Проект системы автоматизированного управления насосными агрегатами станции II подъема комплекса обезжелезивания и деманганации
РЕФЕРАТ
Пояснительная записка содержит 94 стр.
машинописного текста, 15 таблиц, 13 рисунков, список использованных источников
- 24 наименования, 2 приложения.
ДЕМАНГАНАЦИЯ, АВТОМАТИЗАЦИЯ, НАСОСНЫЙ АГРЕГАТ,
ИЗМЕРЕНИЕ, РЕГУЛИРОВАНИЕ, УПРАВЛЕНИЕ, УРОВЕНЬ, ДАВЛЕНИЕ, КОНТРОЛЛЕР, ДАТЧИК,
ЗАЩИТА, SEPAM.
Объектом исследования является насосная станция
II подъема комплекса обезжелезивания и деманганации вод Амурского водозабора в
пласте (г. Комсомольск-на-Амуре).
Целями создания и внедрения АС являются:
- поддержание оптимального давления и расхода в
напорных трубопроводах;
- автоматизация управления
оборудованием насосной станции II подъема;
- своевременное реагирование на
аварийные ситуации;
- исключение влияния человеческого
фактора на процедуру сбора и обработки информации.
В результате создания АС должны быть достигнуты
следующие технические, технологические, производственно-экономические и другие
показатели:
- оптимизация работы насосных станций;
- экономия энергоресурсов и воды;
- безопасность для жизни и здоровья
людей при эксплуатации объекта;
- своевременное обнаружение аварий.
Содержание
ВВЕДЕНИЕ
. ОПИСАНИЕ ТЕХНОЛОГИЧЕСКОГО ПРОЦЕССА
ОБЕЗЖЕЛЕЗИВАНИЯ И ДЕМАНГАНАЦИИ ВОДЫ
.1 Химизм процессов в воде с
участием железа
.2 Методы обезжелезивания воды
.3 Деманганация воды
. ХАРАКТЕРИСТИКИ АВТОМАТИЗИРОВАННОЙ
СИСТЕМЫ УПРАВЛЕНИЯ
. ОПИСАНИЕ ТЕХНОЛОГИЧЕСКОГО
ОБОРУДОВАНИЯ
.1 Структура системы автоматического
управления
.2 Комплекс технических средств
нижнего уровня
.2.1 Выбор средства измерения
давления
.2.2 Выбор электроприводов вращения
для шаровых вентилей и клапанов
.3 Комплекс технических средств
среднего уровня
.3.1 Средство управления и сбора
данных
.3.2 Выбор контроллера
. РАСЧЕТ И ВЫБОР ЭЛЕМЕНТОВ СИЛОВОЙ
ЧАСТИ ЭЛЕКТРОПРИВОДА
.1 Расчет и выбор насосных агрегатов
.2 Разработка структурной схемы
автоматического управления насосными агрегатами
.3 Выбор частотного преобразователя
.4 Выбор силового выключателя
. ВЫБОР СИСТЕМЫ ЗАЩИТЫ
ЭЛЕКТРОПРИВОДА
.1 Защита двигателей насосных
агрегатов
.1.1 Алгоритм работы защиты двигателя
насосных агрегатов
.1.2 Разработка программного
обеспечения для устройства защиты и измерения Sepam
.ОПРЕДЕЛЕНИЕ ЭКОНОМИЧЕСКОЙ
ЭФФЕКТИВНОСТИ ОТ ВНЕДРЕНИЯ СИСТЕМЫ АВТОМАТИЗИРОВАННОГО УПРАВЛЕНИЯ НАСОСНЫМИ
АГРЕГАТАМИ
.1 Характеристика технико-экономической
эффективности модернизации
.2 Критерий экономической оценки
эффективности модернизации
.3 Расчет капитальных вложений на
внедрение проекта САУ НА
.4 Расчет экономического эффекта в
результате внедрения САУ НА
.5 Расчет экономической
эффективности от внедрения САУ НА и срок его окупаемости
. РАЗРАБОТКА МЕРОПРИЯТИЙ ПО БЖД НА
НАСОСНОЙ СТАНЦИИ. ЭЛЕКТРОБЕЗОПАСНОСТЬ
.1 Анализ вредных и опасных
производственных факторов
.2 Опасные факторы, связанные с
использованием электрической энергии
.3 Мероприятия защиты и
предотвращения воздействия повышенного напряжения в электрической цепи на
человека
.4 Требования к персоналу,
допускаемому к обслуживанию электроустановок
.5 Средства защиты
ЗАКЛЮЧЕНИЕ
СПИСОК ИСПОЛЬЗОВАННЫХ ИСТОЧНИКОВ
ПРИЛОЖЕНИЯ
ВВЕДЕНИЕ
О том, что технологические комплексы городского
хозяйства, обеспечивающие жизнедеятельность населения, не могут быть
реализованы без современных средств автоматизации, известно всем и давно.
Действительно, нужно измерять, контролировать основные технологические параметры
процессов, следить за их отклонениями состоянием оборудования. Нужно иметь
возможность дистанционно (из диспетчерского пункта) включать и отключать
отдельные агрегаты, открывать и закрывать задвижки; обеспечивать режимы работы
установок путём поддержания наиболее важных параметров на заранее рассчитанных
значениях.
Реализация этих и многих других функций систем
автоматизации значительно видоизменилась в результате бурного внедрения в
промышленности микропроцессоров, персональных компьютеров и прикладного
программного обеспечения.
Удешевление микропроцессорных устройств и
расширение их функций сделало возможным построение так называемых
«интеллектуальных датчиков», которые вычисляют значения косвенных параметров на
основе прямых измерений по запрограммированным формулам, показывают значения
измеряемых параметров на жидкокристаллических индикаторах, преобразуют
измеряемый параметр в стандартный унифицированный сигнал для его передачи по
каналам связи. Появились новые средства измерительной техники, такие как
ультразвуковые, электромагнитные и кориолисовы расходомеры, радарные и
ультразвуковые уровнемеры и т.п.
Существенным этапом в развитии систем
автоматизации стало появление программируемых логических контроллеров. И если
назначение первых ПЛК сводилось, в основ ном, к реализации функций
«включить-отключить» на основе логических выражений, то в дальнейшем в ПЛК
появились модули автоматического регулирования, реализующие стандартные законы
регулирования. С учётом расширяющихся возможностей программирования современных
ПЛК и так называемых «управляющих процессов» стало возможным создание сложных
многоконтурных систем управления, теория которых была известна давно, но
техническая реализация не вызывала энтузиазма из-за отсутствия технических
средств.
Естественно, при появлении новой техники
возникли трудности с её освоением. Нужно было суметь «запрограммировать» ПЛК в
соответствии с разработанными алгоритмами. Решение было найдено в разработке
специальных методов программирования, понятных широкой массе специалистов по
автоматизации.
При всём многообразии новых технических средств
автоматизации оператор насосной станции наиболее тесно взаимодействует с
современными пультами (панелями, станциями) управления, на мониторах которых
отображаются мнемосхемы технологических процессов с указанием значений наиболее
важных технологических параметров и сопровождением системами сигнализации,
блокировок и защит.
1. Описание
технологического процесса обезжелезивания и деманганации воды
Вода с высоким содержанием железа обладает
отталкивающим вкусом, а использование такой воды в производственном процессе
приводит к появлению ржавых пятен и разводов на готовой продукции. При
производстве бумаги, в текстильной промышленности, в прачечных использование
воды, содержащей железо и марганец, недопустимо. Ионы железа и марганца
загрязняют ионообменные смолы, поэтому при проведении большинства ионообменных
процессов первой стадией обработки воды является их удаление.
Очистка воды от соединений железа является в
ряде случаев довольно сложной задачей, которая может быть решена только
комплексно. Это обстоятельство в первую очередь связано с многообразием форм
существования железа в природных водах. Чтобы определить наиболее действенный и
экономичный для конкретной воды метод обезжелезивания, нужно произвести пробное
удаление железа.
В соответствии с требованиями СНиП метод
обезжелезивания воды, расчетные параметры и дозы реагентов следует принимать на
основе результатов технологических изысканий, выполненных непосредственно у
источника водоснабжения.
1.1 Химизм процессов в воде с
участием железа
В воде поверхностных источников железо находится
обычно в форме органоминеральных коллоидных комплексов, в частности в виде
гуминовокислого железа, и тонкодисперсной взвеси гидроксида железа. В речной
воде, загрязненной кислотными стоками, встречается сульфат двухвалентного
железа FeSO4. Из-за наличия в речной воде растворенного кислорода,
двухвалентное железо Fe2+ окисляется в трехвалентное Fe3+.
При появлении в воде сероводорода H2S образуется тонкодисперсная взвесь
сульфида железа FeS.
Подземные источники воды в подавляющем
большинстве характеризуются наличием растворенного бикарбоната двухвалентного
железа Fe(HCO3)2, который вполне устойчив при отсутствии
окислителей и при рН>7,5. При высокой карбонатной жесткости, рН>10 и
содержании Fe2+>10 мг/л бикарбонат может гидролизоваться с
образованием углекислоты:
Fe(HCO3)2+2H2O=
Fe(OH)2 + 2 H2CO3. (1.1)
Российские санитарные нормы ограничивают общее
содержание железа в воде для хозяйственно-питьевых нужд до 0,3 мг/л. В
некоторых странах допустимое содержание составляет 0,2 мг/л. Фактически
концентрация железа в подземных грунтовых водах находится в пределах от 0,5 до
50 мг/л. В центральном российском регионе, включая Подмосковье, эта величина
изменяется в диапазоне 0,3 - 10 мг/л, наиболее часто 3-5 мг/л, в зависимости от
географического местоположения и глубины источника. Начиная с концентрации
1,0-1,5 мг/л вода имеет неприятный металлический привкус. При уровнях выше 0,3
мг/л железо оставляет пятна на белье и санитарно-технических изделиях. При
концентрации железа ниже 0,3 мг/л запах обычно не ощущается, хотя может
появляться мутность и цветность воды.
Анаэробная (не имеющая контакта с воздухом)
прозрачная грунтовая вода может содержать соединения двухвалентного железа (Fe2+)
до нескольких миллиграммов на литр без ее помутнения при прямой подаче из
источника. Однако при контакте с воздухом, а точнее с кислородом воздуха,
двухвалентное железо окисляется до трехвалентного коллоидного состояния, что
придает воде характерный красно-коричневый оттенок:
4 Fe(HCO3)2 +
O2 + 2 H2O = 4 Fe(OH)3↓ + 8 CO2.
(1.2)
Гидроксид трехвалентного железа Fe(OH)3
коагулирует и переходит в оксид железа Fe2O3. 3 H2O,
выпадающий в виде бурых хлопьев.
Пользователь зачастую наблюдает следующую
картину: в первый момент вода, полученная из скважины, кажется абсолютно чистой
и прозрачной, но в течение нескольких минут она мутнеет (реакция 2) с
появлением специфического оттенка. При отстаивании воды муть оседает, образуя
бурый рыхлый осадок (оксид трехвалентного железа).
Железо способствует также развитию
«железобактерий», которые получают энергию при окислении Fe2+ до Fe3+,
в результате чего в трубопроводах и на оборудовании образуется скопление слизи.
В процессе окисления на 1 мг Fe2+ затрачивается 0,143 мг кислорода
(О2), увеличивается содержание свободной углекислоты на 1,6 мг/л, а
щелочность снижается на 0,036 мг-экв/л
Присутствие в воде солей меди, а также контакт
воды с ранее выпавшим осадком Fe(OH)3, каталитически ускоряет
процесс окисления Fe2+ до Fe3+.
В зависимости от условий (значение рН,
температура, наличие в воде окислителей или восстановителей, их концентрация)
окисление может предшествовать гидролизу, идти параллельно с ним или окислению
может подвергаться продукт гидролиза двухвалентного железа Fe(OH)2
1.2 Методы обезжелезивания воды
Для обезжелезивания поверхностных вод
используются только реагентные методы с последующей фильтрацией.
Обезжелезивание подземных вод осуществляют фильтрованием в сочетании с одним из
способов предварительной обработки воды:
- упрощенная аэрация;
- аэрация на специальных устройствах;
- коагуляция и осветление;
- введение реагентов-окислителей,
таких как хлор, гипохлорит натрия или кальция, озон, перманганат калия.
При мотивированном обосновании применяют и
другие методы, например катионирование, диализ, флотация, электрокоагуляция и
др.
Для удаления из воды железа, содержащегося в
виде коллоида гидроксида железа Fe(OH)3 или в виде коллоидальных
органических соединений, например гуматов железа, используют коагулирование
сульфатом алюминия или железным купоросом с добавлением хлора или гипохлорита
натрия.
В качестве наполнителей для фильтров в основном
используют песок, антрацит, сульфоуголь, керамзит, пиролюзит, а также
фильтрующие материалы, обработанные катализатором, ускоряющим процесс окисления
двухвалентного железа в трехвалентное. В последнее время все большее
распространение получают наполнители с каталитическими свойствами: Manganese
Greensand (MGS), Birm, МТМ и МЖФ.
При наличии в воде коллоидного двухвалентного
железа требуется проведение пробного обезжелезивания. Если отсутствует
возможность осуществить его на первой стадии проектирования, выбирают один из
вышеперечисленных методов на основании проведенного пробного обезжелезивания в
лаборатории или опыта работы аналогичных установок.
1.3 Деманганация воды
Марганец присутствует в земной коре в большом
количестве и обычно он встречается вместе с железом. Содержание растворимого
марганца в подземных и поверхностных водах, бедных кислородом, достигает
нескольких мг/л. Российские санитарные нормы ограничивают уровень
предельно-допустимого содержания марганца в воде хозяйственно-питьевого
назначения до 0,1 мг/л, а в некоторых странах Европы эта величина ниже 0,05
мг/л. Превышение содержания марганца ухудшает органолептические свойства воды.
При уровне выше 0,1 мг/л марганец приводит к появлению пятен на
санитарно-технических изделиях, а также нежелательного привкуса воды. На
трубопроводах образуется пленка, которая отслаивается в виде черного осадка.
В подземных водах марганец находится в виде
хорошо растворимых солей в двухвалентном состоянии. Для удаления марганца из
воды его необходимо перевести в нерастворимое состояние окислением Mn2+
в Mn3+ и Mn4+. Окисленные формы марганца гидролизуются с
образованием практически нерастворимых гидроксидов Mn(OH)3 и Mn(OH)4.
Последний при осаждении на зернистой загрузке фильтра проявляет каталитические
свойства, т.е. ускоряет процесс окисления двухвалентного марганца растворенным
кислородом.
Для эффективного окисления марганца необходимо,
чтобы величина рН очищаемой воды была на уровне 8,0-8,5. В качестве окислителя
применяют перманганат калия, хлор или его производные (гипохлорит натрия),
озон, кислород воздуха.
Глубокая аэрация с последующим фильтрованием
На первом этапе очистки из воды под вакуумом
извлекают свободную углекислоту, что способствует повышению величины рН до
8-8,5. Для этой цели используют вакуумно-эжекционный аппарат, при этом в его
эжекционной части происходит диспергирование воды и ее насыщение кислородом
воздуха. Далее вода направляется на фильтрацию через зернистую загрузку,
например кварцевый песок.
Данный метод очистки применим при окисляемости
исходной воды не выше 9,5 мг О2/л. При этом в воде обязательно присутствие
двухвалентного железа, при окислении которого образуется гидроксид железа,
адсорбирующий Mn2+ и каталитически его окисляющий. Соотношение концентраций [Fe2+]
/ [Mn2+] не должно быть менее 7. Если в исходной воде это
соотношение не выполняется, то в воду дополнительно дозируют сульфат железа
(железный купорос).
Деманганация перманганатом калия
Этот метод применим как для поверхностных, так и
для подземных вод. При введении в воду перманганата калия растворенный марганец
окисляется с образованием малорастворимого оксида марганца согласно следующему
уравнению:
3Mn2+2KMnO4 +
2 H2O = 5 MnO2↓ + 4 H+. (1.3)
Осажденный оксид марганца в виде хлопьев имеет
высокую развитую удельную поверхность примерно 300 м2 на 1 г осадка, что
определяет его высокие сорбционные свойства.
В соответствии с уравнением для удаления 1 мг Mn2+
требуется 1,88 мг перманганата калия. Как уже отмечалось выше, перманганат
обеспечивает удаление из воды не только марганца, но и железа в различных
формах. Также удаляются запахи и улучшаются вкусовые качества воды за счет
сорбционных свойств.
При очистке от марганца подземных вод
параллельно с перманганатом вводят активированную кремневую кислоту из расчета
3-4 мг/л или флокулянты. Это позволяет укрупнить хлопья оксида марганца.
Каталитическое окисление марганца
Как и в процессах очистки от железа, так и при
деманганации предварительное осаждение оксидов марганца на поверхности зерен
фильтрующей загрузки оказывает каталитическое влияние на процесс окисления
двухвалентного марганца растворенным кислородом. В процессе фильтрования
предварительно аэрированной и при необходимости подщелоченной воды на зернах
песчаной загрузки образуется слой осадка гидроксида марганца Mn (OH)4.
Ионы растворенного Mn2+ адсорбируются поверхностью гидроксида
марганца и гидролизуются, образуя оксид трехвалентного марганца Mn2O3.
Последний окисляется растворенным кислородом вновь до Mn (OH)4,
который опять участвует в процессе каталитического окисления. Уравнения реакций
этих процессов можно представить следующим образом:
(OH)4 + Mn(OH)2 = Mn2O3
+ 3 H2O, (1.4)
2 Mn2O3 + 2 O2
+ 8 H2O = Mn(OH)4 ↓. (1.5)
Практическая реализация процессов (1.4) и (1.5)
возможна при использовании каталитических наполнителей. В этом же разделе
приведены требования к исходной воде и рабочие параметры процессов. Можно отметить,
что величина рН очищаемой воды может быть значительно меньше, чем в
традиционных процессах деманганации (8,0-8,5).
Фильтрование через модифицированную загрузку
В пособии указывается, что для повышения ресурса
работы фильтрующей загрузки за счет закрепления пленки катализатора из
гидроксидов железа и оксида марганца на поверхности зерен, а также для снижения
расхода перманганата, предлагается следующий метод.
Перед началом фильтрования через фильтрующую
загрузку последовательно пропускают снизу вверх раствор железного купороса FeSO4
и перманганат калия, а затем ее обрабатывают тринатрийфосфатом Na3PO4
или сульфитом натрия Na2SO3.
Скорость фильтрования исходной воды, подаваемой
сверху вниз, составляет 8-10 м/ч.
Введение реагентов-окислителей
Скорость процесса окисления двухвалентного
марганца реагентами-окислителями из ряда хлор, диоксид хлора ClO2,
гипохлорит натрия, озон в значительной мере зависит от величины рН исходной
воды.
При введении хлора или гипохлорита натрия эффект
окисления достигается в достаточно полной мере при значениях рН не менее
8,0-8,5 и времени контакта окислителя и воды 60-90 минут. В большинстве случаев
обрабатываемая вода должна быть подщелочена. Требуемая доза реагента для
окисления Mn2+ до Mn(OH)4 по стехиометрии составляет 1,3
мг на каждый мг растворенного двухвалентного марганца. Фактические дозы
значительно выше.
Обработка воды озоном или диоксидом хлора
значительно эффективнее. Процесс окисления марганца завершается в течение 10-15
минут при величине рН воды 6,5-7,0. Доза озона по стехиометрии составляет 1,45
мг, а диоксида хлора 1,35 мг на 1 мг двухвалентного марганца. Однако при
озонировании воды озон подвержен каталитическому разложению оксидами марганца,
а поэтому доза должна быть увеличена [5]. При концентрации Mn2+ 0,4
мг/л расход озона составляет 2 мг/мг [Mn2+], а при 0,8 мг/л - 4
мг/мг [Mn2+].
В моем случае будет использоваться очистка вод в
пласте (геотехнологический метод). Технико-экономические сравнения вариантов
очистки подземных вод показывают преимущество подземного способа
обезжелезивания и деманганации: себестоимость 1 м3 воды в 2,5 раза
меньше при очистке подземных вод в пласте по сравнению с традиционными
способами на поверхностных установках.
Технология обезжелезивания и деманганации
подземных вод в водоносном пласте - как и классическая наземная - заключается в
поэтапном окислении растворенных в воде двухвалентных железа и марганца и
переводе их в труднорастворимые формы трехвалентного железа и четырехвалентного
марганца с их последующим удалением путем фильтрации.
Подземная технология очистки воды - точно так же
как и традиционная технология - носит комплексный характер и состоит из целого
ряда физико-химических, катионообменных и микробиологических процессов, которые
могут влиять друг на друга.
При подземном обезжелезивании на участке около
эксплуатационных скважин создаются стабильные зоны (геохимические барьеры), где
происходит окисление растворенных в подземных водах железа и марганца и
отложение их нерастворимых форм в пласте.
При аэрировании воды воздухом происходит
дегазация - удаление избыточных содержаний СО2 и Н2S и
насыщение ее растворенным О2. В результате образования гидроокисла
железа количество СО2 будет возрастать, т.к. при окислении 1 мг Fе2+
выделяется 1.6 мг СО2. На окисление 1 мг Fe2+ расходуется
0,143 мг О2.
В природных условиях величины рН и Eh являются
недостаточно высокими, поэтому для окисления железа и марганца требуется
жизнедеятельность специальных бактерий. Эти железо- и марганцеокисляющие
бактерии обладают способностью использовать окисление железа и марганца в
качестве источника энергии для обмена веществ. Бактерии, которые в качестве
источника энергии могут использовать как железо, так и марганец, должны
окислить в 6 раз больше марганца, чем железа для получения того же количества
энергии. Чем ярче у бактерий выражена склонность к окислению марганца, тем
больше их потребность в органическом углероде (вместо двуокиси углерода),
являющимся источником углерода, необходимого для роста и размножения
железобактерий.
Биохимические окислительно-восстановительные
реакции весьма сходны с химическими, но имеют и отличительные черты.
Катализируемые ферментами, вырабатываемыми живой клеткой, они способны
протекать в отсутствие высоких температур, в то время как для осуществления
ряда химических реакций требуются высокие температуры.
Теоретически окисление Mn в воде кислородом
может происходить при рН в пределах 9 - 9,5. Фактически окисление и осаждение
марганца при размножении микроорганизмов в подземных водах происходит уже при
рН равном 5,8-6,5.
Железобактерии могут развиваться в среде, не
содержащей органических веществ. На 1г синтезированного ими клеточного вещества
они окисляют 279 г двухвалентного железа с образованием 534 г Fe(OH)3.
Соотношение между окисленным железом и ассимилированным из углекислоты
углеродом (500:1) показывает, какое большое количество гидроокиси железа
образуется при автотрофном росте. Гидроокись железа после отмирания бактерий
служит материалом для заполнения порового пространства. Готовое органическое
вещество отмирающих железобактерий используется для синтеза организма
гетеротрофными маганецокисляющими бактериями.
Наиболее изученным представителем нитчатых
бактерий, накапливающих окислы марганца, является Leptothrix (Sphaerolutilus)
discofora, но окисление марганца осуществляют также L. Lopholea, L.
Pseudoochracea, L. cholodnii, L. sideropus, Crenothrix manganifera,
Siderocapsa, Naumanniella. Марганецокисляющие микроорганизмы являются типичными
гетеротрофами.
Продукты химических реакций остаются в
водоносном горизонте. Теоретические расчеты показывают, что при сроке
эксплуатации 100 лет произойдет уменьшение гидравлически эффективного
потенциала пор с 0,1 до максимальной величины 9,0%. Т.е. сроки возможной
эксплуатации водоносного пласта при технологии in situ намного превосходят
сроки эксплуатации самих скважин.
Для обезжелезивания и деманганации подземных вод
в водоносном горизонте применяются односкважинные, дуплетные (двухскважинные)
установки циклического действия, а также многоскважинные установки циклического
или постоянного действия.
Процесс обогащения подземных вод кислородом
воздуха (или закачки-налива аэрированной воды) может осуществляться как
непосредственно через эксплуатационные скважины на односкважинных и дуплетных
установках, так и через специальные инжекционные (наливные или спутниковые)
скважины, расположенные по окружности вокруг каждой эксплуатационной скважины,
на многоскважинных установках.
2. Характеристики
автоматизированной системы управления
В объект управления входят:
- четыре высоковольтных комплектных
распределительных устройств (КРУ) с контроллерами защиты и управления;
- преобразователь частоты;
- три напорные задвижки с
электроприводами;
- станция группового управления (СГУ);
- три шкафа местного управления
задвижками (ШМУЗ);
- посты ручного управления
двигателями.
Целями создания и внедрения СГУ являются:
- Поддержание оптимального давления и расхода в
напорных трубопроводах.
- Автоматизация управления
оборудованием насосной станции II подъема.
- Своевременное реагирование на
аварийные ситуации.
- Исключение влияния человеческого
фактора на процедуру сбора и обработки информации.
СГУ должна включать следующие
организационно-технические подсистемы, обеспечивающие выполнение различных
задач:
- подсистема контроля и управления КРУ
10кВ через контроллер защиты и управления;
- подсистема управления
частотно-регулируемым приводом;
- подсистема управления напорными
задвижками;
- подсистема приема и передачи
информации в сети КРУ 10кВ.
3. Описание
технологического оборудования
.1 Структура системы автоматического
управления
Структура системы логически разделена на три
уровня:
- нижний уровень - уровень датчиков и
исполнительных механизмов;
- средний уровень - уровень
программируемых логических контроллеров (ПЛК);
- верхний уровень - уровень
программно-технических средств оперативного контроля и управления ТП.
Структура системы автоматического управления
представлена на рисунке 3.1.
Рисунок 3.1 - Структура системы автоматического
управления
3.2 Комплекс технических средств
нижнего уровня
3.2.1 Выбор средства измерения
давления
В качестве средств измерения давления выбираем
датчики давления Cerabar T PMC 131. Датчик Cerabar T PMC131-А1В01А1Т
предназначен для измерения абсолютного и избыточного давлений: газов, пара,
жидкостей.
Давление жидкости, воздействующее на диафрагму
датчика, изменяет емкость его электронной схемы, которая формирует выходной
токовый сигнал 4…20 мА, пропорциональный измеряемому давлению.
Технические данные датчика давления приведены в
таблице 3.1.
Таблица 3.1 - Технические характеристики датчика
давления
Наименование
параметра
|
Значение
параметра
|
Вход
|
Измеряемый
параметр
|
Абсолютное
и избыточное давление
|
|
Диапазон
измерений
|
0-16бар
(0-1,6МПа)
|
Выход
|
Выходной
сигнал
|
4…20
мА
|
Точность
|
Нормальные
условия
|
по
DIN IEC 770
|
|
Погрешность
измерений
|
0,5%
|
|
Стабильность
|
0,15%
в год
|
Рабочие
условия эксплуатации
|
Температура
окр. воздуха
|
-20…+85⁰C
|
|
Климатический
класс
|
4К4Н
по DIN EN 60721-3
|
|
Степень
защиты
|
С
разъемом IP65, с кабелем 5м IP68
|
|
Электромагнитная
совместимость
|
Собственные
помехи по EN50081-1 Устойчивость к помехам поEN50082
|
Измеряемая
среда
|
Предельная
температура
|
макс
100⁰C
|
|
Предельное
давление
|
40бар
(4МПа)
|
Напряжение
питания
|
Напряжение
питания, Us
|
11…30В
постоянного тока
|
|
Пульсация
|
5%
|
Реле давления
Реле давления предназначено для
непосредственного пуска насосов с целью поддержания заданной величины давления.
Выбираем реле XMAV12L2135 - датчик давления 12 бар 2 порога.
Технические данные реле давления приведены в
таблице 3.2.
Таблица 3.2 - Технические данные реле давления
Наименование
параметра
|
Значение
параметра
|
Конструктивные
параметры
|
Тип
датчика давления
|
Электромеханич.
датчик давления
|
|
Тип
шкалы
|
Фикс.
дифференциальный
|
|
Тип
контактов
|
1
переключающ. мгновенное действие
|
|
Рабочий
орган
|
перемещаемая
под давлением диафрагма
|
|
Уставка
|
Внешняя
|
|
Способ
работы
|
Регулир.
между двумя пределами
|
Рабочие
условия эксплуатации
|
Контролируемая
жидкость
|
Морская
вода (0...55 °C) Пресная вода (0...55 °C)
|
|
Номинальный
ток [In]
|
B300, AC-15 Ue = 240 V B300, AC-15 Ue = 120 V R300,
DC-13 Ue = 250 V
|
|
Степень
защиты
|
IP54
соответствует EN/IEC 60529
|
|
Предельное
давление
|
27
бар (2,7MПа)
|
|
Давление
разрушения
|
30
бар (3 МПа)
|
|
Рабочая
частота
|
10
цикл/мин
|
|
Температура
окр. сред.
|
-25...55
°C
|
Диапазон
уставок
|
при
падении давления
|
0,3...10,3
бар
|
|
при
увелич. давления
|
1,3...12
бар
|
Прочность
|
Электрическая
|
1000000 циклов,
50/60 Гц,
AC-15, 240 В /3 A, Ith
= 10 A
|
|
Механическая
|
1000000
циклов
|
.2.2 Выбор электроприводов вращения
для шаровых вентилей и клапанов
Электроприводы MODACT MOKED предназначены для
перестановки органов управления с помощью возвратного вращательного движения с
углом поворота выходной части до 90о включая случаи, когда требуется
герметичное запирание в конечных положениях. Типичным примером использования
является управление шаровыми вентилями и клапанами в режиме дистанционного
управления и автоматического регулирования. Устанавливаются непосредственно на
органе управления.
Технические данные электропривода приведены в
таблице 3.3.
Таблица 3.3 - Технические данные электропривода
Наименование
параметра
|
Значение
параметра
|
Рабочие
условия эксплуатации электропривода
|
Напряжение
питания
|
Uп
= 1х220В, f1=50Гц, Uп = 3х220/380В, f1=50Гц
|
|
Рабочее
положение
|
Может
работать в любом рабочем положении
|
|
Самоторможение
|
Обеспечивается
с помощью механического или электромагнитного тормоза электродвигателей.
|
|
Степень
защиты
|
IP
55 или IP 67 по CSN EN 60592
|
|
Рабочий
ход
|
90⁰
|
Рабочие
условия эксплуатации электронного оснащения
|
Система
DMS2.ED
|
содержит
микрокомпьютер, детектор положения, сигнальные светодиоды и 4 кнопки для
установки и контроля электропривода, разъем для подключения детектора
момента, плата питания и интерфейса RS 232.
|
|
Аналоговый
модуль
|
Выходной
сигнал 0/4…20 мА
|
|
Снятие
положения
|
Бесконтактное
магнитное
|
|
Снятие
момента
|
Бесконтактное
магнитное
|
|
Питание
|
Uп=230В,
f=50Гц, Pн=4Вт
|
Исходя из данных таблицы 3.1, 3.2 и 3.3
составляем перечень дискретных и аналоговых сигналов для системы группового
управления.
Перечень дискретных и аналоговых сигналов
приведен в таблице 3.4.
Таблица 3.4 - Перечень дискретных и аналоговых
сигналов
Тип
устройства
|
Сигналы
|
Тип
сигнала для СГУ
|
Количество
|
Задвижка
|
1Открыть
2Закрыть 3Открыта 4Закрыта 5Местное 6 Дистанционное 7 Авария
|
Выход
Выход Вход Вход Вход Вход Вход
|
Сухой
контакт 230В Сухой контакт 230В Сухой контакт 230В Сухой контакт 230В Сухой
контакт 230В Сухой контакт 230В Сухой контакт 230В
|
3
3 3 3 3 3 3
|
СГУ
|
Включить
насос Выключить насос Насос включен Насос выключен Ручной Автоматический
Смешанный
|
Вход
Вход Выход Выход Вход Вход Вход
|
24
В 24 В Индикация Индикация 24 В 24 В 24 В
|
3
3 3 3 3 3 3
|
Датчики
давления
|
Давления
на напоре
|
Вход
|
Аналоговый
4-20 мА
|
2
|
Реле
давления
|
Напор
насоса Всас насоса
|
Вход
Вход
|
24
В 24 В
|
3
3
|
Согласно таблице дискретных и аналоговых
сигналов проведем выбор микроконтроллера, имеющего достаточное количество
дискретных и аналоговых входов и выходов.
3.3 Комплекс технических средств
среднего уровня
3.3.1 Средство управления и сбора
данных
В настоящее время микропроцессорная техника
внедряется во все сферы деятельности человека. И современную автоматизацию
трудно представить без участия в ней микропроцессорных средств. Взять хотя бы
компьютер, знакомый всем со школьной скамьи. А ведь этот самый компьютер - одно
из важнейших программно-технических средств автоматизации.
Есть еще одно микропроцессорное устройство,
хорошо известное в кругу специалистов по автоматизации, - контроллер. Как и
компьютер, контроллер - обязательный компонент любой современной системы
управления.
Контроллер получил свое название от слова
control - управление. Уже из названия становится понятным, что основное назначение
этого устройства - управление. Первая основная область применения контроллеров
(80-е годы прошлого столетия) - дискретные системы управления, в основу
функционирования которых положена логика. Так появилось название этих
устройств, сохранившееся до настоящего времени - программируемые логические
контроллеры (ПЛК).
Следует отметить, что современные ПЛК далеко
ушли в своем развитии от ранних представителей этого класса технических средств
автоматизации. За последние 8-10 лет существенно расширились их функции и
вычислительные возможности. Сегодня ПЛК способны решать задачи по управлению
сложными объектами как в непрерывных, так и в дискретных производствах.
В иерархии уровней АСУТП (автоматизированной
системы управления технологическими процессами) ПЛК занимают определенный
уровень - первый или нижний.
На их основе строятся системы автоматического
управления (САУ) отдельными аппаратами, установками или блоками
технологического процесса. Функционирование САУ происходит без постоянного
присутствия обслуживающего персонала в автоматическом режиме по алгоритмам и
программам, созданным на стадии проектирования системы управления (прикладное
ПО - программное обеспечение).
Объект управления в этой иерархии представлен
измерительными преобразователями (ИП) различных технологических параметров -
давления, уровня, температуры, расхода и т.д., а также исполнительными
устройствами (ИУ) - регулирующими клапанами, кранами, задвижками. С помощью
этих технических средств САУ осуществляют сбор данных, характеризующих состояние
объекта, и реализуют управляющие воздействия на объект в целях обеспечения
заданных (экономически целесообразных) режимов его функционирования.
Уровень оперативно-производственной службы (ОПС)
- в дальнейшем изложении материала второй или верхний уровень АСУТП - реализует
оперативное и режимное управление технологическим процессом. Основные
составляющие этого уровня - оперативный персонал (операторы, диспетчеры,
специалисты) и программно-технические средства. К их числу, прежде всего,
относятся компьютеры, на базе которых создаются автоматизированные рабочие
места (АРМ) операторов и специалистов, и серверы баз данных, в основу
функционирования которых положено прикладное ПО. Присутствие оперативного
персонала на этом уровне и определило само название системы - АСУТП
(автоматизированная система управления технологическим процессом). Понятие
«автоматизированная» по определению предполагает участие человека в управлении.
Таким образом, АСУТП - это человеко-машинная система.
В небольших системах управления локальные ПЛК
могут напрямую по сети взаимодействовать с сервером и АРМ (без интерфейсного
контроллера). Но имеется достаточно большое число проектов АСУТП,
предусматривающих в своей структуре интерфейсные контроллеры (концентраторы).
В зависимости от задач, решаемых системой
управления, контроллеры способны выполнять широкий набор функций. К основным
(базовым) функциям локальных контроллеров относятся:
- сбор и первичная обработка
информации о параметрах технологического процесса и состоянии оборудования;
- хранение технологической и
вспомогательной информации;
- автоматическая обработка
технологической информации;
- формирование управляющих воздействий
- дискретное управление и регулирование;
- исполнение команд с пункта
управления;
- самодиагностика контроллера;
- обмен информацией с верхним уровнем
управления.
-
Функция «Сбор и первичная обработка информации»
подразумевает:
- циклический опрос устройств связи с
объектом (УСО);
- аналогово-цифровое преобразование
сигналов;
- первичную обработку сигналов для
компенсации воздействия помех (фильтрация сигналов);
- определение достоверности информации
по отклонениям сигналов датчиков за пределы измерительного диапазона.
Функция «Хранение технологической и
вспомогательной информации» обеспечивает запись и хранение в памяти
контроллера технологических данных и данных, обеспечивающих заданный режим
работы технологического оборудования. Данная функция также обеспечивает
сохранность информации при отказах технических средств или питания.
Реализация функции «Автоматическая обработка
технологической информации, формирование управляющих воздействий» предполагает
дискретное управление в соответствии с алгоритмами управления, разработанными
на этапе проектирования системы, и регулирование (стабилизация технологических
параметров на заданном уровне) по стандартным (П, ПИ, ПИД) или
специализированным алгоритмам.
Функция «Исполнение команд с пункта управления»
обеспечивает возможность вмешательства оперативного персонала в автоматическое
ведение технологического процесса. При этом оперативный персонал может
осуществлять пуск, отключение, переключение технологического оборудования, а также
выполнять режимное управление процессом - задавать уставки регулирования,
уровни срабатывания блокировок, сигнализаций, алгоритмов автоматического ввода
резервного оборудования.
Функция «Самодиагностика контроллера» включает в
себя проверку работоспособности как технических, так и программных средств
контроллера с оповещением оперативного персонала.
Функция «Обмен информацией» является одной из
важнейших функций контроллера. Эта функция осуществляется в автоматическом
режиме и реализуется специализированными средствами контроллера с
использованием протоколов приема/передачи данных.
3.3.2 Выбор контроллера
Для реализации среднего уровня выбираем
контролер Siemens SIMATIC S7-1200. Программно-логический контроллер Siemens
Simatic S7-1200 - серия универсальных промышленных микроконтроллеров Сименс для
задач автоматизации производства малого уровня. Контроллеры Siemens Simatic
S7-1200 построены по модульному принципу и могут работать в реальном масштабе
времени, применяются для построения простых узлов местной автоматики или узлов
комплексных систем автоматического управления. Контроллеры Siemens Simatic
S7-1200 поддерживают обмен данными через сети Industrial Ethernet/PROFINET, а
также PtP (Point-to-Point) соединения. Программируемые микроконтроллеры Siemens
Simatic S7-1200 имеют компактные пластиковые корпуса со степенью защиты IP20,
могут монтироваться на стандартную 35 мм профильную шину DIN или на монтажную
плату и работают в диапазоне температур от 0 до +50 °C. Они способны
обслуживать от 10 до 284 дискретных и от 2 до 51 аналогового канала
ввода-вывода.
Технические данные контроллера приведены в
таблице 3.5.
Таблица 3.5 - Технические данные
микроконтроллера Siemens Simatic S7-1200
Наименование
|
|
|
|
Центральный
процессор
|
CPU
1211C
|
CPU
1212C
|
CPU
1214C
|
Встроенная
загружаемая память:
|
1
МБ
|
1
МБ
|
2
МБ
|
Расширение
памяти
|
Memory
Card емкостью до 24 Мбайт
|
Встроенная
рабочая память
|
25
КБ
|
25
КБ
|
50
КБ
|
Энергонезависимая
память для сохранения данных
|
2
КБ
|
Адресное
пространство ввода-вывода
|
1024
байт на ввод/ 1024 байт на вывод
|
ПИД
регулирование
|
Поддерживается,
до 16 контуров
|
Скоростные
счетчики
|
3х100
кГц + 1х30 кГц
|
3х100
кГц + 3х30 кГц
|
Импульсные
выходы
|
2х100
кГц, только в моделях с транзисторными выходами
|
Интерфейс
Ethernet
|
1xRJ45,
10/100 Мбит/с
|
Встроенные
входы и выходы
|
2AI
+ 6DI + 4DO
|
2AI
+ 8DI+ 6DO
|
2AI
+ 14DI+ 10DO
|
Количество
каналов системы локального ввода-вывода:
|
|
|
|
каналов
ввода/вывода дискретных сигналов, не более
|
8
/ 6
|
42
/ 40
|
144
/ 140
|
каналов
ввода/вывода аналоговых сигналов, не более
|
2
/ 1
|
10
/ 5
|
34
/ 17
|
Выбираем центральный процессор CPU 1214C который
имеет питание =24В, 14 DI =24В, 10 DO =24В/0.5А, 2 AI 0…10 B/10 бит.
Согласно таблице 4 требуется 2 аналоговых входа,
36 дискретных входов и 12 дискретных выходов. Для получения нужного количества
дискретных входов и выходов выбираем дополнительные модули.
Список дополнительных модулей приведен в таблице
3.6.
Таблица 3.6- Список дополнительных модулей
Наименование
|
Параметры
|
Модули
ввода-вывода дискретных сигналов
|
SM
1221
|
16
DI =24 B
|
|
SM
1223
|
8
DI =24 B + 8 DO =24 B/ 0.5 A
|
Коммуникационные
модули
|
CM
1241
|
RS
485, PtP соединение, протоколы ASCII, USS, Modbus RTU
|
Коммутатор
|
CSM
1277
|
4-канальный
коммутатор Industrial Ethernet, 4 x RJ45, 10/100 Мбит/с
|
Блок
питания
|
PM
1207
|
Вход:
~115/ 230 В, выход: =24 В/ 2.5 А
|
Для программирования всех моделей контроллеров
Siemens S7-1200 используется пакет программ STEP 7 Basic. Программирование
осуществляется на языке LD или FBD. Также есть функция ШИМ.
4. Расчет
и выбор элементов силовой части электропривода
.1 Расчет и выбор насосных агрегатов
В отличие от насосных станций первого подъёма,
подача станций второго подъёма неравномерна в течение суток. На рисунке 4.1
представлен примерный график суточного водопотребления.
Рисунок 4.1- Примерный график
суточного водопотребления
Согласно рисунку 2 максимальное
водопотребление приходится на утренние (с 8 до 10) и вечерние (с 20 до 22)
часы. Насосы выбираются с таким расчётом, чтобы обеспечить максимальную подачу
(расход) в часы пик.
По условиям проекта на станции II
подъема предусмотрена установка 3х насосных агрегатов, каждый из которых должен
обеспечивать максимальный расход воды в часы пик составляющий QH=1000
(м3/ч), максимальный напор НН=80 м, номинальное
КПД ηН =70%.
Мощность насоса в кВт в рабочей
точке определяется по формуле:
, кВт, (4.1)
где
- плотность перекачиваемой среды в
кг/м3, плотность воды составляет 1000 кг/м3.
Тогда:
кВт.
Насосный агрегат выбираем из условия
Из каталога выбираем насосный
агрегат типа 1Д1250 - Д125б.
Насосы центробежные двустороннего входа типа Д и
агрегаты электронасосные на их основе, предназначены для перекачивания воды и
других жидкостей, имеющих сходные с водой свойства по вязкости до 36х10-6
м2/с (36сСт) и химической активности, температурой от 274 до 358К
(от 1 до 85°С), не содержащих твердых включений по массе более 0,05%, размеру
более 0,2 мм и микротвердостью более 6,5 ГПа (650кгс/мм2).Данные
насосные агрегаты оснащены трехфазными асинхронными электродвигателями,
напряжением питания 10 кВ, мощностью 400 кВт.
Характеристики насоса представлены в таблице
4.1. Характеристики асинхронного двигателя насосного агрегата представлены в
таблице 4.2.
Таблица 4.1- Характеристики насоса
Параметр
|
Значение
|
Единица
измерения
|
Подача,
Qн
|
1030
|
м3/ч
|
Напор,
Нн
|
87
|
м
|
Максимальная
потребляемая мощность насоса, Pмах
|
360
|
кВт
|
Частота
вращения nн
|
1450
|
об/мин
|
КПД,ηн
|
0,7
|
-
|
Таблица 4.2 - Характеристики асинхронного двигателя
насосного агрегата
Параметр
|
Значение
|
Единица
измерения
|
Напряжение
питания, Uн
|
6000
|
В
|
Номинальный
ток, Iн
|
47
|
А
|
Номинальная
мощность, Pн
|
400
|
кВт
|
Частота
вращения nн
|
1450
|
об/мин
|
КПД,ηн
|
0,943
|
-
|
Коэффициент
мощности cosφ
|
0,87
|
-
|
Mmax/Mном
|
2,3
|
-
|
Мs/Mном
|
1
|
|
Согласно параметрам двигателя выбираем частотный
преобразователь.
4.2 Разработка структурной схемы
автоматического управления насосными агрегатами
Основным элементом водопроводного узла,
обеспечивающим подачу воды в промышленные и жилые районы городов, является
подсистема подкачки - группа центробежных насосов, приводимых в движение
асинхронными трехфазными двигателями. Задачей подсистемы подкачки является
подача в магистрали определенного объема воды с давлением, не ниже некоторого
требуемого, обычно определяемого необходимым давлением в самой верхней точке
магистрали. Достижение требуемых расхода и давления может осуществляться
несколькими путями: изменением положения задвижек непосредственно на выходном
трубопроводе насоса или изменением частоты вращения. В то время, как метод с
использованием задвижек имеет низкий КПД и увеличивает износ запорного и
насосного оборудования, метод с изменением частоты вращения лишен таких
недостатков. Как правило, валы насосов связаны с роторами электродвигателей
напрямую без понижающих или повышающих редукторов, что означает возможность
изменения скоростей их вращения только лишь путем изменения скорости вращения
ротора двигателя. И в этом случае применение асинхронных электродвигателей в
качестве приводов дает преимущества в управлении и упрощает систему управления
электронасосом.
Проанализируем подсистему подкачки и на её
основе составим структурную схему автоматической системы управления. Питание
электродвигателей осуществляется с локальной подстанции напряжением постоянной
частоты и постоянной амплитуды, далее электродвигатели приводят в действие
центробежные насосы таким образом, что те способны обеспечить максимальный
требуемый напор и требуемый расход воды, причем последний является величиной
переменной. В случае необходимости уменьшения подаваемых объемов воды
используются задвижки на выходных водоводах. Для улучшения КПД подсистемы и
уменьшения энергетических затрат следует отказаться от существующего способа
поддержания гидравлических параметров и разработать систему, мощность которой
будет изменяться динамически.
Анализируя существующую систему видим, что при
постоянном напоре на выходе следует управлять лишь расходом воды, т.е. частотой
вращения крыльчатки насоса и как следствие - частотой вращения ротора привода
насоса. Составим структурную схему системы автоматического управления на основе
сделанных выводов:
Рисунок 4.2- Схема структурная
автоматического управления насосными агрегатами
Система в целом состоит из управляющего
устройства(УУ), получающего уставку U и влияющего на скорость ротора
асинхронного двигателя(АД) и как следствие - на крыльчатку центробежного
насоса(ЦН). Объем воды, перекачанный насосом, проходит некоторый промежуток по
магистрали(М), после чего его величина снимается датчиком и в качестве обратной
связи поступает на элемент сравнения, формируя сигнал рассогласования. Также
следует учесть момент сопротивления ротора двигателя, который будет возмущающим
воздействием в системе управления. Кроме того, для предотвращения аварийной
ситуации целесообразно получать сведения о скорости вращения ротора двигателя,
точнее - о его заклинивании.
В качестве выходной величины системы принят
расход воды. Выберем входной параметр, или иначе - параметр, который будет
отвечать за изменение скорости вращения ротора двигателя.
Как известно, скорость вращения ротора
асинхронного двигателя зависит от частоты питающего напряжения:
об/мин, (4.2)
где: f1 - частота питающего
напряжения,
р - число полюсов, -
скольжение.
Исходя из этого выражения, очевидно,
что осуществлять управление скоростью ротора можно путем изменения частоты
напряжения питания. Такое управление называется частотным и в последнее время
получает широкое распространение. К тому же, широко выпускаются
интеллектуальные частотные преобразователи, позволяющие не только изменять
частоту напряжения, но также программировать в себя определенные законы
управления, что может значительно упростить реализацию системы управления. Для
выбора закона управления необходимо проанализировать передаточную функцию
объекта относительно частоты питающего напряжения. Для этого определим
передаточные функции каждого из звеньев.
Будем искать передаточную функцию асинхронного
двигателя как отношение частоты вращения ротора к частоте питающего напряжения.
В [6] предлагается эту передаточную функцию разбить на две составляющих -
«момент/частота» и «частота/момент» для возможности учета момента
сопротивления, действующего на вал двигателя. Тогда структурная схема при
управлении частотой напряжения статора будет выглядеть так:
Рисунок 4.3 - Структурная схема асинхронного
электродвигателя при управлении частотой питающего напряжения
По данной структурной схеме получим передаточную
функцию по управляющему воздействию:
(4.3)
где
Тм- механическая
постоянная времени двигателя,
Тэ - электромагнитная постоянная времени
двигателя,
- относительное
напряжение статора(к номинальному),
- относительная
частота напряжения статора(к номинальной).
Данная передаточная функция справедлива для
случая, когда потокосцепление статора есть величина постоянная, т.е.
одновременно с изменением частоты питающего напряжения изменяется и его
величина в соответствии с выражением: U1/ω1=const.
Следует отметить, что в современных преобразователях частоты реализован
механизм поддержания постоянного потокосцепления, поэтому передаточная функция
(4.3) может быть использована для описания АД.
Определим передаточную функцию центробежного
насоса и магистрали. Как правило, на практике насос и магистраль рассматривают
как один объект, и с определенной долей точности аппроксимируют общую
передаточную функцию в виде инерционного звена второго порядка с запаздыванием.
Как правило, в разветвленной гидросистеме это колебательное звено, в одиночных
трубопроводах - апериодическое. Для общего случая положим передаточную функцию
равной:
. (4.4)
Т.к. колебательные процессы слабо
выражены вследствие большой инерционности объекта, можно понизить порядок
передаточной функции (4.4).
Получим:
. (4.5)
Параметры передаточной функции зависят от
каждого конкретного случая, поэтому их получают методами идентификации.
На основании (4.3) и (4.5) запишем общую
передаточную функцию объекта:
. (4.6)
Анализируя функцию (4.6) видно, что она имеет
четвертый порядок. Это означает, что регулятор должен иметь возможность
отслеживать ошибку по ускорению, что не представляется возможным во встроенных
в частотный преобразователь ПИД-законах управления. Кроме того, использование
даже дифференциальной составляющей в трубопроводной системе может сильно
ухудшить устойчивость из-за отработки кратковременных возмущений, связанных с
отражением воды от стенок труб, изменением потребления на конечной точке и т.п.
Таким образом, целесообразно использовать ПИ-регулятор с точки зрения
обеспечения максимальной устойчивости, но в этом случае ухудшится время
регулирования, но в данной системе оно не является критичным.
Передаточная функция ПИ-регулятора:
, (4.7)
Точный теоретический расчет
параметров регулятора, при которых будет выполняться условие устойчивости и
требования к заданным показателям качества, выполнить практически невозможно
из-за специфики объекта. Тем не менее, существуют методики расчета
приблизительных параметров регулятора для передаточных функций объектов до
третьей степени. В случае с четвертым порядком функции (4) целесообразно
поступить следующим образом: понизить порядок знаменателя, удалив слагаемое с
наименьшей постоянной времени.
Допустим, что после выполнения этой
процедуры передаточная функция приняла вид:
. (4.8)
Проведем расчет параметров
структурной схемы САУ НА
Двигатель можно разделить на две
части. Механическую и электрическую. Передаточная функция механической и
электрической части имеет вид :
. (4.9)
, (4.10)
где: β - модуль
жесткости линеаризованной механической характеристики асинхронного двигателя,
Тэ - эквивалентная
электромагнитная постоянная времени цепей статора и ротора асинхронного
двигателя,м - механическая постоянная времени.
Модуль жесткости β линеаризованной
механической характеристики, можно рассчитать, как:
, (4.11)
где: Мк - момент
критический,
- угловая скорость асинхронного
двигателя;к - скольжение критическое, его значение можно определить,
как:
. (4.12)
Здесь, sн - номинальное
скольжение асинхронного двигателя. Его можно определить, из следующей формулы:
, (4.13)
где:
- частота вращения идеального
холостого хода асинхронного двигателя, об/мин;
- номинальная частота вращения
асинхронного двигателя, об/мин;
Номинальная частота вращения nн
асинхронного электродвигателя, из паспортных данных равна 1450 об/мин.
Частота вращения идеального
холостого хода n0 асинхронного двигателя, выбирается из стандартного
ряда значений, которая зависит от числа пар полюсов и частоты вращения
двигателя.
Стандартный ряд значений приведен в
таблице 4.3.
Таблица 4.3 - стандартный ряд
значений зависимости числа пар полюсов от частоты вращения двигателя
Число
пар полюсов р
|
1
|
2
|
3
|
4
|
5
|
Частота
вращения идеального холостого хода n0, об/мин
|
3000
|
1500
|
1000
|
750
|
500
|
Из стандартного ряда значений
выбираем частоту вращения идеального холостого хода n0, ближайшую
для номинальной частоты вращения
. Соответственно частоту вращения
идеального холостого хода n0 принимаем равную 1500.
Переведем частоту вращения
идеального холостого хода n0 (об/мин), в угловую скорость ω0 с-1:
. (4.14)
Тогда:
с -1.
Тоже рассчитаем для номинальной
частоты вращения nн двигателя:
, (4.15)
с -1.
Зная значения ω0 и ωн, можно
рассчитать номинальное скольжение асинхронного двигателя sн из
формулы (4.13):
Критический момент Мкр
можно рассчитать, как:
, (4.16)
где λ - кратность
момента,
Мн - номинальный момент
двигателя.
Кратность момента определяется, как
отношение момента номинального двигателя Мн и критического момента
двигателя Мкр:
(4.17)
Кратность момента асинхронного
двигателя, из паспортных данных равна 2,3.Т.е.
.
Номинальный момент двигателя можно
рассчитать, как отношение номинальной мощности двигателя Рн к
номинальной частоте вращения:
(4.18)
Тогда: 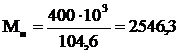
Зная кратность момента λ и
номинальный момент двигателя Мн из формулы (4.16) можно рассчитать
критический момент Мкр:
.
Подставив скольжение асинхронного
двигателя Sн и кратность момента λ в формулу (4.12), рассчитаем
скольжение критическое Sк:
.
Просчитав скольжение критическое sк
и зная момент критический Мкр с частотой вращения идеального
холостого хода ω0, можем
рассчитать модуль жесткости β линеаризованной механической
характеристики, подставив получившиеся значения в формулу (4.11), мы получим:
Механическая постоянная времени Тм
зависит от момента инерции вала двигателя J, редуктора, инерции исполнительного
устройства:
(4.19)
где: J - максимально допустимый
маховой момент механизма (двигателя), кН·м. Из паспортных данных двигателя
J=0,23 кН·м.
Эквивалентную электромагнитную
постоянную времени можно определяется по формуле:
, (4.20)
где: ω0эл.ном - угловая
скорость электромагнитного поля асинхронного двигателя при его номинальной
частоте питания f1ном=50 Гц (
). Для асинхронного двигателя
общепромышленного исполнения
(меньшие значения характерны для
мощных двигателей),
.
Зная допустимый маховой момент и
модуль жесткости, β можно
рассчитать механическую постоянную времени Тм и эквивалентную
электромагнитную постоянную времени Тэ:
c.
с.
Теперь зная механическую постоянную
времени Тм и эквивалентную электромагнитную постоянную времени Тэ
можно подставить их в формулу(6.2):
Рассчитаем параметры насосного
агрегата и магистрали :
(4.21)
где: Qн - номинальный расход воды,
Рн- номинальная мощность насоса.
Тогда:
Так как насос приводится в движение
двигателем без редуктора то постоянная времени насосного агрегата равна
постоянной механической времени двигателя Т1=Тм=0,5с
Для звена с запаздыванием
коэффициент
τ
= Тм
Подставляя все значения в формулу (4.5) получим:
Окончательная передаточная функция
объекта управления примет вид:
Для данной системы методом
Никольса-Зиглера [2] можно рассчитать настройки для ПИ - регулятора:
(4.22)
Согласно [9]
.
Тогда передаточная функция
ПИ-регулятора примет вид:
Как правило, при данных настройках
система бывает устойчивой, однако часто они используются лишь как стартовые настройки
при пуске и наладке регулятора. Процесс наладки заключается в следующим -
выставляются либо полученные настройки, либо значения, меньше их в 2-3 раза, и
постепенно увеличиваются, при этом контролируется выходная величина объекта
управления. Как только выход начинает сильно отклоняться от уставки -
прекращается подбор параметров. Практика показывает, что для достижения
наибольшего быстродействия постоянная времени интегратора должна превышать
рассчитанную в 5-10 раз.
По полученным данным построим структурную
схему САУ НА
Рисунок 4.4 - Схема структурная автоматического
управления насосными агрегатами
С помощью программы Mathcad построим амплитудо-
и фазо-частотные характеристики САУ НА
Рисунок 4.5 - Амплитудо-частотная характеристика
САУ НА
Рисунок 4.6 - Фазо-частотные характеристики САУ
НА
По графикам АЧХ и ФЧХ можно определить, что
система устойчива и имеет запас по амплитуде -30дБ запас по фазе 40⁰.
4.3 Выбор частотного преобразователя
Частотные преобразователи применяются для
регулирования скорости вращения асинхронных электродвигателей благодаря
изменению частоты напряжения питания электродвигателя. Применение
частотно-регулированного привода позволяет осуществлять регулирование скорости
в широком диапазоне, как в процессе работы, так и при разгоне и торможении.
Частотный преобразователь также осуществляет защиту электродвигателя от
перегрузок, что увеличивает срок службы электрической и механической части
оборудования. Экономически обосновано, что применение частотно-регулируемого
привода в различных механизмах позволяет достичь до 60% энергосбережения.
В случае если насосов более одного то нет
необходимости использовать отдельный частотный преобразователь для каждого
насоса, а достаточно иметь только один преобразователь и коммутирующее
устройство. Допустим, насосы имеют характеристики вида 1, а магистраль -
характеристику вида 4(рисунок3). Увеличение подачи и давления производится в
следующем порядке. На начальном этапе в работу включается один насос с
частотно-регулируемым электроприводом. Для обеспечения подачи Q1 его частота
вращения увеличивается до значения ω1. Дальнейший
рост подачи и давления возможен до величин Q3 и Р3 соответственно. Если необходимо
обеспечить дальнейшее увеличение подачи, то происходит переключение питания
электропривода первого насоса с выхода преобразователя частоты на сеть, а к
выходу преобразователя частоты коммутируется электропривод второго насоса и
частота вращения увеличивается до требуемого значения. Например, для
обеспечения подачи и давления Q2' и Р2' соответственно частота вращения второго
насоса должна быть увеличена до значения ω2’. Таким
образом обеспечивается регулирование параметров насосной станции в области,
заключенной между характеристиками 1 и 2. При необходимости дальнейшего
увеличения подачи и давления до значений выше Q3' и Р3' питание электропривода
второго насоса переключается с выхода преобразователя частоты на сеть и в
работу вводится третий насос, управляемый частотно-регулируемым
электроприводом. В этом случае регулирование происходит в области, заключенной
между характеристиками 2 и 3.
Рисунок 4.7 - График комбинированного режима
работы системы подкачки
При снижении подачи и давления коммутация и
регулирование частоты вращения электроприводов насосов происходит в обратном
порядке.
Рассмотренный способ регулирования режима работы
насосной установки обеспечивает плавное и непрерывное изменение подачи и
давления жидкости в широком диапазоне изменения значений регулируемых
параметров от Q1 до Q3'' и характеристики сети от 4 до 4'.
По условиям проекта частотный преобразователь
осуществляет функцию разгона и торможения асинхронного двигателя, по достижению
двигателем номинальной скорости вращения двигатель переключается на прямое
питание от сети.
Исходя из мощности выбранного двигателя а так же
условий пуска двигателя выбираем частотный преобразователь EI-9013.
Преобразователи частоты серии EI повышенной мощности предназначены для
регулирования скорости вращения асинхронных электродвигателей мощностью от 160
до 1000 кВт и номинальным напряжением 0,4 кВ. Нагрузкой электродвигателя могут
служить как насосы, вентиляторы, так и приводы различных механизмов с
постоянным и переменным моментом.
Преобразователи обеспечивают плавный разгон
(торможение) за заданное время и непрерывную работу привода на постоянной
скорости в рабочем диапазоне скоростей вращения. Рабочий диапазон выходной
частоты преобразователя - до 400 Гц.
Технические данные преобразователя частоты
приведены в таблице 4.4.
Таблица4.4 - Технические данные преобразователя
частоты
Модель
EI - 9011 (9013)
|
200Н
|
250Н
|
300Н
|
400Н
|
500H
|
600Н
|
800H
|
1000H
|
1200Н
|
Максимальная
мощность применяемого двигателя, кВт
|
160
|
185
|
220
|
315
|
400
|
500
|
630
|
800
|
1000
|
Выходные
характеристики
|
Полная
мощность преобразователя, кВА
|
200
|
250
|
300
|
400
|
500
|
600
|
800
|
1000
|
1200
|
|
Номинальный
выходной ток, А
|
EI
-9013
|
302
|
340
|
450
|
605
|
800
|
900
|
1200
|
1600
|
1800
|
|
|
EI
-9011
|
302
|
340
|
450
|
605
|
800
|
900
|
-
|
-
|
-
|
|
Максимальное
выходное напряжение
|
Трехфазное
380/400/415/440/460 В (пропорционально входному напряжению)
|
|
Максимальная
выходная частота
|
400
Гц
|
|
Номинальная
выходная частота
|
50
Гц
|
Источник
питания
|
Номинальное
входное напряжение и частота
|
Трехфазное
380/400/440/460 В 50/60 Гц
|
|
Допустимые
отклонения напряжения
|
+
10%, - 15%
|
|
Допустимые
отклонения частоты
|
±
5%
|
Характеристики
цепи управления
|
Метод
управления
|
Синусоидальная
широтно-импульсная модуляция
|
|
Стартовый
крутящий момент
|
150%
при 1Гц
|
|
Полоса
пропускания ПИД-регулятора по скорости
|
5
Гц
|
|
Диапазон
управления частотой
|
от
1,5 до 50 Гц
|
|
Точность
частотных режимов
|
Цифровая
команда: ±0,01% (от -10°С
до +40°С)
|
|
|
Аналоговая
команда: ±0,1% (25°С ±
10°С)
|
|
Разрешение
по частоте
|
Опорный
цифровой сигнал: ± 0,01 Гц
|
|
|
Опорный
аналоговый сигнал: ±0,03 Гц / 60 Гц (11 бит +
код)
|
|
Разрешение
по частоте
|
0,01
Гц
|
|
Запас
по перегрузке
|
150%
от номинального выходного тока (1 минута)
|
|
Сигнал
задания частоты
|
от
-10
до 10 В, от 0 до 10 В, от 4 до 20 мА
|
|
Время
разгона/торможения
|
от
0,01 до 6000 с (Времена разгона/торможения имеют независимые уставки,
возможны 4 ступени)
|
Для уменьшения стоимости проекта и обеспечения
гальванической развязки в цепь питания на входе преобразователя частоты
ставится понижающий трансформатор напряжения 10кВ/0,4кВ, на выходе ставится
повышающий трансформатор напряжения 0,4кВ/10кВ.
4.4 Выбор силового выключателя
Проведем анализ существующих силовых
высоковольтных выключателей.
В настоящее время применяются следующие типы
выключателей 6... 10 кВ: малообъемные масляные (их часто называют также
маломасляными), электромагнитные со щелевыми камерами, вакуумные и элегазовые.
Вакуумные и элегазовые выключатели получили
преимущественное распространение в течение последних 5... 10 лет, в то время
как маломасляные и электромагнитные со щелевыми камерами сейчас практически не
выпускаются, хотя все еще находятся в эксплуатации.
Вакуумные выключатели 6...10 кВ абсолютно
пожаро- и взрывобезопасны, сохраняют свою работоспособность при практически
любых температурах окружающей среды. К достоинствам вакуумных выключателей
можно отнести большой ресурс отключений-включений номинальных токов,
возможность их эксплуатации в агрессивных средах, высокая скорость коммутаций и
готовность к повторным включениям. Следует добавить, что это самый «чистый» тип
выключателя - никаких проблем с загрязнением распредустройства и выделением
небезопасных для экологии веществ, они практически бесшумны в работе. Малые
габариты и возможность произвольного их расположения позволяют уменьшить
размеры распределительного устройства и предоставляют свободу в их компоновке,
например, размещение ячеек в несколько ярусов. Установленные на линейных присоединениях
вакуумники без проблем отключают зарядные токи кабельных или воздушных линий,
находящихся под напряжением.
Но при отключении такими вакуумными
выключателями небольших индуктивных токов (холостой ход трансформатора), есть
вероятность коммутационных перенапряжений. В случае потери вакуума в одной из
дугогасительных камер происходит приваривание контактов - необходим постоянный
контроль отсутствия напряжения на всех трех фазах после отключения
присоединения. Ресурс дугогасительного устройства по отключению токов короткого
замыкания не очень велик.
Элегазовые выключатели как и вакуумные
выключатели полностью пожаро- и взрывобезопасны, и часто, взаимозаменяемы с
этим типом выключателей. Имеют высокую отключающую способность. Элегазовые
выключатели можно устанавливать как в ЗРУ так и в ОРУ. Длительный срок службы
дугогасительного устройства.
Основная сложность при эксплуатации этих
выключателей - SF6 (элегаз, шестифтористая сера), которая сама по себе
недешевая, плюс в обслуживании требуются устройства для очистки, заполнения и
ее перекачки.
Сравнительная характеристика вакуумных и
элегазовых выключателей приведена в таблице 4.5.
Таблица 4.5 - Сравнительная характеристика
вакуумных и элегазовых выключателей
Характеристика
выключателя
|
Элегазовый
VF 12 Изготовитель АВВ
|
Вакуумный
SION Изготовитель Siemens
|
30
|
5
|
Скорость
размыкания контактов, м/с
|
2
|
1,1-0,8
|
Количество
отключений номинального тока отключения до ремонта
|
10000
|
50000
|
Механический
ресурс, циклов «ВО»
|
10000
|
50000
|
Периодичность
технического обслуживания, лет
|
10
|
25
|
Масса
выключателя. Кг
|
110-135
|
38-42
|
Нижнее
значение температуры окружающей среды, °С
|
-10
|
-60
|
Относительная
стоимость, руб.
|
88000
|
75000
|
В отличие от элегазовых вакуумные выключатели:
- не имеют потенциальной способности,
в виду отсутствия элегаза, вызывать, в случае его утечки, аварии с опасными
последствиями, а также угрозу для здоровья обслуживающего персонала;
- не требуют дозаправки дугогасящей
среды (элегаза);
- не требуют специальных средств
диагностирования для контроля технического состояния;
- при температуре ниже минус 20°С не
требует подогрева дугогасящей среды.
Выбираем вакуумный выключатель SION. Они
способны производить все виды коммутационных операций в распределительных сетях
напряжением от 6 до 24 кВ.
Техническая характеристика выключателя приведена
в таблице 4.6.
Таблица 4.6 - Техническая характеристика
вакуумного выключателя
Параметр
|
Значение
|
Единица
измерения
|
Номинальное
напряжение, Uном
|
12000
|
В
|
Номинальный
ток Iн
|
800
|
А
|
Номинальный
ток отключения, Iон
|
20000
|
А
|
Максимальный
ток Imax
|
50000
|
А
|
5. Выбор
системы защиты электропривода
.1 Защита двигателей насосных
агрегатов
обезжелезивание автоматизированное
управление насосный
Для асинхронного двигателя с короткозамкнутым
ротором характерны следующие виды аварийных режимов работы:
- многофазные (трех- и двухфазные) и
однофазные короткие замыкания в обмотках электродвигателя;
- тепловые перегрузки
электродвигателя;
- понижение или исчезновение
напряжение питания;
- обрыв фазы.
Короткие замыкания являются наиболее опасными
аварийными режимами в электроустановках. В большинстве случаев они возникают
из-за пробоя или перекрытия изоляции. Токи короткого замыкания иногда достигают
величин, в десятки и сотни раз превосходящих значения токов нормального режима,
а их тепловое воздействие и динамические усилия, которым подвергаются
токоведущие части, могут привести к повреждению всей электроустановки.
Тепловые перегрузки вызывают в первую очередь
ускоренное старение и разрушение изоляции двигателя, что приводит к коротким
замыканиям, т. е. к серьезной аварии и преждевременному выходу двигателя из
строя.
Защиту от аварийных режимов работы можно
реализовать с помощью релейно-контакторной схемы.
Классические релейно-контакторные схемы защиты
имеют ограниченное быстродействие, малую надежность, большие массогабаритные
показатели, не обеспечивают удаленный контроль за параметрами двигателя и сети,
а так же не позволяют сохранять информацию о произошедшей аварийной ситуации.
В наше время широкое распространение получили
электронные блоки защиты и измерения, позволяющие производить контроль за
основными параметрами электрической сети удаленно. Электронные системы
позволяют обеспечит повышенное быстродействие, сочетать в одном блоке все
необходимые виды защит от аварийных ситуаций, наличие встроенного ПЛК позволяет
адаптировать электронные блоки защиты к любым типам логики управления.
Устройства защиты и измерения Sepam серии 40
предназначены для эксплуатации электрических аппаратов и распределительных
сетей промышленных установок и подстанций для всех уровней напряжения. В
устройствах Sepam серии 40 воплощены наиболее полные, простые и надежные
решения, адаптированные к высоким требованиям применения, когда необходимо
обеспечить измерение токов и напряжения
Для двигателей насосных агрегатов выбираем Sepam
серии M41, для линии электропередач Sepam серии S41.
Функции защиты:
- максимальная фазная токовая защита и
защита от замыканий на землю с регулируемым временем возврата, с переключением
групп активных уставок и логической селективностью;
- защита от замыканий на землю,
нечувствительная к току включения трансформаторов;
- тепловая защита RMS, учитывающая
внешнюю рабочую температуру и работу вентиляции;
- направленная защита в фазах с
коррекцией по напряжению;
- защита по напряжению и частоте
(мин./макс.).
Связь:серии 40 полностью совместим со
стандартом связи Modbus. Все данные, необходимые для дистанционного управления
оборудованием с диспетчерского пункта, доступны благодаря порту связи Modbus,
поддерживающему следующие функции:
- считывание данных измерений,
аварийных сообщений, уставок и т.д.;
- запись команд телеуправления
выключателя и т.д.
Измерения:
- фазный ток, ток нулевой
последовательности, среднее значение тока;
- фазное, линейное напряжение,
напряжение нулевой последовательности;
- частота;
- активная, реактивная и полная
мощность;
- измерение температуры.
На рисунке 5.1 показана функциональная схема
подключения блока защиты Sepam 1000+.На рисунке5.2 показана принципиальная
схема подключения блока защиты Sepam 1000+.
Рисунок 5.1 - Принципиальная схема подключения
блока защиты Sepam
Рисунок 5.2 - Принципиальная схема подключения
блока защиты Sepam
Для защиты двигателей насосных агрегатов
выбираем Sepam серии M41 с установкой следующих видов защиты:
- максимальная токовая в фазах;
- минимальная токовая в фазах;
- тепловая перегрузка;
- максимального напряжения прямой
последовательности;
- минимального напряжения прямой
последовательности;
- максимального напряжения нулевой
последовательности.
Проведем расчет уставок согласно [24] для
параметрирования защиты.
Максимальная токовая в фазах обеспечивает защиту
от токов короткого замыкания. Запускается, когда один, два или три фазных тока
достигают уставки срабатывания. Сигнализация, связанная со срабатыванием
защиты, указывает поврежденную фазу или поврежденные фазы. Данная защита имеет
выдержку времени.
Так как пуск и торможение двигателей насосных
агрегатов осуществляется частотным преобразователем, который обеспечивает
плавный пуск и торможение без превышения пусковыми токами номинальных значений.
Значение тока не должно превышать:
,А, (5.1)
где: Ismax- ток уставки.
Из таблицы 4.2 известно, что Iном= 47А.
Тогда:
,А.
Выдержка по времени срабатывания
защиты согласно [4] Т=0,5с.
Минимальная токовая в фазах
обеспечивает отключение двигателя при обрыве одной фазы, она запускается, когда
ток фазы 1 падает ниже уставки Ismin, защита не чувствительна к
снижению тока (размыкание), вызванному отключением выключателя, имеет
независимую выдержку времени Т (постоянную).
Значение тока не должно быть меньше:
,А. (5.2)
Тогда:
,А.
Тепловая перегрузка. Данная защита
используется для защиты оборудования (двигателей, трансформаторов, генераторов,
линий, конденсаторов) от перегрузок и основана на измерении потребляемого тока.
Согласно ГОСТу 13109-97 колебание
напряжения в питающей электросети допускаются при нормальных значениях пределах
5%, в предельных значениях это 10% от номинального. Причинами могут быть
суточные, сезонные или технологические изменения нагрузки. Из этого следует,
что нормальное напряжение электросети 6кВ может колебаться в пределах от 5700
до 6300 вольт, а предельное отклонение от 5400 до 6600 вольт. Эти колебания
кратковременны.
Для исключения возможного
срабатывания защиты из-за колебания питающего напряжения применяем выдержку по
времени срабатывания защиты.
Защита по минимальному напряжению
прямой последовательности. Данная защита является трехфазной и срабатывает в
соответствии с параметрированием по фазному или линейному напряжению. Защита
запускается, если одно из 3 фазных или линейных напряжений становится меньше
уставки Us/Vs, имеет независимую выдержку времени Т (постоянную). При работе по
фазному напряжению функция указывает поврежденную фазу с помощью аварийной
сигнализации, срабатывающей при повреждении.
Значение минимального напряжения определяется
по формуле :
,В. (5.3)
Из таблицы 4.2 известно, что Uн=
6кВ.
Тогда:
,В.
Выдержка по времени срабатывания
защиты Т=1с
Защита по максимальному напряжению прямой
последовательности является однофазной и срабатывает по фазному или линейному
напряжению. Защита запускается, если одно из вышеуказанных напряжений превышает
уставку Us/Vs, имеет независимую выдержку времени Т (постоянную). При работе по
фазному напряжению функция указывает поврежденную фазу с помощью аварийной
сигнализации, срабатывающей при повреждении.
,В. (5.4)
Из таблицы4,2 известно, что Uн= 6кВ
Тогда:
,В.
Выдержка по времени срабатывания защиты Т=2с
5.1.1 Алгоритм работы защиты
двигателя насосных агрегатов
Измерение контролируемых параметров
осуществляется с помощью трансформаторов тока, трансформаторов напряжения и
датчиков температуры.
Программа контроля и управления защитой
начинается с контроля основных параметров электрической сети.
При возникновении сигнала о превышении током
сети максимально допустимого значения происходит срабатывание защиты по
максимальному току, сигнал с задержкой по времени в 0,5с поступает на
дискретный выход O11, далее посредством вакуумного выключателя происходит
отключение двигателя от питающей сети.
При возникновении сигнала о превышении
допустимого значения напряжения сети происходит срабатывание защиты по
максимальному напряжению, сигнал с задержкой по времени в 2с поступает на
дискретный выход O11, далее посредством вакуумного выключателя происходит
отключение двигателя от питающей сети.
При возникновении сигнала об уменьшении
питающего напряжения на 10% от допустимого значения происходит срабатывание
защиты по минимальному напряжению, сигнал с задержкой по времени в 1с поступает
на дискретный выход O11, далее посредством вакуумного выключателя происходит
отключение двигателя от питающей сети.
При возникновении сигнала об исчезновении тока в
одной из фаз или уменьшении тока на 50% от номинального значения происходит
срабатывание защиты по минимальному току, сигнал с задержкой по времени в 2с
поступает на дискретный выход O11, далее посредством вакуумного выключателя
происходит отключение двигателя от питающей сети.
При возникновении сигнала о превышении
напряжением нулевой последовательности уставки Vsо происходит срабатывание
защиты по максимальному напряжению нулевой последовательности, сигнал с
задержкой по времени в 2с поступает на дискретный выход O11, далее посредством
вакуумного выключателя происходит отключение двигателя от питающей сети.
Согласно описанному алгоритму составим программу
для Sepam 1000+ M41.
5.1.2 Разработка программного
обеспечения для устройства защиты и измерения Sepam
Программа управления защитой написана в среде
SFT2841 на языке Function Block Diagram.
Рисунок 5.3 -Листинг программы в среде SFT2841
на языке Function Block Diagram
Рисунок 5.4
- Схема принципиальная силовой части электропривода
6. Определение
экономической эффективности от внедрения системы автоматизированного управления
насосными агрегатами
.1 Характеристика
технико-экономической эффективности модернизации
Развитие и совершенствование современных
технологических и производственных процессов в промышленности, сельском
хозяйстве, строительстве и других областях народного хозяйства характеризуется
широким использованием средств автоматизации и комплексной механизации. Это
позволяет освободить человека от однообразного и тяжелого труда, повысить
производительность, надежность функционирования технологического оборудования м
качество выпускаемой продукции.
В общем случае автоматизация - это применение
технических средств, экономико-математических методов и систем управления,
освобождающих человека полностью или частично от непосредственного участия в
процессах получения преобразования, передачи и использования энергии,
материалов и информации.
Электрический привод является энергетической
основой технологического и производственного процессов, которые реализуются за
счет механической энергии. В настоящее время в качестве электромеханических
преобразователей используют асинхронные двигатели благодаря их простоте,
надежности и относительно небольшой стоимости.
При создании новых технологических комплексов
применяются системы автоматизированного управления технологическим процессом,
включающие в себя регулируемый электропривод, микропроцессорные средства
автоматизации и информационные средства.
Применение данных систем в работе насосной
станции позволяет обеспечивать:
- бесперебойное водоснабжение;
- стабильное давление в трубопроводах;
- высокая надёжность водоснабжения
(безаварийность);
- качество воды;
- предотвращение возможности
загрязнений поверхностных вод;
- доступный по ценам сервис для
населения.
Каждый из перечисленных аспектов в той или иной
степени связан с необходимостью использования энерго-ресурсосберегающего
оборудования, ведущего к многофакторному положительному влиянию на весь
комплекс предоставляемых предприятием услуг.
Экономический эффект от внедрения станций
управления, оснащённых преобразователями частоты, устройствами плавного пуска,
а также объединения станций управления в единую систему АСУ ТП основан на
следующих факторах:
- прямая экономия от снижения
потребления электроэнергии при регулировании производительности насосных
агрегатов (для разных объектов от 25 до 50%);
- прямая экономия за счёт снижения
непроизводительных утечек воды при оптимизации давления в напорном трубопроводе
(не менее 25 - 30% от общего объёма утечек);
- экономия фонда заработной платы
сокращаемого дежурного персонала;
- резкого снижения аварийности на
сетях (не менее чем в 5 - 10 раз);
- увеличение не менее чем в 3 раза
ресурса и межремонтных сроков насосов, электродвигателей, коммутационного
оборудования;
- снижение затрат на электрическое
отопление на объектах, бытовое обеспечение дежурного персонала;
- резкого увеличения надёжности
системы в целом, за счет устранения «человеческого фактора» и автоматической
диагностики системой всех её элементов и своевременного устранения возможных
аварийных ситуаций.
6.2 Критерий экономической оценки
эффективности модернизации
Критерием экономической эффективности внедрения
Системы автоматизированного управления (САУ) является срок окупаемости,
рассчитываемый по формуле:
, (6.1)
где:
- срок окупаемости проекта,
- капитальные вложения, необходимые
для реализации проекта,
- годовая экономия денежных средств
в результате внедрения проекта.
Для нахождения срока окупаемости
проекта рассчитаем капитальные вложения и годовую экономию от его внедрения.
6.3 Расчет капитальных вложений на
внедрение проекта САУ НА
Капитальные вложения на внедрение проекта
складываются из:
)Прямых расходов:
- стоимость приобретаемого оборудования,
- расходы на оплату труда,
затраченного на внедрение проекта,
- отчисления в фонд социального
страхования.
2)Текущих расходов:
- материальных затрат на эксплуатацию изделия,
- амортизационных отчислений.
Список оборудования САУ представлен в таблице 1.
Таблица 6.1 - Список оборудования САУ
Наименование
|
Кол-во
|
Цена
за ед.(руб.)
|
Стоимость(руб.)
|
1
|
2
|
3
|
4
|
Датчик
давления Cerabar T PMC 131
|
2
|
1000
|
2000
|
Электроприводы
MODACT MOKED
|
3
|
75000
|
225000
|
Контроллер
Siemens SIMATIC S7-1200
|
1
|
23000
|
23000
|
Частотный
преобразователь EI-9013
|
1
|
35000
|
35000
|
Вакуумный
выключатель SION
|
7
|
75000
|
525000
|
Устройства
защиты и измерения Sepam1000+
|
4
|
150000
|
600000
|
Итого:
|
1410000
|
Таким образом, расходы на приобретение
оборудования:
Рассчитаем расходы на оплату труда,
затраченного на разработку проекта САУ-НА и наладку оборудования:
(6.2)
где: Cнч = 265 рублей - стоимость
одного нормо-часа,
Тнч = 600 - трудоемкость проекта в
нормо-часах.
Подставим в формулу (6.2) численные значения:
Отчисления на социальные нужды:
(6.3)
где:
= 28,8% - норма отчислений на
соцстрах.
Тогда:
руб.
Рассчитаем прямые расходы по формуле:
(6.4)
Подставив в (6.4) численные значения, получим:
Найдем текущие затраты. Они состоят
из материальных затрат на обслуживание оборудования и амортизационных
отчислений.
Рассчитаем материальные затраты на обслуживание
оборудования по формуле:
, (6.5)
где: Нмз = 5% - норма материальных
затрат.
Подставив в (6.5) численные значения, получим:
руб.
Рассчитаем амортизационные отчисления линейным
методом по формуле:
, (6.6)
где: а0 - норма амортизационных
отчислений, для силового электротехнического оборудования а0 = 4,4%.
Таким образом:
руб.
Тогда суммарные текущие расходы составят:
(6.7)
Подставив в (6.7) численные значения, получим:
Таким образом, ежегодные текущие затраты
составят 132540 рублей.
6.4 Расчет экономического эффекта в
результате внедрения САУ НА
Расчет суммарной годовой экономии денежных
средств за счет внедрения САУ НА производится по формуле:
(6.8)
где: Эзп - экономия
годового фонда заработной платы;
Эээ - годовая экономия
денежных средств на оплату электроэнергии.
Проект САУ НА предусматривает
внедрение:
1. Системы автоматического управления
задвижками трубопровода.
Это позволяет сократить численность
обслуживающего персонала станции, следовательно, уменьшаются затраты
предприятия на фонд заработной платы.
При расчете годовой экономии фонда заработной
платы принимаем:
- управление задвижками осуществляет
один технический служащий.
- ставка заработной платы технического
служащего - 7 000 рублей (по данным отдела труда и заработной платы).
Таким образом, экономический эффект от внедрения
дистанционного управления в год составляет:
(6.9)
гдe:
- средняя месячная заработная плата
одного работника.
, руб., (6.10)
где:
= 7000руб.- месячная тарифная ставка
работников;
= 5%
- доплаты за условие труда;
= 20%(
)- доплаты
за работу в ночное время;
= 2,2%(
)-доплаты за
работу в праздничные дни;
= 15%(
) - премия;
- 25%(
)-надбавка
за непрерывный стаж работы на предприятии;
- 30%(
)-надбавка
по районному коэффициенту.
Тогда:
Подставив в (6.9) численные
значения, получим:
Таким образом, годовая экономия в
результате внедрения дистанционного управления составит 191 652 рубля.
2.Частотного регулирования скорости
электродвигателей.
Сравнение потерь энергии для двух способов
регулирования мощности - при помощи задвижек и посредством частотного
преобразователя, представлены в таблице 6.1.
Расход энергии представлены за сутки работы трех
насосов мощностью 400кВт каждый. Так как количество потребляемой воды имеет
нелинейную зависимость то режим работы насоса можно разбить на 4 временных
отрезка ночь 01:00-06:00, утро 06:00-10:00, день 10:00-18:00, вечер
18:00-01:00. Расход воды составляет соответственно 20%, 100%, 80%, 100% от
номинального значения для имеющегося насосного агрегата.
Таблица 6.2 - Расход энергии в час при различных
способах регулирования частоты вращения двигателей
Тип
регулирования
|
Потребляемая
энергия кВт*ч
|
|
Ночь
(5часов)
|
Утро
(4часа)
|
День
(8часов)
|
Вечер
(7часов)
|
Суммарная
|
Задвижкой
|
2880
|
4800
|
8640
|
8400
|
24720
|
Частотным
преобразователем
|
960
|
4800
|
6240
|
8400
|
20400
|
Согласно данным таблицы построим график
потребления мощности при различных способах регулирования скорости вращения
насоса.
Рисунок 6.1- Потребление мощности при различных
способах регулирования скорости вращения насоса: 1 - при управлении задвижками;
2-при частотном регулировании; 3-экономия электроэнергии
Как видно из графика, способ регулирования
скорости задвижкой приводит к большим затратам электроэнергии. Поэтому
применение частотного регулирования экономически более эффективно.
Рассчитаем экономию энергии при внедрении
частотного регулирования. При расчете примем следующие условия:
- время работы насосов определяется
исходя из технологического процесса.
- годовая экономия в рублях рассчитана
с учетом тарифа 2,27 рублей за 1 кВт*час.
Рассчитаем годовую экономию денежных средств на
оплату электроэнергии, исходя из стоимости 1 кВтч электроэнергии - 2,27 рублей,
по формуле:
(6.11)
где
- сэкономленная энергия, кВт*ч,
= 2,27 рублей за 1 кВт*час - тариф
электроэнергии.
Подставив в (6.10) численные
значения, получим:
Рассчитаем суммарную годовую экономию денежных
средств в результате внедрения дистанционного управления и частотного
регулирования.
Подставив в формулу (6.7) расчетные
данные из (6.8) и (6.10), получим:
руб.
Таким образом, суммарная экономия
расходов в результате внедрения проекта САУ НА составит 3770988 рублей.
6.5 Расчет экономической
эффективности от внедрения САУ НА и срок его окупаемости
Рассчитаем годовой экономический эффект с учетом
текущих материальных затрат по формуле:
(6.12)
Подставив в формулу (6.12) расчетные
данные, получим:
Срок окупаемости проекта составит:
Вывод.
Таким образом, в результате расчета
экономической эффективности проекта, имеем:
- капитальные полные расходы по внедрению проекта
составят 1603200 рублей;
- ежегодные текущие затраты составят
132540 рублей;
- годовая экономия расходов в
результате внедрения проекта составит 3770988 рублей;
- годовой экономический эффект от
внедрения проекта составит 3638448рублей;
- срок окупаемости проекта 6 месяцев.
7. Разработка
мероприятий по БЖД на насосной станции. Электробезопасность
.1 Анализ вредных и опасных
производственных факторов
При выполнении своих должностных обязанностей на
работника могут воздействовать следующие одиночно и совокупно вредные и опасные
производственные факторы:
- движущиеся машины и механизмы,
подвижные части производственного оборудования;
- запыленность воздуха рабочей зоны;
- повышенная температура поверхностей
оборудования;
- повышенная или пониженная
температура воздуха рабочей зоны;
- повышенный уровень вибрации, шума;
- повышенная подвижность воздуха;
- недостаточная освещенность рабочей
зоны;
- острые кромки, шероховатости на
поверхностях оборудования, инструмента;
- отсутствие или недостаток
естественного света;
- повышенное зрительное напряжение;
- повышенное значение напряжение в
электрической цепи, замыкание которой может произойти через тело человека;
- электромагнитные излучения;
- психофизиологические опасные
факторы: нервно - психические перегрузки;
- повышенная или пониженная влажность
воздуха.
Основным опасным фактором на насосной станции
является повышенное значение напряжение в электрической цепи 10кВ. Вследствие
чего необходимо разработать мероприятия по электробезопасности и ввести группы
допуска для персонала станции при работе с напряжением свыше 1000В.
7.2 Опасные факторы, связанные с
использованием электрической энергии
Факторами опасного и вредного воздействия на
человека, связанными с использованием электрической энергии, являются:
- протекание электрического тока через
организм человека;
- воздействие электрической дуги;
- воздействие биологически активного
электрического поля;
- воздействие биологически активного
магнитного поля;
- воздействие электростатического
поля;
- воздействие электромагнитного
излучения (ЭМИ).
Биологически активными являются электрические и
магнитные поля, напряженность которых превышает предельно допустимые уровни
(ПДУ) - гигиенические нормативы условий труда.
Опасные и вредные последствия для человека от
воздействия электрического тока, электрической дуги, электрического и
магнитного полей, электростатического поля и ЭМИ проявляются в виде
электротравм, механических повреждений и профессиональных заболеваний. Степень
воздействия зависит от экспозиции фактора, в том числе: рода и величины
напряжения и тока, частоты электрического тока, пути тока через тело человека,
продолжительности воздействия электрического тока или электрического и
магнитного полей на организм человека, условий внешней среды.
Экспозиция - количественная характеристика
интенсивности и продолжительности действия вредного фактора.
Электротравмы: локальные поражения тканей
(металлизация кожи, электрические знаки и ожоги) и органов (резкие сокращения
мышц, фибриляция сердца, электроофтальмия, электролиз крови) являются
результатом воздействия электрического тока или электрической дуги на человека.
По степени воздействия на организм человека
различаются четыре стадии:- слабые, судорожные сокращения мышц;- судорожные
сокращения мышц, потеря сознания;- потеря сознания, нарушение сердечной и
дыхательной деятельности;- клиническая смерть, т.е. отсутствие дыхания и
кровообращения.
Профессиональные заболевания проявляются, как
правило, в нарушениях функционального состояния нервной и сердечно-сосудистой
систем. У людей, работающих в зоне воздействия электрического и магнитного
полей, электростатического поля, электромагнитных полей радиочастот, появляются
раздражительность, головная боль, нарушение сна, снижение аппетита, нарушение
репродуктивной функции и др.
7.3 Мероприятия защиты и
предотвращения воздействия повышенного напряжения в электрической цепи на
человека
Перед началом работ необходимо проводить
организационные и технические мероприятия.
К организационным мероприятиям относят выдачу
нарядов, распоряжений и допуска к работе, надзор во время работы, оформление
перерывов в работе, переводов на другое рабочее место и окончание работы.
Наряд - это задание на безопасное производство
работ, определяющее их место и содержание, время начала и окончания,
необходимые меры безопасности, состав бригады и лиц, ответственных за безопасность
выполнения работ. Наряд выписывается на бланке специальной формы. Распоряжение
- это задание на производство работ, определяющее их содержание, место и время,
меры безопасности и лиц, которым поручено выполнение этих работ. Наряды и
распоряжения выдают лица, имеющие группу по электробезопасности не ниже V в
электроустановках напряжением выше 1000 В, и не ниже IV в установках
напряжением до 1000 В. Наряд на работу выписывается под копирку в двух
экземплярах и выдается оперативному персоналу непосредственно перед началом
подготовки рабочего места.
При работе по наряду бригада должна состоять не
менее чем из двух человек - производителя работ и члена бригады. Производитель
работ отвечает за правильность подготовки рабочего места, выполнение необходимых
для производства работ мер безопасности. Он же проводит инструктаж бригады об
этих мерах, обеспечивает их выполнение ее членами, следит за исправностью
инструмента, такелажа, ремонтной оснастки. Производитель работ, выполняемых по
наряду в электроустановках напряжением выше 1000 В, должен иметь группу по
электробезопасности не ниже IV, в установках до 1000 В и для работ, выполняемых
по распоряжению,- не ниже III.
Допуск к работе осуществляется допускающим -
ответственным лицом из оперативного персонала. Перед допуском к работе
ответственный руководитель и производитель работ вместе с допускающим проверяют
выполнение технических мероприятий по подготовке рабочего места. После этого
допускающий проверяет соответствие состава бригады и квалификации включенных в
нее лиц, прочитывает по наряду фамилии ответственного руководителя,
производителя работ, членов бригады и содержание порученной работы; объясняет
бригаде, откуда снято напряжение, где наложены заземления, какие части
ремонтируемого и соседних присоединений остались под напряжением и какие особые
условия производства работ должны соблюдаться; указывает бригаде границы
рабочего места и убеждается, что все им сказанное понято бригадой. После
разъяснений допускающий доказывает бригаде, что напряжение отсутствует,
например, в установках выше 35 кВ с помощью наложения заземлений, а в
установках 35 кВ и ниже, где заземления не видны с места работы,- с помощью
указателя напряжения и прикосновением рукой к токоведущим частям.
С момента допуска бригады к работам для
предупреждения нарушений требований техники безопасности производитель работ
или наблюдающий осуществляет надзор. Наблюдающему запрещается совмещать надзор
с производством какой-либо работы и оставлять бригаду без присмотра во время ее
выполнения. Разрешается кратковременное отсутствие одного или нескольких членов
бригады. При отсутствии производителя работ, если его не может заменить
ответственный руководитель или лицо, выдавшее данный наряд, или лицо из
оперативного персонала, бригада выводится из распределительного устройства,
дверь РУ запирается и оформляется перерыв в работе.
Периодически проверяется соблюдение работающими
правил техники безопасности. При обнаружении нарушений ПТБ или выявлении других
обстоятельств, угрожающих безопасности работающих, у производителя работ
отбирается наряд и бригада удаляется с места работы.
При перерыве в работе на протяжении рабочего дня
бригада удаляется из РУ, после перерыва ни один из членов бригады не имеет
права войти в РУ в отсутствие производителя работ или наблюдающего, так как во
время перерыва могут произойти изменения в схеме, отражающиеся на условиях
производства работ. По окончании работ рабочее место приводится в порядок,
принимается ответственным руководителем, который после вывода бригады
производителем работ расписывается в наряде об их выполнении. Оперативный
персонал осматривает оборудование и места работы, проверяет отсутствие людей,
посторонних предметов, инструмента, снимает заземление и проверяет в
соответствии с принятым порядком учета, удаляет временное ограждение, снимает
плакаты «Работать здесь», «Влезать здесь», устанавливает на место постоянные
ограждения, снимает плакаты, вывешенные до начала работы. По окончании
перечисленных работ наряд закрывается и включается электроустановка.
К техническим мероприятиям относят отключение
напряжения и принятие мер, препятствующих ошибочному или самопроизвольному
включению коммутационной аппаратуры, вывешивание запрещающих плакатов, проверку
отсутствия напряжения, наложение заземлений, вывешивание предупреждающих и
предписывающих плакатов.
В электроустановках напряжением выше 1000 В со
всех сторон, откуда может быть подано напряжение на место работы, при
отключении должен быть видимый разрыв, который осуществляется отключением
разъединителей, отделителей и выключателей нагрузки без автоматического
включения их с помощью пружин, установленных на самих аппаратах. Видимый разрыв
можно создать, сняв предохранители или отсоединив либо сняв шины и провода.
Трансформаторы напряжения и силовые трансформаторы отключаются с обеих сторон,
чтобы исключить обратную трансформацию. Во избежание ошибочного или
самопроизвольного включения коммутационных аппаратов выполняют следующие
мероприятия:
ручные приводы в отключенном положении и
стационарные ограждения запирают на механический замок;
у приводов коммутационных аппаратов, имеющих
дистанционное управление, отключают силовые цепи и цепи оперативного тока;
у грузовых и пружинных приводов включающий груз
или пружины приводят в нерабочее положение.
Во время работы запрещается переставлять или
убирать плакаты и установленные временные ограждения, а также проникать на
территорию огражденных участков.
В электроустановках напряжением выше 1000В
работу с электроизмерительными клещами должны проводить два работника: один -
имеющий группу IV (из числа оперативного персонала), другой - имеющий группу
III (может быть из числа ремонтного персонала). При измерении следует
пользоваться диэлектрическими перчатками. Запрещается наклоняться к прибору для
отсчета показаний.
Работу с измерительными штангами должны
проводить не менее двух работников: один - имеющий группу IV, остальные -
имеющие группу III. Подниматься на конструкцию или телескопическую вышку, а
также спускаться с нее следует без штанги.
Работа должна проводиться по наряду, даже при
единичных измерениях с использованием опорных конструкций или телескопических
вышек.
Работа со штангой допускается без применения
диэлектрических перчаток.
При осмотре электроустановок напряжением выше
1000 В не допускается входить в помещения, камеры, не оборудованные
ограждениями (требования к установке ограждений приведены в Правилах устройства
электроустановок) или барьерами, препятствующими приближению к токоведущим
частям на расстояния менее указанных в таблице 7.1. Не допускается проникать за
ограждения и барьеры электроустановок.
Не допускается выполнение какой-либо работы во
время осмотра.
При замыкании на землю в электроустановках
напряжением 3-35 кВ приближаться к месту замыкания на расстояние менее 4 м в
ЗРУ и менее 8 м - в ОРУ и на ВЛ допускается только для оперативных переключений
с целью ликвидации замыкания и освобождения людей, попавших под напряжение. При
этом следует пользоваться электрозащитными средствами.
Отключать и включать разъединители, отделители и
выключатели напряжением выше 1000 В с ручным приводом необходимо в
диэлектрических перчатках.
Электроустановки осматривают без снятия с них
напряжения. При осмотре электроустановок напряжением 6 - 35 кВ запрещено
приближаться к токопроводящим частям на расстояние менее 0,6 м.
Для осмотра оборудования выше 1000 В открывают
двери камер или ограждений. Оборудование осматривают, стоя перед барьером.
Дефекты выявляют визуально и слух. Во время осмотра нельзя проникать за
ограждения и барьеры или выполнять какие-либо работы.
При необходимости разрешается вход в ячейки и
камеры для осмотра, если расстояние от пола до не огражденных токопроводящих
частей составляет не менее указанного в таблице 7.1.
Таблица 7.1 - Расстояние от пола до
токопроводящих частей
Напряжение,
кВ
|
До
10 включительно
|
35
|
110
|
150-220
|
Расстояние,
м
|
2,5
и более
|
2,75
|
3,5
|
4,2
|
При осмотрах электроустановок напряжением до 35
кВ могут быть обнаружены замыкания на землю. Вблизи места замыкания образуется
зона растекания тока, создаются высокие потенциалы на поверхности пола, земли,
на корпусах оборудования и возникает опасность поражений прикосновения и шага.
Поэтому к месту замыкания нельзя приближаться на расстояние менее 4 метров в
ЗРУ и менее 8 метров в ОРУ. Лишь для оперативных переключений или освобождения
людей, попавших под напряжение, допускается приближаться к месту замыкания (при
условии принятия защитных мер) на расстояния менее указанных.
Отключения и изменения в электрических схемах
производят только по распоряжению старшего дежурного по смене или начальника
электроцеха; в электросетях - диспетчера энергосистемы или электросети; на
промышленных предприятиях - того дежурного, в оперативном управлении которого
находится данное оборудование.
Повышенную опасность для персонала представляют
переключения разъединителей и выключателей.
Разъединители отключают и включают без нагрузки.
Лишь при необходимости допускается отключать разъединителем малые токи
(нагрузочный ток трансформаторов малой мощности, зарядный ток воздушных и
кабельных линий). Разъединители следует включать быстро и до отказа. Если
возникает дуга, ножи надо довести до конца, в противном случае обратный ход
ножа вызовет развитие дуги, в результате этого может произойти несчастный
случай.
Отключать разъединители следует наоборот
медленно, особенно в начальный момент. Если появится дуга при отходе ножей от
губок, разъединитель следует быстро включить обратно. Разъединители отключают
(включают) в диэлектрических перчатках. Разъединители с пофазным управлением и
вертикальным расположением ножей отключают (включают) также в диэлектрических
перчатках, стоя на изолирующем основании и используя изолирующую штангу.
Снимать и устанавливать предохранители следует
при снятом напряжении.
Допускается снимать и устанавливать
предохранители, находящиеся под напряжением, но без нагрузки.
Под напряжением и под нагрузкой допускается
заменять: предохранители во вторичных цепях, предохранители трансформаторов
напряжения и предохранители пробочного типа.
При снятии и установке предохранителей под
напряжением необходимо пользоваться: изолирующими клещами (штангой) с
применением диэлектрических перчаток и средств защиты лица и глаз;
Двери помещений электроустановок, камер, щитов и
сборок, кроме тех, в которых проводятся работы, должны быть закрыты на замок.
Ремонты электрооборудования напряжением выше
1000 В, работа на токоведущих частях без снятия напряжения в электроустановках
напряжением выше 1000 В, а также ремонт ВЛ независимо от напряжения, как
правило, должны выполняться по технологическим картам.
Производитель работ отвечает:
за соответствие подготовленного рабочего места
указаниям наряда, дополнительные меры безопасности, необходимые по условиям
выполнения работ;
за четкость и полноту инструктажа членов
бригады;
за наличие, исправность и правильное применение
необходимых средств защиты, инструмента, инвентаря и приспособлений;
за сохранность на рабочем месте ограждений,
плакатов, заземлений, запирающих устройств;
за безопасное проведение работы и соблюдение
настоящих Правил им самим и членами бригады;
за осуществление постоянного контроля за членами
бригады.
Производитель работ, выполняемых по наряду в
электроустановках напряжением выше 1000 В, должен иметь группу IV.
7.4 Требования к персоналу,
допускаемому к обслуживанию электроустановок
Эксплуатацию электроустановок (ЭУ) должен осуществлять
подготовленный электротехнический персонал.
Обслуживание электротехнологических установок
(электросварка, электролиз, электротермия, и т.п.), а также сложного
энергонасыщенного производственно-технологического оборудования, при работе
которого требуется постоянное техническое обслуживание и регулировка
электроаппаратуры, электроприводов, ручных электрических машин, переносных и
передвижных электроприёмников, переносного электроинструмента, должен
осуществлять электротехнологический персонал. Он должен иметь достаточные
навыки и знания для безопасного выполнения работ и технического обслуживания
закрепленной за ним установки.
Электротехнологический персонал производственных
цехов и участков, осуществляющий эксплуатацию электротехнологических установок
и имеющий группу по электробезопасности II и выше, в своих правах и
обязанностях приравнивается к электротехническому.
Руководители, в непосредственном подчинении
которых находится электротехнологический персонал, должны иметь группу по
электробезопасности не ниже, чем у подчиненного персонала.
Перечень должностей и профессий электро-
технологического персонала, которым необходимо иметь соответствующую группу по
электробезопасности, утверждает руководитель.
Персонал, допущенный к эксплуатации и обслуживанию
электроустановок, должен:
иметь профессиональную подготовку,
соответствующую характеру работы. При отсутствии профессиональной подготовки
такие работники должны быть обучены (до допуска к самостоятельной работе) в
специализированных центрах подготовки персонала;
проходить медицинское освидетельствование.
Состояние здоровья электротехнического персонала, обслуживающего
электроустановки, определяется медицинским освидетельствованием при приёме на
работу и затем проверяется периодически в сроки, установленные органами
здравоохранения. Работники из электротехнического персонала не должны иметь
увечий и болезней в стойкой форме, мешающих производственной работе;
до допуска к самостоятельной работе пройти
обучение приёмам освобождения пострадавшего от действия электрического тока и
оказания первой помощи при несчастных случаях;
пройти обучение на рабочем месте в объеме,
необходимом для данной профессии (должности). Электротехнический персонал до
допуска к самостоятельной работе или при переходе на другую работу (должность),
а также при перерыве в работе свыше одного года, обязан пройти производственное
обучение на рабочем месте. Программу производственного обучения составляет
ответственный за электрохозяйство подразделения и утверждает ответственный за
электрохозяйство предприятия;
пройти проверку знаний МПОТ (ПБ) ЭЭУ, ПТЭЭП и
других нормативно-технических документов (правил и инструкций по технической
эксплуатации, пожарной безопасности, пользованию защитными средствами,
устройства электроустановок) в пределах требований, предъявляемых к
соответствующей должности или профессии. Ему должна быть присвоена
соответствующая группа по электробезопасности и выдано удостоверение
установленного образца;
пройти стажировку на рабочем месте
продолжительностью не менее 2-х недель. Допуск к стажировке и самостоятельной
работе для ИТР оформляется распоряжением по организации, для рабочих - по
подразделению;
получить допуск к самостоятельной работе (в
письменном виде).
.5 Средства защиты
Электроустановки должны быть укомплектованы
испытанными, готовыми к использованию защитными средствами (СЗ), а также
средствами оказания первой медицинской помощи в соответствии с действующими
нормами и правилами.
Средства защиты делятся на следующие классы:
- средства защиты от поражения электрическим
током (электрозащитные средства);
- средства защиты от электрических
полей повышенной напряженности (коллективные и индивидуальные);
- средства индивидуальной защиты.
К электрозащитным средствам относятся:
- изолирующие штанги;
- изолирующие и электроизмерительные клещи;
- указатели напряжения всех видов и
классов;
- бесконтактные сигнализаторы наличия
напряжения;
- изолированный инструмент;
- диэлектрические перчатки, боты и
галоши, ковры, изолирующие подставки;
- защитные ограждения (щиты, ширмы,
изолирующие накладки, колпаки);
- переносные заземления;
- устройства и приспособления для
обеспечения безопасности труда при проведении испытаний и измерений в
электроустановках (указатели напряжения для проверки совпадения фаз, устройства
для прокола кабеля, указатели повреждения кабеля и т.п.);
- плакаты и знаки безопасности;
- прочие средства защиты, изолирующие
устройства и приспособления для ремонтных работ под напряжением в
электроустановках 110 кВ и выше).
Из класса электрозащитных средств выделяются
изолирующие электрозащитные средства, которые в свою очередь подразделяются на
основные и дополнительные.
Основное электрозащитное средство - это СЗ,
применяемое при работе в ЭУ, и изоляция которого длительно выдерживает рабочее
напряжение ЭУ или позволяет прикасаться к токоведущим частям, находящимся под
напряжением.
Дополнительное электрозащитное средство - это
СЗ, которое само по себе при данном напряжении не может обеспечить защиту от
поражения электрическим током, но дополняет основное средство защиты, а также
служит для защиты от напряжения прикосновения и шагового напряжения.
Основные электрозащитные средства
подразделяются:
электрозащитные средства в электроустановках
выше 1000 В (изолирующие штанги, изолирующие и электроизмерительные клещи, указатели
напряжения, устройства и приспособления для обеспечения безопасности при
проведении испытаний и измерений в электроустановках);
электрозащитные средства в электроустановках до
1000 В (изолирующие штанги, изолирующие и электромагнитные клещи, указатели
напряжения, диэлектрические перчатки, изолированный инструмент).
Дополнительные электрозащитные средства
подразделяются:
электрозащитные средства в электроустановках
выше 1000 В (диэлектрические перчатки, диэлектрические боты, диэлектрические
ковры, изолирующие подставки и накладки, изолирующие колпаки, штанги для
переноса и выравнивания потенциала);
электрозащитные средства в электроустановках до
1000 В (диэлектрические калоши, диэлектрические ковры, изолирующие подставки и
накладки, изолирующие колпаки).
Средства коллективной защиты от поражения
электрическим током:
- защитное заземление;
- зануление;
- защитное отключение;
- применение низких напряжений;
- двойная изоляция;
- оградительное устройство;
- сигнализация, блокировка, знаки
безопасности, плакаты.
Ток проходящий по телу человека определяется как
:
ч = Uприк \ Rч. (7.1)
При наличии заземлителя эта зависимость может
быть выражена следующей формулой
ч = Iз * Rз \ Rч, (7.2)
где: Rз - сопротивление растеканию тока
заземлителя, определяемое сопротивлением почвы между заземлителем и землёй.
К средствам индивидуальной защиты, применяемым в
электроустановках, относятся:
- средства защиты головы (каски);
- глаз и лица (очки, щитки);
- органов дыхания (респираторы);
- рук (рукавицы, перчатки);
- средства, страхующие от падения
(пояса, канаты).
Персонал, находящийся в помещениях с действующим
электрооборудованием, а также при обслуживании воздушных ЛЭП, должен надевать
защитные каски.
При выборе конкретных видов СИЗ необходимо
помнить, что СИЗ относятся к видам продукции, подлежащей обязательной
сертификации.
Наличие на насосной станции современных
автоматических электрозащитных средств, соответствующих действующим нормам и
правилами, а так же изложенные выше мероприятия по электробезопасности
позволяют обеспечить надежность срабатывания защит, безопасность производства и
защиту людей от вредного и опасного воздействия электрического тока.
Заключение
Итогом данной дипломной работы стал
разработанный проект системы автоматизированного управления насосными
агрегатами станции 2-го подъема комплекса обезжелезивания и деманганации.
Проект автоматизации управления насосными
агрегатами включает в себя:
- обеспечение автоматического
управления насосными агрегатами клапанами задвижек, что позволит повысить
надежность всей системы и исключить человеческий фактор, а также вывести
человека из опасной рабочей зоны;
- внедрение частотного регулирования скорости
электродвигателей насосных агрегатов позволяет оптимизировать работу насосной
станции в зависимости от количество потребляемых водных ресурсов. Это
существенно сократит расходы электроэнергии при регулировании скорости
двигателей, а так же продлит срок эксплуатации электрического оборудования
вследствие устранения нагревания электродвигателя и силовых цепей;
- внедрение электронного блока защиты
и измерения Sepam 1000+ позволяет обеспечить высокий уровень защиты и
своевременно определение аварийных ситуаций электротехнического оборудования и
двигателей насосных агрегатов, дистанционное управление силовыми выключателями,
а так же производить дистанционные измерения основных параметров электрической
сети и двигателя.
Для проекта произведена оценка экономического
эффекта. Единовременные затраты составили 1603200 рублей. Ежегодный
экономический эффект от внедрения системы автоматического управления составляет
3638448 рублей. Срок окупаемости 6 месяцев.
Разработаны мероприятия по обеспечению БЖД на
насосной станции, которые позволяют повысить безопасность на производстве и
сократить число производственных травм до минимума.
Список
использованных источников
1.Методическое
пособие по водоподготовке. - изд. 3-е, М.: Группа компаний «Импульс», 2004.
.Запольский
А.К., Баран А.А. Коагулянты и флокулянты в процессах очистки воды. - СПб.:
Химия, 1987.- 208 с.
.
Кульский Л.А. Обезвреживание и очистка воды хлором. - М.-Л.: Изд. Министерства
коммунального хозяйства, 1947. - 424 с.
.
Банников В.В. и др. Обеззараживание питьевой воды, приготовление
дезинфицирующих растворов, обезвреживание сточных вод. - М.: НПП Санер, 1996. -
31 с.
.
Кулаков В.В., Сошников Е.В., Чайковский Г.П. Обезжелезивание и деманганация
подземных вод. - Хабаровск: Изд. ДВГУПС, 1998. - 100 с.
.
Башарин А.В., Новиков В.А., Соколовский Г.Г. Управление электроприводами:
учебное пособие для вузов - Л.: Энергоиздат. Ленингр. отд-ние, 1982. - 392 с.,
ил.
.
Москаленко В.В. Система автоматизированного управления электропривода: Учебник.
-М.: ИНФРА-М, 2004.-208с.
.
Белов М.П., Новиков В.А., Рассудов Л.Н. Автоматизированный электропривод
типовых производственных механизмов и технологических комплексов: учебник для
студентов высших учебных заведений. - М.: Издательский центр «Академия», 2007.
- 576с.
.Лукас
В.А. Теория автоматического управления: Учебник для вузов. - М.: Недра, 1990. -
416с.
.
Федоров Ю.Н. Справочник инженера по АСУТП: Проектирование и разработка.
Учебно-практическое пособие. -М.: Инфра-Инженерия, 2008.-928с.
.
Онищенко Г.Б. Электрический привод. Учебник для вузов. -М.: РАСХН. 2003.-320с.
.
Кацман М.М. Электрические машины. - 7-е изд.- М.: Издательский центр «Академия»,
2007.- 496с.
13.
Средства автоматизации [Электронный ресурс]: #"604848.files/image119.gif">
Рисунок
А.1 - Схема гидравлическая насосной станции II подъема
Таблица А.1 - Спецификация оборудования
Поз.
обознач.
|
Наименование
|
Кол.
|
Примечание
|
1A1...1A23
|
Шкаф
местного управления задвижкой ШМУЗ-01
|
23
|
ССМ
35/06-10ATX1.СБ.1
|
FQIT1,
FQIT2
|
Расходомер-счетчик
ультразвуковой, 4-20 мА, RS485Днепр-7-В-801-2-T(4-20)мА-З-RS485-A
|
2
|
|
HS1...HS3
|
Пост
кнопочный КП102
|
3
|
|
LT1
|
Ультразвуковой
измеритель уровня 0...5 м, 4-20 мА, IP68 Optisound 3010 С
|
1
|
|
M1...M3
|
Агрегат
электронасосный 1Д1250-125б
|
3
|
A4-85/37K
- 4 У3, 10кВ
|
MR1,
MR2
|
Датчик
протечки SWF 4.1
|
2
|
|
NSHA1...NSHA4,
NSHA17...NSHA18
|
Электропривод
вращения многооборотный MODACT MONED 52030.90H1NED
|
4
|
|
NSHA7…
NSHA10, NSHA15…NSHA18,
|
Электропривод
вращения однооборотный MODACT MOKED 52327.0E8GED
|
8
|
|
PI1...PI5
|
Манометр
технический показывающий 0…1,6 МПа МП-4У/16
|
7
|
|
PS1...PS3
|
Реле
давления 1.3....12бар, IP54, G1/4 BSP (female) XMAV12L2135
|
3
|
|
PT1,
PT3
|
Датчик
давления G1/2, 4-20 мА, 8...30V, 0...16 бар Cerabar T PMP131-A1B01A1T
|
3
|
|
QE1
|
Датчик
хлора
CCS141-N, CLE 3-mA-2 ppm
|
1
|
|
QIT1
|
Трансмиттер
для измерения свободного хлора CCM253-EP0010 Liquisys M
|
1
|
|
РЧВ1
|
Резервуар
чистой воды
|
1
|
|
Приложение
Б
Рисунок Б.1 - Схема структурная автоматизации
насосной станции II подъема