Разработка технологического процесса механической обработки детали 'Вал промежуточный'
Введение
Основной тенденцией развития современного машиностроительного
производства является его автоматизация в целях значительного повышения
производительности труда и качества выпускаемой продукции.
Автоматизация механической обработки осуществляется путем
широкого применения оборудования с ЧПУ и создания на его основе ГПС,
управляемых от ЭВМ.
При разработке технологических процессов обработки деталей на
автоматизированных участках необходимо решать следующие задачи:
- повышение технологичности деталей;
- повышение точности и качества заготовок; обеспечение
стабильности припуска; совершенствование существующих и создание новых методов
получения заготовок, снижающих их стоимость и расход металла;
- повышение степени концентрации операций и связанное с этим
усложнение структур технологических систем машин;
- развитие прогрессивных технологических процессов и
структурно-компоновочных схем оборудования, разработка новых типов и
конструкций режущего инструмента и приспособлений, обеспечивающих высокую
производительность и качество обработки;
- развитие агрегатного и модульного принципа создания
станочных систем, загрузочных и транспортных устройств, промышленных роботов,
систем управления.
Механизация и автоматизация технологических процессов
механической обработки предусматривает ликвидацию или максимальное сокращение
ручного труда, связанного с транспортировкой, загрузкой, выгрузкой и обработкой
деталей на всех этапах производства, включая контрольные операции, смену и
настройку инструментов, а также работы по сбору и переработке стружки.
Развитие технологии малоотходного производства
предусматривает комплексное решение задачи изготовления заготовок и
механической обработки с минимальными припусками путем коренного
технологического перевооружения заготовительных и механообрабатывающих цехов с
использованием наиболее прогрессивных технологических процессов, созданием
автоматических и комплексно-автоматизированных линий на базе современного
оборудования.
В таком производстве человек освобождается от непосредственного
участия в изготовлении изделия. За ним остаются функции подготовки оснастки,
наладки, программирования, обслуживания вычислительной техники. Увеличивается
доля умственного и сводится и минимуму доля физического труда. Сокращается
численность рабочих. Повышаются требования к квалификации работников,
обслуживающих автоматизированное производство.
1.
Расчет объёма выпуска и определение типа производства
Исходные данные для определения типа производства:
а) объем выпуска деталей в год: N =6000 шт./год;
б) процент запасных частей: в = 5%;
в) процент неизбежных технологических потерь б = 5%;
г) общий объем выпуска деталей в год:
шт./год
д) масса детали: m = 2,5 кг.
Тип производства определяется ориентировочно по табл. 1.
Таблица 1 - Организация производства по массе и объёму выпуска
продукции
Масса детали,
кг
|
Тип
производства
|
|
Е
|
Мс
|
С
|
Кс
|
М
|
1
|
2
|
3
|
4
|
5
|
6
|
<1,0
|
<10
|
10-2000
|
2000-75000
|
75000-200000
|
>200000
|
1,0-2,5
|
<10
|
10-1000
|
1000-50000
|
50000-100000
|
>100000
|
2,5-5,0
|
<10
|
10-500
|
500-35000
|
35000-75000
|
>75000
|
5,0-10
|
<10
|
10-300
|
300-25000
|
25000-50000
|
>50000
|
>10
|
<10
|
10-200
|
200-10000
|
10000-25000
|
>25000
|
В соответствии с таблицей обработка деталей будет
производиться в условиях среднесерийного производства.
Для серийного производства характерно применение
специализированного оборудования, а также станков с числовым программным
управлением и автоматизированных линий и участков на их основе. Приспособления,
режущий и мерительный инструмент могут быть как специальными, так и универсальными.
Научно-методической основой организации серийного производства является
внедрение групповой технологии на базе конструкторской и технологической
унификации. Расстановка оборудования, как правило - по ходу технологического
процесса. В качестве средств межоперационного транспортирования применяются
автоматические тележки.
В серийном производстве количество деталей в партии для
одновременного запуска, допускается определять упрощенным способом:
,
где N - годовая программа выпуска деталей, шт.;
а - число
дней, на которое необходимо иметь запас деталей (периодичность запуска -
выпуска, соответствующая потребности сборки);
шт.
Для изготовления данной детали принимаем двухсменный режим
работы.
2.
Общая
характеристика детали
2.1 Служебное назначение детали
Деталь «Вал промежуточный» работает в условиях динамических
нагрузок. Материал - Сталь 20ХГНМ ГОСТ 4543-71.
Редуктор цилиндрический служит для изменения скорости
вращения при передаче вращательного движения от одного вала к другому. От
работоспособности и ресурса цилиндрического редуктора во многом зависит
обеспечение требуемых функциональных параметров и надежности машины в целом.
Объектом курсового проекта является деталь «вал
промежуточный». Деталь «вал промежуточный» входит в состав редуктора
цилиндрического в качестве вала-шестерни. Назначение детали «вал промежуточный»
- передача крутящего момента с одного на другой вал. Качество вала-шестерни
выше, а стоимость изготовления ниже, чем вала и насадной шестерни. Именно
поэтому все шестерни редукторов выполняют вместе с валом.
Данная деталь имеет ряд основных поверхностей, которые и предназначены
для выполнения ее служебного назначения.
Деталь устанавливается в корпус на подвижные опоры качения, в
качестве которых используются подшипники качения. Судя по посадке в подшипник
характер нагрузки на вал спокойный или с умеренными толчками и вибрацией,
перегрузка до 150% [2].
2.2 Тип детали
Деталь относится к деталям типа тел вращения, а именно -
вал-шестерня (рисунок 1). Основными поверхностями детали, то есть
поверхностями, определяющими конфигурацию детали и основные технологические
задачи по ее изготовлению являются:
наружные цилиндрические поверхности (НЦП),
наружные торцовые поверхности (НТП),
зубчатая поверхность (ЗП), состоящая из НЦП и зубчатых впадин
(ЗВп);
резьбовая поверхность (РП).
К неосновным поверхностям относятся различные фаски и
канавки. Классификация обрабатываемых поверхностей представлена в таблице 2.
Рисунок 1. Эскиз детали
Таблица 2 - Поверхности детали
№ поверхности
|
Вид поверхности
|
Размер
поверхности, мм
|
Квалитет, IT, ITус
|
Шероховатость Ra, мкм
|
1
|
НТП
|
lус = 25
|
11
|
6,3
|
2
|
Фаска
|
0,5х45є
|
h12
|
6,3
|
3
|
НЦП
|
Æ25
|
k6
|
0,4
|
4
|
НТП
|
lус = 35
|
6
|
0,8
|
5
|
Фаска
|
1,6х30є
|
h12
|
6,3
|
6
|
НЦП
|
Æ35
|
u6
|
0,4
|
7
|
НЦП
|
Æ35,3
|
h12
|
6,3
|
8
|
Канавка
|
Æ24,5
|
h12
|
6,3
|
9
|
НЦП
|
Æ37
|
u6
|
0,4
|
10
|
Фаска
|
1х30є
|
h12
|
6,3
|
11
|
Канавка
|
Æ36,5
|
h12
|
6,3
|
12
|
НЦП
|
Æ38
|
u6
|
0,4
|
13
|
НТП
|
lус = 47
|
8
|
1,6
|
14
|
Канавка
|
Æ37,5
|
h12
|
6,3
|
15
|
НЦП
|
Æ47
|
h12
|
6,3
|
16
|
Фаска
|
0,5х45є
|
h12
|
6,3
|
17
|
КП
|
Æ47-Æ42
|
h12
|
6,3
|
18
|
НЦП
|
Æ42
|
h12
|
6,3
|
19
|
НЦП
|
Æ50
|
h12
|
6,3
|
20
|
НЦП
|
Æ42
|
h12
|
6,3
|
21
|
НТП
|
lус = 42
|
8
|
1,6
|
22
|
НЦП
|
Æ35
|
u6
|
0,4
|
23
|
Фаска
|
1,6х30є
|
h12
|
6,3
|
24
|
НТП
|
lус = 35
|
6
|
0,8
|
25
|
Канавка
|
Æ24,5
|
h12
|
6,3
|
26
|
Канавка
|
Æ34,5
|
h12
|
6,3
|
27
|
Фаска
|
1х30є
|
h12
|
6,3
|
28
|
НЦП
|
Æ25
|
k6
|
0,4
|
29
|
НТП
|
lус = 25
|
11
|
6,3
|
30
|
Фаска
|
0,5х45є
|
h12
|
6,3
|
31
|
ЗВп
|
Æ42,058
|
h7
|
0,8
|
32
|
Отв. центровые
|
Æ4
|
h12
|
6,3
|
2.3 Технологичность детали
При анализе детали на технологичность нетехнологичных
элементов конструкции выявлено не было.
Деталь является технологичной по следующим признакам:
- механически обрабатываемые поверхности не
имеют сложной конфигурации;
- конструкция детали позволяет вести за один
установ механическую обработку множества поверхностей;
- конструкция детали обеспечивает свободный
подвод и отвод инструмента, СОЖ в зону резания и из неё, и отвод стружки;
- в конструкции детали предусмотрены канавки
для выхода режущего инструмента;
- в конструкции детали предусмотрены фаски
для облегчения сборочных операций;
- объем выпуска и тип производства позволяют
использовать станки с ЧПУ: токарные, фрезерные, шлифовальные.
.4 Нормоконтроль и метрологическая экспертиза
чертежа детали
Нормоконтроль выполняется согласно ГОСТ 2.111.
Чертёж детали выполнен в масштабе 1:1. Он содержит следующие
характеризующие деталь указания:
- нужное количество сечений и разрезов;
- все необходимые размеры, допуски на размеры и
расположение поверхностей;
шероховатости поверхностей;
марку материала;
технические требования;
значения отклонений соответствуют ГОСТ 25346;
условные обозначения требований по допускам формы и
расположения поверхностей соответствуют ГОСТ 2. 308-79.
При контроле правильности выполнения
чертежа можно выделить следующие недостатки:
- отклонения на чертеже указаны не комбинированным способом
(только числовые значения отклонений), согласно стандартам, добавим квалитеты,
например, Æ
);
на чертеже не показаны центровые отверстия, которые не обходимы
для обработки детали. Примем их согласно ГОСТ 14034-74;
отсутствует шероховатость на поверхности зубчатых впадин;
Анализ обозначения шероховатости:
Чертёж выполнен с применением устаревших стандартов обозначений
шероховатости.
Соблюдение рядов предпочтительности для
сопрягаемых и угловых размеров
Ряды нормальных линейных размеров установлены на основе рядов
предпочтительности чисел по ГОСТ 6636-69.
Таблица 3 - Соблюдение рядов предпочтительности
Размер
|
Соответствие
ряду R20, R40
|
По стандарту
|
Æ25
|
Соответствует
|
R20
|
Æ35
|
Не
соответствует
|
35 (R80)
|
Æ35,3
|
Не
соответствует
|
36 (R20)
|
Æ37
|
Не
соответствует
|
36 (R20)
|
Æ38
|
Соответствует
|
R40
|
Æ47
|
Не
соответствует
|
48 (R40)
|
Æ42
|
Не
соответствует
|
50 (R20)
|
Æ50
|
Соответствует
|
R20
|
Линейные и угловые размеры канавок для выхода шлифовального
круга соответствуют ГОСТ 8820-69.
Размеры и форма центровых отверстий по ГОСТ 14034-74.
Линейные размеры фасок 1, 1,6 соответствуют первому ряду
предпочтительности по ГОСТ 10948-64, фаску с линейным размером 0,5 следует
заменить на 0,6.
Анализ соответствия требований к форме, шероховатости допуску
размера:
Уровень относительной геометрической точности указанных
отклонений принимается нормальным (А). Значения характеристик Ra так же считаем
соответствующим уровню А.
Таблица 4 - Анализ соответствия требований к форме и
шероховатости допуску размера для НЦП
Исполнитель ный
размер
|
Заданные
параметры
|
Тбн,
мкм
|
Расчетные
значения
|
|
Тф,
мкм
|
Ra, мкм
|
Тб,
мкм
|
|
Тфн,
мкм (ГОСТ 24643)
|
Raн, мкм (ГОСТ 2789)
|
|
|
|
|
|
|
|
&
-0,4--
Принято Тф = 4
&
-0,40,020,020
Принято Тф = 4
&
-0,40,020,020
Принято Тф = 4
&
-0,40,020,020
Принято Тф = 4
&
-6,3-
Принято Тф = 50
Из таблицы 4 следует вывод о
несоответствии заданной шероховатости Ra значениям нормативной
шероховатости Raн для поверхностей:
&
, &
,&
. Для этих поверхностей Ra > Raн, это достигается применением отделочных методов обработки
(например, полирование) после выполнения основных операций.
Таблица 5 - Анализ соответствия требований
к форме и шероховатости допуску размера для НТП
Условная длина
|
Условный
квалитет
|
Трус, мкм
|
Заданные
параметры
|
Тбн,
мкм
|
Расчетные
значения
|
|
|
|
Тф, мкм
|
Тб,
мкм
|
Ra, мкм
|
|
Тфн (ГОСТ 24643)
|
 130--6,3- Принято Тф = 40 мкм Принято Ra = 6,3 мкм
|
|
|
|
|
|
|
|
|

16-130,812
Принято Тф = 4 мкм
Таблица 5 (Продолжение) - Анализ соответствия требований к
форме и шероховатости допуску размера для НТП
Из таблицы 4 следует вывод о соответствии
заданной шероховатости Ra значениям нормативной шероховатости Raн.
Значения торцевого биения, которые не
соответствуют нормативным значениям, меняем на нормативные, так как Тб
>Тбн. Для торцев К и Н
допуск биения заменим на нормативный Тб
= 12 мкм. Для торцев М и Л допуск биения оставляем без изменений.
Все имеющиеся на чертеже отраслевые
стандарты меняем на государственные.
Вывод: На чертеже используется устаревшее обозначение
шероховатости и устаревшая форма записи для неуказанных предельных отклонений.
Заменяем их на соответствующие обновленным ГОСТам.
Есть нарушения соответствия точностных и качественных
характеристик. Несоответствующую шероховатость заменяем на нормативную.
Размеры, не подходящие под ряды предпочтительности чисел,
оставляем без изменений, так как они согласуются с размерами других деталей при
сборке.
3. Выбор вида заготовки и его обоснование
Метод получения заготовки детали определяется ее
конструкцией, назначением, материалом, техническими требованиями к изготовлению
и его экономичностью, а так же объемом выпуска. Метод получения заготовки, ее
вид и точность непосредственно определяют точность механической обработки,
производительность труда и себестоимость готового изделия.
Для серийного типа производства целесообразно назначить
заготовку - штамповку, максимально приближенную к конфигурации детали.
Ковка - один из основных методов обработки металлов давлением
(ОМД). Придание металлу необходимой формы, возможно ближе отвечающей
конфигурации будущей детали и получаемой с наименьшими трудозатратами;
исправление дефектов литой структуры; повышение качества металла путем
преобразования литой структуры в деформированную и, наконец, сама возможность
пластического деформирования металлопластичных сплавов - основные аргументы
применения процессов обработки металлов давлением.
Таким образом, улучшение качества металла достигают не только
при его выплавке, разливке и последующей термообработке, но и в процессе ОМД.
Именно пластическая деформация, исправляя дефекты литого металла, и, преобразуя
литую структуру, сообщает ему наивысшие свойства.
К числу технологических процессов малоотходного производства
заготовок относятся: получение точных горячештампованных заготовок с
минимальными отходами в облой, изготовление заготовок холодной объемной
штамповкой или с подогревом. В таблицах 8 и 9 приведены механические свойства и
химический состав материала заготовки.
Таблица 8 - Химический состав материала Сталь 20ХГНМ ГОСТ
4543-71
Химический
элемент
|
%
|
Кремний (Si)
|
0.17-0.37
|
Углерод (C)
|
0.18-0.23
|
Марганец (Mn)
|
0.7-1.1
|
Никель (Ni)
|
0.4-0.7
|
Фосфор (P), не
более
|
0.035
|
Хром (Cr)
|
0.4-0.7
|
Сера (S), не
более
|
0.035
|
Молибден (Mo)
|
0.15-0.25
|
Таблица 9 - Механические свойства материала заготовки
Марка стали
|
При Т=20 С°
|
Термообработка
|
|
sв, МПа
|
sT, МПа
|
d5, %
|
Закалка 860°C,
масло, Отпуск 150 - 180C°, воздух
|
Сталь 20ХГНМ
|
1180-1570
|
930
|
7
|
|
Обозначения:
sв - Предел
кратковременной прочности, [МПа] -
Предел пропорциональности (предел текучести для остаточной деформации), [МПа] -
Относительное удлинение при разрыве, [%]
Заготовку
вала-шестерни можно получить несколькими способами.
Холодным
выдавливанием на прессах. Процесс холодного выдавливания охватывает комбинацию
из пяти видов деформации:
прямого
выдавливания, обратного выдавливания, осадки, обрезки и пробивки. Для холодного
выдавливания заготовок применяют гидравлические прессы, которые позволяют
автоматизировать процесс. Установление максимального усилия в любой точке хода
ползуна на гидравлических прессах позволяет штамповать детали большой длины.
Ковкой на
горизонтально ковочной машине (ГКМ), представляющую собой горизонтальный механический
пресс, в котором, кроме главного деформирующего ползуна есть зажимный, который
зажимает деформируемую часть прутка, обеспечивая ее высадку. Упоры в штампах
ГКМ выполняют регулируемыми, что дает возможность при наладке уточнить
деформируемый объем и получить поковку без облоя. Размерная точность стальных
поковок может достигать 12-14 квалитета, параметр шероховатости поверхности Ra12,5-Ra25.
Определяющими
факторами выбора способа производства заготовок являются:
точность
изготовления заготовки и качество ее поверхности;
наибольшее
приближение размеров заготовки к размерам детали.
Выбор способа
получения заготовки базировался на анализе возможных способов получения,
реализация которых может способствовать улучшению технико-экономических
показателей, т.е. достижению максимальной эффективности при обеспечении
требуемого качества продукции.
Полученные
поковки подвергают предварительной термической обработке.
Целью термической
обработки являются:
устранение
отрицательных последствий нагрева и обработки давлением (снятие остаточных
напряжений, испарение перегрева);
улучшение
обрабатываемости материала заготовки резанием;
подготовка
структуры металла к окончательной ТО, повышающей твёрдость поверхностного слоя
до 45…50 HRC.
После ТО поковки
поступают на очистку поверхности. Эскиз заготовки представлен в графической
части курсового проекта.
Как один из
вариантов получения заготовки примем изготовление заготовок методом холодной
объемной штамповки. Этот способ позволяет получать штамповки, более близкие к
готовой детали по форме и точности размеров, чем штамповки получаемыми другими
способами. В нашем случае, при необходимости изготовления точной детали,
минимальная шероховатость поверхностей которой равна Ra0,4, получение заготовки холодной объемной
штамповкой позволит значительно уменьшить лезвийную обработку, сократить расход
металла и станкоёмкость обработки. Средний коэффициент использования металла
при холодной объемной штамповке 0,5 - 0,6.
4. Разработка маршрутного технологического
процесса изготовления детали
4.1 Определяющим фактором при разработке
маршрутного технологического процесса является тип и организационная форма
производства
Для каждой элементарной поверхности детали назначаем типовой
план её обработки. На базе планов обработки элементарных поверхностей формируем
потенциальные операции, представляющие собой совокупность технологических
переходов одного этапа обработки. Данные сведены в таблицу 10.
Таблица 10 - Разработка маршрутного технологического процесса
№ пов.
|
Обозн. пов. и
её точн.
|
Шерохов. Ra,
мкм
|
Группы станков
|
Планы обработки
|
Этапы обработки
дета-ли
|
Содержание
потен-циальной операции
|
Вид станка в
этапе
|
Кол-во потенц.
уст. в этапе
|
Ус-та-нов
|
№ операции
|
1
|
НТП
|
6,3
|
Группы токарных
станков класса Н, зубофрезерный станок класса Н, группа шлифовальных станков
класса П и В, зубошлифовальный станок класса П
|
Тчр1
|
Эчр
|
Тчр1, Ц32’
|
Токар.
|
4
|
А
|
005
|
|
|
|
|
|
|
Тчр29, Ц32
|
|
|
Б
|
|
|
|
|
|
|
|
Тчр3, Тчр4,Тчр6,
Тчр7,Тчр9, Тчр12, Тчр13
|
Токар.
|
|
А
|
010
|
2
|
Фаска
|
6,3
|
|
Тпч2
|
|
Тчр15,Тчр17,
Тчр18, Тчр19, Тчр20, Тчр21, Тчр22,
Тчр24, Тчр28
|
|
|
Б
|
|
3
|
НЦП
|
0,4
|
|
Тчр3,
Тпч3Тч3, Шп3 Шв3
|
|
|
|
|
|
|
4
|
НТП
|
0,8
|
|
Тчр4, Тпч4,Тч4
Шп4
|
|
|
|
|
|
|
5
|
Фаска
|
6,3
|
|
Тпч5
|
Эпч
|
Тпч2,
Тпч3, Тпч4, Тпч5, Тпч6, Тпч8,
Тпч9, Тпч10, Тпч11,Тпч12 Тпч13,
Тпч14, Тпч16, Тпч27
|
Токар.
|
2
|
А
|
015
|
6
|
НЦП
|
0,4
|
|
Тчр6,
Тпч6, Тч6, Шп6, Шв6
|
|
|
|
|
|
|
7
|
НЦП
|
6,3
|
|
Тчр7
|
|
Тпч21,Тпч22,
Тпч23,Тпч24, Тпч25, Тпч26, Тпч28,
Тпч30
|
|
|
Б
|
|
8
|
Канавка
|
6,3
|
|
Тпч8
|
|
|
|
|
|
|
На основании таблицы 10 выбираем и назначаем экономически
целесообразные методы и виды обработки при выполнении каждого технологического
перехода в соответствии с принятым оборудованием.
Выявляются поверхности, которые можно обработать
комбинированным, групповым методом или совместными элементами переходы
обработки.
После чистового этапа обработки необходимо выполнить
термообработку всего вала - нитроцементацию до твёрдости 80-83HRА, для повышения
износостойкости поверхности вала.
Формируется реальный потенциальный технологический маршрут, в
основу которого закладываются назначенные этапы обработки детали. Содержание
операционного технологического маршрута формируется по принципу максимальной
концентрации при выполнении установов, позиций, переходов. Результаты сводим в
таблицу 11.
Окончательный выбор технологического маршрута может быть
произведен только после определения времени изготовления детали.
Таблица 11 - Реальный предварительный маршрут обработки
Этапы обработки
|
Вид станка в
этапе
|
Тип станка
|
Уточненное
кол-во установов в этапе
|
Пов. установки
|
№ опер.
|
Реальный
предварительный установ
|
Содержание
установа
|
Эчр
|
Токарный
|
УТС настроенный
класс точности Н
|
4
|
19,29
|
005
|
А
|
Тчр1, Ц32’
|
|
|
|
|
12,1
|
|
Б
|
Тчр29, Ц32
|
|
|
|
|
28, 32’
|
010
|
А
|
Тчр3,Тчр4,
Тчр6, Тчр7,Тчр9, Тчр12,
Тчр13
|
|
|
|
|
3,32
|
|
Б
|
Тчр15,Тчр17,Тчр18,
Тчр19,Тчр20, Тчр21, Тчр22, Тчр24,Тчр28
|
Эпч
+ Эч
|
Токарный
|
токарный с ЧПУ,
класс точности Н
|
2
|
28, 32’
|
015
|
А
|
Тпч2,
Тпч3, Тпч4, Тпч5,Тпч6, Тпч8,
Тпч9, Тпч10,Тпч11,Тпч12 Тпч13,
Тпч14, Тпч16, Тпч27, Тч3, Тч4,Тч6,
Тч9, Тч12, Тч13
|
|
|
|
|
3,32
|
|
Б
|
Тпч21,Тпч22,
Тпч23,Тпч24, Тпч25, Тпч26, Тпч28,
Тпч30, Тч21, Тч22, Тч24, Тч28
|
Эч
|
Фрезерный
|
Зубофрезерный
|
1
|
32, 32’
|
020
|
А
|
Фрезерование
зубьев червячной фрезой
|
Это
|
Печь
|
Камерная печь
|
|
|
025
|
|
|
Эп
|
Шлифовальный
|
Зубошлифовальный
станок
|
1
|
32, 32’
|
030
|
А
|
Шп31
|
Эп +
Эв
|
Шлифовальный
|
Шлифовальный с
ЧПУ, класс точности В
|
2
|
32, 32’
|
035
|
А
|
Шп3,Шп4,Шп6,
Шп9,Шп12,Шв3, Шв6, Шв9Шв12
|
|
|
|
|
|
|
Б
|
Шп22,Шп24,Шп28
Шв22Шв28
|
Эотд
|
Шлифовальный
|
Унив.
шлифовальный, класс точности П
|
2
|
32, 32’
|
040
|
А
|
П6,
П9, П12
|
|
|
|
|
|
|
Б
|
П22
|
При формировании таблицы 11 были использованы следующие
положения:
производство среднесерийное, приближённое к мелкосерийному,
поэтому в одной операции формируется несколько установов;
в одной операции возможно совмещение не более чем двух этапов
обработки для увеличения загрузки станка и повышения концентрации переходов;
этапность обработки по возможности не должна быть нарушена.
5. Разработка операционного технологического
процесса обработки детали
5.1 Уточнение выбранного технологического
оборудования
Назначение производственного оборудования производится в
зависимости от размеров детали, её конструктивных особенностей, а также
технических требований, определенных параметров точности и качества
поверхностей.
Подготовку баз будем осуществлять на токарном универсальном
станке 16К20.
Величина 16К20
Наибольшая длина обрабатываемого изделия L, мм
РМЦ 710-710
Высота оси центров над плоскими направляющими станины, мм 215
Пределы чисел оборотов шпинделя, об/мин 12,5 - 1600
Пределы подач, мм/об
Продольных 0,05 -2,8
Поперечных 0,025 - 1,4
Наибольшее усилие, допускаемое механизмом подач, кгс (н)
Продольное
На упоре 800 (7845)
На резце 600 (5884)
Поперечное
На упоре 460 (4510)
На резце 360 (3530)
Мощность электродвигателя главного привода, квт
Основное исполнение 11
Наибольший диаметр изделия, устанавливаемого над станиной, мм 400
Наибольший диаметр обработки над поперечными салазками
суппорта, мм 220
Наибольший диаметр прутка, проходящего через отверстие в
шпинделе, мм 50
Пределы шагов нарезаемых резьб:
Метрических, мм 0,5 - 112
Модульных, модуль 0,5 - 112
Дюймовых, число ниток на один дюйм 56 - 0,5
Питчевых, питч 56 - 0,5
Максимально допустимый вес изделия, устанавливаемого, кг:
В патроне 200
В центрах 460
Коническое отверстие в пиноли задней бабки Морзе №5
Наибольшее перемещение пиноли задней бабки, мм 150
Габариты станка (длин х шир х выс), мм
РМЦ 710 2505 х 1190 х 1500
Вес станка, кг 2835
На черновом, получистовом и чистовом этапах для обработки
вала используется токарный станок с ЧПУ 16К20Ф3, класса точности Н.
Станок предназначен для токарной обработки деталей типа
дисков, колец, заготовок шестерен, муфт, фланцев, крышек, поршней, небольших
корпусных деталей и т.д. На станке можно производить обточку и расточку
цилиндрических, конических и фасонных поверхностей, проточку наружных и
внутренних канавок, подрезку торцев, сверление, рассверливание, развертывание и
зенкерование центральных отверстий.
Техническая характеристика станка
Наибольший
диаметр устанавливаемого изделия над станиной
|
мм.
|
500
|
Наибольшая
длина устанавливаемого изделия в центрах
|
мм.
|
900
|
Наибольший
диаметр обрабатываемого изделия над станиной
|
мм.
|
320
|
Наибольший
диаметр обрабатываемого изделия над суппортом
|
мм.
|
200
|
Наибольший ход
суппортов по оси Х/по оси Z
|
мм.
|
210/905
|
Максимальная
скорость быстрых перемещений:
|
|
|
- продольных
|
мм/мин
|
5000
|
- поперечных
|
мм/мин
|
3000
|
Минимальная /
Максимальная скорость рабочих подач:
|
|
|
- продольных
|
мм/мин
|
1…2000
|
- поперечных
|
мм/мин
|
0,5…1500
|
Регулирование
частот вращения шпинделя
|
|
ступенчатое
|
Количество
ступеней регулирования частот вращения шпинделя
|
|
3
|
Частоты
вращения шпинделя на ступени I/II/III (с эл. двигателем 1500 об/мин)
|
об/мин
|
80/220/660
|
Количество
входных / выходных сигналов
|
|
32/16
|
Число
корректоров
|
|
6
|
Память
управляющих программ
|
байт
|
7900
|
Емкость архива
управляющих программ
|
Кбайт
|
16
|
Максимальное
число кадров управляющих программ
|
|
254
|
Габаритные
размеры станка:
|
|
|
- длина
|
мм
|
3700
|
- ширина
|
мм
|
2260
|
- высота
|
мм
|
1650
|
Масса станка,
кг 3800 Для фрезерования зубьев червячной фрезой выбираем: Зубофрезерный
станок CY-300
|
|
|
Характерные особенности:
Корпус и станина станка сделаны из высококачественного
чугуна, с термообработкой для снятия внутреннего напряжения, корпус никогда не
деформируется и сохраняет высокую точность.
Корпус станка сконструирован из цельного куска чугуна двойной
рамы с высокопрочной арматурой; поэтому достигается выдающаяся жесткость.
Подходит для высокоскоростного резания металла большой толщины.
Крепкая конструкция фрезерной головки и главного шпинделя
оснащена бронзовыми подшипниками, что сопровождается высокой эффективностью
работы, и легкостью настройки.
Благодаря устройству горизонтального перемещения червячную
фрезу легко переместить в горизонтальном направлении.
Скорость шпинделя червячной фрезы бесступенчатая,
регулируемая, легко выбрать наиболее подходящую скорость резания.
С помощью управления рычага по вертикали, могут быть получены
поперечные подачи; высокая скорость для холостого хода, с помощью инверторного
управления и низкая скорость для хода резания; также поставляется с
автоматическим устройством, чтобы остановить поперечную подачу автоматически и
безопасно в любом требуемом положении.
Все главные шестерни коробки передач - высокого класса,
Японского производства, соответствуют 1 классу стандарта JIS.
Бронзовое червячное колесо и двойной ведущий шнек
превосходного качества используются для делительной головки, соответственно
может быть достигнуто отсутствие зазора и точное деление.
Модель CY-300
Макс. диаметр резания 300 мм
Макс. модуль резания М5
Межцентровое расстояние между фрезой и заготовкой 20-220
мм
Вертикальное перемещение суппорта червячной фрезы 240 мм
Диаметр рабочего стола 300 мм
Диаметр центрального отверстия рабочего стола 65 мм
Макс. размер червячной фрезы Ф110х110 мм
Макс. расстояние сдвига червячной фрезы 60 мм
Частота вращения червячной фрезы, бесступенчатая
80-250 об/мин
Главный двигатель 2.2 кВт х 4 пол.
Двигатель для быстрой подачи суппорта червячной фрезы 0,75
кВт
Занимаемая площадь и высота 1860х1100х1950 мм
Примерный вес 3200 кг
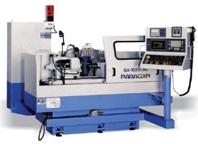
МОДЕЛЬ СТАНКА
|
GU3250CNC
|
РАБОЧИЙ
ДИАПАЗОН
|
Максимальный
диаметр детали, устанавливаемой над станиной, мм
|
320
|
Расстояние
между центрами, мм
|
600
|
Максимальный
обрабатываемый диаметр, мм
|
280
|
Максимальная
длина шлифования, мм
|
520
|
Максимальная
масса заготовки, кг
|
150
|
ШЛИФОВАЛЬНАЯ
БАБКА (Ось X)
|
Перемещения по
оси x, мм
|
200
|
Дискретное
перемещения по оси x, мм
|
0,0001
|
Скорость
быстрых перемещений по оси, мм/мин
|
8000
|
Диапазон поперечных
подач, мм/мин
|
0,0001-6000
|
Мощность
привода шпинделя шлифовальной бабки, кВт
|
3,7
|
Мощность
сервомотора - привода подачи оси x, кВт
|
1
|
ШЛИФОВАЛЬНЫЙ
КРУГ
|
Диаметр х
Ширина х Отверстие, мм
|
405х56х127
|
Максимальная
окружная скорость, м/сек
|
45
|
ПЕРЕДНЯЯ БАБКА
|
Угол поворота
(против часовой стрелки-по часовой стрелке), град
|
90-30
|
Скорость
вращения шпинделя (сервомотор), об/мин
|
0-500
|
Внутренний
конус, типоразмер М.Т.
|
№4
|
ЗАДНЯЯ БАБКА
|
Ход пиноли, мм
|
35
|
Внутренний
конус, типоразмер М.Т.
|
№4
|
СТОЛ (ОСЬ Z)
|
Угол поворота
по часовой стрелке, град
|
+7,5
|
Угол поворота
против часовой стрелки, град
|
-0,5
|
Перемещения по
оси Z, мм
|
630
|
Скорость
быстрых перемещений по оси, мм/мин
|
10000
|
Дискретное
перемещения по оси Z, мм
|
0,0001
|
Диапазон
продольных подач, мм/мин
|
0,001-8000
|
ГИДРОСТАНЦИЯ
|
Емкость бака, л
|
22
|
Мощность
насоса, Вт
|
0,18
|
ГАБАРИТЫ
ИЗДЕЛИЯ
|
Длина, мм
|
3330
|
Ширина, мм
|
2800
|
Высота, мм
|
1890
|
Вес, кг
|
2500
|
На 030 операции используется зубошлифовальный станок 5Д833
Технические характеристики принятого оборудования приведены в
таблице 12.
Таблица12 - Технические характеристики оборудования
Наименование
станка
|
nшпmax, мин-1
|
Nдв, кВт
|
Емкость
магазина инструментов, шт.
|
Размеры рабочей
поверхности стола, мм
|
Габаритные
размеры, мм
|
Вес, кг
|
Класс точности
станка
|
16К20
|
1600
|
11
|
4
|
|
2505х1190х1500
|
2835
|
Н
|
16К20Ф3
|
2500
|
11
|
6
|
|
3700х2260х1650
|
3800
|
Н
|
CY-300
|
250
|
2.2
|
1
|
|
1860х1100х1950
|
3200
|
H
|
GU3250CNC
|
500
|
3.7
|
1
|
|
3330х2800х1890
|
2500
|
В
|
5Д833
|
|
|
|
|
|
|
П
|
5.2 Уточнение схемы установки детали
При обработке на универсальном токарном станке деталь
зажимается в патрон, базами будут являться поверхности 1, 3, 22 (рисунок 2).
Рисунок 2 - Схема установки детали при обработке на УТС
При обработке на токарных станках деталь устанавливается в центра,
так как
> 5 (рисунок 3).
Рисунок 3 - Схема установки детали при обработке на токарных
станках
При обработке на шлифовальных станках деталь устанавливается в
жесткие центры (рисунок 4).
Рисунок 4 - Схема установки детали при обработке на шлифовальных
станках
5.3 Назначение режущего инструмента
Обработка поверхностей ведется стандартным режущим
инструментом. На токарном станке с ЧПУ используются проходные, подрезные и
канавочные (отрезные) резцы со сменными многогранными пластинами из твёрдого
сплава ВК8 (WC-92%; Co-8%, на черновом этапе), ВК3 (WC-97%; Co-3%, на получистовом
этапе), ВК3М (WC-97%; Co-3%, на чистовом этапе, М - мелкозернистый) по ГОСТ 24248-80,
24250-80. Отрезные резцы оснащены напайными пластинами из твердого сплава ВК6.
Для режущих поверхностей инструментов применяем покрытие нитридом титана для
повышения износостойкости.
для зубофрезерования применяем червячные фрезы (с модулем 2,5
мм) ГОСТ 9324-80 из быстрорежущей стали;
На станках с ЧПУ применяется контроль точности выполнения
линейных и диаметральных размеров с применением индикатора контакта в
автоматическом режиме.
.4 Выбор приспособления
Для серийного производства применяем приспособления с
пневмоприводами и гидроприводами, которые способствуют быстродействию
приспособлений, то есть уменьшению вспомогательного времени. На станках
используем приспособления унифицированные и быстропереналаживаемые.
На токарном станке применяется стандартные плавающий и
жесткий центры, а так же поводковое устройство.
На фрезерных станках применяются самоцентрирующие
приспособления цанговая разжимная оправка с пневмоприводом и центра.
На шлифовальном станке применяются центра.
Все приспособления пригодны для обработки всей группы
деталей.
6. Эскизы обработки и схемы установки
деталь технологичность вал
Разновидностью эскизов обработки является операционный эскиз,
технологический эскиз и технологическая наладка. Наиболее предпочтительным для
разработки является технологический эскиз. Он выполняется для каждой
технологической позиции, последняя включает в себя технологические переходы
первого этапа обработки. На эскизах проводят координатные оси, показывают
необходимые точки.
В основе схем установки лежит схема базирования,
представляющая рациональную простановку операционных размеров. Эскизы обработок
вынесем на 2 листа формата А1.
Эскизы схем обработок покажем в таблице 13
Таблица 13 - Эскизы обработок
№ опер.
|
Установ
|
Позиция
инструмента
|
Содержание
операции
|
Оборудование
|
Технологический
эскиз
|
005
|
A
|
I
|
Тчр1, Ц32’
|
УТС настроенный
класс точности Н
|
|
|
Б
|
I
|
Тчр29, Ц32
|
|
|
010
|
А
|
I
|
Тчр3,Тчр4,
Тчр6, Тчр7, Тчр9, Тчр12Тчр13
|
токарный с ЧПУ,
класс точности Н
|
|
|
Б
|
I II
|
Тчр15Тчр17Тчр18,Тчр19,Тчр20,Тчр21,
Тчр22,Тчр24,Тчр28
|
|
|
015
|
А
|
I II
|
Тпч2,Тпч3, Тпч4,Тпч5,Тпч6, Тпч8, Тпч9, Тпч10,Тпч11,Тпч12 Тпч13, Тпч14, Тпч16,Тпч27, Тч3,
Тч4, Тч6, Тч9, Тч12, Тч13
|
токарный с ЧПУ,
класс точности Н
|
|
|
Б
|
I I I
|
Тпч21,Тпч22, Тпч23,Тпч24, Тпч25,Тпч26, Тпч28,Тпч30, Тч21,Тч22
Тч24, Тч28
|
|
|
020
|
А
|
I
|
Фрезерование
зубьев червячной фрезой
|
Зубофрезерный
|
|
025
|
Термообработка
(нитроцементация)
|
030
|
А
|
I
|
Шп31
|
Шлифование
зубьев на зубошлифовальном станке
|
035
|
А
|
I
|
Шп3,Шп4,Шп6,Шп9,Шп12,Шв3,
Шв6,Шв9Шв12
|
Шлифовальный
станок, класс точности В
|
|
|
Б
|
I
|
Шп22,Шп24,Шп28
Шв22Шв28
|
|
|
7. Расчет операционных размеров и размеров
заготовки
Для расчета операционных размеров и размеров заготовки строим
схему линейных внутренних операционных размеров - рисунок 5, и схему
диаметральных размеров и припусков рисунок 6.
7.1 Расчет линейных операционных размеров
Рисунок 5 - Схема линейных операционных размеров
Таблица 14 - Результаты расчета линейных операционных
размеров
№ уравнения
|
Уравнения
|
Элементы
припуска
|
Наименьший
припуск, мм
|
Уравнение
соотношения допусков
|
Допуск искомого
размера, мм
|
Числовое
значение искомой величины, мм
|
|
|
Rz i-1
|
h i-1
|
ДУ i-1
|
ey i
|
|
|
|
|
1
|
A=S2
|
-
|
-
|
-
|
-
|
-
|
|
0,52
|
283,5-0,52
|
2
|
B=S21
|
-
|
-
|
-
|
-
|
-
|
|
0,52
|
266-0,52
|
3
|
C= S21+S20-S2
|
-
|
-
|
-
|
-
|
-
|
TC ≤ Ts21+Ts20+ Ts2
|
1,225
|
266,77-1,225
|
4
|
G=S14
|
-
|
-
|
-
|
-
|
-
|
|
-
|
41min
|
5
|
L=S21-S19
|
-
|
-
|
-
|
-
|
-
|
TL
≤ Ts21+Ts19
|
0,62
|
235,55-0,62
|
6
|
D=S15+S21-S2
|
-
|
-
|
-
|
-
|
-
|
TD≤ Ts15+Ts21+ Ts2
|
1,14
|
156,57-1,14
|
7
|
E=S5-S15
|
-
|
-
|
-
|
-
|
-
|
TE
≤ Ts5+Ts15
|
2,34
|
221,17-2,34
|
8
|
H=S6-S15
|
-
|
-
|
-
|
-
|
-
|
TH≤ Ts6+Ts15
|
1,76
|
189,54-1,76
|
9
|
J=S15+S11-S2
|
-
|
-
|
-
|
-
|
-
|
TJ≤ Ts15+Ts11+ Ts2
|
2,86
|
132,07-2,86
|
10
|
Zs2=S1-S2
|
80
|
500
|
50
|
100
|
0,73
|
S1min= S2max+
Zs2min
|
0,32
|
284,55-0,32
|
11
|
Zs15=S13-S15
|
20
|
100
|
30
|
30
|
0,18
|
S13min=
S15max+ Zs15min
|
0,16
|
156,91-0,16
|
12
|
Zs20=S14-S20
|
10
|
50
|
20
|
20
|
0,1
|
S14min=
S20max+ Zs20min
|
0,13
|
267-0,130
|
13
|
Zs19=S17-S19
|
20
|
100
|
30
|
30
|
0,18
|
S17min=
S19max+ Zs19min
|
0,185
|
235,915-0,185
|
14
|
Zs21=S18-S21
|
10
|
50
|
20
|
20
|
0,1
|
S18min=
S21max+ Zs21min
|
0,130
|
266,23-0,130
|
Zs13=S7-S13
|
40
|
300
|
40
|
50
|
0,43
|
S7min=
S13max+ Zs13min
|
0,250
|
157,59-0,250
|
16
|
Zs14=S12-S14
|
20
|
100
|
30
|
30
|
0,18
|
S12min=
S14max+ Zs14min
|
0,210
|
267,39-0,210
|
17
|
Zs18=S16-S18
|
20
|
100
|
30
|
30
|
0,18
|
S16min=
S18max+ Zs18min
|
0,210
|
266,62-0,210
|
18
|
Zs16=S8-S16
|
40
|
300
|
40
|
50
|
0,43
|
S8min=
S16max+ Zs16min
|
0,320
|
267,37-0,32
|
19
|
Zs17=S9-S17
|
40
|
300
|
40
|
50
|
0,43
|
S9min=
S17max+ Zs17min
|
0,290
|
236,635-0,29
|
20
|
Zs12=S3-S12
|
40
|
300
|
40
|
50
|
0,43
|
S3min=
S12max+ Zs12min
|
0,320
|
268,14-0,32
|
21
|
Zs1=A0-S1
|
80
|
500
|
50
|
100
|
0,73
|
A0min=
Zs1min+ S1max
|
1,4
|
286,68-1,4
|
22
|
Zs3=B0-S3
|
80
|
500
|
50
|
100
|
0,73
|
B0min=
Zs3min+ S3max
|
1,4
|
270,27-1,4
|
Наименьший припуск на обработку Zmin при обработке плоской
поверхности (односторонний припуск) определяются расчетно-аналитическим методом
[5, с. 5].
,
где Rzi-1 - высота микронеровностей поверхности, которая осталась
после выполнения предшествующего этапа (перехода);
hi-1 - глубина дефектного поверхностного слоя оставшегося после
выполнения предшествующего этапа (перехода);
DSi-1
- суммарные отклонения расположения поверхности и отклонения формы, возникающие
при выполнении предшествующего этапа (перехода);
eуi - погрешность при установке на
выполняемом этапе (переходе).
Шероховатость заготовки примем равной Rz=80 мкм
Глубину поверхностного дефектного слоя заготовки примем равной h=200 мкм.
Суммарные отклонения расположения торцовой поверхности заготовки
определим по формуле:
,
где Dн = 1,2 мкм на 1 мм радиуса - отклонение от
перпендикулярности торца фланца к оси поковки
Рассчитаем значения припусков:
Zs2min=80+500+50+100≈0,73
мм
Zs1min=80+500+50+100≈0,73
мм
Zs3min=80+500+50+100≈0,73
мм
Zs7min=80+500+50+100≈0,73
мм
Zs9min=80+500+50+100≈0,73
мм
Zs8min=80+500+50+100≈0,73
мм
Zs13min=40+300+40+50≈0,43
мм
Zs17min=40+300+40+50≈0,43
мм
Zs16min=40+300+40+50≈0,43
мм
Zs12min=40+300+40+50≈0,43
мм
Zs15min=20+100+30+30≈0,18
мм
Zs19min=20+100+30+30≈0,18
мм
Zs14min=20+100+30+30≈0,18
мм
Zs18min=20+100+30+30≈0,18
мм
Zs20min=10+50+20+20≈0,1
мм
Zs21min=10+50+20+20≈0,1
мм
Рассчитаем значения операционных размеров и размеры заготовки:
Определяем значение размера S2
Ts2≤TA, TA=1,3 мм.
Анализируя исходные уравнения, видим, что Ts2 входит в
расчетные уравнения других допусков, следовательно, назначим TA по11-му квалитету.
Ts2=0,52 мкм, S2=283,5-0,52 мм TA=0,52 мкм, A=283,5-0,52 мм;
- Определяем значение размера S21
B=S21=266-0,52
Определяем значение размера S20
TC ≤ Ts21+Ts20+ Ts2 или
0,185 ≤ 0,52+Ts20 +0,52
Ts20=1,225 мм
S20min= Сmin-S21max+ S2min
=248,565-266+282,98=265,545 мм20max= Сmax-S21min+ S2max
=248,75-265,48+283,5=266,77 мм
S20=266,77-1,225мм
- Определяем значение размера S4
G=S4=41min
Определяем значение размера S19
TL ≤ T s21+Ts19
или 0,1 ≤ 0,52+Ts19
Ts19=0,62 мм
S19min= S21min - Lmax=265,48-30,55=234,93
мм19max= S21max - Lmin
=266-30,45=235,55 мм
S19=235,55-0,62мм
- Определяем значение размера S15
TD≤ Ts15+Ts21+ Ts2 или 0,1 ≤ Ts15 +0,52+0,52
Ts15=1,14 мм
S15min= Dmin-S21max+
S2min =138,45-266+282,98=155,43 мм15max= Dmax-S21min+
S2max =138,55-265,48+283,5=156,57 мм
S15=156,57-1,14мм
- Определяем значение размера S5
TE ≤ Ts5+Ts15 или 1,2 ≤ 1,14+Ts5
Ts5=2,34 мм
S5min= S15min +Emin=155,43+63,4=218,83
мм5max= S15max +Emax
=156,57+64,6=221,17 мм
S5=221,17-2,34мм
- Определяем значение размера S6
TH≤ Ts6+Ts15 или 0,62 ≤ 1,14+Ts6
Ts5=1,76 мм
S6min= S15min +Hmin=155,43+32,35=187,78
мм6max= S15max +Hmax
=156,57+32,97=189,54 мм
S6=189,54-1,76мм
- Определяем значение размера S11
TJ≤ Ts15+Ts11+ Ts2 или 1,2 ≤ Ts11 +1,14+0,52
Ts11=2,86 мм
S11min= Jmin-S15max+
S2min =2,8-156,57+282,98=129,21 мм11max= Jmax-S15min+
S2max =4-155,43+283,5=132,07 мм
S11=132,07-2,86мм
- Определяем значение размера S1
Учитывая, что выполняется черновой переход, примем значение Ts1 по 11-му квалитету. Ts1=320 мкм.
S1min= S2max+ Zs2min=283,5+0,73=284,23
мм1max= S1min+ Ts1=284,23+0,32=284,55
мм.
S1=284,55-0,32мм
Определяем значение размера S13
Учитывая, что выполняется получистовой переход, примем значение Ts13 по 10-му квалитету. Ts13=160 мкм.
S13min= S15max+ Zs15min=157,57+0,18=156,75
мм13max= S13min+ Ts13=156,75+0,16=156,91
мм.
S13=156,91-0,16мм
Определяем значение размера S14
Учитывая, что выполняется чистовой переход, примем значение Ts13 по 9-му квалитету. Ts14=130 мкм.
S14min= S20max+ Zs20min=266,77+0,1=266,87
мм14max= S14min+ Ts14=266,87+0,130=267
мм.
S14=267-0,130мм
Определяем значение размера S17
Учитывая, что выполняется получистовой переход, примем значение Ts17 по 10-му квалитету. Ts17=185 мкм.
S17min= S19max+ Zs19min=235,55+0,18=235,73
мм17max= S17min+ Ts17=235,73+0,185=235,915
мм.
S17=235,915-0,185мм
Определяем значение размера S18
Учитывая, что выполняется чистовой переход, примем значение Ts18 по 9-му квалитету. Ts18=130 мкм.
S18min= S21max+ Zs21min=266+0,1=266,1
мм18max= S18min+ Ts18=266,1+0,130=266,230
мм.
S18=266,23-0,130мм
Определяем значение размера S7
Учитывая, что выполняется черновой переход, примем значение Ts7 по 11-му квалитету. Ts7=250 мкм.
S7min= S13max+ Zs13min=156,91+0,43=157,34
мм7max= S7min+ Ts7=157,34+0,25=157,59
мм.
S7=157,59-0,250мм
Определяем значение размера S12
Учитывая, что выполняется получистовой переход, примем значение Ts12 по 10-му квалитету. Ts12=210 мкм.
S12min= S14max+ Zs14min=267+0,18=267,18
мм12max= S12min+ Ts12=267,18+0,210=267,39
мм.
S12=267,39-0,210мм
Определяем значение размера S16
Учитывая, что выполняется получистовой переход, примем значение Ts16 по 10-му квалитету. Ts16=210 мкм.
S16min= S18max+ Zs18min=266,23+0,18=266,41
мм16max= S16min+ Ts16=266,41+0,210=266,62
мм.
S16=266,62-0,210мм
Определяем значение размера S8
Учитывая, что выполняется черновой переход, примем значение Ts8 по 11-му квалитету. Ts8=320 мкм.
S8min= S16max+ Zs16min=266,62+0,43=267,05
мм8max= S8min+ Ts8=267,05+0,320=267,37
мм.
S8=267,37-0,32мм
Определяем значение размера S9
Учитывая, что выполняется черновой переход, примем значение Ts9 по 11-му квалитету. Ts9=290 мкм.
S9min= S17max+ Zs17min=235,915+0,43=236,345
мм9max= S9min+ Ts9=236,345+0,290=236,635
мм.
S9=236,635-0,29мм
Определяем значение размера S3
Учитывая, что выполняется черновой переход, примем значение Ts3 по 11-му квалитету. Ts3=320 мкм.
S3min= S12max+ Zs12min=267,39+0,43=267,82
мм3max= S3min+ Ts3=267,82+0,320=268,14
мм.
S3=268,14-0,32мм
Определяем значение размера A0
Учитывая, что заготовка - штамповка нормальной точности, определим
TEo=TDo=TCo=
TBo = TAo = 1,4 мм0min= Zs1min+ S1max=0,73+284,55=285,28
мм0max= A0min+TAo=285,28+1,4=286,68
мм.
A0=286,68-1,4мм
Определяем значение размера B0
B0min= Zs3min+ S3max=0,73+268,14=268,87
мм0max= B0min+TBo=268,87+1,4=270,27
мм.
B0=270,27-1,4мм
Определяем значение размера C0
C0min= Zs7min+ S7max=0,73+157,59=158,32
мм0max= C0min+TCo=158,32+1,4=159,72
мм.
C0=159,72-1,4мм
Определяем значение размера D0
D0max= Zs9min - S9min+
S2min=0,73-236,345+282,98=46,385 мм0min= D0max - DBo=46,385-1,4=44,985
мм.
D0=46,385-1,4мм
Определяем значение размера E0
E0max= Zs8min - S8min+
S2min=0,73-267,05+282,98=16,66 мм0min= EE0max - EEo=16,66-1,4=15,26
мм.
E0=16,66-1,4мм
7.2 Расчет диаметральных размеров и размеров
заготовки
Результаты расчета размеров заготовки и операционных размеров
расчетно-аналитическим методом для Ш25k6 (
) сведем в таблицу 15.
Рисунок 6 - Схема диаметральных операционных размеров
Таблица 14 - Результаты расчета диаметральных операционных
размеров
Вид заготовки и
план обработки поверхности
|
Элемент
припуска, мкм
|
Допуск размера,
Т, мм
|
2Zmin
|
2Zmax
|
Предельные
размеры
|
Исполнительный
размер
|
|
Rzi-1
|
hi-1
|
ДУi-1
|
еyi
|
|
|
|
Аmax
|
Аmin
|
|
Штамповка
|
80
|
400
|
314
|
-
|
1,4
|
|
|
28,451
|
27,051
|
28,451
|
Черновая
|
40
|
80
|
19
|
300
|
0,21
|
0,91
|
2,52
|
26,141
|
25,931
|
26,141-0,21
|
П/чистовая
|
20
|
30
|
14
|
15
|
0,13
|
0,5
|
0,84
|
25,431
|
25,301
|
25,431-0,13
|
Чистовая
|
10
|
20
|
12
|
6
|
0,052
|
0,14
|
0,322
|
25,161
|
25,109
|
25,161-0,052
|
ТО
|
|
|
|
|
|
|
|
|
|
|
Пов. точн.
|
5
|
10
|
8
|
2
|
0,033
|
0,042
|
0,127
|
25,067
|
25,034
|
25,067-0,033
|
Выс. точн.
|
2,5
|
5
|
4
|
0
|
0,013
|
0,019
|
0,065
|
25,015
|
25,002
|
25
|
Минимальное значение припуска 2Zmin при обработке наружных и
внутренних цилиндрических поверхностей (двухсторонний припуск) определяется:
где Rzi-1 - высота микронеровностей поверхности, которая осталась
после выполнения предшествующего этапа перехода);
h i-1 - глубина дефектного поверхностного слоя,
оставшегося при выполнении предшествующего этапа (перехода);
- суммарные отклонения расположения поверхности и отклонения
формы, возникающие при выполнении предшествующего этапа (перехода);
eyi - погрешность при установке на
выполняемом этапе (переходе).
Шероховатость заготовки примем равной Rz=80 мкм
Глубину поверхностного дефектного слоя заготовки примем равной h=500 мкм
Суммарное отклонение штамповки определим как векторную сумму
кривизны и отклонения центрирования:
,
где ДК=20∙8=160 мкм - кривизна штамповки типа вал (для заготовок
диаметром свыше 25 мм 4 мкм на 1 мм радиуса);
- погрешность при центрировании заготовки (Т - допуск на
диаметральный размер базы заготовки).
Для промежуточных этапов обработки остаточные отклонения
расположения заготовки,
DS = DУзаг´Ку
где DУзаг - кривизна заготовки,
Ку - коэффициент уточнения (Ку = 0,06 - для
чернового этапа, Ку = 0,05 - для получистового этапа, Ку =
0,02 - для чистового этапа), результаты сведем в таблицу 14.
DS чр = 314∙0,06=19 мкм
Погрешность при установке заготовки в радиальном направлении при
закреплении в центрах (при диаметре базы D≥18 мм) еу=300 мкм.
Для промежуточных этапов обработки погрешность закрепления
заготовки,
еу = еузаг´Ку
где еузаг - погрешность закрепления заготовки,
Ку - коэффициент уточнения (Ку = 0,05 - для
получистового этапа, Ку = 0,02 - для чистового этапа), результаты
сведем в таблицу 14.
еу п/ч=300∙0,05=15 мкм.
2Zmax i=2Zmin i+Ti-1+Ti
Найдем значения минимального припуска на каждом этапе обработки:
Zmin чр=2 [80+400+√(3142+3002)]≈0,91
мм
Zmin п/ч=2 [40+80+√(192+152)]≈0,5
мм
Zmin чист=2 [20+30+√(142+62)]≈0,14
мм
Zmin п=2 [10+20+√(122+22)]≈0,042
мм
Zmin в=2 [5+10+√(82+02)]≈0,019
мм.
Определим значение максимального припуска на черновом этапе,
расчеты максимального припуска на остальных этапах покажем в таблице 14.
Zmax чр=0,91+1,4+0,21=2,52 мм
Определяем предельные межпереходные размеры и окончательные
размеры заготовок по формулам:
максимальные размеры
Amax п=Amax в+2Zmin в+Тп=25,015+0,019+0,033=25,067 мм
Amax чист=Amax п+2Zmin п+Тчист=25,067+0,042+0,052=25,161 мм
Amax п/ч=Amax чист+2Zmin чист+Тп/ч=25,161+0,14+0,13=25,431 мм
Amax чр=Amax п/ч+2Zmin п/ч+Тчр=25,431+0,5+0,21=26,141 мм
Amax заг=Amax чр+2Zmin чр+Тзаг=26,141+0,91+1,4=28,451 мм
минимальные размеры
Amin п=Amax в+2Zmin в=25,015+0,019=25,034 мм
Amin чист=Amax п+2Zmin п=25,067+0,042=25,109 мм
Amin п/ч=Amax чист+2Zmin чист=25,161+0,14=25,301 мм
Amin чр=Amax п/ч+2Zmin п/ч=25,431+0,5=25,931 мм
Amin заг=Amax чр+2Zmin чр=26,141+0,91=27,051 мм
7.3 Расчет диаметральных размеров и размеров
заготовки опытно-статистическим методом
Для остальных диаметральных размеров решим данную задачу
опытно - статистическим методом.
Расчет диаметральных размеров для Ш38u6 (
) покажем в таблице 15
Таблица 15 - Расчет
операционных размеров
Вид заготовки и
план обработки поверхности
|
Допуск размера,
Т, мм
|
2Zmin
|
2Zmax
|
Предельные
размеры
|
Исполнительный
размер
|
|
|
|
|
Аmax
|
Аmin
|
|
Штамповка
|
1,4
|
|
|
41,287
|
41,287
|
Черновая
|
0,25
|
0,8
|
2,45
|
39,087
|
38,837
|
39,087-0,25
|
П/чистовая
|
0,16
|
0,25
|
0,66
|
38,587
|
38,427
|
38,587-0,16
|
Чистовая
|
0,062
|
0,15
|
0,212
|
38,277
|
38,215
|
38,277-0,062
|
ТО
|
|
|
|
|
|
|
Пов. точн.
|
0,039
|
0,06
|
0,161
|
38,155
|
38,116
|
38,155
|
Выс. точн.
|
0,016
|
0,04
|
0,095
|
38,076
|
38,060
|
38
|
Определяем предельные межпереходные размеры и окончательные
размеры заготовок по формулам:
максимальные размеры
Amax п=Amax в+2Zmin в+Тп=38,076+0,04+0,039=38,155
мм
Amax чист=Amax п+2Zmin п+Тчист=38,155+0,06+0,062=38,277
мм
Amax п/ч=Amax чист+2Zmin чист+Тп/ч=38,277+0,15+0,16=38,587
мм
Amax чр=Amax п/ч+2Zmin п/ч+Тчр=38,587+0,25+0,25=39,087
мм
Amax заг=Amax чр+2Zmin чр+Тзаг=39,087+0,8+1,4=41,287
мм
минимальные размеры
Amin п=Amax в+2Zmin в=38,076+0,04=38,116 мм
Amin чист=Amax п+2Zmin п=38,155+0,06=38,215 мм
Amin п/ч=Amax чист+2Zmin чист=38,277+0,15=38,427 мм
Amin чр=Amax п/ч+2Zmin п/ч=38,587+0,25=38,837 мм
Amin заг=Amax чр+2Zmin чр=39,087+0,8=39,887 мм
Рассчитанные операционные размеры для Ш35u6 (
) покажем в таблице 16.
Таблица 16 - Расчет операционных размеров
Вид заготовки и
план обработки поверхности
|
Допуск размера,
Т, мм
|
2Zmin
|
2Zmax
|
Предельные
размеры
|
Исполнительный
размер
|
|
|
|
|
Аmax
|
Аmin
|
|
Штамповка
|
1,4
|
|
|
38,287
|
36,887
|
38,287
|
Черновая
|
0,25
|
0,8
|
2,45
|
36,087
|
35,837
|
36,087-0,25
|
П/чистовая
|
0,16
|
0,25
|
0,66
|
35,587
|
35,427
|
35,587-0,16
|
Чистовая
|
0,062
|
0,15
|
0,212
|
35,277
|
35,215
|
35,277-0,062
|
ТО
|
|
|
|
|
|
|
Пов. точн.
|
0,039
|
0,06
|
0,161
|
35,155
|
35,116
|
35,155
|
Выс. точн.
|
0,016
|
0,04
|
0,095
|
35,076
|
35,060
|
35
|
Определяем предельные межпереходные размеры и окончательные
размеры заготовок по формулам:
максимальные размеры
Amax п=Amax в+2Zmin в+Тп=35,076+0,04+0,039=35,155
мм
Amax чист=Amax п+2Zmin п+Тчист=35,155+0,06+0,062=35,277
мм
Amax п/ч=Amax чист+2Zmin чист+Тп/ч=35,277+0,15+0,16=35,587
мм
Amax чр=Amax п/ч+2Zmin п/ч+Тчр=35,587+0,25+0,25=36,087
мм
Amax заг=Amax чр+2Zmin чр+Тзаг=36,087+0,8+1,4=38,287
мм
минимальные размеры
Amin п=Amax в+2Zmin в=35,076+0,04=35,116 мм
Amin чист=Amax п+2Zmin п=35,155+0,06=35,215 мм
Amin п/ч=Amax чист+2Zmin чист=35,277+0,15=35,427 мм
Amin чр=Amax п/ч+2Zmin п/ч=35,587+0,25=35,837 мм
Amin заг=Amax чр+2Zmin чр=36,087+0,8=36,887 мм
Расчет диаметральных размеров для Ш37u6 (
) покажем в таблице 17.
Таблица 17 - Расчет операционных размеров
Вид заготовки и
план обработки поверхности
|
Допуск размера,
Т, мм
|
2Zmin
|
2Zmax
|
Предельные
размеры
|
Исполнительный
размер
|
|
|
|
|
Аmax
|
Аmin
|
|
Штамповка
|
1,4
|
|
|
40,287
|
38,887
|
40,287
|
Черновая
|
0,25
|
0,8
|
2,45
|
38,087
|
37,837
|
38,087-0,25
|
П/чистовая
|
0,16
|
0,25
|
0,66
|
37,587
|
37,427
|
37,587-0,16
|
Чистовая
|
0,062
|
0,15
|
0,212
|
37,277
|
37,215
|
37,277-0,062
|
ТО
|
|
|
|
|
|
|
Пов. точн.
|
0,039
|
0,06
|
0,161
|
37,155
|
37,116
|
37,155
|
Выс. точн.
|
0,016
|
0,04
|
0,095
|
37,076
|
37,060
|
37
|
Определяем предельные межпереходные размеры и окончательные
размеры заготовок по формулам:
максимальные размеры
Amax п=Amax в+2Zmin в+Тп=37,076+0,04+0,039=37,155
мм
Amax чист=Amax п+2Zmin п+Тчист=37,155+0,06+0,062=37,277
мм
Amax п/ч=Amax чист+2Zmin чист+Тп/ч=37,277+0,15+0,16=37,587
мм
Amax чр=Amax п/ч+2Zmin п/ч+Тчр=37,587+0,25+0,25=38,087
мм
Amax заг=Amax чр+2Zmin чр+Тзаг=38,087+0,8+1,4=40,287
мм
минимальные размеры
Amin п=Amax в+2Zmin в=37,076+0,04=37,116 мм
Amin чист=Amax п+2Zmin п=37,155+0,06=37,215 мм
Amin п/ч=Amax чист+2Zmin чист=37,277+0,15=37,427 мм
Amin чр=Amax п/ч+2Zmin п/ч=37,587+0,25=37,837 мм
Amin заг=Amax чр+2Zmin чр=38,087+0,8=38,887 мм
Расчет диаметральных размеров для Ш50h11 (-0,16)
покажем в таблице 18
Таблица 18 - Расчет операционных размеров
Вид заготовки и
план обработки поверхности
|
Допуск размера,
Т, мм
|
2Zmin
|
2Zmax
|
Предельные
размеры
|
Исполнительный
размер
|
|
|
|
|
Аmax
|
Аmin
|
|
Штамповка
|
1,4
|
|
|
52,2
|
50,8
|
51,2
|
Черновая
|
0,16
|
0,8
|
2,36
|
50
|
49,84
|
50-0,16
|
Определяем предельные межпереходные размеры и окончательные
размеры заготовок по формулам:
максимальные размеры
Amax заг=Amax чр+2Zmin чр+Тзаг=50+0,8+1,4=52,2
мм
минимальные размеры
Amin заг=Amax чр+2Zmin чр=50+0,8=50,8 мм
8. Расчет режимов резания
Операция 010 - токарная черновая
Исходные данные:
Заготовка - штамповка
Материал - сталь 20ХГНМ ГОСТ 4543-71
Твердость - 248…293 НВ
Оборудование - токарный патронный с ЧПУ станок модель 16К20Ф3
Эскиз обработки см. чертеж.
Содержание операции:
1. Точить диаметры
а) Ш 26,141 мм
б) Ш 36,087 мм
в) Ш 38,087 мм
г) Ш 39,087 мм
д) Ш 42
е) Ш 50
ж) Ш 47
. Подрезать торцы.
Определяем глубину резания
а) t = 0,65 мм
б) t = 2,09 мм
в) t = 1,09 мм
г) t = 0,6 мм
д) t = 2,3 мм
е) t = 1,2 мм
ж) t = 2,1 мм
Определяем длину рабочего хода
Lр.х. = Lрез. + у + Lдоп., мм [6,
c. 13]
где: Lрез - длина резания,
у - длина подвода, врезания,
Lдоп. - дополнительная
длина резания
а) Lр.х. = Lрез + у +
Lдоп. = 15,36 + 0 + 0 = 15,36 мм.
б) Lр.х. = Lрез + у +
Lдоп. = 41 + 0 + 0 = 41 мм.
в) Lр.х. = Lрез + у +
Lдоп. = 37,6 + 0 + 0 = 37,6 мм.
г) Lр.х. = Lрез + у +
Lдоп. = 31,95 + 0 + 0 = 31,95 мм.
д) Lр.х. = Lрез + у +
Lдоп. = 23,565 + 0 + 0 = 23,565 мм.
е) Lр.х. = Lрез + у +
Lдоп. = 51 + 0 + 0 = 51 мм.
ж) Lр.х. = Lрез + у +
Lдоп. = 4 + 0 + 0 = 4 мм.
Назначение подачи суппортов на оборот
шпинделя [6, с. 51-59]
о = Sт · Кs
а) Sт = 0,25 мм/об
б) Sт = 0,3 мм/об
в) Sт = 0,3 мм/об
г) Sт = 0,3 мм/об
д) Sт = 0,38 мм/об
е) Sт = 0,4 мм/об
ж) Sт = 0,38 мм/об
Кs:
а) 1,35
б) 1,05
в) 1,15
г) 1,35
д) 1
е) 1,15
ж) 1,05о:
а) Sо =0,25 · 1,35 = 0,34 мм/об
б) Sо =0,3 · 1,05 = 0,315 мм/об
в) Sо =0,3 · 1,15 = 0,345 мм/об
г) Sо =0,3 · 1,35 = 0,405 мм/об
д) Sо =0,38 · 1 = 0,38 мм/об
е) Sо =0,4 · 1,15 = 0,46 мм/об
ж) Sо =0,38 · 1,05 = 0,4 мм/обск = 0,35
мм/об [паспорт станка]
Определяем стойкость инструмента [6, с.
60]
Тр = Тн*l, где
l = Lрез/Lр.х. - коэффициент
времени резания,
при l > 0,7 - не
учитывается
Тн - нормированная стойкость инструмента
30 мин.
l = 41/56,36 = 0,74>
0,7;
Тр = 120 мин;
Расчет скорости резания
V = Vтабл · Кv, [3,
с. 114] где
Где: Vтабл - табличная скорость
резания, м/мин;
Кv - коэффициент, зависящий от
стойкости инструмента;
Vтабл = 122 м/мин;
Кv = 0,95;= 122 · 0,95 = 115,9
м/мин
Расчет числа оборотов шпинделя
n = 1000·V/p·D, [6,
с. 105]
а) n = 1000· 115,9/
3,14·26,141 = 1413 об/мин;
б) n = 1000· 115,9/
3,14·36,087 = 1025 об/мин;
в) n = 1000· 115,9/
3,14·38,087 = 965 об/мин;
г) n = 1000· 115,9/
3,14·39,087 = 950 об/мин;
д) n = 1000· 115,9/ 3,14·42 =
820 об/мин;
е) n = 1000· 115,9/ 3,14·50 =
740 об/мин;
ж) n = 1000· 115,9/ 3,14·47 =
790 об/мин;
По паспорту станка принимаем nшп = 1400 об/мин
Уточняем скорость резания
V = n·D·p/1000, [6,
с. 105]
а) V = 1400·26,141·3,14/1000=
114 м/мин;
б) V = 1400·36,087·3,14/1000=
158 м/мин;
в) V = 1400·38,087·3,14/1000=
167 м/мин;
г) V = 1400·39,087·3,14/1000=
172 м/мин;
д) V = 1400·42·3,14/1000= 185
м/мин;
е) V = 1400·50·3,14/1000= 220
м/мин;
ж) V = 1400·47·3,14/1000= 205
м/мин;
Расчет силы и мощности резания
Определение силы резания
Рz = Рzтабл. · К1 · К2 [6,
с. 35-36],
где: Рzтабл - табличная сила
резания, Рzтабл, = 0,6 кН;
К1 - коэффициент, зависящий от
обрабатываемого материала;
К2 - коэффициент, зависящий от
скорости резания и переднего угла при точении.
Рz = 0,6·0,85·1,1 = 0,561 кН
Определяем мощность резания
Nр = Рz · V /60
а) Nр = 0,561·114/60 = 1,1
кВт
б) Nр = 0,561·158/60 = 1,47
кВт
в) Nр = 0,561·167/60 = 1,56
кВт
г) Nр = 0,561·172/60 = 1,6
кВт
д) Nр = 0,561·185/60 = 1,72
кВт
е) Nр = 0,561·220/60 = 2,0
кВт
ж) Nр = 0,561·205/60 = 1,9
кВт
Проверка по мощности двигателя
Nрез.< 1,2*Nдв*h,
где h - КПД станка
Nр < 18·0,85 = 15,3 кВт
Условие выполнено, значит режимы по мощности проходят [6. с.
4]
Основное время:
То =
Длина рабочего хода резца Lр.х. = 64,19 мм, Д = 0 мм;
у = t · ctgц = 0,65 · ctg90 = 0 мм.
а)
То =
= 0,025 мин.
б) То =
= 0,06 мин.
в) То =
= 0,06 мин.
г) То =
= 0,05 мин.
д) То =
= 0,08 мин.
е) То =
= 0,08 мин.
ж) То =
= 0,01 мин.
Операция 035 - шлифовальная
Исходные данные:
Заготовка - обработанный вал: Ш25,067-0,033,
Ш35,155-0,039, Ш37,155-0,039, Ш38,155-0,039
Материал - сталь 20ХГНМ ГОСТ 4543-71
Твердость - 248…293 НВ
Оборудование - Шлифовальный станок с ЧПУ GU3250CNC (Vmax=45 м/сек).
Содержание операции:
Установ А, II:
Шлифовать по программе 4 ступени вала: Ш 25
, Ш 35
, Ш 37
-0,039, Ш 38
Выпишем значения припусков на каждый диаметр в соответствии с
пунктом 7 данной работы:
Ш25: 2Пр=0,067 мм;
Ш35: 2Пр=0,155 мм;
Ш37: 2Пр=0,155 мм;
Ш38: 2Пр=0,155 мм.
Выберем группу и подгруппу обрабатываемого материала:
Для стали 20ХГНМ - группа 2, подгруппа а.
Выберем СОЖ первой группы: Содовый раствор по ГОСТ 10689-70.
Выбор характеристик шлифовального круга:
Для группы обрабатываемости 2а шлифовальный материал - 92А;
Зернистость (по минимальной шероховатости Ra=0,4 мкм) - 20Н;
Твердость (по твердости заготовки 249…293НВ) - СТ2;
Структура - 7.
Выбор частоты вращения заготовки:
При шлифовании ступени Ш25 nT=265 об./мин;
При шлифовании ступени Ш35 nT=240 об./мин;
При шлифовании ступени Ш37 nT=240 об./мин;
При шлифовании ступени Ш38 nT=240 об./мин;
Скорректируем частоту вращения заготовки по формуле:
n= nT∙KП
При шлифовании шейки Ш25 n=265∙0,8=212
об./мин;
При шлифовании шейки Ш35 n=240∙0,8=192
об./мин;
При шлифовании шейки Ш37 n=240∙0,8=192
об./мин;
При шлифовании шейки Ш38 n=240∙0,8=192
об./мин;
Выбор скоростей подач, припуски по ступеням цикла, основного
времени:
При шлифовании шейки Ш25 ST1=0,054
об./мин, Пр1=0,034 мм, ToT=0,09 мин;
При шлифовании шейки Ш35 ST1=0,50
об./мин, Пр1=0,078 мм, ToT=0,011 мин;
При шлифовании шейки Ш37 ST1=0,50
об./мин, Пр1=0,078 мм, ToT=0,011 мин;
При шлифовании шейки Ш38 ST1=0,50
об./мин, Пр1=0,078 мм, ToT=0,011 мин;
Поправочные коэффициенты в зависимости от:
окружной скорости:
Ks1V=1,0 KTv=1,0;
формы шлифуемой поверхности:
Ks1Ш=1,0 KТш=1,0;
податливости технологической системы:
Ks1l=1,0;
KTl =1,0
квалитета детали и заготовки:
Ks1к=1,0 Kпк=1,0 KTv=1,0
Для шейки Ш35:
Ks1к=1,0 Kпк=1,0 KTv=1,0
Для шейки Ш38:
Ks1к=1,0 Kпк=1,0 KTv=1,0
погрешность обработки из за геометрической неточности станка:
Кs1д=1,0 КТд=1,0
шлифовального материала зерен:
Кs1Ш=0,58 KTШ=1,64
группа обрабатываемого материала и твердости круга:
Кs1O=1,0 КTO=1,0
группы СОЖ:
КПЖ=1,0 КТЖ=1,0.
Для каждой шейки:
S1=0,054*1,0*1,0*1,0*1,0*1,0*1,0*1,0*0,58*1,0*1,0=0,03
об/мин.
То=0,09*1,0*1,0*1,0*1,0*1,0*1,0*1,0*1,64=0,11 мин.
Определим значение Sпрод=2400 мм/мин.
n=120 об/мин.
Длина шлифования принимается равной L=70 мм.
9. Управляющая программа
Операция 010: Токарный С ЧПУ 16К20Ф3:
М40
Т1
М3,35,00~,00~,141- 15,36,087- 46,36,087- 52,96,087-
127,99,00,00~,00~,35,00~,00~,141- 15,66,087- 46,395,00- 64,16*,00*- 70,16-
46,00~,00~- 64,16*,00*- 70,16,00- 121,16,00,00~,00~
М3,35- 121,16~,00~*,00*- 127,16- 142,36,00*- 150,96- 157,00-
121,16~,00~*,00*- 127,16- 142,36,00* - 150,96
Z - 157,00
X150,00~
Z3,00~
M9
M5
M30
Заключение
деталь технологичность вал
В ходе данной работы был составлен чертеж детали типа «вал»,
определены расчетным и табличным методами допуски формы, расположения и
шероховатость поверхностей.
Выполнен анализ технологичности детали, а так же анализ
технологичности выбора заготовки в условиях серийного производства.
На основе анализа допусков формы и расположения поверхностей,
а также их шероховатости определена самая точная элементарная поверхность и
сформирован маршрут обработки всех элементарных поверхностей детали типа «вал».
Сформирована последовательность обработки поверхностей детали
и произведен анализ структуры операций на конкретном оборудовании в
соответствии с серийным типом производства.
На основании этого была составлена операционная карта и карта
эскизов обработки поверхностей детали, включая эскизы базирования детали на
каждой операции обработки. В соответствии с технологическим маршрутом были
рассчитаны неизвестные операционные размеры.
Список использованной литературы
1. Метелев Б.А., Куликова Е.А., Тудакова Н.М.
Технология машиностроения. Ч1: комплекс учебно-методических материалов/ Б.А.
Метелев, Е.А. Куликова, Н.М. Тудакова; Нижегород.гос. техн. ун-т Нижний
Новгород, 2007 - 107 с.
2. Горбацевич А.Ф., Шкрет В.А. Курсовое
проектирование по технологии машиностроения, 4-е изд., Москва - Высш. Школа,
1983 - 256 с., ил.
3. Справочник технолога-машиностроителя. В 2-х
т./ Под ред. А.М. Дальского, А.Г. Косиловой и Р.К. Мещерякова, А.Г. Суслова. -
5-е изд., перераб. и доп.-М Машиностроение, 2001. 912 с., ил.
. Общемашиностроительные нормативы времени и
режимов резания для нормирования работ, выполняемых на универсальных и
многоцелевых станках с числовым программным управлением. Ч2, Москва -
Экономика, 1990.
. Расчет припусков: метод. Указания к выполнению
практических работ и разделов в курсовых и дипломн. проектах для студентов
машиностроительных специальностей всех форм обучения/НГТУ; Сост.: Д.С. Пахомов.
Н. Новгород, 2001. - 24 с.
6. Режимы резания
металлов. Справочник. Изд. 3-е, переработанное и дополненное. М.,
«Машиностроение», 1972.
. Техническое
нормирование операций механической обработки детали: Учебное пособие.
Компьютерная версия. /И.М. Морозов. И.И. Гузеев, С.А. Фадюшин. - Челябинск:
Изд. ЮУрГУ. 2003. - 65 с.