Физико-химические характеристики нефти месторождения Карачаганак
Получение
синтетического каучука при переработке нефти месторождения Карачаганак
Содержание
Введение
. Литературный
обзор
.1 История
развития технологии синтетического каучука
1.2 История
открытий, обеспечивших создание технологии СК
1.3 Производства
синтетических каучуков
1.4 Получение мономеров для
синтетических каучуков
1.5 Производства синтетических
каучуков полимеризацией в растворе
.6 Свойства изоперена и
основные методы его получения
.7 Стереоспецифической
полимеризации изопрена
.8 Полимеризация изопрена
.9 Применение
2. Технологическая часть
.1 Физико-химические
характеристики нефти месторождения Карачаганак
.2 Описания поточной схемы
переработки нефти месторождения
.3 Материальные балансы установок,
входящих в поточную схему
Заключения
Список литературы
Введение
Промышленность
синтетического каучука является одной из ведущих отраслей химической и
нефтехимической промышленности.
В настоящее время
на предприятиях, производящих синтетический каучук, благодаря постоянному
совершенствованию существующих и внедрению новых технологических процессов
выпускается более 200 марок синтетических каучуков и латексов, что позволяет
удовлетворять потребности шинной, резинотехнической, электротехнической, легкой
и других отраслей промышленности. Характерной особенностью промышленности
синтетического каучука на современном этапе являются значительные масштабы
производства.
Благодаря успехам в
области химии и технологии, достигнутым в начале 60-х годов, было организовано
производство новых типов синтетических каучуков, обладающих комплексом ценных
эксплуатационных свойств. К ним в первую очередь следует отнести
стереорегулярные изопреновый и бутадиеновый каучуки, полноценно заменяющие
натуральный каучук при изготовлении основной массы шин и резинотехнической
продукции. В промышленности синтетического каучука широко используются мономеры
на основе наиболее экономичного и доступного нефтяного сырья. Современные
производства мономеров и каучуков включают многочисленные технологические
процессы, такие как нефтепереработка, органический синтез, выделение
индивидуальных углеводородов из их смесей, дегидрирование, полимеризация и др.
В области
производства мономеров за последнее десятилетие внедрены новые, более
эффективные методы получения бутадиена - из пиролизной фракции С4 и
окислительным дегидрированием. Предусматривается внедрение одностадийного
способа получения изопрена из изобутилена и формальдегида, а также получение
изопрена через диолы. В производстве изопрена из изопентана предусматривается
внедрение метода окислительного дегидрирования изопентана в изоамилены. В
настоящее время особое внимание обращено на необходимость использования
существующих резервов производства. В промышленности синтетического каучука за
последние годы значительно повысился удельный вес мощностей, введенных за счет
реконструкции и расширения действующих производств, что позволило получить
большую экономию капитальных вложений.
Каучук и резины на
его основе обладают уникальным комплексом свойств: эластичностью в широком диапазоне
температур, высоким сопротивлением истиранию, низкой газопроницаемостью,
хорошими диэлектрическими свойствами, стойкостью ко многим деформациям и ко
многим средам. Области применения резин очень обширны и постоянно
увеличиваются. Ассортимент резиновых изделий включает десятки тысяч
наименований. Около 60% производимого каучука расходуется на резины для
механизированного транспорта: автомашин, самолетов, кораблей и др. Помимо этого
каучук и резины применяются сейчас практически во всех отраслях народного
хозяйства: для обуви, кабелей, резинотехнических и других изделий.
Актуальность. В
сравнении с природным каучуком его синтетический аналог является более выгодным
и перспективным материалом. Во-первых, он более универсален. Современные
способы производства позволяют получить материал, обладающий оптимальными
свойствами для той или иной сферы применения. Кроме того, производство
синтетических каучуков обходится гораздо дешевле. В последние годы
синтетические каучуки нашли широкое применение не только в автомобильной
промышленности, но и в звуко-, тепло-, гидро- и воздух изоляции зданий, а также
в производстве пневматической, гидравлической, медицинской и вакуумной технике.
Кроме того, этот материал широко используется в ракетостроении в качестве
полимерной основы для производства твердого ракетного топлива с порошком
аммиачной селитры в качестве наполнителя.
Цель работы. Получение
синтетического каучука полимеризацией в растворе.
Научная новизна.
Изучена возможность использование растворный полимеризаций для синтеза
эффективные каталитические системы, позволяющие получать стереорегулярные
каучуки СКИ-3 и СКД, который применяется в шинной промышленности.
Каталитические системы Циглера-Натта нашли широкое применение для синтеза
различных эластомеров с широким спектром свойств. Методом растворной
полимеризации с использованием литийорганических соединений, протекающей по
механизму «живых» цепей, получают в промышленности бутадиен-стирольные
термоэластопласты, или статистические сополимеры. Этот метод успешно используется
и при синтезе технически ценных каучуков катионной полимеризацией изобутилена и
его сополимеризацией с изопреном.
1. Литературный обзор
.1 История открытий, обеспечивших создание
технологии СК
В 1825 г. Майкл Фарадей, исследуя пиролиз натурального
каучука, установил, что его простейшая формула C5H8.
В 1835 г. немецкий химик Ф.К. Химмли впервые выделил изопрен C5H8.
В 1866 г. французский химик Пьер Бертло получил бутадиен, пропуская через
нагретую железную трубку смесь этилена и ацетилена.
В 1860-1870-х гг. А.М. Бутлеров выяснил
структуру многих олефинов и многие из них заполимеризовал, в частности
изобутилен под действием серной кислоты.
В 1878 г. русский химик А.А. Кракау открыл
способность полимеризации непредельных соединений под действием щелочных
металлов.
В 1884 г английский химик У. Тилден доказал, что
получал изопрен при термическом разложении скипидара, он же установил состав и
строение изопрена, высказал мысль о том, что склонность изопрена к
полимеризации может быть использована для получена синтетического каучука. В
1870-е гг. французский химик Г. Бушарда выделил из продуктов термического
разложения каучука изопрен, действием на него высокой температуры и соляной
кислоты он получил каучуке образный продукт.
В 1901-1905 гг. В.Н. Ипатьев синтезировал
бутадиен из этилового спирта при высоких 400-500 атмосфернях давлениях. Он же
сумел первым в 1913 г. заполимеризовать этилен, что не удавалось до этого
никому из исследователей.
В 1908 г. М.К. Кучеров получил натрий -
изопреновый каучук (результат опубликовал в 1913 г.).
В 1909 г. С.В. Лебедев впервые продемонстрировал
каучук полученный из дивинила.
Еще в 1899 г И.Л. Кондаков разработал метод
получения диметилбутадиена и доказал, что последний способен превращаться в
каучукоподобное вещество под воздействием света, а также некоторых реагентов,
например натрия. На основе работ Кондакова в Германии в 1916 г. Фриц Гофман
организовал производство т.н. метилкаучука: твёрдого ("Н") и мягкого
("W") синтетического каучука.
В 1910 г Карл Дитрих Гарриес запатентовал способ
полимеризации изопрена под воздействием металлического натрия. Он же в 1902 г.
разработал метод озонирования каучука и этим методом установил строение
различных видов каучуков.
В 1911 г. И.И. Остромысленский получил бутадиен
из ацетальдегида. В 1915 г. Бызов Б.В. получил патент на получение бутадиена
пиролизом нефти.
.2 История создания и развития технологии
синтетического каучука
Начиная еще со второй половины XIX
века, усилия многих химиков разных стран были направлены на изучение способов
получения мономеров и способов их полимеризации в каучукообразные соединения. В
1911 г И. И. Остромысленский предложил получение бутадиена из спирта в три
стадии с выходом 12%. В России эта работа была оценена очень высоко. Дело в
том, что российские химики в противовес западным химикам стремились получить
синтетический каучук из бутадиена, а не изопрена. Возможно, что именно
благодаря этому и наличию в России большой спиртовой базы, в России стало
возможно создание технической базы по производству синтетического каучука.
В 1926 г. ВСНХ СССР объявил конкурс на
разработку технологии получения синтетического каучука, в соответствии с
условиями которого 1 января 1928 г. необходимо было представить описание
процесса и не менее 2 кг каучука полученного по этому способу. Наиболее
разработанными оказались проекты Лебедева С.В. и Бызова Б.В. И в той, и в
другой проектных работах предусматривалось получение синтетического каучука из
бутадиена. Лебедев предлагал получение бутадиена из спирта в одну стадию на разработанном
им катализаторе, обладающим дегидрирующими и дегитратирующими свойствами. Бызов
предлагал получение бутадиена из углеводородов нефти. Несмотря на большие
достижения российских и советских химиков в области переработки нефти, сырьевой
базы для производства бутадиена по методу Бызова не было. Поэтому в январе 1931
года Совет труда и обороны принял решение построить три больших однотипных
завода СК по методу Лебедева. Был создан Ленинградский опытный завод «Литер Б»
(ныне ВНИИСК) на котором в 1931 году была получена первая партия дивинильного
каучука. В 1932-1933 гг. заработали заводы СК в Ярославле, Воронеже, Ефремове,
Казани.
В 1931 г. был пущен завод хлоропренового каучука
в Ереване.
В 1935 г. наступила новая эра в производстве
синтетических каучуков - их стали делать из сополимеров, получаемых радикальной
полимеризацией 1,3-бутадиена в присутствии стирола, акрилонитрила и других
соединений. В 1938 было организовано промышленное производство
бутадиен-стирольных каучуков в Германии, в 1942 - крупное производство
синтетического каучука в США.
Здесь следует отметить, что после 1945 год
наметился постепенный отход от получения бутадиена из пищевого спирта с
постепенным переходом к получению мономеров из нефти.
Каучуки на основе бутадиена и его сополимеров,
решив основную задачу по налаживанию производства покрышек, камер и других
изделий все же не обеспечивали того уровня эксплуатационных свойств, которые
характерны для изделий из натурального каучука. Поэтому поиск путей выхода на
полимеры на основе изопрена не прекращался. В СССР в этой области следует
отметить исследования Ставицкого и Ракитянского по изучению полимеризации
изопрена в присутствии лития, натрия и их органических производных. Полученные
полимеры превосходили по своим эластическим свойствам и прочностью при
растяжении дивинильному каучуку, но все же уступали по показателям натуральному
каучуку.
В 1948 г. Коротков установил, что
физико-механические свойства полимера улучшаются с увеличением содержания
звеньев присоединения в положения цис-1,4, наибольшее количество цис-звеньев
образуется в присутствии литийорганических соединений.
В 1955 г. К. Циглер открыл новые каталитические
системы, ведущие процесс полимеризации по ионному механизму с получением
полимерных материалов, подобных тем, которые получены в присутствии лития. В
дальнейшем эти исследования были углублены в Италии в лаборатории Джулио Натта.
Отечественный промышленный полиизопрен,
полученный на литиевых катализаторах, был назван СКИ, а полученный в
присутствии каталитических систем Циглера-Натта был известен под аббревиатурой
СКИ-3.
В 1956 г. был предложен метод получения
стереорегулярных полибутадиеновых каучуков (СКД), которые по морозостойкости,
устойчивости к истиранию превосходили резины, полученные из натурального
каучука и СКИ-3.
Были получены полимеры на основе двойных
сополимеров этилена и пропилена - СКЭПы (1955-1957). В этих каучуках
отсутствуют двойные связи в структуре полимера, по этой причине резины на их
основе оказываются очень устойчивыми в агрессивных средах, вдобавок они прочны
на истирание.
В 1960-е гг. был освоен промышленный выпуск
каучуков СКД и СКИ-3 в Стерлитамаке, Тольятти, Волжске. В целом все эти
предприятия использовали в качестве исходного сырья мономеры, полученные уже из
нефти, а не из спирта.
Сополимеры бутадиена и изопрена начали быстро
вытеснять натуральный каучук в производстве автомобильных шин. Так, если в 1950
доля К. с. в общем объёме производства натурального и синтетического каучуков
составляла около 22%, в 1960 около 48%, то к 1971 она возросла до ~60% (5 млн.
т синтетического и 3 млн. т натурального каучука), в 1985 г. в мире было
произведено 12 млн т синтетического каучука и только 4 млн т натурального. К
началу 1970-х гг. сложилось мнение, что синтетические каучуки вытеснят
натуральные. Однако в результате нефтяного эмбарго в 1973 г. цены на нефть
резко возросли и одновременно в Малайзии были достигнуты большие успехи в
производстве натурального каучука, позволявшие резко снизить его цену. И по сей
день избавиться от натурального каучука в шинной промышленности не удается.
Так, Японии, не имеющей собственных природных запасов нефти, выгоднее закупать
натуральный каучук в Малайзии и Индонезии. России же, располагающей большими
запасами нефти, ни в коем случае не следует пренебрегать имеющимися
технологиями и мощностями по производству синтетического каучука.
Напряженные разработки в области технологии СК в
СССР и Германии до Второй мировой войны объяснялись тем, что указанные страны
понимали, что в случае войны они будут отрезаны от поставок натурального
каучука. США подходило к вопросу по другому, США стремилось создать у себя
стратегический запас натурального каучука. Как показала жизнь, запасов
оказалось недостаточно, когда Япония вторглась в 1941 г. в Юго-Восточную Азию.
Из уже написанного ясно, что каучук играл важную роль в мировой политике [1].
.3 Производства синтетических каучуков
В промышленности синтез каучуков проводится
полимеризацией мономеров с кратными связями, поликонденсацией
полифункциональных соединений и химической модификацией высокомолекулярных
соединений. Наряду с развитием производства стереорегулярных каучуков СКИ-3 и
СКД успешно развиваются новые направления по созданию высокоэффективных
каучуков с комплексом технически ценных свойств. Одним из таких новых путей является
синтез стереорегулярных ненасыщенных каучуков общего назначения полимеризацией
циклоолефинов с раскрытием кольца. Новым направлением является и синтез
чередующихся, или альтернантные полимеров. Наибольший интерес для
промышленности синтетических каучуков представляют альтернантные сополимеры на
основе бутадиена и пропилена. Металлоорганические катализаторы на основе
соединений цинка или алюминия используются для синтеза каучуков из органических
оксидов путем раскрытия напряженных кислородсодержащих циклов.
Основным методом получения синтетических
каучуков является полимеризация, осуществляемая технологически в массе (блоке),
эмульсии и растворе. В настоящее время традиционная блочная полимеризация,
используемая для получения каучуков типа СКВ, утратила свое значение, уступив
место полимеризации в растворе. Этим методом производят основные типы каучуков
общего назначения и ряд каучуков специального назначения: 1,4-цис-изопреновый
(СКИ-3), 1,4-цис-бутадиеновый (СКД), этилен-пропиленовый (СКЭП) и этилен-пропилен-диеновый
(СКЭПТ), бутилкаучук (БК), статистические сополимеры бутадиена со стиролом
(ДС-СК), бутадиен- (или изопрен-)-стирольные термоэластопласты (ДСТ или ИСТ),
полиизобутилен, цис- или транс-полипентенамеры (ЦПА или ТПА), альтернантные
сополимеры бутадиена с пропиленом (СКБП-А), эпоксидные каучуки (СКПО, СКЭХГ,
СКЭХГ-С), 1,2-полибутадиен (СКД-СР). Полимеризация в растворе может быть
осуществлена в двух вариантах:
1. В применяемом растворителе растворяются
как исходные мономеры, так и образующийся;
2. В растворителе растворяются исходные
мономеры, но не растворяется образующийся полимер, при этом в процессе
полимеризации образуется дисперсия полимера.
Все еще широко используется полимеризация в
эмульсии, этим способом производят бутадиен-стирольные (а-метилстирольные)
каучуки (СКС и СКМС), бутадиен-нитрильные каучуки (СКН), поли-хлоропрен,
фторкаучуки, акрилатные каучуки, эмульсионные каучуки с функциональными
группами, синтетические латексы и некоторые другие каучуки специального
назначения [2].
.4 Получение мономеров для синтетических
каучуков
Важнейшими мономерами для производства каучуков
общего назначения являются бутадиен, изопрен, стирол и а-метил-стирол. Для
производства остальных каучуков специального назначения используются этилен
(этен), пропилен (пропен), алифатические дигалоген - производные,
диорганодихлорсиланы, непредельные фторорга- нические соединения, простые и
сложные олигоэфиры, эфиры акриловой кислоты.
Перспективные для промышленности методы
получения мономеров должны отвечать ряду требований. Главные из них следующие:
) доступность и низкая цена исходного сырья
(ведь 60-70 % от стоимости синтетических каучуков приходится на долю мономера;
) простое оформление технологических процессов;
) низкий расход сырья;
) постоянство качества и высокая чистота
получаемых продуктов.
В настоящее время основные мономеры для
синтетического каучука получают следующими методами.
Бутадиен получают двухстадийным и одностадийным
дегидрированием бутана или бутан содержащих фракций нефтестабилизационных
установок (ЦГФУ), газофракционирующих установок (ГФУ), имеющихся в составе
газобензиновых заводов (ГБЗ) и на нефтеперерабатывающих и нефтехимических
заводах.
Двухстадийное дегидрирование бутана уже давно
освоено на ряде заводов синтетических каучуков, однако затраты на получение
бутадиена этим методом все еще велики. Пути к усовершенствованию метода в
настоящее время видят в поиске более эффективных катализаторов для обеих стадий
дегидрирования и в увеличении производительности реакторов.
На отдельных заводах уже внедрен метод
окислительного дегидрирования н-бутиленов (бутенов) и проводятся работы по
усовершенствованию также внедренного метода одностадийного дегидрирования
бутана под вакуумом. Внедряется процесс выделения бутадиена из пиролизных фракций
С4 с установок пиролиза нефтепродуктов на этилен.
Изопрен получают:
1. дегидрированием изопентана (метилбутана)
или изоамиленов (метилбутенов);
2. из изобутилена и формальдегида через
диметилдиоксан;
. извлечением из пиролизных фракций С5.
Хлоропрен получают двумя способами:
1. димеризацией ацетилена в винилацетилен с
последующим присоединением хлороводорода к винилацетилену;
2. хлорированием бутадиена, с последующей
изомеризацией получаемых хлорорганических продуктов и дегидрохлорированием
выделенного изомера.
Стирол и а-метилстирол получают алкилированием
бензола: для стирола - этиленом, для а-метилстирола - пропиленом (пропеном),
дегидрированием полученных этилбензола и изопропилбензола и последующей
ректификацией продукта дегидрирования - так называемого печного масла.
Изобутилен получают каталитическим
дегидрированием изобутана с применением алюмохромового катализатора. Этот
процесс аналогичен процессам получения н-бутиленов из бутана или изоамиленов из
изопентана. Значительные требования предъявляются к исходному сырью. Особенно
недопустимы заметные примеси изобутилена, так как в процессе дегидрирования
изобутилен частично разлагается с образованием кокса.
Высококонцентрированный изобутилен получают либо
поглощением серной кислотой, либо гидратацией на катион обменных смолах.
Сырье для синтеза мономеров. Производство
мономеров для получения синтетического каучука требует большого расхода
углеводородного сырья (не менее 2 т на 1 т синтетического каучука). Поэтому
важно, чтобы промышленность синтетического каучука была обеспечена на
длительный срок недорогим и качественным сырьем.
Сырьем для синтеза основных мономеров служат
углеводородные и нефтяные газы. К ним относятся природные и попутные газы, газы
стабилизации нефти, нефтезаводские газы и газы деструктивной переработки
нефтепродуктов и др.
.5 Производства синтетических каучуков
полимеризацией в растворе
Преимуществом растворной полимеризации является
возможность использовать для синтеза эффективные каталитические системы,
позволяющие получать стереорегулярные каучуки СКИ-3 и СКД, который применяется
в шинной промышленности. Каталитические системы Циглера-Натта нашли широкое
применение для синтеза различных эластомеров с широким спектром свойств.
Методом растворной полимеризации с использованием литийорганических соединений,
протекающей по механизму «живых» цепей, получают в промышленности
бутадиен-стирольные термоэластопласты, или статистические сополимеры. Этот
метод успешно используется и при синтезе технически ценных каучуков катионной
полимеризацией изобутилена и его сополимеризацией с изопреном.
Технологический процесс полимеризации в растворе
осуществляется по непрерывной схеме, при которой легко отводится теплота,
выделяющаяся в процессе синтеза полимера. Это позволило создать единичные агрегаты
большой мощности, повысить активность и стерео селективность действия
каталитических систем, улучшить технико-экономические показатели процесса
производства растворных каучуков, прежде всего изопренового каучука.
Высокая активность каталитических систем,
используемых в растворной полимеризации, позволяет, в принципе, достигать
высоких конверсий мономеров даже в одном полимеризаторе. Однако значительные
тепловые эффекты, особенно в начальной стадии процесса, высокая вязкость
углеводородных растворов полимеров, протекание побочных процессов, приводящее к
образованию сшитых структур, как правило, требуют проведения процесса в батарее
полимеризаторов. Для выделения растворных каучуков чаще всего используют метод
водной дегазации, а для сушки - червячные машины.
Высокие требования к чистоте исходных мономеров
и растворителя, а также повышенные затраты на регенерацию и транспорт большого
количества растворителя [содержание мономеров в шихте обычно не превышает 25%
масса] удорожают растворные каучуки, однако эти затраты вполне компенсируются
высокими эксплуатационными характеристиками растворных каучуков.
.6 Свойства изоперена и основные методы его
получения
Изопрен один из важнейших мономеров
промышленности синтетический каучук, используется для получения стереорегулярных
изопреновых каучуков и термоэластопластов.
Изопрен является гомологом 1,3-бутадиена, у
которого водород при втором углеродном атоме замещен метильной группой СН3.
При обычных условиях - это легковоспламеняющаяся бесцветная жидкость с
характерным запахом и токсическими свойствами. ПДК изопрена в рабочей зоне 40
мг/м3. Изопрен практически нерастворим в воде, но хорошо растворим в спирте,
эфире и других органических растворителях. Показатели некоторых свойств
изопрена (таблица 1).
Таблица 1 Показатели свойств изопрена
Молекулярная
масса
|
68,11
|
Плотность
г/см3
|
0,681
|
Температура,
°С
|
|
Кипения
|
34,07
|
Плавления
|
-146,7
|
Вспышка
|
-48
|
Самовоспламенения
|
400
|
Теплота,
кДж/моль
|
|
Испарения
|
28,1
|
Полимеризация
|
75,0
|
Концентрационные
пределы при воспламенения паров в смеси с воздухом, % (по объему)
|
1,7-11,5
|
Наличие сопряженной системы двойных связей в
молекуле изопрена определяет ряд его свойств, общих с бутадиеном, в частности
способность к полимеризации. Изопрен при хранении подвержен окислению и
полимеризации. В контакте с кислородом воздуха он образует пероксиды. При
длительном хранении и перед транспортировкой в изопрен вводят ингибитор
(гидрохинон, трет-бутил пирокатехин и др.), а емкости (цистерны) продувают
инертным газом.
Хотя уже давно известно, что изопрен является
основным звеном для построения макромолекул натурального каучука, однако лишь в
последние десятилетия научились синтезировать из изопрена каучук, по комплексу
свойств близкий к натуральному. До организации промышленного производства
стереорегулярного изопренового каучука изопрен использовался в промышленности
синтетического каучука в незначительных количествах. За последние годы были
созданы крупные промышленные производства изопрена. Из большого числа способов
получения изопрена до стадии промышленной реализации доведены следующие:
) из изобутилена и формальдегида;
) двухстадийное дегидрирование
изопентана;
) дегидрирование изоамиленов;
) димеризация пропилена;
) извлечение изопрена из фракции С5 пиролиза
жидких
нефтепродуктов
) из ацетилена и ацетона
В отечественной промышленности применяются пока
только 1, 2 и 5 методы.
Одним из решающих факторов при определении
перспективности того или иного метода синтеза изопрена является наличие
ресурсов и стоимость используемого сырья.
Получение изопрен дегидрированием изопентана.
Метод дегидрирования изопентана (метилбутана) представляет большой интерес,
поскольку сейчас имеются довольно большие ресурсы пентана.
Процесс дегидрирования может быть осуществлен по
одно и двухстадийной схеме.
Сырье для дегидрирование процесса получают либо
в виде пентановой фракции, выделяемой из прямогонного бензина, либо в виде
изопентановой фракции, поступающей с ЦГФУ, либо же в виде изопентан -
изоамиленовой фракции бензина каталитического крекинга.
Процесс получения изопрена двухстадийным
дегидрированием изопентана включает следующие основные операции:
) подготовка и очистка сырья;
) дегидрирование изопентана в изоамилены;
) выделение изопентан-изоамиленовой
фракции;
) разделение изопентан-изоамиленовой
фракции;
) дегидрирование изоамиленов в изопрен;
) разделение изоамилен-изопреновой
фракции;
) концентрирование и очистка
изопрена-сырца.
Подготовка и очистка сырья. Изопентан может быть
получен изомеризацией пентана.
Пентан С5Н12 - бесцветная
легковоспламеняющаяся жидкость. Изопентан - легковоспламеняющаяся жидкость.
Изомеризация пентана в изопентан может быть
представлена уравнением
Процесс проводится в вертикальном цилиндрическом
реакторе с неподвижным слоем гранулированного катализатора в паровой фазе, в
присутствии водорода, циркулирующего в системе. Основные показатели процесса
изомеризации приведены ниже (табл.2)
Таблица 2 Основные показатели процесса
изомеризации
Температура,
°С
|
350-450
|
Давление,
МПа
|
2-4
|
Объемная
скорость подачи жидкого сырья,ч-1
|
1,0
|
Отношение
водород : пентан, моль/моль
|
3:1
|
Массовая
конверсия пентана за 1 проход, %
|
50-60
|
Массовый
выход изопентана на прореагировавший пентан, %
|
90-96
|
Принципиальная схема процесса изомеризации
пентана в изопентан приведена на рисунке 1.
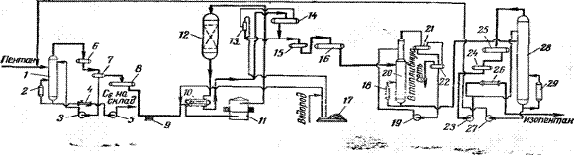
Рисунок 1. Принципиальная схема
процесса изомеризации пентана в изопентан.
Жидкая фракция пентана поступает в
колонну 1 для отделения от тяжелых углеводородов, которые в виде кубовой
жидкости после холодильника 4 насосом 5 откачиваются на склад. Погон колонны 1
- жидкий пентан - поступает в дефлегматор 6 и сливается в сборник 7. Часть
пентана из сборника 7 подается насосом 3 в виде флегмы на колонну 1, а часть
поступает в сборник 8. Жидкий пентан из сборника 8 подается насосом высокого
давления 9 через теплообменник 10 и трубчатую печь 11 в реактор 12. Перед
теплообменником 10 пентан смешивается с циркулирующим газом, содержащим около
85% водорода.. В теплообменнике пентан испаряется, его пары в печи 11
нагреваются до 450°С. Часть пентана (50-60%), проходя сверху вниз через слой
катализатора в реакторе 12, превращается в изопентан.
Реакционный газ из нижней части
реактора 12 охлаждается в теплообменнике 10 и конденсаторе 14 до 40° С, после
чего конденсат разделяется в сепараторе на две фазы: жидкость и
несконденсированный газ. Газ возвращается на смешение с исходной пентановой
фракцией, а жидкость, состоящая из изопентана и н-пентана, поступает в емкость
16. За счет снижения давления в емкости до 1,5-1,6 МПа происходит
дополнительная отдувка газа, а жидкость подвергается двухступенчатой
ректификации в колоннах 20 и 28. В колонне 20 смесь стабилизируется за счет
отгонки легких углеводородов С3 и С4, направляемых в
топливную сеть завода. Кубовая жидкость колонны 20 поступает в колонну 28 и
разделяется на изопентан (верхний продукт) и возвращаемый в цикл (на
изомеризацию) пентан (кубовая жидкость). Изопентан с массовым содержанием
основного продукта 95% через конденсатор 25 поступает в сборник 24, откуда
насосом 23 частично подается на колонну 28 в виде флегмы и частично через
холодильник 26 на склад. Пентан из куба колонны 28 насосом 27 возвращается на
изомеризацию.
Основным аппаратом в данном процессе
является реактор изомеризации. Это вертикальный цилиндрический аппарат
диаметром 2,8 м и высотой около 5,0 м. В его нижней части имеются решетки для
катализатора.
Каталитическое дегидрирование
изопентана в изоамилены. При дегидрировании изопентана протекают различные
реакции. Целевой реакцией является превращение изопентана в смесь трех
изоамиленов (метилбутенов):
При дегидрировании изопентана кроме
основной реакции протекают побочные реакции с образованием легких углеводородов
(С1-С4), тяжелых углеводородов (С6 и выше),
оксида и диоксида углерода и кокса, а также реакции изомеризации. В связи с
этим фракция С5, получаемая из контактного газа, является сложной
смесью углеводородов: трех изоамиленов, изопентана, пентана, амиленов, цис- и
транс-пиперилена, изопрена, циклопентадиена и др. Поэтому выделение из такой
фракции чистых изоамиленов весьма сложно. Поскольку реакция дегидрирования
обратима, то степень превращения изопентана в изоамилены зависит от температуры
реакции.
Изучение различных катализаторов и
вариантов аппаратурного оформления процесса дегидрирования изопентана в
изоамилены привело к заключению, что наиболее выгодным является дегидрирование
изопентана в кипящем слое алюмохромового пылевидного катализатора ИМ-2201. В
связи с этим принципиальная схема дегидрирования изопентана практически не
отличается от схемы дегидрирования бутана в н-бутилены ( рисунок 2).
Рисунок 2. Схема непрерывного
дегидрирования углеводородов на пылевидном катализаторе: 1 - испаритель; 2 -
сепаратор с перегревателем; 3 - печь; 4, 5 - емкости; 6 - воздуходувки; 7 -
топка; 8, 10 - холодильники; 9 - тарельчатый скруббер; 11
сборник; 12 - флорентийский сосуд; 13 - сепаратор; 14, 23 - бункеры; 15, 21- паросборники;
16, 20 - котлы-утилизаторы; 17 - реактор; 18 - закалочный
змеевик; 19 - регенератор; 22 - электрофильтр; 24 - сборник; катализаторной
пыли.
Выделение изопентан-изомиленовой
фракции. Контактный газ, полученный после дегидрирования изопентана и охлажденный
при давлении 0,12 МПа в скруббере до 45 °С, поступает в компрессор,
где при избыточном давлении 0,4 МПа и температуре 35 °С сжижается и
направляется на абсорбцию. Абсорбер орошается тяжелой углеводородной фракцией
(С6 и выше). Неабсорбированный газ (абгаз), состоящий из метана и
водорода, отводится в топливную сеть завода. Насыщенный фракцией С5
абсорбент поступает на десорбционную колонну для выделения фракции С5
в виде погона. Фракция С5 при избыточном давлении 0,3 МПа и
температуре 40-50 °С подвергается ректификации на трех колоннах. Погоном
последней из них является очищенная фракция С5, кубовым остатком -
фракция тяжелых углеводородов (С6 и выше), направляемая на склад.
Разделение изопентан-изоамиленовой
фракции. Разделение изопентан-изоамиленовой фракции производится методом
экстрактивной дистилляции с безводным ДМФА. Принципиальная схема этого процесса
приведена на рисунке 3.
Изопентан-изоамиленовая фракция,
выделенная из контактного газа после дегидрирования изопентана, а также
возвратная изоамиленовая фракция с установки разделения изоамилен-изопреновой
фракции через теплообменники 1, обогреваемые горячим ДМФА из кубовой части
десорбера 5, поступают на экстрактивную дистилляцию с безводным ДМФА
(содержание воды не более 0,5%).
Рисунок 3. Схема разделения
изопентан-изоамиленовой фракции с безводным ДМФА: 1-теплообменник; 2, 3-
колонны экстрактивной дистилляции; 4 - холодильник для ДМФА; 5 - десорбционная
колонна; 6 - емкость для ДМФА; 7 - колонна регенерации ДМФА.
Возвратные (рецикловые) изоамилены
направляются на экстрактивную дистилляцию для вывода изопентана со второй
стадии дегидрирования во избежание его накопления в системе. Экстрактивная
дистилляция проводится в колоннах 2 и 3. Из верхней части колонны 3 отбирается
возвратная изопентановая фракция, содержащая не более 5% примесей изоамиленов,
н-пентана и амиленов, которая после азеотропной осушки поступает на повторное
дегидрирование. Из нижней части колонны 3 ДМФА, частично насыщенный изоамиленами,
направляется в колонну 2, где происходит его окончательное насыщение
изоамиленами. Из нижней части колонны 2 ДМФА с массовым содержанием
углеводородов С5 около 6% поступает на десорбционную колонну 5, в
которой из ДМФА отгоняются изоамилены, содержащие до 5% изопентана. Погон из
колонны 5 после конденсации и охлаждения поступает на склад и на вторую стадию
дегидрирования. Снизу колонны 5 отходит горячий ДМФА, освобожденный от
изоамиленов. Он направляется для обогрева теплообменников 1 и через емкость 6 в
холодильник 4, после которого поступает в верхнюю часть колонны 3 на поглощение
изоамиленов.
В связи с тем, что циркулирующий в
системе ДМФА постепенно загрязняется полимерами и смолами, производят его
регенерацию в двух последовательных колоннах 7. С верха первой колонны
отбираются легкие углеводороды, с верха второй колонны, работающей под
вакуумом, отбирается ДМФА, поступающий в емкость 6, а снизу - тяжелые
углеводороды.
Обогрев колонн 7 производится
паровым конденсатом. Подпитка системы товарным ДМФА осуществляется путем подачи
его со склада на установку регенерации, так как он может содержать
нежелательные примеси.
Дегидрирование изоамиленов в
изопрен. Полученные при дегидрировании изопентана изоамилены на второй стадии
дегидрирования образуют изопрен:
Тепловой эффект данной
эндотермической реакции зависит в основном от структуры исходного изомера и
частично от температуры дегидрирования.
Процесс дегидрирования изоамиленов в
изопрен по технологическому оформлению и применяемым катализаторам не имеет
существенных отличий от процесса дегидрирования м-бутиленов в бутадиен. Для
получения удовлетворительных выходов изопрена процесс осуществляется в
присутствии катализаторов при низком парциальном давлении изоамиленов и высокой
температуре. Для снижения парциального давления изоамиленов процесс проводят
при разбавлении большим количеством водяного пара, который одновременно
является теплоносителем и уменьшает образование кокса на катализаторе.
Катализатор подвергается периодической регенерации паровоздушной смесью для
выжигания кокса и восстановления начальной активности. Параметры процесса
охарактеризованы в таблице 3.
Таблица 3. Параметры процесса
дегидрирования изоамиленов в изопрен при использовании различных катализаторов
Показатели
|
К-16У
|
ИМ-2204
|
Температура
Дегидрирования Регенерации, не более Объемная скорость подачи сырья, ч-1
Разбавление водяным паром, моль : моль Продолжительность Дегидрирования
Регенерации Массовый выход изопрена, % На пропущенное сырье На разложенное
сырье Срок службы катализатора, ч
|
580-640
700 600 1:17 4-12 ч
1 ч 16-20 74-80 -
|
580-620
700 600-700 1:20 5-15
мин 5-15 мин 34 85 8000
|
Ввиду значительного отложения кокса при
дегидрировании, а также для повышения эффективности процесса при использовании
катализатора ИМ-2204 цикл контактирования сокращен до 15 мин. Полный цикл
работы реактора длится 30 мин.
Для дегидрирования изоамиленов в изопрен
применяются реакторы высотой до 2,2 м с неподвижным слоем катализатора.
При работе на катализаторе ИМ-2204 агрегат
дегидрирования состоит из одной двух поточной печи, двух реакторов и двух
котлов-утилизаторов. Перегретые в печи до 530 °С пары изоамиленов перед
поступлением в один из реакторов смешиваются с перегретым в той же печи до 780
°С водяным паром и проходят через слой катализатора сверху вниз. Контактный газ
из реактора поступает в котел-утилизатор, где за счет его охлаждения в
межтрубном пространстве из конденсата получается водяной пар, используемый на
производстве.
После 15-минутного контактирования следует
регенерация катализатора. Для этого подача сырья в реактор прекращается и
реактор продувается паром в линию регенерации для удаления из системы
углеводородов. После продувки паром в реактор подается для регенерации смесь
воздуха с перегретым паром. Объемная скорость подачи воздуха на регенерацию 120
ч-1. По окончании регенерации реактор продувается от воздуха паром в
линию регенерации, после чего снова начинается цикл дегидрирования.
Разделение изоамилен-изопреновой фракции.
Получаемая при дегидрировании изоамиленов изоамилен-изопреновая фракция
содержит помимо изоамиленов и изопрена также изопентан, пентан, м-амилены,
пиперилен, циклспентадиен, углеводороды фракций С2-С3, С6
и выше, ацетиленовые. В связи с близостью температур кипения этих углеводородов
разделение этой фракции обычной ректификацией невозможно. Поэтому для выделения
изопрена и возвратной изоамиленовой фракции, а также для вывода примесей,
отрицательно влияющих на полимеризацию изопрена и качество стереорегулярного
изопренового каучука, применяется двухступенчатая экстрактивная дистилляция с
ДМФА в сочетании с последующей ректификацией получаемого изопрена-сырца.
Применение двухступенчатой экстрактивной дистилляции исключает дополнительную
очистку изопрена-сырца от циклопентадиена и ацетиленовых соединений, так как
они удаляются из изопрена в процессе дистилляции.
Преимущества и недостатки метода. При получении
изопрена из изопентана методом двухстадийного дегидрирования расход изопентана
на 1 т изопрена-ректификата составляет около-2,0-2,4 т.
Главным достоинством метода получения изопрена
двухстадийным дегидрированием изопентана является использование дешевого,
доступного сырья. Недостатки данного метода: многостадийность, большой расход
сырья и энергосредств, сложность очистки изопрена-сырца от нежелательных
примесей, (циклопеопентадиена, карбонильных и ацетиленовых соединений и др.).
Кроме того, образующийся в качестве побочного продукта пиперилен (около 10% от
количества изопрена) не нашел до настоящего времени рационального использования.
.7 Стереоспецифической полимеризации изопрена
При полимеризации изопрена можно, в зависимости
от порядка раскрытия двойных связей, получить звенья четырех типов:
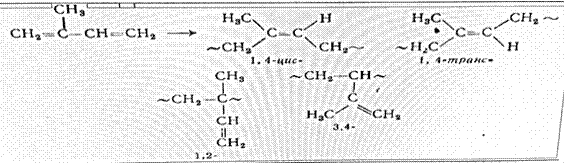
В полимерах из цис-1,4- или
транс-1,4-звеньев вероятно присоединение молекул изопрена «голова к хвосту» (C1-С4),
«голова к голове» (С1-С4) или «хвост к хвосту» (С4-С4);
3,4- или 1,2-полиизопрены могут иметь другое расположение боковых заместителей,
что приводит к получению полимеров нерегулярной структуры. Микроструктура
полиизопренов оказывает решающее влияние на свойства резин на их основе. При
содержании в полимерах до 60% 1,2- и 3,4-звеньев прочность и эластичность
ненаполненных вулканизатов очень малы. При 100%-ном содержании этих звеньев и
каучук и резины из него сильно закристаллизованы. Для цис-1,4-полиизопрена
небольшое содержание структурных неоднородностей сильно влияет на скорость
кристаллизации полимера.
Для исследования микроструктуры
стереорегулярных полимеров используются инфракрасные и магнитнорезонансные
спектры полимеров.
Содержание цис-1,4-звеньев
определяется в основном типом катализатора, применяемого для полимеризации
изопрена. Так, применение циглеровских (на основе тетрахлорида титана и
алюминийалкилов) катализаторов позволяет получить полиизопрен, содержащий до
98% цис-1,4-звеньев, соединенных по принципу «голова к хвосту», с
физико-механическими свойствами близкими к свойствам натурального каучука.
Следует указать, что в натуральный каучук практически 100% цис-1,4-звеньев
соединены по принципу «голова к хвосту». При полимеризации на литий алкильных
катализаторах полимер содержит до 93% цис-1,4-звеньев и по ряду показателей
уступает натуральному каучука. Свойства вулканизатов полиизопрена, и
натурального каучука сравнивается в таблицу 4.
Таблица 4. Сравнивание свойства
вулканизатов полиизопрена и натурального каучука
Показатели
|
Температура,
°С
|
Вулканизат
|
|
|
СКИ
|
НК
|
СКИ
|
НК
|
|
|
иеиаполиенный
|
С
50% технического углерода
|
Условная
прочность при растяжении, Мпа
|
20
100
|
29-32
19-23
|
30-32
20-22
|
25-30
19-20
|
31
21
|
Относительное
удлинение при разрыве, %
|
20
100
|
750-850
850-950
|
750-800
800-900
|
520-570
570-780
|
550
600
|
Сопротивление
раздиру, кН/м
|
20
100
|
-
-
|
-
-
|
100-130
70-75
|
136
60
|
Эластичностью
по отскоку, %
|
20
100
|
66-69
78-80
|
70-72
78-81
|
37-39
52-54
|
40
58
|
|
|
|
|
|
|
|
Вопрос о полной замене натурального каучука
синтетическим цис-1,4-полиизопреном в шинной и резиновой промышленности важно.
Дело в том, что по ряду показателей, таких как когезионная прочность,
клейкость, скорость и глубина кристаллизации СКИ-3 пока еще уступает
натуральному каучуку. Различия в свойствах СКИ-3 и натурального каучука
объясняются некоторыми особенностями их молекулярного строения. Основными их
характеристиками-являются микроструктура полимера, средняя молекулярная масса,
молекулярно-массовое распределение.
Микроструктура СКИ-3 имеет следующие отличия от
микроструктуры натурального каучука: натуральный каучук содержит 94%
полиизопрена и 6% не каучуковых веществ, а СКИ-3 содержит практически 100%
каучукового углеводорода. Кроме того, натуральный каучук содержит полярные
функциональные группы, которые оказывают положительное влияние на его свойства.
Более совершенная микроструктура натуральный каучук оказывает положительное
влияние на некоторые свойства резиновых изделий из натуральных каучуков. Сейчас
проводятся исследования по достижению резинами на основе СКИ-3 качеств, которые
делали бы их полностью равноценными резинам на основе натурального каучука.
Полиизопрен с широким молекулярно-массовым
распределением обладает лучшими технологическими свойствами. Несмотря на
указанную (в таблице 3) разницу в свойствах между натуральным каучуком и
полиизопреном, последний по сумме технологических и физико-механических свойств
можно считать полноценным заменителем натурального каучука. Полиизопрен,
полученный на катализаторах Циглера - Натта, во многих случаях может полностью
заменить натурального каучука в шинной промышленности и производстве
резинотехнических изделий.
1.8 Влияние основных технологических факторов на
структуру и свойства цис-1,4 полиизопрена
Строение и свойства цис-1,4-полиизопрена и
скорость полимеризации зависят от состава катализатора и содержащихся в нем
примесей, наличия примесей в изопрене-ректификате и в растворителе, а также от
температуры полимеризации и условий выделения каучука из полимеризата.
Каталитическая система. Максимальный выход
полимера получается при строго эквимолекулярном соотношении алюминия и титана.
При соотношении А1:Ti > 1 наряду с цис-1,4-полиизопреном образуются
олигомеры - циклические и линейные димеры изопрена, что приводит к снижению
прочности и эластичности вулканизатов.
Приготовление каталитического комплекса является
одной из важнейших стадий процесса, в значительной степени определяющей
скорость полимеризации и структуру получаемого каучука. Образование комплекса
протекает с высокой скоростью, связано с выделением большого количества теплоты
и сопровождается рядом побочных процессов.
Большое влияние на свойства каучука оказывает
чистота исходных компонентов каталитического комплекса. В TiCl4
недопустимо присутствие даже следов НСl,
ТЮСl2,
ССl4,
SiCl4
и VОСl3.
Должен применяться только свежеперегнанный без доступа воздуха TiCl4.
Кислород и вода также разрушают катализатор,
поэтому их содержание в техническом азоте, используемом на всех стадиях
производства каучука СКИ-3, строго регламентируется: массовое содержание
кислорода не должно превышать 0,05%, влаги- 0,001%.
Наиболее сильным ядом для «титанового»
катализатора является циклопентадиен. При его содержании 1,5-10~3 моль/л
катализатор разрушается полностью. На полимеризацию сильно влияют также азот-,
кислород- и серосодержащие соединения. Присутствие диметилформамида или бутилмеркаптана
заметно уменьшают скорость полимеризации и содержание цис-1,4-звеньев в
полиизопрене. К каталитическим ядам откосятся также ацетиленовые и аленовые
углеводороды. Ввиду указанного содержание этих ядов в катализаторе, изопрене,
бутадиене и растворителе строго регламентируется. Допустимое массовое
содержание вредных примесей в изопрене колеблется от 0,002 до 0,0005%, а в
бутадиене от 0,001 до 0,0001%. В растворителе предельно допустимое содержание
примесей (в) следующее: Карбонильные соединения 0,001 %, Пероксидные соединения
0,0005 %, Хлориды 0,0005 %, Азотистые соединения 0,0005 %, Органические и
неорганические кислоты отсутствует.
Растворитель. Полимеризацию изопрена проводят в
инертном растворителе - это необходимо для поддержания системы в жидком
состоянии, облегчения осаждения системы и выделения полученного полимера.
В качестве растворителей используют
алифатические и ароматические соединения, хорошо растворяющие образующийся
полимер, такие как гептан, гексан, циклогексан, бензол. Природа растворителя не
влияет на структуру каучука, но скорость полимеризации и глубина превращения
зависят от скорости растворения полимера в растворителе. Наиболее высокая
скорость полимеризации наблюдается при применении бензола и изопентана.
Наличие воды приводит не только к разрушению
катализатора, но и к нарушению соотношения компонентов каталитического
комплекса и к ухудшению качества каучука. Поэтому при стереорегулярной
полимеризации необходимо возможно более полное устранение воды из реакционной
среды.
Качество мономера. Заметные количества
циклопентадиена в изопрене и растворителе сильно тормозят полимеризацию. Другие
перечисленные выше примеси также уменьшают скорость полимеризации, снижают
содержание в полимере цис-1,4-звеньев, молекулярную массу полиизопрена и
ухудшают качество получаемого каучука.
Температура полимеризации. Реакция полимеризации
изопрена экзотермично, ее можно представить уравнением
nC5H8
> - (C5H8)n
+
75 КДж/моль
Поэтому кроме катализатора и примесей на
скорость полимеризации изопрена и микроструктуру получаемого каучука большое
влияние оказывает температура процесса. Одной из нежелательных побочных реакций
при полимеризации изопрена на комплексных катализаторах Циглера -Натта является
образование высококипящих олигомеров, которые практически невозможно полностью
удалить из полимеризата принятыми в настоящее время методами дегазации.
Оставаясь в каучуках, олигомеры придают им неприятный запах и ухудшают
физикомеханические свойства вулканизатов. Выход олигомеров возрастает с
повышением температуры полимеризации.
Оптимальная температура полимеризации, при
которой образуется минимальное количество олигомеров, составляет 20 °С. Однако
при такой температуре резко снижается скорость реакции. Поэтому на практике
полимеризацию проводят при 25-40 °С и даже немного выше.
Прочие факторы. Скорость полимеризации
пропорциональна концентрации мономера и катализатора в растворе и температуре
процесса. Температура и концентрация мономера в растворе влияют также на
молекулярную массу получаемого полимера: с понижением температуры реакции и
повышением концентрации мономера молекулярная масса каучука повышается. Степень
конверсии мономера не оказывает заметного влияния на свойства СКИ-3.
Процесс получения цис-полиизопрена состоит из
следующих основных стадий:
. полимеризация изопрена;
. дезактивация катализатора, стабилизация
полимера и отмывка полимеризата;
. выделение полимера из полимеризата
(водная дегазация);
. обезвоживание и сушка каучука.
Дополнительными стадиями являются приготовление
каталитического комплекса и регенерация растворителя.
Полимеризация изопрена. Полимеризацию изопрена
проводят непрерывно в батарее из четырех - шести последовательно соединенных
полимеризаторов, причем в первых двух поддерживается температура 25- 30 °С, в
последних 35-40 °С. Реакция полимеризации начинается сразу же после добавления
в полимеризационную шихту катализатора. Ввиду экзотермичности реакции для
получения каучука хорошего качества необходим эффективный отвод теплоты в
условиях высоковязкой реакционной среды. Теплоту реакции отводят путем подачи
охлажденного рассола в рубашки полимеризаторов при непрерывном перемешивании
содержимого полимеризаторов.
Так как образующийся полимер все время
растворяется в растворе, реакционная среда постепенно становится все более
вязкой. При содержании в полимеризате более 10 % полимера перемешивание
затруднено, и это ухудшает отвод теплоты реакции. Вязкость полимеризата зависит
не только от концентрации полимера, но и от его средней молекулярной массы, а
также от типа растворителя. Этот показатель очень важен для аппаратурного
оформления всех стадий процесса получения полиизопрена. От вязкости
полимеризата зависит также скорость и полнота процессов дезактивации и
стабилизации полимера и производительность водной дегазации полимеризата.
При проведении полимеризации содержание мономера
в шихте составляет 12-15%, конверсия мономера 85-90 %• При такой конверсии
полимеризация длится примерно 2-3 ч. Вязкость полимеризата, выходящего из
последнего аппарата и содержащего до 12% полимера, составляет около 3000-4000
МПа-с. Подача шихты и каталитического комплекса на полимеризацию, а также
рассола в рубашки полимеризаторов регулируется автоматически.
Ввиду большой вязкости полимеризата и
необходимости эффективного отвода теплоты, выделяемой при реакции,
полимеризаторы (автоклавы) для полимеризации в растворах должны обладать
достаточной поверхностью охлаждения и иметь устройство для очистки всей
внутренней поверхности от налипающей пленки полимера. Полимеризаторы,
используемые в производстве эмульсионных каучуков, для полимеризации в
растворах непригодны.
Автоклав для высоковязких растворов, применяемый
в отечественной промышленности (рисунок 4), представляет собой вертикальный
цилиндрический аппарат, снабженный рубашкой и спиралевидной мешалкой с
лопастями и скребками, обеспечивающими непрерывное перемешивание и очистку от
полимера всей внутренней поверхности аппарата.
Рисунок 4. Автоклав для полимеризации в
растворах: 1 - вал; 2 - ленточная мешалка; 3 - скребки; 4 - мотор с редуктором;
5 -предохранительное устройство с мембраной; 6 - корпус; 7 - рубашка.
Таблица 5 Краткая характеристика автоклава
Объем,
м3
|
16
|
Площадь
поверхности рубашки, м2
|
45
|
Диаметр,
м
|
2,2
|
Общая
высота, м
|
6,0
|
Частота
вращения мешалки, об/мин
|
30
|
Мощность
мотора, кВт
|
25
|
Расчетная
давления, МПа
|
1,6
|
Корпус, крышка и мешалки, соприкасающиеся с
полимеризатом, изготовлены из нержавеющей стали.
Принципиальная схема получения цис-полиизопрена
приведена на рисунке 5. Охлажденный до -20 °С раствор изопрена поступает в
емкость для приема шихты 1. Шихта и раствор каталитического комплекса
дозировочным насосом 2 подаются в первый из батареи последовательно включенных
полимеризаторов 3. Охлаждение полимеризаторов и регулирование температуры полимеризации
можно осуществлять за счет изменения массы подаваемого рассола в рубашки
полимеризаторов, изменения температуры шихты, поступающей на полимеризацию, и
режима подачи катализатора.
Переток раствора полимера из первого в
последующие по ходу процесса полимеризаторы 3 осуществляется за счет
постепенного уменьшения давления в реакторах.
Дезактивация катализатора, стабилизация полимера
и отмывка полимеризата. По достижении требуемой глубины конверсии изопрена
необходимо дезактивировать катализатор, содержащийся в полимеризате. Для
дезактивации катализатора можно использовать спирты, кислоты, амины и другие
соединения, реагирующие с компонентами каталитического комплекса с образованием
водорастворимых соединений.
Из соображений экономики и эффективности, а
также возможности регенерации дезактиватора из промывной воды в производстве
СКИ-3 в качестве стоппера применяют метиловый или этиловый спирт. Эта стадия
также показана на рисунке 5.
Рисунок 5. Схема получение цис-1,4-полиизопрена:
1 - емкость для приема шихты; 2- дозировочный насос; 3 - полимеризаторы; 4, 8,
13. 17, 20 - насосы; 5 - емкость для метанолотолуольиой смеси; 6,7 - аппараты
для приготовления раствора стабилизатора; 9 - смеситель; 10 ~ отмывая колонна;
11, 21 - конденсаторы; 12 - учредительная емкость; 14 - крошкообразователи; 15
- дегазатор; 16 -емкость для антиагломератора; 18 - отпорная колонна; 19 -
емкость для сбора крошки: 22 - сепаратор.
Раствор дезактиватора готовят смешением метанола
с толуолом в емкости 5, затем насосом 4 смесь подается в аппарат 6. Поскольку
полиизопрен обладает высокой реакционной способностью и в нем имеются примеси
металлов переменной валентности (железа, меди), ускоряющие окислительную
деструкцию, полиизопрен необходимо стабилизировать.
Эффективными стабилизаторами СКИ-3 являются
соединения аминного и фенольного типов. На новых заводах синтетического каучука
применяют смесь 0,5% неозона Д (нафтама-2, фенил-β-нафтиламина)
и 0,5% ДФФД (N1N-дифенил-n-фенилендиамина).
Для получения светлых марок каучука используется ионол (2,6-ди-трет-бутил-4-метилфенол).
Хорошая растворимость стабилизаторов при 40 °С в
дезактиваторе (смеси метанола в толуоле) позволяет совместить дезактивацию
каталитического комплекса и стабилизацию каучука.
В аппаратах 6 и 7 при перемешивании и подогреве
до-40 °С готовят раствор стабилизаторов в дезактиваторе.
Из аппарата 7 готовый раствор стабилизаторов в
дезактиваторе поступает в дозировочный насос 2, а затем - в нижнюю часть
смесителя 9, снабженного Z-образной двух вальной мешалкой. Туда же поступает
одновременно и полимеризат из последнего работающего в батарее полимеризатора
3. В смесителе 9 происходит одновременно разрушение каталитического комплекса и
стабилизация полимера. Удаление из полимеризата разрушенного катализатора и
метанола производится водной экстракцией в отмывочной колонне 10, орошаемой
водой. Отмывку полимеризата производят непосредственно после разрушения
катализатора, так как при хранении не отмытого полимеризата происходит
структурирование полимера. Промывные воды из аппарата 10 направляют на
регенерацию метанола. Отмытый полимеризат из колонны 10 поступает в усреднитель
12. Во избежание потерь паров углеводородов над аппаратом 12 установлен
конденсатор 11, охлаждаемый водой. Конденсат из-аппарата 11 возвращается в
аппарат 12.
Выделение полимера из полимеризата. Выделение
полимера, незаполимеризованного изопрена и растворителя осуществляется в
процессе водной дегазации полимеризата, при которой выделяющийся в виде крошки
полимер дополнительно отмывается. Так как содержание растворителя в
полимеризате значительно превышает содержание незаполимеризованного изопрена,
дегазацию проводят, пока массовое содержание растворителя в каучуке не
уменьшится до 0,5%, что практически исключает присутствие свободного мономера.
Процесс дегазации включает несколько стадий:
эмульгирование отмытого полимеризата водой и паром, введение анти-агломератора,
образование крошки каучука, отгонку растворителя и незаполимеризовавшегося
изопрена - рисунок 5.
Процесс водной дегазации проводят непрерывно в
одну или две ступени. Для предотвращения слипания крошки каучука в отмытый
полимеризат в дегазаторе вводят антиагломератор. В качестве антиагломераторов
можно применять гидроксиды (например, Zn(OH)2), соли жирных кислот
(стеарат кальция) и другие. Дегазацию обычно осуществляют в противотоке острого
водяного пара и дегазируемой крошки каучука в виде дисперсии ее в воде.
Из усреднителя 12 полимеризат насосом 13
подается в крошкообразователи 14, куда для образования крошки каучука подается
острый пар и умягченная вода. Крошка каучука из аппарата 14 и крошка,
увлекаемая парами из дегазатора 15 в отпорную колонну 18 и в емкость 19,
поступает в верхнюю часть дегазатора 15. На дегазацию вместе с полимеризатом
подается также насосом 17 из емкости 16 суспензия антиагломератор а в воде.
Пары растворителя и незаполимеризованного
изопрена, отгоняемые из дегазатора 15, вместе с парами воды поступают сначала в
отпарную колонну 18, а затем в межтрубное пространство конденсатора 21. Там под
небольшим давлением с помощью захоложенной воды происходит конденсация паров
растворителя, изопрена и воды и частичное разделение конденсата на два слоя.
Верхний - масляный слой, состоящий из углеводородов, поступает на окончательную
сепарацию в аппарат 22; нижний - водный слой вместе с нижним слоем из
сепаратора 22 направляется на регенерацию растворенных в нем углеводородов.
Полученная пульпа каучука из аппарата 15
поступает на обезвоживание и сушку.
Обезвоживание и сушка каучука. Пульпа каучука,
получающаяся при водной дегазации и содержащая около 5% каучука, после
предварительного обезвоживания (концентрирования) на виброситах,
вакуум-фильтрах или одно червячном шнековом прессе может быть окончательно
высушена в трехходовой конвейерной сушилке, обогреваемой горячим воздухом
(100-110°С).
В настоящее время в производстве
стереорегулярных каучуков обезвоживание и сушку пульпы каучуков производят
главным образом в экспеллерно-экспандерных (двух шнековых) агрегатах. Эти
агрегаты позволяют увеличить степень механизации и автоматизации процесса
обезвоживания и сушки при одновременном улучшении однородности и качества
каучука. Кроме того, процесс обезвоживания и сушки каучука на двух шнековом
агрегате значительно рентабельней предварительного обезвоживания каучука с
последующей сушкой его в конвейерных сушилках.
Схема обезвоживания и сушки пульпы каучука на
двух шнековом агрегате приведена на рисунке 6.
Рисунок 6. Схема обезвоживания и сушки пульпы
каучука на двухшнековом агрегате: 1 - сборник; 2 - насос; 3 - концентратор
пульпы; 4 - транспортер для подачи пульпы; 5 - экспеллер; 6 - экспандер; 7 -
камера для дополнительной осушки каучука; 8 - калорифер; 9, 11 - горизонтальные
транспортеры; 10 - спиральный вибро подъемник; 12 - вибропитатель; 13 -
загрузочный бункер; 14 - брикетировочный пресс.
После водной дегазации полимеризата пульпа
поступает в концентратор 3, где крошка отделяется от основной массы воды. Вода
сливается в сборник 1 и насосом 2 частично направляется в химзагрязненные
стоки, а частично возвращается в аппарат 3. Крошка каучука, содержащая около
50% влаги, после аппарата 3 шнековым транспортером подается в экспеллер 5, где
отжимается основная масса воды, стекающей в сборник 1. Экспеллер представляет
собой одно червячный шнековый пресс, заключенный внутри фильтрующего цилиндра.
Привод шнека работает от мотора через редуктор.
После экспеллера крошка каучука с влажностью не
более 10% поступает в экспандер 6, где происходит окончательная до сушка
каучука.
Каучук, выходящий из головки экспандера 6 с
остаточной влажностью 0,5-1,0%, поступает на горизонтальный вибротранспортер 9,
заключенный в специальную камеру. В камеру под вибротранспортер подают нагретый
до 140 °С воздух, который после насыщения водяным паром и парами органических
соединений направляют на сжигание. Продукты сгорания выводят в атмосферу.
Горячий воздух досушивает каучук до содержания в нем 0,5% влаги.
Высушенная крошка каучука вибротранспортером 9
подается в зону охлаждения и при температуре 40-50 °С поступает на спиральный
виброподъемник 10. Здесь ее обдувает горячий воздух для удаления влаги с
наружной поверхности. Сухая крошка горизонтальным вибротранспортером 11 и
вибропитателем 12 подается сначала в загрузочный бункер 13 автоматических весов
и далее в брикетированной пресс 14. Брикеты СКИ-3 массой 25-30 кг ленточным
транспортером подают в металлодетектор, где происходит отбраковка брикетов
каучука с включениями железа, затем автоматически заворачивают в полиэтиленовую
пленку (два слоя) и направляют на склад.
Важнейшие узлы агрегата - экспеллер и экспандер
- изображены на отдельных рисунках.
Экспеллер (рисунок 7) снабжен подающим и
разгрузочным конвейерами. Скорость движения шнека питающего конвейера можно
регулировать. Экспеллер работает непрерывно. Обезвоживание каучука происходит
за счет сжатия его шнеком 3, вращающимся внутри фильтрующего цилиндра 2 со
щелями. При изменении размера выпускного отверстия 1 или скорости подачи
каучука изменяется давление шнека на каучук и степень его обезвоживания. Фильтрат
стекает через штуцер. Шнек и фильтр изготавливают из нержавеющей стали, корпус
- из углеродистой стали.
Рисунок 7. Экспеллер для предварительного
обезвоживания крошки каучука: 1- выпускное отверстие; 2 - фильтрующий цилиндр;
3 -шнек; 4 - питающий бункер; 5 -коробка передач.
Экспандер (рисунок 8) представляет собой
горизонтальный шнек 2 с переменным шагом винта, вращающийся в стальном цилиндре
без отверстий 1. Винтами 3 регулируют степень сжатия каучука. Крошка каучука,
проходя по экспандеру в глубь цилиндра, где шаг винта постепенно уменьшается,
сжимается до 5,0 МПа и нагревается вместе с содержащейся в ней водой до 150 °С.
Несмотря на высокую температуру, влага не может испариться и находится в массе
каучука в перегретом состоянии. Для уменьшения потерь теплоты при работе корпус
шнека снабжен рубашкой, обогреваемой паром. При выходе из головки экспандера
вода из каучука мгновенно испаряется за счет дросселирования давления до
атмосферного. Продолжительность пребывания каучука в экспандере около 2 мин,
поэтому структурирования каучука не происходит.
Детали экспандера, соприкасающиеся с каучуком,
изготовлены из нержавеющей стали, остальные части - из углеродистой стали.
Рисунок 8. Шнековый вал экспандера: 1 -стальной
цилиндр; 2-шнек; 3 - винты для регулирования степени сжатии каучука.
В последние годы на заводах синтетического
каучука кроме двух шнековых агрегатов для обезвоживания и сушки каучуков
производительностью до 4 т/ч были установлены агрегаты удвоенной
производительности (до 8 т/ч).
.9 Применение
Изопреновые каучуки, являющиеся каучуками общего
назначения, применяются вместо натурального как самостоятельно, так и в
сочетании с другими эластомерами при изготовлении практически всех резиновых
изделий: шин, разнообразных резинотехнических изделий (транспортерные ленты,
рукава, формовые детали и др.), резиновой обуви. Изопреновые каучуки,
содержащие неокрашивающееся и нетоксичные стабилизаторы (СКИ-3НП), применяют
для изготовления медицинских изделий, резин, контактирующих с пищевыми
продуктами, и изделий широкого потребления (игрушки, мячи и т.д.). Изопреновые
каучуки СКИ-3Д используют в кабельной промышленности для изготовления
электроизоляционных резин, каучук СКИ-3В предназначен для вакуумной техники. На
основе СКИ-3 получают изопреновый латекс и эбониты.
Кроме каучуков, содержащих преимущественно
1,4-цис-звенья, в нашей стране и за рубежом производится 1,4-транс-полиизопрен.
Его синтез осуществляется также полимеризацией изопрена в растворителе на
катализаторах Циглера-Натта. В качестве переходного металла в состав таких
катализаторов чаще всего используется ванадий.
Отечественный транс-полиизопрен выпускается под
торговой маркой СГ, его зарубежным аналогом является канадий полимер,
полисар-Х-414, а природными аналогами - гуттаперча и балата. В отличие от
природных полимеров, синтетические имеют более высокую молекулярную массу и
требует пластикации, они содержат определенное количество гелия. Основное
назначение 1,4-транс-полиизопрена использование в качестве термопластичного
материала в ортопедии и восстановительной хирургии (отечественный материал
поливок), а также в качестве клеев для различных материалов.
Основными потребителями каучука являются шинная
промышленность и производство различных резинотехнических изделий. Ассортимент
выпускаемых в нашей стране резиновых изделий превышает 100 тыс. наименований.
Для комплектации одного современного автомобиля в среднем необходимо 300-500
резиновых изделий (автомашина КамАЗ имеет 800 комплектующих резиновых изделий).
Один самолет содержит 10-2 тыс., а морское судно - до 30 тыс. резиновых
изделий. Для автомобиля средней грузоподъемности около 30 % от себестоимости
составляет удельная стоимость шин, а за время работы машины комплект шин
меняется 5-6 раз. Отсюда становится понятным, какое внимание сегодня следует
уделять повышению качества и работоспособности резиновых изделий.
Мировые мощности по производству изопренового
каучука достигли 1,3 млн. т/год [3].
синтетический каучук полимеризация
нефть
2. Технологическая часть
.1 Физико-химические характеристики нефти
месторождения Карачаганак
Район Карачаганака, открытого в 1988 года,
перспективен на нефтегазонакопление. В настоящее время месторождение
разрабатывается на газоконденсат и природный газ. Продуктивные горизонты
залегают на глубинах более чем 3700 м (пермские в интервале 3700-4500 м,
каменноугольные - 4500-5300 м). Этажи продуктивности достигают 850 м и более.
Коллекторами являются каменноугольные и нижнепермские известняки. По данным
геофизических исследований и лабораторных определений, открытая пористость
карбонатных коллекторов составляет 2-10 %, а в отдельных интервалах - 14 % и
более. Пластовое давление 505 атм. Пластовая температура на глубине 3937 м
достигает 95 °С, на глубине 4050 м - 98 °С.
Приток газа составляет от 26 до 954 тыс. м3/сут,
конденсата - от 22 до 1300 мᶟ/сут. Выход
сырого конденсата колеблется от 416 до 992 см3/м3,
достигая иногда 2108 см3/м3, плотность конденсата
0,623-0,792, в конденсате содержится до 6 % сероводорода и 1-2 % углекислого
газа. Извлекаемые запасы газа конденсата по категории A+B+Ciсоставляет
189,22 млн т. Состав газа и конденсата при режиме сепарации при Р=90 атм., Т=15
°С приведен в таблице1. Плотность газа при этом равнялась 0,888 г/л, конденсата
- 0,623 г/см3.
Таблица 6 Состав газа и конденсата, %
Компоненты
|
Газ
|
Конденсат
|
Сероводород
|
3,26
|
2,29
|
Азот
|
0,73
|
0,07
|
Углекислый
газ
|
4,87
|
0,85
|
Метан
|
86,78
|
2,74
|
Этан
|
5,50
|
3,37
|
Пропан
|
1,78
|
6,66
|
Изобутан
|
0,26
|
2,07
|
0,43
|
5,71
|
Изопентан
|
0,15
|
4,64
|
к-Пентан
|
0,13
|
5,41
|
Гексан
|
0,03
|
14,02
|
Гептан
|
-
|
18,67
|
Октан
|
-
|
11,80
|
Нонан
|
-
|
15,00
|
Декан
|
-
|
6,7
|
Таблица 7 Состав пластового газа, %
|
Скважина
№ 2
|
|
Компоненты
|
3777-3797
м
|
4114-4126
м
|
4154-4343
м
|
Газ
сепарации
|
|
|
1
|
2
|
1
|
2
|
1
|
2
|
|
|
СН4
|
74,60
|
26,41
|
72,62
|
16,45
|
73,80
|
20,35
|
78,96-80,86
|
|
С2Н6
|
6,43
|
5,15
|
5,57
|
6,85
|
6,40
|
5,35
|
5,4-6,54
'
|
|
С3Н8
|
2,46
|
5,93
|
2,96
|
6,30
|
2,60
|
4,85
|
2,13-2,68
|
|
изо-C4H1O
|
0,49
|
1,80
|
0,62
|
1,49
|
0,46
|
1,48
|
0,32-0,52
|
|
н-С4Н10
|
0,86
|
4,30
|
1,28
|
2,89
|
0,91
|
3,46
|
0,54-1,10
|
|
изо-С5Н12
|
-
|
-
|
-
|
-
|
-
|
-
|
0,17-0,32
|
|
н-С5Н12
|
5,36
|
59,48
|
6,41
|
57,6
|
7,18
|
56,82
|
0,13-0,21
|
|
С6
+ высшие
|
-
|
-
|
-
|
-
|
-
|
-
|
0,07-0,26
|
|
N2
|
0,59
|
0,06
|
1,0
|
0,37
|
0,71
|
-
|
0,64-1,17
|
|
С02
|
5,82
|
3,78
|
5,44
|
3,13
|
5,28
|
2,89
|
5,6-6,0
|
|
Н2
|
3,30
|
3,09
|
4,01
|
4,92
|
3,66
|
4,80
|
3,42-3,91
|
|
Всего
|
100,00
|
100,00
|
100,00
|
100,00
|
100,00
|
100,00
|
100
- 100
|
|
Скважина
№ 1
|
Скважина
№ 19
|
4427-4543
м
|
4734-4762,
|
4698-4728
м
|
Газ
сепарации
|
4870-4965
м
|
Газ
сепарации
|
1
|
2
|
1
|
1
2
|
|
1
|
2
|
|
71,85
|
21,59
|
70,38
|
19,70
|
80,47-79,40
|
67,96
|
17,82
|
79,40
|
6,59
|
5,76
|
6,32
|
6,72
|
5,56-6,40
|
6,24
|
5,55
|
6,40
|
3,24
|
6,81
|
2,78
|
7,88
|
2,63-2,04
|
3,06
|
7,54
|
2,04
|
0,77
|
2,08
|
0,57
|
1,73
|
0,55-0,33
|
0,72
|
2,45
|
0,33
|
1,38
|
4,33
|
0,98
|
3,59
|
0,88-0,69
|
1,46
|
4,80
|
0,69
|
-
|
-
|
-
|
-
|
0,08-0,07
|
-
|
-
|
-
|
7,62
|
50,88
|
8,57
|
52,11
|
0,06-0,05
|
10,26
|
54,96
|
0,05
|
-
|
-
|
-
|
-
|
0,04
|
-
|
-
|
-
|
0,67
|
0,31
|
0,60
|
0,30
|
0,73-0,71
|
0,63
|
0,27
|
0,71
|
5,20
|
2,94
|
6,32
|
3,89
|
5,60-6,90
|
6,24
|
3,36
|
6,90
|
3,68
|
5,30
|
3,48
|
4,08
|
3,40-3,41
|
3,39
|
3,35
|
3,41
|
100,00
|
100,00
|
100,00
|
100,00
|
100,00-100,00
|
100,00
|
100,00
|
100,00
|
|
|
|
|
|
|
|
|
|
|
|
|
|
|
|
|
|
Примечание. 1 - пластовый газ, 2 - сырой
конденсат.
При давлении сепарации 80 атм. температура +5
°С, температура и начала кипения конденсата 36 °С. Фракционный состав следующий
(°С): н. к.-36; 10
% - 93; 20 % - 116; 30 % - 137; 40 % -162;
50%-94; 60 % - 230 ; 70 % - 267; 80 % - 285.
Результаты исследований на газоконденсатность
приведены в таблице8. Исследования проводились на большой сепарационной
установке с производительностью 2 млн м3/сут по газу и 1400 м3/сут
по жидкости. Рабочее давление 10 мПа, температура 44 °С.
Физико-химические характеристики и потенциальное
содержание фракций в нефти даны в табл. 11-14.
Таблица 8 Характеристика бензиновых фракций,
выкипающих до 200°С, нефти из скважины № 15
Температураpa
отбора, °С
|
Выход,
%
|
|
Фракционный
состав, °С, при
|
Кислотность,
мг КОН на 100 мл
|
Содержание
|
|
|
|
н.
к.
|
10
|
50
|
90
|
98
|
|
|
Н.
к,-62
|
3,25
|
0,6495
|
-
|
-
|
-
|
-
|
-
|
2,16
|
0,003
|
Н.
к.-85
|
8,3
|
0,6692
|
-
|
-
|
-
|
-
|
-
|
-
|
-
|
Н.
к,-100
|
12,5
|
0,6818
|
30
|
45
|
80
|
98
|
102
|
2,18
|
0,012
|
Н.
к.-120
|
18,1
|
0,6994
|
50
|
65
|
90
|
115
|
120
|
-
|
-
|
Н.
к,-150
|
25,6
|
0,7058
|
50
|
74
|
100
|
135
|
155
|
2,74
|
0,024
|
Н.
к,-180
|
33,1
|
0,7303
|
55
|
75
|
125
|
164
|
182
|
-
|
-
|
Н.
к,-200
|
37,5
|
0,7366
|
60
|
90
|
135
|
190
|
194
|
6,66
|
0,024
|
Таблица 9 Потенциальное содержание фракций в
нефти
Температура
выкипания, °С
|
Выход
на нефть, %
|
|
фракции
|
суммарный
|
н.
к.-62
|
3,25
|
3,25
|
62-95
|
7,6
|
10,85
|
95-122
|
10,6
|
.
21,46
|
122-150
|
7,4
|
28,86
|
150-200
|
11,90
|
40,75
|
200-280
|
54,20
|
280-350
|
8,75
|
62,95
|
350-400
|
10,0
|
72,95
|
400-450
|
9,02
|
81,97
|
Выше
450
|
18,03
|
100
|
Таблица 10 Характеристики керосиновых
дистиллятов
Температура
выкипания, °С
|
Выход
на нефть, %
|
|
Фракционный
состав, °С, при
|
Вязкость,
мм2/с, при
|
Температура,
°С
|
Содержание
серы, %
|
Анилиновая
точка, °С
|
Высота
некоптящей пламени,
|
|
|
|
н.к.
|
10%
|
50
%
|
20°С
|
50°С
|
помутнения
|
застывания
|
вспышки
|
|
|
|
Нефть
из скважины № 14
|
150-280
|
21,5
|
0,8079
|
150
|
188
|
205
|
2,06
|
1,28
|
|
-60
|
66
|
0,507
|
73
|
21,8
|
150-320
|
28,3
|
0,8177
|
160
|
190
|
235
|
2,67
|
1,55
|
-42
|
-50
|
80
|
0,562
|
67
|
20,3
|
Нефть
из скважины № 15
|
150-280
|
26,9
|
0,7930
|
150
|
164
|
188
|
1,62
|
1,06
|
-55
|
-60
|
55
|
0,065
|
60
|
24
|
Таблица 11 Физико-химические характеристики
нефти
Показатели
|
Скважина
|
Скважина
|
Скважина
|
Скважина
|
Скважина
|
|
№
13
|
№
14
|
№
15
|
№
20
|
№29
|
Глубина
перфорации, м
|
5202-5207
|
5120-5170
|
5647-5754
|
5007-5023
|
5164-5174
|
|
0,8495
|
0,8456
|
0,8036
|
0,8160
|
o,86sq
|
Вязкость
при 20 °С, мм2/с
|
12,10
|
18,59
|
3,59
|
5,16
|
94,5
|
Температура
застывания, °С
|
-20
|
-28
|
-15
|
-24
|
2
|
Содержание,
%:
|
|
|
|
|
|
силикагелевых
смол
|
8,85
|
3,38
|
1,17
|
2,2
|
9,02
|
асфальтенов
|
0,70
|
1,3
|
Сл.
|
0,06
|
0,93
|
Серы
|
1,2
|
0,86
|
0,46
|
0,87
|
1,0
|
Азота
|
-
|
0,41
|
0,41
|
-
|
0,62
|
Содержание
парафина, %
|
6,96
|
4,97
|
5,2
|
6,2
|
7,44
|
Температура
его плавления, °С
|
49
|
46
|
46
|
48
|
56
|
Коксуемость,
%
|
2,9
|
1.6
|
0,47
|
0,83
|
3,3
1
|
Кислотное
число, мг КОН на 1 г
|
0,174
|
0,058
|
0,027
|
0,054
|
0,024
1
|
Выход
светлых фракций, %:
|
|
|
|
|
|
до
200 "С
|
28,8
|
24,0
|
40,75
|
36,7
|
22,0
1
|
до
350 °С
|
55,0
|
49,0
|
61,3
|
64,2
|
39,5
1
|
Таблица 12 Физико-химические характеристики
бензиновых фракций
Температура
отбора,. °С
|
Выход
на нефть, %
|
|
|
Содержание
углеводородов, %
|
|
|
|
|
I
ароматических
|
нафтеновых
|
парафиновых
|
|
|
|
|
|
|
суммарное
|
нормального
строения
|
изостроения
|
Нефть
из скважины № 15
|
Н.
к,-62
|
3,25
|
0,6495
|
1,3787
|
-
|
7,59
|
92,41
|
9,38
|
я
3.0
|
62-95
|
7,60
|
0,6962
|
1,3962
|
7,5
|
13,9
|
78,6
|
9,5
|
69,1
|
95-122
|
10,62
|
0,7363
|
1,4132
|
15,6
|
13,5
|
70,9
|
5,21
|
65
Л
|
122-150
|
7,40
|
0,7578
|
1,4252
|
23,94
|
13,69
|
62,37
|
2,90
|
59,4
|
150-200
|
11,90
|
0,7737
|
1,4392
|
31,68
|
10,25
|
58,07
|
7,91
|
50,1
|
Н.
к,-200
|
40,75
|
0,7366
|
1,4194
|
15,74
|
11,79
|
72,47
|
6,98
|
6.1.4
|
Нефть
из скважины № 14
|
Н.
к.-62
|
1,2
|
0,6776
|
1,3840
|
|
11,3
|
88,7
|
88,7
|
|
62-95
|
3,8
|
0,6864
|
1,3940
|
8,6
|
17,8
|
73,6
|
73,6
|
|
95-122
|
4,5
|
0,7255
|
1,4085
|
12,6
|
21,9
|
65,5
|
65,5
|
|
122-150
|
6,5
|
0,7542
|
1,4230
|
20,2
|
19,1
|
60,7
|
60,7
|
|
150-200
|
9,0
|
0,7804
|
1,4380
|
26,3
|
22,1
|
51,6
|
51,6
|
|
Таблица 13 Характеристика легких керосиновых
дистиллятов
Температура
отбора, °С J
|
Выход
на нефть, %
|
|
Фракционный
состав °С, при
|
 , мм2/сТемп-ра
°ССодержание серы. %Высота некоптящего пламени, ммКислотность, мг КОН на 100
мл
|
|
|
|
|
|
|
|
н.к.
|
10
|
50
|
90
|
|
вспышки
в закрытом тигле
|
начала
кристаллизации
|
общей
|
меркаптановой
|
|
|
Нефть
из скважины № 14
|
120-230
|
20,0
|
0,7762
|
120
|
130
|
166
|
210
|
2,00
|
28
|
-70
|
0,277
|
0,003
|
28,5
|
|
120-290
|
29,0
|
0,7972
|
120
|
140
|
200
|
265
|
-
'
|
35
|
-55
|
-
|
0,0031
|
23,8
|
-
|
Нефть
из скважины № 20
|
120-230
|
27,0
|
0,7832
|
120
|
129
|
160
|
190
|
1,31
|
29
|
-60
|
0,43
|
-
|
27
|
|
120-240
|
29,1
|
0,7856
|
120
|
160
|
180
|
225
|
1,37
|
30
|
-60
|
0,44
|
-
|
26
|
-
|
120-342
|
0,8110
|
-
|
-
|
-
|
-
|
2,45
|
-
|
-55
|
0,58
|
-
|
21
|
-
|
Нефть
из скважины № 15
|
120-240
|
27,5
|
0,7766
|
120
|
160
|
175
|
210
|
1,21
|
30
|
-70
|
0,020
|
0,0018
|
28
|
5,5
|
150-250
|
21,6
|
0,7848
|
150
|
166
|
183
|
215
|
1,25
|
50
|
-59
|
0,021
|
0,0025
|
26
|
6,0
|
150-320
|
31,9
|
0,8024
|
150
|
189
|
230
|
280
|
2,28
|
60
|
-
|
0,076
|
-
|
22
|
6,3
|
|
|
|
|
|
|
|
|
|
|
|
|
|
|
|
|
|
|
|
Таблица 14 Потенциальное содержание базовых
масел в нефти
Температура
отбора фракций, °С
|
М
|
Выход
на нефть, %
|
|
Вязкость,
мм2/с, при
|
ИВ
|
|
Температура
застывания, °С
|
|
|
|
|
50°С
|
100°С
|
|
|
|
Нефть
из скважины № 14
|
350-450
|
263
|
13,80
|
0,8797
|
8,41
|
2,94
|
122
|
1,4902
|
-22
|
450
|
489
|
7,41
|
0,8892
|
70,8
|
13,45
|
112
|
1,4802
|
-19
|
Нефть
из скважины № 15
|
350-450
|
243
|
16,13
|
0,8680
|
6,40
|
2,41
.
|
133
|
1,4838
|
-25
|
450
|
334
|
9,8
|
0,8620
|
24,97
|
6,97
|
139
|
1,4740
|
-23
|
Нефть
из скважины № 29
|
350-400
|
247
|
7,29
|
0,8829
|
5,27
|
2,15
|
107
|
1,4912
|
-23
|
400-450
|
303
|
8,62
|
0,8948
|
13,66
|
4,04
|
111
|
1,4959
|
-21
|
Таблица 15 Характеристика дизельных дистиллятов
Температура,
отбора, °С
|
Выход
на нефть, %
|
|
Вязкость,
мм2/с, при
|
Температура,
°С
|
|
|
|
20°С
|
50°С
|
Помутнения
|
застывания
|
Вспышки
|
|
Нефть
скважины № 14
|
180-350
|
1
|
28,4
|
0,8291
|
3,40
|
1,85
.
|
-25
|
-36
|
82
|
200-320
|
2
|
19,3
|
0,8307
|
3,92
|
2,13
|
-25
|
-34
|
93
|
200-350
|
3
|
25,0
|
0,8355
|
4,32
|
2,35
|
-22
|
-31
|
96
|
230-350
|
4
|
20,0
|
0,8385
|
4,55
|
2,38
|
-18
|
-29
|
100
|
|
Нефть
скважины № 15
|
|
180-350
|
5
|
28,15
|
0,8096
|
2,84
|
1,68
|
-32
|
|
85
|
200-320
|
6
|
20,0
|
0,8141
|
3,12
|
1,72
|
-27'
|
-35
|
90
|
200-350
|
7
|
23,75
|
0,8148
|
3,16
|
1,81
|
-27
|
-34
|
95
|
250-350
|
8
|
13,75
|
0,8166
|
3,32
|
1,91
|
-24
|
-32
|
100
|
М
|
Фракционный
состав, °С, при
|
Анилиновая
точка, °С
|
Содержание
серы, %
|
Дизельный
индекс
|
Кислотность
мг КОН на 100 мл
|
|
н.к.
|
10
%
|
50
%
|
90
%
|
|
|
|
|
Нефть
скважины № 14
|
1
|
187
|
180
|
222
|
255
|
300
|
68
|
|
593
|
_
|
2
|
192
|
200
|
232
|
255
|
290
|
70
|
-
|
60,2
|
-
|
3
|
205
|
200
|
242
|
268
|
308
|
72
|
-
|
60.0
|
-
|
4
|
202
|
210
|
245
|
267
|
320
|
73
|
-
.
|
59,7
|
-
|
Нефть
скважины № 15
|
5
|
191
|
180
|
220
|
237
|
285
|
66
|
0,02
|
63
|
.
-.
|
6
|
202
|
200
|
226
|
245
|
275
|
67
|
0.082
|
64
|
|
7
|
204
|
200
|
.
226
|
246
|
285
|
69
|
0.087
|
65
|
6,9
|
8
|
208
|
245
|
252
|
27S
|
285
|
76
|
0,088:
|
69
|
7.2
|
|
|
|
|
|
|
|
|
|
|
|
|
|
|
|
|
|
|
|
|
|
|
Наиболее тяжелой и вязкой является нефть из
скважины, № 29. Нефть из девонских отложений (скв. № 15, интервал перфорации
5647-5754 м) по своим характеристикам существенно отличается от нефтей других
горизонтов. Она маловязкая, легкая, малосмолистая, низкозастывающая,
парафинистая, малосернистая, в ней высоко потенциальное содержание фракций до
350 °С. Основу углеводородного состава широкой бензиновой . фракции н. к.-200
°С составляют парафинистые углеводороды. Легкие фракции нефтей из скважин №
14,15 (н. к,- 120 °С, н. к:-150 °С) по своим показателям, кроме кислотности,
могут служить прямогонными компонентами авиа- и автобензинов.
Фракции н. к,-180°С и н. к. -200°С после
соответствующей очистки могут служить в качестве растворителей для лакокрасочной
промышленности.
Фракция реактивного топлива (120-240°С) нефти из
скважины № 15 имеет низкую температуру начала кристаллизации, обладает хорошими
фотометрическими свойствами, малосернистая, однако из-за малой вязкости и
низкой плотности не отвечает требованиям ГОСТа 10227-62 на реактивное топливо.
Керосиновые фракции из нефти других скважин
содержат повышенное количество общей серы, не соответствующее требованиям
ГОСТа. По остальным физико-химическим характеристикам они отвечают, требованиям
ГОСТа 10227-86 на реактивное топливо ТС-1 или РТ или требованиям ГОСТа 305-82 в
качестве прямогонных компонентов зимних дизельных топлив марки 3, при
необходимости - требованиям ГОСТа 4753-68 на осветительный керосин 30.20.
Таблица 16 Физико-химическая характеристика
масляных дистиллятов и базовых масел (скв. № 15)
Показатели
|
Фракция
350-450 °С
|
Фракция
450 °С
|
|
1
|
2
|
1
|
2
|
Выход
на нефть, %
|
18,75
|
15,73
|
18,3
|
9,8
|
|
0,8379
|
0,8680
'
|
0,8978
|
0,86'
|
Молекулярная
масса
|
320
|
243
|
584
|
354
|
Вязкость,
мм2/с, при:
|
|
50
°С
|
7,13
|
6,40
|
173,5
|
24,9'
|
100
°С
|
3,50
|
2,41
|
38,0
|
6,97
|
Индекс
вязкости
|
-
|
133
|
-
|
139
|
Температура
застывания, °С
|
0
|
-25
|
40
|
-23
|
Содержание
серы, мае. %
|
0,69
|
0,85
|
0,96
|
0,2*
|
|
|
|
|
состав,
%:
|
|
СП
|
71,7
|
56
|
-
|
60,'»
|
Сн
|
23,15
|
27
|
-
|
37,1
|
СА
|
9,62
|
17
|
-
|
1,91
|
Кп
|
0,90
|
1,44
|
-
|
0,81
|
Кн
|
0,63
|
0,93
|
-
|
0,7
1
|
Ко
|
0,275
|
0,51
|
-
|
0',0К
|
Примечание. 1 - исходная фракция, 2 - базовое
масло.
Дизельные дистилляты нефти (скв. № 14) сернистые
и низко застывающие. Фракция 180-350°С по основным характеристикам отвечает
требованиям ГОСТа 305-82 на зимнее топливо. Остальные дизельные дистилляты
могут быть использованы как летнее дизельное топливо после соответствующей
очистки (содержание серы более 0,5 % и завышенная кислотность 5 %). Из числа
аналогичных дистиллятом нефти (скв. № 20) фракция 200-320°С отвечает
требованиям на зимнее топливо, а другие могут быть использованы, согласно ГОСТу
305-82, в качестве летнего дизельного топлива. Значительно отличаются дизельные
дистилляты из нефти скважины № 15, они малосернистые, имеют низкую температуру
застывания. По основным физико-химическим характеристикам (вязкости, температур
застывания, фракционному составу и др.) фракции 200-320°С, 200-350°С отвечают
требованиям холодной климатической зоны, а фракций 240-350°С - на летнее
дизельное топливо для дизелей общего назначения.
Таблица 17 Характеристика остатков нефти
Остаток,
°С, выше
|
Выход
на нефть, %
|
|
Вязкость,
мм2/с, при
|
М
|
Температура,
|
Содержание
серы, %
|
Коксуемость,
%
|
|
|
|
50°С
|
80°С
|
|
засгывания
|
вспышки
|
|
|
Нефть
из скважины № 15
|
240
|
52,7
|
0,8603
|
12,17
|
5,43
|
282
|
9
|
120
|
0,71
|
О,1'1
|
280
|
45,8
|
0,8699
|
15,23
|
6,47
|
302
|
14
|
145
|
0,80
|
0,с
|
320
|
40,6
|
0,8736
|
26,83
|
10,57
|
331
|
17
|
160
|
0,82
|
0,7<>
|
350
|
27,05
|
0,8771
|
41,33
|
14,67
|
396
|
20
|
185
|
0,86
|
«с
|
400
|
27,05
|
0,8856
|
62,28
|
19,22
|
502
|
25
|
215
|
0,94
|
1
|
450
|
18,3
|
0,8978
|
173,5
|
38,90
|
584
|
40
|
262
|
0,96
|
2
|
Нефть
из скважины № 14
|
200
|
73,5
|
0,8840
|
17,8
|
7,7
|
289
|
-12
|
130
|
|
2,7
|
280
|
61,0
|
0,9091
|
38,98
|
13,88
|
311
|
-5
|
165
|
1,16
|
2,8
|
320
|
54,2
|
0,9150
|
67,83
|
20,46
|
347
|
10
|
180
|
-
|
2,9
|
350
|
48,5
|
0,9163
|
71,15
|
23,36
|
439
|
15
|
200
|
1,03
|
3,1
|
400
|
40,0
|
0,9322
|
145,60
|
36,98
|
483
|
20
|
230
|
1,35
|
3,6
|
450
|
31,5
|
0,9436
|
404,22
|
77,30
|
530
|
24
|
245
|
1,15
|
4,6
|
Таблица 18 Групповой углеводородный состав
выкипающих и остаточных фракций
Температура
отбора, °С
|
Содержание
углеводородов, %
|
Промежуточные
фракции и смолы, %
|
|
парафино-нафтеновых
|
ароматических
|
|
|
|
I
группы
|
II
и III
группа
|
IV
группы
|
всего
|
|
Нефть
из скважины № 29
|
200-250
|
84,5
-
|
10,0
|
4,7
|
-
|
14,7
|
0,8
|
250-300
|
80,1
|
4,9
.
|
14,3
|
-
|
19,2
|
0,7
|
300-350
|
79,1
|
8,3
|
10,4
|
-
|
18,7
|
1,6
|
350-400
|
67,04
|
6,2
|
19,89
|
5,87
|
31,96
|
1,0
|
400-450
|
64,43
|
4,68
|
15,98
|
14,10
|
34,76
|
0,81
|
Остаток
выше 450
|
46,06
|
4,14
|
19,74
|
18,06
|
41,94
|
12,0
|
Нефть
из скважины № 15
|
200-250
|
89,6
|
9,2
|
0,3
|
-
|
9,5
|
0,9
|
250-300
|
88,9
|
8,2
|
2,8
|
-
|
11,0
|
0,1
|
300-350
|
86,4
|
7,6
|
5,4
|
-
|
13,0
|
0,6
|
350-450
|
74,82
|
5,18
|
19,33
|
-
|
24,51
|
0,67
|
Остаток
выше 450
|
69,71
|
4,22
|
24,87
|
0,98
|
30,07
|
0,22
|
|
|
|
|
|
|
|
|
|
|
|
|
|
Карбамидной депарафинизацией из фракций 200-320
°С и 200 > 350 °С могут быть получены компоненты арктического дизельного
топлива, при этом выход парафинов составляет 9,3-9,8 %. Исследовании показали,
что жидкие парафины состоят из н-алканов С11-C16.
Вакуумный дистиллят маловязкий (см. 16.). Парафино-нафтеновые
углеводороды в нем составляют 74,8, ароматические - 24,51 % значительная часть
последних приходится на углеводороды II и III гр (19,33 %).
Остаточные базовые масла характеризуются
высокими индекс вязкости (смотреть таблицу 16). Остатки нефти имеют малую
плотность и коксуемость, но довольно высокую температуру застывания [4].
.2 Шифр нефти месторождения
Классификация нефти является базой, которая
позволяет предопределить ассортимент и качество продуктов, подобрать наилучшие
условия переработки тех или иных нефти. С того момента, как добыча нефти и ее
переработка вышли на промышленный уровень, классификация нефти претерпевала
изменения и дополнения. Химическая классификация основана на групповом составе
нефтей. По этой классификации различают следующие нефти: метановая; нафтеновая;
метано-нафтеновая; ароматическая; метано-нафтено-ароматическая;
нафтено-ароматическая. Существует промышленная классификация, основанная на
плотности нефти. В этой классификации выделяют 3 типа нефти: легкие, чья плотность
ниже 0,878 г/см3; утяжеленные - от 0,878 до 0,884 г/см3;
тяжелые - выше 0,884 г/см3
Широкое распространение имела также
технологическая классификация нефти. Согласно этой классификации нефть
подразделяется на три класса по содержанию серы (I<II<III), три типа по
выходу фракций, прогоняющихся до 350С (Т1>Т2>Т3), четыре группы по
потенциальному содержанию базовых масел (М1>М2>М3>М4), две подгруппы
по индексу вязкости (И1>И2) и три вида по содержанию твердого парафина
(П1<П2<П3). В целом нефть характеризуется шифром, составляемым
последовательно из обозначения класса, типа, группы, подгруппы и вида, которым
соответствует данная нефть.
Изучив физико-химические свойства нефти
месторождения Карачаганак, были сделаны следующие выводы:
По содержанию серы: до 2% сернистая. По выходу
светлых фракций, пере прогоняющихся до 3500С: 40%. По потенциальному содержанию
базовых масел: 13,8%. В зависимости от значения индекса вязкости (ИВ) базовых
масел: 121. По содержанию твердых алканов (парафинов): 6,96 %.
Таблица 19 Шифр нефти месторождения Карачаганак
Класс
|
Тип
|
Группа
|
Подгруппа
|
Вид
|
II
|
T2
|
M₄
|
И3
|
П3
|
2%
|
40%
|
13,8%
|
121%
|
6,96
|
.3 Описание поточный схема переработки нефти
месторождения Карачаганак
С учетом
физико-химических свойств нефти Карачаганак предложен топливный вариант
переработки.
Сырая нефть в
количестве 5 млн. т/год направляется на установку электрообессоливания и
обезвоживания, где под действием электрического тока происходит отделение воды,
солей и механических примесей, с последующим разделением на
атмосферно-вакуумной трубчатке.
Газоконденсат направляется для разделение на ГФУ
предельных. Из установки ГФУ предельных пентан направляется на изомеризацию.
При изомеризации пентана получаем изопентан, который является сырьем установки
дегидрирование. Полученный изопрен направляем на полимеризацию, который
продуктом является изопреновый каучук.
Бензиновая фракция направляется на гидроочистку
и после на установку каталический риформинг.
Керосиновая фракция 180-240°С, очищенная на
установке гидроочистки, соответствуют ГОСТу на осветительный керосин. Дизельная
фракция из установки гидроочистки из-за повышенного содержания парафинов
подвергается депарафинизации с целью снижения температуры застывания и
получения жидких парафинов.
Вакуумный газойль фракция 350-500ºС
- подаются на установку гидрокрекинга, с получением следующих продуктов: газа,
содержащего непредельные углеводороды, компонента автомобильного бензина,
компонента дизельного топлива, компонента котельного топлива и сероводород.
Гудрон (фракция выше 500ºС)
с ЭЛОУ-АВТ поступает на установку висбрекинга, с получением основного продукта
- крекинг-остатка. Бензин висбрекинга служит компонентом автобензина; крекинг
остаток - компонент котельного топлива.
.4 Материальные балансы установок, входящих в
поточную схему
Таблица 20 Материальный баланс установки ЭЛОУ
[5]
Наименование
|
Выход
|
Поступило
|
%
|
т/год
|
т/сут
|
кг/час
|
Нефть
сырая
|
100,2
|
5
000 000
|
13698,63
|
328,7671
|
Вода
свежая или конденсат
|
5,0
|
249
500,9980
|
683,5643
|
16,405545
|
Всего
|
105,2
|
5
249 500,9980
|
15439,7088
|
643321,2007
|
Получено
|
|
Нефть
обессоленная
|
99,8
|
4
980 039,9201
|
14
647,1762
|
610
299,0098
|
Соляной
раствор
|
5,4
|
269
461,0778
|
792,5325
|
33
022,1909
|
Всего
|
105,2
|
5
249 500,9980
|
15
439,7088
|
643
321,2007
|
Таблица 21 Материальный баланс установки АВТ
Наименование
|
Выход
|
Поступило
|
%
|
т/год
|
т/сут
|
кг/час
|
Нефть
сырая
|
100
|
4
980 039,9201
|
14
647,1762
|
610
299,00
|
Всего
|
100
|
4
980 039,9201
|
14
647,1762
|
610
299,00
|
Получено
|
|
Газоконденсат
|
3,25
|
161851,297403
|
28
500,9637
|
Бензин
|
29,85
|
1486541,91614
|
4072,7175
|
19
834,7178
|
Керосин
|
8,4
|
418323,353288
|
1146,0913
|
59
199,0039
|
Дизельное
топливо
|
20
|
996007,98402
|
2728,7889
|
94
474,2867
|
Вакуумный
Газойль
|
19,02
|
947203,592803
|
2595,0783
|
116078,8716
|
Гудрон
|
19,48
|
970111,776435
|
2
657,8404
|
11
036,9114
|
Всего
|
100,0
|
4980039,92007
|
14647,1762
|
610299,00
|
Таблица 22 Материальный баланс установки
гидроочистки бензина
Наименование
|
Выход
|
Поступило
|
%
|
т/год
|
т/сут
|
кг/час
|
Бензин
(62-180°С)
|
100,00
|
1
486 541,9161
|
4072,7175
|
97,7452
|
Водород
(100%)
|
0,15
|
2
229,8128
|
6,109076
|
0,1466178
|
Всего
|
100,15
|
1
488 771,7290
|
407,8826
|
9,78918
|
Получено
|
|
Гидроочищенный
бензин
|
99,00
|
1471676,4969
|
4031,9904
|
96,7677
|
Углеводородный
газ
|
0,65
|
9062,5224
|
24,8288
|
0,59589
|
Потери
|
0,50
|
7432,7097
|
20,3635
|
0,4887
|
Всего
|
100,15
|
1
488 171,729
|
4
07,8826
|
9,78918
|
Таблица 23 Материальный баланс установки
гидроочистки керосина
Наименование
|
Выход
|
Поступило
|
%
|
т/год
|
т/сут
|
кг/час
|
Керосин
|
100
|
418223,3532
|
1145,8174
|
27,4996
|
Водород
|
0,25
|
1145,8084
|
3,13920
|
0,0753
|
Всего
|
100,25
|
419369,1616
|
1
148,9566
|
27,5749
|
Получено
|
|
Гидроочищенный
керосин
|
97,90
|
409440,6627
|
1
390,9397
|
57
955,8248
|
Отгон
|
1,10
|
4600,4568
|
15,6285
|
651,1890
|
Углеводородный
газ
|
0,65
|
2718,4517
|
9,2350
|
384,7935
|
Сероводород
|
0,20
|
836,4467
|
2,8415
|
118,39800
|
Потери
|
0,40
|
1773,1437
|
5,6831
|
236,7960
|
Всего
|
100,25
|
419369,1616
|
1148,9566
|
27,5749
|
Таблица 24 Материальный баланс установки
гидроочистки дизельного топлива
Наименование
|
Выход
|
Поступило
|
%
|
т/год
|
т/сут
|
кг/ч
|
Дизельное
топливо
|
100,0
|
996007,9840
|
2
267,3828
|
94
474,2867
|
Водород
|
0,40
|
3984,0319
|
9,0695
|
377,8971
|
Всего
|
100,4
|
999992,0159
|
2
276,4524
|
94
852,1838
|
Получено
|
|
Отгон
|
1,30
|
12948,1037
|
29,4759
|
1
228,1657
|
Углеводородный
газ
|
0,60
|
5976,0479
|
13,6042
|
566,8457
|
Сероводород
|
1,20
|
11952,0958
|
27,2085
|
1
133,6914
|
Потери
|
0,40
|
3984,0319
|
9,0695
|
377,8971
|
Всего
|
100,4
|
999992,0159
|
2
276,4524
|
94
852,1838
|
|
|
|
|
|
|
Таблица 25 Материальный баланс установки
каталитического риформинга
Наименование
|
Выход
|
Поступило
|
%
|
т/год
|
т/сут
|
кг/час
|
Фракция
85-180°С
|
100
|
1471676,4969
|
4031,9904
|
96,7677
|
Всего
|
100
|
1471676,4969
|
4031,9904
|
96,7677
|
Получено
|
|
|
Углеводородный
газ
|
10,0
|
147167,64
|
403,19
|
9,67
|
Головка
стабилизация
|
4,5
|
66225,44
|
181,43
|
4,35
|
Катализат
|
83,7
|
1231793,22
|
3374,77
|
80,99
|
Водосодержащий
газ
|
1,8
|
26490,17
|
72,57
|
1,74
|
В
том числе водород
|
(0,9)
|
13245,08
|
36,28
|
0,87
|
Всего
|
100
|
1471676,4969
|
4031,9904
|
96,7677
|
Таблица 26 Материальный баланс установки
газофракционирующей установки предельных углеводородов
Наименование
|
Выход
|
Поступило
|
%
|
т/год
|
т/сут
|
кг/час
|
Газ
АВТ
|
38,2
|
161851,2974
|
443,4282
|
10,6422
|
Углеводородный
газ каталитического риформинга
|
41
|
147167,64
|
403,19
|
9,67
|
Головка
стабилизации каталитического риформинга
|
14
|
66225,44
|
181,43
|
4,35
|
Всего
|
100
|
375244,37
|
1028,06
|
24,67
|
Получено
|
|
Сухой
газ
|
4,8
|
18011,72
|
49,34
|
1,18
|
Пропановая
фракция
|
24,5
|
91934,87
|
251,87
|
6,04
|
Изобутановая
фракция
|
14,6
|
54785,67
|
150,09
|
3,60
|
Бутановая
фракция
|
36,8
|
138089,92
|
378,32
|
9,07
|
С0
и выше
|
19,3
|
72422,16
|
198,41
|
4,76
|
Всего
|
100
|
375244,37
|
1028,06
|
24,67
|
|
|
|
|
|
|
|
Таблица 27 Материальный баланс установки
изомеризации
Наименование
|
Выход
|
Поступило
|
%
|
т/год
|
т/сут
|
кг/час
|
С5
и выше
|
100
|
72422,16
|
198,41
|
4,76
|
Всего
|
100
|
72422,16
|
198,41
|
4,76
|
Получено
|
|
Углеводородный
газ
|
1,6
|
1158,75
|
3,17
|
0,07
|
Сжиженный
газ
|
16,8
|
12166,92
|
33,33
|
0,80
|
Компонент
автомобильного бензина
|
82,4
|
59675,85
|
163,49
|
3,92
|
В
том числе: Изопентановая фракция
|
(53,4)
|
38673,43
|
105,95
|
2,54
|
|
|
|
|
|
Изогексановая
фракция
|
(22,1)
|
16005,29
|
43,85
|
1,05
|
Гексановая
фракция
|
(6,9)
|
4997,12
|
13,69
|
0,32
|
Всего
|
100
|
72422,16
|
198,41
|
4,76
|
Таблица 28 Материальный баланс установки
производства серы
Наименование
|
Выход
|
|
Поступило
|
%
|
т/год
|
т/сут
|
кг/час
|
|
Сероводород
гидроочистки керосина
|
2,5
|
2,2916
|
0,0549
|
|
Сероводород
гидроочистки дизельного топлива
|
36,6
|
11952,0958
|
32,7454
|
0,7858
|
Сероводород
гидроочистки вакуумного дистиллята
|
6,9
|
19891,2754
|
54,4966
|
1,3079
|
Всего
|
100
|
32679,8179
|
89,5337
|
2,1488
|
Получено
|
|
Сера
техническая
|
93,3
|
30490,2701
|
83,5349
|
2,0048
|
Потери
|
6,7
|
2189,5478
|
5,9987
|
0,1439
|
Всего
|
100
|
32679,8179
|
89,5337
|
2,1488
|
|
|
|
|
|
|
|
Таблица 29 Материальный баланс установки
гидрокрекинга
Наименование
|
Выход
|
Поступило
|
%
|
т/год
|
т/сут
|
кг/час
|
Вакуумный
дистиллят
|
100,0
|
947
203,5928
|
2595,0783
|
62,2818
|
Водород
|
0,80
|
7
577,6287
|
20,7606
|
0,4982
|
Всего
|
100,8
|
954
781,2215
|
2
615,8389
|
62,7801
|
Получено
|
|
Сухой
газ
|
2,60
|
24
627,2934
|
67,4720
|
1,6193
|
Бензиновая
фракция
|
4,60
|
43
571,3652
|
119,3736
|
2,8649
|
Дизельная
фракция
|
43,80
|
414
875,1736
|
1136,6443
|
27,2794
|
Тяжелый
газойль
|
47,70
|
451
816,1137
|
1237,8523
|
29,7084
|
Сероводород
|
2,10
|
19
891,2754
|
54,4966
|
1,3079
|
Всего
|
100,8
|
954
781,2215
|
2
615,8389
|
62,7801
|
Таблица 30 Материальный баланс установки
висбрекинга
Наименование
|
Выход
|
Поступило
|
%
|
т/год
|
т/сут
|
кг/час
|
Гудрон
(>450°С)
|
100,0
|
970111,7764
|
2657,8404
|
63,7881
|
Всего
|
100,0
|
970111,7764
|
2657,8404
|
63,7881
|
Получено
|
|
Углеводородный
газ
|
2,30
|
22312,5708
|
61,1303
|
1,4671
|
Головка
стабилизации
|
3,00
|
29103,3532
|
79,7352
|
1,9136
|
Крекинг
бензин
|
6,70
|
64997,4890
|
178,0753
|
4,2738
|
Крекинг
остаток
|
88,0
|
853698,13632
|
2338,899
|
56,1335
|
Всего
|
100,0
|
970111,7764
|
2657,8404
|
63,7881
|
Таблица 31 Материальный баланс установки
карбамидной депарафинизации
Наименование
|
Выход
|
Поступило
|
%
|
т/год
|
т/сут
|
кг/час
|
Гидроочищенный
Дизельное топливо
|
100,0
|
965131,7364
|
2644,1965
|
63,4607
|
Получено
|
|
Депарафинированное
дизельное топливо
|
90,00
|
868618,5627
|
2379,7768
|
57,1146
|
Жидкий
парафин
|
10,00
|
96513,1736
|
264,4196
|
6,3460
|
Всего
|
100,0
|
965131,7364
|
2644,1965
|
63,4607
|
Таблица 32 Материальный баланс установки
газофракционирующей установки непредельных углеводородов
Наименование
|
Выход
|
Поступило
|
%
|
т/год
|
т/сут
|
кг/час
|
Сухой
газ Гидрокрекинг
|
32,4
|
24627,2934
|
67,7460
|
1,6259
|
Углеводородный
газ висбрекинга
|
29,3
|
22312,5708
|
61,1303
|
1,4671
|
Головка
стабилизации
|
38,3
|
29103,3532
|
79,7352
|
1,9136
|
Всего
|
100,0
|
76043,2174
|
208,3375
|
5,0001
|
Получено
|
|
Сухой
газ
|
30,5
|
23193,1813
|
63,5429
|
1,5250
|
Пропан-пропиле-новая
фракция
|
25,5
|
19391,0204
|
53,1260
|
1,2750
|
Бутан-бутиленовая
фракция
|
37,5
|
28516,2065
|
78,1265
|
1,8750
|
С0
и выше
|
6,5
|
492,8091
|
13,5419
|
0,3250
|
Всего
|
100,0
|
76043,2174
|
208,3375
|
5,0001
|
Таблица 33 Материальный баланс установки
дегидрирование
Наименование
|
Выход
|
Поступило
|
%
|
т/год
|
т/сут
|
кг/час
|
Изопентановая
фракция
|
100
|
38673,43
|
105,95
|
2,54
|
Всего
|
100
|
38673,43
|
105,95
|
2,54
|
Получено
|
|
Газа
|
12,1
|
4679,48
|
12,82
|
0,30
|
Катализат
|
83,7
|
32369,66
|
88,68
|
2,12
|
В
том числе Изо-С5Н10
|
74,9
|
28966,39
|
79,35
|
1,90
|
н-С5Н10
|
3,2
|
1237,54
|
3,39
|
0,08
|
Изопрен
|
1,9
|
734,79
|
2,01
|
0,04
|
Пиперилена
|
3,7
|
1430,91
|
3,92
|
0,09
|
Потери
|
4,2
|
1624,28
|
4,45
|
0,10
|
Всего
|
100
|
38673,43
|
105,95
|
2,54
|
Таблица 34 Материальный баланс установки
полимеризации
Наименование
|
Выход
|
Поступило
|
%
|
т/год
|
т/сут
|
кг/час
|
Изопрен
|
100,0
|
734,79
|
2,01
|
0,04
|
Всего
|
100,0
|
734,79
|
2,01
|
0,04
|
Получено
|
|
Полиизопрен
|
99,4
|
730,38
|
2,00
|
0,04
|
Потери
|
0,6
|
4,40
|
0,01
|
0,002
|
Всего
|
100,0
|
734,79
|
2,01
|
0,04
|
Таблица 35 Материальный баланс установки БСС
Наименование
|
Выход
|
Поступило
|
%
|
т/год
|
Ок.число
|
Катализат
|
75,5
|
1011756,9882
|
90
|
Компонент
автомобильного бензина
|
9,6
|
128542,1118
|
87
|
С0
и выше
|
6,1
|
72422,16
|
70
|
С0
и выше
|
0,4
|
492,8091
|
70
|
Бензин
ГК
|
3,3
|
43571,3652
|
77
|
Бензин
крекинг
|
4,9
|
64997,4890
|
80
|
Всего
бензина
|
100
|
1321782,98
|
87,313
|
ОЧсм = 
=87,313
Таблица 36 Материальный баланс
установки ССДТ
Наименование
|
Выход
|
Поступило
|
%
|
т/год
|
Цет.
число
|
67,68
|
868618,5627
|
40
|
Дизельная
фракция
|
32,32
|
414
875,1736
|
51
|
Всего
ДТ
|
100,0
|
1
283493,7363
|
43,5552
|
ЦЧсм= 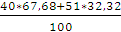
=43,5552
.5 Сводный материальный баланс
Таблица 31 Сводный материальный
баланс
Наименование
|
Выход
|
Получено
|
%
|
т/год
|
т/сут
|
кг/час
|
Нефть
|
100
|
5000,000
|
13698,6301
|
328,7671
|
Итого
|
100
|
5000,000
|
13698,6301
|
328,7671
|
Получено
|
|
Газы
|
8,6
|
430565,457
|
1179,6313
|
28,3111
|
Бензин
|
26,43
|
1321782,98
|
3658,9938
|
87,8158
|
Керосин
|
8,1
|
406440,6627
|
1121,7552
|
26,9221
|
ДТ
|
25,62
|
1283493,736
|
3516,4211
|
84,3941
|
Жидкий
парафин
|
1,9
|
96513,1736
|
264,4196
|
6,3460
|
Сера
|
0,6
|
30490,2701
|
83,5349
|
2,0048
|
Котельное
топливо
|
26,1
|
1305514,250
|
3576,7513
|
85,8420
|
Потери
|
2,50
|
125199,4743
|
343,0122
|
8,2322
|
Всего
|
100
|
5000,000
|
136986,630
|
328,7671
|
Заключение
В промышленности синтез каучуков проводится
полимеризацией мономеров с кратными связями, поликонденсацией
полифункциональных соединений и химической модификацией высокомолекулярных
соединений. Наряду с развитием производства стереорегулярных каучуков СКИ-3 и
СКД успешно развиваются новые направления по созданию высокоэффективных
каучуков с комплексом технически ценных свойств. Одним из таких новых путей
является синтез стереорегулярных ненасыщенных каучуков общего назначения
полимеризацией циклоолефинов с раскрытием кольца. Наиболее доступным и
технологичным из таких полимеров является транс-полипентенамер, получаемый из
циклопентена с использованием каталитических систем на основе
алюминийорганических соединений и галогенидов переходных металлов. Новым
направлением является и синтез чередующихся, или альтернантных полимеров. Наибольший
интерес для промышленности синтетических каучуков представляют альтернантные
сополимеры на основе бутадиена и пропилена. Металлоорганические катализаторы на
основе соединений цинка или алюминия используются для синтеза каучуков из
органических оксидов путем раскрытия напряженных кислородсодержащих циклов
(пропиленоксидные и эпихлоргидриновые каучуки).
Основным методом получения синтетических
каучуков является полимеризация, осуществляемая технологически в массе (блоке),
эмульсии и растворе. В настоящее время традиционная блочная полимеризация,
используемая для получения каучуков типа СКБ, утратила свое значение, уступив
место полимеризации в растворе. Этим методом производят основные типы каучуков
общего назначения и ряд каучуков специального назначения: 1,4-цис-изопреновый.
(СКИ-3), 1,4-цис-бугадиеновый- (СКД),
этилен-пропиленовый (СКЭП) и этилен-пропилен-диеновый (СКЭПТ), бутилкаучук
(БК), статистические сополимеры бутадиена со стиролом (ДС-СК), бутадиен- (или
изопрен-)-стирольные термоэластопласты (ДСТ или ИСТ), полиизобутилен, цис- или
транс-полипентенамеры (ЦПА или ТПА), альтернантные сополимеры бутадиена с
пропиленом (СКБП-А), эпоксидные каучуки (СКПО, СКЭХГ, СКЭХГ-С),
1,2-полибутадиен (СКД-СР).
Изопреновый синтетический каучук является
продуктом радикальной полимеризации мономера-изопрена в растворителе-изопентана
в присутствии каталитического комплекса Циглера-Натта.
Каучук представляет собой стереорегулярный
полимер и имеет ту же молекулярную структуру, что и натуральный каучук.
Список литературы
1. Энциклопедия полимеров в 3 т. М.:
Изд-во «Советская энциклопедия», 1974-1977 г.
. Кирпичников П.А., Береснев В.В.,
Попова Л.М. Альбом технологических схем основных производств промышленности
синтетического каучука. -Л.:Химия.1986.-224 стр.
. Башкатов Т.В., Жигалин Я.Л.
Технология синтетических каучуков. Учебник для техникумов. 2-е изд., Л.: Химия,
1987. - 360 стр.
. Надиров Н.К. Нефть и газ
Казахстана. Часть 2. Алматы, «Гылым» 1995г.
. Рудин М.Г., Драбкин А.Е. Краткий
справочник нефтепереработчика. Ленинград, «Химия» 1980г.
. Эрих В.Н., Расина М.Г., Рудин М.Г.
Химия и технология нефти и газа. Ленинград, «Химия» 1972г.