№
|
Наименование
Эскиз-изделия
|
Марка,
типоразмер
|
Размер мм
|
Масса изделия
|
Расход сырья на
одно изделие
|
Программа
выпуска изделий
|
|
|
|
1
|
b
|
h
|
|
бетон
|
сталь
|
В сут.
|
В смен
|
В год.
|
|
|
|
|
|
|
|
|
|
шт
|
шт
|
шт
|
1
|
колонны
|
ККПI-2
|
11700
|
400
|
500
|
9,3
|
2,1
|
275
|
47
|
16
|
11905
|
1.3
Обоснование выбора способа производства
Изготовление колонн одноэтажных производственных зданий
осуществляется преимущественно целыми элементами. Однако в ряде случаев при
большой высоте зданий и тяжелых нагрузках по условиям транспорта и монтажа
элементов оказывается необходимым членить колонны по высоте на несколько
элементов.
Соединение колонн с фундаментами осуществляется
преимущественно путем заделки стержня колонны в стакан, образованный в верхней
части железобетонного башмака. Стыки тяжелых колонн, состоящих из нескольких
элементов по высоте, выполняются путем сварки арматуры и забетонировки зоны
соединения.
Рациональное решение соединения элементов тяжелых колонн дает
так называемый сухой стык, не требующий забетонировки. Такие стыки могут быть
выполнены при условии изготовления колонны целиком в одной форме, разделенной металлическими
листами на отдельные элементы.
В этих условиях при монтаже колонны соединение элементов
осуществляется установкой одного элемента на другой без подливки бетона. Полное
совпадение смежных плоскостей обеспечивает надежность передачи сжимающих усилий.
Арматура в стыках этого типа соединяется сваркой закладных частей.
С развитием технологии производства сборных железобетонных
конструкций колонны производственных зданий должны получить тенденцию
дальнейшего снижения веса и расхода материалов за счет повышения марки бетона и
широкого применения эффективных сечений.
Производства колонн проходит агрегатно-поточным способом.
Это метод производства ЖБИ с перемещением форм с одного поста
на другой, на которых выполняются определенные виды операций.
Перемещение форм осуществляется мостовыми кранами.
Агрегатно-поточный способ получил широкое распространение
там, где требуется выпуск широкой номенклатуры изделий. Гибкость данного
способа позволяет путем смены и переналадки оборудования осуществлять переход
от выпуска одного типа изделий к выпуску другого.
При агрегатно-поточном производстве технологический процесс
осуществляется последовательно на нескольких постах. При этом формы с поста на
пост передаются не непрерывно действующим конвейером, а специальными внутрицеховыми
транспортными средствами.
Агрегатно-поточный способ производства широко применяется для
изготовления большой номенклатуры изделий на предприятиях средней мощности. При
относительно высокой степени механизации в агрегатно-поточном способе пока
много ручных операций: закладка стержней в установку для электротермического
напряжения арматуры, съем с установки и закладка их в формы, напряжение
стержней гидродомкратами, разравнивание бетонной смеси в форме, операции по
зацепке формы с изделием крюком крана или кран-балки, загрузка камеры
термообработки, укрытие камеры крышкой, выемка изделий из камеры, распалубка и
пр. Все эти операции требуют для обслуживания дополнительный персонал в потоке.
Формование. На поточно-агрегатных и конвейерных линиях
процесс формования изделий происходит в одинаковой последовательности.
Подготовленная форма подается на пост формования, где в нее укладывается
бетонная смесь с помощью бетоноукладчиков или бетонораздатчиков. Затем на этом
же или на следующем посту производится уплотнение бетонной смеси на
виброплощадках. Заглаживание и отделка поверхности бетона осуществляются на
посту формования либо на специальном посту. После этого формы с отформованными
изделиями через определенное время, установленное для одного изделия,
помещаются в камеры пропаривания или подвергаются электропрогреву.
Рисунок 1-Схема агрегатно-поточного метода производства
сборных железобетонных изделий: 1 - раскрытие бортов формы с пропаренной
панелью; 2 - съем прижимного щита кантования панелей; 3 - чистка и смазка
формы; 4 - заполнение формы арматурным каркасом, закладными деталями. столярным
блоком и установка прижимного щита; 5 - заполнение формы легким бетоном и
уплотнение на виброплощадке с пригрузом; 6 - передача формы с панелью на
траверсную тележку; 7 - самоходные тележки для раздачи бетонной и растворной
смесей; 8 - кран-укосина с прижимным щитом; 9 - нанесение декоративного слоя;
10 - осмотр фактуры цветного раствора; 11 - панель, направляемая на доводку и
комплектацию; 12 - пост технического контроля и строповки формы для отправки в
пропарочную камеру; 13 - мостовой кран; 14 - ямные пропарочные камеры
Тепло-влажностная обработка. Щелевые камеры
непрерывного действия применяют при конвейерном способе производства
железобетонных изделий. Их выполняют в виде проходных тоннелей высотой около 1
м, по которым специальными механизмами перемещают формы-вагонетки с изделиями.
Свежеотформованные изделия, перемещаясь вдоль камеры, подвергаются
тепловлажностной обработке в соответствия с заданным температурным режимом.
Небольшая высота камер исключает перепады температуры среды в их поперечном
сечении и создает одинаковые температурно-влажностные условия твердения каждого
изделия. длина камер непрерывного действия определяется производительностью
конвейеров и продолжительностью тепловой обработки. Компоновка камер
непрерывного действия зависят от принятой схемы конвейерной линии. Камеры могут
быть выполнены напольными или заглубленными, причем поверхность перекрытий камер
используется выполнения различных технологических операций по производству
изделий. При необходимости сокращения длины камер непрерывного действия их
выполняют блоками в несколько рядов по горизонтали и вертикали.
Технологический процесс. Технологический процесс
осуществляется на 15 постах. После тепловой обработки и остывания изделий
производят обрезку напрягаемых арматурных стержней машиной. Готовые изделия
транспортируют на пост отделки. Поддоны чистят и смазывают специальной машиной.
Затем укладывают сетки и напрягаемые арматурные сетки, нагретые на установках,
расположенных рядом с постом. Этот пост оборудован переходными мостиками для
переноса нагретой арматуры. После охлаждения стержней укладывают на поддон
подстилающий слой бетонной смеси толщиной 2.3 см. На посту формования поддон
фиксируется и подъемно-опускная секция опускает его на виброплощадку.
Автоматически опускается съемная рама. После нанесения нижнего слоя бетонной
смеси и его уплотнения вводят пуансоны, устанавливают ненапрягаемую, арматуру.
Укладывают оставшуюся часть бетонной смеси и уплотняют при помощи виброплощадки
и вибропригруза. По окончании процесса уплотнения из бетона извлекают пуансоны,
поднимают вибропригруз и раму. Поддон поднимают и по направляющим сталкивают на
следующий пост. Продолжительность формования - 22 мин.
После доводки открытых поверхностей поддон с изделием
транспортируют в щелевую пропарочную камеру, где изделия прогревают глухим
паром с добавлением небольшого количества острого пара. Режим термообработки
следующий: подъем до 85.90°С - 3 ч., изотермический прогрев - , б ч, остывание
- 3 ч.
На посту отделки готовые изделия кантуют, и вывозят на склад
готовой продукции.
1.4
Характеристика технологического оборудования
Виброплощадка. Вибрационные площадки - наиболее
распространённые машины, применяемые для уплотнения бетонной смеси при
изготовлении железобетонных изделий. Классифицируются они по следующим
признакам: характеру колебаний, типу применяемых вибраторов, грузоподъёмности,
способу крепления формы или поддона.
По характеру колебаний бывают виброплощадки с круговыми
гармоническими колебаниями, направленными горизонтальными гармоническими
колебаниями, направленными вертикальными гармоническими колебаниями,
негармоническими ударно-вибрационными колебаниями. По типу вибраторов различают
виброплощадки: с дебалансными бегунками, электромагнитными и гидравлическими
вибраторами.
Для крепления формы к раме виброплощадки применяют
механические, электромагнитные и пневматические устройства.
Электротермический способ натяжения основан на свойстве стали
расширяться (для тонкого стального стержня - удлиняться) при нагревании на 1°
на 0,000012 от первоначальных размеров и опять сокращаться при остывании.
Ямные камеры. Ямные камеры пропаривания используются на
поточно-агрегатных линиях производства железобетонных изделий. Пар поступает в
ямные камеры через перфорированные трубы, укладываемые у пола. Выпуск пара из
труб должен производиться вверх - в пространство между изделиями и стеной.
Диаметр отверстий перфорированных труб принимают в пределах 3…5 мм. Расчетный
расход пара через одно отверстие - 2,4…6,5 кг в 1 ч при давлении 0,02 МПа.
Ямная камера сообщается с атмосферой по вертикальному каналу, снабженному
водяным затвором в целях сохранения давления внутри камер на уровне
атмосферного. Для установки форм в ямные камеры пропаривания применяют стойки с
поворотными кронштейнами. Удельный расход пара при тепловой обработке бетона в
ямных камерах зависит от коэффициента загрузки камер и металлоемкости форм
Пропаривание при нормальном давлении производят в камерах
периодического или непрерывного действия, оно является наиболее экономичным
способом тепловой обработки.
Бетоноукладчик. Изобретение относится к
области строительной техники, в частности к оборудованию для производства
железобетонных изделий и конструкциям бетоноукладчиков. Бетоноукладчик,
согласно изобретению, содержит гидросистему, смонтированный на установленной с
возможностью перемещения пространственной раме приемный бункер с по крайнем
мере одним выходным проемом в днище и лопастным рабочим органом, пульт
управления и по крайней мере один расположенный ниже соответствующего выходного
проема питатель. Питатель выполнен с рабочим органом в виде шнека, который
установлен в охватывающем его корпусе, выполненном в нижней части с проемом в
виде продольной щели, перекрытой снизу в рабочем положении поддоном,
предпочтительно откидным приводным. Технический результат, обеспечиваемый
изобретением, состоит в повышении качества изготавливаемых строительных
конструкций за счет повышения равномерности укладки бетонной смеси и исключения
ее расслаивания при одновременном сокращении энергоемкости, повышении
надежности работы и срока службы оборудования, бетоноукладчика, а также
снижении аварийности при эксплуатации за счет исключения возможности
заклинивания шнеков бетоноукладчика, самопроизвольного открывания поддона его
питателя и обеспечения плавного контролируемого движения бетоноукладчика и
бетонной смеси в шнеках.
Задачей настоящего изобретения является повышение качества
изготавливаемых строительных конструкций за счет повышения равномерности
укладки бетонной смеси и исключения ее расслаивания при одновременном
сокращении энергоемкости, повышение надежности работы и срока службы
оборудования, бетоноукладчика, а также снижение аварийности при эксплуатации за
счет исключения возможности заклинивания шнеков бетоноукладчика,
самопроизвольного открывания поддона его питателя и обеспечения плавного
контролируемого движения бетоноукладчика и бетонной смеси в шнеках.
1.5 Контроль
качества сырьевых материалов, технологического процесса и готовой продукции
При изготовлении колонн контролируется следующие показатели
качества: прочность бетона, морозостойкость бетона, водонепроницаемость бетона,
контроль сварных арматурных и закладных изделий, силу натяжения арматуры,
размеры и отклонение от прямолинейности, перпендикулярности поверхностей
колонн, ширину раскрытия поверхностных технологических трещин, размеры и
положения арматурных и закладных изделий и толщину защитного слоя бетона.
При проверки прочности бетона неразрушающего контроля
фактическую передаточную и отпускную прочность бетона на сжатие определяют
ультразвуковым методом.
Подготовка испытания включает проверку используемых приборов
в соответствии с инструкциями по эксплуатации и установку градуировочных
зависимостей в соответствии с выбранным способом прозвучивания. При
необходимости проведения ультразвуковых испытаний бетона конструкций
непосредственно после термообработки (горячего) для определения отпускной
прочности бетона этих конструкций после их остывания допускается устанавливать
градуировочную зависимость по результатам ультразвуковых измерений горячих
образцов и механических испытаний тех же образцов после их остывания.
Качество поверхности бетона контролируемого участка
конструкции в зоне контакта с ультразвуковыми преобразователями должно
соответствовать требованиям. Допускается проведение измерений времени
распространения ультразвука в конструкциях через облицовочные материалы и
декоративные покрытия по методикам, согласованным с головными
научно-исследовательскими организациями. Сборные линейные конструкции
испытывают, как правило, способом сквозного прозвучивания в поперечном
направлении.
Возраст бетона контролируемых конструкций не должен
отличаться от возраста бетона образцов, испытанных для установления
градуировочной зависимости, более чем на 50 % - при контроле нормируемой
прочности бетона, и 25 % - при определении прочности бетона в процессе
твердения.
Измерение времени распространения ультразвука в бетоне конструкций
следует проводить в направлении, перпендикулярном уплотнению бетона. Расстояние
от края конструкции до места установки ультразвуковых преобразователей должно
быть не менее 30 мм. Измерение времени распространения ультразвука в бетоне
конструкций следует проводить в направлении, перпендикулярном направлению
рабочей арматуры. Концентрация арматуры вдоль выбранной линии прозвучивания не
должна превышать 5 %. Допускается прозвучивание вдоль линии, расположенной
параллельно рабочей арматуре, если расстояние от этой линии до арматуры
составляет не менее 0,6 длины базы. При определении прочности бетона в процессе
его твердения места установки и число зондов или преобразователей устанавливают
в зависимости от конструктивных и технологических особенностей контролируемых
конструкций.
При контроле ускоренного твердения бетона в нескольких
однотипных конструкциях преобразователи устанавливают в конструкции,
находящейся в наименее благоприятных условиях тепловой обработки.
Морозостойкость бетона - способность сохранять
физико-механические свойства при многократном переменном замораживании и
оттаивании.
Морозостойкость бетона определяют в проектном возрасте,
установленном в нормативно-технической и проектной документации, при достижении
им прочности на сжатие, соответствующей его классу.
Морозостойкость бетона колонн следует определять
ультразвуковым методом. Морозостойкость бетона контролируют по результатам
измерения времени распространения ультразвука в образцах в процессе их
попеременного замораживания и оттаивания. Морозостойкость бетона определяют по
критическому числу циклов замораживания и оттаивания, начиная с которого
происходит резкое увеличение времени распространения ультразвука в
контролируемом образце, соответствующее началу интенсивного разрушения материала.
Марку бетона по морозостойкости определяют сравнением полученного значения
критического числа циклов замораживания и оттаивания с установленным в
стандарте его контрольным значением.
Морозостойкость бетона ультразвуковым методом определяют при
помощи специальных стендов или приборов, предназначенных для измерения времени
распространения ультразвука в бетоне и оснащенных дополнительным оборудованием.
Аппаратура для определения морозостойкости должна обеспечивать цифровую
индикацию результатов измерения с дискретностью не более 1,0 мкс и щелевой
способ акустического контакта между контролируемым образцом и
пьезоэлектрическими преобразователями при толщине слоя контактной среды не
более 5 мм. В качестве контактной среды применяют питьевую воду температурой
(18 ± 2)°С.
Образец помещают в испытательную ванну, наполненную водой, и
определяют время распространения в нем ультразвука поочередно по всем каналам
измерения способом сквозного прозвучивания. Направление прозвучивания должно
быть перпендикулярно к направлению укладки бетонной смеси. Образцы бетона
подвергают попеременному замораживанию и оттаиванию. Через указанное число
циклов замораживания и оттаивания в образцах проводят ультразвуковые измерения
и определяют суммарное время распространения ультразвука.
Время распространения ультразвука измеряют после оттаивания
образцов, при этом ориентация образца относительно испытательной ванны должна
оставаться постоянной на протяжении всего испытания. По результатам измерений
для каждого образца находят наименьшее значение суммарного времени
распространения ультразвука.
Критическое число циклов замораживания и оттаивания для
каждого образца М определяют по формуле
Полученное значение М сравнивают с контрольным значением критического
числа циклов замораживания и оттаивания для заданной марки по морозостойкости.
Контролируемый состав бетона считают удовлетворяющим заданной
марке по морозостойкости, если значение М не меньше соответствующего
контрольного значения критического числа циклов замораживания и оттаивания.
Определение водонепроницаемости бетона колонн. Для проведения
испытаний применяют: установку любой конструкции, которая имеет не менее шести
гнезд для крепления образцов и обеспечивает возможность подачи воды к нижней
торцевой поверхности образцов при возрастающем ее давлении, а также возможность
наблюдения за состоянием верхней торцевой поверхности образцов; цилиндрические
формы для изготовления образцов бетона с внутренним диаметром 150 мм и высотой
150; 100; 50 и 30 мм; воду.
Изготовленные образцы хранят в камере нормального твердения
при температуре (20±2)°С и относительной влажности воздуха не менее 95 %. Перед
испытанием образцы выдерживают в помещении лаборатории в течение суток. Диаметр
открытых торцевых поверхностей бетонных образцов - не менее 130 мм.
Образцы в обойме устанавливают в гнезда установки для
испытания и надежно закрепляют. Давление воды повышают ступенями по 0,2 МПа в
течение 1-5 мин и выдерживают на каждой ступени в течение времени. Испытание
проводят до тех пор, пока на верхней торцевой поверхности образца появятся
признаки фильтрации воды в виде капель или мокрого пятна.
Водонепроницаемость каждого образца оценивают максимальным
давлением воды, при котором еще не наблюдалось ее просачивание через образец.
Водонепроницаемость серии образцов оценивают максимальным
давлением воды, при котором на четырех из шести образцов не наблюдалось
просачивание воды.
Ультразвуковые методы контроля качества сварных соединений,
установленные настоящим стандартом, следует применять:
для стыковых однорядных соединений стержней диаметром от 20
до 40 мм из арматурной стали классов A-II и A-III, выполненных ванными и
многослойными способами сварки в инвентарных формах, на стальных
скобах-накладках и подкладках или без формующих и вспомогательных элементов;
для тавровых соединений арматурных стержней диаметром от 8 до
40 мм с пластинами толщиною от 6 до 30 мм, выполненных сваркой под флюсом.
Ультразвуковой контроль следует выполнять при температуре
окружающей среды от плюс 40 до минус 25°С. При температуре окружающей среды от
минус 10 до минус 25°С следует предварительно нагреть контролируемое соединение
до 30-50°С. Ультразвуковому контролю подлежат сварные стыковые соединения
стержней с отношением диаметров в пределах 0,80-1,0.
Ультразвуковые методы контроля позволяют выявить внутренние
дефекты в сварных соединениях без расшифровки их характера и координат.
Характеристикой качества соединения служит величина амплитуды прошедшего через
сварной шов или отражённого ультразвукового сигнала, которая измеряется в
децибелах.
Контроль сварных соединений следует осуществлять методами:
теневым - стыковых соединений стержней, выполненных в инвентарных формах или
без формующих вспомогательных элементов; зеркально-теневым - стыковых соединений
стержней, выполненных на стальных скобах-накладках или подкладках;
эхо-импульсным - тавровых соединений стержней с пластинами, выполненных под
флюсом; фланговые швы в стыковых соединениях, выполненных на стальных
скобах-накладках, ультразвуковому контролю не подлежат.
Для контроля сварных соединений следует использовать
импульсный ультразвуковой дефектоскоп, обеспечивающий работу по раздельной
схеме контроля и имеющий калиброванный аттенюатор с ценой деления не более 2
дБ. Дефектоскоп должен быть снабжен комплектом стандартных образцов и
искателями.
Перед проведением контроля сварные соединения должны быть
очищены от брызг металла, остатков шлака, заусенец, отслаивающейся окалины,
ржавчины, бетона и других загрязнении и подвергнуты внешнему осмотру и обмеру.
При этом забракованные соединения, до исправления обнаруженных дефектов,
ультразвуковому контролю не подлежат.
Перед проведением контроля стыковых соединений стержней
должна быть выполнена подготовка механического устройства, включающая проверку
соосности искателей и стержней.
При контроле стыковых соединений стержней разных диаметров
расстояние между искателями следует выбирать по стержню большего диаметра.
Несоосность искателей и стержней не должна быть более 1,0 мм.
Перед проведением контроля тавровых соединений стержней с пластинами следует в
механическое приспособление-шаблон установить кольцо, ограничивающее зону
сканирования искателя Внутренний диаметр кольца должен превышать диаметр
стержня на 4 - 5 мм. Высота кольца должна быть равна 10-12 мм. Перед
проведением контроля, непосредственно на рабочем месте должна быть настроена
чувствительность дефектоскопа.
В период поиска дефектов в стыковых соединениях стержней
уровень чувствительности дефектоскопа следует повысить на величину 15 дБ по
сравнению с величиной опорного сигнала, полученного на испытательном образце.
Замер максимальной амплитуды сигналов на контролируемом
сварном соединении необходимо проводить в трех точках, перемещая систему
искателей в одной плоскости. В крайних положениях один из искателей следует
помещать вплотную к сварному шву или скобе-накладке. В среднем положении
искатели следует располагать симметрично сварному шву. Результаты трех замеров
амплитуды сигналов следует занести в журнал контроля.
В период поиска дефектов в тавровых соединениях уровень
чувствительности дефектоскопа следует увеличить на 6 дБ по сравнению со
значениями разности амплитуд. При обнаружении дефекта необходимо понизить
уровень чувствительности дефектоскопа до первоначального уровня.
При осуществлении контроля искатель необходимо расположить на
пластине, поместив его внутри ограничительного кольца механического
шаблона-приспособления и производить перемещение искателя на пластине в
пределах ограничительного кольца, фиксируя величину максимальной амплитуды.
Измерение силы натяжения арматуры осуществляется в процессе
ее натяжения или после завершения натяжения. Для измерения силы натяжения
арматуры применяются приборы - ПРДУ, прошедшие государственные испытания и
рекомендованные к массовому выпуску. Перед применением прибор должен быть
проверен на соответствие требованиям инструкции по его эксплуатации. Порядок
проведения измерений должен соответствовать порядку, предусмотренному этой
инструкцией.
Гравитационный метод основан на установлении зависимости между
силой натяжения арматуры и массой грузов, осуществляющих ее натяжение.
Гравитационный метод применяется в тех случаях, когда
натяжение осуществляется грузами непосредственно через систему рычагов или
полиспастов.
Для измерения силы натяжения арматуры измеряют массу грузов,
по которой определяют силу натяжения арматуры с учетом системы передачи силы от
грузов к натягиваемой арматуре, потерь от трения и других потерь, если таковые
имеются. Учет потерь в системе передачи силы натяжения от грузов арматуре осуществляется
динамометром при градуировке системы.
Масса грузов должна измеряться с погрешностью до 2,5%.
Действие прибора ПРДУ при измерении силы натяжения стержневой
арматуры и канатов основано на упругой оттяжке арматурного элемента в середине
пролета между упорами, а при измерении силы натяжения проволоки - на оттяжке ее
на базе упорной рамки прибора. Деформацию пружины прибора измеряют индикатором
часового типа, которая представляет собой показание прибора Упр.
Поперечно оси арматуры создается постоянное перемещение
системы из двух последовательно соединенных звеньев: натянутый арматурный
элемент и пружина прибора.
С увеличением силы натянутой арматуры возрастает
сопротивление поперечной оттяжке и уменьшается ее перемещение, а поэтому
увеличивается деформация пружины прибора, т.е. показания индикатора прибора.
Градуировочная характеристика прибора зависит от диаметра и
длины арматуры при работе на базе формы и только от диаметра - при работе на
базе упорной рамки.
Прибор ПРДУ состоит из корпуса, шарнира с направляющей
трубкой, ходового винта с лимбом и рукояткой, пружины со сферической гайкой,
натяжного крюка, индикатора, упора или упорной рамки.
При измерении силы натяжения стержневой арматуры и канатов
прибор устанавливают упором на стенд, поддон пли форму. Крюк захвата заводят
под стержень или канат и вращением ходового винта за его рукоятку обеспечивают
контакт со стержнем или канатом. Дальнейшим вращением ходового винта создают
предварительную оттяжку арматуры, величину которой фиксируют индикатором.
В конце предварительной оттяжки по риске на корпусе отмечают
положение лимба, жестко соединенного с ходовым винтом, и затем продолжают
вращение ходового винта на несколько оборотов.
После завершения выбранного числа оборотов записывают
показания индикатора. Силу натяжения арматуры определяют по градуировочной
характеристике прибора.
При измерении силы натяжения арматурной проволоки диаметром 5
мм менее, упор заменяют упорной рамкой с базой 600 мм, а крюк захвата - малым
крюком. Силу натяжения проволоки определяют по градуировочной характеристике
прибора при установленной рамке.
При невозможности разместить упор прибора в плоскости между
стенками форм он может быть заметен опорным листом с отверстием для прохода
тяги с крюком.
Для измерения линейных размеров и их отклонений применяют
линейки, рулетки, нутромеры, скобы, штангенциркули, штангенглубиномеры,
индикаторы часового типа, щупы и микроскопы типа МПБ-2.
В необходимых случаях следует применять средства специального
изготовления с отсчетными устройствами в виде индикаторов часового типа,
микрометрических головок и линейных шкал: рулетки со встроенным динамометром,
длиномеры, нутромеры, скобы и клиновые щупы.
Длину, ширину, толщину, диаметр, а также угловые размеры или
их отклонения измеряют в двух крайних сечениях элемента на расстоянии 50 - 100
мм от краев, а при длине или ширине элемента более 2,5 м - и в соответствующем
среднем его сечении.
Отклонения от прямолинейности на лицевой поверхности плоских
элементов измеряют не менее чем в двух любых сечениях элемента, как правило, в
направлении светового потока, падающего на эту поверхность в условиях
эксплуатации.
Отклонения от прямолинейности боковых граней плоских
элементов измеряют в одном из сечений вдоль каждой из граней, а для элементов
цилиндрической формы - вдоль не менее двух образующих, расположенных во взаимно
перпендикулярных сечениях.
Отклонения от прямолинейности ребра элемента измеряют в
сечениях по обеим поверхностям, образующим это ребро, на расстоянии не более 50
мм от него или непосредственно в месте пересечения этих поверхностей.
Для определения защитного слоя бетона и расположение арматуры
используется магнитный метод. Магнитный метод основан на взаимодействии
магнитного или электромагнитного поля прибора со стальной арматурой
железобетонной конструкции.
Толщину защитного слоя бетона и расположение стальной
арматуры в конструкции определяют на основе экспериментально установленной
зависимости между показаниями прибора и указанными контролируемыми параметрами
конструкции.
Для определения толщины защитного слоя бетона и расположения
стальной арматуры в железобетонной конструкции применяют магнитные,
электромагнитные или вихревые приборы, включающие измерительный блок,
измерительный преобразователь и блок питания.
Предел допускаемой погрешности измерения при определении
расположения одиночного арматурного стержня не должен быть более ±10 мм.
До проведения испытаний сопоставляют технические
характеристики применяемого прибора в соответствующими проектными значениями
геометрических параметров армирования контролируемой железобетонной
конструкции.
При несоответствии технических характеристик прибора
параметрам армирования контролируемой конструкции необходимо установить
индивидуальную градуировочную зависимость.
Число и расположение контролируемых участков конструкции
назначают в зависимости от:
цели и условий испытаний;
особенностей проектного решения конструкции;
технологии изготовления или возведения конструкции с учетом
фиксации арматурных стержней;
условий эксплуатации конструкции с учетом агрессивности
внешней среды.
На поверхности конструкции в местах измерений не должно быть
наплывов высотой более 3 мм.
Работу с прибором следует проводить в соответствии с
инструкцией по его эксплуатации.
При толщине защитного слоя бетона меньшей предела измерения
применяемого прибора испытания проводят через прокладку толщиной мм из
материала не обладающего магнетическими свойствами.
Фактическую толщину защитного слоя бетона в этом случае
определяют как разность между результатами измерения и толщиной этой прокладки.
При контроле расположения стальной арматуры в бетоне
конструкции, для которой отсутствуют данные о диаметре арматуры и глубине ее
расположения, определяют схему расположения арматуры и измеряют ее диаметр.
Градуировочную зависимость для определения толщины защитного
слоя бетона устанавливают для конкретной железобетонной конструкции, используя
фрагмент ее армирования с длиной арматурных стержней не менее 400 мм.
Измерения выполняют в практически необходимом диапазоне
толщин защитного слоя бетона через 5-10 мм.
Измерения проводят на специальном стенде при температуре и
влажности окружающей среды, которые установлены как нормальные в
эксплуатационной документации на используемый прибор.
Стенд должен обеспечивать:
проведение испытаний с одиночными арматурными стержнями
требуемых диаметров и с фрагментами армирования этой конкретной конструкции;
установку зазора, имитирующего слой бетона, в диапазоне
измерений прибора с погрешностью не более ±0,2 мм. Зазор образуется прокладками
из материала, не влияющего на показания прибора, или через слой воздуха.
Металлические узлы стенда должны быть расположены на расстоянии, исключающем их
влияние на показания прибора.
Продольные оси преобразователя и образца арматурного стержня
должны быть параллельны между собой и находиться в одной плоскости,
перпендикулярной рабочей поверхности преобразователя прибора.
При установлении градуировочной зависимости применяют
следующий порядок операций:
размещение на стенде образца арматурного стержня требуемого
диаметра или фрагмента армирования конструкции;
установка с помощью прокладок или слоя воздуха необходимого
зазора;
проведение измерений с отсчетом в условных единицах;
фиксация результатов проведенных измерений.
Для установления градуировочной зависимости измерения
необходимо провести не менее чем при трех разных, зазорах.
Таблица 4 - Организация контроля
Объект контроля
|
Контролируемые
параметры материалов, процессов, продукции
|
Метод и
средство контроля
|
Периодичность и
объем контроля
|
Лицо
осуществляющее контроль
|
Входной
контроль
|
1
|
2
|
3
|
4
|
5
|
Сталь
арматурная
|
Вид, класс,
форма и размеры
|
По
сопровождающим документам ГОСТ 10884-94
|
при поставке в
стержнях - не менее 5 % от партии, при поставке в мотках - два мотка
|
Отдел
снабжения, лаборант
|
Бетон
|
Класс, марка,
вид
|
По
сопровождающим документам ГОСТ 26633-91
|
Каждая партия
|
Отдел
снабжения, лаборант
|
Операционный
контроль
|
Чистка, смазка
|
Качество
очистки и смазки
|
Визуальный
осмотр
|
Раз в смену
|
Мастер цеха
|
Армирование
|
Толщина
защитного слоя, правильность установки каркаса и закладных деталей
|
Технический
осмотр, измерительный
|
Каждая форма
два раза в смену по одной формы
|
Бетонщик ОТК
|
Сборка формы
|
Соответствие
формы проектным размерам
|
Обмер рулеткой,
уровнем
|
Раз в квартал
по штучно
|
|
|
Расстояние
между опорами
|
Обмер рулеткой
|
Раз в смену по
одной форме
|
|
Укладка и
уплотнение смеси
|
удобоукладываемость
бетонной смеси
|
ГОСТ 10181.0-81
|
Два раза в
смену по одной пробе
|
|
Равномерность
укладки
|
Толщина слоя,
замер линейкой
|
Раз в смену по
одной форме
|
Мастер цеха
|
|
Время
уплотнения
|
секундомер
|
Раз в смену
|
Мастер цеха
|
|
Средняя
плотность бетонной смеси
|
ГОСТ 10181.0-81
|
Раз в смену по
одной формовке
|
Лаборант
|
|
Прочность
бетона
|
ГОСТ 10180-00
|
Раз в смену из
партии
|
Лаборант
|
Тепловая
обработка
|
Соблюдение
заданного режима тепловлажностной обработки
|
Приборы
автоматического регулирования
|
Каждая камера
|
лаборант
|
Подготовка к
сдачи продукции
|
Внешний вид
изделий
|
визуально
|
Каждая партия
|
|
|
Наличие
дефектов
|
визуально
|
Каждая партия
|
|
|
Правильность
укладки изделий
|
Рулетка, схема
размещения
|
Два раза в
смену
|
Мастер цеха
|
|
Качество
маркировки изделий
|
визуально
|
Постоянно
каждая партия
|
|
Таблица 5 - Технический контроль качества готовой продукции
№
|
Контролируемые
параметры
|
Периодичность
контроля
|
Наименование
методики контроля или контрольного прибора
|
Ед. измерения
|
Показатели
|
Заключение
|
1
|
Прочность
бетона
|
раз в смену
партия
|
Ультразвуковой
метод
|
|
|
В15
|
2
|
Морозостойкость
|
Раз в полгода
партия
|
Ультразвуковой
метод
|
мкс
|
115,7
|
F100
|
3
|
Водонепроницаемость
|
1 раз в полгода
|
Определение по
"мокром пятну"
|
МПа
|
0,4
|
В4
|
4
|
Контроль
сварных арматурных и закладных изделий. Стыковое в инвентарной форме,
горизонтальное
|
1 раз в год
|
Ультразвуковым
методом
|
мм
|
22
|
85
|
Контроль качества бетонных и железобетонных работ
осуществляют на всех этапах их производства, начиная с изготовления бетонной
смеси и кончая твердением уложенного бетона.
Качество готового бетона и железобетонного изделия во многом
зависит от состава бетонной смеси и качества составляющих материалов. Состав
бетонной смеси подбирается в строительной лаборатории из условия получения при
минимальном расходе цемента бетона, имеющего необходимые прочность и свойства.
Схема операционного контроля качества устройства монолитных
бетонных и железобетонных колонн
Допускаемые отклонения:
плоскостей от вертикали или проектного наклона на всю высоту
колонн:
поддерживающих монолитные покрытия и перекрытия - 15 мм;
поддерживающих сборные балочные конструкции - 10 мм;
длины колонн - ±20 мм;
поперечного сечения - +6 мм, - 3 мм;
местных неровностей стен поверхности бетона при проверке
двухметровой рейкой, кроме опорных поверхностей, - 5 мм;
отметок поверхностей и закладных изделий, служащих опорами, -
5 мм.
Минимальная прочность бетона при распалубке стен, МПа:
незагруженных - 0,2-0,3;
загруженных - по проекту или ППР. Приемку конструкций следует
оформлять в установленном порядке актом освидетельствования скрытых работ или
актом на приемку ответственных конструкций.
Приемка колонн, колонны принимают по результатам:
периодических испытаний - по показателям морозостойкости, а
также по водонепроницаемости бетона колонн, предназначенных для эксплуатации в
условиях воздействия агрессивной газообразной среды;
приемо-сдаточных испытаний - по показателям прочности бетона,
соответствия арматурных и закладных изделий рабочим чертежам, прочности сварных
соединений, точности геометрических параметров, толщины защитного слоя бетона
до арматуры, ширины раскрытия поверхностных технологических трещин, категории
бетонной поверхности, правильности нанесения установочных рисок.
2. Расчетная
часть
2.1 Подбор
состава бетона
Марки 300, подвижностью 4см, цемент М400, pц - 3100 кг/м3, pн - 1100 кг/м3;
песок - pп - 2630 кг/м3, pн. сух. - 1568 кг/м3, pн. вл. - 1600 кг/м3,
влажность - 2%; щебень pщ - 2600 кг/м3, pн. сух - 1480 кг/м3, pн. вл. - 1495 кг/м3,
влажность - 1%; V=2 м3.

,
В=168+10=178 л=178 кг/м3
Ц=1,75*178=312 кг/м3





=14,28 л






=406 кг


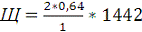
=2307 кг
Ц: В: П: Щ
: 155: 462: 1442
: 0,5: 1,5: 4,6
Ц: В: П: Щ
Режим работы предприятия
Режим работы: по прерывной недели 260 дней, 3 смены.
Расчет складов сырья и готовой продукции
1) Запас цемента на складе
П - годовая производительность в заводе, м3
С1 - среднее расход цемента на м3
Зц - запас цемента в сутки
М - расчетный годовой фонд
) Емкость силоса
N - число силоса
) Склад заполнителя
А) Производительный запас заполнителей
Р - годовая производительность завода
Z1 - средний расход заполнителя по нормам
N - запас заполнителей в сутках
Р1 - годовой фонд вр. Работы образцов
Б) В форме конуса
В) Количество штабелей
C) Требуемая площадь
F= A*m
M - площадь основания;
4) Склад арматуры
А) А=А1* М*1,04= 58*1,04*0,2=12 т
А1 - суточная производительность ЖБК
М - армированной стали на 1 изд.
Б) Площадь складирование
Т - срок хранения, М1 - масса стали размещающий на
склад 1м.
Заключение
В данном курсовом проекте используется агрегатно-поточный
способ производства. Агрегатно-поточный способ изготовления конструкций
характеризуется расчленением технологического процесса на: отдельные операции
или их группы; выполнением нескольких разнотипных операций на универсальных
агрегатах; наличием свободного ритма в потоке; перемещением изделия от поста к
посту; формы и изделия переходят от поста к посту с произвольным интервалом,
зависящим от длительности операции на данном рабочем месте, которая может
колебаться от нескольких минут до нескольких часов.
Достоинство поточно-агрегатного способа - более гибкая и
маневренная технология в отношении использования технологического оборудования,
возможность изготовления широкой номенклатуры изделий с меньшими капитальными
затратами по сравнению с конвейерной технологией. По мимо этого
поточно-агрегатная технология, основанная на применении передвижных агрегатов,
позволяет формовать изделия за несколько проходов, что гарантирует высокое
качество изделий сложной конфигурации и многослойны и позволяет производить
замену устаревшего оборудования без значительной переделки линии. Агрегатно-поточная
технология особенно целесообразна при изготовлении различных по геометрической
конфигурации элементов.
Основное преимущество поточно-агрегатного способа
производства - в универсальности основного технологического оборудования, что
позволяет при незначительной затрате средств и времени, связанных с
изготовлением лишь новых форм, переходить на выпуск нового вида изделий. Этот
способ производства железобетона получил в нашей стране наибольшее
распространение и весьма экономически целесообразен для заводов с широкой
номенклатурой изделий.
Список
литературы
1. ГОСТ
25628-11 "Колонны железобетонные для одноэтажных зданий предприятий.
Технические условия".
2. ГОСТ
26134-11 "Ультразвуковой метод определения морозостойкости".
. ГОСТ
12730.5-07 "Методы определения водонепроницаемости".
. ГОСТ
23858-12 "Бетон и железобетонные изделия. Методы испытания
материалов".
. Ю.М.
Баженов, А.Г. Комар, "Технология бетонных и железобетонных изделий",
М.: Стройиздат, 1984 г.