Расчет зубчатых пар редуктора
ВВЕДЕНИЕ
Курсовой проект по деталям машин является
самостоятельной конструкторской работой студента. В ходе его выполнения
закрепляются знания по курсу « Детали машин и основы конструирования», «
Метрология , стандартизация и сертификация», « Теоретическая механика» и
другие. Приобретаются навыки работы со справочной литературой, государственными
и отраслевыми стандартами.
Объектом проектирования является механический
привод общего назначения. При конструировании привода применяются
распространенные передачи.
1. ПОДБОР ЭЛЕКТРОДВИГАТЕЛЯ И КИНЕМАТИЧЕСКИЙ
РАСЧЁТ ЭЛЕМЕНТОВ ПРИВОДА. РАЗРАБОТКА КИНЕМАТИЧЕСКОЙ СХЕМЫ ПРИВОДА
Выбираем предварительно электродвигатель,
ориентируясь на заданную мощность на выходном валу привода
Назначаем ориентировочное значение общего к.п.д.
привода [Лекции]
= 0,85.
Определяем ориентировочное значение
необходимой мощности электродвигателя [Лекции]
(1.1)
где
- необходимая мощность
электродвигателя, кВт;
Рв - мощность на выходном
валу привода, кВт. (задана)
кВт
Выбираем электродвигатель ориентируясь
на значение мощности
и заданную
синхронную частоту вращения вала двигателя nд [Дунаев, с.
377, табл. 24.8]
Принимаем электродвигатель марки
ГОСТ 19523-81, у которого Рд = 1,1 кВт, nд =920 мин-1.
Определяем угловую скорость вала
выбранного электродвигателя [Лекции]
где wд - угловая
скорость вала выбранного электродвигателя, рад/с.
рад/с
Определяем общее передаточное число
привода [Лекции]
(1.3)
где wв - угловая
скорость выходного вала привода, рад/с. (задана)
Проводим разбивку общего
передаточного числа привода по ступеням редуктора и разрабатываем
кинематическую схему привода
Определяем передаточное число
остальных ступеней привода
(1.4)
где Uр -
передаточное число редуктора.
Так как передаточное число остальных
ступеней привода меньше 4 и выходной вал привода, расположен горизонтально, то
в качестве остальных ступеней привода принимаем ременную (цепную) передачу с
передаточным числом:
Uр.п. (Uц.п.) = Uост. ст. пр = 2
Разрабатываем кинематическую схему
привода
Определяем общий к.п.д. привода
= h1 × h2 × h3 × h4 × hпn, (1.5)
где
- общий к.п.д. привода;
h1 - к.п.д. передачи, h1 =0,94-0,96
[Д, с. 4, табл. 1.1].
Принимаем h1 =0,95 ;
h2 - к.п.д. передачи, h2 = 0,95-0,97
[Д, с. 4, табл. 1.1].
Принимаем h2 = 0,96
n -
количество пар подшипников, n = 2
0,95·0,96·
=0,894
Определяем необходимую мощность
электродвигателя
(1.6)
кВт.
Так как необходимая мощность меньше
номинальной мощности электродвигателя, поэтому принимаем выбранный
электродвигатель.
Определяем угловые скорости валов
привода
(1.7)

рад/с

(1.8)

рад/с
Проверка: w4 = wв ± 4%
Определяем крутящие моменты,
передаваемые валами привода
(1.10)
где Тдв- крутящий момент
на валу двигателя, Н∙м,
Т1Н = Тдв·h1 hп·U (1.11)
Т1Н
=10,45·0,95·0,99·2=19,65 Н×м
Т2Н = Т1Н×h2× hп×U (1.12)
Т2Н
=19,65·0,96·0,99·1,6=29,88 Н×м
Т3Н = Т2Н×h3×hп×U (1.13)
Т3Н = Н×м
Т4Н = Т3Н×h3×hп×U
Н = Т3Н×h3×hп×U
Т4Н = Н×м
Т5Н = Т4Н×h3×hп×U
Т5Н = Н×м
Проверка: Т5Н = Тв
Выполняем график нагрузки в течение
смены
Тпуск = 2·Т1Н,
(1.14)
где Тпуск - пусковой
момент, Н∙м.
Тпуск = 2· 19,65 = 39,3 Н×м
Т1 = Т1Н =
19,65 Н×м
Т2 = Т1Н·
= 19,65·0,5
= 9,8 Н×м
Т3 = Т1Н
= 19,65·0,1
= 1,965 Н×м
t -
продолжительность одной смены, t
= 8 часов.
t1
= к1·t = 0,5·8 = 4
часов
t2
= к2·t = 0,2·8 =
1,6 часов
t3
= к3·t = 0,3·8 =
2,4 часов
2. РАСЧЕТ ЗУБЧАТОЙ ПАРЫ
РЕДУКТОРА на контактную выносливость и на выносливость по напряжениям изгиба
Определяем допускаемые контактные напряжения и
допускаемые напряжения изгиба для материала шестерни и колеса зубчатой пары
редуктора
Выбираем для изготовления шестерни и колеса
зубчатой пары редуктора сталь с термообработкой и назначаем твердости рабочих
поверхностей зубьев шестерни и колеса зубчатой пары редуктора [Кудрявцев,
с. 30, табл. 2.2]
Ш - 40Х , Улучшение НВ = 260-280
К - 40Х , Улучшение НВ = 230-260
Определяем средние твердости рабочих
поверхностей шестерни и колеса зубчатой пары редуктора [Лекции]
(2.1)
где
- средняя твердость рабочих
поверхностей зубьев;
НВmax -
максимальная твердость рабочих поверхностей зубьев;
НВmin -
минимальная твердость рабочих поверхностей зубьев.
Ш -
К -
Определяем предел длительной
контактной выносливости рабочих поверхностей зубьев шестерни и колеса зубчатой
пары редуктора [Кудрявцев,
с. 38, табл. 2.5]
2·
+7 (2.2)
Ш -
2·270+70=610 МПа
К -
2·245+70=560 МПа
Определяем предел выносливости на изгиб для
материала шестерни и колеса зубчатой пары редуктора [Кудрявцев,
с. 43, табл. 2.6]
1,35·
+100 (2.3)
Ш -
1,35·270+100=464,5 МПа
К -
1,35·245+100=430,75 МПа
Выбираем коэффициент безопасности
при расчете по контактным напряжениям [Кудрявцев,
с. 38, табл. 2.5]
[SH] = 1,1 - для шестерни и
колеса зубчатой пары редуктора
Выбираем коэффициент безопасности
при расчете по напряжениям изгиба [Кудрявцев,
с. 43, табл. 2.6.]
[SF] = 1,65 - для шестерни и
колеса зубчатой пары редуктора
Выбираем значение коэффициента,
учитывающего шероховатость рабочих поверхностей зубьев [Кудрявцев, с. 38]
ZR = 1 - для
шестерни и колеса зубчатой пары редуктора
Выбираем значение коэффициента,
учитывающего влияние скорости в зацеплении зубчатой пары редуктора [Кудрявцев, с. 39, рис. 2.19]
ZV = 1,0…1,16.
Принимаем ZV = - для
шестерни и колеса зубчатой пары редуктора
Выбираем значение коэффициента,
учитывающего реверсивность передачи [Лекции]
КС = 1 для нереверсивной
передачи;
КС = 0,8 для реверсивной
передачи.
Принимаем КС
= для шестерни и колеса зубчатой
пары редуктора.
Выбираем базу контактных напряжений
для материалов шестерни и колеса зубчатой пары редуктора [Чернавский, с. 82, рис. 4.6.]
Ш - NHG = 20·
К - NHG = 12,5
Выбираем базу напряжений изгиба для
материалов шестерни и колеса зубчатой пары редуктора [Лекции]
NFG = 4×106
- для шестерни и колеса зубчатой пары редуктора.
Определяем машинное время работы
передачи [Лекции]
S = 365×Lг×24×кгод×ксут×ПВ, (2.4)
где tS - машинное
время, час;
Lг - срок
службы передачи, год;
кгод - коэффициент
использования передачи в течении года;
ксут - коэффициент
использования передачи в течении суток;
ПВ - продолжительность включения.
tS =
365·7·24·0,50·0,66·0,30=6070,68 часов
Определяем наработку для шестерни и
колеса зубчатой пары редуктора [Лекции]
(2.5)
где tS - машинное
время работы передачи;
n - частота
вращения рассчитываемого колеса или шестерни;
мин-1
ш =
60·6070,68·460=167551928
=
=83775964
Выбираем, в зависимости от класса
нагрузки, коэффициент эквивалентности при расчете на выносливость по контактным
напряжениям [Чернавский,
с. 77, табл. 4.1]
КНE = 0,63
Выбираем, в зависимости от класса
нагрузки, коэффициент эквивалентности при расчете на выносливость по
напряжениям изгиба [Чернавский,
с. 77, табл. 4.1]
КFE = 0,725
Определяем эквивалентное число
циклов нагружения шестерни и колеса зубчатой пары редуктора при расчете на
контактную выносливость [Лекции]
HE = KHE×N, (2.6)
Ш - NHE =
0,63·167551928=105557714,6 циклов
К - NHE =
0,63·83775964=52778857,32 циклов
Определяем эквивалентное число
циклов нагружения шестерни и колеса зубчатой пары редуктора при расчете на
выносливость по напряжениям изгиба [Лекции]
FE = KFE×N, (2.7)
Ш - NFE =
0,725·167551928=121475147,8 циклов
К - NFE = 0
,725·83775964=60737573,9 циклов
Определяем
коэффициент долговечности для шестерни и колеса 1-ой и 2-ой ступеней редуктора
при расчете на контактную выносливость [Лекции]
(2.8)
Ш -
К -
Определяем коэффициент долговечности
для шестерни и колеса зубчатой пары редуктора при расчете на выносливость по
напряжениям изгиба [Лекции]
(2.9)
Ш -
К -
Определяем допускаемые контактные
напряжения для материала шестерни и колеса зубчатой пары редуктора [Лекции]
(2.10)
Ш -
Мпа
К -
МПа
Определяем допускаемые напряжения
изгиба для материала шестерни и колеса зубчатой пары редуктора [Лекции]
(2.11)
Ш1 -
МПа
К1 -
МПа
так как ступень редуктора
коническая, то в дальнейшие расчеты вводим меньшее из условных допускаемых
контактных напряжений определенных по формулам:
sНР усл. 1 = 0,43×(sНР ш + sНР к)=0,43·(417,24+413,84)=357,36(2.12)
sНР усл.2 = 1,15×sНР к=1,15·413,84=475,916
Определяем параметры конической
зубчатой пары редуктора и проверяем принятые размеры на выносливость по
контактным напряжениям и напряжениям изгиба
Определяем ориентировочную линейную
скорость в зацеплении конической зубчатой пары редуктора и решаем, какой должна
быть рассчитываемая зубчатая пара - прямозубой или косозубой [Чернавский, с. 95, (4.37)], [Решетов, с. 192]
(2.13)
где n1 - частота
вращения шестерни, мин-1;
Cu -
коэффициент [Чернавский,
с. 95, табл. 4.9.]
T2max - крутящий
момент на валу колеса, Н×мм;
U -
передаточное число конической зубчатой пары редуктора

=1,04
Так как линейная скорость в
зацеплении равна м/с, то принимаем, что коническая зубчатая пара будет
прямозубая
Выбираем величину коэффициента длины
зуба yRe [Лекции]
yRe = 0,25…0,3
Принимаем yRe = 0,3
Выбираем величину коэффициента КНb,
учитывающего неравномерность распределения нагрузки по длине контактных линий
при расчете на контактную выносливость [Лекции]
КНb = 1,04…1,5
при твердости рабочих поверхностей зубьев НВ £ 350
КНb = 1,05…1,5
при твердости рабочих поверхностей зубьев НRC ³ 40
Принимаем КНb =1,3
Выбираем величину коэффициента КНu,
учитывающего влияние динамических нагрузок, возникающих в зацеплении при
расчете на контактную выносливость поверхности зубьев [Лекции]
КНu = 1,1…1,3.
Принимаем КНu =1,2
Выбираем
величину коэффициента КНК, учитывающего нагрузочную способность
конической зубчатой передачи при расчете на контактную выносливость поверхности
зубьев [Лекции]
КНК = 0,85 - для
прямозубой передачи;
КНК = 1,2…1,3 - для
косозубой передачи;
КНК = 1,45 - для передачи
с круговыми зубьями.
Принимаем КНК =0,85
Определяем расчетный внешний диаметр
делительного конуса колеса конической зубчатой пары при yRe = 0,3 [Лекции]
(2.14)
где Т1Н -крутящий момент
на валу шестерни, Н×мм.
3,34·
Полученное значение округляем до
ближайшего стандартного по ГОСТ 12289-76 [Гузенков,
с. 211]
160 мм
Назначаем число зубьев шестерни
конической зубчатой пары редуктора [Лекции]
Z1 = 18…24
Принимаем Z1 =
Определяем число зубьев колеса
конической зубчатой пары редуктора [Лекции]
2 = Z1×U, (2.15)
2 = 20·1,6=32
Уточняем передаточное число [Лекции]
(2.16)
Назначаем угол наклона зубьев b конической зубчатой пары
редуктора
b
= 20…300, обычно кратным 5
Принимаем b =
Примечание Этот пункт выполняется
если рассчитываемая зубчатая пара косозубая или с круговыми зубьями
Определяем углы начальных конусов
шестерни и колеса конической зубчатой пары редуктора [Лекции]
(2.17)
=
1,6=57,995
Определяем расчетный внешний
окружной модуль конической зубчатой пары редуктора [Лекции]
(2.18)
Примечание Если передача прямозубая,
то
расчетный внешний окружной модуль
необходимо округлить до стандартного
значения по ГОСТ 9563-60 [Гузенков, с. 159]
5 мм
Определяем расчетный нормальный
внешний модуль конической зубчатой пары редуктора [Лекции]
(2.19)
Полученное значение округляем до
ближайшего стандартного по ГОСТ 9563-60 [Гузенков,
с. 159]]
5
Примечание Этот пункт выполняется
если рассчитываемая зубчатая пара косозубая или с круговыми зубьями
Определяем внешнее конусное
расстояние конической зубчатой пары редуктора
[Лекции]
Для прямозубой
передачи
(2.20)
Для косозубой и
передач с круговыми зубьями:
(2.21)
=
Определяем ширину венцов шестерни и
колеса конической зубчатой пары редуктора [Лекции]
(2.22)
0,3·94,34=28,3
Полученное значение округляем до
целого числа из ряда нормальных линейных размеров [Гжиров, с. 87]
25
Определяем среднее конусное
расстояние конической зубчатой пары редуктора
[Лекции]
(2.23)
94,34-0,5·25=80,34
Определяем средний модуль конической
зубчатой пары редуктора
Для прямозубой передачи:
(2.24)
Для косозубой и
передач с круговыми зубьями:
(2.25)
5·
Определяем линейную скорость в
зацеплении конической зубчатой пары редуктора, соответствующую среднему
диаметру делительного конуса [Лекции]
(2.26)
где w1 - угловая скорость шестерни конической передачи, рад/с.
м/с
Определяем основные параметры
конической зубчатой пары редуктора [Чернавский, с. 134…138]
Высота головки зуба в среднем
сечении

=
·4,25=4,25

=
·4,25=4,25
где хn1 и хn2 - смещение.
Принимаем хn1 = 0; хn2 = 0.
4,25
4,25
Высота ножки зуба в среднем сечении

=
·4,25=5,31

=
·4,25=5,31
5,31
5,31
Угол ножки зуба
3,71
Угол головки зуба
3,71
3,71
Угол конуса вершин
32,005+3,71=35,715
57,995+3,71=61,705
Угол конуса впадин
32,005-3,71=28,295
57,995-3,71=54,285
Внешняя высота головки зуба
Внешний диаметр вершин зубьев
где
- внешний диаметр делительного
конуса шестерни;
- внешний диаметр делительного
конуса колеса.
20·5=100
32·5=160
100+2·0,066·
=101,668
100+2·0,066·
=100,069
Параметры конической зубчатой пары
редуктора сводим в таблицу 2.1.
Таблица 2.1 - Параметры конической
зубчатой пары редуктора
|
Наименование
параметров
|
Обозначение
|
шестерня
|
колесо
|
1.
|
Число
зубьев
|
Z
|
20
|
32
|
2.
|
Внешний
окружной модуль, мм
|
mte
|
5
|
5
|
3*.
|
Внешний
нормальный модуль, мм
|
mn
|
-
|
-
|
4.
|
Внешнее
конусное расстояние, мм
|
Re
|
94,34
|
94,34
|
5.
|
Среднее
конусное расстояние, мм
|
R
|
81,84
|
81,84
|
6.
|
Ширина
венца, мм
|
b
|
25
|
25
|
7.
|
Угол
делительного конуса, град
|
d
|
32,005
|
57,995
|
8.
|
Угол
конуса вершин зубьев, град
|
da
|
35,795
|
61,785
|
9.
|
Угол
конуса впадин зубьев, град
|
df
|
28,215
|
54,205
|
10*.
|
Угол
наклона зубьев, град
|
b
|
-
|
-
|
Диаметр внешней делительной окружности, мм
|
de
|
100
|
160
|
12.
|
Внешний
диаметр вершин, мм
|
dea
|
101,668
|
100,069
|
|
|
|
|
|
|
Примечание: Строки со звездочкой заполняются
только для косозубой и передач с круговыми зубьями
Определяем силы, действующие в зацеплении
конической зубчатой пары редуктора [Лекции]
Окружная сила
(2.27)
Осевые и радиальные для прямозубой
передачи
(2.28)
490,7·
·
=94,65 Н
490,7·
·
=151,45 Н
Проверяем на контактную выносливость
принятые размеры конической зубчатой пары редуктора [Лекции]
(2.30)
где Т1Н -крутящий момент
на валу шестерни, Н×мм.

Вывод:
Сравниваем прочности шестерни и
колеса и решаем, по какому из колес конической зубчатой пары редуктора будем
вести проверку на выносливость по напряжениям изгиба [Лекции]
- это отношение называется
прочностью
где YF -
коэффициент формы зуба, выбирается для прямозубых передач от действительного
числа зубьев, а для косозубых и передач с круговыми
зубьями в зависимости от
приведенного числа зубьев [Чернавский,
с. 101, табл. 4.13]
Приведенное число зубьев
(2.31)
Ш - YF1 = 4,07
К - YF2 =3,78
Ш -
=37,850
К -
=40,83 , так как прочность шестерни
____меньше_________
чем прочность колеса конической
зубчатой пары редуктора дальнейший расчет будем вести по ___шестерне
______________
Проверяем на выносливость по
напряжениям изгиба принятые размеры конической зубчатой пары редуктора [Лекции]
Для прямозубой конической передачи
(2.32)
3. Расчет
клиноременной передачи с ремнями нормального сечения
Определяем частоту вращения ведущего
(малого шкива) n1, мин-1
920
Выбираем сечение ремня с учетом Рн
и n1 [Гузенков, с. 129. рис 11.6], [Чернавский, с. 266, рис. 9.4].
Принимаем
ремень типа - , с параметрами: [Чернавский, с. 263. табл.
9.4]
Ширина ремня bр = 11 мм;
Высота ремня Т0 = 8 мм;
Площадь поперечного сечения А = 81
мм2.
Выбираем по ГОСТ 20889-80 минимально
допустимый диаметр ведущего (малого) шкива d1 [Чернавский, с. 276. табл.
9.13], [Чернавский, с. 267]
Примечание Диаметр малого шкива
выбрать для угла профиля канавки шкива a
= 38°.
Принимаем d1 = 180 мм
Определяем расчетный диаметр
ведомого (большого) шкива d2, мм
(3.1)
где d1 - диаметр
ведущего шкива, мм;
U -
передаточное число передачи;
ξ - коэффициент скольжения, [Гузенков, с. 131] ξ = 0,01-0,02.
Принимаем ξ = 0,02
2·180·(1-0,02)= 352,8 мм
Полученное значение d2 округляем
до ближайшего стандартного по ГОСТ 20889-88 [Чернавский,
с. 267]
Принимаем d2 = 355 мм
Уточняем передаточное число U’
и проверяем его отклонение ∆ от заданного U
(3.2)
% £ 3%

·100%= 0,6% < 3%
Определяем ориентировочное межосевое
расстояние [Гузенков, с. 136]
(3.3)
где С -
коэффициент, [Гузенков,
с. 136].
Принимаем С = 1,2
а = 1,2·355= 426 мм
Определяем расчетную длину ремня
[Лекции], [Чернавский,
с. 256, формула (9.2)], [Гузенков, с. 136, формула (11.20)].
, (3.4)
2 · 426+
+ (355+180)
+
= 1709,9 мм
Полученное значение округляем до
ближайшего стандартного по ГОСТ 1284.1-89-ГОСТ 1284.3-89 [Чернавский, с.263,
табл. 9.4].
lгост = 1800 мм
Уточняем межосевое расстояние по
стандартной длине ремня, [Лекции], [Чернавский,
с. 262, формула (9.12)], [Гузенков, с. 136, формула (11.21)]
(3.5)
редуктор изгиб зубчатый
напряжение

мм
Определяем угол обхвата ремнем
ведущего шкива [Лекции], [Чернавский,
с. 257, формула (9.3)], [Гузенков, с. 136, формула (11.16)]
(3.6)
Определяем угол между ветвями ремня
[Лекции], [Гузенков, с. 134]
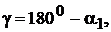
(3.7)
Определяем скорость ремня [Лекции], [Чернавский, с. 257, формула
(9.3)], [Гузенков, с. 135, формула (11.15)]
(3.8)
м/с
Определяем частоту пробегов ремня
[Лекции], [Гузенков, с. 142, формула (11.33)]
(3.9)
где [nn] -
допускаемая частота пробегов, [Лекции], [Гузенков, с. 142]
Принимаем [nn] = 10 c-1
£ 10 c-1
Определяем допускаемую мощность,
передаваемую одним клиновым ремнем [Чернавский,
с. 267, формула (9.14)], [Гузенков, с. 142, формула (11.32)]
(3.10)
где Pо -
допустимая мощность, передаваемая одним ремнем [Чернавский, с. 265, табл. 9.5], [Гузенков, с.
141, табл.11.5)]
Принимаем Pо = 1,69 кВт
Кa - коэффициент, учитывающий влияние
угла обхвата ремнём малого шкива [Чернавский,
с. 267], [Гузенков, с. 140, табл.11.4)];
Принимаем Кa = 0,95
Кl -
коэффициент влияния отношения расчетной длины ремня lp к базовой
длине ремня lo [Чернавский, с. 265, табл.
9.5], [Гузенков, с. 142];
Принимаем Кl = 1
Примечание: условная длина ремня l0 приведена
[Гузенков, с. 128, табл. 11.1].
КZ - коэффициент,
учитывающий неравномерность распределения нагрузки по ремням [Гузенков, с.
142].
При числе ремней Z = 1, КZ = 1;
при числе ремней Z = 2-3 КZ =0,95.
Принимаем КZ = 1
1,69 · 0,95 · 1· 1=1,6
Определяем количество клиновых
ремней Z [Лекции], [Чернавский, с. 267, формула
(9.14)], [Гузенков, с. 142, формула (11.32)]
(3.11)
где Кd -
коэффициент, учитывающий динамические нагрузки и режим работы передачи
[Гузенков, с. 132, табл. 11.2].
Принимаем Кd = 1,5
Принимаем Z = 1
Определяем окружную силу, передаваемую
клиновым ремням Ft, Н [Лекции], [Гузенков, с. 131,
формула (11.3)]
(3.12)
Н
Определяем силы натяжения ведущей F1 и ведомой F2 ветвей, Н
[Лекции], [Гузенков, с. 135, формулы (11.5), (11.6)]
, (3.13)
где Fo - сила
предварительного натяжения ремня, Н [Лекции], [Гузенков, с. 131, формула
(11.4)]
(3.14)
где s0 - напряжение
от предварительного натяжения ремня, МПа [Лекции], [Гузенков, с. 131]
81· 1,5 = 121,5
Примечание: если сила F2
отрицательна, необходимо принять большее значение s0.
Определяем силу
давления ремня на вал шкива Fв, Н [Лекции], [Гузенков, с. 134, формула (11.12)]
(3.15)
121,5·1·
= 242,53
Результаты расчетов сводим в таблицу
3.1.
Таблица 3.1 - Параметры
клиноременной передачи
№
|
Наименование
параметра
|
Обозначение
|
Величина
|
1.
|
Тип
ремня
|
Кордтканевый
клиновой
|
|
2.
|
Ширина
ремня, мм
|
bp
|
11
|
3.
|
Высота
ремня, мм
|
Т0
|
8
|
4.
|
Диаметр
малого шкива, мм
|
d1
|
180
|
5.
|
Диаметр
большого шкива, мм
|
d2
|
355
|
6.
|
Передаточное
число
|
U
|
2
|
7.
|
Межосевое
расстояние, мм
|
a
|
471,9
|
8.
|
Длина
ремня, мм
|
1
|
1800
|
9.
|
Угол
обхвата малого шкива ремнем, град
|
a1
|
158,86
|
10.
|
Угол
между ветвями ремня, град
|
g
|
21,14
|
11.
|
Число
ремней
|
z
|
1
|
12.
|
Число
пробегов
|
n
|
5
|
13.
|
Усилие
давление на вал, Н
|
Fв
|
242,53
|
. ОРИНТИРОВОЧНЫЙ РАСЧЕТ ВАЛОВ
4.1 Расчет ведущего
вала редуктора
Определяем диаметр входного конца вала [Гузенков,
с. 266],
[Лекции]
(4.1)
где dВ расч. - расчетный
диаметр входного конца вала, мм;
ТН - крутящий момент
передаваемый этим валом, Н·мм;
- пониженное допускаемое напряжение
на кручение для материала вала, МПа
Принимаем, что все валы изготовлены
из стали____
= 15…20 МПа
[Гузенков, с.
266] Принимаем
= МПа

мм
Принимаем dВ гост = 18 мм [Чернавский, с. 296]
Определяем диаметр вала под
уплотнение, ориентируясь на диаметр входного конца вала и внутренний диаметр
уплотнения [Дунаев, с. 402. табл. 24.29], [Анурьев Т. 3, с. 204, табл. 30]
В гост ≤ dВ упл.,
В упл. = 22 мм
Определяем
диаметр вала под подшипник, ориентируясь на диаметр вала под уплотнение и
внутренний диаметр подшипника [Дунаев, с. 380. табл. 24.10], [Анурьев Т. 2, с. 116, табл.
96]
В упл. < dВ подш.
dВ подш. = 25 мм
Определяем
диаметр вала под колесо, ориентируясь на диаметр вала под подшипник [Дунаев, с.
137…144]
В подш. ≤ dВ к
В к = 26 мм
4.2 Расчёт ведомого вала редуктора
Определяем
диаметр выходного конца вала

Расчётное
значение dВ расч. округляем
до ближайшего стандартного в большую сторону [Чернавский, с. 296]
dВ гост = 20 мм.
Определяем
диаметр вала под уплотнение, ориентируясь на диаметр выходного конца вала и
внутренний диаметр уплотнения [Дунаев, с. 402. табл. 24.29], [Анурьев Т. 3, с.
204, табл. 30]
В гост ≤ dВ упл.,
В упл. = 24 мм.
Определяем
диаметр вала под подшипник, ориентируясь на диаметр вала под уплотнение и
внутренний диаметр подшипника [Дунаев, с. 380. табл. 24.10], [Анурьев Т. 2, с. 116, табл.
96]
В упл. < dВ подш.,
В подш. = 25 мм
Определяем
диаметр вала под колесо, ориентируясь на диаметр вала под подшипник [Дунаев, с.
137…144]
В подш. ≤ dВ к
В к = 26 мм
.
ОПРЕДЕЛЕНИЕ ОСНОВНЫХ ПАРАМЕТРОВ КОРПУСА РЕДУКТОРА. ЭСКИЗНАЯ КОМПОНОВКА
РЕДУКТОРА И ПРИВОДА В ЦЕЛОМ
5.1 Определяем основные параметры корпуса редуктора
Таблица
5.1- Ориентировочное соотношение размеров основных элементов чугунного и
стального литого корпуса цилиндрического редуктора
Параметры
корпусных деталей
|
Формулы
и размеры (мм)
|
1. Толщина стенки корпуса
Принимаем
δ
=
6 мм
|
|
2.
Толщина стенки крышки
|
δ1
= 0,9·δ = 0,9·6 = 5,4 мм Принимаем δ1
= 6 мм
|
3.
Толщина ребра: в сопряжении со стенкой корпуса; в сопряжении со стенкой
крышки
|
δ2
= (0,8…1)·δ = 1·6 = 6 мм δ3
= (0,8…1)·δ1
= 1·6 = 6 мм
|
4.
Толщина фундаментных лап
|
h =
1,5·d
= 1,5·12 = 18 мм
|
5.
Толщина фланца корпуса
|
h1
= 1,5·d1
=1,5·10 = 15 мм
|
6.
Толщина фланца крышки: для болта с шестигранной головкой
|
h2
= 1,3·d1
= 1,3·10 = 13 мм
|
7.
Толщина подъемных ушей: корпуса; крышки
|
δ4
= 2,5·δ = 2,5·6 = 15 мм δ5
= 2,5·δ1
= 2,5·6 = 15 мм
|
8. Диаметр фундаментных болтов
29,88 = 4,9
мм
9. Диаметр
болтов (винтов) соединения крышки с корпусом редуктора
29,88 = 3,9
Принимаем
d1
= 10 мм
|
|
10.
Диаметры болтов крепления торцевых крышек подшипников и крышки смотрового
отверстия
|
d2
= d3
= 0,5·d1
=
0,5·1 = 0,5 мм Принимаем d2
= d3
= 1 мм
|
11.
Расстояние от стенки корпуса до края фланца фундаментных лап
|
К
= (3,2…3,5)·d = 39,6 мм
Принимаем К = 40 мм
|
12. Расстояние от стенки до края фланца по разъёму
корпуса и крышки: для болта с шестигранной головкой
|
К1
= (2,7…3)·d1
= 3,0·10 = 30 мм Принимаем К1 = 30 мм
|
13.
Расстояние от края фланца до оси болта
|
с1
= 0,5·к1 = 0,5·30 = 15 мм с = 0,5·к = 0,5·40 = 20 мм
|
14.
Расстояние между осями болтов для крепления крышки редуктора к корпусу
|
l
= (10…15)
· d1 =
10·10 = 100 мм
|
. РАСЧЁТ ВЕДУЩЕГО ВАЛА РЕДУКТОРА И ЕГО ОПОР
6.1. Расчёт шпонок
Определяем по эскизной компоновке место
шпоночного соединения
Шпонки установлены на входном конце вала с
диаметром вала 18 мм
Выбираем сечение шпонок в зависимости от
диаметра вала в месте ее установки [9, с. 302…304]
Для диаметра 18 мм под колесом принимаем шпонку
с размерами: b´h´l
= 6×6×25 мм
Проверяем принятые размеры шпонки на прочность
Так вал имеет один и тот же диаметр и передает
один и тот же крутящий момент проверять будем более короткую шпонку
Проверка шпонки на смятие:
(6.1)
где σсм - рабочее
напряжение смятия, МПа;
[σсм] - допускаемое напряжение смятия для материала шпонки,
МПа;
Для стали 45 [σсм] = 100…150
МПа [5, с. 106];
Т - крутящий момент, передаваемый
валом, Н·м;
d - диаметр
вала, м;
к - глубина паза втулки, мм, к =
0,0033 м;
lp - рабочая
длина шпонки, м
(6.2)
где l - длина
паза вала под шпонку, мм
,32 МПа < 100 МПа - условие
выполняется
Проверка шпонки на срез:
(6.3)
где τср - расчетное
напряжение на срез, МПа;
b - ширина
шпонки, мм;
[τср] - допускаемое напряжение
на срез для материала шпонки, МПа
Для стали 45 [τср] = 60…90
МПа [5, с. 106]
,15 МПа < 60 МПа - условие
выполняется
Выбранная шпонка выдерживает
заданную нагрузку и будет работать, т.к. рабочие напряжения смятия и среза не
превышают допустимых.
6.2
Приближённый расчёт вала
Выполняем схему сил действующих на
вал
В
горизонтальной плоскости действуют силы и реакции: RAx; RBx; Fr; Fа; Fв.
В вертикальной плоскости действуют
силы и реакции: RAz; RBz; Ft.
Определяем реакции в опорах вала от
действия горизонтальных и вертикальных сил
;
Строим эпюры изгибающих моментов в
горизонтальной и вертикальной плоскости
В горизонтальной плоскости:
Проверка:
В вертикальной плоскости:
Проверка
Строим эпюру суммарного изгибающего
момента
, (6.4)
где Мсум - суммарный
изгибающий момент, Н·мм.
Точка С
Точка В
Точка A
Точка D
Строим эпюру крутящего момента
Ткр = 19650 Н·мм
Строим эпюру эквивалентного момента
, (6.5)
где Мэкв- эквивалентный
момент, Н·мм;
Ткр- крутящий момент,
Н·мм;
Мсум- суммарный момент,
Н·мм.
Точка С
Точка В
Точка A
Точка А является опасным сечением
вала
Определяем диаметр вала в опасном
сечении [5, с. 267]
, (6.6)
где d - диаметр
вала, мм;
Мэкв - эквивалентный
момент в опасном сечении, Н·мм;
[σиз] -
допускаемое напряжения изгиба, МПа.
Для стали 40Х из которой изготовлен
вал шестерня [σиз] = 90 МПа [5, с. 266, табл. 16.1.]
Полученное значение округляем до
ближайшего стандартного в большую сторону dгост = 14 мм.
Однако при ориентировочном расчете в
данном сечении вала в конструктивных соображениях был принят диаметр вала
равный 25 мм, то его и оставляем
6.3
Уточнённый расчёт вала [5, с. 275…279], [8]
Определяем предел выносливости при
изгибе σ-1 [5, с. 14]
σ-1 = 0,45·σв, (6.7)
где σ-1 - предел
выносливости при изгибе, МПа;
σв - предел
прочности при растяжении, МПа
Для стали 45Х - σв = 1000 МПа
σ-1 = 0,45·1000
= 450 МПа
Определяем предел выносливости при
кручении τ-1 [5, с. 14]
τ-1 = 0,2·σв, (6.8)
где τ-1 - предел
выносливости при кручении, МПа
τ-1 = 0,2·1000
= 200 МПа
Выбираем значение эффективного
коэффициента концентрации напряжений при кручении Кτ (для
шпоночной канавки) [5, с. 270, табл. 16.2]
Кτ = 1,7
Выбираем значения эффективного
коэффициента концентрации напряжений при изгибе Кσ (для
шпоночной канавки) [5. с. 270, табл. 16.2]
Кσ = 2
σа = σи, (6.9)
где σа - амплитуда
цикла при изгибе, МПа;
σи - расчётное
напряжение на изгиб в опасном сечении вала, МПа
(6.10)
где М - изгибающий момент, Н мм;
Wнетто - момент
сопротивления сечения вала по шпоночной канавке, мм3
(6.11)
где d - диаметр вала,
мм;
b - ширина
паза, мм;
t - глубина
паза вала, мм
Определяем амплитуду цикла при
кручении [5, с 269]
τа = 0,5×τк , (6.12)
где τа - амплитуда
цикла при кручении, МПа;
τк - расчётное
напряжение на кручение в рассматриваемом сечении вала, МПа
(6.13)
где T - крутящий
момент передаваемый валом, Н·мм;
Wк. нетто - момент
сопротивления вала, мм3
(6.14)
Выбираем значение коэффициента Кd ,
учитывающего влияние абсолютных размеров поперечного сечения [5, с. 271]
Кd = 0,93
Выбираем значение коэффициента КV,
учитывающего влияние поверхностного упрочнения [5, с. 271, табл. 16.3]
КV = 2,6
Выбираем значение коэффициентов
чувствительности к асимметрии цикла напряжений [5, с. 271]
ψσ = 0,1
ψτ = 0,05
Определяем значения средних
напряжений цикла при изгибе и кручении σт и τт [5. с. 269]
При симметричном цикле изменения
напряжений в сечении вала среднее напряжение цикла при изгибе σm = 0; tm = 9,61 МПа
Определяем
коэффициент запаса прочности при изгибе [5, с. 268]
, (6.15)
где Sσ -
коэффициент запаса прочности при изгибе
Определяем
коэффициент запаса прочности при кручении [5, с. 268]
(6.16)
где Sτ - коэффициент
запаса прочности при кручении
Определяем общий коэффициент запаса
прочности [5, с. 268]
(6.17)
где S - общий
коэффициент запаса прочности;
[S] -
допускаемый коэффициент запаса прочности; [S] = 1,5…2,5
,17 > 2,5 - условие выполняется
6.4 Подбор
и расчёт подшипников качения по динамической грузоподъемности
Определяем радиальную и осевую
нагрузки на подшипники [8]
, (6.18)
где FR -
радиальная нагрузка на подшипник, Н
На подшипник А:
На подшипник D:
Наиболее нагружен подшипник A, по нему и
будем вести расчет на динамическую грузоподъемность подшипников
Определяем
коэффициент осевого нагружения [5, с. 308, табл. 18.2]
, (6.19)
где Со - статическая
грузоподъемность подшипников качения, Н
Для подшипника №205 Со =
7090 Н [6, с. 380, табл. 24.10].
Этому
соотношению соответствует коэффициент осевого нагружения е=0,29
Выбираем коэффициент вращения V [5, с. 307]
Т.к. вращается внутреннее кольцо
подшипника, то следовательно V = 1
Выбираем значения коэффициентов
радиальной и осевой нагрузок X и У [5, с. 308, табл. 18.2]
, (6.20)
Т. к. 0,13 > 0,29, то следовательно
Х = 1
У = 0
Выбираем коэффициент безопасности,
учитывающий характер нагрузки на подшипник [5, с. 307]
При спокойной нагрузке на подшипник
- Кб = 1
Выбираем температурный коэффициент,
учитывающий рабочую температуру нагрева подшипника [5, с. 307]
КТ = 1
Определяем эквивалентную
динамическую нагрузку на подшипник [5, с. 305]
(6.21)
где Р - эквивалентная динамическая
нагрузка на подшипник, Н
Определяем расчётную долговечность
подшипника [5]
(6.22)
где Lh - расчётная
долговечность подшипника, часов;
n - частота
вращения вала, мин-1;
C -
динамическая грузоподъемность подшипника, Н;
C = 11000 Н [6, с.
380, табл. 24.10];
п - показатель степени; для шариковых
подшипников п = 3
Расчётная долговечность подшипника
больше машинного времени работы передачи 29796,18 > 6070,7 часов, то
следовательно, принимаем подшипник №7205
. СМАЗКА ЗУБЧАТЫХ КОЛЁС И
ПОДШИПНИКОВ. ВЫБОР МАРКИ МАСЛА
7.1
Выбираем способ смазывания зубчатых колёс и подшипников [8, с. 347…351]
Смазывание зубчатых пар редуктора
будет осуществляться погружением в ванну с жидким смазочным материалом в нижней
части корпуса редуктора, одного или нескольких колёс. Остальные узлы
смазываются за счёт разбрызгивания масла, погружёнными колёсами. Таким образом
происходит циркуляция масла внутри корпуса.
Подшипники качения будут смазываться
пластичной смазкой ЦИАТИМ-202 или смазкой жировой 1-13 [7, с. 345, табл. 19.2]
7.2
Определяем вязкость масла в зависимости от фактора cз.п. [7, с. 346]
, (7.1)
где ННV - твёрдость
по Виккерсу активных поверхностей зубьев;
σН -
контактные напряжения в зацеплении зубчатых колес, МПа;
V - окружная
скорость в зацеплении зубчатых колес
Выбираем масло И-100А [7, с. 346,
рис. 19.1]. [7, с. 345, табл. 19.1]
7.3
Определяем объём заливаемого масла
(7.2)
где V - объём
масла, л;
L - длина
корпуса редуктора по внутренним стенкам, дм;
B - ширина
корпуса редуктора по внутренним стенкам, дм;
H -
расстояние от дна до верхнего уровня масла, дм
V = 1,5×1,9×0,56 = 1,6 л
Список использованной
литературы
Анурьев
В.И. Справочник конструктора-машиностроителя. В 3-х томах. М.: Машиностроение,
2007, 2009.
Детали
машин/ Под ред. О.А. Ряховского. М.: Изд-во МГТУ им. Н.Э.Баумана, 2007.
Детали
машин: Атлас конструкций/ Под ред. Д.Н. Решетова. М.: Машиностроение, 4.1 и
4.2, 2006.
Дунаев
П.Ф., Леликов О.П. Конструирование узлов и деталей машин. М.: Высшая школа,
2006.
Иванов
М.Н., Финогенов В.А. Детали машин. М.: Высшая школа, 2009.
Иосикевич
Г.Б. Детали машин. М.: Высшая школа, 2008.
Кудрявцев
В.Н. Детали машин. Л.: Машиностроение, 2006.
Кудрявцев
В.Н. Курсовое проектирование деталей машин. М.: Машиностроение, 2007.
Орлов
П.И. Основы конструирования. В 2-х томах. М.: Машиностроение, 2008.
Решетов
Д.Н. Детали машин. М.: Машиностроение, 2009.
Ряховский
О.А., Иванов С.С. Справочник по муфтам. Л.: Политехника, 2008.