Система загрузки доменной печи шихтовыми материалами – агломератом в смеси с коксом
Содержание
доменный печь кокс железорудный
Введение
.
Аналитическая часть
.1
Опытные плавки при загрузке доменных печей смесью кокса и агломерата
.2
Распространение опыта загрузки доменной печи смесью агломерата и кокса на
других заводах
.3
Совершенствование системы загрузки железорудных материалов в смеси с коксом
.4
Влияние смешивания рудного сырья с коксом на газодинамические условия и
технико-экономические показатели доменной плавки
Выводы
.
Основная часть
.1
Исследование работы доменной печи при совместной загрузке железорудных
материалов и кокса в скип
Вводы
Общие
выводы
Библиографический
список
Введение
Одним из наиболее эффективных путей снижения
расхода топлива в доменной плавке является совершенствование загрузки
материалов и распределения их на колошнике для формирования рациональной
структуры столба шихтовых материалов и улучшения использования тепловой и
восстановительной энергии газа.
Кокс и рудное сырье, используемые в доменной
плавке, в современных условиях значительно различаются по крупности, ввиду чего
газопроницаемость шихты в печи существенно зависит от того, в какой мере эти
материалы перемешиваются при загрузке на колошник. От степени их смешивания в
процессе загрузки зависит не только характер взаимного расположения кусков
разной крупности, но и равномерность их распределения по сечению печи, что
влияет на использование газа и на технико-экономические показатели плавки.
В данной дипломной работе проанализирована
работа доменной печи, в зависимости от исходных условий работы печи и способа
загрузки компонентов шихты в скип. Рассмотрены различные методы загрузки
железорудных материалов и кокса в скип.
1. Аналитическая часть
.1 Опытные плавки при загрузке доменных печей
смесью кокса и агломерата
Во многих случаях загрузка рудных материалов и
кокса в доменную печь производится в основном отдельными скипами. Материалы по
сечению печи распределяются неравномерно по количеству и крупности. С
увеличением поперечных размеров печи неравномерность возрастает, что вызывает
чрезмерное "раскрытие" периферии и центра.
Одним из способов получения равномерного
распределения рудной нагрузки по сечению печи, способствующего улучшению
использования газа, является перемешивание рудных материалов и кокса и
последующая совместная загрузка их в смеси.
На моделях и действующих доменных печах
исследовали особенности распределения материалов по сечению и технологии
доменной плавки при загрузке рудных материалов в смеси с коксом [1].
Лабораторные опыты проводили на цилиндре высотой 1200 мм и диаметром 225 мм, моделях
доменной печи объемом 1386 м3 (масштаб 1:20) и засыпного устройства
той же печи в масштабе 1:10. В опытах использовали производственный агломерат с
содержанием до 30% мелочи фракции 0-5 мм, а также агломерат фракций 1-5, 1-10 и
6-10 мм и кокс фракций 20-40, 15-25 и 8-12 мм.
Материалы в цилиндр загружали послойно (при
толщине слоев 0,5 м) и в смеси с помощью засыпного устройства типа
воронка-конус при рудной нагрузке 3,5 кг/кг кокса. Продувку материалов
осуществляли в неподвижном состоянии (после засыпки) и в движении. Состояние
максимально разрыхленного (движущегося) столба материалов в цилиндре создавали
путем закрытия его сверху и вращения на 360° с постоянной скоростью в стойках
вокруг горизонтальной оси, а в модели печи - путем непрерывной разгрузки
материалов с поддержанием постоянного уровня засыпи через промежуточную
емкость.
Исследовали газодинамические характеристики
отдельно кокса фракций 15-25 мм и агломерата 6-10 мм, а также при их загрузке
послойно и в смеси, причем в каждой серии опытов к агломерату добавляли 5%
мелочи 0-5 мм с доведением ее в базовой фракции (6-10 мм) до 40%. Кроме того,
исследовали влияние уменьшения толщины и увеличения числа слоев.
Исследования показали, что газопроницаемость
слоя зависит не столько от порозности в тех пределах, в которых она изменялась,
сколько от размера и характера каналов, образованных межкусковыми промежутками,
по которым движется газ. Это подтверждается данными, полученными при продувке
кокса и агломерата. Средний размер кусков агломерата был в 2,5 раза меньше
среднего размера кокса, хотя их порозности были равны и составляли 0,585 м3/м3.
Потеря напора в слое агломерата была в 5 раз больше, чем в слое кокса (рис. 1,
кривые 1 и 2). Из рис. 1 видно, что как в неподвижном, так и в максимально
разрыхленном (движущемся) слое эта закономерность сохраняется. При переходе из
неподвижного состояния в разрыхленное потери напора в слое кокса и агломерата
уменьшаются в два раза (рис. 1 кривые 1 и 2).
Установлено, что в неподвижном состоянии
послойная загрузка материалов (при отсеве фракции 0-5 мм) снижает их
гидравлическое сопротивление по сравнению с загрузкой в смеси. При разрыхлении
столба материалов гидравлическое сопротивление в смеси несколько ниже, чем при
послойном расположении. Объясняется это тем, что отношение крупности
смешиваемых кусков кокса и агломерата не превышает 2,5. Значительное снижение
потери напора наблюдается при смешивании крупных материалов с более мелкими
(рис. 2, а, б). Характерной особенностью является то, что во всех случаях при
добавлении мелочи 0-5 мм к базовой фракции агломерата послойная загрузка его с
коксом при отсутствии движения материалов позволяет снизить гидравлическое
сопротивление по сравнению со смесью материалов (рис. 2, а). Для движущегося
слоя смесь материалов при любом содержании мелочи в агломерате создает меньшее
гидравлическое сопротивление, чем материалов, загруженных послойно (рис. 2, б).
Рис. 1. Изменение гидравлического сопротивления
материалов в зависимости от количества дутья, способов формирования и состояния
слоя: 1 - агломерат фракции 6-10 мм; 2 - кокс фракции 15-25 мм; 3 - послойная
загрузка; 4 - смесь кокса и агломерата; ------ неподвижный слой; - - - -
движущийся слой
Исследования показали, что в движении степень
разрыхленности смеси на 5-10% больше, чем послойно загруженных материалов,
следовательно, и гидравлическое сопротивление в смеси меньше. Происходит это
потому, что при переходе смеси в движение часть кусочков агломерата
расклинивает куски кокса, что приводит к дополнительному разрыхлению.
Другая часть агломерата (особенно мелочь)
располагается с теневой стороны в неровностях кусков кокса, а также
укладывается в локальных пустотах между крупными кусками кокса, слабо
участвующих в создании сопротивления приходу газов.
Рис. 2. Влияние качества агломерата на
газопроницаемость столба шихты после засыпки (а) и в движении (б): ------
послойная загрузка; - - - - загрузка смеси; цифры у кривых - содержание фракции
0-5 мм в агломерате, %
Для движущегося столба материалов увеличение
числа слоев в результате уменьшения их толщины способствует уменьшению потерь
напора и в пределе смесь агломерата с коксом имеет максимальную
газопроницаемость (рис. 3). При загрузке материалов в смеси они укладываются
плотнее. Смесь занимает объем на 10-15% меньше, чем при послойной загрузке.
Увеличение числа слоев неподвижного материала вызывает рост статического
давления при данном гранулометрическом составе и фракционном соотношении
исследуемых материалов. Однако при определенном соотношении фракций увеличение
числа слоев в неподвижном столбе шихты может улучшить газопроницаемость.
Исследование влияния различных систем загрузок
на распределение материалов по сечению колошника проводили на модели засыпного
устройства. В опытах применяли агломерат фракций 0-12 и 1-5 мм и кокс фракций
15-25 и 8-12 мм. Материалы загружали обычными системами загрузки типа ААККх,
КААКх и опытными - типа (ААА/ККК)х, КККК/АААА. Последние две системы
предусматривают загрузку в один скип 1/4 подачи последовательно: сначала кокс,
затем агломерат (А/К - агломерат вперед) или наоборот (К/А - кокс вперед). При
этом обеспечивалось только частичное смешивание материалов при перегрузке их на
колошник. И, наконец, на колошник загружали предварительно смешанные кокс с
агломератом (смесь).
Рис. 3. Зависимость гидравлического
сопротивления столба шихты от числа слоев материалов (цифры у кривых - число
слоев; см - смесь кокса с агломератом): ------ неподвижный слой; - - - -
движущийся слой
Для оценки распределения материалов по сечению
колошник на 1/2 площади оборудовали наклонным днищем (α=17°),
покрытым
сверху крупнозернистой наждачной бумагой, моделируя поверхность засыпи
материалов в доменной печи. После ссыпания двух-трех подач шихту на колошнике
разделяли листовыми ножами через 1/3 радиуса на три концентрические
полуокружности. Материалы из каждой зоны извлекали, отсортировывали кокс от
агломерата и взвешивали.
Результаты исследования показали, что система
загрузки ААККх способствует наибольшей неравномерности распределения рудной
нагрузки по сечению колошника (рис. 4, кривая 1).
Рис. 4. Распределение рудных нагрузок по сечению
колошника при различных системах загрузки: 1 - ААКК; 2 - КААК; 3 - КККК/АААА; 4
- АААА/КККК
При этом большая часть агломерата
сосредоточивается в периферийной зоне III: рудная нагрузка у оси (зона I) почти
в 6 раз меньше, чем на периферии. Система КААКх раскрывает периферию,
сосредоточивая основную массу агломерата в промежуточной зоне II (рис. 4,
кривая 2). Система (КККК/АААА)х способствует относительно равномерному
распределению материалов, большему раскрытию периферии, значительному снижению
рудной нагрузки в промежуточной зоне II и частичной подгрузке осевой зоны I
(рис. 4, кривая 3). Система (АААА/КККК)х незначительно снижает рудную нагрузку
в промежуточной зоне II, повышая ее в периферийной и осевой зонах (рис. 1.4,
кривая 4). Загрузка смесью агломерата с коксом способствует наиболее равномерному
распределению рудной нагрузки по сечению колошника (рис. 4, кривая 5).
В качестве критерия радиального распределения
материалов использовали значение коэффициента неравномерности Кн,
представляющего собой отношение разности максимальной и минимальной рудных
нагрузок в отдельных зонах к среднему их значению по сечению колошника.
Наибольшая неравномерность распределения
материалов (рис. 5) наблюдается при послойной их загрузке по системе ААККх
(Кн=1,56).
С увеличением степени перемешивания агломерата с
коксом равномерность распределения возрастает, достигая наибольшего значения
при загрузке смеси (Кн=0,56). В последнем случае при ссыпании с большого конуса
относительно мелкий агломерат увлекается кусками кокса по направлению к оси
колошника, обеспечивая более равномерное распределение рудной нагрузки по
сечению.
Рис. 5. Влияние систем загрузок на степень
радиальной неравномерности распределения материалов на колошнике
Первые опытные плавки с применением новой системы
загрузки были проведены в 1971 г. на доменных печах завода им. Дзержинского. На
печи полезным объемом 600 м3 загрузку материалов осуществляли с помощью ручного
управления скипами, в каждый из которых загружали агломерат, а затем кокс
порциями (1/4 их веса в подаче); подача состояла из четырех скипов. Через 7-8 ч
после опытной загрузки общий перепад давления в печи понизился с 1,0 до 0,7
ати, интенсивность плавки повысилась, производительность печи на вторые сутки
возросла на 7%. С ростом интенсивности плавки вагон-весы не успевали загружать
печь и через 2,5 суток опыты были прекращены.
Продолжены они были на доменных печах А и Б
полезным объемом 1386 м3. С целью сокращения загруженности
вагон-весов в опытные периоды массу подачи увеличивали на 16-26%. Загрузку
каждого скипа коксом и управление работой скиповой лебедки осуществляли
вручную. В доопытный период применялась система загрузки 3ААКК 2КААКх, в
опытный (КККК/АААА)х.
Во всех случаях при переходе на загрузку
материалов в смеси наблюдалось повышение нагрева горна, увеличение содержания
кремния в чугуне, что способствовало увеличению рудной нагрузки. На печи А она
возрастала с 3,33 до 3,5 т/т, на печи Б - с 3,19 до 3,60 т/т. При горячем ходе
печи отмечалось некоторое увеличение давления горячего дутья и общего перепада.
Распределение газа по радиусу печи было более равномерным (рис. 6, кривая 2),
использование его улучшилось, в результате содержания СО2 в колошниковом газе
повысилось на 1,2-2,0%.
При выплавке бессемеровского чугуна на печи Б в
опытный период (6 суток) содержание кремния в чугуне возрастало с 1,0 до 1,43%.
Применение новой системы загрузки позволило на четвертые сутки уменьшить расход
кокса на 800 кг/подачу (с 6,9 до 6,1 т) и увеличить рудную нагрузку на 12%. В
этот период отмечалось некоторое раскрытие периферии и подгрузка центральной
зоны печи, температура периферийных газов повысилась на 50-100°С, ход печи стал
более форсированным. В результате суточная производительность возросла на
1,5-2%, расход кокса снизился на 3-5%. Технико-экономические показатели работы
доменных печей А и Б в базовый (в числителе) и опытный (в знаменателе) периоды
приведены ниже (табл. 1.1).
Рис. 6. изменение содержания СО2 в газе по
радиусу колошника доменной печи Б в базовый (1) и опытный (2) периоды
Таблица 1.1.
Показатель
|
Условное
обозначение печи
|
|
А
|
Б
|
Производительность
т/сут
|
|
|
Продолжительность
опытов, сут
|
|
|
Интенсивность
горения кокса, т/м3·сутки
|
|
|
Расход,
кг/т чугуна: кокса металодобавок
|
|
|
Рудная
нагрузка, т/т кокса
|
|
|
Число
подач в сутки (в пересчете на 19 т рудной засыпи в подаче)
|
|
|
Величина
подачи, т: агломерата кокса
|
|
|
Дутье:
расход, м3/мин давление, атм
|
|
|
Общий
перепад давления, ати
|
|
|
Температура,
°С
|
|
|
Расход
природного газа, м3/ч
|
|
|
Расход
кислорода, м3/ч
|
-
|
|
Температура,
°С: колошникового газа переферийного газа
|
|
|
Содержание
в чугуне, %: Si S
|
|
|
Система
загрузки
|
|
|
Основным недостатком в проведении опытных плавок
при загрузке печей смесью рудных материалов с коксом является чрезмерная
загруженность работы вагон-весов. Этот недостаток можно устранить путем
переоборудования рудных течек (рис. 7). Каждая течка 1 выполняется размером не
менее объема скипа и должна иметь вертикальную перегородку 2, разделяющую ее на
две равные части.
Рис. 7. Схема рудного желоба: 1 - желоб; 2 -
перегородка; 3 - механихированые затворы
Обе части рудной течки снизу закрываются
механизированными затворами 3. Такая конструкция рудной течки с отдельными
затворами позволит разгружать вагон-весы, не дожидаясь подхода скипов, а
перегородка обеспечит механическое разделение рудных материалов каждого кармана
вагон-весов на две примерно равные порции. При этом выгрузка рудных материалов
и кокса в каждый скип осуществляется одновременно или поочередно порциями,
обеспечивая получение смеси. При необходимости переход на обычную систему
загрузки осуществляется путем изменения программы работы затворов.
.2 Распространение опыта загрузки доменной печи
смесью агломерата и кокса на других заводах
В Днепродзержинском индустриальном институте
разработана и на доменных печах металлургических заводов (им. Дзержинского и
Криворожского) применена новая система загрузки доменной печи железорудными
материалами в смеси с коксом Смесь агломерата с коксом получали путем
одновременной их загрузки в скип [2].
При загрузке смеси агломерата и кокса плотность
шихты возрастает. Объем смеси на 8-12% меньше, чем при загрузке двумя слоями.
Несмотря на более плотную укладку материалов в смеси при одинаковой высоте
столба, газопроницаемость смешанной шихты лучше, чем при послойной загрузке. Объясняется
это тем, что мелкие фракции агломерата, попадая в локальные пустоты между
крупными кусками кокса, в незначительной степени участвуют в создании
сопротивления проходу газа. С уменьшением содержания мелкой фракции агломерата
разница в сопротивлении смешанной и послойной шихты сокращается.
Опытные плавки на заводе им. Дзержинского
проводили на доменных печах полезным объемом 1386 м3. В течение
всего периода исследований работа печи сопровождалась увеличением нагрева
горна, в результате чего рудная нагрузка повысилась на 5-10%. Центральная часть
печи подгружалась, готовый поток перераспределялся, его использование по
радиусу становилось более равномерным. Благодаря лучшему использованию газового
потока содержание СО2 в колошниковом газе возросло на 1,2-2,0% (рис. 8).
При выплавке бессемеровского чугуна применение
новой системы загрузки позволило на четвертые сутки уменьшить расход кокса на
800 кг/подачу и увеличить рудную нагрузку. В этот период температура
периферийных газов повысилась на 50-100°С, ход печи стал более форсированным, в
результате чего суточная производительность возросла на 1,5-2%, расход кокса
снизился на 3-5%.
Рис.8. Изменение содержания СО2 в газе по
радиусу колошника доменных печей А (а) и Б (б) в базовый (1) и опытный (2)
периоды
Технико-экономические показатели работы печей
завода им. Дзержинского в базовый (в числителе) и опытный (в знаменателе)
периоды приведены в табл.1.2.
Таблица 1.2.
Показатели работы доменной печи № А полезным
объемом 2000 м3 Криворожского металлургического завода
Показатели
|
Периоды
|
|
доопытный
|
опытный
|
послеопытный
|
Производительность
|
3,696
|
3936
|
3820
|
К.
и. п. о, м2/т чугуна
|
0,541
|
0,508
|
0,524
|
Интенсивность,
т/м3· сут: горения кокса проплавления железорудной части шихты
|
0,926
3,37
|
0,89
3,50
|
0,939
3,35
|
Расход:
кокса, кг/т чугуна природного газа, м3/т чугуна кислорода, м3/т чугуна
|
495
117 102
|
451
115 94,0
|
492
108 88,0
|
Рудня
нагрузка, т/т кокса
|
3,63
|
3,94
|
3,48
|
Дутье:
расход, м3/мин температура, °С давление, ати
|
3475
1079 2,96
|
3350
1071 2,90
|
3515
1068 2,87
|
Колошниковый
газ: давление, ати температура, °С содержание, %: СО2 Н2
|
1,65
340 16,8 7,6
|
1,65
340 18,0 7,3
|
1,65
337 16,3 7,6
|
Содержание
в чугуне, % Si Mn S
|
0,71
0,7 0,041
|
0,74
0,71 0,04
|
0,73
0,7 0,042
|
Выход
шлака, кг/т чугуна
|
435
|
426
|
385
|
Основность
шлака СаО:SiО2
|
1,25
|
1,26
|
1,27
|
Следующий этап исследований был продолжен на доменной
печи №А объемом 2000 м3 Криворожского металлургического завода, где
применяется транспортерная подача материалов к скипам.
Всего на доменной печи №А в течение периода
исследований было проведено пять опытных плавок продолжительностью от 1 до 4
сут. Во всех случаях через 6-8 ч после перехода на загрузку смеси агломерата и
кокса, так же как на заводе им. Дзержинского, наблюдался повышенный разогрев
горна, повышалось содержание кремния в чугуне и несколько возрастал нижний
перепад давления. При исходной коксовой колоше 7,7 т расход кокса в подаче при
новой системе загрузки в отдельные сутки снижался на 600 кг, т.е. на 8%.
Газ по сечению печи распределялся более
равномерно, содержание углекислоты в колошниковом газе возросло с 16,5 до 18,7%
(в среднем на 1,6%) (рис. 9).
Рис. 9. Изменение содержания СО2 по радиусу
печи: 1 - при системе загрузки 3ААКК 2КААК; 2 - после 10 подач при системе
загрузки КККК/АААА; 3 - после 80 подач при системе загрузки КККК/АААА; 4 -
после 78 подач при системе загрузки АААА/КККК
Полученные опытные данные о влиянии способа
загрузки материалов в смеси на параметры процесса доменной плавки позволили в
сентябре 1972 г. перед остановкой печи на капитальный ремонт провести более
длительный опытный период.
В период исследований печь работала на
агломерате НКГОКа (75%) и окатышах КЦГОКа (25%).
Данные о химическом составе шихтовых материалов
приведены ниже:
Содержание,
%:
|
Агломерат
|
Окатыши
|
Fe
|
54,5
|
60,0
|
FeO
|
12,6
|
-
|
SiO2
|
9,0
|
8,0
|
Mn
|
0,7
|
-
|
CaO
|
10,9
|
4,1
|
MgO
|
-
|
1,37
|
фракции
5-0 мм
|
22,1
|
7,0
|
Основность
CaO:SiO2
|
1,2
|
0,51
|
Кокс поступал с Криворожского коксохимического
завода следующего состава, %:
Влага
|
2,2-3,1
|
Летучие
|
0,9
|
Зола
|
9,3-9,5
|
М40
|
78,5-79,6
|
Сера
|
1,67-1,75
|
М10
|
6,1-6,7
|
В печи выплавляли передельный чугун с
содержанием кремния 0,7-0,8%.
В опытный период при переходе на систему
загрузки доменной печи смесью шихтовых материалов вскоре после первых подач по
системе А/К А/К А/К А/К подача кокса была уменьшена на 200 кг, через некоторый
период (на 18-й и на 53-й подачах) - еще на 200 кг. Рудная нагрузка возросла с
3,7 до 4,0 т/т кокса. Ход печи при этом был ровный, а общий перепад давления
практически не изменился.
На вторые сутки рудная нагрузка возросла до 4,11
т/т кокса, вследствие чего газопроницаемость столба шихты несколько ухудшилась.
Несмотря на некоторое снижение интенсивности горения кокса (на 4,5%),
производительность печи не только не уменьшилась, а, наоборот возросла, что
объясняется увеличением (на 10%) рудных нагрузок. Интенсивность плавки по руде
при этом повысилась на 4%.
Второй период исследований на доменной печи № А
длился 9 сут; при этом расход кокса снизился с 495-492 до 451 кг/т чугуна, т.
е. на 43 кг/т чугуна (или на 8,7%), производительность возросла с 3696-3820 до
3904 т/сут, т. е. на 146 т/сут (или на 3,9%). Технико-экономические показатели
работы печи в этот период исследования представлены в таблице 1.2.
Содержание СО2 в газе, отобранном по радиусу
колошника, в опытный период возросло с 16,5 до 18,0%. На каждый процент
увеличения углекислоты расход кокса снизился примерно на 30 кг/т чугуна.
Степень использования окиси углерода при этом возросла с 39,4 до 42,3%.
.3 Совершенствование системы загрузки
железорудных материалов в смеси с коксом
Дальнейшее повышение эффективности доменного
производства тесно связано с улучшением использования энергии газов в процессе
плавки. На использование газа существенно влияют качество шихтовых материалов и
загрузка их в печь.
Многочисленные исследования показывают, что при
существующем качестве шихтовых материалов резервы совершенствования загрузки
далеко не исчерпаны. Имеется еще значительный резерв улучшения использования
газа на периферии и в центре. В целом состав газа в печи еще далек от
равновесного.
По данным исследований [2], в условиях комбината
им. Ф.Э. Дзержинского увеличение содержания углекислоты в колошниковом газе на
1% приводит к снижению расхода кокса примерно на 30 кг/т чугуна (улучшению
использования окиси углерода на 3%). Результаты опытных плавок [1, 2, 4]
показывают, что при загрузке железорудных материалов, смешанных с коксом, в
различных условиях плавки достигаются значительное снижение удельного расхода
кокса (на 2-8%) и повышение производительности доменных печей (на 1-4%).
В настоящее время еще распространено убеждение,
что столб шихты из смешанных материалов различной крупности имеет худшую
газопроницаемость, чем расположенных послойно. И только в некоторых работах
[5-7] указывается, что такая шихта может иметь более высокую газопроницаемость.
Различные мнения о газопроницаемости слоя материалов, загруженных в смеси и
послойно, могут быть одинаково справедливы, но только для конкретных условий
при определенных количественных значениях.
Результаты исследований газопроницаемости слоя
материалов, загруженных послойно и в смеси, показали, что при смешивании
материалов существенное уменьшение сопротивления столба шихты наблюдается при
определенных соотношениях мелких и крупных материалов. В частности, при
смешивании производственных агломератов, содержащих 20-30% мелкой фракции (0-5
мм), с коксом потеря напора в слое одинакова. При большем количестве мелочи
газопроницаемость смеси значительно выше, чем при послойном расположении кокса
и агломерата. В этом случае слой мелкого агломерата являлся определяющим в
создании сопротивления проходу газа. При количестве мелочи менее 20%
газопроницаемость смеси была хуже, но незначительно (рис. 10).
Насыпная масса смеси в зависимости от количества
мелкой фракции в агломерате была на 7-25% больше насыпной массы столба шихты с
послойной укладкой. Вследствие этого в одном и том же объеме помещается на
4-13% больше агломерата с незначительно худшей газопроницаемостью, если фракции
0-5 мм меньше 20%, и лучшей, если содержание этой фракции больше 30%.
Рис.10. Зависимость параметров слоя шихты при
раздельной загрузке агломерата и кокса (- - - -) и смесью (-----) от содержания
мелкой фракции в агломерате
Увеличение насыпной массы шихты на 10% (с 1,05
до 1,15 т/м3) эквивалентно улучшению использования объема печи на 5% и
соответственно такому же сокращению удельного расхода кокса. В результате
увеличения активного веса смешанной шихты возникает возможность вести доменную
плавку при более высоких значениях перепада давления. При увеличении насыпной
массы шихты с 1 до 1,15 т/м3 критическая скорость газа в слое, при
которой шихта переходит во взвешенное состояние, возрастает с 7,5 до 8,25 м/с,
а критический перепад давления газа в столбе шихты высотой 1 м увеличивается на
2250 Па [8].
Результаты восьми опытных плавок, проведенных на
комбинатах им. Ф.Э. Дзержинского, "Криворожсталь" и заводе им. Г.И.
Петровского в различные периоды (1971-1982 гг.), показали, что в зависимости от
исходного режима плавки при обычной системе загрузки влияние на газодинамику
процесса при переходе на загрузку материалов в смеси неодинаково.
В случае исходного периферийного или
центрального хода печи переход на загрузку смесью вызывал некоторое увеличение
перепада давления. Количество дутья при этом несколько снижалось до уровня,
обеспечивающего ровный сход шихты. Несмотря на некоторое уменьшение количества
дутья, эффект от загрузки смесью был значительным, производительность возросла,
расход кокса снизился за счет лучшего использования газа и полезного объема
печи.
Некоторый рост перепада давления при загрузке
агломерата с содержанием мелочи около 25% в смеси с коксом объясняется более
равномерным распределением агломерата по сечению и значительным увеличением
рудных нагрузок (на 6-14%). При увеличении рудной нагрузки на 10% интенсивность
горения кокса в среднем понижалась на 5%, интенсивность же плавки по руде
возрастала на 4-5%. В этих условиях производительность увеличивалась на 4,
расход кокса снижался на 8%. Некоторое увеличение перепада давления может
наблюдаться в переходный период перевода с обычной системы загрузки на загрузку
смешанными материалами из-за недостаточного и несвоевременного уменьшения
количества кокса в подаче, в результате чего возникает горячий ход, нарушающий
ровность схода шихты.
Опыт показал, что при переходе на загрузку
смесью расход кокса в подаче после 2 ч работы на новом режиме следует уменьшать
на 2 %, после 4-х - еще на 2, а затем уже корректировать по содержанию кремния
в чугуне.
Увеличение рудной составляющей в объеме печи при
загрузке смесью и более рациональное ее распределение по сечению вызывало
улучшение использования газа, а соответственно и снижение расхода кокса.
Последнее, в свою очередь, приводило к дополнительному повышению рудных
нагрузок. Как правило, содержание СО2 по радиусу печи перераспределялось таким
образом, что общее количество его в газе возрастало. Чаще всего количество СО2
на периферии изменялось незначительно, а к центру печи увеличивалось (рис. 11).
Смешивание материалов, которое обеспечивалось в опытных плавках путем загрузки
в один скип железорудных материалов и кокса, было несовершенным. Если принять
степень смешения агломерата и кокса при равномерном распределении рудной
нагрузки во всем объеме кокса за 1, то в случае опытных плавок она достигала
значения не более 0,5.
Рис. 11. Изменение содержания СО2 по радиусу
печей (1 - Vп = 1386, 2 - 2000 м3) при загрузке по системе 3ААКК 2КААК ( -----)
и смесью (- - - )
Степень смешения была недостаточной, хотя
распределение рудной составляющей по радиусу печи было значительно равномерней,
чем при обычных системах загрузки (рис. 12).
Наблюдения за работой печей при загрузке кокса в
смеси с железорудными материалами по сравнению с работой при обычной системе
загрузки показали, что меняются не только газодинамические условия плавки, но
активизируются массо-теплообменные и физико-химические процессы в слое шихты.
Достигается более равномерный ход процессов в
целом объеме столба шихты и локальных его участках.
Рис. 12. Распределение рудных нагрузок по
сечению колошника
(I - периферия, II - промежуточное сечение, III
- центр) при раздельной загрузке (-----) и смесью (- - - -): 1 - ААКК; 2 -
КААК; 3 - ААКК; 4 - АКЧАК; 5 - КАЧКА; 6 - смесь
Так, в зоне пластического состояния материалов
(1100-1350 °С) слои рудных материалов при обычной загрузке практически плохо
проницаемы и газ в основном проходит через коксовые окна. При загрузке смесью
железорудные материалы в зоне пластического состояния более или менее
равномерно распределены между коксом, через слои которого более равномерно
проходит газ по всему сечению печи (рис. 13). Участки рудных материалов,
находящихся в пластическом состоянии, в этом случае будут лучше обрабатываться
газом, а сопротивление зоны будет меньшим.
Рис. 13. Структура и очертания зон при слоевой
загрузке шихтовых материалов (а) и в смеси (б): 1 - кусковая (сухая) зона
шихты; 2 - пластическая зона; 3 - зона разрыхления; 4 - зона капельного
течения; 5 - зона горения
При отсеве мелочи фракции 0-5 мм
газопроницаемость смеси несколько ниже, чем слоя при раздельной укладке
материалов (см. рис. 1). Тем не менее, загрузка смесью грохоченных материалов в
условиях действующей доменной печи может оказаться еще эффективнее, чем при
наличии в агломерате мелочи, что объясняется резким улучшением газодинамических
условий в определяющей зоне - зоне пластического состояния железорудных
материалов. Отрицательное влияние нижней зоны на ход печи при загрузке
грохоченных рудных материалов в смеси с коксом ослабляется.
Смешивание железорудных материалов с коксом в
существующих потоках шихтоподачи достигается совместной загрузкой их в один
скип или соответствующей укладкой на транспортерной ленте, в промежуточном
бункере с последующей разгрузкой их на колошник.
При загрузке в скип кокс и агломерат подаются
одновременно или поочередно: на дно скипа агломерат, сверху - кокс и наоборот.
Степень смешения в этих случаях различна. Изменение порядка загрузки
используется для регулирования распределения материалов и газа в печи.
Для обеспечения соответствующей скорости
загрузки агломерата и кокса в один скип рудные течки переоборудуются в бункер,
объем которого равен объему скипа. Бункер делится перегородкой на две равные
части, перекрытые снизу затворами с механизмами, работающими в автоматическом
режиме по заданной программе. Новая система загрузки была внедрена и
применяется с 1979 г. на доменной печи № 2 завода им. Г.И. Петровского.
Среднегодовой расход кокса на этой печи снизился на 2%, настолько же возросла
производительность. В отдельные месяцы расход кокса снижался до 5%, а
производительность возрастала на 3,5%.
Кратковременные опытные плавки (до 6 сут.),
которые проводились на доменных печах №11 и 12 комбината им. Ф.Э. Дзержинского,
показали возможность загрузки шихты в смеси при работе на горячем агломерате.
При подаче в один скип горячего агломерата и кокса последний не возгорался,
дымообразование не наблюдалось. Производительность печей возрастала на 2,
расход кокса снижался на 4%. В настоящее время одна из печей комбината
оборудована устройством с гидравлическим приводом для загрузки в один скип
агломерата и кокса по трем программам.
Опытные плавки, проведенные на комбинате
"Криворожсталь" на печах большого объема с транспортерной подачей
материалов к скипам, показали, что на этих печах можно получить наибольший
эффект [2], но система загрузки смесью материалов требует дальнейшей доработки
и исследований, особенно в переходный период и в режиме регулирования. Кроме
этого, требуется дальнейшее исследование работы механизмов, особенно затворов
бункеров и транспортеров, для обеспечения их долговечности и надежности.
.4 Влияние смешивания рудного сырья с коксом на
газодинамические условия и технико-экономические показатели доменной плавки
Кокс и рудное сырье, используемые в доменной
плавке, в современных условиях значительно различаются по крупности, ввиду чего
газопроницаемость шихты в печи существенно зависит от того, в какой мере эти
материалы перемешиваются при загрузке на колошник. От степени их смешивания в
процессе загрузки зависит не только характер взаимного расположения кусков
разной крупности, но и равномерность их распределения по сечению печи, что
влияет на использование газа и на технико-экономические показатели плавки.
Днепродзержинским индустриальным институтом на
заводе им. Петровского исследовано влияния загрузки рудных материалов в смеси с
коксом на работу печи. Предварительно в лабораторных условиях изучили
газопроницаемость слоя, состоящего из фракций различной крупности, при разных
режимах загрузки [4].
Материалы продували компрессорным воздухом (5
ат) в цилиндре диаметром 300 мм и высотой 700 мм с регулированием его расхода.
Перепад давления измеряли на высоте 0,5 м при
расходе воздуха, соответствующем приведенной скорости (в расчете на полное
сечение цилиндра) 0,9 м/с, что обеспечивало соблюдение условий автомодельности
для всего диапазона размеров исследованных фракций.
Загружали агломерат крупностью от 5-0 до 25-15
мм. Для каждой пары исследуемых фракций измеряли перепады давления воздуха в
цилиндре и насыпную массу агломерата при расположении мелкой и крупной фракций
двумя слоями и при их загрузке в смеси. По насыпной плотности можно было судить
о величине порозности при разных условиях загрузки.
Измерения проводили при различном соотношении
фракций. Количество фракций 5-0 мм изменяли от 0 до 100% через каждые 10%.
На рис. 14 приведены результаты исследования
газопроницаемости слоя при загрузке фракций разного размера в комбинации с
фракцией 5-0 мм.
Рис. 14. Изменение перепада давлений (∆Р)
и насыпной массы (γ) агломерата
при послойной укладке (1) и при загрузке в смеси (2) фракция 5-0 мм с более
крупными фракциями а-в (цифры в скобках - мм)
Следует отметить неодинаковый характер
зависимости насыпной массы слоя от содержания мелкой фракции. При загрузке
слоями (1) изменение получается практически линейным. При загрузке в смеси (2)
оно нелинейно. Общая насыпная масса при загрузке обеих фракций в смеси всегда
больше, чем при их послойной укладке; следовательно, порозность слоя при
смешивании фракций разной крупности уменьшается. Наибольшее различие в величине
у по кривым 1 и 2 наблюдалось в серии опытов на рис. 1, в с фракциями 5-0 мм и
25-15 мм, больше всего различавшихся по крупности. При смешивании этих фракций
насыпная масса получается на 11-13% большей, чем при послойной загрузке.
Уменьшение порозности при смешивании материалов
разной крупности не всегда сопровождается ухудшением газопроницаемости. Судя по
кривым ∆Р (рис. 1), смешивание фракции, несмотря на уменьшение
порозности, приводит в большинстве случаев к увеличению газопроницаемости слоя,
причем весьма значительному. Влияние порозности как таковой в данном случае не
является определяющим. Более существенное значение здесь имеет изменение размеров
межкусковых каналов, свободных для прохода газа.
Более заметно проявляется влияние порозности при
содержании мелочи выше 70%, когда при загрузке в смеси получается худшая
газопроницаемость, чем при раздельной.
Таким образом, для материала, содержащего наряду
с более крупными фракциями также и мелочь 5-0 мм, загрузка их в смеси
обеспечивает более высокую газопроницаемость слоя, чем раздельная загрузка.
Аналогичные результаты были получены в тех
случаях, когда вместо фракции 5-0 мм применяли фракцию 3-0 или 5-1 мм.
При смешивании фракции 5-3 мм с более крупными
получили иные результаты (рис. 15). В этих опытах изменение насыпной массы слоя
γ
и перепад давлений ∆Р при смешивании изменились аналогично. Переход от
послойной укладки к загрузке смеси сопровождался уменьшением порозности и
газопроницаемости; лишь в одном случае изменение условий загрузки практически
не повлияло на эти показатели (рис. 15, а).
Следовательно, мнения об увеличении
газопроницаемости слоя при смешивании фракций разной крупности [5-7] и об ее
уменьшении при этом [9] могут быть в равной мере справедливы, но в своих
конкретных условиях.
Анализируя влияние рассматриваемых способов
загрузки на газопроницаемость слоя, следует учесть количественную сторону
явления.
Уменьшение перепада давления на 1 м высоты слоя
в результате смешивания фракций разной крупности с фракцией 5-0 мм при ее
содержании до 30% достигало 600-700 мм вод. ст. или примерно 60-70%.
При удалении мелочи 3-0 м л из агломерата
переход от смешанной с послойной загрузке фракций уменьшал газодинамическое
сопротивление слоя лишь на 30-50 мм вод. ст., или на 20-25%.
Рис. 15. Изменение перепада давлений (∆Р)
и насыпной массы (γ) агломерата
при послойной укладке (1) и при загрузке в смеси (2) фракция 5-3 мм с более
крупными фракциями а-в (цифры в скобках - мм)
Таким образом, относительное изменение перепада
давлений на 1 м высоты слоя для агломерата, содержащего 5-30% мелочи, в 2-3
раза больше, чем без мелочи, а абсолютные значения перепада при наличии мелочи
в 14-20 раз выше, чем при ее отсутствии. Рассортировка агломерата по фракциям с
раздельной их загрузкой обеспечивает повышение газопроницаемости шихты лишь при
условии полного отсева мелочи (5-0 мм).
Для практики важно знать количественное изменение
газопроницаемости при смешивании агломерата и кокса, имеющих реальный
гранулометрический состав.
Перепад давлений в слое из этих материалов
измеряли на установке с цилиндром диаметром 520 мм и высотой 700 мм.
Использовали кокс крупностью 80-40 и агломерат крупностью 40-0 мм, меняя в них
содержание фракции 5-0 мм в агломерате от 0 до 40% через каждые 5%.
Перепад измеряли (рис. 16) при приведенной
скорости газа 0,9 м/с. Смешивание кокса и агломерата реального
гранулометрического состава уменьшило газодинамическое сопротивление слоя на
12-25%.
Рис. 16. Изменение газодинамического
сопротивления реальной шихты в зависимости от содержания мелочи при послойной
укладке кокса и агломерата (1) и при их загрузке в смеси (2)
Исследовали также изменения газопроницаемости
слоя при смешивании кокса с окатышами, содержащими до 10% мелочи. В этих опытах
при смешивании было выявлено на 17-25% большее сопротивление материалов, чем
при послойной укладке (рис. 17). Сопротивление слоя при смешивании изменялось
значительно меньше, чем в опытах с агломератом.
Как известно, повышение равномерности
распределения материалов по сечению печи сопровождается увеличением
газодинамического сопротивления столба шихты. Поэтому смешивание рудного сырья
с коксом, улучшая газопроницаемость ввиду особенностей размещения мелких и
крупных кусков, в то же время должно способствовать снижению газопроницаемости
вследствие более равномерного распределения материалов.
Рис. 17. Изменение газодинамического
сопротивления шихты в зависимости от содержания мелочи при послойной загрузке
кокса и окатышей (1) и при их загрузке в смеси (2)
Фактическое изменение газопроницаемости шихты в
результате смешивания рудных материалов с коксом и влияние такой загрузки на
работу печи может быть установлено только опытным путем.
Более полного смешивания рудного сырья с коксом
в существующих производственных условиях удается достичь при загрузке в один
скип рудной сыпи и кокса, размещаемого сверху. При опрокидывании скипа и
высыпании материалов в приемную воронку и затем на большой конус и в печь
материалы оказываются в значительной степени перемешанными между собой: более
мелкий и тяжелый рудный материал внедряется между кусками кокса. Это подтверждается
результатами исследования на модели засыпного устройства в масштабе 1/10
натуральной величины [1]. Влияние условий загрузки на технико-экономические
показатели доменной плавки исследовали на печи полезным объемом 1033 м3.
Загрузка рудного сырья и кокса в один скип при
существующей схеме шихтоподачи с вагон-весами затруднительна. В частности, при
этом число перемещений вагон-весов увеличивается вдвое, так как в карман
набирается порция рудной сыпи, соответствующая только половине объема скипа.
Это значительно снижает производительность участка загрузки. Для облегчения
работы машинистов вагон-весов массу подачи с переходом на совместную загрузку
рудных материалов и кокса увеличили более чем на 30%, обеспечив предельное
заполнение скипа. Для проведения опытных плавок в электросхему загрузки
потребовалось внести некоторые изменения, обеспечивающие необходимую
согласованность работы вагон-весов и коксовых затворов. Перед опытными плавками
на печи применяли цикличную систему загрузки Р2К2↓ КР2К↓. В опытный
период применяли преимущественно цикличную загрузку, состоявшую из одной подачи
с загрузкой рудных материалов на дно скипа и одной подачи с загрузкой кокса на
дно скипа. При этом, подача состояла из 20,5 т рудной сыпи и 6,5-6,7 т кокса.
Наличие в цикле подачи с загрузкой кокса на дно скипа было обусловлено
стремлением подгрузить периферию, так как при преимущественном использовании
подач с загрузкой рудной сыпи на дно скипа содержание двуокиси углерода на
периферии снижалось, а в осевой и промежуточной зонах повышалось.
Применение цикличных загрузок с различным
соотношением указанных подач дает возможность регулировать распределение рудных
нагрузок по сечению печи. На новом режиме загрузки печь работала 10 дней.
Сравнительный период после опыта тоже продолжался 10 дней.
В течение опытного периода имелись некоторые
обстоятельства, усложнявшие работу печи, что отрицательно влияло на
технико-экономические показатели. Основные трудности были связаны с напряженной
работой машинистов вагон-весов. На протяжении всего опытного периода загрузка
была узким местом в работе печи, что затрудняло устранение возникающих по
разным причинам неполнот. В ряде случаев печь работала на агломерате с рудного
двора, отличающемся повышенным содержанием мелочи. Технико-экономические показатели
работы печи в опытный и сравнительный периоды сопоставлены в табл. 1.3. В
опытном периоде увеличилась интенсивность плавки в результате улучшения
газодинамических условий в печи. При более форсированном ходе перепад давлений
был таким же, как и в сравнительном периоде. Газопроницаемость шихты улучшилась
несмотря на некоторое повышение равномерности распределения материалов,
подтверждавшееся более равномерным распределением содержания двуокиси углерода
по радиусу (рис. 18).
Таблица 1.3.
Технико-экономические показатели работы доменной
печи объемом 1033 м3тпри загрузке рудного сырья в смеси с коксом (I) и при
обычной загрузке (II)
Показатели
|
I
|
II
|
Производительность,
т/сутки *
|
1727
(1732)
|
1669
|
Производительность,
% *
|
103,5
(103,8)
|
100
|
Расход
кокса (сухого), кг/т чугуна *
|
591
(589)
|
601
|
Интенсивность
плавки по коксу, т/м3 ·сутки
|
1,020
|
1,002
|
Доля
подготовленного железорудного сырья, %
|
97,3
|
96,7
|
В
том числе окатышей
|
38,8
|
46,8
|
Содержание
кремния в чугуне, %
|
0,74
|
0,68
|
Выход
шлака, кг/т чугуна
|
518
|
507
|
Основность
шлака (СаО/SiО2)
|
1,25
|
1,25
|
Расход
природного газа, м3/т чугуна
|
85,7
|
85,7
|
Расход
кислорода, м3/т чугуна
|
1,6
|
-
|
Температура
дутья, °С
|
1072
|
1041
|
Избыточное
давление колошникового газа, ат
|
1,01
|
1,01
|
Перепад
давления (дутье-колошник), ат
|
1,20
|
1,20
|
Простои,
%
|
0,45
|
0,5
|
* В скобках - значения, приведенные к условиям
периода обычной работы II.
На опытных плавках удельный расход кокса
снизился при приведении к одинаковым условиям на 12 кг/т чугуна, или на 2,0%, а
производительность печи возросла на 3,8%.
Рис. 18. Распределение содержания двуокиси
углерода в газе по радиусу колошника доменной печи объемом 1033м3 при обычной
послойной загрузке рудного сырья и кокса (1) и при их загрузке в смеси одним
скипом
Можно считать, что смешивание рудного сырья с
коксом при загрузке доменной печи, обеспечивая увеличение газопроницаемости
шихты и более равномерное распределение материалов, способствует улучшению
условий плавки и повышению ее технико-экономических показателей.
Кратковременность опытного периода была
обусловлена значительными трудностями при подаче рудной сыпи и кокса в один
скип.
Можно усилить смешивание материалов и без такой
загрузки. В частности, это достигается путем набора на малый конус двух скипов
материалов: коксового и рудного с расположением кокса под слоем рудной сыпи.
Влияние такой загрузки на показатели доменной
плавки исследовали на печи полезным объемом 700 м3, выплавлявшей
передельный чугун. В обычных условиях на печи применяется система загрузки
Р2К2. При этом подача состоит из 13 т рудных материалов и 3,7-4,1 т кокса.
Соотношение размеров загрузочного устройства на
этой печи таково, что во вращающейся воронке размещается только один скип
материалов. При наборе двух скипов на малый конус значительная часть материала
второго скипа размещается в неподвижной приемной воронке. В связи с этим
электросхему работы распределителя шихты изменили таким образом, чтобы он
вращался только после загрузки на малый конус первого скипа каждой пары.
В течение опытного периода продолжительностью 30
суток применяли различные системы загрузки в сочетании с набором двух скипов на
малый конус.
Наиболее эффективной в смысле смешивания была
загрузка по системе КРКР↓, при которой расположение каждой пары рудного и
коксового скипов на малом конусе благоприятствует смешиванию. Однако ввиду
особенностей электросхемы работы распределителя рудный материал при этом
грузится в печь без вращения воронки.
Чтобы обеспечить равномерность кругового
распределения материалов, эту систему загрузки чаще использовали в комбинации с
системой Р2К2↓ или РКРК↓, что попутно позволяло подгрузить
периферию рудным материалом.
По тем же соображениям использовали систему
загрузки РК2Р↓ и КР2К↓. По эффективности смешивания обе эти системы
уступают системе КРКР↓, так как из двух пар скипов только одна имеет
благоприятное для смешивания расположение рудного материала и кокса. Однако они
более удобны для машинистов вагон-весов.
На рис. 19 приведены кривые радиального
распределения двуокиси углерода при различных системах загрузки.
Наиболее приемлемой по равномерности кругового и
радиального распределения газа, а также по удобству для машинистов вагон-весов
оказалась система загрузки РК2Р↓.
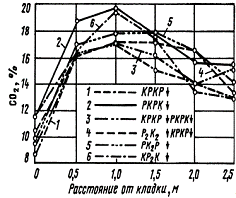
Переход на новый режим загрузки способствовал
улучшению использования газа и повышению газопроницаемости шихты, что позволило
увеличить интенсивность плавки. Это обеспечило повышение производительности
печи на 7,0% при снижении удельного расхода кокса на 2,5% (после приведения к
одинаковым условиям).
В настоящее время на заводе им. Петровского
выполнен проект устройства для загрузки рудного сырья и кокса в один скип. При
этом наряду с последовательной подачей этих материалов в скип предусмотрено и
их одновременное ссыпание.
Показатели работы печи в исследуемый период
приведены в табл.1.4. Для сравнения взяли близкий по условиям доопытный период
продолжительностью 9 суток.
Таблица 1.4.
Показатели
|
I
|
II
|
Производительность,
т/сутки *1
|
1399
(1381)
|
1292
|
Производительность,
% *1
|
108,3
(106,9)
|
100
|
Расход
кокса (сухого), кг/т чугуна *1
|
546
(546)
|
562
|
Расход
кокса (сухого), % *1
|
97,2
(97,2)
|
100
|
Интенсивность
плавки по коксу, т/м3 ·сутки
|
1,229
|
1,165
|
Доля
агломерата в шихте, %
|
100,0
|
100,0
|
Расход
материалов, кг/т чугуна: металлодобавки сырой флюс конверторный шлак
|
21
50 11
|
37
54 54
|
Содержание
кремния в чугуне, %
|
0,78
|
0,79
|
Выход
шлака, кг/т чугуна
|
479
|
493
|
Основность
шлака (СаО/SiО2)
|
1,26
|
1,26
|
Расход
природного газа, м3/т чугуна
|
80
|
86
|
Расход
кислорода, м3/т чугуна
|
21,9
|
24,0
|
Температура
дутья, °С
|
1062
|
1047
|
Избыточное
давление колошникового газа, ат
|
1,06
|
1,08
|
Перепад
давления (дутье-колошник), ат
|
1,03
|
1,01
|
Простои,
%
|
0,33
|
0,15
|
Тихий
ход, %
|
0,38
|
0,19
|
*1 В скобках - после приведения к условиям
периода II.
Выводы
. Разработана новая система загрузки доменной
печи шихтовыми материалами - агломератом в смеси с коксом. В результате применения
новой системы загрузки производительность печей возросла до 4%, а удельный
расход кокса сократился до 9%.
. Исследованиями установлено, что смешивание
железорудных материалов с топливом путем совместной подачи их в скип несколько
изменяет газодинамические условия доменной плавки, активизирует процессы,
уменьшает сопротивление зоны пластического состояния.
. Распределение материалов и газов при такой
загрузке регулируется изменением очередности подачи железорудных материалов и
топлива в скип.
. Результаты опытных плавок на комбинатах им.
Ф.Э. Дзержинского, "Криворожсталь" и работы доменных печей завода им.
Г.И. Петровского показали, что на печах различного объема в зависимости от
условий плавки достигается снижение расхода кокса на 2-8 и повышение производительности
на 2-4%.
. Отработка технологии плавки в новых условиях и
повышение надежности работы механизмов для подачи материалов в скип по
различным программам позволит получить высокие технико-экономические показатели
процесса.
. Изменение условий загрузки фракций разной
крупности оказывает различное влияние на газопроницаемость агломерата в
зависимости от наличия в нем мелочи 5-0 мм. При отсутствии мелочи повышение
газопроницаемости слоя обеспечивается раздельной загрузкой фракций разной
крупности, тогда как при ее наличии улучшение газопроницаемости достигается
путем загрузки этой фракции в смеси с другими.
. Степень изменения газопроницаемости агломерата
при переходе с послойной загрузки разных фракций на одновременную при наличии
мелочи в агломерате значительно больше, чем при ее отсутствии. В частности,
относительное изменение перепада давлений на 1 м высоты слоя для агломерата,
содержащего 5-30% мелочи, в 2-3 раза выше, чем без мелочи, а по абсолютной
величине перепад при наличии мелочи в 14-20 раз выше, чем при ее отсутствии.
. Смешивание кокса крупностью 80-40 мм с
агломератом, содержащим 5-40% фракций 5-0 мм, уменьшает газодинамическое
сопротивление шихты на 12-25%по сравнению с получаемым при послойной укладке
тех же материалов. При смешивании кокса с окатышами, содержащими 10% мелочи,
газодинамическое сопротивление слоя, наоборот, повышается.
. На печи объемом 1033 м3 завода им.
Петровского применение новой системы загрузки способствовало увеличению
газопроницаемости шихты, более равномерному распределению материалов, повышению
производительности и снижению расхода кокса.
. На печи объемом 700 м3 того же
завода смешивание агломерата и кокса путем набора этих материалов на малый
конус двумя скипами обеспечило улучшение газопроницаемости шихты и позволило
форсировать ход.
. В дипломной работе предусматривается
исследование работы доменной печи при совместной загрузке железорудных
материалов и кокса в скип.
2. Основная часть
.1 Исследование работы доменной печи при
совместной загрузке железорудных материалов и кокса в скип
Одним из наиболее эффективных путей снижения
расхода топлива в доменной плавке является совершенствование загрузки
материалов и распределения их на колошнике для формирования рациональной
структуры столба шихтовых материалов и улучшения использования тепловой и
восстановительной энергии газа [10].
В течении ряда лет Днепродзержинским
индустриальным институтом испытан и внедрен на доменных печах завода им. Г.И.
Петровского и Днепровского металлургического комбината (ДМК) принципиально
новый способ загрузки материалов, обеспечивающих смешивание железорудного сырья
с коксом [4, 3].
Для смешивания компонентов доменной шихты, в
отличие от обычно применяемого способа загрузки, производится выдача в один
скип железорудного материала и кокса.
В зависимости от системы подачи материалов к
скипам могут выбираться различные конструктивные решения устройств для
осуществления такого способа загрузки. При транспортерной подаче на колошник
требуется соответствующее обеспечение доз материалов на конвейере. При подаче
железорудного материала по схеме вагон - весы - скип осуществление режима
выдачи в один скип обоих материалов требует переоборудования рудных течек в
бункера с затворами, имеющими привод и работающими в заданном режиме.
Установки с электрическим приводом управления
затворами применяются на трех доменных печах металлургического завода им. Г.И.
Петровского полезным объемом 700 и 1033 м3.
На доменной печи №10 Днепровского
металлургического комбината полезным объемом 1386 м3 введена в
промышленную эксплуатацию установка с гидравлическим приводом управления
затворами рудных бункеров. На этой печи проверена и подтверждена возможность
применения способа загрузки со смешиванием при работе на горячем агломерате -
при подаче его в один скип с коксом дымообразования или возгорания кокса не
происходило.
Условия для смешивания агломерата с коксом
создаются не только при выдаче материалов в скип, но и при последующих
совместных перезагрузках (ссыпаниях), реализуемых обычным двухконусным засыпным
аппаратом. Перемешивание компонентов доменной шихты в процессе загрузки
обеспечивает более равномерное их распределение по сечению колошника, причем,
чем выше достигаемая степень смешивания рудных материалов с коксом, тем
равномернее распределяются они по радиусу колошника. При определенной степени
смешивания рудная нагрузка по радиусу колошника отличается мало.
Степень смешивания материалов в значительной
мере зависит от режима и порядка подачи их в скип. Железорудные материалы и
кокс могут загружаться в скип одновременно, раздельно (каждый первым или
последним) или по различным программам выдачи одного материала относительно
другого для достижения различной степени смешивания. При высокой степени
смешивания материалов на первых стадиях загрузки (в скипе) дальнейшие
перезагрузки могут вызвать выклинивание более мелкого и тяжелого материала из
смеси, что приведет к изменению распределения материалов на колошнике.
На доменной печи №10 ДМК проведена промышленная
проверка и исследование хода плавки при различных режимах, включая поочередную
выдачу в скип кокса и агломерата с определенными задержками времени.
Разработанная схема управления загрузкой работала надежно и без затруднений
обеспечивала изменение режима и переход от одной системы к другой.
Печь выплавляла передельный чугун с содержанием
кремния от 0,64 до 1,07% (по среднемесячным данным), в течении суток колебания
были значительными - от 0,6 до 1,7%. В шихте применялся офлюсованный агломерат
из Криворожских руд (50-52% Fe, 8,6-10,3% FeO, основность CaO/SiO2 = 1,24ч1,27)
при содержании его в шихте от 85 до 100%. Количество мелочи в агломерате
составляло 10,5-14,2%.
Вследствие значительных колебаний состава и
прочности кокса, тепловой и шлаковый режимы плавки были неустойчивыми,
приходилось вести плавку с повышенным нагревом (резервом тепла) , что приводило
к перерасходу кокса и потере производительности. Среднемесячный выход шлака
составлял 480-590 кг/т чугуна, что эквивалентно колебаниям расхода кокса на 50
кг/т чугуна и производительности на 5 %. Основность шлака изменялась в
пределах: CaO/SiO2 = 1,24ч1,29 (CaO+MgO)/SiO2 = 1,38ч1,43, а коэффициент
распределения серы LS составлял 45-56.
Доменная печь работала на дутье, обогащенном
кислородом до 25-27% с вдуванием природного газа в количестве от 80 до 120 м3/т
чугуна. Отношение количества кислорода к природному газу было около 0,4-0,5.
Среднемесячная температура изменялась от 960 до 1150°С, давление колошникового
газа - от 1,3 до 1,5 кПа.
До перехода на загрузку с подачей железорудных
материалов и кокса в один скип на печи применяли системы загрузки 5ААКК 2КААК и
4КААК 3ААКК при уровне засыпи 1,5-1,75 м. при рудной нагрузке 3,5-3,6 т/т
(масса агломерата в подаче 20 т, кокса 5,5-5,6 т) объем этих материалов был
примерно одинаков (по 50%) и насыпная масса шихты составляла 1,09 т/м3.
Содержание СО2 в газе по радиусу колошника изменялось на периферии и в центре
от 11 до 14%, достигая в гребне 21%. Степень использования СО составляло около
40%, температура колошникового газа изменялась от 315 до 350°С.
Первые опытные плавки при переходе на новую
систему загрузки с одновременной подачей агломерата и кокса в скип показали,
что как и в ранее проведенных исследованиях [1-3] повышается
температурно-тепловой уровень процесса (происходит разогрев печи), вызывая
соответствующие изменения содержания кремния в чугуне. В зависимости от
исходных условий начало роста содержания кремния отмечалось через 4-6 часов. В
случае непринятия мер для предотвращения разогрева ход становился горячим,
наблюдалась забивка центральной части печи. Снижение газопроницаемости
центральной части усугублялось плохим качеством железорудных материалов и
кокса, поэтому приходилось переходить на обычный режим загрузки или уменьшать
степень смешивания материалов. На рис. 1 показано характерное изменение
показателей в периоды, когда работа на новых режимах загрузки была
непродолжительной.
Рис. 1. Изменение рудной нагрузки (Рн),
содержания кремния в чугуне(Siч), перепада давления (∆Р), температуры
колошника (Тк) и количества дутья (Vд) в переходные периоды работы печи на
обычной (периоды 1, 3) и совместной (период 2) системах загрузки: К0 - удельный
расход кокса;П - производительность; продолжительность периодов - 1 деление
соответствует 8 ч
Во всех случаях устойчивая длительная работа
печи на режимах загрузки с подачей в один скип агломерата и кокса
обеспечивалась только при заблаговременном снижении расхода кокса и увеличении
рудной нагрузки. При переходе на режим загрузки со смешиванием материалов
количество кокса в подаче сразу уменьшали на 200 кг и затем через несколько
часов, в зависимости от теплового состояния печи, еще на 100-200 кг. В случае
обратного перехода на обычные системы загрузки расход кокса необходимо было
сразу увеличить до исходного уровня.
Исследования показали, что при высокой степени
смешивания материалов (с одновременной подачей в скип агломерата и кокса)
использование газа улучшилось (степень использования СО достигла 45%).
Распределение СО2 по радиусу резко изменилось (рис. 2), повышаясь в центре до
17-20%. Расход кокса постепенно снижался с 525-515 до 490-465 кг/т чугуна, то
есть на 8%.
Рис. 2. Изменение содержания СО2 в колошниковом
газе, рудной нагрузки (Рн) и содержания кремния в чугуне (Siч) при обычной (2)
и совместной (1) системах загрузки в различные периоды (а, б).
продолжительность периодов: 1 деление соответствует 1 сут.
При высокой степени смешивания материалов, в
результате лучшей их обработки газами, температура в горне, как правило,
повышалась, что приводило к изменению теплообменных процессов в нижней и
верхней зонах столба шихтовых материалов. Если при этом резерв тепла не
использовался, то это приводило к горячему ходу и температура повышалась не
только в горне, но и на колошнике.
Уменьшение степени смешивания материалов (при
переходе на поочередную подачу материалов в один скип) снижало эффект экономии
кокса, но газодинамический режим становился менее напряженным. Расход кокса
снижался на 2-4% при сохранении или некотором увеличении производительности. Изменение
степени смешивания материалов позволяло регулировать распределение материалов и
газа в печи. Диаграммы распределения СО2 по радиусу колошника, приведенные на
рис. 3, подтверждают регулирование в широких пределах и возможность разгрузки
центра печи при применении способа загрузки материалов со смешиванием.
Рис. 3. Распределение диоксида углерода по
радиусу колошника при работе печи с загрузкой железорудных материалов и кокса в
один скип по различным программам: 1 - одновременная подача материалов в скип;
2 - подача агломерата через 8 с после начала подачи кокса в скип; 3 - подача
агломерата через 14 с после начала подачи кокса в скип; 4 - подача кокса через
8 с после начала подачи агломерата в скип
Время использования нового способа загрузки на
печи №10 ДМК составило по 6 месяцев в 1984 и 1985 гг. продолжительность опытных
периодов достигала 45-50 суток. Переход на обычные системы загрузки
производился в основном из-за перебоев в поставке кокса (простои из-за отсутствия
кокса по годам соответственно 64 и 60 ч). Технико-экономические показатели
работы печи в периоды исследований, в сравнении с периодами работы на обычных
системах загрузки, приведены в табл. 2.1. При совместной загрузке материалов
достигаются более низкий расход кокса и высокая производительность.В отдельные
периоды, которые характеризовались стабильностью условий и устойчивым тепловым
состоянием горна, при содержании кремния в чугуне около 0,7% расход кокса
снижался до 450-490 кг/т чугуна (табл. 2.2.). Работа печи на новой системе
загрузки показала, что, несмотря на некоторую подгрузку центра, ход печи может
быть ровным при значительном выравнивании и повышении использования газа по
всему сечению колошника.
Таблица 2.1.
Показатели доменной плавки при обычной системе
загрузки (слева) и при работе в режиме смешивания (справа)
Показатель
|
1984
|
1985
|
Продолжительность
периода, мес
|
6/6
|
66/6
|
Производительность,
т/сут (приведенная)
|
2095/2288
(2315)
|
2146/2232
(2225)
|
Расход
кокса, кг/т чугуна (приведенный)
|
546/522
(524)
|
545/510
(501)
|
Расход
природного газа, м3/т
|
103/89
|
108/97
|
Рудная
нагрузка, т/т
|
3,45/3,70
|
3,65/3,74
|
Массовая
доля Fe в шихте, %
|
51,4/51,2
|
51,6/51,8
|
Массовая
доля Si в чугуне, %
|
0,87/0,90
|
0,94/0,96
|
Дутье:
расход, м3/мин температура, °С содержание О2, %
|
2446/2489
1081/1117 26,30/26,1
|
2411/2434
1063/1030 25,60/26,40
|
Давление
колошникового газа, кПа
|
146/140
|
146/145
|
Степень
использования СО, %
|
40,2/41,1
|
40,46/41,88
|
Простои,
%
|
2,73/0,99
|
1,63/2,32
|
Таблица 2.2.
Показатели доменной плавки в лучшие (по расходу
кокса) периоды работы в режиме смешивания
Показатель
|
1984
г.
|
1985
г.
|
|
май
|
июнь
|
май
|
июнь
|
Июль
|
Продолжительность,
сут
|
30
|
30
|
30
|
30
|
30
|
Производительность,
т/сут
|
2360
|
2315
|
2305
|
2398
|
2295
|
Расход:
кокса, кг/т чугуна природного газа, м3/т известняка, кг/т
|
519
85 25
|
506
95 22
|
492
105 9
|
451
101 9
|
501
102 11
|
Рудная
нагрузка, т/т
|
3,54
|
3,83
|
4,0
|
4,06
|
4,96
|
Массовая
доля, %: Fe в рудной части шихты Si в чугуне
|
50,99
0,75
|
50,99
0,85
|
51,67
1,06
|
51,86
0,86
|
52,21
0,81
|
Дутье:
количество, м3/мин давление, кПа температура, °С содержание О2, %
|
2150
230 1140 26,1
|
2107
249 1150 16,8
|
2287
245 1060 26,8
|
2488
260 1071 27,0
|
2554
267 1091 25,9
|
Колошниковый
газ: температура, °С давление, кПа степень использования СО, %
|
329
132 40,32
|
324
135 40,62
|
348
139 41,96
|
327
145 41,50
|
327
146 42,41
|
Исследования показали, что при совместной
загрузке агломерата и кокса в скип в печи формируется структура столба,
существенно отличающаяся от обычно наблюдаемой. При обычных системах загрузки
железорудные материалы и кокс в печи располагаются в основном слоями и
слоистость структуры столба шихты сохраняется практически до зоны плавления.
Физико-химические процессы в слоях протекают неодинаково и неравномерно, что
объясняется различием в газодинамическом сопротивлении слоев кокса и агломерата
по высоте и сечению печи, а также отличием теплофизических и химических свойств
материалов. При слоистой структуре столба шихты возникает необходимость в
создании значительной неравномерности в распределении слоев кокса и агломерата
по сечению печи для обеспечения ровности хода при соответствующей интенсивности
плавки по дутью.
При подаче в один скип агломерата и кокса, и
смешивания их в процессе загрузки насыпная масса шихты возрастала в результате
более плотной укладки материалов и повышения рудных нагрузок.
Для структуры столба при загрузке со смешиванием
характерна большая однородность, чем при послойном расположении агломерата и
кокса. Насыпная масса смеси (1,15-1,5 т/м3) на 7-25% выше, чем при
двухслойной укладке этих материалов (1,05-1,20 т/м3), а порозность
соответственно ниже и составляет 53-35, по сравнению с 57-48%. Таким образом, в
одном и том же объеме печи помещается шихтовых материалов в смеси значительно
больше, чем при послойном их расположении.
Несмотря на более высокую плотность и меньшую
порозность смешанного слоя, газопроницаемость его при равномерном распределении
материалов по сечению может отличаться незначительно (при кусковой шихте) или
быть значительно лучше (при количестве мелочи 0-5 мм в шихте более 30%), чем
при послойной загрузке. Увеличение массы шихты в одном и том же объеме (за счет
агломерата), несмотря на некоторое уменьшение количества дутья, способствовало
лучшему использованию полезного объема печи. Вследствие того, что эффект от
увеличения рудной нагрузки был более значительным, чем влияние снижения
интенсивности плавки по дутью, производительность печи не снижалась.
Формирование структуры столба из смешанной шихты
приводит к более равномерному распределению газовой нагрузки. Газовая нагрузка
на единицу агломерата (va) в смеси возрастает, а на единицу кокса (vк)
снижается, по сравнению со слоистой структурой, из-за уменьшения степени
неравномерности распределения материалов по высоте и сечению печи. В результате
меняется распределение температур ta, tк, tсм соответственно агломерата, кокса,
смеси и перепада давления (∆Р). Характер изменения этих параметров в
слоях агломерата (А), кокса (К), переходном (∆h) и смеси (СМ) представлен
на рис. 4. Из приведенных данных видно, что характеристики отдельных слоев
материалов и смеси значительно отличаются. Теплообмен при слоистой структуре
столба шихты происходит практически в каждом слое материалов раздельно - между
газом и коксом; газом и агломератом, и только на границе материалов (кокса и
агломерата) возможен теплообмен и между твердыми материалами излучением и
теплопроводностью в результате их контакта. Кокс и агломерат при слоевой
структуре шихты в печи прогреваются до различных температур вследствие отличия
в удельных количествах газа, приходящегося на слой коса и агломерата, из-за
неравномерности их распределения, различия в размерах кусков, теплофизических
характеристиках материалов, а также происходящих в них процессах. На
температуру в слое агломерата значительное влияние оказывает тепловой эффект
реакции восстановления [11, 12]. В верхней ступени теплообмена при температурах
700-800°С идет процесс восстановления Fe3O4 до FeO газами СО и Н2,
сопровождающийся поглощением тепла (соответственно 20,96 и 62,41 МДж), что
сказывается на температуре кусочков и слоя агломерата в целом.
Рис. 4. Характеристика слоев шихты при послойном
(а) расположении агломерата и в смеси (б), обозначения в тексте
В нижней зоне теплообмена при 1000-1200°С, где
развито прямое восстановление FeO со значительным поглощением тепла (-152 МДж),
влияние процесса сказывалось еще больше на температуре слоя агломерата, разница
температур в слоях кокса и агломерата достигла значительных величин. Результаты
вертикального зондирования [11, 13] подтверждают, что в области интенсивного
восстановления магнетита и, особенно прямого восстановления вюстита, на кривой
распределения температур по высоте печи наблюдаются температурные остановки и
даже снижение ее на 150°С (рис. 5). Температура в слоях кокса в этих зонах, как
правило, была на несколько градусов выше.
Рис. 5. Зависимость распределения состава (Н2О,
Н2, СО2, СО), количества газа, теплофизических характеристик шихты (С -
теплоемкости, λ - теплопроводности)
по высоте доменной печи в зависимости от температуры в слое агломерата (ta) и
кокса (tк)
Газ, являющийся теплоносителем, выполняет также
функции посредника в массотеплообмене между слоями кокса и агломерата.
Количество его изменяется при переходе от слоя к слою, вследствие различного
газодинамического сопротивления слоев по высоте и сечению печи, что усугубляет
его неравномерность в количестве выполняемой им работы. Теплообмен в слое между
кусками однородных материалов при толщине слоев 100-400 мм практически
отсутствует (температура поверхности примерно одинакова). Скорость нагрева
кусков в определенной степени будет зависеть от их размеров, но при малой
скорости опускания шихты (40-120 мм/мин) значительной разницы в температуре
поверхности больших и малых кусков не наблюдается.
Из рис. 5 видно, что теплоемкость при нагреве до
1000°С меняется для кокса от 0,8 до 1,48 кДж/(кг·К), для агломерата - от 0,6 до
0,96 кДж/(кг·К), то есть теплоемкость кокса примерно в 1,5 раза выше
теплоемкости офлюсованного агломерата. Теплопроводность кокса в отличие от
агломерата с повышением температуры снижается с 0,43 до 0,2 Вт/(м3
К) (агломерата - растет с 0,45 до 0,69 Вт/(м3 К)). Все это не может
не сказаться на условиях теплообмена в отдельных слоях материалов и в смеси.
Разница в теплопроводности агломерата и кокса
при высоких температурах возрастает (теплопроводность офлюсованного агломерата
при 1373 К λ а= 0,729 Вт/(м3·К),
кокса λ
к
= 0,170 Вт/(м3·К), вследствие чего теплообмен на границе слоев между
твердыми материалами (А - К) и в смеси усиливается.
Теоретические и экспериментальные исследования
методом вертикального зондирования печи подтвердили, что тепловое
взаимодействие между кусками кокса и агломерата, находящихся в смеси,
выравнивает температуры не только по сечению кусков, но и в целом уменьшает
разность температур между ними на одном и том же горизонте. Взаимный теплообмен
между коксом и агломератом, находящимся в смеси, выравнивает температуры на
горизонте и обеспечивает более высокий и более равномерный прогрев материалов,
опускающихся на нижние горизонты.
Расчеты по известным уравнениям теплопередачи в
слое кусковых материалов [14, 15] показывают, что смешанные материалы
прогреваются в верхней ступени теплообмена более равномерно, температура
изменяется не так резко, как при послойной загрузке, что свидетельствует о
более активном протекании процессов теплопередачи по высоте печи.
Определение термического КПД, характеризующего
эффективность работы верхней и нижней ступени теплообмена более равномерно, показывает,
что при загрузке в смеси значение его минимальны.
При послойной структуре столба шихты
неравномерность тепловой и химической обработки материалов приводит к
дополнительному перерасходу кокса в результате того, что значительная часть
материалов приходит в горн недостаточно подготовленными. В слое материалов,
находящихся в смеси, создаются более благоприятные условия теплообмена между
ними (особенно в высокотемпературных зонах). Чем выше степень смешивания
агломерата с коксом, тем выше эффект от теплообмена между ними. Расход кокса в
этом случае будет снижаться, даже если общее содержание CO2 в колошниковом газе
не возрастет.
При высокой степени смешивания материалов на
горизонтах высоких температур (выше 950°С) возможно увеличение прямого
восстановления в результате тесного контакта кокса с агломератом. Уменьшение
расхода кокса в этом случае объясняется снижением количества углерода,
расходуемого непосредственно на реакцию прямого восстановления (по сравнению с
косвенным):
+C=Fe+CO-152,2 Мдж 9на 1000 кг Fe требуется 214
кг C) FeO+nC=Fe+CO+(n-1)CO2+13,6 МДж (на 1000 кг Fe - n·214 кг C).
Увеличение же теплопотребности реакции прямого
восстановления в этом случае компенсируется улучшением (активизацией)
теплообмена между коксом, агломератом и газом.
Расчеты показателей прямого и непрямого
восстановления по материальным балансам доменных плавок показывают, что при
смешивании железорудных материалов с коксом чаще наблюдается увеличение степени
прямого восстановления (в среднем с 0,3 до 0,37; хотя имеют место периоды,
когда rd снижается до 0,23). В соответствии с тепловыми балансами плавок
отмечается увеличение удельного расхода тепла на восстановление оксидов с
21-27% при обычной системе загрузки до 25-32% при загрузке в смеси и повышение
коэффициента использования тепла на 5-10%.
В зоне пластического состояния (1100-1350°С)
смешивание материалов способствует сокращению протяженности зоны размягчения,
уменьшению толщины и сплошности непроницаемых для газа пластических слоев.
Участки с размягченными материалами равномернее обрабатываются газом, быстрее
прогреваются, вследствие чего интенсивнее восстанавливается вюститная фаза. Все
эти изменения в процессе предопределили возможность снижения расхода топлива
при загрузке железорудных материалов в смеси с коксом. Практика работы доменной
печи подтверждает правильность этих положений.
Выводы
. При подаче компонентов доменной шихты в один
скип происходит перемешивание их при загрузке и обеспечивается более
равномерное распределение материалов по сечению и высоте столба, вследствие
чего процессы теплообмена и восстановления активизируются и более равномерно
протекают по всему объему.
. В столбе смешанных материалов, по сравнению с
послойной структурой столба шихты, происходит перераспределение удельного
количества газа: на единицу рудного материала - возрастает, кокса - уменьшается
(при неизменном исходном количестве газа), что позволяет увеличивать рудные
нагрузки.
. Новый способ загрузки обеспечивает
формирование более рациональной структуры столба шихтовых материалов и
способствует активизации процессов теплообмена и восстановления.
. При смешанной структуре столба шихты
усиливается взаимный теплообмен железорудными материалами и коксом и создаются
условия для роста степени прямого восстановления, возрастает тепловой КПД и
увеличиваются удельные затраты тепла на восстановление оксидов.
. При совместной загрузке регулирование
распределением материалов и газов по сечению печи осуществляется режимом
загрузки материалов в скип, изменением величины подачи и уровня засыпи. С
увеличением степени смешивания материалов они равномернее распределяются по
сечению печи на уровне засыпи.
. Промышленная проверка показала, что при работе
печи с загрузкой железорудных материалов и кокса в один скип расход кокса
снижается на 2-8%, в зависимости от исходных условий работы печи и степени
смешивания при загрузке.
Общие выводы
. Разработана новая система загрузки доменной
печи шихтовыми материалами - агломератом в смеси с коксом. В результате
применения новой системы загрузки производительность печей возросла до 4%, а
удельный расход кокса сократился до 9%.
. Исследованиями установлено, что смешивание
железорудных материалов с топливом путем совместной подачи их в скип несколько
изменяет газодинамические условия доменной плавки, активизирует процессы,
уменьшает сопротивление зоны пластического состояния.
. Распределение материалов и газов при такой
загрузке регулируется изменением очередности подачи железорудных материалов и
топлива в скип.
. Результаты опытных плавок на комбинатах им. Ф.Э.
Дзержинского, "Криворожсталь" и работы доменных печей завода им. Г.И.
Петровского показали, что на печах различного объема в зависимости от условий
плавки достигается снижение расхода кокса на 2-8 и повышение производительности
на 2-4%.
. Отработка технологии плавки в новых условиях и
повышение надежности работы механизмов для подачи материалов в скип по
различным программам позволит получить высокие технико-экономические показатели
процесса.
. Изменение условий загрузки фракций разной
крупности оказывает различное влияние на газопроницаемость агломерата в
зависимости от наличия в нем мелочи 5-0 мм. При отсутствии мелочи повышение
газопроницаемости слоя обеспечивается раздельной загрузкой фракций разной
крупности, тогда как при ее наличии улучшение газопроницаемости достигается
путем загрузки этой фракции в смеси с другими.
. Степень изменения газопроницаемости агломерата
при переходе с послойной загрузки разных фракций на одновременную при наличии
мелочи в агломерате значительно больше, чем при ее отсутствии. В частности,
относительное изменение перепада давлений на 1 м высоты слоя для агломерата,
содержащего 5-30% мелочи, в 2-3 раза выше, чем без мелочи, а по абсолютной
величине перепад при наличии мелочи в 14-20 раз выше, чем при ее отсутствии.
. Смешивание кокса крупностью 80-40 мм с
агломератом, содержащим 5-40% фракций 5-0 мм, уменьшает газодинамическое
сопротивление шихты на 12-25%по сравнению с получаемым при послойной укладке
тех же материалов. При смешивании кокса с окатышами, содержащими 10% мелочи,
газодинамическое сопротивление слоя, наоборот, повышается.
. На печи объемом 1033 м3 завода им.
Петровского применение новой системы загрузки способствовало увеличению
газопроницаемости шихты, более равномерному распределению материалов, повышению
производительности и снижению расхода кокса.
. На печи объемом 700 м3 того же
завода смешивание агломерата и кокса путем набора этих материалов на малый
конус двумя скипами обеспечило улучшение газопроницаемости шихты и позволило
форсировать ход.
. При подаче компонентов доменной шихты в один
скип происходит перемешивание их при загрузке и обеспечивается более
равномерное распределение материалов по сечению и высоте столба, вследствие
чего процессы теплообмена и восстановления активизируются и более равномерно
протекают по всему объему.
. В столбе смешанных материалов, по сравнению с
послойной структурой столба шихты, происходит перераспределение удельного
количества газа: на единицу рудного материала - возрастает, кокса - уменьшается
(при неизменном исходном количестве газа), что позволяет увеличивать рудные
нагрузки.
. Новый способ загрузки обеспечивает
формирование более рациональной структуры столба шихтовых материалов и
способствует активизации процессов теплообмена и восстановления.
. При смешанной структуре столба шихты
усиливается взаимный теплообмен железорудными материалами и коксом и создаются
условия для роста степени прямого восстановления, возрастает тепловой КПД и
увеличиваются удельные затраты тепла на восстановление оксидов.
. При совместной загрузке регулирование
распределением материалов и газов по сечению печи осуществляется режимом
загрузки материалов в скип, изменением величины подачи и уровня засыпи. С
увеличением степени смешивания материалов они равномернее распределяются по
сечению печи на уровне засыпи.
. Промышленная проверка показала, что при работе
печи с загрузкой железорудных материалов и кокса в один скип расход кокса
снижается на 2-8%, в зависимости от исходных условий работы печи и степени
смешивания при загрузке.
Библиографический список
1.
Логинов В.И., Соломатин С.М., Корж А.Т. Опытные плавки при загрузке доменных
печей смесью кокса и агломерата // Металлург. - 1976. - №4. - С. 14-18.
.
Загрузка доменной печи смесью агломерата и кокса. / В.И. Логинов, С.М.
Соломатин, А.Т. Корж и др. // Черная металлургия. Бюл. НТИ. - 1974. - №17
(733). - С. 33-35.
.
Загрузка железорудных материалов в смеси с коксом. / В.И. Логинов, К.А.
Мусиенко, А.Л. Берин и др. // Металлургическая и горнорудная промышленность. -
1984. - №3. - С. 10-12.
.
Влияние смешивания рудного сырья с коксом на газодинамические условия и
технико-экономические показатели плавки. / В.И. Логинов, А.Л. Берин, С.М.
Соломатин и др. // Сталь. - 1977. - №5. - С. 391-394.
.
Шаповалов М.А. Газопроницаемость доменной шихты. - Теория и практика
металлургии. - 1936. №5. С. 1-9.
.
Орешкин Г.Г. вопросы рационализации работы доменных печей. - Харьков.
Металлургиздат. - 1960. -189 с.
.
Стефанович М.А. Анализ хода доменного процесса. - Свердловск, Металлургиздат.
-1960. - 286 с.
.
Логинов В.И. Аналитическая связь перепадов давления со скоростью газа. -
Металлургия и коксохимия. - 1970. вып. 5. с. 38-42.
.
Фернес С.С. Движение газов через слой кусковых материалов / Домез. - 1932. - №
8 и 9.
.
Работа доменной печи при совместной загрузке железорудных материалов и кокса в
скип. / В.И. Логинов, К.А. Мусиенко, Д.В. Воронков и др. // Сталь. - 1987. -
№12. - С. 7-12.
.
Исследование работы газов и процессов восстановления в доменной печи при
вдувании природного газа методом вертикального и горизонтального зондирования.
/ В.И. Логинов, А.И. Парфенов, Н.В. Голобородько и др. // Сталь. - 1969. - №6.
- С. 484-489.
.
Бабарыкин Н.Н. Влияние восстановительного процесса на теплообмен в доменной
печи // Сталь. - 1981. - №3. - С. 5-9.
.
Исследование работы газов по высоте и радиусу доменной печи при вдувании
природного газа. / В.И. Логинов, С.М. Соломатин, А.И. Парфенов и др. // Сталь.
- 1966. - №11. - С. 978-984.
.
Китаев Б.И., Ярошенко Ю.Г., Лазарев Б.Л. Теплообмен в доменной печи. - М.:
Металлургия, 1966. - 352 с.
.
Ярошенко Ю.Г., Швыдкин В.С. Известия вузов. Черная металлургия, 1967. - №8. -
С. 129-134.