размеры
шахтного поля:
|
|
по падению
|
2400
|
по простиранию
|
7500
|
расстояние до
верхней границы шахтного поля
|
350
|
количество
пластов
|
4
|
мощность
пластов
|
1.2; 1.3; 1.9;
0.9.
|
количество
пластов в одновременной разработке
|
3
|
плотность угля
|
1.3
|
угол залегания
|
18
|
естественная
газоносность угольных пластов, м3/т
|
15
|
относительная
газообильность для шахт бассейна, м3/т. с. д.
|
30
|
коэффициент
дегазации угольных пластов
|
0,2
|
длина лавы
|
190
|
суточное
подвигание очистного забоя
|
3.15
|
кровля
|
Сред. устойч.
к-0,08
|
почва
|
5 к-0.015
|
ДОПОЛНИТЕЛЬНЫЕ
СВЕДЕНИЯ
|
|
расстояние между
пластами
|
90
|
Содержание
курсового проекта
Введение
1. Подсчет балансовых и промышленных запасов, обоснование величины
потерь угля
2. Определение производственной мощности и срока службы шахты
3. Вскрытие шахтного поля
3.1 Выбор способа вскрытия шахтного поля.
4. Выбор способа и схемы подготовки шахтного поля
4.1 Выбор схемы и способа подготовки шахтного поля
5. Определение основных параметров подготовительной выработки
6. Выбор и обоснование системы разработки
6.2 Сплошные системы разработки
7. Определение основных параметров системы разработки. Расчет
нагрузки на очистной забой и обоснование длины лавы
Комбайн очистной КДК 700
Заключение
Список используемой литературы
Введение
Горное дело относится к одному из основных видов человеческой
деятельности, обеспечивающей существование и уровень развития цивилизации.
Горное дело охватывает разведку месторождений полезных ископаемых, их
разработку, первичную переработку добываемого сырья, строительство горных
предприятий и подземных сооружений различного назначения.
Горнодобывающая промышленность - это составная часть горного
дела, цель которой состоит в добыче и первичном обогащении полезного
ископаемого. Эта промышленность поставляет минеральное топливо (уголь, торф,
горючие сланцы, нефть), руды (чёрных, цветных, редких и ценных металлов).
Горнодобывающая промышленность имеет важную роль в экономике государства,
определяет его самостоятельность.
Проектирование, строительство новых и реконструкция
существующих предприятий по добыче твердых полезных ископаемых требует знаний
технологических процессов, понимания и учета горно-геологических условий,
специфики ведения горных работ, требования техники безопасности и охраны труда.
Шахта, как горное предприятие, характеризуется качественными
и количественными параметрами. Качественные характеристики
включают сведения, которые определяют принципиальные особенности предприятий и
могут быть выражены только путем их описания, например, способ вскрытия и
подготовки шахтного поля. Количественные характеристики
(параметры) выражают с помощью чисел. К основным количественным параметрам
относят: производственную мощность, срок службы, балансовые и промышленные
запасы, размеры шахтного поля по простиранию и падению
Курсовая работа показывает, что только на основе глубокой проработки
основных технических решений проектов угольных шахт (схем и способов вскрытия,
подготовки шахтного поля, системы разработки угольных пластов и т.п.) можно
скомпоновать действительно оптимальную технологическую схему на основе
оптимизации качественных характеристик - элементов технологической схемы шахты.
Предложенные и описываемые в данной курсовом проекте расчетные методы оценки
основных качественных характеристик по многим критериям делают более
объективным процесс принятия основных проектных решений.
1. Подсчет
балансовых и промышленных запасов, обоснование величины потерь угля
Часть угольного месторождения, отведенная для разработки
одной шахте, называют шахтным полем.
Шахтное поле включает один или несколько пластов. В последнем
случае запасы отдельных пластов суммируются. Границы шахтного поля или его
участка принимаются в соответствии с утвержденными на момент сбора
геологических материалов. При этом указываются границы в плоскости пласта и по
напластованию пород
По народнохозяйственному применению запасы подразделяют на: геологические,
балансовые, промышленные и забалансовые.
Геологические - общие запасы угля в
пределах шахтного поля, как не предназначенные для разработки, так и
извлекаемые при существующем уровне техники и технологии.
Забалансовые - разработка которых в
настоящее время вследствие некондиционности запасов экономически
нецелесообразна. Запасы, не целесообразные для отработки по
технико-экономическим причинам. Прогноз запасов, не целесообразных для
отработки, производится на вскрытой части поля - непосредственно по данным
геологической документации горных выработок, на невскрытой - на основе
обобщения результатов геологоразведочных и шахтно-геологических работ,
выполняемых маркшейдерско-геологической службой шахты.
Балансовые - запасы, разработка
которых экономически целесообразна сейчас.
, т (1.1)
Zб1=2400*7500*1,7*1,3=28080000 т.,
Zб2=2400*7500*1,3*1,3=30420000 т.,
Zб3=2400*7500*1,9*1,3=44460000 т.,
Zб4=2400*7500*0,2*1,3= 21060000т.,
где S - размер шахтного поля по простиранию, м;
Н - размер шахтного поля по падению, м; п - число рабочих пластов
в шахтном поле; mi - мощность i-го рабочего пласта, м; γ - плотность угля i-го рабочего пласта, т/м3. Для
определения промышленных запасов необходимо установить величину потерь по
каждому из пластов по их источникам: общешахтные (в барьерных и охранных
целиках); эксплуатационные и связанные с геологическими нарушениями.
Промышленные запасы - часть балансовых запасов, за исключением потерь, которая
может быть выдана непосредственно на поверхность и отгружена потребителю,
определяются по формуле:
, (1.2)
Zпр1=28080000-35886240=7806240 т.,
Zпр2=30420000-39106080=8686080т.,
Zпр3=44460000-41030920=3429080т.,
Zпр4=21060000-28978560=7918560т.,
где Zn - проектные потери угля, т.
Проектными потерями является часть балансовых
запасов угля, которая по проекту предусматривается к безвозвратному оставлению
в недрах при отработке всех запасов данной шахты. Они складываются на основании
частных видов потерь: общешахтных, эксплуатационных и вблизи геологических
нарушений.
т, (1.3)
Zп1=15568800+16848000+3469440=35886240т.,
Zп2=16993600+18252000+3860480=39106080т.,
Zп3=24650600+2664000+13716320=41030920т.,
Zп4=12823200+12636000+3519360=28978560т.,
где Zоб - общешахтные потери; Zг. н. - потери, связанные с
геологическими нарушениями пластов; Zэксп - эксплуатационные потери
К общешахтным потерям относятся запасы в
целиках под сохраняемыми объектами на поверхности, в барьерных целиках, в
целиках, служащих для охраны капитальных горных выработок. Эти потери зависят
от схемы вскрытия и конкретных горно-геологических условий месторождения.
Общешахтные потери слагаются из потерь угля
в барьерных (Z1) и охранных (Z2) целиках.
Барьерные целики оставляют у границ
шахтного поля, чтобы исключить возможность вскрытия старых затопленных горных
выработок соседних шахт. Ширина барьерных целиков (I) определяется по
эмпирическим формулам или условно принимается равной 50 м. Охранные целики
оставляют для предотвращения разрушений технологического комплекса на
поверхности, промышленных зданий и сооружений, а также природных объектов.
Потери в охранных целиках при пологом залегании пластов условно составляют 1 -
2%, при крутом - 2 - 4% от балансовых запасов.
(1.4)
Zоб1=1528800+14040000=15568800, т.
Zоб2=1783600+15210000=16993600, т.
Zоб3=2420600+22230000=24650600, т.
Zоб4=1146600+10530000=12823200, т.
, т. (1.5)
Z1.1=2*50 (7500+ (2400-2*50)) *1,2 *1,3=1528800, т.
Z1.2=2*50 (7500+ (2400-2*50)) *1,3 *1,4=1783600, т.
Z1.3=2*50 (7500+ (2400-2*50)) *1,9 *1,3=2420600, т.
Z1.3=2*50 (7500+ (2400-2*50)) *0,1 *1,3=1146600, т.
, т (1.6)
Z2.1= (0,01/0,02) *28080000 =14040000, т.
Z2.2= (0,01/0,02) *30420000 =15210000, т.
Z2.3= (0,01/0,02) *44460000=22230000т.
Z2.4= (0,01/0,02) *21060000=10530000, т.
Потери в целиках вблизи геологических нарушений (Z3) определяются характером
и числом нарушений, их ориентированием по отношению к простиранию пласта. Их
величина в среднем равна 1 - 1,5 % балансовых запасов:
, т (1.7)
Z3.1= (0,01/0,015) *28080000 =16848000т
Z3.1= (0,01/0,015) *30420000=18252000, т
Z3.3= (0,01/0,015) *44460000 =2664000, т
Z3.4= (0,01/0,015) *21060000=12636000, т
К эксплуатационным потерям относятся потери в
целиках и угольных пачках, связанные с системой разработки и технологией горных
работ, и определяются на основе расчетных нормативов. В исключительных случаях,
при сложных горно-геологических условиях залегания пластов (значительные
колебания угла падения, наличие складок и т.п.), величину эксплуатационных
потерь можно принимать исходя из уровня фактических эксплуатационных потерь.
Эксплуатационные потери (Zэ) включают потери по
площади в целиках у горных выработок и по мощности в пачках угля в кровле и
почве пласта, а также потери угля в забоях и при транспортировании. С учетом
потерь от неправильного ведения горных работ величину эксплуатационных потерь
можно принимать: для пластов тонких - 6 - 8 %, средней мощности - 8 - 10 %,
мощных пологих - 10 - 12 %, мощных крутых - 15 - 18 % балансовых запасов за
вычетом общешахтных потерь и потерь около геологических нарушений:
, т (1.9)
Zэксп1= (28080000-15568800-16848000) *0,8=3469440, т.
Zэксп2= (30420000-16993600-18252000) *0,8=3860480, т.
Zэксп3= (44460000-24650600-2664000) *0,8=13716320, т.
Zэксп4= (21060000-12823200-12636000) *0,8=3519360, т.
где Кэп - коэффициент эксплуатационных потерь;
принимается для тонких и весьма тонких пластов - 0,08; средней мощности - 0,12;
мощных пологих - 0,15; мощных крутых - 0, 20.
Промышленные запасы шахтного поля:
, т. (1.10)
Zпр1=28080000-35886240=7806240 т.,
Zпр2=30420000-39106080=8686080т.,
Zпр3=44460000-41030920=3429080т.,
Zпр4=21060000-28978560=7918560т.,
Степень полноты извлечения запасов полезного ископаемого
характеризуется коэффициентом извлечения Сизвл,
который показывает, какую часть балансовых запасов добывают, т.е. выдают на
поверхность. Величина его зависит от горно-геологических условий и колеблется в
широких пределах. По итоговым данным определяется коэффициент извлечения
запасов угля из недр:
(1.11)
Cизвл1= 
Cизвл2=
Cизвл3= 
=0,75
Cизвл4= 
При ориентировочных расчетах рекомендуется этот коэффициент
принимать равным:
для тонких пластов-0,9-0,92;
для пластов средней мощности-0,85-0,88;
для мощных пологих пластов-0,82-0,85;
для мощных крутых пластов-0,75-0,8.
По геологическим данным общий балансовый запас
шахты составлят 
124020000т.
Общие промышленые потери составляют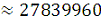
т.
Общешахтные потри составляют
47851200т.
шахтное поле уголь шахта
2.
Определение производственной мощности и срока службы шахты
Различают производственную и проектную
мощности шахты.
Производственная мощность
шахты - максимально возможная в реальных условиях добыча полезного
ископаемого установленного качества в единицу времени (сутки, год),
определяемая исходя из условий производства в рассматриваемом периоде на основе
наиболее полного использования оборудования, рационального режима работы,
эффективной технологии и организации производства при соблюдении требований
безопасности и правил технической эксплуатации. На производственную мощность
оказывают влияние величина запасов, число и мощность угольных пластов, состав и
свойства вмещающих пород, газоносность месторождения и другие факторы.
Производственная мощность шахты складывается из добычи угля в очистных забоях и
получаемой при проведении пластовых выработок. При оптимизации производственной
мощности шахты наиболее выгодное ее значение выбирают, исходя из требований
максимально возможной производительности труда и минимальных затрат на добычу
1т промышленных запасов.
Проектная мощность шахты является
производственным параметром, определение которого требует обязательного учета
конкретных горно-геологических характеристик, а также спроса на конечную
продукцию и перспектив дальнейшего развития шахты.
Проектная мощность - потенциально возможный
объем добычи угля, предусмотренный утвержденный проектом и соответствующий
заложенным решениям по технике, технологии и организации работ, измеряется в
т/год или т/сут.
Количество угля, добываемого в очистном
забое в течении определенного времени называют нагрузкой на очистной
забой.
Срок службы предприятия (шахты) - время, в течение которого
будут извлекаться промышленные запасы.
При проектировании, когда известны горно-геологические и
горнотехнические условия шахты-новостройки, проектную мощность рекомендуется
определить по формуле:
, тыс. т/год, (2.1)
, тыс. т/год
где
- надежность технологической схемы шахты,
включая очистной забой, подземный транспорт, проветривание, околоствольный
двор, подъем, поверхность шахты и пр. При индивидуальной (не блоковой) схеме
отработки запасов, панельной подготовке шахтного поля и подъеме угля по
вертикальным стволам
= 0,75 ¸
0,85=0,88
- коэффициент, учитывающий соотношение количества рабочих пластов
в шахтном поле (
) и находящихся в одновременной отработке
(
):
(2.2)
- коэффициент, учитывающий влияние уровня нагрузки на очистной
забой, условий его работы и пр.:
, (2.3)
- коэффициент, учитывающий условия работы забоев, характерные для
условий данного месторождения:
, (2.4)
- коэффициент, учитывающий устойчивость кровли: при неустойчивой
равен 0,06, средней устойчивости - 0,08, устойчивой - 0,1;
- коэффициент, учитывающий крепость
почвы: при
4 - 0,01, при
= 5 6 - 0,015, при
³7 - 0,02;
- коэффициент, учитывающий нарушенность запасов:
, (2.5)
- объем нарушенных запасов, тыс. т;
- промышленные запасы шахтного поля, тыс.
т;
- коэффициент, учитывающий влияние газа
на мощность шахты,
, (2.6)
- естественная газоносность угольных пластов, м3/т;
- коэффициент дегазации угольных пластов;
- относительная газообильность,
характерная для шахт бассейна, м3/т. с. д.;
. - суммарная мощность одновременно разрабатываемых пластов, м;
- суммарная мощность всех пластов в
шахтном поле, принятых к разработке, м;
- коэффициент, учитывающий глубину разработки
, (2.7)
- расстояние от поверхности до верхней границы шахтного поля, м;
- то же, до нижней границы шахтного поля,
м.
Величина нагрузки на очистной забой
принимается или рассчитывается по формуле
, т/мес., (2.8)
где
- длина очистного забоя, м;
- средняя мощность одновременно
разрабатываемых пластов, м;
- суточное подвигание очистного забоя, м;
- коэффициент извлечения угля по системе
разработки.
Полученный результат следует привести в соответствие с
параметрическим рядом мощностей шахт (0,9; 1, 20; 61,5; 1,8; 2,1; 2,4; 2,7-;
3,0; 3,3; 7 3,6; 3,9; 4,2; 4,5; 4,8; 5,1; 3 5,4; 55,7; 6,0; 6,39; 6,6; 6,9;
7,2; 795. млн. т/год) с учетом расчетного срока службы шахты.
Расчетная проектная мощность шахты
будет находиться между двумя смежными значениями мощности шахты
параметрического ряда:
(2.9)
Для того чтобы сделать выбор из двух значений параметрического
ряда (
или
), необходимо определить срок службы шахты по формуле:
, лет (2.10)
, лет
, лет,
, лет
где
,
- суммарное время на освоение проектной мощности и свертывание
добычи. Принимается в пределах 5-6 лет.
Из полученных значений
и
, с одной стороны, и
и
, с другой, выбирается такое, которое в большей степени отвечает
рекомендациям норм технологического проектирования.
По геологическим данным мощность шахты составляет
тыс. т/год, срок службы шахты при этом
составляет 
60 лет.
3. Вскрытие
шахтного поля
3.1 Выбор
способа вскрытия шахтного поля.
Вскрытием месторождения или шахтного поля
называют проведение комплекса вскрывающих выработок, которые открывают доступ с
поверхности к полезному ископаемому и обеспечивают возможность проведения
основных подготовительных выработок.
Различают схему и способ вскрытия шахтного поля.
Схемой вскрытия называют
пространственное расположение сети вскрывающих выработок (стволы, штольни и
др.) относительно границ шахтного поля (графическое изображение способа
вскрытия).
Способом вскрытия - расположение системы
вскрывающих выработок в шахтном поле относительно горизонтальной плоскости с
учетом их функционального назначения
Основными факторами, определяющими выбор
схемы и способа вскрытия шахтного поля или его части, являются: число
вскрываемых пластов, угол падения пластов, свойства вмещающих пород, расстояние
между пластами, мощность наносов или покрывающей непродуктивной толщи, наличие
плывунов и других водоносных пород, нарушенность месторождения, глубина
разработки, газоносность пластов, рельеф местности, производственная мощность
шахты, размер шахтного поля, срок службы шахты, уровень развития
горнодобывающей техники, подготовка шахтного поля, системы разработки и схемы
вентиляции и др.
Способ вскрытия должен обеспечивать: рациональную разработку
шахтного поля в течение всех этапов работы шахты и получение стабильной
проектной добычи угля на каждом этапе; минимальный объем вскрывающих горных
выработок; минимальные первоначальные капитальные затраты на вскрытие
месторождения и строительство шахты; однотипность транспорта по всем горным
выработкам; возможность периодического обновления горного хозяйства шахты;
выемочный горизонт с достаточно большими запасами угля, чтобы промежутки между
углубками стволов или изменениями элементов схемы были по возможности более
длительными; концентрацию производства и грузопотоков и преимущественное
применение конвейерного транспорта; максимальную производительность труда при
минимальной себестоимости 1т угля; эффективное проветривание горных выработок.
Вскрытие шахтных полей или их частей требует тщательного и
своевременного их исследования и может осуществляться в зависимости от
горно-геологических условий залегания пластов и горнотехнических условий
различными способами. Целесообразность применения того или иного способа
вскрытия также должна быть обоснована экономическим сравнением различных
вариантов, наиболее соответствующих данным условиям.
К основным вскрывающим выработкам относятся
вскрывающие выработки, имеющие непосредственный выход на земную поверхность
(стволы, штольни, шурфы).
К вспомогательным - вскрывающие выработки, не
имеющие непосредственного выхода на земную поверхность (квершлаги, гезенки,
орты, слепые стволы).
Стволы или проходятся сразу на всю глубину шахтного
поля, или постепенно углубляются по мере развития горных работ. В первом случае
имеет место одногоризонтное вскрытие, во втором - многогоризонтное. Преимуществами
вертикальных стволов по отношению к остальным вскрывающим выработкам
являются большое сечение, что очень важно для подачи свежего воздуха в шахту;
меньшие расходы по обслуживанию и поддержанию; возможность совмещения в одном
стволе всех необходимых транспортных операций.
Недостатки вертикальных стволов: большая стоимость
проходки, цикличность подъемных операций; сложность процесса углубки.
Наклонные стволы с конвейерной доставкой
имеют большую пропускную способность, лимитируемую лишь производительностью
установленных конвейеров и временем их непрерывной работы.
Недостатки наклонных стволов: большая, чем у вертикальных
стволов, протяженность и трудоемкость проходки в сложных горно-геологических
условиях.
Существует несколько основных схем вскрытия шахтного поля
(рис.1):
I. Для пологих и наклонных пластов: - вертикальными стволами и
капитальными квершлагами с отработкой всех запасов в шахтном поле на одном
подъемном горизонте бремсберговыми бесступенчатыми уклонными полями; -
вертикальными стволами и погоризонтными квершлагами (при значительных размерах
шахтного поля по падению) с отработкой запасов бремсберговыми и уклонными
полями на каждой выемочной ступени; - главными наклонными и вспомогательными
стволами и капитальными квершлагами.. Для крутонаклонных и крутых пластов -
вскрытие вертикальными стволами и этажными квершлагами.
II. Вскрытие наклонными стволами применяют при
необходимости полной конвейеризации доставки угля на поверхность или при
небольших наносах и размерах шахтного поля.. При горном рельефе поверхности вне
зависимости от угла падения пластов - штольнями.
Кроме перечисленных основных схем вскрытия в каждом
конкретном случае могут рассматриваться и другие прогрессивные, технически
осуществимые схемы вскрытия или их комбинации.
При одногоризонтных способах вскрытия запасы шахтного поля
отрабатываются на один транспортный горизонт, время службы которого
соответствует сроку существования шахты. При многогоризонтных способах вскрытия
запасы отрабатываются на несколько транспортных горизонтов.
Рациональный вариант вскрытия шахтного поля выбирается с
учетом большого количества факторов, главными из которых являются:
геологические, гидрогеологические, топографические, гидрографические,
горнотехнические и экономические.
Выбранный вариант вскрытия должен
удовлетворять требованиям безопасности и удобства ведения работ, быстрого
введения шахты в эксплуатацию, обеспечения заданной производственной мощности,
соответствовать принятой схемы подготовки и разработки угольных пластов.
Правильный выбор схемы и способа вскрытия,
рациональное расположение поверхностных сооружений и подъездных путей,
представляет серьезную инженерную задачу, от решения которой зависит нормальная
деятельность и экономика предприятия.
Выбор схемы и способа вскрытия ведется
последовательно выполняемыми этапами:
вычерчивание в масштабе геологического разреза и
гипсометрический план участка;
проводится конструирование и выбор технически целесообразных
для заданных условий вариантов схем вскрытия;
производится деление шахтного поля на этажи, если схема
подготовки этажная;
проводится деление по падению на выемочные горизонты, если
это позволяют размеры шахтного поля
проводится определение наивыгоднейшего для каждого из
выбранных вариантов параметров вскрытия (размеры вскрывающих выработок, их
длину и количество, вид транспорта, типы крепи);
производится определение по отобранным вариантам основных
объемов первоначальных работ, а также объемы работ будущих периодов по
учитываемым эксплуатационным расходам;
определяется время на сооружение тех объектов шахты, которыми
отличаются сравниваемые варианты;
производится выбор одного варианта
вскрытия путем сравнительной технико-экономической оценки конкурирующих
вариантов.
Рис.3.1 Классификация схем и способов вскрытия
шахтных полей
Рис.3.2 Схемы вскрытия пластового месторождения
По геологическим данным вскрытие шахтного поля проводилась
вертикальными стволами с горизонтальными вспомогательными выработками
(квершлаг).
4. Выбор
способа и схемы подготовки шахтного поля
Выбор схемы подготовки и порядка отработки частей шахтного
поля осуществляется исходя из горно-геологических и горно-технических условий
угольного месторождения, системы разработки угольных месторождений,
технологической схемы выемочного участка и основных его параметров (Lст., lл и т.д.), способа
транспортировки угля, материалов и оборудования и людей, задел по обеспечению
заданного объема добычи. При этом необходимо ориентироваться на схемы
подготовки, рекомендованные параметры технологического проектирования и
передового производственного опыта.
4.1 Выбор
схемы и способа подготовки шахтного поля
На основании исходных данных и норм технологического
проектирования выбирается схема подготовки шахтного поля, в зависимости от
размеров шахтного поля по простиранию и по падению. Выбор схемы подготовки
шахтного поля, ее параметров и конструктивных элементов относится к основным
технико-экономическим вопросам, решаемым при проектировании новых шахт и
горизонтов и планировании горных работ на действующих угольных шахтах.
Неправильное решение этого вопроса ведет к удорожанию добычи 1 т угля,
значительному увеличению первоначальных капитальных затрат на строительство
шахт, ухудшению условий поддержания выработок, увеличению пожароопасности и
другим неблагоприятным последствиям.
Подготовкой шахтного поля называют определённый
порядок проведения выработок, осуществляемый после вскрытия шахтного поля и
обеспечивающий возможность подготовки выемочных полей.
Подготовка выемочного поля (участка) при делении шахтного
поля на панели заключается в проведении и оборудовании всех подготовительных
выработок в ярусе, панели (при горизонтальном залегании пластов), включая
проведение и оборудование ярусных штреков и разрезных печей. Подготовка
выемочного поля при делении шахтного поля на этажи включает в себя работы по
проведению и оборудованию всех подготовительных выработок в выемочном поле,
начиная с участковых бремсбергов или уклонов и заканчивая разрезными печами.
Расположение основных подготовительных выработок относительно
пласта и его элементов. По этому признаку каждая группа способа подготовки
разделяется на подгруппы: индивидуальный - пластовый, полевой,
пластово-полевой; групповой - полевой, пластово-полевой.
При пластовом способе подготовки все основные
подготовительные выработки проводят и поддерживают по каждому из
разрабатываемых пластов полезного ископаемого. Основные его достоинства -
простота технологии проведения выработок и планировки горных работ, меньший
выход породы, чем при полевом и пластово-полевом способах; недостатки -
значительные потери угля в целиках и затруднения с поддержанием выработок.
Пластовую подготовку необходимо применять для разработки пластов, неопасных по
внезапным выбросам и самовозгоранию угля, при боковых породах, смещение которых
не превышает допустимых запасов на осадку контура выработок, соответствующих
податливости применяемой крепи.
Схема подготовки - характерное расположение
объединенных с учетом функционального назначения в единый комплекс
подготавливающих выработок, обеспечивающих деление шахтного поля на готовые к
выемке части.
Существует 4 вида схем подготовки:
. Панельная схема подготовки шахтного поля.
. Комбинированная схема шахтного поля.
. Погоризонтная схема подготовки шахтного поля.
. Этажная схема подготовки шахтного поля.
Этажная схема подготовки шахтного поля - это совокупность
выработок, разделяющих шахтное поле на этажи. Область применения α>25°. Но если размер по простиранию до 4000м, и отрабатываются
газоносные пласты, что требует проведения минимального количества горных
выработок, то этажная схема может применяться и при α<25°. Высота этажа при α<55° 800-400м, при α>55° 120-150м.
Отличительной особенностью этажной схемы подготовки является
деление шахтного поля на этажи, вертикальная высота которых одинакова по всему
простиранию пласта в шахтном поле. Разные по времени отработки этажи могут
иметь различную вертикальную высоту. В зависимости от мощности и газоносности
пластов, склонности угля к самовозгоранию, устойчивости вмещающих пород,
опасности в отношении горных ударов, геологической нарушенности, а также
производственной мощности шахты и других факторов вертикальная высота этажа
принимается не менее 100-120 м.
При этажной схеме подготовки от околоствольного двора или
места пересечения пласта капитальным квершлагом проводят главный откаточный
штрек (пластовый или полевой) обычно на длину до 150м, а из него в середине
шахтного поля - капитальный бремсберг с одним-двумя ходками для доставки грузов
и передвижения людей. От капитального бремсберга в обе стороны проводят этажные
откаточные и вентиляционные штреки с просеками (параллельными штреками),
которые сбивают разрезными печами на расстоянии не менее 40 м от ходков (при
прямом порядке отработки) или у границ этажа (при обратном порядке). После
отработки запасов в первом этаже ведут очистную выемку во втором.
При отработке запасов последнего этажа в бремсберговой части
шахтного поля приступают к подготовке этажей в его уклонной части. С этой целью
на наклонную высоту этажа проводят капитальный уклон и два ходка, остальные
подготовительные выработки проводятся по уже описанной схеме. Схемы
проветривания уклонной части шахтного поля должны быть такими, чтобы свежий
воздух для проветривания подавался из нижней точки уклонного поля по специально
пройденным или предназначенным для этого выработкам.
В основном она используется при разработке пластов с углами
падения более 25°. В некоторых случаях она применяется на пологих пластах: при
вскрытии шахтных полей наклонными стволами, пройденными по пласту; при вскрытии
вертикальными стволами полей с небольшими размерами по простиранию; при
разработке сильногазоносных пластов.
Достоинства этажной схемы подготовки: простота проветривания;
небольшой объем подготовительных выработок; возможность быстрого ввода шахты в
эксплуатацию.
Недостатки - отсутствие возможности для широкого развития
фронта очистных работ, необходимость в проведении этажных откаточных штреков на
всю длину шахтного поля и поддержании их в течение всего периода отработки
этажа.
Этажная система разработки "лава - этаж": 1 -
наклонные выработки; 2 - этажный конвейерный штрек; 3 - просек; 4 - очистной
забой (лава); 5 - этажный вентиляционный штрек; 6 - разрезная печь
Таблица 3.1
Классификация схем и способов подготовки шахтных полей
Схема
подготовки
|
Способ
подготовки
|
Классификационные
признаки
|
Часть шахтного
поля, полученная в результате его деления системой основных подготовительных
выработок, и направление отработки ее относительно элементов залегания пласта
|
Число
разрабатываемых пластов, обслуживаемых одной системой основных
подготовительных выработок на откаточном горизонте
|
Расположение
основных подготовительных выработок относительно пласта и его элементов
|
Погоризонтная
|
Индивидуальный
|
Пластовый
|
|
|
Полевой
|
|
|
Пластово-полевой
|
|
Групповой
|
Полевой
|
|
|
Пластово-полевой
|
Панельная
|
Индивидуальный
|
Пластовый
|
|
|
Полевой
|
|
|
Пластово-полевой
|
|
Групповой
|
Полевой
|
|
|
Пластово-полевой
|
Этажная
|
Индивидуальный
|
Пластовый
|
|
|
Полевой
|
|
|
Пластово-полевой
|
|
Групповой
|
Полевой
|
|
|
Пластово-полевой
|
По геологическим данным способ подготовки шахтного поля будет
проходить при пластовым способе и этажной схемы. Так как простота проветривания;
небольшой объем подготовительных выработок; возможность быстрого ввода шахты в
эксплуатацию.
5.
Определение основных параметров подготовительной выработки
Искусственные сооружения и недрах земли
или на ее поверхности, предназначенные для разработки месторождений полезных
ископаемых или других технических целей и представляющие собой полость в
массиве, называются горной выработкой.
Горные работы - комплекс работ
(процессов) по проведению, креплению и поддержанию горных выработок, а также
выемке и транспортировке полезного ископаемого.
В зависимости от народнохозяйственного
значения различают выработки разведочные, используемые для разведки
месторождений полезных ископаемых, и эксплуатационные, используемые для
эксплуатации месторождений.
К разведочным горным выработкам относятся
траншеи, шурф, штольни, буровые скважины, разведочные квершлаги, штреки,
уклоны, скаты, гезенки и др. Целью проведения разведочных выработок является
опр. деление контуров месторождения полезного ископаемого или определенной его
части, установление элементов и условий залегания полезного ископаемого, его
качества и запасов, а также получение сведений о возможности и целесообразности
промышленной разработки месторождения.
Эксплуатационные горные
выработки - выработки, необходимые для разработки месторождения.
Эксплуатационные выработки, кроме своего основного назначения, выполняют
функции детальной разведки, уточняя и дополняя горно-геологическую
характеристику разрабатываемого месторождения. Подземные эксплуатационные
выработки делятся на вскрывающие, подготовительные и очистные.
К вскрывающим горным выработкам
относятся основные выработки, вскрывающие запасы в шахтном поле (стволы,
штольни, главные квершлаги).
Подготовительные
выработки - выработки, проводимые при подготовке отдельных частей шахтного
поля к очистной выемке. По назначению их подразделяются на выработки главных
или основных направлений (основные и полевые штреки, участковые бремсберги и
уклоны) и прочие подготовительные выработки.
Очистными называют выработки, служащие
для непосредственной добычи полезного ископаемого.
Форма поперечного сечения горной выработки
зависит от назначения срока службы, свойств пересекаемых ею пород, размеров
поперечного сечения, материала и конструкции крепи. По форме сечения различают
выработки: прямоугольную, трапециевидную, арочную, сводчатую, подковообразную с
обратным сводом и без него, а также полигональную, круговую и др. Тип крепи
подготовительных выработок выбирается с учетом запаса сечения на осадку.
Наибольшее распространение получили
трапециевидная и арочная крепи. Площадь поперечного сечения подготовительных
выработок рассчитывается исходя из условий нормальной работы средств транспорта
(электровозы, вагонетки, конвейеры и др.), числа рельсовых путей, наличия
зазоров, предусмотренных "Правилами безопасности в угольных шахтах"
(ПБ) и подачи к очистному забою с допустимыми скоростями необходимого
количества воздуха. Так как все выработки в той или иной мере зависят от
очистных работ, следует учитывать необходимый запас сечения и податливость
крепи на величину ожидаемых смещений пород.
В выработке различают площадь
сечения в свету (площадь по внутреннему контуру выработки), вчерне
(площадь по наружному контуру крепи, включая затяжку боков и кровли
выработки), в проходке (площадь контуру пород, которую принимают
на 3-5% больше площади вчерне), а также размеры выработки до осадки и после
осадки крепи.
Прогрессивными технологическими схемами
разработки пластов на угольных шахтах в выработках, примыкающих к очистному
забою, рекомендуется применять металлические податливые крепи арочной,
трапециевидной или подковообразной формы. Характеристики типовых сечений
различных крепей представлены в табл.5.2.
Площадь поперечного сечения подготовительных выработок в
свету определяется расчетом по факторам допустимой скорости воздушной струи
(проветривания), габаритных размеров подвижного состава и оборудования с учетом
минимально допустимых зазоров, величины усадки крепи после воздействия горного
давления и безремонтного их содержания в течение всего периода эксплуатации.
Ширина выработки в свету, исходя из габаритных размеров применяемого в
выработке оборудования и минимально допустимых зазоров по ПБ, определяется по
формулам.
Расчитываем размеры выработки:
двухпутевая
м; (5.2), B=0,25+1,5+0,2+1,5+0,7=4,15, м;
Типовые сечения подготовительных выработок
Типо-размер
|
Ширина
выработки на высоте 1,8м от почвы (тротуара)
|
Площадь сечения
выработки, м2
|
|
|
в свету после
осадки
|
в свету до
осадки
|
в проходке
|
Арочная форма выработки
|
I II
III IV V
|
2,76 4,04 4,40 4,98 6,72
|
7,1 11,2 12,7
15,5 25,5
|
8,5 12,8 14,5
18,9 29,7
|
10,8 15,9 17,9
22,8 33,2
|
Трапециевидная
форма выработки
|
VI
VII VIII IX
|
2,76 4,04 4,40
6, 20
|
6,9 9,6 10,6
15,6
|
8,7 12,2 13,3
19,7
|
10,4 14,0 15,3
22,9
|
Требуемое сечение выработки в свету по фактору проветривания
проверяется по формуле:
, м2, (5.5)
м2,
где
- суточная нагрузка на лаву, т/сут;
- относительная газообильность лавы, м3/т.
с. д;
- коэффициент запаса воздуха,
; VД - максимально допустимая по ПБ скорость движения воздуха
по выработке, м/с (6 м/с - для подготовительных выработок). Принимается большее
из двух сечений, определенных по габаритам транспорта и по фактору проветривания.
Поперечные сечения горных выработок должны соответствовать типовым сечениям.
При проведении подготовительных выработок предусматривается максимально
возможное применение комбайнового способа проходки или буровзрывного способа на
базе буропогрузочных машин.
Рис.5.2 Схема к определению поперечного сечения
конвейерного штрека
Рассчитываем коэффициент присечки боковых пород:
, м2. (5.7)

, м2.
где
- сечение выработки в проходке, м2;
- сечение выработки по углю, м2.
Площадь угольного забоя равна:
, (5.6)
Кпр=
100%=76,9%
Минимальная высота выработки определяется исходя из размеров
подвижного состава, высоты верхнего строения пути и высоты подвески
коммуникаций и принимается по табл.5.3.
Проведение подготовительных выработок и их последующая
эксплуатация предусматривают расположение в ней, кроме транспортных средств,
следующих коммуникаций: противопожарного и дегазационного (в случае
необходимости) трубопроводов, силовых кабелей, светильников, трубопровода
сжатого воздуха, вентиляционной трубы.
При проведении подготовительной выработки по пласту угля забой
располагают в сечении штрека так, чтобы пласт занимал, как можно большую
площадь сечения и была обеспечена наиболее простая перегрузка угля с конвейера
лавы на штрековое транспортное средство. В этой связи, целесообразна подрывка
почвы пласта.
По данным подготовительной выработки размеры выработки составляет
3,35 м. Сечение выработки в свету составляет 34,65м2. При этом
коэффицент присечки составляет 76,9%.
6. Выбор и
обоснование системы разработки
Под системой разработки угольных месторождений
понимается определенный порядок проведения подготовительных и очистных
выработок в пределах выемочного поля, участка, столба, увязанных в пространстве
и во времени
Система разработки должна обеспечивать безопасное ведение
работ, экономичность разработки, минимальные потери полезного ископаемого.
Рис.6.1 Требования к системам разработки угольных
месторождений
Различают сплошную, столбовую и комбинированную
системы разработки.
Таблица 6.1
Отличительные признаки систем разработки
Отличительные
признаки систем разработки
|
Виды систем
разработки
|
|
сплошные
|
столбовые
|
комбинированные
|
Порядок
проведения подготовительных выработок в выемочном поле (участке, столбе) по
отношению к подвижной плоскости очистного забоя
|
Не разделены во
времени и пространстве
|
Разделены во
времени и пространстве
|
Комбинированное
|
Условия
поддержания выемочных выработок
|
Позади забоя
лавы в зоне интенсивного влияния очистных работ
|
Впереди забоя
лавы в массиве угля или в зоне установившегося горного давления
|
Направление
движения транспортирования угля и очистного забоя
|
Противоположное
|
Совпадает
|
Совпадает или
не совпадает
|
Направление
движения отработанной струи воздуха и очистного забоя
|
- " -
|
Совпадает или
не совпадает
|
То же
|
Рис. 6.3 Элементы и параметры систем разработки
угольных месторождений
Таблица 6.2.
Классификация систем разработки угольных месторождений
Система
разработки
|
Классификационные
признаки
|
Разделение
пласта по мощности на слой
|
Длина очистного
забоя
|
Порядок
проведения подготовительных выработок в выемочном поле (участке, столбе) по
отношению подвижной плоскости очистного забоя
|
Направление
перемещения в пространстве очистного забоя в выемочном поле (участке, столбе)
по отношению к элементам залегания пласта
|
Без разделения
на слои
|
С длинными
забоями
|
Одновременный
(сплошная)
|
По простиранию
|
|
|
|
По падению
|
|
|
|
По восстанию
|
|
|
|
По диагонали
|
|
|
Последовательный
(столбовая)
|
По простиранию
|
|
|
|
По падению
|
|
|
|
По восстанию
|
|
|
|
По диагонали
|
|
|
Одновременно-последовательный
(комбинированная)
|
По простиранию
|
|
|
|
По падению
|
|
|
|
По восстанию
|
|
|
|
По диагонали
|
|
С короткими
забоями
|
Одновременный
(камерная)
|
По простиранию
|
|
|
|
По падению
|
|
|
|
По восстанию
|
|
|
|
По диагонали
|
|
|
Последовательный
(короткими столбами)
|
По простиранию
|
|
|
|
По падению
|
|
|
|
По восстанию
|
|
|
|
По диагонали
|
|
|
Одновременно-последовательный
(камерно-столбовая)
|
По простиранию
|
|
|
|
По падению
|
|
|
|
По восстанию
|
6.2
Сплошные системы разработки
Сущность сплошных систем разработки состоит в одновременном
ведение очистных и подготовительных работ в выемочном поле (участке, столбе),
при этом лава и забои подготовительных выработок движутся в одном направлении,
как правило, от бремсбергов, уклонов или промежуточных квершлагов к границам
выемочного поля (участка, столба). Принципиальная сущность сплошных систем
определяет ряд важных особенностей, главными из которых являются: обеспечение
постоянного динамического равновесия между очистными и подготовительными
работами; поддержание выработок позади очистного забоя в зонах интенсивного
влияния опорного давления.
Сплошные системы разработки могут применяться при любой схеме
подготовки: этажной, панельной и погоризонтной. В зависимости от размеров
выемочного поля по падению пласта в пределах этажа или яруса могут быть
одна-две лавы. Сплошные системы разработки делятся на системы лава-этаж (ярус)
и системы с делением этажа (яруса) на подэтажи (подъярусы).
Пространственная взаимосвязь очистных и подготовительных
выработок обусловливает различные варианты сплошных систем. Опережение
откаточного штрека должно составлять 150-200м, но в каждом случае оно
определяется исходя из конкретных горно-геологических и горно-технических
условий.
Транспортирование угля при наличии в этаже одной лавы происходит
по откаточному штреку. При наличии в этаже двух лав транспортирование может
производиться следующим образом: из верхней лавы уголь транспортируется по
промежуточному (подэтажному) штреку, а из нижней лавы - по откаточному
(конвейерному) штреку.
Лавы при сплошных системах проветриваются обособленно или
последовательно с подсвежением струи.
Для изоляции подэтажей при обособленном проветривании лав
между ними оставляют целик угля. При склонности пласта к самовозгоранию струи
разделяют бутовой полосой, которая возводится между вентиляционным и откаточным
подэтажными штреками. Средняя мощность пластов, отрабатываемых сплошной
системой разработки, для разных бассейнов различна и изменяется от 0,93 до
1,5м. Длина лавы при этих системах составляет в среднем 110-170м.
Областью применения сплошных систем разработки являются в
основном тонкие пласты и реже пласты средней мощности с любыми углами падения,
при отсутствии геологических нарушений, сверхкатегорные по газу и склонные к
внезапным выбросам угля и газа, пласты с пучащими породами почвы, с породами
кровли, позволяющими проводить и поддерживать выработки в зоне влияния
выработанного пространства. Наиболее широко эти системы разработки применяются
в Донецком бассейне (Украина), реже в Кузнецком, Печорском и др.
Достоинствами этих систем разработки являются: быстрый
ввод очистных выработок в работу; малые первоначальные затраты на подготовку
участка; небольшой длины тупиковые выработки, что особенно важно при разработке
весьма газоносных пластов.
Недостатки: сложность поддержания выемочных выработок,
подвергающихся влиянию очистных работ, и в этой связи большие затраты на их
ремонт; отсутствие предварительной разведки пласта подготовительными
выработками, а отсюда опасность неожиданной встречи с геологическими нарушениями;
очистные и подготовительные работы не разделены во времени и пространстве, что
приводит к организационным помехам; ограничение нагрузки на забой по газовому
фактору.
7.
Определение основных параметров системы разработки. Расчет нагрузки на очистной
забой и обоснование длины лавы
К основным параметрам, характеризующим систему разработки,
относят длину очистного забоя, длину столба (выемочного поля), размеры
охранных целиков, разделяющих выемочные выработки, а также нагрузку на
очистной забой.
Длину очистного забоя (лавы) принимают
исходя из длины в поставке комплекта механизированного очистного комплекса или
на основании расчета. В глубоких шахтах длину очистного забоя проверяют по
условию передачи тепла от горных пород и угля шахтному воздуху. В конечном
счете принимают наименьшую длину забоя из сравниваемых значений.
Выбранную длину очистного забоя на каждом пласте
согласовывают с общей линией действующих на шахте очистных забоев. При выборе оптимальной
длины лавы, в основном ориентируются на максимальную нагрузку на забой и
прогрессивные технологические схемы разработки пластов на угольных шахтах и
рекомендации бассейновых научно-исследовательских угольных институтов.
Длину выемочного поля при делении этажа на два
подэтажа и столбовой системе разработки, этажной подготовке и группировании
крутых пластов, а также размер панели по простиранию определяют исходя
из минимизации объемов подготавливающих и выемочных выработок.
Ширину целиков, оставляемых между выработками, обычно
принимают исходя из следующих требований. Ширина целиков, оставляемых между
панельными наклонными выработками не должна превышать 30м, ширина целиков,
предназначенных для охраны панельных бремсбергов (уклонов) со стороны
выработанного пространства 40м, ширина околоштрековых целиков в пределах этажа
15-25м, ширина целиков между длинными столбами, расположенными по падению, на
пластах с углами падения до 120 в пределах 5 - 15м; ширина целиков
между полосами, расположенными по падению, при щитовой выемке крутых мощных
пластов принимается равной 10-20м.
Нагрузка на очистной
забой
- количество полезного ископаемого добываемого при одном работающем очистном
забое, является производной величиной от длины лавы при прочих одинаковых
условиях. Длина лавы является одним из основных параметров системы разработки,
влияющим на технико-экономические показатели работы не только участка, но и
всей шахты. Так, от длины лавы зависят удельная протяженность (на 1000т добычи)
проводимых подготовительных выработок и нагрузка на забой, транспортную
выработку, пласт, увеличивается концентрация горного производства и т.д. Однако
чрезмерное увеличение длины лавы вызывает ряд технических и организационных
затруднений в доставке материалов и оборудования, в передвижении по лаве
рабочих, особенно при небольшой мощности пласта.
Чрезмерно короткие лавы приводят к
увеличению себестоимости 1т угля за счет роста расхода на работы вне лавы:
проведение и поддержание выемочных штреков, транспортировка угля по выработкам
и т.д. Однако при применении современных механизированных комплексов длина лавы
часто предопределяется его конструктивной длиной, поэтому важно определять
нагрузку на очистной забой как производную величину от длины лавы.
Рациональную длину лавы для различных горно-геологических
условий и средств механизации рассчитывают по технологическим и организационным
факторам и проверяют по фактору проветривания. Для комплексно-механизированных
очистных лав длину рассчитывают:

где nс - количество смен по
добыче в сутки; Т - длительность смены, мин.; Тпз - время на
подготовительно-заключительные операции в смену, мин.; Тпз =
15-20мин.; Тп - время учитываемых технологических перерывов в смену,
Тп = 20-30мин.; То - время на отдых, То =
15-20 мин.; Кц - коэффициент надежности технологической схемы
участка; Vр - рабочая скорость подачи комбайна, принимается в соответствии с
табл.1; tв - время на вспомогательные операции по длине лавы, tв = 0,1 мин/м; nц - количество циклов
выемки в течение суток. Коэффициент надежности технологической схемы
определяется по формуле
Коэффициент надежности технологической схемы определяется по
формуле:

где коэффициенты надежности технического
оборудования: Кк - коэффициент готовности комбайна; Ккр - коэффициент
готовности механизированной крепи;
Кз. к - коэффициент готовности
забойного конвейера; Кк. с - коэффициент готовности крепи
сопряжения; Кл. к - коэффициент готовности ленточного конвейера; nк - число конвейеров,
установленных в транспортной выемочной выработке.
Коэффициенты надежности технического
оборудования изменяются в пределах 0,85-0,9.
Длина очистного забоя проверяется по
фактору проветривания в соответствии с зависимостью
, м

,9, м
где Sс - проходная площадь
сечения для струи воздуха, м2; vв - допустимая по ПБ
скорость движения воздуха по лаве, м/с; d - допустимая по ПБ
концентрация метана на исходящей струе лавы, % (1%); Кв - коэффициент,
учитывающий движение воздуха по выработанному пространству за крепью выработки
(при управлении кровлей полным обрушением принимается равным 1,2-1,4); qл - метановыделение из
лавы в исходящую струю воздуха, м3/т суточной добычи; δ - коэффициент, учитывающий предварительную дегазацию пласта; Ке
- коэффициент, учитывающий естественную дегазацию пласта и других источников
выделения метана в период отсутствия добычных работ (для столбовых систем
разработки при управлении кровлей полным обрушением принимается равным 0,8 -
1,2); nц - количество циклов в смену; r - ширина захвата
рабочего органа комбайна, м; m - мощность пласта, м; γ - плотность угля, т/м3.
Площадь сечения лавы, свободная для
прохода воздуха, при применении механизированных крепей определяется по
формулам из табл.1.
Для расчета нагрузки на
комплексно-механизированный очистной забой в табл.1 приведены характеристики
оборудования комплексов, которое может быть использовано на выемочном участке в
зависимости от конкретных горно-геологических условий.
Нагрузка на очистной забой определяется в соответствии с
принятой длиной:
, т/сут.
Q=0,63∙315,9∙1,9∙1,3∙4·3∙0,95=5603,92,
т/сут.,
где С - коэффициент извлечения угля в
лаве, С = 0,95-0,98.
Среднюю нагрузку на лаву увязывают со скоростью крепления
очистного забоя и пропускной способностью доставочных средств. В газовых шахтах
нагрузку проверяют по газовому фактору, определяя максимально возможную
нагрузку при данном уровне метановыделения.
В проекте принимается меньшее из полученных значений. В
случае, если длина лавы получена меньше, чем стандартная длина принятого
компании, необходимо предпринять меры для доведения длины до оптимального
значения. Это, в первую очередь, искусственная дегазация пласта и вмещающих
пород и выработанных пространств. Дегазация - это комплекс
технологических процессов, направленных на предотвращение выделения метана в
атмосферу горных выработок путем его извлечения, улавливания и изолированного
отвода по трубам шахтной дегазационной системы, связывание и нейтрализации
метана в угленосной толще.
Нагрузка на очистной забой составаляет5603,92, т/сут., при длине
лавы 
м
Комбайн очистной КДК 700
Комбайн оснащен бесцепной системой подачи
с частотным регулированием скорости подачи и может применяться в составе
механизированных комплексов типа МДТМ, КМ138, КМ144Б, КМ174, КМ700800,
оснащенных скребковыми конвейерами КСД27, КСД29, КСД210, А30, СПЦ271, СПЦ230,
СП301М90, СП326. Комбайн имеет захват 0,63; 0,8 м и может оснащаться шнеками
диаметром 1800, 2000, 2200 мм.
Основные технические и эксплуатационные
особенности комбайна КДК700 высокая надежность и ресурс, обеспечиваемые
конструктивными параметрами комбайна и использованием высокопрочных материалов;
повышение производительности комбайна до
24 т мин;
увеличение энерговооруженности привода
резания до 710 кВт;
увеличение средней наработки на отказ за
счет применения электрического авторегулируемого привода системы подачи взамен
гидравлического;
обеспечение обслуживания очистных забоев
длиной до 350 м и повышение коэффициента машинного времени вследствие
ускоренного выполнения концевых операций;
снижение трудоемкости технического
обслуживания и текущих ремонтов за счет доступности и удобства
монтажа-демонтажа отдельных блоков без нарушения соединений основных частей
комбайна;
наличие диагностической информации для
сокращения времени поиска повреждений в оборудовании комбайна.
Основные конструктивные особенности
комбайна КДК700 корпус комбайна выполнен в виде единой силовой рамы коробчатой
формы;
основные узлы комбайна выполнены в виде
блочной конструкции;
преобразователь частоты регулируемого
электропривода механизма подачи установлен на комбайне;
наличие системы охлаждения редукторов
режущей части и электрооборудования;
расчетная долговечность силовых элементов
редукторной группы 15000 часов;
комбайн имеет дистанционное, со штрекового
пульта, или беспроводное, с носимого пульта управление, оборудован системой
диагностики и контроля состояния основных узлов, индикации на дисплее
технологической и диагностической информации.
Технические характеристики
Параметр
|
Значение
|
Применяемость
по вынимаемой мощности пласта, м
|
2,0-4,3
|
Производительность,
т/мин
|
- при
сопротивляемости угля резанию 120 кH/м
|
24
|
- при
сопротивляемости угля резанию 240 кH/м
|
18
|
- при
сопротивляемости угля резанию 360 кH/м
|
12
|
Суммарная
номинальная мощность приводов, кВт
|
860
|
в т. ч.:
привода исполнительных органов
|
2х355
|
привода подачи
|
2х60
|
привода насоса
гидросистемы
|
30
|
Номинальное
напряжение, В
|
1140
|
Максимальная
рабочая скорость подачи, м/мин, не менее
|
20
|
Максимальное
тяговое усилие системы подачи, кH, не менее
|
600 (2х300)
|
Средний ресурс
до капитального ремонта, тыс. т
|
1500-2000
|
Габаритные
размеры:
|
- длина по
осям шнеков, мм
|
10450
|
- ширина, мм
|
2020
|
- высота по
корпусу в зоне крепи, мм
|
1500-1700
|
Масса, т., не
более
|
45,0
|
Механизированная крепь MVPO 3500
Секции крепи предназначены для добычи угля методом на завал в
тонких и средне мощных угольных пластах мощностью с 0,8 до 2,1 метров в
различных геологических условиях.
Эти опорные обвальные секции оснащены двумя парами
гидравлических стоек с механическими телескопическими наконечниками.
Регулировка наклона верхняка является разницей по высоте
закрепления забойных и завальных стоек.
Управление отдельных секций - гидравлическое импульсное с
управляемым боковым кожухом.
Ширина отдельных секций 1500 мм. Секции крепи имеют на
верхняке гидродомкраты для центрилировки секции.
Поднимание основания секции производится автоматически при
передвижке секции рычаговым механизмом.
Основные технические параметры:
Рабочий диапазон:
,85 - 2,0 м
Грузоподъемность секции:
000 - 3 500 кН
Количество стоек в секции:
шт
Макс. угол наклона пласта по простиранию:
± 35°
Макс. угол наклона пласта по падению:
± 25°
Основные технические параметры
Исполнение 0,75/2,1
Минимальная высота секции, мм 750
Максимальная высота секции, мм 2100
Рабочий диапазон, мм 850-2000
Максим, угол наклона пласта по простиранию, град. ±35
Максим, угол наклона пласта по падению, град. ±25
Расстояние между секциями, мм 1500
Ширина секции, мм 1460
Макс. сопротивление секции, кН/м2 635
Мин. сопротивление секции, кН/м2 525
Шаг передвижки секции, мм 650-800
Максимальная грузоподъемность секции, кН, 3500
Минимальная грузоподъемность секции, кН 3000
Усилие для передвижения секции, кН 392
Усилие для передвижения конвейера, кН 231
Активный забойный козырек, Да
Рабочее давление, МПа 32
Количество стоек в секции, шт. 4
Грузоподъемность стойки, кН 875
Диаметр стойки, мм 180
Давление на почву, МПа 1,35
Количество функций, со
Масса секции, кг 10700
Горнотехнические показатели работы шахты
1. Количество пластов, n 4 шт
. Угол падения пластов, α, 18 град
. Мощность пластов, m, 1,2; 1,3; 1,9; 0,9; м
. Размеры шахтного поля, м
По простиранию, S 7500 м
По падению, H2400 м
. Площадь шахтного поля, 18000000 км2
. Промышленные запасы, 27839960 Млн. т
. Балансовые запасы, 124020000 Млн. т
. Потери по видам:
Общешахтные потери 47851200 Млн. т
Промышленные потери 
Млн. т
. Проектная мощность шахты,
Млн. т / г
. Полный срок службы шахты, 60 лет
. Нагрузка на очистной забой, 342630 т/ сут
. Число очистных забоев, 2 шт
. Способ вскрытия: Вертикальными стволами, с горизонтальными
вспомогательными выработками.
. Схема вскрытия Вертикальные стволы и квершлаг
. Способ подготовки Пластовый
. Схема подготовки Этажная
. Система разработки Групповой
Заключение
Технологическая схема шахты - совокупность горных
выработок, поверхностных зданий и сооружений с размещенными в них машинами и
механизмами, совместная работа которых должна обеспечивать эффективную и
безопасную добычу угля.
Основа технологической схемы горнодобывающего предприятия -
взаимосвязанное решение вопросов вскрытия, подготовки шахтного поля, системы
разработки и механизации очистных работ, транспорта, подъёма, вентиляции,
энергоснабжения, водоотлива. В связи с этим технологическая схема
горнодобывающего предприятия реализуется в виде цепи последовательно
осуществляемых процессов, которая включает ряд звеньев - основных,
непосредственно создающих поток полезных ископаемых, и вспомогательных,
обеспечивающих его функционирование в заданном режиме. Процессы (и их
составляющие), а также звенья для ряда технологических схем горнодобывающего
предприятия могут быть одинаковыми (способ отбойки, доставки, транспорт,
подъём, аккумулирующие и перепускные выработки, системы канализации энергии и
др.). Реализация вспомогательных процессов (вентиляции, энергоснабжения и
водоотлива) в значительной мере связана с теми же выработками, в которых
осуществляются основные процессы. Главные факторы, определяющие формирование технологической
схемы горнодобывающего предприятия: форма, размеры и глубина залегания полезных
толщ, наличие полезных ископаемых различных видов и сортов, производственная
мощность рудника (шахты), параметры выемочной единицы, тип применяемого
оборудования, очерёдность разработки отдельных участков месторождения,
особенности использования выработанного пространства.
Основные элементы Т.С. Ш.:
очистные забои;
подготовительные забои;
система транспортирования полезного ископаемого;
система доставки людей, материалов и оборудования;
система вентиляции;
система водоотлива;
система дегазации угольных пластов;
шахтный подъем;
поверхностный технологический комплекс;
Главным звеном всего производственного процесса добычи угля
на шахте является очистная выемка, поэтому наряду со своевременным воссозданием
необходимого фронта очистных забоев всеми технологическими звеньями шахты
должна быть обеспечена непрерывная и ритмичная работа забоев на основе научной
организации производства.
Вскрытие шахтных полей производится вертикальными и
наклонными стволами или штольнями, а также их комбинацией. Подготовка к
очистной выемке осуществляется проведением от главных штреков панельных
откаточных и вентиляционных штреков, делящих шахтное поле на отдельные панели.
Её непрерывность достигается использованием выемочных комбайнов в комплексе с
телескопическими (или самоходными) ленточными конвейерами, а в лавах - очистных
комплексов, включающих очистной комбайн, забойный конвейер и механизированную
крепь, в сочетании с конвейерным транспортом по остальным выработкам (включая
наклонный ствол).
Технологическая схема горнодобывающего предприятия
реализуется и оценивается исходя из условия обеспечения установленной
производственной мощности предприятия на основе решений, применяемых по основным
и вспомогательным производственным процессам. Её обоснование в целом
производится исходя из обеспечения: равномерной выдачи продукции; разделения
всего производственного процесса на отдельные рабочие процессы, выполняемые
специализированными звеньями, совмещёнными в той или иной мере во времени;
возможности резервирования; работы всей технологической схемы в соответствии с
заданным темпом как единой производственной единицы; эффективного
функционирования всей технологической схемы путём ликвидации "узких
мест" (даже за счёт мероприятий, не экономичных для каждого звена в
отдельности).
Для формирования и оценки технологической схемы
горнодобывающего предприятия определяют мощность технологических звеньев -
количество и производительность очистных и подготовительных забоев, число и
ёмкость транспортных единиц, типоразмеры оборудования подземного бункерного
комплекса, производительность подъёма. При этом мощность каждого
технологического звена понимается как наибольшая возможная его
производительность при отсутствии помех со стороны других звеньев, а мощность
действующей рудной шахты при данной технологической схеме горнодобывающего
предприятия - как максимальная добыча полезных ископаемых установленного
качества в единицу времени при наиболее полном использовании средств и
возможностей организации производства.
На угольных шахтах технологическая схема горнодобывающего
предприятия характеризуется высоким уровнем комплексной механизации очистных и
подготовительных работ, широким применением конвейерного транспорта угля и
производительных средств колёсного транспорта, эффективной вентиляцией
выработок, использованием средств механизации и автоматизации на
вспомогательных процессах и для обеспечения безопасных и комфортных условий
труда. Доставка людей, материалов и оборудования к рабочим местам производится
колёсным или монорельсовым транспортом.
В угольных шахтах России, КНР и стран Европы получили
распространение технологические схемы горнодобывающего предприятия с длинными
очистными забоями, оборудованными комбайнами флангового действия или стругами,
механизированной или стоечной крепью, скребковыми конвейерами. Управление
горным давлением осуществляется, как правило, полным обрушением пород кровли.
Закладка выработанного пространства применяется при разработке мощных крутых
пластов, представленных самовозгорающимися углями, и для охраны объектов на
земной поверхности. Подготовка очистных забоев производится одиночными или
спаренными выработками, погашаемыми вслед за очистным забоем или используемыми
повторно при отработке соседней лавы. Горизонтальные магистральные выработки
проводят также одиночными или спаренными, чаще полевыми.
Список
используемой литературы
1. Борисов
С.С. Горное дело. - М.: Недра, 2008. - 417с. Бурчаков А.С., Харченко В.А. Выбор
технологических схем угольных шахт. - М.: Недра, 1975. - 274 с.
2. Бурчаков
А.С., Жежелевский Ю.А., Ярунин С.А. Технология и механизация подземной
разработки пластовых месторождений. - М.: Недра, 1989. - 431 с.
. Васючков
Ю.Ф. Горное дело. - М.: Недра, 2010. - 315 с.
. Егоров
П.В., Бобер Е.А., Кузнецов Ю.Н. и др. Основы горного дела. Учебник для вузов. -
М.: Изд-во МГГУ, 2009. - 408 с.
. Казаков
В.Б. Вскрытие, подготовка и системы разработки пластовых месторождений. Учебное
пособие для вузов. М.: 2011 г., - 177 с.
. Килячков
А.П. Технология горного производства. - М.: Недра, 1992. - 415 с.
. Михеев
О.В., Виткалов В.Г., Козовой Г.И., Атрушкевич В.А. Подземная разработка
пластовых месторождений. Теоретические и методические основы проведения
практических занятий. М.: МГГУ. - 2009г. - 487 с.