Проектирование новых деталей литейно-прокатного агрегата
Введение
Одна из важнейших задач современной металлургии состоит в создании
совмещенных процессов непрерывного литья и прокатки. Основное преимущество
такого совмещения заключается в том, что процессы протекают стабильно во
времени. Это максимально упрощает их автоматизацию и улучшает качество проката.
Совмещение позволяет сократить производственные площади, удельные капитальные и
эксплуатационные расходы, снизить расходы металла и энергии, существенно
повысить производительность труда.
На заводе «Электросталь» работает литейно-прокатный агрегат (ЛПА),
созданный и внедренный в результате совместной работы АХК «ВНИИметмаш», завода
«Электросталь» и МГТУ им. Н. Э. Баумана. На агрегате производят катанку из
специальных сталей и сплавов при прямом (без резки слитка) совмещении процессов
непрерывного литья и прокатки.
Целью данной работы является повышение качества проката. Это касается
качества поверхности катанки, улучшение эксплуатационных свойств оборудования.
Кроме того особое внимание уделено увеличению производительности, расширение
сортамента выпускаемой продукции агрегата непрерывной разливки и прокатки стали
СПЦ-3 МЗ «Электросталь».
Чтобы принять решение о том, модернизация какого узла агрегата позволит
нам достичь поставленных целей, проведем анализ существующего технологического
процесса.
Объектом дипломного проектирования является литейно-прокатный агрегат
(ЛПА), его другое название - агрегат непрерывной разливки и прокатки стали и
сплавов (АНРиПСиС), расположенный в сталеплавильном цехе №3 (СПЦ-3) металлургического
завода «Электросталь» (ОАО МЗ «Электросталь») (рис. В.1).
В здании цеха СПЦ-3 размещен только один агрегат АНРиПСиС, который
производит бунтовый прокат круглого профилеразмера Ø
8…10 мм, как
поставляемый заказчику, так и потребляемый внутри завода прокатным цехом №2
(ПЦ-2). Производство характеризуется сложностью марочного состава, включающего
высоколегированные нержавеющие, жаропрочные и коррозионностойкие и прецизионные
сплавы.
Кроме МНЛЗ агрегат АНРиПСиС включает в себя две индукционные установки,
задающую и планетарные клети, шестиклетьевую чистовую группу с моталкой.
1. Научно-исследовательская часть
.1 Технологический процесс ЛПА
Промышленный проволочный ЛПА включает (рис.1.1) индукционную печь, МНЛЗ,
индукционную установку для выравнивания температуры слитка перед прокаткой
(необходима лишь для прокатки отдельных сплавов), сортовой планетарный стан,
летучие ножницы, чистовую группу прокатных клетей, сортовую моталку.
Рис. 1.1. Технологическая схема непрерывного литья и прокатки. 1-
индукционная печь; 2 - МНЛЗ; 3- промежуточная емкость; 4 - кристаллизатор; 5 -
зона вторичного охлаждения; 6 - параллельно-тянущие устройства; 7 - индуктор; 8
- задающая клеть; 9 - планетарный стан; 10 - летучие ножницы; 11 -
автоматический петлерегулятор; 12 - чистовые клети; 13 - моталка
Агрегат оснащен системами гидропривода и централизованной смазки и
представляет собой высокоавтоматизированную технологическую линию, оснащенную
контрольно-измерительными приборами параметров техпроцесса, Специальная
индукционная печь на 12 т служит для выплавки металла из твердой металлической
шихты с добавлением лома марочного состава. Питание индуктора печи током
частотой 1000 Гц от генератора мощностью 500 кВт при напряжении 750 В.
Разливку ведут из сталеразливочного ковша, футеровка которого
предварительно разогрева газовой горелкой до 1000…1100С. Жидкий металл подается
в кристаллизатор 4 из промежуточной емкости 3, в днище которой находится
дозирующий стакан.
МНЛЗ радиального типа с базовым радиусом 3 м предназначена для отливки
слитка сечением 120х140 (125х125) мм и состоит из несущей металлоконструкции,
медного водоохлаждаемого кристаллизатора, установленного на качающейся раме,
механизма качания кристаллизатора, роликовой зоны вторичного охлаждения,
правильно-тянущего устройства 5 (ПТУ), жесткой затравки с механизмом ее
перемещения (табл.1.1).
Таблица 1.1. Основные технические данные и оборудование МНЛЗ
Тип МНЛЗ
|
радиальная
|
Количество ручьев, шт.
|
1
|
Базовый радиус, м
|
3
|
Базовое сечение отливаемой
заготовки, мм
|
60 ´ 80
|
Длина заготовки, мм
|
6000; 12000
|
Металлургическая длина
МНЛЗ, м
|
не менее 22
|
Способ регулирования
расхода металла из промковша
|
с помощью дозаторов
промковша
|
Емкость промковша, т
|
около 12
|
Способ разливки стали
|
открытой струей металла
|
Длина гильзы
кристаллизатора, мм
|
700
|
Тип затравки
|
полужесткая
|
Тип механизма качания
|
рычажный
|
Амплитуда качания
кристаллизатора, мм
|
± 1.5…8
|
Частота качания
кристаллизатора, циклов/мин.
|
до 250
|
Количество плавок в серии,
шт.
|
до 6
|
Вторичное охлаждение
|
водоструйное
|
Тип режущего устройства
|
летучие ножницы
|
Для разливки на МНЛЗ используются углеродистые стали обыкновенного
качества по ГОСТ 380-94 (ст. 3, ст. 5) (табл.1.2).
Таблица 1.2. Основные технологические параметры работы МНЛЗ
Параметр
|
Значение параметра
|
Заданная годовая
производительность МНЛЗ, тыс. тонн стали (по годному)
|
200
|
Средний вес плавки по
годному, т
|
12
|
Фактическое время работы
МНЛЗ, часов в год
|
7200
|
Среднее время разливки 1-й
плавки для базового сечения НЛЗ, мин.
|
37.1
|
Диапазон скоростей
разливки, м/мин.
|
2.5 - 4.5
|
Средняя скорость разливки
стали для базового сечения НЛЗ, м/мин.
|
3.5
|
Среднее время подготовки
МНЛЗ к разливке стали, мин.
|
30
|
Средняя серийность
разливки, плавок
|
4
|
Средняя величина выхода
годного металла, %
|
97.1
|
Зона вторичного охлаждения - это радиальная роликовая проводка,
оборудованная комплексом водораспыляющих форсунок, расположенных вдоль каждой
из четырех граней слитка. Поддерживающие ролики служат для направления затравки
в получаемый слиток. ПТУ содержит две пары приводных тянущих роликов, один -
опорный нижний и один - поворотный, разгибающий холостые ролики. Верхние
тянущие ролики смонтированы в поворотных рычагах, соединенных с гидроцилиндром,
создающим необходимое усилие прижатия роликов к заготовке для отделения
заготовки от затравки и последующего разгибания заготовки в горизонтальное
положение.
Затравка имеет вид криволинейного бруса прямоугольного сечения, ее
головка присоединена к концу переднего стержня и имеет на торце паз типа «ласточкин
хвост». Перед началом разливки затравку вводят в кристаллизатор, а зазоры между
ней и стенками уплотняют асбестом. После заполнения кристаллизатора до
заданного уровня автоматически включается в работу ПТУ и начинается вытягивание
затравки и сцепленного с ней непрерывного слитка. Выходящий слиток охлаждается
водой из форсунок, расположенных по всем четырем граням.
В ПТУ слиток отделяется от затравки, после чего затравку убирают с
технологической оси МНЛЗ механизмом перемещения. На выходе из МНЛЗ отрезают
передний конец слитка, в двух индикаторах выравнивают температуру по сечению.
Слиток поступает в задающую клеть планетарного стана, в которой два
вертикальных валка обжимают ее до требуемого поперечного сечения, а затем - в
рабочую клеть планетарного стана, где площадь поперечного сечения за один
проход уменьшается в 40…50 раз. При планетарной прокатке вследствие больших
деформаций температура металла интенсивно повышается на - 150…170С. Схема
деформации обеспечивает получение проката из слитков без дефектов, так как
можно регулировать режимы проката и температуру.
Основной механизм промышленного сортового планетарного стана -
планетарная клеть (ПК), имеющая сварную скобообразную станину с установленными
в ней четырьмя узлами планетарных валков (ПВ). На лобовинах станины с входной
стороны располагается задающая клеть, а с выходной - тянущие ролики.
Каждый узел планетарных валков смонтирован в разъемном литом коробчатом
корпусе, в котором на подшипниках качения установлен вал сепаратора с приводным
механизмом. По окружности сепаратора на равном расстоянии в расточках
расположены восемь рабочих валков, смонтированных на двух сферических
двухрядных роликовых подшипниках. Узел рабочего валка выполнен в двух
вариантах, позволяющих использовать как цельнокованый валок с осью, так и валок
с насадной бочкой.
Корпуса узлов планетарных валков крестообразно крепятся к призмам,
установленным на лобовых станины. С входной стороны станины проушины корпусов
фиксируют в призме на осях, а с выходной - удерживаются нажимными винтами
механизма настройки. В передней призме смонтирован механизм настройки стана на
заданный размер проката, а также гидромеханизм уравновешивания узлов ПВ с
выборкой зазоров. Привод механизма настройки осуществляется от двигателя через
редуктор, карданный вал и червячную пару. Предусмотрена также индивидуальная
подстройка каждого узла ПВ. Такая конструкция ПК позволяет легко переходить с
одного размера проката на другой при сохранении постоянного положения оси
прокатки. Наибольшее перемещение узлов ПВ выбрано из условия возможности
демонтажа, начиная с любого из них.
Механизм привода сепараторов смонтирован в корпусе узла ПВ. Привод ПК
осуществляют через универсальные шпиндели, на каждом из которых для настройки
симметричности положения рабочих валков установлена муфта, обеспечивающая
индивидуальную регулировку углового положения сепараторов. Сварная станина ПК
представляет собой скобообразную раму, на которой крепятся все узлы. Принятая
схема ПК полностью разгружает станину от воздействия силы прокатки. Чистовая
группа клетей смонтирована с учетом того, что подкат поступает от планетарного
тана с пульсирующей скоростью и имеет периодически изменяющееся сечение
профиля.
В состав чистовой группы входят две отдельно стоящие клети с
индивидуальными приводами, четырех клетьевой блок с групповым приводом и
автоматические петлерегуляторы перед 1-й и 2-й клетями. В отдельно стоящих
клетях производится последовательное обжатие подката в двух взаимно
перпендикулярных направлениях. При этом в значительной степени устраняется
периодичность его профиля. Пульсирующая подача металла от планетарного стана в
первых двух клетях компенсируется петлями.
Компактное расположение оборудования с предельным сокращением межклетевых
интервалов способствует небольшим температурным потерям полосы, и сокращает
длину утолщенных передних и задних концов, прокатываемых без натяжения.
Чередующееся расположение клетей и их наклон позволяют устранить кантовку
полосы при прокатке, упрощают обслуживание клетей и способствует удалению воды
и окалины на валках.
ЛПА имеет системы автоматизации, обеспечивающие направление всем
процессом НЛ и прокатки одним оператором. В автоматическом режиме производится
пуск МНЛЗ: при достижении заданного уровня металла в кристаллизаторе
(контролируется радиоизотопным уровнемером) включаются механизмы МНЛЗ - качания
кристаллизатора, ПТУ, перемещение затравки. Во время работы уровень металла в
кристаллизаторе поддерживается с заданной точностью. Подача воды для охлаждения
слитка в роликовой проводке регулируется в зависимости от скорости вытягивания
слитка из кристаллизатора.
В результате анализа технологического процесса литейно-прокатного
агрегата был сделан вывод, что целесообразнее всего провести модернизацию
чистового блока путем замены старых прокатных клетей на более современные. Это
позволит значительно расширить сортамент и повысить показатели точности
готового изделия, так как данный узел отвечает за качество продукции. Для того
чтобы определить конструкцию клети для замены, проведем анализ существующих в настоящее
время типов клетей.
.2 Анализ конструкции гильзы кристаллизатора
Наиболее эффективными мерами для решения проблем надежности работы
сортовой МНЛЗ при высокоскоростной разливке и получения непрерывнолитых
заготовок с высоким качеством поверхности и макроструктурой, являются меры,
сводящиеся к оптимизации теплового и напряженно-деформированного состояния
формирующейся оболочки слитка в кристаллизаторе путем разработки рациональной
конструкции гильзы, конфигурации ее внутренней полости, режимов и равномерности
охлаждения. Упомянутое выше условие можно реализовать созданием внутреннего
профиля гильзы, основанного на принципе самокомпенсации усадки. С этой целью
гильза в верхней части имеет воронкообразную форму внутреннего поперечного
сечения с вогнутостями синусоидальной формы (рис. 1.2).
Рис. 1.2 Гильза конструкции «ВМ-синус»
При этом амплитуда должна монотонно убывать по длине гильзы до зоны
перехода к формообразующей части. Относительное удлинение синусоиды при ее
выпрямлении вычисляется по следующей формуле:
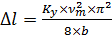
(1.1)
где

-
разница между длиной выпрямленной синусоиды и прямой, равной периоду синусоиды,
мм; vm - амплитуда синусоиды, мм; 2b - период синусоиды, мм; Ку - коэффициент,
учитывающий усадку стали при определенной скорости разливки.
Из
формулы (1.1) видно, что выпрямление выпуклых синусоидальных участков
происходит в соответствии с параболической зависимостью, которая наиболее точно
описывает процесс усадки корочки слитка.
Математическая
модель взаимодействия оболочки непрерывнолитой заготовки с гильзой, имеющей
вогнутости синусоидальной формы.
Для
определения оптимальных параметров гильзы на основе анализа теплового и
напряженно-деформированного состояния оболочки заготовки и ее взаимодействия со
стенками гильзы «ВМ-синус» была разработана математическая модель, учитывающая
взаимосвязь теплового и напряженно-деформированного состояния, неравномерность
теплообмена и затвердевания по периметру поперечного сечения заготовки
вследствие неравномерности толщины газового зазора, теплофизические и
механические свойства стали, обусловленные полями температур, ограниченность перемещений
поверхностных точек оболочки относительно внутренней полости гильзы
кристаллизатора.
Для
построения данной модели было разработано три взаимосвязанных алгоритма
расчета: деформирования грани заготовки в контакте со стенками гильзы,
контактных условий теплообмена между заготовкой и гильзой, температурного
состояния заготовки.
Основные
уравнения деформирования затвердевающей оболочки слитка в кристаллизаторе.
Рассмотрим
изгиб затвердевающей корочки слитка в условиях контакта со стенкой
кристаллизатора. Если представить оболочку сортовой заготовки на одной из ее
граней в конкретный момент деформирования как симметрично нагруженную балку
единичной ширины (рис. 1.3), то для момента в поперечном сечении можно записать

(1.2)
где
q(x) - неравномерно распределенное контактное давление на оболочку слитка, 
-
ферростатическое давление на рассматриваемом горизонте слитка, а - половина
ширины стенки, χ
- координата по оси x, характеризующая
центр тяжести контактного давления на оболочку кристаллизатора.
Рис. 1.3. Схема для расчета изгиба оболочки слитка в плоскости его
поперечного сечения
Здесь и далее формулы для расчета изгиба оболочки заготовки, исходя из
симметрии задачи, представлены для значений х≥0.
Обозначим скорость изменения кривизны данной балки через η
= dk/dt, и k
= 1/ρ, где ρ
- радиус кривизны
синусоидальной поверхности. Один из вариантов модели изгиба
нелинейно-вязкоупругой балки позволяет представить скорость изменения кривизны
как сумму упругой и вязкой составляющей

, (1.3)
где
в пределах упругости при использовании среднего по поперечному сечению модуля
упругости E, упругая составляющая скорости кривизны запишется в виде

, (1.4)

,
где
hs - текущая толщина корочки слитка единичной ширины.
При
изгибе поперечной полоски корочки слитка при распрямлении профиля зависимость
между вязкой составляющей скорости кривизны полоски 
и
моментом М в поперечном сечении корочки можно записать как

,
где
m - экспериментальная постоянная, используемая для описания степенной
зависимости между скоростью деформации и напряжением при ползучести.
Приведенная
изгибная жесткость D при ползучести вычисляется следующим образом

,
где

-
текущая толщина корочки слитка, у - координата перпендикулярная грани. Здесь
использована следующая аппроксимация для деформации ползучести от температуры и
напряжения выражения скорости

,
где
Ас - экспериментально определяемая функция, которая описывает зависимость
скорости деформации от напряжения в зависимости от температуры оболочки слитка.
Координата
нейтральной линии 
определяется
из решения следующего уравнения
В
рассматриваемый момент времени форма изгиба оболочки слитка определяется
следующими соотношениями:
Угол
поворота элемента оболочки -
Отклонение
от прямолинейной формы поперечного сечения -
(x)
= -f(a)+f(x),
где

.
Для
расчета изменения параметров деформированного состояния оболочки слитка во
времени использовалась явная шаговая схема с автоматическим выбором временного
шага из условий устойчивости вычислительного процесса. Кривизна на «n-ом»
временном шаге рассчитывалась по известному напряженно-деформированному
состоянию на предыдущем «n-1» шаге
Математическая
модель температурного состояния заготовки в кристаллизаторе.
Отличительная
особенность кристаллизующихся металлических материалов состоит в наличии
двухфазной зоны, которая представляет собой твердые кристаллиты и жидкую
прослойку. Для решения численной задачи затвердевания и температурного
состояния заготовки в кристаллизаторе с учетом наличия двухфазной зоны и
выделения тепла кристаллизации вводится функция источника тепла в уравнение
нестационарной теплопроводности.

,
(1.5)
где
ср - теплоемкость, ρ
- плотность материала, λ - коэффициент теплопроводности, QSL - функция,
характеризующая пространственно распределенный источник тепла фазового
перехода. Функция QSL прямо пропорциональна скорости затвердевания расплава и
зависит от свойств сплава (в частности от удельной теплоты фазового перехода L*
и интервала кристаллизации). Для того чтобы выразить QSL количественно, обычно
вводится в рассмотрение относительное количество твердой фазы 
в
некотором элементарном объеме расплава в пределах двухфазной зоне. Тогда

. (1.6)
Параметр

для
жидкой фазы равен нулю, для полностью затвердевшей части слитка равен единице и
для двухфазной зоны изменяется от нуля до единицы. Процесс затвердевания
рассматриваем в равновесной постановке (т.е. считать, что диффузионные процессы
в элементарном объеме материала успевают пройти достаточно полно за время
фазового перехода в этом объеме). Равновесная модель затвердевания слитка
позволяет с достаточной точностью исследовать кинетику поля температур при
промышленных скоростях непрерывной разливки.
Численное
решение уравнения теплопроводности было выполнено при следующих начальных и
граничных условиях. В качестве начального условия в окрестности менисковой
поверхности в момент времени t=0 примем для всей расчетной области


, (1.7)
где
Тн - начальная температура заливки металла в кристаллизатор.
В
качестве граничного условия на поверхности заготовки примем уравнение,
отражающее теплообмен между заготовкой и стенками кристаллизатора
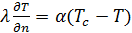
, (1.8)
где
п - нормаль к поверхности заготовки, Тс - температура окружающей среды, α - коэффициент теплоотдачи, учитывающий относительные
количественные вклады тепловой проводимости межконтактной среды при возможном
образовании зазора между поверхностью заготовки и стенками кристаллизатора и
тепловой проводимости через места физического контакта. Методика численного
решения задачи теплопроводности основана на использовании явной
конечноразностной схемы. Коэффициент теплоотдачи определяли по эмпирическим
формулам.
Коэффициент
а в уравнении (1.8) можно записать следующим образом

,
(1.9)
где

, (1.10)
Тsur
- температура поверхности слитка, К; Тс - температура внутренней поверхности
кристаллизатора, К, С=3.53 Вт/(м2 К4) - приведенный коэффициент теплообмена
излучением, зависящий в общем случае от геометрии пространства, разделяющего
поверхности слитка и стенки кристаллизатора, и коэффициентов степени черноты
обеих поверхностей (данный коэффициент получен для простейшего случая плоской
щели), 
-
коэффициент теплоотдачи при контактном теплообмене, определяется по формуле
Шлыкова-Ганина

, (1.11)
где

- предел
прочности менее пластичного материала соприкасающихся поверхностей; 
-
приведенный коэффициент теплопроводности, зависящий от коэффициентов
теплопроводности контактирующих тел, р - контактное давление; φ - относительная площадь контакта, определяет соотношение
между теплообменом излучением и непосредственно контактом.
Оценивая
тепловой поток, возникающий при контакте слитка со стенками кристаллизатора,
следует учесть, что контакт между твердыми телами всегда имеет дискретный
характер, т.е. соприкосновение рассматриваемых поверхностей происходит в
отдельных точках (пятнах) или группах точек. Известно, что даже в условиях
плотного контакта контактная площадь составляет незначительную долю от общей
площади, соприкасающихся поверхностей. Из теории контактного теплообмена
следует, что тепловой поток при подходе к поверхности соприкосновения
разделяется. Часть тепла передается теплопроводностью через точки
непосредственного контакта, а другая - теплопроводностью и лучистым
теплообменом через среду, заполняющую зазоры между слитком и кристаллизатором.
Контактное
давление р определяется суммой ферростатического давления и поверхностных сил
за счет взаимодействия корочки слитка с синусоидальным профилем
кристаллизатора.
Таким
образом, на первом этапе соотношение φ в выражении (9) можно определить, используя экспериментальные данные по
контактному теплообмену в обычных кристаллизаторах, когда контактное давление
фактически является ферростатическим. Оценки для коэффициента контактного
теплообмена для таких кристаллизаторов приведены в работах. В дальнейшем, при
расчете коэффициент теплоотдачи в формуле (9) будет корректироваться в
соответствии с зависимостью теплоотдачи при контактном теплообмене от
контактного давления в конкретной точке поверхности заготовки.
.3 Поиск аналога для проектирования чистовой
клети
Специфической особенностью сортовых станов является наличие большого
числа вариантов прокатных клетей в связи с выпуском широкого диапазона
геометрической и размерной номенклатуры, марочного сортамента и последующего
назначения продукции.
Так, конструкция бесстанинной прокатной клети «SMSMeer», сокращенно HL
(housingless), - это основа современных прокатных станов. Модульная структура
позволяет использовать кассеты для клетей HL во всех возможных конфигурациях:
горизонтальной, вертикальной, наклонной и универсальной. Тем самым, концепция
HL пригодна для черновых, промежуточных и чистовых групп клетей. Габариты
клетей отличаются друг от друга в зависимости от необходимых размеров валков и
шеек валков, режима обжатий, формы калибра, а также характеристики редукторов и
двигателей.
Прокатные клети HL используются в сортопрокатных, проволочных,
мелкосортных станах и комбинированных установках.
Главными признаками конструкции HL являются:
консервативные критерии для расчета компонентов и общая конструкция с
целью достижения компактного, жесткого исполнения деталей,
низкий модуль упругости валков при изгибе (положительное соотношение
диаметров шейки валка и самого валка),
долговечные, многорядные катковые опоры с подушками,
самоустанавливающимися под нагрузкой,
балансировка подушек без зазора,
проводниковый брус сконструирован для простой иточнойналадкипрокатной
арматуры.
Таким образом, самые большие эксплуатационные преимущества - это:
готовый продукт соответствует требуемым допускам по форме и размерам,
благодаря чему плотный контроль веса погонного метра,
экономия времени при смене клетей за счет перевалки вне прокатной линии,
гибкость во время производства, использование того же прокатного блока в
горизонтальной, вертикальной, наклонной и универсальной конфигурации, благодаря
чему малое количество запчастей.
значительное снижение времени и затрат на поддержание оборудования в
рабочем состоянии вследствие небольшого числа компонентов и легкости доступа к
ним, автоматизированная установка очага деформации,
интегрирование в полностью автоматическую систему управления.
Компактные консольные (CL-) клети «SMSMeer» используются самых разных
типоразмеров и имеют широкую область применения. Предпочтительными
возможностями для использования являются: однониточные прокатные станы в
горизонтальном/вертикальном расположении, в разделенных промежуточных группах
двух- или многониточных линий прокатного стана, в качестве сменной клети при
модификациях групп прокатных клетей (в случае проблем с местом установки), в
качестве промежуточных клетей в выходных устройствах для проволоки, на чистовых
линиях.
Преимущества компактных консольных клетей с консольным креплением
валковых валов:
низкие затраты на сооружение фундамента,
низкие затраты на приобретение валков,
незначительный объем сменных и запасныхдеталей.
быстрая обработка валков,
быстрый технический уход,
быстрая замена валков и клетей,
оптимальный доступ,
быстрый монтаж с низкими затратами.
Особые признаки конструкции:
типы клетей с диаметрами валков от 160 мм до900 мм,
модульное исполнение с небольшим весом,
удобство эксплуатации и технического ухода: отсутствие необходимости в
осевой регулировке бандажа валка,
жесткая конструкция клети,
большие диаметры валковых валов (подшипники качения),
незначительный противоизгиб валков,
клеть в кассетной конструкции,
кассеты одного типа клетей не только взаимозаменяемы, но заменяемы также
и в горизонтальных / вертикальных клетях,
предохранительная муфта в качестве защиты от перегрузки,
конструкция допускает большую нагрузку даже при малых диаметрах, тем
самым, она наилучшим образом пригодна для эксплуатации ввысокоскоростных
проволочных блоках даже при низких температурах начала прокатки.
Преимущества по затратам, благодаря:
меньшей потребности в месте для установки прокатного стана,
меньшим и упрощенным фундаментам,
экономии за счет устройств для обработки бандажей валков,
меньшему количеству валковых бандажей на складе,
меньшему количеству основных запчастей (напр., шпиндели),
отсутствию сменных деталей (подушек или комплектных клетей),
ускорению монтажа.
меньшему объему запчастей,
ускорению смены валковых бандажей и программы прокатки,
снижению количества персонала в мастерских по обработке валков,
повышению коэффициента производительности.
Чистовые клети «Сименс ФАИ» («Siemens») установлены на множестве
прокатных станов по всему миру.
Имеются варианты таких станов для широкого спектра сочетаний клетей и
способны удовлетворить практически любую потребность чистовой секции стана.
Усилие прокатки и конструкция калибра подбираются под требования производства.
Клети данного типа высокоскоростные и высокопроизводительные, имеют способность
к переналадке для производства широкого спектра размеров имарок стали при
сохранении по возможности наиболее точных размеров изделия. Клети способны
катать марки стали от углеродистых сталей досложно катаемых термостойких
сплавов. Станы могут поставляться с возможностью сокращения площади сечения в
калибре с 10% до 25% на клеть.
Технические характеристики:
все главные компоненты приводов располагаются ниже нулевой отметки, таким
образом, снижая шум, повышая видимость и удобство обслуживания со стороны
операторовстана;
новая компоновка привода входной стороны обеспечивает упрощенный доступ к
двигателю и не ограничивает размер электродвигателя;
привод входной стороны позволяет отцеплять валы чистовой линии, когда они
не используются для снижения износа высокоскоростных компонентов до минимума;
высококачественные герметизированные станины обеспечивают длительный срок
службы и сокращениерасходов на обслуживание;
станины клетей легко поднимаются для быстрой смены;
разработаны для термомеханической прокатки с возможностью прокатки при
низких температурах;
способность прокатки в крайне узком диапазоне допусков;
валки с покрытием из карбида вольфрама обеспечивают повышенное качество
прутка и более длительный срок службы валков.
Клети кассетного типа («Siemens») благодаря их компактной и жесткой
кассетной конструкции идеально подходят для прокатки изделий с самыми малыми
допусками на размеры. Возможность чрезвычайно быстрой замены кассет в сочетании
с высокой степенью автоматизации создает условия для гибкого и эффективного
производства даже при обработке малых заказных партий.
Особенности:
три возможные схемы расположения валков, обеспечивающие прокатку без
скручивания: горизонтальная, вертикальная и под углом 45° (крестообразная);
низкие издержки производства даже при малых заказных партиях;
наиболее компактная конструкция клети из имеющихся на рынке;
жесткие клети кассетного типа, гарантирующие высокую точность допусков;
быстрая замена кассет с помощью стандартного крана, обслуживающего стан;
открытый доступ к верхней части кассеты;
возможность использования робототехнической системы для замены кассет;
быстрая замена валков без необходимости использования специального
оборудования;
взаимозаменяемые кассеты с горизонтальным, вертикальным и крестообразным
расположением валков, на один и тот же размер.
В сортовых и проволочных станах успешно применяются
редукционно-калибрововочные блоки (RSB -Reducing and Sizing Block) c
трехвалковыми клетями производства «ENCE GmbH» (рис. 1.7).
Рис. 1.7. Трехвалковая клеть с приводными валками
Особенностью данной конструкции является сочетание обжимных и
калибровочных проходов при использовании одного блока клетей (в чистовом блоке
при прокатке прутков и в черновом блоке при производстве катанки).
Все клети блока имеют однотипную конструкцию и являются
взаимозаменяемыми. Приводные валы вращаются в эксцентриковых втулках, что
позволяет выполнять регулирование зазора между валками.
Количество клетей в блоке достигает пяти. Основные технологические
преимущества заключаются в меньшей чувствительности к различным маркам стали с
широким диапазоном коэффициентов температурного расширения, к изменению
натяжения и колебаниям диаметра. При этом обеспечивается высокое качество
поверхности и точность размеров.
Трехвалковые клети конструктивно сложнее и дороже двухвалковых клетей, но
для выполнения производственной программы равноценной по размерному и марочному
сортаменту требуется почти в два раза меньше клетей.
Для черной и промежуточной прокатки применяют двухвалковые реверсивные
подвижные клети, которые полностью автоматизированы и позволяют выпускать
неограниченный сортамент продукции при одном и том же наборе клетей.
В ряде случаев при небольших типоразмерах применяются с консольным
креплением валков различных конфигураций, в том числе горизонтальные,
вертикальные конвертируемые (трансформируемые), универсальные и др. консольные
клети. Преимущества консольных клетей заключаются в их компактности, простой и
быстрой перевалке валков. Однако, в связи с консольным приложением нагрузки
передаваемые усилия прокатки меньше, чем в клетях с двусторонней опорой валков.
Бесстанинные рабочие клети конструкции ВНИИМЕТМАШ характеризуются очень
высокой степенью эксплуатационной надежности и гибкости.
Переналадка высокопроизводительных прокатных клетей в процессе
эксплуатации производится очень быстро, что дает возможность выпускать широкий
ассортимент продукции практически без перерывов в работе. Гибкость линии
обеспечивает возможность прокатки при низкой температуре и выпуска изделий
самых разнообразных профилей из высоколегированных сталей.
Клети снабжены глухими соединительными элементами, можно заменять и
демонтировать за считанные минуты, убирая их из линии прокатки. Верхние и
нижние валки снабжены отдельными гидравлическими нажимными механизмами,
предусмотрены также автоматические системы смазки для роликовых подшипников.
Шпиндельная опора полностью уравновешена. Использование цилиндров переключения,
соединенных со шпиндельными опорами, позволяет производить отсоединение всех линий
инженерного обеспечения, а также шпинделей.
Основные преимущества:
выпуск продукции широкого сортамента по суженным допускам;
малый удельный вес и высокая жесткость клетей в радиальном и осевом
направлениях;
быстрая перевалка клетями с использованием специальных стендов;
рабочие клети каждого типоразмера могут использоваться как в
горизонтальном, так и в вертикальном положении;
конструкция клетей обеспечивает постоянство уровня прокатки для
горизонтальных клетей и постоянство оси прокатки для вертикальных клетей
независимо от диаметра валков и межвалкового зазора;
возможность оснащения линий клетей специальными датчиками и
соответствующими приводами, что позволяет автоматизировать настроечные операции
и реализовать АСУ ТП прокатного производства от подачи заготовки на стан до
взвешивания готового проката, маркировки и отгрузки.
Вывод
Использование того или иного типа клетей обусловливается рядом причин:
величиной усилий прокатки в каждой клети, скоростным, температурным режимами,
производительностью стана. Кроме этого большое внимание уделяется
металлоемкости клетей. В последние десятилетия при проектировании станов для
производства стального мелкосортного проката наметилась устойчивая тенденция -
применять предварительно напряженные и бесстанинные клети. Клети станинной
конструкции в настоящее время применяют исключительно редко.
Трехвалковые клети производства «ENCE GmbH» имеют сложную конструкцию и
применяются достаточно редко, а клети кассетного типа обладают недостаточно
широким сортаментом, поэтому самое пристальное внимание уделено чистовой клети
ВНИИМЕТМАШа, т.к. она имеет наиболее простую конструкцию, и в то же время
обладает необходимой надежностью, прочностью и всеми другими требуемыми
свойствами.
2. Проектно-конструкторская часть
.1 Проектирование нового кристаллизатора МНЛЗ
По своему составу комплекс проектируемого оборудования МНЛЗ состоит из:
основного механического оборудования, обеспечивающего технологический процесс
получения непрерывнолитых заготовок и их последующей обработки; сменного оборудования;
систем снабжения средами; электрооборудования, КИП и А; автоматизированной
системы управления; вспомогательного и специального технологического
оборудования.
Сталеразливочный стенд представляет собой стационарно установленное
двухпозиционное устройство подъемно-поворотного типа. Стенд предназначен для
размещения на нем сталеразливочных ковшей, поворота ковшей из резервного
положения в положение разливки и обратно, подъема и опускания ковшей,
непрерывного взвешивания ковшей с металлом.
Тележки для промежуточного ковша предназначены для перемещения
промежуточного ковша из резервной позиции в рабочую и обратно, удержания
промежуточного ковша при разливке, для подъема и опускания ковша, для
осуществления возможности поперечного перемещения промковша при центрировании
стаканчиков относительно кристаллизаторов
Ковш промежуточный предназначен для приема жидкого металла из
сталеразливочного ковша, распределения его по кристаллизаторам организованной
струей и обеспечения непрерывности струи при разливке способом «плавка на
плавку» во время замены стальковша.
Установка для разогрева промковша предназначена для разогрева футеровки
промковша перед заливкой в него металла и состоит из горелок с механизмом их
перемещения, газовоздухопровода, гидросистемы механизма перемещения горелок,
системы контроля и автоматики.
Металлические конструкции МНЛЗ включают: несущие конструкции, перекрытия
приямков, стойки, балки, балки с монорельсом, обшивку камеры, лестницы и
площадки, несущие конструкции поддерживающих роликов.
Эстакада верхового разливщика с пультом управления включает несущие
конструкции, перекрытия, лестницы и ограждения.
На эстакаде размещено оборудование для контроля и выполнения
соответствующих операций разливщиком.
Площадка обслуживания шиберного затвора стальковша представляет собой
стационарно установленную металлоконструкцию, предназначена для присоединения и
съема гидроцилиндра управления шиберным затвором стальковша.
Чаша шлаковая представляет собой стальную сварную конструкцию,
коробчатого типа, футерованную огнеупорным материалом. Чаша предназначена для
приема металла с отсечных желобов при запуске ручьев МНЛЗ и в случае остановки
вытягивания заготовки.
Чаши аварийные представляют собой сварные конструкции коробчатого типа,
футерованные огнеупорным материалом, и предназначены для приема металла из
промковша в аварийной ситуации.
Чаши переливные представляют собой сварные конструкции коробчатого типа,
футерованные огнеупорным материалом, и предназначены для приема металла из
переливных желобов промковша при его переполнении.
Желоб аварийный предназначен для сбора капель стали и шлака, а также
струи стали в случае «некрытия» шиберного затвора стальковша.
Кристаллизатор предназначен для формирования слитка заданного сечения и
его первичного охлаждения.
Кристаллизатор состоит из корпуса, торцевых крышек, обечайки, медной
гильзы длиной 700 мм, оснащен устройством для смазки рабочих поверхностей
гильзы.
Механизм качания кристаллизатора предназначен для сообщения
кристаллизатору возвратно-поступательного движения по участку круговой
траектории, с радиусом кривизны базовой стенки гильзы кристаллизатора. Целью
качания кристаллизатора является предотвращение зависания корочки слитка на
стенках гильзы и обрыва непрерывнолитой заготовки на выходе из кристаллизатора.
Механизм качания представляет собой четырехзвенный рычажный механизм с
электрическим приводом и состоит из станины, рычагов, узла эксцентрика, привода
и рамы.
Установка поддерживающих роликов предназначена для направления заготовки
и затравки на криволинейном участке между кристаллизатором и ТПМ, а также для
установки секций вторичного охлаждения с коллекторами и форсунками.
Затравка полужесткого типа предназначена для образования временного
"дна" в кристаллизаторе перед началом разливки и последующего вытягивания
заготовки тянуще-правильной машиной.
Установка тянуще - правильных машин (ТПМ) расположена на выходе слитка из
ЗВО и предназначена для вытягивания его из кристаллизатора, выпрямления и
подачи слитка в направлении режущих устройств. ТПМ обеспечивает также
формирование полужесткой затравки по радиусу разливочной дуги МНЛЗ, подачу
затравки в направлении кристаллизатора, вытягивание затравки с заготовкой из
кристаллизатора и отделение головки затравки от кристаллизатора.
Для порезки движущихся НЛЗ на мерные длины и обрезки дефектных концов НЛЗ
предусматривается установка летучих ножниц.
Кристаллизатор, предназначенный для формирования и поддержания корочки
отливаемой заготовки, а также интенсивного отвода тепла от слитка, является
наиболее важным узлом МНЛЗ. Особенностью конструкции кристаллизатора сортовой
машины является наличие обечайки точно сцентрированной на медной гильзе,
которая образует конструкцию «труба в трубе» обеспечивающую проток охлаждающей
воды в зазоре между гильзой и обечайкой.
Кристаллизатор состоит из стального корпуса, медной гильзы, крышек, в
которых гильза фиксируется и уплотняется в корпусе, обечайки, а также
устройства для подачи и равномерного распределения технологической смазки.
Через опорный фланец корпуса кристаллизатора подводится и отводится вода
для охлаждение гильзы и может подаваться вода на 1-ю зону вторичного
охлаждения. В верхней крышке корпуса кристаллизатора гильза зафиксирована
шпонками по четырем граням.
Конструкция нижней крышки должна всегда обеспечивать возможность
свободного удлинения гильзы, чтобы исключить деформацию ее профиля при
температурном расширении в период разливки.
Охлаждающая вода, с высокой скоростью, протекает в зазоре между гильзой и
обечайкой. Установленные в крышках уплотнения из термостойкой резины, исключают
течь воды из кристаллизатора.
На верхней крышке кристаллизатора, вплотную к торцу гильзы, примыкает
устройство для подачи технологической смазки, обеспечивающее ее равномерное
распределения по граням рабочей полости.
При оснащении кристаллизаторов системой ЭМП все элементы конструкции,
расположенные между гильзой и катушками устройства перемешивания, выполняются
из немагнитной стали.
Сборка, настройка и опрессовка кристаллизаторов производится на
специальных стендах в мастерской по подготовке кристаллизаторов.
Для минимизации температуры и термических деформаций стенки гильзы, в
кристаллизаторе поддерживается высокая скорость протока охлаждающей воды (не
менее 12 м/с). Более того, высокая скорость протока необходима для того, чтобы
предотвратить локальные вскипания воды на внешней поверхности гильзы.
Вскипание воды ведет к отложениям накипи на гильзе, что увеличивает
сопротивление теплопередачи от корочки слитка к воде и вызывает перегрев стенок
гильзы (например, отложения известковой накипи толщиной 0.1 мм способствуют
увеличению температуры стенки гильзы почти на 100º С). Повышение температуры медной
стенки выше температур рекристаллизации меди, неизбежно приводит к деформации
стенок гильзы в районе мениска жидкого металла и, соответственно, искажению
профиля рабочей поверхности гильзы.
При обычном ведении процесса разливки температура внутренних стенок
гильзы не превышает 260º С (то есть ниже температуры разупрочнения материала
гильз), однако в случаях низкой скорости протока воды в кристаллизаторе,
неравномерного охлаждения или значительных отложений накипи на внешних
поверхностях гильз температура может повышаться до 300-400º
С и происходит их грубая
деформация.
Другим фактором, влияющим на степень деформации гильзы, является качество
охлаждающей воды. При высоком содержании солей в охлаждающей воде происходит
процесс интенсивного отложения накипи на внешней поверхности гильзы. Отложения
накипи толщиной 20 мкм почти удваивают величину горячей деформации
(выпучивание) гильзы.
Очевидно, также, отрицательное влияние данного фактора на глубину следов
качания, ромбичность, околоугловые трещины, прорывы.
Исходя из этого, предъявляются достаточно жесткие требования к качеству
воды используемой для охлаждения кристаллизаторов.
Конструкция кристаллизатора, отклонения в его сборке могут создавать
предпосылки для того, чтобы скорость протока воды была неоднородной.
Если из-за разности скоростей протока воды в кристаллизаторе одна или
более стенок гильзы становятся горячее чем другие, то гильза, под воздействием
тепловых напряжений, будет деформироваться и принимать непрямоугольную форму.
Подобную форму могут принимать и формирующиеся в гильзе заготовки. Поэтому
важно, чтобы ширина зазора между обечайкой и гильзой кристаллизатора была
постоянной по всей периферии. Для обеспечения этого необходимо, чтобы внешние
размеры гильзы и внутренние размеры обечайки поддерживались в жестких допусках.
Так как обычно ширина водного зазора составляет 3-4 мм, то местное уменьшение
зазора даже на 1 мм может привести к изменению скорости протока воды на 20-30
%. По мере того, как несоосность между гильзой и обечайкой становится более
выраженной, скорость протока воды у поверхности, которая сужает зазор, падает,
а скорость протока у поверхностей, где зазор увеличивается остается неизменной.
Для обеспечения равномерного охлаждения слитка в кристаллизаторе разность
скоростей протока в зазоре между гильзой и обечайкой по разным граням не должна
превышать 1 м/сек.
Неравномерная скорость охлаждающей воды в кристаллизаторе увеличивает
деформацию гильзы и ромбичность НЛЗ. Следовательно, при установке новой гильзы
в кристаллизаторе необходимо произвести тщательную выставку зазора между
гильзой и обечайкой. Выставка равномерного зазора между радиальными и боковыми
гранями гильзы и обечайки выполняется с помощью регулирующих винтов. Величина
зазора между стенками гильзы и обечайки контролируется с помощью концевых мер.
В процессе непрерывной разливки стали температура стенок гильз, несмотря
на их высокую теплопроводность, значительно увеличивается.
В зависимости от скорости протока охлаждающей воды в кристаллизаторе,
толщины стенки гильзы, условий разливки стали (хим. состав стали, скорость
разливки, смазка) в эксплуатационных режимах температуры могут достигать от 200
до 400°С в районе мениска на внутренней
поверхности стенок гильз и от 100 до 200° С в районе мениска на внешней поверхности стенки гильз.
Соответствующие температуры в нижней части гильзы могут составлять от 120
до 200° С и от 75 до 125° С.
При высоких температурах стенок гильз и циклических напряжениях при
разогреве и остывании гильз может происходить их термическая деформация, в
первую очередь в районе мениска металла в кристаллизаторе.
Деформация от циклических температурных напряжений, возникающих при
разогреве и остывании гильз, более значительно проявляется при высокой их
стойкости (вследствие явлений ползучести и размягчения материала гильз).
Следствием деформации гильз является повышенная ромбичность отливаемых
заготовок, пораженности НЛЗ поверхностными трещинами, прорывы НЛЗ по продольным
трещинам.
Для обеспечения интенсивного и равномерного теплоотвода от
затвердевающего слитка в кристаллизаторе важно как можно дольше сохранить
заданный профиль гильзы.
Ранее гильзы кристаллизаторов изготавливали из меди высокой чистоты (Сu -
99.9 %), раскисленной фосфором. Температура рекристаллизации (разупрочнения)
гильз из данного материала составляет около 280 °С.
В последнее время, все большее распространение в качестве материала гильз
получают сплавы Cu-Ag, Cu-Zr-Cr с повышенным сопротивлением деформации.
Повышенное сопротивление деформации гильз из меди с добавками серебра
(температура рекристаллизации около 350 °С) позволяет минимизировать проблемы с качеством НЛЗ,
увеличить их стойкость.
Стойкость гильз кристаллизаторов, в первую очередь, зависит от типа и
толщины износостойкого защитного покрытия на их рабочих поверхностях.
Покрытие может быть одно, двух или трехслойным. Используемые материалы
покрытий гильз - хром, никель, кобальт, полинит.
Наиболее распространенный тип защитного покрытия гильз кристаллизаторов -
однослойное покрытие из твердого хрома.
При данной толщине покрытия стойкость гильз (при отбраковке по износу)
может достигать 8000-12000 тонн разлитой стали.
Необходимо, чтобы толщина защитного покрытия была равномерной и по граням
и по углам гильзы.
Приемлемым уровнем стойкости хромированных гильз считается величина не
менее 6000 тыс. тонн стали.
Важным моментом является высокая чистота, отсутствие дефектов (раковин,
пор, трещин, пузырей) на рабочей поверхности гильз.
Чистота хромированной поверхности гильз должна быть не хуже Rа 0.4-0.8.
Опыт эксплуатации гильз показывает, что повышенная шероховатость,
раковины и поры на поверхности гильз могут вести к биениям слитков, выбросам
капель жидкого металла, прорывам по продольным и поперечным трещинам в
начальный период работы кристаллизаторов.
Основная цель установки поддерживающих роликов - ограничение выпучивания
и ромбичности слитка при высокоскоростной разливке стали. Поддерживающие ролики
под кристаллизатором способствуют более равномерному износу граней гильзы и,
следовательно, увеличению ее ресурса. Поддерживающие ролики под
кристаллизатором, при их удовлетворительной конструкции и выставке, существенно
ограничивают развитие ромбичности НЛЗ.
Последовательность технологических операций по выставке поддерживающих
роликов под кристаллизатором:
установить кристаллизатор на стенд, закрепить и перевести в
горизонтальное положение;
нутромером с цифровым индикатором произвести замер расстояния между
радиальными стенками гильзы, в нижней части кристаллизатора;
выполнить выставку ролика базовой стенки кристаллизатора (по большому
радиусу) по специальному шаблону сопрягая образующую поверхность бочки ролика с
радиальной поверхностью гильзы;
произвести выставку ролика малого радиуса кристаллизатора, относительно
ролика базовой стенки, в размер, соответствующий фактическому размеру в нижней
части гильзы;
выполнить выставку роликов расположенных по прямым граням рабочей полости
кристаллизатора, с помощью специального шаблона, сопрягая образующую
поверхность бочки ролика с плоскостью боковых граней гильзы.
Створ между роликами под кристаллизатором устанавливается на величину 0.1¸0.3 мм относительно внутренних
размеров в нижней части гильзы.
Система охлаждения гильз кристаллизаторов представляет собой замкнутый,
локальный оборотный контур, который включает в себя: водоохлаждаемое
оборудование (кристаллизаторы); водоразборный узел (напорные трубопроводы с
запорной арматурой); циркуляционную насосную станцию; теплообменники;
водоразборный узел; расширительную емкость с системой подпитки; установку
реагентной обработки; систему аварийного охлаждения кристаллизаторов.
В водоразборном узле каждая секция охлаждения кристаллизатора, оснащена
запорной и регулирующей аппаратурой, контрольно-измерительными приборами.
Управление расходом воды первичного охлаждения осуществляется посредством
АСУТП.
Охлаждающая вода постоянно циркулирует в локальном замкнутом контуре и
подвергается обратному охлаждению в теплообменниках.
При соблюдении водно-химического режима эксплуатации, созданная оборотная
система первичного охлаждения обеспечивает выполнение своих главных функций:
надежное снабжение кристаллизаторов водой в соответствии с заданными
параметрами;
нормативные параметры оборотной воды (температуру, содержание взвешенных
веществ, скоростей образования отложений, коррозии металла, биологических
отложений, эффективность реагентной обработки).
В системе используется умягченная или полностью обессоленная вода.
На каждый кристаллизатор оформляется паспорт, в который заносятся
сведения об эксплуатации кристаллизатора на МНЛЗ, стойкости гильз и диаграммы
обмеров рабочей полости гильз.
Обслуживание кристаллизаторов на участке разливки стали производят
операторы МНЛЗ, они же фиксируют в журнале разливки плавок стойкость гильз
кристаллизаторов и заполняют журнал учета движения кристаллизаторов.
Перед установкой на МНЛЗ каждый кристаллизатор подлежит тщательному
осмотру. После разливки каждой серии плавок оператор очищает, с помощью
специальной жидкости, стенки гильз от нагара и визуально оценивает их
состояние.
Отбраковка гильз, обычно, производится в следующих случаях: при высокой
деформации профиля, при наличии значительных дефектов на рабочей поверхности
(особенно в верхней части гильзы), при высоком механическом износе в нижней
части гильз.
При износе в нижней части гильзы на величину более 1 мм могут отмечаться
массовые прорывы металла по трещинам, повышение ромбичности НЛЗ и образование
продольных трещин на поверхности заготовок. Грубые задиры и царапины на рабочих
поверхностях гильзы (особенно, если они расположены в верхней части гильзы и
имеют глубину более 0.5 мм) могут привести к подвисаниям слитка в
кристаллизаторе, обрыву слитка или образованию поверхностных трещин.
Для того, чтобы предотвратить данные отклонения необходимо осуществлять
регулярный контроль за износом гильз с помощью специального прибора. В качестве
подобного диагностического оборудования предлагается прибор MCS - 3000 фирмы
Concast AG. MCS-3000 включает электронный блок, компьютер типа «ноутбук»,
штангу со сменными измерительными головками, калибры для различных сечений
гильз. Данный прибор позволяет измерять внутренние размеры гильз (между
противоположными стенками и углами гильзы) с помощью самоцентрующихся датчиков
при передвижении измерительной головки по гильзе и записывать их в базу данных
компьютера. На дисплей компьютера выводится информация о фактических размерах
гильзы, которые можно сравнить с номинальными значениями. MCS-3000 позволяет
получать распечатки графиков с размерами гильз, которые накапливают в паспорте
кристаллизатора для отслеживания его работы.
С помощью данного прибора возможен обмер гильз в мастерской по подготовке
кристаллизаторов или непосредственно на МНЛЗ во время переподготовки установки.
Обмер гильзы на МНЛЗ выполняется через заданное регламентное время (после
эксплуатации кристаллизатора в течение разливки 50-100 плавок стали) или при
отклонениях процесса разливки из-за кристаллизатора. Обмер гильз на МНЛЗ
позволяет отслеживать изменение их размеров без замены кристаллизаторов, что
существенно сокращает продолжительность переподготовки установки.
Перед проведением обмеров, с помощью прибора MCS-3000, необходимо
произвести тщательную очистку рабочей полости гильзы от нагара от смазки,
скрапин металла, окалины. Для этой цели используется специальная
жидкость-очиститель. Жидкость, с помощью тампона, наносится на рабочие стенки
гильзы. После выдержки в течение около 5-ти минут поверхности гильзы
протираются сухой ветошью. При необходимости, участки поверхности гильзы с
царапинами, задирами, имеющие острые кромки, зачищаются наждачной бумагой. При
проведении обмеров гильз на МНЛЗ, во избежание повреждения измерительной
головки прибора, масленки кристаллизаторов должны быть очищены от скрапин
металла.
Замена кристаллизаторов на МНЛЗ производится по следующим причинам:
достижение гильзой предревизионной стойкости;
два прорыва подряд по трещине в ходе эксплуатации;
ромбичность заготовок выше допустимых значений;
появление течи воды через уплотнения;
утечка смазки или засорение каналов для подачи смазки, которые не удается
прочистить без снятия кристаллизатора;
"чулок" или слиток металла в гильзе после окончания разливки.
Перед отправкой кристаллизатора в ремонт его наружные поверхности очищают
от нагара, масла и скрапа.
Кристаллизатор передают в ремонт вместе с паспортом, в котором заполнены
все графы и указаны причины снятия с МНЛЗ.
Браковочные признаки гильз кристаллизаторов:
дефекты на рабочей поверхности (задиры, раковины, царапины): на
расстоянии 100 - 250 мм от верхнего торца - глубиной более 0.5 мм, на
расстоянии 250 - 800 мм от верхнего торца - глубиной более 1.0;
ступенчатое изменение размеров гильзы по длине - на величину более 0.5 мм
(искажение профиля гильзы определяется по отклонению пика деформации от
заданного профиля в том же сечении);
износ в нижней части гильзы (увеличение размеров с уровня 400-600 до 800
мм) более чем на 1.0 мм.
Основные
рекомендуемые параметры кристаллизаторов для отливки заготовок сечением 60 ´ 80 мм: длина гильзы - 700 мм; радиус внутреннего угла
- 4 мм; величина зазора между гильзой и обечайкой - 3.25 мм; расход охлаждающей
воды - 1700 - 1900 л/мин; рабочее давление воды на кристаллизаторе - 0,8 МПа;
максимальная температура воды на входе в кристаллизатор -
.
Рекомендуемый
материал гильз кристаллизаторов - раскисленная медь с добавками серебра.
Рабочая
поверхность гильз защищена слоем хромированного покрытия толщиной 0.12 - 0.15
мм.
Основной
частью кристаллизаторов сортовых и блюмовых современных МНЛЗ является
водоохлаждаемая гильза, причем вода вдоль гильзы движется по щелевому каналу,
образованному рубашкой охлаждения, которая должна быть расположена концентрично
относительно гильзы.
Известен
кристаллизатор машины непрерывного литья заготовок с прямолинейной осью
кристаллизатора, установленного вертикально.
Недостатком
известного устройства является большая высота машины непрерывного литья - до 45
метров, что требует строительства специальных высотных цехов.
Известен
кристаллизатор машины непрерывного литья заготовок с искривленной осью
кристаллизатора. Это машин радиального литья заготовок. Она лишена недостатка
предыдущей машины и может быть установлена в металлургическом цехе обычной
высоты.
Известны
кристаллизаторы, содержащие гильзу и рубашку охлаждения, в зазор между которыми
подается вода, охлаждающая гильзу.
В
дипломном проекте произведена модернизация кристаллизатора путем замены ранней
конструкции более современной. Новая конструкция дает нам такие плюсы, как:
большая производительность, меньшая себестоимость, легкость обслуживания,
лучшая система охлаждения, меньшая себестоимость и, конечно, улучшенная
поверхность слитка.
Но
и в современных конструкциях есть недостаток. Во всех ранее известных
конструкциях рубашка охлаждения не зажата между верхней и нижней крышками. Это
сделано для того, чтобы она имела возможность во время работы само -
устанавливаться относительно гильзы. Однако, это приводит к тому, что под
действием разницы давления воды (давление в нижней напорной полости на 0,25÷0,3 МПа больше чем в верхней сливной полости), диафрагма,
разделяющая обе полости, всплывает вверх, из- за чего образуется зазор между
диафрагмой и корпусом кристаллизатора. Это приводит к прямому перетеканию на
слив существенной части воды, назначение которой - охлаждать гильзу
кристаллизатора. Потери воды снижают скорость её протекания вдоль гильзы до
уровня, при котором начинает образовываться накипь на наружной стенке гильзы, а
это приводит к образованию трещин и прорывам металла.
Этот
указанный недостаток известной конструкции устранен в предлагаемом устройстве
(рис. 2.1) .
Рис. 2.1. Новый кристаллизатор
Результатом предлагаемой модернизации является поддержание постоянного
зазора между гильзой и ее рубашкой, равномерного по их периметру, а с другой
стороны, полное исключение потери воды, предназначенной для охлаждения гильзы.
Технический результат достигается тем, что в кристаллизаторе, который
содержит гильзу с концентрично установленной относительно неё рубашкой, корпус
с верхней и нижней крышками, образующими замкнутую полость кристаллизатора, а
также диафрагму, связанную с одной из крышек фиксирующими элементами, которая
разделяет замкнутую полость кристаллизатора на напорную и сливную полости, при
этом фиксирующие элементы выполнены в виде шпилек-стяжек, проходящих через
напорную полость. В данном частном случае шпильки-стяжки установлены в
количестве трех штук под углом 120° друг относительно друга и выполнены из пружинной стали с
наружным диаметром шпильки-стяжки Dн = D/(33÷60) (где D - внутренний диаметр корпуса) и
диаметром тела шпильки-стяжки d = Dн / (1,2÷5); зазор между наружной поверхностью
диафрагмы и внутренней поверхностью корпуса равен s1
= 0,10÷0,70 мм на
каждую сторону, а зазор между гильзой и рубашкой составляет s2
= 2,5÷6,0 мм на
сторону с отклонением от номинала не более, чем на ±5%.
Кристаллизатор устроен следующим образом. Гильза 1, в которую
осуществляется разливка металла, установлена вертикально. Корпус
кристаллизатора 2, который совместно с верхней крышкой 3 и нижней крышкой 4
образуют замкнутую полость кристаллизатора. Диафрагмой 5 эта полость разделена
на напорную полость 6 и сливную полость 7. Гильза 1 окружена рубашкой 8,
установленной по отношению к гильзе с зазором s2 = 4÷5 мм. Диафрагма 5 закреплена на крышке
3, установленной со стороны напорной полости, тремя шпильками-стяжками 9, т.е.
проходящими через напорную полость 6. Зазор между наружной поверхностью
диафрагмы 5 и внутренней поверхностью корпуса 2 должен быть в диапазоне 0,10÷0,70
мм. в зависимости от
размера отливаемого слитка. Диаметр каждой шпильки-стяжки 9 определяется как
Dн= D/(33÷60),
где D -диаметр корпуса
2. Небольшой диаметр d, придает шпильке-стяжке большую степень гибкости в
поперечном направлении. Это позволяет выдерживать зазор s2 по всему периметру
рубашки 8 в диапазоне ±5%.
Учитывая тяжелые условия работы шпилек-стяжек 9 и ту среду, которой они
окружены, они должны быть выполнены из пружинной нержавеющей стали. Для подвода
охлаждающей воды имеется патрубок 10, а для отвода - патрубок 11. Охлаждение
гильзы кристаллизатора 1 происходит следующим образом. Через патрубок 10 подают
охлаждающую воду в напорную полость 6 под давлением на 0,2÷0,3
МПа большим, чем в
сливной полости. Через зазор s2 , как показано стрелками 12, вода с большой
скоростью протекает по этому зазору и, тем самым, интенсивно охлаждает гильзу
1. В сливную полость 7 вода попадает, как показано стрелками 13. Диафрагма 5 на
крышке 3 может быть закреплена, например, на трех шпильках-стяжках, что в
наибольшей степени обеспечивает равномерное распределение нагрузки на шпильки.
Данный кристаллизатор предназначен для непрерывного литья прямоугольных
заготовок от 60 х 80 мм. Предложенное техническое решение предотвращает потери
воды, предназначенной для охлаждения гильзы, устраняет перекос рубашки
относительно гильзы и ликвидирует опасность местного перегрева гильзы
кристаллизатора за счет обеспечения равномерного распределения по периметру
гильзы охлаждающей воды и исключения образования накипи на её наружной стенки.
2.2 Проектирование новой чистовой рабочей клети
В новой горизонтальной рабочей клети можно будет прокатывать арматурную
сталь №12, 14, 16, 18, 20, 22, круг диаметром 12…20 мм, квадратный профиль
12…30 эквивалентного сечения; угловую сталь 25х25х4, 28х28х4, 32х32х4, 36х36х4,
40х40х4, арматуру термоупрочненную №12…32.
Техническая характеристика клети следующая:
Момент прокатки, кН·м ………………………………………. 0,7…10,9
Частота вращения валков, об/мин 274…960
диаметр валков - 280…250 мм;
длина бочки валков - 400 мм;
осевая регулировка валков - ± 3,0 мм;
смазка подшипников - густая, закладная.
масса клети - 6,15 т.
скорость прокатки - 4,0….14,0 м/с;
Электродвигатель главного привода клети:
тип - RH450 S8 IMB3
Мощность двигателя номинальная, кВт 525
Частота вращения номинальная, об/мин 742
Шестеренная клеть
Межцентровое расстояние, мм 315
Число зубьев вала-шестерни 39
Модуль передачи нормальный, мм 8
Угол наклона зубьев, b 7°54¢50²
Передаточное число 1
Шпиндель карданный вал типа ЭК1-531-2201010
Максимально допускаемый крутящий момент, кН·м 18
Угол перекоса шпинделя при рабочей нагрузке, не более 2,9°
Осевая регулировка валков, мм ±3
Мотор-редуктор механизма установки раствора валков:
тип 7МЦ 2-60-20-Ф//0,55/4-200-К1
Мощность двигателя номинальная, кВт 0,55
Частота вращения выходного вала, об/мин 69
Передаточное число мотор-редуктора 20
Передаточное отношение специального редуктора
механизма установки раствора валков 40
Механизм уравновешивания подушек- плунжерные гидроцилиндры;
Диаметр плунжера, мм 36
Ход рабочий, мм 20
Количество, шт 8
Гидроцилиндр перемещения клети -СКМ-00-80/56*450-Е 2 0 8 Т S 20
Диаметр поршня, мм 80
Диаметр штока, мм 56
Полный ход, мм 450
Рабочий ход, мм 400
Гидроцилиндр стойки шпиндельной
тип -CD 210 G 40/25-40 Z 1X/01 HBUM 1-1A BOSH REXROTH
Диаметр поршня, мм 40
Диаметр штока, мм 25
Мax раб.ход, мм 40
Усилие, кН 4
Рабочее давление в гидросистеме, МПа 10
Общий вид линии новой горизонтальной клети представлен на рис. 2.2.
Рис. 2.2. Оборудование линии новой горизонтальной клети 280: 1- клеть
рабочая горизонтальная 280; 2 - стойка шпиндельная; 3 - шпиндель; 4 - клеть
шестеренная 315; 5 -редуктор ЦО-450; 6 - плитовина; 7 - рама привода; 8 - рама
двигателя; 9 - электродвигатель
Подвод воды для охлаждения ручьев валков, масла к гидроцилиндрам
перемещения клети, стойки шпиндельной и механизма уравновешивания подушек, а
также смазка подшипников валков осуществляется от соответствующих станций по
трубопроводным магистралям.
Двухвалковая бесстанинная горизонтальная рабочая клеть 280 (рис. 2.3)
устанавливается на направляющих плитовинах и фиксируется гидрозажимами. При
перевалке и в процессе прокатки клеть перемещается гидроцилиндром перемещения
клети в поперечном направлении относительно оси прокатки.
Рис. 2.3. Новая рабочая горизонтальная клеть 280: 1 - узел валков; 2 -
рама; 3 - откидной болт
Узел валков изображен на рис. 2.4.
Рис. 2.4. Узел валков: 1-механизм установки раствора валков; 2-валок
рабочий; 3-подушка верхняя; 4-подушка нижняя; 5-опора левая; 6-опора правая;
7-винт левый; 8-винт правый; 9-гайка левая; 10-гайка правая; 11-опора сферическая;
12-плунжер; 13-крышка стопорная; 14-стакан; 15-стакан; 16-кольцо; 17-калибр.
Рабочие валки установлены в подушках на четырехрядных цилиндрических
роликовых подшипниках.
Осевые нагрузки на каждом валке воспринимаются радиально-упорными
шарикоподшипниками, установленными в корпусе на неприводной стороне клети.
Зазор между нажимными винтами и подушками во время прокатки устраняется
гидроцилиндрами плунжерного типа, установленными в опоры узла валков.
Смазка подшипников качения - пластичная, централизованная. Смазка
поверхностей скольжения опор винтов, резьбы винтов S80x4 и лабиринтов -
пластичная.
Механизм установки раствора валков предназначен для изменения зазора
между валками.
Вращение от мотор-редуктора через муфту зубчатую передается редуктору правому,
а через муфту расцепную - редуктору левому. Корпуса редукторов устанавливаются
на цилиндрические концы винтов узла валков со шпонками. Зубчатые колеса
редукторов передают вращение винтам, с двух сторон которых навинчены гайки с
разным направлением нарезки резьбы.
Гайки зафиксированы от вращения стопорными крышками и штифтуются
совместно с подушками. При вращении винтов зазор между подушками увеличивается
или уменьшается.
Стойка шпиндельная (рис. 2.5) устанавливается на плитовине линии клети и
предназначена для рассоединения клети 280 с карданными валами главного привода,
а так же для поддержки шпинделей при перевалке клети.
Рис. 2.5. Стойка шпиндельная. 1-рама; 2-стул верхний; 3-стул нижний;
4-стержень; 5-гидроцилиндр; 6-болт откидной; 7-гайка стяжная; 8-датчик
положения.
Гидроцилиндр (поз.5) обеспечивает вертикальное перемещение стульев
шпиндельной стойки. Датчик положения (поз.8) фиксирует верхнее положение
стульев и запрещает включать главный привод клети при демонтаже.
При демонтаже рабочей клети из линии стана (перевалке), клеть выдвигается
гидроцилиндром перемещения клети в крайнее положение (удаленное от привода).
Предварительно рабочие валки клети разведены в положение перевалки.
В этом положении поршень гидроцилиндра шпиндельной стойки занимает
крайнее верхнее положение. Фланцы карданных валов касаются стульев. Откидные
болты, соединяющие шпиндельную стойку с рамой клети, убираются, и с помощью
гидроцилиндра перемещения клети шпиндельная стойка совершает перемещение без
клети по направляющим плитовины, стаскивая фланцы карданных валов с концов
валков рабочей клети.
При образовании зазора 200…250 мм между торцами валков и фланцев,
шпиндельная стойка останавливается.
Шпиндели предназначены для передачи вращения и крутящих моментов от
шестеренной клети к валкам рабочей клети.
Шпиндель (рис. 2.6) состоит из раздвижного покупного карданного вала.
ЭК1-531-2201010 (размер по осям шарниров в сжатом состоянии 996мм, ход 400мм),
двух фланцев.
Рис 2.6. Шпиндель.1-фланец; 2-фланец; 3-планка; 4-болт; 5-шайба торцевая;
6-винт установочный.
При сборке шлицевой вал шпинделя должен располагаться со стороны клети.
Сборка шпинделей происходит следующим образом:
На выходные валы шестеренной клети, а также приводные концы рабочих
валков одеваются и крепятся фланцы, в которых закреплены планки. Фланцы
соединяются с карданным валом при помощи прецизионных болтов и гаек, причем паз
должен войти в лопату фланца, надетого на конец приводного валка.
Шпиндели удерживаются шпиндельной стойкой, обеспечивающей сохранение их
положения во время перевалки.
Клеть шестеренная «315» предназначена для передачи крутящего момента двум
валкам рабочей клети. Установлена на раме и крепится к ней болтами. Рама жестко
установлена на фундаменте. В конструкции шестеренной клети использовано
косозубое цилиндрическое зацепление, верхний приводной валок и литой корпус,
состоящий из трех частей.
Все три корпуса стянуты между собой шпильками и болтами. В среднем
корпусе имеется смотровое окно, закрытое крышкой, которое предназначено для
периодического осмотра зубчатого зацепления. В нижнем корпусе выполнено сливное
отверстие, предназначенное для слива отработанного масла.
Шестеренные валки установлены в корпусе на двухрядных конических
роликоподшипниках. Смазка зубчатого зацепления и подшипников качения - жидкая
циркуляционная. Со стороны прокатной клети валы имеют цилиндрические хвостовики
с лысками. С противоположной стороны ведущий вал шестеренной клети через
зубчатую муфту соединен с редуктором.
Редуктор ЦО-450 предназначен для передачи крутящего момента и понижения
частоты вращения от электродвигателя к шестеренной клети.
Редуктор установлен на одной раме с шестеренной клетью.
Корпус редуктора литой, состоящий из двух частей.
Тип редуктора - цилиндрический горизонтальный, одноступенчатый.
Межосевое расстояние - 450мм.
Зубчатое зацепление - цилиндрическое, косозубое. Опоры валов смонтированы
на однорядных конических роликоподшипниках.
Смазка зубчатого зацепления и подшипников качения - жидкая
централизованная.
Валы редуктора соединены через зубчатые муфты с шестеренной клетью и
электродвигателем.
Плитовина предназначена для установки на ней клети и стойки шпиндельной.
Плитовина представляет собой сварную конструкцию, закрепленную на
фундаменте анкерными болтами. В верхней части плитовины имеются направляющие,
необходимые для обеспечения перемещения клети при перевалке и в процессе
прокатки.
В направляющие установлены гидрозажимы, которые фиксируют положение клети
в процессе прокатки. Упоры, установленные на плитовине, определяют положение
клети при монтаже.
На плитовине установлен гидроцилиндр, который через стойку шпиндельную
соединен с клетью. С помощью гидроцилиндра осуществляется горизонтальное
перемещение клети при переходе на прокатку в разных калибрах (т.е. установке
калибра на ось прокатки) и при демонтаже. Датчик, встроенный в гидроцилиндр,
определяет положение клети во время ее перемещения.
Работа линии клети 280 может происходить в различных режимах в
зависимости от сортамента прокатываемого профиля.
Прокатка в клетях чистовой группы осуществляется в соответствии со
схемами прокатки и временной технологической инструкцией.
При производстве проката диаметром более 22 мм рабочие клети чистовой
группы снимаются и на их место устанавливаются транспортные проводки .
Полоса c температурой t=850°… 950°
после петлеобразователя через проводку подается в валки клетей. Валки
охлаждаются водой снаружи. При производстве круга заготовка обжимается в
калибрах круг- овал- круг, при этом перед четными клетями происходит кантовка
заготовки на 90°.
Прокатка производится с минимальным натяжением. При выходе из выпускной клети
проводка снимает профиль с калибра.
Перед началом работы клеть находится в исходном положении:
системы централизованной смазки и водяного охлаждения должны быть
включены;
обеспечено рабочее давление в гидроцилиндрах;
валки выставлены в рабочее положение, обеспечивая необходимый зазор между
калибрами валков, положение валков контролируется датчиком, установленным в
механизме установки раствора валков, при необходимости производится «прожиг»
калибров;
выполнена центровка положения калибров валков относительно оси прокатки;
Основной режим работы линии - автоматический и при необходимости
(например, при настройке механизмов) предусмотрено ручное управление.
Запрещается включение механизма установки раствора валков при затянутом
механизме осевой регулировки.
Перевалка рабочей клети 280 производится после износа калибров или для
замены ее на другую рабочую клеть. Перевалка клети выполняется с помощью
мостового крана грузоподъемностью не менее 8 т.
Процесс перевалки осуществляется следующим образом:
Остановить и отключить электродвигатель привода клети.
Отсоединить подвод смазки и охлаждения.
Отвести вводную и выводную проводки. При необходимости откинуть коллектор
системы охлаждения.
Развести рабочие валки в положение перевалки - 282 ±0,05мм. Это расстояние является
постоянным для всех клетей 280, независимо от степени переточки валков.
Предварительно необходимо ослабить затяжку рычагов механизма осевого
регулирования валков, обеспечив возможность радиального перемещения валков.
Зафиксировать шпиндели в положении перевалки.
Для этого переместить «стулья» стойки шпиндельной в верхнее положение.
При этом поддержка «стула» должна войти в обнижение фланца, соединяющего
шпиндель с рабочим валком. Шпиндельная стойка удерживает шпиндели, сохраняя их
положение во время перевалки.
Отключиь электродвигатель механизма установки раствора валков.
Отсоединить кабель от клемной коробки.
Отключить гидроцилиндры уравновешивания подушек.
Поднять гидрозажимы в верхнее положение, освободив направляющие рамы
клети.
Переместить клеть гидроцилиндром перемещения клети в крайнее положение
(удаленное от привода), до упора.
В таком положении прижимные гайки гидрозажимов попадают в пазы
направляющих рамы клети.
Убрать откидные болты, соединяющие раму клети со стойкой шпиндельной.
Отвернуть винты установочные М24, соединяющие приводные концы валков
рабочих с фланцами карданных валов.
Переместить стойку шпиндельную по направляющим плитовины в сторону
привода, стаскивая фланцы карданов с приводных концов валков рабочей клети.
При образовании зазора 200…250мм между торцами валков и фланцами
карданов, стойку шпиндельную остановить. Клеть находится в положении демонтажа.
Установить шаблон между подушками верхнего валка.
Клеть снимается с плитовины с помощью крана и на передаточной тележке
поступает на участок подготовки клетей, где на специальной площадке узел валков
вынимают из рамы. Перед разборкой клеть должна быть промыта от окалины и масла.
Рис. 2.7. Разборка узла валков клети. 1-валок рабочий; 2-подушка верхняя;
3-корпус; 4-кожух; 5-втулка; 6-втулка; 7-полукольцо; 8-гайка; 9-крышка;
10-втулка; 11-болт специальный.
Далее необходимо отвернуть откидные болты на раме клети, а так же
развести рычаги механизма осевого перемещения валков, освободив опорные
плоскости корпуса радиально-упорного шарикоподшипника.
Затем узел валков с помощью крана установить на стенд клети 280
для предварительной разборки.
На этом стенде снимается узел радиально-упорных подшипников,
установленных в корпусе на неприводной стороне клети (рис. 13).
Операцию производить в следующей последовательности:
снять кожух поз.4;
освободить гайку поз.8, (сняв болт) и отвернуть ее;
снять полукольца поз.7, с втулкой поз.6;
отвернуть болты специальные, поз.11, фиксирующие корпус
шарикоподшипника от проворота;
снять корпус поз.3, с шарикоподшипником вместе с крышкой
поз.9, и втулкой поз.5, на которой насажено внутреннее кольцо упорного
подшипника.
Далее узел валков передается на стенд для смены валков 280. Стенд
предназначен для разборки узла валков и позволяет, в частности, выполнить
замену изношенных валков на новый комплект.
Установку клети с переваленными валками в линию стана производить в
обратном порядке. При монтаже на участке подготовки клетей необходимо выполнить
предварительную осевую регулировку взаимного положения валков.
Выполним поверочный расчёт энергосиловых параметров прокатки.
Пpокатываемый матеpиал-сталь 35ГС
Расчет усилия прокатки.
Определение общего давления металла на валки при прокатке обычно состоит
из решения двух основных задач:
-
вычисление площади соприкосновения прокатываемого металла с валком или, точнее,
проекции этой площади на плоскость, нормальную к равнодействующей усилия на
валки
;
определение
контактного давления (среднего контактного нормального напряжения) на валки
;
Когда
эти величины найдены, общее усилие металла на валки определяют как их
произведение:
,
где
- Н,
- мм2,
- МПа;
Величину
в большинстве случаев найти относительно просто, так
как она зависит от геометрических размеров валков и прокатываемой полосы.
Контактное
давление определяется двумя основными факторами:
механическими
свойствами прокатываемого металла, зависящими в свою очередь от температуры,
степени и скорости деформации металла в очаге деформации;
напряженным
состоянием, зависящим главным образом от геометрических размеров очага
деформации, контактных сил трения, натяжения полосы и внешних зон.
При
линейном напряженном состоянии фактическое сопротивление простому (однородному)
сжатию находиться по уравнению, МПа:
,
где
,
,
- коэффициенты, учитывающие влияние температуры,
степени и скорости деформации на сопротивление деформации;
- предел
текучести материала, МПа.
Влияние
напряженного состояния можно выразить в виде произведения двух коэффициентов,
из которых первый
(коэффициент Лоде) учитывает влияние среднего
нормального напряжения в очаге деформации
, а
второй
- влияние контактных сил трения, внешних зон и
натяжения.
Значение
можно определить по формулам В. С. Смирнова:
а)
при
;
б)
при
,
где
- средняя высота полосы,
;
-
средняя ширина,
;
-
коэффициент внешнего трения при установившемся процессе прокатки.
Коэффициент
трения между прокатываемым металлом и валками зависит от состояния контактных
поверхностей, условий соприкосновения (свойств прокатываемого металла,
температуры прокатки, присутствия окислов, рода смазки, давления и скорости
прокатки) и от характера самого скольжения.
Коэффициент
трения при захвате при горячей прокатке стали (выше 700 ºС) определяется в зависимости от температуры
, ºС по формуле:
,
для
стальных валков
; для чугунных валков с закаленной поверхностью
.
Поправочный
коэффициент
учитывает влияние скорости прокатки. Коэффициент
учитывает химический состав прокатываемого металла.
При
установившемся процессе прокатки коэффициент трения может быть определен по формуле:
.
Коэффициент
напряженного состояния
представляет собой произведение четырех
коэффициентов:
,
где
,
,
,
-
коэффициенты, учитывающие влияние ширины прокатываемой полосы, внешнего трения,
внешних зон и натяжения.
Коэффициент
учитывает перераспределение контактных касательных
напряжений в связи с уширением в тех случаях, когда
, где
- длина
дуги контакта,
;
Коэффициент
- в случае горячей прокатки при отношении
определяют по формуле:
,
когда
отношение
:
.
когда
отношение
:
При
прокатке высоких полос с небольшими обжатиями, когда
, большое влияние на контактное давление оказывают
влияние внешние продольные зоны. Зависимость их влияния в интервале
выражается эмпирическим уравнением:
.
Так
как прокатка ведется без натяжения
.
Как
следует из экспериментальных данных, давление при прокатке в калибрах обычно
выше, чем при прокатке на гладкой бочке, и определяется по формуле, МПа:
,
где
- МПа,
-
коэффициент, учитывающий влияние условия трения и формы калибра на контактное
давление. Этот коэффициент можно найти из выражения:
,
здесь
- угол охвата полосы стенками калибра в плоскости
выхода из валков. При прокатке в сложных фасонных калибрах
.
Момент,
необходимый для привода двух валков, находят по формуле, кН·м:
,
где
вертикальная составляющая усилия прокатки, кН;
- длина дуги контакта, м;
- координата центра тяжести эпюры
относительно оси валков.
Коэффициент
плеча
может меняться в пределах
. Для практических расчетов можно пользоваться
опытными значениями коэффициента
в
зависимости от отношения
, полученные при прокатке сталей без натяжения полосы.
Мощность
прокатки, кВт:
,
где
- кН·м,
-
угловая скорость вращения валков, с-1.
Рассчитаем
энергосиловые параметры для клети 13г.
При
прокатке в калибрах расчет ведем по методу приведенной полосы.
,
где
- площадь поперечного сечения профиля (см. выше),
- ширина калибра.
мм;
мм;
мм;
мм;
;
Определим
коэффициент трения.
,
(стальные
валки);
Для
определения коэффициента
необходимо знать окружную скорость. При
об/мин окружная скорость равна
м/с.
м/с ,
=>
;
Для
стали 35ГС
;
;
;
Для
остальных калибров скорость находиться через коэффициенты вытяжки
, так как прокатка ведется на непрерывном стане:
,
где
;
,
;
Длина
дуги захвата
;
мм;
мм;
мм;
;
=>
Так
как
, то
;
;
;
;
Фактическое
сопротивление деформации
;
Для
Ст 35ГС
МПа;
По
эмпирическим кривым находим
,
,
:
(
);
Относительное
обжатие
,
;
Скорость
деформации
,
где
- окружная скорость, м/с;
- длина
дуги захвата, м;
с-1,
;
МПа;
Контактное
давление:
МПа;
Площадь
контакта:
мм2;
Усилие
прокатки:
*313=241949
Н, (
кН);
Момент
прокатки:
,y - коэффициент плеча равнодействующей силы Р
, по
эмпирической кривой
;
кН·м;
Мощность
прокатки:
,
Угловая
скорость
с-1;
кВт;
Мощность
привода
[Nдв
*0.85]>Nпрпр - мощность прокатки, кВтдв *0.85=525*0.85=446 кВт>Nпр=>
двигатель выбран с достаточным запасом мощности.
Силовой
расчёт винтовой передачи механизма регулировки раствора валков.
Винт:
упорная резьба Æ 80 х 10 мм.
средний
диаметр dср = 77 мм.
Диаметр
пяты трения 100 мм.
Усилие
прокатки 27 т.
Вес
1 валка с комплектом подушек 1100 кг.
Вес
винта 40 кг.
Вес
механизма установки валков 500 кг.
Диаметр
гидроцилиндра уравновешивающего dц = 36 мм.
Давление
100 атм.
Усилие,
развиваемое гидроцилиндром
Суммарное
усилие 8-ми гидроцилиндров равно 8144 кг
Требуемая
скорость перемещения подушки:
при
перевалке V = 0,33 мм/с;
при
регулировке калибров V = 0,05 мм/с.
Определим
необходимую скорость перемещения винта
об/с
- 10 мм/с:
об/с
- 0,33 мм/с (0,05 мм/с)
(при
перевалке)
при
регулировке калибров
(g+r¢) = tg (2,36° + 6,58°) = 0,16
Мкр
= Мкр1 + Мкр2 + Мкртр
Мкр1
= 0,5 F1× d2×tg(g+r¢)
Мкр2
= 0,5 F2× d2×tg(g+r¢)
Мкр2
= 0,5 (1018 + 275) × 0,08 × 0,16 =8,27 кгм
=
(550+125+40) 0,1 × 0,1 × 0,5 = 3,57 кгм
Мкр.=
5 + 8,3 + 3,6 = 17 кгм = 1700 кгсм
Червячная
передача (ступень II):
Принимаем
аw = 100 мм; Z1 = 1; Z2= 40; m = 4; q = 10; c = 0, тогда q×m = 10×4 = 40 мм; d2 = Z2× m = 40×4 = 160 мм
Проверяем
аw= 0,5(Z2 + q + 2c)× m = 0,5(40+10+0) ×4 = 100 мм
= d1+2m =
40 + 8 = 48мм= 40 - 2,4 × 4 = 30,4 мм
в1³ (11 + 0,06× 40) ×4 = 53,6 мм
Принимаем
в1= 60 мм= 160 + 2 × 4 = 168 мм
м2
£ da2 + 2×m= 168 + 8 =
176 мм
в1£ 0,75 da1= 0,75 × 48 = 36 мм
Определим
условный угол обхвата передачи 2d.
При
заданной линейной скорости перемещения подушки 0,05 мм (при регулировке
калибров), осуществляемой передачей винт - гайка, при шаге винта - 10 мм,
окружная скорость вращения винта (минимальная) составит:
об/мин
Скорость
вращения червяка соответственно
=
V2× U = 0,3 × 40 = 12
об/мин
Определим
скорость скольжения червяка
м/с
Определим
КПД червячной передачи
; 
r’= 5030’ ;
= 0,5
Крутящий
момент на червяке
кгм
Крутящий
момент на выходном валу мотор-редуктора
кгм =
35,4 Н.м
Необходимая
мощность двигателя
где
n - максимальные обороты выходного вала мотор-редуктора
об/мин
Максимальная
скорость перемещения подушки в клети 0,35 мм/с - при перевалк).
кВт
Определим:
напряжение
изгиба в зубьях червячного колеса
кг/мм2
коэффициент
запаса по изгибу
контактные
напряжения в зубьях
Прямозубая
передача (I ступень):
Крутящий
момент на валу колеса М = 0,85 кгм.
Конструктивно
принимаем
аw = 120 мм ; m = 4 мм; U =
1;
= 4×30 = 120 мм; da1 = 120 + 8
= 128 мм; dg1= 120 - 10 = 110 мм
Предварительно выбираем
мотор-редуктор 3МП-25М-90-78-310-Ц-У3.
Номинальная мощность эл.
двигателя 0,75 кВт
Допускаемый крутящий момент
на вых. валу мотор-редуктора - 78 Нм.
Передаточное отношение
редукторной части i = 16
Исполнение - фланцевое
Тип - планетарный
модернизированный
Радиус расположения осей
сателлитов - 25 мм
КПД редукторной части 0,95
(НТЦ «Редуктор»)
2.3 Летучие ножницы
Летучие ножницы предназначены для резки металла на ходу («на лету») при
его движении с большой скоростью.
Во многих случаях работоспособность этих ножниц определяет
производительность прокатного стана.
Барабанные ножницы весьма просты по конструкции и надежны в эксплуатации.
Они получили широкое применение для горячей резки широких стальных полос
толщиной до 30 мм., холодной резки стальных полос толщиной до 3 мм. и горячей
резки мелких сортовых профилей.
Устройство и принцип работы этих ножниц состоит в следующем (рис. 2.8):
на двух барабанах по их образующим радиально закреплены ножи (по одному или по
несколько на каждом барабане).
Рис. 2.8. Схема барабанных летучих ножниц: 1 - подающие ролики; 2 -
барабан с ножами; 3 - ножи; 4 - ролики рольганга
Полоса
движется непрерывно и подается к ножницам подающими роликами (или валками
последней клети непрерывного стана) с постоянной скоростью
. При встрече верхнего и нижнего ножей происходит
резание полосы. Для создания разрыва между отрезанными кусками полосы скорость
выходного рольганга должна быть больше скорости полосы перед ножницами.
Так
как барабаны вращаются равномерно с постоянной угловой скоростью и вращающиеся
массы полностью уравновешенны, то эти ножницы позволяют резать металл со
скоростью 15 м/с и выше. Однако эти ножницы имеют следующие недостатки:
)
траекторией движения режущих кромок ножей являются окружности, поэтому при
встрече с горизонтальной движущейся полосой резание будет проходить при
переменном угле и плоскость резанья на полосе не будет вертикальной. Однако
этот недостаток не является существенным при резке тонких полос;
)
резание полосы осуществляется параллельными ножами, т.е. одновременно по всей
ширине ее, вследствие чего возникают большие усилия резания при динамическом их
приложении. Для уменьшения усилия резания желательно один нож делать наклонным
(по принципу гильотинных ножниц) или шевронным, однако при резании широких
полос с большей скоростью, при изменении угла по ширине полосы в процессе
резания, осуществление этого принципа требует увеличения бокового зазора между
ножами, что не всегда желательно.
При
резании металла барабанные летучие ножницы могут работать по двум основным
режимам: периодических запусков и остановок; непрерывного вращения барабанов.
Режим
периодических запусков применяют в двух случаях: при отрезке короткого
переднего конца полосы, некондиционного, имеющего неправильную форму и при
резке полосы на длинные куски, направляемые на холодильник.
При
непрерывном режиме полоса поступает со скоростью
, а
резание происходит периодически через каждые t секунд, поэтому длина отрезаемых
слитков
Таким
образом, длина отрезаемых листов зависит от промежутка времени между
последовательными резами. Введем следующие обозначения:
коэффициент
пропуска реза; он характеризует число оборотов барабана за время между двумя
последовательными резами; например, если рез происходит за каждый оборот, то
; если рез происходит через каждые 2 оборота, когда
барабаны имеют разные диаметры и диаметр нижнего ведущего барабана в 2 раза
меньше диаметра верхнего барабана, то
угловая
скорость ножей барабанов за время между двумя последовательными резами; если
барабаны имеют различные диаметры, то
угловая
скорость приводного барабана меньшего диаметра (нижнего или верхнего).
Очевидно,
что за время между двумя резами нож барабана совершит путь, равный
при окружной скорости
.
Промежуток между резами составит:
поэтому
формула для нахождения длины листов получит следующий вид:
Таким
образом, при постоянной скорости полосы (
) длина
отрезаемого листа зависит от коэффициента пропуска реза и угловой скорости ножа
приводного барабана.
Величину
k можно изменять двумя способами: 1) установкой различного числа ножей на
барабанах; 2) применение барабанов различного диаметра.
Требуемы
различные промежуточные длины можно получить только предварительным подбором
необходимых отношений скорости
, каждое
из которых в процессе резания листов заданной длины должно быть строго
постоянным с целью получения точных допусков по длине листов
Для
поддерживания отношения
постоянным применяют синхронизацию 2-х видов:
электрическую и механическую.
Электрическую
синхронизацию выполняют, когда летучие ножницы установлены за последней клетью
непрерывного стана и имеют свой привод, механически не связанный с приводом
валков клети. В таком случае при помощи различных сельсинных синхронно-следящих
систем обеспечивающих синхронное изменение скоростей двух отдельных
электродвигателей для привода последней клети стана и для привода летучих
ножниц. Однако электрическая синхронизация пока еще не является достаточно
точной и надежной, поэтому она применяется только для летучих ножниц при
горячей резке полосы: заготовки, сорта, когда не требуется большая точность
реза (тем более, что при остывании полосы происходит уменьшение ее линейных
размеров на 4-5%), а также при отрезке только переднего конца.
Механическую
(жесткую) синхронизацию применяют в поточных агрегатах холодной резки рулонной
полосы на лист небольшой длины при непрерывном вращении барабанов ножниц. В
этих случаях в комплект установки летучих ножниц обязательно входят собственно
ножницы и подающие ролики, причем ножницы и подающие ролики имеют привод от
одного общего электродвигателя постоянного тока через различного рода зубчатые
редукторы, жестко связанные между собой муфтами.
Промежуточные
длины и точность резания. При холодной резке рулонной полосы шириной 1000-2350
мм, толщиной 0,2-0,3 мм на листы длиной от 500 до 8000 мм интервалы длин,
согласно ГОСТ, составляют 3-30 мм. Очевидно, что для получения такого широкого
сортамента листов (по длине) требуется широкий интервал синхронизации отношения
скоростей ножей к скорости полосы или скорости подающих роликов.
Для
этого в линии привода ножниц или линии привода подающих роликов устанавливают
многоступенчатый редуктор, который позволяет получить 200-400 различных передаточных
чисел. Так как при работе ножниц максимальное допустимое повышение скорости
ножей по отношению к скорости полосы должно составлять не более 200%, то этот
диапазон различных передаточных чисел должен находиться в пределах от 1 до 2.
Согласно
техническому заданию ножницы должны обеспечить обрезку переднего и заднего
концов (диаметром 20 мм) - отходов заготовки после прокатной планетарной клети,
стоящей в линии УНРС на металлургическом заводе ОАО «Электросталь».
Температура
разрезаемого метала 800 - 500 С°.
Разрезаемые
стали - низколегированные и углеродистые стали.
Общий
вид на листе № 1.
Межцентровое
расстояние режущих барабанов - 500 мм.
Передаточное
число приводной ступени i = 4.067
Рис. 2.9. Кинематическая схема ножниц
Исходные данные:
.максимальная скорость движения - 2,5 м/с
.сечение разрезаемого металла - 20х20 мм
3.площадь
поперечного сечения
.максимальное
сопротивление сдвигу, с учетом захоложенного металла
.максимальное
усилие резания
.расчетное
усилие резанья
Так
как маховой момент вращающихся частей ножниц мал, и кроме того, возможна работа
при весьма малых скоростей движения проката, будет считать, что имеет место
«силовой рез», т.е. рабочая клеть нагружается полными усилиями и моментами от
реза.
Угол
начала резания
Угол
конца резания
Угол,
при котором действует наибольшее усилие резания
Принимают
относительную высоту надреза
Рис. 2.10. Схема механизма резания
По таблицам находим
Определим
момент от максимальных сил резания на верхнем и нижнем валах ножниц
=0, IP=0,
I·7200=720 кг.
Общий
момент от сил резания
Зубчатое
зацепление рабочей клети имеет следующие параметры:
.Межцентровое
расстояние А=500 мм
.Ширина
рабочего венца Вр=100 мм
.Ширина
венца шестерни выбор люфта Вв.л=40мм
.Число
зубьев шестерни Z1=61
.Число
зубьев колеса Z2=61
.Передаточное
число i=1
.Угол
наклона зубьев β=
Расчет
ведем по полному моменту на верхнем валу
Контактные
напряжения в поверхностном слое по «Методике расчета»
Я.Г.
Кистьяна, Машгиз, 1963 г.
,
где
i=1, A=50 см, b=10 см, Мк=355 кг·м
Q=1.9, δ= 1.5, η= 0.5,
ζ=0.38
Проверим
также напряжения на изгиб зубьев колеса
Рассчитаем
приводную ступень зацепления, которая имеет следующие параметры:
.Межцентровое
расстояние А1=311.475
.Ширина
рабочего венца Вр=150 мм
.Число
зубьев шестерни Zш=15
.Число
зубьев колеса Zк=61
.Передаточное
число i=4.067
.Угол
наклона зубьев β=
Расчет
ведем по моменту реза Мрез=1006 кг·м
где
i=4.067, A=31.15 см, b=15 см, Мк=1006 кг·м
=1.5, δ= 1.45, η= 0.8, ζ=0.38
Выполним
расчет валов
)Ведущий
вал.
Рис. 2.11. Расчетная схема

Определим
реакцию на подшипники.
Вертикальная
реакция на опору А1
Вертикальная
реакция на опору Б1
Горизонтальная
реакция на опору А1
Горизонтальная
реакция на опору Б1
Полная
реакция на опору А1
Полная
реакция на опору Б1
Осевая
сила воспринимаемая опорой Б1
Изгибающий
момент в точке В1 приложения силы R в горизонтальной плоскости
Изгибающий
момент в той же точке в вертикальной плоскости
Суммарный
изгибающий момент
Расчетное
сечение для вала-шестерни принимается равным диаметру начальной окружности d0
Касательные
напряжения от кручения
Совместное
действие нагрузок равно σэкв
)Нижний
вал ножниц.
Рис. 2.12. Расчетная схема
Определим
реакции на опорах А2 и Б2
Изгибающий
момент в сечении опоры А2
в
вертикальной плоскости
в
горизонтальной плоскости
Суммарный
момент
Изгибающий
момент в сечении В2 в вертикальной плоскости
в
горизонтальной плоскости
Суммарный
момент
Расчет
ведем по сечению А2
Совместное
действие нагрузок равно σэкв
)Верхний
вал ножниц.
Так
как верхний вал ножниц по конструкции такой же как и нижний, но нагружен
меньшим крутящим моментом и на нем отсутствуют нагрузки от ведущего вала, то
его расчет на прочность не производим.
Рассчитаем
шпонки.
)Верхний
вал.
Шпонка
между валом и режущей головкой установлена на конусе, средний диаметр которого
Размер
шпонки 36х20х140
Между
валом и ступицей колеса установлена d=135мм такая же шпонка 36х20х140
)Нижний
вал.
На
нижнем валу установлены такие же шпонки.
На
шпонке конус
На
шпонке под зубчатым колесом
- для
соединения на конус и для легкопрессовой посадки.
)Ведущий
вал.
Установлена
шпонка 24х14х125 на d=90мм
Проверим
подшипники.
Так
как рабочая клеть ножниц нагружается усилиями реза на очень коротко время,
величина которого несоизмеримо мала со временем разгона ножниц, то проверку
подшипников производим по статической грузоподъемности. Поскольку нагрузка
носит характер удара, то при проверке подшипников берем удвоенную величину
реакции опор.
Ведущий
вал смонтирован на подшипниках с бочкообразными роликами №3522, имеющими
Qст=27000 кг
Реакция
в опоре А1
Коэффициент
запаса по статической нагрузке
Реакция
в опоре Б1
Осевая
сила
Нижний
и верхний валы ножниц смонтированы также на подшипниках с бочкообразными
роликами. Передние опоры имеют подшипники № 3528 с Qцm =44000 кг, а задние
опоры - подшипники № 3524 с Qцm =32000 кг.
Реакция
в опоре А2
Коэффициент
запаса по статической нагрузке
Реакция
в опоре Б2
Осевая
сила
Таким
образом, подшипники имеют достаточный запас прочности.
Расчет
маховых масс ножниц
Маховые
массы ножниц по узлам приводятся ниже:
.Верхний
вал с шестерней…………………………………
.Нижний
вал с шестерней………………………………….
.Верхний
режущий рычаг…………………………………...
.Нижний
режущий рычаг……………………………………
Всего:
.Ведущий
вал - шестерня……………………………………
.Муфта
МЗП - 5………………………………………………
Всего:
Так
как передаточное число приводной ступени i=4.06, то суммарный маховой момент,
приведенный к валу электродвигателя
Пружины
выбора люфта должны удерживать шестерни от раскрытия зазора при разгоне ножниц.
Для определения инерциального момента на верхнем валу определим угловое
ускорение при разгоне ε.
Угол
разгона вала
Время
разгона
Маховый
момент верхнего вала в сборе с шестерней и режущим рычагом
Момент
инерции
Максимальный
момент от инерционных сил:
Для
надежности выбираем коэффициент запаса, равный 2.
Радиус
расположения пружин R=175 мм.
Суммарное
рабочие усилие пружин
Выбираем
число пружин n=4 и коэффициент запаса по максимальному усилию пружины 1.5
По
нормали НМ97-65 выбираем пружину 4х20х5 из проволоки П - 4
ГОСТ
9389 - 60 с рабочей осадкой 10 мм.
3. Технологическая часть
.1 Технология изготовления опорного ролика МНЛЗ
Данная деталь служит для транспортировки заготовок из зоны вторичного
охлаждения МНЛЗ дальше по рабочей линии. Ролик не является водоохлаждаемый. На
один ручей МНЛЗ приходится одна данная деталь. Основным требованием к данной
детали является долговечность, т.к. выход ее из строя приведет к полной
остановке одного из ручьев МНЛЗ. Для этого применяется поверхностное упрочнение
методом деформации обкаткой роликом.
Исходя из условий эксплуатации, к ролику предъявляются следующие
требования:
Предельные отклонения размеров.
а) Поверхности ролика IT 8: IT2 Æ240 p6 Ra 6.3;
Диаметральная точность: IT8 Æ240 p6, обеспечивается токарно-винторезной операцией на
последней стадии обработки детали.
Отклонение формы и взаимного расположения:
допуск полного радиального биения поверхностей бочки относительно базы А,
в качестве которых выбраны самые ответственные поверхности, составляет 0,050
мм;
Шероховатость поверхностей: Ra 6.3- обеспечивается токарно-винторезной
операцией и режимом обработки;
б) Остальные поверхности выполняются от 10 до 14 квалитетов точности и
могут быть легко обеспечены на этапах предварительной обработки поверхности.
в) Шпоночный паз Р9 Ra 3.2 мкм обеспечивается операцией долбления
Выполнение данных технических требований достигается соответствующей
схемой составления технологического процесса: для получения поверхностей по IT8
необходим ряд обработок точением черновая, получистовая и чистовая.
Контроль выполнения данных требований осуществляется методом замера
диаметральных и линейных размеров скобой, калибром, штангенциркуль.
Требования по шероховатости поверхности.
Посадочные поверхности Ra 3.2..
Остальные поверхности Ra 6.3, Ra 12.5.
Ввиду того, что вал представляет собой тело вращения, то в качестве
основной технологической базы при обработке цилиндрических поверхностей
целесообразно выбрать самые точные поверхности, т.е. посадочную поверхность под
подшипник качения. Согласно рабочему чертежу необходимо проконтролировать
диаметральные размеры (средство измерения - микрометр или измерительная скоба)
и радиальное биение (в качестве средства измерения служит индикатор). Радиальное
биение можно определить как наибольшее показание индикатора за один оборот
детали. В качестве измерительной базы- поверхности А.
Технологичная деталь характеризуется:
минимальным расходом металла;
использованием наиболее экономичных методов изготовления с применением
типовых технологических процессов и оснастки при заданном типе производства.
Технологичность детали:
. вал представляет собой тело вращения, поэтому основным видом обработки
является точение. Точность обработки и шероховатости поверхностей детали
соответствуют условиям её эксплуатации;
. форма и размеры детали обеспечивают достаточную жесткость детали и
применение жесткого инструмента, нет необходимости в применении люнета при
токарной обработке;
. в качестве основной технологической базы при обработке цилиндрических
поверхностей выбираем ось вала;
. соблюдается принцип постоянства баз (обрабатывается в центрах);
. унифицированы элементы конструкции детали (фаски, резьбы, канавки);
. обеспечивается свободный подвод режущего инструмента.
. имеется не глубокое отверстие, т.к. это мелкосерийное производство, то
обрабатываем на вертикально-сверлильном станке.
Выбор материала детали вала определяет всю качественную сторону обработки
и эксплуатации вала. Критериями выбора материала валов для транспортировки
заготовок следующие:
Основным требованием к данной детали является долговечность, т.к. выход
ее из строя приведет к полной остановке одного из МНЛЗ. Для этого применяется
поверхностное упрочнение методом деформации обкаткой роликом. Одними из
основных параметров, являются прочность, жесткость, твердость и износостойкость
валов. При выборе материала валов следует учитывать термомеханические условия
их службы. Валы не подвергаются значительным статическим и ударным нагрузкам, а
также термическому воздействию. Обычно вала изготавливаются из сталей
конструкционных легированных. Например: 34ХН1М, 38Х2НМ, 34ХН3М, 38Х2Н2МА,
40Х2Н2МА. Эти стали по своим характеристикам подходят для изготовления валов. В
связи с этим для валов применяется более мягкая термическая обработка, не
приводящая к возникновению существенных остаточных напряжений. Т.к. в данном
стане осуществляется транспортировка заготовки, то есть в процессе больших
усилий не возникает, то в качестве материала для изготовления вала выбрана
Сталь 34ХН1М.
Выбор и обоснование метода получения заготовки: критерии выбора,
схематическое изображение (эскиз заготовки с припусками)
Выбор метода получения заготовки определяется следующими критериями:
) Размеры и конструктивная форма заготовки. Максимальный размер наружной
поверхности - ø280 мм, длина вала - 159 мм; конструктивная форма - ступенчатый
цилиндр.
) Заготовительные свойства материала - материал обладает хорошей
пластичностью.
) Особые требования к материалу детали - необходимо обеспечить
долговечность, т.к. выход ее из строя приведет к полной остановке МНЛЗ.
) Ответственность детали - в детали не должно быть рыхлости, анизотропии
свойств, трещин и других внутренних дефектов.
) Тип производства - единичное.
В качестве основных способов получения заготовки детали целесообразно
рассматривать сортовую прокатку, литье, ковку и штамповку. Материал не обладает
жидкотекучестью, следовательно метод литья нельзя использовать. Получение вала
методом ковки нецелесообразно, ввиду единичного производства и небольших
габаритов.
Поэтому, на основании вышесказанного можно заключить, что наиболее
приемлемой заготовкой для последующей механической обработки является прокат
34ХН1М ГОСТ 8479-70. Эскиз заготовки, с припусками, напусками и допусками
согласно ГОСТ 7829-70, представлен в последнем разделе
Выбор баз и анализ схем базирования для основных операций
При проектировании технологических процессов большое значение, с точки
зрения достижения заданной точности, имеет выбор баз. Обработку заготовки
следует начинать с выбора баз.
При построении маршрута обработки следует придерживаться принципа
постоянства баз, т.е. на всех основных технологических операциях использовать
одни и те же поверхности в качестве технологических баз.
В качестве базы выберем центровые отверстия, полученные после
токарно-винторезной операции. Это позволит на всех основных технологических
операциях использовать одну и ту же поверхность в качестве базы.
3.2 Технология изготовления вала редуктора ЦО-450
Входной вал редуктора ЦО-450 представляет собой тело вращения,
располагается в корпусе редуктора, работает в зацеплении, по средствам шпонок,
с зубчатым колесом и другим зубчатым колесом с целью передачи крутящего момента
от двигателя к приводам.
Входной вал редуктора ЦО-450 это ступенчатый двусторонний вал, имеющий с
двух концов шпоночные пазы для установки зубчатых колес. Шпонки призматические
со скругленными торцами. Так как опоры две, следовательно, справа и слева
предусмотрены опорные цилиндрические шейки. Шейки предназначены для уплотнения
и защиты подшипниковых опор. Также предусмотрены переходные участки (галтели
постоянного радиуса) для снижения концентрации напряжений и увеличения
долговечности. Один торец вала выполняется с фаской для облегчения сборки. На
ступенях вала, предназначенных для установки зубчатых колес, имеются конусные поверхности,
обеспечивающие точность сборки.
К детали предъявляются следующие технические требования:
. Поверхности под подшипники качения
А) Диаметральная точность: IT6 Ø110 k6, обеспечивается обработкой за
несколько переходов, а в частности операцией шлифования за 2 перехода на
последней стадии обработки детали.
Б) Отклонение формы и взаимного расположения: допуск торцевого
биения поверхности вала относительно базы В, в качестве которой выбрана ось
вала, составляет 0.016 мм, допуск радиального биения 0,025, обеспечивается
установкой детали в центрах при обработке поверхности, т.е. за счет совмещения
технологической и измерительной баз;
В) Шероховатость поверхностей: Ral,25 - обеспечивается обработкой за
несколько переходов, а в частности операцией шлифования и режимом обработки;
. Поверхности вала, предназначенные для установки зубчатых колес
А) Диаметральная точность: IT6 Ø120 s6, Ø90 s6 - обеспечиваетея обработкой за
несколько переходов, а в частности операцией шлифования за 2 перехода на
последней стадии обработки детали;
Б) Отклонение формы и взаимного расположения:
Допуск торцевого биения поверхностей вала относительно базы В, в качестве
которой выбрана ось вала, составляет 0.016 мм для Ø120,
0,012 для Ø90,
допуск радиального
биения 0.03 мм для Ø120, 0,025 для Ø90 обеспечивается установкой детали в
центрах при обработке поверхности, т.е. за счет совмещения технологической и
измерительной баз;
В) Шероховатость поверхности: Ra1.25 - обеспечивается обработкой за
несколько переходов, а в частности операцией шлифования и режимом обработки;
. Упорный торец под подшипник качения:
А) Отклонение формы и взаимного расположения:
Допуск симметричности поверхностей паза 32N9 составляет 0,12 мм, паза
25N9 - 0,1 мм (относительно базы В), обеспечивается выверкой заготовки при
фрезеровании;
Б) Шероховатость поверхности: Ra3.2 - обеспечивается выбором режима
обработки;
Остальные поверхности менее ответственны. Их можно обрабатывать по 12-му
квалитету точности IT12 Ra6.3 мкм. Контроль выполнения диаметральных и линейных
размеров осуществляется линейной скобой, калибром, штангенциркулем.
Шероховатость определяем с помощью профилографа или профиломера. В качестве
средства контроля целесообразно применять микрометр или измерительную скобу. В
качестве средства контроля радиального и торцевого биения служит индикатор. В
качестве контроля посадочных поверхностей шпоночных пазов предлагается
использование калибра для контроля симметричности расположения поверхностей.
Схема контроля - см. операцию 055 маршрутного технологического процесса.
Технологичной считают деталь, в которой учтены возможности минимального
расхода металла и использования наиболее экономичных методов изготовления с
применением типовых технологических процессов и оснастки при заданном типе
производства.
Данная деталь технологична по следующим показателям:
Вал представляет собой тело вращения, поэтому основным видом обработки
является точение. Точность обработки и шероховатости поверхностей детали
соовтетствуют условиям её эксплуатации;
Форма и размеры детали обеспечивают достаточную жесткость детали и
применение жесткого инструмента, нет необходимости в применении люнета при
токарной обработке;
В качестве основной технологической базы при обработке цилиндрических
поверхностей выбираем ось вала, при этом происходит совмещение технологической
и измерительной баз;
Все обрабатываемые поверхности имеют свободный подвод и отвод режущего
инструмента, за исключением шпоночных пазов, которые являются закрытыми. Для их
обработки можно использовать только концевую фрезу, причем нужно использовать
разные фрезы, т.к. радиус закругления пазов разный.
Выбор материала детали вала определяет всю качественную сторону обработки
и эксплуатации вала. Критерии выбора материала вала для холодной формовки труб
следуюшие:
критерии, обеспечивающие работоспособность детали;
свойства материала, обеспечивающие технологические характеристики
(прокаливаемость, обрабатываемость, шлифуемость и т.д.).
Одними из основных параметров, определяющие первый критерий, являются
прочность, жесткость, твердость и износостойкость валов. В конечном итоге эти
параметры во многом определяют точность получаемой продукции. Согласно рабочему
чертежу детали, твердость вала составляет 241..286НВ. На рабочих поверхностях
валов по условиям работы не допускаются неметаллические включения, трещины,
черновины, прижоги, шлифовочные трещины и другие поверхностные дефекты. В
металле валов недопустимы трещины и другие дефекты, которые могут вызвать
разрушение вала.
При выборе материала валов следует учитывать термомеханические условия условия
их службы. Валы не подвергаются значительным статическим и ударным нагрузкам, а
также термическому воздействию.
Обычно вала изготавливаются из легированных и углеродистых сталей.
Например: 9ХФ, 60ХН, 9ХН, Сталь 45. Эти стали по своим характеристикам подходят
для изготовления валов.
Данный вал должен быть прочным, износостойким и точным. Деталь
выполняется из стали 45Х ГОСТ 4543-71. Из такой стали изготавливаются валы,
шестерни, болты, шатуны и другие детали, к которым предъявляются требования
повышенной твердости, износостойкости, прочности и работающие при
незначительных ударных нагрузках. Поэтому сталь 45Х нам полностью подходит.
Выбор метода получения заготовки определяется следующими критериями:
Размеры и конструктивная форма заготовки. Максимальный размер наружной
поверхности - Ø130 мм, длина вала - 650 мм; конструктивная форма - ступенчатый
цилиндр.
Заготовительные свойства материала - материал обладает хорошей
пластичностью, также обладает плохими литейными свойствами - использование в
качестве заготовки отливку не целесообразно. Мы можем использовать поковку или
прокат.
Особые требования к материалу детали - необходимо обеспечить высокую
прокаливаемость на значительной глубине.
Ответственность детали - в детали не должно быть рыхлости, анизотропии
свойств, трещин и других внутренних дефектов.
Тип производства - единичное, следовательно поковку брать весьма
нерационально, т.к. изготовление пресс-формы - процесс дорогостоящий и долгий и
это экономически не выгодно.
Таким образом, в качестве заготовки выбираем стальной пруток Ø140
из стали 45Х.
Выбор маршрута обработки производят, исходя из требований, приведенных на
рабочем чертеже и точности заготовки. Требуемая точность готовой детали
достигается за счет правильного проектирования МТП, который состоит из его
основных стадий: операций, установов, переходов. Причем каждый переход
обработки повышает точность детали в среднем на 1..2 квалитета на стадиях
окончательной и чистовой обработки, 2..3 квалитета на стадиях предварительной
обработки.
Учитывая это, составим маршрут обработки следующих основных поверхностей:
Ø110 k6 Ra1,25
Ø120 s6 Ra1,25
Ø90 s6 Ra1,25
Это наиболее ответственные поверхности детали.
Возможны два варианта маршрутов обработки:
Вариант А:
Точение черновое IT12-13 Ra12.5-36;
Точение получистовое IT11-12 Ra3.2-12.5;
Точение чистовое IT8-9 Ra1.4-4.6;
Точение тонкое IT6-7 Ra0.32-1.0.
Вариант Б:
Точение черновое IT12-13 Ra12.5-36;
Точение получистовое IT11-12 Ra3.2-12.5;
Точение чистовое IT8-9 Ra1.4-4.6;
Шлифование предварительное IT7-9 Ra1.0-2.5;
Шлифование чистовое IT6-7 Ra0.5-1.25.
Маршрут обработки будет выглядеть следующим образом:
Ø110 k6 Ra1,25; Ø120 s6 Ra1,25; Ø90 s6 Ra1,25
Точение черновое IT10 Ra6.3;
Точение получистовое IT9 Ra3.2;
Точение чистовое IT8 Ra2.5;
Шлифование предварительное IT7 Ra1.25;
Шлифование чистовое IT6 Ra1.25.
На первой операции точения в качестве черновой базы принимается наружная
цилиндрическая поверхность. При последующей токарной обработке в качестве базы
используются центровые отверстия. На операциях фрезерования за базу принимается
цилиндрическая поверхность и торец. При шлифовании и при контрольной операции в
качестве базы выступают центровые отверстия.
Разработка маршрутной технологии изготовления детали.
Операция 005 Заготовительная
Оборудование: Ленточная пила
Операция 010 Токарно-винторезная
Оборудование: Токарно-винторезный станок
Операция 015 Токарно-винторезная
Оборудование: Токарно-винторезный станок
Операция 020 Токарно-винторезная
Оборудование: Токарно-винторезный станок
Операция 025 Вертикально-фрезерная
Оборудование: Вертикально-фрезерный станок
Операция 030 Слесарная
Оборудование: Верстак
Операция 035 Термическая
Оборудование: Печь
Операция 040 Правка центров
Оборудование: Центрошлифовальный станок
Операция 045 Круглошлифовальная
Оборудование: Круглошлифовальный станок
Операция 050 Маркирочная
Операция 055 Контрольная
Оборудование: Контрольный стенд
4. Организационно-экономическая часть
Конечной целью любого предприятия является получение максимальной прибыли
при минимизации производственных издержек и основных производственных фондов
предприятия.
Своевременное инвестирование в основные фонды является одним из главных
направлений в экономической стратегии предприятия.
Задачей данного раздела дипломного проекта является оценка эффективности
мероприятий по модернизации оборудования литейно-прокатного агрегата.
Необходимо рассчитать затраты по сырью и материалам, ознакомиться с системой
оплаты труда, фондом заработной платы, отчислениями во внебюджетные фонды,
рассчитать общецеховые расходы. На основе полученных данных произвести
сравнение экономических показателей проектируемого и действующего производства,
рассчитать экономический эффект.
Основой решения поставленной задачи является схема принятия решения (рис.
4.1).
Целью предлагаемого ниже технико-экономического расчёта является проверка
экономической эффективности предлагаемой в дипломной работе модернизации
производства и расчет экономических показателей.
Критерием оценки является коэффициент унификации, представляющий собой
отношение конструктивно-преемственных, стандартных и унифицированных деталей и
узлов к их общему количеству в новом оборудовании.
В условиях рынка и постоянно растущего числа конкурентов сокращается
жизненный эффективный срок эксплуатации оборудования. Поэтому его
систематическое обновление и создание новых типов является важной задачей.
Рис. 4.1. Схема принятия решения.
За базовый вариант для сравнения технико-экономических показателей принят
чистовой блок старого образца с рабочими клетями 200, как образец уже
установленный и функционирующий на данном производстве. А в качестве
альтернативы предлагается чистовой блок нового образца с рабочими клетями 280.
Из изложенного следует, что рассматриваемый проект модернизации
отличается целым рядом преимуществ, главным из которых является снижение
себестоимости продукции и увеличение производительности.
Оборудование сталеплавильного цеха предназначено для выплавки стали марок
Ст.3, Ст.5, 35ГС, 25ГС2 из металлического лома с последующей ее разливкой на
МНЛЗ в непрерывно-литую стальную заготовку квадратного сечения размером 60х80
мм и длиной до 12000 мм.
Производительность оборудования составляет по жидкой стали и 200 тыс.
т/год по непрерывно-литой заготовке.
Технологические расчеты показали, что увеличение производительности с 200
тыс. т/год до 260 тыс. т/год возможно на действующей в настоящее время МНЛЗ и
не требует привлечения дополнительных рабочих сил.
Выполним расчет производительности МНЛЗ для базового сечения
непрерывно-литой заготовки.
Средняя продолжительность разливки 1-й плавки
Расчет продолжительности разливки 1-й плавки выполняется по следующей
формуле:
Q
Т1 = --------------- , где:
P ´ m ´ V
Т1 - продолжительности разливки 1-й плавки, мин.- вес жидкого металла в
стальковше (без учета остатка), т
Р - вес одного метра НЛЗ, т (для плотности НЛЗ - 7800 кг/м3)- среднее
количество работающих ручьев МНЛЗ, шт.
(с учетом возможных потерь ручьев в ходе разливки стали)- средняя
линейная скорость разливки, м/мин.
Потери металла при непрерывной разливке:
скрап в промковше при уровне металла 200 мм - около 2.5 т;
обрезь головных и донных НЛЗ (длина обрезаемых участков по 1.0 м) - 0.5
т;
окалина - 4.5 кг/т.
С учетом данных потерь металла вес плавки по жидкому составит 30.9 т,
выход годного металла - 97.1 %.
Таким образом, среднее время разливки 1-й плавки составит:
30.9
Т1 = ----------------------- = 37.1 мин.
0.1219 ´ 1.95 ´ 3.5
Расчет годовой производительности МНЛЗ выполняется по следующей формуле:
60 ´ F ´ Q ´ n
А = К ´
------------------------ , где:
n ´ T1 + T2
- фактическое время работы МНЛЗ, час.- вес 1-й плавки по годному, т-
средняя серийность разливки, плавок- среднее время разливки 1-й плавки, мин.-
среднее время подготовки МНЛЗ к разливке, мин.
К - коэффициент, учитывающий степень загрузки МНЛЗ при эксплуатации
(в первую очередь, учитывающий простои МНЛЗ из-за отсутствия жидкой
стали).
Расчетная производительность МНЛЗ составит:
60 ´ 7200 ´ 30 ´ 4
А = 0.8 ´
------------------------------ = 232.4 тыс. тонн.
4 ´ 37.1 + 30
Производительность цеха на данный момент составляет 200 тыс. т/год
непрерывно-литой заготовки квадратного сечения 60×80 мм и длиной до 12 000 мм.
Проектом предусматривается увеличение производительности на 33% и доведение
её до 260 тыс. т/год.
Годовой фонд календарного времени: 365 дней или 8 760 часов. Регламентом
предусмотрено 15 дней или 360 часов остановки на капитальный ремонт.
Эффективный фонд времени работы установки: 8 400 часов в год.
Часовая производительность:
Сменная производительность:
Суточная производительность:
Месячная производительность:
Результаты расчета производительности МНЛЗ сведены в табл. 4.1
Таблица 4.1. Производительность МНЛЗ ОАО «Электросталь».
Наименование показателя
|
До модернизации
|
После модернизации
|
Годовая производительность,
т/год
|
200 000
|
260 000
|
Часовая
производителльность, т/час
|
23,8
|
30,95
|
Сменная
производителльность, т/смену
|
190,4
|
247,62
|
Суточная
производителльность, т/сутки
|
571,2
|
742,8
|
Месячная
производителльность, т/мес.
|
16 700
|
21 700
|
Переменные затраты - виды расходов, величина которых изменяется
пропорционально изменению объемов продукции (сумма затрат на сырье, основные и
вспомогательные материалы, топливо и все виды энергетических затрат (табл.
6.3)). Состав переменных затрат на 1 т продукции показан на рис. 4.2.
Постоянные затраты - затраты, которые не зависят от величины объёма
выпуска: заработная плата с начислениями в различные фонды, амортизация,
затраты на ремонт оборудования, общезаводские и цеховые расходы (табл. 4.2).
Таблица 4.2 Переменные затраты из расчета на производство 1 тонны
непрерывно-литой заготовки.
Поз.
|
Наименование статей
расходов
|
Сумма
|
1
|
Сырье и материалы
|
9 730,05
|
2
|
Футеровка
|
930,98
|
-
|
Отходы от пр-ва и брак ( -
)
|
- 91,59
|
3
|
Теплоэнергия (собст.
котельная).
|
7,95
|
4
|
Эл.энергия
|
1 305,71
|
5
|
Вода-водооборотный цикл
|
304,16
|
6
|
Кислород газообразный
|
531,79
|
7
|
Азот газообразный
|
1,90
|
8
|
Аргон газообразный
|
14,56
|
9
|
Сжатый воздух
|
45,08
|
10
|
Природный газ
|
93,68
|
11
|
Услуги по транспортировке
газа
|
7,16
|
|
Итого:
|
23 542,44
|
Увеличение объёмов производства приводит к уменьшению постоянных
расходов, приходящихся на единицу продукции, что повышает прибыль с единицы
продукции. На практике используется понятие условно-постоянные затраты, так
как, хотя данный вид расходов присутствует даже во время простоя предприятия,
их величина может быть изменена в зависимости от величины выбранного периода
времени.
В сумме переменные и постоянные затраты составляют общие (табл. 4.3).
Таблица 4.3. Условно-постоянные затраты из расчета на 1 месяц.
Поз.
|
Наименование статей
расходов
|
Сумма
|
1
|
Фонд оплаты труда основных
рабочих
|
4 500 000,00
|
2
|
Единый социальный налог
|
1 179 000,00
|
3
|
Цеховые расходы
|
37 148 456,83
|
|
Итого:
|
42 827 456,83
|
Таблица 4.4. Общие затраты при производстве непрерывно-литой заготовки.
|
До модернизации
|
После модернизации
|
Наименование статей
расходов
|
Сумма
|
|
На 1 тонну продукции
|
Объем выпуска (т/мес.)
|
|
|
16 700
|
21 700
|
Переменные затраты:
|
Сырье и материалы
|
9 730,05
|
162 491 835
|
210 810 180
|
Футеровка
|
930,98
|
15 541 366
|
20 202 266
|
Отходы от производства и
брак (-)
|
- 91,59
|
1 529 553
|
1 987 503
|
Теплоэнергия (собств.
котельная).
|
7,95
|
132 765
|
172 515
|
Электроэнергия
|
1 305,71
|
21 805 357
|
50 033 907
|
Вода (водооборотный цикл)
|
304,16
|
5 079 472
|
6 600 272
|
Кислород газообразный
|
531,79
|
8 880 893
|
11 539 843
|
Азот газообразный
|
1,90
|
31 730
|
41 230
|
Аргон газообразный
|
14,56
|
243 152
|
315 952
|
Сжатый воздух
|
45,08
|
752 836
|
978 236
|
Природный газ
|
93,68
|
1 564 456
|
2 032 856
|
Услуги по транспортировке
газа
|
7,16
|
119 572
|
155 372
|
Итого, переменных
|
12 881,41
|
215 119 547
|
279 526 597
|
Условно-постоянные
затраты(в мес.):
|
ФОТ - основных рабочих
|
4 500 000,00
|
ЕСН
|
1 179 000,00
|
Цеховые расходы
|
37 148 456,83
|
Итого условно-постоянных
|
42 827 456,83
|
Общие затраты:
|
Всего затрат на выпуск
|
257 947 000
|
322 354 100
|
в том числе на 1 тонну:
|
15 447,31
|
14 855,03
|
|
|
|
|
|
Оценка экономической эффективности от реализации проекта по модернизации
оборудования
Выход
продукта увеличился с 200 тыс. т/год до 250 тыс. т/год. Товарную продукцию (
) до и
после реализации проекта по увеличению производительности определяем по
формуле:
где Q
- количество выработанной продукции, т/сут.;
Ц
- цена целевого продукта
Таким
образом, товарная продукция до и после внедрения проекта по модернизации
составит:
Прибыль
(до и после внедрения проекта по модернизации) рассчитывается по формуле:
где СС
- общие затраты на производство продукции в сутки, руб./сут.
Рентабельность
основной продукции находим по формуле:
где Ц
- цена 1 т целевой продукции, руб./т;
С
- себестоимость продукции, руб./т
Таким
образом:
Прирост
прибыли от реализации проекта по увеличению производительности составит:
Таблица
4.5. Сравнение технико-экономических показателей работы литейно-прокатного
агрегата до и после внедрения проекта по модернизации.
Наименование показателей
|
До модернизации
|
После модернизации
|
Выработка целевой
продукции, т/год
|
200 000
|
250 000
|
Товарная продукция,
руб./сут
|
|
|
Себестоимость одной тонны
продукции, руб./т
|
15 447,31
|
|
Прибыль, руб./т
|
|
|
Численность персонала, чел.
|
150
|
150
|
Рентабельность целевой
продукции, %
|
6,5
|
10,1
|
Экономия от снижения себестоимости:
где С1 - себестоимость одной тонны продукции до внедрения проекта;
С2 - себестоимость одной тонны продукции после внедрения проекта;

-
выработка основной продукции после внедрения проекта.
Годовой
экономический эффект составит:
Процент
снижения себестоимости составит:
Прирост
прибыли (
) на весь
выпуск произойдёт за счёт снижения себестоимости тонны товарной продукции и
составит:
По
предварительным расчетам затраты на модернизацию (Зм) составят 2 500 000 руб.
Исходя из этого рассчитаем количество тонн товарной продукции, которое
необходимо произвести, чтобы покрыть затраты на модернизацию:
При
производительности 250 тыс. т/год затраты на внедрение проекта модернизации
окупятся за короткий период времени.
Таким
образом, приведённые выше технологические и экономические расчеты показали, что
в результате внедрения проекта модернизации производства с привлечением
незначительных дополнительных капиталовложений, производительность увеличится с
200 тыс. т/год до 260 тыс. т/год; сократится доля постоянных расходов в
структуре себестоимости продукции на 33%; себестоимость основного продукта
снизится на 4%.
Прирост
прибыли при работе модернизированного цеха с производительностью 260 тыс. т/год
составит 35 608 800 руб/год. Срок окупаемости проекта менее месяца.
За
базу для сравнения принимаем показатели оборудования, которое используется в
настоящее время на ОАО «Электросталь» в г. Электросталь.
Экономический
эффект от модернизации получается за счет повышения производительности и
соответствующего снижения условно-постоянной части расходов по переделу. Он
равен 153 922 800 тыс. руб.
На
основе полученных результатов и оценки состояния рынка производится построение
графика увеличения жизненного цикла продукта (рис. 4.5).
Рис.
4.5. График увеличения жизненного цикла продукта.
литейный прокатный кристаллизатор ролик
5. Охрана труда и экология
5.1 Анализ вредных и опасных факторов при работе ЛПА
ЛПА состоит из:
участка расплавки металла в индукционной печи;
кристаллизатора;
рольганга с правильными роликами;
индукторов для подогрева металла;
задающей клети;
планетарного стана;
группы чистовых клетей;
моталки;
склада готовой продукции.
Применение агрегата непрерывной разливки и прокатки стали существенно
улучшает условия труда в сравнении с существующей технологией за счет более
полной автоматизации и механизации всех процессов.
Однако, даже в полностью механизированном цехе вопросы охраны труда не
снимаются (хотя приобретают качественно новый характер), так как остаются
операторы, наладчики, ремонтники, обслуживающие производство постоянно или
периодически.
При эксплуатации данного агрегата возникает ряд опасных и вредных
факторов, которые необходимо предотвратить для обеспечения полной безопасности
обслуживающего персонала, а так же, для создания нормальных условий труда,
наиболее благоприятных для работающих.
Тепловое излучение
Температура металла во время разливки составляет примерно 1500 ºС. Во время прокатки она снижается до
1100-1150 ºС. Т.е. во время всего технологического процесса существует
опасность вредного воздействия тепловых лучей на человека, а так же случайного соприкосновения
его с раскаленным металлом.
Воздух рабочей зоны
Все технологические процессы производства чугуна, стали, цветных и редких
металлов, а также связанные с их последующей обработкой, сопровождаются
образованием значительных количеств аэрозолей и газов. В атмосферу цеха наряду
с пылью выносятся оксиды углерода и серы, соединения хлора, фтора и другие
составляющие перерабатываемого сырья. Их количество зависит от
металлургического процесса, его интенсивности, конструкции агрегата,
физико-химической характеристики компонентов шихты и других факторов.
Производства черной металлургии по убыванию вредности загрязнителей воздуха
располагаются в следующей последовательности: агломерационное, коксохимическое,
доменное, сталеплавильное, прокатное и пр.
Т.к. ЛПА совмещает в себе сталеплавильное и прокатное производство, то
выделение вредных веществ в атмосферу цеха происходит в достаточно значительной
степени.
В связи с тем, что требование полного отсутствия токсичных веществ на
рабочих местах часто нереально или трудно выполнимо, особую значимость
приобретает гигиеническая регламентация содержания вредных веществ в воздухе
рабочей зоны (ГОСТ 12.1.005-88). Вредные вещества могут привести к нарушению
здоровья, если их концентрация в воздухе превышает определенную для данного
вещества величину - ПДК. Предельно допустимая концентрация вредного вещества в
воздухе рабочей зоны (ПДК) - концентрация, которая при ежедневной 8-ч работе в
течение всего рабочего стажа не может вызвать заболевания или отклонения в
состоянии здоровья работающего или его потомства. Для веществ, обладающих
действием на кожу, обосновывается предельно допустимый уровень загрязнения ими
кожи, мг/м3 в соответствии с ГН 2.2.5.563-96.
В качестве технических мер защиты от вредных веществ в нашем случае можно
применить: автоматизацию и дистанционное управление вредными технологическими
процессами, герметизацию печи, применение местных вытяжных устройств. Воздух
для приточной вентиляции должен быть достаточно чистым, при необходимости
очищенным. Общеобменная вентиляция применяется лишь в дополнение к местным
отсосам. Необходимы средства очистки воздуха, загрязненного пылью и газами.
СНиП 2.2.4.548-96 - Устанавливают гигиенические требования к показателям
микроклимата рабочих мест производственных помещений с учетом интенсивности
энергозатрат работающих, времени выполнения работы, периодов года и содержат
требования к методам измерения и контроля микроклиматических условий.
Показатели микроклимата должны обеспечивать сохранение теплового баланса
человека с окружающей средой и поддержание оптимального или допустимого
теплового состояния организма. Показателями, характеризующими микроклимат в
производственных помещениях, являются:
температура воздуха;
температура поверхностей;
относительная влажность воздуха;
скорость движения воздуха;
интенсивность теплового облучения.
Но рекомендуется придерживаться оптимальных показателей микроклимата на
рабочих местах производственных помещений, т.к. они более приемлемы для работы
человека.
.2 Производственное освещение, шум, вибрация
Естественное и искусственное освещение нормируется по СНиП 23.05-95.
Производственные здания и рабочие площадки металлургических предприятий
освещаются естественным светом небосвода (прямым и отраженным) и искусственным
от электроламп, а также совмещенным. Освещение должно обеспечивать санитарные
нормы освещенности на рабочих местах, равномерную яркость, отсутствие резких
теней и блесткости, постоянство освещенности во времени и правильность
направления светового потока.
Проектом предусмотрено два вида освещения: рабочее и аварийное. Аварийное
освещение предусмотрено для продолжения работ при аварийном отключении рабочего
освещения, а также для эвакуации людей в случае пожара или аварии. Минимальная
освещенность при этом принята не менее 10% от нормируемой рабочей освещенности
Наиболее характерным из вредных факторов работы прокатного стана является
шум.
СНиП 2.2.4/2.1.8.562-96 - данный документ регламентирует шум на рабочих
местах, в помещениях жилых, общественных зданий на территории застройки.
Шумы возникают в результате работы электродвигателей, узлов стана,
перемещения бунтов катанки, плавки стали и т.п. Наиболее сильным по
интенсивности является непосредственно сама прокатка из-за технологических
особенностей планетарной прокатки.
Постоянный шум характеризуется уровнем звукового давления в октановых
полосах со среднегеометрическими частотами.
Шум не только ухудшает внимание работников, но и утомляет их. При
превышении допустимого уровня шум может создать условия невозможные для работы.
В нашем цехе шум можно охарактеризовать как постоянный, широкополосный,
низкочастотный (от 500 Гц до 1 кГц) со звуковым давлением 134 дБ, что превышает
предельно допустимый уровень звука в 85 дБ, устанавливаемый СНиП
2.2.4/2.1.8.562-96.
С целью защиты от шума необходимо:
рабочим обязательно применение СИЗ: берушей, наушников, шлемов.
СНиП 2.2.4/2.1.8.566-96 устанавливают классификацию, нормируемые
параметры, предельно допустимые значения производственных вибраций.
Постоянные вибрации могут вызвать виброболезнь, проявляющуюся в патологии
сосудов конечностей, подверженных вибрациям. При виброболезни происходит
сужение сосудов, в результате чего ухудшается снабжение кровью конечностей.
Виброболезнь усугубляется в холоде. Сотрясение организма при частотах колебания,
совпадающих с собственными частотами органов, приводит к их травмам.
При работе прокатного стана неизбежно возникают вибрации. Их вызывают
вращающиеся с большой скоростью части оборудования, движения и удары заготовок,
различные технологические процессы в машинах и агрегатах. В связи с
технологическими особенностями планетарной прокатки вибрацию можно
охарактеризовать как общую постоянную, низкочастотную. Или, согласно СНиП
2.2.4/2.1.8.566-96 - общая вибрация 3 категории (технологическая вибрация, воздействующая
на человека на рабочих местах стационарных машин или передающаяся на рабочие
места, не имеющие источников вибрации).
При частотном (спектральном) анализе нормируемыми параметрами являются
средние квадратические значения виброскорости (ν) и виброускорения (α)
В нашем случае для снижения вибрации применяются следующие методы:
балансировка неуравновешенных вращающихся масс, нанесение на вибрирующие
поверхности вязкоупругих материалов, применение виброизоляции.
Расчет освещения рабочего места конструктора.
Измерение и оценка освещенности проводились в соответствии со СНиП
23-05-95 «Нормы проектирования. Естественное и искусственное освещение», ГОСТ
17677-82 «Светильники. Общие технические условия», ГОСТ 24940-97 «Здания и
сооружения. Методы измерения освещенности».
На рабочем месте используется совмещенное освещение, т.е. сочетание
естественного и искусственного освещения.
Источником искусственного освещения на рабочем месте
инженера-конструктора являются 6 светильников, имеющие по одной люминесцентной
лампе ЛБ40, расположенные в 2 ряда по 3 светильника каждый (высота подвеса
светильника h1св = 2,5 м), а также 2 светильника, расположенные непосредственно
на рабочих столах (высота подвеса светильника h2св = 0,5 м).
Система искусственного освещения - комбинированная.
Стены помещения обиты светлыми панелями, потолок окрашен белой краской.
В соответствии со СНиП 23-05-95 для II б разряда зрительной работы в
операторской комнате Енорм=500 лк.
Расчет освещения производится для комнаты площадью S=30 м2, длина которой
а =6,0 м, ширина в =5,0 м, высота h=3,45 м.
Световой поток одной лампы ЛБ 40 составляет Fл,= 3000 лм [2].
Рассчитаем фактическую освещенность на рабочем месте с помощью точечного
метода расчета [7] по формуле
где - коэффициент добавочной освещенности, = 1,3;
- условная освещенность, определяется по графику
пространственных изолюкс, зависящих от высоты подвеса светильника и расстоянии
от проекции оси светильника до расчетной точки, лк;- световой поток лампы ЛБ
40, лм;
Кз - коэффициент запаса, учитывающий снижение освещенности, вследствие
старения ламп, запыления и загрязнения светильников, Кз = 1,5.
Определим расстояние L, м, от проекции светильников до расчетной точки=
0,= 1,5 м,= 3,0 м,= 2,0 м,=
2,5 м,=
3,6 м,= 0,= 3,0 м.
= 180 лк.
Фактическая освещенность на рабочем месте по формуле составит:
лк.
На данном рабочем месте инженера-конструктора производственная
освещенность, равная Еф= 465 лк, не соответствует нормативному значению
Енорм=500 лк. Таким образом, необходимо разработать мероприятия по улучшению
уровня освещенности.
В качестве естественного освещения на рабочем месте инженера используется
боковое освещение. Имеется два оконных проема, каждый из которых 2 м в ширину.
=EBH/EHAP*100,
Естественная освещенность замеряется с помощью люксметра Ю-116 на
расстоянии 1, 2, 3, 4, 5 метра от окна. Измерения производят в светлое время
суток, в солнечную погоду. Точки замера естественной освещенности в помещении
указаны в Приложении В. По формуле (4) для каждой из точек подсчитываем
значение коэффициента естественной освещенности (КЕО).
где ЕВН, ЕНАР - соответственно освещенности внутри здания и снаружи.
Освещенность, измеренная с помощью люксметра Ю-116 снаружи здания,
составляет ЕНАР=10400 лк
Результаты измерений и расчетов естественной освещенности представлены в
таблице и на рисунке 5.1.
Таблица 5.1. Зависимость коэффициента естественного освещения от
расстояния до окна
Расстояние от окна L, м
|
Коэффициент естественного
освещения (КЕО), %
|
Норматив КЕО, %, согласно
СниП 23-05-95
|
0
|
820
|
7,9
|
4,2
|
1
|
630
|
6,06
|
4,2
|
2
|
540
|
5,2
|
4,2
|
3
|
390
|
3,75
|
4,2
|
4
|
270
|
2,6
|
4,2
|
5
|
210
|
2,02
|
4,2
|
Нормируемое значение
КЕОнор=4,2
=КЕОнор-КЕОфак = 4,2-2,6 = 1,6
5.3 Электробезопасность
Электрические установки представляют большую потенциальную опасность,
обусловленную тем обстоятельством, что органы чувств человека не могут на
расстоянии обнаружить наличие электрического напряжения на оборудовании.
В работе ЛПА участвует достаточно много различных электроустановок.
Наиболее мощными из них являются привода планетарной клети, задающей клети и
индукционная сталеплавильная печь. Сепараторы планетарной клети приводятся во
вращение от двух двигателей постоянного тока типа ДП-92 мощностью 135 кВт при
напряжении 220 В или 270 кВт при напряжении 440 В. Двигатель привода задающей
клети постоянного тока типа ДП-42 мощностью 21 кВ.
Все это обуславливает необходимость обязательного соблюдения правил по
охране труда (правила безопасности) при эксплуатации электроустановок ПОТ
РМ-016-2001 РД 153-34.0-03.150-00.
Электрооборудование стана должно соответствовать ГОСТ 12.2.007.10-87,
ГОСТ 12.2.007.0-78 и ГОСТ 12.1.019-79. Должны быть предусмотрены места
независимого защитного заземления стана, электродвигателей, пульта, шкафов
управления, нагревательного трансформатора. Места заземления должны иметь
специальные знаки, обозначенные согласно указаниям на чертежах.
Изоляция токоведущих частей электрооборудования стана выполняется в
соответствии с ГОСТ 21657-83.
Сопротивление изоляции в любой точке электрооборудования, не соединенного
электрически с землей, должно быть не ниже 1 МОм, а изоляция электрических
машин - не менее 0.5 МОм. Для аварийного выключения стана на пульте управления
должна быть предусмотрена кнопка ручного управления аварийной остановки всех
типов приводов стана «Стоп аварийный». Схема электроприводов должна
обеспечивать защиту от самопроизвольного включения всех механизмов стана при
восстановлении внезапно исчезнувшего напряжения.
Двери шкафов управления станом должны закрываться на ключ и на ее
наружной стороне должен быть знак электрического напряжения, обозначенный по
ГОСТ 12.4.026-76.
Все электродвиатели стана должны иметь автоматические выключатели,
выполняющие так же роль предохранителей при перегрузке двигателей по
максимальному току.
В ЛПА используются индукционные печи, трансформаторы и т.п. Все это
является источником электромагнитных полей и может явиться причиной
профессиональных заболеваний. Опасность воздействия ЭМП усугубляется тем, что
они не обнаруживаются органами чувств.
СанПиН 2.2.4.1191-03 устанавливают санитарно-эпидемиологические требования
к условиям производственных воздействий ЭМП.
В нашем случае для защиты персонала от ЭМП можно применить следующие
способы и средства: дистанционное управление, экранирование рабочего места,
рациональное размещение оборудования в рабочем помещении, применение СИЗ.
5.4 Травмобезопасность
Травмы работников прокатного цеха могут возникнуть в результате:
наезда транспорта межцехового сообщения и ПТМ;
неудовлетворительного содержания рабочего места;
нарушения технологического процесса;
неисправности в работе оборудования;
нарушения правил техники безопасности.
Для предотвращения травм предъявляются следующие требования безопасности
к конструкции стана:
. В стане должны быть электрические и механические блокировки,
исключающие аварии и поломки механизмов, обеспечена возможность быстрой
остановки стана.
. Все муфты и смежные зубчатые колеса должны быть закрыты защитными
кожухами, сетчатыми или сплошными в соответствии с ГОСТ 9.032-74, ГОСТ
9.104-79, ГОСТ 15150-69.
. Все площадки, лежащие ниже уровня пола, должны быть перекрыты настилами
и плитами, имеющими рифленую поверхность. Опасные участки стана должны иметь
сетчатые ограждения.
. Органы управления должны быть снабжены надписями и символами,
указывающими объект, к которому они относятся.
. Органы управления станом должны размещаться на пульте управления в
соответствии с ГОСТ 22269-76.
. Символы органов управления производственным оборудованием должны быть в
соответствии с ГОСТ 124.040-76.
. Рабочее место оператора должно быть расположено вне стана.
. На деталях и сборочных единицах стана массой более 50 кг должны быть
предусмотрены специальные захватные устройства для строповки при
транспортировке и монтаже.
. Оборудование стана должно быть окрашено в соответствии с ГОСТ 9.032-74,
ГОСТ 9.104-79, ГОСТ 15150-69.
5.5 Пожарная безопасность
Строительные материалы по стойкости к действию огня делятся согласно СНиП
2.01.02-85 на три группы:
несгораемые;
трудносгораемые;
сгораемые.
Производственные здания прокатных цехов выполняют из несгораемых
материалов, сохраняющих постоянную массу при действии огня, металла, бетона,
кирпича, гипсовых и гипсоволоконных плит. Ниже приводится характеристика
данного производства с точки зрения пожарной безопасности.
Характеристика производства
|
Категория производства
|
Характеристика используемых
веществ
|
Пожароопасное
|
Г
|
Несгораемые вещества в
горячем, раскаленном или расплавленном состоянии, процесс обработки которых
сопровождатся выделением пламени
|
Необходимая огнестойкость зданий прокатных цехов определяется в
соответствии со СНиП 2.01.02-85 с учетом категории производства, этажности
здания и его площади. Вышеуказанные нормы предусматривают пять степеней
огнестойкости здания, которые определяются огнестойкостью элементов зданий.
Здания прокатных и механических цехов выполняются не ниже 2-ой степени
огнестойкости. В соответствии с ГОСТ 12.1.004-91: «ССБТ пожарная безопасность.
Общие требования» вероятность возникновения пожара в течение года не должна
превышать 10-6.
Обеспечение пожарной безопасности промышленных предприятий достигается
строгим соблюдением пожарных требований, регламентированных СНиП 20.90-2-85 и
СНиП 2.01.02-85, требований пожарной безопасности для промышленных предприятий,
правилами устройства электроустановок.
Для тушения пожара линия прокатки оборудована порошковыми огнетушителями,
предназначенными для тушения различных материалов, установок (в том числе
находящихся под напряжением до 1000 В).
5.6 Оценка труда литейщика
Оценку труда проводим по Руководству Р 2.2.2006-05 «Руководство по
гигиенической оценке факторов рабочей среды и трудового процесса. Критерии и
классификации условий труда», раздел 5.10 «Тяжесть и напряженность трудового
процесса»
Классы условий труда по показателям тяжести трудового процесса:
Показатели тяжести
трудового процесса
|
Значение параметра
|
Классы условий труда
|
1. Физическая динамическая
нагрузка (единицы внешней механической работы за смену, кг х м)
|
1.1. Физическая
динамическая нагрузка (единицы внешней механической работы за смену, кг х м)
|
до 2 500 кг х м
|
2
|
1.2.1. При перемещении груза
на расстояние от 1 до 5 м.
|
до 12 500 кг х м
|
1
|
1.2.2. При перемещении
груза на расстояние более 5 м.
|
до 24 000 кг х м
|
1
|
2. Масса поднимаемого и
перемещаемого груза в ручную (кг)
|
2.1. Подъем и перемещение
(разовое) тяжести при чередовании с другой работой(до 2х раз в час)
|
до 15 кг
|
2
|
2.2. Подъем и перемещение
(разовое) тяжести в течение рабочей смены
|
до 15 кг
|
2
|
2.3.Суммарная масса грузов,
перемещаемых в течении каждого часа смены
|
|
|
2.3.1.С рабочей поверхности
|
250 кг
|
1
|
2.3.2. С пола
|
до 100 кг
|
1
|
3.Стереотипные рабочие
движения (количество за смену)
|
3.1. При локальной нагрузке
(с участием мышц кистей и пальцев рук)
|
40 000
|
2
|
3.2. При региональной
нагрузке(при работе с преимущественным участием мышц рук и плечевого пояса)
|
20 000
|
2
|
4. Статическая нагрузка -
величина статической нагрузки за смену при удержании груза, приложение усилий
(кгс х с)
|
4.1.Одной рукой
|
до 36 000
|
2
|
4.2.Двумя руками
|
до 70 000
|
2
|
4.3.С участием мышц корпуса
|
|
|
5. Рабочая поза
|
5.1. Рабочая поза
|
Периодическое, до 50%
времени смены, нахождение в неудобной и/или фиксированной позе; Пребывание в
вынужденной позе (на коленях, на корточках, и т.п.)до 25% времени смены.
Нахождение в позе стоя до 80% времени смены.
|
3.1.
|
6. Наклоны корпуса
|
6.1. Наклоны корпуса.
|
51 - 100
|
2
|
7. Перемещение в
пространстве, обусловленные технологическим процессом, км
|
7.1. По горизонтали
|
до 8
|
2
|
7.2. По вертикали
|
до 2,5
|
2
|
Классы условий труда по показателям напряженности трудового процесса.
Показатели напряженности
трудового процесса
|
Значение параметра
|
Классы условий труда
|
Интеллектуальные нагрузки
|
1.1. Содержание работы
|
Решение простых задач по
инструкции
|
2
|
1.2. Восприятие
сигналов(информации) и их оценка.
|
Восприятие сигналов с
последующей коррекцией действий и операций
|
2
|
1.3. Распределение функций
по степени сложности задания
|
Обработка, выполнение
задания и его проверка.
|
2
|
1.4. Характер выполняемой
работы
|
Работа по установленному
графику с возможной его коррекцией по ходу деятельности.
|
2
|
Сенсорные нагрузки.
|
2.1. Длительность
сосредоточенного наблюдения (% времени от смены)
|
51-75
|
3.1
|
2.2. Плотность
сигналов(световых, звуковых) и сообщений в среднем за час работы
|
76-175
|
3.1
|
2.3. Число производственных
объектов одновременного наблюдения
|
6-10
|
1
|
2.4.Размер объекта
различения в мм при длительности сосредоточенного наблюдения (% от времени
смены)
|
5-1,1 мм - более 50%; 1-0,3
мм - до 50% Менее 0,3 мм - до 25%
|
2
|
2.5. Работа с оптическими
приборами при длительности сосредоточенного наблюдения(% времени смены)
|
до 25
|
1
|
2.6. Наблюдение за экранами
видеотерминалов (часов в смену)
|
до 2
|
1
|
2.7. Нагрузка на слуховой
анализатор
|
Разборчивость слов и
сигналов от 70 до 50 %. Имеются помехи, на фоне которых речь слышна на
расстоянии 2 м
|
3.1
|
2.8. Нагрузка на голосовой
аппарат (суммарное количество часов, наговариваемое в неделю)
|
до 20
|
2
|
Эмоциональные нагрузки
|
3.1. Степень
ответственности за результат собственной деятельности. Значимость ошибки.
|
Несет ответственность за
функциональное качество вспомогательных работ (заданий). Влечет за собой
дополнительные усилия со стороны вышестоящего руководства
|
2
|
3.2. Степень риска для
собственной жизни
|
вероятна
|
3.2
|
3.3. Степень
ответственности за безопасность других лиц
|
возможна
|
3.2
|
3.4. Количество конфликтных
ситуаций, обусловленных профессиональной деятельностью, за смену
|
1-3
|
2
|
Монотонность нагрузок
|
4.1. Число элементов,
необходимых для реализации простого задания ли в многократно повторяющихся
операциях.
|
9-6
|
2
|
4.2. Продолжительность (в
сек) выполнения простых заданий или повторяющихся операций
|
более 100
|
1
|
4.3. Время активных действий(
в % от смены). В остальное время - наблюдение за ходом производственного
процесса
|
19-10
|
2
|
4.4. Монотонность
производственной обстановки (% от времени смены)
|
менее 75
|
1
|
Режим работы
|
5.1. Фактическая
продолжительность рабочего дня
|
8-9 ч.
|
2
|
5.2. Сменность работы
|
Трехсменная работа (работа
в ночную смену)
|
3.1
|
5.3. Наличие
регламентированных перерывов и их продолжительность
|
Перерывы регламентированы,
недостаточной продолжительности: от 3 до 7% рабочего времени.
|
2
|
|
|
|
|
|
Итак,
из всех показателей, характеризующих напряженность труда, 5 относятся к классу
3.1 <#"810321.files/image345.jpg">
Рис. П.1. Новый кристаллизатор
Рис. П.2. Барабан летучих ножниц
Рис. П.3. Барабаны верхний и нижний летучих ножниц
Рис. П.4. Механизм резания летучих ножниц
Рис. П.5. Вал летучих ножниц
Рис. П.6. Летучие ножницы
Рис. П.7. Опорный ролик МНЛЗ
Рис. П.8. Кристаллизатор
Рис. П.9. Маршрут изготовления опорного ролика