Проектирование привода цепного конвейера
Содержание
1. Кинематический расчет привода и
выбор электродвигателя
.1 Выбор электродвигателя
1.2 Крутящие моменты и угловые
скорости валов редуктора
1.3 Выбор материала и расчёт
допускаемых контактных напряжений
1.4 Расчет допускаемых напряжений
изгиба
2. Расчет цилиндрической косозубой
передачи тихоходной ступени
.1 Расчёт передачи на контактную
выносливость
2.2 Проверка передачи по критерию
контактной выносливости
2.3 Проверка зубьев колес на
изгибную прочность
3 Расчет цилиндрической шевронной
передачи быстроходной ступени
.1 Расчёт передачи на контактную
выносливость
3.2 Проверка передачи по критерию
контактной выносливости
3.3 Проверка зубьев колес на
изгибную прочность
4. Расчёт валов редуктора
.1 Предварительный расчёт валов
4.2 Выбор и проверка шпонок и шлицов
на смятие
4.3 Эскизная компоновка редуктора
4.4 Расчёт промежуточного вала
4.5 Проверка подшипников качения
промежуточного вала
4.6 Расчёт выходного вала
4.7 Проверка подшипников качения
промежуточного вала
5. Выбор муфты
. Выбор сорта масла
Список использованных источников
1. Кинематический расчет привода и выбор
электродвигателя
.1 Выбор электродвигателя
Назначаем степень точности передач: 9 степень
точности.
Определяем ориентировочно общий КПД привода:
,
где
- КПД быстроходной ступени,
- КПД
тихоходной ступени,
- КПД
цепной передачи. В зависимости от степени точности принимаем приближенные
значения КПД передач с учетом потерь в подшипниках:
,
Тогда Общий
КПД равен:
Ориентировочная мощность двигателя:

В общем машиностроении большинство
машин приводят в движение от трехфазных асинхронных двигателей. Принимаем
электродвигатель 4А132М4 со следующими техническими характеристиками: P = 11 кВт,
= 1460
об/мин (что соответствует синхронной скорости
= 1500 об/мин).
Делительный диаметр тяговой
звездочки:
Угловая скорость вращения тяговой
звездочки:
;
Частота вращения тяговой звездочки:
В этом случае общее передаточное
отношение привода:
В соответствии с ГОСТ’ом 2185-81 и
12289-66, примем передаточное число цепной передачи
[2]. Тогда
передаточное число редуктора
.
Из рекомендаций по разбивке общего
передаточного числа редуктора по ступеням, найдём передаточное число
быстроходной ступени
[2]. Примем
ближайшее передаточное число по ГОСТу
. Передаточное число тихоходной
ступени
.
Примем ближайшее передаточное число
по ГОСТу
.
Действительное передаточное число редуктора
. Тогда действительное передаточное
число цепной передачи
.
.2 Крутящие моменты и угловые скорости валов
редуктора
· входного вала
· промежуточного вала
· выходного вала
Расчёт зубчатых колёс редуктора
1.3 Выбор материала и расчёт допускаемых
контактных напряжений
Так как материал и вид термической обработки для
шестерён и зубчатых колес не задан, то осуществим его выбор самостоятельно.
Для шестерён примем сталь 40Х (
); для
зубчатых колес - 40Х (
). При этом
следует соблюдать условие:
. Вид ТО - улучшение. Улучшение -
это термический вид обработки, состоящий закалки с высоким отпуском.
Определение допускаемого контактного напряжения
для косозубой и шевронной передач:
,
где
и
- пределы контактной выносливости
активных поверхностей зубьев, соответствующие базовому числу циклов перемены
напряжений соответственно для шестерни и для колеса:
SH -
коэффициент безопасности при расчете на контактную прочность, SH = 1,1 (стр.
130, [1]); КHL - коэффициент долговечности,
учитывающий влияние срока службы и режима нагрузки передачи:
где NHО - базовое
число циклов контактных переменных напряжений,
[2]; NHЕ - расчётное
число циклов перемены напряжений.
Ресурс работы привода
Расчетное число циклов для
напряжений изгиба:
,
где
- коэффициент эквивалентной
нагрузки,
Так как NH0 < NHЕ1 , NH0 < NHЕ2, NH0 < NHЕ3, то КHL1 = КHL2 =КHL3=1.
Тогда для шевронной и косозубых
передач:
1.4 Расчет допускаемых напряжений изгиба
где
и
- пределы изгибной выносливости при
базовом числе циклов соответственно для шестерни и для колеса, зависят от
материала и вида ТО [2]:
SF -
минимальный коэффициент запаса прчности, SF1 = SF2 = 1,75 , при
условии, что зубчатые колёса изготовлены из поковок (стр. 131, [1]); KFC -
коэффициент, учитывающий влияние двухстороннего приложения нагрузки, для
нереверсивных передач KFC = 1 (стр.
133, [1]); КFL -
коэффициент долговечности, рассчитывается с учетом базового числа нагружения NFО (для стали NFО = 4∙106)
и эквивалентного числа циклов нагружения при постоянной работе NFЕ ;
где m -
показатель степени корня (при HB ≤ 350
значение m = 6; при HB > 350
значение m = 9);
Тогда для шевронных и косозубых
передач:
2. Расчет цилиндрической косозубой
передачи тихоходной ступени
Расчёт редуктора начинаем с
тихоходной ступени, потому что она является наиболее нагруженной. Так как
заданная схема редуктора с раздвоенной тихоходной ступенью, то расчет будем
производить по одной ступени. Для второй ступени расчеты и результаты будут
аналогичными.
.1 Расчёт передачи на контактную выносливость
Определяем предварительное межосевое расстояние
зубчатой передачи из условия контактной выносливости:
где Ка - числовой
вспомогательный коэффициент, для косозубых колес Ка = 430 МПа1/3;
ybа -
коэффициент ширины зубчатого колеса, ybа = 0,315
(таблица 4.8, [1]); К*Нβ -
коэффициент, учитывающий неравномерность распределения нагрузки по длине
контактной линии, К*Нβ = 1,15;
- момент на
одной шестерне раздвоенной тихоходной передачи,
.
.
Согласно ГОСТ 2185-81 принято
стандартное межосевое расстояние аw2 = 180 мм
[2]. Определение предварительного модуля передачи:
.
Согласно ГОСТ 9563-60 принят
стандартный модуль из первого ряда m2 = 3 мм [2].
- предварительное число зубьев
шестерни,
где β*2 - предварительный
угол наклона линии зуба на делительной окружности колеса, принимаем β*2 = 12º;
.
Принимаем
Принято число зубьев шестерни
, число
зубьев колеса
.
Определяем истинный угол наклона линии зуба на
делительной окружности колеса β2:
Определение фактического передаточного числа и
погрешности передачи:
Определение делительных диаметров
колес:
Определение диаметров окружностей
вершин:
а2 - делительное
межосевое расстояние:
,
и
отличаются
на 0,004 мм, поэтому смещение вводить не будем.
Определение диаметров окружностей
впадин:
Определение диаметров начальных
окружностей колес:
Определение высоты зубьев колес:
Определение ширины колеса:
Согласно ГОСТ 6636-69 (П.4, [1]),
принята ширина колеса
, ширина
шестерни:
bW3 = bW4 + (3..5) =
63 мм.
Определение окружной скорости в
зацеплении:
Степень точности нашей передачи: 9
(таблица 4.5, [1]).
Определение окружной силы:
Определение радиальной и осевой
силы:
Так как данная схема редуктора с
раздвоенной тихоходной ступенью и направление линии зуба на цилиндрических
косозубых передачах разное (левое и правое), то общая осевая нагрузка будет
равна нулю.
2.2 Проверка передачи по критерию контактной
выносливости
Определение расчетного контактного напряжения:
,
где ZM -
коэффициент, учитывающий механические свойства материалов сопряженных зубчатых
колес, для стальных зубчатых колес ZM = 275 (Н1/2/мм);
ZН -
коэффициент, учитывающий форму сопряженных поверхностей зубьев в полюсе
зацепления:
;
Ze -
коэффициент, учитывающий суммарную длину контактных линий, для косозубых колес:
,
где εα -
коэффициент торцевого перекрытия передачи, определяемый по следующей формуле:,
,
;
;
- удельная расчетная окружная сила,
Н/мм:
,
где КНa -
коэффициент, учитывающий неравномерность распределения нагрузки между зубьями;
согласно ГОСТ 21354-75 принят КНa =1,22 (рис.
4.1, [1]);
КНb -
коэффициент неравномерности распределения нагрузки по ширине венца и значения ybd -
коэффициента ширины шестерни:
;
согласно ГОСТ 21354-75 принят КНb =1,1;
КНV -
коэффициент, учитывающий динамическую нагрузку, возникающую в зацеплении
поверхностей зубьев; зависит от значения окружной скорости зацепления V = 1,08 и
степени точности s = 9, принят КНV = 1,01
(таблица 4.6, [1]);
.
Контактная выносливость передачи
обеспечена.
2.3 Проверка зубьев колес на изгибную прочность
Определение расчетных напряжений изгиба:
где
- коэффициент нагрузки:
,
КFa
-
коэффициент, учитывающий неравномерность распределения нагрузки между зубьями;
для косозубых со степенью точности равной 9, КFa=1
(стр. 134, [1]);
КFb
-
коэффициент, учитывающий неравномерность распределения нагрузки по ширине
венца, согласно ГОСТ 21354-75 принят КFb
=
1,08 (таблица 4.4, [1]);
КFV -
коэффициент, учитывающий динамическую нагрузку, возникающую в зацеплении
поверхностей зубьев
(таблица
4.7, [1]).
YF -
коэффициент, учитывающий форму зуба, определяется по таблице 4.12 [1], в
зависимости от эквивалентного числа зубьев:
;
По эквивалентному числу зубьев шестерни Z3
=
26 принят YF3
=
3,9 и по эквивалентному числу зубьев колеса Z4
= 104 принят YF4
= 3,6;
Yb
- коэффициент, учитывающий наклон зуба; для косозубой передачи:
Ye
-
коэффициент, учитывающий перекрытие зубьев; для косозубых колес принят Ye
=
1;
Условия изгибной прочности зубьев
обеспечены.
3. Расчет цилиндрической шевронной передачи
быстроходной ступени
.1 Расчёт передачи на контактную выносливость
Определяем предварительное межосевое расстояние
передачи из условия контактной выносливости:
Ка = 430 МПа1/3;
К*Нβ = 1,25;
коэффициент ширины в соответствии с
примечанием [2],
, принимаем
;,
.
Согласно ГОСТ 2185-81 принято
стандартное межосевое расстояние аw = 140 мм.
Определение предварительного модуля
передачи:
.
Согласно ГОСТ 9563-60 принят
стандартный модуль m = 2,5 мм.
- предварительное суммарное число
зубьев,
где β*-
предварительный угол наклона линии зуба на делительной окружности колеса,
принимаем β* = 30º;
.
Принимаем
Принято число зубьев шестерни
, число
зубьев колеса
.
Таблица 1 - Основные параметры
цилиндрической косозубой передачи тихоходной ступени
№
п/п
|
Наименование
|
Обоз-ние
|
Значение
|
Размерность
|
1
|
Вращающий
момент на промежуточном валу
|
Т2
|
155,41
|
|
2
|
Вращающий
момент на тихоходном валу
|
Т3
|
596,77
|
|
3
|
Частота
вращения промежуточного вала
|
n2
|
324,44
|
мин-1
|
4
|
Частота
вращения тихоходного вала
|
n3
|
81
|
мин-1
|
5
|
Угловая
скорость вращения промежуточного вала
|
33,97с-1
|
|
|
6
|
Угловая
скорость вращения тихоходного вала
|
8,5с-1
|
|
|
7
|
Допускаемое
контактное напряжение
|
531МПа
|
|
|
8
|
Допускаемые
напряжения изгиба
|
шестерни
|
310МПа
|
|
|
|
|
колеса
|
270МПа
|
|
|
9
|
Межосевое
расстояние
|
аw2
|
180
|
мм
|
10
|
Делительное
межосевое расстояние
|
а2
|
180,004
|
мм
|
11
|
Модуль
|
m2
|
3,0
|
мм
|
12
|
Числа
зубьев
|
шестерни
|
Z3
|
23
|
-
|
|
|
колеса
|
Z4
|
92
|
-
|
13
|
Угол
наклона линии зуба
|
 Град.
|
|
|
14
|
Угол
профиля исходного контура
|
α2
|
Град.
|
|
15
|
Фактическое
передаточное число
|
иФ
|
4
|
-
|
16
|
Делительные
диаметры
|
шестерни
|
d3
|
72,0025
|
мм
|
|
|
колеса
|
d4
|
288,007
|
мм
|
17
|
Диаметры
окружностей вершин
|
шестерни
|
dа3
|
78,0025
|
мм
|
|
|
колеса
|
dа4
|
294,007
|
мм
|
18
|
Диаметры
окружностей впадин
|
шестерни
|
df3
|
64,5025
|
мм
|
|
|
колеса
|
df4
|
280,507
|
мм
|
19
|
Диаметры
начальных окружностей
|
шестерни
|
dW3
|
72,0025
|
мм
|
|
|
колеса
|
dW4
|
288,007
|
мм
|
20
|
Высота
зубьев
|
шестерни
|
6,75мм
|
|
|
|
|
колеса
|
6,75мм
|
|
|
21
|
Ширина
|
шестерни
|
63мм
|
|
|
|
|
колеса
|
60мм
|
|
|
22
|
Расчетное
контактное напряжение
|
525МПа
|
|
|
23
|
Расчетные
напряжения изгиба
|
шестерни
|
90МПа
|
|
|
|
|
колеса
|
83МПа
|
|
|
24
|
Окружная
скорость зацепления
|
V
|
1,22
|
м/с
|
25
|
Окружная
сила
|
4317Н
|
|
|
26
|
Радиальная
сила
|
1710Н
|
|
|
27
|
Осевая
сила
|
1266Н
|
|
|
Определяем истинный угол наклона линии зуба на
делительной окружности колеса β:
Определение фактического передаточного числа и
погрешности передачи:
Определение делительных диаметров
колес:
Определение диаметров окружностей
вершин:
а - делительное межосевое
расстояние:
,
и
отличаются
на 0,0015 мм, поэтому смещение вводить не будем.
Определение диаметров окружностей
впадин:
Определение диаметров начальных
окружностей колес:
Определение высоты зубьев колес:
Определение ширины колеса:
Согласно ГОСТ 6636-69 (таблица П.4,
[1]), принята ширина колеса
, ширина шестерни:
bW1 = bW2 + (3..5) =
60 мм.
Степень точности нашей передачи: 9.
Так как эта передача шевронная, то
осевая нагрузка будет компенсироваться, но при этом нужно учесть то, что
подшипники необходимо использовать роликовые радиальные с короткими
цилиндрическими роликами.
3.2 Проверка передачи по критерию контактной
выносливости
Определение расчетного контактного напряжения:
,
где ZM = 275 (Н1/2/мм);
;
,
;
;
,
где КНa =1,6;
;
согласно ГОСТ 21354-75 принят КНb =1,2;
КНV - в
зависимости от значения окружной скорости зацепления V = 3,89 и
степени точности s = 9, принят КНV = 1,05
(таблица 4.6, [1]);
.
Контактная выносливость передачи не
обеспечена.
Увеличим ширину зубчатого колеса и
шестерни
.
Контактная выносливость передачи
обеспечена.
3.3 Проверка зубьев колес на изгибную прочность
Определение расчетных напряжений изгиба:
КFa=1;
КFb = 1,16;
.
По эквивалентному числу зубьев шестерни Z1
=
26 принят YF1
=
3,9 и по эквивалентному числу зубьев колеса Z2
= 117 принят YF2
= 3,6;
Ye
=
1;
Условия изгибной прочности зубьев
обеспечены.
Таблица 2 - Основные параметры
шевронной передачи быстроходной ступени
№
п/п
|
Наименование
|
Обозначение
|
Значение
|
Размерность
|
1
|
Вращающий
момент на промежуточном валу
|
Т1
|
71,95
|
|
2
|
Вращающий
момент на тихоходном валу
|
Т2
|
310,82
|
|
3
|
Частота
вращения входного вала
|
n1
|
1460
|
мин-1
|
4
|
Частота
вращения промежуточного вала
|
n2
|
324,44
|
мин-1
|
5
|
Угловая
скорость вращения входного вала
|
152,89с-1
|
|
|
6
|
Угловая
скорость вращения промежуточного вала
|
33,97с-1
|
|
|
7
|
Допускаемое
контактное напряжение
|
531МПа
|
|
|
8
|
Допускаемые
напряжения изгиба
|
шестерни
|
310МПа
|
|
|
|
|
колеса
|
270МПа
|
|
|
9
|
Межосевое
расстояние
|
аw
|
140
|
мм
|
10
|
Делительное
межосевое расстояние
|
а
|
140,0015
|
мм
|
11
|
Модуль
|
m
|
2,5
|
мм
|
12
|
Числа
зубьев
|
шестерни
|
Z1
|
18
|
-
|
|
|
колеса
|
Z2
|
81
|
-
|
13
|
Угол
наклона линии зуба
|
 Град.
|
|
|
14
|
Угол
профиля исходного контура
|
α
|
Град.
|
|
15
|
Фактическое
передаточное число
|
иФ
|
4,5
|
-
|
16
|
Делительные
диаметры
|
шестерни
|
d1
|
50,9107
|
мм
|
|
|
колеса
|
d2
|
229,0923
|
мм
|
17
|
Диаметры
окружностей вершин
|
шестерни
|
dа1
|
55,9107
|
мм
|
|
|
колеса
|
dа2
|
234,0923
|
мм
|
18
|
Диаметры
окружностей впадин
|
шестерни
|
df1
|
44,6607
|
мм
|
|
|
колеса
|
df2
|
222,8423
|
мм
|
19
|
Диаметры
начальных окружностей
|
шестерни
|
dW1
|
50,9107
|
мм
|
|
|
колеса
|
dW2
|
229,0923
|
мм
|
20
|
Высота
зубьев
|
шестерни
|
5,625мм
|
|
|
|
|
колеса
|
5,625мм
|
|
|
21
|
Ширина
|
шестерни
|
63мм
|
|
|
|
|
колеса
|
60мм
|
|
|
22
|
Расчетное
контактное напряжение
|
525МПа
|
|
|
23
|
Расчетные
напряжения изгиба
|
шестерни
|
78МПа
|
|
|
|
|
колеса
|
72МПа
|
|
|
24
|
Окружная
скорость зацепления
|
V
|
3,89
|
м/с
|
25
|
Окружная
сила
|
2827Н
|
|
|
26
|
Радиальная
сила
|
1164Н
|
|
|
27
|
Осевая
сила
|
1473Н
|
|
|
4. Расчёт валов редуктора
.1 Предварительный расчёт валов
Предварительный расчет валов ведем
по условию допускаемого напряжения на кручение:.
. Принимаем
Предварительные диаметры валов:
;
;
,
и согласно ГОСТ 6636-69 принимаем
,
. Диаметр
быстроходного вала принимаем равным
, где
- диаметр конца вала двигателя,
. Тогда
.
Для тихоходного вала:
= d1+
= 32 мм -
диаметр вала под крышкой подшипника,
=
+ 3 = 35 мм - диаметр вала под
подшипником,
=
+ 5 = 40 мм - диаметр переходного
участка вала.
Шестерню для этого вала, так как её
размеры не особо на много отличаются от размеров вала, сделаем по схеме
«вал-шестерня».
Для промежуточного вала:
=
- диаметр вала под подшипником,
=
+ 5 = 40 мм - диаметр вала под
шестернями.
- диаметр вала под колесом.
- диаметр упорного участка.
Для выходного вала:
= d3+
= 57 мм -
диаметр вала под крышкой подшипника,
=
+ 3 = 60 мм - диаметр вала под
подшипником,
=
+ 5 = 65 мм - диаметр переходного
участка вала
=
+ (3-5) = 70 мм - диаметр вала под
колесом.
Для ведомого вала с
= 35 мм
принимаем роликовые радиальные подшипники с короткими цилиндрическими роликами
лёгкой узкой серии («на плавающей основе») по ГОСТ 8328 - 75: 2207 со
следующими параметрами:
d, мм
|
D, мм
|
B, мм
|
C0, кН
|
C, кН
|
35
|
72
|
17
|
17,6
|
31,9
|
По наружному диаметру подшипника D
= 72 мм выбрана крышка торцевая Крышка 21 - 72 ГОСТ 18511 - 73.
Для промежуточного вала с
= 35 мм
принимаем шариковые радиальные однорядные подшипники лёгкой серии по ГОСТ 8338
- 75: 207 со следующими параметрами:
d, мм
|
D, мм
|
B, мм
|
C0, кН
|
C, кН
|
35
|
72
|
17
|
13,9
|
25,5
|
По наружному диаметру подшипника D
= 72 мм выбрана крышка торцевая глухая Крышка 21 - 72 ГОСТ 18511 - 73.
Для выходного вала с
= 60 мм
принимаем шариковые радиальные однорядные подшипники лёгкой серии по ГОСТ 8338
- 75: 212 со следующими параметрами:
d, ммD, ммB, ммC0, кНC, кН
|
|
|
|
|
60
|
110
|
22
|
31,5
|
52,0
|
По наружному диаметру подшипника D
= 110 мм выбрана крышка торцевая Крышка 21 - 110 ГОСТ 18511 - 73.
.2 Выбор и проверка шпонок и шлицов на смятие
· Для колеса на промежуточном валу:
В соответствии с ГОСТ 23360-78 выбираем шпонку
призматическую:
Диаметр
вала, мм
|
Размеры
сечений шпонок
|
глубина
паза t,
мм
|
|
b
|
h
|
|
Свыше
44 до 50
|
14
|
9
|
5,5
|
Напряжение смятия:
,
где z - число
шпонок, z = 1;
- рабочая длинна шпонки, принимаем
;
- допустимое напряжение смятия,
Условие прочности выполнено.
Обозначение призматической шпонки:
Шпонка 14´9´50
· Для шестерен на промежуточном валу:
В соответствии с ГОСТ 23360-78 выбираем шпонку
призматическую:
Диаметр
вала, мм
|
Размеры
сечений шпонок
|
глубина
паза t,
мм
|
|
b
|
h
|
|
Свыше
38 до 44
|
12
|
8
|
5
|
Напряжение смятия:
,
z = 1;
;
Условие прочности выполнено.
Обозначение призматической шпонки:
Шпонка 12´8´50
· Для колес на выходном валу:
В соответствии с ГОСТ 1139 - 80 выбираем шлицы
прямобочные лёгкой серии:
Напряжение смятия рассчитывается по формуле:
,
где
- момент на одном колесе
раздвоенной тихоходной передачи,
;
.
Условие прочности выполнено.
Обозначение шлица прямобочного с
центрированием по наружному диаметру:
.
.3 Эскизная компоновка редуктора
При эскизном проектировании определяем
расположение деталей передачи, расстояние между ними. Эскизную компоновку
редуктора выполним на миллиметровке формата А2.
вал редуктор цилиндрический шпонка
4.4 Расчёт промежуточного вала
§ Окружное усилие:
шестерни -
колеса -
Радиальное усилие:
шестерни -
колеса -
§ Осевое усилие:
шестерни -
колеса -
Так как колесо шевронное, то все
осевые усилия будут взаимокомпенсироваться, и поэтому в расчётах не будем их
учитывать.
Все действующие силы -
пространственные, поэтому для удобства расчетов, систему координат XYZ разобьём на
две подсистемы координат:
· XOZ - система
(плоскость), в которой действуют усилия
,
,
,
и реакции
опор RAZ и RBZ (неизвестные);
· XOY - система
(плоскость), в которой действует усилия
,
и реакции
опор RAY и RBY
(неизвестные).
Для плоскости ХOZ:
- условие равновесия;
;
;
Проверка:
Расчёты выполнены правильно.
Построение эпюр:
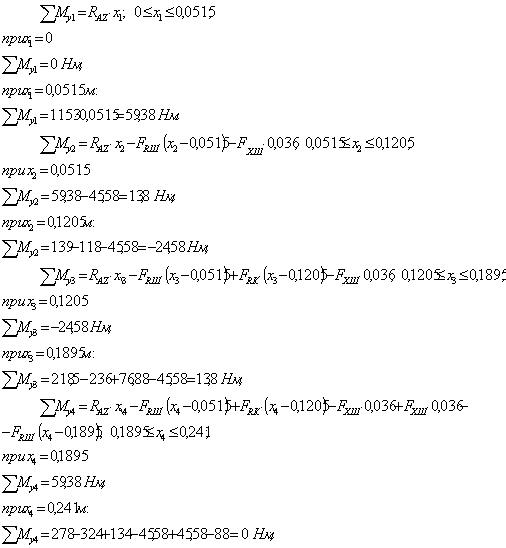
- условие равновесия;
;
;
Проверка:
Расчёты выполнены правильно.
Построение эпюр:
Суммарный изгибающий момент
определяется методом геометрического суммирования:
- моменты в опасных сечениях вала;
M = max(
);
МИЗГmax = M1 = M3 = 163,5 Нм.
Наибольшие изгибающие моменты МИЗГmax = 163,5 Нм
находятся в сечениях вала под шестернями.
Расчетное напряжение изгиба в
опасном сечении вала:
,
где b* -
коэффициент перегрузочных моментов, принят b
= 3,0 - для двигателя 4А132М4
Расчетное напряжение кручения в
опасном сечении вала
.
Расчетное напряжение
растяжения/сжатия от осевой силы
Определение эквивалентного
напряжения по III теории
прочности
,
где
- допускаемое напряжение изгиба;
Материал вала - сталь 40Х:
- предел текучести;
- предел прочности;
- пределы выносливости при изгибе и
кручении;
- допускаемый запас статической
прочности;
Коэффициенты запаса прочности по напряжениям
изгиба и кручения
,
где
,
- среднее напряжение изгиба и
амплитуда цикла;
- среднее
напряжение кручения и амплитуда цикла;
- коэффициенты чувствительности
материала, учитывающие влияние постоянной составляющей цикла на усталостную
прочность, приняты
(таблица
7.1, [1]);
коэффициент
упрочняющей технологии, принят
(шлифование), (рис. 15.6, [3]);
- масштабные
факторы, учитывающие влияние абсолютных размеров вала на предел выносливости,
приняты
(рис. 15.5,
[3]);
-
эффективные коэффициенты концентрации напряжений при изгибе и кручении,
обусловленные различными факторами концентрации напряжений (шпоночный паз),
приняты
(таблица
15.1, [3]).
Общий расчетный запас выносливости:
4.5 Проверка подшипников качения промежуточного
вала
Для расчета принят подшипник легкой серии типа
207 (шариковые радиальные однорядные подшипники лёгкой серии ГОСТ 8338 - 75).
Определение эквивалентной динамической нагрузки
на подшипник:
,
где Х и Y -
коэффициенты осевой и радиальной нагрузок соответственно, принимаются в
зависимости от типа подшипника, так как подшипник 207 радиальный, то Х = 1, Y = 0; V -
коэффициент вращения кольца, V = 1 (вращается внутреннее кольцо); R -
радиальная нагрузка на подшипник, H; КБ
=1,1 - 1,2 - коэффициент безопасности, принят КБ =1,2; КТ
- температурный коэффициент, вводимый в расчет, когда t >100 C° , при t ≤100 C° КТ
=1.
Определение опорных реакций в
подшипниках
Определение расчетной долговечности выбранного
подшипника типа 207, с динамической грузоподъемностью С = 25500 Н
,
где m -
показатель степени кривой выносливости, определяемый формой тела качения, m = 3 - для
шарикоподшипника радиально-упорного; m = 3,33 -
для роликоподшипника радиально-упорного.
Определение заданного ресурса
работы:
Определение расчетного ресурса работы выбранного
подшипника типа 207;
Условие долговечности выполнено.
4.6 Расчёт выходного вала
§ Окружное усилие
§ Радиальное усилие
§ Осевое усилие
§ Усилие, возникающее на консоли вала от
соединительной муфты:
Будем рассматривать плоскости:
· XOZ - система
(плоскость), в которой действуют усилия
,
и реакции
опор RAZ и RBZ (неизвестные);
· XOY - система
(плоскость), в которой действует усилия
,
и реакции
опор RAY и RBY
(неизвестные).
Для плоскости ХOZ:
- условие равновесия;
;
;
Проверка:
Расчёты выполнены правильно.
Построение эпюр:
Для плоскость XOY:
- условие равновесия;
;
;
Проверка:
Расчёты выполнены правильно.
Построение эпюр:
Суммарный изгибающий момент
определяется методом геометрического суммирования:
- моменты в опасных сечениях вала;
M = max(
);
МИЗГmax =
= 576 Нм.
Наибольшие изгибающие моменты МИЗГmax = 576 Нм
находятся в сечениях вала под правым колесом.
Расчетное напряжение изгиба в
опасном сечении вала:
,
Расчетное напряжение кручения в
опасном сечении вала
.
Расчетное напряжение
растяжения/сжатия от осевой силы
Определение эквивалентного
напряжения по III теории
прочности
,
где
- допускаемое напряжение изгиба;
Материал вала - сталь 40Х:
- предел текучести;
- предел прочности;
- пределы выносливости при изгибе и
кручении;
- допускаемый запас статической
прочности;
Коэффициенты запаса прочности по напряжениям
изгиба и кручения
,
где
,
;
;
;
(шлифование);
;
.
Общий расчетный запас выносливости:
Так как получился большой запас
прочности, то диаметры валов можно уменьшить. Но перед этим необходимо
проверить, выполняется ли условие долговечности подшипников.
Проверка подшипников качения
промежуточного вала
Для расчета принят подшипник легкой
серии типа 212 (шариковые радиальные однорядные подшипники лёгкой серии ГОСТ
8338 - 75).
Определение эквивалентной
динамической нагрузки на подшипник:
,
где Х = 1, Y = 0;
V = 1
(вращается внутреннее кольцо);
КБ =1,2;
КТ =1.
Определение опорных реакций в
подшипниках
Определение расчетной долговечности выбранного
подшипника типа 212, с динамической грузоподъемностью С = 52000 Н
,
Определение расчетного ресурса работы выбранного
подшипника типа 212;
Так как условие долговечности
выполнено с заметным запасом, то можно выходной вал уменьшить. Каждую ступень
вала уменьшим на 5 см. Тогда выберем другие подшипники. Для вала с
= 55 мм
принимаем шариковые радиальные однорядные подшипники лёгкой серии по ГОСТ 8338
- 75: 211 со следующими параметрами:
d, мм
|
D, мм
|
B, мм
|
C0, кН
|
C, кН
|
55
|
100
|
21
|
25
|
43,6
|
По наружному диаметру подшипника D
= 100 мм выбрана крышка торцевая Крышка 21 - 100 ГОСТ 18511 - 73.
Определяем расчетную долговечность выбранного
подшипника типа 211, с динамической грузоподъемностью С = 43600 Н
,
Определение расчетного ресурса работы выбранного
подшипника типа 211;
Условие долговечности выполнено.
5. Выбор муфты
Муфта, соединяющая вал ротора электродвигателя и
входной конец быстроходного вала редуктора выбрана в зависимости от диаметра
вала ротора (d1=38,0
мм).
Принята муфта упругая втулочно-пальцевая Муфта
250 - 38 - 1 - УЗ ГОСТ 21424-93 (том 2, стр. 314, [4]).
Должно выполняться условие:
,
где
- номинальный крутящий момент;
,
где k - коэффициент режима работы
для привода конвейера, k = 1,3 (стр. 274, [5]).;
.
Условие выполнено.
6. Выбор сорта масла
Принимаем, что цилиндрическая
передача редуктора смазывается погружением колеса только тихоходной ступени
(т.к.
, (стр. 148,
[5])) в масляную ванну на глубину 20…30 мм, подшипники - масляным туманом.
Ориентировочно определяем
необходимую вязкость смазочного материала по эмпирической формуле (8.9 , [1]):
n50»n1/
,
где n50 -
рекомендуемая кинематическая вязкость смазочного материала при температуре 50°С и заданной средней окружной
скорости передачи V, м/с;
v1 -
рекомендуемая вязкость при V = 1 м/с, с термически обработанной
поверхностью зубьев (улучшение) v1=260…280 мм2/с
(стр. 337, [5]).
Принято масло ИТП-200, с номинальной
кинематической вязкостью при 50°С
220 - 244
.
Объем масляной ванны принимают
таким, чтобы обеспечить отвод выделяющейся в зацеплении теплоты к стенкам
корпуса. Для двухступенчатого цилиндрического редуктора объем масляной ванны
рекомендуется принимать таким, чтобы на 1 кВт передаваемой мощности приходилось
0,35…0,7 л масла, т.е.
. На
практике же объем масляной ванны принимается исходя из опыта эксплуатации
конкретных механизмов в конкретных условиях, и может существенно отличаться от
приведенных значений.
Список использованных источников
1 Чернилевский,
Д. В.Детали машин. Проектирование приводов технологического оборудования / Д.
В. Чернилевский - М.: Машиностроение, 2002. - 560 с., ил.
Детали
машин и основы конструирования: Методические указания и задания на курсовое
проектирование / Санкт-Петербургский горный институт. Сост.: А. В. Большунов,
Е. С. Кузнецов, Г. В. Соколова, И. П. Тимофеев. СПб, 2001. - 54 с.
Детали
машин: Учебник для студентов высших учебных заведений / М. Н. Иванов - М.:
Высшая школа, 1991. - 383с., ил.
Анурьев
В. И. «Справочник конструктора-машиностроителя: В 3-х томах», - М.:
Машиностроение, 1978.
Дунаев
П. Ф., Леликов О. П. «Конструирование узлов и деталей машин: Учеб. пособие для
машиностроит. спец. вузов». - М.: Высш. шк., 1985.