Показатель
|
Эталонная СТО
|
Расчетная СТО
|
|
|
|
Численность
производственных рабочих Р
|
75
|
|
63 2860 870 12500 5490
|
Площадь
производственно- складских помещений S п ,
м2
|
3490
|
|
|
Площадь
административно-бытовых помещений S
а , м2
|
1070
|
|
|
Площадь
территории S т , м2
|
14175
|
|
|
Число
комплексно обслуживаемых автомобилей в год N
|
4920
|
|
|
3.
Исследовательская часть
3.1 Современные методы диагностики
дизельных двигателей
Выбор измерений определяется наличием оборудования для
диагностики и необходимыми затратами времени. Для электронных систем с
самодиагностикой сначала считывают информацию из памяти неисправностей.
Преимущество метода состоит в легком доступе к информации и возможности
предварительной диагностики всех имеющихся электронных блоков. Разумеется,
эффект от применения этого метода не должен переоцениваться, т. к. блок
управления контролирует другие блоки большей частью лишь по конечному
результату. Рано или поздно любой механик сталкивается с ситуациями, когда при
неудовлетворительно работающем двигателе из памяти неисправностей может
поступать сообщение о том, что они отсутствуют. В этом случае механик
целенаправленными измерениями должен проверять блоки, которые не определяются
самодиагностикой. Например, проверку работы механизмов двигателя и системы
впрыска топлива придется осуществлять измерением компрессии и давления подачи
топлива. При жалобах на плохой пуск, низкую мощность двигателя или дымный
выхлоп рационально провести замер дымности ОГ дымомером типа «Хартридж».
Преимущество такого замера - в легком доступе к выпускной трубе.
Большая часть блоков управления поставляется с так называемым
перечнем параметров, куда входят все измеряемые величины, обрабатываемые блоком
управления. Эти величины при опросе датчиков проверяются на достоверность.
Комбинируя различные данные результатов проверки, механик, имеющий большой опыт
измерений и хорошо знающий систему управления, может определить дальнейшие шаги
проверки. В особенно сложных случаях рекомендуется зарегистрировать проведенные
измерения, включая результаты их обработки, и соответствующим образом
распечатать. Только действуя последовательно, методом исключения исправных
блоков, можно выделить неисправный конструктивный элемент. Когда дефектный блок
будет установлен - либо обнаружением в памяти неисправностей, либо с помощью
соответствующих тестов - дефектная часть блока должна быть определена
дальнейшими измерениями. Например, блок измерения температуры охлаждающей жидкости
состоит из датчика температуры охлаждающей жидкости, электрических проводов,
соединительных колодок и соответствующей части блока управления. В памяти
неисправностей может оказаться испорченным один из вышеназванных конструктивных
элементов. Измерением напряжения или сопротивления неисправный конструктивный
элемент может быть окончательно определен и заменен. Такой метод проверки может
потребовать очень много времени, однако в сложных случаях он является
единственным, действительно приводящим к положительному результату.
3.1.1 Самодиагностика
Уже первые электронные системы впрыска топлива включали
самодиагностику. В ремонтных мастерских с появлением двигателей, оснащенных
системой впрыска, поя-вилась надежда, что одним лишь опросом памяти неисправностей
подозрительный конструктивный элемент может быть обнаружен и заменен, а данные
о нем удалены из памяти неисправностей. Традиционные измерения и методы
диагностики, требующие больших затрат, должны были бы остаться в прошлом. Опыт
все эти надежды разрушил: очень часто на явно неисправных транспортных
средствах самодиагностика не определяет никаких повреждений или неправильно
устанавливает причину неисправности. При гидродинамических или механических
неисправностях самодиагностика либо ничего не выдает, либо выдает неправильные
заключения.
Ограниченные возможности системы самодиагностики можно
продемонстрировать на примере датчика температуры. Мерой температуры для блока
управления служит падение напряжения на термисторе с отрицательным
температурным коэффициентом NTC. Разработчик устанавливает допустимый диапазон
температур, например, от -40 до +140 "С (рис. 3.1.1).
Рис. 3.1.1 Контролируемое блоком управления напряжение
сигнала датчика с отрицательным температурным сопротивлением (NTC). В заштрихованной
области блок управления не регистрирует неисправность
Для блока управления все сигналы, соответствующие этому
диапазону температур, находятся в области напряжений от 0,5 до 4,5 В. Только
когда напряжение выходит из этой зеленой области, блок управления устанавливает
ошибку, которая соответствует либо короткому замыканию (U5= 0 В), либо обрыву (U5= 5 В). Однако, если
из-за повышенного переходного сопротивления в электрическом разъеме измеряется
слишком низкая температура, а напряжение сигнала при этом не вышло из «зеленой
области», блок управления посчитает эту информацию правильной и будет
использовать ее, например, при расчете начала впрыскивания топлива или величины
пусковой подачи топлива. Эти соображения относятся ко всем датчикам, у которых
величина напряжения сигнала является мерой таких физических величин, как расход
воздуха, давление наддува, положение педали подачи топлива и т. д. Отсюда
следует, что сообщение блока управления «неисправность отсутствует» не всегда
означает исправность блока. Даже если память неисправностей содержит сообщение
о дефекте в блоке, необходимо быть начеку. При помощи системы самодиагностики
блок управления производит мониторинг узла, который в нашем примере состоит из
датчика температуры, жгута проводов с разъемами и блока питания. Прежде чем
заменить датчик температуры, нужно с помощью дальнейших измерений убедиться,
что неисправность действительно связана с дефектом датчика температуры, а не с
дефектом жгута проводов или блока управления. Эти измерения будут иметь тем
большее значение, чем выше стоимость неисправной детали. Очевидно, при
включении и работу самодиагностики «электронные мозги» блока управления ни в
коем случае не должны отключаться. Тем не менее в существующих в настоящее
время системах нельзя отказываться от использования самодиагностики. Остается
надеяться, что с широким внедрением протокола бортовой диагностики (OBD) глубина самодиагностики
существенно расширится.
Рассмотрим еще несколько указаний по рациональному использованию
самодиагностики.
Если в сложном случае неисправности возможно предположение,
что ранее уже было несколько безуспешных поисков неисправности, память
неисправностей следует стереть и провести пробные поездки - до тех пор, пока
неисправность не возникнет снова. Тем самым можно избежать опасности, что
память неисправностей покажет их во всех тестах, которые, например, проводились
с рассоединенными разъемами.
В сложных случаях может оказаться рациональным опрашивать
память неисправностей всех имеющихся на транспортном средстве систем. В
настоящее время электрооборудование, оснащенное бортовым контроллером связи CAN, позволяет, например,
обнаружить неполадки в питании блока управления - одну из наиболее часто
встречающихся неисправностей у дизельных двигателей Volkswagen с непосредственным
впрыском и турбонаддувом, возникающих из-за дефектов реле. Сам блок управления
не может регистрировать нарушение питания, т. к. в этот момент из-за неполадок
в питании у него не работает память. Одновременно нарушается обмен данными с
другими блоками управления, что регистрируется работающими блоками управления
как ошибки в передаче данных.
Многие блоки управления (например, на автомобилях Mercedes-Benz) при появлении ошибок
фиксируют рабочее состояние двигателя, например температуру, частоту вращения
коленчатого вала, скорость и пройденный путь автомобиля. Последующая оценка
граничных условий позволит быстрее выявить неисправность и воспроизвести ее при
испытательной поездке.
3.1.2 Таблица данных
Все современные блоки управления передают на считывающее
устройство замеренные параметры, относящиеся к наиболее значимой части
самодиагностики. Имея таблицу этих данных, можно за короткое время получить
полную информацию о работе блока управления, даже если память неисправностей не
заполнена. Многие блоки управления показывают также соответствующие заданные
параметры и дают быстрое сравнение заданных и действительных значений.
Данные можно вызвать для всех рабочих состояний двигателя,
начиная с включения выключателя стартера и свечей накаливания. Если автомобиль
долгое время не запускался, стоит обратить внимание на все значения измеряемой
температуры - охлаждающей жидкости, топлива и воздуха на впуске (строки 4,18 и
19, табл. 3.1.1). После длительной стоянки автомобиля измеряемые величины
температуры должны отличаться от заданных не более чем на 2 °С. Если эта
величина превышена, датчик температуры должен быть протестирован, в частности,
с использованием термометра. В процессе прогрева двигателя показания
температуры могут проверяться, как и все другие величины, на логичность
изменения. Например, начало впрыскивания должно оставаться вблизи установочного
угла поворота коленчатого вала и смещаться в направлении «раньше» с ростом
частоты вращения коленчатого вала. При полном выходе из строя датчика, к
примеру датчика температуры, показания будут различаться в зависимости от
производителя и модели. У большей части производителей автомобилей в этом
случае будет отображаться значение -50 °С, которое сразу бросится в глаза.На
некоторых моделях автомобилей Volkswagen появляется либо последнее измеренное значение
параметра, либо значение «по умолчанию», по которому блок управления делает
расчеты. Показания моделей автомобилей Volkswagen следует принимать с
особенной осторожностью - с учетом логичности изменений.
При работе двигателя с перебоями стоит обратить внимание на
отклонение от заданной величины подачи топлива (строки с 24-й по 26-ю, табл.
3.1.1). Для выравнивания работы двигателя по цилиндрам блок управления изменяет
подачу топлива в отдельных цилиндрах до тех пор, пока все цилиндры не будут
работать одинаково. Такое регулирование по цилиндрам осуществляется по сигналам
датчика ВМТ. В 3 строках с 24-й по 26-ю (табл. 3.1.1) отклонение подачи топлива
указывается по отношению к опорному цилиндру. В системах впрыска, оснащенных
датчиком подъема иглы распылителя форсунки, опорным является цилиндр, в который
установлена форсунка с этим датчиком.
В аккумуляторных системах впрыска или системах с
насос-форсунками рассчитывается средняя подача топлива и указывается отклонение
по отдельным цилиндрам. Если в каком-либо цилиндре возникла серьезная
неисправность, блок управления попытается изменением подачи топлива по
цилиндрам выровнять работу двигателя на режиме холостого хода. Величину допуска
для отклонения в подаче топлива по цилиндрам указывает производитель. По опыту
автора, причину неисправности необходимо искать при отклонении подачи топлива
больше чем на 1,5 мг/цикл или на 30 % от базовой величины подачи (строка 2,
табл. 3.1.1).
Табл. 3.1.1. Данные дизельного двигателя Volkswagen TDI мощностью 66 кВт,
полученные на режиме холостого хода
Оценка отклонений подачи топлива дает возможность быстро
найти дефектный цилиндр, что особенно эффективно для аккумуляторной системы
впрыска или системы с насос-форсунками, т. к. в этих системах нельзя обнаружить
неисправность путем последовательного отсоединения по цилиндрам трубок высокого
давления. Если неисправный цилиндр найден по большому отклонению подачи
топлива, измерением компрессии в цилиндрах следует установить, идет ли речь о
неисправности гидравлики форсунок или об ошибке в работе других механизмов
двигателя. Типичные неисправности в электросхеме должны быть зарегистрированы в
памяти неисправностей блока управления.
При всех преимуществах, которые дает просмотр таблицы данных,
у этого метода диагностики имеются определенные ограничения по скорости
передачи данных от блока управления в принимающие устройства и датчики.
Считается, что чем больше передается данных, тем медленнее идет обновление
измеряемых величин и тем менее точно определяются отклонения от заданных
значений.
Функционирование исполнительных механизмов, действующих по
команде блока управления, может быть предварительно определено визуально или на
слух. Однако, хотя этот способ поиска неисправностей производит впечатление на
клиентов, его эффективность сильно ограничена. Реле, например, может щелкать и
при наличии сгоревших контактов, а гидравлический или пневматический клапан
может срабатывать не только под действием злектрических команд. В любом случае
при оценке закрытых конструктивных элементов без диагностики исполнительных
механизмов не обойтись.
.1.3 Поиск неисправностей с использованием
дымомера типа “Хартридж”
Дымомер типа «Хартридж» имеется в распоряжении крупных
мастерских для предварительной оценки дымности отработавших газов (далее ОГ)
без больших затрат времени. Для большинства приборов по измерению дымности ОГ
имеются специальные программы по поиску неисправности, включающие постоянные измерения
действительных значений дымности ОГ, проводимые при пуске двигателя и на режиме
холостого хода. Для определения дымности ОГ при полной нагрузке и максимальной
(ограничиваемой регулятором) частоте вращения коленчатого вала регистрируются
показания дымомера на режимах свободного ускорения.
Прибор для измерения дымности ОГ типа «Хартридж» оценивает
отработавшие газы на просвет, т. е. точно так же, как это определяет своим
зрением человек, поэтому этот прибор иногда называют «калиброванным глазом».
Непрозрачность ОГ определяется наличием частиц сажи, несгоревшего топлива,
моторного масла и водяного пара (рис. 3.1.2.).
Рис. 3.1.2. Факторы дымности ОГ и состав отработавших частиц.
Характеристики дымления дизельного двигателя.
Выброс сажи увеличивается с ростом нагрузки на двигатель,
сопровождаемым обогащением топливо-воздушной смеси. Граница прекращения
дымления соответствует составу смеси при коэффициенте избытка воздуха λ = 1,2. Исправный дизельный двигатель на холостом ходу частиц
сажи (твердых частиц) почти не выбрасывает. Усиленный выброс твердых частиц или
несгоревшего топлива указывает на нарушения процесса сгорания, вызванные плохой
подготовкой топливо-воздушной смеси, например, из-за неисправных распылителей форсунок,
ошибочно установленного начала подачи или высокого расхода масла при износе
деталей ЦПГ. Нарушения процесса сгорания могут приводить к повышенному дымлению
на всех рабочих режимах. Большинство дымомеров позволяют регистрировать
изменение непрозрачности ОГ в зависимости от частоты вращения коленчатого вала,
обеспечивая возможность поиска неисправности на режимах свободного ускорения
(рис. 3.1.3.).
Рис. 3.1.3. Типичные кривые дымности ОГ и частоты вращения
коленчатого вала при свободном ускорении
Кривая дымности ОГ определена на всех рабочих режимах
двигателя. Точка 1 (рис. 3.1.3.) характеризует дымность на холостом ходу - у
исправного дизельного двигателя с отключенной рециркуляцией ОГ она должна быть
менее 5 %, соответственно, k = 0,12 м-1.
Превышение этого значения дымности ОГ свидетельствует о нарушениях процесса
сгорания. В этом случае нужно проверить аппаратуру впрыскивания, распылители
форсунок и момент начала подачи топлива. Неплотность прилегания поршневых колец
также вызывает повышенное дымление, что можно объяснить, с одной стороны,
низким давлением в конце такта сжатия, с другой стороны, повышенным расходом
масла. Точка 2 (рис. 3.1.3.) характеризует максимальное дымление на полной
нагрузке. Так как дизельный двигатель на режимах свободного ускорения работает
с полной нагрузкой только в течение короткого времени, наибольшая подача
топлива происходит также очень недолго. В исправном двигателе изменение
непрозрачности ОГ приблизительно соответствует изменению подачи топлива. У
современных дизельных двигателей максимальное дымление приблизительно
соответствует k =1,0 м-1.
Более точные сведения о значении дымления двигателя на полной нагрузке
указываются в табличке автомобиля (рис. 3.1.4.)
Рис.3.1.4. Места нанесения коэффициента поглощения k для автомобилей: a - Peugeot, б - Ford Transit, в - Volkswagen Lupo
в обрамленном прямоугольнике приводится значение k, которое было установлено
на режиме полной нагрузки при утверждении типа транспортного средства. Тот
факт, что контрольное значение k можно обнаружить под
капотом каждого автомобиля, значительно облегчает применение этого метода
испытания. Если измеренное значение в точке 2 (рис. 3.1.3.) находится выше
контрольной величины, двигатель получает при полной нагрузке слишком большое
количество топлива или слишком малое количество воздуха. Прежде чем делать
выбор между этими возможными неисправностями, желательно спросить клиента о
мощности двигателя. Если мощность двигателя находится в допусках для серийной
продукции, а значение дымности ОГ при этом слишком завышено, это означает, что
двигатель получает при полной нагрузке слишком мало воздуха. Тогда при поиске
причины неисправности следует пройти по пути всасываемого двигателем воздуха,
начиная с проверки внешнего вида воздушного фильтра. Затем измерением давления
наддува при полной нагрузке проверяют турбокомпрессор. Частой причиной
повышенного дымления являются неисправности в системе рециркуляции ОГ. На
режиме полной нагрузки рециркуляция ОГ обычно отключается. Если клапан
рециркуляции ОГ из-за механической или электрической неисправности открыт на
режиме полной нагрузки, двигатель выбрасывает густой черный дым, т. к. ОГ в
системе рециркуляции вытесняют из впускного трубопровода свежий воздух.
Действие клапана рециркуляции может быть проверено визуально или измерением с
помощью дымомера при открытом клапане системы рециркуляции ОГ (рис. 3.1.5).
Рис. 3.1.5. Кривые дымности ОГ и частоты вращения коленчатого
вала при свободном ускорении с постоянно открытым клапаном рециркуляции ОГ
На полное открытие клапана рециркуляции ОГ (с помощью ручного
вакуумного насоса) двигатель должен реагировать повышенным дымлением. Если
дымление было сильным и при контрольном измерении с открытым клапаном
рециркуляции ОГ осталось неизменным, значит клапан рециркуляции ОГ «завис» и
должен быть тщательно проверен. У большинства дизельных двигателей величина
расхода воздуха используется блоком управления для расчета полной подачи
топлива. Такие двигатели на недостаток воздуха, который создает открытый клапан
рециркуляции ОГ, реагируют потерей мощности и черным дымом (рис. 3.1.6 и рис.
3.1.7).
Рис.3.1.6. Кривые дымности ОГ и частоты вращения коленчатого
вала при свободном ускорении исправного двигателя Volkswagen 1.9TDI
Рис.3.1.7. Кривые дымности ОГ и частоты вращения коленчатого
вала при свободном ускорении двигателя Volkswagen 1.9TDI с постоянно открытом
клапаном рециркуляции ОГ
Точно так же сопротивление на выходе выпускной трубы приведет
к низкому давлению наддува и снижению мощности двигателя. Если дымление на
режиме полной нагрузки заметно ниже нормального значения, подача топлива на
этом режиме является слишком низкой. Так как блоки управления при любой
неисправности (из соображений безопасности) снижают подачу на полной нагрузке,
всякий раз необходимо сначала просмотреть память неисправностей. При
незаполненной памяти неисправностей проверяется давление подкачки, создаваемое
насосом низкого давления , и затем с помощью таблицы данных или осциллографа
проверяются все замеренные датчиками величины, необходимые блоку управления для
расчета подачи на полной нагрузке. Сюда относятся датчики расхода воздуха,
давления наддува и температуры всасываемого воздуха и топлива.
Если дымность в точке 3 (рис. 3.1.3.) слишком высока при
срабатывании ограничителя оборотов коленчатого вала, проблемы связаны не с
величиной подачи, а с частотой вращения коленчатого вала. При допустимом
дымлении на холостом ходу и полной нагрузке следует сначала проверить
функционирование регулятора начала подачи.
Претензии клиента в этом случае могут быть следующими:
двигатель не развивает мощность и дымит. Потери мощности можно определить по
медленному достижению максимальной частоты вращения и «скругленной» кривой
частоты вращения коленчатого вала. На слишком поздно установленное начало
подачи топлива указывают высокие значения дымности ОГ на всех режимах и
недостаток мощности.
Однако видимое изменение значения дымности ОГ можно
установить только при точно определенной погрешности начала подачи. Не все
двигатели реагируют одинаково на неправильно установленное начало
подачи. Если начало подачи лишком раннее, величина дымности ОГ снижается на
холостом ходу, однако увеличивается на режиме полной нагрузки.
Величина дымления находится слишком высоко наряду с уже
упомянутыми нарушениями сгорания, которые вызываются неисправностями в
аппаратуре впрыскивания, речь может идти о повышенном расходе масла или плохом
качестве топлива. При повышенном расходе масла значения дымности ОГ находятся
высоко на всех режимах - двигатель выпускает синий дым. Плохое качество топлива
также является причиной высоких значений дымности ОГ во всех трех точках (рис.
3.1.3.). Двигатель выбрасывает черный дым при ощутимо сниженной мощности. При
подозрении на плохое качество топлива пробы на запах из горловины топливного
бака недостаточно (хотя самая распространенная причина - заправка автомобиля
бензином, а не дизельным топливом). Для надежности необходимо запустить
двигатель, «питая» его из емкости с проверенным топливом. Если все симптомы
повышенной дымности ОГ исчезли, причина определена. Что касается
заправки автомобиля по ошибке бензином, то, т. к. бензин не имеет смазывающих
свойств дизельного топлива, современные системы впрыска высокого давления
реагируют на это частичными отказами или прекращением работы. Особенно
восприимчивы к переходу на бензин распределительные топливные насосы высокого
давления и насосы высокого давления аккумуляторной системы впрыска. Рядный
топливный насос высокого давления и насос-форсунки в этом случае не пострадают,
благодаря тому что в этих системах кулачковый вал смазывается моторным маслом.
Поиск неисправности с дымомером типа «Хартридж», как и
просмотр памяти неисправностей, хорошо подходят для предварительного
определения дефектов, т. к. в течение короткого времени дают направление для
дальнейших проверок. По сравнению с памятью неисправностей поиск с дымомером
имеет преимущество в том, что позволяет оценивать конечный продукт процесса
сгорания и, таким образом, показывает результат как механических дефектов, так
и неисправностей в системе топливоподачи. Поиск неисправностей по измерениям
дымности ОГ приведен в табл. 3.1.2.
.1.4 Относительное определение источника дымления
Если дымность ОГ на режиме холостого хода превышает 5 % (или
коэффициент поглощения k превышает величину 0,1 м-1 и есть
подозрение, что неисправность может быть связана с дефектом одного из цилиндров
двигателя, следует последовательно отключать цилиндры отсоединением
трубопроводов высокого давления и при этом фиксировать значения дымности ОГ.
Если после отключения одного из цилиндров спустя самое позднее 10 с значение
дымности ОГ явно снизится, это означает, что найден дефектный цилиндр,
приводящий к повышенной дымности ОГ (табл. 3.1.3. и рис. 3.1.8.).
Табл. 3.1.2. Поиск неисправностей по измерениям дымности ОГ:
н - нормальная величина, + - высокое значение, - - низкое значение
Табл. 3.1.3. Измерение относительной дымности. При отключении
дефектного цилиндра с неплотно установленной форсункой дымность снизилась в
среднем с 17 до 3%.
Рис. 3.1.8. Кривые дымности ОГ и частоты вращения коленчатого
вала при свободном ускорении дизельного двигателя с неплотно установленной
форсункой в одном из цилиндров
Этот метод испытания особенно пригоден для систем с
насос-форсунками и аккумуляторных систем впрыска, потому как элементы
насос-форсунок и, соответственно, форсунки аккумуляторной системы по своей
конструкции не могут быть проверены каким-либо иным способом. У двигателей с
насос-форсунками для отключения цилиндра требуется отсоединить штекер от
соответствующего электромагнитного клапана. В аккумуляторной системе впрыска
понадобится дополнительная, электрически исправная форсунка, которую
присоединяют вместо проверяемой форсунки. У некоторых двигателей Mercedes Benz,например,
восьмицилиндровых с аккумуляторной системой или предназначенных для грузовых
автомобилей с системой насос-форсунок, цилиндры можно отключать по отдельности
специальным пробником с соответствующей управляющей программой.
3.1.5 Проверка пусковой подачи
При возникновении проблем холодного пуска дизельного
двигателя станции технического обслуживания ограничиваются проверкой
компрессии, свечей накаливания и подачи топлива. При этом работники сервиса
часто забывают, что для уверенного холодного пуска дизельному двигателю
необходима определенная пусковая подача, которая при частоте вращения
коленчатого вала, приводимого стартером, может осуществляться ТНВД с
механическим регулированием. Системы с электронным регулированием задают
пусковую подачу в зависимости от температуры охлаждающей жидкости. До внедрения
в практику автосервисов приборов для измерения дымности ОГ пусковая подача
могла быть проверена только на стендах для испытания топливных насосов. Прибор
для измерения дымности ОГ используют следующим образом: запускают двигатель и
наблюдают изменение дымности ОГ после того, как двигатель выйдет на режим
холостого хода. У топливных насосов с механическим регулированием предельная
величина дымности ОГ должна составлять минимум 50 % или k = 2,0м-1 . При
более низких значениях дымности ОГ могут появиться затруднения при холодном
пуске. При слишком низкой подаче на режиме полной нагрузки снижается также
пусковая подача. У пятицилиндровых вихрекамерных двигателей Audi (код двигателя CN) пусковая подача
регулируется с помощью температурного датчика в виде сильфона. В таких
двигателях, как и при использовании топливной аппаратуры с электронным
управлением, дымление пуска следует проверять при двух значениях температуры. У
прогретого двигателя дымность при пуске должна находиться в пределах от 20 до
35 % или k=0.6-1.0 м-1 (рис. 3.1.9.)
Рис. 3.1.9. . Кривые дымности ОГ и коэффициента поглощения на
режиме холодного при -10° С и на рабочем режиме прогретого двигателя с
электронным регулированием
При проверке пусковой подачи дизелей, оснащенных TIIИД с электронным
регулированием, имитируется температура -5 °С установкой в разъем
датчика температуры резистора сопротивлением ~10 кОм и запускают
двигатель. При этом дымность ОГ при пуске должна увеличиться минимум до 50 % .
При более низких значениях дымности ОГ в некоторых блоках управления (например,
двигателей BMW) пусковая подача регулируется специальным тестером (Modic III или DIS). Перед
изменением пусковой подачи необходимо с помощью диагностического прибора
проверить датчик температуры.
У некоторых распределительных ТНВД фирмы Bosch пусковая подача
регулирует-с я винтом с внутренним шестигранником, который представляет собой
упор для рычага, расположенного на боковой стороне насоса (рис. 3.1.10).
Рис. 3.1.10. Для установки пусковой подачи в регулировочный
винт вставлен шестигранный ключ
Пусковую подачу уменьшают поворотом винта по часовой стрелке.
Однако этот рычаг нельзя путать с рычагом холостого хода, который находится на
другой стороне насоса. Действие рычага пусковой подачи можно отличить по тому,
что он полностью прекращает работу двигателя, поэтому его также называют
рычагом останова.
.2.1 Момент начала подачи топлива
Установка начала подачи топлива влияет на шум сгорания, мощность
двигателя, расход топлива и содержание вредных веществ в ОГ. Если подача
топлива начинается слишком рано, двигатель работает жестко, с сильным шумом
сгорания, низким расходом топлива, но повышенным содержанием оксидов азота в
ОГ. При слишком ранней установке начала подачи увеличивается и дымность, потому
что увеличенная задержка воспламенения приводит к низкой температуре цикла.
Резкое нарастание давления сгорания может вызвать повреждение
кривошипно-шатунного механизма. На позднее начало подачи топлива двигатель
реагирует потерей мощности, увеличенным расходом топлива и повышенным
дымлением. При позднем завершении сгорания увеличивается температура ОГ, а
следовательно, риск повреждения выпускных клапанов и турбокомпрессора. Таким
образом, в данном случае большую роль играют проверка и точная установка начала
подачи топлива.
3.2.2 Статическая установка начала подачи
Регулирование ТНВД с механическим регулированием
осуществляется в основном при помощи механического инструмента на неработающем
двигателе. Таким образом производится регулирование предварительного хода
плунжера у распределительных ТНВД фирмы Bosch. Этот же метод может
применяться и для распределительных ТНВД этой фирмы с электронным
регулированием - у насосов типа VP 37/36 (рис.3.2.1.).
Рис. 3.2.1. Измерение предварительного хода плунжера у
распределительного ТНВД типа V37 с электронным регулированием фирмы Bosch
У распределительных ТНВД типа ДРС с радиальными плунжерами
фирмы Lucas ход плунжера не может быть измерен непосредственно. Здесь
оценивается величина начала подачи по положению ротора. Приваренный к ротору
шип должен приподнять штифт индикатора на определенную величину (рис. 3.2.2. и
рис. 3.2.3.).
Рис.3.2.2. Измерение начала подачи топлива на насосах типа DPC фирмы Lucas
а - измерительный щуп в исходном положении, индикатор
выставлен на ноль
б - измерительный щуп в положении начала подачи топлива
Рис. 3.2.3. Измерительный инструмент для регулирования ТНВД
типа DPC фирмы Lucas
Шип приваривается к ротору с определенным допуском, поэтому
требуемое значение устанавливается на заводе индивидуально для каждого насоса и
заносится в табличку, укрепленную на рычаге управления. Без учета этой
контрольной величины установка начала подачи невозможна.
С возрастанием точности изготовления насосов стал применяться
т. н. метод разметки, особенно у аппаратуры впрыскивания с электронным
управлением. При этом коленчатый для распределительный валы, а также топливный
насос при сборке двигателя блокируются штифтами, которые удаляются после
установки зубчатого ремня или цепи привода механизма газораспределения. Этот
метод экономит время и дает достаточную точность, т. к. электронные устройства
могут компенсировать ошибку установки до 4°.
3.2.3 Динамическое измерение начала подачи
Так же, как у бензиновых двигателей, начало подачи топлива на
работающем дизеле может контролироваться и устанавливаться. В качестве измерителя
применяют зажимной датчик, который устанавливается на топливопроводе высокого
давления первого цилиндра. Топливопровод высокого давления расширяется при
увеличении давления в начале подачи топлива примерно на 0,001 мм по диаметру.
Пьезопленка датчика также растягивается, меня свое электрическое сопротивление.
Сигнал обрабатывается в измерительном приборе и, при определенном уровне,
выраженном в процентах от максимальной величины, можно считать, что началась
подача топлива.
Теперь можно определять начало подачи топлива, освещая
вспышкой метку ВМТ первого цилиндра на маховике или шкиве коленчатого вала.
Если на двигатель установить отдельный датчик ВМТ, начало подачи топлива можно
непосредственно считывать с дисплея прибора. Преимуществами этого метода
являются быстрая готовность к измерению и возможность проверять
функционирование регулятора начала подачи (рис. 3.2.4.).
Рис. 3.2.4. Зависимость опережения впрыскивания (в градусах
угла поворота коленчатого вала), измеренного зажимным датчиком, расположенным
вблизи от ТНВД от частоты вращения коленвала
Импульсный датчик регулятора (датчик RI)
У автомобилей Mercedes-Benz серии 124/190D зажимной датчик заменен
индуктивным датчиком RI, который заворачивается в соответствующее
резьбовое Отверстие корпуса топливного насоса (рис. 3.2.5. и рис. 3.2.6.).
Рис. 3.2.5. Монтаж датчика типа RI на рядном ТНВД
Рис. 3.2.6. Монтаж датчика типа RI на распределительном
ТНВД
Штифт в регулирующей втулке рядного ТНВД или во вращающейся
втулке ротора распределительного ТНВД фирмы Lucas вырабатывает при
прохождении датчика и сигнал, который оценивается как начало подачи топлива. На
результат измерения влияет также место установки датчика. Волна давления,
двигаясь к распылителю форсунки в начале подачи топлива со скоростью 1350 м/с,
достигает распылителя через несколько градусов угла поворота коленчатого вала.
Большинство производителей рекомендуют монтировать датчик по возможности ближе
к топливному насосу. Однако есть и исключения: у автомобилей PSA (Peugeot, Citroen) зажимной датчик установлен
в форсунке. Уровень срабатывания триггера в этом случае составляет 15 %.
3.3.1 Измерение давления в дизельных двигателях
Неисправности, возникающие в аппаратуре впрыскивания и не
определяющиеся в большинстве случаев самодиагностикой, могут быть обнаружены с
помощью манометра. Каждая аппаратура впрыскивания имеет контура высокого и
низкого давления. В контуре низкого давления находится электрический или
механический подкачивающий насос, который подает топливо через фильтр в
контур высокого давления. При проблемах с пуском или при потере мощности
следует провести измерение давления под качки на проблемном рабочем режиме.
3.3.2 Измерение давления в дизельной аппаратуре
впрыскивания
У распределительных насосов Bosch в присоединительном
штуцере топливопровода обратного слива находится дроссельное отверстие, которое
вместе с клапаном управления давлением поддерживает давление в полости насоса.
С адаптером, выполненным из штуцера обратного слива и гайки топливопровода
высокого давления, можно измерить давление в насосе (рис. 3.3.1.).
Рис. 3.3.1. Адаптеры для измерения давления в
распределительных насосах Bosch
Адаптер подходит ко всем распределительным топливным насосам Bosch, которые имеют резьбу M12x1,5 (рис. 3.3.2 и рис.
3.3.3.) в штуцере обратного слива.
Рис. 3.3.2. Подсоединение адаптера к ТНВД типа VP37
Рис. 3.3.3. Подсоединение адаптера к ТНВД типа VP44
Автомобили BMW с распределительным ТНВД VP37 снабжены электрическим
подкачивающим насосом в топливном баке, Насос работает при включенном
выключателе стартера и свечей накаливания и создает давление от 0,2 до 0,3 бар.
Для ТНВД EPIC фирмы Lucas требуются два адаптера. Один адаптер - от ТНВД с электронным
регулированием двигателя Mercedes 2,2 (ОМ 604). Второй адаптер - от ТНВД двигателя
Ford Transit (рис. 3.3.4.).
Рис. 3.3.4. ТНВД EPIC фирмы Lucas. Стрелки указывают на места подключения
манометров
Эти насосы требуют минимального давления - в 5,6 бар. Обычно
устанавливают 7 бар. Все распределительные ТНВД имеют гидравлическое устройство
регулирования начала подачи, поэтому давление подкачки должно проверяться также
при высокой частоте вращения коленчатого вала.
У двигателей Volkswagen, оснащенных системой насос-форсунок, имеется
проверочный штуцер с резьбой M12, при подсоединении к которому манометра можно измерить
давление подкачки (рис. 3.3.5.).
Рис. 3.3.5. Измерение давления подкачки у двигателей Volkswagen, оснащенных системой
насос-форсунок
Избыточное давление при пуске должно составлять минимум 1,0
бар, на режиме холостого хода - 3 бар и при максимальном частоте коленчатого
вала, ограничиваемом регулятором, - 8 бар. У двигателей с аккумуляторной
системой впрыска манометр присоединяют между насосами низкого и высокого
давления (рис. 3.3.6.).
Рис. 3.3.6. Измерение давления в контуре низкого давления у
двигателей Mercedes с аккумуляторной системой впрыска
Избыточное давление при пуске должно составлять по меньшей
мере 1,0 бар, на режиме холостого хода - 2,5 бар и на всех других рабочих
режимах - 3,0 бар. У двигателей Rover и BMW с аккумуляторной
системой впрыска топлива низкое давление контролируется блоком управления с
помощью датчика давления, который располагается в топливном фильтре. Давление
можно проверить по протоколу данных устройства при чтении памяти
неисправностей.
Для стабилизации давления в системе обратного слива топлива у
двигателей с аккумуляторной системой впрыска поддерживается давление от 0,6 до
0,9 бар (FIAT) или 0,7 бар (Peugeot).
3.3.3 Измерение давления наддува
Большинство современных дизельных двигателей оборудуются
турбокомпрессорами, которые снабжают двигатель, особенно при полной нагрузке,
достаточным количеством воздуха. Большее количество воздуха в камере сгорания
позволяет впрыскивать большее количество топлива и увеличить мощность, а при
меньшей подаче топлива - снизить выброс сажи.
Поэтому давление наддува, являясь параметром, определяющим
величину полной нагрузки, должно проверяться прежде всего при жалобах клиента
на пониженную мощность. Для проверки давления наддува присоединяют манометр к
соответствующему штуцеру впускного трубопровода и измеряют давление на
соответствие данным производителя. Измерение без нагрузки не может дать
требуемого результата, т. к. турбокомпрессор обеспечивает необходимое давление
наддува только при достаточно большом количестве ОГ. Короткий период полной
нагрузки на режимах свободного ускорения также не является достаточным для
измерения давления наддува, т. к. рост частоты вращения турбины не успевает за
увеличением частоты вращения коленчатого вала. Поэтому измерение давления
наддува можно осуществить при поездке с более постоянной полной нагрузкой и при
средней частоте вращения коленчатого вала. Если испытательный стенд с беговыми
барабанами отсутствует, следует провести пробную поездку на дороге.
Не только слишком низкое, но и слишком высокое давление
наддува может привести к снижению мощности, т. к. блок управления при
превышении предельного значения давления наддува, с целью защиты
турбокомпрессора, снижает подачу топлива. При значениях давления наддува, не
соответствующих данным производителя, необходимо проверять весь двигатель.
Только если установлено, что все узлы и механизмы, окружающие турбокомпрессор,
в порядке, можно будет заменять дорогой агрегат.
3.3.4 Проверка утечек из камеры сгорания
Пусковые свойства и качество сгорания у дизельного двигателя
сильно зависят от достигаемого давления сжатия. Поэтому утечки из камеры
сгорания должны проверяться при каждом более тщательном поиске неисправности.
К классическим методам такой проверки относятся проверка
компрессии при пусковой частоте вращения коленчатого вала и тест падения
давления. Оба метода требуют большого подготовительного времени т.к.
требуется получить доступ к камере сгорания через отверстия, предназначенные
для форсунок или свечей накаливания. Измерение устройством для проверки
компрессии проводится при пусковой частоте вращения коленчатого вала без
воспламенения в цилиндрах. Получаемая величина давления должна быть не менее 25
бар. При этом условия измерения, близки к рабочему режиму двигателя. Риск
ошибки измерения незначителен.
3.3.5 Проверка компрессии в цилиндрах оценкой
сигнала частоты вращения коленчатого вала.
У некоторых тестеров проверка компрессии в цилиндрах
производится оценкой изменения не силы тока стартера, а частоты вращения
коленчатого вала при проворачивании двигателя (рис. 3.3.7.).
Для регистрации частоты вращения используется датчик
положения коленчатого вала. При исправном двигателе колебания частоты вращения
коленчатого вала во всех цилиндрах одинаковы. Метод имеет два преимущества: не
требуется присоединять никаких дополнительных датчиков, т. к. используются уже
имеющиеся на двигателе. При использовании данного метода возможно опознание
цилиндров (рис. 3.3.8.). Для гарантийной автомастерской это самый быстрый метод
проверки компрессии в цилиндрах
Рис. 3.3.7. Проверка компрессии в цилиндрах по кривой
изменения частоты вращения коленчатого вала. Самое большое изменение частоты
вращения наблюдается на такте сжатия шестого цилиндра, самое маленькое на такте
сжатия третьего цилиндра
.
Рис. 3.3.8. Числовые значения (в %) и диаграмма изменения
частоты вращения коленчатого вала по цилиндрам
Вышеописанные методы проверки компрессии в цилиндрах по
электрическим сигналам все больше вытесняют классические испытания с
использованием манометра, т. к. первые дают правильные результаты уже
через несколько минут. Однако в случае определения неисправности этими методами
следует провести, например, классический тест падения давления для большей
гарантии и правильности результатов.
3.4.1 Аккумуляторная система впрыска топлива
фирмы Bosch
Аккумуляторную систему впрыска топлива (Common Rail System) специалисты оценивают
как систему будущего, т. к. она предоставляет разработчикам наибольшие
возможности при выборе давления, а также при формировании законов впрыскивания.
Таким образом, благодаря этой системе будут наиболее полно выполняться
ограничения по шуму работы двигателя и токсичности ОГ, а также требования по
мощности. Серьезную конкуренцию аккумуляторным системам, возможно,
составят системы с насос-форсунками, которые могут оказаться дешевле для
двигателя с небольшим числом цилиндров. Все другие системы впрыска топлива
на дальнюю перспективу можно рассматривать лишь как промежуточные
решения. Аккумуляторная система впрыска топлива первого поколения вошла в серию
с 1998 года.
В настоящее время аккумуляторные системы впрыска
топлива, применяемые на автомобилях Audi, BMW, Daimler-Chrysler (рис. 3.4.1.), FIAT, Peugeot и Rover, в основном идентичны.
Рис. 3.4.1. Аккумуляторная система впрыска топлива двигателя
автомобиля Mercedes 200CDI
3.4.2 Система подачи топлива
В двигателе Mercedes топливо нагнется в систему из топливного бака
шестеренчатым топливоподкачивающим насосом (рис. 3.4.2. и рис. 3.4.3.).
Рис. 3.4.2. Система подачи топлива аккумуляторной системы
впрыска
А - давление подкачки топлива 2.5-3.0 бар С - линия обратного
слива топлива
D - линия высокого давления 250-1350 бар F - впускной топливопровод
Рис. 3.4.3. Топливные насосы двигателя Mercedes 200CDI
- шестеренчатый топливоподкачивающий насос 2 - трехплунжерный
ТНВД 3 - электромагнитный клапан
Во впускном топливопроводе (рис. 3.4.2) находятся
предварительный подогреватель топлива и топливный фильтр. Топливо подается к
ТНВД под давлением от 2,5 до 3,0 бар. При превышении допустимого давления
клапан, расположенный в шестеренном насосе, связывает подводящий и отводящий
контуры. Другие производители дизелей используют шиберные роликовые
электронасосы, подобные тем, что применяются в системах впрыска топлива
бензиновых двигателей. В дизельных двигателях BMW на магистрали низкого
давления устанавливается датчик давления. В двигателях Mercedes на линии подвода топлива
к ТНВД расположен электромагнитный клапан останова двигателя, который
срабатывает в случае необходимости аварийной остановки двигателя.
Дизельное топливо, подаваемое в ТНВД, выполняет функцию
охлаждения и смазки трущихся пар насоса. Поэтому категорически не следует
проводить продолжительное проворачивание коленчатого вала дизеля при отсутствии
топлива в топливном баке. Для обеспечения смазывания ТНВД топливом, особенно
при пуске двигателя, на входе в насос располагается предохранительный клапан,
который обеспечивает подвод топлива к плунжеру давления, начиная с 0,5 бар.
Количество топлива, подаваемого топливным насосом высокого
давления, намного превышает требуемое для впрыскивания топлива.
Производительность подачи топлива меняется за счет действия электромагнитных
клапанов регулирования давления и отключения плунжерной секции. В последнем
случае (примерно до 2/3 от полной нагрузки) трехплунжерный ТНВД работает только
с двумя плунжерными секциями. Благодаря отключению плунжерной секции снижаются
затраты мощности на ТНВД и температуру топлива на сливе, т. к. меньшее
количество топлива отдает меньше энергии при переходе от высокого
давления к низкому. Недостатками такого решения является возникновение
колебаний давления в аккумуляторе и крутящего момента в приводе насоса.
Отключение плунжерных секций применяется на двигателях FIAT и Peugeot. ТНВД с отключением
плунжерной секции внешне отличаются по наличию электромагнитного клапана на
секции.
Топливо из ТНВД по топливопроводу высокого давления поступает
в аккумулятор высокого давления. С одной стороны аккумулятора в корпус завернут
датчик давления, с другой - электромагнитный клапан регулирования давления.
Датчик регистрирует давление в аккумуляторе, которое блоком управления сравнивается
по полю характеристик с заданным. При отклонении давления от требуемого блок
управления изменяет скважность подачи электрического питания к электромагниту
клапана регулирования давления. Шарик клапана (рис. 3.4.4.) прижимается к седлу
усилием пружины и электромагнита.
Рис. 3.4.4. Электромагнитный клапан регулирования давления
- давление в аккумуляторе высокого давления 2 - слив топлива
3 - электромагнит
Сила пружины рассчитана на давление до 100 бар, что
значительнее ниже давления в линии высокого давления (250-1350 бар), поэтому
только при приложении усилия электромагнита шарик не отойдет от седла, отделяя
аккумулятор от линии слива. Клапан регулирования давления может быть установлен
либо на аккумуляторе, либо на ТНВД.
От аккумулятора короткие топливопроводы высокого давления
подводятся к форсункам, которые имеют собственную систему управления
процессом впрыскивания топлива (рис. 3.4.5.).
Игла распылителя форсунки в нерабочем состоянии прижимается к
седлу пружиной распылителя - это предотвращает попадание воздуха в форсунку при
пуске двигателя.
Рис. 3.4.5. Процесс впрыскивания топлива
Когда ТНВД создает давление в аккумуляторе, оно действует как
на конусную поверхность иглы, так и на поршень управляющего клапана. Поскольку
площадь рабочей поверхности поршня на 50 % больше площади конусной поверхности
иглы, игла распылителя продолжает прижиматься к седлу. Для начала впрыскивания
топлива якорь электромагнита управляющего клапана сдвигается, приподнимая шарик
над конусным седлом. Таким образом, отводящее дроссельное отверстие
управляющего клапана открывается, пропуская топливо из зоны над поршнем
управляющего клапана в линию слива топлива. Давление на поршень управляющего
клапана падает, т.к. подводящее дроссельное отверстие управляющего клапана
имеет меньшее сечение, чем отводящее. Давление в аккумуляторе поднимает иглу
распылителя, обеспечивая впрыскивание топлива в камеру сгорания. Если
управляющий клапан закрывается, на его поршень снова действует полное давление
аккумулятора. Игла распылителя запирается гидравлически. Благодаря
использованию электрогидравлического управления процессы впрыскивания топлива
могут происходить за короткие промежутки времени. Становится возможным процесс
предварительного впрыскивания топлива, с помощью которого достигаются более мягкая
работа двигателя. Цикловая подача определяется продолжительностью
открытия управляющего клапана и давлением в аккумуляторе. Так как большая часть
топлива под высоким давлением поступает на линию обратного слива, его
температура может повышаться до 140 °С. Поэтому па автомобилях с
пластмассовыми топливными баками должны предусматриваться охладители топлива,
отбирающие тепло в охлаждающую жидкость. Температура охлаждающей жидкости
снижается благодаря использованию дополнительного радиатора, устанавливаемого
перед радиатором топлива.
Датчики и исполнительные механизмы по техническому уровню
должны соответствовать элементам современной аккумуляторной системы впрыска
топлива. Типичными датчиками, применяемыми в таких двигателях, являются датчик
давления в аккумуляторе высокого давления и датчик Холла на распределительном
валу. Последний служит для распознавания номера цилиндра, т.к. форсунки должны
регулироваться индивидуально. Наряду с обычными исполнительными механизмами,
такими как пневматический редуктор для управления рециркуляцией ОГ, механизмы
управления турбокомпрессором и отключением впускного канала, применяются
характерные для аккумуляторной системы впрыска топлива исполнительные механизмы
для форсунки, электромагнитных клапанов регулирования давления, отключения
секции насоса и останова двигателя.
3.5 Поиск неисправностей в аккумуляторной системе
.5.1 Самодиагностика
В аккумуляторной системе впрыска топлива применяется
простейший метод самодиагностики. Блок управления следит за выходом из строя
электрических блоков и передает результаты в память неисправностей. В
зависимости от значимости ошибки впрыскивание топлива продолжается или
двигатель останавливается. С помощью соответствующего тестера данные памяти
неисправностей могут считываться или удаляться. Если значение реального
давления в аккумуляторе высокого давления и значение предписанное, хранящееся в
памяти блока управления, не совпадают, наличие нарушений уплотнения сопряжений
в системе высокого давления бесспорно. С помощью соответствующего теста
проверяются вероятные открытые места негерметичности, после чего остается
проанализировать внутренние нарушения уплотнения сопряжений в форсунках,
электромагнитном клапане регулирования давления и ТНВД.
Коррекция режима холостого хода предназначена для компенсации
отклонений по цилиндрам в механике двигателя и гидравлике системы впрыска
топлива, возникающих при серийном производстве. Неравномерность работы
двигателя по цилиндрам блок управления проверяет с помощью датчика ВМТ. Если
какой-то цилиндр отличается больше чем на 30 % от заданного значения, это
считается ненормальным и блок управления пытается исправить отклонение
значительным увеличением цикловой подачи топлива в данный цилиндр.
Механические повреждения, такие как, например, прогар
выпускного клапана, могут быть выявлены путем замера компрессии, оцениваемой по
протеканию величины силы тока в стартере. Если никаких механических
неисправностей не обнаружено, возможно, неисправна форсунка. Для проверки
форсунки соседних цилиндров меняются местами. Если отклонение цикловой подачи
подтверждается, неисправная форсунка должна быть заменена.
3.5.2 Гидравлическое испытание форсунок
Если коленчатый вал двигателя начинает вращаться
неравномерно, наряду с проверкой механики следует протестировать и форсунки.
Альтернативой может быть метод замера количества топлива, отводимого от
форсунок. Для этого топливопроводы обратного слива топлива соединяются, а общий
топливопровод запирается зажимом. Вместо общего топливопровода подсоединяются
трубки, идущие к мерному устройству.
Двигатель запускается и работает с той частотой вращения
коленчатого вала, которая показалась некомфортной. Через несколько минут
сравнивают по цилиндрам количество топлива, ушедшего на слив.
Различия до 30%, особенно при работе на режиме холостого
хода, соответствуют норме. При номинальной частоте вращения коленчатого вала
количество топлива на сливе не должно превышать 150 см3 в минуту на
одну форсунку. Если эта цифра превышена, форсунка дефектна и должна быть
заменена. При наличии прибора для измерения расхода топлива, ранее применяемого
при эксплуатации системы впрыска топлива K-Jetronic, его можно использовать
и для замера количества топлива, сливаемого форсункой (рис. 3.5.1.).
Рис. 3.5.1. Прибор для замера топлива, сливаемого форсункой
марки Bosch
Третьей возможностью проверки форсунок является замер
дымности ОГ. У исправных двигателей с аккумуляторной системой впрыска топлива
дымность ОГ на режиме холостого хода почти равна нулю. Если замеренная дымность
ОГ на режиме холостого хода превышает значение k=0.12м-1, то можно
предположить ухудшение процесса сгорания. Если механические дефекты двигателя
отсутствуют, причиной неполадок может являться только форсунка. При демонтаже
форсунки она не должна выниматься за трубки высокого давления. Следует
использовать специальное приспособление с зажимными любами. Перед установкой на
место форсунка должна обрабатываться специальным составом, чтобы она не
прикипела к металлу головки блока цилиндров из-за контактной коррозии. При
любых работах с элементами системы высокого давления следует точно
придерживаться приложенных инструкций. Например, для фиксации форсунок их
затягивают только определенным крутящим моментом. С использованием дымомера
возможны и другие методы проверки аккумуляторной системы впрыска топлива.
Значения максимального коэффициента поглощения, характеризующего величину
дымности ОГ на режимах свободного ускорения, лежат в пределах 0,3-1,0 м-1
(см. рис. 3.5.2.).
Рис. 3.5.2. Кривые дымности ОГ и частоты вращения коленчатого
вала двигателя Mercedes 200CDI при свободном ускорении
При получении больших значений следует проверить поступление
воздуха в двигатель, исправность форсунок и датчиков, что оказывает влияние на
формирование цикловой подачи топлива. Особенно важно проверить датчик давления
в аккумуляторе высокого давления. Если датчик показывает слишком малые
значения, то блок управления, воздействуя на клапан регулирования давления,
повышает давление в аккумуляторе и, соответственно, цикловую подачу топлива. В
связи с этим датчик давления в аккумуляторе является базисным элементом. При
пуске прогретого двигателя максимальный коэффициент поглощения не достигает
величины 0,3 м-1. Если при пуске холодного двигателя максимальный
коэффициент поглощения не увеличивается, добавлением сопротивления примерно
15кОм имитируют на температурном датчике температуру порядка -10 °С. Если
величина дымности изменяется, как показано на рис. 3.5.3. следует проверить
температурный датчик и, по необходимости, его заменить.
Рис. 3.5.3. Кривые дымности ОГ и частоты вращения коленчатого
вала двигателя Mercedes 200CDI при холодном пуске
4. Технологический раздел
.1 Исходные данные для проектирования
Тип производства - единичное.
Чертеж детали изображен на рисунке 4.1.1.
Рис. 4.1.1 . Чертеж детали
1. HB 200…240
2. Радиусы скруглений 1,6мм max.
3. Неуказанные
предельные отклонения размеров: валов -t, остальных
t/2 среднего класса точности по СТ СЭВ 302-76
4.2 Выбор маршрута обработки
поверхности детали
Рассмотрим формирование вариантов маршрута обработки
отверстия диаметром 48 мм по 7 квалитету точности. Предварительные методы
обработки представлении на рис.4.2.1.
Рис. 4.2.1. Проектирование маршрута обработки.
________ варианты маршрута; -------- выбранный
маршрут.
Принимаем маршрут: заготовка, предварительное
зенкерование, протягивание. Выбранный маршрут обусловлен тем, что достигается
наибольшей точности, при мало количестве операций. Одновременно протягивается
шпоночный паз.
4.3 Расчет припусков
.3.1 Расчет одностороннего припусков
на обработку левого торца заготовки
Принимаем
К = 1,2
а)
составляющая
а равна 3000 мкм.
б)
На = 150 мкм
в)
Та = 100 мкм
г)
мкм, неперпендикулярность торца
д)
, погрешность установки
Припуск
на точение
4.3.2
Расчет одностороннего припусков на обработку правого торца заготовки
а)
составляющая
а равна 740 мкм, т.к. левый торец заготовки подрезан,
но возможны неровности.
б)
На = 150 мкм
в)
Та = 100 мкм
г)
мкм, пространственные отклонения правого торца учтены
составляющей
а.
д)
, погрешность установки
Припуск
на точение
4.3.3
Расчет двустороннего припуска на обработку поверхности заготовки
принимаем
К = 1,2.
а)
определяем составляющий
a.
допуск
на диаметральный размер из проката обычной точности, в расчет принимаем минусовое
отклонение размера
a =2000 мкм.
б)
На = 150 мкм, Та = 150 мкм.
в)
а=0, т.к. длинна вала незначительна, погрешность зацентровки
не учитываем.
г)
кривизна заготовки в ее среднем сечении
,
где,
l=0.5*L=0.5*58=29
мм
мкм/мм
мкм.
д)
погрешность установки:
,
,
погрешность базирования (3Х кулачковый патрон);
мкм,
погрешность закрепления;
,
погрешность положения.
Следовательно,
погрешность установки:
мкм
Следовательно,
двухсторонний припуск на черновое точение:
4.3.4
Определение операционного припуска и размера заготовки
Операционный
припуск:
Z0=Z1+Z2
Z0=3.8+0.914=4.714 мм=5 мм
Длинна
заготовки:
Lзаг=58+5=63
0,74 мм.
Диаметр
заготовки:
dЗАГ=148+4=152 мм, принимаем из стандартного ряда dЗАГ=160
мм.
4.4
Расчет режимов резания для револьверной операции
Определить
штучное время для обработки вала на размер d=148,12 мм, l=58
мм с шероховатостью Rz80 при dЗАГ=160
мм.
Расчет
длины рабочего хода суппорта:
LР.Х= LРЕЗ +y+LДОП
Где, LРЕЗ=37 мм, длина резанья; y=10 мм подвод, врезание и пробег
инструмента.
LР.Х= 37+10=47 мм.
Глубина резанья:
мм
назначаем
число проходов i=2, тогда t=3 мм.
Назначение
подачи суппорта на оборот шпинделя Sо=0,5 мм/об.
Стойкость
инструмента:
Тр=Тм*
,
Где,
Тр=Тм=50, т.к.
.
Скорость
резанья:
V=Vтабл*К1*К2*К3 м/мин
Где К1=0,9 - коэффициент зависящий от
обрабатываемого материала ст.45;
К2=1 - коэффициент зависящий от марки и
твердости сплава;
К3=1 - коэффициент зависящий от вида
обработки;
Vтабл=120 м/мин - табличная скорость.
V=120*0,9*1*1=108 м/мин.
Расчет числа оборотов шпинделя станка:
об/мин,
, об/мин,
по
паспорту станка n=250об/мин.
Скорость
резанья:
м/мин,
м/мин.
Расчет
основного машинного времени:
мин,
мин.
Вспомогательное
время:
мин,
где
мин - вспомогательное время на снятие и установку;
мин -
вспомогательное время связанное с переходом.
мин.
Дополнительное
время:
мин,
мин.
Штучное
время:
мин,
мин.
5. Охрана труда и окружающей среды
.1 Анализ системы управления охраной
труда и окружающей среды
Систему управления охраной труда и окружающей на
проектируемом предприятии разработана в соответствии с требованиями ГОСТ Р
12.0.006-2002 ССБТ. Основные элементы которой представлены на рис 5.1.1.
Рис. 5.1.1 .Элементы системы управления охраной труда
и окружающей среды.
Табл.5.2.1. Опасные и вредные производственные факторы
на рабочих местах участка ТО и ТР
Опасности и вредности
|
Источники возникновения
|
Основные регламентирующие
документы
|
1. Электрический ток
|
Электроприборы,
электропроводка, стенды.
|
ГОСТ 12.1.038-82 ССБТ ГОСТ
50571.1-93 ГОСТ 12.1.030-81 ССБТ
|
2. Подвижные части машин и
механизмов
|
Двигающиеся части агрегатов
(кран балка), инструмент и приспособления
|
ГОСТ 12.2.003-74 ССБТ ГОСТ
12.2.061-81 ССБТ ГОСТ 12.2.062-81 ССБТ
|
3. Пожароопасность
|
Горючие жидкости, пары
топлива, неисправная проводка
|
ГОСТ 12.1.004-91 ССБТ ГОСТ
12.4.009-83 ССБТ ГОСТ 25829-79 ССБТ СНиП 2.03.02-85
|
4. Несоответствие норм
микроклимата
|
Наличие сквозных проходов,
недостаточное отопление
|
ГОСТ 12.1.005-88 ССБТ СНиП
2.04.05-84
|
5. Вредные выбросы
|
Продукты выбросов ДВС, пары
бензина и моющих средств
|
ГОСТ 12.1.005-88 ССБТ ГОСТ
12.1.007-76 ССБТ
|
Работающие двигатели,
станки, приборы
|
ГОСТ 12.1.003-83 ССБТ ГОСТ
12.1.028-80 ССБТ (СТСЭВ 1413-78)
|
7. Вибрация
|
Вентиляция, стенды и
оборудование
|
ГОСТ 12.1.012-9О ССБТ ГОСТ
12.4.094-88 ССБТ ГОСТ 12.4.002-74 ССБТ ГОСТ 12.4.093-80 ССБТ
|
8. Освещение
|
Недостаточность освещения.
|
СНиП 23-05-95
|
.3 Несоответствие норм микроклимата
Нормирование параметров воздуха рабочей зоны
осуществляется согласно ГОСТ 12.1.005 ССБТ. «Воздух рабочей зоны. Общие
санитарные требования к воздуху рабочей зоны». Работы, выполняемые на участке
ТО и ТР, относятся к средней степени тяжести. Для создания безопасных условий
труда участке ТО и ТР в соответствии с санитарными требованиями
предусматриваются нормы микроклиматических условий в зависимости от
температуры, относительной влажности, скорости движения воздуха, времени года,
характера помещения, избыткам тепла и степени тяжести выполняемой работы.
Параметры и нормы микроклимата на участке приведены в
табл.5.3.1.
Табл.5.3.1. Оптимальные величины микроклимата
Период года
|
Категория работ
|
Оптимальная температура, °С
|
Средняя температура на
участке ТО и ТР, °С
|
Допустимая относительная
влажность, %
|
Средняя влажность на
участке ТО и ТР, %
|
Допустимая скорость
движения воздуха, м/с
|
Средняя скорость движения
воздуха на участке ТО и ТР, м/с
|
Холодный
|
Средней тяжести
|
18-20
|
19
|
До 75
|
70
|
0,2
|
Не более 0,3
|
Теплый
|
|
21-23
|
22
|
При 25°С Не более 65
|
70
|
0,3
|
0,2-0,4
|
Расчёт воздушной завесы шиберного типа
Для обеспечения заданной температуры воздуха в помещении, в холодный
период года, на въездных воротах производственного корпуса предусмотрена воздушная
завеса, схема которой приведена на рис.5.3.1.
Рис.5.3.1. Схема воздушной завесы.
Общий расход воздуха, подаваемого завесой шиберного типа, определяется по
формуле:
, кг/ч
где
- отношение расхода воздуха, подаваемого завесой, к
расходу воздуха, проходящего через проём при работе завесы;
;
-
коэффициент расхода проёма при работе завесы,
;
-
площадь открываемого проёма, оборудованного завесой, м2;
м2;
-
разность давлений с воздуха с двух сторон наружного ограждения на уровне
проёма, Па;
,
где
- поправочный коэффициент на ветровое давление;
;
,Па
где
- расчётная высота, т.е. расстояние по вертикали от
центра проёма до уровня нулевых давлений, м;
м ;
-
плотность наружного воздуха, кг/м3;
кг/м3;
-
плотность внутреннего воздуха, кг/м3;
кг/м3;
Па.
,Па;
где
- расчётный аэродинамический коэффициент,
[СНиП
2.01.07-85];
-
расчётная скорость ветра для холодного времени года, м/с;
м/с ;
Па;
Па.
-
плотность, кг/м3, смеси подаваемой завесой и наружного воздуха при
температуре
кг/м3.
кг/ч
Принимаем
к установке завесы типа ЗВТЗ-5 суммарной производительностью по воздуху
кг/ч. Для принятого решение получим F=14
и вычисляем:
;
Требуемую
температуру воздуха, подаваемой завесой, находим по формуле:
,
где
- отношение теплоты, теряемой с воздухом, уходящим
через открытый проём наружу, к тепловой мощности завесы;
;
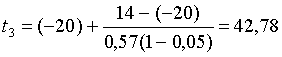
Тепловая
мощность калориферов воздушно-тепловой завесы:
, Вт
где
- коэффициент ;
-
температура воздуха забираемого для завесы,
;

;
Вт
Полученная тепловая мощность не превышает табличной (522200)
5.4 Вредные вещества
Вредные вещества нормируются согласно ГОСТ 12.0.007 -
99. Основными источниками выделения вредных веществ на участке ТО и ТР
являются: пары топлива и смазочных материалов; (табл.5.4.1.).
Таблица 5.4.1. Предельно допустимые значения
концентрации вредных веществ в воздухе рабочей зоны участка ТО и ТР
Наименование вредных
веществ
|
Предельно допустимая
концентрация, мг/м3
|
Класс опасности
|
Окислы азота (пересчет на N2O5) (пары)
|
5
|
2
|
Пары дизельного топлива
|
9
|
3
|
Пары эксплутационных
жидкостей
|
5
|
3
|
Альдегиды
|
5
|
2
|
Окись углерода (пары)
|
20
|
4
|
Едкие щелочи (р-ры в
пересчете на NaOH)
|
0,5
|
2
|
Бензин топливный (в
пересчете на С)
|
100
|
2
|
В результате проведенного анализа и замеров
установлено, что системы вентиляции и отопления исправны и работают в заданных
режимах. Техническое обслуживание данных систем периодическое согласно графику
службой главного механика СТО. В связи с этим метеорологические условия участка
ТО и ТР находятся в пределах норм, установленных ГОСТом.
5.5 Шум и вибрация
Шум нормируется в соответствии с ГОСТ 12.1.083 - 83
«ССБТ. Шум. Общие требования безопасности». Нормируемый параметр - уровень
звукового давления. Основными источниками шума на участке ТО и ТР являются
пневматические и электромеханические гайковерты. Характеристики и допустимые
уровни шума на рабочих местах (табл.5.5.1. ).
Табл. 5.5.1. Звуковое давление, уровни звука и
эквивалентные уровни звука
Вид трудовой деятельности
|
Уровни звукового давления,
дБ, в октавных полосах со среднегеометрическими частотами, Гц
|
Уровни звука и
эквивалентные уровни звука, дБ
|
|
31,5
|
63
|
125
|
250
|
500
|
1000
|
2000
|
4000
|
8000
|
80
|
Выполнение работ на
постоянных рабочих местах в производственных помещениях
|
107
|
95
|
87
|
82
|
78
|
75
|
73
|
71
|
69
|
|
|
|
|
|
|
|
|
|
|
|
|
|
Нормирование вибрации осуществляется в соответствии с
ГОСТ 12.1.0 12 - 90 «Вибрационная безопасность» табл.5.5.2.
Табл.5.5.2. Предельно допустимые величины вибраций на
участке ТО и ТР
Вибрация
|
Категория вибрации
|
Нормативы корректирования
по частоте и эквивалентные корректированные значения
|
|
|
Виброускорение
|
Виброскорость
|
|
|
м/с-2
|
ДБ
|
м/с-2·10-2
|
ДБ
|
Локальная Общая
|
3 типа «а»
|
0,1
|
100
|
0,2
|
92
|
Оборудование участка ТО и ТР проходит своевременную
балансировку, а все установки базируются на виброгасящих фундаментах.
.6 Освещение
На участке применяется искусственное освещение,
нормируемое по СНИП 23-05-95 .(Табл.5.6.2.)
Табл.5.6.2.
Характеристика зрительной
работты
|
Разряд зрительной работы
|
Подразряд зрительной работы
|
Характеристика фона
|
Освещенность, лк
|
|
|
|
|
При системе
комбинированного освещения
|
При системе общего
освещения
|
|
|
|
|
Всего
|
От общего
|
|
Средней точности
|
IV
|
а
|
Темный
|
300
|
200
|
200
|
5.6.1 Проектирование искусственного
освещения
Помещение производственного участка относится к
разряду IIIа. Контраст объекта различения с
фоном - малый. По освещенности - характер объекта различения с фоном темный.
Минимальное значение освещенности 200 лк. Геометрия помещения учитывается
индексом помещения:
где
а и b - длина и ширина помещения соответственно, м,
h - расчетная
высота (подвеска над расчетной поверхностью), м.
Коэффициент
отражения потолка Рn = 0,7; стен Рc = 0,3;
расчетной поверхности Рp = 0,1. Выбираем светильник с Г-2 глубокой КСС(рис. ),
= 73.
Рис.5.6.1.
Кривая силы света
Находим
отношение L/h = 0,77 и, учитывая, что высота помещения h =
3,6 м, находим расстояние между светильниками L = 2,7м. Зная
параметры своего помещения, вычисляем, что при таком расстоянии на агрегатном
участке можно расположить 10 светильников. Необходимый световой поток от каждой
лампы определяется по формуле:
где
Еn -
нормативное значение освещенности, Еn = 200 лк (СНиП 23-05-95);
S - площадь помещения, S = 108 м2
Кз - коэффициент запаса, учитывающий снижение
светового потока за счет запыленности, для светильников с люминесцентными
лампами К3 =1,4;
Z- коэффициент неравномерности освещенности, для
люминесцентных ламп, Z =
1,1;
N - число светильников, N = 10;
-
коэффициент использования светового потока,
= 73.
Выбираем
светильник со световым потоком 5200 лм, ЛБ - 80 мощностью 80 Вт, допустимое
отклонение - 10 %...+20 %. В нашем случае +12 %. Выбираем светильники ЛСП102х80/ДОЗ-0,1.
5.7
Электробезопасность
Нормирование
электробезопасности осуществляется по ГОСТ 12.1.038 - 90 «ССБТ.
Электробезопасность. Предельно допустимые уровни напряжений прикосновения и
токов». Предельно допустимые уровни напряжений прикосновения и токов приведены
в табл.5.7.1. .
Табл.
5.7.1. Предельно допустимые уровни напряжений прикосновения и токов
Напряжение прикосновения и
ток, протекающий через тело
|
U, В
|
I, mA
|
|
Не более
|
Переменный 50 Гц
|
2
|
0,3
|
Предельно допустимые уровни напряжений прикосновения и
токов (табл. 5.7.2.) при аварийном режиме установок напряжением до 1000 В с
глухозаземленной или изолированной нейтралью и выше 1000 В с изолированной
нейтралью.
Табл.5.7.2.
Род тока
|
Нормируемая величина
|
Предельно допустимые
уровни, не более, при продолжительности воздействия тока t, c
|
|
|
0.1
|
0.2
|
0.4
|
0.6
|
0.8
|
1.0
|
<1,0
|
Переменный 50 Гц
|
U, В I,mA
|
340 400
|
160 190
|
120 140
|
95 105
|
75 75
|
60 50
|
20 6
|
Предельно допустимые уровни напряжений прикосновения и
токов при аварийном режиме установок с частотой тока 50 Гц напряжением 1000 В с
глухим заземлением нейтрали (табл.5.7.3.).
Табл.5.7.3.
Продолжительности
воздействия тока t, c
|
Предельно допустимые уровни
напряжений прикосновения U, B
|
До 0.1
|
500
|
0,2
|
400
|
0,5
|
200
|
0,7
|
130
|
1,0
|
100
|
Свыше 1,0 до 5,0
|
65
|
По ГОСТ 12.1.19-79
1 обеспечение недопустимости токоведущих
частей, находящихся под напряжением, для случайного прикосновения. С этой целью
токоведущие части необходимо располагать, на недоступной высоте, широко
применяется ограждение и изоляция токоведущих частей;
2 применение защитного заземления и
зануления электроустановок;
3 автоматическое отключение, применение
пониженного напряжения, двойной изоляции и др.;
4 применение специальных защитных
средств - переносных приборов и приспособлений, средств индивидуальной защиты;
5 четкая организация безопасной эксплуатации
электроустановок.
.8 Пожарная безопасность
Пожаробезопасность нормируется по ГОСТ 12.1.004-91
«ССБТ. Пожарная безопасность» и ГОСТ 12.3.047.-98 «Пожарная безопасность
технологических процессов. Общие требования. Меры контроля.».
Производственный корпус по пожарной опасности можно
разбить по зонам следующих категорий:
Зона ТО и ТР - «В»;
Шиномонтажный участок - «В»;
Участок диагностики - «В»;
В соответствии с классификацией НПБ 105-95 помещение
участка ТО и ТР относится к категории «В» по пожарной безопасности. Здание СТО
оборудовано железобетонными капитальными стенами и железобетонными
перекрытиями.
Огнестойкость зданий по требованиям СНИП 2.01.02
-85(6.10)
Табл.5.8.1.
Степень огнестойкости
|
Несущие стены
|
Чердачные перекрытия
|
Внутренние стены
|
II
|
Несгораемые (2,4 ч)
|
Трудно сгораемые (0,76 ч)
|
Трудно сгораемые (0,3 ч)
|
5.8.1 Технические средства по
своевременному обнаружению пожара
Для своевременного обнаружения пожара используется
электрическая пожарная сигнализация автоматического действия в соответствии с
ГОСТ 12.3.047-98. Пожарная сигнализация осуществляется с помощью электрической
пожарной сигнализации (ЭПС) автоматического действия. В ЭПС используются
автоматические извещатели теплового действия типа ЭПС - 038, по две штуки на
каждый участок. Сигнал о пожаре поступает на пульт мастера зоны ТР,
производственного корпуса. Помимо автоматической пожарной сигнализации
установлен ручной пожарный извещатель ИПР на высоте 1,5 м от пола.
.8.2 Технические средства по тушению
пожара
В помещении участка ТО и ТР спроектирована система
внутреннего пожаротушения. Сеть противопожарного водоснабжения
предусматривается от существующего водопровода производственного корпуса.
Установка пожарных кранов производится на отметке 1,35 м от пола. Система
внутреннего противопожарного водопровода запроектирована из стальных
водогазопроводных труб по ГОСТ 3262-75. Расход воды на внутреннее пожаротушение
и число струй, одновременно подаваемых от пожарных кранов, определены в
соответствии со СПиН 2.04.09-81 и составляют: 2х2,5 л/с.
5.8.3 Первичные средства
пожаротушения
В помещении участка ТО и ТР в соответствии с ГОСТ Р
12.3.047-98 установлены средства первичного пожаротушения: ящики с сухим песком
из расчета 0,5 м3, укомплектованы лопатой, различные пены и порошки, щиты с противопожарным
инвентарем. Пожарные щиты снабжены необходимым оборудованием. Предельная зона,
защищаемая одним пожарным щитом, составляем 800 кв.м. Тип щита - ЩП-В. Для
ликвидации возгораний в помещении участка установлены водопенный и порошковый
огнетушители (ОУ-5, ОУ-80, ОВП У-250, ОВП -100) по ГОСТ 12.4.009 (табл.
5.8.2.).
Табл.5.8.2. Распределение средств пожаротушения
Категория помещения
|
Предельная защищаемая
площадь, м2
|
Класс пожара
|
Пенные огнетушители 10 л
|
Порошковые вместимостью, л
|
Хладоновые огнетушители, 2л
|
Углекислотные огнетушители
|
|
|
|
|
2
|
5
|
10
|
|
2
|
5
|
В
|
400
|
А
|
2++
|
4+
|
2++
|
1+
|
-
|
-
|
2+
|
|
|
Д
|
-
|
-
|
2+
|
1++
|
-
|
-
|
-
|
|
|
(Е)
|
-
|
-
|
2++
|
1+
|
2+
|
4+
|
2++
|
5.8.4 Эвакуационные пути
Для безопасной эвакуации людей на случай возникновения
пожара в помещении участка ТО и ТР в соответствии со СНиП 2.09.02-85
располагаются два рассредоточенных эвакуационных выхода с шириной участков
путей эвакуации не менее 1 м.
5.9 Охрана окружающей среды
.9.1 Расчет выбросов загрязняющих веществ
В расчете рассматривается загрязняющие вещества:
·
оксид углерода (CO);
·
углеводороды (CH);
·
оксиды азота (в
пересчете на диоксид азота NO2);
·
сажа (C);
Выброс iго вещества одним автомобилем кй
группы в день:
При выезде с территории СТО
где,
- удельный выброс iго вещества при прогреве двигателя автомобиля кй
группы, г/мин.
-
пробеговый выброс iго
вещества при движении по территории СТО с относительно постоянной скоростью,
г/км.
-
удельный выброс iго
вещества при работе двигателя на холостом ходу, г/мин.
- время
прогрева двигателя, мин
- пробег
по территории СТО одного автомобиля в день при выезде, км.
,
- время работы двигателя на холостом ходу при выезде
с СТО, мин.
где,
- пробег по территории СТО одного автомобиля в день ,
км.
Выбросы
загрязняющих веществ при прогреве и работе двигателя на холостом ходу
автомобилями с бензиновыми и дизельными двигателями соответствуют ситуации,
когда на СТО не проводится работа по контролю токсичности ОГ в соответствии с
ГОСТ 17.2.2.03-87 и ГОСТ 21393-75.
Валовой
выброс iго
вещества автомобилями рассчитывается раздельно для каждого периода года.
, кг.
Где,
-
количество автомобилей кй группы на СТО
-
количество рабочих дней в расчетном периоде
- период
года (теплый, холодный, переходный)
Для
определения общего валового выброса валовые выбросы iго вещества суммируются по периодам года:
, кг.
Максимальный
разовый выброс iго
вещества (
) определяется по формуле:
, г/с
Максимальный разовый выброс рассчитывается для холодного периода года.
Данные по расходу топлива при прогреве и работе двигателя на холостом
ходу соответствуют ситуации, когда на СТО не проводится работа по контролю
токсичности ОГ в соответствии с ГОСТ 17.2.2.03-87 (kхх = 1).
I. Выбросы
CO
а)
теплый период:
г,
г;
б)
холодный период:
г,
г;
в)
переходный период:
г,
г.
MТ = 0,7*(5,37 + 3,92)*200*50*10-3 = 64,8 кг;
MП = 0,7*(6,4 + 4,02)*75*50*10-3 = 27,3 кг;
MО = MТ + MХ +MП = 64,8 +
34,3 + 27,3 =126,4 кг.
г/с
II. Выбросы CH
а)
теплый период:
г,
г;
б)
холодный период:
г,
г;
в)
переходный период:
г,
г.
MТ = 0,7*(0,68 + 0,48)*200*50*10-3 = 8,12 кг;
MХ = 0,7*(0,87 + 0,52)*90*50*10-3 = 4,8 кг;
MП = 0,7*(0,81 + 0,5)*75*50*10-3 = 3,4 кг;
MО = MТ + MХ +MП = 8,12 +
4,8 + 3,4 = 16,32 кг.
, г/с.
III. Выбросы NO2
а)
теплый период:
г,
г;
б)
холодный период:
г,
г;
в)
переходный период:
г,
г.
MТ =0,7*(2,2 + 1,7)*200*50*10-3 = 27,3 кг;
MХ =0,7*(2,04 + 1,54)*90*50*10-3 = 11,2 кг;
MП = 0,7*(1,94 + 1,47)*75*50*10-3 = 8,9 кг;
MО = MТ + MХ +MП = 27,3
+11,2 +8,9 = 47,4 кг.
, г/с.
IV. Выбросы C
а)
теплый период:
г,
г;
б)
холодный период:
г,
г;
в)
переходный период:
г,
г.
MТ = 0,7*(0,1 + 0,08)*200*50*10-3 = 0,126 кг;
MХ = 0,7*(0,19 + 0,1)*90*50*10-3 = 0,203 кг;
MП = 0,7*(0,18 + 0,09)*75*50*10-3 = 0,189 кг;
MО = MТ + MХ +MП = 0,126
+ 0,203 + 0,189 = 0,518 кг.
, г/с.
Выбросы
вредных веществ за один год приведены в табл.5.9.1.
Табл.5.9.1.
Вредное вещество
|
CO
|
CH
|
NO2
|
C
|
Кол-во, кг
|
126,4
|
16,32
|
47,4
|
0,518
|
.9.2 Очистные сооружения
СТО потребляет значительное количество пресной воды.
Она используется для хозяйственно-бытовых и производственных нужд, а также для
устройства внутреннего пожаротушения.
Наиболее крупными потребителями являются посты мойки,
где только на один автомобиль ежедневно приходится 0,5...2 м3 воды. Для
сокращения расхода воды в последнее время широко внедряют системы оборотного
водоснабжения, которые позволяют повторно использовать воду после ее очистки в
специальных устройствах. При этом чистая вода расходуется только на восполнение
потерь из-за испарения и утечки вместе с остатками грязи. Снижению расхода воды
способствует и применение синтетических моющих средств. Очищают
производственные сточные воды и ливневые стоки в очистных сооружениях СТО. Так
как в сточных водах в основном преобладают механические частицы и
нефтепродукты, процесс очистки значительно упрощается. Механическая очистка
осуществляется путем действия центробежных сил - фильтрованием. В
гидроцилиндрах вода получает вращательное движение (рис.5.9.1. ).
Рис. 5.9.1. Схема очистки сточных вод на гидроциклонах
«Кристалл»
- моечная канава; 2 - металлический бункер для сбора
осадка; З - приемный резервуар сточных вод; 4 - накопитель осадка; 5 - насосы -
ВЕС; б - безнапорный гидроциклон - ГС - 5О0; 7 - плавающая воронка для сбора
нефтепродуктов; 8 - резервуар для сбора нефтепродуктов; 9 - промежуточный
резервуар чистой воды; 10 - напорный фильтр - «Полимер - 300»; 11 - резервуар
чистой воды.
При этом более тяжелые частицы за счет центробежных
сил отбрасываются к стенкам и опускаются на дно гидроциклона, а легкие примеси
и нефтепродукты собираются в центре и всплывают на поверхность воды.
Фильтрование применяют для очистки сточных вод от тонкодисперсионных
загрязнений. Процесс фильтрования используется, как правило, на заключительных
стадиях очистки воды. В качестве элементов в установках используются гранулы
полипропилена и сипрона, обладающие высокой адсорбционной и адгезионной
способностью к нефтепродуктам.
Применение механической очистки воды предпочтительно
потому, что она является наиболее простой в изготовлении, обслуживании и не
требует дополнительных затрат на расходные материалы.
Песколовки - сооружения для задержки песка и других
минеральных взвесей.
W = q / U
где W-
площадь сечения рабочей части песколовки,м2
q - расход сточных вод, м3 /с,
U - скорость потока сточных вод, U = 0,3 м /с,
L - длина рабочей части песколовки, м,
t - время протока, t = 30 с.
Тогда W = 1
/ 0,3 = 3,33 м2, L
= 0,3 × 30 = 9м.
Сток из моечной канавы поступает в металлический
бункер, где тяжелые частицы оседают на его дно (крупность задерживаемых частиц
26 мм). Бункер расположен в непосредственной близости от мойки автомобилей.
Из бункера поступает в приемный резервуар З и насосами
5 перекачивается в безнапорный гидроциклон б (гидравлическая крупность
задерживаемых частиц - 18 мм) и самотечно поступает в промежуточный резервуар
чистой воды 9. Нефтепродукты в безнапорном гидроциклоне улавливаются плавающей
воронкой и поступают в резервуар для сбора нефтепродуктов 8, а осадок - в
накопитель осадков 4.
Из промежуточного резервуара 9 вода проступает в
напорные фильтры 10, где полностью очищаясь поступает в резервуар чистой воды
11. Из резервуара 11 чистая вода подается на мойку водяным насосом 5.
Нефтепродукты поступают в нефтесборник 12. Степень очистки по схеме составляет:
по взвеси - 99%;
- по нефтепродуктам - 88,5%.
6. Экономико-организационный раздел
Затраты инвестора при организации СТО делятся на две основные
группы - единовременные и текущие (эксплуатационные).
В состав единовременных затрат входят затраты на
строительство зданий, сооружений, прокладку инженерных коммуникаций,
технологическое оборудование и т.д.
Стоимость 1 м2 с учетом затрат на коммуникации
может быть принята о 8000 до 12000 рублей для зданий, выполненных из
быстровозводимых конструкций, и 17000.. .20000 рублей для зданий из
железобетона.
Затраты на приобретение и монтаж технологического
оборудования могут быть приняты в пределах 220000...460000 рублей на 1 рабочий
пост (меньшие значения для оборудования отечественного производства). В эти
суммы включены затраты на оснащение производственных участков и затраты на
монтаж оборудования.
Основные статьи текущих затрат и их удельные значения
приведены в табл.6.1.
Таблица 6.1. - Удельные текущие затраты
№ п.п.
|
Наименование
затрат
|
Единицы
измерения
|
Годовые
удельные затраты
|
1
|
Ремонт зданий,
оборудования и коммуникаций
|
руб./пост
|
50000... 70000
|
2
|
Аренда
земельного участка
|
руб./м2
|
300
|
3
|
Электроэнергия
|
руб./пост
|
15000... 20000
|
4
|
Отопление
|
руб./м2
|
30...40
|
5
|
Вода для
питьевых и технологических нужд
|
руб./пост
|
700... 1000
|
6
|
Расходные
материалы
|
руб./пост
|
25000... 30000
|
7
|
Амортизация
зданий, сооружений и оборудования
|
руб./м2
|
400... 600
|
8
|
Заработная
плата
|
руб./чел.
|
80000.. 120000
|
9
|
Накладные
расходы (реклама, охрана окружающей среды и др.)
|
руб.
|
6 - 10 % от
суммы текущих затрат
|
Для нашего примера результаты расчета единовременных и
текущих затрат приведены в табл.6.2.
Таблица 6.2. - Расчет единовременных затрат
№ п.п.
|
Наименование
затрат
|
Единица
измерения
|
Принятые
удельные затраты
|
Абсолютные
затраты, руб.
|
1
|
Строительство
здания станции с коммуникациями
|
руб./м2
|
18000
|
3730∙18000=67140000
|
2
|
Технологическое
оборудование с монтажом
|
руб./пост
|
400000
|
16∙400000=6400000
|
Итого
|
73540000 рублей
|
Таблица 6.3. - Расчет текущих затрат за год
№ п.п.
|
Наименование
затрат
|
Единица
измерения
|
Принятые
удельные затраты
|
Абсолютные
затраты, руб.
|
1
|
Ремонт здания,
оборудования и коммуникаций
|
руб./пост
|
60000
|
16∙60000=960000
|
2
|
Аренда
земельного участка
|
руб./м2
|
300
|
12500∙300=3750000
|
3
|
Электроэнергия
|
руб./пост
|
16000
|
16∙16000=256000
|
4
|
Отопление
|
руб./м2
|
30
|
30∙3730=111900
|
5
|
Вода для
питьевых и технологических нужд
|
руб./пост
|
800
|
16∙800=
12800
|
6
|
Расходные
материалы
|
руб./пост
|
27000
|
16∙27000=432000
|
7
|
Амортизация
зданий, сооружений и оборудования
|
руб./м2
|
400
|
3730∙400=1492000
|
8
|
Заработная
плата
|
руб./чел.
|
120000
|
63∙120000=7560000
|
9
|
Накладные
расходы (реклама, охрана окружающей среды и др.)
|
руб.
|
6 % от суммы
текущих затрат
|
874482
|
Итого
|
15449182
|
Одним из важнейших показателей проекта является срок
окупаемости единовременных вложения. Чем он меньше, тем эффективнее
используются инвестиции в организацию предприятия. В настоящее время приемлемым
является срок окупаемости 3-4 года.
Для расчета срока окупаемости предварительно необходимо
определить доходы и прибыль станции технического обслуживания.
Доход СТО за год в рублях:
Д =ТСТО∙Н,
где ТСТО - годовой объем работ,
нормо-ч (приравниваем чел.-ч. к нормо-ч);
Н- стоимость нормо-часа в рублях.
Для нашего проектируемой СТОА принимаем стоимость нормо-часа
Н = 1400 руб. При этом доход станции за год составит: Д = 324802∙1400
= 49920800 руб. Прибыль за год в рублях:
П = Д-Р,
где Р - текущие затраты за год, руб. Р = 15449182
руб. Таким образом, прибыль СТОА будет равна: П = 49920800-15449182=
34471618 руб.
В прибыль проектируемой СТО также входит прибыль от продажи
запчастей и автопринадлежностей и принимается в размере 60…90% прибыли от
выполняемых работ:
Пзч =(0,6...0,9)∙П.
Пзч = 0,6 х 34471618=20682970.8 руб..
Прибыль проектируемой СТО с учетом прибыли от продажи
запасных частей составит:
ПСТО=П+Пзч
ПСТО =34471618+20682970.8=55154588.8 руб.. Чистая
прибыль без налогов в рублях:
ЧП=ПСТО -
где ЧП - чистая прибыль,
НП - действующая ставка налога на прибыль, %. НП = 20%. То
есть чистая прибыль СТОА будет равна:
ЧП = 55154588.8-0.20∙55154588.8=41917500руб.
Определение реальной ценности и окупаемости проекта
производится с учетом дисконтирования, то есть приведения экономических
показателей разных лет к сопоставимому во времени виду с помощью коэффициентов
дисконтирования, основанных на формуле сложных процентов.
Предварительно рассчитаем чистый дисконтируемый доход:
ЧДД = (ЧП + А) ∙Кд,
где А - величина амортизации зданий, сооружений и
оборудования,руб.;
Кд - коэффициент дисконтирования, который
принимается для: первого года работы - 0,77; второго - 0,59; третьего - 0,46 и
четвертого -0,35.
Реальная ценность проекта (в руб.) рассчитывается по годам:
-й год РЦПР1=ЧДД1-ЕДЗ;
2-й год РЦПР2 = РЦПР1 + ЧДД2;
3-й год РЦПРЗ=РЦПР2+ЧДД3;
4-й год РЦПР4 = РЦПРЗ + ЧДД4,
где ЕДЗ - величина единовременных затрат, руб. Для нашего
примера (первый год эксплуатации): ЧДД =(41917500 ∙ 0,77 =
32276475руб.
РЦПР1 =32276475-73540000 =
-41263252 руб; Результаты расчета для последующих лет даны в табл.6.4.
Таблица 6.4. - Показатели работы СТОА при единовременном
вводе мощностей
Показатели
|
Годы
|
|
0
|
1
|
2
|
3
|
4
|
Единовременные
затраты, руб.
|
73540000
|
0
|
0
|
0
|
0
|
Текущие
затраты, руб.
|
0
|
15449182
|
15449182
|
15449182
|
15449182
|
Доход, руб.
|
0
|
49920800
|
49920800
|
49920800
|
49920800
|
Прибыль, руб.
|
0
|
55154588.8
|
55154588.8
|
55154588.8
|
55154588.8
|
Прибыль после
налогообложения, руб.
|
0
|
41917500
|
41917500
|
41917500
|
41917500
|
Коэффициент
дисконтирования
|
1
|
0,77
|
0.59
|
0,46
|
0.35
|
Чистый
дисконтированный доход, руб.
|
0
|
32276475
|
24731325
|
19282050
|
14671125
|
Реальная
ценность проекта, руб
|
-73540000
|
-41263252
|
-16532200
|
2749850
|
17420975
|
Как видно из табл.6.4. , при единовременном вводе мощностей и
неизменных величинах дохода и текущих затрат по годам проект окупит себя на
третий год после ввода в эксплуатацию.
Значение срока окупаемости в 3 года является вполне приемлемым,
то есть проект СТО для инвестора будет выгоден.
Вывод
По итогам работы мы делаем вывод, что данный проект реконструкции СТО
выгоден для инвесторов. Срок окупаемости нашего проекта составляет 3 года, что
является хорошим результатом. Впоследствии СТО будем приносить неплохую прибыль
и иметь хорошие резервы для расширения территории и развития дилерства.
Список используемой литературы
Учебно-методическая литература
. Напольский Г.М. Технологическое
проектирование АТП и СТОЛ. М:
Транспорт, 1993.
. Суханов Б.Н., Бозьих И.О., Бедарев
Ю.Ф. Техническое обслуживание и ремонт автомобилей. Пособие по дипломному
проектированию. М.:
Транспорт, 1991.
. Афанасьев Л.Л., Колясинский Б.С.,
Маслов А.А. Гаражи и станции
технического обслуживания
автомобилей. Альбом чертежей. М.:
Транспорт, 1980.
. Клейнерман Л.Л.; Денисов В.Г.;
Дорохин Н.Б. Проектирование предприятий автомобильного транспорта. Методическое
указание по
выполнению курсового и дипломного
проекта для студентов
специальности 1500200 дневного и
заочного отделения.
. Табель технологического
оборудования и специализированного инструмента для АТП. ЦБНТН Минавтотранса
РСФСР, 1983.
. Анурьев В.Н. Справочник
конструктора-машинострйтеля: В 3-х томах. Т.1 - 5-е изд., перераб. и доп. - М.:
Машиностроение, 1978 г. - 728 с, ил.
. Анурьев В.И. Справочник
конструктора-машиностроителя: В 3-х томах. Т.2 - 5-е изд., перераб. и доп. -
М.: Машиностроение, 1978 г. - 559 с, ил.
. Павлов Я.М. детали машин., изд-во
«Машиностроение», 1969 г. 448 с, табл. 55, ил. 250.
. Феодосьев В.И. Сопротивление
материалов. - 8-е изд., стереотип. - М. :Наука. Главная редакция
физико-математической литературы, 1979. -
с. .
. Основы проектирования и
эксплуатации технологического оборудования:
Учебное пособие! В.И. Петров, А.Л.
Клейнерман, Н.Б. дорохин - Тула:
Тул. гос. ун-т, 2000. - 160с.
. И.А. Коганов, А.А. Станкеев. Расчёт
припусков на механическую обработку. Учебное пособие. Тульский политехнический
институт, 1973 год, 193 с.
. Салон А.И. Охрана труда на
предприятиях автомобильного транспорта:
Учебник для студентов автомоб. для.
вузов. - 3-е и-зд., перераб. и доп. -
М.: Транспорт, 1985.-351с.
. Кузнецов Ю.М. Охрана труда на
автотранспортных предприятиях: Учеб. для учащихся автотрансп. техникумов. - М.:
Транспорт, 1990. - 288 с.
.Охрана труда в машиностроении:
Учебник для машиностроительных
вузов. Е. Я. Юдин, С. В. Белов и др;
Под редакцией Е. Я. Юдина, - 2-е издание, перераб. и доп. -: Машиностроение,
1983, 432 с, ил.
. Справочная книга по охране труда в
машиностроении: Г.В.Бектобеков, Н.Н.Борисова, В.И.Коротков и др.; Под общ. ред.
О.Н.Русака - Л.:
Машиностроение. Ленинградское
отделение, 1989. 541 с: ил.
Нормативные материалы
. Положение о ТО и ТР подвижного
транспорта. М.: Транспорт, 1986
. СНиП 23-05-95
.МУ 2.24.706-98
. ГОСТ 12.1.003-96
. СН 2.2.4/2.1.8.562-96
. ГОСТ 12.1.038-82
.СНиПII-12-77
. ГОСТ 12.1.012-90
. СН 2.2.4/2.1.8.566-96
. ГОСТ 12.1.030-81