Проект реконструкции электросталеплавильного цеха
ВЕДОМОСТЬ ОБЪЕМА ДИПЛОМНОГО ПРОЕКТА
Формат
|
Обозначение
|
Наименование
|
Кол-во
листов
|
Примечание
|
А4
|
|
Задание
к дипломному проекту
|
1
|
|
А4
|
|
Пояснительная
записка
|
|
|
А4
(CD)
|
|
План-схема
ЭСПЦ-2
|
1
|
Приведена
на электронном носителе
|
А3
(CD)
|
|
Машина
непрерывного литья заготовок до реконструкции
|
1
|
Приведена
на электронном носителе
|
А4
(CD)
|
|
Кристаллизатор
диаметр 200
|
1
|
Приведена
на электронном носителе
|
А4
(CD)
|
|
Зона
вторичного охлаждения
|
1
|
Приведена
на электронном носителе
|
А3
(CD)
|
|
Машина
непрерывного литья заготовок после реконструкции
|
1
|
Приведена
на электронном носителе
|
А4
(CD)
|
|
Спецчасть
|
1
|
Приведена
на электронном носителе
|
А4
(CD)
|
|
Технологическая
схема плавки марки 40Х
|
1
|
Приведена
на электронном носителе
|
А4
(CD)
|
|
Технико-экономические
показатели
|
1
|
Приведена
на электронном носителе
|
РЕФЕРАТ
Дипломная работа: 162 с., 15 рис., 55 табл., 23
источников, 7 прил.
МНЛЗ, ЛИТАЯ ЗАГОТОВКА круглого сечения,
гильзовый кристаллизатор, круглофакельное вторичное охлаждение.
Объектом исследования является
электросталеплавильный цех №2, входящий в состав РУП «БМЗ».
Целью дипломной работы является проект
реконструкции электросталеплавильного цеха, путем изменения технологического
процесса разливки стали, предусматривающий мероприятия, способствующие
повышению качества литой заготовки и увеличению производства МНЛЗ на 20%.
Проект реконструкции включает в себя изменение
конструкции кристаллизатора и секций зоны вторичного охлаждения для уменьшения
количества некоторых видов дефектов МНЛЗ, получения круглой заготовки,
увеличения скорости затвердевания слитка и более мягкого, равномерного
охлаждения литой заготовки.
Анализ технико-экономических показателей данного
проекта показал, что реконструктивные мероприятия в ЭСПЦ-2 имеют положительный
эффект.
кристаллизатор
электросталеплавильный разливка сталь
СОДЕРЖАНИЕ
ВВЕДЕНИЕ
.
ОБОСНОВАНИЕ РЕКОНСТРУКЦИИ ЦЕХА
.1
Краткая история республиканского унитарного предприятия «Белорусский
металлургический завод
.2
Анализ современных МНЛЗ - особенности конструкций, области применения с точки
зрения изготовления литых заготовок различного сечения
.3.1
Применение гильзового кристаллизатора
.3.2Применение
новой конструкция вторичного охлаждения заготовки с применением
комбинированного: водяного и водовоздушного охлаждения круглофакельными
форсунками
.4
Выводы
.
ТЕХНОЛОГИЧЕСКАЯ ЧАСТЬ
.1
Полное описание конструктивных элементов МНЛЗ до реконструкции
.1.1
Описание технологического процесса
.2
Описание конструктивных элементов МНЛЗ после реконструкции
.3
Планировочное расположение МНЛЗ в цехе
.
ТЕХНОЛОГИЯ ПРОИЗВОДСТВА СТАЛИ МАРКИ 40Х
.1
Технические требования и химический состав легированной среднеуглеродистой
стали 40Х
.2
Технология выплавки стали 40Х на ДСП-3
.3
Технология раскисления и легирования стали 40Х на выпуске
.4
Технология обработки металла на установке «ковш-печь»
.4.1
Основные требования к разливаемому металлу
.5
Технологический расчет производства стали марки 40Х
.5.1
Баланс металла по электросталеплавильному производству
.5.2
Отходы в электросталеплавильном цехе
.5.3
Отходы в прокатных цехах
.5.4
Расчет материального баланса плавк
.5.5
Период плавления шихты
.5.6
Окислительный период плавки
.5.7
Количество газов периода плавления и окисления
.5.8
Расчёт расхода раскислителей и легирующих на выпуске
.5.9
Расчёт расхода раскислителей и легирующих на «печь-ковше»
.6
Тепловой баланс плавки
.6.1
Количество тепла, необходимое для расплавления и нагрева стали
.6.2
Количество теплоты, необходимое для нагрева шлака
.6.3
Определение тепловых потерь
.
СПЕЦИАЛЬНАЯ ЧАСТЬ
.1
Разработка новой технологии вторичного охлаждения с применением круглофакельных
водовоздушных форсунок
.1.1
Расчёт зоны вторичного охлаждения
.2
Расчет основных параметров МНЛЗ
.
ОРГАНИЗАЦИОННО-ЭКОНОМИЧЕСКАЯ ЧАСТЬ
.1
Организация производства. Структура управления ЭСПЦ-2
.1.1
Мероприятия по повышению квалификации рабочих и инженерных кадров
.1.2
Методы стимулирования работы сотрудников
.2
Расчет инвестиций
.3
Расчет себестоимости продукции
.3.1
Расчет затрат на материалы
.3.2
Затраты на топливо и энергию на технологические цели
.3.3
Расчет фонда заработной платы и отчислений на социальные нужды
.3.4
Определение общепроизводственных, общехозяйственных и коммерческих расходов
.3.5
Расчет расходов по организации, обслуживанию и управлению производством
.4
Расчет технико-экономических показателей цеха
.5
Заключение
.
ОХРАНА ТРУДА
.1
Производственная санитария, техника безопасности, пожарная профилактика
.1.1
Характеристика техпроцесса с точки зрения воздействия на работающих опасных и
вредных производственных факторов
.1.2
Метеорологические условия
.1.3
Вентиляция
.1.4
Производственное освещение
.1.5
Шум, вибрация
.1.6
Электробезопасность
.1.7
Требования безопасности к технологическому процессу, к конструкции оборудования
.1.8
Санитарно-бытовые помещения
.1.9
Пожарная профилактика
.1.10
Расчет интенсивности теплового облучения на рабочем месте сталевара
.
ЭКОЛОГИЧЕСКАЯ БЕЗОПАСНОСТЬ ПРОИЗВОДСТВА
.1
Экология сталеплавильного цеха
.2
Газо- и пылевыделения из электроплавильных печей
ЗАКЛЮЧЕНИЕ
СПИСОК
ИСПОЛЬЗОВАНЫХ ИСТОЧНИКОВ
ПРИЛОЖЕНИЕ
А Кристаллизатор диаметр 200
ПРИЛОЖЕНИЕ
Б Машина непрерывной разливки стали до реконструкции
ПРИЛОЖЕНИЕ
В Машина непрерывной разливки стали после реконструкции
ПРИЛОЖЕНИЕ
Г План - схема ЭСПЦ-2
ПРИЛОЖЕНИЕ
Д Технологическая схема плавки стали 40Х
ПРИЛОЖЕНИЕ
Ж Зона вторичного охлаждения
ПРИЛОЖЕНИЕ
К Технико-экономические показатели проекта
ВВЕДЕНИЕ
Наряду со снижением себестоимости выпускаемой
продукции, одной из основных проблем, стоящих перед специалистами черной
металлургии, является проблема получения качественной непрерывнолитой
заготовки, которая во многих случаях неразрывно связана с возникновением
вмикро- и макроструктуре заготовки различного рода напряжений. Немаловажную
роль в решении этих сложных и многоплановых задач играет своевременное и
тщательное изучение передового мирового опыта и результатов наиболее
перспективных исследований в области энергосбережения и устранения дефектов,
полученных при производстве стали и литой заготовки.
Именно целью данной работы и является внедрение
в существующий технологический процесс разработок новейших технологий разливки
стали, способных снизить количество дефектов литой заготовки с получением
конечной продукции высокого качества и сократить затраты на производство литой
заготовки.
Объектом исследования является сталеплавильный
цех №2, входящий в состав РУП «БМЗ». В качестве агрегатов реконструкции приняты
начальный и конечный - машина непрерывного литья заготовок №3 (МНЛЗ - 3).
Осуществить на практике данный замысел на базе
имеющегося оборудования ЭСПЦ - 2 станет возможным с применением на агрегате
МНЛЗ - гильзовых кристаллизаторов и круглофакельного вторичного охлаждения.
Внедрение предлагаемых технологий, а также
реализация всех запланированных мероприятий, позволит не только снизить затраты
на производство, но и получить стабильно высокое качество конечного продукта -
стальной заготовки круглого сечения всего марочника легированных сталей, тем
самым значительно улучшив приоритетные направления в области повышения качества
продукции РУП «БМЗ» на мировом рынке, и дав возможность в будущем обеспечивать
трубопрпокатное производства трубной заготовкой диаметром 200 мм собственного
производства.
1. ОБОСНОВАНИЕ РЕКОНСТРУКЦИИ ЦЕХА
.1 Краткая история республиканского унитарного
предприятия «Белорусский металлургический завод»
Республиканское унитарное предприятие
«Белорусский металлургический завод» (РУП «БМЗ») является унитарным
предприятием государственной формы собственности, с момента строительства и
ввода первого комплекса в эксплуатацию в ноябре 1984 года является уникальным
высокотехнологичным предприятием металлургической отрасли.
Завод спроектирован и построен “под ключ”
фирмами “Фест-Альпине” (Австрия) и “Даниели” (Италия). 19 марта 1982г. был
заключен контракт на проектирование и строительство завода и всей необходимой
инфраструктуры. 10 сентября 1982г. был заложен «первый камень» под строящимся
сталеплавильным цехом. Строительство осуществлялось в 4-е очереди. Первая
очередь сдана в эксплуатацию в ноябре 1984г., вторая - в ноябре 1987г., третья
- в марте 1991г., 15 сентября 2000г. введен в эксплуатацию новый прокатный стан
150, в июле 2007 года введен в эксплуатацию трубопрокатный цех. В результате
окончательно сформировался технологический профиль и специализация РУП «БМЗ»
как предприятия «европейского типа» с высоким уровнем технологии и
предопределили направления его стратегического развития на перспективу. Из
мини-завода Белорусский металлургический завод превратился в уникальное
предприятие, которое не только выплавляет качественную сталь, но и превращает ее
суперпрочный металлокорд.
Первые производственные мощности БМЗ были
введены в эксплуатацию 15 октября 1984 года выпуском первой плавки и её
разливкой
на
машине непрерывного литья заготовок. Эта дата считается официальным
днем
рождения завода. Проектная мощность электросталеплавильного цеха на тот момент
составляла 750 тыс. тонн выплавляемой стали или 720 тыс. тонн непрерывнолитой
заготовки в год и была впервые достигнута в 1986 году, когда было произведено
731 тыс. тонн продукции.
С вводом в эксплуатацию дуговой сталеплавильной
печи № 3 в 1991 году проектная мощность сталеплавильного комплекса увеличилась
до 1 040 тыс. тонн в год. В настоящее время уже имеется результат по превышению
проектных мощностей сталеплавильного производства почти в 1,7 раза - более 1
776 тыс. тонн литой заготовки в 2004 году. Разработана, освоена и внедрена
технология производства всей гаммы сталей присущих современному классическому
электросталеплавильному производству. Это сталь для легированного
конструкционного проката, рессорно-пружинного проката, штамповые стали. В
дополнение к марочнику сталей, предусмотренному проектом и базирующемуся, в
основном, на союзных ГОСТах, освоена технология производства десятков новых
марок сталей по стандартам США, Японии, Кореи и практически всех ведущих
государств Европы.
Предметом деятельности Унитарного предприятия
«Белорусский металлургический завод» является производство стали, проката
черных металлов, металлокорда, бортовой латунированной проволоки, товаров
народного потребления, стройматериалов, выполнение работ и оказание услуг,
расширение ассортимента и повышение качества производимой продукции и
оказываемых услуг.
Структура основного производства завода
представлена отделением переработки лома, сталеплавильным, прокатным,
трубопрокатным и метизным производствами, а также вспомогательными, ремонтными
и энергетическими цехами и службами, аналитическими и испытательными центрами [
1 ].
Сталеплавильное производство:
В состав сталеплавильного производства входят:
копровый цех (КЦ) и два электросталеплавильных цеха (ЭСПЦ - 1; ЭСПЦ - 2).
Состав копрового цеха: отделение по переработке
лома, отделение производства извести, отделение шлакопереработки.
Состав электросталеплавильного цеха ЭСПЦ - 1:
печное отделение, оборудованное двумя стотонными дуговыми печами с
трансформатором 95 МВ·А (ДСП-1) и 95 МВ·А (ДСП-2); участок внепечной обработки
стали, оборудованный агрегатом «ковш-печь» с установкой «Velco» для вдувания
ТШС; отделение разливки, в состав которого входят две разливочные шестиручьевые
машины радиального типа с сечением кристаллизатора 125х125мм и 140х140мм,
комплекс оборудования по футеровке, сушке и разогреву сталеразливочных и
промежуточных ковшей, склад заготовок.
Состав электросталеплавильного цеха ЭСПЦ - 2:
печное отделение, оборудованное одной стотонной дуговой электропечью (ДСП) с
трансформатором 95 МВ·А; участок внепечной обработки стали (УВОС),
оборудованный установками «ковш-печь» и «Velco», двумя вакууматорами:
циркуляционного и камерного типа; отделение разливки, оборудованное
реконструированной одной разливочной четырехручьевой машиной радиального типа с
сечением кристаллизаторов 250х300 мм и 300х400 мм и диаметром 200 мм комплекс
оборудования по футеровке, сушке и разогреву вакууматора, стальковшей и
промковшей, склад заготовок.
Прокатное производство:
Прокатное производство представлено
сортопрокатным цехом, имеющим в своем составе: сортовой стан “850”,
мелкосортный стан “320”,
проволочный
стан “150” и трубопрокатным цехом .Состав сортового стана “850”:
подогревательная печь, нагревательная печь, гидросбив, реверсивная клеть, пила
горячей резки, холодильник, колодцы замедленного охлаждения.
Состав мелкосортного стана “320”: нагревательная
печь, черновая, промежуточная и чистовая группы, трасса термического упрочнения
проката, делительные ножницы, холодильник, участок упаковки и маркировки
проката, ножницы холодной резки.
Состав проволочного стана “150”: нагревательная
печь, черновая и две промежуточные группы, десятиклетьевой проволочный стан,
линия двухстадийного охлаждения катанки, участок упаковки и маркировки катанки.
Состав трубопрокатного цеха: участок горячей
прокатки труб, линия предварительной отделки, участок термообработки, финишная
линия отделки.
Метизное производство:
В состав метизного производства завода входят два
сталепроволочных цеха с производством металлокорда: СтПЦ-1 с ПМК (“Micord») и
СтПЦ-2 с ПМК («Pluscord”), а также сталепроволочный цех №3 (СтПЦ-3) с участком
товаров народного потребления.
СтПЦ-1 и СтПЦ-2 оснащены: линиями травления и
бурирования катанки, агрегатами патентирования и латунирования проволоки,
станами для волочения проволоки на сухой и жидкой смазке, машинами одинарной и
двойной свивки прядей и металлокорда, а также оплеточными станками. В СтПЦ-1
имеется агрегат бронзирования, для производства бортовой проволоки.
СтПЦ-3 оснащен: станами для волочения на сухой
смазке, гвоздильными автоматами, станками для производства товаров народного
потребления.
В состав вспомогательных цехов завода входят:
цех ремонта металлургического оборудования; цех ремонта
электрометаллургического оборудования, цех ремонта энергетического
оборудования; энергетический цех; газокислородный цех; автотранспортный цех;
цех железнодорожного транспорта; цех благоустройства и складское хозяйство.
1.2 Анализ современных МНЛЗ - особенности
конструкций, области применения с точки зрения изготовления литых заготовок
различного сечения
В мировом производстве черных металлов улучшение
качества непрерывнолитых заготовок, наряду с совершенствованием технологии
выплавки и внепечной обработки, достигается в результате использования
расходуемых материалов требуемого качества, надежной защиты жидкого металла при
разливке от вторичных процессов окисления, использования кристаллизатора новых
конструкций и механизма качания, применения физических методов воздействия на
процесс формирования внутреннего строения слитка в виде электромагнитного поля
и мягкого обжатия в зоне затвердевания, автоматизации и оперативного контроля
процесса разливки.
Основным функциональным звеном, определяющим процесс
в непрерывной разливке заготовок является кристаллизатор, включающий медную
водоохлаждаемую гильзу, установленную в ее корпусе, который может совершать
возвратно-поступательные движения с заданной частотой и амплитудой.
Кристаллизатор имеет систему контроля (поддержания) уровня металла и систему
подачи охлаждающей воды в зазор между внешней поверхностью гильзы и рубашкой в
корпусе. Важнейшим элементом обеспечивающим эффективность работы
кристаллизатора является гильза, под средством которой происходит отвод тепла
от затвердевающей заготовки к охлаждающей жидкости непосредственно формируется
геометрическая форма заготовки. Обеспечение устойчивого контакта поверхности
заготовки с внутренней поверхностью гильзы является едва ли не важнейшей
задачей для равномерного формирования твердой корочки и геометрической формы
заготовки.
В последнее два десятилетия наибольшее
распространение для МНЛЗ получила концепция так называемой «параболической»
формы внутренней полости гильзы кристаллизатора, которая в максимальной степени
учитывает усадку заготовки по мере ее движения вниз, что позволяет
минимизировать величину воздушного зазора между заготовкой и стенками гильзы.
Известно, что воздушный зазор имеет термическое сопротивление на порядок выше,
чем термическое сопротивление стенки гильзы и может составлять 35-50 % общего
термического сопротивления в системе отвода тепла от жидкой стали к охлаждающей
воде. Соответственно увеличение воздушного зазора тормозит рост твердой
корочки, а при неравномерном воздушном зазоре по граням и углам возможна
деформация профиля заготовки. Именно поэтому ряд разработчиков и производителей
гильз (например “Europa Metalli”, “Abax”) предпочитают иметь в нижней части
гильзы повышенную конусность, которая как бы гарантирует контакт заготовки с
поверхностью нижней части гильзы. Вместе с тем, как показывает опыт
эксплуатации таких гильз, основной причиной их выхода из строя является
сравнительно быстрый износ в нижней части, который начинается с истирания
защитного покрытия, а затем и непосредственно тела медной гильзы.
Для разливки круглой заготовки при выборе
конструкции гильзы основное внимание уделяется ее верхней части. В ней при
литье может возникнуть овальность заготовки из-за разнотолщинности,
обусловленной разной величиной газового зазора, что связано с влиянием ряда
тепловых и физических воздействий, которые изменяют равномерность теплоотвода
от оболочки по периметру.
На МНЛЗ-2 Волжского трубного завода в 2006г
проведена реконструкция оборудования зоны кристаллизации для разливки круглых
заготовок диаметром 156 мм где в реконструированные кристаллизаторы
фирмы «SMS Demag» были установлены гильзы для
круглого сечения «ВНИИМЕТМАШ», что позволило достичь максимальной скорости
разливки 3,5 м/мин, снизить брак с 4,5 % до 0,18 %, овальность заготовки
уменьшить с 0,46 % до 0,01 % и исключить затраты на доработку заготовок перед
отправкой заказчику. При реконструкции МНЛЗ на металлургическом заводе
«ТМК-Решица» (Румыния) использовались гильзы кристаллизаторов для круглой
заготовки сечением 177 мм, разработанные и изготовленные «ВНИИМЕТМАШ» и
получены аналогичные результаты.
Основные поставщики гильз большого квадратного и
круглого сечения: «EM Moulds s.r.l.», «KME Germany AG & Co. KG», «Рочес
ЗАО», «ОллГрадо ООО», «Anssen Metallurgy Group Co LTD», «GPO Impex LLP», «AGC
Technologies GmbH», «ВНИИМЕТМАШ».
Функциональная зона вторичного охлаждения
является крайне важной с точки зрения качества заготовки. Это, в первую
очередь, относится к предотвращению формирования различного рода термических
внутренних напряжений в твердом каркасе заготовки. Вторичное охлаждение
(режимы) может влиять на геометрическую форму заготовки, формирование трещин,
осевую пористость и ликвацию. Высокая эффективность метода водовоздушного
охлаждения объясняется тем, что благодаря высокой кинетической энергии с
металлом одновременно контактирует большое количество распыленной воды. При
одном и том же расходе воды площадь теплообмена между водой и заготовкой
увеличивается: с одной стороны, вода мелко распылена и число капель очень
велико, а с другой, - эти капли равномерно распределяются по поверхности
заготовки, так как факел имеет устойчивую форму конуса. Известно, что
соотношение воздух-вода не является единственным и решающим фактором влияния на
коэффициент теплоотдачи. В виду этого фирмой «Lecher Gmbh» (Германия),
являющейся одним из лидеров в производстве форсунок в мире, производились
исследования зависимости коэффициента теплоотдачи в зависимости от
давления
воды в форсунке. Установлено, что в случае давления воды 400 кПа для форсунки
11/90-40-40 наблюдается прекращение поступления воздуха в смеситель форсунки
(воздух вытесняется жидкостью) и с этого момента начинается уменьшение
коэффициента теплоотдачи. В свою очередь применение современных форсунок серии
100.259 (Master-Cooler), позволяет устойчиво работать, в данном случае при
максимальном давлении жидкости до 550 кПа, что обеспечивает эффективное
охлаждение заготовки. Форсунки этой серии позволили обеспечить стабильную
работу МНЛЗ и исключить прорывы металла. Кроме того данный вид форсунок был
специально сконструирован для получения максимальных значений коэффициентов
теплоотдачи в диапазоне 500-600 кПа. Последние результаты в области
исследования и разработок двухкомпонентных распыляющих систем привели к
созданию форсунок с минимальным расходом воздуха и одновременно с широким
расходом регулирования. При постоянном давлении воздуха 2,5 бар возможно
достижение соотношения 1:23. Это соотношение в 2-3 раза больше, чем у
однокомпонентных форсунок. Новым решением, которое получило развитие в
последние годы, стала вертикальная прокладка труб квадратного сечения для
воздушных и водяных подводов. Форсунки в таком исполнении с предусмотренным
подсоединением крепятся на вертикальных пластинах. Обвязка с подводящими
трубками становится больше не нужна. Все распылители в этом случае находятся за
пределами корпуса сегмента и подсоединены непосредственно к подводящему
коллектору. Такой метод подсоединения и крепления форсунок, испытанный фирмой
«Lecher Gmbh» (Германия), позволил гибко располагать их по ширине заготовки с
тем, чтобы получить равномерность распределения охладителя и более эффективное
охлаждение на различных зонах (установка форсунок в шахматном порядке). Фирмой
«Lecher Gmbh» рекомендуется конструкция «Split Pipe», позволяющая отделять
переднюю часть с распылителем от корпуса форсунки, а также автоматически
фиксировать направление струи. Это особенно важно для верхних сегментов,
находящихся вблизи кристаллизатора.
Следующим преимуществом такой конструкции можно
назвать то, что смеситель находится непосредственно на коллекторе и готовая
водовоздушная смесь подается к соплу форсунки. Это позволяет компактно
располагать и свободно охватывать любое межроликовое расстояние. В целом
разработанное фирмой «Lecher Gmbh» вторичное охлаждение заготовки распыленной
водовоздушной дисперсией значительно улучшило теплопередачу, обеспечив при этом
более интенсивный рост затвердевшей корки и более равномерное охлаждение
заготовки, что позволило повысить скорость вытягивания заготовки на 15-20% и
снизить количество брака заготовки по продольным и диагональным трещинам.
На машинах непрерывного литья Оскольского
электрометаллургического комбината (ОАО «ОЭМК») разливают сталь широкого
сортамента марок. Разливка высокоуглеродистой стали, в большей степени склонной
к образованию дефектов, требует мягкого и равномерного вторичного охлаждения.
Широко применяемая в настоящее время система водяного вторичного охлаждения
блюмов не позволяет обеспечить плавного снижения температуры поверхности по длине
заготовки и равномерное ее охлаждение по ширине из-за наличия участков
локального переохлаждения. Обеспечить мягкое и равномерное вторичное охлаждение
непрерывнолитых блюмов сечение 300х360 мм позволяет водовоздушная система
вторичного охлаждения, разработанная «ВНИИМЕТМАШ».
Система основана на принципе образования
водовоздушной смеси в коллекторах в непосредственной близости от форсунок.
Новая система вторичного охлаждения обеспечивает повышение качества
трещиночествительной стали и снижения брака по раскатанной трещине с 0,02 % до
0 %, снижения доработки поверхности с 31 % до 14 %. Кроме других возможностей,
режим мягкого обжатия представляет собой особо
эффективное
средство устранения нежелательных сегрегационных эффектов и, следовательно,
повышения качества непрерывнолитых заготовок. Это достигается за счет
уменьшения толщины заготовки в зоне завершения кристаллизации в результате
приложения внешних усилий до величины нормальной термической усадки, что
позволяет выровнять резкий перепад объемов и предотвратить всасывание
сегрегированного остаточного расплава. В то время как этот процесс уже
используется при разливке слябов, геометрические параметры заготовок
квадратного сечения, несмотря на положительные результаты испытаний, не
позволили реализовать его на практике. Впервые данный режим обработки был
успешно испытан и реализован на МНЛЗ SO компании Saarstahl AG.
Совместно с фирмой Маннесман Демаг была
разработана концепция проектирования и расчета "блока мягкого
обжатия" (SR) для шестиручьевой МНЛЗ. Для определения влияния обжатия по
толщине на структуру металла от клети к клети, в некоторых опытах применяли
следующий порядок: четыре отрезка блюма обжимали по толщине в различном числе
клетей SR. Сначала применяли только клеть № 1, затем клети № 1 +2, затем клети
№ 1 + 2 + 3 и наконец все четыре клети. В каждом случае от блюма отбирали
пробу. По продольным серным отпечаткам высокоуглеродистой стали с 0,8 % С при
обжатии за проход в первой клети 1 мм, во второй 2 мм, в третьей 3 мм и в
четвертой 2,5 мм были сделаны следующие выводы о влиянии мягкого обжатия: при
суммарном обжатии 3 мм, достигавшемся в клети № 2, уже отмечалось уменьшение
ликвации по продольной оси затвердевания, однако V- образная ликвация была еще
очень заметной; при суммарном обжатии 6 мм, достигавшемся в клети № 3, осевая
ликвация уже была в значительной мере устранена; это относится и к V-образной
ликвации; достигнутое в третьей клети усреднение химического состава сердцевины
блюма уже было настолько хорошим, что дальнейшее увеличение суммарного обжатия
до 8,5 мм в клети №4 не дало никакого дополнительного улучшения,
обнаруживаемого по серным отпечаткам, однако микропористость уменьшилась.
Шестиручьевая МНЛЗ криволинейного типа компании
Saarstahl AG в Фёльклингене введена в эксплуатацию в апреле 2004 г. Заложенные
в проекте параметры МНЛЗ (радиус кривизны 11м, многоточечное выпрямление)
позволяют удовлетворять жесткие требования в отношении качества поверхности и
внутренней структуры заготовки. К особенностям агрегата относятся кристаллизаторы,
обеспечивающие очень высокую скорость разливки (до 4 м/мин) в закрытом режиме,
система резонансных колебаний с гидравлическим приводом и высокомощные
устройства для перемешивания расплава в кристаллизаторе и ручье,
функционирующие в широком диапазоне частот, проводки для точного направления и
высокоэффективного охлаждения заготовки с использованием высокого давления и
двухкомпонентного агента. Размеры поперечного сечения заготовки составляют
150x150 мм при длине 8-15,5 м или 180x180 мм при длине 6-13 м. Основным
элементом агрегата является узел мягкого обжатия в сегментном исполнении.
Вместо традиционных тянущих роликов агрегат располагает шестью имеющими
гидравлический привод сегментами на ручей, которые обеспечивают точную
установку зазора и распределение усилий в зоне завершения кристаллизации и,
следовательно, целенаправленное влияние на формирование внутренней
микроструктуры заготовки. Дополнительно имеется динамическая расчетная модель
DSC (Dynamic Solidification Control - динамический контроль кристаллизации), с
помощью которой определяются оптимальные параметры процессов вторичного
охлаждения и мягкого обжатия.Возможности режима мягкого обжатия для уменьшения
ликвации в средней части заготовки ограничены способностью к удлинению корочки
на границе твердой и жидкой фаз. Так как повышенная нагрузка на корочку в зоне
фронта кристаллизации приводит к образованию внутренних трещин, величина
отдельных стадий деформации не должна превышать максимально допустимого
значения. Соответствующее предельное значение можно установить экспериментально
и путем расчета [ 2 ].
.3 Реконструктивные мероприятия по улучшению
качества заготовки
Одной из основных проблем, стоящих перед
специалистами черной металлургии при получении заготовок высокого качества,
является проблема получения чистотой стали. Немаловажную роль в решении этой
задачи играет своевременное и тщательное изучение передового мирового опыта и
результатов наиболее перспективных исследований в области снижения и устранения
дефектов, полученных при производстве стали.
Реконструктивные мероприятия, обеспечивающие
повышение производительности цеха, снижение энергоемкости производства стали и
повышение качества литой заготовки, согласно тематике данного дипломного
проекта разрабатываются на базе существующего оборудования ЭСПЦ - 2 РУП «БМЗ».
На агрегате МНЛЗ с целью улучшения качества
внутренней структуры слитка и повышения производительности машины предлагается:
изменение конструкции кристаллизатора,
применение гильз позволяющих получить заготовку круглого сечения;
применение электромагнитного перемешивания в
кристаллизаторе разработанное фирмой Danieli Rotelec;
изменение конструкции секций зоны вторичного
охлаждения (ЗВО), применение комбинированного: водяного и водовоздушного
охлаждения круглофакельными форсунками;
применение системы мягкого обжатия заготовки.
.3.1 Применение гильзового кристаллизатора
Многоконусная конструкция трубчатой гильзы
кристаллизатора и толщина ее стенки преследуют цель предотвращения остаточной
деформации под воздействием температуры. Деформация гильзы кристаллизатора
могла бы привести к значительному снижению срока службы кристаллизатора и
повлечь за собой появление глубоких следов качания и дефектов формы у
заготовок.
Гильза кристаллизатора имеет многоконусную
конструкцию, для того чтобы компенсировать усадку заготовки и поддерживать
контакт между заготовкой и кристаллизатором. Правильный выбор многоконусной
конструкции обеспечивает максимальный контакт до самого низа кристаллизатора и
тем самым снижает возможность трещинообразования и дефектов формы, таких как
овальность, скошенность стенок и вмятины.
Конструкция кристаллизатора предусматривает
высокую скорость воды в зазоре. Это направлено на поддержание температуры меди
на достаточно низком уровне, чтобы избежать закипания воды, в особенности возле
мениска. Неконтролируемое кипение характеризуется нестабильной теплопередачей с
периодическими изменениями температуры медной стенки.
Подобная ситуация ведет к остаточной деформации
гильзы. Более того, повышение температуры стенки способствует осаждению
растворенных солей. Возникновение кипения зависит не только от скорости воды,
но также и от давления в зазоре кристаллизатора. Фактически, существует хорошо
известная связь между температурой кипения и давлением.
Ширина зазора между гильзой кристаллизатора и
рубашкой находится в диапазоне 3,25 - 4,00 мм. с высокой точность по допускам.
Это решение является оптимальным с точки зрения предъявляемых требований к
высокой скорости воды и практических ограничений, существующих вследствие падения
давления в кристаллизаторе. Для обеспечения постоянства водяного зазора,
водяная рубашка подвергается механической обработке с узким допуском (
приложение А).
Рекомендуется применение опорных роликов под
кристаллизатором. Для каждого сечения предусматриваются два ряда опорных
роликов. Эти ролики предназначены для вывода заготовки из кристаллизатора. При
отсутствии направления хода заготовки она может оцарапать стенку дна
кристаллизатора, сокращая тем самым срок его службы и вызывая появление дефектов
[ 2 ].
Практический опыт работы на аналогичных
разливочных машинах показал, что при правильной эксплуатации и
техобслужиавании, средний срок службы медной трубчатой гильзы кристаллизатора
составляет более 250 плавок.
Конструкция кристаллизатора показана на рисунке
1.1
Рисунок 1.1 - Кристаллизатор круглого сечения
диаметром 200 мм
Новая конструкция кристаллизатора обеспечит:
постоянство водяного зазора между гильзой и
рубашкой;
высокую скорость протока воды в зазоре;
высокую точность центровки медной гильзы;
установку катушки электромагнитного
перемешивания.
Применение новой конструкция вторичного
охлаждения заготовки с применением комбинированного: водяного и водовоздушного
охлаждения круглофакельными форсунками
Конструкция обеспечивает быструю и правильную
скорость затвердевания и предотвращает появление металлургических дефектов как
поверхностных, так и внутренних. Это достигается путем:
снижения подогрева поверхности в конце
охлаждения струйным душированием.
сведения к минимуму разницы в скорости
охлаждения между центром и углами граней слитка путем соответствующего
расположения душирующих форсунок.
Регулировка расхода: по 2 независимой системы
для каждой зоны каждого ручья, для обеспечения сбалансированного охлаждения
блюма (внутренний-внешний радиус, боковые стороны) отдельный контур для
внутренного - внешнего радиуса и отдельный контур для боковых сторон.
Система охлаждения подразделяется на ряд
независимых зон охлаждения в зависимости от требований по разливаемым размерам,
скорости разливки и маркам стали. Каждая зона охлаждения управляется
индивидуально с помощью системы автоматики 2-го уровня.
Такая конструкция преследует цель обеспечения
идеального режима охлаждения (который характеризуется минимальными механическими
напряжениями), позволяющим постепенно сократить коэффициент теплопередачи от
кристаллизатора к концу зоны охлаждения, где охлаждение
происходит
только путем естественной конвекции воздуха и излучения. По этому же принципу
определяется и оптимальная длина охлаждения. Такое распределение интенсивности
охлаждения является наиболее эффективным с точки зрения длины в жидком
состоянии и средней температуры заготовки.
Проект системы струйного душирования основан на
математической модели затвердевания и теплопередачи. Компьютерные программы
определяют наилучшее расположение системы струйного душирования на основе
предварительно рассчитанного теоретического режима теплопередачи [2].
Выводы
Использование новой конструкции кристаллизатора
позволит получить:
постоянство водяного зазора между гильзой и
рубашкой;
высокую скорость протока воды в зазоре;
высокую точность центровки медной гильзы;
возможность установки катушки электромагнитного
перемешивания (ЭВМ);
возможность получения круглой заготовки
диаметром 200 мм для использования при производстве бесшовных горячекатаных
труб в трубопрокатном цехе;
снижения трещинообразования и дефектов формы
(овальность, скошенность стенок и вмятины);
возможность увеличения скорости разливки и
перегрев в промковше без негативных последствий.
Усовершенствование системы вторичного охлаждения
позволит достичь:
снижения подогрева поверхности в конце
охлаждения струйным душированием;
сведения к минимуму разницы в скорости
охлаждения между центром и углами граней слитка;
уменьшение механических напряжений;
быструю и правильную скорость затвердевания.
Кроме этого, смотря в будущее, есть все
основания полагать, что внедрение предложенных технологий, а также реализации
всех запланированных мероприятий, позволит получить стабильно высокое качество
конечного продукта всего марочника сталей, тем самым значительно улучшив
приоритетные направления в области повышения качества продукции, а также
увеличить объем выпускаемой продукции РУП «БМЗ» на мировом рынке.
. ТЕХНОЛОГИЧЕСКАЯ ЧАСТЬ
.1 Полное описание конструктивных элементов МНЛЗ
до реконструкции
МНЛЗ представляет собой современную установку
для получения сортовой заготовки методом непрерывной разливки стали (приложение
Б).
Технические характеристики существующей на
заводе МНЛЗ до реконструкции приведены в таблице 2.1 [ 3 ].
Таблица 2.1 - Технические характеристики МНЛЗ до
реконструкции
Наименование
параметра
|
Показатель
|
1
|
2
|
Годовое
производство, т
|
690
000
|
Вес
плавки, т
|
100
|
Тип
машины
|
радиальная
установка с прямым кристаллизатором разработка фирмы Фест-Альпине
|
Количество
ручьев
|
4
|
Сечение
слитка, мм
|
250х300
прямоугольное сечение
|
|
300х400
прямоугольное сечение
|
Расстояние
между ручьями, мм
|
1300
/ 1500 / 1300
|
Радиус
разливочной дуги, м
|
10
|
Скорость
разливки, м/мин
|
0,5
- 1,5 (в зависимости от марки и сечения)
|
Металлургическая
длина (max), м
|
28,9
|
Скорость
машины для транспортировки затравки, м/мин
|
5
|
Длина
блюмов, мм
|
2500
- 5500
|
Скорость
рольганга, м/мин
|
30
|
Скорость
передвижения, м/мин: Поперечный транспортер блюмов
|
до
72 - ручной режим; 42 - автоматика.
|
Схема МНЛЗ показана на рисунке 2.1
-сталеразливочный ковш, 2-промежуточный ковш,
3-стопор КР-1111, 4-стакан-дозатор, 5- стопорный механизм; 6- кристаллизатор,
7-зона изгиба, 8- разливочная дуга, 9,10,11 -тянущий трайбаппарат №№1,2,3,
12-правильная зона; 13-промежуточный рольганг; 14- машина газокислородной резки
(МГКР); 15-рольганг газокислородной резки.
Рисунок 2.1 - Схема МНЛЗ (до реконструкции)
Краткая характеристика и технологические
параметры конструктивных элементов МНЛЗ:
подъемно поворотный сталеразливочный стенд
служит для перемещения сталеразливочного ковша с металлом после внепечной
обработки.
промежуточный ковш (позиция 2 рисунка 2.1)
выполняет функции приемной камеры для поддержания ферростатического давления
стали на постоянном уровне на протяжении всего процесса разливки и
распределение по ручьям.
Технические характеристики промежуточного ковша
приведены в таблице 2.2.
Таблица 2.2 - Технические характеристики
промежуточного ковша
Наименование
параметра
|
Показатель
|
Вместимость,
т
|
25
|
Максимальная
вместимость, т
|
29
|
Высота
перелива, мм
|
1050
|
Глубина
ванны жидкого металла, мм
|
1000
|
Общая
масса, т
|
50
|
тележка промковша используется для
транспортировки промковша от участка загрузки до участка разливки. Основные
параметры тележки промковша приведены в таблице 2.3
Таблица 2.3 - Основные параметры тележки
промковша
Наименование
параметра
|
Показатель
|
Тип
|
подъемный,
с ходовыми путями и гидравлическим блоком
|
Скорость
тележки промковша, м/мин
|
2-20
|
Ход,
мм
|
9300
|
кристаллизатор (позиция 6 рисунка 2.1)
предназначен для охлаждения поступающей из промковша жидкой стали с помощью
водоохлаждаемых медных плит, и определяет поперечное сечение ручья. Технические
характеристики кристаллизатора приведены в таблице 2.4.
Таблица 2.4 - Технические характеристики
кристаллизатора
Наименование
параметра
|
Показатель
|
Основные
размеры, мм: длина
|
2850
|
ширина
|
1250
|
высота
|
965
|
Основные
составные части
|
водяной
короб; вставка пластины; перекрытие кристаллизатора.
|
Нижняя
кромка медной плиты на горячем формате, мм:
|
300х400
|
250х
300
|
Ширина
нижней кромки медной плиты, мм
|
409
|
309,5
|
Толщина
блюма, мм
|
308,5
|
257
|
Длина
кристаллизатора медная плита, мм
|
800
|
800
|
регулирование уровня в кристаллизаторе
В целях оптимизации уровня качества при
разливке, очень важно поддерживать постоянный уровень стали в кристаллизаторе,
для этого используется изотопный излучатель автоматического поддержания уровня
металла в гильзе кристаллизатора (САПУ).
катушка электромагнитного перемешивания
Система электромагнитного перемешивания металла
в кристаллизаторе наружного типа состоит из катушек, установленных с наружной
стороны кристаллизатора, на балансирной станине, вместе со специальной системой
водяного охлаждения.
устройство подачи шлакообразующей смеси для
смазки кристаллизатора.Располагается на тележке промковша и служит для
автоматической подачи порошка в кристаллизатор в процессе разливки с целью
предотвращения налипания расплавленной стали на гильзе кристаллизатора,
предотвращения окисления стали, изоляции поверхности стали, защиты от
поглощения посторонних включений и регулирования теплопередачи.
механизм качания используется для создания
вертикального колебательного движения, которое, в свою очередь, передается на
кристаллизатор и закрепленные на нем опорные валки.
Механизм качания состоит из сменной рамы,
привода качания, стола качания, направляющей стола качания, рамы основания
механизма качания.
В устройстве механизма качания закреплены
кристаллизатор и зона изгиба. Кристаллизатор поднимается и опускается,
амплитуда качания постоянна и составляет ±3 мм, а частота
колебаний может настраиваться от 50 до 200 мин-1.
Качание кристаллизатора и стола качания
осуществляется с помощью эксцентриковых кривошипно-шатунных механизмов,
расположенных с фиксированной и незакрепленной сторон, которые работают
синхронно посредством валов и муфт и связаны с редукторами и двигателем
привода. Частота вращения двигателя и число движений качания зависит от
скорости.
Эксцентриковое качание подается на кристаллизатор
с помощью поршня, верхний подшипник которого привинчен к столу качания. Ход
привода механизма качания задан постоянно с помощью эксцентрикового вала с
амплитудой 3 мм.
Основные параметры приведены в таблице 2.5.
Таблица 2.5 - Основные параметры механизма
качания
Наименование
параметра
|
Показатель
|
Основные
размеры, мм: длина
|
2580
|
ширина
|
1250
|
высота
|
1500
|
Масса,
кг
|
5080
|
зона изгиба (позиция 6 рисунка 2.1)
Основными составными частями сегмента являются:
внешние рамы с роликами; внутренние рамы с
роликами; боковые направляющие ролики ручьев; верхние и нижние подшипники;
опорные ролики; трубопроводы охлаждающей воды.
Внешние и внутренние рамы представляют собой
сварную стальную конструкцию. Ролики установлены на консолях, которые крепятся
на внешних и внутренних дугах. Опорные ролики центрируются и закрепляются
фланцевой плитой на верхней части внешней рамы.
Направляющие ролики ручьев, корпусы подшипников,
внешние и внутренние рамы охлаждаются изнутри. Зазор между роликами (зазор
разливки) можно настроить с помощью прокладок на роликах и на раме внутренней
дуги. Формат разливки настраивается с помощью прокладок для форматов разливки.
Верхняя подвеска сегмента установлена на сменной раме устройства механизма
качания. Нижняя опора опирается в разливочной дуге.
В таблице 2.6 приведены технические параметры
зоны изгиба.
Таблица 2.6 - Технические параметры зоны изгиба
Наименование
параметра
|
Показатель
|
1
|
2
|
Основные
размеры, мм: длина
|
3965
|
ширина
|
1210
|
высота
|
Масса,
кг: - для сечения 250 х 300 мм - для сечения 300 х 400 мм
|
7290
7620
|
Направляющие
ролики ручьев:
|
250х
300
|
300х400
|
Внутренние
дуги диаметр, мм/ количество
|
165/9
|
165/9
|
разливочная дуга (позиция 8 рисунка 2.1)
Задачей разливочной дуги является направление
поступающего из кристаллизатора в тянущее устройство и правильную зону. Кроме
того, разливочная дуга применяется в виде направляющей конструкции для
затравки. Направление ручья осуществляется 8 роликами на наружной дуге.
Направление затравки во время ее ввода
осуществляется размещенными между опорными роликами наружной и внутренней дугах
направляющими для затравки.
Основными составными частями разливочной дуги
являются:
рама разливочной дуги с внутренним охлаждением;
верхняя и нижняя опоры;
ролики внешней дуги; ролики внутренней дуги;
направляющая холодной затравки. Их технические параметры приведены в таблице
2.7.
Таблица 2.7 - Технические параметры разливочной
дуги
Наименование
параметра
|
Показатель
|
1
|
2
|
Разливочная
дуга/основные размеры рамы, мм: длина
|
не
более 9063
|
Рама
разливочной дуги:
|
внутреннее
охлаждение водой
|
ширина,
мм
|
не
более 1270
|
высота,
мм
|
не
более 2169
|
Масса,
кг
|
8530
|
Рама
разливочной дуги:
|
внутреннее
охлаждение водой
|
тянущий трайбаппарат (позиции 9,10,11 рисунка
2.1)
Предназначены для ввода и вывода затравки и транспортировки
горячего слитка. Их параметры приведены в таблице 2.8.
Таблица 2.8 - Основные параметры тянущих
трайбаппаратов
Наименование
параметра
|
Показатель
|
1
|
2
|
Высота,
мм
|
3957
|
Длина,
мм
|
1695
|
Ширина,
мм
|
954
|
Максимальная
скорость разливки, м/мин
|
0.5
- 1.0
|
Максимальная
скорость ввода затравки, м/мин
|
5
|
Максимальное
усилие вытяжки горячего слитка, т
|
25
|
Максимальное
усилие вытяжки затравки, т
|
17
|
Максимальный
движущий момент редукторов, Нм
|
1040
|
Диаметр
валка, мм
|
450
(400)
|
Передаточное
число
|
i
= 400
|
Минимальное
сечение разливочного отверстия кристаллизатора, мм
|
155
|
Максимальное
сечение разливочного отверстия кристаллизатора, мм
|
380
|
Гидравлическое
давление, Па
|
160
|
Гидроцилиндр
диаметр/ход, мм
|
140/450
|
Масса
на узел (без электродвигателей), кг: тянущего трайбаппарата №1, №2
|
5553
|
тянущего
трайбаппарата №3
|
4732
|
-промежуточный рольганг(позиция 13 рисунка 2.1)
предназначен для транспортировки затравки и/или горячего слитка между тянущими
трайбаппаратами №2, №3.
Основные узлы промежуточного рольганга:
комплекты роликов; рама рольганга; прогоны; боковые направляющие; трубопроводы
для охлаждающей воды; смазочные трубопроводы; перекрытия. Их основные параметры
приведены в таблице 2.9.
Таблица 2.9 - Основные параметры промежуточного
рольганга
Наименование
параметра
|
Показатель
|
Высота,
мм
|
600
|
Длина,
мм
|
2560
|
Ширина,
мм
|
800
|
Масса,
кг
|
7790
|
шаг
роликов, мм
|
1080
|
диаметр
роликов, мм
|
250
|
ширина
бочки, мм
|
450
|
количество
роликов, шт
|
12
|
машина газо-кислородной резки (МГКР) (позиция 14
рисунка 2.1) служит для разделения литой заготовки на мерные длины.
В таблице 2.10 показаны ее технические
характеристики.
Таблица 2.10 - Технические характеристики МГКР
Наименование
параметра
|
Показатель
|
1
|
2
|
Количество
машин, шт.
|
4
|
Диаметр
мерительного ролика, мм
|
1000
|
Скорость
передвижения машины
|
|
быстрое,
мм/мин
|
12063
|
медленное,
мм/мин
|
4000
|
Скорость
передвижения резака
|
|
быстрое,
мм/мин
|
1822
|
надрез,
мм/мин
|
100
|
резание
(мах), мм/мин
|
500
|
Давление
|
|
режущий
кислород, Па
|
8
|
кислород
для нагрева, Па
|
2,0-3,0
|
газ
для нагрева, Па
|
1,6-2,0
|
газ
дежурного пламени, Па
|
0,7-2,0
|
кислород
дежурного пламени, Па
|
1,5-2,0
|
рольганг газокислородной резки (позиция 15
рисунка 2.1) предназначен для транспортировки не отрезанных или отрезанных
блюмов, а также для транспортировки вводимой и выводимой затравки. Над
рольгангом находится машина газокислородной резки, перемещаемая в направлении
ручья.
боковой шлеппер предназначен для передачи блюмов
с ручьев на рольганг передаточного пролета или на накопительный стол с
захватками.
накопительный стол с захватками расположен сбоку
от шлеппера предназначен для накопления блюмов прямоугольного сечения,
предназначенных для процесса медленного охлаждения.
Состоит из приемного стола, захватов, подвижных
траверс.
холодильник с шагающими балками расположен на
конечном отрезке участка разгрузки заготовок. Холодильник на шагающих балках
предназначен для охлаждения заготовок круглого сечения.
стол-накопитель для заготовок круглого сечения
располагается за холодильником и убирает заготовки в конце машины [ 4 ].
.1.1 Описание технологического процесса
Жидкий металл поставляется из сталеплавильного
цеха в двухстопорном сталеразливочном ковше с огнеупорной футеровкой.
Сталеразливочный ковш устанавливается мостовым
краном в определенной позиции на поворотный стенд МНЛЗ. Отверстие в дне ковша
закрыто шибером. С целью установки ковша в разливочную позицию поворотного
стенд поворачивается на 180° и ковш располагается над промковшом. Промковш
оборудован огнеупорной футеровкой. Для уменьшения тепловых потерь промковш
закрывается крышкой с огнеупорной футеровкой.
При помощи двух тележек промковши перемещаются
между позициями разливки и разогрева в направлении, перпендикулярном по
отношению к направлению разливки. Каждая из тележек также оснащена
гидравлическим подъемным устройством. В позициях разогрева находятся
стационарные разогревающие горелки, а также стационарные станции для разогрева
погружных стаканов.
В целях защиты разливочной струи от вторичного
окисления между сталеразливочным ковшом и промковшом расположена труба из
огнеупорного материала.
После открытия шибера сталеразливочного ковша
жидкий металл поступает в промковш, из которого распределяется на четыре ручья.
Подача металла из промковша в кристаллизатор
автоматически регулируется стопором. По погружным стаканам с огнеупорной
футеровкой, расположенной в нижней части промковша, жидкий металл поступает
затем в кристаллизатор.
Рабочие стенки кристаллизатора охлаждаются и
выполнены из медных пластин длиной 800 мм, с мультиплакированными рабочими поверхностями.
При достижении жидким металлом определенного
уровня в кристаллизаторе, стопоры последовательно открываются и жидкий металл
равномерно распределяется по всему кристаллизатору.
Уровень жидкого металла в кристаллизаторе
регистрируется радиоктивным измерительным устройством, на основании чего
регулируется подача жидкого металла в кристаллизатор путем подъема и опускания
стопора. Процесс разливки начинается после достижения в кристаллизаторе
определенного уровня жидкой стали.
Чтобы можно было начать разливку необходима
затравка. Затравки исполнены в виде так называемых универсальных затравок,
оснащаемых соответствующими головками и переходными звеньями и представляет
собой цельную конструкцию, которая вводится в кристаллизатор. Между головкой
затравки, находящейся в кристаллизаторе, и медными пластинами кристаллизатора
имеется уплотнение в виде огнеупорных шнуров, предотвращающее утечку жидкого
металла при заполнении кристаллизатора.
В кристаллизаторе начинается затвердевание
жидкого металла с
образованием
корочки слитка, которая не разрушается под действием ферростатического давления
и усилия вытяжки на выходе из кристаллизатора. Для предупреждения “зависания”
корочки в кристаллизаторе, последний осуществляет возвратно-поступательные
движения в вертикальном направлении, вырабатываемые приводом механизма качания
(синусоидальная форма кривой).
С целью защиты от теплоизлучений и от вторичного
окисления зеркало жидкого металла в кристаллизаторе покрывается изолирующими и
покровными шлаковыми смесями (ШОС) на плавиковой основе. Которая служит в
качестве смазочного средства между корочкой непрерывнолитого слитка и стенками
кристаллизатора.
При плавлении ШОС образуется смазочная пленка. В
выбор подходящего смазочного средства оказывает решающее влияние на качество
поверхности слитка.
После выхода из кристаллизатора расположена зона
вторичного охлаждения где слиток подвергается охлаждению. Интенсивность
охлаждения слитка автоматически регулируется в соответствии с поведением
разливаемых марок стали при затвердевании.
Образующийся водяной пар собирается в
холодильной камере и отсасывается из нее двумя вентиляторами через цеховую
крышу.
Частично затвердевший непрерывно-литой слиток
сначала поступает в радиальную зону (разливочная дуга), а затем, после выхода
из зоны правки (правильной зоны), вновь переводится в горизонтальную зону.
Движение непрерывнолитого слитка осуществляется
тремя трайбаппаратам, их ролики приводные с гидравлическим регулированием
вытягивают непрерывно-литой слиток из кристаллизатора. Затвердевание слитка
происходит не позднее, чем за тянущим трайбаппаратом № 3.
За тянущим трайбаппаратом № 3 следует устройство
для отделения затравки, отделяющее затравку от горячего слитка. Отделение
затравки от кристаллизатора осуществляется автоматическим устройством. По
окончании процесса отделения затравка вытягивается со скоростью рольганга и
вынимается из технологической линии при помощи подъемного приспособления.
Отделение затравки от слитка может быть выполнено также машиной для газовой
резки.
Вытягиваемый со скоростью разливки
непрерывнолитой слиток через рольганг для газовой резки передается к машине для
газовой резки (горелки, работающие на природном газе и кислороде) с
приспособлением для измерения длины и режется на требуемые мерные длины.
Разрезанные на мерные длины заготовки через
отводящие рольганги транспортируются в рабочую зону поперечного транспортера.
Снятие заготовок и их транспортировка на рольганг для горячего посада
осуществляются поперечным транспортером.
На участке поперечного транспортера заготовка
подвергаются маркировке цифрами и буквами на маркировочной машине, а также
взвешивается, и передается в прокатный цех или на промежуточное хранения за
пределами МНЛЗ.
МНЛЗ работает в автоматическом режиме.
Важнейшие рабочие параметры регистрируются и
индицируются на дисплеях [ 4 ].
.2 Описание конструктивных элементов МНЛЗ после
реконструкции
По мере совершенствования изделий машиностроения
в настоящее время возрастают и требования к качеству металла со стороны
потребителей, что влечет за собой необходимость совершенствования технологии и
оборудования для производства стали, а также увеличения производительности
существующей МНЛЗ, получения поверхности заготовки более высокого качества, без
трещин, снижение брака и улучшения макроструктуры заготовки.
Современный технологический процесс производства
качественной высокоуглеродистой, среднеуглеродистой, легированной сталей и
сталей кордового назначения, как правило, включает непрерывную разливку. Ввиду
этого макро- и микроструктура непрерывнолитой заготовки, следовательно,
получение из нее конечной продукции круга или цельнотянутой трубы или катанки
или металлокорда имеет ряд характерных особенностей, в значительной мере
определяющих конечное качество продукции.
К числу основных дефектов литой заготовки,
разливаемой на МНЛЗ-3 РУП «БМЗ» можно отнести:
продольные трещины по кромкам (прорывы);
осевая пористость и ликвация;
диагональные трещины, ромбичность;
краевое точечное загрязнение (неметаллические
включения);
подусадочная ликвация.
Также с пуском в эксплуатацию собственного
трубного производства, возникла необходимость в получении более дешевой трубной
заготовки диаметром 200 мм путем ее непрерывной разливки.
С целью гарантированного получения более
качественной заготовки (блюма) и получения нового вида продукции, литая круглая
заготовка (диаметром 200 мм) из углеродистой, легированной качественной и
трубной марок стали со скоростью разливки от 0,7 до 2,1 м/мин, РУП «БМЗ» был
предложен ряд реконструкционных мероприятий (согласно разделу 1).
Главная цель которых - достижение
технологического решения:
высокое качество продукции;
высокая производительность;
максимальная простота в эксплуатации;
эксплуатационная надежность;
максимальная гибкость удовлетворения различной
рыночной коньюктуры.
Проведение реконструкции позволит достичь на
МНЛЗ следующих технических характеристик (таблица 2.11, 2.12 ), (приложение В).
Таблица 2.11 - Технические характеристики МНЛЗ
после реконструкции
Наименование
параметра
|
Показатель
|
1
|
2
|
Годовое
производство, т
|
841
000
|
Тип
машины
|
криволинейный
|
Количество
ручьев
|
4
|
Радиус
машины, м
|
13
(технология многоточечной правки)
|
Точки
разгиба, м
|
(13-18-34)
многоточечная правка
|
Расстояние
между ручьями, мм
|
1300-1500-1300
|
Оснастка
для разливки сечений, мм
|
200
круглое сечение
|
|
250х300
прямоугольное сечение
|
|
300х400
прямоугольное сечение
|
Вместимость
стальковша, т
|
110
|
Вместимость
промковша, т
|
25
|
Форма
промковша
|
дельтообразная
|
Уровень
стали в промковше, мм
|
100,
рабочий уровень
|
Контроль
уровня промковша
|
метод
взвешивания
|
Способ
разливки
|
через
погружные стаканы
|
Управление
струей
|
стопорный
механизм
|
Гильза
кристаллизатора длина, мм
|
780,
криволинейного типа
|
Смазка
кристаллизатора
|
порошок
(ШОС)
|
Электромагнитное
перемешивание
|
в
кристаллизаторе
|
Механизм
качания кристаллизатора
|
гидравлический
|
Частота
качания кристаллизатора
|
25-250
качаний в минуту
|
Вторичная
система охлаждения:
|
|
первая
зона
|
(опорные
ролики) вода
|
вторая
зона
|
воздух
и вода
|
третья
зона
|
воздух
и вода
|
четвертая
зоны
|
воздух
и вода
|
Тянуще-правильный
агрегат
|
9
модулей (для каждого ручья)
|
Скорость
извлечения, м/мин
|
0,25-5,00
|
Тип
затравки
|
гибкий
|
Длина
резки, м
|
|
круглое
сечение 200 мм
|
от
4,0 до 9,6
|
сечение
250х300, 300х400 мм
|
от
2,5 до 5,5
|
Таблица 2.12-Технические характеристики
кристаллизатора после реконструкции:
Наименование
параметра
|
Показатель
|
Тип
|
Вставка
кристаллизатора - цилиндрической формы (CuAg)
|
Длина
кристаллизатора, мм
|
780
|
Конус
|
DANAM
|
Сечение,
мм
|
диаметр
200
|
250х300
|
300х400
|
Необходимый
первичный расход на ручей, л/мин
|
1800
|
2250
|
3400
|
Зазор
протока воды, мм
|
3,25
|
3,25
|
4,00
|
Давление
воды на входе кристаллизатора, Па
|
8
|
8
|
8
|
Падение
давления, Па
|
4
|
2,5
|
2,3
|
Максимальная
температура воды на входе, °С
|
35
|
35
|
35
|
Тип
гильзы
|
Медная
гильза- трубчатый (CuAg)
|
Длина
гильзы, мм
|
780
|
Сечение,
мм
|
диаметр
200
|
250х300
|
300х400
|
Количество,
конусов
|
02
|
04
|
04
|
Конус
1, мм
|
300
(1,90 %)
|
190
(2,40 %)
|
190
(2,40%)
|
Конус
2, мм
|
480
(1,60%)
|
210
(1,20%)
|
210
(1,20%)
|
Конус
3, мм
|
-
|
380
(0,50%)
|
380
(0,50%)
|
Размер
дна, мм
|
диаметр
205
|
254х305
|
310х410
|
Толщина
гильзы, мм
|
16
|
24
|
28
|
Внутренний
радиус, мм
|
-
|
10
|
10
|
Водяной
зазор, мм
|
3,25
|
3,25
|
4
|
Для транспортировки круглых заготовок диаметром
200 мм был спроектирован холодильник на шагающих балках.
Для правильного расчета холодильника на шагающих
балках, важно определить наиболее неблагоприятный случай с учетом следующих
условий:
средняя расчетная температура заготовки на входе
в холодильник составляет 900 °C;
максимальная скорость разливки для 4 ручьев;
максимальная температура на выходе 600 °C.
Общая длина холодильника 16 м, шаг позиций укладки
на холодильнике 300 мм. Температура заготовки на выходе (наихудший случай):
выше 600°C (5,5 м) [5].
Планировочное расположение МНЛЗ в цехе
Установка непрерывной разливки стали со
встроенным зданием снабжения средами расположена в сталеплавильном цехе -
пролет D/E, между колоннами 1-4 - и в прокатном цехе - пролет E/F до колонны 5.
Вспомогательное оборудование, как, например,
хозяйство промковшей и опорная мастерская с необходимыми складскими участками
находятся в сталеплавильном цехе - пролет D/E между колоннами 4-7.
Складские участки для промежуточного хранения
блюмов в аварийных ситуациях расположены в зоне прокатного цеха.
Все реконструкционные мероприятия планируется
провести на базе существующего оборудования ЭСПЦ - 2 РУП «БМЗ» без каких либо
изменений в планировке цеха (приложение Г).
. ТЕХНОЛОГИЯ ПРОИЗВОДСТВА СТАЛИ МАРКИ 40Х
.1 Технические требования и химический состав
легированной среднеуглеродистой стали 40Х
Из стали 40Х на РУП «БМЗ» согласно ГОСТу 4543-71
производится заготовка круг, которая применяется в машиностроении для
производства конструкционных деталей и механизмов (оси, валы, вал- шестерни,
плунжеры, штоки, коленчатые и кулачковые валы, зубчатые венцы и другие
улучшаемые детали повышенной прочности.
Вид поставки - сортовой прокат, в том числе
фасонный: ГОСТ 4543-71, ГОСТ 2590-71, ГОСТ 2591-71, ГОСТ 2879-69, ГОСТ
10702-78.
Шлифованный пруток и серебрянка ГОСТ 14955-77.
Полоса ГОСТ 103-76, ГОСТ 82-70.
Технологические свойства: трудносвариваемая,
флокеночуcтвительная, склонна к отпускной хрупкости.
Основными механическими характеристиками круга
диаметром 80-120 мм из стали 40Х являются временное сопротивление разрыву и
сужение поперечного сечения при испытании на растяжение, отражающие возможность
упрочнения и пластичность. Технические требования к заготовке кругу диаметром
80-120 мм, должны соответствовать требованиям, изложенным в ГОСТ 4543-71
(таблица 3.1), [ 6 ].
Таблица 3.1 - Химический состав стали марки 40Х
по ГОСТ 4543-71
Марка
стали 40Х
|
Содержание
элементов, %
|
|
|
С
|
Si
|
Mn
|
P
|
S
|
Cr
|
Ni
|
Cu
|
|
max
|
0,36
|
0,17
|
0,50
|
-
|
-
|
0,80
|
-
|
-
|
0,44
|
0,37
|
0,80
|
0,035
|
0,035
|
1,10
|
0,30
|
0,30
|
3.2 Технология выплавки стали 40Х на ДСП-3
Сталь 40 Х выплавляется в ДСП-3 одношлаковым
процессом, с жидким стартом - завалкой шихты на "болото" (оставление
части металла и шлака 5-10 тонн от предыдущей плавки). После слива предыдущей
плавки производится операция по заправке печи огнеупорными материалами и
подварке порога печи.
Для заправки печи используется магнезитовый
порошок. Заправка производится сухим материалом, либо увлажненным водным
раствором жидкого стекла, с помощью лотков, вручную, или штатными средствами
заправки. Порог рабочего окна должен быть очищен от остатков металла и шлака.
Порог заправляется (подваривается) сухим магнезитовым порошком или доломитом,
либо порошком фракции, не превышающей 20 мм, из переработанных второгнеупоров.
Загрузка металлошихты, состоящей из лома черных
металлов и передельного чугуна, осуществляется с помощью специальных корзин в
два приема - завалка (основная) и подвалка. Шихтовка плавок для стали 40 Х
производится по 3 вариантам с использованием легированного лома в количестве,
обеспечивающим содержание легирующих элементов в жидком металле на нижнем
пределе (таблица 3.2).
Таблица 3.2 - Рекомендуемые варианты шихтовок для
стали 40Х
Шихтовка
|
1
вариант
|
2
вариант
|
3
вариант
|
Углеродистый
лом 2А, 3А
|
45-55
|
70-80
|
85-95
|
Пакеты
8А, 9А
|
10-15
|
-
|
10-15
|
Легированный
лом Б-1,3
|
30-40
|
30-40
|
-
|
Оборотный
углеродистый лом
|
5-10
|
-
|
5-10
|
Сразу после выпуска плавки присаживается известь
массой от 1000 до 1500 кг, а затем коксовая мелочь или кокс с размером фракции
от 25 до
мм массой от 300 до 350 кг.
Завалка металлошихты в печь производится после
закрытия шибера и засыпки канала эркера. При ведении плавки с
"болотом" для ускорения плавления лома укладыватся кислородное
"копье" под металлошихту. Во избежание зашлакования выходного
отверстия кислородного копья подается кислород для отдува с минимальным
расходом 250 м3/ч. Далее производят процесс завалки металлошихты из корзины в печь.
После загрузки металлошихты в печь заводится
свод, опускаются графитированные электроды и производится расплавление шихты в
автоматическом режиме, за счет образования электродуги и использования энергии
топливно-кислородных горелок (ТКГ). В автоматическом режиме осуществляется
также энергетический режим (переключение ступеней напряжения) и присадка
шлакообразующих материалов.
После расходования от 1000 до 1500 кВт·ч
электроэнергии производится включение газокислородных горелок с инжектором.
Суммарный расход природного газа на все горелки поддерживается автоматически
составляет 1750 м3/ч, кислорода около 8500 м3/ч газа, угля - 15-40
кг/мин.Продолжительность работы горелок от 15 до 18 мин.
После расхода электроэнергии от 7000 до 10000
кВт·ч в печь присаживают коксовую мелочь или кокс с размером фракции от 25 до
40 мм массой 400кг разовыми порциями до 50 кг, присадка извести массой до 4,0
тонн производится отдельными порциями массой от 200 до 300 кг.
При вдувании кислорода через копье, находящееся
под шихтой, после отработки 7000 кВт·ч электроэнергии его массовый расход
повышают от 1200 до 1500 м3/ч. После отработки 17000-20000 кВт·ч производится
подвалка металлошихты. Масса подвалки составляет 50-60 т.
Расплавление подвалки производится также в
автоматическом режиме.
Сразу после окончания работы дверной горелки и
подрезки шихты, в
рабочее окно вводится фурма «МАРК-4» и
производится продувка жидкого расплава кислородом с расходом от 1800 до 2400
м3/ч и эркерной горелкой с расходом от 1200 до 1500 м3/ч.
Цель данной технологической операции заключается
в интенсификации процесса расплавления шихты, поскольку кипение (перемешивание)
ускоряет нагрев ванны и усредняет расплав по температуре и химическому составу.
Для повышения устойчивости горения дуг, защиты футеровки и водоохлаждаемых
элементов печи от прямого излучения при помощи манипулятора и эркерной горелки
подается угольная пыль фракцией с расходом от 15 до 40 кг/мин в количестве от
300 до 600 кг на плавку, с таким расчетом, чтобы поддерживать шлак во
вспененном состоянии до конца плавки, который необходим для экранирования
электродуги.
После отработки 17000-20000 кВт·ч производится
подвалка металлошихты. Масса подвалки составляет 50-60 т. Расплавление подвалки
производится также в автоматическом режиме.
Включение печи и зажигание дуги производят на 19
ступени напряжения с последующим переходом на 22-24 ступень.
Сразу после окончания работы дверной горелки и
подрезки шихты, в рабочее окно вводится фурма «МАРК-4» и производится продувка
жидкого расплава кислородом с расходом от 1800 до 2400 м3/ч и эркерной горелкой
с расходом от 1500 до 1900 м3/ч. С началом подачи кислорода в печь
осуществляется присадка извести отдельными порциями массой от 100 до 200 кг до
1,5 тонн.
В процессе всей выплавки стали в ДСП-3 производится
донная продувка ванны металла по методу "VRD" азотом или аргоном в
автоматическом режиме. В течение всего окислительного периода шлак
поддерживается во вспененном состоянии, что позволяет производить
технологический процесс удаления фосфора и небольшой части серы из
металла,
которая в процессе плавки переходит в шлак. Шлак самотеком скачивают через
порог рабочего окна в шлаковую чашу, не допуская схода металла.
После расплавления металлошихты, при температуре
1560-15800С отбирается проба, которая отправляется в лабораторию по
пневмопочте. В пробе металла спектральным методом определяется массовая доля
химических элементов: углерода, кремния, серы, фосфора, меди, никеля, марганца,
хрома согласно требованиям нормативно-технической документации (НТД).
Доводка плавки производится на 22-19 ступенях
напряжения. За период доводки плавки должно быть окислено не менее 0,10 %
массовой доли углерода. Продолжительность кислородного рафинирования зависит от
массовой доли углерода в металле и содержания серы (соответственно менее 0,2% и
0,030%).
По окончании окислительного периода и нагрева
металла перед выпуском измеряют температуру и отбирают пробу металла на
химический анализ. По окончанию окислительного периода и нагрева металла до
температуры 1660-16800С производится его выпуск в сталеразливочный ковш,
который предварительно прогретый до состояния красного каления (температура не
менее 8000С) устанавливается на сталевозе. Рекомендуемая массовая доля углерода
в металле перед выпуском не менее 0,10 %. Перед выпуском стали из печи
производится расчет количества науглероживателя, раскислителей, легирующих на
плавку на нижний марочный предел для заданной марки стали и загружается в
расходный бункер заранее взвешенными порциями. После выпуска полупродукта
плавка передается на участок внепечной обработки [ 7 ].
Технические характеристики и технологические
показатели ведения плавки в ДСП-3 представлены в таблице 3.3.
Таблица 3.3 - Технико - технологические
характеристики ДСП - 3
Наименование
параметра
|
Показатель
|
1
|
2
|
Технические
характеристики
|
Вместимость
печи, т
|
100
|
Активная
мощность трансформатора, МВ·А
|
75
|
Максимальный
ток, кА
|
72
|
Внутренний
диаметр кожуха, мм
|
6400
|
Внутренний
диаметр охлаждающих стенок, мм
|
6455
|
Высота
кожуха над уровнем окна, мм
|
2600
|
Высота
окна над уровнем площадки, мм
|
700
|
Размеры
рабочего окна, мм
|
1250х1000
|
Диаметр
электрода, мм
|
610
|
Диаметр
делительной окружности, мм
|
1400
|
Ход
электрода, мм
|
4200
|
Высота
подъема свода, мм
|
400
|
Угол
поворота свода, град
|
76
|
Угол
наклона печи на слив металла, град
|
38
|
Угол
наклона печи на слив шлака, град.
|
12
|
Охлаждение
электрододержателей
|
вода
|
Расход
воды на охлаждение механических деталей, м3 /ч
|
230
|
Поворотный
механизм печи и механизм подъема и поворота свода
|
водно-глюколевая
смесь
|
Рабочее
давление, мПа
|
14
|
Регулировка
электродов и управление заслонкой окна
|
гидравлическое
|
Рабочее
давление, мПа
|
6
|
Угол
наклона печи на слив металла при выпуске на "болото", град
|
10
|
Угол
наклона печи на слив металла при выпуске "начисто", град
|
25
|
.3 Технология раскисления и легирования стали
40Х на выпуске
Раскисление и легирование стали 40Х
осуществляется в ковше во время выпуска присадками науглероживателя, алюминия,
ферросилиция, силикомарганца. Быстродействующий клапан на подачу аргона в ковш
должен быть открыт перед началом выпуска. Присадки науглероживателей и
раскислителей в ковш осуществляются через транспортную систему подачи
материалов, заранее взвешенными порциями.
Информация о количестве присаживаемых материалов
вводится в ЭВМ в отчет о плавке.
Материалы для присадки в ковш набираются в
промежуточный бункер-наполнитель и вводятся в следующей последовательности. Для
проведения предварительного двухстадийного углеродного раскисления за 10-15
минут до слива металла, в бункер набирается коксовая мелочь или науглероживатель
тип “С” в количестве от 60 до 150 кг, после чего данный материал отдается на
дно ковша.
Далее в бункер набираются следующие материалы:
известь 300-400 кг, коксовая мелочь 50-100 кг из расчёта получения в аргонной
пробе содержания углерода 0,20-0,25 %; затем ферросилиций (FeSi75) - 250 - 300
кг из расчёта получения содержания кремния 0,17 - 0,20 %, затем (SiMn78) -
400-600 кг из расчёта получения содержания марганца 0,40 - 0,50 %.
При наполнении ковша 35-40 тоннами металла,
производится отдача чушкового алюминия в количестве 12-28 кг. После наполнения
1/3 ковша металлом (40-50т) присаживают порцию шлакообразующих, раскисляющих и
легирующих материалов указанных выше. После полного наполнения ковша 105-110
тонн присаживается плавиковый шпат в количестве 70-100 кг.
Проведение такой технологии предварительного
углеродного раскисления и легирования металла на выпуске, позволит получить
химический состав стали 40Х на нижнем значении требований ГОСТа сразу же после
выпуска металла в ковш.
Выпуск металла заканчивают при наполнении ковша
на высоту не менее 400 мм и не более 200 мм от верхнего среза по футеровке.
Далее ковш с металлом передается на аргонную
установку, где металл продувается аргоном в течение не менее 5 мин. Отбирается
проба металла на полный химический анализ и производится замер температуры,
после чего плавка передается на установку «ковш-печь» для ведения дальнейшей
внепечной обработки [ 8 ].
3.4 Технология обработки металла на установке
«ковш-печь»
По прибытию ковша на установку “печь-ковш”, в
последовательности, определяемой диалогом АСУТП "Начало плавки",
вводятся данные о плавке. После подключения продувочных фурм к трассе
регулируется подача аргона.
Производится визуальная оценка интенсивности
продувки металла.
Продувка металла аргоном устанавливается с
расходом до 300 л/мин и не должна приводить к выбросам металла и шлака из
стальковша и оголению зеркала металла.
Продолжительность продувки составляет 3 - 5 мин.
Далее опускается свод, производится измерение температуры стали для последующего
выбора ступени напряжения. Ступень напряжения в пределах от 9 до 11
устанавливается для поддержания температуры, а в пределах от 12 до 15 - для
нагрева металла.
При внепечной обработке на установке “печь-ковш”
первоначально наводится белый рафинировочный шлак присадками извести в
количестве 6 - 10 кг/т и плавикового шпата 1,0 -
1,5 кг/т. Продолжительность наведения рафинирующего шлака составляет от 5 до 15
минут, при этом покровный шлак сформированный присадками шлакообразующих
материалов с основностью (CaO:CaF2 = 4:1) доводят до получения отношения
кратности шлака к металлу 1,2:100.
Далее производится раскисление шлака присадками
раскисляющей смеси АКС порцией по 40-60 кг на плавку, ввод алюминия в металл
при необходимости осуществляется в первую очередь трайбаппаратом из расчёта
получения его в металле 0,012-0,030 %. Для ввода 0,01% Al в
зависимости от массы жидкого металла в ковше от 100т до 120т необходимо
присадить AlCa проволоку в количестве от 200 до 250м.
После производится корректировка химического
состава стали присадками науглероживателя и ферросплавов. При корректировке
содержания кремния необходимо учитывать кремний, вносимый силикокальцием при
дальнейшей обработке. При корректировке стали по содержанию химических
элементов во время отдачи ферросплавов в ковш расход инертного газа необходимо
увеличить на 30-50 л/мин (но не более 300 л/мин.) и выдержать не менее 5 минут.
В течение всей внепечной обработки металл
продувается аргоном, при необходимости допускается кратковременное включение катушки
ЭМП. Далее плавка передается на циркуляционный вакууматор «RH» или в
вакуумкамеру «VD».
Температура металла для среднеуглеродистой
легированной стали 40Х перед вакуумированием должна быть 1575-1600˚С, на
15-40˚С выше температуры отдачи плавки на МНЛЗ.
Вакуумная обработка металла на вакууматоре RH
начинается не ранее, чем за 60 мин, а на вакууматоре VD не ранее, чем за 80
мин, до передачи плавки на МНЛЗ. Длительность вакуумной обработки: -
на RH не менее 15мин; - на VD не менее 20мин. При
остаточном разряжении: - на RH - 1,5 мПа не менее 7 мин; - на VD - 1.5 мПа не
менее 10 мин.
После вакуумирования отбирается проба шлака на
полный химический анализ и производится замер содержания водорода в металле
датчиками “Hydris”.
Содержание FeO+MnO в шлаке должно быть не более
1,5%. Содержание водорода в металле не должно превышать 3,0%, при содержании
водорода более 3,0% производится повторное вакуумирование, при отсутствии
возможности повторного вакуумирования плавка передается на МНЛЗ с обязательным
посадом в колодцы замедленного охлаждения после прокатки на стане 850.
При необходимости допускается корректировка
химического состава
стали
по содержанию углерода проволокой с углеродным наполнителем, но не более чем на
0,05% и алюминия проволокой по замеру активности кислорода датчиком “Celox”.
После вакуумирования плавка опять передается на
установку «печь-ковш», где далее производится корректировка по алюминию.
После корректировки по алюминию катанкой
присаживают трайбаппаратом силикокальциевую проволоку для модификации
неметаллических включений.
Необходимое количество проволоки рассчитывается
по компьютерной программе “SiCa”:
= (0,0144∙S+0,00686∙Al+0,000012∙T)∙M/2,56∙b∙b∙h
(3.1)
где: L - необходимая длина
проволоки, м; - cодержание S в металле перед присадкой SiCa, %;
Аl - содержание
алюминия в металле перед присадкой, %;
Т - температура металла в стальковше перед
присадкой, оС;
М - масса жидкого
металла в ковше, т;
,56 - эмпирический расчетный коэффициент;
b -степень усвоения Са, (принимать 8%); -содержание
Ca в SiCa, (30%);
h -степень наполнения порошковой проволоки, 1
погонный м - 0,225 кг (0,195кг).
Ввод проволоки в металл осуществляется при
отключенной установке подогрева. Скорость ввода проволоки 3,0 -
3,5 м/с. После присадки силикокальция металл продувается аргоном без оголения
зеркала металла в течение не менее 5 минут.
Допускается кратковременный подогрев после
присадки порошковой проволоки с SiCa для поддержания требуемой температуры
металла.
Перед передачей ковша на МНЛЗ-3 поверхность металла
утепляется одной из нижеперечисленных смесей в следующих количествах:
утепляющая смесь П-1, П-3180 - 200 кг;
утепляющая смесь ТИС 3К100 - 150 кг;
зола рисовой шелухи (лузги)100 -
120 кг.
После проведения всей внепечной обработки и
получения заданного химического состава, металл передается с требуемой
температурой 1545 - 1555°С на МНЛЗ-3.
При разливке стали методом “плавка на плавку”
допускается снижение температуры металла в стальковше перед началом разливки на
10-15°С
(кроме 1-й плавки в серию) [ 9 ].
Технологические параметры внепечной обработки
легированной стали 40Х представлены в таблице 3.4.
Таблица 3.4 - Технологические параметры
внепечной обработки легированной стали 40Х
Время
обработки мин
|
Печь
- ковш
|
общее
|
40-60
|
|
|
под
током
|
21-28
|
|
Вакууматор
RH
|
общее
|
15
|
|
Общее
время внепечной обработки
|
76-103
|
Удельный
расход материалов, кг/т
|
CaО
|
3,0-3,2
|
|
Раскисляющая
смесь (АКС)
|
0,38-0,4
|
|
SiСa
|
0,65-0,7
|
Содержание
в шлаке, %
|
(FeO+MnO)
|
0,3-0,5
|
Основность
шлака
|
белого
|
2,8-2,9
|
|
низкоосновного
|
1,6-1,8
|
Интенсивность
продувки аргоном, л/мин
|
200-250
|
Содержание
в расплаве, %
|
[H]
|
1,5-2,5
|
|
[O]
|
14-16
|
.4.1 Основные требования к разливаемому металлу
Для разливки стали 40Х на МНЛЗ-3, металл подают
после корректировки его температуры и усреднения по химическому составу на
установке внепечной обработки стали «ковш-печь».
Технологические параметры разливки стали 40Х на
МНЛЗ-3 приведены в таблице 3.5.
Таблица 3.5 - Температура металла и
технологические параметры разливки стали 40Х (проектный вариант)
В
печи перед выпуском, °С
|
1660-1680
|
В
сталеразливочном ковше перед началом разливки на МНЛЗ, ˚С
|
1545-1560
|
В
промежуточном ковше, ˚С
|
1510-1525
|
Температура
ликвидус, ˚С
|
1485-1499
|
Применяемые
ШОС
|
Scorialit
189, 163
|
Группа
охлаждения
|
2
|
Химический состав используемых при разливке
стали 40Х смесей указан в таблице 3.6.
Химический состав утеплителей приведен в таблице
3.7.
Таблица 3.6 - Химический состав ШОС,
используемых при разливке стали 40Х
Тип
ШОС
|
Массовая
доля химических элементов, %
|
|
SiO2
|
СаО+
MgO
|
MnO
|
Al2O3
|
Na2O+K2O
|
Fe2O3
|
Н2О
|
F
|
С
(общ.)
|
Scorialit-C
163-79/H
|
24,0
- 26,0
|
23,5
- 25,5
|
< 0,2
|
11,5
- 13,5
|
2,5
- 4,0
|
3,0
- 5,0
|
< 0,8
|
5,0
- 6,5
|
23,0
- 25,0
|
Scorialit-C
189/Е 2
|
30,0
- 32,0
|
18,5
- 20,5
|
< 0,1
|
4,5
- 6,0
|
9,5
- 11,5
|
1,0
- 2,5
|
< 0,8
|
3,5
- 5,0
|
23,0
- 25,0
|
Таблица 3.7 - Химический состав утеплителей
используемых при разливке стали 40Х
Тип
утеплителя
|
Массовая
доля химических элементов, %
|
|
SiO2
|
CaO
|
Al2O3
|
Na2O+K2O
|
MgO
|
Wр,
не более
|
С
|
Fe2O3
|
П-2,
П-3
|
22
- 30
|
47
- 60
|
3
- 7
|
0
- 20
|
3
- 7
|
< 0,6
|
4
- 6
|
0,5
|
Зола
рисовой шелухи
|
90-95
|
-
|
1,5
|
-
|
-
|
-
|
< 5
|
-
|
Зола
рисовой лузги
|
92-94
|
-
|
-
|
-
|
-
|
1,5
|
11-18
|
-
|
Присадка утеплителя в промковш производится
после наполнения его металлом в количестве от 5 до 7 т. Удельный расход
утеплителя для первых плавок в серии должен составлять от 0,4 до 0,6 кг, для
последующих от 0,2 до 0,4 кг на одну тонну жидкой стали.
Измерение температуры металла в промковше
производят 3 раза (в начале, в середине и в конце разливки) или непрерывно. При
температуре металла в промковше на верхнем пределе допуска, разливка
производится со скоростью равной нижнему температурному пределу допуска для
соответствующей марки стали и сечения заготовок.
Размер обрези головной части заготовки
составляет 600-700 мм, а хвостовой части - 1200-1700 мм. Порез заготовки на мерную
длину осуществляется, согласно задания производственного отдела.
.5 Технологический расчет производства стали
марки 40Х
.5.1 Баланс металла по электросталеплавильному
производству
Для составления баланса металла необходимо
определить количество отходов, образующихся в электросталеплавильных и
прокатных цехах. Отходы, которые не могут быть использованы в качестве шихты
для плавки стали в электропечах, называют невозвратимыми отходами. Количество
отходов зависит от многих факторов: сортамента продукции, ёмкости печей, типа
МНЛЗ, качества шихтовых материалов, тщательности исполнения технологий и многих
других факторов, в том числе и от квалификации персонала. Чем меньше количество
отходов, тем меньше расход металлошихты на 1т годного, тем рентабельней работа
предприятия.
.5.2 Отходы в электросталеплавильном цехе
Возвратимые отходы в электросталеплавильном цехе
представляют собой обрезь заготовок, отливаемых на МНЛЗ и скрап.
Отходы в виде скрапа возникают в следствие
образования козелков в сталеразливочных ковшах, в промежуточных ковшах при
разливке на МНЛЗ и т.д. Количество скрапа колеблется в пределах 0,5 - 1% от
массы жидкой стали. Количество обрези заготовок - при разливке стали на МНЛЗ
зависит от сечения заготовки, емкости печи, числа ручьев.
Невозвратимые отходы в ЭСПЦ представляют собой
угар металла в печи в результате испарения в зоне электрических дуг и окисления
его поступающим в печь кислородом.
При наличии в цехе МНЛЗ дополнительно появляется
угар при резке металла газорезками на мерные заготовки.
Величина угара в печах в большой степени зависит
от качества шихты:стружка, мелкий ржавый скрап окисляются больше, в связи с
этим, величина угара возрастает. Угар увеличивается при продувке расплава
кислородом. Величина угара обычно колеблется от 6% до 9%, а иногда поднимается
и до 11-12% от массы загружаемой металлической шихты.
Выход годного определяет расход шихты на 1т
заготовок и определяется по формуле:
¦ = SШ / SQ(3.2)
где SШ - потребность в
шихте с учетом потерь на возвратимые и невозвратимые отходы;
SQ - годовое производство заготовок.
Для ЭСПЦ, в соответствии с формулой 3.2,
величина ¦ всегда больше 1, в зависимости от сортамента
сталей и технологии она колеблется в пределах 1,09 - 1,2. В соответствии с этим
обратная величина - выход годного составляет 83-92%.
.5.3 Отходы в прокатных цехах
При прокатке заготовки также образуются
возвратимые и невозвратимые отходы. Первые могут использоваться в качестве
шихты для электропечей. Для оценки количества отходов в прокатных цехах
необходимо располагать данными о выходе годного (ВГ) или о коэффициенте расхода
(КР) и схемой прокатки металла. Выход годного определяется потерями при
прокатке: угаром при нагреве заготовки перед прокаткой, обрезью концов, включая
потери при зачистке, браком и недокатом.
Выход годного считают в процентах от массы
заготовки:
ВГ = 100 - П(3.3)
где П - потери, %.
Другой показатель - коэффициент расхода (КР),
характеризует расход заготовки на 1т годного. Он представляет собой величину,
обратную выходу годного :
КР = 100 / (ВГ)(3.4)
Выход годного из заготовок на современных
сортовых станах (в соответствии с формулой 3.3) колеблется в среднем от 91% до
96%, при чем большие значения относятся к мелкосортным, полосовым и проволочным
станам.
В соответствии с формулой 3.4
КР = 100 / (91-96) = 1,099 - 1,041.
В таблице 3.8 приведена принятая на РУП “БМЗ”
классификация выплавляемых марок сталей.
Таблица 3.8- Сортамент сталей, выплавляемых на
РУП “БМЗ”
Наименование
группы
|
Марки
стали
|
Производство,
т/год
|
1
|
2
|
3
|
Рядовая
|
Ст1сп,
Ст2сп, Ст3сп, Ст5сп, 460В и т.д.
|
1105040
|
Низколегированная
|
460В(32),
460(40), 35ГС, 35Г, 25Г2С и т.д.
|
128511
|
Качественная
|
1026,
20, 40, 2С45 и т.д.
|
133916
|
Легированная
|
09Г2С,
ШХ 15, 25ХГТ, 40Х и т.д.
|
44138
|
Никельсодержащая
|
817М40,
20ХГНМ, 20ХН3А, 40ХН и т.д.
|
12049
|
Кордовая
|
70К,
70Б, 70РМЛ, 75К и т.д.
|
95819
|
Высокопрочная
кордовая
|
80К,
85К
|
53803
|
Итого
|
|
1573176
|
В таблице 3.9 приведены основные характеристики
прокатных станов РУП “БМЗ”.
Таблица 3.9 - Характеристика прокатных станов
РУП “БМЗ”
Агрегат
|
Характеристика
|
Годовое
производство, т
|
Стан
850
|
Крупносортовой,
одноклетьевой, реверсивный. Сортамент: круг 80-150мм, квадрат 100х100;
125х125мм.
|
404592
|
Стан
320
|
Мелкосортовой,
непрерывный, 20 клетьевой. Сортамент: круг 20-80мм, квадрат 20х20 - 80х80мм,
шестигранник 20/80мм, арматура,
|
662868
|
Стан
150
|
Проволочный,
непрерывный, 26 клетьевой. Сортамент: катанка 4-10мм, арматура 5,5-12,5мм.
|
357081
|
Опираясь на сортамент выплавляемых в цехе марок
сталей, выбранное сечение заготовок, отливаемых на МНЛЗ, рассчитываем
количество возвратимых и невозвратимых отходов и потребность в шихте на 1т
заготовки. Результаты расчетов сводятся в таблицу 3.10.
Таблица 3.10-Собственные отходы ЭСПЦ-1,2 и
потребность в металлошихте
Группа
марок
|
Произ-водство,
т/год
|
Скрап
%
|
Скрап,
т
|
Угар,
%
|
Всего,
т/год
|
Потреб-ность
м/шихте, т/год
|
1
|
1105040
|
0,5
|
5525,2
|
7
|
77352,8
|
82878
|
1187918
|
2
|
128511
|
0,5
|
642,56
|
8
|
10280,88
|
10923,4
|
139434,4
|
3
|
133916
|
0,5
|
669,58
|
8
|
10713,28
|
11382,9
|
145298,9
|
4
|
44138
|
0,5
|
220,69
|
9
|
3972,42
|
4193,1
|
48331,1
|
5
|
12049
|
0,5
|
60,2
|
9
|
1084,4
|
1144,6
|
13193,6
|
6
|
95819
|
0,5
|
479
|
10
|
9581,9
|
10060,9
|
105879,9
|
7
|
53803
|
0,5
|
269,01
|
10
|
5380,3
|
5649,3
|
59452,3
|
Всего
|
1573176
|
0,5
|
7866,2
|
-
|
118365,9
|
126232,
|
1699408
|
Данные таблиц 3.8, 3.9 и 3.10 совместно с
принятой на заводе схемой прокатки позволяют составить баланс металла по заводу
и определить годовую потребность в привозном ломе (таблица 3.11).
Таблица 3.11 - Величина обрези и угара при
газорезке заготовок отливаемых на МНЛЗ
Сечение
мм
|
Производство,
т
|
Обрезь,
%
|
Обрезь,
т
|
Угар,
%
|
Угар,
т
|
Всего,
т
|
круглое
200
|
1125761
|
0,4
|
4503
|
0
|
0
|
4503,4
|
250х300
|
255880
|
1,6
|
4094,08
|
0,6
|
1535,3
|
5629,4
|
300х400
|
191226
|
1,8
|
3442
|
0,8
|
1529,8
|
4971,8
|
Всего
|
1572867
|
3,8
|
12039,08
|
1,4
|
3065,1
|
15104,6
|
С учетом величины обрези и угара на МНЛЗ (данные
таблиц 3.10 и 3.11) потребность в металлошихте составляет 1714512,7т.
Следовательно, выход годного в общем по ЭСПЦ-1,2
составляет 91,7%.
Составим баланс металла (таблица 3.12).
Таблица 3.12 - Баланс металла по прокатным
цехам, тыс.тонн
Статьи
балансов
|
Группа
марок стали
|
Сумма
тыс. т
|
|
1
|
2
|
3
|
4
|
5
|
6
|
7
|
|
Стан
850
|
отходы
|
5,7
|
0
|
2,9
|
1,4
|
0,2
|
2,2
|
1
|
14,9
|
угар
|
1,2
|
0
|
0,6
|
0,3
|
0,2
|
0,5
|
0,2
|
3,3
|
Годный
прокат
|
102,3
|
0
|
128,55
|
42,43
|
11,6
|
93,11
|
52,6
|
428
|
Поступило
|
109,2
|
0
|
132,05
|
44,1
|
12,04
|
95,8
|
53,8
|
447,1
|
Стан
320
|
отходы
|
16,2
|
2,4
|
0,04
|
0
|
0
|
0
|
0
|
186,4
|
угар
|
1,9
|
0,3
|
0
|
0
|
0
|
0
|
0
|
2,3
|
Годный
прокат
|
541
|
79,4
|
1,4
|
0,14
|
|
|
|
641,9
|
Поступило
|
559,1
|
82,1
|
1,44
|
0,14
|
0
|
0
|
0
|
662,8
|
Стан
150
|
отходы
|
7,6
|
0,7
|
0,3
|
0,3
|
0
|
2,1
|
1
|
12
|
угар
|
1,3
|
0,1
|
0,1
|
0
|
0
|
0,3
|
0,2
|
2
|
Годный
прокат
|
219,1
|
19,7
|
9,5
|
8
|
0
|
59,8
|
28
|
345
|
Поступило
|
228
|
20,5
|
9,9
|
8,3
|
|
62,2
|
29,2
|
357
|
Выход годного составляет:
Для стана 850 (428906/447106)·100 = 95,9%
Для стана 320 (641931/662871)·100 = 96,8%
Для стана 150 (345081/357081)·100 = 96,6%
В среднем для прокатных станов выход годного
составляет 96,4 %.
Сквозной выход годного на участках ЭСПЦ -
прокатные станы составляет 88,39 %.
В таблице 3.13 покажем общее количество
возвратимых отходов.
Таблица 3.13 - Общее количество возвратимых
отходов, тонн
Источник
|
Группы
марок стали
|
Сумма,
т
|
|
1
|
2
|
3
|
4
|
5
|
6
|
7
|
|
Из
ЭСПЦ
|
печи
|
5522,17
|
642,2
|
669,36
|
220
|
60
|
475
|
265
|
7866,24
|
МНЛЗ
|
12039,08
|
Из
прокатных цехов
|
Со
стана 850
|
5700
|
1500
|
2900
|
1400
|
200
|
2200
|
1000
|
14900
|
Со
стана 320
|
16200
|
2400
|
40
|
0
|
0
|
0
|
0
|
18640
|
Со
стана 150
|
7600
|
700
|
300
|
300
|
0
|
2100
|
1000
|
12000
|
Всего
|
65445,32
|
Годовая потребность в привозном ломе рассчитаем
по формуле:
ГПлом=ГПмет.ш. - ГПвозр.отх (3.5)
Следовательно, годовая потребность в привозном
ломе в соответствии с формулой 3.5:
ГПлом= 1714512,7 - 65445,32 = 1649067 т/г
.5.4 Расчет материального баланса плавки
Для упрощения расчет ведется на 100 кг.
металлошихты. Химический состав шихтовых материалов приведен в таблице 3.14.
Химический состав применяемых шлакообразующих приведен в таблице 3.15. Состав
металлошихты в завалку представлен в таблице 3.16.
Таблица 3.14 - Химический состав шихтовых
материалов
Состав
шихты, %
|
С
|
Si
|
Mn
|
P
|
S
|
Cr
|
Ni
|
Сu
|
|
|
|
|
не
более
|
Углеродистый
лом 2А,3А
|
0,3
|
0,2
|
0,4
|
0,05
|
0,05
|
-
|
0,2
|
0,3
|
Легированный
лом Б1,Б3
|
0,7
|
0,6
|
0,7
|
0,03
|
0,03
|
1,1
|
0,3
|
0,3
|
FeSiMn
75
|
0,05
|
12
|
75,0
|
0,35
|
0,03
|
-
|
-
|
|
FeMn
78
|
7,0
|
2,0
|
78,0
|
0,35
|
0,03
|
-
|
|
-
|
FeSi
65
|
-
|
65
|
0,4
|
0,05
|
0,02
|
-
|
|
-
|
FeCr
850
|
8,0
|
2,0
|
-
|
0,03
|
0,08
|
65
|
-
|
Науглероживатель
тип «С»
|
99,0
|
-
|
-
|
-
|
0,04
|
-
|
-
|
-
|
Кокс
|
80,0
|
-
|
-
|
-
|
2,0
|
-
|
|
|
Таблица 3.15 - Химический состав шлакообразующих
ШОС
%
|
СаО
|
MgO
|
SiO2
|
Al2O3
|
Fe2O3
|
P2O5
|
CO2
|
S
|
Al
|
CaF2
|
Известь
|
92
|
3,3
|
2,5
|
1,0
|
0,60
|
0,10
|
0,20
|
0,01
|
-
|
-
|
Плавиковый
шпат
|
0,40
|
-
|
3,1
|
0,2
|
0,8
|
-
|
0,3
|
0,2
|
-
|
95,0
|
АКС
|
-
|
-
|
-
|
53-75
|
-
|
-
|
-
|
-
|
23-35
|
-
|
3.5.5 Период плавления шихты
Таблица 3.16 - Химический состав металлошихты в
завалку
Материал
|
Вескг
|
C
|
Si
|
Mn
|
P
|
S
|
Cr
|
Ni
|
Cu
|
Fe
|
Лом
2А,3А
|
70
|
0,21
|
0,14
|
0,28
|
0,035
|
0,035
|
-
|
0,14
|
0,21
|
68,95
|
Лом
Б1,Б3
|
30
|
0,21
|
0,18
|
0,21
|
0,009
|
0,009
|
0,33
|
0,09
|
0,09
|
28,87
|
Всего
|
100
|
0,42
|
0,32
|
0,49
|
0,044
|
0,044
|
0,33
|
0,23
|
0,3
|
97,82
|
Во время плавления в печь загружают [ 10 ]:
Известь - 4%; кокс - 0,4%
Во время плавления окисляются следующие
элементы:
Углерод
угар углерода шихты составит 20% :0,42 · 0,2 =
0,084 кг;
останется углерода в металле: 0,42 - 0,084 =
0,336 кг.
Кремний
угар кремния составит 70%:
перейдет в шлак кремния 0,32 · 0,7 = 0,224;
останется кремния в металле 0,32 - 0,224 = 0,096
кг.
Марганец
угар марганца составит 50%:
перейдет марганца в шлак 0,49 · 0,5 = 0,245 кг;
останется марганца в металле 0,49 - 0,245 =
0,245 кг.
Хром
Угар хрома составит 10%:
перейдёт хрома в шлак 0,33 ∙ 0,1 = 0,033
кг;
останется хрома в металле 0,33 - 0,033 = 0,297
кг.
Фосфор
угар фосфора составит 60%:
перейдет фосфора в шлак 0,044 · 0,6 = 0,0264 кг;
останется фосфора в металле 0,044 - 0,0264 =
0,0176 кг.
Сера
можно принять, что сера содержащаяся в металле
не выгорает.
Железо
угар железа составит 2%:
перейдет в шлак и улетучивается в зоне дуг
7,82·0,02=1,9564кг;
останется в ванне 97,82 - 1,9564 = 95,863 кг.
Количество кислорода, необходимого для окисления
примесей металла в период плавления, представлено в таблице 3.17.
На основании материального баланса принимаем,
что из 2 кг окислившегося железа 85% окисляется до Fe2O3 и улетучивается в зоне
электрических дуг. Оставшиеся 12% окисляется до FeO, 3% до Fe2O3, которые переходят
в шлак.
Таблица 3.17 - Количество кислорода,
необходимого для окисления примесей, кг
Элемент
|
Окисляется
|
Химическое
уравнение
|
Требуется
кислорода
|
1
|
2
|
3
|
4
|
С
|
0,084
|

|
|
Si
|
0,224
|

|
|
Mn
|
0,245
|
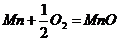
|
|
Cr
|
0,033
|

|
|
1
|
2
|
3
|
4
|
P
|
0,0264
|
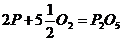
|
|
Fe
|
1,9564
· 0,88
|
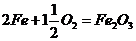
|
|
Fe
|
1,9564
· 0,12
|
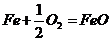
|
|
Всего
|
2,568
|
|
1,277
кг
|
Расчет кислорода производим для области
концентраций [C] ≥ 0,1%;
[O%] = 0,006+
(3.5)
По формуле (3.5)
[O%] = 0,006+
0,0149%.
Содержание кислорода в металле
0,0149 % :
[O] мет = 0,0149 · 4,5 = 0,067 FeO;
т.е. приближенно 96 · 0,067 : 100 =
0,0643 кг FeO, для чего потребуется:
кислорода 0,0643 · 16 : 72 = 0,0143
кг;
железа 0,0643 - 0,0143 = 0,05 кг.
Общая потребность в кислороде 1,277
+ 0,0143 = 1,291 кг.
Количество железа к моменту
расплавления составит
[Fe ] = 97,82 - 1,9564 - 0,05 =
95,81 кг.
Состав металла в первой пробе по
расплавлении показан в таблице 3.18
Таблица 3.18 - Состав металла в
первой пробе по расплавлении
Элемент
|
кг
|
%
|
1
|
2
|
3
|
С
|
0,336
|
0,345
|
Si
|
0,096
|
0,098
|
Mn
|
0,245
|
0,252
|
S
|
0,044
|
0,045
|
P
|
0,0176
|
0,018
|
Cr
|
0,297
|
0,305
|
Ni
|
0,23
|
0,236
|
FeO
|
0,0643
|
0,066
|
Fe
|
95,81
|
98,64
|
Итого
|
97,13
|
100,000
|
Шлак периода плавления
Поступает в шлак из металла, кг:
0,224 ∙ 60 : 28 = 0,48;0,245 · 71: 55 =
0,316;O3 0,033 ∙ 152 : 104 = 0,048;O5 0,0264 ∙ 142 : 62 =
0,06;,9564 ∙ 0,12 ∙ 72 : 56 = 0,30;O31,9564 ∙ 0,03 ∙
160 : 112 = 0,083.
Поступает в шлак с известью (количество извести
4 кг), кг:
CaО4 · 92 :
100 = 3,68;
MgO4 · 3,3 : 100 = 0,132;· 2,5 : 100
= 0,10;O34 · 1,0 : 100 = 0,04;O34 · 0,6 : 100 = 0,024;O54 · 0,1 : 100 = 0,004.
Расход электродов примем 3 кг на 1т садки или
0,3 кг на 100 кг:
в
период плавления расходуется 60% или 0,18 кг на 100 кг садки; в окислительный
период расходуется 40% или 0,12 кг на 100 кг садки.
Состав шлака периода плавления представлен в
таблице 3.19
Таблица 3.19 - Состав и количество шлака периода
плавления
Источник
поступления
|
Металл
|
Известь
|
Итого
|
|
|
|
кг
|
%
|
CaO
|
-
|
3,68
|
3,68
|
69,65
|
MgO
|
-
|
0,132
|
0,132
|
2,49
|
SiO2
|
0,48
|
0,1
|
0,58
|
10,97
|
Al2O3
|
-
|
0,04
|
0,04
|
0,757
|
FeO
|
0,30
|
-
|
0,30
|
5,67
|
Fe2O3
|
0,083
|
0,04
|
0,123
|
2,328
|
MnO
|
0,316
|
-
|
0,316
|
5,98
|
P2O5
|
0,06
|
0,004
|
0,064
|
1,211
|
Cr2O3
|
0,048
|
-
|
0,048
|
0,908
|
Всего
|
1,287
|
3,996
|
5,283
|
100
|
.5.6 Окислительный период плавки
Углерод
Для хорошей дегазации металла окисляют около
0,3% С; удаляется углерод до содержания его 0,12% С. Вес металла к концу
окислительного периода составит 94 кг. К концу окислительного периода в металле
должно быть углерода приблизительно
[С] =96 · 0,12 : 100 = 0,115 кг; выгорит 0,336 -
0,115 = 0,221 кг.
Марганец
К концу периода останется в металле
приблизительно 0,20% Mn, или
[Mn] =96 · 0,20 : 100 = 0,192 кг; окислится
0,245 - 0,192 = 0,053 кг.
Кремний
При продувке кислородом окисляется весь кремний
т.е. окисляется
,096 кг.
Хром
угар хрома составит 10%:
перейдёт хрома в шлак 0,297 ∙ 0,1 = 0,0297
кг;
останется хрома в металле 0,297-0,0297 = 0,267
кг.
Фосфор
Считаем, что к концу окислительного периода в металле
останется 0,005 % Р:
[Р] = 96 · 0,005 : 100 = 0,0048 кг;
окислится 0,0176 - 0,0048 = 0,0128 кг.
Сера
При основности шлака выше 2 и непрерывном
обновлении состава шлака можно рассчитывать, что из металла будет удалено
0,0010 кг серы. Останется в металле 0,044 - 0,0010 = 0,034 кг.
Железо
Угар железа составит 1%. Перейдет в шлак и
улетучивается в зоне электрических дуг:96,61 · 0,01 = 0,9661 кг;
останется в ванне 96,61 - 0,9661 = 95,64 кг.
Потребность в газообразном кислороде
Расчет количества кислорода необходимого для
окисления примесей металла в период доводки, приведен в таблице 3.20.
Таблица 3.20 - Количество кислорода,
необходимого для окисления примесей в период доводки
Элемент
|
Окисляется,
кг
|
Химическое
уравнение
|
Требуется
кислорода, кг
|
1
|
2
|
3
|
4
|
Углерод
|
0,221
|

|
|
Кремний
|
0,096
|

|
|
Марганец
|
0,053
|
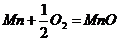
|
|
Фосфор
|
0,0010
|
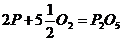
|
|
Хром
|
0,0297
|

|
|
Железо
|
0,9661
· 0,88
|
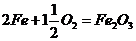
|
|
Железо
|
0,9661
· 0,12
|
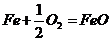
|
|
Всего
|
1,4067
|
|
0,8297
|
На основании материального баланса принимаем,
что из 0,9661 кг окислившегося железа 85% Fe окисляется до Fe2O3 и
улетучивается в зоне электрических дуг. Оставшиеся 12% окисляется до FeO, 3% до
Fe2O3, которые переходят в шлак.
Количество закиси железа в жидкой стали
По формуле Феттерса и Чипмана в металле,
содержащем 0,12% С, должно находится в растворе:
[%FeO] = (0,0124 + 0,05 · 0,12) : 0,35 = 0,052%
(0,0115% О)
Принимается содержание кислорода в металле
равным 0,0177% или 0,08% FeO.
Металл в конце периода плавления содержал 0,066%
FeO. Необходимо повысить содержание закиси железа на
,080 - 0,066 = 0,014 %;
или 96 ∙ 0,014 : 100 = 0,0134 кг FeO,
на что потребуется:
кислорода 0,0134 · 16 : 72 = 0,0029 кг;
железа 0,0134 - 0,0029 = 0,0105 кг.
Вес шлака окислительного периода
Подлежит удалению из металла 0,005% Р. Для
удаления фосфора при
нарастающей температуре металла требуется
основность шлака 2 - 2,5 и обновление его. Учитывая это обстоятельство,
принимаем среднее содержание Р2О5 во вновь наведенном шлаке 0,5%. Вес вновь
наводимого шлака:
(0,005 : 0,5) · (142:62) ·100 = 2,29 кг
Принимаем, что шлак окислительного периода
удален на 70%. Остается шлака в печи 5,283 · 0,3 = 1,584 кг;
Общий вес шлака окислительного периода 2,29 +
1,584 =3,874 кг.
Потребность в извести
Чтобы определить количество присаживаемой
извести, принимаем:
основность CaO/SiO2 = 2,
сумму CaO + MgO + MnO = 65%
Закись марганца вносится:
шлаком периода плавления 0,316 · 0,3 = 0,0948
кг,
окисляющимся марганцем из металла 0,053 · 71 :
55 = 0,068 кг,
всего вносится 0,0948 + 0,068 = 0,1628 кг MnO
Оксид магния вносится:
шлаком периода плавления 0,132 · 0,3 = 0,0396
кг;
если обозначить известь через «х», то известь
внесет х 0,033 кг MgO.
всего вносится MgO 0,0396 + 0,033х кг
Оксид кальция вносится:
шлаком периода плавления 3,68 · 0,3 = 1,104 кг,
известью 0,92∙х.
всего вносится оксида кальция 1,104 + 0,92х
MnO + MgO + CaO = 3,86 · 0,65 = 2,509 кг
или 0,1628 + 0,0396 + 0,033х + 1,104 + 0,92х =
2,509 кг
потребуется извести: х = 1,26 кг.
Кремнезем вносится:
шлаком периода плавления 0,58 · 0,3 = 0,174 кг;
окисляется кремния из металла 0,096 · 60 : 28 =
0,205 кг;
известью 1,26 · 0,025 = 0,315 кг;
всего вносится 0,694 кг SiO2.
требуется кремния для получения основности :
[Si] = (1,104 + 0,92 · 1,26) : 2 = 1,1316 кг
Оксид хрома вносится:
шлаком периода плавления 0,048 · 0,3 = 0,0144
кг;
окисляется хрома из металла 0,0297 · 152 : 104 =
0,043 кг;
всего вносится 0,0144 + 0,043 = 0,0574 кг Cr2O3.
Поступление в шлак железа
,3 · 0,3 = 0,09 кг FeO,
из шлака периода плавления 0,123 · 0,3 = 0,0369
кг Fe2O3;
вносится известью 1,26 · 0,006 = 0,0075 кг
Fe2O3;
итого вносится FeO 0,09 кг и Fe2O3 0,0444 кг.
Для окисленности шлака требуется:
железа 0,09 · 56 : 72 = 0,07 кг;
,0444 · 112 : 160 = 0,031 кг;
кислорода 0,09 - 0,07 = 0,2 кг;
,0444 - 0,031 = 0,0134 кг.
Данные о весовом количестве и химическом составе
шлака приведены в таблице 3.21.
Таблица 3.21 - Вес (кг) и состав шлака
окислительного периода
Оксид
|
Источники
поступления
|
Итого
|
|
из
шлака периода плавления
|
из
металла
|
из
извести
|
кг
|
%
|
CaO
|
1,104
|
-
|
1,159
|
2,263
|
60,63
|
MgO
|
0,0396
|
-
|
0,041
|
0,0806
|
2,159
|
MnO
|
0,0948
|
0,068
|
-
|
0,1628
|
4,361
|
SiO2
|
0,174
|
0,205
|
0,315
|
0,694
|
18,59
|
Al2O3
|
0,012
|
-
|
0,0126
|
0,0246
|
0,659
|
FeO
|
0,09
|
0,09
|
-
|
0,18
|
4,82
|
Fe2O3
|
0,123
|
0,0444
|
0,0075
|
0,1749
|
4,68
|
P2O5
|
0,064
|
0,0293
|
0,00126
|
0,0945
|
2,53
|
Cr2O3
|
0,0144
|
0,043
|
-
|
0,0574
|
1,537
|
S
|
-
|
0,0010
|
0,00126
|
0,00226
|
0,06
|
Всего
|
1,701
|
0,437
|
1,537
|
3,7324
|
100
|
Выход и состав металла к концу окислительного
периода приведен в таблице 3.22.
Таблица 3.22 - Выход и состав металла к концу
окислительного периода
Элемент
|
кг
|
%
|
1
|
2
|
3
|
Углерод
|
0,115
|
0,119
|
Кремний
|
0,000
|
-
|
Марганец
|
0,192
|
0,199
|
Хром
|
0,267
|
0,276
|
Никель
|
0,23
|
0,238
|
Фосфор
|
0,0048
|
0,0049
|
Сера
|
0,034
|
0,035
|
Закись
железа 96 · 0,08 : 100
|
0,0768
|
0,079
|
Железо:
в печи в конце плавления Расходуется на образование закиси и оксида железа
0,0105 + 0,07 + 0,031
|
95,64
|
99,05
|
|
0,1115
|
|
Всего
железа
|
95,528
|
|
Всего
стали
|
96,44
|
100
|
.5.7 Количество газов периода плавления и
окисления
При окислении углерода металла образуется окись
углерода в количестве
[СО] = (0,084 + 0,221) · 28/12 = 0,711 кг.
В течение плавления и окисления расходуется
графитированных электродов на 100 кг шихты 0,18 + 0,12 = 0,3 кг
или [С] = 0,3 · 0,99 = 0,29 кг
Сгорает углерода кокса, данного в завалку для
вспенивания шлака
[Скокс] = 0,4 · 0,8 = 0,32 кг
На основании анализа опытных плавок считаем, что
углерод окисляется следующим образом: 70% до СО и 30% до СО2.
С образованием оксида углерода сгорает (0,29 +
0,32) · 0,7 = 0,427 кг С;
и образуется 0,427 · 28/12 = 0,996 кг СО;
на что потребуется 0,996 - 0,427 = 0,569 кг
кислорода.
С образованием углекислого газа сгорает
(0,29+0,32) · 0,3 = 0,183 кг С;
и образуется 0,183 · 44/12 = 0,671 кг СО2;
на что требуется 0,671 - 0,183 = 0,488 кг
кислорода.
Для периодов плавления и окисления требуется
кислорода
[О2] = 1,291 + 2,106 + 0,0029 + 0,2 + 0,0134 =
3,6133 кг.
Всего требуется кислорода 3,6133 + 0,569 + 0,488
= 4,6703 кг.
Принимается, что 50% кислорода поступит с
воздухом (в основном в период плавления).
Потребуется газообразного кислорода 4,6703 · 0,5
= 2,335 кг.
Считая использование кислорода равным 85%,
находим, что в плавление и окислительный период необходимо подать газообразного
кислорода: 2,335 : 0,85 = 2,74 кг, или технического кислорода (98% О2);
[О2 ] = 2,74 : 0,98 = 2,80 кг; или 2,8 · 22,4/32
= 1,96 м3.
С кислородом вносится азота около 2%, т.е. 2,8 -
2,74 = 0,06 кг.
Для окислительных процессов используется
кислорода воздуха:
[О2 ] = 4,6703 · 0,5 = 2,335 кг, или 2,335 ·
22,4/32 = 1,634 м3;
кислороду сопутствует азот (включая аргон и
прочие газы):
[N2 ] = 2,335 · 77/23 = 7,817 кг, или 1,634 ·
79/21 = 6,14м3;
объем воздуха составит 1,634 + 6,14 = 7,774 м3;
вес воздуха составит 2,335 + 7,817 = 10,152 кг.
При нагреве извести выделяется, кг:
СО2 (4+1,26) · 0,002 = 0,0105;
Н2О (4+1,26) · 0,002 = 0,0105.
Влага, вносимая воздухом
Допускается, что температура воздуха 20ºС,
давление - 760 мм, относительная влажность 70%. По таблицам находится, что
упругость насыщенного водяного пара при 20ºС
равна 17.5 мм рт. ст.
Упругость водяных паров в воздухе составит 17,5
· 0,7 = 12,25 мм.
Количество влажного атмосферного воздуха при
температуре 20ºС и давлении 760 мм
будет равно
= 6,128 · (273+20)/273 · (760/760-12,25) = 6,680
м3.
Точка росы t при р = 12,25 мм лежит около 14ºС;
вес водяного пара в 1 м3 атмосферного воздуха:
= 0,29 · (р/273) = 0,29 · (12,25/273+14) =
0,0120 кг;
воздух внесет с собой влаги 0,012 · 6,680 = 0,08
кг.
всего влаги 0,0105 + 0,080 = 0,0905 кг.
Водяной пар будет восстановлен оксидам углерода
по реакции
Н2О + СО = Н2 + СО2.;
при этом образуется водорода 0,0905 · 2/18 =
0,01 кг;
потребуется оксида углерода 0,0905 · 28/18 =
0,14 кг;
образуется углекислого газа 0,14 · 44/28 = 0,22
кг.
В периоды плавления и окислительный
израсходовано газообразного кислорода 2,74 кг. Из этого количества ушло в
атмосферу печи 15% или
[О2] = 2,74 · 0,15 = 0,411 кг.
Свободный кислород будет окислять оксид углерода
с образованием углекислого газа по реакции СО + ½ О2
= СО2.;
образуется СО2 0,411 ·44/16 = 1,13 кг;
для этого требуется СО 1,13 - 0,411 = 0,719 кг.
Все проделанные расчеты сведем в таблицы 3.23,
3.24.
Таблица 3.23 -Сводная таблица газов для периодов
плавления и окислительного
Наименование
|
кг
|
%
|
1
|
2
|
3
|
Оксид
углерода
|
0,848
|
7,87
|
Углекислый
газ
|
2,031
|
18,86
|
Водород
|
0,01
|
0,092
|
Азот
|
7,877
|
73,15
|
Всего
|
10,766
|
100
|
Таблица 3.24 - Материальный баланс
окислительного периода
Израсходовано
|
кг
|
Получено
|
кг
|
Углеродистый
лом 2А, 3А
|
70
|
Металла
|
96,44
|
Легированный
лом Б1, Б3
|
30
|
Шлака
|
7,43
|
Извести
|
5,26
|
Газов
|
10,766
|
Электродов
|
0,3
|
Угар
железа
|
3,54
|
Воздуха
|
10,232
|
Невязка
(0,46%)
|
0,41
|
Газообразный
кислород
|
2,80
|
|
|
Всего:
|
118,59
|
|
118,59
|
.5.8 Расчёт расхода раскислителей и легирующих
на выпуске
Расчёт ведём (на 96 кг, масса стали на выпуске)
по формуле :
GFeCn=
=
(3.6)
Следовательно по формуле 3.6 рассчитаем
количество вносимой коксовой мелочи (С = 80%).кокс = (0,2 - 0,115) · 96/ (80 ·
0,75) = 0,136 кг
с ним внесётся [С] = 0,136 · 80/100 = 0,108 кг;
[S] = 0,136 · 2 : 100 = 0,0027 кг
Вносим FeSi 65
GFeSi 65 = (0,14 · 96)/(65 · 0,8) = 0,258 кг;
с ним внесётся:
[Si] = 0,258 · 65/100 = 0,167 кг;
[Mn] = 0,258 · 0,4/100 = 0,001 кг;
[P] = 0,258 · 0,05/100 = 0,0001 кг;
[S] = 0,258 · 0,02/100 = 0,00005 кг;
[Fe] = 0,258 · 24,5/100 = 0,063 кг.
Вносим FeSiMn 75=
(0,55 - 0,192) · 96/((75·0,85)+(12·0,8)) = 0,468 кг;
с ним внесётся:
[Si] = 0,468 · 12/100 = 0,056 кг;
[Mn] = 0,468 · 75/100 = 0,351 кг;
[С] = 0,468 · 0,05/100 = 0,0002 кг;
[P] = 0,468 · 0,35/100 = 0,0016 кг;
[S] = 0,468 · 0,03/100 = 0,00014 кг;
[Fe] = 0,468 · 12/100 = 0,056 кг.
Конечный состав металла после выпуска (кг):
[С] = 0,115 + 0,108 + 0,0002 = 0,225 кг;
[Si] = 0,167 + 0,056 = 0,223 кг;
[Mn] = 0,192 + 0,001 + 0,351 = 0,544 кг;
[P] = 0,0048 + 0,0001 + 0,0016 =
0,0065 кг;
[S] = 0,034 + 0,0027 + 0,00005 +
0,00014 = 0,0368 кг;
[Fe] = 96,44 + 0,063 + 0,056 = 96,56
кг.
3.5.9 Расчёт расхода раскислителей и легирующих
на «печь-ковше»
Вносим FeCr 850
850 = (0,9 - 0,267) · 96/65= 0,934 кг
с ним внесётся
[Сr] = 0,934 · 65/100 = 0,607 кг;
[С] = 0,934 · 8/100 = 0,0747 кг;
[Si] = 0,934 · 2/100 = 0,0186 кг;
[Mn] = 0,934 · 0,4/100 = 0,0037 кг;
[P] = 0,934 · 0,03/100 = 0,00028 кг;
[S] = 0,934 · 0,08/100 = 0,00074 кг;
[Fe] = 0,934 · 25/100 = 0,2335 кг.
Вносим науглероживатель тип «С» (С = 99%)
тип С = (0,302 - 0,225)·96/(99·0,75) = 0,1 кг;
с ним внесётся
[С] = 0,1 · 99 : 100 = 0,099 кг;
[S] = 0,1 · 0,04 : 100 = 0,00004 кг.
Массовая доля Al в металле после раскисления
алюминием приближенно равна
[Al] = Alчушк. · (1- угар) = 0,028 · (1- 0,85) =
0,0042 кг, или
,0042 · 93/100 = 0,0039%.
Исходя из остаточной концентрации алюминия в
металле [Al] = 0,0039%, в плавку на 100т вносим 95 м силикокальциевой проволоки
(из расхода 100 м на 100 т металла) или на 100 кг садки 0,095 м
силикокальциевой проволоки.
Вносим SiCa (в 1 м. погонном - 225 гр. - SiCa
или 400 гр. всей проволоки чистого веса)
= 0,095 · 0,225 = 0,0213 кг или 0,095 · 0,400 =
0,038 кг.
с ним внесётся [Si] = 0,0213 · 60/100 = 0,0127
кг.
Вносим Al проволоку ( в 1 м погонный - 180 гр.
Al)
= 0,095 · 0,180 = 0,0171 кг.
с ним внесётся [Al] = 0,0171 · 100/100 = 0,0171
кг.
Конечный состав металла, кг:
[С] = 0,225 + 0,074 + 0,099 = 0,398 кг;
[Si] = 0,223 + 0,0186 + 0,0127 = 0,2543 кг;
[Mn] = 0,544 + 0,0037 = 0,547 кг;
[Сr] = 0,267 + 0,607 = 0,874 кг
[P] = 0,0065 + 0,00028 = 0,0068 кг;
[S] = 0,0368 + 0,00074 + 0,00004 -
0,0105 = 0,027 кг;
[Fe] = 96,56 + 0,2335 = 96,79 кг.
Представим конечный состав металла в таблице
3.25.
Таблица 3.25 - Окончательный состав металла к
концу плавки
Элемент
|
кг
|
%
|
Углерод
|
0,398
|
0,401
|
Кремний
|
0,2543
|
0,256
|
0,547
|
0,551
|
Фосфор
|
0,0068
|
0,0068
|
Хром
|
0,874
|
0,881
|
Никель
|
0,23
|
0,232
|
Алюминий
|
0,0171
|
0,017
|
Сера
|
0,027
|
0,027
|
Железа
|
96,79
|
97,67
|
Всего
стали
|
99,1
|
100
|
Технологическая схема плавки представлена в
приложении Д.
Обработка стали ТШС
Состав ТШС: СаО - 75%; CaF2 - 25%.
Расход ТШС 6 кг/т. Обработка стали производится
в ковше с магнезитовой футеровкой.
Концентрация алюминия в стали Al = 0,017%.
Количество оксидов, образующихся при
раскисленнии 1т стали покажем в таблице 3.26.
Таблица 3.26 - Количество оксидов, образующихся
при раскислении (расчет ведется на 1т стали)
Элемент
|
Концентрация
в стали, %
|
Вводится
в металл с учетом угара, %
|
Угар
элемента, %
|
Образуется
оксидов, кг
|
Mn
|
0,547
|
0,643
|
0,096
|
1,239
|
Si
|
0,254
|
0,317
|
0,063
|
1,35
|
Al
|
0,017
|
0,085
|
0,068
|
1,33
|
Итого
|
|
3,919
|
Образуется оксидов:
[Mn] + [O] = (MnO);
Δ Mn = 1000 ·
0,096/100 = 0,96 · 71/55 = 1,239 кг;
[Si] + 2[O] = (SiO2);
Δ Si = 1000 ·
0,063/100% = 0,63 · 60/28 = 1,35 кг;
[Al] + 3[O] = (Al2O3);
Δ Al = 1000 ·
0,068/100% = 0,68 · 102/52 = 0,133 кг.
Изменение состава рафинировочного шлака к концу
обработки представлено в таблице (3.27)
Таблица 3.27 - Изменение состава рафинировочного
шлака
Материал
|
ТШС
|
АКС
|
Продукты
раскисления
|
Футеровка
|
Итого
|
Состав
шлака, %
|
1
|
2
|
3
|
4
|
5
|
6
|
7
|
Количество,
кг
|
6
|
0,4
|
3,919
|
2
|
12,32
|
100
|
CaO
|
4,5
|
-
|
-
|
-
|
4,5
|
36,52
|
CaF2
|
1,5
|
-
|
-
|
-
|
1,5
|
12,17
|
Рассчитываем значения Ls и ηs
для магнезитово - углеродистой футеровки:
КAl = [Al]2 · [a0]3
= 10-13;(3.7)
где a0 =
%;
LgLs = - 2,78 + 0,86 ·
- lg
0,0029;(3.8)
гдеLs = 28,5 - коэффициент
распределения серы;
λ =
;(3.9)
Используя формулы 3.7 - 3.9 получим:
Ls = - 2,78 +
0,86·((36,52+0,05·15,42)/(10,96+0,6·13,07)) - lg 0,0029 =
= -2,78 + 1,705 + 2,53 = 1,455;
λ = 0,0103;
Определим степень десульфурации ηS и
соответственно [S] :
ηS =
;(3.10)
[S] = ([S]нач
- ηS
· [S]нач);
(3.11)
Тогда используя формулы 3.10 и 3.11
получим:
ηS = ((0,0103·28,5)/(1+0,0103·28,5))
= 0,227;
[S] = 0,0375 - 0,227 · 0,0375 =
0,028 % (0,027 кг).
Итоговые параметры материального
баланса плавки приведены в таблице 3.28.
Таблица 3.28 - Материальный баланс
плавки (на 100 кг)
Израсходовано,
кг
|
Получено,
кг
|
Углеродистый
лом 2А,3А
|
70
|
Жидкая
сталь
|
99,1
|
Легированный
лом Б1,Б3
|
30
|
Шлак
|
7,43
|
Извести
|
5,26
|
Потери
с газами
|
10,766
|
Электродов
|
0,3
|
Угар
железа
|
3,54
|
Воздуха
|
10,232
|
Невязка
(0,26%)
|
0,31
|
Кислорода
|
2,80
|
|
|
FeSi
65
|
0,258
|
|
|
FeSiMn
17
|
0,468
|
|
|
FeCr
850
|
0,934
|
|
|
Al
чушковый
|
0,028
|
|
|
Науглераживатель
тип «С»
|
0,1
|
|
|
SiСа
|
0,0213
|
|
|
Коксовая
мелочь
|
0,136
|
|
|
Al
(проволока)
|
0,0171
|
|
|
ТШС
(СаО : CaF2)
|
0,6
|
|
|
Всего:
|
121,154
|
Всего:
|
121,154
|
.6 Тепловой баланс плавки
Расчёт ведется на 1т стали.
Тепловой баланс плавки в ДСП выглядит следующим
образом [ 11 ]:эл + Qхим + Qмет. и шл. + Qгор = Qст + Qшл + Qотх. газ. +
Qпотерь; (3.12)
гдеQэл - тепло, получаемое от горения
электрических дуг;хим - тепло, получаемое от экзотермических реакций окисления
примесей;мет. и шл. - тепло, получаемое от остатка части жидкого металла и
шлака от предыдущей плавки (болото);гор шл - тепло, получаемое от
газокислородных горелок;ст - тепло расплавленной стали;шл - тепло
расплавленного шлака;отх. газ - тепло потерянное с отходящими газами;потерь - тепло
потерянное по различным причинам.
Все расчеты сводятся в таблицу 3.29.
.6.1 Количество тепла, необходимое для
расплавления и нагрева стали
-й период (плавления) :
ст.пл. = [Ств · (Тликв - Тнач) + gскр. + Сжидк·
(Тпл - Тликв)] · Млома; (3.13)
гдеQст.пл. - количество теплоты, необходимое
затратить для расплавления и нагрева до Тпл = 1550 ˚С.
Сжидк, Ств - соответственно теплоемкости твердой
и жидкой стали (Ств = 0,75 МДж/т·°С; Сжидк = 0,85 МДж/т·°С);лома - масса
металлошихты, Mлома = 1,12т;
Тнач - начальная температура загружаемого лома,
Тнач = 20 ˚С;
Тликв - температура ликвидус для данного состава
лома, Тликв = 1502 0C;- скрытая теплота плавления g = 240 КДж/кг.
Тогда с помощью формулы 3.13 получим:лома= [0,75
· (1502 - 20) + 240 + 0,85 · (1560 - 1502) = 1400,8 МДж/т; или Wст. = 383,7
кВт·ч; (1 кВт·ч = 3,65 МДж.).
-й период (окислительный или доводки)
ΣQ =
ΣQст.+
Qшл (3.14);ст.ок. = Сжидк · (Твып -Тпл) ·Мст. (3.15);
где Мст. =1,12-масса жидкой стали в конце
окислительного периода, т;ст.ок.- количество теплоты, необходимое для нагрева
стали до температуры выпуска, МДж;
Твып, Тпл - соответственно температуры стали
перед выпуском и после расплавления, Твып = 1660; Тпл = 1560 ˚С.
Следовательно, используя формулы 3.14 и 3.15
получим:
ст.ок.= 0,85 · (1660 - 1560) · 1,12 = 95,2
МДж/т;
или Wст.ок. = 26,08 кВт·ч.
ΣQ = 1400,8 + 95,2 =
1496 МДж/т
или ΣWст.
= 409 кВт·ч.
.6.2 Количество теплоты, необходимое для нагрева
шлака
Количество теплоты, необходимое для нагрева
шлака находим используя формулы:
шл = Сшл · Твып. · Мшл;(3.16)
гдеСшл - теплоемкость шлака, Сшл = 2,1 МДж/т Ìград;
Мшл - масса шлака, Мшл = 0,1 т;
ΣQок. = Qст.ок. +
Qшл. (3.17)
Используя формулы 3.16-3.17 получим:
шл = 2,1 · 1660 · 0,1 = 348,6 МДж/т или Wшл =
95,5 кВт·ч.
ΣQок. = 1496 + 348,6
= 1844,6 МДж/т; или Wст.ок. = 505,4 кВт·ч.
Однако с учетом теплового и электрического КПД
реальное количество теплоты составит:
эл = ΣQ/ηэл
· ηм
(3.18)
Тогда Qэл = 1844,6/(0,9 · 0,8) = 2562 МДж/т; или
Wэл = 701,9 кВт·ч.
Тепло от химических реакций окисления примесей и
самого железа:
хим = qССО·Δ[C]+qSiSio2
·Δ[Si]+qMnMnO·Δ[Mn]+qPP2O5·Δ[P]+
+ qFeFeO·Δ[Fe](3.19)
где qRRnОm - удельное количество теплоты при
окислении 1-ого килограмма элемента MДж/т;
Δ[R]- количество
окислившегося элемента, кг.
Подставив данные в формулу 3.19 получим:
хим = ((0,42 - 0,119) · 11,2 · 12) + (0,32 ·
11,2 · 26) + ((0,49- 0,199) · 11,2 · 7,5) + ((0,044- 0,005) · 11,2 · 30) +
((97,82 - 95,2) · 11,2 · 4,5) = 303,2 МДж/т; или W хим = =83,07 кВт·ч.
.6.3 Определение тепловых потерь
Расчет тепловых потерь ведем по формулам:
потерь = Qэл. - Qст. + Qшл;(3.20)потерь = Qэл. -
Qст. + Qме. и шл.;(3.21)
Доля тепловых потерь (от суммы всех потерь за
плавку):
с отходящими газами - 35
÷ 50%;
- через рабочее окно - 10
÷ 15%;
- через электроды - 3
÷ 5%;
- через футеровку и стеновые панели - 30
÷ 35%.
тогда подставив данные в формулы 3.20-3.21
получим
потерь = 2562 - (1496 + 313,3) = 752,7
МДж/т.отх.газов = 752,7 · 0,45 = 338,7 МДж/т.потерь = 752,7 · (0,15 + 0,05 +
0,503) = 378,7 МДж/т.
В таблице 3.29 показываем тепловой баланс
плавки.
Таблица 3.29 - Тепловой баланс плавки
Приход
тепла
|
МДж/т
|
Расход
тепла
|
МДж/т
|
1
|
2
|
3
|
4
|
Qэл.
|
1774
|
Qст.
|
1496
|
Qхим.
|
303,2
|
Qшл.
|
348,6
|
Qмет.и
шл
|
313,3
|
Qотх.газов
|
338,7
|
Qгор
|
171,5
|
Qпотерь
|
378,7
|
Всего
|
2562
|
Всего
|
2562
|
4. СПЕЦИАЛЬНАЯ ЧАСТЬ
.1 Разработка новой технологии вторичного
охлаждения с применением круглофакельных водовоздушных форсунок
Теплофизические и термомеханические процессы,
происходящие внутри затвердевающего слитка и в итоге определяющие
кристаллическую структуру блюма и его внутренние и поверхностные дефекты, в
значительной степени зависят от условий отбора тепла с поверхности слитка в
зоне вторичного охлаждения. Создание возможности управления тепловым состоянием
формирующегося слитка за счёт регулирования внешней системы вторичного
охлаждения делает возможным прогнозирование качества конечного продукта и путём
минимизации дефектов поверхности слитка и дефектов его внутреннего строения
получить высококачественный непрерывнолитой блюм для всего марочного
сортамента.
На МНЛЗ-3 РУП «БМЗ» в зоне вторичного охлаждения
используется классическое водяное плоскофакельное охлаждение. Зона вторичного
охлаждения разбита на три секции, в каждой из которых имеется свой расход воды,
характеризуемый различным числом форсунок. В третьей ЗВО движущийся слиток
начинает деформироваться и в дальнейшем перемещается по дуге, близкой к
четверти окружности. В результате этого в слитке возникают механические
напряжения за счет изгиба слитка, которые накладываются на термические
напряжения, возникающие в ЗВО. Анализирую ситуацию можно уверено сказать, что
позиция механических и термических напряжений создает нелинейную картину
распределения напряжений в слитке, что в конечном итоге приводит к формированию
трещин в слитке, тем самым отрицательно влияя на качество получаемого слитка.
Для устранения данного вида дефекта, в данном
проекте предлагается применить водовоздушную систему охлаждения, взамен
применяемой водяной, с переходом на круглофакельное форсуночное охлаждение
взамен плоскофакельному (рисунок 4.1) (приложение Ж).
Рисунок 4.1- Геометрическая схема
круглофакельного (предлагаемая) и плоскофакельного (стандартная) водяного
охлаждения на участке ЗВО МНЛЗ-3
К форсункам предъявляются следующие требования:
гарантированное получение расчётного коэффициента теплоотдачи, равномерное
распределение коэффициента теплоотдачи по ширине факела, постоянная геометрия
факела при изменении расхода теплоносителя, широкий диапазон расходов воды,
надёжность работы форсунок в жёстких условиях [ 12 ].
Для обеспечения мягкого и равномерного
вторичного охлаждения непрерывнолитых блюмовых заготовок предлагается применить
водовоздушную систему вторичного охлаждения. Для смешивания воды и
воздуха
предлагается устройство со смешиванием внутри камеры. Распылительное устройство
в данном случае состоит из отдельной смесительной камеры с патрубками,
расположенными под углом 90° для подвода воды и воздуха (рисунок 4.2).
,2- патрубки для подвода воздуха и воды; 3 -
болт для технического дробления воды; 4 - корпус распылителя; 5 -
круглофакельная форсунка
Рисунок 4.2 - Распылительное устройство
На рисунке 4.3 представлены фотографии ряда
форсунок прогрессивной конструкции, дающие наилучшее распределение коэффициента
теплоотдачи по площади орошаемой поверхности.
Рисунок 4.3 -Варианты исполнения форсунок,
позволяющих охлаждать поверхность непрерывнолитых заготовок водовоздушным
туманом
Соосно с водяным патрубком внутрь камеры
ввинчивается специальный болт для предварительного механического дробления
водяного потока, а также очистки полости камеры в случае ее засорения.
В подводящих воду и воздух патрубках
внутри камеры выполнены сужающие каналы. Применение таких распылительных
устройств позволит снизить потребление воздуха на дробление 1 м3 воды со 100 -
140 до 25 м3 и формировать водовоздушную смесь при изменении расходов воды в
потоке в соотношении 1:18. Стабильное формирование водовоздушного потока будет
обеспечиваться при повышенном давлении воды (около 0,7 МПа) и воздуха (более
0,3 МПа) на входе в смесительную камеру. Максимальный расход воды на один ручей
составляет примерно 33 м
/ч, а
воздуха - около 830 м
/ч. Для
подачи водовоздушной смеси по касательной к поверхности от центра заготовки к
узким граням смесь подают в полость форсунки, после этого смесь через выпускные
отверстия весьма сложной конфигурации в виде потока конусновидной формы
распределяются по охлаждаемой поверхности (рисунок 4.4) [ 13 ].
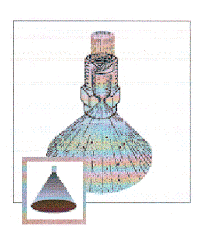
а- полость форсунки; б- поток
охладителя конусновидной формы
Рисунок
4.4 - Форсунка с круглым водовоздушным факелом
Конструкция данной водовоздушной форсунки,
позволяет формировать
поток охладителя с углом раскрытия факела по
большой оси около 155 - 160, по малой - 35 - 40 (рисунок 4.5). Площадь
выходного сечения форсунки составляет 25 мм. Форсунка устанавливается над
поверхностью заготовки на
высоте
~ 0,3м и обеспечивает охлаждение около 80-85% площади межроликового пространства.
Расход воздуха на распыление 1м
воды составляет в среднем 12- 20 м
.

Рисунок 4.5 -Сформированный поток охладителя с
углом раскрытия факела предлагаемой форсунки
Для получения оптимальной модели
круглофакельного охлаждения были рассчитаны поля напряженности слитка. На
основе этих расчетов была спроектирована математическая модель
термонапряженного слитка получаемого на МНЛЗ-3. Расчет проекции нормальных
напряжений на вертикальной оси слитка производился исходя из допущения, что
каждый элемент горизонтального слоя слитка деформируется одинаково. В начальный
момент времени все элементы модели имели одинаковую высоту, соответствующую
вертикальному шагу конечно-разностной сетки Δу.
В процессе моделирования шаг сетки изменялся в соответствии с изменениями
высоты горизонтального слоя элементов, т.е. вертикальный шаг сетки -
неравномерный. В момент кристаллизации металла внутри элемента шаг сетки,
соответствующий данному элементу, фиксировался в качестве начальной высоты
данного элемента. Относительная деформация элемента определялась с учетом
изгиба заготовки и порядковых номеров элемента в плоскости изгиба по всей длине
слитка. Таким образом, моделирование напряжений сводилось к перерасчету
вертикального шага конечно-
разностной сетки по напряжениям и накоплению
пластических деформаций. При компьютерном моделировании использовались
теплофизические данные легированной стали и слиток размером 250x300 мм.[ 14 ]
Для оценки эффективности данной системы были
проведены эксперименты с опробованием новой технологии охлаждения слитка. В
качестве исходных данных по параметрам разливки среднеуглеродистой легированной
стали использовали следующие технологические данные: температура заливки
1550°С; скорость вытяжки слитка 0,71 м/мин.
Для анализа напряженного состояния использовали
продольное сечение Z=0,04 м, которое находилось вблизи поверхности слитка. В
этом сечении по длине слитка было выделено несколько направлений, положения
которых в пространстве определялись значением Хп. Были проанализированы точки X
находящиеся на различных расстояниях Х=0,005 - 0,075 м от поверхности слитка.
На рисунке 4.7 представлено распределение продольных
напряжений в точке X=0,005м по длине слитка для плоскофакельного и
круглофакельного охлаждения.
В интервале 1 < L < 4 м как в случае
круглофакельного, так и плоскофакельного охлаждения изменения напряжений носят
колебательный характер изменения температуры. Причем колебания при
круглофакельном охлаждении слитка почти в два раза меньше соответствующих
колебаний при плоскофакельном охлаждении. Это свидетельствует о том, что
круглофакельное охлаждение способствует сглаживанию продольных напряжений по сравнению
с плоскофакельным. Например, для точки Х=0,015 м напряжения при круглофакельном
охлаждении почти в два раза меньше напряжений, возникающих при плоскофакельном
охлаждении. Причем это наблюдается на протяжении всей зоны вторичного
охлаждения (рисунок 4.7).
Рисунок 4.7 - Распределение продольных напряжений в сечении Z=0,04 м для
участка слитка 250x300 мм (L-длина) при 1-круглофакельном и 2- плоскофакельном
форсуночном охлаждении ЗВО МНЛЗ при: а) X = 0,005 м,
б) X = 0,015 м
На рисунке 4.8 представлено распределение
напряжений на участке ЗВО для точек Х=0,025 м и Х=0,035 м. Для точки,
находящейся ближе к поверхности четко прослеживается снижение напряжений,
соответствующих случаю круглофакельного охлаждения в сравнении с
плоскофакельным. Причем это хорошо видно для растягивающих напряжений.

Рисунок 4.8 - Распределение продольных
напряжений в сечении Z=0,04 м для участка слитка 250x300 мм (L - длина) при 1 -
круглофакельном и 2 - плоскофакельном форсуночном охлаждении ЗВО МНЛЗ при: а) X
= 0,025 м,
б) X = 0,035 м
На участке 2,5 < L < 5 м напряжения носят
колебательный характер, что связано с чередованием водяной и воздушной зон и
хорошо согласуется с подобными колебаниями, представленными на рисунке 4.8.
Для точки Х=0,035 м, находящейся ближе к центру,
различие в растягивающих напряжениях при круглофакельном и плоскофакельном
охлаждении наблюдается для участка 4 < L < 6 м. Причем различие в
напряжениях по длине слитка изменяются не линейно, что связано с началом изгиба
слитка, который находится в интервале 3-4 м.
На рисунке 4.9 представлено распределение
продольных напряжений в точках Х=0,045 м и Х=0,055 м. Для этих точек различие в
напряжениях, сформированных при круглофакельном и плоскофакельном охлаждении,
незначительны на участке 0 < L < 2,5 м и начинают проявляться после 4
метров. Чем ближе анализируемая точка к середине выделенной поверхности, тем
длиннее участок, на котором напряжения при круглофакельном и плоскофакельном
охлаждении близки.
Рисунок 4.9- Распределение продольных напряжений
в сечении Z=0,04 м для участка слитка 250x300 мм (L - длина) при 1 -
круглофакельном и 2 - плоскофакельном форсуночном охлаждении ЗВО МНЛЗ при: а) X
= 0,045 м,
б) X = 0,055 м
На основе исследований было установлено, что
развитие напряжений в слитке при вытягивании влияют размеры зон вторичного
охлаждения, расположение охлаждающих и не охлаждающих роликов.
Конфигурация и размеры роликов изменяют тепловые
свойства среды, из-за чего изменяется коэффициент теплоотдачи между слитком и
охлаждающей средой. Это приводит к пилообразному изменению температуры
(образованию локальных напряжений, связанных с наличием многократных фазовых
превращений), что было установлено в результате расчетов.
На рисунке 4.10 (а) представлено детальное
изображение участка охлаждения, из которого можно видеть, что градиенты
температуры сглаживаются для второго (предлагаемого) по сравнению с первым
вариантом. Аналогичные изменения наблюдаются на участке слитка от 2 м до 4 м
вытягиваемого слитка (рисунок 4.10 (б)).
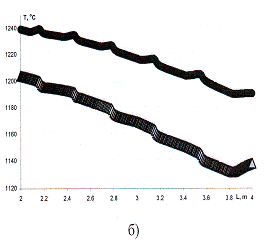
Рисунок 4.10 - Зависимость изменения температуры поверхности слитка
Уменьшение пилообразности температуры может
свидетельствовать о снижении уровня напряжений на поверхности слитка.
Таким образом, на основе выполненных расчетов и
исследований процесса формирования напряжений в слитке размером 250х300мм было
установлено,
что предлагаемый вариант в сравнении с базовым обеспечивает снижение напряжений
в слитке. Предлагаемый вариант отличается от базового увеличением водовоздушной
зоны за счет уменьшения воздушных прослоек, находящихся между зоной
кристаллизатора и в ЗВО-1, ЗВО-2, ЗВО-3 между роликами. При этом, применив
круглофакельные форсунки, можно снизить интенсивность охлаждения в 1,5 раза,
так как площадь измененной поверхности получается увеличенной в 1,5 раза. В
этом случае сглаживаются перегибы на температурных кривых слитков.
Использование круглофакельных форсунок в ЗВО
позволит создать дополнительное охлаждение неохлаждаемых роликовых узлов,
позволит увеличить ресурс стойкости роликовой секции и увеличить срок службы
подшипников в роликах. Кроме того, использование круглофакельного охлаждения
позволит увеличить длину зоны вторичного водяного охлаждения до 2,6-2,7м, за
счёт уменьшения воздушных прослоек между роликами в трёхсекционной зоне
вторичного охлаждения. В свою очередь это обеспечит равномерное охлаждение
слитка, предотвратит образование локальных напряжений, связанных с наличием
многократных фазовых превращений, что приведет к снижению и более равномерному
распределению термических напряжений по всей поверхности слитка и как следствие
уменьшение поверхностных дефектов слитка и улучшение макроструктуры отливаемой
заготовки.
В результате предлагаемых мероприятий
предполагается:
- индекс продольных трещин
(суммарная длина продольных трещин на площади 1м
) на круге и заготовке снизится с 6
до 1;
поражённость заготовок по
поверхностным трещинам снизится более чем в 2,5 раза;
глубина залегания трещин снизится до
2-3мм;
объём зачистки заготовки снизится на
80-90%.
.1.1 Расчёт зоны вторичного
охлаждения
При водовоздушном охлаждении
выделяют несколько зон, отличающихся по механизму теплоотвода: зона орошения
водой, зона натекания воды перед роликом, участок контактного охлаждения
роликом, зона конвекции и излучения на воздухе.
Остановимся на теплоотдачи в факеле
водовоздушной форсунки. Схема форсуночного охлаждения представлена на рисунке
4.12.
Рисунок 4.12- Влияние установочных
размеров форсунок на распределение плотности орошения
Основные геометрические параметры
зоны орошения:
-расстояние
от форсунки до заготовки;
β-
угол
раскрытия факела;
-расстояние
от крайней боковой точки заготовки до факела форсунки;
-полуширина
факела форсунки;
-перекрытие
факелов форсунок;
Данные
параметры связаны простейшими геометрическими соотношениями :
=h
tg
;(4.1)
=K
a
;(4.2)
где
K
-коэффициент
перекрытия.
Расстояние
между форсунками при их симметричном расположении относительно оси заготовки
рассчитывается по формуле:
ф
= 2a
- h
.(4.3)
где
Lф -расстояние между форсунками.
При
расчёте установочных расстояний принимаем во внимание, что:
боковые
стороны заготовки не должны переохлаждаться;
необходимо
стремится к равномерности охлаждения.
Первое
условие определяет величину параметра b
,второе накладывает ограничения на
коэффициент K
.
Зададим
параметры d
=200мм, β=100
, K
=0,65,
следовательно
= d
/ K
(4.4)
= a
/ tg
(4.5)
Откуда
рассчитаем расстояние между форсунками, подставив все данные в формулы 4.3-4.5:
a
=200/0,65=307,7мм
= 307,7/ tg
=258,6ммф
=2 · 307,7-258,6=356,8мм
Расход
охладителя (воды) в зоне вторичного охлаждения зависит от сечения заготовки,
марки стали и скорости разливки.
Расчет
расхода воды по зонам ЗВО для заготовки круглого сечения диаметром 200 ведем по
формуле 4.6, а все расчеты сводим в таблицу 4.1:
=
WН2О / Vg · Q(4.6)
где
G -расстояние между форсунками;Н2О - общий расход воды, л/мин;- скорость
разливки , м/мин;- вес заготовки, кг.
Таблица
4.1 - Расход воды по зонам ЗВО для заготовки диаметром 200 мм
Расход
воды л/мин
|
Скорость,
м/мин
|
|
0
|
0.25
|
0.5
|
0.75
|
1
|
1.25
|
1.5
|
1.75
|
2
|
2.25
|
2.5
|
1
|
2
|
3
|
4
|
5
|
6
|
7
|
8
|
10
|
11
|
12
|
Вторичное
охлаждение группа марок сталей 1
|
Контур
1 (боковые)
|
6
|
11
|
16
|
22
|
27
|
31
|
35
|
40
|
45
|
51
|
57
|
Контур
2 (радиальные)
|
6
|
11
|
16
|
22
|
27
|
31
|
35
|
40
|
45
|
51
|
57
|
Контур
3 (боковые)
|
5
|
10
|
15
|
20
|
24
|
28
|
32
|
38
|
43
|
48
|
54
|
Контур
4 (радиальные)
|
5
|
10
|
15
|
20
|
24
|
28
|
32
|
38
|
43
|
48
|
54
|
Контур
5 (боковые)
|
5
|
5
|
5
|
8
|
10
|
12
|
14
|
16
|
19
|
21
|
24
|
Контур
6 (радиальные)
|
5
|
5
|
5
|
8
|
10
|
12
|
14
|
16
|
19
|
21
|
24
|
Контур
7 (боковые)
|
5
|
5
|
5
|
8
|
10
|
10
|
12
|
12
|
12
|
13
|
15
|
Контур
8 (радиальные)
|
5
|
5
|
5
|
8
|
10
|
10
|
12
|
12
|
12
|
13
|
15
|
Общий
|
42
|
62
|
82
|
116
|
142
|
162
|
186
|
212
|
238
|
266
|
300
|
расход
л/кг
|
|
1,04
|
0,69
|
0,65
|
0,60
|
0,54
|
0,52
|
0,51
|
0,50
|
0,50
|
0,50
|
Вторичное
охлаждение группа марок сталей 2
|
Контур
1 (боковые)
|
6
|
11
|
16
|
22
|
26
|
30
|
35
|
37
|
41
|
47
|
52
|
Контур
2 (радиальные)
|
6
|
11
|
16
|
22
|
26
|
30
|
35
|
37
|
41
|
47
|
52
|
Контур
3 (боковые)
|
5
|
10
|
12
|
15
|
20
|
25
|
30
|
35
|
40
|
48
|
51
|
Контур
4 (радиальные)
|
5
|
10
|
12
|
15
|
20
|
25
|
30
|
35
|
40
|
48
|
51
|
Контур
5 (боковые)
|
5
|
5
|
8
|
10
|
12
|
14
|
14
|
14
|
16
|
17
|
20
|
Контур
6 (радиальные)
|
5
|
5
|
8
|
10
|
12
|
14
|
14
|
14
|
16
|
17
|
20
|
Контур
7 (боковые)
|
5
|
5
|
5
|
8
|
10
|
10
|
12
|
12
|
12
|
13
|
15
|
Контур
8 (радиальные)
|
5
|
5
|
5
|
8
|
10
|
10
|
12
|
12
|
12
|
13
|
15
|
Общий
|
42
|
62
|
82
|
110
|
136
|
158
|
182
|
196
|
218
|
250
|
276
|
расход
л/кг
|
|
1,04
|
0,69
|
0,62
|
0,57
|
0,53
|
0,51
|
0,47
|
0,46
|
0,47
|
0,46
|
4.2 Расчет основных параметров МНЛЗ
Скорость разливки определим по формуле:
= К · (1 + r) / r; (4.7)
где К - коэффициент марки стали К = 0,13 -
0,30;- радиус круглой заготовки, м.
Расчет производительности одного ручья определим
по формуле:
П1 = ρме
· F · V · 60;(4.8)
гдеП1 - производительность одного ручья, кг/ч;-
площадь сечения заготовки, м2 (F=πr²=3,14
· 0,1²=0,0314);-
скорость разливки, м/мин;
ρ ме - плотность
металла, 7450 кг/м3.
Подставив данные в формулы 4.7-4.8 получим:
= 0,13 · (1 + 0,100)/0,100 = 1,43 м/мин;
П1= 7450 · 0,0314 · 1,43 · 60 = 20071 кг/ч =
20,07 т/ч;
Время разливки на 1 ковш:
τ = М / (N · V · m · φ)(4.9)
где М - масса металла в ковше, кг - 100000;-
масса 1-го погонного метра заготовки, кг,
φ - коэффициент,
учитывающий потери времени на разливке, мин - 0,9;- количество ручьев, 4;
V - скорость разливки, м/мин.
Толщина корки:
σ корки = К
= К
(4.10)
где К - коэффициент затвердевания,
24-33 мм/мин 0,5, для 100т плавки;
τ - время кристаллизации, мин.;
Н - расстояние от данной точки до
уровня металла в кристаллизаторе;
Подставив данные в формулы 4.9-4.10
получим:
τ =100000 / 4 · 1,43 · 486 ·
0,9 = 39,97 мин;
σ корки = 31
= 31,4 мм.
Полное время затвердевания
заготовки:
τ = (а/2К)2 (4.11)
где К - коэффициент затвердевания,
0,028 мм/мин0,5 .
Определение металлургической длины
установки на МНЛЗ осуществляется по формуле:
жидк = К · а2 · V(4.12)
где К-коэффициент, зависящий от
величины отношения b/a (К= 260)
Подставив данные в формулы 4.11-4.12
получим:
τ = (0,100 / 2 ·
0,028)2 = 17,36 минжидк = 260 · 0,12 ·1,43 = 17,55 м
принимаем L жидк = 18 м.
Годовая производительность МНЛЗ
рассчитаем используя формулу :
Р = 1440 · n · M · Ф · φ1 / (n (τ 1 + τ2))(4.13)
где Р - производительность МНЛЗ,
тыс.т/г;- количество плавок в серии, шт;
τ 1 - время разливки одного
ковша;
τ2 - пауза, время подготовки
МНЛЗ к приёму следующей серии, 40 мин;
φ1 - коэффициент, учитывающий
загрузку оборудования, 0,8;
Ф - фонд рабочего времени в году,
сут.;
Ф = 365 - (Тпл +Ттр) (4.14)
где Тпл - планово-предупредительный
ремонт, 20 сут.;
Ттр - время текущего ремонта, 20
сут.;
М - масса металла в ковше, 100 т.
Следовательно используя формулы 4.13
и 4.14 получим:
Ф = 365 - (20 +20) = 340 суток
Р = 1440 · 7 · 100 · 340 · 0,8/ (4 ·
(39,97 + 40)) = 841857 т/г.
По производственным данным, плановая
производительность МНЛЗ №3 на 2009 год составляет 690200 тонн литой заготовки.
Принимая это за фактическую производительность, увеличение выпуска МНЛЗ
составит:
- (841857 · 100 / 690200) ≈
22%
5. ОРГАНИЗАЦИОННО-ЭКОНОМИЧЕСКАЯ ЧАСТЬ
.1 Организация производства. Структура
управления ЭСПЦ-2
В ЭСПЦ-2 организационная структура представлена
децентрализованным управлением производства. Начальник цеха назначается и
освобождается от должности приказом генерального директора предприятия по
представлению главного сталеплавильщика производства. Начальник цеха
осуществляет управление производством и связь с производственными участками
непосредственно и через, своих заместителей. Ежедневно проводится утреннее
оперативное совещание, где старшие мастера, участков отчитываются за прошедшие
сутки по выполнению производственных и качественных показателей, намечаются
мероприятия на текущие сутки, доводится оперативная информация, разбираются
случаи нарушений, допущенные при ведении технологического процесса.
Заместитель начальника цеха по
электросталеплавильному производству осуществляет руководство производством
через начальников и старших мастеров.
Для эффективного руководства участком,
систематического выполнения установленных производственных показателей,
успешного проведения воспитательной работы в коллективе назначается мастер. В
ЭСПЦ-2 на каждом участке руководство бригадами осуществляют непосредственно
мастера.
Коллектив цеха имеет сложную, развивающуюся
структуру: социально-классовую (основные и вспомогательные рабочие, специалисты
с высшим и средним образованием, инженеры, техники, служащие); социально -
демографическую (мужчины, женщины разных возрастных
групп, молодежь); социально-профессиональную и
квалификационную структуру, определяющуюся разделением труда, технологическими
и организационными особенностями.
Управление цехом является системным, охватывает
все стороны производственной, экономической, научно-технической, социальной и
экологической деятельности и регламентируется нормативными документами.
Управление цехом осуществляется на демократических началах; к управлению широко
привлекаются трудовой коллектив, профсоюзные и общественные организации цеха.
Управление материальными и трудовыми ресурсами
направлено на оперативное решение вопросов планирование, организации
производства и оплаты труда, а также на достижение плановых технико-экономических
показателей и оплаты труда, а также на достижение плановых
технико-экономических показателей и снижение себестоимости продукции.
Работа в ЭСПЦ-2 ведется по плану, утвержденному
главным инженером завода. В ноябре-декабре месяце цех получает предварительное
годовое производственное задание на объем и сортамент выпускаемой продукции с
учетом фирм-потребителей на следующий год.
На основании полученного производственного
задания начальник планово-производственного отдела совместно с заместителями и
начальниками участков определят необходимое количество оборудование, материалов
для выполнения данного объема выпуска продукции. Начальник
планово-производственного бюро составляет и представляет в производственный
отдел недельные графики работы оборудование, а также технические отчеты по
цеху.
Структура управлением цеха представлена на
рисунке 5.1
Рисунок 5.1 - Структура управлением цеха
.1.1 Мероприятия по повышению квалификации
рабочих и инженерных кадров
С целью обеспечения эффективной деятельности
всех подразделений завода (включая ЭСПЦ-2) и наполнения их специалистами
высокой культуры и профессиональной компетентности, а также профессиональными
кадрами требуемого уровня квалификации; сохранения и развития профессионального
потенциала и конкурентоспособности кадров; обеспечения кадровой поддержки
инновационных процессов; подготовки резерва руководящих кадров и резерва кадров
необходимой квалификации -на заводе ежегодно утверждается план-график
профессионального обучения рабочих и инженерных кадров.
Обучение персонала завода организуется по двум
направлениям:
непрерывное обучение руководящих работников и
специалистов;
непрерывное профессиональное обучение рабочих
(служащих).
Непрерывное профессиональное обучение руководящих
работников и специалистов носит непрерывный характер и осуществляется в течении
всей трудовой деятельности с целью усовершенствования и самоусовершенствования
уровня уже полученного высшего или среднего специального образования,
совершенствования профессионального мастерства в соответствии с требованиями
научно-технического и социально-экономического развития и включает в себя
следующие виды:
систематическое самостоятельное обучение
(самообразование);
обучение на предприятии (по месту работы);
повышение квалификации;
переподготовка;
стажировка.
Потребность в обучении определяется из нужд
производства, с учетом его перспективного научно-технического развития и
проводится не реже 1 раза в 5 лет.
Подготовка будущих руководителей осуществляется
путем создания из перспективных работников с лидерскими качествами резерва
руководителей. Обучение резерва руководителей производиться в соответствии с
Системой подготовки руководящих работников и специалистов.
Для повышения эффективности и качества труда
рабочих на производстве учебным центром применяются следующие виды обучения:
профессиональная подготовка рабочих;
переподготовка;
повышение квалификации рабочих;
курсы целевого назначения.
Непрерывное профессиональное обучение рабочих
(служащих) производится по двум формам: групповой и индивидуальный.
Обучение рабочих (служащих) производится по
учебным программам, разработанным и утвержденным в установленном порядке,
сопровождается текущей аттестацией и завершается итоговой аттестацией,
состоящей из одного или 2-х этапов:
выполнение квалификационной пробной работы;
теоретический экзамен.
При успешном прохождении итоговой аттестации
рабочему (служащему) присваивается соответствующая квалификация по профессии и
при профессиональной подготовке (переподготовке) выдается свидетельство
установленного образца.
Квалификационный разряд (класс, категория)
устанавливаются в соответствии с программой, по которой проводилось обучение.
Обучение может быть организовано с отрывом и без
отрыва от производства.
Повышение квалификации рабочих осуществляется на
основании заявок с периодичностью не реже 1 раза в 4 года, но не ранее года
работы по имеющейся квалификации.
По другим видам периодичность обучения
устанавливается предприятием с учетом производственной необходимости.
.1.2 Методы стимулирования работы сотрудников
Показатели, условия и порядок премирования
служащих и рабочих ЭСПЦ-2 разработаны в соответствии с Трудовым кодексом
Республики Беларусь и иными актами законодательства Республики Беларусь в целях
усиления материальной заинтересованности работников в результатах своего труда
и повышения эффективности деятельности цеха.
Показатели, условия и порядок премирования
работников ЭСПЦ-2 утверждаются для цеха положением и устанавливают круг
премируемых работников, основные показатели премирования, основания уменьшения
размеров и лишение премий, периодичность и источники выплаты премии,
предусматривают дифференцированный подход к премированию в зависимости от
личного вклада каждого работника в результаты производственно-хозяйственной деятельности
цеха и завода.
Премия представляет собой дополнительные
(денежное) вознаграждение, выплачиваемое работнику сверх основного заработка
при достижении установленных показателей премирования в размерах
предусмотренных системой оплаты труда.
Специальные и разовые премии поощрительного
характера (за внедрение новых видов техники и технологии, за экономию
энергоресурсов, сбор сдачу цветного лома, отходов цветных и драгоценных
металлов и др.) выплачиваются на основании действующих положений.
С целью материальной заинтересованности
работников цеха работникам соответствующих профессий устанавливается доплата:
персоналу ремонтных служб за фактическое
снижение нормы простоя оборудования и агрегатов;
служащим за снижении установленного уровня брака
производимой продукции;
за непосредственное участие в подготовке, а
также своевременную и качественную отгрузку экспортного металла (литой
заготовки) в страны дальнего зарубежья (на экспорт);
Доплата за своевременную подготовку и отгрузку
продукции на экспорт производиться в следующем порядке:
начальникам смен и сменным рабочим из расчета
0,8% за каждую 1 (одну) тысячу тонн отгруженной литой заготовки на экспорт при
условии выполнения установленного плана отгрузки;
заместителю начальника цеха по производству,
мастеру участка по отгрузке литой заготовки и дневным рабочим из расчета 0,2%
за каждую 1 (одну) тысячу тонн отгруженной литой заготовки на экспорт при
условии выполнения установленного плана отгрузки.
.2 Расчет инвестиций
Инвестиции состоят из капитальных вложений и
оборотных средств. Капиталовложения состоят из вложений в здания, техническую
оснастку и инструмент, производственный инвентарь и сопутствующих
капиталовложений.
Капиталовложения в производственное здание
рассчитывается по формуле 5.1:
Кзд = Sзд ∙ Цзд(5.1)
гдеКзд - капиталовложение в производственное
здание, млн. руб.;зд - площадь цеха, м2 (по производственным данным составляет
9400,8 м2);
Цзд - стоимость 1 м2 производственной площади,
руб. (по заводским данным 22 551 272 руб);
Кзд.б,п = 9400,8 ∙ 22 551 272 = 212 000
млн. руб.
Капиталовложения в технологическое оборудование:
Коб = ∑mпр ∙ Цj ∙ Кд (5.2)
гдеКоб-капиталовложения в технологическое
оборудование, млн. руб.;пр - принятое количество оборудования, шт;
Цj - цена единицы оборудования, руб.
Стоимость оборудования:
ДСП 38120 млн. руб;
МНЛЗ 36740 млн. руб;
Кристаллизаторы в сборе 1031 млн. руб;
Зона вторичного охлаждения1501 млн. руб.
Кд - коэффициент дополнительных затрат на
транспортные расходы, устройство фундамента и монтаж оборудования равен 1,15)
Подставив все данные в формулу 5.2 получим:
Коб.б = (38120 + 36740) ∙ 1,15 = 86089
млн. руб.;
Коб.п = (38120 + 36740 + 1031 + 1501) ∙
1,15 = 89001 млн.руб.
Капиталовложения в транспортные средства:
Коб = ∑mпр ∙ Цj ∙ Кд (5.3)
гдеКоб - капиталовложения в транспортные
средства, млн. руб.;пр - принятое количество оборудования, шт.;
Цj - цена единицы оборудования, руб. (по
заводским данным стоимость сталевоза составляет 900 млн. руб.;
Кд - коэффициент дополнительных затрат на
транспортные расходы, устройство фундамента и монтаж оборудования равен 1,15)
Используя формулу 5.3 рассчитаем:
Коб.б,п = 900 ∙ 1,15 = 1035 млн. руб.;
Капиталовложения в техоснастку и инструмент
учитываются в себестоимости продукции.
Капиталовложения в производственный инвентарь
укрупнено принимаются как 1 ÷ 2 % от
стоимости оборудования, следовательно:
Кпр.инв. б = 86089 ∙ 1,5/100 = 1291 млн.
руб.;
Кпр.инв. п = 89001 ∙ 1,5/100 = 1335 млн.
руб.
Стоимость нормируемых оборотных средств
укрупнено принимается
как 30% полной себестоимости годового объема
выпуска продукции.
Все инвестиции сводим в таблицу 5.1.
Таблица 5.1 - Величина инвестиций по вариантам
проекта
Наименование
групп инвестиций
|
Базовый
вариант
|
Проектный
вариант
|
|
Кол-во
|
Сумма,
млн. руб.
|
Кол-во
|
Сумма,
млн. руб.
|
Здания
и сооружения, м2.
|
1
|
212000
|
1
|
212000
|
Рабочие
машины и оборудование, шт.
|
1
|
86089
|
1
|
89001
|
Транспортные
средства, шт.
|
1
|
1035
|
1
|
1035
|
Производственный
инвентарь
|
1291
|
1335
|
Итого
основных фондов
|
3
|
300415
|
3
|
303371
|
Оборотные
средства
|
|
187949
|
|
180812
|
Всего
инвестиций
|
|
488364
|
|
484183
|
.3 Расчет себестоимости продукции
.3.1 Расчет затрат на материалы
Затраты на основные материалы рассчитываются на
1 тонну стали с учетом стоимости возвратных отходов:
См = qmi ∙ Цм ∙ Ктз - q0 ∙
Ц0(5.4)
гдеСм - затраты на основные материалы, млн.
руб.;- норма расхода материала, кг/т;
Цм - оптовая цена материала, руб/кг;
Ктз - коэффициент транспортно - заготовительных
расходов, Ктз = 1,05);- количество реализуемого отхода материала, кг/т;
Ц0 - цена отходов, руб/кг;
Оборотным, реализуемым отходом материала
является только стальной лом.
Результаты всех расчетов затрат на основные и
вспомогательные материалы (формула 5.4) приведены в таблице 5.2.
Таблица 5.2 - Ведомость затрат на основные и
вспомогательные материалы
Наименование
материала
|
Норма
расхода на 1 т
|
Цена
1 т руб.
|
Сумма
расхода на 1 т руб.
|
Годовая
потребность, т
|
Сумма
затрат млн.руб.
|
|
1
|
2
|
3
|
4
|
5
|
6
|
|
Проектный
вариант
|
Металлошихта
|
1,12
|
375989
|
421107,68
|
941920
|
396649,746
|
|
Отходы
|
0,032
|
87378
|
2796,096
|
26912
|
75,2485356
|
|
Всего
задано:
|
1,088
|
288611
|
314008,768
|
915008
|
287320,535
|
|
добавочные
|
0,0752
|
38263
|
2877,3776
|
63243,2
|
181,974567
|
|
электроды
610
|
0,00324
|
52682
|
170,68968
|
2724,84
|
0,46510207
|
|
электроды
400
|
0,00028
|
38571
|
10,79988
|
235,48
|
0,00254316
|
|
вода
оборотная
|
0,045
|
30000
|
1350
|
37845
|
51,09075
|
|
кислород
|
0,0304
|
87408
|
2657,2032
|
25566,4
|
67,9351199
|
|
вода
техническая
|
0,00084
|
32638
|
27,41592
|
706,44
|
0,0193677
|
|
вспомогательные
|
0,00225
|
103245
|
232,30125
|
1892,25
|
0,43957204
|
|
огнеупоры
|
0,012
|
215800
|
2589,6
|
10092
|
26,1342432
|
|
Итого
|
|
|
747827,93
|
|
684373,591
|
|
Базовый
вариант
|
металлошихта
|
1,15
|
375989
|
432387,35
|
793500
|
343099,36
|
|
отходы
|
0,032
|
87378
|
2796,096
|
22080
|
61,7378
|
|
всего
задано:
|
1,118
|
288611
|
322667,1
|
771420
|
248911,85
|
|
добавочные
|
0,0763
|
38263
|
2919,4669
|
52647
|
153,70117
|
|
электроды
610
|
0,00324
|
52682
|
170,68968
|
2235,6
|
0,3815938
|
|
электроды
400
|
0,00028
|
38571
|
10,79988
|
193,2
|
0,0020865
|
|
вода
оборотная
|
0,045
|
30000
|
1350
|
31050
|
41,9175
|
|
кислород
|
0,0304
|
87408
|
2657,2032
|
20976
|
55,737494
|
|
вода
техническая
|
0,00084
|
32638
|
27,41592
|
579,6
|
0,0158903
|
|
вспомогательные
|
0,00225
|
103245
|
232,30125
|
1552,5
|
0,3606477
|
|
огнеупоры
|
0,01311
|
215800
|
2829,138
|
9045,9
|
25,592099
|
|
Итого
|
|
|
768047,56
|
|
529952,8
|
|
|
|
|
|
|
|
|
|
|
.3.2 Затраты на топливо и энергию на технологические
цели
Затраты на технологическое топливо Стт (руб/т)
определяются:
Стт = qт ∙ Кпт ∙ Кн ∙ Цт(5.5)
гдеqт - удельный расход топлива (природного
газа), (21 м3/т);
Кпт - коэффициент потерь топлива, (Кпт ≈
1,05);
Кн - коэффициент неравномерности загрузки
оборудования,
(Кн ≈ 1,1 - 1,5);
Цт - цена топлива, (469,84 руб/т);
Удельные затраты на топливо (природный газ) по
базовому и проектному вариантам (используя формулу 5.5) равняются:
Стт б,п = 21 ∙ 1,05 ∙ 1,1 ∙
469,84 = 11395,97 руб/т
Годовые затраты на топливо (природный газ):
по базовому варианту: 11395,97 ∙ 690000 =
7863,22 млн.руб;
по проектному варианту: 11395,97 ∙ 841000
= 9584,01 млн. руб.
Затраты на технологическую электроэнергию Стэ
(руб)
рассчитываются по формуле:
Стэ = qэ ∙ Цэ (5.6)
где qэ - норма расхода электроэнергии, (qэб =
0,490 квт∙ч/т), эп = 0,388 квт∙ч/т);
Цэ - цена 1 квт∙ч электроэнергии, (Цэ =
140619 руб/квт∙ч);
Затраты электроэнергии по вариантам проекта,
используя формулу 5.6 равняются:
Базовый вариант:
Удельные : Стэ = 0,490 ∙ 140619 = 68903
руб/т;
Годовые: 38903 ∙ 690000 = 47543,28
млн.руб.
Проектный вариант:
Удельные : Стэ = 0,388 ∙ 140619 = 54560
руб/т;
Годовые: 54560 ∙ 841000 = 45885,1 млн.руб.
.3.3 Расчет фонда заработной платы и отчислений
на социальные нужды
Основная зарплата рабочих - повременщиков Зрп
(руб) определяется:
Зрп = (1+Кпдс) ∙ ∑Зрi ∙ Чспi ∙
Fэф (5.7)
гдеКпдс - коэффициент премий и доплат (по
заводским данным
Кпдс = 0,35);
Зрi - средняя часовая тарифная ставка, (по
заводским данным 6000 руб/ч);
Чспi - численность работающих;эф - эффективный
годовой фонд рабочего времени рабочих, ч
Подставив данные в формулу 5.7 получим:
Зрп б,п = (1+0,35) ∙ (6000 ∙ 120 ∙
1936 + 6000 ∙ 51 ∙ 1803) = 2626,61 млн. руб/г
Зрп б = 2626,61/690000 = 3806 руб/т;
Зрп п = 2626,61/841000 = 3123 руб/т.
Дополнительная заработная плата для рабочих
принимается 7%:
Зрп доп б,п = 2626,61 ∙ 7/100 = 183,86
млн.руб./год
Зрп доп б = 3806 ∙ 7/100 = 266,42 руб/т;
Зрп доп п = 3123 ∙ 7/100 = 218,61 руб/т.
Фонд заработной платы руководителей,
специалистов и служащих
определяется:
Зрсс = (1+Кд) ∙ Ч ∙ Зм ∙
12(5.8)
гдеЗрсс - фонд заработной платы руководителей,
специалистов и служащих, млн. руб.;
Кд - коэффициент доплат, Кд = 0,05;
Зм - среднемесячные оклады, (руководители - 3
млн. руб., специалисты - 1,5 млн. руб., служащие - 1 млн. руб.);
- число месяцев в году.
Используя формулу 5.8 найдем:
Зрссб,п = (1+0,05) ∙ (6 ∙ 3 ∙
12 + 15 ∙ 1,67 ∙ 12 + 10 ∙ 1 ∙ 12) = 680,84 млн.руб./г
Зрссб = 636,3 / 690000 = 922,17 руб/т;
Зрссп = 636,3 / 841000 = 756,59 руб/т.
Годовой фонд заработной платы работающих сводим
в таблицу 5.3.
Таблица 5.3 - Годовой фонд заработной платы
работающих по вариантам проекта
Категория
работающих
|
Удельная
заработная плата, руб/т
|
Годовой
фонд основной заработной платы, млн. руб.
|
Годовой
фонд дополнительной заработной платы, млн. руб.
|
Итого
|
|
Основная
|
Дополните-
льная
|
|
|
|
Базовый
вариант
|
Производ.
рабоч.
|
3806
|
266,42
|
2626,61
|
183,86
|
2810,47
|
Руководители
Специалисты Служащие
|
922,17
|
|
680,84
|
|
680,84
|
Итого
|
4728,17
|
266,42
|
3307,45
|
183,86
|
3491,31
|
Проектный
вариант
|
Производ.
рабоч.
|
3123
|
218,61
|
2626,6
|
183,86
|
2810,47
|
Руководители
Специалисты Служащие
|
756,59
|
|
680,84
|
|
680,84
|
Итого
|
3879,59
|
218,61
|
3307,45
|
183,86
|
3491,31
|
Отчисления в фонд социальной защиты населения
(35% от ФОТ)следовательно:
Отч сз б,п = 3491,311 ∙ 35/100 = 1221,95
млн. руб/г
Отчисления в фонд занятости (1% от ФОТ):
Отч фз б,п = 3491,311 ∙ 1/100 = 34,91 млн.
руб/г
.3.4 Определение общепроизводственных,
общехозяйственных и коммерческих расходов
Амортизация оборудования и транспортных средств
определяется:
А = ∑Цбj ∙ mпрj ∙
(Haj/100)(5.9)
гдеА - амортизация оборудования, млн. руб.;
Цбj - балансовая цена оборудования, млн.
руб.;прj - количество оборудования, шт.;- норма амортизационных отчислений
(принимается 10%).
Используя формулу 5.9 получим:
Аб = (86089 ∙ 1 ∙ (10/100)) + (1035 ∙
1 ∙ (10/100)) = 8712,4 млн. руб.;
Ап = (89001 ∙ 1 ∙ (10/100)) + (1035 ∙
1 ∙ (10/100)) = 9003,6 млн. руб.
Стоимость вспомогательных материалов принимается
равной 0,5 - 1% от стоимости оборудования, следовательно:
Свсм б = 86089 ∙ 0,5/100 = 430,44 млн.
руб.;
Свсм п = 89001 ∙ 0,5/100 = 445,01 млн.
руб.
Затраты на силовую энергию состоят из:
Плата за установленную мощность:
Сэм = Wy ∙ Ц ∙ Квр ∙ КN ∙
Кпс,(5.10)
Стоимость потребляемой энергии:
Сэп = Цэ ∙ Fg∙ Квр ∙ КN ∙
(Кпс/η),(5.11)
гдеWy - суммарная установленная мощность
оборудования,
(Р = 4650 кВт);
Квр - коэффициент загрузки оборудования по
времени, (Квр =0,9);
КN - коэффициент загрузки оборудования по
мощности, (КN = 0,9);
Кпс - коэффициент потерь электроэнергии,( Кпс =
1,03);
η - коэффициент
мощности, (η =0,65);
Цэ - стоимость 1 кВт.ч электроэнергии (Цэ =
289,29 руб).
Зсэ, б,п = 4650 ∙ 25000 ∙ 0,9∙
0,9∙ 1,03 = 97 млн. руб.
Содержание оборудования рассчитываем:
Зоб..= Свсм ∙ Зсэ, б,п(5.12)
Используя формулу 5.12 получим:
в базовом варианте: Зоб.б.= 430,44+97 = 527,44
млн. руб.;
в проектном варианте: Зоб.пр.= 445,01+97 =
542,01 млн. руб.
Текущий ремонт оборудования определяется в
размере 5% от балансовой стоимости, следовательно:
Трб = 86089 ∙ 5/100 + 1035 ∙ 5/100 =
4356 млн. руб.;
Трп = 89001 ∙ 5/100 + 1035 ∙ 5/100 =
4502 млн. руб.
Расходы на внутризаводское перемещение грузов
определяется как 10% от стоимости транспорта:
Рп б,п = 1035∙10/100 = 10,35 млн. руб.
Износ малоценных и быстроизнашивающихся
инструментов укрупнено принимается в размере 100 тыс. руб/1 рабочего:
Имб.п = 100000 ∙ 120 = 12 млн. руб.
Составляем смету расходов на содержание и
эксплуатацию оборудования (таблица 5.4).
Таблица 5.4 - Смета расходов на содержание и
эксплуатацию оборудования
Наименование
статей
|
Сумма,
млн. руб.
|
|
базовый
вариант
|
проектный
вариант
|
1
|
2
|
3
|
Амортизация
оборудования и транспортных средств
|
8712,4
|
9003,6
|
Содержание
оборудования
|
527,44
|
542,01
|
Основная
и дополнительная заработная плата рабочих
|
2810,47
|
2810,47
|
Текущий
ремонт оборудования, транспортных средств и ценного инструмента
|
4356
|
4502
|
Внутризаводское
перемещение грузов
|
10,35
|
10,35
|
Износ
малоценных инструментов и приспособлений
|
12
|
12
|
Всего,
в том числе:
|
16428,66
|
16880,4
|
Материальные
затраты:
|
4905,79
|
5169,83
|
Амортизационные
отчисления
|
8712,4
|
9003,6
|
Расходы
на оплату
|
2810,47
|
2810,47
|
.3.5 Расчет расходов по организации,
обслуживанию и управлению производством
Затраты на содержание аппарата управления
включают основную и дополнительную заработную плату руководителей, специалистов
и служащих:
По базовому и проектному вариантам:
Зрб.п =636,3 + 44,541 = 680,841 млн. руб.;
Амортизация зданий, сооружений и инвентаря определяется
по формуле:
А = ∑Цбj ∙ mпрj ∙
(Haj/100)(5.13)
гдеА - амортизация зданий, сооружений и
инвентаря, млн. руб.;
Цбj - балансовая цена зданий, млн. руб.;прj -
количество зданий, шт.;- норма амортизационных отчислений, (принимается 1,2 %).
Используя формулу 5.13 получим:
Аб,п = (212000 ∙ 1 ∙ (1,2/100)) =
2544 млн. руб.;
Расход на содержание зданий, сооружений и
инвентаря Рзд б,п укрупнено определяется в стоимости 7 у.е./м2.
Следовательно по базовому и проектному
вариантам:
Рзд б,п = 9400,8 ∙ 7 ∙ 2850 =
187,546 млн. руб.
Расходы на текущий ремонт зданий и сооружений
Рр.зд принимаются в размере 1,5% от их стоимости, инвентаря - 10%.
По базовому варианту:
Рр.зд б =212000 ∙ 1,5/100 + 1291 ∙
10/100 = 3309 млн. руб.;
По проектному варианту:
Рр.зд п =212000 ∙ 1,5/100 + 1335 ∙
10/100 = 3314 млн. руб.
Расходы на испытания, опыты, исследования,
рационализация и изобретательство Рпроч принимаются в размере 100 у.е. на
одного работающего.
По базовому и проектному вариантам:
Рпроч б,п =171 ∙ 100 ∙ 2850 = 48,74
млн. руб.
Расходы по охране труда Рот принимаются в
размере 70 у.е. на одного работающего.
По базовому и проектному вариантам:
Рот б,п =171 ∙ 70 ∙ 2850 = 34,11
млн. руб.
Износ малоценного и быстроизнашиваемого
инвентаря Из принимается в размере 50 у.е. на одного работающего.
По базовому и проектному вариантам:
Из б/п =171 ∙ 50 ∙ 2850 = 24,36 млн.
руб.
Все расходы по организации, обслуживанию и
управлению производством сводим в таблицу 5.5.
Таблица 5.5 - Расчет расходов по организации,
обслуживанию и управлению производством
Наименование
статей
|
Сумма,
млн. руб.
|
|
Базовый
вариант
|
Проектный
вариант
|
Содержание
аппарата управления
|
680,841
|
680,841
|
Амортизация
зданий, сооружений инвентаря
|
2544
|
2544
|
Содержание
зданий, сооружений, инвентаря
|
187,546
|
187,546
|
Текущий
ремонт зданий, сооружений, инвентаря
|
3309
|
3314
|
Испытания,
опыты, исследования, рационализация и изобретательство
|
48,74
|
48,74
|
Охрана
труда
|
34,11
|
34,11
|
Износ
малоценного и быстроизнашивающегося инвентаря
|
24,36
|
24,36
|
Прочие
расходы (2% от суммы п.1-7)
|
136,57
|
136,71
|
Всего
в том числе:
|
6965,167
|
6970,307
|
Материальные
затраты (сумма п.3-8)
|
3740,32
|
3747,46
|
Амортизационные
отчисления
|
2544
|
2544
|
Расходы
на оплату труда
|
680,841
|
680,841
|
Общехозяйственные расходы принимаются в размере
60% от основной заработной платы производственных рабочих (в том числе
материальные затраты - 65%, амортизация - 20%, зарплата - 15%).
Коммерческие расходы - 3% от производственной
себестоимости.
В таблице 5.6 проводим калькуляцию полной
себестоимости годового выпуска продукции.
Таблица 5.6 - Калькуляция полной себестоимости
годового выпуска продукции
Наименование
калькуляционных статей
|
Сумма
затрат, млн. руб.
|
|
Базовый
вариант
|
Проектный
вариант
|
Итого
|
Затраты
на основные и вспомогательные материалы
|
529952
|
516001,27
|
-13950
|
Топливо,
энергия, технологические цели
|
47543,28
|
37646,4
|
-9896
|
Основная
заработная плата производственных рабочих
|
3806
|
3806
|
0
|
Налоги,
отчисления в бюджет и внебюджетные фонды
|
1256,86
|
1256,86
|
0
|
Износ
инструментов и приспособлений целевого назначения
|
12
|
12
|
0
|
Общепроизводственные
расходы в том числе
|
23393,8
|
24145,7
|
751.9
|
Материальные
затраты
|
8646,11
|
8917,29
|
271.18
|
Амортизационные
отчисления
|
11256,4
|
11737,1
|
480.7
|
Расходы
на оплату труда
|
3491,311
|
3491,311
|
0
|
Итого
цеховая себестоимость
|
605964
|
582868
|
-23096
|
Общехозяйственные
расходы, в т ч
|
2283,6
|
2283,6
|
0
|
Материальные
затраты
|
1484,34
|
1484,34
|
0
|
Амортизационные
отчисления
|
456,7
|
456,7
|
0
|
Расходы
на оплату труда
|
342,54
|
342,54
|
0
|
Производственная
себестоимость
|
608248
|
585152
|
-23096
|
Коммерческие
расходы
|
18247
|
17555
|
-692
|
Полная
себестоимость годового выпуска продукции
|
626495
|
602707
|
-23788
|
.4 Расчет технико-экономических показателей цеха
Годовой объем выпуска продукции в отпускных
ценах (Q, млн. руб.) определяется по формуле:= Сп,б ∙ (1+Рс/100), (5.14)
где Сп,б - полная себестоимость годового объема
выпуска продукции по базовому варианту, млн. руб.;
Рс - рентабельность продукции в процентах к
себестоимости (20% от Сп,б ).
Прибыль от реализации продукции (Пр, млн. руб.)
определяется по формуле:
Пр = (Q - Сп - 0,20 ∙ (3+1,4+А))/1,2
,(5.15)
где Сп - полная себестоимость годового объема
выпуска продукции по проектному или базовому варианту, млн. руб.;
,20 - ставка налога на добавленную стоимость;
З - фонд заработной платы по вариантам, млн. руб.;
А - амортизация основных фондов, млн. руб.
Чистая прибыль определяется:
Пч = (Пр-0,01Ф0) ∙ (1-Нп/100),(5.16)
гдеФ0 - стоимость основных фондов по вариантам,
млн. руб.;
Нп - ставка налога на прибыль, 24%.
Подставив данные в формулы 5.14-.516 получим:
б= 626495∙ (1+20/100) = 751794 млн. руб.п=
6027075∙ (1+20/100) = 723248 млн. руб.
Прб = (751794 - 626495 - 0,20 ∙
(3491,311+1,4+2544))/1,2 = 103410 млн. руб.;
Прп = (751794 - 602707 - 0,20 ∙
(3491,311+1,4+2544))/1,2 = 123233 млн. руб.
Пчб = (103410-0,01∙300415) ∙
(1-24/100) = 76308 млн. руб.;
Пчп = (123233-0,01∙303371) ∙
(1-24/100) = 91352 млн.руб.
Рентабельность производства (Р,%) по вариантам
определяется по формуле:
Р = (Пч/И) ∙ 100(5.17)
гдеПч - годовая чистая прибыль по вариантам,
млн. руб.;
И - величина инвестиций, млн. руб.
Период возврата инвестиций определяется:
Т = И/Пч(5.18)
Подставив данные в формулы 5.17 и 5.18 получим:
Рб = 76308/488364 ∙ 100 = 15,6 %
Рп = 91352/486106 ∙ 100 = 18,9 %
Тб = 488364/76308 = 6,4года.
Тп = 484183/91352 = 5,3 года.
В таблице 5.7 приводим технико - экономические
показатели проекта
Таблица 5.7 - Технико - экономические показатели
проекта
Показатели
|
Варианты
|
|
Базовый
|
Проектный
|
1
|
2
|
3
|
Годовой
объем выпуска продукции В натуральном выражении, т В стоимостном выражении,
млн. руб.
|
690000
751794
|
841000
723248
|
Стоимость
инвестиций, млн. руб.
|
488364
|
484183
|
В
том числе основных фондов, млн. руб.
|
300415
|
303371
|
Численность
работающих, чел
|
171
|
171
|
В
том числе производственных, чел
|
120
|
120
|
Фонд
заработной платы, млн. руб.
|
3491,311
|
3491,311
|
Среднемесячная
заработная плата 1 работающего, млн. руб.
|
1,7
|
1,7
|
Производительность
труда 1 работающего, млн. руб./чел
|
4396
|
4396
|
Фондоотдача,
руб/руб
|
2,5
|
2,5
|
|
Себестоимость
годового объема, млн. руб.
|
626495
|
602707
|
|
Себестоимость
единицы продукции, млн руб
|
0,91
|
0,72
|
|
Прибыль
чистая, млн. руб.
|
76308
|
91352
|
|
Рентабельность
производства, %
|
15,6
|
18,9
|
|
Период
возврата инвестиций, лет
|
6,4
|
5,3
|
|
|
|
|
|
|
Анализ технико-экономических показателей данного
проекта показал, что реконструктивные мероприятия в ЭСПЦ-2 имеют положительный
эффект.
Себестоимость единицы продукции снизилась на
0,19 млн.руб. Рентабельность производства при этом увеличилась на 3,3 %. Период
возврата инвестиций составил 5,3 лет.
Все технико - экономические показатели проекта
представлены в приложении К.
. ОХРАНА ТРУДА
На предприятиях, где присутствует
электросталеплавильное производство, существует большое количество опасных и
вредных производственных факторов, таких как запыленность, загазованность, шум,
вибрация, тепловое излучение, недостаточная освещенность и ряд других, которые
создают неблагоприятные условия труда и способствуют развитию профессиональных
заболеваний, повышению производственного травматизма, а также увеличивают общую
заболеваемость работающих.
.1 Производственная санитария, техника
безопасности, пожарная профилактика
.1.1 Характеристика техпроцесса с точки зрения
воздействия на работающих опасных и вредных производственных факторов
Одним из вредных веществ, часто находящимся в
воздухе металлургических цехов, является пыль. В металлургических цехах пыль
образуется при процессах подготовки шихтовых материалов, при плавке, печной и
внепечной обработке стали, сушке стальковшей, при футеровке сталеплавильных
агрегатов. Токсические вещества выделяются при выплавке и разливке стали, сушке
ковшей, изготовлении футеровки и при других процессах производства стали.
Наиболее токсичными веществами электросталеплавильного производства являются
диоксины и фураны - хлорсодержащие органические соединения, образующиеся при нагреве
шихты, загрязнённой пластмассами на основе ПВХ, например, бытового или
автомобильного лома.
К вредным веществам, встречающимся в
металлургии, относятся оксид углерода и сернистый газ. Вредные вещества,
образующиеся при ведении процесса плавки в электросталеплавильных печах,
приведены в таблице 6.1.
Таблица 6.1 - Вредные вещества процесса плавки
Вещества
|
ПДК,
мг/м3
|
Класс
опасности
|
Медь
|
1
|
2
|
Свинец
|
0,01
|
1
|
Сода
кальцинированная
|
2
|
3
|
Железа
оксид
|
6
|
4
|
Алюминия
оксид
|
2
|
3
|
Хрома
оксид
|
1
|
3
|
Водорода
хлорид
|
5
|
2
|
Сурьма
металлическая (пыль)
|
0,5
|
2
|
Хлор
|
1
|
2
|
Диоксид
кремния (пыль) >70%
|
1
|
3
|
Диоксид
кремния (пыль) <2%
|
10
|
4
|
Чугун
|
6
|
4
|
Углерода
оксид
|
20
|
4
|
Для снижения пылеобразования при
погрузочно-разгрузочных работах на шихтовом дворе по стенам бункеров смонтированы
трубопроводы с форсунками для распыления воды сжатым воздухом. На участке ДСП-3
и УВОС печи укрываются специальными пылегазоулавливающими укрытиями.
Кроме того участки выплавки и разливки
оборудованы общеобменной вентиляцией, на рабочих местах сталеваров, подручных
сталевара, разливщиков установлены устройства воздушного душирования. Работа
сталеваров и подручных сталеваров в течение смены чередуется с перерывами для
отдыха в специально оборудованных комнатах. [ 19 ]
Очистка выбросов от ДСП и МНЛЗ производится в
пылегазоулавливающих (ПГУ) установках грубой и тонкой очистки. Все работающие
используют средства индивидуальной защиты: респираторы, защитные очки, каски,
беруши, наушники.
.1.2 Метеорологические условия
Метеорологические условия (микроклимат) на
рабочем месте определяются температурой воздуха, относительной влажностью,
скоростью движения воздуха и интенсивностью теплового облучения от нагретых
поверхностей.
Благоприятные (комфортные) метеорологические
условия на производстве являются важным фактором в обеспечении высокой
производительности труда и в профилактике заболеваний.
Категория выполняемой работы (по энергозатратам
организма) на участках ДСП-3 и УВОС, МНЛЗ-3, 2 в ЭСПЦ-2 - средней тяжести IIб.
Для данной категории энергозатраты составляют
201-250 ккал/час, т.е. 233-290 Вт. ЭСПЦ - 2 - это помещение со значительным
избытком явного тепла.
Оптимальные нормы микроклимата для сталеваров и
подручных сталеваров приведены в таблице 6.2.
Таблица 6.2 - Оптимальные нормы микроклимата
Период
года
|
Категория
работ
|
Температура,
0С
|
Скорость
движения воздуха, м/с,
|
Холодный
|
Средней
тяжести IIб
|
17-20
|
60-40
|
0,3
|
Теплый
|
Средней
тяжести IIб
|
20-22
|
60-40
|
0,4
|
Допустимые параметры микроклимата для сталеваров
и подручных сталеваров приведены в таблице 6.3.
Таблица 6.3 - Допустимые параметры микроклимата
Период
года
|
Категория
работ
|
Темпе-ратура,
0С
|
Относитель
ная влажность, %
|
Скорость
движения воздуха, м/с,
|
Температу-ра
воздуха вне раб. мест, 0С
|
Холодный
|
Средней
тяжести IIб
|
15-21
|
75
|
0,4
|
13-23
|
Теплый
|
Средней
тяжести IIб
|
16-27
|
55-75
|
0,2-0,5
|
15-29
|
Меры защиты от интенсивных тепловых излучений:
теплоизоляция
нагретых
поверхностей, экранирование тепловых излучений, воздушное душирование, орошение
воздуха в летнее время. Рабочие используют защитный суконный костюм с вачегами
(рукавицы) согласно ГОСТ 12.4.103-83 и сапоги с голенищами типа ТР по ГОСТ
12.4.032-95.
Для защиты головы применяется каска, для защиты
лица и глаз - специальные защитные очки (марки 034-У, 034-В1, 034-В2) , очки
защитные козырьковые (марки П-2, П-3, ОК1, ОК3) и защитные щитки.
При высокой интенсивности теплового излучения в
течение смены устраиваются перерывы, рабочие снабжаются газированной
подсоленной водой (от 0,2 до 0,5 % хлористого натрия) из расчета 4-5 литров на
человека в смену.
Работники проходят предварительные и
периодические медицинские осмотры в целях предупреждения и ранней диагностики
заболеваний. [ 20 ]
.1.3 Вентиляция
Воздухообмен в цехе производится с
использованием естественной и механической вентиляции согласно СНБ 4.02.01-03.
Естественная вентиляция осуществляется через
окна, форточки, фонари. Механическая вентиляция - приточная и вытяжная.
Одним из основных мероприятий по оптимизации
параметров микроклимата и состава воздуха в производственных помещениях
является обеспечение надлежащего воздухообмена.
Напротив рабочей площадки в продольной стене
оборудованы приточные отверстия в виде открывающихся фрамуг, которые
обеспечивают свободное поступление свежего воздуха в глубь помещения. При этом
свежий воздух не перемешивается, а вытесняет загрязненный воздух, находящийся в
помещении. Для более эффективного удаления СО, СО2 вредных выбросов при плавке
шихты в ДСП применяется замкнутая система вытяжных устройств, обеспечивающая
наиболее полное удаление контаминантов из объема печи.
Для этого в верхней части здания предусмотрена
вытяжная система (щелевые воздухозаборники и др.) производительностью около 165
м3/мин. Наряду с этим используются также вытяжные колпаки, производительность
которых составляет 120 м3/мин.
Наличие вентилятора в системе выведения пыли
непосредственно из объема дуговой электропечи обеспечивает производительность
системы 12 м3/мин. При разливке стали, полученной в дуговой электропечи,
воздушный поток от пыли очищают путем расположения кожухов вентиляционной
системы над разливаемым металлом с последующим пропусканием воздушного потока,
содержащего пыль, через рукавные фильтры или электрофильтры. Для очистки
воздуха от пыли в ЭСПЦ применяют пылеосадительные камеры и фильтры различной
конструкции.
Защита от вредных выделений (смазок, кислот,
металлической пыли и т.д.) осуществляются с помощью установок местной
вентиляции систем аспирации, а также производится герметизация узлов и емкостей
оборудования, которые являются источниками выделения вредных веществ.
Образующиеся в процессе плавки газы представляют
собой смесь моно- и диоксида углерода, непрореагировавшего кислорода и азота
подсасываемого через рабочее окно воздуха. Наиболее эффективным способом
удаления газов из рабочего пространства дуговых печей является прямой газоотсос
механической тягой через сводовое газоотводящее отверстие диаметром 600...900
мм.
.1.4 Производственное освещение
Нормальные условия работы в производственных
помещениях ЭСПЦ обеспечиваются достаточным освещением рабочих зон, проходов и
проездов, для чего применяется общее естественное освещение, искусственное
освещение и локальные осветительные установки. Естественное освещение
используется в дневное время суток. Оно обеспечивает хорошую освещенность,
равномерность; вследствие высокой диффузности (рассеивания) благоприятно
действует на зрение. В ЭСПЦ-2 применяют верхнее и комбинированное естественное
освещение с двухсторонними фонарями вертикального и наклонного остекления.
Боковое естественное освещение осуществляется
через окна в наружных стенах, верхнее - через светоаэрационные фонари. Верхнее
остекление производится из светорассеивающего стекла, которое обеспечивает
равномерную освещенность цеха. Остекление, находящееся на уровне глаз выполнено
из обычного прозрачного стекла. Отношение площади остекления к площади пола на
основных участках ЭСПЦ обычно составляет 12 - 15 %, в складских и подсобных
помещениях 10 %. В ЭСПЦ применяется комбинированный тип естественного
освещения.
Установленное в ЭСПЦ осветительное оборудование
обеспечивает освещённость производственных участков согласно нормам зрительных
работ.
Согласно ТКП 45-2.04-153-2009 определяется
разряд зрительной работы, а также нормативное значение минимальной
освещенности. На участках предусмотрены следующие виды искусственного
освещения: рабочее (общее, комбинированное), дежурное, аварийное (освещение
безопасности и эвакуационное аварийное освещение).
Источниками искусственного освещения являются
газоразрядные лампы, лампы накаливания, люминесцентные лампы.
Применяемые типы светильников: газоразрядные
лампы - РСП 10, РСП 18; лампы накаливания - УПМ 15, УПД, НСП 22; люминесцентные
лампы - ЛСП 17, ПВЛМ.
Минимальная высота подвеса над полом при общем
искусственном освещении - 5м. Очистка стекол на окнах аэрационных фонарях
осуществляется не реже 4-х раз в год. [ 21 ]. Нормы освещенности приведены в
таблице 6.4.
Таблица 6.4 - Нормы освещенности отдельных
участков ЭСПЦ - 2
Наименование
участка
|
Разряд
зрительных работ
|
Общая
система освещения, освещенность, лк
|
Боковое
естественное освещение, КЕО,%
|
ДСП
- 3
|
7
|
200
|
1
|
УВОС
|
7
|
200
|
1
|
Склад
готовой продукции
|
8а
|
200
|
1
|
.1.5 Шум, вибрация
Источники интенсивного шума и вибрации в ЭСПЦ-2:
участок ДСП-3 и УВОС - дуговая сталеплавильная электропечь; установка внепечной
обработки стали - “ковш-печь”, вакууматор RH и VD.
Уровень шума согласно ГОСТ 12.1.003-83, СанПиН
2.2.4/2.1.8.10 - 32 - 2002 не превышает 80 дБА.
Средства защиты от шума: изолирующие кожухи,
глушители, противошумные укрытия. На участке с повышенным шумом оборудуются
комнаты психологической разгрузки. Рабочими используются индивидуальные
средства защиты: беруши, наушники. [ 21 ]
Уровень общей технологической вибрации в
производственных помещениях не превышает 92 дБ, а локальная вибрация не
превышает 112 дБ согласно ГОСТ 12.1.012-2004 и СанПиН 2.2.4/2.1.8.10 - 33 -
2002.
Средствами защиты от вибрации, применяемыми при
выполнении техпроцесса, являются: виброизолирующий фундамент, герметичные
изолирующие кожухи.
Средства индивидуальной защиты работающих:
специальные антивибрационные рукавицы, обувь с амортизированными подошвами.
.1.6 Электробезопасность
По опасностям поражения участок ДСП-3 и УВОС,
МНЛЗ-3 совмещают два и более фактора, свойственных помещениям с повышенной
опасностью и относятся к особо опасным помещениям (класс III).
С целью защиты от поражения электрическим током
в цехе проложен
общий
контур заземления. Корпуса оборудования, установленного на участках
подсоединены к этому контуру. Сопротивление контура заземления 4 Ом ГОСТ
12.1.030-81. Кроме этого на оборудовании изолированы все токоведущие части
тралей подъемно-транспортного оборудования и размещены на недоступной высоте.
Транспортные подстанции находятся в отдельных помещениях.
Освещение переносными лампами осуществляется
напряжением 36 В. Широко применены устройства защитного отключения. Рабочими
используются средства индивидуальной защиты - диэлектрические перчатки,
резиновые коврики, инструмент с изолированными рукоятками. [ 20 ]
.1.7 Требования безопасности к технологическому
процессу, к конструкции оборудования
При работе оборудования опасными зонами являются
пространства вокруг движущихся элементов (ДСП, “печь-ковш”, сталевозы,
конвейеры, подъемно-транспортные машины, технологический автотранспорт, и т.д.;
места с наличием опасности поражения электрическим током; воздействия тепловых
и электромагнитных излучений, шума, вибрации, вредных паров, газов, пыли).
Производственное оборудование соответствует ГОСТ
12.3.027-2004 «Работы литейные», ГОСТ 12.2.046.0-2004 «Оборудование
технологическое для литейного производства».
Все движущиеся части оборудования ограждены.
Размеры ячеек сетчатых ограждений подвижных узлов, доступных для случайного
прикосновения имеют размер менее 10х10 мм. Ограждения массой более 6 кг имеют
рукоятки для удержания их при съеме. Калитки ограждений снабжены концевыми
выключателями.
Крепления защитных устройств надежны, исключают
самооткрывание. Предусмотрены предохранительные устройства, исключающие
внезапные перегрузки, переход движущихся частей за установленные границы,
чрезмерное повышение давления пара, воды, газа, величины электрического тока,
выход других контролируемых параметров за пределы допустимых значений.
Рабочее место и органы управления
металлургического оборудования соответствуют ГОСТ 12.2.064-81. Конструкция
пультов исключает возможность случайного включения.
Конвейеры оборудуются системой аварийной
остановки по всей длине конвейера. Все конвейеры оборудованы звуковым сигналом
перед началом движения за 30 секунд.
При высоте выступающих частей до 70 мм
допускается их сплошная окраска желтым цветом. Окраска внутренней поверхности и
предупреждающие знаки по наружной поверхности дверей, в которых располагаются
механизмы передач при наладке металлургического оборудования, требующие периодического
доступа выполнены ГОСТ 12.4.026-76.
Металлургическое оборудование окрашивается в
желтый цвет.
Быстродвижущиеся части машины окрашиваются в
красный цвет, медленно движущиеся - в желтый, вентустановки, металлические
конструкции - алюминиевой краской, ограждения и колонны в желтый цвет [ 20 ].
.1.8 Санитарно-бытовые помещения
Согласно ТКП 45-3.02-209-2010 процесс
металлургии чугуна относится к 3-ей группе производственных процессов.
Исходя из этого, состав санитарно-бытовых
помещений следующий: гардеробные, душевые, умывальные, уборные, сушильные,
курительные
комнаты, комнаты личной гигиены женщин
(предусмотрены в случае численности женщин - 15 человек), комнаты отдыха и
психологической разгрузки. Расчет производится на 100 человек работающих.
Требуемые площади санитарно-бытовых помещений
составляют: гардеробные - 50 м2; душевые - 80 м2; умывальные
- 20 м2; уборные - 15 м2; сушильные - 20 м2; курительные - 3 м2; комнаты отдыха
и психологической разгрузки - 90 м2.
Бытовые помещения размещены в цехе на свободных
местах, используя в первую очередь свободные объемы здания. Такие решения
снижают стоимость строительства бытовых помещений, улучшают условия
обслуживания рабочих и приближаются к рабочим местам.
Гардеробные, душевые и т.д. помещения располагаются
вне цеха. Они располагаться в местах с наименьшим выделением вредности, в
отдельных корпусах или пристройках здания.
Помещения, требующие подачи воды и отвода
сточных вод, необходимо размещать рядом или друг над другом с целью сокращения
длины линий водопровода и канализации.
.1.9 Пожарная профилактика
Пожарная безопасность обеспечена мерами пожарной
профилактики и активной пожарной защиты. В проектируемом цехе пожарная
профилактика включает комплекс мероприятий, необходимых для предупреждения возникновения
пожара или уменьшение его последствий.
Все элементы проектируемого цеха относятся по
признаку пожарной опасности к категории Г2, НПБ 5-2005. Их выполняют из
несгораемых материалов, обеспечивающих 1 степень огнестойкости (СНиП
2.01.02-85, СНБ2.02.01-98, ТКП 45-3.02-90-2008), состоящих из несгораемых
несущих и
наружных
стен, лестничных клеток и полок.
Первичные средства пожаротушения в цехе
представлены огнетушителем ОВП-10, ОУ -2, ОУ- 5, ведра, ящики с песком, багры,
лопаты. На случай возникновения пожара должна быть обеспечена возможность
безопасной эвакуации людей, находящихся в помещении. Число эвакуационных
выходов из здания не менее двух.
Пожарная безопасность предусматривает такое
состояние объекта, при котором исключалось бы возникновение пожара, а в случае
его возникновения предотвращалось бы воздействие на людей опасных факторов
пожара и обеспечивалась защита материальных ценностей.
Пожарная безопасность обеспечивается системами
предотвращения пожара и пожарной защиты, включающими комплекс организационных
мероприятий и технических средств.
Возможные причины пожаров: неисправность
электрооборудования, нарушение технологического процесса, несоблюдение
технологического режима, несоблюдение графика планового ремонта, неисправность
запорной аппаратуры, отсутствие заглушек на ремонтируемых аппаратах, искры при
электрогазосварочных работах.
Так как высота здания имеет более 10 м, то через
каждые 100 м по наружному периметру установлены пожарные лестницы шириной 0,7 м
на расстоянии от земли 2м согласно ТКП 45-2.02-22-2006.
Массовый выход людей при пожаре осуществляется
через эвакуационные выходы, ширина которых в свету составляет не менее 1 м.
Ширина дверей эвакуационных путей не менее 0,8
м. Высота прохода по путям эвакуации составляет не менее 2м. Эвакуационные
выходы расположены в наружных стенах по периметру здания через 72 м.
В качестве путей эвакуации используются также
проезды и проходы. Ворота открываются наружу. Предусмотрен пожарный трубопровод
и пожарные гидранты снаружи здания.
Участки с легковоспламеняющимися веществами
оснащены асбестовыми материалами. Цех оборудован пожарной сигнализацией.
.1.10 Расчет интенсивности теплового облучения
на рабочем месте сталевара
Данные к расчету:
источник излучения ДСП-100;
температура жидкого металла Т=1873 К;
площадь рабочего окна F = 3,75 м²;
-расстояние от центра излучающей поверхности
до облучаемого объекта L = 2 м.
Расчет интенсивности теплового излучения
проводим по формуле:
= {3,26·(F)1/2· [(T/100)4 - 100]}/L2(6.1)
Подставив данные в формулу 6.1 получим:
= {3,26· (3,75)1/2· [(1873/100)4 - 100]}/22 =
2117 Bт/м2
Согласно нормам ГОСТ 12.1.005-88. ССБТ
интенсивность теплового облучения работающих возле открытых источников не
должна превышать 140 Вт/м², что
значительно меньше расчетной интенсивности, следовательно необходимо принять
соответствующие меры защиты. т.е. поставить защитные экраны и выдать меры
личной защиты: рукавицы, каски, очки или щитки, спецодежду, спецобувь.
. ЭКОЛОГИЧЕСКАЯ БЕЗОПАСНОСТЬ ПРОИЗВОДСТВА
.1 Экология сталеплавильного цеха
Самым весомым по уровню запыленности и объемом
пылегазовых потоков является участок выплавки металла. Наиболее интенсивные
выделения загрязняющих веществ приходятся на процесс окисления металла.
Плавка стали в дуговых печах обеспечивает
высокое качество металла, стабильность свойств, невысокий угар дорогостоящих
легирующих компонентов, однако сопровождается интенсивным пылегазообразованием.
Газы под воздействием избыточного давления прорываются через зазоры плавильного
агрегата в окружающую атмосферу и приводят к загрязнению воздушного бассейна.
Высокая температура газов и дисперсность пыли, значительные колебания объемов
выбросов в различные периоды плавки, перемещение электродов, пода и свода при
эксплуатации - все это затрудняет создание надежной и эффективной системы
отбора и очистки выбросов от электродуговой печи.
Интенсивность пылегазообразования при плавке
стали в дуговых печах зависит от ведения технологического процесса, вида
шихтовых материалов, расхода электродов, состава футеровки и других
показателей. При отсутствии системы уплотнения (герметизации) печи газы
фильтруются через неплотности свода, электродные зазоры, желоб и рабочее окно.
В зависимости от системы отбора газов
неорганизованные выбросы могут составлять до 40 % общего объема. Следует
различать первичные газы, образующиеся непосредственно в объеме печи, и
вторичные, поступающие на очистку, в которых концентрация пыли и газообразных
компонентов в десятки раз меньше вследствие разбавления воздухом. Количество и
состав газов, поступающих на очистку, определяются емкостью печи, режимом
плавки и способом отбора газов.
За счет выгорания углерода из металла, угара
электродов, а также загрязнений, вносимых скрапом, образования газов при
разложении флюсов и окисления присадок в электродуговой печи в среднем за
плавку выделяется 350 ÷ 500 м3
первичных газов на 1 т металлозавалки. При крупной, чистой шихте выбросы
снижаются до 100 м3/т.
Газы, образующиеся при плавке стали в дуговых
печах, состоят из оксидов углерода (СО и СО2), азота (NО и NO2) серы (SO2 и
SO3). В небольших концентрациях присутствуют цианиды, фториды, пары воды и
некоторые продукты деструкции органических веществ. Основная доля указанных
газов образуется в зоне горения дуги. Часть газов выделяется из расплава в
период кипения и доводки металла. Объем выбросов загрязняющих веществ в
атмосферу от электродуговой печи приведен в таблице 7.1.
Таблица 7.1 - Объем выбросов загрязняющих
веществ в атмосферу от электродуговой печи
Емкость
печи, т.
|
Произво-дитель-ность
печи, т/ч
|
Объем
техноло- гичес- ких газов, м3/т
|
Объем
отходящих газов, м3/ч
|
Удельные
выделения загрязняющих веществ, кг/ч
|
|
|
|
|
пыль
|
оксид
углеро- да
|
окислы
азота
|
окислы
серы
|
100
|
92
|
270
|
19700
|
72,8
|
26,93
|
4,8
|
1,63
|
Кроме большого количества токсичных газов в
дуговой печи образуется чрезвычайно много дисперсной пыли. Удельные выбросы
пыли зависят в основном от состава и качества шихты, а также от интенсивности
плавки, т.е. подводимой мощности. Поскольку основными источниками образования
пыли в дуговой печи являются продукты взаимодействия
(окисления, испарения, сублимации) шихты,
футеровки, флюсов и материала электродов с плазмой электрической дуги, а также
физико-химических превращений в расплаве, то состав и свойства пыли
претерпевают существенные изменения в различные периоды плавки. Общие потери от
испарения компонентов могут достигать 1 % от веса металлозавалки. При этом угар
легкоплавких элементов с высокой упругостью паров, как правило, превышает
потери остальных компонентов.
Химический состав пыли отличается многокомпонентностью
и значительно изменяется в зависимости от периодов плавки и марки выплавляемой
стали по таблице 7.2.
Таблица 7.2 - Содержание химических элементов
при выплавке в ДСП
Период
плавки
|
Химический
состав, вес, %
|
|
С
|
SiO2
|
CaO
|
MgO
|
MnO
|
FeO
|
Fe2O3
|
Расплавление
шихты
|
0,9-2,0
|
10-20
|
0,6-1,5
|
1,0-2,0
|
1,0-3,0
|
6-10
|
50-75
|
Раскисление
и доводка расплава
|
0,8-2,0
|
15-30
|
1,0-3,0
|
1,0-2,0
|
1,0-3,0
|
6-12
|
40-65
|
Пыль, выбрасываемая электродуговыми печами,
относится к III-IV классам дисперсности, хотя в отдельные периоды плавки в
газоход могут попадать довольно крупные частицы - продукты разрушения
футеровки, пригар и т.д. Поскольку основным источником образования пыли
является электрическая дуга, то первичная пыль, состоящая из оксидов, имеет
чрезвычайно мелкие размеры.
Плавка стали в электродуговых печах
сопровождается интенсивным образованием вредных газообразных веществ и
дисперсного аэрозоля, характеристики и количество которых существенно зависят
от целого ряда технологических и конструктивных факторов. При недостаточно
надежной герметизации печи в плавильном пролете литейного цеха создаются
повышенные уровни запыленности: в рабочей зоне
вокруг печи - до 40 мг/м3, над печью - 700 мг/м3 и под крышей цеха - до 60
мг/м3. Значительно превышает при этом санитарные нормы и концентрация окиси
углерода и азота.
7.2 Газ- и пылевыделения из электроплавильных
печей
Выплавка стали в дуговой электропечи
сопровождается значительными выделениями газов при высокой температуре и
загрязненных пылью.
Газы в духовых электропечах образуются при
выгорании углерода металла и сгорания электродов.
Для расчета и конструирования систем газоочистки
необходимо определить основные параметры, характеризующие газовыделение. К ним
следует отнести объем, интенсивность выделения, химический состав, температуру
газов и содержание в них пыли, ее химический и гранулометрический состав.
Количество газов и интенсивность их выделения в
значительной степени будут зависеть от марки выплавки стали, периода и
особенностей технологии ведения плавки, емкости печи. На основании опытных
данных установлено, что в различные периоды плавки выделение газов
неравномерно.
В окислительный период происходит бурное
выделение газов, значительно отличающихся по составу и содержанию пыли в них от
газов, выделяющихся в период расплавления и восстановления.
Химический состав газов также колеблется в
зависимости от периода плавки. Кроме указанных химических соединений в
отходящих газах может содержаться сернистый ангидрид SO2 в пределах 1
÷ 9 мг/м3.
В связи с тем, что количество и химический
состав технологических газов изменяется в зависимости от марки стали, для
правильного определения действительно характеристика газов следует в каждом
отдельном случае знать, какие сорта стали предполагается варить в проектируемой
печи. Запыленность газов также не постоянна во времени. В период расплавки
содержание пыли в отходящих газах относительно невелико, а размеры пылинок
довольно значительны (5 ÷ 20 мкм). В
окислительный период наряду с интенсивным выделением газов происходит и интенсивное
пылеобразование.
Примерный химический состав пыли, %
е2О3 = 56,8; Мn2О3 = 10; Аl203 = 5; SiO2 = 6,9;
СаО = 6,9; МgО = 5,8
При проектировании системы газоочистки расчет
объема выделяющихся газов ведется на период, характеризуемы интенсивным газо- и
пылевыделением, то есть окислительный период.
При расчете объема технологических газов
необходимо руководствоваться следующими данными:
а) в окислительный период выгорает 0,3 ÷
0,6 % С металла (в зависимости от марки выплавляемой стали) с образованием СО;
б) выгорает углерод электродов в количестве 0,14
кг на 100 кг садки с образованием 70 % СО и 30 % СО2.
Полученный объем газов необходимо увеличить на
60 ÷
70 %. Помимо образовавшейся смеси СО + СО2 в печь подсасывается атмосферный
воздух через рабочее окно. В существующих конструкциях сталеплавильных печей не
предусмотрены специальные устройства для улавливания и удаления образующихся в
период плавки газов. В связи с этим при незначительном повышении давления в
рабочем пространстве печи технологические газы, через имеющиеся неплотности в
печи, просачиваются в помещение и загрязняют атмосферу цеха.
Поэтому необходимо устанавливать системы
улавливания (отсосы) газов на дуговых электропечах. К системе отсоса
предъявляются следующие требования:
а) естественное или принудительное удаление
газов через аэрационные шахты в перекрытии зданий, расположенные
непосредственно над печами;
б) удаление газов через зонт, расположенный над
печью, с принудительным отводом от него;
в) принудительный отвод газов непосредственно из
рабочего пространства печи.
Метод естественного удаления газов наиболее
прост, но имеет существенные недостатки. Совершенно недостаточна эффективность
удаления газов. Кроме того, выходящие потоки воздуха могут захватывать только
мелкую пыль, а основная ее часть остается в атмосфере цеха, что ухудшает
условия труда обслуживающего персонала. Накопление пыли на техническом
оборудовании приводит к преждевременному его износу и повышению
эксплуатационных расходов. При таком методе удаления запыленных газов исключается
возможность их очистки, что приводит к загрязнению окружающей среды.
С целью уменьшения распространения удаляемых
газов внутри помещения над печами устанавливают вытяжные колпаки и зонты.
Способ удаления газов при помощи зонтов более
совершенен, так как при этом отсасывается значительная часть газов. Однако
применение вытяжных зонтов не обеспечивает необходимой чистоты атмосферы цеха.
Они требуют больших скоростей отсоса газа, а это приводит к большим недососам
воздуха [ 22 ].
Наиболее эффективно применение отсосов
непосредственно из рабочего пространства печи. Именно такой метод применяется
на ДСП-3 РУП «БМЗ».
Где для прямого отвода газов на своде печи
предусмотрено водоохлаждаемое устройство (колено), которое через подвижную
муфту обеспечивает поступление горячего газа в трубопровод.
Для охлаждения отходящих газов предусмотрен
трубный холодильник с принудительной вентиляцией, где горячие газы поднимаются
через первую ступень холодильника в отражательный колпак. А после - охлажденный
газ поворачивается и проходит через вторую ступень вниз во входной бункер.
Из-за чего отходящий газ теряет около 75% тепла и его температура не превышает
1560 С.
Охлаждающий же воздух нагнетается из атмосферы
осевыми вентиляторами. Накапливающаяся в холодильнике пыль собирается и
постоянно подается в бункерах на скребковый транспортер через шлюзовые
питатели.
Газы, отсасываемые из укрытия печи, колпака или
зонда соединяются с охлажденным газом от электропечи позади холодильника в
канале смешивания. Количество отходящего газа из укрытия печи устанавливается
регулирующими заслонками так, чтобы температура газа перед камерой фильтра не
превышала 125°С. При увеличении температуры газа свыше 125°С предусмотрено
автоматическое открывание заслонки “аварийного воздуха” для всасывания воздуха
из атмосферы.
В качестве сепаратора пыли на ДСП используют
рукавный фильтр- обеспыливающий агрегат с автоматической очисткой рукавов с
помощью импульсов сжатого воздуха.
Рукава фильтра омываются потоком газа снаружи.
Обеспыленный газ отсасывается из внутреннего
пространства рукавов и подается через канал чистого воздуха к вентилятору.
Для обеспечения требуемого отсоса отходящих
газов на установке предусмотрено два радиальных дымососа.
Выброс очищенного газа в атмосферу производится
через дымовую трубу высотой 60 метров.
Транспортировка образующейся пыли из-под
холодильника газа и из-под камер фильтров производится скребковыми
транспортерами пыли. Пыль собирается в накопительном бункере. Из бункера пыль
подается в автотранспорт для отгрузки за пределы цеха.
При оборудовании духовых печей дополнительными
устройствами для герметизации рабочего пространства (уплотнение зазоров у
электродов, уплотнение рабочего окна и т.д.) метод отсоса дымовых из рабочего
пространства позволяет полностью исключить выбивание газов в цех и обеспечить
требуемую очистку их от пыли.
Диаметр отверстия в своде устанавливают из
условия беспрепятственного отвода всех образующихся газов.
Печной патрубок может быть как водоохлаждаемым ,
так и футерованным. Однако футерованный патрубок быстро зарастает плавильной
пылью, в результате чего уменьшается его проходное сечение [ 23 ].
ЗАКЛЮЧЕНИЕ
Итогом проделанной дипломной работы является
проект реконструкции электросталеплавильного цеха, путем изменения
технологического процесса разливки стали, предусматривающий мероприятия,
способствующие повышению качества литой заготовки и увеличению производства
МНЛЗ на 20%.
Проект реконструкции включает в себя изменение
конструкции кристаллизатора и секций зоны вторичного охлаждения для уменьшения
количества некоторых видов дефектов МНЛЗ и увеличения производительности
машины.
Применение гильзового кристаллизатора позволит
обеспечить:
постоянство водяного зазора между гильзой и
рубашкой;
высокую скорость протока воды в зазоре;
высокую точность центровки медной гильзы;
возможность установки катушки электромагнитного
перемешивания;
возможность получения круглой заготовки
диаметром 200 мм для использования при производстве бесшовных горячекатаных
труб в трубопрокатном цехе;
снижения трещинообразования и дефектов формы
(овальность, скошенность стенок квадрата и вмятины).
Применение комбинированного: водяного и
водовоздушного охлаждения круглофакельными форсунками позволит:
снижения подогрева поверхности в конце
охлаждения струйным душированием;
сведения к минимуму разницы в скорости
охлаждения между центром и углами граней слитка путем расположнения душирующих
форсунок;
обеспечить мягкое и равномерное вторичное
охлаждение непрерывнолитых заготовок;
обеспечить быструю и правильную скорость затвердевания;
снижение брака по раскатанной трещине;
снижение внутренних и поверхностных дефектов.
Анализ технико-экономических показателей данного
проекта показал, что реконструктивные мероприятия в ЭСПЦ-2 имеют положительный
эффект.
Себестоимость единицы продукции снизилась на
0,19 млн.руб. Годовой экономический эффект составил 15044,1 млн.руб.
Рентабельность производства при этом увеличилась на 3,3 %. Период возврата
инвестиций составил 5,3 лет.
СПИСОК ИСПОЛЬЗОВАНЫХ ИСТОЧНИКОВ
1.
Н.В.Андрианов, Фотоальбом «Сэрца краiны, магутны аплот-Беларускi металургiчны
завод 1984-2009», Мн, УП «Белта», 2009 - с 1 -37.
.
А.В.Демин РУП «БМЗ», Современное состояние технологий при разливке стали в
области качества, Литье и металлургия, 2010, №3 - с 99- 146.
.
Технологическая инструкция «Непрерывная разливка стали на МНЛЗ, ТИ
840-С-18-2004, г. Жлобин, 2004 - 31с.
.
Технологическая инструкция «Непрерывная разливка стали на МНЛЗ, ТИ
840-С-18-2001, г. Жлобин, 2001 - 20с.
.
Технологическая инструкция «Непрерывная разливка стали на МНЛЗ, ТИ
840-С-18-2010, г. Жлобин, 2010 - 40с.
.
Технологическая карта «Выплавка, внепечная обработка и разливка качественной
углеродистой стали», ТК 840-С-02-2006, г.Жлобин, 2006.- 4с.
.
Попандопуло И.К., Михневич Ю.Ф. Непрерывная разливка стали. - М.: Металлургия,
1990. - 296 с.
.
Григорьев В.П., Нечкин Ю.М., Егоров А.В. и др. Конструкции и проектирование
агрегатов сталеплавильного производства. - М.: МИСИС, 1995. - 512с.
.
Лузгин В.П.,Вишкарев А.Д.Учебное пособие №1513. МИСИС, 2000.- 56с.
.
Поволоцкий Д.Я., Кудрин В.А., Вишкарев А.Ф. Внепечная обработка стали - М.:
«МИСИС», 1995. - 256 с.
.
И.В. Земсков, к.т.н. Г.И. Столяров (БГПА). Особенности непрерывного литья
заготовок из хромистых сталей. Сталь, 2003. - №2, с 45-48
.
С. Шатохин. Современные водовоздушные форсунки для зоны вторичного охлаждения
МНЛЗ. Металлургическая и горнорудная промышленность, 2002.- №10, 37с
.
В.С. Есаулов, В.А. Николаев (ИЧМ). Водовоздушное охлаждение непрерывнолитых
заготовок на МНЛЗ. Электрометаллургия, 2004.-№10, с
.
Н.Чичко, Н.В. Андрианов. Белорусский национальный технический университет, РУП
“Белорусский металлургический завод”. Численное моделирование температур и
напряжений в слитке при плоскофакельном и круглофакельном вторичном охлаждении.
Сталь, 2004 .- №10, с 236-240.
.
Положение о непрерывном профессиональном обучении руководящих работников и
специалистов. П-840-16-5-2007, г.Жлобин, 2007 -9с.
.
Положение о непрерывном профессиональном обучении рабочих (служащих).
П-840-16-6-2007, г.Жлобин, 2007 -9с.
.
Показатели, условия и порядок премирования и оплаты труда работников
электросталеплавильного цеха №2 за основные результаты финансово-хозяйственной
деятельности, г.Жлобин, 2007 -8с.
.
Кожевников Е.А., Астраханцев С.Е., Ридецкая И.Н. Практическое пособие по
выполнению экономического раздела дипломного проекта. - Гомель: ГГТУ, 2001 -
18с.
.
Малькевич М.М., Вербовой И. В., Бурчков Л. П. Пособие общественного инспектора
по охране труда.- 2-е изд.перераб.и доп. СП-б.,Универсал, 2001.-45с.
.
Общая инструкция по охране труда для работающих на РУП «БМЗ». БТИ 33-01-2010.
г. Жлобин, 2010 - 163с.
.
Инструкция по охране труда для сталеваров, подручных сталевара ДСП-3. БТИ
59-01-2010, г. Жлобин, 2010 - 17с .
.
Н.Ф.Невар, Конспект лекций «Отраслевая экология», Мн, БНТУ, 2010 - 121с.
.
Производственно-технологическая инструкция «Эксплуатация ПГУ ДСП-3»
ПТИ-840-С2-111-2007, г.Жлобин, 2007 - 9с.
ПРИЛОЖЕНИЕ А Кристаллизатор диаметр 200
ПРИЛОЖЕНИЕ Б Машина непрерывной разливки стали
до реконструкции
ПРИЛОЖЕНИЕ В Машина непрерывной разливки стали
после реконструкции
ПРИЛОЖЕНИЕ Г План - схема ЭСПЦ-2
ПРИЛОЖЕНИЕ Д Технологическая схема плавки стали
40Х
ПРИЛОЖЕНИЕ Ж Зона вторичного охлаждения
ПРИЛОЖЕНИЕ К
Технико-экономические показатели проекта
Показатели
|
Варианты
|
|
Базовый
|
Проектный
|
Годовой
объем выпуска продукции В натуральном выражении, т В стоимостном выражении,
млн руб
|
690000
751794
|
841000
723248
|
Стоимость
инвестиций, млн руб
|
488364
|
484183
|
В
том числе основных фондов, млн руб
|
300415
|
303371
|
Численность
работающих, чел
|
171
|
171
|
В
том числе производственных, чел
|
120
|
120
|
Фонд
заработной платы, млн руб
|
3491,311
|
3491,311
|
Среднемесячная
заработная плата 1 работающего, млн руб
|
1,7
|
1,7
|
Производительность
труда 1 работающего, млн руб/чел
|
4396
|
4396
|
Фондоотдача,
руб/руб
|
2,5
|
2,5
|
Себестоимость
годового объема, млн руб
|
626495
|
602707
|
Себестоимость
единицы продукции, млн руб
|
0,91
|
0,72
|
Прибыль
чистая, млн руб
|
76308
|
91352
|
Рентабельность
производства, %
|
15,
6
|
18,
9
|
Период
возврата инвестиций, лет
|
6,
4
|
5,
3
|