Электрификация и автоматизация технологических процессов строительства коллектора подземных коммуникаций в условиях ОАО СУ-70 'ГПР-1'
Введение
электропривод вентиляторный локомотивный
Целью дипломного проекта является электрификация и
автоматизация технологических процессов строительства кабельного коллектора от
ТЭЦ №8 под Волгоградским проспектом г. Москвы.
В дипломном проекте приводятся горно-технологические
характеристики объекта, производится расчет исходных параметров механического
оборудования, рассматриваются вопросы о безопасности ведения проходческих
работ, производятся расчеты технико-экономических показателей.
Основными задачами дипломного проекта являются:
· анализ технологической характеристики
подземного коллектора;
· выбор проходческого комплекса,
механического оборудования электрооборудования;
· оценка экономической эффективности
строительства подземного коллектора;
· проектирование и выбор систем
электроснабжения, электропривода и автоматизации.
Специальный вопрос содержит оценку энергетических показателей
и разработку комплексных мероприятий направленных на энергосбережение.
. Горно-технологическая часть
.1
Подземный коллектор
Проектируемый кабельный коллектор будет находиться в
Юго-Восточном административном округе г. Москвы, и будет проходить под
существующими автомобильными дорогами.
Строительство участка коллектора осуществляется от ТЭЦ №8 до
городской подстанции № «127».
Строительство основной трассы коллектора осуществляется
закрытым способом (методом щитовой проходки) на длине 294 м с помощью
механизированного проходческого щитового комплекса Lovat-3.6. Приняты сечения
следующих габаритов: щитовая проходка - щит диаметром 3,6 м.
Продольный профиль коллектора составлен на основании
изысканий
«Мосинжстройпроект». Положение коллектора в профиле
определено согласно существующих и проектируемых подземных коммуникаций,
отметок земли, условием работы прокладываемых в нем коммуникаций, а также
гидрогеологических условий по трассе коллектора.
1.2 Инженерно-геологические условия строительства
В соответствии с заключением об инженерно-геологических и
гидрогеологических условиях строительства, в траншеях и щитов будут разрабатываться
древнеаллювиальные и флювиогляциальные пески I группы по трудности
разработки, супеси и суглинки II группы, а также мореные суглинки со щебнем свыше
10% - III группы.
Грунтовые воды заключены в аллювиальных песках и будут
вскрыты при земляных работах.
При обнаружении несоответствия геологических и
гидрогеологических условий в натуре с данными проекта, надлежит силами
специализированной организации произвести дополнительную разведку, а вопрос о
дальнейшем производстве работ решить по согласованию с заказчиком и проектной
организацией.
В связи с недоступностью просадок земной поверхности и
горно-геологическими условиями для строительства коллектора принята щитовая
проходка.
.3 Щитовая проходка
Шахты для щитовой проходки запроектированы круглого и прямоугольного
сечений. Размеры шахт приняты с учётом габаритов камер, монтажа и демонтажа
щита, а также монтажа труб в тоннеле.
В соответствии с заключением об инженерно-геологических
условиях участков строительства, проходка шахт принята в грунтах I, II и III категории. При проходке
шахт разработка грунта производится заходками, с временным креплением,
экскаватором с грейферным ковшом и вручную, с подъёмом грунта краном в бадьях.
Крепление круглых шахт приняты инвентарными швеллерными поясами.
Тип креплений выбран исходя из размеров шахт, их назначения и
физико-механических свойств грунтов.
По окончании проходки монтажной шахты, щит Æ = 3.6 м, опускается в
шахту краном РДК-25, грузоподъёмностью 25 тонн.
После ввода щита в забой, приступают к обустройству шахты -
устройству лестниц, подъёмного отделения, монтажу необходимых трубопроводов.
Конструкция тоннеля принята из железобетонных блоков, с
устройством монолитной железобетонной рубашки, торкрета по сетке, а на
отдельных участках трассы и с устройством металлоизоляции.
Врезка щита
В начале работ сооружается «стена в грунте», затем происходит
выемка грунта в монтажной камере.
Врезка щита в грунтовый массив осуществляется в следующей
последовательности:
за основной «стеной в грунте» сооружается три дополнительные
неармированные стены из бетона марки В10 на известковом щебне толщиной 600 мм;
в сечении сооружаемого тоннеля вырубается бетон основной
«стены в грунте» и вырубаются балки;
в монтажной камере устанавливаются упоры (временный и
постоянный) для надвижки щита до забоя и его врезки;
на специальной площадке монтируется и подготавливается к
работе щит «Lovat»;
после его надвижки (за щитом) - на металлоконструкциях, на
длине монтажной камеры, монтируется основание шириной в два блока обделки под 2
рельсовый путь;
монтируется первичный ленточный конвейер;
придвигается щит вплотную ко лбу забоя;
включается ротор и другие необходимые системы и начинается
проходка технологического отхода.
Технологический цикл работы щита включает в себя следующие
операции:
разработка породы в забое;
дозированная выдача грунта из забоя;
транспортировка разработанного грунта вагонетками с помощью
электровоза;
наращивание силового кабеля и трубопроводов для водопровода,
водоотлива, сжатого воздуха, вентиляции;
разрушение и удаление валунов;
лазерный контроль за передвижением щита в тоннеле;
компьютерный контроль параметров роботы тоннелепроходческого
комплекса;
транспортирование блоков обделки блоковозками;
монтаж обделки блокоукладчиком;
нагнетание тампонажного раствора за обделку.
1.4 Электрооборудование и автоматика,
сигнализация загазованности, производственная громкоговорящая связь,
диспетчеризация
Коллектор оснащён системой сигнализации загазованности на
базе шахтной аппаратуры «Метан», а также производственной громкоговорящей связью,
выполненной аппаратами ПГС-3. Сигнализация и управление работой
технологического оборудования коллектора выведена в диспетчерскую, которая
будет запроектирована после решения вопроса о её местоположении уточненном (в
проекте предусмотрен выход к диспетчерской от камеры №15).
Для диспетчеризации используются щиты производства СП
«Москоллектор».
1.5
Озеленение
Проект разработан с учётом планировочного решения,
существующей и проектируемой сети подземных коммуникаций. Проектом
предусматривается посадка зелёных насаждений. Восстановление газона в границах
рабочей зоны предусматривается в проекте организации строительства и включено в
общую смету.
1.6 Организационно - технологическая схема
строительства
Строительство закрытого перехода предусмотрено щитовой
проходкой.
Трасса проектируемого кабельного коллектора проходит под
существующими автомобильной дорогой, Волгоградский проспект. Шахты для щитовой
проходки запроектированы прямоугольного сечения. Для производства работ
вскрываются монтажные и демонтажные котлованы прямоугольного сечения.
Разработка котлованов ведется в креплениях стальными трубами с устройством
поясов и распорок. В связи с неблагоприятными гидрогеологическими условиями
проектом организации строительства предусмотрено строительное водопонижение
эжекторными иглофильтрами, устанавливаемыми по периметру рабочего и приемного
котлованов. Водопонизительные установки располагаются в развитии.
Щитовую проходку под существующими автомобильной дорогой
необходимо вести с особой осторожностью с постоянным креплением лба забоя.
1.7 Дорога
Асфальтобетонное покрытие до начала основных работ должно
быть разобрано и отправлено на переработку. После окончания строительных работ
асфальтобетонное покрытие восстанавливается.
1.8
Сети уличного освещения
Проектом предусматривается переустроить сети уличного
освещения с учётом очередности производства работ с последующим восстановлением
по постоянной схеме.
. Механическое оборудование и транспорт
.1 Водоотливные установки
Расчет исходных параметров для выбора
оборудования
Насосы выбираем по расчетным значениям подачи Qр и напора Hр.
В соответствии с Правилами безопасности необходимая
подача насосов определяется следующим образом:
где Т - регламентируемое отраслевыми Правилами безопасности
нормативное время откачки суточного притока воды. Для горных предприятий Т =
20.
Расчетный напор насосов численно равен сопротивлению внешней сети
при расчетной подаче. При определении расчетного напора разницей диаметров
нагнетательного и всасывающего трубопроводов пренебрегают. Поэтому
где Нг - геодезическая высота подъема воды, м;
λP - расчетный коэффициент линейных
гидравлических сопротивлений;
L - полная длина трубопровода, включая всасывающий трубопровод, м;
Dp - расчетный диаметр нагнетательного трубопровода, м;
Vэ -
экономически целесообразная скорость движения воды по трубопроводу, м/с;
g - ускорение силы тяжести, м/с2 (g=9,8 м/с2).
Геодезическая высота подъема воды
HГ = Hш + Hвс+ Hп, м,
где Hвс - высота всасывания, предварительно принимается равной 4-5
м;
Hп - высота
переподъема воды на поверхности (Hп =1 м).
HГ =15 + 4+
1=20 м.
Полную длину трубопровода для шахтной установки можно
определить по формуле:
L= Hш + Hп + lвс+ lнк+ lтх + l1, м,
где lвс = 8 - 12 м - длина всасывающего трубопровода (lвс= 8 м);
lнк = 20 -30 м - длина трубопровода в насосной
камере (lнк= 20 м);
lтх = 15 - 20 м - длина трубопровода в трубном ходке
(lтх = 15 м);
l1 = 75 м - длина трубопровода на поверхности до
места сброса воды.
L = 15 + 1 + 8 + 20 + 15 + 5 = 64 м.
Расчетный диаметр нагнетательного трубопровода определяется по
значению экономически целесообразной скорости движения воды
В соответствии с нормами технологического проектирования
горнодобывающих предприятий скорость движения воды по нагнетательным
трубопроводам не должна превышать 3 м/с. С достаточной для практических
расчетов точностью она определяется по эмпирической формуле:
Коэффициент линейных гидравлических сопротивлений для
трубопроводов водоотливных установок определяется по формуле:
Сумму коэффициентов местных гидравлических сопротивлений принимаем
равной ∑ξр = 20.
Для выбора труб находим толщину стенок, которая с учетом
коррозионного износа определяется по формуле
где 1,18 - коэффициент, учитывающий минусовой допуск толщины
стенки;
δ0 - минимальная по условиям прочности толщина стенки трубы, мм;
δкв - скорость коррозионного износа внутренней поверхности
трубы, мм/год, принята равной 0,1 мм/год;
t = 10 - 15 лет - срок службы трубопровода (t = 15 лет).
Минимальная по условиям прочности толщина стенки трубы
определяется следующим образом:
δ0 =1875·Рр·Dр /σв, мм,
где Рр - расчетное давление воды в трубопроводе
Рр = 10-6·ρ·g·Нр, МПа;
где ρ - плотность воды, кг/м3;
σв - временное сопротивление
разрыву для стали, из которой изготовлены трубы, МПа, (σв = 412 Мпа для марки стали Ст4сп).
Рр = 10-6 · 1020 · 9,8 · 23,2 = 0,23
МПа;
δ0 = 1875 · 0,23 · 0,054 /
412 = 0,056 мм;
Выбор основного оборудования водоотливной установки
По значениям Qр и Hр.
Выбираем два консольных насоса типа К 45/30 со следующими характеристиками:
диаметр рабочего колеса D2 = 168 мм;
напор H =30 м;
подача Q = 45 м3/ч;
частота n = 2900 об/мин;
КПД η = 72%.
По значениям Dp и δр выбираем для нагнетательного става трубы
стальные горячедеформированные бесшовные (ГОСТ 8732 - 78). Внутренний диаметр
труб - 100 мм, наружный - 114 мм.
Для всасывающего трубопровода принимаем аналогичные трубы большего
диаметра.
Определение режима работы насосов
Задаваясь расходом Q (м3/с) в интервале от 0 до 1,2 Qp по формуле расчета
характеристики внешней сети определим для каждого значения Qi величину Hci. Данные расчета сводим в
табл. 1. Характеристика внешней сети рассчитывается по формуле:
С = HГ + RС·Q2,
где RС - обобщенный коэффициент сопротивления внешней
сети
где λ - коэффициент
линейных гидравлических сопротивлений (λ =0,042);
DH - внутренний диаметр выбранного
стандартного нагнетательного трубопровода;
∑ξ - сумма коэффициентов местных сопротивлений
(∑ξ = 20);
Таблица 1
Qi, м3/ч
|
0
|
9,6
|
19,2
|
28,8
|
38,4
|
48
|
57,6
|
Qi, м3/с
|
0
|
0,0026
|
0,0053
|
0,008
|
0,0106
|
0,0133
|
0,016
|
Hci, м
|
17
|
17,42
|
18,7
|
20,9
|
23,9
|
27,9
|
32,8
|
По данным табл. 1 строим характеристику внешней сети.
Рис. 2.1. Характеристика внешней сети
Выбор привода насоса и определение энергоемкости
водоотлива
Необходимая мощность электродвигателя насоса определяется
следующим образом:
где ρ = 1020 кг/м3
- плотность перекачиваемой воды.
С учетом частоты вращения насоса выбираем асинхронный двигатель с
короткозамкнутым ротором 4А100L2УЗ со
следующими характеристиками:
номинальная мощность Pн = 5,5 кВт;
напряжение U = 220/380 В;
частота вращения n = 3000
об./мин.;
КПД η = 87,5%;
коэффициент мощности cosφ =0,83.
Годовой расход электроэнергии на водоотлив определяется по
формуле:
где ηэд - КПД электродвигателя;
ηэс = (0,92 - 0,96) - КПД электросети;
N - количество дней в году с максимальным притоком воды;
Тн - число часов работы водоотливной в сутки при
откачке нормального притока воды, Тн = Qн /Qд =960 / 45 = 21,3 ч.;
Tmax = Q max /2Qд = 1320 / 2·45
= 14,7 ч.
где Tmax - число часов работы водоотливной
установки в сутки при откачке максимального притока воды,
2.2 Вентиляторные установки
Вентиляция выработки производится вентилятором ВМ-6М. Техническая
характеристика вентилятора:
производительность Qв = 340 м3 / мин.;
полное давление Hв = 2000 Па;
КПД вентилятора ηв = 0,76;
габариты 1050х730х750 мм;
масса 350 кг;
тип электродвигателя ВРМ132М2;
мощность электродвигателя Pд = 13
кВт;
скорость вращения вала n =3000
об/мин.
Среднегодовой расход электроэнергии на вентиляцию рассчитывается
по формуле:
.3 Локомотивная откатка
Так как строительство подземного коллектора производится в
городских условиях, то применяется аккумуляторный электровоз модели АК-2у со
следующими характеристиками:
·
масса
- 2,2 т;
·
сила
тяги -3,3 кН;
·
скорость
- 3,95 км/ч;
·
ток -
75 А;
·
ширина
колеи - 600 мм.
Характеристика вагонетки со съемным опрокидным кузовом БК -
1,0:
·
вместимость
-1 м3;
·
грузоподъемность
- 1,9 т;
·
масса
порожней вагонетки - 0,63 т.
3. Безопасность труда
.1 Общие сведения
Объект производства работ закрытым способом на
рассматриваемом участке строительства кабельного коллектора относится к опасным
производственным объектам. В камерах и тоннеле могут возникнуть условия для
появления вредных и опасных факторов. Для их предупреждения и ликвидации
организуются специальные мероприятия.
В настоящее время существуют и с каждым годом
усовершенствуются нормативные базы, технология и техника производства
строительных работ, ужесточаются требования охраны труда и технике
безопасности, более полно проводятся геотехнические исследования.
3.2 Анализ опасных факторов
Обрушение кровли забоя
кабельных коллекторов
При строительстве подземных сооружений
самым распространенным опасным фактором является обрушение горных пород кровли.
При строительстве, тоннелей закрытым
способом обрушение породы происходит чаще всего в результате вывала в забое или
в непосредственной близости от него.
Обрушению способствует также наличие
геологических нарушений, неоднородность массива, наличие сыпучих пород,
близость водоносного горизонта, неравномерное изменение плотности пород. По
геологическим данным строительство коллектора пересекает водоносный горизонт,
что увеличивает опасность обрушений.
Обрушение породы может произойти
непосредственно в плоскости переднего торца обделки. При этом нарушится
прочность находящейся впереди породы вследствие скопления грунтовых вод,
которые могут проникать в грунт с поверхности в результате ливней и таяния
снега. Причинами обрушения породы могут быть также понижение уровня грунтовых
вод и извлечение из забоя валунов и крупных каменистых включений.
Пожар в монтажной камере
и тоннеле
При строительстве подземных выработок
пожары относятся к наиболее экстремальным видам аварий: при ограниченном
количестве путей эвакуации людей и подходов к очагу возгорания практически
каждый случай открытого горения влечет опасность отравления выделяющимися
газами.
На участке строительства кабельного
коллектора источником пожара и одновременно объектом горения может служить
изоляция проложенных кабелей с напряжением, возможно возгорание аварийного
запаса деревянных материалов. Кроме того, пожар в подземной выработке может
произойти из-за неправильного производства сварочных работ.
Затопление и обводнение
горных выработок.
Прорывы подземных вод и плывуна в забое
выработки также относятся к опасным факторам. Основной опасностью
представляется ведение работ в зоне пересечения тоннеля с водоносным
горизонтом. Вероятность прорыва воды в неустойчивых водонасыщенных грунтах, при
проходке городских тоннелей ниже уровня грунтовых вод в условиях повышенного
гидростатического давления достаточно велика. Это может привести к частичному
или полному затоплению выработки, вызывая поломку горнопроходческого
оборудования, травмы и гибель людей. При этом изменяется естественный
водоприток что может привести к перегрузке водоотлива и остановке работ.
Также обводненность горных пород снижает
прочность песчаника на 20%, а глин - на 70%, что увеличивает опасность
обрушения пород.
Загазирование подземных выработок при
строительстве кабельного коллектора может быть вызвано выделением газа из
горных пород при недостаточности или неправильным использовании вентиляции.
Дополнительным источником загазирования
подземных выработок может стать пожар.
Производственный
травматизм
Производственный травматизм квалифицируется как нарушение
анатомической целостности или физиологических функций тканей или органов
человека, вызванное внезапным внешним воздействием при исполнении им
производственных обязанностей.
Основными производственными травмами являются: поражение
электрическим током, ушиб и переломы конечностей, ожоги, поражение глаз,
отсечение конечностей.
Причинами травматизма являются, в основном, ошибочные
действия персонала или природные явления, способствующие возникновению
опасности на строительном объекте.
Если последними человечество еще не научилось управлять в
промышленных масштабах, то ошибочные действия персонала мы в силах свести к
минимуму. На предприятии необходимо применять организационные и технические
меры по предупреждению травматизма, например, проведение инструктажей и
обучения работников охране труда и промышленной безопасности, применение
оградительных, изолирующих, предохранительных, блокирующих, сигнализирующих и
других устройств, защищающих человека во время производственного процесса,
применение средств индивидуальной защиты, воспитание личной и коллективной
ответственности, производственной культуры.
3.3 Анализ вредных факторов
Общие сведения
Вредные факторы производственной среды, имеющие накопительное
действие при постоянном воздействии на организм человека могут привести к
хроническим заболеваниям или раннему наступлению нетрудоспособности.
Горные работы, а тем более, работы в подземных условиях
связаны с проявлением ряда вредных факторов, оказывающих негативное влияние на
здоровье и самочувствие работающих.
В подземных условиях невозможно обеспечить полностью
требований, предъявляемых законодательством по аттестации рабочих мест, можно
лишь стараться свести к минимуму их воздействие.
Так, анализируя условия работы горнорабочих - проходчиков,
результаты аттестации рабочих мест на участке строительства кабельного
коллектора под Волгоградским, можно отметить наличие вредных факторов, которые
в последующем могут привести к профзаболеваниям и получению групп инвалидности
горнорабочими, подвергавшимися их воздействию.
Вибрация при работе оборудования
Вибрация при постоянном воздействии может привести к развитию
виброболезни у рабочих, суть которой состоит в разрушении межсуставной ткани и
функциональных нарушениях. При строительстве тоннелей основным источником
вибрации являются перфораторы.
По итогам аттестации рабочих мест вибрация от колонковых
перфораторов отнесена к 3 категории, подпункту «А» (на постоянных рабочих
местах производственных помещений предприятий). По виброфактору шахта считается
условно аттестованной, с выполнением предписанных рекомендаций.
Наличие шума
При проведении бурильных и откаточных работ уровень шума в
забое достигает значений 50ДцБ, что может привести к снижению порога слуха у
рабочих. Воздействие шума может усугубляться его типом. Так по временной
характеристики шум при ведении работ в забое отнесен к непостоянному
импульсному шуму, а по спектральной характеристике к тональному шуму с ярко
выраженными дискретными тонами.
Освещение подземных выработок
В условиях подземных выработок существует проблема отсутствия
коэффициента искусственного освещения. Это является основной причиной снижения
остроты зрения работающих в подземных горных выработках людей. Освещения в
подземных горных выработках не хватает, несмотря на отсутствие работ высокой
точности и постоянной работы резервного освещения. Освещенность выработок
местами не превышает 200 люксов и люди работают в полумраке.
Микроклимат подземного пространства объекта
строительства
Микроклимат рабочих мест в подземном пространстве различен в
зависимости от времени года, но, как правило, обладает большой влажностью, а в
зимний период времени носит охлаждающий характер, в летний период нагревающий.
Скорость воздуха и давление находятся в пределах нормы и отвечают требованиям
аттестации. Остальные параметры микроклимата - температура и влажность - сильно
зависят от времени года и могут отклоняться по своим значениям в ту или иную
сторону.
Профессиональные заболевания
Острое профессиональное заболевание возможно в виде ожога
глаз ультрафиолетовым излучением при выполнении сварочных работ, при отравлении
хлором, оксидом углерода и др.
Хронические профессиональные заболевания развиваются после
многократного и длительного воздействия вредных производственных факторов,
например, вибрации, производственного шума и др.
Неблагоприятные (вредные) условия труда создаются
запыленностью, загазованностью, повышенной влажностью, производственным шумом,
вибрацией, неудобной рабочей позой, тяжёлым физическим трудом и др.
В зависимости от вида производственных вредностей могут
развиться такие заболевания как пневмокониозы, повреждение кожных покровов,
нарушение опорно-двигательного аппарата, виброболезнь, шумовая болезнь
(тугоухость) и др.
В России в настоящее время ежегодно регистрируется до 12-13
тысяч профессиональных заболеваний. Для сравнения, примерно такое же количество
регистрируется в Финляндии, а в США сотни тысяч (более 500) профессиональных
заболеваний в год. Очевидно, что сравнительно небольшое количество ежегодно
устанавливаемых профессиональных заболеваний в России вызвано не лучшими
условиями труда, а недостатками в диагностике профессиональных заболеваний на
ранней стадии их развития и низкой личностной оценкой своего здоровья.
.4 Законодательство
Российской Федерации в области промышленной безопасности и охраны труда
Общие сведения
Правовое регулирование вопросов охраны
труда и промышленной безопасности на всех строительных объектах, в том числе и
опасных производственных объектах, к которым относится участок строительства
кабельного коллектора под Волгоградским проспектом, осуществляется Конституцией
Российской федерации, федеральными законами, другими нормативными актами
органов государственной власти и управления.
Основными нормативными актами
регулирующими трудовые отношения и вопросы охраны труда являются Кодекс законов
о труде Российской Федерации (РФ) и Основы законодательства РФ об охране труда.
В области промышленной безопасности таким документом является Федеральный закон
«О промышленной безопасности опасных производственных объектов». Ряд аспектов
промышленной безопасности и охраны труда регулируется федеральными законами «Об
охране окружающей природной среды», «О недрах», «О санитарно-эпидемиологическом
благополучии населения», «О защите населения и территорий от чрезвычайных
ситуаций природного и техногенного характера» и др.
Вопросы ответственности за нарушение
законодательства в области промышленной безопасности и охраны труда
регулируются Кодексом РСФСР об административных правонарушениях
(административная ответственность), Уголовным кодексом Российской Федерации
(уголовная ответственность), Гражданским кодексом Российской Федерации
(материальная ответственность
Нормативные документы
Для обеспечения безопасности работников во время трудового
процесса, улучшения условий труда и правильного регулирования отношений между
работниками и работодателем в ОАО «Террикон» создана служба охраны труда,
которая обеспечивает соблюдение всех нормативно-правовых документов в области
охраны труда в строительстве подземных сооружений и смежных работ. Основными из
них являются следующие документы:
. Конституция РФ
2. Кодекс РСФСР об административных
правонарушениях. От 20.06.84 г. с последующими изменениями и дополнениями.
3. Гражданский кодекс Российской
Федерации Ч. 1 от 21.10.94 г. №174-ФЗ; Ч. 2 от 26.01.1996 г. №15-ФЗ.
4. Трудовой кодекс РФ от 10.06.06 г.
5. «О промышленной безопасности опасных
производственных объектов» Федеральный закон №116-ФЗ от 21 июля 1997 г.
6. Федеральный закон «О внесении
изменений и дополнений в закон «О недрах». От 03.03.95 г. №27-ФЗ.
7. Закон РСФСР «Об охране окружающей
природной среды». От 19.12.91 г. №2061.
8. Федеральный закон «Об
экологической экспертизе». От 23.11.96 г.
№174-ФЗ.
9. Закон РСФСР «О
санитарно-эпидемиологическом благополучии населения». От 30.03.99 г. №52-ФЗ.
10. Федеральный закон «О защите
населения и территорий от чрезвычайных ситуаций природного и техногенного
характера». От 21.12.94 г.
11. Федеральный закон «О
лицензировании отдельных видов деятельности». От 25.09.98 г. №158-ФЗ.
12. Закон Российской Федерации «О
страховании». От 27.11.92 г. №4015-1.
13. Федеральный закон «О пожарной
безопасности». От 21.12.94 г. №69-ФЗ.
14. «Об основах охраны труда в
Российской Федерации». Федеральный закон РФ №181-ФЗ
. «О бюджете Федерального фонда
обязательного медицинского страхования на 1999 год» Федеральный закон от 01.05.1999
№91-ФЗ
16. Указ Президента Российской
Федерации «О государственных надзорных органах» от 12.11.92 г., №1355.
17. Указ Президента Российской
Федерации «О государственном надзоре и контроле за соблюдением законодательства
Российской Федерации о труде и охране труда» от 4.05.94 г., №850.
. Положение «О Федеральной
инспекции труда при Министерстве труда Российской Федерации (Рострудинспекции).
Указ Президента РФ от 20.07.94 г.
. Положение «О Федеральном горном и
промышленном надзоре России». Указ Президента РФ от 18.02.93 г., №234.
. Правила возмещения работодателями
вреда, причиненного работникам увечьем, профессиональным заболеванием, либо
иным повреждением здоровья, связанными с исполнением ими трудовых обязанностей.
Постановление Верховного Совета РФ от 24.12.94 г. с последующими изменениями и
дополнениями.
. «О государственной экспертизе
условий труда». Постановление СМ РСФСР от 3.12.90 г., №557.
. «О мерах по улучшению условий
труда». Постановление Правительства РФ от 26.08.95 г., №843.
. «О регистрации объектов в
государственном реестре опасных производственных объектов». Постановление
Правительства РФ от 24.11.98 г., №1371.
. «Об организации и осуществлении
производственного контроля за соблюдением требований промышленной безопасности
на опасном производственном объекте. Постановление Правительства РФ от 10.03.99
г., №263.
25. О применении технических устройств
на опасных производственных объектах». Постановление Правительства РФ от
25.12.98 г., №1540.
26. Положение о декларации
безопасности промышленного объекта Российской Федерации. Постановление
Правительства РФ от 1.07.95 г., 3 675.
. Изменения и дополнения №980-ПП от
6 декабря 2005 г. К постановлению Правительства Москвы №857-ПП от 7 декабря
2004 г.
. ПБ 03-428-02 «Правила
безопасности при строительстве подземных сооружений»
. Правила устройства и безопасной
эксплуатации грузоподъемных кранов.
. «Правила подготовки и
производства земляных работ, обустойства и содержания строительных площадок в
г. Москве», утвержденные постановлением Правительства Москвы №857-ПП от 7
декабря 2004 г.
. ГОСТ 12.0.002-80 ССБТ. «Термины и
определения»
. ГОСТ 12.0.003-88 ССБТ. «Опасные и
вредные производственные факторы»
. ГОСТ 12.2.061-81 ССБТ.
«Оборудование производственное. Общие требования безопасности к рабочим местам»
. ГОСТ 12.2.064-81 ССБТ. «Органы
управления производственным оборудованием. Общие требования безопасности»
. ГОСТ 12.1.003-83 ССБТ. «Шум.
Общие требования безопасности»
. ГОСТ 12.1.050-86 ССБТ. «методы
измерения шума на рабочих местах»
. ГОСТ 12.1.012-90 ССБТ.
«Вибрационная безопасность, общие требования»
. ГОСТ 12.4.011-89 ССБТ «Средства
защиты работающих. Общие требования и классификация»
. ГОСТ 12.2.062-81 ССБТ
«Оборудование производственное. Ограждения защитные»
. ГОСТ 12.4.026-01 ССБТ «Цвета специальные
и знаки безопасности»
. ГОСТ 16310-80 «Соединения сварные
из полиэтилена и винипласта. Основные типы, конструктивные элементы и размеры».
. ГОСТ 12.3.009-76 (СТ СЭВ 3518-81)
«Система стандартов безопасности труда. Работы погрузочно-разгрузочные. Общие
требования безопасности».
. ГОСТ 21807-76х
«Бункеры (бадьи) переносимые вместимостью до 2 м3 для бетонной
смеси. Общие технические условия».
. СП 12-136-2002 «Безопасность
труда в строительстве. Решения по охране труда и промышленной безопасности в проектах
организации строительства и проектах производства работ»
. СНиП 12-03-2001 «Безопасность
труда в строительстве. Часть 1. Общие требования»
. СНиП 12-04-2002 «Безопасность
труда в строительстве. Часть 2. Строительное производство».
. СНиП 12-01-2004 «Организация
строительства»
. СНиП 23-05-95 «Естественное и
искусственное освещение»
. СНиП 3.01.03-84 «Геодезические
работы в строительстве»
. СНиП 3.02.01-87 «Земляные
сооружения. Основания и фундаменты»
. СНиП 3.02.03-84 «Подземные горные
выработки»
. СНиП 3.05.03-85 «Тепловые сети»
. СНиП 3.03.04-85 «Наружные сети и
сооружения водоснабжения и канализации»
. СНиП 11-01-2003 «Инструкция о
порядке разработки, согласования, экспертизы и утверждения градостроительной
документации»
. МГСН 6.01-03 «Бестраншейная
прокладка коммуникаций с применением микротоннелепроходческих комплексов и
реконструкция трубопроводов с применением специального оборудования»
. ГН 2.2.5.1313-03 «Предельно
допустимые концентрации (ПДК) вредных веществ в воздухе рабочей зоны»
. ГН 2.2.5.1314-03 «Ориентировочные
безопасные уровни воздействия (ОБУВ) вредных веществ в воздухе рабочей зоны»
. ГН 1.1.725-98 «Перечень веществ,
продуктов, производственных процессов, бытовых и природных факторов,
канцерогенных для человека»
. ГН 1.2.1841-04 «Дополнения и
изменения 1к ГН 1.1.725-98 «Перечень веществ, продуктов, производственных
процессов, бытовых и природных факторов, канцерогенных для человека»
. ГН 2.2.5.563-96 «Предельно
допустимые уровни (ПДУ) загрязнения кожных покровов вредными веществами»
. СН 2.2.4/2.1.8.566-96
«Производственная вибрация, вибрация в помещениях жилых и общественных зданий»
. СанПиН 2.2.2.540-96
«Гигиенические требования к ручным инструментам и организации работ»
. МУ 2.2.4.706-98/ МУ ОТ РМ 01-98.
«Оценка освещенности рабочих мест»
. РД-07-226-98 «Инструкции по
производству геодезическо-маркшейдерских работ при строительстве коммунальных
тоннелей и инженерных коммуникаций подземным способом» (с изменением (РДИ
07-470 (226) - 02), утвержденным Постановлением Госгортехнадзора России
(Ростехнадзора) 27.06.2002 г. №39.
. МТСК-6 «Московский
территориальный строительный каталог. Организация и технология строительства»
Выводы: в разделе безопасности труда был произведен
анализ опасных и вредных факторов горного производства, воздействующих на
персонал проектируемого коллектора, рассмотрены меры безопасности по
эксплуатации горного оборудования и транспортных средств, борьбе с пылью и
вредными газами. Также в этом разделе рассмотрены электробезопасность,
противопожарные мероприятия в коллекторе и на промплощадке.
. Технико-экономические показатели
На данном объекте строительства принят круглосуточный режим
работы. При таком режиме работы строительство ведется 6 дней в неделю,
круглосуточно в 4 смены по 6 часов (3 - рабочие, 1 - ремонтная).
Таблица 4.1. График работы
Режим работы
|
4 смены
|
Продолжительность
смены
|
6 часов
|
Запланированный
перерыв
|
0,2 часа
|
Рабочая неделя
|
6 дней
|
Проходческие работы ведутся в течение 4 месяцев, поэтому
число рабочих дней составит:
Др =Дк - В-П = 120 - 18 - 4 = 98 дн.,
где Др - число рабочих дней в течение срока
строительства;
Дк - календарное число дней (срок строительства);
В-число выходных дней в течение срока строительства;
П - число праздничных дней в течение срока строительства.
Для рабочих вспомогательных служб и ИТР, которые находятся на
объекте в течение 6 месяцев, число рабочих дней составит:
Д'р =182 - 26 -5 = 151 дн.
4.1
Мощность и оценка основных фондов
Капитальные затраты на здания, сооружения, определяем по
укрупненным показателям. Затраты на оборудование определяем по ценам
действующих прейскурантов. Стоимость оборудования включает в себя номинальную
стоимость, затраты на транспортировку 4,5%, монтаж 8%, хранение 1,2%, запасные
части 3,8%. Действительна стоимость оборудования составляет 117,5% от стоимости
по прейскуранту.
Основные производственные фонды оцениваются в 23762 тыс. руб.
Месячная производительность проходческих работ составляет
Амес = 1231,8 м3 / мес.
Под фондоемкостью при ведении ГПР принимается показатель,
определяющий стоимость основных производственных фондов, приходящихся на
единицу годового выпуска продукции. При ведении проходческих работ единицей
продукции является м3 грунта, а вместо годового объема продукции
принимается срок строительства, поэтому фондоемкость определяем по следующей
формуле:
где Фосн - стоимость основных фондов, руб.;
Амес - месячная производительность проходческих работ,
м3 / мес.;
n - число месяцев, в течение которых ведется строительство;
Фондоотдача на ГПР характеризует количество продукции т.е.
проходки производимой в единицу времени в расчете на 1 руб. стоимости основных
производственных фондов и определяется по формуле:
4.2 Себестоимость и материальные затраты
Материальные затраты рассчитаны по формулам приведены в
таблице 4.2.
Таблица 4.2
Ед. изм.
Ст-ть за ед.
тыс руб
Расход
Общая ст-ть тыс
руб
Тюбинговое
кольцо
шт
8800
100
880000
Доска обрезн.
м
716,4
135
96714
Брус
м
720
60
43200
Цемент
т
35
250
87500
Песок
т
180
100
18000
Рельс
Пг.м
233,33
400
93332
Трубы
Пг.м
246
200
49200
Неучт. мат
-
-
-
1600
ИТОГО
-
-
-
1269546
.3 Численность рабочих и фонд заработной платы
Численность рабочих:
Nя - явочная численность рабочих
Nя = Nсп.р /Kсп = 56 / 1,2 ≈ 47 чел.;
где Kсп = 1,2 коэффициент списочного состава.
Рабочие (работают 4,5 месяца) 56 чел. средняя заработная
плата в день составляет 617 руб.
Руководители 8 чел. с средней заработной платой в день 727
руб.
Инженерно технический персонал 7 чел. средняя заработная
плата в день составляет 643 руб.
Служащие 3 чел. заработная плата в день 530 руб.
Итого фонд заработной платы составляет 4876 тыс. руб.
4.4 Производительность труда
Производительностью труда называют показатель, оценивающий
количество продукции, произведенной одним работником в единицу времени.
Определяем среднемесячную производительность труда по формуле:
где nм - число месяцев, в течение которых ведется строительство;
Nсп.р -
списочная численность рабочих.
Величиной, обратной производительности труда, является
трудоемкость работ. Определим количество чел.-смен, затрачиваемых на выемку
1000 м3 породы следующим образом:
где Nя - явочная численность рабочих равна 47 чел.
Асут - суточная производительность проходческих
работ, м3/сут. (Асут = 47,4 м3/сут.).
Рассчитываем удельное электропотребление
4.5 Фондовооруженность труда
Фондовооруженность труда - показатель, характеризующий
степень оснащенности труда основными производственными фондами. Он определяется
делением балансовой стоимости основных производственных фондов на
среднесписочное число работников:
.6 Электровооруженность труда
Показатель электровооруженности труда определяется в виде
отношения расхода электроэнергии на одного рабочего в год:
Эт=Э/Nсп×tр=(177×24×120)/74×6=1148кВт /чел.,
где Э - количество потребленной электроэнергии.
Таблица 4.3. Основные технико-экономические показатели
Наименование
|
Условные
обозначения
|
Ед. измерения
|
Численный
показатель
|
Основные
производственные фонды
|
Фосн
|
Тыс. руб
|
23762
|
Месячная
производительность
|
Амес
|
м3/мес.
|
1231,8
|
Списочный
состав
|
Nсп
|
Чел.
|
74
|
Фондоотдача
|
Ф
|
Руб. в год/руб.
|
5,4×10-3
|
Производительность
труда
|
Пм
|
М3/мес.×чел.
|
24,7
|
Фондоемкость
|
Фе
|
Руб./руб.
|
18732
|
Фондовооруженность
|
Фв
|
Тыс. руб
|
1247
|
Удельное
электропотребление
|
Эу
|
кВт×ч/м3
|
87,6
|
Электровооруженность
труда
|
Эт
|
кВт/чел
|
1148
|
Трудоемкость
|
Т
|
Чел.-см/м³
|
992
|
5. Автоматизированный электропривод
.1 Основные характеристики объекта управления
Основные производственные процессы, проходящие в рабочем
пространстве выработки коллекторного тоннеля, сопровождаются выделением
большого количества вредных и опасных газов (СО2; окислы азота и др.) и пыль.
Это связано с тем, что согласно принятой технологии ведения работ, проходка
тоннелей осуществляется с использованием буровзрывного способа.
Как известно, в тех выработках, в которых могут находиться
люди, согласно требованиям ПБ, воздух должен содержать по объему О2 не менее
20% и СО2 не более 0,5%.
Для снабжения работающих в забое людей достаточным
количеством воздуха необходима искусственная вентиляция, которая обеспечивала
бы приток свежего и удаление отработанного воздуха, из выработки.
Для этих целей на участке используется главная вентиляторная
установка ГВУ, состоящая из 2-ух вентиляторов - главного и резервного (для аварийного
включения при неисправности главного вентилятора). Установка выбрана в разделе
«Механическое оборудование».
Согласно поставленным условиям ГВУ обеспечивает необходимым
количеством воздуха Qв=15м3/с при частоте оборотов вращения n=3000 об/мин.
В качестве привода ГВУ применяем АДКЗ типа ВРМ132М2. Он
обеспечивает минимальную скорость движения воздуха 7 м/с. Вентиляторная
установка, как и большинство турбомашин, имеет вентиляторный характер нагрузки,
относится к низкодинамичной системе, имеет продолжительный режим работы с
постоянной нагрузкой.
Рабочая механическая характеристика в этом случае
определяется соотношением:
М=М0+сωª;
где М0 - начальный момент статического сопротивления,
обусловленный силами трения М0 = (0,02-0,05) Мном;
с - коэффициент пропорциональности между моментом и угловой
скоростью;
ω - угловая скорость вала
механизма;
а - показатель степени, характеризующий среду в которой
работает турбомашина.
.2 Сравнение и выбор системы электропривода
Актуальные задачи дальнейшего повышения эффективности работы
завода не могут быть решены без автоматизации производственных процессов.
Вследствие этого повышаются требования к системам управления и электроприводам,
являющихся одной из важных частей технологического процесса в
машиностроительном производстве.
Основным критерием выбора привода является
технико-экономическое сравнение вариантов, при выполнении которого должны
учитываться преимущества и недостатки приводов.
Выбор вариантов электроприводов возможен за счёт
использования при сравнении таких критериев, как относительная стоимость
приводов, требуемая мощность привода и максимальный момент при пуске, уровень
управляемости.
Асинхронный двигатель с коротко замкнутым ротором благодаря
своей простоте, дешевизне, малым габаритным размерам и высоким КПД широко
используется в нерегулируемом электроприводе различных машин и установок.
Осуществляем выбор электропривода вентилятора. Примем
асинхронный двигатель марки ВРМ132М2.
Система
электропривода РКС
Частота вращения ротора асинхронного двигателя зависит от
угловой скорости вращающегося магнитного поля статора и скольжения. Угловую
скорость асинхронного двигателя при постоянной нагрузке можно считать функцией
двух переменных: угловой скорости вращающегося поля (синхронной скорости) и
напряжения на кольцах ротора. Поэтому скорость двигателя можно регулировать
изменением напряжения на кольцах ротора или изменением скорости вращающегося
магнитного поля статора.
Напряжение на кольцах ротора можно изменять, включая
добавочные сопротивления или вводя дополнительную э. д. с. в цепь ротора. При
введении добавочного активного сопротивления в цепь ротора, ток в роторе
уменьшается. При этом уменьшается момент двигателя, и скорость его начнет
снижаться.
При работе в зоне малых скоростей характеристики становятся настолько
мягкими, что небольшое изменение статического момента вызывает значительное
изменение угловой скорости. Вследствие этого по условию поддержания стабильных
значений угловой скорости двигателя приходится обычно ограничивать диапазон
регулирования.
Регулирование скорости введением добавочного сопротивления в
цепь ротора неэкономично, так как снижение скорости вращения связано с
потерями, пропорциональными скольжению двигателя. Поэтому реостатное
регулирование скорости применяют для установок, в которых время работы с малой
скоростью незначительно. Это позволяет снизить стоимость и габариты аппаратуры
в результате использования пускового реостата в качестве регулировочного.
Если момент нагрузки рабочей машины зависит от скорости, в
частности пропорционален ω², то
электрические потери в цепи ротора имеют максимум при скорости ω=0,67ω
. Поэтому для таких машин реостатное
регулирование находит применение.
В качестве регулировочного сопротивления используют жидкостные или
металлические реостаты. В последнем, наиболее распространенным случае число
возможных скоростей электропривода определяется числом ступеней пускового
реостата, переключаемых в приводах небольшой мощности обычно с помощью силовых
контроллеров барабанного или кулачкового типа. Такая система управления
встречается на лебедках, обслуживающих неответственные объекты, и шахтных
электровозах.
Для мощных приводов применяют релейно-контакторные системы
управления с автоматическим пуском двигателей в функции времени или тока по
схемам, аналогичным схемам управления нерегулируемых приводов, или с
комбинированным пуском в функции тока и времени. Основной отличительной
особенностью таких схем регулируемого электропривода является наличие
командоконтроллера вместо кнопочного пульта управления
Система электропривода АВК
Управление асинхронным двигателем путем изменения сопротивления,
включенного в цепь ротора, связано с потерями энергии, пропорциональными
скольжению. Для мощных двигателей, кроме того, резко возрастают размеры и
стоимость коммутационной аппаратуры в роторной цепи. Более экономичным способом
является применение каскадных схем включения, обеспечивающих возможность
использования энергии потерь скольжения.
В каскадных схемах в цепь ротора асинхронных двигателей вводят
добавочную э. д. с., направленную согласно или встречно с э. д. с. ротора и
имеющую одинаковую с ней частоту.
Если добавочная э. д. с. и э. д. с. ротора совпадают по фазе
(находятся в противофазе), ток ротора увеличивается (уменьшается), что приводит
к возрастанию (снижению) вращающего момента двигателя. При постоянном
статическом моменте это вызовет увеличение (уменьшение) скорости до значения,
при котором момент двигателя станет равным статическому.
Таким образом, меняя величину и направление добавочного э. д. с.
можно регулировать скорость вращения асинхронного двигателя в сторону
уменьшения ее (свыше синхронной скорости).
При регулировании скорости вниз от синхронной добавочной э. д. с.
находится в противофазе с э. д. с. ротора и угол сдвига тока ротора и
добавочного э. д. с. превышает 90 электрических градусов. Источник добавочной
э. д. с. при этом преобразует энергию потерь скольжения в механическую или
электрическую энергию промышленной частоты.
В зависимости от способа преобразования этой энергии каскадные
схемы разделяют на электрические и электромеханические каскады. В электрических
каскадах энергия скольжения за вычетом потерь в цепи преобразователя отдается в
сеть, а в электромеханических каскадах преобразуется в механическую энергию,
подводимую к валу привода.
Для преобразования энергии скольжения раньше использовались
электрические машины (одноякорные преобразователи, двигатель-генераторные
агрегаты), включаемые в цепь ротора асинхронного двигателя, поэтому такие схемы
получили название каскадных схем, или электромашинных каскадов. Чтобы не
согласовывать по фазе и частоте, в настоящее время энергию скольжения
преобразует сначала в энергию постоянного тока с помощью вентильного
преобразователя. При использовании электрических машин для последующего
преобразования энергии электропривод называют вентильно-машинным каскадом.
Схемы, в которых преобразование энергии скольжения осуществляется только с
помощью вентильных преобразователей, называют асинхронно-вентильными каскадами.
Электромашинные каскады находят ограниченное применение, в
частности для привода мощных вентиляторных установок. Это объясняется
необходимостью использования вспомогательных машин, мощность которых соизмерима
с мощностью регулируемого асинхронного двигателя. Таким же недостатком обладают
и вентильно-машинные каскады.
Электропривод
системы ПЧ-Д с АИН
Общие
сведения
Регулирование скорости вращения изменением частоты питающего
напряжения является по существу единственным способом регулирования для
синхронных двигателей, а для асинхронных обеспечивает наилучшие показатели по
сравнению со всеми другими способами и позволяет использовать наиболее простой
тип двигателя - асинхронный двигатель с короткозамкнутым ротором.
Однако изменение частоты влияет и на механические
характеристики двигателя. При уменьшении частоты момент возрастает по сравнению
с номинальным режимом, а при увеличении частоты снижается.
Для получения нормальных режимов работы, обеспечивающих
полное использование двигателя, необходимо одновременно с изменением частоты менять
и амплитуду напряжения, подводимого к статору.
Для осуществления такого регулирования необходим
преобразователь, позволяющий плавно изменять частоту переменного тока при
одновременном изменении его напряжения по определенному закону, в общем случае представленному
нелинейной функцией.
Применявшиеся с этой целью до настоящего времени
электромашинные преобразователи не отвечают этим требованиям, обладают малым
быстродействием, а по габаритам и экономичности уступают электроприводам
постоянного тока. Поэтому они используются очень редко, преимущественно в тех
случаях, когда применение электропривода постоянного тока становится
затруднительным (при очень мощных и быстроходных установках, для одновременного
регулирования нескольких двигателей и т.п.).
Появление вентильных преобразователей частоты на управляемых
кремниевых вентилях делает перспективным применение электропривода с
регулированием частоты. При этом обеспечивается возможность регулирования
скорости двигателя вверх и вниз от основной скорости.
В настоящее время вентильные преобразователи частоты (ВПЧ),
обеспечивающие высокое быстродействие и возможность раздельного изменения
частоты и напряжения, получают широкое применение. Большое количество
разработанных схем вентильных преобразователей частоты может быть разделено на
два основных типа, свойства которых определяют область их использования.
К первому типу относятся преобразователи с промежуточным
звеном постоянного тока, осуществляющие выпрямление переменного тока
промышленной частоты и последующее преобразование в переменный ток необходимой
частоты и напряжения.
Ко второму типу относятся преобразователи с непосредственной
связью (или непосредственные преобразователи частоты), у которых функции
выпрямления и инвертирования совмещены и выполняются вентилями одновременно.
Преобразователи частоты со звеном постоянного тока позволяют
изменять выходную частоту в широких пределах (от долей герца до нескольких
килогерц) при любой частоте питающей сети. Поэтому они могут применяться для
электроприводов механизмов, требующих большого диапазона изменения скорости
вверх и вниз от основной синхронной, или для быстроходных приводов, питающихся
от источников повышенной частоты и работающих со скоростью в несколько десятков
тысяч оборотов в минуту.
Непосредственные преобразователи частоты позволяют получать
выходную частоту, начиная примерно от половины частоты питающей сети и ниже,
т.е. при промышленной частоте 50 Гц максимальная выходная частота не превышает
25 Гц. В связи с этим они могут быть использованы для электропривода установок,
у которых помимо основной, высокой скорости необходимо иметь пониженную
скорость вращения при высокой ее стабильности и необходимости длительной работы
с этой скоростью. Преимуществом непосредственных преобразователей является большая
надежность работы по сравнению с преобразователями со звеном постоянного тока.
Из перечисленных выше систем электроприводов для
вентеляторной установки наиболее целесообразно использовать электропривод
системы ПЧ-Д с АИН
Применение
частотно-регулируемого электропривода в системах вентиляции
Высокую эффективность внедрения
частотно-регулируемого электропривода можно получить при использовании его в
насосных, вентиляторных, нагнетательных установках за счет следующих его
преимуществ:
экономия электроэнергии (до 50%);
экономия транспортируемого продукта за
счет снижения непроизводительных расходов (до 25%);
снижение аварийности пневматической сети
путем поддержания минимально необходимого давления;
снижение аварийности сети и самого
агрегата за счет применения плавного пуска;
повышение надежности и снижение
аварийности электрооборудования за счет устранения ударных пусковых токов;
снижение уровня шума, создаваемого
установкой;
удобство автоматизации;
удобство и простота внедрения.
Перечисленные сферы применения
частотно-регулируемых электроприводов, являясь наиболее простыми по технической
реализации, тем не менее дают значительный экономический эффект и
характеризуются небольшим (от 0,5 до 5 лет) сроком окупаемости.
5.3
Расчет статических характеристик электропривода установки вентилятора местного
проветривания системы ПЧ-Д с АИН
Для расчета статических характеристик асинхронного двигателя
с короткозамкнутым ротором в случае с преобразователем частоты с инвертором
напряжения необходимо знание следующих параметров:
- активное сопротивление обмотки фазы статора;
- приведенное активное сопротивление обмотки фазы ротора;
- индуктивное сопротивление обмотки фазы статора;
- приведенное индуктивное сопротивление обмотки фазы ротора;
- индуктивное сопротивление намагничивающей цепи.
Для расчета принят асинхронный электродвигатель с
короткозамкнутым ротором типа ВРМ132М2 со следующими паспортными данными:
Р2н=13 кВт; U1н=220,380,660В; nн=2919 об/мин (n0=3000 об/мин); l=Мкр/Мном=2,9;
рn = 1; Jдв = 0,135 кг · м2; hном = 0,897; cos jном = 0,85; Qном=15 м3/с; Qср=11 м3/с.
. Номинальный ток фазы статора:
,
где U1н = 380 В-фазное напряжение статора.
. Линейный номинальный ток статора:
= 25,905 А.
3. Из условия Iпч ≥ Iлн выбираем преобразователь частоты типа FDU 40-03, для которого Iпч=30 А > Iлн = 25,905 А.P=15кВт. Стоимость 61000
руб.
. Номинальное скольжение двигателя:
5. Активное сопротивление фазы статора:
. Угловая скорость магнитного поля статора двигателя:
7. Номинальный и критический моменты двигателя:
где ωн - номинальная угловая скорость вала
двигателя:
8. Индуктивное сопротивление короткого замыкания:
. Индуктивные сопротивления статора и приведенное ротора:
. Приведенное активное сопротивление фазы ротора
. Номинальный приведенный ток ротора:
12. Номинальный коэффициент мощности роторной цепи:
Тогда
. Номинальный ток намагничивающего контура:
. Номинальная ЭДС фазы статора:
15. Индуктивное сопротивление намагничивающей цепи:
. Коэффициенты рассеяния статора и ротора:
17. Общий коэффициент рассеяния:
18. Определение величин «b», «c», «d», «e»:
При этом
19. Определение коэффициентов А(n,b), В(b), С(b), необходимых для расчета электромеханических и механических
характеристик.
где b - абсолютное скольжение двигателя;
- относительная частота тока статора;
- номинальная частота питающей сети.
. Критическое скольжение при n < 1.0:
. Критическое скольжение при n ³ 1.0.
Причем в диапазоне n = 1.4-1.0 эта
величина практически не меняется, поэтому используем n = 1.4:
. Для получения семейства характеристик задаемся относительной
частотой n: 1.4; 1.2; 1.0; 0.8; 0.6; 0.4; 0.2. Для
этих относительных частот задаемся параметром абсолютного скольжения b от 0 до 1,0, включая величины
номинального и критических скольжений. Расчет коэффициентов сводим в табл. 5.1,
используя данные, полученные в п. 19.
Таблица 5.1. Расчет коэффициентов А(n,b), В(b), С(b)
β
|
0
|
0,027
|
0,171
|
0,2
|
0,336
|
0,4
|
0,6
|
0,8
|
1
|
B(β)
|
0,667
|
0,671
|
0,839
|
0,903
|
1,332
|
1,61
|
2,789
|
4,44
|
6,562
|
C(β)
|
0,000294
|
0,0011
|
0,032
|
0,044
|
0,124
|
0,177
|
0,397
|
0,707
|
1,104
|
A (n=1,4)
|
1,444
|
1,523
|
3,149
|
3,723
|
7,518
|
9,932
|
20,071
|
34,14
|
52,139
|
A (n=1,2)
|
1,061
|
1,124
|
2,351
|
2,779
|
5,603
|
7,396
|
14,911
|
25,324
|
38,636
|
A (n=1,0)
|
0,737
|
0,786
|
1,669
|
1,974
|
3,972
|
5,236
|
10,524
|
17,837
|
27,176
|
A (n=0,8)
|
0,471
|
0,508
|
1,104
|
1,306
|
2,623
|
3,453
|
6,91
|
11,679
|
-
|
A (n=0,6)
|
0,265
|
0,29
|
0,656
|
0,777
|
1,558
|
2,046
|
4,07
|
-
|
-
|
A (n=0,4)
|
0,118
|
0,133
|
0,325
|
0,387
|
0,775
|
1,015
|
-
|
-
|
-
|
A (n=0,2)
|
0,029
|
0,036
|
0,112
|
0,134
|
-
|
-
|
-
|
-
|
-
|
. Уравнения электромеханической и механической характеристик
для вентиляторного закона частотного регулирования при n < 1.0:
;
.
При n ³ 1.0:
Угловая скорость вала двигателя вычисляется по формуле:
.
Используя данные табл. 5.1, расчет электромеханических и
механических характеристик сводим в табл. 5.2.
Графический вид электромеханических и механических характеристик,
построенных по данным табл. 5.2, представлен на рис. 5.1 и рис. 5.2.
Таблица 5.2. Расчет статических характеристик двигателя для
вентиляторного закона частотного регулирования
β
|
0
|
0,027
|
0,171
|
0,2
|
0,336
|
0,4
|
0,8
|
1
|
|
|
|
|
|
ν=1,4
|
|
|
|
|
ω, с-1
|
439,82
|
431,34
|
386,1
|
376,99
|
334,26
|
314,2
|
251,3
|
188,5
|
125,6
|
I1,
A
|
6,416
|
12,08
|
45,737
|
49,138
|
57,974
|
60,025
|
63,309
|
64,712
|
65,451
|
М, Нм
|
0
|
27,956
|
85,619
|
84,702
|
70,481
|
63,1
|
47,143
|
36,954
|
30,247
|
|
|
|
|
|
ν=1,2
|
|
|
|
|
ω, с-1
|
376,99
|
368,5
|
323,26
|
314,15
|
271,43
|
251,3
|
188,5
|
125,66
|
62,8
|
I1,
A
|
6,93
|
13,017
|
49,012
|
52,654
|
62,17
|
64,399
|
66,247
|
67,315
|
68,125
|
М, Нм
|
0
|
32,46
|
98,32
|
97,522
|
81,051
|
73,104
|
54,392
|
42,702
|
34,986
|
|
|
|
|
|
ν=1,0
|
|
|
|
|
ω, с-1
|
314,16
|
305,67
|
260,43
|
251,32
|
208,6
|
188,5
|
125,6
|
62,8
|
0
|
I1,
A
|
7,591
|
14,212
|
53,098
|
57,037
|
67,408
|
69,867
|
73,891
|
75,664
|
76,619
|
М, Нм
|
0
|
27,904
|
141,35
|
153,71
|
174,98
|
172,39
|
149,3
|
125,06
|
118,17
|
|
|
|
|
|
ν=0,8
|
|
|
|
|
ω, с-1
|
251,33
|
242,84
|
197,6
|
188,49
|
145,76
|
125,6
|
62,8
|
0
|
|
I1,
A
|
6,263
|
12,068
|
58,767
|
66,196
|
91,347
|
98,895
|
112,66
|
119,04
|
|
М, Нм
|
0
|
38,695
|
115,39
|
114,12
|
95,285
|
86,046
|
64,521
|
41,45
|
|
|
|
|
|
ν=0,6
|
|
|
|
|
ω, с-1
|
188,5
|
180,01
|
134,77
|
125,66
|
82,938
|
62,8
|
0
|
|
I1,
A
|
4,697
|
9,051
|
44,075
|
49,647
|
68,51
|
74,171
|
84,498
|
|
М, Нм
|
0
|
15,696
|
79,511
|
86,465
|
98,428
|
96,973
|
83,981
|
|
|
|
ν=0,4
|
|
|
|
|
|
ω, с-1
|
125,66
|
117,18
|
71,94
|
62,83
|
20,1
|
0
|
|
I1,
A
|
3,131
|
6,034
|
29,383
|
33,098
|
45,673
|
49,447
|
|
М, Нм
|
0
|
6,976
|
35,338
|
38,428
|
43,745
|
43,09
|
|
|
|
ν=0,2
|
|
|
|
ω, с-1
|
62,83
|
54,34
|
9,11
|
0
|
|
I1,
A
|
1,565
|
3,017
|
14,691
|
16,549
|
|
М, Нм
|
0
|
1,744
|
8,834
|
9,607
|
|
Рис. 5.1. Электромеханические характеристики
Построение вентиляторной характеристики.
М=М0+С·ω²;
где: С=Mн-Мо/ωн2
М0=(0,05-0,07)· Мн;
Данные расчет приведены в таблице 5.3.
Таблица 5.3
ω, сˉ¹
|
0
|
50
|
100
|
200
|
300
|
350
|
М, Нм
|
0
|
7
|
13
|
29
|
50
|
63
|
Рис. 5.2. Механические характеристики
5.4 Расчет системы управления электроприводом по
схеме ПЧ-Д
Структурная схема электропривода без системы управления
состоит из последовательно соединенных безынерционных, инерционных и интегриру
- ющих звеньев с внутренней обратной связью по угловой скорости (рис.).
Преобразователь частоты представлен инерционным звеном. Суммарный момент
инерции электропривода принимаем равным удвоенному значению момента инерции
двигателя, т.е. JΣ = 2·Jдв = 2 · 0,135 = 0,27 кг·м2.
В общем случае эта величина определяется согласно расчетам, принятым в теории
электропривода. Напряжения и токи в системе управления приняты в соответствии с
Государственным стандартом приборов.
Структурная и принципиальная схемы электропривода
представлены на рис. 5.3 и 5.4 соответственно.
. При номинальном напряжении на входах блоков управления ПЧ Uун=10В, создается
напряжение U1н=380В. Тогда коэффициент усиления преобразователя ориентировочно:
где Uун - номинальное напряжение сигнала управления,
подаваемого на входы блоков управления выпрямителем и инвертором.
. Коэффициент передачи внутренней обратной связи по скорости:
. Коэффициент передачи звена тока статора:
4. Коэффициент передачи звена момента:
. Индуктивность рассеяния обмоток статора и ротора:
6. Индуктивность намагничивания:
. Полная индуктивность обмоток статора и ротора:
. Номинальный ток в цепи постоянного тока преобразователя частоты:
где
- коэффициент передачи мостового
инвертора по току;
Iпчн = 40 А - номинальный ток преобразователя.
9. По номинальному току выбираем сглаживающий дроссель типа
ФРОС-65/0,5:
Активное сопротивление сглаживающего дросселя:
. Эквивалентная индуктивность системы ПЧ-Д:
. Эквивалентное активное сопротивление системы ПЧ-Д:
. Электромагнитная постоянная времени системы ПЧ-Д с АИН:
Структурная схема электропривода представлена на рис 5.3.
Рис. 5.3. Структурная схема электропривода системы ПЧ-Д13.
Расчет параметров контура регулирования тока
Коэффициент передачи замкнутого контура регулирования тока
для I1м = 2I1н= 2·14,956 = 29,912 А и максимального задающего Uзтм = 9В на входе РТ:
Необходимое значение коэффициента обратной связи по току:
Для измерения тока статорной цепи использован трансформатор тока,
для которого I1т ≥ I1м, т.е. I1т = 40 А
> I1м = 29,912 А. Коэффициент передачи трансформатора тока:
где Im1, Im2 - номинальные токи первичной и вторичной обмотки трансформатора
тока.
Требуемая величина коэффициента усиления датчика тока:
Входные сопротивления должны быть приняты одинаковыми R1т=R2т.
Постоянная времени контура регулирования тока равна
удвоенному значению малой, некомпенсируемой постоянной времени Тпч:
тогда постоянная времени регулятора тока:
Задаваясь величиной емкости Сот=1 мкФ, находим
Сопротивление резистора в цепи обратной связи операционного
усилителя:
. Расчет параметров контура регулирования частоты.
Максимальная ЭДС холостого хода в статорной цепи двигателя:
где wм - максимальная угловая скорость вала двигателя с
учетом перерегулирования в двукратноинтегрирующей системе (d=43%).
Коэффициент передачи замкнутого контура регулирования частоты
при
Uзчм = 9 В и Eм =566,427 В:
Коэффициенты передачи обратной связи по частоте Коч
и датчика ЭДС Кдэ:
.
Постоянная времени регулятора частоты в
двукратноинтегрирующей системе:
Задаваясь величиной емкости Соч= 0,5 мкФ, находим:
Усилитель регулятора частоты должен быть охвачен дополнительной
обратной связью со стабилитронами или блоком ограничения напряжения РЧ
величиной Uрчм = Uзтм = 9 В.
5.5 Расчет экономии электроэнергии
. Годовое потребление электроэнергии при нерегулируемом
приводе:
кВт·ч/год
где Тгод = 8760 ч - число часов работы, вентилятора в
год.
. Количество сэкономленной энергии при использовании регулируемого
электропривода:
кВт·ч/год
где
=11 м3/с - средняя подача
воздуха;
=15 м3/с - номинальная подача воздуха.
. Годовая экономия средств, при использовании регулируемого
электропривода:
рублей/год
=1.74 руб./кВт·ч - стоимость электроэнергии(тариф).
. Затраты на приобретение ПЧ 61000 рублей
. Затраты на монтаж и наладку:
рублей
. Суммарные затраты:
рублей
. Срок окупаемости применяемого преобразователя частоты:
года
Из приведенного расчета следует, что преобразователь частоты
окупится через 8,5 месяцев со дня пуска в эксплуатацию.
При применения частотно-регулируемого
электропривода, он и является наиболее простыми и удобным по технической
реализации, но тем не менее дает значительный экономический эффект и
характеризуются небольшим сроком окупаемости.
Принципиальная схема указанна на рисунке
5.4:
Рис. 5.4. Принципиальная схема электропривода системы ПЧ
Принципиальная схема электропривода реализована на принципе
частотного управления. В ее основе лежит преобразователь частоты и автономным
инвертором напряжения. Схема имеет два контура регулирования - контур
регулирования тока и контур регулирования частоты. Для реализации этих обратных
связей использованы ДТ-датчик тока и ДЭ-датчик ЭДС. Обратные связи выполнены
отрицательными для устойчивости работы системы и как следствие - регулирования
скорости. В схеме представлены два регулятора - регулятор частоты и регулятор
тока. Оба регулятора выполнены на основе ПИ-регулятора и имеют в своей базе
операционный усилитель. ФП-функциональный преобразователь создает необходимый
закон частотного управления (вентиляторный). Для управления инвертором и
управляемым выпрямителем в схеме имеются блок управления инвертором БУИ и блок
управления выпрямителем БУВ.
6. Средства автоматизации
электроустановок при строительстве коллектора г. Москвы
.1 Автоматизация
водоотлива
Автоматизация водоотливных установок заключается в
обеспечении автоматического выполнения всех операций по заливке насосов, их
пуску и остановке, контроля над работой насосов и сигнализации, переключению
различных задвижек и клапанов.
Основными задачами автоматизации процесса откачки воды из
подземных выработок являются следующие:
обеспечение нормального функционирования водоотлива без
постоянного присутствия обслуживающего персонала;
пуск и остановка насосов в зависимости от уровня воды в
водосборнике в пределах регулировочной емкости;
автоматическое управление насосными агрегатами;
автоматическое включение резервных насосных агрегатов при
неисправности и автоматическом отключении работавших;
быстрое переключение с автоматического управления на ручное.
Кроме того, система автоматизации процесса откачки воды из
подземных выработок должна обеспечивать:
аварийный останов насосов при снижении или потери
производительности, перегреве подшипников, исчезновении напряжения в цепях
управления, коротких замыканиях;
местное (ручное) управление отдельными агрегатами для
наладочных и ремонтных работ;
блокировки, исключающие возможность: пуска насосного агрегата
при не залитом насосе, включения моторного привода задвижки до пуска насосного
агрегата, останова насосного агрегата до полного закрытия задвижки,
дистанционного включения насосов при отсутствии воды в водосборнике, повторного
включения аварийного отключившегося насоса до устранения причины аварийного
отключения;
контроль производительности насосов, перегрева подшипников и
положения задвижек;
сигнализацию: в камере водоотлива - об аварийном отключении
насосного агрегата и о наличии напряжения в цепях управления; в диспетчерском
пункте - о работе насосных агрегатов (световую), об аварийном отключении
насосных агрегатов (обезличенный сигнал), аварийном уровне воды в водосборнике,
неисправности сигнальных цепей (световую и звуковую) и о наличии напряжения в
цепях управления.
Автоматизация процесса проветривания
Вентиляторы местного проветривания (ВМП) применяются для
подачи свежего воздуха в подготовительные выработки. Согласно п. 175 ПБ ВМП
должны работать непрерывно, а в случае их остановки или нарушения вентиляции
напряжение с электрооборудования, находящегося в тупиковой части выработки,
должно быть снято.
Автоматизация процесса проветривания определяется способом
проветривания и технологической схемой вентиляторных установок, которые
принципиально отличаются друг то друга методом реверсирования воздушной струи.
Основные задачи автоматического управления вентиляторами
следующие:
обеспечение необходимых технологических режимов работы
различных типов вентиляторов при различных технологических схемах проветривания
без постоянного присутствия обслуживающего персонала;
обеспечение оперативного регулирования режима работы
вентилятора для поддержания оптимального режима проветривания;
автоматизация вентиляторов, оборудованных различными типами
приводных двигателей;
работа установки в нормальном и реверсивном режимах;
регулирование производительности вентилятора;
автоматический ввод в работу резервного вентилятора в случае
аварийного отключения работавшего агрегата;
автоматический ввод резерва питания низковольтных цепей;
подача предупредительной звуковой и световой сигнализации;
защитное отключение вентиляторной установки;
контроль: длительности разгона двигателя; положения ляд,
шиберов, лопаток направляющего и спрямляющего аппаратов; депрессии и
производительности вентиляторов; температуры обмоток электродвигателя,
подшипников двигателя и вентилятора; наличия напряжения на станции управления;
остановки вентилятора.
Нормальный режим вентиляции обеспечивается с помощью
аппаратуры контроля воздуха АКВ-2П.
Аппаратура АКВ-2П осуществляет автоматический непрерывный
контроль количества воздуха, поступающего к забою тупиковой выработки, и
защитное отключение электроэнергии при нарушении нормального режима ее
проветривания. Для этого аппаратура блокируется с групповым коммутационным
аппаратом (пускателем, автоматическим выключателем), питающим
электрооборудование выработки. Аппаратура АКВ-2П обеспечивает:
выдержку времени 5 - 10 мин на включение электрооборудования
выработки от момента установления нормального режима ее проветривания;
автоматическое с выдержкой времени 1 - 2 мин отключение
электроэнергии с электрооборудования выработки и невозможность ее включения при
нарушении нормального режима проветривания;
мгновенное автоматическое отключение электроэнергии при
отключении ВМП;
местную световую сигнализацию о нормальном и аварийном
режимах проветривания забоя тупиковой выработки.
6.2 Обоснование выбора вида автоматизации
При строительстве коллектора строительно-механизированным
управлением целесообразно внедрить систему автоматизации процесса откачки воды
из подземных выработок, поскольку работы по проходке тоннеля ведутся в условиях
среднего водопритока в шахту. Выбранная система автоматизации водоотливных
установок поможет существенно облегчить работу обслуживающего персонала, а
также повысить надежность процесса откачки поступающей воды.
6.3 Сравнение систем автоматизации водоотлива
Взрывобезопасная аппаратура автоматизации
водоотливных установок ВАВ.1М
Взрывобезопасная аппаратура ВАВ предназначена для
автоматического, дистанционного и местного управления, главными
высоковольтными, низковольтными водоотливными установками, а также
автоматического и местного управления одиночными водоотливными установками
шахт, опасных по газу и пыли.
В автоматическом режиме аппаратура включает насосные агрегаты
в зависимости от уровня воды в водосборнике; обеспечивает включение
электродвигателей насосов с выдержкой времени при параллельной работе насосных
агрегатов для исключения наложения пусковых токов и гидравлического удара;
включает резервный насос при выходе из строя рабочего; заливает погружным или
вспомогательным насосом главные насосы и осуществляет контроль заливки во
времени, контроль работы по производительности и защиты от аварийных режимов.
Аппаратура построена по блочному принципу. Элементы
управления одним насосным агрегатом выделены в отдельный узел и смонтированы на
отдельной панели со штепсельным разъемом. Источник питания искробезопасных
цепей, элементы контроля аварийного уровня и сигнализации выполнены также в
виде отдельных блоков со штепсельными разъемами. Работа узла управления
насосными агрегатами не зависят от функционирования других узлов управления.
Схема аппаратуры реализована на многоконтактных герметизированных реле
закрытого типа в сочетании с полупроводниковым элементами.
В зависимости от условий применения и комплектности поставки
аппаратура изготовляется в трех модификациях: ВАВ.1.1М, ВАВ.2.1М, ВАВ.3.1М.
Аппаратура автоматизации водоотливных установок
изготавливается по техническим условиям ТУ 12.0165709.026-89. Один комплект
аппаратуры предназначен для автоматизации до трех насосных агрегатов. При
большем количестве насосных агрегатов аппаратура позволяет стыковку комплектов.
Комплект аппаратуры ВАВ
- Блок управления насосами БУВ.1М - предназначен для выбора
режима работы насосов, обработки сигналов, поступающих от датчиков с
последующей выдачей команд на исполнительные устройства, а также для
сигнализации о состоянии водоотливной установки.
Табло сигнальное водоотлива СТВ.1М - предназначено для приема
и отображения информации о состоянии водоотливной установки. Техническая
характеристика:
Термодатчик ТДЛ.1М - предназначен для контроля нагрева
подшипников.
Реле производительности РПН.1М - предназначено для контроля
работы насоса.
Реле давления РДВ.1М - предназначено для контроля заливки главного
насоса по давлению.
Датчик электродный ЭД.1М - предназначен для замыкания цепи
управления в схеме автоматизированной водоотливной установки.
Привод задвижки П3.1М - предназначен для открытия задвижек
нагнетательных трубопроводов. Привод может применяться для управления другими
механизмами с вращательным движением подсоединительного звена, в условиях
опасных по газу и пыли.
Пускатель автоматики ПРА - предназначен для упрощения и
защиты привода задвижек.
Аппаратура автоматизации водоотливной установки
АВО-3
Для автоматизации водоотлива применяют типовую аппаратуру
АВ0-3. Эта аппаратура используется в том случае, если приводной двигатель
насосной установки является низковольтным. Система автоматизации АВ0-3
предусматривает заливку главных насосов и всасывающего трубопровода перед
пуском с помощью вспомогательного погружного заливочного насоса.
В данном случае рассматриваем устройство и схему аппаратуры
управления одиночным насосом АВ0-3, обеспечивающую:
1. Автоматическую работу насоса;
2. Автоматическую заливку насоса с помощью погружного
заливочного насоса;
. Остановку насоса при его неисправности;
. Ручное (местное) управление насосом с кнопочного
поста на магнитном пускателе при переводе рукоятки переключателя режима в
положение «Ручное управление»;
. Сигнализацию (световую и звуковую) о неисправности
насоса, аварийном уровне воды в водосборнике, целости сигнальной цепи и наличия
питания в аппаратуре управления.
В комплект аппаратуры АВ0-3 входят: аппарат управления АУО-3,
блок сигнальный БСО-1, реле производительности флажковое РПФВ-1К, заливочный
погружной насос ЗПН, три электродных датчика ЭД и гудок переменного тока
ГПРВ-2М. Аппаратура выполнена во взрывобезопасном исполнении, цепи электродных
датчиков искробезопасные.
Управление всеми операциями по заливке насоса и его пуску
производится с помощью реле времени, состоящего из синхронного микро-двигателя
М (рис. 1) и соединенных с его валом профилированных дисков, которые при
вращении воздействуют на контакты (диаграмма замыканий контактов реле времени).
При повышении уровня воды в водосборнике до электрода верхнего уровня В2
замкнется цепь реле управления К1. Реле включается и контактом К1.2 блокируется
во включенном положении через электрод нижнего уровня В3. Контакт К1.1 включит
реле К2, а контакт К1.3 - двигатель реле времени. Диски придут во вращение и
разомкнется контакт КТ.2 в цепи электрода В2.
Замыкающий контакт К2.1 включит реле гидравлической защиты
К3, которое контактом К3.1 включит пускатель заливочного насоса, а контактом
К3.2 подготовит цепь для включения пускателя главного насоса. Через 63 с, что
соответствует повороту дисков на 1100 от исходного положения,
замкнется контакт КТ.5 моторного реле времени в цепи управления пускателя
главного насоса и двигатель насоса включится.
Рис. 6.1. Аппаратура АВ0-3
Работа насоса контролируется флажковым реле
производительности BV типа РПФВ-1К, представляющим собой датчик релейного действия,
устанавливаемый на горизонтальном участке всасывающего трубопровода. При
определенной скорости потока, соответствующей номинальной производительности
насоса, флажок через систему рычагов воздействует на контактную группу, в
результате чего замыкается контакт BV в цепи реле К3.
Через 23 с после пуска насоса, т.е. через 86 с после начала
цикла, контактные диски повернутся на 1500. При этом разомкнутся
контакты КТ.3, КТ.4 и КТ.6. Контакт КТ.3 отключит двигатель М реле времени и
диски остановятся. Контакт КТ.6 отключит пускатель заливочного насоса и заливка
главного насоса прекратится. При размыкании контакта КТ.4 катушка реле
гидравлической защиты К3 будет питаться только через контакт BV реле производительности.
В таком состоянии все элементы аппаратуры автоматизации будут
находиться, пока уровень воды не опустится ниже электрода В3. При этом реле К1,
К2, К3 и пускатель главного насоса отключатся и двигатель насоса остановится.
Размыкающий контакт К2.2 включит двигатель реле времени, который приведет диски
в исходное положение (поворот на 1800). В этом положении двигатель М
отключится контактом КТ.1. Контакт КТ.2 в цепи электрода верхнего уровня В2
замкнется и аппаратура автоматизации полностью придет в исходное состояние.
Если главный насос за 23 с не достигнет номинальной
производительности (контакт BV не замкнется), реле К3 отключится и контактом
К3.2 произведет остановку насоса. Размыкающий контакт К3.3 включит аварийное
реле К4, которое своим контактом К4.1 отключит сигнальное реле К5,
установленное в сигнальном блоке БСО-1, вследствие чего погаснет лампа НL1 с белым светофильтром,
загорится лампа HL2 с красным светофильтром и включится гудок НА. Диспетчер
(оператор) снимает звуковой сигнал переключением тумблера SA1.
Аварийная сигнализация срабатывает также при повышении уровня
воды до электрода верхнего уровня В1.
При случайном кратковременном исчезновении напряжения во
время работы насоса пускатель его отключится и насос остановится. Отключатся
также все реле. При появлении напряжения двигатель насоса сразу не включится,
так как цепь реле К1 разомкнута контактом КТ.2, а также вследствие того, что
уровень воды находится ниже электрода В2. Включится только двигатель М реле
времени через размыкающий контакт К2.2 и собственный контакт КТ.1, который
отключит двигатель М в исходном положении дисков. Контакт КТ.2 замкнется и
подготовит цепь реле К1. Включение насоса произойдет только после того, как
уровень воды поднимется до электрода В2.
Вывод: при строительстве перегонного коллектора для
откачки поступающей в выработки воды используются насосные установки с
низковольтными приводными электродвигателями, к тому же работы ведутся в
условиях не опасных по газу и пыли, поэтому для автоматизации насосных
установок наиболее приемлема аппаратура автоматизации АВО-3, которая
обеспечивает надежную работу насосных агрегатов и отвечает основным требованиям
автоматизации процесса откачки воды из подземных выработок.
Экономическая эффективность от автоматизации управления
насосными агрегатами достигается исключением холостой работы насосов и
сокращением времени на их запуск, что приводит к уменьшению расхода
электроэнергии, это особенно существенно при больших притоках воды. Снижается
расход на материалы и запасные части.
Дальнейшее совершенствование автоматизации водоотлива должно
идти по пути применения регулируемых насосных агрегатов, что обеспечит их
работу в оптимальных режимах и в периоды минимальной нагрузки энергосети.
Новые системы автоматизации должны обеспечивать экономию электроэнергии,
увеличение надежности работы и срока службы насосных агрегатов, возможность
использования их при различных технологических схемах откачки воды, повышение
готовности установок к работе.
Важнейшим результатом автоматизации является облегчения труда
обслуживающего персонала и повышение безопасности труда.
7. Электроснабжение
.1 Расчет электрического
освещения подземной выработки
Предварительно принимаем к установке
светильники типа РВЛ-20М:
= 127 В,
= 20 Вт,
= 980 лм,
= 0,7,
= 0,6.
Коэффициент приведения светового потока:
.
Горизонтальная освещенность в точке равноудаленной от 2
светильников:
лк.
К установке принимаем светильники РВЛ-20М, т.к. выполняется
условие:
лк.
Количество светильников:

шт.
Мощность осветительного трансформатора:
кВ·А.
К установке принимаем агрегат пусковой АБК-4.
Сечение осветительного кабеля:
мм
.
К установке принимаем кабель КГЭШ 3х6+1х4.
.2 Расчет электрической
нагрузки участка и выбор мощности силового трансформатора ПУПП
В состав проходческого механизированного
комплекса входят: погрузочная машина RME-137SE, предохранительная лебедка 1ЛП, вентилятор
местного проветривания ВМ-6М, агрегат пусковой АБК-4.
Составляем спецификацию
электрооборудования участка с указанием электромеханических параметров
двигателей.
Таблица 7.1. Спецификация основного
электрооборудования участка
Оборудование Тип двигателя
кВт
,
об/мин
А % 
|
|
|
|
|
|
|
|
RME-137SE
|
Исполнительный
орган
|
ВАО2 280L4
|
200
|
1500
|
210
|
94
|
0,89
|
6,5
|
2,4
|
|
Перегружатель
|
ВАО2 280S4
|
132
|
1500
|
170
|
94
|
0,88
|
6,5
|
2,4
|
|
Конвейер
|
ВА 200М4
|
37
|
1500
|
45
|
92
|
0,88
|
6
|
1,8
|
|
Насос
маслосистемы
|
ВА 200М4
|
37
|
1500
|
45
|
92
|
0,88
|
6
|
1,8
|
|
Насос орошения
|
ВА 180S4
|
22
|
1500
|
40
|
91
|
0,87
|
6
|
1,9
|
Предохранительная
лебедка 1ЛП
|
ВР 180М4
|
18,5
|
1800
|
33,5
|
81
|
0,88
|
5,7
|
1,9
|
Водоотливная
установка
|
4А100L2Y3
|
5.5
|
3000
|
7.2
|
87
|
0.83
|
5,2
|
2
|
Вентилятор
ВМ-6М
|
ВРМ132М2
|
13
|
3000
|
25
|
98
|
0,91
|
6
|
2,3
|
АБК-4
|
|
4 кВ∙А
|
|
|
|
|
|
|
Итого
|
|
469
|
|
|
|
|
|
|
Так как электродвигатели исполнительного
органа и перегружателя имеют большую установленную мощность и отличаются
тяжелыми условиями пуска, то их целесообразно выделить в отдельную группу и
подключить к отдельной транформаторной подстанции.
) Коэффициент спроса для первой группы:
Расчетная электрическая нагрузка:
кВт;
квар;
кВ∙А.
К установке принимаем трансформатор ТСШВ-630/6.
кВ∙А
кВ∙А.
2) Коэффициент спроса для второй группы:
Расчетная электрическая нагрузка:
кВт;
квар;
кВ∙А.
К установке принимаем трансформатор ТСШВ-160/6.
кВ∙А
кВ∙А.
.3 Выбор сечения и проверка кабелей в нормальном режиме работы
электрооборудования
Целью расчета является выбор сечения магистрального кабеля,
питающего РП-НН участка, и выбор сечения гибких кабелей, по которым
осуществляется питание электродвигателей машин и механизмов.
Проверка кабелей в нормальном режиме работы проводится по
допустимой потере напряжения на зажимах наиболее удаленного мощного двигателя.
Напряжение сети: 660В;
Расстояние от ПУПП до РПП участка: LМК=50 м;
Расстояние от РПП до двигателей ТПК RME-136SE: LГК=250 м;
Коэффициент мощности: cosφсв = 0,6.
Составим однолинейную схему питания горных машин на добычном
участке (рис. 7.1). Предварительно принимаем передачу и дальнейшее
распределение электроэнергии от ПУПП №1 и ПУПП №2 по двум магистральным кабелям
до РП-НН №1 и РП-НН №2.
Расчетный ток нагрузки магистральных кабелей:
А;
А.
Для питания РП-НН №1 предварительно принимаем к установке два
кабеля ЭВТ 3х70+1х10, для которых выполняется условие:
А,
для кабеля типа ЭВТ при 200С
=1,06.
Для питания РП-НН №2 предварительно принимаем к установке один
кабель ЭВТ 3х35+1х10, для которого выполняется условие:
А.
Рис. 7.1. Однолинейная схема питания горных машин
Коэффициент загрузки трансформатора ТСШВ-630/6:
.
Активная и реактивная составляющие полного напряжения короткого
замыкания:
;
.
Потери напряжения в трансформаторе ТСШВ-630/6:
В.
Коэффициент загрузки трансформатора ТСШВ-160/6:
.
Активная и реактивная составляющие полного напряжения короткого
замыкания:
;
.
Потери напряжения в трансформаторе ТСШВ-160/6:
В.
РП-НН №1:
1) Для двигателя исполнительного органа
А, предварительно принимаем к установке
гибкий экранированный кабель КГЭШ 3х50+1х10+3х4 (
= 200 А).
Параметры гибкого кабеля с учетом 10% удлинения:
Ом;
Ом;
В.
2) Для двигателя перегружателя
А, предварительно принимаем к установке гибкий экранированный
кабель
КГЭШ 3х50+1х10+3х4 (
= 200 А).
Параметры гибкого кабеля с учетом 10% удлинения:
Ом;
Ом;
В.
РП-НН №2:
3) Для двигателя конвейера
А, предварительно принимаем к установке гибкий экранированный
кабель КГЭШ 3х10+1х6+3х2,5 (
= 75 А).
Параметры гибкого кабеля с учетом 10% удлинения:
Ом;
Ом;
В.
4) Для двигателя насоса маслосистемы
А, предварительно принимаем к установке
гибкий экранированный кабель КГЭШ 3х10+1х6+3х2,5 (
= 75 А).
Параметры гибкого кабеля с учетом 10% удлинения:
Ом;
Ом;
В.
5) Для двигателя насоса орошения
А, предварительно принимаем к установке гибкий экранированный
кабель КГЭШ 3х6+1х4+3х1,5 (
= 58 А).
Параметры гибкого кабеля с учетом 10% удлинения:
Ом;
Ом;
В.
) Для двигателя лебёдки
А, предварительно принимаем к установке гибкий экранированный
кабель
КГЭШ 3х6+1х4+3х1,5 (
= 58 А).
Параметры гибкого кабеля с учетом 10% удлинения:
Ом;
Ом;
В.
7) Для двигателя водоотливной установки
А, предварительно принимаем к установке
гибкий экранированный кабель КГЭШ 3х10+1х6+3х2,5 (
= 75 А).
Параметры гибкого кабеля с учетом 10% удлинения:
Ом;
Ом;
В.
8) Для двигателя вентилятора
А, предварительно принимаем к установке гибкий экранированный
кабель
КГЭШ 3х6+1х4+3х1,5 (
= 58 А).
Параметры гибкого кабеля с учетом 10% удлинения:
Ом;
Ом;
В.
Параметры магистральных кабелей, питающих РП-НН №1 и РП-НН
№2:
Ом;
Ом;
Ом;
Ом.
Максимальные потери напряжения в
магистральных кабелях:
В;
В.
В.
Минимальное сечение для магистральных кабелей:
мм
,
мм
,
Окончательно к установке принимаем:
для питания РП-НН №1 два кабеля ЭВТ 3x70+1х10;
для питания РП-НН №2 кабель ЭВТ
3х35+1х10.
Таблица 7.2. Сечение и тип кабелей,
питающих электроустановки участка
Оборудование
участка
|
Ток, А
|
Длина кабеля, м
|
Тип кабеля
|
, Ом , Ом
|
|
Исполнительный
орган
|
210
|
250
|
КГЭШ
3х50+1х10+3х4
|
0,122
|
0,019
|
Перегружатель
|
170
|
250
|
КГЭШ
3х50+1х10+3х4
|
0,122
|
0,019
|
Конвейер
|
45
|
250
|
КГЭШ
3х10+1х6+3х2,5
|
0,611
|
0,029
|
Насос маслосистемы
|
45
|
250
|
КГЭШ
3х10+1х6+3х2,5
|
0,611
|
0,029
|
Насос орошения
|
40
|
250
|
КГЭШ
3х6+1х4+3х1,5
|
1,02
|
0,034
|
Предохранительная
лебедка 1ЛП
|
33,5
|
150
|
КГЭШ
3х6+1х4+3х1,5
|
0,611
|
0,021
|
Водоотливная
установка
|
7.5
|
100
|
КГЭШ
3х10+1х6+3х2,5
|
0,244
|
0,012
|
Вентилятор
ВМ-6М
|
25
|
50
|
КГЭШ
3х6+1х4+3х1,5
|
0,204
|
0,007
|
7.4 Расчет участковой
сети в пусковом режиме работы электрооборудования
Двигатель ВАО2 280L4 исполнительного органа:
= 200 кВт,
= 210 A,
= 1365 А,
= 3055 Н·м,
= 1500 об/мин
получает питание от силового трансформатора ТСШВ-630/6 по
двум магистральным кабелям ЭВТ 3x70+1х10
(
= 50 м), приходящим на РП-НН №1 и гибкому
кабелю KГЭШ Зх50+1х10+3х4 (
= 250 м).
Номинальная нагрузка на РП-НН: 332 кВт.
Номинальное напряжение сети: 660 В.
Номинальный момент двигателя комбайна:
Н·м.
Минимально допустимое напряжение на зажимах двигателя в пусковом
режиме:
В.
Параметры силового трансформатора:
Ом;
Ом;
Ом.
Параметры магистрального и гибкого кабелей:
Ом,
Ом;
Ом,
Ом.
Мощность группы двигателей, работающих в нормальном режиме:
кВт.
Потеря напряжения в сети от двигателей, работающих в нормальном
режиме:
Фактическое напряжение на зажимах двигателя ТПК в пусковом режиме:
Параметры участковой сети отвечают условиям пускового режима
работы электрооборудования, т.к. выполняется условие:
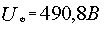
7.5 Расчет токов
короткого замыкания в участковой сети
В состав проходческого механизированного
комплекса входит электрооборудование, параметры которого указаны в табл. 7.3.
Таблица 7.3. Электрооборудование участка
Оборудование
|
Ток, А
|
Пусковой ток, А
|
Тип кабеля
|
, Ом , Ом
|
|
Исполнительный
орган
|
210
|
1365
|
КГЭШ
3х50+1х10+3х4
|
0,122
|
0,019
|
Перегружатель
|
170
|
1105
|
КГЭШ
3х50+1х10+3х4
|
0,122
|
0,019
|
Конвейер
|
45
|
270
|
КГЭШ
3х10+1х6+3х2,5
|
0,611
|
0,029
|
Насос маслосистемы
|
270
|
КГЭШ
3х10+1х6+3х2,5
|
0,611
|
0,029
|
Насос орошения
|
40
|
240
|
КГЭШ
3х6+1х4+3х1,5
|
1,02
|
0,034
|
Предохранительная
лебедка 1ЛП
|
33,5
|
191
|
КГЭШ
3х6+1х4+3х1,5
|
0,611
|
0,021
|
Водоотливная
установка
|
7.2
|
37.4
|
КГЭШ
3х10+1х6+3х2,5
|
0,244
|
0,012
|
Вентилятор ВМ-6М
|
25
|
150
|
КГЭШ
3х6+1х4+3х1,5
|
0,204
|
0,007
|
РП-НН №1
|
380
|
-
|
2 ЭВТ 3х70+1х10
|
0,008
|
0,004
|
РП-НН №2
|
222
|
-
|
ЭВТ 3х35+1х10
|
0,031
|
0,005
|
Рис. 7.2. Схема распределения
электроэнергии по участку
Рис. 7.3. Схема замещения
Параметры силового трансформатора ТСШВ-630/6:
Ом;
Ом;
Ом.
Параметры силового трансформатора ТСШВ-160/6:
Ом;
Ом;
Ом.
1) Полное сопротивление до точки К1
на шинах РП-НН №1:
Ом.
Трехфазный ток короткого замыкания в точке K1:
А.
Параметры автоматического выключателя АВ-400ДО:
;
В;
;
А;
;
А.
Ток уставки максимальной защиты:
А,
А.
Коэффициент чувствительности:
;
2) Полное сопротивление до точки К2
на шинах РП-НН №2:
Ом.
Трехфазный ток короткого замыкания в точке
K2:
А.
Параметры автоматического выключателя АФВ-1А:
;
В;
;
А;
;
А.
Ток уставки максимальной защиты:
А,
А.
Коэффициент чувствительности:
;
3) Точка К3:
Ом.
А.
Магнитный пускатель ПВИ-320А:
;
В;
;
А;
,
А.
Токи уставки максимальной защиты:
А,
А.
Коэффициент чувствительности:
.
4) Точка К4:
Ом.
А.
Магнитный пускатель ПВИ-250Б:
;
В;
;
А;
,
А.
Токи уставки максимальной защиты:
А,
А.
Коэффициент чувствительности:
.
5) Точка К5:
Ом.
А.
Магнитный пускатель ПВИ-63Б:
;
В;
;
А;
,
А.
Токи уставки максимальной защиты:
А,
А.
Коэффициент чувствительности:
.
6) Точка К6:
Ом.
А.
Магнитный пускатель ПВИ-63Б:
;
В;
;
А;
,
А.
Токи уставки максимальной защиты:
А,
А.
Коэффициент чувствительности:
.
7) Точка К7:
Ом.
А.
Магнитный пускатель ПВИ-63Б:
;
В;
;
А;
,
А.
Токи уставки максимальной защиты:
А,
А.
Коэффициент чувствительности:
.
8) Точка К8:
Ом.
А.
Магнитный пускатель ПВИ-63Б:
;
В;
;
А;
,
А.
Токи уставки максимальной защиты:
А,
А.
Коэффициент чувствительности:
.
9) Точка К9:
Ом.
А.
Магнитный пускатель ПВИ-125Б:
;
В;
;
А;
,
А.
Токи уставки максимальной защиты:
А,
А.
Коэффициент чувствительности:
.
10) Точка К10:
Ом.
А.
Магнитный пускатель ПВИ-125Б:
;
В;
;
А;
,
А.
Токи уставки максимальной защиты:
А,
А.
Коэффициент чувствительности:
.
Результаты расчета токов КЗ, выбора
аппаратуры и уставок максимальной токовой защиты приведены в табл. 7.4.
Таблица 7.4. Результаты расчета токов КЗ
Оборудование
участка
|
Ток, А
|
Пусковой ток, А
|
, ААппарат , А
|
|
|
|
Исполнит.орган
|
210
|
1365
|
2430
|
ПВИ-320А
|
1400
|
1,7
|
Перегружатель
|
170
|
1105
|
2430
|
ПВИ-250Б
|
1200
|
2,1
|
Конвейер
|
45
|
270
|
524,3
|
ПВИ-63Б
|
280
|
1,8
|
Насос
маслосистемы
|
45
|
270
|
524,3
|
ПВИ-63Б
|
280
|
1,8
|
Насос орошения
|
40
|
240
|
395,6
|
ПВИ-63Б
|
250
|
1,6
|
Предохранит.
лебедка 1ЛП
|
33,5
|
191
|
525,1
|
ПВИ-63Б
|
200
|
2,6
|
Водоотливная
установка
|
7.2
|
37.4
|
1142
|
ПВИ-125Б
|
300
|
3,8
|
Вентилятор ВМ-6М
|
25
|
150
|
1312
|
ПВИ-125Б
|
250
|
5,2
|
РП-НН №1
|
348,4
|
-
|
12450
|
АВ-400ДО
|
1600
|
7,8
|
РП-НН №2
|
101
|
-
|
3320
|
АВФ-1А
|
450
|
7,4
|
7.6 Расчет
высоковольтного участка кабельной сети до ПУПП
Целью расчета является определение сечения
питающего ПУПП высоковольтного кабеля, выбор устанавливаемой высоковольтной
ячейки КРУ, выбор уставки срабатывания защиты от токов короткого замыкания в
сети 6 кВ.
Передвижная участковая подземная
подстанция (трансформатор ТСШВ-630/6/0,69) получает питание от шин 6кВ
по кабелю протяженностью 500 м.
РП-ВН укомплектовано ячейками КРУВ-6.
На ГПП установлен трансформатор ТМН-1000/35/6.
Расчетный ток нагрузки участка -
= 348,4 А;
Пусковой ток наиболее мощного электродвигателя
=1365 А;
Годовое число часов использования максимальной нагрузки
=5600 ч.
Номинальный ток нагрузки со стороны высокого напряжения:
А,
А.
Сечение кабеля с учетом
принимаем равным 16 мм², т.к.
А
для кабеля марки ЭВТ 3x16+1x10.
Ожидаемый ток отключения КЗ:
кА,
где
=100 МВ·А (для КРУВ-6).
Сечение кабеля по термической устойчивости току КЗ:
мм².
Так как
мм² >
=16 мм², то предварительно выбираем кабель ЭВТ
3х35+1х10.
Сечение кабеля по экономической плотности тока:
мм², где
= 2,7 А/мм² при
= 5600 ч.
Расчетные сопротивления участка высоковольтной сети:
Ом;
Ом;
Ом;
Ом.
Установившийся ток короткого замыкания на
вводе ПУПП:
А.
Ом.
Выбор параметров КРУВ-6:
; 80 А > 57,7 A;
; 9600 А > 6069 A;
; 100 МВА > 66,1 МВА;
МВ·А.
Расчет уставки защиты от токов короткого замыкания:
А;
А;
А;
.
Выбранная уставка соответствует требованиям по надежности и
чувствительности защиты от токов короткого замыкания в высоковольтной
электрической сети.
7.7 Расчет основных
энергетических показателей участка шахты
Получасовая максимальная нагрузка участка
= 690 кВт;
Расход активной электроэнергии за месяц
= 53928 кВт·ч;
Расход реактивной электроэнергии за месяц
= 71712 квар·ч;
Месячная производительность участка П = 2700 м3;
Ставка за мощность а = 634,55 руб./кВт∙ч/мес;
Ставка за энергию b
= 1,52 руб./кВт·ч;
Списочный состав рабочих
= 41 чел.;
Количество рабочих дней в месяц
= 30;
Продолжительность рабочей смены
= 7 ч.;
Количество рабочих смен в сутки
= 2.
Средняя месячная нагрузка участка:
кВт;
квар.
Средневзвешенный коэффициент мощности:
,
=
.
Реактивная мощность, которую необходимо компенсировать:
квар.
Удельный расход электроэнергии:
кВт·ч/м3.
Электровооруженность труда:
кВт·ч/(чел. ч).
Стоимость электроэнергии:
руб.
Удельная стоимость электроэнергии: Zу = 9,6 руб./кВт·ч.
8. Методологические основы проведения
энергоаудита (энергетического обследования)
Введение
В
2009 году принят федеральный закон №261-ФЗ «Об энергосбережении и о повышении
энергетической эффективности и о внесении изменений в отдельные законодательные
акты Российской Федерации». Данный закон регулирует отношения по
энегросбережению и повышению энергетической эффективности. В законе введено
новое понятие энергоаудита - энергетическое обследование. Энергетическое
обследование - это сбор и обработка информации об использовании энергетических
ресурсов в целях получения достоверной информации об объеме используемых
энергетических ресурсов, о показателях энергетической эффективности, выявления
возможностей энергосбережения и повышения энергетической эффективности с
отражением полученных результатов в энергетическом паспорте. Вместе с тем
понятие энергоаудита не противоречит по сути понятию «энергетическое обследованию».
Поэтому в дипломном проекте в дальнейшем будем применять термин «энергоаудит»,
что соответствует наименованию этапа дипломного проекта (см. п. 5 задания по
дипломному проекту).
Энергетический аудит (энергоаудит) - это
технико-экономическое инспектирование систем энергогенерирования,
энергораспределения и энергопотребления предприятия с целью определения
возможностей экономии затрат на потребляемые ТЭР, разработки
технических, организационных и экономических мероприятий, помогающих
предприятию достичь реальной экономии денежных средств и энергоресурсов
8.1 Общие положения
Вопрос о проведении энергоаудита предприятия обычно решается
непосредственно с руководством организации, заинтересованной в повышении своей
экономической эффективности. Первый контакт рекомендуется устанавливать
непосредственно с ее ответственным руководителем.
Проводится начальное ознакомление с системой генерирования,
распределения и энергопотребления на предприятии, выявляются места
нерационального энергопотребления, оценивается потенциал энергосбережения,
намечается состав бригады энергоаудита и оценивается объем предполагаемой
работы. Как правило, энергообслуживающий персонал предприятия хорошо знает
различие проектной и исполнительной схем энергоснабжения, нарушение правил эксплуатации
установленного энергетического оборудования, ведущие к дополнительным потерям
энергии, имеет свое видение решения проблемы энергосбережения. Персонал
предприятия лучше всех знает сложившуюся реальную картину на предприятии и
должен понять, что выявление нерациональных энергопотерь не приведет к штрафным
для него санкциям. Энергоаудитор - представитель не карающей, а помогающей
организации.
Собирается информация по энергопотреблению за прошедшие
периоды времени. Сбор и накопление информации рекомендуется производить с
использованием стандартных форм.
Общее энергопотребление организацией различных
энергоносителей (как правило, отражаемое в финансовой отчетности предприятия в
разделе оплаты энергоносителей) разбивается по отдельным цехам, группам технологических
процессов, отдельным основным процессам и установкам, видам продукции (как
составляющие себестоимости). Этот ознакомительный этап завершается
формированием таблицы энергопотребления. При этом используются стационарные
средства учета предприятия, проводятся
дополнительные измерения в узловых точках предприятия с
помощью переносных приборов, используются расчетные методы.
Опытный энергоаудитор, которым, как правило, является
специалист энергоснабженец, может быстро выявить места возможной экономии энергии
по:
- завышенным температурам уходящих газов и разогретых
поверхностей, свидетельствующих о наличии плохой теплоизоляции;
- низкому значению cos
асинхронного
электропривода, свидетельствующему о его недогрузке и неэкономичном режиме
работы системы.
Все выявленные возможности экономии энергии должны быть
внесены в перечень рекомендаций с указанием приоритета на реализацию,
определяемому технико-экономическим расчетом.
Возможности решения по экономии ТЭР, имеющие более высокий
приоритет по условию экономической эффективности, прорабатываются более
детально технически, организационно и экономически.
Отчет по энергоаудиту передается руководству предприятия.
Предварительно целесообразно провести его обсуждение с
сотрудниками предприятия, которые имеют отношение по характеру их служебной
деятельности к энергосбережению и реализации энергосберегающих предложений,
учесть их критические замечания и получить их поддержку. Важно своевременно,
без проволочек передать отчет, так как при переносе сроков принятия решения
теряется эффект новизны и увеличивается вероятность принятия руководством
отрицательного решения по реализации энергосберегающих мероприятий.
В настоящее время уже издано большое количество методической
литературы по энергоаудиту. Не смотря на то, что многие методики существенно
отличаются, порядок проведения энергетического обследования предприятия можно
представить следующим образом:
1. Энергоаудит электротехнических и электромеханических
систем;
- анализ системы электроснабжения и электропотребления;
- анализ режимов работы трансформаторных подстанций;
анализ системы КРМ;
обследование основного электропотребляющего
оборудования;
обследование системы освещения;
электробаланс и оценка потерь в системе электроснабжения.
2. Энергоаудит теплотехнических и технологических систем;
анализ тепловых схем;
- аудит котельной;
обследование систем отопления;
тепловой баланс;
анализ режимов работы холодильного оборудования;
анализ режимов работы систем водоснабжения и канализации;
обследование компрессорного оборудования, системы
разводки сжатых газов.
Результаты труда «Энергоаудитора» во многом зависят от
профессиональных навыков его специалистов. Профессиональные навыки
подразумевают знание технических, экономических и управленческих аспектов, а
также техники безопасности. Проблемой, как правило, является отсутствие на
предприятиях внутреннего учета. Поэтому аудиторская организация должна быть
оснащена комплектом портативного измерительного оборудования, оборудования, позволяющего
фиксировать фактическое энергопотребление без врезки в обследуемые системы и
без остановки работающего оборудования. Определив и решив общие вопросы
энергоаудита, необходимо разобрать подробнее этапы его проведения.
8.2 Этапы энергоаудита
Первый этап энергоаудита - оценка
энергопотребления и затрат
Первый, ознакомительный этап энергоаудита посвящен знакомству
с предприятием и сбору и анализу имеющейся на предприятии, полезной для
энергоаудита, информации.
Определение текущего потребления всех энергоресурсов и затрат
на них является необходимой исходной информацией. Она необходима для анализа
проблем энергоиспользования и правильной расстановки приоритетов для достижения
наилучших результатов энергоаудита. Какая же информация потребуется и может
быть полезной для энергоаудита. Прежде всего, это потребление всех
энергоресурсов по месяцам на протяжении последних 12 или более месяцев. Обычно
такая информация представляется в табличном виде.
Информация об энергоресурсах представлена в абсолютных единицах
измерения. Значимость их невозможно сопоставить. Чтобы выяснить, доля каких
энергоресурсов в общем потреблении наиболее значительна, на использование каких
энергоресурсов нужно обратить внимание прежде всего, информация об
электропотреблении должна быть представлена в другом виде.
Необходимо определить энергоэквивалент для каждого
энергоресурса.
Энергоэквивалент [Гдж] - это теплотворная
энергия ресурса, выраженная в одноименных единицах Гдж (или Гкал) с помощью
переводного коэффициента энергосодержания.
Энергосодержание [Гдж/сд] - количество
энергии (Гдж) в единице энергоресурса.
Вопрос о ценах на энергоресурсы является очень важным при
проведении энергоаудита, особенно в условиях рыночных взаимоотношений между
поставщиками и потребителями энергоресурсов. Правильный выбор поставщика и
условия договора на поставку может сказаться на итоговой стоимости используемых
энергоресурсов.
Не последнюю роль играет и выбор типа используемого
энергоресурса, особенно в условиях нестабильных, часто меняющихся цен. Например,
в последнее время на российском рынке появился большой выбор радиационных
отопителей с прямым сжиганием газа. Во многих случаях переход от традиционных
систем парового и водяного отопления на такие отопители дает значительную
экономию в стоимости энергоресурсов.
При рассмотрении структур тарифов на энергоресурсы нужно
учесть все факторы, которые в конечном итоге определяют, сколько предприятие
платит за энергоресурсы:
- изменение цены в течение года
дифференцированные тарифные ставки
штрафные санкции
другие выплаты
Наиболее сложной обычно является структура тарифов на
электроэнергию, которая зависит от вида размера потребителя, региона.
Поскольку цены на электроэнергию являются комплексными, для
оценки потенциала экономии в потреблении электроэнергии необходимо получить
следующую информацию:
- полная установленная мощность электрооборудования;
- суточные графики нагрузки;
годовые (сезонные) изменения нагрузки;
средняя величина коэффициента мощности;
возможность комплексации реактивной мощности;
- структура энергопотребления
(технологические процессы, освещение и др.).
Для оценки эффективности использования энергоресурсов и
наглядности представляемой информации могут быть получены различные типы
удельных затрат.
В результате ознакомительного этапа энергоаудиторы должны
иметь:
- представление о предприятии и основных технологических
процессах;
- общую стоимость затрат предприятия на энергоресурсы.
Важно не забыть расходы на воду, стоки и канализацию;
структуру затрат по энергоносителям;
сезонные изменения в потреблении энергоресурсов и их
стоимости;
структуру цен на каждый энергоресурс.
Основной результат Первого этапа - определение наиболее значимого
энергоресурса в стоимостном выражении.
Основное правило, которого следует придерживаться при
проведении энергоаудита - чем более высокая доля энергоресурса в общей
стоимости, тем больше времени должно быть запланировано для определения
эффективности его использования на предприятии.
Второй этап энергоаудита - оценка энергетических
потоков
По результатам первого этапа энергоаудита мы знаем стоимость
и потребление каждого энергоресурса на предприятии. Следующим логическим шагом
будет определить, куда же идут энергоресурсы, как они используются.
Цели второго этапа энергоаудита «Оценка энергетических
потоков»:
- определение для каждого энергоресурса наиболее значимых
потребителей по затратам и объемам потребления;
- распределение потребления каждого энергоресурса по
основным
потребителям;
Чтобы правильно понять, где и для чего расходуются энергоресурсы,
необходимо разобраться в производственных технологических процессах. Обычно это
достигается путем обсуждения с руководством производственных цехов, мастерами и
технологами, обследованием технологических линий предприятия и составлением схем
(диаграммы) технологических процессов. Для каждого элемента такой схемы следует
определить потоки энергоресурсов, сырья, продукции, промышленных стоков и
потерь. Основываясь на имеющейся информации и визуальном наблюдении, оценить
величину энергопотоков и потерь, а также составить перечень основных
потребителей энергоресурсов (как для основных процессов, так и для
вспомогательных).
Если для оценки энергетических потоков имеющейся информации
недостаточно, необходимо использовать локальные счетчики, там, где они имеются,
или специальное переносное оборудование для энергоаудита.
Часто небольшая экономия у крупного потребителя бывает более
значительной (и достижимой), чем большая экономия у небольшого потребителя. Это
не означает, что следует игнорировать небольших потребителей, но начальные
усилия следует концентрировать на областях, наиболее вероятных для получения
значительной экономии энергоресурсов.
После того, как удалось разобраться в основных
технологических процессах, необходимо составить список основных потребителей
энергоресурсов предприятия, чтобы на следующем этапе сосредоточиться на их
детальном обследовании. Наиболее крупными потребителями энергии на горных
предприятиях обычно являются:
- энергоемкие агрегаты основного технологического процесса
(экскаваторы, угольные и проходческие комбайны, драги, технологические насосы и
др.);
- вентиляторные установки (главного проветривания и
др.);
компрессорные установки;
водоотливные установки;
транспорт (подъемные и конвейерные установки,
автомобильный транспорт и др.);
система освещения;
система отопления (котлы паровые и водогрейные и
др.).
В процессе обследования основных технологических агрегатов
необходимо сформировать идеи о том, как можно улучшить эффективность их работы
и снизить потери энергии.
Таким образом, в результате Второго этапа должны быть:
- определены наиболее значимые потребители по затратам и
объемам потребления для каждого энергоресурса;
- определены их энергетические характеристики и
составлены агрегатные балансы.
Третий этап энергоаудита - критическое
рассмотрение потоков
Целью данного этапа является составление балансов
энергопотребления по основным переделам производства и в целом по предприятию и
критический анализ всех статей расхода для того, чтобы предложить пути снижения
затрат на энергоресурсы.
Основные задачи анализа энергетических балансов отдельных
установок, процессов и предприятия в целом следующие:
оценка фактического уровня энергоиспользования и определение
возможностей его повышения;
определение размеров и установление основных причин потерь
энергии во всех элементах энергетического хозяйства;
выявление внутрипроизводственных резервов экономии топлива и
энергии;
- определение выхода и использования вторичных энергетических
ресурсов;
- оценка эффективности использования различных видов и
параметров энергоносителей в отдельных установках и процессах;
- изучение влияния внедрения новой техники и технологии на
показатели энергоиспользования предприятия;
- исследование возможностей интенсификации и улучшения
энергетических режимов работы оборудования;
- совершенствование нормирования и планирования
энергопотребления;
- разработка перспективных планов повышения экономичности
энергохозяйства предприятия на 5-10 летний период.
Обязательным условием получения оптимальных решений повышения
экономичности энергохозяйства является комплексный подход к анализу
энергоиспользования, т.е. совместное рассмотрение технологических и
энергетических схем, исследование взаимосвязей между отдельными участками
энергохозяйства, получение режимов работы оборудования и оценка влияния всех
факторов на энергетическую экономичность предприятия.
Сравнение показателей энергоиспользования изучаемых объектов
- основной прием анализа. Главными объектами анализа должны являться отдельные
статьи составленных энергетических балансов. Необходимость поэлементного
рассмотрения балансов определяется тем, что только при этом обеспечиваются
наиболее полное выявление внутрипроизводственных резервов и конкретное
проектирование мероприятий по их реализации. Размер резервов экономии энергии
необходимо определять сопоставлением достигнутого уровня энергоиспользования с
потенциально возможным и реально достижимым в условиях данного предприятия.
Четвертый этап энергоаудита - разработка
энергосберегающих проектов
Результатом третьего этапа является множество идей о способах
снижения потребления энергоресурсов предприятия, возникших в результате анализа
энергетических балансов. На данном этапе необходимо обобщить эту информацию,
выбрать лучшие идеи, рассчитать стоимость предлагаемых мероприятий и
разработать сводный список проектов.
На основании опыта рекомендуется придерживаться следующей
последовательности:
- составить список всех потребителей каждого энергоресурса,
по которым имеются предлагаемые энергосберегающие мероприятия;
- составить список всех возможных энергосберегающих
мероприятий;
повторить ту же последовательность действий для
систем распределения каждого энергоресурса;
повторить ту же последовательность действий для систем
преобразования энергии - котельных, компрессорных и т.п. Для очень крупных
систем и потребителей, возможно, для упрощения анализа, имеет смысл разбить их
на части;
доработать энергосберегающие мероприятия в проекты.
Основной «продукт» энергоаудита - проект по энергосбережению
- должен быть не обособленным документом, выражающим лишь точку зрения
энергоаудитора, а руководством к действию для предприятия.
Проект должен учитывать все реалии предприятия (наличие
финансовых и производственных ресурсов, планов по расширению или изменению
технологии), мнение всех заинтересованных специалистов предприятия и
согласовываться с руководством.
Пятый этап энергоаудита - экспертиза
энергосберегающих проектов
Поскольку в результате энергоаудита предлагаются не только
простые энергосберегающие мероприятия, не требующие больших капитальных затрат,
но и серьезные дорогостоящие проекты, необходима тщательная экспертиза
предлагаемых проектов и определение всех возможных последствий их внедрения.
Экспертизе проектов посвящается пятый этап энергоаудита.
Цели пятого этапа энергоаудита:
- убедиться, что проекты реализуемы технически и не имеют
побочных эффектов;
- рассчитать затраты и выгоды от проекта.
Оценку эффективности проекта удобно начинать с составления
двух списков. Затраты по проекту включает в себя:
- капитальные затраты на закупку оборудования;
- стоимость монтажа и наладки оборудования;
затраты на обслуживание оборудования;
другие возможные затраты.
Выгоды от проекта:
- снижение энергопотребления;
- увеличение производительности оборудования;
улучшение качества продукции;
снижение выбросов в окружающую среду;
снижение эксплуатационных расходов;
другие возможные выгоды.
Для определения затратной части проекта необходимы знание
стоимости предлагаемого оборудования и монтажных работ, а также условий
инвестирования. Необходимо провести маркетинговые исследования поставщиков
оборудования и источников финансирования. Стоимость монтажных работ зависит от
возможности выполнения монтажа собственными силами предприятия или привлечения
специализированных организаций.
Выгоды от проекта необходимо рассчитать в стоимостном
выражении. Снижение электропотребления дает уменьшение затрат на оплату
энергоресурсов. Увеличение производительности оборудования дает снижение
себестоимости, а улучшение качества продукции дает возможность продать ее
дороже.
Чем ниже стоимость проекта и чем больше выгод он даст, тем
привлекательнее проект. Но для оценки проекта, в который инвестируются крупные
суммы денег, такого критерия недостаточно. Наиболее простым способом
экономической оценки инвестиционного проекта, а также сравнения двух
альтернативных проектов, является метод окупаемости инвестиций.
Метод окупаемости заключается в оценке дополнительной прибыли
за год, которая получается в результате инвестиций. «Период окупаемости»
является периодом времени, в течение которого происходит накопление
дополнительной прибыли, равной сумме первичных инвестиций. Чем меньше период
окупаемости, тем привлекательнее проект. Многие компании устанавливают
максимальный период окупаемости, при превышении которого проект не
рассматривается. Помимо факторов, влияющих на экономическую эффективность
проекта, при его представлении должны быть указаны и факты, дающие другие,
нефинансовые выгоды, а также риски, связанные с изменением цен на
энергоресурсы, надежность и т.п.
Шестой этап энергоаудита - представление
результатов
Цель этого, заключительного этапа энергоаудита - отчитаться
перед предприятием - заказчиком о выполненной работе. Результатом является
энергетический паспорт и отчет о проведенном энергоаудите.
.3 Потребление энергоресурсов
Данные о общем потреблении энергоресурсов, выявленные на
первом этапе энергоаудита, сведены в таблице 8.1
Таблица 8.1. Общее потребление энергоресурсов
Месяц
(2010-2011 гг.)
|
ЭНЕРГОРЕСУРС
|
|
Электроэнергия,
кВт·ч
|
ГСМ, кг
|
Диз. топливо, л
|
Сжат. возд., м3
|
Декабрь
|
140586
|
410
|
13356
|
8788
|
Январь
|
152459
|
456,8
|
13254
|
8788
|
Февраль
|
142477
|
395
|
13623
|
8788
|
Март
|
142852
|
432
|
13875
|
8788
|
Апрель
|
8659
|
260
|
4950
|
8788
|
ВСЕГО
|
641150
|
1957
|
60565
|
39546
|
В результате второго этапа энергоаудита были определены
наиболее значимые потребители по затратам и объемам потребления энергоресурсов,
данные сведены в таблицу 8.2
Таблица 8.2. Расход электроэнергии
Направление
использования
|
Кол-во
|
Мощность кВт
|
Наработанные
часы, час
|
Потребление эл.
эн., тыс. кВт·ч
|
%
|
Проходческий
комплекс
|
1
|
260
|
1960
|
509,6
|
82,5
|
Пневмобетонный
узел
|
1
|
18,5
|
764
|
14,1
|
2,2
|
Маслостанция
|
3
|
41
|
1372
|
56,25
|
9,2
|
Вентилятор
|
1
|
13
|
2352
|
30,6
|
5,1
|
Итого:
|
6
|
332.5
|
6448
|
641,15
|
100
|
Вывод: в результате проведенных исследований на втором
этапе выявлено, что наибольшее количество энергии потребляет проходческий
комплекс (82.5%)
На шестом этапе энергоаудита идет представление результатов
проделанной работы, данные по каждому ресурсу, его потреблению, их процентное
соотношение и стоимость сведены в таблицу 8.3
Потребление энергоресурсов и их стоимость Таблица 8.3
Энергоресурс
|
Единица
|
Потребление
|
Энергосодерж.,
Гдж/ед
|
Энергет.
эквивалент, Гдж
|
% энергии
|
Стоимость, руб.
|
% стоимости
|
Тыс. руб. / Гдж
|
Электроэнергия
|
кВт·ч
|
641150
|
0,0036
|
2309
|
47,34
|
1115601
|
79,5
|
483,15
|
Дизельное
топливо
|
Л
|
1957
|
0,0401
|
78,5
|
1,61
|
32877,6
|
2,3
|
418,12
|
ГСМ
|
Кг
|
6056
|
0,0411
|
2489,6
|
51,1
|
254352,7
|
18,1
|
102,2
|
ВСЕГО
|
|
|
|
4877,1
|
100
|
1402831,3
|
100
|
|
9. Определение энергетических показателей
основных энергоемких установок технологических комплексов
.1 Расчет основных энергетических показателей
технологических процессов производства
Таблица 9.1. Спецификация основного
электрооборудования участка
Оборудование Тип двигателя
кВт
,
об/мин
А % 
|
|
|
|
|
|
|
|
RME-137SE
|
Исполнительный
орган
|
ВАО2 280L4
|
200
|
1500
|
210
|
94
|
0,89
|
6,5
|
2,4
|
|
Перегружатель
|
ВАО2 280S4
|
132
|
1500
|
170
|
94
|
0,88
|
6,5
|
2,4
|
|
Конвейер
|
ВА 200М4
|
37
|
1500
|
45
|
92
|
0,88
|
6
|
1,8
|
|
Насос
маслосистемы
|
ВА 200М4
|
37
|
1500
|
45
|
92
|
0,88
|
6
|
1,8
|
|
Насос орошения
|
ВА 180S4
|
22
|
1500
|
40
|
91
|
0,87
|
6
|
1,9
|
Предохранительная
лебедка 1ЛП
|
ВР 180М4
|
18,5
|
1800
|
33,5
|
81
|
0,88
|
5,7
|
1,9
|
Водоотливная
установка
|
4А100L2Y3
|
5.5
|
3000
|
7.2
|
87
|
0.83
|
5,2
|
2
|
Вентилятор
ВМ-6М
|
ВРМ132М2
|
13
|
3000
|
25
|
98
|
0,91
|
6
|
2,3
|
Коэффициент спроса для каждой группы
электроустановок
При механизированном проведении подготовительных работ машинами
с индивидуальной крепью и отсутствием блокировки очередности пуска
электродвигателей коэффициент спроса определяется по формуле:
Kc = 0,286 + 0,714
,
где
- номинальная мощность наибольшего
электродвигателя, в группе электроприемников, питающихся от одной шахтной ПУПП;
- сумма номинальных мощностей электроприемников на участке.
Коэффициент спроса первой группы - 0,72;
Коэффициент спроса второй группы - 0,47;
Суммарная установленная и расчетная нагрузка для каждой группы
электроприемников и шахты в целом.
Расчетная нагрузка определяется:
Ррасч = кс ·
, кВт.
Расчетная нагрузка проходческого щита:
Ррасч = кс ·
= 0,72 · 200 = 144 кВт.
Расчетная нагрузка перегружателя:
Ррасч = кс ·
= 0,72 · 132= 95,04 кВт.
Расчетная нагрузка конвейера:
Ррасч = кс ·
= 0,47· 37 = 17,4кВт
Расчетная нагрузка вентилятора:
Ррасч = кс ·
= 0,47 · 13 = 6,11 кВт.
Расчетная нагрузка лебедки:
Ррасч = кс ·
= 0,47· 37 = 17,4кВт.
Расчетная нагрузка насоса орошения:
Ррасч = кс ·
=0,47
=10,34кВт
Расчетная нагрузка водоотливной установки:
Ррасч = кс ·
= 0,47·5,5 =2,58кВт.
Расчетная нагрузка маслостанции:
Ррасч = кс ·
= 0,47·37=17,4кВт
Технологический расход электроэнергии
,
где
- расчетная мощность i-ой группы электроприемников, кВт;
- продолжительность работы i-ой группы электроприемников за расчетный период времени, ч.
Для проходческого щита:
= 144*20 = 2880 кВт·ч.
Для перегружателя:
=95,04*20 =1900,8 кВт·ч.
Для лебедки:
= 8,7*14 = 121,8 кВт·ч.
Для вентилятора:
= 6,13*24 =147,12 кВт·ч.
Для насоса маслосистемы:
= 17,4*20 =348,6кВт·ч.
Для конвеера:
= 17,4*20 =348кВт·ч.
Для насоса орошения:
= 10,34 *20 =206,8кВт·ч.
Для водоотливной установки:
= 2,58*24 =61,92кВт·ч.
.2 Расчет производительности основных технологических установок
Производительность проходческого щита Lovat - 3,6
Теоретическая производительность Q (м3/ мин) проходческого щита:
Q = 60
SB ·VП ·γ = 60
3,6
2,4
1,3 = 674 т/ час,
где SB - сечение выработки, м2
VП -
скорость перемещения исполнительного органа в направлении перемещения забоя
выработки, м/с;
γ = 1,3 - плотность полезного ископаемого,
т/ м3.
Техническая производительность щита:
Qт = Qх· Kт = 674
0,45 =303,3 т/ час,
где Kт - коэффициент технически возможной непрерывности работы щита.
Kт =
,
где
- коэффициент готовности (комплексный
показатель надежности) щита, равный 0,75-0,8;
- время простоев щита за рабочий цикл, зависящее от конструкции и
его рабочего инструмента, мин;
- чистое время работы за цикл по разрушению пород забоя, мин.
Qэ = Qх· Kэ х
= 674 х 0,36х· 4= 971 т/ смену,
где Kэ -коэффициент непрерывности работы, учитывающий все виды
простоев при работе.
Kэ = А ·
·
,
где А=0,8 - коэффициент, учитывающий регламентированные перерывы в
работе;
- время простоев за цикл по организационно-техническим причинам,
из-за обмена вагонеток, отсутствия электроэнергии, несовмещенности во времени
операций по возведению отделки и др.
Производительность вентилятора
Таблица 9.2. Технические характеристики вентилятора
Марка
вентилятора
|
ВМ-6М
|
Тип приводного
двигателя
|
ВРМ132М2
|
Мощность
двигателя Рдв, кВт
|
13
|
Частота
вращения вентилятора nв,об/мин
|
3000
|
Подача
вентилятора Qв, м/с
|
11
|
КПД двигателя η
д
|
0,99
|
КПД вентилятора
η в
|
0,75
|
Qcм =3600 ·
· Qв = 3600 · 6 ·11 = 237,5 тыс. м3 / смену,
где
= 6 - время работы вентилятора в смену, ч.
Производительность водоотлива
Таблица 9.3. Технические характеристики водоотлива
Марка насосаК
45/30
|
|
Тип приводного
двигателя
|
4А100L2УЗ
|
Мощность
двигателя Рдв, кВт
|
5,5
|
Частота
вращения nв,об/мин
|
3000
|
Подача насоса Qн, м3/ч
|
48
|
КПД двигателя η
д
|
0,87
|
КПД насосной
установки η в
|
0,63
|
Qэ = Qн ·
= 60 · 6 = 288 м3 / смену.
.3 Удельный расход электроэнергии по технологическим участкам
Удельный расход электроэнергии по технологическим участкам
определяется по формуле:
ωТ =
,
где Wpi - технологический расход электроэнергии
группой электроустановок, кВт ч;
Qpi - производительность технологического
оборудования участка, т, м3, тыс. м3 и т.д.
Удельный расход электроэнергии комплекса Lovat - 3,6:
ωТ п.к =
=
= 2,96кВт · ч/ т.
Удельный расход электроэнергии лебедки:

ω



3,04 кВт·ч/тыс. м
.
Удельный расход электроэнергии вентилятора:
ω


0,6 кВт·ч/м
.
Удельный расход электроэнергии маслостанции:
ω
кВт·ч/т.
Удельный расход перегружателя:
ω
кВт·ч/т
Удельный расход конвеера:
ω
кВт·ч/т
Удельный расход насоса орошения:
ω
кВт·ч/т
Удельный расход водоотливной системы:
ω
кВт·ч/т
Таблица 9.4. Основные энергетические показатели
технологических установок и комплексов
Электроприемники
кВт
P
кВтt
чW
кВт·чQ
*ω
кВтч/*
|
|
|
|
|
|
|
|
RME-137SE
|
Исполнительный
орган
|
200
|
0,72
|
144
|
5
|
2880
|
971
|
2,96
|
|
Перегружатель
|
132
|
0,72
|
95,04
|
5
|
1900,8
|
971
|
2,007
|
|
Конвейер
|
37
|
0,47
|
17,4
|
5
|
348
|
971
|
0,35
|
|
Насос
Маслосистемы
|
37
|
0,47
|
17,4
|
5
|
348
|
971
|
0,43
|
|
Насос орошения
|
22
|
0,47
|
10,34
|
5
|
206,8
|
971
|
0,21
|
Предохранительная
лебедка 1ЛП
|
18,5
|
0,47
|
17,4
|
3,5
|
121,8
|
40
|
3,04
|
Водоотливная
установка
|
5.5
|
0,47
|
2,58
|
6
|
61,92
|
288
|
4,52
|
Вентилятор
ВМ-6М
|
13
|
0,47
|
6,11
|
6
|
147,12
|
237,5
|
0,61
|
* - единица измерения производительности (т; м³;
тыс м³)
Таблица 9.5. Параметры кабельных линий
Оборудование
участка
|
Ток, А
|
Длина кабеля, м
|
Тип кабеля
|
Сечение S мм2
|
Исполнительный
орган
|
210
|
250
|
КГЭШ
3х50+1х10+3х4
|
50
|
Перегружатель
|
170
|
250
|
КГЭШ
3х50+1х10+3х4
|
50
|
Конвейер
|
45
|
250
|
КГЭШ
3х10+1х6+3х2,5
|
10
|
Насос
маслосистемы
|
45
|
250
|
КГЭШ
3х10+1х6+3х2,5
|
10
|
Насос орошения
|
40
|
250
|
КГЭШ
3х6+1х4+3х1,5
|
6
|
Предохранительная
лебедка 1ЛП
|
33,5
|
150
|
КГЭШ
3х6+1х4+3х1,5
|
6
|
Водоотливная
установка
|
7.5
|
100
|
КГЭШ
3х10+1х6+3х2,5
|
10
|
Вентилятор
ВМ-6М
|
25
|
50
|
КГЭШ
3х6+1х4+3х1,5
|
6
|
Силовой трансформатор ТСШВ-630/10/6
S
=630кВа;
= 3,5%; I
= 3%;
P
= 4,7 кВт;
P
= 2,8 кВт.иловой трансформатор ТСШВ-160/10/6
S
= 160 кВА;
= 3,5%; I
= 4,5%;
P
= 1,7 кВт;
P
= 1,33 кВт.
9.4 Расчет и анализ составляющих электробаланса технологических
установок
Уравнение электробаланса, устанавливающее равенство между
поступлением и расходом электроэнергии в общем виде определяется по формуле:
W
= W
+
W
+
W
+
W
, кВт ч,
где W
- подводимая к установке электроэнергия;
W
- полезный расход энергии
W
- потери энергии в линиях и электрических
сетях;
W
- потери электроэнергии в рабочей машине;
W
- потери электроэнергии в
преобразовательной установке (электродвигателе, трансформаторе, инверторе и
т.д.).
Потери электроэнергии в электрической сети
Потери активной мощности и электроэнергии в кабеле, питающем
проходческий щит Lovat - 3,6:
P
10,6 кВт;
W
=
P
T
= 10,6 · 5 = 53 кВт·ч,
где P
- номинальная активная мощность двигателя
установки, кВт;
Q
- реактивная мощность двигателя установки, квар;
U
- напряжение питания установки, кВ;
L - длина
линии, км;
R
- сопротивление линии, Ом;
T
- продолжительность времени работы за расчетный период, ч.
Таблица 9.6. Потери мощности и электроэнергии
Объект потерь
|
Потери P, кВтПотери W,
кВт·ч
|
|
Исполнительный
орган
|
10,6
|
53
|
Перегружатель
|
2,6
|
13
|
Конвейер
|
1,09
|
5,45
|
Насос
маслосистемы
|
1,09
|
5,45
|
Насос орошения
|
1,12
|
5,6
|
Предохранительная
лебедка 1ЛП
|
0,28
|
0,98
|
Водоотливная
установка
|
0,007
|
0,044
|
Вентилятор ВМ-6М
|
0,014
|
0,084
|
РП-НН №1
|
7,2
|
36
|
РП-НН №2
|
4,1
|
2,46
|
Потери активной мощности и электроэнергии в
трансформаторах
Потери в трансформаторе ТСШВ-630/6:
кВт;
кВт·ч,
где
P
,
P
- активные потери холостого хода и в меди при номинальной
нагрузке, кВт;
β=0,63 - коэффициент загрузке
трансформатора;
T
- полное число часов работы трансформатора за расчетный период,
ч;
T
- число часов максимума потерь по активной мощности за расчетный
период времени, ч.
Потери в трансформаторе ТСШВ - 160/6
кВт;
кВт·ч.
Потери электроэнергии в вентиляторе местного проветривания
Потери в пусковом режиме
при торможении противовключением
при динамическом торможении
при реверсировании двигателя
где К=1 - для двигателей постоянного тока параллельного
возбуждения;
К=2 - для асинхронных двигателей;
hп, hр, hт - соответственно число пусков, торможений и реверсов в час;
GD2 - момент
инерции двигателя или механизма
no - частота вращения двигателя при
идеальном холостом ходе.
Потери электроэнергии в двигателях
Таблица 9.7
Оборудование
|
Потери, кВт·ч
|
|
пусковые
|
Торможение
противовкл.
|
Динам.
торможение
|
реверс
|
Лебедка ЛВД-11
|
1,9 · 10-3
|
0,011
|
1,9 · 10-3
|
8,55· 10-3
|
Вентилятор
ВМ-6М
|
1,3 · 10-4
|
1,9 · 10-4
|
1,3 · 10-4
|
6,4· 10-4
|
Исполнительный
орган
|
11,9
|
12,7
|
11,9
|
15,6
|
Перегружатель
|
0,85
|
5,1
|
0,85
|
6,8
|
Насос
маслосистемы
|
6,6· 10-2
|
0,4
|
6,6· 10-2
|
1,5
|
Конвеер
|
6,3· 10-2
|
0,5
|
6,3· 10-2
|
1,2
|
Насос орошения
|
2,3· 10-2
|
0,14
|
2,3· 10-2
|
0,9
|
Водоотливная
установка
|
2,06· 10-3
|
1,2· 10-2
|
2,06· 10-3
|
1,8· 10-2
|
Полезный расход электроэнергии при осуществлении
технологического процесса в течение учетного периода
WT = WЭ -
, кВт·ч,
где WT - расход энергии на технологический процесс,
кВт·ч;
- сумма потерь электроэнергии при осуществлении технологического
процесса, кВт·ч.
На основании расчетов составляющих электробаланса производится
оценка энергоэффективности работы технологических агрегатов с помощью коэффициента
полезного действия
Для отдельных электроустановок составляющие электробалансов можно
определить по эмпирическим зависимостям, полученным в результате
математического моделирования и статистического анализа режимов потребления
электрической энергии.
9.5 Мероприятия, направленные на повышение
энергоэффективности
Основные мероприятия по экономии электрической энергии и, как
следствие, по снижению удельного расхода электроэнергии делятся на три группы:
-я группа - мероприятия по повышению производительности шахт
за счёт совершенствования технологии отдельных производственных процессов и
повышения надёжности технологических схем;
-я группа - технологические и организационно - технические
мероприятия, направленные на снижение потребления активной энергии отдельными
технологическими процессами, технологическими объектами и электроустановками;
повышение степени загрузки и коэффициента полезного действия (к.п.д.)
оборудования;
-я группа - технические и организационные мероприятия,
направленные на снижение потерь электрической энергии во всех элементах системы
электроснабжения, рационализацию электропривода и электрических сетей.
Снижение
энергозатрат на ведение проходческих работ
Повышение скорости проходки
Экономия электроэнергии (кВт·ч) при повышении скорости
проходки за счёт увеличения машинного времени работы оборудования (повышение
надёжности технологической схемы, лучшая организация труда и т.д.) определяется
по формуле:
ΔW=ΣωiВМП ·Δtji,
где ωiВМП - суточное потребление
электроэнергии i-м ВМП, кВт·ч/сут;
Δtji - сокращение времени
проведения j-й подготовительной выработки, обусловившее уменьшение
продолжительности работы i-го ВМП, сут.
где nсут - количество рабочих (по проходке) дней
(суток) в году, сут;j - длина j-й выработки, м;
ΔVпр=ΔVпр2 - ΔVпр1; К=Vпр2 /Vпр1
пр1; Vпр2 - скорость проходки
соответственно до и после внедрения мероприятий по повышению темпов проведения
подготовительной выработки, м/месяц.
Технические и организационные мероприятия по
снижению энергозатрат при проведении подготовительных выработок.
К таким мероприятиям относятся:
применение при проходке облегчённых конструкций с меньшей
энерговооружённостью (с учётом малой загрузки конвейеров при проведении подготовительных
выработок по сравнению с конвейерами, транспортирующими груз из очистных
забоев);
применение новых конструкций двухбарабанных исполнительных
органов для щитов тяжёлого типа;
применение установок для бурения шпуров вращательно-ударного
действия с электроприводом вместо пневматических бурильных машин.
Экономия времени на ведение проходческих работ:
где nсут=98 - количество рабочих дней на проходку;пр=294
м - длина прходки;1пр=3,3 м/сут - скорость проходки;2пр=3,89
м/сут - скорость проходки после увеличения (график позволяет увеличить скорость
проходки с 3,3 м/сут до 4,65 м/сут)
Общее время работы 4 месяца, следовательно:1пр=3,3·30=99
м/месяц2пр=3,89·30=116 м/месяц.
Таким образом получается, что:
Δt =15,4 суток - это
сокращенное время проведения проходческих работ.
Экономия электроэнергии определяется по формуле:
ΔWпр=Wсут(nсут-Δt)=2389,5 (98-15,4)=36840 кВт·ч.
где Wсут - суточный расход электроэнергии на
ведение проходческих работ (в чистом виде):
сут=Рр·tр=177·13,5=2389,5
кВт·ч
Таким образом, экономия электроэнергии на ведение
проходческих работ составляет ΔWпр=36840кВт·ч.
Мероприятия по повышению энергоэффективности
водоотливных установок
Основные мероприятия по экономии электрической
энергии:
. уменьшение притока воды в шахту:
. предупреждением проникновения воды в шахту с
поверхности;
При выборе типа и производительности насосов для работы на
заданный трубопровод должны соблюдаться паспортные параметры насосов.
Необходимо стремиться к тому, чтобы точка пересечения индивидуальной
характеристики насоса и характеристики трубопровода лежали в зоне максимального
к.п.д.
При работе насосов с завышенным напором часть напора гасится
в трубопроводе и бесполезно теряется при сбрасывании воды на поверхность. В
этом случае необходимо:
снять часть промежуточных секций (если насосы секционные);
рассмотреть возможность установки насосов с меньшим напором.
Указанные мероприятия позволят сместить точку пересечения
индивидуальной характеристики насоса о характеристикой трубопровода в зону
максимального к.п.д (см. рис. 9.1) и обеспечат работу водоотливной установки с
меньшим удельным расходом электроэнергии.
4. Уменьшение потерь напора в трубопроводе (снижение
его сопротивления).
Потери напора в трубопроводе оказывают существенное влияние
на энергетические показатели водоотливной установки.
Наиболее эффективного уменьшения потерь напора в трубопроводе
позволит добиться выполнение следующих мероприятий:
) Увеличение сечения труб по всей длине или на отдельных
участках путем замены старых труб.
Потери напора в трубопроводе (м) выражаются формулами:
для труб на прямом участке
h=(0,083·λтрξ·L·Q2)/d5;
для местных сопротивлении
h=(0,083·ξ·Q2)/d4,
где λтр - коэффициент трения
воды о стенки труб (для шахтной воды λтр=0,03);
L - длина участка трубопровода, м;
Q - количество пропускаемой воды, м3/cек;
d - диаметр трубопровода, м;
ξ - коэффициент местного
сопротивления (принимается по табл. 9.9).
Таблица 9.9. Значения коэффициента местного сопротивления
Местное
сопротивление
|
Значение
коэффициента
|
Задвижка
|
0,5
|
Закруглённое
колено на 90°
|
0,3
|
Обратный клапан
|
5,0
|
В случае изменения параметров трубопровода с использованием
формул определяется разность потерь напора (м) на каждом участке как
Δh=h1 - h2,
где h1, h2 - потери напора на участке трубопровода до и
после его реконструкции, м.
Тогда суммарное снижение потерь напора (м) будет равно
ΔhΣ=Δh1+Δh2+ … +Δhn
где Δh1, Δh2,…, Δhn - величина снижения
потерь непора на отдельных, участках трубопровода, м.
Снижение потерь напора в трубопроводе приведет к смещению
рабочей точки установки с соответствующим изменением её к.п.д. (см. рис. 9.1).
Размер экономии электроэнергии (кВт · ч), которая может быть
получена от снижения сопротивления трубопровода, подсчитывается по формуле:
0,00286 (Q1·H1·η2 - Q2·H2·η1) tн
ΔW=,
η1 · η2 · ηd · ηс
где Q1, Q2 - подача насосной установки соответственно до и
после изменения сопротивления трубопровода (определяется по показаниям расходомера),
м3 /ч;
Н1, H2 - полный напор водоотливной установки
соответственно до и после изменения сопротивления трубопровода (определяется по
показаниям манометра), м;
η2, η2 - к.п.д. водоотливной установки до и после изменения
сопротивления трубопровода. При известных значениях Q1, Q2 и H1, H2 величины η1 и η2 определяются положением
точки пересечения (А, В) характеристики насоса и трубопровода (см. рис. 9.1);
ηd, ηс - к.п.д. соответственно двигателя и сети (изменяются
незначительно, поэтому в расчетах принимаются равными: ηа - номинальному значению двигателя; ηс= 0,95 - 0,97); tн - время работы насосов за расчётный период, ч.
При выполнении аналитических расчетов величину Н2 следует
определять как
Н2=Н1 - ΔhΣ
где ΔhΣ - суммарное снижение
потерь напора, м.
) Включение на параллельную работу резервного нагнетательного
става;
Такое включение следует осуществлять при снижении
производи-тельности насоса по сравнению с номинальной на величину более 20%.
При этом уменьшается сопротивление трубопровода и экономия электроэнергии может
составить 7-10% от потребляемой.
) ликвидация в трубопроводе излишней арматуры и ненужных
поворотов или снижение их сопротивления сглаживанием острых углов.
) сокращение длины трубопровода:
путем изменения его конфигурации;
за счет работы насоса на вертикальную скважину вместо
наклонного става по уклону.
) регулярная (не реже одного раза в год) очистка трубопровода
от накопившихся осадков.
Повышение
к.п.д. насосной установки
Для этого необходимо:
соблюдать график планово-предупредительных ремонтов;
осуществлять качественный ремонт насоса, запорной и
распределительной арматуры, всасывающих устройств;
следить за сальниковой набивкой в подшипниках и уплотнениях;
следить за степенью износа турбинок, направляющих аппаратов,
разгрузочного устройства и при превышении допустимых пределов износа
осуществлять замену изношенных элементов насосной установки.
замена насосов старых типов на новые, имеющие более высокий
к.п.д.
Расчёт экономии электроэнергии (кВт·ч), которая может быть
получена при этом, следует производить по формуле:
(η2 - η1)
ΔW=
0,00286 H·Q·tн,
η1 · η2 · ηd · ηс
где Н - напор, определяемый по показаниям манометра, м;
Q - фактическая подача насоса, м3/ч;
η1, η2 - к.п.д. соответственно старого и нового насосов;
tн - время работы насоса за расчётный период, ч.
Рассмотрим экономию электроэнергии водоотливных установок за
счёт изменения производительности насосов.
Суммарная номинальная мощность насосов:
Рн=1*5,5=5,5 кВт.
Производительность насосов:1=7 м3/чел.,
тогда ω1=P1/Q1;1=10 м3/чел.,
тогда ω2=P2/Q2.
н1=Pн1·tн=5,5·245=1347,5
кВт·ч,
где tн=nсут ·nсм·tсм=98·2·5=245
ч - время работы водоотливной установки.
Мероприятия по повышению энергоэффективности
вентиляторных установок
Основные мероприятия по экономии электрической
энергии:
-
повышение эксплуатационного к.п.д. вентиляторной установки
Допущение дефектов при монтаже и наладке вентиляторной
установки приводит к снижению эксплуатационного к.п.д., оценить которое можно
использованием следующих значений:
работа осевого вентилятора с перевернутым рабочим колесом
снижает к.п.д. на 20-40%;
несоблюдение радиального и осевого зазоров между рабочим
колесом и входным патрубком центробежных вентиляторов, а также радиального
зазора между рабочими лопатками и цилиндрической обечайкой корпуса осевого
вентилятора снижает к.п.д. на 5-10%;
снятие обтекателя на входе осевого вентилятора снижает его
к.п.д. на 10%;
укороченный диффузор или его отсутствие на выходе осевого
вентилятора снижает к.п.д. на 6%;
рассогласование в углах установки лопаток направляющего
аппарата (более 5°) приводит к снижению к.п.д. вентилятора на 5-10%.
Устранением указанных дефектов можно добиться
соответствующего повышения эксплуатационного к.п.д. вентилятора.
Значения к.п.д. принимаются равными; ηс= 0,93 - 0,97; ηм= 0,95-0,97.
Значение ηа зависит от типа
двигателя (асинхронный, синхронный), а также фактической загрузки двигателя,
характеризуемой коэффициентом загрузки β, который определяется с
помощью выражения:
β=Pс/Pн.с,
где Рс - фактическая мощность (кВт), потребляемая
двигателем из сети при данной загрузке, определяемая:
по показателям приборов (счётчиков, амперметров и
вольтметров), включённых в цепь статора двигателя;
аналитически;
Рн.с - мощность, потребляемая двигателем из сети
(кВт) при номинальной загрузке, определяемая как Рн.с=Рн./ηн, где ηн - номинальный к.п.д.
двигателя.
Входящая в это выражение мощность Рс (кВт)
рассчитывается как:
Рс=(ΔWcч · Кcч)/24,
где ΔWcч - разность показаний
установленного на вводном уотройстве счётчика активной энергии за сутки, дел.;
Кcч= Ктт · Ктн - коэффициент
счётчика;
Ктт, Ктн - коэффициенты трансформации
трансформаторов тока и напряжения.
Значения к.п.д. вентилятора η1 (η2) определяются по данным
замеров как
η1,2 =(Q·H)/(1000·Рс)
С этой целью необходимо увеличивать площади поперечного
сечения вентиляционных выработок (путем перекрепления), улучшать
аэродинамические свойства выработок (применением затяжки, обшивки, штукатурки
стен, скашивания углов на поворотах воздушой струи, установкой обтекателей на
расстрелах и т.д.), снижать местные сопротивления (уборкой завалов в выработка
неиспользуемого оборудования, вагонеток), проводить дополнительные
вентиляционные выработки.
Периодические депрессионные съемки шахтных вентиляционных
сетей дают картину распределения общешахтной депрессии и позволяют выявить
места резкого увеличения аэродинамического сопротивления горных выработок. На
основе анализа материалов депрессионных съемок необходимо разрабатывать
мероприятия по снижения депрессии отдельных выработок и устранению или
уменьшению местных сопротивлений.
Величина депрессии горной выработки hг.в (Па) определяется по
формуле:
где α - коэффициент
аэродинамического сопротивления, кг·с/м4;
L - протяженность горной выработки, м;
Р - периметр горной выработки, м;
Q - количество воздуха, подаваемого по горнов выработке, м3/с.
Величина депрессии, затрачиваемой на преодоление местных
сопротивлений (загромождённость выработок, резкие повороты, изменение сечения
выработок и т.д.), hм.с (Па) подсчитывается по формуле:
hм.с=0,598·ξ·V²,
где ξ - коэффициент местного
сопротивления (табл. 9.10);
V - скорость воздушной струи, м/с
Таблица 9.10. Значения коэффициента местного сопротивления ξ
Наименование
местных сопротивлений
|
ξ
|
Поворот струи
на 20°
|
0,1
|
То же при
сглаживании внутренних углов
|
0,0084
|
Поворот струи
на 40°
|
0,3
|
То же при
сглаживании внутренних углов
|
0,025
|
Поворот струи
на 60°
|
0,55
|
То же при
сглаживании внутренних углов
|
0,046
|
Поворот струи
на 90°
|
1,4
|
То же при
сглаживании внутренних углов
|
0,52-0,75
|
Сопряжение
выработок тройником
|
2,0
|
То же при
скошенных углах
|
1,0
|
Сужение
выработок при переходе ствола, Сбойки в вентиляционный канал
|
0,6
|
То же при
скошенных стенках на 14-25°
|
0,22-0,12
|
Отдельно
стоящая вагонетка
|
0,84-3,36
|
После определения по формулам величин ожидаемого снижения
депрессии при осуществлении мероприятий по упорядочению вентиляционной сети
рассчитывается возможная экономия электрической энергии (кВт·ч) как:
Q [Η·η2 - (Н-ΔН)·η1]·tв
ΔW=
1000·η1·η2·ηd·ηс·ηм
где Н - первоначальная депрессия вентиляционной сети шахты,
Па;
η1, η2 - к.п.д. вентилятора до и после уменьшения депрессии
вентиляционной сети шахты (определяются с использованием выражений);
ΔН - ожидаемое снижение
депрессии вентиляционной сети шахты, Па;
Q - подача вентилятора, сохраняемая постоянной при помощи
регулирования режима работы, м3/с.
Согласование (периодическое, нe реже одного раза в
полгода) режима работы вентилятора с характеристикой сети.
Для достижения экономичной работы вентиляторной установки в
процессе её эксплуатации и технического обслуживания необходимо стремиться к
тому, чтобы характеристика вентиляционной сети шахты пересекала индивидуальную
характеристику вентилятора в правой (устойчивой) ветви, возможно ближе к точке,
соответствующей режиму работы вентилятора с максимальным значением к.п.д.
Отклонение от оптимального режима работы вентилятора влечет
за собой уменьшение к.п.д., причем расход электроэнергии на потери в самом
вентиляторе резко возрастает.
Индивидуальные характеристики вентилятора определяются его
типом, конструктивными параметрами, качеством монтажа и являются практически
неизменными для конкретной установки.
Способы согласования режима работы вентилятора о
характеристикой сети могут быть различными в зависимости от типа вентилятора,
технологической схемы вентиляторной установки, регулировочных свойств
электропривода и т.д.
Для согласования режима работы вентилятора с характеристикой
сети следует также осуществлять:
) Изменение угла установки лопаток рабочего колеса
осевых вентиляторов.
Это мероприятие следует осуществлять при увеличении объема
очистных, подготовительных работ, изменении параметров вентиляционной сети и
т.д.
Экономия электрической энергии, которая может быть получена
за счет улучшения режима работы вентилятора (кВт·ч), определится из выражения:
(Q1·Η1·η2 - Q2·Η2·η1)·tв
ΔW=
1000·η1·η2·ηd·ηс·ηм
где Q1 - подача вентилятора до и после изменения режима
его работы (может определяться как порезультатам замеров, так и по совмещенным
характеристикам вентилятора и вентиляционной сети), м3/с;
Η1, Η2 - давление до и после изменения режима (определяется так же), Па;
η1,η2 - к.п.д. вентилятора до и после изменения режима работы.
Изменением к.п.д. ηd, ηс, ηм переходе на новый режим
работы вентиляторов при выполнении практических расчетов можно пренебречь.
) Снятие лопаток с одного колеса двухступенчатого
вентилятора и изменение (в случае необходимости) на другом колесе угла
установки лопаток
Для повышения к.п.д.недостаточно загруженных двухступенчатых
осевых вентиляторов, работающих с низким к.п.д. на вентиляционную сеть с малой
депрессией, может оказаться целесообразным полностью снять лопатки с одного
колеса, а на другом увеличить угол установки лопаток до величины,
обеспечивающей сохранение необходимой подачи и давления вентилятора. Следует
иметь ввиду, что фактический к.п.д. двухступенчатого вентилятора с одним
рабочим колесом окажется несколько ниже, чем к.п.д. одноступенчатого
вентилятора сравнимых параметров, т.к. при снятии лопаток с одного колеса
ухудшаются его аэродинамические характеристики. Несмотря на это, рекомендуемая
операция в ряде случаев позволит повысить к.п.д. вентиляторной установки и
добиться на этой основе экономии электрической энергии.
) Изменение угла установки лопаток направляющего
аппарата.
Экономичное регулирование производительности центробежных
вентиляторов следует осуществлять изменением угла положения лопаток
направляющего аппарата в пределах от 60° до 70°. При больших углах величина
к.п.д. вентилятора становится меньше 0,6. Регулируя производительность
центробежных вентиляторов двустороннего всасывания, необходимо обеспечить
установку лопаток обоих направляющих аппаратов под строго одинаковым углом. В
противном случае на роторе вентилятора появляется осевое усилие, приводящее к
дополнительным потерям мощности и энергии в подшипниках с одновременным
сокращением срока их службы.
) Изменение положения закрылков лопаток рабочего
колеса центробежных вентиляторов.
По сравнению с применяемым в настоящее время способом
регулирования, изложенным в п. 3, регулирование подачи вентиляторов поворотом
закрылков рабочего колеса позволит, согласно расчётам института ВВИИм им. М.Х.
Федорова уменьшить расход электроэнергии вентиляторной установкой примерно на
6%.
) Повышение активной загрузки привода вентилятора.
Это мероприятие может быть осуществлено заменой существующего
электродвигателя на двигатель меньшей мощности, либо на двигатель с меньшей
частотой вращения. В ряде случаев на стадии развития шахты наибольший эффект
может Быть получена результате замены электродвигателя на двигатель меньшей
мощности и с меньшей частотой вращения (при условии, что вентилятор
обеспечивает необходимое шахте давление и подачу).
Среднесуточная фактическая загрузка электродвигателя
вентилятора Рс определяется по показаниям счетчика, установленного
на вентиляторной установке. Затем по паспортным данным двигателя Рн
и ηн определяется мощность,
потребляемая из сети при номинальной загруке, как Рн.с=Рн./ηн, и рассчитывается коэффициент загрузки двигателя β.
При β≤0,4÷0,5 следует рассматривать
вопрос замены электродвигателя на на двигатель меньшей мощности, величина
которой ориентировочно может быть определена из выражения:
Рс=(Q·H)/(1000·η).
К установке принимаем двигатель мощностью Рн'
≥Рс (при той же частоте вращения).
Ожидаемая экономия электроэнергии (кВт·ч) при осуществлении
указанного мероприятия подсчитывается по формуле:
Η · Q · tв
ΔW=
(1/ηd1-1/ηd2),
1000·η·ηс
где ηd1, ηd2 - фактический к.п.д. электродвигателя до и после
проведения мероприятий.
) Проведение модернизации вентиляторов и реконструкции
вентиляторной установки.
При проведении модернизации вентиляторов следует
предусматривать комплекс технических мероприятий, направленных на повышение
экономичности работы вентилятолрной установки (замену рабочего колеса, подрезку
или удлинение лопаток, увеличение длины диффузора и т.д.)
В случае реконструкции установки следует предусматривать:
замену вентиляторов старых типов с низким к.п.д. на
вентиляторы нового типа, имеющие более высокие технико - экономические показатели;
применение в качестве электропривода систем регулируемого
электропривода (например, каскадных схем), обеспечивающих плавное и экономичное
регулирование частоты вращения вентилятора (а следовательно, подачи и даления)
в соответствии с регламентированными Правилами безопасности, а также
изменяющимися параметрами вентиляционной сети и самой вентиляторной установки.
Экономия электроэнергии вентиляторных установок
за счёт повышения эксплуатационного к.п.д.
где Рвент=1·13 кВт=13 кВт - суммарная мощность
вентиляторной установки;
tвент=nдней ·nсм·tсм=98·2·7=1372
ч - время работы вентиляторной установки;т.в.=Р ·tв=13·1372=17836
кВт·ч;
η1=0,65 - эксплуатационное
к.п.д. до проведения мероприятия;
η2=0,75 - эксплуатационное
к.п.д. после проведения мероприятия.
Таким образом экономи электроэнергии за счёт повышения
эксплуатационного к.п.д. составит ΔW=3567
кВт·ч.
Экономия электроэнергии в кабельных линиях
Основные мероприятия по экономии электрической энергии в
электрических сетях указаны в приведенной ниже структурной схеме рис. 9.3.
Рис. 9.3.
Потери активной мощности
и энергии
W (кВт· ч) в трехфазных воздушных линиях и кабелях определяются из
выражений
= 3 I2 R ·10-3,
=
R ·10-3
или
,
где I - расчетный ток линии, А; R =
- активное сопротивление провода или жилы
кабеля, Ом;
ρ - удельное сопротивление
материала провода при 20 0С (для алюминия 0,026-0,029; для меди 0,0175-0,018;
для стали 0,10-0,14 Ом.мм2/ м);
L - длина линии, м;
S - cечение проводника, мм2
P, Q - соответственно расчетная активная и реактивная мощность линии,
кВт, квар;
U - линейное напряжение, кВ;
Тр - продолжительность работы за расчетный период,
ч.
Потери активной мощности в трехфазных линиях в сетях могут
быть определены также с использованием специальных таблиц
При переводе сетей на более высокое напряжение экономия
электрической энергии (кВт ч) в воздушных и кабельных линиях определяется из
выражения
;
,
где I1, I2 - значения тока в сети
соответственно при низшем и высшем напряжении, А;
S1, S2 - cечение проводов при
низшем и высшем напряжении, мм2;
При проведении реконструкции сетей без изменения напряжения (I1 =I2 = I).
Экономия электроэнергии достигается за счет
замены сечения проводов
замены материала проводов
сокращения длины линий.
Расчет экономии электроэнергии (кВт · ч) следует выполнять с
использованием выражения
,
которое будет иметь следующий вид в случае
замены сечения проводов (ρ1 = ρ2 = ρ; L1= L2 = L)
;
замены материала проводов (L1= L2 = L; S1 = S2 = S)
;
сокращения длины линий (ρ1 = ρ2 = ρ; S1 = S2 = S)
;
- замены сечения проводов и материала (L1= L2 = L)
.
Приближение источников питания к потребителям позволит
осуществлять
питание отдельно стоящих мощных электроустановок или групп
электроустановок не от стационарной, а от передвижной подстанции, максимально
приближенной к электроприемникам;
питание участков и горизонтов шахт с поверхности от передвижной
комплектной трансформаторной подстанции кабелями, проложенными по скважинам.
Применение такого варианта питания подземных электроустановок
должны предшествовать технико-экономические расчеты вариантов электроснабжения
использованием типовых методик
Приближение источников питания к потребителям позволит уменьшить
протяженность низковольтной сети и увеличить протяженность высоковольтной.
Ожидаемая экономия электроэнергии может быть определена при этом с
использованием выражения
.
Экономия электроэнергии в двигателях
Основные мероприятия по экономии электрической энергии при работе
электродвигателей указаны в приведенной ниже структурной схеме рис. 9.3.
Рис. 9.4
Увеличение средней загрузки рабочих машин приводит к снижению
удельного расхода электроэнергии. Значение коэффициента загрузки β можно рассчитать как
β
,
где P
- фактическая мощность (кВт),
потребляемая двигателем из сети при данной загрузке, определяемая:
по показателям приборов (счетчиков, амперметров и вольтметров),
включенных в цепь статора двигателя;
аналитически по методике P
- мощность, потребляемая двигателем из
сети (кВт) при номинальной загрузке, определяемая как
P
,
где η
- номинальный к.п.д. двигателя.
Ориентировочное значение экономии электрической энергии,
получаемое в результате повышения загрузки рабочих машин, можно определить по
приведенным на рис. Кривым K
= f (β), где K
- коэффициент увеличения удельного расхода
электрической энергии, %.
K
,
где ∆W
- фактическое значение удельного расхода
электроэнергии за фиксированный промежуток времени, кВт.ч/мин (час, сутки и
т.д.); ∆W
- удельный расход энергии при отсутствии
холостого хода и загрузке β=1, кВт.ч/мин (час, сутки и т.д.);
K
=
- коэффициент использования рабочей
машины;
Т
- машинное время, ч;
Т
- время холостой работы, ч.
Правильный выбор электродвигателя по типу и мощности на стадии
проектирования и эксплуатации, который предполагает
выбор электродвигателей по мощности в соответствии с режимом
работы механизма (установки);
установку двигателей закрытого типа только в тех местах, где она
регламентируется Правилами устройства электроустановок или ПТЭ угольных и
сланцевых шахт. Установка таких двигателей в условиях окружающей среды,
допускающих эксплуатацию двигателей, открытого или защищенного типа, имеющих
лучшие энергетические показатели, будет приводить к необоснованным потерям
электроэнергии;
при прочих равных условиях отдавать предпочтение перед двигателями
с фазным ротором короткозамкнутым асинхронным двигателям, имеющим более высокие
энергетические показатели (к.п.д. и Cosφ).
Замена мало загруженных электродвигателей на двигатели меньшей
мощности.
При средней загрузке электродвигателя менее 45% номинальной мощности
замена его менее мощным всегда целесообразна и проверка расчетами не требуется.
При загрузке электродвигателя более 70% номинальной мощности
замена его нецелесообразна.
При загрузке электродвигателя в пределах 45-70% номинальной
мощности целесообразность его замены должна быть подтверждена уменьшением
суммарных потерь электрической энергии в электродвигателе и сети в результате
проведенной замены согласно выражению
,
где
η
, η
- к.п.д. сравниваемых двигателей при
заданной загрузке, о.е.;
tg φ
, tg φ
- тангенсы углов φ
и φ
, соответствующие значениям коэффициента
мощности cos φ
и cos φ
; K
- коэффициент потерь, кВт/квар.
Необходимые для расчета ориентировочные значения к.п.д. и cosφ асинхронных двигателей в зависимости от коэффициента загрузки β определяются путем умножения приведенных в табл. значений в
относительных единицах (о.е.) на номинальные (по паспорту).
Таблица 9.11. Ориентировочные значения к.п.д. и асинхронных
двигателей в зависимости от загрузки
β, о.е.
|
0,1
|
0,2
|
0,3
|
0,4
|
0,5
|
0,6
|
0,7
|
0,8
|
0,9
|
1,0
|
η, о.е.
|
0,48
|
0,68
|
0,79
|
0,86
|
0,93
|
0,97
|
1,0
|
1,01
|
1,01
|
1,0
|
cos φ
|
0,34
|
0,56
|
0,70
|
0,79
|
0,87
|
0,93
|
0,97
|
1,0
|
1,0
|
1,0
|
Замена малозагруженных двигателей, встроенных в механизмы,
настолько дорога и сложна, что она практически нецелесообразна.
Повышение качества ремонта двигателей.
При проведении ремонта двигателей недопустимо снижение их
энергетических показателей (к.п.д. и cos φ), которое может иметь место при
обточке роторов;
уменьшении числа проводников в пазу;
расточке пазов;
выжигании обмоток.
Снижение энергетических показателей двигателей по сравнению с
номинальными данными в процессе их эксплуатации будет приводить к
увеличению мощности холостого хода, а следовательно, к
повышенному потреблению активной энергии;
повышенному потреблению реактивной энергии (в случае
увеличения при ремонте воздушного зазора между статором и ротором),
сопровождаемому указанными в п. отрицательными последствиями.
Выбор двигателей с более высокими энергетическими
показателями.
Заключение
В дипломном проекте выполнены основные задачи:
· на основании анализа технологической
характеристики выбран проходческий комплекс Lovat 3.6
· по результатам расчётов выбрано основное
механическое оборудование: консольный насос типа К 45/30, вентилятор ВМ-6М,
аккумуляторный электровоз модели АК-2у.
· рассмотрены вопросы безопасного ведения
проходческих работ, а также мероприятия по охране труда и предотвращению
аварийных ситуаций;
· рассчитаны основные технико-экономические
показатели строительства коллектора.
В специальной части дипломного проекта произведён расчёт
системы электроснабжения, на основании которого выбрано основное
электрооборудование. Также было произведено сравнение и выбор систем
автоматизированного электропривода вентеляторной установки. Решены задачи
автоматизации процесса откачки воды. В специальном вопросе дипломного проекта
было рассмотрено:
· анализ энергетических показателей
· расчет производительности основных
технологических установок
· разработаны мероприятия направленные на
повышение энергоэффективности
Результатом дипломного проекта является обоснование способов
экономии энергоресурсов при городском подземном строительстве.
Список используемой литературы
1.
В.Е. Меркина, С.Н. Власова, О.Н. Макарова. Справочник инженера тоннельщика -
М.:Транспорт, 1993.
.
А.П. Гришко, В.И. Шелоганов. «Стационарные машины и установки: Учебное пособие
для вузов». М.: Издательство МГГУ, 20043. Пухов Ю.С. Транспортные машины. - М.:
Недра, 1996.
.
Зайко А.В. «Проходческие щиты». - М.: МГГУ, 1992.
.
Под ред. Ушакова. «Охрана труда» - М.: Недра, 1986.
.В.
Моссаковский, М.А. Ревазов, Ю.А. Маляров «Экономика горной промышленности.» -
М.: Недра, 1988.
.
Костюк В.С., Переслегин Н.Г., Шитилов Ю.В., Фащиленко В.Н. «Автоматизированный
электропривод». - М.: МГУ 1981.
.
Фащиленко В.Н. «Регулируемый электропривод насосных и вентиляторных установок
горных предприятий.» - М: Горная книга 2011
.
Пичуев А.В., Петуров В.И., Чеботаев Н.И «Электрофикация горного производства в
задачах и примерах.» - М: Горная книга 2012
.
Плащанский Л.А. «Основы электроснабжения.» - М.: МГГУ, 2005.
.
Неклепаев Б.Н., Крючков С.А. «Электрическая часть станций и подстанций:
Справочные материалы для курсового и дипломного проектирования.» - М.:
Энергоатомиздат, 1989.
.
Федоров А.А., Ристхейн Э.М. «Электроснабжение промышленных предприятий». - М.;
Энергия, 1981 г.
.
Плащанский Л.А. «Основы электроснабжения. Пособие по курсовому и дипломному
проектированию». - М.; МГИ, 1994 г.
.
Дзюбан В.С. «Аппараты защиты от токов утечки в шахтных электрических сетях». М.:
Недра, 1982
.
Шипунов Н.В. «Защитное отключение». М.: Энергия, 1968
.
Долин П.А. «Основы техники безопасности в электроустановках». М.: Энергия,
1979.
.
Колосюк.П «Защитное отключение рудничных электроустановок». М.: Недра, 1980.
.
Фролкин В.Г. «Быстродействующая защита шахтных участковых сетей». М.: Недра,
1986.
.
Пичуев А.В., Плащанский Л.А. Методические указания для практических занятий по
дисциплине «Основы электроснабжения». - М.; МГГУ, 1995 г.
.
Ягудаев Б.М., Шишкин Н.Ф., Назаров В.В. «Защита от электропоражения в горной
промышленности». М.: Недра, 1982.
Щуцкий
В.И., Жидков В.О., Ильин Ю.Н. «Защитное шунтирование однофазных повреждений
электроустановок». М.: Энергоатомиздат, 1986.