Параметр
|
Значение
|
Передаточное
число
|
45
|
Допускаемый
крутящий момент на выходном валу, Н∙м
|
3300
|
Длина,
мм.
|
1300
|
Высота,
мм.
|
600
|
Ширина,
мм.
|
350
|
Диаметр
быстроходного конического конца вала, мм.
|
40
|
Длина
быстроходного конического конца вала, мм.
|
85
|
Диаметр
тихоходного цилиндрического конца вала, мм.
|
70
|
Длина
тихоходного цилиндрического конца вала, мм.
|
138
|
.4 Выбор тормоза
Исходя из большого передаточного числа
редуктора, тормоз в данном случае не требуется, т.к. при остановке будет
происходить самоторможение.
.5 Выбор быстроходной муфты
Муфту выбираем по максимальному крутящему
моменту на быстроходном валу и диаметрам быстроходных валов электродвигателя и
редуктора.
Требуемый передаваемый крутящий момент муфтой
[18, стр.250]:
(2.10)
где Кр - коэффициент,
зависящий от характера нагрузки, Кр = 1,25 [18,стр.251,табл 10.26];
Т - крутящий момент на валу, Н∙м.
По справочнику [18, стр.428,табл.
К25] выбираем согласно исходных данных муфту с торообразной оболочкой: Муфта
200-II-38-II-40-У2 ГОСТ
20884-93.
У которой 200 - максимальный
передаваемый крутящий момент (Н∙м), II -
исполнения посадочного места под вал (коническое), 32 и 40 - посадочные
диаметры валов (мм) электродвигателя и редуктора соответственно.
.6 Выбор тихоходной муфты
Тихоходную муфту также выбираем по
максимальному крутящему моменту на тихоходном валу и диаметрам тихоходных валов
редуктора и барабана.
По [9, стр.301, табл П.6.1]
выбираем, согласно исходных данных, зубчатую муфту типа МЗ по ГОСТ 5003-83:
Муфта МЗ 6300-I-70-I-95-У2
(Муфта МЗ №4) ГОСТ 5003-83.
У которой 6300 - максимальный
передаваемый крутящий момент (Н∙м), I -
исполнения посадочного места под вал (цилиндрическое), 70 и 95 - посадочные
диаметры валов (мм) редуктора и вала барабана соответственно.
.7 Проектный расчет вала приводного
барабана
Проектный расчет вала ведем по
напряжениям кручения [τ]к = 20 Н/мм2
по методике представленной в [18, стр.110].
.7.1 Выбор материала
Для изготовления вала применяем по
рекомендации [18] Сталь 45 со следующими характеристиками: термообработка -
улучшение; твердость поверхности - 235..262 HRC; предел
прочности - 780 МПа; предел текучести - 540 МПа; предел выносливости при
симметричном цикле - 335 МПа.
.7.2 Определение основных
геометрических размеров
Расчет ведем согласно методике
представленной в [18. стр.112].
Минимальный диаметр вала [18.
стр.112]:
(2.11)
Принимаем согласно стандартных
линейных размеров по ГОСТ 6636-69 диаметр выходного конца вала d1 = 95 мм.
Длина выходного конца вала
определяем по формуле:
(2.12)
Диаметры под подшипники d2 и d5:
Высота буртика t = 5 мм.
[18. стр.114,табл. 7.1]
(2.13)
Длина ступени l2 под
подшипник и уплотнение:
(2.14)
Принимаем согласно стандартных
линейных размеров по ГОСТ 6636-69 длина ступени l2 = 160 мм.
Длина ступени l5 под
подшипник равна ширине подшипника.Диаметры под ступицы барабана:
Ориентировочная фаска ступицы f = 3 мм.
[18. стр.114,табл 7.1].
(2.15)
Принимаем согласно стандартных
линейных размеров по ГОСТ 6636-69 диаметр вала под ступицы барабана d3 = d4 = 120 мм.
Длина ступеней l3 и l4 под ступицы
барабана:
(2.16)
Принимаем согласно стандартных
линейных размеров по ГОСТ 6636-69 длину участка вала под ступицы барабана l3 = l4 = 145 мм.
Остальные линейные размеры принимаем
конструктивно. Компоновочная схема вала барабана представлена на рисунок 2.2.
Компоновочная схема вала в масштабе 1:1 представлена на миллиметровке в
приложении.
.7.3 Предварительный выбор
подшипников
Подшипники выбираем по диаметру вала
в месте посадки подшипников. Предварительно выбираем радиальные сферические
шариковые подшипники легкой серии 1221 ГОСТ 28428-90 с шириной В = 36 мм, d = 105 мм, D = 190 мм.
.7.4 Выбор корпуса и крышек
подшипника
Для герметизации подшипников, осевой
фиксации и восприятия осевых нагрузок применяют корпуса и крышки.
Корпус и крышки подшипников выбираем
в зависимости от диаметра наружного кольца подшипника D.
Выбираем: Корпус [1, стр.288] УМ-190
по ГОСТ 13218.3-80; Крышки торцовые с отверстием для монтажного уплотнения [1,
стр.255]. Крышка 1,2 190х105 ГОСТ 18512-73; Крышка торцовая глухая [1,
стр.262]. Крышка 2,2-190 ГОСТ 18511-73.
.7.5 Выбор шпонки для посадки муфты
Исходя из диаметра вала под муфту d1 = 105 мм.
выбираем из справочника по [5, стр.450, табл. К42] стандартную шпонку: 25×14×140 ГОСТ
23360-78.
Для соединений призматическими
шпонками основным условием является расчет на смятие [5, стр.265]:
(2.17)
где lр - рабочая
длина шпонки, мм.;
t - глубина
врезания шпонки в вал, t = 9 мм. [таблица К42, 5, стр.450];
[s]см
- допускаемое напряжение смятия, Н/мм2.
Рабочая длина шпонки определяется по
формуле:
(2.18)
Шпонка по прочности пригодна.
.7.6 Выбор шпонки для посадки
ступицы барабана
Исходя из диаметра вала под ступицу d3 = 120 мм.
выбираем из справочника по таблице 2 [1, стр.810] стандартную шпонку: 32×18×125 ГОСТ
23360-78.
Рабочая длина шпонки :
, t = 11 мм.
[1, стр.810,табл 2].
Проверим шпонку по формуле (17):
Шпонка по прочности пригодна.
.8 Проверочный расчет вала
приводного барабана
Расчет ведем согласно методике [5] и
схеме представленной на рис. 2.3.
.8.1 Определение усилия на барабане
от натяжения ленты при транспортировке груза
Окружное усилие на барабане [2,
стр.433]:
(2.19)
Натяжение сбегающего конца ленты [2,
стр.433]:
(2.20)
где μ -
коэффициент трения;
α - угол обхвата барабана.
При использовании стального барабана
и сухой окружающей среды
μ = 0,3 [2, стр.394], угол
обхвата барабана α = 250о
(см. п.2.1).
Натяжение набегающего конца ленты
[2, стр.433]:
(2.21)
Отсюда нагрузка на барабане от натяжения
ленты при транспортировании груза:
(2.22)
2.8.2 Силы действующие на вал
барабана
Консольная сила от муфты [5,
стр.101]:
(2.23)
Усилия от ступиц найдем через
нагрузку на барабан.
Из условия действующих моментов [3,
стр.96] действующие силы от ступиц барабана:
(2.24)
2.8.3 Реакции опор
2.8.4 Изгибающие моменты
.8.5 Крутящие моменты
Крутящие моменты на одном валу
всегда численно равны.
.8.6 Приведенные моменты
На основании 3-й гипотезы прочности
определяем приведенные моменты по формуле:
(2.25)
где М - суммарный изгибающий момент,
Н∙м;
Мк - крутящий момент, Н∙м;
α - коэффициент, учитывающий
различие в характеристиках циклов напряжений изгиба и кручения, Сталь 45 α = 0,579.
.8.7 Проверка подшипников
Предварительно выбраны подшипники
1221 ГОСТ 28428-90 (см. п.2.7.2) со следующими характеристиками:
d = 105 мм., D = 190 мм.,
В = 36 мм., Cr = 68,9 кН,
С0r = 40,5 кН.
Наибольшую нагрузку испытывает
подшипник в точке В (Рисунок 2.3).
Радиальная нагрузка на подшипник в
данной точке RB = 9240,65
Н.
Исходя из того, что осевой нагрузкой
на подшипник, согласно расчетных данных, можно пренебречь, эквивалентная
нагрузка:
(2.26)
где V -
коэффициент вращения, V = 1 [5, стр.142];
Kб -
коэффициент безопасности, Kб = 1,4 [5,
стр.271];
Kt -
температурный коэффициент, Kt = 1 [5,
стр.271];
Определяем расчетную динамическую
грузоподъемность и проверяем условие пригодности:
(2.27)
где Lh - срок
службы привода, Lh = 21900 ч. (см. п.2.2);
Условие пригодности Сrp ≤ Сr
выполняется.
Определяем базовую долговечность
подшипника:
(2.28)
Условие пригодности L10h ≤ Lh
выполняется.
Подшипник 1221 ГОСТ 28428-90
пригоден.
.8.8 Проверка опасного сечения
Исходя из эпюры приведенных моментов
(см. Рисунок 2.3) и геометрии вала, опасное сечение находится в районе левой
ступицы барабана (со стороны муфты). Расчет ведем по методике приведенной в [5,
стр.267].
.8.9 Определяем коэффициент запаса
прочности для нормальных напряжений
Нормальные напряжения в опасном
сечении:
(2.29)
где М - изгибающий момент в
рассматриваемом сечении,
;
W - осевой
момент инерции сопротивления сечения вала, ослабленный шпоночным пазом, мм3.
Осевой момент инерции сопротивления
сечения вала, ослабленной шпоночным пазом:
(2.30)
где d - диаметр
вала в рассматриваемом сечении d = 120 мм (см. п. 2.7.2.);
b - ширина
шпоночного паза, b = 32 мм (см. п. 2.7.4.);
t - глубина
шпоночного паза, t = 11 мм (см. п. 2.7.4.).
Отсюда нормальные напряжения в
опасном сечении:
Коэффициент концентрации нормальных
напряжений:
(2.31)
где Ks - эффективный
коэффициент концентрации напряжений, Ks = 1,9
таблица 11.2 [5, стр.271];
Kd -
коэффициент влияния абсолютных размеров поперечного сечения, Kd = 0,62
таблица 11.3 [5, стр.272];
KF -
коэффициент влияния шероховатости, KF = 1,0
таблица 11.4 [5, стр.272]
Предел выносливости по нормальным
напряжениям:
(2.32)
где s-1 - предел
выносливости при симметричном цикле изгиба, Н/мм2. Предел
выносливости при симметричном цикле изгиба для Стали 45
s-1 = 335 Н/мм2 (см. п.
7.1.).
Определяем коэффициент запаса по
касательным напряжениям:
(2.33)
.8.10 Определяем коэффициент запаса
прочности для касательных напряжений
(2.34)
где Т - вращающий момент в
рассматриваемом сечении, Н∙м;
Wp - полярный
момент инерции сопротивления сечения вала, ослабленного шпоночным пазом, мм3.
Полярный момент инерции
сопротивления сечения вала, ослабленного шпоночным пазом:
(2.35)
Касательные напряжения в опасном
сечении:
Коэффициент концентрации нормальных
напряжений:
(2.36)
где Kr -
эффективный коэффициент концентрации напряжений, Kr = 1,6 [5,
стр. 271 табл. 11.2];
Kd -
коэффициент влияния абсолютных размеров сечения;
KF -
коэффициент влияния шероховатости.
Предел выносливости по касательным
напряжениям:
(2.37)
где τ-1 = 0,58∙s-1 - предел
выносливости при симметричном цикле, Н/мм2. Для Стали 45 τ-1 = 0,58∙335
= 194,3 Н/мм2 (см. п. 2.7.1.).
Определяем коэффициент запаса по
касательным напряжениям:
(2.38)
.8.11 Расчетный коэффициент запаса
прочности
Расчетный коэффициент запаса прочности
(2.39)
где [S] = 1,6 …
2,1 - допускаемый коэффициент запаса прочности.
Так как 3,72 ≥ 2,1 условие
прочности выполняется.
.9 Разработка гидропривода
секторного затвора узла загрузки удобрений
Разработать гидропривод секторного
затвора узла загрузки удобрений. Электромеханическую передачу необходимо
заменить на гидравлическую, наиболее рационально выбрать гидроаппаратуру и
обеспечить минимум потерь в гидросистеме.
Проектирование гидропривода
базируется на применении стандартной гидроаппаратуры. При выполнении дипломной
работы используются материалы таких курсов, как физика, высшая математика,
теоретическая механика, детали машин, техническое черчение, математическое
моделирование.
2.9.1 Определение нагрузочных и
скоростных параметров гидродвигателя
Для расчета и выбора гидродвигателя необходимо
знать максимальное осевое усилие, максимальную линейную скорость.
Для подъема и опускания секторного затвора с
помощью проектируемого гидропривода, заданы следующие параметры:
максимальное осевое усилие, Н - 6000 Н;
максимальная линейная скорость, м/с - Vmax
= 0,077 м/с.
В нашем случае используем гидроцилиндр
поступательного движения. Наибольшее распространение в гидравлике имеют
гидроцилиндры поршневые двухстороннего действия с односторонним штоком.
.9.2 Определение нагрузочных параметров и выбор
гидроцилиндра
Основными параметрами гидроцилиндра являются
диаметры поршня и штока, ход поршня и рабочее давление.
Ход поршня определяем, исходя из величины
наибольшего перемещения рабочего органа (РО) и ГОСТ 6540-68 (5).
Ход поршня равен 400 мм.
Рабочим давлением Р необходимо задаться,
руководствуясь техническими характеристиками привода существующих станков или
роботов, стандартных гидроцилиндров, насосов и рядом номинальных давлений
регламентируемых ГОСТ 6540- 68. При этом необходимо учесть, что ориентировочно
должно выполняться соотношение
Р=
Рн.
где Рн - давление,
создаваемое насосом.
В нашем случае Рн =6,3
МПа. Из условия, находим Р1=
Рн ,
рабочее давление Р1=
6,3 = 4,2 МПа. Давление Р2
принимаем равным 0,5 МПа. [2]
Диаметр поршня D гидроцилиндра
определяется по формуле :
,
где р
и р
- давление соответственно в
напорной и сливной полостях ГЦ;
Величина p1 принимается
равной рабочему давлению, т.е. p1 = p.
Противодавление выбирается из
диапазона p2=(0.3...0.9) МПа.
Значения y1 и y2 принимаются
с учетом выбранной конструкции ГЦ.
Если ГЦ с односторонним штоком, то
для обеспечения равенства скоростей быстрых ходов при БП необходимо применять
дифференциальную схему включения; при этом y1 =0, y2 =1/(2)1/2
мм.
Из этого условия определяем диаметр
штока:
мм.
По полученным значениям из
справочника выбираем стандартный гидроцилиндр: гидроцилиндр поступательного
движения двухстороннего действия с односторонним штоком ГЦП 63×40×400.
Давление, МПа:
Номинальное 6,3
Максимальное 8
страгивания 0,4
холостого хо да 0,32
Номинальное усилие, кН:
толкающее 17,6
тянущее 10,54
Скорость пере мещения, м/мин:
максимальная 18
минимальная (при выдви жении штока) 0,032
Масса, кг 20
Выбранный гидроцилиндр проверяем на устойчивость
работы, исходя из требуемой длины хода.
Гидроцилиндр ГЦП 63×40×400
удовлетворяет условиям на устойчивость.
Проверяю выбранный гидроцилиндр по условию
обеспечения максимального осевого усилия при рабочем ходе, т.е F1ст³
F1;
где F1ст
и F1
- эффективные площади в напорной полости соответственно стандартного и
расчетного гидроцилиндра.
, м2,
м2.
, м2,
м2.
Так как Fст > F выбор
сделан правильно.
.9.3 Составление принципиальной схемы привода
Гидропривод, показанный на схеме работает
следующим образом. Насос 2 через фильтр 1 засасывает рабочую жидкость из
гидробака 5 и нагнетает её по напорной магистрали через обратный клапан 3 в
распределитель 6. Распределитель (в данном случае реверсивный золотник) в
зависимости от того, в какое положение установлен его плунжер, направляет жидкость
по одному из участков исполнительной магистрали в полость гидроцилиндра 8.
Рисунок 2.4 - Принципиальная схема
гидропривода: 1 - Фильтр щелевой 25-80-1 по ГОСТ 21329-75; 2 - Насосная
установка 2МП Г48-84 УХЛ
4Г49-33 по
ТУ-053-1806-86; 3 - Обратный клапан встраиваемый типа МКОВ 16/3 по
2-053-1738-86; 4 - Предохранительный клапан Г54-34М; 5 - Гидробак; 6 -
Гидрораспределитель типа ВММ6.44 ВРУХЛ; 7 - Дроссель с обратным клапаном типа
ДК-С12 по ТУ2-053-1651-83; 8 - Гидроцилиндр ГЦП 63×40×400
Под действием давления жидкости
поршень движется в цилиндре, и шток перемещает приводимый механизм. Из
противоположной полости силового гидроцилиндра жидкость по второму участку
исполнительной магистрали подходит к распределителю, который направляет ее по
сливной магистрали в бак 5. В конце каждого хода поршня плунжер золотника
переставляется в другое крайнее положение, тем самым изменяется на
противоположное направление движения жидкости в участках исполнительной
магистрали, а следовательно, и направление движения штока. При нормальной
нагрузке насоса предохранительный клапан 4 закрыт и вся жидкость, нагнетаемая
насосом, поступает в силовой гидроцилиндр и гидродвигатель. Затяжка
регулировочной пружины предохранительного клапана производится так, что он
открывается при превышении давления нагнетания предельно допустимой величины и
перепускает жидкость на слив по вспомогательной линии. После снижения нагрузки
до нормы предохранительный клапан закрывается и восстанавливается нормальная
работа гидропривода. Так, срабатывая периодически, предохранительный клапан
предохраняет элементы гидропривода от недопустимых нагрузок при пиковых
возрастаниях сопротивления движению штока силового гидроцилиндра.
Клапан 4 предназначен для создания
постоянного давления, сниженного по сравнению с давлением, развиваемым насосом.
При повышении давления в системе клапан открывается и пропускает масло на слив.
Если давление падает ниже того, на которое настроена пружина, клапан
закрывается.
.9.4 Расчет и выбор насосной
установки
Максимальный расход жидкости
необходимый для питания гидроцилиндра.
Где QБП, QБО -
максимальные расходы жидкости,
VДmax - максимальная
скорость поршня,
F1СТ, F2СТ -
эффективные площади.
,
,
где D - диаметр
поршня, мм.;
d - диаметр
штока, мм.
мм2
мм2
м3/с
м3/с
Зная соотношение 0,001 м3/с
= 60 л/мин., получаем
л/мин.,
л/мин.,
Выбор насосной установки произвожу
по наибольшему из расходов.
Qн
Qмах
Определяю величину требуемого
давления на выходе из насоса.
, МПа,
где 
- потери давления в линии при
рабочем ходе.
Предварительный выбор насосной
установки производим, приняв
Из справочника [2] выбираем насосную
установку 2МП Г48-84 УХЛ
4Г49-33 по
ТУ-053-1806-86.
Основные параметры:
Подача, л/мин,18
Давление на выходе из насоса, МПа:
Номинальное, МПа6,3
Минимальное, МПа2,5
Мощность приводного электродвигателя, кВт 3,8
где М- исполнение по расположению и количеству
агрегатов - один агрегат за щитом,
Г48-84 - обозначение насосной установки,
УХЛ - климатическое исполнение,
Г12-32 - тип комплектующего насоса,
A112МА6 - тип
комплектующего электродвигателя,
Г49-33 - номер насосного агрегата.
.9.5 Выбор гидроаппаратуры
Предохранительный клапан Г54-32М по ТУ2-053-1628
- 83 резьбового присоединения [2].
Диаметр условного прохода 10 мм.
Номинальное давление настройки 6,3 МПа.
Расход масла:
Qном
= 32 л/мин;
Qmax
= 50 л/мин;
Qmin
= 1 л/мин.
Суммарные утечки, не более 65 см3/мин.
Масса, кг, не более 2,3
Фильтр щелевой 25-80-1 ГОСТ 21329-75 [2].
Номинальная тонкость фильтрации, мкм80
Номинальная расход, л/мин.25
Номинальное давление, МПа 6,3
Номинальный перепад давлений, МПа0,09
Масса кг.4,5
Обратный клапан встраиваемый типа МКОВ 16/3 по
2-053-1738-86 [2].
Диаметр условного прохода D = 16 мм.
Давление на входе, МПа
номинальное32
максимальное42
Давление на выходе, МПа32
Давление открывания, МПа не менее0,05
Дроссель с обратным клапаном типа ДК-С12 по
ТУ2-053-1651-83.
Диаметр условного прохода, мм. 12
Расход масла, л/мин:
номинальный (Qном) 25
максимальный (Qmах)
40
Давление минимальное, МПа0,6
Потеря давления при полностью открытом дросселе
и
Qном.
МПа, не более0,3
Потеря давления в обратном клапане при Qном.
МПа,
не более 0,3
Масса, кг5
Гидрораспределитель типа ВММ6.44ВРУХЛ по ГОСТ
24679-81, [2]
Исполнение по давлению - 25 МПа
Диаметр условного прохода - 6 мм;
- исполнение по гидросхеме;
ММ - ручное управление;
Исполнение по способу установки золотника:
гидравлический возврат
Расход масла:
Qном
= 16 л/мин;
Qmax
= 30 л/мин.
Давление: Pном
= 32МПа;
.9.6 Выбор внутреннего диаметра трубопровода
Внутренний диаметр трубопровода определяется по
формуле [1]:
= 4,6
,
где Q- расход
масла, [ л/мин];
-
рекомендуемая скорость течения жидкости, [ м/с].
Минимально допустимая толщина стенки [1]:
,
где Р- максимальное давление
жидкости.
- предел прочности на растяжение,
= 340 МПа.
- коэффициент безопасности
2
Для напорной линии при давлении 6,3
МПа скорость равна 3,2 м/с, для сливных линий
= 2м/с. [4].
На основании расчётных данных
и
выбираем
стандартные трубы или рукава, у которых внутренний диаметр и толщина стенки (
) являются
ближайшими к расчётным [2]. Для монтажа стальных труб при давлении до 6,3 МПа
применяются стальные прецизионные трубы с развальцовкой по ГОСТ 9567-75 .
Выбираем трубопровод в напорной
линии для участков от насосной установки до плиты ГУ.
Для участка 3-4.
=4,6
= 10,5 мм.
Принимаем: Труба 14×1 ГОСТ
9567-75.
Проверяем по толщине стенки
= 0,25мм.‹1 мм,
следовательно труба выбрана верно.
Труба 14×1 ГОСТ
9567-75.
Соединение концевое: штуцер 2-14-М
ОСТ2Г93-4-78.
Соединение проходное: тройник 2-14
ОСТ2 Г93-9-78.
Для участка 4-9
Труба 14×1 ГОСТ
9567-75.
Соединение концевое: штуцер 2-14-М
ОСТ2Г93-4-78.
Соединение проходное: тройник 2-14
ОСТ2 Г93-9-78.
Для участка 4-5, 6-7.
=4,6
= 9,72мм.
Принимаем: Труба 12×0,6 ГОСТ
9567-75.
Проверяем по толщине стенки
= 0,22 мм.‹1 мм,
следовательно труба выбрана верно.
Труба 12×0,6 ГОСТ
9567-75.
Соединение концевое: штуцер 2-12-М
ОСТ2Г93-4-78.
Соединение концевое: штуцер 2-12-М
ОСТ2Г93-4-78.
Для участка 8-10.
Труба 12×0,6 ГОСТ
9567-75.
Соединение концевое: штуцер 2-12-М
ОСТ2Г93-4-78.
Соединение концевое: штуцер 2-12-М
ОСТ2Г93-4-78.
Для участка 11-12.
Труба 12×0,6 ГОСТ
9567-75.
Соединение концевое: штуцер 2-12-М
ОСТ2Г93-4-78.
Соединение концевое: штуцер 2-12-М
ОСТ2Г93-4-78.
Для участка 12-13.
Труба 12×0,6 ГОСТ
9567-75.
Соединение концевое: штуцер 2-12-М
ОСТ2Г93-4-78.
Соединение концевое: штуцер 2-12-М
ОСТ2Г93-4-78.
Выбираем трубопровод в сливной линии
для участка 14-15.
=4,6
= 13,8 мм.
Рукав высокого давления I-18-6.3/4,2У
по ГОСТ 6286-73
Соединение концевое: штуцер 2-18-М
ОСТ2Г93-4-78.
Для участка 16-17
=4,6
= 13,8 мм.
Принимаем: Труба 18×1 ГОСТ
9567-75
Проверяем по толщине стенки
= 0,29мм.‹1 мм,
Труба 18×1ГОСТ
9567-75.
Соединение концевое: штуцер 2-18-М
ОСТ2Г93-4-78.
Выбираем трубопровод во всасывающей
магистрали для участков 1-2 от гидробака до насоса.
= 4,6
= 13,8 мм.
Принимаем: Труба 18×1 ГОСТ
9567-75
Проверяем по толщине стенки
= 0,29мм.‹1 мм,
Труба 18×1ГОСТ
9567-75.
Соединение концевое: штуцер 2-18-М
ОСТ2Г93-4-78.
Соединение проходное: штуцер 2-18-М
ОСТ2Г93-4-78.
.9.7 Разработка конструкции
гидроблока управления
В нашем случае в конструкцию
гидроблока управления входят следующие аппараты: гидрораспределитель типа
ВММ6.44ВРУХЛпо ГОСТ 24679-81 и клапан обратный встраиваемый типа МКОВ 16/3 по
2-053-1738-86. Данные аппараты компонуются на специальной плите, к которой
прикрепляются посредством стандартных крепежных деталей.
При проектировании гидроблока управления
обеспечена компактность, технологичность конструкции, удобство сборки, а также
возможность установки его на оборудовании (на задней стенке плиты предусмотрены
резьбовые крепежные отверстия).
Диаметры отверстий в плите соответствуют
диаметрам отверстий в аппаратах, которые к нему присоединяются. На основе
компоновки выполняют сборочный чертеж гидроблока управления, на котором
проставляются габаритные, присоединительные и установочные размеры. На основе
сборочного чертежа блока управления выполняется рабочий чертеж корпуса.
.9.8 Определение потерь давления в аппаратуре и
трубопроводах
Потерю давления в гидроаппаратах определяем по
формуле[4]:
где А и В - коэффициенты
аппроксимации экспериментальной зависимости от потерь давления ;
Где
- потери давления в аппарате при
номинальном расходе, МПа;
- перепад давления открывания или
настройки;
- номинальный расход аппарата, м3/с.
Дроссель с обратным клапаном типа
ДК-С12 по ТУ2-053-1651-83
= 8,59 л/мин
= 0,000143 м3/с;
= 0,3 МПа
= 25 л/мин =
0,000417 м3/с
= 359,71 ∙ 0,000143 +
864553,31 ∙ 0,0001432 = 0,0691 МПа.
Гидрораспределитель типа
ВММ6.44ВРУХЛ по ГОСТ 24679 -81
= 14,3 л/мин = 0,000238 м3/с;
=0,3МПа
= 63 л/мин =
0,00105 м3/с
= 142,86 ∙ 0,000238 +
136054,42 ∙ 0,0002382 = 0,0417 МПа. Обратный клапан встраиваемый
типа МКОВ 16/3 по 2-053-1738-86.
= 18 л/мин =
0,0003 м3/с;
= 0,18 МПа
= 32 л/мин =
0,000533 м3/с
= 0,05 МПа
= 121,95 ∙ 0,0003 + 228873,24
∙ 0,00032 = 0,0571 МПа
Суммарные потери для напорной линии:
= 0,0417 + 0,0571 = 0,0988 МПа.
Суммарные потери для сливной линии:
МПа.
Гидрораспределитель типа ВММ6.44ВРУХЛ по ГОСТ
24679 -81
= 14,3 л/мин = 0,000238 м3/с;
=0,3МПа
= 63 л/мин =
0,00105 м3/с
.9.9 Определение потерь в
гидроаппарате
Потерю давления в гидроаппаратах
определяем по формуле [4]:
где А и В - коэффициенты
аппроксимации экспериментальной зависимости от потерь давления ;
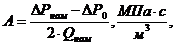
Где
- потери давления в аппарате
при
номинальном расходе, МПа;
- перепад давления открывания или
настройки;
- номинальный расход аппарата, м3/с.
Дроссель с обратным клапаном типа
ДК-С12 по ТУ2-053-1651-83
= 8,59 л/мин
= 0,000143 м3/с;
= 0,3 МПа
= 25 л/мин =
0,000417 м3/с
= 359,71 ∙ 0,000143 +
864553,31 ∙ 0,0001432 = 0,0691 МПа.
Гидрораспределитель типа
ВММ6.44ВРУХЛ по ГОСТ 24679 -81
= 14,3 л/мин = 0,000238 м3/с;
=0,3МПа
= 63 л/мин =
0,00105 м3/с
= 142,86 ∙ 0,000238 +
136054,42 ∙ 0,0002382 = 0,0417 МПа.
Обратный клапан встраиваемый типа
МКОВ 16/3 по 2-053-1738-86.
= 18 л/мин =
0,0003 м3/с;
= 0,18 МПа
= 32 л/мин =
0,000533 м3/с
= 0,05 МПа
= 121,95 ∙ 0,0003 + 228873,24
∙ 0,00032 = 0,0571 МПа
Суммарные потери для напорной линии:
= 0,0417 + 0,0571 = 0,0988 МПа.
Суммарные потери для сливной линии:
МПа.
Гидрораспределитель типа ВММ6.44ВРУХЛ по ГОСТ
24679 -81
= 14,3 л/мин = 0,000238 м3/с;
=0,3МПа
= 63 л/мин =
0,00105 м3/с
Таблица 2.4 - Потери давления в
гидроаппаратах
Этапы
цикла
|
Линия
|
Аппарат
|
Qдейств,
м3/с
|
QАП,
м3/с
|
АБ
|
|
|
|
|
Быстрый
подвод
|
Напорная
|
Обратный
клапан
|
0,0003
|
0,000533
|
0,18
|
121,95
|
228873,24
|
0,0571
|
0,0988
|
|
|
Распределитель
|
0,000238
|
0,00105
|
0,3
|
142,86
|
136054,42
|
0,0417
|
|
|
Сливная
|
Распределитель
|
0,000238
|
0,00105
|
0,3
|
142,86
|
136054,42
|
0,0417
|
0,1108
|
|
|
Дроссель
|
0,000143
|
0,00417
|
0,3
|
359,71
|
864553,31
|
0,0691
|
|
.9.10 Потери давления по длине
Потери давления по длине обусловлены вязким
трением жидкости при ее течении в трубопроводе.
За рабочую жидкость принимаем минеральное масло
ИГП-3 8 ГОСТ ТУ 38101413-78 класс вязкости по ISO
3448-68, группа по ISO
6743/4-1981-НМ - масло с антикоррозионными, антиокислительными и
противоизносными присадками:

=35-40мм2/с;
=890т/м3
,
=-
Определяем режим течения жидкости по числу
Рейнольдса [3]:
,
где u-
фактическая скорость жидкости, [м/с];
V -
кинематический коэффициент вязкости, [м2/с].
Затем сравниваем это число с
, если
то режим
течения - ламинарный, если
то режим турбулентный.
Для гладких круглых труб, а также
для отверстий в корпусе гидроблока управления -
=2300.
Для участка 3-4:
− режим ламинарный
гдеQ - расход
жидкости в линии, [
];
f - площадь
внутреннего сечения, [м2]:
Потери давления на вязкое трение
[4]:
где hе - потери
напора по длине,
pg - удельный
вес жидкости, [ кг/м3]
где
- плотность рабочей жидкости, [кг/м3];
- коэффициент гидротрения на i участке;
- длина
участка, [м];
- внутренний диаметр трубопровода,
[м];
- фактическая скорость,[ м/с].
при ламинарном режиме
Рассчитываем потери на участке 3-4:
= 1235,5;
Расчеты для других участков
производим по аналогичной схеме, и результаты заносим в таблицу 2.4.
Таблица 2.4 - Потери давления по
длине при рабочем подводе
Этапы
цикла
|
Линия
|
Участок
|
Qmax, м3/с
|
dст,
м
|
fст,
м2
|
uф,
м/с
|
Re
|
λ
|
L, м
|
ΔРe, МПа
|
Быстрый
подвод
|
Напорная
|
3-4
|
0,0003
|
0,012
|
0,00011
|
2,73
|
819
|
0,0781
|
0,5
|
0,0108
|
|
|
4-5,6-7
|
0,000238
|
0,0108
|
0,00009
|
2,64
|
712,8
|
0,0897
|
0,5
|
0,0129
|
|
|
8-10
|
0,000238
|
0,0108
|
0,00009
|
2,64
|
712,8
|
0,0897
|
1,2
|
0,0309
|
|
Сливная
|
11-12
|
0,000143
|
0,0108
|
0,00009
|
1,59
|
429,3
|
0,1491
|
1,2
|
0,0186
|
|
|
12-13
|
0,000143
|
0,012
|
0,00011
|
1,3
|
390
|
0,1641
|
0,5
|
0,0051
|
|
|
14-15
|
0,000143
|
0,018
|
0,00025
|
0,95
|
427,5
|
0,1497
|
7
|
0,0233
|
Суммарные потери для напорной (
и сливной
линии (
).
= 0,0546 МПа
= 0,047 МПа
.9.11 Местные потери давления
Местные потери (
)
складываются из потерь в различных местных сопротивлениях и определяются по
формуле [1]:
Затем сравниваем это число с
, если
то режим
течения - ламинарный, если
то режим турбулентный.
Для гладких круглых труб, а также
для отверстий в корпусе гидроблока управления -
=2300.

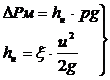
,
где
- фактическая скорость жидкости, м/c;
- коэффициент местных потерь;
- потери
напора местные,
-удельный вес жидкости, кг/м3;
- плотность рабочей жидкости, кг/м.
Коэффициенты
определяются
по справочнику и заносятся в таблицу 6.3 , где суммируются для напорной и
сливной линий.
Определяем местные потери для
участка 3-4:
Расчёт для остальных участков рассчитываем
аналогично, и результаты заносим в таблицу 2.5.
Местные потери (
)
складываются из потерь в различных местных сопротивлениях и определяются по
формуле [1]:
Затем сравниваем это число с
, если
то режим
течения - ламинарный, если
то режим турбулентный.
Суммарные потери для напорной (
) и сливной
линии
= 0,0107 МПа.
Рмс = 0,0054 МПа.
Заключительным этапом расчета является расчёт
суммарных потерь давления в напорной и сливной линии [1]:
По результатам расчёта уточняем
расчёт и выбор насосной установки по давлению.
Предварительный выбор насосной
установки 2МП Г48-84 УХЛ
4Г49-33 по
ТУ-053-1806-86 сделан правильно.
ленточный конвейер
гидропривод
3. Технологическая
часть
.1 Разработка технологического процесса
изготовления детали фланец с применением станков с ЧПУ
.1.1 Описание, назначение и конструкция детали
Деталь - фланец, служит в качестве части
сборного корпуса. Деталь ограничена габаритными размерами Ø120
мм. ширина 28 мм. Наружная поверхность тела вращения ступенчатая. Также имеется
восемь аксиальных отверстий, из них четыре отверстия ступенчатые Ø11
мм., и четыре гладких Ø7 мм. Деталь
изготавливается из конструкционной углеродистой стали 45, химический состав и
механические свойства приведены в таблице 3.1 и 3.2. Шероховатость
обрабатываемых поверхностей от RZ
40 до RZ
2,5. Наиболее сложным для обработки является отверстие Ø80H9
(+0,074) и наружная ступень Ø35Js6.
Радиальное биение поверхности относительно общей оси поверхности не более 0,02
мм.
Таблица 3.1 - Химический состав стали 45 (%).
С
|
Si
|
Mn
|
S
|
P
|
Ni
|
Cr
|
|
|
|
не
более
|
|
|
0,4-0,5
|
0,17-0,37
|
0,5-0,8
|
0,045
|
0,3
|
0,3
|
Таблица 3.2 - Механические свойства стали 45
ГОСТ 1050-88.
sт, мПа
|
sвр, мПа
|
s,%
|
y, %
|
а
н, Вж/см2
|
|
не
менее
|
|
горячекатаная
|
отожженная
|
360
|
610
|
16
|
40
|
50
|
241
|
197
|
.1.2 Технологический контроль чертежа детали
Рабочий чертеж обрабатываемой детали содержит
все необходимые сведения, дающие полное представление о детали, то есть все
проекции, разрезы, совершенно четко и однозначно объясняющие её конфигурацию, и
возможные способы получения заготовки. На чертеже указаны все размеры с
необходимыми отклонениями, требуемая шероховатость обрабатываемых поверхностей,
что для данной детали достаточно. Чертеж содержит все необходимые сведения о материале
детали. Рабочий чертеж соответствует действующим на сегодняшний день
стандартам.
.1.3 Анализ технологичности конструкции детали
Основной задачей анализа является проработка
технологичности конструкции обрабатываемой детали, снижение трудоёмкости,
возможность обработки высокопроизводительными методами.
Деталь - фланец имеет простую форму тела
вращения, в целом конструкция детали технологична, это подтверждается тем, что
материал, из которого изготовлена деталь Сталь 45, технологически дешевая, она
хорошо обрабатывается лезвийными инструментами, хорошо обрабатывается
шлифованием. Здесь используются обычные методы обработки детали: токарная,
фрезерная, сверлильная, и шлифовальная. Также могут применяться типовые станки,
стандартные инструменты и приспособления. Для получения отверстий требуется
станок с ЧПУ. Для контроля данной детали применяются универсальные средства
измерения. Для обработки детали используется минимум слесарной обработки. Все
вместе взятое дает невысокую трудоемкость, невысокую стоимость изготовления
этой детали, что соответственно дает представление о технологичности
конструкции.
.1.4 Выбор метода изготовления и формы заготовки
Метод выполнения заготовки для изготовления
деталей определяется исходя из назначения и конструкции детали, условиями её
работы и представляемыми требованиями к ней. Выбрать заготовку, значит
установить способ её получения, наметить припуски на обработку каждой
поверхности, рассчитать размеры и указать допуски на неточность изготовления.
Для рационального изготовления заготовки с минимальной себестоимостью
необходимо учитывать все вышеперечисленные данные.
Выбор метода выполнения заготовки определяется
назначением и конструкцией заданной детали, материалы, технические требования,
а также, что немаловажно, экономичность изготовления и снижение трудоемкости.
Для изготовления детали будем рассматривать
несколько вариантов получения заготовки:
Вариант 1: заготовка из круглого проката
(Рисунок 3.1.).
Рисунок 3.1 - Эскиз заготовки из проката
Объем заготовки определяется по формуле:
(3.1)
где D - диаметр
заготовки, см.;
h - длина
заготовки, см.
Массу заготовки определяем по
формуле:
(3.2)
гдеp
- удельный вес стали, равен 7,85 г/см3.
Вариант 2: заготовка из поковки
(Рисунок 3.2.).
Рисунок 3.2 - Эскиз заготовки из
поковки
Объем поковки определяется по
формуле:
(3.3)
где
- объемы отдельных частей
заготовки, см3.
Массу заготовки определяем по
формуле:
.
Вариант 3: заготовка из поковки
(Рисунок 3.3.).
Рисунок 3.3 - Эскиз заготовки из
поковки
Объем поковки определяется по
формуле:
где
- объемы отдельных частей
заготовки, см3.
Массу заготовки определяем по
формуле:
.
Определяем стоимость заготовки по 1
варианту.
Масса заготовки Мg = 3,18 кг.
Стоимость заготовки определяется по
формуле:
(3.4)
гдеС1 - стоимость 1 тонны заготовок,
принятых за базу, руб.;
Q - масса заготовки,
кг.
Определяем стоимость заготовки по 2
варианту.
Масса заготовки Мg = 1,81 кг.
Стоимость заготовки определяется по
формуле:
(3.5)
Где
- коэффициенты, зависящие от класса
точности, группы сложности, массы, марки материала и объема производства
заготовок;
С1 - стоимость 1 тонны
заготовок, принятых за базу, руб.;
Q - масса заготовки,
кг.;
g - масса детали,
кг.;
Sотх.
- стоимость 1 тонны стружки, руб.
Определяем стоимость заготовки по 3
варианту.
Масса заготовки Мg = 2,09 кг.
Стоимость заготовки определяется по
формуле:
Где
- коэффициенты, зависящие от класса
точности, группы сложности, массы, марки материала и объема производства
заготовок;
С1 - стоимость 1 тонны
заготовок, принятых за базу, руб.;
Q - масса заготовки,
кг.;
g - масса детали,
кг.;
Sотх.
- стоимость 1 тонны стружки, руб.
Вариант изготовления заготовки из
круглого проката отличается повышенной металлоемкостью, требует больше
трудоемкости на изготовление детали. Поковка (вариант 2) позволяет получить
более точную заготовку, но требует повышенных затрат при начальной подготовке
производства и повышенной трудоемкости. Заготовка из поковки (вариант 3),
обладает меньшими затратами, требует меньшей трудоемкости, чем заготовки из
поковки и круглого проката. С точки зрения экономии металла, стоимость
заготовки - поковки (вариант 3) ниже, чем стоимость заготовки из круглого
проката и поковки (вариант 2).
Таким образом, для дальнейшего
проектирования выбираем заготовку - поковку (вариант 3).
.1.5 Выбор структуры и плана
технологического процесса
Технологический процесс обработки
детали предусматривает несколько стадий. Если рассматривать данный процесс
укрупнено, то необходимо выделить черновую обработку и окончательную
(абразивными инструментами). Каждая из этих стадий разбивается на необходимое
количество технологических операций.
В описании технологического процесса
не указывают такие операции как смазка, упаковка, нанесение специальных
покрытий и т.д.
Вычерчиваем эскиз детали и
обозначаем обрабатываемые поверхности.
Рисунок 3.4 - Эскиз детали
Таблица 3.3 - План маршрута
обработки детали
Операция
|
Переход
|
1.
Токарная с ЧПУ
|
1.1.
Подрезать торец. 1.2. Точить Ø 80. 1.3. Сверлить отверстие Ø18. 1.4.
Точить Ø
35. 1.5.
Снять фаску 1×45о. 1.6.
Дать риску Ø50±0,2.
|
2.
Токарная с ЧПУ
|
2.1.
Подрезать торец в размер 28 мм. 2.2. Точить Ø 120. 2.3.
Расточить выборку Ø70.
2.4.
Расточить выборку Ø80Н9(+0,074).
2.5. Снять фаску 1,5×45о. 2.6.
Дать риску Ø100±0,2.
|
3.
Фрезерная С ЧПУ
|
3.1.
Фрезеровать фаску 5×45о.
|
4.
Вертикально -сверлильная с ЧПУ
|
4.1.
Сверлить 8 отверстий Ø7.
4.2.
Произвести цековку Ø11
на
4 отв.
|
5.
Круглошлифовальная
|
5.1.
Шлифовать Ø35Js6 5.2.
Шлифовать Ø80Н9(+0,074)
|
6.
Внутришлифовальная
|
|
.1.6 Выбор типа производства и формы организации
технологического процесса.
Тип производства определяется по величине
коэффициента загрузки оборудования по формуле:
, (3.6)
Где ΣТ - общая
норма времени на обработку детали;
tв - время за
которое производится выпуск изделия, (мин.), и определяется по формуле:
, (3.7)
гдеFд -
действительный годовой фонд времени работы оборудования, час. (при двухсменной
работе равен 4015 часов);
N - годовая
программа выпуска равна 1000 штук;
Расчет нормы времени.
Токарная операция.
Фрезерная операция.
Вертикально - сверлильная операция.

Шлифовальная операция.
ΣТ = 22,3 мин.
Этот коэффициент соответствует
мелкосерийному типу производства. Для данного типа производства наиболее
характерной является групповая форма организации производства, которую и
применим в качестве базовой организационной формы технологического процесса для
изготовления детали “фланец”.
Штучно-калькуляционное время
определяем по формуле:
, (3.8)
где φк -
коэффициент, учитывающий вспомогательное и дополнительное время.
φк = 1,98 -
для мелкосерийного производства.
Таблица 3.4 - Штучно-калькуляционное
время
Операция
|
То,
мин.
|
φк
|
Тш.к.,
мин.
|
Токарная
|
11,4
|
1,98
|
22,6
|
Фрезерная
|
2,4
|
1,98
|
4,75
|
Сверлильная
|
2,2
|
1,98
|
4,4
|
Шлифовальная
|
6,3
|
1,98
|
12,5
|
Итого:
|
|
|
44,25
|
.1.7 Выбор и расчет припусков на механическую
обработку
Припуски имеют очень важное значение в процессе
разработки технологических операций механической обработки деталей. Правильное
значение припусков на обработку заготовки обеспечивает экономию материала и
трудовых ресурсов, качества выпускаемой продукции.
Расчет припуска на механическую обработку Ø120
мм.
Величину минимального припуска на механическую
обработку определяем по формуле:
(3.9)
где RZ = 350 мкм.
- величина неровностей поверхности;
Т = 250 мкм. - величина дефектного
слоя;
р - величина пространственных
отклонений (коробление, смещение оси заготовки), р = 400 мкм.
При установке в трехкулачковый
патрон с упором в торец погрешность закрепления и установки на переходе ε = 400.
Допуск на обработку заготовки - 0,3
мм.
Величину максимального припуска на
механическую обработку определяем по формуле:
(3.10)
Рисунок 3.5 - Схема расположения
припусков и допусков при механической обработке
.1.8 Технические характеристики
выбранного оборудования
Выбор оборудования осуществляется на основании
таких данных, как метод обработки, точность обработки, расположение размеров
обрабатываемых поверхностей, габаритных размеров заготовки, количество
инструментов в наладке станка, обеспечение заданной производительности, эффективность
использования станка по времени, мощности и др.
В процессе обработки детали используется
несколько видов станков. Краткая характеристика последних приведена ниже.
Токарная операция.
Для токарной программной операции выбираем
станок с ЧПУ модели 16К20Ф3С35.
Технические характеристики станка:
наибольший диаметр обрабатываемой детали:
над станиной - 400 мм., над суппортом - 200 мм.
расстояние между центрами - 1000 мм.
число оборотов шпинделя - 35…1600 об/мин.
число скоростей по программе - 9.
Пределы рабочих подач:
продольная - 0…1200 мм/об., поперечная - 0…600
мм/об.
число подач - 2.
число управляемых осей координат:
всего - 2, одновременно - 2.
количество инструментов - 6.
дискретность отсчета:
поперечного хода - 0,005 мм., продольного хода -
0,01 мм.
Фрезерная операция.
Выбираем вертикально-фрезерный станок 6Р10.
Технические характеристики станка:
наибольшее перемещение стола
продольное - 500 мм.; поперечное - 160 мм.;
вертикальное - 300 мм.;
число скоростей шпинделя - 12.
подача стола:
продольная - 25…120 мм.; поперечная - 25…120
мм.; вертикальная - 12,5…560 мм.;
мощность электродвигателя - 3 кВт.
Вертикально-сверлильная операция.
Выбираем вертикально-сверлильный станок модели
2Р135Ф2-1.
Технические характеристики станка:
наибольший условный диаметр сверления в стали -
35 мм.
рабочая поверхность станка - 4400×710
мм.
вылет шпинделя - 200 мм.
наибольший ход шпинделя - 200 мм.
конус Морзе шпинделя - 3.
число скоростей шпинделя - 12.
частота вращения шпинделя - 45…2000 об/мин.
подача шпинделя - 0,1…1,6 об/мин.
мощность электродвигателя - 2,2 кВт.
Круглошлифовальная операция.
Выбираем круглошлифовальный станок 3Е12
Технические характеристики станка:
наибольшие размеры обрабатываемой заготовки:
диаметр 200 мм.
длина 500 мм.
наибольшие размеры шлифовального круга - 350×40×127.
- частота вращения шпинделя шлифовальной бабки -
1900…2720 мин-1.
Внутришлифовальная операция
Выбираем универсальный внутришлифовальный станок
3К228В
Технические характеристики станка:
диаметр шлифуемых отверстий - 50…200 мм.;
наибольшая длина шлифования - 200 мм.;
наибольший диаметр устанавливаемого изделия -
560 мм.;
частота вращения шпинделя изделия - 560 мм.;
частота вращения внутришлифовального шпинделя -
4500…12000 об/мин.;
частота вращения торцевого шпинделя - 4000
об/мин.
мощность электродвигателя - 5,5 кВт.
3.1.9 Выбор режущих инструментов
Выбор режущих инструментов осуществляется в
зависимости от метода обработки, формы и размеров обрабатываемой поверхности,
ее точности, шероховатости, от обрабатываемого материала, заданной
производительности и периода стойкости. Режущие инструменты должны обладать
высокой режущей способностью (стабильной размерной стойкостью при высоких
режимах резания), обеспечить возможность быстрой и удобной замены, наладки в
процессе работы, формировать транспортабельную стружку и отводить ее от зоны
обработки без нарушения нормальной работы оборудования.
Выбор режущего инструмента выполнен по методике
изложенной в [3, с.240; 5, с.522, с.180].
Выбранные режущие инструменты приведены в
таблице 3.5.
Таблица 3.5 - Режущие инструменты
Операция
|
Наименование
перехода
|
Инструмент
|
Материал
режущей части
|
ГОСТ
инструмента
|
|
Токарная
с ЧПУ
|
1.1.
Подрезать торец.
|
Резец
токарный подрезной
|
Т15К6
|
ГОСТ
18877-73
|
|
|
1.2.
Точить Ø
80.
|
Резец
проходной упорный отогнутый
|
Т15К6
|
ГОСТ
18879-73
|
|
|
1.3.
Сверлить отверстие Ø18.
|
Сверло
спиральное Ø18.
|
Р6М5
|
ГОСТ
10902-77
|
|
|
1.4.
Точить Ø
35.
|
Резец
проходной упорный отогнутый
|
Т15К6
|
ГОСТ
18879-73
|
|
|
2.1.
Подрезать торец в размер 28 мм.
|
Резец
токарный подрезной
|
Т15К6
|
ГОСТ
18877-73
|
|
|
2.2.
Точить Ø
120.
|
Резец
токарный проходной прямой
|
Т15К6
|
ГОСТ
18880-73
|
|
|
2.3.
Расточить выборку Ø70.
|
Резец
токарный расточной
|
Т5К10
|
ГОСТ
18882-73
|
|
|
2.4.
Расточить выборку Ø80Н9(+0,074)
|
Резец
токарный расточной
|
Т5К10
|
ГОСТ
18882-73
|
|
Фрезерная
с ЧПУ
|
3.1.
Фрезеровать фаску 5×45о.
|
Фреза
торцевая
|
Р6М5
|
ГОСТ
10902-77
|
|
Сверлильная
с ЧПУ
|
4.1.
Сверлить 8 отверстий Ø7.
|
Сверло
спиральное Ø7.
|
Р6М5
|
ГОСТ
10902-77
|
Круглошлифовальная
|
4.2.
Произвести цековку Ø11
на
4 отв.
|
Зенкер
Ø11.
|
Р6М5
|
ГОСТ
10902-77
|
|
5.1.
Шлифовать Ø35Js6.
|
Круг
шлифовальный ПП450×203×50
24А16С28К5
|
Белый
электрорунд на керамической связке
|
ГОСТ
9473-80
|
Внутришлифовальная
|
5.2.
Шлифовать Ø80Н9(+0,074)
|
Круг
шлифовальный ПП70×20×10
24А16С28К5
|
Белый
электрорунд на керамической связке
|
ГОСТ
9473-80
|
|
|
|
|
|
|
|
.1.10 Выбор приспособлений и вспомогательных
инструментов
Станочное приспособление выбираем с условием
того, чтобы обеспечивали требуемое базирование и надежное закрепление детали на
операциях, высокую жесткость установленной на станке детали, учитывая
возможность автоматизации обработки и других требований.
Выбор приспособления производим и заносим в
таблицу 3.6.
Таблица 3.6 - Выбор приспособлений
№
|
Операция
|
Приспособление
|
1
|
Токарная
|
Патрон
токарный трехкулачковый. Державка для расточного резца.
|
2
|
Фрезерная
|
Поворотный
стол. Тиски машинные универсальные.
|
3
|
Шлифовальная
|
Патрон
самоцентрирующий.
|
.1.11 Выбор средств измерения и контроля
Выбираем средства измерения и контроля размеров,
в зависимости от типа производства и величины допуска контролируемого параметра
для каждой операции.
Для токарной обработки выбираем: микрометр
рычажный МР75-100 ГОСТ 14710-89, биение мер, профилометр.
Для фрезерной обработки выбираем индикатор
часового типа ИЧ-5, С=0,01.
Для сверлильной обработки выбираем
штангенциркуль ШЦ I - 125 - 0,1
ГОСТ 166-80.
Для шлифовальной обработки выбираем индикаторный
нутромер.
.1.12 Специализированный участок по изготовлению
фланцев и его планировка
Потребное количество оборудования определяем по
формуле:
, (3.11)
Где mp - расчётное
количество станков, шт.
Штучное время, затраченное на обработку
определяем по формуле:
, (3.12)
Где То - время
затраченное на операцию, мин.;
Фобр. - коэффициент вида
обработки равен.
Находим время затраченное на токарную операцию
(Фобр. = 2,14)
Принимаем mp = 1 -
токарный станок.
Находим время затраченное на фрезерную операцию
(Фобр. = 1,84)
Принимаем mp = 1 -
вертикально-фрезерный станок.
Находим время затраченное на
сверлильную операцию (Фобр. = 1,84)
Принимаем mp = 1 -
сверлильный станок.
Находим время затраченное на круглошлифовальную
операцию (Фобр. = 2,10)
Принимаем mp = 1 -
круглошлифовальный станок.
Находим время затраченное на внутришлифовальную
операцию (Фобр. = 2,10)
Принимаем mp = 1 -
внутришлифовальный станок.
.1.13 Выбор режимов резания
Расчет ведется одновременно с
заполнением операционных и маршрутных карт технологического процесса. Режим
резания устанавливаем, исходя из особенностей обрабатываемой детали и
характеристики режущего инструмента и станка. Результаты сводим в таблицу.
Приведем расчет на примере технологического перехода - подрезка торца Ø120. Для чего
выбираем проходной резец с механическим креплением пластин из твердого сплава
Т5К10 с углом в плане f=45Å
. Глубина резания:
(3.13)
Где
D - наибольший диаметр заготовки, мм.;- наименьший диаметр заготовки, мм.
.
Назначаем подачу:о=0,1 мм/об.;
Принимаем
из стандартного ряда станка: Sо=0,1 мм/об.;
.
Расчет скорость резания:
(3.14)
гдеCV -
коэффициент, скорости резания; CV = 273
x, y, m -
показатели степени скорости резания;
КV -
коэффициент, качества обработки;
КV = КmV КnV КMV КfV КOV,(3.15)
где
КmV -
коэффициент, качества материала - 1
КnV -
коэффициент, состояния поверхности заготовки - 0,8
КMV -
коэффициент, материал режущей части - 1
КfV -
коэффициент, параметры резца - 1
КOV -
коэффициент, вид обработки - 1,18
КV =
1·0,8·1·1·1,18 = 0,944
Период
стойкости инструмента T = 60мин;=273 · 0,944 / 600,2·2,50,15 ·0,10,2
= 159,7 м/мин;
.
Определяем частоту вращения:
n=1000*V/π*d, об./мин.;
(3.16)
гдеV
- скорость резания, м/мин.;- наибольший диаметр заготовки, мм.; =1000·159,7 /
3,14·120 = 423,7 об./мин.;
принимаем
по паспорту станка: n = 500 об./мин.;
Рассчитанные
режимы резания операций заносим в таблицу 3.7.
Таблица
3.7 - Режимы резания
Операция
|
Технологические
переходы
|
Элементы
режимов резания
|
|
|
t, мм.
|
S, мм/об.
|
V,м/мин.
|
n, об/мин.
|
Токарная
с ЧПУ
|
Подрезать
торец Ø
120
|
2,5
|
0,1
|
159,7
|
500
|
|
Точить
Ø
80
|
2,5
|
0,15
|
145
|
630
|
|
Сверлить
отверстие Ø18
|
4
|
0,1
|
56,7
|
220
|
|
Точить
Ø
35
|
2,5
|
0,15
|
145
|
630
|
|
Подрезать
торец
|
2,5
|
0,1
|
185
|
500
|
|
Точить
Ø
120
|
2,5
|
0,15
|
145
|
400
|
|
Расточить
выборку Ø70,
за
2 прохода предварительно.
|
4
|
0,6
|
91,7
|
400
|
|
Расточить
выборку Ø70,
окончательно
|
2
|
0,1
|
162,3
|
800
|
|
Расточить
выборку Ø80,
предварительно.
|
4
|
0,6
|
91,7
|
400
|
|
Расточить
выборку Ø80,
окончательно.
|
1
|
0,05
|
206,8
|
1000
|
Фрезерная
с ЧПУ
|
Фрезеровать
фаску 5×45о.
|
|
0,05
мм/зуб
|
50
|
250
|
Сверлильная
с ЧПУ
|
Сверлить
8 отверстий Ø7
|
|
0,08
|
25
|
220
|
|
Зенкеровать
Ø11
на
4 отв.
|
|
0,12
|
30
|
160
|
Круглошлифовальная
|
Шлифовать
Ø35
Js6
|
|
30
м/сек
|
35
м/сек.
|
70
|
Внутришлифовальная
|
Шлифовать
Ø80Н9(+0,074)
|
|
35
м/сек
|
25
м/сек.
|
65
|
.1.14 Разработка управляющей программы для
токарной обработки детали на станке с ЧПУ модели 16К20Ф3С5
Составим программу для обработки фланца на
токарно-универсальном станке 16К20Ф3С5 с ЧПУ.
Программа состоит из следующих проходов:
1. Подрезать торец
2. Точить Ø
120 мм.
. Расточить выборку Ø
70 мм.
. Расточить выборку Ø
80 мм.
Инструмент:
1. Резец токарный проходной прямой Т5К10 ГОСТ
18877-73.
2. Резец токарный подрезной Т5К10 ГОСТ
18877-73.
. Резец токарный расточной Т5К10 ГОСТ
18882-73.
Разработаем схему наладки станка содержащую
изображение заготовки с контуром обрабатываемой поверхности, настроечные
размеры, схему базирования заготовки, положение начальной точки траектории
режущего инструмента, инструменты в начальном положении с их траекториями
движения.
№ 001G27T101S500M104
- вводится абсолютная система координат
№ 002G58Z+000000F70000
- смещение 0 вдоль координат Z.
№ 003X+000000
- смещение 0 вдоль координат X.
№ 004G26
- вводится относительная система координат.
№ 006Z-03000F70000
- перемещение вдоль оси Z
на 30 мм.
№ 007X-08200
- перемещение вдоль оси X
на 82 мм.
№ 008X-07800F10200
- перемещение вдоль оси X
на 78 мм.
№ 009Z+03000F70000
- перемещение вдоль оси Z
на 30 мм.
№ 010X+16000
- перемещение резца в начальное положение.
№ 011G40F10100L31
- обработка детали первым резцом закончена.
№ 012Т102 - вывод второго инструмента.
№ 013G26
- обнуление погрешностей.
№ 014G01F10100L32
- вводится линейный интерполятор перемещений.
№ 015X-02000F70000
- перемещение вдоль оси X
на 20 мм.
№ 016Z-04200
- перемещение вдоль оси Z
на 42 мм.
№ 017X+02000F70000
- перемещение вдоль оси X
на 20 мм.
№ 018Z+04200
- перемещение резца в начальное положение.
№ 019G40F10100L32
- обработка детали вторым резцом закончена.
№ 020T103
- вывод третьего инструмента.
№ 021G26
- обнуление погрешностей.
№ 022G01F10200L33
- вводится линейный интерполятор перемещений.
№ 023X-08000F70000
- перемещение вдоль оси X
на 80 мм.
№ 024Z-03250
- перемещение вдоль оси Z
на 32,5 мм.
№ 025X-04000
- перемещение вдоль оси X
на 40 мм.
№ 026Z+00500
отвод резца от детали на 5 мм.
№ 027X-04000F70000
- перемещение вдоль оси X
на 40 мм.
№ 028Z-00500
- перемещение вдоль оси Z
на 5 мм.
№ 029X-04000
- перемещение вдоль оси X
на 40 мм.
№ 030Z+07500F70000
- перемещение вдоль оси Z
на 7,5 мм.
№ 031Z+02750F70000
- перемещение вдоль оси Z
на 27,5 мм.
№ 032X+04000F70000
- перемещение резца в начальное положение.
№ 033G40F10200L33
- обработка детали 3-им инструментом закончена.
№ 034G25X+999999F70000
- возвращение суппорта в ноль станка.
№ 035M105
- выключение шпинделя.
№ 036G25Z+999999
- возвращение суппорта в ноль станка.
№ 037M002
- конец программы.
.2 Расчет и конструирование резца
.2.1 Выбор типа резца
В ходе проведения дипломной работы необходимо
рассчитать по формулам и сконструировать токарный проходной прямой правый
резец. Резец рассчитываем для чернового обтачивания наружного диаметра детали
типа «Фланец» диаметром D
= 125 мм. до диаметра D
= 120 мм, длиной 12 мм. Параметр шероховатости обработанной поверхности Ra
=
40. Материал заготовки сталь 45, σв
= 610 МПа. Припуск на обработку (на сторону) h
= 2,5 мм. на длине 12 мм. Заготовка поковка. Обработку производим на
токарно-винторезном станке модели 16К20.
По справочнику выбираем резец и устанавливаем
его геометрические элементы. Тип резца токарный проходной, прямой правый.
Материал рабочей части пластины - твердый сплав Т5К10 ГОСТ 38882-74. Материал
корпуса резца - сталь 50 ГОСТ 1058-74. Эскиз обработки приведен на Рисунок 3.7.
Геометрические элементы резца: форма передней
поверхности криволинейная с отрицательной фаской (тип VI),
ширина радиусной лунки А = 4 мм., радиус лунки R
= 10 мм. [15, с.297, табл. 8.9]. Передний угол γ=12°;
передний угол на упрочняющей фаске γф=-5°;
главный задний угол α=8°; угол
наклона главной режущей кромки λ=0;
главный угол в плане ф=60°; вспомогательный угол в плане ф1=30°;
радиус вершины r=1 мм.
Рисунок 3.7 - Эскиз обработки
.2.2 Определение скоростей и сил при резании
Определяем глубину резания черновую. Припуск
снимаем за один проход. Тогда:
(3.17)
мм.
Назначаем подачу [15,с.266,табл.11].
Для параметра шероховатости поверхности Rz=40 мкм,
обработки стали резцом с радиусом при вершине г=1 мм, S0=0,8-1,3
мм/об. Учитываем поправочный коэффициент на подачу равный 0,8: S0=(0,8/1,3)*0.8=0,64…1,04
мм/об. Принимаем значение Sо=0,84 мм/об.
Корректируем подачу по паспортным
данным станка 16К20 S0=0,8 мм/об.
Назначаем период стойкости резца
Т=45 мин.
Определяем скорость резания по
формуле полученной из ([15] с.265).
(3.18)
Ку - общий поправочный коэффициент,
равный произведению поправочных коэффициентов, учитывающих изменённые условия
обработки. Определяем значение этих коэффициентов.
КМv
- поправочный коэффициент, учитывающий изменение механических свойств
обрабатываемого материала ([15] с. 108-113):
По [15, с.314 табл.8.20] находим значение
коэффициента Сv
и показателей степеней m,
xv, уv
формулы. Для наружного точения, твердого сплава Т5К10 и Sо=0,84
мм/об.: Сv
=259,
xv=0,18, уv=0,45,m=0,15.
Учитываем поправочные коэффициенты на скорость
резания.
,(3.19)
По условию δв =610МПа
Определяем общий поправочный
коэффициент на скорость главного движения резания:
,(3.20)
КПv -
поправочный коэффициент, учитывающий состояние поверхности заготовки ([15]
с.108-113). КПу = 1 так как заготовка поковка.
КИv -
поправочный коэффициент, учитывающий изменение материала рабочей части
инструмента. КИу=1, так как принят твердый сплав;
Кфv -
поправочный коэффициент, учитывающий изменение главного угла в плане φ, Кфv=0,92, так
как φ=60°;
КОv -
поправочный коэффициент, учитывающий вид обработки, КОv=1 так как
осуществляется наружное продольное растачивание.
Подставив все найденные величины в
формулу, получим:
В единицах СИ:
Определяем частоту вращения шпинделя,
соответствующую найденной скорости:
(3.21)
Корректируя частоты вращения
шпинделя по паспортным данным станка модели 16К20, устанавливаем действительное
значение частоты вращения п = 400мин -1
(3.22)
В единицах СИ:
Определяем главную составляющую силы
резания:
(3.23)
КРz
- общий поправочный коэффициент, равный произведению отдельных поправочных
коэффициентов, учитывающих измененные условия обработки. Определяем значения
этих коэффициентов.
КМрz
- поправочный коэффициент, учитывающий изменение механических свойств
обрабатываемого материала;
По табл. 8.26 ([15] с.318) находим значение
коэффициента СРz,
и показателей степеней формулы хрz,
урz,
nрz.
Для наружного точения резцом из стали 50, σв=610
МПа: СРz=320;
хрz=0,96;
урz=0,71;
nрz=0,12.
Учитываем поправочные коэффициенты на силу
резания.
, (3.24)
Показатель степени - np определяем
по ([15] с.318). Для обработки конструкционной стали резцом с пластиной
твердого сплава Т5К10 nр=0,75. По
условию δВ=610 МПа.
Тогда:
(3.25)
КФPz -
поправочный коэффициент, учитывающий изменение главного угла в плане ф. Для
ф=60° и резца из быстрорежущей стали КФPz =0,94;
Кγрz -
поправочный коэффициент, учитывающий изменение переднего угла γ. Кγрz =1, так как
γ
=10°;
Кλpz -
поправочный коэффициент, учитывающий изменение угла наклона главной режущей
кромки λ, Кλpz =1, так как
λ,=0.
Подставляем все найденные величины в
формулу:
В единицах СИ:
Pzv =9,81×290=2844,9 Н
Определяем мощность, затрачиваемую
на резание:
(3.26)
где Рz - в кгс, υД - в м/мин;
В единицах СИ:
(3.27)
где Рz - в Н, υД - в м/с;
Проверяем, достаточна ли мощность
привода станка. Необходимо проверить выполнения условия:
Мощность (кВт) на шпинделе станка по
приводу:
(3.28)
В паспортных данных станка находим: Nд=10 кВт, η=0,75.
Следовательно,
т.е.
обработка фланца возможна.
.2.3 Определение сечения державки
В качестве материала корпуса резца
выбираем сталь 50 ГОСТ 1050-88 с δв= 650 МПа
(65 кгс) и допустимое напряжение на изгиб δиз=200 МПа (20
кгс).
При условии, что h = 1.6 ∙
b, то ширина
прямоугольного сечения корпуса резца в единицах СИ:
(3.29)
где l - вылет
резца, l=65 мм
δиз = 200*106
Па.
м.
Принимаем ближайшее большее значение
корпуса b = 16 мм. и
руководствуясь приведенными соотношениями, получим высоты корпуса резца h = 1,6∙b = 1,6∙16
= 25,5 мм. Принимаем h = 25 мм.
Проверяем прочность и жесткость
корпуса резца:
Максимальная нагрузка допускаемая
прочностью резца:
(3.30)
В единицах СИ:
Максимальная нагрузка, допускаемая
жесткостью резца:
(3.31)
Где f -
допускаемая стрела прогиба резца при черновом точении,
f = 0,1*10-3
м;
Е=2∙105 МПа = 2∙1011
Па = 20000 кгс/мм2;
l - вылет
резца;
J - момент
инерции прямоугольного сечения корпуса,м4;
(3.32)
В единицах СИ:
,
Резец обладает достаточными
прочностью и жесткостью, так как
>2844,9 <4369,6 Н
.2.4 Выбор габаритных размеров резца
Согласно исходным условиям для
черновой обработки детали по справочнику ([15], с.297) выбираем форму резца, у
которого передняя поверхность криволинейная с отрицательной фаской.
Конструктивные размеры резца берем
по СТ СЭВ 190-75; общая длина резца L = 150 мм;
расстояние от вершины резца до боковой поверхности в направлении лезвия n = 6 мм;
радиус кривизны вершины лезвия резца rв = 1 мм; l = 16 мм.
Геометрические элементы лезвия резца
выбираем по ([15] с.297); ширина радиусной лунки А=4 мм., радиус лунки R=10 мм.
Передний угол γ=12о; передний
угол на упрочняющей фаске γ=-5о; главный
задний угол α=8°; угол наклона
главной режущей кромки λ=0; главный
угол в плане ф=60°; вспомогательный угол в плане ф1=30°; радиус
вершины r=1 мм.
По ГОСТ 5688-61 принимаем: качества
отделки (параметры шероховатости) передней и задней поверхности лезвия резца Ra=0,2 и
опорной поверхности корпуса Ra=0,4;
предельные отклонения габаритных размеров L=150H16, h=25h14, b=16h4; марка
твердого сплава Т5К10; материал державки сталь 50 по ГОСТ 1050-88. В качестве
крепления режущей пластинки выбираем материал припоя - латунь Л68 по ГОСТ 15527-70.
4. Безопасность
и экологичность проекта
.1 Анализ опасных и вредных факторов в цехе
погрузки удобрений
В цехе загрузки удобрений возникают вредные
производственные факторы, влияющие на человека и окружающую среду. Цех
спроектирован для загрузки удобрений в автомобили «Белаз». Готовое удобрение
ленточным конвейером подается в бункер, когда бункер заполняется удобрением,
подъезжает автомобиль «Белаз» и удобрения загружаются в него.
При выполнении технологического процесса
загрузки удобрений возникают физически опасные и вредные производственные
факторы: движущиеся ленты и вращающиеся ролики ленточных конвейеров, привод
конвейера, вибрация, запыленность, могут превышать предельно допустимые
значения. Из-за повышенной запыленности, возможно ухудшение освещенности, а
также шум, вибрация.
При проведении оценки монотонности труда
выявлено присутствие психофизиологических небезопасных и вредоносных
производственные моментов. Физиологические статические и динамические
перегрузки у персонала, нервно-психические перегрузки, интеллектуальное
перенапряжение, перенапряжение анализаторов слуха, зрения у технологического
персонала: операторов на постах управления. Результаты влияния
психофизиологических небезопасных и вредоносных производственных моментов - завышенная
утомляемость, рассеянное забота, растет возможность принятия работающими
неверных заключений.
Эти факторы оказывают вредное воздействие на
организм человека, возникают снижение его работоспособности, увеличение его
травматизма и возможно профессиональных заболеваний, таких как заболевания
дыхательных путей, легких, заболевания органов зрения и слуха.
4.2 Меры по обеспечению безопасных и здоровых
условий труда
Транспортирующие машины считаются неотъемлемой
частью современного производства, так как с их помощью осуществляется
механизация основных технологических процессов и вспомогательных работ.
Конструкция конвейера исключает возможность
падения транспортируемых материалов и предусматривает ограждения и блокировки с
учетом требований настоящих Правил. Категорически запрещено включать и
использовать конвейеры, движущиеся и вращающиеся части которых (лента, барабан,
ролики) засыпаны транспортируемым материалом. Конвейер имеет предохраняющее
устройство, отключающие приводы при перегрузке.
Конвейер, транспортирующий порошкообразные
пылящие материалы, а еще материалы, выделяющие пары и газы, или материалы с
большой температурой, оборудуются системами пылеподавления, вентиляции или
аспирации и тепловой защитой зависящих от физико-химических свойств материалов
и конструкции конвейера.
В местах прохода людей и проезда транспортных
средств под магистралью конвейеров поставлены сплошные защитные огораживания
для улавливания падающих с сборочного потока материалов и изделий. Рабочая
ветвь сборочного потока, размещенного в наклонной галерее, ограждена со стороны
прохода, устроены настилы с поперечинами. Приводные, натяжные и отклоняющие
барабаны, натяжные прибора, канаты и блоки натяжных приборов, ременные,
червячные, муфтовые и иные передачи на конвейерах ограждены. Грузы натяжных
приборов ограждены. Во время работы сборочного потока вход в огражденную зону
исключен.
Системой сборочного потока учтен доступ к
составляющим, блокам и контрольным устройством сборочного потока, требующим
повторяющейся испытания, а еще к приборам регулировки и смазки без снятия
огораживания.
Для предотвращения обратного хода ленты привод
ленточного конвейера оснащен автоматическими тормозными устройствами.
Пробуксовывание ленты конвейера устраняется
натяжкой ленты натяжными приборами после очистки барабанов и ленты. Подсыпать
канифоль и другие материалы в целях устранения пробуксовки ленты запрещается.
Для предупреждения воспламенения ленты приводные
станции конвейеров оборудованы тепловыми датчиками, сблокированными с приводом.
Электрокабели, по которым подается напряжение к электродвигателям расположены
так, что они обеспечивают их надежную эксплуатацию и не перекрывают проходы.
Кабели защищены от теплового воздействия и механических повреждений.
Для защиты от шума персонал обеспечивается
средствами индивидуальной защиты. К ним относятся шумоизолирующие наушники и
беруши. Для снижения запыленности проводится постоянно уборка пыли и
мероприятия по снижению запыленности.
Шкафы с электрооборудованием всегда закрываются.
Все открытые проемы, галереи, лестницы и
площадки имеют ограждения в соответствии с нормами. Проходы, пешеходные мостики
и дорожки соответственно обозначены. В цехе применяется система запрещающих,
предупреждающих и информационных знаков, утвержденная Министерством промышленности
РФ. Знаки устанавливаются в соответствующих им значению местах.
В цехе имеются запасные выходы и план эвакуации
персонала при авариях.
В цехе расположена система пожарного
водоснабжения с гидрантами. У каждого гидранта находится пожарный шкаф с рукавами
и пожарный ящик с песком и ведром. На случай возникновения пожара, каждое
рабочее место оснащено огнетушителями.
Большое внимание в цехе уделяется проведению
мероприятий информативного характера:
Инструкции для работников по профессиям и на
отдельные виды работ разрабатываются в соответствии с перечнем составленным
службой охраны труда. Требования ИОТ доводятся до сведения работников под
роспись работника и лица проводившего инструктаж в журнале регистрации
инструктажей или наряде- допуске. Внеплановые инструктажи проводятся при
изменении или вводе в действие новой ИОТ.
Все вновь принимаемые рабочие и
инженерно-технические работни ки до начала производственной деятельности
проводят первичный инструктаж, а затем теоретическое и практическое обучение на
рабочих местах.
Сроки стажировки устанавливаются на основании
письменного рас поряжения администрации в зависимости от опыта, об
разовательного уровня и квалификации. До получения допуска, обучающийся не
имеет право самостоятельно выполнять какие-либо работы, ему может поручаться
выполнение отдельных операций под контролем работника, за которым он закреплен.
Заключение квалификационной комиссии является
обязательным ус ловием допуска к самостоятельной работе. При получении
неудовлетворительной оценки, комиссией устанав ливается новый срок обучения (не
более месяца) и дата повторной проверки знаний. При получении
неудовлетворительной оценки при повторной проверке знаний квалификационной
комиссией делается вы вод о его непригодности к выполнению обязанностей по
данному ра бочему месту и служит основанием для его перевода на другую работу,
а в случае его несогласия - для увольнения в соответствии с действующим
законодательством.
Периодичность проверки знаний для рабочих - один
раз в год.
Внеочередная проверка знаний у рабочих может
быть проведена в следующих случаях [12]:
·
при
введении в действие новых или переработанных инстру кций по безопасному
выполнению работ;
·
при
нарушении правил техники безопасности или инструкции по безопасным методам
работы;
·
после
несчастного случая или аварии, происшедших на производстве из-за нарушения
работающими правил темники безопасности;
·
при
установлении фактов неудовлетворительного знания ра ботающими инструкций по
рабочему месту. Периодичность проверки знаний ИТР по технике безопасности один
раз в три года.
В случае неудовлетворительных знаний работник
может быть оставлен в занимаемой должности на срок не более 3-х месяцев, при
неудовлетворительных знаниях ТБ при повторной проверке он переводится на другую
работу в порядке перевода, установленном в законодательстве.
Внеочередную проверку знаний ИТР проходит в следующих слу чаях [12]:
·
при
переводе ИТР временно или постоянно на другую дол жность, требующую
дополнительных знаний по технике безопасности;
·
по
требованию органов Государственного надзора, вышесто ящей организации и решению
руководства производством при недоста точных знаниях работниками правил и норм
по технике безопасности.
Для приёма пищи в столовых производства
работникам предоставляется обеденный перерыв, продолжительностью до 60 минут.
Запрещается приём пищи на рабочем месте. Так же в течении рабочего дня
работнику предоставляются перерывы для отдыха и оправления естественных
надобностей.
Общее время перерывов 30 минут - два перерыва по
5 минут перед обеденным перерывом и два по 10 минут после обеденного перерыва.
Каждый работник ОАО “Аммофос” ежегодно проходит
медицинский осмотр для выявления профзаболеваний и последующего его лечения,
при необходимости.
Кроме выше перечисленных мер в цехе действуют
инструкции по охране труда и технике безопасности. Каждый работник обязан знать
инструкции и соблюдать их. Нарушение ТБ и ИОТ влечет за собой наказание, вплоть
до увольнения работника или ответственного за соблюдение ТБ.проверки знаний для
рабочих - один раз в год.
Внеочередная проверка знаний у рабочих может
быть проведена в следующих случаях [12]:
·
при
введении в действие новых или переработанных инстру кций по безопасному
выполнению работ;
·
при
нарушении правил техники безопасности или инструкции по безопасным методам
работы;
·
после
несчастного случая или аварии, происшедших на производстве из-за нарушения
работающими правил темники безопасности;
·
при
установлении фактов неудовлетворительного знания ра ботающими инструкций по
рабочему месту. Периодичность проверки знаний ИТР по технике безопасности один
раз в три года.
В случае неудовлетворительных знаний работник
может быть оставлен в занимаемой должности на срок не более 3-х месяцев, при
неудовлетворительных знаниях ТБ при повторной проверке он переводится на другую
работу в порядке перевода, установленном в законодательстве.
Внеочередную проверку знаний ИТР проходит в следующих случаях [12]:
·
при
переводе ИТР временно или постоянно на другую должность, требующую
дополнительных знаний по технике безопасности;
·
при
введении новых или переработанных нормативных документов по безопасности труда;
·
по
требованию органов Государственного надзора, вышестоящей организации и решению
руководства производством при недоста точных знаниях работниками правил и норм
по технике безопасности.
Для приёма пищи в столовых производства
работникам предоставляется обеденный перерыв, продолжительностью до 60 минут.
Запрещается приём пищи на рабочем месте. Так же в течении рабочего дня
работнику предоставляются перерывы для отдыха и оправления естественных
надобностей.
Общее время перерывов 30 минут - два перерыва по
5 минут перед обеденным перерывом и два по 10 минут после обеденного перерыва.
Каждый работник ОАО “Аммофос” ежегодно проходит
медицинский осмотр для выявления профзаболеваний и последующего его лечения,
при необходимости.
Кроме выше перечисленных мер в цехе действуют
инструкции по охране труда и технике безопасности. Каждый работник обязан знать
инструкции и соблюдать их. Нарушение ТБ и ИОТ влечет за собой наказание, вплоть
до увольнения работника или ответственного за соблюдение ТБ.
4.3 Расчет искусственного освещения на посту
оператора
На посту оператора загрузки удобрений следует
ограничивать прямую блесткость от источников освещения, при этом яркость
светящихся поверхностей (окна, светильники и др.), находящихся в поле зрения,
должна быть не ниже 400 лк., таким образом на посту оператора ставятся
газоразрядные лампы.
Определяем требуемый световой поток ламп,
обеспечивающий оптимальные условия труда при выполнении зрительных работ:
,(4.1)
где Ф - световой поток, лм;
Е - освещенность, лк;
S - площадь
освещаемого объекта, ширина - 3 метра, высота - 8 метров,
S = 3 х 8 =
24 м2;
к - коэффициент запаса, учитывающий
запыление светильников и снижение светоотдачи источников света в процессе
эксплуатации, с учётом содержания более 10мг/м3 пыли для
газоразрядных ламп примем к = 2,0;
z -
коэффициент неравномерности освещения, для газоразрядных ламп z=1,1;
N- число
необходимых светильников,
(4.2)
L -
расстояние между светильниками, L=1,45м,
М - расстояние между рядами М=2…3
метра;
;
u -
коэффициент использования светового потока:
, (4.3)
А,В - длина и ширина помещения,
Нр - расстояние
светильников;
,
принимаем индекс I=2, тогда u =0.34…0,57;
y -
коэффициент затенения, y=1;
.
4.4 Меры по обеспечению безопасности персонала в
условиях чрезвычайной ситуации
В цехе загрузки удобрений ОАО «Аммофос» возможны
следующие чрезвычайные ситуации:
- Внезапное обрушение здания или сооружений;
- Пожар в кабельных подвалах, в камерах
трансформаторов, транспортерной галерее конвейеров, на оборудовании.
Причины возникновения чрезвычайных ситуаций -
нарушение техники пожаробезопасности, использование неисправного оборудования,
природные факторы.
Все сотрудники цеха проходят обучение действиям
в условиях чрезвычайных ситуаций.
Все новые принимаемые рабочие и
инженерно-технические работни ки до начала производственной деятельности
проходят первичный инструктаж, а затем теоретическое и практическое обучение
действиям на рабочих местах в составе рабочих расчётов. Рабочий, хорошо
прошедший стажировку на рабочем месте и проверку знаний, получает удостоверение
на право самостоятельной работы. Рабочие проходят проверку знаний - один раз в
год. Запрещается допускать к работе лиц, не ознакомленных с планом ликвидации
аварий и не знающих его в части относящейся к месту работы.
В цехе имеются планы ликвидации аварий в
соответствии с требованиями Инструкции по составлению планов ликвидации аварий,
утвержденной ГГТН РФ.
Планы ликвидации аварий пересматриваются и
утверждаются ежегодно за месяц до начала следующего года.
При возникновении чрезвычайной ситуации работник
обязан:
·
осуществить
безаварийную остановку оборудования;
·
оповестить
по телефонному аппарату или через посыльных всех работников в столовой, на
соседних участках, в лаборатории, работников сторонних организаций;
·
знать
номера телефонов экстренных вызовов скорой помощи, по жарной команды и военизированной
газоспасательной службы; оповестить необходимые службы о возникновении
чрезвычайной ситуации;
·
оказывать
первую помощь при ожогах, отравлениях, при по ражении электротоком,
механических травмах; оказать при необходимости первую помощь себе и пострадавшим;
·
исполнять
действия в составе рабочего расчёта,
·
при
получению команды на эвакуацию осуществить безаварийную остановку производства
мини мальным количеством персонала; организованно следовать в безопасную зону
или же в убежище;
·
при
следовании в убежище необходимо соблюдать маршруты движения по всей территории
и в границах производства, в связи с наличием огромного количества
трубопроводов с агрессивными жидкостями как внутри производства, так и на
межцеховых коммуникациях.
·
Не
покидать убежища до поступления сообщения о ликвидации чрезвычайной ситуации и
разрешения покинуть убежище.
Причины возникновения чрезвычайных ситуаций -
нарушение техники пожаробезопасности, применение неисправного оборудования,
природные факторы.
4.5 Меры по охране окружающей среды
Решение вопросов охраны окружающей среды
являются обязательной частью работающих и внедряемых в Обществе систем
управления: системы качества (СК), системы менеджмента качества (СМК), системы
управления окружающей средой (СУОС), системы управления промышленной
безопасностью (СУПБ). Контроль в области охраны окружающей среды выполняется на
всех этапах управления и рассматривает:
- качественное выполнение процедур СУОС,
- прохождение внутренних аудитов выполнения
требований законодательных и нормативных актов,
- регулярное наблюдение соответствия действующим
законодательным и нормативным актам.
Политика ОАО «Аммофос» в последнее время всё
больше направлена на изучение производственной среды работников. Происходит
внедрение различных рационализаторских предложений имеющих экологический
характер.
Ведущими источниками загрязнения окружающей
среды являются:
·
технологические
процессы, происходящие с выделением грязных горючих и удушающих газов;
·
оборудование
потребляющее воду для охлаждения и промывки рабочих органов оборудования
(масло-эмульсионных жидкостей);
·
системы
смыва пыли, канализация;
·
твёрдые
бытовые отходы (неметаллический производственный мусор).
·
лом
черных и цветных металлов.
Главные мероприятия по охране окружающей среды
ОАО «Аммофос» ориентированы на защиту атмосферы и защиту водяного бассейна и
исполняются централизованно для всех цехов производства.
Заключение
Узел загрузки удобрений способен своевременно
осуществлять функции загрузки удобрения в автомобили БелАЗ в соответствии с
технологической схемой.
В цехе загрузки удобрений находится бункер с
секторным затвором, оборудованным электрогидравлическим приводом открывания и
закрывания секторного затвора. Применение секторного затвора с электрогидравлическим
приводом позволило: улучшить плавность и точность хода в работе секторного
затвора, улучшить качество загрузки удобрений, облегчить труд оператора.
В разработанной конструкции привода открывания и
закрывания секторного затвора использованы стандартные узлы и изделия, которые
производятся на территории Российской Федерации, что ведёт к увеличению степени
стандартизации и унификации. В свою очередь повышение степени стандартизации
позволяет значительно повысить ремонтопригодность секторного затвора.
Детали привода секторного затвора (фланец и др.)
достаточно технологичны. Их можно обрабатывать на типовом стандартном
оборудовании стандартным режущим инструментом, используя универсальные типовые
приспособления.
В проектируемом приводе Узел загрузки удобрений
способен своевременно осуществлять функции загрузки удобрения в автомобили
БелАЗ в соответствии с технологической схемой.
В цехе загрузки удобрений находится бункер с
секторным затвором, оборудованным электрогидравлическим приводом открывания и закрывания
секторного затвора. Применение секторного затвора с электрогидравлическим
приводом позволило: улучшить плавность и точность хода в работе секторного
затвора, улучшить качество загрузки удобрений, облегчить труд оператора.
В разработанной конструкции привода открывания и
закрывания секторного затвора использованы стандартные узлы и изделия, которые
производятся на территории Российской Федерации, что ведёт к увеличению степени
стандартизации и унификации. В свою очередь повышение степени стандартизации
позволяет значительно повысить ремонтопригодность секторного затвора.
Детали привода секторного затвора (фланец и др.)
достаточно технологичны. Их возможно обрабатывать на типовом обычном
оборудовании с обычным режущим инструментом, применяя универсальные типовые
приспособления.
В проектируемом приводе ленточного конвейера для
сыпучих грузов цеха загрузки удобрений, заменили существующий редуктор на
редуктор с более прочным корпусом, замена фланцевой муфты на зубчатую муфту,
позволило значительно повысить надежность привода ленточного конвейера по
сравнению с базовым вариантом.
Конструкция ленточного конвейера исключает
возможность падения транспортируемых материалов и предусматривает ограждения и
блокировки с учетом требований настоящих Правил. Конструкцией конвейера
предусмотрен безопасный доступ персонала к элементам, блокам и контрольным
устройством конвейера, требующим периодической проверки при эксплуатации и
безопасной замены вышедших из строя узлов и деталей оборудования.
В ходе проведения расчета инвестиционного
проекта были произведены расчеты, в результате которых выявили, что для
увеличения дохода предприятия ОАО «Аммофос» цеха загрузки удобрений необходимо
снизить удельные затраты на 15 % производство продукции без изменения
технологии производства. В результате для снижения удельных затрат нам
потребуются более значительные инвестиции, но в результате мы сможем получить
более значительный доход, чем при увеличении объема выпуска продукции на 5 % и
при постоянных удельных затратах. При этом чистая прибыль предприятия составит
966,10 млн.руб./год, срок окупаемости инвестиционного проекта цеха загрузки
удобрений ОАО «Аммофос» составит 2,4 года.
Применяемые в соответствии с характером работы
средства индивидуальной защиты, обеспечивают безопасность, охрану здоровья и
работоспособность работающих.
Оборудование цеха загрузки удобрений не является
источником загрязнения окружающей среды.
Список использованных источников
1. Абрамов, Е.И. Элементы
гидропривода. / Е.И. Абрамов, К.А. Колесниченко, В.Т. Маслов - К: Техника. -
1969. - С. 319
. Анурьев, В.И. Справочник
конструктора-машиностроителя: В 3 т.-М. / Анурьев В.И // Машиностроение. -
2001.
. Аршинов, В.А. Резание металлов и
режущий инструмент. Изд. 3 - е - М. / В.А. Аршинов, Г.А Алексеев // Машиностроение.
- 1975. - С. 440
. Блюмберг, В.А. Справочник токаря /
В.А. Блюмберг, Е.И. Зазерский Е.И Машиностроение. - 1981. - С. 406
. Бреш, Л.С. Гидравлический привод
агрегатных станков и автоматических линий / Л.С. Бреш Машиностроение. - 1988. -
С. 512
. Вайнсон, А.А.
Подъемно-транспортные машины: Учебник для вузов по специальности
«Подъемно-транспортные машины, строительные дорожные машины и оборудование» /
А.А. Вайнсон Машиностроение. - 1989. - С. 536
. Долин, П.А. Справочник по технике
безопасности / П.А. Долин Энергоатомиздат. - 1984. - С. 350
. Долин, П.А. Основы техники
безопасности в электроустановках / П.А. Долин П.А. Энергия. - 1978. - С. 150
. Курсовое проектирование
грузоподъемных машин / С.А Казак [и др.] Высшая школа. - 1989. - С. 319
. Справочная книга для
проектирования электротехнического освещения / Г.М. Кнорринг, Ю.Б. Оболенцев [и
др.] Энергия - 1976. - С. 384
. Редукторы. Справочное пособие /
Г.Н. Краузе [и др.] Машиностроение - 1989. - С. 144
. Безопасность технологических процессов
и производств / П.П. Кукин, В.Л. Лапин [и др.] Высшая школа - 1999. - С. 225
. Лесенко, Г.Г.
Инженерно-технические средства безопасности труда / Г.Г Лесенко Техника - 1983.
- С.256
. Нефёдов, Н.А. Машиностроение /
Н.А. Нефёдов, К.А. Осипов 1990. - С. 448
. Ординарцев, И.А. Справочник
инструментальщика / И.А. Ординарцев Машиностроение - 1987. - С. 846
. Методические указания к выполнению
курсовой работы «Режущий инструмент» / Вологда - 2001. - 31с.
. Свешников, В.К. Станочные
гидроприводы / В.К. Свешников, А.А. Усов Машиностроение. - 1988. - С.512
. Шейнблит, А.Е. Курсовое
проектирование деталей машин / А.Е. Шейнблит Янтар. Сказ. - 2004 - С. 454
. Шичков, А.Н. Оценка внутренней
стоимости предприятия / Вологда: ВоГТУ. А.Н Шичков - 2003. - 278 с.