Оборудование и технологии предприятия по производству комплектов изделий для сборного домостроения
.
Отчет по
производственной практике
Оборудование
и технологии предприятия по производству комплектов изделий для сборного
домостроения
Студентка
Н.Д.
Крашенинникова
ВВЕДЕНИЕ
В современных условиях производство строительных
материалов является одним из важнейших направлений нашей отечественной
промышленности. Это объясняется ежегодно повышающимися темпами строительства и
дефицитом высококачественных стройматериалов.
ОАО «Бетфор» - одно
из крупнейших в стране и на Урале предприятий по производству железобетонных
изделий, а также бетонных и растворных смесей для строительства объектов
различного назначения.
С момента основания основным направлением
деятельности предприятия было производство комплектов изделий для сборного
домостроения, так назваемых панельных домов.
Наша производственная (механическая) практика
прошла на Заводе ЖБИ «Бетфор», который был переименован в "ЛСР.
Строительство-Урал". Мы были ознакомлены с производством в 7-ом и 9-ом
цехах.
Мне необходимо было изучить арматурное отделение
7-го цеха, а именно установку для сварки закладных деталей под слоем флюса.
Дополнительным заданием было рассмотреть систему очистки воздуха на установке
сварки под слоем флюса.
1. О ПРЕДПРИЯТИИ
История развития
Завод железобетонных изделий им. Ленинского
комсомола расположен на восточной окраине города Екатеринбурга в районе,
прилегающему к озеру Шарташ и парку “Каменные палатки”.
Производственные цеха и службы занимают около
110 га площади.
Завод является промышленной базой Свердловского
домостроительного комбината по производству деталей для строительства
крупнопанельных домов в пяти, двенадцати и шестнадцати этажном исполнении.
В состав завода входят 13 цехов, четыре из
которых производят железобетонные изделия: один производит товарный бетон и
раствор, два обеспечивают основное производство конструктивным бетоном и
арматурой, ремонтно-механический цех, электроремонтный участком КИП и
Автоматики, ремонтно-строительный, транспортно-хозяйственный и паросиловой.
Сырье и материалы в основном завод получает
железнодорожным транспортом, а часть автомобильным. Щебень для производства
бетонов всех фракций завод получает с Шарташского карьера, расположенного в
полутора километрах от завода. Песок для мелкого заполнителя для
конструктивного бетона поступает с Махневского Гидромеханизированного карьера
Свердловской области, расположенного около двухсот километров от завода. Песок
для производства растворов поступает с Пышминского карьера. Основная масса
цемента поступает с Сухоложского цементного завода, а известь с Дружининского
карьера. В производстве легкого бетона используется зола-унос от
электрофильтров Рефтинской ГРЭС, расположенной также в Свердловской области.
Первые шаги 1957-1967 гг.
апреля 1957 года:
введен в эксплуатацию главный корпус завода по
производству железобетонных плит перекрытий с законченным производственным
циклом;
заводу присвоено имя Ленинского Комсомола.
Начиная с «нуля», коллектив завода, приобретал
опыт по ходу освоения производства, привлекая молодых специалистов, подготовка
которых активно началась во многих средних, высших учебных заведениях.
С момента основания приоритетным направлением
деятельности предприятия было производство комплектов изделий для сборного
домостроения.
год:
начало производства комплектов изделий для массового
строительства 5-этажных домов.
В середине 60-х годов основным направлением
деятельности завода стал выпуск комплектов изделий для массовой застройки
микрорайонов 5-этажными домами серии 2П, 1-468. Резкое увеличение объемов
строительства, а также повышение требований по комфортности жилья и
архитектурной выразительности, потребовало максимального наращивания темпов
производства изделий для строительства панельных домов.
год:
укомплектовано продукцией завода строительство
185 тыс. м2 жилья.
Бурное развитие 1967-1977 гг.
год:
освоено производство изделий для строительства
9-этажных домов и укомплектовано строительство 200 тыс. м2 жилья.
год:
построен и введен в эксплуатацию цех по
производству объемных элементов - санитарно-технических кабин, шахт лифтов, элементов
кровли, лоджий др. с законченным технологическим циклом;
освоено производство изделий для строительства
12-этажных домов;
укомплектовано строительство 334 тыс. м2
жилья.
год:
изготовлен первый комплект 16-этажного дома и
укомплектовано строительство 385 тыс. м2 жилья.
год:
начало реконструкции производства с целью
перехода на выпуск изделий для блок-секционного строительства домов 9-16 этажей
серии 141СВ с максимальной заводской готовностью;
укомплектовано строительство 460 тыс. м2
жилья в год.
Массовое производство 1977-1987 гг.
год:
в условиях реконструкции и без снижения объемов
производства завершено строительство первого 9-этажного дома новой серии 141СВ.
год:
завершение реконструкции производственных
мощностей предприятия.
-1987 годы:
заводом достигнуты максимальные объемы
комплектации строительства жилья - 461 тыс. м2.
Расширение деятельности 1987-1997 гг.
год:
начало застройки микрорайонов «Синие Камни» и
«Ботанический» домами производства завода «Бетфор».
год:
завод ЖБИ «Бетфор» по объемам производства
железобетона и деталей крупнопанельного домостроения стал первым по величине
предприятием строительной индустрии страны.
год:
сокращен объем крупнопанельного строительства;
освоено производство газозолобетонных блоков для
строительства зданий различной этажности, в том числе для индивидуального
строительства;
освоено производство железобетонной продукции
общественного назначения - свай, перемычек, бордюров, элементов теплотрасс,
заборных плит, гаражных изделий, плит дорожных покрытий и т.д.;
проведена приватизация завода и зарегистрировано
предприятие ОАО «Бетфор».
год:
заводу вручен сертификат Российской Федерации
«Лидер российской экономики».
Новый этап 1997-2008 гг.
год: ориентируясь на рынок сбыта, предприятие
совместно с рядом проектных организаций предложило строителям новое поколение
жилых домов, которое позволяет сочетать преимущества крупнопанельного
домостроения с возросшими требованиями к архитектурной выразительности и
повышенной комфортности зданий. Такие дома получили название Домостроительная
система «Бетфор».
год:
сдан в эксплуатацию первый 10-этажный дом,
построенный по «Домостроительной системе «Бетфор».
по новой системе укомплектовано строительство
80,5 тыс. м2 жилья.
год:
завод вошел в состав крупного строительного
холдинга «НОВА-ГРУПП», в который кроме производственных предприятий, входят
проектные и строительные организации, что обеспечивает полный цикл работ от
разработки проекта до сдачи объекта под ключ.
-2005 гг:
реконструкция производства, введение новых
производственных линий: Бельгийские линии по производству плит перекрытий
пустотного настила, изготавливаемых методом безопалубочного формования, и Линия
по производству изделий для каркасных зданий (преднапряженных балок и колонн).
год:
введена в эксплуатацию универсальная конвейерная
линия немецкой фирмы «ЕВАWЕ»,
по производству изделий различного назначения, таких как: внутренние несущие
стеновые панели, трехслойные наружные стеновые панели, плиты лоджий, лестничные
площадки и др.
В 2008 г. на строительный рынок Свердловской
области пришел крупный федеральный игрок - «Группа ЛСР». Выход на строительный
рынок Екатеринбурга «ЛСР» осуществила путем покупки активов регионального
игрока - холдинга «НоваГрупп».
В марте 2013 года Завод ЖБИ "Бетфор"
переименован в "ЛСР. Строительство-Урал" в связи с развитием
федерального бренда ЛСР - одного из крупнейших строительных холдингов России.
Штат "ЛСР. Строительство-Урал" насчитывает более 1000 квалифицированных
сотрудников.
В числе выпускаемой продукции предприятия -
плиты перекрытия, сваи, ригели и прочие железобетонные изделия. Универсальная
конвейерная линия немецкой фирмы «ЕВАWЕ»
по производству изделий различного назначения и новое оборудование ведущих европейских
производителей позволяют выпускать изделия с идеально ровной геометрией и
качеством поверхностей.
Производственные мощности предприятия
составляют:
- производство конструкций
для индустриального домостроения - 200000
м2/год;
производство ЖБИ для
возведения объектов разного назначения - 130 000
м2/год
;
- производство бетонных блоков - 10 тыс.
м3/год;
производство изделий из ячеистого
бетона (БГМ) - 125 тыс. м3/год;
производство товарных бетонных и
растворных смесей - 145 тыс. м3/год.
2.АРМАТУРНОЕ ОТДЕЛЕНИЕ
.1 Общие сведения
Данный технологический процесс разработан на
производство арматурных изделий, закладных деталей и соединительных элементов,
предназначенных для железобетонных изделий и изготавливаемых в арматурном цехе
завода.
Арматурные изделия, закладные детали и
соединительные элементы должны изготавливаться в соответствии с требованиями
альбомов рабочих чертежей «Крупнопанельные жилые дома серии 137С. Часть 10.
Разделы на все железобетонные изделия. Раздел 10.14.1. закладные детали,
строповочные петли и соединительные элементы».
Сетки сварные изготавливаются в соответствии с
требованиями ГОСТ 23279-85 на многоточечных контактных машинах.
Тяжелые сетки изготавливаются на вертикальных
установках контактной сваркой.
Плоские, объемно- пространственные каркасы и
закладные детали изготавливаются в соответствии с требованиями ГОСТ 10922-90:
плоские каркасы - на одноточечных контактных машинах
и на автоматизированной линии;
объемно - пространственные каркасы - на
вертикальных и горизонтальных установках контактной точечной сваркой;
закладные детали сваркой под слоем флюса - на
машинах полуавтоматах;
закладные детали рельефной сваркой - на
одноточечных контактных машинах.
Ограждения лоджий изготавливаются ручной дуговой
сваркой на посту 3 между осями Г-Д/Е в соответствии с требованиями ГОСТ
10922-90.
Готовые закладные детали металлизируются
сварочной проволокой из алюминия или алюминиевых сплавов на посту 9 между осями
Б/В-Т.
Режим работы цеха
Количество рабочих суток в год 254
Количество рабочих смен в сутки 3
Количество рабочих часов в смену 8
Объем выпускаемой продукции, т:
Годовой -8000
Суточный -31.5
Сменный -10.5
Состав бригады, чел.
Профессия
|
Разряд
|
1 смена
|
2 смена
|
3 смена
|
Всего
|
Сварщик
арматурных сеток и каркасов
|
4 3 2
|
2 7 5
|
2 7 5
|
2 7 5
|
33 21 15
|
Электросварщик ручной дуговой
сварки
|
5
|
9
|
9
|
9
|
27
|
Сварщик на полуавтоматах
|
3
|
1
|
1
|
1
|
3
|
Арматурщик
|
3
|
4
|
4
|
4
|
12
|
Стропальщик
|
3
|
1
|
1
|
1
|
3
|
Антикоррозионщик
|
4
|
1
|
1
|
2
|
Металлизаторщик
|
4
|
1
|
1
|
1
|
2
|
Машинист мостового крана
|
5 4 3
|
2 1 1
|
2 1 1
|
2 1 1
|
6 3 3
|
Итого:
|
|
|
|
|
130
|
Рисунок 2.1 - Арматурное отделение седьмого цеха
Рисунок 2.2 - Арматура в седьмом цехе
2.2 Нормы
проектирования арматурных цехов
Проектирование цеха начинается
с технологических расчетов, в которых определяются:
количество арматурной стали;
количество резов;
количество свариваемых точек;
количество гибок стержней и
плоских каркасов;
количество свариваемых
пространственных каркасов.
Количество потребного
материала, объем работ по каждому виду арматуры заносится в ведомость объемов
работ, которая является исходной для выбора оборудования, определения его
количества и планировочного решения.
Для облегчения подсчетов
объемов арматурных работ рекомендуется виды изделий группировать по технологическому
признаку их изготовления.
При определении количества
арматурной стали, согласно нормам технологического проектирования ОНТП 07-85
(общесоюзные нормы технологического проектирования предприятий сборного
железобетона), к общему весу стали, добавляется 4% на отходы. На действующих
предприятиях отходы арматуры колеблются в пределах 2 - 10 %.
Расчет количества оборудования
по всем видам технологического процесса производится на основании часовых норм
выработки (производительность оборудования). Ведомость расчета оборудования
составляется на основании ведомости объема арматурных работ и распределении их
видам сварочных машин.
Коэффициенты использования
оборудования
Правильно-отрезные
станки = 0,7;
Стыкосварочные
автоматизированные станки = 0,85;
Многоэлектродные
машины неавтоматизированные = 0,75;
Одноэлектродные
сварочные станки = 0,25.
Схема технологического процесса
изготовления арматурных элементов.
Рисунок 2.3 - Схема
технологического процесса изготовления арматурных элементов: 1 -
заготовительные операции; 2 - сварочные операции; 3 - операции доработки; 4 -
сборочные операции.
2.3 Компоновка оборудования арматурного цеха
Изготовление арматурных
элементов ведется несколькими потоками, поэтому расстановка оборудования в цехе
производится соответственно потоком, образуя тем самым поточные
механизированные линии. Машины и агрегаты поточной линии устанавливаются в
строгой последовательности технологического процесса.
Одна поточная линия
создается
для изготовления легкой арматурной сетки.
Вторая поточная
линия - для тяжелой арматуры.
Между поточными линиями вдоль
цеха располагается транспортный проезд:
шириной 3,0 - 3,5 м при
транспортировании арматуры вагонетками;
шириной 2,0 - 2,5 м при
транспортировании арматуры кран-балками.
Оборудование в цехе размещается
в следующей последовательности:
) Бухты с арматурной сталью,
стержневая арматура складируется в начале поточной линии, на специально
подготовленной площадке.
) На расстоянии 1 - 1,5 м от
склада устанавливаются размоточные устройства (вертушки).
) На расстоянии 2,0 - 2,5 м от
вертушек располагают правильно-отрезные станки. Их устанавливают параллельно
друг другу:
для легкой арматуры;
для тяжелой арматуры.
Расстояние между ними 1 - 1,5
м; расстояние от стены - не менее 1,5 м.
) Приемные стеллажи заготовок
арматурной стали монтируются по потоку длиной от 3,5 до 5 м.
В некоторых случаях за
приемными стеллажами правильно-отрезных станков ставятся отрезные станки для
коротких стержней или машины для механического упрочнения прутков (упрочнение
вытяжкой).
) Гибочный станок,
обслуживающий обе линии.
) На расстоянии 4,0 - 5,0 м от
гибочных станков располагают многоточечные сварочные машины и одноточечные
сварочные машины сварки сеток шириной до 700 мм и плоских каркасов из тяжелой
арматуры с приемными столами или рольгангами длиной до 6,0 м.
Расстояние от стены этих
станков не ближе 0,8 - 1,0 м.
) Далее монтируются установки
для сборки пространственных каркасов. -Площадь для подвесных сварочных машин со
сборочным постом составляет от 60 до 100 м2, в зависимости от
сложности изделия.
) Во второй половине пролета
монтируются многоточечные сварочные машины (для сварки больших сеток) и
гибочный станок (для гибки сеток).
Площадь занимаемая
многоточечной сварочной машиной вместе с заготовительным участком и складом
готовой сетки составляет 200 м2.
Площадь для гибочного станка -
60 м2 (при длине 12 м).
Требования ОНТП для арматурных
цехов
) Запас арматурной стали на
складе, расчетные сутки = 20 - 25 суток.
) Масса металла, размещаемого
на 1 м2 площади склада:
сталь в бухтах = 1,2 т;
сталь в прутках и сортовой
прокат = 3,2 т;
полосовая сталь = 2,1 т;
сетки в рулонах = 0,4 т;
) Коэффициент, учитывающий
неполноту использования площади склада для хранения арматурной стали на
стеллажах и в закрытых складах вместимостью:
до 500 т = 3;
более 500 т = 2.
) Запас, ч., полуфабрикатов
между отделениями арматурного цеха:
сеток, закладных и анкерных
деталей = 8;
плоских каркасов = 4;
готовых арматурных каркасов в
цехе = 8;
товарных арматурных сеток и
каркасов на складе = 24 - 100.
) Высота хранения сеток и
каркасов:
в горизонтальном положении =
1,5 м;
в вертикальном положении = 4 м.
) Усредненная масса арматурных
сеток и каркасов, размещаемых на 1 м2 площади, при хранении в цехе
(с учетом проходов):
для стали D до 14 мм =0,04 т;
для стали D более 14 мм =0,15
т.
) Отходы арматурной стали,
классов, %:
А240; A300; A400; B500; Bр500 =
2;
- А600;
A800; A1000 = 3;
Aт600;
Aт800;
Aт1000;
Aт1200
= 6;
- B1500; Bp1500; К1400; К1500 =
7.
) Отходы листовой и сортовой
стали для закладных деталей, % при использовании:
полосы = 2%;
листа = 5%.
2.4Транспортирование
арматурных изделий
Механизированный способ является обязательным
при работе с грузам массой более 50 кг, а также при подъеме груза на высоту
более 3 м.
При подъеме и перемещении кранами арматурных
каркасов и сеток должны выполняться следующие требования:
грузозахватные приспособления (канаты, стропы,
траверсы) должны быть предварительно проверены на контрольную нагрузку;
во избежание выпадения стропы из крана во время
подъема или отпускание арматуры каждый крюк должен быть снабжен
предохранительной скобой;
длинномерные грузы, например пучки арматурных
стержней, следует поднимать в горизонтальном положении не менее чем двумя
самозатягивающимися петлевыми стропами, плотно облегающими поднимаемый груз;
перед подъемом грузовой канат крана должен
находиться в вертикальном положении под центром тяжести груза.
Запрещается подтаскивать груз при косом
натяжении каната. При отсутствии данных о положении центра тяжести поднимаемого
груза его следует установить путем пробных подвешиваний.
Элементы опалубки, арматурные сетки и отдельные
стержни арматурных изделий должны быть до подъема скреплены между собой.
При подъеме арматурных каркасов и длинномерных
грузов и сеток необходимо пользоваться оттяжками из прочного пенькового каната
или тонкого стального троса.
Переносить поднимаемую арматуру над людьми
запрещается.
Снимать стропы с поднятых и установленных
арматурных каркасов можно лишь после их надежного закрепления.
Оставлять на весу устанавливаемую арматуру
запрещается.
Общие требования по
технике безопасности
К производству работ по изготовлению арматурных
изделий и закладных деталей допускаются лица, не моложе 18 лет, годные по состоянию
здоровья, прошедшие обучение по программе технической эксплуатации
оборудования, сдавшие экзамены по технике безопасности и имеющие 2-ю группу
допуска по электробезопасности.
Все работающие и вновь поступившие на
предприятие независимо от стажа, опыта работы и квалификации проходят
инструктаж по технике безопасности по инструкциям, утвержденным главным
инженером предприятия.
Вводный инструктаж проводит инженер по технике
безопасности или главный инженер предприятия в специально оборудованном для
этого помещении, оснащенном наглядными пособиями.
Арматурная сталь в цехе должна храниться в
штабелях высотой не более 1,2 м.
Между штабелями должен быть проход не менее 1 м.
Сетки, каркасы плоские и закладные детали должны
складироваться и храниться на специальных стеллажах или в контейнерах.
Бухты арматурной стали должны храниться в
штабелях, рассортированными по наименованию проката, маркам и диаметру. Высота
штабеля не должна превышать 1,5 м, а ширина проходов между ними должна быть не
менее 1 м. допускается хранить бухты арматурной стали в приямках, оборудованных
ограждениями.
Листовая сталь и разновидность проката должны
рассортированы по наименованию проката, маркам, диаметру и храниться в штабелях
и стеллажах.
Высота штабеля листовой стали не должна превышать
1,5 м с установкой ограничителей для исключения послойного смещения.
Ширина главных проходов должна быть не менее 1,5
м.
Ширина второстепенных проходов, используемых для
ремонта, осмотра и смазки оборудования, должна быть не менее 0,8 м с учетом
выступающих частей станков и максимальных размеров обрабатываемых изделий.
Проезды для цехового транспорта должны иметь
ширину, превышающую не менее чем на 1 м максимальные габариты груженых
транспортных средств.
Запрещается загромождать проходы и проезды цеха арматурными
стержнями, каркасами и другими материалами и предметами.
До начала работы каждому рабочему необходимо:
выяснить какие неисправности были в течение
предыдущей смены;
убедиться в исправности оборудования, приборов и
предохранительных устройств;
особое внимание обратить на целостность изоляции
токопроводящих проводов и обеспечить защиту их от случайных повреждений
арматурой;
надеть спецодежду, спецобувь и другие средства
защиты.
Средства защиты должны соответствовать
требованиям «Типовых отраслевых норм бесплатной выдачи спецодежды, спецобуви и
предохранительных приспособлений». Спецодежда для рабочих должна
соответствовать требованиям ГОСТ 12.4.011-89.
Все рабочие, занятые производством работ, должны
быть в касках, соответствующих требованиям ГОСТ 12.4.087-84.
Электропроводка к станкам и оборудованию должна
быть проложена в заземленных металлических трубах.
Шкафы с электроаппаратурой обязательно
запираются на замок. Ремонтировать, регулировать и осматривать
электроаппаратуру разрешается только дежурному электрику.
Движущиеся нерабочие детали механизмов, если они
представляют опасность, необходимо ограждать.
3.УСТАНОВКА СВАРКИ
ЗАКЛАДНЫХ ДЕТАЛЕЙ ПОД СЛОЕМ ФЛЮСА
На заводе используют установку для сварки
закладных деталей под флюсом типа АДФ-2001 (рисунок 3.1, 3.2)
Основные
характеристики:
Наименование
параметра
|
Значение
|
Напряжение
питающей сети при частоте 50Гц, В
|
380
|
Номинальный
сварочный ток, при ПВ=60%
|
2000
|
Максимальная
скорость подачи стержня, мм/с
|
15
|
8
- 40
|
Длина
свариваемых стержней (в долях диаметров), мм
|
10
- 30
|
Максимальная
производительность сварок/час (при d = 20 мм)
|
220
|
Толщина
свариваемого плоского элемента, мм
|
5
- 40
|
Рабочее
давление воздуха в пневмосистеме, кгс/см2
|
4
- 5
|
Расход
воздуха, м3/ч
|
30
|
Расход
воды, л/ч
|
100
|
Емкость
бункера для флюса, дм3
|
12
|
Габаритные
размеры
|
1150*890*1790
|
Масса,
кг
|
385
|
Состав установки:
·
механизм зажатия пластин;
·
механизм зажатия арматурного
стержня;
·
механизм
вертикального перемещения стержня по заданному циклу;
·
стол;
·
пневматическое устройство;
·
блок управления процессом сварки;
·
комплект проводов и шлангов;
Рисунок 3.1, 3.2 - Установка типа АДФ-2001
1.1 Сварочный
процесс дуговой сварки стержней состоит из следующих циклов (таблица 3.1):
1. Привариваемая пластина
прижимается к поверхности стола.
2. Стержень позиционируется на
поверхности пластины и пневмозажимом фиксируется в головке, место сварки
засыпается флюсом.
3. После включения сварочного
тока стержень отрывается от пластины и возбуждается дуга.
4. По истечении времени горения
дуги стержень электроприводом осаживается на заданную глубину в сварочную
ванну.
5. После кристаллизации
сварного соединения происходит отключение всех компонентов - стержень и
пластина освобождаются.
3.2 Сущность
процесса сварки под флюсом
Сущность процесса сварки под флюсом
определяет его особенности по сравнению с ручной дуговой сваркой.
Производительность по сравнению с
ручной сваркой увеличивается в 5-12 раз. При сварке под флюсом ток по
электродной проволоке проходит только в ее вылете (место от токоподвода до
дуги).
Поэтому можно использовать
повышенные (25-100 А/
) по сравнению с ручной дуговой
сваркой (10-20 А/
) плотности сварочного тока без
опасения значительного перегрева электрода в вылете и отслаивания обмазки, как
в покрытом электроде.
Использование больших сварочных
токов резко повышает глубину проплавления основного металла и появляется
возможность сварки металла повышенной толщины без разделки кромок. При сварке с
разделкой кромок уменьшается угол разделки и увеличивается величина их
притупления, т.е. уменьшается количество электродного металла, необходимого для
заполнения разделки. Металл шва обычно состоит приблизительно на 2/3 из
переплавленного основного металла (при ручной дуговой сварке соотношение
обратное). В результате вышесказанного растут скорость и производительность
сварки. Под флюсом сваривают металл толщиной 2-60 мм при скорости однодуговой
сварки до 0,07 км/ч. Применение многодуговой сварки позволяет повысить се
скорость до 0,3 км/ч.
Высокое качество металлов шва и
сварного соединения достигается за счет надежной защиты расплавленного металла
от взаимодействия с воздухом, его металлургической обработки и легирования
раздавленным шлаком. Наличие шлака на поверхности шва уменьшает скорость
кристаллизации металла сварочной ванны и скорость охлаждения металла шва. В
результате металлический шов не имеет пор, содержит пониженное количество
неметаллических включений. Улучшение формы шва и стабильности его размеров,
особенно глубины проплавления, обеспечивает постоянные химический состав и
другие свойства на всей длине шва. Сварку под флюсом применяют для изготовления
крупногабаритных резервуаров, строительных конструкций, труб и т.д. из сталей,
никелевых сплавов, меди, алюминия, титана и их сплавов.
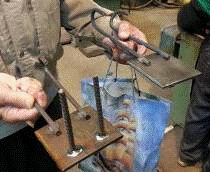
Рисунок 3.3, 3.4 - Готовые закладные детали
Экономичность процесса определяется
снижением расхода сварочных материалов за счет сокращения потерь металла на
угар и разбрызгивание (не более 3%, а при ручной сварке достигают 15%),
отсутствием потерь на огарки. Лучшее использование тепла дуги при сварке под
флюсом по сравнению с ручной сваркой уменьшает расход электроэнергии на 30-40
%. Повышению экономичности способствует и снижение трудоемкости работ по
разделке кромок под сварку, зачистке шва от брызг и шлака. Сварка выполняется с
применением специальных автоматов или полуавтоматов. Условия работы позволяют
сварщику обходиться без щитков для защиты глаз и лица. Повышаются общий уровень
и культура производства.
Недостатками способа является
повышенная жидкотекучесть расплавленного металла и флюса. Поэтому сварка
возможна только в нижнем положении при отклонении плоскости шва от горизонтали
не более чем на 10-15°. В противном случае нарушится формирование шва, могут
образоваться подрезы и другие дефекты. Это одна из причин, почему сварку под
флюсом не применяют для соединения поворотных кольцевых стыков труб диаметром
менее 150 мм. Кроме того, этот способ сварки требует и более тщательной сборки
кромок под сварку и использования специальных приемов сварки. При увеличенном
зазоре между кромками возможно вытекание в него расплавленного металла и флюса
и образование в шве дефектов.
3.3Технические
требования по изготовлению закладных деталей
.5.1. Закладные детали должны изготавливаться в
соответствии с требованиями ГОСТ 10922-90.
.5.2. Отклонения размеров и параметров закладных
деталей от проектных не должны превышать, мм:
а) габаритных размеров плоских элементов ±5;
б) расстояния между плоскими элементами деталей
типа «закрытый столик» при расстоянии:
до 250 ±4;
свыше 250 ±5;
в) положение в плане плоских элементов деталей
типа «закрытый столик» - 4;
г) размер анкерных стержней по длине для деталей
типа «открытый столик» - ±10;
д) расстояния от одного из крайних анкерных
стержней до любого другого анкерного стержня - ±5.
Толщина плоских элементов закладных деталей
должна быть в пределах допускаемых отклонений на прокат.
.5.3. Элементы закладных деталей из полосового,
сортового проката должны иметь плоские поверхности.
Отклонение от плоскостности наружных лицевых
поверхностей плоских элементов, закладно детали не должна превышать 3 мм.
.5.4. Угол между поверхностью плоского элемента
и анкерным стержнем закладной детали должен быть в пределах установленных ГОСТ
14098-91.
.5.5. Кромки плоских элементов закладных деталей
должны быть очищены от грата и шлака после огневой резки.
.5.6. На элементах закладных деталей не должно
быть отслаивающейся ржавчины и окалины, а также следов масла, битума и других
загрязнений.
.5.7. Типы, конструкции и размеры сварных
соединений, выполняемых контактной и дуговой сваркой стержней, а также
листового и фасонного проката должны соответствовать требованиям ГОСТ 14098-91.
.5.8. Сварные соединения, выполняемые контактной
сваркой, должны быть окружены гратом. Свищи в соединениях, смятие стержней
электродами на глубину более 0,1 диаметра, подплавление и поджоги под
электродами при контактной сваркой не допускаются.
.5.9. При сварке закладных деталей пол слоем
флюса используют флюс марки АН-348А соответствующий требованиям ГОСТ 9087-81.
Флюс должен быть изготовлен из однородных зерен.
Содержание инородных частиц (не растворившихся частиц сырьевых материалов,
футеровки, угля, графита, кокса, металлических частиц и др.) должно быть не
более 0,5% от массы флюса.
Флюс марки АН-348А должен быть стекловидным
цветом от желтого до коричневого.
.5.10. Металлизацию закладных деталей необходимо
производить в соответствии с требованиями СНиП 3.04.03-85;
Алюминиевая проволока для металлизации закладных
деталей должна соответствовать требованиям ГОСТ 7871-75.
3.4 Расход
материалов

=Д*
*
,
где: 
- расчетная масса наплавленного
металла, кг/м;

- коэффициент, выражающий отношение
массы израсходованного флюса к массе сварочной проволоки и зависящий от типа
сварочного соединения и способа сварки.
Коэффициент 
при сварке под слоем флюса и
электрошлаковой сварке:
Сварка
|
Швы
стыковые и угловых соединений
|
Швы
тавровых соединений без скоса и со скосом кромок
|
|
Без
скоса кромки с отбортовкой
|
Со скосом кромки
|
|
Автоматическая Полуавтоматическая
|
1,3 1,4
|
1,2 1,3
|
1,1 1,2
|
3.5Требования к
процессам сварки под флюсом
Сварочное оборудование,
предназначенное для сварки под флюсом на стационарных постах, должно иметь:
а) приспособление для
механизированной засыпки флюса в сварочную ванну;
б) флюсоотсос с
бункером-накопителем и фильтром (при возврате воздуха в помещение) для уборки
использованного флюса со шва.
Стационарные установки для
электродуговой сварки флюсом должны быть оснащены местными отсосами.
Отсосы должны быть расположены
непосредственно у места сварки (на расстоянии не более 40 мм от зоны дуги в
сторону формирования шва). Рекомендуется применять отсосы щелевидной формы.
Скорость воздушного потока
должна быть 4 - 9 м/с в зависимости от требуемого объема отсасываемого воздуха.
Стационарные установки для
сварки под слоем флюса должны быть обеспечены механизированными устройствами
для очистки шва от шлаковой корки с одновременным его сбором. Ручная уборка
флюса (в респираторе) допускается только в случаях, когда применение
флюсоотсосов не представляется возможным. В системе сбора и подачи флюса должна
быть предусмотрена очистка выбрасываемого воздуха от пыли и газов. При засыпке
флюса в бункер автомата должны быть приняты меры по защите работающего и
окружающих рабочих мест от запыления. Для предупреждения повышенного выделения
аэрозоля газов, применяющихся при механизированной и автоматической сварке,
флюс должен быть сухим, не загрязненным посторонними веществами (смазывающими
маслами, осколками флюсовой корки и т.д.). При сварке под флюсом автоматами,
передвигающимися по рельсовому пути, должны быть обеспечены надежность и
правильность закрепления рельсового пути на изделии или на стенде, а также
надежность крепления обратных и боковых роликов ходового механизма. Рабочие
места сварщиков при сварке труб и других крупногабаритных конструкций должны
быть оборудованы специальными кабинами с подачей приточного воздуха, тепло- и
звукоизоляцией наружных поверхностей и пультом управления сварочным процессом.
4. СИСТЕМА ОЧИСТКИ
ВОЗДУХА НА УСТАНОВКЕ СВАРКИ ПОД СЛОЕМ ФЛЮСА
Постоянное развитие получают технологические
процессы, связанные с обработкой металлов. Одним из видов обработки металлов
является электросварка, которая подразделяется на механизированную в углекислом
газе, ручную дуговую, автоматическую дуговую под флюсом, контактную.
Электросварка сопровождается выделением
сварочного аэрозоля, содержащего мелкодисперсную твердую фазу и газы.
Интенсивность выделений зависит от характеристики процесса, марки сварочных материалов
и свариваемого металла. При этом определяющее влияние оказывает состав
сварочного материала.
Сварочный аэрозоль содержит соединения железа,
марганца, никеля, хрома, алюминия, меди и других веществ, а также газы (оксиды
азота, оксид и диоксид углерода, озон, фтористый водород).
В соответствии с ГОСТ 12.3.003-86 (Работы
электросварочные. Требования безопасности) не допускается проведение сварки при
не работающей местной вытяжной вентиляции.
В таблице 4.1 приведены предельно допустимые
концентрации вредных веществ в воздухе рабочей зоны сварочных цехов,
регламентированные ГОСТ.
Таблица 4.1 - ПДК вредных веществ в воздухе
рабочей зоны сварочных цехов
Наименование
вещества
|
ПДК,
мг/ мКласс
опасностиАгрегатное состояние (а-аэрозоль, п- пары)Примечание
|
|
|
|
Содержание
марганца в сварочных аэрозолях, масс %
|
До
20
|
0,20
|
2
|
а
|
|
До
20-30
|
0,10
|
2
|
а
|
|
Хроматы,
бихроматы
|
0,01
|
1
|
а
|
в
пересчете на Cr )
|
Оксид
хрома ( )1,002а
|
|
|
|
|
Никель
и его оксиды
|
0,05
|
1
|
а
|
в
пересчете Ni
|
Оксид
цинка
|
0,50
|
2
|
а
|
|
Титан
и его двуоксид
|
10,00
|
4
|
а
|
|
Алюминий
и его сплавы
|
2,00
|
2
|
а
|
|
медь
металлическая
|
1,00
|
2
|
а
|
|
Вольфрам
|
6,00
|
3
|
а
|
2,00
|
4
|
а
|
|
двуоксид
азота
|
2,00
|
2
|
п
|
|
Озон
|
0,10
|
1
|
п
|
|
Оксид
углерода
|
20,00
|
4
|
п
|
|
втористый
водород
|
0,05
|
1
|
п
|
|
Соли
фтористоводородной кислоты:
|
Хорошо
растворимые(NaF, KF)
|
0,20
|
2
|
а
|
по
HF
|
Плохорастворимые
(AI ), NaAIFd)0,502апо HF
|
|
|
|
|
Сварочные участки оснащаются
вытяжной вентиляцией, удаляющей выше-указанные загрязнения от рабочих мест, с
последующей очисткой этого воздуха.
Сварочные посты могут быть, как
фиксированные (стационарные), так и нефиксированные (например,
сборочно-сварочные цеха крупно-габаритных металлоизделий.
Для нефиксированных сварочных
участков могут быть использованы передвижные фильтровентиляционные
пылеулавливающие агрегаты, которые в данном случае должны быть оснащены
консольно-поворотным вытяжным устройством, позволяющим максимально близко
приближать вытяжную воронкут к месту сварки, а значит и источнику выделения
загрязнений. Нефиксированные сварочные участки могут также оснащаться
централизованной системой вытяжной вентиляции, которая в свою очередь
оснащается консольно-поворотными устройствами с большим радиусом (5-7 метров)
действия.
На заводе ЖБИ «Бетфор» установлены
фиксированные сварочные участки, которые оснащаются централизованными вытяжными
системами. Для удаления и очистки воздуха от стационарных сварочных постов
могут быть также использованы специализированные столы сварщика FTW, оснащенные
фильтровентиляционными агрегатами.
Вытяжной воздух, удаляемый от установок
сварочных постов, должен подвергаться очистке с целью выполнения требований ПДВ
(предельно-допустимого выброса) при выбросе очищенного воздуха в атмосферу или
более эффективной очистке воздуха в случае осуществления рециркуляции
очищенного воздуха.
сварка флюс деталь
Рисунок 4.1 - Централизованная вытяжная система
ЗАКЛЮЧЕНИЕ
В
ходе механической практики на заводе ЖБИ «Бетфор» я ознакомилась с большим
разнообразием продукции, выпускаемым данным предприятием. Также изучила
арматурное отделение (в цехе №7). Важно отметить, что мной была рассмотрена
установка сварки закладных деталей под слоем флюса, система очистки воздуха от
данной установки.
И в заключении хотелось бы еще раз отметить, что
сегодня завод ЖБИ "БЕТФОР" переименован в "ЛСР.
Строительство-Урал"- лидер рынка крупнопанельного строительства, одно из
крупнейших предприятий Урала по производству железобетонных изделий, бетонных и
растворных смесей для строительства объектов различного назначения.
БИБЛИОГРАФИЧЕСКИЙ СПИСОК
1) Капустин Ф.Л. Оформление
учебных текстовых и графических документов: методические указания / Ф.Л.
Капустин, С.Ф. Шишкин, А.Б. Лошкарев, Е.Ю. Васина. Екатеринбург: ГОУ ВПО
УГТУ-УПИ, 2006.
) Капустин Ф.Л., Спиридонова
А.М., Владимирова Е.Б. и др. Сквозная программа учебной, производственной и
преддипломной практики. Е.: ГОУ УГТУ-УПИ, 2002.
) Карта технологического
процесса производства арматурных изделий и закладных деталей КТП 36-9-89.
Екатеринбург: Министерство строительства в районах Урала и западной Сибири
СССР, ТСО «СРЕДУРАЛСТРОЙ», производственно-технологическое объединение
«ПРОГРЕСС», 1989.