Модернизация конструкции четырехвалковой листогибочной машины для производства труб и обечаек большого диаметра
СОДЕРЖАНИЕ
ВВЕДЕНИЕ
1. АНАЛИЗ ЛИТЕРАТУРНЫХ ИСТОЧНОКОВ. ЦЕЛЬ И ЗАДАЧИ РАБОТЫ
2. КОНСТРУКТОРСКАЯ ЧАСТЬ
.1 Описание работы машины
.2 Разработка кинематической схемы привода
.3 Энерго - кинематический расчет привода
.3.1 Определение общего коэффициента полезного действия
привода
2.3.2 Выбор электродвигателя
.3.3 Определение максимальной мощности на приводном валу
.4 Определение передаточного числа
.5 Определение частоты вращения приводного вала
.6 Определение угловой скорости и крутящего момента на
приводном валу
.7 Выбор червячного редуктора
.7.1 Выбор редуктора главного привода
.7.2 Выбор мотор-редуктора привода подачи валков
.8 Ориентировочный расчет и конструирование главного
приводного вала
.9 Проектирование стакана
.10 Выбор муфт
.10.1 Редуктор - вал приводной
.10.2 Мотор-редуктор - вал соединительный
.11 Эскизная компоновка вала
.12 Проверка шпоночного соединения
.13 Проверка вала на выносливость
.14 Проверка подшипников качения
.15 Проектирование винтовой пары
.15.1 Кинематический расчет
.15.3 Расчет винтовой пары на прочность
.16 Расчет клиноременной передачи главного привода
.16.1 Расчет диаметров ведущего и ведомого шкивов
.16.2 Выбор типа ремня по окружной скорости
.16.3 Уточнение передаточного числа с учетом упругого
скольжения
.16.4 Определение межосевого расстояния
.16.5 Определение расчетной длины
.16.6 Оценка долговечности ремня
.17 Расчет прижимного усилия
. ИМИТАЦИОННЫЕ ИССЛЕДОВАНИЯ НАПРЯЖЕННО-ДЕФОРМИРОВАННОГО
СОСТОЯНИЯ ОСНОВАНИЯ УСТАНОВКИ ЧЕТЫРЕХВАЛКОВОЙ ЛИСТОГИБОЧНОЙ МАШИНЫ
3.1 Использование трехмерных моделей для расчета изделий
методами имитационного моделирования
3.2 Расчет напряженно-деформированного состояния
. ТЕХНОЛОГИЧЕСКАЯ ЧАСТЬ
.1 Описание конструкции детали и её назначение
.2 Анализ технологичности конструкции детали
.3 Выбор типа производства
.4 Выбор заготовки
.5 Выбор маршрута обработки
.6 Расчет и выбор припусков на обработку
.7 Выбор оборудования
.8 Выбор режущих инструментов
.9 Выбор измерительных инструментов
.10 Расчет и выбор режимов резания
.11 Расчет технического нормирования времени операций
. ПРОЕКТИРОВАНИЕ УЧАСТКА МЕХАНОСБОРОЧНОГО ЦЕХА ДЛЯ
ИЗГОТОВЛЕНИЯ ДЕТАЛИ ТИПА КРЫШКА
.1 Определение типа и формы организации производства
.2 Определение годовой производственной программы
.3 Выбор формы специализации участков
.4 Определение количества основного оборудования
механического участка
5.5 Определение состава и количества производственных рабочих
механического участка
5.6 Предварительное определение производственной площади
участка
.7 Разработка структуры механического участка
.8 Определение расхода инструмента
.9 Организация и планирование ремонтных работ на участке
.10 Определение численности ремонтного персонала участка
.11 Разработка плана участка и схемы расположения
технологического оборудования
ЗАКЛЮЧЕНИЕ
СПИСОК ИСПОЛЬЗОВАННЫХ ИСТОЧНИКОВ
ПРИЛОЖЕНИЕ 1. СПЕЦИФИКАЦИИ
ПРИЛОЖЕНИЕ 2. МАРШРУТНЫЕ КАРТЫ
ВВЕДЕНИЕ
Машиностроительное производство на данный момент времени находится далеко
не на первом месте среди отраслей народного хозяйства Российской Федерации. Еще
не давно предприятия машиностроения работали только с использованием
оборудования достаточно устаревшего, поэтому возникла необходимость развития и
модернизации. В последние годы ситуация стала меняться. На предприятиях
происходит внедрение новых технологий, которые позволяют выйти на новый уровень
производства и создавать продукцию высокого качества, способную конкурировать
на международном рынке.
Вологодская область является одним из промышленных центров. Большое
значение для нашей области и страны имеют такие предприятия, как ОАО
«Северсталь» г.Череповец, Вологодский подшипниковый завод, Вологодский оптико -
механический завод и другие предприятия.
Металлургические предприятия, как ООО «ССМ - Тяжмаш» постоянно ставят
перед собой задачи по увеличению выпуска продукции и повышению ее качества.
Решению этих задач должны способствовать следующие факторы:
реконструкция, механизация и автоматизация производственного
оборудования;
улучшение технологических процессов;
повышение квалификации рабочих.
В работе будет рассмотрена четырехвалковая листогибочная машина
(предназначение, конструкция, производительность и многое другое), приведены
расчеты оценки структуры затрат производства; анализ различных факторов,
действующих при ее эксплуатации.
1. АНАЛИЗ ЛИТЕРАТУРНЫХ ИСТОЧНИКОВ. ЦЕЛИ И ЗАДАЧИ РАБОТЫ
Четырехвалковая листогибочная машина в основном предназначена для гибки
толстостенных крупногабаритных цилиндрических обечаек. В конструкции машины
предусмотрена возможность наклонной установки боковых валков для гибки
отдельных видов конических обечаек.
В основе данного процесса гибки лежит развальцовка и прокат металлов.
Прокат - это вид обработки давлением, при котором процесс деформации металла
осуществляется сдавливанием его между вращающимися валками. Окончательные
размеры и форма сечения полученного прокаткой изделия определяются профилем
отверстия между сжимающими металл валками.
Валки для прокатки изготовляют из углеродистой и легированной стали, а
также из высокопрочного чугуна с отбеленным поверхностным слоем. Они бывают
гладкими и калиброванными, т.е. имеющими ручьи определенного профиля. Ручей -
это профиль выреза на боковой поверхности валка. Калибр - профиль, составляемый
смежными ручьями двух валков. Предварительное обжатие заготовок производят в
обжимных и черновых калибрах, окончательный профиль проката получают в чистовых
калибрах.
Существуют три вида прокатки: продольная, поперечная и
поперечно-винтовая. При продольной прокатке заготовка деформируется между двумя
валками, которые вращаются в разные стороны, а заготовка движется поступательно
перпендикулярно осям валков.
Это основной вид проката, им производят более 90 % прокатной продукции, в
том числе весь сортовой и листовой прокат.
При поперечной прокатке валки вращаются в одном направлении и придают
вращение заготовке. Направление вращения заготовки противоположно направлению
вращения валков, а ось вращения параллельна оси вращения валков. Заготовка
деформируется, вращаясь и перемещаясь вдоль оси валков. Поперечная прокатка
применяется для производства профилей периодического сечения.
При поперечно - винтовой (косой) прокатке валки расположены под углом,
вращаются в одну сторону и придают заготовке одновременно вращательное и
поступательное движение. При этом за счет перекоса валков заготовка получает не
только поперечную, но и продольную деформацию. Этим видом проката производят
бесшовные трубы, периодические виды проката, шары.
Прокатку осуществляют на специальных машинах - прокатных станах,
устройство которых зависит от вида прокатываемых изделий и их размеров.
Основными частями прокатного стана являются привод, передаточный механизм и
рабочие клети с прокатными валками.
Прокатные станы классифицируют:
по числу валков в клетях (трехвалковые - триостаны, четырехвалковые -
кваростаны и т. д. );
по направлению вращения валков (нереверсивные - с постоянным направлением
вращения, реверсивные - с переменным направлением вращения валков);
по назначению (обжимные, черновые, сортовые, листовые, рельсовые,
трубопрокатные и т. д.);
по размеру (мелкосортные, среднесортные, крупносортные).
Крупные прокатные станы называют блюмингами или слябингами, на них
стальные слитки (массой 5 - 15 тонн и более ) прокатываются в квадратные
заготовки - блюмы, используемые для сортового проката, и прямоугольные листовые
заготовки - слябы, используемые для листового проката. Рабочие клети сортовых
станов могут располагаться в линию параллельно друг другу или последовательно
друг за другом.
Станы с последовательным расположением клетей называют непрерывными, так
как заготовка идет последовательно из одной клети в другую без поворотов и
возвратов. Полунепрерывные станы - станы, сочетающие последовательное и
параллельное расположение клетей. Непрерывные станы дают широкую возможность
механизации и автоматизации процесса и применения высоких скоростей прокатки.
Продукцией прокатного производства являются как готовые изделия (балки,
трубы, рельсы и др.), так и заготовки для последующей обработки ковкой,
штамповкой, волочением или резанием.
Вся продукция прокатного производства делится на четыре группы:
сортовой прокат;
листовой прокат;
трубы;
специальные виды проката.
Сортовой прокат делится на простой (квадрат, круг, шестигранник,
прямоугольник) и фасонный (уголок, двутавр, швеллер, рельс и др.) Листовой
прокат делят на толстолистовой (толщина листа 4-160 мм ) и тонколистовой
(толщина менее 4 мм ). Листы толщиной менее 0,2 мм называются фольгой.
Прокаткой получают трубы бесшовные и со швом (сварные швы). Наиболее
распространенным способом получения бесшовных труб является прокатка заготовки
круглого сплошного сечения сначала на специальном трубопрокатном прошивном
стане поперечно - винтовой прокатки, в котором заготовка получает винтообразное
движение, вследствие чего внутри ее образуется полость, а затем на стане
продольной прокатки, где из полой заготовки получают трубу требуемых размеров.
Сварные трубы изготавливают печной, газовой и электрической сваркой из
горячекатаной ленты низкоуглеродистой стали на непрерывных прокатных станах.
К специальным видам проката относятся периодический прокат, колеса,
кольца, шары. Периодический прокат имеет закономерно изменяющееся, периодически
повторяющийся по длине сечение. Полученные периодической прокаткой профили
представляют собой цепь деталей, имеющих различную форму и размеры ( шатуны,
оси, валы, рычаги и др.) и являющихся заготовками для последующей ковки и
штамповки. Производительность ковки и штамповки из заготовок периодического
проката на 25-35 % выше, чем из обычного проката, расход штампов ниже, экономия
металла 20-30%.
Гнутые профили, используемые в строительстве зданий, получают прокаткой
стального листа, ленты, швеллеров, уголков на роликогибочных станах
периодического и непрерывного действия. Прокаткой цветных металлов и их сплавов
получают полосы, листы, ленты, трубы и другие профили. В основном этот процесс
прокатки состоит из тех же операций, что и прокатка стали.
Прокатка бывает горячей и холодной. Наибольшее распространение имеет
горячая прокатка. Холодную прокатку применяют для получения тонких изделий,
например листов малой толщины, стальных полос. Возникающий при этом наклеп
устраняется последующим отжигом.
Процесс бесслитковой прокатки заключается в совмещенных разливке и
прокатке полуфабрикатов из цветных металлов и их сплавов ( листов, лент, полос
), которые получают заливкой жидкого металла в зазор между двумя охлаждаемыми
водой вращающимися валками. Этот способ удешевляет и упрощает изготовление
изделий, так как исключаются отливка слитков и подготовка их к прокатке.
Производство труб с одним сварным швом включает в себя следующие работы:
гибка цилиндрических обечаек на листогибочных вальцах;
прихватка заготовок;
односторонняя сварка с обратным формированием шва на подушке;
нагрев в печи ( нормализация );
обрезка концевых участков;
торцовка и снятие фасок.
Основным формоизменяющим оборудованием, относимым к прокатному, является
формовочное ( непрерывные станы подгибки кромок, прессы и гибочные вальцы ) и
сварочное оборудование ( станы наружной и внутренней сварки ).
Формовочные прессы имеют ряд преимуществ по сравнению с листогибочными
вальцами при изготовлении заготовки для труб большого диаметра. Формовочные
прессы позволяют формовать заготовку длиной 12-18 мм, производительность их в 3
раза выше гибочных вальцев; точность геометрической формы заготовки выше, что
облегчает процесс сварки. Однако листогибочные вальцы проще по конструкции и
значительно уменьшают удельные капиталовложения. Благодаря этому чаще всего в
производстве применяются вальцы.
При гибке в вальцах лист изгибается вдоль продольной оси между тремя или
четырьмя валками. Лист, опираясь на боковые валки, прогибается под действием
верхнего валка и вследствие его вращения принимает цилиндрическую форму.
Диаметр заготовки определяется установкой верхнего валка большего диаметра
относительно нижних валков. В трехвалковых вальцах получают заготовку, имеющую
прямолинейные участки по краям листа. При использовании четырехвалковых вальцов
благодаря соответствующей установке крайних холостых валков получают заготовку
более правильной формы.
Заготовка для цилиндрических обечаек выполняется прямоугольной, со строго
параллельными продольными кромками шириной, подсчитанной с учетом требующегося
зазора. Если для сварки продольного шва требуется разделка кромок, она
производится у плоской заготовки.
Заготовка заводится в машину до упора в противоположный боковой валок
(рисунок 1а). Перемещением вверх нижнего валка заготовка зажимается между
верхним и нижним валками, производится гибка заготовки на узком участке путем
сжатия боковых валков (рисунок 1б,1в).
Включением вращения валков, заготовка до самой кромки сгибается на
конечный радиус. После этого валки устанавливаются по симметричной, сгибается
средний участок заготовки на промежуточный радиус (рисунок 1г ). Подгибка
второго конца заготовки осуществляется тем же способом, как и первого. Затем за
один - два пропуска заготовка сгибается на окончательный радиус (рисунок
1д,1е). Количество пропусков зависит от марки стали заготовки и квалификации
гибщика.
В машиностроении одним из наиболее важных этапов производства является
конструкторская подготовка производства. Конструкторская подготовка
производства - это важнейший этап создания нового изделия. От организации КПП
зависят качество выпускаемых машин, их надежность и экономическая
эффективность. КПП является не только техническим, но и экономико - организационным
этапом.
Правильная организация КПП в большей степени зависит от технических
требований, поставленных перед конструкторами. Она оказывает решающее влияние
как на технологическую подготовку производства, так и на технико-экономические
показатели работы предприятия.
Опыт показывает, что процессы и темпы внедрения достижений науки и
техники в производство наиболее эффективны, когда конструкторская подготовка
органически связывается с научной, технологической и организационной
подготовкой производства.
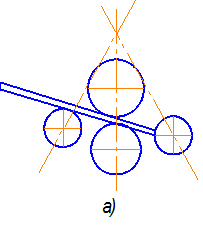
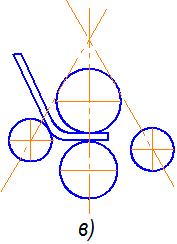

Рисунок 1.1- Процесс гибки обечаек
На практике в машиностроительном производстве станки и оборудование
подвергаются физическому и моральному износу.
Физический износ обуславливается старением узлов и деталей, усталостью
материалов и другими причинами, постепенно приводящими оборудование в нерабочее
состояние. Физический износ устраняется в результате проведения плановых
ремонтов оборудования.
Моральный износ определяется экономическим старением машин, заключающимся
в том, что машины аналогичной конструкции и назначения начинают выпускаться
дешевле или внедряется новая, технически более совершенная конструкция машины и
эксплуатация старых моделей машин становится экономически нецелесообразной.
Средством преодоления морального износа является модернизация оборудования.
Под модернизацией находящегося в эксплуатации оборудования понимается
приведение его в соответствии с современными требованиями путем внесения
частичных изменений и усовершенствований в конструкцию машин с целью повышения
их эффективности в производственных условиях.
Расширение технологических возможностей машин осуществляется вследствие:
внесения частичных изменений в конструкцию машины (станка );
оснащения станков приспособлениями, не предусмотренными их конструкцией,
в результате которых возрастает количество операций, которые могут быть
выполнены на станке.
Повышение точности машин производится в следующих направлениях:
повышения кинематической точности путем внесения изменений в
кинематическую схему, установки или усовершенствования коррекционных устройств;
повышения геометрической точности за счет установки подшипников
повышенной точности;
уменьшения температурных деформаций с помощью введения циркуляционной
смазки, установки температурных компенсаторов.
Повышение надежности станков осуществляется :
применением защитных устройств, предохраняющие узлы и детали станков от
загрязнения песком, стружкой и абразивом;
улучшением системы смазки трущихся поверхностей деталей и узлов;
проведением мероприятий по снижению износа ходовых винтов, винтов подачи,
а также гаек к ним, путем применения защитных устройств, принудительной системы
смазки, повышения качества термообработки.
Результатом получения наибольшего экономического эффекта целесообразно
проводить модернизацию по нескольким направлениям, исходя из конкретных
требований производства.
Целью данной работы является модернизация четырехвалковой листогибочной
машины. Суть модернизации заключается в изменении конструкции машины, вследствие
чего она сможет гнуть стальные листы от 10 до 16 мм. Такие цилиндрические
обечайки позволят изготовлять трубы, которые станут прочные, что способствует
их меньшему износу, т.е. продукция будет более долговечна.
Исходя из поставленной цели необходимо решить следующие задачи:
спроектировать привод перемещения и вращения валков;
изменить ход нижнего прижимного валка;
увеличить мощность на приводном валу;
провести необходимые проверочные расчеты;
доказать экономически целесообразность данного проекта.
2. КОНСТРУКТОРСКАЯ ЧАСТЬ
2.1 Описание работы машины
В четырехвалковой листогибочной машине (рисунок 2.1) в двух сварно -
литых станинах расположены четыре валка: приводной верхний валок, нижний и два
боковых. Правая 1 и левая 2 станины установлены на общей раме 4.
Основной привод машины 3 (привод перемещения и вращения валков) -
механический. Привод верхнего валка от электродвигателя через червячный
редуктор.
Тихоходный вал редуктора выполнен полым. Сквозь отверстие этого вала
проходит конец верхнего приводного валка, который соединен с механизмом
наклона.
Для передачи вращения на верхний валок предусмотрена кулачковая муфта 5.
Правая полумуфта жестко соединена с концом полого тихоходного вала редуктора
посредством болтов. Левая полумуфта постоянно прижата к правой пружинами.
Регулировка пружин производится механизмом переключения 6. Правый и левый
подшипники верхнего валка соединены соответственно с правой и левой станинами
посредством оси.
Нижний валок предназначен, в основном, для увеличения тягового усилия
между заготовкой и верхним приводным валком. Прижим нижнего валка к верхнему
через заготовку осуществляется электродвигателем 7. С помощью нижнего валка и
прижимного устройства производится также подгибка кромок в заготовке
Регулировка боковых валков машины осуществляется от двух самостоятельных
электродвигателей через червячный редуктор и винтовую пару. Боковые валки
расположены в сферических опорах, что позволяет устранить защемление концов
валка в подшипниках и дает возможность наклонной установки валков при гибке
конических обечаек. Для обеспечения синхронности движения правого и левого
ползунов с боковым валком ведущие валы червячных редукторов соединены
промежуточным валом. На правом конце промежуточного вала установлена сцепная
пневматическая муфта, Посредством которой может быть отключен механизм
регулировки правого ползуна. Таким образом, положение боковых валков может
регулироваться одновременно (включаются оба электродвигателя) или каждый валок
регулируется самостоятельно (включается один электродвигатель). Кроме того,
благодаря сцепной зубчатой муфте, установленной на промежуточном валу.
достигается наклонная установка боковых валков.
Между электродвигателем и редуктором установлена предохранительная муфта,
которая срабатывает при давлении бокового валка на верхний выше допустимого,
обусловленного прочностью механизма регулировки.
Для наблюдения за установкой боковых валков предусмотрены указатели хода
валков, установленных на правой станине. Указатели посредством троса и роликов
соединены с правыми ползунами боковых валков.
Рисунок 2.1 - Четырехвалковая листогибочная машина
2.2 Разработка кинематической схемы привода
На рисунке 2.2 представлена кинематическая схема, рассчитываемого привода
Рисунок. 2.2 - Кинематическая схема привода:1 - электродвигатель;2 -
ременная передача;3 - редуктор;4 - муфта;5 - подшипники.
2.3 Энерго - кинематический расчет привода
.3.1 Определение общего коэффициента полезного
действия привода
Целью энерго-кинематического расчета является подбор электродвигателя на
основании потребной мощности, а также определения передаточного числа ступени
привода, исходя из частот вращения вала электродвигателя и вала исполнительного
органа машины.
Значения параметров принимаются на основе следующих рекомендаций:
мощность на приводном валу Р=5,5кВт;
частота вращения приводного вала nП.В.≈14 об/мин.
Для определения общего КПД привода определяем источник потерь мощности
при передаче от электродвигателя к исполнительному органу. В механических
передачах потери мощности возникают во всех типах передач, в подшипниках и
соединительных муфтах.
В данном приводе источником потерь будет: две пары подшипников, муфта,
червячная передача, ременная передача. Общий КПД для данного привода
определяется по формуле:
, (2.1)
где
- КПД
пары подшипников качения;
- КПД
муфты;
- КПД
червячной передачи;
- КПД
ременной передачи.
Подставим
значения в формулу и получим общий КПД привода:
2.3.2 Выбор электродвигателя
Потребная
мощность приводного электродвигателя определяется по формуле:
, (2.2)
где
Рр - расчетная мощность электродвигателя, кВт;
РП.В.
- мощность на приводном валу, кВт;
η - КПД привода;
, (2.3)
При
выборе электродвигателя должно соблюдаться условие
. Принимаем электродвигатель 4А132М6У3.
Мощность
электродвигателя
.
Синхронная
частота вращения вала nЭД=970 об/мин.
Диаметр
вала dЭД=32мм.
2.3.3 Определение максимальной мощности на приводном
валу
Максимальную
мощность на приводном валу определяем по формуле:
, (2.4)
где
Рмах - максимальная мощность на приводном валу, Н;
РЭД
- мощность электродвигателя, РЭД =7,5 кВт;
η - КПД привода;
.
2.4 Определение передаточного числа
Общее
передаточное число определяется по формуле:
; (2.5)
где
u - передаточное число;эд - асинхронная частота вращения вала
электродвигателя,П.В. - требуемая частота приводного вала, n=14 об/мин;
.
Из
стандартного ряда передаточных чисел червячных редукторов выбираем
.
2.5 Определение частоты вращения приводного вала
Частота
вращения приводного вала определяется по формуле:
, (2.6)
.
2.6 Определение угловой скорости и крутящего
момента на приводном валу
Угловая скорость на приводном валу определяется по формуле
, (2.7)
где
ωП.В. - угловая скорость приводного вала, с-1;П.В. -
уточненная частота приводного вала, nП.В.=12,12об/мин;
.
Крутящий
момент на приводном валу определяется по формуле:
, (2.8)
где
ТП.В. - крутящий момент на приводном валу, Нм;
РЭД
- мощность электродвигателя, Вт;
η - КПД привода;
ωП.В. - угловая скорость приводного вала, с-1.
Угловая
скорость на приводном валу - 1,27 с-1;
Крутящий
момент на приводном валу - 4570 Нм.
2.7 Выбор червячного редуктора
.7.1 Выбор редуктора главного привода
Червячный
редуктор выбираем для следующих условий работы:
частота
вращения электродвигателя n=970 об/мин;
передаточное
число редуктора u=80;
момент
на приводном валу Т=4570 Нм.
Определяем
расчетный момент:
, Нм,
(2.9)
где
Тр - расчетный крутящий момент на тихоходном валу редуктора, Нм;
ТП.В.
- крутящий момент на приводном валу, Нм;
κ - коэффициент условий работы.
Подбор
редуктора осуществляется с учетом необходимой схемы сборки, расположения
червячной пары и способа крепления.
По
таблице подбираем редуктор 1ЦЗУ-315-80-22-УЗ, для которого
.
2.7.2 Выбор мотор - редуктора привода подачи валков
-
крутящий момент на выходном валу T=320 Нм
По
ТУ2-056-232-80 выбираем мотор-редуктор 1МЦ2С-80-112-К-У3, для которого частота
вращения выходного вала 112 об/мин.
2.8 Ориентировочный расчет и конструирование главного
приводного вала
Определяем
минимальный диаметр приводного вала:
, (2.10)
где
d - минимальный диаметр приводного вала;
ТП.В.
- крутящий момент на приводном валу, Нм;
-
(15…25)МПа
Подставим
значения в формулу:
.
Определяем
диаметр под подшипник:
, (2.11)
где
dп - диаметр под подшипник;
Получим
.
Принимаем
dП1=100мм.
Диаметр
буртика определяется из следующего выражения:
, (2.12)
где
dбп - диаметр буртика.
На
левом конце вала принимаем диаметр 70мм, на который запрессуем втулку с двумя
шариковыми упорными подшипниками. Диаметр под шариковый радиальный подшипник
dП2=80мм. Рабочий эскиз вала приведен на рисунке 2.3.
Рисунок 2.3 - Рабочий эскиз вала
2.9 Проектирование стакана
В данной конструкции стакан необходим для фиксации подшипников.
Толщина стенки δ=7,5 мм, диаметр резьбы d=М8 и число винтов крепления
стакана к корпусу z=4 по табл. 7.1 (Чернилевский с.172) в зависимости от
диаметра отверстия под подшипник D=80мм. Толщину фланца δ2≈1,2δ.
Высоту t упорного
заплечика согласуют с размерами подшипника.
δ2=1.2*7.5=9мм,
Тогда принимаем δ2=10 мм;=8.5мм;
Принимая С≈d, h=(1,0…1,2)d, получаем минимальный диаметр фланца
стакана D=D+(4…4,4)d. Необходимо, чтобы отверстия под болт стакана совпадали с
отверстиями крышки ГОСТ 18511 - 73.ф=80+(4…4,4)*8=112…115,2 мм.
Чтобы обеспечить сопряжение торцов фланца стакана и корпуса по плоскости,
на наружной цилиндрической поверхности стакана перед торцом фланца делают
канавку. Канавку выполняют и перед заплечиком стакана, по торцам которого
устанавливают кольцо подшипника. Для неподвижных после установки в корпус
стаканов применяют посадки H7/k6 или H7/m.
2.10 Выбор муфт
Выбор муфты производится на основе диаметров соединяемых валов и
максимального крутящего момента.
2.10.1 Редуктор - вал приводной
Диаметр тихоходного вала редуктора d2=100 мм, диаметр концевого участка
приводного вала d=70мм. Выбираем стандартную муфту МУВП 50 - 40 - 1.1 - У3 ГОСТ
12080-66. Параметры полумуфты:d=100мм; D=150мм; D1=200мм; L=100мм; l=40мм.
Эскиз полумуфты приведен на рисунке 2.4.
2.10.2 Мотор- редуктор - вал соединительный
Концевой участок вала соединительного 30 мм. В соответствии с этим
условием выбираем муфту. Устанавливаем стандартную полумуфту МУВП 35-32-1.1-У3
ГОСТ 12080-66. Параметры полумуфты : d=35; D1=80мм; D2=100мм; l1=80мм; B=9мм;
n=6. Вторую полумуфту необходимо конструировать.
Рисунок 2.4 - Эскиз полумуфты
2.11 Эскизная компоновка вала
На эскизной компоновке определяют расположение деталей, уточняют
расстояние между ними. Непосредственно определяют расстояние между точками, где
приложены реакции опор и сила Fм, возникшая от несоосности валов. Эскизная
компоновка вала представлена на рисунке. 2.5.
Рисунок 2.5 - Эскизная компоновка вала
2.12 Проверка шпоночного соединения
.12.1 Редуктор - вал приводной
Шпонка 12×12×100 ГОСТ 23360-78
Шпоночное соединение проверяется из условия:
, (2.13)
, (2.14)
где
[σсм] - допустимое напряжение на смятие, [σсм] =200 МПа;
ТП.В. - передаваемый крутящий
момент, ТП.В. =4570 Нм;- диаметр вала, d=100 мм;- глубина шпоночного паза,
h=12мм;- длина шпонки, l=100мм;- ширина шпонки, b=12мм;- рабочая длина шпонки
.
Выбранная шпонка выдержит
передаваемые напряжения, т.к соответствует условию
.
2.12.2 Мотор-редуктор - соединительный вал
Шпонка 10×8×70 ГОСТ 23360-78
Т=320Нм - крутящий момент на выходном валу
Определим напряжение на смятие:
,
.
Выбранная
шпонка соответствует условию.
2.13 Проверка вала на выносливость
.13.1 Определение реакций в опорах
Определение
силы от несоосности валов:
, (2.15)
Определение
реакций в опорах А и В:
, (2.16)
, (2.17)
Определение
изгибающих моментов:
, (2.18)
, (2.19)
где
Fм - сила от несоосности валов, Н;
ТП.В.
- крутящий момент на приводном валу, Нм;, RB - реакции в опорах А и В, Н;, lBC,
lAB - длины участков вала, м;
МA,
МB - изгибающие моменты, Нм.
Подставим
данные значения в формулы и получим:
Реакции
в опорах:
Изгибающие
моменты:
.
По
полученным данным построим эпюры. Эпюры изгибающих и крутящих моментов
представлены на рисунок 2.6.
Рисунок
2.6 - Эпюры изгибающих и крутящих моментов
2.13.2 Определение напряжений изгиба и кручения
Определяем
осевой момент сопротивления сечения:
, (2.20)
Определение полярного момента сопротивления сечения:
, (2.21)
Определение
напряжений изгиба:
, (2.22)
Определение
напряжений кручения:
, (2.23)
где
W - осевой момент сопротивления сечения вала, мм3;- полярный момент
сопротивления сечения вала, мм3;
σИ - напряжения изгиба, Н/мм3;
τК - напряжения кручения, Н/мм3.
Подставим
значения в формулы:
;
;
Необходимо
произвести проверочный расчет на выносливость.
2.13.3 Проверочный расчет на выносливость
Для
того, чтобы проверить вал на выносливость необходимо рассчитать коэффициенты
запаса прочности по нормальным и касательным напряжениям .
; (2.24)
; (2.25)
; (2.26)
где
[S] - допустимое значение коэффициента запаса прочности;
Sσ - коэффициент запаса прочности по нормальным напряжениям;
Sτ - коэффициент запаса прочности по касательным напряжениям;
σ-1 и τ-1
- пределы выносливости соответственно при
изгибе и кручении, Н/мм2;
σа и τа - амплитуда напряжений цикла;
σm и τm - среднее напряжение цикла;
ψσ и ψτ - коэффициенты, учитывающие влияние
постоянной составляющей цикла напряжений на сопротивление усталости;
кd - масштабный фактор;
кF - коэффициент влияния шероховатости;
Найдем коэффициенты запаса прочности по касательным и нормальным
напряжениям и подставим в общую формулу:
Полученный
результат соответствует условию S›[S], следовательно вал выдержит применяемые
напряжения.
2.14 Проверка подшипников качения
.14.1 Параметры подшипников качения
Шариковый
упорный подшипник ГОСТ 6874 - 75 8109.
Параметры
подшипника: d=40мм, D=60мм, H=13мм, r=1мм, C=27000H, Co=53000H;
Шариковые
радиальные подшипники ГОСТ 7242 - 70 №80208.
Параметры
подшипника: d=40мм, D=80мм, H=18мм, r=2мм, C=32000H, Co=17800H, m=0.36кг;
Шариковые радиально-упорные
подшипники ГОСТ 7242-91=100мм; D=150мм; H=20мм; r=2мм; C=35100H; Co=19800H;
m=0.46кг.
2.14.2
Определение эквивалентной нагрузки
1) Шариковый упорный
подшипник
, (2.27)
где Ра - эквивалентная
динамическая осевая нагрузка, Н;- осевая нагрузка на подшипники, Fa=505Н;
кσ - коэффициент безопасности; кσ=1,3
кТ - температурный
коэффициент; кТ=1,4
.
) Шариковый радиальный
подшипник
Расчет производится по более
нагруженной опоре В.
, (2.28)
где Pr - эквивалентная
динамическая радиальная нагрузка, Н;
Х - коэффициент радиальной
нагрузки, Х=1;
У - коэффициент осевой
нагрузки, У=0;- радиальная нагрузка на подшипник, RB=2589Н;
кσ - коэффициент безопасности; кσ=1,3;
кТ - температурный
коэффициент; кТ=1,4;- осевая нагрузка на подшипник, Fa=505 Н;- коэффициент
вращения, V=1.
.
2.14.3
Определение долговечности подшипников
Расчетную долговечность
подшипника определяют по формуле:
, (2.29)
где n - частота вращения
кольца, n=12,12 об/мин;- базовая динамическая радиальная грузоподъемность
подшипника, Н;- эквивалентная динамическая радиальная нагрузка;
Р=919 Н- показатель степени,
m=3.
1) Шариковый упорный подшипник
В одной опоре установлены два одинаковых упорных подшипника, поэтому
базовая динамическая радиальная нагрузка равна:
, (2.30)
Подставив
значения в формулу получаем:
2) Шариковый радиальный подшипник:=32000H; n=12,12об/мин; Pr=4712H,
Тогда получим:
Подшипник
пригоден для машины, если расчетная долговечность больше или равна требуемой
L10h≥Lh.
Рекомендуемое
значение Lh=20000…30000ч.
Выбранные
подшипники удовлетворяют условию.
2.15 Проектирование винтовой пары
В четырехвалковой листогибочной машине винтовые пары служат для
регулировки валков. Они расположены в станинах. В данном дипломном проекте необходимо
уменьшить ход нижнего и боковых валков.
2.15.1 Кинематический расчет
Угловая скорость ω и частота вращения nП.В. связаны со
скоростью поступательного движения v зависимостями
, (2.31)
, (2.32)
где Рр - шаг резьбы, мм;- число заходов резьбы;-
скорость поступательного движения, мм/с.
КПД винтовой пары в случае преобразования
вращательного движения в поступательное, с учетом дополнительных потерь (в
резьбе из - за ошибок изготовления и потерь в опорах) определяется:
, (2.33)
где Ψ=30˚ - угол подъема винтовой линии (резьбы);
ρ=5˚- приведенный угол трения.
Определение
скорости поступательного движения:
где
nП.В.=12,12 об/мин - частота вращения приводного вала;=3мм - шаг
трапецеидальной резьбы;=1 - число заходов резьбы;
Определение
угловой скорости:
где
ω
- угловая скорость;
.
2.15.2 Определение среднего диаметра резьбы винтовой
пары
Зависимость
между мощностью Р на ведущем звене, необходимая для создания на ведомом звене
осевой силы Fa находят из уравнения:
, (2.34)
, (2.35)
где
Р - мощность на ведущем звене, Вт;- осевая сила, Н;
ηв-п - КПД винтовой пары.
Средний
диаметр резьбы определяют по формуле:
, мм,
(2.36)
где
γ=1,2…2,5
для неразъемных гаек;
γ=2,5…3,5 для разъемных;
[p]=12МПа
- допускаемое давление между рабочими поверхностями резьбы винта и гайки для
стали по бронзе и антифрикционному чугуну;- осевая сила, Fa =370Н.
2.15.3 Расчет винтовой пары на прочность
Тело
винта проверяют на прочность в зависимости от вида нагружения. Если винт
испытывает сжатие, то во избежание продольного изгиба необходимо обеспечить
запас устойчивости. Запас устойчивости проверяется из условия:
, (2.37)
где
[ny] ≥4; по формуле Ясинского (при λ0≤λ≤λпред)кр - критическая осевая сила, Н;- осевая сила,
Fa=370Н.
Критическая
осевая сила определяется по формуле:
, (2.38)
, (2.39)
где
λ
- гибкость винта;
μ - коэффициент длины;
ι - длина винта;-радиус инерции сечения винта (
).
Значения
a, b,
λ0, λпред берутся в справочных
таблицах.
.
Следовательно
винт диаметром 70 мм выдержит осевую нагрузку.
2.15.4 Проектирование гайки
Размеры
опорного фланца гайки проверяют на срез и на смятие:
, мм,
(2.40)
где
НГ - длина гайки, мм;
ψГ - коэффициент высоты гайки;- средний диаметр
трапецеидальной резьбы, мм.
, мм
Полученный результат
округляют до ближайшего стандартного значения. Следовательно принимаем НГ=95мм.
Так как осевая сила мала,
диаметр винта больше расчетного примерно в 10 раз и запас прочности винта
ny=150 при [ny] ≥4, нет смысла проводить расчет наружного диаметра гайки
и высоты заплечика из условий прочности на удельные давления.
2.16
Расчет клиноременной передачи главного привода
Важным этапом при
проектировании механического привода является расчет и конструирование
клиноременной передачи, которая обычно располагается сразу после двигателя,
т.е. является быстроходной ступенью механизма. При выборе типа ремня
целесообразно в первую очередь рассмотреть возможность использования плоского
ремня как наиболее дешевого и доступного в эксплуатации.
2.16.1
Расчет диаметров ведущего и ведомого шкивов
Диаметр ведущего шкива
определяется:
(2.41)
где Т - момент на ведущем
шкиве, Нм
, (2.42)
Тогда получим:
Диаметр
ведомого шкива без учета упругого скольжения определяется:
, (2.43)
Долговечность
ремня и коэффициент полезного действия передачи снижаются с уменьшением
параметров шкивов, поэтому диаметр ведущего шкива следует принимать возможно
большим. По ГОСТ 20889-88 принимаем диаметр равный 180мм.
2.16.2 Выбор типа ремня по окружной скорости
Окружная
скорость ремня определяется по формуле:
(2.44)
По
ГОСТ 12843-96 выбираем ремень Б-2000. Число ремней 3.
2.16.3 Уточнение передаточного числа с учетом
упругого скольжения
Определяется
по формуле:
, (2.45)
где
=0,01…0,02 - коэффициент упругого скольжения
2.16.4 Определение межосевого расстояния
Межосевое
расстояние находится из зависимости:
, (2.46)
где
=1,5 - коэффициент, зависящий от способа натяжения
ремня(автоматическое натяжение).
2.16.5 Определение расчетной длины ремня
Расчетная
длина ремня для открытой передачи определяется:
, (2.47)
где
Получим
расчетную длину:
Вычисленный
результат округляют до ближайшего стандартного значения. Принимаем расчетную
длину ремня равную 1700мм.
2.16.6 Оценка долговечности ремня
Долговечность
ремня проверяется из условия:
, с -1
(2.48)
где
- расчетная частота пробега ремня в секунду;
=3…6 -
допускаемая частота пробега ремня.
Следовательно
выбранный ремень соответствует условию долговечности.
.17 Расчет прижимного усилия
В четырехвалковой листогибочной машине нижние валки при перемещении
создают прижимное усилие, которое действует на прямоугольную стальную
заготовку, а верхний валок прижимает ее своим весом, в результате чего
происходит гибка заготовки. При этом на обрабатываемый лист действуют силы
зажима (рисунок 2.7.).
Рисунок 2.7 - Силы, действующие на обрабатываемый лист
Сила R может быть разложена на нормальную V и касательную Р составляющие.
При уменьшении сил N или V ниже определенного значения наступит
проскальзывание. Во избежании этого необходимо развить усилие зажима:
N = k Q /(2×μ),Н, (2.49)
=1,25...1,6 - коэффициент запаса силы сжатия;- вес верхнего валка;
μ=0,12...0,15 - коэффициент трения между контактными
поверхностями.г =mq=314×9,8=20977,2 Н
N = 1,5× 2097,2
/(2×0,12)=13107,5 Н
Скольжение отсутствует при условии, что сила трения F на контактных
поверхностях равна касательной силе валка или превышает ее:
=Р = N×μ ≥ Qг×μ/2, Н, (2.50)
Во время возрастания усилия зажима происходит скольжение рабочих площадок
на поверхности обечайки, что может привести к ее повреждению. Поэтому зажимное
усилие должно быть развито полностью.
В этом случае:
=Р = Q×μ×u×η/2, Н, (2.51)
где u=2N/Q - передаточная функция зажимного устройства,
η - КПД прижимного устройства.=2×754,93/2097,2=0,72.
F=Р = 2097,2×0,12×0,72×0,74/2=67,09
Н
Результирующая сила находится по формуле:
(2.52)
Правильность
расчета проверяется из условия:
≥
[k]
где
k - коэффициент запаса зажатия;
= N×2×μ/Qг
[k]
- допустимый коэффициент запаса зажатия;
[k]=1,25...1,6
k = 13099,5×2×0,13/2097,2
= 1,63
Следовательно, расчеты проведены верно.
3. Имитационные исследования напряженно -
деформированного состояния основания установки четырехвалковой листогибочной
машины
.1 Использование трёхмерных моделей для расчёта
изделий методами имитационного моделирования
привод вал скольжение прочность
Имитационное моделирование - создание электронной модели проектируемого объекта и
экспериментирование с ней при заданных ограничениях. Цель таких экспериментов - это определение оптимальных параметров
модели.
Различают два метода имитации:
ᅳ Кинематическая - имитация процесса движения элемента
объекта с целью определения столкновений (коллизий);
ᅳ Динамическая - имитация процесса исследования
поведения объекта при изменении действующих нагрузок и температур. В этом
случае определяется теплонапряжённое состояние объекта, а также определение
напряжённо -
деформированного состояния объекта.
Для определения напряжённо - деформированного состояния могут использоваться методы
имитационной физики, достаточно хорошо разработана теория метода математической
физики. Эти методы позволяют получить достаточно точные результаты, только лишь
при достаточно простой конфигурации объекта. При сложной конфигурации объекта в
САПР используется метод конечных элементов (МКЭ).
Совершенство конструкции, ее надежность, а также механические,
энергетические, прочностные и другие характеристики закладываются на этапе
конструирования, таким образом, от принятия правильных конструкторских решений
во многом зависит качество работы и конкурентоспособность создаваемого
механического оборудования. Основными техническими характеристиками материалов,
влияющими на работоспособность конструкции , являются следующие характеристики:
Прочность - способность материала сопротивляться нагрузкам без
разрушения. Количественной характеристикой является предел прочности sb, под которым понимается напряжение,
приводящее к разрушению материала.
Упругость - свойство материала восстанавливать свои форму и размеры после
снятия нагрузки. Основной количественной характеристикой упругости служит
перемещение под действием единичной нагрузки, которое в свою очередь не зависит
от модуля упругости Е и коэффициента Пуассона m.
Пластичность - свойство материала сохранять значительные пластические
деформации после снятия нагрузки. Характеризуется пределом текучести sr - напряжением, при котором величина
остаточной пластической деформации не превышает 0,2 %.
Выносливость - способность материала сопротивляться разрушению от
усталости. Количественно характеризуется пределом выносливости s -1, равным наибольшему напряжению,
которое образец выдерживает без разрушения при неограниченном числе
симметричных циклов нагружения.
Для разработки современных машин, которые будут конкурентоспособными по
отношению к зарубежным аналогам, необходимо внедрять компьютерную технологию
проектирования. Это единственный путь, который способен поднять качество
проектирования и создать оптимальные по весу, энергопотреблению и ряду других
параметров конструкции.
Для реализации этих и других задач и предназначена русскоязычная Система
автоматизированного расчета и проектирования в машиностроении и строительстве
АРМ Win Machine - российская разработка, адресованная инженерам и
конструкторам, занятым конструированием нового и модернизацией существующего
механического оборудования.
АРМ Win Machine включает эффективные и надежные алгоритмы и программы
расчета:
энергетических и кинематических параметров;
прочности, жесткости и устойчивости;
выносливости;
надежности и износостойкости;
динамических характеристик.
3.2 Расчет напряженно-деформированного состояния
основания
Имитация проводится путем приложения соответствующих нагрузок в пяти
областях детали. Выбор области приложения нагрузки обусловлен количеством
ступеней данной детали.
Расчет детали «Основание» проводится с использованием модуля APM
Structure 3D программного комлекса APM WinMachine. Модуль APM Structure 3D
предназначен для расчета напряженно-деформированного состояния стержневых,
пластинчатых, оболочечных и твердотельных конструкций, а также их произвольных
комбинаций. APM Structure 3D организован таким образом, что в его рамках можно
рассчитать все многообразие существующих конструкций, собирая их из
вышеперечисленных макроэлементов. Конструкции и их элементы могут быть
импортированы в редактор конструкций через DXF-формат из 2D и 3D графических
редакторов или напрямую через модуль APM STUDIO с подготовленной
конечно-элементной сеткой и вариантами закрепления и нагружения. Внешняя
нагрузка, так же как и условия закрепления конструкции, могут быть
произвольными как по характеру, так и по местоположению.
Модуль позволяет решать следующие задачи:
определение полей эквивалентных напряжений и их составляющих;
расчет линейных, угловых и результирующих перемещений;
определение внутренних усилий;
расчет устойчивости и формы потери устойчивости;
определение частот собственных колебаний и собственных форм;
расчет вынужденных колебаний;
автоматический подбор сечений из условий прочности, жесткости,
устойчивости для металлоконструкций машиностроительного назначения;
проектирование узлов металлоконструкций;
автоматическая генерация номенклатуры элементов, составляющих
конструкцию.STUDIO - модуль моделирования и импорта (поддерживается импорт из
формата STEP) трехмерных поверхностных и твердотельных моделей с инструментами
указания опор и приложения различных нагрузок и встроенным генератором
разбиения на конечно-элементную сетку. Основное назначение модуля - подготовка
смоделированной или импортированной геометрии к конечно-элементному анализу в
модуле APM STRUCTURE 3D.
Прежде всего необходимо сформировать твердотельную модель детали. Модель
детали представлена на рисунке 3.1.
Рисунок 3.1 - Модель детали «Основание»
После этого выбирается материал детали. Это является важным шагом,
поскольку от выбора материала будут зависеть физические свойства будущего
изделия. APM WinMachine обладает обширной библиотекой материалов. Для данной
детали выбирается углеродистая сталь. Следующим шагом будет разбиение детали на
конечные элементы. Здесь мы можем выбрать размеры конечных элементов, что
влияет на точность вычислений (см. рисунок 3.2).
Рисунок 3.2 - Разбиение модели на конечные элементы
На рисунке 3.3 показан выбор размера конечных элементов.
Рисунок. 3.3 - Выбор размера конечных элементов
После разбиения детали на КЭ укажем редактору, на каких поверхностях
закрепляется деталь, какие силы действуют на нее и т.д. (рисунок 3.4)
Произведём статический анализ, зададим ограничения и действующие силы.
Действующие силы и ограничения приведены на рисунке 3.5
.
Рисунок 3.4 - Фиксация детали
Рисунок 3.5 - Действующие силы и ограничение
Расчитываем форму колебаний основания в зависимости от частоты
электродвигателя, установленного на машине. Частота электродвигателя 1000 Гц.
Расчитываем собственную частоту основания. Результаты расчетов приведены в
приложении. Форма колебаний основания приведена на рисунке 3.6.
Рисунок 3.6 - Форма колебаний основания
После этого выполняем команду Run, запуская основной расчет программы. После
в дереве появляются папки: Stress, Displacement, Strain, Deformation, Design
Check.
В первой папке Stress находится расчет статического напряжения, деталь
закрашивается в цвета, которые меняются в зависимости от величины нагрузки на
различных участках. Расчет статистического напряжения приведен на рисунке 3.7.
Рисунок 3.7 - Статическое напряжение
Проведем расчет основания на устойчивость. Результаты расчета приведены
на рисунке 3.8.
Рисунок 3.8 - Коэффициент потери устойчивости
Аналогично проводим исследования для остальных областей воздействия на
деталь.
По цветной легенде, находящейся около рисунка, можно определить
максимальные значения того или иного параметра и сделать соответствующие выводы
о прочностных характеристиках детали.
В ходе расчетов, проведенных методом имитационного моделирования, были
получены аппроксимированные результаты: наибольшие значения статического
напряжения и деформационного растяжения лежат в пределах, определенных
разработчиком как допустимые при указанных нагрузках, деталь имеет необходимый
запас прочности, требуемый для безопасного использования изделия в целом.
Результаты расчета подтверждают, что деталь
«Основание» спроектирована верно - максимальное напряжение не превышает
допустимого, а максимальная деформация не критична, коэффициент запаса
прочности находится в пределах от 1 до 10 (равен 5,3)
4. Технологическая часть
Эффективность производства, его технический прогресс, качество выпускаемой
продукции во многом зависят от опережающего развития производства нового
оборудования, машин станков и аппаратов, от всемирного внедрения методов
технико-экономического анализа, обеспечивающих решение технических вопросов и
экономическую эффективность конструкторских и технологических разработок.
Механическая обработка является основным методом изготовления деталей в
машиностроении. Использование типовых операций механической обработки в
технологическом процессе (токарных, сверлильных, фрезерных и др.) наиболее
характерно в изготовлении деталей машин.
Темой работы является разработка технологического процесса механической
обработки детали.
Все вопросы технологии и ее организации, разрабатываемые в дипломном
проекте, должны отвечать реальным целям, стоящим перед производством.
Необходимо показать сущность и значение организации труда, совершенствования
технологии на основе использования новых достижений науки и техники и методы
улучшения использования рабочего времени
4.1 Назначение и конструкция детали
Деталь, разрабатываемая в выпускной работе - крышка - является составной частью приводного
вала. Крышка служит для герметизации подшипниковых узлов.
Данная деталь принадлежит к классу дисков с центральным сквозным
ступенчатым отверстием. Наиболее точным является центральное отверстие Ø
52, для установки
манжеты. Имеется 3 паза для крепления детали к корпусу вала. Крышка
изготовляется из стали 45 ГОСТ 1058-88. Химический состав и механические
свойства стали 45 приведены соответственно в таблицы 4.1 и 4.2.
Таблица 4.1 - Химический состав стали 45 (ГОСТ 1050-88), %
С
|
Si
|
Mn
|
S
|
P
|
Ni
|
Cr
|
|
|
|
не более
|
|
|
0,40-0,50
|
0,17-0,37
|
0,50-0,80
|
0,045
|
0,045
|
0,30
|
0,30
|
Таблица 4.2 - Механические свойства стали 45
, МПа
, МПа
, %ψ, %ан,
Дж/см2НВ (не более)
|
|
|
|
|
|
не менее
|
|
горячекатанной
|
отожженной
|
360
|
610
|
16
|
40
|
50
|
241
|
197
|
Эскиз детали приведен на рисунке 4.1.
Рисунок 4.1 - Эскиз детали
4.2 Анализ технологичности детали
Технологичность конструкции рассматривается как совокупность свойств
конструкции изделия, определяющих ее приспособленность к ремонте для заданных
показателей качества, объема выпуска и условий выполнения работ.
Технологический
анализ конструкции обеспечивает улучшение технико-экономических показателей
разрабатываемого технологического процесса. Поэтому технологический анализ -
один из важнейших этапов технологической разработки, в том числе и дипломного
проектирования.
Каждая деталь должна изготовляться с минимальными трудовыми и
материальными затратами. Эти затраты можно сократить в значительной степени от
правильного выбора варианта технологического процесса, его оснащения,
механизации и автоматизации, применения оптимальных режимов обработки и
правильной подготовки производства. На трудоемкость изготовления детали
оказывают особое влияние ее конструкция и технические требования на
изготовление.
Основные задачи, решаемые при анализе технологичности конструкции
обрабатываемой детали, сводятся к возможному уменьшению трудоемкости и
металлоемкости, возможности обработки детали высокопроизводительными методами.
Таким образом, улучшение технологичности конструкции позволяет снизить
себестоимость ее изготовления без ущерба для ее служебного назначения.
Технологичность конструкции детали определяем по соотношению
положительных и отрицательных элементов (технологичных и нетехнологичных
элементов)
Нетехнологичные и технологичные элементы конструкции детали:
1. Материал технологичен.
2. Достаточно сложная конструкция.
3. Обычные виды обработки.
. Возможно использования типовых станков.
. Возможно применение стандартных инструментов.
. Возможно применение стандартных приспособлений.
. Устойчивость детали средняя.
. Сложный контроль пазов детали.
. Обычный расход материала.
. Деталь нетрудоемкая.
При изготовлении крышки применяются типовые
металлорежущие станки. Рационально выбран материал детали - хорошая
обрабатываемость резанием. Применение стандартных инструментов и средств
измерения. Кроме того основная доля обработки приходится на токарную операцию.
По произведенной качественной оценке можно сделать вывод, что деталь вполне
технологична.
4.3 Выбор типа производства
Тип производства характеризуется коэффициентом закрепления операций за
одним рабочим местом или единицей оборудования.
(4.1)
где
- число различных операций;
- число
рабочих мест, на которых выполняются данные операции.
Типы
производства характеризуются следующими коэффициентами закрепления операций:
Массовое……………………………………………1
Крупносерийное
……………………………… св. 1до 10
Среднесерийное
……………………………… от 10 до 20
Мелкосерийное
………………………………. от 20 до 40
Единичное
……………………………………….. св. 40
Для
предварительного определения типа производства можно использовать годовой объем
выпуска и массы деталей.
В
данном случае:= 1,6 кг - масса детали;
Nг = 2000 шт. - годовая программа выпуска.
Тип производства выбираем по таблице 4.3.
Таблица 4.3 - Зависимость типа производства от объема выпуска и массы
детали
Масса детали, кг
|
Тип производства
|
|
Единичное
|
мелкосерийное
|
средне- серийное
|
крупно- серийное
|
массовое
|
<1,0 1,0¸2,5 2,5¸5,0 5,0¸10,0 >10,0
|
<10 <10 <10 <10 <10
|
10¸2000 10¸1000 10¸500 10¸300 10¸200
|
1500¸100000 1000¸50000 500¸1000 300¸25000 200¸10000
|
75000¸200000 50000¸100000 35000¸75000 25000¸50000 10000¸25000
|
>200000 >100000 >75000 >50000 >25000
|
Исходя из справочных данных, выбираем среднесерийное производство. В
среднесерийном производстве выпускаются изделия ограниченной номенклатуры,
изготавливаемые периодически повторяющимися партиями со сравнительно большим
объемом выпуска, по сравнению с мелкосерийным производством. На рабочих местах
выполняется несколько периодически повторяющихся операций. Технологические
особенности серийного производства изменяются в зависимости от номенклатуры,
трудоемкости и количества изделий в партии деталей.
4.4 Выбор заготовки
При выборе вида заготовки необходимо учитывать не только эксплуатационные
условия работы детали, ее размеры и форму, но и экономичность ее производства.
Если при выборе заготовок возникают затруднения, какой метод изготовления
принять, тогда производят технико - экономический расчет двух или нескольких
выбранных вариантов.
Метод выполнения заготовок для детали определяется назначением и
конструкцией детали с учетом технологических свойств материала, техническими
требованиями, серийностью выпуска, формы детали и заготовки, а также
экономичностью изготовления. Заготовку желательно выбирать с таким расчетом,
чтобы ее форма была максимально приближена к форме готового изделия, поскольку
это значительно облегчит последующую обработку.
При выборе заготовки для заданной детали главным критерием является
обеспечение заданного качества готового изделия при его минимальной
себестоимости.
Исходные данные, необходимые для выбора вида заготовки и способа ее
получения:
материал заготовки - Сталь 45 ГОСТ 1050-88 ;
плотность материала - 7850 кг/м3;
масса детали, кг - 1,6 кг;
годовая программа - 2000 шт.
Определим стоимость одной заготовки, проведя технико-экономический расчет
двух вариантов изготовления заготовки:
- штамповка ГОСТ 7505-74;
- прокат сортовой ГОСТ 2590-7.
) Заготовка методом штамповки
Припуски штамповки на диаметр:
, мм,
(4.2)
где
DP - расчетный диаметр штамповки, мм;- номинальный диаметр, мм;- припуск на
штамповку, мм.
мм;
мм.
Припуски
штамповки на длину:
мм;
ааааааааааа (4.3)
где
LP - расчетная длина , мм; ааааааааааа- длина участка детали, мм;- припуск на
штамповку, мм.
мм.
Определим
объем полученной штамповки:
, мм3;
(4.4)
где
D - диаметр обрабатываемой поверхности заготовки, мм;- длина обрабатываемой
поверхности заготовки, мм;
Определим
массу заготовки:
, кг,
(4.5)
где
m - масса штамповки, кг;=7850 кг/м3 - плотность стали;шт - объем штамповки, м3.
Масса
заготовки при штамповке:
кг.
)
Заготовка из круглого проката:
Припуски
на прокат:
при
черновом точении припуск на обработку 4 мм;
при
чистовом 1 мм;
при
шлифовании 0,4мм.
,мм,
(4.6)
где
DP - расчетный диаметр проката, мм;- максимальный диаметр детали, мм;- припуск
на обработку, мм.
мм;
мм;
мм.
Принимаем
диаметр проката Dпр=160мм.
Припуск
на подрезку торца:
, мм,
(4.7)
где
LP - расчетный припуск заготовки, мм;- номинальная длина детали, мм;- припуск
на подрезку торца, мм;
мм.
Объем
заготовки из проката равен:
, мм3,
(4.8)
, мм3
Масса
заготовки равна:
, кг,
(4.9)
кг.
Определим
коэффициенты использования материала:
, (4.10)
где
К - коэффициент использования материала;Д - масса детали, кг;З - масса
заготовки, кг;
Заготовка
методом штамповки:
Заготовка
из проката:
.
Определим
себестоимость заготовки методом штамповки:
,руб.,
(4.11)
где
С - базовая стоимость 1т заготовок, руб.;- масса заготовки, кг;- масса детали,
кг;- стоимость 1т отходов, руб.;; kc; кв; кМ; кп - коэффициенты, зависящие от
класса точности, группы сложности, массы, марки материала и объема производства
заготовок.
За
базу принимаем стоимость одной тонны штамповок С=573 руб. (штамповки из
конструкционной легированной стали массой до 2 кг, нормальной степени точности
по ГОСТ 7503-73, 1-ой группы сложности, 2-ой группы серийности. Прейскурант №
25-01,1981 г.)
кт - коэффициент, зависящий от точности кт = 1
км - коэффициент для легированных сталей кс = 1,13;
кс - коэффициент, зависящий от сложности заготовки
кс=0,77;
кв- коэффициент, зависящий от массы заготовки,
км = 1,29.
Подставим данные значения в формулу и определим
стоимость заготовки методом штамповки:
руб.
Стоимость
заготовки из проката определяем по формуле:
, руб.,
(4.12)
где
Q - масса заготовки, кг;- цена 1 кг материала заготовки, руб;- масса готовой
детали, кг;отх - цена 1 т отходов, руб.
руб.
Из технико-экономического расчета видно, что заготовка
полученная из проката более экономична, но коэффициент использования материала
при получении заготовки методом горячей штамповки выше на 50%. В случае
использования проката требуется выполнить дополнительную отрезку, правку,
токарную и сверлильную обработки до размеров штампованной заготовки, что
приводит к увеличению стоимости изготовления детали. Поэтому принимаем
заготовку методом штамповки.
4.5 Выбор маршрута обработки
Основные операции при изготовлении данной детали следующие:
токарная (точение детали по контуру, растачивание выборки);
сверлильная (сверление отверстий);
фрезерная (фрезерование пазов);
шлифовальная (окончательная обработка в размер с требуемой шероховатостью
поверхностей);
Маршрут обработки детали приведен в таблице 4.4.
4.6 Расчет и выбор припусков
на обработку
Величина припуска влияет на себестоимость изготовления
детали. При увеличенном припуске повышаются затраты труда, расход материала и
другие производственные расходы, а при уменьшенном приходится повышать точность
заготовки, что также увеличивает себестоимость изготовления детали. Величина
припусков на механическую обработку зависит от метода получения заготовки,
марки материала заготовки, точности и шероховатости обрабатываемой поверхности,
модели и типа оборудования, приспособления и инструмента.
Таблица 4.4 -Маршрут обработки крышки
Операция
|
Переход
|
№ операции
|
Наименование
|
№ перехода
|
Содержание
|
005
|
Токарная (обработка с одной
стороны)
|
01 02 03 04 05 06 07
08
|
точить Æ 151 мм на длину l = 33 мм; подрезать торец в размер
31; расточить отверстие Æ44 на длину l = 29мм;
расточить отверстие Æ52 на длину l = 26мм; расточить выборку Æ110 на длину l = 19мм; расточить отверстие Æ120на длину l = 9мм; подрезать торец; расточить
уклон 45° на длину l=5мм; точить фаску 1*45°.
|
010
|
Токарная (обработка с
другой стороны)
|
01 02
|
точить Æ 151 мм на длину l = 33 мм; точить конус 45° на длину l = 27 мм
|
015
|
Сверлильная
|
|
Сверлить 3 отверстия Æ 7 мм длиной l = 20 мм
|
020
|
Фрезерная
|
|
Фрезеровать паз 12х12.
|
Рассчитаем припуски для обработки поверхности
диаметром 151 мм.
Технологический маршрут обработки поверхности состоит
из 3-х операций:
- обтачивание;
сверление;
шлифование.
Для данной поверхности расчёт проводим аналитическим
методом, а для остальных табличным.
Суммарное отклонение определяем по формуле:
, мкм,
(4.13)
, мкм;
(4.14)
где
ρсм=1 - величина отклонения расположения;
ρкор - величина деформации заготовки;
∆к - идеальная кривизна заготовки в мкм на 1 мм длины;
∆к = 1,5 мкм/мм;
D - диаметр заготовки, D=151мм.
мкм;
мкм.
Величина
остаточного суммарного расположения заготовки после выполнения перехода:
,мкм,
(4.15)
где
- коэффициент уточнения;
-
суммарное отклонение расположения заготовки.
- после чернового обтачивания р1=
0,06 * 1025 = 61,5 мкм;
после чистового обтачивания р2 = 0,04
* 1025=41 мкм;
после шлифования р3 = 0,02 * 1025
=20.5 мкм.
Расчет минимальных значений припусков произведём по
формуле:
, мкм,
(4.16)
где Rzi-1 - шероховатость на предыдущее переходе;
Тi-1 - глубина дефектного слоя на предыдущем
переходе;- погрешность установки заготовки на предыдущем переходе.
мкм;
мкм;
мкм;
мкм.
Производим
расчёт размера диаметров, начиная с предельного минимального размера, заданного
чертежом, путем последовательного прибавления расчетного минимального припуска
каждого технологического перехода:
, мм;
(4.17)
мм;
мм;
мм;
мм.
Округлим расчётные размеры:
мм;
мм;
мм;
мм;
мм.
Определяем наибольшие предельные размеры di max:
значения допуска для доводки δ4 = 0,019 мм;
для шлифовки δ3 = 0,030 мм;
для чистового обтачивания δ2 = 0,19 мм;
для чернового обтачивания δ1 = 0,46 мм; δзаг=1.
Наибольший предельный размер:
, мм,
(4.18)
мм;
мм;
мм;
мм;
мм.
Определяем
предельные размеры припусков
и
:
, мм
(4.19)
мм;
мм;
мм;
мм;
мм;
мм;
мм;
мм.
Определим
общие припуски z0min и z0max:
мм;
мм.
Проводим
проверку правильности выполнения расчётов:
, (4.20)
, (4.21)
,119-0,108=0,03-0,019
,011=0,011
;
;
.
Сводим данные в таблицу 4.5 и на основании проведённых расчётов строим
схему графического расположения припусков и допусков по обработке поверхности ø149+0,021+0,002 .
Таблица 4.5 - Результаты расчета припусков, допусков и промежуточных
размеров
Техно-логические переходы
обработки поверх-ности
|
Элменты припуска, мкм
|
Расчётный припуск, мкм
2Zmin
|
Расчётный размер, мм dр
|
Допуск, мкм δ
|
Предельный размер, мм
|
Предельный припуск, мкм
|
|
Rz
|
T
|
ρ
|
|
|
|
dmin
|
dmax
|
2*Zmin
|
2*Zmax
|
Заготовка
|
150
|
200
|
1025
|
|
151,338
|
1000
|
151,38
|
152,38
|
|
|
Черновое точение
|
50
|
50
|
61,5
|
2×1375
|
149,624
|
460
|
149,63
|
149,5
|
1750
|
3250
|
Чистовое точение
|
30
|
30
|
41
|
2×161,5
|
151,302
|
190
|
149,31
|
149,14
|
320
|
590
|
Шлифовка
|
10
|
20
|
20,5
|
2×101
|
149,102
|
30
|
149,11
|
149,09
|
200
|
360
|
Схема расположения полей припусков, допусков и промежуточных размеров
приведена на рисунке 4.2.
Рисунок
4.2 - Схема графического расположения припусков
.7 Выбор оборудования
) Токарная
операция
Токарная операция выполняется на токарно-винторезном станке
мод. 16К20.
Техническая характеристика данного станка
наибольший диаметр обрабатываемой детали, мм 400;
наибольшая длина продольного перемещения, мм 900;
наибольшая длина поперечного перемещения суппорта, мм 250;
диапазон скоростей вращения шпинделя, об\мин 12,5-2000;
число скоростей 22;
наибольшая скорость продольной подачи, мм\мин 1200;
диапазоны скоростей подач, мм\мин
продольная 3
- 1200;
поперечная 1,5
- 600;
скорость быстрого хода, мм\мин
продольная 4800;
поперечная
2400;
мощность электродвигателя главного движения, кВт 10.
Оснастка: токарный трехкулачковый патрон, вращающийся центр.
2)
Сверлильная операция
В качестве технологического оборудования назначаем вертикально-сверлильный
станок мод. 2Н125.
Основные характеристики станка
корпус Морзе шпинделя
№ 3;
наибольший диаметр сверления по стали, мм 25;
количество операций частот вращения шпинделя 12;
частота вращения шпинделя, мин-1
45-2000;
величина подачи, мм/об
0,1…0,6;
количество ступеней подач 9;
мощность электродвигателя, кВт 2,2.
Оснастка: приспособление на станке, поводковый патрон, вращающиеся
центра.
) Фрезерная операция
Станок для обработки пазов концевыми и шпоночными фрезами. Класс точности
станков П.
Основные характеристики станка:
ширина фрезеруемого паза, мм
6…32;
наибольшая длина фрезеруемого паза, мм 600;
наибольшая разбивка паза, мм 1,0;
частота вращения шпинделя, мин-1:
;315;400;500;630;800;1000;1250;1600;2000;3150
количество поперечных подач фрезерной головки 18;
поперечная подача фрезерной головки, мм\мин
;5; 6,3; 8; 10; 12,5; 16; 20; 25; 31,5; 40; 50; 63; 80; 100; 125; 160;
200
мощность электродвигателя, кВт:
главного движения
2,2;
привода подач
1,5.
Оснастка: приспособление на станке (тиски, делительная головка).
4) Круглошлифовальная
операция
Круглошлифовальная операция выполняется на круглошлифовальном станке
мод.3Т160.
Основные характеристики станка
наибольшие размеры обрабатываемой заготовки, мм
диаметр 280;
длина 700;
конус Морзе передней бабки, №5;
наибольшие размеры шлиф. круга 750х130х305;
диаметр шлиф. круга для внутреннего шлифования, мм 16,32,52;
частота вращения шпинделя круга, об/мин 1250;
частота вращения шпинделя изделия, об/мин 55… 620;
мощность электродвигателя главного движения, кВт 17;
габариты станка, мм 3754х4675;
категория ремонтной сложности 30.
Оснастка: центра круглошлифовального станка, поводковый патрон.
4.8 Выбор режущего инструмента
При разработке технологического процесса выбор режущего инструмента в
значительной мере предопределяется методами обработки, свойствами
обрабатываемого материала, требуемой точностью обработки и качества
обрабатываемой поверхности.
Режущий инструмент необходимо выбирать по соответствующим стандартам и
справочной литературе взависимости от методов обработки деталей.Правильный
выбор режущей части инструмента имеет большое значение для повышения
производительности и снижения себестоимости обработки.
1) Токарная
операция
В качестве режущего инструмента применяем стандартный режущий инструмент
. Необходим черновой и чистовой резец. Раздельное применение необходимо для
повышения точности обработки. При черновом больше глубина резания и повышенный
износ.
Все инструменты оснащены пластинками твердого сплава Т15К6.
Режущие инструменты:
проходной упорный правый с механическим креплением твердосплавной
пластиной ГОСТ 18872-73;
расточной резец для глухих отверстий ГОСТ 18880-73;
расточной резец для сквозных отверстий ГОСТ 18873-73;
упорно-проходной резец ГОСТ 18877-73;
2)
Сверлильная операция
- сверло 2301-0404 ГОСТ 2092-77 общего назначения под сверление отверстия
Æ 7 мм.:
диаметр сверла, мм 8,0;
длина спиральной части сверла, мм 60;
длина сверла, мм 95;
материал режущей части Р6М5.
) Фрезерная операция
Режущий инструмент ы:
фреза концевая Æ 12 мм ГОСТ 17025-71;
материал режущей части ВК-15.
4)
Круглошлифовальная операция
Режущий инструмент:
абразивный круг прямоугольного профиля 25А20ПСМ1
4.9 Выбор измерительного инструмента
При проектировании технологического процесса для межоперационного и
окончательного контроля обрабатываемых поверхностей необходимо использовать
стандартный измерительный инструмент, учитывая тип производства. Затраты по
эксплуатации измерительных инструментов обычно малы и в расчетах экономической
эффективности не учитываются.
) Токарная операция
штангенциркуль ШЦ 3-125-0,05 ГОСТ 164-80;
шаблон фасочный 1*45°.
) Сверлильная операция
калибр-пробка ГОСТ 16780-71.
) Фрезерная операция
калибр-пробка ГОСТ 16780-71;
штангенциркуль ШЦ-1 0-150 ГОСТ 164-80.
) Круглошлифовальная операция
микрометр гладкий ГОСТ 6507-78
прибор для измерения параметров шероховатости поверхности (профилометр
цеховой с отсчетом цифровым и индуктивным преобразователем).
4.10 Расчет режимов резания
Расчет ведется одновременно с заполнением операционных или маршрутных
карт технологического процесса. Совмещение этих работ исключает необходимость
дублирования одних и тех же сведений в различных документах, так как в
операционных картах должны быть записаны данные по оборудованию, способу
обработки, характеристике обрабатываемой детали и другие, которые используются
для расчетов режимов резания.
Выбор режимов резания осуществляется по таблицам режимов. Для нескольких
наиболее характерных переходов (например, для одного перехода определенной
операции) - расчетно-аналитическим методом.
Режимы резания зависят от обрабатываемого материала, от материала режущей
части инструмента, от шероховатости и конфигурации обрабатываемой поверхности,
от величины припуска на обработку, от требуемой производительности операции, от
режима замены и периода стойкости режущего инструмента.
Определим режимы резания для подрезки торца Æ 151 мм:
Глубина резания определяется по формуле:
=
; мм, (4.22)
заг - максимальный диаметр
заготовки, мм;- диаметр детали, мм.
Получаем
t
=
мм.
Величину
подачи назначаем= 0,4 - 0,5 мм/об.
Окончательно
принимаем= 0,4 об/мин.
Скорость
резания
=Vт*К1*К2*К3;
м/мин, (4.23)
где Vт - табличная скорость, выбирается из карты;
К1 - коэффициент, зависящий от размеров обработки, выбирается из карты;
К2 - коэффициент, зависящий от состояния обрабатываемой поверхности и ее
твердости, определяется из таблицы;
К3 - коэффициент, зависящий от материала и его стойкости, определяется из
таблицы коэффициента К3.
Подставим данные значения в формулу и определим скорость
резания:=70*1*1,2*1=84м/мин.
Результаты расчетов приведены в таблице 3.6.
Таблица 3.6 - Таблица результатов расчетов режимов резания
Переход
|
V, м/мин
|
n, мин-1
|
S, мм/об
|
t, мм
|
Токарная операция
(обработка с одной стороны)
|
точить Æ 151 подрезать торец расточить отверстие Æ44 расточить отверстие Æ52 расточить выборку Æ110
расточить отверстие Æ120 подрезать торец расточить уклон 45° точить фаску 1*45°
|
90 80 80 80 80 80 70 100 70
|
500 500 500 500 250 250 710
250 250
|
0,1 0,2 0,1 0,1 0,2 0,2
0,17 0,17 0,05
|
2 1 3 4 29 5 2 5 1
|
Токарная операция
(обработка с другой стороны)
|
точить Æ 151 точить конус 45°
|
90 120
|
720 250
|
1 5
|
1,8 20,4
|
Сверлильная операция
|
25
|
1000
|
0,1
|
7
|
Фрезерная операция
|
фрезеровать паз 12х12
|
40
|
315
|
0,1
|
12
|
Шлифовальная операция
|
шлифовать торец Æ 149 шлифовать конус 45°
|
0,72 0,72
|
1250 1250
|
6 0,5
|
0,2 0,2
|
4.11 Расчет технической нормы времени
Техническая норма времени на обработку заготовки является одним из
основных параметров для расчета стоимости изготовляемой детали, числа
производственного оборудования, заработной платы рабочих и планирования
производства.
Техническое нормирование времени представляет собой установление
технически обоснованных ресурсов: энергии, материала, инструментов, рабочего
времени и т.д.
Приведем пример расчета для токарной операции. Расчет ведем по справочным
данным.
В серийном производстве норма штучно-калькуляционного времени Тш-к
определяется по формуле:
(4.24)
где
Тп-з - подготовительно-заключительное время, мин;- количество деталей в
настроечной партии, шт.;
То
- основное время, мин;
Ту.с.
- время на установку и снятие детали, мин;
Тз.о.
- время на закрепление и открепление детали, мин;
Туп
- время на приемы управления, мин;
Тиз
- время на измерение детали, мин;- коэффициент, учитывающий нормирование
вспомогательного времени в серийном производстве;
Тоб.от.
- время на обслуживание рабочего места и время перерывов, мин.
Количество
деталей в настроечной партии определяется по формуле:
, (4.25)
где
Nг - годовая программа, шт;
а
- периодичность запуска, принимаем равной 2 дня;- число рабочих дней в году.
шт.
Справочные
данные:
мин;
время
на включение станка кнопкой равно
Ту.п.
= 0,22 мин;
время
на измерение детали
Тиз
=0,22 мин.
Рассчитываем
техническую норму времени для первого перехода:
мин.
Расчеты
по технической норме времени сводим в таблицу 4.7
Таблица
4.7 - Таблица технических норм времени
Наименование операций
|
То
|
Тв
|
Тот
|
Т п-з
|
Тш-к
|
|
|
Ту.с.+ Тз.о.
|
Туп
|
Тиз
|
|
|
|
I Токарная
|
4,707
|
0,16
|
0,22
|
0,22
|
4.05
|
4
|
9,965
|
II Токарная
|
2,477
|
0,12
|
0,18
|
0,22
|
3,9
|
4
|
7,58
|
Сверлильная
|
1,069
|
0,09
|
0,16
|
0,074
|
3,39
|
4
|
6,702
|
Фрезерная
|
1,14
|
0,09
|
0,16
|
0,074
|
3,39
|
4
|
5,28
|
IКруглошлифовальная
|
0,72
|
0,08
|
0,06
|
0,17
|
0,61
|
4
|
2,15
|
IIКруглошлифовальная
|
0,4
|
0,01
|
0,06
|
0,17
|
0,61
|
4
|
1,7
|
5. Проектирование механического участка для
обработки детали типа «крышка подшипника»
.1 Определение типа и формы организации
производства
В зависимости от размера производственной программы, характера продукции
(массы, размеров и т.д.), а также технических и экономических условий
осуществления производственного процесса различают три типа производства:
единичное (индивидуальное), серийное и массовое.
В соответствии с ГОСТ 14.004 - 83, показателем для определения типа
функционирующего производства является коэффициент закрепления операций:
Кзо =
(5.1)
где: Чоп - число технологических операций, подлежащих выполнению цехом
или участком;
Спр - число рабочих мест, выполняющих эти операции.
Согласно ГОСТ 14.004 - 83:
для массового производства коэффициент Кзо = 1;
для крупносерийного 1 ≤ Кзо ≤ 10;
для среднесерийного 10 ≤ Кзо ≤ 20;
для мелкосерийного 20 ≤ Кзо ≤ 40.
Далее необходима проверка принятых решений после определения количества
основного оборудования. В данном курсовом проекте мы проектируем
машиностроительный участок мелкосерийного производства.
После определения типа производства устанавливают форму его организации.
Форма организации производства может быть поточной и не поточной. Далее она
будет определять способ расположения оборудования и рабочих мест, схему
движения обрабатываемых объектов и т.д.
Для мелко и среднесерийного производства принимается не поточная форма
организации.
Для серийного производства количество деталей в партии запуска
определяется упрощенным способом:
(5.2)
где: D - количество деталей по годовой программе с запасными частями,
шт.;
t - число дней, на которые необходимо иметь страховочный запас деталей
для бесперебойной работы (сборки). Нормальным считается:
- для
крупных деталей (св. 20 кг) - на 2 - 3 дня;
- для
мелких 5 - 10 дней.
Ф - число рабочих дней в году, 250 - 260.
Полученное количество деталей округляется до большего.
5.2 Определение годовой производственной
программы
Проектирование по приведенной программе также предусматривает наличие
разработанных технологических процессов, но только для деталей - представителей
групп, объединенных по признаку конструктивного или технологического сходства.
В этом случае, все подлежащие изготовлению изделия приводятся к нескольким
типовым, являющимся наиболее характерными для каждой группы. Проектирование по
приведенной программе характерно для цехов мелко и среднесерийного
производства.
Для определения приведенной программы все изделия разбивают на группы по
конструктивным или технологическим признакам. Группа представляется одним
типовым изделием - представителем, к которому предъявляются следующие
требования:
- число
изделий - представителей должно быть преобладающим в годовой программе:
- их
общая трудоемкость должна составлять значительную часть от общей трудоемкости
данной группы.
Расчет приведенной программы заключается в определении условного объема
выпуска деталей - представителей. Вместо всей номенклатуры деталей, входящих в
группу.
Для каждого наименования деталей расчет производится по формуле:
(5.3)
где:- заданный объем выпуска деталей i - го наименования;пр i -
коэффициент приведения деталей i - го наименования, характеризующий
трудоемкость данной детали по сравнению с деталью - представителем:
(5.4)
K1 - коэффициент приведения по массе; для геометрически подобных деталей.
(5.5)
- масса приводимой детали, кг;пр - масса детали - представителя, кг;-
коэффициент приведения по серийности:
(5.6)
пр и Ni - программа выпуска соответственно детали - представителя и
приводимой детали;
α - показатель степени, равный 0,15 для
объектов легкого и среднего машиностроения и 0,2 для объектов тяжелого
машиностроения;
Исходя из материалов, имеющихся в распоряжении студента и руководителя
производственную программу цеха (фонд производственного времени цеха) можно
задать в нормо-часах. Трудоемкость (станкоемкость) одного производственного
участка на основании данных производственной деятельности машиностроительных
предприятий может составлять 25000 ÷ 50000 станко-ч., а трудоемкость цеха - от
250000 до 750000 станко-час. При курсовом проектировании и работе над ВКР
программа цеха должна соответствовать малому цеху (100 ÷
150 единиц основного
оборудования), т.е. составлять 400000 ÷ 550000 нормо-час.
Так как годовая производственная программа точно не установлена, то
основываясь на производственном опыте проектирования механического цеха и
участков мелкосерийного производства, принимаем годовую программу
проектируемого участка 100000 нормо-час.
5.3 Выбор формы специализации участка
При подетальной специализации на участках изготавливают детали сходной
конструкции, независимо от того, к какому узлу они принадлежат. Основное
оборудование располагается по ходу технологического процесса на участках,
которые получают название по виду производимой продукции. Подетальная специализация
характерна для средне и крупносерийного производства.
Технологическая форма специализации чаще всего используется в единичном,
мелко - среднесерийном производстве. При этом участки специализируют по типам
оборудования. Последовательность расположения таких участков однородных станков
на площади цеха определяется последовательностью обработки большинства типовых
деталей. Основное достоинство технологической специализации - большая гибкость
производства при освоении новых изделий и большие возможности регулирования
загрузки оборудования. Технологическая специализация цехов и участков
применяется, главным образом, или для деталей, технологический процесс
изготовления состоит из одной-двух операций, или для сосредоточения однотипных
сложных в наладке операций (например, операции обработки зубьев зубчатых
колес). В данном проекте принимаем подетальную форму специализации участка.
5.4 Определение количества основного
оборудования механического участка
Состав основного оборудования механического цеха устанавливается на
основе технологического процесса изготовления детали - представителя
(представителей). В данном проекте деталь-представитель «крышка».
Технологический процесс изготовления данной детали представлен в таблице
5.1.
Работа выполняется в несколько этапов.
. Рассчитывается общее количество основного технологического оборудования
участка:
(5.7)
где:
Тпр - заданная годовая программа участка в нормо-ч, (100000).
Фд - действительный годовой фонд времени работы единицы оборудования в
часах
Таблица 5.1 - Технологический процесс изготовления детали «крышка»
Номер операции
|
Наименование операции
|
Тип и модель оборудования
|
Время, мин
|
Инструмент
|
|
|
|
tшк
|
режущий
|
мерительный
|
005
|
Токарная
|
токарно-винторезный станок
с ЧПУ 16К20Ф3С5
|
17,54
|
Резец: расточной;
подрезной;
|
Штангенциркуль
|
015
|
Сверлильная
|
вертикально-сверлильный
станок мод. 2Н125
|
6,702
|
сверло Æ 7 мм 2301-0404 ГОСТ 2092-77
|
калибр-пробка ГОСТ 16780-71
|
020
|
Фрезерная
|
Станок для обработки пазов
концевыми и шпоночными фрезами
|
5,28
|
фреза концевая Æ 12 мм ГОСТ 17025-71
|
Штангенциркуль
|
Для разных видов оборудования этот фонд может составлять:
- для двухсменного режима работы 3800 ÷ 4015 часов (4000),
для односменного - 1900 ÷ 2010 часов.
. Распределяется по операциям оборудование участка изготовления детали -
представителя (представителей), технологический процесс которой разработан.
Для этого составляем расчетную таблицу 5.2.
Распределение производится пропорционально трудоемкости выполнения
операций, то есть штучно - калькуляционному времени, затрачиваемому на
выполнение каждой операции.
Штучно - калькуляционное время, суммированное по всем операциям:
(5.8)
где: Nпр - количество операций технологического процесса.
Таблица 5.2 - Распределение по операциям оборудования участка
изготовления «крышка»
Номер операции
|
Наименование операции
|
Тип и модель оборудования
|
tшк, мин
|
Т∑к, мин
|
δТпр, ч/мин
|
ΔТпр, ч
|
Фд, ч
|
Ср
|
005
|
Токарная
|
токарно-винторезный станок
с ЧПУ 16К20Ф3С5
|
17,54
|
33,7
|
2967,36
|
24480,1
|
4000
|
8,6
|
015
|
Сверлильная
|
вертикально-сверлильный
станок мод. 2Н125
|
6,702
|
|
|
46290,8
|
4000
|
11,5
|
020
|
Фрезерная
|
Станок для обработки пазов
концевыми и шпоночными фрезами
|
5,28
|
|
|
18902,1
|
4000
|
4,7
|
ИТОГО
|
100000
|
|
24,8
|
Далее подсчитывается число нормо-часов заданной годовой программы
участка, приходящейся на одну минуту суммарного штучно - калькуляционного
времени:
(5.9)
Затем для каждой операции технологического процесса определяется часть
годовой производственной программы, приходящаяся на оборудование, выполняющее
эту операцию:
Например, для токарной с ЧПУ:
(5.10)
Расчетное количество оборудования (с точностью до сотых долей),
необходимого для выполнения каждой операции:
Например, для токарной с ЧПУ:
(5.11)
3. Для участка изготовления детали - представителя составляется ведомость
оборудования, таблица 5.3.
Суммарные расчетные значения ∑Ср для каждой модели округляются до
большего целого - принятого количества Спр.
Определяется коэффициент загрузки оборудования каждого вида:
Для токарной с ЧПУ:
(5.12)
Полученное значение принимается как средний коэффициент загрузки по
участку.
Таблица 5.3 - Ведомость оборудования производственного участка
Номер операции
|
Наименование операции
|
Тип и модель оборудования
|
tшк, мин
|
Т∑к, мин
|
δТпр, ч/мин
|
ΔТпр, ч
|
Фд, ч
|
Ср
|
005
|
Токарная
|
токарно-винторезный станок
с ЧПУ 16К20Ф3С5
|
17,54
|
33,7
|
2967,36
|
24480,1
|
4000
|
8,6
|
015
|
Сверлильная
|
вертикально-сверлильный
станок мод. 2Н125
|
6,702
|
|
|
46290,8
|
4000
|
11,5
|
020
|
Фрезерная
|
Станок для обработки пазов
концевыми и шпоночными фрезами
|
5,28
|
|
|
18902,1
|
4000
|
4,7
|
ИТОГО
|
100000
|
|
24,8
|
После суммирования расчетного ∑Ср.общ и принятого Спр количества
оборудования по участку определяется средний коэффициент загрузки:
(5.13)
4. Пересчитывается общее количество производственного оборудования
участка.
Общее количество оборудования цеха, полученное в п.1 пересчитывается с
учетом среднего коэффициента загрузки. Ранее расчет Спр.ц был выполнен исходя
из 100 % загрузки оборудования. Зная фактическую загрузку оборудования, его
потребное количество можно скорректировать следующим образом:
(5.14)
5.5 Определяется состав и количество
оборудования каждого типоразмера, для проектируемого механического участка
Результаты представлены в таблице 5.4.
Таблица 5.4 - Ведомость производственного оборудования участка по
изготовлению детали «крышка»
№ п/п
|
Тип оборудования
|
Модель
|
Расчетное количество
оборудования
|
Принятое количество
оборудования
|
Коэффициент загрузки
|
|
|
|
∑Ср
|
Спр
|
Кз
|
005
|
Токарная
|
токарно-винторезный станок
с ЧПУ 16К20Ф3С5
|
17,3
|
18
|
0,97
|
015
|
Сверлильная
|
вертикально-сверлильный
станок мод. 2Н125
|
2,8
|
3
|
0,96
|
020
|
Фрезерная
|
Станок для обработки пазов
концевыми и шпоночными фрезами
|
4,7
|
5
|
0,94
|
ИТОГО
|
24,8
|
26
|
0,95 средний
|
5.5 Определение состава и количества
производственных рабочих механического участка
На данном механическом участке к работникам основного производства
относятся: токари, фрезеровщики, шлифовщики.
Число производственных рабочих определяется для каждого вида оборудования
по формуле:
(5.15)
где Тст.ч - суммарная станкоемкость изготовления деталей на данном типе
оборудования на участке (в цехе);
Фд.р. - действительный (эффективный) годовой фонд времени рабочего, ч
(при проектировании можно задать в пределах 1630 ÷ 1830 ч);
Км - коэффициент многостаночного обслуживания, т.е. среднее количество
станков, обслуживаемых одним рабочим.
Коэффициент многостаночного обслуживания принимается равным 1 для всех
видов универсальных станков. Для автоматизированного оборудования
рассчитывается по формуле:
(5.16)
где tо, tв - составляющие штучного времени, мин;пер - время на переходы
рабочего между станками; при расчетах можно принять 0,5 мин.
При детальных расчетах численность производственных рабочих
рассчитывается по принятому количеству единиц оборудования.
(5.17)
где Фд - действительный годовой фонд времени работы единицы оборудования,
ч; 4000
Спр - принятое количество единиц оборудования данной модели;
Кз - коэффициент загрузки оборудования.
Принимается расчетное значение для соответствующего типа оборудования, а
если его нет, то среднее значение по участку.
Для токарной:
Для
сверлильной:
Для
фрезерной:
Количество
наладчиков определяется:
(5.18)
где ∑Спр - принятое количество станков данной группы;
Нобсл - норма обслуживания станков одним наладчиком,
Для токарных станков:
Для
сверлильных станков:
Для
фрезерных станков:
После
расчета численности рабочих осуществляется их распределение по сменам и
составляется ведомость работающих, таблица 5.5.
Таблица
5.5 - Ведомость работающих на участке
№
|
Количество работающих
|
Всего
|
|
|
в первую смену
|
во вторую смену
|
|
1
|
Производственные рабочие
Итого
|
30
|
30
|
60
|
2
|
Вспомогательные рабочие: -
наладчик Итого
|
4
|
3
|
7
|
3
|
Руководители: - начальник
участка - старший мастер -мастер смены Итого
|
1 1 1
|
1
|
1 1 2
|
Всего работников
|
37
|
34
|
71
|
5.6 Предварительное определение производственной
площади участка
На данном этапе рассчитываются ориентировочные размеры производственной
площади участка.
Производственная площадь участка рассчитывается как:
= 20 · 28 = 560 м2
где: Sуд.пр - удельная площадь, приходящаяся на 1 производственный
станок, м2,уд.пр принимается из расчета 20 - 25 м2 на 1 станок.
5.7 Разработка структуры механического участка
Структура механического участка - логические взаимоотношения уровней его
управления и функциональных служб, построенные в такой форме, которая позволяет
наиболее эффективно реализовывать технологические процессы изготовления
деталей. Структура проектируемого участка должна определяться содержанием
технологического процесса изготовления деталей.
Система обеспечения состоит из систем:
инструментального обеспечения;
ремонтного обслуживания;
В систему инструментального обеспечения входят:
инструментально - раздаточный склад (ИРС) и (или) инструментально -
раздаточная кладовая (ИРК).
5.8 Определение расхода инструмента
Методы расчета расхода инструментальной оснастки различаются в
зависимости от типа производства.
Для серийного производства рассчитывается машинное время работы
инструмента на токарном станке до полного его износа по формуле:

где: L
- допустимая величина стачивания рабочей части инструмента при переточке, мм:-
средняя величина слоя, снимаемого с рабочей части инструмента при каждой
переточке, мм;ст - стойкость инструмента (время машинной работы инструмента
между двумя его переточками), час.
Средние
нормативы износа и стойкости режущих инструментов принимаются по таблице 5.6.
Аналогично
рассчитывается машинное время работы инструмента на сверлильном станке до
полного его износа:
Машинное
время износа инструмента на фрезерном станке:
В
мелкосерийном производстве для токарного станка расход режущего инструмента за
год рассчитывается по формуле:
(4.2)
где: kу - коэффициент случайной убыли инструмента (принимается по
статистическим данным и колеблется в пределах от 0,05 до 0,1)
Для сверлильного станка расход режущего инструмента за год:
Для
токарного станка расход режущего инструмента за год:
Норма
износа измерительного инструмента на программу (штангенциркуля) m0 может быть
определена по формуле:
= 10 · 3100 · 2,5 = 7750
где dизн - величина допустимого износа в мкм по нормативным документам;ст
- норматив стойкости измерительного инструмента (число промеров на 1 мкм износа
инструмента);р - коэффициент ремонта (равен числу восстановительных ремонтов,
Расход мерительного инструмента (штангенциркуля) определяется по формуле:
Расход мерительного инструмента (пробка) определяется по формуле:
Результаты
расчета среднегодового расхода инструмента представлены в таблице 5.6.
Таблица
5.6 - Ведомость расхода инструмента
№
|
Операция
|
Инструмент
|
Вид инструмента
|
Расход, шт.
|
005
|
Токарная
|
Режущий
|
Резец токарный проходной
(черновой)
|
1667
|
|
|
|
Резец токарный проходной
(чистовой)
|
1558
|
|
|
Мерительный
|
Штангенциркуль
|
1
|
010
|
Сверлильная
|
Режущий
|
Сверло
|
40
|
|
|
Мерительный
|
калибр-пробка
|
1
|
020
|
Фрезерная
|
Режущий
|
Фреза
|
913
|
|
|
Мерительный
|
калибр-пробка
|
2
|
5.9 Организация и планирование ремонтных работ
на участке
Структура ремонтного цикла между двумя капитальными ремонтами (КР) для
станков массой до 10 т, устанавливаемых на проектируемом участке состоит из 5
осмотров (О) и 4 текущих ремонтов(ТР), таблица 5.7:
КР-О-ТР-О-ТР-О-ТР-О-ТР-О-КР.
Таблица 5.7 - Структура межремонтного цикла металлорежущих станков
Вид оборудова-ния
|
Группа оборудова-ния
|
Масса, тн
|
Структура межремонтного цикла
|
Количество текущих ремонтов
|
Количество плановых
осмотров
|
Металло-режущие станки
|
Токарные, фрезерные,
шлифовальные и др.
|
до 10
|
КР-О-ТР-О-ТР-О-ТР-О-ТР-О-КР
|
4
|
5
|
Определяем среднюю ремонтную сложность станков на участке, данные сводим
в таблицу 5.8.
Таблица 5.8 - Средняя категория сложности ремонта металлорежущих станков
№
|
Оборудование
|
Средняя категория сложности
ремонта
|
1
|
Токарные станки с ЧПУ
|
13
|
2
|
Токарно - револьверные
станки
|
10
|
3
|
Токарно - карусельные
станки
|
24
|
4
|
Токарные автоматы
|
18
|
5
|
Сверлильные станки
|
8
|
6
|
Фрезерные станки
|
10
|
7
|
Расточные станки
|
12
|
8
|
Плоскошлифовальные станки
|
10
|
9
|
Круглошлифовальные станки
|
10
|
10
|
Внутришлифовальные станки
|
9
|
11
|
Протяжные
|
12
|
12
|
Прочие
|
13
|
Для токарных станков приведенное количество ремонтных единиц Nпр равно:
Nпр = ΣNi · Ri = (21 · 13) = 237
где Ni - количество единиц оборудования i - го вида;- категория сложности
ремонта i - го технологического оборудования.
Для сверлильных станков приведенное количество ремонтных единиц равно:
пр = ΣNi · Ri = (4 · 12) = 48
Для фрезерных станков:
Nпр = ΣNi · Ri = (3 · 10) = 30
Рассчитываем продолжительность ремонтного цикла, длительность ремонтного
цикла в календарном времени, длительность межремонтного периода и периодичность
межосмотрового обслуживания.
Ремонтный цикл для металлорежущих станков:
Трц = 16800 · βом · βпи · βто · βв · βд · βкм = 16800 · 1 ·1,1 ·1 ·1 ·1 ·1 =
18480 час =
где: 16800 - нормативный ремонтный цикл, час;
βом - коэффициент, учитывающий род
обрабатываемого материала, для стали - 1;
βпи - коэффициент, учитывающий условия
эксплуатации оборудования, для нормальных условий - 1,1;
βто, βв, βд, βкм - коэффициенты, учитывающие
точность, возраст, долговечность и категорию массы, принимаем равными - 1.
Межремонтный период Тмр и периодичность технического обслуживания Тто
определяются по формулам:
где dт и dТО - число текущих ремонтов и технических обслуживаний.
Далее определяем необходимые объемы ремонтных работ для каждой единицы
технологического оборудования механического участка.
Средний годовой объем ремонтных работ по видам (слесарные, станочные,
сварочные, покрасочные и т.п.) по ремонту и межремонтному обслуживанию можно по
формуле:
Для токарных станков:
где:
qk, qТ, qо - трудоемкости соответственно капитального ремонта, текущего ремонта
и осмотров на одну ремонтную единицу.
Для
сверлильных станков:
Для
фрезерных станков:
5.10 Определение численности ремонтного
персонала участка
Количество станочников и наладчиков определяется как:
где
Qраб - средний годовой объем станочных, слесарных и прочих работ, час;
Кв
- коэффициент выполнения норм (1,1 ÷ 1,2).
Полученные данные сводим в таблицу 5.9.
5.11 Разработка плана участка и схемы
расположения технологического оборудования
Определяем общую площадь участка.
При расстановке оборудования необходимо стремиться к рациональному
использованию подкрановых площадей, для чего все станки следует распределить по
группам в зависимости от размеров и массы изготавливаемых деталей и размещать
эти группы в пролетах, оборудованных крановым оборудованием соответствующей
грузоподъемности. Оборудование может устанавливаться в пролете в два, три и
четыре ряда в зависимости от его размеров и ширины пролета. При расположении в
два ряда вдоль пролета посредине предусматривается проезд для транспорта, при
трех рядах продольных проездов может быть два или один. В последнем случае
проезд образуется между одинарным сдвоенным рядами оборудования.
Таблица 5.9 - Ведомость технологического оборудования участка подлежащего
обслуживанию и ремонту обслуживанию и ремонту
Оборудование
|
Количество
|
Средняя категория сложности
|
Приведенное количество
ремонтных единиц
|
Структура межремонтного
цикла
|
Продолжительность
межремонтного цикла, лет
|
Длительность межремонтного
периода, месяцев
|
Периодичность
межосмотрового обслуживания, месяцев
|
Среднегодовой объем
ремонтных работ, час
|
|
|
|
|
|
|
|
|
слесарных
|
станочных
|
прочих
|
Токарный
|
9
|
13
|
117
|
КР-О-ТР-О-ТР-О-ТР-О-ТР-О-КР
|
4,9
|
12
|
5
|
2790
|
Сверлильный
|
4
|
12
|
48
|
КР-О-ТР-О-ТР-О-ТР-О-ТР-О-КР
|
5
|
12
|
5
|
1144
|
Токарный
|
12
|
12
|
120
|
КР-О-ТР-О-ТР-О-ТР-О-ТР-О-КР
|
5
|
12
|
5
|
2862
|
Фрезерный
|
3
|
10
|
30
|
КР-О-ТР-О-ТР-О-ТР-О-ТР-О-КР
|
5
|
12
|
5
|
715
|
Итого
|
28
|
47
|
315
|
-
|
-
|
-
|
-
|
7511
|
План разработанного участка показан на рисунке 5.1.
Рисунок 5.1- План участка машиностроительного цеха
Заключение
В представленной работе была проведена модернизация четырехвалковой
листогибочной машины. Проект состоит из пяти основных разделов: анализ
литературных источников, конструкторская часть, технологическая часть,
проектирование участка машиностроительного цеха.
В процессе выполнения работы были рассмотрены следующие задачи:
спроектирован привод перемещения и вращения валков листогибочной машины;
изменен ход движения прижимных валков;
разработана винтовая и клиноременная передачи;
проведены необходимые расчеты на выносливость.
В технологической части проекта была рассмотрена комплексная деталь,
составлен маршрут её обработки, подобраны режущие инструменты, рассчитаны
режимы резания, выбраны станочные и инструментальные приспособления, средства
измерения и контроля размеров. При выборе режущего инструмента предпочтение
отдавалось режущему инструменту из твердого сплава.
В заключении можно сделать вывод, что модернизация машин и оборудования в
целом решает задачи повышения технологического уровня машиностроения,
увеличения производительности и получения высоких технико - экономических
показателей продукции.
Список используемой литературы
1 Анурьев,
В. И. Справочник конструктора-машиностроителя : в 3 т. . Т. 1 / В. И. Анурьев ;
под ред. И. Н. Жестковой . - 8-е изд., перераб. и доп. . - Москва :
Машиностроение , 2001 . - 920 с.
Анурьев,
В. И. Справочник конструктора-машиностроителя : в 3 т. . Т. 2 / В. И. Анурьев ;
под ред. И. Н. Жестковой . - 8-е изд., перераб. и доп. . - Москва :
Машиностроение , 2001 . - 900 с.
Анурьев,
В. И. Справочник конструктора-машиностроителя : в 3 т. . Т. 3 / В. И. Анурьев ;
под ред. И. Н. Жестковой . - 8-е изд., перераб. и доп. . - Москва :
Машиностроение , 2001 . - 858 с.
Иванов,
М. Н. Детали машин : учеб. для втузов / М. Н. Иванов, В. А. Финогенов . -
Москва : Абрис , 2013 . - 406, [1] с.
Дунаев,
П. Ф. Конструирование узлов и деталей машин : учеб. пособие для вузов / П. Ф.
Дунаев, О. П. Леликов . - 10-е изд., стер. . - Москва : Academia , 2007 . -
495, [1] с.
Барановский
Ю.В. Режимы резания металлов.: cправочник / под ред. Ю.В. Барановского. - 3-е
изд., перераб. и доп. - Москва: Машиностроение, 1972. - 409с.
Егоров,
М. Е. Технология машиностроения : учебник для машиностроит. вузов и фак. / М.
Е. Егоров, В. И. Дементьев, В. Л. Дмитриев ; под ред. М. Е. Егорова . - 2-е
изд., доп. . - Москва : Высш. шк. , 1976 . - 534 с.
Горбацевич,
А. Ф. Курсовое проектирование по технологии машиностроения : учебное пособие
для вузов / А. Ф. Горбацевич, В. А. Шкред . - Изд. 5-е, стер. ; Перепеч. с 4-го
изд. 1983 г. . - Москва : Альянс , 2007 . - 255, [1] с.
Горбунов
В.И. Обработка металлов резанием, металлорежущий инструмент и станки/ В.И.
Горбунов. - Москва: Машиностроение, 1981.- 287с.
Добрыднев
И.С. Курсовое проектирование по предмету технология машиностроения / И.С.
Добрыднев. - Москва: Машиностроение, 1984. - 359с.
Справочник
технолога-машиностроителя : в 2 т. . Т. 2/ Ю. А. Абрамов, В. Н. Андреев, Б. И.
Горбунов и др. / под ред. А. Г. Косиловой, Р. К. Мещерякова . - 4-е изд.,
перераб. и доп. . - Москва : Машиностроение , 1986 . - 495 с.
Охрана
окружающей среды : учебник для вузов / Белов С. В., Барбинов Ф. А., Козьяков А.
Ф.; под ред. С. В. Белова . - 2-е изд., испр. и доп. . - Москва : Высш. шк. ,
1991 . - 319 с.
Новиков
Ю.В. Охрана окружающей среды.: учеб. пособие / Ю.В. Новиков. - Москва: Высш.
шк., 1987. - 287с.
Организация,
планирование и управление производством : практикум (курсовое проектирование):
учеб. пособие для вузов / под ред. Н. И. Новицкого . - Москва : КНОРУС , 2006 .
- 319, [1] с.
Детали
машин: методические указания к курсовому проекту "Энергокинематический
расчет привода": ФПМ: специальности: 150200, 120100, 210200, 170400 /
сост.: В. П. Полетаев, А. А. Усов . - Вологда : ВоГТУ , 2003 . - 24 с.
Детали
машин : методические указания к курсовому проекту "Расчет подшипников
качения на долговечность": ФПМ: специальности: 120100, 120700, 150200 /
сост.: В. П. Полетаев, А. А. Усов . - Вологда : ВоПИ , 1997 . - 27 с.
Детали
машин: методические указания к курсовому проекту "Энергокинематический
расчет привода": ФПМ: специальности: 150200, 120100, 210200, 170400 /
сост.: В. П. Полетаев, А. А. Усов . - Вологда : ВоГТУ , 2003 . - 24 с. :
Детали
машин : методические указания к курсовому проекту "Расчет плоскоременной
передачи": ФПМ, ЗДО: специальности: 150200, 120100, 210200, 170400 /
сост.: В. П. Полетаев, А. А. Усов . - Вологда : ВоГТУ , 2005 . - 19 с.
19 Методические
рекомендации по оформлению выпускных квалификационных работ, курсовых
проектов/работ для студентов очной, очно - заочной (вечерней) и заочной форм
обучения [Электронный ресурс] . Вып. 4 / сост.: Тритенко А. Н., Сафонова О. В.,
Дурягина Н. В. - Вологда : ВоГУ , 2016 . - 120 с. Режим доступа:
<#"898071.files/image277.jpg">