Модернизация уплотнений поршня гидроцилиндров
Аннотация
В данном дипломном проекте были затронуты вопросы
работы гидропривода одноковшового экскаватора четвертой размерной группы ЭО
4225, выполняется модернизация гидросистемы, осуществляется подбор
гидроаппаратов.
Реферат
Модернизация гидропривода одноковшового экскаватора ЭО 4225
Цель проекта - борьба с пульсациями давления и негативными вибрациями в
гидроприводе машины.
В процессе работы рассмотрено влияние температуры рабочей жидкости на
параметры и характеристики гидравлического привода. Произведен патентный поиск
гидроаккумуляторов и уплотнений поршня гидроцилиндров. Выполнены прочностные
расчеты и гидравлический расчет гидропривода одноковшового экскаватора.
Существующая методика гидравлического и теплового расчетов гидропривода
адаптирована к программе MathCAD.
Также были выполнены расчеты виброизоляторов и экономический расчет.
Техническое предложение
Целью дипломного проекта является модернизация
гидропривода одноковшового экскаватора четвертой размерной группы ЭО 4225.
Разработка заключается в следующем: установка нового устройства -
гидроаккумулятора, модернизация уплотнений поршня гидроцилиндров.
Введение
Гидравлический привод применяется на дорожно-строительных,
подъемно-транспортных, сельскохозяйственных, лесозаготовительных и лесохозяйственных,
мелиоративных, транспортных и других самоходных машинах различного
технологического назначения. Основные преимущество гидропривода: плавность и
равномерность движения рабочих органов, возможность получения больших
передаточных отношений, возможность бесступенчатого регулирования скоростей в
широком диапазоне. А также простота преобразования вращательного движения в
возвратно-поступательное и возвратно-поворотное, малый момент инерции,
обеспечивающий быстрое реверсирование, легкость стандартизации и унификации
основных элементов, небольшой вес и малые габариты гидрооборудования. Высокий
КПД, мгновенность передачи командных импульсов, простота предохранительных
устройств и их высокая надежность; легкость управления и регулирования,
самосмазываемость оборудования также относятся к преимуществам гидропривода.
Гидравлический привод применяется на многих машинах: экскаваторах,
бульдозерах, автогрейдерах, скреперах, валочно-трелевочных и
валочно-пакетирующих машинах. Установлено на погрузчиках, автокранах,
зерноуборочных машинах. Также для привода рабочего оборудования, колесного или
гусеничного движителя, выносных опор и рулевого управления. В настоящее время
около 90% самоходных машин различного технологического назначения оснащено
гидроприводом. В дальнейшем процент гидрофицированных машин еще более
увеличится.
В настоящее время в нашей стране так же, как и в зарубежных странах,
практически невозможно назвать такую отрасль промышленности или сельского
хозяйства, в которых не применялся бы гидропривод.[1]
Гидроприводом оснащено большинство лесных, дорожно строительных и
мелиоративно-строительных машин.
1. Общая часть
.1 Назначение и техническая характеристика машины
Полноповоротный одноковшовый универсальный
гидравлический экскаватор на гусеничном ходу тракторного типа ЭО-4225
изготавливается в соответствии с ГОСТ 17343-71 и предварительно разрыхленных
скальных и мерзлых грунтов IV
категорий с величиной кусков не более 400 мм, в диапазоне температур окружающей
среды от минус 40 до плюс 40 град.С.
Экскаватор используется для разработки карьеров, рытья
котлованов, траншей, каналов, а также для погрузки грунта и сыпучих материалов.
Специальные рабочие органы: гидромолот, клещевой
захват и рыхлитель, позволяют производить вскрышные работы на мерзлых и скальных
грунтах.
Конструкция экскаватора предусматривает возможность
работать со следующими видами сменного рабочего оборудования : обратная лопата,
обратная лопата с моноблочной стрелой, обратная лопата с удлиненной рукоятью,
оборудование прямого копания, оборудование прямая лопата унифицированная с
обратной лопатой, грейфер, грейфер многочелюстной, грейфер с удлинителем,
грейфер для глубоких колодцев, рыхлитель, гидромолот, оборудование
захватно-клещевого типа с трезубым рыхлителем.
Конструкция ходовой части предусматривает возможность
установки уширенных башмаков, что обеспечивает снижение удельного давления на
грунт и улучшает условия передвижения и работы экскаватора на слабых и
переувлажненных грунтах.
Экскаватор состоит из трех основных частей: тележки,
состоящей из гусеничного хода и ходовой рамы; опорно-поворотного устройства;
поворотной платформы с механизмами и агрегатами гидросистемы и рабочего
оборудования.
Опорной базой экскаватора является тележка. Привод
тележки осуществляется механизмом передвижения. На тележку через поворотную
роликовую опору опирается поворотная платформа, вращение которой осуществляется
механизмом поворота. Базовые узлы экскаватора и рабочее оборудование
изготовлены из низколегированных сталей.
Силовая установка состоит из дизельного двигателя и
гидронасоса, установлена в задний части поворотной платформы.
Рабочее оборудование включает в себя: стрелу, рукоять
и ковш. Гидроцилиндры приводят в действие рабочее оборудование. Гидромоторы
осуществляют привод механизма поворота, поворотной платформы и механизма
передвижения экскаватора. Управление рабочими органами и передвижением
осуществляется с помощью рычагов и педалей механизма гидроуправления
расположенного в кабине оператора.
Конструкция кабины машиниста также включает в себя
системы отопления, вентиляции, кондиционирования, что обеспечивает нормальные
условия работы оператора.
1.2 Принципиальная гидравлическая схема экскаватора
Гидравлический привод экскаватора является сложной
функциональной системой, в которой использованы различные по назначению
гидравлические устройства, обеспечивающие требуемые условия работы экскаватора.
Принципиальная схема гидропривода экскаватора
определяет полный состав элементов и связей между ними и дает детальное
представление о принципах работы экскаватора.
Одной из основных задач современного отечественного
экскаваторостроения является правильный выбор схемы гидропривода. К
гидроприводу экскаватора предъявляется ряд требований: правильный выбор
механических характеристик; обеспечение стабильной работы в переходных режимах;
обеспечение необходимых скоростей рабочего движения; получение наилучших
энергетических показателей; достижение наибольших значений КПД элементов
привода; обеспечение удобства управления; обеспечение достаточной
долговечности.
Признавая необходимость выполнения этих требований,
нужно отметить, что применение любой схемы гидропривода может быть признано
рациональным, если она:
1) обеспечивает выполнение экскаватором
необходимых технологических операций при проведении земляных и скальных работ;
2) обеспечивает наиболее высокие
технико-экономические показатели экскаваторов.
Гидропередачи отдельных механизмов должны обеспечивать
следующие требования:
1) такую продолжительность рабочих
операций, которая соответствовала бы минимальной продолжительности рабочего
цикла экскаватора, отвечающего требованиям стандартов;
2) рабочие усилия и скорости экскаватора
в соответствии с требованиями стандартов;
3) минимальные затраты энергии и
максимальный КПД при выполнении рабочих операций;
4) ограничение максимальных скоростей и
ускорений;
5) ограничение динамических нагрузок до
минимально возможных;
6) независимость действия и возможность
совмещения не менее трех рабочих операций;
7) надежность и долговечность;
8) безопасность работы;
9) нормальную работу машины при таких
условиях: температуре окружающего воздуха от - 45 до 45 °С; тряске, вибрации,
воздействии центробежных сил, крене и дифференте; запыленности окружающего
воздуха;
10) долговечность всех агрегатов, уплотнений,
шлангов и других элементов гидропривода; возможность регулирования, наладки и
мелкого ремонта в условиях эксплуатации; возможность плавного бесступенчатого
регулирования скоростей всех приводов;
11) плавное трогание и остановку машины.
Гидравлическая схема экскаватора насыщена гидроэлементами
и функциональные связи между ними очень сложны. Поэтому при изучении назначения
элементов гидропривода и их взаимодействия схему разобьем на составные части.
Как было сказано, гидропривод состоит из
гидропередачи, системы гидроуправления и вспомогательных устройств. На эти
составные части разобьем гидросхему и рассмотрим устройство всех элементов в их
взаимодействии как в составных частях гидросхемы, так и в полной гидросхеме.
Рабочая жидкость из гидробака 1 насосом 59 или 57 (секциями А и В) подается
к гидрораспределителям 36 и 50 с гидроуправлением. При нейтральном положении
золотников гидрораспределителей напорные линии гидронасоса соединены со сливом.
Рабочие полости гидроцилиндров и гидромоторов поворота и хода заперты.
От секции А насоса 59 или 57 рабочая жидкость поступает в распределитель
36, а от секции В - в распределитель 50.
Секция 24 через центральный коллектор 19 управляет левым гидромотором 28
механизма передвижения, а секция 48 правым гидромотором.
Секция 30 управляет подачей второго потока, в распределитель 50 для
получения ускоренного движения подъема стрелы, рукояти и ковша. Секция 33
управляет гидромотором механизма поворота экскаватора влево и вправо.
Секция 34 управляет движением гидроцилиндра ковша 43 при включении
педалей блока 52. Сливная крышка 35 служит для объединения сливных и
переливного каналов гидрораспределителя в один канал, который соединен отводом
со сливной магистралью.
Золотник 44 управляется педалью блока 52 и служит для опускания стрелы
под действием собственного веса при нейтральном положении секции 45, и
обеспечивает «плавающее» положение рабочего оборудования, необходимое при
производстве планировочных и зачистных работ.
Золотник опускания стрелы 44, крепится к рабочей секции 45. Опускание
стрелы может производится также принудительно на режиме насоса путем включения
золотника 45 на опускание стрелы. Для обеспечения плавного опускания стрелы на
режиме насоса в поршневом трубопроводе гидроцилиндров стрелы установлен
дроссель 38.
Промежуточная секция 46 необходима для совмещения двух рабочих операций,
выполняемых от одного гидрораспределителя 50 подъема или опускания стрелы с
поворотом рукояти или ковша по последовательной схеме. При совмещении указанных
операций рабочая жидкость, сливающая из штоковых или поршневых полостей
гидроцилиндров стрелы, поступает через обратный клапан промежуточной секции 47
или 49 в гидроцилиндры рукояти или ковша. Секция 47 управляет движением
гидроцилиндра рукояти в трубопроводе штоковой полости которого, установлен
дроссель 42, который служит для предотвращения резкого опускания рукояти под
собственным весом.
Секция 49 управляет движением гидроцилиндра ковша 43.
Напорная секция 23 распределителей имеет предохранительный клапан,
отрегулированный на давление 28 МПа, который предотвращает перегрузку насоса 59
(секции А и В) при включении золотника стрелы, рукояти или ковша не позволяет
течь рабочей жидкости в обратном направлении.
Перепускные клапаны блока перепускных клапанов 25 и 31, установленные на
рабочих секциях 24, 33 и 48, разгружают гидромоторы от пиковых давлений при
торможении или разгоне.
Предохранительные клапаны блока перепускных клапанов 25, установленные на
рабочих секциях хода, отрегулированы на давление 25 МПа, а клапаны секции 33
механизма поворота - на давление 160 МПа и запломбированы.
Предохранительные клапаны 37 разгружают полости гидроцилиндров,
трубопроводы и гидрораспределители от чрезмерных реактивных давлений в запертых
полостях гидроцилиндров, возникающих при копании ковшом. Клапаны отрегулированы
на давление 40 МПа.
Предохранительный клапан 20 защищает от перетяжки гусеничные ленты
ходового механизма во время движения и настроен на давление 28 МПа.
Предохранительные клапаны 9 защищают от перегрузки насосы 4 и 7, и
настроены на 35 МПа.
Обратные клапаны 39 предназначены для подачи потока рабочей жидкости в
одном направлении от сливной линии к поршневой полости гидроцилиндров стрелы 40
или штоковой полости гидроцилиндра рукояти 41 в том случае когда в этих
полостях гидроцилиндров создается разрежение в случае срабатывания
предохранительных клапанов 37. Они установлены в трубопроводах.
В сливной линии установлены линейные фильтры 14, и калорифер с
вентилятором. Привод вентилятора осуществляется от гидромотора 8, питаемого
шестеренным гидронасосом 7, установленном на ДВС 58.
Предохранительный клапан 12 установленный в гидросистеме параллельно
калориферу 10, предотвращает повышение давления перед калорифером при низкой
температуре рабочей жидкости.
Для механизированной заправки жидкостью основного бака 1 и гидросистемы
имеется распределитель 66, при переключении которого соединяется заправочная
емкость 2 с гидронасосом 7, который подает ее через фильтры 63 в бак 1.
Для управления золотниками рабочих секций 24, 30, 33, 34, 45, 47, 48 и 49
в кабине машиниста на пульте установлены блоки гидроуправления 55, 53 и 52,
которые при включении дают гидравлический сигнал на включение золотника
гидрораспределителя. В кабине машиниста установлено 5 блоков управления из них
три рычажных и два педальных.
Для питания блоков управления, нульустановителя гидронасоса 59 и тормозов
механизма поворота и хода служит вспомогательная гидросистема, состоящая из
шестеренного насоса установленного на ДВС, гидроклапана 9, манометра 13 и
пневмогидроаккомулятора 6.
Давление в гидросистеме контролируется по показаниям манометров 13, 17 и
18, включаемых кранами 15 и 16. Для защиты манометров 13 и 18 от повреждения в
их линии установлен демпфер 11 который успокаивает колебания рабочей жидкости.
Для сообщения гидробака 1 с атмосферой установлен клапан-сапун 62, который
поддерживает в баке избыточное давление для ускоренной подачи рабочей жидкости
в насос 59 или 57. На сливном трубопроводе бака 1 крепится датчик температуры,
который дает электрический сигнал на указатель температуры рабочей жидкости,
установленный в кабине машиниста.
Для предотвращения утечек рабочей жидкости из гидросистемы, в случае
обрыва трубопровода предусмотрена установка реле уровня масла 60 которое
сигнализирует о понижении уровня масла в баке 1 ниже критического, путем подачи
электрического сигнала на электроуправляемый золотник 61 для снятия давления
управления. При этом рабочее движение экскаватора прекращается, а насос 59 с
нульустановителем понижает подачу рабочей жидкости в напорную линию до
минимального количества.
При заполнении масляного бака 1 до необходимого уровня сигнализатор
уровня масла включает электроуправляемый золотник и подает давление в систему
управления экскаватором. В гидросистеме установлен пневмогидроаккомулятор 6 с
обратным клапаном 5, который обеспечивает накопление энергии рабочей жидкости и
позволяет поддерживать необходимое рабочее давление в системе управления в
моменты включения двух золотников блоков управления и подачу сигнала на
регулятор насоса 59. Обратный клапан 5 запирает поток жидкости в обратном
направлении.
При остановке двигателя за счет накопленной энергии жидкости в
пневмогидроаккомуляторе можно произвести включение золотника опускания рабочего
оборудования. Для гидропривода механизмов экскаватора, может использоваться,
как основной вариант, гидронасос 59 с нульустановителем и нерегулируемый
гидромотор хода 28, и запасной вариант, гидронасос 57 без нульустановителя и
регулируемый гидромотор хода 29.
Работа гидросистемы натяжения гусениц.
Гидравлическая система обеспечивает натяжение и сдавание гусениц при
попадании твердых предметов между гусеничной лентой и ведущим или натяжным
колесом. Натяжение гусеничных лент осуществляется автоматически, путем отвода
части рабочей жидкости, подаваемой на механизм передвижения. При включении
привода хода рабочая жидкость от гидрораспределителей через коллектор 9 по
трубопроводам 8 подается на гидромоторы 6 хода, приводя их во вращение. При
включении любого гидромотора, независимо от направления, рабочая жидкость через
систему клапанов «ИЛИ» 7 и 11 и через обратный клапан 12 попадает на блок
клапанов 3, а от него по трубопроводам 2- к гидроцилиндрам 1 натяжения гусениц,
автоматически приводя их в натяжку. Обратный клапан 12 блокирует слив рабочей
жидкости из гидроцилиндров натяжения при отключении привода хода, то есть
удерживает гусеницы в натянутом состоянии, когда механизм передвижения не
работает. В случае чрезмерного повышения давления в гидроцилиндрах натяжения
гусениц, например при попадании твердых предметов между гусеничной лентой и
натяжным или ведущим колесом (стопорная нагрузка), давление превысит величину
настройки предохранительного клапана 4, и в блоке клапанов 3, клапан 4
откроется и рабочая жидкость из гидроцилиндров 1 натяжения через бачок 5
(гаситель давления) по дренажному трубопроводу 10 гидромоторов хода через
коллектор 9 сбросится в бак рабочей жидкости 14. Дроссель 13, установленный в
клапане 12, снимает динамические перегрузки на гидроцилиндры натяжения при
включении привода хода.
1.3 Влияние температуры рабочей жидкости на
работоспособность и эффективность гидрофицированной машины
Виды внешних воздействий на работу гидропривода.
Эффективность работы гидравлического привода определяется объемным КПД и
подачей насосов, потерями энергии на трение в гидрооборудовании и потерями
давления в гидросистеме, интенсивностью изнашивания деталей и связанную с ней
долговечностью гидрооборудования, сроком службы рабочей жидкости. Эти параметры
в конечном итоге определяют время цикла, производительность и эффективность
использования гидрофицированной машины. Установление качественной и
количественной зависимостей параметров гидропривода от температуры и
определение на их основе оптимального теплового режима, представление на их
основе оптимального теплового режима является сложной технической задачей.
Климатические условия эксплуатации влияют на
работоспособность и эффективность гидропривода в основном через состояние
рабочей жидкости, определяемое ее вязкостью, содержание механических примесей,
газов и влаги, а также модулем упругости. Кроме того, климатические условия
влияют на изменение зазоров в сопряжениях гидрооборудовании, условиях
взаимодействия поверхностей трения, физико-механические свойства деталей,
нагрузки на гидродвигателях. Все перечисленные факторы, действуя одновременно,
усиливают влияние друг на друга и, в конечном итоге определяют качественную и
количественную зависимости параметров и характеристик гидропривода от
климатических условии эксплуатации.
Как известно, рабочие жидкости передают энергию от
насоса по трубопроводам к гидравлическим двигателям, обеспечивая смазку
поверхностей трения, защиту деталей от коррозии, отвод тепла и удаление
продуктов износа из зон трения. Таким образом, за счет рабочей жидкости
осуществляется функционирование гидрооборудования, поэтому состояние жидкости во
многом определяет эффективность гидравлического привода.
В качестве рабочих жидкостей в гидроприводах
самоходных машин применяют минеральные масла с различными улучшающими их
эксплуатационные свойства присадки. Наибольшее распространение получили: в гидроприводах
с аксиально-поршневыми насосами МГ-15В (ВМГЗ зимнее), МГЕ-46В (МГ-30 летнее),
МГ-20 (для стационарных установок в закрытых помещениях); в гидроприводах с
шестеренными насосами М-8В2 (зимнее) и М-10В2 (летнее). Как уже отмечалось,
рабочие жидкости в современных гидроприводах эксплуатируются в широком
диапазоне температур - от минус 50 до плюс 100 °С при давлении в напорной
гидролинии до 32 МПа и разрежении во всасывающей гидролинии до 0,03 МПа.
Жидкость контактирует с полимерами, цветными и черными металлами, на которых в
связи с износом отсутствуют защитные - описные пленки, на жидкость воздействуют
длительные вибрации, в гидросистему попадают из окружающей среды влага и
абразивные частицы. Все это создает весьма неблагоприятные условия эксплуатации
и сокращает срок службы рабочей жидкости.
Прежде всего, срок службы жидкости зависит от
интенсивности и химического разложения, которое происходит в результате
окисления масла кислородом воздуха. Каталитическое воздействие при этом
оказывает температура, нерастворенный воздух и абразивные частицы. Повышение
температуры после плюс 40 °С на каждые 8-10 °С ускоряет интенсивность окисления
масла в два раза.
Процесс окисления и окислительной полимеризации под
воздействием высокой температуры (выше плюс 60 °С) является основным фактором
старения масла, при котором выделяются и выпадают в осадок органические кислоты
и асфальто-смолистые вещества.
Процесс окисления особенно активен при наличии в
жидкости гидросистемы растворенного и эмульгированного воздуха. Так, при
адиабатическом сжатии воздушно-масляной эмульсии, например, до 7 МПа
температура воздуха в микроскопическом пузырьке повышается до 700 °С (с
начальной температуры 0 °С). Такая высокая температура учитывает множество
микроскопических пузырьков, резко интенсифицирует в локальных зонах процессы
карбонизации масла.
За один цикл от всасывания до слива в гидробак рабочая
жидкость претерпевает различные по характеру нагрузки. Во всасывающей
гидролинии на жидкость воздействует разрежение, которое способствует интенсивному
выделению кавитации. В насосах, особенно шестеренных, на жидкость воздействует
чрезвычайно высокое контактное давление. В течение небольшого времени (10-5 с)
контактное давление может достигать2·103МПа.
При прохождении жидкости под давлением с высокой
скоростью через каналы и зазоры направляющей и регулирующей гидроаппаратуры и
другие местные сопротивления происходит многократная деформация (смятие)
жидкости. Этот процесс усиливает вибрации трубопроводов и гидропривода в целом,
происходящая под действием реверсирования и пульсации потока жидкости.
Деформация жидкости в конечном итоге вызывает механическую деструкцию масла,
которая сопровождается уменьшением вязкости, ухудшением смазывающих свойств и
потемнением масла. По требованиям ряда зарубежных фирм, изготавливающих
самоходные машины, рабочая жидкость полежит замене при изменении вязкости на
±10% по отношению к первоначальной. Наличие механических примесей (загрязнений)
в гидросистеме способствует увеличению окисления масла, особенно в момент
образования частиц износа, когда повышены их поверхностно-активные свойства. В
качестве основных источников и причин загрязнений рабочей жидкости необходимо
выделить следующее: загрязнение гидросистемы в период изготовления
гидрооборудования и сборки гидроприводов; загрязнение гидросистемы в процессе
заправок и дозаправок рабочей жидкостью в условиях эксплуатации; загрязнение
гидросистемы в процессе эксплуатации машины.
При строгом соблюдении правил эксплуатации
гидрофицированных машин основное количество механических примесей в рабочей
жидкости появляется в результате износа и коррозии деталей гидрооборудования.
Как при абразивном, так и при усталостном изнашивании взаимодействующих
поверхностей насосов, гидродвигателей, распределителей и регулирующих гидроаппаратов
происходит отделение микрообъемов металла, которые в последствии сортируются
жидкостью по гидросистеме.
Содержание загрязнений растет на каждом этапе
транспортировки рабочей жидкости от нефтеперерабатывающего завода и заправочной
станции. Оно также увеличивается после заправки жидкости в гидросистему по мере
наработки машины, а затем уровень загрязнений стабилизируется.
За счет насыщения рабочей жидкости воздухом происходит
уменьшение ее объемной упругости, возникает интенсивное пенообразование, а в
конечном итоге появляется кавитация в гидронасосах. Процесс интенсивного
пенообразования начинается при вязкости жидкости 300·10-6 м2/с, что для масла
МГ-15В (ВМГЗ) соответствует минус 23 °С.
Влага в рабочей жидкости приводит к образованию
стойкой воздушной масляной эмульсии, в результате чего ухудшаются смазывающие
свойства масел, происходит их интенсивное окисление, повышается трение, более
интенсивно протекает коррозия и кавитационные явления.
Под действием влаги происходит помутнение рабочей
жидкости, по нормам зарубежных фирм допустимое содержание влаги в гидросистемах
строительных машин составляет примерно 0,1% по весу.
Таким образом, в рабочих жидкостях гидросистем
самоходных машин всегда присутствуют механические примеси, влага,
адсорбированные и нерастворенный воздух, и под влиянием их, а также под
влиянием температуры, давления, вибрации, химически агрессивных поверхностей
деталей гидрооборудования минеральные масла претерпевают значительные
изменения, что отрицательно сказывается на их физико-механических свойствах, а
в конечном итоге работоспособности и эффективности гидравлического привода.
.3.1 Влияние температуры на трение в гидрооборудовании
Трение в гидрооборудовании оказывает существенное
влияние на работоспособность гидравлического привода. Например, повышение силы
трения в гидродвигателях (гидроцилиндрах и гидромоторах) снижает полезные
усилия на штоке и валу, тем самым уменьшает грузоподъемность или усилие резания
грунта. Повышение силы трения в насосах увеличивает потребную мощность ДВС, что
приводит к перерасходу топлива и снижению ресурса двигателя. Повышение силы
трения в плунжерах распределителей увеличивает усилия на рукоятках и педалях
управления, что повышает утомляемость оператора и ухудшает эргономические
показатели машины. Повышение силы трения в направляющей и регулирующей
гидроаппаратуре снижает ее быстродействие. В конечном итоге повышение сил
трения снижает производительность машины, увеличивается износ сопряженных
деталей и сокращает ресурс гидрооборудования.
Рассмотрим причины увеличения силы трения уплотнений
при положительных и отрицательных температурах. Увеличение силы трения при
температуре ниже 0°С связано прежде всего с повышением сил внутреннего трения,
которые характеризуются предельным напряжением сдвига одного слоя жидкости
относительно другого.
Увеличение силы трения при температурах выше плюс 20
°С обусловлено одновременным ростом гистерезисной и адгезионной составляющих
силы трения. С повышением температуры повышается эластичность резины,
вследствие чего растет фактическая площадь контакта и увеличивается адгезионная
составляющая силы трения. Улучшение эластичности резинового уплотнения приводит
к увеличению глубины деформируемого поверхностного слоя, так как уменьшается
сопротивление внедрению шероховатостей твердой поверхности цилиндра.
Увеличение глубины деформируемого слоя повышает
гистерезисные потери в уплотнительном элементе. Суммарное увеличение двух
составляющих объясняет повышение силы трения при положительных температурах.
Кроме того, на повышение силы трения значительное влияние оказывает вязкость
масла. С уменьшением вязкости защитные свойства масла ослабевают, и в зоне
контакта уплотнения происходит разрыв масляной пленки, образуются зоны сухого
трения, на которых увеличивается молекулярные взаимодействие контактирующих
поверхностей, т. е. повышается адгезионная составляющая трения.
.3.2 Влияние температуры на потери давления в
гидрооборудовании и трубопроводах
При низких температурах резко снижаются полезные
усилия на рабочих органах гидрофицированных машин, что оказывается на их
грузоподъемности и производительности. Главной причиной этого являются потери
давления в гидрооборудовании, трубопроводах и всасывающей гидролинии насосов.
Эти потери вызываются трением жидкости о стенки трубопроводов и каналов
гидооборудования; деформацией потока жидкости, вызываемой завихрениями в
местных сопротивлениях, изменением скорости и направления потока; инерцией
вязкой жидкости. На преодоление этих сил затрачивается энергия, которая
определяет потери давления в гидросистеме. Эти потери увеличиваются при
увеличении вязкости жидкости и могут привести не только и снижению полезных
усилий на выходные звенья когда давления жидкости в гидродвигателях
недостаточно даже для холостого перемещения рабочего оборудования. Такая
ситуация нередко наблюдается при температурах ниже минус 25 °С в гидроприводах
с шестеренными насосами, в которых используется моторное масло М-8В2. Следует
отметить, что механизм потерь давления во всасывающей и напорной гидролиниях
имеет некоторое различие. Если во всасывающем трубопроводе потери давления
связаны с трением и инерцией вязкой жидкости, то в напорном и сливном
трубопроводах - с трением и деформацией потока жидкости.
Это различие объясняется характером движения жидкости:
во всасывающем трубопроводе направление потока постоянно, ответвлений нет,
изгиб меньше, ограничена и скорость потока; в напорном трубопроводе поток
разветвляется на несколько частей, на его пути встречается большое количество
изгибов и местных сопротивлений, при переключении направляющей и регулирующей
гидроаппаратуры происходит изменение направления и реверсирование потока, за
счет повышенных скоростей (5 м/с и более) наблюдаются завихрения.
Хотя по величине потери давления в напорных
гидролиниях значительно выше, чем во всасывающих, последние оказывают более
существенное влияние на работоспособность гидравлического привода.
Конструкция всасывающего трубопровода и
месторасположения гидробака на машине оказывают влияние на кавитацию. Чем
меньше диаметр, больше шероховатость внутренней поверхности и количества
изгибов трубопровода, чем ниже расположен гидробак по отношению к насосу, тем
раньше, начинается кавитация. Исключить или значительно уменьшить
гидравлические потери во всасывающем трубопроводе можно на стадии проектирования
гидропривода, применяя следующие конструктивные мероприятия:
-увеличение диаметра и уменьшение длины трубопровода;
уменьшение количества и величины местных
сопротивлений;
уменьшение шероховатости внутренней поверхности
трубопровода;
применение всасывающих патрубков коноидальной формы;
расположение гидробака выше всасывающей линии насоса;
применение гидробаков с внутренним давлением выше
атмосферного;
установка дополнительного насоса подпитки;
оптимизация температуры (вязкости) рабочей жидкости.
1.3.3 Влияние климатических условий на
эксплуатационную производительность гидрофицированных машин
Применение гидрофицированных самоходных машин в
северных районах сдерживается исключительно низкой эффективностью
гидравлического привода в зимний период. Например, бульдозер не мог
осуществлять планировку снега при температуре воздуха минус 24 °С, даже через
час с момента пуска машины. Причинами этого явились неуправляемое движение
отвала при действии внешней нагрузки и недостаточное усилие резания.
Аналогичная картина наблюдается и при работе других машин. На практике в
Восточной Сибири, Якутии на дальнем Востоке часто для поддержания
работоспособности гидропривода на определенном уровне в суровых климатических
условиях двигатели машин не глушат с ноября по март месяц. Это ведет к
перерасходу топлива, преждевременному износу двигателя и гидронасоса,
загрязнению окружающей среды. Из всех факторов, определяющих климатические
условия, наибольшее влияние на технико-экономические показатели оказывает
температура. Остальные факторы влияют опосредованно через температуру.
Например, при увеличении скорости ветра, существенно изменяются условия
теплообмена гидропривода с окружающей средой и уменьшается температура рабочей
жидкости. При увеличении прочности разрабатываемого грунта, ухудшении состояния
дорог или повышении глубины снежного покрова ухудшается режим работы
гидропривода, т. к. возрастают нагрузки на гидродвигатель, что в свою очередь,
приводит к повышению давления в гидросистеме и увеличению температуры рабочей жидкости.
Таким образом, температура окружающей среды и рабочей
жидкости является главным фактором, определяющим технико-экономические
показатели гидрофицированных машин.
Нами выделено три основных направления, по которым
температура воздействует на гидравлический привод. Под влиянием температуры (в
диапазоне от минус 50 °С до плюс 80 °С) значительно изменяется состояние
рабочей жидкости: в сотни и тысячи раз повышается вязкость, увеличивается
плотность, повышаются загрязненность и содержание влаги. За счет насыщения
жидкости газо-воздушной фазой, уменьшаются модуль объемной упругости и скорость
распространения импульса, увеличиваются динамическая податливость и коэффициент
объемного расширения. При изменении температуры происходит изменение величины
зазоров в подвижных соединениях и натягов в неподвижных. За счет деформации и
изменения размеров деталей происходит повышение сил трения или защемления
подвижных элементов в направляющей и регулирующей гидроаппаратуре, подсос
воздуха во всасывающей гидролинии и насыщение рабочей жидкости воздухом. Все
это вызывает ухудшение динамики гидропривода и металлоконструкции, заклинивание
гидроаппаратуры, разрушение гидрооборудования.
Изменение температуры оказывает отрицательное влияние
на физико-механическое свойство материалов гидрооборудования, особенно
полимеров. Изменяется характер контакта поверхностей трения, повышается сила
трения и износ деталей гидрооборудования.
.4 Методы повышения эффективности работы гидропривода
Проблема повышения эффективности гидравлического
привода решается на стадии его проектирования, изготовления и эксплуатации.
.4.1 Применение материалов повышенной прочности для
изготовления ответственных деталей гидрооборудования
В качестве примера этого направления повышения
работоспособности можно отметить применение более стойких металлов в насосах,
регулирующей и направляющей гидроаппаратуре для изготовления деталей,
подверженных кавитационной эрозии. Применение хладностойких сталей для
изготовления штоков и проушин гидроцилиндров, валов насосов и гидромоторов,
применение прочных и морозостойких полиуретановых и резинотканевых уплотнений
гидрооборудования, которые имеют высокую прочность, сохраняют достаточную
эластичность в широком диапазоне температуры и не подвержены интенсивному
старению и вулканизации.
1.4.2 Применение новых, более совершенных конструкций
гидрооборудования
Даже небольшие изменения конструкции существующего
гидрооборудования позволяют повысить их работоспособность при экстремальных
температурах. Например, применение эластичных прокладок и изменение посадок в
соединении штуцер-корпус распределителя позволяет уменьшить низкотемпературное
разрушение последнего. Уменьшение концентраторов напряжений на валу насосов и
гидромоторов также позволяет сократить их поломки в период пуска при прецизионных
соединениях направляющей и регулирующей аппаратуры. Применение соответствующих
посадок в гидроаппаратуре исключает случаи низкотемпературного защемления
подвижных элементов в зазорах и тем самым предотвращает возможные аварийные
ситуации.
1.4.3 Разработка современных гидравлических систем
Применение рациональной разводки гидравлической
системы, уменьшение протяженности и изгибов всасывающей, напорной и сливной
гидролиний за счет рационального расположения гидрооборудования на машине,
использования электрогидравлического способа управления и объединения функций
двух-трех гидроаппаратов в одном позволяет уменьшить потери энергии в
гидролиниях и увеличить полезные усилия на гидродвигателях при низких
температурах окружающей среды и рабочей жидкости. К этому методу следует
отнести, например, использование гидрозамков или дросселей с обратными
клапанами, предназначенных для исключения быстрого самопроизвольного опускания
рабочего оборудования, применения вторичных предохранительных клапанов, а также
клапанов с различными логическими функциями. Кроме того, существенно повысить
работоспособность гидрофицированных машин можно применением регулируемых
аксиально-поршневых насосов с так называемым ноль-установителем, который при
пуске насоса автоматически уменьшает угол наклона блока цилиндров и тем самым
обеспечивает минимальную подачу жидкости.
Это позволяет уменьшить типовые давления в период
пуска и, как следствие, крутящий момент на валу, что в конечном итоге исключает
задиры и заклинивание в поршневой группе насоса. Таким образом, прогрев
двигателя внутреннего сгорания и разогрев рабочей жидкости в гидросистеме могут
быть осуществлены при минимальной подаче насоса и минимальных нагрузках.
.4.4 Применение маловязких рабочих жидкостей
Всесоюзным научно-исследовательским институтом
нефтяной промышленности (ВНИИНП) совместно с Всесоюзным научно
исследовательским и проектно-конструкторским институтом промышленных
гидроприводов и гидроавтоматики ВНИИ гидропривод и Всесоюзный
научно-исследовательский и институтом строительного и дорожного машиностроения
(ВНИИстройдормаш) разработаны гидравлические масла ВМГЗ и МГ. Эти масла созданы
с целью уменьшения номенклатуры рабочих жидкостей, обеспечения
работоспособности гидроприводов самоходных машин, эксплуатируемых на открытом
воздухе в различных климатических условиях. Применение этих масел, особенно в
гидросистемах с аксиально-поршневыми насосами, позволило расширить
географическую зону эксплуатации и отказаться от двенадцати сортов масел,
использовавшихся ранее. Длительный период эксплуатации гидрофицированных машин
показал, что масла ВМГЗ и МГ обладают хорошими эксплуатационными свойствами:
обеспечивают защиту металлических поверхностей трения от задиров и износа,
удовлетворительно предотвращают коррозию, слабо образуют смолистые осадки,
имеют хорошие антипенные свойства.
Однако необходимо отметить, что маловязкие минеральные
масла при температурах выше плюс 35°С не обеспечивают достаточную защиту
поверхностей трения, что приводит к повышенным внутренним и наружным утечкам
рабочей жидкости, что, в свою очередь, снижает объемный КПД гидронасосов и
гидромоторов и производительность гидрофицированных машин.
.4.5 Повышение уровня технического обслуживания
Анализ длительного опыта эксплуатации
гидрофицированных самоходных машин показывает, что уровень технического
обслуживания является важным фактором повышения эффективности. Причем для
машин, эксплуатируемых в суровых климатических условиях, тщательность и
своевременность технического обслуживания особенно необходима.
.4.6 Оптимизация теплового режима гидропривода
Это направление следует считать наиболее радикальным,
т. к. оно позволяет решить проблемы работоспособности гидропривода в комплексе.
Оптимальный тепловой режим дает возможность уменьшить потери давления жидкости
в гидросистеме и потери на трение в гидрооборудовании увеличить долговечность
гидрооборудования, повысить объемный КПД и производительность машин; исключить
кавитацию и ее отрицательные последствия. Кроме того, регулирование температуры
способствует сохранению химической стабильности рабочей жидкости, уменьшает
наружные утечки, а главное, позволяет использовать в гидроприводе одно масло в
течение всего года. Все это достигается с помощью искусственного поддержания
температуры (вязкости) минерального масла в оптимальном диапазоне, граничные
температуры которого зависят от конструкции гидропривода и марки используемой
рабочей жидкости. Для регулирования температуры рабочей жидкости в гидросистему
вводится дополнительное устройство, которое при низких температурах за счет
специальных подогревателей или тепла, выделяемого двигателем внутреннего
сгорания, способствует интенсивному разогреву масла, а при высоких температурах
увеличивает теплообмен гидропривода с окружающей средой за счет ввода
дополнительных поверхностей теплоотдачи, обдува гидросистемы, применения
масляных радиаторов.
Следует помнить, что все шесть рассмотренных методов
повышения работоспособности гидропривода ни в коем случае не исключают и не
заменяют полностью друг друга, а органично сочетаются между собой. Поэтому при
проектировании гидроприводов машин, предназначенных для эксплуатации в районах
с суровым и резко континентальным климатом, необходимо учитывать возможность
сочетания всех методов.
В заключение необходимо отметить, что в настоящее
время предпусковой разогрев рабочей жидкости находит широкое применение на
отечественных и зарубежных машинах.
2. Патентный поиск
.1 Описание принципиальных схем авторских свидетельств
и патентов
.1.1 Конструкция гидропневмоаккумулятора (Ас 1325202 А1
СССР, F 15 В 1/04, 1980) представлена на
рисунке 2.1.1.
Рисунок 2.1.1 - Конструкция гидропневмоаккумулятора с
поплавковым разделителем сред
Гидропневмоаккумулятор (см. рисунок 2.1.1) содержит поплавковый
разделитель 1, установленный в корпус 2 с образовании газовой 3 и жидкостной 4
полостей, и отсечной клапан 5, затвор 6 которого размещён на разделителе, а
седло 7 на штуцере 8 подвода жидкости.
Особенность представленной конструкции гидропневмоаккумулятора заключается
в повышении его надёжности. Надёжность повышена путём адаптации к работе в
условиях смещения корпуса от его вертикальной оси. Выбираем данную модель ввиду
новизны и большей чем в остальных конструкциях надежности.
2.1.2 Конструкция гидропневмоаккумулятора (Ас 1809177
А1 СССР, F 15 В 1/04, 1977) представлена на
рисунке 2.1.2.
Рисунок 2.1.2 - Гидропневмоаккумулятор
Данная конструкция гидропневматического аккумулятора
содержит: 3-верхняя полусфера, 7-нижняя полусфера; 4,5-фигурные кольца,
8-резиновая мембрана, 6 - резиновое уплотнительное кольцо, 1-штуцер подвода
давления газа; 2-резиновое кольцо трубчатой формы, 9-штуцер подвода и отвода
жидкости.
Особенность изобретения заключается в том, что обе
половины корпуса гидропневмоаккумулятора выполнены из одинаковых штампованных
заготовок в виде полусфер 3 и 7 механически обработанных на краях, а затем
сваренных в конце сборки. Полусферы сжимают сферический поясок из двух
одинаковых фигурных колец 4 и 5, между которыми по периферийной кольцевой
канавке зажата мембрана 8, образующая газовую и гидравлическую полости.
Со стороны корпуса в пояске имеется разгрузочная
проточка, сообщающая через канал, выполненный в конце пояска, с газовой
полостью гидропневмоаккумулятора, а со стороны гидравлической полости в
сферическом пояске в кольцевой проточке установлено уплотнительное кольцо.
Штуцер для подвода газа снабжён кольцевой канавкой, глухим осевым отверстием с
выходящими из него сквозными боковыми отверстиями и резиновым кольцом трубчатой
формы, закреплённым одним концом в кольцевой канавке штуцера и герметизирующим
его боковые отверстия.
К числу достоинств данной конструкции можно отнести
повышенную надёжность, которая достигнута выполнением пояска в виде двух
фигурных колец 4 и 5 (см. рисунок 2.1.2), на одной стороне которых выполнены
уступы, а на другой стороне в торцах выполнены кольцевые канавки. Также к
достоинствам можно отнести простоту изготовления и сборки конструкции и
повышение герметичности подвода газа в газовую полость гидропневмоаккумулятора.
Данная конструкция вновь разработанной уступает в
следующем: повышенные габаритные показатели, что повлияло бы на возможность
установки в гидроприводе станка.
.1.3 Конструкция гидропневмоаккумулятора (Ас 361583 Япония, F 156 1/02, 1968) представлена на
рисунке 2.1.3
Гидропневмоаккумулятор (см. рисунок 2.1.3) содержит корпус 1 и
закреплённый в нём эластичный разделитель 2, изготовленный из резины. Отверстие
3 в корпусе сообщает жидкостную полость гидропневмоаккумулятора с магистралью
гидросистемы. В отверстии 3 закреплено седло 4 запорного клапана. На нижнем
конце разделителя расположен жёсткий затвор 9 клапана, взаимодействующий с
седлом 4. Заодно с затвором выполнен закрытый цилиндр 10 жидкостного
амортизатора, в котором размещён поршень 8. Между внутренней поверхностью
цилиндра и поршня имеется кольцевой зазор 11. Шток 7 проходит через центральное
отверстие в торцовой стенки цилиндра 10с зазором 12. Поршень разделяет полость
цилиндра на штоковую 10 и бесштоковую 14 полости, заполняемые рабочей жидкостью
из полости гидропневмоаккумулятора.
Рисунок 2.1.3 - Конструкция гидропневмоаккумулятора
Достоинства этого гидропневмоаккумулятора заключается
в особенностях его конструкции. Наличие жидкостного двухполостного амортизатора
обеспечивает более полное опорожнение жидкостной полости при вытеснении
жидкости, смягчения удара при посадке затвора на седло клапана, а также
предотвращение неправильной деформации разделителя.
Данная конструкция вновь разработанной уступает в следующем: сложность
изготовления, повышенные требования при сборке, а также увеличенное время на
опорожнение жидкостной полости.
2.1.4 Конструкция гидропневмоаккумулятора (Ас 386156
СССР, F 15 В 1/04, 1971) представлена на
рисунке 2.1.4
Рисунок 2.1.4 - Конструкция гидропневмоаккумулятора
Данная конструкция гидропневмоаккумулятора содержит:
корпус 1, эластичную диафрагму 2, выпускной клапан 3, запорный конус 4, седло
5, пружину 6, штуцер 7, разгрузочные канавки 8 и 9, стопорное кольцо 10,
направляющий стержень.
Подобный гидропневмоаккумулятор отличается выбранного
тем, что на одной из взаимодействующих поверхностей впускного клапана или
эластичной диафрагмы выполнены разгрузочные канавки. Такое выполнение
гидропневмоаккумулятора позволяет предотвратить присасывания диафрагмы и
клапана при отсутствии противодавления жидкости и тем самым повысить его
долговечность.
Данная конструкция уступает выбранной нами в следующем: сложность при
сборке и изготовлении, большие массогабаритные показатели, что ограничивает
диапазон его применения. Большая вероятность неполного опорожнения. Большое
время срабатывания и разрядки.
2.1.5 Конструкция гидропневмоаккумулятора (Ас 108605
СССР, F 15 В 1/04, 1956) представлена на
рисунке 2.1.5
Рисунок 2.1.5 - Конструкция шарового
гидропневмоаккумулятора
Шаровой гидропневмоаккумулятор (см. рисунок 2.1.5) состоит из корпуса 1,
резиновой диафрагмы 2, разделяющей воздушную 3 и гидравлическую камеры 4 и
сферического козырька 5.
Шаровой гидропневмоаккумулятор отличается тем, что с
целью устранения неполной разрядки, над сливным отверстием гидравлической
камеры установлен сферический козырёк с мелкими отверстиями.
Данная конструкция вновь разработанной уступает в следующем: большие
габариты и замедленную реакцию диафрагмы на ударное повышение давления.
2.2 Описание принципиальных схем авторских
свидетельств и патентов на уплотнения гидроцилиндров
В мировой практике накоплен большой опыт применения силовых
гидроцилиндров в качестве исполнительных элементов гидроприводов. Наряду с
определенными преимуществами по сравнению с механическим, электрическим и
пневматическим приводами, гидропривод имеет и некоторые недостатки, к которым в
первую очередь следует отнести сложность обеспечения герметичности подвижных
соединений, особенно соединений поршня и штока (с возвратно - поступательным
движением). Несмотря на то, что узлы уплотнений подвижных соединений занимают
сравнительно небольшую часть гидроцилиндра, именно от них зависит безотказная
работа последнего, а также дальнейшее развитие гидропривода в направлении
увеличения скоростей, температур и давлений, повышения надежности и
экологической безопасности.. В связи с этим ведущие области в области уплотнительной
техники отечественные и зарубежные фирмы проводят широкие теоретические и
экспериментальные исследования, на основании которых разрабатывают и выпускают
уплотнения отличающиеся улучшенными характеристиками.
2.2.1 Уплотнение (Пат. 5197746 США. МКИ F16j 15/46) поршня
гидроцилиндра, разработанное фирмой Leber Corp. (США) рис.
2.2.1
Рисунок
2.2.1 (Пат. 5197746 США. МКИ F16j 15/46) поршня гидроцилиндра, разработанное фирмой Leber Corp (США) отличается большим ресурсом
Оно
состоит из разрезного металлического пружинного кольца 2 и упругого резинового
кольца 3 круглого поперечного сечения. В кольцевой канавке трапецевидного
поперечного сечения с одной наклонной боковой стенкой поршня 1 размещается
кольцо 3. которое деформируется при установке и обеспечивает начальное поджатие
кольца 2 к внутренней поверхности корпуса гидроцилиндра. Под действием давления
рабочей жидкости в полости корпуса гидроцилиндра резиновое кольцо 3
вдавливается в зазор между дном кольцевой канавки поршня 1 и
скошеннойвнутренней поверхностью кольца 2, обеспечивая повышение контактного
давления в подвижном соединении и увеличение герметизирующей способности
уплотнения.
2.2.2
Уплотнение (А.С. 1829865 СССР, МКИ F16j 15/00) штока
гидроцилиндра, рис. 2.2.2
Рисунок
2.2.2 Уплотнение (А.С. 1829865 СССР, МКИ F16j
15/00) штока гидроцилиндра
Надежно
работает при давлении до 250 МПа. Оно состоит из двух колец: 1 (из шести
частей) и 6 (из трех частей), которые стягиваются браслетными пружинами 3 и 4;
при этом обеспечивается как плотное прилегание частей колец друг другу, так и
колец в целом к штоку 7 гидроцилиндра. Кольца 1 и 6 установлены в полости,
образованной расточкой в корпусе 5 и крышкой 2 на рабочих поверхностях колец
выполнены кольцевые пазы а и б трапецеидального поперечного сечения,
заполненные антифрикционным материалом спеченным с основным материалом колец.
Кольца 1 и 6 изготовляют из антифрикционного материала (например, из
бериллиевой бронзы), твердость и прочность которого значительно превышает
твердость и прочность антифрикционного материала (например, оловянистой
бронзы), заполняющего кольцевые пазы а и б.
Под
действием давления р рабочей жидкости кольца 1 и 6 дополнительно прижимаются к
поверхности штока 7; задний торец кольца 1 прижимается к крышки 2, внутренние
торцы 1 и 6 прижимаются одно к другому, обеспечивая надежную герметизацию
подвижного и неподвижных соединений.
.2.3
Уплотнение (Пат. 2062377 РФ, МКИ F16j 15/18) поршня гидроцилиндра, рис.2.2.3
Рисунок
2.2.3 Уплотнение (Пат. 2062377 РФ, МКИ F16j 15/18) поршня гидроцилиндра
Состоит
из пакета притертых по боковым поверхностям одинаковых пружинных разрезных
колец 7, изготовленных из металлов и неметаллических материалов, обладающих
достаточной жесткостью с концентрическими наружной и внутренней поверхностями.
Пакет
колец 7 установлен на обойму 4 из эластичного материала, например резины,
расположенную в канавке поршня 6. Для обеспечения высокой герметичности
подвижного соединения поршня 6 с корпусом 5 разрезы сопрягаемых колец 7
установлены со смещением на 90°. Для сжатия колец 7 в осевом направлении
предусмотрена пластичная пружина 3, сила сжатия которой регулируется с помощью
поджимной гайки 2, навинчиваемой на резьбу штока 1. Боковые поверхности колец 7
сопрягаются между собой, образуя полость а, в которые вытесняется материал
обоймы 4 в виде кольцевых выступов б, обеспечивая некоторую подвижность колец
7. Таким образом обеспечивается высокая степень герметичности в подвижном
соединении между кольцами 7 и внутренней поверхностью корпуса 5, а также в
неподвижном соединении между наружной поверхностью обоймы 4 и кольцами 7.
Описанное уплотнение отличается большим сроком службы.
.2.4
(Заявка на пат. 00693, Междунар. РСТ, МКИ F16j
9/06)
Рисунок
2.2.4 Заявка на пат. 00693, Междунар. РСТ, МКИ F16j
9/06
Многокольцевое
уплотнение размещается на канавке а (рис. 4) поршня 5 и состоит из двух
резиновых колец 4 и 6 круглого поперечного сечения, расположенных на дне
канавки а, промежуточного кольца 3. Рабочая уплотняющая поверхность д кольца 3
выполняется с малым углом наклона, причем зазор между поверхностью д и рабочей
поверхностью г корпуса 2 гидроцилиндра увеличивается по направлению к канавке
в. Конструкция уплотнения обеспечивает рациональное распределение давлений на рабочей
поверхности д с максимальным давлением на кромках б и е.
Полимерные
материалы на основе политетрафторэтилена, применяемые для изготовления
уплотнений подвижных соединений гидроцилиндров, отличаются высокими
антифрикционными свойствами и износостойкостью, но на ряду с этим они
недостаточно упруги, склонны к текучести и релаксации напряжений, что не
позволяет создавать необходимое контактное давление и компенсировать изменение
зазоров в подвижном соединении.
Применяя
манжеты данной конструкции наряду со стандартными уплотнениями поршня
гидроцилиндра можно увеличить надежность и долговечность подвижного соединения
поршень - стенка гидроцилиндра. И обеспечить наибольшую герметичность.
.2.5
Резиновая манжета (Пат. 2027930, РФ, МКИ F16j
15/32) V-образного поперечного сечения, рис. 2.2.5
Рисунок
2.2.5 Резиновая манжета (Пат. 2027930, РФ, МКИ F16j
15/32) V-образного поперечного сечения
Она
состоит из внутренней уплотнительной губы в контактирующей с дном кольцевой
канавки поршня 2, наружной уплотнительной губы а, контактирующей с внутренней
цилиндрической поверхностью корпуса 3, и опорной части 1. Уплотнительные губы а
и б имеют переменную толщину, плавно увеличивающуюся от конца контактной кромки
к месту б соединения с опорной частью 1. Ширина поперечного сечения манжеты в
месте соединения уплотнительных губ с опорной частью на 4-15% больше ширины
зазора между уплотняемыми поверхностями корпуса 3 гидроцилиндра и канавки на
поршне 2.
3. Расчет гидропривода машины
.1 Исходных данные
Для расчета гидропривода необходимо знать:
1 принципиальную гидравлическую схему
машины;
2 техническую характеристику машины;
3 величины усилий на гидродвигателях;
4 величины скоростей штока
гидроцилиндров и вала гидромоторов;
5 номинальное давление в гидросистеме;
6 длину напорной, сливной и всасывающей
гидролиний;
коэффициенты местных сопротивлений напорной, сливной и
всасывающей гидролиний;
7 высоту всасывания насоса;
8 граничные температуры окружающего
воздуха;
9 режим работы гидропривода;
10прототип машины.
.2 Выбор рабочей жидкости
От правильности выбора рабочей жидкости зависит
работоспособность гидропривода и долговечность гидрооборудования. Даже
оптимально спроектированный гидропривод может оказаться неработоспособным или
малоэффективным, если жидкость не будет соответствовать условиям эксплуатации.
Марку масла выбирают исходя из условий эксплуатации,
типа насоса и ответственности гидросистемы. Чем ниже температура окружающего
воздуха, тем менее вязкую жидкость следует выбирать, и наоборот.
Для гидроприводов самоходных машин масла выбираются по
следующим основным показателям: диапазону температур; соответствию вязкости
жидкости номинальному давлению; климатическим условиям эксплуатации
гидропривода; срокам эксплуатации машины; продолжительности работы гидропривода
в течение суток; соответствию рабочей жидкости резиновым уплотнениям; стоимости
жидкости. Важнейшим из этих показателей следует считать диапазон температуры
(вязкости) масла.
Рабочую жидкость выбирают также с учетом типа насосов.
Для шестеренных гидронасосов всех марок в качестве рабочих жидкостей используют
моторное масло М - 8В2 (зимой), М - 10В2 (летом); для аксиально-поршневых
насосов ВМГЗ (зимой), МГ - 30 (летом); для машин, работающих в закрытых
помещениях, - МГ - 20. В качестве заменителя масел ВМГЗ и МГ-30 могут быть
использованы соответственно масла АМГ - 10 и ИС - 30.
В данном случае для гидропривода работающего в условиях от - 40 до + 40
целесообразно применять в качестве рабочей жидкости масло МГ - 30 (летом) и
ВМГЗ (зимой).
.3 Расчет мощности и подачи насоса
Мощность насоса рассчитаем по формуле (3.3.1)
(3.3.1)
Где
z - число одновременно работающих гидроцилиндров;
Т
- усилие на штоке, Н;
υn - скорость
перемещения поршня, м/с;
D - диапазон
регулирования;
ηгмн - гидромеханический КПД насоса;
ηгмц - гидромеханический КПД цилиндра.
Вт
Рассчитаем подачу насоса по формуле (3.3.2)
, (3.3.2)
м3/с.
Определение
типоразмера насоса
Рабочий объем насоса можно определить по
формуле(3.3.3):
(3.3.3)
Где
z - число одновременно работающих насосов;
qн - рабочий
объем насоса, см /об;
nн - число
оборотов вала насоса, об/мин;
D - диапазон
регулирования;
ηобн - объемный КПД насоса.
Для
расчетов используем среднее число оборотов вала насосов n =
1700 об/мин
, см3/об
Выбираем
регулируемый аксиально-поршневой насос 312.20, его параметры практически
совпадают с расчетными.
3.4 Выбор направляющей и регулирующей гидроаппаратуры
Выбор элементов гидроаппаратуры производим по
номинальному давлению, номинальной подаче насоса и условному проходу.
Выбираем гидрораспределители Р-20 с управлением от
двух электромагнитов и условным проходом Dу=20мм.
В качестве предохранительных клапанов выбираем
предохранительные клапаны МКПВ - 4/3 Ф2В и МКПВ - 4/3 П3.
В данной гидросистеме использованы обратные клапаны
тарельчатого типа. Место установки преимущественно на гидролиниях управления
гидрораспределителями параллельно с регулируемым дросселем. Предназначены для
пропускания жидкости только в одном направлении, при обратном потоке жидкости
клапаны закрываются. Выбираем клапан типа Г51-24 с диаметром условного прохода Dу=20 мм на номинальный расход рабочей
жидкости QH = 80 л/мин
.5 Выбор фильтра
Для очистки рабочей жидкости от механических примесей в гидроприводах
самоходных машин применяют различные фильтрующие устройства (фильтры).
Выбор унифицированных фильтров осуществляется по
номинальному потоку жидкости и требуемой номинальной тонкости фильтрации.
По внутреннему диаметру сливной магистрали выбираем
фильтр 1.1.32-25, который обеспечивает достаточно высокую тонкость фильтрации и
обеспечивает необходимую пропускную способность для заданного потока жидкости.
3.6 Расчет диаметров трубопроводов
Определим диаметры напорного, сливного и всасывающего
трубопровода. Для этого зададимся приблизительными скоростями потока жидкости в
этих гидролиниях. Примем следующие скорости потока жидкости:
в напорном трубопроводе υн = 4 м/с;
в сливном трубопроводе υс = 2 м/с;
во всасывающем трубопроводе υв = 1 м/с;
Диаметр трубопроводов можно определить по формуле
(3.6.1):
(3.6.1)
Где QH -
подача насоса, л/мин;
υ - скорость потока жидкости, м/с;
,м
,м
,м
В
соответствии с ГОСТ 16516-80 выбираем стандартные диаметры трубопроводов,
которые используем в дальнейших расчетах dН = 16 мм; dС =
20 мм; dВС = 32 мм.
Теперь
уточним действительные скорости потока жидкости в напорном, сливном и
всасывающем трубопроводах по формуле (3.6.2)
(3.6.2)
получаем действительные скорости потока жидкости в
трубопроводах:
υн=3,4 м/с υс=2,2 м/с υв=0,85м/с. Эти значения скоростей
будем учитывать в дальнейших расчетах.
.7 Расчет всасывающего трубопровода
Расчет проведем по формуле (3.7.1)
Запишем уравнение Бернулли:
(3.7.1)
Где Р0 - атмосферное давление, Па;
ρ - плотность жидкости, кг/м3;
g - ускорение свободного падения, м/с2;
hB - высота всасывания, м;
υB - скорость потока жидкости во
всасывающем трубопроводе, м/с;
ζ - коэффициент местных сопротивлений
всасывающего трубопровода;
bВ - поправочный коэффициент, учитывающий влияние вязкости
жидкости на местные потери;
λВ - коэффициент трения жидкости о
стенки всасывающего трубопровода;
lВ - длина всасывающего трубопровода, м;
dB - диаметр всасывающего трубопровода, м.
Произведем расчет потерь давления в диапазоне
температур от минус 10 градусов до 80 градусов Цельсия.
Все полученные данные внесем в таблицу (таблица 3.7.1)
Число Рейнольдса определим по формуле (3.7.2) при
температуре жидкости tЖ =
10°С
(3.7.2)
Где
ν - вязкость жидкости, м2/с.
Аналогичным образом определим числа Рейнольдса для других температур.
Полученные данные занесем в таблицу (3.7.1)
Так как число Рейнольдса для диапазона температур от
-40˚С до 80˚С меньше 2300, то режим течения будет ламинарным.
Коэффициент Дарси для ламинарного режима течения можно определить по формуле
(3.7.3.
Определим коэффициент Дарси для температуры 0˚С:
, (3.7.3)
Из
графика зависимости поправочного коэффициента b от числа
Рейнольдса определим поправочный коэффициент bВ и результаты
занесем в таблицу (3.7.1).
При
температуре жидкости tж = 10˚С
Па
По
полученным результатам строим график (рисунок 3.7.1) зависимости давления во
всасывающей камере насоса от температуры при высоте всасывания h1 =
+0,5 м и h2 = - 0,5 м.
Из
построенных графиков видно, что давление во всасывающей камере насоса при
размещении гидробака на 0,5 м выше всасывающей камеры насоса дает существенный
положительный эффект. При температуре выше 50˚С давление во всасывающей
камере насоса превышает атмосферное. Расчет показал, что при проектировании
гидрофицированных машин целесообразно размещать гидробак на высоту 0,5 м выше
уровня насоса, что в свою очередь позволяет повысить всасывающую способность
насосов.
Рисунок
3.7.1 - Зависимость давления во всасывающей камере насоса от температуры
1- высота всасывания плюс 0,5 м
2- высота всасывания минус 0,5м.
.8 Расчет потерь давления в напорной и сливной
гидролиниях
Путевые
потери давления определяем по формулам (3.8.1) и (3.8.2)
(3.8.1)
Где
ΔРП.Н. - потери давления в напорной гидролинии, МПа;
ΔРП.С. - потери давления в сливной гидролинии, МПа.
(3.8.2)
Где
λН, λС -
коэффициенты трения жидкости в напорной и сливной гидролиниях;
lН, 1С - длины
напорной и сливной гидролиний, м;
dH, dС -
диаметры напорной и сливной гидролиний, м;
υH, υС -
скорости потока жидкости в напорном и сливном трубопроводах, м/с;
ρ - плотность жидкости, кг/м3.
Как и при расчете давления во всасывающем трубопроводе, занесем все
переменные параметры в таблицу (3.8.1), полученные из графиков или расчетным
путем.
По графику зависимости поправочного коэффициента b от числа Рейнольдса находим
поправочные коэффициенты bН и bC для напорной и сливной гидролинии.
Рассчитаем путевые потери давления в напорном и
сливном трубопроводах:
При температуре жидкости tЖ = 0°С
МПа
Местные
потери давления определяем по формулам (3.8.3) и (3.8.4)
, (3.8.3)
(3.8.4)
Где
ζН и ζС -
коэффициенты местных сопротивлений в напорном и сливном трубопроводах;
bH и bC -
поправочные коэффициенты, учитывающие влияние вязкости жидкости на местные
потери давления в напорном и сливном трубопроводах;
υH и υC - скорости потока жидкости в напорном и сливном трубопроводах, м/с;
ρ - плотность жидкости, кг /м3.
Определим
число Рейнольдса при температуре tж = 20 ˚С для напорного и сливного трубопровода
по формулам (3.8.5) и (3.8.6)
, (3.8.5)
(3.8.6)
Аналогичными
расчетами определим число Рейнольдса и для других температур и результаты
расчета занесем в таблицу (3.8.1).
Определим
коэффициенты гидравлического трения для напорного и сливного трубопроводов.
Результаты занесем в таблицу (3.8.1).
При
температуре жидкости tж = 20 ˚С:
,
,
.
Рассчитаем
местные потери давления при температуре рабочей жидкости tж =
20 ˚С:
МПа.
На основании расчетных данных строим график (рисунок 3.8.1)
Таблица 3.8.1 - Зависимость потерь давления в гидросистеме экскаватора от
температуры рабочей жидкости.
Параметры
|
Температура рабочей жидкости,
ºС
|
|
|
|
|
|
|
|
-40
|
-20
|
0
|
20
|
40
|
60
|
80
|
 6002551407254209
|
|
|
|
|
|
|
|
897893883875868856840
|
|
|
|
|
|
|
|
   0,770,330,180,090,070,040,035
|
|
|
|
|
|
|
|
1,250,530,290,150,110,040,039
|
|
|
|
|
|
|
|
98230419816108729396524
|
|
|
|
|
|
|
|
6014125750066718004000
|
|
|
|
|
|
|
|
831,81,51,311
|
|
|
|
|
|
|
|
1252,71,71,61,11
|
|
|
|
|
|
|
|
∑∆Pп,
МПа
|
4,577
|
1,051
|
0,611
|
0,399
|
0,206
|
0,18
|
∑∆Рм, МПа
|
0,702
|
0,267
|
0,156
|
0,115
|
0,107
|
0,08
|
0,077
|
∑∆Р, МПа
|
5,279
|
2,215
|
1,207
|
0,726
|
0,506
|
0,286
|
0,257
|
∑ΔР, МПа
t,°С
Рисунок
3.8.1 - Зависимость потерь давления в гидросистеме экскаватора от температуры
.9 Расчет КПД гидропривода экскаватора
Общий КПД гидропривода определяется произведением гидравлического,
механического и объемного КПД по формуле
(3.9.1)
Гидравлический
КПД определяется по суммарным потерям давления
(3.9.2)
где
Рном - номинальное давление насоса, МПа
∑ΔР - суммарные потери давления в гидросистеме, МПа
При
температуре жидкости 20 ˚С гидравлический КПД равен:
Определим
значения гидравлического КПД при других температурах и результаты занесем в
таблицу (3.9.1)
Механический
КПД определяется по формуле:
(3.9.3)
Из паспортных данных аксиально-поршневого насоса марки
НП-90 определим его механический КПД. Механический КПД гидромотора при давлении
32 МПа равен 0,94. Механический КПД распределителей принимаем равным единице.
Объемный
КПД гидропривода определится как произведение объемных КПД насоса -
, распределителя -
и
гидроцилиндра -
:
(3.9.4)
В формуле (3.9.4) объемные КПД распределителей и
гидроцилиндров можно принимать равным 1, так как внутренние утечки по отношению
к подаче насоса пренебрежительно малы.
Значение объемного КПД насоса принимаем по линейному
закону (с увеличением температуры жидкости КПД уменьшается в связи с
увеличением утечек).
По паспортным данным значение объемного КПД насоса
312.20 при номинальном режиме работы принимаем равным = 0,92.
При температуре жидкости tЖ = 20°С
Результаты
расчета при всех температурах заносим в табл. 3.9.1 и определяем общий КПД
гидропривода станка.
Далее
строим график в координатах
(рисунок
3.9.1), который показывает оптимальный диапазон температур рабочей жидкости, в
котором КПД гидропривода достигает максимального значения.
Таблица
3.9.1 - Зависимость КПД гидропривода от температуры
КПД
|
Температура рабочей
жидкости, ˚С
|
|
-40
|
-20
|
0
|
20
|
40
|
60
|
80
|
Гидравлический
|
0,5
|
0,74
|
0,85
|
0,97
|
0,99
|
0,99
|
0,99
|
Механический
|
0,85
|
0,85
|
0,85
|
0,85
|
0,85
|
0,85
|
0,85
|
Объемный
|
0,52
|
0,73
|
0,86
|
0,85
|
0,80
|
0,7
|
0,56
|
Общий
|
0,22
|
0,46
|
0,62
|
0,7
|
0,67
|
0,58
|
0,47
|
Рисунок
3.9.1 - Зависимость общего КПД гидропривода от температуры рабочей жидкости
3.10 Расчет и выбор гидромотора
Крутящий момент на валу гидромотора определяют по формуле (3.10.1):
, (3.10.1)
где:
qм - рабочий объем гидромотора, см3/об;
Рном
- номинальное давление в гидросистеме, МПа.
Н∙м.
3.11 Выбор вместимости гидробака и определение площади
теплоизлучающих поверхностей
Предварительно вместимость бака выбираем исходя из рекомендации по
формуле:
(3.11.1)
Где
QН - минутная подача насоса, л/мин.
л
После
предварительного выбора объема бака согласовываем его значение по ГОСТ
12448-80и выбираем вместимость бака 63 литра. Определим площадь теплоотдачи
бака по формуле
, (3.11.2)
м2
3.12 Расчет площади теплоотдачи гидрооборудования
Определим площадь теплоизлучающих поверхностей комбайна по формуле
(3.12.1)
Где
Fб - площадь теплоотдачи, м2;
αб - поправочный коэффициент.
м2
3.13 Тепловой расчет
Расчет выполняется для температуры рабочей жидкости 20 ˚С.
Количество тепла, выделяемое гидроприводом, можно определить по формуле:
(3.13.1)
где ηобщ - общий КПД гидропривода;
NH - мощность привода насоса, Вт;
kп - коэффициент продолжительности работы под нагрузкой;
kд -
коэффициент использования номинального давления.
Вт
Установившуюся
температуру рабочей жидкости можно определть по формуле
, (3.13.2)
Где
Кгн - коэффициент теплоотдачи;
tо.max -
максимальная температура окружающей среды.
˚С
Так
как установившаяся температура рабочей жидкости на 27 градусов превышает
допустимую (70˚С), то в гидроприводе необходимо применить устройство для
отвода тепла
Площадь
теплообменника можно определить по формуле (2.13.3):
(2.13.3)
м2.
Определим
текущую температуру рабочей жидкости в гидроприводе по формуле
(3.13.4)
В
формуле (3.13.4) неизвестной величиной остается средняя удельная теплоемкость,
которую можно определить по формуле:
(3.13.5)
Где
Сж = 1,85·103 - теплопроводность рабочей жидкости Дж/(кг·˚С);
mго - масса
гидрооборудования, кг;
mж - масса
рабочей жидкости, кг;
Сго
- теплоемкость материала (стали), Дж/(кг·˚С).
Определим
массу жидкости, полагая, что ее объем в гидросистеме превышает объем жидкости в
гидробаке Vб в 1,5 раза:
(3.13.6)
Где
ρ
- плотность жидкости, кг/м3.
кг,
.
Придавая
значения времени τ,
определим текущую температуру в соответствии с формулой (3.13.4)
Через
τ
= 1200с после начала работы:
˚С
Через
τ
= 2400с после начала работы:
Через
τ
= 3600с после начала работы:
Через
τ
= 4800с после начала работы:
Через
τ
= 6000с после начала работы:
Через
τ
= 7200с после начала работы:
По
результатам расчета строим график в координатах tж - τ (рисунок 3.13.1)
Рисунок
3.13.1 Зависимость температуры рабочей жидкости в гидроприводе экскаватора от
времени работы: 1 - с теплообменником 2 - без теплообменника
4. Прочностные расчеты
4.1 Расчет толщины стенки корпуса гидропневмоаккумулятора
на прочность
При расчете толщины стенки S
корпуса поплавкового гидропневмоаккумулятора на прочность можно применить
формулу:
; (4.1.1)
где:
D - внутренний диаметр аккумулятора, м;
σ - допускаемое напряжение на разрыв для материала, кг/см2;
Рmax -
давление в конце зарядки, кг/см2;
μ - коэффициент Пуассона (для сталей μ = 0,33).
Допускаемое
напряжение на разрыве σ
для корпуса из стали 45 для расчета
примем равной 600 кгс/см2.
см.
Толщина
стенки корпуса гидропневмоаккумулятора не должна быть менее чем 0,22 см.
4.2 Расчет толщины стенки трубопровода на прочность
При расчете стенок трубопровода на прочность должно соблюдаться условие
(4.2.1)
где
К =
;
r1 и r2 -
внутренний и наружный радиус трубы;
-
допускаемое напряжение при разрыве;
n - коэффициент
запаса прочности.
Преобразовав
формулу (4.2.1) получим:
(4.2.2)
В
нашем случае:
Р
= 35 МПа, n = 3,
= 296
МПа.
Из
формулы (4.2.2) получаем наименьшее значение наружного радиуса r2 в
соответствии с формулой (4.2.3)
м.
Отсюда
толщина стенки будет определятся по формуле:
м.
Для
дальнейших расчетов принимаем трубопровод с наружным диаметром равным 30 мм и
толщиной стенки 7 мм.
.3 Расчет резьбы присоединительной трубки
гидроцилиндра на прочность
Резьба присоединительной трубки нагружена только осевой силой.
Следовательно, расчет проведем только на растяжение в соответствии с условием
прочности (4.3.1)
(4.3.1)
Где
- осевая нагрузка, эквивалентная продольной силе, Н;
-
минимальный наружный диаметр резьбы, м;
-
расчетное напряжение при растяжении, Па;
-
допускаемое напряжение при растяжении, Па.
Определим
силу, действующую вдоль оси трубки
по
формуле (4.3.2):
(4.3.2)
где:
Р - максимальное давление в трубопроводе, Па;
d - диаметр
присоединительной части, м.
Н.
Допускаемое
напряжение при растяжении для присоединительной трубки из стали Ст3 найдем из
выражения (4.3.3)
, (4.3.3)
где:
- предел текучести материала, Па;
-
допускаемый коэффициент запаса прочности.
Принимаем
для стали предел текучести
равным
225∙106Па и коэффициент прочности
равным
2, тогда:
Па.
Определим
минимальный наружный диаметр резьбы по формуле (4.3.4):
, (4.3.4)
где:
- максимальный внутренний диаметр резьбы, м.
Для
расчетов принимаем присоединительную трубку с трубной резьбой ¾ и с внутренним диаметром 14 мм.
м.
Расчетное
напряжение при растяжении найдем в соответствии с условием (4.3.1):
МПа
В
соответствии с расчетными данными условие прочности выполняется:
5. Технологическая часть
Технологическое проектирование произведено на деталь штуцер. Был выполнен
анализ технологичности конструкции; выбран метод получения заготовки и
рассчитаны ее размеры; разработаны маршрутный и операционный технологические
процессы изготовления детали; на все переходы (операции) назначены режимы
резания; все операции механической обработки пронормированы.
5.1 Назначение и конструкция детали
Штуцер представляет собой цилиндрическую ступенчатую полую деталь.
Изготавливается из стали 45 ГОСТ 1050 - 88.
Штуцер предназначен для подвода рабочей жидкости в полость
гидроаккумулятора с целью накопления гидравлической энергии.
5.2 Анализ технологичности конструкции
1. На чертеже имеется достаточное количество обоснованных служебным
назначением допусков, размеров, формы и взаимного расположения поверхностей,
шероховатости поверхностей по ГОСТ 23346-82.
. Достаточная степень использования унифицированных элементов,
способствующих применению прогрессивных технологических процессов, стандартного
или нормализованного режущего инструмента по ГОСТ 18878-73.
3. Возможен удобный подвод режущего инструмента к обрабатываемой
поверхности.
. Конструкция предусматривает наличие комплекта баз или создание
искусственных баз, гарантирующих надежную установку и закрепление детали в
процессе ее обработки.
. Конструкция детали предусматривает также удобство контроля
детали в процессе ее изготовления.
5.3 Выбор метода получения заготовки
При выборе заготовок для заданной детали назначают метод ее получения,
определяют конфигурации, размеры, допуски, припуски на обработку и формируют
технические условия на изготовление.
Главным при выборе заготовки является обеспечение заданного качества
готовой детали при ее минимальной себестоимости. Выбор заготовки также связан с
конкретным технико-экономическим расчетом себестоимости готовой детали,
выполняемым для заданного объема годового выпуска с учетом других условий
производства.
Технологические процессы получения заготовок определяются
технологическими свойствами материала, конструктивными формами, размерами
деталей и программой выпуска.
В качестве заготовки выбираем сортовой прокат круглого сечения.
Материал заготовки сталь 45.
5.4 Расчет припусков на заготовку
Припуски на заготовку, а также на обработку наиболее точных поверхностей
определяют расчетно-аналитическим методом.
Припуски на обработку остальных поверхностей назначают по справочным
таблицам.
Определение припусков расчетно-аналитическим методом выполняют в
следующем порядке.
1. Выбираем маршрут обработки отдельной поверхности.
При выборе маршрута обработки поверхностей необходимо использовать точные
характеристики различных технологических методов обработки. Выбирают вариант
обработки поверхности, обеспечивающий требуемые точность и шероховатость поверхности.
Необходимо обработать поверхность штуцера диаметром 60мм. Запишем
технологический процесс обработки поверхности:
Заготовка - Н 16, RZ =
125 мкм
Точение однократное - H 14, RZ = 32 мкм
2. В графу «Наименование операции (переходов)» записывается намеченный
технический процесс обработки поверхности, для которой рассчитывался припуск.
3. В графах «Квалитет допуска размеров» и «Параметр шероховатости »
указываются параметры шероховатости и точности изготовления поверхности на
каждой операции (переходе). Если на последней операции (переходе) выполняется
размер, заданный чертежом, то значение квалитета допуска и параметра
шероховатости указывается по чертежу.
4. Элементы
припуска (RZ - высота неровностей профиля, мкм; h -
глубина дефектного поверхностного слоя, мкм;
-
Суммарные отклонения расположения поверхности, мкм;
- погрешность установки заготовки, мкм.).
Суммарное отклонение расположения поверхности рассчитывается по формуле
(5.3)
где
- коэффициент кривизны;
l - длина
заготовки;
Погрешность
установки рассчитывается по формуле
(5.4)
где
- погрешность установки заготовки, мкм;
,
- коэффициенты
мкм.
5. Рассчитывается минимальный припуск на обработку по следующей
формуле
(5.5)
где
2Zmin - минимальный припуск, мм;
RZ - высота
неровностей профиля, мкм;
h - глубина
дефектного поверхностного слоя, мкм;
-
суммарные отклонения расположения поверхности, мкм;
-
погрешность установки заготовки, мкм.
мкм
6. Определяется расчетный размер на каждой операции. Расчет следует
вести от конечной операции (перехода). В графу «Расчетный размер» записывается
наименьший предельный размер. Затем к этому размеру прибавляется расчетный
припуск, засчитанный для этой операции (перехода). Таким образом, получается
расчетный размер для предшествующей операции. Далее к этому полученному размеру
прибавляется расчетный припуск, рассчитанный для данной операции. В результате
получается расчетный размер для всех операции (переходов). Таким образом,
получается размер заготовки или необходимый межпереходный размер.
. Далее на расчетный размер каждой операции (перехода) назначается
допуск согласно заданному квалитету и записывается в графу «Допуск на
выполняемый размер».
8. Для определения минимального принятого размера необходимо
расчетный размер на каждой операции округлить до знака назначенного допуском.
Для определения небольшого принятого размера необходимо к значению минимального
принятого размера прибавить допуск, назначенный на расчетный размер для каждой
операции.
Рассчитанный размер заносим в графы «Предельные размеры».
9. Определяют минимальный и максимальный значения припусков:
, (5.6)
, (5.7)
Рассчитанные
таким образом припуски записываем в графах «Предельные значения припуска» для
каждой операции. Внизу таблицы после всех расчетов в графах «2Zmax»
и «2Zmin» записываются значения минимального и максимального
общих припусков:
, (5.8)
, (5.9)
10. Проверяется правильность произведенных расчетов по формуле:
(5.10)
где
Тз и Тд - допуски на линейные размеры соответственно заготовки и детали, мм;
,71-2=0,90-0,190
,71=0,71
Проверка
показала, что расчеты были произведены, верно.
В
качестве заготовки выбран сортовой прокат круглого сечении диаметром ø62
Масса
заготовки:
(5.1)
Где
m - масса заготовки, кг;
V - объем
заготовки, см3;
ρ - плотность материала заготовки, кг/см3.
Коэффициент
использования материала:
(5.2)
где Ким
- коэффициент использования материала;
mд - масса
детали, кг;
mз - масса
заготовки, кг.
,
т.к.
с одной заготовки получается 15 деталей, то коэффициент использования материала
умножаем на 15:
5.5 Разработка технологического маршрута изготовления
детали
Технологический маршрут изготовления штуцера приведен в технологической
карте (См. прил.Б).
Механическая обработка производится на токарной операции.
В маршрут введены вспомогательные операции:
) Заготовительная операция - для отрезки заготовки необходимого размера
) Транспортирование - для передачи заготовки из цеха в цех.
) Промывка - для очистки детали.
) Контроль - для проверки на соответствие всех размеров готовой детали
чертежу.
5.6 Проектирование операционного технологического
процесса изготовления детали
На всех операциях установка заготовки осуществляется в трехкулачковом
самоцентрирующем патроне.
Заготовка базируется по наружной поверхности.
Операционный технологический процесс приведен на листе.
Выбор оборудования. При составлении технологического
маршрута обработки и при его технико-экономическом обосновании выбирают
конкретную модель станка в зависимости от: вида обработки, точности и жесткости
станка, габаритных размерах станка, мощность станка, частоты вращения шпинделя,
скорости подачи, возможности механизации (автоматизации) операции, цены станка.
При этом учитывается тот факт, что разные станки дают разную точность
обработки.
Выбираем токарно-револьверный станок 1365
Выбор режущего инструмента. Конструкция, размеры
инструмента для заданной операции зависят от вида обработки, размеров
обрабатываемой поверхности, свойств материала заготовки, требуемой точности
обработки и шероховатости обрабатываемой поверхности. При обработке детали из
стали 45 применяется в качестве материала режущей части инструмента твердый
сплав. Марку твердого сплава для обработки стали 45 выбирают по таблице: Т15К6.
5.7 Расчет и назначение режимов резания
Для первого перехода:
Глубина резания t:
При однократном точении и отсутствии ограничений по мощности
оборудования, жесткости системы СПИД глубина резания принимается равной
припуску на обработку.
t=0,53
мм
Подача S
При однократном точении подача принимается максимально допустимой по
мощности оборудования, жесткости системы СПИД, прочности режущей пластины и
прочности державки.
S=0,6÷1,2 мм/об.
Принимаем S=0,9 мм/об.
Скорость резания V:
скорость резания при нагруженном продольном точении рассчитывают по
эмпирической формуле:
, (5.11)
где
V - скорость резания, м/мин;
Cv, m, x, y -
коэффициенты [табл.17[3]]
Т
- стойкость, мин;
Kv=KmvKnvKuv
где
Knv = 0,9= 1
м/мин
Сила
резания PZ:
При
нагруженном продольном точении силу рассчитывают по формуле
(5.12)
где
PZ - сила резания, Н;
Cp, x, y, n -
табл.22, гл. 4 [3];
Kp - поправочный
коэффициент;
Где
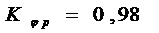
(при
);
(при
)
(при
);
(при
;
Мощность
резания N:
Мощность
резания рассчитывают по формуле:
(5.13)
где
N - мощность резания, кВт.
Число
оборотов вращения шпинделя рассчитывают по формуле
(5.14)
где
n - число оборотов вращения шпинделя, об/мин;
об/мин
По
паспортным данным токарно-рвольверного станка 1365 принимаем n=450
об/мин.
Уточненная
скорость:
м/мин
На
остальные переходы и режимы резания назначены по нормативам:
Токарная
. t=0,6 S=0,65 V=87,6 n=450
. t=0,6 S=0,6 V=115 n=1300
. t=0,6 S=0,6 V=115 n=1100
. t=0,6 S=0,6 V=115 n=700
. t=0,6 S=0,6 V=115 n=600
. t=0,3 S=0,05 V=29 n=600
. t=0,35 S=0,08 V=19 n=700
. t=2 S=0,15 V=170 n=250
. t=0,6 S=0,6 V=115 n=1300
. t=0,3 S=0,05 V=29 n=600
. t=0,6 S=0,65 V=87,6 n=450
. t=0,6 S=0,65 V=87,6 n=450
. t=60 S=0,15 V=170 n=250
. t=0,6 S=0,65 V=87,6 n=450
5.8 Расчет нормы времени
Расчет норм времени на обработку сводится к определению штучного времени
на заданную операцию на обработку одной детали.
Штучное время:
(5.15)
где
Тшт - штучное время, мин
Топ
- оперативное время, мин;
Тоб
- время на обслуживание рабочего места, мин;
Тпер
- время на перерывы, мин;
Оперативное
время:
(5.16)
где
Топ - оперативное время, мин;
То
- основное время, мин;
Тв
- вспомогательное время, мин.
Основное
время:
(5.17)
где
То - основное время, мин;
i - число
проходов в технологической операции;
где
l - расчетная длина обработки, мм;
n - частота
вращения шпинделя, об/мин;
S - подача,
мм/об.
Основное
время на токарную операцию:
То=0,12+0,09+0,08+0,015+0,057+0,041+0,025+0,21+0,69+0,027+0,22+0,025+0,56+0,96+0,12+0,43=3,67
мин.
Вспомогательное
время:
(5.18)
где
Тв - вспомогательное время, мин;
Тус
- время на установку заготовки, мин;
Туп
- время на прием управления станком и смену инструмента, мин;
Тп
- время, связанное с переходом, мин;
Тизм
- время на контроль измерения, мин.
Значения
Tв назначаются по картам общемашиностроительных
нормативов.
Вспомогательное
время для токарной операции:
Тв=0,5+3,66+1,11+0,24=5,51
мин.
Оперативное
время на токарной операции:
То=3,67+5,51=9,18
мин.
Время
на обслуживание рабочего места при выполнении токарной операции:
Тоб=0,04∙То=0,04∙9,18=0,37
мин
Время на перерывы при выполнении токарной операции:
Тпер=0,04∙Топ=0,04∙9,18=0,37 мин
Норма штучного времени на всю токарную операцию:
Тшт=9,18+0,37+0,37=9,92 мин
6. Экономическая часть
.1 Технико-экономическое обоснование
В настоящее время выпускается достаточное количество
гидромашин и гидроаппаратуры с высокими удельными показателями и КПД, но
гидроприводы в целом не отличаются высоким КПД. При этом наблюдается не только
перерасход энергии, но и снижение показателей надежности и долговечности гидросистем
вследствие утечек и других потерь энергии, за счет вибрации и пульсаций
давления, которые способствуют интенсивному изнашиванию силовых элементов
гидромашин.
В данном дипломном проекте рассматриваем повышение
производительности гидрофицированного экскаватора четвертой размерной группы,
который предназначен для выполнения земляных работ в грунтах, а также
погрузочно-разгрузочных работ. В данном экскаваторе, также одной из
существенных проблем является невысокая эффективность рабочего оборудования, при
постоянной работе экскаватора понижается КПД гидропривода и производительность
копания.
Технически эффективным решением проблемы является установка устройства
гидроаккумулятора на рабочее оборудование. Это позволяет обеспечивать
увеличение скорости подъема рабочего оборудования в два раза без изменения
параметров насоса и гидравлической системы.
.2 Расчет КПТУ
Оценка технического уровня изделия начинается с отбора
базового варианта. Формируем модель на стадии научных исследований с
параметрами соответствующими прогнозам и тенденциям развития техники в этом
направлении, а также требованиям технического задания.
Комплексный показатель технического уровня (КПТУ)
определяют для оценки технического уровня проектируемой гидросистемы
оборудования с учетом всей совокупности параметров изделия:
(6.2.1)
где bi -
коэффициент значимости i-гo параметра;
qi - относительные единичные показатели качества;
n - количество показателей качества.
или
(6.2.2)
где pHi, pБi - абсолютные значения i-гo показателя
качества соответственно новой и базовой моделей.
Выбирают вид формулы исходя из того, что увеличение
относительного показателя будет соответствовать улучшению качества изделия.
Коэффициенты значимости показывают значимость каждого i-гo параметра на величину полезного эффекта в целом. Наибольшее
распространение получил метод на основе экспериментальных оценок. Согласно
этому методу:
1. вводим обозначения показателей качества: Х1, Х2;
2. составляем квадратную матрицу смежности размеров n х n и проводим сравнения их важности для изделия относительно
друг друга. При этом используем знаки "<", ">", и
"=";
3. заменяем знаки коэффициентами
предпочтительности cxi,
соответственно"<" на 0,5, ">" на 1,5, и
"="на 1;
. находим построчно суммы ∑аi;
. определяем абсолютные значимости Вi путем метрического умножения строк в
квадратной матрице на вектор-столбец ∑аi;
. рассчитываем относительные значимости
параметров bi по формуле
(6.2.3)
Введем
обозначение показателей:
X1 -
производительность;
X2 - КПД
гидропривода;
Строим
матрицу смежности (табл.6.2.1) сравнив попарно все параметры. Заменяем знаки
"<", ">", "=" на коэффициенты
предпочтительности cxi (соответственно 0,5; 1,5; 1).
Таблица 6.2.1 - Матрица смежности
|
Х1
|
Х2
|
Σai
|
Bi
|
bi
|
Производительность
|
1
|
0,5
|
1,5
|
2,75
|
0,367
|
КПД гидропривода
|
1,5
|
1
|
2,5
|
4,75
|
0,633
|
Σ
|
|
|
4
|
7,5
|
1
|
Рассчитываем абсолютные значения Bi, затем относительные bi (вычисляются в долях единицы),
значения заносим в матрицу смежности (табл. 6.2.1)
В1=1·1,5 + 0,5·2,5 = 2,75 (6.2.4)
В2 =1,5·1,5 + 1·2,5 = 4,75 (6.2.5)
Относительные единичные показатели качества qi определяем по формуле:(6.2.2).
Данные для расчета КПТУ проектируемого оборудования заносим в таблицу 6.2.2.
гидропривод
одноковшовый экскаватор
Таблица 6.2.2 - Данные расчета КПТУ оборудования экскаватора
Номенклатура основных
параметров
|
Единицы измерения
|
Значение параметров
|
qi
|
bi
|
qi∙bi
|
|
|
Базовая
|
Новая
|
|
|
|
Производительность
|
м3/ч
|
100,4
|
112
|
1,12
|
0,367
|
0,411
|
КПД гидропривода
|
|
0,75
|
0,81
|
1,08
|
0,633
|
0,684
|
КПТУ
|
|
|
|
|
1
|
1,66
|
Полученное в результате расчетов значение КПТУ новой модели составляет
1,66, а это значит что, новое изделие более совершенно по сравнению с базовой
моделью.
6.3 Расчет затрат на производство и эксплуатацию
экскаватора
Приведенные затраты на производство и эксплуатацию экскаватора
рассчитываем по формуле:
Зпр = И + Ен ·К (6.3.1)
где Зпр - затраты на производство, руб/год;
И - эксплуатационные издержки или затраты на
эксплуатацию, руб/год;
Ен
- нормативный коэффициент сравнительной эффективности
;
Зпр = 180392,38 + 0,5 · 993828,4 = 677306,6
К - капитальные вложения в технику, руб.
К = Цн + kм +kтр (6.3.2)
где Цн - цена, руб;
kм - коэффициент, учитывающий затраты на монтаж, руб;
kтр - коэффициент, учитывающий затраты на транспортировку,
руб.
К = 355694,7 + 620236 + 17897,7 = 993828,4
kм =0,15·Цн (6.3.3)
kтр =0,05·Цн (6.3.4)
Цн = Сн + П (6.3.5)
где Сн - себестоимость, руб.
kм =0,15 · 3934440 = 590166,
kтр = 0,05 · 3934440 = 196722,
Цн
=
+
=
355694,7.
П
- нормативная прибыль на одно изделие, руб.
(6.3.6)
где Н - норматив рентабельности (норматив образования
прибыли принимаем 50%),
См - сумма прямых материальных затрат в себестоимости
оборудования (сырье, материалы, комплектующие изделия), руб.
.3.1 Расчет себестоимости
Себестоимость - это затраты, связанные с изготовлением
(включая разработку) и реализацией.
Так как известны данные о составе материальных затрат,
предназначенных для использования в новом изделии, используем метод укрупненных
нормативов.
(3.6.7)
где Ск.и - сумма прямых материальных затрат на
комплектующие изделия, руб;
Созп - основная заработная плата рабочих, руб;
кизн - коэффициент, учитывающий косвенные расходы, kизн = (30 ÷ 60);
kк - коэффициент, учитывающий косвенные расходы, куда входят:
1 расходы на содержание и эксплуатацию
оборудования (80 ÷ 120);
2 цеховые расходы (50 ÷ 80);
3 общезаводские расходы (80 ÷ 100);
4 kпр - коэффициент прочих расходов, kпр = (4 ÷ 14);
kд - коэффициент, учитывающий дополнительную заработную плату,
kд =(10 ÷ 12);
kт - коэффициент, учитывающий внепроизводственные расходы. В
среднем по отрасли, можно принять равным 10.
6.3.2 Расчет затрат на материалы
См= См.о + См.в (6.3.8)
где См.о - затраты на основные материалы, руб.
См.в - затраты на вспомогательные материалы. При
укрупненных расчетах принимают в размере 10 ÷ 15% от стоимости основных
материалов;
(6.3.9)
где
- потребность в i-ом материале,
кг/шт;
- оптовая
цена материала, руб/кг;
- оптовая
цена реализуемых отходов, руб/кг;
-
коэффициент, учитывающий транспортно-заготовительные расходы, принимаем
= 1,03 ÷ 1,05;
-
количество реализуемых расходов i-гo материала, кг;
Цены
на материал принимают на основе прейскурантов оптовых цен табл. 6.3.1
Таблица
6.3.1 - Затраты на основные материалы
|
Норма
|
Оптовая це-
|
Суммарные
|
Наименование и марка
материалов
|
расхода,
|
на,
|
затраты на
|
|
т
|
руб/т.
|
Материалы,
|
|
|
|
руб.
|
Лист стальной г/катанный,
ст.З
|
0,160
|
15940
|
2550,4
|
от 2 до 20мм.
|
|
|
|
Лист стальной г/катанный
|
0,427
|
21600
|
9223,2
|
09Г2С-4СВ ГОСТ 19281-89,
|
|
|
|
от 2 до 20мм.
|
|
|
|
Продолжение таблицы 6.3.1
|
|
|
|
Швеллер горячекатаный,
|
0,314
|
16400
|
5149,6
|
ГОСТ 9240-89,
|
|
|
|
№ 5, 6, 8, 12, 14, 16, 18а,
20, 24, 27.
|
|
|
|
Трубы бесшовные
горячекатаные,
|
0,213
|
20970
|
4466,61
|
ГОСТ 8731-87
|
|
|
|
диаметром 54, 57, 60, 76,
89, 102, 108,
|
|
|
|
114, 127, 133, 159, 168,
219, 273, 325,
|
|
|
|
426мм.
|
|
|
|
Балка г/катанная, стЗ
|
0,240
|
18000
|
4320
|
№10,12,14,16,18,20,30
|
|
|
|
См.о= (0,16·15940·1,04-30·1,2) +
(0,427·21600·1,04-35·1,2) + (0,314·16400·1,04-16·1,2) + +
(0,213·20970·1,04-16·1,2) + (0,24·18000·1,04-14·1,2) = 26610 (руб.);
См.в = 0,13·26610 = 3459;
См =26619 + 3459 = 30078
Затраты на материалы при проектировании базовой и
проектируемой модели оборудования одинаковы.
.3.3 Расчет затрат на комплектующие изделия
Затраты на комплектующие изделия определяют по их
потребному количеству и оптовым ценам на них:
, (6.3.10)
где
- потребность в i-ом виде
комплектующих изделий;
- оптовая
цена i-гo вида комплектующих изделий, руб;
Таблица
6.3.2 - Затраты на комплектующие изделия
Наименование комплектующих
изделий
|
Кол-во шт.
|
Цена за единицу, руб.
|
Сумма затрат, руб.
|
Гидрораспределитель Р80
|
1
|
11070
|
11070
|
Манометр 20МПа
|
2
|
640
|
1280
|
Фильтр FS5000 0.025 BS GT12
|
1
|
3700
|
3700
|
Рукава высокого давления DIN2SN12
|
6
|
125
|
750
|
Гидроцилиндр ковша
|
2
|
15000
|
30000
|
Гидроцилиндр стрелы
|
2
|
25000
|
50000
|
Гидрозамок VNR/B/SO/SE-15
|
2
|
1270
|
2540
|
Насос 224.25 (Завод
«Пневмостроймашина»)
|
1
|
15850
|
15850
|
Ковш 0,6
м3
|
1
|
12000
|
12000
|
Затраты на комплектующие изделия для базовой модели:
Ск.и =(11070 + 1280 + 3700 + 750 + 30000 + 50000 +
2540 + 15850 + 12000)·4,04 = 130030
6.3.4 Расчет основной заработной платы рабочим
Основная заработная плата рабочих, занятых
изготовлением оборудования может быть определена методом удельных весов:
(6.3.11)
где
ti - трудоемкость i-гo
вида работ, нормо-час;
n - количество
видов работ при изготовлении оборудования;
сн.ч.
- средняя стоимость одного нормо-часа, включая выплаты из премиальных фондов,
руб.
Усредненные
значения сн.ч. (с учетом часовых тарифных ставок, средних для соответствующих
работ, разрядов и доплат-премиальных, по районному коэффициенту и др.)
приведены в [6.3.2].
Таблица
6.3.3 - Трудовые затраты и фонд заработной платы основных производственных
рабочих
Наименование операции
|
Часовая тариф-
|
Норма времени
|
Тарифный
|
или вида работ
|
ная ставка,
|
на операцию,
|
фонд з/п,
|
|
руб/ч.
|
ч.
|
руб.
|
Сборка
|
110
|
11
|
1210
|
Регулировка и обкатка
|
250
|
2
|
500
|
Окраска
|
140
|
7
|
980
|
Изготовление присоеди-
|
100
|
14
|
1400
|
нительной арматуры
|
|
|
|
Изготовление гидроци-
|
210
|
36
|
7560
|
линдров
|
|
|
|
Изготовление составных
|
180
|
52
|
9360
|
|
|
|
Созп= 1210 + 500 + 980 + 1400 + 7560 + 9360 = 21010
6.3.5 Расчет затрат на эксплуатацию
Для целей технико-экономического анализа при
проектировании экскаватора необходимо принимать во внимание те статьи
эксплуатационных расходов, значение которых изменяется с применением вариантов
конструкторских решений. Таким образом, затраты на эксплуатацию можно
определить по формуле:
И = Зл + Здт + Зтр (6.3.12)
где И - затраты на эксплуатацию, руб/год;
Зл - амортизационные отчисления, руб/год;
Здт - затраты на дизельное топливо, руб/год;
Зтр - затраты на текущий ремонт, руб/год.
И = 73180,58 + 93415 + 13796,8 = 180392,38,
(6.3.13)
где Na -
годовая норма амортизации, %;
К - капитальные вложения потребителя на приобретение,
транспортировку, монтаж оборудования, руб.
.
(6.3.14)
где Нч - норма расхода дизтоплива машины, на которой
установлен гидроаккумулятор, час;
Цл - цена на диз. топливо за литр, руб;
Т - время работы гидроаккумултора за год, час;
Здт =17·17,5·314 = 93415.
Зтр= Сэл + Зн + Зм (6.3.15)
где Сэл - стоимость заменяемых элементов, руб/год;
Зн - заработная плата наладчиков, руб/год;
Зм - затраты на материалы, расходуемые при ремонте,
руб/год.
Зтр = 11100 + 2608 + 88,8 = 13796,8,
(6.3.16)
где
Nэл - количество заменяемых элементов в год, шт;
Цэл
- цена элемента i-го вида, руб.
Сэл
= 820 +1050 + 8450 + 780 = 11100.
(6.3.17)
где Sн -
часовая тарифная ставка наладчика, руб/час;
k1, k2, k3- коэффициенты, учитывающие
соответственно доплаты к основной заработной плате (премии, районный
коэффициент и др.). Можно принять k1 = 1,6, k2 =1,1, k3 =1,14
ti - затраты времени на затрату i-гo элемента.
Зн = 200·1,6·1,1·1,14·(1 + 1,5 + 2 + 2) = 2608,
Затраты на материалы, расходуемые при ремонте
принимаем в пределах 0,5÷1,0 % от Сэл.
Зм = 0,008·Сэл (6.3.18)
Зм= 0,008·11100 = 88,8.
.4 Расчет оптовой цены экскаватора с учетом КПТУ
Одним из направлений совершенствования ценообразования
на новую технику является более полный учет в цене технического уровня и
качества изделия.
В соответствии с отраслевой методикой ценообразования
оптовая цена оборудования определяется по формуле:
Цн = Цб·[1 + (КПТУ - 1)·0,7]·0,9 (6.4.1)
где Цн,Цб - цены соответственно нового и базового
оборудования, руб;
,7 - коэффициент учета полезного эффекта в цене нового
экскаватора;
,9 - коэффициент удешевления, корректирующий
прейскурантную цену базового оборудования и характеризующий моральное старение
базового изделия за период проектирования и освоения новой техники.
Цн = 1010000·[1 + (1,66-1)·0,7]·0,9 = 1328958.
.5 Выбор оптимального варианта конструкторского
решения
Критерием оптимальности применения является
интегральный показатель качества, учитывающий влияние, как технического уровня
изделия, так и затраты на его изготовление. Он выражается через формулу:
(6.5.1)
где U -
интегральный показатель качества;
Зпр - приведенные затраты на изготовление и
эксплуатацию;
;
.
Таким образом модернизация экскаватора дает вполне
ощутимый экономический эффект, так как рост качества опережает рост затрат на
изготовление проектируемого изделия. Получение результаты расчетов приведем в
сводной таблице (6.5.1)
Таблица 6.5.1 Технико-экономические показатели экскаватора ЭО 4225
Наименование показателей
|
Ед. измерений
|
Значение показателей
|
|
|
проектируемая
|
базовая
|
1. Технические: КПД
Производительность КПТУ
|
м3/ч
|
0,81 112 1,66
|
0,75 104
|
Показатели
эффективности: - затраты на производство - затраты на эксплуатацию -
приведенные затраты - интегральный показатель качества руб/год руб/год
руб/год руб
,38
,6
|
|
Цена с учетом КПТУ
|
руб
|
1328958
|
7. Безопасность и экологичность проекта
Целью раздела "Безопасность и экологичность
проекта" является разработка безопасной и надежной конструкции
гидравлического привода машин и механизмов, которые исключают или снижают
возможность производственного травматизма, профессиональных заболеваний,
пожаров и взрывов, аварий и загрязнения окружающей среды.
Одним из перспективных направлений экономического и
социального развития России является развитие производства новой техники для
выполнения земельно-строительных, подъемно-транспортных,
погрузочно-разгрузочных, лесозаготовительных и другим машинам циклического
действия.
Целью дипломного проекта является: «Модернизация
гидропривода одноковшового экскаватора ЭО - 4225 Ковровец».
Рассматриваемый экскаватор ЭО-4225 предназначен для
выполнения земляных работ на грунтах 1 - 4 категорий по ГОСТ 17343-71 и предварительно
разрыхленных скальных и мерзлых грунтов с величиной кусков не более 400мм, в
диапазоне температур окружающей среды -40 до +40С0. Экскаватор применяют для
разработки карьеров, рытья котлованов, траншей, каналов, погрузки грунта и
сыпучих материалов.
Сущность модернизации заключается в том, что при
установке дополнительного оборудования в виде гидроаккумулятора, снижаются
нежелательные колебательные процессы в гидросистеме, уменьшается пульсация
жидкости и как следствие падает уровень шума и вибрация.
.1 Недостатки машины по обеспечению её безопасной
эксплуатации
Полностью безопасных и безвредных машин не существует.
Одной из целей данного проекта является уменьшение опасности и вредности при
эксплуатации и обслуживании экскаватора ЭО-4225.
На основе анализа опыта эксплуатации гидромашин
(гидрооборудования, отдельных узлов и элементов) выявлены следующие характерные
опасности и вредности, возникающие при их работе:
аккумулирование потенциальной энергии внутри машины
жидкостями и газами под давлением, упругими элементами (пружинами);
опасности связанные с погрузочно-разгрузочными
работами;
опасности удара элементами гидропривода;
поступление вибрации на оператора за период рабочего
дня, что очень плохо сказывается на здоровье человека;
опасности, обусловленные выбросом жидкости, которая
оказывает на организм человека токсичное действие и, кроме того, создаёт
опасность возникновения пожара;
опасности обусловленные погодными условиями,
эксплуатация проектируемого гидропривода предполагается в интервале температур
от -40° С до +40° С;
опасности, связанные с выбросом вредных веществ в
атмосферу;
опасность воздействия шума на оператора за счет
нахождения кабины на одной платформе с ДВС (двигатель внутреннего сгорания).
Так же в задачу охраны труда входит сведение к
минимальной вероятности поражения или заболевания работающего с одновременным
обеспечением комфорта, при максимальной производительности труда.
7.2 Проектные решения по обеспечению безопасности
труда на проектируемом оборудовании
Для безопасного ведения работ всех видов обслуживающий
персонал должен строго соблюдать правила техники безопасности при эксплуатации,
техническом обслуживании и ремонте экскаватора. Нарушение этих правил может
привести к несчастным случаям, связанным с получением различных травм (ушибов,
ранений, ожогов кислотой, от действия электрического тока и.т.д.) и привести к
понижению трудоспособности.
Находящаяся рабочая жидкость внутри гидропривода при
изменении температуры окружающей среды изменяет свою вязкость. Это влечет за
собой низкую проходимость рабочей жидкости по трубопроводу, тем самым может
привести к образованию пробок в трубопроводе и к разрыву рукавов высокого
давления. Таким образом, в гидросистеме может произойти повышение давления, что
чревато разрушением элементов гидропривода. И как следствие, это может повлечь
за собой травматизм.
Средствами борьбы с этими опасностями могут служить:
1установка устройства гидроаккумулятора;
2использование маловязких рабочих жидкостей;
3выполнение всех инструкций по эксплуатации машин оснащенных
гидроприводом.
При отсутствии на машине устройств гидроаккумулятора
при эксплуатации в районах с низкой температурой окружающей среды, повышается
износ гидрооборудования и риск выхода из строя элементов гидропривода,
вследствие чего возможно несанкционированное опускание исполнительного
механизма и травмирование посторонних лиц. В гидроприводах применяются элементы
с подвижными частями и деталями, которые могут нанести повреждение человеку при
скачке давления в гидросистеме, либо при перемещении органов управления
исполнительных механизмов.
Во избежание травматизма принимаются следующие меры:
- установка устройства гидроаккумулятора;
- применение в гидроприводе предохранительных
клапанов;
применение гидрозамков.
При высоких давлениях в гидроприводе возможны утечки
рабочей жидкости, которые в свою очередь могут нанести вред здоровью человека,
а так же попасть на двигатель машины, и как следствие, привести к возгоранию
экскаватора. Кроме того, при длительной работе экскаватора, элементы рабочего
оборудования могут нагреваться, при попадании рабочей жидкости на них
происходит испарение вредных веществ.
Во избежание подобных ситуаций предпринимают следующие
меры:
- обеспечение герметичности уплотнений (ГОСТ
9833-73) и манжет (ГОСТ 14896-84);
4 ежедневной проверки трубопроводов и
рукавов высокого давления;
5 предоставление оператору средств
индивидуальной защиты.
- в качестве рабочих жидкостей для гидросистемы
экскаватора выбраны минеральные масла МГ15В (зимой) и МГЕ46В (летом), которые
соответствуют всем техническим требованиям, не имеют неприятного запаха и не
несут вреда при попадании на кожу человека. Температура вспышки соответствует
требованиям пожаробезопасности и составляет 175 °С, что на 95 °С выше
максимальной.
- для предотвращения попадания рабочей жидкости
на рабочие органы, установлены защитные кожухи и рабочие органы расположены
так, чтобы жидкость не попадала на них.
Обслуживающий персонал должен работать в специальной
одежде, соответствующей климатическим условиям, иметь помещения для отдыха и
обогрева, сокращение рабочего дня и увеличение продолжительности отпуска при
температуре воздуха ниже допустимых величин (время пребывания на рабочих местах
регламентируют СанПиН 2.2.4.518-98).
При работе на экскаваторе происходит выделение вредных
веществ. Они в виде токсинов или паров проникают в организм человека через
органы дыхания и кожный покров. Последствиями воздействия вредных веществ на
организм человека могут быть:
6 отравления;
7 ожоги;
8 изменение световосприятия зрения;
9 другие отклонения в состоянии
здоровья работающих.
Для предотвращения неблагоприятного воздействия
вредных веществ на организм человека и нормализации санитарно-гигиенического
состояния воздушной среды используют:
10максимально возможную герметизацию источников выделения вредных веществ;
11обеспечение работающих средствами индивидуальной защиты органов дыхания и
кожного покрова.
Периодичность испытаний гидросистемы - два раза в год
и обслуживание оператором - ежедневно. Испытания проводятся при давлении 30 МПа.
Включение смазывающего устройства в гидросистеме
машины обеспечивает значительную экономию рабочей жидкости и создает
экономичный режим работы насоса.
Рабочие характеристики поддерживаются за счет
выбранного насоса, поддерживается расход и давление в гидросистеме машины, а
температура рабочей жидкости остается в допустимых пределах из-за выбранного
бака.
Органы управления находятся в кабине и осуществляются
рычагами, которые соответствуют требованиям эргономики, чтобы не было
самопроизвольного пуска. Установка запускается поэтапно, сначала запускается
двигатель с ключа, а потом рычагами осуществляется управление машиной.
Всё это в комплексе ведет к оптимизации работы
гидропривода, тем самым, уменьшая вредное воздействие на окружающую среду и
человека. Устранены вибрационные воздействия за счет плавности работы рабочего
органа. Исключены гидроудары и резкие подъемы и опускания рабочих органов.
7.3 Обеспечение безопасности в аварийных и
чрезвычайных ситуациях
При возникновении пожара необходимо снять напряжение с
электрооборудования и заглушить двигатель. Для тушения пожара в кабине
экскаватора предусмотрены углекислотные или порошковые огнетушители.
Оператор должен опустить стрелу и прекратить работу в
случае:
12внезапной просадки или сползания машины в котлован при работе на бровке;
13деформации металлоконструкций, разгерметизации гидросистемы,
возникновения посторонних шумов и стуков в механизмах;
14сильного снегопада, тумана, грозы.
Сигнализация о разгерметизации и опасном повышении
давления гидропривода осуществляется при помощи специально установленного
манометра, кроме того при повышении температуры выше 70°С включается
теплообменник.
При высоком давлении рабочая жидкость вытекает
мгновенно и может нанести травму человеку, а также попасть на двигатель машины
и привести к возгоранию. Для предотвращения этих явлений с целью повышения
безопасности, надежности и экологичности проведен расчет на прочность наиболее
опасных участков (глава 4).
7.4 Охрана окружающей среды при эксплуатации
гидропривода и технологических процессах изготовления узлов и деталей
гидропривода
При эксплуатации гидропривода особое внимание нужно
уделять проблеме экологии, так как рабочие жидкости изготавливаются на нефтяной
основе, а нефть является сильным загрязнителем окружающей среды. При попадании
в воду даже небольшого ее количества, вода становится непригодной для
использования, а на месте ее пролива в почву, долго не растет трава.
Наибольший объем проливаемой жидкости приходится на
время ее сезонной смены или дозаправки. Чтобы минимизировать эти утечки рабочую
жидкость следует заливать в гидросистему при помощи специальных
маслозаправочных станций. В их отсутствии пользоваться глубокими воронками с
металлической сеткой. Запрещается доливать рабочую жидкость во время работы двигателя
экскаватора, курить, пользоваться открытым огнем, принимать пишу.
При сезонной замене отработанной рабочей жидкости
производится ее утилизация и отправка на переработку. Перед отправкой на
утилизацию, рабочая жидкость должна быть аккуратно слита из масляного бака,
гидравлических цилиндров и маслопроводов.
С целью предупреждения возможного разрыва
трубопроводов и возникновения утечек рабочей жидкости через уплотнение
сальников, рукавов и трубопроводов гидроагрегатов, следует ежедневно
осуществлять осмотр машины, устранять малейшие подтеки масла, подтягивать
хомуты и соединительные элементы. Отходы производства при изготовлении детали,
то есть стружка, идут на утилизацию, а затем на переплавку.
В соответствие с ГОСТ 12.0.003 "Опасные и вредные
производственные факторы. Классификация" в рабочей зоне при механической
обработке детали имеют место выделения вредных веществ (см. таблицу 7.4.1)
Таблица 7.4.1 - Выделение вредных веществ
Вид обработки
|
Вредное вещество
|
Удельное выделение
|
Точение
|
Аэрозоли эмульсона
|
0,04 ÷ 0,25 г/ч
|
Сверление
|
Аэрозоли эмульсона
|
0,06 г/ч
|
Предельно допустимая концентрация (ПДК) выделяемых
вредностей при механической обработке определим в соответствии с ГОСТ
12.1.005-88, их значения занесём в таблицу 7.4.2:
Таблица 7.4.2 - Выделяемые вредности при механической
обработке
Наименование вещества
|
Агрегатное состояние
|
ПДК, мг/см3
|
Класс опасности
|
Пыль оксида ванадия
|
Твёрдое
|
0,5
|
II
|
Масло минеральное (на
нефтяной основе)
|
Аэрозоль
|
5
|
III
|
При механических операциях: точение, сверление образуется
пыль, мелкая стружка с повышенным содержанием абразивных включений, вредные для
здоровья аэрозоли жидкостей и т.д. Для снижения степени воздействия вредных
веществ и обеспечения безопасной работы предусмотрительно используем:
устройство для отсоса пыли в виде вытяжных зондов или
вытяжных панелей;
возможность отсоса из зоны обработки загрязнённого
воздуха;
оснащение присоединяемыми к станкам индивидуальными
станками, устройствами (включающими пылестружкогазоприёмники и отсасывающие
устройства);
при необходимости зона обработки должна закрываться
кожухом, к которому присоединяется воздуховод отсасывающей системы.
7.5 Инструкция по безопасности эксплуатации
гидропривода по ГОСТ 12.0.004
На машине работает один оператор. Присутствие
посторонних лиц и предметов на экскаваторе во время работы запрещено, также как
и нахождение кого бы то ни было в радиусе его зоны действия. Лица, не имеющие
соответствующей квалификации и не прошедшие инструктажа по технике
безопасности, к работе на экскаваторе не допускаются. Персонал должен строго
соблюдать правила техники безопасности при эксплуатации, техническом
обслуживании и ремонте экскаватора. Нарушение этих правил может привести к
несчастным случаям, связанным с получением различных травм (ушибов, ранений,
ожогов кислотой, от действия электрического тока и.т.д.) и потерей
трудоспособности.
При эксплуатации полноповоротного одноковшового
экскаватора ЭО-4225 необходимо пользоваться инструкцией по безопасной
эксплуатации экскаватора, утвержденной ОАО «Воронежский механический завод».
.6 Расчет виброизоляторов
Функционирование экскаватора обеспечивается
гидроприводом, при работе которого наблюдается вибрация. Она может быть снижена
тремя способами: воздействием силы на источник вибрации, воздействием на
колебательную систему и виброизоляцией. Наиболее распространенным методом
борьбы с вибрацией является применение для вибрирующего оборудования
виброизоляторов, представляющих собой либо пружину, либо резиновые втулки. На
экскаваторе используются виброизоляторы в виде резиновых втулок, установленных
на гидроцилиндрах в проушине, где осуществляется закрепление с рабочим органом.
Основное их назначение - защита рабочего оборудования от вибраций и защита
работающего от вибрирующего рабочего оборудования. Расчет виброизоляторов сводится
к определению их геометрических параметров: высоты, площади, числа и марки
резиновых прокладок.
Экскаватор весом Р = 25600 Н с числом оборотов вала
насоса п = 1500 об/мин.
Определим частоту вынужденных колебаний:
Гц.
Собственная
частота насоса рассчитывается по формуле:
,
Гц.
Находим
статическую осадку резиновой втулки
где
g - ускорение свободного падения, м/с2.
м.
Высоту втулки рассчитываем по формуле (м):
,
где Gy -
динамический модуль упругости резиновой втулки, н/м2;
-
допустимая нагрузка на сжатие резиновой втулки, Н/м2;
Из
рекомендаций [1, с. 87] выбираем в качестве втулки марку резины 2566, у которой
[
]= 9,8·104 Н/м2 и Gy = 24,5·105
Н/м2.
м.
Втулка
чрезмерно толста. Принимаем соотношение частот вынужденных и собственных
колебаний, равное 2. Отсюда:
Гц
Тогда
статическая осадка
м.
Высота
втулки при этом
м.
Общую
площадь втулок, укладываемых под основание экскаватора, рассчитываем по
формуле:
,
где Р - вес вибрирующего агрегата, Н;- число втулок,
шт.
Число
втулок можно принять равным 4, тогда площадь каждой втулки:
м2.
При
квадратной форме сечения ее сторона будет составлять 0,255 м.
Определим
коэффициент передачи:
.
Оптимальное
соотношение
.
Снижение
уровня колебаний и вибраций определим по формуле:
,
дБ
Вывод:
Исходя из расчета виброизоляторов, становится очевидным, что при установке
виброизолятора в виде резиновых втулок, установленных на гидроцилиндрах в
проушине, где осуществляется закрепление с рабочим органом, происходит защита
рабочего оборудования от вибраций.
7.7 Средств индивидуальной защиты
Таблица 7.7.1 - Климатические регионы (пояса) в России
Климатический регион (пояс)
|
Средняя температура воздуха
зимних месяцев, °С
|
Средняя ветра из вероятных
м/с
|
скорость наиболее величин,
|
IA (особый)
|
-25
|
6,8
|
1Б (IV)
|
-41
|
1,3
|
II (III)
|
-18
|
3,6
|
III (II)
|
-9,7
|
5,6
|
Гигиенические требования к теплоизоляции СИЗ.
Наш регион относится к климатическому региону 1Б и IV поясу со средней температурой
воздуха зимних месяцев -35°С и средней скоростью ветра 1,3 м/с [5], (СанПиН
2.2.4.518-98).
Требовании к теплоизоляции СИЗ применительно к
климатическим регионам представлены в таблице 7.7.2.
Таблица 7.7.2 - Требовании к теплоизоляции СИЗ
применительно к климатическим регионам
Климатический регион (пояс)
|
Теплоизоляция СИЗ, °С ·
м2/Вт (не менее)
|
|
Головы
|
ног
|
рук
|
IA (особый)
|
0,397
|
0,437
|
0,497
|
1Б (IV)
|
0,447
|
0,572
|
0,551
|
II (III)
|
0,329
|
0,422
|
0,403
|
III (II)
|
0,295
|
0,332
|
0,377
|
Расчет теплоизоляции комплекта индивидуальных средств
защиты работающих от охлаждения и времени допустимого пребывания на холоде.
Сущность метода заключается в оценке теплозащитной
функции одежды на основании величин ее теплоизоляции и показателей теплового
состояния человека в реальных условиях трудовой деятельности и/или в условиях,
моделирующих эту деятельность (в микроклиматической камере). Теплоизоляция
комплекта одежды определяется на основе результатов измерения температуры кожи
и плотности сухого теплового потока с поверхности тела в заданных условиях
испытания.
Теплоизоляция одежды определяется с участием человека.
Она может быть определена также расчетным методом исходя из технических
параметров пакета материалов (толщины и воздухопроницаемости):
для расчета теплоизоляции одежды используются средние
значения теплового потока из величин, зарегистрированных в период его
относительной стабилизации (но не менее чем из четырех) *, и температуры кожи в
конце исследования;
теплоизоляция одежды (комплекта) в целом (Iк) рассчитывается по формуле (7.7.1):
(7.7.1)
Где Тск - средневзвешенная температура кожи, °С;
Тв - температура окружающего воздуха, °С;
qcn - средневзвешенный тепловой поток, Вт/м2.
Датчик в области лба размещается под головным убором.
Теплоизоляция отдельных предметов одежды (головной
убор, рукавицы, обувь, костюм и т.д.) определяется по формуле (7.3.2):
(7.7.2)
где Тлк - температура кожи той или иной области тела
(локальная), °С;
Тв - температура окружающего воздуха, °С;
qлп - тепловой поток с поверхности той или иной области тела
(локаль-ный), Вт/ м ;
- датчики для измерения температуры кожи и
теплового потока располагаются на поверхности тела человека;
- средневзвешенная температура кожи рассчитывается по
формуле (7.7.3)
Тек = 0,0886 · Т1 + 0,34 (Т2 + ТЗ + Т4 + Т5) / 4 +
0,134 · Т6 + 0,045 · Т7 + 0,203 (Т8 + Т9) / 2 + 0,125 · Т10 + 0,0644 · Т11, (7.7.3)
Где Т1 ÷ Т11 - соответственно температура
кожи лба, груди, спины, живота, поясницы, плеча, тыла кисти, бедра (верх),
бедра (низ), голени, тыла стопы;
- средневзвешенный тепловой поток рассчитывается
аналогично определению средневзвешенной температуры кожи.
Расчетный метод определения теплоизоляции одежды (вид
одежды: комбинезон или куртка и брюки):
- измеряется толщина пакета материалов одежды
(включая "комнатную" одежду) при давлении 2 г·с/см2, и по аналогии
рассчитывается ее средневзвешенное значение;
- теплоизоляция одежды в относительно спокойном
воздухе рассчитывается по формуле (7.7.4) (применительно к человеку,
находящемуся в покое в положении "стоя"):
IК = 0,125 + 0,044 · σ - 0,000678 ·
σ (7.7.4)
где Iк -
теплоизоляция одежды в относительно спокойном воздухе (штиль);
σ - средневзвешенная толщина пакета
материалов одежды, мм;
Теплоизоляция одежды в условиях ветрового воздействия,
IКВ, определяется из формулы (7.7.5):
IКВ= Iк
[100 - [(0,07 · В + 2) · V +
5]] / 100 (7.7.5)
где В - величина воздухопроницаемости верхнего слоя
одежды (основного) или в комплекте с используемой ветрозащитной прокладкой, дм3/м2
· с (при перепаде давления 5 мм вод. ст.);
V - скорость ветра, м/с;
- снижение Iкв, % под воздействием движений человека в процессе трудовой деятельности
(может быть установлено в процессе исследований).
Определим, какую теплоизоляцию будет иметь одежда,
имеющая средневзвешенную толщину σ =15 мм, воздухопроницаемость В =30
дм3/м2·с при скорости ветра V =1,3
м/с.
qлп = 0,155 °С·м2/Вт,
Iк= 0,125 + 0,044 · 15 - 0,000678 · 15=0,775,
Iкв= 0,775 [100 - [(0,07·30 + 2)·1,3 + 5]] /100= 0,695
Одежда считается соответствующей условиям
эксплуатации, если средние значения всех наиболее важных показателей теплового
состояния человека не выходят за границы оптимального или допустимого. Число
выходов отдельных величин показателей за граничные значения не должно превышать
20% от их общего количества.
.8 Электробезопасность
В соответствии с Правилами технической эксплуатации электроустановок
потребителей и Правилами техники безопасности при эксплуатации электроустановок
потребителей машинисты экскаваторов должны иметь квалификационную группу не
ниже второй, а обслуживающие машины электромонтеры - не ниже третьей. Лица,
относящиеся ко второй квалификационной группе, должны знать устройство
электроустановок; опасность воздействия электрического тока на человека; основные
требования техники безопасности, иметь общее представление о назначении и
применении защитных средств; уметь практически оказывать первую медицинскую
помощь.
При поражении электрическим током различают электрические травмы
(наружные поражения тканей) и электрический удар (поражения внутренних
органов).
В частности, по требованиям электробезопасности
экскаваторы должны быть оборудованы:
электростартером для пуска основного или пускового
двигателя;
устройством отключения АКБ;
защитными колпачками на открытых клеммах
электрооборудования кроме подключенных на «массу»;
розеткой для подключения переносной лампы мощностью не
менее 20 Вт;
отдельными контейнерами или отсеками для АКБ, что
исключит попадание токопроводящих и горючих материалов на батареи, а паров электролита
- в кабину;
дополнительной защитой изоляции от механических
повреждений в местах перехода через острые углы и кромки деталей.
.9 Пожаробезопасность
На экскаваторе должны находиться средства
пламегашения, к которым есть свободный доступ и которые можно снять с
крепления, не применяя инструмент.
Выпускная система двигателя должна обеспечивать
гашение искр до выхода отработавших газов в атмосферу, струя отработавших газов
не должна попадать на оператора или горючие материалы.
При возникновении пожара опустите рабочее оборудование
на землю, остановите двигатель, повернув ключ включателя стартера против
часовой стрелки до упора, отключите «массу» аккумуляторов и немедленно покиньте
экскаватор.
При пожаре горящее топливо и масла нельзя тушить
водой. Следует применять огнетушитель, забрасывать пламя землей или песком.
Нельзя подходить к открытому огню в промасленной одежде.
Соблюдайте особую осторожность при обслуживании
аккумуляторных батарей. Нельзя курить и пользоваться открытым огнем; не
допускайте образования искры вблизи батареи: это может привести к пожару или
взрыву, т.к. аккумуляторы выделяют легковоспламеняющиеся газы.
Чтобы избежать возникновения искры вблизи батареи,
провод, ведущий к «массе», всегда подсоединяйте последним, а отсоединяйте первым.
Не допускайте, чтобы какой-нибудь металлический предмет или соединительный
провод одновременно прикасался бы к положительному полюсу батареи и к другой
металлической детали экскаватора. При таком касании искра может вызвать взрыв.
Чтобы определить степень разряженности аккумуляторов, пользуйтесь вольтметром
(нагрузочной вилкой) или ареометром. Перед подключением или отключением
аккумуляторов убедитесь в том, что включатель «массы» отключен.
Постоянно следите за состоянием изоляции и надежностью
крепления электрических проводов. Искрение в местах повреждения изоляции и
ослабление крепления может привести к пожару.
В случае возгорания электропроводки немедленно
отключите «массу» аккумулятора!
При обслуживании двигателя и топливной системы
экскаватора:
Немедленно устраняйте все обнаруженные течи топлива и
масла. Насухо протрите все загрязненные места на экскаваторе.
Никогда не открывайте горловину топливного бака и не
заливайте топливо в бак при работающем двигателе. Не курите, обслуживая
топливную систему. В холодное время года не пользуйтесь открытым огнем для
прогрева топливопроводов и поддона дизеля. Пары топлива опасны, искры или
открытое пламя могут привести к их взрыву или пожару.
Следите, чтобы во время работы дизеля вблизи
выпускного коллектора и глушителя не было легковоспламеняющихся материалов.
Используйте только рекомендованные сорта топлива.
Никогда не смешивайте дизельное топливо с бензином, спиртом и т.д. это может
привести к пожару или взрыву.
Список используемых источников
1. Каверзин
С. В. Курсовое и дипломное проектирование по гидроприводу самоходных машин:
Учебное пособие.-Красноярск: ПИК «Офсет», 1997 384с.
. Каверзин С.
В., Лебедев В. П., Сорокин Е. А. Обеспечение работоспособности гидравлического
привода при низких температурах Красноярск: 1997.-240с.
. Справочник
технолога-машиностроителя, том 1 / Под ред. Косиловой А. Г., Мещерякова Р. К.:
Машиностроение, 1985.-696 с.
. Справочник
технолога-машиностроителя, том 2 / Под ред. Косиловой А. Г., Мещерякова Р. К.:
Машиностроение, 1986.-496 с.
. Чекмарев А.
А., Осипов В. К. Справочник по машиностроительному черчению.- М.: Высшая школа,
1994. -671 с.
.
Общестроительные нормативы режимов резания для технического нормирования работ
на металлорежущих станках. Токарные, карусельные, токарно - револьверные,
алмазно - расточные, сверлильные, строгальные, долбежные, фрезерные станки. М.:
Машиностроение, 1974.-416 с.
.
Общестроительные нормативы времени вспомогательного, на обслуживание рабочего
места и подготовительно - заключительного на работы, выполняемые на
металлорежущих станках, издание 2-е. М.: Издательство НИИ труда, 1984.-460с.
. Анурьев В.
И. Справочник конструктора - машиностроителя, том 1. М.: Машиностроение,
1978.-728 с.
. Анурьев В.
И. Справочник конструктора - машиностроителя, том 2. М.: Машиностроение,
1978."553 с.
. Анурьев В.
И. Справочник конструктора - машиностроителя, том 3. М.: Машиностроение,
1978.-557 с.
. Башта Т. М.
Машиностроительная гидравлика. М.: Машиностроение, 1971.-672 с.
. Навроцкий
К.Л. Теория и проектирование гидро- и пневмоприводов: Учебник для студентов
вузов по специальности (Гидравлические машины, гидроприводы и
гидропневмоавтоматика). Машиностроение. 1991. -384 с
. Емелина
З.Г., Емелин Д.Г. Безопасность жизнедеятельности: Учебное пособие. Красноярск
ИПЦ КГТУ, 2000. 183 с.
. Руденко
П.А. и др. Проектирование и производство заготовок в машиностроении: Учеб.
Пособие / П.А. Руденко, Ю.А. Харламов, В.М. Плескач; Под общ. ред. В.М.
Плескача. - К.: Высшая шк., 1991. - 247 с.: ил.
. Технология
машиностроения: В 2 т. Т.1. Основы технологии машиностроения: Учебник для вузов
/ В.М. Бурцев, А.С. Васильев, А.М. дальский и др.; Под ред. А.М. Дальского. -
М.: Изд-во МГТУ им. Н.Э. Баумана, 1998. - 564с., ил
. Технология
машиностроения: В 2 т. Т.2. Основы технологии машиностроения: Учебник для вузов
/ В.М. Бурцев, А.С. Васильев, А.М. дальский и др.; Под ред. А.М. Дальского. -
М.: Изд-во МГТУ им. Н.Э. Баумана, 1998. - 564с., ил
. Примеры
расчетов гидропривода: Метод. Указания для студентов специальностей 1211 -
(Гидравлические машины, гидропривод и гидропневмоавтоматика) и 1709 -
(Подъемно-транспортные, строительные и дорожные машины) / Сост. П.М. Кондратов;
КГТУ. Красноярск, 1998. 83 с.
.
Металлорежущие станки. Учеб. Пособие для втузов Н.С. Колев, Л.В. Красниченко,
Н.С. Никулин и др. - 2-е изд., перераб. и доп. - М.: Машиностроение, 1980. -
500 с., ил.
. С.В.
Каверзин, А.С. Каверзина, С.В. Подсосов. Гидравлические баки самоходных машин
(проектирование, расчет, эксплуатация). Красноярск ИПЦ КГТУ 2001. 75с.
. Стандарт
предприятия. СТП КГТУ 01-02. Т. В. Васильченко Красноярск КГТУ 2005. 52с.
.
Безопасность и экологичность проекта: Метод. Указания по дипломному
проектированию для студентов направления «Гидравлическая, вакуумная и
компрессорная техника» (спец. 121100). В.Я. Кондрасенко, Л.Н. Горбунова, О.Н.
Ледяева. Красноярск: ИПЦ КГТУ, 2004. 24с.
.
Безопасность жизнедеятельности в техносфере: Учеб. пособие. О.Н. Русак, Л.Н.
Горбунова, В.Я. Кондрасенко и др. Красноярск: ИПЦ КГТУ, 2001. 431с.