Умови експлуатації
|
|
Об’єкт
діагностування
|
|
Режими та процеси
ТО і ремонту
|
|
Режими і процеси
діагностування
|
|
|
|
|
|
|
|
Економічні
показники
|
|
Технічний стан і
ефективність об’єкта
|
|
Нормативні
показники
|
|
Методи і засоби
діагностування, ТО і ремонту
|
Рис. 2.1 Схема формування технологічних процесів
діагностування автомобілів в умовах експлуатації
Об’єкт діагностування характеризується переліком його
складових елементів, їх функціональним призначенням і взаємодією,
закономірностями зміни параметрів технічного стану і економічними показниками,
діагностичними параметрами та їх зв’язками із структурними параметрами і,
наприкінці, пристосованістю агрегатів і механізмів до діагностування
(контролепридатністю) [13].
Закономірності зміни технічного стану об’єкта діагностування
обумовлюють його надійність і затрати на відновлення. Вказані вимірювання
можуть бути неперервними і дискретними. В результаті цих вимірювань відповідно
виникають поступові (накопичувальні) і неочікувані відмови. Неочікування
відмови відбувається через випадкові причини, що викликають значні зміни
технічного стану об'єкта.
Діагностичні параметри являють собою фізичні величини,
адекватні структурним параметрам, що використовуються для виміру технічного
стану механізму, що діагностується, без його розбирання.
З усього багатоманіття можливих діагностичних параметрів вибирають
і використовують з практичною метою лише ті параметри, які відповідають вимогам
однозначності, стабільності, широти вимірювань, доступності і зручності
вимірювання, інформативності і технологічності. Зміст перерахованих вимог
графічно показаний на рис. 2.2 [14].
Рис. 2.2 Графічна ілюстрація основних вимог до діагностичних
параметрів за: а - однозначністю; б - стабільністю; в - діапазоном вимірювання;
1, 2 - криві неоднозначної залежності, 3 - крива однозначної залежності, 4 -
рівний коридор розсіювання, 5 - коридор розсіювання, що збільшується, 6 - крива
більшої широти вимірювання, 7 - крива меншої широти виміру
Вимоги однозначності передбачають дотримання умов, коли
кожному значенню структурного чи функціонального параметру відповідає
одне-єдине значення діагностичного параметра. Так, параметри кривих 1 і 2 (рис.
2.2, a) не відповідають критерію
однозначності, а параметри кривої 3 - відповідають, тобто діагностичному
параметру Д2 можуть відповідати чотири різні значення структурного
параметра (S2’, S2’’, S2’’’,
S2’’’’), параметру Д1 - два значення
структурного параметра (S1’, S1’’),
а будь - якому діагностичному параметру Д3 відповідає одне значення
структурного параметра S3.
Вимоги стабільності встановлює можливу величину відхилення
діагностичного параметра від свого середнього значення, що характеризує
розсіювання параметра при незмінних значеннях структурних параметрів і умовах
їх виміру.
Вимоги ширини вимірювання встановлює діапазон виміру
діагностичного параметра, що відповідає заданій величині зміни структурного
параметра. Чим більший діапазон зміни діагностичного параметра, тим вища його
інформативність. На рис. 2.2, в параметр кривої 6 має більшу
широту зміни діагностичного параметру ∆Д4, ніж параметр кривої
7 ∆Д5. Аналітично умова показується наступною залежністю:
, (2.1)
Тому перед вибором діагностичного параметра необхідно
проаналізувати його залежність від структурного параметра, вияснити
взаємозв’язок між ними та визначити інформативність діагностичного параметра.
Отримання інформації про технічний стан об’єкта за допомогою
будь-якого діагностичного параметра пов’язане з матеріальними затратами.
Економічна цілеспрямованість цих затрат залежить, з однієї сторони, від вартості
діагностичних засобів, а з другої - від ймовірностей відмов і вартості їх
усунення, тобто вартості ремонту. Тому кінцева оцінка раціональної повноти
інформації визначається вартісними критеріями і критеріями надійності об’єкта
діагностування.
Класифікацію діагностичних параметрів можна подати за такою
схемою (рис. 2.3) [14].
Діагностичні параметри являють собою фізичні величини,
адекватні структурним параметрам, що використовуються для визначення технічного
стану механізмів, що діагностуються без їхнього розбирання. Як вже було
розглянуто з всіх можливих діагностичних параметрів вибирають ті, які
відповідають вимогам однозначності, стабільності, чутливості і інформативності.
Рис. 2.3 Класифікація діагностичних параметрів
Чутливість Кч діагностичного параметру, тобто його
приріст dS при зміні dU структурного параметру, буде [14]:
, (2.2)
Однозначність діагностичного параметру означає відсутність
екстремуму (
) в діапазоні від початкового Uн до граничного Uгр
значень структурного параметра.
Інформативність є одним із найважливіших властивостей
діагностичних параметрів. Вона дозволяє знизити вихідну невизначеність
(ентропію) технічного стану об’єкта діагностування за рахунок відомостей,
отриманих в результаті вимірювання даного діагностичного параметру. Ентропія об’єкта
Н(x) характеризується деяким числом n його технічних станів, кожне з яких може
відбутися з цією чи іншою ймовірністю Рі, що залежить від надійності
об’єкта. Якщо вимірювання даного діагностичного параметра дозволяє повністю
вирішити діагностичну задачу, то його інформативність Iх дорівнює
ентропії об’єкту Н(x) [14]:
, (2.3)
Практично при діагностуванні механізмів автомобіля часто
використовують декілька діагностичних параметрів. При цьому значення Рі
різні, а зв’язки між структурними і діагностичними параметрами неоднозначні. В
подібних випадках інформативність діагностичного параметра можна оцінити по
об’єму представлених ним відомостей про виявлення несправності об’єкта. Для
цього порівнюють розподіл величин діагностичного параметра, виміряного у
достатньо великій кількості справних і несправних об’єктів. Якщо діагностичний
параметр малоінформативний, то розподіли відрізняються незначно. Це означає, що
параметр не дозволяє відрізнити справний об’єкт від несправного. Чим більша
різниця розподілів, тим вища інформативність даного параметра. Різницю
розподілів оцінюють за допомогою коефіцієнта інформативності [14]:
, (2.4)
де
,
- відповідно ймовірності попадання спостереження в даний
діапазон ознаки j при справному (А) і несправному (В) стані об’єктів;-
кількість діапазонів розподілу величин діагностичного параметра.
.2 Узагальнена блок-схема діагностування АТЗ
Діагностування автомобіля в цілому і
по його елементах повинно проводитися у визначеному порядку, що використовує
послідовні, умовні перевірки. З цією метою весь автомобіль можна розділити на
рівні (рис. 4).
Перший рівень містить у собі загальне
діагностування автомобіля з метою визначення його основних вихідних показників
продуктивності й економічної ефективності.
На другому рівні діагностуються
частини автомобіля, такі, як двигун, електроустаткування, трансмісія, ходова
частина, рульове керування, гальмові системи і додаткове устаткування в цілому.
У третій рівень входить
діагностування агрегатів механізмів, систем, приладів, пристроїв.
Четвертий рівень містить у собі
діагностування рухливих з’єднань типу: деталь з деталлю, деталь із зовнішнім
середовищем.
На п'ятому рівні розглядаються окремі
деталі.
Використання запропонованої
класифікації дозволяє більш строго підійти до розгляду всіх наступних
матеріалів, почавши з загального діагностування автомобіля і закінчивши цей
процес з’єднань і при необхідності деталями, зокрема, для підвіски автомобіля.
Сучасні досягнення в області розвитку
методів і засобів діагностування дозволяють проводити оцінку стану на перших
трьох рівнях, а забезпеченість засобами діагностування четвертого рівня складає
не більш 20%.
Діагностувати окремі деталі навряд чи
доцільно, тому що істотні зміни елементів автомобіля відбуваються в рухливих і
інших з’єднань під час робочих процесів.
Контроль стану деталей проходить звичайно при розбиранні під
час поточного і капітального ремонтів.
.3 Діагностування агрегатів і систем АТЗ і автомобіля в
цілому
Під загальним діагностуванням розуміється діагностування
автомобіля по параметрах, що характеризує його загальний технічний стан без виявлення
конкретної несправності чи відмови за принципом «придатний - непридатний»,
«справний - несправний».
Продуктивність чи кількість вантажів або пасажирів,
перевезених автомобілем на визначену відстань за одну годину, за зміну, за рік
залежить, крім інших причин, і від технічного стану автомобіля. Такі параметри,
як потужність двигуна, тягове зусилля, інтенсивність розгону автомобіля
впливають на показники продуктивності.
Паливна економічність автомобіля характеризується витратами
палива на різних режимах і залежить від технічного стану тих елементів
автомобіля, які беруть участь у переміщенні автомобіля. Таким чином, знаючи
тягове зусилля на колесах автомобіля, інтенсивність розгону і витрати палива на
режимах холостого ходу, руху і розгону, можна судити про загальний технічний
стан автомобіля.
Попередній технічний стан визначається по параметрах
суб'єктивного діагностування за допомогою органів чуттів і застосування
найпростіших засобів для посилення сигналу.
Інтенсивність розгону автомобіля може бути визначена на
дорозі при русі на прямій передачі на мінімальній швидкості, шляхом різкого
натискання на педаль керування дроселем і візуальною оцінкою часу розгону до
визначеної швидкості. При цьому візуально оцінюється робота двигуна на
мінімальній частоті обертання в режимі холостого ходу, герметичність систем
мащення, охолодження і живлення.
Аналогічно може бути визначена величина вибігу з максимальної
швидкості до нульової. за кольором відпрацьованих газів, роблять висновки про
склад робочої суміші. Чорний вихлоп говорить про збагачену суміш.
На ходу автомобіля перевіряється робота зчеплення, коробки
передач, трансмісії. Шуми і стукоти можуть прослухуватися стетоскопом з
визначенням конкретного місця чи стукоту шуму, перевіряється гальмовий шлях,
уповільнення при гальмуванні й одночасність гальмування коліс.
Для об'єктивного діагностування автомобіля в цілому,
здійснюваного за допомогою контрольно-вимірювального устаткування і приладів,
застосовуються стенди з біговими барабанами, оснащеними гальмовою установкою і
витратомірами.
Рис. 2.4 Рівні діагностування автомобіля
Перевірка роботи ходової частини проходить за допомогою
спеціальних діагностичних засобів. Ходова частина автомобілів працює в
несприятливих умовах у зв'язку з постійним контактом з поверхнею дороги і
наявністю пилу і бруду. Тому при виконанні щоденного обслуговування роблять
зовнішній огляд, перевіряють затягування гайок кріплення коліс, періодично -
тиск повітря в шинах. При ТО-1 визначають стан і кріплення елементів підвісок.
Основні діагностичні роботи з елементів ходової масті
виконуються при ТО-2. Перевіряють відповідність кутів сходження, розвалу і
повороту коліс нормативним значенням, а також кути нахилу шворнів. В елементах
переднього моста визначають люфти в шкворневих з'єднаннях і підшипниках маточин
керованих коліс. При нерівномірному зносі протектора шин необхідно перевірити
збалансованість коліс, визначити пружність підвіски і дію амортизаторів.
Причиною нерівномірного і прискореного зносу шин може бути перекос осей.
При діагностуванні ходової частини варто звертати особливу
увагу на технічний стан елементів підвіски - ресор і амортизаторів. Від їхньої
працездатності залежать плавність ходу, стійкість і безпека руху автомобіля.
Недостатня плавність ходу втомлює водія і пасажирів, збільшує динамічні
навантаження на елементи автомобіля, скорочує термін його служби і знижує
продуктивність.
Установлено, що на задню і передню підвіску припадає до 10%
від загального числа поточних ремонтів автомобіля.
Найбільш часто зустрічаються несправності і відмовлення
підвіски: поломка ресорних листів і пружин, знос пальців і втулок ресор, знос
гумового буфера - обмежувача ходу моста, знос амортизаторів, втулок
стабілізаторів і т.п.
Зовнішнім проявом розглянутих відмов є поява стукотів і шумів
при русі автомобіля і слабо загасаючі коливання кузова при наїзді на перешкоду.
Загальний технічний стан підвіски може бути оцінене по
величині загасання коливань, викликаних, наприклад, скиданням колеса автомобіля
з невеликої висоти. Загасання вільних коливань виникає внаслідок тертя листів
ресори, тертя в елементах шарнірів, в амортизаторі і шинах.
При візуальному огляді елементів підвіски перевіряють:
- наявність поломок і тріщин пружин, листів ресор,
кронштейнів і провушин ресор;
- люфт у сполученні важелів, стійки амортизаторів і
ресор;
зазор між кузовом і кронштейнами осей важелів
передньої підвіски;
якість гумових упорів.
Пружні властивості пружин і ресор визначають найпростішим
способом - шляхом виміру спеціальною лінійкою стріли прогину.
Діагностування пружин або ресор і амортизаторів безпосередньо
на автомобілі може здійснюватися за допомогою площадок чи барабанних стендів. У
першому випадку колеса автомобіля встановлюються на окремі площадки, яким
спеціальний збудник створює коливання у вертикальній площині. Після вимикання
збудника реєструючий пристрій, записує процес загасання коливань. По величині
амплітуди визначається технічний стан амортизатора й у випадку відхилень -
характер несправності.
3. Експериментальні дослідження за
надійністю конструкцій підвісок легкових АТЗ
.1 Програма та методика проведення досліджень
На погіршення технічного стану автомобілів впливають різні
чинники. Основні з них наведені у розділі 1. Дослідженню впливу на надійність
кожної групи чинників присвячено достатньо уваги [15]. Однак, оскільки система
експлуатації АТЗ - це динамічна система як з боку змін їх конструкцій, так і
дорожніх умов та умов і режимів використання, закономірності зниження
показників експлуатаційних властивостей АТЗ, їх технічного стану видозмінюються
і, отже, вони потребують постійних подальших досліджень. Тим більше з
урахуванням дії законів ринкової економіки в галузях машинобудування,
автомобільного транспорту, технічного сервісу, будівництва і утримання доріг.
На основі результатів досліджень повинні коректуватися як
стратегічні, так і тактичні напрями розвитку конструкцій АТЗ, автодорожньої
мережі, якості дорожніх одягів тощо. Найістотніший вплив останнього на
інтенсивність погіршання технічного стану легкових АТЗ проявляється на
елементах їх підвісок, що напряму знижує, крім цього, рівень безпеки
транспортних процесів.
Для визначення показників експлуатаційної надійності
елементів підвісок легкових автомобілів у магістерській кваліфікаційній роботі
було використано дані раніше проведених досліджень, які базувалися на
автомобілях “Таврія”, “Славута”, “Ланос”, “Сенс” (Запорізький автозавод) і
“Шевроле” (виробництва Росії), що експлуатуються у місті Львові.
При проведенні досліджень інформація про експлуатаційну
надійність елементів їх підвісок збиралась впродовж півроку 2009 року за результатами діагностування
технічного стану їх на лінії інструментального контролю Bosch SDL-260 на
станції технічного обслуговування Відкритого акціонерного товариства
“Галичина-Авто” (м. Львів).
Електронна діагностична лінія динамічної перевірки
автомобілів фірми Bosch
SDL-260 (Німеччина) забезпечує вимірювання гальмівної сили робочої і стоянкової
гальмівних систем, сумарного сходження коліс обох осей і дає оцінку стану
підвіски автомобіля за амплітудою коливання після гальмування. Лінія
складається з вимірювальних платформ, пристрою визначення сумарного сходження
коліс, спеціалізованого дисплея і принтера.
Давачі вимірюють силу, прикладену до поверхні платформи, що
виникає при гальмуванні автомобіля, який випробовується. Гальмівні зусилля
сканується давачами протягом всього часу гальмування і обробляється
комп’ютерним блоком, при цьому значення максимальної гальмівної сили в (Н)
висвітлюється на дисплеї лінії. Усі поточні значення гальмівної сили з
інтервалом у 0,05 сек. видаються на принтер і показуються на роздруківці.
Дисплей обладнаний колірним індикатором (червоний, жовтий, зелений)
ефективності гальмування і нерівномірності гальмівних сил коліс за осями.
Величина сумарного сходження коліс кожної осі автомобіля
визначається при проїзді автомобіля, який випробовується через пристрій
визначення сумарного сходження коліс. Пристрій складається з 2-х установлених
паралельно платформ - рухомої і нерухомої. Поперечне відхилення рухомої
платформи, викликане наявністю кута сходження, вимірюється за допомогою
вбудованого давача і обробляється комп’ютерним блоком. Величина сумарного
сходження коліс у (мм) висвітлюється на дисплеї і роздруковується на принтері.
Динамічний метод вимірів дозволяє легко визначати гальмівні зусилля навіть на
автомобілях з постійним повним приводом коліс.
Інформація про динамічні коливання автомобіля після його
зупинки на вимірювальних платформах роздруковується на принтері і дозволяє
оцінити ефективність роботи підвіски автомобіля, який випробовується.
Швидкість автомобіля під час проходження тесту складає 5 - 10
км/год. Інформація про швидкість автомобіля, який випробовується, автоматично
вимірюється і роздруковується на принтері. Введення необхідних даних і керування
лінією легко здійснюється майстром сервісу безпосередньо з автомобіля за
допомогою пульта дистанційного керування.
Програма проведення досліджень включала:
а) збирання інформації про вхідні потоки СТО - час та
кількість надходжень АТЗ на обслуговування (усунення несправностей та відмов),
їх пробіг, особливості прояву дефектів за інформацією від водіїв;
б) діагностування підвісок АТЗ на лінії інструментального
контролю і виявлення причин їх відмов;
в) опрацювання методами математичної статистики даних про
вхідні потоки АТЗ на СТО та результатів діагностування елементів підвісок;
г) узагальнення отриманих результатів.
Спостереження і збір відповідної інформації виконувались від
моменту прийняття автомобіля на обслуговування із спілкуванням з водієм на предмет
встановлення прояву несправностей, виконання діагностичних операцій на лінії
інструментального контролю й опрацювання їх результатів з розбиранням дефектних
вузлів підвісок і оцінюванням їх технічного стану, до моменту завершення
замінних операцій і внесення відповідних записів у комп’ютерну базу даних СТО і
супроводжувальну документацію. На основі цієї бази даних отримано масиви
статистик щодо експлуатаційної надійності підвісок цих АТЗ.
Були зроблені наступні висновки:
. Процеси втрати працездатності підвісок мають випадкову
природу і характеризуються нестабільністю виникнення відмов та значними
дисперсією, середньоквадратичним відхиленням і коефіцієнтом варіації
нерівномірності.
. Великий діапазон розкиду цих показників за окремими
конструктивними елементами підвісок та марок автомобілів вказує, очевидно, на
безпосередній вплив на їх надійність низької якості дорожніх покрить, значних
кривини вуличної мережі у плані та інтенсивності транспортних потоків на ній.
. Отримані результати можуть стати основою в обґрунтуванні
відповідних інженерних рішень щодо підвищення або: а) рівня стабільності
завантаження ремонтно-технологічного і діагностичного обладнання СТО; б)
параметричної надійності підвісок АТЗ; в) якості дорожніх покрить.
. Визначення пріоритетного напрямку руху інженерної думки
щодо підвищення експлуатаційної надійності АТЗ повинно здійснюватись за
показниками порівняльних характеристик “ціни їх надійності” та інвестицій на
утримання і розвиток мережі автодоріг і об’єктів інфраструктури технічного
сервісу автомобілів.
Згідно пункту 4 висновків у магістерській кваліфікаційній
роботі здійснено додаткове опрацювання результатів досліджень для визначення
оптимальної періодичності ТО підвіски легкових автомобілів “Сенс” і “Ланос” з
огляду на техніко-економічний критерій, а саме на основі мінімуму затрат на
виконання чергового діагностування та поточного ремонту [17].
.2 Особливості конструкцій підвісок досліджуваних автомобілів
Конструкції підвісок досліджуваних автомобілів “Славута” і
“Таврія” та “Сенс” і “Ланос” є однаковими, а їх окремі деталі не відрізняються
від деталей підвіски “Шевроле”.
Передня підвіска всіх АТЗ - незалежна, важільно-телескопічна,
складається із таких основних елементів - амортизаційного стояка (переднього
стояка), на якому встановлена пружина і буфер стиску (пружні елементи
підвіски), кулака і важеля з штангою із кульовим шарніром.
Роль демпферного пристрою виконує гідравлічний телескопічний
амортизатор. Стабілізатор поперечної стійкості представляє собою пружний
П-подібний стрижень, розміщений в переді за рухом автомобіля.
Конструкція передньої підвіски
автомобіля “Сенс” і “Ланос” є однаковою, її основні елементи показані на рис.
3.1 [16].
Рис. 3.1 Елементи конструкції
підвіски переднього колеса автомобілів “Ланос”:
- захисний ковпачок; 2, 3, 24, 37, 43
- гайки; 4, 20, 29, 32, 36 - шайби; 5 - верхня опора амортизаторної стійки; 6 -
упорна шайба; 7 - пластмасова опора; 8 - захисна склянка; 9 - верхня опорна
чашка; 10 - пружина підвіски; 11 - буфер ходу стиску; 12 - стопорне кільце; 13
- підшипник маточини; 14 - маточина колеса; 15 - гальмівний диск; 16 - стопорна
шайба; 17 - фасонна гайка; 18, 19 - гвинт; 21 - захисний кожух; 22 - втулка
заднього шарніра важеля підвіски; 23 - чека; 25, 40 - кронштейни; 26, 28, 31,
39 - болти; 27 - кульова опора; 30 - втулка стабілізатора; 33 - важіль
підвіски; 34 - втулка переднього шарніра важеля підвіски; 35 - елемент корпуса
кузова автомобіля; 38 - розпірна втулка; 41 - подушка стрижня стабілізатора; 42
- стрижень стабілізатора; 44 - гайка корпуса стійки; 45 - шток; 46 - циліндр;
47 - корпус стійки; 48 - нижня опорна чашка; 49 - поворотний важіль; 50 -
поворотний кулак
У верхній опорі стійки амортизаторної
встановлений гумовий пружний елемент, що забезпечує хитання стійки при роботі
підвіски і гасіння вібрацій, а також упорний кульковий підшипник, який служить
упором верхньої опорної чашки пружини і забезпечує поворот стійки.
До середньої частини корпуса стійки
приварений поворотний важіль, за який здійснюється поворот стійкі, необхідний
для повороту колеса при зміні напряму руху автомобіля.
Корпус стійки виконаний разом з
поворотним кулаком. До поворотного кулака кріпиться захисний кожух гальмівного
диска. Усередині отвору поворотного кулака за допомогою стопорних кілець
закріплений дворядний підшипник маточини колеса.
Нижній кінець поворотного кулака шарнірно з'єднаний з важелем
підвіски за допомогою кульової опори. Палець кульової опори закріплений у
поворотному кулаку за допомогою гайки, а корпус опори приклепаний до важеля
підвіски.
Задня підвіска автомобіля Lanos незалежна. Її балка складається з
двох подовжніх важелів, пружно зв'язаних поперечним з'єднувачем. Важелі і
з'єднувач мають У-подібний перетин; з'єднувач зміщений від осі коліс вперед і
розташований поблизу шарнірних кріплень важелів до кузова автомобіля. Така
конструкція балки задньої підвіски має велику жорсткість на згин і малу - на
кручення, що забезпечує переміщення коліс при русі по нерівностях дороги
практично незалежно один від другого. Балка підвіски виконує функцію
направляючого пристрою. Пружним пристроєм є дві кручені спіральні пружини. Роль
демпферного пристрою виконують гідравлічні телескопічні амортизатори.
Стабілізатор поперечної стійкості являє собою пружний стрижень.
Елементи конструкції задньої підвіски автомобіля Lanos представлені на рис. 3.2.
Рис. 3.2. Елементи конструкції
пружного, направляючого і демпферного пристроїв задньої підвіски:
- захисний ковпачок; 2 - гайка; 3 -
верхня (нижня) обойма подушки; 4 - верхня подушка амортизатора; 5 - нижня
подушка амортизатора; 6 - втулка; 7 - амортизатор; 8 - болт; 9 - верхня опорна
чашка; 10 - пружина підвіски; 11 - нижня опорна чашка; 12 - важіль; 13 -
з'єднувач
.3 Оцінка надійності конструкцій підвісок та визначення
періодичності їх ТО
У дослідженнях бралися до уваги лише ті конструктивні
елементи підвісок, які найчастіше відмовляли:
- амортизатор задній,
- верхня опора переднього стояка,
кульовий шарнір передньої підвіски,
підшипники маточин коліс.
Протягом досліджуваного періоду (1.03.09-9.09.09) на СТО надійшли автомобілі з причин дефектів у
перерахованих вище за порядком конструктивних елементах у кількості 144
одиниць. З них 21 автомобіль “Сенс”, які мали пробіги в межах - 3100-42100 км, та
15 автомобілів “Ланос” - відповідно з пробігами в межах 4100-49120 км.
Основні дефекти елементів підвісок за результатами опитування
водіїв - стукіт у підвісці і підтікання рідини з верхньої частини
амортизаторів.
З використанням в середовищі Statistica 6.0 на основі отриманих масивів
даних (додаток А) за відомою методикою було розраховано числові характеристики
розподілів та побудовано гістограми розподілу пробігів автомобілів “Сенс” і
“Ланос” на відмови через втрату працездатності їх підвісок із спробою
узгодження їх з законами розподілів.
На основі отриманого масиву статистичних даних було складено
варіаційний ряд, шляхом розташування значень пробігу автомобілів “Сенс” і
“Ланос” на відмови елементів їх підвіски у порядку зростання. Далі визначалися
кількість інтервалів статистичного ряду і їх ширину, математичне сподівання,
дисперсія, середньоквадратичне відхилення і коефіцієнт варіації пробігу на
відмови.
Розрахунки, наприклад, для пробігу на відмови підвіски разом
автомобілів “Сенс” і “Ланос” наведені в таблиці статистичного ряду (таблиця
3.1).
Таблиця
3.1
Статистичний ряд розподілу пробігу автомобілів “Сенс” і
“Ланос” (разом) на відмови елементів їх підвіски
Показники
|
Інтервали, k
|
Сума
|
|
1
|
2
|
3
|
4
|
5
|
6
|
|
Величина інтервалу,
тис. км
|
3,10-10,77
|
10,77-18,44
|
18,44-26,11
|
26,11-33,78
|
33,78-41,45
|
41,45-49,12
|
-
|
Середина інтервалу,
тис. км
|
6,935
|
14,605
|
22,275
|
29,945
|
37,615
|
45,285
|
|
Частота попадання
поточних пробігів в інтервали
|
9
|
6
|
7
|
4
|
6
|
4
|
36
|
Емпірична частість
|
0,250
|
0,167
|
0,194
|
0,111
|
0,167
|
0,111
|
1,000
|
Математичне
сподівання пробігу на відмови, тис. км
|
1,734
|
2,434
|
4,331
|
3,327
|
6,269
|
5,032
|
23,6
|
Дисперсія пробігу
на відмови, тис. км
|
65,55
|
12,104
|
0,141
|
5,165
|
34,984
|
54,553
|
172,5
|
На основі даних таблиці 3.1 визначаємо:
- математичне сподівання пробігу на відмови - 23,6 тис. км;
- дисперсія пробігу на відмови - 172,5 тис. км;
середньоквадратичне відхилення - 13,1 тис. км;
коефіцієнт варіації - 55,6%.
На рис. 3.3. показано гістограми розподілу пробігів
автомобілів “Сенс” і “Ланос” на відмови через втрату працездатності їх
підвісок. На рис. 3.3, а показано спробу узгодження з розподілом Вейбула, а на
рис. 3.3, б - нормальним.
Через великий розкид і нерівномірність пробігів автомобілів
“Сенс” і “Ланос” на відмови узгодження їх з законами розподілу неможливе.
Значення математичного сподівання пробігів на відмови для автомобілів “Сенс”
складає 23271 км (21 автомобіль) і автомобілів “Ланос” - 27566 км (15
автомобілів). При коефіцієнтах варіації відповідно 69% і 97%.
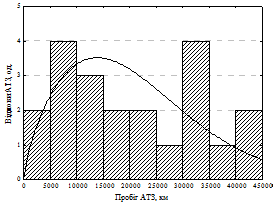
а) б)
Рис. 3.3 Гістограми розподілу пробігів автомобілів “Сенс” (а)
і “Ланос” (б) на відмови через втрату працездатності їх підвісок
На рис. 3.4 показано об’єднану гістограму розподілу пробігів
автомобілів “Сенс” і “Ланос” на відмови через втрату працездатності їх
підвісок.
Рис. 3.4 Гістограма розподілу пробігів АТЗ автомобілів
“Ланос” і “сенс” на відмови через
втрату працездатності їх підвісок із узгодженням за експоненціальним законом
Результатом проведених досліджень стало отримання
математичного сподівання пробігу автомобілів “Сенс” і “Ланос” на відмови, яке
склало 23,6 тис. км.
Результати будуть використані при плануванні оптимальної
періодичності технічного обслуговування підвісок АТЗ за мінімальних сумарних
затрат з критерієм оптимізації періодичності ТО з використанням мінімуму
функції сумарного ризику.
Порівнювалися також аналогічні показники експлуатаційної
надійності конструкцій підвісок окремих марок вітчизняних та закордонних
автомобілів (табл. 3.2). За показниками розподілів інтервалів вхідних потоків
лінії інструментального контролю СТО
та інтенсивності відмов
найнадійнішими є конструкції
підвісок автомобілів "Ланос" (
=9,38 дн;
=0,12 од/дн).
технічний надійність підвіска автомобіль
Таблиця
3.2
Показники надійності конструкцій підвісок автомобілів “Ланос”
і “сенс”
Автомобілі
|
Кількість АТЗ, од
|
Інтервали між
замовленнями/щоденні надходження
|
|
|
, дн/ ,
од/дн
|
, дн/ ,
од
|
, дн/ ,
од
|
, %/ ,
%
|
"Сенс"
|
21
|
6,19/0,17
|
96,04/45,21
|
9,80/26,47
|
158,32/155,29
|
"Ланос"
|
15
|
9,38/0,12
|
172,70/62,32
|
13,14/20,42
|
140,16/170,17
|
4. Теоретичні дослідження параметрів
систем та агрегатів АТЗ та складання математичної моделі їх діагностування
.1 Обґрунтування структурних параметрів систем та агрегатів
АТЗ для визначення фактичного рівня їх технічного стану
Успішне розв’язання задач діагностування технічного стану
автомобілів можливе за наявності науково обґрунтованих, перевірених на практиці
і зручних у використанні, методів та засобів визначення технічного стану
агрегатів, систем і спряжень машин та прогнозування їх ресурсу.
Для діагностування автомобіля використовують різні методи і
різноманітні діагностичні засоби, які безперервно вдосконалюються завдяки
новітнім досягненням науки і техніки [18, 19, 20, 21]. Застосування ЕОМ різко
розширило можливості діагностики. Доведено, що чим досконаліші методи
діагностування і засоби діагностики, тим точніше і вірогідніше буде визначений
дійсний технічний стан автомобіля і залишковий ресурс його роботи.
В основі діагностування лежить встановлення зміни
конструктивно-технологічних параметрів машини за рядом ознак діагностичних
параметрів, які необхідно вимірювати. Вимірювання їх здійснюються за зовнішніми
ознаками, які відтворюють зміну технічного стану систем і спряжень машини.
Деякі зовнішні ознаки одночасно є параметрами, що характеризують робочі процеси
машини [22]. Стосовно до АТЗ ці ознаки наступні: потужність двигуна, витрата
палива чи моторної оливи, гальмівний шлях автомобіля і т.п. Вони вимірюються,
як правило, під час роботи автомобіля і часто на найбільш характерних робочих
режимах, що відповідають експлуатаційним режимам, чи близьких до них.
Параметри робочих процесів машини найповніше і комплексно
відтворюють технічний стан агрегату, механізму чи машини в цілому [18, 19, 20,
21, 23].
Зовнішні ознаки технічного стану АТЗ - стукіт, шум, вібрація,
димність, нагрів і т.п. - показують стан окремого механізму чи спряження -
окремого елемента АТЗ (чи системи). Деякі з цих параметрів можуть бути виміряні
в неробочому, статичному стані механізму чи системи, коли система чи механізм
не виконують свої прямі функції. Такі виміри легше здійснити на практиці, але
вони не завжди вичерпно показують технічний стан елемента машини, який в
робочому режимі під час експлуатації може відрізнятися від стану, коли механізм
не працює.
Одна з особливостей діагностичних параметрів складальних
одиниць механізмів і агрегатів автомобіля полягає в тому, що вони представлені
як механічними, так і електричними сигналами. Стосовно ходової частини
автомобіля Daewoo “Ланос”, то у його підвісці
відсутні електричні сигнали, оскільки його конструкція не передбачає жодних
електричних систем, наприклад, керованого рівня чи ходу підвіски, контролю за
зносом шин чи тиску у них [16].
діагностичні параметри, які вимірюють
під час проведення діагностування, вибирають з множини принципово можливих
параметрів деякої обмеженої кількості для дослідження інформативності ознак,
сформованих на цих параметрах. Від правильного вибору параметрів залежить
якість діагностування.
Якщо розглядати процес діагностування ходової частини
автомобіля, то найскладнішим є діагностика підвіски автомобіля. Вона вимагає
застосування спеціальних приладів для визначення справності її елементів і
правильної постановки діагнозу. Про це засвідчує велика кількість несправностей
щодо ходової частини автомобіля (табл. 4.1).
Звичайно, велика кількість ознак ускладнює процес
діагностування і вимагає складних діагностичних засобів, які повинні в своїй
пам’яті мати допустимі числові значення параметрів технічного стану. В таблиці
4.2 подані значення основних даних для регулювання і контролю підвіски
автомобілів сімейства Daewoo “Ланос” [16].
Таблиця
4.1
Основні ознаки несправностей, можливий діагноз і прилади для
перевірки ходової частини автомобіля
Вид
|
Ознака несправності
|
Діагноз
(несправність)
|
Прилад для
перевірки
|
Ходова частина
автомобіля
|
Плямистий знос шин
передніх коліс
|
- незадовільна
робота передніх амортизаторів; - послаблені різьбові з’єднання кріплення
передньої підвіски; - значний від’ємний кут поздовжнього нахилу осі повороту
передніх коліс; - значний дисбаланс керованих коліс; - значний зазор у
підшипниках маточини керованих коліс; - биття гальмівного диску; - значне
радіальне чи осьове биття шин; - значний знос втулок важеля підвіски; -
значне від’ємне чи додатне сходження керованих коліс.
|
Bosch SDL-260, балансувальний
стенд
|
|
Зношення
центральної частини протектора
|
- експлуатація шин
при підвищеному тиску у шинах
|
Манометр
|
Ходова частина
автомобіля
|
Зношення зовнішніх
частин протектора
|
- експлуатація шин
при пониженому тиску у шинах; - неправильна робота кермової трапеції.
|
Манометр, ПКО-4
|
|
Конусне зношення
шин керованих коліс
|
- великий розвал
коліс при збільшеному сходженні керованих коліс
|
Bosch SDL-260
|
|
Прискорене зношення
шин керованих коліс
|
- велике сходження
керованих коліс
|
Bosch SDL-260
|
|
Зношення шин задніх
коліс з правої частини
|
- задній міст
повернений за годинниковою стрілкою
|
Bosch SDL-260
|
|
Зношення шин задніх
коліс з лівої частини
|
- задній міст
повернений проти годинникової стрілки
|
Bosch SDL-260
|
|
Зношення внутрішніх
частин протектора коліс заднього моста
|
- балка заднього
моста деформована так, що колеса мають великий від’ємний розвал
|
Bosch SDL-260
|
|
Слід від задніх і
передніх коліс не співпадає
|
- задній міст
зміщений
|
Bosch SDL-260
|
Ходова частина
автомобіля
|
Зношення зовнішніх
частин протектора коліс заднього моста
|
- балка заднього
моста деформована так, що колеса мають великий додатній розвал
|
Bosch SDL-260
|
|
Зношення шин коліс
заднього моста рівномірний, але пришвидшений відносно переднього моста
|
- балка заднього
моста деформована так, що наявне сходження задніх коліс
|
Bosch SDL-260
|
|
Автомобіль на
великій швидкості відводить то вліво, то вправо
|
- задній міст
зміщений
|
Bosch SDL-260
|
|
Автомобіль
відводить вліво або вправо
|
- різний кут
поздовжнього нахилу осі повороту передніх коліс; - різний розвал передніх
коліс
|
Bosch SDL-260
|
Ходова частина
автомобіля
|
Крен кузова
|
- поломка витків
пружини з того боку, куди нахилений кузов; - залишкова деформація пружин
|
Візуально
|
|
Підтікання рідини
із амортизаторів
|
- усадка
ущільнюючого кільця резервуара чи послаблення затягування гайки; - знос
гумових сальників штока; - задири або риски на штоці; - знос штока; -
недостатня кількість рідини
|
Візуально
|
|
Постійні пробої
задньої підвіски і удари при переїзді нерівностей
|
- перевантажений
автомобіль; - пружини втратили пружність; - поломка витків пружини; -
незадовільна робота амортизаторів
|
Bosch SDL-260
|
|
Пробої які
супроводжуються металевими стуками
|
- пошкоджені гумові
відбійники, які обмежують хід підвіски
|
Візуально
|
Ходова частина
автомобіля
|
Скрип у передньому
мості
|
- знос гумових
втулок; - відсутність змащення в кульових шарнірах
|
Візуально
|
|
На великій
швидкості кермо вібрує
|
- великий дисбаланс
передніх коліс; - змінені кути встановлення передніх коліс
|
Bosch SDL-260,
балансувальний стенд
|
|
Незадовільне
зусилля при ході віддачі
|
- нещільне
прилягання клапана віддачі; - поломка чи надмірний знос ущільнюючих кілець; -
задири на поршні, кільцях чи циліндрі
|
Візуально
|
|
Незадовільне
зусилля при ході стиску
|
- деформація
тарілки великого клапана; - наявність нерівностей під тарілку на корпусі
клапана стиску; - нещільне перекриття клапана стиску через попадання
сторонніх предметів
|
Візуально
|
|
Стуки і скрипи в
амортизаторі
|
- ослаблення
кріплення або не співпадають осі кріплення; - завелика кількість рідини в
амортизаторі;
|
Візуально
|
Таблиця
4.2
Основні дані для регулювання і контролю підвіски автомобілів
сімейства Daewoo “Ланос”
Назва параметру
технічного стану
|
Значення параметра
|
Передня підвіска
|
Відстань від
опорної поверхні до передньої частини важеля, мм
|
195
|
Відстань від опорної
поверхні до задньої частини важеля, мм
|
191
|
Кут розвалу
передніх коліс
|
-1°10'…20'
|
Різниця між кутами
розвалу передніх коліс
|
1°
|
Кут сходження
передніх коліс (завантаження автомобіля - 2 особи)
|
-10'…10'
|
Кут поздовжнього
нахилу осі повороту колеса (кермове колесо без підсилювача)
|
30'…2°30'
|
Кут поздовжнього
нахилу осі повороту колеса (кермове колесо з підсилювачем)
|
1°45'…3°45'
|
Різниця між кутами
поздовжнього нахилу осі повороту передніх коліс, не більше
|
1°
|
Задня підвіска
|
Довжина різі штока
амортизатора над торцем гайки кріплення, мм
|
9,0
|
Кут розвалу задніх
коліс
|
-2°…-1°10'
|
Різниця між кутами
розвалу задніх коліс
|
30'
|
Кут сходження
задніх коліс (завантаження автомобіля - 2 особи)
|
-10'…40'
|
Різниця між кутами
сходження задніх коліс, не більше
|
15'
|
Аналізуючи дані таблиці 4.1, всі параметри технічного стану
(структурні параметри), зміна яких призводить до виникнення несправності, можна
розділити на групи, в залежності від способу їх вимірювання: ті, що вимірюються
зносами, градусами та тиском. Тут одразу помітна різниця між контролем тиску у
шинах і визначенні інших показників.
Можна зробити висновок, що для підвіски легкового автомобіля
основними показниками технічного стану механізму є величини зносу його
елементів. Це не дає змогу виміряти їх без розбирання механізму, тому вимагає
застосування складних технічних засобів.
Зазвичай вплив параметрів на технічний стан системи є різний,
тому з всіх параметрів необхідно виділити ті, що найбільш впливають на зміну
працездатності системи.
.2 Формулювання робочої гіпотези щодо вибору параметрів
діагностування систем та агрегатів АТЗ
Як показують дані попереднього підрозділу (табл. 4.1, 4.2),
для визначення технічного стану підвіски легкового автомобіля використовують 12
параметрів діагностування.
Відхилення кожного з них від нормативних меж засвідчує
відповідний рівень зниження технічного стану і, очевидно, зниження
працездатності підвіски АТЗ.
При організації технологічного процесу діагностування
ставиться задача раціональної мінімізації числа контрольно - вимірювальних
операцій, підвищення точності вимірювання діагностичних параметрів і,
відповідно, встановлення діагнозу [18]. При цьому потрібно дотримуватись
загальної умови мінімізації витрат на експлуатацію, обслуговування і ремонт
об’єкту, що діагностується.
Як вказувалось в розділі 1, технічне діагностування
направлене на вирішення 3-х основних задач: визначення працездатності об’єкта,
виявлення і усунення відмови й несправності, визначення залишкового ресурсу.
Кожному з 3-ох випадків відповідає визначений методологічний підхід, що
забезпечує побудову свого алгоритму діагностування.
Побудові алгоритму діагностування передує аналіз статистичних
даних на відмовах і несправностях, що найчастіше повторюються. На основі даних
аналізу розробляють структурні схеми за ланцюгом: об’єкт, що діагностується
(автомобіль) - агрегат - система, механізм - вузол - елемент - структурний
параметр.
Число ланок у ланцюзі в кожному конкретному випадку (в
залежності від системи і агрегату) може мінятися. Кожна ланка визначає рівень пошуку
чи технологічного кроку, спрямованого на встановлення несправності. Наприклад,
в наведеній на рис. 4.1 спрощені схемі рівнів алгоритму діагностування АТЗ при
пошуку несправності їх 7.
Ці рівні укрупнені стосовно підвіски автомобіля, решту систем
і механізмів упущено:
·
перший
(найвищий) рівень пошуку передбачає визначення загального технічного стану
автомобіля;
·
другий
рівень пошуку включає в себе контроль основних агрегатів автомобіля: 1.1 -
двигун; 1.2 - ходова частина; 1.3 - коробка передач; 1.4 - гальмівна система;
1.5 - трансмісія; 1.6 - кузов;
·
на
третьому рівні здійснюється пошук несправностей по вузлах, механізмах і
системах окремих агрегатів: 2.1 - рама (несучий кузов) автомобіля; 2.2 -
колеса; 2.3 - підвіска; 2.4 - мости;
·
четвертий
рівень відповідає контролю основних вузлів, з яких складається механізм, що
діагностується (в окремих випадках допускається агрегат) або система,
наприклад, для передньої підвіски: 3.1 - важіль підвіски в зборі; 3.2 - стійка
передньої підвіски в зборі; 3.3 - стабілізатор поперечної стійкості в зборі;
3.4 - маточина колеса в зборі;
·
на
п’ятому рівні контролюють деталі систем і механізмів, за якими в процесі
експлуатації спостерігається найбільше число відмов і несправностей: 4.1 -
верхня опора амортизаційної стійки; 4.2 - пружина; 4.3 - амортизатор; 4.4 -
нижня опорна чашка; 4.5 - верхня опорна чашка;
Рис. 4.1 Спрощена схема рівнів алгоритму діагностування АТЗ
при пошуку несправності
·
шостому
рівню відповідає контроль елементів і спряжень, що визначаються на основі
аналізу статистичних даних із врахуванням критеріїв експлуатаційної надійності:
5.1 - клапан віддачі - сідло; 5.2 - ущільнююче кільце - шток; 5.3 - ущільнююче
кільце - циліндр; 5.4 - клапан стику - сідло;
·
на
сьомому рівні контролюють структурні параметри, які визначають технічний стан
системи чи механізму: 6.1 - задири на поверхні штока; 6.2 - цілісність
ущільнюючого кільця; 6.3 - геометричні розміри ущільнюючого кільця; 6.4 -
геометричні розміри штока (діаметр, конусність, овальність).
В складніших схемах, подається взаємозв’язок між структурними
і діагностичними параметрами, який дозволяє за зміною діагностичного параметру
визначити в яких деталях відбулася відмова чи несправність. Мабуть, такі схеми
вимагатимуть опрацювання великої кількості статистичних даних і складних
діагностичних засобів для зчитування параметрів.
Важливим у скороченні тривалості, трудомісткості та вартості
діагностування буде вибір обмеженої кількості параметрів діагностування, зняття
фактичних показників яких і порівняння з нормативними, повинні дати однозначну
відповідь щодо регулювань (заміни, ремонту) систем в цілому [24, 25, 26, 27,
28].
Отже, можна висунути таку гіпотезу: існує один або декілька
параметрів технічного стану (структури) у системах, які функціонально і
однозначно впливають на якість перебігу робочих процесів у системах. Серед
всієї сукупності структурних параметрів ці декілька, за умови використання
відповідних технічних засобів діагностування, бази знань і бази даних дадуть
змогу оперативно прийняти рішення щодо подальших ремонто-обслуговувальних та
діагностувальних дій.
В загальному прийнято, що для повної перевірки підвіски
автомобіля необхідно провести наступні операції [16]:
1.
сходження передніх і задніх коліс;
3.
Кути
поздовжнього нахилу осі повороту передніх коліс;
4.
Різниця
між кутами поздовжнього нахилу осі повороту передніх коліс;
5.
Відстань
від опорної поверхні до задньої частини важеля;
6.
Відстань
від опорної поверхні до передньої частини важеля;
7.
Стан
втулок стабілізатора передніх коліс;
8.
Стан
втулок важеля підвіски передніх коліс;
9.
Стан
кульових шарнірів передніх коліс;
10.Стан підшипників маточин передніх і задніх коліс;
11.Стан амортизаторів передніх і задніх коліс;
12.Стан верхніх і нижніх опор стояків передніх і задніх коліс;
13.Стан пружин підвіски передніх і задніх коліс.
Кути розвалу передніх і задніх коліс та поздовжнього нахилу
осі повороту передніх коліс не регулюються, а їх номінальні значення
досягаються заміною відповідних деталей.
Звичайно, перевірка, регулювання і визначення всіх цих
параметрів вимагає значних зусиль і затрат. Тому необхідно зменшити кількість
перевірок, але, одночасно, не зменшуючи інформативності проведення діагностування.
Отже, з урахуванням висунутої гіпотези, з всієї вибірки
діагностичних параметрів, виділяємо найосновніші:
·
сходження
передніх коліс;
·
розвал
передніх коліс;
·
стан
амортизаторів передніх і задніх коліс;
·
стан
підшипників маточин передніх і задніх коліс.
Кожен з цих параметрів характеризує декілька параметрів
технічного стану і впливає на показники роботи підвіски автомобіля Daewoo “Ланос”.
На мою думку, саме за допомогою цих чотирьох діагностичних
параметрів можна оцінювати стан підвіски легкового автомобіля Daewoo “Ланос” - справний чи
несправний. Ці чотири діагностичних параметри охоплюють всю номенклатуру
структурних параметрів. Таким чином, контролюється загальний стан підвіски
автомобіля.
Загальний вигляд алгоритму діагностування, згідно з висуненою
гіпотезою зображений на рис. 4.2.
.3 Формалізація станів складальних одиниць систем та
складання математичної моделі їх діагностування (матричний підхід) на прикладі
підвіски АТЗ
Моделювання складної системи як
єдиного цілого здійснити переважно не вдається через її складність. Тому під
час моделювання в системі виділяють елементи, які надалі розглядаються як
неподільні одиниці; неперервною незалежною змінною залишається тільки час.
Рис. 4.2 Алгоритм пошуку несправності згідно висуненої
гіпотези
Поведінку більшості фізичних
підсистем можна охарактеризувати за допомогою фазових змінних. Фазова змінна -
це величина, що характеризує фізичний або інформаційний стан модельованого
об'єкта.
Так, в електричній підсистемі фазовою
змінною є струми і напруги, у механічній - сили і швидкості. Закони
функціонування елементів підсистеми задаються компонентними рівняннями, які
описують зв'язок фазової змінної різного типу для кожного елемента технічної
системи. У більшості фізичних підсистем можна виділити три типи найпростіших
елементів:
• елементи дисипації (розсіювання)
енергії (елементи типу опір R),
• елементи накопичення потенціальної
енергії (елементи типу С);
• елементи накопичення кінетичної
енергії (відповідно елементи типу І).
Сукупність цих елементів і джерел
фазових змінних типу напруги (падіння потенціалів) Е та потоку І може виступати
в ролі об'єктів математичної моделі технічної системи практично довільного
рівня складності. Аналогії між внутрішніми компонентами і фазовими змінними
підсистем технічних систем різної фізичної природи наведені в табл. 4.3.
Конструкція підвіски вимагає
використання не тільки компонентів і фазових змінних механічної поступальної
(пружина, важіль, стабілізатор, кермова трапеція, кульовий шарнір) та обертової
підсистем (підшипник маточини), а і гідравлічної підсистеми (амортизатор).
Тепловим потоком при терті у
елементах розсіювання енергії (амортизатор і пружина) на даному етапі можна
знехтувати.
Таблиця 4.3
Компоненти і фазові змінні підсистем
технічних систем
Підсистема
|
Фазові змінні
|
Компоненти
|
|
Сила
|
Швидкість
|
Опір тертя
|
Маса
|
Пружність
|
Механічна
поступальна
|
Сила
|
Швидкість
|
Опір тертя
|
Маса
|
Пружність
|
Електрична
|
Струм
|
Напруга
|
Опір
|
Ємність
|
Індуктивність
|
Механічна
обертальна
|
Момент сил
|
Кутова швидкість
|
Опір тертя
|
Момент інерції
|
Обертальна
гнучкість
|
Гідравлічна/пневматична
|
Розхід рідини/ газу
|
Тиск
|
Опір тертя
|
Гідравлічна ємність
|
Гідравлічна
індуктивність
|
Теплова
|
Тепловий потік
|
Температура
|
Тепловий опір
|
Теплоємність
|
Немає фізичного змісту
|
На підставі аналізу літературних джерел, за основу
математичного відтворення особливостей функціонування підвіски автомобіля було
вирішено взято матричний підхід, який дозволяє визначати присутність одиничних
і кратних дефектів в лінійних електричних колах.
Метод розрахований на електричні кола, що складаються з
резисторів, кількість яких практично необмежена. Глибина діагностування
визначається числом доступних вузлів електричного кола.
Було запропоновано замінити механічно-гідравлічну підсистему
підвіски на еквівалентну електричну для подальшого застосування матричного
підходу. Покажемо метод на прикладі визначення справності передньої підвіски
легкового автомобіля.
Представимо принципову спрощену схему передньої підвіски
легкового автомобіля “Ланос” та еквівалентну їй принципово електричну схему
передньої підвіски у вигляді опорів із джерелом живлення (рис. 4.1):
а) б)
Рис. 4.3. Принципова спрощена схема передньої підвіски легкового
автомобіля “Ланос” (а) та еквівалентна їй принципова електрична схема передньої
підвіски у вигляді опорів із джерелом живлення (б) (розшифрування позначень у
тексті)
На рис. 4.3, а прийнято такі позначення: 1 - верхня опора
амортизаторної стійки, 2 - верхня опорна чашка, 3 - амортизатор, 4 - пружина
підвіски, 5 - корпус амортизаторної стійки, 6 - підшипник маточини, 7 -
поворотний кулак, 8 - важіль, 9 - втулка переднього шарніра важеля підвіски; F - сила, яка діє від нерівностей
дороги.
На рис. 4.3, б прийнято такі еквівалентні електричні
позначення: R1 - еквівалентний електричний опір
верхня опорної чашки, R2 - еквівалентний електричний опір амортизатора, R3 - еквівалентний електричний опір
пружини підвіски, R4 - еквівалентний електричний
опір підшипника маточини; U - еквівалентна електрична напруга, яка діє від нерівностей дороги.
Звичайно, врахувати всі опори неможливо і для наочності
методу непотрібно. Тому на рис. 4.3 показана принципова схема опорів, на якій R1
- опір вимикача, R2 - додатковий опір, R3 -
опір провідників, R4 - опір первинного кола котушки
запалення.
Для зручності розрахунків приймемо наближені значення: R1
= 2 Ом, R2 = 0,5 Ом, R3 = 0,5 Ом, R4
= 1 Ом.
Процедура пошуку дефектів включає 2 етапи:
А. Підготовчий етап.
1.
Задаємося
кратністю дефекту k = 1, пошук якого буде здійснюватися.
2.
Вибірково
вибираються пари контрольних виводів (n). Їх число повинно перевищувати
кратність дефекту (n > k), тому n = 2 (рис. 4.4).
3.
Виходячи
з номінальних значень елементів кола, вираховуються номінальні значення напруги
на вибраних парах контрольних виводів (V01, V02,…, V0n
) при заданій напрузі:
01 = Vдж = 5 В;1 = I2 = I3
= I4 = V01 / R1 = 5 / 2 = 2,5 А;02 =
I4 R4 = 2,5 · 1 = 2,5 В
Рис. 4.4 Принципова еквівалентна електрична схема для
визначення справності підвіски: Vдж - напруга тестера, Vдж =
5 В (реально джерело збурення), I0, I1, I2, I3,
I4 - номінальні значення сили струму, на відповідних елементах
підвіски
4.
Здійснюється
перехід до спряженої схеми (рис. 4.5).
а) б)
Рис. 4.5 Спряжена схема: а - під’єднання одиничного джерела
струму до виводів 1-1’; б - під’єднання одиничного джерела струму до
виводів 2-2’
5.
Рахуючи,
що одиничне джерело струму почергово під’єднується до пар контрольних виводів,
вираховуються значення напруг на всіх елементах електричного кола (V1,
V2,…, Vр), де р - число елементів кола.
Знаходимо значення напруги, якщо одиничне джерело під’єднання
до виводів 1-1’:11 = 1 В21
= ¼ В31
= ¼ В41
= ½ В
Знаходимо значення напруги, якщо одиничне джерело під’єднання
до виводів 2-2’:12 = ½ В22 = 1/8 В32
= 1/8 В42 = ¼ В
6.
Із
отриманих значень напруг складаємо матриці Z, розмірністю n·k. Число таких
матриць дорівнює числу комбінацій можливих дефектів з заданою кратністю:

7.
Для всіх
матриць Z визначається вираз
= Z (ZT • Z)-1 ZT
8.
По
обрахованих значеннях Z всі можливі дефекти розбиваються на класи еквівалентних
дефектів (дефекти з однаковим значенням Z належать одному класу).
Отримаємо чотири класи еквівалентності дефектів:
). Z12, Z132). Z24, Z34
). Z234). Z14
Б. Метрологічний етап.
9.
В схемах
проводяться виміри напруги на вибраних контрольних парах виводів (Vm1,
Vm2,…, Vmn).
Припустимо, що значення напруги будуть: V11 = 4 В,
V11 = 3,5 В.
10.Складаються матриці V0 і Vm:
V0 = [5 2,5]; Vm = [4 3,5]
11.Вираховується матриця ∆V
∆V = V0 - Vm (4.1)
В нашому випадку: ∆V = [1 -1]m
12.Якщо виконується рівність ∆V = 0, то рахується, що дефект в колі
відсутній.
13.При нерівності ∆V ≠ 0 рахується, що в колі присутній дефект.
В такому випадку для всіх матриць Z визначається вираз
(Z - 1) ∆Vm (4.2)
1.
При
виконанні рівності (Z - 1) ∆Vm = 0 робиться висновок, що в
колі присутній дефект заданої кратності, що належить даному класу еквівалентності
дефектів.
В нашому випадку вираз Z3 рівний нулю, тому робимо
висновок, що в колі присутній дефект кратності один, а дефектними елементами є
опори R2 і R3.
2.
При
нерівності (Z - 1) ∆Vm ≠ 0 необхідно перейти до дефектів
більш високої кратності і повторити процедуру пошуку дефектів з початку.
5. Порівняльні дослідження
періодичності діагностування АТЗ
.1 Вибір бази та методу порівняльних досліджень
Для оцінки технічного стану важливо своєчасно встановити
момент настання передвідмовного стану агрегату або системи автомобіля, за якого
для відновлення працездатності необхідно провести профілактику або заміну
окремих деталей, щоб запобігти відмові.
Розглядається модель передвідмовного технічного стану
агрегату або системи автомобіля, в основу якої покладені закономірності зміни
діагностичних параметрів з пробігом та оптимальна періодичність діагностування
[17].
Передвідмовним вважається стан, за якого діагностичний
параметр
(
- пробіг автомобіля) досягає
гранично-допустимого значення
на момент пробігу [17]:
(5.1)
де
- середній пробіг на відмову, км;
- оптимальна періодичність діагностування, км.
Отже, згідно з (5.1) передвідмовний стан завжди буде
своєчасно виявлений.
Оптимальну періодичність діагностування
прийнято вибирати з огляду на
техніко-економічний критерій, а саме на основі мінімуму затрат на виконання
чергового діагностування
та поточного ремонту
[17]. На практиці користуються
графічним методом визначення оптимальної періодичності діагностування
на основі побудованих кривих
залежності коефіцієнта оптимальності
від відношення затрат
для різних законів розподілу відмов.
Коефіцієнт оптимальності
показує, у скільки разів оптимальна періодичність
діагностування більша або менша за середній пробіг на відмову. Задавши
відношення затрат
, з графіка знаходять значення
. Оптимальна періодичність
діагностування дорівнює:
(5.2)
Зауважимо, що техніко-економічне обґрунтування вибору
оптимальної періодичності діагностування справедливе для всіх агрегатів та
механізмів автомобіля, крім тих, що забезпечують безпеку руху.
У найтривалішому (нормальному) експлуатаційному періоді,
згідно з даними статистичних спостережень, відмови розподілені відповідно до
експоненційного закону. Коефіцієнт оптимальності
не залежить від параметрів закону
розподілу та визначається графічно [17].
Користуючись діагностичними картами агрегатів автомобіля,
можна отримати аналітичну залежність зміни діагностичного параметра від
пробігу. У загальному вигляді її зображають співвідношенням [17]:
, (5.3)
де
- номінальне значення параметра;
,
- const (
- інтенсивність зміни параметра,
якщо
=1, зменшена у
разів,
- показник степеня, який визначає
характер зміни параметра).
Формула (5.3) дає можливість встановити гранично-допустиме
значення параметра
, що відповідає пробігу
. Для цього спочатку знаходять
та
згідно з (5.2) та (5.1).
Задача прогнозування працездатного стану на період до
наступного діагностування розв'язується на основі моделі, яка базується на
теоремі Байєса [17].
Якщо відомі значення показників надійності - інтенсивності
раптових
та зношувальних
відмов, а також закономірності зміни
діагностичних параметрів, необхідно визначити ймовірність відсутності відмови у
період пробігу з моменту останнього діагностування
до наступного
(
- періодичність діагностування), за
умови, що жоден діагностичний параметр за цей час не вийде за межі
гранично-допустимого значення
.
Апостеріорна ймовірність (така, що ґрунтується на досвіді)
відсутності відмови за умови, що передвідмовний стан не настане протягом
пробігу [
;
], визначається за формулою Байєса:
(5.4)
де
,
- гіпотези, відповідно, про виникнення та відсутності відмов
протягом періоду прогнозування [
;
];
,
- апріорні ймовірності (такі, що наявні до проведення
досліджень) подій
та
;
- гіпотеза про те, що передвідмовний стан не настане
протягом періоду прогнозування [
;
], жоден діагностичний параметр не досягне
граничнодопустимого значення;
- умовна ймовірність того, що передвідмовний стан не настане
(гіпотеза
) за умови відсутності відмов (гіпотеза
);
- умовна ймовірність того, що передвідмовний стан не настав,
за умови виникнення відмови (гіпотеза
).
За даними статистичних спостережень, для основного
(найтривалішого) періоду експлуатації інтенсивності раптових та зношувальних
відмов не залежать від пробігу (
,
). Апріорна ймовірність відсутності відмови протягом періоду
прогнозування [
;
] описується експоненційним законом [17]:
. (5.5)
Оскільки гіпотези
та
несумісні (
), то ймовірність виникнення відмови:
(5.6)
Аналогічно умовна ймовірність того, що передвідмовний стан не
настав протягом [
;
], але виникла раптова відмова:
(5.7)
Ймовірність того, що передвідмовний стан не настав
(діагностичний параметр не досяг гранично-допустимого значення), за умови
відсутності відмови протягом пробігу [
;
], визначається:
(5.8)
де
- інтенсивність зміни діагностичного параметра, що
розглядається, а
- відносна його зміна [0<
<1].
Якщо параметр з напрацюванням зростає (
<
), тоді
(5.9)
у протилежному випадку (
>
):
(5.10)
де
- значення діагностичного параметра на момент
діагностування.
З врахуванням (5.5) - (5.10) апостеріорна ймовірність
відсутності відмови (5.4) матиме вигляд
(5.11)
Отже, співвідношення (5.11) дає змогу розрахувати ймовірність
відсутності відмови (прогноз працездатного стану) агрегатів автомобіля на
період до наступного діагностування.
Результати прогнозування обґрунтовують рішення стосовно
можливих позапланових ремонтно-профілактичних робіт для забезпечення
нормативного ресурсу основних агрегатів.
На основі попередньо розрахованого гранично-допустимого
значення діагностичного параметра
та відомої аналітичної
закономірності його зміни з пробігом (5.3), визначають ймовірність відсутності
відмови [Р] за формулою (5.11) протягом усього нормативного ресурсу пробігу.
Для прийняття рішення про необхідність можливих позапланових
ремонтно-профілактичних робіт для конкретного вилученого з експлуатації
автомобіля спочатку визначають ймовірність відсутності відмови
за формулою (5.11) і порівнюють її з
[Р]. Якщо
[Р], то для даного автомобіля позапланових робіт не
проводять, в протилежному випадку їх виконують одразу ж після діагностування
для зменшення інтенсивності зношування деталей агрегату.
Зауважимо, що ймовірність відсутності відмови [Р] можна
використати для розв’язання багатьох інших задач, зокрема планування заміни
деталей агрегату; формування комплекту запасних частин та інструменту, що
необхідно мати в спорядженому автомобілі; планування обсягів робіт зон ТО та ПР
тощо.
На практиці на станціях діагностування зручно користуватись
побудованими на підставі співвідношення (5.11) за різних значень відносної
зміни діагностичного параметра (5.9), (5.10) параметричними кривими ймовірності
відсутності відмови агрегату, за даним параметром, протягом всього нормативного
ресурсу пробігу. Попередньо, для визначення [Р], зручно користуватись графічною
залежністю зміни діагностичного параметра з пробігом (5.3).
Вибір стратегії керування працездатним станом автомобіля
ґрунтується на визначенні оптимальної періодичності контрольно-діагностичних
перевірок.
Даний підхід дає можливість встановити таку періодичність
діагностування, яка, з одного боку, зменшує затрати на ТО та ПР, з другого -
дає змогу підтримувати працездатність автомобіля на оптимальному рівні.
Критерієм оптимізації такого керування є мінімум функції сумарного ризику [17]:
(5.12)
де
- ризик аварійної відмови деталей агрегату на період
прогнозування;
- ризик передчасного (марного) діагностування агрегату
(визначаються у грошовому еквіваленті). Своєю чергою
;
(5.13)
де
,
- відповідно затрати на усунення аварійної відмови (грн.) та
затрати на одне діагностування (грн.);
- ймовірність виникнення аварійної
відмови агрегату у період прогнозування;
- кількість діагностичних перевірок
протягом цього ж періоду.
Отже, формула (5.12) з врахуванням (5.13), набуває вигляду:
.(5.14)
Без істотних втрат точності розрахунків густину розподілу
ймовірності відмов, яка описується розподілом Вейбулла, можна замінити
нормальним розподілом Гауса [17]. Тоді ймовірність аварійної відмови системи
задається співвідношенням [17]:
(5.15)
де
,
- відповідно математичне сподівання та середньоквадратичне
відхилення значень діагностичного параметра протягом періоду прогнозування;
- гранично-допустиме значення діагностичного
параметра.
Середньоквадратичне відхилення значень діагностичного
параметра можна обчислити так:
, (5.16)
де
- коефіцієнт варіації діагностичного параметра;
- середня зміна діагностичного
параметра протягом періоду експлуатації між двома контрольними перевірками:
, (5.17)
де
- номінальне значення діагностичного параметра,
- середня кількість діагностичних
перевірок впродовж всього періоду ресурсу (до ремонту агрегату). Зауважимо, що
середню зміну діагностичного параметра
можна також визначити,
використовуючи співвідношення (5.5).
Математичне сподівання значення діагностичного параметра на
період прогнозування:
, (5.18)
де
- значення діагностичного параметра на момент
діагностування.
Значення діагностичного параметра за умов появи відмови є
обмежене внаслідок конструктивних особливостей агрегату, отже:
. Межу
можливих значень нормально
розподіленої випадкової величини
можна встановити на підставі правила
“трьох сигм”. Тоді ймовірність аварійної відмови системи (5.15)
визначатиметься:
(5.19)
Тут верхня межа інтегрування
залежить від тривалості періоду
прогнозу, що дорівнює технічним обслуговуванням.
Ймовірність аварійної відмови не визначається через
елементарні функції, а обчислюється за допомогою функції Лапласа
:
(5.20)
З врахуванням (5.16)-(5.20) критерій ризику (5.12) та функція
ризику (5.14) матимуть вигляд:
, (5.21)
де
, (5.22)
,
Співвідношення (5.21), (5.22) дають змогу розрахувати
кількість контрольно-діагностичних перевірок
, які можна не проводити з моменту
останнього діагностування, коли діагностичний параметр дорівнює
. Отже, встановлено період
експлуатації, протягом якого агрегат перебуватиме в працездатному стані (залишковий
ресурс). Це дає можливість змінювати періодичність виконання
контрольно-діагностичних операцій вилученням
перевірок з наперед запланованої їх
кількості
. На практиці зручно користуватись графічною залежністю
=
, яку можна побудувати на підставі
співвідношень (5.21), (5.22) для різних значень діагностичного параметра
.
Зауважимо, що співвідношення (5.21), (5.22) справедливі для
двох випадків зміни діагностичного параметра з пробігом - як для зростання (
), так і для зменшення параметра (
).
Крім того, на підставі даної моделі можна визначити
залишковий ресурс агрегату за розглянутим діагностичним параметром. Визначивши
, залишковий ресурс знайдемо за
формулою
, (5.23)
де
- періодичність діагностувань.
.2 Результати порівняльних досліджень, їх аналіз та
оптимізація періодичності ТО на прикладі передньої підвіски автомобіля Lanos
Для визначення оптимальних пробігів в програмі Маthcad, яка
дозволяє проводити розрахунки за трьома попередніми методиками. Програма
наведена у додатку Б.
За основу було взято коливання підвіски автомобіля після його
гальмування при перевірці на діагностичному комплексі Bosch SDL-260.
З урахуванням початкового значення затухаючих коливань
=2 і граничного значення
=5, яке відповідає повністю
несправному амортизатору, меж коефіцієнта варіації
=55,6% (підрозділ 3.3)
нерівномірності розподілу пробігів на відмову підвісок легкових автомобілів
використано програму у середовищі Mathcad
і розраховано кількість пропусків діагностувань
підвіски легкового автомобіля у
циклі ТО-2 (згідно Положення-98-20 тис. км).
Втрати (збитки) і витрати (
,
) брались
з розрахунку значень, що
відповідають чинній вартості діагностування на діагностичному комплексі Bosch SDL-260 (34 грн.) і витратам за
усунення несправності
(160 грн).
Відповідними обчисленнями знайдено залежність коефіцієнта
оптимальності
від співвідношень
для коефіцієнта варіації
=55,6%
[17].
Коефіцієнт оптимальності
враховує грошові витрати, пов’язані
з проведенням ТО-2 і із збитками за усунення несправності. На зміну його значень
матиме вплив коефіцієнт варіації нерівномірності розподілу пробігів на відмову
підвісок легкових автомобілів
.
Чим останній більший, тим для різних співвідношень витрат і
збитків буде більший коефіцієнт оптимальності
і, отже,
матиме значення, близькі до
середнього пробігу АТЗ
.
Для прикладу, на підставі розробленої методики визначено
кількість пропусків виконання діагностувань з періодичністю
залежно від значень кількості
затухаючих коливань підвіски k для одного коефіцієнта варіації
(рис. 5.1).
При цьому у розрахунках коефіцієнта оптимальності взято
максимальні значення втрат
. Періодичність
змінювалася залежно від коефіцієнта
оптимальності
, значення якого у свою чергу залежать від коефіцієнта
варіації
.
Для великих значень коефіцієнта варіації, відбувається ріст
періодичності
за рахунок нестабільності зміни відмов підвісок легкових
автомобілів з пробігом і росту ризику
настання перевищення
гранично-допустимого значення
=5.
Рис. 5.1 Зміна можливих пропусків виконання діагностувань з
періодичністю
залежно від значень кількості затухаючих коливань підвіски
5.3 Оцінка результатів порівняльних досліджень
Отримані результати вказують, що якщо, наприклад, оптимальний
пробіг АТЗ з коефіцієнтом варіації
=55,6% (підрозділ 3.3)
нерівномірності розподілу пробігів на відмову підвісок легкових автомобілів:
тис. км
і значення кількості затухаючих коливань підвіски Z=3, то можна зробити k=2 пропуски проведення ТО (див. рис.
5.1) в інтервалі пробігу
тис. км. При цьому залишковий пробіг складе
16,6 тис км.
Якщо ж значення кількості затухаючих коливань підвіски 4,
можна пропустити в цьому ж інтервалі пробігу 1 пропуск проведення діагностувань
k.
Якщо АТЗ має значення кількості затухаючих коливань підвіски
більше 5, то пропуски проведення діагностувань з позицій оптимальних витрат і
не перевищення гранично-допустимого значення неприпустимі.
6. ОХОРОНА ПРАЦІ
Ремонтне виробництво є особливо несприятливим з точки зору
техніки безпеки, пожежної безпеки та виробничої санітарії. Це обумовлено тим,
що автомобілі, які надходять в ремонт та технічне обслуговування можуть бути
забруднені речовинами, шкідливими для здоров’я людини, горючими матеріалами, а
пошкоджені деталі можуть бути причиною травмування. Специфікою ремонтного
виробництва є також те, що робітники постійно працюють з різними об’єктами
ремонту і виконують різні операції, їх робочі місця, як правило, не є
постійними.
Поліпшення умов праці є одним із резервів росту її
продуктивності та екологічної ефективності виробництва, а також подальшого
покращення соціального стану і здоров’я працівників.
Проблема поліпшення умов праці безпосередньо пов’язана з
санітарно-побутовими умовами, режимом роботи і медичним обслуговуванням
працівників, організацією відпочинку, харчування та інших факторів.
Збитків, яких сьогодні завдає виробничий травматизм і
професійні захворювання на виробництві, можна позбавитись за рахунок розробки
спеціальних заходів додержання вимог трудового законодавства, спеціальних
нормативних та інших документів, а також впровадження в виробництво найновіших
досягнень науки і передового досвіду з охорони праці.
.1 Структурно-функціональний аналіз технологічних процесів розбирання
автомобіля
Технологічний процес заміни вузлів і агрегатів включає
наступні операції:
- миття і очищення деталей агрегатів і вузлів та кріпильних
деталей;
виконання допоміжних операцій для створення доступу до
вузлів, що потребують заміни;
готування і встановлення технологічного обладнання;
- виконання основних операцій заміни агрегатів і вузлів;
- контроль технічного стану агрегатів, вузлів та деталей;
- транспортування знятих вузів деталей для їх заміни.
У процесі виконання вище перелічених операцій можуть виникати
такі травмонебезпечні ситуації:
під час миття, очищення деталей та зливання технологічних
робочих матеріалів:
· розбризкування мийного розчину або технологічних
матеріалів і попадання їх на обличчя , руки та інші відкриті ділянки тіла;
· загоряння мийного розчину на основі
горючих матеріалів або технологічних рідин;
· забруднення робочого місця;
- під час виконання допоміжних операцій для створення доступу
до агрегатів і вузлів, що потребують заміни:
· наявність на деталях відколи, зазубрин і стружки;
· падіння деталей і складальних
одиниць;
· зіскакування ключів з граней гайок;
- підготовка і встановлення технологічного обладнання:
· намотування одягу на обертові деталі обладнання
(силовий гвинт);
· затискання одягу або частин тіла елементами
обладнання, падіння, перекидання обладнання;
· наїзд мобільним обладнанням на
перешкоди, виконавців робіт або на інших присутніх осіб;
- виконання основних операцій заміни агрегатів і вузлів:
· наявність на деталях відколи, зазубрин і стружки;
· зіскакування ключів з граней гайок;
· падіння деталей і складальних одиниць;
- під час виконання основних операцій заміни агрегатів і
вузлів:
· зіскакування ключів з граней гайок;
· наявність на деталях гострих кромок і
відшарування металу;
· падіння деталей зі стола;
- під час контроль технічного стану агрегатів, вузлів та
деталей:
· випадання з рук мірного інструменту та пристроїв для
дефектування;
· неправильне використання інструментів
та пристроїв;
- під час транспортування знятих вузів деталей для їх заміни:
· падіння деталей і складальних одиниць з обладнання;
· перекидання обладнання разом з
транспортованими вузлами;
· наїзд мобільним обладнанням на
виконавців робіт або на інших присутніх осіб;
· наїзд мобільним обладнанням на інше
обладнання, автомобілі або їх складові частини;
Небезпечні умови операції (НУ):
· використання шкідливих для здоров’я мийних розчинів
(НУ1):
· використання легкозаймистих речовин
(НУ2):
· несправні інструменти (НУ3):
· несправне обладнання (НУ4):
· порушення вимог безпеки праці (НУ5):
Небезпечні дії (НД):
· розбризкування мийного розчину, витікання
технологічних рідин (НД1):
· користування інструментом, що
спричинює іскроутворення, значний нагрів або відкритого полум’я, паління
цигарок (НД2):
· та використання відкритого полум’я
(НД3):
· потрапляння горючих матеріалів на
нагріті деталі:
· використання несправного обладнання
(НД5):
Небезпечна ситуація (НС):
· потрапляння агресивних речовин на шкіру та в очі (НС1):
· займання горючих речовин (НС2):
· зіскакування інструментів з деталей
(НС3):
· падіння деталей, інструментів
обладнання або непередбачена траєкторія їх руху (НС4):
· необачні або невмілі дії виконавця
(НС5)
На підставі співставлення небезпечних умов операцій (НУ),
небезпечних дій (НД), та небезпечних ситуацій (НС) складаємо модель процесу.
.2 Вимоги безпеки до території, приміщень, обладнання і
виробничих процесів ремонтних майстерень
Територія ремонтних майстерень, виробничих,
санітарно-побутових та інших приміщень повинна відповідати технологічному
процесу ремонтного виробництва та вимогам санітарних норм проектування.
Поверхня має бути вирівняна й спланована так, щоб забезпечити відведення
стічних вод до водостоків від будівель, майданчиків, проїздів та пішохідних
доріжок. Ширина дороги для руху техніки і пішохідних доріжок до майстерні,
санітарно-побутових, допоміжних і інших приміщень при однобічному русі повинна
бути на 1,8 м, а при двобічному - на 2,7 м більша за ширину
сільськогосподарської машини. Ширина пішохідних доріжок має бути не менша 1,5
м.
Майданчики для зберігання автомобілів, тракторів, комбайнів
та іншої сільськогосподарської техніки повинні бути рівними, з твердим
покриттям (асфальт, бетон та ін.).
Виробничі процеси, які супроводжуються забрудненням робочої
зони шкідливими речовинами (отруйні гази, пари, пил і т.д.), треба проводити в
окремих приміщеннях, обладнаних вентиляцією.
Підлога в приміщеннях цехів повинна бути щільною, з твердим
покриттям, зручним для очищення і ремонту. В приміщеннях, де користуються
водою, підлогу влаштовують з похилом для стоку. На оглядових ямах та естакадах
треба встановлювати напрямні для коліс автомобілів і тракторів, а також
обладнувати з двох боків сходи для спуску в яму. На естакадах по всій довжині
мають бути поручні висотою не менш як 1м.
Усі зовнішні входи та виходи, в’їзди у виробничі приміщення
обладнують тамбурами для запобігання протягам і тепловим завісам.
Дахи та карнізи будівель у зимовий час треба регулярно
очищати від снігу та льоду.
Проходи між стелажами, полицями, шафами у складських
приміщеннях повинні бути шириною не менше 1м.
Висновки
1.
Аналіз
сучасного стану з технічним станом автомобілів показує, що технічна
експлуатація їх, зокрема, діагностування, відстає від навіть нормативних
колишніх союзних, не кажучи про відомі прогресивні закордонні аналоги.
2.
Оскільки
на підвіску легкових автомобілів припадає велика кількість відмов під час їх
комерційної експлуатації, досліджуються можливості вдосконалення діагностування
їх технічного стану з використанням комп’ютеризованих засобів.
3.
З метою
встановлення істотних структурних параметрів діагностування підвіски легкових
автомобілів проведено аналіз конструкції підвіски автомобіля Daewoo «Ланос», усіх можливих
параметрів технічного стану, а також параметрів діагностування; обґрунтовано
параметри технічного діагностування підвіски автомобіля, скоротивши їх
кількість з 13-ти до 4-ох.
4.
На
підставі аналізу літературних джерел, за основу математичного відтворення
особливостей функціонування механізму підвіски взято матричний підхід і
виконано відповідні розрахунки за допомогою них (приклад таких розрахунків
показаний для випадку перевірки справності передньої підвіски автомобіля).
5.
На
основі підходу планування оптимальної періодичності діагностування АТЗ за
мінімального ризику, встановлена періодичність діагностування підвіски для
автомобілів Daewoo «Ланос», яка, з одного боку,
зменшує затрати на ТО та ПР, з іншого дає змогу підтримувати працездатність АТЗ
на оптимальному рівні.
6.
Визначено
міжконтрольні пробіги АТЗ для автомобілів Daewoo «Ланос» за кількістю затухаючих
коливань підвіски, коли сума втрат від усунення несправності і затрат на
виконання діагностування на діагностичному комплексі Bosch SDL-260 будуть мінімальними.
Встановлені кількість пропусків проведення діагностувань із визначеною періодичністю
на середньому пробігу, коли кількість коливань не перевищує встановлених меж.
Список використаних джерел
1. Аринин
И.Н. Диагностирование технического состояния автомобилей. - М.: Транспорт,
1988. - 176 с.
2. Положення
про технічне обслуговування і ремонт дорожніх транспортних засобів
автомобільного транспорту. - К.: Мінтранспорт України, 1998. - 11 с.
. ГОСТ
18322-78 (СТ СЄВ 5151-85) Система техничного обслуживания и ремонта техники.
Термины и определения. - М.: Изд-во стандартов, 1986. - 13 с.
. Техническая
эксплуатация автомобилей: Под. ред. проф. Говорущенко Н.Я. - Харьков: Изд-во
"Вища школа" при Харьк. ун-те, 1984. - 312 с.
5. Зарубин
Л.Г. Устройство, обслуживание, ремонт и эксплуатация автомобилей Ford Mondeo. -
Вильнюс: Изд-во “Аргус”, 1996. - 295 с.
. Канарчук
В.Є., Лудченко О.А., Чигринець А.Д. Основи технічного обслуговування і ремонту
автомобілів: Підручник. У 3-х кн. - К.: Вища школа, 1994. - Книга 1: Теоретичні
основи. Технологія. - 344 с.
7. Говорущенко
Н.Я., Варфоломеев В.Н. Оптимизация периодичности диагностирования
автомобилей//Матер. междунар. конфер. “Новые технологии в
машино-приборостроении и на транспорте”. - Севастополь: СГТУ. - 2001. - С.
288-296.
. Техническая
эксплуатация автомобилей: Учебник для вузов / Под ред. Крамаренко Г. В. - 2-е
изд., перераб. и доп. - М.: Транспорт, 1983. - 488 с.
. Прудовский
Б.Д., Ухарский В.Б. Управление технической эксплуатацией автомобилей по
нормативным
показателям. - М.: Транспорт, 1990. - 239 с.
10. Техническая
эксплуатация автомобилей: Учебник для вузов/Кузнецов Е.С., Воронов В.П., Болдин
А.П. и др. Под. ред Кузнецова Е.С. - 3-е изд., перераб. и доп. - М.: Транспорт,
1991. - 413 с.
. Технология
ремонта дорожных машин и основы проектирования ремонтных предприятий. Учебное
пособие для вузов/Зеленков Г.И., Дехтеринский Л.В., Крившин А.П. - 2-е изд.,
перераб. и доп. - М.: Высшая школа, 1981. - 496 с.
. Мирошников
Л.В. Теоретические основы технической диагностики автомобилей. Учеб. Пособие. -
М.: Высшая школа, 1976. - 126 с.
. Мозгалевский
А.В., Гаскаров Д.В. Техническая диагностика. - М.: Высшая школа, 1985. - 207 с.
. Харазов
А.М. Диагностическое обеспечение технического обслуживания и ремонта
автомобилей: Справ. пособие.- М.: Высшая школа, 1990. - 208 с.
. Губинский
А.И. Надежность и качество функционирования эргатических систем. - М.: Наука,
1982. - 270 с.
16. Илюшин
А.Е. Daewoo Lanos, Assol: Седан и хэтчбек: вып. с 1996 г.: Бензиновые двигатели:
Эксплуатация. Обслуживание. Ремонт: цветные электросхемы. - Ростов-на-Дону: ЗАО
”Изд-во ДОН-ПРЕСС”, 2005. - 250
с.
17. Гогайзель
А.В. Игровое моделирование систем обеспечения работоспособности
автотранспортных средств: Учебн. Пос. - К.: УМК ВО, 1988. - 88 с.
. Спичкин
Г.В., Третьяков А.М. Практикум по диагностированию автомобилей: Учеб. пособие.
- 2-е изд. перераб. и доп. - М.: Высшая школа, 1986. - 439 с.
. Технические
средства диагностирования: Справочник / Клюев В.В., Пархоменко П.П., Абрамчук
В.Е. и др. Под. общ. ред. Клюева В.В. - М.: Машиностроение, 1989. - 672 с.
. Харазов
А.М. Диагностическое обеспечение технического обслуживания и ремонта
автомобилей: Справ. пособие.- М.: Высшая школа, 1990. - 208 с.
21. Яринский
В.В. Пересядемо на Деу? // Журнал "MotorNews". - 2000. - № 5. - С. 10-12.
22. Аринин
И.Н. Техническая диагностика автомобилей. - М.: Транспорт, 1991. - 146 с.
. Макаров
Р.А. Средства технической диагностики машин. - М.: Машиностроение, 1981. - 223
с.
. Биргер
И.А. Техническая диагностика. - М.: Машиностроение, 1988. - 182 c.
. Говорущенко
Н.Я., Туренко А.Н. Системотехника транспорта (на примере автомобильного тр-та).
Часть 2. - Харьков, 1998. - 219 с.
. ГОСТ
23564-79. Техническая диагностика. Показатели диагностирования. - Введ.
01.01.80. - М.: Изд-во стандартов, 1989. - 16 с.
. Доценко
Б.И. Диагностирование динамических систем. - К.: Техніка, 1983. - 157 с.
. Никитин
Г.А. Исследование алгоритмов и разработка аппаратуры автоматизированого
контроля и диагностики автомобилей: Автореф.дис… к-та техн. наук: 01.02.74 /
Челябинский политехн. ин-тут. - Челябинск, 1984. - 24 с.
ДОДАТОК А
Статистичні дані надходжень і відмов елементів підвісок
автомобілів “Ланос” і “Сенс”
Амортизатор задній
Дата
|
Пробіг, км
|
Інтервали, дні
|
АТЗ
|
01.03.2009
|
|
|
|
|
|
09.03.2009
|
1
|
32100
|
8,00
|
8.1
|
сенс
|
01.08.2009
|
1
|
16000
|
1,00
|
24.5
|
сенс
|
01.08.2009
|
2
|
9900
|
0,50
|
0.1
|
сенс
|
17.08.2009
|
1
|
33000
|
16,00
|
16.1
|
сенс
|
23.08.2009
|
1
|
42100
|
6,00
|
6.1
|
сенс
|
01.03.2009
|
|
|
|
|
|
15.03.2009
|
1
|
25094
|
4,00
|
14.1
|
ланос
|
10.06.2009
|
1
|
49120
|
|
27.3
|
ланос
|
18.06.2009
|
1
|
24100
|
8,00
|
8.1
|
ланос
|
02.09.2009
|
1
|
4100
|
32,00
|
16.3
|
ланос
|
Шарнір кульовий
передньої підвіски
|
01.06.2009
|
|
|
|
|
|
17.06.2009
|
1
|
35000
|
16,00
|
16.1
|
Ланос
|
08.08.2009
|
1
|
40603
|
7,00
|
21.2
|
Ланос
|
Верхня опора
переднього стояка
|
|
|
01.06.2009
|
|
|
|
|
|
15.06.2009
|
1
|
32000
|
14,00
|
14.1
|
сенс
|
18.06.2009
|
1
|
6484
|
3,00
|
3.1
|
сенс
|
20.06.2009
|
1
|
10025
|
2,00
|
2.1
|
сенс
|
20.06.2009
|
3
|
21100
|
0,33
|
0.1
|
сенс
|
08.08.2009
|
1
|
36760
|
7,00
|
18.2
|
сенс
|
02.09.2009
|
1
|
26450
|
1,00
|
25.1
|
сенс
|
05.09.2009
|
1
|
19700
|
3,00
|
3.1
|
сенс
|
01.06.2009
|
|
|
|
|
|
20.06.2009
|
1
|
11050
|
19,00
|
19.1
|
Ланос
|
17.08.2009
|
1
|
41320
|
16,00
|
27.2
|
Ланос
|
01.09.2009
|
1
|
16790
|
15,00
|
15.1
|
Ланос
|
Підшипник маточини
колеса
|
17.06.2009
|
|
|
|
|
|
17.06.2009
|
1
|
12456
|
1,00
|
0.1
|
сенс
|
18.06.2009
|
1
|
3400
|
1,00
|
1.1
|
сенс
|
01.08.2009
|
1
|
9900
|
1,00
|
13.2
|
сенс
|
04.08.2009
|
1
|
34520
|
3,00
|
3.1
|
сенс
|
06.08.2009
|
1
|
41300
|
2,00
|
2.1
|
сенс
|
06.08.2009
|
2
|
9500
|
0,50
|
0.1
|
сенс
|
25.08.2009
|
1
|
11540
|
19,00
|
19.1
|
сенс
|
04.09.2009
|
1
|
24711
|
10,00
|
10.1
|
сенс
|
01.08.2009
|
|
|
|
|
|
02.08.2009
|
1
|
20000
|
1,00
|
1.1
|
ланос
|
06.08.2009
|
1
|
49070
|
4,00
|
4.1
|
ланос
|
06.08.2009
|
2
|
46000
|
0,50
|
0.1
|
ланос
|
08.08.2009
|
1
|
9050
|
2,00
|
2.1
|
ланос
|
|
|
|
|
|
|
|
|
ДОДАТОК Б
Програма в середовищі Маthcad для визначення технічного стану
підвіски автомобіля
Вводимо початкові дані
Вводимо значення середнього пробігу на відмову і
періодичності проведення діагностування
Проводимо розрахунок
Рис. Б.1 Залежність зміни коливань підвіски від пробігу АТЗ
Рис. Б.2. Визначення ймовірність того, що передвідмовний стан
не настав, за умови відсутності відмови протягом пробігу
Розрахунок за методикою мінімального ризику, вводимо виміряне
значення
Максимальна кількість пропусків проведення діагностувань:
Типові системи технічного
обслуговування - 2
При обґрунтуванні режимів ТО автомобілів застосовують такі
методи визначення періодичності ТО автомобілів:
1. Метод визначення періодичності ТО за допустимим рівнем
безвідмовності
2. Метод визначення періодичності за допустимим
значенням і закономірністю зміни параметра технічного стану
. Техніко-економічний метод
. Економіко-імовірнісний метод
. Метод статистичних випробовувань
. За параметрами технічного стану
. За найбільшою продуктивністю
. За зовнішнім виглядом автомобіля, створенням безпеки
руху
. Метод коректування періодичності залежно від напрацювання
10. Метод визначення періодичності профілактичного
обслуговування після безвідмовної роботи
км пробігу
11. Профілактичне обслуговування здійснюється після
загального напрацювання
пробігу, незалежно від проміжних відмов
. Поглиблене профілактичне обслуговування з введенням
операцій поточного ремонту після k-ої відмови
. Метод визначення оптимальної періодичності ТО за
витратою палива
Структурні параметри систем та
агрегатів АТЗ
У загальному
прийнято, що для повної перевірки підвіски автомобіля необхідно перевірити:
1. сходження передніх і задніх коліс;
2. Розвал передніх і задніх коліс;
. Кути поздовжнього нахилу осі повороту передніх
коліс;
. Різниця між кутами поздовжнього нахилу осі повороту
передніх коліс;
. Відстань від опорної поверхні до задньої частини
важеля;
. Відстань від опорної поверхні до передньої частини
важеля;
. Стан втулок стабілізатора передніх коліс;
. Стан втулок важеля підвіски передніх коліс;
. Стан кульових шарнірів передніх коліс;
. Стан підшипників маточин передніх і задніх коліс;
. Стан амортизаторів передніх і задніх коліс;
. Стан верхніх і нижніх опор стояків передніх і задніх
коліс;
. Стан пружин підвіски передніх і задніх коліс.
З урахуванням висунутої гіпотези, з всієї вибірки
діагностичних параметрів, виділяємо найосновніші:
·
сходження
передніх коліс;
·
розвал
передніх коліс;
·
стан
амортизаторів передніх і задніх коліс;
·
стан
підшипників маточин передніх і задніх коліс.
Оцінка надійності конструкцій підвісок та визначення
періодичності їх ТО
а)
б)
Рис. Гістограми розподілу пробігів автомобілів “Сенс” (а) і
“Ланос” (б) на відмови через втрату працездатності їх підвісок
ДОДАТОК В
ДОПОВІДЬ
Шановний пане голово! Шановні члени комісії!
Дійсним інструментом введення режиму економії є зниження
затрат на технічне обслуговування і ремонт автомобілів за рахунок широкого
використання засобів діагностування, тобто визначення технічного стану
автомобілів і їх агрегатів без розбирання з метою прогнозування можливостей їх
подальшої безвідмовної роботи чи застосування ощадних технологій технічного
обслуговування і ремонту. Необхідність діагностування зумовлена і тим, що під
час експлуатації автомобіля несправності більшою частиною визначаються лише тоді,
коли дія їх є значною.
Тому актуальним є розроблення теми магістерської
кваліфікаційної роботи: (читай з аркуша 1). ”Оптимізація системи технічного
обслуговування і ремонту автомобільних транспортних засобів за результатами
діагностування їх технічного стану”
У роботі сформульована мета - обґрунтування періодичності
виконання технічного обслуговування і ремонту АТЗ та підвищення рівня технічної
експлуатації автомобілів (на прикладі підвіски легкового автомобіля).
На сьогоднішній день при обґрунтуванні режимів ТО автомобілів
застосовують наступні методи визначення періодичності ( читай з аркуша 2).
Діагностування автомобіля в цілому і за його елементами
повинно проводитися у визначеному порядку, що використовує послідовні, умовні
перевірки. З цією метою весь автомобіль можна розділити на рівні у вигляді
блок-схеми діагностування (читай з аркуша 3). Перший рівень містить у собі
загальне діагностування автомобіля з метою визначення його основних вихідних
показників продуктивності й економічної ефективності. На другому рівні
діагностуються частини автомобіля, такі, як двигун, трансмісія, ходова частина
тощо. У третій рівень входить діагностування агрегатів, механізмів, систем.
Четвертий рівень містить у собі діагностування рухливих з’єднань. На п'ятому
рівні розглядаються окремі деталі.
Використання запропонованої класифікації дозволяє більш
строго підійти до розгляду всіх наступних матеріалів, почавши з загального
діагностування автомобіля і закінчивши цей процес з’єднаннями і за необхідності
деталями, зокрема, для підвіски автомобіля.
В загальному прийнято, що для повної перевірки підвіски
автомобіля необхідно провести наступні операції (читай з аркуша 4):
Отже, з урахуванням висунутої гіпотези, з всієї вибірки
діагностичних параметрів, було виділено найосновніші:
·
сходження
передніх коліс;
·
розвал
передніх коліс;
·
стан
амортизаторів передніх і задніх коліс;
·
стан
підшипників маточин передніх і задніх коліс.
Кожен з цих параметрів характеризує декілька параметрів
технічного стану і впливає на показники роботи підвіски автомобіля.
На нашу думку, саме за допомогою цих чотирьох діагностичних
параметрів можна оцінювати стан підвіски автомобіля - справний чи несправний.
Ці чотири діагностичних параметри охоплюють всю номенклатуру структурних параметрів.
Таким чином, контролюється загальний стан підвіски автомобіля.
Згідно мети роботи було проведено аналіз критеріїв визначення
періодичності профілактичних робіт і проаналізовано методи визначення
періодичності технічного обслуговування автомобілів, а також використаних при
цьому характеристик експлуатаційної надійності автомобілів.
Для визначення показників експлуатаційної надійності
елементів підвісок легкових автомобілів у магістерській кваліфікаційній роботі
було опрацьовано дані проведених досліджень, які базувалися на автомобілях
“Таврія”, “Славута”, “Ланос”, “Сенс” і “Шевроле”.
При проведенні досліджень інформація про експлуатаційну
надійність елементів їх підвісок збиралась впродовж половини 2009 року за
результатами діагностування технічного стану їх на лінії інструментального
контролю Bosch SDL-260 на станції технічного обслуговування відкритого
акціонерного товариства “Галичина-Авто”.
Для визначення пробігів до ТО підвісок, в програмі Маthcad
розроблено програму для визначення періодичності діагностування передньої
підвіски автомобіля Наведено фрагмент. За основу було взято коливання підвіски
автомобіля після його гальмування при перевірці на діагностичному комплексі Bosch SDL-260.
На основі проведених досліджень до уваги бралися лише ті
конструктивні елементи підвісок, які найчастіше відмовляли: амортизатор задній,
верхня опора переднього стояка, кульовий шарнір передньої підвіски, підшипники
маточин коліс.
З використанням середовища Statistica 6.0 на основі отриманих масивів
даних відмов елементів підвісок було розраховано числові характеристики
розподілів та побудовано гістограми розподілу пробігів автомобілів “Сенс” і
“Ланос” на відмови через втрату працездатності їх підвісок із узгодження їх з
законами розподілів ( показуй на аркуші 5).
В результаті отримано значення математичного сподівання
пробігу на відмови - 23,6 тис. км і коефіцієнта варіації - 55,6 %.
На основі аналізу статистичних даних по відмовах розробляють
структурні схеми за ланцюгом: об’єкт, що діагностується (автомобіль) - агрегат
- система, механізм - вузол - елемент - структурний параметр.
Число ланок у ланцюзі в кожному конкретному випадку (в
залежності від системи і агрегату) може мінятися. Кожна ланка визначає рівень
пошуку чи технологічного кроку, спрямованого на встановлення несправності.
Розроблено схему семи рівнів алгоритму діагностування АТЗ при пошуку
несправності (читай з аркуша 6).
Важливим у скороченні тривалості, трудомісткості та вартості
діагностування буде вибір обмеженої кількості параметрів діагностування, зняття
фактичних показників яких і порівняння з нормативними, повинні дати однозначну
відповідь щодо регулювань (заміни, ремонту) систем в цілому.
Було висунуто гіпотезу, що існує один або декілька параметрів
технічного стану (структури) у системах, які функціонально і однозначно
впливають на якість перебігу робочих процесів підвісці АТЗ. Вони дадуть змогу
оперативно прийняти рішення щодо подальших ремонто-обслуговувальних та
діагностувальних дій.
загальний вигляд схеми алгоритму діагностування АТЗ при
пошуку несправності, згідно з висуненою гіпотезою наведено на аркуші 7 (читай з
аркуша 7).
Конструкція підвіски вимагає використання не тільки
компонентів і фазових змінних механічної поступальної (пружина, важіль) та
обертової підсистем (підшипник маточини), а і гідравлічної підсистеми
(амортизатор).
Було запропоновано замінити механічно-гідравлічну підсистему
підвіски на еквівалентну електричну для подальшого застосування матричного
підходу. Для цього схему передньої підвіски легкового автомобіля “Ланос”
замінено еквівалентною їй електричною схемою передньої підвіски у вигляді
опорів із джерелом живлення.
Процедура пошуку дефектів включає 2 етапи (читай з аркуша 8).
Підготовчий етап - задаємо кратністю дефекту, вибираємо пари
контрольних виводів. Вираховуємо номінальні значення напруги на вибраних парах
контрольних виводів. Здійснюється перехід до спряженої схеми. Рахуючи, що
одиничне джерело струму почергово під’єднується до пар контрольних виводів,
вираховуються значення напруг на всіх елементах кола. Із отриманих значень напруг складаємо
матриці. Число таких матриць дорівнює числу комбінацій можливих дефектів з
заданою кратністю. Для всіх матриць Z визначається вираз (читай з аркуша 8) і
всі можливі дефекти розбиваються на класи еквівалентних дефектів.
Метрологічний етап - в схемах проводяться виміри напруги на
вибраних контрольних парах виводів, вираховується матриця ∆V. Якщо
виконується рівність ∆V = 0, то рахується, що дефект в колі відсутній.
Розглянемо модель передвідмовного технічного стану агрегату
або системи автомобіля, в основу якої покладені закономірності зміни
діагностичних параметрів з пробігом та оптимальна періодичність діагностування.
Вибір стратегії керування працездатним станом автомобіля
ґрунтується на визначенні оптимальної періодичності контрольно-діагностичних
перевірок. Даний підхід дає можливість встановити таку періодичність
діагностування, яка, з одного боку, зменшує затрати на ТО та ПР, з другого -
дає змогу підтримувати працездатність автомобіля на оптимальному рівні.
Критерієм оптимізації такого керування є мінімум функції сумарних ризиків -
ризик аварійної відмови деталей агрегату на період прогнозуванняі ризик
передчасного діагностування агрегату (читай з аркуша 9).
Методика дозволяє розрахувати кількість
контрольно-діагностичних перевірок, які можна не проводити з моменту останнього
діагностування. Отже, встановлено період експлуатації, протягом якого агрегат
перебуватиме в працездатному стані (залишковий ресурс). Це дає можливість
змінювати періодичність виконання контрольно-діагностичних операцій вилученням
проміжних перевірок з наперед запланованої їх кількості.
На підставі розробленої методики визначено кількість
пропусків виконання діагностувань з визначеною періодичністю залежно від
значень кількості затухаючих коливань підвіски для одного коефіцієнта варіації
(читай з аркуша 10)
Висновки
З метою встановлення істотних структурних параметрів
діагностування підвіски легкових автомобілів проведено аналіз конструкції
підвіски автомобіля Daewoo
«Ланос», усіх можливих параметрів технічного стану, а також параметрів
діагностування; обґрунтовано параметри технічного діагностування підвіски
автомобіля, скоротивши їх кількість з 13-ти до 4-ох.
На підставі аналізу літературних джерел, за основу
математичного відтворення особливостей функціонування механізму підвіски взято
матричний підхід і виконано відповідні розрахунки за допомогою них (приклад
таких розрахунків показаний для випадку перевірки справності передньої підвіски
автомобіля).
На основі підходу планування оптимальної періодичності
діагностування АТЗ за мінімального ризику, встановлена періодичність
діагностування підвіски для автомобілів Daewoo «Ланос», яка, з одного боку, зменшує
затрати на ТО та ПР, з іншого дає змогу підтримувати працездатність АТЗ на
оптимальному рівні.
Визначено міжконтрольні пробіги АТЗ для автомобілів Daewoo «Ланос» за кількістю
затухаючих коливань підвіски, коли сума втрат від усунення несправності і
затрат на виконання діагностування на діагностичному комплексі Bosch SDL-260 будуть мінімальними.
Встановлені кількість пропусків проведення діагностувань із визначеною
періодичністю на середньому пробігу, коли кількість коливань не перевищує
встановлених меж.