Энергетическая установка танкера дедвейтом 7000 т
СОДЕРЖАНИЕ
Список сокращений
Введение
. Описание судна
. Выбор главного двигателя
. Расчет валопровода
. Проектирование систем
. Анализ ресурсов и выбор схемы утилизации тепловых потерь ГД
. Выбор вспомогательных и утилизационного котла
. Опреснительная установка
8. Судовая электростанция
9. Обоснование компоновки и расположения оборудования судовой
энергетической установки
. Монтаж оборудования
. Защита окружающей среды при эксплуатации СЭУ
. Оценка экономической эффективности СЭУ
Заключение
РЕФЕРАТ
Данный проект содержит листов, 12
рисунков, 25 таблиц, 3 приложения.
ЭНЕРГЕТИЧЕСКАЯ УСТАНОВКА, СИСТЕМЫ
СЭУ, АВТОМАТИЗИРОВАННОЕ ПРОЕКТИРОВАНИЕ, АГРЕГАТИРОВАНИЕ, ОБОРУДОВАНИЕ,
ОПТИМИЗАЦИЯ, МОДУЛЬ, МОДЕЛИРОВАНИЕ, БЛОЧНАЯ КОМПОНОВКА, ФУНКЦИОНАЛЬНЫЙ БЛОК.
Объектом разработки является СЭУ
танкера, расположение энергетического оборудования в машинно-котельном
отделении судна.
Цель работы: разработать
энергетическую установку танкера, изучить типы расположения оборудования и
выбрать оптимальный. Оценить экономическую эффективность выбранной установки.
Проектирование ЭУ выполнялось с
помощью программ САПР СЭУ. Выбор расположения оборудования осуществлялся с
помощью методов компьютерного проектирования, на основе предыдущих разработок.
Метод таблиц относительных координат и абсолютных габаритов позволяет перенести
на новое проектирование опыт, накопленный предыдущими поколениями
проектировщиков. Метод визуализации позволяет проверить допустимость
расположения на любом сечении помещения МКО.
СПИСОК СОКРАЩЕНИЙ
СЭУ - судовая энергетическая
установка
МКО - машинно-котельное отделение
САПР ЭУ - система
автоматизированного проектирования энергетических установок
СЭС - судовая электростанция
ГД - главный двигатель
МОД - малооборотный двигатель
СОД - среднеоборотный двигатель
МДМ - максимальная длительная
мощность
ОДР - область допустимых режимов
ПК - пропульсивный комплекс
ОУ - опреснительная установка
ЦПУ - центральный пост управления
ВКУ - вспомогательная котельная
установка
ВПГ - вспомогательный парогенератор
ГРЩ - главный распределительный щит
РКД - рабоче-конструкторская
документация
ВВЕДЕНИЕ
Судовая энергетическая установка
(СЭУ) предназначена для обеспечения движения судна и снабжения необходимой
энергией всех судовых потребителей. За счет выработки в необходимом количестве
трех видов энергии - механической, электрической и тепловой, СЭУ обеспечивает
функционирование судна по прямому назначению - перевозку грузов и различной
техники, работу других подсистем судна, жизнедеятельность людей на судне -
экипажа и пассажиров. Основные качества транспортных судов - безопасность
плавания, мореходность и провозоспособность - в значительной мере
обеспечиваются СЭУ. От СЭУ также существенно зависят экономические показатели
транспортного судна, уровень его строительной стоимости и текущих
эксплуатационных затрат.
Затраты на СЭУ составляют 20-35%
общей строительной стоимости судна и 35-50% затрат на содержание судна на ходу.
В связи с этим проектирование СЭУ является одним из важнейших этапов
проектирования судна в целом.
Основными направлениями развития СЭУ
являются: снижение затрат на топливо и затрат труда на обслуживание, увеличение
экономичности СЭУ, повышение эффективности использования судов.
СЭУ представляет собой комплекс
технических средств, обеспечивающих:
Взаимодействие главного двигателя и
движителя (гребного винта) для обеспечения движения судна;
Выработку энергии и передачу ее ко
всем судовым потребителям;
Функционирование общесудовых систем
и устройств, включая бытовые системы, обеспечивающие условия обитаемости в
служебных и жилых помещениях.
В данном проекте представлен расчет
энергетической установки. Исходя из основных габаритов судна, его назначения и
дальности плавания подобран главный двигатель, вспомогательный двигатель,
утилизационный котел и оборудование. При расчетах использован комплекс программ
САПР ЭУ. Разработаны схемы расположения оборудования в МКО.
1. ОПИСАНИЕ СУДНА
Тип судна - танкер, предназначенный
для перевозки на коротких линиях нефтепродуктов, в основном топлив и смазочных
масел, а так же сырой нефти, с возможностью одновременной перевозки и выгрузки
до пяти сортов топлива.
В качестве корпуса приняты
характеристики корпуса танкера проекта 17120. Архитектурно- конструктивный тип
танкера: одновинтовое, однопалубное судно с баком и ютом, кормовым
расположением энергетической установки, жилых помещений и постов управления, с
двойным дном, двойными бортами и одной продольной переборкой в грузовой части.
Судно проектируется в соответствиями
с Правилами Морского Регистра Судоходства России на классе КМ*Л2 IAI.
Район плавания неограниченный.
Водоизмещение
|
D=10 300 т
|
Дедвейт
|
Dw=7 000 т
|
Эксплуатационная скорость
|
Us=14,2 уз
|
Наибольшая длина
|
Lmax=109,0 м
|
Длина между перпендикулярами
|
Lпп=102,0 м
|
Наибольшая ширина
|
B=18,6 м
|
Расчетная осадка
|
T=7,0 м
|
Высота борта
|
Hб=9,5 м
|
Дальность плавания
|
L=6000 миль
|
Численность экипажа
|
20 чел
|
Мощность СЭС
|
Pэл=500 кВт
|
Автономность плавания по запасам
топлива и провизии составляет 60 суток.
Остойчивость судна при всех
эксплуатационных случаях нагрузки, включая случаи частичного заполнения танков,
а также при погрузке/выгрузке одновременно всех танков удовлетворяет Правила
Регистра.
Для обеспечения непотопляемости
корпус судна разделен на 8 водонепроницаемых отсеков. Непотопляемость
обеспечивается во всех случаях нагрузки в соответствии с Правилами Регистра.
. ВЫБОР ГЛАВНОГО ДВИГАТЕЛЯ
Одной из основных задач
проектирования СЭУ является правильный выбор главного двигателя.
Исходными данными для этого служат:
тип и назначение судна, районы плавания, режимы работы установки, условия
размещения двигателя, а так же требования Регистра.
Основными требованиями к ГД являются
достаточная для обеспечения заданной скорости полного хода мощность и
массогабаритные показатели. При удовлетворении этих требований на выбор типа
двигателя могут влиять:
конструктивные особенности,
обеспечивающие удобство монтажа и обслуживания в условиях судна;
показатели надежности (ресурс,
вероятность безотказной работы и трудоемкость технического обслуживания),
влияющие на стоимость ремонтов и время использования двигателя по назначению в
период срока службы;
стоимость создания и экономичность
режимов, наиболее характерных для эксплуатации судна;
возможность работы на экономичных
сортах топлива и масел;
виброакустические характеристики
судна;
длительность реверса.
В судостроении применяются в
качестве главных двигателей: дизельные, паротурбинные, газотурбинные и
комбинированные установки.
На танкерах применяется в основном
дизельная установка. Для данного проекта можно применить установки с МОД или с
СОД.
Установки с СОД характеризуют:
широкие возможности расположения дизелей в МКО, высокая экономичность при
работе на промежуточных режимах, меньшие массогабариты по сравнению с МОД.
Недостатки - большое количество цилиндров, требующих обслуживания при
проведении плановых осмотров и ремонтов, повышенная шумность и необходимость
применения редуктора.
Установки с МОД обладают высокой
экономичностью, большими агрегатными мощностями и моторесурсом, могут работать
на тяжелом топливе. Но установки с МОД имеют неблагоприятные массогабаритные
показатели.
В данном проекте выбрана установка с
МОД. Это связано с конструктивной простотой и высокой надежностью передачи,
высоким КПД передачи (частично компенсирующим снижение пропульсивного КПД),
низкими расходами на эксплуатационное обслуживание.
Главный двигатель и оборудование
выбрано с помощью программного комплекса WYBOR2001.
Определяется сопротивление движению
судна с заданной скоростью. Для работы комплекса необходимо в таблице исходных
данных указать сопротивление движению судна. Расчеты сопротивления на основе
модельных испытаний производятся с учетом допущений, которые приводят к
погрешностям до 20-30%. Поэтому в данном случае целесообразней будет рассчитать
сопротивление, исходя из имеющихся данных о судне, взятом за прототип.
кН
Далее следует решить
вопрос о числе винтов, создающих упор, обеспечивающий движение судна. Основным
критерием такого выбора является удельная нагрузка на винт - отношение упора,
создаваемого винтом к площади его диска. На морских транспортных судах осадка
судна, ограничивающая диаметр винта, значительна, поэтому удельная нагрузка
далека от предельных значений и по нагрузке может быть применен один винт,
перерабатывающий весь упор движущий судно с высоким К.П.Д. В данном случае
принимаем один винт, как и в судне прототипе.
Определение главного
параметра выбора двигателя - его эффективной мощности, измеряемой на выходном
фланце двигателя.
Мощность может быть
найдена с использованием зависимости:
кВт
где kз - коэффициент
запаса мощности, отражающий возможное возрастание сопротивления, например, при
движении в сложных метеорологических условиях;- сопротивление движению судна,
приходящееся на анализируемый винт, кН; - скорость движения судна, м/с;
- пропульсивный
коэффициент;
Мощность энергетической
установки судов ледового плавания должна быть не меньше определенной по
следующим зависимостям, принятым в соответствии с Правилами Регистра РФ:
где f1 - коэффициент
влияния типа винта. В случае применения ВФШ f1=1,1. В случае применения ВРШ
f1=0,9;- коэффициент влияния типа носового образования.
В любом случае
произведение
должно
быть не менее 0,85;- коэффициент влияния ширины корпуса:
- ширина судна, м;и Ne0-
коэффициент, отражающие влияние категории ледового усиления и водоизмещения
приведены в табл.1
Таблица 1.
Коэффициенты,
учитывающие влияние ледового класса
Ограничение
|
Параметр
|
Категория ледового усиления
|
|
|
ЛУ2
|
ЛУ3
|
ЛУ4
|
ЛУ5
|
ЛУ6
|
ЛУ7
|
ЛУ8
|
ЛУ9
|
Dт
|
f4
|
0,18
|
0,22
|
0,26
|
0,3
|
0,36
|
0,42
|
0,47
|
0,5
|
|
Ne0, кВт
|
0
|
370
|
740
|
2200
|
3100
|
4000
|
5300
|
7500
|
D>т
|
f4
|
0,11
|
0,13
|
0,15
|
0,2
|
0,22
|
0,24
|
0,25
|
0,26
|
|
Ne0, кВт
|
2100
|
3070
|
4040
|
5200
|
7300
|
9400
|
11600
|
14700
|
-
|
Neмин, кВт
|
740
|
740
|
1000
|
2600
|
3500
|
5000
|
7200
|
10000
|
В любом случае величина мощности
пропульсивного комплекса судна с ледовым классом не может быть меньше
указанного в последней строке табл.1.
Производится проверка допустимости
ПК по удельной нагрузке на винты:
где Dв - диаметр винта;р
- расчетная осадка судна;- допустимое отношение диаметра винта к осадке.
Значение kD определяется формой кормового образования судна и расположением
винта относительно диаметральной плоскости. Для речных судов kD = 0,7 - 0,8 -
для не буксирных судов с простой формой кормы, 1 - для тех же судов с
туннельной кормой и 1,1 - 1,15 - для буксиров - толкачей с туннельными
обводами. Меньшие значения соответствуют винтам, расположенным по бортам,
большие - винтам, расположенным в диаметральной плоскости. Для морских судов kD
= 0,6 - 0,65 в случае применения двухвальной установки и 0,7 - 0,75 для
одновальной установки;уддоп- максимально допустимое значение удельной нагрузки
на лопасти винтов. Его значение можно принять в пределах 180 для буксиров
толкачей и 260 для не буксирных судов, кВт/м2.
В случае если полученные
значения превосходят допустимые, то число движителей следует увеличить.
Найденная эффективная
мощность позволяет выбрать двигатель из типоразмерного ряда малооборотных или
среднеоборотный двигателей.
В табл.2 приведены
характеристики типоразмерного ряда малооборотных дизелей типа
МС фирмы MAN.
На двигатели этой фирмы
приходится до 70% продаж малооборотных дизелей на мировом рынке. Данные
относятся к типоразмерному ряду 2002 года.
Таблица 2 Характеристики
типоразмерного ряда ДВС типа МС
J
|
Марка
|
Nц
|
Zц
|
Dц
|
Sц
|
n max
|
n min
|
bе
|
Pе max
|
Pе min
|
1
|
2
|
3
|
4
|
5
|
6
|
7
|
8
|
9
|
10
|
11
|
1
|
K98MC
|
5720
|
6-14
|
0,98
|
2,66
|
94
|
84
|
0,171
|
18,2
|
14,6
|
2
|
K98MC-C
|
5710
|
6-14
|
0,98
|
2,4
|
104
|
94
|
0,171
|
18,2
|
14,6
|
3
|
S90MC-С
|
4890
|
6-9
|
0,9
|
3,188
|
76
|
61
|
0,167
|
19
|
15,2
|
4
|
L90MC-С
|
4880
|
6-12
|
0,9
|
2,916
|
83
|
62
|
0,167
|
19
|
12,2
|
5
|
K90MC
|
4570
|
4-12
|
0,9
|
2,55
|
94
|
71
|
0,171
|
18
|
11,5
|
6
|
K90MC-C
|
4570
|
6-12
|
0,9
|
2,3
|
104
|
89
|
0,171
|
18
|
14,4
|
7
|
S80MC-С
|
3880
|
6-8
|
0,8
|
3,2
|
76
|
57
|
0,167
|
19
|
11,5
|
8
|
S80MC
|
3640
|
4-12
|
0,8
|
3,056
|
79
|
59
|
0,167
|
18
|
11,5
|
9
|
L80MC
|
3640
|
4-10
|
0,8
|
2,592
|
93
|
70
|
0,174
|
18
|
11,5
|
10
|
K80MC-C
|
3610
|
6-12
|
0,8
|
2,3
|
104
|
89
|
0,171
|
18
|
14,4
|
11
|
S70MC-C
|
3110
|
4-8
|
0,7
|
2,8
|
91
|
68
|
0,169
|
19
|
12,2
|
12
|
S70MC
|
2810
|
4-8
|
0,7
|
2,674
|
91
|
68
|
0,169
|
18
|
11,5
|
13
|
L70MC-С
|
3110
|
4-8
|
0,7
|
2,36
|
108
|
91
|
0,17
|
19
|
15,5
|
14
|
L70MC
|
2830
|
4-8
|
0,7
|
2,268
|
81
|
0,174
|
18
|
11,5
|
15
|
S60MC-C
|
2260
|
4-8
|
0,6
|
2,4
|
105
|
79
|
0,17
|
19
|
12,2
|
16
|
S60MC
|
2040
|
4-8
|
0,6
|
2,292
|
105
|
79
|
0,170
|
18
|
11,5
|
17
|
L60MC-С
|
2230
|
4-8
|
0,6
|
2,022
|
123
|
105
|
0,171
|
19
|
15,2
|
18
|
L60MC
|
1920
|
4-8
|
0,6
|
1,944
|
123
|
92
|
0,171
|
17
|
10,9
|
19
|
S50MC-C
|
1580
|
4-8
|
0,5
|
2
|
127
|
95
|
0,171
|
19
|
12,2
|
20
|
S50MC
|
1430
|
4-8
|
0,5
|
1,91
|
127
|
95
|
0,171
|
18
|
11,5
|
21
|
L50MC
|
1330
|
4-8
|
0,5
|
1,62
|
148
|
111
|
0,173
|
17
|
10,9
|
22
|
S46MC-С
|
1310
|
4-8
|
0,46
|
1,932
|
129
|
108
|
0,174
|
19
|
15,2
|
23
|
S42MC
|
1080
|
4-12
|
0,42
|
1,764
|
136
|
115
|
0,177
|
19,5
|
15,6
|
24
|
L42MC
|
995
|
4-12
|
0,42
|
1,36
|
176
|
132
|
0,1768
|
18
|
11,5
|
25
|
S35MC
|
740
|
4-12
|
0,35
|
1,40
|
173
|
147
|
0,178
|
19,1
|
15,3
|
26
|
L35MC
|
650
|
4-12
|
0,35
|
1,05
|
210
|
178
|
0,177
|
18,4
|
14,7
|
27
|
S26MC
|
400
|
4-12
|
0,26
|
0,98
|
250
|
212
|
0,179
|
18,5
|
14,8
|
Столбцы табл.2 содержат следующие
характеристики типоразмеров базовых цилиндров:
- J - нумерация типоразмеров
цилиндров;
- фирменное обозначение типоразмера
цилиндра, включающее буквенный и цифровой код. Последний отражает диаметр
цилиндра в сантиметрах. Буквенный код отражает принадлежность к ряду МС и
конструктивный тип цилиндра: S - сверхдлинноходовой (S/D >
), L - длинноходовой, K - с
нормальным отношением хода поршня к диаметру ок. 2.5, K - C - короткоходовой;
- максимальная длительная
цилиндровая мощность, кВт;
- допустимый диапазон числа
цилиндров в составе агрегата Zц;
- диаметр цилиндра, м;
- ход поршня, м;
- частота на режиме максимальной
длительной мощности(МДМ),об/мин;
- частота на нижней границе области
допустимых номинальных режимов (ОДР), об/мин;
- удельный расход топлива на режиме
МДМ, кг/кВт·час;
- среднее эффективное давление на
режиме МДМ (максимальное), бар;
- среднее эффективное давление на
нижней границе ОДР, бар.
Выбор главного двигателя из
типоразмерного ряда производится по максимальному режиму движения с наибольшей
скоростью (на режиме испытаний на скорость) в соответствии со следующей
зависимостью:
Для выбранного агрегата
главного двигателя необходимо рассчитать параметры длительного
эксплуатационного режима. На этом режиме для движения судна потребляется
мощность в соответствии со следующей зависимостью:
Это требуемая мощность,
определенная выше, но без учета коэффициента запаса мощности.
Для выбора допустимого
варианта данных таблицы 2 достаточно, но для выбора оптимального варианта из
допустимых нужны массогабаритные характеристики. Для определения массы и длины
агрегатов можно использовать линейные аппроксимации следующего вида:
где Gа и Lа - масса и
длина агрегата, включающего Zц одинаковых цилиндра; Gа6 и Lа6 - масса и длина
шестицилиндрового агрегата; Gц и Lмц - масса и межцентровое расстояние для
цилиндра данного типоразмера.
Коэффициенты
аппроксимационных зависимостей для определения массы и длины агрегатов МОД типа
МС в функции числа цилиндров приведены в таблице 3.
Таблица 3
Массогабаритные
характеристики двигателей типа МС
J
|
Марка
|
Gаб
|
Gц
|
Lаб
|
Lмц
|
Hгаб
|
Hрем
|
Bфр
|
1
|
2
|
3
|
4
|
5
|
6
|
7
|
8
|
9
|
1
|
K98MC
|
1143
|
163
|
12,865
|
1,75
|
13,9
|
15,1
|
4,64
|
2
|
K98MC-C
|
1102
|
157
|
12,865
|
1,75
|
13,49
|
14,53
|
4,37
|
3
|
S90MC-С
|
1074
|
156
|
12,087
|
1,602
|
11,6
|
16,23
|
5
|
4
|
L90MC-С
|
1077
|
160
|
12,4
|
1,602
|
14,7
|
15,6
|
4,936
|
5
|
K90MC
|
1074
|
149
|
12,38
|
1,602
|
13,75
|
15,82
|
4,936
|
6
|
K90MC-C
|
986
|
140
|
12,447
|
1,602
|
13,03
|
14,5
|
4,286
|
7
|
S80MC-C
|
872
|
108
|
10,899
|
1,424
|
12,95
|
16,04
|
5
|
8
|
S80MC
|
885
|
113,4
|
11,377
|
1,424
|
12,95
|
15,86
|
4,824
|
9
|
L80MC
|
791
|
107,5
|
11,232
|
1,424
|
11,52
|
13,78
|
4,388
|
10
|
K80MC-C
|
736
|
106,3
|
11,104
|
1,424
|
12,26
|
13,41
|
4,088
|
11
|
S70MC-C
|
555
|
74
|
8,971
|
1,19
|
11,64
|
13,92
|
4,39
|
12
|
S70MC
|
562
|
77,3
|
9,669
|
1,246
|
11,62
|
13,97
|
4,25
|
13
|
L70MC-С
|
538
|
71,8
|
8,971
|
1,19
|
11,36
|
12,55
|
3,842
|
14
|
L70MC
|
525
|
71
|
9,5
|
1,246
|
10,36
|
12,55
|
3,842
|
15
|
S60MC-C
|
358
|
51
|
7,688
|
1,02
|
10,08
|
11,95
|
3,77
|
16
|
S60MC
|
371
|
49,3
|
8,252
|
1,068
|
9,72
|
11,8
|
3,478
|
17
|
L60MC-C
|
347
|
49,5
|
7,688
|
1,02
|
8,2
|
11,08
|
3,228
|
18
|
L60MC
|
357
|
44,5
|
8,092
|
1,068
|
8,6
|
3,228
|
19
|
S50MC-C
|
207
|
29,5
|
6,392
|
0,85
|
7,88
|
10,04
|
3,15
|
20
|
S50MC
|
225
|
29,3
|
7,06
|
0,89
|
8,26
|
9,89
|
2,95
|
21
|
L50MC
|
215
|
28,3
|
7,06
|
0,89
|
7,24
|
8,77
|
2,71
|
22
|
S45MC
|
171
|
21
|
5,881
|
0,782
|
7,89
|
9,59
|
2,924
|
23
|
S42MC
|
143
|
20
|
5,694
|
0,748
|
6,92
|
8,95
|
2,67
|
24
|
L42MC
|
123
|
16,5
|
6,325
|
0,748
|
7,4
|
7,4
|
2,46
|
25
|
S35MC
|
75
|
10,88
|
4,72
|
0,6
|
5,42
|
7,08
|
2,2
|
26
|
L35MC
|
67
|
9,75
|
4,685
|
0,6
|
4,79
|
5,75
|
1,98
|
27
|
S26MC
|
42
|
5,88
|
3,95
|
0,49
|
4,3
|
5,25
|
1,88
|
Дополнительно к указанным выше
характеристикам шестицилиндрового агрегата и одного цилиндра табл.3 включает в
себя также: Bфр - ширину двигателя по фундаментной раме и вертикальные габариты
- физический H габ и ремонтный Hрем. Последний представляет собой минимально
необходимое расстояние от опоры фундаментной рамы до гака грузоподъемного
устройства для разборки двигателя, м. Эти характеристики позволяют определить
вертикальные размеры МКО и расположение двигателя по длине с учетом сужения
корпуса в кормовой оконечности.
Данные таблиц и указанные расчеты
включены в модули САПРа, необходимые для выбора главного двигателя. От
проектировщика требуется заполнить файл исходных данных, которые представлены в
таблице 4:
В табл. 4. представлены следующие
переменные, кодирующие отдельные особенности и характеристики судна и СЭУ:
CY - переменная, кодирующая тип
судна. Предусмотрены следующие значения этой переменной: 1- танкер; 2- балкер;
3- нефтерудовоз; 4- универсальный сухогруз; 5- рефрижиратор; 6- лесовоз; 7-
контейнеровоз; 8- лихтеровоз; 9- ролкер; 10- метановоз; 11- химовоз; 12-
газовоз комбинированный; 13- газовоз изотермический.
DPR - полное водоизмещение
судна-прототипа - вес судна с номинальной загрузкой по грузовую марку, т;
D0 - водоизмещение судна порожнем -
без груза Рг, запасов Gз, снабжения Gсн и команды Gком, т. Разница DPR и D0 -
переменная часть водоизмещения - дедвейт:
DW = DPR - D0 = Рг + Gз + Gсн +
Gком.
В рассматриваемой модели
водоизмещение судна принято постоянным, а возможные изменения массы двигателя
GDW, винта GW и валопровода GWAL, а также запасов топлива Gз приводят к
изменению грузоподъемности:
Рг =
Dпр-D0-Kгр[(GDW-GDWпр)-(GW-GWб)-(GWAL-GWALб)-(Gз-Gзб)],
при наличии возможности размещения
дополнительного груза. Последнее учитывается введением Kгр - коэффициента
использования свободного тоннажа. Индексом «б» обозначены параметры базового
варианта - судна-прототипа;
RPR - сопротивление движению
судна-прототипа на VPR;
VPR - скорость судна-прототипа;
VSU - то же, проектируемого судна.
Если задано VSU = 0.0, то происходит пересылка значения VSU = VPR;
K3 - коэффициент запаса мощности -
отношение мощности на эксплуатационном режиме и режиме наибольшей скорости или
обратное отношение. Если K3 < 1, то в п.п. 4, 5, 6 заданы параметры
максимального режима. Если K3 >1 это признак задания параметров
эксплуатационного режима и для определения Ne треб его нужно увеличить в K3
раз;
NEG - загрузка электростанции на
ходовом режиме. Если задано NEG = 0.0, то это признак необходимости определить
эту мощность по корреляционным зависимостям;
TSU - осадка судна в гpузу;
HB - высота борта;
LCYD- длина судна между
перпендикулярами;
KOB - коэффициент общей полноты
корпуса;
KD - максимально допустимое
отношение диаметра винта к осадке;
NEPR- мощность главного двигателя
судна-прототипа, отдаваемая на винт на VPR;
NPR - частота на режиме VPR;
BEGD- удельный расход топлива
двигателя судна-прототипа;
GDB - масса двигателя
судна-прототипа;
LPL - дальность плавания судна в
круговом рейсе;
LED - класс ледового усиления судна.
Переменная принимает следующие значения: 0- без ледовых усилений, 1- Л3, 2- Л2,
3- Л1, 4- УЛ, 5- УЛА.
WINT- тип движителя. Возможны два
значения: 1 - применен винт фиксированного шага, 2 - применен ВРШ;
TCS - код наличия и типа ТКС.
Возможны следующие значения: 0 -
ТКС отсутствует, 1 - ТКС в наличии и
работает на коленвал, 2 - ТКС работает на дизель-генератор, частично или
полностью исключая на него расход топлива;
TWG - код наличия и тип
валогенератора. Возможны следующие значения: 0 - валогенератор отсутствует, 1 -
применен валогенератор с гидромеханической стабилизацией частоты, 2 - применен
валогенератор со статической стабилизацией частоты;
IZVR- доступно ли изменение заданной
скорости. Возможны два значения этой переменной: 0 - заданную скорость менять
нельзя, 1 - возможна некоторая оптимизация скорости в пределах дополнительного
запаса мощности одного цилиндра;
TRGD- выбран типоразмер цилиндра с J
= TRGD. J - индекс типоразмера цилиндра (см. табл. цилиндров МС). Если задано
TRGD = 0, то просматривается применение всех типоразмеров цилиндров из
типоразмерного ряда. Если задано TRGD > 0, то расчет будет выполнен только
для одного типоразмера, но подробный, с оптимизацией положения режимной точки и
анализом экономики.
Таблица 4.
Исходные данные для выбора двигателя
────────────────────────────────────────────────────────────────────────┐
ФАЙЛ
ISX.DAT - ИСХОДНЫЕ ДАННЫЕ ДЛЯ ВЫБОРА ДВИГАТЕЛЯ ИЗ ТИПОРЯДА МС │
────┬──────────────────────────────────┬────────┬──────────┬────────────┤
Nпп│
НАИМЕНОВАНИЕ ПЕРЕМЕННОЙ │ОБОЗНАЧ.│ РАЗМЕРН. │ЧИСЛ.ЗНАЧЕН.│
────┼──────────────────────────────────┼────────┼──────────┼────────────┤
1
│ Код типа судна │ CY │ - │
1│
2
│ Полное водоизмещение судна │ DPR │ т │
10300.00│
3
│ Водоизмещение судна порожнем │ D0 │ т │
3300.000│
4
│ Сопротивл.движению судна на VPR │ RPR │ кН │
263.000│
5
│ Скорость судна-прототипа │ VPR │ узл │
14.200│
6
│ Скор. проектир.судна │ VSU │ узл │
14.200│
7
│ Коэф.запаса мощности │ K3 │ - │
0.85│
8
│ Мощн.электростанции на ходу │ NEG │ кBт │
500.000│
9
│ Осадка судна в гpузу │ TSU │ м │
7.00│
10
│ Высота борта │ HB │ м │
9.500│
11
│ Длина судна между перпендикуляр.│ LCYD │ м │
102.000│
12
│ Коэффициент общей полн. корпуса │ KOB │ - │
0.754│
13
│ Мах.допуст.отношение Dвинта/TSU │ KD │ - │
0.700│
14
│ | Параметры | Мощность на VPR │ NEPR │ кBт │
3360.000│
15
│ | гл.двигателя| Частота -"- │ NPR │ об/мин │
115.000│
16
│ | судна - | Уд.расх.топл-"- │ BEGDB │ г/кВт*ч │
179.0│
17
│ | - прототипа | Масса │ GDB │ т │
67.0000│
18
│ Дальность плавания │ LPL │ мили │
6000.0│
19
│ Код класса ледового усиления │ LEDUS │ - │
2│
20
│ Код типа винта ( 1- ВФШ, 2- ВРШ)│ WINT │ - │
1│
21
│ Наличие и тип ТКС ( 0, 1, 2 ) │ TCS │ - │
0│
22
│ Наличие и тип валогенератора(0-2)│ TWG │ - │
0│
23
│Скорость задана жестко(0-ДА,1-НЕТ)│ IZVR │ - │
0│
24
│ Тип ГТН 0-обычный, 1-экономичный │ GTN │ - │
1│
25
│Выбран типоразм.цилиндраДВС(0-НЕТ)│ TRGD │ - │
0│
────┴──────────────────────────────────┴────────┴──────────┴────────────┘
Кроме файла ISX.DAT подлежит
заполнению файл CONSTANT.DAT включающий не часто изменяемые величины. Он
представлен в табл. 5:
Таблица 5
№ п/п
|
Наименование переменной
|
Обозначение
|
Размерность
|
Значение
|
1
|
Код типа СЭУ
|
CEY
|
-
|
1
|
2
|
Код степени автоматизации
|
AWT
|
-
|
1
|
3
|
Число валопроводов на судне
|
WAL
|
-
|
1
|
4
|
Код района расположения МКО
|
RAS
|
-
|
1
|
5
|
Код доли стали повышенной прочности в составе корпуса судна
|
ST
|
-
|
0
|
6
|
Число судов в составе серии
|
NC
|
-
|
1
|
7
|
Код бассейна эксплуатации судна
|
BASS
|
|
3
|
8
|
Количество членов экипажа
|
ZE
|
-
|
0
|
9
|
Код марки топлива, используемого на длительном ходовом режиме
|
TOP
|
-
|
2
|
10
|
Класс перевозимого груза
|
KLASS
|
-
|
7
|
11
|
Код наличия утилизации теплоты
|
REG
|
-
|
1
|
12
|
Дисковое отношение винта
|
TET
|
-
|
0.75
|
13
|
Годовой период эксплуатации судна
|
TGOD
|
cут/год
|
340
|
14
|
Ставка за пользование капиталом
|
EN
|
1/год
|
0,15
|
15
|
Коэффициент использования свободного тоннажа
|
KGR
|
-
|
1
|
16
|
Коэффициент использования грузоподъемности
|
AGR
|
-
|
0,95
|
17
|
Коэффициент пересчета руб./долл в 1983 г.
|
INDD
|
руб/долл
|
0,62
|
18
|
Длительность стоянки без грузовых операций для танкера
|
TST
|
cут/рейс
|
4
|
19
|
Длительность стоянки с грузовыми операциями для танкера
|
TSTG
|
cут/рейс
|
0,75
|
20
|
Длительность стоянки с мойкой для танкера
|
TSTM
|
cут/рейс
|
2
|
21
|
Доля стоянки без грузовых операций для сухогруза
|
AST
|
-
|
1
|
22
|
Доля стоянки с грузовыми операциями для сухогруза
|
ASTG
|
-
|
0,5
|
Возможные значения переменных файла
CONSTANT.DAT:
: 1 - СЭУ с МО ДВС;2 - СЭУ с СО
ДВС;3 - ПТУ;4 - ГТУ;5 - ГТУ с ТУК;
энергетическая установка танкер
AWT: 1 - класс автоматизации A1; 2 -
A2; 3 - без автоматизации;: 1 - чисто кормовое расположение; 2 - промежуточное;
3 - среднее;: 0 - до 30% стали повышенной прочности; 1 - до 50%; 2 - более 50%;
: 1- Черноморский бассейн; 2- Каспийский; 3- Балтийский; 4- Северный; 5- Дальневосточный;
6- Сахалинский; 7- Арктический; 8- Камчатский; : 1- мазут марки М-40; 2-
моторное топливо марки ДМ; 3- моторное топливо марки ДТ; 4- дизельное топливо
марки ДЛ;
Количество членов экипажа может быть
задано прямо в табл.. Если оно неизвестно пользователю, то следует задать в
поз.8 ZE = 0. Это является признаком необходимости применения формул,
аппроксимирующих табличные данные в функции типа судна и его дедвейта DW.
Принимается число членов экипажа, ближайшее большее целое от значения в
соответствии с этими зависимостями.
По этим данным программный комплекс
WYBOR2001 предлагает несколько вариантов двигателя, для каждого из которых
производятся расчеты технических и технико-экономических показателей. Т.о.
можно выбрать наиболее предпочтительный вариант.
Файл GD_MC_AL.LST (здесь приведены
все агрегаты из типоразмерного ряда МАН типа МС 2001г., обеспечивающие
получение заданной эксплуатационной скорости и с мощностью, превышающей
требуемую не более, чем на мощность одного цилиндра данного типоразмера):индекс
типоразмера цилиндра,его обозначениечисло цилиндров в агрегатемаксимальная
длительная мощность,кВтдостижимая скорость при МДМ,узлыудельный расход топлива
на экспл.режиме,кг/квт*ч,LDR,HRPR- масса,т, длина,м, и рем.высота,м,
двигателяудельные приведенные затраты,долл./тонно-миличисло рейсов за год
эксплуатациипервоначальная стоимость СЭУ,долларыстоимость израсходованного
топлива,доллары за рейс= 26 типоразмер ДВС L35MC = 5 NEL= 3250.0 VD= 14.20 BE=
0.177= 57.25 LDR= 4.09 LMKO= 13.19 HRPR= 4.79=0.01573188 ZRE=13.960 KY= 4266.4
ZT= 347355.= 27 типоразмер ДВС S26MC = 8 NEL= 3200.0 VD= 14.13 BE= 0.179= 53.76
LDR= 4.93 LMKO= 13.99 HRPR= 4.30=0.01570416 ZRE=13.960 KY= 4215.7 ZT= 347355.
Программой выбраны два агрегата: 8
S26MC и 5 L35MC. Они обеспечивают достижение эксплуатационной скорости.
Выполним уточненный расчет для
агрегатов J= 26 и 27, последовательно подставив в последнюю строку файла
ISX.DAT (табл. 4) индексы двигателей - цифры 26 и 27 и каждый раз обращаясь к
программе WYBOR2001.EXE.
Результаты приведены ниже:
Вариант при J=26:= 263000.0 NEPR=
3360.0 VPR= 14.200 VSU= 14.200= 500.0 TWG= 0 TCS= 0 ZW= 1= 7.000 HB= 9.500
LMKOB= 13.37 KD= 0.7000= 224096.9 NETR= 3109.142 NERR= 2642.77 VR= 13.1078=
11.4 GWALB= 10.2 GDB= 67.0 GZTB= 230.6
Характеристики винта на режимах М, Р
и L3диаметр винта,мотносительная поступь V/N*DW- упор винта R/(1-TP),кНскорость
воды в диске винта VR*(1-WT),м/скоэффициент упора P/RO*N**2*DW**4коэффициент
упора-скорости V*DW*SQRT(RO/P)коэфф.нагрузки по упору 8*KT/PI*LP**2
(0.4<CTA<7.)- к.п.д.винта в свободной воде 1.876-1.235*CTA**0.1-
коэффициент влияния неравномерности на момент- коэффициент попутного потока-
коэффициент засасыванияпропульсивный коэффициентежим M - при DW=DWMAX= 4.9000
LP= 0.5142 P= 298477.06= 8.1861 KT= 0.1812 KDE= 2.2327= 0.5703 CTA= 1.7444 IQ=
0.9667= 0.3755 TP= 0.2492 KPROP= 0.70926ежим P- рабочий на винтовой проходящей
через MДM= 3.5424 LP= 0.3472 P= 285537.66= 7.4796 KT= 0.1810 KDE= 1.6141=
0.4637 CTA= 3.8248 IQ= 0.9605= 0.4294 TP= 0.2152 KPROP= 0.66402ежим P- рабочий
на винтовой проходящей через MДM= 3.5411 LP= 0.3471 P= 285525.84= 7.4786 KT=
0.1811 KDE= 1.6135= 0.4636 CTA= 3.8284 IQ= 0.9604= 0.4295 TP= 0.2151 KPROP=
0.66395=26 L35MC ОГРАНИЧЕНИЯ ВЫПОЛНЕНЫ, РЕЖИМ P
0 0
Экономические характеристики
судна,СЭУ и двигателя
Удельные приведенные
затраты,доллары/т*мили- UDPZ=0.0158926
Годовые приведенные затраты,доллары
в год - GPZ = 9410293.
Годовая транспортная
работа,тонномили/год - GTR = 592117376.
Годовой доход от перев.груза
тыс.долл./год - DOX = 13508.
Грузоподемность судна,тонны - GRP =
7069.
Годовой период эксплуатации,
сутки/год - TGOD= 340.
Число рейсов за год - ZRE = 13.960
Длительность рейса,час - STK =
584.535
Длительность ходовых режимов,час -
TPL = 422.535
Годовые текущие расходы,доллары в
год - GR = 7203083.
Текущие расходы за рейс,доллары за
рейс - CR = 515987.
Расходы на топливо, " - ZT =
360543.
Расходы на масло, " - SM = 94.
Расходы на амортизацию,ремонт и
снабжение,"- CA = 127841.
Расходы навигационные, " - CH =
8170.
Расходы косвенные, " - CK =
6547.
Число членов экипажа, человек - ZE =
26
Расходы на экипаж, " - CE =
12791.6
Стоимость главного двигателя,
тыс.долларов - KD = 724.4
Стоимость механич.оборудования МКО,
" - KM = 2213.8
Стоимость энергетической установки,
" - KY = 4266.4
Стоимость металлического корпуса
судна," - KMK= 2425.0
Стоимость оборудования корпуса судна,
" - KOK= 4804.9
Стоимость корпуса судна, " - KK
= 7229.9
Стоимость работ судостр.предприятия,
" - KRA= 1190.9
Стоимость судна установившейся
серии, " - KC = 14714.7
Стоимость серийного судна " -
SCP= 20600.6
Число цилиндров в агрегате - ZC= 5
Максимальная длительная мощность,кВт
- NEL1= 3250.000
Мощность на винт на режиме Р - NERR=
2320.426
Нагрузка двигателя на
экспл.режиме(Э)- NERD= 2320.426
Нагрузка двигателя на режиме СМДМ -
NESP= 2729.620
Эффективное давление на Э отн.к PеL1
- PEOTN= 0.7990
Частота на режиме МДМ - NL1 =
210.000
Частота на режиме L3 - NL3 = 178.000
Частота на режиме P - NR = 187.656
Частота на режиме СМДМ - NSP =
198.134
Оптимальная частота при DW=DWMAX -
NM = 100.191
Достижимая скорость на режиме
МДМ,узл- VD = 14.201
Требуемая мощность
валогенератора,кВт- NWGT= 0.000
Располагаемая мощность для привода
ВГ- NWGR= 536.421
Принятый типоразмер валогенератора -
NWGF= 0.000
Мощность турбокомпаунда,кВт - NTCS=
0.000
Мощность турбокомпаунда на винт -
NTCW= 0.000
Коэффициент запаса мощности фактич.
- KZR = 0.7139
Удельный расход топлива на НМДМ -BEN
= 0.17700
Удельный расход топлива на
реж.оптим.- BEO = 0.17539
Удельный расход топлива на
экспл.реж.- BE = 0.17129
Удельн.расх.топл. на привод
эл.генер.- BEWD= 0.19800
Масса гребного винта для режима Р,т.с-
GGW = 4.421
Стоимость движителя для
реж.Р,тыс.долл-KWIN= 12.539
Масса валопровода -"-- GWAL=
6.361
Диаметр гребного вала, м DGR = 0.320
Масса запаса топлива на гл.двигатель
- GZT = 181.938
Масса двигателя,тонны -"-- GD =
57.250
Разница перем.масс по ср. с
прототип.- DG = -69.311
Доп.доход от перевозок при изм.массы
- DDOX= 132.435
Длина машинного отделения,метры -
LMKO= 13.195
Длина двигателя,метры - LDR = 4.09
Ширина двигателя по фундаментной
раме- DRD = 1.98
Ремонтный габарит по высоте,метры -
HRGD= 4.79
Допустимо снижение частоты и
увеличение диам. винта= 3.6357 LP= 0.3598 P= 286390.69= 7.5504 KT= 0.1817 KDE=
1.6566= 0.4732 CTA= 3.5739 IQ= 0.9611= 0.4240 TP= 0.2175 KPROP= 0.66890= 176.39
NRO= 178.00 NEO= 2337.75= 4.76
Вариант при J=27:= 263000.0 NEPR=
3360.0 VPR= 14.200 VSU= 14.200= 500.0 TWG= 0 TCS= 0 ZW= 1= 7.000 HB= 9.500
LMKOB= 13.37 KD= 0.7000= 224096.9 NETR= 3109.142 NERR= 2642.77 VR= 13.1078=
11.4 GWALB= 10.2 GDB= 67.0 GZTB= 230.6
Характеристики винта на режимах М, Р
и L3диаметр винта,мотносительная поступь V/N*DW- упор винта R/(1-TP),кНскорость
воды в диске винта VR*(1-WT),м/скоэффициент упора P/RO*N**2*DW**4коэффициент
упора-скорости V*DW*SQRT(RO/P)коэфф.нагрузки по упору 8*KT/PI*LP**2
(0.4<CTA<7.)- к.п.д.винта в свободной воде 1.876-1.235*CTA**0.1-
коэффициент влияния неравномерности на момент- коэффициент попутного потока-
коэффициент засасыванияпропульсивный коэффициентежим M - при DW=DWMAX= 4.9000
LP= 0.5142 P= 298477.06= 8.1861 KT= 0.1812 KDE= 2.2327= 0.5703 CTA= 1.7444 IQ=
0.9667= 0.3755 TP= 0.2492 KPROP= 0.70926ежим P- рабочий на винтовой проходящей
через MДM= 3.2107 LP= 0.3046 P= 282544.75= 7.2012 KT= 0.1811 KDE= 1.4629=
0.4262 CTA= 4.9703 IQ= 0.9580= 0.4506 TP= 0.2069 KPROP= 0.64228ежим P- рабочий
на винтовой проходящей через MДM= 3.2111 LP= 0.3047 P= 282548.37= 7.2016 KT=
0.1811 KDE= 1.4631= 0.4263 CTA= 4.9686 IQ= 0.9580= 0.4506 TP= 0.2069 KPROP=
0.64231=27 S26MC ОГРАНИЧЕНИЯ ВЫПОЛНЕНЫ, РЕЖИМ P
0 0
Экономические характеристики
судна,СЭУ и двигателя
Удельные приведенные затраты,доллары/т*мили-
UDPZ=0.0158977
Годовые приведенные затраты,доллары
в год - GPZ = 9407799.
Годовая транспортная
работа,тонномили/год - GTR = 591769216.
Годовой доход от перев.груза
тыс.долл./год - DOX = 13500.
Грузоподемность судна,тонны - GRP =
7065.
Годовой период эксплуатации,
сутки/год - TGOD= 340.
Число рейсов за год - ZRE = 13.960
Длительность ходовых режимов,час -
TPL = 422.535
Годовые текущие расходы,доллары в
год - GR = 7209504.
Текущие расходы за рейс,доллары за
рейс - CR = 516447.
Расходы на топливо, " - ZT =
361539.
Расходы на масло, " - SM = 97.
Расходы на амортизацию,ремонт и
снабжение,"- CA = 127325.
Расходы навигационные, " - CH =
8170.
Расходы косвенные, " - CK =
6525.
Число членов экипажа, человек - ZE =
26
Расходы на экипаж, " - CE =
12791.6
Стоимость главного двигателя,
тыс.долларов - KD = 717.6
Стоимость механич.оборудования МКО,
" - KM = 2186.3
Стоимость энергетической установки,
" - KY = 4215.7
Стоимость металлического корпуса
судна," - KMK= 2424.6
Стоимость оборудования корпуса
судна, " - KOK= 4804.9
Стоимость корпуса судна, " - KK
= 7229.5
Стоимость работ судостр.предприятия,
" - KRA= 1190.9
Стоимость судна установившейся
серии, " - KC = 14655.3
Стоимость серийного судна " -
SCP= 20517.4
Число цилиндров в агрегате - ZC= 8
Максимальная длительная мощность,кВт
- NEL1= 3200.000
Мощность на винт на режиме Р - NERR=
2398.587
Нагрузка двигателя на
экспл.режиме(Э)- NERD= 2398.587
Нагрузка двигателя на режиме СМДМ -
NESP= 2822.005
Эффективное давление на Э отн.к PеL1
- PEOTN= 0.8254
Частота на режиме МДМ - NL1 =
250.000
Частота на режиме L3 - NL3 = 212.000
Частота на режиме P - NR = 227.022
Частота на режиме СМДМ - NSP =
239.741
Оптимальная частота при DW=DWMAX -
NM = 100.191
Достижимая скорость на режиме
МДМ,узл- VD = 14.128
Требуемая мощность
валогенератора,кВт- NWGT= 0.000
Располагаемая мощность для привода
ВГ- NWGR= 458.347
Принятый типоразмер валогенератора -
NWGF= 0.000
Мощность турбокомпаунда,кВт - NTCS=
0.000
Мощность турбокомпаунда на винт -
NTCW= 0.000
Коэффициент запаса мощности фактич.
- KZR = 0.7496
Удельный расход топлива на НМДМ -BEN
= 0.17900
Удельный расход топлива на
реж.оптим.- BEO = 0.17782
Удельный расход топлива на
экспл.реж.- BE = 0.17448
Удельн.расх.топл. на привод
эл.генер.- BEWD= 0.19800
Масса гребного винта для режима
Р,т.с- GGW = 3.325
Стоимость движителя для
реж.Р,тыс.долл-KWIN= 10.058
Масса валопровода -"-- GWAL=
5.470
Диаметр гребного вала, м DGR = 0.300
Масса запаса топлива на гл.двигатель
- GZT = 191.571
Масса двигателя,тонны -"-- GD =
53.760
Разница перем.масс по ср. с
прототип.- DG = -65.154
Доп.доход от перевозок при изм.массы
- DDOX= 124.494
Длина машинного отделения,метры -
LMKO= 13.995
Длина двигателя,метры - LDR = 4.93
Ширина двигателя по фундаментной
раме- DRD = 1.88
Ремонтный габарит по высоте,метры -
HRGD= 4.30
Допустимо снижение частоты и
увеличение диам. винта= 3.3227 LP= 0.3196 P= 283548.34= 7.2999 KT= 0.1818 KDE=
1.5140= 0.4395 CTA= 4.5322 IQ= 0.9589= 0.4431 TP= 0.2097 KPROP= 0.65049= 220.46
NRO= 212.00 NEO= 2429.14= 3.66
Как видно из сравнения результатов
для данного проекта оптимальным является двигатель 5L35MC: у него лучшие
показатели по удельному расходу топлива на ходовом режиме - на 1,9% меньше, чем
у 8S26MC, благоприятные габаритные показатели (длина меньше на 0,8 м). Выбираем
этот двигатель.
J
|
Марка
|
Nа
|
Zц
|
Dц
|
Sц
|
Gа
|
Lа
|
bеэ
|
Hгаб
|
Bфр
|
26
|
5L35MC
|
3250
|
5
|
0,35
|
1,05
|
57,25
|
4,085
|
0,1713
|
4,79
|
1,98
|
27
|
8S26MC
|
3200
|
8
|
0,26
|
0,98
|
53,76
|
4,93
|
0,1745
|
4,3
|
1,88
|
. РАСЧЕТ ВАЛОПРОВОДА
Валопровод служит для передачи
крутящего момента от главных двигателей гребному винту и для передачи упора
винта корпусу судна через главный упорный подшипник, встроенный обычно в корпус
малооборотного двигателя (или редуктора в случае применения СОД).
На проектируемом судне
предусматривается одна линия валопровода. Состав валопровода:
Гребной вал
Гребной винт
Промежуточный вал
Дейдвудное устройство опорного
подшипника.
Гребной вал предусматривается
сплошным (с расточкой по оси вала) из углеродистой стали с откованными
совместно с ним фланцами. Главный упорный подшипник в ГД встроен в ГД. Для
поддержания гребного и промежуточного валов предусматривается подшипник
скольжения опорный самоустанавливающийся, расположенный на гребном валу.
Дейдвудное устройство
предусматривается с дейдвудной трубой сварной с одним дейдвудным подшипником,
залитым баббитом на масляной смазке. Конструкцией уплотнения и системой смазки
предусматривается дренаж протечек масла (забортной воды) внутрь судна при
нарушении герметичности уплотнений.
Комплексное проектирование валопровода
включает ряд основных этапов:
определение прочных размеров в
соответствии с формулами, приведенными в Правилах Регистра РФ;
разработка конструкции валопровода;
расположение элементов ПК в МКО и
расстановка опор валопровода;
проверочный расчет сложного
напряженного состояния и определение запасов прочности;
расчет колебаний валопровода.
Основной расчетный размер
валопровода в соответствии с Правилами Регистра РФ это диаметр промежуточного
вала. Для его определения следует использовать такую зависимость:
где F- коэффициент,
учитывающий тип главного двигателя. Для ротативных, в том числе турбинных
двигателей F=95, а для поршневых двигателей, в том числе ДВС F=100;
- отношение Ne -
мощности, кВт, к n - частоте, об/мин, на расчетном режиме двигателя. Это
отношение представляет из себя величину вращающего момента, выраженного во
внесистемных единицах кВт/(об/мин) и развиваемого двигателем на расчетном
режиме эксплуатации.
Прочие размеры
валопровода назначаются в долях от dпр. В частности упорный вал, проходящий
через отдельно стоящий (выносной) главный упорный подшипник, должен иметь на
расстоянии до одного диаметра от упорного гребня диаметр не меньше
На
большем расстоянии от упорного гребня диаметр можно постепенно уменьшить до
размера промежуточного вала.
Кормовая оконечность
гребного вала должна иметь диаметр не меньше определенного по следующей
зависимости:
Параметры этой
зависимости, кроме коэффициента k, рассмотрены выше и представляют из себя
составляющие формулы для диаметра промежуточного вала. Коэффициент усиления
гребного вала k зависит от способа крепления винта на конусе. Если используется
бесшпоночное соединение, то k принимается равным 1,22. В случае применения
шпонки, предотвращающей проворачивание гребного винта на конусе, сечение
гребного винта ослабляется и необходимо применение k=1,26.
Указанные размеры валов
рассчитаны для случая применения материалов с вр=400 МПа.
При наличии у судна
категории ледового усиления найденные значения диаметров следует увеличить в
соответствии со следующей зависимостью
Коэффициенты усиления,
выраженные в процентах, принимаются в соответствии с табл.5.
Таблица 5
Ледовые усиления валов
судовых валопроводов
Тип валов
|
Категория ледового усиления
|
|
ЛУ1 и 2
|
ЛУ3
|
ЛУ4
|
ЛУ5
|
ЛУ6
|
ЛУ7
|
ЛУ8 и 9
|
Промежуточный и упорный
|
0
|
4
|
8
|
12
|
13,5
|
15
|
*
|
Гребной
|
5
|
8
|
15
|
20
|
25
|
30
|
*
|
Примечание * - коэффициенты усиления
согласовываются с Регистром РФ особо.
Для всех судов с ледовыми
ограничениями кроме ЛУ1 диаметр гребного вала в кормовом подшипнике не должен
быть меньше рассчитанного по такой формуле:
где a - коэффициент
влияния размеров ступицы гребного винта, равный 10,8 при Dст
0,25
Dв и 11,5 при Dст>0,25 Dв;- ширина спрямленного цилиндрического сечения
лопасти на радиусе0,25 Rмах для цельнолитых винтов и 0,35 Rмах для ВРШ, где
Rмах= Dв/2, м;- наибольшая толщина сечения лопасти на том же радиусе, м;
лоп - временное
сопротивление материала лопастей гребного винта, МПа;
вал - временное
сопротивление материала гребного вала, МПа.
Полученные в результате
всех пересчетов значения диаметров следует согласовать с рядом предпочтительных
диаметров шеек судовых валопроводов. Это сложный ряд, основанный на
арифметической прогрессии с переменным шагом. Он представлен в табл.6.
Таблица 6
Ряд предпочтительных
диаметров шеек судовых валопроводов. Размеры в мм.
Диапазон диаметров
|
90 -140
|
140 - 300
|
320 - 420
|
420 - 570
|
570 - 780
|
780 - 1100
|
Шаг прогрессии
|
5
|
10
|
20
|
Переменный 30/20
|
30
|
40
|
При выборе окончательного значения
диаметра для каждого из валов принимается ближайший больший к расчетному значению
диаметр из ряда предпочтительных чисел.
При наличии отверстия вдоль оси вала
с диаметром до 40% от наружного диаметра компенсация снижения прочности не
требуется. При необходимости сделать отверстие большего диаметра этот диметр do
не должен быть больше определенного по следующей зависимости:
где d - диаметр вала без отверстия;ф - фактический диаметр вала с
отверстием.
Диаметр соединительных болтов для фланцев валопровода должен быть
не менее определенного по следующей формуле:
где dпр - окончательно принятый диаметр промежуточного вала, мм;
в - временное сопротивление материала вала, МПа;
б - временное сопротивление материала болта, МПа. На значенияб
наложено ограничение:в
б
1,7·в.
В любом случае б
1000
МПа.
Толщины фланцев валов судовых валопроводов не должна быть меньше
0,2 dпр или диаметра соединительного болта. Из двух рассмотренных значений
принимается большее. В случае навешивания гребного винта на фланец гребного
вала толщина этого фланца должна быть не меньше 0,25 dгр. При расчетах
ограничений на толщины фланцев принимаются окончательные значения
соответствующих диаметров - после введения всех усилений и округления;
Разработка конструкции валопровода преследует цель построение
расчетной схемы для реализации последующих этапов проектирования. В процессе
разработки конструкции нужно определиться с типом и расположением опорных
подшипников, размерами и конструкцией дейдвудных устройств, конструкцией
отдельных валов.
Проверочный расчет сложного напряженного состояния и определение
запасов прочности производится с целью проверки прочности валопровода.
Расчетные зависимости Правил Регистра учитывают только одну нагрузку -
вращающий момент двигателя и равный ему и противоположно направленный
реактивный момент винта. Прочие нагрузки учитываются при проверке прочности.
Сначала нужно составить расчетную схему с указанием всех
действующих нагрузок, в том числе:
распределенных нагрузок,
сосредоточенных сил - веса гребного винта и сил от сосредоточенных
масс на пролетах,
реакций опор валопровода,
указанных выше моментов,
пульсирующие нагрузки от работы винта в косом потоке за корпусом
судна и др.
На рис.10 представлена расчетная схема валопровода в соответствии
с рис.9.
На рис.10 представлены следующие
нагрузки, действующие на валопровод:
- вращающий момент
двигателя Mкр, равный
,
кНм, и реактивный момент винта Mр, с точностью до моментов трения в сальниках и
подшипниках равный Mкр;
распределенные нагрузки
qгр и qпр, равные весу погонного метра соответ-ствующих валов
,
кН/м;
вес гребного винта Gгв,
который можно определить, например, с помощью формулы Ф.М. Кацмана [11]: в=
т,
(2.21)
где Dв - диаметр
гребного винта, м; - дисковое отношение винта; l0 - длина ступицы, м.
Ориентировочные значения l0 можно определить по статистическим оценкам: l0
0,2
Dв или 3 dгр;
реакции опор валопровода
R1 - R3. Реакция кормового подшипника промежуточного вала отсутствует, так как
он монтажный. Для определения реакций опор следует привлечь программное
обеспечение расчета статически неопределимых балок, например, метод конечных
элементов [12];
упор винта Pгв =
и
равное ему и противоположно направленное усилие в упорном подшипнике, движущее
судно;
моменты от работы винта
в косом потоке за корпусом судна: 1 в вертикальной плоскости и 2 в
горизонтальной плоскости. Поток, стекающий с корпуса на винт, на самом деле
прямой, но для винта в связи с его вращением этот поток становится косым, от
чего создаются дополнительные моменты. Данные о дополнительных моментов от
работы винта в косом потоке являются экспериментальными и зависят от сложной
совокупности параметров, в том числе от формы кормового образования и числа
лопастей винта. В первом приближении эти величины можно найти по рекомендациям
[11];
пульсационные
составляющие упора и дополнительных моментов, возникающие вследствие работы
винта с конечным числом лопастей в потоке за корпусом судна. Эти составляющие
можно определить по данным [11] и их амплитудные значения следует добавит к
величинам, определенным в предыдущем абзаце.
Облегчением расчета
фактических напряжений валопровода является то, что можно заранее указать
расчетное сечение с наибольшим значение напряжения. Это - сечение расположено
на кормовой опоре в расчетной точке приложения реакции. Для этого сечения
следует определить нормальные, касательные и эквивалентные напряжения с учетом
дополнительных монтажных напряжений и сравнить их с допускаемыми. Коэффициент
запаса прочности должен лежать в заданных пределах;
Расчет колебаний
валопровода производится с целью по возможности избежать появления резонансных
явлений и снижения надежности валопровода вследствие действия знакопеременных
резонансных нагрузок. В случае, если этого избежать не удается, необходимо
установить запретные зоны частот, ограничивающие напряжения от резонанса.
Расчеты колебаний
валопроводов самостоятельная и сложная процедура. В процессе разработки
варианта ПК её удается решить только в первом приближении и только ограниченно.
Производится расчет низших частот колебаний наиболее проблемных участков
валопровода. Обычно это - консоль гребного вала и пролет наибольшей длины.
Собственная частота колебаний гребного вала в вертикальной плоскости, с-1,
определяется в соответствии со следующим выражением:
грв=0,159
,
(2.22)
где EI - изгибная
жесткость гребного вала, Нм2; L - расстояние между опорами гребного вала, м; lк
- длина консоли гребного вала - расстояние между точками приложения усилий -
реакции кормовой опоры и веса винта, м; M
- сумма массы гребного
винта и присоединенных масс воды, кг; Iм
- момент инерции
гребного винта и присоединенных масс воды.; q - интенсивность распределенной
нагрузки на гребном валу, кг/м; коэффициент податливости кормовой опоры. Он
может быть принят равным 1 - 1,5 для металлических подшипников; 2,5 для бакаута
и синтетических материалов; 4 - для резинометаллических подшипников.
Частота первого тона
собственных колебаний пролета промежуточного вала, свободно лежащего на опорах,
определяется по такой формуле, с-1:
пр=
,
(2.23)
где Lпр - длина пролета
наибольшей длины на промежуточном валу, м; P - упор винта на максимальном
режиме, кН; Pкр =
-
критическая сила при продольном изгибе, кН.
Полученные значения
собственных частот сравниваются с частотами возмущающих сил - частотой вращения
главного двигателя на режиме МДМ nmax, лопастной частотой винта - произведением
nmax на число лопастей винта; произведением nmax на число цилиндров в составе
агрегата двигателя. Если собственные частоты на 20 и более % больше частоты
возмущающих сил, то резонанса на наиболее опасных низких частотах не будет. В
противоположном случае требуется более точный, но и более сложный расчет. Более
детальное исследование колебаний выходят за рамки вопроса.
Валопровод
рассчитывается с помощью комплекса программ WAL RAZM, учитывающего проверку
валопровода на прочность и резонансные частоты.
Для применения модуля
WAL_RAZM следует подготовить данные в соответствии с таблицей
────────────────────────────────────────────────────────────────────────
ФАЙЛ
WAL_RAZM.DAT - ИСХОДНЫЕ ДАННЫЕ ДЛЯ КОМПЛЕКСА ПРОГРАММ WAL_RAZM
────┬──────────────────────────────────┬────────┬─────────┬─────────────
Nпп│
НАИМЕНОВАНИЕ ПЕРЕМЕННОЙ │ОБОЗНАЧ.│ РАЗМЕРН.│
ЗНАЧЕНИЕ
────┼──────────────────────────────────┼────────┼─────────┼─────────────
1.
│ Mощность на номинальном режиме │ NEL │ кBт │
3250.000
2.
│ Частота вращения номинальн.режим│ NL │ об/мин │
210.000
3.
│ Упор винта " " " │ P │
кН │ 290.867
4.
│ Длина ахтерпика (>50.-дл.судна) │ LAP │ м │
102.000
5.
│ Длина главного двигателя │ LGD │ м │
4.085
6.
│ Диаметр винта │ DW │ м │
3.542
7.
│ Дисковое отношение винта │ TETA │ - │
0.750
8.
│ Временн.сопр.матер.гребного вала │ BGR │ МПа │
500.000
9.
│ Временн.сопр.матер.промежут.вала │ BPR │ МПа │
550.000
10.│
Временн.сопр.матер.соедин.болтов │ BBOL │ МПа │
600.000
11.│
Код класса ледового усиления │ LU │ - │
2
12.│Код
смазки дейдвуда:1-масло/2-вода│ SMD │ - │
1
13.│
Наличие шпонки гр.в.:1-есть/2-нет│ JW │ - │
1
14.│
Число болтов фланца пром.вала │ ZB │ - │
8
15.│Схема
турбокомпаундной системы 0-2│ TKS │ - │
0
16.│
Наличие валогенератора 0/1 │ TWG │ - │
0
17.│Схема
валопр.(0-?,1/2-опор в дейдв│ SXW │ - │
2
────────────────────────────────────────────────────────────────────────
В табл. заданы следующие переменные,
оказывающие влияние на характеристики валопровода:
NEL - эффективная мощность двигателя
на режиме МДМ, кВт;
NL - частота на режиме МДМ, об/мин;
P - упор винта на режиме испытания
на скорость, кН;
LAP - длина ахтерпика, м. Если эта
длина неизвестна, то можно задать LAP равной длине судна LSU, в этом случае
будет применена аппроксимирующая зависимость длины ахтерпика в функции длины
судна;
LGD - длина главного двигателя, м;
DW - диаметр винта, м;
TETA- дисковое отношение винта;
BGR - предел длительной прочности
материала гребного вала, МПа;
BPR - то же для материала
промежуточного вала, МПА;
BBOL- то же для материала
соединительных болтов, МПа;
LU - код класса ледового усиления.
Предусмотрены следующие 8 значений LU: 0- без ледовых усилений, 1 - Л3, 2 - Л2,
3 - Л1,4 - УЛ, 5 - УЛА, 6 - средний вал ледокола, 7 - бортовой вал ледокола;
SMD - код смазки дейдвуда: 1 -
масло, 2 - вода;
JW - наличие шпонки гребного вала: 1
- есть, 2 - нет;
ZB - число болтов фланца
промежуточного вала;
TKS - код турбокомпаундной системы:
0 - нет, 1 - есть и работает на винт, 2 - есть и работает на дизель-генератор;
TWG - код наличия валогенератора: 0
- нет, 1 - есть;
SXW - код схемы валопровода,
численно равный числу опор в дейдвудной трубе. Если это число неизвестно
проектировщику, то следует задать SXW=0, в этом случае будет проанализирована
возможность размещения в дейдвудной трубе одной или двух опор и решение будет
принято программой. Анализ распространяется и на задание проектировщика (1 или
2). Если последнее ошибочно, то оно корректируется.
На основании этих данных с помощью
программы рассчитывается:
с использованием формул Регистра РФ
определяются прочные размеры валопровода. Формулы учитывают лишь одну из
нагрузок, действующих на валопровод - передаваемый крутящий момент, поэтому
результаты нуждаются в проверке;
производится конструирование
валопровода. По найденным размерам размещаются опоры, строится расчетная схема
для проверки прочности методами сопротивления материалов;
выполняется расчет прочности
валопровода как статически неопределимой балки с нахождением реакций опор,
сложного напряженного состояния в расчетном сечении на кормовой опоре с учетом
амплитудных значений пульсирующих нагрузок от работы винта в косом потоке за
корпусом судна. Коэффициенты запаса прочности должны лежать в заданных пределах
- они ограничены как снизу, так и сверху;
рассчитываются колебания
валопровода. Если низшие тона колебаний консоли гребного вала и пролета
наибольшей длины значительно (более чем на 20%) превосходят частоты возмущающих
сил - лопастной частоты zл * nв и частоты двигателя zц * nв, то на этом анализ колебаний
заканчивается - резонанса не будет. В противоположном случае расчеты продолжают
путем уточненного анализа собственных частот, оценок резонансных напряжений и
установления запретных зон оборотов. Последнее крайне нежелательно;
проектируется монтаж валопровода с
целью оптимизации нагрузок на опоры за счет их вертикального перемещения.
Результаты расчетов приведены в
табличной форме (см табл.).
*************************************************************************
ФАЙЛ
WAL_RAZM.REZ - РЕЗУЛЬТАТЫ РАБОТЫ КОМПЛЕКСА ПРОГРАММ WAL_RAZM I
*************************************************************************
NппI
НАИМЕНОВАНИЕ ПЕРЕМЕННОЙ IОБОЗНАЧ.I РАЗМЕРН.I ЗНАЧЕНИЕ I
*************************************************************************
1.
I Диаметр промежуточного вала I DPR I м I 0.2400
2.
I Диаметр гребного вала I DGR I м I 0.3400
3.
I Диаметр упорного вала I DUP I м I 0.2634
4.
I Толщина облицовки гребного вала I SOBL I м I 0.0169
5.
I Длина ахтерпика I LAP I м I 4.2398
6.
I Длина гребного вала I LGW I м I 6.9448
7.
I Длина консоли I LK I м I 0.7820
8.
IСумарная длина промежуточных валовI LPRS I м I 5.0218
9.
I Длина промежуточного вала I LPR I м I 5.0218
10
I Число опор валопровода I ZOP I - I 4.0000
11.I
Число опор промежуточного вала I ZPR I - I 1.0000
12.I
Расстояние между опор гребн.вала I LMOPG I м I 3.8498
13.I
Минимально допустимое расстояние I LMOPG1I м I 3.2070
14.I
Максимально допустимое расстояниеI LMOPG2I м I 8.1633
15.I
Расстояние между опор промеж.валаI LMOPR I м I 2.5109
16.I
Минимально допустимое расстояние I LMOPR1I м I 2.6944
17.I
Максимально допустимое расстояниеI LMOPR2I м I 6.8586
18.I
Толщина фланца гребного вала I TFLG I м I 0.0850
19.IТолщина
фланца промежуточного валаI TFLPR I м I 0.0500
20.I
Диаметр соединительных болтов I DB I м I 0.0500
21.I
Диаметр гребного винта I DGW I м I 3.5420
22.I
Диаметр ступицы гребного винта I DST I м I 0.7084
23.I
Длина ступицы гребного винта I LST I м I 0.6800
24.I
Масса гребного винта I GGW I кг I 4478.2739
25.I
Длина главного двигателя I LGD I м I 4.0850
26.I
Ремонтный габарит гребного вала I LREM I м I 6.9448
27.I
Длина МКО I LMKO I м I 13.5298
*************************************************************************
По полученным данным можно
разработать эскиз расположения двигателя и валопровода в МКО.
Программа WAL_RAZM подготавливает
данные для расчета валопровода как статически неопределимой балки:
.8 0.782 8000.0 4 210.
.34000 0.13600 3.84980 0.10000
0.00000
.24000 0.09600 3.67045 0.10000
0.00000
.26340 0.10536 1.45970 0.10000
0.00000
.37 3250.00 4
.000 3.541 0.750 1.000
В таблице данных представлены:
4474.8 - вес винта, кг; 0.782 - длина консоли гребного вала, м; 8000.0 -
плотность материала валов, кг/м3; 4 - число опор валопровода, включая жесткую
заделку в упорном подшипнике, встроенном в двигатель; 210. - максимальная
частота ГД;
Далее приведены три строки,
характеризующие пролеты валопровода - вторая строка - пролет гребного вала
(внутри дейдвуда): 0.34000 - наружный диаметр гребного вала, м; 0.13600 -
диаметр расточки вала, м; 3.84980 - длина пролета, м; последние цифры в данном
расчете не учитываются. Строки третья и четвертая то же для двух пролетов на
промежуточном валу.
Пятая строка содержит: 318.37 - упор
винта, кН; 3250.00 - максимальную мощность ГД, кВт; 4 - число лопастей винта.
Так как число цилиндров - 5, то число лопастей должно быть другим во избежание
резонанса. Принимаем четырех лопастной винт.
В последней строке
приведены:196200.000 - модуль упругости материала валов, МПа;
.541 - диаметр винта, м; 0.750 -
дисковое отношение винта; 1.000 - относительная жесткость опор валопровода.
Эти данные позволяют рассчитать
валопровод как статически неопределимую балку и параметры монтажа валопровода
(последние не рассчитываем). Ниже приведены результаты расчета валопровода как
статически неопределимой балки.
ИCXOДHЫE ДAHHЫE= 4474.8 LK= 0.782 G=
8000.0 N= 4 NB=210.0P L L1 M
.34000 0.13600 3.84980 0.10000
0.00000
.24000 0.09600 3.67045 0.10000
0.00000
.26340 0.10536 1.45970 0.10000
0.00000ПOPHЫE MOMEHTЫ И PEAKЦИИ(KHM) R(KH)
.749 62.274
.654 8.702
.377 11.376
.732 -0.194= 8378. GS= 8375.= 318.37
КН N= 3250.00 КВТ Zл= 4
БЭKB= 106.67140 (эквивалентное
напряжение в точке приложения силы на кормовой опоре)= 196200.
DB=3.5410 FB=0.7500 AL=1.0000
ЫHУЖДEHHЫE И COБCTBEHHЫE ЧACTOTЫ=
210.0 NL= 840.0 (лопастная частота - произведение NB на Zл)= 1104.0
(собственная частота консоли гребного вала) NSPR= 2231.5 (собственная частота
наибольшего пролета на линии валопровода - в данном случае гребного вала)
. ПРОЕКТИРОВАНИЕ СИСТЕМ
Системой называется совокупность
специализированных трубопроводов с механизмами, аппаратами, приборами и
устройствами, предназначенная для выполнения определенных функций, связанных с
эксплуатацией СЭУ. Любые системы судовой энергетической системы должны обладать
соответствующей надежностью и живучестью.
Под надежностью системы понимают ее
свойство сохранять во времени в установленных пределах все значения параметров,
характеризующих способность выполнять требуемые функции в заданных режимах и
условиях применения.
Надежность системы обуславливается
следующими свойствами:
Безотказность - свойство сохранять
работоспособность в течении некоторого промежутка времени без вынужденных
перерывов.
Долговечность - свойство системы
сохранять работоспособное состояние до наступления предельного состояния при
установленной системе тех. обслуживания и ремонта. Долговечность системы
зависит от долговечности ее элементов.
Ремонтопригодность - совокупность
конструктивно-технологических свойств объекта, определяющих его
приспособленность к выполнению всех видов технического обслуживания и ремонта.
Под конструктивно-технологическими свойствами понимается доступность элементов
системы, их контролепригодность, простота монтажа и демонтажа, степень
унификации и стандартизации.
Для повышения надежности систем
используется:
Применение в системах минимального
числа оборудования, при этом оборудование подбирается высокоэффективное,
экономичное и надежное, обладающее необходимым запасом производительности и
мощности.
Выбор рациональной схемы
резервирования отдельных элементов и участков системы.
Применение схем, позволяющих
использовать теоретически действующее оборудование в качестве резервного.
Улучшение качества механизмов и
систем в целом путем улучшения конструкции отдельных узлов и деталей, а так же
применения более стойких материалов.
Улучшение технологии изготовления
отдельных элементов системы и её монтажа в корпусе судна путем применения
блоков и агрегатов, собираемых на общем фундаменте в цехе.
Рациональное расположение механизмов
в МКО, обеспечение минимальной длины трасс трубопроводов, использование
стандартных унифицированных деталей и элементов.
Своевременное проведение
профилактических ремонтов и осмотров, повышение квалификации обслуживающего
персонала.
Основными системами ДУ являются:
топливная, масляная, охлаждения, сжатого воздуха и газоотвода. Оборудование
систем подбирают в соответствии с нормативными документами, рекомендациями
поставщиков основного энергетического оборудования, данными по опыту
эксплуатации и данными по номенклатуре поставляемых промышленностью образцов.
Системы судовых энергетических установок должны обеспечить подвод и отвод
рабочих тел к местам потребления и производства их в заданном количестве и определенного
качества. Исходя из анализа этих функций систем, происходит их функциональное
проектирование - определение подач, напоров, расходов, емкостей,
производительностей, сечений, поверхностей и других характеристик.
В основу расчета систем положены рекомендуемые
фирмами характеристики вспомогательного оборудования, приведенные в таблице.
Следует отметить, что рекомендации фирмы-производителя двигателя по параметрам
рабочих тел энергетических систем - расходам, тепловым потокам, температурам и
давлениям обеспечивают стабильный расчетный температурный режим двигателя и
этим самым являются способом обеспечения гарантируемого ресурса.
Таблица
Характеристики оборудования систем
двигателей типа МС
J
|
Марка
|
Wтц
|
Wтп
|
Wпр
|
Wзв
|
Wмо
|
Wм
|
Wмр
|
Qизл
|
1
|
2
|
3
|
4
|
5
|
6
|
7
|
8
|
9
|
10
|
26
|
0,33
|
0,17
|
5,67
|
21,7
|
8,5
|
15.
|
*0.17
|
1,8
|
27
|
S26MC
|
0,33
|
0,1
|
4,
|
17,5
|
6,2
|
10.8
|
-
|
2,0
|
J
|
Марка
|
Gвоз
|
Gгаз
|
Tгаз
|
Qво
|
Qмо
|
Qпр
|
Qт
|
|
1
|
2
|
11
|
12
|
13
|
14
|
15
|
16
|
17
|
|
26
|
L35MC
|
1.47
|
1.5
|
265.
|
235.
|
58.3
|
100.
|
8.7
|
|
27
|
S26MC
|
0.85
|
0.866
|
260.
|
141.7
|
58.3
|
76.7
|
8.7
|
|
|
|
|
|
|
|
|
|
|
|
|
|
|
|
|
|
|
|
|
* - подача насоса гидропривода
выхлопных клапанов;
В таблице приведены требуемые
характеристики оборудования систем, обслуживающих двигатель из ряда МС, из
расчета на один цилиндр соответствующего типоразмера.
-индекс типоразмера цилиндра;
- маркировка цилиндров, включающая
буквенный и цифровой код;
- Wтц - подача циркуляционного
топливного насоса, м3/ч;
- Wтп - подача топливоподкачивающего
насоса, м3/ч;
- Wпр - подача насоса пресной воды,
м3/ч;
- Wзв - подача насоса забортной
воды, м3/ч;
- Wм - проток забортной воды через
маслоохладитель, м3/ч;
- Wм - подача главного масляного
насоса, м3/ч;
- Wмр - подача насоса смазки
распредвала, м3/ч. В случае если в данной графе стоит прочерк - насос
отсутствует, а смазка распредвала - консистентная. Если в этой графе стоит
звездочка, то кроме применения консистентной смазки распредвала еще применен
гидропривод выхлопного клапана, подача которого в столбце 9 и указана, м3/ч;
- потери теплоты в помещение МКО от
теплоты сжигаемого в двигателе топлива, %;
- Gвоз - pасход продувочного
воздуха, кг/сек;
- Gгаз - pасход выхлопных газов,
кг/сек;
- Tгаз - темпеpатуpа газов, 0С;
- Qво - отвод теплоты от
продувочного воздуха, кВт;
- Qмо - отвод теплоты с
циркуляционным маслом, кВт;
- Qпр - отвод теплоты от пресной воды,
кВт;
- Qт - расход теплоты на подогрев
топлива, кВт.
Параметры таблицы отнесены к режиму
МДМ.
Насосы должны обеспечивать напор не
ниже заданного в таблице, а температура рабочих тел не должна превосходить
указанных здесь же величин.
Параметры рабочих тел
Наименование насосов
|
Pнаг
|
Tmax
|
Топливный подкачивающий
|
0,4
|
100
|
Топливный циркуляционный
|
1,0
|
150
|
Смазки циркуляционный
|
0,4
|
60
|
Смазки распредвала
|
0,3
|
60
|
Забортной воды
|
0,25
|
50
|
Пресной воды
|
0,3
|
100
|
В таблице приведены рекомендуемые
значения параметров шести основных насосов энергетических систем двигателей
типа МС: наг - давление нагнетания, МПа; - температура наибольшая, 0С.
Проектирование систем состоит в
умножении строки, соответствующей выбранному типоразмеру цилиндра ДВС типа МС,
на число цилиндров в составе агрегата.
Для проектирования систем следует
подготовить исходные данные в соответствии со следующей таблицей.
Исходные данные модели
функционального проектирования систем
────────────────────────────────────────────────────────────────────────
ФАЙЛ
SMC1_ISX.DAT - ИСХОДНЫЕ ДАННЫЕ ДЛЯ КОМПЛЕКСА ПРОГРАММ SIST_MC
────┬──────────────────────────────────┬────────┬─────────┬─────────────
Nпп│
НАИМЕНОВАНИЕ ПЕРЕМЕННОЙ │ОБОЗНАЧ.│ РАЗМЕРН.│
ЗНАЧЕНИЕ
────┼──────────────────────────────────┼────────┼─────────┼─────────────
1.
│ Mощность гл.дв.на номин. режиме │ NE │ кBт │
2379.646
2.
│ Частота вращ.гл.дв.на ном.режиме │ NR │ об/мин │
189.238
3.
│ Cкорость хода судна │ VSU │ узлы │
14.200
4.
│ Дальность плавания │ LPL │ мили │
6000.000
5.
│Mощность электрогенератора на ходу│ NDG │ кBт │
500.000
6.
│ Mарка топлива гл. двигателя │ MTG │ - │
1
7.
│ Mарка топлива дизельгенератора │ MTW │ - │
1
8.
│ Типоразмер главного двигателя │ TRGD │ - │
26
9.
│ Число цилиндров гл. двигателя │ IZ │ - │
5
────────────────────────────────────────────────────────────────────────
Топливная система.
Предназначена для приема, хранения,
перекачки, очистки, подогрева, подачи топлива к главным и вспомогательным двигателям
внутреннего сгорания и парогенераторам, а так же для передачи его на берег и
другие суда. Большинство дизелей для пуска, на переходных режимах и перед
остановкой используют дизельное легкое топливо, а на основных режимах плавания
используют тяжелое топливо марки МТ-100, вязкостью 700 сСТ при температуре 50
°С. Поэтому необходимо предусматривать системы легкого и тяжелого топлива.
Топливная система обеспечивает
подготовку и перекачку топлива, обеспечивает замер расхода топлива на ГД и
вспомогательном ДГ.
Топливная система состоит из
подсистем:
Приема, хранения и перекачки,
обеспечивающие прием топлива с берега или других судов, распределение его по
емкостям основного запаса, перекачку топлива из одной цистерны в другую,
заполнение отстойных и расходных цистерн, а так же выдачу топлива на берег.
Очистки, обеспечивающая повышение
качества топлива путем изменения его физического состояния (отстаивание,
сепарация, гомогенизация).
Подачи топлива к потребителям.
Результаты расчета по топливной
системе
************************************************************************
ФАЙЛ
SMC2_REZ.DAT - РЕЗУЛЬТАТЫ РАБОТЫ КОМПЛЕКСА ПРОГРАММ SISTEMA I
************************************************************************
NппI
IОБОЗН.I НАИМЕНОВАНИЕ ПЕРЕМЕННОЙ IРАЗМI ЗНАЧЕНИЕ I
************************************************************************
1.I
ТР I BT I ЧАСОВОЙ РАСХОД ТОПЛИВА IT/Ч I 0.421197
2.I*ТР
I VRZTTI ОБЪЕМ РАСХОДНОЙ ЦИСТЕРНЫ ТЯЖ. ТОПЛ. IM**3I 7.980582
3.I*ТР
I VRZLTI " " " ЛЕГ. ТОПЛ. IM**3I 1.596116
4.I
ТР I VSM I " СМЕСИТЕЛЬНОЙ ЦИСТЕРНЫ IM**3I 0.075816
5.I*ТР
I WTPH I ПОДАЧА ТОПЛИВОПОДКАЧИВАЮЩЕГО НАСОСА IT/Ч I 0.850000
6.I*ТР
I HTPH I НАПОР " " IМПА I 0.400000
7.I
ТР I NTPH I МОЩНОСТЬ " " IКВТ I 0.148698
8.I
ТР I WZTH I ПОДАЧА ЦИРКУЛЯЦИОННОГО ТОПЛ. НАСОСА IT/Ч I 0.000000
9.I
ТР I HZTH I НАПОР " " " IМПА I
0.000000
10.I
ТР I NZTH I МОЩНОСТЬ " " " IКВТ I
0.000000
11.I
ТР I QTP I РАСХОД ТЕПЛА НА ПОДОГРЕВ ТОПЛИВА IКВТ I 153.000000
12.I*ТР
I FTP I ПОВЕРХНОСТЬ ПОДОГРЕВАТЕЛЯ ТОПЛИВА IM**2I 11.730000
13.I
ТХ I SRT I РАСХОД ТОПЛИВА ЗА РЕЙС IТ/РЕI 195.767792
14.I
ТХ I ZTT I ЗАПАС ТЯЖЕЛОГО ТОПЛИВА I " I 180.106369
15.I
ТХ I ZLT I " ЛЕГКОГО " I " I
45.026592
16.I
ТХ I VZAZ I ОБЪЕМ ЦИСТЕРНЫ АВАРИЙНОГО ЗАПАСА IM**3I 11.970873
17.I*ТХ
I WTPEHI ПОДАЧА ТОПЛИВОПЕРЕКАЧИВАЮЩЕГО НАСОСАIТ/Ч I 10.917436
18.I*ТХ
I HTPEHI НАПОР " IМПА I 0.300000
19.I
ТХ I NTPEHI МОЩНОСТЬ " IКВТ I 1.432412
20.I
ТХ I VPERZI ОБЪЕМ ПЕРЕЛИВНОЙ ЦИСТЕРНЫ IМ**3I 1.995145
21.I
ТХ I WZAPRI ИНТЕНСИВНОСТЬ ЗАПРАВКИ IТ/Ч I 91.199997
22.I
ТХ I TPOGRI ДЛИТЕЛЬНОСТЬ ПОГРУЗКИ ТОПЛИВА I Ч I 2.146577
23.I
ТХ I DTRPTI ДИАМЕТР ТРУБОПРОВОДА ПОГРУЗКИ ТОПЛ. I M I 0.242789
24.I
ТО I VOZ I ОБЪЕМ ОТСТОЙНОЙ ЦИСТЕРНЫ IМ**3I 11.970873
25.I*ТО
I WSTT I ПРОИЗВОДИТЕЛЬНОСТЬ СЕПАРАТОРА Т Т IТ/Ч I 1.364679
26.I
ТО I WHSTTI ПОДАЧА НАСОСА СЕПАРАТОРА Т Т IT/Ч I 1.569381
27.I
ТО I HHSTTI НАПОР " IМПА I 0.300000
28.I
ТО I NHSTTI МОЩНОСТЬ " IКВТ I 0.247091
29.I*ТО
I WSLT I ПРОИЗВОДИТЕЛЬНОСТЬ СЕПАРАТОРА Л Т IМ**3I 1.364679
30.I
ТО I WHSLTI ПОДАЧА НАСОСА СЕПАРАТОРА Л Т IT/Ч I 1.569381
31.I
ТО I HHSLTI НАПОР " IМПА I 0.300000
32.I
ТО I NHSLTI МОЩНОСТЬ " IКВТ I 0.247091
33.I
ТО I QSEP I РАСХОД ТЕПЛА В ПОДОГРЕВАТЕЛЕ СЕП-РА IКВТ I 68.233971
34.I*ТО
I FPSTTI ПОВЕРХНОСТЬ ПОДОГР. СЕПАРАТОРА T T IM**2I 5.231271
35.I
ТО I FPSLTI " " " Л Т I " I
5.231271
36.I
ТО I WGOM I ПРОИЗВОДИТЕЛЬНОСТЬ ГОМОГЕНИЗАТОРА IT/Ч I 0.932018
37.I
ТО IWFILTRI ПРОИЗВОДИТ. ПОЛНОПОТОЧНОГО ФИЛЬТРА IT/Ч I 0.932018
38.I*ТО
I VZGRTI ОБЪЕМ ЦИСТЕРНЫ ГРЯЗНОГО ТОПЛИВА IM**3I 0.475929
39.I
ТО I VZPR I ОБЪЕМ ЦИСТЕРНЫ ПРОТЕЧЕК ТОПЛИВА IM**3I 0.166575
40.I*ТО
I WHGRTI ПОДАЧА НАСОСА ГРЯЗНОГО ТОПЛИВА IT/Ч I 0.317286
41.I
ТО I VOTX I ОБЪЕМ ЦИСТЕРНЫ ОТХОДОВ СЕПАРАЦИИ IM**3I 1.010874
ЦИСТЕРНЫ ОТХОДОВ СЕПАРАЦИИ IM**3I
1.010874
В состав системы подобраны:
Топливоподкачивающий насос ШФ
2-25-1,4/4Б-13;
Два циркуляционных насоса ШФ
2-25-0,8/16Б-13, подключены параллельно;
Топливоперекачивающий насос 3В 16/25-1-10/16Б-2;
Насос грязного топлива ШФ
0,6-25-0,36/25Б;
Сепаратор тяжелого топлива СЦ-1,5-4М
Сепаратор легкого топлива СЦ-1,5-4М
На рисунке показана примерная
принципиальная схема топливной системы. Из цистерн общего запаса тяжелое
топливо подается в отстойные цистерны через фильтры грубой очистки.
Все топливные цистерны оборудуются
воздушными трубами, имеющими выход на открытую палубу. Кроме того,
предусматривают переливные трубы для перетекания топлива в случае переполнения
цистерны. В топливные цистерны устанавливают змеевиковые подогреватели для
подогрева топлива. После отстаивания топливо подают на сепараторы, и после
сепарации поступает в расходную цистерну. Дизельное топливо также сепарируют
перед его подачей в расходную цистерну легкого топлива. Из расходных цистерн
топливо топливоподкачивающим насосом подается в обогреваемую смесительную
цистерну, при этом проходит через обогреваемый фильтр. Из смесительной цистерны
топливо циркуляционными топливными насосами подается в обогреватель для
снижения вязкости, через фильтры и поступает в топливные насосы высокого
давления.
Вискозиметр регулирует вязкость
топлива путем воздействия на паровой клапан, который изменяет подачу пара в
топливо-подогреватель.
Система циркуляционной смазки.
Предназначена для приема, хранения,
и перекачки, смазки главного и вспомогательных двигателей, а так же других
механизмов.
В целях восстановления рабочих
свойств масел применяют систему регенерации масел в циркуляционных системах
смазки. Регенерация осуществляется с помощью отстаивания, сепарации, фильтрации
и добавления многофункциональных присадок в масло. Циркуляционное масло
охлаждают в маслоохладителях, прокачиваемых забортной водой.
Таблица Результаты расчета по
масляной системе
NппI
IОБОЗН.I НАИМЕНОВАНИЕ ПЕРЕМЕННОЙ IРАЗМI ЗНАЧЕНИЕ I
************************************************************************
1.I
СЦ I QZ I ТЕПЛООТВОД С МАСЛОМ ОТ ГЛ.ДВИГАТЕЛЯ IКВТ I 291.500000
2.I*СЦ
I WGMH I ПОДАЧА ГЛАВНОГО МАСЛЯНОГО НАСОСА IТ/Ч I 75.000000
3.I*СЦ
I HGMH I НАПОР " " " IМПА I 0.600000
4.I
СЦ I NGMH I МОЩНОСТЬ " " " IКВТ I
19.444445
5.I*СЦ
I VSZZ I ОБЪЕМ СТОЧНО-ЦИРКУЛЯЦИОННОЙ ЦИСТЕРНЫIM**3I 15.750001
6.I
СЦ I T2M I ТЕМПEРАТУРА МАСЛА ПЕРЕД МАСЛООХЛАД. IГРАДI 55.000000
7.I*СО
I WSM I ПРОИЗВОДИТЕЛЬНОСТЬ СЕПАРАТОРА МАСЛА IT/Ч I 1.968750
8.I
СО I QPSM I РАСХОД ТЕПЛА В ПОДОГРЕВАТЕЛЕ СЕПАР. IКВТ I 56.054691
9.I*СО
I FPSM I ПОВЕРХНОСТЬ ПОДОГРЕВАТЕЛЯ СЕПАРАТОРАIM**2I 0.070000
10.I
СО I WHSM I ПОДАЧА НАСОСА СЕПАРАТОРА МАСЛА IТ/Ч I 2.362500
11.I
СО I HHSM I НАПОР " " " IМПА I
0.400000
12.I
СО I NHSM I МОЩНОСТЬ " " " IКВТ I
0.408333
13.I
СО I WFGO I ПРОИЗВОДИТЕЛЬН. ФИЛЬТРА ГРУБ.ОЧИСТ. IТ/Ч I 75.000000
14.I*СО
I WFTO I " " ТОНК. " I " I
75.000000
15.I
СО I WBF I " " БАЙПАСНОГО I " I
6.000000
16.I
СХ I ZZM I ЗАПАС ЦИРКУЛЯЦИОННОГО МАСЛА I T I 11.572974
17.I
СХ I VZZM I ОБЪЕМ ЦИСТЕРН ЗАПАСА ЦИРКУЛЯЦ.МАСЛА IM**3I 13.887569
18.I
СХ I VZGM I ОБЪЕМ ЦИСТЕРНЫ ГРЯЗНОГО МАСЛА IM**3I 10.125000
19.I
СХ I WMPEHI ПОДАЧА МАСЛОПЕРЕКАЧИВАЮЩЕГО НАСОСА IT/Ч I 12.187500
20.I
СХ I HMPEHI НАПОР " " IМПА I 0.300000
21.I
СХ I NMPEHI МОЩНОСТЬ " " IКВТ I 1.685185
22.I
СХ IVZSEPMI ОБЪЕМ ЦИСТЕРНЫ СЕПАРИРОВАННОГО МАСЛАIM**3I 13.887569
В систему входят:
Главный масляный насос 3В
125/16-3-80/4Б;
Сепаратор MARX 204;
Маслоохладитель кожухотрубный ОКН
26,9-420-2.
На рисунке показана принципиальная
схема смазки дизелей.
Под главным двигателем 1 расположена
сточная система 2 циркуляционного масла. С помощью насосов 4 масло проходит
через фильтр 3, поступает в маслоохладитель 5. На каждом масляном насосе должен
быть перепускной предохранительный клапан, ограничивающий повышение давления.
После маслоохладителя установлен автоматический клапан, регулирующий
температуру масла. После маслоохладителя масло попадает в главную масляную
магистраль. Проходит через сдвоенный масляный фильтр и подается на смазку
подшипников и охлаждение поршней. Сдвоенный масляный фильтр необходим для того,
чтобы один из фильтров можно было отключать для очистки от грязи. Параллельно
основному контуру циркуляции масла в системе смазки имеется независимый контур
сепарации масла. Из сточной цистерны масло для лучшей очистки в сепараторе
проходит через подогреватель. Очищенное масло возвращается в сточную цистерну.
Система охлаждения.
Служит для отвода теплоты от ДВС,
передач, компрессоров, опорных и упорных подшипников валопровода и других
механизмов.
Системы охлаждения выполняют
проточными и замкнутыми. Проточные системы применяются для охлаждения рабочих
сред в теплообменных аппаратах, в них применяют забортную воду. Замкнутые
системы используют для отвода теплоты от ДВС, т.к. при температурах 50-55 °С
начинается выпадение солей из забортной воды.
При проектировании систем охлаждения
учитывать требования Регистра РФ. В каждом машинном отделении должно быть
предусмотрено не менее двух приемных кингстонов забортной воды, один из них
днищевой. За кингстонами устанавливают фильтры, очистка которых должна
производиться без прекращения работы насосов забортной воды.
************************************************************************
ФАЙЛ
SMC2_REZ.DAT - РЕЗУЛЬТАТЫ РАБОТЫ КОМПЛЕКСА ПРОГРАММ SISTEMA I
************************************************************************
NппI
IОБОЗН.I НАИМЕНОВАНИЕ ПЕРЕМЕННОЙ IРАЗМI ЗНАЧЕНИЕ I
************************************************************************
1.I
ПР I QT I ТЕПЛОТА ВЫД. В ГЛ.ДВ. ОТ СГОР.ТОПЛ. IКВТ I 4855.469730
2.I
ПР I QPW I " ОТВОДИМАЯ С ПРЕСНОЙ ВОДОЙ I " I 592.222229
3.I
ПР I WHPW I ПОДАЧА НАСОСА ПРЕСНОЙ ВОДЫ IТ/Ч I 28.350000
4.I
ПР I HHPW I НАПОР " " " IМПА I
0.250000
5.I
ПР I NHPW I МОЩНОСТЬ " " " IКВТ I
0.002940
6.I
ПР I VWRZ I ОБЪЕМ ВОДЫ В РАСШИРИТЕЛЬНОЙ ЦИСТЕРНЕIM**3I 0.594912
7.I
ПР I VRZ I ОБЪЕМ РАСШИРИТЕЛЬНОЙ ЦИСТЕРНЫ IM**3I 0.773385
8.I
ПР I VRB I ОБЪЕМ РАСТВОРНОГО БАЧКА IM**3I 0.107084
9.I
ПР I TPR1 I ТЕМПЕРАТУРА ПРЕСН.ВОДЫ ПЕРЕД ГЛ.ДВИГIГРАДI 75.010826
10.I
ПР I TPR2 I ТЕМПЕРАТУРA ПРЕСН.ВОДЫ ЗА ГЛ.ДВИГIГРАДI 80.000000
************************************************************************
ФАЙЛ
SMC2_REZ.DAT - РЕЗУЛЬТАТЫ РАБОТЫ КОМПЛЕКСА ПРОГРАММ SISTEMA I
************************************************************************
NппI
IОБОЗН.I НАИМЕНОВАНИЕ ПЕРЕМЕННОЙ IРАЗМI ЗНАЧЕНИЕ I
************************************************************************
1.I
ЗВ I WHZW I ПОДАЧА НАСОСА ЗАБОРТНОЙ ВОДЫ IT/Ч I 96.000000
2.I
ЗВ I HHZW I НАПОР " " " IМПА I
0.250000
3.I
ЗВ I NHZW I МОЩНОСТЬ " " " IКВТ I
9.930728
4.I
ЗВ I TZW1 I ТЕМПЕРАТУРА ЗАБ.ВОДЫ НАЧАЛЬНАЯ IГРАДI 32.000000
5.I
ЗВ I TZW2 I ТЕМПЕРАТУРА ЗАБ.ВОДЫ ЗА МАСЛООХЛАД. IГРАДI 33.935978
6.I
ЗВ I QW I ОТВОД ТЕПЛОТЫ ОТ ПРОДУВОЧН. ВОЗДУХА IКВТ I 1175.000000
7.I
ЗВ I WZWO I РАСХОД ЗАБ.ВОДЫ ЧЕРЕЗ ВОЗДУХООХЛАД. IT/Ч I 60.000000
8.I
ЗВ I WZOPWI " " " ОХЛ.ПРЕСН.ВОДЫIТ/Ч I
0.000000
9.I
ЗВ I WZORWI " " " МАСЛООХЛ.РАСПР.ВАЛАIT/Ч I
0.000000
10.I
ЗВ I QRW I ОТВОД ТЕПЛОТЫ ОТ " " " IКВТ I
0.000000
11.I
ЗВ I TZW3 I ТЕМПЕРАТУРА ЗАБ.ВОДЫ В ОТЛИВНОМ КОЛЛI " I 51.954178
12.I
ЗВ I DTMO I СРЕДН.ТЕМПЕР.НАПОР В МАСЛООХЛАДИТЕЛЕIГРАДI 15.532011
13.I
ЗВ I DTOPWI " " " В ОХЛАД.ПРЕСН.ВОДЫ I " I
34.560337
14.I
ЗВ I FMO I ПОВЕРХНОСТЬ ГЛАВНОГО МАСЛООХЛАДИТЕЛЯIM**2I 20.108242
15.I
ЗВ I FOPW I " " ПРЕСНОЙ ВОДЫ I " I
15.993501
В состав системы входит:
Насос пресной воды НЦВ40/20Б;
Насос забортной воды НЦВ100/20А;
Охладитель пресной воды
кожухотрубный ОКН 15,8-420-5.
На рисунке показана принципиальная
схема системы охлаждения двигателя пресной водой. Центробежный насос 2 подает
воду водо-водяной охладитель 4, после которого она поступает в полости рабочих
втулок и крышки ГД. Нагретая вода от двигателя подается снова к насосу 2.
Наиболее высоко расположенный участок этого трубопровода соединен с
расширительной цистерной 13, которая сообщается с атмосферой. Расширительная
цистерна должна располагаться выше двигателя и подключается к всасывающей линии
насоса, обеспечивая компенсацию изменения объема воды при колебаниях
температуры и подпор на всасывании насоса. В ее верхнюю часть отводятся трубки
удаления воздуха из верхних точек полостей охлаждения ДВС и магистралей. Через
расширительную цистерну пополняется система пресной водой, вводятся присадки,
снижающие отложение накипи и коррозию в полостях ДВС. Растворы приготовляют в
растворном бачке, и затем спускают в расширительную цистерну. Для регулирования
температуры, поступающей к двигателю, служит термостат, перепускающий воду
помимо охладителя. Циркуляционная система имеет стояночный насос 3, включенный
параллельно основному насосу 2 (он резервируется).
На предыдущем рисунке представлена
принципиальная схема системы охлаждения забортной водой. Последняя принимается
через бортовой 1 или донный кингстон 15. От кингстона через фильтры 14 вода
поступает к насосу охлаждающей воды 3, который подает ее на маслоохладитель 5 и
водоохладитель 7, а также на охлаждение компрессоров, подшипников валопровода и
другие нужды. Нагретая вода после водоохладителя 6 отводится за борт через
отливной забортный клапан 10. При чрезмерно низкой температуре забортной воды и
при попадании битого льда в приемные кингстоны часть нагретой воды можно
перепустить 13 во всасывающую магистраль. Регулирование производится клапаном
9. Охлаждающая система имеет резервный насос, включенный параллельно основному
насосу.
Система сжатого воздуха
Сжатый воздух используется для
запуска главных и вспомогательных двигателей, реверса главных двигателей при
отсутствии других средств реверса (ВРШ, реверс-редуктора и др.). У нас этих
средств нет, поэтому МОД с ВФШ делают реверсивным и используют сжатый воздух
для реверса. Кроме того сжатый воздух более низких параметров используют для
бытовых и технических нужд - пневмоцистерн, подачи сигналов (сирена),
пневмоинструмента, продувания забортных отверстий.
На схеме представлены 5 - главные
компрессора, 6 - подкачивающий компрессор, влаго-маслоотделитель 4, баллоны 3
главных двигателей 1, баллоны дизель-генераторов 7, баллон хознужд 9 (может и
не быть), бытовые потребители питаются либо от хозбаллона, либо от одного
главного баллона через дроссельные клапана, снижающие давление от 32 атм до 2-3
атм.
Требуемое давление сжатого воздуха
зависит от потребителей. Для пуска двигателей требуется воздух под давлением
2,5 - 3,0 МПа. Для общесудовых нужд необходим сжатый воздух под давлением
0,8-1,0 МПа.
К системам сжатого воздуха Правилами
Регистра предъявляются определенные требования. Для пуска главных двигателей
должно быть предусмотрено не менее двух баллонов равной емкости, для пуска
вспомогательных допускается установка баллона на каждый ДГ. Вместимость
баллонов должна обеспечивать для реверсивного ДВС не менее двенадцати пусков с реверсами
для каждого двигателя. Для вспомогательных двигателей вместимость баллонов
должна обеспечивать не менее шести пусков двигателя наибольшей мощности. Для
вспомогательных нужд устанавливают отдельные баллоны низкого давления.
Приняты два главных компрессора
HC-54A производительностью по 46 нм3/час.
Так как главные компрессора
невелики, то подкачивающий не нужен.
. АНАЛИЗ РЕСУРСОВ И ВЫБОР СХЕМЫ
УТИЛИЗАЦИИ ТЕПЛОВЫХ ПОТЕРЬ ГД (УЗЛОВОЙ ВОПРОС)
Общие сведения
Не смотря на то, что малооборотные
энергетические установки на сегодняшний день помимо того, что позволяют
использовать более дешёвое тяжёлое топливо, являются самыми экономичными
двигателями. Однако и в них ещё имеются определённые резервы, дающие
возможность повысить эффективность установки.
Около половины энергии сжигаемого в
дизелях топлива теряется с выхлопными газами, с охлаждением пресной воды и
смазочного масла, а также излучается в окружающую среду. Даже в свете
продолжающегося неуклонного роста эффективности дизелей утилизация части этих огромных
потерь способно существенно повысить эффективность СДУ. Именно поэтому
утилизация вторичных энергоресурсов широко применяется на практике.
Потери теплоты с выхлопными газами
частично позволяет использовать утилизационный парогенератор, который вырабатывает
некоторое количество пара необходимого для эксплуатации судна, на получение
которого во вспомогательных парогенераторах необходимо сжигать топливо.
Потери тепла с пресной водой, после
прохода через рубашки и крышки цилиндров, полезно используют в утилизационных
опреснительных установках, которые позволяют не только полностью обеспечить
судно пресной водой, но и сократить массу запасов рабочих тел.
Однако создание эффективной системы
утилизации тепловых потерь сопряжено со значительными трудностями по выбору
оптимальной схемы, оптимального сочетания параметров, необходимости обеспечить
компенсацию дополнительных расходов. Предложено большое число вариантов схем
систем утилизации как раздельных для отдельных теплоносителей, так и
совместных, комплексных. Выполнен ряд диссертаций, выпущен ряд монографий,
однако ввиду сложности проблемы не только не установлены границы применения тех
или иных решений, но даже существует путаница в понимании физических процессов.
На рис. 5.1 представлена обобщенная
схема системы утилизации теплоты судовой дизельной установки, принятая в
соответствии с работами А.Г.Курзона, Д.Иорданова и Г.Д.Седельникова. Схема
предусматривает все мыслимые технические решения в этом направлении, в том
числе утилизацию теплоты газов, продувочного воздуха, пресной воды и даже
масла, применение валогенератора и утилизационного турбогенератора,
турбокомпаундной системы работающей на винт, пропульсивной паровой
утилизационной турбины, наличие двух ступеней давления пара, использование пара
среднего и низкого давления как для целей теплофикации, так и в турбинах после
перегрева.
Наличие в составе реальной схемы
утилизации одновременно всего многообразия элементов, представленных на рис.
5.1, исключено, как ввиду дублирования их функций, так и вследствие высоких
капитальных затрат, которые навряд ли будут оправданы. На ряде судов
потребность в таком количестве тепловой энергии отсутствует. Малооборотные
двигатели имеют слишком низкий температурный потенциал выхлопных газов, что
затрудняет реализацию утилизационных циклов с паровыми турбинами. В этом смысле
схема, представленная на рис. 5.1, может быть названа обобщенной - на ней
отражено все, что только можно придумать, а в реальном проектировании будут
применяться схемы, получаемые усечением обобщенной.
На рис. 5.1 представлены: 1- главный
двигатель; 2- валогенератор; 3 - передача; 4 - пропульсивная паровая турбина
(ППТ); 5 - силовая газовая турбина (ТКС); 6 - газовая заслонка; 7 - шибер
перепуска газов; 8 - масляный насос турбоагрегата; 9 - маслоохладитель
турбо-агрегата; 10 - дизель-генератор дополнительный; 11 - дизель-генератор
основной; 12 - вспомогательный парогенератор (ВПГ); 13 - утилизационный
парогенератор (УПГ); 14 - испарительная секция первой ступени (низкого)
давления пара;15 - испарительная секция второй ступени (среднего) давления
пара; 16 - пароперегреватель первой ступени давления пара; 17 -
пароперегреватель второй ступени давления пара; 18 - сепаратор второй ступени
давления пара; 19 - питательный клапан первой ступени давления пара; 20 -
сепаратор первой ступени давления пара; 21 - утилизационный турбогенератор
(УТГ); 22 - общесудовые потребители пара; 23 - конденсатор пара обще- судовых
потребителей; 24 - конденсатор УТГ; 25 - конденсатный насос УТГ; 26 - эжектор
конденсатора УТГ с холодильником; 27 - теплый ящик; 28 - питательный насос ВПГ
и УПГ; 29 - подогреватель питательной воды второй ступени давления пара; 30 -
циркуляционный насос второй ступени давления пара; 31 - газо-турбонагнетатель;
32 -высокотемпературная секция охладителя продувочного воздуха (ВТС); 33 -
низко-температурная секция охладителя продувочного воздуха (НТС); 34 - конечный
водоохладитель; 35 - циркуляционный насос пресной воды; 36 - высокотемпературные
потребители теплоты пресной воды; 37 - низкотемпературные потребители теплоты
пресной воды; 38 - эжектор конденсатора ППТ с холодильником; 39 - конденсатный
насос конденсатора ППТ; 40 - конденсатор ППТ; 41 - движитель.
Задачи эскизного проектирования
систем утилизации достаточно ограничены: нужно выполнить анализ получения в
системе утилизации наибольшего возможного количества электрической энергии,
сравнить это количество с нагрузкой автономного дизель-генератора и сделать
вывод о целесообразности ее применения. В случае, если ходовой дизель-генератор
может быть заменен не полностью, систему устанавливать не стоит, так как
дизель-генератор не может эффективно эксплуатироваться при нагрузке менее 70%
от номинала.
Включение различных вариантов
подогрева питательной воды за счет пресной воды, продувочного воздуха и масла
не влияет на мощность утилизационного турбогенератора. На рис. 5.2 представлена
диаграмма температурных напоров в системе утилизации теплоты выхлопных газов
среднеоборотных двигателей, рассматриваемых в качестве альтернативного варианта
малооборотным двигателям. На судне были установлены малооборотные дизеля. В
качестве альтернативных могут быть использованы два среднеоборотных двигателя,
работающих каждый на свой движитель, с номинальной мощностью Neн=5430 кВт,
температура выхлопных газов T1= 390 0С. На длительном эксплуатационном режиме
соответственно 4860 кВт и 365 0С.
Система утилизации одноконтурная.
Здесь приведены данные по варианту с давлением пара в сепараторе Ps=0.8 МПа,
соответствующему максимуму энергии пара УПГ и наибольшей мощности
утилизационного турбогенератора. Этому давлению соответствует температура
насыщения Ts=170,4 град.С. Температура перегретого пара Tпп = 335 град.С. Она
принята на 30 град. меньше температуры газов на входе в УПГ. Как видно из
рис.5.2 при меньших температурных напорах в пароперегревателе интенсивность
охлаждения газов снижается, что приводит к росту площади и удорожанию
поверхности теплообмена.
Как видно из рисунка, отвод теплоты
в экономайзере не влияет на количество пара, получаемого в испарительной
секции, так как это количество лимитируется минимально допустимым температурным
напором в конце процесса испарения - (T3 - Ts) = 25-30 град С. Если не греть
воду в экономайзере, температура в конце секции испарения не увеличится,
значит, не увеличится и количество получаемого пара, и мощность УТГ.
Одновременно, если греть воду не в экономайзере, а в системе утилизации
теплоты, например продувочного воздуха, то газы будут выброшены в атмосферу не
охлажденными, а затраты на обустройство аппаратов утилизации теплоты останутся
неоправданными.
Минимальный температурный напор в
испарительной секции также ограничен по той же причине роста поверхности
испарения и увеличения стоимости УПГ. По некоторым данным этот напор (T3 - Ts)
может быть уменьшен до 20 0С. Дискуссия на эту тему беспредметна, поскольку
эффективность системы утилизации - объект экономического анализа, а не утверждений
и рассуждений. В каждом конкретном случае следует показать насколько изменится
поверхность, увеличится масса и стоимость УПГ и как изменится экономика судна.
Отдельно следует рассмотреть процесс
в экономайзере. Питательная вода поступает в УПГ с температурой Tпв ок.120 0С.
Теплота, необходимая для подогрева этой воды до Tэк = Ts - Tн, где Tн
- недогрев до состояния насыщения, необходимый для надежной работы питательного
клапана, изображена в масштабе отрезком I1 - Iпв. На такую же величину уменьшится
теплота выхлопных газов, что приведет к снижению температуры газов от T3 = 200
0С до Tух ок. 193 0С. Хотелось бы уменьшить эту температуру для увеличения
эффективности утилизационного цикла.
Однако этого сделать нельзя в связи
с выпадением капелек конденсата на поверхностях охлаждения с температурой
меньше температуры точки росы. Дополнительно обращаем внимание на то, что точка
росы определяется не как средняя температура газов в пучке, а как локальная
температура на поверхности теплообмена. Вследствие градиентов температур,
необходимых для передачи теплоты в реальном времени, температура на поверхности
ниже температуры газов в пристеночном слое.
Кроме этого следует учесть
переменные режимы работы пропульсивного комплекса. При снижении мощности
отдаваемой на движение падают и температура и расход выхлопных газов.
Уменьшаются и температуры по тракту УПГ. Таким образом, повышается вероятность
возникновение на поверхности экономайзера состояния близкого к конденсации
водяных паров в выхлопных газах - точки росы.
Во избежание начала процессов
низкотемпературной коррозии и снижения ресурса УПГ, принято за правило иметь на
входе в экономайзер температуру воды не ниже температуры точки росы. Последняя
представлена на рис. 5.3 в функции содержания в выхлопных газах сернистых
соединений.
Как видно из рисунка принятая нами
температура Tпв = 120 0С соответствует весьма низкому серосодержанию менее
0,3%. Переход на современные высоковязкие сорта топлива приведет к возрастанию
наименьшей допустимой температуры питательной воды до Tпв = 135 и более 0С.
Для сравнения на рис.5.2 приведены
также температуры на выходе из малооборотного двигателя типа МС - номинальные,
соответствующие режиму МДМ и эксплуатационные - соответствующие длительному
режиму эксплуатации. Как видно из рисунка температурные напоры падают и не
сильно превосходят таковые же на выходе из секции испарения. О перегреве пара
не приходится и думать, а это затрудняет работу турбогенератора вследствие
наличия влажности пара не только в последних ступенях, но и на входе в УТГ.
Таким образом выхлопные газы малооборотных дизелей способны обеспечить
получение лишь насыщенного пара, пригодного для использования в системах
теплофикации.
Теплофикационные схемы - получение
пара для целей подогрева различных потребителей полезны всегда, так как
расходовать пар нужно, на его производство тратится топливо во вспомогательном
котле, а последний работает на сниженной нагрузке только лучше. Конечно, здесь
также вредны излишества. Если номинальная производительность УПГ больше, чем
расход на длительном режиме, то мы будем платить за излишние, не используемые
поверхности. Однако это лишь теоретическое замечание.
В результате выполненного анализа
можно сформулировать минимальные задачи эскизного проектирования систем
утилизации теплоты:
определить количество и температуру
выхлопных газов главного двигателя на длительном ходовом режиме эксплуатации;
найти количество пара, получаемое
при подаче выхлопных газов на отдельные типоразмеры из ряд стандартных
утилизационных котлов;
оценить возможное количество
электроэнергии, получаемое от найденного количества пара в утилизационном
турбогенераторе, тоже стандартном;
рассмотреть возможность замены
ходового дизель-генератора на утилизационный турбогенератор. При неполной
замене оценить коэффициент загрузки генератора. Он должен быть не ниже 0,7. При
меньших значениях загрузки основного генератора применение турбогенератора
нецелесообразно;
если от турбогенератора отказались,
сравнить производительности УПГ и ВПГ и подобрать УПГ с близкими характеристиками
для полной или частичной замены ВПГ на длительном ходовом режиме.
Проблема проектирования и анализа
(исследования) возможностей системы утилизации тепловых потерь главных судовых
двигателей состоит в том, что эти характеристики заданы в базе данных (см.
раздел 4. Системы СЭУ) в соответствии с проспектами фирм-производителей
двигателей на режиме номинальной МДМ - точка L1 на диапазоне допустимых МДМ, а
систему утилизации нужно создавать для режима длительной эксплуатационной
мощности - ДЭМ, продолжительность которого составляет до 95% ходового времени.
Режим же НМДМ может вообще никогда не использоваться, так как существует
настройка на СМДМ, кроме того максимальная мощность (СМДМ) используется крайне
редко.
Методика пересчета параметров с
режима НМДМ на режим ДЭМ приведена в проспектах на двигатели. Для
типоразмерного ряда МС эта методика изложена ниже.
К номинальным параметрам выхлопных
газов вносятся поправки на соответствующие конкретные условия и конструкцию
двигателя с использованием следующих зависимостей:отр = Mн Nо/Nн Mа10-2
(1+dMб/100) (1+dMв/100) Nр/Nо (1+dMг/100);
отр = Tн + dTа + dTб + dTв + dTг,
град.С,
где: Mотр, Тотр, Nр - расход, кг/ч,
температура отработавших газов, 0С, и эффективная мощность, кВт, на основном
расчетном длительном эксплуатационном режиме; Мн, Tн, Nн - то же на режиме L1
(МДМ); Nо - эффективная мощность на спецификационном режиме настройки агрегата
МОД на номинальные характеристики, кВт; Mа - коэффициент влияния на массу газов
отклонения спецификационного режима от режима L1 (МДМ), %; dTа - поправка к
температуре на отклонения спецификационного режима от режима L1 (МДМ); dMб,dTб
- поправки на отклонение начальных параметров от стандарта ИСО; dMв,dTв -
поправки на отклонение длительного режима эксплуатации от спецификационного
режима; dMг,dTг - поправки на наличие ТКС.
Номинальные параметры могут быть
определены с помощью таблиц раздела 4. Температура на выходе из ГТН задана
прямо: Tн = Tг, 0С.
Мощность и расход газа следует
умножить на число цилиндров в составе агрегата:
н = Nц * Zцил; Mн = Gгаз * Zцил.
Поправки на отклонение
спецификационного режима от режима номинальной МДМ представлены на рис.5.4.
Графики, приведенные на рис.5.4,
могут быть описаны следующими зависимостями, принятыми в соответствии с
проспектом фирмы MAN - B&W:
а = 100 - 14.9388 * (Ln(n) -
Ln(N));а = 35.5195 * Ln(n) + 14.9410 * Ln(N) - 232.3792,
где n, N - отношение частоты(n) и
мощности(N) на спецификационном режиме к параметрам точки L1 - режима
номинальной МДМ, %.
Напомним одновременно, что
увлекаться снижением спецификационного режима по сравнению с режимом МДМ не
следует. Хотя проектировщику фирмой представлена определенная свобода в выборе
режима оптимизации, но масса, габариты и стоимость определяются точкой L1.
Использовать же режим номинальной МДМ после оптимизации двигателя на режиме
пониженной мощности будет невозможно.
Согласно ИСО стандартные параметры
окружающей среды составляют: температуры воздуха Tв и забортной воды Tзв - 27
град.С, давление воздуха - 0.1 МПа, противодавление на выхлопе - 0.003 МПа.
Поправки к расходу и температуре газов на выходе из газотурбонагнетателя в
зависимости от отклонения фактических параметров от их стандартных значений
представлены в табл.5.1.
Таблица 5.1
Поправки к параметрам выхлопных
газов ДВС типа МС
Параметры среды
|
Увеличение параметров среды на каждые
|
Поправки к параметрам газа на выходе из газотурбонагнетателя
|
|
|
к расходу, %
|
к температуре, 0С
|
Температура воздуха
|
10 0С
|
-4.1%
|
+16 0С
|
Температура забортной воды
|
10 0С
|
+1.9%
|
+1 0С
|
Давление воздуха
|
10 кПа
|
-0.3%
|
+0.1градС
|
Противодавление выхлопа
|
1 кПа
|
-1.1%
|
+5град.С
|
Аппроксимируя данные табл.5.4 можно
получить общую зависимость для поправок на отклонение параметров окружающей
среды от стандарта ИСО:
б
=-0.41(Tмо-27)-0.3(Pб-0.1)+0.19(Tзв-27)-1100(dP-0.003);б =
1.6(Tмо-27)-100(Pб-0.1)+0.1(Tзв-27)-5000(dP-0.003);
где: Tмо,Pб, Tзв,dP - фактические
значения параметров окружающей среды - температуры в МКО, давления воздуха,
температуры забортной воды и противодавления газовыхлопного тракта.
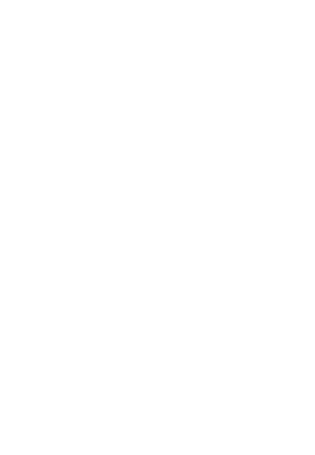
Они могут быть описаны следующими
зависимостями, приведенными в проспекте фирмы. Для винта фиксированного шага:в
= 0.0055 Nр2 - 1.15 Nр + 60;в = 0.005 Nр2 - 0.72 Nр + 22.
Для винта регулируемого шага:в =
0.0055 Nр2 - 1.22 Nр + 67;в = 0.0043 Nр2 - 0.63 Nр + 20,
где Nр - эффективная мощность на
основном длительном эксплуатационном режиме в процентах от мощности на режиме
оптимизации, %;
Наличие ТКС снижает массу газа
приблизительно на 8% и увеличивает температуру ориентировочно на 30 град.С.
Номинальное количество теплоты,
отводимой от двигателя с охлаждением продувочного воздуха, пресной водой,
охлаждающей рубашки и крышки цилиндров, и с маслом может быть определено по
таблице раздела 4, где они обозначены Qvoz, Qhol, Qm и заданы в кВт на каждый
цилиндр данного типоразмера. Изменение этих величин при отклонении режима от
номинального (L1, НМДМ) представлено на рис. 5.6 а, б, в.
Расчет ресурсов утилизации
Количество вторичных энергоресурсов
малооборотной дизельной установки можно определить путём применения
программного комплекса RESURSY, который решает задачи определения количества и
температуры, пресной воды, выхлопных газов и отвод тепла от продувочного
воздуха главного двигателя на длительном ходовом режиме эксплуатации.
Исходные данные для двигателя 5L35MC
представлены в табл. 5.2.
Таблица 5.2
────────────────────────────────────────────────────────────────────────┐
ФАЙЛ
MTG_MOD.DAT - ДАННЫЕ ДЛЯ РАСЧЕТА Gг и Tг ВЫХЛОПНЫХ ГАЗОВ МОД │
────┬──────────────────────────────────┬────────┬──────────┬────────────┤
Nпп│
НАИМЕНОВАНИЕ ПЕРЕМЕННОЙ │ОБОЗНАЧ.│ РАЗМЕРН. │ЧИСЛ.ЗНАЧЕН.│
────┼──────────────────────────────────┼────────┼──────────┼────────────┤
1
│ Мощность на режиме оптимизации │ Nо │ % │
84.000│
2
│ Частота на режиме оптимизации │ n │ % │
94.350│
3
│ Температура воздуха в МКО │ Tv │ град.С │
27.000│
4
│ Барометрическое давление │ Pv │ МПа │
0.100│
5
│ Температура забортной воды │ Tw │ град.С │
27.000│
6
│ Противодавление на выхлопе │ dPвых│ МПа │
0.003│
7
│ Мощность на длит.режиме(% от No)│ Nр │ % │
85.000│
8
│ Частота на длит.режиме(% от n) │ OBP │ % │
94.712│
9
│ Темпер.продув.возд.в коллекторе │ Tvн │ град.С │
50.000│
10
│ Температура пресной воды передГД│ Tпрв │ град.С │
70.000│
11
│ Температура циркул.масла передГД│ Tм │ град.С │
42.000│
12
│ Код типоразмера цилиндра │ TRGD │ - │
26│
13
│ Число цилиндров МОД в агрегате │ Zцил │ - │
5│
14
│ Признак наличия ТКС │ TCS │ - │
0│
15
│ Код типа движителя │ WINT │ - │
1│
────┴──────────────────────────────────┴────────┴──────────┴────────────┘
После обращения к модели RESURSY
могут быть получены параметры рабочих тел систем СЭУ на длительном
эксплуатационном режиме. Результаты представлены ниже.
Расчет ресурсов утилизации ДВС типа
МС (МОД ДКРН) на длительном эксплуатационном режиме
ИСХОДНЫЕ ДАННЫЕ (файл MTG_MOD.DAT)=
84.000 N= 94.350 TV= 27.000 PV= 0.100= 27.000 DP2= 0.003 NP= 85.000 OBP=
94.712= 50.000 TPR= 70.000 TM= 42.000= 5 TRGD= 26 TCS= 0 WINT= 1
РЕЗУЛЬТАТЫ РАСЧЕТА
Материальый и энергетический баланс
систем
на один цилиндр МОД ДКРН типа МС
типоразмера J = 26
на режиме номинальной МДМ (L1) по
данным фирмы MAN-B&W
.470 - расход продувочного воздуха,
кг/с;
.500 - расход выхлопных газов,
кг/час;
.000 - температура выхлопных газов,
град.С;
.670 - расход пресной воды, м3/ч;
.200 - общий расход забортной воды,
м3/ч;
.000 - расход циркуляционного масла,
м3/ч;
.170 - расход масла смазки
распредвала, м3/ч;
.000 - отвод теплоты от продувочного
воздуха, кВт;
.000 - расход забортной воды через
охл.воздуха.м3/ч;
.300 - отвод теплоты от
циркуляционного масла, кВт;
.170 - расход забортной воды через
охл.пр.воды м3/ч;
.000 - отвод теплоты от пресной
воды, кВт./
Баланс агрегата МОД на длительном
эксплуатационном режиме
.389 - расход выхлопных газов, кг/с;
.254 - температура выхлопных газов,
град.С;
.850 - расход продувочного воздуха,
кг/с;
.041 - температура продувочного
воздуха, град.С;
.818 - отвод теплоты от продувочного
воздуха, кВт;
.350 - расход пресной воды в системе
охлажд., м3/ч;
.652 - темпер.пресной воды на выходе
из ГД, град.С;
.000 - темпер.пресной воды на входе
в ГД, град.С;
.464 - отвод теплоты от пресной
воды, кВт;
.000 - расход циркуляционного масла
м3/ч;
.987 - температура масла на выходе,
град.С;
.939 - отвод теплоты с маслом, кВт.
Поправочные коэффициент количества и
температуры газов
.264 -4.671 - MA, DTA (режим
оптимизации)
.000 0.000 - DMB, DTB (отличие от
условий ИСО)
.988 -3.075 - DMC, DTC (отклонение
от режима оптимизации)
.000 0.000 - DMG, DTG (наличие ТКС)
Поправочные коэффициент к расходам
тепла
.389 - QVO (продувочного воздуха)
.893 - QPO (пресной воды)
.859 - QMO (циркуляционного масла)
Определение паропроизводительности
утилизационного парогенератора
Для танкеров важна возможность
получения наибольшего количества теплоты в системах утилизации, так как расход
пара на подогрев груза (на длительном режиме) весьма велик.
Рассмотрим также и другие
возможности получения теплоты в системах утилизации, в том числе утилизацию
теплоты продувочного воздуха, а также снижение параметров пара УПГ по сравнению
с ВПГ. Эти параметры обычно приравниваются для возможности использования
единого сепаратора для сбора и расходования пара в системе питания потребителей
в соответствии со схемой, представленной на рис.5.7.
Потребители тепловой энергии на
танкере нуждаются в подогреве до различных температур, а следовательно и
различных температурах теплоносителя. В наиболее высокой температуре греющего
пара нуждается тяжелое топливо.
Таблица 5.5
Вязкость отечественных марок топлива
ГОСТ
|
Марка топлива
|
Вязкость, сСт
|
Температура, оС
|
ГОСТ 305-73
|
Л
|
3,5 - 6
|
20
|
ГОСТ 1667-68
|
ДТ
|
36
|
50
|
ГОСТ 1667-68
|
ДМ
|
150
|
|
ГОСТ 10585-75
|
Ф5
|
36,2
|
|
ГОСТ 10585-75
|
Ф12
|
89
|
|
ГОСТ 10585-75
|
40
|
59
|
80
|
ГОСТ 10585-75
|
100
|
118
|
|
В табл. 5.5 приведена вязкость
отечественных марок топлива. В зарубежной практике существует тенденция
использования на грузовых судах наиболее тяжелых и вязких марок топлива в
соответствии со стандартом ISO. Вместе с тем имеется возможность работы на
высоковязком топливе типа RMK55 (М-100 по отечественному стандарту) не только
вспомогательных котлов, но и двигателей внутреннего сгорания как малооборотных,
так и среднеоборотных и даже высокооборотных.
В табл. 5.5 приведена вязкость марок
топлива в соответствии с отечественными стандартами. В связи с использованием
на отечественных судах двигателей, изготовленных
по лицензиям зарубежных фирм, а
также возможностью бункеровки в зарубежных портах высоковязким топливом в
соответствии со стандартом ISO должна быть предусмотрена возможность работы на
указанных марках топлива.
Для перекачки, сепарации и
качественного распыления тяжелого топлива при впрыске его в цилиндр дизеля
требуется снижение вязкости, что достигается подогревом его до температур
указанных в табл. 5.6. Для обеспечения эффективной передачи теплоты от греющего
пара необходим температурный напор - превышение температуры греющего пара над
температурой нагреваемого рабочего тела. На практике его принимают равным 25-30
оС.
Таблица 5.6
Температура топлива при обработке и
использовании
Марка топлива
|
Температура топлива, оС
|
|
Перед перекачкой
|
Перед сепарацией
|
Перед форсунками
|
Моторное ДТ
|
5 - 10
|
40 - 60
|
65 - 75
|
Мазут флотский: Ф-5
|
5 - 10
|
40 - 60
|
65 - 75
|
Ф-12
|
10 - 25
|
55 - 80
|
85 - 95
|
Дизельный мазут ДМ
|
30 - 50
|
80 - 85
|
100 - 110
|
Топочный мазут: М-40
|
60 - 70
|
110 - 120
|
130 - 135
|
М-100
|
80 - 90
|
130 - 140
|
150 - 155
|
Таким образом, если на длительном
ходовом режиме в качестве топлива для главного двигателя используют мазут
М-100, то греющий пар должен иметь температуру не ниже 180 оС. В системах
теплоснабжения применяется насыщенный пар, обладающий более высоким
коэффициентом теплоотдачи по сравнению с перегретым паром и горячей водой. В
результате вспомогательная котельная установка должна генерировать насыщенный
пар с температурой 180 oС и соответствующим давлением насыщения 1 МПа.
В случае если для главного двигателя
используется топливо М-40, то его необходимо нагреть до 130-135 оС, и ВКУ
должна вырабатывать пар с температурой 160 оС и давлением насыщения 0,62 МПа.
Если принять, что температурный напор снижается до 20 оС, то допустимо
использовать котлы с давлением 0,5 МПа и температурой насыщения 152 оС.
Прочие потребители пара требуют
более умеренных параметров. Особенно это относится к потребителям, применяемым
для обогрева помещений и подогрева груза на танкерах. Безусловно,
непосредственная подача в системы бытового потребления пара даже насыщенного
пара с давлением 5 - 7 атм невозможна вследствие излишне высокой температуры.
Подобный пар может использоваться в паропреобразователях для получения пара и
горячей воды с допустимыми параметрами.
На рис. 5.7 приведены требуемые
температуры подогрева различных марок топлива для снижения вязкости,
необходимой для впрыска в ДВС.
Существующая практика проектирования
судовых вспомогательных теплоэнегретических установок состоит в приравнивание
параметров утилизационного котла параметрам вспомогательного. Поскольку во
вспомогательных котлах получается насыщенный пар, то речь идет о давлении
насыщения и соответствующей давлению температуре насыщения. В табл. 5.8
приведена вырезка из таблиц характеристик водяного пара (состояние насыщения по
давлениям) для диапазона, представляющего интерес для судовой энергетики.
Использование одинаковых параметров
позволяет использовать общую емкость для накопления и расходования пара
поступающего от вспомогательного и утилизационного котлов. Кроме этого на
сухогрузных судах возможно обойтись только паром утилизационного котла на
ходовых режимах для покрытия всех потребностей судна. Для танкеров же это
весьма неэкономный способ, так как от утилизационного котла получают
теплопроизводительность в два и более раза меньшую, чем это могло бы быть при
снижении параметров пара. Допустимо ли это? Рассмотрим характеристики
потребителей пара на танкерах и возможность снижения давления и температуры
пара, получаемого в утилизационном котле.
В табл. 5.8 приведены составляющие
паровой нагрузки танкера пр. 17120 на длительном ходовом режиме. Именно на этом
режиме следует получить максимальное количество тепловой энергии от системы
утилизации тепловых потерь главного двигателя.
Таблица 5.8
Паровые нагрузки танкера пр.17120 на
длительном ходовом режиме
№ пп
|
Наименование потребителей
|
Wном кг/ч
|
Ход с обогревом груза
|
|
|
|
kз
|
kо
|
Wфакт
|
1
|
Обогрев цистерн запаса тяжелого топлива
|
383
|
0,8
|
0,3
|
92
|
2
|
Обогрев отстойных цистерн тяжелого топлива
|
120
|
0,8
|
0,5
|
48
|
3
|
Обогрев расходных цистерн тяжелого топлива
|
200
|
0,5
|
0,5
|
50
|
4
|
Подогрев топлива перед сепарацией
|
120
|
0,6
|
1
|
72
|
5
|
Подогреватели топлива ГД
|
70
|
0,8
|
1
|
56
|
6
|
Подогреватели топлива ДГ
|
100
|
0,3
|
1
|
30
|
7
|
Подогреватели пресной воды ДГ
|
200
|
0,3
|
1
|
40
|
8
|
Подогреватели пресной воды ГД
|
200
|
-
|
-
|
-
|
9
|
Обогрев циркуляционной масляной цистерны ГД
|
120
|
-
|
-
|
-
|
10
|
Подогреватель масла ДГ
|
150
|
0,6
|
1
|
90
|
11
|
Подогреватель топлива ВПГ
|
62
|
1
|
0,5
|
31
|
Итого по группе 1: Механизмы и аппараты СЭУ
|
|
|
|
509
|
12
|
Система кондиционирования воздуха
|
450
|
0,8
|
1
|
340
|
13
|
Общесудовая вентиляция
|
785
|
0,5
|
1
|
392
|
14
|
Паровое отопление
|
150
|
1
|
1
|
150
|
15
|
Хозяйственное пароснабжение
|
400
|
1
|
0,7
|
280
|
16
|
Обогрев балласта
|
1515
|
-
|
-
|
-
|
17
|
Обогрев груза
|
1600
|
1
|
1
|
1600
|
18
|
Разогрев груза
|
3950
|
-
|
-
|
-
|
19
|
Подогрев забортной воды для мойки танков
|
5000
|
-
|
-
|
-
|
Итого по группе 2: Механизмы и аппараты судовых систем
|
|
|
|
2762
|
Итого в сумме по группам 1 и 2
|
|
|
|
3271
|
Итого в сумме с 3% утечек
|
|
|
|
3369
|
Количество и нагрузка работающих ПГ
|
|
УПГ300+ВПГ3000
|
Количество и производительность резервных ПГ
|
|
ВПГ 6300
|
Как видно из таблицы наибольшее
количество пара расходуется на подогрев перевозимого груза, подогрев и
увлажнение воздуха в системах вентиляции и кондиционирования. Все эти
потребители нуждаются в температуре пара значительно более низкой, чем та,
которая нужна для подогрева тяжелого топлива для двигателей. Для последнего
необходимо менее 100 кг/ч пара и из-за этого небольшого количества приходится
держать повышенное давление во всей системе, ставить паропреобразователи для
большего количества пара и недополучать пар в системе утилизации теплоты
выхлопных газов.
На танкерах могут перевозиться
различные грузы, причем в разных рейсах разные. Система подогрева груза должна
быть рассчитана на наиболее вязкий груз, перевозка которого на данном судне
вероятна. К таким грузам относятся мазуты. Их характерные температуры приведены
в табл. 5.9 [3, 4].
Таблица 5.9
Характерные температуры высоковязких
грузов
Марки мазутов
|
Температура, оС
|
|
застывания, не ниже
|
остывания, не ниже
|
перед откачкой
|
в конце разогрева
|
вспышки
|
20
|
5
|
10
|
20
|
40
|
60
|
40
|
10
|
15
|
30
|
50
|
80
|
60
|
15
|
20
|
40
|
55
|
90
|
80
|
20
|
25
|
50
|
60
|
100
|
100
|
25
|
30
|
60
|
65
|
105
|
Система подогрева перевозимого груза
должна обеспечивать поддержание температуры груза на уровне предотвращающем
застывание - хотя бы на 5 оС выше температуры застывания груза. Эта температура
должна быть ниже температуры вспышки паров жидких грузов на 15 оС [3, 5]. Таким
образом вязкие грузы следует подогревать теплоносителем от утилизационных
устройств до температуры не выше 30 - 40 оС и для этого нужно иметь температуру
теплоносителя не ниже 60 - 70 оС. Это может быть вода с атмосферным давлением и
не обязательно кипящая. Конечно пар более удобен в использовании, так как не
нуждается в насосе для перемещения. Пар с атмосферным давлением (вакуумные
паровые системы более сложны, чем водяные) имеет температуру 100 оС это хорошо
по сравнению с водяной системой с минимально необходимой температурой, так как
температурный напор увеличен и площади греющих змеевиков могут быть уменьшены.
Такой пар в системе утилизации получить несложно и в большом количестве. Оценим
эту возможность.
В табл. 5.10 приведен расход пара на
теплообменные аппараты общесудовых систем при температуре наружного воздуха
-200 С.
Таблица 5.10
Наименование потребителей
|
Расход пара, кг/час
|
|
Ход судна с обогревом груза
|
Ход судна с разогревом груза
|
Ход судна с мойкой танков
|
Система кондиционирования воздуха
|
450
|
450
|
450
|
Вентиляция
|
785
|
785
|
785
|
Паровое отопление
|
150
|
150
|
150
|
Хозяйственное пароснабжение
|
400
|
400
|
400
|
Грузовая система
|
1600
|
11000
|
Итого:
|
3250
|
11810
|
13310
|
В системе утилизации теплоты
выхлопных газов действует ограничение по температуре точки росы, представленной
на рис. 5.3. Это ограничение состоит в том, что температура насыщения пара,
получаемого в утилизационном котле не должна быть ниже температуры точки росы
для топлива, используемого в главных двигателях на длительном ходовом режиме
плюс 10 оС - запас на возможное снижение температуры на переменных режимах.
Учитывая, что в соответствии с табл. 5. все марки тяжелого топлива содержат до
5% серы, что с учетом коэффициенты избытка воздуха и его теоретически
необходимого количества для сжигания топлива приводит к содержанию сернистых
соединений в выхлопных газах в пределах до 0,2%. Этому содержанию серы
соответствует температура насыщения пара 120 + 10 = 130 оС, а с учетом необходимого
температурного напора между газами и кипящей водой (не менее 20 оС), получаем
температуру выхлопных газов на выходе из УПГ равной 150 оС.
Учитывая различные потребности
различных потребителей в параметрах пара предлагаем применять раздельную схему
ВКУ, включающую три различных источника тепловой, работающих на разные группы
потребителей. Схема такой установки представлена на рис. 5.8.
При снижении температуры газов до
этой температуры в системе утилизации теплоты выхлопных газов двигателя 5L35MC
на длительном эксплуатационном режиме может быть получено следующее количество
пара с давлением 5 атм:
УПГ = Gг cpг (tнач - tкон)/r = 6.389
3600 1 (257,254 - 150) / 2116 = 1165,8кг/ч.
Конечно, следует выполнить анализ
возможности снять соответствующего количества теплоты в утилизационном
парогенераторе. Возможно, для этого потребуется внести изменения в поверхность
нагрева котла и сечение газохода, но это второй вопрос. Сейчас из уравнения
теплового баланса мы выяснили возможность увеличения количества получаемого
пара при условии получения принятой температуры уходящих газов.
В системе утилизации тепловых
потерь, отводимых с охлаждением продувочного воздуха, отсутствует ограничение
по температуре точки росы, так как воздух чистый. Мы можем получать пар с атмосферным
давлением в количестве:
ОПВ = Gв cpв (tнач - tкон)/r
=22539.85 1 (170 - 120) / 2258,4 = 499 кг/ч..
Обогрев груза полностью обеспечен за
счет системы утилизации теплоты газов и продувочного воздуха, кроме этого в
обратном рейсе пар из системы утилизации можно использовать на общесудовые
нужды. Это позволит сэкономить 91,6 кг/ч топлива. За рейс танкера пр. 17120
будут сэкономлены 38,6 тонн топлива, на эту величину можно увеличить
провозоспособность и за год эксплуатации получить дополнительный доход в
размере:
,8 (180 + 0,023 6000) 13.96 = 163,6
тыс. у.е./год.
Такой дополнительный доход
оправдывает установку высокотемпературной секции охлаждения продувочного
воздуха и применение раздельных систем обогрева груза с тремя ступенями
давления:
атмосферная, питаемая паром от
высокотемпературной секции;
с давлением 5 атм., питаемая паром
от утилизационного котла;
с давлением 10 атм., питаемая паром
от вспомогательного котла.
По видимому, предпочтительной
является единая система с атмосферным давлением, питаемая от общего сборника
пара, в который пар поступает прямо из высокотемпературной секции охлаждения
продувочного воздуха, и от двух преобразователей пара: 5 атм. - 1 атм. и 10
атм. - 1 атм.
Подогрев тяжелого топлива
осуществляется только от вспомогательного котла. Параметры пара утилизационного
котла не обеспечивают требуемого подогрева тяжелого топлива. Это может создать
проблемы в балластном пробеге. Для решения этой проблемы целесообразно выбрать
вспомогательные котлы не одинаковой производительности и меньший из них
эксплуатировать в балластном пробеге. Таким образом предпочтительной является
раздельная схема ВКУ, обеспечивающая получение дополнительной прибыли в размере
163,6 тыс. у.е./год..
. ВЫБОР ВСПОМОГАТЕЛЬНЫХ И
УТИЛИЗАЦИОННОГО КОТЛОВ
На судах для обеспечения
хозяйственно-бытовых нужд (отопление, душевые, камбуз, прачечные и пр.) и для
подогрева масла и некоторых сортов топлива требуются пар или горячая вода. Для
этих целей используются вспомогательные котельные установки.
Расчетная мощность вспомогательной
котельной установки на ранних стадиях проектирования определяется суммированием
расходов пара на крупные потребители, для определения которых можно
использовать зависимости от характерных параметров судна и СЭУ.
Требуемый расход пара на общесудовые
нужды:
На танкере значительное
количество тепла расходуется на подогрев груза и подогрев забортной воды для
мытья танков.
Расход пара на подогрев
груза (формула Юнга):
Таким образом получаем
приблизительное количество пара, которое нам необходимо получить:
=k·(D1+D2)=1.04·(1,21+3,81)=1,04·5,02=5,224т/ч,
где k=1,03-1,05 -
коэффициент, учитывающий утечки пара. Более точные данные дают таблицы нагрузки
судна - прототипа - танкера пр. 17120, представленная в табл.6.1.
Таблица 6.1
Потребности танкера
пр.17120 в паре на режимах эксплуатации
Режимы эксплуатации танкера
|
Потребность в паре, кг/час
|
С учетом работы утилизации, кг/час
|
Ход с обогревом груза
|
3370
|
1705
|
Ход с разогревом груза
|
5790
|
4125
|
Мойка танков
|
8151
|
6486
|
Стоянка без грузовых операций
|
3880
|
3880
|
Стоянка с грузовыми операциями
|
2796
|
2796
|
На ходовых режимах раздельная
система утилизации теплоты, см. раздел 5, вырабатывает 1665 кг/ч пара для
вспомогательных и технических нужд судна.
Выберем два вспомогательных котла
КАВ2,5/7 и КАВ4/7
Марка
|
КАВ2,5/7
|
Марка парогенератора, указывающая на принадлежность к ряду
парогенераторов КАВ и далее номпнальные паропроизводительность и давление
пара в кг/см2
|
D
|
2,5
|
Номинальная паропроизводительность, т/ч
|
P
|
0,7
|
Рабочее давление в коллекторе парогенератора, мпа
|
|
80
|
Коэффициент полезного действия парогенератора на номинальном
режиме (отношение количества теплоты переданное пару к низшей теплоте сгорания
топлива)
|
S
|
67,9
|
Поверхность теплообмена, м2
|
B
|
2407
|
Ширина, мм
|
L
|
2780
|
Длина, мм
|
H
|
3712
|
Высота, мм
|
Gс
|
6,45
|
Масса котла, не заполненного водой
|
Gр
|
7,6
|
Масса котла, приготовленного к работе, т
|
В качестве утилизационного котла
выберем котел с глубокой утилизацией теплоты с производительностью на 1,2 т/ч.
Это может быть КУП400Р.
Альтернативой несколько устаревшим
котлам КАВ могут служить котлы СНВ фирмы Аалборг (Швеция).
Характеристики вспомогательных
котлов фирмы Аaлборг (Швеция)
Т/р ВПГ
|
Wп, т/ч
|
Dк, м
|
H, м
|
Dтр, м
|
Gc, т
|
Gв, м3
|
CHB 2500
|
2,5
|
1,9
|
4,15
|
0,3
|
7,7
|
3,8
|
CHB 4000
|
4
|
2,2
|
4,67
|
0,35
|
10,4
|
5,6
|
В таблице указаны следующие
характеристики котлов типа CHB: Wп - паропроизводительность, т/ч; Dк и H -
диаметр и высота барабана котла, м; Dт - диаметр газоотводной трубы, м;; Gс-
сухая масса котла, т;; Gв- масса воды в котле, т. Коэффициент полезного
действия котлов типа CHB составляет ок. 85%.
. ОПРЕСНИТЕЛЬНАЯ УСТАНОВКА
На морских судах широко применяются
утилизационные опреснительно-испарительные установки (ОУ). За счет
использования теплоты пресной воды, охлаждающей двигатели, которую всё равно
нужно охлаждать после прохода через рубашки и крышки цилиндров, утилизационные
ОУ позволяют не только полностью обеспечить судно пресной водой по цене на порядок
дешевле поставляемой с берега, но и сократить массу запасов рабочих тел,
увеличить провозоспособность и эффективность судов.
Для определения производительности
ОУ следует учесть все регулярные потери пресной воды на судне, в том числе:
потери воды в системе охлаждения
пресной водой главных и вспомогательных двигателей, около 270 л/сутки на каждые
1000 кВт включенной мощности;
расход пресной воды на
технологические нужды судна. Например, на каждую тонну замороженной рыбы на
судах-рефрежираторах расходуется до 100 кг пресной воды для целей глазирования.
Ещё больше этот расход на рыбопромысловых и консервных базах;
утечки пара и конденсата в системах
парогенераторов, продувание котлов. Они определяются расчетной
производительностью котлов и составляют до 1.5 - 3% от последней;
расходы пресной (питьевой и
мытьевой) воды членами экипажа и пассажирами судов. По санитарным нормам эта
величина составляет от 180 до 240 литров в сутки на человека. На судах
повышенной комфортности эта норма увеличивается до 500 л/сут.
Требуемая производительность Qоу т
определяется с использованием зависимостей для рассмотренных выше статей
расходования воды на судне:
оу = Kз·(Dн·Zл + Dдв·Nе/1000 +
Dпг·Wпг · 0.24 + Dт·Iт),т/сут,
где з - коэффициент запаса
производительности равный 1.25 - 1.5, примем равным 1,3;н=0,5 т/сут на человека
- санитарная норма расходования воды;л=22 - число людей на судне, включая
команду и пасажиров;дв=0,27 т/сут на 1000 кВт включенной мощности- коэффициент
потерь воды из систем охлаждения двигателей; е=2379 кВт - суммарная мощность
двигателей, работающих на длительном эксплуатационном режиме;пг=1,5%-
коэффициент потерь пресной воды из систем вспомогательного
парогенератора;пг=1,2 т/ч - паропроизводительность вспомогательного
парогенератора;т - нормативы расходования пресной воды на технологические нужды
судна, литров на единицу измерителя;т - измеритель расходования пресной воды на
технологические нужды судна.
Расход на технологические нужды
судна не учитываем, т.к. эта величина на данном судне незначительна.
Т.о. необходимая производительность
опреснительной установки:
оу = 1,3·(0,5·22 + 0,27·2379/1000 +
1,5·1,2 · 0,24)=15,7 т/сут.
По найденной производительности и
температуре охлаждающей воды, прошедшей через ГД, можно определить подходящую
опреснительную установку, используя диаграмму допустимых режимов установок
АФГУ.
В данном случае это установка
AFGU1-S15.
Таблица
Характеристики установки
Wоу
|
15
|
Номинальная производительность, т/сут.
|
W1
|
58
|
Наибольший расход греющей воды, м3/ч
|
T1
|
75
|
Температура, соответствующая наибольшему расходу воды, 0С
|
W2
|
31
|
Наименьший расход греющей воды, м3/ч
|
T2
|
86
|
Соответствующая наименьшему расходу воды температура, 0С
|
Pэл
|
6,5
|
расход электроэнергии на работу установки, кВт
|
L
|
1,86
|
Длина, м
|
B
|
1,07
|
Ширина, м
|
H
|
1,67
|
Высота, м
|
Gр
|
1600
|
Рабочая масса установки, кг
|
8. СУДОВАЯ ЭЛЕКТРОСТАНЦИЯ
Назначение судовой электростанции
состоит в генерации тока необходимых параметров и распределении его по
потребителям. Основными элементами электростанции являются источники энергии (первичные
двигатели и генераторы тока), распределительные устройства (главный
распределительный щит и местные распределительные щиты) и электрическая сеть.
Задачами при проектировании судовой
электростанции являются выбор рода тока, напряжения и частоты, определение
мощности и количества генераторов, выбор типа их привода, разработка схем
распределения электроэнергии. В настоящее время большинство потребителей
используют переменный ток. Применение переменного тока позволяет использовать
синхронные генераторы, асинхронные короткозамкнутые электродвигатели, получать
любое напряжение с помощью трансформаторов, использовать серийное оборудование
и питание на стоянках от береговой сети.
В соответствии с Правилами Регистра
на судах устанавливается аварийный источник электроэнергии. В качестве такого
источника используют независимый дизель-генератор, который размещают в
отдельном помещении вне шахты МКО, расположенном выше палубы переборок и
имеющим выход на открытую палубу. Аварийный дизель-генератиор должен иметь независимые
обслуживающие системы, радиаторное охлаждение и свой распределительный щит.
Расходная топливная цистерна должна обеспечивать его работу на грузовых судах
не менее 18 часов.
Выбор числа и мощности генераторов
произведен по таблице режимов нагрузки электростанции. Потребляемая мощность по
режимам обозначена в таблице 18.
Таблица 18
Нагрузка электростанции
Наименование режима
|
Потребляемая мощность, кВт
|
Стоянка без грузовых операций
|
241,89
|
Стоянка с грузовыми операциями
|
726,69
|
Маневры (съемка с якоря)
|
893,03
|
Ходовой режим
|
413,14
|
Ходовой режим с обогревом груза
|
444,38
|
Ходовой режим с мойкой танков
|
444,38
|
Аварийный режим (пожар или пробоина)
|
418,78
|
Аварийный режим
|
81,55
|
На основании таблицы приняты:
Основная электростанция в составе
трех дизель-генераторов L16/24.
Характеристики ДГ L16/24
Число цилиндров
|
6
|
Nэл - номинальная электрическая мощность, отдаваемая в сеть,
кВт. Допустима перегрузка на 10% от Nн, ограниченная во времени;
|
515
|
Nе - эффективная мощность приводного двигателя, кВт.
|
540
|
Gраб - масса агрегата дизельгенератора, приготовленного к
действию, т
|
10.5
|
Lдг - длина наибольшая габаритная, мм
|
4616
|
Lсод - длина агрегата двигателя, мм
|
3026
|
Bфр - ширина по фундаментной раме, мм
|
1000
|
Bм/о - минимально допустимое межосевое расстояние
дизельгенераторов, поставленных рядом
|
1800
|
Hгаб - габаритная высота, мм.
|
2226
|
Одна аварийная электростанция в
составе одного аварийного дизель-генератора АГДФ 100/1500, работающего на
аварийный распределительный щит.
Характеристики АГДФ 100/1500
Мощность, кВт
|
100.0
|
Удельный расход топлива, кг/кВт·ч
|
0.2690
|
Удельный расход масла, кг/кВт·ч
|
1.850
|
Масса, т
|
3.40
|
Длинна, мм
|
3100
|
Ширина, мм
|
1150
|
Высота, мм
|
1650
|
. ОБОСНОВАНИЕ КОМПОНОВКИ И
РАСПОЛОЖЕНИЯ ОБОРУДОВАНИЯ СУДОВОЙ ЭНЕРГЕТИЧЕСКОЙ УСТАНОВКИ (КОНСТРУКТИВНЫЙ
УЗЕЛ)
Основные типы расположения и
компоновки СЭУ
Качество расположения энергетической
установки в МКО транспортного судна оказывает определенное влияние на
эффективность грузоперевозок, трудоемкость, затраты на постройку и себестоимость
судна, удобство эксплуатации, технического обслуживания и ремонтных работ,
надежность и долговечность СЭУ, безопасность труда обслуживающего персонала,
затраты энергии на собственные нужды СЭУ и другие аспекты эффективности судна.
Для транспортных судов наиболее
очевидно требование максимально возможного сокращения длины помещений СЭУ при
соблюдении всех ограничительных требований и предоставлении достаточного
пространства для обеспечения удобного обслуживания и ремонта оборудования СЭУ,
а также общесудового оборудования, расположенного в МКО. За счет этого могут
быть увеличены размеры грузовых помещений и увеличена грузовместимость, на
большинстве судов определяющая провозоспособность.
Наиболее экономически оправдано
расположение СЭУ на транспортном судне в одном помещении - машинно-котельном
отделении (МКО). При этом сокращается длина МКО вследствие наложения ремонтных
зон различных механизмов и отсутствия дополнительных проходов и переходов.
Обычно это требование на гражданских судах может быть реализовано, так как
размеры МКО не противоречат требованиям к непотопляемости судна. Последняя
обеспечивается при затоплении определенного числа смежных отсеков, оговоренного
Правилами Регистра РФ.
Из основного помещения МКО обычно
выгораживают помещение центрального поста управления (ЦПУ), которое, по
условиям обитаемости и работоспособности персонала, должно иметь пониженный
уровень шума по сравнению с помещением МКО. Также, иногда, особенно часто на
речных судах, выделяют помещение основного оборудования судовой электростанции
- дизель-генераторов, имеющих, в связи с применением высокооборотных приводных
двигателей, повышенный уровень шума. Оба эти помещения имеют эффективную
акустическую изоляцию, а опорные связи - амортизацию, предотвращающую
распространение шума через корпусные конструкции.
Помещение МКО, включая цистерны
расходуемых рабочих тел СЭУ, обычно занимает все пространство поперек судна -
от борта до борта и все помещения по высоте - в пределах основного корпуса, а
также в пределах надстройки - в шахте МКО. По размещению МКО по длине судна
выделяют следующие типы расположений:
чисто кормовое, когда помещение МКО
непосредственно примыкает к переборке ахтерпика;
смещенное к средней части судна,
когда между переборкой ахтерпика и помещением МКО располагают обычно один, реже
большее число грузовых помещений;
среднее, когда помещение МКО
размещают в средней части судна;
носовое, когда помещение МКО
размещают ближе к носовой оконечности судна.
Расположение оборудования в МКО
должно обеспечивать выполнение следующих требований:
обеспечение удобства при проведении
обслуживания и ремонта. Это требование реализуется путем предоставления
пространства для разборки оборудования (ремонтных габаритов), ремонтных
площадок, грузоподъемных средств, подходов и проходов, транспортных
магистралей, снижением объемов сопутствующих ремонтных работ, доступностью мест
ремонта, облегчением локализации отказов и др.;
сокращение длины связей
(трубопроводов и кабельных трасс) между оборудованием;
выполнение требований техники безопасности
и охраны труда обслуживающего персонала;
предотвращение распространения шума
и вибрации механизмов и ограничение воздействия этих факторов на персонал;
обеспечение пожаробезопасности. Эти
требования реализуются группой методов - от вывода дыхательных труб топливных и
масляных цистерн на открытую палубу до выделения отдельных помещений для
опрессовки форсунок, запрещением прокладки водяных трубопроводов над
электрооборудованием и щитами, топливных трубопроводов над нагретыми узлами и
электрооборудованием и др.;
обеспечение надежной работы
оборудования при крене, дифференте, изменении осадки, качке судна;
уменьшение массы фундаментов под
механизмы МКО, достигаемое простотой их конструкции и согласованием их с
основными элементами конструкции корпуса;
расположение общего центра масс СЭУ
вблизи диаметральной плоскости во избежание возникновения кренящего момента и
необходимости принятия твердого балласта для его компенсации;
расположение общего центра масс СЭУ
по возможности в нижней части МКО для улучшения остойчивости судна;
приближением энергетических запасов
к главным и вспомогательным двигателям, т.е. их расположением вблизи МКО для
сокращения размеров топливных трубопроводов. Запасы тяжелого топлива следует
отделять от забортного пространства пустыми цистернами во избежание
переохлаждения топлива и потери текучести. Ввиду значительной массы запасов
топлива и их расходования по мере выполнения рейса следует предусматривать
мероприятия по удифферентовке судна при различной степени расходования запасов.
Выделяют определенные типовые схемы
расположения главного оборудования - для одновальных и многовальных установок,
а также в зависимости от типа судовых движителей и формы кормового образования.
Основное оборудование СЭС на транспортных судах располагается часто в корму от
главных двигателей на нижней платформе над линией валопровода. Иногда, при
отсутствии здесь достаточного пространства, дизель-генераторы смещают на один
из бортов или располагают побортно от главного двигателя в трюме. Вариантов
расположения основного оборудования СЭС достаточно много.
Основное оборудование ВКУ -
вспомогательные парогенераторы (ВПГ) располагают чаще всего на верхней
платформе в корму от главных двигателей. Иногда на морских судах при
недостаточной высоте борта и невозможности развить требуемое количество
платформ, ВПГ выносят в отдельное помещение на главной палубе в корму от шахты
МКО. Утилизационные котлы обычно располагают в шахте МКО по ходу газовыхлопного
тракта главных двигателей.
Вспомогательное оборудование
располагают в МКО на свободных площадях одним из двух основных способов:
россыпью, когда каждый элемент СЭУ в
том виде, в каком он поставляется на судостроительное предприятие, без
дополнительной доработки, устанавливается на несущие конструкции отдельно от
оборудования, с которым он будет взаимодействовать в процессе работы. В
качестве несущей конструкции в зависимости от массы элемента СЭУ может быть
использован индивидуальный судовой фундамент или конструкция судовых
перекрытий. Эти элементы связывают с другими, взаимодействующими с ними в
процессе функционирования, при помощи энергетических связей - трубопроводов и
кабелей;
функциональное агрегатирование, под
которым понимают объединение на общей несущей конструкции совокупности
оборудования взаимодействующего при выполнении определенной функции.
Типовой состав функционального
блока: оборудование, выполняющее определенную законченную функцию, внутренние
трубопроводы, арматура, контрольно-измерительные приборы, элементы управления и
автоматики, несущая конструкция. В качестве последней могут выступать -
фундаментная рама, легкий каркас или цистерна. В состав функциональных
агрегатов энергетических систем могут входить: насосы, теплообменные аппараты,
сепараторы, фильтры, арматура, внутренние трубопроводы, соединяющие между собой
оборудование взаимодействующее при выполнении функции агрегата,
контрольно-измерительные приборы и элементы автоматического регулирования,
управления и сигнализации. Функциональные агрегаты собираются в цехе, не
обязательно на судостроительном предприятии, на специальном участке
агрегатирования, снабженном вспомогательным технологическим оборудованием, типа
кантователей, гайковертов, оборудования диагностики и пр. В собранном виде
функциональные агрегаты поступают на судно, расположенное на стапеле или на
участке достройки. Там агрегаты крепятся на корпусные конструкции и соединяются
магистральными трубопроводами с другими агрегатами, главным и основным
оборудованием, цистернами, участками приема и сдачи рабочих тел. Кроме этого
агрегаты соединяются магистральными кабелями с групповыми электрическими щитами
или главным распределительным щитом (ГРЩ).
В соответствии с рассмотренным,
выделяют два основных типа компоновки вспомогательного оборудования - россыпью
либо в составе функциональных агрегатов. Кроме этого отдельный тип компоновки -
зональное агрегатирование, применяемое ко всему оборудованию, располагаемому в
МКО, независимо от принадлежности к СЭУ и степени законченности выполняемой
функции, а также к общесудовому оборудованию, располагаемому в других частях
судна. При зональном агрегатировании оборудование, намеченное к установке в
определенной зоне МКО, крепится к корпусным конструкциям установленным в данной
зоне. В состав зонального агрегата могут входить как оборудование, установленное
россыпью, так и в виде функциональных агрегатов, как взаимодействующее между
собой, так и относящееся к различным системам и не взаимодействующее. Зональный
агрегат собирают на пристапельном участке судостроительного предприятия. В него
включают также внутренние трубопроводы, в том числе транзитные. В собранном
виде зональный агрегат поступает на стапель, где он сваривается с другими
зональными агрегатами и плоскостными и объемными корпусными конструкциями,
образуя МКО в целом.
Зональное агрегатирование -
прогрессивный технологический прием, сокращающий стапельный период постройки
судна. Обычно зональные агрегаты - это крупные блоки массой несколько десятков
и более тонн. Зональное агрегатирование не противоречит функциональному.
Например, в виде зональных агрегатов изготавливают помещение основного
оборудования СЭС - дизель-генераторов или ВКУ - вспомогательных парогенераторов
с их вспомогательными механизмами. Основное отличие при зональном
агрегатировании состоит в использовании для крепления оборудования достаточно
крупных корпусных конструкций - платформ, палуб или секций двойного дна,
возможно с помощью местных фундаментов.
Обоснование типа расположения МКО по
длине судна
На транспортных судах наиболее
широко распространено расположение главного оборудования СЭУ и МКО в целом в
кормовой оконечности судна. Причина к этому - расположение именно здесь - за
кормой судна винта - судового движителя, использующего пограничный слой,
накапливающийся на корпусе, для повышения своей энергетической эффективности.
Вследствие такого расположение КПД винта одновальной установки на 25 - 30% выше
КПД винта в свободной воде. Кормовому расположению винта водоизмещающих судов
нет альтернативы.
При чисто кормовом расположении МКО
длина валопровода получается минимальной и КПД валопровода наиболее высоким.
Грузовые помещения получаются совмещенными, что облегчает их эксплуатацию. Это
наиболее широко распространенный тип расположения главного оборудования СЭУ и
МКО в целом. Обычно выше помещений МКО располагают надстройку, включающую
ходовую рубку, жилые, общественно-бытовые и служебные помещения, шахту
газо-воздушных трубопроводов.
Вследствие сужения корпуса в
кормовой оконечности длина МКО несколько увеличивается по сравнению с
расположением МКО в средней части судна, иногда существенно, например,
вследствие разборки валопровода внутрь судна.
Однако прочие преимущества такого
размещения МКО перевешивают некоторое увеличение длины. Сужающаяся форма
кормовой оконечности не вполне удобна для размещения генеральных грузов, контейнеров,
автотехники, грузов на поддонах и прочих грузов с прямоугольной формой
габарита. Совмещенное расположение грузовых помещений облегчает проведение
грузовых операций на танкерах, универсальных сухогрузах, ролкерах, балкерах и
контейнерных судах.
Эти и другие преимущества кормового
расположения сделали его в последние годы безальтернативным, несмотря на
некоторые дополнительные недостатки, в частности недостаточную
удиферентованность судна при переменной загрузке.
В случае применения второго типа
расположения ПК - смещение к средней части судна, в корму от МКО делают один
грузовой или технологический отсек. Такое размещение МКО позволяет более
компактно разместить оборудование пропульсивной установки особенно для случая
двухвальной установки. В этом случае расположить рядом два двигателя с
требуемым расстоянием между ними в сужающихся обводах корпуса в кормовой
оконечности не представляется возможным. Отсюда и возникает смещение главных
двигателей к средней части, где заострение корпуса судна уже не так существенно
влияет на ширину МКО.
Следует обратить внимание на то, что
проведение валопровода через грузовые трюма делает необходимым организацию
выгородки - коридора гребного вала с подкреплениями достаточными для восприятия
веса груза. Наличие коридора уменьшает полезные объемы таких трюмов и
затрудняет размещение в них крупногабаритных грузов.
Среднее расположение МКО на морских
грузовых судах встречается крайне редко вследствие присущих ему недостатков -
длинного и тяжелого валопровода, необходимости организации коридора валопровода
в грузовых отсеках в корму от МКО, снижения КПД от
большого числа подшипников и
переборочных сальников. Единственное преимущество - лучшая удиферентованность
судна на режимах с различной загрузкой - в грузу и в балласте. На некоторых
судах это преимущество является важным, что и определяет применение среднего
расположения МКО.
Носовое расположение МКО находит
применение на быстроходных судах с наклонным валопроводом - на судах на
подводных крыльях и воздушной подушке скегового типа. На указанных судах
перемещение МКО ближе к носовой оконечности позволяет уменьшить при заданном
клиренсе угол уклона валопровода. Косинус этого угла определяет полезную часть
упора, движущего судно. На некоторых буксирных судах смещение МКО в сторону
носовой оконечности используется для компенсации дифферентующего момента от
натяжения буксирного троса. На водоизмещающих транспортных судах такое
расположение не находит применения вследствие присущих ему недостатков.
Обоснование способа компоновки оборудования
энергетических комплексов
Каждый из указанных способов
компоновки вспомогательного оборудования обладает совокупностью преимуществ и
недостатков по сравнению с другими. В частности расположение россыпью, имеет
несомненные преимущества по свободному доступу со всех сторон к каждому из
элементов СЭУ, что весьма важно при проведении технического обслуживания и
ремонта.
В период перестройки экономической
формации, продолжающейся и в настоящее время, качество производимого
отечественного оборудования снизилось, упала его надежность. Доступность
оборудования для ремонта стала важным фактором, обеспечивающим некоторое
повышение ремонтопригодности и компенсацию снижения прочих составляющих
надежности.
Расположение оборудования россыпью
увеличивается длительность постройки судна ввиду длительного монтажа и
испытаний каждого из элементов СЭУ на объекте. Совместные испытания возможны
только после монтажа всего взаимодействующего оборудования. Это является
существенным недостатком такой компоновки.
Особая приспособленность к
проведению восстановительных работ на судне актуально только в случае
применения ненадежного оборудования. По нашему мнению эта особенность
отечественного оборудования не может быть постоянной. Или отечественное
производство энергетического оборудования перестроится и будет производить
качественные и надежные механизмы, или оно отомрет в конкурентной борьбе с
передовыми предприятиями зарубежья. Третьего в развивающемся глобальном мире не
дано.
Объединение в функциональный агрегат
оборудования выполняющего законченную функцию по обеспечению главных и
вспомогательных двигателей определенного вида рабочим телом - топливом, маслом
или водой обеспечивает сокращение длины магистральных трубопроводов, соединяет
оборудование, ответственное за выполнение функции, пространственно в одной
зоне, чем облегчается обнаружение и устранение отказов, способствует сокращению
сроков постройки судна за счет проведения монтажа и испытаний агрегата в цехе
параллельно с другими работами, облегчает монтаж и повышает его качество за
счет специализации производства, наличия монтажных приспособлений,
измерительных средств и квалифицированных работников, создает условия для
организации агрегатного ремонта по регламенту - замены агрегатов во время
стоянки в порту.
Этот, несомненно прогрессивный
способ, в то же время он не лишен недостатков. Значительная затесненность
монтажа не способствует удобству проведения ремонтных работ в условиях судна.
Кроме этого нарушаются требования к взаимному расположению элементов гидравлических
сетей - расстояние между ними меньше требуемого для выравнивания нарушений
равномерности потока в трубопроводах. Это несколько снижает надежность
оборудования и требует применения эрозионно-стойких трубопроводов - литых из
цветных металлов и сплавов или футерованных пластическими материалами.
В целом преимущества функционального
агрегатирования существенно превышают его недостатки и делает его весьма
перспективным, особенно при условии организации специализированного
производства функциональных агрегатов.
На рис. приведена современная
функциональная схема агрегатирования малооборотных дизельных установок с МОД
ДКРН типа MC. На рис.3.2 обозначены: 1 - главный двигатель; 2 - блок насосов
гидропривода выхлопных клапанов; 3 -- деаэратор топлива; 4 - блок циркуляционных
топливных насосов; 5- блок топливоподкачивающих насосов; 6 - блок насосов
забортной воды; 7 - цистерна цилиндрового масла; 8 - напорная цистерна смазки
газотурбонагнетателя (ГТН); 9 - блок смазки ГТН; 10 - блок охлаждения
двигателей пресной водой; 11 - блок маслоохладителей; 12 - баллоны пускового
воздуха главных двигателей; 13 - блок воздушных компрессоров; 14 - блок
циркуляционных масляных насосов; 15 - блок сепарации масла; 16 - блок перекачки
масла; 17 - растворный бачек; 18 - расширительная цистерна; 19 - функциональный
блок сточной масляной цистерны.
Функциональное агрегатирование
впервые последовательно было применено на танкере пр.1559.
Головное судно "Великий
Октябрь" в соответствии с этим проектом было построено на Балтийском
заводе в 1967г. Все последующие суда в большей или меньшей степени используют
этот принцип. На танкере пр.1596 типа "Командарм Федько" впервые были
применены унифицированные агрегаты, разработанные Херсонским ЦКБ.
Зональное агрегатирование - это
технологический прием, обеспечивающий сокращение стапельного периода постройки
судна за счет производства работ по сварке и насыщению блоков на пристапельном
участке. Зональные агрегаты могут включать как оборудование россыпью, так и объединенное
в функциональные блоки. Масса зональных блоков ограничивается возможностями
грузоподъемных средств завода - строителя по перемещению и установке блоков на
стапель для дальнейшей сварки с другими зональными блоками. В зонах стыков
требуется освобождение пространства ориентировочно равного 0,5 м для
перемещения сварочных автоматов при соединении блоков на стапеле. Это
пространство позднее может быть заполнено оборудованием.
. МОНТАЖ МЕХАНИЧЕСКОГО ОБОРУДОВАНИЯ
Современное судно насыщенно
многообразным оборудованием, которое различается по конструкции, массе,
габаритным размерам и требованиям к точности монтажа.
Объем механомонтажных работ для
транспортного судна составляет 6-10% от общей трудоемкости их постройки.
Массогабаритный показатель в значительной
степени определяет вид поставки оборудования, влияет на выбор технологического
процесса, средств технологического оснащения и трудоемкость монтажа.
К части механического оборудования
(главным механизмам, валопроводу) предъявляют повышенные требования к точности
базирования на судне. Допуски на их центровку измеряются десятыми и даже сотыми
долями миллиметра, что на один-два порядка выше требований точности
изготовления и сборки корпусных конструкций. В узлах крепления механизмов к
фундаментам применяют компенсирующие звенья, обычно называемые подкладками,
которые компенсируют отклонения в расположении фундаментов на судне и позволяют
согласовывать допуски на размеры корпусных конструкций с более жесткими
допусками на базирование механического оборудования. Механизмы, как правило,
прикрепляются к фундаментам болтами.
Номенклатура механомонтажных работ
весьма разнообразна и включает в общем случае обработку опорных поверхностей
судовых фундаментов, расконсервацию и погрузку механизмов на судно, их центровку,
пригонку компенсирующих звеньев, обработку отверстий под болты и закрепление
механизмов.
Сам характер монтажных работ,
выполняемых в стесненных условиях, затрудняет их механизацию из-за
ограниченного доступа средств монтажа к объекту монтажа.
Для улучшения условий выполнения
механомонтажных работ необходим перенос возможно большего их объема с судна в
цех.
Этому в полной мере отвечает
агрегатирование, которое предусматривает создание вне судна сборочно-монтажных
единиц путем их компоновки из стандартного или унифицированного оборудования,
обладающего свойствами размерной и функциональной взаимозаменяемости (модулей).
Применяют различные формы
агрегатирования:
Агрегатирование в одном корпусе -
наиболее прогрессивная форма механизмов, например двигателей внутреннего
сгорания, паропроизводящих установок. Позволяет создать жесткую моноблочную
конструкцию, которая в большей степени удовлетворяет требованиям надежности и
технологичности;
Агрегатирование на общей
фундаментной раме. Позволяет выполнить компоновку нескольких механизмов в один
агрегат, например насос-дизель-генератор. Однако эта форма агрегатирования
недостаточно технологична.
Агрегатирование на каркасе объемной
конструкции. Широко применяется при компоновке агрегатов из нецентруемого
оборудования и дает возможность создать легкую опорную конструкцию, на которой
собирают механизмы.
Типовой технологический процесс
монтажа механического оборудования включает следующие этапы:
Подготовка монтажных баз
Погрузка и транспортировка
оборудования на судне;
Базирование оборудования на судне;
Установка компенсирующих звеньев
между опорными поверхностями оборудования и фундамента;
Крепление оборудования на
фундаменте;
Контроль качества монтажа.
Подготовка монтажных баз.
Тщательная подготовка общей базы
предупреждает возможные трудоемкие переделки фундаментов, необходимость в
которых выявляется после погрузки и цетровке механизмов на судне. Подготовка
общей базы состоит из нанесения плазовых точек на корпусные конструкции,
проверки наличия осевых рисок на фундаменте, контроля правильности его
установки на судне и обработки опорных поверхностей.
Фундаменты изготовляют в пределах
допусков и устанавливают с разрешаемым смещением и непараллельностью
относительно базовых плоскостей судна и оси валопровода. До погрузки
оборудования фундаменты грунтуют, окрашивают и сдают на конструкцию.
Погрешности изготовления и установки делают положение фундамента на судне
нестабильным. Эти неточности переносятся на монтируемое оборудование.
Координаты фундаментов задают
расстояниями от опорной поверхности и осевых рисок до основных плоскостей ил
конструкций судна, принятых за базу отсчета. Положение фундамента под главный
двигатель проверяют так же относительно оси валопровода, материализованной
струной, которую натягивают между плазовыми точками, нанесенными на переборках
машинного отделения.
Опорную поверхность фундамента
обрабатывают для обеспечения качественного сопряжения подкладок с фундаментом.
Фундаменты обрабатывают в цехе или на судне переносными фрезерными станками и
пневматическими шлифовальными машинами. Отступления от общей плоскостности
нормируются в виде допускаемых уклона и ступенчатости планок фундамента.
Отклонения в расположении фундамента по высоте относительно оси валопровода
компенсируют подкладками, в зависимости, от конструкции которых предъявляют
различные требования к качеству обработки фундаментов. Плоскостность опорной
поверхности планок проверяют лекальной линейкой и щупом. Пластинка толщиной
0,10 мм не должна проходить между проверяемой поверхностью и линейкой.
Необходимо провести подготовку
базовой системы механизма. Она состоит в проверке наличия осевых рисок на
механизмах, расконсервации и контроле отсутствия механических повреждений
опорных поверхностей, сопрягаемых с фундаментом. Поверхности лап и фундаментных
рам должны находиться в одной плоскости и обработаны с шероховатостью не грубее
4-го класса. Места прилегания гаек и шайб болтов подрезают с соблюдением
перпендикулярности к оси отверстия.
Погрузка оборудования на судно.
Основное требование при транспортно-погрузочных
операциях - обеспечение отсутствия деформаций механизмов. Оборудование должно
поступать на монтаж с установленными заглушками на отверстия и фланцы
патрубков, чтобы избежать попадания посторонних предметов. Арматуру и приборы,
которые мешают погрузке и могут быть повреждены, снимают и маркируют с
указанием номеров механизма и судна. Погрузку выполняют одним или несколькими
кранами в зависимости от массы механизма.
Базирование оборудования
Требования к точности расположения
оборудования на судне зависят от его связи с координатами корпуса и базовыми
механизмами. При окончательном положении оборудования необходимо выполнить
следующие требования:
Обеспечить соосность главного
двигателя и валопровода;
Отклонение положения двигателя от
осевых рисок фундамента разрешается не более ±1мм
Расстояние между опорными
поверхностями механизма и фундамента должно быть достаточным для установки
компенсирующих звеньев заданной толщины;
Расстояние от механизма дол
соседнего оборудования должно быть не не менее 10 мм при жестком креплении и
более 30 мм при установке на амортизаторы.
Положение оборудования определяют
путем совмещения ориентирующих элементов базовой системы механизма и общей
технологической базы судна. Оборудование перемещают гидропакетами, домкратами
или отжимными болтами. Приспособления должны иметь достаточную
грузоподъемность, количество точек опоры выбирают из условия отсутствия
деформации корпуса механизма.
При базировании оборудования, строго
связанного с координатами судна, к каковым относится главный двигатель,
используют центровку оптическим методом.
Схема оптической центровки главного
двигателя
Главные двигатели ориентируют на
судне по оси валопровода, материализованной двумя точками А и Б (см рис.),
координаты которых берут с плаза. Плазовые точки необходимо нанести на
корпусные конструкции с точностью до ±1 мм от размеров, указанных в чертежах.
Применяемая оптическая оснастка
должна обеспечивать высокую точность измерений. Центровку выполняют методом
визирования. Вначале необходимо отцентровать оптический прибор 8 по оси
вращения вала механизма 6. Эту операцию выполняют путем проектирования сетки 5
прибора на вспомогательную мишень 3 или контрольные мишени 2 и 4, установленные
на оси валопровода. Прибор фокусируют на мишень и отмечают положение проекции
центра его перекрестия. Вал механизма поворачивают на 180° и снова проектируют
перекрестие прибора на мишень. Определяют величину несовпадения перекрестий,
которую устраняют, перемещая прибор регулировочными винтами 7 на кронштейне 9.
Оптический прибор будет сцетрованным с осью механизма, если при проворачивании
вала центры перекрестий прибора и мишени совпадают.
Величина несовпадения не должна
превышать толщины линий перекрестий мишени:
=0,025L
Где L - расстояние наблюдения, м.
После этого приступают к центровке
механизма по оси валопровода. Контрольные мишени обычно устанавливают на
кормовой переборке машинного отделения и шергене 1, не связанном с корпусом
судна. Носовая мишень имеет отверстие для наблюдения за кормовой.
Центровку механизма выполняют путем
проектирования перекрестия оптического прибора на каждую из мишеней и
перемещения механизма отжимными приспособлениями 11 дол совмещения перекрестий.
При этом контролируют так же не параллельность механизма валопровода, которая
не должна превышать
,
где a=0,10-0,15 -
коэффициент допускаемой непаралельности механизма оси валопровода;АБ -
расстояние между мишенями, м.
Перемещение механизма
вдоль оси валопровода ограничивают путем совмещения поперечных рисок 10 на
механизме и 12 на фундаменте. Вращение механизма вокруг оси исключают,
ограничивая его крен.
Таким образом,
базирование главного двигателя считается выполненным, если:
несовпадение перекрестий
прибора и носовой мишени
то же на кормовой мишени
несовпадение поперечных
рисок
крен механизма k≤1.0
vv на 1 м его ширины.
Установка компенсирующих
звеньев.
Подкладки должны
обеспечивать надежное крепление и минимальную трудоемкость монтажа
оборудования. При выборе материала основное значение имеет неизменяемость
механических характеристик и формы подкладок под нагрузкой при различных
температурных условиях эксплуатации. Для главного двигателя будем использовать
подкладки из пластмассы ФМВ (формируемая малоусадочная волокнистая).Форму с
массой заводят между опорными поверхностями фундамента и рамой отцентрованного
механизма, который находится на отжимных болтах. Болт, смазанный тонким слоем
солидола, заводят в отверстия рамы, массы и фундамента. Для уплотнения форму
обжимают струбциной до тех пор, пока масса не выйдет в монтажные зазоры.
Подогрев подкладок выполняют при помощи термоэлектронагревателей. После
отверждения пластмассы выворачивают отжимные болты и механизм крепят фундаментными
болтами.
Крепление оборудования.
Правильное
конструктивное оформление узлов крепления обеспечивает надежность и
ударостойкость механизмов. Крепление состоит из простых болтов и призонных
цилиндрических болтов. Для облегчения установки и демонтажа призонным болтам
иногда придают пологую конусность 1:500. Для неподвижности оборудования
необходимо, чтобы нагрузки, сдвигающие механизм плоскости крепления, были в два
раза меньше силы трения от затяжки фундаментных блоков.
Технология крепления
простыми и призонными болтами отличается подготовкой отверстий, требованиями к
посадке и способу установки болтов.
Сверление отверстий.
Наиболее трудоемко сверление по разметке, выполненной путем перенесения
положения отверстий с основания отцентрованного механизма на фундамент. Для
возможности сверления механизм снимают. Разметку можно упростить, применив
шаблон или макет. Если позволяет конструкция, то сверление осуществляют через
отверстия в лапах механизма.
Подрезание отверстий.
Для плотного прилегания головки и гайки болта фундамент и лапу вокруг отверстия
подрезают облицовочной зенковкой.
Развертывание отверстий.
Отверстия для призонных болтов должны быть изготовлены по 2-му классу точности
и иметь шероховатость не грубее 5-го класса. После сверления их дополнительно
черновыми и чистовыми развертками. Призонные болты изготовляют индивидуально
для каждого отверстия. Стержень болта обрабатывают по фактическому диаметру
отверстия с допускаемым отклонением, обеспечивающим плотную посадку 2-го класса
точности, и шероховатостью не грубее 7-го класса.
Установка призонных
болтов. Посадку болтов выполняют с предварительным охлаждением до температуры
ниже -100°С или ручной запрессовкой ударами кувалды. Первый способ более
технологичен. В этом случае исключаются задиры и уменьшение натяга из-за среза
и смятия микронеровностей, характерных для запрессовки болтов.
Контроль качества
монтажа.
Качество монтажа
определяется правильным расположением оборудования на судне, соответствием его
крепления требованиям чертежа и отсутствием деформаций в статическом состоянии.
Монтаж двигателей внутреннего сгорания выполняется без разборки, контролируя
распределение нагрузок от действия силы тяжести механизма на его опорный
фланец. Метод контроля основан на следующем. Вначале находят стендовые значения
нагрузок. Для этого н азаводе-изготовителе динамометрами измеряют нагрузки на
опорный фланец механизма, поднимая его параллельно опорной поверхности
сборочного стенда. Значения нагрузок заносят в формуляр. При монтаже н а
судовом фундаменте в опорный фланец механизма снова вворачивают динамометры и
действуя ими как отжимными болтами, регулируют нагрузки, добиваясь их
совпадения с формулярными значениями. Отклонение монтажных нагрузок от
стендовых величин не должно превышать ±5%.
. ЗАЩИТА ОКРУЖАЮЩЕЙ СРЕДЫ
ПРИ ЭКСПЛУАТАЦИИ СЭУ
Суда и их энергетические
установки являются значительным источником загрязнения окружающей среды.
Источниками загрязнения на судах являются отработавшие газы двигателей и
парогенераторов, сбросы топлива и масел, льяльных, трюмных, балластных вод,
отходы после очистки танков, тепловое радиационное излучение, отходы реакторных
установок, твердые и пищевые отходы. Огромный вред биосфере наносит загрязнение
вод мирового океана нефтепродуктами. Они вызывают гибель морской флоры и фауны,
в частности фитопланктона, который является основным потребителем углекислого
газа и обеспечивает поступление 50 % всего кислорода, поступающего в атмосферу.
Задача сохранения
окружающей среды заключается в том, чтобы не превысить допустимый уровень загрязнения.
Эта задача может решаться в основном по двум направлениям:
создание систем,
работающих по замкнутому циклу и позволяющих утилизировать основную массу
доходов
очистка и снижение
токсичности сбросов, неизбежно поступающих в биосферу.
В данном разделе
рассмотрим способы борьбы с загрязнением моря нефтепродуктами.
Причиной образования
льяльных вод в МКО являются главным образом протечки нефтепродуктов через
арматуру, фланцевые соединения и уплотнения насосов топливных и масляных
систем, а также протечки забортной и пресной воды. Кроме льяльных вод при
эксплуатации СЭУ имеются отходы нефтепродуктов вследствие их фильтрации,
сепарации, перелива, слива масел, разборки механизмов при ремонте и т.д.
Накопления в льялах и колодцах загрязненных вод происходит вследствие мойки
настилов и механизмов, стока конденсата при отпотевании стенок МКО, внутренней
чистки и продувании парогенераторов, протечек в обшивке корпуса судна.
Емкость сточной цистерны
для сбора грязного топлива, шлама и других отходов топлива на танкерах с ДУ
можно определить по формуле:
г.т.=Ω·Neуст,
м3
где Ω=0,10-0,12
опытный коэффициент, примем равным 0,10уст=3250 кВт, мощность
установки.г.т=0,10·3250=3,250 т3 - объем сточной цистерны для проектируемой ЭУ
Расположение льял,
сборных колодцев, цистерн и других емкостей зависит от конструкции корпуса,
типа энергетической установки, и ее мощности. Льяла рекомендуется размещать по
бортам МКО.
Поступление льяльных вод
зависит от водоизмещения судна, типа установки, ее мощности и технического
состояния. Количество льяльных вод можно принимать в зависимости от
водоизмещения (см. табл.). В среднем эта величина может составлять от 0,02 до
0,5% водоизмещения судна в сутки. Количество льяльных вод на стоянке,
накапливающихся на стоянке, составляет 50-70% количества этих вод на ходу
судна. При продолжительности рейса 20-30 суток и более на судах скапливается
большое количество льяльных вод. Содержание нефтепродуктов в них составляет в
среднем 2000-3000мг/л, притом, что верхний допускаемый предел составляет 15
мг/л.
Таблица
Количество льяльных вод
на ходу судна
Водоизмещения судна, т
|
|
м3/сут
|
% от водоизмещения
|
До 1500
|
0,3-8,0
|
0,02-0,5
|
1500-4000
|
8,0-20
|
~0,5
|
4000-10 000
|
20-30
|
0,5-0,3
|
10 000-25 000
|
30-50
|
0,3-0,2
|
25 000-100 000
|
50-60
|
0,2-0,06
|
В идеальном случае, при высоком
качестве уплотнений, отсутствии протечек и правильном обслуживании количество
льяльных вод и их концентрация должны быть минимальны. К этому следует
стремиться при проектировании энергетических установок.
На транспортных судах используется
большое количество трюмных, промывочных и балластных вод. Балластными водами
заполняют трюмы и топливные цистерны после их опорожнения для удифферентовки,
обеспечения остойчивости и других мореходных качеств судна. Значительный балласт
принимают танкеры в обратном рейсе - до 30% и более от водоизмещения. При этом
в танках, где находится балласт, остается не менее 0,5% перевозимых
нефтепродуктов. Перед новым заполнением танки необходимо освободить от
балласта, который может содержать до 5000 мг/л нефти, т.е. иметь концентрацию в
350 раз больше допустимой.
Для предотвращения загрязнения моря
нефтепродуктами на всех транспортных судах устанавливаются системы очистки
льяльных и других загрязненных вод. При использовании дизельного и моторного
топлив плотностью до 0,95 г/см3 наиболее эффективными являются двухступенчатые
системы грубой и тонкой очистки. Грубая очистка осуществляется в сепарирующих
устройствах отстойного типа, в которых от воды отделяются грубодисперсные
частицы нефтепродуктов. Тонкая очистка производится в фильтрах коалесцирующего
типа.
На рис показана схема системы
двухступенчатой очистки загрязненных нефтепродуктами вод. Из сборных колодцев
(льял) 1 насосы 2 (основной или резервный) подают загрязненные воды в фильтр грубой
очистки 3 с вертикальным движением жидкости. Емкость этого фильтра должна быть
равна (или несколько больше) суточному объему поступающих загрязненных вод.
Благодаря этому обеспечивается отстой нефтепродуктов между двумя периодическими
откачиваниями. В фильтре 3 посредством змеевика 9 предусматривается обогрев
смеси насыщенным паром низкого давления. С ростом температуры смеси объем нефти
увеличивается быстрее, чем объем воды, в результате чего возникает подъемная
сила, действующая на частицы нефти. Всплывшие нефтепродукты через клапанное
устройство, отделяющее нефть от воды, переходят в нефтесборник 5, откуда
удаляются в цистерну 4 сточных нефтепродуктов. Температура подогрева может
поддерживаться в пределах от 35 до 50°С.
После грубой очистки смесь поступает
в сепаратор 6 тонкой очистки коалесцирующего типа. Принцип действия таких
сепараторов состоит в укрупнении частиц нефти путем их слияния при прохождении
через коалесцирующий материал и последующего их отделения от воды под действием
массовых сил. В качестве коалесцирующих материалов могут применяться шерсть,
стекловолокно, синтетические волокна. В настоящее время широко используется
полипропилен.
Выделившиеся из смеси в сепараторе 6
нефтепродукты перетекают в нефтесборник 5, откуда удаляются в цистерну 4
сточных нефтепродуктов, а очищенная вода поступает в контрольную цистерну 8 и
после проверки сбрасывается за борт. Через трубку 7 из нефтесборника удаляется
воздух, а через клапан 10 производится осушение системы. Нефтесборник 5 снабжен
датчиками нижнего и верхнего уровня, автоматическим устройством для подогрева
смеси, сброса нефти в цистерну 4 и выпуска воздуха.
Стоки из льял МО, за исключением
стоков из льял, расположенных в районе грузовых насосов нефтяного танкера, не
должны смешиваться с остатками нефтяного груза. Нефтяные остатки, которые по
концентрации нефтепродуктов не могут быть сброшены в море, сохраняются на
борту, сжигаются во вспомогательных ПГ, сливаются в приемные устройства на
берегу или передаются на специальные суда.
. ОЦЕНКА ЭКОНОМИЧЕСКОЙ ЭФФЕКТИВНОСТИ
СЭУ
Оптимизацию технических решений чаще
всего осуществляют на основе экономической оценки, используя показатель
экономической эффективности. Принимаемые решения должны быть технически
допустимыми и оптимальными - лучшими из возможных по значению критерия
оптимальности.
Для морских транспортных судов
критерием оптимальности является критерий экономической эффективности, в
качестве которого применяется норма прибыли - отношение ежегодной прибыли от
эксплуатации судна П к капитальным вложениям в его создание Kс:
.
Годовой объем прибыли
можно представить как разницу между доходами от эксплуатации судна Д и
расходами на его функционирование Р:
Доходы от эксплуатации
судна поступают в виде платы за перевозку грузов:
где Рг -
грузоподъемность судна, т; Kгп - коэффициент технического использования
грузоподъемности - средневзвешенный коэффициент загрузки судна; Lпл - величина
линии, на которой эксплуатируется судно,мили; Fr - фрахтовая ставка, зависящая
от вида перевозимого груза и бассейна эксплуатации судна, долл.за тонно-милю. В
случае перевозки разнородных грузов необходимо осреднение этой величины; Zр -
среднее число рейсов за год.
Расходы, связанные с
эксплуатацией судна, разделяют на первоначальные, или единовременные, и
текущие, или постоянные. Первые выступают в виде капитальных вложений -
стоимости постройки или приобретения судна Кс. Годовые текущие расходы Ртек -
сумма расходов на топливо Рт, смазочные и обтирочные материалы Рсм, амортизацию
Ра, текущий ремонт Рр, снабжение Рсн, содержание экипажа Рэк, навигационные Рн
и косвенные Ркос расходы:
Различия между
капитальными и текущими расходами достаточно условны. Судовладелец, как
правило, не имеет свободных денег и приобретает суда на капитал, взятый под
проценты в банке. За пользование капиталом производятся ежегодные платежи:
где Но - норматив
годовых отчислений за пользование капиталом, равный в общем случае учетной
банковской ставке.
Таким образом,
фактическими расходами на эксплуатацию судна являются так называемые "приведенные
затраты" - сумма текущих расходов и платы за пользование капиталом,
вложенным в постройку судна:
где Ен - прогноз учетной
банковской ставки.
Последовательное
применение модулей WERT, LOHN, DOXOD позволяет рассчитать первоначальную
стоимость судна, двигателя, текущие расходы и доход от эксплуатации судна.
Далее можно сконструировать комплексный показатель эффективности.
Базовый модуль WERT
предназначен для определения первоначальной стоимости морского транспортного
судна, его энергетической установки и главного двигателя, а также массы
энергетической установки в рабочем состоянии и сухой массы главного
оборудования СЭУ. В основу разработки модуля положена типовая методика
определения капитальных вложений и корреляционные зависимости показателей
стоимости, массы и габаритов в функции главных параметров судна и СЭУ. В
соответствии с этой методикой себестоимость Кс судна установившейся серии может
быть определена как сумма четырех слагаемых с поправочными коэффициентами,
учитывающими определенные особенности судна и СЭУ:
где Kэу - стоимость
энергетической установки;мк - стоимость металлического корпуса;ст -
коэффициент, учитывающий долю стали повышенной прочности в составе корпуса;ок -
стоимость оборудования корпуса судна; р - стоимость работ судостроительного
предприятия по монтажу, наладке и испытаниям при постройке судна;
Пki -произведение
коэффициентов, учитывающих класс ледового усиления kл, район расположения СЭУ
на судне kр, класс автоматизации производственных процессов на судне ka2, число
kв и тип движителей kдв; гд - стоимость главного двигателя; мо - стоимость
механического оборудования МКО; а1 - коэффициент, учитывающий степень
автоматизации СЭУ.
Слагаемые этого выражения
являются функциями измерителей стоимости - в основном массы соответствующих
конструктивно-технических групп оборудования, а для главных двигателей и СЭУ в
целом - максимальной длительной мощности, а также типов соответствующих
объектов (судов и СЭУ).
Стоимость очередного
j-ого судна серии Kcj определяется с учетом поправки kj, зависящей от
порядкового номера j и массы корпуса судна:
Для работы модуля
необходимо заполнить файл исходных данных.
Таблица 22
────────────────────────────────────────────────────────────────────────┐
ФАЙЛ
WERT-ISX.DAT - исходные данные для автономного прогона WERT │
────┬──────────────────────────────────┬────────┬──────────┬────────────┤
Nпп│
НАИМЕНОВАНИЕ ПЕРЕМЕННОЙ │ОБОЗНАЧ.│ РАЗМЕРН. │ЧИСЛ.ЗНАЧЕН.│
────┼──────────────────────────────────┼────────┼──────────┼────────────┤
1
│ Код типа судна ( 1 - 13 ) │ CY │ - │
1│
2
│ Код типа СЭУ ( 1 - 5 ) │ CEY │ - │
1│
3
│ Код ледового класса судна (1-7) │ LED │ - │
2│
4
│ Код степени автоматизации (1-3) │ AWT │ - │
2│
5
│ Код района расположения МКО(1-3)│ RAS │ - │
1│
6
│ Число валопроводов на судне(1-2)│ WAL │ - │
1│
7
│ Код типа движителя (1-ВФШ,2-ВРШ)│ WINT │ - │
1│
8
│ Код доли стали повышен.прочности│ ST │ - │
0│
9
│ Код наличия регенерации теплоты │ REG │ - │
0│
10
│ Число судов в составе серии │ NC │ - │
10│
11
│ Полное водоизмещение судна │ D │ т.с. │
10300.00│
12
│ Водоизмещение судна порожнем │ DP │ т.с. │
3300.00│
13
│ Номин. мощность двигателя (НМДМ)│ NEL1 │ кВт │
3250.00│
14
│ Частота на режиме НМДМ │ NL1 │ об/мин │
210.00│
15
│ Масса двигателя │ GD │ т.с. │
57.25│
────┴──────────────────────────────────┴────────┴──────────┴────────────┘
В
результате работы модуля получаем следующие показатели:
Измерители
стоимости судна,СЭУ и двигателя.
Масса
металлического корпуса судна,тыс.тонн - GKOR = 2.825
Масса
оборудования корпуса, " " - GOK = 0.499
Суммарная
масса оборудованного корпуса, " - GSUM = 3.324
Мощность
двигателя, тыс.кВт - MO = 3.250
Масса
двигателя, тыс.тонн - GD = 0.057
Масса
механического оборудования МКО" " - GMO = 0.582
Масса
энергетической установки, " " - GY = 0.639
Стоимостные характеристики судна,СЭУ и двигателя.
Стоимость главного двигателя, тыс.долларов - KD = 724.4
Cтоимость механич.оборудования MKO, " - KM = 2213.8
Cтоимость энергетической установки, " - KY = 2938.2
Cтоимость металлического корпуса судна," - KMK= 2417.6
Cтоимость оборудования корпуса судна, " - KOK= 4804.9
Cтоимость оборудованного корпуса судна," - KK = 7222.4
Cтоимость работ судостр.предприятия, " - KRA= 1190.9
Cтоимость судна установившейся серии, " - KC = 13165.5
Cтоимость серийного судна " - SCP= 14620.3
Базовый модуль LOHN предназначен для
определения текущих расходов за рейс транспортного судна на основе отраслевой
методики определения себестоимости эксплуатации, согласно которой Р - текущие
затраты за рейс складываются из суммы расходов на топливо РТ, на смазку Рсм,
амортизацию Ра, текущий ремонт Рр, снабжение Рсн, на экипаж Рэк, навигационные Рн
и косвенные расходы и Ркос.
Таблица
────────────────────────────────────────────────────────────────────────┐
ФАЙЛ
LOHN-ISX.DAT - исходные данные для автономного применения LOHN │
────┬──────────────────────────────────┬────────┬──────────┬────────────┤
Nпп│
НАИМЕНОВАНИЕ ПЕРЕМЕННОЙ │ОБОЗНАЧ.│ РАЗМЕРН. │ЧИСЛ.ЗНАЧЕН.│
────┼──────────────────────────────────┼────────┼──────────┼────────────┤
1
│ Код типа судна ( 1 - 13 ) │ CY │ - │
1│
2
│ Код типа СЭУ ( 1 - 5 ) │ CEY │ - │
1│
3
│ Код бассейна экспл. судна (1-7) │ BASS │ - │
3│
4
│ Код марки топлива на ход.режиме │ KT(1)│ - │
1│
5
│ Число членов экипажа(0-аппрокс.)│ ZE │ - │
20│
6
│ Код наличия регенерации теплоты │ REG │ - │
0│
7
│ Класс перевозимого груза │ KLASS │ - │
5│
8
│ Стоимость постройки судна │ KC │ тыс.долл.│
14620.300│
9
│ Дедвейт судна │ DW │ т.с. │
7000.000│
10
│ Мощность гл.двигат.на экспл.реж. │ NERR │ кВт │
2379.646│
11
│ Удельный расход топл.главн.двигат│ BEGD │ г/кВт*ч│
177.000│
12
│ Мощность электрогенератра на ходу│ NWD1 │ кВт │
400.000│
13
│|Мощность электроген|без гр.операц│ NWD2 │ кВт │
200.000│
14
│| на стоянке |с груз.операц│ NWD3 │ кВт │
400.000│
15
│ Удельный расход топл.вспом.двигат│ BEWD │ г/кВт*ч│
200.000│
16
│ Расход топлива Всп. П Г на ходу│ BK1 │ кг/ч │
100.000│
17
│|Расход топлива ВПГ |без гр.операц│ BK2 │ кг/ч │
20.000│
18
│| на стоянке |с груз.операц│ BK3 │ кг/ч │
400.000│
19
│ Годовой период эксплуатации судна│ TGOD │ сут/год │
330.000│
20
│ Дальность плавания судна │ LPL │ мили │
6000.000│
21
│ Средняя эксплуатац.скорость судна│ VSR │ узлы │
14.140│
22
│ Процент.ставка за польз.капиталом│ EN │ 1/год │
0.150│
23
│ Длит. стоянки без гр.оп.(танкер) │ TST │ сут/рейс│
4.000│
24
│ Длительн.стоянки с гр.оп.(танкер)│ TSTG │ сут/рейс│
0.750│
25
│ Длительн.стоянки с мойкой(танкер)│ TSTM │ сут/рейс│
2.000│
26
│Отн.доля стоянки без гр.оп.(ун.сух│ AST │ - │
0.200│
27
│ Отн.доля стоянки с гр.оп.(ун.сух)│ ASTG │ - │
0.000│
────┴──────────────────────────────────┴────────┴──────────┴────────────┘
Результаты
работы модуля LOHN описываются следующими переменными, имеющими одинаковую
pазмеpность - доллары за рейс:
Эксплуатационные расходы по судну
Число рейсов за год - ZRE = 13.508
Длительность рейса,час - STK = 586.3
Длительность ходовых режимов,час - TPL = 424.3
Транспортная работа,тысячи тонномиль в год - GTR = 567327.4
Доход от перевозок груза,тыс.долларов в год- DOX = 21983.9
Годовые текущие расходы,тыс.долларов в год - GR = 6657.8
Годовые приведенные затраты по судну, -"- - GPZ = 8850.9
Текущие расходы за рейс,доллары за рейс - CR = 492887.8
Расходы на топливо, " - ZT = 368247.4
Расходы на масло, " - SM = 160.3
Расходы на амортизацию,ремонт и снабжение,"- CA = 91007.2
Расходы навигационные, " - CH = 12805.0
Расходы косвенные, " - CK = 5246.3
Расходы на экипаж, " - CE = 15421.7
Число членов экипажа, человек - ZE = 20
ЗАКЛЮЧЕНИЕ
В ходе проекта была рассчитана ЭУ
танкера дедвейтом 7 000 тонн с малооборотным двигателем. Был произведен выбор
оборудования, в которое входит: дизель-генераторы, утилизационные котлы,
опреснительная установка, насосы и другое оборудование.
Рассмотрены основные системы СЭУ:
топливная, масляная, пускового воздуха, охлаждения забортной и пресной водой.
Приведены их принципиальные схемы и краткое описание.
В проекте рассмотрены принципы
расположения оборудования в МКО, обеспечивающие достижение целей проектирования
- сокращение размеров МКО при удовлетворении ограничительных требований на
функционирование оборудования и обеспечение удобной и безопасной эксплуатации
СЭУ. Приведены примеры расположения СЭУ в МКО основными способами. В результате
проведенной работы был найден оптимальный вариант расположения оборудования в
блочной компоновке, составлена таблица относительных координат для расположения
энергетического оборудования россыпью.
Технологическая часть содержит
материал по технологии монтажа ГД, раздел по охране окружающей среды - защиту
морской среды от загрязнения льяльными водами. В экономическом разделе
рассчитаны первоначальная стоимость судна, текущие расходы на эксплуатацию и
доход от эксплуатации.
СПИСОК ИСПОЛЬЗУЕМОЙ ЛИТЕРАТУРЫ
1. Б.Л. Троицкий, Е.А. Сударева, «Основы проектирования
судовых энергетических установок», Л., Судостроение, 1987.
. П.И.Козлов и др, «Судовые энергетические установки», Л.,
Судостроение, 1969.
. Н.В. Голубев, «Проектирование энергетических установок
морских судов», Л., Судостроение, 1980.
. В.И. Козлов, «Судовые дизельные установки с МОД»,
учебное пособие, Л., ЛКИ, 1990.
. А.Г. Даниловский, «Проектирование расположений
энергетических установок транспортных судов», С-Пб, СПбГУВК, 2004.
. А.Г.Даниловский, «Судовые энергетические установки.
Автоматизированное проектирование», С-Пб, 2004.
. В.С. Кравченко, «Монтаж судовых энергетических
установок», Л., Судостроение, 1975.
. В.Ф. Соколов, «Основы технологии судостроения», С-Пб,
Судостроение, 1995.
. Ф.Л. Юдицкий, «Защита окружающей среды при эксплуатации
судов», Л., Судостроение, 1978.
. В.А. Маркевич, «Средства защиты моря от загрязнения при
эксплуатации СЭУ», учебное пособие, Л., ЛКИ, 1983.