Расчет привода ленточного конвейера
Содержание
Введение
. Расчет
энергокинематических параметров привода
.1 Выбор
электродвигателя
.2 Определение
передаточных ступеней привода
.3 Определение
чисел оборотов валов
.4 Определение
вращающихся моментов на валах
.5 Определение
угловых скоростей
. Расчет
клиноременной передачи
. Выбор
твердости, термообработки, материала колес
. Определение
допускаемых напряжений
. Проектный
расчет редуктора
. Проверочный
расчет редуктора
. Определение
консольных сил
. Проектный
расчет валов
. Предварительный
выбор подшипников
. Выбор
муфты
. Определение
реакций в подшипниках. Построение эпюр изгибающих и крутящих моментов
. Проверочный
расчет подшипников
. Проверочный
расчет валов
. Выбор
шпонок. Проверочный расчет шпонок на смятие
. Выбор
смазочного материала
. Посадка
подшипников
Введение
В данной работе требуется спроектировать горизонтальный одноступенчатый
редуктор. Закрытая косозубая передача, левый наклон зубьев. Открытая передача -
клиноременная нормального сечения Б. В редукторе находится 2 пары роликовых
конических подшипников на тихоходном и быстроходном валах, установленных по
схеме враспор.
Подшипники смазываются картерным способом в результате разбрызгивания
масла вращением колеса. Смазывание зацепления осуществляется жидким маслом
картерным непроточным способом (окунанием). Масло заливают в редуктор через
люк, а сливают - через специальное отверстие сбоку, закрываемое пробкой с
конической резьбой. Для отслеживания уровня масла, применяется круглый
маслоуказатель. Для обеспечения точности сборки крышки и основания и исключения
возникновения несоосности резьбовых отверстий применяют установочные штифты.
Чтобы обеспечить легкую разборку редуктора применяют отжимной винт.
Кинематическая схема
Привод ленточного конвейера
1) Эл. Двигатель
) Клиноременная передача
) Цилиндрический редуктор (косозубый)
) Муфта
) Барабан конвейера
Производство мелкосерийное
Исходные данные
Окружное усилие на барабане
Ft, кН
|
2,35
|
Окружная скорость ленты
конвейера V, м/с
|
0,85
|
Диаметр барабана Dб,
м
|
0,25
|
Срок службы редуктора Lh,
ч
|
12000
|
Синхронная частота вращения
двигателя, об/мин
|
750
|
. Расчет силовых и кинематических параметров привода
.1 Выбор электродвигателя
Требуемая мощность рабочей машины:
вых=Ft·V=
Общий коэффициент полезного действия привода:
hобщ =hр.п. · hред. · hопор · hмуф
hр.п. = 0,96
- КПД ременной передачи
hред.= 0,97 -
КПД цилиндрической передачи, hопор = 0,99-
КПД подшипников качения, hмуф 0,98 -
КПД соединительной муфты
hобщ = hрем · hр.п. · hопор · hмуф = 0,94*0,97*0,99*0,98=0,9035
Требуемая мощность двигателя
Выбираем
двигатель 4АМ112МВ8У3, Pном= 3кВт , nном= 700 об/мин
1.2
Определение передаточных ступеней привода
Частота
вращения на выходе (барабана конвейера):
Частота
вращения на входе (электродвигателя):
Общее
передаточное отношение:
общ = Uр.п. * Uред.ред= Uобщ /
Uр.п. = 10,78 / 3 = 3,59 (редуктора)
р.п.
= 3(ременной передачи)
1.3
Определение чисел оборотов валов
(вал
двигателя)
(быстроходный
вал редуктора)
(тихоходный
вал редуктора)
1.4
Определение крутящих моментов на валах привода

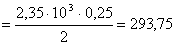
(вал
рабочей машины)
=
(тихоходного
вала)
(
быстроходного вала)
(вал
двигателя)
1.5
Определение угловых скоростей
c-1(вал
двигателя)
c-1
(быстроходный вал редуктора)
c-1
(тихоходный вал редуктора)
c-1(вал
рабочей машины)
Параметр
|
Электродвигатель (Входной
вал)
|
Быстроходный вал
|
Тихоходный вал
|
Барабан (Выходной вал)
|
|
|
|
|
|
n , (мин-1)
|
700
|
233,33
|
64,94
|
64,94
|
ω,
(с-1)
|
73
|
24,4
|
6,8
|
6,8
|
T ,( Н*м)
|
29,89
|
86,08
|
299,72
|
299,75
|
U
|
|
Uр.п. = 3
|
Uред = 3,59
|
Uобщ = 10,78
|
. Расчет клиноременной передачи
при Рном= P1 = 3 кВт и nном= 700 об/мин
- принимаем клиновой ремень нормального сечения Б. d1 min = 125 мм
(минимально допустимый диаметр ведущего шкива) d1 = 140 мм
(расчетный диаметр ведущего шкива)
Диаметр ведомого шкива:
ε = 0,02 - коэффициент скольжения
2 = 400 мм
(стандарт)
Фактическое передаточное
число:
отклонение Uф от
заданного U:
Ориентировочное межосевое
расстояние:
Н = 10,5 мм - высота сечения
клинового ремня
Расчетная длина ремня:
мм
= 1600 мм (стандарт)
Значение межосевого
расстояния по стандартной длине:
Угол обхвата ремнем ведущего
шкива:
Скорость ремня:
Частота пробега ремня:
Допускаемая мощность передаваемая
клиновым ремнем:
[Pп]=[P0]
· Ср · Сa · Сl
· Сz
[P0]=1,61 кВт
допускаемая приведенная мощность, передаваемая одним клиновым ремнем
СР=0,9 коэффициент
динамичности нагрузки и длительности работы
Сa=0,89 коэффициент угла обхвата
Сl=0,96
коэффициент влияния отношения расчетной длины к стандартной, l/l0=0,71
Сz= 0,9
коэффициент числа ремней в комплекте клиноременной передачи
[Pп]= 1,61 ·
0,9 · 0,89 · 0,96 · 0,9 = 1,1 кВт
Число клиновых ремней:
Принимаем 3 клиновых ремня.
Сила предварительного
натяжения:
Окружная сила передаваемая
комплектом клиновых ремней:
Сила натяжения ведущей ветви:
1= F0
= 199,8 +
= 297,8H
Сила натяжения ведомой ветви:
2=F0
=199,8-
= 101,8H
Сила давления ремней на вал:
Fоп=2*z*F0*sin
=2*3*199,8*sin
=1118,8H
Проверочный расчёт
σmax= σ1+σи+σv ≤ [σp] = 10
Н/мм2,
σ1 = F0/А+
F1/(2zА),
σ1 =
199,8/138 + 297,8/(2*3*138) =1,45+0,71 = 2,16
, А=138мм2;
σи=Еи*h/d1,σи=80*10,5/140=840/140=6
(Н/мм2),
где Еи - модуль
продольной упругости при изгибе, Еи=80 мм2;
σv=ρ*V2*10-6, ρ=1250 кг/мм3 , σv= 1250*(5,1)2*10-6=0,03(Н/мм2);
Тогда σmax= 2,16 + 6 + 0,03 = 8,19 ≤ [σp], [σp] = 10
(Н/мм2).
Параметры клиноременной
передачи
|
Значение
|
|
Значение
|
Тип ремня
|
Б
|
Частота пробегов ремня,U
|
3,2(с-1)
|
Сечение ремня
|
Нормальное
|
Диаметр ведущего шкива d1
|
140
|
Количество ремней, z
|
3
|
Диаметр ведомого Шкива d2
|
400
|
Межосевое расстояние, а
|
351,9
|
Максимальное напряжение σmax, Н/мм2
|
8,19
|
Длина ремня ,l
|
1600 мм
|
Предварительное натяжение
ремня F0, , Н/мм2
|
199,8
|
Угол обхвата малого шкива, α1
|
137,9
|
Сила давления ремня на вал
Fоп, Н
|
1111, 8
|
3. Выбор твердости, термообработки, материала колес
привод
вал консольный скорость
Выбираем материал: сталь 40Х.
Термообработка - улучшение.
Интервал твердости зубьев шестерни: НВ1 = 269…302
Интервал твердости зубьев колеса: НВ2 = 235…262
Средняя твердость для шестерни: НВ1ср=285,5
Средняя твердость для колеса: НВ2ср= 248,5
Механические характеристики стали для шестерни:
sв = 900 Н/мм2,
s-1 = 410 Н/мм2 , sт = 750 Н/мм2
Механические характеристики стали для колеса:
sв = 790 Н/мм2,
s-1 = 375 Н/мм2 , sт = 640 Н/мм2
Предельное значение диаметра и толщины обода или диска шестерни:пред
= 125 мм, Sпред = 80 мм
Предельное значение диаметра и толщины обода или диска колеса:пред =
200 мм, Sпред = 125 мм
4. Определение допускаемых напряжений
Коэффициент долговечности для зубьев шестерни:
HO1
= 25 млн. циклов,1 = 573 ω1Lh
= 573* 24,4 *12000 = 168 млн. циклов
т.к.
N1 >NHO1 , то КНL1 = 1
Коэффициент
долговечности для зубьев колеса:
HO2
= 16,5 млн. циклов,2 = 573 ω2Lh
= 573* 6,8 *12000 = 47 млн. циклов
т.к.
N2 >NHO2 , то КНL2 = 1
Допускаемое
контактное напряжение для зубьев шестерни:
[s]H1= КНL1 * [s]HО1
[s]HО1 = 1,8 * НВср1 + 67 = 1,8 *285,5 + 67 = 580,9
Н/мм2
[s]H1 = 1* 580,9 = 580,9 Н/мм2
Допускаемое
контактное напряжение для зубьев колеса:
[s]H2 = КНL2 * [s]HО2
[s]HО2 = 1,8 * НВср2 + 67 = 1,8 *248,5 + 67 = 514,3
Н/мм2
[s]H2 = 1* 514,3 = 514,3 Н/мм2
Допускаемое
контактное напряжение для передачи:
[s]H= min ([s]H2, [s]H1) = 514,3 Н/мм2
Определение
допускаемых напряжений изгиба.
Коэффициент
долговечности для зубьев шестерни:
FO1
= 4 млн. циклов,1 = 573 ω1Lh
= 573* 24,4 *12000 = 168 млн. циклов
т.к.
N1 >NFO1 , то КFL1 = 1
Коэффициент
долговечности для зубьев колеса:
HO2
= 4 млн. циклов,2 = 573 ω2Lh
= 573* 6,8 *12000 = 47 млн. циклов
т.к.
N2 >NFO2 , то КFL2 = 1
Допускаемое
напряжение на изгиб для зубьев шестерни:
[s]F1 = КFL1 * [s]FО1
[s]FО1 = 1,03 * НВср1 = 1,03 * 285,5 = 294,1 Н/мм2
[s]F1 = 1* 293,55 = 294,1 Н/мм2
Допускаемое
напряжение на изгиб для зубьев колеса:
[s]F2= КFL2 * [s]FО2
[s]FО2 = 1,03 * НВср2 = 1,03 *248,5 = 255,96 Н/мм2
[s]F2= 255,96 = 255,96 Н/мм2
Таблица
Элемент передачи
|
Марка стали
|
Dпред
|
Термообработка
|
HB1cp
|
σв
|
σ-1
|
[σ]Н
|
[σ]F
|
|
|
Sпред
|
|
HB2cp
|
Н/мм2
|
Шестерня
|
40Х
|
125
|
Улучшение
|
285,5
|
900
|
410
|
580,9
|
294,1
|
Колесо
|
40Х
|
125
|
Улучшение
|
248,5
|
790
|
375
|
514,3
|
255,96
|
. Проектный расчет редуктора
Межосевое расстояние:
Ка
- вспомогательный коэффициент, для косозубой передачи Ка = 43
ψа = 0,3
коэффициент ширины венца колеса для шестерни= 3,59 передаточное число редуктора
Т2
= 299,72 Н·м вращающий момент на тихоходном валу
[s]H= 514,3 Н/мм2, допускаемое контактное
напряжение колеса с менее прочным зубом
КНβ = 1 коэффициент неравномерности нагрузки зуба
аw = 130мм (стандарт)
Модуль зацепления:
m= 5,8 - вспомогательный коэффициент для косозубых
передач
мм -
делительный диаметр колеса2 = ψa · аw
= 0,3 * 130 = 39 = 40мм - ширина венца колеса
[s]F= 255,96 Н/мм2- допускаемое напряжение изгиба
колеса с менее прочным зубом
мм
мм (гост)
Угол
наклона зубьев для косозубых передач:
βmin=
arcsin
= arcsin
= 10,1º
Суммарное число зубьев шестерни и колеса:
Принимаем
Действительная
величина угла наклона зубьев:
βmin=arccos
=12,3329 º
Определяем
число зубьев шестерни:
Определяем
число зубьев колеса
Фактическое
передаточное число:
Отклонение
фактического от заданного передаточного числа:
Определяем
фактическое межосевое расстояние:
мм
Определяем
фактические основные параметры передачи:
Диаметр
делительной окружности шестерни:
мм
Диаметр
делительной окружности колеса:
мм
Диаметр
вершин зубьев шестерни и колеса:
мм
мм
Диаметры
впадин шестерни и колеса:
мм
мм
Ширина
венца колеса и шестерни:
мм
мм
Параметр
|
Шестерня
|
Колесо
|
Диаметр
|
Делительный
|
57,32
|
202,68
|
|
Вершин зубьев
|
61,32
|
206,68
|
|
Впадин зубьев
|
52,52
|
197,88
|
Ширина венца
|
44
|
40
|
6. Проверочный расчет редуктора
Межосевое расстояние:
мм
Диаметр заготовки шестерни:пред = 125 мм, Dзаг= da1+6
мм, Dзаг= 61,32 + 6 = 67,32 ммзаг
Dпред ; 67,32
125 - удовлетворяется неравенствопред
=125мм, толщина диска заготовки колеса закрытой передачи Sзаг=b2
+4 мм,заг= 40+4=44 (мм).заг
Sпред ; 44 ≤ 125 -
удовлетворяется неравенство
Контактные напряжения зубьев:
К
= 376 - вспомогательный коэффициент для косозубых передач
Н -
окружная сила в зацеплении
КНα -
коэффициент учитывающий распределение нагрузки между зубьями, зависит от
окружной скорости
=
, м/с
=
= 0,7
1 м/с
9 степень точности
КНα =1,11
КНβ = 1- коэффициент неравномерности нагрузки зуба
КНV=
1,01 - коэффициент динамической нагрузки
[Н/мм2]
Проверка
напряжения изгиба зубьев колеса
F2 - коэффициент формы зуба колеса, определяется
интерполированием в зависимости от эквивалентного числа зубьев колеса
V2
= 106
YF2 = 3,6
-
коэффициент, учитывающий наклон зуба
Проверка
напряжения изгиба зубьев шестерни
F1
- коэффициент учитывающий форму
зуба и концентрацию напряжений, определяется интерполированием в зависимости от
эквивалентного числа зубьев колеса
V1
=
;
V1
= 30
YF1 =
3,8
Проектный
расчет
Параметр
|
Значение
|
Параметр
|
Значение
|
Межосевое расстояние, аw
(мм)
|
130
|
Угол наклона зубьев
|
12,3329
|
Модуль зацепления, m (мм)
|
2
|
Диаметр делительной
окружности, мм: шестерни d1 колеса d2
|
57,32 202,68
|
Ширина зубчатого венца, мм:
Шестерни, b1 Колеса, b2
|
44 40
|
Диаметр окружности вершин,
мм: шестерни dа1 колеса dа2
|
61,32 206,68
|
Число зубьев : Шестерни, z1
Колеса, z2
|
28 99
|
Диаметр окружности впадин,
мм : шестерни df1 колеса df2
|
52,52 197,88
|
Вид зубьев
|
косозубые
|
|
|
Параметр
|
Допускаемое значение
|
Расчётные значения
|
Примечания
|
Контактные напряжения σ , Н/мм2
|
514,3
|
512,4
|
Недогрузка 0,4%
|
Напряжения изгиба σF1, Н/мм2
|
294,1
|
133,2
|
Недогрузка 54,7%
|
Напряжения изгиба σF2, Н/мм2
|
255,96
|
126,2
|
Недогрузка 50,7%
|
. Определение консольных сил
α = 200 - угол зацепления
Окружная сила на колесе (и шестерне):
Н
Радиальная
сила на колесе:
Fr2 = Ft2 * tgα/cos
= 2957,3 * 0,36/0,9769 = 1101,8H
Радиальная
сила на шестерне:r1 = Fr2= 1101,8H
Осевая
сила на колесе:
a2=Ft2*tgβ=646,6Н
Осевая
сила на шестерне:a2= Fa1=646,6Н
Консольная
сила клиноременной передачи:
Fоп=2*z*F0*sin
=2*3*199,8*sin
=1118,8H
Консольная
сила от муфты (на тихоходном валу):
8.
Проектный расчет валов
Выбираем
материал: Сталь 40х
Термообработка:
улучшение
Твердость: НВ = 269…302
Допускаемые напряжения: sв = 900 Н/мм2,
s-1 = 410 Н/мм2 , sт = 750 Н/мм2
Допускаемое напряжение на кручение для шестерни:
[τ]k= 10
Н/мм2
Допускаемое напряжение на кручение для вала колеса:
[τ]k= 20 Н/мм2
вал-шестерня
-я ступень вала под открытую передачу
1 = 36 мм (стандарт)1=(1,2)*d1 -
под шкив
l1=42мм, фаска
с=1,6мм
-я ступень вала2 =
d1 + 2t = 36 + 2 * 2,5 = 41 мм , при t = 2,52 = 40 мм
(стандарт)2=1,5d2=60мм, l2 = 60 (стандарт)
-я ступень вала3 =
d2 + 3,2r = 40 + 3,2 * 2,5 = 48 мм, при r = 2,53 = 48 мм
(стандарт)3 = 84 мм получили конструктивно
-я ступень вала4
=d2 = 40 мм4 = Т + c = 25,5 + 1,6 = 27,1 мм4=
28 мм (стандарт)
вал колеса
-я ступень вала под открытую
передачу
1 = 42 мм (стандарт)1=1,2*d1 -
под полумуфту1=50 мм
-я ступень вала2 =
d1 + 2t = 42 + 2 * 2,8 = 47,6 мм , при t = 2,82 = 50 мм
(стандарт)2= 1,25d2=62,5 мм2= 63 мм
-я ступень вала3 =
d2 + 3,2r = 50 + 3,2 * 3 = 59,6 мм, при r = 33 = 60 мм
(стандарт)3 = 84 мм
-я ступень вала4 =
d2 = 50 мм4 = Т + c = 29,5 + 1,6 = 32 мм (стандарт)
-я ступень вала (распорная
втулка)5 = d3+ 3f, при f = 2,55 = 60 + 3*2 =
82 мм5 = 82 (стандарт)
9. Предварительный выбор
подшипников
Для быстроходного вала:
Если Fa<0,25FR,
то можно выбирать радиальные шариковые однорядные подшипники.a =
646,6 H, FR=1101,8 H, 0,25*FR = 274,5 H, Fa>0,25FR
следовательно тип подшипника - роликовый конический, серия средняя:
Типоразмер - 7308,= 40 мм, D
= 90 мм, T = 25,5 мм, r = 2,5 мм, Cr = 61 кН, Cоr= 46 кН
Для тихоходного вала колеса
берем роликовые конические подшипники средней серии:= 50 мм, D = 110 мм, Т =
29,5 мм, r = 3 мм, Cr = 96,6 кН, Cоr= 75,9 кН
Размеры ступеней валов
редуктора
Вал sв=900H/мм2,
s-1=410Н/мм2
sт=750Н/мм2
|
Размеры ступеней, мм
|
Подшипники
|
|
d1
|
d2
|
d3
|
d4
|
d5
|
Типо-размер
|
d×D×T мм
|
Cr, кН
|
C0r, кН
|
|
l1
|
l2
|
l3
|
l4
|
l5
|
|
|
|
|
Быстроходный
|
36
|
40
|
48
|
40
|
-
|
7308
|
40х90х25,5
|
61
|
46
|
|
62
|
80
|
84
|
28
|
-
|
|
|
|
|
Тихоходный
|
42
|
50
|
60
|
50
|
82
|
7310
|
50х110х29,5
|
96,6
|
75,9
|
|
80
|
78
|
84
|
32
|
10
|
|
|
|
|
10. Выбор муфты
Определение расчетного момента и выбор муфт
Тр = Кр*Т2≤Т
где Кр- коэффициент режима нагрузки, для ленточных конвейеров,
Кр = 1,4; [табл. 10.26]
Т2- вращающий момент на тихоходном валу редуктора, Т2 =
299,72 Н·м;
Тр= 1,4*299,72 = 419,6 Н·м
Выбираем Т = 500 Н·м
Выбираем упругую втулочно-пальцевую муфту.
11. Определение реакций в подшипниках. Построение эпюр
изгибающих и крутящих моментов
1) Тихоходный вал
Дано:
) Вертикальная плоскость
а) определяем опорные реакции, Н;
Проверка:
б) строим эпюру изгибающих моментов относительно оси Х в характерных
сечениях 1..3, Н∙м :
)Горизонтальная плоскость:
а) определяем опорные реакции , Н;
Проверка:
б) строим эпюру изгибающих моментов относительно оси Y в характерных
сечениях 1..4, Н∙м:
) Строим эпюру крутящих моментов ,Н∙м:
Определим суммарные радиальные реакции:
Определяем
суммарные изгибающие моменты в наиболее нагруженных сечениях:
2) Быстроходный вал
Дано:
1. Вертикальная плоскость
а) определяем опорные реакции ,Н :
Проверка
б)
строим эпюру изгибающих моментов относительно оси Х в характерных сечениях 1..4
, Н∙м;
2. Горизонтальная плоскость:
а) определяем опорные реакции , Н :
б)
строим эпюру изгибающих моментов относительно оси Y в характерных сечениях 2..4
, Н∙м;
3. Строим эпюру крутящих моментов ,Н∙м:
Определим суммарные радиальные реакции:
Определяем
суммарные изгибающие моменты в наиболее нагруженных сечениях:
.
Проверочный расчет подшипников
Пригодность
подшипников определяется сопоставлением расчетной динамической грузоподъемности
, Н, с базовой
, Н, или
базовой долговечности
, ч, с требуемой
, ч, по
условиям
или
.
Расчетная
динамическая грузоподъемность
, Н, и
базовая долговечность
, ч, определяются по формулам:
,
где
- эквивалентная динамическая нагрузка, Н
(1/табл.9.1);
-
показатель степени,
, т.к. используются роликовые подшипники;
-
коэффициент надежности. При безотказной работе
;
-
коэффициент, учитывающий качество влияние качества подшипника и качества его
эксплуатации,
- для роликовых конических;
- частота вращения внутреннего кольца подшипника
соответствующего вала, об/мин (табл.1);
Быстроходный
вал:
Подшипник
7308 ГОСТ 27365 - 87:
a) Определяем осевые составляющие радиальных нагрузок:
) По табл. 9.6. определяем осевые нагрузки подшипников.
) Определяем отношения :
) По соотношениям
и
выбираем соответствующие формулы для определения RE;
e) Определяем динамическую грузоподъемность по большей
эквивалентной нагрузке RE;
Подшипники 7308 ГОСТ 27365 - 87 пригодны для работы на быстроходном
валу.) Определяем долговечность подшипника:
Тихоходный
вал:
Подшипник
7310 ГОСТ 27365 - 87:
a) Определяем осевые составляющие радиальных нагрузок:
) По табл. 9.6. определяем осевые нагрузки подшипников.
) Определяем отношения :
) По соотношениям
и
выбираем
соответствующие формулы для определения RE;
e) Определяем динамическую грузоподъемность по большей
эквивалентной нагрузке RE;
Подшипники 7310 ГОСТ 27365 - 87 пригодны для работы на быстроходном
валу.) Определяем долговечность подшипника:
13.
Проверочный расчет валов
Цель
расчета - определить коэффициенты запаса прочности в опасных сечениях вала и
сравнить их с допускаемыми:
,
где
[s] = 1,3…1,5 при высокой достоверности расчета.
Расчетная схема валов.
Опасные сечения вала.
Намечаются два опасных сечения на каждом из валов - на 2-й и 3-й ступени.
Определение источников концентрации напряжений в опасных сечениях.
Опасное
сечение 2-й ступени быстроходных и тихоходных валов определяют два
концентратора напряжений - посадка подшипника с натягом и ступенчатый переход
галтелью
между 2-й и 3-й ступенью с буртиком
;
Концентрация
напряжений на 3-й ступени быстроходного вала определяется соотношением диаметра
впадин шестерни
и диаметра 3-й ступени вала
, т.е.
-
концентратор напряжений шлицы.
Концентрация
напряжений на 3-й ступени тихоходного вала определяется посадкой колеса с
натягом и шпоночным пазом.
Расчет валов на усталостную прочность.
1. Определение
напряжений в опасных сечениях вала,
.
Нормальные
напряжения изменяются по симметричному циклу, при котором амплитуда напряжений
равна расчетным напряжениям изгиба
:
,
где
- суммарный изгибающий момент в рассматриваемом
сечении, Н·м;
- осевой
момент сопротивления сечения вала, мм3.
Касательные
напряжения изменяются по нулевому циклу, при котором амплитуда цикла
равна половине расчетных напряжений кручения
:
,
где
- крутящий момент Н·м;
-
полярный момент инерции сопротивления сечения вала, мм3.
Для
3-й ступени быстроходного вала:
;
;
;
;
Для
2-й ступени быстроходного вала:
;
;
;
;
Для
3-й ступени тихоходного вала:
;
;
;
;
Для
2-й ступени тихоходного вала:
;
;
;
;
2. Определение коэффициентов концентрации нормальных и касательных
напряжений.
,
где
и
-
эффективные коэффициенты концентрации напряжений (1/табл.11.2);
- коэффициент влияния абсолютных размеров поперечного
сечения (1/табл.11.3);
- коэффициент влияния шероховатости (1/табл.11.4);
-
коэффициент влияния поверхностного упрочнения (1/табл.11.5).
Для
валов без поверхностного упрочнения:
-я
ступень быстроходного вала:
Т.к.
концентратором напряжений являются шлицы, то
,
,
,
.
;
;
-я
ступень быстроходного вала:
Для
ступенчатого перехода галтелью:
,
,
,
;
;
;
Для
посадки подшипника с натягом:
и
Учитываем
наиболее опасный концентратор напряжений, т.е. посадку с натягом.
;
;
-я
ступень тихоходного вала:
Для
шпоночного паза, выполненного концевой фрезой:
;
; 
; à
;
;
Для
посадки колеса с натягом:
; и
;
Учитываем
наиболее опасный концентратор напряжений, т.е. посадку с натягом.
;
;
-я
ступень тихоходного вала:
Для
ступенчатого перехода галтелью:
;
;
; à
;
;
Для
посадки подшипника с натягом:
и
;
Учитываем
наиболее опасный концентратор напряжений, т.е. посадку с натягом.
;
;
3. Определение пределов выносливости в расчетном сечении вала.
;
,
где
и
-
пределы выносливости гладких образцов при симметричном цикле изгиба и кручения,
.
-я
ступень быстроходного вала:
;
;
-я
ступень быстроходного вала:
;
;
-я
ступень тихоходного вала:
;
;
-я
ступень тихоходного вала:
;
;
4. Определение коэффициентов запаса прочности по нормальным и
касательным напряжениям.
;
;
-я
ступень быстроходного вала:
;
;
-я
ступень быстроходного вала:
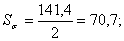
;
-я
ступень тихоходного вала:
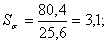
-я
ступень тихоходного вала:


;
5. Определение общего коэффициента запаса прочности в опасных
сечениях.
-я
ступень быстроходного вала:
;
-я
ступень быстроходного вала:
;
-я
ступень тихоходного вала:
;
-я
ступень тихоходного вала:
;
14. Проверочный расчет шпонок на смятие
Условие прочности:
,
где
- окружная сила на шестерне или колесе, Н;
-
площадь смятия,
,
где
- рабочая длина шпонки со скругленными торцами,
;
-
стандартные размеры (1/табл.К42);
-
допускаемое напряжение на смятие,
;
, так как колесо выполнено из стали, и происходит
колебание нагрузки. вращающий момент на валу -M
Диаметр вала d, мм
|
Сечение шпонки, мм
|
Фаска мм
|
Глубина паза, мм
|
Длина шпонки l, мм L=lст-6
|
|
b
|
h
|
|
вала t1
|
Ступица t2
|
|
60
|
12
|
8
|
0,4…0,6
|
5
|
3,3
|
60
|
Т.е.
. Выбранная шпонка удовлетворяет условиям прочности.
Шпонка
под шкив быстроходного вала
:
Таблица
Диаметр вала d, мм
|
Сечение шпонки, мм
|
Фаска мм
|
Глубина паза, мм
|
Длина шпонки l, мм L=lст-10
|
|
b
|
h
|
|
вала t1
|
Ступица t2
|
|
36
|
10
|
8
|
0,4…0,6
|
5
|
3.3
|
53
|
Т.е.
. Выбранная шпонка удовлетворяет условиям прочности.
1) Шпонка под муфту тихоходного вала
:
Диаметр вала d, мм
|
Сечение шпонки, мм
|
Фаска мм
|
Глубина паза, мм
|
Длина шпонки l, мм L=lст-9
|
|
b
|
h
|
|
вала t1
|
ступицаt2
|
|
42
|
12
|
8
|
0,4…0,6
|
5
|
3,3
|
71
|
Т.е.
. Выбранная шпонка удовлетворяет условиям прочности.
.
Выбор смазочного материала
Для
смазывания зубчатого зацепления применим способ непрерывного смазывания жидким
маслом окунанием.
По
тСмазкааблице устанавливаем вязкость масла. При контактных напряжениях в зубьях
sн =512,4 Н/мм2 и скорости до v = 2 м/с.
Выбираем жидкое масло И-Г-А-68 с кинематической вязкостью 68
/с.
Объем
масляной ванны определяем из расчета 0,8 л на 1 кВт передаваемой мощности. Т.к.
передается 3 кВт мощности от двигателя, то объем масла составляет
.
При
окунании в масляную ванну колеса
, где
- модуль зацепления. Т.е.
. Проектируем основание корпуса в соответствии
необходимым уровнем масла для смазывания закрытой передачи.
Контроль
уровня масла осуществляется с помощью круглого маслоуказателя.
Слив
масла осуществляется с помощью пробки с конической резьбой, сливное отверстие
сбоку.
Выбираем
для подшипников смазку жидким маслом. Смазка осуществляется разбрызгиванием с
помощью зубчатого колеса.
16. Посадка подшипников
Для
быстроходного вала
à
Для
подшипника 7308 ГОСТ 27365 - 87:
;
Для
тихоходного вала
Для
подшипника 7310 ГОСТ 27365 - 87:
;
Т.к.
оба неравенства выполняются, то для обоих подшипников для внутреннего кольца
выбираем посадку
, для наружного кольца подшипника выбираем посадку
.