Автоматизация устройства абразивной зачистки
РЕФЕРАТ
Настоящая выпускная квалификационная работа
посвящена модернизации автоматического управления станком на устройстве
абразивной зачистки крупносортного цеха ОАО “ЕВРАЗ НТМК”. Актуальность проекта
обусловлена необходимостью повышения надёжности работы данного устройства,
стремлением к уменьшению простоев и снижением затрат на ремонты.
В выпускной квалификационной работе
спроектирована принципиальная схема системы управления, подобрано необходимое
оборудование, модули ПЛК. Также написана управляющая программа на языке Step7.
Произведено исследование работоспособности написанной программы, соответствие
её выполнения технологическому процессу. Рассмотрен вопрос обмена данными между
контроллерами и исполнительными механизмами и выбрано необходимое для этого
оборудование, а также сделан расчёт экономической целесообразности
предлагаемого внедрения.
Выпускная квалификационная работа содержит
пояснительную записку на 111 листах, приложения на 23 листах и включает в себя:
рисунков, 6 таблиц.
Графическая часть проекта выполнена на 6 листах
формата А1.
ПЕРЕЧЕНЬ УСЛОВНЫХ ОБОЗНАЧЕНИЙ И ТЕРМИНОВ
КСЦ - Крупносортный цех
УАЗ - устройство абразивной зачистки
НТМК - Нижнетагильский металлургический комбинат
ВКР - выпускная квалификационная работа
ОТК - отделение технологического контроля
РКС - релейно-контакторные схемы
ПЛК - программируемый логический контроллер
ПО - программное обеспечение
ТП - технологический процесс
FC - Function Block- Organization
Block- Data Block- Supervisory Control And Data Acquisition- Windows Control
Center- personal computer- human machine interface (человеко-машинный
интерфейс)-
процессор
ПЛК
MMC - micro memory card
НТП - нормирующий термопреобразователь
ПЭВМ - промышленная электронно-вычислительная
машина
ВВЕДЕНИЕ
ОАО «Нижнетагильский металлургический комбинат»
одно из крупнейших металлургических предприятий мира с полным технологическим
циклом. НТМК первым в СССР построил конвертерный цех, освоил выплавку чугуна из
ванадийсодержащего сырья, разработал оригинальную технологию термообработки
рельс, построил первую машину непрерывного литья заготовок, самый крупный
универсально-балочный стан.
В конце 80-х годов ХХ века НТМК достиг наивысших
показателей по производству продукции. При этом комбинат уступал другим
российским и мировым производителям по уровню технологии (преобладал
мартеновский способ выплавки стали, незначителен объем стали, разливаемой на
установках непрерывного литья и т.д.).
После получения полной хозяйственной
самостоятельности в 1992 году прежде всего была разработана программа
технического перевооружения. За этот период введены в эксплуатацию две доменных
печи, четыре машины непрерывного литья заготовок, комплекс внепечной обработки
стали, вакуммирования и десульфурации, новая нагревательная печь с шагающим
подом, несколько слиткоразрезных станков Вагнера, новые линии прессования в
огнеупорном производстве, новая производственная линия в колёсопрокатном стане
и т.д. Общая сумма капитальных вложений составила превысила $ 3 миллиарда.
Реконструкция позволила вывести из эксплуатации
ряд устаревших производственных мощностей, улучшить производственные и
финансово-экономические показатели работы комбината.
ОАО «НТМК» занимает пятое место в России по
выпуску продукции чёрной металлургии. Основной вид деятельности - производство
и реализация металлопроката. ОАО «НТМК» производит около 10 % общего выпуска
проката в России.
Основной задачей ОАО «НТМК» является увеличение
массы продукции, повышение эффективности, качества и уменьшение потерь металла
и энергии.
Именно для решения основных задач ОАО «НТМК»
принято решение руководством крупносортного цеха и электротехнической
лаборатории о модернизации станка УАЗ. Модернизация позволит избавиться от
значительных простоев на данном участке, повысить выпуск продукции, так как
решается вопрос об «узком месте» на данном участке. Частые ремонты, технические
обслуживания установки нарушают нормальную работу цеха. Также это приводит к
дополнительным затратам. Принятое решение о модернизации вызовет капитальные
затраты на закупку и монтаж нового оборудования, но срок окупаемости составит
около 1-2 лет, что является очень выгодным для предприятия.
Модернизация направлена на применении
программируемых логических контроллеров, взамен старым установленным
релейно-контакторных схем. ПЛК имеет явное преимущество по надёжности и
современности перед РКС. Аналогичные модернизации проводятся по множеству
электрооборудования в разных цехах комбината. В настоящее время РКС в состоянии
морального износа. А также, установленные РКС на данном устройстве физически
очень изношены.
Всеми этими факторами обусловлена актуальность и
относительная новизна темы данной ВКР.
ОБЗОР ЛИТЕРАТУРНЫХ ИСТОЧНИКОВ
Станок обдирочно-шлифовальный предназначен для
зачистки круглого проката. В настоящее время станок автоматизирован на уровне
релейно-контакторного управления, что имеет ряд недостатков при современных
условиях производства. Низкая надёжность реле и сложность поиска причин
отказов, ограниченный срок службы, связанный с «подгоранием» контактов.
До существующей релейно-контакторной схемы
управление осуществлялось вручную операторами. В дипломном проекте будет
разработано управление станком с помощью программируемых логических
контроллеров.
Различают три вида автоматизации:
. Ручное управление
При ручном управлении человек непосредственно
воздействует на органы управления, наблюдая за ходом технологического процесса;
. Автоматизированное управление
При автоматизированном управлении находят
широкое применение автоматические устройства, но процесс управления протекает
при активном участии человека, как на этапе анализа состояния объекта , так и
при реализации управляющих воздействий;
. Автоматическое управление
При автоматическом управлении заданное состояние
объекта поддерживается с помощью специальных автоматических устройств, а
человек выполняет функции наладчика или ремонтника. Функцию управления человек
берёт на себя только в аварийных ситуациях.
Токарный станок, у которого оператор может
индивидуально осуществлять выполнение всех линейных перемещений салазок и задней
бабки, используя элементы ручного управления.
эти перемещения могут быть остановлены как по
команде самого оператора, так и посредством установленного упора с ручной
регулировкой;
оператор может запускать и прекращать вращение
шпинделя;
изменение частоты вращения шпинделя может
выполняться с помощью ручного управления.
Ручное управление - неавтоматический режим
работы станка, при котором оператор управляет станком без использования
предварительно запрограммированных числовых данных, например, с помощью кнопочного
выключателя или джойстика;
Работа станка в ручном режиме: (manual modes of
operation): Работа станка, управляемого оператором вручную, без
последовательности, определенной заранее введенной программой.
Станок может выполнять следующий автоматический
цикл: постоянство окружной скорости.
. Релейно-контакторные схемы
Переключательные элементы, позже получившие
название "реле", появились в начале прошлого века, истоки же их -
аналогичные элементы неэлектрической природы - создавались еще ранее.
В середине 30-х годов начала зарождаться т е о р
и я релейно-контактных схем, т. е. схем, состоящих из нескольких релейных
элементов. В нашей стране слово в этой области было сказано В. И. Шестаковым, в
диссертации которого - она называлась "Некоторые математические методы
конструирования и упрощения двухполюсных схем класса А" (1938 г.) - для
анализа и расчета релейно-контактных схем были использованы методы алгебры
логики. Работы Шестакова, по-видимому, опередили аналогичные исследования,
выполненные известным специалистом по информатике и кибернетике Клодом
Шенноном.
Для автоматического управления работой станков
широко применяют электрические релейно-контактные схемы, состоящие из
электрических контактов, соединенных в определенной последовательности, и
регулирующих устройств, на которые эти контакты воздействуют.
Структурная схема автоматизированного управления
насосных агрегатов, являясь замкнутой цепью воздействия отдельных элементов,
должна включать:
измерительные датчики и реле, реагирующие на
изменение неэлектрических величин;
преобразователи импульса изменения
неэлектрической величины в электрическую;
усилители, увеличивающие мощность
преобразованной величины для приведения в действие исполнительного механизма;
исполнительный механизм, выполняющий необходимые
операции для поддержания в заданном режиме параметра, на который настроено
автоматизированное управление.
Все указанные элементы, независимо от места их
установки, связаны одной общей схемой, которая составляется в соответствии с
технологическим заданием и должна обеспечить определенную последовательность
выполнения операций рабочими механизмами, а также необходимые блокировки.
Основным принципом работы релейно-контактной
схемы является последовательность действия отдельных ее элементов. Все
элементы, входящие в релейно-контактную схему, можно разделить на три основные
группы: приемные, промежуточные и исполнительные. Каждая релейно-контактная
схема состоит из схемы цепи главного тока и схемы цепи управления. Кроме того,
релейно-контактные схемы подразделяют на принципиально свернутые и
принципиально развернутые. В принципиально свернутых схемах каждый аппарат
показан как единое целое (при этом сохраняется конструктивное единство каждого
аппарата). В принципиально развернутых схемах каждый аппарат условно
разделяется на составные части (обмотки, контакты), которые размещаются в
разных местах схемы по признаку включения в отдельные электрические цепи.
Интеллектуальное реле
Системы автоматики и управления старого образца
(релейно-контакторные) не отличались особой надежностью и ремонтопригодностью.
Состоящие из десятков, а то и сотен элементов, исполнительных узлов и
сигнальных ламп, соединенные километрами проводов, такие системы требовали
очень точной и длительной настройки, периодических планово-ремонтных
мероприятий, постоянной замены вышедших из строя реле, контакторов, клемников и
т.д.
За последние годы в области электроавтоматики и
КИПиА произошла революция, перевернувшая представления людей о понятии
автоматизация. Появились очень надежные, дешевые и многофункциональные
электронные блоки, заменяющие собой целые шкафы релейно-контакторных схем. Эти
новые блоки, так называемые интеллектуальные реле, способны воплотить в себе,
практически, любую задачу. Основной их особенностью является простота монтажа,
наладки и настройки. Вся схема исполнительной автоматики программируется внутрь
блока при помощи обычного компьютера, без всякого дополнительного оборудования.
Делается это быстро и оперативно, что дает возможность изменить любой параметр
в уже работающей системе. Благодаря совместимости с компьютером и малому числу
составных частей (сам блок является основной исполнительной единицей), новые
системы автоматики становятся максимально гибкими, надежными, малогабаритными,
и, самое главное, несоизмеримо дешевыми, по сравнению со старыми аналогами.
Программируемое (интеллектуальное)
реле - разновидность программируемых логических контроллеров
<#"653919.files/image001.gif">
Рис. 1.1. Общий вид коммуникацонного
модуля
S7-200
При этом все контроллеры S7-200
могут выступать как равноправные устройства генерирующие запросы и отвечающие
на них.
При работе в сети типа MPI (для
организации взаимодействия с ПЛК типа S7-300 или S7-400) ПЛК S-200 будет
выступать как ведомое устройство.
Имеются центральные ПЛК с питанием
+24В, ~120~230В.
Также имеются модули типа SIPLUS
S7-200 работающие в расширенном температурном диапазоне и высокой влажности.
Взаимодействие с пользователем
В системах на базе S7-200 HMI
интерфейс (взаимодействие с пользователем) может быть реализован следующим образом:
Панели текстовые и графические
Панели подключаются по интерфейсу
PPIинтерфейс на PC: реализуется средствами программ Protool или WinCC.
Монтаж ПЛК с модулями осуществляется
на стандартную профильную 35мм DIN рейку.
В качестве альтернативного крепления
на модуле предусмотрены крепления на щит в виде «ушек» по болты. Сочленение
модулей расширения с ПЛК и остальными модулями происходит при помощи гибкого
кабеля на боковой стороне каждого модуля (расположены под пластиковой
заглушкой).
Программирование всегда ведется из
программы STEP 7 MicroWin, отличаются только способы загрузки программы в ПЛК.
Через кабель PC / PPI
Через Industrial Ethernet при
наличии в системе коммуникационного модуля CP243-1.
Через модемную связь при наличии в
системе коммуникационного модуля CP241.
При программировании используется
программа STEP7 MicroWin на языках LAD, STL или FBD. Также в MicroWin
осуществляется настройка панелей оператора TD200 и TD400, а также
коммуникационных модулей.
Пакет STEP 7 MicroWin имеет
множество встроенных библиотек и мастеров настройки модулей.
Необходимо отметить, что на данный
момент SIEMENS рекомендует для замены ПЛК SIMATIC S7-200 ПЛК SIMATIC S7-1200.
S7-1200 обладают большими возможностями. К ним можно отнести: меньший размер
корпусов, больший размер памяти, большее число поддерживаемых входов в системе
и меньшую цену.
Для написания программы используется
пакет STEP 7 BASIC, в которой интегрированы средства написания и отладки
программ для ПЛК, а также пакет WinCCBasic для создания HMI на базе панелей KT
и KTP.
Также STEP 7 BASIC не поддерживает
язык программирования STL.S7-300
Рис. 1.2. Общий вид ПЛК Siemens
S-300
Модульные программируемые
контроллеры для решения задач автоматизации среднего уровня сложности. Являются
наиболее яркими и наверное самыми востребованными представителями ПЛК фирмы
SIEMENS. Существенные возможности для расширения до 32 модулей (4 ряда по 8
модулей в каждом) позволяют обслуживать огромное количество сигналов (до 8200
дискретных и 512 аналоговых). Набор встроенных технологических функций
позволяет решать задачи скоростного счета, измерения частоты или длительности
периода, ПИД-регулирования, позиционирования, перевода части дискретных выходов
в импульсный режим.
Монтаж осуществляется на профильную
шину S7-300. Фиксация в рабочих положениях осуществляется винтами. Объединение
модулей в единую систему выполняется с помощью шинных соединителей (входят в
комплект поставки каждого модуля), устанавливаемых на тыльную часть
корпуса.S7-400.
Модульный программируемый контроллер
для решения сложных задач автоматического управления.
В системах S7-400 возможна замена
модулей расширения без выключения контроллера за счет расположения шины
непосредственно в стойке. Также на ПЛК S7-400 возможно построение так
называемых H - систем (систем двойного резервирования) имеющих два CPU
программа в которых выполняется параллельно и переключение между управляющими
контроллерами происходит без прерывания технологического процесса.
Программирование и настройка также
как и S7-300 осуществляется из пакета STEP 7.S7-1500 новое решение от SIEMENS.
Просто неограниченные возможности за
счет увеличенного быстродействия и огромного количества памяти. Время
выполнения логической операции 1 нс. Скорость обмена по внутренней шине до 400
Мб/с. Также изменилась качество программой поддержки ПЛК. Теперь в программе
хранятся и символьные имена и комментарии, поддержка 64-битных данных.
Монтаж осуществляется либо с помощью
шинных соединителей как S7-300 либо на активную встроенную шину.
Модули
Произвольный порядок размещения
модулей в монтажных стойках. Фиксированные посадочные места занимают только
модули блока питания, CPU и коммуникационного модуля. Наличие съемных
соединителей позволяет производить быструю замену модулей без демонтажа их
внешних цепей и упрощают выполнение операций подключения внешних цепей модулей.
Возможна установка в систему так называемых Dummy модулей для резервирования
места в системе под дальнейшее расширение. Эти модули не выполняют никаких
функций кроме обеспечения целостности шины системы.может быть реализован как на
базе панелей оператора так и на базе PC программами Protool или WinCC.
Программирование осуществляется из среды STEP7 Professional (на данный момент
интегрирована со средой разработки HMI WinCC). Запись и отладка программы
возможна через любой доступный в системе интерфейс.
Рис. 1.3. Расположение модулей ПЛК
Siemens
.2 Удаленное управление и мониторинг
(аббр.
<#"653919.files/image004.gif">
Станок состоит из ряда узлов,
объединенных для выполнения определенных задач, а именно:
Узлы, предназначенные для загрузки и
разгрузки заготовок «Механизм загрузки», «Гидроцилиндр механизма
загрузки»-2шт., «Механизм сброса», «Гидроцилиндр сброса» - 4шт., « Стеллаж
промежуточный».
Узлы, предназначенные для
перемещения, зажима и вращения заготовки - «Путь рельсовый», «Стол», «Привод»,
«Ролик натяжной», «Гидроцилиндр натяжения», «Подвод питания к столу», « Ролик
приводной»-8шт., «Механизм зажима» - 8шт., «Привод роликов» и др., входящие в
комплекс «Стол».
Узлы, обеспечивающие
зачистку заготовки и перемещение шлифовальной бабки - «Станина бабки
шлифовальной», «Бабка шлифованная», «Головка шлифовальная», « Шпиндель»,
«Гидроцилиндр прижима круга», «Гидроцилиндр перемещения бабки шлифованной»,
«Кожух круга шлифовального» и др. узлы, входящие в комплекс «Привод
инструмента».
Узлы, обеспечивающие работу
оператора на станке - «Кабина», «Кресло оператора», «Пульт управления» и ряд
других узлов.
Дополнительные узлы, предназначенные
для обеспечения работы станка или создания удобств обслуживания. Это
гидроагрегаты, гидро- и электрооборудование, «Механизм замены круга»,
подогреватель в кабине оператора и ряд других узлов.
Компоновка станка
Стол станка перемещается по
рельсовому пути. Перпендикулярно движению
стола перемещается бабка
шлифовальная по основанию.
С другой стороны против бабки
шлифовальной расположена кабина оператора.
На передней части шлифованной бабки
в опоре качается шлифовальная головка в передней части которой, в расточке,
установлен шпиндель с шлифовальным крутом.
Слева от оператора установлен
стеллаж промежуточный, а с другой стороны рельсового пути механизм загрузки. За
путем рельсовым, слева от оператора установлены буфера и ролик натяжной,
который перемещается от гидроцилиндра натяжения, обеспечивая постоянное
натяжение троса при его вытяжке.
За путем рельсовым справа от
оператора установлен привод с барабаном, на который наматывается или
сматывается при движении стола соответствующие ветви каната.
Управление станком осуществляется из
кабины оператора с помощью пульта управления. Пульт управления включает в себя
две панели с кнопками управления, переключателями, сигнальными лампами,
регуляторами температуры, амперметром и вольтметрами. Функциональные назначения
нанесены на панелях пульта около аппаратов.
Конструктивные особенности отдельных
узлов
Путь рельсовый.
Путь рельсовый предназначен для
перемещения по нему стола, на котором производится абразивная зачистка
заготовки. Путь рельсовый представляет собой крановые рельсы, закрепленные при
помощи болтов и планок на шпалах, выполнены из швеллеров. Каждая шпала крепится
фундаментными болтами и подлита бетоном.
Стол.
Стол предназначен для установки на
нем заготовки, вращения её и зажима в процессе обработки и сброса после
обработки. Стол представляет собой сварную конструкцию из швеллеров и листов,
выполненную в виде рамы. Сверху на столе крепятся узлы привода роликов, ролики
приводные, механизм зажима, механизм сброса, трубопровод , гидроагрегат стола,
гидроцилиндры сброса , а также гидро- и электроаппаратура. С боку стола
крепится кронштейн токоподвода. Стол установлен на колесах, которые
перемещаются по рельсовому пути.
Механизм сброса.
Механизм сброса установлен на столе
и представляет собой ваз установленный на опорах и поворачивающийся от
гидроцилиндров. На вазу закреплены рычаги сброса, которые выполняют функции
загрузки и выгрузки. Стол при этом находится в зоне загрузки - выгрузки.
Ролики приводные.
Ролики приводные установлены на
столе и представляют собой сварной корпус, внутри которого расположена
центральная шестерня, передающая вращение на две связанные с ней шестерни на
одном вату с роликами. Все приводные ролики соединены между собой валами,
которые получают вращение от привода роликов.
Привод роликов.
Привод роликов установлен в правой
части стола и служит для передачи вращения через приводные ролики на заготовку.
В приводе роликов установлены редуктор и электродвигатель со встроенным
тормозом, который служит для мгновенной остановки при провороте её на угол.
Механизм зажима.
Механизм зажима предназначен для
зажима заготовки во время выборочной зачистки и сплошной зачистки строчками и
устанавливается на узле «Ролики приводные». Механизм зажима представляет собой
основание, на котором крепится гидроцилиндр. Шток гидроцилиндра закреплен на
основании и в корпусе роликов приводных. Для различных диаметров заготовок
предусмотрены сменные губки.
Подвод питания к столу.
Подвод питания к столу предназначен
для подвода электроэнергии к гидроагрегату стола, приводу роликов и
представляет собой тележку на 4-х колесах, в средней части которой закреплена
ось, на которой вращается барабан. В передней и задней части тележки
установлены ролики для канатов.
Барабан перемещается по
направляющим. На шпалах пути рельсового
установлена плита с коробкой, в
которой закреплены кабели, которые обходя барабан, закреплены вторым концом на
колодке, закрепленной на задней стенке стола, кроме этого вокруг роликов на
тележке проходят канаты, которые одними концами закреплены на столе, другими на
шпале пути рельсового. При перемещении стола канаты сообщают перемещение
тележке с барабаном. Натяжение канатов осуществляется тягой, установленной на
кронштейне стола.
Станина бабки шлифовальной.
Станина бабки шлифовальной
представляет собой сварную конструкцию коробчатой формы, выполненную из листов.
Сверху на станину устанавливаются рельсы, по которым перемещается бабка
шлифовальная. На верхней поверхности станины установлен на кронштейне
гидроцилиндр перемещения бабки шлифовальной. В верхней части установлен сварной
пылестружкоприемник для обеспечения направления факела шлифовального круга при
работе. В проём боковой стенки станины вкатывается тележка с бункером для сбора
металлоабразивных отходов.
Бабка шлифовальная.
Бабка шлифовальная выполнена сварной
конструкции, коробчатой формы, установленной на колесах, на которых
перемещается по рельсам станины. Сверху, в расточках на оси, устанавливается
головка шлифовальная и гидроцилиндр прижима шлифовального круга. Сбоку, на
верхней поверхности, устанавливается датчик подхвата шлифовального круга и
кронштейн фиксатора шлифовальной головки.
Головка шлифовальная.
Головка шлифовальная выполнена литой
конструкции и представляет собой приклон, который устанавливается на бабку
шлифовальную. Передняя часть корпуса шлифовальной головки сделана разъемная. В
разъеме устанавливается шпиндель. Сверху, на приклон, монтируется на
подмоторной плите электродвигатель привода шлифовального круга Натяжение ремней
осуществляется при помощи винта. На торце корпуса шлифовальной головки
закреплен кронштейн, шарнирно связанный с гидроцилиндром прижима шлифовального
круга. На корпусе шлифовальной головки монтируется кожух шлифовального круга и
кожух ременной передачи.
Шпиндель.
Шпиндель смонтирован в гильзе на
двух роликоподшипниках и одном упорно-радиальном подшипнике. Шлифовальный круг
на планшайбе устанавливается на переднем, а шкив узкой клиноремённой передачи
на заднем конических концах шпинделя. Гильза шпинделя крепится в корпусе
шлифовальной головки крышкой и фиксируется в осевом направлении своими буртами.
Смазка опор осуществляется консистентной смазкой ВНИИП-228ГОСТ12330-77 или
Старт ТУ3810/986-84. Контроль нагрева опор производится термопарами.
Механизм установки хода бабки
шлифовальной.
Механизм установки хода бабки
шлифовальной, определяющий крайние положения бабки шлифовальной, представляет
собой сварной корпус, установленный на боковой стенке станины бабки
шлифовальный, внутри которого находятся конечники, на которые воздействуют
лепестки, закрепленные на одной оси с подпружиненными рычагами. При перемещении
шлифовальной бабки кулаки, расположенные на штанге, поочередно воздействуют на
соответствующий рычаг, который, поворачиваясь на оси, дает команду на остановку
бабки шлифовальной.
Привод стола.
Привод стола представляет собой
основание, на котором на кронштейне установлен гидромотор, связанный
втулочно-пальцевой муфтой с редуктором, тихоходный зал которого зубчатой муфтой
соединен с барабаном, на котором выполнена винтовая нарезка определенного
профиля, в которую укладывается при наматывании приводной канат, перемещающий
стол.
Механизм загрузки.
Механизм загрузки служит для выдачи
на стол только одной заготовки. Механизм состоит из сварных стоек, связанных
между собой швеллерами. На стойках сверху закреплены направляющие, на которые
укладываются заготовки. Спереди на стойках крепится вал, на котором
устанавливаются отсекатели. Отсекатель имеет две лопасти, каждая из которых
предназначена для своего диапазона обрабатываемых заготовок. На концах валов
установлены рычаги, которые связаны со штоками гидроцилиндров загрузки. Для
переналадки на обработку соответствующих диаметров необходимо вынуть шпонку
связывающую рычаг с диском, провернуть диски до совпадения очередного
шпоночного паза с рычагом и закрепить шпонку. Для обеспечения нахождения торцев
укладываемых заготовок в одной плоскости на механизме загрузки предусмотрен
боковой щит.
Стеллаж промежуточный.
Стеллаж промежуточный состоит из
сварных стоек связанных между собой швеллерами. На стойках сверху закреплены
направляющие, по которым катятся до упора обработанные заготовки. На крайнюю
правую стойку крепятся конечники узла «Установка конечных выключателей стола».
Кабина.
Кабина является рабочим местом
оператора. Своими остекленными частями кабина обращена к рабочей зоне и зоне
загрузки. Одно из окон может открываться для выполнения рабочим осмотра
заготовки. Кабина выполнена из отдельных щитов скрепленных между собой. Каждый
щит имеет двойные звукоизолирующие стенки. В кабине расположен пульт управления
с рукоятками управления. Оператор находится в кресле, которое имеет возможность
перемещаться по кабине.
Механизм замены круга.
Механизм замены круга предназначен
для замены изношенного шлифовального крута новым и представляет собой сварную
стойку, на которой установлены шарнирно закрепленные рычаги. В расточке рычага
установлено сварное ложе с открывающейся передней стенкой. Ложе имеет
возможность регулировки для установки его по высоте. Механизм замены круга
имеет фиксаторы, которые фиксируют его в исходном положении. Для замены
изношенного круга рычаг с ложем и установленным на нем новым шлифовальным
крутом подводится к планшайбе шпинделя. После того как новый круг закреплен на
планшайбе, открывается передняя стенка ложа и ложе вместе с шарнирными рычагами
отводится в исходное положение и фиксируется. Передняя стенка закрывается.
Датчик подхвата шлифовального крута.
Датчик подхвата шлифовального круга
представляет собой механизм
аварийного
провала шлифовального круга, состоящий из электромагнитной муфты и
бесконтактного конечника. В расточке корпуса установлен вал, на наружном конце
которого жестко закреплен барабан с намотанным на него канатом. Внутри корпуса
на валу установлен свободно рычаг с лепестком. Рычаг выполняет роль полумуфты,
вторая часть которой в этот момент отведена эл. магнитом, при касании
шлифовальным крутом заготовки, включается. Канат одним концом жестко закреплен
на кронштейне, установленном на корпусе шлифовальной головки, а на втором конце
висит противовес. При опускании круга более положенного лепесток дает команду
бесконтактному датчику на отвод круга.
Ролик натяжной.
Узел предназначен для изменения направления и
натяжения каната привода стола осуществляемою при помощи гидроцилиндра,
укрепленного на основании узла.
Основание узла сварено из швеллеров. На верхней
части его на платиках установлены направляющие для колес, ось которых является
также осью вращения ролика. Эта ось закреплена в корпусе, к которому крепится
шток гидроцилиндра натяжения. Перемещая штоком гидроцилиндра корпус с колесами,
а, следовательно, и ролик с канатом по направляющим, происходит натяжение
каната. Полный ход гидроцилиндра соответствует тому, что канат выбран, так как
он в процессе эксплуатации вытягивается, при этом через конечный выключатель
дастся команда на останов стола. Необходимо укоротить канат или поставить
новый.
Рукоятки управления крестовые.
Рукоятки управления крестовые (покупные изделия)
крепятся на пульте управления. Каждая рукоятка имеет 4 фиксированных положения.
Одна из них управляет перемещением стола ( вправо-влево) и шлифовальной бабки (
вперед - назад), а другая - зажимом-разжимом изделия и вращением изделия в
обеих направлениях.
Электрооборудование станк
- электропривод вращения шлифовального круга
(М1);
электрооборудование гидроагрегата привода инструмента,
состоящее из привода насосов (М2, М3), вентилятора и насоса теплообменника (М4,
М6), регулятора усилия прижима шлифовального круга (М5) и нагревателя масла в
баке гидроагрегата (ЕН1…ЕН4);
электрооборудование гидроагрегата привода
перемещения стола, состоящее из привода насосов скорости стола 1-ой, 2-ой, 3-ей
ступени (М8, М9, М10), насоса управления (М11), вентилятора и насоса
теплообменника (М12, М17), регулятора скорости стола внутри ступени (М13) и
нагревателя масла в баке гидроагрегата (ЕН5…ЕН8);
электрооборудование кантователя в составе
привода насоса (М14), нагревателя масла в баке гидроагрегата (ЕН9…ЕН12) и
привода вращения заготовки (М15 со встроенным тормозом YL1);
электрооборудование кабины, включающее освещение
кабины (EL2), звуковую сигнализацию (НА), освещение станка (EL3, EL4), обогрев
кабины (Е1), пульт управления с аппаратами управления всеми составными частями
станка и педаль для опускания шлифовальной головки (SQ23);
электрооборудование электрошкафа с аппаратами
электроавтоматики станка;
конечные выключатели, датчики температуры и
гидрораспределители
управления гидроприводами.
Сведения о системе питания
Питание электрооборудования станка
осуществляется от трёхфазной сети переменного тока 380В, 50Гц. В станке
применяются следующие напряжения переменного тока:
силовые цепи 380В;
цепи управления 110В;
цепи сигнализации световой 22В;
цепи сигнализации звуковой 220В;
цепи питания регуляторов температуры 220В;
переносное освещение 12В;
освещение станка, кабины 220В;
обогрев кабины 220В.
Постоянного тока:
цепи управления 24В;
- цепи питания бесконтактных выключателей,
магнитов гидрораспределителей 24В.
Цепи питания регуляторов температуры (А1…А4),
освещения кабины (EL2), обогрева кабины (Е1), звуковой сигнализации (НА) и
освещения станка (EL3,EL4) подключены на напряжение 220В через разделительный
трансформатор TV3.
Гидросистема. Общие сведения
Гидропривод станка, состоящий из 3-х агрегатов,
обеспечивает:
- кантование, зажим и сброс заготовки;
поперечное перемещение шлифовальной бабки,
подъем и опускание инструмента, перемещение цилиндров механизма загрузки;
перемещение стола и натяжение троса.
Описание работы стола.
Гидроагрегат кантования, зажима и сброса
изделия.
При включении электродвигателя М насосной
установки для разгрузки насоса включается УА24 гидрораспределителя Р1, а при
включении для работы цилиндров кантования и сброса цилиндров зажима УА24
отключается. Кантование и сброс заготовки осуществляется гидроцилиндрам и
Ц1...Ц4, перемещение которых синхронизированно валом. Зажим и разжим заготовки
осуществляется гидроцилиндрами Ц5...Ц12. Управление поворотом рычагов механизма
сброса, рычагами зажима производится, гидрораспледелителями Р2 и РЗ.
Зажим заготовки происходит при включенном УА23 -
контролируется РД2. Отвод рычагов зажима происходит при включенном УА22 -
контролируется РД1. При повороте рычагов механизма сброса гидроцилиндрами
Ц1...Ц4 рычаги занимают промежуточное положение, обеспечивающее прием заготовки
со стеллажа загрузки.
После приема заготовки происходит опускание
рычагов механизма сброса в нижнее положение гидроцилиндрами Ц1...Ц4 до укладки
заготовки на ролики поворотные, после чего происходит зажим заготовки
гидроцилиндрами Ц5...Ц12 (при включенном УА20). После отвода рычагов зажима
включается УА21 и происходит сброс заготовки на стол загрузки. Включается УА20
и рычаги отводятся в исходное положение - загрузка.
По окончанию зажима и достижению наибольшего
давления в линии 13 срабатывает реле давления РД2 и подает команду на
электромагнит УА24 гидрораспледелителя Р1, разгружающий насос с Q=I10,4л/мин.
Клапан давления КД2 смягчает удар при сбросе заготовки на рычаги и обеспечивает
их плавное опускание.
Настройка клапанов давления в гидроприводе
кантования, зажима и сброса заготовок:
КД2 - настраивается экспериментально на величину,
обеспечивающую безударное падение заготовки на рычаги и плавное отпускания.
реле давление РД 1; РД2 настроить на 0,1... 0,2
МПа больше рабочих давлений.
Система смазки
Описание системы смазки.
Все вращающиеся и трущиеся детали станка смазаны
при сборке. Однако, при длительной эксплуатации, при замене и регулировке
подшипников следует пополнять или полностью заменять их смазку в соответствии с
техническими требованиями сборочных чертежей.
Резервуары редукторов заливаются жидкой смазкой
в соответствии с указаниями эксплутационных документов.
2.3 Требования к системе автоматизации
Работа станка допускается:
кнопка аварийного отключения SB2 в верхнем
положении,
включён вводной автомат,
окно кабины закрыто,
ключ переключателя SA4 в положении 1(включено),
нажата кнопка SB1,
прозвучала звуковая предупредительная
сигнализация.
Подогрев масла в баках должен осуществляться
автоматически при снижении температуры ниже допустимой и окончание подогрева
при достижении необходимой температуры (измерители-регуляторы А1-А4).
Работа двигателя шлифовального круга.
При условии включения кнопки SB10, кожух круга
закрыт, шлифовальная головка находится вверху, подшипники не имеют перегрева и
не производится замена шлифовального круга.
Необходим плавный разгон круга, обеспечиваемый
переключением звезды на треугольник.
Защита от кратковременных и длительных
перегрузок (с предотвращением ложного срабатывания).
Движение шлифовальной головки.
Работа станка начинается с исходного положения
головки.
Движение шлифовальной головки вниз начинается по
команде от педали, головка зажата, механизм смены круга в исходном положении,
фиксатор головки выведен.
Контроль перегрузки.
При режиме постоянного вращения заготовки, то
разрешение движения при разжатой заготовке. Подвод головки до касания с
заготовкой происходит на низком давлении гидрораспределителей.
За время отскока головка уходит вверх в случае
провала головки.
Перемещение стола.
Скорость стола должна изменяться по ступеням с
регулировкой внутри каждой ступени. Движение при выбранном тросе, рычаги сброса
заготовки внизу, рычаги загрузки внизу, нет движения головки вверх, заготовка
зажата.
С исходного положения движение стола возможно
только вправо.
Вращение и поворот заготовки.
Переключателем должна обеспечиваться возможность
либо постоянного вращения, либо кратковременного поворота заготовки.
Постоянное вращение заготовки возможно при
разжатой заготовке.
Загрузка заготовки.
Загрузка происходит при исходном положении
стола, рычаги сброса заготовки со стола в среднем положении.
Режим «Наладка» - цикл загрузки можно
осуществить в любом положении стола и рычагов сброса загрузки со стола.
Приём и выгрузка заготовки.
При скатывании заготовки на рычаги стола они
должны располагаться в горизонтальном положении.
Для обработки заготовки стол находится в
исходном положении, рычаги зажима заготовки разведены.
Рычаги в среднем положении - готовность к приёму
следующей заготовки.
Зажим и разжим заготовки.
В режиме «Работа» зажим и разжим заготовки
возможен только в нижнем положении рычагов стола.
Предусмотреть световую сигнализацию о положениях
и режиме работы всех механизмов, контроля температуры масла в баках, засорении
фильтров, включении вводного автомата.
Предусмотреть 2 режима работы станка:
работа
наладка
Управление станком осуществляется из кабины
оператора с помощью пульта управления.
3. КОНСТРУКТОРСКАЯ ЧАСТЬ
.1 Проектирование принципиальной схемы
В данном проекте целесообразно оставить прежнюю
силовую часть, так как изменение и проектирование цепей управления не требует
замен двигателей, трансформаторов, магнитных пускателей и прочих элементов.
В силовой части добавляем на главный привод (М1
- шлифовальный круг) контроль по токам двигателя (Simocode). Это необходимо для
более современного и точного управления на переключении асинхронного двигателя
М1 звезда-треугольник при его разгоне и вспомогательная защита.
Источники питания также остаются исходными,
изменяется их назначение. К цепи постоянного тока 24В добавляется назначение
питания ПЛК. А цепи 110В переменного тока разгружаются от неиспользования в
модернизируемой версии промежуточных реле.
Номинальное напряжение магнитных пускателей
равно 110В переменного тока. Управлять ими необходимо через промежуточные реле
на 24В постоянного тока, т.к. номинальное напряжение на входах/выходах ПЛК
В постоянного тока. Выход ПЛК подаёт напряжение
на промежуточное реле (=24В), который своим контактором замыкает цепь питания
магнитного пускателя (110В). См. лист 3.
Блокировка дверей электрошкафа на срабатывание
главного вводного автомата остаётся прежней. Аналогично и освещение кабины,
звуковая сигнализация, освещение станка и обогрев кабины остаются без
изменений. Нецелесообразно управлять этими устройствами через программируемый
логический контроллер. На листе 3 обозначена неизменяемая часть установки.
В виду того, что выключатели конечного
положения, индуктивные датчики, электромагниты в системе гидроуправления имеют
номинальное напряжение 24В постоянного тока технически удобно оставлять их без
изменений, подключая напрямую к входам/выходам ПЛК дискретного значения.
Нормально закрытые контакты тепловых защит на
всех 15ти двигателях размещаем на дискретных входах ПЛК. Которые при превышении
двигателем допустимой температуры нагрева будут блокировать работу этого
двигателя при размыкании.
Кнопки, педаль, крестовые переключатели также
подключаем к дискретному входу ПЛК.
Лампочки, электромагниты гидросистемы подключаем
к выходу ПЛК (=24В). Для магнитных пускателей, одного силового электромагнита
(110В), звонка громкого боя ( НА) в сети 220В, и мотор-редуктора вводим 21
промежуточное реле KV.
Необходимо учесть резерв на модулях входа/выхода
ПЛК, принятый около 10%.
Для датчиков аналогового типа устанавливаем
модуль аналоговых входов (Analog input). Сюда относятся измерители-регуляторы
температуры, которые измеряют температуру (подшипников, масла в баках
гидросистемы) и в зависимости от её значений запускают либо отключают
подогреватели.
Сами датчики ВТ1…ВТ5 остаются неизменными,
присоединяются к темропреобразователям сопротивлений, откуда уже в нужных диапазонах
токов (4…20мА) сигнал поступает на модуль аналогового входа.proV в цепи питания
двигателя М1 устанавливаем для контроля токов этого двигателя. Заменяем
устаревший принцип управления скоростью двигателя по времени на новый по
величине тока в двигателе. Скорость изменяется при переключении обмотки
двигателя со звезды на треугольник. Устройства SIMOCODE proV также обеспечивают
дополнительную защиту и распространены на ОАО «ЕВРАЗ НТМК».
Указатели усилия прижима шлифовального круга и
скорости стола из старой цепи =24В подключаются к новой =24В. Сами механизмы
без изменений.
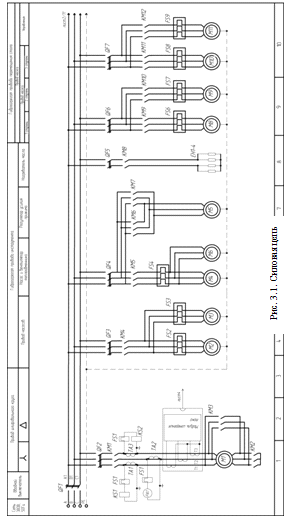

Рис.
3.4. Схема SIMOCODE ProV
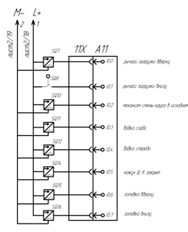
Рис. 3.5. Модуль входов IB0, IB1
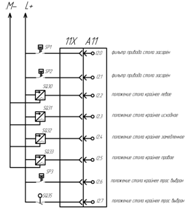
Рис. 3.6. Модуль входов IB2, IB3

Рис. 3.7. Модуль входов IB4, IB5

Рис. 3.8. Модуль входов IB6, IB7
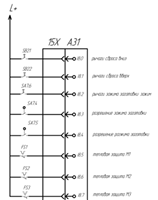
Рис. 3.9. Модуль входов IB8, IB9
Рис. 3.10. Модуль входов IB10, IB11

Рис. 3.11. Модуль выходов QB12, QB13
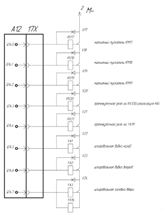
Рис. 3.12. Модуль выходов QB14, QB15

Рис. 3.13. Модуль выходов QB16, QB17
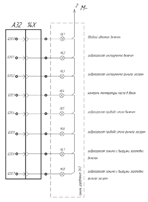
Рис. 3.14. Модуль выходов QB20, QB21
3.2 Выбор оборудования
По возможности при выборе элементов пользуемся
исключённым оборудованием из старой установки, которое необходимо для установки
на модернизированную (реле =24В, 110В). Также в первую очередь используем
оборудование со склада, элементы ПЛК после реконструкции Конвертерного цеха,
Дымососной.
Выбор ПЛК целесообразнее производить из линейки
Siemens, в связи с широкой распространённостью этого производителя на НТМК.
Обслуживающий и оперативно-ремонтный персонал комбината имеет навыки диагностики
проблем ПЛК Siemens и обучен работе с ними. Немецкий производитель
предоставляет большое количество разнообразной аппаратуры для технологических
процессов и промышленности. Богатый опыт в системах автоматизации вызывает
доверие у потенциальных заказчиков техники.
Для установки ПЛК на станке используем имеющийся
шкаф управления S7-300. В наличии блок питания SIMATIC S7-300, PS 307.
Первоначально выбирается центральный процессор
для контроллера. Так как управление необходимо осуществлять одним только
станком, правильнее выбрать распространённый процессор CPU315-2 DP, который
справится с технологической программой данного станка.
Подсчитав необходимое количество входов и
выходов, подбираем модули ввода и вывода дискретных сигналов. Для 79 входных
дискретных сигналов и необходимого резерва устанавливаем 3 модуля по 32 входа
(1 модуль в наличии). Для 57 выходных дискретных сигналов устанавливаем 1
модуль вывода на 32 выхода и 2 модуля на 15 выходов (1 модуль в наличии).
Необходимое количество аналоговых входов равно
6. используем имеющийся модуль на 8 аналоговых входов.
Чтобы обеспечить удобство и быструю замену в
случае выхода из строя модулей ввода/вывода, подключаем их через фронтштеккеры.
промежуточное реле для мотор-редуктора, 21
промежуточных реле для включения цепи магнитных пускателей.
Нормирующий преобразователь НТП2 выбираем по
типу датчика.
Реле перегрузки подключается к трансформаторам
тока на 5А, с отдельным питанием на 220В.
ММС - модуль - карта памяти для программы.
Таблица 1
Перечень элементов
Поз.
обозн.
|
Наименование
|
Кол.
|
Примечание
|
|
|
|
|
|
Шкаф
управления S7-300 в составе:
|
|
|
PS1
|
Блок
питания SIMATIC S7-300, PS 307, вход: ~120/230В; выход: =24В/5А. В комплекте
с изолированной скобой для подключения питания к интерфейсному модулю
|
1
|
6ES7307-1EA00-0AA0
|
|
CPU315-2
DP
|
1
|
315-2AG10-0AB0
|
A11, A21, A31
|
SM
321, модуль ввода дискретных сигналов: оптоэлектронное разделение внешних и
внутренних цепей, 32 входа =24В
|
3
|
6ES7321-1BL00-0AA0
|
A12
|
SM
322, модуль вывода дискретных сигналов: гальваническое разделение внешних и
внутренних цепей, 32 выхода =24В
|
1
|
6ES7322-1BL01-0AA0
|
A22, A32
|
SM
322, модуль вывода дискретных сигналов: гальваническое разделение внешних и
внутренних цепей, 16 выходов =24В
|
2
|
6ES7322-1BH01-0AA0
|
A13
|
SM
331, модуль ввода аналоговых сигналов: гальваническое разделение внешних и
внутренних цепей, 8 входов +-5В/+-10В/1…5В/+-20мА/0(4)…20мА.
|
1
|
6ES7331-7КF02-0AB0
|
11Х,13Х, 15Х,17Х
|
40
полюсный фронтальный соединитель с подключённым жгутом
|
4
|
6ES7922-3BC50-0AC0
|
12Х,
14Х, 16X
|
20
полюсный фронтальный соединитель с подключённым жгутом
|
2
|
6ES7922-3BC50-0AB0
|
КV30
|
Реле
промежуточное, 110В, 50Гц
|
1
|
РЭП34-31-11
УХЛ4
|
КV1…КV12 КV14… КV21 КV22
|
Реле
промежуточное, 24В с розеткой типа 2
|
21
|
РП21М-003-УХЛ4
|
V1…V40
|
Диод
|
40
|
КД209А
|
A1.1,
A1.2 A2…A4
|
Нормирующий
преобразователь
|
5
|
ЕН8
ТМТ182
|
А111
|
SIMOCODE
proV модуль измерения тока
|
1
|
3UF7103-1AA00-0
|
А112
|
SIMOCODE
proV базовый модуль
|
1
|
3UF7010-1AB00-0
|
1
|
953-8LG11-0AA0
|
- выделены элементы в налички
3.3 Написание управляющей программы
Используем стандартную программу написания для
ПЛК Siemens - Step7. С помощью симулятора PLCSIM проверяем правильность
написания и проводим отладку программы.
Создание конфигурации оборудования. С учётом
выбранных элеметнов и модулей ПЛК, в программе Step7 задаём HardWare Config.
Для всех входов и выходов в соответствии со
схемой в пункте 3.1 присваиваем символьные имена к адресам в программе.
Отображаем в таблице символов. При необходимости ввода меркеров, добавляем их в
таблицу на этапе проектирования.
При написании программы используется язык LAD
как более наглядный и схожий по построению с релейно-контакторным видом
управления.
Рис. 3.17. Таблица символов
Рис. 3.18. Таблица символов (продолжение)
Рис. 3.19. Таблица символов (продолжение)
Перед началом работы на станке по условиям
безопасности необходимо подать звуковую сигнализацию. Промежуточное реле на
которую расположено на выходе Q12.3 - KV20. Самоподхват сигнализации после
нажатия на кнопку «Пуск» обеспечивается SR-триггером. Действие по времени
звуковой сигнализации ограничиваем таймером S_ODT, который через заданный
промежуток времени при подаче на него сигнала подаёт сигнал на свой выход.
Таймер в программе заменяет реле времени в исходной оперативной схеме.
Рис. 3.20. Сигнализация
Меркер М4.2 собирает условия подачи «1» на
меркер М4.3, который в свою очередь обеспечивает условие работы для всей
остальной схемы.
Рис. 3.21. Условия М4.2
Рис. 3.22. Условия М4.3
Для условия работы всей схемы М4.3 проверяет
условия на срабатывание «Ключ», не нажатия «Стоп аварийный», не открытое Окно и
предыдущие условия из М4.2.
Поддержание оптимальной температуры масла в
баках гидроагрегатов выполнялось через реле KV34. Используем для этого действия
меркер М4.4. Те же условия включения схемы, но без таймера и отдельные кнопки
подают «1» на данный меркер.
Рис. 3.23. Условия М4.4
Охлаждение бака гидропривода инструмента
осуществляется двумя условиями: нет перегрева двигателей М4, М5=FS4; есть
сигнал «1» меркера превышения температуры М4.5. При срабатывании Q12.4
запускается промежуточное реле KV5 и соответственно магнитный пускатель КМ5.
Рис. 3.24. Магнитный пускатель приводов М4, М6
Меркер М4.5 формируется через сравнение
заданного «нормального» значения температуры и реального значения, снятого с
датчика ВТ3.
Преобразование аналогового сигнала:
Рис. 3.25. Действие FC105
Сравнение:
Рис. 3.26. Условия М4.5
Аналогично нагрев бака гидропривода инструмента.
Изменение в сравнении.
Рис. 3.27. Действие нагревателя при снижении
температуры
Пуск насосов на гидроприводе инструмента.
Рис. 3.28. Магн. пускатель насоса М2, М3
На магнитный пускатель КМ4 подаётся питание при
выполнении основных условий (ключ, окно, стоп), меркеров М4.3- отработка
звуковой сигнализации перед пуском, М4.4 - поддержания оптимальной температуры масла,
также кнопок на данный механизм (Стоп, пуск), Q12.7 - не работает подогрев,
FS2,FS3 - нет перегрева двигателя.
Формирование разрешения на замену шлифовального
круга.
Рис. 3.29. Действие М4.6
Основная программа выполняется в блоке OB1.
Функциональные блоки разумно создать для каждого механизма, также это удобно
для написания программы по заданному алгоритму РКС.
Создаём FB4-FB13:
Рис. 3.30. Фрагмент таблицы символов (FB)
Для гидропривода инструмента DB4, который
выполняется при условиях на EN.
Рис. 3.31. Data Block гидропривода инструмента
Для привода шлифовального круга необходимо
несколько условий:
нажатие кнопки Замена» (в случае замены), нет
вращения шлифовального круга (КМ1), конечный выключатель крайнего левого
положения стола замкнут, конченый выключатель «Бабка сзади» замкнут, для
«самоподхвата» (удержания триггера) два замкнутых конечных выключателя:
исходное положение механизма смены круга и фиксатор головки выведен. Контроль
перегрузки обеспечивается таймером вместо исходного реле времени, запускается
KS1 - контактом токового реле.
Рис. 3.32. Структура FB5 Шлифовального круга
Рис.3.33. Функция шлифовального круга в OB1
Аналогично созданы и остальные функциональные
блоки FB6-FB13, которые вызываются в организационном блоке OB1.
4. ИССЛЕДОВАТЕЛЬСКАЯ ЧАСТЬ
Для исследования правильности работы
спроектированной установки воспользуемся симулятором S7-PLCSIM.
При не нажатом «Пуске» схемы нет сигнала на
работу.
Рис. 4.1. Действие М4.1, М4.2
Для начала работы нажимаем «Пуск» I4.1 и видим,
что включается предупредительная звуковая сигнализация М4.1 и начинается отсчёт
времени М4.2.
Рис. 4.2. Симулятор PLCSIM
Рис. 4.3. Действие М4.1, М4.2
Вставляем ключ I4.2 в схему и замыкаем
промежуточный меркер М4.3.
Рис. 4.4. Действие симулятора на М4.3
Рис. 4.5. Действие М4.3
Рис. 4.6. Действие FC105
Убеждаемся в том, что не срабатывает подогрев
без превышения температуры Network 6-7.
Рис. 4.7. Команда сравнения на температуре (не
выполняется)
Нет запуска на охлаждение:
Рис. 4.8. Проверка запуска привода М5
Проверка на подогрев при снижении температуры
ниже допустимого уровня.
Рис. 4.9. Команда сравнения на температуре
(выполняется)
Насосы КМ4 не запускаются, пока идёт подогрев
масла, остальные условия выполнены:
Рис. 4.10. Условия запуска привода М2, М3
Проверка работоспособности функционального блока
FB5 - управление шлифовальным кругом (замена, контроль перегрузки).
Рис. 4.11. Выполнение FB5 Шлифовального круга
5. ОРГАНИЗАЦИОННО-ЭКОНОМИЧЕСКАЯ ЧАСТЬ
Модернизация устройства абразивной зачистки
круглого проката в выходной линии Крупносортного цеха требует такие
приобретения, как:
Техническая документация;
Комплект оборудования ПЛК и модулей;
Комплект оборудования, необходимого для
доработки существующих элементов измерения:
нормирующие термопреобразователи; ;
Комплект программного обеспечения (ПО);
Монтаж, надзор на месте за пуско-наладочными
работами, обучение, руководство по эксплуатации и техническому обслуживанию.
5.1 Определение капитальных затрат
Капитальные затраты для УАЗ складываются из
нескольких составляющих:
стоимость оборудования
стоимость монтажных и демонтажных работ
стоимость проектной части
стоимость смежных расходов (документы)
Таблица 2
Стоимость оборудования
Наименование
|
Кол-во,
шт.
|
Цена
|
Стоимость,
р.
|
Блок питания
SIMATIC S7-300, PS 307 6ES7307-1EA00-0AA0
|
1
|
140,98
у.е.
|
40*140,98*1=
5 640,00
|
CPU315-2
DP 315-2AG10-0AB0
|
1
|
1
431,00 у.е.
|
40*1
431,00*1= 57 240,00
|
SM
321, модуль ввода дискретных сигналов, 32 входа 6ES7321-1BL00-0AA0
|
2
|
311,64
у.е.
|
40*311,64*2=
24 932,00
|
SM
322, модуль вывода дискретных сигналов, 32 вых. 6ES7322-1BL01-0AA0
|
1
|
431,42
у.е.
|
40*431,42
*1= 17 256,00
|
SM
322, модуль вывода дискретных сигналов, 16 вых. 6ES7322-1BH01-0AA0
|
1
|
215,18
у.е.
|
40*215,18
*1= 8 607,00
|
SM
331, модуль ввода аналоговых сигналов, 8вх. 6ES7331-7КF02-0AB0
|
1
|
595,72
у.е.
|
40*595,72*1=
23 828,00
|
40
полюсный фронштеккер 6ES7922-3BC50-0AC0
|
2
|
35,72
у.е.
|
40*35,72*2=
2 860,00
|
20
полюсный фронштеккер 6ES7922-3BC50-0AB0
|
2
|
22,68
у.е.
|
40*22,68*2=
1 814,00
|
Нормирующий
преобразователь ЕН8 ТМТ182
|
5
|
53,5
у.е.
|
40*53,5*5=
10 700,00
|
SIMOCODE
proV модуль измерения тока 3UF7103-1AA00-0
|
1
|
185,15
у.е.
|
40*185,15
*1= 7 406,00
|
SIMOCODE
proV базовый модуль 3UF7010-1AB00-0
|
1
|
450,80
у.е.
|
40*450,80
*1= 18 032,00
|
ММС
- модуль 128кB 953-8LG11-0AA0
|
1
|
49,33
у.е.
|
40*49,33*1=
1 973,00
|
ИТОГО
|
19
|
4
507,16 у.е.
|
185
926,00
|
Принимаем среднюю величину 1 у.е. = 40 руб.
В таблице приведено необходимое количество
нового оборудования, не учитываются используемые модули, которые имеются на
складе после реконструкции.
КОБ = 185 926 руб.
Таблица 3
Стоимость монтажных и демонтажных работ
Наименование работ
|
Трудоёмкость,
чел/час
|
Цена,
руб. за 1чел/час
|
Стоимость
работ, руб.
|
Демонтаж
релейного шкафа и подключений
|
12
|
80
|
960
|
Монтаж
ПЛК, интерфейса, подключение датчиков и реле
|
24
|
80
|
1920
|
Установка
ПО, настройка работы станка
|
32
|
120
|
3840
|
Цена работ рассчитывается исходя из месячного
оклада электромонтёров для монтажа/демонтажа и настройка работы станка с ПЛК из
месячного оклада инженера-электроника.
КМОНТ = 960+1920+3840 = 6720 руб.
Стоимость проектной части
Так как модернизация станка УАЗ производится
внутри предприятия без привлечения проектных организаций стоимость проектной
части принимается как месячная заработная плата инженера-электроника 1
категории.
Оклад = 18 800 руб.
Премия = 25%*18 800 = 4 700 руб.
Уральский коэф. = 15%*18 800 = 2820 руб.
Подоходный налог = 13%*(18 800+2820) = 2810 руб.
Заработная плата = 18 800+4 700+2820-2810 =
23510 руб.
КПРОЕКТ = 23510 руб.
Стоимость смежных расходов
В смежные работы по модернизации станка
включается оформление и документация.
Примем равной 1000 руб.
КСМ = 1000 руб.
ИТОГО капитальных затрат:
К = КОБ + КМОНТ + КПРОЕКТ + КСМ
К = КОБ + КМОНТ + КПРОЕКТ + КСМ
5.2 Определение эксплуатационных расходов
Ежегодные текущие затраты на станке УАЗ
складываются из следующих составляющих:
амортизационные отчисления
годовые затраты на материалы
годовые затраты на рабочую силу
стоимость потерь электроэнергии
Расчёт амортизационных отчислений
Установим, что на всё приобретаемое оборудование
относятся амортизационные отчисления.
Са = ра * Коб*
Са = 0,08 * 185 926,00 = 14 875,00 (руб./год)
Коб* = 185 926,00 руб.
ра = 0,08
где Коб* - доля оборудования, подлежащего
амортизации
ра - нормативный коэф. амортизации
Расчёт годовых затрат на материалы
Исходная схема УАЗ отмечается крайней
ненадёжностью и периодически выходит из строя. При этом часто приходится
заменять реле или контакторы для восстановления работоспособности.
Средняя стоимость реле на 110В: 250 руб
Средняя стоимость реле на 24В: 185руб
Примем, по 1 реле на каждый ремонт
СМ1 = (250+185)*12 = 5220 руб./год
В спроектированной установке схема не требует
многих промежуточных реле, но остаются другие согласующие реле на включение
магнитных пускателей и электромагниты в гидросистемах.
СМ2 = 185*1 = 185 руб./год
Расчёт годовых затрат на рабочую силу
Исходная установка относительно часто выходит из
строя. На восстановление её работоспособности существует группа электромонтёров
для данного участка цеха.
Рассчитать трудочасы на восстановление сложно и
возможно только приближённым грубым методом. Примем, что существующая штатная
должность электромонтёра 4 разряда будет исключена, либо полставки должности
переведены на другие работы.
Оклад = 13 200 руб.
Премия = 50%*13 200 = 6 600 руб.
Уральский коэф. = 15%*13 200 = 1980 руб.
Подоходный налог = 13%*(13 200+1980) = 1970 руб.
Заработная плата = 13 200+6 600+1980-1970 = 19
810 руб./мес
Годовые расходы = ЗП*12 = 19 810 руб.*12 =
237720 руб./год.
СЗП1 = 237720 руб./год*0,5 ставки = 118860
руб./год.
Модернизированная установка затрат на рабочую
силу почти не требует, допустим периодическое исправление и настройка программы
управления отнимет у инженера-электроника 80 часов в год.
Т.е. ЗП*0,5 = 23510 руб.*0,5 = 11755 руб./год.
СЗП2 = 11755 руб./год.
Расчёт потерь электроэнергии
В разделе 6 «Энергосбережение» была подсчитана
экономия электроэнергии за счёт применения ПЛК Siemens. Разница в потреблении
электроэнергии у исходной и модернизированной установки около 200 Вт.
Примем количество дней работы установки (без
дней на ремонты и планово-предупредительные работы в цехе) равным 320.
Примем количество часов работы установки в сутки
(без времени на обед и перерывы) равным 20.
Исходная установка:
Wгод1 = 350 * 20 * 320 = 2 240(кВт*ч)
Сn1 = ЦЭ* Wгод1 = 2,8 * 2 240 = 6 270 (руб.)
Модернизированная установка:
год2 = 150 * 20 * 320 = 960 (кВт*ч)
Сn2 = ЦЭ* Wгод2 = 2,8 * 960 = 2 688 (руб.)
гдегод - разница в годовом потреблении электроэнергии;
ЦЭ - цена электроэнергии;
Сn - стоимость эл.эн.
Получаем разность Сп1 - Сп2 = 3582 руб./год.
Общие ежегодные затраты:
С = СА + СМ + СЗП + СП
С1 = 0,00 + 5220,00 + 237 720,00 + 6 270,00 =
130 350,00
С2 = 14 875,00 + 185,00 + 11 755,00 + 2 688,00 =
29 503,00
.3 Составление итоговой таблицы
технико-экономических показателей
Таблица 4
Таблица технико-экономических показателей
Показатель
|
Ед.
изм.
|
Значение
|
|
|
базовый
|
проектный
|
1)
Капитальные затраты
|
1.1.
Ст-ть оборудования
|
руб.
|
-
|
185
926
|
1.2.
Ст-ть монтажн. работ
|
руб.
|
-
|
6
720
|
1.3.
Ст-ть проектн. части
|
руб.
|
-
|
23
510
|
1.4.
Ст-ть смежн. расх.
|
руб.
|
-
|
1
000
|
ИТОГО
капит. затрат
|
руб.
|
-
|
217
156
|
2)
Эксплуатационные расходы
|
2.1.
Амортизац. отчисл.
|
руб.
|
-
|
14
875
|
2.2.
Затраты на материалы
|
руб.
|
5
220
|
185
|
2.3.
Затраты на раб. силу
|
руб.
|
118
860
|
11
755
|
2.4.
Оплата эл.эн.
|
руб.
|
6
270
|
2
688
|
ИТОГО
экспл. расходов
|
руб.
|
130
350
|
29
503
|
3)
Годовой экономический эффект
|
3.1.
Разница тек. расходов
|
руб.
|
100
847
|
3.2.
Эк. эффект от расхода ЗИП и материала
|
руб.
|
5
035
|
3.3.
Эк. эффект от обслуживания
|
руб.
|
107
105
|
3.4.
Эк. эффект от расхода электроэнергии
|
руб.
|
3
582
|
3.3.
Количество ремонтов
|
раз/год
|
12
|
1
|
Срок
окупаемости
|
лет
|
2,15
|
Вывод: Срок окупаемости намного
меньше нормативного (7 лет), следовательно, установка нового оборудования на
УАЗ, его модернизация будет экономически эффективна для предприятия.
6. ЭНЕРГОСБЕРЕЖЕНИЕ
Вопросы энергосбережения всегда были
актуальны для ОАО «НТМК».
Доля энергозатрат в себестоимости
продукции комбината: 2009 год - 9%, 2010 г. - 11%. Рост доли энергозатрат в
себестоимости связан, в первую очередь, с ростом тарифов на закупные
энергоресурсы.
Приоритетные направления
энергосбережения:
снижение расхода энергоресурсов при
производственных процессах;
замещение закупных энергоресурсов
собственным производством (э/э ТЭЦ иГУБТ, использование в качестве топлива
доменного и коксового газов и т.д.);
-сокращение непроизводительных потерь
энергоресурсов в процессе транспортировки и потребления.
Достижение значимого эффекта от энергосбережения
возможно при условии реализации не только технических решений, но и применении
более
совершенного
механизма управления энергосбережением - системы энергетического менеджмента.
Страны, внедрившие у себя стандарты в области системы энергоменеджмента,
добились устойчивой экономии до 20% потребления энергоресурсов в
промышленности.
Позитивный опыт применения энергоменеджмента и
потребность придания работе по
энергосбережению системности и комплексности неизбежно ведут квнедрению системы
энергоменеджмента в соответствии со стандартом.
Режим энергосбережения особенно актуален для
механизмов, которые часть времени работают с пониженной нагрузкой, - конвейеры,
насосы, вентиляторы и т.п. Кроме снижения расхода электроэнергии, экономический
эффект от применения частотно-регулируемых электроприводов достигается путем
увеличения ресурса работы электротехнического и механического оборудования, что
становится дополнительным плюсом.
6.1 Уменьшение потребления электроэнергии в
оперативной схеме
Уменьшение потребления электроэнергии в
оперативной схеме модернизируемой установки УАЗ происходит за счёт смены
управления с релейно-контакторных элементов на ПЛК.
Сравним мощность исходной схемы с промежуточными
реле, реле времени и мощность потребления проектируемого ПЛК со своими
промежуточными реле.
Расчёт энергопотребления исходной схемы
управления:
Реле времени РСВ15-1, 110В, 50Гц, кол-во: 8 шт.
= 5,5*8 = 44 Вт
Реле промежуточное, 24В, РП21М-003-УХЛ4,
РП21М-004-УХЛ4, кол-во: 24 шт.
= 4*24 = 96 Вт
Реле промежуточное, 110В, 50Гц, РЭП34-31-11
УХЛ4, РЭП34-44-11 УХЛ4, кол-во: 23 шт.
= 8*23 = 184 Вт
Расчёт энергопотребления проектируемой схемы
управления:
Расчёт энергопотребления ПЛК:
Для определения мощности и определения
технических данных воспользуемся каталогом продукции Siemens.
Данные каталога приведены в Приложении.
-2 DP= IU = 24В*0,850А = 20,4 Вт
321, модуль ввода дискретных сигналов:
оптоэлектронное разделение внешних и внутренних
цепей, 32 входа =24В
6ES7321-1BL00-0AA0= 6,5 Вт
322, модуль вывода дискретных сигналов:
гальваническое разделение внешних и внутренних
цепей, 32 выхода =24В
6ES7322-1BL01-0AA0= 6,6 Вт
322, модуль вывода дискретных сигналов:
гальваническое разделение внешних и внутренних
цепей, 16 выходов =24В
6ES7322-1BH01-0AA0= 4,9 Вт
322, модуль ввода аналоговых сигналов:
гальваническое разделение внешних и внутренних
цепей, 8 входов +-5В/+-10В/1…5В/+-20мА/0(4)…20мА.
6ES7331-7КF02-0AB0= 1 Вт
Суммарная потребляемая мощность:
-2 DP = 20,4 Вт
321, 6ES7321-1BL00-0AA0, кол-во: 3шт.= 6,5 Вт *
3 = 19,5 Вт
322, 6ES7322-1BL01-0AA0, кол-во: 1шт.= 6,5 Вт *
1 = 6,6 Вт
322, 6ES7322-1BH01-0AA0, кол-во: 2шт.
P = 4,9 Вт
* 2 = 9,8 Вт
331, 6ES7331-7КF02-0AB0
P = 1 Вт * 1 = 1 Вт
РПЛК = 20,4+19,5+6,6+9,8+1 = 57,3 (Вт)
Расчёт энергопотребления спроектированных
промежуточных реле:
Реле промежуточное 110В, 50Гц РЭП34-31-11 УХЛ 4,
кол-во: 1 шт.
= 8 Вт
Реле промежуточное 24В, РП21М-003-УХЛ4, кол-во:
21 шт.
= 4*21 = 84 Вт
РСУММ2 = 56,3 + 8 + 84 = 148 Вт
Подсчитаем разницу в электропотреблении исходной
установки и спроектированной:
РРАЗН = РСУММ1 - РСУММ2 = 324 Вт - 148 Вт = 176
Вт
Разность потребляемой мощности отличается более
чем в два раза в пользу спроектированной системы управления.
.2 Уменьшение потребления электроэнергии за счёт
применения устройства плавного пуска
Установим целесообразность установки устройства
плавного пуска.
Для этого сравним моменты инерции двигателя
главного привода шлифовального круга и момент инерции шлифовального круга.
Таблица 5
Момент инерции двигателя М1, 4АМ250S4УП УЗ,
75кВт, 380/660В, 50Гц, исп. 1М1081:
Момент инерции шлифовального круга
ПП 630х80х305:
Т.к.
, почти в 5 раз, то целесообразно
установить устройства плавного пуска на главный привод М1.
Двигатель работает без остановки в
течение смены, кроме больших перерывов более 30мин. Энергоэффективно
останавливать двигатель в технологических перерывах пока он работает в
холостую. А так как условия запуска с большим моментом инерции нагрузки тяжелы
желательно применить устройство плавного пуска. Выберем из каталога Siemens
серии Sirius:Sirius 3RW40 - устройства плавного пуска, плавного останова и
защиты.
Применение SIRIUS для 3-фазного
двигателя
Устройства плавного пуска мощностью
от 5.5 до 250 кВт (при 400 В) подходят для стандартного применения в 3-фазных
сетях. Очень маленький размер, низкие потери электроэнергии и простота в
использовании - это только 3 из многих преимуществ применения устройств
плавного пуска SIRIUS 3RW40.
Полупроводниковые устройства
плавного пуска SIRIUS 3RW40 подходят для плавного пуска/останова 3-фазных
асинхронных двигателей. Благодаря фазовому ток ограничивается во всех 3 фазах в
течение всего процесса пуска. Кроме этого, благодаря специальному методу
управления исключаются являющиеся нежелательными составляющие постоянного тока,
характерные для всех устройств плавного пуска с управлением по двум фазам. В
итоге, можно не только осуществить 2-фазный пуск двигателя до 250 кВт (при 400
В), но и избежать бросков тока и вращающего момента, которые возникают при
использовании устройств пуска «звезда-треугольник».
Рис. 6.1. Устройство плавного пуска
SIRIUS
Подберём необходимое устройство
Sirius:
Таблица 6
Мощность
электродвигателя, Pн, кВт, Uпит=380 В, 3 фазы
|
Ток
номинальный УПП, А
|
Код
устройства
|
75
|
134
|
3RW4055-6BB44
|
7. БЕЗОПАСНОСТЬ ПРИ ЭКСПЛУАТАЦИИ И РЕМОНТАХ
ОБОРУДОВАНИЯ
7.1 Общая
характеристика объекта с точки зрения безопасности
Объектом рассмотрения, в данной ВКР, является
крупносортный цех ОАО «НТМК», участок линии выходной обработки круглого
проката. Характеристиками условия труда на рабочем месте, являются:
. Пыль;
. Шум;
. Работа в действующих электроустановках;
. Движущиеся машины и механизмы;
. Подвижные части производственного
оборудования;
. Передвигающиеся изделия, заготовки;
. Повышенная запыленность и
загазованность воздуха рабочей зоны;
. Повышенная или пониженная температура
поверхностей оборудования, материалов;
. Повышенная или пониженная температура
воздуха рабочей зоны;
. Повышенный уровень шума на рабочем месте;
. Отсутствие или недостаток естественного света;
. Недостаточная освещенность рабочей зоны;
. Повышенная пульсация светового потока;
. Работа в зоне влияния электрического поля;
. Работа в зоне влияния магнитного поля
7.2 Обоснование эффективности автоматизации с
точки зрения безопасности человека
Автоматизация имеет исключительно большое
значение для успешного решения конструкций машиностроительных изделий с точки
зрения культуры труда. Она дает возможность конструктору и проектировщику
эффективно и притом экономично решать вопросы конструирования машин и устройств
с точки зрения безопасности в отношении рабочего травматизма и охраны здоровья
обслуживающего персонала и, не в последнюю очередь, оказывает влияние на
внешний вид проектируемого машиностроительного изделия. Влияние автоматизации
на внешний вид проектируемого изделия может сказываться как тогда, когда данная
машина или другое оборудование конструируется как полностью автоматизированное,
так и тогда, когда данное машиностроительное изделие должно изготовляться на
автоматической линии или автоматизированным производственным процессом. Таким
образом, конструктор и проектировщик должны интересоваться автоматизацией и с
указанных точек зрения, и с точки зрения общественных результатов внедрения
автоматизации и влияния автоматизации на человека, который будет управлять автоматизированным
оборудованием.
Применение средств автоматизации и
дистанционного контроля исключает
такие факторы воздействия на человека как:
утомление;
монотонность операций;
персептивная и интеллектуальная нагрузка;
окружающая среда;
биомеханические и физиологические факторы.
Также автоматизация повышает точность и
стабильность работы, исключает несчастные случаи по ошибке оператора. Если
из-за неполадки агрегат переводится в безопасный режим, то благодаря встроенной
системе диагностики можно будет быстрее установить причину и раньше возобновить
работу.
В данной ВКР по модернизации Устройства
абразивной зачистки система автоматического управления на релейно-контакторных
схемах заменяется на более совершенные системы с ПЛК, позволяющие избавиться от
промежуточных рели и их контактов.
В среднем обслуживание данного устройства при
выходе из строя производится раз в месяц. Работы эл.-монтёров по восстановлению
работоспособности занимают от 4 до 12 часов. Модернизация обеспечит
бесперебойную работу установки, т.к. в схеме не будет промежуточных реле, реле
времени. Следовательно, внедрение проектируемой автоматической системы приведёт
к улучшению условий труда обслуживающих работников по следующим вредным и
опасным производственным факторам:
1. Пыль;
. Работа в действующих электроустановках;
. Движущиеся машины и механизмы;
. Повышенная запыленность и
загазованность воздуха рабочей зоны;
. Отсутствие или недостаток естественного света;
. Недостаточная освещенность рабочей зоны;
. Работа в зоне влияния электрического поля;
. Работа в зоне влияния магнитного поля
Главный исключаемый фактор - работа в
действующих электроустановках, т.к. при замене и ремонте предшествующих реле
необходимо работать по близости к токопроводящим, сторонним проводящим и
открытопроводящим частям.
7.3 Категория
помещения по электробезопасности
Питание в КСЦ приходит с трансформаторной
подстанции, напряжение 6кВ., с двух секций шин. После чего, понижающим
трансформатором снижается до 400 В., откуда сниженное напряжение попадает в
электропомещение, также два ввода приходят на щиты распределительные. Далее
питающее напряжение подаётся непосредственно на электроустановку, управляющие
привода и т.д.
Электропомещение в отношении опасности поражения
электрическим током относится к особо опасным. Так как выявлено наличие двух и
более условий повышенной опасности. Существует возможность одновременного
прикосновения человека к металлоконструкциям зданий, имеющим соединения с
землёй, технологическим аппаратам - это, например, корпуса электрошкафов,
механизмов с одной стороны, и к металлическим корпусам электрооборудования
(открытым проводящим частям) - с другой. Также на поверхностях возле установки
УАЗ оседает токопроводящая пыль, которая вращением шлифовального круга
снимается с металлической заготовки. Местами присутствуют токопроводящие полы
из железным плит или просто земляных.
Данное электропомещение снабжено системой
кондиционирования для поддержания температуры в пределах нормы вентиляции.
Элементы управления устройства УАЗ расположены на посту управления, с точки
зрения электробезопасности помещения без повышенной опасности. Шкафы управления
автоматикой установки находятся на посту управления, доступ к шкафам имеют
только электротехнический персонал, все шкафы запираются.
По надёжности электроснабжения КСЦ относится к
потребителям I категории. В данном случае перерыв в электроснабжении может
повлечь за собой значительный материальный ущерб, а также расстройство сложного
технологического процесса. Пониженное напряжение или его отсутствие может
привести к браку изделий, например, на прокатной клети Стана «650» или при
нагреве заготовок. Поэтому для предотвращения таких случаев предпринимаются
следующие меры: использование резервного ввода, использование источников
бесперебойного питания.
.4 Алгоритмические и программные решения,
обеспечивающие безопасность персонала при работе с объектом автоматизации
Открытие дверей на входе в рабочую зону
установки приводит к срабатыванию внешней сигнализации. Двери электрошкафа
связаны с главным вводным автоматом QF1, который размыкается при открытии
дверей.
Рис. 7.1. Блокировка дверей электрошкафа
модернизация автоматический станок
контроллер
Применяется заземление всех двигателей и
трансформаторов установки, показанное на схемах пунктирной линией PE.
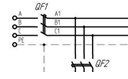
Рис. 7.2. Фрагмент заземления из схемы
При нажатии кнопки «Пуск» программа должна
давать сигнал на включение сигнализации.
Рис. 7.3. Фрагмент программы (безопасность)
Сигнализация отрабатывает время, устанавливаемое
таймером Т1.
Рис. 7.4. Фрагмент программы
Меркер М4.3, выполняющий функцию реле KV33 в
исходной схеме, отвечает за работу всей всей установки. Он блокирует
положительный сигнал на все исполнительные механизмы.
Необходимо выполнение условий безопасности:
окно кабины (SQ24) закрыто, I3.1;
кнопка аварийного отключения SB2 находится в
верхнем положении, I4.3;
ключ SA4 повёрнут в положение 1 (включено),
I4.2.
Проверка работоспособности условий защит:
Рис. 7.5. Проверка на симуляторе
Нажат I4.1 - Пуск, I4.2- повёрнут ключ, нет Стоп
I4.3 и не открыто Окно I3.1. Подаётся плюс на М4.2, позволяющий сработать
таймеру на звуковой сигнализации и отключить её, замкнув М4.3 после заданного
времени.
Аналогично выполняются и другие условия
безопасности при работе на станке:
Включение шлифовального круга возможно при
условии, что кожух круга закрыт, шлифовальная головка находится вверху и не
производится замена шлифовального круга;
Движение шлифовальной головки возможно при
условии исходного положения головки, головка зажата, механизм смены круга в
исходном положении, фиксатор головки выведен.
7.5 Рекомендации по организации рабочего места
оператора автоматизированной системы управления
Рабочее место оператора должно обеспечивать:
удобную рабочую позу, точность движений, соответствие санитарно-гигиеническим
требованиям. Основой рабочего места оператора является пульт с органами
управления и индикаторными панелями. Особенности его технологического решения
определяются спецификой работы оператора. Основным требованием при размещении
индикаторных, регистрирующих элементов и органов управления является облегчение
сбора информации и ее переработки человеком. Учитывается, что моторное поле
(поле движений) разделяется на максимальные, минимальные, нормальные и
оптимальные рабочие зоны операторов, работающих в горизонтальной и вертикальных
плоскостях при работе сидя(рис. 7.6.). В горизонтальной плоскости поле делится
на зону основных движений оператора с легкой доступностью и хорошим обзором
(оптимальное рабочее пространство) и зону вспомогательных движений
(максимальное рабочее пространство). Оптимальное рабочее пространство
ограничено дугами, описываемыми каждой рукой оператора при вращении в локтевом
суставе - зона I (рис. ). Максимальное рабочее пространство ограничено дугами,
описываемыми вытянутыми руками с поворотом в плечевом суставе (зона II). Органы
управления располагают так, чтобы по возможности свести рабочие движения к
движениям предплечья, пальцев кисти руки, исключить движения плечевого сустава,
перекрестную работу рук, равномерно распределить работу между правой и левой
рукой, с учетом того фактора, что правой рукой выполняются наиболее
ответственные операции, требующие наибольшей силы и точности.
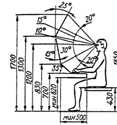
Рис.7.6. - зона основных движений; II - зона
вспомогательных движений; III - зона вне пределов досягаемости, но в пределах
видимости приборов.
Наиболее важные индикаторные элементы исходя из
анализа деятельности оператора располагаются в центре на уровне глаз оператора
или несколько ниже. Целесообразно выполнять группировку индикаторных элементов,
передающих информацию об одном объекте, либо связанных общей задачей по
функциональному назначению. Группирование может выполняться разделением
приборов определенными промежутками, выделением групп различной окраской,
заключением групп в рамки и т.д.Показания должны читаться слева направо.
Надписи к элементам выполняют краткими, ясными и размещают горизонтально.Плоскость
поверхности, где располагаются индикаторы, перпендикулярна линии взора, что
достигаются наклоном рабочих панелей (рис. 1).Микроклимат в помещении пункта
управления должен благоприятствовать работе персонала. Рекомендуется
температура воздуха 18-24 °С, влажность от 30 до 80 %, скорость движения
воздуха - не более одного метра в секунду.
Управление станком осуществляется из кабины
оператора с помощью пульта управления. Пульт управления включает в себя две
панели с кнопками управления, переключателями, сигнальными лампами,
регуляторами температуры, амперметром и вольтметрами. Функциональные назначения
нанесены на панелях пульта около аппаратов. Их обозначения в соответствии со
схемой электрической принципиальной показаны на рис.
Рис.7.7. Панель регуляторов и указателей
Рис.7.8. Панель управления
Перспективной разработкой по данному станку
будет создание SCADA-системы для мониторинга технологического процесса. Это
позволит избавиться от физических кнопок и переключателей, облегчит работу
оператора.
Охрана труда при работе с персональными ЭВМ
Требования в области охраны труда в полной мере
выполняются на рабочем месте оператора:
помещение для эксплуатации ПЭВМ имеет естественное
и искусственное освещение;
естественное и искусственное освещение
соответствовать требованиям действующей нормативной документации СанПиН. Окна в
помещениях, где эксплуатируется вычислительная техника, ориентированы на и
северо-восток. Оконные проемы оборудованы регулируемыми жалюзи;
площадь на одно рабочее место пользователей ПЭВМ
с ВДТ на базе плоских дискретных экранов (жидкокристаллические, плазменные)
составляет не менее 4,5 м2;
помещение оборудовано защитным заземлением в
соответствии с техническими требованиями по эксплуатации;
в помещении обеспечиваются оптимальные параметры
микроклимата для категории работ 1а и 1б в соответствии с действующими
санитарно-эпидемиологическими нормативами микроклимата производственных
помещений;
шумящее оборудование (печатающие устройства,
серверы и т.п.), уровни шума которого превышают нормативные, размещается вне
помещения с ПЭВМ;
высота рабочей поверхности стола составляет 750
мм, есть необходимое пространство под столом для расположения ног.
ЗАКЛЮЧЕНИЕ
Модернизация установки УАЗ повышает надёжность
его работы, снижает количество его ремонтов и обслуживания. Как следствие,
явный экономический эффект от модернизации, который подтверждён в 5м разделе.
В выпускной квалификационной работе подобрано
необходимое новое электрооборудование, выбраны модули ПЛК, написана управляющая
программа работы установки для процессора ПЛК. Произведено исследование
работоспособности написанной программы, а также сделано обоснование
экономической целесообразности предлагаемого внедрения. Обеспечены достаточные
условия безопасности и блокировки в программе. Все принятые технические решения
подтверждены соответствующими расчетами.
Модернизация, в частности в системах
автоматизации актуальна для ОАО «НТМК», как важный шаг в повышении качества
продукции, снижения её себестоимости, а, следовательно, повышения
конкурентоспособности продукции комбината.
БИБЛИОГРАФИЧЕСКИЙ СПИСОК
Проектирование
автоматизированного электропривода промышленных установок и систем
энергообеспечения предприятий, организаций и учреждений: метод. указания к
дипломному проектированию / авт.-сост. В.Л. Тимофеев; Федер. агентство по
образованию, ГОУ ВПО «УГТУ-УПИ имени первого Президента России Б.Н. Ельцина»,
Нижнетагил. технол. ин-т (фил.). - Нижний Тагил: НТИ (ф) УГТУ-УПИ, 2009. - 28
с.
Автоматизация
с помощью программ Step7 LAD и FBD. Программируемые контроллеры Simatic
S7-300/400 / Ганс Бергер: Нюрнберг, 2001.- Язык программирования промышленных
контроллеров SIMATIC S7. Учебное пособие / ЦПП Евраз-Урал - Нижний Тагил, 2012.
- 186 с.
Безопасность
жизнедеятельности. Технические расчеты параметров электробезопасности: учеб.
пособие по выполнению раздела ВКР / авт.-сост. В.В. Гоман; Федер. агентство по
образованию, ГОУ ВПО «УГТУ-УПИ имени первого Президента России Б.Н. Ельцина»,
Нижнетагил. технол. ин-т (фил.). - Нижний Тагил: НТИ (ф) УГТУ-УПИ, 2010. -
с.
Должностные
инструкции для обслуживающего и ремонтного персонала по КСЦ, ДИ Р 117 004.21.
Каталог
Siemens CA01русская редакция / Сименс. - Г.: Эрланген, 2012.
Руководство
по эксплуатации: станок обдирочно-шлифовальный / ОАО «Воронежский
станкостроительный завод» - В., 2009.
Технические
и экономические расчеты в курсовых и дипломных проектах/ В.Л. Тимофеев, О.Н.
Баркова, И.Н. Исаев. Нижний Тагил: НТИ(ф) УГТУ-УПИ, 2006.
Руководство
по эксплуатации: 2ТРМ1 / ОВЕН - Москва, 2010.