Отримання товарних дизельних палив методом оксидаційного знесірчування
ЗМІСТ
ВСТУП
.
Огляд літератури
1.1 Склад та
властивості прямогонних дизельних фракцій
1.1.1 Вуглеводні прямогонних дизельних фракцій
.1.2 Сірчисті сполуки
.1.2.1 Елементна сірка і сірководень
.1.2.2 Меркаптани
.1.2.3 Сульфіди
.1.2.4 Дисульфіди
.1.2.5 Тіофен і його похідні
.2 Способи очищення прямогонних дизельних фракцій
.2.1 Стан та перспективи випуску низькосірчистих палив
.2.2 Фізико-хімічні методи
.2.2.1 Адсорбція і ректифікація
.2.2.2 Селективна екстракція
.2.2.3 Комплексоутворення
.2.3 Хімічні методи
.2.3.1 Сульфування
.2.3.2 Алкілування
.2.3.3 Гідроочищення
.2.3.4 Оксидаційне очищення
. ОБ’ЄКТИ ТА МЕТОДИКИ ПРОВЕДЕННЯ ЕКСПЕРИМЕНТІВ
.1 Характеристика вихідної сировини та допоміжних
речовин
.2 Опис лабораторної установки оксидаційного
знесірчування дизельних фракцій
.3 Методики проведення досліджень та аналізу
результатів
.4 Визначення вмісту загальної сірки в твердому осаді
і кубовому залишку
. ЕКСПЕРЕМЕНТАЛЬНА ЧАСТИНА
.1 Вплив тиску
.2 Знесірчування різних типів сировини
. ТЕХНОЛОГІЧНА ЧАСТИНА
.1 Оптимальні параметри процесу оксидаційної очистки
.2 Матеріальний баланс процесу
.3 Обгрунтування вибору технологічної схеми установки
оксидаційної очистки
.4 Опис принципової технологічної схеми установки
оксидаційної очистки
. ЕКОНОМІЧНА ЧАСТИНА
.1 Техніко-економічне обгруниування
.2 Розрахунок витрат на проведення досліджень
.3 Розрахунок вартості сировини і матеріалів
.4 Розрахунок витрат на електроенергію для
технологічних цілей
.5 Вартість апаратури та обладнання
.6 Вартість орендної плати
.7 Розрахунок чисельності працюючих і фонду заробітної
плати
.8 Визначення вартості проведених досліджень
.9 Економічний ефект досліджень
. ОХОРОНА ПРАЦІ
.1 Потенційно небезпечні фактори при роботі у хімічній
лабораторії
.2 Заходи забезпечення безпеки експлуатації лабораторного
обладнаня і проведення лабораторних досліджень
.3 Санітарно гігієнічні заходи
.3.1 Метеорологічні умови
.3.2 Опалення, вентиляція та система кондиціювання
.3.3 Система освітлення
.3.4 Системи водопостачання і каналізації
.5 Засоби індивідуального захисту
.6 Заходи пожежної профілактики
.7. Опис небезпечних ділянок технологічної схеми
установки оксидаційного знесірчування ДП
.8. Розрахунок системи вентиляції
.9 Розрахунок природного освітлення
. ЦИВІЛЬНА БЕЗПЕКА
.1 Вступ
7.2 Розрахунок надлишкового тиску вибуху
.3 Попередження і унеможливлення надзвичайної ситуації
ВИСНОВКИ
СПИСОК ВИКОРИСТАНОЇ ЛІТЕРАТУРИ
ВСТУП
Зростання жорсткості
вимог до екологічних властивостей палив призводить до зменшення в них
допустимої кількості сірчистих сполук. Ілюстрацією цього положення може бути
допустимий вміст сірки у дизельному пальному (ДП), що випускається у США: з
2009 року максимальний вміст сірки у них повинен не перевищувати 10 ppm (0,001
% мас.). Ідентичні або навіть жорсткіші вимоги висуваються до палив, що
випускаються у країнах Євросоюзу.
На даний момент
єдиною широко використовуваною промисловою технологією очищення нафтової
сировини від сполук сірки є гідроочищення (ГО). Але цей метод має ряд
недоліків, основними з яких є:
- у процесі використовується порівняно складне
обладнання, розраховане на тиск 7 МПа і вище, що автоматично вимагає великих
капітальних затрат при будівництві нової установки;
оскільки одним з продуктів процесу є сірководень, то
паралельно з гідроочищенням вимагається будівництво установок очищення газів
від H2S та його утилізації (виробництва сірки або сірчаної кислоти);
для глибокого гідроочищення вимагається використання
чистого водню, що автоматично спричиняє до будівництва поряд з вищезгаданими
установками ще й блок виробництва водню;
при гідроочищенні поряд із сірчистими сполуками
усуваються також всі інші гетероатомні речовини та гідрується частина
ароматики, що автоматично спричинює до зниження у очищеному продукті речовин,
здатних сорбуватися на металічних поверхнях;
сполуки ряду тіофену та інші конденсовані сірчисті
сполуки, що можуть міститися у сировині, не піддаються гідроочищеню через
просторові затруднення, які виникають при їх контакті з каталізаторами.
У зв’язку з цими недоліками необхідно створювати якісно нові
технології очищення нафтових фракцій. До таких процесів можна віднести
оксидаційне знесірчування (ОЗ) нафтової сировини.
Суть методу полягає в окисненні сірчистих сполук до
сульфонів, сульфоксидів та, можливо, сульфокислот, які порівняно з іншими
компонентами сировини проявляють чітко виражені полярні властивості. Це
дозволяє відділяти їх від інших сполук, що містяться в нафтових фракціях,
адсорбцією або екстракцією. Крім цього, враховуючи те, що сульфоксиди, сульфони
та сульфокислоти мають, порівняно з відповідними вихідними сірчистими
сполуками, вищу температуру кипіння, їх можна усувати із суміші звичайною
перегонкою.
Відомі оксидаційні процеси переробки нафтових фракцій можна
розділити на три групи:
технології, спрямовані на демеркаптанізацію палив;
процеси, головною метою яких є одержання нафтових
сульфоксидів
та сульфонів, як кінцевих продуктів;
технології, спрямовані на зменшення загального вмісту сірки у
сировині;
Але, застосовуючи оксидаційний метод вилучення сірки з
прямогонних фракцій можна зменшити кількість сірки не більше, ніж на 80 %. Тому
отримувати паливо, що відповідало б європейським стандартам (вміст сірки -
0,0005-0,0015 % мас.), при знесірчуванні сировини ( з вмістом сірки більшим від
0.01 % мас.) методом окиснення - неможливо.
З іншого боку, на сьогодні в Україні дозволено випуск
дизельних палив з вмістом сірки навіть до 0,2 % мас. А саме, на території нашої
держави є три заводи (АТ «НПК-Галичина», м. Дрогобич; ВАТ «Нафтохімік
Прикарпаття», м. Надвірна; ВАТ «Херсоннафтопереробка», м. Херсон), які не мають
установок гідроочищення дизельних фракцій і можуть переробляти тільки
низькосірчисту вітчизняну нафту. У випадку використання «важких»
високосірчистих російських нафт вищевказані підприємства не здатні випускати ДП
з вмістом сірки до 0,2 % мас.
У випадку знесірчування прямогонноі сировини оксидаційним
методом отримується паливо з вмістом сірки менше 0.2 % мас., а також отримане
паливо має кращі змащуючі властивості, ніж продукти гідрогенізації.
Продукти окиснення (концентрати сірчистих сполук) можуть
використовуватися, як мастильно-охолоджуючі рідини, вартість яких на 10-20 %
перевищує вартість товарних дизельних палив. Тому, якщо собівартість процесу
вилучення сірки оксидаційним методом не буде перевищувати собівартість процесу
гідроочищення, то даний метод може знайти промислове використання.
Запропонована технологічна схема процесу дає можливість
отримувати товарне дизельне пальне, вміст сірки у якому не перевищує 0,2 % мас.
Отриманий основний продукт (ДП) має значно кращі змащуючі властивості та меншу
собівартість, ніж гідрогенізат установки гідроочистки.
дизельний оксидаційний знесірчування очистка
1. ОГЛЯД ЛІТЕРАТУРИ
Для того, щоб провести аналіз технологій десульфуризації
прямогонних нафтових фракцій, які вже існують,а також для вивчення напрямків в
яких ці технології можуть розвиватися, треба розглянути склад цих фракцій,
вивчити його вплив на екологічні властивості палив, а також поведінку окремих
вуглеводнів у ході експлуатації та під час знесірчування і після нього.
Світові вимоги до товарних палив відрізняються від тих, які
діють в нашій державі. Тому їх необхідно порівняти і встановити чи можуть
вітчизняні заводи виробляти такі палива.
.1 Склад та властивості прямогонних дизельних фракцій
Як правило, межі википання прямогонних дизельних фракцій
становлять 180-350 ºС. В основу цих фракцій входять такі
групи вуглеводнів: алкани (парафіни), циклоалкани (нафтени), арени (ароматичні)
і гетероатомні сполуки ( в основному сірчисті, кисневмісні і азотисті). Також
тут можуть міститися конденсовані речовини - “смоли”, але їхня кількість
невелика. Основу фр. 180-350 ºС становлять вуглеводні, а
основною причиною незадовільних властивостей є сірчисті сполуки. Тому нижче
розглянуто склад, властивості, а також можливий вміст у прямогонних дизельних
фракціях вуглеводнів та окремих груп сірчистих сполук.
.1.1 Вуглеводні прямогонних дизельних фракцій
Зазвичай кількість алканів у прямогонних дизельних фракціях,
які отримані внаслідок атмосферної чи вакуумної перегонки, складає 55-60 %
[1,2]. Якщо палива отримані із сірчистих нафт, то в них переважають нормальні
алкани, а вміст ізоалканів може бути різним і не залежить від типу нафти.
Алкани, а особливо н-парфіни приводять до втрати рухливості палива при
понижених температурах, але алканові веглеводні мають хороші екологічні
властивості і високе цетанове число.
Розчинні у паливі кисневмісні продукти ( переважно кислоти),
які утворюються при окисненні алканів, можуть викликати корозію конструкційних
матеріалів, а особливо сплавів кольорових металів [2-4].
Нафтени містяться у прямогонних дизельних фракціях у
кількості 15-50 % [1,2]. Переважна частина бі-, три- і тетрациклічних
циклоалканів зосереджена у фракціях, які википають при температурах вищих від
350-400 ºС [2], а от нафтени, які виділені з
фракцій, що киплять до 300 º С в основному моноциклічні з
невеликими боковими ланцюгами. Так як циклоалкани мають добрі експлуатаційні і
екологічні властивості, то вони є найбажанішими компонентами дизельних палив.
Під час окиснення нафтенів утворюються такі ж сполуки, що і при окисненні
алканів, а саме: альдегіди, спирти, кетони, гідропероксиди, а також кислоти і
оксикислоти.
Найбільша кількість аренових вуглеводнів знаходиться у
висококиплячих фракціях дизельних палив [1,2]. А в середньому, у прямогонних
дизельних фракціях, вміст аренів складає 10-40 % мас. і ця кількість зростає з
підвищенням температури їх википання. Тут арени переважно представлені
похідними бензолу, а також можуть зустрічатися похідні нафталіну. Конденсованих
аренових вуглеводнів в дизпаливах небагато, приблизно 0.1-1.3 % мас [4].
Залежно від кількості бічних ланцюгів і від їх будови
змінюється схильність аренів до окиснення, а також їхня термічна стабільність.
Метилзаміщені і незаміщені арени є більш стабільні ніж алкани [2]. Чим більша
кількість бічних ланцюгів, тим краще арени будуть окиснюватися [3]. Арени з
ненасиченими бічними ланцюгами окиснюються найкраще, з подальшим ущільненням.
Але у прямогонних нафтових фракціях вони майже не зустрічаються, а тільки
можуть бути продуктами вторинних процесів переробки нафти [1,2,5,6]. Арени
окиснюються через стадію утворення гідропероксидів. В результаті утворюються
сполуки, у яких кисневі функціональні групи знаходяться (переважно) в бічних
ланцюгах і відділені від кільця двома-трьома вуглецевими атомами. Ці продукти
виступають, як слабкі інгібітори процесу окиснення. Фенол і його похідні
алкілфенольного типу є набагато кращими антиокисниками, але ці сполуки
утворюються у менших кількостях [7-10].
При збільшенні, у прямогонних дизельних фракціях, циклічності
аренів їх окиснення супроводжується накопиченням великої кількості нерозчинних
продуктів у порівнянні з моноциклічними аренами.
.1.2 Сірчисті сполуки
У прямогонних дизельних фракціях загальний вміст сірчистих
сполук змінюється від кількох десятих відсотка до 50-10 % мас. [2]. Сірчисті
сполуки у нафті і нафтопродуктах представлині елементною, меркаптановою,
сірководневою, сульфідною, дисульфідною і тіофеновою формами.
При згорянні сірчистих сполук утворюються оксиди сірки, які є
забрудниками довкілля. А тому сполуки сірки є небажані у паливі (погані
екологічні властивості).
Але, взаємодіючи з гідропероксидами, які є основним джерелом
утворення вільних радикалів [11, 12], усі сірчисті сполуки гальмують окиснення
вуглеводнів. Активність такої взаємодії залежить від того, яка будова сірчистих
сполук. Найактивніше з гідропероксидами реагують меркаптани, а найважче -
тіофени. Проміжне місце займають сульфіди і дисульфіди.
Так як спирти, сульфоксиди і вода були знайдені в первинних
продуктах окиснення, то першу стадію взаємлдії сірчистих сполук з
гідропероксидами можна подати таким сумарним рівнянням (на прикладі реакції
окиснення сульфідів) [12,13]:
(1.1)
Так само перебігають процеси взаємодії гідропероксидів з іншими
сірчистими сполуками.
При зберіганні, чи використанні пального з високим вмістом
сірки можливе утворення твердих радикалів, внаслідок подальших окиснювальних
перетворень продуктів окиснення вуглеводнів з пероксидами.
Далі розглянуто поведінку сірчистих сполук під час гідрування
та окиснення та їх склад і співвідношення у прямогонних нафтових фракціях.
.1.2.1 Елементна сірка і сірководень
У прямогонних дизельних фракціях елементна сірка міститься в
кількостях 1´10-4¸7´10-4 % мас.
При взаємодії елементної сірки з вуглеводнями, у прямогонних
дизельних фракціях, може утворюватися сірководень, а також він може бути у
вільному стані. Сірка і сірководень є дуже корозійноактивними по відношенню до
чорних і особливо кольорових металів. Оскільки вміст елементарної сірки, як
правило, є дуже малим, то у нормах на товарні палива не допускається
присутність тільки сірководню [10, 14].
.1.2.2 Меркаптани
Кількість меркаптанів становить 40-75 % мас. від усіх
сірчистих сполук фракції. Переважно меркаптани знаходяться у легких фракціях
нафти. Їхній вміст різко зменшується із зростанням температури кипіння фракції,
а у тих фракціях які википають вище 300 ºС, меркаптани майже відсутні.
У прямогонних дизельних фракціях присутні, як алканові ( етилмеркаптан,
децилмеркаптан), так і аренові (фенілмеркаптан, бензилмеркаптан) меркаптани
[1,2].
Алканові меркаптани нормальної будови, є більш стійкими ніж
їх ізомери, особливо при високих температурах, а вищі гомологи алканових
меркаптанів термічно є менш стабільними ніж нижчі. Аренові меркаптани є ще
більш стійкі до дії високої температури [15].
Меркаптани представляють собою реакційно здатні сполуки. Вони
схильні до таких перетворень як: термічний розклад, окиснення, ущільнення,
взаємодія з кольоровими металами (особливо з міддю і її сплавами, викликаючи
таким чином їх корозію і руйнування [5] ). Також вони легко утворюють солі
металів (меркаптиди), які дуже погано розчиняються в паливах. В ході процесу
гідроочищення меркаптани пертворюються на відповідні вуглеволні і сірководень.
Якщо меркаптани окиснювати киснем повітря, або іншим слабким
окисником, то утворюються дисульфіди, а якщо сильним окисником (озоном,
пероксидом водню), то утворюються сульфокислоти (через стадію утворення
сульфокислот) [16,17]. Можливе також утворення сульфенових або сульфінових
кислот, які можуть досить легко окиснюватися.
Отже, меркаптани - це сполуки з найвищою з-поміж усіх
гетероорганічних сполук прямогонних дизельних фракцій хімічною активністю, що
зумовлює їх високу корозійну активність і схильність до окиснення в умовах
експлуатації, тому їх вміст у паливах обмежується окремо.
.1.2.3 Сульфіди
Сульфіди, в нафтових фракціях, знаходяться як аліфатичної,
так і циклічної будови.
Сульфіди мають більшу термічну стабільність, ніж меркаптани і
дисульфіди.
Вміст сульфідів лінійної будови у прямогонних дизельних
фракціях може становити 2¸40 % мас. від усіх сірчистих сполук
[1, 2].
Під час процесу гідроочищення сульфіди перетворюються на
сірководень і два відповідні алкани. Це проходить через стадію утворення меркаптану.
Також з сульфідів можуть утворюватися алкани і меркаптани, але при недостачі
водню.
Однією з найвіжливіших реакцій лінійних сульфідів є
окиснення. При наявності кисню повітря, кисню, пероксиду водню сульфіди досить
активно окиснюються з утворенням сульфоксидів [18-24].
Якщо у м’яких умовах сульфіди озонувати, то через стадію
сульфоксидів будуть утворюватися сульфони ( їх вихід до 90 %) [25,26-28]. Якщо
ж створити більш жорсткі умови, то руйнуються зв’язки C-S і утворюються
ненасичені, кисневмісні вуглеводневі сполуки і сірчана кислота [16].
Циклічні сульфіди (тіофан і його похідні) можуть міститися в
кількості до 40-50 % від загальної кількості сірчистих сполук, які є в паливах
середніх нафтових дистилятів [16]. Але сам тіофан в паливах практично відсутній.
Під час гідрування тіофанів з розривом кільця, утворюються
меркаптани, які в подальшому можуть гідруватися до алканів.
Також тіофани досить легко окиснюються киснем з утворенням
сульфоксидів і сульфонів, яке супроводжується розривом кільця [23].
Хоч і вміст сульфідів окремо не лімітується, все ж їх
присутність не є бажаною у товарних дизельних паливах.
.1.2.4 Дисульфіди
В прямогонних дизельних фракціях дисульфіди є в кількості не
більше 7-15 % мас. від загального вмісту сірки у фракції [2]. Вміст дисульфідів
зростає при збільшенні молекулярної маси і температури кипіння нафтових
фракцій, але до певної межі, так як дисульфіди є термічно нестійкими
речовинами.
В ході процесу гідрування дисульфіди перетворюються в
меркаптани, які надалі гідруються до відповідних алканів. Але, якщо буде
недостача водню, то гідрування може припинитися на стадії отримання
меркаптанів.
Легко взаємодіючи з озоном і пероксидом водню дисульфіди
утворюють ангідрид сульфонової кислоти (RSO2OSO2R) і
тіолсульфонат (RSO2SR), сильфони та сульфоксиди.
Присутність дисульфідів гальмує реакції окиснення
вуглеводнів. Це відбувається внаслідок їхньої взаємодії з гідропероксидами, з
утворенням стабільних радикалів, які потім вступають в реакції конденсації. В
результаті утворюються тверді нерозчинні осади.
.1.2.5 Тіофен і його похідні
Тіофен практично не зустрічається в прямогонних дизельних
фракціях. Але в них може міститися різна кількість похідних тіофену. Кількість
тіофенових структур збільшується при зростанні температури кипіння фракції.
Тіофен має найвищу термічну стабільність порівняно з усіма
сірчистими сполуками з однаковою молекулярною масою. Також порівняно з
меркаптанами, сульфідами і дисульфідами, тіофен і його аренові похідні є більш
стабільні до дії окисників. При озонуванні тіофен утворює сульфоксиди і
сильфони [26].
В процесі гідроочистки, тіофен найважче, з усіх сірчистих
сполук, піддається гідруванню і відділенню сірки. А деякі похідні тіофену
навіть залишаються стабільними в процесі ГО. Оскільки тіофен має високу термічну
стабільність і низьку реакційну здатність, то його вміст в товарних дизельних
паливах окремо не лімітується [16,17].
Роблячи висновок з проведеного аналізу періодичної і
патентної літератури, можна сказати, що у прямогонних дизельних фракціях може
міститися досить велика кількість сірчистих сполук, представлених всіма типами
цих речовин. У середніх нафтових дистилятах основу сірчистих сполук складають
циклічні та аліфатичні сульфіди. Але із зростанням температури википання
фракцій вміст тіофенових структур збільшується.
Такі технологічні показники, як концентрація фактичних смол,
кислотність, коксивність 10-% залишку можуть погіршуватися, оскільки при
зберіганні сірчисті сполуки схильні до реакцій окиснення і ущільнення. Але
основним недоліком присутності у паливах сірковмісних компонентів є те, що при
їх використанні (спалюванні) утворюється діоксид сірки, який є забрудником
атмосфери.
.2 Способи очищення прямогонних дизельних фракцій
В останні 10-20 років невпинно зростали вимоги до екологічних
властивостей палив. А особливо це стосується вмісту в паливах сірки [29-36].
Тому перед тим, як розглядати технології очищення нафтових фракцій, які вже
існують і ті технології, які тільки розробляються, необхідно проаналізувати ці
вимоги і подивитися, як вони впливають на роботу нафтопереробних заводів (НПЗ).
.2.1 Стан та перспективи випуску низькосірчистих палив
Найжорсткіші обмеження по вмісту сірки висуваються до
автомобільних палив, а саме до дизельних палив і бензинів. Наведемо приклад
допустимого вмісту сірки у пальному, що випускається у США: з січня 2006 року
допускається вміст сірки до 30 ppm у бензинах [29,32] та до 15 ppm у дизельних
паливах [34,35], а з 2009 року максимальний вміст сірки у них повинен не
перевищувати 10 ppm [32,35]. Такі ж, а можливо і жорсткіші вимоги до палива
ставляться у Європі [37-39].
Що стосується України, то тут не висуваються такі жорсткі
вимоги до дизельних палив (ДП). Але з 2006 року вміст сірки повинен не
перевищувати 0.2 % мас. (2000 ppm) [40].
Оскільки міняються вимоги щодо екологічних властивостей
стосовно ДП, то це приводить до того, що нафтопереробні підприємства вимушені
змінювати технологію виробництва. Так, деяким НПЗ доводиться вводити зовсім
нові агрегати. В першу чергу, це стосується установок гідроочистки прямогонних
дизельних фракцій, оскільки на сьогоднішній день вони є єдиною широко
використовуваною технологією вилучення сірки з вуглеводневої сировини. Але
метод гідроочищення і самі установки гідро очистки, в свою чергу, мають ряд
недоліків, які описані у вступній частині. Наприклад для виробництва дизельного
палива з вмістом сірки 0.05 % мас. і менше з високо сірчистої сировини
необхідне використання глибокої десульфуризації з тиском водню не менше 4 МПа.
Також погіршуються такі експлуатаційні властивості ДП як змащувальні,
термоокиснювальні, стабільність при зберіганні, внаслідок проведення глибокого
гідроочищення. Наприклад стабільність і антиокислювальні властивості
погіршуються після глибокого вилучення всіх гетероатомних сполук. Тоді
гідроочищене ДП проявляє приблизно у 10 разів більшу схильність до накопичення
гідро пероксидів, ніж паливо із вмістом сірки 0.2 % мас. [41].
На сьогоднішній день немає якоїсь чіткої і універсальної
класифікації десульфуризаційних процесів, оскільки існує багато методів
очищення від гетероатомних сполук.
Наявні технології можна розділити на дві великі групи: з
використанням водню та без нього. Або їх можна поділити на категорії за
ступенем вилучення органічних сполук сірки. Але такі підходи до класифікації не
є поширеними [126].
Дивлячись на те, як перетворюються сірчисті сполуки всі
процеси можна розділити на три групи:
перетворення із руйнуванням органічних сполук сульфуру. У
цьому випадку вихідні речовини перетворюються до газоподібних, або твердих
продуктів сірки, а відновлена вуглеводнева частина залишається в
нафтопродуктах;
процеси, внаслідок яких сірчисті сполуки або продукти їх
перетворення відокремлюються від потоків НПЗ;
поєднання двох попередніх методів. А саме, коли виділені з
сировини сіркоорганічні сполуки у подальшому зазнають перетворень у окремому
реакторі, а вуглеводнева частина, яка при цьому утворюється, повертається в
очищену сировину.
Найбільш правильно було б розділити процеси на дві групи:
хімічні та фізико-хімічні. У першій групі були б технології внаслідок яких
відбувається вилучення сірчистих сполук за рахунок їх докорінного перетворення
у інші види речовин. А у другій - технології за рахунок фізичних процесів або
утворення слабких хімічних зв’язків з допоміжними реагентами. Тоді
сіркоорганічні речовини вилучалися б у тому вигляді, в якому вони присутні у
вихідній сировині. Хоча у роботі [42] усі процеси вилучення сірчистих сполук
класифікують на каталітичні і фізико-хімічні. При цьому до останніх відносять
типові фізичні перетворення (екстракція, адсорбція) і процеси , в яких
проходить перетворення, наприклад окиснення. А це, на мій погляд, не зовсім
правильно.
.2.2 Фізико-хімічні методи
До фізико-хімічних методів видалення сірчистих сполук можна
віднести: адсорбцію, ректифікацію, селективну екстракцію, комплексоутворення.
.2.2.1 Адсорбція і ректифікація
Завдяки використанню різних адсорбентів (силікагелю,
активованого вугілля, оксиду алюмінію, глинистих матеріалів, нікелю нанесеного
на його оксиди [21,43-49] ) адсорбційні методи дозволяють вилучити з прямогонних
дизельних фракцій сірчисті сполуки. Адсорбційна активність сірчистих сполук
зростає в наступному ряді: тіофени < аліфатичні меркаптани < аліфатичні
дисульфіди < аренові і циклічні меркаптани < аренові дисульфіди <
аліфатичні і циклічні сульфіди [16]. Так як арени і сірчисті сполуки мають
порівняно однакову адсорбційну здатність [50,51], то основна частина сірчистих
сполук виділяється у вигляді сірчисто-аренових концентратів [43,44,50]. А в
подальшому, використовуючи ректифікацію, можна збільшити вміст сірчистих сполук
в цих концентратах.
Також адсорбцію можна ефективно використовувати для очищення
продуктів гідроочистки, якщо компоненти, які треба вилучити є в невеликій
кількості. Тоді в сировині, здебільшого, зосереджуються схильні до поляризації
похідні тіофену, які погано піддаються гідруванню (тому залишаються у продуктах
після гідроочищення), але добре сорбуються на твердих адсорбентах.
Адсорбцію ( чи хемосорбцію) можна ефективно поєднувати з
іншими процесами (наприклад, гідруванням). Ці процеси часто називають
«реакційною адсорбцією» [42]. Тоді адсорбенти, головним чином, зв’язують
продукти перетворення сіркоорганічних сполук вихідної речовини, а також, як
правило, паралельно виконують роль каталізатора. У якості таких
адсорбентів-каталізаторів використовуються оксиди цинку та нікелю [42, 53] або
нікель молібденові оксиди [42], що нанесені на силікагель. Також цей процес
можна розглядати як один з видів гідрочистки.
Таким чином, поєднуючи адсорбцію з ректифікацією збільшують
концентрацію сірчистих сполук в аренових концентратах. Але внаслідок подібної
адсорбційної здатності сірчистих сполук і ароматики, а також малої ємності
твердих сорбентів, повністю видлити небажані компоненти ці методи не
дозволяють.
Якщо ж використовувати адсорбцію після або у поєднанні з
процесами гідрування, то цей метод буде ефективним.
.2.2.2 Селективна екстракція
Для того, щоб вилучити сірковмісні сполуки з прямогонних
дизельних фракцій методом екстракції можна використовувати ацетон, оцтову
кислоту, фурфурол, фенол, диметилформамід, етанол, анілін, оцтовий ангідрид,
полі етиленгліколі, складні гетероатомовмісні органічні суміші, які називають
іонними рідинами (суміш хлоридів заліза та імідазоліуму, BF4, (C4H9)4NBr·2C6H11NO).
Можна вилучити від 50 до 100 % сірчистих сполук, але це залежить від типу
розчинника і кількості циклів екстракції [54,55-60].
Але в цих процесів є суттєві недоліки. Так розчинники, які
використовуються, мають порівняно малу розчинну здатність, а також, паралельно
з сіркоорганічними речовинами екстрагують ароматику. Деякі розчинники досить
важко відділити від екстрактів і рафінатів [42,61,62]. Через це екстракти треба
направляти на знесірчування ( наприклад, гідроочищення), а після цього
ароматичні сполуки повертати назад у нафтові потоки. Тобто, в такому випадку,
використовуючи екстракцію ми зменшуємо продуктивність установок ГО.
Можна збільшити розчинну здатність або селективність
розчинника. Тоді треба використовувати їх суміші (ацетон-етанол [56], різні
гліколі [57] ). Але це ускладнює схему відділення розчинників від екстракту.
Досить часто технології, у яких сірчисті сполуки спочатку
перетворюються хімічно ( за допомогою окиснення), а потім вилучаються за
допомогою селективних розчинників [42,59,60], також відносять до процесів
екстракції. Але в цьому випадку основною стадією треба вважати процес окиснення
(хімічне перетворення).
Для вилучення сульфідів з метою отримання з них сульфоксидів
використовують процес екстракції сірчистих сполук сірчаною кислотою
[19,23,63,64]. Але тоді також проходить сульфування сірчистих сполук та
ароматики. Щоб отримати найкращі результати необхідно використовувати
двоступеневу екстракцію. При цьому на першій стадії беруть 86 %-ну, а на другій
- 91 %-ну сірчану кислоту [65]. Тоді сірчана кислота добре розчиняє сульфіди і
не вилучає інші сіркові сполуки і вуглеводні.
З вище сказаного видно, що процес екстракції є ефективним
лише при поєднанні його з хімічними процесами, або використовуючи сірчану
кислоту. При сірчанокислій екстракції небажані сполуки усуваються лише частково,
а при цьому ще й сульфуються аренові вуглеводні. Також виникає проблема з
утилізацією кислих відходів. Ці недоліки роблять даний метод промислово не
привабливим.
Ще можна використовувати іонні рідини. Це дозволяє вилучити
майже всю сірку. Але більша частина цих методів є поєднанням екстракції і
окиснення. Їх апробація проводилася лише на модельних сумішах, які є лише
схожими до гідрогенізатів з досить малим вмістом сірки; застосування дорогих
речовин робить їх непривабливими з технологічної точки зору.
.2.2.3 Комплексоутворення
З галогенідами металів (титану, кобальту, ртуті, паладію,
алюмінію), галогенами і галоїд похідними сполуками, азотнокислим сріблом,
2,4,5,7-тетранітро-9-флоуреном [34,66-70,71,72], сіркові сполуки утворюють
стабільні комплекси. Після відділення при нагріванні ці комплекси руйнуються, а
також погано розчиняються у вуглеводнях.
Розчинні комплекси утворюються внаслідок взаємодії
дисульфідів з ацетатом ртуті. При подальшій обробці розчином хлористого натрію
вони переходять у нерозчинний стан. Схильність до комплексоутворення
зменшується із збільшенням молекулярної маси дисульфідів. Ця закономірність
пропорційна збільшенню частки вуглеводневої частини. Для інших сіркових сполук
це явище також є характерне [16]. Внаслідок утворення комплексів з азотнокислим
сріблом отримують чисті сульфіди [19,24,45,70].
Для отримання сірчистих сполук із високосірчистої дистилятної
фракції був розроблений спосіб їх виділення у вигляді комплексів із хлоридами
кобальту, нікелю, цину, заліза, алюмінію, титану і олова з подальшим їх
розділенням рідинною адсорбцією [24, 44, 69]. Також був встановлений найбільш
ефективний комплексоутворювач - тетрахлорид олова.
Такий метод дозволяє виділяти велику кількість сірчистих
сполук ( до 74 % від їх вмісту у фракції). Але він має і ряд недоліків:
використання дорогих і досить часто шкідливих
реагентів;
велика витрата реагентів;
громіздкість апаратурного оформлення;
Даний метод використовувався тільки в лабораторній практиці,
тому що залежно від сировини разом із сірковими сполуками комплекси можуть
утворювати ароматичні і азотовмісні речовини.
Як підсумок щодо використання фізико-хімічних методів для
усунення сірчистих сполук з нафтових фракцій, можна сказати, що вони можуть
бути ефективними тільки у поєднанні з хімічними процесами і при цьму останні
відіграють ключову роль. Це пояснюється тим, що сіркові сполуки мають подібні
фізичні властивості з ароматичними вуглеводнями.
.2.3 Хімічні методи
Сульфування, алкілування, гідроочищення, окиснення - це
хімічні методи видалення сірчистих сполук. Їхня суть полягає в наступному: в
одному випадку сіркові сполуки розкладаються на вуглеводневу частину та
газоподібні компоненти, які містять сірку ( Н2S, SO2), а в іншому - проходить
перетворення всіх органічних сполук сірки і тоді вони набувають нових
властивостей. Вони стають водорозчинними або полярними, збільшується їхня
температура кипіння або схильність до поляризації. Внаслідок цього за допомогою
вище перерахованих методів, продукти перетворення органічних сполук сірки можна
ефективно виділити з реакційної суміші.
.2.3.1 Сульфування
Для очищення дистилятів і нафтових залишків, у
нафтопереробній промисловості, давно використовують концентровану сірчану
кислоту. «Кислий гудрон», який при цьому утворюється є побічним продуктом. Він
складається з непрореагованої сірчаної кислоти, продуктів сульфування,
окислення, ущільнення ненасичених, ароматичних та гетероорганічних сполук. Для
збільшення повноти вилучення сірки застосовують багатоступеневе сульфування
сировини [16].
Даний метод є не селективним. Проходять незворотні втрати
аренів, кисневмісних та інших речовин, а також великі виходи «кислих гудронів»
. Також до недоліків можна віднести проблему утилізації цих гудронів, значні
витрати сірчаної кислоти, погіршення експлуатаційних властивостей, додаткові
стадії очищення. Тому цей метод в даний час в промисловості не
використовується.
.2.3.2 Алкілування
Сірчисті сполуки (у першу чергу тіофенова сірка) алкілується
ненасиченими вуглеводнями С6-С8 в присутності каталізаторів (BF3, AlCl3,
ZnCl2, SbCl5, що нанесені на силікагель, оксид алюмінію
чи кремнію) [42]. Продукти алкілування відділяються від реакційної суміші
ректифікацією, внаслідок того, що вони можуть мати до 170 ºС вищу температуру кипіння,
ніж відповідні їм вуглеводні. В результаті даного методу ступінь вилучення
сіркових сполук є більшим, ніж 99.5 %.
Але в сировині також є ароматичні вуглеводні і ненасичені
вуглеводні ( останні присутні, якщо сировина вторинного походження), які також
проявляють схильність до алкілування. Тому отриманий алкілат є концентратом
сірчистих, ароматичних та олефінових речовин. Через це, після алкілування і
виділення продуктів за допомогою ректифікації, останні направляються на
гідроочистку . Таким чином, можна сказати, що процес алкілування є стадією
підготовки сировини до гідроочищення, а це дозволяє зменшити продуктивність
установки, затрати на проведення процесу, витрату водню.
.2.3.3 Гідроочищення
Процеси гідроочищення це - процеси в ході яких, прямогонні
дизельні фракції обробляють воднем або водневмісними газами в присутності
каталізатора, для вилучення з цих фракцій небажаних сполук.
На даний час цей процес є найпоширенішим методом очищення
прямогонних фракцій, він широко застосовується в промисловості і постійно
вдосконалюється [1, 5, 77, 78].
При гідроочищенні майже всі аліфатичні сірчисті сполуки
переходять в сірководень. При цьому утворюється ненасичений вуглеводень.
Тіофани і тіофени гідруються з утворенням відповідних аліфатичних вуглеводнів і
сірководню [1, 5, 77]. Якщо є недостача водню, то одні сірчисті сполуки можуть
переходити в інші. Так, меркаптани можуть утворювати сульфіди або замість
насичених - ненасичені:
2RSH + H2 ® RSR + H2S,
(1.2)+ H2 ® R`H + R`CH=CHR` + H2S.
(1.3)
Детально поведінка сірчистих сполук під час гідрування була
розглянута у підрозд. 1.1.2.
При гідроочищенні азот і кисневмісні сполуки переходять у
аміак і воду, з одночасним утворенням відповідних вуглеводнів [1, 5].
Умови процесу: температура - 320-430 К, тиск - 3-10 МПа,
об’ємна швидкість подачі сировини - 2-5 год-1 і більше, витрата
водню - 100-900 м3/м3 сировини.
Нижнє значення температури процесу обмежується швидкістю
знесірчення, а верхнє - початком закоксовування каталізатора [1, 5, 75, 76].
Каталізаторами даного процесу виступають альюмо-кобальт-молібденові (АКМ) і
альюмо-нікель молібденові (АКМ). Каталізатор АКМ майже не викликає
гідрокрекінгу вуглеводнів, він має високу активність і селективність за
кінцевою реакцією знесірчення і є активним при насиченні ненасичених
вуглеводнів. Каталізатор АНМ є менш активним при насиченні ненасичених, але
сприяє насиченню аренів і проявляє більшу активність при гідруванні азотистих
сполук. Так як, гідрування аренів ( при використанні АНМ) зменшує
енргомісткість товарного дизельного палива, то у процесах гідроочистки
прямогонних дизельних фракцій переважно використовують каталізатор АКМ. Але
якщо стоїть завдання зменшити в сировині кількість ароматичних вуглеводнів (
для покращення метанового числа або екологічних властивостей палива), то тоді
використовують каталізатор АНМ.
Оскільки, активність каталізатора досить сильно пов’язана з
типом реактора [42, 142] ( особливо щодо конденсованих тіофеново-ароматичних
сполук), то каталізатор вибирається у кожному конкретному випадку окремо.
Так як, з кожним роком збільшуються вимоги до екологічних
властивостей палив, то це приводить до підвищення жорсткості процесів, а саме
до підвищення парціального тиску водню в системі, збільшення температури,
необхідно використовувати чистий водень замість водневмісного газу. Ці фактори вимагають
збільшення енергетичних затрат і зміни технології процесу. Тому всі роботи, які
проводяться по удосконаленню процесу можна розділити на три групи:
створення нових реакторних блоків;
удосконалення каталізаторів;
розробка підвидів установок гідроочистки ( їх
комбінація з іншими процесами), наприклад, «реактивна адсорбція», про яку
згадувалося вище;
Серед тих каталізаторів, які вже розроблені або удосконалені
є: ІС-44, KF-752, HR 416, HR 448, CoMo STARS, NiMo STARS, CoMo CENTIEL, NiMo
CENTIEL, NEBULA, АКВФС, АКФС, АМФС, РК-222, РК-231, РК-442, ГО-70Н [42, 75,
78-87]. Хоча використання цих каталізаторів дає хороші результати (вихід рідких
продуктів після гідроочищення становить 97-98 % мас., а ступінь знесірчення
більше 99 %), та все ж їхня ефективність значною мірою залежить від якості
сировини [42].
Тому на даний час розробляються і впроваджуються каталізатори
на основі благородних металів (платина, паладій) [42]. Ці каталізатори
зменшують кількість сірки до 6 ppm і менше, а також дозволяють усувати до 75 %
ароматики. Але каталізатори на основі благородних металів можна використовувати
на другій стадії очищення, тобто коли основна кількість органічної сірки
видалена з сировини, тому що дані метали є дуже чутливі до сірчистих сполук.
Для того щоб удосконалити (модернізувати) реакторні блоки
установок гідроочистки використовуються такі методи:
для зменшення дезактивації каталізатора за рахунок
його частої регенерації, використовують реактори з киплячим шаром;
додаткове введення водню в реактор у місці виходу
сировини та проміжне виведення газоподібних продуктів. Ці заходи дозволяють
збільшити концентрацію реагенту (водню) на виході з реактора і зменшити
кількість сірководню. А це сприяє поглибленню реакцій гідрування;
Але всі ці заходи приводять до ускладнення апаратурного
оформлення процесу. А якщо ще й використовувати киплячий шар, то треба
випускати зовсім нові форми каталізаторів. Тому майже всі установки
гідроочистки використовують реактори з стаціонарним шаром каталізатора.
Хоча процес гідроочистки, безумовно має переваги (високий
ступінь вилучення сірки, достатня селективність процесу, високий вихід рідких
продуктів), та все ж існують і недоліки, на які треба звернути увагу.
Сучасні процеси гідроочищення потребують дорогих
каталізаторів і використання чистого водню, який стає все дорожчим і
дефіцитнішим. Колись, коли проходило порівняно неглибоке вилучення сірки, можна
було використовувати водневмісний газ, в якому вміст водню становив 25-30 %
мас. Дефіцит водню пояснюється тим, що внаслідок модернізації установок
риформінгу, зменшилося його виробництво на НПЗ. Тому нафтопереробні заводи
вимушені створювати окремі установки по виробництву водню.
В технологічній схемі ГО є обов’язкові вузли, для очищення
вуглеводневого і водневмісного газів від сірководню, який в свою чергу
необхідно переробляти в сірку чи сірчану кислоту.
Внаслідок гідроочищення майже повністю руйнуються
гетероатомні сполуки, які здатні утворювати захисні плівки на поверхні металів.
А це, веде до погіршення протизношувальних властивостей палив. При ГО також
погіршується хімічна стабільність палива ( дівищується його здатність до
окиснення, погіршуються змащуючи властивості, стабільність при зберіганні),
внаслідок видалення, в ході процесу, природних антиоксидантів (дисульфідв, фенолів)
[1, 10, 48]. В цьому випадку продуктами окиснення є розчинні у паливі
вуглеводневі кислоти, які викликають корозію обладнання. Тобто при ГО корозійна
активність палив може, навіть, збільшитися [5, 10, 88]. Тому до гідроочищених
палив необхідно додавати присадки, які є досить дорогими.
Ще одним недоліком цього процесу є неможливість усунення
сірки, яка знаходиться у вигляді конденсованих сполук на основі похідних
тіофену. Це відбувається через те, що при їх контакті з каталізатором виникають
просторові затруднення.
Таким чином, всі ці недоліки приводять до високої вартості
будівництва установок ГО і суміжних їй технологій. Також погіршуються
експлуатаційні властивості дизельних палив [88-91]. А якщо, в сировині наявні
конденсовані сполуки тіофенового ряду, то це веде до неможливості отримання
палив з вмістом сірки 10-15 ppm.
.2.3.4 Оксидаційне очищення
Оскільки, описаний вище, процес гідроочищення має суттєві
недоліки, то необхідно було шукати якісь принципово нові напрямки очистки
прямогонних нафтових фракцій від сіркових сполук. Одним з таких напрямків є
розробка процесів, які ґрунтуються на окисненні сірчистих сполук.
Даний метод базується на реакції окиснення, а саме сірчистих
сполук до сульфоксидів або, навіть, сульфокислот. Ці продукти окиснення можна
відділити від інших вуглеводнів ректифікацією, адсорбцією чи екстракцією.
Також велося вивчення [92] окиснення сірки органічних сполук
в присутності метанолу. В результаті утворювалися газоподібні продукти (SO2 та
H2S). Але при використанні цього методу, ступінь вилучення сірки становив 40 %.
Тому від нього відмовилися.
В якості окисника, для окиснення прямогонних дизельних
фракцій, можуть виступати різні речовини: розчини пероксиду водню, азотної
кислоти, діоксид азоту, озон, органічні гідропероксиди, кисень, супероксид
калію [42, 93-97]. Найбільшу швидкість окиснення мають аліфатичні сульфіди. При
цьому, послідовно або паралельно утворюються сульфоксиди і сильфони. Трохи
повільніше меркаптани окиснюються до дисульфідів.
Якщо створити жорсткі умови ( високі температури або
підібрати сильний окисник, наприклад, перманганат калію чи концентрований
пероксид водню), то меркаптани можуть окислюватися до сульфокислот або, навіть,
до сірчаної кислоти [45].
Аналогічно аліфатичним сульфідам досить легко окиснюються тіофани
з розривом кільця та утворенням сульфонів і сульфоксидів [17].
Тіофени пероксидом водню або іншими сильними окисниками
(наприклад, надкислотами) можна окиснити до сульфонів [16, 42, 98].
Розглянувши, як проходить окиснення різних типів сіркових сполук,
можна сказати, що в основному продуктами окиснення є сильфони і сульфоксиди.
Вони мають у своєму складі полярні групи S=О і О=S=О, а тому проявляють яскраво
виражені основні властивості. Тому адсорбція чи кислотна екстракція цілком
підходить для їхнього відділення від інших сполук. А також, завдяки тому, що їх
температура кипіння на 30-200 градусів [99] вища ніж у відповідних вуглеводнів,
ми можемо використовувати звичайну перегонку, для відділення їх від реакційної
маси.
Після вивчення реакцій окиснення сіркових сполук, а також
властивостей продуктів, які при цьому отримуються [11, 23, 24, 42, 63, 84-87,
93-98, 100-105], був запропонований цілий ряд процесів оксидаційної переробки
нафтових фракцій від сіркових сполук. Їх можна поділити на три групи:
процеси, спрямовані на демеркаптанізацію палив;
процеси, метою яких є отримання нафтових
сульфоксидів та сильфонів;
процеси, основним завданням яких є зменшення
загального вмісту сірки в сировині;
Оксидаційна демеркаптанізація палив є найбільш вивчена технологія
і вона досить широко використовується в промисловості. Так як, вміст
меркаптанової сірки в дизельних фракціях є не великий, то цей метод
використовують переважно для прямогонних гасових і бензинових фракцій. В основі
даного процесу лежить реакція окиснення меркаптанів киснем повітря в лужному
середовищі в присутності твердого каталізатора. В результаті цього меркаптани
переходять в дисульфіди. Останні залишаються в розчиненому стані в очищеному
паливі. Даний процес складається з таких стадій: попередня обробка лугом,
демеркаптанізація, промивання і фільтрування. Стадія демеркаптанізації
проходить в реакторі з каталізатором при тиску 0.14-0.7 МПа і температурі 40-60
ºС [110-113].
Витрати на будівництво установки окислювальної
демеркаптанізації є приблизно у 12 разів менші, ніж на будівництво установки
гідроочистки, а собівартість продуктів - менша на 17 % [114].
В процесі оксидаційної демеркаптанізації використовують різні
каталізатори. Наприклад: УВКО-3 - вуглецеве волокно з нанесеним каталізаторним
комплексом [111] ( процес безлужної каталітичної окислювальної
демеркаптанізації), полімерний фталоціаніновий каталізатор КС. До переваг
останнього можна віднести зручність у експлуатації, стабільну активність,
тривалий термін служби, робота без заміни, підживлення чи регенерації протягом
п’яти років. Але він не дуже ефективний при окисненні високомолекулярних
меркаптанів середніх дистилятних фракцій. Тому було запропоновано проводити
демеркаптанізацію цих фракцій використовуючи такі каталізатори як: фталоцианінові
комплекси Со чи Fe [114, 117, 118], оксидні цинк-мідні каталізатори Д-49,
ГИАП-10-2, ГИАП-15 [111, 119, 120]. Але всі ці налагодження не усунуло всіх
недоліків процесу, а саме, не вдалося повністю уникнути використання лужного
розчину у процесі та зменшити вміст загальної сірки в очищуваній сировині.
Процеси другої групи - це процеси оксидаційного вилучення
сіркових сполук з прямогонних нафтових фракцій. Метою цього, є отримання цінних
продуктів, а саме нафтових сульфоксидів і сульфонів.
Сильфони і сульфоксиди мають унікальні властивості,
наприклад, полярність. Тому вони широки використовуються у різних галузях
промисловості. Так, у нафтопереробній - як селективні розчинники, у
нафтовидобувній - як сировина для отримання високоефективних інгібіторів утворення
твердих нафтових відкладів, для отримання інгібіторів корозії металів,
протизадирних та антиокислювальних присадок до палив та олив, як пластифікатори
при виробництві полімерів, як мастильно - охолоджуючі рідини при обробці
металів, тощо [16, 43, 121-127, 128].
Вперше ідею виробництва сульфоксидів з нафтової сировини
запропонував Р.Д. Оболєнцев [129]. Подальша робота показала, що сульфіди і
продукти їх окиснення розчиняються в сірчаній кислоті з утворенням сульфонієвих
комплексів. Ці дослідження стали основою для процесів отримання сульфідів і
сульфоксидів з нафтової сировини [130]. Пізніше було запропоновано
використовувати пероксид водню, для окиснення дизельної фракції, в присутності
кислот, карбонільних речовин або сполук металів [131]. Сильфони і сульфоксиди
також можна отримати з оливних дистилятів. Оскільки сульфідна сірка в даній
сировині складає близько половини від загальної, то основна увага зверталася
саме на її окиснення [132]. В цьому випадку ступінь окиснення сульфідів
становив до 76 % мас.
Найперспективнішими напрямком оксидаційного знесірчування ( з
метою вилучення сірчистих сполук) є третій напрямок. Над окисненням сіркових
сполук у дистилятних паливах вищезгаданими розчинниками, працювали і працюють
багато авторів [11, 18-23, 42, 52, 59, 60, 93-97, 100-105, 133-137].
Даний напрямок має два варіанти: вилучення сірчистих сполук,
що залишилися у сировині після гідроочищення і окиснювальне очищення
(облагородження) прямогонних нафтових фракцій.
Проте більшість робіт присвячена першому варіанту. У деяких
випадках каталізатори ГО забезпечують високий ступінь вилучення сірчистих
сполук і дозволяють отримати ДП з вмістом сірки 10-15 ppm [138]. У інших -
шляхом гідроочищення неможливо досягнути бажаних результатів [138, 139]. В
основному це пов’язано з присутністю в сировині конденсованих тіофенових
структур. Оскільки в процесі ГО неможливо вилучити ці структури, то останнім
часом ведуться роботи по оксидаційному доочищенні палив [42, 59, 60, 75, 97,
105, 139-143]. Тоді пропонується використовувати процес для доочищення
гідроочищених палив, з метою отримання палив із вмістом сірки 0.2-10 ppm.
Реакційне середовище можна обробляти ультразвуком [42, 100],
для збільшення глибини вилучення сірки і покращення селективності процесу.
Але, в більшості робіт, які присвячені доочищенню
гідрогенізатів, як сировина бралися модельні суміші ( розчини бензотіофену,
дибензотіофену і їх похідних у толуолі). Також використовувалися складні
комплексні каталізатори (наприклад, Q4W10O32
(Q = (CH3)3NC16H33, (CH3)3NC14H29,
(CH3)3NC12H25 і (CH3)3NC10H21),
H3PW12O40·14H2O) та вищезгадані
іонні рідини [42, 59, 60, 97, 105].
Перші спроби оксидаційного очищування прямогонних фракцій
згадані у роботах [133-137]. Ступінь вилучення сірки становить 25-36 % для
фракції 240¸270 0С, 69 % - для фракції 200¸240 0С і 100 % -
для фракцій 80¸140 0С та 140¸200 0С. Усунені в
процесі окиснення сірчисті сполуки переходять, очевидно, в лужний розчин, тому
виникає проблема його утилізації. До того ж, не вивчено впливу умов процесу на
експлуатаційні показники продуктів. Для пришвидшення процесу окиснення
запропоновано проводити процес у присутності каталізатора (хлорна мідь, 0,005¸0,08 % від маси фракції) та в
окиснювальній колоні барботажного типу [135]. Дана модифікація застосовувалась
для знесірчення дизельної фракції 200¸300 0С. Середній ступінь
сіркоочищення 50¸55 % досягається при 160 0С і співвідношенні
нафтопродукту до лужного розчину 1:1.
Для повного окиснення сірчистих сполук прямогонних дизельних
фракцій пропонується використовувати надоцтову кислоту з подальшою екстракцією
утворених продуктів [42]. Ступінь вилучення сірчистих сполук при цьому сягав
97,6 %.
У роботі [128] наведені результати досліджень некаталітичного
оксидаційного знесірчування прямогонних гасових (легких дизельних) фракцій та
показано можливість з сировини, яка википає в межах 140-280 (300) 0С,
з вмістом сірки 0,15-0,46 % мас. отримувати товарні реактивні палива (РП).
Знесірчування проводилося у присутності води, використання якої дозволяло
зменшити інтенсивність окиснення вуглеводневого середовища [128], хоча при
глибокому окисненні «темних» нафтових дистилятів та гудрону застосування води
дозволяло навпаки збільшити глибину окиснення сировини [144].
Отримані запропонованим методом [128] РП мали кращі змащуючи
властивості, ніж аналогічні продукти, одержані на установці гідроочистки.
Продукти окиснення (концентрати сірчистих сполук) за своїми характеристиками
відповідали певним видам мастильно-охолоджучих рідин, що використовуються при
обробці металів.
Отже, методи оксидаційнго очищення прямогонних сірчистих
фракцій є досить перспективним, хоч і містять ряд недоліків: довготривалість
процесу (до 3 год), наявність додаткових стадій (відстоювання, промивання,
просушування), які ускладнюють процес, використання лугу, каталізатора, дорогих
реагеннтів.
Відділення продуктів окиснення від очищених фракцій переважно
проводять за допомогою адсорбції або екстракції, що робить метод досить
громіздким. Крім того, більшість всіх досліджень знесірчування дизельних палив
оксидаційним методом спрямовані на вивчення процесу доочищення продуктів ГО.
Лише у небагатьох з них розглядається можливість одержання товарних дизельних
палив одразу з прямогонної сировини. У цих останніх роботах не наведено даних
(за виключенням кінцевого вмісту сірки у продуктах) про те, які експлуатаційні
властивості будуть мати отримані таким чином ДП (наприклад, змащуючі,
антиокиснювальні тощо). Крім того, у проаналізованих відомостях про процеси
оксидаційного очищення не наведено інформації про характеристики самого
оксиданту (окисненого продукту до виділення з нього сульфонів та сульфоксидів).
Аналіз опрацьованих робіт по оксидаційному знесірчуванню
нафтових фракцій показує, що ефективними вони можуть бути лише у випадку
використання їх як стадії доочищення продукту після установки ГО.
Порівняння описаного вище процесу некаталітичного окиснення
легких дизельних (гасових) фракцій [128] з окисненням важчої прямогонної
сировини [133-137] також показує, що використання «ширших» та «важчих» фракцій
буде утруднювати процес оксидаційного знесірчування. Пояснюється це наступними
чинниками:
зі збільшенням температури кипіння фракцій
зменшується різниця між температурами випаровування вихідних сірчистих речовин
та їх окиснених аналогів [99]; це, а також розширення фракційного складу
ускладнює виділення продуктів окиснення ректифікацією;
у «важчій» сировині міститься більше сполук схильних
до поляризації, які можуть адсорбуватися разом з сульфонами чи сульфоксидами на
полярних адсорбентах, що спричинює, у свою чергу, складність розділення
продуктів окиснення адсорбцією;
у «важчій» сировині міститься більша кількість
тіофенової сірки, яка гірше окиснюється ніж відповідні сполуки меркаптанового,
сульфідного та дисульфідного рядів.
Проаналізувавши дані, можна сказати, що для знесірчування
прямогонних нафтових фракцій ( у першу чергу дизельних) до європейських
стандартів, необхідно використовувати каталізатори і дорогі сильні окисники.
Але, так як в нашій країні дозволено випускати дизельні
палива з вмістом сірки до 0.2% мас, то такий вміст сірки можна досягнути
використовуючи оксидацій не знесірчення без каталізаторів і дорогих реагентів.
2. ОБ’ЄКТИ ТА МЕТОДИКИ ПРОВЕДЕННЯ ЕКСПЕРИМЕНТІВ
.1 Характеристика вихідної сировини та допоміжних речовин
Для проведення досліджень було відібрано наступні проби
прямогонних дизельних фракцій та один зразок гідрогенізату.
Таблиця 2.1 Характеристики вихідної
сировини
Назва показника
|
Норма відповідно до [168]
|
Значення для широких прямогонних дизельних фракцій
|
Значення для гідрогенізату з ВАТ «Укртат-нафта»
(м.Кременчук)
|
|
|
з ВАТ „НПК-Галичина” (м.Дрогобич) (ШДФ1)
|
з ВАТ „Нафтохімік Прикарпаття” (м. Надвірна) (ШДФ2)
|
з ВАТ „Нафтохімік Прикарпаття” (м. Надвірна) (ШДФ3)
|
|
Цетанове число, не менше
|
45
|
45
|
47
|
50
|
-
|
Фракційний склад, °С: 50 % переганяється за
температури , 0С, не вище 96 % переганяється за температури , 0С, не вище
|
275 370
|
275 346
|
268 355
|
266 365
|
281 358
|
В’язкість кінематична при 20 0С, мм2/с
|
3,0-5,5
|
5,2
|
5,1
|
4,7
|
-
|
Температура застигання, 0С, не вище
|
-10
|
-16
|
-15
|
-3
|
-9
|
Температура спалаху у закритому тиглі, 0С, не нижче
|
45
|
78
|
77
|
64
|
-
|
Вміст загальної сірки, % мас., не більше
|
0,2
|
0,25
|
0,35
|
0,67
|
0,055
|
Вміст меркаптанової сірки, % мас., не більше
|
0,010
|
0,013
|
0,008
|
0,009
|
0,001
|
Вміст сірководню
|
відсутній
|
відсутній
|
відсутній
|
відсутній
|
-
|
Випробування на мідній пластинці
|
витримує
|
витримує
|
витримує
|
не витримує
|
Витримує
|
Концентрація фактичних смол, мг/100см3, не більше
|
30
|
28
|
2
|
25
|
12
|
Кислотність, мгКОН/100см3, не більше
|
5,0
|
2,8
|
4,2
|
1,8
|
0
|
Йодне число, г йоду/100 г, не більше
|
5,0
|
3,74
|
1,54
|
1,13
|
-
|
Зольність, % мас., не більше
|
0,010
|
0,030
|
0,007
|
0,004
|
-
|
Коксівність 10 %-го залишку, %, не більше
|
0,25
|
0,23
|
0,11
|
0,05
|
0,01
|
Коефіцієнт фільтрованості, не більше
|
3,00
|
0,15
|
1,20
|
1,24
|
-
|
Вміст механічних домішок
|
відсутні
|
відсутні
|
відсутні
|
-
|
Вміст води
|
відсутні
|
відсутні
|
відсутні
|
відсутні
|
-
|
Густина при 20 °С, кг/м3, не більше
|
850
|
838
|
849
|
844
|
839
|
Як видно з наведених у табл. 2.1 даних, жодна з вихідних
широких дизельних фракційне не відповідає вимогам до товарних дизельних палив
щодо вмісту загальної сірки у них. Окрім того, ШДФ1 має завищену (в 3 рази)
зольність; вміст меркаптанової сірки у ній також перевищує норму. ШДФ3 має
незадовільну температуру застигання.
Перша та третя широкі дизельні фракції мають досить високий
вміст фактичних смол, а друга - кислотність.
Для вибору правильного підходу до організації процесу
знесірчування зразки сировини було розігнано на окремі фракції, характеристики
яких подано у табл. 2.2-2.4.
Таблиця 2.2 Характеристика вузьких фракцій ШДФ1
Показник
|
Фракція п.к.¸320 °С
|
Фракція > 320 °С
|
Густина при 20 °С, кг/м3
|
832
|
869
|
Вміст загальної сірки, % мас.
|
0,16
|
0,67
|
Концентрація фактичних смол, мг/100см 3
|
24
|
49
|
Кислотність, мгКОН/100см3
|
0,8
|
11,5
|
Вихід, % мас., на ШДФ
|
79,4
|
20,6
|
Таблиця 2.3 Характеристика вузьких фракцій ШДФ2
Показник
|
Фракція п.к.¸280 °С
|
Фракція > 280 °С
|
Густина при 20 °С, кг/м3
|
825
|
871
|
Вміст загальної сірки, % мас.
|
0,15
|
0,56
|
Концентрація фактичних смол, мг/100см 3
|
1,5
|
2,7
|
Кислотність, мгКОН/100см3
|
1,5
|
12,0
|
Вихід, % мас., на ШДФ
|
67,5
|
32,5
|
Таблиця 2.4 Характеристика вузьких фракцій ШДФ3
Показник
|
Фракція п.к.*¸280 °С
|
Фракція 280¸350 °С
|
Фракція > 280 °С
|
Фракція п.к.¸350 0С
|
Густина при 20 °С, кг/м3
|
821
|
856
|
861
|
839
|
Вміст загальної сірки, % мас.
|
0,32
|
0,87
|
0,98
|
0,57
|
Концентрація фактичних смол, мг/100см 3
|
7,5
|
15,0
|
435,0
|
11,9
|
Кислотність, мгКОН/100см3
|
1,6
|
5,9
|
11,3
|
3,5
|
Вихід, % мас., на ШДФ
|
47,2
|
35,3
|
52,8
|
82,5
|
Вміст окремих груп сірки, % мас.на загальну -
меркаптанової - сульфідної аліфатичної - залишкової (тіофенової та
тіофанової)
|
3,12 53,13 43,75
|
0,92 58,85 40,23
|
- - -
|
- - -
|
*Початок кипіння - 165 0С.
Як видно з наведених даних, основна маса сірки та сполук,
здатних до реакцій конденсації, зосереджена у важчих фракціях: при збільшенні
температури википання фракцій зростає вміст сірки та концентрація фактичних
смол.
Окрім того, результати, наведені у табл. 2.2-2.4 показують,
що у випадку потреби одержання товарного ДП з вмістом сірки до 0,2 % мас. при
використанні ШДФ1 достатньо знесірчувати лише фр. > 320 °С, яка становить близько 20 %
мас., ШДФ2 - фр. > 280 °С, яка становить менше 50 % мас. від загальної
кількості.
У випадку використання як сировини прямогонної дизельної
фракції з дуже високим вмістом сірки (ШДФ3) навіть найлегші фракції мають
загальний вміст сірки, більший від 0,2 % мас., а отже знесірчуванню треба
піддавати або всі окремі фракції, або цілу сировину.
Як видно з табл. 2.4, основна маса сірки у дистилятних
фракціях п.к.¸280 °С та 280¸350 °С представлена аліфатичними
сульфідами. Менший вміст залишкової сірки у фр. 280¸350 °С (порівняно з фр. п.к.¸280 °С) пояснюється, очевидно,
більшим вмістом циклічних сульфідів у фр. п.к.¸280 °С.
.2 Опис лабораторної установки оксидаційного знесірчування
дизельних фракцій
Установка оксидаційного знесірчування дизельних фракцій, що
створена на кафедрі хімічної технології переробки нафти та газу НУ “Львівська
політехніка”, показана на рис. 2.1 [145, 144].
Установка складається з реакторного блоку, системи стиснення
і очистки повітря, охолодження і вловлювання газоподібних продуктів реакції і
приладів для регулювання та вимірювання температури, тиску, витрат і ін..
Реакційна суміш завантажується в реактор (1) барботажного
типу об`ємом до 0,7 л, який виготовлений з нержавіючої сталі Х18Н10 і
обладнаний штуцером для підводу повітря та фланцем, яким кріпиться до
холодильника (2). Температура в середині реактора контролюється за допомогою
термопари (5) і регулюється ЛАТРом (13). Відпрацьоване повітря, що виводиться з
реактора, проходить холодильник (2), в який для охолодження подається вода. У
холодильнику (2) в основному конденсуються пари палива і води, що виносяться з
реактора. При потребі, перемішування реакційної суміші в реакторі здійснюється
за допомогою пропелерної мішалки. Електродвигун (3) приводу мішалки
розташований в герметичному стальному корпусі, який кріпиться до верхньої
частини холодильника (2). В корпусі є прохідний ізолятор (4), через який
підводиться електричний струм до двигуна. Електродвигун працює в умовах
підвищеного тиску повітря, що виключає сальниковий пристрій в реакторі.
Конструкція реактора дозволяє тримати в системі тиск до 6 МПа при температурі
623 К.
Вертикальне переміщення реакційної суміші в реакторі
досягається за рахунок встановленої в корпусі реактора циліндричної труби (6).
При роботі мішалки здійснюється циркуляція реакційної суміші в напрямку: вгору
- по внутрішньому простору труби - вниз у простір між корпусом реактора і
труби.
Перед початком досліду у реактор (1) з балону (15) подається
азот для видалення з реактора повітря та запобігання передчасного окислення
реакційної суміші. Подача азоту регулюється вентилем (12/6). Одночасно
відбувається нагрівання реакційної суміші в реакторі за допомогою
електронагрівача (14).
Після досягнення заданого тиску подача азоту припиняється.
Повітря, яке подається на окиснення в реактор (1),
нагнітається компресором (10), накопичується у ресивер (9), де очищується від
води та оливи. Доосушується повітря у адсорбері (8), проходячи через шар
силікагелю. Тиск у ресивері (9) контролюється манометром (11/2). Витрата повітря
вимірюється ротаметром (7/1) та регулюється вентилем (12/2). Тиск повітря
контролюється манометром (11/1). Для запобігання попадання продуктів реакції і
парів води в корпус електродвигуна (3) можна створювати зворотній тиск шляхом
подачі туди стиснутого повітря або азоту. У цьому випадку витрата повітря
вимірюється ротаметром (7/2) і регулюється вентилем (12/3).
Після досягнення у реакторі (1) заданої температури через
вентиль (12/1) у реактор подається повітря. Тиск у реакторі (1) підтримується
на заданому рівні за рахунок відбору частини газів окиснення через вентиль
(12/4) у балон (16), тиск в якому контролюється за допомогою манометра (11/3).
Якщо гази не відбиралися, то через вентиль (12/4) вони викидалися в атмосферу.
Температура реакційної суміші заміряється термопарою (5) та
регулюється ЛАТРом (13).
Після завершення досліду подача повітря в реактор (1)
припиняється, вимикається нагрів та перекривається відбір газу у балон (16).
Після цього в реактор з балону (15) знову подається азот для видалення із
системи непрореагованого кисню і припинення реакцій окиснення. Від штуцера з
низу реактора (1) від’єднують трубку, по якій подається азот та повітря, і
реактор занурюють у ємність з холодною водою для швидкого охолодження
реакційної суміші. При досягненні реакційною сумішшю температури 303¸313 К охолодження
припиняється, надлишковий тиск стравлюється через вентилі (12/4 і 12/5),
реактор (1) від’єднують від фланця з холодильником (2), і реакційна суміш
вивантажується з реактора у мірну посудину і зважується. За результатами
зважувань складався матеріальний баланс процесу.
Рис. 2.1. Схема лабораторної
установки 1 - реактор, 2, - холодильники, 3 - електродвигун, 4 - ущільнення, 5
- термопара, 6 -труба, 7 -ротаметр, 8 - ресивер, 9 -ресивер, 10 -компресор, 11
- манометр, 12 -вентиль, 13 -ЛАТР, 14 -електронагрівач, 15 -балон з азотом, 16
- балон для збору газів, 17 - реометр, 18 - поглинач СО2, 19 -
газовий лічильник
2.3 Методики проведення досліджень та аналізу результатів
У випадку окиснення вихідної сировини з водою, водну фазу
відділяли, а окиснену прямогонну дизельну фракцію (оксидат) розділяли та
аналізували, за наведеною нижче схемою (див. рис.2.2).
Рис. 2.2. Схема
дослідження оксидату, одержаного при окисненні прямогонної дизельної фракції.
Перегонка (відповідно до схеми, поданої на рис. 2.2.)
здійснювалася на установці без дефлегмації; для адсорбційного розділення
продуктів використовувався проявний метод, адсорбент - силікагель марки АСК.
Для порівняння ефективності адсорбентів використовувалися також флоурісил та
відбілююча глина.
Силікагель попередньо промивався водою, а потім сушився при
150 0С протягом 12 год. Співвідношення адсорбент : рідка фаза
оксидату становило 1:1. Для десорбції очищеного палива використовувався бензол,
концентрату сірчистих сполук - спиртобензол.
Маса оксидату, Gокс, г, визначається за формулою:
окс. = Gм.п.+окс. - Gм.п., (2.1)
де:Gм.п.+окс., Gм.п. - маси мірної
посудини з оксидатом та порожньої мірної посудини, відповідно, г.
Маса утвореного в процесі окиснення твердого осаду, Мосаду,
г, визначається за формулою:
Gосаду = Gф.+осад - Gф., (2.2)
де:Gф.+осад, Gф. - маси фільтру з
осадом та чистого фільтру, відповідно, г.
Маса очищеної прямогонної дизельної фракції (дистиляту), Gдист.,
г, та кубового залишку, Gкуб., г, визначалась після проведення
перегонки оксидату за формулами:
Gдист. = Gпр.+дист. - Gпр.
та Gкуб. = Gп.к.+куб. - Gп.к., (2.3,
2.4)
де:Gпр.+дист., Gпр., Gп.к.+куб.,
Gп.к. - маси прийомника з дистилятом, порожнього прийомника,
перегонної колби з кубовим залишком та порожньої перегонної колби, відповідно,
г.
Вихід оксидату, твердого осаду, дистиляту та кубового залишку
визначається як відношення їх маси до маси вихідної прямогонної дизельної
фракції, % мас.:
Хокс. = Gокс. / Gсир., Хосаду
= Gосаду / Gсир., (2.5,
2.6)
та
Хдист. = Gдист. / Gсир., Хкуб.
= Gкуб. / Gсир., (2.7,
2.8)
де:Gсир. - маса вихідної прямогонної дизельної
фракції, г.
При розрахунках матеріальних балансів процесу втратами при
перегонці/адсорбційному розділенні рідкої фази оксидату нехтували.
Показниками, що визначалися в оксидаті та очищеному паливі,
були вміст загальної сірки [146] та фактичних смол [147], кислотність [148].
Другий показник характеризує кількість утворених продуктів ущільнення та
окиснення, схильних до подальшої конденсації та смолоутворення під час
експлуатації чи зберігання продуктів; третій -кількість кислих розчинних у
паливі компонентів.
Крім того у сировині та кінцевих продуктах визначалися
наступні показники: вміст меркаптанової сірки [149], фракційний склад [150],
густина [151], в’язкість кінематична при 20 0С [152], температура
застигання [153],змащувальні властивості [154], температура спалаху у закритому
тиглі [155], вміст сірководню [149], йодне число [156], зольність [157],
коксивність 10 %-го залишку [158], вміст механічних домішок [159] та води
[160], випробування на мідній пластинці [161].
Вміст окремих груп органічної сірки (сірководню, меркаптанів,
дисульвідфі, аліфатичних сульфідів) визначався відповідно до методик, наведених
у [162].
Розрахунок кількості сировини, що може виноситися у ході
процесу з реактора з повітрям та парами води проводили у наступній
послідовності. Враховуючи незначну відмінність між характеристиками сировини,
обчислення проводили для ШДФ3.
Кількість парів, G, кг, що виноситься з реактора, визначали
за наступною формулою [163]:
G = (gпов. × Рн.п. × М) / (Р - Рн.п.)
/ 29 , (2.9)
де: М - молекулярна маса суміші парів прямогонної дизельної
фракції і води;пов. - кількість повітря, яка пройшла через реактор,
кг; середня витрата повітря становила gпов. = 0,0255 кг;
Рн.п. - загальний тиск насичених парів суміші
прямогонної дизельної фракції і води (випадку її присутності), Па;
Р - загальний тиск у реакторі окиснення, Па;
- молекулярна маса повітря.
Загальний тиск насичених парів суміші прямогонної дизельної
фракції і води, Рн.п., визначався, згідно закону Рауля-Дальтона:
Рн.п. = S РПДФ і × x`ПДФ і + Рводи
, (2.10)
де: x`ПДФ і , - мольні частки і-го компонента
прямогонної дизельної фракції в рідині;
Рводи - тиск насичених парів води при 240 0С;
Рводи = 2381137,5 Па [76];
РПДФ і - тиск насичених парів і-го компонента
сировини при 240 0С, Па.
Вихідну сировину умовно розділяли на три рівні за масою
фракції. Масу сировини, завантаженої у реактор приймали рівною середній масі,
що використовувалась під час досліджень (0,3375 кг). Тиск насичених парів
сировини (кожної з трьох фракцій), при заданій температурі, визначали за
графіком Кокса [163,76] для певного вуглеводню, що відповідає кожній фракції.
Молекулярна маса фракцій розраховувалася за формулою Воїнова [163,76] (середня
температура кипіння першої фракції приймалася 173 0С, другої - 202,5
0С, третьої - 267 0С). Відповідно до молекулярної маси
можна прирівняти кожну фракцію до певного вуглеводню. У нашому випадку - С12,
С15 і С18 відповідно. Отже, за графіком Кокса [163,76]: РС12
= 469000 Па., РС15 = 169000 Па, РС18 = 37800 Па.
Мольні частки фракцій сировини (відповідних їм вуглеводнів) в
рідині розраховували, знаючи їхні молекулярні маси та кількість при
завантаженні в реактор. Результати розрахунків зведено у табл. 2.5.
Таблиця 2.5 Розрахунок мольної частки, xi`, компонентів
суміші
Компонент
|
Мі
|
Gі, кг
|
ni = Gі / Мі
|
xi` = ni / S ni
|
С12
|
129
|
0,1125
|
0,00087
|
0,3948
|
С15
|
148
|
0,1125
|
0,00076
|
0,3441
|
С18
|
195
|
0,1125
|
0,00058
|
0,2612
|
Сума
|
-
|
0,3375
|
0,00221
|
1,0000
|
Тоді S РПДФ і × x`ПДФ і = 253166 Па.
За рівнянням (2.10) знаходили значення загального тиску
насичених парів суміші прямогонної дизельної фракції і води: Рн.п. =
2634304 Па.
Для визначення молекулярної маси суміші парів прямогонної
дизельної фракції і води використовували отримані вище значення тисків
насичених парів і значення молекулярної маси вихідної сировини, розрахованої за
формулою Крега [163,76] (Мсировини=201): y`ПДФ =
253166/2634304 = 0,0961; y`в.п. = 2381138/2634304 = 0,9039, де
253166 - парціальний тиск нафтових парів. Молекулярна маси суміші парів
прямогонної дизельної фракції і води становила: М = 0,0961 × 201 + 0,9039 × 18 = 36.
Для визначення оптимального значення тиску розраховували
частку відгону при різних його значеннях і максимальній запланованій
температурі досліджень (240 0С) та температурі виходу
відпрацьованого повітря з реакторного блоку (40 0С) (для двох
випадків - у присутності води та без неї).
Для цього вибрано мінімальне значення тиску у реакторі
(2700000 Па), нижче якого (теоретично) реакційна суміш при 240 0С
буде перебувати у пароподібному стані, і розраховано кількість парів, G, кг, що
виноситься з реактора, за формулою (2.9): G= (0,0255 × 2700000 × 36) / (2700000 - 2634304) /
29 = 1,27 кг. З цієї кількості на частку парів сировини припадає: GПДФ
= 1,27 × 0,0961 = 0,12 кг. Маючи величину завантаженої прямогонної
дизельної фракції (0,3375 кг), було знайдено кількість відгону, е, %, за
пропорцією: е = GПДФ × 100 / Gзавант. = 0,12 × 100 / 0,3375 = 36,14 %.
Аналогічно проведено розрахунки кількості відгону в інтервалі
3,0-5 МПа з кроком 0,5, а також для випадку, коли процес проводиться без води.
Рис. 2.3. Залежність частки відгону сировини від тиску при
240 0С.
На основі отриманих результатів побудовано графічну
залежність кількості відгону парів вихідної сировини з повітрям від загального
тиску в реакторі окиснення (див. рис. 2.3.) при температурі 240 0С.
З рис. 2.3. видно, що при 240 0С і тисках до 3 МПа
значення часток відгону є досить великими, що, практично, може призвести до
значних втрат прямогонної дизельної фракції з повітрям. При тиску 3 МПа і 240 0С
частка відгону становить 6,87 %. Збільшення тиску у реакторі понад 3 МПа
суттєвого впливу на зменшення частки відгону не виявляє. Для того, щоб суттєво
зменшити втрати при дослідженнях процесу відпрацьоване повітря після реактора
проходить холодильник-конденсатор, в якому охолоджується до 40 0С
При цьому, частина парів прямогонної дизельної фракції конденсується і
повертається у реактор. При температурі виходу відпрацьованого повітря з
реакторного блоку (40 0С), згідно аналогічних розрахунків, частка
відгону сировини з повітрям не перевищуватиме 0,002 % навіть при тисках 0,5
МПа. З іншого боку зрозуміло, що на практиці (у зв’язку з низькими
коефіцієнтами тепловіддачі парів та газів) втрати легких фракцій у лабораторних
умовах будуть більшими, ніж теоретично розраховані.
Для опису співвідношення повітря:сировина, тривалості та
площі контакту між ними використовували поняття «об’ємна швидкість подачі»
(ОШП), яка чисельно дорівнювала відношенню витрати оксиданту (м3/хв)
до об’єму сировини (м3) - W, хв-1.
Для опису характеру руху оксиданту, тривалості та площі
контакту між повітрям та сировиною (у випадку проведення процесу без
перемішування) використовували поняття лінійної швидкості (ЛШ) руху оксиданту,
V, м/с. Для спрощення моделі опису процесу ЛШ розраховували на порожнє січення
реактора, як відношення витрати оксиданту, м3/с, до площі реактора,
м2.
З цією ж метою застосовували визначення «фіктивний час
контакту», який розраховували, як відношення висоти шару сировини м, до ЛШ, м/с
(tф, с). При наявності
перемішування рідкого реакційного середовища, яке проводилося з метою
збільшення міжфазової поверхні сировина:вода (каталізатор):повітря, його
інтенсивність характеризувалася з допомогою модифікованого критерія Рейнольдса,
що розраховувався відповідно до методик [144,164].
Залежність значення критерію Рейнольдса від частоти
перемішування наведена у роботі [144,164] та подана у табл. 2.6.
Таблиця 2.6 Залежність модифікованого критерію Рейнольдса від
частоти обертів мішалки
Частота обертів мішалки, об/хв
|
Reм за водою
|
0
|
0
|
500
|
5000
|
2000
|
19000
|
4000
|
38000
|
При цьому реактор та мішалка мали наступні геометричні
параметри: відношення діаметра реактора до діаметра циркуляційної труби -
D/d=2,27; відношення діаметра циркуляційної труби до діаметра мішалки - d/d1=1,32;
відношення висоти реактора до висоти циркуляційної труби - H/h=2,47; кут нахилу
лопастей мішалки - 35-45 0.
.4 Визначення вмісту загальної сірки в твердому осаді і
кубовому залишку
Вміст загальної сірки в твердому осаді і кубового залишку
визначався на основі методики [165,166]. Визначення сірки цим методом базується
на тому, що при спалюванні наважки продукту в потоці повітря вільна сірка і
сірка, яка входить до складу сірчистих сполук, згоряють з утворенням діоксиду
сірки. Останній, при виході з пічки, поглинається водним розчином сірчаної
кислоти й окисняється пероксидом водню до сірчаної кислоти.
За кількістю мілілітрів їдкого натру, витраченого на
титрування утвореної сірчаної кислоти, вираховується вміст загальної сірки у
твердому осаді чи кубовому залишку.
Вміст сірки у продукті обчислювали за формулою:
S = (16 . N . (V1-V0))/
(10 . a), (2.11.)
де:V1 - об'єм рідкого натру, витраченого на
титрування розчину в приймачі після проведення досліду, мл;0 - об'єм
рідкого натру, витраченого на титрування розчину в приймачі до проведення досліду,
мл;- нормальність розчину гідроксиду натрію, (г-екв/л);- маса наважки вугілля,
г.
За результат аналізу приймали середнє арифметичне двох
паралельних визначень.
3. ЕКСПЕРЕМЕНТАЛЬНА ЧАСТИНА
Розрахунки, наведені в розд. 2, показали, що для перебування
реакційного середовища в рідкому стані, необхідно підтримувати тиск на рівні 3
МПа. Тому, для того, щоб перевірити чи справді необхідно проводити процес в
рідкій фазі, треба провести ряд досліджень по знессірчуванню сировини за різних
тисків, тобто встановити на основі експериментальних даних, як буде проходити
процес у гомогенній паровій фазі та гетерогенній рідкій.
Крім того у роботах [128,167] описано, що додавання води може
позитивно впливати на процес ( покращувати селективність, збільшувати ступінь вилучення
сірки). Тому подальше дослідження проводили, як в присутності води, так і без
неї.
.1 Вплив тиску
Для досліджень використовувалася фр. > 320 0С,
отримана з ШДФ1 (характеристику вихідної сировини див. у табл. 2.2). Чинники
процесу підтримували близькими до відомих оптимальних умов оксидаційного
знесірчування прямогонних гасових фракцій, описаних у [164]: температура - 180 0С;
тривалість процесу - 30 хв.; об’ємне співвідношення повітря:сировина - 1,65 хв-1,
лінійна швидкість руху оксиданту - 0,03 м/с. Процес проводили без перемішування
реакційного середовища. Співвідношення вода:сировина становило 1:1 (за
об’ємом). Для розділення рідкої фази оксидату використовувалася перегонка;
дистилят (очищене паливо) переганяли до «класичної» температури кінця кипіння
дизельних палив - 350 0С.
Отримані результати подано у табл. 3.1-3.3 та на рис. 3.1
Як видно з отриманих результатів (див. табл. 3.1), суттєве
значення тиск, у першу чергу, має на вихід рідкого продукту окиснення. Оскільки
при тисках 0,5 та 1,0 МПа випаровується практично вся сировина (див. підрозд.
2.3), то за цих умов вихід рідкої фази оксидату є значно нижчим, ніж при 2,5
МПа та більше. Це пояснюється тим, що при 0,5-1,0 МПа система охолодження та
конденсації внаслідок низьких коефіцієнтів тепловіддачі парів та газів не
спроможна на задовільному рівні сконденсувати та охолодити останні.
Таблиця 3.1 Вплив тиску на вихід основних продуктів при
знесірчуванні фр. > 320 0С ШДФ1
№
|
Тиск, МПа
|
Вихід, % мас., на сировину
|
|
|
рідкої фази оксидату
|
твердої фази оксидату
|
очищеного палива (дистиляту)
|
концентрату рідких продуктів окиснення (КРПО),
(кубового залишку)
|
1
|
0,5
|
94,81
|
0,00
|
83,46
|
11,35
|
2
|
1,0
|
96,04
|
0,08
|
85,62
|
10,42
|
3
|
2,5
|
98,37
|
0,28
|
89,23
|
9,14
|
4
|
3,0
|
98,32
|
0,78
|
89,41
|
8,91
|
5
|
4,0
|
97,15
|
1,23
|
87,40
|
9,75
|
Таблиця 3.2 Вплив тиску на якість рідкої фази оксидату,
отриманої при знесірчуванні фр. > 320 0С ШДФ1
№
|
Тиск, МПа
|
Назва показника
|
|
|
Вміст загальної сірки, %мас
|
Вміст фактичних смол, мг на 100см3
|
Кислотність, мг КОН на 100 см3
|
1
|
0,5
|
0,68
|
63
|
-
|
2
|
1,0
|
0,65
|
68
|
-
|
3
|
2,5
|
0,60
|
76
|
-
|
4
|
3,0
|
0,59
|
92
|
-
|
5
|
4,0
|
0,59
|
99
|
-
|
Таблиця 3.3 Вплив тиску на якість очищеного палива,
отриманого при знесірчуванні фр. > 320 0С ШДФ1
№
|
Тиск, МПа
|
Назва показника
|
|
|
Вміст загальної сірки, % мас
|
Вміст фактичних смол, мг на 100см3
|
Кислотність, мг КОН на 100 см3
|
1
|
0,5
|
0,58
|
52
|
15,6
|
2
|
1,0
|
0,58
|
48
|
16,3
|
3
|
2,5
|
0,42
|
35
|
18,7
|
4
|
3,0
|
0,35
|
33
|
20,0
|
5
|
4,0
|
0,34
|
34
|
38,9
|
Рис. 3.1. Залежність ступеня вилучення сірки від тиску
процесу
Дані табл. 3.1. також свідчать про те, що при проведенні
процесу у паровій фазі (тиски 0,5 і 1,0 МПа) збільшується вихід кубового
залишку, що отримується при перегонці рідкої фази оксидату (РФО). Причиною
цього є низька селективність окиснення у паровій фазі (окиснюється більша
кількість вуглеводнів, які при перегонці переходять у КРПО).
Підтверджується це тим (див. табл. 3.2 та 3.3), що при
окисненні за низьких тисків (0,5 та 1,0 МПа) проміжні продукти окиснення
(речовини, з яких утворюються фактичні смоли) розподілені рівномірно по всій
сировині (після відділення кубового залишку від рідкої фази оксидату вміст
фактичних смол зменшується незначно). При високих тисках (2,5 МПа та більше)
фактичні смоли зосереджуються у фракціях, що википають при температурах,
більших від 350 0С.
При перебігу процесу в паро-газовій фазі (тиски 0,5-1,0 МПа)
ступінь вилучення сірки (див. рис. 3.1) є незначним. Пояснюється це, у першу
чергу, низьким виходом очищеного палива (випаровуються низькокиплячі
малосірчисті фракції). Внаслідок цього вміст сірки у окисненій рідкій частині
може навіть зростати порівняно з вихідною сировиною (див. табл. 3.2 та рис.
3.1). Крім того, окиснення у паровій фазі проходить менш інтенсивно з
обриванням реакцій на проміжній стадії: у очищеному паливі високий вміст
фактичних смол, вихід твердої фази оксидату (ТФО) є низьким.
При збільшенні тиску до 2,5 МПа і далі інтенсифікуються
реакції окиснення як сірки, так вуглеводневої частини. При чому окиснення
проходить більш повно: зменшується вміст проміжних продуктів ущільнення та
окиснення (фактичних смол), а зростає вихід кінцевих (твердої фази).
Збільшення тиску від 3,0 МПа до 4,0 МПа на ступінь вилучення
сірки фактично не впливає (див. рис. 3.1), проте суттєво інтенсифікує реакції
окиснення та ущільнення (різко зростають вихід твердого залишку та кислотність
очищеного палива).
Слід відмітити, що останній показник зростає у всьому
інтервалі досліджуваних тисків (див. табл. 3.3). Пояснюється це тим, що кислоти
дизельних фракцій порівняно термічно нестабільні сполуки, які розкладаються при
підвищених температурах з утворенням газоподібних продуктів [2,16]. Зрозуміло,
що зростання тиску сприяє збільшенню швидкості дифузії кисню в рідке середовище
та перешкоджає реакціям розкладу з утворенням газоподібних продуктів, що, у
кінцевому випадку, сприяє зростанню кислотності отриманого палива.
Отже, виходячи із проведених досліджень і розрахунків та
враховуючи потребу досягнення максимальних ступеня вилучення сірчистих сполук й
виходу очищеного палива, оптимальними слід підтримувати тиски 2,5-3,0 МПа.
3.2 Знесірчування різних типів сировини
Порівняння отриманих результатів [167], а також аналіз
літературних даних, який наведено в розд. 1, показує, що сировина з більшим
вмістом S і важчим фракційним складом знесірчується гірше ніж сировина з меншим
вмістом S і легшим фракційним складом.
Тому в даному розділі наведено порівняння ефективності
вилучення сірки з різних типів широких дизельних фракцій чи їх окремих частин.
Експерименти проводилися як у присутності води так і без неї.
У першому випадку співвідношення вода сировина підтримували рівним 1:1 (об.).
Інші фіксовані чинники становили: температура - 180 0С; тривалість
процесу - 30 хв.; тиск - 3.0 МПа; ОШП - 1,65 хв-1; ЛШ - 0,0030 м/с.
Процес проводили без перемішування реакційного середовища. Для розділення
рідкої фази оксидату використовувалася перегонка; дистилят (очищене паливо)
переганяли до «класичної» температури кінця кипіння дизельних палив - 350 0С
або кінця кипіння відповідних вузьких фракцій, за виключенням гідрогенізату,
кінець кипіння якого становив 360 0С.
Отримані результати за присутності у реакційній системі води
подано у табл. 3.4-3.6; без води - у табл. 3.7-3.9.
Таблиця 3.4 Вихід основних продуктів при проведенні
досліджень за присутності води
№
|
Сировина
|
Вихід, % мас. на сировину
|
|
|
рідкої фази оксидату
|
твердої фази оксидату
|
очищеного палива (дистиляту)
|
КРПО (кубового залишку)
|
1
|
ШДФ1
|
98,94
|
0,25
|
90,83
|
8,11
|
2
|
Фр. > 320 0C ШДФ1
|
98,37
|
0,28
|
89,23
|
3
|
ШДФ2
|
98,11
|
0,08
|
87,80
|
10,31
|
4
|
ШДФ3
|
98,51
|
0,49
|
87,37
|
11,14
|
5
|
Фр. 280-350 0C ШДФ3
|
98,01
|
0,21
|
93,57
|
4,44
|
Таблиця 3.5 Якість рідкої фази оксидату, отриманої при
знесірчуванні за присутності води
№
|
Сировина
|
Назва показника
|
|
|
Вміст загальної сірки, %мас
|
Вміст фактичних смол, мг на 100см3
|
Кислотність, мг КОН на 100 см3
|
Ступінь знесірчування, %
|
1
|
ШДФ1
|
0,23
|
61
|
-
|
8,00
|
2
|
Фр. > 320 0C ШДФ1
|
0,60
|
76
|
-
|
10,45
|
3
|
ШДФ2
|
0,35
|
33
|
29,8
|
0,00
|
4
|
ШДФ3
|
0,67
|
46
|
6,2
|
0,00
|
5
|
Фр. 280-350 0C ШДФ3
|
0,81
|
41
|
33,55
|
6,90
|
Таблиця 3.6 Якість очищеного палива, отриманого при
знесірчуванні за присутності води
№
|
Сировина
|
Назва показника
|
|
|
Вміст загальної сірки, % мас.
|
Вміст фактичних смол, мг на 100см3
|
Кислотність, мг КОН на 100 см3
|
Ступінь знесірчування, %
|
1
|
ШДФ1
|
0,17
|
12
|
8,4
|
32,00
|
2
|
Фр. > 320 0C ШДФ1
|
0,42
|
35
|
18,7
|
37,31
|
3
|
ШДФ2
|
0,29
|
7
|
9,2
|
17,14
|
4
|
ШДФ3
|
0,58
|
9
|
4,8
|
13,43
|
5
|
Фр. 280-350 0C ШДФ3
|
0,65
|
20
|
4,1
|
25,29
|
Таблиця 3.7 Вихід основних продуктів при проведенні
досліджень без води
№
|
Сировина
|
Вихід, % мас. на сировину
|
|
|
рідкої фази оксидату
|
твердої фази оксидату
|
очищеного палива (дистиляту)
|
КРПО (кубового залишку)
|
1
|
ШДФ1
|
96,05
|
3,49
|
84,23
|
11,82
|
2
|
Фр. > 320 0C ШДФ1
|
94,28
|
4,21
|
80,95
|
13,33
|
3
|
ШДФ3
|
97,27
|
2,35
|
84,60
|
12,67
|
4
|
Фр. 280-350 0C ШДФ3
|
97,22
|
2,39
|
91,94
|
5,28
|
5
|
Фр. п.к.-280 0C ШДФ3
|
97,05
|
1,61
|
92,90
|
4,15
|
6
|
Гідрогенізат
|
98,42
|
0,43
|
95,24
|
3,18
|
Таблиця 3.8 Якість рідкої фази оксидату, отриманої при
знесірчуванні без води
№
|
Сировина
|
Назва показника
|
|
|
Вміст загальної сірки, %мас
|
Вміст фактичних смол, мг на 100см3
|
Кислотність, мг КОН на 100 см3
|
Ступінь знесірчування, %
|
1
|
ШДФ1
|
0,22
|
298
|
-
|
12,00
|
2
|
Фр. > 320 0C ШДФ1
|
0,55
|
315
|
-
|
17,91
|
3
|
ШДФ3
|
0,65
|
124,0
|
15
|
2,99
|
4
|
Фр. 280-350 0C ШДФ3
|
0,83
|
237
|
45,4
|
4,60
|
5
|
Фр. п.к.-280 0C ШДФ3
|
0,23
|
16,0
|
8,4
|
28,13
|
6
|
Гідрогенізат
|
0,016
|
34
|
-
|
70,91
|
Таблиця 3.9 Якість очищеного палива, отриманого при
знесірчуванні без води
№
|
Сировина
|
Назва показника
|
|
|
Вміст загальної сірки, % мас.
|
Вміст фактичних смол, мг на 100см3
|
Кислотність, мг КОН на 100 см3
|
Ступінь знесірчування, %
|
1
|
ШДФ1
|
0,17
|
39
|
16,1
|
32,00
|
2
|
Фр. > 320 0C ШДФ1
|
0,39
|
45
|
39,6
|
41,79
|
3
|
ШДФ3
|
0,60
|
39
|
8,1
|
10,45
|
4
|
Фр. 280-350 0C ШДФ3
|
0,65
|
41
|
10,5
|
25,29
|
5
|
Фр. п.к.-280 0C ШДФ3
|
0,18
|
6,3
|
5,4
|
43,75
|
6
|
Гідрогенізат
|
0,008*
|
11
|
2,1
|
85,45
|
*Дистилят піддавали залуговуванню; вихід продуктів
залуговування становив 0,71 % мас. на дистилят; вміст сірки у незалугованому
дистиляті становив 0,008 % мас.
На основі отриманих у табл. 3.4-3.9 даних прослідковується
чітка залежність (як для широких дизельних фракцій, так і для окремих їх
вузьких частин): ступінь вилучення сірки зростає зі зменшенням її вмісту у
вихідній сировині. Для прикладу, ступені вилучення сірки з очищеного палива,
отриманого за присутності води, для ШДФ1, ШДФ2 та ШДФ3 складають відповідно
32,00; 17,14; 13,43. При цьому вмісти сірки у вихідних зразках сировини
становлять для ШДФ1 - 0,25 % мас.; ШДФ2 - 0,32 % мас.; ШДФ3 - 0,67 % мас. Така
ж тенденція спостерігається і при проведенні знесірчування без води: для
гідрогенізату (вміст сірки у вихідній сировині - 0,055 % мас.) ШДФ1 і ШДФ3
ступені вилучення сірки становлять 85,45; 32,00; 10,45. Аналогічно поводять
себе окремі вузькі фракції ШДФ 3: ступінь вилучення сірки з фр. п.к.-280 0С
значно більший від ступеня вилучення з фр. 280-350 0С
Порівняння дослідів 1 і 2, 4 і 5 табл. 3.4-3.5 та дослідів 1
і 2, 3-5 табл. 3.7-3.8 показує, що використання сировини вужчого фракційного
складу дозволяє збільшити ступінь вилучення сірки, можливо, за рахунок більш
ефективного вилучення продуктів окиснення.
Як видно з отриманих результатів при знесірчуванні ШДФ1
вдається отримати товарне ДП з вмістом сірки до 0,2 % мас.
При змішуванні отриманого дистиляту з фр. > 320 0C
ШДФ1 та вихідної «головної» фр. п.к.-320 °С ШДФ1 , одержували паливо, вміст
загальної сірки у якому становив 0,23 % мас. Тому було проведено ряд пошукових
досліджень при вищих температурах.
Окиснення фр. > 320 °С ШДФ1 при збільшенні температури до
220 °С
(180-220 °С - оптимальні межі температур для проведення подібного процесу
знесірчування прямогонних гасових фракцій ), тривалості процесу - 30 хв.; тиску
- 3.0 МПа, об’ємному співвідношенні повітря:сировина- 1,65 хв-1 та
співвідношенні вода:сировина, рівному 1:10 дозволило отримати дистилят з
вмістом сірки 0,31 % мас. (див. табл. 3.10 та 3.11).
Таблиця 3.10 Вихід основних продуктів при знесірчуванні фр.
> 320 0С ШДФ1
Вихід, % мас., на сировину
|
рідкої фази оксидату
|
твердої фази оксидату
|
очищеного палива (дистиляту)
|
КРПО (кубового залишку)
|
96,03
|
1,85
|
84,29
|
11,74
|
Таблиця 3.11 Характеристики рідкої фази оксидату та очищеного
палива, отриманих при знесірчуванні фр. > 320 0С ШДФ1
№
|
Продукт
|
Назва показника
|
|
|
Вміст загальної сірки, % мас.
|
Вміст фактичних смол, мг на 100 см3
|
Кислотність, мг КОН на 100 см3
|
Ступінь вилучення сірки, %
|
1
|
Рідка фаза оксидату
|
0,49
|
97
|
-
|
26,87
|
2
|
Очищене паливо
|
0,31
|
49
|
18,5
|
53,73
|
Одержану знесірчену фракцію змішували надалі з прямогонною
фракцією п.к¸320 °С і отримували паливо, вміст сірки у якому становив 0,18 %
мас. і відповідав вимогам до ДП марки Л - 0,2 - 62. Тобто з ШДФ1 можна отримувати
товарні палива з вмістом сірки до 0,2 % мас. як шляхом знесірчування цілої
фракції, так і окремої її частини.
Як видно з отриманих даних, за умов досліджень з ШДФ2 не
вдається отримати паливо з вмістом сірки 0,2 % мас. та менше. Збільшення
температури процесу до 220 0С та зменшення кількості води
(співвідношення вода:сировина становило 1:10) за інших однакових умов дає змогу
одержувати продукт (див. табл. 3.12-3.13), який за вмістом сірки практично
відповідає вимогам до ДП марки Л - 0,2 - 62.
Таблиця 3.12 Вихід основних продуктів при знесірчуванні ШДФ2
Вихід, % мас., на сировину
|
рідкої фази оксидату
|
твердої фази оксидату
|
очищеного палива (дистиляту)
|
КРПО (кубового залишку)
|
94,92
|
2,51
|
84,60
|
10,32
|
Таблиця 3.13 Характеристики рідкої фази оксидату та очищеного
палива, отриманих при знесірчуванні ШДФ2
№
|
Продукт
|
Назва показника
|
|
|
Вміст загальної сірки, %мас
|
Вміст фактичних смол, мг на 100см3
|
Кислотність, мг КОН на 100 см3
|
Ступінь вилучення сірки, %
|
1
|
Рідка фаза оксидату
|
0,32
|
67
|
33,6
|
8,57
|
2
|
Очищене паливо
|
0,21
|
9
|
11,4
|
40,00
|
Отримані результати (див. табл. 3.9) також показують, що при
використанні гідрогенізату вдається вилучати більше, ніж 85 % сірки, що
залишилась після процесу гідроочистки та отримувати паливо з вмістом сірки до
0,05 % мас. Вміст фактичних смол та кислотність палива після оксидаційного
очищення та наступним оброблення лугом гідрогенізату також відповідали вимогам
до товарних продуктів.
При використані ШДФ3 або її окремих частин процес
оксидаційного знесірчування проходить менш інтенсивно (порівняно з ШДФ1 або
ШДФ2), за винятком застосування найлегшого дистиляту (фр. п.к.-280 0C).
В останньому випадку вдається вилучати близько 50 % загальної сірки.
Це можна пояснити, виходячи з наступних міркувань:
зі збільшенням температури кипіння фракцій
зменшується різниця між температурами випаровування вихідних сірчистих речовин
та їх окиснених аналогів; вказаний чинник та розширення фракційного складу
утруднює виділення продуктів окиснення ректифікацією;
- у «важчій» сировині міститься більша кількість
тіофенової сірки, яка, порівняно з сполуками меркаптанового, сульфідного та
дисульфідного рядів, окислюється повільніше.
Метою подальших досліджень - є вивчення способів розділення
продуктів гідрогенізаційного знесірчування прямогонних та гідроочищених
дизельних фракцій.
4. ТЕХНОЛОГІЧНА ЧАСТИНА
.1 Оптимальні параметри процесу оксидаційної очистки
На основі експериментальних даних (див. табл. 3.10) вибрано
наступні оптимальні умови:
температура процесу 220 0С;
- тиск в реакторі 3.0 МПа;
- об’ємна швидкість подачі оксиданту 0.0275 с-1;
тривалість процесу 30 хв.;
співвідношення Н2О: ПДФ 1:10.
4.2 Матеріальний баланс процесу
Для розрахунку матеріального балансу
використовувалися наступні величини.
Об’ємна швидкість подачі оксиданту
складає 0.0275 с-1. Тоді (при розрахунку на 100 кг сировини),
знайдемо об’єм сировини за формулою:
Vсир. = G / r, (4.1)
де: G - маса сировини, кг.;
r - густина сировини, кг / м3, r = 888 кг / м3.сир.
= 100 / 888 = 0.11 м3.
Секундна витрата оксиданту:сек. = 0.11 · 0.0275 = 0.003 м3
/ сек.
Тоді об’єм оксиданту розраховується за формулою:
V = Vсек. · t, (4.2)
де: Vсек. - секундна витрата оксиданту, м3
/ сек.;
t - час досліду, сек., t = 30 хв.
V = 0.003 · 1800 = 5.4 м3.
Кількість повітря розраховується за формулою:
Gпов. = V · rпов., (4.3)
де:V - об’єм оксиданту, м3
rпов. - густина повітря, кг / м3.,
r = 1.29 кг / м3.пов.
= 5.4 · 1.29 =
6.97 кг.
Об’ємне співвідношення ПДФ : вода - 10 : 1.
Об’єм сировини - 0.1126 м3.
Об’єм води - 0.01126 м3.
Для розрахунку матеріального балансу використовувалися дані
про вихід продуктів після проведення оксидаційного знесірчування фр. > 320 ºС ШДФ1 (табл. 3.10).
У зв’язку з тим, що кубовий залишок планується
використовувати як мастильно-змащуючі рідини, то продуктивність установки (100
тис. т/рік) приймаємо виходячи з потреб цих рідин.
Приймаємо, що кількість робочих днів в році - 310.
Матеріальний баланс процесу наведено в таблиці 4.1:
Таблиця 4.1 Матеріальний баланс
процесу
Показники
|
Кількість
|
|
% мас. на сир.
|
кг / год.
|
Тис. т / рік
|
Надійшло:
|
|
|
|
Фракція > 320 ºС
|
100.00
|
13440.86
|
100.00
|
Вода
|
11.23
|
1510.00
|
11.23
|
Повітря
|
6.97
|
936.83
|
6.97
|
118.20
|
15887.69
|
118.20
|
Одержано:
|
|
|
|
Очищене дизельне паливо
|
84.29
|
11329.71
|
84.29
|
Кубовий залишок
|
11.74
|
1578.02
|
11.74
|
Твердий залишок
|
1.85
|
248.66
|
1.85
|
Відпрацьоване повітря + гази окислення + втрати +
вода
|
20.32
|
2731.30
|
20.32
|
Всього:
|
118.20
|
15887.69
|
118.20
|
.3 Обгрунтування вибору технологічної схеми установки
оксидаційної очистки
Власний досвід з окиснення дизельних фракцій у лабораторних
умовах, а також, аналіз літературних даних [128,166] показує, що процес
оксидаційної очистки може бути успішно реалізований при правильному вирішенні
наступних технологічних стадій:
1)
забезпечення
надійного контакту оксиданту із сумішшю прямогонної дизельної фракції і води;
2)
рекуперація
енергії стиснених газоподібних продуктів окиснення;
3)
відділення
окисненої прямогонної дизельної фракції від водної та твердої фаз;
4)
забезпечення
ефективного розділення окисненої прямогонної дизельної фракції від продуктів
окиснення сірчистих сполук, з метою отримання товарного дизельного палива.
5) нагрів вихідної прямогонної дизельної фракції і води до
температури процесу і рекуперація тепла продуктів реакції;
Принципова блок-схема процесу оксидаційної очистки, з
врахуванням різних методів розділення оксидату, подана на рис. 4.1.
Нагрів сировини до температури процесу доцільно здійснювати
за рахунок тепла продуктів реакції, що дозволить значно зменшити енергетичні
затрати на реалізацію процесу. Для цього може бути використане стандартне
теплообмінне обладнання. Контакт сировини і води з повітрям може відбуватись у
апаратах різної конструкції: куби періодичної дії; змієвиковий реактор;
пустотіла колона; колона з сітчастими тарілками; суміщення змієвикового
реактора і колони. Пустотіла колона має, в порівнянні з іншими реакторами,
найвищу інтенсивність окиснення (за виключенням колони з сітчастими тарілками)
та найменші затрати металу на одиницю сировини [169-171].
Рис.4.1. Принципова блок-схема процесу оксидаційної очистки.
Оскільки, в процесі окиснення прямогонної дизельної фракції
утворюється мілкодисперсний твердий осад і існує ймовірність попадання його
після фільтрування з оксидатом у ректифікаційну колону, а також, необхідність
перегонки 95¸96 % мас. на завантаження колони, то для ректифікації
пропонується використовувати колону, подібну до ректифікаційної колони
установки каталітичного крекінгу.
Для регенерації енергії стиснених газоподібних продуктів
окиснення можуть використовуватись апарати, подібні до апаратів утилізації
тепла димових газів установок каталітичного крекінгу або газових турбін. Газова
турбіна дозволяє отримати велику потужність в одному агрегаті. При цьому вона
має малі габарити і порівняно малу масу на одиницю потужності [10].
Інші апарати є типовим серійним обладнанням НПЗ та хімічних
виробництв.
.4 Опис принципової технологічної схеми установки
оксидаційної очистки
Принципову технологічну схему установки оксидаційної очистки
прямогонних дизельних фракцій подано на рис. 4.2.
Сировина помпою (1) двома потоками прокачується через
теплообмінник (2) і холодильник-конденсатор (20), де підігрівається за рахунок
тепла нижнього і верхнього продукту колони (19), догрівається до потрібної
температури водяною парою в теплообміннику (3) і подається через маточник у
колону окиснення (4) під розподільчу тарілку. Помпою (5) в колону (4)
подається, також, вода, яка вводиться на розподільчу тарілку під рівень рідини
у колоні. Оскільки, вода подається у колону з температурою меншою на 30¸50 ° від температури реакції, то
це дозволяє зменшити температуру в зоні сепарації і зменшити винос парів
палива. Вниз колони (4) компресором (6) через маточник подається оксидант
(повітря). Для запобігання виносу краплинок рідини з парами верх колони (4)
обладнаний відбійними елементами.
Газоподібні продукти окиснення охолоджуються у
холодильнику-конденсаторі (7) і подаються у сепаратор (8), де від них
відділяється волога. Із сепаратора (8) газоподібні продукти окиснення надходять
у турбодетандер (9), де енергія стиснених газів перетворюється у механічну
роботу. Остання використовується для роботи електрогенератора (10). В процесі
пуску установки для приводу турбодетандера (9) встановлена парова турбіна (11),
яку після виходу турбодетандера на режим зупиняють. Відпрацьовані стиснені
гази, які виходять з газового тракту турбодетандера (9), охолоджуються у
холодильнику-конденсаторі (12) і після відділення конденсату, який збирається у
ємності (13), виводяться з установки.
Рідкі продукти окиснення з колони (4), під тиском, подаються
у сепаратор (15), у якому відбувається відділення водної фази від оксидату
(окисненої прямогонної дизельної фракції). Відділена водна фаза пропускається
через фільтри (16), які працюють почергово, для відділення твердої фази. Після
проходження фільтрів водна фаза надходить у ємність (14), звідки помпою (5)
повертається на рециркуляцію у колону (4). Оксидат пропускається через фільтри
(17), також, для відділення твердої фази, підігрівається водяною парою у
теплообміннику (18) і вводиться у живильну секцію ректифікаційної колони (19).
У колоні (19) відбувається відгонка очищеного палива від
кубового залишку. Пари верху колони конденсуються у холодильнику-конденсаторі
(20), доохолоджуються у холодильнику (21) і збираються в ємності (22), у якій
відбувається відділення від очищеного палива захопленої з парами вологи.
Частина очищеного палива помпою (23) подається на верх колони (19), як холодне
зрошення, а балансова кількість виводиться на доочистку від кислих сполук.
Нижній продукт (кубовий залишок) колони (19) забирається
помпою (25), віддає своє тепло вихідній сировині і виводиться з установки.
Частина його підігрівається водяною парою в теплообміннику (24) і подається, як
гаряче зрошення, у колону (19) та для запобігання осадження частинок
захопленого осаду на дно колони. Оскільки, є можливість попадання осаду у
колону (19), в її нижній частині встановлено каскадні тарілки, і дно колони є
конічної форми.
Рис. 4.2. Принципова технологічна схема установки
оксидаційної очистки: 1, 5, 23, 25 - помпи; 2, 3, 18, 24 - теплообмінники; 4 -
колона окиснення; 6 - компресор; 7, 12, 20 - холодильники-конденсатори; 8, 13,
15 - сепаратори; 9 - турбодетандер; 10 - електрогенератор; 11 - парова турбіна;
14, 22 - ємності; 16, 17 - фільтри; 19 - ректифікаційна колона; 21 -
холодильник; І - вихідна ПГФ; ІІ - повітря; ІІІ - свіжа вода; ІV - очищене
паливо на доочистку; V - кубовий залишок; VI - відпрацьоване повітря; VІІ -
водяна пара; VІІІ - стоки; IX - тверда фаза.
5. ЕКОНОМІЧНА ЧАСТИНА
.1 Техніко-економічне обгруниування
Зростання жорсткості вимог до екологічних властивостей палив
призводить до зменшення в них допустимої кількості сірчистих сполук.
Ілюстрацією цього положення може бути допустимий вміст сірки у дизельному
пальному (ДП), що випускається у США: з 2009 року максимальний вміст сірки у
них повинен не перевищувати 10 ppm (0,001 % мас.). Ідентичні або навіть
жорсткіші вимоги висуваються до палив, що випускаються у країнах Євросоюзу.
На даний момент єдиною широко використовуваною промисловою
технологією очищення нафтової сировини від сполук сірки є гідроочищення (ГО).
Але цей метод має ряд недоліків, основними з яких є:
у процесі використовується порівняно складне
обладнання, розраховане на тиск 7 МПа і вище, що автоматично вимагає великих
капітальних затрат при будівництві нової установки;
оскільки одним з продуктів процесу є сірководень, то
паралельно з гідроочищенням вимагається будівництво установок очищення газів
від H2S та його утилізації (виробництва сірки або сірчаної кислоти);
для глибокого гідроочищення вимагається використання
чистого водню, що автоматично спричиняє до будівництва поряд з вищезгаданими
установками ще й блок виробництва водню;
при гідроочищенні поряд із сірчистими сполуками
усуваються також всі інші гетероатомні речовини та гідрується частина
ароматики, що автоматично спричинює до зниження у очищеному продукті речовин,
здатних сорбуватися на металічних поверхнях;
сполуки ряду тіофену та інші конденсовані сірчисті
сполуки, що можуть міститися у сировині, не піддаються гідроочищеню через
просторові затруднення, які виникають при їх контакті з каталізаторами.
У зв’язку з цими недоліками необхідно створювати якісно нові
технології очищення нафтових фракцій. До таких процесів можна віднести
оксидаційне знесірчування (ОЗ) нафтової сировини. Суть методу полягає в
окисненні сірчистих сполук до сульфонів, сульфоксидів та, можливо,
сульфокислот, які порівняно з іншими компонентами сировини проявляють чітко
виражені полярні властивості. Це дозволяє відділяти їх від інших сполук, що
містяться в нафтових фракціях, адсорбцією або екстракцією. Крім цього,
враховуючи те, що сульфоксиди, сульфони та сульфокислоти мають, порівняно з
відповідними вихідними сірчистими сполуками, вищу температуру кипіння, їх можна
усувати із суміші звичайною перегонкою.
.2 Розрахунок витрат на проведення досліджень
В табл. 5.1.наведені статті витрат на проведення наукових
досліджень.
Таблиця 5.1. Статті витрат на проведення наукових дослідженя
Стаття витрат
|
Розрахункова формула
|
Складові
|
Сировина і матеріали 
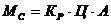
-
ціна сировини і матеріалів;
-
норма витрати на одиницю продукції по всіх компонентах;
-
ціна на сировину та матеріали;
- об’єм продукції.
|
|
Електроенергія 

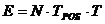
-
ціна споживчої електроенергії;
-
потужність електричних приладів;
-
годинний фонд часу дослідження;
- тариф.
|
|
Заробітна плата виробничого персоналу 
-
фонд заробітної плати;
-
кількість чоловік;
-
денний фонд часу;
- денна ставка по категорії робіт.
|
|
|
Відрахування на соціальні затрати
|
 - відрахування від заробітної плати у фонд соціального
страхування
|
|
Амортизаційні відрахування 
-
амортизаційні відрахування;
-
початкова вартість використаного обладнання;
- квартальна норма амортизаційних
відрах.
|
|
|
Накладні витрати
|
 - накладні витрати 20% суми попередніх статей;
|
|
.3 Розрахунок вартості сировини і матеріалів
Витрати на сировину і матеріали, які були витрачені на
проведення експериментів, визначаються за такою формулою:
,
(5.1.)
де:
- витрата і-того виду матеріальних ресурсів;
-
ціна і-того виду матеріальних ресурсів.
Вартість сировини і матеріалів, необхідних для проведення досліджень,
наведена в табл. 5.2.
Таблиця 5.2. Вартість сировини використаної для досліджень, з
розрахунку на 100 л готового продукту
№ п/п
|
Сировина
|
Загальна кількість витраченої сировини, л.
|
Вартість за 1 л, грн.
|
Вартість витрат на сировину, грн.
|
1
|
ШДФ1 з ВАТ «НПК Галичина» (м. Дрогобич).
|
25.00
|
2.00
|
50.00
|
2
|
ШДФ2 з ВАТ «Нафтохімік Прикарпаття» (м. Надвірна)
|
25.00
|
2.00
|
50.00
|
3
|
ШДФ3 з ВАТ «Нафтохімік Прикарпаття » (м. Надвірна)
|
25.00
|
2.00
|
50.00
|
4
|
Гідрогенізат з ВАТ «Укрнафта» (м. Кременчук)
|
25.00
|
2.70
|
67.50
|
5
|
Всього
|
--
|
--
|
217.5
|
.4 Розрахунок витрат на електроенергію для технологічних
цілей
Витрати на електроенергію визначаються за формулою:
(5.2.)
де:
- потужність електроспоживачів, кВт;
-
фонд роботи електричного обладнання, год;
-
тариф, грн./кВт·год.
Таблиця (5.3.) Витрати на електроенергію для технологічних цілей
№ п/п
|
Назва обладнання
|
Потужність обладнання, кВт
|
Час роботи, год.
|
Тариф, грн./кВт·год
|
Сума витрат, грн.
|
1
|
Компресор
|
4.0
|
20.0
|
0.2364
|
18.91
|
2
|
ЛАТР
|
0.2
|
60.0
|
0.2364
|
2.84
|
3
|
Ваги аналітичні
|
0.05
|
7.0
|
0.2364
|
0.08
|
4
|
Сушильна шафа
|
1.6
|
75.0
|
0.2364
|
28.37
|
5
|
Електродвигун
|
3.0
|
25.0
|
0.2364
|
17.73
|
6
|
Електронагрівач
|
1.5
|
60.0
|
0.2364
|
21.28
|
7
|
Витяжна шафа
|
3.0
|
140.0
|
0.2364
|
99.29
|
8
|
Всьго
|
--
|
--
|
--
|
188.50
|
.5 Вартість апаратури та обладнання
Вартість апаратури взята з каталогу «Реактиви. Хімічний
посуд. Лабораторне обладнання» за 2009 р., науково-виробничої фірми «Сфера Сім»
(м. Львів) і наведена в табл. 5.4.
Таблиця 5.4. Вартість апаратури та обладнання необхідного для
проведення досліджень
№ п/п
|
Назва
|
Кількість
|
Ціна обладнання, грн.
|
Загальна вартість обладнання, грн.
|
1
|
Компресор
|
1
|
5300
|
5300
|
2
|
ЛАТР
|
1
|
2950
|
2950
|
3
|
Ваги аналітичні
|
1
|
7056
|
7056
|
4
|
Ваги технічні
|
1
|
2230
|
2230
|
5
|
Сушильна шафа
|
1
|
5750
|
5750
|
6
|
Електронагрівач
|
1
|
2600
|
2600
|
7
|
Витяжна шафа
|
1
|
14200
|
14200
|
8
|
Реактор
|
1
|
9750
|
9750
|
9
|
Ротаметр
|
2
|
1700
|
3400
|
10
|
Манометр
|
5
|
1540
|
7700
|
11
|
Вентиль
|
6
|
950
|
5700
|
12
|
Балон з азотом
|
1
|
3450
|
3450
|
13
|
Балон для збору газів
|
1
|
2600
|
2600
|
14
|
Ресивер
|
1
|
3400
|
3400
|
15
|
Колби плоскодонні на 500 мл
|
5
|
13.50
|
67.50
|
16
|
Колби конічні на 50 мл
|
10
|
6.40
|
64.00
|
17
|
Колби конічні на 100 мл
|
10
|
7.10
|
71.00
|
18
|
Всього
|
--
|
--
|
76288.50
|
Розрахунок амортизаційних відрахувань проводимо з розрахунку,
що квартальна норма амортизаційних відрахувань рівна 6 %:
грн.
(5.3.)
.6 Вартість орендної плати
Оплата за оренду 1 м2 приміщення складає 123.0
грн. за місяць. Площа лабораторії в якій проводилися дослідження становить 28 м2.
За час проведення досліджень ( 3 місяці), оплата за оренду приміщення складає:
грн.
(5.4.)
.7 Розрахунок чисельності працюючих і фонду заробітної плати
У проведенні досліджень приймали участь:
дипломник з розміром стипендії - 590 грн/місяць.
керівник науково-дослідної роботи (доцент) - 29.93 грн/год.
Термін проведення роботи - 3 місяці.
Загальний фонд заробітної плати становить:
грн.
(5.5.)
Відрахування на соціальні заходи складають 36.4 % від
загального фонду заробітної плати:
грн.
(5.6.)
.8 Визначення вартості проведених досліджень
Розрахунок вартості проведення досліджень приводимо у таблиці
5.5.
Таблиця 5.5. Загальна вартість досліджень
№ п/п
|
Вартість затрат
|
Сума,грн.
|
1
|
Вартість сировини і матеріалів
|
217.50
|
2
|
Вартість електроенергії
|
188.50
|
3
|
Загальний фонд заробітної плати
|
2727.76
|
4
|
Відрахування на соціальні заходи
|
992.90
|
5
|
Вартість оренди приміщення
|
10332.00
|
6
|
Амортизаційні відрахування
|
4577.31
|
7
|
Разом
|
19035.97
|
8
|
Накладні витрати (20 % прямих)
|
3807.19
|
9
|
Всього
|
22843.16
|
Собівартість продукції:
(5.7.)
де: -
- затрати на сировину при виготовленні 1 л продукції;
-
питома вага на сировину в собівартості продукції, (75 %).
грн.
Ціна 1 кг продукту:
(5.8.)
де: -
- рентабельність (
).
грн.
.9 Економічний ефект досліджень
Пропоновану технологію процесу оксидаційного очищування
прямогонних дизельних фракцій можна реалізовувати у кількох напрямках:
- як альтернативу процесу гідроочищення;
- для одержання компоненту дизельного пального з
хорошими змащуючими властивостями;
для доочищення фракцій дизельного пального після
гідроочищення.
У другому випадку реалізація процесу є можливою лише тоді,
коли оксидаційний процес є щонайменше не дорожчим від гідрогенізаційного, а у
першому - коли переважає його за техніко-екномічними показниками.
Порівняти капітальні затрати на будівництво двох установок
досить важко, проте можна перечислити основні технологічні блоки самих
установок та суміжні інсталяції по виробництву вихідних реагентів і переробці
побічних продуктів.
Установка гідроочистки та паралельні їй технології
складаються з:
- установки виробництва водню;
- реакторного блоку;
вузла розділення (ректифікації) продуктів;
очищення газів від сірководню;
залуговування рідких продуктів;
установки виробництва сірки;
блоку допалювання газів з установки виробництва
сірки.
Установка оксидаційної очистки та суміжні технології
будуть складатися:
- вузла розділення (ректифікації) продуктів;
залуговування рідких продуктів;
адсорбційного доочищення/розділення дистиляту,
отриманого при ректифікації;
вузла змішування концентратів рідких продуктів
окиснення (приготування МОР);
блоку допалювання газів окиснення.
Як видно з вищенаведених даних набір установок є дещо меншим
при проведенні оксидаційного очищення і, очевидно, вимагає менших капітальних
затрат.
Основними складовими собівартості очищеного палива є вартість
сировини та побічних продуктів і експлуатаційні затрати. Виходи цільового
продукту (дизельного палива) при оксидаційному очищенні є дещо меншими від виходів
при гідроочищенні, у першу чергу, за рахунок втрат нафтопродукту з
відпрацьованим повітрям та отримання більшої кількості побічних продуктів.
Проте втрати у промисловості, як правило, є значно меншими, ніж втрати у
лабораторних умовах. Окрім того, собівартість побічних продуктів при
оксидаційному знесірчуванні перевищує аналогічний показних при гідроочищуванні.
Для визначення економічного ефекту дослідження порівняємо
сумарні енергетичні затрати і вартість основних продуктів.
Для процесу гідроочистки, норми енергетичних затрат і виходи
основних продуктів взяті з [76]. Для процесу оксидаційного знесірчування вище
сказані велечини отримані на основі лабораторних досліджень. Оскільки, тиск в
процесі гідроочистки приблизно в два рази менший ніж в процесі оксидаційного
знесірчування, то кількість електроенергії на оксидаційне знесірчування
витрачається приблизно в два рази менше (з розрахунку на 1000 кг сировини).
Всі розрахунки проведені на 1000 кг сировини. Результати
наведені в таблиці 5.6., 5.7., 5.8. та 5.9.
Таблиця 5.6. Сума реалізації продуктів (на 1000 кг. сировини)
в процесі гідроочистки
Стаття
|
Одиниці вимір.
|
Кількість
|
Ціна одиниці, грн.
|
Вартість, грн.
|
1. Очищене паливо
|
кг
|
965.00
|
5.95
|
5741.75
|
2. Вуглеводневі гази + Н2S
|
кг
|
30.00
|
0.96
|
28.80
|
3. Втрати
|
кг
|
5.00
|
--
|
--
|
Разом
|
кг
|
1000.00
|
--
|
5770.55
|
Таблиця 5.7. Енергетичні затрати (на 1000 кг. сировини) в
процесі гідроочистки
Стаття
|
Одиниці вимір.
|
Кількість
|
Ціна одиниці, грн.
|
Вартість, грн.
|
1. Вода оборотня
|
м3
|
7.00
|
0.29
|
2.03
|
2. Електроенергія
|
кВт∙год
|
17.50
|
0.5846
|
10.23
|
3. Паливний газ
|
м3
|
24.34
|
1.25
|
30.43
|
4. ВВГ
|
кг
|
75.00
|
0.96
|
72.00
|
5. Каталізатор
|
кг
|
0.018
|
200.00
|
3.60
|
Разом
|
--
|
--
|
--
|
118.29
|
Таблиця 5.8. Сума реалізації продуктів (на 1000 кг. сировини)
в процесі оксидаційного знесірчування
Стаття
|
Одиниці вимір.
|
Кількість
|
Ціна одиниці, грн.
|
Вартість, грн.
|
1. Очищене паливо
|
кг
|
842.90
|
5.95
|
5015.26
|
2. Концентрат рідких продуктів окислення (КРПО)
|
кг
|
117.40
|
7.14
|
838.24
|
Тверда фаза (комп. бітуму)
|
кг
|
18.50
|
3.00
|
55.50
|
3. Втрати
|
кг
|
21.20
|
--
|
--
|
Разом
|
кг
|
1000.00
|
--
|
5909.00
|
Таблиця 5.9. Енергетичні затрати (на 1000 кг. сировини) в
процесі оксидаційного знесірчування
Стаття
|
Одиниці вимір.
|
Кількість
|
Ціна одиниці, грн.
|
Вартість, грн.
|
1. Вода свіжа
|
м3
|
20.00
|
0.58
|
11.60
|
2. Вода оборотня
|
м3
|
7.00
|
0.29
|
2.03
|
3. Електроенергія
|
кВт∙год
|
8.75
|
0.5846
|
5.12
|
4. Паливний газ
|
м3
|
9.76
|
1.25
|
12.20
|
5. Адсорбент
|
кг
|
0.45
|
9.80
|
4.41
|
Разом
|
--
|
--
|
--
|
35.36
|
Як видно, з табл. 5.6., 5.7., 5.8. та 5.9. дохід процесу
оксидаційного знесірчування приблизно на 200 грн. більший ніж процесу
гідроочистки, а енергетичні витрати оксидаційного знесірчування приблизно в два
рази менші порівняно з гідроочисткою ( з розрахунку на 1000 кг. сировини).
Виходячи з цього, можна порахувати економічний ефект дослідження:
тис.
грн. (5.9.)
6. ОХОРОНА ПРАЦІ
Темою даної дипломної роботи є оксидаційне знесірчування
прямогонних та гідроочищених дизельних палив. Очевидно, що метою проведення
наукових досліджень є отримання дизельних палив, які б відповідали всім вимогам
щодо якості товарних нафтопродуктів. В ході досліджень використовувалася
сировина різного фракційного складу, а також даний процес проводився при різних
тисках, температурах та в присутності води і без неї.
В процесі виконання даних робіт є ряд небезпечних факторів,
що можуть призвести до нещасних випадків при невиконанні правил безпеки
поведінки в хімічній лабораторії. Метою даного розділу є виявлення
небезпечностей, зазначення методів захисту від них, а також визначення
оптимальних умов праці в даній лабораторії
В табл. 6.1.наведені дані про токсичність і пожежо-,
вибухонебезпечність речовин, які наявні в процесі.
.1 Потенційно небезпечні фактори при роботі у хімічній
лабораторії
Так як, в лабораторії кафедри хімічної технології нафти та
газу проводяться дослідження із використанням горючих, вибухонебезпечних і
токсичних речовин, то вона належить до хімічних лабораторій із підвищеною
небезпекою [172]. Тому для безпечної роботи, необхідно дотримуватися правил
техніки безпеки в лабораторії. Незнання і порушення цих правил, може привести
до пожеж, вибухів, а як наслідок, до отруєнь, опіків та інших важких наслідків.
Небезпечними і шкідливими факторами процесу оксидаційного
знесірчування є:
- наявність обладнання, що працює під тиском;
Таблиця 5.1 Дані про токсичність і вибухо-,
пожежонебезпечність речовин процесу
Речовина
|
Густина парів відносно повітря
|
ГДК мг/м3
|
Характеристика впливу речовини на організм людини
|
Температура, ºС
|
Концентраційні границі вибуху, об %
|
Група вибухо небезпечності суміші
|
Категорія вибухоне безпечності суміші
|
Питомий електричний опір, Ом/м
|
Схильність до
|
Засоби пожежогасіння
|
|
|
|
|
Спалаху
|
Само займання
|
НГВ
|
ВГВ
|
|
|
|
Само займання
|
Утв. перок. сполук
|
|
Дизельне паливо
|
7.4
|
300
|
Пари викликають головний біль, нудоту
|
+ 30
|
≈ 380
|
--
|
--
|
Т2
|
II А
|
> 106
|
Є
|
Немає
|
Ящики з піском, вода, вогнегасники
|
- наявність нагрівного обладнання;
наявність обладнання, що працює під напругою;
- наявність горючих, легкозаймистих та токсичних
речовин;
наявність скляного посуду ( як з термосила, так і
простого).
В даному процесі найбільш небезпечними факторами є:
температура (160-280 ºС) і тиск (до 3 МПа).
Згідно нормативу НА ПБ Б. 03.002-2007 за пожежонебезпечністю
хімічна лабораторія відноситься до приміщень категорії “В”.
Згідно ПБЕ-ДНАОП 0.00-1.32-01 воно класифікується, як
приміщення класу 2, тобто як приміщення, в якому вибухонебезпечне середовище
створюється лише при аварії і тиск вибуху перевищує 5 МПа.
Згідно санітарної класифікації технологічних процесів дане
дослідження відносять до III класу, а саме до такого де є процеси з явними
хімічними забрудненнями.
За санітарними нормами проектування промислових підприємств
СН245-71 лабораторія відноситься до V класу із санітарно-захисною зоною більшою
або рівною 50 м.
.2 Заходи забезпечення безпеки експлуатації лабораторного
обладнаня і проведення лабораторних досліджень
Наукові дослідження здійснюються у хімічній лабораторії кім.
116 VIII навчального корпусу НУ «Львівська політехніка».
Планування, розміщення, санітарно-технічне обладнання
хімічної лабораторії повинні узгоджуватися з санітарними СН-245-71 та
протипожежним СНиП 2.09.02-85 нормами проектування. Згідно норм СН-245-71 для
одного працюючого відводиться 5 м2 площі (14 м3 об’єму)
без врахування витяжної шафи. Виходячи з цього, плануємо лабораторію з робочими
місцями для трьох наукових співробітників.
В хімічній лабораторії повинна бути: приточно-витяжна
вентиляція, система нагрівання, система водопостачання і каналізація,
підведення електроенергії для освітлення і роботи лабораторних приладів,
забезпечення дистильованою водою.
Під час роботи в шкідливих та небезпечних умовах працівники
повинні приступати до роботи тільки у засобах індивідуального захисту
(бавовняний халат, шкіряне взуття, захисні окуляри, респіратор, гумові
рукавички, спеціальний фартух, захисна маска), які мають бути наявні в
лабораторії; зберігати та приймати їжу тільки у відведених для цього місцях;
після робіт помити забруднені частини тіла.
При роботі можливий вплив таких небезпечних і шкідливих
виробничих чинників:
. Фізичних:
травмування гострими кромками при руйнуванні скляного
обладнання і тари;
небезпечне значення напруги в електричному ланцюзі, замикання
якого може здійснитися крізь тіло людини;
підвищена та понижена температура повітря робочої зони;
підвищена рухомість повітря.
. Хімічних:
отримання хімічних опіків;
токсична та подразнююча дія речовин на організм людини,
зокрема на шкіряні покрови, слизові оболонки, органи дихання.
Кожен співробітник лабораторії повинен знати, які речовини,
матеріали, обладнання знаходяться в можливій зоні виникнення пожежі і які
засоби пожежогасіння можна використовувати.
Перед початком роботи необхідно перевірити та одягти засоби
індивідуального захисту, перевірити справність приладів і обладнання, включити
загально обмінну припливно-витяжну вентиляцію за 15-20 хв. до початку роботи, а
при виявленні несправностей обладнання сповістити свого керівника та не
приступати до роботи до усунення виявлених несправностей.
Особливої уваги заслуговує робота з електроприладами. При
роботі з ними слід берегтися від термічних опіків та уражень електричним
струмом, тому всі електроприлади в лабораторії повинні бути справними і
зануленими або заземленими. До підключених елетроприладів не слід доторкатися
вологими руками. Перед початком роботи необхідно перевірити справність усіх
електричних приладів [173].
Змішування або розведення хімічних речовин, що
супроводжується виділенням тепла, виконувати в термостійкому або порцеляновому
посуді.
При нагріванні хімічних речовин у пробірці необхідно її
спрямовувати в бік від себе й осіб, які знаходяться поруч . При збовтуванні
розчину у колбах і пробірках закривати їх корками. При виконанні робіт не
залишати запалені пальники та інші нагрівальні прилади без нагляду.
Відходи кислот, лугів та інших небезпечних речовин зливати
тільки в спеціальні тари. Не зберігати речовини невідомого походження без
напису і етикеток.
При роботі з органічними розчинниками, які використовуються в
процесі, злив чи перелив розчинників необхідно обов’язково проводити під
витяжною шафою. Кількість розчинників, які знаходяться в лабораторії, не
повинна перевищувати денної потреби лабораторії. Запаси розчинників необхідно
зберігати в спеціальному сховищі (на складі).
Співробітники, які приступають до нового виду
вогненебезпечної чи вибухонебезпечної роботи, повинні попередньо отримати
вказівки по техніці безпеки від свого керівника.
Куріння дозволяється тільки у спеціально відведених місцях.
Велику небезпеку для організму людини становлять сильнодіючі
отруйні речовини. Тому до роботи із сильнодіючими отруйними речовинами
допускаються тільки висококваліфіковані робітники. На робочому місці повинні
знаходитися індивідуальні засоби захисту органів дихання і шкіри, необхідні
дегазуючі речовини і засоби для надання першої допомоги.
Більша частина робіт в хімічній лабораторії пов’язана з
використанням скляного посуду. З точки зору техніки безпеки скло має ряд
недоліків, основні з яких крихкість і невисока стійкість до різких перепадів
температури. Більша частина нещасних випадків трапляється при порушенні правил
роботи зі склом, а саме травми різної важкості, пожежі та вибухи (при пролитті
горючих рідин, окисників), отруєння і хімічні опіки ( при потраплянні токсичних
речовин в атмосферу чи на шкіру людини).
З міркувань безпеки, враховуючи, що тиск всередині реактора
до 3,0 МПа, дослідна установка поміщається в захисний вертикальний металевий
ящик, відкритий з однієї сторони для доступу до установки. Установка
розміщується біля витяжної шафи, під якою проводиться наливання реагентів та
виливання продуктів із реактора, повернута відкритою стороною до стіни. Реактор
вкритий ізоляцією, що захищає від можливих опіків при доторканні до нього.
Температура регулюється автоматично за допомогою вимірювача-регулятора. Кисень
подається в установку з балону через редуктор.
В роботі використовувалися дизельне паливо, яке легко
випаровуються і створюють вибухонебезпечні суміші із повітрям. Слід уникати
його розливу та розбризкування.
Особливі вимоги ставлять до роботи з вогне- та
вибухонебезпечними речовинами. Всі роботи з легкозаймистими горючими рідинами
проводять у витяжній шафі при увімкненій вентиляції. При роботі з
вибухонебезпечними речовинами використовують захисні екрани і інші захисні
засоби згідно інструкції. Просочені ЛЗР та ГР тканини треба збирати в металеві
ящики, які щільно закриваються кришками. Необхідно приймати заходи, щоб звести
ймовірність проливу до мінімуму і обмежити кількість рідини, яка може вилитись.
Пролиті ЛЗР та ГР повинні збиратися, а місця проливу засипатися піском.
Електроосвітлення повинно бути у вибухобезпечному виконанні.
В лабораторії знаходиться таке електрообладнання: сушильна
шафа, електрична плита, аналітична вага, прилад для вимірювання температури,
установка для проведення окиснення. Всі електроприлади повинні бути заземлені
[174]. В особливо важких умовах експлуатації знаходиться ізоляція
електрообладнання, яке постійно працює у витяжній шафі, тому важливу роль в
системі заходів по зменшенню електротравматизму повинен відігравати контроль
ізоляції і профілактика її пошкоджень. Опір ізоляції повинен періодично
перевірятись. Частини обладнання, які неможливо ізолювати, повинні бути важко
доступними. Все електрообладнання повинно позначатися згідно ГОСТ 12.3.020-76.
В лабораторних приміщеннях не допускається зберігання навіть
невеликих кількостей легкозаймистих речовин з температурою кипіння нижче 50°С. Зберігання інших
легкозаймистих речовин допускається в товстостінних пляшках місткістю не більше
1 л, які оснащені герметичними корками. Пляшки з легкозаймистими речовинами
поміщають в спеціальні металеві ящики з написом «ЛЗР», встановлені подалі від
джерел тепла. Забороняється виливати відходи легкозаймистих речовин в
каналізацію. Лабораторія повинна бути забезпечена первинними засобами
пожежегасіння.
Після закінчення роботи працюючий повинен вимкнути
електроприлади, постачання води та газу, привести в порядок робоче місце.
.3 Санітарно гігієнічні заходи
.3.1 Метеорологічні умови
Метеорологічні умови, а саме температура, вологість і
швидкість руху повітря, визначають теплообмін організму людини і здійснюють
суттєвий вплив на функціональний стан різних систем організму, самопочуття,
працездатність і здоров’я.
Незалежно від метеорологічних умов вміст у повітрі шкідливих
речовин не повинен перевищувати їх гранично допустимі концентрації, приведені у
[175].
Згідно ДСН 3.3.6.042-99 №42 від 01.12.09, робота в
лабораторії відноситься до категорії робіт Iб (роботи, що виконуються стоячи
або пов’язані з ходінням та супроводжуються деяким фізичним напруженням ).
Відповідно до цієї категорії передбачені наступні метеорологічні умови
(табл.6.2.).
Таблиця 6.2. Оптимальні метеорологічні умови
Показник
|
Холодний період року
|
Теплий період року
|
Температура, 0С
|
21-23
|
22-24
|
Відносна вологість, %;
|
60-40
|
60-40
|
Швидкість руху повітря, м/с
|
0,1
|
0,2
|
.3.2 Опалення, вентиляція та система кондиціювання
В лабораторії діють такі системи вентиляції: механічна,
проточна, локально-витяжна. Повітрообмін повинен становити не менше 20 м3/год
на одну людину. Швидкість руху повітря, яке втягується в шафу через робочий
отвір повинна бути не менше 0,5-0,7 м/с при видаленні парів і газів, що
володіють малою токсичністю, і 1-1,5 м/с при видаленні сильнодіючих шкідливих
речовин (пари свинцю, ртуті, ціанідні сполуки і інші). Шафа освітлюється
електричними лампами у вибухобезпечному виконанні. Дерев’яні частини з
внутрішньої сторони повинні бути облиті негорючим матеріалом з метою
запобігання попадання полум’я пальників. Витяжна шафа встановлюється впритул до
негорючих стінок.
Для забезпечення оптимальних метеорологічних умов в холодний
період року, в лабораторії передбачено центральне парове опалення.
Звичайні системи вентиляції не здатні підтримувати всі
параметри повітря в межах, що забезпечують комфортні умови в зонах перебування
людей. Цю роль виконує кондиціонування, що є більш досконалою формою механічної
вентиляції та автоматично підтримує мікроклімат на робочому місці незалежно від
умов навколишнього середовища. Під кондиціонуванням розуміють нагрівання або
охолодження, зволоження або осушка повітря і очистка від пилу. Розрізняють системи
комфортного кондиціонування, що забезпечують в приміщенні постійні комфортні
для працюючого умови, і системи технологічного кондиціонування, які призначенні
для підтримки в виробничому приміщені визначених технологічним процесом умов.
Кондиціонування повітря потребує в порівнянні з вентиляцією
значних одноразових витрат, однак ці витрати швидко окупляться, так як
підвищують продуктивність праці, та фізіологічний стан працюючих.
.3.3 Система освітлення
Одним із важливих елементів сприятливих умов праці є
раціональне освітлення приміщення і робочого місця. В хімічній лабораторії
використовується природне і штучне освітлення. Освітлення виконують відповідно
до будівельних норм і правил ДБНВ.2.5-28-2006. Нормативна освітленість в
лабораторії становить 300 лк, так як дослідні роботи відносяться до III
розряду, високого класу точності.
Електричне освітлення здійснюється за рахунок ламп
розжарювання у звичайному виконанні, під витяжною шафою в вибухо-
пожежобезпечному виконанні.
.3.4 Системи водопостачання і каналізації
Витяжна шафа і робочі столи обладнані комунікаціями для
підведення гарячої і холодної води, газу і електроенергії. Підведення води
здійснюється по трубах, розміщених в доступних для огляду та ремонту
спеціальних каналах. Водопровідна система обладнана вентилями і кранами, які
знаходяться у легкодоступних місцях. Це дозволяє у разі необхідності в окремих
випадках швидко відключити подачу води для всієї лабораторії. Для відведення
стічних вод без попередньої обробки служить система каналізації. Раковини для
стічних вод розміщені під витяжною шафою і поза її межами. Місцева обробка
сильно кислих і сильно лужних стоків є обов’язковою також, як і для стоків, які
містять токсичні леткі речовини. Не допускається зливати в лабораторні раковини
органічні розчинники. Їх необхідно збирати в окрему посудину і зберігати під
витяжною шафою окремо від інших реактивів.
Водопостачання і каналізація повинні відповідати санітарним
нормам і правилам.
Кожна лабораторія повинна бути обладнана вмивальним куточком
з умивальником, а також шафами для одягу. Умивальники повинні бути оснащені
змішувачами гарячої і холодної води. Біля кожного умивальника повинен бути
гачок для рушника і посуд для рідкого чи полички для звичайного мила. В
лабораторії повинні бути побутові приміщення: санвузол, душ, кімната
відпочинку, роздягальня.
.4 Шум і вібрація
Виробниче обладнання та інструменти, які створюють шум при
роботі, необхідно конструювати у відповідності з вимогами ДСН 3.3.6.037-99
Для боротьби з шумом застосовують такі основні заходи:
зменшення шуму в джерелі;
звукоізоляція;
віброізоляція;
звукопоглинання;
архітектурно-планувальні заходи;
засоби індивідуального захисту.
Для послаблення шуму зменшуємо амплітуду коливань,
зрівноважуємо обертові частини механізмів, замінюємо металічні деталі деталями
з великим значенням внутрішнього тертя (пластик, гума, фетр). В приміщеннях
лабораторії рівень звуку і еквівалентні рівні звуку не повинні перевищувати 60
дБ.
Робота обладнання супроводжується виникненням вібрації, яка
передається на підлогу, столи, робочі зони іншого обладнання. При надмірно
інтенсивній і тривалій вібрації на людину може виникнути погіршення фізичного
стану працюючого. Найбільш ефективним заходом боротьби з вібрацією є усунення
її джерела. Зменшення вібрації може бути досягнуто шляхом:
урівноваження мас;
зміною маси або жорсткості;
застосування матеріалів з великим внутрішнім тертям;
віброізолюючих втулок і муфт, пружинних і гумових
амортизаторів.
Вібрація нормується згідно ДСН 3.3.6.039-99
.5 Засоби індивідуального захисту
Засоби індивідуального захисту застосовують тоді, коли безпека праці не
може бути досягнута технічними або організаційними засобами. Їх поділяють на
засоби захисту органів дихання, спецодяг, засоби захисту рук, голови, обличчя,
очей, органів слуху, шкіри.
В процесі досліджень застосовували такі засоби індивідуального захисту:
халат бавовняний;
гумові рукавиці;
захисні окуляри;
щиток - маска.
Для захисту органів дихання у лабораторії передбачено респіратор і
фільтруючий протигаз.
.6 Заходи пожежної профілактики
Робота в хімічній лабораторії практично завжди пов’язана з
можливістю виникнення спалахів, пожеж чи вибухів. За пожежонебезпечністю
хімічна лабораторія відноситься до приміщень категорії “В” згідно нормативу НА
ПБ Б. 03.002-2007.
Згідно ПБЕ-ДНАОП 0.00-1.32-01 приміщення класифікується, як
приміщення класу 2, тобто як приміщення, в якому вибухонебезпечне середовище
створюється лише при аварії і тиск вибуху перевищує 5 МПа.
В лабораторії передбачено застосування захисних засобів від
дії статичної електрики:
всі апарати, трубопроводи, де є діелектричні сполуки, повинні
бути заземлені;
обмежено турбулентність потоків,лінійна швидкість в трубах
< 1-1,5 м/с;
додавання мікрокількостей речовин, які зменшують опір;
з’єднання всіх металічних комунікацій, апаратів в єдину
електричну систему шляхом встановлення металічних перемичок.
При виникненні пожежі в лабораторії повинні бути засоби
пожежегасіння. До них відносять:
сирий пісок - згідно з нормами протипожежної безпеки
наявність піску в кожній лабораторії є обов’язковою. Пісок використовують в тих
випадках, коли вода не є ефективним засобом пожежегасіння. Пісок знаходиться в
металевому ящику;
азбестове полотно використовують для гасіння пожежі, якщо
нема заперечення з боку властивостей речовини. Це - найдоступніший засіб
пожежегасіння.
вуглекислотні вогнегасники є обов’язковим елементом, який
повинен бути наявним у кожній хімічній лабораторії.
Необхідно застосувати систему блискавкозахисту ІІ-б (ІІ
категорія, б-тип захисту) по РД 34-87 для будівель і споруд, що згідно ПУЕ
відносяться до класів 2 та 22.
Основними обов’язками всіх співробітників хімічної
лабораторії при виявленні спалаху чи пожежі є:
негайне попередження по телефону пожежної команди, або
включення пожежної сигналізації;
винесення з приміщення лабораторії в безпечне місце всіх
вогне-і вибухонебезпечних речовин, а також балонів з газами;
перекриття всіх вентилів, кранів систем газопостачання,
вентиляції, знеструмлення всіх електричних вузлів;
організація робіт по ліквідації пожежі;
у випадку займання одягу - гасіння полум’я азбестовою
ковдрою.
При проектуванні і будівництві споруд повинні передбачатись
евакуаційні шляхи і виходи на випадок виникнення в будівлі пожежі або аварії. В
корпусі повинно бути не менше двох шляхів евакуації. Ширина шляху евакуації
повинна бути достатньою для евакуації людей, вибирається в залежності від
кількості працюючих. На кожному поверсі є план евакуації. На шляху евакуації
повинно бути освітлення (автономне джерело освітлення)[176].
.7 Опис небезпечних ділянок технологічної схеми установки
оксидаційного знесірчування ДП
Дана технологічна схема, як і усі, має певні ділянки з
підвищеною небезпекою. Недотримання правил техніки безпеки на них, може привести
до нещасних випадків.
Так як, процес проходить під тиском, то у схему включений
компресор, а також ряд насосів, для перекачування сировини і продуктів процесу.
Дані апарати повинні знаходитися в спеціальних металевих, захисних каркасах, а
також необхідно регулярно (відповідно до графіка ремонтних робіт) проводити їх
обслуговування.
Оксидаційне знесірчування відбувається за рахунок підвищених
температур ( колона окиснення). А для нагріву і охолодження сировини і
продуктів процесу ,на схемі передбачені теплообмінники і
холодильники-конденсатори. Працівникам необхідно бути дуже обережними і чітко
дотримуватися правил техніки безпеки при роботі і обслуговуванні цих апаратів.
Як і вбудь якому процесі, в процесі оксидаційного
знесірчування, є багато електроприладів. При роботі з ними слід берегтися від
термічних опіків та уражень електричним струмом, тому всі електроприлади
повинні бути справними і зануленими або заземленими.
Всі трубопроводи, вентилі, крани, засувки повинні бути
справними і неушкодженими, для того, щоб не виникло нещасних випадків при їх
обслуговуванні.
Усі ємності і резервуари, які є в межах даної установки
повинні бути герметичними, щоб не відбувалося витікання сировини і продуктів
процесу.
.8 Розрахунок системи вентиляції
Параметри приміщення:
ширина а = 4 м.
довжина b = 7 м.
висота h = 4.5 м.
Речовина, яка випаровується - дизельне паливо.
Кількість дизельного палива, яка випаровується за одну годину
q = 14.70 г/год.
. Кількість припливного повітря (L), яке необхідно подати у
приміщення для нормалізації повітрообміну, м3/год.:
,
(6.1.)
де:
і
-
відповідно, ГДК і фактична концентрація шкідливої речовини в повітрі робочої
зони, мг/м3;
-
кількість речовини, що виділяється в приміщенні мг/год.
м3/год.
. Кратність повітрообміну (К), год-1.:
,
(6.2.)
де:
-
об’єм приміщення, м3.
м3.
Тоді:
год-1.
.9 Розрахунок природного освітлення
. Площа світлових отворів (S0), м2:
,
(6.3.)
де:
- нормоване значення КПО з врахуванням світлового
поясу;
-
площа підлоги приміщення,
=28 м2;
-
коефіцієнт запасу,
=2;
-
світлова характеристика вікон з врахуванням геометричних пропорцій приміщення,
=9.5;
-
коефіцієнт, який враховує затемнення вікон будинками, які стоять напроти,
=1.4;
-
загальний коефіцієнт світлопроникання;
-
коефіцієнт, який враховує відбивання світла від поверхні,
=1.15;
Нормоване значення КПО (
)
з врахуванням світлового поясу:
%,
(6.4.)
де:
- коефіцієнт світлового клімату,
=0.85;
-
нормоване значення КПО, яке залежить від розряду зорової роботи,
=1.0 %;
Загальний коефіцієнт світлопроникання:
,
(6.5.)
де:
- коефіцієнти, що враховують: конструктивні
особливості вікон, рам, товщину скла, штори, жалюзі, витрати світла в
сонцезахисних конструкціях, витрати світла в сонцезахисній сітці;
,
,
,
,
.
Відстань від верху вікна до розрахункової точки:
м.
(6.6.)
Відношення ширини приміщення до його довжини:
(6.7.)
Відношення ширини приміщення до відстані від верху вікна до
розрахункової точки:
(6.8.)
Відношення відстані від низу вікна до розрахункової точки до
ширини приміщенння:
(6.9.)
Тоді:
м2.
(6.10.)
2. Кількість вікон (n):
,
(6.11.)
. Загальна довжина вікон, м:
м.
(6.12.)
. Периметр приміщення, м:
м.
(6.13.)
В результаті обрахунків встановлено, що загальна довжина
вікон приміщення не перевищує периметр, тому для забезпечення нормативного
значення КПО для V-го розряду зорової роботи згідно ДБН 2.5.28-2006 «Природне
та штучне освітлення», необхідно 5 світлових отворів площею 2.88 м2
кожен.
7. ЦИВІЛЬНА БЕЗПЕКА
.1 Вступ
В даному розділі, об’єктом дослідження є хімічна лабораторія
кафедри ХТНГ. В ній проводилися експерименти даної дипломної роботи, тема якої
«Оксидаційне знесірчування прямогонного та гідроочищеного дизельного палива ».
Вона розташована на першому поверсі, навчального корпусу №8, Національного
університету «Львівська політехніка». Площа лабораторії становить 28 м2.
В лабораторії, в середньому, перебуває три особи.
Хімічна лабораторія є об’єктом підвищеної небезпеки через
наявність багатьох небезпечних факторів. Так, як і в будь-якій хімічній
лабораторії, в ній зберігаються різноманітні речовини, багато з яких є
отруйними та вибухопожежонебезпечними, а це - головні фактори небезпеки. Також
до небезпечних факторів можна віднести наявність балонів зі стисненими газами,
зокрема азотом та киснем, наявність газового обладнання (пальники), а також
електричної пічки.
Основні отруйні та вибухонебезпечні речовини наявні в
лабораторії наведені в табл. 7.1.
Таблиця 7.1. Характеристика отруйних та вибухонебезпечних
речовин, які наявні в лабораторії
Речовина
|
Максимальна Кількість, л
|
ГДК мг/м3
|
Клас отруйності
|
Температура спалаху, ºС
|
Концентр. межі вибуху, % об.
|
|
|
|
|
|
НГВ
|
ВГВ
|
Дизельне паливо
|
50.0
|
--
|
--
|
--
|
--
|
--
|
Оцтова кислота
|
3.0
|
5
|
ІІІ
|
38
|
5.0
|
16.0
|
Сірчана кислота
|
4.0
|
1 (пари)
|
ІІ
|
-
|
-
|
-
|
7.2 Розрахунок надлишкового тиску вибуху
В хімічній лабораторії може скластися багато небезпечних
ситуацій, які несуть загрозу здоров’ю людини. Але найнебезпечнішою та
найімовірнішою є така ситуація, яка може скластися у випадку розливу дизельного
палива, а це може спричинити пожежу. Дана ситуація ускладнюється присутністю
балону з киснем, який при розгерметизації, значно посилить горіння. Також,
окрім пожежі, можлива ще більш небезпечна ситуація - вибух. Він може відбутися
у випадку утворення вибухової суміші дизельного палива з повітрям, при його
випаровуванні.
Для визначення критеріїв вибухопожежної небезпеки, при
винекнені такої ситуації, як розрахунковий варіант, вибираємо найбільш
несприятливий варіант такої ситуації, при якому у вибуху бере участь все наявне
в лабораторії дизельне паливо (50 літрів).
Проведемо розрахунок надлишкового тиску при вибуху дизельного
палива в приміщенні [177]. Вихідні дані для розрахунку наведені в табл.7.2 та
табл.7.3.
Таблиця 7.2 Характеристика горючої речовини
Горюча речовина
|
Об’єм ГР, м3
|
Густина ГР, кг/м3
|
Хімічна формула
|
Молярна маса, кг/кмоль
|
Температура повітря, оС
|
Густина повітря, кг/м3
|
Маса ГР, кг
|
Дизельне паливо
|
5∙10-2
|
850
|
|
209.70
|
20
|
1,29
|
42.50
|
Таблиця 7.3 Характеристика приміщення
Приміщення
|
Площа приміщення, м2
|
Об’єм приміщення, м3
|
Площа випаровування, м2
|
Тиск в приміщенні, кПа
|
Лабораторія
|
28
|
126
|
28
|
101
|
Надлишковий тиск при вибуху обчислюється за наступною
формулою:
(7.1.)
де: Δр - тиск вибуху, кПа;- маса горючої
речовини у вибуховій суміші, кг;- теплота згорання цієї речовини, кДж/кг;-
безрозмірний коефіцієнт, який враховує, що не вся горюча речовина, яка
знаходиться у вибуховій суміші, знаходиться в області вибуховості.
рo - тиск в приміщенні, кПа;- вільний об’єм
приміщення, м3. Приймають як 0,8 від геометричного об’єму
приміщення;
ρ - густина вибухової суміші
(приймають рівною густинні повітря), кг/м 3;
с - теплоємність вибухової суміші (приймають рівною
теплоємності повітря), кДж/кг∙К;o - початкова температура, К;-
безрозмірний коефіцієнт, який враховує неадіабатичність вибуху.
с≈1,01кДж/кг∙К; К = 3; Q = 46000 кДж/кг; z = 0,3
- як для рідин.
Вільний об’єм приміщення:
V=Vпр·0,8=126·0,8=100,8 м3 (7.2.)
Обчислюємо, яка маса дизельного палива випарується при
проливі 50 л.
(7.3.)
де:
,
кг/м2∙с - питома швидкість випаровування,
де: η - коефіцієнт, що залежить від швидкості і
температури повітряного потоку над поверхнею випаровування. Приймаємо η = 2.
М - молярна маса рідини, що випаровується, кг/кмоль;
Рп - тиск насиченої пари при розрахунковій температурі,
визначається за довідниковими даними, кПа. Приймаємо рівне 18 кПа;- площа
випаровування (при розливі 1л рідини рівна 1 м2), м2;
τ - час випаровування (приймається рівним часу повного
випаровування, але на більше 3600с), с.
Отже, випарується все дизельне паливо.
Надлишковий тиск вибуху:
(7.4.)
Ударна хвиля вибуху, надлишковий тиск якого 513.13 кПа,
приводить до смерті.
Вибух такої сили спричиняє повну деформацію несучих
конструкцій, руйнування більшої частини перекриттів, стін і устаткування.
Відновлення елемента не можливе [178].
.3 Попередження і унеможливлення надзвичайної ситуації
Для попередження і унеможливлення описаної вище надзвичайної
ситуації (пожежі чи вибуху), необхідно здійснювати наступні заходи. А саме дотримуватися
двох основних принципів вибухопожежобезпеки [178]:
- робити все можливе, щоб в лабораторії не було джерел
запалювання;
- робити все можливе, щоб не утворилась вибухова
суміш;
Якщо розглядати ці принципи конкретніше, то можна
сформулювати такі вимоги:
- перед тим, як приступати до нового виду
вогненебезпечної, чи вибухонебезпечної роботи, необхідно попередньо пройти
інструктаж по техніці безпеки у свого керівника;
- всі роботи з легкозаймистими горючими рідинами
проводять у витяжній шафі при увімкненій вентиляції. При роботі з
вибухонебезпечними речовинами використовують захисні екрани і інші захисні
засоби згідно інструкції. Просочені ЛЗР та ГР тканини треба збирати в металеві
ящики, які щільно закриваються кришками. Необхідно бути дуже обережним, щоб
звести імовірність проливу до мінімуму, а також обмежити кількість рідини, яка
може вилитись. Розлиті ЛЗР та ГР необхідно негайно зібрати, а місця проливу
засипатися піском. Електроосвітлення повинно бути у вибухобезпечному виконанні;
у лабораторії категорично забороняється куріння;
- якщо лабораторні операції проводити неправильно, а
також в аварійних ситуаціях, можливе потрапляння парів легкозаймистих речовин в
атмосферу та утворення пожежовибухонебезпечних концентрацій. Тому будь-які
роботи з легкозаймистими речовинами необхідно проводити у витяжній шафі
(вентиляція - це ефективний засіб для попередження утворення
пожежовибухонебезпечних концентрацій горючих парів);
- реактиви слід зберігати у спеціально відведених
місцях, зокрема, у товстостінних пляшках, об’ємом не більше 1 л з герметичними
пробками. В лабораторних приміщеннях не допускається зберігання навіть
невеликих кількостей легкозаймистих речовин з температурою кипіння нижче 50°С. Зберігання інших
легкозаймистих речовин допускається в товстостінних пляшках місткістю не більше
1 л, які оснащені герметичними корками. Пляшки з легкозаймистими речовинами
поміщають в спеціальні металеві ящики з написом «ЛЗР», встановлені подалі від
джерел тепла. Забороняється виливати відходи легкозаймистих речовин в
каналізацію. Лабораторія повинна бути забезпечена первинними засобами
пожежегасіння;
До первинних засобів пожежегасіння відносять [178]:
- сирий пісок. Його використовують у тому випадку, коли
вода є не ефективним засобом пожежегасіння. Пісок слід зберігати в металевому
ящику;
- азбестове полотно. При гасінні пожежі його
використовують в тому випадку, коли нема заперечення з боку властивостей
речовини;
вуглекислотні вогнегасники. Це є обов’язковий елемент,
який повинен бути наявним у кожній хімічній лабораторії;
- на випадок виникнення пожежі чи аварії, в будівлі
повинні бути передбачені евакуаційні шляхи і виходи. В корпусі повинно бути не
Ширина шляху евакуації повинна бути достатньою для евакуації людей (вибирається
в залежності від кількості працюючих). На кожному поверсі є план евакуації. На
шляху евакуації повинно бути освітлення (автономне джерело освітлення).
ВИСНОВКИ
1. В процесі написання даної дипломної роботи був проведений
огляд літератури, під час якого розглянуто процеси знесірчування вуглеводневої
сировини.
2. Як сировину, було відібрано і проаналізовано три
прямогонні фракції і один гідрогенізат.
. Для характеристики, та оцінки ефективності
оксидаційного знесірчування дизельного палива розраховано та опрацьовано
методики досліджень і визначення показників якості сировини й продуктів
процесу.
. Виходячи із проведених досліджень і розрахунків та
враховуючи потребу досягнення максимальних ступеня вилучення сірчистих сполук й
виходу очищеного палива, оптимальними слід підтримувати тиски на рівні 2,5-3,0
МПа.
. В ході досліджень різних типів сировини встановлено,
що при використанні сировини з порівняно низьким вмістом сірки, вдається
отримати очищене паливо з вмістом сірки < 0.2. % мас.
Отримані результати також показують, що при використанні
гідрогенізату вдається вилучити більше ніж 85 % сірки, що залишилася після
процесу гідроочистки та отримати паливо з вмістом сірки до 0.05 % мас.
При використанні ШДФ або її важчих фракцій, оксидацій не
знесірчування проходить менш інтенсивно, що можна пояснити наступними
причинами:
зі збільшенням температури кипіння фракцій
зменшується різниця між температурами випаровування вихідних сірчистих речовин
та їх окиснених аналогів; вказаний чинник та розширення фракційного складу
утруднює виділення продуктів окиснення ректифікацією;
- у «важчій» сировині міститься більша кількість
тіофенової сірки, яка, порівняно з сполуками меркаптанового, сульфідного та
дисульфідного рядів, окислюється повільніше.
6. На основі результатів досліджень фр. > 320
ºС ШДФ1,
складено матеріальний баланс.
7. Було розроблено принципову технологічну схему процесу.
. В ході написання економічної частини були визначені
статті витрат на проведення дослідження у лабораторних умовах та розраховано
економічний ефект досліджень.
Показано, що оксидаційне знесірчування буде дешевшим
порівняно з процесом гідроочищення.
. В розділі охорони праці, описані потенційно небезпечні
фактори при роботі у хімічній лабораторії, вказано заходи забезпечення безпеки
експлуатації лабораторного обладнання і проведення лабораторних досліджень,
санітарно-гігієнічні заходи і засоби індивідуального захисту.
. В розділі цивільної безпеки об’єктом дослідження була
лабораторія, в якій проводилися дослідження.
Як варіант небезпечної ситуації, був розглянутий вибух 50 л. дизельного
палива і проведений розрахунок надлишкового тиску вибуху. Описано заходи, які
необхідно здійснювати, для попередження і унеможливлювання згаданої
надзвичайної ситуації.
СПИСОК ВИКОРИСТАНОЇ ЛІТЕРАТУРИ
1. Магарил Р.З. Теоретические основы процессов
переработки нефти. - М.: Химия, 1996. - 543 с.
2. Химия нефти и газа / Под ред. Проскурякова
В.А. - Л.: Химия, 1989. - 422 с.
. Черножуков Н.И., Крейн С.Э. Окисляемость
минеральных масел / Н.И. Черножуков, С.Э. Крейн - Гостоптехиздат, 1955. - 385
с.
. Большаков Г.Ф. Образование гетерогенной
системы при окислении углеводородных топлив. - Новосибирск: Наука, 1990. - 312
с.
. Смидович Е.В. Технология переработки нефти и
газа. Ч.2. - М.: Химия, 1980. - 328 с.
. Большаков Г.Ф., Чертков Я.Б. Топлива для реактивных
двигателей / Г.Ф. Большаков, Я.Б. Чертков - Л.: Недра, 1964. - 157 с.
. Кружалов Б.Д., Голованенко Б.И. Совместное
получение фенола и ацетона / Б.Д. Кружалов, Б.И. Голованенко - М.:
Государственное науч.-техн. изд-во хим. литературы, 1963. - 197 с.
. Кулиев А.М. Химия и технология присадок к
маслам и топливам. - М.: Химия, 1972. - 358 с.
. Нейланд О.Я. Органическая химия. - М.: Высшая
школа, 1990. - 750 с.
10. Гуреев А.А. Химмотология / Гуреев А.А., Фукс
И.Г., Лашхи В.Л. - М.: Химия, 1986. - 366с.
11. Караулова Е.Н. Химия сульфидов нефти. - М.:
Наука, 1970. - 202 с.
. Эмануэль Н.М. Цепные реакции окисления
углеводородов в жидкой фазе / Эмануэль Н.М., Денисов Е.Т., Майзус З.К. - М.:
Наука, 1965. - С. 291.
. Большаков Г.Ф. Физико-химические основы образования
осадков в реактивных топливах. - Л.: Химия, 1972. - 232 с.
. Школьников В.М. Топлива, смазочные материалы,
технические жидкости. Ассортимент и применение.: Справочник. - М.: Техинформ,
1999. - 596 с.
. Химия органических соединений серы / Под ред.
Беленького Л.И. - М.: Химия, 1988. - 318 с.
. Большаков Г.Ф. Сероорганические соединения
нефти. - Новосибирск: Наука, 1986. - 246 с.
. Чертков Я.Б. Современные и перспективные
углеводородные реактивные и дизельные топлива. - М.: Химия, 1968. - 355 с.
. ХІV Научная сессия по химии и технологии
органических соединений серы и сернистых нефтей / [Л.Б. Авдеева, А.В. Машкина,
А.Х. Шарипов, та ін.] - Рига: Зинатне, 1976. - 245-246 с.
. Каталитическое окисление сульфидов дистиллата
190¸360
°С нефти в сульфоксиды кислородом
воздуха / [А.В. Машкина, А.Х. Шарипов, Н.К. Ляпина, та ін. ] - М.: Нефтехимия,
1984. - 106-114 с.
. Окисление сульфидов нефти пероксидом водорода
в присутствии карбонильных соединений / [А.Х. Шарипов, Р.М. Масагутов, З.А.
Сулейманова, та ін.] - М.: Нефтехимия, 1989. - 551-555 с.
. Дудина Р.И. Исследование жидкофазного
окисления нефтяных сульфидов кислородом воздуха в присутствии хлорида меди /
Дудина Р.И., Авдеева Л.Б, Власова Л.В. - М.: Нефтехимия, 1979. - 462-467 с.
. Жидкофазное окисление диэтилсульфида
кислородом в медьсодержащих катализаторах / [Г.В. Варнакова, А.В. Машкина, Н.П.
Кирик, та ін ] - М.: Кинетика и катализ, 1984. - 837-841 с.
. Окисление сульфидов и сульфоксидов
кислородом, катализируемое галогенидами меди в растворе ацетона / [А.В.
Машкина, Г.В. Варнакова, Л.М. Загряцкая, та ін. ] - М.: Кинетика и катализ,
1981. - 607-612 с.
. Гальперн Г.Д. Гетероатомные компоненты нефти.
- М.: Успехи химии, 1976. - 1395-1427 с.
. Караулова Е.Н. Химия сульфидов нефти. - М.:
Наука, 1970. - 202 с.
. Получение сульфоксидов озонолизом сульфидов в
эфирных растворителях. Т. XIX, № 2 / [В.Н. Одиноков, О.С.Куковинец, Г.Ю.
Ишмуратов, та ін.] - М.: Нефтехимия, 1979. -- 269-272 с.
. D. Jerchel, L. Dippelhofer, D. Renner. /
Chem. Ber. - 1954. - V. 87. - 947 р.
. L. Ostrowski, W. Leśniański. / Roczn. Chem. - 1957. -
V. 31. - 1327р.
. EPA-Gasoline RIA, Regulatory Impact
Analysis-Control of Air Pollution from New Motor Vehicles: Tier 2 Motor Vehicle
Emissions Standards and Gasoline Sulfur Control Requirements. US Environmental
Protection Agency, Air and Radiation, EPA420-R-99-023. December 1999.
. EPA-RFG-II, Phase II RFG Report on
Performance Testing. US Environmental Protection Agency, Air and Radiation,
EPA420-R-99-025. April 1999.
. Directive of the European Parliament and of
the Council. Brussels COM. 2001. 11.05.
. EPA, Control of Air Pollution from New Motor
Vehicles Amendment to the Tier-2/Gasoline Sulfur Regulations. US Environmental
Protection Agency. April 13, 2001.
33. Dixson-Decleve, S. World Refining.
September/October 2004, 14, 7-19.
. EPA-Diesel RIA, Regulatory Impact Analysis:
Heavy-duty Engine and Vehicle Standards and Highway Diesel Fuel Sulfur Control
Requirements. United States Environmental Protection Agency, Air and Radiation,
EPA420-R-00-026. December 2000.
35. EPA, EPA Gives the Green Light on Diesel Sulfur
Rule, Press Release. United States Environmental Protection Agency. February
28, 2001.
. Ohmes, R. Hydrocarbon processing. February
2005, 84 (2), 39-43.
37. Anonymous.
Lukoil Confirms 10-ppm ULSD Production at Perm Refinery
<http://proquest.umi.com.libproxy.rpi.edu/pqdweb?index=24&did=887992471&SrchMode=3&sid=3&Fmt=3&VInst=PROD&VType=PQD&RQT=309&VName=PQD&TS=1129151401&clientId=8470&aid=2>.
World Refining. Houston. Jul 2005, 15, 4-17.
. Anonymous.
Lithuanian Refiner Investing for 'Sulfur-Free' Gasoline
<http://proquest.umi.com.libproxy.rpi.edu/pqdweb?index=41&did=842544031&SrchMode=3&sid=2&Fmt=3&VInst=PROD&VType=PQD&RQT=309&VName=PQD&TS=1129160647&clientId=8470&aid=1>.
World Refining. Houston. Apr/May 2005, 15, 3-14.
. Anonymous.
Czech Refiner Claims 10-ppm Sulfur Fuels Production
<http://proquest.umi.com.libproxy.rpi.edu/pqdweb?index=30&did=795993121&SrchMode=3&sid=4&Fmt=4&VInst=PROD&VType=PQD&RQT=309&VName=PQD&TS=1129161222&clientId=8470&aid=1>.
World Refining. Houston. Jan/Feb 2005, 15, 1-14.
40. ДСТУ 3868-99 Паливо дизельне. Технічні умови. -
Заменяет: ГОСТ 305-82. Введ. 8 квітня 1999 р. № 179: - УкрНДІНП «МАСМА», ТК 38.
41. Окисляемость и стабилизация экологически
чистого дизельного топлива. № 3. / [Т.В. Попова, Т.П. Вишнякова, В.В. Юречко,
В.И.Фролов] - М.: ХТТМ, 1995. -- 18-20 с.
42. Babich I. V.,
Moulijn J. A. Science and technology of novel processes for deep
desulfurization of oil refinery streams: a review // Fuel. <http://www.sciencedirect.com.libproxy.rpi.edu/science?_ob=JournalURL&_cdi=5726&_auth=y&_acct=C000035878&_version=1&_urlVersion=0&_userid=659639&md5=0650e92b0ecc570279d4acd93a0bd89f>2003,
82 (6 <http://www.sciencedirect.com.libproxy.rpi.edu/science?_ob=IssueURL&_tockey=%23TOC%235726%232003%23999179993%23380566%23FLA%23&_auth=y&view=c&_acct=C000035878&_version=1&_urlVersion=0&_userid=659639&md5=1e433a6a7b9034c0fea1acea15b86ea8>),
607-631.
43. Химия нефти / Под ред. Сюняева З.И. - Л.: Химия,
1984. - 359 с.
44. Мин Р.С. Хроматографическое выделение сернистых
соединений нефти через комплексы с хлоридами металлов. / Р.С. Мин, Л.Н. Бауер -
М.: НПНХ, 1997. - № 3, 20-23 с.
. Ляпина Н.К. Химия и физико-химия
сераорганических соединений нефтяных дистиллятов. - М.: Химия, 1984. - 118 с.
. Технология катализаторов / Под ред. Мухленова
И.П. - Л.: Химия, 1989. - 271 с.
. Черножуков Н.И. Технология переработки нефти
и газа. Ч.3. Очистка и разделение нефтяного сырья, производство товарных
нефтепродуктов. - М.: Химия, 1978. - 423 с.
48. Nina Kolbe, Oliver van Rheinberg and Jan T.
Andersson. Influence of Desulfurization Methods on the Phenol Content and
Pattern in Gas Oil and Diesel Fuel // Energy Fuels, 2009, 23 (6), pp 3024-3031.
49. Oliver van
Rheinberg, Klaus Lucka, Heinrich Köhne, Thomas Schade and Jan T.
Andersson<http://www.sciencedirect.com/science?_ob=ArticleURL&_udi=B6V3B-4S9NDTD-1&_user=10&_coverDate=10%2F31%2F2008&_alid=1011401746&_rdoc=18&_fmt=high&_orig=search&_cdi=5726&_docanchor=&view=c&_ct=120&_acct=C000050221&_version=1&_urlVersion=0&_userid=10&md5=1386708fb7941678cceba74f3dcc9c5b>
Selective removal of sulphur in liquid fuels for fuel cell applications //
Fuel, Volume 87, Issues 13-14, October 2008, Pages 2988-2996
50. Journal of
Molecular Catalysis A: Chemical, Volume 160, Issue 2, 31 October 2000, Pages
409-427 Xiaoliang Ma and Harold H. Schobert.
. Каталитическое
окисление сульфидов средних дистиллятов сернистой нефти / [Шарипов А.Х.,
Нигматуллин В.Р., Нигматуллин И.Р., Закиров Р.В.] - М.: ХТТМ, 2006. - № 6. -
45-51 с.
. Savage,
David W.
<http://www.patentstorm.us/inventors-patents/David_W__Savage/1793059/1.html>
Kaul, Bal K.
<http://www.patentstorm.us/inventors-patents/Bal_K__Kaul/1659922/1.html>
Dupre, Gerald D. <http://www.patentstorm.us/inventors-patents/Gerald_D__Dupre/2009858/1.html>
O'Bara, Joseph T.
<http://www.patentstorm.us/inventors-patents/Joseph_T__O_Bara/1659923/1.html>Wales,
William E. <http://www.patentstorm.us/inventors-patents/William_E__Wales/1793063/1.html>
Ho, Teh C.
<http://www.patentstorm.us/inventors-patents/Teh_C__Ho/941641/1.html> US
Patent 5454933 - Deep desulfurization of distillate fuels US Patent Issued on
October 3, 1995 <http://www.patentstorm.us/patents-by-date/1995/1003/1.html>
Estimated Patent Expiration Date: October 3, 2012
. Khare,
Gyanesh P.
<http://www.patentstorm.us/inventors-patents/Gyanesh_P__Khare/704502/1.html>
Engelbert, Donald R.
<http://www.patentstorm.us/inventors-patents/Donald_R__Engelbert/1490271/1.html>
Cass, Bryan W. <http://www.patentstorm.us/inventors-patents/Bryan_W__Cass/908146/1.html>
US Patent 6056871 - Transport desulfurization process utilizing a sulfur
sorbent that is both fluidizable and circulatable and a method of making such
sulfur sorbentUS Patent Issued on May 2, 2000
<http://www.patentstorm.us/patents-by-date/2000/0502/1.html>Estimated
Patent Expiration Date: January 12, 2019.
. Химия и
физика нефти и нефтехимический синтез / [Улендеева А.Д., Никитина Т.С., Ляпина
Н.К. и др]. - Уфа: 1976. - 219-223 с.
55. Funakoshi,
Izumi
<http://www.patentstorm.us/inventors-patents/Izumi_Funakoshi/2885428/1.html>
Aida, Tetsuo
<http://www.patentstorm.us/inventors-patents/Tetsuo_Aida/2885429/1.html>
US Patent 5753102 - Process for recovering organic sulfur compounds from fuel
oil US Patent Issued on May 19, 1998
<http://www.patentstorm.us/patents-by-date/1998/0519/1.html> Estimated
Patent Expiration Date: October 3, 2015Estimated Expiration Date is calculated
based on simple USPTO term provisions. It does not account for terminal
disclaimers, term adjustments, failure to pay maintenance fees, or other
factors which might affect the term of a patent.
56. 133. US Patent
5582714 - Process for the removal of sulfur from petroleum fractions US Patent
Issued on December 10, 1996 <http://www.patentstorm.us/patents-by-date/1996/1210/1.html>
Estimated Patent Expiration Date: March 20, 2015 Forte, Paulino
<http://www.patentstorm.us/inventors-patents/Paulino_Forte/1549565/1.html>
57. 134. Horii, Yuji
<http://www.patentstorm.us/inventors-patents/Yuji_Horii/2051424/1.html>
Onuki, Hitoshi
<http://www.patentstorm.us/inventors-patents/Hitoshi_Onuki/2051425/1.html>
Doi, Sadaaki
<http://www.patentstorm.us/inventors-patents/Sadaaki_Doi/2051426/1.html>
Mori, Toshiatsu <http://www.patentstorm.us/inventors-patents/Toshiatsu_Mori/2051427/1.html>
Takatori, Takeo
<http://www.patentstorm.us/inventors-patents/Takeo_Takatori/2051428/1.html>
Sato, Hideaki
<http://www.patentstorm.us/inventors-patents/Hideaki_Sato/2051429/1.html>
Ookuro, Tsuyoshi <http://www.patentstorm.us/inventors-patents/Tsuyoshi_Ookuro/2051430/1.html>
Sugawara, Toru
<http://www.patentstorm.us/inventors-patents/Toru_Sugawara/2051431/1.html>
US Patent 5494572 - Desulfurization and denitration of light oil by extraction
US Patent Issued on February 27, 1996
<http://www.patentstorm.us/patents-by-date/1996/0227/1.html> Estimated
Patent Expiration Date: June 2, 2015
58. Nan Hee Ko, Je Seung Lee, Eun Soo Huh, Hyunjoo
Lee, Kwang Deog Jung, Hoon Sik Kim and Minserk Cheong. Extractive
Desulfurization Using Fe-Containing Ionic Liquids // Energy Fuels, 2008, 22
(3), pp 1687-1690.
59. Huaming Li,
Lining He, Jidong Lu, Wenshuai Zhu, Xue Jiang
<http://pubs.acs.org/doi/abs/10.1021/ef800797n?prevSearch=desulfurization&searchHistoryKey=>
, Yan Wang <http://pubs.acs.org/doi/abs/10.1021/ef800797n?prevSearch=desulfurization&searchHistoryKey=>
and Yongsheng Yan
<http://pubs.acs.org/doi/abs/10.1021/ef800797n?prevSearch=desulfurization&searchHistoryKey=>.
Deep Oxidative Desulfurization of Fuels Catalyzed by Phosphotungstic Acid in
Ionic Liquids at Room Temperature //Energy Fuels, 2009, 23 (3), pp 1354-1357.
. Dishun Zhao,
Zhimin Sun, Fatang Li, Ran Liu and Haidan Shan
<http://pubs.acs.org/doi/abs/10.1021/ef800162w?prevSearch=desulfurization&searchHistoryKey=>
Oxidative Desulfurization of Thiophene Catalyzed by (C4H9)4NBr·2C6H11NO
Coordinated Ionic Liquid // Energy Fuels, 2008, 22 (5), pp 3065-3069.
61. Красногорская Н.Н. Экстракция средних нефтяных
фракций / Красногорская Н.Н., Габдикеева А.Р., Грушевенко А.Э. - М.: Химия,
1989. - 72 с.
62. Экстракционная технология производства
экологически чистых дизельных и реактивных топлив / [Гайле А.А., Сомов В.Е.,
Семенов Л.В., Залищевский Г.Д., Варшавский О.М., Колдобская Л.Л., Кайфаджян
Е.А].-ХТТМ. - 1999. - № 5. - С. 3-7.
. Чертков Я.Б. Сернистые и кислородные
соединения нефтяных дистиллятов /Я. Чертков, Спиркин В.Г. - М.: Химия, 1971. -
312 с.
. Чертков Я.Б. Применение серной кислоты для
извлечения сероорганических соединений из нефтяных фракций / Чертков Я.Б.,
Спиркин В.Г., Демишев В.Н. - Нефтехимия. - 1965. - Т. 5, № 5. - С. 741.
. Улендеева А.Д. Химия и физика нефти и
нефтехимический синтез / Улендеева А.Д., Никитина Т.С., Ляпина Н.К. - Уфа,
1976. - С. 219-223.
. А.с. 1502602 СССР, МКИ С 10 G 29/2, 29/06.
Способ очистки нефтепродуктов от сероорганических соединений / Р.С. Мин, И.А.
Савинова, А.Н. Плюснин (СССР). - № 4328034/23-04; Заявл. 17.11.87; Опубл.
23.08.89; Бюл. № 31, 1989. - 2 с.
. А.с. 1505960 СССР, МКИ С 10 G 29/12. Способ
очистки нефтепродуктов от сероорганических соединений / С.М. Лещев, С.Ф. Фукс,
Е.М. Рахманько (СССР). - № 4322728/23-04; Заявл. 29.10.87; Опубл. 7.09.89; Бюл.
№ 33, 1989. - 3 с.
. Взаимодействие водного раствора ацетата ртути
с меркаптанами, сульфидами и дисульфидами.: Сообщение II / VI Научная сессия по
химии сераорганических соединений нефтей и нефтепродуктов / Данилова Т.А.,
Тиц-Скворцова И.Н., Насыров И. - Уфа. - 1961. - С. 77-78.
. Использование реакции комплексообразования
для разделения и концентрирования сернистых соединений нефти / Материалы IV
Междунар. конф. “Химия нефти и газа”. / Бауер Л.Н., Мин Р.С. - Т.1. Секция А. -
Томск. - 2000. - С. 88-91.
. Никитина В.С. Выделение сульфидов из
сернистых концентратов нефти / Никитина В.С., Ляпина Н.К., Улендеева А.Д.
Нефтехимия. - 1970. - Т. X, № 4. - С.594-598.
. Valérie Meille, Emmanuelle
Schulz, Michel Vrinat and Marc Lemaire A new route towards deep
desulfurization: selective charge transfer complex formation // Chem. Commun.,
1998, 305 - 306.
. Alexandra Milenkovic, Emmanuelle Schulz, Valérie Meille, David Loffreda,
Michel Forissier, Michel Vrinat, Philippe Sautet, and Marc Lemaire. Selective
Elimination of Alkyldibenzothiophenes from Gas Oil by Formation of Insoluble
Charge-Transfer Complexes // Energy Fuels, 1999, 13 (4), pp 881-887.
73. Суханов В.П. Каталитические процессы в
нефтепереработке / Суханов В.П. - М.: Химия, 1979. - 344 с.
74. National Petroleum Council Study: Proposed
Regulations // Oil & Gas Journal. - 2000. - July 17. - pp. 60-63.
75. Diehl F., Chapus N., Kasztelan S., Morel F. New
challenges in catalyst selection // Hydrocarbon Engineering. - 1999. - V. 4, №
3. - pp. 67-70.
76. Рудин М.Г. Краткий справочник
нефтепереработчика / Рудин М.Г., Драбкин А.Е. - Л.: Химия, 1980. - 327 с.
77. Catalytic hydrodesulfurization of gas oil and model
sulfur compounds over commercial and laboratory-made CoMo and NiMo catalysts:
Activity and reaction scheme Catalysis Today, Volume 39, Issues 1-2, 3 December
1997, Pages 13-20 Emmanuel Lecrenay, Kinya Sakanishi and Isao Mochida.
78. Матвейчук А. Каталитические процессы
нефтепереработки: реальность и надежды / Матвейчук А. - Нефть России. - 1997. -
№ 9. - С. 42-46.
79. Активизация катализатора гидроочистки ГО-30-7
элементной серы в реакторе с радиальным вводом сырья / [ Крылов В.А., Штерман
Б.М., Дианов В.Ф., Аликин А.Г.]. - НПНХ. - 1991 - № 8. - С. 9-11.
. Цеолитсодержащие катализаторы в процессе
гидроочистки нефтяных фракций / [Алиев Р.Р., Овсянников В.А., Григорьев Н.А.,
Вязков В.А.]. -НПНХ. - 1993. - № 8. - С. 9-11.
. Сидельковская В.Г. Роль цеолитного компонента
в улучшении каталитических, эксплуатационных и регенерационных свойств
катализаторов гидроочистки / Сидельковская В.Г., Алиев Р.Р. ХТТМ. - 1994. - №
4. - С. 14-18.
. Хвостенко Н.Н. Перевод установки гидроочистки
дизельного топлива Л-24/6 на новый алюмоникельмолибденовый катализатор /
Хвостенко Н.Н., Овчинников В.Н., Лебедев Б.Л. - НПНХ. - 1997. - № 1. - С .
21-22.
. Колесников И.М. Гомогенно-каталитическое
гидродесульфирование нефтяных фракций / Колесников И.М., Колесников С.И.,
Рахман Арифур. - ХТТМ. - 1995. - № 1. - С. 9-11.
. Предсульфидирование катализаторов
гидроочистки элементной серой вне реактора / [Насиров Р.К., Дианова С.А.,
Ковальчук Н.А., Насиров И.Р.]. - ХТТМ. - 1998. - № 6. - С. 19-22.
. Производство малосернистых дизельных топлив
на Ново-Уфимском НПЗ с применением отечественных катализаторов гидроочистки /
[Халманских П.В., Беликов Д.О., Муниров А.Ю., Мухарямов Ф.С., Мотов М.В.]. -
НПНХ. - 1999. - № 2. - С. 13-15.
. Отечественные катализаторы для производства
дизельного топлива с улучшенными экологическими характеристиками / [Смирнов
В.К., Сайфуллин Н.Р., Калимуллин Н.Р., Ганцев В.А., Мотов М.В.]. - ХТТМ. -
1999. - № 4.- С.6-9.
. Смирнов В.К. Новые катализаторы для
гидрооблагораживания нефтяных фракций / Смирнов В.К., Капустин В.М., Ганцев
В.А. - ХТТМ. - 2002. - № 3. - С. 3-7.
. Улучшение стабильности углеводородных топлив
с помощью антиокислительных присадок / [Вишнякова Т.П., Голубева И.А., Попова
Т.В., Попандопуло И.В., Терехин С.Н., Харитонов В.В.]. - ХТТМ. - 1990. - № 7. -
С. 28-30.
. Спиркин В.Г. Противоизносные свойства
дизельных топлив с улучшенными экологическими характеристиками / Спиркин В.Г.,
Мурашев С.В. - ХТТМ. - 1999. - № 3. - С. 29-30.
. Митусова Т.Н. Влияние качества дизельных
топлив на их противоизносные свойства / Митусова Т.Н., Полина Е.В., Калинина
М.В. - НПНХ. - 1999. - № 4. - С.8-11.
91. Улучшение смазочных свойств дизельных топлив /
[Митусова Т.Н., Логинов С.А., Полина Е.В., Рудяк К.Б., Капустин В.М.]. - ХТТМ.
- 2002. - № 3. - С. 24-25.
92. Frederick, Ford John Arrowsmith, Rayne Timothy
George, Adlington Dennis United States Patent 3341448. Inventors: Frederick,
Ford John Arrowsmith, Rayne Timothy George, Adlington Dennis. Publication Date:
09/12/1967 Desulphurization of hydrocarbons using oxidative and
hydro-treatments.
93. А.с. 1549985 СССР, С 10 G 27/12. Способ очистки
легких углеводородных фракций от сернистых соединений / З.А. Сулейманова, В.М.
Колычев, М.А. Паис и др. (СССР). - № 4335292/23-04; Заявл. 26.11.87; Опубл.
15.03.90; Бюл. № 10, 1990. - 3 с.
94. Лукъяница В.Г. Окисление нефтяных сульфидов
диоксидом азота / Лукъяница В.Г., Гальперн Г.Д. - Нефтехимия. - 1985. - Т. XXV,
№ 1. - С. 103-109.
. Лунин В.В. Обессеривание и деметаллизация
тяжелых фракций нефти путем озонолиза и радиолиза / Лунин В.В., Французов В.К.,
Лихтерова Н.М. - Нефтехимия. - 2002. - Т. 42, № 3. - С. 195-202.
. Превращение углеводородов нефти под действием
пучка активных электронов и озона / [Лунин В.В., Лихтерова Н.М., Торховский
В.Н., Саенко В.Б., Богачева А.Н., Калиничева О.Н.]. - ХТТМ. - 1999. - № 4. - С.
38-43.
. Ngo Yeung Chan, Ting-Yang Lin and Teh Fu Yen.
Superoxides: Alternative Oxidants for the Oxidative Desulfurization Process
Energy Fuels, 2008, 22 (5), pp 3326-3328.
98. J. G.Schulz,
<http://www.patentstorm.us/inventors-patents/Johann_G__Schulz/1767676/1.html>
J. J. Stanulonis,
<http://www.patentstorm.us/inventors-patents/John_J__Stanulonis/3337126/1.html>
W. R.Wajert,
<http://www.patentstorm.us/inventors-patents/William_R__Wajert/3454765/1.html>US
Patent 4280818 - Novel compositions of matter and process for utilizing same US
Patent Issued on July 28, 1981
<http://www.patentstorm.us/patents-by-date/1981/0728/1.html> Estimated
Patent Expiration Date: February 22, 2000
. Справочник
химика: В 3 т. - Л.: Госхимиздат, Лен-ое отдел., 1963. - Т 1.: Общие сведения,
строение вещества, физические свойства важнейших веществ, краткие сведения по
лабораторной технике. - 1070 с.
. Anonymous.
Shake the sulfur right out of fuel // Chemical Engineering Progress
<http://www.encyclopedia.com/Chemical+Engineering+Progress/publications.aspx?pageNumber=1>
May 1, 2001Copyright American Institute of Chemical Engineers May 2001.
. Yasuhiro
Shiraishi, Takayuki Hirai, and Isao Komasawa. A Deep Desulfurization Process
for Light Oil by Photochemical Reaction in an Organic Two-Phase Liquid−Liquid
Extraction System // Ind. Eng. Chem. Res., 1998, 37 (1), pp 203-211.
. System
Yasuhiro Shiraishi, Yasuto Taki, Takayuki Hirai, and Isao Komasawa. Visible
Light-Induced Deep Desulfurization Process for Light Oils by Photochemical
Electron-Transfer Oxidation in an Organic Two-Phase Extraction // Ind. Eng.
Chem. Res., 1999, 38 (9), pp 3310-3318.
. Yasuhiro
Shiraishi, Yasuto Taki, Takayuki Hirai, and Isao Komasawa. Visible
Light-Induced Desulfurization Process for Catalytic-Cracked Gasoline Using an
Organic Two-Phase Extraction System // Ind. Eng. Chem. Res., 1999, 38 (12), pp
4538-4544.
. Yasuhiro
Shiraishi, Takayuki Hirai, and Isao Komasawa. Photochemical Desulfurization and
Denitrogenation Process for Vacuum Gas Oil Using an Organic Two-Phase
Extraction System // Ind. Eng. Chem. Res., 2001, 40 (1), pp 293-303
. Deep
desulfurization of fuels catalyzed by surfactant-type decatungstates using H2O2
as oxidant <http://www.sciencedirect.com/science?_ob=ArticleURL&_udi=B6V3B-4V2PMN4-1&_user=10&_coverDate=03%2F31%2F2009&_alid=1011416203&_rdoc=13&_fmt=high&_orig=search&_cdi=5726&_st=13&_docanchor=&view=f&_ct=15&_acct=C000050221&_version=1&_urlVersion=0&_userid=10&md5=56a8be33e4e631e6e86740915d31aab4>
// Fuel, Volume 88, Issue 3, March 2009, Pages 431-436 Xue Jiang, Huaming Li,
Wenshuai Zhu, Lining He, Huoming Shu, Jidong Lu.
. Хроматографическое
выделение сульфоксидов из окисленных дистиллатов сернистых нефтей / [Караулова
Е.Н., Гальперн Г.Д., Аристова Л.Д., Бардина Т.А., Коршунова В.М.]. -
Нефтехимия. - 1965. - Т. V, № 5. - С. 753-759.
. Шарипов А.Х.
Получение концентратов сульфоксидов и сульфидов из нефтяного сырья (обзор) /
Шарипов А.Х. - Нефтехимия. - 1988. - Т. XXVIII, № 6. - С. 723-735.
. Шарипов А.Х.
Получение нефтяных серосодержащих реагентов для гидрометалургии / Шарипов А.Х.
- ХТТМ. - 1997. - № 3. - С. 9-17.
. Шарипов А.Х.
Концентраты сульфоксидов из нефтяного сырья. / Шарипов А.Х., Нигматуллин В.Р.,
Нигматуллин И.Р. ХТТМ. - 2002. - № 3. - С. 41-43.
. Asselin
G.F., Stormont D.H. Treating light refinery products // Oil and Gas J. - 1965.
- V. 63, №.1. - pp. 90-93.
. Демеркаптанизация
углеводородных фракций / [Безворотный П.В., Аликин А.Г., Мазгаров А.М.,
Вильданов А.Ф., Бажирова Н.Г.]. - НПНХ. - 1999. - № 7. - С.14-17.
. Petrolieri
D`Italia. - 1973. - V.20. - № 7. - P. 51-52.
. Соркин Я.Г.
Особенности переработки сернистых нефтей и охрана окружающей среды / Соркин
Я.Г. - М.: Химия, 1975 -294 с.
. Шарипов А.Х.
Окислительное обессеривание меркаптансодержащего сырья / Шарипов А.Х. - ХТТМ. -
1998. - № 4. - С. 9-13.
. Обезвреживание
технологических конденсатов на установке КТ-1 Павлодарского ПНЗ. / [мадуллина
А.Г., Куницын Б.М., Хрущева И.К., Орлова Л.Н., Вайнбендер В.Р., Котвицкий
В.Ф.]. - ТМ. - 1990. - № 10. - С. 32-33.
. Гетерогенно-каталитическая
емеркаптанизация легкого углеводородного сырья / [Ахмадулина А.Г., Кижаев Б.В.,
Нургалиева Г.М., Шабаева А.С., Тугуши С.О., Харитонов Н.В.]X. - 1994. - № 2. -
С. 39-41.
. Шарипов А.Х.
Использование полифталоцианина кобальта в процессах демеркаптанизации топлив и
газов / Шарипов А.Х. - М.: ЦНИИТЭ нефтехим, 1993. - С. 38-46.
. Шарипов А.Х.
Полифталоцианин кобальта как катализатор окисления меркаптанов / Шарипов А.Х.,
Кириченко Ю.В. - ХТТМ. - 1999. - № 1. - С. 33-35.
. Жадановский
Н.Б. Процесс демеркаптанизации топлив на окисно-цинковых катализаторах.
Переработка нефти: Тем. обзор. / Жадановский Н.Б., Беридзе Г.Ю., Дыдыкина З.Н.
- М.: ЦНИИТЭнефтехим. - 1989.
. Евдокимов
Е.В. Активация окисдноцинкового катализатора газом риформинга / Евдокимов Е.В.,
Путилова К.Л. - ХТТМ. - 1990. - № 3. - С . 11.
. Никитин Ю.Е.
Химия экстракции сульфоксидами / Никитин Ю.Е., Муринов Ю.И., Розен А.М. -
Успехи химии. - 1976. - Т. XLV. - Вып. 12. - С. 2233-2252.
. Утилизация
продуктов демеркаптанизации углеводородного сырья / [Ахметов Л.И., Колбин А.М.,
Исмагилов Ф.Р., Подшивалин А.В., Туктарова И.О.]. - ХТТМ. - 1999. - № 3. - С.
8-9.
. Шарипов А.Х.
Оксиды органических сульфидов для нефтепереработки и нефтехимии / Шарипов А.Х.
- ХТТМ. - 2001. - № 1. - С. 43-49.
. Научная
сессия по химии и технологии органических соединений серы и сернистых нефтей. /
Гарипов Т.В., Червяков Д.К. - Рига: Зинатне. - 1976. - С. 70.
. Научная
сессия по химии и технологии органических соединений серы и сернистых нефтей. /
Радцева Г.Е., Ряховская Н.Н., Шарипов А.Х. - Рига: Зинатне. - 1976. - С. 103.
. Шарипов А.Х.
Новое в получении концентратов сульфоксидов и сульфонов из нефтяного сырья /
Шарипов А.Х. - Нефтехимия. - 1991. - Т. 31, № 3. - С. 275-283.
. Химия
процессов экстракции / [Николаев А.В., Торгов В.Г., Андриевский В.Н. Гальцова
Э.А.] - М.: Наука, 1970. - С. 75-80.
. Панів П.М.
Оксидаційна некаталітична очистка прямогонних гасових фракцій: Дис. канд. техн.
наук: 05.17.07 - хімічна технологія палива та пально-мастильних матеріалів.
Львов - 2002. - 183 с.
. Obolentzev
R.D. - In Seventh World Petroleum Congress. Proceedings. London, Elsevier Publ.
Co., 1967. - V. 9. - P. 109-110.
. Шарипов А.Х.
Промышленные схемы получения концентратов сульфоксидов из нефтяного сырья /
Шарипов А.Х. - ХТТМ. - 1991. - № 4. - С. 2-5.
. Каталитическое
окисление сульфидов средних дистиллятов сернистой нефти / [Шарипов А.Х.,
Нигматуллин В.Р., Нигматуллин И.Р., Закиров Р.В.]. - ХТТМ. - 2006. - № 6. - С.
45-51.
. Шарипов А.Х.
Каталитическое окисление сульфидов масляных фракций органическими
гидропероксидами / Шарипов А.Х., Нигматуллин В.Р. - ХТТМ. - 2006. - № 1 - С.
38-40.
. Обессеривание
нефтей и нефтепродуктов методом окисления: VI Научная сессия по химии
сераорганических соединений нефтей и нефтепродуктов. Проскуряков В.А.,
Розенталь Д.А., Васильева Г.М., Семенов В.Д. - Уфа. - 1961. - С. 26.
. Работы в
области химии и технологии топлива : Сб. науч. тр. - М.-Л.: Химия, 1964. - С.
168-172.
. Работы в
области химии и технологии топлива : Сб. науч. тр. - М.-Л.: Химия, 1964. - С.
173-178.
. Химия
сераорганических соединений, содержащихся в нефтях и нефтепродуктах : Сб. науч.
тр. - М.-Л.: Химия, 1964. - Т. 7. - С. 192-195.
. А. с. СССР,
кл. 23 b, 1/05, (С 10 g) / Способ очистки нефти и нефтепродуктов от сернистых
соединений. / Проскуряков В.А., Розенталь Д.А., Васильева Г.М. - № 161845;
Заявл. 23.06.61; Опубл. 1.04.64. Бюл. № 8, 1964. - 4 с.
. Алиев Р.Р.
Гидроочистка смесевого дизельного топлива на секции 100 комплекса Г-43-107
Бакинского НПЗ им. Гейдара Алиева / Алиев Р.Р. -Нефтепереработка и нефтехимия.
- 2008. - № 1. - С. 14-19.
. Danhong
Wang. Oxidative desulfurization of fuel oil. Part I. Oxidation of
dibenzothiophenes using tert-butyl hydroperoxide // Applied Catalysis A^
General. - 2003. - N 253. P. 91-99.
. Larivé J.F. Low sulfur fuels in Europe: an analysis
// Hydrocarbon Engineering. - 2001. - V. 6, № 4. - pp. 15-20.
. Morris P.,
Baade W.F., Jordan R.L. Increasing capacity with cleaner fuels // Hydrocarbon
Engineering. - 2001. - V. 6, № 7. - pp. 23-28.
. Criterion
Catalysts and Technologies L.P. Low sulfur solutions // Hydrocarbon
Engineering. - 2001. - V. 6, № 9. - pp. 25-31.
. Levy R.E.,
Rappas A.S., Decanio S.J., Nero V.P. UniPure`s ASR-2 Desulphurization Process
Provides Cost-Effective Solution for Ujtra-Low-Sulfur Refined Products // World
Refining. - 2001. - V. 12, №.4. - pp. 24-32.
. Гуменецкий
В.В. Исследование окисления асфальтенов, смол и масел кислородом воздуха в
водном растворе: Дисс… канд. техн. наук.: 05.17.07.- Львов, 1976. - 245 с.
. Антонишин
В.И., Гуменецкий В.В. Методика деструктивного окисления высокомолекулярных
соединений нефти и анализа полученных продуктов. - Весн. ЛПИ, Сер. Химия и
химическая технология. Львов, 1974. - № 82. - С. 94-100.
. ГОСТ
19121-73. Нефтепродукты. Метод определения содержания серы сжиганием в лампе. -
Взамен ГОСТ 1771-48, ГОСТ 8657-57; Введ. 01.07.74. - М.: Изд-во стандартов,
1987. - 7 с.
. ГОСТ
8489-85. Топливо моторное. Метод определения фактических смол (по Бударову). -
Взамен ГОСТ 8489-58; Введ. 01.07.86. - М.: Изд-во стандартов, 1987. - 3 с.
. ГОСТ
5985-79. Нефтепродукты. Метод определения кислотности и кислотного числа. -
Взамен ГОСТ 5985-59; Введ. 01.01.80. - М.: Изд-во стандартов, 1987. - 8 с.
. ГОСТ
17323-71. Топливо для двигателей. Метод определения меркаптановой и
сероводородной серы потенциометрическим титрованим. Введ. 07.12. 71. - - М.:
Изд-во стандартов, 1991. - 35 с.
. ГОСТ
2177-82. Нефтепродукты. Метод определения фракционного состава. - Взамен ГОСТ
2177-66; Введ. 01.01.83. - М.: Изд-во стандартов, 1987. - 25 с.
. ГОСТ
3900-85. Нефть и нефтепродукты. Метод определения плотности. - Взамен ГОСТ
3900-47; Введ. 20.12.85. - М.: Изд-во стандартов, 1991. - 37 с.
. ГОСТ 33-82.
Нефтепродукты. Метод определения кинематической и расчет динамической вязкости.
- Взамен ГОСТ 33-66; Введ. 01.01.83. - М.: Изд-во стандартов, 1987. - 11 с.
. ГОСТ
5066-56. Топлива моторные. Метод определения температуры помутнения, начала
кристализации и кристализации. - Взамен ГОСТ 5066-52; Введ. 01.06.56. - М.:
Изд-во стандартов, 1987. - 13 с.
. ГОСТ
9490-75. Материалы смазочные жидкие и пластичные. Метод определения смазывающих
свойств на четырехшариковой машине. - Взамен ГОСТ 9490-60; Введ. 01.01.78. -
М.: Государственный комитет СССР по стандартам, 1981. - 9 с.
. ГОСТ
6356-75. Нефтепродукты. Продукты химические органические. Метод определения
температуры вспышки в закрытом тигле. - Взамен ГОСТ 6356-52; Введ. 01.07.77. -
М.: Изд-во стандартов, 1975. - 5 с.
. ГОСТ
2070-82. Нефтепродукты светлые. Метод определения йодных чисел и содержания
непредельных углеводородов. - Взамен ГОСТ 2070-55; Введ. 01.07.83. - М.: Изд-во
стандартов, 1987. - 6 с.
. ГОСТ
1461-75. Нефть и нефтепродукты. Метод определения зольности. - Взамен ГОСТ
1461-59; Введ. 01.07.76. - М.: Изд-во стандартов, 1987.-7 с.
. ГОСТ
19932-74. Нефтепродукты. Метод определения коксуемости. - Взамен ГОСТ 5061-49 и
ГОСТ 5987-51; Введ. 01.07.75. - М.: Изд-во стандартов, 1987. - 5 с.
. ГОСТ
6370-83. Нефть, нефтепродукты и присадки. Метод определения механических
примесей. - Введ. 12.04. 83. - М.: Изд-во стандартов, 1988. - 6 с.
. ГОСТ
2477-65. Нефть и нефтепродукты. Метод определения содержания воды. - Взамен
ГОСТ 1044-41; Введ26.06.65. - М.: Изд-во стандартов, 1972.-7 с.
. ГОСТ
6321-69. Топливо для двигателей. Метод испытания на медной пластинке. - Взамен
ГОСТ 6321-52; Введ. 01.11.70. - М.: Изд-во стандартов, 1975. - 2 с.
. Рыбак Б.М.
Анализ нефти и нефтипродуктов / Рыбак Б.М. - Москва: Государственное
научно-техническое издательство нефтяной и горно-топливной литературы, 1962 -
347 с.
. Гуревич И.Л.
Общие свойства и первичные методы переработки нефти и газа. - М.: Химия, 1972.
- 359 с.
. Гайванович
В.И. Исследование окисления высокомолекулярных соединений нефти кислородом
воздуха в водно-эмульсионной среде и в бензольном растворе: Дисс… канд. техн.
наук.: 05.17.07.- Львов, 1980. - 225 с.
. Пиш’єв С.В.
Оксидаційна десульфуризація високосіркового низькометаморфінізованого вугілля :
дисертація… канд. техн. наук. : 05.17.07. - Львів, 1999. - 149с.
. Pysh’yev
S.V., Bratychak M.M., Lazorko O.I. Investigation of straight-run diesel oil
fractions with sulfur high content oxidative desulphurization // Chemistry and
Chemical Technology. - 2008. - V. 2, №.4. - pp. 309-316
. Pysh’yev
S.V., Bratychak M.M., Lazorko O.I. Temperature and water effect on the
oxidative desulphurization of straight-run diesel fraction with a high sulphur
content // Chemistry and Chemical Technology. - 2009. - V. 3, №.2. - pp. 163-1
. ДСТУ 3868-99
Паливо дизельне. Технічні умови. - Заменяет: ГОСТ 305-82. Введ. 8 квітня 1999
р. № 179: - УкрНДІНП «МАСМА»), ТК 38.
. Касьянов
А.А., Сухоруков А.М., Дьяченко С.А., Грудников И.Б., Кузнецова Н.С., Прокопюк
С.Г. Опыт реконструкции битумной установки // ХТТМ. - 1999. - № 4. - С. 25-26.
. Ипполитов
Е.В., Грудников И.Б. Технология производства битумов. Недавняя история и давние
проблемы // ХТТМ. - 2000. - № 4. - С. 18-24.
. Груцкий
Л.Г., Пранович А.А., Питиримов В.В., Грудников И.Б., Ипполитов Е.В., Колесов
В.В., Чистяков В.Н. Окислительная колонна битумной установки // ХТТМ. - 2000. -
№ 6. - С. 11.
. ГОСТ
12.0.003-74. ССБТ. Опасные и вредные производственные факторы. Классификация.
. Правила
устройства электрооборудования. - М. Энергоатомиздат. 1987.
. ГОСТ
12.3.002-75. ССБТ. Процессы производственные. Общие требования безопасности.
. СН 245-71.
ДНАОП 0.03.-3.01-71. Санитарные нормы проектирования промышленных предприятий.
- М.: Стройиздат, 1972.
. СНиП
2.04.01-85. Внутренний водопровод и канализация зданий. Нормы проектирования.
. Методичні
вказівки до дипломного проектування з розділу «Цивільна безпека» для студентів
хімічного профілю/ Укл. С.М. Орел. - Львів: Видавництво - НУ «Львівська
політехніка», 2002. - 64 с.
. Оцінка
обстановки у надзвичайних ситуаціях. Навчальний посібник. В.Є. Гончарук, С.І.
Качан, С.М. Орел, В.І. Пуцило. - Львів: - Видавництво НУ «Львівська
політехніка», 2004. - 184 с.