Производство модифицированного арболита
Содержание
Введение
. Аналитический обзор
.1 Состояние и перспективы развития производства и применения
арболита в строительстве
.2 Анализ образования и переработки твердых промышленных и
бытовых отходов в Красноярском крае
.3 Анализ возможности использования твердых промышленных и
бытовых отходов в производстве арболита
. Программа и методика исследований
.1 Теоретические взгляды на технологию производства и
структурообразование арболита
.2 Программа и методика проведения эксперимента
.3 Анализ процесса рециклинга твердых промышленных и бытовых
отходов в производстве арболитовых изделий
.4 Выбор основных характеристик моделей
. Результаты экспериментальных исследований
.1 Лабораторные установки для проведения исследований
.2 Сырье и материалы
.3 Последовательность проведения экспериментов
.4 Методики определения физико - механических показателей
арболитовых блоков
.5 Результаты экспериментальных исследований
. Экология города Лесосибирска
.1 Состав и характеристики состава загрязняющих веществ в
городе Лесосибирск
.2 Оценка и анализ системы загрязняющих веществ в
Унифицированной программе расчета загрязнения атмосферы "Эколог",
вариант "Стандарт"
. Экономическая часть
Заключение
Библиографический список
Введение
Социально-экономическое развитие, стимулируемое ростом численности
населения планеты, сопровождается обострением негативных проблем, лежащих в
сфере экологии и безопасности жизнедеятельности. Наибольшую остроту приобретают
загрязнения и захоронения твердых промышленных и бытовых отходов.
Необходимость выполнения требований санитарных норм и норм пожарной
безопасности обусловило появление компаний по рециклингу твердых промышленных и
бытовых отходов. Однако данный тип отходов можно использовать в производстве
строительных материалов, путем введения их в структуру в качестве вторичного
сырья.
Вместе с тем рециклинг твердых промышленных и бытовых отходов в широких
промышленных масштабах остается не реализованным, что связано, в том числе, с
недостаточной эффективностью известных технических решений.
В настоящей работе научно обосновывается возможность использования
твердых промышленных и бытовых отходов в производстве арболитовых изделий. В
результате решения данной проблемы возникает ряд задач:
. Проанализировать применение арболитовых изделий в строительстве.
. Проанализировать образование и переработку твердых промышленных
и бытовых отходов.
. Спланировать и реализовать однофакторные эксперименты по
определению зависимостей физико-механических свойств арболитовых изделий от
процентного соотношения фракционного состава стекла, полиэтилентерефталата,
коры и вермикулита.
1. Аналитический обзор
.1 Состояние и перспективы развития производства и применения
арболита в строительстве
Арболит - легкий бетон, получаемый на минеральном вяжущем и органическом
целлюлозном заполнителе растительного происхождения, химических добавок и воде.
Поэтому арболиту присущи прочность, огнестойкость, биостойкость бетона и
небольшая плотность, теплопроводность, легкость обработки режущим инструментом
и гвоздимость древесины.
Арболит (ГОСТ-19222-84) имеет марки 5,10,15,25,35,50 и в зависимости от
средней плотности в высушенном до постоянной массы состоянии подразделяются на:
Теплоизоляционный со средней плотностью до 500 кг./м3;
Конструкционный со средней плотностью от 500 до 800 кг./м3.
Благодаря положительным свойствам арболитовые изделия нашли
широкое применение в строительстве. Это стеновые панели и блоки, плиты покрытия
для совмещенных кровель плиты перекрытия, усиленные железобетонными брусками
или несущей основой, перегородочные плиты для первых этажей культурно-бытовых
зданий и магазинов, тепло- и звукоизоляционные плиты, объемно-пространственные
конструкции, монолиты и т.п. Имелся опыт производства и применения в жилищном
строительстве плит сборной стяжки под линолеум и паркет.
Арболит зарекомендовал себя отличным стеновым материалом. Благодаря
крупнопористой структуре этот легкий бетон обладает ценными, особенно для
сельскохозяйственного строительства, качествами: высокой теплоизолязией и
способностью поддерживать осушающий режим в помещениях, не конденсируя влаги на
поверхности и не повышая влагосодержания в стенах.
Арболит нашел широкое применение в сельском жилищном строительстве.
Эффективность применения арболита в качестве стенового материала обусловлена
его малой средней плотностью, хорошими тепло- и звукоизоляционными свойствами.
В настоящее время наибольшее распространение получило строительство
крупноблочных домов из арболита 115 серии, наименьшее - крупнопанельных домов с
панелями размером на комнату.
Наиболее перспективные проекты жилых домов 115 серии из крупных
арболитовых блоков следующие
ТП 183-115-119/1.2 «Одноэтажный одноквартирный трехкомнатный
дом»;
ТП 183-115-54 «Одноэтажный двухквартирный трехкомнатный дом»;
ТП 141-115-5/75 «Двухэтажный двухквартирный блокированный в двух
уровнях, четырехкомнатный дом».
Основные стеновые блоки имеют следующие размеры 290×180
мм, 290×580
мм, толщина наружных
стеновых блоков принимается 240 и 280 мм. Толщина внутренних блоков 200 мм.
Стеновые блоки изготавливают из арболита М25, он с двух сторон офактуривается
цементным раствором. Марка по прочности на сжатие наружного слоя 100. Марка
раствора внутреннего отделочного слоя 50. Толщина фактурного слоя 10 мм.
Панели из арболита для жилищного строительства имеют максимальный размер
400×250×300
мм (ПН 48-1-30), толщина
наружных панелей для температуры наружного воздуха до -40°С составляет 300 мм.
Особенность арболита по сравнению с такими аналогичными материалами, как
фибролит, деревобетон, ксилолит и др., состоит в том, что для его получения
пригодна более широкая номенклатура органических целлюлозных заполнителей
различной природы (древесная дробленка, костра льна и конопли, сечка тростника,
стеблей хлопчатника, рисовой соломы и др.), т.е. отходы производства, запасы
которых в нашей стране практически не ограничены.
В сельскохозяйственном строительстве изделия из арболита широко
применяются в виде стеновых панелей и блоков. Haкоплен определенный опыт
применения арболита при строительстве промышленных сооружений, жилых и культурно-бытовых
зданий. На основе арболита можно также получать плиты покрытия и перекрытия,
плиты основания под линолеум и паркет, теплоизоляционные изделия,
пространственные конструкции и др.
За рубежом использование отходов деревообработки для получения строительных
материалов, подобных арболиту, на минеральном вяжущем и органическом
целлюлозном заполнителе получило широкое распространение. Эти материалы,
вырабатываемые по различным технологиям, имеют фирменные названия:
"дюризол" в Швейцарии, "вундстроун" в США,
"чентери-боад" в Японии, "дюрипанель" в Германии,
"велокс" в Австрии. Изделия хорошо зарекомендовали себя и широко
применяются при возведении одноэтажных и высотных зданий различного назначения
. Отечественный и зарубежный опыт свидетельствует о том, что по строительным,
экономическим и эксплуатационным свойствам арболит является эффективным
строительным материалом. Поэтому арболиту в нашей стране уделяется большое
внимание.
Производство и применение арболита позволяет снизить материалоемкость,
энергоемкость, массу здания и удельные капитальные затраты на изготовление 1 м2
стенового материала по сравнению с бетоном на пористых заполнителях.
Одновременно решается и другая важная народнохозяйственная задача - защита
окружающей среды от загрязнения отходами промышленного и сельскохозяйственного
производства.
При современных темпах развития капитального строительства наблюдается
интенсивный рост потребления местных материалов и продуктов их переработки. В
то же время рост перерабатывающей промышленности опережает рост объема
лесозаготовок, что истощает запасы леса в традиционных районах лесозаготовок, а
освоение лесов в северных и восточных районах страны требует больших
дополнительных капитальных вложений на строительство дорог.
Неполное использование отходов лесоматериалов - большая экономическая
потеря для народного хозяйства. Известно, что коэффициент выхода продукции при
переработке древесины крайне низок. Так, для получения 1 м3 погонажных изделий
расходуется 2,8-3,3 м3, для выработки 1 м3 фанеры - 4 м3, на изготовление
мебельных изделий, соответствующих в пересчете 1 м3 древесины, более 5 м3, а на
изготовление несущих клееных деревянных конструкций (КДК), содержащих 1 м3
древесины, расходуется 2,6-2,8 м3 бревен 2-го и 3-го сорта. Необходимо изыскивать
пути рационального и эффективного использования древесных отходов, в том числе
и для создания строительных материалов, тем более что из 1 м3 отходов древесины
(в плотных м3) можно получить более 2 м3 строительных материалов, например
фибролита, арболита, древесностружечных плит и др.
Известно, что коэффициент выхода продукции при переработке древесины
крайне низок. Так, для получения 1 м3 погонажных изделий расходуется 2,8-3,3
м3, для выработки 1 м3 фанеры - 4 м3, на изготовление мебельных изделий,
соответствующих в пересчете 1 м3 древесины, более 5 м3, а на изготовление
несущих клееных деревянных конструкций (КДК), содержащих 1 м3 древесины,
расходуется 2,6-2,8 м3 бревен 2-го и 3-го сорта. Необходимо изыскивать пути
рационального и эффективного использования древесных отходов, в том числе и для
создания строительных материалов, тем более что из 1 м3 отходов древесины (в
плотных м3) можно получить более 2 м3 строительных материалов, например
фибролита, арболита, древесностружечных плит и др.
Один из наиболее эффективных и рентабельных способов использования
древесных отходов - выпуск арболита, так как технология его относительно
несложна, а производство не требует больших капитальных вложений. Эффективность
применения арболита и практически неограниченные сырьевые возможности дают
право рассматривать развитие производства арболита не как временную меру для
ликвидации дефицита в стеновых материалах, а как одно из 4 важных направлений в
освоении местных строительных материалов. Применение арболита обеспечивает снижение
расхода цемента. На изготовление 1 м2 стены из арболита (приведенной толщины по
теплозащите) требуется цемента на 30-35 кг меньше, чем при использовании
керамзитобетона (хотя расход вяжущего на 1 м3 конструкций у арболита несколько
больше), что обусловлено значительным уменьшением толщины стены из этого
материала из-за его более высоких теплофизических свойств.
Применение арболита для ограждающих конструкций позволяет также сократить
энергозатраты. Арболитовая стена благодаря крупнопористой структуре материала
обеспечивает высокое термическое сопротивление конструкции, а это дает
возможность тратить меньше энергии на отопление. Последнее обстоятельство имеет
особое значение для животноводческих помещений, где для поддержания нормальных
условий требуются большие эксплуатационные затраты на вентиляцию.
Эффективность применения конструкций и изделий из арболита определяется
возможностью существенного снижения массы зданий и сооружений и повышения их
теплозащиты, уменьшения перевозок за счет использования местных материалов,
снижения стоимости строительства. 1 м3 древесных отходов, использованных при
производстве арболита, заменяет в строительстве 1,5 м3 пиловочника. При
приведенной толщине стены по условиям теплопередачи масса ее 1 м2 из арболита в
7-8 раз меньше, чем из кирпича, и в 2-3 раза меньше, чем из керамзитобетона.
Эффективность применения арболита обусловлена также уменьшением удельных
капитальных вложений на создание производственной базы, которые в 2 раза
меньше, чем при организации выпуска панелей из бетона на пористых заполнителях.
Изделия из арболита небольшой средней плотности (400-800 кг/м3) обладают
ценными строительными свойствами: они хорошо пилятся, гвоздятся, держат
штукатурку и шурупы, обрабатываются режущим инструментом, трудно сгораемы и
биостойки. Большое народнохозяйственное значение имеет развитие производства
арболитовых конструкций в нефтедобывающих районах Западной и Восточной Сибири,
а также в районах Крайнего Севера и Дальнего Востока, где осваиваются богатые
природные ресурсы, а жилищное и промышленное строительство сдерживается из-за
недостатка природных и искусственных минеральных пористых заполнителей для
изготовления бетона. При строительстве малоэтажных зданий конструкции и изделия
из арболита эффективно заменяют кирпич, керамзитобетон, ячеистые бетоны и
древесину, а по ряду эксплуатационных свойств превосходят их. Интересно
сопоставить стены из разных материалов, имеющие эквивалентную толщину,
обеспечивающую одинаковую теплозащиту.
1.2 Анализ образования и переработки твердых промышленных и
бытовых отходов в Красноярском крае
Красноярский край, занимаемый центральное положение в азиатской части
Российской Федерации и протянувшийся от берегов Северного Ледовитого океана до
Саянских гор на 3 тысячи километров, в силу наличия богатых природных ресурсов
(недра, воды, лес) играет одну из ключевых ролей в российской экономике.
Среди субъектов РФ, входящих в состав Сибирского федерального округа,
Красноярский край имеет неблагоприятную экологическую среду, обусловленную,
прежде всего, своими природными особенностями. Край занимает первое
место по количеству выброшенных вредных веществ в атмосферу (45%), объему
забранной воды из водных объектов (30%) и объему сброса сточных вод (32%). На
территории края имеются и «экологически опасные точки», прежде всего на
территории Норильского промышленного района.
Таблица 1.1 - Основные экологические показатели, антропогенного
воздействия на окружающую среду Красноярского края
Показатель
|
2009
|
2010
|
2011
|
1.Общекраевые выбросы
загрязняющих веществ в атмосферный воздух всего, тыс.тонн, в том числе
|
2872,6
|
2812,5
|
2897
|
стационарные
|
2478,6
|
2446
|
2491
|
передвижные
|
393,97
|
366,1
|
406,6
|
2.Общекраевые сбросы
сточных вод, млн. куб.м
|
2905
|
2341,8
|
2172,
|
3.Образование отходов, по
краю, всего (1-5классы), млн. тонн
|
321,8
|
298,2
|
302,7
|
в т.ч.отходы 5 класса,
млн.тонн
|
320,28
|
295,6
|
300,1
|
% населения края проживает в городах с очень высоким уровнем загрязнения
воздуха. Города Норильск, Минусинск, Лесосибирск и Красноярск входят в список
городов России с наиболее загрязненным атмосферным воздухом.
В крае значительное развитие получили такие обрабатывающие производства
как металлургическое, химическое, обработка древесины. На территории края
производится и распределяется электроэнергия, добываются полезные ископаемые,
осуществляется производство нефтепродуктов и пр.
К предприятиям, оказывающим наиболее существенное воздействие на водные
объекты, относятся:
Заполярный филиал ОАО ГМК «Норильский никель» (его деятельность
оказывает негативное влияние на все элементы окружающей среды);
Структурные подразделения ОАО «Енисейская ТГК -13»;
Предприятия, входящие в состав ОАО Объединенной компании
«РУСАЛ»;
Оптовые генерирующие компании (ОГК-4 и ОГК-6);
Предприятия топливно-энергетического комплекса;
Предприятия тепловодораспределения (коммунального хозяйства);
Среди них - предприятия нефтяного комплекса (ОАО «Ачинский
нефтеперерабатывающий завод ВНК»), предприятия лесного комплекса в г.
Лесосибирске, добывающие предприятия - ЗАО «ЗДК «Полюс» в п. Северо-Енисейске.
По сути эти же предприятия оказывают наибольший вклад в загрязнение
атмосферного воздуха путем выброса загрязняющих веществ (от 81 до 93% от общего
валового выброса).
Основной объем отходов образуется при добыче полезных ископаемых (около
94% от общего количества образующихся отходов). При добыче полезных ископаемых,
в основном это 5-й класс опасности преимущественно, вскрышные породы - 99,9%.
За последние годы отмечается рост образования отходов в данной отрасли. Второе
место по образованию отходов занимают отрасли обрабатывающих производств - 5,2
%. Наибольшее количество промышленных отходов образуется в Северо-Енисейском и
Мотыгинском районах, городах Ачинск и Лесосибирск.
В целом зоны экологического неблагополучия, вызванного антропогенным
воздействием на окружающую среду, четко соответствуют размещению пяти основных
промышленных районов края: Норильского, Красноярского, Ачинско-Назаровского,
Канского, Минусинского, которые предопределены размещением природных ресурсов,
транспортной сетью, размещением населения.
Основные целями и задачами в области охраны окружающей среды,
определенными в «Стратегии социально-экономического развития Российской
Федерации до 2020 года» к 2012 году должны быть на 20% сокращены объемы
загрязнения воздуха и водных объектов, а также образование отходов, а к 2020
году необходимо на 40% сократить уровень энергоемкости предприятий, снизить
число «экологически опасных точек» и сократить численность городского
населения, проживающего в условиях неблагоприятной окружающей среды.
Приближение к этой цели возможно только с помощью контрольно-надзорной
деятельности, так как в рамках контрольной проверки устанавливаются соблюдение
предприятиями обязательных нормативно-правовых требований, выявляются
(пресекаются) нарушения природоохранного законодательства конкретным
природопользователем.
На территории Красноярского края продолжает увеличиваться показатель
образования и накопления отходов.
Таблица 1.2 - Образование отходов на территории Красноярского края, млн.
тонн (вместе с Норильским промрайоном)
Класс отходов
|
Год
|
|
2005
|
2006
|
2007
|
2008
|
2009
|
2010
|
2011
|
Отходы 1-5класса
|
132,5
|
193,1
|
289,9
|
233,3
|
321,8
|
298,2
|
302,79
|
Отходы 1-4 класса
|
0,8
|
1,3
|
1,34
|
1,4
|
1,52
|
2,6
|
2,6
|
Отходы 5 класса
|
131,7
|
191,8
|
288,56
|
231,9
|
320,28
|
295,6
|
300,19
|
Объем отходов, образовавшихся в 2010 году, по сравнению с 2009 годом
увеличился незначительно всего на 1,5 %, что косвенно свидетельствует о
незначительном росте производства на территории Красноярского края в 2010 году.
Наибольшее количество отходов (более 1 млн. т) образуют предприятия и
организации городов: Ачинск, Красноярск, Назарово, Норильск и муниципальных
районов: Ачинский, Курагинский, Мотыгинский, Северо-Енисейский.
Динамика образования отходов в городах Красноярского края показывает, что
из 17 городов увеличение образования отходов зафиксировано только в 7 из них. В
городах Бородино Енисейск, Железногорск, Заозерный, Зеленогорск, Игарка, Канск,
Красноярск, Минусинск, Шарыпово объемы образования отходов в 2010 году
снизились.
Таблица 1.3 - Образование отходов в пределах основных городов
Красноярского края , тыс.тонн
Город
|
2009
|
2010
|
2011
|
Ачинск
|
10 054,8
|
10 676,6
|
11 012,3
|
Енисейск
|
129,7
|
121,7
|
115,4
|
Железногорск
|
25,8
|
34,1
|
43,1
|
Зеленогорск
|
308,4
|
344,1
|
386,5
|
Канск
|
58,2
|
41,1
|
32,6
|
Красноярск
|
112 215,6
|
89 201,7
|
78 201,7
|
Лесосибирск
|
632,5
|
990,4
|
1 320,3
|
Назарово
|
7,5
|
3 318,4
|
3 589,4
|
Таблица 1.4 - Образование отходов в основных отходообразующих районов
Красноярского края, тыс. тонн
Район
|
2009
|
2010
|
2011
|
Емельяновский
|
69,8
|
84,4
|
101,3
|
Енисейский
|
1617,4
|
1000,6
|
854,3
|
Канский
|
67,1
|
69,9
|
73,5
|
Кежемский
|
6,5
|
14,3
|
28,5
|
Козульский
|
4,4
|
3,6
|
2,5
|
Краснотуранский
|
2,5
|
33,7
|
48,4
|
Курагинский
|
1 594,7
|
11 246,7
|
11 589,3
|
Минусинский
|
43,3
|
36,6
|
30,5
|
Мотыгинский
|
6 827,6
|
12 800,6
|
15 500
|
Назаровский
|
419,0
|
318,7
|
286,4
|
Нижнеингашский
|
3,9
|
3,9
|
4,5
|
Новоселовский
|
0,6
|
30,5
|
38,4
|
Северо-Енисейский
|
130 189,2
|
137 009,6
|
144 586,2
|
Сухобузимский
|
48,4
|
27,6
|
25,3
|
Туруханский
|
70,0
|
88,4
|
96,4
|
Ужурский
|
181,9
|
208,9
|
234,5
|
Шарыповский
|
227,7
|
233,4
|
248,3
|
Эвенкийский
|
20,6
|
9,6
|
5,9
|
Таймырский (Долгано -
Ненецкий) и Норильск
|
33 153,3
|
4,4*
|
-
|
* без г.Норильска
Таблица 1.5 - Количество образовавшихся отходов в 2009-2010 гг. по видам
экономической деятельности, (млн т)
Виды экономической
деятельности
|
Количество отходов
|
|
2010 г.
|
2011 г.
|
Всего отходов по отраслям экономики
|
298,2
|
302,8
|
Добыча полезных ископаемых,
в том числе:
|
250,9
|
252,2
|
добыча
топливно-энергетических полезных ископаемых
|
110,7
|
91,3
|
добыча полезных ископаемых,
кроме топливно-энергетических
|
140,2
|
160,9
|
Обрабатывающие
производства, в том числе:
|
44,4
|
47,9
|
металлургическое
производство и производство готовых металлических изделий
|
43,3
|
46,4
|
обработка древесины и
производство изделий из дерева
|
0,73
|
1,08
|
производство прочих
неметаллических минеральных продуктов (известь, цемент, кирпич, стекло, бетон)
|
0,19
|
0,30
|
производство пищевых
продуктов
|
0,07
|
0,07
|
целлюлозно-бумажное
производство
|
0,02
|
0,02
|
химическое производство
|
0,004
|
0,002
|
Производство и
распределение электроэнергии, газа и воды
|
1,26
|
1,41
|
Строительство
|
0,22
|
0,10
|
Транспорт и связь
|
0,11
|
0,10
|
Предоставление прочих
коммунальных, социальных и персональных услуг
|
0,11
|
0,013
|
Прочие виды экономической
деятельности
|
0,24
|
1,10
|
Данные об образовании отходов производства и потребления в 2011 году по
видам экономической деятельности, представленные в таблице, свидетельствуют,
что основной объем отходов образуется при добыче полезных ископаемых. В 2011 г.
это составило 83,5 % от общего количества образовавшихся отходов. При добыче
полезных ископаемых, кроме топливно-энергетических, основная доля отходов
приходится на 5-й класс опасности (преимущественно, вскрышные породы) - 99,99
%.
Следующее место по образованию отходов занимают отрасли обрабатывающих
производств - 15,8 %, при этом отходы металлургического производства составляют
основную долю в данной отрасли - 96,9 %.
Третье место по образованию отходов занимают предприятия производства и
распределения электроэнергии, газа и воды, объем отходов которых, составляет
0,47 % от общего количества образовавшихся отходов. На 5-й класс опасности
отходов приходится 97 % отходов данной отрасли.
Отходы 1 и 2 классов опасности для окружающей среды образовывается
преимущественно на предприятиях транспорта и связи - 22,2 и 111,4 т
соответственно; на предприятиях производства и распределения электроэнергии,
газа и воды - 17,9 и 12,0 т.
Наибольшее количество отходов 3-го класса опасности образовалось в 2011
году на предприятиях сельского хозяйства (124,0 тыс. т), что составляет 66,0 %
от общего количества образовавшихся отходов 3-го класса опасности.
На предприятиях жилищно-коммунального хозяйства образуются
преимущественно отходы 4-го и 5-го классов опасности.
Таблица 1.6 - Предприятия - основные источники образования отходов
Наименований предприятий
|
Объемы образования отходов,
тыс. т
|
|
2009 г.
|
2010 г.
|
2011 г.
|
ЗАО «Золотодобывающая
компания «Полюс»
|
101958
|
95733
|
110043
|
ОАО ГМК «Норильский никель»
|
н/д
|
33123
|
35484
|
ООО «Соврудник»
|
13424
|
20143
|
21568
|
ООО Артель старателей
«Прииск Дражный»
|
15529
|
13926
|
5133
|
ОАО «РУСАЛ Ачинск»
|
13499
|
9992
|
10631
|
ОАО «Горевский ГОК»
|
4015
|
3966
|
826
|
0,1
|
1617
|
482
|
ОАО «Енисейская ТГК
(ТГК-13)
|
610
|
492
|
582
|
ОАО «Лесосибирский ЛДК № 1»
|
321
|
287
|
274
|
Филиал ОАО «ОГК-6»
Красноярская ГРЭС-2
|
407
|
259
|
317
|
ОАО «ОГК-4» филиал
«Тепловые сети», филиал «Березовская ГРЭС»
|
250
|
228
|
233
|
ООО «Новоангарский
обогатительный комбинат»
|
222
|
14
|
н/д
|
ОАО «РУСАЛ Красноярский
алюминиевый завод»
|
150
|
132
|
133
|
Таким образом видно, что количество отходов всех классов опасности
возрастает ежегодно. В результате этого необходима их утилизация, переработка
либо захоронение. Согласно программам росприроднадзора в Красноярском крае
замечены большие нарушения в сфере утилизации бытовых и твердых промышленных
отходов. Возникает необходимость постройки все новых полигонов для отходов, это
связано в первую очередь с большим периодом распада сложных материалов. Без
решения данной проблемы не минуемо наступит экологическая катастрофа. Для
предотвращения этого необходима разработка новых способов переработки и
утилизации отходов. В данной работе представлен способ переработки твердых
промышленных и бытовых отходов в наполнитель для арболитовых изделий,
используемых в строительной индустрии.
1.3 Анализ возможности использования твердых промышленных и
бытовых отходов в производстве арболита
Промышленность строительных материалов - базовая отрасль строительного
комплекса. Она относится к числу наиболее материалоемких отраслей
промышленности. Материалоемкость определяется отношением количества или
стоимости израсходованных на производство продукции материальных ресурсов к
общему объему продукции. Учитывая, что многие минеральные и органические отходы
по своему химическому составу и техническим свойствам близки к природному
сырью, а во многих случаях имеют и ряд преимуществ (предварительная термическая
обработка, повышенная дисперсность и др.), применение в производстве
строительных материалов промышленных отходов является одним из основных
направлений снижения материалоемкости этого массового многотоннажного
производства. В то же время снижение объемов разрабатываемого природного сырья
и утилизация отходов имеет существенное экономико-экологическое значение. В
ряде случаев применение сырья из отвалов промышленных предприятий практически
полностью удовлетворяет потребности отрасли в природных ресурсах.
Первое место по объему и значению для строительной индустрии принадлежит
доменным шлакам, получаемым в качестве побочного продукта при выплавке чугуна
из железных руд. В настоящее время доменные шлаки являются ценным сырьевым
ресурсом для производства многих строительных материалов и прежде всего
портландцемента. Использование доменных шлаков как активного компонента цемента
позволяет существенно увеличить его выпуск. Европейскими нормами разрешается
вводить в портландцемент до 35% доменного гранулированного шлака, а в шлакопортландцемент
- до 80%. Ввод доменных шлаков в сырьевую смесь увеличивает производительность
печей и снижает расход топлива на 15%. При использовании доменных шлаков для
производства шлакопортландцемента снижаются топливно-энергетические затраты на
единицу продукции почти в 2 раза, а себестоимость - на 25-30%. Кроме того, шлак
как активная добавка значительно улучшает ряд строительно-технических свойств
цемента.
Доменные шлаки стали сырьем не только для традиционных, но и для таких
сравнительно новых эффективных материалов, как шлакоситаллы - продуктов,
полученных методом каталитической кристаллизации шлакового стекла. По
прочностным показателям шлакоситаллы не уступают основным металлам, существенно
превышая стекло, керамику, каменное литье, природный камень. Шлакоситаллы в 3
раза легче чугуна и стали, они имеют прочность на истирание в 8 раз выше, чем у
каменного литья и в 20-30 раз, чем у гранита и мрамора.
По сравнению с доменными пока значительно в меньшей степени используются
сталеплавильные шлаки и шлаки цветной металлургии. Они являются большим
резервом получения строительного щебня и могут быть с успехом использованы в
производстве минеральной ваты, портландцемента и других вяжущих материалов,
бетонов автоклавного твердения.
Большим количеством отходов в виде различных шламов характеризуется
глиноземное производство. Несмотря на отличия в химическом составе шламов,
остающихся после выщелачивания А1203 из природного глиноземсодержащего сырья,
все они содержат 80-85% гидратированного двухкальциевого силиката. После
обезвоживания этот минерал обладает способностью твердеть как при нормальной
температуре, так и в условиях тепловлажностной обработки. Наиболее
крупнотоннажный отход глиноземного производства - нефелиновый (белитовый) шлам
- с успехом используется для производства портландцемента и других вяжущих,
материалов автоклавного твердения и др. При применении нефелинового шлама в
производстве портландцемента расход известняка сокращается на 50--60%,
производительность вращающихся печей повышается на 25-30%, а расход топлива
снижается на 20-25%.
Большое количество отходов в виде золы и шлаков, а также их смесей
образуется при сжигании твердых видов топлива. Их выход составляет: в бурых
углях - 10-15%, каменных углях - 5-40%, антраците - 2-30%, горючих сланцах -
50-80%, топливном торфе - 2-30%.
В производстве строительных материалов обычно используются золы сухого
удаления и золошлаковая смесь из отвалов. Область применения золошлакового
сырья в производстве строительных материалов чрезвычайно разнообразна. Наиболее
значительными направлениями использования топливных зол и шлаков являются
дорожное строительство, производство вяжущих, тяжелых и ячеистых бетонов,
легких заполнителей, стеновых материалов. В тяжелых бетонах золы используют, в
основном, в качестве активной минеральной добавки и микронаполнителя, что
позволяет снизить расход цемента на 20-30%. В легких бетонах на пористых
заполнителях золы применяют не только как добавки, снижающие расход цемента, но
и как мелкий заполнитель, а шлаки в качестве пористого песка и щебня. Золы и
шлаки используются также для изготовления искусственных пористых заполнителей
легких бетонов. В ячеистых бетонах зола применяется как основной компонент или
добавка для снижения расхода вяжущего.
Все большее применение в промышленности строительных материалов находят
отходы угледобычи и углеобогащения. На углеобогатительных фабриках угольных
бассейнов ежегодно образуются миллионы тон отходов, которые с успехом могут
быть использованы для получения пористого заполнителя и кирпича. Использование
отходов углеобогащения в качестве топливной и отощающей добавки при
изготовлении керамических изделий позволяет сократить расход условного топлива
на 50-70 кг на 1000 шт. кирпича и повысить его марку. При строительстве дорог
отходы угледобычи могут широко использоваться в конструкции дорожной одежды.
Ценнейшее сырье для арболитовых изделий представляют собой отходы
горнорудных предприятий и предприятий нерудной промышленности. Можно привести
немало примеров эффективного использования вскрышных пород, отходов обогащения
руд, отсевов дробления как сырья для получения вяжущих, автоклавных материалов,
стекла, керамики, фракционированных заполнителей. Эксплуатационные расходы на
получение 1 м3 щебня из отходов горнорудных предприятий в 2-2,5 раза ниже, чем
на добычу его из карьеров.
Значительным выходом отходов, представляющих интерес для производства
арболитовых изделий, характеризуется химическая промышленность. Основными из
них являются фосфорные шлаки и фосфогипс. Фосфорные шлаки - отходы при возгонке
фосфора в электропечах - перерабатываются, в основном, в гранулированные шлаки,
шлаковую пемзу и литой щебень. Гранулированные электротермофос-форные шлаки
близки по структуре и составу к доменным и так же с высокой эффективностью
могут использоваться в производстве цементов. На их основе разработана
технология шлакоситаллов. Использование фосфорных шлаков в производстве
стеновой керамики позволяет повысить марку кирпича и улучшить другие его
свойства.
Потребности промышленности строительных материалов в гипсовом сырье
практически в полной мере можно удовлетворить за счет гипсосодержащих отходов
промышленности и, в первую очередь, фосфогипса. К настоящему времени разработан
ряд технологий получения строительного и высокопрочного гипса из фосфогипса,
реализованных пока недостаточно. Этому в определенной мере способствует
существующая ценовая политика на природное сырье, не поощряющая в полной мере
альтернативных вторичных сырьевых ресурсов. В Японии, где нет собственных
запасов природного гипсового сырья, для получения разнообразных гипсовых
изделий фосфогипс используют практически полностью.
Применение фосфогипса эффективно также в производстве портландцемента,
где он не только позволяет, как и природный гипсовый камень, регулировать сроки
схватывания цемента, но, будучи введенным в сырьевую смесь, выполняет роль
минерализатора, снижающего температуру обжига клинкера.
Большая группа эффективных строительных материалов изготавливается из
отходов древесины и переработки другого растительного сырья. С этой целью
используют опилки, стружку, древесную муку, кору, сучья, костру и т. д. Все
древесные отходы можно разделить на три группы: отходы лесозаготовительной
промышленности, отходы лесопильного производства и отходы деревообрабатывающей
промышленности.
Из отходов древесины, полученных на различных стадиях ее переработки,
изготовляют древесноволокнистые и древесно-стружечные плиты, арболит, ксилолит,
опилкобетон, ксилобетон, фибролит, королит, древесные пластики. Все эти
материалы в зависимости от области применения разделяют на
конструкционно-теплоизоляционные, теплоизоляционные и отделочные.
Применение материалов на основе древесных отходов, наряду с высокими
технико-экономическими показателями, обеспечивает архитектурную
выразительность, хороший воздухообмен и микроклимат помещений, улучшенные
теплотехнические показатели.
Значительный объем отходов, которые могут служить вторичными сырьевыми
ресурсами, образуется на самих предприятиях строительных материалов. Это,
наряду с отходами производства нерудных материалов, стекольный и керамический
бой, цементная пыль, отходы производства минеральной ваты и др. Комплексное
использование сырья на большинстве предприятий позволяет создавать безотходные
технологии, при которых полностью сырьевые ресурсы перерабатываются в
строительные материалы.
Существенные резервы для развития сырьевого потенциала в производстве
строительных материалов представляют отходы городского хозяйства. В передовых
странах мира в составе твердых бытовых отходов превалируют макулатура, полимерные
продукты, текстиль, стекло. Имеется многолетний опыт производства на базе этих
отходов картона, волокна, строительных пластмассовых изделий и др.
Таким образом широкая утилизация отходов в производстве строительных
материалов требует решения ряда организационных и научно-технических проблем.
Необходима региональная каталогизация отходов с указанием их полной
характеристики. Требует развития стандартизация отходов как сырьевых ресурсов в
производстве конкретных строительных материалов. Масштабы утилизации
промышленных отходов и отходов городского хозяйства будут расширяться по мере
внедрения комплекса технических мер по стабилизации их состава, повышению
степени технологической подготовки (снижение влажности, гранулирование и др.).
Огромное значение имеет экономическое стимулирование, включающее вопросы
ценообразования, финансирования, материального стимулирования.
Многие из перечисленных веществ можно использовать для производства
арболитовых изделий. В данной дипломной работе представлена возможность использования
твердых промышленных и бытовых отходов в производстве арболитовых изделий.
2. Программа и методика исследований
.1 Теоретические взгляды на технологию производства и
структурообразование арболита
Исследования показали, что сроки твердения арболита и
его прочность зависят от химического состава древесины. Установлено, что
наиболее вредное воздействие оказывают легкорастворимые простейшие сахара:
сахароза, глюкоза, фруктоза и часть гемицеллюлозы, способной в определенных
условиях превратиться в эти сахара. В меньшей степени опасны крахмал, танины и
смолы. Щелочная среда цементного теста способствует выделению «цементных ядов»,
количество которых колеблется в значительных пределах в зависимости от породы
древесины, условий и сроков ее хранения (табл. 1).
Было выявлено, что воздействие водорастворимых веществ
древесины на твердеющий цемент проявляется в стабилизирующем эффекте.
Таблица 2.1- Химический состав некоторых пород
древесины, %
Состав
|
Ель
|
Сосна
|
Осина
|
Бук
|
Целлюлоза (определяемая по
хлорному методу без пентозанов)
|
58,3
|
55,6
|
54,1
|
47,9
|
Лигнин (определяемый по
сернокислотному методу)
|
28,3
|
26,5
|
20,1
|
22,5
|
Гемицеллюлоза
(легкогидролизуемые пентозаны)
|
10,3
|
9,6
|
22,4
|
26
|
Экстрактивные вещества,
растворимые в горячей воде
|
1,9
|
2,3
|
2,3
|
2,4
|
«Цементные яды», состоящие в основном из углеводных
групп НОСН, осаждаясь на поверхности частичек минералов цемента 3CaOSi02 (трехкальциевый силикат) и
ЗСаО-А1203 (трехкальциевый алюминат), образуют тончайшие оболочки, которые
затрудняют ход процессов гидратации цемента. Для уменьшения отрицательно,
влияния водорастворимых экстрактивных и легкогидролизуемых веществ на прочность
деревоцементных композиций были предложены различные способы и технологические
приемы. Сущность, которых заключалась в частичном удалении этих веществ из
древесного заполнителя, в переводе простейших сахаров в нерастворимые или
безвредные для цемента соединения, в ускорении твердения портландцемента (т. е.
в сокращении времени их воздействия на процессы твердения) и др.
Невысокая прочность арболита при значительном расходе
портландцемента объясняется не только отрицательным влиянием экстрактивных и
легкогидролизуемых веществ, содержащихся в древевесном заполнителе (как и в
других органических целлюлозных заполнителях), на процессы структурообразования
арболита, но также отрицательным влиянием объемно-влажностных деформаций и
давления набухания древесного заполнителя в процессе твердения и высыхания
арболита при эксплуатации во влагопеременных условиях.
При изготовлении древесной дробленки для производства
арболита предпочтение отдается тем породам древесины, в которых меньше
водорастворимых экстрактивных веществ, которые являются медлителями твердения
портландцемента. Поэтому в производстве арболита в основном применяют дробленку
из ели, сосны, пихт. Древесина лиственницы из-за высокого содержания в ней
экстрактивных веществ и, как следствие, высокой химической активности считается
малопригодной. Кроме того, она подвержена большим влажностным деформациям по
сравнению с другими хвойными порода (таблице 2).
Таблица 2.2 - Усушка древесины
Тангенциальная усушка
древесины
|
Порода
|
ранней
|
поздней
|
Уп/Ур*
|
Ель Сосна Лиственница
|
8,1 8,05 7,87
|
10,3 11,26 13,87
|
1,27 1,39 1,76
|
* - усушка соответственно поздней и ранней древесины
К специфическим свойствам органического целлюлозного
заполнителя, отрицательно влияющим на процессы структурообразования, т.е.
прочность и стойкость арболита к влагопеременным воздействиям, относятся:
повышенная химическая активность; значительные объемные влажностные деформации и
развитие давления набухания; резко выраженная анизотропия; высокая
проницаемость; низкая адгезия по отношению к цементному камню; значительная
упругость при уплотнении смеси.
Эти специфические свойства древесного заполнителя в
разной степени влияют на процессы структурообразования и физико-механические
свойства арболита, однако для получения высококачественных изделий и
конструкций должны учитываться в их технологии.
Полиэтилентерефталат (ПЭТФ) - твердое вещество без
запаха, плотность 1,38-1,40г/см3,температура плавления 255-2650С,температура
размягчения 245-2480С, температура стеклования 70-800С.
Полиэтилентерефталат характеризуются высокой
прочностью и ударной вязкостью, устойчив к истиранию и многократным деформациям
при растяжении и изгибе.
Стекло - вещество и материал, один из самых древних и,
благодаря разнообразию своих свойств, - универсальный в практике человека.
Физико-химически - твёрдое тело, структурно- аморфно, изотропно; все виды
стёкол при формировании преобразуются в агрегатном состоянии - от чрезвычайной
вязкости жидкого до так называемого стеклообразного - в процессе остывания со
скоростью, достаточной для предотвращения кристаллизации расплавов, получаемых
плавлением сырья (шихты).
Полиэтилентерефталат и стекло, являются пассивным
неволокнистым компонентам, которые оказывают значительное влияние на
образование связей в арболите следовательно, и на физико-механические свойства
арболита. Очевидно, что размер частиц вводимого неволокнистого компонента будет
оказывать определенное влияние на свойства готовой продукции. Однако,
представленные теоретические предположения необходимо подтвердить
экспериментальным путем. Для этого требуется провести планирование
эксперимента, выбрать основные характеристики моделей, разработать
математические модели с нормализованными значениями факторов.
2.2 Программа и методика проведения эксперимента
Важнейшей составной частью научного исследования
является построение математической модели объекта. Математическая модель - это
совокупность математических зависимостей, описывающих функционирование системы.
Построенная математическая модель объекта является хорошим инструментом
исследования. С ее помощью определяют интересующие исследователя характеристики
объекта, результаты влияния на него тех или иных факторов, оптимальные режимы
функционирования и способы управления объектом.
Выбор методов исследований. Экспериментальные методы исследований
объединяются под названием «планирование эксперимента». Планирование
эксперимента - это совокупность приемов, позволяющих исследователю правильно
построить эксперимент и получить адекватное описание интересующего процесса.
Для решения поставленных задач используются методы
математического планирования с целью получения математического описания
процесса. Уравнение математического описания могут быть получены тремя
методами: аналитическим, экспериментальным и экспериментально-аналитическим.
Аналитический метод, являющийся наиболее наглядным и
достоверным, основан на знании физико-химических и других закономерностей,
присущих исследуемому объекту. Поэтому он применим только для хорошо изученных
процессов. Экспериментально-аналитический метод заключается в определении
неизвестных коэффициентов уравнений, отражающих известные физические явления.
Экспериментальные методы получения математических моделей применяют для
сложных многофакторных процессов, которые теоретически изучены недостаточно.
Математические зависимости, полученные этим методом, не отражают физической
сущности объекта, только устанавливают количественные соотношения между его
входными и выходными факторами.
Экспериментальные исследования делятся на пассивные и
активные. Полученное при пассивном эксперименте уравнение регрессии,
справедливо только в том узком диапазоне изменений входных параметров, какой
существовал во время проведения эксперимента.
При активном эксперименте объекту наносятся
искусственные возмущения и измеряются соответствующие им значения выходных
исследуемых параметров. Величина и сочетание возмущающих воздействий вводится в
объект в соответствии с определенным планом, оптимальным по какому-либо критерию.
По сравнению с традиционным методом математические
планы эксперимента значительно сокращают необходимое число опытов и более
равномерно исследуют факторное пространство. Но они могут быть использованы
только при условии нормального закона распределения исходных параметров.
Планирование однофакторного
эксперимента. Для
решения задачи определения наиболее значимых факторов был проведен
однофакторный эксперимент для получения математических моделей вида Y=f(X1). Метод обработки результатов
эксперимента с целью описания объекта - метод наименьших квадратов .
Эксперимент состоит из N
опытов, равноотстоящих друг от друга на шаг h. Уравнение в общем виде для однофакторных экспериментов
Y=B0+B1X1 +B11X12, (2.1)
Для вычисления трех неизвестных коэффициентов данного уравнения
необходимо решить систему из трех линейных уравнений

(2.2)
Поставив вычисленные значения в уравнение общего вида,
получим искомую математическую модель.
Для определения процентного содержания компонентов в древесноволокнистой
композиции, без ухудшения физико - механических характеристик готовых
древесноволокнистых плит, были проведены однофакторные эксперименты, целью которых
являлось получение регрессионных зависимостей вида (2.1), которые с
достаточной точностью описывали бы результаты экспериментов. Коэффициенты
уравнения (2.1) определялись при решении системы из трех линейных уравнений с
тремя неизвестными (2.2). Входными параметрами для проведения эксперимента
являются, фракционный состав стекла и полиэтилентерефталата и их процентное
содержание в композиции а.с.в. Уровни варьирования взяты из литературных
источников.
2.3 Анализ процесса рециклинга
твердых промышленных отходов в производстве арболитовых изделий
Регрессионный анализ процесса обработки вторичного
волокна производится по представленной ниже схеме.
1. Определение среднего значения функций отклика по строкам
(математические ожидания)

, (2.3)
где n -
число параллельных опытов;
Yu1 - значение функции отклика параллельных опытов.
. Вычисление построчных дисперсий.
Для определения величины разброса случайных величин относительно
математического ожидания вычисляем значения построчных дисперсии Su по следующей формуле
, (2.4)
где
- среднее значение параллельных опытов.
3. Проверка однородности выборочных оценок с
использованием критерия Кохрена
, (2.5)
где
- наибольшее из вычисленных значений построчных дисперсии;
Gm - табличное значение критерия Кохрена.
Табличное значение критерия Кохрена определяется
согласно выбранному уровню значимости q, числу степеней свободы f и по
количеству выборок u.
Если условие выполняется, то дисперсии однородны, т.е. полученные
экспериментальные данные находятся в доверительном интервале.
. Вычисление (оценка) дисперсии воспроизводимости среднего
значения функции
, (2.6)
. Определение значимости коэффициентов
регрессии
Значимость полученных, согласно уравнению (2.4), коэффициентов уравнений
регрессии определяем по критерию Стьюдента
, (2.5)
где tp -
расчетное значение критерия Стьюдента;
- дисперсия коэффициентов регрессии,
оценка которой производится по формуле
, (2.6)
(2.7)
где
- табличное значение критерия Стьюдента при уровне
значимости q и числе степеней свободы f.
Коэффициенты регрессии, не удовлетворяющие условию
(2.7), считаются незначимыми (равными нулю) и соответствующие члены из
уравнения регрессии исключаются.
. Проверка адекватности математической модели
соответствующему технологическому процессу.
По результатам проверки адекватности модели можно
принять или отвергнуть гипотезу о том, соответствует ли построенная модель
результатам эксперимента, и, следовательно, пригодна ли она для описания
объекта. Проверка адекватности модели осуществляется в четыре этапа.
Определяют сумму квадратов, характеризующую
адекватность модели Sад.
Она рассчитывается по формуле
, (2.8)
где n -
число дублированных опытов;
- среднее значение результатов
эксперимента в j-й серии
дублированных опытов, j=1,2,…N;
- величина отклика, рассчитанная по уравнению
регрессии для j-го опыта.
Вычисляют число степеней свободы fад дисперсии адекватности по формуле
fад =N-p, (2.9)
где N -
число опытов;
р - число значимых коэффициентов регрессии.
Вычисляют дисперсию адекватности Sад по формуле
, (2.10)
С помощью F -
критерия Фишера проверяют однородность дисперсии адекватности
и дисперсии воспроизводимости S2{y}. При этом вычисляют отношение по формуле
, (2.11)
где S2{y} - дисперсия воспроизводимости
эксперимента, рассчитывается по формуле (2.6).
Полученное значение сравнивают с табличным, найденным
при выбранном уровне значимости q и для чисел степени свободы fад и fy. Если выполняется соотношение то модель считается адекватной
и может быть использована для описания объекта.
Fрасч.<Fтабл. (2.12)
Для математического анализа и интерпретации полученных моделей лучше
всего пользоваться уравнениями в нормализованных значениях факторов.
Необходимость математического анализа на ряду с регрессионным обуславливается
тем, что для квадратичной модели степень влияния фактора на изменение отклика
не является постоянной. Она различна в разных точках диапазона варьирования
данного фактора, а при наличии парных взаимодействий определяется еще и
уровнями факторов, входящих в эти взаимодействия. Степень влияния фактора Х1
на изменение отклика в некоторой точке Х1 =
определяется величиной частной производной
, взятой в точке
, то есть выражением
= b1 + 2b11
+ b12Х 2. Как видно, значение этого выражения
определяется как уровнем фактора Х1 =
, так и значением фактора Х2.
Если же сравнивать факторы по максимальной степени их слияния в диапазоне
варьирования, то, в общем случае, для i-го фактора критерием является максимальное по модулю
значение величины
, которое равно
.
Обращаясь к уравнению параболы общего вида
Y = b0 + biXi + biiXi2, (2.13)
будем учитывать некоторые факты:
) Если bii > 0, то
уравнение (3.21) описывает вогнутую функцию (ветви параболы направлены вверх),
а если bii < 0 - выпуклую.
) Абсцисса вершины параболы равна XiB = - bi / 2bii.
) Если имеет место соотношение
½bi½ > 2½bii½, (2.14)
то вершина параболы находится вне диапазона варьирования фактора Хi и, следовательно, уравнение
описывает монотонную функцию. Если при этом bi > 0, то эта функция монотонно возрастающая, а если
bi < 0 - монотонно убывающая.
) При наличии соотношения
½bi½ < 2½bii½, (2.15)
функция имеет экстремум внутри диапазона варьирования фактора Xi - максимум при bii < 0 или минимум при bii > 0.
Реализация описанной схемы регрессионного и математического анализа и
оценка степени влияния каждого входного технологического фактора на выходные
величины осуществлена с применением программы Microsoft Excel 2010.
2.4 Выбор основных характеристик моделей
Факторы, влияющие на исследуемый процесс можно разделить на три группы:
управляемые, контролируемые, неконтролируемые.
Управляемые факторы однофакторных эксперимента:
-Fc - фракционный состав стекла, г.;
Fп -
фракционный состав полиэтилентерефталата, г.;
Fк -
фракционный состав коры, г.;
Fв -
фракционный состав вермикулита, г.;
-Сс
- концентрационный компонент стекла в основной композиции к а.с.в, %;
Сп - концентрационный компонент полиэтилентерефталата в основной
композиции к а.с.в , %;
-Ск
- концентрационный компонент коры в основной композиции к а.с.в, %;
-Св
- концентрационный компонент вермикулита в основной композиции к а.с.в, %.
Контролируемые факторы однофакторного эксперимента:
-Og - огнезащищенность, мин;
Pr -
прочность готового блока, МПа;
Pl -
плотность готовой блока, кг/м3.
К неконтролируемым факторам эксперимента относились не указанные выше
геометрические характеристики процесса.
Таким образом, программа экспериментальных исследований должна состоять
из четырех разделов:
. Планирование и реализация однофакторных исследований по определению
зависимости прочности, Pr,
плотности, Pl, огнезащищенности , Og, арболитового блока от фракционного состава стекла и его процентного
содержания в основной композиции в виде функциональных зависимостей:
Pr = f (Fc), (2.16)
Pr = f (Сс), (2.17)
Pl = f (Fc), (2.18)
Pl = f (Сс), (2.19)= f (Fc), (2.20)=
f (Сс), (2.21)
2. Планирование и реализация однофакторных исследований по определению
зависимости прочности, Pr,
плотности, Pl, огнезащищенности , Og, арболитового блока от фракционного состава
полиэтилентерефталата и его процентного содержания в основной композиции в виде
функциональных зависимостей:
Pr = f (Fп), (2.22)
Pr = f (Сп) (2.23)
Pl = f (Fп), (2.24)
Pl = f (Сп), (2.25)
Og = f (Fп), (2.26)= f (Сп), (2.27)
3. Планирование и реализация однофакторных исследований по определению
зависимости прочности, Pr,
плотности, Pl, огнезащищенности , Og, арболитового блока от фракционного состава коры и его
процентного содержания в основной композиции в виде функциональных
зависимостей:
Pr = f (Fк), (2.28)
Pr = f (Ск) (2.29)
Pl = f (Fк), (2.30)
Pl = f (Ск), (2.31)
Og = f (Fк), (2.32)= f (Ск), (2.33)
4. Планирование и реализация однофакторных исследований по определению
зависимости прочности, Pr,
плотности, Pl, огнезащищенности , Og, арболитового блока от фракционного состава вермикулита и
его процентного содержания в основной композиции в виде функциональных
зависимостей:
Pr = f (Fв), (2.34)
Pr = f (Св), (2.35)
Pl = f (Fв) (2.36)
Pl = f (Св), (2.37)
Og = f (Fв), (2.38)= f (Св), (2.39)
Таким образом, активный однофакторный эксперимент был принят нами в
качестве основного метода получения математического описания рециклинга твердых
промышленных и бытовых отходов в производстве арболитовых изделий.
3. Результаты экспериментальных исследований
.1 Лабораторные установки для проведения исследований
Мельница МР - 4. Устройство МР-4 предназначено для измельчения кусковых материалов,
являющимися отходами производства в виде пластика, коры, хвои, веток хвойных
и/или лиственных деревьев, макулатура, полиэтилен, РТИ, макулатура, твердый
листовой материал растительного происхождения.
Таблица 3.1 - Характеристика устройства
Высота с питателем для
крупных габаритов измельчаемого материала, мм.
|
550
|
Высота с питателем для
широкого листового материала, мм.
|
310
|
Ширина, мм.
|
360
|
Длина, мм.
|
750
|
Электродвигатель
трехфазного тока Напряжение, В. Мощность, кВт Частота вращения ротора электродвигателя,
об/мин Частота вращения ведущего вала устройства, об/мин
|
220 2 1500 900
|
Масса, кг.
|
55
|
На рисунке 3.1 показано устройство МР - 4 для измельчения отходов
производства. Основными элементами устройства являются ротор 1 и статор-корпус
2. Ротор 1 и приводной шкив 3 жестко связанны с валом 4, на котором свободно
посажены внутренние обоймы подшипников 5. Наружные обоймы подшипников 5
установлены в корпусе 2. В пазах ротора 1 закреплены ножи 6 при помощи клиньев
7 и винтов 8. В корпусе 2 закреплена сменная колосниковая решетка 9, с
отверстиями круглого сечения, диаметр которых определяет размеры измельченных
частиц.
Измельчение осуществляется режущими кромками ножей 6 ротора 1 и режущей
кромкой 11 питателя 12, где между режущими кромками (поз. 10 и 11)
устанавливается минимально возможный зазор b= 0,1-1 мм. Питатель 12 закреплен на корпусе 2, с
некоторым межосевым смещением a,
который образован между продольной осью симметрии О1-О2 питателя 12 и
вертикальной диаметральной осью симметрии О-О ротора 1.
Рисунок 3.1 - Устройство МР - 4
Решение поставленной задачи осуществляется путем подачи измельчаемого
материала в зону измельчения устройства, в ориентируемом состоянии, которое
осуществляется за счет питателя (воронки), форма сечения отверстия которого
соответствует форме поверхности поперечного сечения измельчаемого материала.
Например, при измельчении пластиковых бутылок питатель должен иметь круглое
отверстие, через которое по очереди поступают бутылки, а при измельчении
плоской ленты питатель должен иметь прямоугольное отверстие (щель), через
которое непрерывно подается лента с прямоугольным поперечным сечением. Высота
питателей должна быть не менее 5d
и/или 5c, где d- диаметр отверстия питателя, c-ширина щели питателя.
На рисунке 3.1 показаны устройства для измельчения отходов производства.
Основными элементами устройства являются ротор 1 и статор-корпус 2. ротор 1 и
приводной шкив 3 жестко связанны с валом 4, на котором свободно посажены
внутренние обоймы подшипников 5. Наружные обоймы подшипников 5 установлены в
корпусе 2. В пазах ротора 1 закреплены ножи 6 при помощи клиньев 7 и винтов 8.
В корпусе 2 закреплена сменная колошниковая решетка 9, диаметр отверстий
которой ограничивает размер измельченных частиц.
Измельчение отходов производства материалы в устройстве осуществляется
режущими кромками 10 ножей 6 ротора 1 и режущей кромкой 11 питателя 12, где
между режущими кромками 10 и 11 устанавливается минимально возможный зазор b= 0,1-1 мм. Питатель 12 закреплен на
корпусе 2, с некоторым отрезком (a),
который образован между продольной осью симметрии О1О2 питателя 12 и
вертикальной диаметральной осью симметрии ОО ротора 1.
Величина отрезка (а) определяется опытным путем. Отрезок (а) может быть
установлен от оси симметрии О-О ротора 1- направо или налево.
Установлено, что при большой величине правого отрезка (а) материал для
измельчения не подается в зону измельчения устройства (материал выбрасывается
из питателя).
Установлено, что при большой величине левого отрезка (а) материал для
измельчения подается из питателя в зону измельчения устройства с большой
скоростью, которая превышает скорость измельчения материала в устройстве, что
приводит к остановке вращения ротора.
Установлено, что для измельчения материала величина отрезка (а) должна
быть определенна опытным путем, при котором скорость подачи материала из
питателя должна соответствовать скорости измельчаемого материала в устройстве.
Бетоносмеситель Prorab ECM-63. Модель оборудована двигателем мощностью 220 Вт, который
для безопасности находится в защищённом кожухе. Двигатель питается от сети: 220
В, 50 Гц.
Барабан бетономешалки имеет максимальный объём 63 литра, что позволяет
вмещать до 48 литров готовой смеси. После завершения работы обязательно нужно
проводить чистку барабана.
Материалы для приготовления бетона загружаются в загрузочное отверстие
диаметром 267 мм. Скорость перемешивания составляет 27,5 оборотов в минуту.
Наклон барабана (например, для залива бетона) осуществляется с помощью
специальной рукоятки наклона.
Эксплуатацию модели можно осуществлять только в условиях следующего
температурного режима: +5 С° - + 35 С°.
Для безопасной эксплуатации рабочее место должно быть максимально чистым
и хорошо освещённым.
Вес инструмента составляет 25 кг. А габариты: 1110х550х935 мм. Для
удобства транспортировки бетономешалка оборудована одной опорной и одной
колёсной стойкой (с двумя колесами).
Рама бетономешалки PRORAB ECM 63 усилена металлическими откосами, которые
обеспечивают жесткость и прочность конструкции.
Наличие колес позволяет быстро и легко перемещать бетономешалку в любое
удобное место. Управление наклоном барабана бетономешалки осуществляется
вручную с помощью специальной удобной рукоятки. Устойчивость благодаря наличию
опорной ножки.
Класс защиты IP45D. Цельный чугунный венец. Электрический привод.
Рисунок 3.2 - Бетоносмеситель Prorab ECM-63
Устройство и принцип работы ФВГ-2
Конструкция прибора, представленная на рисунке 1, имеет следующие
основные элементы:
- механизма привода сит,
- реле времени,
- поддон,
- набор сит,
- крышка,
- пружины крепления.
Рисунок 3.3 - Конструкция фракционатора ФВГ - 2
Работа прибора основана на гирационном разделении волокна по фракциям.
Электродвигатель через клиноременную передачу вращает центральный вал с
эксцентриком, на котором через подшипники закреплена планшайба с роликовым
упором, не позволяющим вращаться планшайбе. За счет эксцентриситета, планшайба,
на которой жестко крепятся поддон, сита и крышка, создает колебания вдоль
прибора с частотой около 400 колебаний в минуту.
При работе прибор создает значительную вибрацию, поэтому устанавливать
прибор необходимо на жесткое основание, исключающее смещение прибора
Вибропресс стром - уникум. Назначение.
1. Установка «СТРОМ» предназначена для производства
различных типов строительных блоков, кирпичей, и тротуарной плитки для
индивидуального строительства. дома, дачи, гаража и благоустройства
приусадебного хозяйства.
1.2. Установки «СТРОМ» созданы на основе модульности конструкции,
что расширяет их возможности при оснащении дополнительной оснасткой.
1.3. Установки должны работать при температуре окружающей
среды не ниже 5 градусов по Цельсию. Установки «СТРОМ» соответствуют
техническому исполнению «У» категории «3» по ГОСТ 15150-69.
. Блок-формы
2. Виброплощадка
. Электродвигатель с грузом (эксцентриком)
Рисунок 3.4 - Устройство вибропресса стром - уникум
Подготовка установки к работе и порядок работы.
Рисунок 3.5 - Схема формы вибропресса
1. При подготовке к работе необходимо расконсервировать установку в
соответствии с. Перед включением установки в сеть необходимо:
• изучить и выполнять требования настоящего паспорта;
• убедиться в соответствии напряжений электровибропривода и
питающей электросети « проверить надежность крепления и затяжку всех резьбовых
соединений;
• удостовериться в отсутствии повреждений токопроводящего
кабеля и штепсельной вилки;
2. Перед началом работы виброплощадка устанавливается на равном месте. Во
избежание появления боковых колебаний установка виброплощадки с уклоном не
допускается.
3. На виброплощадку устанавливаются три блок-формы (1) на подставках (2).
Подставка (2) необходима для предотвращения выпадения рабочей смеси из формы
(1). А так же для перемещения блок-формы при выемке отформованного блока из
блок-формы.
4. Подключить электрооборудование к электрической сети с помощью
прилагаемого токопроводящего кабеля со штепсельной вилкой. С целью защиты от
перегрузок и коротких замыканий электропривод рекомендуется подключать к сети
через автомат.
5. Формы заполняются рабочей смесью на 1\4 часть. При необходимости
внутрь блок-форм устанавливается дополнительная оснастка, делящая полость на
равные части. Для производства изделий имеющих толщину 5 - 15 см форма
заполняется рабочей смесью на данную высоту.
6. Нажатием кнопки «Пуск» пускового устройства включается
электродвигатель.
7. Формы заполняются рабочей смесью до верхнего края.
8. Время уплотнения смеси - 2 минуты. По окончании формования
электропривод отключается, блок-формы снимаются с виброплощадки д 11
расформовки - переносятся на ровное место (лист рубероида или тонкий слой
сухого песка), подставка выдёргивается из-под формы, форма снимается с изделия.
Перед заполнением формы рабочей смесью внутренние стороны формы для
облегчения выемки необходимо смазать отработанным маслом. Данная операция
выполняется перед началом работы и в последующем повторяется после каждого
восьмого изготовленного блока.
Порядок работы при использовании сменной оснастки блок -
форм.
После заполнения формы раствором и окончания вибрации электродвигатель
выключается, поверхность блока выравнивается и производится расформовка и
выемка изделия.
Для повышения прочности стен рекомендуется использовать различную арматуру.
Установку (1) устанавливают на ровное место, заполняют три блок-формы
рабочий смесью на 1\4 часть каждой, после чего в них устанавливают оснастку,
делящую полость формы на 2-8 равных частей (2).
В формы добавляется рабочая смесь с одновременным включением
электровибратора для её уплотнения, поверхность изделия равняется, после чего
электровибратор отключается и производится расформовка и выемка изделия.
Рисунок 3.6 - Схема формы для пустотелого блока
3.2 Сырье и материалы
Органический целлюлозный заполнитель.
Многие органические
целлюлозные заполнители, в том числе и древесина (древесный заполнитель),
наряду с присущими им ценными свойствами (малая средняя плотность, хорошая
смачиваемость, легкость обработки, в частности дроблением и др.), имеют и
отрицательные качества, которые затрудняют получение арболита высокой прочности
из высокопрочных компонентов (цементный камень и древесина).
Технологическое древесное сырье поставляется на
предприятие как отдельно по породам, так и в смешанном виде в различных
соотношениях.
Диаметр заготовок сырья в круглом виде устанавливается
от 5 до 15 см. Заготовки диаметром более 15 см подлежат расколке части,
наибольшая линия раскола по торцу не должна превышать 15 см.
В технологическом сырье допускаются пороки древесины
(по ГОСТ 2140-81 с изм.), в том числе гниль внутренняя заболонная мягкая и
наружная трухлявая, если она занимает не более 6% площади торца дровяного сырья
или 5% общего объёма партии.
Дрова и кусковые отходы укладывают, принимают и
учитывают в соответствии с ГОСТ 3243-46 (с изм.). Древесное технологическое
сырье в круглом виде хранят в соответствии с ГОСТ 9014.0-75 (с изм.).
Кусковые отходы древесины должны измельчаться в щепу и
выдерживаться в кучах под навесом не менее 1 мес. при положительной
температуре.
Применение свежесрубленной древесины всех пород для
производства арболита допускается при соблюдении следующих требований:
показатель пригодности (удельный расход цемента на единицу прочности арболита
при сжатии) должен быть не более 15; содержание водорастворимых редуцирующих
веществ не более 2%.
При дроблении и рассеве необходимо применять древесину
равновесной относительной влажности не более 39%, при влажности выше этого
предела нарушается нормальная работа дробилок, сит и грохотов.
Органическими заполнителями служат измельченная
древесина из отходов лесозаготовок, лесопиления и деревообработки хвойных (ель,
сосна, пихта) и лиственных (береза, осина, бук, тополь) пород, костра конопли и
льна, измельченные стебли хлопчатника и измельченная рисовая солома.
Размеры древесных частиц измельченной древесины не
должны превышать по длине 40, по ширине 10, а по толщине 5 мм. Содержание
примеси коры в измельченной древесине не должно быть более 10%, а хвои и
листьев - более 5% по массе сухой смеси заполнителя. Содержание водорастворимых
редуцирующих веществ в измельченной древесине не должно превышать 2% (данный
показатель не является браковочным признаком).
Фракционный состав органического заполнителя должен
находиться в следующих пределах:
Размеры отверстий контрольных сит, мм 20, 10, 5, 2,5,
менее 2,5
Полные остатки на контрольных ситах, % по массе до 5,
20-40, 40-75, 90-100, до 10.
Вяжущие вещества. Вяжущие вещества, применяемые для
приготовления арболита по ГОСТ 19222-84, должны удовлетворять требованиям
следующих Стандартов: портландцемент и быстротвердеющий портландцемент - ГОСТ
10178-76 (с изм.); цемент сульфатостойкий - ГОСТ 22266-76 с изм.);
портландцемент белый - ГОСТ 965-78; портландцемент цветной-ГОСТ 15825-80.
Марка цемента должна быть не ниже 300 - для
теплоизоляционного арболита и 400 - для конструкционного.
При возможности выбора портландцемента предпочтение
отдается алитовым цементам, содержащим в основном трехкальциевый силикат. Такой
цемент обеспечивает в первые сутки более интенсивный набор прочности по
сравнению с белитовым цементом.
С увеличением тонкости помола портландцемента
прочность цементного камня возрастает. Средний размер зерен портландцемента
примерно 40 мкм. Глубина гидратации зерен через 6-12 мес. твердения обычно не
превышает 10-15 мкм. Таким образом, при обычном помоле портландцемента 30-40%
клинкерной части его не участвует в твердении и формировании структуры камня. С
увеличением тонкости помола цемента возрастает содержание клеящих веществ -
гидратов минералов и повышается прочность цементного камня. Цементы должны
иметь тонкость помола, характеризуемую остатком на сите № 008 не более 15 %.
Тонкость помола цемента характеризуется также удельной поверхностью
(см2/г) - суммарной поверхностью зерен (см2) в 1 г цемента. Удельная
поверхность цементов 2500-3000 см2/г. Для повышения активности цемента и
получения быстротвердеющего цемента тонкость помола повышают. Условно считают,
что прирост удельной поверхности цемента на каждые 1000 см2/г повышает
активность на 20-25%.
Химические добавки. В арболитовую смесь химические
добавки вводят для повышения марочной прочности; ускорения процессов твердения;
улучшения технологических свойств арболитовой смеси (удобоукладываемость,
однородность) повышения защитных свойств арболита по отношению к стали арматуре
(ингибиторы коррозии стали); улучшения строительных свойств.
Добавками служат химические вещества, которые
локализуют замедляющее действие экстрактивных веществ, содержащихся в
органическом целлюлозном заполнителе, или покрывают частицы заполнителя
водонепроницаемой пленкой препятствующей соприкосновению вредных веществ
заполнителя с цементным тестом. Многие добавки являются также ускорителями
твердения арболита, что позволяет сократить срок воздействия вредных веществ на
гидролиз гидратацию цемента.
При использовании древесного заполнителя химическая добавка выбирается в
зависимости от его активности - содержания сахара в водорастворимых
экстрактивных веществах. При применении заполнителя из хвойной выдержанной
древесины (атмосферное хранение в течение 3 мес. и более) эффективным
ускорителем твердения арболита является хлорид кальция и комплексные добавки на
его основе, а для заполнителя из свежесрубленной древесины -сульфат алюминия и
комплексные добавки на его основе. Если используют заполнитель из смешанных
пород древесины или лиственницы, наиболее эффективны комплексные добавки:
хлорид кальция + жидкое стекло и хлорид кальция + известь.
Выбор и дозирование химических добавок для арболита оcyществляется заводской лабораторией с
учетом конкретных условий вида заполнителя.
Химические добавки в арболитовую смесь вводят в виде
водных растворов взамен воды затворения или частично заменяя ее. Для
поддержания принятого водоцементного отношения (В/Ц) количество воды,
содержащееся в растворах, учитывается при расчете состава, арболитовой смеси.
Вода для приготовления растворов химических добавок и корректировки В/Ц
арболитовой смеси должна удовлетворять требованиям ГОСТ 23732-79.
Растворы химических добавок готовят в специальных
установках или емкостях с учетом коррозионной агрессивности этих растворов.
Для ускорения растворения химических веществ при
приготовлении растворов рекомендуется подогревать воду до 40-70°С перемешивать
растворы.
Перед использованием раствора следует определять его
плотность, в соответствии с которой устанавливают дозировку. При необходимости
плотность корректируют добавлением в раствор воды и химической добавки.
Плотность растворов определяют при температуре 18-20°С ареометром со шкалой от
1 до 1,4 г/см3 или денсеметром.
Количественное соотношение компонентов химических
добавок устанавливают с учетом конкретных свойств применяемых материалов для
приготовления арболитовой смеси. Его корректируют в переходе на другие сырьевые
материалы.
арболит производство рециклинг отходы
Таблица 3.1 - Содержание хлорида кальция в растворах
Концентрация раствора, %
|
Плотность раствора при
20°С, г/см3
|
Содержание безводного
СаС12, кг
|
|
|
в 1 л раствора
|
в I кг раствора
|
1
|
2
|
3
|
4
|
2
|
1,015
|
0,02
|
0,02
|
4
|
1,032
|
0,041
|
0,04
|
6
|
1,049
|
0,063
|
0,06
|
8
|
1,066
|
0,085
|
0,08
|
1,084
|
0,108
|
0,1
|
12
|
1,102
|
0,132
|
0,12
|
14
|
1,12
|
0,157
|
0,14
|
16
|
1,139
|
0,182
|
0,16
|
17
|
1,148
|
0,195
|
0,17
|
18
|
1,158
|
0,209
|
0,18
|
19
|
1,168
|
0,222
|
0,19
|
20
|
1,178
|
0,236
|
0,2
|
21
|
1,18
|
0,25
|
0,21
|
22
|
1,198
|
0,264
|
0,22
|
23
|
1,208
|
0,278
|
0,23
|
24
|
1,218
|
0,293
|
0,24
|
25
|
1,228
|
0,307
|
0,25
|
26
|
1,239
|
0,322
|
0,26
|
Вода для затворения бетона и раствора отделочных слоев
должна удовлетворять требованиям ГОСТ 23732-79.
Вермикулит. Для придания арболитовым блокам специфических свойств в качестве
наполнителя применяли вспученный вермикулит.
Вермикулит - минерал из группы гидрослюд, имеющих слоистую структуру.
Продукт вторичного изменения (гидролиза и последующего выветривания) темных
слюд биотита и флогопита. Представляет собой крупные пластинчатые кристаллы
золотисто - желтого или бурого цвета. При нагревании из пластинок образуются
червеобразные столбики или нити золотистого или серебристого цвета с поперечным
делением на тончайшие чешуйки (вспученный вермикулит). В нашей дипломной работе
был использован вспученный вермикулит по ГОСТ 12865 - 67 плотностью 100 кг/м3.
В соответствии с указанным стандартом, вспученный вермикулит выпускается трех
фракционных составов: крупный - с размером фракций от 5 до 10 мм; средний - с
размерами фракций от 0.6 до 5 мм; мелкий - с размером фракций до 0,6 мм. В
результате предварительных экспериментов было установлено, что добавление
вспученного вермикулита крупного и среднего фракционного состава даже в очень
малых долях (5-6%) оказывает резко негативное воздействие на прочностные
характеристики арболитовых блоков.
Полиэтилентерефталат (ПЭТФ) - твердое вещество без
запаха, плотность 1,38-1,40г/см3,температура плавления 255-2650С,температура
размягчения 245-2480С, температура стеклования 70-800С.
Полиэтилентерефталат характеризуются высокой
прочностью и ударной вязкостью, устойчив к истиранию и многократным деформациям
при растяжении и изгибе.
Стекло - вещество и материал, один из самых
древних и, благодаря разнообразию своих свойств, - универсальный в практике человека.
Физико-химически - твёрдое тело, структурно- аморфно, изотропно; все виды
стёкол при формировании преобразуются в агрегатном состоянии - от чрезвычайной
вязкости жидкого до так называемого стеклообразного - в процессе остывания со
скоростью, достаточной для предотвращения кристаллизации расплавов, получаемых
плавлением сырья (шихты).
Полиэтилентерефталат и стекло, являются пассивным
неволокнистым компонентам, которые оказывают значительное влияние на
образование связей в арболите следовательно, и на физико-механические свойства
арболита. Очевидно, что размер частиц вводимого неволокнистого компонента будет
оказывать определенное влияние на свойства готовой продукции. Для этого
требуется провести планирование эксперимента, выбрать основные характеристики
моделей, разработать математические модели с нормализованными значениями
факторов.
3.3 Последовательность проведения экспериментов
В соответствии с планами экспериментов исследования проводились по
следующему направлению.
При проведении однофакторного эксперимента изменяли значения одного из
факторов (С, F), не учитывая влияние остальных, при
всех прочих равных условиях, затем определяли физико - механические показатели
готового арболитового блока и проводили испытания по определению параметров
пожарной опасности.
Этапы проведения эксперимента:
. Подготовка оборудования. Перед тем как начать заготовку сырья для
проведения эксперимента необходимо подготовить оборудование. Для снижения
вибрации и предотвращения повреждения пола лаборатории под оборудование
укладываются резиновые коврики, на которые в последующем устанавливается
вибропресс и бетоносмеситель.
. Установка и проверка оборудования. Перед тем как установить
оборудование необходимо проверить работоспособность и исправность рабочих
узлов. После его установки на резиновые коврики проверяется его
работоспособность путем кратковременного включения и выключения.
. Заготовка сырья. Для проведения экспериментов щепа, которая
соответствует ГОСТ 15815 - 83 "Щепа технологическая. Технические
условия", доставлялась с предприятия ОАО "Лесосибирский ЛДК №1".
После доставки в лабораторию щепы определялась ее влажность. Размол щепы и
полиэтилентерефталата осуществлялся на мельнице МР - 4 следующим образом.
Измельчение осуществляется путем подачи материала в рубящую зону
устройства через питатель, который ориентирует поступающие кусковые отходы,
форма сечения и размеры питателя (воронки) должны соответствовать поперечному
сечению кусков измельчаемого материала. Например, при измельчении пластиковых
бутылок питатель должен иметь круглое отверстие, через которое по очереди
поступают бутылки, а при измельчении плоской ленты питатель должен иметь
прямоугольное отверстие-щель, через которое непрерывно подается лента с
прямоугольным поперечным сечением. Высота питателей должна быть не менее 5c, где c-ширина щели питателя,
соответствующая толщине измельчаемого материала +1 мм: (с=δ+1, мм).
Величина межосевого смещения а определяется опытным путем.
При увеличении смещения а материал для измельчения втягивается из
питателя в зону измельчения устройства с большой скоростью, которая может
превысить скорость измельчения материала в устройстве, что приведёт к остановке
вращения ротора.
Изменением а регулируется скорость втягивания материала из
питателя в зону измельчения, которая должна соответствовать скорости
измельчаемого материала в устройстве.
Перед пуском устройства для измельчения заданного материала закрепляют
питатель 12 на корпусе 2 то отрезки (а), полученные опытным путем, при котором
скорость подачи материала из питателя соответствует скорости выхода
измельченного материала из устройства.
Рисунок 3.3 - Схема размалывающей мельницы МР - 4
При работе устройства измельчаемый материал подается из питателя 12 на
вращающий ротор 1 (в ориентируемом состоянии) где режущая кромка 10 каждого
ножа 6, по очереди врезается и срезает часть материала с помощью режущей кромки
11 питателя 12. Материал, подвергнутый измельчению, проваливается в бункер
через отверстия в колосниковой решетки.
. Изготовление арболитовых блоков. Производится расчет необходимого
количества сырья для изготовления образцов. Взвешивается необходимое количество
щепы и закладывается во включенный бетоносмеситель. По плану эксперимента
выбирается вторичное сырье, взвешивается необходимое количество и засыпается во
включенный бетоносмеситель с щепой. Затем добавляется связующее вещество. В
нашем эксперименте в качестве связующего вещества используется портландцемент
марки М 400 ДО. После перемешивания в течении 5 минут добавляются хлористый
кальций и жидкое натриевое стекло. Вся масса перемешивается в течении 2 минут.
После этого добавляется вода, температуры 20-30 0С равномерными малыми
порциями, для воизбежания образования комков и оседания на стенках
бетоносмесителя, и перемешивается в течении 5 минут. Под бетоносмеситель
устанавливается плоская емкость и вся смесь извлекается из бетоносмесителя,
путем его наклонения с помощью рукоятки.
На установленный вибропресс ставятся формы, предварительно смазанные
машинным маслом, для более легкого извлечения блока. В формы заливается
арболитовая смесь и слегка придавливается крышками для начального уплотнения.
Включается вибропресс, смесь уплотняется, и после 20 секунд вибропресс
выключается. Готовые формы с арболитовыми блоками снимаются с вибропресса и
укладываются. После выдержки в течении 3 дней блоки изымаются из форм,
оборачиваются пищевой пленкой и выдерживаются в течении 25 дней при температуре
25 0С и влажности воздуха 70%. Формы очищаются и эксперимент повторяется
согласно плану.
3.4 Методики определения физико-механических показателей
арболитовых блоков
Определение плотности образцов. Образцы взвешиваются после выдержки
в течении 28 суток. По одному образцу укладываем на весы, фиксируем массу и
вычисляем плотность по формуле

(3.1)
где
ρ
- плотность образца, кг/м3;
m - масса образца, кг;
V - объем образца, м3.
Методика
определения параметров пожарной опасности арболитовых блоков.
Образец
исследуемого материала закрепляют в держателе и при помощи шаблона проверяют
положение образца относительно его вертикальной оси. Включают прибор для
регистрации температуры, зажигают газовую горелку и регулируют расход газа так,
чтобы контролируемая в течение 3 мин температура газообразных продуктов горения
составляла (200±5) °С.
Держатель
с образцом вводят в камеру за время не более 5 с и испытывают в течение (300±2)
с или до достижения максимальной температуры отходящих газообразных продуктов
горения материала, при этом регистрируют время ее достижения. Если при
испытании максимальная температура не превышает 260°С, то продолжительность
испытания составляет (300±2) с. После чего горелку выключают. Образец
выдерживают в камере до полного остывания (комнатной температуры). Остывший
образец извлекают из камеры и взвешивают.
Если
при испытании максимальная температура превысила 260°С, то продолжительность
испытания определяется временем достижения максимальной температуры. Горелку
выключают, образец извлекают из камеры и после остывания взвешивают.
Максимальное
приращение температуры (Δtmax) вычисляют
по формуле
Δtmax = tmax - t0, (3.2)
где
tmax - максимальная температура газообразных продуктов горения исследуемого
материала, °С;- начальная температура испытания, равная 200°С.
Потерю
массы образца
(Δm) в процентах вычисляют по
формуле
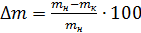
, (3.3)
где
mн - масса образца до испытания, г;к - масса образца после испытания, г.
По
значению максимального приращения температуры Δtmax и потере массы Δm материалы классифицируют:
трудногорючие
- Δtmax
< 60°C и Δm <60%;
-
горючие - Δtmax
> 60°С или Δm
> 60 %.
Горючие
материалы подразделяют в зависимости от времени достижения максимальной
температуры газообразных продуктов горения τ исследуемого материала tmax на:
трудновоспламеняемые
τ
> 4 мин;
средней
воспламеняемости - 0,5 < τ < 4 мин;
легковоспламеняемые
- τ
< 0,5 мин.
Методика
определения прочности при сжатии арболитовых блоков.
Предел
прочности при сжатии Rc, МПа вычисляют для каждого образца по формуле

(3.4)
где
Р - разрушающая нагрузка, Н.
Для
определения разрушающей силы необходимо выпилить из арболитового блока образец
размером 5×5×10
см, установить его в пресс и подать
нагрузку согласно плану эксперимента. После определения первых трещин на
образце нагрузку прекращают и нагрузку фиксируют.
3.5
Результаты экспериментальных исследований
На первом этапе исследований была спланирована и проведена серия
однофакторных экспериментов по определению зависимости плотности Pl от массовой доли стекла Cc, вспученного вермикулита Св, коры Ск
и полиэтилентерефталата Сп, с размером фракций 2,2;10;30 мм.
После обработки результатов эксперимента, по фракции 2,2 мм, в пакете
программ Microsoft Excel 2007 были получены следующие регрессионные
зависимости:

, (3.5)

, (3.6)

, (3.7)

; (3.8)
Анализ зависимостей позволяет говорить о большем влиянии линейной
составляющей, чем квадратичной. Более наглядное представление о представленных
зависимостях дают графики, построенные по полученным уравнениям (рисунки
3.4-3.6).
Рисунок 3.4 - Зависимость плотности от содержания вторичного вещества,
фракции 2,2 мм, в общем объеме сухой массы
Как видно из представленных графиков, с увеличением объемной доли стекла,
коры и вермикулита параметры плотности увеличиваются, а с использованием
полиэтилентерефталата - уменьшается. Например, при значении Сс= 12,5% плотность
арболитовых блоков составляет 880,6 кг/м3, а при Сс = 37,5% плотность составит
1108 кг/м3, при этом марка арболитового блока увеличивается. При увеличении
концентрации п/э свыше 20% марка готового арболитового блока снижается, что
негативно сказывается на физико - механических характеристиках. При
использовании стекла, коры и вермикулита арболит входит в группу
конструкционных блоков, что позволит использовать данный тип блоков для
строительства самонесущих стен и зданий более высокой этажности.
После обработки результатов эксперимента, по фракции 10 мм, в пакете
программ Microsoft Excel 2007 были получены следующие регрессионные зависимости:

, (3.9)

, (3.10)

; (3.11)
Рисунок
3.5 - Зависимость плотности от содержания вторичного вещества, фракции 10 мм, в
общем объеме сухой массы
Анализ
графических зависимостей на рисунках 3.4 и 3.5 показал следующее. При
увеличении содержания вторичного сырья, в общей массе, наблюдается увеличение
плотности на 3-5 %.
После обработки результатов эксперимента, по фракции 30 мм, в пакете
программ Microsoft Excel 2007 были получены следующие регрессионные
зависимости:

, (3.12)

, (3.13)

; (3.14)
Анализ
графиков на рисунке 3.6 показал, что наблюдается линейная закономерность
увеличения плотности от содержания вторичного сырья. При увеличении фракции
плотность увеличивается на 5-10 %, это объясняется высокой степенью плотности
засыпания.
Рисунок
3.6 - Зависимость плотности от содержания вторичного вещества, фракции 30 мм, в
общем объеме сухой массы
На втором этапе исследований была спланирована и проведена серия
однофакторных экспериментов по определению зависимости прочности при сжатии Pr от массовой доли стекла Cc, вспученного вермикулита Св, коры Ск
и полиэтилентерефталата Сп, с размером фракций 2,2;10;30 мм.
После обработки результатов эксперимента, по фракции 2,2 мм, в пакете
программ Microsoft Excel 2007 были получены следующие регрессионные
зависимости:

, (3.15)

, (3.16)

, (3.17)

; (3.18)
Анализ зависимостей позволяет говорить о большем влиянии линейной
составляющей, чем квадратичной. Более наглядное представление о представленных
зависимостях дают графики, построенные по полученным уравнениям (рисунки
3.7-3.9).
Рисунок 3.7 - Зависимость прочности при сжатии от содержания вторичного
вещества, фракции 2,2 мм, в общем объеме сухой массы
Как видно из представленных графиков, с увеличением объемной доли стекла
и коры параметры прочности при сжатии увеличиваются, а с использованием
вермикулита и полиэтилентерефталата - уменьшается. Например, при значении Сс=
12,5% прочность при сжатии арболитовых блоков составляет 1,1 МПа, а при Сс =
37,5% прочность составит 0,9 МПа, при этом марка арболитового блока
уменьшается. При увеличении концентрации вермикулита свыше 20% марка готового
арболитового блока снижается, что негативно сказывается на физико -
механических характеристиках. При использовании стекла, коры и вермикулита
арболит входит в группу конструкционных блоков, что позволит использовать
данный тип блоков для строительства самонесущих стен и зданий более высокой
этажности.
После обработки результатов эксперимента, по фракции 10 мм, в пакете программ
Microsoft Excel 2007 были получены следующие регрессионные
зависимости:

, (3.19)

, (3.20)

; (3.21)
Анализ
графических зависимостей на рисунках 3.7 и 3.8 показал следующее. При
увеличении содержания стекла и коры, в общей массе, наблюдается увеличение
прочности на 5-10 %.
Рисунок
3.8 - Зависимость прочности при сжатии от содержания вторичного вещества,
фракции 10 мм, в общем объеме сухой массы
После обработки результатов эксперимента, по фракции 30 мм, в пакете
программ Microsoft Excel 2007 были получены следующие регрессионные
зависимости:

, (3.22)

, (3.23)

; (3.24)
Анализ
графиков на рисунке 3.9 показал, что наблюдается линейная закономерность
увеличения плотности от содержания вторичного сырья. При увеличении фракции
прочности увеличивается на 5-12 %, это объясняется высокой степенью плотности
засыпания.
Рисунок
3.9 - Зависимость прочности при сжатии от содержания вторичного вещества,
фракции 30 мм, в общем объеме сухой массы
На третьем этапе исследований была спланирована и проведена серия
однофакторных экспериментов по определению зависимости огнезащищенности Og от массовой доли стекла Cc, вспученного вермикулита Св, коры Ск
и полиэтилентерефталата Сп, с размером фракций 2,2;10;30 мм.
После обработки результатов эксперимента, по фракции 2,2 мм, в пакете
программ Microsoft Excel 2007 были получены следующие регрессионные
зависимости:

, (3.25)

, (3.26)

, (3.27)

; (3.28)
Анализ зависимостей позволяет говорить о большем влиянии линейной
составляющей, чем квадратичной. Более наглядное представление о представленных
зависимостях дают графики, построенные по полученным уравнениям (рисунки
3.10-3.12).
Рисунок 3.10 - Зависимость огнезащищенности от содержания вторичного
вещества, фракции 2,2 мм, в общем объеме сухой массы
Как видно из представленных графиков, с увеличением объемной доли коры и
вермикулита параметры огнезащищенности увеличиваются, а с использованием
полиэтилентерефталата и мтекла - уменьшается. Например, при значении Сс= 12,5%
огнезащищенность арболитовых блоков составляет 1,8 часа, а при Сс = 37,5%
огнезащищенность составит 1,3 часа, при этом марка арболитового блока
снижается. При увеличении концентрации стекла свыше 20% марка готового
арболитового блока снижается, что негативно сказывается на физико -
механических характеристиках. При использовании стекла и коры арболит входит в
группу конструкционных блоков, что позволит использовать данный тип блоков для
строительства самонесущих стен и зданий более высокой этажности.
После обработки результатов эксперимента, по фракции 10 мм, в пакете
программ Microsoft Excel 2007 были получены следующие регрессионные
зависимости:

, (3.29)

, (3.30)

; (3.31)
Рисунок
3.11 - Зависимость огнезащищенности от содержания вторичного вещества, фракции
10 мм, в общем объеме сухой массы
Анализ
графических зависимостей на рисунках 3.4 и 3.5 показал следующее. При
увеличении содержания стекла и полиэтилентерефталата, в общей массе,
наблюдается уменьшение огнезащищенности на 10-25 %.
После обработки результатов эксперимента, по фракции 30 мм, в пакете
программ Microsoft Excel 2007 были получены следующие регрессионные
зависимости:

, (3.32)

, (3.33)

; (3.34)
Анализ
графиков на рисунке 3.12 показал, что наблюдается линейная закономерность
увеличения огнезащищенности от содержания вторичного сырья. При увеличении
фракции огнезащищенность уменьшается на 5-10 %, это объясняется высокой
степенью плотности засыпания.
Рисунок
3.12 - Зависимость огнезащищенности от содержания вторичного вещества, фракции
30 мм, в общем объеме сухой массы
Выводы. В третьей главе представлено описание лабораторных установок, сырья и
материалов, использованных при проведении экспериментальных исследований,
описаны методики определения параметров плотности, прочности при сжатии и
огнезащищенности арболитовых блоков, представлены результаты экспериментов.
Полученные в работе уравнения, описывающие исследуемые процессы
подготовки арболитовых блоков, адекватны, по ним построены функции откликов в
виде графических зависимостей, для которых выполняется основное требование:
экспериментальные точки в совокупности лежат достаточно близко к кривой,
являющейся графиком искомой зависимости. Поэтому данные уравнения, на наш
взгляд, позволяют прогнозировать получение качественных арболитовых блоков в
зависимости от процентного содержания вторичного сырья и фракционного состава
твердых промышленный и бытовых отходов ; при известных значениях конструктивных
и технологических параметров лабораторных установок и, варьируя значения
массовой доли вторичного сырья в арболитовой массе, не только определять
физико-механические и геометрические показатели арболитовых блоков, но и
снизить параметры пожарной опасности арболита, изготовленного из нее, по ГОСТ
12.1.044-89 «Пожаровзрывоопасность веществ и материалов. Номенклатура
показателей и методы их определения» до трудновоспламеняемых.
4. Экология г. Лесосибирска
4.1 Состав и характеристики состава загрязняющих веществ в г.
Лесосибирске
На основании многочисленных предварительных исследований установлено, что
жители г. Лесосибирска и близлежащих поселков ощущают отрицательное влияние в
той или иной степени (статистические данные министерства здравоохранения
Красноярского края по г. Лесосибирску свидетельствуют о высоком проценте
онкологических заболеваний) в результате производственной деятельности крупных
и мелких предприятий, расположенных в черте города, в виде загрязняющих веществ
таких как: бензин, углерод (сажа), бензол, свинец и его неорганические
соединения, бенз(а)пирен, формальдегид, диоксид азота, диоксид серы, пыль
неорганическая, содержащая <20% оксида кремния, взвешенные вещества, фенол,
оксид углерода, оксид азота.
Бензин - горючая смесь лёгких углеводородов с температурой кипения от 30 до 180
°C.
Образование возможно в транспортных цехах, топливных станциях,
автозаправочных станциях и др. от разлива топлива, работы двигателя внутреннего
сгорания, при заправке транспортных средств.
Легкое отравление парами бензина может наступить после 5-10 мин
пребывания человека в атмосфере с концентрацией паров бензина в пределах
900-3612 мг/м³. При этом появляются головная боль, головокружение,
сердцебиение, слабость, психическое возбуждение, беспричинная вялость, легкие
подергивания мышц, дрожание рук, мышечные судороги.
При непродолжительном вдыхании воздуха с концентрацией паров бензина
5000-10000 мг/м³ уже через несколько минут появляются головная боль,
неприятные ощущения в горле, кашель, раздражение слизистых оболочек носа, глаз.
Кроме того, первыми признаками острого отравления парами бензина являются
понижение температуры тела, замедление пульса и другие симптомы.
При концентрации паров бензина в воздухе свыше 2,2% (30 г/м³)
после 10-12 вдохов
человек отравляется, теряет сознание; свыше 3% (40 г/м³)
происходит молниеносное
отравление (2-3 вдоха) - быстрая потеря сознания и смерть.
Углерод (Сажа) - аморфный углерод, продукт неполного сгорания или
термического разложения углеводородов в неконтролируемых условиях.
Углерод поступает в окружающую среду в виде сажи в составе выхлопных
газов автотранспорта, при сжигании угля на ТЭС, при открытых разработках угля,
подземной его газификации, получении угольных концентратов и др. Концентрация
углерода над источниками горения 100-400 мкг/м³, крупными городами 2,4-15,9 мкг/м³,
сельскими районами 0,5 -
0,8 мкг/м³. С газоаэрозольными выбросами АЭС в атмосферу поступает
(6-15)·109 Бк/сут 14СО2.
Высокое содержание углерода в атмосферных аэрозолях ведет к повышению
заболеваемости населения, особенно верхних дыхательных путей и легких.
Профессиональные заболевания - в основном антракоз и пылевой бронхит. В воздухе
рабочей зоны ПДК, мг/м³: алмаз 8,0, антрацит и кокс 6,0, каменный уголь 10,0,
технический углерод и углеродная пыль 4,0; в атмосферном воздухе максимальная
разовая 0,15, среднесуточная 0,05 мг/м³.
Токсическое действие 14С, вошедшего в состав молекул белков (особенно в
ДНК и РНК), определяется его радиационным взаимодействием с β-частицами (14С (β)
→ 14N), приводящим
к изменению химического состава молекулы. Допустимая концентрация 14С в воздухе
рабочей зоны ДКА 1,3 Бк/л, в атмосферном воздухе ДКБ 4,4 Бк/л, в воде 3,0·104
Бк/л, предельно допустимое поступление через органы дыхания 3,2·108 Бк/год.
Сажа входит в категорию частиц, опасных для лёгких, так как частицы менее пяти
микрометров в диаметре не отфильтровываются в верхних дыхательных путях.
Бензол - органическое химическое соединение, бесцветная жидкость с приятным
сладковатым запахом. Простейший ароматический углеводород. Бензол входит в
состав бензина.
Содержание бензола в воздухе обычно составляет от 3 до 160 мкг/м3; более
высокие концентрации отмечены в крупных городах. В непосредственной близости от
заправочных станций, промышленных предприятий, использующих или производящих
бензол, его концентрация в воздухе может достигать нескольких сотен мкг/м3. В
селитебной зоне концентрация бензола обычно составляет 3-30 мкг/м3 и зависит в
основном от интенсивности движения транспорта.
Поступление с воздухом является основным источником попадания бензола в
организм. Около 50 % бензола, содержащегося во вдыхаемом воздухе, абсорбируется
легкими.
При хроническом воздействии бензол накапливается в жировой ткани. В
высоких концентрациях (более 3200 мг/м3) нейротоксичен. Хроническое воздействие
близких к порогу токсичности концентраций приводит к поражению костного мозга и
развитию постоянной пангемоцитопении (низкое содержание всех форменных
элементов крови); в тяжелых случаях развивается летальная апластическая анемия,
вызванная ингибированием костного мозга. При профессиональном контакте
(воздействие бензола в концентрации от нескольких десятков до нескольких сотен мг/м3)
развиваются и другие патологические изменения крови (например, тромбоцитопения,
лимфопения). При этом исследования на животных показали, что гематотоксичностью
обладают метаболиты бензола. Гематотоксические эффекты сопровождаются учащением
хромосомных аберраций.
При непродолжительном вдыхании паров бензола не возникает немедленного
отравления. В больших дозах бензол вызывает тошноту и головокружение, а в
некоторых тяжёлых случаях отравление может повлечь смертельный исход. Первым
признаком отравления бензолом нередко бывает эйфория. Пары бензола могут
проникать через неповрежденную кожу. Если организм человека подвергается
длительному воздействию бензола в малых количествах, то хроническое отравление
бензолом может стать причиной лейкемии и анемии.
Свинец и его не органические соединения - Свинец - металл, который испаряется
при температуре свыше 400 °С.
Основными источниками загрязнения окружающей среды свинцом являются
автотранспорт, использующий свинец содержащий бензин, и стационарные источники
предприятий цветной металлургии.
Средние концентрации свинца в воздухе крупных городов составляют 0,5 - 1
мкг/м3 при ПДК 0,3 мкг/м3.При вдыхании эти частицы попадают в легкие.
Свинец и его неорганические соединения в зависимости от их агрегатного
состояния и характера контакта с ними могут проникать в организм через
дыхательные пути, желудочно-кишечный тракт и частично кожные покровы. В
производственных условиях наиболее часто они поступают в организм через
дыхательные пути в виде пыли, аэрозоля и паров. В желудочно-кишечный тракт
свинец и его соединения попадают преимущественно при бытовых интоксикациях,
реже - на производствах, где не соблюдаются правила личной гигиены.
Проникновение свинца через дыхательный тракт является самым опасным для
организма. Всасывание свинца происходит на всем протяжении дыхательных путей,
откуда он проникает непосредственно в кровь. Свинец относится к ядам с
выраженным кумулятивным действием. Местом депонирования свинца являются главным
образом кости, печень, почки. В меньшей степени свинец откладывается в
селезенке, в головном мозге, лимфоузлах.
По степени воздействия на организм человека свинец относится к 1-му
классу опасности как чрезвычайно опасный. Свинец и его соединения токсичны. При
сильном отравлении наблюдаются боли в животе, в суставах, судороги, обмороки.
Свинец может накапливаться в костях, вызывая их постепенное разрушение,
осаждается в печени и почках.
Бенз(а)пирен - химическое соединение, представитель семейства
полициклических углеводородов, вещество первого класса опасности.
Образуется при сгорании углеводородного жидкого, твёрдого и газообразного
топлива (в меньшей степени при сгорании газообразного топлива).
Наиболее высокая концентрация бензапирена в воздухе отмечена в городах и
поселках, где есть предприятия металлургии и нефтехимии, - там она может
превышать предельно допустимую концентрацию (1 нанограмм в кубометре воздуха) в
10, 15, а то и в 60 раз.
В окружающей среде накапливается преимущественно в почве, меньше в воде.
Из почвы поступает в ткани растений и продолжает своё движение дальше в
трофической цепи, при этом на каждой её ступени содержание БП в природных
объектах возрастает на порядок.
Контроль содержания бенз(а)пирена в природных продуктах производится
методом жидкостной хроматографии.
Бенз(а)пирен - канцерогенное вещество, 1 класса опасности, которое
расценивается медиками как однозначно провоцирующее раковые заболевания.
Вещество имеет хорошую проникающую способность в клетки живых организмов.
Человек может получить его не только через кожу, но и через дыхательные пути и
с пищей. БП обладает способностью накапливаться в живых организмах, провоцируя
в дальнейшем онкологические заболевания. В организме бенз(а)пирен частично
окисляется, давая производные фенольного и хинонного типа, также обладающими мутагенной
активностью, а частично выводится из организма в неизменном виде.
Формальдегид - бесцветный газ с резким запахом, хорошо растворимый в воде,
спиртах и полярных растворителях.
Источником образования формальдегида в городах главным образом является
автомобильный транспорт, в результате работы двигателей которого формальдегид
выделяется в выхлопах совместно с другими недогоревшими углеводородами. Помимо
автотранспорта источником формальдегида являются деревообрабатывающие
предприятия, автозаводы, химические и кожевенные производства. Негативное
воздействие формальдегида обусловлено его высокой реакционной способностью.
Фоновые концентрации составляют несколько мкг/м3, в городском воздухе
достигают величин 0,005-0,01 мг/м3. Вблизи промышленных источников - выше.
Кратковременные пиковые концентрации в застроенных городских районах (в часы
пик или в условиях фотохимического смога) примерно на порядок выше.
Формальдегид токсичен: приём внутрь 60-90 мл является смертельным.
Симптомы отравления: бледность, упадок сил, бессознательное состояние,
депрессия, затруднённое дыхание, головная боль, нередко судороги по ночам.
При остром ингаляционном отравлении: конъюнктивит, острый бронхит, вплоть
до отёка лёгких. Постепенно нарастают признаки поражения центральной нервной
системы (головокружение, чувство страха, шаткая походка, судороги). При
отравлении через рот: ожог слизистых оболочек пищеварительного тракта (жжение,
боль в глотке, по ходу пищевода, в желудке, рвота кровавыми массами),
геморрагический нефрит, анурия. Возможны отёк гортани, рефлекторная остановка
дыхания.
Хроническое отравление у работающих с техническим формалином проявляется
похуданием, диспепсическими симптомами, поражением центральной нервной системы
(психическое возбуждение, дрожание, атаксия, расстройства зрения, упорные
головные боли, плохой сон). Описаны органические заболевания нервной системы
(таламический синдром), расстройства потоотделения, температурная асимметрия.
Отмечены случаи бронхиальной астмы.
Азота диоксид - газ, красно-бурого цвета, с характерным острым запахом или
желтоватая жидкость.
Диоксиды азота образуются, в основном, в процессе сгорания органического
топлива при высоких температурах и затем в атмосфере трансформируются в NO2.
Значительное количество оксидов азота производится тепловыми электростанциями,
металлургическими предприятиями, крупными и мелкими котельными и
автотранспортом.
В промышленных районах и городах наблюдается концентрация NO2 в пределах
0,4-0,8 мг/м3, а при образовании смога - до 1 мг/м3.
При малых концентрациях, составляющих всего 0,23 мг/м3, человек ощущает
присутствие этого газа. Эта концентрация является порогом обнаружения диоксида
азота. Однако способность организма обнаруживать NO2 пропадает после 10 минут
вдыхания, но при этом ощущается чувство сухости и першения в горле. Хотя и эти
признаки исчезают при продолжительном воздействии газа в концентрации, в 15 раз
превышающей порог обнаружения. Таким образом, NO2 ослабляет обоняние. Диоксид
азота воздействует не только на обоняние, но и ослабляет ночное зрение -
способность глаза адаптироваться к темноте. Этот эффект же наблюдается при
концентрации 0,14 мг/м3, что, соответственно, ниже порога обнаружения.делает
человека более восприимчивым к патогенам, вызывающим болезни дыхательных путей.
У людей, подвергшихся воздействию высоких концентраций диоксида азота, чаще
наблюдаются катар верхних дыхательных путей, бронхиты, круп и воспаление
легких. Кроме того, диоксид азота сам по себе может стать причиной заболеваний
дыхательных путей. При этом стенки альвеол и кровеносных капилляров становятся
настолько проницаемыми, что пропускают сыворотку крови в полость легких. В этой
жидкости растворяется вдыхаемый воздух, образуя пену, препятствующую
дальнейшему газообмену. Возникает отек легких, который зачастую ведет к
летальному исходу. Длительное воздействие оксидов азота вызывает расширение
клеток в корешках бронхов (тонких разветвлениях воздушных путей альвеол),
ухудшение сопротивляемости легких к бактериям, а также расширение альвеол.
Некоторые исследователи считают, что в районах с высоким содержанием в
атмосфере диоксида азота наблюдается повышенная смертность от сердечных и
раковых заболеваний.
Сера диоксид в нормальных условиях представляет собой бесцветный газ с
характерным резким запахом (запах загорающейся спички).
Рисунок 4.1 - Диоксид серы (SO2)
(Д.с.) - SO2, бесцветный газ с резким запахом, один из главных
загрязнителей атмосферы. Д.с. образуется при сжигании ископаемого топлива на
предприятиях топливно-энергетического комплекса и в двигателях внутреннего
сгорания, а также на предприятиях нефтехимического комплекса. Образуется при
сгорании угля и нефти, в металлургических производствах, при переработке
содержащих серу руд (сульфиды), при различных химических технологических
процессах. Среди источников образования первое место занимает уголь, который
дает 70% антропогенных выбросов. В процессе горения сера превращается в
сернистый газ, а часть серы остается в золе в твердом состоянии.
Таблица 4.1 - Основные характеристики диоксида серы
Наименование характеристики
|
Величина
|
Общие
|
Систематическое
|
Оксид серы (IV)
|
Химическая формула
|
SO2
|
Относительная молекулярная
масса
|
64,054 а.е.м.
|
Молярная масса
|
64,054 г/моль
|
Физические свойства
|
Плотность вещества
|
2,927 г/л
|
Состояние (ст.усл.)
|
бесцветный газ
|
Термические свойства
|
Температура плавления
|
-75,5 0С
|
Температура кипения
|
-10,01 0С
|
Химические свойства
|
Растворимость в воде
|
11,5 г/100 мл
|
Классификация
|
Номер CAS
|
[7446-09-5]
|
Под давлением сжижается при комнатной температуре. Растворяется в воде с
образованием нестойкой сернистой кислоты; растворимость 11,5 г/100 г воды при
20 °C, снижается с ростом температуры. Растворяется также в этаноле, серной
кислоте. SO2 - один из основных компонентов вулканических газов.
Д.с. пагубно влияет на растения, так как проникает в лист и вступает в
реакцию с железом, входящим в состав хлорофилла, вызывает распад хлорофилла и
гибель растения. Загрязнение атмосферы Д.с. - главная причина кислотных дождей.
Во всем мире идет поиск возможностей уменьшения выбросов Д.с. в
атмосферу. В странах Западной Европы за последние 20 лет удалось сократить
объем выбросов Д.с. с 65 до 40 млн. т. в год, однако за счет увеличения
выбросов Д.с. Индией, Китаем и странами СНГ в глобальном масштабе общее количество
выбросов Д.с. практически не уменьшилось. В РФ в 1995 г., несмотря на некоторый
спад производства, количество выбросов Д.с. по сравнению с 1980 г. возросло в
1,5 раза.
Количество Д.с., которое выбрасывается в атмосферу на единицу
национального продукта, зависит от уровня технологии и экологической
безопасности предприятий страны. Так, в последние годы существования СССР на
единицу национального продукта выбрасывалось Д.с. в 19 раз больше, чем в
Японии.
Загрязнение Д.с. во многом связано с <экспортом> загрязнения, т. е.
трансграничным переносом загрязнений атмосферными потоками. Поскольку в Европе
преобладает западный перенос, то многие страны получают по преимуществу
<импортные> кислотные дожди. Европейская часть РФ получает с запада Д.с.
примерно в 5 раз больше, чем производит сама. В аналогичном положении находятся
и такие страны, как Швеция и Норвегия. Содержимое серы в неочищенной нефти
также довольно большой, в зависимости от места происхождения (0,1-2%). При
сгорании нефтяных продуктов сернистого газа образуется значительно меньше, чем
при сгорании угля.
Источниками образования двуокиси серы могут быть также отдельные области
промышленности, главным образом металлургическая, а также предприятия из
производства серной кислоты и переработки нефти. На транспорте загрязнения
соединениями серы относительно незначительное.
При среднесуточной концентрации сернистого газа 0,1-0,2 мг/м3 у населения
наблюдается обострение заболеваний верхних дыхательных путей. Резкое увеличение
числа случаев заболеваемости бронхитами у людей старше 55 лет отмечается на
следующий день после повышения среднесуточной концентрации сернистого газа до
0,7 мг/м3. Чувствительность по отношению к SO2 весьма различна у отдельных
людей, животных и растений.
Диоксид серы очень токсичен. Симптомы при отравлении сернистым газом -
насморк, кашель, охриплость, сильное першение в горле и своеобразный привкус.
При вдыхании сернистого газа более высокой концентрации - удушье, расстройство
речи, затруднение глотания, рвота, возможен острый отёк лёгких.
При кратковременном вдыхании оказывает сильное раздражающее действие,
вызывает кашель и першение в горле.
Получение. Промышленный способ получения - сжигание серы или
обжиг сульфидов, в основном - пирита
<#"810572.files/image075.jpg">
Рисунок 4.2 - Спектр поглощения SO2 в ультрафиолетовом диапазоне
Относится
к кислотным оксидам <#"810572.files/image076.gif">, (5.1)
где П - годовой объем производства, м3/год;
Пчас - производительность линии, тонн/час;
N -
продолжительность смены, час;
n -
количество смен, шт.;
Д - количество рабочих дней в году, дни.
Произведем расчет
П=0,95∙7∙3∙350= 7000 м3/год
Потребность в щепе составляет 300 кг на производство 1 м3 арболита.
Сменная потребность в сырье равна 1995 кг. Тогда годовой запас сырья составит
2100000 кг.
Производительность цеха конструкционного арболита будет составлять 7000
м3 в год.
Расчет капитальных вложений.
В данном пункте учитываем капиталовложения по установленному оборудованию
и техническим средствам. Стоимость устанавливаемого оборудования берется по
данным учёта и сводятся в таблицу 5.2
Таблица 5.2 - Расчет капиталовложений
Наименование затрат и
оборудования
|
Объем работ или количество
оборудования
|
Стоимость
|
|
|
единицы, руб.
|
всего, руб.
|
1
|
2
|
3
|
4
|
Устройство приемное ДН-20
|
1
|
7000
|
7000
|
Машина рубильная с
конвейером подачи ДУ-2
|
1
|
250000
|
250000
|
Бункер щепы ДБО-60
|
1
|
167000
|
167000
|
Дробилка молотковая ДМ-1
|
1
|
220000
|
220000
|
Бункер древесной дробленки
ДБО-60
|
1
|
135000
|
135000
|
Устройство для замачивания
дробленки ПА1.022
|
1
|
35000
|
35000
|
Подъемник скиповый
ПА1.020.200
|
1
|
46000
|
46000
|
Смеситель для приготовления
арболитовой смеси СБ-62
|
1
|
80000
|
80000
|
Смеситель ц/п раствора
СБ-80
|
1
|
60000
|
60000
|
Секция склада цемента с
системой подачи ДСМ.07
|
11
|
10000
|
110000
|
Компрессор ДБВ-1 Расходный
бункер цемента
|
1
|
75000
|
75000
|
Устройство для хим. добавки
|
1
|
80000
|
80000
|
Фильтр рукавный РФ-30
|
1
|
50000
|
50000
|
Дозатор цемента
АВДЦ-425/1200М
|
1
|
110000
|
110000
|
Дозатор жидкости ДБЖ-400
|
1
|
110000
|
110000
|
1
|
135000
|
135000
|
Формовочная линия ЛВ-24
|
1
|
1490000
|
1490000
|
Конвейер роликовый ЛВ-125М
|
1
|
956000
|
956000
|
Конвейер роликовый ТЛ-10
|
1
|
925000
|
925000
|
Захват для изделия СМЖ-46А
|
1
|
224000
|
224000
|
Доставка и монтаж
|
|
|
510000
|
Итого
|
|
|
5775000
|
Стоимость оборудования составляет 5775000 рублей, включая доставку и
монтаж.
Расход сырья и материалов для производства конструкционного арболита в
натуральном выражении представлен в таблице 5.3
Таблица 5.3 - Расход сырья и материалов для производства
модифицированного арболита в натуральном выражении
Наименование
|
По плану
|
|
на 1 м3
|
на потребителя
|
1 Технологическая щепа, кг
|
300
|
2100000
|
2 Цемент, кг
|
300
|
2100000
|
3 Сернокислый алюминий, кг
|
12
|
84000
|
4Вода, л
|
400
|
2800000
|
Итого
|
1012
|
7084000
|
Расход сырья и материалов для производства конструкционного арболита в
стоимостном выражении представлен в таблице 5.4.
Таблица 5.4 - Расход сырья и материалов для производства
модифицированного арболита в стоимостном выражении
Наименование
|
По плану
|
|
на 1 м3, руб.
|
на потребителя, руб.
|
1 Технологическая щепа
|
300
|
2100000
|
2 Цемент
|
1050
|
7350000
|
3 Сернокислый алюминий
|
144
|
1008000
|
4 Вода
|
8
|
56000
|
Итого
|
1502
|
22355900
|
Цемент планируется закупать на Красноярском Цементном Заводе, сернокислый
алюминий - в ООО «МДМ ХИМ» в г. Красноярске. Транспортные расходы по доставке
цемента сернокислого алюминия из Красноярска составят (стоимость доставки
одного вагона 30000 руб.):
ТР = 36 вагонов∙30000 = 1080000 руб.
Расчет себестоимости продукции. Себестоимость включает затраты
предприятия на ее производство и реализацию. Величина себестоимости отражается
в калькуляциях себестоимости продукции в виде общей суммы затрат и затрат на
единицу продукции. По проектам строительства (реконструкции) цехов определяют
цеховую себестоимость продукции.
В калькуляции себестоимости учитываются статьи затрат, в свою очередь по
отдельным из них дополнительно составляют сметы затрат (на транспортно-заготовительные
расходы по сырью, затраты по сушке пиломатериалов, цеховые и общезаводские
расходы и т. п.).
Расчет стоимости электроэнергии для технологических нужд. Электроэнергия для технологических
нужд формируется суммой потребляемой энергии всех машин и агрегатов с учетом
коэффициента использования оборудования и рассчитывается по формуле
Цэ = ЦкВт∙Nоб∙N∙n∙Д∙Кисп, (5.2)
где ЦкВт - стоимость одного кВт - 0,72 р.;
Nоб-мощность
оборудования, кВт;
N -
продолжительность смены, час;
n -
количество смен, шт.;
Д - количество рабочих дней в году, дни;
Кисп - коэффициент использования оборудования.
Цэ = 0,72∙40∙8∙3∙350∙1 = 241920 руб.
Расчет стоимости электроэнергии для хозяйственных нужд. Для освещения цеха для производства
арболита используются лампы накаливания марки НБ 220-1500. Потребное количество
светильников рассчитаем по формуле
N=
шт., (5.3)
где E - требуемая горизонтальная
освещенность, лк;
S -
площадь помещения, м2;
Кз - коэффициент запаса;
U -
коэффициент использования;
Фл - световой поток лампы.
N=
шт.
Мощность лампы накаливания НБ 220-1500 составляет 1,5 кВт. Тогда
стоимость электроэнергии хозяйственных нужд рассчитаем по формуле
(5.4)
где ЦкВт - стоимость одного кВт - 0,72 р.;
Nоп -
мощность осветительного прибора, кВт;
n -
количество осветительных приборов.
- продолжительность смены, ч;
- количество смен;
- количество рабочих дней в году;
Цэ = 0,72∙(1,5∙32)∙7 ∙3∙350= 254016 руб.
Таблица 5.5 - Расход электроэнергии для производства модифицированного
арболита в стоимостном выражении
Наименование
|
По плану
|
|
на 1 м3, руб.
|
на потребителя, руб.
|
1 Для технологических нужд
|
34,56
|
241920
|
2 Для хозяйственных нужд
|
36,28
|
254016
|
Итого
|
70,85
|
495936
|
Расчет фонда заработной платы. На данном предприятии в статью
затрат по заработной плате входят: основная и дополнительная заработная плата
основных и вспомогательных рабочих, а также управленческого и служебного
персонала.
Количество работающих в цехе - 30 человек, заработная плата одного
рабочего в месяц в среднем составляет 15000 руб. Следовательно, заработная
плата 30 рабочих за год составит:
З/п за год = 15000∙30∙12 = 5400000 руб.
З/п на 1 м3 = 5400000/7000 = 771,42 руб.
Страховые взносы составят:
СВ = 5400000∙30,8 % = 1663200 руб.
СВ на 1 м3 = 1663200/7000= 237,6 руб.
Расходы на содержание и эксплуатацию оборудования составляют 20 % от
стоимости оборудования.. Подставляя значения, получаем
А=5265000∙0,2= 1053000 руб.
А на 1 м3 =1053000/7000= 150,4 руб.
Расходы на подготовку и освоение производства приняты в размере 10%
стоимости оборудования.
Зос=5265000
0,1= 526500 руб.
Зос на 1 м3 =526500/7000= 75,2 руб.
Общепроизводственные расходы составляют 20% от суммы заработной платы и
амортизации.
Рц=6555000∙0,2= 1311000 руб.
Рц на 1 м3 =1311000/7000= 187,28 руб.
Прочие расходы составят 5 % от стоимости оборудования, следовательно:
ПР = 5265000∙5 % = 263250 руб.
ПР на 1 м3 = 263250/7000= 37,6 руб.
Внепроизводственные расходы составляют 4 % от производственной
себестоимости.
Пвн = 28232307∙0.04 = 1129292,28 руб.
Пвн на 1 м3 = 1129292,28 /7000= 161,32 руб.
Себестоимость производства арболита представлена в таблице 5.5
Таблица 5.5 - Калькуляция себестоимости продукции
Статьи затрат
|
По проекту
|
|
всего, руб.
|
на 1м3, руб.
|
Сырье по оптовым ценам
|
22355900
|
1502
|
Расход на электроэнергию
|
495936
|
70,848
|
Заработная плата
|
5400000
|
771,42
|
Страховые взносы
|
1663200
|
237,6
|
Расходы на содержание и
эксплуатацию оборудования
|
1053000
|
150,4
|
Расходы на подготовку и
освоение производства
|
526500
|
75,2
|
Общепроизводственные
расходы
|
1311000
|
187,28
|
Прочие производственные
расходы
|
263250
|
37,6
|
Внепроизводственные расходы
|
1129292,28
|
161,32
|
Итого
|
22355900
|
3193,7
|
Данная полная себестоимость рассчитана на 1 м3 продукции. Стоимость 1 м3
будет равна 3193,7, при экспортной цене 3700 р./м3.
Расчет прибыли. Прибыль рассчитываем по формуле
П = (Ц - С) × А, (5.5)
где Ц - цена единицы продукции, руб;
С - себестоимость единицы продукции;
А - объём производства, т.
Прибыль по проекту будет равна
ПП= (3700-3193,7) · 7000 = 3544100 руб.
Принимаем размер налога 20 % с прибыли. Чистую прибыль рассчитываем по
формуле
П = Пп × 0,8.
(5.6)
Подставляя значения в формулу получаем
П = 3544100× 0,8= 2835280 руб.
Технико-экономические показатели
Основные технико-экономические показатели приведены в таблице 5.6
Таблица 5.6 - Технико-экономические показатели
Показатель
|
Проект
|
Капиталовложения, тыс. руб.
|
5775
|
Валовый выпуск арболита, м
3:
|
7000
|
Себестоимость 1 м 3
арболита, руб.
|
3060,9
|
Потребность в сырье, т.
|
7084
|
Число работающих, человек
|
30
|
Выпуск продукции на одного
рабочего, м 3
|
233,33
|
Прибыль, руб.
|
2835280
|
Экономический расчет производства модифицированного арболита
с использованием твердых промышленных и бытовых отходов.
Для производства модифицированного арболита требуются следующие
компоненты: щепа, вяжущий компонент - портландцемент марки М400,вторичные
минералы, а также вода. В качестве отходов будут использованы кора, вермикулит
вспученный, полиэтилентерефталат и стекло фракций 2,2;10;30 мм в количестве 25
% от общего объема сухой массы (Vсм).
В данном случае в качестве основного компонента будет использована
технологическая щепа .
Производственная мощность. Базовые данные для расчета производственной программы
цеха по производству модифицированного арболита.
Найдем производительность завода по следующей формуле
, (5.7)
где П - годовой объем производства, м3/год;
Пчас - производительность линии, тонн/час;
N -
продолжительность смены, час;
n -
количество смен, шт.;
Д - количество рабочих дней в году, дни.
Произведем расчет
П=0,95∙7∙3∙350= 7000 м3/год
Потребность в щепе составляет 225 кг на производство 1 м3 арболита.
Сменная потребность в сырье равна 1500 кг. Тогда годовой запас сырья составит
1575000 кг.
Производительность цеха модифицированного арболита будет составлять 7000
м3 в год.
Расчет капитальных вложений.
В данном пункте учитываем капиталовложения по установленному оборудованию
и техническим средствам. Стоимость устанавливаемого оборудования берется по
данным учёта и сводятся в таблицу 5.7.
Таблица 5.7 - Расчет капиталовложений
Наименование затрат и
оборудования
|
Объем работ или количество
оборудования
|
Стоимость
|
|
|
единицы, руб.
|
всего, руб.
|
1
|
2
|
3
|
4
|
Устройство приемное ДН-20
|
1
|
7000
|
7000
|
Машина рубильная с
конвейером подачи ДУ-2
|
1
|
250000
|
250000
|
Бункер щепы ДБО-60
|
1
|
167000
|
167000
|
Дробилка молотковая ДМ-1
|
1
|
220000
|
220000
|
Бункер древесной дробленки
ДБО-60
|
1
|
135000
|
135000
|
Устройство для замачивания
дробленки ПА1.022
|
1
|
35000
|
35000
|
Подъемник скиповый
ПА1.020.200
|
3
|
46000
|
138000
|
Смеситель для приготовления
арболитовой смеси СБ-62
|
1
|
80000
|
80000
|
Смеситель ц/п раствора
СБ-80
|
1
|
60000
|
60000
|
Секция склада цемента с
системой подачи ДСМ.07
|
11
|
10000
|
110000
|
Компрессор ДБВ-1 Расходный
бункер цемента
|
1
|
75000
|
75000
|
Устройство для хим. добавки
|
1
|
80000
|
80000
|
Фильтр рукавный РФ-30
|
1
|
50000
|
50000
|
Дозатор цемента
АВДЦ-425/1200М
|
1
|
110000
|
110000
|
Дозатор жидкости ДБЖ-400
|
1
|
110000
|
110000
|
Дозатор хим. добавки
425/1200М
|
1
|
135000
|
135000
|
Формовочная линия ЛВ-24
|
1
|
1490000
|
1490000
|
Конвейер роликовый ЛВ-125М
|
1
|
956000
|
956000
|
Конвейер роликовый ТЛ-10
|
1
|
925000
|
925000
|
Захват для изделия СМЖ-46А
|
1
|
224000
|
224000
|
Дробилка АМД - 600 ДУ
|
1
|
120360
|
120360
|
Бункер твердых промышленных
отходов и бытовых отходов
|
1
|
167000
|
167000
|
Доставка и монтаж
оборудования
|
|
|
510000
|
Итого
|
|
|
5990000
|
Стоимость оборудования составляет 5990000 рублей, включая доставку и
монтаж.
Расход сырья и материалов представлен в таблице 5.9.
Таблица 5.9 - Расход сырья и материалов для производства
модифицированного арболита в натуральном выражении
Наименование
|
По плану
|
|
на 1 м3
|
на потребителя
|
1
|
2
|
3
|
1 Технологическая щепа, кг
|
225
|
1575000
|
2 Цемент, кг
|
300
|
2100000
|
3 Сернокислый алюминий, кг
|
12
|
84000
|
4 Твердые промышленные и
бытовые отходы, кг
|
25% от Vсм
|
25% от Vсм
|
5Вода, л
|
400
|
2800000
|
Итого
|
925
|
6559000
|
Расход сырья и материалов для производства модифицированного арболита в
стоимостном выражении представлен в таблице 5.10.
Таблица 5.10 - Расход сырья и материалов для производства
модифицированного арболита в стоимостном выражении
Наименование
|
По плану
|
|
на 1 м3, руб.
|
1 Технологическая щепа
|
225
|
1575000
|
2 Цемент
|
1050
|
7350000
|
3 Сернокислый алюминий
|
144
|
1008000
|
4 Твердые промышленные и
бытовые отходы
|
-
|
-
|
5 Вода
|
8
|
56000
|
Итого
|
1457
|
10199000
|
Цемент планируется закупать на Красноярском Цементном Заводе, сернокислый
алюминий - в ООО «МДМ ХИМ» в г. Красноярске. Транспортные расходы по доставке
цемента, вспученного вермикулита и сернокислого алюминия из Красноярска
составят (стоимость доставки одного вагона 30000 руб.):
ТР = 47 вагонов∙30000 = 1410000 руб.
Расчет себестоимости продукции. Себестоимость включает затраты
предприятия на ее производство и реализацию. Величина себестоимости отражается
в калькуляциях себестоимости продукции в виде общей суммы затрат и затрат на
единицу продукции. По проектам строительства (реконструкции) цехов определяют
цеховую себестоимость продукции.
В калькуляции себестоимости учитываются статьи затрат, в свою очередь по
отдельным из них дополнительно составляют сметы затрат (на
транспортно-заготовительные расходы по сырью, затраты по сушке пиломатериалов,
цеховые и общезаводские расходы и т. п.).
Расчет стоимости электроэнергии для технологических нужд. Электроэнергия для технологических
нужд формируется суммой потребляемой энергии всех машин и агрегатов с учетом
коэффициента использования оборудования и рассчитывается по формуле
Цэ = ЦкВт∙Nоб∙N∙n∙Д∙Кисп, (5.8)
где ЦкВт - стоимость одного кВт - 0,72 р.;
Nоб-мощность
оборудования, кВт;
N -
продолжительность смены, час;
n -
количество смен, шт.;
Д - количество рабочих дней в году, дни;
Кисп - коэффициент использования оборудования.
Цэ = 0,72∙50∙8∙3∙350∙1 = 302400 руб.
Расчет стоимости электроэнергии для хозяйственных нужд. Для освещения цеха для производства
арболита используются лампы накаливания марки НБ 220-1500. Потребное количество
светильников рассчитаем по формуле
N=
шт., (5.9)
где E - требуемая горизонтальная
освещенность, лк;
S -
площадь помещения, м2;
Кз - коэффициент запаса;
U -
коэффициент использования;
Фл - световой поток лампы.
N=
шт.
Мощность лампы накаливания НБ 220-1500 составляет 1,5 кВт. Тогда
стоимость электроэнергии хозяйственных нужд рассчитаем по формуле
(5.10)
где ЦкВт - стоимость одного кВт - 0,72 р.;
Nоп -
мощность осветительного прибора, кВт;
n -
количество осветительных приборов.
- продолжительность смены, ч;
- количество смен;
- количество рабочих дней в году;
Цэ = 0,72∙(1,5∙32)∙7 ∙3∙350= 254016 руб.
Таблица 5.11 - Расход электроэнергии для производства модифицированного
арболита в стоимостном выражении
Наименование
|
По плану
|
|
на 1 м3, руб.
|
на потребителя, руб.
|
1 Для технологических нужд
|
38,02
|
302400
|
2 Для хозяйственных нужд
|
36,28
|
254016
|
Итого
|
74,3
|
520128
|
Расчет фонда заработной платы. На данном предприятии в статью
затрат по заработной плате входят: основная и дополнительная заработная плата
основных и вспомогательных рабочих, а также управленческого и служебного
персонала.
Количество работающих в цехе - 34 человек, заработная плата одного
рабочего в месяц в среднем составляет 15000 руб. Следовательно, заработная
плата 34 рабочих за год составит:
З/п за год = 15000∙34∙12 = 6120000 руб.
З/п на 1 м3 = 6120000/7000= 874,3 руб.
Страховые взносы составят:
СВ = 6120000∙30,8 % = 2068560 руб.
СВ на 1 м3 = 2068560/7000= 295,5 руб.
Расходы на содержание и эксплуатацию оборудования составляют 20 % от
стоимости оборудования.. Подставляя значения, получаем
А=5990000∙0,2= 1198000 руб.
А на 1 м3 =1198000 /7000= 171,14 руб.
Расходы на подготовку и освоение производства приняты в размере 10%
стоимости оборудования.
Зос=5990000
0,1= 599000 руб.
Зос 1 м3 =599000/7000= 85,57 руб.
Общепроизводственные расходы составляют 20% от суммы заработной платы и
амортизации.
Рц=7318000∙0,2= 1463000 руб.
Рц 1 м3 =1463000/7000= 209 руб.
Прочие расходы составят 5 % от стоимости оборудования, следовательно:
ПР = 599000∙5 % = 29950 руб.
ПР 1 м3 = 29950 /7000= 42,8 руб.
Внепроизводственные расходы составляют 4 % от производственной
себестоимости.
Пвн = 28444667∙0.04 = 1137786,7 руб.
Пвн 1 м3 = 1137786,7 /7000= 162,5 руб.
Себестоимость производства арболита представлена в таблице 5.12
Таблица 5.12 - Калькуляция себестоимости продукции
Статьи затрат
|
По проекту
|
|
всего, руб.
|
на 1м3, руб.
|
Сырье по оптовым ценам
|
10199000
|
1457
|
Расход на электроэнергию
|
520128
|
74,3
|
Заработная плата
|
6120000
|
874,3
|
Страховые взносы
|
2068560
|
295,5
|
Расходы на содержание и
эксплуатацию оборудования
|
1198000
|
171,14
|
Расходы на подготовку и
освоение производства
|
599000
|
85,57
|
Общепроизводственные
расходы
|
1463600
|
209
|
Прочие производственные
расходы
|
299500
|
42,8
|
Внепроизводственные расходы
|
1137786,3
|
162,5
|
Полная себестоимость
|
21426300
|
3060,9
|
Данная полная себестоимость рассчитана на 1 м3 продукции. Стоимость 1 м3
будет равна 3060,9, при экспортной цене 3700 р./м3.
Расчет прибыли. Прибыль рассчитываем по формуле
П = (Ц - С) × А, (5.11)
где Ц - цена единицы продукции, руб;
С - себестоимость единицы продукции;
А - объём производства, т.
Прибыль по проекту будет равна
ПП= (3700-3060,9) · 7000 = 4972100 руб.
Принимаем размер налога 20 % с прибыли. Чистую прибыль рассчитываем по
формуле
П = Пп × 0,8.
(5.12)
Подставляя значения в формулу получаем
П = 4972100× 0,8= 3977680 руб.
Экономическая эффективность проекта. Экономическая эффективность проекта
оценивается коэффициентом общей эффективности
(5.13)
где П - величина прибыли по проекту, тыс. руб;
К - капиталовложения по проекту, тыс. руб.
Подставляя значения в формулу, получаем
Э К =
.
Срок окупаемости капиталовложений, лет, определяется по формуле
Ток = К/П; (5.14)
Подставляя значения в формулу, получаем
Ток =5895360/3977680 руб. = 1,45 лет.
При разовой инвестиции расчет чистого приведенного дохода (эффекта), NPV, тыс. руб., можно представить
формулой
NPV =
= PV - IC,
(5.15)
где Р1, Р2, Рк, ….., Рn -
годовые денежные поступления в течение n - лет;
IC -
стартовые инвестиции (капитальные вложения);
I -
ставка сравнения;
PV -
общая накопленная величина дисконтированных поступлений.
При NPV > 0, проект следует принять; при NPV < 0, проект следует отвергнуть; при NPV = 0, проект не прибылен, но и не
убыточен. Коэффициент дисконтированной стоимости принимается равный 12 %.
Расчет чистой дисконтированной стоимости представлен в таблице 5.13
Таблица 5.13 - Расчет чистой дисконтированной стоимости
Период времени, год
|
Платежи и поступления, руб.
|
Коэффициент дисконтирования
(12 %)
|
Чистая текущая стоимость
разных лет, руб.
|
Кумулятивная чистая текущая
стоимость, руб.
|
0
|
-5895360
|
1
|
-5895360
|
-5895360
|
1
|
3977512
|
0,892
|
3551350
|
-2223650
|
2
|
3977512
|
0,797
|
3170848,21
|
947198,21
|
Срок окупаемости капиталовложений с учетом дисконтированной стоимости
составляет 2 года.
Технико-экономические показатели
Основные технико-экономические показатели приведены в таблице 5.14
Таблица 5.14 - Технико-экономические показатели
Показатель
|
Проект
|
1
|
2
|
Капиталовложения, тыс. руб.
|
5895
|
Валовый выпуск арболита, м
3:
|
7000
|
Себестоимость 1 м 3
арболита, руб.
|
3060,9
|
Потребность в сырье, т.
|
5313
|
Число работающих, человек
|
34
|
Выпуск продукции на одного
рабочего, м 3
|
205,88
|
Прибыль, руб.
|
3977680
|
Коэффициент общей
эффективности
|
0,689
|
Срок окупаемости
капиталовложений, год
|
1,45
|
Таким образом основная цель заключалась в комплексном
использовании отходов лесопиления и увеличение ассортимента выпускаемой
продукции. Предприятие получит прибыль в размере 4972100 руб. Капиталовложения
окупятся за 1,75 года, с учетом временного коэффициента. Исходя из этого,
проект можно считать эффективным. В результате внедрения мероприятий,
разработанных в дипломной работе, производительность цеха составит 7000 м 3. Из
данного расчета можно сделать вывод, что при равных капиталовложениях
производство модифицированного арболита с использованием отходов промышленности
принесет прибыль на конец года больше на 2136820 рублей, при одинаковом объеме
производства. Срок окупаемости сократится на 0,58 года.
Заключение
В результате выполненных исследований по приданию специальных свойств
арболитовым блокам, изготовленным способом вибропрессования, получены следующие
результаты:
. На основании анализа исследований в области производства арболитовых
блоков был определен круг задач, подлежащих изучению.
. По результатам предварительного эксперимента было изучено влияние
фракционного состава и массовой доли твердых промышленных и бытовых отходов в
арболитовой массе на параметры прочности на сжатие, огнезащищенности и
плотности готовой продукции.
. На базе экспериментальных исследований разработаны математические
модели, адекватно описывающие процесс получения арболитовых блоков пониженной
пожарной опасности.
. Анализ полученных математических зависимостей позволил определить
оптимальные по различным критериям технологические режимы, применение которых
приводит к получению арболитовых блоков пониженной пожарной опасности с
необходимыми физико-механическими характеристиками.
. На основании результатов исследований была разработана композиция для
получения арболитовых блоков пониженной пожарной опасности способом
вибропрессования.
. Предложена технология для производства арболитовых блоков пониженной
пожарной опасности.
6. Выполнена оценка экономической эффективности производства
древесноволокнистых плит пониженной пожарной опасности. Сумма капитальных
вложений составит 5895 тыс. руб. Себестоимость 1м3 арболитовых блоков
пониженной пожарной опасности - 3060,9 руб. Прибыль предприятия при выпуске 7
тыс.м3. арболитовых блоков пониженной пожарной опасности составит 3977,68 тыс.
руб. в год, при сроке окупаемости 1,45 лет и экономической эффективности
капитальных вложений 0,68.
Библиографический список
1 Абрамкин, В.В. Методические указания к дипломному
проектированию для студентов всех форм обучения [Текст] / В.В. Абрамкин. -
Красноярск СибГТУ, 2004. - 22 с.
2 Арустамов, Э.А. Безопасность жизнедеятельности:
Учебник. - 2-е изд., перераб. и доп. [Текст] / Э.А. Арустамов. - М.:
Издательский дом «Дашков и К», 2000. - 678 с.
Агафонова, И.П. Деревообрабатывающая промышленность
России: современное состояние и пути достижения необходимого уровня развития
Текст] / И.П. Агафонов // Деревообраб. пром-сть. - 2003. - № 4. - С. 19-23.
Бельков, В.В. Лесные ресурсы края и их использование
[Текст] / В.В. Бельков // Инвестиционный потенциал лесного комплекса
Красноярского края. - Красноярск: СибГТУ, 2003. - С. 23-31.
5 Головков, С.И. Энергетическое использование
древесных отходов [Текст] / С. И. Головков, И.Ф. Коперин, В.И. Найденов. - М.:
Лесн. пром-сть,2004. - 224 с.
6 Грачев, А.А. Энергетическая ценность отходов
древесины [Текст] / А. Грачев // Дерево-RU. - 2006. - № 1. - С. 124-125.
Гомонай, М.В. Древесное биотопливо: брикеты и
гранулы [Текст] / М.В. Гомонай. - М.: МГУЛ, 2007. - 90 с.
8 Горошко, С.К. Экономика безотходных технологий
лесного комплекса [Текст] / С.К. Горошко. - М.: Лесн. пром-сть, 2003. - 184 с.
9 Ермолина, Т.В. Система вузовской учебной
документации. Дипломное проектирование, требования к выполнению и
представлению. [Текст] / Т.В. Ермолина. - Красноярск: Сиб ГТУ, 2002. - 28 с.
10 Загорье, A.M. Вторичные энергосырьевые ресурсы
лесоперерабатывающей промышленности [Текст] / A.M. Загорье, Р.Ю.
Зах. - М.: Лесн. пром-сть. - 2002. - 84 с.
11 Комплексная химическая переработка древесины [Текст]
/И.Н. Коверинский [и др.]. - Архангельск: АГТУ, 2002. - 347 с.
12 Коробов, В.В. Переработка низкокачественного сырья
[Текст] / В.В. Коробов, Н.П. Рушнов. - М.: Экономика, 2004. - 288 с.
13 Лапкаев, А.Г. Безопасность жизнедеятельности.
Безопасность труда: Учебное пособие для студентов вузов. Издание 2-е
(дополненное и переработанное). [Текст] / А.Г. Лапкаев. - Красноярск: РИЦ
СибГТУ, 2008. - 632 с.
14 Миронов, Г.С. Комплексное использование древесины.
Переработка вторичных древесных ресурсов [Текст] / Г.С. Миронов. - Красноярск:
СибГТУ, 2001. - 70 с.
15 Михайлов, Г.М. Пути улучшения использования
вторичного древесного сырья [Текст] / Г.М. Михайлов, Н. А. Серов - М.: Лесн.
пром-сть, 2005. - 224 с.
16 Мосягин, В.И. Вторичные ресурсы лесного комплекса
[Текст] / В.И. Мосягин. - СПб.: СПбЛТА, 2006. - 232 с.
Никишов, В.Д. Комплексное использование древесины
[Текст] / В.Д. Никишов. - М.: Лесн. пром-сть, 2005. - 180 с.
18 Обливин, Л.Г. Безопасность жизнедеятельности в лесопромышленном
производстве и лесном хозяйстве: Учебник [Текст] / В.Н. Обливин, А.С. Щербаков.
- М.: ГОУ ВПО МГУЛ, 2009. - 650 с.
19 Пучков, Б.В. Использование древесных отходов для
производства плит [Текст] / Б.В. Пучков. - М.: МГУЛ, 2005. - 56 с.
20 Репях, С.М. Основные направления рационального
использования древесных отходов [Текст] / С.М. Репях, Р.А. Степень, В.В.
Шелепков // Вестник СибГТУ. - 2001. - №2. - С. 86-93.
21 Савицкая, Г.В. Анализ хозяйственной деятельности
предприятия: Учебник. - 4-е изд., перераб. и доп. [Текст] / Г. В. Савицкая. -
М.: ИНФРА-М, 2008. - 512 с.
22 Состояние лесных ресурсов и их хозяйственное
использование // Природные ресурсы Красноярского края. - Красноярск: КНИИГиМС,
2001.- С. 156-158.
23 Твердая, Л.А. Технико-экономический анализ
хозяйственной деятельности предприятий. [Текст] / Л.А. Твердая. - Красноярск:
СибГТУ, 2005. - 104 с.
24 Тацюн, М.В. О мерах по обеспечению
конкурентоспособности лесопромышленного производства России [Текст] / М.В.
Тацюн // Лесн. пром-сть. - 2004. - № 1. - С. 2-4.
25 Холод, Н. И. Экономико-математические методы и
модели. [Текст] / Н.И. Холод. - М.: БГЭУ, 2008. - 412 с.
26 Холькин, Ю.И. Технология гидролизных производств
[Текст] / Ю.И. Холькин. - М.: Лесн. пром-сть, 2001. - 496 с.
27 Храмова, Л.Н. Эколого-экономическая оценка
рационального использования вторичных ресурсов [Текст] / Л. Н. Храмова, Р. А.
Степень, С. В. Соболев//Вестник КраГУ - 2006 - №5. -с. 131-137.
Храмова, Л.Н. Проблема использования твердых отходов
деревообрабатывающих предприятий города Лесосибирска [Текст] / Л. Н. Храмова //
Непрерывное экологическое образование и экологические проблемы Красноярского
края Сб мат VI региональной научно-практической конференции - Красноярск
СибГТУ, 2001 - с. 79-81.
Храмова, Л.Н. Состояние и пути утилизации отходов
деревообработки [Текст] / Л.Н. Храмова // Химико-лесной комплекс - проблемы и
решения Сб мат Всероссийской научно-практической конференции -Красноярск
СибГТУ, 2002 - ТII - с. 296-301.
Храмова, Л.Н. Оценка эколого-экономической ситуации
на предприятиях города Лесосибирска [Текст] / Л.Н. Храмова // Непрерывное
экологическое образование и экологические проблемы Красноярского края Сб мат
VII региональной научно-практической конференции -Красноярск СибГТУ, 2002 - 124
с.
Храмова, Л.Н. Эколого-экономическая оценка
рационального использования вторичных ресурсов в Ангаро-Енисейском регионе
[Текст] / Л Н Храмова, С В Соболев, Р А Степень// Красноярск СибГТУ, 2006 - 134
с.
Черняева, Г.Н. Утилизация древесной биомассы [Текст]
/ Г.Н. Черняева, С.Я. Долгодворова, Р.А. Степень. - Красноярск: ИЛиД СО АН
СССР, 2007.- 166 с.
Чистова, Н.Г. Система вузовской учебной документации
для студентов [Текст]: Сборник учебных конструкторских документов. Учебное
пособие по оформлению, составлению и представлению конструкторской документации
в Лесосибирском филиале СибГТУ студентам специальностей 2602.00 «Технология
деревообработки», «Лесоинженерное дело», 0608.00 «Экономика природопользования
и охраны окружающей среды» всех форм обучения / Н.Г. Чистова, Л.А. Трофимук, Л.Н.
Журавлева, В.В. Силин. - Лесосибирск: Лесосибирский филиал Сибирского
государственного технологического университета; СибГТУ, 2004. - 104 с.
34 Шапкин, А.С. Математические методы и модели
исследования операций. [Текст] / А.С. Шапкин, Н.П. Мазаева. - М.: Дашков и К,
2006. - 400 с.
35 Шварцман, Г.М. Производство древесностружечных плит
[Текст] / Г.М. Шварцман, Д.А. Щедро. - М.: Лесн. пром-сть, 2002. - 320 с.
36 Щербаков, А.С. Безопасность жизнедеятельности в
лесопромышленном производстве и лесном хозяйстве: Учебник. [Текст] / А.С.
Щербаков, В.Н. Обливин, Л.Г. Казаков, Л.И. Никитин, А.А. Гуревич, Н. Г. Гренц.
- М.: ГОУ ВПО МГУЛ, 2009. - 650 с.
37 Эколого-экономические проблемы многоцелевого
лесопользования / отв. ред. И.В. Семечкин. - Красноярск: ИЛиД СО АН СССР,
2005.-162 с.