Нормирование точности геометрических параметров изделия 'Редуктор коническо-цилиндрический'
МИНОБРНАУКИ РОССИИ
ГЛАЗОВСКИЙ ИНЖЕНЕРНО-ЭКОНОМИЧЕСКИЙ
ИНСТИТУТ
(филиал) ФГБОУ ВО «ИжГТУ имени М. Т.
Калашникова»
КАФЕДРА «СПЕЦИАЛЬНЫЕ ИНЖЕНЕРНЫЕ
НАУКИ»
КУРСОВАЯ РАБОТА
по дисциплине «Нормирование точности»
ТЕМА Нормирование точности
геометрических параметров изделия «Редуктор коническо-цилиндрический»
Оглавление
Введение
. Нормирование точности гладких соединений
. Контроль размеров гладкими калибрами
. Расчет допусков и посадок подшипников качения на вал и
корпус
. Нормирование точности шпоночного соединения
. Нормирование точности метрической резьбы
. Нормирование точности цилиндрической зубчатой передачи
. Выбор универсальных средств измерения
Заключение
Список литературы
Введение
При создании приводов различных механизмов в условиях современной
промышленности необходимо бывает изменить скорость вращения элементов
трансмиссионных узлов и передаваемых ими крутящих моментов. Для этих целей
служат специальные устройства - редукторы, вариаторы, мультипликаторы.
Основной задачей редуктора является увеличение крутящего момента и в то
же время - уменьшение частоты вращения на выходном валу.
Это обуславливает их необходимость в различных приводах, поскольку там
требуется не только обеспечение заданной скорости, но и создание значительного
тягового усилия, что без редукторов является практически возможным
Цель работы: назначить точность геометрических параметров редуктора в
соответствии с государственными стандартами и тем самым обеспечить его
нормальное функционирование на протяжении срока службы.
Достигнуть поставленной цели можно через решение следующих задач:
. Назначение посадок гладких цилиндрических соединений деталей редуктора.
. Проектирование предельных калибров для контроля размеров деталей,
входящих в состав гладких цилиндрических соединений в условиях серийного
производства.
. Назначение допусков и посадок подшипников качения на валы и корпуса
редуктора.
. Назначение параметров точности деталей, входящих в состав соединений
сложного профиля: резьбовых, шпоночных, и т.п.
. Назначение параметров точности цилиндрических зубчатых передач.
. Выбор и обоснование выбора универсальных средств измерений для контроля
деталей редуктора.
Объектом представленной работы является точность и взаимозаменяемость
изделий машиностроения, а предметом - редуктор
коническо-цилиндрический.
1.
Нормирование точности гладких соединений
Таблица 1.1
Исходные данные по D
Наименование исходных данных
|
Значения исходных данных
|
Номинальный размер соединения
|
D=120 мм
|
Название деталей, входящих в соединение
|
Вал ведомый и колесо зубчатое цилиндрическое
|
Вид посадки
|
|
В соединение входят зубчатое колесо и вал. Выбираем систему отверстия,
т.к. внутренние поверхности получить с заданной точностью сложнее (требуется
специальный инструмент определенного диаметра).
Посадка
считается легкопрессовой посадкой, имеет минимальный
гарантированный натяг. Применяется придля центрирования тяжело нагруженных и
быстро вращающихся крупногабаритных деталей. Требует дополнительного крепления.
) Определение предельных отклонений сопрягаемых деталей
Для отверстия D = 120Н7, TD = 35 мкм, EI = 0, ES =
35 мкм
Для вала d = 120p6, Td = 22 мкм, ei =
37 мкм, es = 59 мкм
Назначена посадка
2) Определение предельных размеров отверстия и вала
Предельные размеры отверстия:
(1.1)
(1.2)
(1.3)
Предельные размеры вала:
(1.4)
(1.5)
(1.6)
3) Расчет характеристик посадки
Максимальный натяг:
(1.7)
Минимальный натяг:
(1.8)
Средний натяг:
(1.9)
Допуск посадки:
(1.10)
(1.11)
Рис.1.1 Схема расположения полей допусков вала и отверстия посадки по D
4) Назначение шероховатости и допусков формы поверхности
Значение шероховатости определяем методом подобия. Для отверстия 7
квалитета диаметром 120 мм значение шероховатости Ra=1,6 мкм, для вала 6 квалитета диаметром 120 мм Ra = 0,8 мкм.
Допуск формы цилиндричности для отверстия L120Н7 Тф= 16 мкм, для вала L120р6 Тф = 10 мкм.
. Контроль
размеров гладкими калибрами
калибр нормирование точность вал
Исходные данные для проектирования калибров
Контролируемая поверхность
|
Контролируемый размер
|
Калибр
|
Отверстие
|
|
Пробка
|
Вал
|
|
Скоба
|
По номинальному размеру вала (отверстия) и по квалитету точности
выбранной посадки найдем отклонения и допуски для калибра-скобы (пробки), а
также на контркалибры К-И, К-ПР, К-НЕ. Допуски и отклонения гладких калибров
определены по ГОСТ 24853-81. Найденные значения указаны в табл. 2.2.
Таблица 2.2
Допуски и отклонения гладких калибров, мкм
Наименование параметров
|
Пробка
|
Скоба
|
|
Обозначение
|
Величина
|
Обозначение
|
Величина
|
Размер сдвига поля допуска
|
z
|
5
|
z1
|
5
|
Размер выхода допуска на износ
|
Y
|
4
|
Y1
|
4
|
Допуск на изготовление калибра
|
H
|
6
|
H1
|
6
|
Допуск на изготовление контркалибра
|
Hp
|
2,5
|
Hp
|
2,5
|
1) Проектирование калибра-пробки
Для калибра-пробки выбираем схему расположения полей допусков для
размеров до 180 мм, квалитетов с 6-го по 8-й
Расчет исполнительных размеров калибра-пробки
Исполнительные и предельные размеры пробки согласно схеме расположения
полей допусков подсчитываются по формулам:
(2.1)
(2.2)
(2.3)
(2.4)
(2.5)
(2.6)
(2.7)
Расчет исполнительных размеров калибра-скобы
(2.8)
(2.9)
(2.10)
(2.11)
(2.12)
(2.13)
(2.14)
Расчет контркалибра для контроля скобы
Для контроля размеров калибров-скоб используют контркалибры.
Исполнительные размеры контркалибров, согласно схеме расположения полей
допусков, подсчитываются по формулам
(2.15)
(2.16)
(2.17)
Рис.2.1 Эскиз контркалибра для скобы
Рис.2.2 Расположение полей допусков для скобы и контркалибра
Рис.2.3. Расположение полей допусков для пробки
2)Технические требования к калибрам
Допуск цилиндричности для пробок ТО = Н/3 = 2 мкм. Шероховатость рабочих
поверхностей: пробки - Ra =
0,16 мкм, скобы Ra = 0,08 мкм.
Шероховатость торцов Ra =
1,6 мкм, шероховатость фасок Ra =
0,8 мкм. Материал калибров - сталь Х, твердость HRC 87…63 обеспечить закалкой.
Рис.2.4 Скоба
Рис.2.5 Пробка проходная
3. Расчет
допусков и посадок подшипников качения на вал и корпус
Таблица 3.1
Исходные данные для подшипников качения
Условное обозначение подшипника
|
7620
|
Радиальная нагрузка R, кН
|
12
|
Коэффициент перегрузки К
|
1,8
|
Вращающаяся деталь
|
Вал
|
Конструкция вала
|
Сплошной
|
Конструкция корпуса
|
Разъёмный
|
1) Расшифровка условного обозначения подшипника
Условное обозначение подшипника - 7620 - подшипники роликовые
радиально-упорные по ГОСТ 27365-87.
- код внутреннего диаметра
- серия по диаметру
- тип подшипника
- конструктивное исполнение
- серия по ширине
- класс точности
Конструктивные размеры подшипника
Рис.3.1 Геометрические параметры подшипника по ГОСТ 27365-87
T=77,5
мм D=215 ммB=73 мм
d=100
мм r =r1=4 мм
Определим отклонения внутреннего и наружного колец подшипника для
нулевого класса:
Вращающаяся деталь - вал, следовательно, внутренне кольцо подшипника
испытывает циркуляционную нагрузку, наружное кольцо испытывает местное нагружение.
2) Расчет интенсивности радиальной нагрузки
Вращающееся кольцо подшипника испытывает циркуляционный вид нагружения,
что требует обеспечения неподвижного соединения с сопрягаемой деталью. Величина
минимального натяга зависит от интенсивности радиальной нагрузки, определяемой
по формуле:
(3.1)
К2 = 1 - коэффициент, учитывающий ослабление посадочного натяга при
пониженной жесткости вала или корпуса (для жесткой конструкции К2 = 1).
К3 = 1 - коэффициент неравномерности распределения радиальной нагрузки
между рядами тел качения в двурядных роликоподшипниках и сдвоенных
шарикоподшипниках при наличии осевой нагрузки на опору (для однорядных
подшипников К3 = 1).
3) Выбор полей допусков
Для циркуляционно-нагруженного кольца подберем посадку в зависимости от
диаметра, интенсивности радиальной нагрузки и класса точности. Посадка
для внутреннего кольца подшипника
Для местно-нагруженного кольца подберем посадку в зависимости от
диаметра, класса точности и величины перегрузки. Посадка для наружного кольца
подшипника
4) Определение предельных размеров
Внутреннее кольцо:
Вал:
Минимальный натяг:
Максимальный натяг:
Средний натяг:
Отверстие корпуса:
Наружное кольцо:
Минимальный зазор:
Максимальный зазор:
Средний зазор:
Рис.3.1 Схема расположения полей допусков внутреннего кольца подшипника и
вала
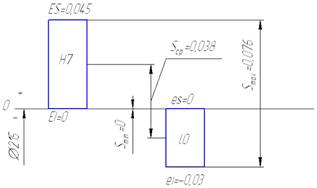
) Технические требования на рабочие поверхности вала и
корпуса
Шероховатость сопрягаемых поверхностей вала, отверстия и торцов
заплечиков Ra = 1,6 мкм.
Допуски формы и расположения поверхностей:
а) Допуски круглости и профиля продольного сечения:
для вала Тф = 6 мкм
для отверстия Тф = 9 мкм
.Нормирование
точности шпоночного соединения
Таблица 4.1
Исходные данные для расчета шпоночного соединения
Диаметр вала, мм
|
120
|
Ширина и высота шпонки b•h,
мм (по ГОСТ 23360)
|
32•18
|
Шпонка
|
Крепежная
|
Тип производства
|
Серийное
|
Количество шпонок в соединении
|
1
|
) Определение размеров шпонки
Найдем размеры шпоночного соединения по ГОСТ 23360-78
b=32
мм - ширина шпонкиS1max = 0,6мм - радиус скругления или
фаска
h=18
мм - высотаt1 = 11+0,2 - глубина паза на валу
l =
90…360 мм - длина шпонки t2 =
7,4+0,2 - глубина паза во втулке
Smin= 0,6мм - фаска
) Выбор посадки шпонки в пазы вала и втулки
Предельные отклонения шпонки:
а) Ширина шпонки b = 32h9(-0,062)
б) Высота шпонки h = 18h11(-0,11)
в) Длина шпонки l = 100h14(-0,87)
г) Длина паза под шпонку L = 100H15(+1,4)
Выбор посадок шпонки в пазы вала и втулки зависит от типа производства и
назначения шпонки. В данном соединении шпонка крепежная, соединение плотное,
производство - серийное.
Принимаем: паз вала -
паз втулки -
Рис.4.1 Расположение полей допусков на ширину шпонки b
3) Расчет допусков взаимного расположения шпоночного
паза
Допуск параллельности равен 0,5Т9, допуск симметричности - 2Т9 от
номинальной ширины шпонки.
Т0= 0,5∙62 = 31 мкм, Т4 = 2∙62 = 124 мкм. Допуск
симметричности зависимый, т.к. производство серийное.
5.
Нормирование точности метрической резьбы
Таблица 5.1
Исходные данные для расчета метрической резьбы
Болт
|
М24х170 ГОСТ 7798-70
|
Гайка
|
М24 ГОСТ 5915-70
|
Длина свинчивания
|
Нормальная
|
)Расшифровка условного обозначения резьбы
Резьба метрическая, номинальный диаметр d = 24 мм, шаг крупный. Определяем шаг по таблице: Р = 3 мм.
)Определение основных размеров профиля
По ГОСТ 24705 определяем основные размеры профиля:
наружный диаметр резьбы d = 24
мм
внутренний диаметр D1 = d1= d-4+0,752 = 20,752 мм (5.1)
средний диаметр D2 = d2 = d - 2 +0,051 = 22,051 мм (5.2)
диаметр по дну впадин d3 = d - 4 + 0,319 = 20,319 мм (5.3)
теоретическая высота витка Н = 0,866Р = 2,598 мм (5.4)
рабочая высота витка Н1 = 0,541Р = 1,623 мм (5.5)
3)Назначение степени точности и поля допусков
Т.к. длина свинчивания нормальная, а средний класс точности получил
наибольшее распространение, то назначаем предпочтительные поля допусков для
болта -6g, для гайки - 6Н.
Определим числовые значения допусков и отклонений:
Таблица 5.2
Числовые значения допусков и отклонений
Номинальный размер, мм
|
Обозначение поля допуска
|
Величина допуска Т, мкм
|
ES, мкм
|
Наибольший предельный размер, мм
|
EI, мкм
|
Наименьший предельный размер, мм
|
d = 24
|
6g
|
-48
|
23,952
|
-423
|
23,577
|
d2 = 22,051
|
6g
|
200
|
-48
|
22,003
|
-248
|
21,803
|
d1 = 20,752
|
-
|
-
|
-
|
20,752
|
-
|
-
|
D = 24
|
-
|
-
|
-
|
-
|
0
|
24
|
D2 = 22,051
|
6Н
|
265
|
265
|
22,316
|
0
|
22,051
|
D1 = 20,752
|
6Н
|
500
|
500
|
21,252
|
0
|
20,752
|
Рис.5.1 Профиль резьбы
Рис.5.2. Расположение полей допусков по профилю резьбы болта 6g и гайки 6Н
6.
Нормирование точности цилиндрической зубчатой передачи
Таблица 6.1
Исходные данные для зубчатой передачи
Вид изделия
|
Редуктор
|
Межосевое расстояние а, мм
|
315
|
Модуль m,
мм
|
6
|
Исходный контур
|
ГОСТ 13755-81
|
Коэффициент смещения исходного контура х
|
0
|
Окружная скорость V, м/с
|
9
|
Число зубьев z
|
81
|
Угол наклона зубьев β
|
8˚7’
|
Ширина зубчатого венца В, мм
|
125
|
Температура допустимого нагрева зубчатой передачи t1
|
+70˚C
|
Температура допустимого нагрева корпуса t2
|
+40˚C
|
)Определение геометрических параметров зубчатого колеса
Делительный диаметр
(6.1)
Диаметр вершин
(6.2)
Диаметр основной окружности
(6.4)
Количество охватываемых зубьев при измерении длины общей нормали
(6.5)
Длина общей нормали
(6.6)
2) Назначение степени точности
Передача является передачей общего назначения. Для них не устанавливаются
повышенные требования ни по одному из требований. По табл. назначаем 8-ую
степень точности.
Вид сопряжения определяется наименьшим гарантированным боковым зазором.
Гарантированный боковой зазор получается как сумма температурных и силовых
деформаций:
(6.7)
Для передачи общего назначения jn1 = 0,02m=0,12
мм (6.8)
Боковой зазор, соответствующий температурной компенсации, определяется по
формуле:
(6.9)
3)Выбор контрольного комплекса зубчатого венца
Учитывая, что зубчатая передача 8-ой степени точности, выбираем 3-ий
комплекс.
Для контроля кинематической точности принимаем
и
Для контроля плавности работы принимаем
и
Для контроля контакта зубьев принимаем
Для контроля бокового зазора принимаем
и
Таблица 6.2
Контрольный комплекс для зубчатой передачи 8-С
Контролируемый параметр
|
Обозначение параметра
|
Допускаемые значения, мкм
|
Средства измерения
|
Допуск на колебание измерительного межосевого расстояния за
оборот зубчатого колеса
|
|
125
|
Межцентромер
|
Допуск на колебание длины общей нормали
|
|
80
|
Нормалемер
|
Длина общей нормали
|
W
|
167,8 мм
|
Нормалемер
|
Допуск на колебание измерительного межосевого расстояния на
одном зубе
|
|
40
|
Межцентромер
|
Допуск на погрешность профиля зуба
|
|
28
|
Эвольвентомер
|
Допуск на направление зуба
|
|
32
|
|
Верхнее предельное отклонение измерительного межосевого
расстояния
|
|
40
|
Межцентромер
|
Нижнее предельное отклонение измерительного межосевого
расстояния
|
|
-200
|
Межцентромер
|
4)Определение требований к базовым поверхностям колеса
Точность диаметра вершин зубьев
(6.10)
Допуск на радиальное биение по вершинам зубьев Fd = 0,6Fr =
0,6∙80=48 мкм (6.11)
Принимаем Fd = 50 мкм
Торцовое биение базового торца на диаметре 0,75d=368 мм находим расчетом, определив
= 32 мкм по
, по
табл. принимаем
= 50 мкм (6.12)
. Выбор
универсальных средств измерения
Таблица 7.1
Исходные данные по выбору средств измерения (СИ)
Контролируемая поверхность
|
Вал
|
Исполнительный размер
|
|
Контролируемая поверхность
|
Отверстие
|
|
1)Выбор СИ для вала
Произведем выбор СИ по метрологическим факторам, учитывая, что
контролируется вал. По ГОСТ 8.051 определяем для размера 120 допуск на
изготовление IT и допускаемую погрешность измерения δ:
IT =
22мкм, δ
= 6 мкм
Выбираем возможное измерительное средство. Это скоба рычажная на стойке
СР-25 (код 9) с параметрами:
цена деления отсчетного устройства i = 0,002мм
предельная погрешность измерения Δ=5 мкм
)Выбор СИ для отверстия
По ГОСТ 8.051 определяем для размера 120 7-го квалитета допуск на
изготовление IT и допускаемую погрешность измеренияδ
IT =
35мкм, δ
=10 мкм
Выбираем возможное измерительное средство. Это нутромер индикаторный
НИ-10 (код 18) с параметрами:
цена деления отсчетного устройства i = 0,001 мм
предельная погрешность измерения Δ = 6,5 мкм
Заключение
Итогом выполненной работы стал комплект конструкторской документации для
контроля редуктора с назначенными параметрами геометрической точности элементов
в соответствии с государственными стандартами в области обеспечения точности
изделий машиностроения.
В ходе работы были назначены посадки гладких цилиндрических соединений
деталей редуктора, спроектированы предельные калибры для контроля размеров
деталей, входящих в состав гладких цилиндрических соединений, назначены допуски
и посадки подшипников качения на валы и в корпуса. Назначены параметры точности
деталей, входящих в состав соединений сложного профиля, назначены параметры
точности цилиндрических зубчатых передач. А также обоснованно выбраны универсальные
средства измерений для контроля изготовления деталей.
Список
литературы
1. Кайнова, В.Н. Нормирование точности
изделий машиностроения: учеб.пособие / В.Н. Кайнова [и др.]; НГТУ. Н.Новгород,
2007.−207с.
2. Блинов И.А. Методические указания по выполнению курсовой
работы по дисциплине «Нормирование точности»: учеб.пособие/ И.А. Блинов; ГИЭИ,
Глазов, 2013.-106 с.
3. ГОСТ 1643-81. Основные нормы взаимозаменяемости. Передачи
зубчатые цилиндрические. Допуски.