(округленное до ближайшего
целого )-
|
|
|
|
13
|
Уточненное межосевое
расстояние ay, мм 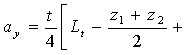 , мм -
|
|
|
14
|
Монтажное межосевое
расстояние а м = 0.996 аy, мм  -0,996∙1271,1=1266
|
|
|
15
|
Нагрузка на валы Qв = 1.15 Кg Ft , H -1,15∙4703,7=5409,3
|
|
|
Вывод: цепь ПР - 31,75 - 8900 ГОСТ 13568 -75 подходит по заданным
условиям работы.[2]
Расчет клиноременной передачи
Рисунок 6 - Схема ременной передачи
Исходные данные:
. Передаточное отношение uрп = 4.
. Крутящий момент на ведущем валу T1 = 28,2 Н∙м.
. Частота вращения ведущего вала n1 = 950 об/мин.
. Мощность на ведущем валу N1 = 2,8 кВт.
Определим расчётный передаваемый крутящий момент Т1Р, Н·м
Т1Р =Т1 ·сР. (43)
где сР - коэффициент, учитывающий динамичность нагружения
передачи и режим её работы. Для лёгкого режима работы при числе смен равной
единице сР =1. [2]
Т1Р = 28,2 · 1 = 28,2 Н·м.
В зависимости от полученной величины выбираем сечения Z и A.
T1Р
= <30Н·м, T1Р = 15-60 Н·м,
d1min = 63 мм, d1min = 90 мм,
HР = 6 мм. HР =8мм.
ГОСТ 1284.1-89. [2]
Действительный диаметр ведущего шкива d1, мм выбираем исходя из соотношения:
d1
>d1min.
(44)
Принимаем для сечения Z: d1= 71 мм, для сечения А: d1 = 100 мм ГОСТ 20889-88. [2]
Расчётный диаметр ведомого шкива d2Р, мм
2Р =d1 · Uрп. (45)
Для Z: d2р = 71·4
= 284 мм.
Для А: d2р
= 100·4 = 400 мм.
Действительный диаметр
ведомого шкива d2, мм
выбирается исходя из условия:
d2 <d2р.
(46)
Принимаем для сечения Z d2
= 280 мм, для сечения А d2 = 400 мм. [2]
Действительное передаточное
отношение u
u
=
, (47)
где
ε =
0,01÷0,02 - коэффициент упругости
скольжения.
Для
Z: u =
= 4.
Для
А: u =
= 4,06.
Минимальное
межосевое расстояние amin, мм
amin =0,55(d1
+d2 )+Hр. (48)
Для
Z: amin =
0,55·(71 + 280) + 6 = 199,05 мм.
Для
А: amin =
0,55·(100 + 400) + 8 = 283 мм.
Расчётная
длина ремня Lр, мм
Lр =2·amin
+0,·5·π·(d1 +d2 )+0,25·(d2-d1
)2/amin (49)
Для
Z: Lр =
2·199,05 + 0,5·3,14·(71 + 280) + 0,25·(280-71)2/199,05 = 1004мм.
Для
А: Lр = 2·283
+ 0,5·3,14·(100+400)+0,25·(400-100)2/283 = 1430,5мм.
Действительную
длину ремня выбираем исходя из условия L, мм
>Lр
(50)
Для
сечения Z принимаем L= 1120 мм, для сечения А принимаем L=1600мм. ГОСТ
1284.1-89. [2]
В
зависимости от действительной длины ремня принимаем значение коэффициента сL,учитывающего
длину ремня для сечения Z cL =
0,93; для сечения А сL =
0,98 ГОСТ 1284.3-96. [2]
Межцентровое
расстояние равно a, мм
a=amin +0,5·(L-Lр
).
(51)
Для
Z: а = 199,05 +0,5·(1120-1004) = 257,05мм.
Для
А: a = 283 +0,5·(1600-1430,5) = 367,8 мм.
Угол
обхвата ремнём меньшего шкива α1, º
α1 =180-57·(d2
-d1 )/a. (52)
Для
Z: α1 = 180-57·(280-71)/199,05 = 120º.
Для
А: α1 = 180-57·(400-100)/283 = 119,5º.
В
зависимости от полученного значения принимаем значение коэффициента сα, учитывающего угол обхвата для сечения Z сα = 0,89; А сα=0,89. [2]
Скорость
ремня υ,
м/с
υ = (π·d1 ·n1)/(60·103).
(53)
Для
Z: υ
= (3,14·71·950)/(60·103) = 3,5 м/с.
Для
А: υ = (3,14·100·950)/(60·103) = 4,9 м/с.
Число
ремней передач z
z = (N1 ·cр)/(N0·cL·cα·ck),
(54)
где
N0 -
мощность, передаваемая одним ремнём. Выбирается в зависимости от сечения ремня,
его скорости и диаметра ведущего шкива. Для сечения Z при d1= 71 мм, υ = 3,5 м/с, N0 = 0,42 кВт. Для сечения А d1 =
100 мм, υ
= 4,9 м/с, N0 = 0,64 кВт. [2]
Сk -
коэффициент, учитывающий число ремней передач. Предварительно принимаем сk =1.
Для
Z: z = (2,8·1)/(0,42·0,93·0,89·1) = 8.
Для
А: z = (2,8·1)/(0,64·0,98·0,89·1) = 5.
Принимаем
для сечения Z z = 8, для сечения А z = 5.
Сила,
нагружающая валы передач F, H
F=2·F0sin(α1/2).
(55)
где
F0-
предварительное напряжение ремня.
F0=0,5·Ft/φ. (56)
где
φ
= 0,45÷0,55 - коэффициент тяги.
Ft -окружное
усилие.
Ft = (2·103
·T1 )/d1. (57)
Для
сечения Z
t = 2·103 ·28,2/71
= 794,4 H.
Для
сечения А
t = 2·103·28,2/100
= 564 H.
Для
сечения Z:
F0 = 0,5·794,4/0,5 = 794,4H.
Для
сечения А
F0 = 0,5·564/0,5 = 564 H.
F для сечения Z=
2·794,4 · sin (120/2) = 1375,9 H.
F для сечения А
F = 2·564 · sin
(119,5/2) = 974,4H.
Условия
выбора к установке ремня:
.
Значение силы (F), нагружающей вал передачи, также должно быть
наименьшим.
Исходя
из значений z и F принимаем к установке ремень сечения А.
Анализ
результатов расчета показывает, что целесообразнее по конструктивным
соображениям принять ремень типа А с числом ремней 5.
.4 Выбор и расчет шпоночных соединений
Диаметр приводного вала d, мм
в месте посадки определяем по формуле:
, мм;
(58)
где
T4 -
крутящий момент на приводном валу, Н∙мм
[τк] -
допускаемое напряжение при кручении, МПа
[τк] = 25
МПа. [4]
Рисунок
7 - Размеры шпонки
Таблица
5 - Стандартные длины шпонки
Таблица
6 - Габаритные размеры шпонок
мм.
Принимаем
диаметр вала 74 мм;
диаметр
вала под подшипник 75 мм (ГОСТ 6636-69). [4]
Сечение
шпонки b
h: 20×12;
Глубина
паза: вала t1=7,5 мм,
втулки t2=4,9 мм.
[4]
Расчёт
шпоночного соединение на смятие lp, мм
, (59)
где
T4 -
передаваемый вращающий момент, Н∙мм; d - диаметр вала
в месте установки шпонки; lp - рабочая длина шпонки; при стальной ступице и
спокойной нагрузке допускаемое напряжение смятия [; z - количество
шпонок, шт; [4]
мм.
Условие
прочности на срезМПа
МПа.
Полная
длина шпонки l, мм:
l=lp+b, мм ; (61)
l=98,7+20=118,7
мм
Принимаем
к установке шпонку длиной 125 мм. [4]
Принимаем
по стандарту шпонку с размерами: 20×12×125. [4]
3. Рекомендации по выбору масла и смазки всех узлов привода
Зацепление цилиндрических редукторов обычно смазываются жидким маслом.
Способы смазки: картерный, централизованный или струйный. Для нашего вида
редуктора рекомендуется картерный способ. Способ смазывания выбирается в
зависимости от окружной скорости. При окружных скоростях не превышающих 12 м/с,
применяется картерное смазывание погружением в масляную ванну редуктора, если
требуется охлаждение путем централизованного подвода охлажденного масла.
Температура масла в ванне редуктора допускается до 65°С и только в редких
случаях 85°С. Зубчатое колесо должно быть погружено в масляную ванну не более
чем на 2/3 высоты зуба. Картерный проточный способ смазывания состоит в том,
что в ванну редуктора с одной стороны подается масло, а с другой отводится и
одновременно происходит охлаждение его. Для очистки масла от грязи и других
примесей применяют сетчато-пластинчатые фильтры. Охлаждение масла
осуществляется в трубчатых холодильниках, по трубкам которого проходит
охлажденная вода.
Для сохранения физико-химических свойств масла при длительной
эксплуатации, а так же для лучшего его отстоя, в смазочную систему добавляют
баки-отстойники емкостью от 8 до 20-кратной минутной производительности насоса.
Масло подается сверху не зависимо от направления вращения зубчатых колес.
Давление в смазочной системе поддерживается примерно 1…1,5 атм., на выходе из
сопла - 0,5…0,8 атм.
Подшипники смазываются маслом, разбрызгиванием колес. Подшипники
конической шестерни смазываются, разбрызгиваемым конической передачей.
Циркуляционная смазка применяется при больших скоростях передачи
(
м/с), а также в редукторах небольшой мощности и
скорости, если конструкция не позволяет осуществить картерную смазку. Масло из
картера или специального бака подается насосом в места смазки по трубопроводу
через сопла или при широких звездочках через коллекторы.
Для
очистки и охлаждения масла устанавливают фильтры, охладители и другие
устройства.
В
среднескоростных цепных передачах, не имеющих герметичных картеров, можно
применять пластичное внутришарнирное или капельное смазывание. Пластичное
внутришарнирное смазывание осуществляется периодически, через 120-180 часов,
погружением цепи в масло, нагретое до температуры, обеспечивающей его
разжижение. Пластичный смазочный материал применяют при скорости цепи до 4 м/с,
а капельное смазывание - до 6 м/с. Для смазывания цепной передачи мы
использовали периодическую смазку.
Подшипники
приводного вала целесообразно смазывать индивидуально густой (пластичной)
смазкой. Также для смазывания подшипников нашего приводного вала используем
пластичную смазку. В этом случае подшипник закрывают с внутренней стороны
защитным или маслосбрасывающим кольцом. Свободное пространство внутри
подшипникового узла заполняют густой смазкой. Через каждые три месяца
производят добавку свежей смазки, а через год - разборку, промывку узла и
сборку со свежей смазкой.
Для
подачи в подшипники густой смазки применяют пресс-масленки по ГОСТ 19853-74.
Смазка подается под давлением специальным шприцем. Для густой смазки используют
также колпачковые масленки.
Для
индивидуального подвода жидкой смазки к подшипникам имеются масленки различных
конструкций. Самой распространенной из них является пресс-масленка по ГОСТ
19853-74. Широкое применение находит также наливная масленка.
Диаметр
отверстия для подвода смазки в корпусе, крышке, стакане обычно принимают равным
диаметру резьбы для масленки и выполняют его сверлом под резьбу.
В
крышках подшипников для подвода смазки выполняют канавки, а на торце делают
один-два паза. В стаканах также выполняют канавки и сверлят одно-два поперечных
отверстия. [5]
4. Краткое описание порядка сборки, работы и обслуживания основных
элементов привода
Привод шнекового питателя включает в себя электродвигатель, являющийся
источником механической энергии. С вала электродвигателя с частотой вращения
равной 950 об/мин передается вращающий момент через ременную передачу (u=5) на цилиндрический редуктор.
Выходной вал редуктора передает вращающий момент через цепную передачу
(Т=528,07Н∙м), приводящая в движение рабочий орган машины.
Порядок сборки привода описывается по сборочным чертежам.
На раму 2 устанавливают электродвигатель 32 и цилиндрический редуктор 17.
На вал электродвигателя одевается ведущий шкив 6 ременной передачи. На входной
вал редуктора одевается ведомый шкив 7. Электродвигатель и редуктор
устанавливаются на раму, производят натяжение ременной передачи 18 натяжной
плитой 5. Электродвигатель и редуктор устанавливают на пазы рамы и наживляют
болтами 12, 13 с надетыми на них гайками 15 и 16. На ведомый вал редуктора
одевается ведущая звёздочка 8 цепной передачи 19. На приводной вал одевается
ведомая звёздочка 9 , которая фиксируется концевой шайбой. После установки
звёздочек происходит установка цепей и их натяжение при помощи натяжного
устройства 4.
После установки всех элементов привода осуществляется монтаж кожа и
натяжных устройств; выполняется контроль уровня масла в редукторе.
При пуске в работу привода необходимо его вначале обкатать без нагрузки в
течение не менее 1 часа. Обслуживание привода заключается в том, что необходимо
следить за количеством масла в редукторе ведь от этого зависит долговечность
его работа.
Порядок работы привода шнекового питателя заключается в следующем: от
электродвигателя типа 4А112MA6УЗ
по ГОСТ 12139-84 мощностью 3 кВт и частотой вращения 950 об/мин через ременную
передачу передается крутящий момент на быстроходный вал цилиндрического
редуктора марки ЦУ-200-5-12У2 по ГОСТ 21426-75 с передаточным числом 5. Частота
вращения быстроходного вала - 111,29 об/мин. На тихоходный вал редуктора
насаживаем ведущую звездочку цепной передачи. Непосредственно через цепную
передачу крутящий момент передается на приводной вал. Частота вращения
приводного вала - 1991,67об/мин.
5. Требования техники безопасности к проектируемому объекту
Важную роль в обеспечении безопасной эксплуатации оборудования
принадлежит его безопасной конструкции, оснащенной необходимой
контрольно-измерительной аппаратурой, приборами безопасности, блокировочными
устройствами, автоматическими средствами сигнализации и защиты, позволяющими
контролировать соблюдение нормальных режимов технологического процесса, а также
исключающими возможность возникновения аварий и несчастных случаев.
В процессе работы категорически запрещается техническое обслуживание
привода (устранение неполадок, доливка или смена масла в редукторе, смазка
цепной передачи и т.д.).
Конструкция привода шнекового питателя должна обеспечивать безопасную
эксплуатацию. Элементы механической и электрической части машины выполняются в
требуемом климатическом исполнении. В обязательном порядке устанавливается
защитное заземление. Электродвигатель, пускорегулирующую аппаратуру и приводную
и натяжную станции защищают от попадания капельной влаги посредством установки
кожухов. Для того чтобы не нарушать тепловой режим электродвигателя, в месте его
установки кожух перфорируют.
Механические передачи приводной станции снабжаются защитными кожухами.
Привод шнекового питателя устанавливается на прочное, тщательно
выровненное основание. В обязательном порядке приводная станция и опорные
конструкции закрепляют анкерными болтами во избежание смещения от заданного
проектного положения в процессе эксплуатации.
Расположение и установка оборудования в технологическом цехе
осуществляется с соблюдением следующих условий: последовательность расстановки
оборудования по технологической схеме, обеспечение удобства и безопасности
обслуживания и ремонта, максимального естественного освещения и поступления
свежего воздуха. [6]
Заключение
В ходе выполнения курсового проекта на тему «Расчет привода шнекового
питателя» я ознакомился с принципом ее действия и назначением. В расчетной
части по заданным параметрам был рассчитан привод машины, т. е. подобран
электродвигатель, цилиндрический редуктор. Также были рассчитаны клиноременная
передача и цепная передача.
Список используемой источников
1 Классификация хлебопекарных
предприятий и оборудования / Машины с шнековыми питателями - 09.08.11. - Режим
доступа: http://www.backerei.ru
<http://www.backerei.ru>
2 Методические указания к
выполнению курсового проекта по дисциплине «Прикладная механика» для студентов
технологических специальностей: - Могилев, 2002.
3 Анурьев, В.И. Справочник конструктора - машиностроителя /
В.И. Анурьев. - в 3-х томах. - М.: Машиностроение, 1975. - Т. 3. - 526с.
Методические указания к курсовому проекту по курсу «Детали
машин и основы конструирования» для студентов специальностей Т.05.04. и
Т.05.07., «Кинематический расчет привода» / В.Г. Харкевич, В.А. Кеворкянц. -
Могилев, 1999.
Дунаев П.Ф. Конструирование узлов и деталей машин: Учеб.
Пособие для вузов. - 3-е изд. перераб. и доп. - М.: Высш. Школа, 1978. - 352с.
Никитин, В.С. Охрана труда на предприятиях пищевой
промышленности / В.С. Никитин, Ю.М. Бурашников. - М.: Агропромиздат, 1991. -
350с.: ил.