Вывернуть
пробки из сливных отверстий коробки передач
<#"803965.files/image010.gif"> (44)
где: αu -
коэффициент использования авто,
αт - коэффициент технической
готовности авто,
ДРГ - дни работы в году в АТП,
ДКГ - календарные дни в году,
Кu -
коэффициент учитывая снижения используемой техники, исправных авто в рабочие
дни АТП по эксплуатационным причинам.
Кu = 0,93-0,97
принимаем: Кu = 0.95
αт - коэффициент технической
готовности зависит от простоя авто в зоне обслуживания и ТР.
(45)
где: αт -
коэффициент технической готовности зависит от простоя авто в зоне обслуживания
и ТР,
dТОТР -
расчетное значение простоя подвижного состава, ТО и ТР,
dКР -
продолжительность простоя в КР,
LКР -
расчетный пробег до КР,
LCC -
среднесуточный пробег.
dТОТР = dнТОТР * К4
(46)
где: dТОТР -
расчетное значение простоя подвижного состава, ТО и ТР,
dнТОТР -
нормативное значение простоя подвижного состава, ТО и ТР,
dнТОТР = 0,5
- 0,55 принимаем: dнТОТР = 0,5
К4 - среднее значение коэффициента
корректирования нормативной продолжительности простоя в ТО и ТР в зависимости
от пробега с начала эксплуатации.
dТОТР = 0,5 *
0,7 = 0,35
dКР = dКРН =25 дн.
αт = 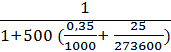 = 0,82
αu =  = 0,78
Определение годового пробега по
парку
LПГ = αu * LСС * АП *
ДРГ (47)
где: LПГ - годовой
пробег по парку,
αu = 0,78,
LСС = 500 км,
АП = 132 ед.,
ДРГ = 365 дн.
LПГ = 0, 78 *
500 * 132 * 365 = 18790200 км
Годовая трудоемкость ТР по АТП
Годовая трудоемкость ТР по АТП определяется по
следующей формуле:
ТгТР =  (48)
где: LПГ - годовой пробег по парку,
км;
tтр -
расчетная трудоемкость ТР;
tтр = 8,25
чел.час/1000 км;
ТГТР = 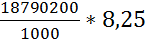
ТГТР = 155019,15 чел.час/1000 км.
Расчет трудоемкости постовых работ
Ti = ТГТР * σi (49)
где: ТГТР - годовая трудоемкость;
σi -
коэффициент трудоемкости по данному виду работ.
. Контрольно диагностические работы:
σК-Д=0,017
TК-Д =
155019,15 * 0,017 = 2635,32 чел.час
. Регулировочные работы:
σРЕГ=0,018
TР =
155019,15 * 0,018 = 2790,34 чел.час
. Разборо-сборочные работы:
σРАЗ.СБ=0,26
TР-С =
155019,15 * 0,26 = 40304,97 чел.час
Расчет трудоемкости участковых работ
. Агрегатные работы:
σАГР=0,17
TАГР =
155019,15 * 0,17 = 26353,25 чел.час
. Электротехнические работы:
σЭЛ.ТЕХ=0,085
TЭЛ-ТЕХ =
155019,15 * 0,085 = 13176,62 чел.час
. Ремонт приборов системы питания:
σСИСТ.ПИТ=0,03
TСИС.ПИТ =
155019,15 * 0,03 = 4650,57 чел.час
. Шиномонтажные работы:
σШ-Ж=0,03
TШ-Ж =
155019,15 * 0,03 = 4650,57 чел.час
. Шиноремонтные работы:
σШ-Р=0,01
TШ-Р =
155019,15 * 0,01 = 1550,19 чел.час
. Медницкие работы:
σМЕД=0,02
TМЕД =
155019,15 * 0,02 = 3100,22 чел.час
. Жестяницкие работы:
σЖЕСТ=0,012
TЖЕСТ =
155019,15 * 0,012 = 1860,22 чел.час
. Сварочные работы:
σСВАР=0,012
TСВАР =
155019,15 * 0,012 = 1860,22 чел.час
. Кузнчено-рессорные работы:
σК.РЕСС=0,03
TКУЗ-РЕС =
155019,15 * 0,03 = 4650,57 чел.час
. Слесарно-механические работы:
σСЛ.МЕХ=0,08
TСЛ-МХ =
155019,15 * 0,08 = 12401,53 чел.час
. Арматурные работы:
σАРМ=0,045
TАРМ =
155019,15 * 0,045 = 6975,86 чел.час
. Обойные работы:
σОБ=0,026
TОБ =
155019,15 * 0,026 = 4030,49 чел.час
. Аккумуляторные работы:
σАКБ=0,01
TАКБ =
155019,15 * 0,01 = 1550,19 чел.час
. Малярные работы:
σМАЛ=0,08
TМАЛ =
155019,15 * 0,08 = 12401,53 чел.час
2.15 Расчет состава
рабочих в зоне ТР
Рассчитываем явочное и штатное число рабочих по
постам и участкам:
РЯ = ТТР / Фрм (50)
РШТ = ТТР / Фрв (51)
где: РЯ - явочное число рабочих;
Фрм - годовой производственной фонд рабочего
времени;
Фрм = 1981;
РШТ - штатное число производственных рабочих;
Фрв - годовой фонд рабочего времени одного
производственного рабочего;
Фрв = 1820;
Постовые работы:
. Контрольно диагностические работы:
РЯ = 2635,32 / 1981 = 1,33 чел.
РШТ = 2635,32 / 1820 = 1,44 чел.
. Регулировочные работы:
РЯ = 2790,34 / 1981 = 1,40 чел.
РШТ = 2790,34 / 1820 = 1,53 чел.
. Разборо-сборочные работы:
РЯ = 40304,97 / 1981 = 20,34 чел.
РШТ = 2635,32 / 1820 = 22,14 чел.
Участковые работы:
. Агрегатные работы:
РЯ = 26353,25 / 1981 = 13,3 чел.
РШТ = 26353,25 / 1820 = 14,47 чел.
. Электротехнические работы:
РЯ = 13176,62 / 1981 = 6,65 чел.
РШТ = 13176,62 / 1820 = 7,23 чел.
. Ремонт приборов системы питания:
РЯ = 4650,57 / 1981 = 2,34 чел.
РШТ = 4650,57 / 1820 = 2,55 чел.
. Шиномонтажные работы:
РЯ = 4650,57 / 1981 = 2,34 чел.
РШТ = 4650,57 / 1820 = 2,55 чел.
. Шиноремонтные работы:
РЯ = 1550,19 / 1981 = 0,76 чел.
РШТ = 1550,19 / 1820 = 0,85 чел.
. Медницкие работы:
РЯ = 3100,38 / 1981 = 1,56 чел.
РШТ = 3100,38 / 1820 = 1,7 чел.
. Жестяницкие работы:
РЯ = 1860,22 / 1981 = 0,93 чел.
РШТ = 1860,22 / 1820 = 1,02 чел.
. Сварочные работы:
РЯ = 1860,22 / 1981 = 0,93 чел.
РШТ = 1860,22 / 1820 = 1,02 чел.
. Кузнечно-рессорные работы:
РЯ = 4650,57 / 1981 = 2,34 чел.
РШТ = 4650,57 / 1820 = 2,55 чел.
. Слесарно-механические работы:
РЯ = 12401,53 / 1981 = 6,26 чел.
РШТ = 12401,53 / 1820 = 6,81 чел.
. Арматурные работы:
РЯ = 6975,86 / 1981 = 3,52 чел.
РШТ = 6975,86 / 1820 = 3,83 чел.
. Обойные работы:
РЯ = 4030,49 / 1981 = 2,03 чел.
РШТ = 4030,49 / 1820 = 2,21 чел.
. Аккумуляторные работы:
РЯ = 1550,19 / 1981 = 0,78 чел.
РШТ = 1550,19 / 1820 = 0,85 чел.
. Малярные работы:
РЯ = 12401,53 / 1981 = 6,26 чел.
РШТ = 12401,53 / 1820 = 6,81 чел.
Таблица № 12 Распределение рабочих по постам и
участкам.
Виды
работ
|
Стр.
П %
|
Ттр.
П чел. час
|
Ря.
чел.
|
Рш.
чел.
|
Принято
рабочих
|
Рабо
-чих в одну смену
|
Норма
пло -щади на 1 чел.
|
Мини
-мальная площадь участка
|
Постовые
работы
|
Контрольно
- диагностические
|
1,7
|
2635.32
|
1,33
|
1,44
|
2
|
1
|
-
|
-
|
Регулировочные
|
1,8
|
2790.34
|
1,40
|
1,53
|
2
|
1
|
-
|
-
|
Разборо
- сборочные
|
26
|
40304.97
|
20,34
|
22,14
|
22
|
11
|
-
|
-
|
ИТОГО
|
29,5
|
45730.63
|
23,07
|
25,11
|
26
|
13
|
-
|
132
|
Участковые
работы
|
Агрегатные
|
17
|
26353.25
|
13,3
|
14,47
|
14
|
7
|
13
|
91
|
Электротехнические
|
8,5
|
13176.62
|
6,65
|
7,23
|
6
|
3
|
10
|
30
|
Аккумуляторный
|
1
|
1550,19
|
0,78
|
0,85
|
2
|
1
|
10
|
10
|
Ремонт
системы питания
|
3
|
4650.57
|
2,34
|
2,55
|
2
|
1
|
12
|
12
|
Шиномонтажные
|
3
|
4650.57
|
2,34
|
2,55
|
2
|
1
|
10
|
10
|
Шиноремонтные
|
1
|
1550.19
|
0,76
|
0,85
|
2
|
1
|
10
|
10
|
Медницкие
|
2
|
3100.38
|
1,56
|
1,7
|
2
|
1
|
24
|
24
|
Жестяницкие
|
1,2
|
1860.22
|
0,93
|
1,02
|
2
|
1
|
24
|
24
|
Сварочные
|
1,2
|
1860.22
|
0,93
|
1,02
|
2
|
1
|
24
|
24
|
Кузнечно
- рессорные
|
3
|
4650.57
|
2,55
|
2
|
1
|
24
|
24
|
Слесарно
- механические
|
8
|
12401.53
|
6,26
|
6,81
|
6
|
3
|
10
|
30
|
Арматурные
|
4,5
|
6975.86
|
3,52
|
3,83
|
4
|
2
|
12
|
24
|
Малярные
(рассчитывается по длине автобуса)
|
8
|
12401.53
|
6,26
|
6,81
|
6
|
3
|
-
|
132
|
Обойные
|
2,6
|
4030.49
|
2,03
|
2,21
|
2
|
1
|
10
|
10
|
ИТОГО
|
60,6
|
99212,19
|
50
|
54,45
|
54
|
27
|
243
|
576
|
2.16 Подбор
технологического оборудования и оснастки
Таблица № 13 Технологическое оборудование.
№
по порядку
|
Оборудование,
приборы, приспособления
|
Тип,
модель
|
Краткая
характеристика
|
Принятое
количество
|
Размеры
|
Производственные
цеха
|
Электротехническое
отделение
|
1
|
Ларь
|
Собственного
изготовления
|
Для
отходов
|
1
|
500х
500х 500
|
2
|
Умывальник
|
-
|
-
|
2
|
500х
500х 500
|
3
|
Секционный
стеллаж
|
Собственного
изготовления
|
Для
хранения оборудования
|
2
|
1400х
500х 1200
|
4
|
Ларь
|
Собственного
изготовления
|
Для
обтирочного материала
|
2
|
400х
300х 500
|
5
|
Прибор
|
Э
- 204
|
Для
проверки КИП
|
2
|
325х
275
|
6
|
Стенд
|
-
|
Для
проверки приборов
|
1
|
-
|
7
|
Стол
|
Собственного
изготовления
|
Для
приборов
|
2
|
1100х
300х 600
|
8
|
Стенд
|
532М
|
Контрольно
- испытательный, 0,5 кВт
|
1
|
1545х
885х 600
|
9
|
Стол
|
Стэнли
|
Конторский
|
2
|
1100х
600х 600
|
10
|
Подставка
|
Собственного
изготовления
|
Под
оборудование
|
2
|
800х
500 х600
|
11
|
Станок
|
-
|
Сверлильный
0,35 Вт
|
1
|
-
|
12
|
Пресс
|
-
|
Реечный
ручной
|
1
|
800х
500х 1200
|
13
|
Верстак
|
ОГ-8-132
|
Слесарный
|
1
|
1200х
800х 600
|
14
|
Тиски
|
-
|
Слесарные
|
1
|
-
|
15
|
Тумбочка
|
Собственного
изготовления
|
Для
хранения инструментов
|
2
|
700х
500х 800
|
16
|
Станок
|
МВ-01
|
электрозаточной
18 кВт
|
1
|
460х
260х 455
|
17
|
Станок
|
ЦКБ-Р-105
|
Проточки
коллекторов 400 Вт
|
1
|
1700х
500
|
18
|
Станок
|
НС-12А
|
Настольно-сверлильный
0,37 кВт
|
1
|
770х
465
|
19
|
Шкаф
|
НП-014
|
Сушильный
|
3
|
650х
650х 1600
|
20
|
Установка
|
-
|
Для
мойки и сушки деталей 3 кВт
|
2
|
1200х
700х 950
|
21
|
Круглый
вращающийся стол
|
Собственного
изготовления
|
Для
ремонта агрегатов
|
2
|
Ǿ1200
|
22
|
Приспособление
|
-
|
Для
отвертывания башмаков
|
2
|
-
|
23
|
Приспособление
|
-
|
Для
разборки и сборки генераторов
|
2
|
-
|
24
|
Полка
|
-
|
Для
инструментов
|
2
|
-
|
25
|
Прибор
|
Э-236
|
Для
проверки якорей генераторов
|
1
|
264х
196
|
Слесарно-механическое
отделение
|
26
|
Слесарный
верстак
|
-
|
самодельный
|
4
|
1400х
800х 600
|
|
27
|
Слесарные
тиски
|
-
|
заводские
|
4
|
-
|
|
28
|
Токарно-винторезный
станок
|
1К62Б
|
Заводского
изготовления 10 кВт
|
1
|
-
|
|
29
|
Полка
|
-
|
Для
инструментов
|
1
|
-
|
|
30
|
Инструментальный
шкаф
|
-
|
самодельный
|
4
|
555х
455х 800
|
|
31
|
Универсально-заточной
станок
|
-
|
Заводского
изготовления 1,4 кВт
|
2
|
-
|
|
32
|
Шлифовальный
станок
|
-
|
Заводского
изготовления
|
1
|
-
|
|
33
|
Стеллаж
для деталей
|
-
|
Заводского
изготовления
|
3
|
1400х
800х 500
|
|
34
|
Универсально-фрезеровальный
станок
|
-
|
Заводского
изготовления 3 кВт
|
2
|
-
|
|
35
|
Станок
отрезной
|
-
|
Заводского
изготовления 3,5 кВт
|
1
|
-
|
|
36
|
Вертикально-сверлильный
|
-
|
Заводского
изготовления 4 кВт
|
1
|
-
|
|
37
|
Проверочная
плита
|
-
|
Заводского
изготовления
|
1
|
1000х
750х 750
|
|
38
|
Настольно-сверлильный
станок
|
-
|
Заводского
изготовления 3 кВт
|
2
|
800х600х1650
|
|
39
|
Пресс
ручной
|
-
|
Заводского
изготовления
|
1
|
800х
600х 1650
|
|
Отделение
по ремонту двигателей
|
40
|
Моечная
установка
|
ОРМ-12
|
Для
мойки двигателей 43,6 кВт
|
2
|
1670х
1540х 1550
|
|
41
|
Моечная
установка
|
ОМ-1316
|
Для
мойки деталей 30 кВт
|
2
|
1250х
620х 800
|
|
42
|
Станок
|
278Н
|
Для
расточки гильз, 2,2 кВт
|
2
|
1200х
700х 1800
|
|
43
|
Станок
|
3833М
|
Для
полировки гильз, 2,8 кВт
|
2
|
1400х
300х 1600
|
|
44
|
Верстак
с пневматикой
|
СД-3701-04
|
5
кВт
|
1
|
1250х
800х 1800
|
|
45
|
Тумбочка
|
СД-3701-08
|
Для
инструментов
|
3
|
600х
522х 800
|
|
46
|
Прибор
|
2211М
|
для
правки и проверки шатунов
|
1
|
300х
250х 350
|
|
47
|
Шкаф
|
Собственного
изготовления
|
Для
деталей шатунно-поршневой группы
|
1
|
600х
522х 1600
|
|
48
|
Прибор
для определения упругости
|
КИ-40
|
Пружин
клапанов и поршневых колец
|
1
|
300х
250х 350
|
Стенд
|
ПИМ-1357-05Б
|
Для
опрессовки поршневых колец
|
1
|
800х
600х 800
|
|
50
|
Стеллаж
|
Собственного
изготовления
|
Для
хранения приборов и приспособлений
|
3
|
930х
600х 500
|
|
51
|
Станок
|
М-3
|
Для
притирки клапанов
|
2
|
1600х
585х 800
|
|
52
|
Станок
|
ОПР-823
|
Для
шлифования клапанов 0,37 кВт
|
1
|
935х
600х 800
|
|
53
|
Стенд
|
БОШ
2-3211
|
Для
ремонта дизельных форсунок, типа Common Rail 3 кВт
|
1
|
1300х
845х 600
|
|
54
|
Шкаф
|
-
|
Для
деталей газораспределительного механизма
|
3
|
800х
460х 1600
|
|
55
|
Стенд
|
СК
(ЭК-7В)
|
Для
обкатки и испытания компрессоров 80 кВт
|
1
|
884х
710х 600
|
|
56
|
Стенд
|
-
|
Для
сборки и разборки головок цилиндров двигателей
|
1
|
1060х
520х 600
|
|
57
|
Стенд
|
СИ-МН-37
|
Для
испытания масляных насосов дизелей 37 кВт
|
1
|
800х
480х 750
|
|
58
|
Стеллаж
|
Собственного
изготовления
|
Для
хранения масляных и водяных насосов
|
2
|
930х
600х 400
|
|
59
|
Умывальник
|
-
|
-
|
2
|
500х
500х 600
|
|
60
|
Ларь
|
-
|
Для
отходов
|
2
|
500х
500х 500
|
|
61
|
Стол
|
Стэнли
|
Конторский
|
2
|
1180х
620х 800
|
|
62
|
Ларь
|
-
|
Для
обтирочных материалов
|
2
|
800х
400х 600
|
|
63
|
Стеллаж
|
ПИ-033П
|
Для
хранения двигателей
|
1
|
1500х
1200х 300
|
|
64
|
Кран-балка
|
-
|
Для
перемещения агрегатов 8,74 кВт
|
1
|
9000х
200
|
|
65
|
Стенд
|
Р-660-1
|
Для
разборки дизельных двигателей грузовых авто и автобусов
|
1
|
1460х
810х 1070
|
|
Медницкое
отделение
|
66
|
Верстак
|
ВС-2
|
Для
ремонта топливных баков
|
1
|
1400х
800х 400
|
67
|
Стенд
- верстак с ванной
|
-
|
Для
ремонта радиаторов
|
1
|
1600х
900х 550
|
68
|
Шкаф
вытяжной
|
-
|
Для
распайки и поправки радиаторов
|
1
|
1300х
950х 1800
|
69
|
Установка
|
-
|
Для
очистки радиаторов от накипи, 0,8 кВт
|
1
|
1250
х100 х600
|
70
|
Стеллаж
|
Р-522А
|
Для
радиаторов и топливных баков
|
1
|
2000х
800х 400
|
71
|
Стеллаж
|
-
|
Для
деталей
|
3
|
1400х
450х 400
|
Сварочно-жестяницкое
отделение
|
72
|
Верстак
|
-
|
Жестяницкий
|
2
|
800х
600х 400
|
73
|
Пост
|
-
|
Для
сварочных работ
|
2
|
3000х
1500х 400
|
74
|
Станок
|
-
|
Передвижной
шлифовальный 2,6 кВт
|
2
|
800х
400х 500
|
75
|
Штатив
|
-
|
Для
баллона с кислородом
|
1
|
800х
300х 600
|
76
|
Стеллаж
|
-
|
Для
крыльев
|
1
|
1700х
1300х 400
|
77
|
Тележка
- стенд
|
-
|
Для
ремонта кабин
|
1
|
1650х
1200х 300
|
78
|
Площадка
|
-
|
Для
листового материала
|
1
|
1200х
950х 450
|
79
|
Аппарат
|
-
|
Для
точечной сварки, 6 кВт
|
1
|
700х
500х 500
|
80
|
Станок
|
-
|
Вертикально
-сверлильный, 4 кВт
|
1
|
700х
500х 1600
|
81
|
Плита
|
-
|
правочная
|
1
|
1500х
1000х 900
|
Шиномонтажное
и вулканизационное отделение
|
82
|
Борторасширитель
|
-
|
Пневматический
|
1
|
1200х
800х 600
|
83
|
Стенд
|
-
|
Для
правки дисков колес, 0,75 кВт
|
1
|
400х
800х 900
|
84
|
Стенд
|
Ш-509
|
Для
демонтажа и монтажа шин, 3,5 кВт
|
1
|
1600х
1600х 1200
|
85
|
Камера
|
6008
|
Для
сушки колес и покрышек
|
2
|
1500х
1500х 1580
|
86
|
Стеллаж
|
-
|
Одноярусный
|
1
|
2150х
750х 150
|
87
|
Верстак
|
Ш-903
|
Слесарный
|
2
|
1400х
800х 600
|
88
|
Ларь
|
-
|
Для
отходов
|
1
|
500х
500х 500
|
89
|
Тиски
|
-
|
Слесарные
|
2
|
60х40
х40
|
90
|
Вешалка
|
Ш-503
|
Для
камер
|
2
|
1500х
250х 1600
|
91
|
Электровулканизационный
аппарат
|
-
|
Для
ремонта камер, 1 кВт
|
1
|
800х
600 600
|
92
|
Ванна
|
Ш-902
|
Для
проверки камер
|
1
|
Ø1200
|
93
|
Клеемешалка
|
6178
|
Ручная
|
1
|
800х
600х 600
|
Пост
ТР
|
|
94
|
Кран-балка
|
ЭД-2
|
Грузоподъемность
2 тонны подвесного типа, 1,6 кВт
|
1
|
9000х
200
|
|
95
|
Инструментальный
шкаф
|
Собственного
изготовления
|
Для
хранения инструмента
|
1
|
600х
500
|
|
96
|
Слесарный
верстак
|
Собственного
изготовления
|
-
|
1
|
1100х
600
|
|
97
|
Грузоподъемная
тележка
|
Собственного
изготовления
|
Грузоподъемность
400кг
|
1
|
700х
500
|
|
98
|
Подставка
|
модель
П248
|
Подставка
под КПП/двигатель
|
2
|
300х
300
|
|
99
|
Гидравлический
автоматический домкрат
|
П310
|
Передвижной,
универсальный, грузоподъемность 3500кг
|
1
|
710х
380
|
|
100
|
Установка
для сбора отработавших масел
|
С-508
|
Передвижная,
емкость 50 кг
|
1
|
Ø
700
|
|
101
|
Бак
маслораздаточный
|
133М
|
Передвижная,
Механический, емкость 45 кг
|
2
|
Ø
650
|
|
102
|
Установка
компрессорная
|
1101-Б5
|
Стационарная
с электроприводом от 220В, 3,2кВт
|
1
|
800х
510
|
|
103
|
Нагнетатель
для пластических смазок
|
М-390
|
Передвижной,
с электроприводом от 220В, 2,3кВт
|
1
|
500х
510
|
|
104
|
Установка
для сверления
|
Р-175
|
Универсальная,
1,3кВт
|
1
|
600х
450
|
|
105
|
Комплект
инструментов
|
2446
|
Для
производства разборочно-сборочных работ
|
1
|
-
|
|
106
|
Комплект
инструментов
|
ПИМ-1516
|
Для
производства крепежных работ
|
1
|
|
107
|
Приспособление
для извлечения срезанных шпилек
|
ПИМ-490М
|
-
|
1
|
-
|
|
108
|
Точило
настольное
|
ЗЕ-631
|
Стационарная,
1,1кВт
|
1
|
600х
450
|
|
109
|
Тележка
инструментальная
|
ОРГ-70-7878
|
передвижная
|
1
|
700х
450
|
|
110
|
Ларь
для чистой ветоши
|
Собственного
изготовления
|
-
|
1
|
500х
500
|
|
111
|
Бак
для мусора
|
Собственного
изготовления
|
-
|
3
|
500х
500
|
|
112
|
Электрогайковерт
для гаек колес
|
И-303М
|
Передвижной,
универсальный, 2,3кВт
|
1
|
510х
480
|
|
113
|
Тележка
для снятия и установки колес грузовых автомобилей
|
П217
|
Передвижная
с механическим приводом
|
1
|
1200х
750
|
|
114
|
Приспособление
|
Р-154
|
Для
высверливания шпилек полуосей грузовых а/в 0,6кВт
|
1
|
-
|
|
115
|
Прибор
|
ЦКБ-К-303
|
Для
проверки установки фар, питание от АКБ U=12В
|
1
|
800х
750
|
|
Арматурное
отделение
|
|
116
|
Сварочный
трансформатор
|
СТШ-300
|
Для
ручной сварки, 20,5 кВт
|
1
|
670х
666
|
|
117
|
Сварочный
верстак
|
-
|
Для
сварочных работ
|
1
|
750х
1500
|
|
118
|
Верстак
|
ОГ-8-132
|
слесарный
|
1
|
1200х
800
|
|
119
|
Тиски
|
-
|
слесарные
|
1
|
-
|
|
120
|
Молот
ковачный
|
МА-4132
|
-
|
1
|
2275х
930
|
|
121
|
Печь
камерная
|
СНО-6.12
|
58
кВт
|
1
|
600х
1200
|
|
122
|
Набор
молотков
|
-
|
-
|
1
|
-
|
|
123
|
Набор
кувалд
|
-
|
-
|
1
|
-
|
|
Обойное
отделение
|
|
124
|
Стол
|
Собственного
изготовления
|
-
|
1
|
1200х
800
|
|
125
|
Швейная
машина
|
Класс
23А
|
Для
тяжёлых и средних работ по коже 0,27 кВт
|
1
|
520х
250
|
|
126
|
Швейная
машина
|
Класс
97
|
Для
шитья хлопчатобумажных, шелковых, шерстяных и льняных тканей 0,4 кВт
|
1
|
1100х
650
|
|
127
|
Стеллаж
|
-
|
Для
тканей и чехлов
|
2
|
1000х
500
|
|
Агрегатное
отделение
|
|
128
|
Стеллаж
|
Собственного
изготовления
|
Для
деталей
|
2
|
550х
100
|
|
129
|
Настенный
шкаф
|
-
|
Для
приборов и инструментов
|
2
|
100х
50
|
|
130
|
Ларь
|
Собственного
изготовления
|
Для
обтирочных материалов
|
3
|
150х
200
|
|
131
|
Кран-балка
|
Тельфер
Кран
|
Для
перемещения тяжеловесных грузов и материалов, 8,74 кВт, грзпд. 2 тонны.
|
1
|
5000х
150
|
|
132
|
Ларь
|
Собственного
изготовления
|
Для
отходов
|
2
|
150х
150
|
|
133
|
Станок
|
Р-185
|
Для
расточки тормозных барабанов 1,1 кВт
|
1
|
250х
250
|
|
134
|
Верстак
|
КС-006
|
Слесарный
|
2
|
250х
550
|
|
135
|
Тиски
|
-
|
Слесарные
|
2
|
50х
50
|
|
136
|
Раковина
|
-
|
Для
мытья рук
|
1
|
200х
100
|
|
137
|
Станок
|
Z-5112В1
|
Сверлильный,
1 кВт
|
1
|
150х 150
|
|
138
|
Стенд
|
Р-746
|
Для
разборки и регулировки сцеплений
|
1
|
250х
350
|
|
139
|
Пресс
|
AHP
|
Гидравлический8
кВт
|
1
|
700х
650
|
|
140
|
Пресс
|
Н-3620
|
Верстачный
|
1
|
200х
300
|
|
141
|
Стенд
|
Р-223
|
Для
ремонта карданных валов и рулевых механизмов
|
1
|
700х
950
|
|
142
|
Стенд
|
ТТН-410
|
Для
наклепки \ расклепки тормозных накладок
|
1
|
300х
250
|
|
143
|
Стенд
|
РР-3
|
Для
ремонта редукторов задних мостов
|
1
|
400х
500
|
|
144
|
Стенд
|
ЛПН-078
|
Для
ремонта КПП, главных передачи и раздатки, 117 кг
|
1
|
750х
150
|
|
145
|
Стенд
|
СУ-179
|
Для
ремонта передних и задних мостов
|
1
|
750х
200
|
|
146
|
Ванна
|
ИПКС-114ЦМ(Н)
|
Передвижная,
моечная
|
1
|
350х
400
|
|
147
|
Телефон
и радио
|
-
|
1
кВт
|
1
|
50х
50
|
|
|
|
|
|
|
|
|
|
|
|
|
|
|
|
2.17 Расчет
производственных площадей
По зоне ТР:
FЗДАНИЯ = FПОСТА
+ ∑FУЧАСТКОВ, м2 (52)
∑FУЧАСТКОВ=FАГР
+ FЭЛ + FРЕМ.СИСТ
+ FШИН.РЕМ + FШИН.МЖН
+ FМЕД + FЖЕСТ
+ FСВАР +
FК.РЕСС + FСЛ.МЕХ
+ FАРМ + FОБ
+ FАКБ + FМАЛ,
м2 (53)
Расчет площади поста:
FПОСТА= LПОСТА
* ВПОСТА, м2 (54)
принимаем: ВПОСТА=6м
LПОСТА=LАВТО
* П+а * (П+1), м (55)
где: LАВТО
- длина автомобиля в проекции;
LАВТО = 18 м;
П - количество постов;
а=1,5 - 2м;
принимаем: а = 2м;
LПОСТА =
18*1+2(1+1)=22 м
FПОСТА=22*6=132 м2
Расчет площади участков:
FУЧАСТКА=fУЧАСТКА
* РУЧАСТКА, м2 (56)
где: fУЧАСТКА
- норма площади на одного человека, на данном участке;
РУЧАСТКА - количество принятых рабочих на данном
участке;
. Агрегатный участок.
FАГР=7 * 13= 91 м2
. Электротехнический участок.
FЭЛ=3 * 10= 30 м2
. Участок ремонта системы питания.
FСИСТ.ПИТ=1 * 12= 12
м2
. Шиноремонтный участок.
FШИН.РЕМ=1 * 10= 10
м2
. Шиномонтажный участок.
FШИН.МНЖ=1 * 10= 10
м2
. Медницкий участок.
FМЕД=1 * 24= 24 м2
. Жестяницкий участок.
FЖЕСТ=1 * 24= 24 м2
. Сварочный участок.
FСВАР=1 * 24= 24 м2
. Кузнечно-рессорный участок.
FК.РЕСС=1 * 24= 24
м2
. Слесарно-механический участок.
FСЛ.МЕХ=3 * 10= 30
м2
. Арматурный участок.
FАРМ=2 * 12= 24 м2
. Обойный участок.
FОБ=1 * 10= 10 м2
. Аккумуляторный участок.
FАКБ=1 * 10= 10 м2
. Малярный участок.
(рассчитывается по длине автобуса)
FМАЛ= LПОСТА
* ВПОСТА, м2 (57)
FМАЛ=22 * 6= 132 м2
∑FУЧАСТКОВ
= 91+30+12+10+10+24+24+24+24+30+24+10+10+132 = 455 м2
FЗДАНИЯ = 132 + 455
= 587 м2
Планирование рабочего места слесаря, по ремонту
агрегатов.
рис. 8 Планирование агрегатного участка
. Стеллаж, 2. Настенный шкаф, 3. Ларь для
обтирочных материалов, 4. Кран-балка, 5. Ларь для отходов, 6. Станок для
расточки тормозных барабанов и тормозных накладок, 7. Верстак слесарный, 8.
Тиски слесарные, 9. Раковина для мытья рук, 10. Станок сверлильный, 11. Стенд
для разборки и регулировки сцепления, 12. Пресс гидравлический, 13. Пресс
верстачный, 14. Стенд для ремонта карданных валов и рулевых механизмов, 15.
Стенд для наклепки/расклепки тормозных накладок, 16. Стенд для ремонта
редукторов задних мостов, 17. Стенд для ремонта КПП, раздатки и ГП, 18. Стенд
для ремонта передних и задних мостов, 19. Ванна передвижная, моечная, 20.
Телефон и радио.
3. КОНСТРУКТОРСКИЙ РАЗДЕЛ
3.1 Общие сведения
Анализ существующих приспособлений
Ранее, для расточки отверстий использовали
подручные средства:
Различные метчики;
Зубило;
Напильники;
Кувалду.
Что приводило к сильным повреждениям и сколам
отверстий в КПП.
Предлагаемое же приспособление экономит время, и
позволяет растачивать отверстия без деформации полуоси, различных сколов,
уменьшился травматизм на рабочем месте.
Предлагаем уже существующую бор-штангу для
расточки отверстий под опорные подшипники КПП. Применение этого приспособления
должно облегчить процесс и повысить качество разборочных работ, что приведет к
повышению производительности труда.
Технические требования к изделию:
иметь простую конструкцию;
быть недорогим и быстро окупаться;
легко подвергаться ремонту в случае
неисправности.
Разработка эскиза приспособления.
рис. 9 Эскиз бор-штанги
1. Бор-штанга нижняя, для расточки отверстия под
вторичный вал; 2. Бор-штанга верхняя, для расточки отверстия под первичный вал;
3. Кронштейн для крепления бор-штанги в отверстии, левый; 4. Кронштейн для
крепления бор-штанги в отверстии, правый; 5. Болт, фиксирующий кронштейн на
поверхности; 6. Регулятор кронштейна; 7. Болт-фиксатор бор-штанги в отверстии;
8. Один из резаков на верхней бор-штанге; 9.Рычаг вращения бор-штанги.
Инструкция по эксплуатации приспособления.
Бор-штанга состоит из:
Верхней и нижней бор-штанг;
Переднего кронштейна;
Наружной и внутренней верхних втулок.
Для расточки отверстий под опорные подшипники на
автобусе МАЗ-105 пользуясь данным приспособлением необходимо:
- вставить бор-штангу в отверстия;
- закрепить их на корпусе КПП;
- вращать с вышеуказанным усилием, до плавной
расточки отверстия.
3.2 Основной расчет
Данные для расчета.
Наиболее нагруженным элементом является вал -
бор-штанга, т.к. работает на кручение.
Цель расчета:
- Определить соответствует ли марка стали, заявленным
требованиям;
- Проверить соответствует ли выбранные
геометрические параметры требованиям.
Выбранная марка стали: сталь 45
[τКР]=1500 * 103 Н/м2
- принял из таблицы «механические свойства и допускаемые напряжения сталей» при
термообработке в нормальных условиях.
Р = 15 кВт - среднее значение мускульной силы
человеческой руки.
Проводим расчет на кручение.
Расчет.
. Проверочный расчет:
Проверяется основная нагрузочная способность:
τКР≤ [τКР]
(58)
τКР = 9,55Р * 106 /
0,2 d3n
(59)
где:
[τКР] = 1500*103 Н/м2
- табличное значение;
n = 10 об/мин -
среднее количество оборотов в минуту.
Р = 15 кН - среднее значение мускульной силы
человеческой руки.
τКР = 9,55 * 15 *
106 / 0,2 * 853 * 10 = 116,63*103 Н/м2
Вывод: т.к. 1500*103 Н/м2 ≥ 116,63*103,
условие τКР≤
[τКР]
выполняется.
. Проектный расчет:
Проверяется диаметр штанги:
[d]
≥ d (60)
d = 3√9,55Р *
106 / 0,2n * [τКР]
(61)
=
3√9,55 * 20 * 106 / 0,2 * 10 * 1500 * 103 = 4 мм.
Вывод:
т.к. 85 ≥ 4, условие [d] ≥ d
выполняется.
.
Проверочно - уточненный:
Проверяется
силовая нагрузка штанги:
[Р]
≤ Р (62)
Р
= 0,2 d3n * [τКР] / 9,55 *
106, кВт (63)
Р
= 0,2 * (85*10-3)3 * 10 * 1500 * 103 / 9,55 * 106 = 0,02 кВт = 20 Вт.
Вывод:
т.к. 20 ≥ 15, условие [Р] ≤ Р выполняется.
Вывод:
Из расчетов следует, что выбранный диаметр, мощность и расчет на кручение
соответствуют заданным нагрузкам и не вызовут неисправности или поломки в
процессе эксплуатации.
3.3 Техника безопасности при работе с бор-штангой
Выполнять
работы со штангой в следующем порядке :
.Необходимо
плотно зафиксировать устройство на корпусе КПП. В случае неправильной установки
на деталь необходимо снять приспособление и установить заново.
.Использовать
штангу только для расточки отверстий в корпусе КПП.
.При
работе со штангой необходимо использовать средство индивидуальной защиты
(перчатки и очки).
4. ЭКОНОМИЧЕСКИЙ РАЗДЕЛ
4.1 Исходные данные для
выполнения курсового проекта
Таблица № 14 Исходные данные для выполнения
курсового проекта
Показатели
|
Величина
показателя
|
1.
Марка автомобиля /автопоезда/автобуса.
|
МАЗ-105
|
2.Среднесписочное
количество автомобилей /автопоездов/ в парке, ед.
|
132
|
3.
Коэффициент выпуска автомобилей /автопоездов/ на линию, Кв.
|
0,78
|
4.
Среднесуточный пробег, км.
|
500
|
5.
Техническое состояние автомобилей, пробег с начала эксплуатации в долях от
нормативного пробега до капитального ремонта: - до
капитального ремонта автомобиля - 66 %
|
200
|
6.
Годовой пробег всех автомобилей, тыс.км.
|
18790200
|
7.
Автомобиле - дни в работе, а-дн.
|
56940
|
8.
Количество технических обслуживаний в сутки:
|
123
|
Е
О, ед.
|
103
|
ТО-1,
ед.
|
15
|
ТО-2,
ед.
|
5
|
9.
Режим работы АТП, дн.
|
7
|
10.
Режим работы укрупненной производственной бригады, смен
|
2
|
12.
Снижение затрат на техническое обслуживание и текущий ремонт автомобилей /в
результате внедрения орг.тех.мероприятия/ на 1000 км пробега, тенге.
|
107
|
13.
Срок окупаемости капитальных вложений в мероприятие, год.
|
1,83
|
.2 Смета
затрат и калькуляция себестоимости
Себестоимость продукции представляет собой
денежное выражение всех затрат на выполнение запланированного объема работ.
Определение затрат приходящихся на единицу
продукции называется калькуляцией себестоимости. При калькулировании
себестоимости все затраты в зависимости от их характера и целевого назначения
распределяются по статьям. Смета затрат при выполнении технического
обслуживания включает в себя основную и дополнительную заработную плату
производственных рабочих с отчислениями во внебюджетные фонды, затраты на
запасные части, материалы и цеховые расходы.
Определение по статьям калькуляции.
При определении себестоимости отдельных видов
продукции (работ, услуг) чаще используется: группировка затрат на единицу
продукции по статьям калькуляции. В качестве типовой группировки применяется
следующая номенклатура статей калькуляции прямые и косвенные (накладные)
расходы:
Прямые расходы:
- Сырье и материалы;
Полуфабрикаты комплектующие изделия;
Вычитаются возвратные отходы;
Топливо и: электроэнергия на технологические
цели;
Основная з/п производственных рабочих;
Дополнительная з/п производственных рабочих;
Отчисления во внебюджетные фонды;
Расходы на подготовку и основание производства.
Накладные или косвенные расходы:
- Общие производственные расходы;
- Расходы на содержание и эксплуатацию
оборудование;
Цеховые расходы.
- Общехозяйственные расходы;
- Общезаводские непроизводственные расходы.
Общепроизводственные расходы.
Расходы на содержание и эксплуатацию
оборудования:
Амортизация оборудования;
ремонт оборудования;
электроэнергия, топливо;
расходы на содержание рабочих мест;
расходы внутри заводского перемещения груза;
износ инструментов общего назначения.
Цеховые расходы:
з/п цехового персонала;
амортизация ремонт и содержание здание, цеха;
расходы на охрану труда и технику безопасности;
потери от простоев по вине цехов:
потери от порчи материальных ценностей при
хранении в цехах.
Общехозяйственные расходы
затраты аппарата управления с отчислениями во
внебюджетные фонды;
почтовые, телеграфные, канцелярские расходы;
командировочные расходы;
амортизация и содержания легковых автомобилей;
расходы на содержания вычислительных центров.
Общезаводские и производственные расходы
Расходы на рекламу;
представительские расходы - транспортное
обслуживание гостей,
буферное обслуживание гостей,
культурно-зрелищная программа,
затраты на перевозчика;
расходы на транспортировку готовой продукции;
потери от простоев не по вине цеха.
Распределение рабочих по разрядам
Ниже приведены процентные отношения разрядов в
бригаде, количество рабочих данного разряда в бригаде и почасовая ставка для
данного разряда.
Распределение рабочих по разрядам
Таблица № 15 Распределение рабочих по разрядам
Разряд
|
Зона
ЕО
|
Зона
ТО-1
|
Зона
ТО-2
|
Зона
ТР
|
Производственные
участки
|
Всего
рабочих
|
|
1см
|
2см
|
3см
|
1см
|
2см
|
3см
|
1см
|
2см
|
3см
|
1см
|
2см
|
3см
|
1см
|
2см
|
3см
|
|
1
разряд
|
|
2
|
2
|
|
|
|
|
|
|
1
|
1
|
|
1
|
1
|
|
8
|
2
разряд
|
|
1
|
1
|
1
|
1
|
|
3
|
3
|
|
8
|
8
|
|
12
|
12
|
|
50
|
3
разряд
|
|
|
|
1
|
1
|
|
1
|
1
|
|
1
|
1
|
|
9
|
9
|
|
24
|
4
разряд
|
|
|
|
1
|
1
|
|
1
|
1
|
|
1
|
1
|
|
4
|
4
|
|
14
|
5
разряд
|
|
|
|
1
|
1
|
|
1
|
1
|
|
1
|
1
|
|
1
|
1
|
|
8
|
6
разряд
|
|
|
|
1
|
1
|
|
1
|
1
|
|
1
|
1
|
|
|
|
|
6
|
ИТОГО
|
|
3
|
3
|
5
|
5
|
|
7
|
7
|
|
13
|
13
|
|
27
|
27
|
|
110
|
На основании полученных данных заполняем таблицу:
Таблица № 16 Тарифная ставка рабочих
Разряд.
|
Количество
человек
|
Тарифная
ставка.
|
Размер
оплаты.
|
1
|
8
|
72,15
|
577,2
|
2
|
50
|
87,95
|
4397,5
|
3
|
24
|
96,2
|
2308,8
|
4
|
14
|
108,6
|
1520,4
|
5
|
8
|
125,1
|
1000,8
|
6
|
6
|
145,95
|
875,7
|
Итого.
|
110
|
-
|
10680
|
Среднечасовая тарифная ставка:
С ср.час.= 97,09 тенге
Расчет трудовых затрат
Определяем заработную плату за
фактически отработанное время (нормированную зарплату).
Зн=Сср.час*Фр*Чфр (64)
Зн= 97,09 * 1820 * 110 = 19437418 тенге
Сср.час - среднечасовая тарифная ставка, тенге.
Фр - фонд рабочего времени в году.
Чр - фактически численность рабочих.
Определяем основную заработную плату
производственных рабочих.
Зосн = Зн+П+ Дбр+Дн (65)
где:
П - размер премии
Дбр - доплата бригадиру;
Дн - доплата за работу в ночное время
Зосн= 19437418 + 5831225,4+ 239066,1 +
2129280,79 = 27636990,29 тенге
Для рабочих - сдельщиков при составе бригады
5-10 человек размер доплаты за бригадирство 10% от нормируемой заработной платы
(3), свыше 10 человек - 15% от нормируемой заработной платы при условии
выполнения норм выработки.
Для рабочих-повременщиков, при составе бригады
свыше 5 человек доплата за бригадирство составляет 10% от нормированной
зарплаты при условии выполнения бригадой нормативных заданий.
Доплата за работу в ночное время принимается 35%
от среднечасовой тарифной ставки, доплата в вечернюю смену - 20% от
среднечасовой тарифной ставки.
Определяем премию в размере 20-40% от
нормированной заработной платы:
П = Зн*(от 0,2 до 0,4) (тен.) (66)
(принимаю 0,3 тенге)
П = 19437418 * 0,3 = 5831225,4
Доплата бригадиру - 15 % от его з/пл.
Дбр = Фр*Часовую тарифную ставку бригадира*
кол-во бригад*0,15 (тенге) (67)
Дбр= 1820 * 145,95 * 6 * 0,15 = 239066,1 тенге
Доплата за работу в ночное время.
Дн = Сср.час.*(0,35*Чр в ночное время+0,2*Чр
вечером)*Фр (тенге) (68)
Дн= 97,09 * (0,35 * 3 +0,2 * 55) * 1820 =
2129280,79 тенге
Определяем плановой фонд заработной
платы рабочих:
Зобщ=Зосн+Здоп+ НЗ (69)
где:
Зосн - основная заработная плата, тенге.
Здоп - дополнительная заработная плата, тенге.
О - начисление на заработную плату, тенге.
Зобщ= 27636990,29 + 2763699,03 + 3009668,24 =
33410357,56 тенге
Дополнительная зарплата
рассчитывается в размере 10% от основной зарплаты:
Здоп=Зосн*0,1 (тенге) (70)
Здоп= 27636990,29 * 0,1 = 2763699,03 тенге
Начисление на заработную плату:
НЗ =( (Зосн+Здоп) - 10%) * 11% (71)
НЗ = ( (27636990,29 + 2763699,03) - 10%) * 11% =
3009668,24 тенге
Итого трудовые затраты (ТЗ):
(общий фонд заработной платы производственных
рабочих)
ТЗ = Зосн+Здоп+ НЗ (72)
ТЗ = 27636990,29 + 2763699,03 + 3009668,24 =
33410357,56 тенге
Определяем среднемесячную заработную плату
одного производственного рабочего:
Зсред мес.=(Зосн+Здоп) / (Чф*12мес )(тенге) (73)
Зсред= (27636990,29 + 2763699,03) / (110 * 12) =
23 030,83 тенге
Определяем фонд заработной платы
вспомогательных рабочих, руководителей, служащих и других служащих
Основная заработная плата
вспомогательных рабочих
Звсп=Сср.мес всп.*Чвсп* Кпр*12мес (тенге) (73)
Звсп= 12121,2 * 28 * 1,3 * 12 = 5294540,16 тенге
Число вспомогательных рабочих:
Чвсп= 0,25 * Чр =110 * 0,25 = 28 человек
Кпр - коэффициент премии (от 1,2 до 1,4),
принимаю 1,3.
Ccр.мес.всп -
среднемесячная заработная плата вспомогательных рабочих
Сср.мес.всп=168час.*Сср.час.всп (тенге) (74)
Сср.мес.всп= 168 * 72,15 = 12121,2 тенге
Сср.час.всп - среднечасовая тарифная ставка
вспомогательных рабочих.
час. - среднее количество часов, которое
необходимо отработать за месяц.
Определяем зарплату руководителей:
Зр = Ор*Чр * Кпр* 12мес (тенге) (75)
Зр= 90000 * 7 * 1,3 * 12 = 9828000 тенге
Ор - оклад руководителей - от 80000 до 140000
тенге, принимаю 90000 тенге.
Чр=Пр*(Чфр+Чвс)= 0,05 * (110+28) = 7 человека
(76)
Пр - процент руководителей в АТП (от 3 до 7%),
принимаю 5%.
Определяем зарплату служащих
Зсл = Осл*Чс* Кпр*12мес (тенге) (77)
Зсл = 40000 * 14 * 1,3 * 12 = 8736000 тенге
Число служащих: Чс = Пс*(Чфр+Чвс) = 0,1 * (110 +
28) = 14 человек (78)
Устанавливаем оклад служащих Осл =20000-60000
тенге, принимаю 40000 тенге.
Пс -процент служащих в АТП (от 7 до 12%), принимаю
10 %.
Определяем зарплату других служащих
Здр.сл. = Одр.сл.*Чдрс.*Кпр.*12мес. (тенге) (79)
Здр.сл. = 40000 * 220 * 1,3 * 12 = 137280000
тенге
Чдрс. = Пдрс.*(Чфр+Чвс) + Чводителей = 0,1 *
(110+28) + 206 = 220 человек (80)
Пдрс- процент других служащих в АТП (от 5 до
10%), принимаю 10%.
Оклад других служащих Одр.сл =30000-70000 тенге,
принимаю 40000 тенге.
Определяем дополнительную заработную плату,
которая принимается:
- для вспомогательных рабочих - 9%,
- для руководителей - 15%,
- для служащих - 11%,
- для других служащих - 9%.
ЗДвсп. = Звсп.*0,09(тенге) ЗДвсп = 5294540,16 *
0,09 = 476508, 61 тенге(81)
ЗДрук. = Зрук.*0,15(тенге) ЗДрук.= 9828000 *
0,15 = 1474200 тенге (82)
ЗДслуж.=Зслуж.*0,11(тенге) ЗДслуж.= 8736000 *
0,11 = 960960 тенге (83)
ЗДдр.сл.=Здр.сл.*0,09(тенге) ЗДдр.сл.= 137280000
* 0,09 = 12355200 тенге (84)
Определяем начисление на заработную плату:
НЗвсп.вн.ф. = 11%*((Звсп.осн.+Звсп.доп.)-10%)
(тенге) (85)
НЗвсп.вн.ф.= 11% * ((5294540,16 + 476508, 61) -
10%) = 571333,83 тенге
НЗрук.вн.ф. = 11%*((Зрук.осн.+Зрук.доп.)-10%)
(тенге) (86)
НЗрук.вн.ф.= 11% * ((9828000 + 1474200) - 10%) =
1118917,8 тенге
НЗслуж.вн.ф. = 11%*((Зслуж.осн.+Зслуж.доп.)-10%)
(тенге) (87)
НЗслуж.вн.ф.= 11% * ((8736000 + 960960)-10%) =
959999,04 тенге
НЗдр.сл.вн.ф.= 11% *((Здр.сл. осн.+Здр.сл.доп.)
-10%) (тенге) (88)
НЗдр.сл.вн.ф.= 11% ((137280000 + 12355200)-10%)
= 14813884,8 тенге
Определим годовой фонд заработной платы всех
категорий работников:
Звсп.г.=Звсп.+Зд.всп.+НЗвсп.вн.ф.(тенге) (89)
Звсп.г.= 5294540,16 + 476508, 61+ 571333,83 =
6342382,6 тенге
Зрук.г. = Зрук.+Зд.рук.+НЗрук.вн.ф.(тенге) (90)
Зрук.г.= 9828000 + 1474200 + 1118917,8 =
12421117,8 тенге
Зслуж.г.=Зслуж.+Зд.служ.+НЗслуж.вн.ф.(тенге)
(91)
Зслуж.г.= 8736000 + 960960 + 959999,04 =
10656959,04 тенге
Здр.сл.г. =
Здр.сл.+Зд.др.сл.+НЗдр.сл.вн.ф.(тенге) (92)
Здр.сл.г. = 137280000 + 12355200 + 14813884,8 =
164449084,8 тенге
Итого годовой фонд зарплаты:
Зг=ТЗ+ Звсп.г+ Зрук.г+ Зслуж.г+ Здр.сл.г= (93)
,56 +6342382,6+ 12421117,8+10656959,04
+164449084,8= 227279901,8
Затраты на материалы и запасные
части
Затраты на материалы и запасные
части для проведения техническихобслуживаний и текущего ремонта определяют,
исходя из запланированного числа часов работы машины в год и стоимости
материалов и запасных частей отнесённой к одному часу работы (автомобиля)
машины.
Если неизвестна норма затрат материалов, то
можно воспользоваться следующими нормами:
Для текущего ремонта (технического
обслуживания) стоимость материалов составляет 100 - 120% от трудовых затрат
производственных рабочих:
р.м.то.
= Т.З.*1,2
(тенге)
(94)
Ср.м.то.= 33410357,56 * 1,2 = 40092429,07 тенге
Запчасти:
Сзч = 33410357,56 * 0,10 = 3341035,76 тенге
Определяем затраты на ремонтные
материалы:
Ср.м. = Срм.то.+Сзч (тенге) (96)
Ср.м. = 40092429,07 + 3341035,76 = 43433464,83
тенге
Определяем
транспортно-заготовительные расходы:
Т.З.Р. = Ср.м.*К1+Сзч*К2 (тенге) (97)
Т.З.Р.= 43433464,83*0,11 + 3341035,76 *0,04 =
4911322,56 тенге
К1 = 0,11 - коэффициент
транспортно-заготовительных расходов по материалам;
К2 = 0,04 - коэффициент
транспортно-заготовительных расходов по запчастям;
Определяем издержки на
вспомогательные материалы
Топливо и электроэнергия для технологических
целей
Расход электроэнергии, кВт-час.
Qэт = (
Ру*Фоб*К3*Кс) / (Кпс*Кп);(кВт-час) (98)
эт = (692,15 * 5840 * 0,8 * 0,20) / (0,95 * 0,9)
= 756426,85 квт-час.
Ру - суммарная установленная мощность
электроприёмников, кВт. (принимается
из технологического раздела курсовых проектов по
ТО и ТР);
Ру = 692,15 кВт/час.
Фоб - действительный фонд годового рабочего
времени оборудования, 2920 час.;
Фоб = t*n*Дрг
= 8*2*365 = 5840 часов (99)
К3 - коэффициент загрузки оборудования
(0,6-0,9), принимаю 0,8;
n - количество смен
t - продолжительность
смены, часы
Дрг - количество рабочих дней в году, дни
Кс - коэффициент спроса (0,15-0,25), принимаю
0,20;
Кпс - коэффициент, учитывающий потери в сети
(0,92-0,95), принимаю 0,95;
Кп - коэффициент, учитывающий потери в двигателе
(0,85-0,9), принимаю 0,9;
Затраты на электроэнергию, тенге.
Сэт = Qэт*Ц
квт.час. (100)
Сэт = 756426,85 * 11 = 8320695,35 тенге
Цквт. час. - тарифная плата за 1 квт. Час - 11
тенге.
Затраты на охрану труда составляют
2-3% от трудовых затрат.
Сохр = ТЗ*0,02 (101)
Сохр = 33410357,56 * 0,02 = 668207,15 тенге
Затраты на текущий ремонт
производственных помещений принимаются
-1,6% от стоимости здания, принимаю
1%.
Стоимость
здания определяется по формуле:
|
|
|
Сзд
= Ц*V(тенге) (102) Сзд = 10080 * 20000 = 201600000 тенге где:
|
Ц
- цена 1м3 объёма здания,принимаем___20000____тенге
|
|
|
V
- объём здания, м3
|
|
|
Затраты
на текущий ремонт здания
|
|
|
Срем
зд = Сзд * % затрат на ремонт = (201600000 * 1) / 100 = 2016000 тенге (103)
|
Объемные
показатели здания:
|
|
|
Объем
здания
|
|
10080
м3
|
Площадь
здания
|
|
1344
м2
|
Объем
зоны ЕО
|
|
1890
м3
|
Площадь
зоны ЕО
|
|
252
м2
|
длина
зоны ЕО
|
|
42
м
|
ширина
зоны ЕО
|
|
6
м
|
высота
зоны ЕО
|
|
7,5
м
|
Объем
зоны ТО-1
|
|
1890
м3
|
Площадь
зоны ТО-1
|
|
252
м2
|
длина
зоны ТО-1
|
|
42
м
|
ширина
зоны ТО-1
|
|
6
м
|
высота
зоны ТО-1
|
|
7,5
м
|
Объем
зоны ТО-2
|
|
1890
м3
|
Площадь
зоны ТО-2
|
|
252
м2
|
длина
зоны ТО-2
|
|
42
м
|
ширина
зоны ТО-2
|
|
6
м
|
высота
зоны ТО-2
|
|
7,5
м
|
Объем
зоны постов ТР
|
|
990
м3
|
Площадь
зоны постов ТР
|
|
132
м2
|
длина
зоны постов ТР
|
|
22
м
|
ширина
зоны постов ТР
|
|
6
м
|
высота
зоны постов ТР
|
|
7,5
м
|
Объем
зоны производственных помещений ТР
|
|
3420
м3
|
Площадь
зоны производственных помещений ТР
|
|
455
м2
|
длина
зоны производственных помещений ТР
|
|
76
м
|
ширина
зоны производственных помещений ТР
|
|
6
м
|
высота
зоны производственных помещений ТР
|
|
7,5
м
|
Затраты на содержание и текущий
ремонт оборудования составляет 3-7% от стоимости оборудования, принимаю 5%.
Стоимость оборудования приблизительно
принимается из расчёта 2000-4000 тенге на 1 кв.м площади цеха.
Стоимость оборудования:
об = Fзд
* Соб1 (тенге)= 1344 * 2000 = 2688000 тенге (104)
Соб1 - Стоимость оборудования из расчёта на 1
кв.м площади цеха 2000-4000 тенге, принимаю 2000 тенге.
Затраты на содержание оборудования:
обор= Соб*%= (2688000 * 5) / 100 = 134400 тенге
(105)
Амортизационные отчисления принимаются в
процентах от балансовой стоимости соответствующих основных фондов.
Для здания -10%
Азд = 0,1 Азд = 0,1*Сзд
Азд= 201600000 * 0,1 = 20160000 тенге (106)
Для оборудования - 9%.
Аобор = 0,09. Аобор = 0,09*Собор
Аобор = 2688000 * 0,09 = 241920 тенге (107)
Затраты на осветительную энергию:
Sэл.осв.=
Ц*Wэл.осв.(тенге)
(108)
эл.осв. = 11*67200 = 739200 тенге
эл.осв.
= 25*F*Тосв.
/ 1000(тенге)
(109)
эл.осв. = (25*1344*2000) / 1000 = 67200 тенге
Wэл.осв. - расход
электроэнергии на кВ.м площади, кВт/час
Тос. - число часов использования осветительной
нагрузки в год.ч.
При двухсменном режиме работы Тос. = 2000 часов,
при односменной 800 часов.
- расход осветительной электроэнергии на кВ.м,
Вт.
Затраты на воду на бытовые и прочие
нужды.
воды = Цвод*Qвод (тенге) (110)
воды = 3810,21 * 126,5 = 481991,31 тенге
Цвод - стоимость 1 м3 воды, 126,5 тенгевод. -
расход воды, м3
Расход воды:
вод = Qбн+Qтц = 2810,21 + 1000 = 3810,21 (111)
Расход воды на бытовые нужды:
бн = ((Рв*Чр+Р пл*Fзд)*Р пн*Др.) / 1000 л (112)
бн = ((40*110+1,5*1344)* 1,2*365) / 1000 =
2810,21 тг.
Рв - норма расхода воды на 1 производственного
рабочего на бытовые нужды
в сутки:
Р пл - л/кв.м - норма расхода на 1 кв.м площади;
Р пн- коэффициент, учитывающий расход воды на
прочие нужды;
Др. - дни работы производственных
подразделенийтц - расход воды на технологические цели в год : 1000л
Qвод = 3810,21 тенге
л - норма расхода воды на 1 производственного
рабочего на бытовые нужды
в сутки:
,5 л - л/кв.м - норма расхода на 1 кв.м площади;
,2 - коэффициент, учитывающий расход воды на
прочие нужды;
Др. - дни работы производственных подразделений
в год = 365
Затраты на отопление.
отоп = Цп*Qп
(тенге) (113)
отоп = 1122 * 2822,40 = 3166732,8 тенге
Qп - расход пара, Т
Цп - стоимость 1 т. пара, условно = 1122 тенге
п = (qн*Vзд*Фг.ф.)
/ (540*1000)(т) (114)
п = (30*10080*5040) / (540*1000) = 2822,40 тенге
qн - удельный расход
пара, 25-35 ккал/час, принимаю 30 ккал/час.
- тепло, отдаваемое за 1 кг пара при его
конденсации, ккал.
Фг.ф. - отоп. период. счет*мес*дни*часы;
7*30*24= 5040
Затраты на канализацию
Ск = (Qт.ц.
+ Qб.н.) * Цк (тенге)
(115)
Ск = (1000 + 2810,21) * 122 = 464845,38 тенге
Qт.ц. - расход воды
на технологические цели (м3);
Qб.н. - расход воды
на бытовые нужды (м3);
Цк - тарифная плата за спуск 1 м3 воды: в
канализацию 122 (тенге).
Затраты на ремонт и износ
малоценного и быстроизнашивающегося имущества.
Сиз = Соб * К (тенге) (116)
Сиз = 2688000 * 0,08 = 215040 тенге
Соб - стоимость оборудования, (тенге)
К - коэффициент, учитывающий соотношение между
затратами по данной статье и стоимостью оборудования участка (К=0,08) (для
вновь проектируемого производственного объединения).
Или
из.ин.
= n*Чфр
(тенге)
(117)
из.ин. = 1000 * 110 = 110000 тенге
n -нормативные
затраты на одного рабочего - 1000
Затраты на спецодежду
сп.од.
= n*Чфр
(тенге)
(118)
сп.од. = 2000 * 110 = 220000 тенге
n - нормативные
затраты на одного рабочего - 2000
Затраты на сжатый воздух
С сж.в. = Q
сж.в. * Ц сж.в. = 6806,52 * 575/1000 = 3913,75 тенге (119)
сж.в. - расход сжатого воздуха;
Цсж.в. - стоимость 1м3 сжатого воздуха 575 тенге
за 1000 м3
сж.в.= 1,5 * (q*n*Ки*8)+(0,3*0,14*8)) *
Др (120)
сж.в = 1,5 * ((0,4*9*0,42*8)+(0,3*0,14*8)) * 365
= 6806,52 тенге
Ки - коэффициент использования
воздухоприемником; Ки = 0,42
Др - дни (365,256).
Пневмо инструменты:расход q=0,4
количество пневмоинструмента n=9
Таблица № 17 Смета общепроизводственных расходов
№
п/п
|
Наименование
|
Сумма
затрат в тенге.
|
Процентное
соотношение
|
1.
|
Амортизация
зданий
|
20160000
|
70,71
|
2.
|
Текущий
ремонт зданий
|
2016000
|
7,07
|
3.
|
Амортизация
оборудования
|
241920
|
0,85
|
4.
|
Текущий
ремонт оборудования
|
134400
|
0,47
|
5.
|
Затраты
на освещение
|
739200
|
2,59
|
6.
|
Затраты
на водоснабжение для бытовых нужд
|
481991,31
|
1,69
|
7.
|
Затраты
на канализацию
|
464845,38
|
1,63
|
8.
|
Затраты
на отопление
|
3166732,8
|
11,11
|
9.
|
Затраты
на охрану труда и технику безопасности
|
668207,15
|
2,34
|
10.
|
Затраты
на ремонт и износ малоценного и быстроизнашивающегося имущества
|
215040,00
|
0,75
|
11.
|
Затраты
на спецодежду
|
220000,00
|
0,77
|
12
|
Затраты
на сжатый воздух
|
3913,75
|
0,01
|
|
ИТОГО:
|
28512250,39
|
100
%
|
Определяем общехозяйственные расходы
К общехозяйственным расходам относятся расходы
по управлению предприятием в целом. В их состав входят следующие виды затрат:
1. Расходы по содержанию аппарата управления
включающие:
- зарплату аппарата управления с
отчислениями во внебюджетные фонды;
- командировочные расходы;
почтово-телеграфные расходы;
амортизация и расходы на содержание
легковых автомобилей;
расходы на содержание вычислительных
центров и т.п.
2. Общехозяйственные расходы, включающие:
- зарплату персонала, не относящегося к
аппарату управления, с отчислениями во внебюджетные фонды;
- амортизацию, ремонт, содержание зданий
и сооружений общезаводского характера;
расходы на изобретательство и рационализацию;
износ МБП;
расходы на подготовку кадров и т.п.
3. Налоги, сборы, отчисления, включаемые в
себестоимость продукции (работ, услуг).
4. Общезаводские непроизводственные
расходы, включающие:
- недостачи и потери от порчи
материальных ценностей и готовой продукции при хранении их на общезаводских
складах;
- потери от простоев, не по вине цехов и
т.п.
Общепроизводственные расходы и общехозяйственные
расходы списываются на себестоимость продукции (работ, услуг)
Общехозяйственные расходы.
Рассчитываются путем умножения нормированной
заработной платы на коэффициент 1,3.
Ох.р.= Зн*1,3 (тенге) (121)
Ох.р.= 19437418 * 1,3 = 25268643,4 тенге
Составляем калькуляцию себестоимости
технического обслуживания:
Таблица № 18 Калькуляция себестоимости
технического обслуживания:
N п/п
|
Статьи
калькуляции
|
Сумма
в тенге
|
1
|
Основные
материалы.
|
43
433 464,83
|
2
|
Транспортно-заготовительные
расходы
|
4
911 322,56
|
3
|
Вспомогательные
материалы
|
3
341 035,76
|
4
|
Топливо
и энергия для технологических целей
|
8
320 695,35
|
5
|
Основная
заработная плата производственных рабочих (З осн.)
|
27
636 990,29
|
6
|
В
том числе нормированная заработная плата
|
19
437 418,00
|
7
|
Дополнительная
заработная плата производственных рабочих
|
2
763 699,03
|
8
|
Начисления
з.р.
|
3009668,24
|
9
|
Итого
трудовые затраты
|
33
410 357,56
|
10
|
Годовой
фонд зарплаты вспомогательных рабочих
|
6
342 382,60
|
11
|
Годовой
фонд зарплаты цеховых руководителей, служащих и других служащих
|
187527161,64
|
12
|
Итого
прямые затраты (п.1 + п.2 + п.3 + п.4 + п.9+ п.10 + п.11)
|
287
286 420,30
|
13
|
Общепроизводственные
расходы
|
28
512 250,39
|
14
|
Общехозяйственные
расходы
|
25
268 643,40
|
15
|
Итого
производственная себестоимость (п.12 +п.13 + п.14)
|
341
067 314,09
|
16
|
Коммерческие
расходы (п. 15* 0,02) 0,02 - коэффициент коммерческих расходов
|
6
821 346,28
|
17
|
Итого
коммерческая себестоимость (п.16 + п.15)
|
347
888 660,37
|
18
|
Прибыль
(28% от коммерческой себестоимости) (п.17* 0,28)
|
97
408 824,90
|
19
|
Оптовая
цена, стоимость ТО (ТР;КР) (п.18 + п.17)
|
445
297 485,27
|
20
|
Налог
на добавленную стоимость (НДС-12% от оптовой цены)(п.19*0,12)
|
53
435 698,23
|
21
|
Отпускная
цена (п.19 + п.20)
|
498
733 183,50
|
22
|
Торговая
надбавка (25%)(п.21* 0,25)
|
124
683 295,88
|
23
|
Рыночная
цена1(п.21 + п.22)
|
623
416 479,38
|
Стоимость обслуживания автопарка -
297 485,27 тенге
Себестоимость обслуживания 1 автомобиля -
705 336,57 тенге
Себестоимость 1 обслуживания -
989,94 тенге
Минимальный план на 1 автомобиль -
939,32 тенге
На основании полученных данных:
Технико-экономические показатели
дипломного проекта:
Таблица № 19 Технико-экономические показатели
проекта
№
п/п
|
Наименование
показателей
|
Единица
измерения
|
Величина
показателя
|
1.
|
Годовая
производственная программа
|
Чел.ч
|
400400
|
Число
производственных рабочих
|
Чел.
|
110
|
3.
|
Число
вспомогательных рабочих
|
Чел.
|
28
|
4.
|
Число
руководителей и служащих
|
Чел.
|
21
|
5.
|
Общее
число служащих
|
Чел.
|
220
|
6.
|
Общее
количество работающих
|
Чел.
|
379
|
7.
|
Общегодовой
фонд заработной платы работников
|
тенге
|
227
279 901,80
|
8.
|
В
том числе основных производственных рабочих
|
тенге
|
33
410 357,56
|
9.
|
Среднемесячная
заработная плата одного производственного рабочего
|
тенге
|
23
030,83
|
10.
|
Среднемесячная
заработная плата одного работающего
|
тенге/чел.
|
49
973,59
|
11.
|
Себестоимость
обслуживания одного автомобиля в год
|
тенге/авт.
|
2
583 843,29
|
12.
|
Себестоимость
одного обслуживания
|
тенге/обсл.
|
5
989,94
|
13.
|
Себестоимость
текущего ремонта
|
тенге
|
2
150 400,00
|
14.
|
Производительность
труда в расчете на одного рабочего
|
тенге/чел.
|
5
667 422,54
|
15.
|
Фондоотдача
|
тенге/чел.
|
3,05
|
16.
|
Фондоемкость
|
тенге/чел.
|
0,33
|
17.
|
Фондовооруженность
|
тенге/чел.
|
24
436,36
|
18.
|
Прибыль
|
тенге
|
97
408 824,90
|
19.
|
Стоимость
работ
|
тенге
|
445
297 485,27
|
20.
|
Уровень
рентабельности в целом
|
%
|
21,88
|
21.
|
В
том числе по затратам
|
%
|
28,00
|
Находим строки 11, 14-21 исходя из формул:
.=стоимость работ : число работающих
.=стоимость работ : стоимость основных средств
.=1: фондоотдачу
.=стоимость оборудования : численность рабочих
.=строка 19 из предыдущей таблицы
.=строка 20 из предыдущей таблицы
.=прибыль : стоимость работ*100
.=прибыль : полную себестоимость*100
Штатный состав АТП
Таблица № 20 Штатный состав АТП
Руководители
|
7
|
чел
|
Служащие
|
14
|
чел
|
Производственные
рабочие
|
110
|
чел
|
Вспомогательные
рабочие
|
28
|
чел
|
Водители
|
220
|
чел
|
ВСЕГО
|
379
|
чел
|
4.3 Расчет
экономической эффективности от внедрения приспособления
Назначение, описание и область применения
приспособления
Предлагаем уже существующую бор-штангу для
расточки отверстий под опорные подшипники КПП. Применение этого приспособления
должно облегчить процесс и повысить качество разборочных работ, что приведет к
повышению производительности труда.
Технические требования к изделию:
иметь простую конструкцию;
быть недорогим и быстро окупаться;
легко подвергаться ремонту в случае
неисправности.
Бор-штанга состоит из:
Верхней и нижней бор-штанг;
Переднего кронштейна;
Наружной и внутренней верхних втулок.
Себестоимость до внедрения
приспособления.
С1 = Р1*(1+(Нц / 100)), тенге (122)
С1= 388,36 * (1+ (140 / 100)) = 932,06 тенге
Р1 - расценка работы 1
Нц - цеховые расходы, в % условно принимаются
120-140%;
принимаем: 140%.
Р1 = ССР.Ч. * НВР, тенге (123)
Р1= 97,09 * 4 = 388,36 тенге
Сср.ч. - среднечасовая тарифная ставка, в тенге
Нвр. - норма времени, в чел.ч.(принимается по Тн
и Р, вып.5 или по ВНиР); принимаем: 4 чел.час.
Себестоимость работы после внедрения
приспособления.
С2 = Р2*(1+(Нц / 100))+(П / К)*(1 / Т+Э / 100) ,
тенге (124)
С2 = 194,18 * (1+(140 / 100)) + (3500 / 69) * (1
/ 1+ 20 / 100) = 526,9 тенге
Р2 - расценка после внедрения стенда
Р2=ССР.Ч* НВР , тенге (125)
Р2= 97,09 * 2 = 194,18 тенге
Нвр - после внедрения стенда норма времени,
чел.ч.;
принимаем: 2 чел.час.
П - ориентировочная стоимость приспособления с
учетом коэффициента инфляции
П = Б * У, тенге (126)
П = 700 * 5 = 3500
Б - число, учитывающее сложность приспособления
Для простого: Б=700;
средней сложности: Б=1000;
сложное: Б=1300;
принимаем: Б=700.
У - количество узлов и деталей в приспособлении
(по чертежам);
К - годовая программа принимается по заданию или
рассчитывается;
К = 69 раз.
Б - сколько раз приспособление применяем в день
на одну машину;
Т - срок службы приспособления;
Принимается Т = 1 - 3 года,
Принимаем: Т = 1 год.
Э - процент расходов, связанных с внедрением в
производство;
Принимается Э = 20 - 40%,
принимаем: Э = 20%.
С2 - себестоимость ремонта после внедрения
приспособления
1. Условно-годовой экономический эффект от
внедрения приспособления
Ен - коэффициент сравнительной экономической
эффективности капитальных
Вложений во внедрение данного приспособления.
Принимается Ен = 0,16
ЭУЧ = К*(С1 - С2) + ЕН * П, тенге (127)
ЭУЧ.= 69 * (932,06 - 526,9) + 0,16 * 3500 =
28516,04 тенге
Срок окупаемости капитальных затрат на внедрение
данного приспособления:
То = П / ЭУЧ, л (128)
То = 3500 / 28516,04 = 0,12 л
Номинальный срок окупаемости:
Тн = Ддр * То, л (129)
Тн =1,83 * 0,12 = 0,22 г.
Ддр = 1,83 г
5. ОХРАНА ТРУДА
5.1 Охрана труда на
предприятии
Правила по охране труда на автомобильном
транспорте являются отраслевым нормативным документом, действие которого
распространяется на автотранспортные предприятия независимо от их ведомственной
принадлежности и форм собственности, и частных лиц, осуществляющих перевозку
грузов и пассажиров, техническое обслуживание и ремонт автотранспорта.
а) Функции по охране труда и ответственность
руководителя, специалистов и других работников.
Руководитель работ обязан обеспечить:
безопасную эксплуатацию производственных зданий,
сооружений, оборудования, безопасность технологических процессов;
режим труда и отдыха работников, установленный
законодательством;
работников необходимым количеством
санитарно-бытовых помещений и оборудования, контролировать их работу и
использование по прямому назначению;
на каждом рабочем месте условия труда в
соответствии с требованиями трудового кодекса РК от 15 мая 2007 года;
разработку и выполнение мероприятий по охране
труда;
проведение предварительных при поступлении на
работу и периодических медицинских осмотров;
проведение сертификации рабочих мест и
производственных объектов по охране труда;
разработку инструкций по охране труда и
обеспечение ими всех работников;
обучение, проведение своевременных инструктажей
по охране труда;
работников качественной специальной одеждой;
возмещение вреда, причиненного здоровью
работникам вследствие неблагоприятных и опасных условий труда;
информировать работников о состоянии условий и
охраны труда на рабочем месте;
распределение функций по охране труда между
специалистами;
своевременно расследовать несчастные случаи на
производстве;
необходимые меры по обеспечению жизни и здоровья
персонала при возникновении аварийных ситуаций;
обязательное социальное страхование от
несчастных случаев;
выполнять функции по охране труда, возложенные
на них руководителем предприятия.
Основной принцип в области безопасности и охраны
труда - это приоритет жизни и здоровья работников по отношению к результатам
производственной деятельности.
При этом работодатели обязаны обеспечивать
здоровые и безопасные условия труда для своих работников, принимать все меры по
предотвращению рисков на рабочих местах, обучать работников правилам и нормам
охраны труда и выполнять другие требования законодательства.
Структура и численность службы безопасности и
охраны труда определяются в соответствии с задачами и функциями.
Служба безопасности и охраны труда ликвидируется
только в случае прекращения производственной деятельности предприятия.
Основные цели и задачи службы безопасности и
охраны труда: разработка и осуществление комплекса социально-экономических,
организационно-технических, санитарно-гигиенических и лечебно-профилактических
мероприятий по созданию и обеспечению безопасных и здоровых условий труда на
производстве.
Служба безопасности и охраны труда предприятия в
соответствии с установленными задачами:
- обеспечивает разработку, внедрение и
эффективное функционирование системы управления охраной труда на предприятии;
координирует работу функциональных и
производственных подразделений предприятия в вопросах безопасности труда и
взаимодействует с уполномоченным территориальным органом по труду;
организует работу постоянно действующей комиссии
предприятия по безопасности труда;
совместно с соответствующими отделами и службами
осуществляет контроль за состоянием безопасности и охраны труда и своевременно
обеспечивает каждого работника достоверной и полной информацией о состоянии
условий и охраны труда на рабочем месте, полагающимся при этом; средствах
индивидуальной защиты, льготах и компенсациях;
руководит организацией и проведением аттестации
рабочих мест по условиям труда.
контролирует безопасность велений
производственных процессов и работ, техническое состояние и правильность
эксплуатации производственного оборудовании, зданий и сооружений, бытовых
помещений;
контролирует своевременность и качество обучения
работающих безопасным методам работы, проведение инструктажей и проверок знаний
рабочих, правильность ведения журналов регистрации инструктажей;
контролирует наличие и правильность ведения
технической документации по вопросам охраны труда, предусмотренной стандартами,
правилами и другими нормативными документами для подразделений предприятия;
разрабатывает программы вводного инструктажа
рабочих и инженерно-технических работников, проводит вводный инструктаж
поступающих на предприятие работников;
выдает предписания руководителям подразделений и
другим должностным лицам об устранении выявленных недостатков в работе и нарушений
правил и норм безопасности. Эти предписания могут быть отменены только
распоряжением руководителя (владельца) предприятия;
проводит анализ общего состояния условий труда в
подразделениях, а также нарушений правил и норм безопасности, инструкций по
безопасному ведению работ, анализирует эффективность проводимых мероприятий и
принятых решений;
участвует в расследовании несчастных случаев на
производстве, профзаболеваний и аварий, ведет их учет;
по результатам анализа несчастных случаев
совместно с работниками соответствующих подразделений разрабатывает мероприятия
по их предупреждению и осуществляет контроль за выполнением.
Уровни шума
Звуки различной частоты без корреляции по фазе -
это шум. Уровни звука и эквивалентные уровни звука на рабочих местах в
производственных помещениях не должны превышать 75 дБА. ГОСТ 53695-2009. При
разработке новых технологических процессов, при проектировании, изготовлении,
эксплуатации машин и оборудования, производственных зданий применяются все
необходимые меры для снижения уровня шума до требуемых величин.
В процессе работы маховичного накопителя
основной шум исходит от электрических машин. В результате возникает шум
механического и электромагнитного происхождения - шум, возникающий вследствие
вращения больших масс и электромагнитных процессов в роторе и статоре.
Воздействие шума на организм может проявляться в
виде специфического поражения органов слуха, нарушений со стороны ряда органов
и систем, снижением производительности труда, повышения уровня травматизма.
Для защиты от шума конструкции
звукоизолируются согласно ГОСТ 23499-2009
<https://www.google.com/url?sa=t&rct=j&q=&esrc=s&source=web&cd=4&ved=0CEAQFjAD&url=http%3A%2F%2Fwww.estateline.ru%2Flegislation%2F1453%2F&ei=Q8aWU8euKIuBywO_gIKwBg&usg=AFQjCNGHFahO8HfbFaJBsM2knHOefVooSw&bvm=bv.68693194,d.bGQ&cad=rja>.
Вибрация.
Механические колебания оборудования и его узлов,
коммутаций и сооружений при дозвуковых и частично звуковых частотах называются
вибрацией.
Различают локальную (местную) вибрацию,
передающуюся через руки, и общую вибрацию, передающуюся через опорные
поверхности на тело человека.
Локальная вибрация, сопровождающая работу с
ручным механизированным инструментом, может вызывать мышечные и костные
деформации, нарушение кровоснабжения и чувствительности кожи, а в отдельных
случаях - вибрационную болезнь.
Общая вибрация может вызывать существенные
нарушения функций организма, а при большой интенсивности при определенном
диапазоне частот - разрыв тканей, сотрясение мозга, нарушение сердечной
деятельности и нервной системы.
Гигиенические нормы вибрации, воздействующей на
человека на постоянных рабочих местах в производственных помещениях,
установлены ГОСТ 53573-2009.
Рабочее место оператора на БЩУ по вибрации
относится к категории 3(в) - вибрация на рабочих местах работников умственного
труда и персонала, не занимающегося физическим трудом.
В таблице приведены санитарные нормы
одночисловых показателей вибрационной нагрузки на оператора для длительности
смены 8 часов:
Таблица № 21 Вид и категория вибрации
Вид
вибрации
|
Категория
вибрации
|
Нормативные,
корректированные по частоте и эквивалентные корректированные значения
|
|
|
Виброускорения
|
Виброскорости
|
|
|
М/с2
|
дБ
|
М*102/с
|
дБ
|
Локальная
|
-
|
2
|
126
|
2
|
112
|
Общая
|
3(в)
|
0,014
|
83
|
0,028
|
75
|
Электробезопасность
На блочном щите управления находится множество
электрических приборов работающие при переменном токе и напряжении 220В. При
неосторожном обращении с токоведущими частями оборудования при нарушении
электроизоляции и оголении проводов возникает опасность поражения электрическим
током.
Блочный щит управления относится к помещениям с
повышенной опасностью поражения электрическим током, так как все оборудование и
несущие конструкции - металлические. Для предотвращения поражения электрическим
током используют изоляцию. Это одна из основных защитных мер. Наименьшая
величина сопротивления изоляции проводов относительно земли для
электроустановок напряжением до 1000 В должна быть не менее 50000 Ом. Мерой
защиты от поражения электрическим током служит защитное заземление Rз=4 Ом.
Все это обеспечивает условия работы в помещении,
соответствующие ГОСТ 12.1.019-2009.
Во избежание электротравм при работе с
электроприборами, оператору необходимо соблюдать правила эксплуатации всех
приборов.
Величина силы поражающего тока в зависимости от степени
воздействия на человека подразделяют на три подгруппы:
безопасная для жизни человека - I ≤ 0,02А;
опасная для жизни человека - I=0,05А;
смертельная для жизни человека - I >0,1А.
На каждом предприятии приказом должно быть
назначено лицо из числа специалистов, ответственное за общее состояние и
эксплуатацию всего электрохозяйства предприятия.
Все электрооборудование должно иметь надежное
защитное заземление, неисправности, могущие вызвать искрение, короткое
замыкание, нагревание проводов, должны немедленно устраняться.
Во всех защитных устройствах должны
устанавливаться только калиброванные предохранители.
Оборудование должно устанавливаться так, чтобы
на электродвигатель не попадали стружка, вода, масло, эмульсия.
Переносные электроинструменты применять только
полностью исправные, напряжением не свыше 36В и частотой 200Гц, в виде
исключения без повышенной опасности можно использовать электроинструмент
напряжением до 220В с соблюдением следующих правил:
надежное заземление корпуса инструмента;
обязательно использовать диэлектрические
резиновые перчатки;
все токоведущие части электроинструмента должны
быть закрыты и недоступны для прикосновения.
Изоляция проводов должна систематически
проверяться, ее сопротивление относительно земли для напряжения 230 В и частоты
50 Гц должно быть не менее 8 кОм и для напряжения 400 В - 15 кОм.
Токоведущие линии должны располагаться на высоте
не менее 2,5м.
Проверка состояния надземной части заземляющих
устройств должна проводиться не реже одного раза в три месяца и при каждой
перестановке оборудования.
Освещенность
На блочном щите управления используется только
исскуственное освещение.
Искусственное освещение осуществляется с помощью
ламп накаливания НБ-220.60 в сочетании со светильниками рассеянного света типа
"люцетта", подающими 40-60% светового потока вниз. Освещенность
поверхностей объекта осуществляется искусственным светом 300 люксов.
Выполняемые работы относятся к разряду работ
малой точности (наименьший размер объекта различения 1-5 мм), разряд зрительных
работ -V (СНиП РК 3.02-04-2009).
5.2 Техника
безопасности при проведение ТО и ремонта
Техническое обслуживание (ТО-1 и ТО-2) и ремонт
автомобилей (ТР и КР) производится на специально отведенных постах, оснащенных
необходимыми устройствами, приборами и приспособлениями.
Автомобили, направленные на посты технического
обслуживания, должны быть вымыты, очищены от грязи. Постановка автомобилей на
посты ТО осуществляется под руководством мастера.
После постановки автомобиля на пост необходимо:
а) затормозить его стояночным тормозом;
б) выключить зажигание (перекрыть подачу топлива
и дизелей);
в) рычаг переключения передач, поставить в
нейтральное положение;
г) на рулевое колесо повесить табличку:
«Двигатель не пускать - работают люди!».
При обслуживании автомобиля на подъемнике на
пульте управления подъемником должна быть вывешена табличка: «Не трогать - под
автомобилем работают люди!»
В поднятом положении плунжер гидравлического
подъемника должен надежно фиксироваться упором от самопроизвольного опускания.
В помещениях технического обслуживания с
поточным движением автомобилей обязательно устройство сигнализации,
сигнализирующий о начале движения автомобилей.
Пуск двигателя автомобиля на постах ТО
разрешается только водителю-перегонщику или бригадиру.
Работники, производящие обслуживания, должны
обеспечиваться исправными приспособлениями и инструментами.
При необходимости выполнения работ под
автомобилем вне эстакады, работники должны обеспечиваться лежаками.
Для снятия и установки деталей, узлов и
агрегатов массой 15 кг и более необходимо пользоваться подъемно-транспортными
механизмами.
Для перегонки автомобилей на посты диагностики
должен быть выделен специальный водитель-перегонщик.
В зоне ТО запрещается:
а) применять для обтирки и мытья
легковоспламеняющиеся жидкости;
б) хранить легковоспламеняющиеся жидкости в
количествах, больше сменной необходимости;
в) заправлять автомобили топливом;
г) загромождать проходы и выходы из помещений;
д) хранить отработанное масло и порожнюю тару из
под топлива.
5.3 Организация
пожарной безопасности на предприятии
Степень огнестойкости одноэтажных зданий
Таблица № 22 Степень огнестойкости одноэтажных
зданий
Количество
автомобилей в эксплуатации
|
Количество
постов для обслуживания автомобилей
|
Степень
огнестойкости
|
Более
100
|
Более
30
|
II
|
От
51 до 100
|
От
11 до 30
|
III
|
От
21 до 50
|
10
и менее
|
IV
|
20
и менее
|
10
и менее
|
V
|
Огнестойкость зданий высотой в 2 этажа и более
независимо от количества обслуживаемых автомобилей не должна быть ниже II
степени.
Устройство наземных резервуаров для хранения
жидкого топлива на территории АТП запрещается.
В помещении зоны ТО должны быть несгораемые
стены, перегородки и покрытия с пределом огнестойкости не менее 1 ч, предел
огнестойкости внутренних дверей и ворот должен быть не менее 0,75 ч.
Запрещается хранить в одном помещении баллоны с
кислородом и баллоны с горючими газами.
В зоне ТО должны отводиться специальные места
для курения.
Разводить костры на территории АТП запрещается.
Пожарная охрана совместно с администрацией АТП
должна разработать:
план эвакуации людей и техники при пожаре;
инструкции на случай пожара.
Весь пожарный инвентарь должен содержаться в
исправном состоянии и храниться на видном месте, к нему должен быть обеспечен
свободный доступ.
Пожарный инвентарь зоны ТО передается под
ответственность ответственным лицам (бригадирам, мастерам).
Использование пожарного инвентаря в
хозяйственных целях и других не связанных с пожаротушением категорически
запрещается.
Пожарные краны во всех помещениях должны быть
оборудованы рукавами и стволами, заключенными в шкафчики.
В помещениях для и ремонта автомобилей должны
быть густопенные огнетушители из расчета - один огнетушитель на 50 м2 площади,
но не менее двух на каждое отдельное помещение.
Кроме того, по согласованию с местной пожарной
охраной устанавливают щиты с противопожарным инвентарем (лопата, лом, пожарный
топор, ключ от водопроводного крана, по два пожарных багра и ведра) и бочки с
водой возле каждого щита.
В зимнее время огнетушители помешаются в
ближайшее оттапливаемое помещение, а в пунктах, где они висели, вывешиваются
таблички с их местонахождением.
Ящики с пожарным песком должны быть окрашены в
красный цвет и плотно закрыты.
Водоснабжение для тушения пожара автомобилей,
должно осуществляться от наружных пожарных гидрантов или из водоемов.
Данное автотранспортное предприятие относится к
категории «А», взрывопожароопасности.
Таблица № 23 Категория взрывопожароопасности.
Категория
помещения
|
Характеристика
веществ и материалов, находящихся (обращающихся) в помещении
|
А
взрывопожароопасная
|
Горючие
газы, ЛВЖ с температурой вспышки не более 280С в таком количестве, что могут
образовывать взрывоопасные парогазовоздушные смеси, при воспламенении которых
развивается расчетное избыточное давление взрыва в помещении, превышающее 5
кПа. Вещества и материалы, способные взрываться и гореть при взаимодействии с
водой, кислородом воздуха или друг с другом в таком количестве, что расчетное
избыточное давление взрыва в помещении превышает 5 кПа
|
Чтобы обеспечить пожаробезопасность на
предприятии, на каждом посту имеются пожарные щиты, в помещении имеются
огнетушители, с расчетом 1 огнетушитель на 20 м2. Также, в здании (и в
некоторых производственных участках) имеются аварийные выходы на случай ЧП.
5.4 Охрана окружающей
среды на предприятии
Охрану окружающей среды на автотранспортном
предприятии можно назвать крайне серьезным мероприятием, т.к. оно относится к
экологически опасным.
Негативное влияние на окружающую среду может
оказываться за счет:
достаточно большого количества производственных
отходов ;
существенных объемов загрязнения воды, которое
происходит в результате мойки автомобилей;
объемов загазованного воздуха и т.п.
Для снижения отрицательного влияния производства
на окружающую среду указанных выше факторов мы предлагаем:
уменьшение объема загрязнения воды при помощи
внедрения двухэтапного процесса мойки: на первом этапе - водой из отстойников
(отработанная вода после ее частичной очистки применяется повторно), и на
втором - чистой, используемой впервые, водой.
увеличение зеленых насаждений на границах АТП,
как метод борьбы с загрязнениям воздуха;
частичную или полную переработку отработавшего
масла (при восстановлении в первую очередь механическим путем удаляют свободную
воду и твердые частицы, затем идет теплофизическая фаза: выпаривание, вакуумная
перегонка).
Очистка вод промышленных стоков, сбрасываемых в
водоемы, является важнейшим техническим мероприятием. Организации, выполняющие
строительные работы и эксплуатирующие технику и автомобили, обязаны сооружать
очистные устройства с искусственной или естественной очисткой. Сброс сточных
вод допускается, если содержание различных вредных веществ в них не превышает
предельно допустимых концентраций (ПДК), установленных органами санитарного и
рыбного надзора. Очистка сточных вод выполняется различными методами:
естественного отстаивания, флотации, электрокоагуляции, магнитной обработки и
химической очистки. Наиболее широко применяется метод естественного
отстаивания, однако он эффективен при размерах частиц более 0,01 мм.
Загрязнение поверхности земли и водоемов при
техническом обслуживании и ремонте машин происходит при нарушении правил
эксплуатации. Для сохранения окружающей среды необходимо: посты мойки и
технического обслуживания оборудовать грязеотстойниками и
маслобензоуловителями; сливать отработавшее масло и технические жидкости в
специальные емкости с последующей отправкой их на восстановление/утилизацию;
исключать утечку нефтепродуктов при их транспортировке, хранении и выдаче; все
отходы эксплуатационных материалов технического обслуживания собирать и
складировать в специально отведенных местах с последующей уборкой в
установленном порядке.
Атмосфера загрязняется выхлопными газами
двигателей внутреннего сгорания. При работе двигателей внутреннего сгорания в
среднем на 1 кг топлива приходится 650 м3 выхлопных газов, токсичность которых
регламентируется содержанием оксидов углерода, азота, углеводородов и сажи.
Нормы содержания вредных веществ отработавших
газах, кВт/час
Таблица № 24 Нормы содержания вредных веществ
отработавших газах
Правила
ЕЭС
|
NOx
|
CO
|
CH
|
Твердые
частицы
|
ECR-4900
|
1982
|
18
|
14
|
3,5
|
Не
реглам.
|
ЕВРО-0
|
1988
|
14,4
|
11,2
|
2,5
|
Не
реглам.
|
ЕВРО-1
|
1993
|
8
|
4,5
|
1,1
|
0,36
|
ЕВРО-2
|
1996
|
7
|
4
|
1,1
|
0,15
|
ЕВРО-3
|
2000
|
5,0
|
2,0
|
0,6
|
0,1
|
Список литературы
1.
«Положение о техническом обслуживании и ремонта подвижного состава
автомобильного транспорта». М. Транспорт, 1986г.
.
Броневич Г.Н., «Курсовое и дипломное проектирование по специальности
строительные машины и оборудование».
.
Крупицкий Э.Н. «Справочник молодого слесаря».
.
Миллер Г.Э. «Техническое нормирование».
.
Алексанин А.Г., Быстрицкий Я.Е. «Охрана труда».
.
Суханов Б.Н.; Борзых И.О.; Бедарев Ю.Ф. «Техническое обслуживание и ремонт
автомобилей. Пособие по дипломному проектированию». М. Транспорт,1991
.
Карагодин В.И.; Митрохин Н.Н. «Ремонт автомобилей и двигателей». М. Мастерство;
Высшая школа, 2001г.
.
Клебанов Б.В. «Проектирование производственных участков АТП». М. Транспорт,
1975г.
.
Шестопалов С.К. «Ремонт грузовых автомобилей». М. Транспорт, 2000г.
.
Родичев В.А. «Грузовые автомобили». М. Проф.Обр.Издат, 2000г.
.
«Правила по охране труда на предприятиях автомобильного транспорта». М.
Транспорт, 1985г.
.
«Краткий автомобильный справочник». М. Транспорт,1994г.
.
Шестопалов С.К. «Устройство и техническое обслуживание грузовых автомобилей». -
М.: Транспорт, - 2000г.
.
«Общесоюзные нормы технологического проектирования предприятий автомобильного
транспорта». ОНТП-01-91,Минавтотранс, 1991г.
.
Барашков И.В. и Звонков Б.П. «Бригадная, организация ТО и ТР автомобилей».
.
Боровских Ю.Л. и др. «ТО и ТР автомобилей».
.
Радин Ю.А. и др. «Справочное пособие авторемонтника».
.
Стрюков Б.Ф. «Экономика и планирование эксплуатации, и ремонт дорожных машин».
.
«Методические указания по выполнению курсового проекта по экономике».
.
«Нормативы численности рабочих, занятых ТО и текущим ремонтом подвижного
состава и др. транспорта».
Похожие работы на - Повышение эффективности технического обслуживания и текущего ремонта в АТП на 132 единицы техники, экономический расчет эффективности проекта
|