Модернизация системы управления и автоматики электропривода насосного агрегата при гидротранспортировании минерального сырья в условиях ГРО 'Катока' (Ангола)
Федеральное агентство по образованию
Государственное образовательное
учреждение высшего профессионального образования
Санкт-Петербургский государственный
горный институт
им. Г.В. Плеханова (технический
университет)
Допускается к
защите в ГАК
Зав.кафедрой Э
и ЭМ
/ / проф.
Козярук А. Е.
“ ” ___июня
2008 г.
ДИПЛОМНЫЙ ПРОЕКТ
ДП. 03. 1592. 08
ПОЯСНИТЕЛЬНАЯ ЗАПИСКА
Тема: “Модернизация системы
управления и автоматики электропривода насосного агрегата при
гидротранспортировании минерального сырья в условиях ГРО «Катока» (Ангола)» ”
Автор:
студент гр. / ЭР-03-1 / /_____________________/ /Рибейро Жозе/
Руководитель
проекта: / Доцент / /_________________/ /Маларев В. И./
Рецензент: /
Профессор, д.т.н./ /__________________/ / Сарвин А. А. /
Консультанты:
/ Э и ЭМ / /
Профессор, д.т.н. / /__________________/ / Козярук А. Е./
/ ГТМ / /
Профессор, д.т.н. / /___________________/ / Николаев А.К./
Санкт-Петербург
год
Федеральное
агентство по образованию
Государственное
образовательное учреждение высшего профессионального образования
Санкт-Петербургский
государственный горный институт
им. Г.В.
Плеханова (технический университет)
Кафедра Э и ЭМ_
Допускается к защите в ГАК
Зав.кафедрой Э и ЭМ
/ / проф. Козярук А. Е.
“ ” ___июня 2008 г.
ЗАДАНИЕ НА
ПРОЕКТИРОВАНИЕ
студенту Рибейро Жозе уч. группа. ЭР-03-1
Тема: “Модернизация системы управления и автоматики электропривода
насосного агрегата при гидротранспортировании минерального сырья в условиях ГРО
«Катока» (Ангола)’’ ”
_____________________________________________________________
_____________________________________________________________
_____________________________________________________________
Исходные данные: Документация ГРО «Катока» __________________
_____________________________________________________________
_____________________________________________________________
Требования к графической части проекта и пояснительной записке содержатся
в Методических указаниях по проектированию.
Срок сдачи законченного проекта: 30 Мая 2008 г
Руководитель работа: / Доцент / /_________________/ /Маларев В. И./
Дата выдачи задания: 06 Марта 2008 г
Аннотация
Дипломный проект посвящен модернизации систем управления и автоматики
электропривода насосного агрегата при гидротранспортировании минерального сырья
в условиях ГРО «Катока» (Ангола), и разработке для него системы управления для
снижения потребления электроэнергии и для улучшения технико-экономических
показателей. В проекте также представлена автоматизированная система управления
насосом с использованием нечеткой логики и выявлены ее преимущества.
Работа содержит 105 страниц пояснительной записки, 36 рисунок, 22 таблиц
и список литературы, включающий 19 источник.
The Summary
graduation
is devoted to about the modernisation of control systems and the automatics of
electric drive of the pumps aggregation in system hydraulic transport of
mineral raw material in circumstances SMC-Lda «Катока» (Angola), to and
development for him control systems for the reduction of the consumption of
electric energy and for the improvement of technical-economic indexes. In
project also is presented automated control system by pump with using of
undistinct logic and detected of its advantage.
Work contains: 105 pages of explanation message, 36 pictures,
22 tables and list of literature, including 19 sources.
Содержание
Аннотация
Введение
I. ОБЩАЯ ЧАСТЬ
. Общая
характеристика предприятия
.1 История
развития алмазодобывающей промышленности Анголы
.2 Экономическое
и финансовое положение предприятия
.3 Горно-геологическая
характеристика месторождения
.4 Технология
ведения горных работ
.5 Технология
добычных работ
.6 Система
разработки карьера
.7 Взрывные
работы в карьере
.8 Вскрышные
и отвальные работы
.9 Технологический
процесс
. Гидротранспорт
хвостов
.1 Технологическая
схема
.2 Расчет
гидротранспортной установки и выбор землесоса
.3 Грунтовые
насосы типа ГрТ 8000/71
. Электропривода
насосного агрегата
.1 Техническое
задание на электропривод грунтового насоса ГрТ-8000/71
.2 Описание
штатного электропривода
.3 Выбор
электродвигателя
.4 Алгоритм
работы системы управления
.5 Выбор
закона управления
.6 Система
управления насосом с преобразователем частоты
.7 Моделирование
скалярной системы частотного управления АД
.8 Результаты
моделирования
.9 Описание
преобразователя частоты PowerFlex 7000
. Электроснабжение
на предприятии
.1 Главные
понизительные подстанции и источники питания
.2 Силовое
электрооборудование
.3 Аппаратура
управления
.4 Выполнение
электрических сетей
.5 Заземление
.6 Расчет
электроснабжения насоса выбор сечения жил кабеля, питающего двигатель
.7 Расчет
токов короткого замыкания
.8 Выбор
коммутационной и защитной аппаратуры
.9 Выбор
разъединителей
II. СПЕЦИАЛЬНАЯ ЧАСТЬ
. Система
управления насосом с использованием нечеткой логики
.1 Нечеткая
логика. Основные определения и свойства
.2 Операции
с множествами
.3 Объединение
множеств
.4 Системы
автоматического регулирования с фаззи-регуляторами
.5 Фаззифицирование
.6 Фаззи-логические
преобразования
.7 Дефаззифицирование
.8 Обоснование
применения нечетких систем управления в трубопроводном гидротранспорте
.9 Актуальность
использования нечетких систем управления в области гидротранспорта сырья
.10 Нечеткая
модель системы гидротранспорта
III. ЭКОНОМИЧЕСКАЯ ЧАСТЬ
. Определение
экономической эффективности
.1 Факторы,
влияющие на экономическую эффективность
.2 Плата
за электроэнергию. Затраты по базовому варианту
.3 Суммарные
затраты по базовому варианту
.4 Затраты
по предлагаемому варианту
.5 Суммарные
затраты по предлагаемому варианту
.6 Экономический
эффект от внедрения широтно-импульсного преобразователя фирмы PowerFlex 7000
IV. БЕЗОПАСНОСТЬ ЖИЗНЕДЕЯТЕЛЬНОСТИ
. Характеристика
условий и анализ потенциальных опасностей
.1 Анализ
травматизма
.2 Борьба
с шумом
.3 Борьба
с пылью
.4 Электробезопасность
.5 Пожарная
безопасность
.6 План
ликвидации аварии
.7 Чрезвычайная
ситуация и меры по ее ликвидации
V. ЭКОЛОГИЯ ГОРНОГО ПРОИЗВОДСТВА
. Экологическая
устойчивость территории
.1 Охрана
окружающей среды
.2 Охрана
воздушного бассейна0
.3 Санитарно-защитная
зона
.4 Мероприятия
по снижению выбросов вредных веществ в атмосферу
.5 Охрана
поверхностных и подземных вод от загрязнения и истощения
.6 Мероприятия
по охране и рациональному использованию водных ресурсов
.7 Охрана
недр
.8 Мероприятия
по охране почв и рекультивации нарушенных земель
.9 Контроль
радиационной обстановки на объектах комбината
Заключение
Список
используемой литературы
ВВЕДЕНИЕ
Горная промышленность является одной из важнейших составляющих экономики
Ангола, непосредственно влияющей на формирование бюджета страны.
В экономике Анголы алмазы являются основными стратегическими ресурсами,
формирующими значительную долю валового национального продукта и валютных
поступлений страны. При любых достижениях в области реформирования промышленности
страны, упрочнение её позиций на мировом рынке алмазов будет оставаться
приоритетной государственной задачей на длительную перспективу.
Геологические ресурсы страны изучены ещё недостаточно, но можно
утверждать, что в её недрах содержится около пятой части мировых запасов
алмазов. Поэтому рациональное и эффективное освоение коренных алмазоносных
месторождений является одной из важнейших проблем алмазодобывающей
промышленности Анголы. Целью этого подхода является укрепление позиций страны
на мировом алмазном рынке и проведение на нём такой политики, которая отвечала
бы стабильности мировой алмазодобывающей индустрии.
Для реализации этой цели, компании непрерывно занимаются поиском подходов
к модернизации, обновление основных звеньев технологического процесса добычи,
транспортирования и переработки минерального сырья, а также реструктуризации и
реорганизации управления производством в новых условиях, стремятся сделать
производство эффективным, вопросы контроля разработки месторождений и
оптимизации добычи алмаз давно являются первостепенными задачами.
Наиболее острой проблемой сегодня является быстрый рост издержек
производства.
Работа предприятий в рыночных условиях диктует свои правила: хочешь быть
конкурентоспособным - сокращай затраты, снижения энергопотребления, удельной
энергоёмкости и металоёмкости процесса; изменяй форму деятельности. И как
следствие этого, совершенствуется структура предприятий, и разрабатываются
мероприятия по наращиванию объемов добычи алмаз в целях обеспечения роста
прибыли и улучшения благосостояния работников алмазодобывающих предприятий.
Возможности динамичного и эффективного развития алмазодобычи на крупном
коренном месторождении алмазов в современных политико-экономических условиях
Анголы продемонстрированны на примере производственной деятельности
Горно-рудного Общества «Катока». Ангола.
I. Общая часть
1. Общая характеристика предприятия “ГРО Катока”
Горно-рудное Общество «Катока» - первый в Анголе горно-обогатительный
комплекс на коренном кимберлите. ГРО «Катока» в Анголе - один из самых
современных промышленных объектов в Африке, который входит в число 10
крупнейших эксплуатируемых месторождений мира, обеспечивающих более 70%
мирового объема добычи алмазов. При разработке месторождения используются
высокотехнологичные методы добычи и обогащения алмазной руды.
В административно-географическом отношении кимберлитовая трубка «Катока»
располагается на северо-востоке республики Ангола в северо-западной части
провинции Южная Лунда. Трубка по своим размерам представляет собой одно из
крупнейших коренных месторождений алмазов в мире. Она находится в 30 км к
северу от города Сауримо - административного центра провинции в 800 км к
востоку от столицы Республики Ангола города Луанды (рис.1.1.).
Рис.1.1. Географическое расположении концессии ГРО «Катока»
Масштабы бизнеса предприятия ГРО «Катока» на алмазном рынке Анголы весьма
существенны. Оно было основано 16 сентября 1993 г. при долевом участии
российских - «Алроса», ангольских - ЕНДИАМА, бразильских - «Одебрешт» и позже,
в 1997 г. на завершающей фазе 1 этапа Проекта, израильских - «Диамонти
Файненшинг» капиталов.
Ввиду отсутствия должных условий безопасности в регионе, строительство
комплекса началось лишь в 1995 г. Обогатительная фабрика и карьер начали
эксплуатироваться в 1997 г. Первые алмазы «Катоки» были получены в 1997 г. а
добытый за время эксплуатации крупнейший ювелирный алмаз весил 108 карат.
Концепция развития ГРО «Катока» предполагала две фазы и включала
геолого-разведочные работы с целью подсчёта запасов алмазов в месторождении.
Первая фаза с предполагаемым сроком в 9 лет включала:
§ Разработку месторождения до глубины 60 м, переработку 1.620 000 т руды и
добычу 940 000 карат алмазов с годовой стоимостью порядка 70,5 млн. долл.США.
§ Инвестиции на инсталляцию и развитие проекта в 94 млн.долл. США, включая
15 млн. долл. США на геолого-разведку до глубины 600 м.
§ Геолого-разведочные работы имели своей целью подсчёт запасов алмазов до
указанной глубины, как основы для составления ТЭО (Технико- экономическое
обоснование) для второй фазы Проекта.
ТЭО первой фазы базировалось на следущих показателях (таб.1.1).
Таблица 1.1
Показатели ТЭО первого этапа Проекта ГРО «Катока» (в млн. долл.США)
Доходы
|
497,5
|
Расходы
|
387,1
|
Инвестиции
|
94,0
|
Производственные расходы
|
266,9
|
Прочие расходы
|
26,2
|
Производственный результат
(прибыль)
|
110,4
|
Роялти
|
24,9
|
Налог на производство
|
34,2
|
Чистая прибыль
|
51,3
|
Вторая фаза - инвестиции, связанные с созданием второго обогатительного
модуля мощностью 3 или 4 млн.т. и увеличением мощности ГРО "Катока"
соответственно до 6,0 или 7 млн.т. руды в год. Инвестиции второго направления
связаны главным образом со строительством второго обогатительного модуля и
объектов его обеспечения (второй дробильный комплекс, объекты производственного
водоснабжения, хвостового хозяйства, охраны и др.); созданием нового, более
мощного карьерного хозяйства (приобретением высокопроизводительной
горнотранспортной техники под увеличенные объемы выемки горной массы);
перевооружением энергохозяйства (переходом на новый источник электроснабжения),
расширением департаментов оборудования и поставок; некоторым расширением других
обслуживающих служб и социальной сферы.
1.1 История развития алмазодобывающей промышленности Анголы
Алмазы в Анголе были открыты в 1907 году бельгийским геологом Жанотом из
Международного Горного Общества Конго в аллювии р. Каминини. Эта находка
подтвердила возможность открытия промышленно-алмазоносных отложений в Конго и в
Анголе. Позже, в 1912 году, геологами той же компании Жонстоном и Мак Веем в
аллювии р. Мусалала на северо-востоке Анголы были найдены 7 алмазов. Имеются
упоминания о более ранних старательских разработках и торговле алмазами в ХIХ веке в провинциях Куанго и Маланже.
Находки алмазов в Конго и на северо-востоке Анголы способствовали
учреждению в марте 1913 г. первой компании, которая была уполномочена проводит
систематические поиски алмазных месторождений - РЕМА (Горно-поисковая компания
Анголы). Она получила лицензию на 5 лет на право разведки и разработки алмазных
месторождений в зоне, ограниченной на СВ границей сираны, на З- меридианом 19о
и на юге-паралелью 11о, которая была продлена в 1918 г. ещё на 5 лет. В
начальный период поиски проводились в бассейнах р.р. Шикапа и Луашиму. Первые
положительные результаты были получены при поисках алмазов в бассейне р.р.
Шиумбе и Луембе, где в течение 3 лет в аллювиальных отложениях были
подтверждены промышленные запасы в 3 млн. карат.
В октябре 1917 г. была учреждена Алмазодобывающая Компания Анголы- DIAMANG с участием международного капитала,
которой были переданы горные права компании РЕМА. В декабре 1920 г. Высший
Комиссариат Анголы подписал контракт с DIAMANG, согласно которому площадь концессии увеличивалась, а
срок горной лицензии продлевался до 30 лет. В 1921-1928 г.г. DIAMANG эксклюзивно проводил
геолого-поисковые работы на всей территории Анголы площадью в 1256 тыс. км2. В
1928 г., ввиду выделения резервной территории правительства Анголы в прибрежной
полосе площадью в 224,7 тыс. км2, площадь концесии сократилась до 1025 тыс.
км2, что составило 82% территории страны. В 1937 г. действие лицензии DIAMANG было продлено ещё на 30 лет. В 1967
г. DIAMANG получила эксклюзивное право на
огранку алмазов на всей территории Португалии и её колоний. В Португалии была
построена первая ограночная фабрика.
Важной вехой было выделение в 1926 г. Единой Зоны Охраны для разработки
месторождений, контролируемых DIAMANG,
ограниченной с севера границей страны, на востоке - р. Кассаи и юге -
паралелью, проходящей через г.Сауриму до р. Лушику. Другое важное право было
конституировано, как выделение «площадей разработки» с маркировкой границ
горных участков. Их разработка разрешалась лишь по согласованию с
контролирующим органом- Дирекцией Горно-геологической службы соответствующих
Планов производства, регулируемых Горным законодательством страны. Декретом от
07. 1937 г. были упрощены правила горного отвода для местных артелей, которым
устанавливался срок лицензии на геологоразведку и эксплуатацию участков
площадью до 50 тыс.км2. К 1971 г. DIAMANG владел правом на разведку и разработку 27 таких участков,
площадь которых составила 975 тыс. км2, или 78% территории Анголы.
С 1971 г. DIAMANG занимался
главным образом алмазодобычей. В связи с чем возникла необходимость продолжения
геологических исследований, разведки и разработки алмазных месторождений на
остальной территории страны. В этих целях был учреждён Консорциум CODIAMA с равным участием DIAMANG и De Beers и 10% участия государства. Тогда, объёмы производства
DIAMANG, достигшие максимума в 1971 г. в
2413 тыс. карат, снизидись в 1975 г. до 970,6 тыс. карат.
Алмазодобывающая промышленность Анголы после 1975г.,- года независимости
Анголы, вступила в полосу глубокого кризиса, который объяснялся не только
сложившейся политико-экономической ситуацией, но и массовым оттоком из страны
квалифицированных специалистов в области организации и управления в
алмазодобыче.
Другой негативный фактор - это продолжающаяся гражданская война, которая
провоцирует нестабильность в алмазоносных районах, разрушение инфраструктуры
горно-добывающей отрасли и неблагоприятный инвестиционный климат в экономике
Анголы.
В 1985 г. DIAMANG заключила
контракт с фирмой MATS,
финансируемой Де Бирс, для управления горно-добычными работами. Но эта попытка
реорганизации алмазодобывающего сектора успеха не имела, и было принято решение
о ликвидации DIAMANG ввиду её технической и экономической
несостоятельности.
После ликвидации DIAMANG,
все её права и функции перешли к государственному предприятию ENDIAMA, учреждённому в 1986 г. Среди
различных мероприятий по реорганизации и развитию алмазодобывающего сектора,
отметим следующие:
§ Заключение контракта на проведение работ с фирмой RST (Roan Selection Trust) для разработки алмазов в бассейне р. Кванго в 1986
г.
§ Заключение контракта на проведение работ с фирмой SPE (Sociedade Portuguesa de Empreendimentos) для добычи алмазов в зоне Лукапа в
1989 г.
§ Развитие собственного Проекта по алмазодобыче в регионе Нзаи.
§ Заключение контракта с бразильской фирмой OMSI (ODEBRECHT) на эксплуатацию месторождения в
районе Лузамба в 1990 г.
Широкое развитие горных работ по добыче алмазов на СВ страны, привело
значительным изменениям в деятельности ENDIAMA, которая состояла в организации электроснабжения,
ремонта, снабжения продовольствием, торговли, авто- и авиатранспорта для
развития производства. Это способствовало её реорганизации в конце 90-х годов в
холдинг, включающий ряд алмазодобывающих предприятий - SML, SDM e SMCatoca. Эти мероприятия привели к
положительным эффектам в области организации производства, стабилизации
социальной обстановки и снижению миграции в регионе алмазодобычи, которая
провоцировала незаконные старательские разработки и нелегальную торговлю
алмазами.
Ситуация в регионе осложнилась в 1992 г. из-за нового обострения
гражданской войны в бассейне р.Куанго, где начались несанкционированные
механизированные разработки и незаконная торговля алмазами. Чтобы
стабилизировать ситуацию, в других районах региона также была разрешена
разработка и комерциализация алмазов через различные учреждённые для этого
фирмы. В течение этого периода объём нелегального экспорта алмазов достигал, по
разным оценкам, от 500 до 800 млн. карат в год, что сказывалось негативно на
структуре макроэкономики страны. Наиболее эффективной попыткой стабилизировать ситуацию
и реформировать алмазодобывающий сектор явилось учреждение в конце 1999 г.
Сбытовой Организации
Анголы - SODIAM, которая
осуществляет комерциализацию алмазов через один канал.
SODIAM
с 51% участия своего капитала учредила в этом же году фирму ASCORP, которая в настоящее время
осуществляет закупку всех добытых в стране алмазов, включая и неформальный их
рынок.
Что касается выдачи лицензий на геологоразведку и эксплуатацию алмазных
месторождений, заключённые ранее контракты были ограничены максимальной
площадью в 3000 км2, что позволяло более эффективно контролировать разработку
концессий и сократить возможное истощение запасов алмазов ввиду незаконной их
добычи.
В отношении добычи алмазов старателями «гаримпейрус» готовится ряд
законодательных акций для организации и узаконивания их деятельности. Среди
этих актов следует упомянуть выделение площадей под старательскую разработку, а
также норм кредитования старателей и разработку руководящего Горного Кодекса
старателя.
На основе вышеупомянутых мер были созданы благоприятные условия для
развития алмазодобывающего сектора и роста в последние годы производства
алмазов на горно-добывающих предприятиях, превысившего старательскую добычу.
В общем объёме промышленного производства алмазов в 1999-2000 г.г. Проект
«Катока», являющийся первым опытом эксплуатации коренного кимберлитового
месторождения алмазов в Анголе, занимает первую позицию с 70% по объёму и 45%
по стоимости добычи в стране.
Другой показательный факт, характеризующий позитивные изменения и интерес
зарубежных инвесторов к алмазодобыче в Анголе - это начало эксплуатации новых
коренных месторождений, как Каматуе, Кмафука-Камазамба, что даёт уверенность в
том, что в короткий срок Ангола может достичь привелигерованного положения в
мировой алмазодобыче.
Анализ производства алмазов в Анголе в последние 20 лет, показывает 68%
увеличение его объёмов, с 2356 тыс. карат в1970 г. до 4348 тыс. карат в 2000 г.
При этом отмечается три критических момента в развитиии алмазодобычи в этот
период.
§ До 1975 г. алмазодобывающий сектор характеризовался хотя и низким
уровнем, но стабильного производства.
§ С 1975 г. по 1998 г. - период нестабильного производства, связанный с
обострениями военной обстановки и активностью незаконной старательской
эксплуатации алмазных залежей, порождавшей нелегальную торговлю и
дезорганизацию рынка, нестабильность и бесконтрольность цен на алмазы.
§ 1998-2000г.г.- период реорганизации алмазодобывающей промышленности,
совпавший с началом эксплуатации трубки «Катока», ростом производства алмазов
на горных предприятиях и его преобладанием над старательской добычей.
Строительство осуществлялось силами отечественных предприятий и росиских
фирм. Большая часть инфраструктуры города создана совместими ангольскими и
бразиискими строителями, а комбината (фабрика 1,2), и технологические линии на
всех
переделах созданы силами отечественных и россиских строительных и
монтажных организаций. Все промышленные объекты комбината построены с учетом
розы ветров, их удаленность от границ города составляет 10-15 километров.
В 1997 году была пущена первая очередь комбината (Модуль 1), в 2005 -
вторая комбината (Модуль 2).
По
результатам геологоразведочных работ за 1997-2000 годы утверждены запасы руды и
алмазов месторождения «Катока» до глубины 600 м (таб. 1.2.).
Таблица 1.2.
Запасы руды и алмазов месторождения «Катока» до глубины 600 м
Категории В+С1
|
Геологические запасы
|
Извлекаемые запасы
|
Руда
|
220 819 310 т
|
226 287 320 т
|
Среднее содержание
|
0,55 кар/т
|
0,54 кар/т
|
Всего алмазов
|
122 775 240 карат
|
122 770 380 карат
|
Стоимость алмазов
|
73 $/кар.
|
73 $/кар.
|
Общая стоимость
|
$ 8 962 592 520
|
$ 8 962 237 740
|
Категории В+С1+C2
|
|
|
Руда
|
272 680 260 т
|
278 420 540 т
|
Среднее содержание
|
0,60 кар./т
|
0,59 кар./т
|
Всего алмазов
|
165 153 790 кар.
|
165 147 230 кар.
|
Стоимость алмазов
|
73 $/кар.
|
73 $/кар.
|
Общая стоимость
|
$ 12 056 226 670
|
$ 12 055 747 790
|
1.2 Экономическое и финансовое положение предприятия
Горно-рудное Общество «Катока» создавался и начинал хозяйственную
деятельность в экономических условиях, кардинально отличающихся от тех, в
которых работает в настоящее время.
Развитие показателей деятельности ГРО «КАТОКА» с начала промышленной
эксплуатации месторождения ( 1997 г.) характеризуется положительной динамикой.
Проектная мощость предприятия 1600 тыс.т. уже в 1999 г. была превышена на
25%; объем переработанной руды составил в 1999 г. 2000,0 тыс.т. а в 2000 г.
2592 тыс.т.
В прошедшем 2000 г. выручка Компании составила $153.2 млн. По сравнению с
1999 годом выручка возросла на 20%, а чистая прибыль на 52%. Объем добычи
алмазов ГРО «КАТОКА» в 2000 г. увеличен на 24%, а средняя цена на реализованные
алмазы была несколько выше уровня 1999 г. Таких высоких показателей удалось
достичь благодаря эффективному менеджменту, увеличению объемов производства, а
также удачной конъюнктуре рынка необработанных алмазов.
Программой работы предприятия на 2001 и 2008 г.г. намечена годовая
производительность по переработке руды 2900 тыс.т. и 3000 тыс.т. и объемы
реализации алмазов в стоимостном выражении $165,6 млн.и $168,5 млн. с ростом к
2000 г. 8 % и 10 % соответственно.
Все намеченные на первое полугодие 2001 г. показатели выполнены,
финансовый результат превысил бюджетные проектировки. За период 1997 - 2000
г.г. получено выручки от реализации продукции в сумме $356,6 млн., чистой
прибыли $49,4 млн. В 2000 г. полностью завершены расчеты по займам (включая
проценты), полученным для обеспечения начала производственной деятельности.
Информация о динамике объемов производства, о прибыльности и движении
денежных средств демонстрирует способность менеджмента ГРО «КАТОКА» в
эффективном управлении предприятием и его высокопроизводительным производством.
Эффективная работа в течение 2007-2008 г.г., планируемый рост производства и
прибыли на последующие два года - хорошие индикаторы дальнейшего развития горнорудного
проекта «Катока». Наличие большого объема балансовых разведанных по
месторождению запасов является надежной гарантией для функционирования
предприятия в течение длительного срока - около 40 лет.
Результаты технической и финансово-экономической оценки перспектив
освоения месторождения трубки «Катока» обосновывают техническую возможность и
экономическую целесообразность увеличения мощности ГРО «Катока» к 2012 г. до
6,0 или 8,0 млн.т. руды в год и 3,6 или 4,3 млн. кар. алмазов, с уставным
капиталом $ 171,2 млн. что состоиляет чистой прибыли $167,6 млн.
Максимальное увеличение прибыли путем повышения эффективности работы по
всем важнейшим направлениям производственной и финансовой деятельности,
упрочение положения на рынке алмазов главные целевые задачи, стоящие перед
предприятием.
Важнейшим условием успешного решения указанных задач является разработка
и реализация специальной инновационной стратегии (политики) в непосредственной
связи с общей стратегией развития компании. Фактически все основные стратегические
цели могут быть достигнуты только в результате последовательной и
целенаправленной инновационной политики.
Инновационная политика компании предполагает объединение целей
научно-технической и инвестиционной политики и направлена на внедрение новых
техники и технологий для повышения эффективности производственной детельности
на всех этапах производства алмазов, а также в области сбыта продукции и
менеджмента.
Основной элемент стратегии предприятия ГРО «Катока» - активное
наращивание объемов производства, обеспечение устойчивого финансового состояния
комнпании и конкурентных преимуществ её продукции.
Составной частью инновационной политики ГРО « Катока» являются кратко-,
средне- и долгосрочные цели и задачи, качественные и количественные ориентиры,
как основа для разработки маркетинговой, инвестиционной, технологической и
организационной и других функциональных стратегий развития компании.
Другая важная для предприятия задача - научиться работать себе не в
убыток, а этого можно добиться, только снижая издержки производства и повышая
качество продукции. Большое внимание уделяется снижению затрат на
энергоносители, составляющие 46% материальных затрат.
1.3 Горно-геологическая характеристика месторождения
Трубка «Катока» расположена на правом склоне долины среднего течения реки
Лова, одного из притоков реки Шикапа. Месторождение располагается в
естественной эрозионной котловине, сформированной ручьем Катока, протекающим
непосредственно по трубке. Котловина замкнута с севера, востока и юга, открыта
на запад; абсолютные отметки рельефа дневной поверхности изменяются от +1025 до
+950 м. в русле Ловы.
Климат района тропический с характерными в течение года двумя основными
сезонами: сезон дождей, продолжающийся с сентября до мая, и сухой сезон,
длящийся с мая по август. Наиболее дождливый период приходится на ноябрь -
март, когда в сутки выпадает до 55,6 мм, то есть до 4-5% годовой нормы. Число
дождливых дней в году 75-90.
Температура воздуха отличается стабильностью: средняя минимальная
температура 16 °С, средняя максимальная 28 0С, при колебании средних месячных
температур от 20 0С до 23 0С. Относительная влажность воздуха изменяется от 30%
весной до 70% - 80% летом.
Площадь выхода кимберлитов под наносы равна примерно 67 гектарам. Трубка
изометрическая: размеры по осям - 900 x 900 м. До глубины 130-150 м контакты с вмещающими породами крутые,
падение их 75°-850 внутрь рудного тела. До начала горных работ непосредственно
на поверхность кимберлиты выходили в северо-западной части трубки, остальная ее
часть была перекрыта песчано-глинистыми отложениями, мощность которых меняется
от 0-5 метров на западе до 50-55 метров на востоке (рис.1.2.).
Гнейсы и кимберлиты трубки Катока перекрыты чехлом
песчаных и песчано-глинистых отложений. В пределах карьерного поля породы
перекрывающего чехла разделяются на два слоя. Мощность верхнего слоя
(представлен песками формации Калахари) относительно постоянна и равна примерно
20 м. Пески обычно плотного сложения, в основании имеют 0,5-1-метровый слой
галечника. Ниже до подстилающих гнейсов залегают межформационные пески и
супеси. Пески обводнены, граница высачивания воды находится на отметках 970-980
м. Пески интенсивно разрушаются фильтрационным потоком, и с ними связаны
основная масса нарушений целостности уступов и берм.
Центральная часть кимберлитового поля имеет форму
чаши, глубина которой в центре превышает 250 м. Эта чаша выполнена
полимиктовыми песчаниками, возникшими при выветривании кимберлитов,
формировании перекрывающих пород и образовавшими вулканогенно-осадочный
комплекс. Породами, вмещающими трубку, являются гнейсы. В верхней части
приблизительно в отметках +970 м. породы сильно выветрелые и представлены
глинистыми сапролитами невысокой прочности. Их мощность не превышает 10 метров.
С глубиной, ниже отм.+960м, прочность гнейсов возрастает до очень значительной.
Так, вскрытые в 2001 году гнейсы в южной части карьера ниже отметки +965 м. не
поддаются рыхлению механическим способом и отрабатываются с 2002 года с
применением буровзрывных работ.
Периферийная часть трубки, разрабатываемая в настоящее
время, представлена порфировыми кимберлитами, цвет которых меняется от
кирпично-красного до серовато - зеленого.
Карьером вскрыты кимберлиты коры выветривания, которые
характеризуются малой прочностью, повышенной трещиноватостью, наличием
многочисленных зеркал скольжения. Кимберлит на контакте с межформационными
песками увлажнен. С глубиной прочность порфировых кимберлитов увеличивается.
Центральную часть трубки составляют автолитовые кимберлитовые брекчии.
На территории карьерного поля установлено несколько
типов подземных вод:
§ Ненапорные воды в перекрывающих породах
(межформационных песках и супесях);
§ трещинные воды вмещающих гнейсов;
§ трещинные и порово-трещинные воды
кимберлитов.
Суммарный приток из ненапорного водоносного горизонта
в межформационных песках составляет 170-190 м3/час. Фильтрация воды из песков
происходит крайне неравномерно.
Нет детальных данных по вмещающим и перекрывающим
породам. Данные о породах, в которых будет отстраиваться борта карьера,
практически отсутствуют, поэтому можно только предполагать, что единственной
или преобладающей вмещающей породой является гнейс.
В 2002 г. при проведении наземной съемки были
зафиксированы геофизические аномалии на участке, прилегающем к трубке Катока с
востока и юго-востока. В результате заверки этих аномалий выявлены два
кимберлитовых тела (№1 и №3) трубочного типа, которые большей своей частью
расположены в пределах карьерного поля. В процессе развития горных работ они
будут вовлечены в разработку, и в слагающих их породах будут формироваться
уступы карьера.
В настоящее время произведена заверка этих аномалий
весьма низкая алмазоносность трубок «Аномалия 1» и «Аномалия 3» не позволяет
рассматривать их в качестве промышленно значимых объектов. Вероятнее всего,
основной объем кимберлитовых пород данных трубок, вовлеченных в разработку
карьером «Катока», по результатам эсплуатационной разведки будет представлять
собой вскрышу. Определенная их часть, с содержанием алмазов 0,10-0,15кар/т,
будет отнесена к непромышленным рудам и складирована в спецотвал. Блоки руд, в
которых среднее содержание алмазов превысит 0,15кар/т (бортовое содержание),
предполагается включать в обогатительный процесс совместно с балансовыми рудами
тр. Катока. При этом, прирост балансовых запасов следует ожидать
незначительным, чтобы повлиять на стратегию их отработки.
В настоящее время в отвалы вывозятся породы системы
Калахари, межформационные пески, близкие к ним вулканогенно-осадочные породы и
выветрелые гнейсы коры выветривания. Данные по прочности отвальной массы
получены только по двум скважинами. Породы, вывозимые в отвал увлажнённые, что
создаёт трудности в формировании отвалов. Для создания более высокого яруса (до
20 м), производится отсыпка пионерного яруса из крепких гнейсов или из
необводнённых песков формации Калахари с высотой яруса до 3-5 м. Крепкие породы
(Гнейс) добываются и вывозятся для последующего дробления на дробилку, или
используются для ремонта дорог и берм внутри карьера. При росте
производительности карьера по добыче, так же пропорционально возрастает объём
вскрышных работ. Интенсивность работ, а также сложные геофизические показатели
пород, вызывают необходимость применение отвалообразующего комплекса.
1.4 Технология ведения горных работ
В связи с тем, что вскрышные породы в основном слагаются из песчаных и
песчано-глинистых отложений большого объёма водонасышенных песков, наличием
обильных осадков, а также отсутствием достаточного количества щебня (все дороги
на проекте и в карьере покрыты гравийным материалом), на проекте, вынуждены использовать
автосамосвалы повышенной проходимости фирмы «Катерпиллар», «Volvo». Это автосамосвалы марки D 400, Саt 740, Volvo-А40.
Горно-погрузочная техника представлена погрузчиками Liebher 330, экскаваторами Саt 375 LМЕ (2ед), Саt 5080
(2ед), Liebher 984 (4ед), на вспомогательных
работах Саt 3З0 (1ед), на бункерах фабрик
работают погрузчики Саt
980(2ед), Саt 988(1ед).
Бульдозерная техника представлена гусеничными бульдозерами Саt D7R, D9R, D10R, и колёсными бульдозерами Саt 824.
Сущность применяемой технологии разработки месторождения заключается в
следующем:
В рабочей зоне карьера формируются участки временно нерабочих бортов
(целиков), чередующихся с рабочими горизонтами по их разносу; В разносе верхних
горизонтов временно нерабочие борта одновременно с его формированием
посредством приведения во временно нерабочее положение ниже расположенных
рабочих горизонтов.
В отсыпке заградительных валов для улавливания камнепада на горизонтах
через интервалы по глубине, равные высоте участков временно нерабочего борта; В
устройстве в постоянном или полустационарном борту карьера на горизонтах
размещения заградительных валов транспортных берм и формировании в рабочем
борту систем съездов с горизонтов размещения заградительных валов на
нижерасположенные рабочие горизонты в пределах интервала по глубине, равного
высоте участков временно нерабочего борта.
Это технология ведения горных работ позволяет размещать систему съездов в
каждом целике в положении, обеспечивающем минимальное расстояние
транспортирования из забоев до транспортных берм в постоянном борту карьера или
до приемных бункеров дробильно-конвейерного комплекса (после ввода этого в
работу) и достаточную стационарность трассы, а также обеспечивает возможность
работы с максимальным результирующим углом наклона рабочего борта и создает
условия для высокопроизводительной и безопасной работы технологического
оборудования.
1.5 Технология добычных работ
Согласно утверждённой горно-транспортной части в карьере
предусматривается развитие транспортной системы разработки с внешним
отвалообразованием вскрышных пород и комбинированной добычей руды через
усреднительные перегрузочные пункты.
Основной объём горной массы вывозится из карьера автомобильным
транспортом, автосамосвалами большой грузоподъёмности; 93,2% всей рудной массы
на обогатительную фабрику транспортируется автомобильнным транспортом с
перегрузочных пунктов, 6,7% рудной массы вывозится непосредственно из забоя на
складке. 15% вскрышной породы (скальной) транспортируется из забоя
непосредственно в Восточный автодорожный отвал.
1.6 Система разработки карьера
В настоящий момент применяется углубочная транспортная
система разработки с внешними отвалами, на основе использования
экскаваторно-автомобильного комплекса.
Технологическая схема включает прямую разработку
массива вскрышных пород экскаваторами с емкостью ковша 5-7 м и погрузкой в
автосамосвалы грузоподъемностью 36 т. Рыхление крепких пород (гнейсов)
буровзрывным способом - обуриваются буровым станком «IngersoII-Rand СМ 6950», и применяются штатные ВМ, которые
производятся в Анголе. Разработка производится без буровзрывного способа
рыхления массива, участки с твердыми разновидностями кимберлита подвергаются
рыхлению при помощи бульдозера Саt D10R. Буровзрывное рыхление рудного массива производится только в
исключительных случаях с пониженным удельным расходом ВВ, когда нет возможности
производить механическое рыхление массива.
Параметры системы разработки:
§ высота рабочего уступа -
5-10 м,
§ высота временно нерабочего уступа - 10 м; и 30 м на
восточном борту в отметках 1010 -980 м (рис.1.3).
§ угол наклона уступа - 450, 600, 750
(в крепких гнейсах), 300 на строенном уступе (рис.1.3).
§ ширина рабочих площадок 30
- 60 м;
§ ширина транспортных и предохранительных берм - 20 - 30
м.
При проектировании, в текущем и на предельных контурах
карьера произойдёт изменение параметров уступов. Так с отметок +1010 м до отм.
+980 м. В предельное положение будет поставлен строенный уступ Н=30 м под углом
300 , ширина берм гор +970 и +960 будут равняться 30 метрам, а на крепких рудах
и кальных гнейсах ниже отметки +950 м. углы уступа изменятся до 60°, а ниже 920
отм. до 75°. Что сократит объёмы вскрышных работ, при сохранении стойчивости
борта карьера.
На западном борту карьера, со стороны р. Ловы на гор.+
950, +940, составлены в промконтуре бермы, шириной 27м и углом 35°.
В течении 2007 года на восточном борту карьера уже
произведена постановка уступа с гор +1010 до +980 одним строенным уступом
высотой 30 метров и с уклоном 30 град. Для формирования упорной и дренажной
базы, выемку рыхлых пород производить на глубину 3-5 м (или до твёрдого
материала) ниже уровня стояния, и только потом отстраивать берму и проезжую
часть из гнейса или руды заново.
В противном случае удержать массив невозможно. Откос
уступа соответственно принимает более пологое положение, ~35° -40°, что
необходимо учесть при дальнейшем проектировании.
1.7 Взрывные работы в карьере
На карьере применяется короткозамедленное многорядное,
бескапсюльное взрывание с помощью детонирующего шнура.
На бурении взрывных скважин в карьере используется
буровой станок «INGERSOLL-RED» СМ-695. Частые поломки бурового
станка привели к отставанию работы карьера по буровзрывным работам.
Неритмичность поставок взрывчатых материалов также сказалось на отставании
буровзрывных работ. В ноябре 2007 года введен в эксплуатацию новый буровой
станок «ATLAS COPCO». С вводом его в эксплуатацию карьер рассчитывает
увеличить объем буровзрывных работ.
На 2009 год предусматривается производство взрывных
работ в объёме 800 000 м3 со средним расходом ВВ 0,5 кг\м3. Объём бурения
составит порядка 50000 погонных метров взрывных скважин. В связи с увеличение
объемов взрывания возникла необходимость увеличении емкости расходного склада
ВМ. Существовавший склад вмещал 10 тонн взрывчатых материалов и 5 тонн средств
взрывания. В ноябре 2007 года емкость склада была увеличена до 30 тонн
взрывчатых материалов.
Взрывные скважины бурят станками ATLAS COPCO с использованием долот диаметром 244,5 мм.
Максимальная производительность бурового станка при средней стойкости долот 128
м равна 37 тыс. м скважин в год.
Для эффективной работы экскаваторов необходимо обеспечить степень
дробления пород до dср = 20-30 см.
1.8 Вскрышные и отвальные работы
Вскрытие рабочей зоны карьера осуществляется
автомобильными съездами, приуроченными, в основном, к западному выезду. Через
западный выезд осуществляется связь рабочих горизонтов, расположенных ниже
отметки 950 м, с обогатительной фабрикой, северным и южным отвалами и рудным
складом.
Верхняя часть южного и северного торцов карьера вскрыта ризонтальными
рабочими площадками по рельефу топографической поверхности. В настоящее время
площадки трансформировались в горизонтальные бермы. Связь горизонтов
осуществляется по этим бермам, выходящим на основную технологическую дорогу.
Связь рабочих горизонтов внутри карьера осуществляется по временным
автомобильным съездам. Для выемки вскрыши в автомобильные отвалы применяются
бульдозеры Саt D7R, D9R, D10R, и Саt 824.
Автосамосвалы разгружают горную массу преимущественно под откос отвала
через предохранительный вал, высотой 1,3 метра. Бульдозер сталкивает оставшуюся
на разгрузочной площадке горную массу под откос, при этом формируется
поверхность разгрузочной площадки с уклоном 3° и предохранительный вал по всей длине фронта
разгрузки. В соответствии с этим, предусмотрено применение различных
технологических схем отработки пород покрывающей толщи, руды и вмещающих
скальных пород:
1.9 Технологический процесс
В карьере используются экскаваторы: Саt 375 LМЕ
(2ед), Саt 5080 (2ед), Liebher 984 (4ед), на вспомогательных работах Саt 3З0 (1ед), буровые станки
INGERSOLL-RED СМ-695, ATLAS COPCO. Рудная масса из забоя доставляется
автосамосвалами «Катерпиллар», «Volvo».
D 400, Саt 740, Volvo-А40.
на перегрузочные усреднительные склады, откуда погрузчики Саt 980(2ед), Саt 988(1ед), подается на дробильно-обогатительную фабрику.
Рудная масса с содержанием негаборитных валуков вывозится автосамосвалами
на пневматические дробилки с целью их дальнейшего использования.
Система геофизического опробования при разведке, бурении и складировании
перед подачей рудной массы на дробильно-обогатительную фабрику обеспечивает её
требуемое качество.
Таблица 1.3.
Основные показатели работы карьера кимберлить трубка «Катока»
Показатель
|
2004
|
2005
|
2006
|
2007
|
Вскрыша эксплуатационная,
млн.куб.м/г.
|
По плану Фактически %
|
5,5 6,0 109,0
|
6,4 6,0 93,8
|
6,8 6,2 91,1
|
10,0 7,7 77,8
|
Добыча руды, млн.т:
|
По плану Фактически %
|
2,0 2,17 108,5
|
2,7 2,9 107,4
|
3,6 4,4 122,2
|
4,3 4,6 106,9
|
Горная масса, млн.т:
|
По плану Фактически %
|
7,5 8,17 109,1
|
9,1 8,9 97,8
|
10,4 8,7 83,6
|
14,3 12,4 86,7
|
Текущий коэффициент
вскрыши, млн.куб.м/г.
|
По проекту Фактически
|
2,8 2,8
|
2,4 2,1
|
1,9 1,7
|
2,3 1,7
|
Глубина карьера по замкн.
контуру,
|
140
|
200
|
250
|
310
|
Исходным сырьем для обогатительной фабрики являются алмазосодержающии
руды.
Технологический процесс дробления руды включает в себя:
§ мельницы мокрого сомоизмельчения ММС-50X 23P
предназначена для дезинтергация кимберлитов для раскрытия алмазов.
§ Односпиральный классификатор 1КСН-24 предназначен для гидравлической классификации
разгрузки мельницы по граничному зерну 1,4 мм и вывода в отвал рудного
материала мельче 1,4 мм.
§ Грохот фирмы “Vibromech” модели
Н2-48-21 предназначена для классификация по крупности песков классификатором
1КСН-24.
Компоновка технологического оборудования корпуса крупного дробления
позволяет с помощью трёх пластинчатых питателей подавать дробленую руду из трёх
дробилок ММС-50Х 23Р на любой из двух ленточных конвейеров и таким образом
непрерывно обеспечивать рудой корпус среднего и мелкого дробления. Благодаря
применению новых высокопроизводительных дробилок СД-3000Т и КЛЩ-3000Т при трех
стадиальной схеме дробления впервые на крупной дробильной фабрике по
переработке руды получена в замкнутом цикле дробления конечная крупность
материала - 1,4 мм.
Горизонтальное расположение всех дробилок среднего и мелкого дробления
существенно упростило транспортную схему замкнутого цикла, обеспечило
независимую работу дробилок, облегчило условия ремонта дробилок и грохотов.
Технологическая схема обогащения включает три стадии измельчения: одна
стадия-магнитной сепарации, две операции классификации, по классу +25мм, +13мм,
+5мм, и -1,4 мм и операцию доводки концентрата методом рентгенной сепарации
алмазов. Концентрат направляют в корпус извлечения, а пустые породы в
замкнутном цикле на грохочение.
Хвосты руды и магнитной сепарации подаются в пульпонасосную, откуда с
помощью грунтовых насосов Ду500 по пульпопроводам диаметром 1200 мм
направляются в хвостохранилище.
Высокая техническая оснащённость ГРО «Катока» имеет и обратную сторону; в
структуре себестоимости очень велики издержки на ремонт и обслуживание,
амортизацию и эксплуатацию машин и механизмов (автотранспортные систем), на
долю чего приходится до 60 % общей энергоемкости и материалоемкости процесса.
Поэтому мы предлагаем рассмотреть возможность внедрения перспективного
направления гидротранспорта пульпы на УОФ, что существенно повысит
эффективность деятельности ГРО «Катока».
2. Гидротранспортные системы
Гидравлический транспорт на предприятиях горной промышленности является
важным звеном технологического процесса добычи и переработки минерального
сырья. Этот вид транспортирования обеспечивает передачу насыпных материалов без
перегрузки по трассам сложного профиля и большой протяженности.
Транспортирование твердых материалов в потоке воды, как пpавило, является более экономичным,
чем перевозки этих материалов железнодорожным или автомобильным транспортом.
Перспективность гидравлического трубопроводного транспорта твepдыx материалов обусловливается не только высокой экономичностью,
но и такими показателями, как непрерывность транспортного процесса, высокая
производительность, экологичность и возможность полной автоматизации всего
процесса [5].
2.1 Технологическая cистемы
гидротранспорта
Работа системы гидротранспорта приведена на схема 2.2., включающих 2
«нормальных» режима работы и 2 «аварийных» режима работы.
«Нормальный» режим работы предусматривает 2
последовательно включенных грунтовых насоса (пара насосов) при всех открытых
задвижках прямой напорной линии. При этом частота вращения каждого насоса
синхронно регулируется в диапазоне n = 540-380 1/мин своим ЧРП (частотно-регулируемые преобразователя) PowerFlex 7000 (зона №1 + зона №2 на графике
совместной работы насосов с трубопроводами) в зависимости от уровня пульпы в
зумпфе [4].
«Аварийный» режим работы предусматривает 2
последовательно включенных грунтовых насоса (пара насосов ) при открытых
задвижках «Z»-o6paзной напорной
линии (используются 2 узла переключений). При этом возможны два варианта
работы:
§ управление каждым насосом выполняет
свой ЧРП. Частота вращения каждого насоса регулируется в диапазоне n=540-380 1/мин своим ЧРП (зона №1 +
зона №2 на графике совместной работы насосов с трубопроводами);
§ при выходе из строя одного ЧРП,
управление насосами выполняет оставшийся рабочий ЧРП, который разгоняет 1-й
насос до постоянной частоты вращения n=540 1/мин, переключается на 2-й насос и регулирует частоту его вращения
в диапазоне n=540-380 (зона №2 на графике
совместной работы насосов с трубопроводами).
График совместной работы грунтовых насосов с
трубопроводами приведен на (рис. 2.1.). Рекомендуемая область работы грунтовых
насосов по условиям гидротранспорта в зависимости от качества пульпы
(гранулометрический состав, удельный вес частиц, нагрузка по выходу твердого,
количество воды) находится в области расходов Q=2400м3/ч-7900м3/ч.
Оптимальный режим работы уточняется в режиме отладки
системы гидротранспорта и ориентировочно составляет Q≈2700-8000m3/ч (при работе грунтовых насосов на трубопровод ГрТ 8000).
Рис.2.1. График совместной работы грунтовых насосов с
трубопроводами
§ одно ступенчатые - без промежуточных насосных станций;
§ многоступенчатые, вьшолняемые с промежуточными емкостями (зумпфами) или
без них (по схеме "насос в насос"').
Технологическая схема хвостового хозяйства, представляеть собой: хвосты
магнитной сепарации (1) и сливы дешламаторов (2) самотеком попадают в
пульпонасосную (3), где распределяются по зумпфам. Всего зумпфов 12 - по числу
установленных грунтовых насосов (4). Грунтовые насосы типа ГрТ - 8000/71,
мощностью 3150 кВт, приводятся в движение асинхронными двигателями (5) типа
АО2-21-49-16Т1, мощностью 3150 кВт. В одновременной работе находятся 3 или 4
насоса (в зависимости от подачи пульпы), еще 4 находятся в резерве, а
оставшиеся в ремонте. Это связано с большим износом насосов, поэтому
применяется двукратное резервирование. Количество резервных насосов определяет
оператор ЦДП ГТС.
Рис.2.2. Технологическая схема хвостового хозяйства
Управление насосами производится: с панельной операторской станции и с
центрального диспетчерского пункта гидротехнических сооружений (ЦДП ГТС),
расположенного в контейнере управления на площадке пульпонасосной станции.
Пульпонасосная станция включает четыре системы
технологического оборудования:
§ основную технологическую систему (систему
гидротранспорта); система предназначена для подачи хвостовой пульпы в
хвостохранилище на реке Луитэ.
§ систему обеспечения грунтовых
насосов; система предназначена для подачи технической воды на гидроуплотнение и
охлаждение понижающих редукторов грунтовых насосов.
§ систему промывки внутристанционных
пульповодов и зумпфа; система предназначена для промывки технической водой
рабочей линии внутристанционных пульповодов и грунтовых насосов со сбросом
промывочной воды в дренаж. При плановой или аварийной остановке всей системы
гидротранспорта также выполняется промывка зумпфа со сливом воды в дренаж.
§ дренажную систему; система
предназначена для сбора и сброса дренажной воды в действующее хвостохранилище
на реке Чикоа. Дренажная вода собирается дренажным лотком и отводится в
дренажный приямок. Далее из дренажного приямка вода отводится в самотечном
режиме. При переполнении дренажного приямка вода откачивается дренажным
насосом.
В пульпонасосной станции предусматривается две аварийные емкости
размерами в плане 30×30 м высотой 9,0 м. Сливы с полов в заглубленной части
перекачиваются в зумпф песковыми насосами ПВП 250/28 - три штуки (два рабочих,
один резервный).
На случай затопления заглубленной части ПНС на незатопляемой отметке
+1,00 м устанавливается вертикальный артезианский вертикальный насос типа
20А-18 1-1, производительность 600 м3/час, напором 28 м.
Перекачивание пульпы в хвостохранилище (6) осуществляется по 2 стальным
трубопроводам, диаметром 1200 мм каждый (1 в работе, 1 в резерве). Емкость
хвостохранилища составляет 410 млн.куб.м., а площадь составляет 25 кв.км. В
качестве хвостохранилища используется река Чикоа. Укладка хвостов
осуществляется на резервуар (дыки) при помощи распределительного пульповода,
для сброса излишков воды при помощи распределительного пульповода, который
оборудован выпусками диаметром 125 мм, врезанными по длине пульпопровода через
10-12 м. После отстаивания, вода забирается из хвостохранилища и используется
вновь на технологические нужды (рис.2.3.).
Рис. 2.3. Функциональная схема системы управления пульповодом
2.2. Расчет гидротранспортной установки и выбор землесоса
Важнейшими исходными параметрами при paсчете системы гидротрантранпорта, оnpеделяющими как ее энергетические показатели, так и
конструктивно-технологическое оформление являются длина и профиль трассы
трубопровода.
Длина трубопровода может быть от нескольких до десятков километров, чем в
итоге опредляются затраты энергии на перeмещение расчетного грузопотока твердого материала. При
наличии чередующихся спусков и подъемов трубопровода по его длине всю трассу
целесобразно рассматривать как состоящую из отдельных элементов,
характеризующися двумя параметрами - длина элемента и уклоном, который может
быть положительным или отрицательным по отношению к напраилению
транспортирования [5].
Определим основные параметры гидротранспортной установки по следующим
данным. Расстояние транспортирования 15000 м, геодезический перепад высот
трассы z = +25 м, геодезический высота
всесывания z = 5 м. Объемная производительность
установки по пульпе, Vп=8000
м3/ч, плотность твердого материала 3,0 т/м3, плотность пульпы 1,6 т/м3,
концентрация гидросмеси, s =
0,6, диаметр трубы 1200 мм, средневзвешенный диаметр частиц твердого, dср = 0,12 мм
Гидравлическая крупность:
(2.1)
Критическая
скорость движения пульпы: (2.2)
Критический
диаметр трубопровода: (2.3)
Таким
образом, принятый диаметр трубопровода больше критического, а это значит что
пересчет не требуется.
Число
Рейнольдса: (2.4)
=
1*10-6 м2/с - кинематическая вязкость
Коэффициент
гидравлических сопротивлений для чистой воды: (2.5)
Удельные
потери напора при движении чистой воды: (2.6)
Удельные
потери при движении пульпы: (2.7)
Необходимый
напор гидротранспортной установки: (2.8)
Мощность
электропривода: (2.9)
В практике гидравлического транспорта на предприятиях горной
промышленности используются насосы различного принципа действия (динамические и
объемные) Наиболее широко применимы насосы центробежного типа ГРТ, ГРК, ГРУ,
характеризующиеся невысокими развиваемыми давлениями при высоких расходах
перекачиваемых гидросмесей. Поэтому исходя из расхода, требуемого напора и
мощности, принимаем 4 грунтовых насоса типа ГрТ 8000/71, еще 4 насоса этого же
типа находятся в резерве, а еще 4 в ремонте. То есть потребуется две насосных
станции. Это связано с тем, что в процессе работы происходит быстрый износ
землесоса, поэтому применяется двукратное резервирование.
2.3 Грунтовые насосы типа ГрТ 8000/71
Область применения: горно-обогатительные и горно-металлургические
предприятия, теплоэлектростанции, предприятия по производству цемента, алмазо-
и золотодобывающие предприятия, технологические предприятия, технологические
линии дробления, обогащения полезных ископаемых и т.п.
Рис.2.4. Внешний вид насоса ГрТ 8000/71
Центробежные грунтовые насосы (рис.2.4) конструктивно выполнены в виде
консольного одноступенчатого насоса, горизонтально расположенного на отдельной
стойке, с приводом от электродвигателя через упругую муфту. Рабочее колесо
закрытого типа.
Предназначены для перекачивания гравийных, песчано-гравийных, шлаковых,
золошлаковых и других абразивных гидросмесей с водородным показателем pH 6-8,
плотностью до 1600 кг/м3, с температурой до 70° С.
Насосы имеют ряд конструктивных исполнений, обеспечивающих повышенный
ресурс работы при названных условиях эксплуатации:
§ установка внутреннего корпуса (исполнение Т);
§ увеличение размеров (25% от номинального) проходного сечения (исполнение
Т);
§ применение износостойкого сплава ИЧХ28М2 (исполнение А);
§ футеровка абразивным материалом на органической связке - корундирование
(исполнение К).
Рабочее колесо (2) (рис.2.5.) выполнено с большим количеством мощных
отбойных лопаток на обоих дисках. Отбойные лопатки расположены таким образом,
что защищают области наиболее интенсивного износа дисков, так как они работают
аналогично колесу вихревого насоса. Кроме того, они предотвращают попадание
абразивных частиц в пазухи между колесом и корпусом, обеспечивая постоянный
минимальный перепад давления в переднем уплотнении насоса.
Для эффективной работы отбойных лопаток предусмотрена возможность
регулирования зазора между торцовой поверхностью отбойных лопаток и передним
бронедиском (3) (без разборки насоса) с помощью специальной регулировочной
шпильки, размещенной на опорной стойке (10).
В пространство между колесом и корпусом (1) подводится промывающая вода,
выносящая частицы из пазухи между колесом и корпусом.
горный алмазодобывающий землесос преобразователь
Рис. 2.5. Основные узлы насоса ГрТ 8000/71: 1 - внутренний корпус, 2 -
рабочее колесо, 3 - защитный диск, 4 - передняя половина корпуса, 5 - задняя
половина корпуса, 6 - гайка рабочего колеса, 7 - сальник, 8 - вал, 9 - упругая
муфта, 10- опорная стойка.
Уплотнение вала в месте выхода его из корпуса насоса - мягкий сальник
(7). Для охлаждения и предохранения от износа в сальниковое уплотнение через
кольцо сальника подаётся техническая вода под давлением, превышающим давление в
зоне уплотнения на 0,5 - 1 кгс/см2.
3. Электропривода насосного агрегата
3.1 Техническое задание на электропривод
грунтового насоса
Техническое задание на комплектный регулируемый элекропривод грунтового
насоса ГрТ 8000/71, находящегося на горно-обогатительной фабрик, для
перекачивания гравийных, песчано-гравийных, и других абразивных гидросмесей с
водородным показателем pH 6-8, плотностью до 1600 кг/м3, с температурой до 70°
С. «ГРО Катока-Ангола».
Назначение: Электропривод предназначен для регулирования
производительности насосной станции путем изменения частоты вращения приводного
электродвигателя.
Технические характеристики.
Напряжение питания,
кВ.........................................................……….6
Привод регулируемый, нереверсивный
Требования к качеству электрической энергии……………Кнл ≤ 5%
Диапазон регулирования……………………...……..……………..1:3
Статические характеристики:
Установившаяся скорость, рад/с………………………………..38,22
Преобразователь частоты:
Электропривод насосной станции снабжается преобразователем частоты фирмы
«Rockwell Automation» типа PowerFlex 7000 со встроенной защитой от
перегрузки, перенапряжения и низкого значения напряжения, перегрева,
кратковременного отказа в цепи питания, от замыкания на землю со стороны
выхода.
Напряжение на выходе преобразователя частоты, В….…..0 - 6000
Максимальная мощность подключаемого электропривода,.кВт….3200
Частота питающей сети, Гц……………………..……….…………50
Требования к САР и автоматизации:
Статическая точность, %…..……….…………...…….……………± 5
Динамическая точность, %...…………..……...…….……………± 10
Посты управления:
Местное со щита управления, непосредственно на самой установке.
Дистанционное - из операторской.
Виды защит:
Максимальная токовая (1,5Iном)
Минимальная (± 5%)Uном
Тепловая
Защита при обрывах фазы первичной питающей сети
Защита по току электродвигателя (1,5 А) при повторной перегрузке в
течение 30 сек. и двукратной перегрузке в течение 6 сек. с запретом повторного
включения;
защита при отклонении напряжения первичной питающей сети выше 25 % и ниже
25 % от номинального значения;
защита при коротком замыкании обмоток электродвигателя или жил
подводящего силового кабеля ( Iуст
=[5-7]*Iном)
Защита при турбинном вращении насоса;
Защита подшипников двигателя и насоса от перегрева свыше 70ºС
Защита от снижения давления масла в подшипниках двигателя и насоса
Сигнализация:
Индикация пуска и останова электродвигателя
Обобщенная индикация срабатывания защит
Сигнализация технологических защит:
Давление в подшипниках ниже нормы
«Температура подшипников свыше 70ºС»
«Температура охлаждающей воды свыше нормы»
«Уровень в зумпфе ниже критического»
«Питающая задвижка открыта»
«Питающая задвижка закрыта»
Вид и род сигналов (0-4) В, (10-20) мА “Сухой контакт”
Условия эксплуатации:
Диапазон температур................……………………...... .(-40 - +40)°С
Относительная влажность.............…………………... .80% при 20°С
Климатическое исполнение оборудования ……….……………....Т1
Коэффициент запыленности для двигателя, мг/м3…………………3
Степень защиты от внешних воздействий двигателей ……..….IP54
Степень защиты для шкафов управления ………..…….……….IP22
Механические перегрузки: устанавливается при внешних источниках,
создающих вибрацию не выше 35 Гц и максимальном ускорении 5 м/с2. Ударные
нагрузки отсутствуют.
Требования по надежности
Коэффициент готовности ..........................................................….0,92
Время среднее восстоновления,
ч..................................................….1
Гарантийный срок эксплуатации,
ч.........................................…20000
Среднее время между кап. ремонтами, лет..............................…………..5
Гарантии изготовителя:
Гарантийный срок
службы.........................................................2 года.
Назначенный срок
службы.........................................................20 лет.
Минимальное время между кап. ремонтами...............................5
лет.
3.2 Описание штатного
электропривода
Штатный электропривод является нерегулируемым. При нажатии кнопки пуска с
поста управления включается электродвигатель мощностью 3150 кВт, который в свою
очередь приводит в действие исполнительный механизм - насос типа ГрТ 8000/71.
Электропривод снабжен автоматическим выключателем 4000 А и контактором на
3200 А. Штатный электропривод не имеет устройства плавного пуска и
регулирующего устройства. Вследствие этого оборудование не защищено от пусковых
токов и не имеет возможности контроля объемов перекачиваемой
технологической жидкости.
Для эксплуатации принят насос типа ГрТ 8000/71. конструктивно выполнены в
виде консольного одноступенчатого насоса, горизонтально расположенного на отдельной
стойке, с приводом от электродвигателя через упругую муфту. Рабочее колесо
закрытого типа.
Основные характеристики насоса представлены в табл. 3.1.
Таблица 3.1
Технические параметры насоса ГрТ 8000/71
Подача насоса,
м3/ч
|
Напор насоса, м
|
Скорость вращения,
об/мин
|
Потребляемая
мощность,кВт
|
Номинальный КПД
%
|
Диаметр(направляющего)нагнетательного
патрубка, мм
|
Диаметр
всасывающего патрубка,мм
|
Рамер проходного
сечения,мм
|
8000
|
71
|
375
|
3150
|
74
|
680
|
700
|
310
|
3.3 Выбор электродвигателя
Выбор типа двигателя сделан на основе технико-экономического сравнения
различных двигателей переменного тока. Должны быть сопоставлены их
электрические и механические свойства, первоначальная стоимость самих
двигателей и аппаратуры управления, эксплуатационные расходы.
При выборе нерегулируемого типа двигателя можно ограничиться сравнением
трёх типов двигателей переменного тока: 1) асинхронного с короткозамкнутым
ротором, 2) асинхронного с фазным ротором и 3) синхронного.
Приведённые выше соображения показывают значительные технико-экономические
преимущества двигателей с короткозамкнутым ротором. При лёгких условиях пуска,
то есть при малом значении статического момента при трогании и малом моменте
инерции, может быть использован простейший короткозамкнутый двигатель.
Поэтому, для привода насоса применяют асинхронные двигатели с
короткозамкнутым ротором, выполненные в защищённом, закрытом или рудничном
исполнении.
Необходимая мощность двигателя N (кВт) для привода насоса определяется по формуле:
(3.1)
где: k- коэффициент запаса мощности
двигателя, k=1,1;
Q-
фактическая подача насоса, м3/ч;
H-
фактический развиваемый напор с учётом высоты всасывания, м;
hр- КПД установки;
r- плотность откачиваемой воды, кг/м3.
кВт,
Выбираем
асинхронный двигатель АО2-21-49-16Т1.
Требуемая мощность двигатель 3150 кВт, скорость вращения рабочего органа
составляет 375 об/мин. Следовательно, выбранный электродвигатель удовлетворяет
характеристикам насоса.
Характеристики двигателя АО2-21-49-16Т1 приведены в табл.3.2.
Таблица 3.2
Технические параметры двигателя АО2-21-49-16Т1
Номинальная
мощность
|
Номинальное
напряжение
|
Номинальный ток
статора
|
Синхронная
частота вращения
|
Номинальный
коэффициент мощности
|
Номинальный КПД
|
Номинальное скольжение
|
Кратность
максимального момента
|
Кратность
пускового момента
|
Кратность
пускового тока
|
Рном, кВт
|
Uном, В
|
I Л ном,
А
|
nо, об/мин.
|
сos φном
|
ηном, %
|
S
|
=ʎ
|
|
|
3150
|
6000
|
374
|
375
|
0,85
|
95,3
|
0,026
|
2,0
|
1,2
|
5,0
|
Расчет
параметров двигателя
В номинальном
режиме:
R1’ =
0,10; X1’ = 0,012; R’’2=0,0037; X’’2=0,0011,
Хµ=19,6
пр к.з. R2П=0,027; RК.П.=0,039; XК.П.=
0,16.
Максимальной допустимый маховый момент, кг . м2 = 105000
Номинальный ток двигателя:
IН=
A. (3.2)
Рис.3.1.
Г-образная схема замещения АД для номинального режима.
Параметры
Г - образной схемы замещения АД для номинального режима в относительных
единицах:
1
=
Ом, (3.3)
R 1=
Ом (3.4)
Коэффициент
перевода относительных единиц в физические:
=
=
= 9,26
(3.5)
Взаимная
индуктивность статора и ротора, приведенная к статору, и индуктивность фазы
обмотки статора:
=
Гн; (3.6)
Ls =
Гн. (3.7)
Активное
сопротивление и индуктивное сопротивление рассеяние фазы обмотки статора:
=
r1 = R1 C = 2,39 ∙ 9,26 = 22,13 Ом; (3.8)
х1
= Х1 С = 0,286 . 9,26 = 2,648 Ом (3.9)
Поправочный
коэффициент для параметров Г-образной схемы замещения:
σг =
=
(3.10)
Активное
сопротивление и индуктивное сопротивление рассеяния ротора, приведенное к
статору:
=
Ом. (3.11)
Ом
(3.12)
Индуктивность
фазы обмотки ротора, приведенная к статору:
=
Гн. (3.13)
Через
первичные параметры определяется переходная индуктивность асинхронной машины.
Переходная
индуктивность статора и ротора:
’s = Ls - 
Гн.
(3.14)
L'r = Lr -
Гн. (3.15)
Постоянная
времени обмотки ротора и статора:
'r =
С. (3.16)
Ts =
С. (3.17)
Коэффициент
магнитной связи статора и ротора:
=
. (3.18)
Kr=
(3.19)
Расчет
механической характеристики двигателя
Номинальное и критическое скольжение (таб.3.2):
Синхронная частота вращения ротора:
ωc=
рад*с (3.20)
Кратность
пускового и критического моментов (таб.3.2):
Номинальный
момент двигателя:
Мн=9570
Нм. (3.21)
Пусковой
момент двигателя по справочным данным:
п=1.2∙Мн=1,2
∙ 82530 = 99036 Нм. (3.22)
Критический
момент:
Мк=2,0
∙ Мн = 2,0 . 82530= 165060 Нм. (3.23)
3.4 Алгоритм работы системы управления
Пуск насоса осуществляется следующим образом:
а) открыть питающую задвижку, загорается сигнал «Питающая задвижка
открыта» (HL 11) на щите оператора;
б) открыть вентили маслосмазки и гидроуплотнения;
в) при нормальном давлении в системе маслосмазки загорается сигнал «Готовность»
(HL 2) на ЩО;
г) нажать кнопку «Пуск» (SB 2)
на ЩО, загорается сигнал «Работа» (HL 3);
д) открыть напорную задвижку
Плановое отключение насоса осуществляется нажатием кнопки «Стоп» (SB 3) на ЩО.
Аварийное отключение с места осуществляется нажатием кнопки «Стоп» (SB 1), а со ЩО - кнопкой «Стоп» (SB 3).
Автоматическое отключение происходит при срабатывании защит в камере КРУ,
защит преобразователя частоты, аварийном перегреве подшипников (свыше 70ºС), снижении давления в системе
маслосмазки подшипников, отсутствии напряжения в цепях управления, отсутствии
пульпы в зумпфе.
Однако монитор АСУ ТП фабрики предоставляет возможность наблюдения и
управления текущим состоянием технологического процесса фабрики. Весь
технологический процесс отображен на восьми мнемосхемах, которые регистрируют
состояние отдельных переделов фабрики: «Рудоподготовка», «РЛС», «Отсадка»,
«Доводка», «ГТС», «Общефабричные параметры».
Для выполнения управляющих воздействий над технологическим оборудованием,
монитор АСУ ТП отображается текущий режим объекта, один из трех: «Местный»,
«Дистанционный», «Автоматический».
Аварийный останов оборудования работает всегда, когда оборудование
находится либо в дистанционном, либо в автоматическом режимах.
Управляющие воздействия на объект возможны только в режиме
«Дистанционный». В этом режиме становятся доступны команды «Пуск»/«Стоп» и если
необходимо окошко ввода заданного положения шибера.
Силовая схема электропривода (рис. 3.2), и схема цепей управления,
сигнализации и блокировок (рис.3.3.)
Таблица 3.3.
Таблица электрооборудования
Обозначение
|
Наименование
|
Кол.
|
Примеч.
|
M
|
Электродвигатель
АО2-21-49-16У1
|
1
|
Р=3150кВт, 6 кВ
|
QS
|
Разъединитель РВЛ 6/400
|
|
|
В
|
Вакуумный выключатель
ВМП-10
|
1
|
|
ТА1, ТА2
|
Трансформатор тока ТЛМ-6
|
2
|
|
KА1 - КА4
|
Реле токовое РТ-40/20
|
2
|
|
KK1, КК2
|
Реле тепловое
|
2
|
|
KL1-KL3
|
Реле промежуточное ПМЛ
110004
|
3
|
|
YA1
|
Электромагнит включения
|
1
|
|
YA2
|
Электромагнит отключения
|
|
|
SB1, SB3
|
Кнопка управления КУФ
|
2
|
|
SB2
|
Кнопка управления КУ
|
1
|
|
НL1
|
Светодиод
|
1
|
зеленый
|
НL2-HL11
|
Светодиод
|
10
|
красный
|
R
|
Сопротивление ПЭВ-5
|
1
|
|
FU
|
Предохранитель ПКЭ
|
1
|
|
Рис. 3.2. Силовая схема электропривода. Рис.3.3. Схема цепей управления,
сигнализации и блокировок
3.5 Выбор закона управления
Потери энергии в технологическом процессе зависят от технологической
нагрузки, определяемой потребителем, и потерь напора на оборудовании насосной
станции которые определяются гидравлическим сопротивлением элементов схемы. Для
организации технологического процесса с минимальными энергетическими потерями
необходимо, в первую очередь, снизить потери напора между трубопроводом
насосного агрегата и сетью потребителей. Кроме того, в процессе
функционирования в зависимости от режимов работы системы может меняться
давление перед насосом, создаваемое источником водоснабжения.
Такой характер взаимосвязи параметров требует установки в системе
дроссельных регулирующих элементов - регулирующих клапанов (иногда их роль
выполняют напорные задвижки агрегатов). Эти элементы создают дополнительное
гидравлическое сопротивление и позволяют обеспечить стабильное давление в
сетевом трубопроводе. При использовании дроссельных элементов происходит
распределение напора на элементах системы.
На величину потерь при дроссельном регулировании влияет не только
регулирующий элемент: чаще всего на этапе проектирования выбирается насосный
агрегат с определённым запасом напора, а при замене насосных агрегатов новое
оборудование может иметь несколько завышенные характеристики. Кроме того,
диапазон изменения входных давлений (перед всасывающим патрубком насосного
агрегата) оказывает влияние на величину давления за насосным агрегатом. Все эти
обстоятельства приводят к тому, что потери энергии в ходе технологического
процесса становятся достаточно большими, достигающими 45 и более процентов от
номинальной мощности агрегата.
Для решения задачи минимизации потерь, связанных с регулированием
давления в сети, необходимо исключить дополнительные гидравлические
сопротивления на участке от насосного агрегата до сетевого трубопровода, то
есть необходимо полностью открыть всю запорно-регулируюшую арматуру. Это можно
сделать, если процесс регулирования давления передать насосному агрегату.
Теория работы нагнетателей (насосов и вентиляторов) доказывает, что изменение
частоты вращения привода нагнететеля изменяет его напорные характеристики,
кроме того, напор создаваемый нагнетателем, пропорционален квадрату частоты
вращения агрегата.
Если организовать работу привода насосного агрегата таким образом, чтобы
он при изменении параметров технологического процесса (расхода в сети и
давления на входе агрегата) изменял частоту вращения, то в итоге можно без
существенных потерь энергии стабилизировать давление в сети потребителей. При
таком способе регулирования исключаются потери напора (нет дроссельных
элементов), а значит, и потери гидравлической энергии.
Способ регулирования давления в сети путём изменения частоты вращения
привода насосного агрегата снижает энергопотребление ещё и по другой причине.
Собственно насос как устройство преобразования энергии имеет свой коэффициент
полезного действия - отношение механической энергии, приложенной к валу, к
гидравлической энергии, получаемой в напорном трубопроводе насосного агрегата.
В соответствии с теорией подобия максимум коэффициента полезного действия
с уменьшением частоты вращения несколько снижается и смещается влево. Анализ
требуемого изменения частоты насосного агрегата при изменении расхода в сети
показывает, что с уменьшением расхода требуется снижение частоты вращения. В
этом случае КПД насоса выше, чем при работе на номинальной частоте вращения.
Таким образом, снижение частоты вращения в соответствии с технологической
нагрузкой позволяет не только экономить потребляемую энергию на исключении
гидравлических потерь, но и получить экономический эффект за счёт повышения
коэффициента полезного действия самого насоса - преобразования механической
энергии в гидравлическую.
Применение частотного регулирования приводов позволяет существенно
уменьшить и эксплуатационные затраты, связанные с обслуживанием агрегатов и
систем. Например, снижение перепада давления между всасывающим и напорным
патрубками насосного агрегата увеличивает срок службы сальниковых уплотнений,
практически исключая гидроудары и обеспечивает стабильность давлений в
трубопроводах сетей, а также минимизирует затраты на обслуживание.
Технология управления асинхронными двигателями, обеспечивающая
энергосбережение, обусловлена их конструктивными особенностями и техническими
параметрами, а также характеристиками нагрузки.
Использование частотно-регулируемого электропривода в насосных станциях
по перекачке жидкости имеет ряд отличительных особенностей, связанных с
массовым использованием центробежных конструкций насосов, которые отличаются
тем, что для них расход пропорционален частоте оборотов крыльчатки, давление
пропорционально квадрату числа оборотов, а потребляемая мощность - кубической
степени. В соответствии с формулами приведения центробежных насосов эти
параметры эмпирически можно выразить следующим образом:
Q/Q0 = n/n0, H/H0 = (n/n0)2, N/N0 = (n/n0)3, (3.24)
Характеристики пропорциональности:
(3.25)
Где,
Q - расход, Н- напор, R- сопротивление сети, n(ω) - частота вращения,мощность потребляемая
электродвигателем.
Поскольку подача питательного насоса пропорциональна частоте вращения
двигателя, а напор, развиваемый насосом пропорционален квадрату частоты
вращения двигателя, для обеспечения требуемой точности поддержания давления в
системе частоту вращения двигателя необходимо поддерживать с точностью не хуже ± 0,65% wзад. Это возможно только при
использовании в составе преобразователя частоты двухконтурной системы
регулирования.
Исходя из этого выбираем электропривод с системой скалярного управления
асинхронных короткозамкнутый двигателей.
Функциональная схема системы управления питательным насосом имеет вид:
Рис.3.4. Функциональная схема системы управления электроприводом
питательного насоса
3.6 Система управления насосом с
преобразователем частоты
К категории механизмов, у которых момент зависит от скорости и имеет
квадратичную зависимость в первую очередь, относятся центробежные насосы.
Благодаря квадратичной характеристике U/f и возможности её
динамического выбора преобразователь позволяет управлять насосами с наибольшей
эффективностью, приближаясь к их естественной характеристике и тем самым
сокращая потери энергии. Необходимо также более подробно отметить уже
упоминавшуюся ранее функцию динамического выбора характеристики U/f. При снижении нагрузки на валу двигателя и, соответственно,
уменьшении тока статора, преобразователь снижает напряжение на статоре
двигателя, сохраняя частоту неизменной. Благодаря снижению напряжения
уменьшаются потери энергии в статоре двигателя, а значит и общие потери энергии
в приводной системе становятся ниже. При возрастании нагрузки на валу двигателя
процесс протекает в обратной последовательности и ПЧ возвращается на
номинальную характеристику.
Наличие программируемого ПИД-регулятора позволяет организовать
автоматический контроль за аналоговым сигналом приходящим с датчика обратной
связи (например давления, температуры, уровня). Программируемые релейные выходы
позволяют организовать работу насосной станции в веерном режиме (что позволяет
уменьшить мощность насосов за счет увеличения их количества), постоянно контролируя
количество включенных насосов, что позволяет существенно уменьшить расход
электроэнергии и увеличить ресурс насосов. Необходимо отметить также наличие
пропускаемых частот, настраиваемых пользователем и позволяющих избежать
резонанса в механизме и двигателе. Из функций, полезных при управлении
насосами, следует также отметить возможность "подхвата" вращающегося
двигателя и возможность автоматического перезапуска при исчезновении питания
или рестарта при аварийном отключении. Преобразователь может перезапускаться до
10 раз с задержкой перед включением от 5 до 25 секунд, что достаточно для
подавляющего большинства насосов.
Преобразователи могут комплектоваться дополнительным внешним фильтром
радиочастот, применение которого позволяет ПЧ с запасом отвечать самым жёстким
требованиям по электромагнитной совместимости (ЭМС). Совокупность качеств
преобразователя частоты делает его отличным выбором для управления
центробежными насосами, а наличие разнообразных модулей расширения позволяет
создавать на его базе локальные системы управления и/или интегрировать ПЧ в уже
существующие системы управления.
Современные преобразователи частоты позволяют создавать системы
управления (СУ) без дополнительных аппаратных средств, так как имеют
программное функция обеспечение для встроенного в привод микроконтроллера.
Сегодня нельзя найти отрасль, где не применялись бы частотно-регулируемые
электроприводы с приводными асинхронными двигателями. Большинство
производственных машин и механизмов общепромышленного применения (насосы, вентиляторы,
конвейеры, компрессоры и т.п.) требуют относительно небольшого диапазона и
невысокой точности регулирования скорости (до 1:20), относительно низкого
быстродействия. В этом случае используют электроприводы с системой скалярного
управления асинхронных двигателей, т.е. с взаимосвязанным регулированием
частоты и значения питающего напряжения ( U/f ), ( рис.3.5).
Рис.3.5. Структурная схема электропривода со скалярным управлерием с
датчиком скорости
Регулятор тока
В системах автоматического управления электроприводами широко
используются различного рода регуляторы тока, напряжения, скорости.
Рассмотрим ПИ-регулятор тока и запишем его передаточную функцию. Если в
цепь обратной связи операционного усилителя включены последовательно резистор
Rо.с.
и конденсатор Со.с., во входную цепь-резистор R1, тогда Zo.c.=(Ro.c.+1)/Co.c.p , а Z1=R1 и передаточная функция усилителя имеет вид:
, где Т1=Rо.с.С
, Т2=R1С, (3.26)
Для
большенства технологических процессов при использовании стандартного
ПИ-регулятора заранее можно считать, что АСР будет устойчива. Пропорциональная
составляющая мгновенно “ отрабатывает “ основную “ часть “ входного сигнала,
тогда как затем интегральная составляющая постоянно “ приводит “ выходной
сигнал к заданному значению.
На
рис.3.6. представлена принципиальная схема ПИ-регулятора, выполненная на
операционном усилителе.
Рис.3.6. Схема регулятора тока.
Регулятор скорости
Если в цепь обратной связи включить резистор Ro.c., а во входную
цепь-резистор R1, тогда Zo.c.=Ro.c., а Z1=R1 и передаточная функция усилителя
будет иметь вид:
. (3.27)
В
этом случае операционный усилитель выполняет масштабное преобразование входного
напряжения с коэффициентом k и называется пропорциональным ( П ). П-регулятор
безинерционен. Коэффициент усиления регулятора k является
параметром его настройки и численно равен перемещению регулирующего органа,
которое осуществляет регулятор при отклонении регулируемой величины на единицу
ее изменения.
На
рис.3.7. представлена принципиальная схема П-регулятора, выполненная на
операционном усилителе.
Рис.3.7.
Схема регулятора скорости.
Питание на электродвигатель подается от трехфазной сети линейным
напряжением 380 В (частота 50 Гц). Силовая цепь содержит автоматический
выключатель Mitsubishi, 3P, 400 А (QF1),
частотный преобразователь типа PowerFlex 7000.
Все функции регулирования и защиты осуществляет частотный преобразователь
и работает в автоматическом режиме. Имеется возможность ручного управления
пуском, остановом и регулированием частоты.
Преобразователь частоты - это электронное устройство для плавного
бесступенчатого регулирования скорости вращения вала асинхронного двигателя. В
простейшем случае частотного регулирования управление скоростью вращения вала
осуществляется с помощью изменения частоты и амплитуды трехфазного напряжения,
подаваемого на двигатель. Большинство современных преобразователей частоты
построено по схеме двойного преобразования. Они состоят из следующих основных
частей:
§ звена постоянного тока;
§ силового трехфазного импульсного инвертора;
§ системы управления.
Применение частотно регулируемого электропривода позволяет достичь
преимуществ по сравнению с традиционными методами регулирования: уменьшение
энергопотребления до 35-50%; устранение пусковых токов и перегрузок двигателя
на период пуска; отсутствие дополнительных потерь при регулировании; уменьшение
механического износа и увеличение срока службы оборудования и снижение затрат
на его обслуживание и ремонт. ПЧ строится с использованием транзисторов с
изолированным затвором (IGBT),
(Рис. 3.8.).
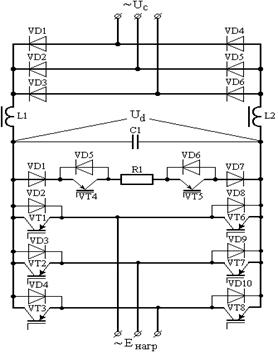
В
ПЧ входное напряжение 220/380 В, с частотой 50 Гц преобразуется в выходное
импульсное напряжение посредством широтно-импульсной модуляции (ШИМ), которая
формирует в обмотках двигателя синусоидальный ток частотой от 0 до 400 Гц.
Увеличением частоты и амплитуды напряжения, подаваемого на обмотки асинхронного
двигателя, обеспечивается плавное регулирование скорости вращения вала
электродвигателя. Для обеспечения высокой жесткости механической характеристики
двигателя и достаточной перегрузочной способности необходимо одновременно с
частотой тока регулировать напряжение с тем, чтобы магнитный поток оставался
постоянным. Отсутствие необходимости в электрическом торможении и реверсе
привода упрощает структуру ПЧ и позволяет выполнить его на базе автономного
инвертора напряжения. При изменении частоты вращения вала двигателя новая
рабочая точка располагается в зоне устойчивой работы насоса и при этом КПД не
превышает 0,9 максимального его значения. При изменении частоты напряжение
изменяется так, чтобы отношение максимального момента двигателя к моменту
сопротивления на его валу было постоянным. При постоянстве перегрузочной
способности номинальные коэффициенты мощности и КПД двигателя на всем диапазоне
регулирования частоты вращения практически не изменяются. Энергия, потребляемая
электроприводом, пропорциональна частоте вращения в третьей степени, отсюда
следует, что если в процессе управления производительность при питании приводного
двигателя от ПЧ снижена частота напряжения от 50 до 40 Гц, то потребление
энергии уменьшается почти в 2 раза.
3.7 Моделирование скалярной системы
частотного управления АД
При реализации скалярной системы частотного управления преобразователь
частоты реализует следующий закон управления:
(3.28)
Для
анализа стационарных режимов работы питательного насоса в составе комплекса
может быть использовано упрощенное представление асинхронного приводного
двигателя питательного насоса в виде:
,
(3.29)
где
; рп - число пар полюсов двигателя;
- эквивалентная постоянная времени двигателя; JS - суммарный
момент инерции ротора двигателя и механизма; Мк и Sк - критический
момент и критическое скольжение двигателя соответственно; wо - выходная частота преобразователя частоты; wr -
частота вращения ротора двигателя.
Идеальный
преобразователь частоты при этом может быть представлен в виде, показанном на
рис.3.9. Закон управления в модели может быть реализован с помощью двух
дополнительных блоков умножения.
Рис.3.9.
Структурная схема идеального преобразователя частоты.
На
выходе этих звеньев включаются два усилительных звена с переменным
коэффициентом усиления, пропорциональным амплитудному значению выходного
напряжения преобразователя частоты Um. Задающее воздействие
преобразователя частоты может быть представлено задатчиком интенсивности,
предназначен для задания сигнала по скорости с заданной интенсивностью
нарастания разгона и торможения.
Преобразователь
частоты с системой широтно-импульсной модуляции выходного напряжения может быть
представлен нелинейной моделью, в которой идеальный преобразователь частоты
реализует входное управляющее воздействие.
Модель
преобразователя частоты с ШИМ включает в себя следующие основные элементы
системы:
§ генератор пилообразных импульсов несущей частоты;
§ формирователь фазных опорных сигналов;
§ блок выходного каскада реального преобразователя частоты с
§ ШИМ - модуляцией кривой выходного напряжения.
На рис.3.10 приведена структурная схема генератора пилообразных импульсов
несущей частоты.
Рис.3.10. Генератор пилообразных импульсов несущей частоты с входным
косинусоидальным сигналом (а) и с входным синусоидальным сигналом (б).
На рис.3.11. приведена структурная схема формирователя опорных
напряжений.
Рис.3.11. Структурная схема формирователя фазных опорных сигналов.
Функции sin ωопt и cos ωопt получаются на выходе модели идеального преобразователя
частоты (рис.3.11) с единичной максимальной выходной амплитудой. Символом (*)
обозначены единичные сигналы на выходе формирователя. На рис.3.12 приведена
структурная схема выходного каскада преобразователя частоты с ШИМ-модуляцией
выходного напряжения.
Рис.3.12. Структурная схема выходного каскада преобразователя частоты с
ШИМ-модуляцией.
Если объединить структурные схемы (рис.3.11. - 3.12.), в общую модель, то
получится математическая модель реального преобразователя частоты. Эта модель
приведена на (рис.3.13.).
Рис. 3.13. Структура схема реального преобразователя частоты с ШИМ -
Модуляцией кривой выходного напряжения
Система регулирования частотно-регулируемого электропривода с системой
скалярного управления, реализующая режим постоянства мощности, включает в себя
внешний контур с регулятором мощности, стабилизирующий мощность на предельном
уровне Рпред = (2 × 10) МВт, и внутренний контур с
регулятором амплитудного значения тока статора двигателя. Для формирования
сигналов обратных связей в системе должен быть предусмотрен вычислитель
ненаблюдаемых координат. В данном случае по информации, полученной путем
прямого измерения мгновенных значений (фазные напряжения и токи статора асинхронного
двигателя и частота вращения ротора двигателя) вычисляется величина полной и
полезной мощности электропривода.
Вычислитель ненаблюдаемых координат в системе скалярного управления
строится в соответствии со следующим математическим описанием:
(3.30)
Структурная
схема вычислителя ненаблюдаемых координат электропривода приведена на
(рис.3.14.).
Рис.3.14.
Структурная схема вычислителя ненаблюдаемых координат электропривода.
Блок
регуляторов в системе скалярного управления, обеспечивающего режим стабилизации
мощности включает в себя П - регулятор механической мощности двигателя и ПИ -
регулятор амплитудного значения тока статора. Структурная схема блока
регуляторов приведена на( рис.3.15.).
Рис.3.15.
Структурная схема блока регуляторов.
Полученный
на выходе блока регуляторов сигнал ωоп подается на вход структурной схемы идеального
преобразователя частоты, реализующего закон частотного управления, вместо
сигнала задатчика интенсивности. На выходе идеального преобразователя частоты
при этом формируются тригонометрические функции вида cos ωопt и sin ωопt. Эти сигналы поступают на вход модели реального
преобразователя частоты с ШИМ - модуляцией выходного напряжения.
На
основании вышеизложенных положений, опираясь на систему уравнений состояния
двигателя, разботаем схему моделированию привода насоса, с помощью пакета
прикладной программы Matlab/Simulink, схемой, представленной на (рис.3.16.).
Рис.3.16.
Структурная схема насосной установки.
Модель
состоит из следующих элементов:
Задатчика интенсивности;
Блока ограничения;
Генератора импульсов;
Дискретного ШИМ генератора;
Источника напряжения переменного тока;
ШИМ инвертора;
Блок измерения параметров двигателя
Система автоматического регулирования;
Модель двигателя;
Модель насосной нагрузки;
Модель трубопроводов.
§ Модель насосной нагрузки состоит из двух блоков и моделирует
сопротивление вращению на валу двигателя от насоса. Здесь коэффициент:
(3.31)
§ Модель трубопроводов представляет собой совокупность блоков, которые
моделируют сопротивления движению жидкости в трубопроводах. Здесь коэффициент:
. (3.32)
3.8
Результаты моделирования
Переходные процессы в системе скалярнаго управления электроприводом
насосного агрегата представлены на (рис.3.17.).
Рис.3.17. Переходные процессы систем в режиме пуск, разгон и
моделирования внешнего воздействия
Моделирование
проводилось с фиксированным шагом
.
Анализ
полученных диаграмм показывает, что предпалагаемый электропривод позволяет:
§ Осуществить плавный разгон двигателя до номинальной частоты вращения при
пуске, при этом скачок электромагнитного момента не превышает критического
значения;
§ Осуществить плавное регулирование частоты вращения в заданном диапазоне;
§ Производился пуск двигателя с вентиляторной нагрузкой до номинальной
скорости.
§ Двигатель разгоняется до номинальной скорости в течение 1,5 секунд. Он
приводит в движение насос, который перекачивает минеральные серья. Через 1,5
секунды с начала пуска насос обеспечивает необходимое давление, равное 5,8 МПа.
При этом
момент сопротивления равен моменту номинальному.
§ После разгона до номинальной скорости происходит наброс и сброс давления.
§ Из рис.3.17. видно, что все эти возмущения отрабатываются примерно за
одну секунду, после чего давление выравнивается и устанавливается равным
заданию.
3.9 Описание преобразователя частоты PowerFlex 7000
Таблица 3.4. Технические характеристики ПЧ PowerFlex 7000
Питающая сеть
|
Силовые цепи:
|
3х6 кВ, +10%, 50(60) Гц ±
2%
|
Цепи управления:
|
3х380 В, +10%, -15%, 50(60)
Гц ± 2% (с заземленной либо изолированной нейтралью)
|
Сеть питания
электродвигателя
|
Выходное
напряжение:
|
3х(0…6 кВ) ± 2% (значение
максимального выходного напряжения программируется)
|
Выходная
частота:
|
0…50 Гц ± 0,1% (значения
максимальной и минимальной частоты программируются)
|
Параметры
электропривода
|
Ток перегрузки:
|
110% номинального значения
в течение 120 с Среднеквадратичное значение тока не должно превосходить
номинальное за время усреднения 10 мин.
|
Коэффициент
мощности двигателя
|
0,8 - 1,0
|
Коэффициент
полезного действия
|
0,97
|
Коэффициент мощности на
стороне питающей сети
|
0,95
|
Сопротивление электрической
изоляции гальванически не связанных частей электропривода между собой и
относительно корпуса, не менее:
|
для цепей с номинальным
напряжением 220 В и 380 В
|
не менее 5 МОм
|
для цепей с напряжением до
60 В
|
не менее 5 МОм
|
для силовых цепей,
относительно корпуса
|
не менее 100 МОм
|
Электрическая прочность
изоляции (кроме силовых трансформаторов и реакторов)
|
для цепей с номинальным напряжением
380 В
|
2500 В, 50 Гц, 1
мин.
|
для цепей управления
напряжением 60 В
|
1500 В, 50 Гц, 1
мин.
|
Кратковременное допустимое
отклонение напряжения питающей сети
|
40%
|
Условия
окружающей среды
|
рабочая
температура
|
+1 …+40°С,
|
влажность (без
конденсации)
|
до 80%.
|
В
электроприводах PowerFlex 7000
реализованы:
§ оптимизированные
алгоритмы высокочастотного ШИМ-управления,
§ законы
частотного регулирования АД. Это обеспечивает работу АД во всевозможных
режимах.
Электроприводы
PowerFlex 7000 обеспечивают:
§ плавный пуск;
§ длительную
работу в заданном диапазоне частот вращения и нагрузок;
§ реверсирование движения;
§ торможение и останов.
§ защиту
электрического и механического оборудования в аварийных и нештатных режимах.
Предусматривают
работу в ручном и автоматическом режимах.
Для приема
управляющих и задающих сигналов и управления внешними устройствами
электропривод содержит:
§ 6 - дискретных входов;
§ 2 - аналоговых входа;
§ 6 - программируемых релейных выходов;
§ 4 - аналоговых выхода.
Также
электропривод PowerFlex 7000 поддерживает обмен данными с
внешними устройствами и с дистанционным пультом управления на расстояние до
1000 м. Обмен данными происходит через интерфейс RS485 в соответствии с протоколами «Modbus», «Profibus», CAN.
Электропривод
PowerFlex 7000 состоит из 4-х электрических
модулей, представленных на структурной схеме (рис.3.18). В первом модуле
размещена высоковольтная батарея конденсаторов фильтра звена постоянного тока.
В остальных трёх модулях размещены компоненты преобразователя частоты, построенного
по схеме выпрямитель - инвертор напряжения с широтно-импульсной модуляцией
(ШИМ). Каждый модуль содержит два плеча диодного выпрямителя (фаза сети) и два
плеча инвертора (фаза двигателя). Модули соединены между собой по трёхфазной
системе питания и инвертирования при помощи шин или кабелей. На боковых стенках
силовых модулей закреплены шкафы питания вентиляторов системы охлаждения
привода.
Система
управления размещена в отдельном шкафу вертикального исполнения и связана с
силовыми модулями при помощи экранированных сигнальных кабелей. Там же
установлены коммутационные аппараты питания собственных нужд.
Силовые ключи
инвертора построены на запираемых (GTO) тиристорах. В связи с относительно высоким уровнем выпрямленного
напряжения в каждом плече
установлено
по 4 прибора 55-го класса. Это позволяет повысить надёжность устройства, а так
же обеспечить «мягкую» аварийную остановку преобразователя в случае выхода из
строя одного прибора.
Для
управления тиристорами использован способ переключения по эмиттеру со
встроенным низковольтным МОП драйвером. Обратный ток управляющего электрода
возникает за счёт быстрого отключения цепи катода и естественного перевода
анодного тока в цепь управляющего электрода.
Рис.3.18. Структурная схема преобразователя частоты PowerFlex 7000
О текущем
состоянии электропривода можно узнать по состоянию элементов индикации либо по
информации, выводимой на ЖК-дисплей ПУ-4.
Элементы
индикации электропривода сообщают о:
§ включенном/отключенном состоянии;
§ нормальном/аварийном режиме работы;
§ наличии
напряжения силовой питающей сети;
§ наличии напряжения собственных нужд;
§ вышедшем
из строя тиристоре инвертора.
Графический
ЖК-дисплей предназначен для контроля программных параметров и индикации текущих
значений, таких как:
§ текущая частота выходного напряжения;
§ текущее выходное напряжение;
§ выходной ток преобразователя;
§ напряжение
в звене постоянного тока;
§ величина уставки технологического параметра;
§ фактическое
значение величины технологического параметра;
§ текущее время;
§ текущий режим работы.
На ЖК-дисплей
ПУ информация выводится в виде легко распознаваемых знаков или текстовых
сообщений. Для удобства пользователя вся выводимая информация сведена в
функциональные группы.
Электроприводы
PowerFlex 7000 предусматривают работу в ручном
и автоматическом режимах.
В ручном
режиме привод отрабатывает заданное оператором значение частоты и напряжения и
поддерживает соответствующую скорость двигателя.
В
автоматическом режиме регулирование частоты вращения электродвигателя
происходит в замкнутой системе. Регулирование осуществляется встроенным
программным ПИД-регулятором по сигналам с датчиков обратной связи (датчик
скорости, датчик технологического параметра и т.п.).
В особом
подрежиме автоматического режима (в режиме работы по таймеру) регулирование
осуществляется на основании запрограммированных значений интервалов времени и
соответствующих им величин технологического параметра.
Управление
может осуществляться с местного встроенного пульта или с пульта дистанционного
управления. В
автоматическом режиме требуемое значение технологического параметра задаётся:
§ потенциометром «задание» системы управления;
§ с помощью
клавиатуры пульта управления;
§ с помощью
команды по каналу последовательной связи.
Значение
сигнала обратной связи стандартного типа принимается по соответствующему
аналоговому входу.
В ручном
режиме задание выходной частоты производится:
§ потенциометром «задание»;
§ с помощью
клавиатуры пульта управления;
§ с помощью
команды по каналу последовательной связи;
§ дистанционно унифицированным сигналом.
Выбор
источника управляющего сигнала осуществляется путём программирования
соответствующих параметров.
Для
подключения внешних устройств система управления содержит (табл. 3.5):
Таблица 3.5. Входы и выходы ПЧ PowerFlex 7000
Дискретные входы
|
6 (сигнал типа "сухой
контакт", Rнагр=2 кОм, I=10...20 мА)
|
Аналоговые входы
|
2 (0...10В; 0(4)...20 мА)
по согласованию с Заказчиком количество входов может быть увеличено до 6
|
Программируемые
релейные выходы
|
6 ("сухой
контакт", 250 В, 0,3 А)
|
Аналоговые
выходы
|
4 (0...10В; 0(4)...20 мА)
субмодуль аналоговых выходов поставляются по согласованию с Заказчиком
|
Шесть
дискретных входов электропривода PowerFlex 7000 гальванически развязаны (помехозащищены). Они могут быть настроены
на прием логических сигналов, управляющих:
§ выбором текущего режима;
§ выбором текущего источника задания;
§ выбором
текущего источника обратной связи;
§ выбором
текущих темпов разгона-торможения;
§ выбором
направления вращения ротора двигателя;
§ выбором
текущего номера фиксированного ручного задания из заданного ряда;
§ СТАРТОМ;
§ СТОПОМ;
§ блокировками
№ 1 или № 2, обеспечивающих останов по запрограммированному Пользователем
алгоритму;
При настройке
ЭП, любой дискретный вход (с сохранением настроек на функции) может быть
заменен Пользователем специальной ячейкой оперативной памяти (логический
коммутатор с №, соответствующим № дискретного входа), содержимое которой может
быть программно изменено.
Шесть
аналоговых входов электропривода PowerFlex 7000 гальванически развязаны (помехозащищены). Они могут быть настроены на прием сигналов, используемых как:
§ альтернативный
источник задания ручного режима № 1;
§ альтернативный
источник задания ручного режима № 2;
§ альтернативный
источник задания автоматического режима № 1;
§ альтернативный
источник задания автоматического режима № 2;
§ источник обратной связи № 1;
§ источник обратной связи № 2.
При
настройке, любой аналоговый вход (с сохранением настроек на функции) может быть
заменен Пользователем специальным 16-разрядным регистром в оперативной памяти
(кодовый регистр с №, соответствующим № аналогового входа). Содержимое регистра
может быть программно изменено.
Шесть
дискретных (релейных) выходов электропривода PowerFlex 7000 гальванически развязаны
(помехозащищены). Они могут быть настроены на выдачу сигналов (прямых или
инверсных - переключающийся контакт) для:
§ аварийной
сигнализации с целью оповещения персонала;
§ блокировки смежного технологического оборудования;
§ отображения
различных фаз работы электропривода;
§ включения/выключения дополнительных двигателей;
Четыре
аналоговых выхода электропривода PowerFlex 7000 гальванически развязаны (помехозащищены). Они могут быть настроены
на выдачу сигнала, эквивалентного одному из текущих параметров преобразователя:
§ текущей выходной частоты;
§ текущего значения тока двигателя;
§ текущего значения выходной мощности.
В
электроприводе PowerFlex 7000 предусмотрена возможность увеличения числа
входов/выходов с помощью дополнительных встраиваемых субмодулей расширения.
Внешнее
управляющее устройство имеет возможность дистанционной настройки
электропривода, а также считывания специальными командами протокола
дистанционного цифрового управления следующей информации о:
§ текущем
состоянии дискретных входов вместе с информацией о том, какие входы заняты
функциями электропривода;
§ текущем
состоянии логических коммутаторов вместе с информацией о том, какие из них
заняты функциями электропривода;
§ текущем состоянии аналоговых входов;
§ текущем состоянии кодовых регистров;
§ текущем
состоянии релейных выходов вместе с информацией о том, какие выходы заняты
функциями электропривода.
Для питания
внешних цепей управления содержит изолированный (нестабилизированный) источник
питания 24 В (0,2 А).
4. Электроснабжение на предприятии
Месторождение «Катока» входит в пятёрку крупнейших алмазных трубок мира.
Диаметр трубки равен приблизительно 900 м. запасы её оцениваются в 400-500
млн.карат. Электроснабжение предприятия осуществляется от собственной дизельной
электростанции в составе 8-ми генераторов по 1,36 МВт и 8 генераторов по 1,46
МВт суммарной мощностью 22,56 МВт. В пределах жилого посёлка ГРО «Катока»
располагаются две ДЭС мощностью 0,55 и 0,4 МВт, служащие резервом при остановке
или профилактике головной ДЭС.
В настоящее время суточное потребление электроэнергии ГРО «Катока»
составляет 75-80 тыс.кВтч, ориентировочно 75-80 % от общего объёма
электропотребления приходится на производственные нужды, остальную часть
потребляет жилой посёлок. График суточного потребления электроэнергии
достаточно выровненный, потребляемая мощность в среднем составляет 3,7-3,9 МВт,
максимум 4.4 МВт. Один раз в неделю каждая из обогатительной фабрик
останавливается на плановую профилактику.
4.1 Главные понизительные подстанции и источники питания
В соответствии с рекомендованной главной электрической схемой
электроснабжение установки осуществляется от двух независимых
взаимнорезервирующих воздушных линий 35/6 кВ, обеспечивая электроснабжение по I категории надежности. Рис. 4.1.
На подстанции предусматривается установка двух трехфазных двухобмоточных
трансформаторов типа ТДНС-63000/110, мощностью по 63000 кВА; напряжением 115±9´1,78%/11/6,6 кВ с регулированием напряжения
под нагрузкой. Охлаждение трансформатора масляно-воздушное, с естественной
циркуляцией масла и принудительной циркуляцией воздуха. Полная масса
трансформатора составляет 23,5 тонны, транспортная - 19,5 тонны, масла - 6,5
тонны.
От ГПП-I по токопроводам 10 кВ получают
питание цеховые трансформаторные подстанции и двигатели мельниц мощностью 2500
кВт; по токопроводам 6 кВ - двигатели 250 и 500 кВт конвейеров корпуса
обогащения и корпусов дробления, 400 кВт дробилок, вентиляторов, 500 и 630 кВт
насосов корпуса обогащения отделения сгущения, пульпонасосной, 1000 кВт мельниц
корпуса обогащения и 3150 кВт землесосы пульпонасосной.
На напряжение 6 кВ приняты трансформаторные подстанции канализационной
насосной №3, предзаводской площадки и АБК.
Подстанции ТП3, ТП4, ТП5 корпуса обогащения - 10 кВ. Подстанции ТП2
корпуса среднего и мелкого дробления, ТП6, ТП7, ТП8, корпуса обогащения 6 кВ.
Загрузка обмоток трансформатора 1Т и 2Т в нормальном режиме на напряжении
10 кВ - около 0,6 и на напряжении 6 кВ - 0,5. В аварийном режиме при выходе из
строя одного из трансформаторов загрузка обмоток 10 кВ и 6 кВ оставшегося в
работе трансформатора ГПП-1 соответственно 1,14 и 0,85 с учетом коэффициента
совмещения максимума - 0,95.
Токопроводы 6 и 10 кВ приняты жёсткими симметричными с шинами профиля
“круглая труба” из сплава АДЗ1Т; по территории от ТПП-1 в корпусе обогащения и
токопровод 10 кВ в корпусе обогащения - на подвесных изоляторах (токопровод 6
кВ в корпусе обогащения - на опорных в связи с недостаточной шириной коридора
токопровода).
Для токопроводов приняты следующие виды защит:
1. Защита от многофазных повреждении, действующая без выдержки
времени. Эта защита должна быть отстроена от коротких замыканий за реакторами
на отвлетвениях и, по возможности охватить весь токопровод.
2. Защита от многофазных повреждений с выдержкой времени, отстроена
от токов нагрузки и самозапуска электродвигателей. Защита должна охватывать
весь токопровод и осуществить резервирование защит, действующих при коротких
замыканиях.
Распределительные подстанции подключаются к токопроводам через
выключатели, не рассчитанные на отключение короткого замыкания до реакторов,
поэтому отключение таких повреждений должно производиться защитами
токопроводов.
4.2 Силовое электрооборудование
Питание электроприемников ~380/220В осуществляется от трансформаторных
подстанций ТП3-3, ТП4-4, ТП5-3, ТП3-4, ТП3-5, ТП4-4, ТП4-5, ТП5-4, ТП5-5;
электроприемников напряжением 6кВ от распределительных подстанций ТП6, ТП7,
ТП8; электроприемников напряжением 10кВ от распределительных подстанций ТП3,
ТП4, ТП5.
4.3
Аппаратура управления
По условиям окружающей среды пульпонасосная относится к категории влажных
помещений. В соответствии с условиями окружающей среды и заданием, вся основная
аппаратура управления и защиты устанавливается на щитах станций управления и
размещается в специальных помещениях (ПСУ), для которых предусмотрена подача
воздуха с избыточным давлением. В помещениях секций управления располагаются
также преобразователи частоты для двигателей грунтовых насосов 2ГрТ-8000/71.
4.4 Выполнение
электрических сетей
Силовые и контрольные сети, в основном, выполнены кабелями с алюминиевыми
жилами, резиновой изоляцией, в резиновой негорючей оболочке марок АНРГ и АКНРГ.
Для электроприемников напряжением выше 1000В применены кабели с
алюминиевыми жилами с пластмассовой изоляцией марки АВВБ и АВВБГ для напряжения
6 кВ и ААШВ для напряжения 10 кВ. Для передвижных и вибрирующих
электроприемников применены гибкие кабели марки КРПТ.
4.5 Заземление
Все электроконструкции, корпуса электродвигательных аппаратов и т.п.,
нормально не находящихся под напряжением, но могущие оказаться под ним,
вследствие повреждения изоляции, заземляются. Присоединение к заземляющему
устройству корпусов электроприемников производится при помощи стальных полос,
четвертой жилы кабеля.
4.6 Расчет электроснабжения насоса, выбор сечения жил кабеля,
питающего двигатель
Для определения сопротивления сети необходимо предварительно выбрать
сечения кабелей и проводов, для чего надо знать значения расчетных токов.
Выбор сечения жил кабелей и проводов производится в соответствии с
условием
каб ≤ Iкаб.доп и Iпров ≤ Iпров.доп
Определим расчетный ток:
в кабеле двигателя АО2-21-49-16Т1:
А (4.1)
Проверка
кабеля по потере напряжения:
(4.2)
Где,
ro - удельное активное сопротивление кабеля (1,125
Ом/км);
хо
- удельное индуктивное сопротивление кабеля (0,071 Ом/км);
l = 160 м -
длина кабеля.
DU < DUдоп.
Выбранный
кабель удовлетворяет условию по потере напряжения, принимаем кабель ААБл-3X240мм2
4.7 Расчет токов короткого
замыкания
Найдем ток трехфазного к.з. в точках К1, Для этого определим
сопротивления элементов цепи, приведенные к базисному напряжению Трансформатор
ТМН-6300/110 Sном=6,3 МВ×А; Uв=110 кВ; Uн=6
кВ; Pк=48 кВт; Uк%=10,5 % Базовая мощность
Sб =
200 МВ.А. Сопротивление питающей системы Xс = 0. Длина кабеля L = 160 м
На рисунке 4.1., показана схема электроснабжения насосов ГрТ 8000/71.
Рис. 4.1. Схема электроснабжения насосного отделения пульпонасосной
(высоковольтная часть)
Сопротивление трансформатора участковой подстанции:
Ом (4.3)
Ом (4.4)
Сопротивление кабельной линии.
X = Xо l = 0,071*0,16=0,011 Ом (4.5)
R = Ro l = 1,125*0,16=0,18 Ом (4.6)
Асинхронный двигатель с короткозамкнутым ротором:
P=3150
кВт; cosj=0,85; Кп.т.=5,7
Ом (4.7)
кВ ,А
(4.8)
Рис.4.2. Схема замещения
Сопротивление от источника питания до точки К-1
S=X1+X2+X3+X4=0,198+0,66+0,024+0,011=0,89
Ом (4.9)
RS=R2+R3+R4=0,048+0,062+0,18=0,29
Ом (4.10)
Мощности короткого замыкания
МВ.А
(4.11)
Ток
в точке Кз
кА
(4.12)
с (4.13)
Ударный ток определяется по формуле
кА
(4.14)
где
kу - ударный коэффициент
Расчет
токов к.з. в точке к-1 с учетом АД
кА
(4.15)(3)1=I(3)c+I(3)g=4+3,2=7,2 kA (4.16)S2=X1+X2+X3=0,198+0,66+0,024=0,882 Ом
(4.17)(3)уд=KyÖ2*I(3)g=Ö2*1,7*3,2=7,6 kA (4.18)=1+e-0.01/0.026 =1,7
(4.19)
c
(4.20)(3)=iус(3)+iуд(3)=7,7+7,6=15,3 кА
(4.21)
Аналогичные расчеты проводим для остальных линий и точек.
4.8 Выбор коммутационной и
защитной аппаратуры
Для включения и отключения электродвигателя привода насоса в рабочем
режиме, к.з. и перегрузках служит высоковольтный выключатель.
Условия выбора высоковольтных выключателей (табл.4.1).
Таблица 4.1. Основные параметры вылючатели
Проверяемая величина
|
Обозначение
|
Формула
|
Номинальное напряжение, кВ
|
Uн
|
Uн³Uнр 6 кВ =6 кВ
|
Номинальный ток, кА
|
Iн
|
Iн³Iн.р. 630 А>342 А
|
Номинальный ток отключения,
кА
|
Iном.отк.
|
Iн.отк.³Iн.отк.рас 20 кА> 7,2 кА
|
Номинальная мощность
отключения, кВА
|
Sн.отк.
|
Sн.отк.³Sн.отк.р 4000 кВА> 3889 кВА к
|
Номинальный ток
динамической стойкости, кА
|
Iу
|
iy³iу.расч.
|
Ток термической стойкости,
кА
|
Iн.т.с.
|
Iн.т.с.³I
|
(4.22)
Выбираем
масляный выключатель типа ВМП-10-630. Его технические характеристики приведены
в таб. 4.2
Таблица
4.2. Технические характеристики масляного выключателя ВМП -10-630
Тип
|
Uном кВ
|
Iном А
|
Предельн.сквоз. ток
|
Ток терм. стойкости,кА(Uс)
|
Ток отк- люч. кА
|
Соб- ствен. Время окл. Сек.
|
Врем вкл. с при- водом
|
|
|
|
действ.зн-е
|
ампл. Зн-е
|
|
|
|
|
ВМП
|
6
|
630
|
20
|
52
|
20
|
20
|
0,1
|
0,3
|
4.9 Выбор разъединителей
Разъединители
служат для отключения цепи без нагрузки, а также для обеспечения видимого
разрыва при производстве ремонтных работ.
Условия выбора разъединителей указаны в таб. 4.3.
Таблица 4.3. Основные параметры разъединители
Величина
|
Обозначение
|
Формула
|
Номинальное напряжение кВ
|
Uн
|
Uн³Uн.т. 6 кВ = 6кВ
|
Номинальный ток, А
|
Iн
|
Iн³Iн.т. 400 А > 342 A
|
Допустимый ударный ток кА
|
iн.дин.
|
iн³iуд.р.
|
Ток термической стойкости
кА
|
Iн.т.с.
|
Iн.т.с.³I t/tт.с.
|
Исходя из этих условий выбираем разъединитель типа РВЛ-6/400 (табл. 4.4).
Таблица 4.4. Технические характеристики разъединителя РВЛ-6/400
Тип
|
Uном кВ
|
Iном А
|
Предельный сквозной ток
к.з. кА
|
Ток термической Стойкости
кА(н.с.)
|
|
|
|
амплитудное
|
действующее
|
|
РВЛ6/400
|
6
|
400
|
50
|
29
|
16
|
II.
СПЕЦИАЛЬНАЯ ЧАСТЬ
5. Система управления насосом с использованием нечеткой логики
.1 Нечеткая логика. Основные определения и свойства
Теория нечетких множеств представляет собой расширение классической
теории множеств. Она нечеткая, но ни в коем случае не неточная. Она
организована и математически строго обоснована, как и классическая теория
множеств, которая в ней содержится и является ее частью. Для облегчения
понимания нечеткой теории множеств важно заметить, что человек, когда он
размышляет, часто не считает правильным или просто не может принять решение
«да» или решение «нет». Он принимает некоторое промежуточное решение: «немного
да» или / и «немного нет». Вполне понятно, что между экспериментальными
величинами или состояниями да / нет, истина / ложь, включено / выключено, один
/ ноль могут быть промежуточные состояния (величины), которые как раз и
являются очень важными и очень нужными.
Любой элемент нечеткого множества может полностью принадлежать некоторому
нечеткому множеству (фаззи-множеству) или принадлежать только в определенной
степени. Поэтому может быть введена очень важная для нечетких множеств
количественная мера - степень принадлежности. При этом используются, как
правило, только нормализованные множества.
В нормализованном множестве (или нормальном) множестве степень
принадлежности всех элементов множества находятся (лежат) в диапазоне между 0 и
1
mA(x) Î [0, 1], т.е. max mA(x) = 1 x Î X, (5.1)
где X - основное множество.
Для того чтобы получить нормализованное (нормальное) множество достаточно
разделить все значения функции принадлежности на ее максимальное значение. В
дальнейшем изложении будем рассматривать только нормализованные множества,
максимальное значение функции принадлежности которых равно 1. Наглядное
представление нормированного четкого множества A, которое является подмножеством основного множества G (A Ì G) дано на рисунке 5.1, а изображение нечеткого нормированного
(нормального) множества B (B подмножество G) - на (рис.5.2) в виде Венн-диаграмм
[7].
Рис.5.1. Нормированное четкое множество А
Рис. 5.2. Изображение нечеткого нормированного (нормального) множества В
При введении математического понятия «нечеткое» множество часто в
качестве наглядных примеров приводят обычное «человеческое» применение
какого-нибудь обыденного понятия, категории.
5.2 Операции с множествами
Покажем, как выполняются операции объединения, пересечения и др. с
четкими и нечеткими множествами.
Пусть A, B - нечеткие нормализованные множества; mA(x), mB(x) - степени принадлежности элемента x к нечеткому множеству A, B; x -
рассматриваемый элемент; G -
множество всех элементов, x -
основное множество.
min{...}
- минимум оператор; выбирается минимум (элемент с минимальным значением) из
фигурных скобок.
max{...}
- максимум оператор; выбирается максимум из фигурных скобок.
Отметим,
что операциям с множествами: объединение множеств, пересечение множеств, а
также операции дополнение множества можно поставить в соответствие операции
алгебры логики. Если A и B множества, то объединению A È B соответствует операция
дизъюнкции (табл.5.1) a Ú b, пересечению множеств A Ç B соответствует операция
конъюнкции a Ù b, а так называемое дополнение множества
в алгебре логики соответствует инверсии
(табл.5.2.). Рассмотрим эти операции с множествами.
Таблица
5.1.
Логические
операции с множествами
a
|
b
|
a Ù b
|
a Ú b
|
a ® b
|
a ¨ b
|
a Ä b
|
0
|
0
|
0
|
0
|
1
|
1
|
0
|
0
|
1
|
0
|
1
|
1
|
0
|
1
|
1
|
0
|
0
|
1
|
0
|
0
|
1
|
1
|
1
|
1
|
1
|
1
|
1
|
0
|
Таблица 5.2.
Алгебра
логики инверсии
a
|
0
|
1
|
10
|
|
|
5.3 Объединение множеств
È B = { (x); m A È B (x))} " x Î G, (5.2)
где множество G - основное
(универсальное) множество, т.е. множество всех элементов x.
Или подробней объединение множеств A, B запишется в виде
A È B = { (x); m A È B (x))| m A È B (x) > 0 } " x Î G, (5.3)
где m A È B (x) := max { m A (x); m B (x) } " x Î G.
Знак := означает « по определению равно»; в более подробной записи
объединение множеств A È B свойство m A È B (x) > 0
указывает на то, что также как, например, для нечеткого множества A носителем S (A) этого множества
является тот элемент x,
степень принадлежности которого больше нуля
Î S (A) Û m A (x) > 0, здесь Û - знак эквивалентности.
Рассмотрим объединение множеств для четкой логики. Пусть x Î C и x Î D, где C и D четкие множества, и m C (x) = 1, m D (x) = 0.
Объединение m C È D (x) = max { m C (x); m D (x) } = max { 1, 0 } = 1, что означает x Î C È D.
5.4
Системы автоматического регулирования с фаззи-регуляторами
При синтезе логических систем автоматического управления (САУ) таких, как
системы управления насосными агрегатами, воздуходувками, лифтами, движением по
железным дорогам - используется математических аппарат классической логики -
алгебры логики. В качестве управляющих устройств для систем логического
управления обычно применяются специализированные микроконтроллеры или
управляющие компьютеры общепромышленного назначения. Существуют
специализированные алгоритмические языки (например «ПРОЛОГ»), которые
применяются при создании управляющих программ САУ. Использование таких языков и
специально созданных программ делает возможным синтезировать для каждого
конкретного случая программу непосредственно на основе технологического
задания, которые представляются обычно для этого в записи по специальной форме.
При синтезе непрерывных САР с фаззи-регуляторами, таких, например, как
система стабилизации выходного параметра сложного технологического процесса
успешно применяется нечеткая логика, лингвистические переменные,
терм-множества. Область применения фаззи-регуляторов - это, прежде всего
автоматическое регулирование тех технологических процессов, строгое
математическое описание которых для целей автоматического управления методами
классической математики представляется очень трудным или даже практически
невозможным.
Для многих сложных технологических процессов, в том числе в
горно-обогатительной, металлургической, химической промышленности часто
используются комбинированные САР. Комбинированную систему, например систему
стабилизации выходного параметра сложного объекта регулирования, можно считать
в некоторой мере характерным и общим примером САР: она имеет замкнутую цепь
регулирования и разомкнутые цепи.
5.5 Фаззифицирование
Фаззифицирование - это превращение измеренных (четких) значений переменной,
или иным образом полученных данных - сигналов от каких-либо устройств,
например, сенсоров, от операторов агрегатов и процессов в категории нечеткой
логики.
Полученные с определенной точностью четкие значения величин или данные
переводятся на язык нечетких множеств - фаззи - множеств, и любая степень
принадлежности mi
определяется далее уже этим нечетким множеством.
Другая формулировка этого определения: фаззифицирование выявляет, в какой
степени данное значение, измеренное или иным образом полученное, имеет
определенное множеством свойство (качество).
Если это лингвистическое терм - множество, то надо определить, к какому
терму и в какой степени относится текущее полученное значение лингвистической,
например входной, переменной.
На рис.5.3, показан «блок фаззифицирования». Простейшая функция
принадлежности изображена на рисунке внутри блока условно в графической форме и
символически изображает процедуру преобразования в этом блоке. Терм-множество
записано в виде m (А, В, С), где mА, mВ, mС - функции принадлежности отдельных терм.
Рис. 5.3. «Блок фаззифицирования»
5.6
Фаззи-логические преобразования
При фаззифицировании получены исходные данные в форме нечетких множеств,
функций принадлежности и степеней принадлежности элементов множеств. Теперь на
основе логических правил ЕСЛИ <предпосылка>, ТОГДА <результат> с
применением необходимых операций И, ИЛИ и др. выполняются основные фаззи -
логические вычисления, в результате которых получаем решение задачи в категориях
нечеткой логики. Схема этой процедуры показана в виде блока преобразований на
(рис.5.4.).
Порядок действий по созданию и работе алгоритма логических преобразований
следующий:
1 Устанавливаются правила переработки
фаззи - информации;
2 Устанавливается механизм переработки
фаззи-информации, необходимость использования операторов И, ИЛИ, НЕ, g-оператора и т.д.;
3 Проводятся вычисления в соответствии
с п.2 для получения степеней принадлежности результирующих множеств.
Рис. 5.4. Схема процедуры фаззи-логических преобразований
5.7 Дефаззифицирование
Дефаззифицирование - это преобразование нечетких данных в конкретные
числа, четкие значения величин.
Схематически указанное преобразование изображено на рис.5.5. На входы
поданы результирующие множества из блока преобразований в виде функций
принадлежности mрез
1, mрез 2, …, mрез n, на выходе численное решение, например в нашем случае,
величина регулирующего воздействия Y.

Существуют различные методы транспонирования нечетких результирующих
множеств в конкретные числа и искомые четкие математические характеристики. Для
каждого конкретного случая (алгоритма) на основе опыта выбирается, или, даже
можно сказать, подбирается после проверки первых результатов наиболее
подходящий метод. Если использовать для решения одной и той же задачи различные
методы дефаззифицирования одних и тех же нечетких характеристик, то могут быть
получены несколько различные выходные данные.
Метод центра тяжести
При дефаззифицировании используется в качестве значения выходной величины
значение координаты (абсциссы) центра тяжести площади результирующего
множества.
Вычисление абсциссы центра тяжести плоской фигуры (рис.5.6) выполняется
по формуле 5.4.
xs =
, (5.4)
где
xs - координата (абсцисса) центра тяжести, xa -
начальное значение абсциссы площади, xe - конечное значение абсциссы
площади, f (x) - функция, ограничивающая площадь фигуры.
Рис.
5.6. Вычисление абсциссы центра тяжести плоской фигуры
Во
многих сложных случаях вычисления по этой формуле необходимо выполнять с
применением численного интегрирования. Поэтому широко используется упрощенная
формула 5.5, в которой интеграл заменен суммой:
»
, (5.5)
где;
xs - абсцисса центра тяжести, xi - абсцисса
среднего значения (центрального значения) выходного множества, например его
терма, Hi - степень принадлежности - «высота отсечения» -
выходного множества, i = 1, 2, …, n - порядковый номер выходного
множества - действующего логического правила.
Метод
среднего значения максимума
В
этом случае за выходное четкое значение принимают абсциссу среднего значения
максимальной величины выходного множества, например, при лингвистических
переменных - функцию принадлежности выходного терма с максимальной площадью.
Метод
дефаззифицирования при синглетон
Вычисление
выходной четкой величины при дефаззифицировании множеств единичной мощности
обычно проводится по той же упрощенной формуле.
Кроме
того, существует метод среднего значения для синглетон. Он используется обычно
при 5 - 9 или большем количестве выходных результирующих множеств синглетон.
Расчет тогда проводится по формуле 5.6:
=
, (5.6)
где,
mi -
выходные функции принадлежности единичной мощности, xi0 - абсцисса
действующего («отсеченного») значения синглетон.
Использование
упрощенной формулы вычисления центра тяжести для MAX / MIN
метода и для синглетон дает одинаковые результаты. Такой же результат получаем
и при применении этой формулы для выходных множеств в нашем примере, полученных
по методу MAX-произведение. Очевидно также, что при использовании в
последнем случае точной формулы для определения абсциссы центра тяжести
результат будет другой.
Также
совершенно другой результат дает формула уравновешивающего метода - среднего
значения для синглетон, использование которой для нашего примера было бы неоправданно.
Существует
еще несколько проверенных, широко используемых на практике методов
дефаззифицирования. Они применяются для решения различных сложных, специальных
задач. Кроме того, создаются новые методы в соответствии с условиями той или
иной задачи и в связи с необходимостью получения тех или иных результатов,
например, усредненных, упрощенных, с учетом определенных акцентов, связанных с
особыми режимами исследуемого процесса и т.д.
5.8 Обоснование применения нечетких систем управления в трубопроводном
гидротранспорте
Гидравлический транспорт применяется в горной
промышленности для перемещения твердых сыпучих материалов потоком жидкости. Он
характеризуется рядом преимуществ по сравнению с другими видами транспорта,
однако целесообразность его использования обусловлена режимом эксплуатации
оборудования гидротранспортной системы. Исследованию процессов, происходящих
при транспортировании двухфазной среды, посвящено немало научных исследований,
проведенных специалистами различного профиля. Весь спектр работ можно
достаточно четко разделить на два направления: теоретические и эмпирические.
Теоретические работы посвящены преимущественно анализу неких идеализированных
моделей, применение которых на практике в ближайшем будущем довольно
сомнительно. Поиск эмпирического или полуэмпирического описания
функционирования гидравлического транспорта дает ощутимые практические
результаты. Эмпирические исследования порождают методики описания и способы
решения задач, которые могут использоваться в достаточно узких рамках. Эти
ограничения, прежде всего, связаны с широким разнообразием гидротранспортных
систем, которые иногда имеют уникальный характер.
Известно, что любая гидротранспортная система имеет
оптимальный (или близкий к оптимальному) режим эксплуатации. На практике
преобладающее большинство систем функционирует в режимах, далеких от
оптимального, а часто и в неустойчивых. Это приводит к значительному удорожанию
транспортных расходов и к аварийным ситуациям, которые могут повлечь за собой
не только экономический, но и экологический ущерб. В связи с этим возникает
необходимость поиска эффективных методик, которые позволили бы математически
описать и в дальнейшем автоматизировать управление процессами гидротранспорта.
В настоящее время основу управления гидротранспортными
системами составляют человеческие знания, то есть опыт, накопленный
квалифицированными специалистами в данной отрасли. Также значительную роль
играют лабораторные исследования и промышленные испытания, ориентированные на
конкретный вид транспортируемого сырья и конфигурацию технологического
оборудования.
Одной из существенных проблем автоматизации
гидравлического транспорта является отсутствие контрольно-измерительной
аппаратуры, которая отвечала бы требованиям управления. Это обусловлено
трудностями измерения физических параметров двухфазной среды (давления,
плотности, расхода, уровня). Существующие датчики с удовлетворительными
характеристиками - это в основном зарубежные дорогостоящие приборы.
Отечественные аналоги значительно уступают им в точности и надежности. Поэтому
большинство параметров гидросмеси измеряется либо косвенным путем, либо
оценивается "на глазок" опытным персоналом.
Таким образом, мы выделили две существенные преграды
для автоматизации гидротранспорта - отсутствие универсальных методик расчета и
проблемы с контрольно-измерительной аппаратурой. В связи с этим следует
отметить ограниченные возможности применения классической теории
автоматического управления для процессов гидротранспорта. Существующая ситуация
в области управления гидротранспортными системами свидетельствует о том, что
большинство задач контроля и управления решаются человеком-специалистом
(экспертом). Качественный характер оценок эксперта и разработанных им правил
принятия решений создают предпосылки для возможности применения искусственного
интеллекта (ИИ) для управления в гидротранспортных системах.
Развитие теоретических и прикладных аспектов
кибернетики, математического программирования, теории автоматического
управления дает реальную возможность замены одного из наиболее
"слабых" звеньев в управлении - человека на производственные системы
с ИИ. Таким образом, ставится задача замены специалиста-эксперта или лица,
принимающего решения (ЛПР), некоторой системой управления с ИИ, которая
выполняла бы его функции. Построение высокоинтеллектуальной системы управления
является достаточно сложной задачей, которую необходимо решать поэтапно.
Рассмотрим последовательность шагов создания системы
управления, предназначенной для конкретных условий работы. Пусть требуется создать
производственную систему с ИИ для управления магистральной гидротранспортной
системой (ГТС) рудника. Для этого необходимо выполнить ряд задач: изучить
теоретические сведения о функционировании ГТС, выявить качественную картину
работы объекта;
§ выполнить инженерные расчеты основных
параметров объекта, используя конкретные данные (количественная оценка);
собрать и обработать экспериментальный материал;
§ собрать и обработать экспертные
данные;
§ создать математические модели
основных звеньев ГТС, четко определить ограничения и критерии (если планируется
использование нечеткой логики для создания системы управления, то
целесообразным является построение нечетких математических моделей элементов
ГТС);
§ построить укрупненный алгоритм
управления ГТС;
§ детально разработать алгоритмы
управления отдельными звеньями ГТС;
§ внедрить локальные алгоритмы
управления в режиме советчика и обучить нейронные сети, если предполагается их
использование;
§ преобразовать алгоритмы для условий
самостоятельного функционирования (на данном этапе на ЛПР возлагается задача
согласования работы локальных алгоритмов);
§ синтезировать разработанные локальные
алгоритмы в единую глобальную систему управления. Синтез может осуществляться
поэтапно путем группирования алгоритмов, наиболее тесно связанных между собой
технологически. На завершающей стадии этого этапа созданная глобальная система
должна функционировать параллельно работе ЛПР и группы экспертов. Здесь система
проходит окончательную проверку и апробацию, в ходе которых устанавливается ее
адекватность, оптимальность, надежность и другие характеристики. Если для
создания системы были использованы нейронные сети, то этот этап совпадает с
последней стадией их обучения;
§ обеспечить самостоятельное
функционирование созданной системы управления.
Выполнение первых трех пунктов является стандартной инженерной задачей,
изучение которой здесь не представляет интереса. Рассмотрим детально следующие
два взаимосвязанных этапа - сбор, обработку экспертных данных и создание на их
основе математических моделей звеньев ГТС.
В данном дипломном проекте предложено использовать нечеткие системы
управления в условиях ГРО «Катока»
5.9 Актуальность использования нечетких систем управления в
области гидротранспорта сырья
Основным технологическим оборудованием напорной ГТС являются насосы,
которые предназначены для создания избыточного давления гидросмеси для
преодоления гидравлических сопротивлений, возникающих при ее движении в
трубопроводе. В рассматриваемой ГТС (ГРО «Катока», респ. Ангола), применяются
центробежные грунтовые насосы. На магистральном трубопроводе (от пульпонасосной
до хвостохранилища), который имеет протяженность 15 км, установлены
центробежные грунтовые насосы ГрТ 8000/71. Непосредственный интерес для решения
задач автоматизации ГТС, предлагаем представить задача на исследование работы
насоса при перекачивании гидросмеси. Как известно, при работе на гидросмеси
напор, развиваемый насосом, возрастает. Существует множество методик расчета
расходно-напорных характеристик центробежных насосов при работе на пульпе.
Однако результаты вычислений по разным методикам отличаются друг от друга до
полутора раз, что вызывает некоторые сомнения и неопределенность выбора
адекватной методики расчета. Построение характеристики насоса по гидросмеси
основывается на налогичной характеристике при работе на чистой воде, которая
должна приводится в паспортных данных насоса. У некоторых насосов такая
характеристика вообще не приводится, а известна лишь рабочая точка с
номинальными значениями расхода и напора. Таким образом, создание
математического описания работы насоса на основе точных числовых данных
является проблематичным. В связи с этим предлагается методика создания нечеткой
математической модели центробежного насоса на основе экспертных данных
качественного характера.
5.10 Нечеткая модель системы
гидротранспорта
Выходным управляемым параметром насоса является
избыточное давление (напор). Величина напора зависит от расхода гидросмеси, ее
плотности гранулометрического состава, а также от конструктивных особенностей
самого насосного агрегата. Наиболее существенное влияние на динамику работы
насос оказывает изменение плотности и расхода гидросмеси. Ha основе экспертных знаний были
установлены предельные границы возможных колебаний расхода (Qmin, Qmax) и плотности (pmin, pmax)
гидросмеси. Также определены номинальные (соответствующие математическому
ожиданию) значения этих же параметров. Для составления нечетких логических
правил описания модели четкие переменные Q и р фаззифицируются в пределах установленных границ (min - max). Для фаззификации был выбрано семь лингвистических
переменных - "очень малое" (ОМ), "малое" (М), "ниже
среднего" (НС), "среднее" (С), "выше среднего" (ВС),
"большое" (Б) и "очень большое" (ОБ). Использование
подобного лингвистического отображения параметров не дает четкого
математического описания, но создает наглядное адекватное представление о
качественных характеристиках объекта. С учетом выделенных лингвистических
переменных строятся функции принадлежности µ входных переменных Q и р (рис. 5.7).
Рис. 5.7. Функции принадлежности входных переменных - а -расход (Q); б - плотность (p)
Следующим этапом создания нечеткой модели является
формирование на основе данных эксперта базы знаний. Она представляет собой
таблицу соответствия выходных переменных входным. Поскольку основой создания
базы значений является человеческий опыт, то данные в ней представлены в
лингвистической форме с использованием введенных лингвистических переменных
(табл. 5.3). Для программной реализации нечеткой модели на ЭВМ база знаний
представляется не в табличной форме, а в виде набору лингвистических правил
(уравнений) вида:
Если..., то...
В математической форме эти правила записываются с
использованием логических операций булевой алгебры: (И), (ИЛИ) (таб.5.3.).
Таблица 5.3. База знаний нечеткой модели центробежного насоса
Q ρ
|
ОМ
|
М
|
НС
|
С
|
ВС
|
Б
|
ОБ
|
ОМ
|
ВС
|
ВС
|
С
|
НС
|
НС
|
М
|
ОМ
|
М
|
Б
|
Б
|
ВС
|
С
|
НС
|
НС
|
М
|
НС
|
ОБ
|
ОБ
|
Б
|
ВС
|
С
|
НС
|
НС
|
С
|
ОБ
|
ОБ
|
Б
|
Б
|
ВС
|
С
|
НС
|
ВС
|
ОБ
|
ОБ
|
ОБ
|
Б
|
ВС
|
С
|
С
|
Б
|
ОБ
|
ОБ
|
ОБ
|
ОБ
|
Б
|
ВС
|
С
|
ОБ
|
ОБ
|
ОБ
|
ОБ
|
ОБ
|
ОБ
|
Б
|
ВС
|
Запишем, например, логическое уравнение для значения
давления Н, соответствующего среднему (С) уровню: 'j
Если ((Q=HС^р= OM)V(Q=С^р=M)V
V(Q = ВС^р= HС)V(Q= Б^р=С)V(Q = Б^р = BС)V (5.7)
V(Q =OБ^p=ВС)V(Q = OБ^pБ)) то Н=С.
Данная форма записи наглядна для понимания логического
вывода правил, но для практического применения это уравнение должно
записываться с учетом значений функций принадлежности, которые определяются
согласно (рис.5.1.), тогда выражение (5.7) примет вид (5.8):
(5.8)
где
Н* - значение давления, выраженное в числовой форме. Преобразование
лингвистического значения переменной в числовое называется дефаззификацией.
Существует
достаточно много методов дефаззификации. В данном случае целесообразно
применить метод весового осреднения.
Система
управления пульповодом на подводящем трубопроводе установлены датчики расхода и
плотности, а на отходящем - датчики давления. Сигналы с датчиков поступают на
контроллер RSLogix5000 фирмы Rokwell Automation (Rokwell Software), который работает по
нечеткому алгоритму (рис.5.8.). В него заложена база знаний, показанная в
таб.5.3.
Рис. 5.8. Обучающееся управление по обобщенной функции
принадлежности
После обработки сигналов по нечеткому алгоритму, он
выдает управляющие сигналы на преобразователи частоты (ПЧ), которые, в свою
очередь, управляют частотой вращения двигателей (АД), изменяя таким образом,
напор и подачу грунтовых насосов ГрТ 8000/71.
III.
ЭКОНОМИЧЕСКАЯ ЧАСТЬ
6. Определение экономической эффективности о модернизации и
автоматизация ЭП. Конвейерной установки
Экономический эффект от модернизации автоматической системы управления
электропривода конвейерной установки образуется в результате более
рационального использования технологических процессов; оптимизации
распределения технологических потоков; сокращение трудоемкости учетных задач;
повышение оперативности работ.
Все это способствует повышению уровня аналитической и нормативной работы,
большей обоснованности решений. Модернизация системы позволяет определять ряд
аналитических показателей, расчет которых затруднен: фондо материало и
трудоемкость. Использование их для планирования и анализа позволяет более четко
устанавливать затраты на производство продукта и пути их снижения, определять
влияющие структурные изменения на конечных показателях работы предприятия. При
расчете экономической эффективности учитывают экономический эффект,
достигаемый в результате оптимизации производства и снижения трудоемкости
решения учетных задач.
Основной эффект от модернизации автоматики - стабилизация и оптимизация
технологического режима, следовательно, повышение производительности установок,
сокращение норм расхода.
Экономическую эффективность автоматизации технологических процессов определяет
изменение следующих технико-экономических показателей:
§ уменьшение расходных коэффициентов по сырью, и материалам;
§ повышение надежности работы конвейер и системы электроснабжения, так как
исключаются механические, электромагнитные , возникающие при пусках, которые
при прямых пусках могут в 6-8 раз превысить номинальные значения;
§ нарастание пускового тока плавно с заданным ограничением;
§ возможность осуществлять практически неограниченное число пусков
конвейер;
§ возможность запуска от газотурбинных, газопоршневых, дизельных
электростанций и других источников без увеличения их мощности для обеспечения
запуска электродвигателей;
§ увеличение межремонтных промежутков и сроков эксплуатации оборудования;
§ исключение просадки напряжения сети в режиме пуска электродвигателей, что
обеспечивает надежную работу подключенного к сети оборудования.
§ повышение качества продукции за счет приближения режимных параметров к
технологическим ограничениям при уменьшении их разброса и более точного
поддержания заданных режимов, оптимальной их корректировки;
§ сокращение при проектировании количества однотипного технологического
оборудования и промежуточных емкостей в результате единичной мощности
конвейеров, сокращение числа приборов КИПиА путем использования систем
централизованного контроля и регулирования, а также непосредственного цифрового
управления;
§ улучшение условий труда, повышение безопасности труда, сокращение
травматизма.
6.1 Факторы, влияющие на экономическую эффективность
Определяем экономическую эффективность от внедрения электропривода на
основе ЧПР PowerFlex 7000 фирмы Rokwell Automation
(Roсkwell Software), и электродвигателя с короткозамкнутым ротором для
ленточную конвейер типа WEG-330.
Факторы, сказывающиеся на экономической эффективности:
1. Сокращение числа отказов в работе привода, а значит увеличение
производительности конвейеров;
2. Сокращение времени ремонта электропривода;
3. Сокращение времени на проведение профилактических и регламентных
работ;
4. Увеличение надёжности электропривода конвейеров за счёт
применения асинхронного двигателя с короткозамкнутым ротором;
. Уменьшение капиталовложений на создание электропривода;
6. Сокращение потребления электроэнергии за счёт увеличения КПД.
При экономической оценке считаем, что с внедрением широтно-импульсного
преобразователя фирмы Rokwell Automation, и электродвигателя с короткозамкнутым
ротором высвобождения обслуживающего персонала не произойдёт, не изменится
заработная плата, облегчится лишь обслуживание конвейеров установки.
6.2 Плата за электроэнергию. Затраты по базовому варианту
Стоимость потреблённой электроэнергии рассчитывается по формуле:
, (6.1)
где а - стоимость 1 кВт заявленной мощности (1,66 Долларов США); В -
стоимость 1 кВт/ч электроэнергии (0,025 $/кВт . час); W - расход активной мощности.
(6.2)
где Тм - число часов работы конвейер в месяц (600 часов); Руст - мощность
двигателя привода Л.К.
кВт (6.3)
кВт .
час;
$/месяц.
Годовая плата за электроэнергию составит:
$/год
(6.4)
6.3 Суммарные затраты по базовому варианту
Общие затраты по базовому варианту составят:
Долларов
США. (6.5)
Где,
- Амортизационные отчисления, к - капитальные затраты
по базовому, к = 1 360 Долларов США; 0,05 - норма амортизационных отчислений.
Тогда:
Долларов США.
6.4 Затраты по предлагаемому варианту
Затраты на электроэнергию составят:
кВт
кВт .
час;
Внедрение
частотно управляемого электропривода «PowerFlex 7000» позволит снизить
потребление электроэнергии на 20% ежемесячно. Таким образом:
Долларов
США.
Годовая плата за потреблённую электроэнергию составит:
Долларов
США.
Капитальные затраты по предлагаемому варианту, представлены в таб.6.1
Долларов
США. (6.6)
Где,
Цоб - цена оборудования (ЧПР Power Flex 7000);
Км.д.
- коэффициент, учитывающий расходы на Монтаж, доставка, и наладка
Амортизационные
отчисления составят:
$.
Таблица 6.1.
Капитальные затраты по предлагаемому варианту
Затраты
|
Цена (Долларов США)
|
Преобразователь частоты PowerFlex 7000
|
144000
|
Монтаж, доставка, наладка
|
800
|
Зарплата рабочих и соц.
Страхование
|
360
|
Материалы и запасные части
|
600
|
Прочие расходы
|
200
|
ВСЕГО
|
145960
|
6.5 Суммарные затраты по предлагаемому варианту
Суммарные годовые затраты по предложенному варианту составят:
Долларов
США /год.
6.6 Экономический эффект от внедрения широтно-импульсного
преобразователя фирмы PowerFlex 7000
Годовая прибыль при внедрении предлагаемого варианта равна:
; (6.7)
где Сг1 и Сг2 - суммарные годовые затраты по базовому и предлагаемому
варианту соответственно.
Долларов
США /год.
Срок окупаемости находится по формуле:
, лет;
(6.8)
где кз - капитальные затраты по предложенному варианту; П - годовая
прибыль.
Срок окупаемости составит:
года.
Годовой экономический эффект составит:
(6.9)
где Еq =0,3 ¸ 0,5; кз - кап. затраты по предлагаемому
варианту.
Для сравнения базового и предлагаемого вариантов составим таб.6.2.
Таблица 6.2.
Технико-экономические показатели
Показатель
|
Ед. изм.
|
Варианты
|
|
|
Базовый
|
Предлагаемый
|
Капитальные затраты
|
$
|
---
|
145960
|
Экон. плата за
электроэнергию кВт. час
|
$/год
|
660799
|
528639
|
суммарные затраты
|
$/год
|
660867
|
535937
|
Экономический эффект
|
$/год
|
81141
|
Срок окупаемости
|
год
|
1,2
|
IV.
БЕЗОПАСНОСТЬ ЖИЗНЕДЕЯТЕЛЬНОСТИ
7. Характеристика условий и анализ потенциальных опасностей
Проектом предусмотрено проведение мероприятий по автоматизации
конвейерной линии в цехах дробильно-обогатительной фабрики на ГРО ”Катока”.
Мероприятия включают монтажные, пусконаладочные работы в условиях вредного
производства.
При проведении работ основными вредными факторами являются:
§ недостаточная освещенность (10 лк);
§ опасность поражения током;
§ шум (более 98 дБА);
§ вибрация (более 10-15 дБА);
§ повышенная запыленность (более 80% - 2,1 мг/м3).
Кроме того, существует потенциальная опасность травмирования вращающимися
частями машин и механизмов, валами вращения электродвигателей, редукторов,
конвейеров, муфтами соединения электрических приводов.
При проведении работ возможны следующие чрезвычайные ситуации:
§ возгорание электропроводки и электрооборудования;
§ пожары в цехах фабрики;
§ обрушение конструкции здания.
Для района проведения работ существует потенциальная опасность
возникновения чрезвычайной ситуации, связанной с высоким температурой
окружающего воздуха +35,1 0 С, сильные дождей, ураганные ветры и другие
стихийные бедствия, могущие нарушить снабжение фабрики рудой, материалами,
электроэнергией, сорвать доставку на работу и с работы людей и создать тем
самым напряженную обстановку.
7.1
Анализ травматизма
Анализ проводится за период с 2005 по 2006 г. статистическим методом,
путем группировки в таблицы по следующим пунктам:
§ коэффициенты частоты, табл.7.1.;
§ по стажу, табл.7.2.
§ по возрасту, табл.7.3;
§ по тяжести, табл.7.4.
В таблицу 7.1. сведены коэффициенты частоты и тяжести травматизма.
|
2006
|
2007
|
Коэффициент частоты, Кч
|
4,49
|
3,63
|
Коэффициент тяжести, Кт
|
23,35
|
24,32
|
Потеря дней
трудоспособности
|
794
|
681
|
Среднесписочная численность
трудящихся
|
3378 (278 женщин)
|
3442 (322 женщин)
|
Таблица 7.2. Анализ травматизм по стажу
Травматизм по стажу
|
2006
|
2007
|
от 0 до 5 лет (из них до 1
года)
|
13 (3)
|
12 (4)
|
от 5 до 10 лет
|
12
|
6
|
от 10 до 15 лет
|
5
|
5
|
от 15 до 20 лет
|
2
|
3
|
от 20 лет и выше
|
2
|
2
|
Таблица 7.3. Анализ травматизм по возрасту
Травматизм по возрасту
|
2006
|
2007
|
до 18 лет
|
-
|
1
|
с 18 до 25 лет
|
3
|
1
|
с 26 до 30 лет
|
2
|
1
|
с 31 до 40 лет
|
10
|
18
|
с 41 до 50 лет
|
16
|
7
|
от 51 до 60 лет
|
3
|
-
|
Из анализа травм по возрасту и стажу работы пострадавшего видно, что в
2005г. больше всего травм допустили люди в возрасте около 40 лет (18 случаев),
но с небольшим стажем работы по профессии до 5 лет (12 случаев). Это говорит о
том, что рабочий персонал без профессиональных навыков часто подвергается
риску, полагаясь на свой богатый жизненный опыт.
Таблица 7.4. Анализ травматизм по тяжести
Травматизм по
тяжести20062007
|
|
|
Всего несчастных случаев
|
34
|
28 (1 подросток)
|
Легкие
|
25
|
20
|
С тяжелым исходом
|
7
|
7
|
Со смертельным исходом
|
2
|
1
|
Мероприятия по снижению травматизма на дробильно-обогатительной фабрике:
§ Результаты анализа травматизма за прошедшие четыре года довести до
сведения всех работников фабрики.
§ Руководителям и специалистам фабрики в своей профилактической работе по
охране труда и технике безопасности учитывать вывод данного анализа
травматизма.
§ При проведении экзаменационных проверок знаний, очередных инструктажа по
технике безопасности, а также перед выдачей заданий особое внимание уделять
работникам в возрасте 40-50 лет, со стажем работы 10-20 лет.
§ Выделение дополнительных средств для устранение неисправностей машин,
механизмов и т.п., а также улучшение условий труда на рабочем месте.
§ Ежесменное обследование рабочих мест механиками, энергетиками,
ст.мастерами и мастерами, проводить в наиболее травмоопасное время, т.е. с
11.00 до 14.00 и с 16.00 до 18.00.
7.2
Борьба с шумом
С целью снижения шума и защиты от шума в корпусе мелкого и среднего
дробления используются:
§ средства звукоизоляции, звукопоглощения и снижения ударного шума конусных
дробилок типа КСД и КМД;
§ пластинчатые питатели вместо вибропитателей;
§ грохоты с ограждениями повышенной звукоизоляцией;
§ малошумные футеровки в местах перегрузки руды с подвижных конвейеров,
дробилок, грохотов;
§ звукоизолированные кабины наблюдения для машинистов кранов, подвижных
конвейеров и дробилок.
В качестве индивидуальных средств защиты от шума используются
противошумные наушники типа “ВЦНИИО-2” и противошумные вкладыши типа “ФП”.
7.3 Борьба с пылью
Источниками пыли являются узлы пересыпа руды с конвейера на конвейер, в
бункер, грохота, вторичное пылеобразование, которое характерно для всех цехов
фабрики. Для предотвращения распространения пыли все перегрузочные устройства,
течки, воронки закрыты кожухами с местными отсосами, подсоединенные к
аспирационной системе.
Борьба с производственной пылью осуществляется путём внедрения ряда
санитарно-гигиенических мероприятий:
§ вентиляция и аспирация воздуха;
§ герметизация оборудования, в процессе работы которого происходит
выделение вредных веществ;
§ гидроподавление пыли в узлах перегрузки руды;
§ гидросмыв рабочих площадок.
В комплексе мероприятий для создания нормальных санитарно-гигиенических
условий труда предусмотрено укрупнение системы аспирации пылящих точек
герметизированного технологического оборудования с устройством ёмких укрытий и
применением мокрой очистки выбрасываемого воздуха.
Воздухообмен рассчитан на борьбу с влаговыделением и поддержанием
нормальных параметров микроклимата. В холодное время года для защиты от
проникновения холодного воздуха с улицы в цеха фабрики ворота снабжены
тепловыми завесами, а приточный воздух подогревается в камерах калориферов.
В местах, где запыленность воздуха превышает ПДК (4 мг/м3), трудящиеся
обеспечены противопылевыми респираторами "Лепесток - ШБ-1" или
РУ-60М.
Практика показывает, что создание нормальных условий труда достигается
лишь при осуществлении целого комплекса мероприятий, как-то: герметизация
оборудования, увлажнение руды, аспирация, приточно-вытяжная вентиляция,
применение средств индивидуальной защиты. Технологическое оборудование, работа
которого сопровождается пылевыделением (дробилки, грохоты и т.д.) снабжены
встроенными герметизированными укрытиями, подключенными к аспирации.
В случае использования загрязненной воды производится ее осветление и
бактериологическая очистка. Расход воды в корпусе крупного дробления 2500 л/смену.
7.4 Электробезопасность
При эксплуатации электрооборудования, дробилок ремонтные работы и уход за
ними производятся персоналом в полном соответствии с “Правилами технической
эксплуатации электроустановок потребителя (ПТЭ и ПТБ) и по технике
безопасности, действующие на ГРО “Катока”. Все работы по монтажу, ремонту,
ликвидации неисправности производятся при полном снятии напряжения, а именно:
. с главного электропривода;
. с электропривода распределителя питания материала;
. со стеллажа сопротивлений;
В электрооборудование главного привода входит:
. электродвигатель;
. щит станции управления;
Напряжение подается только после выполнения всех требований по
заземлению. Заземляются:
. Корпуса электрических машин (находящихся в цеху, дробилке);
. Каркасы щитов управления.
Каждый заземляющий элемент присоединен к заземлению или заземляющей
магистрали.
Максимальное сопротивление заземления, измеренное в любой (в том числе и
наиболее удалённой от главных заземлителей) точки заземляющей сети, не
превышает 4 Ом.
Система защитного отключения состоит из коммутационного аппарата,
осуществляющего отключение сети с повреждённой изоляцией от источника питания
(автоматический выключатель), и аппарата защиты (реле утечки), выполняющий
контроль состояния изоляции сети относительно земли.
Для защиты от токов утечки применяют аппараты типа РУ-380 (устройство
автоматического контроля изоляции). Время отключения повреждённой сети не
превышает 0,2 с (согласно ПТЭ и ПТБ).
Применяется также система сигнализации, оповещающая об изменении режима
работы оборудования. Чтобы не произошло воспламенения или поломки двигателей
из-
за попадания пыли, применяют машины, имеющие оболочку, защищающие их
внутреннюю полость, а также двигатели во взрывобезопасном исполнении.
Для контроля прочности и целостности изоляции периодически проводят ее
проверку специальными приборами - мегаомметрами. Исправная изоляция
обеспечивает достаточную защиту от поражения током при прикосновении к
изолированному проводу.
Все доступные токоведущие части изолируются и ограждаются.
Вращающиеся соединительные муфты имеют защитные кожуха.
Все проходы к электрооборудованию и доступ к нему свободны и достаточны
для обслуживания и ремонта.
Лица, обслуживающие электрические грузоподъемные механизмы, электрокары,
электросварочное оборудование и т.д. и имеют допуск, это:
§ тельферист-стропольщик - I кв.
гр - 36В;
§ машинисты кранов - II кв.
гр. - 220-238 В;
§ электросварщик - II кв.
гр - 220-238 А;
§ дробильщики - II кв. гр. -
220-238 В.
Также надо отметить, что в качестве переносного освещения на рабочих
местах используется освещение U = 36
В, а в особо опасных местах и помещениях (дробилках) не выше 12 В. Переносным
освещением пользуются работники I кв.
гр. и выше.
7.5 Пожарная безопасность
Содержание производственных помещений и противопожарного оборудования в целом
отвечают действующим “Типовым правилам пожарной безопасности на промышленных
предприятиях”. Цех дробильный и подсобные помещения, склады обеспечены
первичными средствами тушения и пожарным инвентарем.
Пожарная техника для защиты объектов. Основные виды.