Проектирование колеса тихоходной ступени механической передачи привода
Содержание
Введение
. Понятие об
универсальных электроприводах
.1
Классификация универсальных приводов
.2
Характеристика привода П-1,1
.3 Правила
эксплуатации и техники безопасности
.
Проектирование зубчатого колеса
.1 Зубчатые
передачи
.1.1 Общие
сведения о зубчатых передачах
.1.2
Классификация зубчатых передач
.1.3 Критерии
расчёта эвольвентных зубьев
.1.4 Силы в
зубчатом зацеплении
2.1.5 Расчёт
зубьев на контактную выносливость
2.1.6 Расчёт
зубьев на изгиб
2.2
Валы и оси
2.2.1
Назначение, виды и разновидности
.2.2 Расчёт
вала на объёмную прочность
.3 Опоры
валов и осей - подшипники
.3.1
Подшипники скольжения
.3.2
Подшипники качения
.3.3 Расчёт
номинальной долговечности подшипника
.3.4 Методика
выбора подшипников качения19
.
Кинематический расчет привода
. Расчет
косозубой цилиндрической передачи
.1 Выбор
материалов и допускаемых напряжений
4.2
Геометрический расчет косозубой передачи
4.3
Проверочный расчет
.4 Силы,
действующие в зубчатом зацеплении
5.
Технико-экономические показатели
Заключение
Список
использованной литературы
Введение
В машиностроении широко используются различные конструкции приводов.
Привод - устройство для привидения в действие от двигателя разных
технологических машин. Редуктор - механизм, для уменьшения частоты вращения и
увеличения вращающего момента. Редуктор является законченным механизмом,
соединенным с двигателем и рабочей машиной муфтами ли другими разъемными
устройствами. Соединение вала машины с валом электродвигателя возможно лишь в
относительно редких случаях, когда частоты вращения этих валов одинаковы.
Кинематическая схема привода может включать, помимо редуктора, открытые
зубчатые передачи, цепные или ременные передачи.
Требуемая мощность электродвигателя определяйся с поправкой на КПД узлов
привода. Так как для рассчитываемого привода подходят двигатели с различными
частотами вращения, то следует рассмотреть несколько вариантов и остановиться
на оптимальном, соответствующем конкретным условиям работы.
В ходе выполнения работы применяются как аналитические, так и графические
методы решения инженерных задач на разных этапах подготовки конструкторской
документации.
1. Понятие об универсальных электроприводах
Электроприводом называется машинное устройство, используемое для
приведения в движение машины. Он состоит из электрического двигателя,
передаточного механизма и пульта управления.
На предприятиях общественного питания наряду с машинами, предназначенными
для выполнения одной какой-либо операции, широко применяются универсальные
приводы с набором сменных механизмов, выполняющих целый ряд операций по
обработке продуктов.
Универсальные приводы используют преимущественно в небольших предприятиях
общественного питания, в мясных, овощных и кондитерских цехах.
Универсальным приводом называется устройство, состоящее из электродвигателя
с редуктором и имеющее приспособление для переменного подсоединения различных
сменных механизмов. Он состоит из электродвигателя с редуктором, на котором
могут закрепляться и попеременно работать различные по назначению съемные
механизмы: мясорубка, взбивалка, овощерезка, мясорыхлитель и другие машины.
Отсюда привод получил свое название - "универсальный".
Применение универсальных приводов значительно увеличивает
производительность труда, снижает капитальные затраты, увеличивает коэффициент
полезного действия оборудования, уменьшает роль человека в обработке продукта,
что отвечает современным тенденциям и требованиям развития в сфере
общественного питания.
.1 Классификация универсальных приводов
К универсальным привалам общего назначения относятся и универсальные
малогабаритные приводы УММ-ПР с электродвигателем переменного тока, УММ-ПС с
электродвигателем постоянного тока, которые используют на транспорте (судах и
вагонах-ресторанах).
Все универсальные приводы имеют буквенные обозначения. Первая буква П
обозначает привод, вторая - название цеха: М - мясной, X - холодный, Г -
горячий, У - универсальный, для холодного цеха ПХ-0,6, для горячего цеха ПГ-0,6
и для мясного цеха ПМ-1,1. На приводы общего назначения: ПУ-0,6 и П-11
устанавливаются сменные механизмы, которые имеют буквенные обозначения: первая
буква М - механизм сменный, вторая М - мясорубка, В - механизм взбивальный, О -
механизм овощерезательный.
На больших предприятиях общественного питания, где имеется цеховое
деление, используют специализированные универсальные приводы:
Привод ПМ-1.1 специализированный для мясо-рыбного цеха выпускается в
односкоростном или двухскоростном варианте, с частотой вращения вала 170 или
1400 об/мин и мощностью двигателя 1,1 кВт. Он имеет комплект сменных исполнительных
механизмов, которые могут быть использованы только в мясо-рыбных цехах
предприятий.
Привод ПХ-0,6 специализированный для холодных цехов. Состоит из
односкоростного привода П-0,6 и комплекта сменных исполнительных механизмов,
которые могут быть использованы в холодных цехах.
Привод ПГ-0,6 специализированный для горячих цехов, состоит из
полноскоростного привода П-0,6 и комплекта сменных исполнительных механизмов,
которые могут быть использованы в горячих цехах.
Привод П-П универсальный состоит из двухступенчатого зубчатого редуктора,
двухскоростного двигателя. Частота вращения приводного вала привода составляет
ПО и 330 об/мин. На горловине привода расположена рукоятка с кулачком для
крепления сменных исполнительных механизмов. Переключатель скоростей
электродвигателя, пусковая кнопка и кнопка возврата гешевого реле смонтированы
на пульте управления.
1.2 Характеристика привода П-1,1
Привод универсальный П-1,1 предназначен для механизации основных
процессов переработки пищевых продуктов на предприятиях общественного питания.
Этот привод выпускается двухскоростными, с частотой вращения приводного вала
170 и 1400 об/мин и односкоростными, с частотой вращения 170 об/мин и мощностью
двигателя 1,1 кВт.
Односкоростной привод представляет собой редуктор с прифланцованным к
нему электродвигателем. Электродвигатель и редуктор закрыты кожухом. Картер
отлит с корпусом редуктора как одно целое. Крепление сменных механизмов в
горловине редуктора осуществляется двумя винтами, что существенно увеличивает
затраты времени при фиксации и снятии сменных механизмов и является не вполне
практичным и удобным способом крепежа насадок к приводу.
Двухскоростной привод имеет односкоростной двигатель и два независимых
выходных вала, вращающихся с различной частотой. Первый выходной вал -
внутренний (монолитный) - соединен с валом электродвигателя. Внутренний вал
вращается с частотой 1400 об/мин. Через внутренний вал вращение передается
только косторезке или рыбочистке, что существенно ограничивает производительные
возможности данного привода. Второй выходной вал - наружный (пустотелый) -
вращается с частотой 170 об/мин. К пустотелому валу присоединяют мясорубку,
фаршемешалку, размолочный механизм и мясорыхлитель. Устройство остальных
деталей и узлов аналогично устройству их в односкоростных приводах.
Рис. 1.1 - Универсальный привод общего назначения П-1,1 (1 - редуктора, 2
- картер, 3 - электродвигатель, 4 -кожух, 5 - зубчатое колесо, 6 - приводной
вал, 7 - переключатель скоростей)
.3 Правила эксплуатации и техники безопасности
Подготовку к работе универсального привода проводит повар, закрепленный
за данной машиной, который перед началом работы обязан выполнить требования
техники безопасности и соблюдать при работе с машиной безопасность труда.
Вот поэтому перед началом работы проверяется правильность установки
универсального привода, исправность сменного механизма и правильность его
сборки и крепления с помощью винтов-зажимов. При установке корпуса сменного
механизма в горловине привода контролируют, чтобы конец рабочего вала механизма
попал в гнездо привода вала редуктора универсального привода. Проверяется
наличие ограждающих устройств, заземления или зануления.
Убедившись в исправности сменного механизма и привода, производят пробный
пуск па холостом ходу. Привод должен работать с небольшим шумом. В случае
неисправности привод останавливают и устраняют причину неисправности.
Регулировать скорость вращения в процессе работы разрешается только при наличие
вариатора в конструкции машин.
Приготовленные продукты загружать в сменные механизмы нужно только после
включения универсального привода, исключение составляет только взбивальный
механизм, у которого сначала загружают в бачок продукты, а затем включают
универсальный привод.
При работе запрещается перегружать сменный механизм продуктами, так как
это приводит к ухудшению качества или порче продуктов, а так же к поломке
машины. Особое внимание нужно уделить строгому соблюдению правил безопасности
при работе с универсальным приводом, т.к. неосторожность приводит к травмам
обслуживающего персонала.
Категорически запрещается работать на машине без наличия соответствующих
предохранительных устройств, а также подталкивать продукты в горловину сменного
механизма руками.
Осмотр универсального привода и установленного сменного механизма, а так
же устранение неполадок разрешается проводить только после выключения
электродвигателя универсального привода и его полной остановки.
После окончания работы универсальный привод выключают и отключают от
электросети. Только потом можно снимать сменный механизм для разборки, промывки
и сушки.
Профилактический и текущий ремонт универсального привода и сменных
механизмов проводят специальные работники согласно заключенного договора.
2. Проектирование зубчатого колеса
.1 Зубчатые передачи
.1.1 Общие сведения о зубчатых передачах
Наиболее распространенные передачи в современном машиностроении -
зубчатые передачи. Основные их достоинства - высокий к.п.д., компактность,
надежность работы, простота эксплуатации, постоянство передаточного отношения,
большой диапазон передаваемых мощностей (от тысячных долей до десятков тысяч
киловатт). К основным недостаткам зубчатых передач относятся сравнительная
сложность их изготовления (необходимость в специальном оборудовании и инструментах)
и шум при неточном изготовлении и высоких окружных скоростях. При больших
расстояниях между осями ведущего и ведомого валов зубчатые передачи получаются
громоздкими и применение их в этих случаях нерационально.
2.1.2 Классификация зубчатых передач
Рис. 2.1 - Виды зубчатых передач
Наиболее распространены передачи с внешним зацеплением.
Достоинства.
. Возможность передачи практически любых мощностей (до 50 000 кВт и
более) при весьма широком диапазоне окружных скоростей (от долей м/с до 30...
150 м/с). При высоких скоростях применяют передачи с косыми зубьями (рис. 2.1,
б, e) изготовленные с высокой точностью и
тщательно смонтированные.
. Постоянство передаточного отношения. В исключительных случаях применяют
зубчатые передачи с переменным передаточным отношением, получающимся при
некруглых зубчатых колесах.
. Компактность, надежность и высокая усталостная долговечность передачи.
. Высокий КПД (0,97.. .0,99) при высокой точности изготовления и монтажа,
низкой шероховатости рабочей поверхности зубьев, жидкой смазке и передаче
полной мощности. При невыполнении указанных условий КПД может понизиться на
20... 40%.
. Простота обслуживания и ухода.
. Сравнительно небольшие силы давления на валы и их опоры.
. Может быть изготовлена из самых разнообразных материалов, металлических
и неметаллических.
Недостатки.
. Ограниченность передаточного отношения.
. Является источником вибрации и шума, особенно при низком качестве
изготовления и монтажа и значительных скоростях.
. При больших перегрузках возможна поломка деталей (пробуксовки
исключены).
. Относительная сложность изготовления высокоточных зубчатых колес.
Зубчатые передачи классифицируются:
а) по конструктивному оформлению:
открытые, не имеющие защитного кожуха и масляной ванны;
полуоткрытые, имеющие защитный кожух;
закрытые, имеющие картер и крышку, хорошо изолирующие передачу от внешней
среды; картер служит масляной ванной передач (редукторы, коробки переменных
передач и др.);
б) по окружной скорости:
тихоходные (итах = 3.. .4 м/с);
среднескоростные (4 м/с < 15 м/с);
высокоскоростные (v >
15 м/с);
в) по взаимному расположению осей валов:
при валах с параллельными осями - цилиндрические (прямозубые - рис 2.1,
а, косозубые - рис. 2.1, б, шевронные - рис. 2.1, в);
при валах с пересекающимися осями - конические (прямозубые и косозубые -
рис. 2.1, д,е или с криволинейными зубьями - рис. 2.1, ж);
при валах со скрещивающимися осями - винтовые (рис. 2.1, з), гипоидные
(рис. 2.1, и).
Прямозубыми называются колеса (передачи), направление каждого зуба
которых совпадает с образующей начальной поверхности (цилиндра или конуса).
Косозубыми называются зубчатые колеса, направление каждого зуба которых
составляет некоторый постоянный угол с образующей начальной поверхности.
Шевронными называются колеса, зубчатый венец которых образуется из двух рядов
косых зубьев противоположного направления. Конические колеса могут быть
прямозубыми, косозубыми и с круговым зубом.
Косозубые передачи обладают рядом достоинств по сравнению с прямозубыми:
благодаря наличию угла наклона β зубья вступают в зацепление по своей
длине b постепенно, что обеспечивает более
равномерную и плавную работу, и, естественно, снижение шума механизма
вследствие большего коэффициента перекрытия. У косозубых колес минимальное
число зубьев zk
min, при котором
не происходит подрезания, меньше, чем у прямозубых (zk min = zmincos3β). Косозубые передачи позволяют
подобрать при заданном межосевом расстоянии за счет изменения угла наклона β пару колес со стандартным модулем.
К недостаткам косозубых передач следует отнести более сложное
изготовление колес по сравнению с прямозубыми и появление дополнительного
осевого усилия, передаваемого на опоры. Для устранения осевого усилия можно
применять шевронные зубчатые колеса. Венец шевронного колеса состоит из
участков с правым и левым направлением зубьев. Зубья такого колеса могут быть
нарезаны на одном ободе или венец состоит из жесткого соединения двух косозубых
колес с разным направлением наклона зубьев. Шевронные колеса сложнее в
изготовлении косозубых.
2.1.3 Критерии расчёта эвольвентных зубьев
Поскольку колёса в зацеплении взаимодействуют своими зубьями, то весьма
часто в эксплуатации наблюдаются различные повреждения их рабочих поверхностей.
Усталостное выкрашивание является наиболее серьёзным и распространённым
дефектом поверхности зубьев даже для закрытых хорошо смазываемых и защищённых
от загрязнения передач.
На рабочих поверхностях появляются небольшие углубления, которые затем
превращаются в раковины.
Выкрашивание носит усталостный характер и вызвано контактными
напряжениями, которые изменяются по отнулевому пульсирующему циклу.
Выкрашивание приводит к повышению контактного давления и нарушению работы
передачи. В открытых передачах поверхностные слои истираются раньше, чем в них
появляются усталостные трещины, поэтому выкрашивание появляется весьма редко.
Для предупреждения выкрашивания необходимо повышать твёрдость материала
термообработкой либо повышать степень точности передачи, а также правильно
назначать размеры из расчёта на усталость по контактным напряжениям.
Абразивный износ является основной причиной выхода из строя передач при
плохой смазке. Это, в первую очередь, открытые передачи, а также закрытые, но
находящиеся в засорённой среде: в горных, дорожных, строительных, транспортных
машинах. У изношенных передач повышаются зазоры в зацеплении и, как следствие,
усиливаются шум, вибрация, динамические перегрузки; искажается форма зуба;
уменьшаются размеры поперечного сечения, а значит и прочность зуба.
Основные меры предупреждения износа - повышение твёрдости поверхности
зубьев, защита от загрязнения, применение специальных масел. В расчёте на
контактную выносливость абразивный износ учитывается занижением допускаемых
контактных напряжений.
Заедание происходит в высоконагруженных и высокоскоростных передачах. В месте
контакта зубьев возникает повышенная температура, приводящая к молекулярному
сцеплению металла с последующим отрывом. Вырванные частицы затем царапают
трущиеся поверхности.
Обычно заедания происходят вследствие выдавливания масляной плёнки между
зубьев при совместном действии высоких давлений и скоростей.
Меры предупреждения здесь те же, что и при абразивном износе.
Рекомендуется также фланкирование зубьев, правильный выбор сорта масла и его
охлаждение.
Другой, реже встречающийся, но не менее опасный вид поломок - излом
зуба. Такая поломка связана с напряжениями изгиба, также имеющими отнулевой
пульсирующий характер. Излом зуба может привести к весьма тяжким последствиям
вплоть до разрушения валов и подшипников, а иногда и всего механизма. Для
предупреждения излома проводится расчёт зуба по напряжениям изгиба. Такой
расчёт для закрытых передач выполняется в качестве проверочного после расчёта
на контактные напряжения. Для открытых передач, где высока вероятность
случайных перегрузок, этот расчёт выполняется как проектировочный.
Усталостное выкрашивание, абразивный износ и заедание обусловлены
поверхностной прочностью, а излом - объёмной прочностью зубьев.
Поскольку поверхностные повреждения - главный вид поломок для закрытых
передач, то расчёт на контактную выносливость выполняют в качестве
проектировочного; расчёт на изгиб - в качестве проверочного. Для открытых
передач всё наоборот, т.к. режим работы временный или даже разовый, а
перегрузки значительные.
.1.4 Силы в зубчатом зацеплении
Фактически, движение передаётся зубчатым зацеплением посредством силы
нормального давления в точке контакта зубьев Fn , которая определяется, как интеграл
от контактных напряжений sк по всей
площади S контакта зубьев Fn = ∫s(sк)
dS.
Однако этот интеграл вычислить практически невозможно, т.к. неизвестен
точный вид функции sк.
Используют другой приём: ещё неизвестную силу нормального давления Fn сначала раскладывают на три ортогональных
проекции:
осевую силу Fa ,
направленную параллельно оси колеса;
радиальную силу Fr , направленную по радиусу к центру колеса;
окружную силу Ft , направленную касательно к делительной окружности.
Легче всего вычислить силу Ft , зная передаваемый вращающий момент Мвр и делительный
диаметр dw
Ft = 2MВр
/ dw.
Радиальная сила вычисляется, зная угол зацепления aw
Fr = Ft tgaw.
Осевая сила вычисляется через окружную силу и угол наклона зубьев b
Fa = Ft tgb.
Наконец, если необходимо, зная все проекции, можно вычислить и модуль
нормальной силы
Fn = (Fa2 + Fr2
+ Ft2)½
= Ft
/(cosαw
cosβ).
Нормальная сила распределена по длине контактной линии, поэтому, зная
длину lS контактной линии, можно вычислить
удельную погонную нормальную нагрузку
qn = Fn / lΣ ≈ Ft /(b εαkε cosαw cosβ),
где ea -
коэффициент перекрытия, ke - отношение минимальной длины контактной линии к средней.
Для двух цилиндрических колёс в зацеплении одноимённые силы равны, но
противоположны. Окружная сила для шестерни противоположна направлению вращения,
окружная сила для колеса направлена в сторону вращения.
Аналитическими методами теории прочности можно получить точное решение
для вычисления напряжений в контакте двух эвольвентных профилей.
Однако это слишком усложнит задачу, поэтому на малой площадке контакта
геометрия эвольвентных профилей корректно подменяется контактом двух цилиндров.
Для этого случая используют формулу Герца-Беляева:
Здесь Епр - приведённый модуль упругости материалов шестерни и
колеса
Епр = 2 Е1 Е2 / ( Е1 + Е2),
rпр -
приведённый радиус кривизны зубьев
/rпр = 1/r1 ± 1/r2, r1,2 = 0,5dW 1,2 sin aW ,
n - коэффициент Пуассона, qn - удельная погонная нормальная нагрузка, [s]HE - допускаемые контактные напряжения с учётом
фактических условий работы.
Расчёт зубьев на контактную выносливость для закрытых передач (длительно
работают на постоянных режимах без перегрузок) выполняют как проектировочный. В
расчёте задаются передаточным отношением, которое зависит от делительных
диаметров и определяют межосевое расстояние Аw (или модуль m), а через него и все геометрические параметры зубьев. Для открытых
передач контактные дефекты не характерны и этот расчёт выполняют, как
проверочный, вычисляя контактные напряжения и сравнивая их с допускаемыми.
зубчатый редуктор подшипник эвольвентный
2.1.6 Расчёт зубьев на изгиб
Зуб представляют как консольную балку переменного сечения, нагруженную
окружной и радиальной силами (изгибом от осевой силы пренебрегают).
При этом окружная сила стремится изогнуть зуб, вызывая максимальные
напряжения изгиба в опасном корневом сечении, а радиальная сила сжимает зуб,
немного облегчая его напряжённое состояние.
sA =
sизг А - sсжатия А.
Напряжения сжатия вычитаются из напряжений изгиба. Учитывая, что
напряжения изгиба в консольной балке равны частному от деления изгибающего
момента Mизг на момент сопротивления корневого
сечения зуба W, а напряжения сжатия это сила Fr, делённая на площадь корневого
сечения зуба, получаем:
.
Здесь b - ширина зуба, m - модуль зацепления, YH - коэффициент прочности зуба.
Иногда используют понятие коэффициента формы зуба YFH = 1 / YH.
Таким образом, получаем в окончательном виде условие прочности зуба на
изгиб:
sA
= qn YH / m ≤ [s]FE .
Полученное уравнение решают, задавшись свойствами выбранного материала.
Допускаемые напряжения на изгиб (индекс F) и контактные (индекс H) зависят от свойств материала, направления приложенной
нагрузки и числа циклов наработки передачи
[s]FE = [s]F KF KFC /
SF; [s]HE = [s]H KH / SH.
Здесь [s]F и [s ]H
- соответственно пределы изгибной и контактной выносливости; SF и SH - коэффициенты безопасности,
зависящие от термообработки материалов; KFC учитывает влияние двухстороннего
приложения нагрузки для реверсивных передач; KF и KH - коэффициенты долговечности,
зависящие от соотношения фактического и базового числа циклов наработки.
Фактическое число циклов наработки находится произведением частоты вращения
колеса и срока его службы в минутах. Базовые числа циклов напряжений зависят от
материала и термообработки зубьев.
2.2 Валы и оси
2.2.1 Назначение, виды и разновидности
Колёса передач установлены на специальных продолговатых деталях круглого
сечения. Среди таких деталей различают оси и валы.
Ось - деталь, служащая для удержания колёс и центрирования их вращения.
Вал - ось, передающая вращающий момент.
Не следует путать понятия "ось колеса", это деталь и "ось
вращения", это геометрическая линия центров вращения.
Формы валов и осей весьма многообразны от простейших цилиндров до сложных
коленчатых конструкций. Форма вала определяется распределением изгибающих и
крутящих моментов по его длине. Правильно спроектированный вал представляет
собой балку равного сопротивления.
Рис. 2.4 - Основные типы валов и осей
Валы и оси вращаются, а следовательно, испытывают знакопеременные
нагрузки, напряжения и деформации. Поэтому поломки валов и осей имеют усталостный
характер.
Причины поломок валов и осей прослеживаются на всех этапах их
"жизни".
. На стадии проектирования - неверный выбор формы, неверная оценка
концентраторов напряжений.
. На стадии изготовления - надрезы, забоины, вмятины от небрежного
обращения.
. На стадии эксплуатации - неверная регулировка подшипниковых узлов.
Для работоспособности вала или оси необходимо обеспечить:
объёмную прочность (способность сопротивляться Mизг и Мкрут);
поверхностную прочность (особенно в местах соединения с другими
деталями);
жёсткость на изгиб;
крутильную жёсткость (особенно для длинных валов).
Все валы в обязательном порядке рассчитывают на объёмную прочность.
Схемы нагружения валов и осей зависят от количества и места установки на
них вращающихся деталей и направления действия сил. При сложном нагружении
выбирают две ортогональные плоскости (например, фронтальную и горизонтальную) и
рассматривают схему в каждой плоскости. Рассчитываются, конечно, не реальные
конструкции, а упрощённые расчётные модели, представляющие собой балки на
шарнирных опорах, балки с заделкой и даже статически неопределимые задачи.
При составлении расчётной схемы валы рассматривают как прямые брусья,
лежащие на шарнирных опорах. При выборе типа опоры полагают, что деформации
валов малы и, если подшипник допускает хотя бы небольшой наклон или перемещение
цапфы, его считают шарнирно-неподвижной или шарнирно-подвижной опорой.
Подшипники скольжения или качения, воспринимающие одновременно радиальные и осевые
усилия, рассматривают как шарнирно-неподвижные опоры, а подшипники,
воспринимающие только радиальные усилия, - как шарнирно-подвижные.
Такие задачи хорошо известны студентам из курсов теоретической механики
(статики) и сопротивления материалов.
2.2.2 Расчёт вала на объёмную прочность
Данный расчет состоит из 3-х этапов:
1. Предварительный расчёт валов
Выполняется на стадии проработки Технического Задания, когда известны
только вращающие моменты на всех валах машины. При этом считается, что вал испытывает
только касательные напряжения кручения
tкр = Мвр
/ Wp £ [t]кр,
где Wp - полярный момент сопротивления
сечения.
Для круглого сечения: Wp = pd3/16, [t]кр = 15 ¸ 20 Н/мм2.
Условие прочности по напряжениям кручения удобно решать относительно
диаметра вала
.
Это
- минимальный диаметр вала. На всех других участках вала он может быть только
больше. Вычисленный минимальный диаметр вала округляется до ближайшего большего
из нормального ряда. Этот диаметр является исходным для дальнейшего
проектирования.
2. Уточнённый расчёт валов
На данном этапе учитывает не только вращающий, но и изгибающие моменты.
Выполняется на этапе эскизной компоновки, когда предварительно выбраны
подшипники, известна длина всех участков вала, известно положение всех колёс на
валу, рассчитаны силы, действующие на вал.
Чертятся расчётные схемы вала в двух плоскостях. По известным силам в
зубчатых передачах и расстояниям до опор строятся эпюры изгибающих моментов в
горизонтальной и фронтальной плоскостях. Затем вычисляется суммарный изгибающий
момент
Далее
рассчитывается и строится эпюра эквивалентного "изгибающе-вращающего"
момента
где
α
= 0,75 или 1 в зависимости от принятой
энергетической теории прочности [5], принимаемый большинством авторов равным 1.
Вычисляется эквивалентное напряжение от совместного действия изгиба и
кручения
sэкв = Мэкв
/ Wp.
Уравнение также решается относительно минимального диаметра вала

Полученный
в уточнённом расчёте минимальный диаметр вала принимается окончательно для
дальнейшего проектирования.
3. Расчёт вала на выносливость
Выполняется как проверочный на стадии рабочего проектирования, когда
практически готов рабочий чертёж вала, т.е. известна его точная форма, размеры
и все концентраторы напряжений: шпоночные пазы, кольцевые канавки, сквозные и
глухие отверстия, посадки с натягом, галтели (плавные, скруглённые переходы
диаметров).
При расчёте полагается, что напряжения изгиба изменяются по симметричному
циклу, а касательные напряжения кручения - по отнулевому пульсирующему циклу.
Проверочный расчёт вала на выносливость по существу сводится к
определению фактического коэффициента запаса прочности n, который сравнивается с допускаемым
Здесь ns и nt - коэффициенты запаса по нормальным и
касательным напряжениям
где
s-1 и τ-1 -
пределы выносливости материала вала при изгибе и кручении с симметричным
циклом; kσ и
kτ - эффективные коэффициенты концентрации напряжений
при изгибе и кручении, учитывающие галтели, шпоночные канавки, прессовые
посадки и резьбу; εα и ετ - масштабные коэффициенты диаметра вала; sa и τa -
амплитудные значения напряжений; sm и τm - средние напряжения цикла (sm= 0, τm= τa); ψσ и ψτ -
коэффициенты влияния среднего напряжения цикла на усталостную прочность зависят
от типа стали. Вычисление коэффициентов запаса прочности по напряжениям
подробно излагалось в курсе "Сопротивление материалов", в разделе
"Циклическое напряжённое состояние".
Если
коэффициент запаса оказывается меньше требуемого, то сопротивление усталости
можно существенно повысить, применив поверхностное упрочнение: азотирование,
поверхностную закалку токами высокой частоты, дробеструйный наклёп, обкатку
роликами и т.д. При этом можно получить увеличение предела выносливости до 50%
и более.
2.3 Опоры валов и осей - подшипники
Валы и оси поддерживаются специальными деталями, которые являются
опорами. Назначение подшипника состоит в том, что он должен обеспечить надёжное
и точное соединение вращающейся (вал, ось) детали и неподвижного корпуса.
Следовательно, главная особенность работы подшипника - трение сопряжённых
деталей.
По характеру трения подшипники разделяют на две большие группы:
подшипники скольжения (трение скольжения);
подшипники качения (трение качения).
2.3.1.Подшипники скольжения
Подшипник скольжения представляет собой корпус, имеющий цилиндрическое
отверстие, в которое вставляется вкладыш или втулка из антифрикционного
материала (часто используются цветные металлы), и смазывающее устройство.
Между валом и отверстием втулки подшипника имеется зазор, который
позволяет свободно вращаться валу. Для успешной работы подшипника зазор
предварительно рассчитывается.
Рис. 2.5- Подшипник скольжения
Основным элементом таких подшипников является вкладыш из антифрикционного
материала или, по крайней мере, c
антифрикционным покрытием. Вкладыш устанавливают (вкладывают) между валом и
корпусом подшипника.
Трение скольжения безусловно больше трения качения, тем не менее, достоинства
подшипников скольжения заключаются в многообразных областях использования:
- в разъёмных конструкциях;
при больших скоростях вращения (газодинамические подшипники в
турбореактивных двигателях при n > 10 000 об/мин);
при необходимости точного центрирования осей;
в машинах очень больших и очень малых габаритов;
в воде и других агрессивных средах.
Недостатки таких подшипников - трение и потребность в дорогих
антифрикционных материалах.
Кроме того, подшипники скольжения применяют во вспомогательных, тихоходных,
малоответственных механизмах.
Характерные дефекты и поломки подшипников скольжения вызваны трением:
температурные дефекты (заедание и выплавление вкладыша);
абразивный износ;
усталостные разрушения вследствие пульсации нагрузок.
Большинство радиальных подшипников имеет цилиндрический вкладыш, который,
однако, может воспринимать и осевые нагрузки за счёт галтелей на валу и
закругления кромок вкладыша. Подшипники с коническим вкладышем применяются
редко, их используют при небольших нагрузках, когда необходимо систематически
устранять ("отслеживать") зазор от износа подшипника для сохранения
точности механизма.
Для правильной работы подшипников без износа поверхности цапфы и втулки
должны быть разделены слоем смазки достаточной толщины. В зависимости от режима
работы подшипника в нём может быть:
жидкостное трение, когда рабочие поверхности вала и вкладыша разделены
слоем масла, толщина которого больше суммы высот шероховатости поверхностей;
при этом масло воспринимает внешнюю нагрузку, изолируя вал от вкладыша,
предотвращая их износ. Сопротивление движению очень мало;
полужидкостное трение, когда неровности вала и вкладыша могут касаться
друг друга и в этих местах происходит их схватывание и отрыв частиц вкладыша.
Такое трение приводит к абразивному износу даже без попадания пыли извне.
2.3.2 Подшипники качения
Подшипники качения работают преимущественно при трении качения и состоят
из двух колец, тел качения, сепаратора, отделяющего тела качения друг от друга,
удерживающего на равном расстоянии и направляющего их движение.
Рис.2.6 - подшипник качения
Принцип их конструкции заключается в наличии между валом и корпусом
группы одинаковых круглых тел, называемых телами качения.
Это могут быть или шарики, или ролики (короткие толстые либо длинные
иглообразные), или конические ролики, или бочкообразные, или даже спиралевидные
пружины. Обычно подшипник выполняется как самостоятельная сборочная единица,
состоящая из наружного и внутреннего колец, между которыми и помещены тела
качения.
Тела качения во избежание ненужного контакта друг с другом и равномерного
распределения по окружности заключены в специальную кольцеобразную обойму -
сепаратор.
В некоторых конструкциях, где приходится бороться за уменьшение радиальных
габаритов, применяются т.н. "бескольцевые" подшипники, когда тела
качения установлены непосредственно между валом и корпусом. Однако нетрудно
догадаться, что такие конструкции требуют сложной, индивидуальной, а,
следовательно, и дорогой сборки-разборки.
Достоинства подшипников качения:
низкое трение, низкий нагрев;
экономия смазки;
высокий уровень стандартизации;
экономия дорогих антифрикционных материалов.
Недостатки подшипников качения:
- высокие габариты (особенно радиальные) и вес;
высокие требования к оптимизации выбора типоразмера;
слабая виброзащита, более того, подшипники сами являются генераторами
вибрации за счёт даже очень малой неизбежной разноразмерности тел качения.
2.3.3 Расчёт номинальной долговечности подшипника
Номинальная долговечность это число циклов (или часов), которые подшипник
должен проработать до появления первых признаков усталости. Существует
эмпирическая (найденная из опыта) зависимость для определения номинальной
долговечности
Ln = ( C / P )a, [млн. оборотов],
где С - грузоподъёмность, Р - эквивалентная динамическая нагрузка, a = 0,3 для шариков, a = 0,33 для роликов.
Номинальную долговечность можно вычислить и в часах
Lh = (106 / 60 n) Ln ,
[часов],
где n - частота вращения вала.
Эквивалентная динамическая нагрузка это такая постоянная нагрузка, при
которой долговечность подшипника та же, что и при реальных условиях работы.
Здесь для радиальных и радиально упорных подшипников подразумевается радиальная
нагрузка, а для упорных и упорно-радиальных - центральная осевая нагрузка.
Эквивалентная динамическая нагрузка вычисляется по эмпирической формуле
P = (V X Fr + Y Fa) KБ KТ,
где Fr , Fa - радиальная и осевая реакции опор; V - коэффициент вращения вектора
нагрузки (V = 1 если вращается внутреннее
кольцо, V = 1,2 если вращается наружное
кольцо); X, Y - коэффициенты радиальной и осевой нагрузок, зависящие от
типа подшипников, определяются по справочнику;
КБ - коэффициент безопасности, учитывающий влияние
динамических условий работы (КБ = 1 для передач, КБ = 1,8
для подвижного состава),
КТ - коэффициент температурного режима (до 100оС КТ
=1).
.3.4 Методика выбора подшипников качения
Опытный проектировщик может назначать конкретный тип и размер подшипника,
а затем делать проверочный расчёт. Однако здесь требуется большой конструкторский
опыт, ибо в случае неудачного выбора может не выполниться условие прочности,
тогда потребуется выбрать другой подшипник и повторить проверочный расчёт.
Методика выбора состоит из пяти этапов:
. Вычисляется требуемая долговечность подшипника исходя из частоты
вращения и заданного заказчиком срока службы машины.
. По найденным ранее реакциям опор выбирается тип подшипника (радиальный,
радиально-упорный, упорно-радиальный или упорный), из справочника находятся
коэффициенты радиальной и осевой нагрузок Х, У.
. Рассчитывается эквивалентная динамическая нагрузка.
. Определяется требуемая грузоподъёмность C = P*L(1/α).
. По каталогу, исходя из требуемой грузоподъёмности, выбирается
конкретный типоразмер ("номер") подшипника, причём должны выполняться
два условия:
- грузоподъёмность по каталогу не менее требуемой;
внутренний диаметр подшипника не менее диаметра вала.
3. Кинематический расчет привода
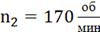
Передаточное
отношение зубчатой передачи составит
Принимаем
значение U=4 из ряда нормальных предпочтительных значений.
Определим
крутящие моменты на валах привода:
быстроходный
вал:
Tб=9550∙
=9550∙
=14,9 Н∙м;
где
- кпд пары подшипников качения
тихоходный
вал привода:
TТ=
=
= 28,62 Н∙м.
- кпд
зубчатого зацепления
4.
Расчет косозубой цилиндрической передачи
.1
Выбор материалов и допускаемых напряжений
Выбираем
в качестве материала колеса - сталь 45, с термообработкой в виде нормализации,
с твердостью Н2=192…240 HB. Имеющую следующие механические
характеристики: предел прочности σв=750 Н/мм2
и предел текучести σт=450 Н/мм2.
Выбираем
в качестве материала шестерни сталь 45, с термообработкой в виде нормализации,
с твердостью Н1=207…255 HB. Имеющую следующие механические
характеристики: предел прочности σв=600 Н/мм2
и предел текучести σт=320 Н/мм2.
Определим
средние значения твердости шестерни Н1 ср и колеса Н2 ср:
Н1
ср=0,5∙(Н1 min + H1 max)=0,5∙(207+255)=231
HB.
Н2
ср=0,5∙(Н2 min + H2 max)=0,5∙(192+240)=216
HB.
Необходимая
разность твердостей шестерни и колеса обеспечена.
Определим
числа циклов перемены контактных напряжений для шестерни NHO1 и NHO2
:HO1=14∙106,HO2=12∙106.
Определим
эквивалентное число циклов перемены напряжений для шестерни
N1=
где
Lh, ч -
долговечность (расчетный срок службы)
n1 = 698 мин-1 - частота вращения шестерни.
Определим
эквивалентное число перемены напряжений для колеса N2
N2=
где
n2 = 170
мин-1 - частота вращения колеса.
Определим
допускаемые напряжения:
[σH]1=1,8∙Н1
ср+ 67 = 1,8∙231+67=482,8 Н/мм2,
[σH]2=1,8∙Н2
ср+67 = 1,8∙216+67=455,8 Н/мм2.
Определим
допускаемые контактные напряжения для зубьев шестерни [σH]1 и
колеса [σH]2
:
[σH]1=
KHL1[σH]1=1·482,8=482,8
Н/мм2,
[σH]2=KHL2[σH]2=1·455,8=455,8
Н/мм2.
Принимаем
в качестве расчетного допускаемого контактного напряжения [σH]2=
455,8 Н/мм2.
Принимаем
число циклов перемены напряжений изгиба NF0=4∙106 .
Так
как N1 > NFO и N2 > NFO, принимаем значения коэффициентов долговечности при
расчете на изгиб для шестерни KFL1=1 и
колеса KFL2=1.
Определим
допускаемые напряжения изгиба [σ]F0:
Н/мм2
Н/мм2
Определим
допускаемые напряжения изгиба для зубьев шестерни [σF]1 и
колеса [σF]2
:
[σF]1=
KFL1[σ]FO1=1·238=238
Н/мм2,
[σF]2=KFL2[σ]FO2=1·222=222
Н/мм2.
В
качестве расчетного выбираем [σF]2 =222 Н/мм2.
4.2
Геометрический расчет косозубой передачи
Принимаем
приведенный модуль упругости для стальных колес Епр=2,1∙105
Н/мм2 .
Принимаем
коэффициент ширины колеса относительно межосевого расстояния передачи
=0,315.
Принимаем
предварительное значение коэффициента неравномерности распределения нагрузки по
ширине колеса K’Hβ=1,07
Определяем
предварительное значение межосевого расстояния передачи из условия контактной
усталости зубьев
мм
Определим
предварительное значение ширины зубчатого колеса передачи:
b’2=
∙ аwБ =0,315∙68,7=21,6 мм.
Принимаем
стандартное значение ширины зубчатого колеса из ряда нормальных линейных
размеров b2=36 мм.
Определение
диапазона рекомендуемых значений нормального модуля передачи: m’n=(0,01…0,02)∙аwБ=(0,01…0,02)∙68,7=0,69…1,37
мм.
Принимаем
стандартное значение нормального модуля mn=1
мм. .
Принимаем
значение коэффициента осевого перекрытия εβ=1,1
Определим
минимальное значение угла наклона зубьев передачи
βmin=arcsin
=arcsin
=5,51°
Принимаем
βmin=8°.
Z’1=
=
=27,2.
Принимаем
число зубьев шестерни Z1=27>Zmin=18.
Определим
предварительное значение числа зубьев колеса.
Z’2= Z’1∙U’=27∙4=108.
Принимаем
число зубьев колеса Z2=108.
Определим
действительное передаточное число зубчатой передачи.
U=
=
= 4.
Определим
отклонение действительного передаточного числа передачи U от
заданного U’.
ΔU=
∙100%=
∙100%=0
% < [
]=3%.
Определим
действительно значение межосевого расстояния передачи:
мм.
Принимаем
70 мм.
Определим
действительное значение угла наклона зубьев колес передачи:
β=arccos
= arccos
=15,36° .
Полученный
результат наклона зубьев β=15,36°
входит в рекомендуемые пределы 8°≤β≤20°.
Определим
делительные диаметры шестерни d1 и колеса
d2
d1=
=
= 28 мм,
d2=
=
= 112 мм.
Проверим
выполнение условия:
=
=70 мм = аWБ =70 мм.
Определим
диаметры окружностей вершин зубьев шестерни da1 и колеса da2 :
da1= d1+2∙mn= 28+2∙1=30 мм,
da2= d2+2∙mn=112+2∙1=114 мм.
Определим
диаметры окружностей впадин зубьев шестерни df1 и колеса df2
df1=d1-2,5∙mn =28-2,5∙1=25,5 мм,
df2=d2-2,5∙mn=112-2,5∙1=109,5 мм.
Определим
диапазон рекомендуемых значений ширины шестерни
b’1=b2+(2…5)=36+(2…5)=37…41 мм.
Принимаем
значение ширины шестерни b1=40 мм,
входящее в диапазон рекомендуемых значений.
4.3
Проверочный расчет
Определим
окружную скорость зубчатых колес:
V=
=
=1,02 м/с.
Назначим
степень точности передачи ST=9, исходя из полученного значения скорости V=1,02
м/с [3, с.21, табл.15].
Определим
значение коэффициента ширины шестерни относительно ее диаметра.
ψbd=
=
.
Принимаем
значение коэффициента неравномерности распределения нагрузки по ширине колеса KHβ=1,12.
Принимаем
значение коэффициента динамической нагрузки передачи KHV=1,05.
Определим
коэффициент нагрузки передачи.
KH= KHβ∙ KHV=1,12∙1,05=1,176.
Определим
коэффициент торцевого перекрытия:
=
=1,67.
Определим
значение коэффициента повышения прочности косозубой передачи по контактным
напряжениям, по сравнению с прямозубой передачей:
ZHβ=
=
=0,773.
Принимаем
угол зацепления αω=20°.
Определим
действительные контактные напряжения в зацеплении зубчатых колес:
σH=1,18∙ZHβ∙
=
=1,18∙0,768∙
= 459,3 Н/мм2.
Определим
отклонение действительного контактного напряжения в зацеплении зубчатых колес σH
от расчетного допускаемого [σH]
∙100%=
∙100%= -0,76 %.
Так
как
, то условие по контактным напряжениям выполняется
Определим
эквивалентные числа зубьев шестерни Zv1 и колеса Zv2
Zv1=
=
=30, Zv2=
=
=120.
Принимаем
значения коэффициентов формы зубьев шестерни уF1=3,8 и колеса уF2=3,6.
Определим
значение коэффициента, учитывающего наклон зубьев передачи:
yβ=1-
=1-
=0,89.
Определим
значение коэффициента повышения прочности косозубой передачи по напряжениям
изгиба по сравнению с прямозубой передачей:
ZFβ=
=
=0,72.
Принимаем
значение коэффициента неравномерности распределения нагрузки по ширине колеса KFβ=1,17.
Принимаем
значение коэффициента динамической нагрузки передачи KFV=1,13.
Определим
коэффициент нагрузки передачи:
KF= KFβ∙ KFV=1,17∙1,13=1,32.
Определим
менее прочное звено по отношениям
,
.
Менее
прочным звеном передачи является зубчатое колесо, так как для него указанное
отношение получилось меньше. Исходя из этого, проверочный расчет на
сопротивление усталости зубьев при изгибе проводим для зубчатого колеса
передачи.
Определим
действительное напряжение изгиба для зубьев колеса σF2 и сравним с допускаемым
напряжением изгиба колеса [σF2].
σF2=
σF2=
=61,67 Н/мм2
[σF]2=222
Н/мм2.
Прочность
зубьев колеса по напряжениям изгиба обеспечена.
4.4
Силы, действующие в зубчатом зацеплении
FtБ=
=
= 1064,3 Н.
Определим радиальную силу зубчатых колес:
FrБ= FtБ∙
=1064,3∙
= 387,2 H.
Определим
осевую силу в зацеплении зубчатых колес:
FaБ=FtБ∙tgβ=1064,3 ∙tg(15,36°)=292,3
H.
5. Технико-экономические показатели
Важным показателем совершенства конструкции является условие равной
прочности и равной долговечности всех элементов, поскольку наличие в
конструкции хотя бы одного недостаточно прочного или недостаточно долговечного
элемента снижает надежность конструкции в целом.
Экономические аспекты при проектировании проявляются при выборе
материалов, термообработки, упрочняющей технологии, формы и способов
изготовления детали. Технологичность деталей и узлов является одним из
важнейших условий в создании машин с оптимальными технико-экономическими показателями.
При серийном производстве наиболее экономичным является формообразование
деталей, методом литья или пластическим деформированием (обработка давлением).
При этом ускоряется процесс производства, уменьшается расход материалов и
снижаются затраты на электроэнергию и инструмент.
Экономичность, надежность, долговечность КПД, виброактивность,
интенсивность шума и другие показатели редуктора в большой степени зависят от
изнашивания рабочих поверхностей. Трение и изнашивание наносят огромный ущерб
народному хозяйству. Установлено, что 85…90% машин выходят из строя в
результате изнашивания деталей и только 10…15% - по другим причинам, например,
из-за поломок, которые в свою очередь являются следствием изменений условий
работы, вызванное износом сопряженных поверхностей, особенно это касается
износа зубьев редуктора, который снижает их изгибную прочность и выносливость.
Поэтому при расчете зубчатой передачи были использованы все рекомендации по
ГОСТ 21354-87, позволяющие максимально уменьшить износ зубчатых колес и
увеличить их надежность, предусмотрены защитные устройства, предупреждающие
попадание абразивных частиц в зону контакта.
Выбранный материал для зубчатых колес является одним из наиболее
распространенных и относительно недорогих материалов, пригодных для
производства зубчатых колес.
Для снижения коррозийно-механического изнашивания использованы
рекомендации последних исследований по вопросу смазки и смазочных устройств.
Эти исследования убедительно доказывают, что усовершенствованные смазки
являются наиболее эффективной мерой, направленной на повышение несущей
способности и долговечности редуктора.
Заключение
В данной работе были рассмотрены основные типы зубчатых передач,
приведены краткие сведения из геометрии и кинематики эвольвентных зубчатых зацеплений,
описаны основные виды разрушения зубьев и методы производства зубчатых колес.
Так же были кратко рассмотрены основные составляющие зубчатых редукторов: валы,
оси и подшипники качения и скольжения.
Особое внимание было уделено зубчатой передаче универсального привода
П-1,1. Был произведен кинематический расчет передачи, выбран материал для
зубчатых колес и определены допускаемые напряжения. Так же были рассчитаны
геометрические размеры зубчатых колес, определены усилия в зацеплении и
проведен проверочный расчет на контактную и изгибную прочность.
В работе приведено технико-экономическое обоснование проектных решений.
Список использованной литературы
1. Анурьев
В.И. Справочник конструктора-машиностроителя в 3-х т, т.2: изд. 8-е перераб. и
доп. Под ред. И.Н. Жестковой. - М.: Машиностроение, 2001. - 912 с.
. Курсовое
проектирование деталей машин: Учеб. пособие для учащихся машиностроит. спец.
вузов./ Чернавский С.А., Ицкович Г.М и др. - 3-е изд., перераб. и доп. - М.:
Машиностроение, 1989. 416 с.
. Соколов В.
И. Основы расчета и конструирования машин и аппаратов пищевых производств:
Учебник для втузов по специальности «Машины и аппараты пищевых производств». -
М.: Машиностроение, 1983. - 447 с.