Сварка корпуса питателя
СОДЕРЖАНИЕ
ВВЕДЕНИЕ
Ι. Описание и
назначение конструкции «корпус питателя»
ΙΙ.
Выбор материала для сварной конструкции
ΙΙΙ.
Обоснованный выбор способа сварки с учетом современных технологий
ΙV. Выбор
сварочного оборудования и инструментов. Выбор сварочных материалов
VΙ. Выбор
режима сварки
VΙΙ.
Технология изготовления сварной конструкции
VΙΙΙ.
Контроль качества сварной конструкции
ΙX.
Экономическая часть. Организация рабочего места электросварщика
XΙ. Охрана
труда и техника безопасности
XΙΙ.
Используемые источники информации
ВВЕДЕНИЕ
В современном сварочном
производстве характерны разнообразие способов дуговой сварки, широкий масштаб
их применения в различных отраслях промышленности и привлечение большого числа
рабочих.
Успехи в разработке и
производстве покрытых электродов обусловили высокую производительность ручной
дуговой сварки сталей, не уступающих механизированной сварке под флюсом и в
углекислом газе, поэтому этот способ широко применяют в отрасли. При
изготовлении стальных корпусов судов сварки под флюсом позволило в основном
механизировать выполнение швов в нижнем положении. Однако на корпусах
современных судов более половины объема сварочных работ выполняются в
положениях, отличных от нижнего. Механизация сварки этой группы швов в
значительной мере осуществляется за счет сварки в углекислом газе электродной
проволокой диаметром от 0,8 до 1,4 мм. /1/
Механизированная сварка в
углекислом газе получила широкое применение при изготовлении стальных судовых
трубопроводов диаметром 22 мм и более, приварке к трубопроводам фланцев,
штуцеров. При изготовлении трубопроводов из медно-никелевых сплавов применяют
механизированную сварку в азоте плавящимся вольфрамовым электродом. На заводах
освоена и широко применяется ручная аргонодуговая сварка неплавящимся вольфрамовым
электродом и механизированная сварка плавящимся электродом сплавов алюминия и
титана.
Внедрение в производство
большой номенклатуры конструкционных и сварочных материалов, способов дуговой
сварки обусловило необходимость исследования влияния технологии сварки на
характер излучения электрической дуги с целью определения его опасности для
органов зрения, эффективности выпускаемых промышленных средств защиты глаз и
соответствия параметров отечественных светофильтров физиологическим
особенностям органов зрения.
Выше перечисленные способы
сварки широко применяемые не только в судостроении, но и в других отраслях
промышленности, значительно отличающихся друг от друга в связи с чем позволяют
более полно исследовать влияние технологии сварки на излучение электрической
дуги и определить его интенсивность в различных областях спектра
/3/.
Данными способами сварки изготавливают различные
конструкции, цистерны, вахтовые автобусы, автобусы, прицепы и так далее. Для
изготовления какого-либо сваренного изделия используют приспособления,
обеспечивающие надежное закрепление деталей, быструю и точную установку по
упорам в заданной последовательности и должно быть удобно в эксплуатации,
которые могут быть ручными, механизированными и автоматизированными.
Использование приспособления повысит
производительность труда, сократит время производства сварной конструкции,
повысит качество сборки-сварки, облегчит труд рабочего
/6/.
.
ОПИСАНИЕ И НАЗНАЧЕНИЕ КОНСТРУКЦИИ «КОРПУС ПИТАТЕЛЯ»
Конструкция «корпус питателя»
предназначена для предохранения деталей от воздействия внешней среды. А также
конструкция «корпус питателя» ограждает все детали, входящие в него, от
постороннего влияния и защищает рабочих от травмирования
/2/.
Корпуса служат не только для размещения и
крепления в них узлов и деталей механизмов, но и для защиты их от механических
повреждений и попадания пыли и влаги, они все в какой-то степени
герметизированы. От конструкции корпуса зависят точность и надежность работы
механизма, его размеры, масса и внешний вид, удобство и безопасность
эксплуатации.
Сварные конструкции
Строительные Машиностроительные Трубопроводы
конструкции конструкции
Рис.1.1 Классификация сварных
конструкций
К машиностроительным сварным
конструкциям относятся конструкции, расчет и конструирование которых
производится на машиностроительных заводах. Машиностроительные конструкции в
свою очередь условно подразделяются на 5 групп (рис.1.2):
Машиностроительные конструкции (сварные)
Нестандартное Детали
машин Рамы
оборудование
приспособлений
Бункеры Затворы
Кожухи Рамы под Каркасы Этажерки
(корпуса) оборудование
Емкостные
Котлы Аппаратура Специальные Емкости
приспособления
Рис.1.2 Классификация
машиностроительных конструкций
К первой относятся емкостные
конструкции, среди которых можно выделить несколько подгрупп: котлы, посудины и
аппараты, специальное оборудование, емкости.
К группе разных конструкций
относятся: рамы под оборудование, опорные конструкции, трубопроводы
/4/.
К нестандартному оборудованию
условно отнесены конструкции разнообразных бункеров, затворов, кожухов и др.
Сварные корпуса изготавливают при мелкосерийном
и единичном производствах. Их выполняют из металлопроката (листов, полос,
уголков, профилей). Корпус после сварки подвергают отжигу для снятия локальных
(в местах сварки) внутренних напряжений. И только после отжига рекомендуют
производить механическую обработку плоскостей и отверстий. Толщина стенок
определяется типом сварки и усилиями, возникающими при обработке корпуса после
сварки. Жесткость корпуса можно увеличить ребрами, располагаемыми снаружи у
мест крепления подшипников.
Корпуса по степени защиты от воздействия
окружающей среды классифицируют как обыкновенные защитные, пыленепроницаемые, брызгонепроницаемые
и взрывобезопасные. Важен выбор степени герметизации - полная герметичность
корпусов усложняет и удорожает конструкцию. Основные элементы герметичных
корпусов, которые необходимо уплотнять, - крышки, смотровые стекла,
электрические вводы и подвижные соединения
/10/.
Сварная конструкция «корпус» (черт. 640С -
371СБ, габаритные размеры - 1900х1610х780, масса - 3370 кг.) состоит из:
Фланец (поз.1) 2 шт.
Корпус питателя (правый) (поз.2) 1 шт.
Ребро (поз.3) 18 шт.
Ребро (поз.4) 1 шт.
Рисунок 1.1. - Корпус питателя: 1 - фланец, 2 -
корпус питателя (правый), 3 - ребро, 4 - ребро..
ВЫБОР МАТЕРИАЛА ДЛЯ СВАРНОЙ КОНСТРУКЦИИ
Для всех деталей сваркой конструкции «корпус
питателя» выбираем сталь Ст3сп3.
Таблица 2.1 Характеристика материала Ст3сп3
Марка:
|
Ст3сп3
|
Классификация:
|
Сталь
конструкционная углеродистая обыкновенного качества
|
Применение:
|
несущие
элементы сварных и не сварных конструкций и деталей, работающих при
положительных температурах
|
Таблица 2.2 Химический состав в % материала
Ст3сп3.
C
|
Si
|
Mn
|
Ni
|
S
|
P
|
Cr
|
N
|
Cu
|
As
|
0.14-0.22
|
0.05-0.15
|
до
0.3
|
до
0.05
|
до
0.04
|
до
0.3
|
до
0.008
|
до
0.3
|
до
0.08
|
При работе с этим материалом необходимо
произвести оценку свариваемости металла.
Свариваемостью называется способность металла
или сочетания металлов образовывать при установленной технологии сварки
соединения, отвечающее требованиям, обусловленным конструкции и эксплуатации
изделия /5/.
Основным элементом в углеродистых
конструкционных сталях является углерод. С увеличением количества углерода в
стали повышается ее прочность и твердость, уменьшается пластичность и вязкость.
Марганец и кремний повышают прочность и твердость, и способствует закаливанию
стали.
По свариваемости стали условно подразделяются на
4 группы:
а) I - хорошосвариваемые, стали с эквивалентным
содержанием углерода Сэкв.≤ 0,25%
б) II - удовлетворительно свариваемые, стали с
эквивалентным содержанием Сэкв.≥ 0,25-0,35%
в) III - ограниченно свариваемые, стали с
эквивалентным содержанием Сэкв.≥ 0,35-0,45%
г) IV -плохо свариваемые, стали с эквивалентным
содержанием Сэкв.≥ 0,45%.
Эквивалентное содержания углерода определяется
по формуле:
Сэк. = С + Mn/20 + Ni/15
где, С, Мn, Ni - химические элементы, %.
Таблица 2.4 Свариваемость металла
Свариваемость
|
без
ограничений
|
-
сварка производится без подогрева и без последующей термообработки
|
ограниченно
свариваемая
|
-
сварка возможна при подогреве до 100-120 град. и последующей термообработке
|
трудносвариваемая
|
-
для получения качественных сварных соединений требуются дополнительные
операции: подогрев до 200-300 град. при сварке, термообработка после сварки -
отжиг
|
Для сварки корпуса питателя
выбираем сталь Ст3сп3 относится к III
группе свариваемости с содержанием углерода 0,03%, по раскислению - спокойная
/9/.
ІІІ. ОБОСНОВАННЫЙ
ВЫБОР СПОСОБА СВАРКИ С УЧЕТОМ СОВРЕМЕННЫХ ТЕХНОЛОГИЙ
Дуговая сварка в защитных газах - это сварка,
при который дуга и металл находятся в защитном газе, который подается в зону
свариваемости с помощью специальных приспособлений. Этот вид сварки широко
применяют при изготовлении машиностроительных и строительных конструкций.
Основные преимущества сварки в защитных газах:
высокая продуктивность (в 2 раза больше по
сравнению с ручной дуговой сваркой покрытыми электродами), низкая стоимость при
использовании защитных газов;
возможность свариваемости в разных
пространственных положениях;
маленькая зона термического воздействия и
относительно не большая деформация выбора последствия высокой степени
концентрации дуги;
высокое качество защиты, нет необходимости
защиты шва при многослойном сваривании;
допустимость процесса сварки металла разной
толщины, возможность наблюдения за образованием шва;
высокое качество свариваемых металлов и их
сплавов разной толщины.
Недостатки сварки в защитных газах:
открытая дуга, которая повышает опасность
поражения зрения световым излучением;
необходимость защиты зоны сваривания от
сквозняка, что усложняет сварку в монтажных условиях;
потеря металла на разбрызгивание, наличие
газовой аппаратуры, в некоторых случаях водного охлаждения горелок.
Основными разновидностями сварки являются:
сварка в углекислом газе и аргонодуговая сварка.
Рисунок 3.1. - Схемы сварки в защитных газах: а,
б, в - не плавящимся электродом на постоянном токе прямой полярности; не
плавящимся электродом на переменном токе; плавящимся электродом на постоянном
токе обратной полярности; 1 - сварочный преобразователь, 2 - амперметр, 3 -
вольтметр, 4 - балластный реостат, 5 - наконечник, 6 - вольфрамовый электрод, 7
- редуктор расходомер газа, 8 - баллон с жатым газом, 9 - трансформатор, 10 -
осциллятор, 11 - механизм подачи проволоки, 12 - электродная плавящаяся
проволока, 13 - контакт контактора, 14 - катушка с проволокой.
IV. ВЫБОР
СВАРОЧНОГО ОБОРУДОВАНИЯ И ИНСТРУМЕНТОВ
Для сварки корпуса питателя применяем сварочный
полуавтомат УСП 180.
Он предназначен для сварки низкоуглеродистых
сталей в среде углекислого газа автоматически подаваемым плавящимся электродом.
Совмещение надежного, мощного источника питания и устройства подачи проволоки в
едином корпусе на колесах - преимущество данного полуавтомата.
Таблица 4.1. - Характеристики полуавтомата УСП
180
Названия
характеристик
|
Числовое
назначение
|
Напряжение
питания сети, В Максимальный сварочный ток, А Регулирование сварочного тока
Толщина свариваемо металла, мм Скорость подачи сварочной проволоки, м/ч
Защитный газ Режим сварки Номинальный режим работы, ПН% Диаметр электродной
проволоки, мм Габариты, мм Масса, кг
|
380
180 Ступенчатое 1…6 120…960 Углекислота Постоянные, прерывистый 60 0,8…1,2
750х530х670 105
|
Источник питания -
универсальный сварочный выпрямитель ВДУ-504. Используется как при ручной
дуговой сварке, так и при сварке в среде защитных газов.
Таблица 4.2 - Технические
характеристики универсальных сварочных выпрямителей ВДУ- 504
Характеристика
|
Тип
ВДУ-504
|
Напряжение,
В
|
220/380
|
Номинальный
сварочный ток при ПР 60%, А
|
500
|
Номинальное
рабочее напряжение, В
|
46
|
Напряжение
холостого хода, В
|
72-76
|
Пределы
регулирования сварочного тока, А
|
100-500
|
Пределы
регулирования рабочего напряжения, В
|
18-50
|
кдд,%
|
82,5
|
Масса,
кг
|
V.
ВЫБОР СВАРОЧНЫХ МАТЕРИАЛОВ
При полуавтоматической сварке в среде защитных
газов применяются сварочная проволока и защитный газ.
В зависимости от назначения применяется
проволока сварочная сплошного сечения и порошковая, наплавочная сплошного
сечения. По виду поверхности низкоуглеродистая и легированная проволока
подразделяется на неомедненную и омедненную. Проволока может изготавливаться из
стали, выплавленной электрошлаковым или вакуумно-дуговым переплавом или
вакуумно-индукционных печах.
Проволока сварочная, применяемая при сварке в
углекислом газе должна соответствовать ГОСТ 2246-70. Поверхность проволоки
должна быть чистой и гладкой, без трещин, расслоений, ржавчины, окалины, масла
и других загрязнений, не должна иметь резких перегибов во избежание заедания ее
в спирали гибкого шланга держателя.
Рассмотрим характеристики сварочной проволоки Св
08Г2С ГОСТ 2246-70. Ее применяют для изготовления конструкции из
низколегированных сталей с повышенными требованиями к металлу шва по ударной
вязкости при отрицательной температуре.
Таблица 5.1. - Химический состав наплавленного
металла
Хим.элемент
|
С
%
|
Si %
|
Mn %
|
Мо
%
|
S %
|
P %
|
Содержание
|
0,12
|
0,75
|
1,9
|
0,65
|
0,07
|
0,027
|
Таблица 5.2. - Механический состав металла шва
δв
|
δm
|
δ5
|
ψ
|
КСU
|
КСV
|
МПа
|
%
|
Дж/см
при t°С
|
|
|
20
|
-20
|
943
|
777
|
15,5
|
-
|
109
|
-
|
Проволоку Св 08Г2С ГОСТ2246-70 применяют также
для сварки конструкции из легированной стали повышенной и высокой прочности с
временным сопротивлением разрыву 690-980 МПа, сварка может производиться во
всех пространственных положениях.
Рассмотрим также сварочную проволоку Св-12Х13
ГОСТ3456-70. Ее применяют для сварки конструкций из хромистых сталей и наплавке
уплотнительных поверхностей стальной арматуры.
Таблица 5.3. - Химический состав наплавленного
металла
С
|
Si
|
Mn
|
Mo
|
Ni
|
Cr
|
S
|
P
|
0,13
|
0,62
|
0,86
|
-
|
0,42
|
12,2
|
0,013
|
0,023
|
Таблица 5.4. - Механические свойства металла шва
δв
|
δm
|
δ5
|
ψ
|
КСU
|
КСV
|
МПа
|
|
%
|
|
Дж/см
при t°С
|
|
|
|
|
20
|
-20
|
650
|
20,3
|
-
|
103
|
-
|
|
|
|
|
|
|
|
Из выше предложенных проволок
применяем сварочную проволоку Св 08Г2С потому что данная проволока применяется
для сварки конструкции из легированной стали повышенной и высокой прочности с
временным сопротивлением разрыву 690-980 МПа, сварка может производится во всех
пространственных положениях. Также Мn
и Si положительно
влияют на свойства металла шва - компенсируют дополнительное окисление металла
при сварке и образованию пор.
. РАСЧЕТ
РЕЖИМОВ
СВАРКИ
Для получения сварного шва
требуемых размеров и формы необходимо выбрать соответствующий режим сварки.
В зависимости от свариваемого метала, его
толщины и требований предъявляемых к сварному соединению выбираем режим сварки.
Ввиду более высокой стабильности дуги применяется преимущественно постоянный
ток обратной полярности. Помимо параметров режима на стабильность горения дуги,
форму и размеры шва большое влияние оказывает характер расплавления и переноса
электродного металла в сварочную ванну. Характер переноса электродного металла,
зависит от материала и диаметра электрода, состава защитного газа и ряда других
факторов.
Таблица 6.1. - Ориентировочные параметры вылета
электрода, расстояние от наконечника горелки и поверхностью металла и расход
углекислого газа в зависимости от диаметра электрической проволоки
Диаметр
электродной проволоки, мм
|
Вылет
электрода, мм
|
Расстояние
от наконечника горелки до поверхности свариваемого металла, мм
|
Расход
СО2, дм3/мин.
|
1,6
- 2,0
|
15
- 25
|
15
- 20
|
15
- 20
|
При сварке в углекислом газе основные типы
сварных соединений и их конструктивные элементы выбирают по ГОСТ 14771-76 .
Источником питания дуги служит сварочный выпрямитель , сварка конструкции
ведется постоянным током обратной полярности. Согласно табл.6.2. выбираем
диаметр проволоки 2 мм, силу тока 280-380 А. согласно табл.6.1. и 6.2. выбираем
расход газа 18 л/мин. Характерный режим сварки металла толщиной 6 мм, это ток
280-380 А, скорость сварки 18-24 м/ч, длина дуги 2 мм, вылет электрода 15 - 25
мм, диаметр проволоки 2 мм.
С увеличением скорости сварки
уменьшаются все геометрические размеры шва. Её устанавливают в зависимости от
толщины метала и условий нормального формирования шва. При очень большой
скорости сварки конец электрода может выйти из зоны защиты и окислиться на
воздухе. Маленькая скорость сварки приводит к увеличению сварочной ванны и
увеличивает возможность образование пор в металле.
Скорость сварки составляет
15-80м/час.
С увеличением вылета электрода
ухудшается стойкость горения дуги и формирование шва, а также увеличивается
разбрызгивание жидкого металла. При сварке с очень маленьким вылетом ухудшается
наблюдение за процессом сварки и часто подогревает газовое сопло и
струеподводящий контактный наконечник. Кроме вылета электрода необходимо
выдерживать определённое расстояние от сопла горелки до поверхности металла,
поскольку с увеличением этого расстояния ухудшается газовая защита зоны сварки
и возможно попадание кислорода и азота воздуха в расплавленный метал, что
приводит к появлению газовых пор. Величину вылета электрода, а также расстояние
от сопла горелки до поверхности металла устанавливают в зависимости от
выбранного диаметра электродной проволоки.
Таблица 6.2. - Ориентировочные
режимы полуавтоматической сварки без раздела кромок низкоуглеродистых сталей в
СО2 проволокой Св08 - Г2С и постоянным током обратной полярности
Толщина
металла шва, мм
|
Ширина
зазора, мм
|
Кол-во
слоев
|
Диаметр
проволоки, мм
|
Сила
сварного тока, А
|
Напряжение
дуги, В
|
Скорость
сварки, мм/ч
|
Расход
газа, л/мин.
|
8,0-12,0
|
1,8-
2,2
|
2
|
2,0
|
350
|
30
|
16-30
|
18-20
|
VII. ТЕХНОЛОГИЯ
ИЗГОТОВЛЕНИЯ СВАРНОЙ КОНСТРУКЦИИ
корпус питатель
сварной конструкция
Процесс последовательного
соединения и скрепления сборочных деталей между собой прихватками или болтами
для образования отправочного элемента называют сборкой.
Сборка
сварочной
конструкции «корпуса питателя» - это одна из главных операции при изготовлении
конструкции. Собранные детали конструкции сначала прихватывают, а потом
сваривают. В некоторых случаях сборочные операции чередуются со сварочными.
Технология сборки конструкций зависит от имеющегося в цехе оборудования и
способа производства /1/.
Технологический процесс сборки
независимо от способа производства должен удовлетворять следующим требованиям:
соблюдение требуемой последовательности сборки и сварки; применение
необходимого инструмента и приспособлений, повышающих производительность труда
сборщика; увязка сборочных операций с операциями по сварке; проведение
послеоперационного контроля качества сборки; соблюдение допусков на размеры
конструкций; соблюдение правил техники безопасности. Сведения о процессе сборки
записывают в технологические карты сборки сборочных единиц и общей сборки
конструкции. Если при изготовлении конструкции операции сборки чередуются с
операциями сварки, то технологический процесс сварки описывают в той же
технологической карте /3/.
Процесс сборки конструкций под
сварку охватывает следующие виды работ: раскладку поданных под сборку деталей
на стеллажах в непосредственной близости к месту сборки; собственно сборку,
т.е. размещение отдельных деталей во взаимном расположении, указанном на чертеже;
закрепление деталей между собой или прикрепление мелких деталей к основным
крупным сначала зажимными или распорными приспособлениями, а затем короткими
швами (прихватками) и подготовка собранной конструкции
к сварке.
Особенностью сборки сварной конструкции
«корпус» является то, что все элементы металлоконструкции устанавливают в одной
горизонтальной плоскости и выдерживают параллельность и перпендикулярность
элементов «корпуса питателя» друг к другу.
В зависимости от формы,
размеров элементов и типа производства применяются следующие способы сборки
конструкций под сварку: сборка по предварительной разметке; по
упорам-фиксаторам; по шаблонам-копирам; по контрольным отверстиям в собираемых
элементах, в кондукторах, на поточных линиях.
Таблица 7.1 Зависимость
прихваток от толщины металла и длины сварного шва.
Толщина
металла, мм
|
<5
|
>5
|
Длина
шва, мм
|
<
150-200
|
>200
|
Длина
прихваток, мм
|
<5
|
>
20-30
|
Расстояние
между
|
50-100
|
>
300-500
|
прихватками,
мм
|
|
|
Сборка - сварка:
поз:1=2,2=1,3=18,4=2
общая сборка
поз:1=2,2=1(30Л),3=18,4=2
. На входящих в сборку деталях заточить
места под сварку шириной 20 мм, L=33,20 м
. Собрать узел с полной подгонкой по
месту, прихватить.
. Контроль ОТК
. Подогрев корпуса питателя в местах
сварки до t=120-150 град.
. Подготовить места под сварку. Варить
п/а в CO2. Швы зачистить. Длинные швы варить от середины на края
обратноступенчатым способом участками приблизительно по 300 мм.
Нестандартные швы №4 - типа У4=250-280;U=26-30
св-08г2с 1.6: Т1 Н 10 L 1.7 n=2=250-280;U=26-30 св-08г2с 1.6: Т1 Н 10 L 0.5
n=1=250-280;U=26-30 св-08г2с 1.6: Т3 Н 8 L 0.1 n=20=212-238;U=22-26 св-08г2с
1.6: Т3 В 8 L 0.15 n=20=250-280;U=26-30 св-08г2с 1.6: Т5 Н 30 L 0.5
n=1=320-350;U=30-34 св-08г2с 1.6: У4 Н 28 L 1.7 n=2=320-350;U=30-34 св-08г2с
1.6: У4 Н 28 L 0.5 n=2
. Заточить сварные швы. L=4,40 м
. Править после сварки.
. Разметка под м.о
. Произвести дробеструйную очистку
поверхностей изделия.
. Выполнить слесарные работы подготовки
поверхностей под окрашивание.
. Подготовить поверхности под покрытие.
Покрытие согл. ТУ черт. - S=18,0 м2
. Сдать ОТК.
Выполненные сварные швы заносим
в табл. 7.2. - сварные швы
Таблица.7.2. - Сварные швы
№
шва
|
ГОСТ
|
Наименование
|
Примечание
|
1
|
14771
- 76
|
Т1
- Δ10
|
|
2
|
|
Т3
- Δ8
|
|
3
|
23518
- 79
|
Т5
|
|
VIII.
КОНТРОЛЬ КАЧЕСТВА СВАРНОЙ КОНСТРУКЦИИ
Сварку подвергают проверке для определенных
возможных отклонений от технических условий, предъявляемых данному виду
изделий. Изделие считается качественным, если отклонения не превышают
допустимых норм. В зависимости от вида сварочных соединений и условий
дальнейшей эксплуатации, изделия после сварки подвергают соответствующему
контролю. Контроль может быть предварительным, когда проверяют качество
исходных материалов, подготовку свариваемых поверхностей, состояние оснастки и
оборудования. К предварительному контролю относят также сварку опытных
образцов, которые подвергают соответствующим испытаниям. При этом в зависимости
от условий эксплуатации опытные образцы подвергают металлографическим
исследованиям и неразрушающим или разрушающим методам контроля.
Под текущим контролем понимают проверку
соблюдения технологических режимов, стабильность режимов. При текущем контроле
проверяют качество положений послойных швов и их зачистку. Окончательный
контроль осуществляют в соответствии с техническими условиями. Дефекты,
обнаруженные в результате контроля, подлежат исправлению.
Испытание аммиаком применяют также при
двустороннем доступе к конструкции изоляции. Этим методом рекомендуется
проверять плотность сварных швов метало изоляции фундаментных плит и покрытий
сооружений. Для этого швы на видимой поверхности изоляции окрашивают раствором
фенолфталеина или азотнокислой ртути (5%-ный раствор), а во внутреннее
пространство между метало изоляцией и основанием нагнетают 1%-ную смесь аммиака
с воздухом под давлением не менее 6,6 кПа через отверстия, равномерно
распределенные по площади изоляции. Для предотвращения выхода
аммиачно-воздушной смеси из-под изоляции по ее периметру устраивают асфальтовый
или битумный замок. Проницаемость сварных швов определяют по изменению окраски
суспензии фенолфталеина, образующей на поверхности дефектного шва
красно-фиолетовые пятна (при использовании азотнокислой ртути - черные пятна).
Выборочный контроль засверливанием проводят с
целью определения качества провара и отсутствия внутренних дефектов.
Засверливание выполняют сверлом, диаметр которого на 6 мм больше ширины шва, с
таким расчетом, чтобы был захвачен основной металл, а затем отверстия
протравливают 10%иым раствором двойной соли хлорной меди и аммония в воде в
течение 1-3 мин. Осадок меди удаляют водой или 5%-ным раствором надсернокислого
аммония. Затем осматривают отверстие невооруженным глазом или при помощи лупы.
Прочность сварных швов определяют механическими
испытаниями на растяжение и изгиб (ГОСТ 6996-66)
/3/.
Контроль качества «корпуса питателя»:
1. Проверить
качество сварки внешним осмотром;
2. Проверить
размеры измерительной линейкой;
Замерить катеты швов
измерительным шаблоном.
IX.
ЭКОНОМИЧЕСКАЯ ЧАСТЬ
.Расчет постоянных затрат на 1 изделие «корпус
питателя».
. Арендная плата составляет 1000 грн.
. Патент на изготовление металлоизделий
составляет - 100 грн.
. Плата за телефонные услугу - 100 грн.
. Стоимость необходимого оборудования за
месяц.
. Стоимость необходимого инвентаря за
месяц
. Постоянные затраты в месяц составляют.
+1000+100+416,7+34,7=2551,4 грн.
. Расчет количества изделий,
изготовляемых за месяц:
определяем фонд времени за 1 месяц (Фм)
Фм =
,
где Фрв - фонд рабочего времени за
год (2012ч\часов)
- количество месяцев в году
Фм =
(час)
количество изделий, изготовленных за
1 месяц:

,
где t - время,
затраченное на изготовление 1 изделия
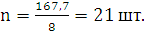
4. Постоянные затраты на одно изделий
составляют:
Зпост =
=121,49 грн.
. Расчет переменных затрат на
единицу изделия.
1. Затраты на сырье (металл)
См = Ц * S,
где Ц - цена 1 м2 металла грн.
S - площадь металла,
м2
См = 400 * 3 = 1200 грн.
. Расчет стоимости электродов:
Сэл = Цэд * n,
где Цэд - цена одного электрода, грн.
n - количество
электродов
Сэд = 0,15 * 400 = 60 грн.
. Транспортные расходы:
Тр = 
= 
= 48 грн.
4. Затраты на воду:
Зв = 
,
где Цв = цена 1 м3
воды, грн.
n =
количество изделий за месяц
Зв = 
= 54,5 грн.
5. Затраты на электроэнергию на 1 изделие:
Зэ = 
,
где Цэ - цена одного
кВт электроэнергии,
Рэ - расход электроэнергии в месяц,
n -
количество изделий на месяц.
Зэ = 
= 4,43 грн.
6. Затраты на заработную плату:
Зз.п. = 
* t1изд
,
где Зм
- месячная
заработная плата, грн.
Фм - фонд рабочего времени за 1
месяц ( 167,7 ч)
Т1изд - затраты времени на 1
изделие, час
Зз.п. = 
* 5 = 500 грн.
7. Отчисления на социальное страхование:
Сс = 
Сс = 
= 8,05 грн.
8. Переменные затраты на 1 изделие:
Зпер. = См+Сэд+Тр.+Зв+Зэ+Ззп+Сс
Зпер. = 1200+60+48+54,5+4,43+500+8,05=1874,98
грн.
. Себестоимость одного изделия
составляет:
С = Зпост + Зпер
С = 121,49+1874,98 = 1996,47 грн.
Х. ОРГАНИЗАЦИЯ РАБОЧЕГО МЕСТА
ЭЛЕКТРОСВАРЩИКА
Рабочее место сварщика - это
участок производственной площади, оснащенный оборудованием и другими средствами
труда, соответствующими характеру работ, выполняемых на этом месте
Рациональная организация
рабочего места заключается в следующем:
- выбор
оснащения, оборудования, инструмента, приспособлений;
- создание
безопасных и санитарно-гигиенических условий труда;
- поддержание
чистоты и порядка, рациональное обслуживание рабочего места;
- сварочное
место оборудовано постом ручной дуговой сварки, которое имеет выпрямитель ВДУ -
504. На сборочном месте находится кондуктор, в котором производится сборка и
сварка. Деталь перемещается с помощью мостового крана, грузоподъемностью 5т.
Сварочным постом называется
рабочее место сварщика, оборудованное комплектом соответствующей аппаратуры и
приспособлений /3/.
Рис. 10.1 Рабочее место сварщика
- источник электропитания; 2 - кабели; 3 -
электрододержатель; 4- ящик для электродов; 5- стол; 6- ящик для инструментов;
7- вытяжная вентиляция; 8 - противопожарный
инвентарь выложенным из кирпича, цемента, бетона.
Высота рабочего стола сварщика - в пределах
0,6-0,7 м, материал -толстый листовой металл. Для защиты глаз и лица сварщика
используются щитки или маски из фибры или спецфанеры. Защиту от вредных
излучений при сварке хорошо обеспечивают светофильтры темно-зеленого цвета
(типа С). Для различных режимов сварки используются различные классы
светофильтров типа С. Это определяется инструкциями, прилагаемыми к
светофильтрам.
От правильной организации
рабочего места в значительной мере зависит как обеспечение высокой
производительности труда сварщиков, так и надёжное качество сварных швов и
соединений. Рабочие места сварщиков в зависимости от выполняемой работы и
габаритов свариваемых изделий, могут быть расположены в специальных сварочных
кабинах или непосредственно у этих изделий (требования к организации рабочих
мест сварщиков регламентированы ГОСТ 12.3.003-75).
Для защиты рабочих от излучения
дуги в постоянных местах сварки устанавливают для каждого сварщика отдельную
кабину размером 2x2,5 м. Стенки кабины могут быть сделаны из тонкого железа,
брезента. Брезент должен быть пропитан огнестойким составом. Стенки окрашивают
в светло-серый цвет красками, хорошо поглощающими ультрафиолетовые лучи
(цинковые или титановые белила, желтый крон). Освещенность кабины должна быть
не менее 80-100лк. Кабину оборудуют местной вентиляцией с воздухообменом 40 м
/ч на каждого рабочего. Вентиляционный отсос должен располагаться так, чтобы
газы, выделяющиеся при сварке, проходили мимо сварщика. Пол в кабине должен
быть из огнестойкого материала (кирпич, бетон, цемент). Под ногами сварщиков
должен находиться резиновый коврик. Сварку деталей производят на рабочем столе.
Крышку стола изготавливают из чугуна толщиной 20-25 мм. Сварочный пост оснащен
выпрямителем и необходимым инструментом сварщика и средствами индивидуальной
защиты сварщика (маски, щитки, респираторы)
/5/.
XI.
ОХРАНА ТРУДА И ТЕХНИКА БЕЗОПАСНОСТИ
Нарушение техники безопасности при проведении
сварочных работ часто приводит к самым печальным последствиям - пожарам,
взрывам и как следствие травмам и гибели людей.
Так же при сварке возможны следующие травмы -
поражение электрическим током, ожоги от шлака и капель металла, травмы
механического характера.
Для предотвращения всех этих положений важно
неукоснительно соблюдать меры предосторожности.
1. Надежная изоляция всех, проводов,
связанных с питанием источника тока и сварочной дуги, устройство геометрически
закрытых включающих устройств, заземление корпусов сварочных аппаратов.
Заземлению подлежат: корпуса источников питания, аппаратного ящика,
вспомогательное электрическое оборудование. Сечение заземляющих проводов должно
быть не менее 25 мм2. Подключением, отключением и ремонтом сварочного
оборудования занимается только дежурный электромонтер. Сварщикам запрещается производить
эти работы
/7/.
. Применение в источниках питания
автоматических выключателей высокого напряжения, которые в момент холостого
хода разрывают сварочную цепь и подают на держатель напряжение 12 В.
. Надежное устройство
электрододержателя с хорошей изоляцией, которая гарантирует, что не будет
случайного контакта токоведущих частей электрододержателя со свариваемым
изделием или руками сварщика (ГОСТ 14651-69). Электрододержатель должен иметь
высокую механическую прочность и выдерживать не менее 8000 зажимов электродов.
.Работа в исправной сухой спецодежде
и рукавицах. При работе в тесных отсеках и замкнутых пространствах обязательно
использование резиновых галош и ковриков, источников освещения с напряжением не
свыше 6-12 В.
. При работе на электронно-лучевых
установках предотвращение опасности поражения лучами жесткого рентгеновского
(почти полное) поглощение вредных излучении, связанных с горением дуги. Особую
опасность в смысле поражения глаз представляет световой луч квантовых
генераторов (лазеров) так как даже отраженные лучи лазера могут вызвать тяжелое
повреждение глаз и кожи. Поэтому лазеры имеют автоматические устройства,
предотвращающие такие поражения, но при условии строгого соблюдения
производственной инструкции операторами-сварщиками, работающими на этих
установках
/7/.
Защитные стекла, вставленные в щитки
и маски, снаружи закрывают простым стеклом для предохранения их от брызг
расплавленного металла. Щитки изготовляют из изоляционного металла - фибры,
фанеры и по форме и размерам они должны полностью защищать лицо и голову
сварщика (ГОСТ 1361-69).
Для ослабления резкого контраста
между яркостью дуги и малой яркостью темных стен (кабины) последние должны быть
окрашены в светлые тона (серый, голубой, желтый) с добавлением в краску окиси
цинка с целью уменьшения отражения ультрафиолетовых лучей дуги, падающих на
стены.
При работе вне кабины для защиты
зрения окружающих, работающих сварщиков и вспомогательных рабочих должны
применяться переносные щиты и ширмы /9/.
Предотвращение опасности поражения
брызгами расплавленного металла и шлака. Образующиеся при дуговой сварке брызги
расплавленного металла имеют температуру до 1800 град. С. при которой одежда из
любой ткани разрушается. Для защиты от таких брызг обычно используют спецодежду
(брюки, куртку и рукавицы) из брезентовой или специальной ткани. Куртки при
работе не следует вправлять в брюки, а обувь должна иметь гладкий верх, чтобы
брызги расплавленного металла не попадали внутрь одежды, так как в этом случае
возможны тяжелые ожоги.
Для защиты от соприкосновения с
влажной, холодной землей и снегом, а также с холодным металлом при наружных
работах и в помещении сварщики должны обеспечиваться теплыми подстилками,
матами, подколенниками и подлокотниками из огнестойких материалов с эластичной
прослойкой.
Предотвращение отравления вредными
газами и аэрозолями, выделяющимися при сварке. Высокая температура дуги (6000-
8000° С) неизбежно приводит к тому, что часть сварочной проволоки, покрытий,
флюсов переходит в парообразное состояние. Эти пары, попадая в атмосферу цеха,
конденсируются и превращаются в аэрозоль конденсации, частицы которой по
дисперсности приближаются к дымам и легко попадают в дыхательную систему
сварщиков. Эти аэрозоли представляют главную профессиональную опасность труда
сварщиков. Количество пыли в зоне дыхания сварщика зависит главным образом от
способа сварки и свариваемых материалов, но в известной степени определяется и
типом конструкций. Химический состав электросварочной пыли зависит от способов
сварки и видов основных и сварочных материалов /7/.
Существуют строгие требования в
области вентиляции при сварочных работах. Для улавливания сварочного аэрозоля
на стационарных постах, а где это возможно, и на нестационарных нужно
устанавливать местные отсосы в виде вытяжного шкафа вертикальной или наклонной
панели равномерного всасывания стола с подрешеточным отсосом и др. При сварке
крупногабаритных серийных конструкций на кондукторах, манипуляторах и т. п.
местные отсосы необходимо встраивать непосредственно в эти приспособления. При
автоматической сварке под флюсом, в защитных газах, электрошлаковой сварке
применяют устройства с местным отсосом газов.
При использовании баллонов со
сжатыми газами необходимо соблюдать установленные меры безопасности: не бросать
баллоны, не устанавливать их вблизи нагревательных приборов, не хранить вместе
баллоны с кислородом и горючими газами, баллоны хранить в вертикальном
положении. При замерзании влаги в редукторе баллона с СО2 отогревать его только
через специальный электроподогреватель или обкладывая тряпками, намоченными в
горячей воде. Категорически запрещается отогревать любые баллоны со сжатыми
газами открытым пламенем, так как это почти неизбежно приводит к взрыву
баллона.
При производстве сварочных работ на
емкостях, ранее использованных, требуется выяснение типа хранившегося продукта
и наличие его остатков. Обязательна тщательная очистка сосуда от остатков
продуктов и 2-3-кратная промывка 10%-ным раствором щелочей, необходима также
последующая продувка сжатым воздухом для удаления запаха, который может вредно
действовать на сварщика /3/.
Категорически запрещается продувать
емкости кислородом, что иногда пытаются делать, так как в этом случае попадание
кислорода на одежду и кожу сварщика при любом открытом источнике огня вызывает
интенсивное возгорание одежды и приводит к ожогам со смертельным исходом.
Взрывоопасность существует и при
выполнении работ в помещениях, имеющих большое количество пылевидных
органических веществ (пищевой муки, торфа, каменного угля). Эта пыль при
определенной концентрации может давать взрывы большой силы. Помимо тщательной
вентиляции для производства сварочных работ в таких помещениях требуется
специальное разрешение пожарной охраны /5/.
Предотвращение пожаров от
расплавленного металла и шлака. Опасность возникновения пожаров по этой причине
существует в тех случаях, когда сварку выполняют по металлу, закрывающему
дерево либо горючие изолировочные материалы, на деревянных лесах, вблизи легко
воспламеняющихся материалов и т. п. Все указанные варианты сварки не должны допускаться.
Предотвращение травм, связанных со
сборочными и транспортными операциями (травмы механического характера). Важное
значение имеет внедрение комплексной механизации и автоматизации, что
значительно уменьшает опасность травм такого рода.
Основные причины травматизма при
сборке и сварке: отсутствие транспортных средств для транспортировки тяжелых
деталей и изделий; неисправность транспортных средств; неисправность такелажных
приспособлений; неисправный инструмент: кувалды, молотки, гаечные ключи, зубила,
отсутствие защитных очков при очистке швов от шлака; отсутствие спецодежды и
других защитных средств /1/.
Меры безопасности в этом случае: все
указанные средства и инструменты следует периодически проверять; такелажные
работы должны производить лица, прошедшие специальный инструктаж; от рабочих
необходимо требовать соблюдения всех правил по технике безопасности, включая
работу в спецодежде, рукавицах; использование средств индивидуальной вентиляции
(где это необходимо) и т. д. Важное значение имеет внедрение комплексной
механизации и автоматизации, что значительно уменьшает опасность травм такого
рода
/10/.
Чтобы было удобно работать сварщикам
нужно соблюдать следующие рекомендации:
1. Сборку и сварку крупногабаритных
секций следует выполнять на специализированных местах, постелях, стендах, при
этом должны быть обеспечены достаточные проходы с каждой стороны конструкции.
. При сварке объемных секций на
высоте необходимо устраивать леса с расположением сварочного оборудования вне
рабочего места сварщика.
. Все оборудование, которое при
неисправном состоянии может оказаться под напряжением, должно иметь
индивидуальное заземление с выводом к общему защитному заземлению.
. Все сварочные установки должны
находиться под наблюдением наладчика-монтера. Исправлять дефекты
электросварочного оборудования имеет право только монтер-наладчик.
XII.
ИСПОЛЬЗУЕМЫЕ ИСТОЧНИКИ ИНФОРМАЦИИ
1. Гуменюк І.В. «Технологія
електродугового зварювання», Київ: «Грамота», 2006.
2. Думов
С.И. - «Технология электрической сварки плавлением» - М: Машиностроение, 1987.
. Китаев
А.М. «Сварочная книга сварщика » - М: Машиностроение, 1985.
. Куркин
А.С. «Сварочные конструкции» - М: Машиностроение, 1991.
. Методическое
пособие по курсовому проектированию, НМТ,2003
. Николаев
Г. А., Винокуров В. А., Сварные конструкции. Справочник технолога: Учебн. для
вузов
/
Под
ред. Г. А. Николаева. - М:
Высш. шк., 2000. - 446с.: ил.
8. Нормативы на полуавтоматическую сварку
в среде защитных газов - М: Экономика, 1989.
9. Ольшанский
Н.А. , Николаев Г.А. Специальные методы сварки. М.:
Машиностроение,
1995. - 232 с.
. Рыморов
К.С. «Механизация и автоматизация сварочного производства» - М: Машиностроение,
1990.