Страна
|
Индекс МПК
|
Номера просмотренных патентов
|
Выявленные аналоги
|
Россия
|
G01K 7/01 G01K 7/02 G01K 7/16 G01K 7/32
|
№№ 2207529 - 2448335
|
№ 2207529 «Цифровой термометр», № 2328710 «Цифровой
термометр», № 2373502 «Устройство для измерения температуры теплоносителя», №
2411469 «Телеметрическое устройство для измерения температуры», № 2445589
«Способ измерения температуры поверхности и измеритель температуры», №
2447411 «Способ измерения температуры, термоэлектронно-механический
преобразователь с автоэлектронной эмиссией и способ его изготовления», №
2447412 «Устройство для измерения температуры», № 2448335 «Термокоса»
|
2.4 Анализ результатов поиска
Рассмотрим более подробно аналоги, перечисленные в таблице 2.1.
Цифровой термометр (патент № 2207529) содержит термопреобразователь с
частотным выходом, первый и второй генераторы частот, реверсивный и суммирующий
счетчики, три элемента «И», триггер, блок индикации и преобразователи частоты в
код и кода в частоту. В устройство также введен регистр, кодовый вход которого
соединен с выходом реверсивного счетчика, прямой динамический вход записи - с
выходом триггера, а выход - с кодовым входом преобразователя кода в частоту.
Техническим результатом является повышение быстродействия цифрового термометра.
Изобретение (патент № 2328710) относится к измерительной технике,
предназначено для работы с термопреобразователями с частотным выходным сигналом
и может быть использовано при измерениях температуры, например, в
теплосчетчиках для повышения точности измерения температуры при одновременном
упрощении устройства. Цифровой термометр содержит два термочувствительных
пьезорезонатора, помещенных в защитные капсулы и включенных в частотозадающие
цепи измерительных автогенераторов, выходы которых соединены с первыми входами
блоков формирования разностной частоты, вторые входы которых соединены с
выходом опорного автогенератора, и третьим с - таймерным входом вычислительного
блока. Первый и второй счетные входы, которого соединены с выходами первого и
второго блоков формирования разностной частоты, а четвертый вход соединен с
выходом ПЗУ, вход которого соединен с первым выходом вычислительного блока,
второй выход которого, в свою очередь, соединен с входом блока индикации.
Технический результат - повышение точности измерения температуры при
одновременном упрощении устройства.
Изобретение (патент № 2373502) относится к термометрии, а именно к
контактным датчикам для измерения температуры, и может быть использовано в
нефтяной, газовой, химической, пищевой промышленности, а также в коммунальном
хозяйстве для измерения температуры среды, находящейся в трубопроводах,
независимо от диаметра трубы. Предложено устройство для измерения температуры
теплоносителя, включающее расположенную в трубопроводе капсулу, представляющую
собой стакан со ступенчатым дном, причем донная ступень выполнена в виде
наружного глухого тонкостенного патрубка. На внутренней боковой поверхности
патрубка выполнена резьба, на которой жестко закреплена вставка, выполненная в
виде снабженного внешней резьбой стержня, снабженного продольной сквозной
прямоугольной канавкой, при этом во внутренней полости капсулы установлен
измерительно-передающий модуль. Модуль состоит из измеряющей температуру
печатной платы, снабженной хвостовиком с закрепленным на нем
термочувствительным элементом на конце, и печатной платы беспроводной связи,
включающей элемент инициализации. В зоне верхнего основания корпуса установлены
элемент питания и антенна для передачи информации на счетчик тепловой энергии
и/или индикатор температуры. Технический результат - повышение точности
измерения, упрощение конструкции, обеспечение надежности работы устройства и
удобство пользования потребителем тепла.
Телеметрическое устройство для измерения температуры (патент № 2411469)
предназначено: для измерения температуры и учета теплопотребления в
труднодоступных местах и/или опасных местах. Сущность изобретения:
телеметрическое устройство для измерения температуры содержит источник
постоянного напряжения, термочувствительный элемент, катушку индуктивности, два
полевых транзистора разной проводимости. Стоки полевых транзисторов соединены
между собой. Изменение температуры контролируемого объекта вызывает изменение
емкостной составляющей термочувствительного элемента, выполненного в виде
пьезоэлектрика, что приводит к изменению резонансной частоты колебательного
контура, образованного термочувствительным элементом и катушкой индуктивности.
Телеметрическая информация передается по элементам объекта контроля с помощью
акустических волн. Технический результат - создание устройства для измерения
температуры, в котором отсутствует необходимость в электрической линии связи с
потребителем информации о температуре объекта контроля в контролируемой зоне.
Способ измерения температуры поверхности и измеритель температуры (патент
№ 2445589). Сущность изобретения заключается в использовании потока
электромагнитного излучения видимого диапазона и малой интенсивности от
излучателя, например лазера, предварительно расфокусированного устройством и
направленного на нагретую поверхность. Часть падающего излучения отражается от
поверхности детали, фокусируется устройством на фотоприемник, например
фотодиод, где под действием этого излучения вырабатывается сигнал в виде
электрического напряжения или тока. Уровень этого сигнала определяется
величиной отраженного излучения, которое зависит от температуры поверхности.
Сравнивая получаемый с фотоприемника сигнал с эталонным сигналом, определяют температуру
исследуемой поверхности. Измеритель температуры содержит излучатель
электромагнитных волн, например лазер, расфокусирующее и фокусирующее
устройства, фотоприемник, усилитель, компаратор, схему «И», генератор линейно
изменяющегося напряжения, генератор импульсов образцовой частоты, двоичный
счетчик импульсов, дешифратор, цифровое устройство сравнения, устройство памяти
эталонных кодов, устройство индикации. Технический результат - создание
измерителя температуры во всем диапазоне возможных температур.
Способ измерения температуры, термоэлектронномеханический преобразователь
с автоэлектронной эмиссией и способ его изготовления (патент № 2447411).
Техническое решение заключается в том, что определяют изменения параметров
термочувствительного элемента в зависимости от изменения температуры и
определяют текущее значение температуры по величине указанных параметров. В
качестве термочувствительного элемента используют биморфный элемент,
размещенный в электрическом поле, а о текущем значении температуры судят по
изменению тока эмиссии в зависимости от механической деформации биморфного
элемента от температуры. В качестве биморфного элемента используют
преобразователь, первый слой выполнен из окисла ванадия, а второй - из
вольфрама. Термоэлектронномеханический преобразователь с автоэлектронной
эмиссией содержит один чувствительный элемент с одной полупроводниковой
структурой и электронную схему. Чувствительный элемент размещен на основании
преобразователя с зазором относительно токопроводящей площадки, на поверхности
которой сформирован, по меньшей мере, один вискер. В биморфном элементе
выполнены отверстия. Два и более биморфных элемента объединены в матричную
структуру на общем кристалле. Электронная схема содержит электронные ключи и
мультиплексоры опроса строк и столбцов, связанные с общим видеовыходом.
Устройство для измерения температуры (патент № 2447412). Изобретение
относится к измерительной технике и может быть использовано в телеметрической
системе. Заявлено устройство для измерения температуры, содержащее термометр
сопротивления и задающий резистор, общая точка которых соединена с общей шиной,
генератор стабильного тока, шесть электронных ключей, генератор прямоугольных
импульсов, три усилителя. Дополнительно в устройство введен RC-фильтр. Электронные
ключи разбиты на три группы по два ключа в каждой группе. В устройство также
введен запоминающий конденсатор, который одним выводом подключен к объединенным
между собой выходам электронных ключей второй группы, а другим - к входу
первого усилителя. Технический результат: повышение помехоустойчивости
устройства.
Термокоса (патент № 2448335). Изобретение относится к термометрии, а
именно к датчикам температуры, и предназначено для одновременного измерения
температуры в нескольких точках объекта, расположение которых определяется
конструкцией объекта. Термокоса содержит последовательно расположенные датчики
температуры, соединенные между собой гибким кабелем, обеспечивающим
электрическое соединение датчиков температуры, разъем для подключения к устройству
считывания, хранения, обработки и отображения данных, при этом каждый датчик
температуры заключен в защитный корпус. Технический результат - снижение
времени термической реакции, повышение точности измерения и надежности, а
также возможность расширенного диапазона использования.
Патентные исследования показали, что на сегодняшний день существует
достаточно большое количество устройств измерения температуры различных
моделей, отличающихся принципом действия, информативностью и точностью
получаемых данных, что свидетельствует о высокой востребованности подобных
устройств и развитии исследований в данном направлении.
Сравнение датчиков, рассмотренных при патентных исследованиях с датчиком
температуры TST01-2,0-П, показало, что данный датчик температуры является
наиболее подходящим для разрабатываемой системы по совокупности причин:
- серийное производство;
- простота конструкции;
минимальные габаритные размеры;
наличие цифрового выхода;
низкая стоимость.
автоматический электрообогрев трубопровод гидратообразование
3. Система автоматизации куста газоконденсатных скважин
.1 Цели создания автоматизированной системы управления
Основными целями создания автоматизированных систем управления
технологическими процессами являются:
- комплексная автоматизация объектов Кшукского и Нижне-Квакчикского
газоконденсатных месторождении, создание на базе АСУ ТП малолюдной и
энергосберегающей технологий, позволяющих повысить рентабельность и
эффективность производства;
- выполнение установленных производственных заданий, снижение
непроизводительных потерь материально-технических и топливно-энергетических
ресурсов и сокращение эксплуатационных расходов;
обеспечение противоаварийной и противопожарной защиты объектов с
целью повышения экологической безопасности производства;
обеспечение надежной и эффективной работы основных и
вспомогательных производственных объектов за счет оптимального управления
режимами их работы.
Основной задачей создания АСУ ТП является превращение технологических
объектов в автоматизированные производственные звенья, работающие в заданных
режимах под оперативным контролем вышестоящих уровней управления [1].
Структурная схема автоматизации куста газоконденсатных скважин № 1
Нижне-Квакчикского ГКМ. Основными методами, позволяющими осуществить поставленные
цели и задачи, являются [2]:
- оптимизация структуры АСУ, исключающая избыточность технических
средств, снижение трудоемкости технического и ремонтного обслуживания систем
управления;
- выявление предаварийных и аварийных ситуаций в оперативном режиме;
автоматизация сбора, обработки и представления информации
оперативному персоналу.
АСУ ТП объектов Кшукского и Нижне-Квакчикского газоконденсатных
месторождений обеспечивает функционирование технологического оборудования в
заданном режиме без постоянного присутствия обслуживающего и эксплуатирующего
персонала на объектах.
Отслеживание текущего режима работы оборудования и управление
технологическим процессом осуществляется автоматически на основании заложенных
алгоритмов управления. При этом оперативному персоналу предоставляется
возможность наблюдения за ходом процесса и управления режимами работы
оборудования с автоматизированных рабочих мест производственного персонала.
На АРМ персонала отображается текущий режим работы технологического
оборудования, аварийные и предупредительные сообщения системы при отклонениях
наиболее важных технологических параметров за допустимые границы,
диагностическая информация о работоспособности комплекса технических средств, а
также отчеты установленной формы.
3.2 Основные технические решения
В качестве основных принципов при определении архитектуры построения АСУ
ТП приняты следующие:
- децентрализация функций сбора, обработки информации и выработки
управляющих воздействий, максимальное их приближение к месту возникновения
информации и её использования;
- распределенность и возможность использования информации
различными подсистемами;
модульность построения технических и программных средств;
создание многоуровневой системы оптимального управления
технологическим процессом;
функционирование без постоянного присутствия обслуживающего
персонала для систем управления большинства технологических объектов;
стандартизация взаимосвязей (функциональная, программная,
конструктивная) между уровнями управления.
Структура АСУ ТП обеспечивает выполнение функций контроля и оптимального
управления производством в целом, а также управление отдельными установками,
как при нормальной работе, так и в нештатных ситуациях.
АСУ ТП построена по иерархическому принципу и включает в себя два взаимосвязанных
уровня:
- нижний уровень - уровень систем автоматизированного управления
технологическим оборудованием, функционирующий в автоматическом режиме без
присутствия человека.
Системы управления данного уровня включают в себя датчики, преобразователи,
исполнительные механизмы, системы локальной автоматики и станции
автоматического управления, реализуемые на базе программируемых логических
контроллеров;
- верхний уровень - уровень операторной, в которой размещается
оперативно-производственная служба, реализуется на базе персональных
компьютеров с организацией автоматизированных рабочих мест персонала. Уровень
ОПС размещаются в операторной служебного корпуса.
Требования к структуре и функционированию системы обусловлены
топологическим расположением контролируемых и управляемых технологических
объектов обустройства Нижне-Квакчикского месторождения и необходимостью
обеспечения высокого уровня надежности систем и объекта управления в целом.
3.3 Функционирование автоматизированной системы управления
АСУ ТП является восстанавливаемой и обслуживаемой многофункциональной
системой. АСУ ТП функционирует в режиме реального времени в непрерывном
круглосуточном режиме.
АСУ ТП функционирует в одном из следующих режимов:
- автоматический;
- автоматизированный (с рабочего места оператора);
местный (от местных щитов управления, от местных кнопок при
пуско-наладочных, ремонтных работах).
Переключение между местным и дистанционным (от АСУ ТП) режимами работы
исполнительных механизмов производится переключателями с силовых щитов
управления. Переключение между автоматическим и автоматизированным режимами
управления производится оператором с пульта управления.
Система телемеханики газовых скважин и газопроводов функционирует в
автоматическом режиме и не требует постоянного присутствия обслуживающего
персонала.
Управление объектами СТМ осуществляется с пульта оператора, который
располагается в операторной служебного эксплуатационно-ремонтного блока УКПГ.
Передача информации системы телемеханики осуществляется по оптоволоконному
кабелю.
АСУ ТП Кшукского и Нижне-Квакчикского ГКМ предназначена для
автоматизированного контроля и управления основными и вспомогательными
процессами добычи и подготовки газа для обеспечения бесперебойной подачи
запланированных объемов газа в межпромысловый газопровод с наименьшими
эксплуатационными затратами.
Технологические процессы характеризуются большим количеством переменных
состояния и управления, воздействием на объект многочисленных возмущений,
связанных с плановыми переключениями технологических аппаратов и применением
взрывоопасных и пожароопасных продуктов. Все это в совокупности предъявляет
повышенные требования к АСУ ТП.
Технологические процессы являются непрерывными. Однако для выполнения
технологического регламента существует возможность осуществления программно -
логического управления по пуску и останову объекта.
Управление технологическим процессом добычи и переработки газа связано с
получением, переработкой и анализом большого объема информации. Организация
потоков информации - одно из необходимых условий рационального функционирования
системы управления. Потоки информации замыкаются через производственный
процесс и охватывают все элементы производства [3].
Технологический процесс обработки информации в АСУ ТП включает:
- сбор и подготовку данных;
- передачу данных;
обработку и хранение данных;
выдачу данных пользователю.
Основным методом сбора данных в АСУ ТП является автоматический. В этом
случае осуществляется прямое измерение технологического параметра,
преобразование сигнала и передача сигнала в управляющий контроллер.
Информационная модель системы включает:
- график информационной взаимосвязи задач и комплексов задач АСУ ТП;
- состав оперативных документов, необходимых для формирования
соответствующих массивов на машинных носителях;
состав выходных документов, формируемых в результате решения
задачи.
Для решения задач всех информационных уровней используется единая система
классификации и кодирования информации, единая система документации и единая
нормативно - справочная информационная база на машинных носителях.
АСУ ТП УКПГ по выполняемым функциям является интегрированной
организационно-технологической системой и функционально состоит из следующих
подсистем:
- распределенная система управления УКПГ;
- система противоаварийной защиты УКПГ;
АСУ ТП построена по иерархическому принципу и включает следующие уровни
управления:
- уровень оперативно-производственных служб. К нему относятся серверы,
АРМы, коммуникационное оборудование уровня ОПС, панели резервного управления,
пульт экстренного останова;
- уровень систем автоматического управления.
Ниже приведен перечень функций системы в соответствии с разделением на
подсистемы и включает в себя информационные функции и функции управления,
которым соответствует функциональность АСУ ТП. Выбор ПТК обусловлен
соответствием его мощности объемам автоматизации, а также особенностями
функционирования автоматизируемых объектов.
АСУ ТП УКПГ на уровне ОПС выполняет следующие функции:
- дистанционное управление технологическими объектами. Дистанционное
управление обеспечивает возможность выполнения с АРМа оператора следующих
операций:
1) регулирование расхода газа на выходе УКПГ с автоматическим
регулированием на нижнем уровне управления расхода газа по технологическим
ниткам, газосборным шлейфам и скважинам;
2) отключение технологического участка (линии) для проведения
регламентных и ремонтных работ;
) управление исполнительными механизмами;
- предоставление оператору информации о состоянии объекта управления. РСУ
обеспечивает отображение параметров, принимаемых с уровня САУ и от смежных
систем на мнемосхемах со звуковой и световой сигнализацией об отклонении
параметров за заданные границы и сигнализацией состояния исполнительных
механизмов;
- сбор и архивирование данных о технологическом процессе, и
выполнение процедур обмена с вышестоящим уровнем управления;
автоматическое протоколирование нарушений заданных режимов
работы оборудования и отклонений параметров за пределы технологических уставок;
формирование и печать отчетных документов автоматически (отчеты,
протоколы событий, действий оператора, аварийных и предупредительных сигналов)
либо по запросу пользователя (отчеты, протоколы, графики, копии экранов);
ведение технологической базы данных.
Обеспечена автоматическая запись параметров поступающих с уровня САУ и
действий оператора, которые фиксируются в соответствующем журнале;
- конфигурирование ПТК АСУ ТП УКПГ;
- синхронизация времени всех компонентов системы, использующих
временные отметки и характеристики с привязкой к шкале единого времени U.T.C.;
комплексный контроль состояния работоспособности объектов и
инженерных сооружений на основе организации и построения единого
информационного пространства для всех ключевых служб и подразделений,
участвующих в процессе управления, контроля состояния и эксплуатации объектов
(наработки, количество пуском, отказов, ремонтов, данные по учету ресурсов,
паспортизация, анализ эффективности производства);
ключевым компонентом информационно-аналитической системы
является формируемая в процессе реализации проекта Единая информационная база
данных, содержащая всю необходимую информацию для организации процесса
планирования, контроля и оперативного управления производственным процессом
обеспечения экономической эффективности и экологической безопасности проводимых
мероприятий по обслуживанию компонентов ИУС, полевого КИПиА и технологического
оборудования.
АСУ ТП на уровне САУ выполняет следующие функции:
- сбор и обработку информации, поступающей от датчиков и исполнительных
механизмов, в том числе:
1) циклический опрос входов модулей ввода-вывода системы;
) аналогово-цифровое преобразование сигналов;
) первичную обработку сигналов для компенсации воздействия помех;
) определение достоверности информации по диапазонам измерения;
- регулирование параметров технологического процесса. Данная функция
должна выполняться автоматически на основе уставок и текущей величины
регулируемого параметра;
- взаимообмен информацией с уровнем ОПС.
Система противоаварийной защиты выполняет следующие функции:
- выявление предаварийных ситуаций;
- автоматическая блокировка технологического оборудования в
соответствии с алгоритмами блокировок и защит;
предоставление оператору информации о состоянии датчиков и
исполнительных механизмов системы ПАЗ, а также выдача аварийных и
предупредительных сигналов.
3.4 Функции системы телемеханики
Программно-технические средства автоматизации и диспетчерского управления
для территориально - распределенных объектов системы телемеханики (кусты
газовых скважин, газопроводы) обеспечивают:
- телемеханический контроль основных параметров (температуры, давления,
дебита скважин, параметров тока и напряжения секций комплектно-трансформаторной
подстанции, параметров тока и напряжения, а также регулирование напряжения
станции катодной защиты), характеризующих технологический процесс и состояние
объекта;
- работу технологических объектов в условиях нормальной
эксплуатации в автоматическом режиме с заданными параметрами технологического
процесса без постоянного присутствия обслуживающего персонала;
автоматическое управление электроприводными кранами по резкому
понижению давления (порыв трубопровода) с одновременным отключением
соответствующих скважин;
телеуправление с пульта управления УКПГ отдельными объектами;
телесигнализацию об отклонениях основных технологических
параметров от заданных значений, аварийного отключения выключателей КТП;
телесигнализацию недопустимо низкой температуры, пожара и
несанкционированного доступа в блок-боксы телемеханики;
автоматизированный контроль функционирующих объектов и
оборудования, анализ режимов работы, оценку работы и состояния технологического
оборудования, оперативное обнаружение и локализацию неисправностей и аварийных
ситуаций, реализацию поступающих команд.
3.5 Система противоаварийных защит
Алгоритмы работы объектов предназначены для автоматического,
дистанционного управления и регулирования технологических процессов. Система
позволяет сократить трудозатраты и минимизировать численность эксплуатационного
персонала, предотвратить возможность неправильных или несанкционированных
действий оператора, а также выполняет функции оперативного контроля
технологического режима установок, высокоэффективного и безопасного управления
технологическими процессами объектов системы телемеханики, обеспечения противоаварийной
и противопожарной защиты, повышения экологической безопасности производства.
АСУ ТП Кшукского и Нижне-Квакчикского газоконденсатных месторождений
выполняются как единые, законченные, управляющие и информационные системы для
объектов основного и вспомогательного технологического процесса,
предназначенные для работы как в автоматическом режиме без присутствия
обслуживающего персонала, так и в режиме управления с диспетчерского пункта.
Система противоаварийных защит включает в себя:
- систему противоаварийных защит по технологическим параметрам;
- систему противопожарной защиты;
систему экстренного останова.
Функции противоаварийной защиты предлагается осуществлять на принципах:
- многоуровневой противоаварийной защиты, верхний уровень которой
ориентируется на остановку в целом;
- взаимного влияния отдельных агрегатов и установок;
диагностики приборов и технологического оборудования.
Многоуровневая противоаварийная защита подразумевает разграничение защит
технологического оборудования по уровням, каждый из которых определяется своими
условиями запуска и процедурой выполнения. Концептуально (структурно или
функционально) выделяются следующие уровни:
- первый уровень - остановка технологического комплекса в целом;
- второй уровень - остановка отдельных технологических блоков;
третий уровень - остановка отдельного технологического
оборудования (технологической линии или агрегата).
Указанные уровни предусматривают иерархическую соподчиненность, когда
запуск противоаварийной защиты первого уровня предусматривает автоматическую
инициализацию уровней 2 и 3. Условия запуска того или иного уровня определяются
таким образом, что если при остановке отдельного агрегата необходимо отключить
технологическую линию, запускается защита второго уровня.
Запуск противоаварийных защит предусматривается:
- вручную оператором;
- автоматически при подтверждении оператором;
автоматически без подтверждения оператора.
Подтверждение оператором предполагает учет временной задержки, после
которой противоаварийная защита будет запущена автоматически. Предусматривается
также режим отключения автоматического запуска противоаварийных защит, что
должно быть зафиксировано в журнале действий оператора. Запуск противоаварийной
защиты отключает режим регулирования (осуществляется в рамках комплексного
управления технологическим оборудованием). Данное решение обуславливает
требование к обеспечению устойчивости технологического процесса при решении задач
комплексного управления.
Необходимость в наличии комплексных противоаварийных защит определяется:
- взаимосвязанностью основного технологического оборудования;
- возможностью возникновения аварии на объекте, обеспечивающем
непрерывную работу основного технологического оборудования.
Источниками автоматического запуска противоаварийных защит являются:
- обнаружение подтвержденного пожара (срабатывание двух шлейфов пожарной
сигнализации в одной защищаемой зоне) в основных блоках технологического
оборудования;
- обнаружение второго порога загазованности в блоках
технологического оборудования.
Системы управления технологическими процессами осуществляют контроль за
технологическими параметрами на предмет соответствия условиям запуска
противоаварийных защит, как отдельных агрегатов, блоков так и установки в целом
и выполнение противоаварийных защит.
Система пожарогазобезопасности осуществляет пожарообнаружение,
газообнаружение, пожаротушение и выдает в АСУ ТП сигналы на запуск
противоаварийных защит тех или иных установок.
3.6 Основные решения в части автоматизации объекта
Технологической схемой обвязки эксплуатационных скважин куста
предусмотрено:
- регулирование расхода газа (дебита) по каждой скважине;
- автоматическое отключение скважин в случае порыва шлейфа;
автоматическое отключение кустов скважин при повышении на 10 %
или при понижении на 20 % давления по отношению к рабочему;
термокарманы для замера температуры газа на устьях (до и после
регулятора расхода газа) для контроля за режимом работы скважин;
возможность проведения работ по глушению скважин,
гидравлическому разрыву пласта, соляно-кислотной обработке, а также по
исследованию скважин;
отвод газа на факел при продувке скважин;
замер дебита каждой скважины.
Для выполнения этих требований в обвязке скважин кустов предусматриваются
следующие технические решения.
Выкидные линии скважин подключаются к коллектору и оборудуются замерными
устройствами для замера дебита каждой скважины.
В обвязке каждой скважины куста после замерного устройства предусматривается
регулятор расхода газа, позволяющий производить регулирование дебита скважины.
Для проведения газодинамических исследований скважин на факельной линии
куста предусматривается узел подключения передвижной установки для исследования
скважин, производства экспериментального завода ООО «ТюменНИИгипрогаз». Для
подключения замерного сепаратора предусматриваются задвижки с ручным
управлением. Подключение выполняется быстроразъемными соединениями. После
окончания работ и отключения замерного сепаратора указанные задвижки
пломбируются в закрытом положении.
Подача газа после замерной установки производится в выходной коллектор
куста скважин, освобождение от давления газа сепаратора, входящего в состав
этой установки, производится на горизонтальный факел. Сброс жидкости при
исследовании скважин от сепаратора производится в специальный контейнер.
Предусматривается местный и дистанционный контроль давления и
температуры потока в трубопроводе.
С целью предупреждения возможного гидратообразования в шлейфах и обвязке
скважин в период их ввода в эксплуатацию предусматривается подача метанола
через блоки дозирования ингибитора БРМ 4 во все шлейфы, НКТ и в затрубное
пространство каждой скважины. БРМ 4 предназначен для ручного и дистанционного
управления расходом метанола. Метанол подается от насосной, расположенной на
площадке УКПГ.
Для удобства проведения ремонтных работ на трубопроводах обвязки
фонтанной арматуры предусмотрена установка фланцевых разъемов.
Продувка скважин и трубопроводов при ремонтных и профилактических работах
предусматривается на горизонтальный факел. Для перевода жидкой части потока в
газообразное состояние и для регулирования скорости продувки на факельном
трубопроводе на расстоянии 10 метров от факела устанавливается дроссель с
ручным управлением. В качестве горизонтального факела предусматривается
горизонтальная горелка с ручным розжигом.
При глушении скважин подача задавочной жидкости предусматривается от
передвижного задавочного агрегата. Для снижения расчетного давления шлейфа на
общем газовом коллекторе на кустовой площадке предусмотрена установка
регулятора давления и предохранительного клапана (для защиты шлейфа от
превышения давления).Газ от предохранительного клапана сбрасывается в амбар.
Давление настройки предохранительного клапана 15,8 МПа.
Спецификация оборудования автоматизации куста скважин № 1 представлена в
таблице 3.1.
Таблица 3.1 - Спецификация оборудования автоматизации куста скважин № 1
Позиция
|
Наименование
|
Кол-во
|
Примечание
|
1 - 8
|
Термометр биметаллический показывающий ТБ-2Р
|
8
|
|
9 - 16
|
Преобразователь температуры Метран-286-06
|
8
|
1ExdIICT5X
|
17 - 20
|
Преобразователь температуры Метран-286-04
|
4
|
1ExdIICT6
|
21
|
Преобразователь температуры Метран-286-01
|
1
|
Устанавливается в БТП
|
22
|
Манометр показывающий МП4-У-У2-40 МПа
|
1
|
|
23
|
Манометр показывающий МП4-У-У2-10 МПа
|
1
|
|
24 - 34
|
Датчик избыточного давления Метран-150TG-5
|
11
|
1ExdIICT5
|
35-1 - 38-1
|
Устройство сужающее БСУ 100/25 УХЛ1
|
4
|
|
35-2 - 38-2
|
Датчик разности давлений Метран-150CD-2
|
4
|
1ExdIICT5
|
В таблицах 3.2 и 3.3 описан объем автоматизации объекта и перечни
выходных и входных сигналов.
Таблица 3.2 - Объем автоматизации, перечень выходных сигналов
Объект
|
Наименование команды управления
|
Параметры нагрузки
|
|
|
Напряжение
|
Коммутируемый ток
|
Задвижки Зд.1, Зд.2 - 2 шт.
|
Открыть
|
24 В
|
2 А
|
|
Закрыть
|
24 В
|
2 А
|
|
Стоп
|
24 В
|
2 А
|
Соленоидный клапан в БРМ4
|
Открыть/закрыть
|
24 В
|
0,65 А
|
Регулирующие клапаны КлР1, КлР2, КлР3, КлР4, КлР5
|
Регулирование
|
|
4-20 мА
|
Таблица 3.3 - Объем автоматизации, перечень входных сигналов
Наименование параметра
|
Диапазон измерения
|
Предупредительная уставка сигнализации
|
Аварийная уставка сигнализации
|
Управление
|
Тип датчика
|
Тип сигнала
|
Кол-во сигналов
|
Режим управления задвижкой Зд.1, Зд.2 - местный
|
НО
|
|
|
|
AUMA MATIC (Зд.1-, Зд.2)
|
DI 24 VDC
|
2
|
Режим управления задвижкой Зд.1, Зд.2 - дистанцион.
|
НО
|
|
|
|
|
DI 24 VDC
|
2
|
Состояние привода задвижки Зд.1, Зд.2 - неисправность
|
НЗ
|
|
|
|
|
DI 24 VDC
|
2
|
Состояние привода задвижки Зд.1, Зд.2 - готовность
|
НО
|
|
|
|
|
DI 24 VDC
|
2
|
Состояние задвижки Зд.1, Зд.2 - открыта
|
НО
|
|
|
|
|
DI 24 VDC
|
2
|
Состояние задвижки Зд.1, Зд.2 - закрыта
|
НО
|
|
|
|
|
DI 24 VDC
|
2
|
Состояние задвижки Зд.1, Зд.2 - заклинивание
|
НО
|
|
|
|
|
DI 24 VDC
|
2
|
Давление газа в трубопроводе на УКПГ перед (по ходу газа)
Зд.1,МПа
|
0 … 16
|
L1=17,6
|
L2=14,4 H2=12,8
|
При H2, L2 закрыть Зд.1
|
Метран-150TG
|
(4 ... 20) мА, HART
|
1
|
Давление газа в трубопроводе на УКПГ перед (по ходу газа)
КлР5, МПа
|
0 … 20
|
L1=18,2
|
L2=16,16 H=22,23
|
При H, L2 закрыть Зд.1
|
Метран-150TG
|
(4 ... 20) мА, HART
|
1
|
Давление метанола в трубопроводе с УКПГ после (по ходу метанола)
Зд.2, МПа
|
0 … 16
|
L1=14,4
|
L2=12,8 Н=17,6
|
При Н, L2 закрыть Зд.2
|
Метран-150TG
|
(4 ... 20) мА, HART
|
1
|
Несанкционированный доступ в БТП
|
|
|
|
|
SQ1
|
DI 24 VDC
|
1
|
Температура в БТП, єС
|
-50 … 500
|
|
+5
|
|
Метран-286-01
|
(4 ... 20) мА, HART
|
1
|
Пожар в БТП
|
|
|
|
|
|
DI 24 VDC
|
1
|
Неисправность прибора пожарной сигнализации
|
|
|
|
|
|
DI 24 VDC
|
1
|
Контроль работы КТП
|
|
|
|
|
|
DI 24 VDC
|
1
|
Режим управления регулятором КлР1, КлР2, КлР3, КлР4, КлР5-
местный
|
НО
|
|
|
|
AUMA MATIC (КлР1, КлР2, КлР3, КлР4, КлР5)
|
DI 24 VDC
|
5
|
Режим управления регулятором КлР1, КлР2, КлР3, КлР4, КлР5 -
дистанционный
|
НО
|
|
|
|
|
DI 24 VDC
|
5
|
Состояние привода регулятора КлР1,иКлР2, КлР3, КлР4, КлР5-
неисправность
|
НЗ
|
|
|
|
|
DI 24 VDC
|
5
|
Состояние привода регулятора КлР1,иКлР2, КлР3, КлР4, КлР5-
готовность
|
НО
|
|
|
|
|
DI 24 VDC
|
5
|
Состояние регулятора КлР1, КлР2, КлР3, КлР4, КлР5- открыт
|
НО
|
|
|
|
|
DI 24 VDC
|
5
|
Состояние регулятора КлР1-- закрыт
|
НО
|
|
|
|
|
DI 24 VDC
|
5
|
Давление газа до и после КлР1, КлР2, КлР3, КлР4, МПа
|
0 … 25
|
|
|
|
Метран-150TG
|
(4 ... 20) мА, HART
|
8
|
Температура газа в трубопроводе ГС1 до КлР1, КлР2, КлР3,
КлР4, °С
|
-50 … 500
|
|
|
|
Метран-286-06
|
(4 ... 20) мА, HART
|
4
|
Температура в КШОЭ № 1,2,3,4, °С
|
-50 … 500
|
|
+5
|
|
Метран-286-04
|
(4 ... 20) мА, HART
|
4
|
Расход, м3/ч
|
0,4-9,6
|
|
|
Регулиров. КлР1-4
|
Метран-150CD
|
(4 ... 20) мА, HART
|
4
|
Функциональная схема автоматизации куста газоконденсатных скважин № 1
представлена на рисунке 3.2.
.7 Организация канала передачи информации
Для организации канала передачи информации между установкой комплексной
подготовки газа и кустом газовых скважин № 1 применена волоконно-оптическая
линия связи на воздушных линиях электропередач, для передачи информации по
которой служит оптический самонесущий кабель марки
ОКЛЖ-01-6-16-10/125-0,36/0,22-3,5/18-20,5. Прокладка оптического кабеля
выполнена методом подвеса к элементам ВЛ при помощи линейной арматуры.
ВОЛС выполнено по технологии «кольцо» с использованием различных волокон
одного кабеля и «горячим» резервом оборудования. Данное решение базируется на
семействе PDH-мультиплексоров НТЦ «НАТЕКС» - FlexGain FOM4/FOM4E/FOM16E/FOM16OG
и позволяет строить оптические PDH-сети пропускной способностью до 1 Гбит/с с
подключением на уровне потоков Е1 Ethernet 10/100/1000BaseT к оборудованию
доступа и системам передачи: гибким мультиплексорам, кросс-коннекторам n·64
кбит/с, радиорелейным системам, xDSL-модемам и т.д. Мультиплексоры семейства
FlexGain предназначены для передачи от 4 до 16 потоков Е1 G.703 или смешанного
TDMIP-трафика по одному или двум волокнам оптического кабеля.
.8 Оборудование автоматизации объекта
Интеллектуальный датчик избыточного давления Метран 150TG. Внешний вид
датчика представлен на рисунке 3.4.
Рисунок 3.4 - Интеллектуальный датчик избыточного давления Метран 150TG
На объекте используется 11 приборов данной марки, они предназначены для
измерения давления газа и метанола в трубопроводах куста ГКС № 1.
Датчик имеет максимальный диапазон измерений 5-ой категории: от 0 до 68
МПа, давление перегрузки 100 МПа. Предел допускаемой основной погрешности
±0,075. Дополнительная погрешность датчиков, вызванная воздействием
электромагнитных помех не превышает ±1% от диапазона изменения выходного
сигнала.
Настройка и управление датчика осуществляется дистанционно при помощи
управляющего устройства, поддерживающего HART-протокол.
Датчик состоит из сенсорного модуля и электронного преобразователя.
Сенсорный модуль состоит из измерительного блока и платы аналого-цифрового
преобразователя. Давление подается в камеру измерительного блока, преобразуется
в деформацию чувствительного элемента и изменение электрического сигнала.
Электронный преобразователь преобразует электрический сигнал в соответствующий
выходной сигнал. В сенсорном модуле моделей 150TG используется тензорезистивный
тензомодуль на кремниевой подложке. Чувствительным элементом тензомодуля
(рисунок 3.5) является пластина 1 из кремния с пленочными тензорезисторами (структура
КНК).
Рисунок 3.5 - Устройство датчика Метран 150TG 1-чувствительный элемент;
2-разделительная мембрана; 3- разделительная жидкость
Давление через разделительную мембрану 2 и разделительную жидкость 3
передается на чувствительный элемент тензомодуля. Воздействие давления
преобразуется в деформацию чувствительного элемента, вызывая при этом изменение
электрического сопротивления его тензорезисторов и разбаланс мостовой схемы.
Электрический сигнал, образующийся при разбалансе мостовой схемы, измеряется
АЦП и подается в электронный преобразователь. Электронный преобразователь
преобразует это изменение в выходной сигнал [4].
Функционально канал преобразования сигнала измерительного блока (рисунок
3.6) состоит из АЦП, блока памяти АЦП, микроконтроллера с блоком памяти,
цифро-аналогового преобразователя (ЦАП), стабилизатора напряжения, фильтра
радиопомех, встроенной регулировки «нуля» и «диапазона», HART-модема. Кроме
того, в электронные преобразователи входит ЖКИ - индикатор и блок защиты от
переходных процессов.
Рисунок 3.6 - Функциональная схема датчика Метран 150TG
Конструктивно АЦП, блок памяти АЦП размещаются на плате АЦП, которая
установлена в сенсорном модуле. Сенсорный модуль имеет также встроенный
температурный сенсор для коррекции температуры. Остальные элементы
функциональной схемы размещаются в корпусе электронного преобразователя. Плата
АЦП принимает аналоговые сигналы тензомодуля, пропорциональные входной измеряемой
величине (давлению) (Uр) и температуре (Ut), и преобразовывает их в цифровые
коды. Энергонезависимая память предназначена для хранения коэффициентов
коррекции характеристик сенсорного модуля и других данных о сенсорном модуле.
Микроконтроллер, установленный на микропроцессорной плате, принимает
цифровые сигналы с платы АЦП вместе с коэффициентами коррекции, производит
коррекцию и линеаризацию характеристики сенсора, вычисляет скорректированное
значение выходного сигнала датчика и передаёт его в ЦАП. ЦАП преобразует
цифровой сигнал, поступающий с микроконтроллера, в выходной аналоговый токовый
сигнал. HART-модем, установленный на микропроцессорной плате, предназначен для
выделения HART сигнала из токовой петли 4-20мА и преобразование его в
стандартный цифровой сигнал, а также для осуществления обратной операции −
преобразование цифрового сигнала в HART сигнал и замешивание его в токовую
петлю.
Блок регулирования «нуля» и « диапазона» предназначен для установки точек
аналогового выходного сигнала 4 и 20мА на выбранные значения давления.
Настройка датчиков осуществляется по цифровому каналу связи.
Интеллектуальные датчики давления серии Метран-150 CD (рисунок 3.7) предназначены для
непрерывного преобразования в унифицированный токовый выходной сигнал и/или
цифровой сигнал в стандарте протокола HART входных измеряемых величин:
избыточного давления; абсолютного давления; разности давлений.
В АСУ ТП куста ГКС № 1 данный датчик используется для измерения расхода
газа методом перепада давления в выкидной линии скважины (от 0,4 до 9,6 тыс. м3/ч).
На объекте установлено 4 датчика.
Рисунок 3.7 - Интеллектуальные датчики давления серии Метран-150
Датчики
измерения перепада давления применяются комплектно с первичным преобразователем
расхода БСУ-100/25 (сужающим устройством <#"793973.files/image005.jpg">
Рисунок 3.8 - Интеллектуальный преобразователи температуры Метран-286
Данные датчики предназначены для измерения температуры газа в
трубопроводах ГКС № 1, измерения температуры воздуха в блок-боксе БТП и шкафах
КШО-Э, в общей сложности на объекте установлено 13 датчиков Метран-286.
Управление датчиком осуществляется дистанционно. Связь с управляющими
устройствами осуществляется:
- по аналоговому каналу - передачей информации об измеряемой температуре
в виде постоянного тока 4-20 мА;
- по цифровому каналу - в соответствии с HART протоколом в
стандарте Bell-202.
Сигнал первичного преобразователя температуры преобразуется в
унифицированный выходной сигнал постоянного тока 4-20 мА с наложенным на него
цифровым сигналом HART версии 5 с физическим интерфейсом Bell-202 с помощью
электронного модуля, встроенного в корпус первичного преобразователя.
Диапазон измерений Метран-286: от минус 50 °С до плюс 500 °С. Предел
допускаемой основной приведенной погрешности по аналоговому и цифровому сигналу
±0,15% [5].
Измеряемый параметр - температура в Метран-286 с помощью
термопреобразователями сопротивления преобразуется в изменение омического
сопротивления платинового чувствительного элемента. Аналоговый сигнал преобразуется
с помощью АЦП в дискретный сигнал. Дискретный сигнал с помощью
микропроцессорного преобразователя обрабатывается с целью:
- линеаризации номинальной статической характеристики преобразования;
- перестройки диапазонов измерений в пределах рабочего диапазона
температур;
самодиагностики составляющих узлов, детектирования обрыва или
короткого замыкания.
С выхода МП дискретный сигнал поступает на ЦАП, осуществляющий
преобразование дискретного сигнала в унифицированный токовый аналоговый сигнал
4-20 мА, а также на блок частотного модулятора, преобразующий дискретный сигнал
в частотно-модулированный и наложенный на аналоговый сигнал.
Блок управления Auma Matic (схема
управления MSPE 31700-FG8YС KMS TP204/209) предназначен для управления
промышленной арматурой, вентилями, задвижками, заслонками или кранами [6]
(рисунок 3.9).
Рисунок 3.9 - Многооборотные электроприводы AUMA MATIC
Блок БРМ 4 - блок дозирования ингибитора. Блок БРМ 4 представлен на
рисунке 3.10.
Рисунок 3.10 - Блок дозирования ингибитора
Применяется при подготовке газа к транспортировке, предназначен для
ручного и дистанционного управления расходом ингибитора. Блок дозирования
ингибитора является составной частью системы подачи ингибитора в скважины
кустов. Регулируемая среда - метанол.
АСУ ТП реализована на базе оборудования производства компании GE IP. Для
шкафов управления локальных САУ используется ПТК Rx3i PACSystem.
Применяемый ПТК обладает следующими качествами:
модульный принцип построения;
- высокий срок эксплуатации;
возможность интеграции с другим оборудованием с помощью
стандартных сетей связи и программного обеспечения.
В составе ПТК шкафов управления и шкафов УСО используются модули
платформы Rx3i:
- универсальная базовая плата;
- модуль питания;
сетевой модуль Ethernet;
модуль аналогового ввода;
модуль дискретного ввода 24 VDC;
модуль дискретного вывода 24 VDC;
сетевой комплект Ethernet.
.9 Функции программного обеспечения
Программное обеспечение контроллеров функционирует под управлением
микропроцессора, выполняющего операции булевой логики.
Инструментальное программное обеспечение выполняет следующие операции в
каждом цикле:
- подготовительные, включающие расчет времени цикла, определение режима
выполнения, обновление таблиц ошибок;
- запись во внутренние регистры памяти аналоговых и дискретных
данных;
выполнение прикладной программы (алгоритмов пользователя);
реализацию законов регулирования;
обработку запросов от программных устройств резервированного
сервера и интеллектуальных модулей;
обработку сбоев и отказов модулей;
проверку целостности прикладной программы пользователя подсчетом
контрольной суммы.
Программирование контроллера (конфигурирование CPU, модулей ввода/вывода
и специализированных модулей), а также отладка прикладных программ пользователя
осуществляется с помощью сервисного программного обеспечения - пакета Logic Developer PLC Profession Edition.
Прикладное программное обеспечение контроллера выполняет следующие
операции в каждом цикле:
- опрос и обработка информации от модулей ввода-вывода;
- анализ входных данных, формирование блока данных для передачи их
на резервированный сервер уровня ОПС;
регулирование параметров технологического процесса по уставкам
поступающим с уровня ОПС;
формирование и выдача на исполнительные механизмы выходных сигналов
по заложенным алгоритмам;
выполнение расчетных функций;
выполнение алгоритмов противоаварийных блокировок.
Разработка специального программного обеспечения (прикладных программ
пользователя) ПЛК производится на языке релейной логики с использованием
редактора релейно-контактной логики (LD). Каждая операция реализуется
функциональным блоком. Программа состоит из строк. Строка представляет собой
последовательность функциональных блоков.
Редактирование программ включает следующие операции со строками или
функциональными блоками: вставка, замена, уничтожение, копирование, поиск.
Просмотр таблиц, регистров обеспечивает просмотр и корректировку значений
регистров в режиме on-line в процессе функционирования контроллера.
Регистры обеспечивают взаимодействие системного математического
обеспечения с прикладными программами пользователя.
В начале цикла инструментальное математическое обеспечение записывает в
регистры данные, полученные от модулей дискретных и аналоговых входов, а
прикладное программное обеспечение (алгоритмы пользователя) выполняет
обработку. В конце цикла инструментальное математическое обеспечение читает
данные из регистров и передает их модулям дискретных и аналоговых выходов.
Адреса регистров задаются в процессе конфигурирования контроллера.
Контроллер имеет следующие типы регистров:
- %AI - аналоговые входные переменные;
- %AQ - аналоговые выходные переменные;
% I - дискретные входные переменные;
%Q - дискретные выходные переменные;
%M - дискретные внутренние регистры (кратковременная память);
%R - аналоговые внутренние регистры;
%T - дискретные временные (рабочие) регистры (оперативная
память);
%S - дискретные регистры статуса и ошибок - только чтение
(системные данные - диагностика);
%G - данные, получаемые или передаваемые коммуникационными
модулями (глобальные данные);
%W - память слов (режим слов).
Сбор аналоговых и дискретных параметров выполняется циклически. Обработка
параметров ведется в течение периода опроса. Обмен данными с вышестоящим
уровнем выполняется через внутренние регистры контроллера.
Синхронизация времени контроллера выполняется автоматически. Инициатором
является верхний уровень управления, передающий значения своего времени на
контроллер. В соответствии с переданным временем контроллер корректирует
показания своего таймера.
АРМ инженера является ключевым рабочим местом, обеспечивающим изменение
конфигурации АСУ ТП. АРМ инженера оснащена программным обеспечением,
позволяющим реализовать рабочее место специалиста на базе трех системных блоков
(сервер основной, резервный и АРМ инженера) и консоли управления включающей
монитор, клавиатуру, манипулятор типа «мышь».
Программное обеспечение АРМа инженера обеспечивает инженера информацией
обо всех имеющихся ресурсах системы, позволяет получить универсальный доступ к
обзору всех производственных переменных. Общее и прикладное ПО АРМа инженера
позволяет:
- добавить/удалить необходимые элементы системы с изменением или без их
характеристик;
- изменить шкалы, границы сигнализации, названия и другие
параметры настройки технологических переменных;
создать или отредактировать существующие алгоритмы обработки
данных;
создать или отредактировать существующие алгоритмы регулирования
параметров технологических процессов;
создать или отредактировать существующие алгоритмы формирования
команд управления;
создать или отредактировать существующие логические алгоритмы
определения состояния объектов;
создать или отредактировать существующие алгоритмы диагностики
элементов системы;
создать или отредактировать существующие алгоритмы противоаварийных
блокировок и сигнализации;
создать или отредактировать существующие математико-логические
расчёты;
создать новые или откорректировать существующие мнемосхемы, в
том числе с использованием библиотечных и шаблонных элементов;
изменить правила формирования и глубину исторической БД;
документировать данные проектов.
Ниже
на рисунке 3.11 представлен чертеж формы документа видеокадра "Куст ГКС №
1 Нижне-Квакчикского ГКМ".
Рисунок 3.11 - Чертеж формы документа видеокадра "Куст ГКС № 1
Нижне-Квакчикского ГКМ"
3.10 Описание алгоритмов регулирования системы
Комплекс алгоритмов управления технологическими процессами УКПГ Кшукского
и Нижне-Квакчикского ГКМ обеспечивают формирование общей стратегии совместного
управления технологически связанным газопромысловым оборудованием для
достижения стабильного, безопасного, надежного и качественного функционирования
автоматизированного технологического комплекса.
Комплексные алгоритмы управления технологическим оборудованием УКПГ
выделены в АСУ ТП в качестве функциональной подсистемы и реализуются в виде
прикладного программного обеспечения на базе принятого программно-технического
комплекса.
В реализуемой алгоритмической иерархии комплексные алгоритмы занимают
промежуточное положение между локальными алгоритмами управления
технологическими аппаратами и алгоритмами противоаварийной защиты. В состав
комплексных алгоритмов входят:
- алгоритм обеспечения требуемого термобарического режима
низкотемпературных сепараторов;
- алгоритм автоматического поддержания заданного давления в
низкотемпературном сепараторе;
алгоритм автоматического поддержания температуры газа в
низкотемпературном сепараторе;
алгоритм автоматического поддержания уровня жидкостей в
емкостях;
алгоритм автоматического регулирования давления газа по УКПГ;
алгоритм автоматического поддержания расхода газа по УКПГ;
3.10.1 Алгоритм автоматического регулирования давления
Автоматическое поддержание заданного давления газа осуществляется за счет
изменения степени открытия клапана-регулятора КлР5. В зависимости от
рассогласования между заданным давлением газа и текущим измеренным значением
происходит изменение положения регулирующего клапана, на величину dA.
Графическое описание алгоритма представлено на рисунке 3.12.
При выполнении неравенства:
, (3.1)
Рисунок 3.12 - Блок-схема алгоритма автоматического поддержания давления
газа
Выполняется процедура повышения давления, а при:
, (3.2)
выполняется
процедура понижения давления. В случае если рассогласование между заданным и
текущим измеренным значением давления газа превышает величину dP·N, то шаг
открытия (закрытия) клапана увеличивается в K раз. Когда текущее измеренное
значение давления станет меньше dP·N, то значение шага опять станет равно
значению dA.
Измеряемые
параметры:
- P -текущее измеренное значение давления газа после регулирующего
клапана;
- A - текущее положение клапана-регулятора.
Заданные параметры:
Pзад - заданное значение давления газа;
- dP - нечувствительность по давлению;
dA - шаг открытия/закрытия клапана-регулятора;
K - коэффициент увеличения шага изменения положения
клапана-регулятора;
N - коэффициент увеличения зоны нечувствительности (значение
уточняется в процессе наладки).
Изначально проводится проверка условия:
. (3.3)
В
случае, если
, (3.4)
шаг
изменения положения клапана-регулятора равен dA.
Если
, (3.5)
шаг
изменения положения клапана-регулятора равен dA·K.
При выполнении условия (3.2) клапан-регулятор закрывается на величину
шага изменения положения клапана-регулятора. При выполнении условия (3.1)
клапан-регулятор открывается на величину шага изменения положения
клапана-регулятора. Выполняется временная задержка t.
3.10.2 Алгоритм автоматического поддержания расхода газа
Автоматическое поддержание заданного расхода газа осуществляется за счет
изменения степени открытия клапана-регулятора КлР1 - КлР4. В зависимости от
рассогласования между заданным расходом газа и текущим измеренным значением
происходит изменение положения регулирующего клапана, на величину dA.
Графическое описание алгоритма представлено на рисунке 3.13.
Рисунок 3.13 - Блок-схема алгоритма автоматического поддержания расхода
газа на выходе коллектора сырого газа КГС № 1
При
, (3.6)
выполняется
процедура повышения расхода, а при:
, (3.7)
выполняется
процедура понижения расхода. В случае если рассогласование между заданным и
текущим измеренным значением расхода газа превышает величину dF·N, то шаг
открытия (закрытия) клапана увеличивается в K раз. Когда текущее измеренное
значение расхода станет меньше dF·N, то значение шага опять станет равно
значению dA.
Измеряемые
параметры:
- F -текущее измеренное значение расхода газа после регулирующего
клапана;
- A - текущее положение клапана-регулятора.
Заданные параметры:
Fзад - заданное значение расхода;
- dF - нечувствительность по расходу;
dA - шаг открытия/закрытия клапана-регулятора;
K - коэффициент увеличения шага изменения положения
клапана-регулятора;
N - коэффициент увеличения зоны нечувствительности.
Изначально проводится проверка условия:
|
.. (3.8)
В
случае, если:
|
,, (3.9)
шаг
изменения положения клапана-регулятора равен dA. Если
|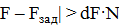
, (3.10)
то
шаг изменения положения клапана-регулятора равен dA·K.
При
выполнении условия (3.6) клапан-регулятор закрывается на величину шага
изменения положения клапана-регулятора. При выполнении условия (3.7)
клапан-регулятор открывается на величину шага изменения положения
клапана-регулятора.
4. Разработка системы автоматического регулирования
.1 Гидратообразование в трубопроводах природного газа
В нефтедобывающей и нефтехимической промышленности трубопроводы
различного калибра и назначения зачастую дают сбои из-за пробок, сужения
проходного сечения и высокой вязкости транспортируемых жидкостей. Обогрев
трубопроводов устраняет опасность их разрушения при замерзании.
Одной из важнейших проблем при эксплуатации трубопроводов транспорта газа
является образование газогидратов. Отлагаясь на внутренних стенках труб,
гидраты резко уменьшают их пропускную способность и могут привести к аварийной
остановке эксплуатации газопровода. Затраты нефтегазовых компаний на
предупреждение и борьбу с газогидратными пробками составляют значительную часть
стоимости эксплуатации месторождений. Поэтому сокращение эксплуатационных
затрат на предупреждение и борьбу с гидратообразованием в промысловых системах
добычи газа вызывает немалый интерес со стороны многих добывающих и
эксплуатирующих компаний нефтегазовой отрасли [7].
Гидраты углеводородных газов являются неустойчивыми соединениями
углеводородов с водой и представляют собой белые кристаллы, внешне похожие на
снег или лед. Они состоят из одной или нескольких молекул газа (метана,
пропана, углекислого газа и др.) и воды. Основными факторами, определяющими
условия образования гидратов, являются состав газа, его давление, температура,
полное насыщение газа парами воды.
Газовые гидраты в качестве причины, осложняющей эксплуатацию
газопроводов, впервые (в 1934 г.) назвал американец Е.Г. Хаммершмидт [9]. Им
было установлено, что газовые гидраты могут образовываться и накапливаться в
газопроводах, вызывая их закупорку (рис. 4.1, рис. 4.2).
Рисунок 4.1 - Газогидратная пробка, извлеченная из трубопровода
Рисунок 4.2 - Схема образования гидратов в горизонтальной трубе: 1 -
газопровод; 2 - гидраты
Наиболее часто закупорки газопровода происходят в зимний период в связи
значительным охлаждением движущегося в трубопроводе газового потока.
Образование гидратов может иметь место на всех газопроводах, за исключением
транспортирующих газ с точкой росы паров воды ниже минимальной рабочей температуры.
К технологическим факторам, влияющим на образование гидратов, относят:
- недостаточно тщательные продувки газопровода перед пуском;
- отсутствие конденсатосборников и продувочных патрубков в
пониженных местах газопровода или нерегулярное удаление из них скапливающейся
жидкости;
недостаточную очистку газа до подачи его в магистральный
газопровод.
Способы предупреждения образования гидратов:
Поддержание температуры потока газа выше температуры гидратообразования с
помощью подогревателей, теплоизоляции трубопроводов и подбора режима
эксплуатации, обеспечивающего максимальную температуру газового потока.
Понижение температуры точки росы газа:
- уменьшением давления при транспорте газа (при этом наряду с понижением
температур точек росы снижается также температура начала образования гидратов);
- нейтрализацией воды, выпадающей в жидком виде;
очисткой газа от паров воды - газоосушка.
Уменьшение давления при транспорте газа обычно используется только для
ликвидации гидратных пробок, но не как средство предупреждения образования
гидратов, потому, что это связано с одновременным уменьшением пропускной
способности газопровода.
Для понижения точки росы газа нейтрализацией выпадающей воды в поток газа
вводят ингибиторы. В качестве ингибиторов гидратообразования используются
метанол и этиленгликоль. Эффективность их применения зависит от условий
гидратообразования. Ингибиторы, введенные в поток природного газа, частично
поглощают водяные пары и переводят их в раствор, не образующий гидратов или же
образующий их при более низких температурах.
Уменьшение плотности газа извлечением из него тяжелых углеводородов. При
этом увеличивается давление и снижается температура, при которых начинают
образовываться гидраты.
4.2 Гидратообразование в трубопроводе сброса газа с предохранительного
клапана
Для снижения расчетного давления шлейфа на общем газовом коллекторе на
кустовой площадке предусмотрена установка регулятора давления и
предохранительного клапана (для защиты шлейфа от превышения давления).
Газ от предохранительного клапана сбрасывается в амбар по трубопроводу
Ш89х8 (труба - 09Г2С, Рисп = 36,88 МПа, протяженность 90 м),
выделенному красным цветом на рисунке 4.3. Давление настройки
предохранительного клапана 15,8 МПа.
Рисунок 4.3 - Трубопровод сброса газа с предохранительного клапана
В процессе проведения наладочных работ и пробной эксплуатации
технологических систем куста газоконденсатных скважин № 1 Нижне-Квакчикского
ГКМ выявлено следующее: при отработке сброса газа с предохранительного клапана
наблюдается скапливание в трубопроводе сбросной линии гидратов углеводородов
содержащихся в добываемом газе (конденсат, метанольная вода и т.д.). Причиной
образования скоплений гидратов в трубопроводе является отсутствие естественного
положительного наклона трубопровода сбросной технологической линии.
Вместе с тем, климат в районе Нижне-Квакчикского газоконденсатного
месторождения характеризуется холодной, ветреной, малооблачной погодой. Самый
холодный месяц - февраль, средняя месячная температура которого составляет
минус 14,8 °С, а абсолютный минимум достигает минус 45 °С. Температура наиболее
холодной пятидневки - минус 31 °С. Определено, что имеющейся теплоизоляционной
окожуховки трубопровода для недопущения образования гидратных пробок в
трубопроводе в период отрицательных температур недостаточно.
Образование гидратных пробок в трубопроводе сброса газа с
предохранительного клапана общего газового коллектора куста газоконденсатных
скважин № 1 повлечет к разрушению технологического трубопровода сбросной линии
и невозможности выполнить защиту шлейфа общего газового коллектора от повышения
давления в случае возникновения нештатных ситуаций.
Целесообразно использовать для обогрева трубопровода электрическую
кабельную систему обогрева с целью компенсации тепловых потерь
теплоизолированных трубопроводов.
С учетом климатических условий и физико-химических свойств добываемого
газа в рабочем режиме необходимо поддерживать положительную температуру не ниже
плюс 5 °С. При этом управление нагревом необходимо осуществлять по сигналам,
поступающим от системы управления. Главным звеном в цепи управления является
регулятор температуры, который реализует заданный алгоритм управления обогревом
трубопровода. Регулятор контролирует температуру наружного воздуха посредством
датчика температуры воздуха. На основе полученной информации регулятор
управляет мощностью обогрева объекта (от 0% до 100%). Регулятор температуры
автоматически включает обогрев системы и управляет мощностью обогрева при температуре
ниже плюс 10 °С и автоматически отключает обогрев при температуре трубы выше
плюс 10 °С (защита от перегрева).
4.3 Борьба с гидратообразованием. Электрическая кабельная
система
В состав системы обогрева (рисунок 4.4) входят:
- нагревательная часть: нагревательные кабели и
аксессуары для их крепления на трубопроводе, локальные элементы подогрева узлов
трубопровода (фланцев, вентилей, насосов);
- распределительная сеть, обеспечивающая
питание для всех элементов греющей части и передачу сигналов от датчиков до
контроллера: силовые и информационные кабели, распределительные коробки и
крепежные элементы;
Рисунок 4.4 - Типовая система электрообогрева трубопровода
- система управления: шкаф управления, терморегулятор,
датчики температуры трубы и воздуха, пускорегулирующая и защитная аппаратура.
В соответствии с поставленной задачей
(терморегулирование электрообогрева сбросного трубопровода Ш89х8, протяженность
90 м от предохранительного клапана) в состав разрабатываемой системы войдут:
- шкаф управления - установить в блок-боксе БТП в
отсеке автоматики (минимизация затрат на прокладку силового кабеля);
- датчик температуры трубы и распределительная
коробка - установить в месте наиболее уязвимом к остыванию;
три секции саморегулирующейся нагревательной
ленты по 30 м (две распределительные коробки);
датчик температуры воздуха - установить на
стенке блок-бокса БТП;
кабель контрольный - 220 м;
кабель электропитания - 420 м.
4.3.1 Выбор нагревательного кабеля
В зависимости от области применения используются нагревательные кабели
различной конструкции, рассчитанные на разные диапазоны температур.
Резистивные - в этих кабелях тепло выделяется
нагревательной жилой, окруженной изоляцией, экранами и защитными оболочками
(рисунок 4.5). Они запитываются с двух или с одного конца (двухжильные кабели).
К разновидностям этого типа относятся, в частности, плоские нагревательные
ленты типа Логнлайн, бронированные, армированные и спиральные кабели.
Резистивные кабели используются секциями определенной длины, зависящей от
исполнения кабеля и напряжения питания.
Рисунок 4.5 - Резистивный нагревательный кабель
Простота конструкции, высокая технологичность и
относительно низкая стоимость. Монтаж нагревательных секций на объекте занимает
мало времени и не сложен. Плоское сечение двухжильных кабелей и лент
обеспечивает хороший тепловой контакт с обогреваемой поверхностью. Они
позволяют обогревать трубопроводы длиной до нескольких километров при питании с
одного конца.
При этом существует необходимость использования секций
строго заданной длины. Кабели Логнлайн зачастую требуют для питания
высоковольтного оборудования и соблюдения, связанных с этим мер безопасности.
Зональные - специфическая разновидность резистивных
кабелей (рисунок 4.6). Тепло выделяется в нагревательной спирали, имеющей через
равные расстояния контакт с двумя токопроводящими жилами, благодаря чему
формируются зоны тепловыделения, соединенные параллельно. Вся конструкция
окружена изоляцией, экранами и защитными оболочками. Запитываются с одного
конца. Используются отрезками, кратными длине зоны.
Рисунок 4.6 - Зональный нагревательный кабель
Возможность использования произвольными (с точностью до метра) длинами
(до 200 м), отрезаемыми на объекте по месту. Высокие рабочие температуры (у
кабелей марки AHT - до плюс 350 °С). Тепловыделение, не зависящее от
температуры. Возможность использования концевого участка до первого зонного
контакта в качестве «холодного» монтажного конца.
Необходимость знания точного местонахождения зонных контактов и учет
«зонной кратности» длины при проектировании.
Саморегулирующиеся - тепло выделяется в полупроводящей
пластмассе, заполняющей пространство между двумя токопроводящими жилами
(рисунок 4.7). При повышении температуры сопротивление пластмассы возрастает и
тепловыделение падает, благодаря чему создается эффект саморегулирования.
Конструкция окружена электроизолирующими и защитными оболочками и экранами.
Запитываются с одного конца.
Рисунок 4.7 - Саморегулирующаяся нагревательная лента
Возможность использования произвольными (от 20 см) длинами, отрезаемыми
«по месту». В ряде случаев не требуют использования регулирующей аппаратуры. Не
перегреваются и не перегорают даже при самопересечении, так как каждый участок
кабеля сам приспосабливается к окружающим условиям теплоотдачи.
Стартовый ток при низкой окружающей температуре существенно (в
полтора-два раза) превышает номинальный рабочий ток системы обогрева, что
необходимо учитывать при расчете питающей сети и защитных устройств.
Практическая невозможность обеспечить форсированный обогрев, например.
По результатам анализа предложенных типов нагревательного кабеля
определено, что наиболее подходящим в особенности в условиях существующей
необходимости максимального обеспечения безаварийной эксплуатации объекта
повышенной опасности, выбором является саморегулирующееся нагревательная лента.
Для разрабатываемой системы необходима саморегулирующееся электрическая
нагревательная лента удовлетворяющая следующим требованиям:
- автоматическая регуляция тепловыделения в ответ на изменение температуры
трубы;
- нарезка нужной длины без ущерба для характеристик;
- стойкость к перегреву и перегоранию даже при самопересечении;
- высокое тепловыделение;
- рабочее напряжение 220 В;
- высокая прочность к механическим воздействиям;
- включение в максимальном температурном диапазоне.
Вышеуказанные параметры определены на основании
следующих исходных данных:
- диаметр трубопровода - 89 мм;
- толщина теплоизоляции трубопровода - 60 мм;
расчетные теплопотери - 21,6 Вт/м.
Наиболее подходящей данным критериям является лента типа ВТС
производства компании ООО «ССТ». А именно 30ВТС2-ВР, так как обладает
следующими характеристиками:
- максимальная температура плюс 120 °C;
- максимально допустимая температура без нагрузки (1000 часов
суммарно) 190 °C;
- минимальная температура монтажа минус 30 °C;
- электропитание - 220 - 240 В;
- максимальное сопротивление защитной оплетки не более 10
Oм/км;
- линейная мощность от 15 до 60 Вт/м;
- медная луженая оплетка;
- оболочка из фторполимера.
ВTС одобрена для использования в безопасных и
взрывоопасных зонах согласно мировым стандартам, а также стандартам ГОСТ Р
51330 и ГОСТ Р МЭК 62086. Также саморегулирующееся тепловая лента ВTС фирмы ООО
«ССТ» получил широкое распространение на объектах ОАО «Газпром». Конструкция
саморегулирующейся тепловой ленты ВTС представлена на рисунке 4.8.
Рисунок 4.8 - Конструкция саморегулирующейся тепловой
ленты ВTС
Согласно расчетам производителя, для трубопровода
диаметром 89 мм и протяженностью 90 м потребуется установить три секции
саморегулирующейся ленты по 30 м. В связи с чем, потребуется монтаж двух
распределительных коробок.
4.3.2 Выбор датчиков температуры
В качестве чувствительных элементов разрабатываемой системы необходимы
два датчика температуры, один предназначен для определения температуры воздуха,
другой необходим для измерения температуры трубы.
Основным критерием выбора датчиков являются такие параметры как:
- температурный диапазон (принимая во внимание климатические показатели
Нижне-Квакчикского ГКМ, необходимый диапазон измерения датчика находится в
районе от минус 45 до плюс 30 °С);
- форм-фактор;
соотношение «цена-качество».
По результатам проведенного анализа предложений различных производителей
средств измерений, таких как «OJ Electronics» (Дания), «FuehlerSysteme eNET
International GmbH» (Германия), ООО "ССТ" (Россия) и ПГ «Метран»
(Россия) можно сделать вывод, что спектр предложений требуемых датчиков
температуры, с достаточно широким диапазоном и точностью измерений (погрешность
не более ±1°С) достаточно широк. Цена на данные приборы варьируется в районе от
300 до 1000 рублей. Наработка на отказ составляет не менее 100 000 часов, срок
службы 10 лет.
В связи с незначительной стоимостью и с учетом положительного опыта
эксплуатации датчиков температуры трубы TST01-2,0-П (рисунок 4.9) на технологических
трубопроводах объектов Нижне-Квакчикского ГКМ, остановим выбор на данном
приборе. При этом необходимо отметить, что данные датчики находятся в наличии
на объекте.
Рисунок 4.9 - Датчик температуры трубы TST01-2,0-П
Ниже представлены основные характеристики датчика:
- выполнен в герметичном пластиковом корпусе;
- чувствительный элемент - цифровой полупроводниковый датчик
(DS18В20);
диапазон измеряемых температур от минус 55 до плюс 60 °С;
точность измерения температуры ±0,05 °С;
стоимость - 365 р.
Принцип действия цифровых датчиков температуры DS18В20 фирмы
"Dallas" основан на подсчете количества импульсов, вырабатываемых
генератором с низким температурным коэффициентом во временном интервале,
который формируется генератором с большим температурным коэффициентом.
Счетчик инициализируется значением, соответствующим минус 55 °C
(минимальной измеряемой температуре). Если счетчик достигает нуля перед тем,
как заканчивается временной интервал (это означает, что температура больше
минус 55 °C), то регистр температуры, который также инициализирован значением
минус 55 °C, инкрементируется. Одновременно счетчик предустанавливается новым значением,
которое задается схемой формирования наклона характеристики. Эта схема нужна
для компенсации параболической зависимости частот генераторов от температуры.
Счетчик снова начинает работать, и если он опять достигает нуля, когда интервал
еще не закончен, процесс повторяется снова. Схема формирования наклона
загружает счетчик значениями, которые соответствуют количеству импульсов
генератора на один градус Цельсия для каждого конкретного значения температуры.
По окончанию процесса преобразования регистр температуры будет содержать
значение температуры.
Далее более подробно о принципах работы кварцевых термометров. Кварцевые
термометры - это автогенераторные преобразователи с частотным выходом,
использующие в качестве чувствительного элемента пьезоэлектрический резонатор с
сильной зависимостью частоты от температуры. Преимущество использования
термочувствительных кварцевых резонаторов, прежде всего, заключается в их
высокой чувствительности, высокой стабильности и простоте использования. Сигнал
от резонаторов, возможно, сразу обрабатывать в цифровой форме, что удешевляет
процесс контроля температуры. Измерение температуры с помощью
термочувствительных кварцевых резонаторов основано на использовании анизотропии
кристалла кварца. Выбирая соответствующую ориентацию среза пьезоэлемента
относительно кристаллографических осей, можно изменять его термочастотную
характеристику, которая в общем случае является нелинейной функцией температуры
и описывается выражением [9].
где

-
температурный коэффициент частоты;
Т
и Т0 - калибровочное и опорное значение температуры;
f0 - резонансная частота при температуре Т0.
В широком диапазоне температур температурная частотная характеристика
кварцевого резонатора с достаточной точностью аппроксимируется полиномом
третьей степени (m = 3).
Для измерения температуры необходимы кварцевые резонаторы с максимальным
температурным коэффициентом чувствительности и монотонным изменением
температурной частотной характеристики на рабочем участке. Современные
кварцевые термочувствительные резонаторы имеют чувствительность 2 Гц/°С и 4
Гц/°С для резонаторов с опорной частотой, равной 32 и 64 кГц соответственно.
Диапазон измеряемых температур ограничен снизу азотными температурами, а
сверху - примерно величиной от плюс 150 до 200 °С. Ограничение определяется
наличием провалов добротности резонаторов при использовании искусственного
кварцевого сырья, а также уменьшением крутизны преобразования при понижении
температуры. Для достижения высокой точности измерения температуры необходима
индивидуальная градуировка с учетом нелинейных членов в аппроксимирующем
полиноме, однако, в настоящее время это не является сложной задачей.
Микропроцессор пересчитывает значение частоты, поступающее с кварцевого
преобразователя, в значение температуры по индивидуальной градуировочной
характеристике. Существуют термометры позволяющие измерять температуру в
диапазоне от минус 30 до плюс 100 °С с точностью 0,06 °С.
Типовой кварцевый термометр состоит из трех основных узлов:
чувствительного элемента, частотного преобразователя и специального вычислителя
(микроконтроллер). Созданный на базе кварцевых резонаторов цифровой термометр
можно использовать как многоканальную систему контроля температуры. Можно
осуществить передачу частоты с преобразователя температуры на расстояния до
нескольких сотен метров.
DS18B20 цифровой термометр с программируемым разрешением (рисунок 4.10),
от 9 до 12-bit, которое может сохраняться в EEPROM памяти прибора.
Рисунок 4.10 - Датчиков температуры DS18B20
DS18B20 обменивается данными по 1-Wire шине и при этом может быть как
единственным устройством на линии, так и работать в группе. Все процессы на
шине управляются центральным микропроцессором. Диапазон измерений от минус 55°C
до плюс 125°C и точностью 0,5°C в диапазоне от минус 10°C до плюс 85°C. В
дополнение, DS18B20 может питаться напряжением линии данных (“parasite power”),
при отсутствии внешнего источника напряжения.
Каждый DS18B20 имеет уникальный 64-битный последовательный код, который
позволяет, общаться с множеством датчиков DS18B20 установленных на одной шине.
Такой принцип позволяет использовать один микропроцессор, чтобы контролировать
множество датчиков DS18B20, распределенных по большому участку.
Описание выводов датчика DS18B20 дается в таблице 4.1.
На рисунке 4.11 показана блок-схема DS18B20.
Таблица 4.1 - Назначение выводов
Вывод
|
Символ
|
Описание
|
1
|
GND
|
Общий (земля)
|
2
|
DQ
|
Ввода/вывода (Input/Output pin) данных. По этой линии
подается питание в режиме работы с паразитным питанием.
|
3
|
VDD
|
VDD Вывод питания. Для режима работы с паразитным питание
VDD необходимо соединить с общим проводом.
|
Рисунок 4.11 - Структурная схема датчика DS18B20
64-битовый ROM запоминает уникальный последовательный код прибора.
Оперативная память содержит 2-байтовый температурный регистр, который хранит
значение температуры по окончанию температурного преобразования. Два
однобайтовых регистра температуры, контроля температуры (триггерной схемы TH и
TL), и к регистру конфигурации. Регистр конфигурации позволяет пользователю
устанавливать разрешающую способность цифрового преобразователя температуры к
9, 10, 11, или 12 битам, это и влияет на время конвертирования температуры. TH,
TL и регистры конфигурации энергонезависимы (EEPROM), таким образом, они
сохранят данные, когда прибор - выключен. B20 использует исключительно 1-Wire
протокол - при этом формируется соединение, которое осуществляет коммуникацию на
шине, используя всего один управляющий сигнал. Шина должна быть подключена к
источнику питания через «подтягивающий» резистор, так как все устройства
связаны с шиной, используют соединение через Z-состояния или вход открытого
стока. Используя эту шину микропроцессор (устройство управления) идентифицирует
и обращается к датчикам температуры, используя 64-битовый код прибора.
Поскольку каждый прибор имеет уникальный код, число приборов, к которым можно
обратиться на одной шине, фактически неограниченно.
Другая особенность DS18B20 - способность работать без внешнего питания.
Эта возможность предоставляется через подтягивающий резистор. Высокий сигнал
шины заряжает внутренний конденсатор (CPP), который питает прибор, когда на
шине низкий уровень. Этот метод носит название «Паразитное питание». При этом
максимальная измеряемая температура составляет плюс 100 °C. Для расширения
диапазона температур до плюс 125 °C необходимо использовать внешнее питание.
Основной функциональный блок DS18B20 это его температурный
преобразователь. Разрешающая способность температурного преобразователя может
быть изменена пользователем и составляет 9, 10, 11, или 12 битов, соответствуя
приращениям (дискретности измерения температуры) 0,5 °C, 0,25°C, 0,125°C, и
0,0625°C, соответственно. Разрешающая способность по умолчанию установлена
12-бит. В исходном состоянии DS18B20 находится в состоянии покоя (в неактивном
состоянии). Чтобы начать температурное измерение и преобразование, подается
команда начала конвертирования температуры [0х44]. После конвертирования,
полученные данные запоминаются в 2-байтовом регистре температуры в оперативной
памяти, и DS18B20 возвращается к неактивному состоянию. Если DS18B20 включен с
внешним питанием, ведущий может контролировать конвертирование температуры
(после команды [0х44]) по состоянию шины. DS18B20 будет формировать (ответ на
слот времени чтения от устройства управления) логический «0» когда происходит
температурное преобразование. И логическую «1», когда конвертирование
выполнено. Если DS18B20 включен с паразитным питанием, эта технология
уведомления не может быть использована, так как шину нужно подать высокий
уровень (напряжение питания) в течение всего времени температурного
преобразования. В этом случае устройство управления должно самостоятельно
контролировать время конвертирования.
Выходные температурные данные DS18B20 калиброваны в градусах Цельсия.
Температурные данные запоминаются как 16-битовое число со знаком (рисунок
4.12).
Рисунок 4.12 - Формат регистра температуры
Биты признака (S) указывают, является ли температура положительная или
отрицательная: для положительных S = 0, а для отрицательных чисел S = 1. Если
DS18B20 будет настроен для конвертирования 12-битной разрешения, то все биты в
температурном регистре будут содержать действительные данные. Для 11-битной
разрешающей способности, бит 0 не определен. Для 10-битной разрешающей
способности, биты 1 и 0 неопределенны, и для 9 битной разрешающей способности
2, 1 и 0 не определенны.
В таблице 4.2 представлены примеры данных цифрового выхода и
соответствующей температуры, для 12- битной разрешающей способности.
Таблица 4.2 - Соответствие данных цифрового выхода температуре
Температура
|
Цифровой выход (двоичный)
|
Цифровой выход (Hex)
|
+125°C
|
0000 0111 1101 0000
|
07D0h
|
+85°C
|
0000 0101 0101 0000
|
0550h
|
+25.0625°C
|
0000 0001 1001 0001
|
0191h
|
+25.0625°C
|
0000 0000 1010 0010
|
00A2h
|
+0.5°C
|
0000 0000 0000 1000
|
0008h
|
0°C
|
0000 0000 0000 0000
|
0000h
|
-0.5°C
|
1 111 111 111 111 000
|
FFF8h
|
-10.125°C
|
1 111 111 101 011 110
|
FF5Eh
|
-25.0625°C
|
1 111 111 001 101 110
|
FE6Fh
|
-55°C
|
1 111 110 010 010 000
|
FC90h
|
После того, как DS18B20 выполнит температурное преобразование,
температурное значение - сравнивается со значением, записанным в регистры TH и
TL. Регистры TH и TL энергонезависимы (EEPROM), таким образом, они сохранят
данные, когда устройство обесточено. К TH и TL можно обратиться через байты 2 и
3 согласно карте памяти.
4.3.3 Монтаж системы автоматического регулирования обогрева
Греющие секции смонтировать на поверхности трубы, пустив по низу.
Электропитание подвести к нагревательным секциям через коробки
соединительные РТВ401 (рисунок 4.13), которые предназначены для подключения к
силовой сети саморегулирующихся нагревательных лент.
Рисунок 4.13 - Коробка соединительная РТВ401
Коробка крепится непосредственно на трубопроводе. Коробка позволяет
выполнить подключение до 2 ниток саморегулирующихся нагревательных лент к силовому
кабелю.
Конструкция корпуса обеспечивает защиту от проникновения влаги и пыли
IP66 и высокую коррозионную стойкость. Кабельный ввод коробки предназначен для
подключения небронированных силовых кабелей диаметром от 7 до 18 мм или
бронированных силовых кабелей диаметром от 12,5 до 20,5 мм (сечение от 1,5 до
10 ммІ).
На площадку куста газоконденсатных скважин № 1 подведена линия
электропередачи ВЛ-10 кВ, электроснабжение потребителей электроэнергии на
напряжение 0,4 кВ предусмотрено от блок-бокса БТП-Э-Меркурий-А с
трансформатором 25 кВА. Кабели, питающие трехфазные потребители должны
содержать пять проводников:
фазные проводники (три штуки);
нулевой рабочий проводник;
защитный (заземляющий проводник).
Из всего многообразия кабельной продукции, представленной на современном
рынке, жестким требованиям электро и пожаробезопасности соответствуют только
два типа кабелей: ВВГ и NYM. С учетом положительного опыта эксплуатации кабеля
типа ВВГ решено использовать его. Внутренние сети должны быть выполнены кабелем,
не распространяющим горение, то есть с индексом «НГ» (СП - 110 - 2003 п. 14.5).
Кроме того, электропроводки должны быть с пониженным дымовыделением, на что
указывает индекс «LS». С учетом максимальной пусковой нагрузки 4,59 кВт и
протяженностью кабельной линии сечение одной жилы примем 2,5 мм2.
Для питания электрощита использовать кабель ВВг-НГ-LS 5х2,5. Электропитание
электрогреющих секций выполнить кабелем Вббшв 4х4 (напряжение питания 220В,
протяженность кабельной линии 240 м). На рисунке 4.14 представлена схема
организации электроснабжения греющих секций.
Рисунок 4.14 - Схема энергообеспечения
Для подключения контрольных кабелей от контроллера до датчика температуры
трубы использовать коробку соединительную РТВ403 (рисунок 4.15), которая
предназначена для подключения кабелей системы управления электрообогревом.
Коробка позволяет выполнить подключение 1 или 2-х кабелей управления.
Конструкция корпуса обеспечивает защиту от проникновения влаги и пыли IP66 и
высокую коррозионную стойкость. Кабельные вводы коробки предназначены для
подключения небронированных кабелей диаметром от 7 до 18 мм и бронированных
кабелей диаметром от 12,5 до 20,5 мм.
Рисунок 4.15 - Коробка соединительная РТВ403
Датчик температуры трубы и распределительную коробку
установить в месте наиболее уязвимом к остыванию. Выполнить прокладку
сигнального кабеля КВВГЭ 4х4) от контроллера САУ КГС № 1 до датчиков
температуры (рисунок 4.16).
Рисунок 4.16 - Принципиальная схема прокладки
кабельных линий
Управление нагревом необходимо осуществлять по сигналам, поступающим от
системы управления. Главным звеном в цепи управления является контроллер
PACSystems RX3i, который должен реализовать заданный алгоритм управления
обогревом трубопровода.
Контроллер PACSystems RX3i (рисунок 4.17) предлагает единый механизм
управления и универсальную среду программирования для обеспечения переносимости
приложений между различными аппаратными платформами и сближения систем
управления.
Рисунок 4.17 - Контроллер PACSystems RX3i
Высокопроизводительный контроллер с микропроцессором 300 МГц Intel и 10
МБайт пользовательской памяти, что исключает необходимость дополнительных
контроллеров и упрощает управление.
Универсальная объединительная панель с высокоскоростной шиной PCI,
работающей на частоте 27 МГц для быстрого переноса данных для комплексного
ввода-вывода и последовательной шиной для простого ввода-вывода, что
оптимизирует производительность и ваши вложения. Универсальная объединительная
панель поддерживает также функцию горячей замены для минимизации времени
простоя.
Широкий диапазон модулей ввода-вывода (доступно более 40 типов) для
простых и сложных приложений; также доступны различные сетевые модули.
Контроллер PACSystems RX3i обладает платформой для резервирования,
предоставляя ориентированное на пользователей решение высокой степени
доступности по достижению наилучших характеристик.
В качестве устройства коммутации мощности применить реле управления
К-6-22Z (производства фирмы ABB).
Регулятор контролирует температуру наружного воздуха посредством датчика
температуры воздуха. На основе полученной информации о температуре трубы
регулятор управляет мощностью обогрева объекта (от 0% до 100%). Регулятор
температуры автоматически включает обогрев системы и управляет мощностью
обогрева при температуре трубы ниже плюс 10 °С и автоматически отключает
обогрев при температуре трубы выше плюс 10 °С (защита от перегрева).
4.4 Алгоритм управления нагревом
Для обеспечения равномерного и своевременного нагрева трубопровода
необходимо задать рабочую характеристику контроля температуры, а именно две
температуры и соответствующие им проценты выходной мощности системы обогрева.
По ним контроллер рассчитывает свою температурно-мощностную кривую (рисунок
4.18).
Рисунок 4.18 - Температурно-мощностная характеристика
Затем контроллер переходит в режим стабилизации температуры. В результате
температура трубы поддерживается в заданном диапазоне с минимально возможными
энергозатратами, независимо от изменения температуры окружающего воздуха.
Алгоритм управления обогревом трубопровода сбросной линии газа с
предохранительного клапана СППК5 куста газоконденсатных скважин № 1
Нижне-Квакчикского ГКМ представлен на рисунке 4.19
Рисунок 4.19 - Алгоритм регулирования температуры
трубопровода
В соответствии с алгоритмом разработана программа на
языке ST, которая позволит контроллеру
PACSystems RX3i осуществлять изменение мощности обогрева трубопровода в
соответствии с температурными параметрами на объекте. Листинг программы
представлен ниже.
if T_ tr <10 then
if T_vozd<=-20
then W:=l00;
elsif W:=(10 - T_vozd)*3,33;
end_if;_if;
if T_tr>=10 then W:=0;
end_if;
5. Охрана труда и техника безопасности
Темой данного дипломного проекта, как уже было отмечено ранее, является
автоматизация куста газоконденсатных скважин № 1 Нижне-Квакчикского
газоконденсатного месторождения расположенного в Соболевском районе Камчатского
края (на западном побережье полуострова Камчатка) в 50 км севернее п.
Соболево. Ближайшими населенными пунктами являются п. Крутогоровский,
расположенный в 45 км к северо-западу, п. Соболево, расположенный в 50 км к
югу. От г. Петропавловск-Камчатский месторождение находятся на удалении 300 км.
В целях обеспечения охраны труда и техники безопасности, в данном разделе
дана характеристика производственной среды, в которой будет монтироваться,
эксплуатироваться и ремонтироваться автоматизированная система управления
технологическим процессом (описанная в технической части дипломного проекта), а
именно система автоматического управления обогревом технологических
трубопроводов. Также проводится анализ производственных опасностей и
вредностей, рассматриваются мероприятия по безопасной эксплуатации оборудования
автоматизации.
Охрана труда и техника безопасности должны выполняться при всех видах
работ, связанных с производственным процессом, монтажом, обслуживанием и
наладкой средств автоматизации куста газоконденсатных скважин № 1 Нижне-Квакчикского
ГКМ.
Несоблюдение требований безопасности производства может привести к
производственным травмам и авариям на объекте.
.1 Анализ потенциальных опасностей и производственных вредностей
На основании РД 00158758-161-94 скважины куста № 1 Нижне-Квакчикского ГКМ
расположены на одной прямой линии с шагом 40 м.
В соответствии с Положением о классификации чрезвычайных ситуаций
природного и технического характера, утвержденного Постановлением Правительства
РФ № 304 от 21.05.2007 на объекте возможно возникновение чрезвычайных ситуаций
локального характера (зона чрезвычайной ситуации не выходит за пределы
территории объекта при этом количество пострадавших составляет не более 10
человек).
При монтаже, наладке, эксплуатации и ремонте оборудования автоматизации
куста газоконденсатных скважин № 1 Нижне-Квакчикского ГКМ не исключена также
возможность возникновения следующих опасностей:
- воздействие
загрязненного воздуха на площадке и блок-боксе КТП на организм работающих
(таблица 5.1);
взрывопожароопасность, обусловленная тем фактом, что в производственной
среде возможно выделение взрывопожароопасных смесей. Классификация объектов на
площадке по взрывопожароопасности приведена в таблице 5.2;
опасность воздействия при проливе ингибитора - метанола, что приводит к
отравлениям при обслуживании технологического оборудования;
- природный
газ подается под высоким давлением до 19 мПа, температура может достигать до 20
°С.
Технологические процессы на площадке куста газоконденсатных скважин № 1
Нижне-Квакчикского газоконденсатного месторождения происходят под высоким
давлением (давление в устье добывающей скважины может достигать 19 мПа). В
случае разрушения оборудования скважин (противофонтанного оборудования, осадной
колонны) фактором дальнейшего развития аварии является невозможность быстрой
остановки процесса выхода газа из устья скважины или из поверхности земли.
Развитие газопроявления может привести к выбросу из скважины газа или
промывочного раствора и к аварийному истечению (фонтану), которое создает пожароопасную
ситуацию.
Таблица 5.1 Взрывопожароопасные и токсические свойства веществ куста
газоконденсатных скважин № 1 Нижне-Квакчикского ГКМ (полуостров Камчатка)
Наименование вещества на рассматриваемом объекте
|
Агрегатное состояние
|
Класс опасности веществ
|
Температура, °С
|
Концентрационный предел взрываемости, % объем
|
Характеристика токсичности (воздействие на организм
человека)
|
Предельно допустимая концентрация веществ в воздухе
|
|
|
|
Вспышки
|
Самовоспламенения
|
Нижний предел
|
Верхний предел
|
|
|
Природный газ
|
Г
|
4
|
-
|
537
|
4,5
|
13,5
|
В больших количествах обладает наркотическим действием
|
50 (ОБУВ)
|
Метанол
|
Ж
|
3
|
11
|
436
|
6
|
34,7
|
Сильный и весьма опасный нервный яд
|
5
|
Конденсат газовый
|
Ж
|
4
|
-44
|
380
|
1,4
|
8
|
Пары оказывают вредное воздействие на центральную нервную
систему
|
37
|
Таблица 5.2 Взрывопожарная и пожарная опасность, санитарная
характеристика производственных зданий, помещений и наружных установок куста
газоконденсатных скважин № 1 Нижне-Квакчикского ГКМ (полуостров Камчатка)
Наименование производственных зданий, помещений, наружных
установок
|
Категории взрывопожароопасной и пожарной опасности зданий и
помещений (НПБ 105-03)
|
Классификация зон внутри и вне помещений
|
|
|
Класс
взрывопожароопасной
или пожарной зоны (ПУЭ и ПБ 08- 624-03)
|
Категории и группа взрывопожароопасных
смесей (ГОСТ 12.1.011- 78) Р51330.5-99 Р52330.11-99
|
Устья скважин
|
Ан
|
В-1 г
|
IIA-T1
|
КИП, операторные щиты управления
|
Д
|
|
|
Основные возможные причины аварий на скважинах площадки куста скважин № 1
Нижне-Квакчикского ГКМ (полуостров Камчатка):
- несоответствие конструкции скважины геологическим условиям (не
учитываются залегания и пластовые давления вскрываемых горизонтов, глубина
залегания подверженных гидроразрыву пород и др.);
- некачественное цементирование кондукторов, промежуточных и
эксплуатационных колонн;
негерметичность резьбовых соединений и нарушения целостности
обсадных колонн, а также дефекты устьевого оборудования;
разрушение в результате воздействия агрессивных сред и высоких
давлений (выход из строя элементов оборудования происходит преимущественно в
скважинах, в добываемой продукции которых содержится минерализованная вода);
разгерметизация оборудования из-за коррозии, дефекта
изготовления, усталости металла, механического повреждения;
ошибки персонала при ведении технологического процесса;
нарушения техники безопасности при проведении работ по
техническому обслуживанию оборудования, при огневых и сварочных работах, а
также наладке оборудования КИП и автоматики;
неисправность и неправильная эксплуатация противовыбросового
оборудования.
Причинами разгерметизации трубопроводов могут быть:
- остаточные напряжения в материале трубопроводов в сочетании с
напряжениями, возникающими при монтаже и ремонте;
- превышение давления;
коррозия;
образование ледяных пробок, размораживание.
Технологические процессы на площадке куста газоконденсатных скважин № 1
Нижне-Квакчикского ГКМ, для поддержания которых используются технические
средства автоматизации (термопреобразователи, манометры и т. д.), изложенные в
технической части дипломного проекта, характеризуются следующими особенностями:
- содержимым
технологического оборудования являются: природный газ, газовый конденсат и
метанол, оказывающие неблагоприятное воздействие на человека;
- приводом задвижек на технологических трубопроводах являются
электродвигатели с питающим напряжением до 380 В, а также другие средства
(электрообогреватели, трансформатор тока и др.), которые могут быть источниками
поражения электрическим током. По степени опасности поражения электрическим
током объект относится к особо опасным, так как имеется сырость, токопроводящие
полы и металлоконструкции;
- основная часть оборудования работает под избыточным давлением, которое
может достигать до 19 мПа и вызвать порыв трубопроводов.
Первичные преобразователи (преобразователь температуры Метран-286,
давления Метран-150TG и 150CD), контроллер и вторичные приборы
автоматизации, находятся непосредственно в зоне с возможным образованием
взрывоопасных смесей.
Отказ или поломки оборудования КИП и автоматики могут являться фактором
позднего обнаружения утечки газа, из-за отсутствия запах газа.
Основные физические проявления аварии и сопровождающие их поражающие
факторы при загидрачивании сбросной линии газа (объект модернизации) согласно
СТО Газпром 2-2.3-400-2009:
- разрыв трубопровода со срывом его концов с опор с воспламенением газа и
образованием струевого пламени (поражающие факторы: разлет осколков, ВВС,
скоростной напор струи газа, прямое воздействие пламени, тепловое излучение);
- разрыв трубопровода со срывом его концов с опор без
воспламенения газа, истекающего в виде свободной(ых) струи(й) из концов
разрушенного трубопровода (поражающие факторы: разлет осколков, ВВС, скоростной
напор струи газа, загазованность).
5.2 Мероприятия по обеспечению безопасных и безвредных
условий труда на площадке куста газоконденсатных скважин
Надежная и взрывобезопасная эксплуатация технологического оборудования
достигается за счет своевременного распознавания предаварийных ситуаций и
комплексной защите объекта управления.
Для обеспечения надежной и безопасной эксплуатации технологического
оборудования, а также для предупреждения возникновения чрезвычайных ситуаций
предусмотрены следующие мероприятия:
- управление технологическими операциями осуществляется автоматически;
- технологические схемы и комплектация основного оборудования
гарантируют непрерывность производственного процесса за счет оснащения
технологического оборудования системами автоматического регулирования,
блокировки и сигнализации;
генеральный план объекта выполнен с соблюдением противопожарных
разрывов между сооружениями в соответствии со СНиП II-89-80* «Генеральные планы промышленных предприятий» и ВНТП
03/170/567-87 «Противопожарные нормы проектирования объектов Западносибирского
нефтегазового комплекса»;
технологического оборудование выбрано в соответствии с заданными
технологическими параметрами, что уменьшает вероятность образования
взрывоопасных смесей;
применение блочно-комплектного оборудования заводского
изготовления, как более надежного в эксплуатации;
запорная арматура для газа принята по классу герметичности
затвора А по ГОСТ 9544-93;
соединения труб предусмотрено выполнить сваркой;
предусмотрен 100% контроль качества физическими методами сварных
соединений трубопроводов;
выбор материалов труб и деталей технологических трубопроводов
произведен по температуре наиболее холодной пятидневки района эксплуатации
(минус 31 °С);
для защиты от превышения рабочего давления на отдельном
технологическом оборудовании установлены предохранительные клапаны;
для площадки куста газоконденсатных скважин предусмотрен уровень
автоматизации, при котором обеспечивается безаварийная работа в условиях
нормальной эксплуатации без постоянного присутствия обслуживающего персонала;
принятая степень автоматизации обеспечивается наличием
необходимых средств контроля и управления;
применение оборудования, не соответствующего по категории
исполнения климатическим условиям не допускается.
Для обеспечения стабильности кустовых оснований площадки скважин № 1
Нижне-Квакчикского ГКМ выполнены мероприятия по инженерной подготовке
территории, которая запроектирована исходя из природно-климатических и
грунтовых условий района.
Оставшаяся после проведения строительных работ песчаная полоса вокруг
куста является противопожарной преградой.
Продувка скважин и трубопроводов при ремонтных и профилактических
работах предусматривается на горизонтальный факел. Горизонтальный факел
установлен в факельном амбаре в обваловании выстой 1,5 м на расстоянии 100 м от
оси куста скважин. Для предотвращения эрозии обваловки амбара от струи и
пламени горящего газа длина амбара составляет 24 м, ширина - 6 м.
5.2.1 Мероприятия по технике безопасности на площадке куста
газоконденсатных скважин № 1 Нижне-Квакчикского ГКМ (полуостров Камчатка).
Во избежание несчастных случаев при обслуживании оборудования куста
газоконденсатных скважин № 1 Нижне-Квакчикского ГКМ (полуостров Камчатка),
персонал должен иметь соответствующую подготовку, пройти производственный
инструктаж, быть ознакомлен с общими правилами техники безопасности и с
безопасными методами работы на поручаемом ему для обслуживания оборудования, а
также с методами оказания первой помощи. По окончании инструктажа направляемые
на работу сдают экзамен по технике безопасности в соответствии с ПБ 08-624-03,
ПУЭ, ПТЭ и получают удостоверение с присвоенной квалификационной группы, дающее
им право работать по обслуживанию действующих электроустановок.
Большинство технических средств, на базе которых построена система
автоматизации технологических процессов куста газоконденсатных скважин № 1
Нижне-Квакчикского ГКМ, являются потребителями электрической энергии. Поэтому в
первую очередь отметим мероприятия по обеспечению электробезопасности:
- к
работе допускаются лица, имеющие допуск к данному виду работ (в частности, к
работе с напряжением до 1000 В);
- все
работы, связанные с монтажом, наладкой, обслуживанием и ремонтом ТСА, должны
производиться в соответствии со следующими нормативно-техническими документами:
а) «Правила технической эксплуатации электроустановок потребителей»
(ПТЭ);
б) «Правила техники безопасности при эксплуатации электроустановок
потребителей» (ПТБ);
в) «Правила устройства электроустановок» (ПУЭ);
- изоляцией
электрических устройств в соответствии с техническими условиями;
- все
части устройств, находящихся под напряжением размещены в корпусах,
обеспечивающих защиту обслуживающего персонала от прикосновения к деталям,
находящимся под напряжением, а открытые токоведущие части располагаются на
недоступной высоте;
- надежным креплением технических средств автоматизации при их монтаже на
объекте автоматизации.
Корпуса устройств заземляются в соответствии с ГОСТ 12.2.007-75
(сопротивление заземляющего устройства не должно превышать 4 Ом).
Измерение сопротивления заземляющего устройства производится не реже
одного раза в год.
Работы, связанные с ремонтом технических средств автоматизации куста
скважин № 1 Нижне-Квакчикского ГКМ, располагаемых во взрывоопасной зоне,
необходимо производить только при отключенном напряжении питания.
Отметим мероприятия по обеспечению взрывобезопасности оборудования:
- всё
оборудование и коммуникации испытаны на механическую прочность повышенным
давлением;
- защита
оборудования и коммуникаций от прямых ударов молний и вторичных проявлений
молний;
- заземление всех металлических нетоковедущих частей электрооборудования, а
также строительных металлоконструкций.
5.2.2 Мероприятия по промышленной санитарии на площадке куста
газоконденсатных скважин
К мероприятиям по промышленной санитарии относятся требования к
спецодежде, требования к освещению, микроклимату, к шуму и вибрации на рабочем
месте, требования к организации и оборудованию рабочего места.
Все работники, обслуживающие оборудование, обеспечиваются защитной
спецодеждой - костюм хлопчатобумажный, рукавицы, сапоги в соответствии с ГОСТ
12.4.011 -89 ССБТ «Средства защиты работающих». Также в соответствии с
«Типовыми нормами бесплатной выдачи сертифицированных специальной одежды,
специальной обуви и других средств индивидуальной защиты работникам, занятым на
работах с вредными и (или) опасными условиями труда, а также на работах,
выполняемых в особых температурных условиях или связанных с загрязнением, в
организациях нефтегазового комплекса», утвержденными приказом № 443 от 6 июля
2005 г. Министерством здравоохранения и социального развития РФ, в качестве
защитных мероприятий от воздействия метанола на человека в проекте
предусмотрено применение специализированных средств индивидуальной защиты:
защитные очки, резиновые перчатки, спецодежда и обувь.
Для устранения воздействия на организм работающих вредных веществ
предусмотрена выдача противогазов при аварийной ситуации на площадке куста
газоконденсатных скважин.
Система производственного освещения площадки обеспечивает:
- соответствие
уровня освещенности рабочих мест характеру выполняемой зрительной работы;
- постоянство
освещенности во времени.
5.2.3 Мероприятия по пожарной безопасности на площадке куста
газоконденсатных скважин
Требования по пожарной безопасности регламентируются согласно ППБ 01-03
«Правила пожарной безопасности» и ВППБ 01-04-98. В целях профилактики пожаров
на территории площадки куста скважин № 1 Нижне-Квакчикского ГКМ необходимо:
- чтобы
персонал был ознакомлен с технологическими процессами на объекте, инструкциями
по противопожарной безопасности и устройством средств пожаротушения, а также
обучен действиям в сложившейся опасной ситуации;
- принять меры по устранению источников зажигания в местах возможного
образования взрывопожароопасных смесей;
- использованный обтирочный материал хранить в специальном металлическом
ящике с крышкой.
Система обеспечения пожарной безопасности объекта предусматривает,
прежде всего, предотвращение пожара, т.е. устранение причин его возникновения и
обеспечивается комплексом организационно-технических мероприятий, изложенных в
данном перечне. Также осуществляется постоянный контроль за эксплуатацией
взрывоопасных и пожароопасных установок.
Минимальные расстояния между сооружениями площадки куста скважин № 1
Нижне-Квакчикского ГКМ с учетом их пожарной опасности и степени огнестойкости
приняты по нормам СНиП II-89-80*,
ВНТП 01/87/04-84, ВНТП 03/170/567-87, СНиП 2.07.01-89, НПБ 11-98*. Расстояние
от факельного ствола до границы сооружений принято 100 м.
На основании нормативных документов приняты:
- уровень ответственности зданий и сооружений согласно приложению 7 СНиП
2.01.07-85* - II;
- класс функциональной пожарной опасности по СНиП 21-01-97*;
степень огнестойкости зданий по СНиП 21-01-97*;
- класс конструктивной пожарной опасности по СНиП 21-01-97*.
На въезде на кустовую площадку скважин № 1 Нижне-Квакчикского ГКМ
предусмотрена площадка размещения пожарной техники размером 20 на 20 м.
Система оповещения организована в соответствии с требованиями ПНБ 104-03.
В помещении КТП устанавливается автоматическая установка пожаротушения.
Электрооборудование, контрольно-измерительные приборы, средства
блокировки и автоматика выполнены во взрывозащищенном исполнении(Ex) и имеют уровень взрывозащиты - 1
(взрывобезопасный), по виду взрывозащиты применяется оборудование с
искробезопасной электрической сетью (i).
Молниезащита зданий и сооружений объектов выполнена в соответствии с
требованиями «Инструкции по устройству молниезащиты зданий, сооружений и
промышленных коммуникаций» СО153-34.21.122-2003.На площадке куста скважин № 1
Нижне-Квакчикского ГКМ установлена мачта прожекторная с молниеотводом (общая
высота 32 м).
Исполнение оборудования и средств автоматизации, размещенных во
взрывоопасных зонах, соответствует классификации помещений и наружных установок
по взрывоопасной и пожарной опасности в соответствии с ПЭУ и ППБ 01-03, НПБ
105-03.
Контроль загазованности реализован на базе газоанализатора СГОЭС
производства ЗАО «Электростандарт-прибор», г. Гатчина. Для опробования и съема
звуковой и световой сигнализации используется пост управления кнопочный
взрывозащищенный КУ-91-1ExdT5
фирмы ОАО «ВЭЛАН» г Зеленокумск. Для звукового и светового оповещения
применяется оповещатель звуковой взрывозащищенный «ExOПП3-2В» и оповещатель ТСВ-1-12-А-Т-К/Ч соответственно
фирмы НПК «Эталон», г. Волгодонск.
5.3 Расчет критериев пожарной опасности и определение категории скважин
куста газоконденсатных скважин
.3.1 Исходные данные
Характеристика веществ и материалов, обращающихся (находящихся) на
площадке:
Природный газ (по метану СН4): горючий газ. Молярная масса: 16,043
кг/кмоль. Нижний концентрационный предел распространения пламени (НКПР): 5,28%
(об.). Расчетная температура воздуха tp = 29 °С - абсолютная
максимальная температура воздуха согласно СНиП 23-01-99. Характеристика
технологического процесса:
В состав скважины входят:
- трубопровод с газом, диаметром 100 мм, длиной 4 м, давлением 1МПа,
производительность 1500 м3/час;
- трубопровод с метанолом диаметром 50 мм.
Отключение автоматическое, без резервирования, расчетное время
отключения принимается согласно НПБ 105-03 равным 120 с.
5.3.2 Расчет критериев пожарной опасности
Расчет выполняется в соответствии с НПБ 105-03. За расчетную аварийную
ситуацию принимается разгерметизация трубопровода с газом на площадке куста
газоконденсатных скважин № 1 Нижне-Квакчикского ГКМ.
Определяется объем газа, выделившегося в результате расчетной аварии, м3:
,(5.1)
,(5.2)
где V1Т - объем газа, вышедшего из
трубопровода до его отключения, м3;
,(5.3)
где q - расход газа, м3/с;
T - расчетное время отключения, с;
V2Т
- объем газа,
вышедшего из трубопровода после его отключения, м3;
(5.4)
где P - давление в трубопроводе, кПа;
r - внутренний радиус трубопроводов,
м;
L -
длина трубопровода от аварийного аппарата до задвижек, м.
м3(5.5)
Определяется плотность газа при расчетной температуре, кг/м3:
,(5.6)
где М - молярная масса, кг/кмоль;
V0 - молярный объем, м3/кмоль;
tр - расчетная температура, °С.
Определяется масса выделившегося при аварии газа, кг:
(5.7)
Горизонтальный размер зоны, ограничивающий область концентраций,
превышающих нижний концентрационный предел распространения пламени,
определяется по формуле:
(5.8)
Определяется приведенная масса газа mпр, кг:
,(5.9)
где Qсг - удельная теплота сгорания газа,
Дж/кг;
Z -
коэффициент участия горючих газов в горении;
Q0 - константа, Дж/кг;
m -
масса горючих газов, поступивших в результате аварии в окружающее пространство,
кг.
Избыточное давление, развиваемое при сгорании газовоздушной смеси,
определяется по формуле:

(5.10)
5.3.3 Определение категории наружной установки по пожарной опасности
Определение категорий наружных установок осуществляется путем
последовательной проверки их принадлежности к категориям, приведенным в НПБ
105-03. В соответствии с НПБ 105-03 скважины добывающие эксплуатирующие
относятся к категории Ан, т.к. горизонтальный размер зоны, ограничивающей
газовоздушную смесь с концентрацией горючего выше НКПР, превышает 30 м и
расчетное избыточное давление при сгорании газовоздушной смеси на расстоянии 30
м от наружной установки превышает 5 кПа.
6. Расчет экономического эффекта внедрения системы
.1 Краткая характеристика предложения
Для снижения расчетного давления шлейфа на общем газовом коллекторе
кустовой площадки № 1 Нижне-Квакчикского ГКМ предусмотрена установка регулятора
давления и предохранительного клапана (для защиты шлейфа от превышения
давления).
Газ от предохранительного клапана сбрасывается в амбар по трубопроводу
Ш89х8 (труба - 09Г2С, Рисп = 36,88 МПа, протяженность 90 м).
Давление настройки предохранительного клапана 15,8 МПа.
В процессе проведения наладочных работ и пробной эксплуатации
технологических систем куста газоконденсатных скважин № 1 Нижне-Квакчикского
ГКМ выявлено следующее: при отработке сброса газа с предохранительного клапана
наблюдается скапливание в трубопроводе сбросной линии гидратов углеводородов
содержащихся в добываемом газе (вода, метанольная вода и т.д.). Причиной
образования скоплений гидратов в трубопроводе является отсутствие естественного
положительного наклона трубопровода сбросной технологической линии.
Одной из важнейших проблем при эксплуатации трубопроводов транспорта газа
является образование газогидратов. Наиболее часто закупорки газопровода
происходят в зимний период в связи значительным охлаждением движущегося в
трубопроводе газового потока.
Вместе с тем климат в районе Нижне-Квакчикского газоконденсатного
месторождения характеризуется холодной, ветреной, малооблачной погодой. Самый
холодный месяц - февраль, средняя месячная температура которого составляет
минус 14,8 °С, а абсолютный минимум достигает минус 45 °С. Температура наиболее
холодной пятидневки - минус 31 °С. Определено, что имеющейся теплоизоляционной
окожуховки трубопровода для недопущения образования гидратных пробок в
трубопроводе в период отрицательных температур недостаточно.
Образование гидратных пробок в трубопроводе сброса газа с
предохранительного клапана общего газового коллектора куста газоконденсатных
скважин № 1 повлечет к разрушению технологического трубопровода сбросной линии
и невозможности выполнить защиту шлейфа общего газового коллектора от повышения
давления в случае возникновения нештатных ситуаций.
В соответствии с поставленной задачей
(терморегулирование электрообогрева сбросного трубопровода Ш89х8 09Г2С
протяженность 90 м от предохранительного клапана) в состав разрабатываемой
системы войдут:
- шкаф управления - обусловлено необходимостью
установки контроллера терморегуляции, устройств и оборудования аварийного
автоматического отключения при возникновении короткого замыкания, а также
возникновении тока утечки на землю (30 мА), шкаф установить в блок-боксе КТП в
отсеке автоматики (минимизация затрат на прокладку кабеля электропитания);
- датчик температуры трубы и распределительная
коробка - установить в месте наиболее уязвимом к остыванию;
три секции саморегулирующейся нагревательной
ленты по 30 м (две распределительные коробки);
датчик температуры воздуха - установить на
стенке блок-бокса КТП;
кабель контрольный - 220 м;
кабель электропитания - 420 м;
Регуляция температуры обогрева трубопровода
предусматривается на основе алгоритма, заложенного в контроллер системы
автоматизации кустовой площадки ПТК Rx3i PACSystem.
6.2 Расчет экономической эффективности
Исходные данные для расчета экономического эффекта
представлены в таблице 6.1.
Таблица 6.1 - Исходные данные для расчёта
экономического эффекта
Показатель
|
Значение
|
Суточная добыча газа, тыс. м3/сут.
|
174,40
|
Себестоимость добычи природного газа, руб./тыс. м3
|
4,89
|
Ставка неустойки за несвоевременную подачу газа (от
себестоимости), %
|
50
|
Ставка налога на прибыль, %
|
20
|
Стоимость ремонтных работ, тыс.руб.
|
75
|
Средняя продолжительность ремонта, час.
|
16
|
Количество монтируемых систем, шт.
|
1
|
Стоимость монтажа системы, тыс.руб./шт.
|
7,20
|
Стоимость приобретения оборудования и материалов системы,
тыс.руб.
|
160,65
|
Для начала на основании исходных данных рассчитаем общую величину затрат
на внедрение системы обогрева трубопровода сбросной линии куста
газоконденсатных скважин № 1 Нижне-Квакчикского ГКМ.
,(6.1)
где Зпр - величина затрат на оборудование и его доставку до
объекта, тыс.р.
Зм - затраты на монтаж системы, тыс.руб.
N -
количество приобретаемых и монтируемых систем, шт.
(6.2)
Общая величина затрат на предлагаемое проектное решение составит 167,85
тыс.р.
Далее определим величину полученных результатов от внедрения системы
обогрева трубопровода сбросной линии куста газоконденсатных скважин.
Данный трубопровод, как участник технологической цепочки, непосредственно
не участвует в процессе добычи и транспортировки природного газа до УНТС УКПГ
Нижне-Квакчикского ГКМ и далее потребителю, а предназначен для защиты шлейфа от
превышения давления на общем газовом коллекторе куста скважин в случае
аварийных ситуаций. Соответственно результаты от внедрения указанной системы
определены совокупностью экономических выгод от предотвращения аварийных
ситуаций и разрушения технологического оборудования куста скважин и
следовательно, несвоевременной перекачки природного газа потребителю (Рt).
, (6.3)
где Сдоб - объем суточной перекачки газа, 1000 м3;
- часов в сутках, час;
Трем - продолжительность ремонтных работ, час;
Цдоб - себестоимость добычи газа, руб./1000 м3;
Ндоб - неустойка за несвоевременную поставку газа, д.е;
Црем - средняя сметная стоимость ремонтных работ.
Величина экономии составит:
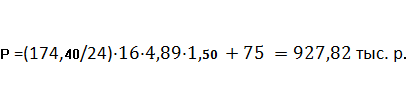
(6.4)
Согласно статистическим данным, приведенным в СТО Газпром 2-2.3-400-2009
доля аварий произошедших на газопроводах неочищенного газа (наиболее подходящих
по классификации) за 38 лет составляет 3,2% от общего количества аварий. Что
составляет порядка одной аварии за 8 лет.
Рг = 927,816/8 = 115,98 тыс.р. (6.5)
Общая величина годового экономического эффекта составит:
Э = 167,85 - 115,977 = 51,97 тыс.р. (6.6)
Чистая прибыль предприятия:
ЧП = Э·(1-Н), (6.7)
где Н - налог на прибыль предприятий и организаций.
ЧП = 51,97· (1-0,2) = 41,60 тыс.р. (6.8)
Таблица 6.2 - Сводные показатели расчета экономического эффекта
Показатель
|
Значение
|
Общая величина затрат на внедрение системы, тыс.руб.
|
167,85
|
Общая величина полученных результатов от внедрения системы,
тыс.руб.
|
927,82
|
Годовая величина полученных результатов от внедрения
системы, тыс.руб.
|
115,98
|
Годовой экономический эффект внедрения, тыс.руб.
|
51,97
|
Чистая прибыль предприятия, тыс.руб.
|
41,60
|
6.3 Расчет показателей инвестиционного проекта
Для того чтобы система была эффективной, затраты на текущий ремонт должны
составлять не более 10% от капитальных вложений. Внедряемая система имеет
высокую степень надежности.
Величина амортизационных отчислений:

, (6.9)
где NA - норма амортизационных отчислений,
%;
К - капитальные вложения, тыс. руб.
Норма амортизационных отчислений NA = 10% с учетом планового срока
обновления системы 10 лет.
Результаты расчета эксплуатационных затрат приведены в таблице 6.3.
Таблица 6.3 - Расчет эксплуатационных затрат
Наименование
|
Стоимость, тыс. руб.
|
Затраты на текущий ремонт
|
16,79
|
Амортизационные отчисления
|
16,79
|
Итого:
|
33,58
|
Одним из показателей экономической эффективности является чистый
дисконтный доход (ЧДД), который определяется как сумма текущих эффектов за весь
расчетный период. Проект считается прибыльным и его следует принять, если
чистый дисконтный доход (ЧДД) больше нуля.
На практике часто пользуются следующей формулой для определения ЧДД:

(6.10)
где t - год расчетного периода;
N -
плановый срок обновления системы, лет;
ЧП - чистая прибыль в году t,
руб.;
бt - коэффициент дисконтирования.
В качестве начального года расчетного периода принимается год начала
финансирования работ по осуществлению мероприятия. Конечный год tN расчетного периода определяется
моментом завершения установленного жизненного цикла проектируемой системы,
зависящий от планового срока обновления средств автоматизации по условиям их
использования или срока службы (с учетом морального старения).
Приведение разновременных затрат и результатов всех лет периода
реализации мероприятия к расчетному году осуществляется путем умножения их
величины за каждый год на коэффициент дисконтирования, рассчитываемый по
формуле:

(6.11)
где r - величина ставки дисконта, r =10%.
Важным фактором, влияющим на оценку эффективности проекта, является
ставка дисконта.
В результате расчетов получаем, что ЧДД > 0 (таблица 6.4),
следовательно, применение системы целесообразно с экономической точки зрения.
Предложенная система автоматического регулирования температуры трубы
сбросного газопровода может быть рекомендована к внедрению, что подтверждено
расчетом экономической эффективности.
Таблица 6.4 - Расчет показателей эффективности инвестиционного проекта
внедрения системы
Показатель
|
Год
|
Итого
|
|
0
|
1
|
2
|
3
|
4
|
5
|
6
|
7
|
8
|
9
|
10
|
|
Затраты на внедрение, тыс.руб.
|
167,85
|
-
|
-
|
-
|
-
|
-
|
-
|
-
|
-
|
|
|
167,85
|
Денежный поток, тыс.руб.
|
-
|
-
|
-
|
-
|
-
|
-
|
-
|
-
|
927,82
|
-
|
-
|
927,816
|
Эксплуатационные издержки, тыс.руб.
|
-
|
33,58
|
33,58
|
33,58
|
33,58
|
33,58
|
33,58
|
33,58
|
33,58
|
33,58
|
33,58
|
335,8
|
Валовая прибыль, тыс.руб.
|
-
|
51,97
|
51,97
|
51,97
|
51,97
|
51,97
|
51,97
|
51,97
|
51,97
|
51,97
|
51,97
|
|
Чистая прибыль, тыс.руб.
|
-
|
41,60
|
41,60
|
41,60
|
41,60
|
41,60
|
41,60
|
41,60
|
41,60
|
41,60
|
41,60
|
4160
|
Коэффициент дисконтирования
|
-
|
0,91
|
0,48
|
0,32
|
0,24
|
0,20
|
0,16
|
0,14
|
0,12
|
0,11
|
0,10
|
-
|
Чистый дисконтированный поток, тыс.руб.
|
-167,85
|
37,82
|
19,8
|
13,42
|
10,15
|
8,16
|
6,82
|
5,86
|
5,14
|
4,57
|
4,12
|
-
|
ЧДД
|
115,86
|
Индекс доходности
|
1,69
|
Срок окупаемости, лет
|
на 6-ой год эксплуатации в соответствии с денежными
потоками
|
Внутренняя норма доходности, %
|
17,5
|
Заключение
В данном дипломном проекте была рассмотрена система автоматизации куста
газоконденсатных скважин № 1 Нижне-Квакчикского газоконденсатного
месторождения.
Приведенное в первом разделе технологическое описание куста
газоконденсатных скважин дает полное представление об особенностях его работы и
взаимосвязи с другими объектами Кшукского и Нижне-Квакчикского месторождений.
Анализ существующего уровня автоматизации рассматриваемого куста скважин
показал, что он находится на достаточно высоком уровне, позволяющем обеспечить
протекание всех технологических процессов на объекте без присутствия
эксплуатационного персонала. В тоже время в процессе проведения наладочных
работ и пробной эксплуатации технологических систем куста газоконденсатных
скважин № 1 Нижне-Квакчикского ГКМ выявлено скапливание в трубопроводе сбросной
линии гидратов углеводородов содержащихся в добываемом газе (конденсат, метанольная
вода и т.д.). В связи с чем, предложено внедрение автоматической системы
регулирования обогрева трубопровода.
Проведённый технико-экономический анализ
свидетельствует о том, что внедрение системы автоматического управления
обогревом трубопровода позволит увеличить ресурс работы рассматриваемой
технологической линии за счет непрерывного измерения и регулирования его
температурных параметров.
Анализ безопасности проекта свидетельствует о снижении
вероятности возникновения аварийных ситуаций на кусте скважин № 1 в результате
предотвращения процессов гидратообразования в трубопроводе.
Для обеспечения безопасной эксплуатации куста газоконденсатных скважин №
1 Нижне-Квакчикского ГКМ разработанная система должна являться неотъемлемой
частью данного объекта.
Список использованных источников
1 Ананенков А.Г. АСУ ТП промыслов газоконденсатного
месторождения крайнего севера/ А.Г. Ананенков, Г.П. Ставкин, Э.Г. Талыбов. -
М.: Недра, 1998. - 221 с.
Горев С.М. Автоматизация технологических процессов в нефтяной
и газовой промышленности. Курс лекций. Ч. 1. - Петропавловск-Камчатский: Камчат ГТУ, 2003. - 121 с.
3 Кулиев А.М. Оптимизация процессов газопромысловой
технологии/ А.М. Кулиев, В.Г. Тагиев. - М.: Недра, 1984. - 200 с.
4 Датчик давления Метран-150: руководство по эксплуатации.
Челябинск: ПГ «Метран», 2012.
Преобразователь температуры Метран - 286: руководство по
эксплуатации. Челябинск: ПГ «Метран», 2008.
Программированное устройство Rx3i PACSystem: руководство по
эксплуатации. Компания GE Fanuc Automation North America, Inc., 2005.
Бекиров Т.М. Сбор и подготовка к транспорту природных газов/
Т.М. Бекиров, А.Т. Шаталов. - М.: Недра, 1986. - 261 с.
Комиссарчик, В.Ф. Автоматическое регулирование
технологических процессов: учебное пособие. - Тверь: 2001. - 247 с.