Технология изготовления коробчатой конструкции
Содержание
Введение
. Технология изготовления коробчатой
конструкции.
.1 Назначения конструкции.
.2 Сварочные материалы.
.3 Подготовка металла к сварке.
.4 Сварочное оборудование.
.5 Режимы сварки.
.6 Техника сварки.
.6.1 Сборка изделия.
.6.2 Наложение сварных швов
.7 Мероприятия по уменьшению
деформации.
.8 Контроль сварного изделия.
. Техника безопасности при
выполнение сварочных работ.
Список используемой литературы
Введение
Сварка принадлежит к числу великих русских
изобретений. Она чудесно преобразила лицо многих технологических процессов
производства машин и механизмов, строительства судов и сооружений, играет
важную роль в освоении космоса.
Сварка сыграла важную роль в выполнении первых
пятилеток, индустриализации нашей страны, в оснащении Советской Армии могучей
боевой техникой в грозные годы Великой Отечественной войны, в восстановлении и
подъёме народного хозяйства в послевоенный период.
В настоящее время сварка превратилась в крупный
самостоятельный вид производства. Она применяется для создания и возведения
принципиально новых конструкций и сооружений, для ремонта машин и аппаратов,
для получения изделий со специальными свойствами. Сварные конструкции несут
свою службу при сверхвысоких и сверхнизких температурах, при давлениях,
значительно превосходящих атмосферное, и в условиях космического вакуума.
Современные достижения в области сварки позволяют соединять не только металлы,
но и пластмассы, стекло, керамику и другие материалы. При этом свариваемые
элементы могут иметь размеры от нескольких микрон в производстве изделий
электронной техники до десятков метров в машиностроении и строительстве
Создание и продвижение в жизнь всё новых и новых
материалов с всё более ярким спектром их характеристик неразрывно связано с
усложнением и постоянным развитием служебных свойств машин и механизмов в самом
широком смысле их понятий. И здесь без сварки не обойтись никаким образом.
Молодость сварки, её широта и универсализм,
высокая экономическая эффективность служат залогом дальнейшего плодотворного
развития сварочной науки и техники.
1 Технология изготовления коробчатой конструкции
.1 Назначения конструкции
Мангал самое распространенное решение устройства
для жарки мяса на открытом огне. Его конструкция проста до элементарного.
Классический мангал представляет собой металлический ящик на ножках. В
отдельных случаях этот ящик может иметь двойное дно с поддувалом. Готовые
мангалы продаются как в строительных гипермаркетах, так и в хозяйственных
отделениях рынков. Авторские кованые мангалы нередко можно встретить в
специальных каталогах и в сети Интернет. Если вы желаете видеть на своем
участке нечто оригинальное, то ничего лучшего кованого мангала пока не
придумали
.2 Сварочные материалы
УОНИ 13/55
Используются для сварки стали углеродистой и
низколегированных сталей.
Цели для которых используются эти электроды:
Электроды предназначены для сварки ответственных
конструкций из сталей низколегированных и углеродистых, когда повышены
требования по пластичности и также ударной вязкости к металлу сварных швов. Сварка
происходит во всех положениях пространственных, кроме положения вертикально
сверху вниз, при помощи постоянного тока обратной полярности.
Рис.4 Электроды уони 13/55
.3 Подготовка металла к сварке
В подготовку металла под сварку входит правка,
разметка и наметка, резка и обработка кромок, холодная и горячая гибка. Правка
производится преимущественно на станках, а иногда вручную. Листовой, полосовой
и профильный прокат правят на вальцах, которые чаще всего имеют семь или девять
валков.
Вальцы оборудуются двумя роликовыми столами для
загрузки и выхода металла в процессе правки. При правке листы пропускают через
вальцы от 3 до 5 раз. Наряду с машинной правкой иногда применяют ручную правку.
Последнюю производят на чугунных или стальных правильных плитах ударами молота,
кувалды и при помощи винтового пресса. Правку угловой стали производят на
углоправильных вальцах или на ручных винтовых прессах, а двутавров и швеллеров
- на приводных или ручных правильных прессах. Разметка и наметка. При
индивидуальном производстве выправленный металл поступает на разметку, а при
массовом и серийном производстве поступает для наметки. Перед разметкой и
наметкой поверхность металла грунтуется меловой краской на клею.
При разметке однотипных деталей для массового и
серийного производства пользуются металлическими или фанерными шаблонами.
Разметка при помощи шаблонов называется наметкой. Инструментами для выполнения
разметки и наметки служат чертилка из закаленной стали, кернеры, стальные
линейки и угольники, стальные циркули и рейсмусы, молотки, клямеры, струбцины,
стальные рулетки и др.
Резка. Резка металла на заготовки производится
механическим способом на ножницах и пилах или газокислородным пламенем.
Механическая резка производится в основном на ножницах и применяется
преимущественно для прямолинейного реза листов толщиной до 20 мм. Наибольшее
применение имеют гильотинные ножницы с ножами длиной от 1 до 3 м и
пресс-ножницы с длиной ножей до 700 мм.
Для криволинейного реза толщин до 6 мм
применяются роликовые ножницы с дисковыми ножами. Для прямолинейного реза
больших толщин и для криволинейного реза толщин свыше 6 мм применяется
преимущественно газокислородная резка ручная, полуавтоматическая и
автоматическая. Для холодной резки стержней круглого и других сечений
применяются круглые (циркульные) зубчатые и фрикционные пилы.
Обработка кромок под сварку. Обработка и скос
кромок под сварку производятся механическим путем на кромкострогальных и
продольно-строгальных станках или газокислородным пламенем. При небольшом
объеме работ иногда применяют рубку пневматическим зубилом. Гибка. Гибка
листового, полосового и широкополосового металла производится на листогибочных
трехвалковых и четырехвалковых вальцах. На холодную гибку поступают листы с подготовленными
кромками и вырезанными отверстиями малых диаметров. Гибка профильного металла
производится на правильно-гибочных прессах и роликовых гибочных станах.
Наименьший допустимый радиус гибки стали в холодном состоянии рекомендуют брать
равным 25-кратной толщине листа или высоте симметричного профиля. Если радиус
холодной гибки меньше 25 толщин деформируемой стали, то возможны надрывы
наружных волокон.
Гибка больших толщин и гибка обечаек малого
диаметра, при средней толщине листа, производится горячим способом в
кузнечно-прессовых цехах. Нагрев деталей производится до температуры
1000-1100°С, при которой металл легко поддается деформированию. Подготовку
кромок под сварку и вырезку больших отверстий производят после горячей гибки
.4 Сварочное оборудование
Рис.2 Выпрямитель сварочный ВД-306 С1
Сварочный выпрямитель типа ВД-306 С1
предназначен для ручной дуговой сварки покрытыми электродами изделий из сталей
на постоянном токе.
Регулирование сварочного тока осуществляется механическим
перемещением обмоток трансформатора с указанием сварочного тока по шкале на
лицевой панели.
Выпрямитель ВД-306 С1 рекомендуется для
применения в условиях цехов промышленных предприятий .
Выпрямитель имеет следующие основные технические
решения:
• Плавная регулировка сварочного тока в
пределах двух ступеней переключения
• Защита от тепловой перегрузки
• Класс изоляции Н
• Быстроразъемные, безопасные токовые
разъемы
• Принудительное охлаждение
.5 Режимы сварки
Режимы ручной дуговой сварки имеют основные и
дополнительные параметры. Основные параметры - диаметр электрода; сила, род и
полярность сварочного тока; напряжение дуги.
Дополнительные - состав и толщина покрытий,
число проходов, положение шва в пространстве.
Диаметр электродов зависит от толщины металла,
положения шва в пространстве, катета шва. Сила сварочного тока зависит oт
выбранного диаметра электрода. Пpи сварке швов в нижнем положении величину токa
подсчитывают по эмпирическим формулам Iсв = Кdэ Или Iсв = (20 +6dэ)dэ
Пpи сварке на вертикальной плоскости уменьшают
силу тока на 10-15 %, а в потолочном положении уменьшают на 15-20 % по
сравнению со значением, выбранным для нижнего положения.
.6 Техника сварки
В процессе сварки швов в нижнем положении
сварщик совершает электродом три основных движения: подает электрод вниз для
поддержания постоянной длины дуги по мере плавления электрода; перемещает
электрод вдоль оси шва для заполнения разделки шва, а также производит концом
электрода поперечные движения для получения валика шва заданной ширины.
Рис.3 Положение швов в пространстве
В процессе сварки швов в нижнем положении
сварщик совершает электродом три основных движения: подает электрод вниз для
поддержания постоянной длины дуги по мере плавления электрода; перемещает
электрод вдоль оси шва для заполнения разделки шва, а также производит концом
электрода поперечные движения для получения валика шва заданной ширины. Схемы
движения конца электрода представлены на рис. 78. Неправильное ведение электрода
при сварке может привести к непроварам и пористости шва.
Для получения провара и хорошо сформированного
шва амплитуда поперечных колебаний электрода не должна превышать двух-трех
диаметров электрода. При сварке тонкого металла и первых слоев многослойного
шва электрод ведут без поперечных колебаний. По положению в пространстве швы
разделяют на нижние, вертикальные и потолочные Наиболее удобной для выполнения
является сварка в нижнем положении
металл сварка трещина напряжение
1.6.1 Сборка изделия
Подготовка и сборка элементов конструкции под
сварку во многом предопределяют качество сварных соединений и их надежность.
Вместе с тем не следует предъявлять излишних требований к подготовке и сборке
деталей под сварку. Рациональной технологией сборки является такая технология
сборки деталей, которая обеспечивает необходимое качество сварного соединения и
шва при минимальных требованиях к сборке.
С увеличением толщины свариваемых кромок
увеличиваются высота, длина и шаг прихваток. Поперечное сечение прихватки не
должно превышать 1/8 сечения полного шва. В местах резких переходов, в острых
углах, на окружностях с малым радиусом и в других местах концентрации
напряжений установка прихваток не разрешается. Прихватки также не следует
устанавливать вблизи отверстий, на расстоянии менее 10 мм от отверстия или от
края детали.
При прихватке фланцев, цилиндров, шайб,
трубчатых соединений и т. п. прихватки следует располагать симметрично. В
случае двусторонней прихватки деталей прихватки следует располагать в шахматном
порядке. Прихватки следует ставить в такой последовательности, которая
исключает или сводит до минимума коробление листов. Прихватку длинных листов
начинают с постановки прихваток на одном, а затем на другом концах соединений,
третью прихватку ставят в середине. Остальные прихватки ставят между ними.

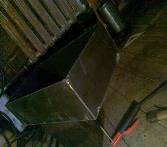
Рис.4 Сборка изделия на прихватках.
.6.2 Наложение сварных швов
При этом вначале осуществляется сварка узлов, из
которых в дальнейшем собирается и сваривается сложное изделие. Особенно
продуманно следует выбирать порядок сварки двухсторонних швов.
Для уменьшения внутренних напряжений и
предупреждения образования трещин обе стороны надлежит сваривать одновременно.
Поэтому конструкции из легированной стали весьма полезно сваривать в поворотном
приспособлении.
Для борьбы с напряжениями и трещинами
рекомендуется применять способ обратной деформации, а также местный или общий
подогрев.
При многослойной сварке валики следует
накладывать по возможности одинакового сечения и длины. Это необходимо для
уменьшения зоны закалки свариваемой стали. А зона отпуска показана радиальной
штриховкой. Между штриховкой и границей валика располагается зона закалки. При
наложении последующих валиков зона закалки ранее наложенных валиков
нагревается, вследствие чего происходит ее отпуск. В результате такого метода
сварки вся зона термического влияния может быть равномерно отпущена.
Если валики наложены разного сечения и в
различном положении, зоны отпуска будут не полностью перекрывать зоны закалки
предыдущих валиков и в шве останутся большие прослойки закаленной стали.

Рис. 5 Наложение сварных швов
.7 Мероприятия по уменьшению деформации
Образование остаточных напряжений и деформаций
при сварке вызывается одной и той же причиной, именно появлением внутренних
усилий при местном нагреве металла до пластического состояния. Оба эти явления
находятся во взаимной связи между собой, но пpoявляются при сварке конструкций
в различной степени и во многих случаях в противоположных направлениях.
В сварных конструкциях, изготовленных без
заметных искривлений, остаточные напряжения растяжения достигают весьма высоких
значений. Наоборот, в сильно деформированных при сварке конструкциях величина остаточных
напряжений растяжения понижена. Вследствие этого некоторые мероприятия по
уменьшению остаточных деформаций противоположны мероприятиям по уменьшению
остаточных напряжений. Все же в числе мероприятий по уменьшению остаточных
напряжений растяжения есть такие, которые ведут к уменьшению деформаций.
Мероприятия по борьбе с деформациями можно разделить на три вида:
конструктивные, технологические, проводимые в процессе сварки, и
технологические, проводимые после сварки.
Основное внимание при изготовлении сварных
конструкций необходимо сосредоточить на мероприятиях конструктивных и
технологических, выполняемых в процессе сварки. Что касается мероприятий по
уменьшению деформаций после сварки, которые главным образом сводятся к холодной
и горячей правке искривленных сваркой изделий, то применение их на практике
нерационально. Холодную или горячую правку после сварки можно применять только
в крайних случаях, так как холодная и горячая правка, помимо дополнительных
трудоемких операций, приводят к увеличению остаточных напряжений растяжения в
активной зоне и к исчерпыванию пластических свойств в металле шва. Последнее
понижает вибрационную и ударную выносливость сварных конструкций и приводит
иногда к разрывам и трещинам в процессе правки или эксплуатации. Для ответственных
конструкций холодная и горячая правка не опасна и безвредна только в том
случае, если после правки производится снятие напряжений путем термического
отпуска.
.8 Контроль сварного изделия
Визуальный контроль качества.
Визуальным контролем (ВИК-ом) проверяют качество
подготовки и сборки заготовок под сварку, качество выполнения швов в процессе
сварки и качество готовых сварных соединений. Обычно внешним осмотром
контролируют все сварные изделия независимо от применения других видов
контроля.
Визуально-измерительный контроль во многих
случаях достаточно информативен и является наиболее дешевым и оперативным
методом контроля. Контроль заготовки и сборки. Внешнему осмотру подвергают
свариваемые материалы для выявления (определения отсутствия) вмятин, заусенцев,
окалины, ржавчины и т. п. Проверяют качество подготовки кромок под сварку и
сборку заготовок.
К основным контролируемым размерам собранных под
сварку деталей (изделий) относят зазор между кромками и притупление кромок -
для стыковых соединений без разделки кромок; зазор между кромками, притупление
кромок и угол их разделки - для соединений с разделкой кромок; ширину нахлестки
и зазор между листами - для нахлесточных соединений; зазор между листом и
кромкой, угол между свариваемыми элементами, а также притупление и угол скоса
кромок - для тавровых соединений; зазор между свариваемыми элементами и угол
между ними - для угловых соединений.
Детали, узлы или изделия, собранные под сварку с
отклонением от технических условий или установленного технологического
процесса, бракуют. Средства, порядок и методика визуального контроля
предусматриваются технологическим процессом производства или нормативной
документацией.
Наблюдение за процессом сварки. На этом этапе
сварщик помимо контроля режимов сварки (тока, напряжения, скорости сварки и т.
п.) и стабильности горения дуги следит за правильностью выполнения валиков в
многослойных швах. Особенно важным на этом этапе является тщательный осмотр
первого слоя при любом количестве слоев. Качество сварки первого слоя оценивают
при необходимости с помощью лупы, а для оценки качества конструкций
ответственного назначения иногда применяют также капиллярную дефектоскопию.
Осмотр готовых изделий. Внешним осмотром
невооруженным глазом или с помощью лупы выявляют прежде всего дефекты швов в
виде трещин, подрезов, пор, свищей, прожогов, наплывов, непроваров в нижней
части швов. Многие из этих дефектов, как правило, недопустимы и подлежат
исправлению. При осмотре выявляют также дефекты формы швов, распределение
чешуек и общий характер распределения металла в усилении шва.
Внешний вид поверхности шва характерен для
каждого способа сварки, а также для пространственного положения, в котором
выполнялась сварка. Равномерность чешуек характеризует работу сварщика, его
умение поддерживать постоянную длину дуги и равномерную скорость сварки.
Неравномерность чешуек, разная ширина и высота шва указывают на колебание
мощности дуги, частые обрывы и неустойчивость горения дуги в процессе сварки. В
таком шве возможны непровары, поры, шлаки и другие дефекты. При сварке в
вертикальном и потолочном положениях сварные швы имеют резко выраженную
Неравномерность чешуек, бугры, седловины и наплывы. При сварке в защитных газах
в вакууме внешняя поверхность швов гладкая, блестящая, без чешуек и имеет вид
полоски расплавленного металла. В сварных швах, выполняемых из титана и других
активных материалов, контролируют цвет и величину зоны цветов побежалости. Сварные
швы часто сравнивают по внешнему виду со специальными эталонами. Геометрические
параметры швов измеряют с помощью шаблонов или измерительных инструментов.
Тщательный внешний осмотр - обычно весьма
простая операция, тем не менее может служить высокоэффективным средством
предупреждения и обнаружения дефектов. Только после проведения визуального
контроля и исправления недопустимых дефектов сварные соединения подвергают
контролю другими физическими методами (рентгеновский контроль, ультразвуковой
контроль и т.д.) для выявления внутренних дефектов.
Рис.6 Набор инструментов визуального осмотра.
. Техника безопасности при выполнение сварочных
работ
При работе с металлами необходимо строго
соблюдать правила техники безопасности. Для защиты лица и глаз сварщика от
лучей сварочной дуги и брызг металла и от подсвечивания от дуги рядом
работающего сварщика служат щитки и маски или шлемы, изготавливаемые согласно
данным ГОСТ. Щиток и маски должны быть такого размера и формы, чтобы ни одна
часть лица не была обнаженной.
В рамку, через которую сварщик наблюдает за
дугой, вставляются два стекла: защитное, или светофильтр, и покровное с
номинальными размерами каждого 52 X 102 X 2,5 мм. Покровное - наружное -
бесцветное, служит для защиты светофильтра от металлических брызг. Щитки и
маски должны поставляться комплектно со светофильтром и покровным стеклом.
Нельзя пользоваться случайными цветными
стеклами, так как они не всегда могут хорошо защищать глаза от невидимых
ультрафиолетовых лучей сварочной дуги, которые вызывают хронические заболевания
глаз.
Защитные стекла вкладываются в рамку с
внутренней стороны щитка и удерживаются пружинками. Покровное стекло нужно
менять каждые 5-10 дней.
Проходы между группами сварочных трансформаторов
должны иметь Ширину не менее 1 м. Расстояние между сварочными трансформаторами,
стоящими рядом в одной группе, составляет не менее 0,1 м, между сварочным
трансформатором и ацетиленовым генератором- не менее 3 метров.
Регулятор сварочного тока может размещаться
рядом со сварочным трансформатором или над ним. Установка последнего над регулятором
тока запрещается.
В качестве обратного провода, соединяющего
свариваемое изделия с источником сварочного тока, может служить стальная шина
любого профиля при условии, что ее сечение обеспечивает безопасное по условию
нагрева протекания сварочного тока.
Список используемой литературы
1.Андреев
В.В. Инвентарные источники питания сварочной дуги // Сварщик .- 1999. -№ 6 . -
с. 25-29.
.Виноградов
В.С. Оборудование и технология дуговой автоматической и механической сварки/
В.С. Виноградов. - М. :Высш.Шк., 2000. - 319с.
.Волченко
В.Н. Контроль качества сварных конструкций / В.Н. Волченко. - М.:
Машиностроение, 1986. - 152с.
.Кобозев
В.А. Сварочные трансформаторы - В.А. Кобозев, В.В. Коваленко.- Ставрополь:
[б.и.], 1998- 227с.
.Оборудование
для дуговой сварки: справочное пособие/ под ред. В.В Смирнова -Л.:
Энергоатомиздат, 1986.-656 с.
.Розаренов
Ю.Н. Оборудование для электрической сварки плавлением /Ю.Н. Розаренов .- М.:
Машиностроение, 1987.- 207 с.