Разработка технологического процесса ремонта КПП Hyundai Solaris
КУРСОВОЙ ПРОЕКТ ПО
«Техническому обслуживанию
автомобилей»
на ТЕМУ:
РАЗРАБОТКА ТЕХНОЛОГИЧЕСКОГО ПРОЦЕССА
РЕМОНТА КППSOLARIS
Содержание
Введение
. Расчетно-технологическая часть
.1 Техническая характеристика автомобиля
.2 Корректирование пробегов автомобиля
.3 Расчет числа технологических воздействий
.4 Расчет числа дней простоя
.5 Расчет числа технических воздействий на парк автомобилей
за год
.6 Расчет числа технических воздействий за сутки
.7 Расчет годового объема работ ЕО, ТО, ТР и диагностики
.8 Расчет трудоемкости участка
.9 Расчет количества рабочих в агрегатном участке
.10 Подбор оборудования и оснастки производственных участков
.11 Обоснование технологической планировки производственного
участка
. Организационный раздел
.1 Выбор метода организации труда в агрегатном участке
.2 Организация технологического процесса ремонта КПП
.3 Мероприятия по охране труда в агрегатном участке
.4 Мероприятия по охране окружающей среды
.5 Мероприятия по пожарной безопасности в агрегатном участке
. Конструкторская часть
.1 Сравнительный анализ существующего технологического
оборудования
.2 Устройство и работа предлагаемого оборудования
.3 Техника безопасности при работе с оборудованием
Заключение
Литература
Приложение
Введение
Автомобильная промышленность является ведущей отраслью
отечественного машиностроения, определяющей экономический и социальный уровень
развития страны. Ситуацию в российской автомобильной промышленности в последние
несколько лет можно охарактеризовать как неоднозначную. С одной стороны,
происходил бурный рост рынка, вызванный, в том числе, ростом покупательской
способности населения, развитием потребительского кредитования и укреплением
национальной валюты. С другой стороны, постоянно сокращалась доля отечественных
производителей на автомобильном рынке при одновременном усилении конкуренции
внутри ценовых сегментов.
Во многом рост связан с продолжающимся ростом спроса в Китае и Индии,
одновременно с восстановлением рынка в США, а также общемировым ростом спроса
на премиальные бренды. Восстановление в ЕС происходит медленными темпами из-за
завершения действия многочисленных схем утилизации. Мировое производство
впервые может превысить 80 млн штук.
Восстановление внутреннего производства.
Существенно увеличившийся спрос на автомобили, государственные программы
стимулирования, а также инвестиции автопроизводителей в новые мощности дали
возможность заметно нарастить объемы производства.
За первые девять месяцев 2011 года было произведено 1,26 миллиона
легковых автомобилей, что на 54% больше, чем за аналогичный период 2010 года.
Динамика прироста производства иностранных брендов существенно выше
динамики производства традиционных российских брендов.
По результатам 2011 года мы ожидаем, что в России будет произведено
порядка 1,7 миллиона легковых автомобилей, что на 41% больше объема выпуска
2010 года и является абсолютным историческим максимумом.
Рынок автокредитования в России.
По итогам 2011 года ожидается, что доля автомобилей, купленных в кредит,
в общих продажах легковых автомобилей возрастет до 43% и достигнет 17,1 млрд
долларов в денежном выражении. Это немного меньше докризисного значения, когда
рынок достигал значения в 19,4 млрд долларов.
По сравнению с 2010 годом, когда было выдано автокредитов на сумму 10,1
млрд долларов, прирост должен составить около 69%.
В 2012 году мы ожидаем рост ставок по автокредитам, в первую очередь, на
те автомобили, которые участвовали в программе льготного кредитования, что
потенциально может негативно сказаться на продажах автомобилей в кредит.
Заключение
За первые девять месяцев 2011 года рынок легковых автомобилей показал 45%
рост в количественном выражении благодаря росту потребительской уверенности,
программам государственной поддержки, увеличению доступности кредитования.
В дальнейшем мы ожидаем замедления темпов роста и полагаем, что в 2011
году объем продаж новых легковых автомобилей не превысит 2,5 млн штук.
Благодаря вводу новых мощностей и увеличению использования существующих
2011 год может стать рекордным годом по объему производства легковых
автомобилей в России, может быть выпущено около 1,7 млн легковых автомобилей.
Кризис 2008 года показал, что Россия не изолирована от общемировых
экономических процессов. В случае развития ситуации по негативному сценарию
динамика российского автомобильного рынка может существенным образом
измениться.
В текущих экономических условиях игроки автомобильного рынка могут
рассчитывать на долгосрочный рост, но при этом должны быть готовыми быстро
отреагировать на возможные изменения.
автомобиль технический пробег
1. Расчетно-технологическая часть
.1 Техническая характеристика автомобиля
Таблица 1
Количество мест
|
5
|
Габаритные размеры, мм
|
Длина
|
4370
|
|
Ширина
|
1700
|
|
Высота
|
1470
|
Колесная база, мм
|
2570
|
Клиренс, мм
|
160
|
Двигатели
|
Gamma 1,4
|
Gamma 1,6
|
Объем, см3
|
1396
|
1591
|
Максимальная мощность, л.с. при об/мин
|
107 / 6300
|
123 / 6300
|
Максимальный крутящий момент, Нм приоб/мин
|
135,4 / 5000
|
155 / 4200
|
Топливный бак, л
|
43
|
Трансмиссия
|
5МТ
|
4АТ
|
5МТ
|
4АТ
|
Время разгона 0-100 км/ч, с
|
11,5
|
13,2
|
10,2
|
11,2
|
Максимальная скорость, км/ч
|
190
|
170
|
190
|
180
|
Расход топлива, л
|
Городской цикл
|
7,6
|
8,5
|
7,9
|
8,6
|
|
Загородный цикл
|
4,9
|
5,2
|
4,9
|
5,2
|
Задачей технологического расчета является определение
необходимых данных (производственной программы, численности рабочих, количества
постов и площадей) для разработки планировочного решения производственного
подразделения АТП и организации технологического процесса ТО и ТР подвижного
состава.
При выполнении этого раздела руководствуемся
«Положением о ТО и ремонте подвижного состава автомобильного транспорта»,
учебником И.С. Туревского «Техническое обслуживание автомобилей», а также
существующими методическими указаниями.
Исходные данные для расчета, выданные проекта, заносим
в табл. 2.
Таблица 2. Исходные данные
Исходные данные
|
Условные обозначения
|
Данные для расчета
|
Единица измерения
|
Марка автомобиля
|
-
|
Hyundai Solaris
|
-
|
Списочное число автомобилей
|
Ас
|
600
|
шт.
|
Пробег с начала эксплуатации в долях единицы от пробега
до капитального ремонта базовых агрегатов Lкр
|
-
|
0,1
|
шт.
|
Среднесуточныйпробег
|
lсс
|
420
|
км
|
Число дней работы АТП в году
|
Дргп
|
365
|
дни
|
Число дней работы подразделения в году
|
Дргу
|
365
|
дни
|
Плановый коэффициент технической готовности (от 0,85 до
0,92)
|
aт
|
0,9
|
-
|
Категория эксплуатации
|
-
|
|
-
|
Климат
|
-
|
Умеренно холодный
|
-
|
.2 Корректирование нормативных пробегов
нормативы, установленные Положением, для эталонных условий
эксплуатации, необходимо корректировать умножением на соответствующие
коэффициенты.
Корректирование нормативов технического обслуживания и ремонта подвижного
состава в зависимости от условий эксплуатации осуществляется с применением
коэффициента k1 (табл. 2, 3 приложения 1) в соответствии с их
классификацией, которая включает пять категорий условий эксплуатации. Выбранные
коэффициенты корректирования внести в табл. 2.
Таблица 3. Применение коэффициентов корректировки нормативов ТО и ТР и их
значения (пример заполнения)
Корректируемый параметр
|
Коэффициент
|
|
k1
|
k2
|
k3
|
k4
|
k41
|
k5
|
Периодичность ТО-1, км
|
1,0
|
-
|
0,9
|
-
|
-
|
-
|
Периодичность ТО-2, км
|
1,0
|
-
|
0,9
|
-
|
-
|
-
|
Трудоемкость ЕО, чел.-ч
|
-
|
1,0
|
-
|
-
|
-
|
0,8
|
Трудоемкость ТО-1, чел.-ч
|
-
|
1,0
|
-
|
-
|
-
|
0,8
|
Трудоемкость ТО-2, чел.-ч
|
-
|
1,0
|
-
|
-
|
-
|
0,8
|
Трудоемкость ТР, чел.-ч
|
1,0
|
1,0
|
1,1
|
0,4
|
-
|
0,8
|
Простои в период ТО-2 и ТР, дней на 1000 км пробега
|
-
|
-
|
-
|
-
|
0,7
|
-
|
Трудоемкость технического обслуживания и текущего ремонта и расход
запасных частей корректируют с учетом модификации подвижного состава и
особенностей организации его работы (автомобили с прицепами, самосвалы и т.д.)
с применением коэффициента k2 (табл. 4 приложения 1).
Природно-климатические условия учитывают, используя коэффициент k3
при определении периодичности ТО, удельной трудоемкости текущего ремонта,
который изменяется с учетом агрессивности окружающей среды (табл. 5 приложения
1). Корректирование нормативов осуществляют для серийных моделей автомобилей, в
конструкции которых не учтены специфические особенности работы в данных
районах.
Районирование территорий по природно-климатическим условиям приведено в
табл. 6 приложения 1. Для районов, не указанных в этом регионе, коэффициент
корректирования равен 1,0.
Пробег автомобиля с начала эксплуатации учитывают при определении
трудоемкости текущего ремонта. С этой целью вводят коэффициент k4
(табл. 7 приложения 1).
Уровень концентрации подвижного состава (число АТС), а также технологическую
совместимость (не менее 25 автомобилей в группе) учитывает коэффициент k5
(табл. 8 приложения 1).
Продолжительность простоя в период технического обслуживания и ремонта в
зависимости от пробега с начала эксплуатации измеряется с помощью коэффициента k¢4 (табл. 7 приложения 1).
Коэффициент корректирования нормативов периодичности ТО:
kто =k1×k3=
где
kто - коэффициент корректирования периодичности ТО; k1 -
коэффициент, учитывающий категорию условий эксплуатации; k3 -
коэффициент, учитывающий природно-климатические условия.
Коэффициент
корректирования нормативов трудоемкости ТО:
= k2×k5=0,9
где
k
- коэффициент корректирования трудоемкости ТО; 5
- коэффицииент, учитывающий количество автомобилей на автотранспортном
предприятии.
Коэффициент корректирования нормативов трудоемкости ТР:
k
= k1×k2×k3×k 4×k5=0,352=0,3
где
k4 - коэффицииент, учитывающий пробег с начала эксплуатации.
Периодичность
ТО-1, скорректированная в соответствии с условиями эксплуатации, равна:
= L
×kто=5000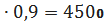
км
где
L
- пробег до ТО-1, скорректированный в соответствии с
условиями эксплуатации, км;
-
нормативный пробег до ТО-1, км.
Периодичность
ТО-2, скорректированная в соответствии с условиями эксплуатации, равна:
= L
×kто=20000
км.
где
L
- пробег до ТО-2, скорректированный в соответствии с
условиями эксплуатации, км;
-
нормативный пробег до ТО-2, км.
Скорректированные
пробеги до ТО-1 и ТО-2 должны быть кратными среднесуточному пробегу и между
собой.
Кратность
пробега до ТО-1 среднесуточному пробегу равна:
1 = L
/ lсс=4500/420=10,7=11
где
i1 - кратность пробега до ТО-1 среднесуточному пробегу; сс
- среднесуточный пробег, км.
Плановый
пробег до ТО-1, который используется для дальнейших расчетов, равен:
1 = lсс×i1=420 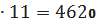
км.
где
L1 - плановый пробег до ТО-1.
При
этом L1 должен быть круглым целым числом, не отличающимся от L
более чем на 10 %.
Кратность
пробега до ТО-2 пробегу до ТО-1 равна:
2 = L
/L1=18000/4620=3,9
где
i2 - кратность пробега до ТО-2 пробегу до ТО-1.
Плановый
пробег до ТО-2 равен:
2 = L1×i2=4620 
18480 км
где
L2 - плановый пробег до ТО-2, км.
При
этом L2 должен быть круглым целым числом, не отличающимся от L
более чем на 10 %.
.3
Расчет числа технологических воздействий
Для
расчета числа технических воздействий на автомобиль и парк определяют годовой
пробег одного автомобиля:
г = Дрг×lсс×aт=365
км
где
Lг - годовой пробегодного автомобиля, км;
Дрг
- число дней работы АТП в год;
lсс
- среднесуточный пробег одного автомобиля, км;
aт - плановый коэффициент технической готовности.
Число
технических воздействий определяют по группам автомобилей, имеющим одинаковую
периодичность обслуживания.
Число
ТО-2 равно:
2=
=137970/18480=7,6
где
N2 - число ТО-2 на один автомобиль в год.
Число
ТО-1 равно:
1 =
- N2=137970/4620-8=22
где
N1 - число ТО-1 на один автомобиль в год; N2 - число ТО-2
на один автомобиль в год.
Число
ЕО равно:
ео=
Lг/ lсс=137970/420=328
где
Nео - число ЕО на один автомобиль в год.
Число
автомобилей, диагностируемых в процессе текущего ремонта согласно [1],
принимают равным 10 % от программы ТО-1 за год. Таким образом, количество Д-1
на один автомобиль в год:
Д1 = 1,1N1 + N2=32
где
NД1 - количество Д-1 на один автомобиль в год с учетом числа
технических воздействий (ТО-1 и ТО-2).
Число
автомобилей, диагностируемых при текущем ремонте, принимают равным 20 % от
годовой программы ТО-2.
Таким
образом, количество Д-2 на один автомобиль в год:
Д2 = 1,2N2=9,6
10
где
NД2 - количество Д-2 на один автомобиль в год с учетом числа
технических воздействий (ТО-2).
.4
Расчет числа дней простоя автомобиля
Расчет
числа дней простоя автомобиля в период ТО-2 и текущего ремонта, коэффициента
выпуска автомобиля на линию, коэффициента нерабочих дней автомобиля и годового
пробега парка автомобилей АТП
Число
дней простоя одного автомобиля в период ТО-2 и текущего ремонта (затраты
времени на ТО-1 при этом не учитывают поскольку ТО-1 выполняют без снятия автомобиля
с линии - в межсменное время):
Др=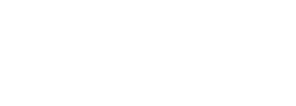
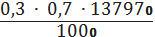
= 28,97
дней
Коэффициент
выпуска, определяющий долю календарного времени, в течение которого автомобиль
(или парк автомобилей) осуществляет транспортную работу (перевозит грузы,
пассажиров и т.п.) на линии:
=0,9
=0,9
где
a в -
коэффициент выпуска автомобиля на линию;
a т - плановый коэффициент технической готовности
автомобиля (по заданию);
Дн
- число дней в году, в течение которых исправный автомобиль не используется в
транспортной работе по организационным причинам (выходные и праздничные дни,
отсутствие работы, персонала, стихийные бедствия), дни;
Дн=
Дк - Дрг= 365 - 365 = 0дн.
где
Дрг - число дней работы АТП в году, дней;
Дк
- число календарных дней в году (Дк = 365 дней).
.5
Расчет числа технических воздействий на парк автомобилей за год
Число
ТО-1, проводимых автотранспортным предприятием за год:
= Ас×N1= 600 
где
N
- число ТО-1 на парк автомобилей в год;
Ас
- списочное число автомобилей на АТП.
Число
ТО-2, проводимых автотранспортным предприятием за год:
= Ас×N2= 600 
8 = 4800
где
N
- число ТО-2 на парк автомобилей в год.
Число
операций ежедневного технического обслуживания, проводимых автотранспортным
предприятием за год:
= Ас×Nео= 600 
328 =
196800
где
N
- число операций ежедневного технического
обслуживания на парк автомобилей в год.
Количество
Д-1, проводимых автотранспортным
предприятием за год:
= Ас×NД1= 600 
32 =
19200
где
N
- количество Д-1 на парк автомобилей в год.
Количество
Д-2 в автотранспортном предприятии за
год:
= Ас×NД2= 600 
10 =
6000
где
N
- количество Д-2 на парк автомобилей в год.
.6
Расчет числа технических воздействий за сутки
Число
ТО-1 в сутки:
N
= 
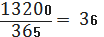
где
N
- число ТО-1 в сутки.
Число
ТО-2 в сутки:
= 

где
N
- число ТО-2 в сутки.
Число
ежедневного технического обслуживания в сутки:
= 

где
N
- число операций ежедневного технического
обслуживания в сутки.
.7
Расчет годового объема работ ЕО, ТО, ТР и диагностики
Таблица
4
Трудоёмкость ЕО,чел-час
|
0,35
|
Трудоёмкость ТО-1,чел-час
|
2,5
|
Трудоёмкость ТО-2,чел-час
|
10,5
|
Трудоёмкость ТР, чел час
|
3,0
|
Трудоемкость ежедневного технического обслуживания, чел.-ч:
tео=t
×k2×k5=0,35 
чел.-ч
где
tео - скорректированная трудоемкость
ежедневного технического обслуживания, чел.-ч;
t
- нормативная трудоемкость ежедневного технического
обслуживания, чел.-ч (табл. 10 приложения 1).
Трудоемкость
ТО-1, чел.-ч:
1 = t
×k2×k5=2,5
чел.-ч
где
t1 - скорректированная трудоемкость ТО-1,
чел.-ч;
t
- нормативная трудоемкость ТО-1, чел.-ч (табл. 10
приложения 1).
Трудоемкость
ТО-2, чел.-ч:
2 = t
×k2×k5= 10,5
чел.-ч
где
t1 - скорректированная трудоемкость ТО-2,
чел.-ч;
t
- нормативная трудоемкость ТО-2, чел.-ч (табл. 10
приложения 1).
Трудоемкость
текущего ремонта, чел.-ч:
тр=
t
×k1×k2×k3×k4×k5= 3,0 
чел.-ч
где
tтр - скорректированная удельная трудоемкость
текущего ремонта, чел.-ч/1000 км пробега;
t
- нормативная удельная трудоемкость текущего ремонта,
чел.-ч/1000 км пробега (табл. 10 приложения 1).
Годовой
объем работ ежедневного технического обслуживания, чел.-ч:
= N
×tео=196800 
чел.-ч
где
T
- объем работ ежедневного технического обслуживания в
год, чел.-ч;
- число ЕО на парк автомобилей в год;ео -
скорректированная трудоемкость ежедневного технического обслуживания, чел.-ч.
Годовой
объем работ по ТО-1, чел.-ч:
T
= N
×t1= 13200 
чел.-ч
где
T
- объем работ ТО-1 в год, чел.-ч;
- число ТО-1 на парк автомобилей в год;1 -
скорректированная трудоемкость ТО-1, чел.-ч.
Годовой
объем работ по ТО-2, чел.-ч:
Т
= N
×t2=4800
чел.-ч
где
Т
- объем работ ТО-2 в год, чел.-ч;
- число ТО-2 на парк автомобилей в год;2 -
скорректированная трудоемкость ТО-2, чел.-ч.
Годовой
объем работ по текущему ремонту, чел.-ч:
= (tтр×L
)/1 000=
чел.-ч
где
T
- объем работ ТР в год, чел.-ч; тр - скорректированная удельная
трудоемкость одного ТР на 1 000 км пробега, чел.-ч/1 000 км;
L
-годовой пробег парка автомобилей, км;
L
= Lг×Ас=137970 
км
где
Lг - годовой пробег одного автомобиля, км;
Годовой
объем постовых работ по текущему ремонту, чел.-ч:
= kп×T
= 0,40
чел.-ч
где
kп - доля
постовых работ в годовом объеме работ по текущему ремонту (kп = 0,40).
Годовой
объем работ на производственных участках текущего ремонта, чел.-ч:
= kу×T
=0,6
чел.-ч
где
kу - доля
работ на производственных ремонтных участках в годовом объеме работ по текущему
ремонту (kу = 0,6).
Работы
по диагностированию являются неотъемлемой частью работ по техническому
обслуживанию. Поэтому годовой объем работ Д-1 составляет 10…12 % годового
объема работ ТО-1, а годовой объем работ Д-2 составляет сумму, состоящую из 10
% годового объема работ по ТО-2 и 12 % годового объема по текущему ремонту.
Суммарный
объем работ по ТО и ремонту на автотранспортном предприятии в год:
то-тр=
T
+ T
+ T
+ T
=
55104+26400+40320+869211= 991035ч.ч.
1.8
Расчет трудоемкости участка
В
соответствии с заданием на курсовое проектирование необходимо спроектировать
агрегатный участок, текущего ремонта, и для расчета численности
ремонтно-обслуживающего персонала необходимо применить следующее соотношение:
Тi
=аi×T
=
= 7301,4
ч.ч.,
где
T
- общий объем работ по текущему ремонту,
осуществляемый на участках, в отделениях или цехах текущего ремонта (60 % от
общего объема ТР);
аi - доля работ по текущему ремонту
на агрегатном участке (табл. 11).
.9
Расчет количества рабочих в агрегатном участке
Число
рабочих мест


= 4
где
Рт - число рабочих мест, ед.;
Тi
- объем работ на заданном для проектирования подразделении
автотранспортного предприятия (зона, участок, отделение или цех), чел.-ч;
Фт- фонд рабочего времени рабочего
места, чел.-ч.
Окончательно
принимаем технологически необходимое количество Рабочих в размере РТ
= 1. Годовой фонд времени рабочего места Фт(в
часах) для 40-часовой рабочей недели приведен в табл. 12.
Численность
рабочих по штатному расписанию:

5 чел.
где
hш - коэффициент штатности, равный 0,89.
Таблица
с разрядами
Профессия
|
количество
|
В т.ч. по разрядам
|
|
|
1
|
2
|
3
|
4
|
5
|
Моторист
|
2
|
-
|
-
|
-
|
1
|
1
|
Слесарь по ремонту агрегатов
|
3
|
-
|
-
|
2
|
1
|
-
|
1.10 Подбор оборудования и оснастки производственных участков
Подбор оборудования осуществляем по техническим характеристикам
стандартного гаражного оборудования, исходя из перечня выполняемых работ на
участке, учитывая количество рабочих постов и типа обслуживаемых автомобилей.
Технологическое оборудование представлено в таблице 5.
Таблица 5. Ведомость технологического оборудования
Технологическое оборудование
|
№
|
Наименование оборудования
|
Кол-во
|
Габаритные размеры, мм
|
Площадь, м2
|
Энергоемкость, кВт
|
Стоимость, р/шт
|
Марка или модель
|
1
|
Станок для расточки Тормозных барабанов
|
1
|
1080х800
|
0,9
|
1,8
|
289500
|
Р185
|
2
|
Радиально-сверлильный Настольный станок
|
1
|
450х450
|
0,2
|
0,8
|
1150
|
ВС- 43
|
3
|
Стенд для разборки и регулировки сцепления
|
1
|
900х530
|
0,5
|
-
|
36550
|
Р- 746
|
4
|
Гидропресс 40 т
|
1
|
1570х800
|
1,3
|
5,5
|
400000
|
ГП-36
|
5
|
Стенд для ремонта редукторов задних мостов
|
1
|
1100х600
|
0,7
|
-
|
38300
|
Р-620
|
6
|
Стенд для клёпки тормозных накладок
|
1
|
860х500
|
0,4
|
1,8
|
95000
|
PN-1
|
7
|
Подвесная кран-балка
|
1
|
60х6000
|
0,4
|
2,1
|
115600
|
ЭК-Б-1
|
8
|
Настольно-верстачный пресс 3т
|
1
|
680х340
|
0,2
|
1,5
|
52000
|
ОКС-918
|
9
|
Стенд для ремонта КПП
|
1
|
1020х790
|
0,8
|
-
|
67000
|
П-201У
|
10
|
Стенд для ремонта передних и задних мостов
|
1
|
1260х860
|
1,08
|
-
|
55000
|
СМ 2450
|
11
|
Вертикально-сверлильный станок
|
1
|
870x1110
|
1
|
2
|
157000
|
2С132
|
12
|
Заточный станок
|
1
|
210х210
|
0,04
|
0,6
|
2530
|
AIKEN MG
|
13
|
|
|
|
Fоб=7,52 м2
|
N = 16,1 кВт
|
|
|
В работе агрегатного участка предусматриваем широко использовать
разнообразный современный универсальный, специализированный ручной и
механизированный инструмент, приспособления. Ведомость технологической оснастки
представлена в таблице 6.
Таблица 6. Ведомость технологической оснастки
Технологическая оснастка
|
№ п/п
|
Наименование оборудования
|
Кол-во
|
Габаритные размеры, мм
|
Площадь, м2
|
Энергоемкость, кВт
|
Стоимость, р/шт
|
Марка или модель
|
1
|
Разводной ключ
|
2
|
|
|
|
320
|
Jonnesway
|
2
|
Кусачки
|
4
|
|
|
|
150
|
Matrix
|
3
|
Пассатижи
|
5
|
|
|
|
180
|
Matrix
|
4
|
Плоскогубцы
|
5
|
|
|
|
330
|
Force
|
5
|
Молоток
|
5
|
|
|
|
400
|
Gross
|
6
|
Домкрат подкатной
|
2
|
|
|
|
2400
|
Full star
|
7
|
Электродуговая сварка
|
1
|
|
|
4,0
|
9200
|
Торус 250
|
8
|
Дрель
|
2
|
|
|
0,6
|
1400
|
Sparke
|
9
|
Болгарка
|
2
|
|
|
0,9
|
2500
|
Bosch
|
10
|
Киянка
|
4
|
|
|
|
650
|
Stayer
|
11
|
Напильник
|
5
|
|
|
|
180
|
АСС
|
Подбор организационной оснастки осуществляем исходя из перечня работ
выполняемых в агрегатном участке, учитывая количество рабочих мест и количество
одновременно работающих в наиболее загруженную смену. Ведомость организационной
оснастки представлена в таблице 7.
Таблица 7. Ведомость организационной оснастки
Технологическое оборудование
|
№ п/п
|
Наименование оборудования
|
Кол-во
|
Габаритные размеры, мм
|
Площадь, м2
|
Энергоемкость, кВт
|
Стоимость, р/шт
|
Марка или модель
|
1
|
Стеллаж для деталей
|
2
|
1400х600
|
0,8
|
-
|
3990
|
Пром Металл Комплектация
|
2
|
Ларь для обтирочных материалов
|
1
|
800х400
|
0,3
|
-
|
2800
|
ОАО ”АСО”
|
3
|
Передвижная моечная ванна
|
1
|
450х900
|
0,4
|
-
|
3500
|
ВМП-400
|
4
|
Телефон и радио
|
1
|
55х35
|
0,002
|
0,15
|
1690
|
Voxtel E105
|
5
|
Раковина для мытья рук
|
1
|
45х50
|
0,002
|
-
|
1800
|
BAUMAN
|
6
|
Слесарный верстак
|
1
|
1300х700
|
0,9
|
-
|
18990
|
Sivik КС 008
|
7
|
Настенный шкаф для приборов и инструментов
|
1
|
540х360
|
0,2
|
-
|
4690
|
Ferrum 30
|
8
|
Ларь для отходов
|
1
|
600х340
|
0,2
|
-
|
2750
|
ОАО "АСО"
|
9
|
Тиски
|
2
|
70х50
|
0,04
|
-
|
9900
|
Matador
|
|
|
|
|
Fоб=3м2
|
N = 16,1 кВт
|
|
|
Расчет площади производственного участка
Состав помещений определяется размером АТП и производственными
программами по эксплуатации, техническому обслуживанию и ремонту. В
соответствии с нормами проектирования на АТП и СТО должны предусматриваться
отдельные производственные помещения для размещения следующих зон и производственных
участков: участка уборочно-моечных работ; зоны технического обслуживания и
текущего ремонта; агрегатно-механического; ремонта приборов системы питания и
электрооборудования; кузовного и окрасочного.
На СТОА допускается размещать в одном помещении с постами технического
обслуживания и ремонта следующие участки: агрегатно-механический, ремонта
приборов системы питания и электрооборудования.
В помещениях кузовных работ допускается размещать посты для выполнения
работ непосредственно на автомобиле.
Определение требуемой для размещения оборудования агрегатного участка в
соответствии с технологическими и санитарно-техническими нормами
производственной площади производим по формуле:
10,5 ∙
4 = 42м2
где
fоб - площадь, оборудования и
организационной оснастки в плане, составляет 10,5.м2;
Кп
- коэффициент плотности расстановки оборудования, Кп = 3 - 4,5.
С учетом размещения агрегатного участка в основном
производственном корпусе АТП, определим и скорректируем необходимую площадь с
учетом стандартной строительной сетки колонн. Выбираем стандартную строительную
сетку 6х9 м, общей площадью в 54 м2.
Превышение расчетной площади помещения, выбранного для
размещения агрегатного участка над принятой, определим по формуле:
м2
Превышение расчетной площади над принятой должно находится в пределах
нормы до 20%, при общей площади помещения менее 100 м2. Принимаем
высоту помещения с учетом того, что в участке располагается подъемное
оборудование, и требуемое расстояние для подвеса светильников Hу =
4,2 м.
1.11 Обоснование технологической планировки
производственного участка
Разработка планировочного решения участка производится
в соответствии с технологией работ, требованиями научной организации труда,
строительных норм и правил.
Наружная несущая стена помещения выполнена из кирпича
и имеет толщину 380 мм, внутренние стены предусматриваем выполнить из плоских
панелей армированного легкого бетона толщиной 150 мм.
Предусматриваем установить на участке двухпольные
двери шириною 1490 мм, и три оконных проема шириной 1800 мм. Расстановку
оборудования производим с учетом нормативных требований безопасности,
противопожарной защиты, эргономики, санитарно-технических норм.
При размещении оборудования учитываем требования к
удобству монтажа и обслуживания, соблюдая нормативные расстояния между
отдельными видами оборудования, оборудования и элементами здания.
2. Организационный раздел
.1 Выбор метода организации труда
При выборе метода организации труда в агрегатном участке необходимо
учитывать комплекс выполняемых работ при ТР и техническом обслуживании, так при
проведении электротехнических, диагностических, сварочных и шинных работ
рабочие участков привлекаются в зоны ТО-1 и ЕО, однако фактически они принадлежат
участкам.
Рабочие участка не смогут сформировать полноценную бригаду и поэтому они
входят в состав специализированной бригады, дополненной рабочими других
участков.
Рабочими местами в участке являются: стенд для обкатки
КПП, стенд для сборки-разборки агрегатов, слесарный верстак,
радиально-сверлильный настольный станок, вертикально-сверлильный станок, стенд
для ремонта передних и задних мостов, стенд для ремонта редукторов задних
мостов, стенд для разборки и регулировки сцепления. На которых выполняют работы
по сборке-разборке агрегатов.
Работы в участке распределяются между рабочими бригадиром, каждый рабочий
несет индивидуальную ответственность за порученную ему работу.
.2 Организация технологического процесса ремонта КПП
Независимо от объема работ по разборке коробки передач
всегда нужно исполнять следующие рекомендации:
после установки коробки передач стоит контролировать
уровень масла. Величина масла Sae 80, ApiGl-4; Gl-5 составляет 3,1 л;
всегда следует подменять все бумажные прокладки, уплотнительные
кольца круглого сечения и манжеты валов. Место промеж кромками манжет перед
монтажом всегда смазывать пластичной смазкой;
досконально расчистить все уплотняющие плоскости. При
использовании герметика наносить его размеренно и следить за тем, чтобы не
забивались вентиляционные отверстия; -
всегда подменять все пружинные упорные или упорные
кольца. Пружинные упорные кольца при монтаже не распространять слишком сильно и
всегда следить за тем, чтобы они действительно попадали в канавку;
болты и гайки, используемые для фиксации задней крышки
и картера, отворачивать и зажимать крест-накрест. Все самостопорящиеся гайки и
болты нужно подменять. Следить за соблюдением моментов затяжки;
игольчатые подшипники устанавливать маркировкой наружу
стороной, с которой применяется оправка;
все подшипники смазывать перед монтажом; - внутренние
кольца конических роликовых подшипников перед монтажом нагревать до 100° С. Не
путать промеж собой внутренние и внешние кольца разнообразных подшипников.
Конические роликовые подшипники одного вала подменять всегда в комплекте;
HyundaiSolaris разборка коробки передач - толщину компенсационных шайб всегда
измерять микрометром в нескольких местах. Устанавливать только шайбы без
заусенцев и других изъянов;
кольца синхронизатора контролировать на изнашивание и
при надобности подменять согласно указаниям в соответствующем разделе. Перед
монтажом досконально смазывать их маслом, чтобы они при первом же пуске не
начали работать всухую.
Рис. 1. Части картера коробки передач и картера
сцепления: 1 - болт, 25 Н·м; 2 - приводной фланец, правый; 3 - пружина; 4 -
регулировочная шайба; 5 - коническое кольцо; 7 - болт, 25 Н·м; 6 - картер
сцепления; 8 - шестерня привода спидометра; 9 - направляющая втулка; 10 -
дифференциал; 11 - магнит; 12 - установочный стержень; 13 - коническое кольцо;
14 - регулировочная шайба; 15 - пружина; 16 - приводной фланец; 17 - болт, 25
Н·м; 18 - упорное кольцо; 19 - шестерня, пятая передача; 20 - картер коробки
передач; 21 - установочный стержень
Рисунок 2.
Фиксация фланца коробки передач при отвинчивании
болтов Hyundai Solaris разборка коробки передач - демонтировать приводные
фланцы с картера коробки, для чего расположить под фланцем две лопатки,
используемые для снятия шин. Обращайте внимание на то, что левый и правый
фланцы отличаются друг от друга по длине и имеют разную маркировку. Фланец в
картере коробки передач (левая сторона) - наиболее короткий; - демонтировать на
обеих сторонах пружину 15 (рисунок. 3), регулировочную шайбу 14 и коническое
кольцо 13. Бурт конического кольца обращен в сторону регулировочной шайбы; -
применяя рисунок. 2, открутить три болта 1 задней крышки 2 и демонтировать
прокладку 3; - палец переключения передач зафиксировать на валу управления и
включить пятую передачу. Для этого отстранить внутрь тягу вилки переключения
коробки передач и развернуть ее влево. Демонтаж вилки переключения передач: 1 -
гайка; 2 - болт вилки - согласно рисунок. 5. ослабить контргайку 1 под
переключающей вилкой и открутить болт 2 с шаровой головкой.
Демонтировать вилку 5 (рисунок 2) подключения пятой
передачи одновременно со скользящей муфтой 4; - еще поставить скользящую муфту
на ступицу синхронизатора. Демонтаж частей шестерни пятой передачи
(заблокировать передачи в соответствии со стрелками 1, 2 и 3).
Рисунок 3.
Открутить болт А (рис. 4) для шестерни пятой передачи.
Для этого включить пятую передачу (стрелка 1), а также вторую передачу. Для
подключения второй передачи повторять пеpедвижения по стрелкам 2 и 3; - еще
демонтировать ступицу переключения для пятой передачи и выключить вторую передачу;
- демонтировать фиксатор 6 (см. Рисунок 2). Здесь может быть размещено упорное
кольцо. При монтировании фиксатор допустимо заместить пружинным упорным кольцом
соответствующего размера.
Фиксация ступицы синхронизатора на валу с участием
упорного кольца (стрелка) Hyundai Solaris разборка коробки передач поставить
съемник под шестерню 9 пятой передачи и демонтировать ступицу 7 синхронизатора
с шестерней; - демонтировать игольчатый подшипник 10; поставить отвертку под
регулировочную шайбу 12 для шестерни пятой передачи и демонтировать с вала
шайбу одновременно с опорной втулкой 11 игольчатого подшипника; демонтировать
пружинное упорное кольцо 21 (см. Рисунок 3) и демонтировать шестерню 20 пятой
передачи с вала. Шестерню отжимать или с участием двух отверток, установленных
на двух противоположных друг другу сторонах, или соответствующим съемником.
Демонтаж пружинного кольца - открутить болты картера
сцепления от картера коробки передач; демонтировать картер сцепления. В
уплотняющую плоскость вставлены 2 установочных штифта и, возможно, потребуется
нанести несколько ударов резиновым молотком, чтобы разделить картер на две
части. Другой вариант: выбить установочные штифты бородком через картер.
Демонтаж уплотняющей заглушки сбоку коробки передач - извлечь уплотнительные
заглушки из боковой стороны коробки передач. Они вынимаются с участием киянки.
На рисунке 4 показано, как размещается приспособление. Взамен инструмента
771/38 допустимо ввернуть болт М7х35 мм. Для этого нужно спилить головку болта
и осуществить скос в резьбе, чтобы привернуть проставку 771/15; - демонтировать
вал устройства переключения передач. Если потребуется, применять бородок в
соответствии с рисунок. 10; рис. 10. Выбивание бородком вала устройства
переключения передач HyundaiSolaris разборка коробки передач.
Демонтаж пальца переключения передач: 1 - палец; 2 -
консоль - извлечь пружину (указанное стрелкой область на рисунок 4),
содержащуюся промеж пальцем 1 переключения передач и переключающей консолью 2
(рис. 4), и демонтировать палец переключения передач. Под ним распологается
болт, удерживающий переключающую консоль и втулку; - отделить тумблер фонарей
заднего хода. Близко находятся три болта фиксации передачи заднего хода.
Открутить дaнные болты; - демонтировать тяги вилок подключения пятой передачи и
заднего хода, а также рычаг подключения заднего хода. Демонтаж тяг вилок
переключения передач: 1 - тяга вилки подключения пятой передачи; 2 - тяга вилки
подключения заднего хода; 3 - рычаг подключения заднего хода
Рис. 4. Демонтаж валов коробки передач: 1 - вал
передачи заднего хода; 2 - шестерня заднего хода; 3 - тяга вилки переключения
первой/второй передачи; 4 - ведомый вал; 5 - первичный вал; 6 - тяга вилки
переключения третьей/четвертой передачи
Рисунок 5
При выполнении следующей манипуляции применять рисунок
5. Прежде выбить вал 1 передачи заднего хода. Далее извлечь из картера коробки
передач первичный вал 5, ведомый вал 4, тягу 3 вилок переключения первой/второй
передач, тягу 6 вилок переключения третьей/четвертой передачи, шестерню 2
подключения заднего хода и вал 1.
Демонтаж первичного и ведомого вала Первичный вал
может сниматься одновременно с ведомым валом. Если нужно заместить первичный
вал или конический роликовый подшипник, то приводной вал необходимо
регулировать снова, как изложено ниже. Для демонтажа первичного и ведомого вала
нужно осуществить следующее (рисунок 6).