Подготовительный цех и основное производство шинного завода по выпуску покрышек
Реферат
В данном дипломном проекте спроектирован шинный завод,
включающий в себя подготовительный цех и основное производство по выпуску
покрышек размером 21.00 РЗЗ мощностью 0,06 млн. шин в год.
В технологической части диплома обоснованы рецептуры резиновых
смесей, описаны технологические процессы производства шин, произведён
конструкторский расчёт запаса прочности каркаса.
В расчётной части диплома рассчитаны материальные балансы
резиновых смесей и их ингредиентов, а также произведён расчёт требуемого количества
оборудования.
В разделе по безопасности и экологичности разработаны
мероприятия по улучшению трудовой деятельности и уменьшению загрязнений
окружающей среды.
В экономической части представлены расчёты прибыльности
предприятия.
Диплом состоит из пояснительной записки, которая включает _
страницу, 90 таблиц, 1 рисунок, а также графическую часть, состоящую из 4
листов формата А-1подготовительного цеха и основного производства, 4 листов
разреза шинного завода и 1-го по безопасности проекта.
Введение
Шинная промышленность - одна из ведущих отраслей
нефтеперерабатывающей и нефтехимической промышленности. Развитию шинной
промышленности придается большое значение, так как от качества шин зависит
работа автомобильного и авиационного транспорта, строительных, дорожных,
сельскохозяйственных и других машин.
При использовании пневматических шин повышается скорость
движения, комфортность передвижения и проходимость машин в различных дорожных
условиях. Хорошая амортизация достигается благодаря эластичности резины и
упругости сжатого воздуха, находящегося в шинах.
Шинный завод представляет собой сложное предприятие с большим
количеством самого разнообразного оборудования, оснащенного системами
автоматизации и контрольно-измерительными приборами [36,45].
Необходимость повышения производительности труда в
горнорудной промышленности и гидротехническом строительстве, усиленное и
развитие добычи полезных ископаемых высокоэффективным открытым способом,
освоение районов Крайнего Севера, Сибири и Дальнего Востока определили пути
дальнейшего развития карьерного транспорта и строительно-дорожной техники в
направлении создания машин большой единичной мощности. Для обеспечения
возрастающих объемов перевозок горных масс разработано семейство новых
карьерных автомобилей-самосвалов и автопоездов грузоподъемностью 75, 110, 120 и
180 тонн, объединенных под общим названием карьерных автосамосвалов особо
большой грузоподъемности.
КГШ, работающие при скоростях до 50 км/ч широко применяют для
строительных, дорожных и подъемно-транспортных машин. В зависимости от
назначения и условий эксплуатации они могут иметь дорожный, повышенной
проходимости или карьерный рисунок протектора.
Совершенствование и разработка новых шин для
специализированного карьерного автомобильного транспорта обусловлены нуждами
горнодобывающих и сырьевых отраслей народного хозяйства, научно-технический
прогресс в которых связан с дальнейшим расширением наиболее эффективного
открытого способа добычи полезных ископаемых.
Организация производства таких шин требует разработки новых
материалов, технологических процессов и оборудования для их изготовления [45].
1. Технико-экономическое обоснование
Проектируемое предприятие целесообразно строить в районе
города Кемерово, с учетом направления преобладающих ветров (так называемой розы
ветров). Это расположение обусловлено близостью поставщиков сырья и материалов,
а также близким расположением потребителей готовой продукции (Кузбасс).
Необходимые для технологического процесса ингредиенты будут
поступать из Барнаула (технический углерод), Нижнекамска (каучуки), Кемерово
(корд и химические реактивы) и других городов, в которых выпускается
необходимое сырье.
Большинство видов основного сырья завод будет получать по
железнодорожной магистрали.
Перевозка грузов, поступающих на предприятие с соседних
районов, предусматривается за счет автомобильного хозяйства города, и частично,
внутризаводским транспортом.
Источником водоснабжения является река Томь; источником
хозяйственно-бытовых нужд и противопожарного водоснабжения принимается городской
водопровод. Снабжение предприятия энергетическими ресурсами (паром,
электроэнергией) предусматривается от ТЭЦ.
На проектируемом предприятии предусмотрено непрерывное
производство, поэтому график работы четырехсменный.
Комплектование инженерно-технического подразделения
производится в порядке вольного найма по трудовому контракту, приглашением
молодых специалистов, окончивших обучение в ВУЗах.
2. Стандартизация
Данный проект выполнен в соответствии с СТП 3.4.204-01, СТП
3.4.205-01 и СТП 3.4.105-01.
Все разделы, предусмотренные в дипломном проекте, выполнены в
соответствие с требованиями Российских стандартов:
ГОСТ 2106-68ЕСКД. Текстовые документы.
ГОСТ 2.301-68ЕСКД. Форматы
ГОСТ 2.302-68ЕСКД. Масштаб.
ГОСТ 2.303-68ЕСКД. Линии.
ГОСТ 2.305-68ЕСКД. Изображение - виды, разрезы, сечения.
ГОСТ 2.306-68ЕСКД. Обозначение графических материалов и
правила их нанесения на чертёж.
ГОСТ 2.109-73. Основные требования к чертежам.
ГОСТ 2.120-73. Технический проект.
ГОСТ 21.110-95 СПДС. Правила выполнения спецификации
оборудования, изделий и материалов.
ГОСТ 21.204-93 СПДС. Условные графические обозначения и
изображение элементов генеральных планов и сооружений.
ГОСТ 8.417-81 ГСИ. Единицы физических величин.
ГОСТ 7.1-84. Библиографическое описание произведений печати.
3. Назначение и характеристика выпускаемой продукции
Шина 21.00 РЗЗ, модели Ф-330 с карьерным рисунком протектора
является крупногабаритной и эксплуатируется на автомобилях «БелАЗ».
Таблица 3.1 Техническая
характеристика шины 21.00.РЗЗ
Наименование
показателя
|
|
Условное
обозначение
|
21.00.РЗЗ
|
Рисунок
протектора
|
Карьерный
|
Наружный
диаметр, мм
|
1950
|
Ширина профиля,
мм
|
540
|
Статический
радиус, мм
|
880±15
|
Норма слойности
|
32
|
Максимально
допустимая нагрузка, кг
|
12000
|
Внутреннее
давление, соответствующее максимальной нагрузке, кПа
|
600±25
|
Средний ресурс,
км
|
33000
|
Обозначение
профиля обода
|
15,00-33/3,0
|
Максимальная
скорость, км/ч
|
50
|
Масса шины, кг
не более
|
505
|
4. Технологическая часть
.1 Обоснование рецептур резиновых смесей
.1.1 Обоснование рецептуры резиновой смеси шифра ПД-167,
предназначенной для изготовления беговой части протектора
Для пневматических шин важными характеристиками являются:
потери на качение, их сцепление с мокрой и обледенелой дорогой и долговечность.
Во многом это зависит от свойств покровных резин, в частности беговая часть
протектора вступает в непосредственный контакт с дорогой и воспринимает все ее
неровности. Она работает в режиме заданных напряжений, подвергается
значительному истиранию, атмосферному воздействию, температурному воздействию,
поэтому протекторные резины должны обладать высокой прочностью при растяжении,
также сопротивлением раздиру, истиранию и разрастанию трещин, стойкостью к
механическим повреждениям, атмосферостойкостью.
Крупногабаритные шины эксплуатируются в карьерах, где
покрытие дорог неусовершенствованное, и работают они в условиях высоких местных
напряжений и при больших нагрузках. Отсюда следует, что протекторные резины
крупногабаритных покрышек должны помимо всего обладать высокой износостойкостью
при абразивном износе, стойкостью к сколам и трещинам, иметь малые
гистерезисные потери.
Высокая прочность и стойкость при абразивном износе, а также
стойкость к сколам, низкие гистерезисные потери и хорошую стойкость при
усталостном износе обеспечивает применение натурального каучука (70,0 м.ч.). С
технологической точки зрения применение НК повышает конфекционную клейкость
резиновой смеси.
Комбинация каучуков СКИ-3 (30,0 м.ч.) и НК (70,0 м.ч.)
придает покрышке достаточно хорошее сцепление с дорогой, малое теплообразование
в процессе эксплуатации и износостойкость на дорогах с неусовершенствованным
покрытием. Вулканизующая система должна обеспечивать высокую скорость
вулканизации в главном периоде, широкое плато вулканизации и минимальную
реверсию свойств резин в процессе вулканизации, так как данная покрышка
является крупногабаритной и для достаточной вулканизации необходим длительный
нагрев. Также вулканизующая система должна обеспечивать безопасность обработки
резиновых смесей. Поэтому для протекторных резин крупногабаритных шин
характерно использование «эффективных» и «полуэффективных» вулканизующих
систем.
В качестве вулканизующего агента используют серу (1,0 м.ч.),
ускорителями в данной системе являются сульфенамид М (1,0 м.ч.) и гексол ЗВ
(0,5 м.ч.). Сульфенамид М очень хорошо распределяется в эластомерной матрице.
Он является ускорителем высокой активности, резиновые смеси обладают большим
индукционным периодом и широким платом вулканизации, что обеспечивает большую
стойкость к подвулканизации и стойкость к реверсии. Гексол ЗВ (0,5 м.ч.)
позволяет получить широкий спектр связей, что повышает устойчивость к тепловому
старению, донором серы в этой системе является N,N-дитиодиморфолин (1,5 м.ч.).
Его применение позволяет получать при высоких температурах вулканизаты с
уменьшенным числом полисулъфидных связей, обладающие высокими прочностными и
динамическими свойствами, высокой теплостойкостью и стойкостью к тепловому
старению и обеспечивает значительно меньшую склонность к подвулканизации
резиновой смеси. Активатором в данной вулканизующей системе являются цинковые
белила (4,0 м.ч.), что способствует получению резин с высокими прочностными и
физико-механическими показателями.
Использование активного высокоструктурного технического
углерода ТУ-245 (45,0 м.ч.) обуславливает повышение модуля жесткости резин,
износостойкости и сопротивления раздиру. Кремнекислотный наполнитель Улътрасил
VN-3 (10,0 м.ч.) обеспечивает покрышке высокую устойчивость к сколам.
Для лучшей диспергации порошкообразных ингредиентов применяют
стеарин (3,0 м.ч.). Он также является вторичным активатором вулканизации,
взаимодействует с оксидом цинка, образуя стеарат цинка, который хорошо
диспергируется в матрице каучука и в свою очередь активирует ускоритель
вулканизации.
Для улучшения технологических свойств в резиновую смесь
вводят жидкие мягчители. Масло ПН-6 (4,0 м.ч.) улучшает шприцуемость заготовок,
снижая энергозатраты и температуру при обработке этих смесей. Содержание масла
ПН-6 существенно ниже по сравнению с обычно применяемыми дозировками с целью
повышения упругопрочностных свойств и износостойкости протекторных резин. Такой
мягчитель, как канифоль (2,0 м.ч.) улучшает технологические свойства резины, не
ухудшая при этом физико-механические показатели готового изделия, и придает детали
хорошую конфекционную клейкость.
Применение высокоактивных типов технического углерода при
низком содержании мягчителей приводит к быстрому повышению температуры смесей
при смешении в условиях ограниченного охлаждения резиносмесителей, а также при
дальнейшей обработке смесей, поэтому для резин на основе НК применяют
антискорчинги. Бензойная кислота (0,5 м.ч.) и сантогард РVI (0,15 м.ч.)
предотвращают преждевременную вулканизацию, но не влияют на скорость
вулканизации в главном периоде.
Для предотвращения или замедления разрушения резины
протектора в процессе эксплуатации в нее вводят стабилизаторы. Комбинация
диафена ФП (1,0 м.ч.) и ацетонанила Р (2,0 м.ч.) защищает резину от теплового
старения, атмосферных воздействий, придает большую динамическую устойчивость.
Таблица 4.1 - Рецептура резиновой смеси для беговой части
протектора
Ингредиенты
|
Массовые части
|
Массовые
проценты
|
Плотность, кг/м3
|
Объемные части
|
Объемные
проценты
|
Навеска, кг
|
|
|
|
|
|
|
1 ст
|
2 ст
|
1
|
2
|
3
|
4
|
5
|
6
|
7
|
8
|
НК, RSS1-3,
SMR-5, SMR-10. Вязкость по Муни (60±5) усл.ед.
|
70
|
39,85
|
920,00
|
76,09
|
49,50
|
80,30
|
|
СКИ-3. 1 группа
|
30,00
|
17,08
|
920,00
|
32,61
|
21,21
|
34,41
|
|
Сера
|
1,00
|
0,57
|
2200,00
|
0,45
|
0,30
|
|
1,04
|
Сульфенамид М
|
1,00
|
0,57
|
1370,00
|
0,73
|
0,47
|
|
1,04
|
N,N'-дитиоморфолин
|
1,50
|
0,85
|
1290,00
|
1,16
|
0,76
|
|
1,56
|
Гексол ЗВ, ЗВИ
|
0,50
|
0,28
|
1270,00
|
0,39
|
0,26
|
|
0,5
|
Бензойная
кислота
|
0,50
|
0,28
|
1200,00
|
0,42
|
0,27
|
0,57
|
|
Сантогард PVI
|
0,15
|
0,09
|
1530,00
|
0,10
|
0,06
|
|
0,16
|
Цинковые белила
|
4,00
|
2,28
|
5350,00
|
0,75
|
0,49
|
4,59
|
|
Стеариновая
кислота
|
3,00
|
1,71
|
870,00
|
3,45
|
2,24
|
3,44
|
|
Канифоль
сосновая
|
2,00
|
1,14
|
1040,00
|
1,92
|
1,25
|
2,29
|
|
Масло ПН-6Ш
|
4,00
|
2,28
|
970,00
|
4,12
|
2,68
|
4,59
|
|
Диафен ФП
|
1,00
|
0,57
|
1250,00
|
0,80
|
0,52
|
|
1,04
|
Ацетонанил Р,
РГ
|
2,00
|
1,14
|
1080,00
|
1,85
|
1,20
|
|
2,08
|
Ультрасил VN3
|
10,00
|
5,69
|
2500,00
|
4,00
|
2,60
|
11,48
|
|
Углерод
технический П 245
|
45,00
|
25,62
|
1810,00
|
24,86
|
16,17
|
51,62
|
|
Маточная смесь
|
|
|
|
|
|
|
175,3
|
Итого
|
175,65
|
100,00
|
|
153,71
|
100,00
|
193,29
|
182,7
|
Плотность смеси 1 стадии = 1137 кг/м3;
Плотность смеси 2 стадии = 1142 кг/м3.
Таблица 4.2 - Нормы контроля резиновой смеси для беговой
части протектора
Вязкость при
100ºС,
усл.ед.
|
Темпера-тура
вулканизации,ºС
|
Продолжительность
вулканизации, мин
|
Условное
напряжение при удлинении 300%, МПа
|
Условная
прочность при растя-жении, МПа, не менее
|
Относитель-ное
удлинение при разрыве, %
|
Сопротивление
раздиру, КН/м, не менее
|
Твердость по
Шору, А
|
|
|
|
|
|
|
|
|
|
|
|
|
|
|
|
|
|
|
|
|
|
|
|
|
|
|
|
|
|
|
|
|
70 ± 5
|
155
|
20 ± 0,5
|
12,7 ± 2,0
|
21,6
|
500 ± 75
|
88
|
65 ± 5
|
.1.2 Обоснование рецептуры резиновой смеси шифра ПД-168,
предназначенной для изготовления подканавочного слоя протектора
Основным режимом работы для подканавочного слоя протектора
грузовых шин является режим заданной энергии цикла. Этот слой воспринимает
основную массу толчков и ударов от неровностей дороги. В связи с этим резина
подканавочного слоя должна обладать высокой прочностью, усталостной
выносливостью, стойкостью к тепловому старению и стойкостью к разрастанию
трещин, а резиновая смесь - конфекционной клейкостью.
Необходимую прочность, хорошую эластичность и высокие
динамические показатели придает подканавочному слою НК (100,0 м.ч.). Он так же
обеспечивает необходимую конфекционную клейкость детали. Для подканавочного
слоя существенно важно малое теплообразование, что в данном случае
обеспечивается низкими гистерезисными потерями резин на основе НК.
Для подканавочного слоя характерно использование
«полуэффективных» систем вулканизации для придания высокой устойчивости к
тепловому старению. В качестве вулканизующих агентов для ненасыщенных
карбоцепных каучуков обычно используется сера (1,0 м.ч.). Роль основного
ускорителя здесь выполняет сульфенамид Ц (1,0 м.ч.), имеющий большой
индукционный период для безопасной обработки и высокую скорость вулканизации в
основном периоде вулканизации. Донором серы в вулканизующей системе является
N,N-дитиодиморфолин (1,5 м.ч.), благодаря чему уменьшается дозировка серы,
значительно упрощается процесс ее диспергации и образуется множество
теплоустойчивых поперечных связей с низкой полисульфидностью. Активатором
вулканизующих агентов являются цинковые белила (7,0 м.ч.). Повышенное
содержание оксида цинка необходимо для увеличения теплоотдачи резины
подканавочного слоя.
Наполнение ведут техуглеродом П-323 (50,0 м.ч.), он несколько
менее активен, чем техуглерод П-245, используемый в беговой части протектора,
для повышения динамических характеристик, для снижения внутреннего трения,
гистерезисных потерь.
Диспергирование порошкообразных ингредиентов упрощается в
присутствии стеариновой кислоты (2,5 м.ч.), которая также является вторичным
активатором вулканизации.
Для придания хорошей обрабатываемости смеси в нее добавляют
масло ПН-6 (4,0 м.ч.), что необходимо при высоком наполнении техуглеродом. Так
же в смесь вводят канифоль (3,0 м.ч.) для улучшения технологических свойств,
повышения клейкости без ухудшения физико-механических показателей вулканизата.
Из-за склонности НК к подвулканизации появляется
необходимость в использовании замедлителей подвулканизации. В этой смеси в
качестве антискорчинга применяется фталевый ангидрид (0,5 м.ч.), который по
эффективности действия превосходит бензойную кислоту, и в тоже время, имеет
невысокую стоимость.
Подканавочный слой находится между беговой частью протектора
и брекером, жесткий температурный режим эксплуатации обуславливает введение
стабилизаторов. Зарекомендовавшая себя комбинация стабилизаторов ацетонанил Р
(1,5 м.ч.) и диафен ФП (1,0 м.ч.) обеспечивает резине высокую устойчивость к
термоокислительному старению и усталостную выносливость.
Таблица 4.3 - Рецептура резиновой смеси для подканавочной
части протектора
Ингредиенты
|
Массовые части
|
Массовые
проценты
|
Плотность, кг/м3
|
Объемные части
|
Объемные
проценты
|
Навеска, кг
|
|
|
|
|
|
|
1 ст
|
2 ст
|
1
|
2
|
3
|
4
|
5
|
6
|
7
|
8
|
НК, RSS1-3,
SMR-5. Вязкость по Муни (60±5) усл.ед.
|
100,00
|
57,80
|
920,00
|
108,70
|
71,34
|
115,00
|
|
Сера
|
1,00
|
0,58
|
2200,00
|
0,45
|
0,30
|
|
1,05
|
Сульфенамид Ц
|
1,00
|
0,58
|
1360,00
|
0,74
|
0,48
|
|
1,05
|
N,N'-дитиоморфолин
|
1,50
|
0,87
|
1290,00
|
1,16
|
0,76
|
|
1,57
|
Фталевый
ангидрид
|
0,50
|
0,29
|
1600,00
|
0,31
|
0,21
|
0,58
|
|
Цинковые белила
|
7,00
|
4,05
|
5350,00
|
1,31
|
0,86
|
8,04
|
|
Стеариновая
кислота
|
2,50
|
1,45
|
870,00
|
2,87
|
1,89
|
2,87
|
|
Канифоль
сосновая
|
3,00
|
1,73
|
1040,00
|
2,88
|
1,89
|
3,46
|
|
Масло ПН-6Ш
|
4,00
|
2,31
|
970,00
|
4,12
|
2,71
|
4,60
|
|
Диафен ФП
|
1,00
|
0,58
|
1250,00
|
0,80
|
0,53
|
|
1,05
|
Ацетонанил Р,
РГ
|
1,50
|
0,87
|
1080,00
|
1,39
|
0,91
|
|
1,57
|
Углерод
технический П 323
|
50,00
|
28,90
|
1810,00
|
27,62
|
18,13
|
57,46
|
|
Маточная смесь
|
|
|
|
|
|
|
175,3
|
Итого
|
173,00
|
100,00
|
|
152,36
|
192,1
|
181,
|
Плотность смеси 1 стадии = 1130 кг/м3;
Плотность смеси 2 стадии = 1135 кг/м3.
Таблица 4.4 - Нормы контроля резиновой смеси для
подканавочной части протектора
Вязкость при
100ºС,
усл.ед.
|
Темпера-тура
вулкани-зации,ºС
|
Продолжитель-ность
вулканизации, мин
|
Условное
напряжение при удлинении 300%, МПа
|
Условная
прочность при растя-жении, МПа, не менее
|
Относитель-ное
удлинение при разрыве, %
|
Сопротив-ление
раздиру, КН/м, не менее
|
Твердость по
Шору, А
|
|
|
|
|
|
|
|
|
|
|
|
|
|
|
|
|
|
|
|
|
|
|
|
|
|
|
|
|
|
|
|
|
75 ± 5
|
155
|
20 ± 0,5
|
14,7 ± 2,0
|
23,5
|
500 ± 75
|
118
|
65 ± 5
|
.1.3 Обоснование рецептуры резиновой смеси шифра ПД-169,
предназначенной для изготовления боковины протектора
Такой элемент покрышки как боковина работает преимущественно
в режиме заданных деформаций, подвергается постоянным циклическим нагрузкам и
воздействию атмосферы. В связи с этим, основными требованиями к резинам боковин
является усталостная выносливость и атмосферостойкость в сочетании с
необходимой прочностью связи с каркасом и прочности стыка, стойкость к
механическим повреждениям.
Для стойкости к тепловому старению используют комбинацию
каучуков НК (70,0 м.ч.) и СКМС-30 АРК (30,0 м.ч.), в которой НК придает оптимальную
прочность детали, а СКМС-30 АРК придает каркасность, кроме того, резины на его
основе при введении активных наполнителей характеризуются высокой механической
прочностью.
В таком соотношении резины на основе этих каучуков обладают
высокой усталостной выносливостью, что необходимо для работы боковины в
динамическом нагружении.
Учитывая, что резина боковин работает в режиме заданной
деформации, с целью снижения напряжений в резине и, соответственно, повышения
ее работоспособности при выборе содержания вулканизующей группы, следует
стремиться к созданию резин с относительно низким модулем при сохранении их
прочностных свойств. В связи с этим содержание серы (1,0 м.ч.) в смеси
невысокое. В качестве ускорителя взят сульфенамид Ц (1,5 м.ч.), обладающий большим
индукционным периодом и высокой скоростью вулканизации в основном периоде.
Активатором вулканизации являются цинковые белила (5,0 м.ч.).
Наполнение резины осуществляется низкоструктурным активным
техническим углеродом П-323 (35,0 м.ч.), для обеспечения высокой прочности и
сопротивления раздиру. Невысокая дозировка незначительно увеличивает модуль
резины и обеспечивает ей достаточные динамические показатели.
Стеариновая кислота (1,5 м.ч.) облегчает диспергирование
вулканизующей группы и техуглерода, является вторичным активатором
вулканизации.
Для улучшения обрабатываемости в резину вводим мягчители.
Канифоль (3,0 м.ч.) улучшает технологические свойства, не ухудшая при этом
технические свойства резины, так же придает конфекционную клейкость. Жидкий
мягчитель масло ПН-6 (6,0 м.ч.) снижает вязкость системы, улучшая
технологические свойства смеси.
Так как НК при обработке смеси склонен к подвулканизации, в
нее введен в качестве антискорчинга фталевый ангидрид (0,5 м.ч.).
Так как боковина подвергается воздействию ультрафиолета,
кислорода, озона и усталостных нагрузок, в ее рецептуре присутствуют
стабилизаторы. Защитный воск ЗВ-1 (2,0 м.ч.), как физический антиозонант в
процессе эксплуатации выпотевает на поверхность, образуя пленку, и защищает
боковину от воздействий атмосферы. Противоутомитель диафен ФП обеспечивает
боковине высокое сопротивление к старению под воздействием динамических
нагружений, так же повышает устойчивость к термоокислительному старению.
Таблица 4.5 - Рецептура резиновой смеси для боковины
протектора
Ингредиенты
|
Массовые части
|
Массовые
проценты
|
Плотность, кг/м3
|
Объемные части
|
Объемные
проценты
|
Навеска, кг
|
|
|
|
|
|
|
1 ст
|
2 ст
|
1
|
2
|
3
|
4
|
5
|
6
|
7
|
8
|
НК, RSS1-3,
SMR-5, SMR-10. Вязкость по Муни (60±5) усл.ед.
|
70,00
|
44,44
|
920,00
|
76,09
|
52,44
|
83,80
|
|
СКМС-30АРК
|
30,00
|
19,05
|
930,00
|
32,26
|
22,23
|
35,90
|
|
Сера
|
1,00
|
0,63
|
2200,00
|
0,45
|
0,31
|
|
1,10
|
Сульфенамид Ц
|
1,50
|
0,95
|
1360,00
|
1,10
|
0,76
|
|
1,65
|
Фталевый
ангидрид
|
0,50
|
0,32
|
1600,00
|
0,31
|
0,22
|
0,60
|
|
Цинковые белила
|
5,00
|
3,17
|
5350,00
|
0,93
|
0,64
|
5,99
|
|
Стеариновая
кислота
|
1,50
|
0,95
|
870,00
|
1,72
|
1,19
|
1,80
|
|
Канифоль
сосновая
|
3,00
|
1,90
|
1040,00
|
2,88
|
1,99
|
3,59
|
|
Масло ПН-6Ш
|
6,00
|
3,81
|
970,00
|
6,19
|
4,26
|
7,19
|
|
Защитный воск
ЗВ-1
|
2,00
|
1,27
|
906,00
|
2,21
|
1,52
|
2,39
|
|
Диафен ФП
|
2,00
|
1,27
|
1250,00
|
1,60
|
1,10
|
|
2,20
|
Углерод
технический П 323
|
35,00
|
22,22
|
1810,00
|
19,34
|
13,33
|
41,90
|
|
Маточная смесь
|
|
|
|
|
|
|
168,5
|
Итого
|
157,50
|
100,00
|
|
145,09
|
100,00
|
183,9
|
173,
|
Плотность смеси 1 стадии = 1077 кг/м3;
Плотность смеси 2 стадии = 1085 кг/м3.
Таблица 4.6 - Нормы контроля резиновой смеси для боковины
протектора
Вязкость при
100ºС,
усл.ед.
|
Темпера-тура
вулкани-зации,ºС
|
Продолжитель-ность
вулканизации, мин
|
Условное
напряжение при удлинении 300%, МПа
|
Условная
прочность при растя-жении, МПа, не менее
|
Относитель-ное
удлинение при разрыве, %
|
Сопротив-ление
раздиру, КН/м, не менее
|
Твер-дость по
Шору, А
|
|
|
|
|
|
|
|
|
|
|
|
|
|
|
|
|
|
|
|
|
|
|
|
|
|
|
|
|
|
|
|
|
50 ± 5
|
155
|
20 ± 0,5
|
6,9 ± 2,0
|
22,0
|
650 ± 75
|
74
|
60 ± 5
|
4.1.4 Обоснование рецептуры резиновой смеси шифра КД-46,
предназначенной для обрезинивания слоев каркаса, бортовой ленты, крыльевой
ленты, для изготовления прослоек каркаса
Резина каркаса работает преимущественно в режиме постоянной
деформации и для обеспечения продолжительной работы каркасных резин,
целесообразно иметь сравнительно невысокий модуль упругости (в пределах 10-14
МПа). Более того, каркас должен обладать высокой прочностью связи резины с
кордом и прочностью связи между слоями каркаса. Формирование прочной
адгезионной связи в системе резина - корд невозможна без удовлетворительного
затекания резиновой смеси в кордное полотно в процессе обрезинивания, поэтому
резиновая смесь должна обладать комплексом пластоэластических и
упруговязкостных характеристик. Кроме того, обкладочные резины для текстильного
корда должны обладать высоким уровнем конфекционной клейкости и стабильностью
при хранении.
Для обеспечения равномерного распределения нитей корда в
процессе формования на второй стадии сборки резиновая смесь должна обладать
определенным уровнем упругих свойств, который, главным образом, зависит от типа
полимера. Достаточный модуль упругости независимо от направления каландрования,
обеспечивает натуральный каучук (100,0 м.ч.). Он придает каркасу высокие
динамические показатели, помимо этого, резины на основе НК обладают сродством к
текстильному корду, а так же повышенной конфекционной клейкостью, что важно для
слоев каркаса.
Вулканизующий агент сера (2,2 м.ч.) содержится в достаточном
количестве. Сульфенамид Ц (0,8 м.ч.) является ускорителем высокой активности и
большим индукционным периодом обеспечивает безопасную обработку при обрезинке
текстильною корда. Модификатор малеимид Ф (2,5 м.ч.) обеспечивает стойкость к
реверсии, позволяя длительно вулканизовать покрышку без ухудшения свойств
резины. Активатор цинковые белила (5,0 м.ч.) позволяет получать резины с хорошими
физико-механическими показателями.
Степень наполнения каркасных резин и тип применяемого
техуглерода определяется получением, главным образом, оптимальных усталостных
характеристик. В связи с этим, резина наполнена техуглеродом П-323 (40,0 м.ч.)
в небольшом количестве, достаточном для обеспечения прочностных свойств.
Минеральный наполнитель ультрасил VNЗ (5,0 м.ч.) вводится для повышения адгезии
к текстильному корду.
Все порошкообразные ингредиенты диспергируются гораздо лучше
в присутствие стеариновой кислоты (2,0 м.ч.), которая так же является вторичным
активатором вулканизации.
Для улучшения технологических свойств смеси и снижения
энергозатрат при обработке вводится масло ПН-6 (5,0 м.ч.) в качестве жидкого
мягчителя. Канифоль (2,5 м.ч.) в свою очередь так же улучшает технологические
свойства смеси, не оказывая существенного влияния на свойства вулканизата,
кроме того, увеличивает конфекционную клейкость резиновой смеси. Такой
мягчитель как АСМГ (5,0 м.ч.) улучшает технологические свойства резиновой смеси,
повышает качество прессовки корда.
Ввиду того, что каркасные резины в процессе эксплуатации
постоянно деформируются, для обеспечения их работы в процессе эксплуатации, в
их состав вводятся стабилизаторы. Противоутомитель диафен ФП (1,0 м.ч.)
обеспечивает резинам высокую усталостную выносливость и повышает их
сопротивление к термоокислительному старению.
Таблица 4.7 - Рецептура резиновой смеси для слоев каркаса,
прослоек каркаса, для бортовой и крыльевой ленты
Ингредиенты
|
Массовые части
|
Массовые
проценты
|
Плотность, кг/м3
|
Объемные части
|
Объемные
проценты
|
Навеска,кг
|
|
|
|
|
|
|
1 ст
|
2 ст
|
1
|
2
|
3
|
4
|
5
|
6
|
7
|
8
|
НК, RSS1-3,
SMR-5, SMR-10. Вязкость по Муни (60±5) усл.ед.
|
100,00
|
58,48
|
920,00
|
109,00
|
70,42
|
114,07
|
|
Сера
|
2,20
|
1,29
|
2200,00
|
1,00
|
0,65
|
|
2,28
|
Сульфенамид Ц
|
0,80
|
0,47
|
1360,00
|
0,59
|
0,38
|
|
0,83
|
Малеимид Ф
|
2,50
|
1,46
|
703,00
|
3,56
|
2,30
|
|
2,60
|
Ультрасил VN3
|
5,00
|
2,92
|
2500,00
|
2,00
|
1,29
|
5,72
|
|
Цинковые белила
|
5,00
|
2,92
|
5350,00
|
0,93
|
0,60
|
5,72
|
|
Стеариновая
кислота
|
2,00
|
1,17
|
870,00
|
2,30
|
1,49
|
2,29
|
|
Канифоль
сосновая
|
2,50
|
1,46
|
1040,00
|
2,40
|
1,55
|
2,86
|
|
Масло ПН-6Ш
|
5,00
|
2,92
|
970,00
|
5,15
|
3,33
|
5,72
|
|
Мягчитель АСМГ
|
5,00
|
2,92
|
1010,00
|
4,95
|
3,20
|
5,72
|
|
Диафен ФП
|
1,00
|
0,58
|
1250,00
|
0,80
|
0,52
|
|
1,04
|
Углерод
технический П 323
|
40,00
|
23,39
|
1810,00
|
22,10
|
14,28
|
45,75
|
|
Маточная смесь
|
|
|
|
|
|
|
170,
|
Итого
|
171,00
|
100,00
|
|
154,79
|
100,00
|
187,85
|
176,
|
Плотность смеси 1 стадии = 1062 кг/м3;
Плотность смеси 2 стадии = 1104 кг/м3.
Таблица 4.8 - Нормы контроля резиновой смеси для слоев
каркаса
Вязкость при
100ºС,
усл.ед.
|
Температура
вулканизации,ºС
|
Продолжительность
вулканизации, мин
|
Условное
напряжение при удлинении 300%, МПа
|
Условная
прочность при растя-жении, МПа, не менее
|
Относительное
удлинение при разрыве, %
|
|
|
|
|
|
|
|
|
|
|
|
|
|
|
|
|
|
|
|
|
|
|
|
|
55 ± 5
|
155
|
15 ± 0,5
|
10,8 ± 2,0
|
22,0
|
500 ± 75
|
.1.5 Обоснование рецептуры резиновой смеси шифра БД-57,
предназначенной для обрезинки металлокорда покрышки и прослоек брекера, для
обрезинки металлокорда бортовой ленты и для ее прослоек
Брекерная резина в процессе эксплуатации работает в
сложно-напряженном состоянии. Высокая и надежная прочность связи в резино-
металлокордном композите в значительной мере определяется составом брекерных
резин. К брекерным резинам, кроме требований высокой адгезии к металлокорду,
являющихся приоритетными, предъявляются и другие. К резиновым смесям -
необходимая вязкость, стойкость к подвулканизации, высокая клейкость,
отсутствие выцветания серы в процессе хранения. Резины должны иметь высокую
скорость вулканизации, удовлетворительные прочностные и усталостные свойства,
необходимую стойкость к старению, твердость, соответствующую конструкции шин.
Для обеспечения надлежащей прочности и стабильности в данном
режиме эксплуатации, брекерную резину изготавливают на основе НК (100,0 м.ч.).
Более того, резины на основе НК обладают повышенной конфекционной клейкостью.
Вулканизация этой резины осуществляется серой (3,4 м.ч.).
Серы содержится повышенное количество, так как часть ее концентрируется у
поверхности металла, образуя прочный межфазный слой нестехиометрического
сульфида меди, что повышает прочность связи резины с кордом. Помимо этого
увеличенное содержание серы позволяет получить резину с высоким модулем, для
обеспечения необходимой твердости, соответствующей конструкции шин. При
введении большого количества серы, она без труда растворяется в каучуке при
температуре смешения, но при остывании смеси растворимость серы в каучуке
уменьшается, и она может выцветать на поверхность. Для предотвращения этого
явления, часть молотой серы заменяют на полимерную серу (0,95 м.ч.), которая
ввиду высокой молекулярной массы не диффундирует на поверхность. В качестве
ускорителя в этой вулканизующей системе используют сульфенамид М (0,6 м.ч),
придающий резиновой смеси большой индукционный период. Широкое плато
вулканизации обеспечивается применением малеимида Ф (5,0 м.ч.), который придаст
резинам стойкость к реверсии при длительной вулканизации. Активатор
вулканизации -цинковые белила (8,0 м.ч.) - содержится в несколько увеличенной
дозе, так как часть его расходуется на стабилизацию адгезионных связей.
Брекерная резина наполнена активным техуглеродом П-323 (55,0
м.ч.) для обеспечения требуемого модуля жесткости брекера, прочности связи его
с металлокордом и высокого модуля.
Стеарат натрия (1,0 м.ч.) вводится для облегчения диспергации
порошкообразных ингредиентов и в качестве вторичного активатора вулканизации.
Содержание кислоты в рецептуре оказывает существенное влияние на начальную
адгезию и сохранение ее в различных условиях старения, особенно при тепловом и
влажном старении. В связи с этим увеличение концентрации стеариновой кислоты
выше 0,5 - 1,0 м.ч. нецелесообразно. Нафтенат кобальта (2,0 м.ч.) применяется в
качестве промотора адгезии. Соединения кобальта повышают плотность поперечных
связей в резине, а также способствуют образованию промежуточного адгезионного
слоя на границе резина-металлокорд.
Для улучшения технологических свойств смеси в нее вводят
ароматическое масло ПН-6 (4,0 м.ч.), которое снижает вязкость системы и
уменьшает теплообразование и энергозатраты при обработке. Смола SР-1077 (5,0
м.ч.) играет роль твердого мягчителя, не ухудшая эксплуатационных характеристик
резины. Мягчитель АСМГ (3,0 м.ч.) облегчает затекание резиновой смеси между
проволоками и улучшает качество прессовки корда.
Модификатор НФА-К (0,75 м.ч.) улучшает каучук-сажевое взаимодействие
и способствует снижению гистерезисных потерь при использовании активных
наполнителей, что позволяет снизить теплообразование в брекере.
С учетом склонности НК к подвулканизации, разумно
использование замедлителей подвулканизации. Сантогард РVI (0,2 м.ч.) способен
обеспечить требуемую стойкость к преждевременной вулканизации.
Стабилизатор диафен ФП (1,0 м.ч.) играет роль преимущественно
противоутомителя и защищает резину от термоокислительного старения. Его
применение необходимо из-за высокого теплообразования в брекере.
Таблица 4.9 - Рецептура резиновой смеси для обкладки брекера
Ингредиенты
|
Массо-вые части
|
Массовые
проценты
|
Плотность, кг/м3
|
Объем-ные части
|
Объемные
проценты
|
Навеска, кг
|
|
|
|
|
|
|
1 ст
|
2 ст
|
3 ст
|
1
|
2
|
3
|
4
|
5
|
6
|
7
|
8
|
9
|
НК, RSS1-3,
SMR-5. Непластицированный
|
100,00
|
52,67
|
920,00
|
108,70
|
62,21
|
104,00
|
|
|
Сера
|
3,40
|
1,79
|
2200,00
|
1,55
|
0,88
|
|
|
3,10
|
Сера полимерная
|
0,90
|
0,47
|
1950,00
|
0,46
|
0,26
|
|
|
0,83
|
Сульфенамид М
|
0,60
|
0,32
|
1370,00
|
0,25
|
|
|
0,50
|
Малеимид Ф
|
5,00
|
2,63
|
703,00
|
7,11
|
4,07
|
|
|
4,60
|
Модификатор
НФА-К
|
0,75
|
0,40
|
580,00
|
1,29
|
0,74
|
|
|
0,69
|
Нафтенат
кобальта
|
2,00
|
1,05
|
580,00
|
3,45
|
1,97
|
2,08
|
|
|
Сантогард PVI
|
0,20
|
0,11
|
1530,00
|
0,13
|
0,07
|
|
|
0,18
|
Цинковые белила
|
8,00
|
4,21
|
5350,00
|
1,50
|
0,86
|
8,3
|
|
|
Стеарат натрия
|
1,00
|
0,53
|
850,00
|
1,18
|
0,67
|
1,04
|
|
|
Смола SP-1077
|
5,00
|
2,63
|
470,00
|
10,64
|
6,09
|
5,19
|
|
|
Масло ПН-6Ш
|
4,00
|
2,11
|
970,00
|
4,12
|
2,36
|
4,15
|
|
|
Мягчитель АСМГ
|
3,00
|
1,58
|
1010,00
|
2,97
|
1,70
|
3,11
|
|
|
Диафен ФП
|
1,00
|
0,53
|
1250,00
|
0,80
|
0,46
|
|
|
0,92
|
Углерод
технический П 323
|
55,00
|
28,97
|
1810,00
|
30,39
|
17,39
|
57,11
|
|
|
Маточная смесь
|
|
|
|
|
|
|
185,
|
162,
|
Итого
|
189,85
|
100,00
|
|
174,72
|
100,00
|
185,
|
185
|
173,
|
Плотность смеси 1 стадии = 1089кг/м3;
Плотность смеси 2 стадии = 1090 кг/м3.
Таблица 4.10 - Нормы контроля резиновой смеси для обкладки
брекера
Вязкость при
100ºС,
усл.ед.
|
Темпера-тура
вулкани-зации,ºС
|
Продолжитель-ность
вулканизации, мин
|
Условное
напряжение при удлинении 300%, МПа
|
Условная
прочность при растя-жении, МПа, не менее
|
Относительное
удлинение при разрыве, %
|
Прочность связи
по методу блоков с металлокордом, КН/м
|
67 ± 5
|
155
|
20 ± 0,5
|
18,6 ± 2,0
|
19,6
|
350 ± 75
|
49
|
4.1.6 Обоснование рецептуры резиновой смеси шифра ИД-19,
предназначенной для изоляции проволоки бортового кольца
Жесткий нерастяжимый борт в процессе эксплуатации
обеспечивает плотную посадку покрышки на обод колеса. Нерастяжимость борта
обеспечивает металлическая проволока, а обкладочная резина должна обеспечивать
монолитность конструкции. Исходя из этого, резина бортового кольца должна
обладать сродством к латунированной проволоке, высокой прочностью и твердостью.
Для качественного обрезинивания проволоки, смесь должна быть каркасной и
обладать необходимой упругостью.
Для бортового кольца применяются резины на основе НК (100,0
м.ч.), для совулканизуемости с остальными деталями покрышки и для обеспечения
конфекционной клейкости детали, для обеспечения прочности связи с
латунированной проволокой.
Требуемый комплекс свойств достигается вулканизацией
элементарной серой (1,2 м.ч.) в комплексе с полимерной (4,8 м.ч.). Полимерная
сера используется для предотвращения выцветания вулканизующего агента на
поверхность, кроме того, она увеличивает адгезию. В общем, содержание серы
увеличено для обеспечения высокого модуля жесткости, и ввиду того, что часть ее
расходуется на образование слоя нестехиометрического сульфида меди на границе
резина-металл. Ускоритель вулканизации сульфенамид Ц (0,6 м.ч.) обладает
широким индукционным периодом и высокой скоростью вулканизации в основном
периоде. Другой ускоритель тиазол 2МБС (0,2 м.ч.) имеет несколько меньший
индукционный период и в процессе вулканизации покрышки бортовое кольцо
приобретает жесткость на начальной стадии, что предотвращает его сдвиг.
Цинковые белила (10,0 м.ч.) являются активатором в данной системе и участвуют в
создании промежуточного адгезионного слоя на поверхности латуни.
Для обеспечения высокого модуля и твердости резины бортового
кольца, производится ее высокое наполнение активным техуглеродом П-245 (30,0
м.ч.) и техуглеродом средней активности П-514 (30,0 м.ч.).
Для улучшения диспергации сыпучих ингредиентов в матрице
каучука вводится стеариновая кислота (2,0 м.ч.), она так же является вторичным
активатором вулканизации.
Для обеспечения необходимого комплекса технологических
свойств в смесь вводятся мягчители. Масло ПН-6 (5,0 м.ч.) уменьшает вязкость
системы и позволяет обрабатывать смеси с высоким наполнением. Канифоль сосновая
(3,0 м.ч.) является твердым мягчителем и повышает клейкость. Такой мягчитель,
как АСМГ (10,0 м.ч.) улучшает затекаемость резиновой смеси между проволоками бортового
кольца, а так же шприцуемость, не влияя на физико-механические показатели
вулканизата.
В смесях на основе НК целесообразно использование
антискорчингов. Сантогард РVI (0,3 м.ч.) обеспечивает достаточную стойкость
композиции к подвулканизации.
Для продления срока эксплуатации покрышки в резиновую смесь
вводят стабилизатор диафен ФП (1,0 м.ч.), который хотя и является
преимущественно противоутомителем, защищает резину и от других факторов
старения.
Таблица 4.11 - Рецептура резиновой смеси для обрезинивания
проволоки бортового кольца
Ингредиенты
|
Массовые части
|
Массовые
проценты
|
Плотность, кг/м3
|
Объемные части
|
Объемные
проценты
|
Навеска, кг
|
|
|
|
|
|
|
1 ст
|
2 ст
|
1
|
2
|
3
|
4
|
5
|
6
|
7
|
8
|
НК, RSS1-3,
SMR-5, SMR-10, SMR-20. Вязкость по Муни (60±5) усл.ед.
|
100,00
|
50,48
|
920,00
|
108,70
|
64,43
|
103,62
|
|
Сера
|
1,20
|
0,61
|
2200,00
|
0,55
|
0,32
|
|
1,14
|
Сера полимерная
|
4,80
|
2,42
|
1950,00
|
2,46
|
1,46
|
|
4,55
|
Сульфенамид Ц
|
0,60
|
0,30
|
1360,00
|
0,44
|
0,26
|
|
0,57
|
Тиазол 2МБС
|
0,20
|
0,10
|
1520,00
|
0,13
|
0,08
|
|
0,19
|
Цинковые белила
|
10,00
|
5,05
|
5350,00
|
1,87
|
1,11
|
10,36
|
|
Сантогард PVI
|
0,30
|
0,15
|
1530,00
|
0,20
|
0,12
|
|
0,28
|
Стеариновая
кислота
|
2,00
|
1,01
|
870,00
|
2,30
|
1,36
|
2,07
|
|
Канифоль
сосновая
|
3,00
|
1,51
|
1040,00
|
2,88
|
1,71
|
3,11
|
|
Масло ПН-6Ш
|
5,00
|
2,52
|
1040,00
|
4,81
|
2,85
|
5,18
|
|
Мягчитель АСМГ
|
10,00
|
5,05
|
970,00
|
10,31
|
6,11
|
10,36
|
|
Диафен ФП
|
1,00
|
0,50
|
1080,00
|
0,93
|
0,55
|
|
0,95
|
Углерод
технический П 514
|
30,00
|
15,14
|
1810,00
|
16,57
|
9,82
|
31,08
|
|
Углерод
технический П 234
|
30,00
|
15,14
|
1810,00
|
16,57
|
9,82
|
31,08
|
|
Маточная смесь
|
|
|
|
|
|
|
180,
|
Итого
|
198,10
|
100,00
|
|
168,72
|
100,00
|
197,3
|
187,4
|
Плотность смеси 1 стадии = 1159 кг/м3;
Плотность смеси 2 стадии = 1174 кг/м3.
Таблица 4.12 - Нормы контроля резиновой смеси для
обрезинивания проволоки бортового кольца
Вязкость при
100ºС,
усл.ед.
|
Температура
вулканизации,ºС
|
Продолжитель-ность
вулканизации, мин
|
Условное
напряжение при удлинении 300%, МПа
|
Условная
прочность при растяжении, МПа, не менее
|
Относи-тельное
удлине-ние при разрыве, %
|
|
|
|
|
|
|
|
|
|
|
|
|
|
|
|
|
|
|
|
|
|
|
|
|
67 ± 5
|
155
|
20 ± 0,5
|
18,6 ± 2,0
|
20,0
|
350 ± 75
|
.1.7 Обоснование рецептуры резиновой смеси шифра БД-56,
предназначенной для обрезинивания металлокорда бортового кольца для
дополнительного крыла
В процессе эксплуатации покрышки бортовое кольцо практически
не деформируется, обеспечивает жесткую посадку покрышки на обод колеса. Поэтому
резина бортового кольца должна иметь высокую прочность связи с металлокордом
бортового кольца, обладать повышенной твердостью и быть устойчивой к
термоокислительному старению.
Для бортового кольца используют НК (100,0 м.ч.), так как он
наиболее стабилен при любых режимах эксплуатации и обладает высокой прочностью.
Вулканизацию проводят элементарной серой (3,4 м.ч.) с
небольшим добавлением полимерной серы (0,9 м.ч.), которая не выцветает на
поверхность при хранении. Общее содержание серы завышено, так как часть ее
затрачивается на образование промежуточного адгезионного слоя
нестехиометрического сульфида меди на поверхности латуни, так же большое
количество серы обеспечивает высокий модуль резины. Ускорителем в данной
системе является сульфенамид М (0,6 м.ч.) с широким индукционным периодом.
Цинковые белила (8,0 м.ч.) играют роль активатора и участвуют в образовании
промежуточного слоя на границе резина - латунированная проволока.
Резина бортового кольца наполнена активным техническим
углеродом П-323 (50,0 м.ч.), для обеспечения высокого модуля резины и
обеспечения твердости. Кремнекислотный наполнитель улътрасил (10,0 м.ч.)
повышает адгезию резины к латуни.
Стеарат натрия (1,0 м.ч.) облегчает диспергацию
порошкообразных ингредиентов, вводимых на первой стадии смешения, в матрице
каучука и играет роль вторичного активатора вулканизации.
Чтобы облегчить обработку резиновой смеси в нее вводят
мягчители. Масло ПН-6ш (4,0 м.ч.) является жидким мягчителем и уменьшает
вязкость системы, снижая энергозатраты на обработку резиновой смеси. Основным
условием высокой работоспособности бортовой резины является стабильность ее
упруго-прочностных свойств и твердости в различных условиях термоокислительного
старения, поэтому в рецептуре применяют усиливающую фенолформальдегидную смолу
SР-1077 (5,0 м.ч.). Мягчитель АСМГ (3,0 м.ч.) повышает затекаемость резиновой
смеси в структуру металлокорда бортового кольца.
Модификатор РУ (2,0 м.ч.) увеличивает адгезию резины к
поверхности латунированной проволоки и является отвердителем смолы SР-1077.
Промотор адгезии нафтенат кобальта (2,0 м.ч.) в процессе вулканизации
внедряется в слой оксида цинка на поверхности латуни, что приводит к уменьшению
электропроводности пленки оксида цинка и снижает скорость диффузии ионов меди
через эту пленку, способствуя образованию необходимого количества
нестехиометрического количества сульфида меди на границе резина-латунь. То
есть, введение ионов кобальта оправдано как в состав латунного покрытия, так и
в эластомерную композицию.
Для обеспечения стойкости резины к подвулканизации
используется сантогард РVI (0,2 м.ч.), что делает обработку смеси безопасной.
Стойкость резины к старению и деструкции повышается с
применением таких стабилизаторов как диафен ФП (1,0 м.ч.).
Таблица 4.13 - Рецептура резиновой смеси для бортового кольца
Ингредиенты
|
Массо- вые
части
|
Массовые
проценты
|
Плотность, кг/м3
|
Объемные части
|
Объемные
проценты
|
Навеска, кг
|
|
|
|
|
|
|
1 ст
|
2 ст
|
3 ст
|
1
|
2
|
3
|
4
|
5
|
6
|
7
|
8
|
9
|
НК, RSS1-3,
SMR-5. непластицированный
|
100,00
|
52,33
|
920,00
|
108,70
|
64,27
|
103,52
|
|
|
Сера
|
3,40
|
1,78
|
2200,00
|
1,55
|
0,91
|
|
|
3,22
|
Сера полимерная
|
0,90
|
0,47
|
1950,00
|
0,46
|
0,27
|
|
|
0,85
|
Сульфенамид М
|
0,60
|
0,31
|
1370,00
|
0,44
|
0,26
|
|
|
0,57
|
Модификатор РУ
|
2,00
|
1,05
|
1270,00
|
1,57
|
0,93
|
|
|
1,89
|
Ультрасил VN3
|
10,00
|
5,23
|
2500,00
|
4,00
|
2,37
|
10,36
|
|
|
Нафтенат
кобальта
|
2,00
|
1,05
|
580,00
|
3,45
|
2,04
|
2,07
|
|
|
Сантогард PVI
|
0,20
|
0,10
|
1530,00
|
0,13
|
0,08
|
|
|
0,19
|
Цинковые белила
|
8,00
|
4,19
|
5350,00
|
1,50
|
0,88
|
8,29
|
|
|
Стеарат натрия
|
0,52
|
850,00
|
1,18
|
0,70
|
1,03
|
|
|
Смола SP-1077
|
5,00
|
2,62
|
470,00
|
10,64
|
6,29
|
5,18
|
|
|
Масло ПН-6Ш
|
4,00
|
2,09
|
970,00
|
4,12
|
2,44
|
4,14
|
|
|
Мягчитель АСМГ
|
3,00
|
1,57
|
1010,00
|
2,97
|
1,76
|
3,11
|
|
|
Диафен ФП
|
1,00
|
0,52
|
1250,00
|
0,80
|
0,47
|
|
|
0,95
|
Углерод
технический П 323
|
50,00
|
26,16
|
1810,00
|
27,62
|
16,33
|
51,79
|
|
|
Маточная смесь
|
|
|
|
|
|
|
189,38
|
172,97
|
Итого
|
191,10
|
100,00
|
|
169,13
|
100,00
|
189,38
|
189,38
|
180,64
|
Плотность смеси 1 стадии = 1114 кг/м3;
Плотность смеси 2 стадии = 1129 кг/м3.
Таблица 4.14 - Нормы контроля резиновой смеси для бортового
кольца
Вязкость при
100ºС,
усл.ед.
|
Темпера-тура
вулкани-зации,ºС
|
Продолжитель-ность
вулканизации, мин
|
Условное
напряжение при удлинении 300%, МПа
|
Условная
прочность при растя-жении, МПа, не менее
|
Относитель-ное
удлинение при разрыве, %
|
Прочность связи
по методу блоков с металлокордом, КН/м
|
67 ± 5
|
155
|
20 ± 0,5
|
18,6 ± 2,0
|
19,6
|
350 ± 75
|
49
|
.1.8 Обоснование рецептуры резиновой смеси шифра ФД-20,
предназначенной для промазки ленты спиральной обертки бортового кольца
Обертка бортового кольца применяется для придания кольцу
большей жесткости и прочности, чтобы оно сохраняло форму. Поэтому резина,
которой промазана текстильная оберточная лента, должна обладать высокой
конфекционной клейкостью, сродством к текстильному полотну и малой усадкой.
За основу резины берут комбинацию каучуков НК (50,0 м.ч.) и
СКИ-3 (50,0 м.ч.). Натуральный каучук используется в резинах всех прилежащих
деталей, это придает композиции конфекционную клейкость. СКИ-3 применяется для
снижения стоимости смеси и ввиду его доступности. Так же в смесь добавляют
регенерат РКТ (30,0 м.ч.) для улучшения технологичности смеси и еще большего
удешевления.
Вулканизующий агент - сера (2,4 м.ч.) - содержится в
нормальной дозировке. В качестве ускорителей вулканизации взяты сульфенамид Ц
(0,6 м.ч.) и 2-меркаптобензтиазол (0,4 м.ч.). Сульфенамид Ц имеет большой
индукционный период и высокую скорость вулканизации в основном периоде,
2-меркаптобензтиазол имеет небольшой индукционный период и резина обертки
частично свулканизовывается раньше, это исключает смещение кольца при
вулканизации. Цинковые белила (5,0 м.ч.) присутствуют в рецептуре как активатор
вулканизации.
Наполнение производится техуглеродом средней активности П-514
(30,0 м.ч.), который не очень сильно повышает модуль жесткости резины и более
доступен. Другой наполнитель - обогащенный мел (20,0 м.ч.) - улучшает обработку
смеси и облегчает промазку текстильного полотна.
Стеариновая кислота (1,0 м.ч.) предназначена для облегчения
диспергации порошкообразных ингредиентов и является вторичным активатором
вулканизации.
Для улучшения технологических свойств в смесь вводится масло
ПН-6 (8,0 м.ч.), оно уменьшает вязкость системы и снижает энергозатраты при
обработке смеси. Канифоль (3,0 м.ч.) является твердым мягчителем, она также
облегчает обработку, не оказывая влияния на свойства вулканизата, кроме того,
придает смеси дополнительную клейкость. Стирол - инденовая смола (15,0 м.ч.)
тоже является твердым мягчителем, она облегчает затекание резины между
волокнами бязи при промазке и придаст конфекционную клейкость. Для крепления
резины к различным материалам используют систему на основе резорцина.
Модификатор РУ (3,0 м.ч.) обеспечивает хорошую адгезию резины к бязи.
Для сохранения свойств резины в процессе эксплуатации
производится ее стабилизация диафеном ФП (0,5 м.ч.), который замедляет процессы
старения.
Таблица 4.15 - Рецептура резиновой смеси для спиральной
обертки бортового кольца
Ингредиенты
|
Массовые части
|
Массовые
проценты
|
Плотность, кг/м3
|
Объем-ные части
|
Объем-ные
проценты
|
Навеска,кг
|
|
|
|
|
|
|
1 ст
|
2 ст
|
1
|
2
|
3
|
4
|
5
|
6
|
7
|
8
|
НК, RSS1-3,
SMR-5, SMR-10, SMR-20. Вязкость по Муни (60±5) усл.ед.
|
50,00
|
22,84
|
920,00
|
54,35
|
28,68
|
45,95
|
|
СКИ-3 II группа
|
50,00
|
22,84
|
920,00
|
54,35
|
28,68
|
45,95
|
|
Регенерат РКТ
|
30,00
|
13,70
|
1200,00
|
25,00
|
13,19
|
27,57
|
|
Сера
|
2,40
|
1,10
|
2200,00
|
1,09
|
0,58
|
|
2,03
|
2-меркаптобензтиазол
|
0,40
|
0,18
|
1500,00
|
0,27
|
0,14
|
|
0,34
|
Сульфенамид Ц
|
0,60
|
0,27
|
1360,00
|
0,44
|
0,23
|
|
0,51
|
Модификатор РУ
|
3,00
|
1,37
|
1270,00
|
2,36
|
1,25
|
|
2,53
|
Цинковые белила
|
5,00
|
2,28
|
5350,00
|
0,93
|
0,49
|
5,00
|
|
Стеариновая
кислота
|
1,00
|
0,46
|
870,00
|
1,15
|
0,61
|
0,92
|
|
Канифоль
сосновая
|
3,00
|
1,37
|
1040,00
|
2,88
|
1,52
|
2,80
|
|
Углеводородные
смолы
|
15,00
|
6,85
|
1050,00
|
14,29
|
7,54
|
13,78
|
|
Масло ПН-6Ш
|
8,00
|
3,65
|
970,00
|
8,25
|
4,35
|
7,35
|
|
Диафен ФП
|
0,50
|
0,23
|
1250,00
|
0,40
|
0,21
|
|
0,42
|
Мел природный
обогащенный
|
20,00
|
9,14
|
2800,00
|
7,14
|
3,77
|
18,38
|
|
Углерод
технический П 514
|
30,00
|
13,70
|
1810,00
|
16,57
|
8,75
|
27,57
|
|
Маточная смесь
|
|
|
|
|
|
|
178,97
|
Итого
|
218,90
|
100,00
|
|
189,48
|
100,00
|
195,33
|
184,8
|
Плотность смеси 1 стадии = 1149 кг/м3;
Плотность смеси 2 стадии = 1155 кг/м3.
Таблица 4.16 - Нормы контроля резиновой смеси для спиральной
обертки бортового кольца
Вязкость при
100ºС,
усл.ед.
|
Температура
вулканизации,ºС
|
Продолжительность
вулканизации, мин
|
Условное
напряжение при удлинении 300%, МПа
|
Условная
прочность при растя-жении, МПа, не менее
|
Относительное
удлинение при разрыве, %
|
|
|
|
|
|
|
|
|
|
|
|
|
|
|
|
|
|
|
|
|
|
|
|
|
55 ± 5
|
155
|
15 ± 0,5
|
10,8 ± 2,0
|
22,0
|
500 ± 75
|
.1.9 Обоснование рецептуры резиновой смеси шифра НШ-18,
предназначенной для изготовления наполнительного шнура для борта
Наполнительный шнур в покрышке придает борту монолитность,
обеспечивает отсутствие включений воздуха в крыле покрышки. Поэтому
наполнительная резина борта должна быть каркасной, с хорошей конфекционной
клейкостью, должна обладать твердостью в соответствие с конструкцией покрышки.
Наполнительный шнур играет роль промежуточного звена между жестким бортовым
кольцом и боковиной, работающей в динамике.
Резина борта выполняется на основе НК (100,0 м.ч.) из-за его
высокой когезионной прочности, кроме того, резины на основе НК обладают хорошей
конфекционной клейкостью. Добавка термоэластопластов ТЭП ДСТ-30Р (5,0 м.ч.)
увеличивает твердость резины, повышает каркасность смеси и улучшает когезионную
прочность, обеспечивает каркасность борта.
В качестве вулканизующего агента используется полимерная сера
(5,0 м.ч.), повышенная дозировка которой обеспечивает высокий модуль резине
наполнительного шнура. Полимерная сера не выцветает на поверхность, как обычная
и лучше распределяется по матрице каучука. Это обеспечивает прочную связь
наполнительного шнура с другими деталями. Ускоритель сульфенамид М (0,9 м.ч.)
обеспечивает высокую скорость вулканизации в главном периоде, а тиазол-2МБС
(0,2 м.ч.) вводится, чтобы не произошел сдвиг крыла при вулканизации.
Активатором являются цинковые белила (5,0 м.ч.).
Для обеспечения необходимой твердости резины, производится ее
наполнение техуглеродом П-514 (40,0 м.ч.) и П-234 (20,0 м.ч.). Применение
углерода средней активности обосновано тем, что он не сильно завышает модуль
жесткости, и резина работает в деформационном режиме с меньшим
теплообразованием. Активный техуглерод обеспечивает необходимую твердость.
Другой наполнитель - ультрасил VN3 (5,0 м.ч.) обеспечивает высокую адгезию
детали к металлу и предотвращает образование и разрастание трещин.
Стеариновая кислота играет роль диспергатора сыпучих
ингредиентов и роль вторичного активатора.
Для обеспечения технологичности смеси в нее вводят мягчители.
Канифоль (2,0 м.ч.) улучшает технологические свойства смеси и придает
дополнительную клейкость. Мягчитель АСМГ (5,0 м.ч.) улучшает обрабатываемость
смеси. Углеводородная стирол - инденовая смола (3,0 м.ч.) также играет роль
твердого мягчителя, улучшая обрабатываемость смеси. Такая комбинация мягчителей
позволяет получить ровное монолитное изделие при шприцевании.
Для резин на основе НК необходимо использование антискорчинга,
здесь его роль играют: бензойная кислота (0,3 м.ч.) и сантогард РVI (0,3 м.ч.),
которые предотвращают преждевременную подвулканизацию.
Модификатор РУ (2,0 м.ч.) придает резиновой смеси
дополнительное сродство к текстильному корду и металлу. Его присутствие
обусловлено необходимостью повысить прочность связи между деталями борта
покрышки.
Стойкость к старению резине обеспечивает комбинация
стабилизаторов: диафен ФП (0,5 м.ч.) преимущественно является
противоутомителем, а ацетонанил Р (0,5 м.ч.) преимущественно придает
термоокислительную стойкость.
Таблица 4.17 - Рецептура резиновой смеси для наполнительного
шнура
Ингредиенты
|
Массовые части
|
Массовые
проценты
|
Плотность, кг/м3
|
Объемные части
|
Объемные
проценты
|
Навеска, кг
|
|
|
|
|
|
|
1 ст
|
2 ст
|
3 ст
|
1
|
2
|
3
|
4
|
5
|
6
|
7
|
8
|
9
|
НК, RSS1-3,
SMR-5. непластицированный
|
100,00
|
50,84
|
920,00
|
108,70
|
64,52
|
105,48
|
|
|
ТЭП ДСТ - 30Р
|
5,00
|
2,54
|
920,00
|
5,43
|
3,23
|
5,29
|
|
|
Сера
|
5,00
|
2,54
|
1950,00
|
2,56
|
1,52
|
|
|
4,75
|
Сульфенамид М
|
0,90
|
0,46
|
1370,00
|
0,66
|
0,39
|
|
|
0,85
|
Тиазол 2МБС
|
0,20
|
0,10
|
1520,00
|
0,13
|
0,08
|
|
|
0,19
|
Ультрасил VN3
|
5,00
|
2,54
|
2500,00
|
2,00
|
1,19
|
5,29
|
|
|
Модификатор РУ
|
2,00
|
1,02
|
1270,00
|
1,57
|
0,93
|
|
|
1,90
|
Бензойная
кислота
|
0,30
|
0,15
|
1200,00
|
0,25
|
0,15
|
0,31
|
|
|
Цинковые белила
|
5,00
|
2,54
|
5350,00
|
0,93
|
0,55
|
5,29
|
|
|
Сантогард PVI
|
0,30
|
0,15
|
1530,00
|
0,20
|
0,12
|
|
|
0,29
|
Стеариновая
кислота
|
2,00
|
1,02
|
870,00
|
2,30
|
1,36
|
2,11
|
|
|
Канифоль
сосновая
|
2,00
|
1,02
|
1040,00
|
1,92
|
1,14
|
2,11
|
|
|
Мягчитель АСМГ
|
5,00
|
2,54
|
1010,00
|
4,95
|
2,94
|
5,29
|
|
|
Ацетонанил Р,
РГ
|
0,50
|
0,25
|
1080,00
|
0,46
|
0,27
|
Углеводородные
смолы
|
3,00
|
1,53
|
1050,00
|
2,86
|
1,70
|
3,17
|
|
|
Диафен ФП
|
0,50
|
0,25
|
1250,00
|
0,40
|
0,24
|
|
|
0,47
|
Углерод
технический П 514
|
40,00
|
20,34
|
1810,00
|
22,10
|
13,12
|
41,09
|
|
|
Углерод
технический П 234
|
20,00
|
10,17
|
1810,00
|
11,05
|
6,56
|
20,50
|
|
|
Маточная смесь
|
|
|
|
|
|
|
192,95
|
177,81
|
Сумма
|
196,70
|
100,00
|
|
168,48
|
100,00
|
192,95
|
192,95
|
186,72
|
Плотность смеси 1 стадии = 1153 кг/м3;
Плотность смеси 2 стадии = 1167 кг/м3.
Таблица 4.18 - Нормы контроля резиновой смеси для
наполнительного шнура
Вязкость при
100ºС,
усл.ед.
|
Температура
вулканизации,ºС
|
Продолжительность
вулканизации, мин
|
Условное
напряжение при удлинении 300%, МПа
|
Условная
прочность при растя-жении, МПа, не менее
|
Относительное
удлинение при разрыве, %
|
|
|
|
|
|
|
|
|
|
|
|
|
|
|
|
|
|
|
|
|
|
|
|
|
67 ± 5
|
155
|
20 ± 0,5
|
18,6 ± 2,0
|
19,6
|
350 ± 75
|
.1.10 Обоснование рецептуры резиновой смеси шифра БЛД-21,
предназначенной для прослоек бортовой ленты
К резине для прослоек бортовой ленты предъявляются следующие
требования: она должна иметь хорошую адгезию к текстильному корду и
металлокорду, а также обладать удовлетворительной конфекционной клейкостью.
Резину для прослоек бортовой ленты изготавливают на основе НК
(65,0 м.ч.) и СКМС-30 АРК (35,0 м.ч.). Прочность и конфекционная клейкость
обеспечивается натуральным каучуком, а необходимая жесткость и теплостойкость
метилстирольным каучуком. Термоэластопласты ТЭП ДСТ-ЗОР (5,0 м.ч.) придают
резине необходимую твердость, улучшают обрабатываемость резиновой смеси и
обеспечивают ее каркасность.
Вулканизующий агент - сера полимерная (2,8 м.ч.) не выцветает
на поверхность при хранении, обеспечивая сохранение конфекционной клейкости
изделия. Ускоритель - сульфенамид М (0,9 м.ч.) имеет широкое плато вулканизации
и широкий индукционный период, позволяет безопасно обрабатывать смесь.
Активатор вулканизации - цинковые белила (3,0 м.ч.).
Для обеспечения высокой прочности и модуля, необходимой
твердости резины, смесь наполняют активным техуглеродом П-234 (55,0 м.ч.).
Диспергатором сыпучих ингредиентов служит стеариновая кислота
(2,0 м.ч.), она также является вторичным активатором.
Масло ПН-6 (5,0 м.ч.) играет роль жидкого мягчителя, облегчая
обработку смеси. Канифоль сосновая (2,0 м.ч.) вводится как твердый мягчигель и
повышает клейкость. Стирол - инденовая смола (2,0 м.ч.) также улучшает
технологические свойства.
Сантогард РVI (0,3 м.ч.) выполняет в смеси функцию
замедлителя подвулканизации.
Стабилизатор диафен ФП (5,0 м.ч.) предотвращает быстрое
старение резины, являясь химическим антиозонантом высокой активности и
противоутомителем.
Таблица 4.19 - Рецептура резиновой смеси для прослоек
бортовой ленты
Ингредиенты
|
Массовые части
|
Массовые
проценты
|
Плотность, кг/м3
|
Объемные части
|
Объемные
проценты
|
Навеска, кг
|
|
|
|
|
|
|
1 ст
|
2 ст
|
1
|
2
|
3
|
4
|
5
|
6
|
7
|
8
|
НК, RSS1-3,
SMR-5. Вязкость по Муни (60±5) усл.ед.
|
65,00
|
30,43
|
920,00
|
60,87
|
38,53
|
70,80
|
|
СКМС-30 АРК
|
35,00
|
19,02
|
930,00
|
37,63
|
23,82
|
38,12
|
|
ТЭП ДСТ-30Р
|
5,00
|
2,72
|
920,00
|
5,43
|
3,44
|
5,44
|
|
Сера полимерная
|
2,80
|
1,52
|
1950,00
|
1,44
|
0,91
|
|
2,76
|
Сульфенамид М
|
0,90
|
0,49
|
1370,00
|
0,66
|
0,42
|
|
0,88
|
Цинковые белила
|
3,00
|
1,63
|
5350,00
|
0,56
|
0,35
|
3,26
|
|
Сантогард PVI
|
0,30
|
0,16
|
1530,00
|
0,20
|
0,12
|
|
0,29
|
Стеариновая
кислота
|
2,00
|
1,09
|
870,00
|
2,30
|
1,46
|
2,17
|
|
Канифоль
сосновая
|
2,00
|
1,09
|
1040,00
|
1,92
|
1,22
|
2,17
|
|
Масло ПН-6Ш
|
5,00
|
2,72
|
970,00
|
5,15
|
3,26
|
5,44
|
|
Углеводородные
смолы
|
2,00
|
1,09
|
1050,00
|
1,90
|
1,21
|
2,17
|
|
Диафен ФП
|
5,00
|
2,72
|
1250,00
|
4,00
|
2,53
|
|
4,93
|
Углерод
технический П 234
|
65,00
|
35,33
|
1810,00
|
35,91
|
22,73
|
59,91
|
|
Маточная смесь
|
|
|
|
|
|
|
171,78
|
Итого
|
184,00
|
100,00
|
|
157,98
|
100,00
|
189,55
|
180,64
|
Плотность смеси 1 стадии = 1115 кг/м3;
Плотность смеси 2 стадии = 1129 кг/м3.
Таблица 4.20 - Нормы контроля резиновой смеси для прослоек
бортовой ленты
Вязкость при
100ºС,
усл.ед.
|
Температура
вулканизации,ºС
|
Продолжительность
вулканизации, мин
|
Условное
напряжение при удлинении 300%, МПа
|
Условная
прочность при растя-жении, МПа, не менее
|
Относительное
удлинение при разрыве, %
|
|
|
|
|
|
|
|
|
|
|
|
|
|
|
|
|
|
|
|
|
|
|
|
|
65 ± 5
|
155
|
20 ± 0,5
|
19,6 ± 2,0
|
21,0
|
450 ± 75
|
.1.11 Обоснование рецептуры резиновой смеси шифра ЕКД-39,
предназначенной для изготовления ездовой камеры
Камера покрышки поддерживает постоянное давление воздуха
внутри нее, поэтому она должна отвечать следующим требованиям: высокая
газонепроницаемость стенки камеры, позволяющая надежно сохранять внутреннее
давление в шине: высокая пластичность и низкая остаточная деформация,
обеспечивающая малую разнашиваемость камеры в процессе эксплуатации, что
приводит к образованию складок, особенно при перемонтаже камер; высокая
усталостная выносливость и стойкость к старению, особенно по сопротивлению
раздиру, так как это определяет ремонтопригодность камер после проколов;
герметичность и высокая прочность стыка и вентиля камеры, отсутствие
посторонних включений в теле камеры.
Высокой газонепроницаемостью, усталостной выносливости
обладает бутилкаучук БК-1675Т (100,0 м.ч.). Поэтому он так часто применяется
для производства ездовых камер. Кроме того, БК не склонен к подвулканизации и
может безопасно обрабатываться. Для понижения остаточной деформации, повышения
когезионной прочности, морозостойкости, снижения хладотекучести, повышения скорости
вулканизации вводят ХБК-НТ 1068 (2,0 м.ч.).
Сера (2,0 м.ч.) вводится как вулканизующий агент. Комбинация
ускорителей: тиазол 2МБС (0,5 м.ч.) и тиурам Д (1,0 м.ч.) обеспечивает высокую
скорость вулканизации и образование широкого спектра различных поперечных
связей, что придает резине теплостойкость. Активатор вулканизующих агентов -
цинковые белила (5,0 м.ч.).
Наполняют резину техуглеродом средней активности П-514 (55,0
м.ч.), это придает резине достаточную прочность, усталостную выносливость при
эксплуатации и достаточное сопротивление раздиру.
Диспергирование сыпучих ингредиентов облегчается при введении
стеариновой кислоты (1,0 м.ч.), которая также играет роль вторичного
активатора.
Для придания смеси удовлетворительных технологических
свойств, в нее вводят совместимый с БК жидкий мягчитель - стабилойл-18 (20,0
м.ч.). Это неароматическое масло и оно не образует пор в камере. В качестве
твердого мягчителя используется октофор N (2,0 м.ч.), который улучшает
обрабатываемость смеси, не снижая технических показателей вулканизата и
повышает клейкость.
Таблица 4.21 - Рецептура резиновой смеси для ездовой камеры
Ингредиенты
|
Массовые части
|
Массовые
проценты
|
Плотность, кг/м3
|
Объемные части
|
Объемные
проценты
|
Навеска, кг
|
|
|
|
|
|
|
1 ст
|
2 ст
|
1
|
2
|
3
|
4
|
5
|
6
|
7
|
8
|
Бутилкаучук
БК-1675Т
|
100,00
|
53,05
|
910,00
|
109,89
|
64,31
|
124,30
|
|
Хлорбутилкаучук
ХБК НТ-1066
|
2,00
|
1,06
|
910,00
|
2,20
|
1,29
|
2,49
|
|
Сера
|
2,00
|
1,06
|
2200,00
|
0,91
|
0,53
|
|
1,87
|
Тиазол 2МБС
|
0,50
|
0,27
|
1520,00
|
0,33
|
0,19
|
|
0,47
|
Тиурам Д
|
1,00
|
0,53
|
1350,00
|
0,74
|
0,43
|
|
0,94
|
Цинковые белила
|
5,00
|
2,65
|
5350,00
|
0,93
|
0,55
|
6,21
|
|
Стеариновая
кислота
|
1,00
|
0,53
|
870,00
|
1,15
|
0,67
|
1,24
|
|
Октофор N, Na
|
2,00
|
1,06
|
1070,00
|
1,87
|
1,09
|
2,49
|
|
Стабилойл-18
|
20,00
|
10,61
|
890,00
|
22,47
|
13,15
|
24,86
|
|
Углерод
технический П 514
|
55,00
|
29,18
|
1810,00
|
30,39
|
17,78
|
68,36
|
|
Маточная смесь
|
|
|
|
|
|
|
173,20
|
Итого
|
188,50
|
100,00
|
|
170,88
|
100,00
|
229,95
|
176,48
|
Плотность смеси 1 стадии = 1095 кг/м3;
Плотность смеси 2 стадии = 1103 кг/м3.
Таблица 4.22 - Нормы контроля резиновой смеси для ездовой
камеры
Пластич-ность,
усл. ед.
|
Темпера-тура
вулкани-зации,ºС
|
Продолжитель-ность
вулканиза-ции, мин
|
Условное
напряжение при удлинении 300%, МПа
|
Условная
прочность при растя-жении, МПа, не менее
|
Относитель-ное
удлинение при разрыве, %
|
Сопротив-ление
раздиру, КН/м, не менее
|
Относитель-ное
остаточное удлинение, % н/б
|
|
|
|
|
|
|
|
|
|
|
|
|
|
|
|
|
|
|
|
|
|
|
|
|
|
|
|
|
|
|
|
|
0,45±0,05
|
165±1
|
10 ± 1
|
4,4± 1,5
|
5,8
|
650 ± 150
|
29
|
30 ± 10
|
.1.12 Обоснование рецептуры резиновой смеси шифра 9ЛО-53,
предназначенной для изготовления ободной ленты
Ободная лента предохраняет камеру от повреждения ободом
колеса, она должна быть эластичной и стойкой к порезам, стойкой к тепловому
старению.
Основу резины для ободной ленты составляют следующие каучуки:
СКИ-3 (50,0 м.ч.), СКД (30,0 м.ч.) и СКМС-30 АРКМ-15 (20,0 м.ч.). СКИ-3 придает
необходимую прочность, СКД - стойкость к механическим повреждениям,
морозостойкость, а СКМС - теплостойкость. Эта комбинация отвечает необходимым
требованиям и недорога. Добавка регенерата РКТ (30,0 м.ч.) улучшает
технологические свойства, придаст пластичность смеси и еще больше снижает
стоимость резины.
Вулканизующим агентом является сера (1,3 м.ч.). Ускорители:
сульфенамид Ц (1,2 м.ч.), обладающий высокой скоростью вулканизации,
индукционным периодом и широким плато вулканизации, и тиазол 2МБС (0,2 м.ч.),
который обеспечивает сохранение формы изделия в начальном периоде вулканизации.
Активатор вулканизации - цинковые белила (3,0 м.ч.).
Для создания резины, обладающей невысоким модулем жесткости,
применяется полуусиливающий техуглерод П-514 (50,0 м.ч.).
Стеариновая кислота (1,0 м.ч.) облегчает диспергирование
сыпучих ингредиентов и является вторичным активатором вулканизации.
Для улучшения обрабатываемости смеси в нее вводят жидкий
мягчитель масло ПН-6 (12,0 м.ч.) и канифоль (2,0 м.ч.), как твердый мягчитель.
В качестве антискорчинга в смеси присутствует фталевый
ангидрид (0,5 м.ч.) предотвращая подвулканизацию.
Защитный воск ЗВ-1 (1,0 м.ч.) является физическим
антиозонантом и, выцветая на поверхность, образует защитную пленку, придавая
стойкость к действию атмосферы. Комбинация диафена ФП (0,5 м.ч.) и ацетонанила
Р (1,5 м.ч.) придает резине стойкость к усталостному износу и
термоокислительному старению.
Таблица 4.23 - Рецептура резиновой смеси для ободной ленты
Ингредиенты
|
Массовые части
|
Массовые проценты
|
Плотность, кг/м3
|
Объемные части
|
Объемные
проценты
|
Навеска, кг
|
|
|
|
|
|
|
1 ст
|
2 ст
|
1
|
2
|
3
|
4
|
5
|
6
|
7
|
8
|
СКИ-3 II группа
|
50,00
|
24,49
|
920,00
|
29,82
|
47,51
|
|
СКД II марка
|
30,00
|
14,69
|
910,00
|
32,97
|
18,09
|
28,50
|
|
СКМС-30 АРКМ-15
|
20,00
|
9,79
|
930,00
|
21,51
|
11,80
|
19,00
|
|
Регенерат РКТ
|
30,00
|
14,69
|
1200,00
|
25,00
|
13,72
|
28,50
|
|
Сера
|
1,30
|
0,64
|
2200,00
|
0,59
|
0,32
|
|
1,14
|
Сульфенамид Ц
|
1,20
|
0,59
|
1360,00
|
0,88
|
0,48
|
|
1,05
|
Тиазол 2МБС
|
0,20
|
0,10
|
1520,00
|
0,13
|
0,07
|
|
0,17
|
Фталевый
ангидрид
|
0,50
|
0,24
|
1600,00
|
0,31
|
0,17
|
0,47
|
|
Цинковые белила
|
3,00
|
1,47
|
5350,00
|
0,56
|
0,31
|
2,86
|
|
Стеариновая
кислота
|
1,00
|
0,49
|
870,00
|
1,15
|
0,63
|
0,95
|
|
Канифоль
сосновая
|
2,00
|
0,98
|
1040,00
|
1,92
|
1,06
|
1,90
|
|
Масло ПН-6Ш
|
12,00
|
5,88
|
970,00
|
12,37
|
6,79
|
11,40
|
|
Защитный воск
3В-1
|
1,00
|
0,49
|
906,00
|
1,10
|
0,61
|
0,95
|
|
Диафен ФП
|
0,50
|
0,24
|
1250,00
|
0,40
|
0,22
|
|
0,44
|
Ацетонанил Р,
РГ
|
1,50
|
0,73
|
1080,00
|
1,39
|
0,76
|
|
1,32
|
Углерод
технический П 514
|
50,00
|
24,49
|
1810,00
|
27,62
|
15,16
|
47,51
|
|
Маточная смесь
|
|
|
|
|
|
|
175,08
|
Итого
|
204,20
|
100,00
|
|
182,26
|
100,00
|
189,55
|
179,20
|
Плотность смеси 1 стадии = 1115 кг/м3;
Плотность смеси 2 стадии = 1120 кг/м3.
Таблица 4.24 - Нормы контроля резиновой смеси для ободной
ленты
Пластич-ность,
усл.ед.
|
Темпера-тура
вулкани-зации,ºС
|
Продолжитель-ность
вулканизации, мин
|
Условная
прочность при растяжении, МПа, не менее
|
Относительное
удлинение при разрыве, %
|
Твердость по
Шору, А
|
0,45±0,05
|
155±2
|
10 ± 0,5
|
7,8
|
550 ± 150
|
55 ± 10
|
.1.13 Обоснование рецептуры резиновой смеси шифра ЕВД-40,
предназначенной для обрезинивания пятки вентиля
Вентильная резина должна быть газонепроницаемой и
теплостойкой, также она должна иметь высокую прочность связи с латунированным
корпусом вентиля.
Основу резины составляют два каучука: СКИ-3-01 (75,0 м.ч.) и
ХБК НТ-1068 (25,0 м.ч.). СКИ-3-01 обладает высокой когезионной прочностью, а
ХБК придает газонепроницаемость, кроме того, обладает сродством к металлу,
благодаря своей полярности.
Вулканизующим агентом является сера (3,0 м.ч.), несколько
увеличенная дозировка обусловлена тем, что сера участвует в образовании
промежуточного адгезионного слоя нестехиометрического сульфида меди на
поверхности латунированного вентиля. Ускоритель - сульфенамид Ц (1,2 м.ч.),
обеспечивающий высокую скорость вулканизации. Активатором являются цинковые
белила (20,0 м.ч.), их содержание завышено, так как часть расходуется на
создание слоя на поверхности латуни, который обеспечивает прочность связи
резины и металлом.
Наполнение ведется среднеактивным техугдеродом П-514 (35,0
м.ч.), чтобы модуль жесткости резины был невысоким. Минеральный наполнитель
БС-120 (25,0 м.ч.) вводится для придания смеси хорошей адгезии к металлу и
улучшения теплоотвода, повышает сопротивление раздиру.
Удовлетворительные технологические свойства обеспечивает
твердый мягчитель АСМГ (2,0 м.ч.).
Функцию антискорчинга в смеси выполняет бензойная кислота
(0,5 м.ч.).
Модификатор РУ (1,0 м.ч.) на основе резорцина вводится для
повышения сродства к металлу.
Для зашиты от атмосферных воздействий в смесь вводится
физический антиозонант защитный воск ЗВ-1 (2,0 м.ч), который, выпотевая на
поверхность, создает защитный слой и предотвращает воздействие различных
факторов старения.
Таблица 4.25 - Рецептура резиновой смеси для обрезинивания
пятки вентиля
Ингредиенты
|
Массовые части
|
Массовые
проценты
|
Плотность, кг/м3
|
Объемные части
|
Объемные
проценты
|
Навеска, кг
|
|
|
|
|
|
|
1 ст
|
2 ст
|
1
|
2
|
3
|
4
|
5
|
6
|
7
|
8
|
СКИ 3-01
|
75,00
|
39,54
|
920,00
|
81,52
|
53,77
|
106,02
|
|
Хлорбутилкаучук
ХБК НТ-1068
|
25,00
|
13,18
|
910,00
|
27,47
|
18,12
|
35,34
|
|
Сера
|
3,00
|
1,58
|
2200,00
|
1,36
|
0,90
|
|
3,16
|
Сульфенамид Ц
|
1,20
|
0,63
|
1360,00
|
0,88
|
0,58
|
|
1,27
|
Белая сажа
БС-120
|
25,00
|
13,18
|
2100,00
|
11,90
|
7,85
|
35,34
|
|
Цинковые белила
|
20,00
|
10,54
|
5350,00
|
3,74
|
2,47
|
28,27
|
|
Бензойная
кислота
|
0,50
|
0,26
|
1200,00
|
0,42
|
0,27
|
0,71
|
|
Модификатор РУ
|
1,00
|
0,53
|
1270,00
|
0,79
|
0,52
|
|
1,05
|
Мягчитель АСМГ
|
2,00
|
1,05
|
1010,00
|
1,98
|
1,31
|
2,83
|
|
Защитный воск
3В-1
|
2,00
|
1,05
|
910,00
|
2,20
|
1,45
|
2,83
|
|
Углерод
технический П 514
|
35,00
|
18,45
|
1810,00
|
19,34
|
12,76
|
49,48
|
|
Маточная смесь
|
|
|
|
|
|
|
194,68
|
Итого
|
189,70
|
100,00
|
|
151,60
|
100,00
|
260,82
|
200,16
|
Плотность смеси 1 стадии = 1242 кг/м3;
Плотность смеси 2 стадии = 1251 кг/м3.
Таблица 4.26 - Нормы контроля резиновой смеси для
обрезинивания пятки вентиля
Пластич-ность,
усл.ед.
|
Темпера-тура
вулкани-зации,ºС
|
Продолжитель-ность
вулканизации, мин
|
Условное
напряжение при удлинении 300%, Мпа
|
Условная
прочность при растя-жении, МПа, не менее
|
Прочность связи
с корпусом вентиля, Н
|
Сопротив-ление
раздиру, КН/м, не менее
|
Твердость по
Шору, А
|
0,3±0,05
|
165±1
|
10 ± 1
|
9,84±2,5
|
11,8
|
98
|
49
|
60 ± 5
|
.1.14 Обоснование рецептуры резиновой смеси шифра ДД-7,
предназначенной для изготовления диафрагмы
Поскольку диафрагма предназначена для формования покрышки при
вулканизации и создания эффекта прессовки, она должна обладать высокой
стойкостью к старению, низкой остаточной деформацией, газонепроница-емостью,
высокой теплостойкостью, эластичностью, высокой усталостной выносливостью и
паростойкостью.
Большинство требований обеспечивается применением в качестве
основы резиновой смеси бутилкаучука (100,0 м.ч.), так как он мало ненасыщенный
каучук - с высокой плотностью упаковки макромолекул. Наирит ДН (5,0 м.ч.)
вводится как донор хлора для смоляной вулканизации.
Вулканизацию бутилкаучука проводят смолами типа Амберол
St-137 (8,0 м.ч.), для получения теплостойких связей. Цинковые белила (3,0
м.ч.) вводятся как ускоритель вулканизации. Модификатор гексол ЗВ (0,3 м.ч.)
способствует образованию теплостойких связей и является донором хлора для
смоляной вулканизации.
Наполнение резиновой смеси производят техуглеродом П-245
(25,0 м.ч.) и П-514 (25,0 м.ч.), такая комбинация обеспечивает достаточную
динамическую усталостную выносливость. Кроме того, техуглерод П-245 придает
стойкость к разрастанию трещин и стойкость к пару.
Для обеспечения хорошего диспергирования сыпучих
ингредиентов, в смесь вводится стеариновая кислота (3,0 м.ч.).
Удовлетворительные технологические свойства смеси позволяет
получить применение жидкого мягчителя стабилойл-18 (5,0 м.ч), который совместим
с БК и не ведет к порообразованию.
Таблица 4.27 - Рецептура резиновой смеси для диафрагмы
Ингредиенты
|
Массовые части
|
Массовые проценты
|
Плотность, кг/м3
|
Объемные части
|
Объемные
проценты
|
Навеска, кг
|
|
|
|
|
|
|
1 ст
|
2 ст
|
1
|
2
|
3
|
4
|
5
|
6
|
7
|
8
|
Бутилкаучук
БК-1675Т
|
100,00
|
57,37
|
910,00
|
109,90
|
65,08
|
137,50
|
|
Наирит ДН
|
5,00
|
2,87
|
1220,00
|
4,10
|
2,43
|
6,87
|
|
Амберол St -137
|
8,00
|
4,59
|
460,00
|
17,39
|
10,30
|
|
7,98
|
Гексол ЗВ, ЗВИ
|
0,30
|
0,17
|
1270,00
|
0,24
|
0,14
|
|
0,29
|
Цинковые белила
|
3,00
|
1,72
|
5350,00
|
0,56
|
0,33
|
4,12
|
|
Стеариновая
кислота
|
3,00
|
1,72
|
870,00
|
3,45
|
2,04
|
4,12
|
|
Стабилойл 18
|
5,00
|
2,87
|
890,00
|
5,62
|
3,33
|
6,87
|
|
Углерод
технический П 514
|
25,00
|
14,34
|
1810,00
|
13,81
|
8,18
|
34,37
|
|
Углерод
технический П 234
|
25,00
|
14,34
|
1810,00
|
13,81
|
8,18
|
|
Маточная смесь
|
|
|
|
|
|
|
165,81
|
Итого
|
174,30
|
100,00
|
|
168,88
|
100,00
|
228,27
|
174,08
|
Плотность смеси 1 стадии = 1087 кг/м3;
Плотность смеси 2 стадии = 1088 кг/м3.
Таблица 4.28 - Нормы контроля резиновой смеси для диафрагмы
Пластич-ность,
усл.ед.
|
Темпера-тура
вулкани-зации,ºС
|
Продолжитель-ность
вулканизации, мин
|
Условное
напряжение при удлинении 300%, МПа
|
Условная
прочность при растя-жении, МПа, не менее
|
Относительное
удлинение при разрыве, %
|
Твер- дость по
Шору, А
|
0,4±0,05
|
155±2
|
90 ± 0,5
|
5,2±1,2
|
9,8
|
675±75
|
55 ± 5
|
Таблица 4.29 - Рецепт смеси для пластикации натурального
каучука
Наименование
ингредиентов
|
Массовые части
|
Массовые
проценты
|
Плотность, кг/м3
|
Объемные части
|
Объемные
проценты
|
Навеска, кг
|
|
|
|
|
|
|
|
|
|
|
|
|
|
|
НК
непластицированный
|
100,00
|
99,30
|
920,00
|
108,70
|
99,65
|
165,03
|
|
|
|
|
|
|
|
Ренацит 7
|
0,70
|
0,70
|
1860,00
|
0,38
|
0,35
|
1,16
|
Всего
|
100,70
|
100,00
|
|
109,07
|
100,00
|
166,18
|
Плотность смеси = 923 кг/м3.
Таблица 4.30 - Рецепт пропиточного состава ПР-01-02-01-308,
для пропитки анидного, вискозного и капронового корда.
Наименование
материалов
|
На 100 м.д.
каучука, м.д.
|
Массовая доля
сухого остатка, %
|
Масса навески,
кг
|
|
|
|
На 1000 кг
состава
|
По массе сухого
остатка
|
1
|
2
|
3
|
4
|
5
|
Каучук в виде
латекса ДБА-1(100%)
|
50,00
|
40,30
|
|
|
Каучук в виде
латекса СКД-1с (100%)
|
50,00
|
40,30
|
|
|
Смола СФ-282
(100%)
|
16,50
|
13,28
|
|
|
Формальдегид
(100%)
|
6,60
|
5,32
|
|
|
Едкий натр
(100%)
|
0,99
|
0,80
|
|
|
Аммиак водный
(25%)
|
3,82
|
|
|
|
Вода умягченная
|
826,63
|
|
|
|
Латекс ДБА-1
(30%)
|
|
|
174,60
|
52,38
|
Латекс СКД-1с
(30%)
|
|
|
174,60
|
52,38
|
Поликонденсированный
раствор смолы СФ-282 (5%)
|
|
|
504,80
|
25,24
|
Аммиак водный
(25%)
|
|
|
4,00
|
|
Вода умягченная
|
|
|
142,00
|
|
Итого
|
954,54
|
100,00
|
1000,00
|
130,00
|
.2 Обоснование выбора и описание технологического процесса
приготовления резиновых смесей
4.2.1 Подготовка и развеска каучука
В основном НК поступает на заводской склад в кипах массой
около 100 кг. Практически установлено, что оптимальными условиями хранения
являются температура 10-15º С и относительная
влажность воздуха 70-75%. При хранении каучука важно соблюдать постоянство
температуры и влажности воздуха, так как если на поверхности каучука будет
присутствовать конденсат, процесс окисления каучука ускоряется в несколько раз.
Для предотвращения быстрого старения каучуков, для их
хранения используют деревянные склады, а также деревянные поддоны и контейнеры.
Некоторые из каучуков, используемых в данном производстве,
перед введением в технологический процесс, требуют предварительной обработки:
для кристаллизующихся каучуков (таких как НК, СКИ-3) необходима
декристализация, НК кристаллизуется при температуре от 10º С и ниже, для высокомолекулярных малопластичных каучуков
(например, НК) предусмотрена пластикация.
В данном проекте, предусмотрена декристализация каучуков
токами высокой частоты на установках непрерывного действия. Установка
высокочастотного разогрева состоит из генераторов токов высокой частоты, камер
высокочастотного разогрева, устройств, для защиты от радиопомех, конвейеров,
устройств, для контроля получения кип НК и контроля степени его разогрева.
Производительность установки 40 кип в час.
Для пластикации НК используется метод физико-химической
пластикации, при этом каучук перерабатывают в резиносмесителе с добавкой
промотора пластикации ренацита 7.
При введении в технологический процесс изготовления резиновых
смесей, кипы каучука разрезаются дисковыми ножами и дозируются с помощью
автоматических систем ДАС-З00, каждая из которых занята развеской отдельного
вида каучука. Эта система снабжена ножевыми устройствами (грубой и тонкой
резки), способными срезать навеску каучука с точностью до 0,2 кг.
От установки ДАС-300 каучук, пройдя весы - транспортер, по
линии ПТК подается к резиносмесителям в подвесных контейнерах.
Транспортная система подвесного толкающего конвейера состоит
из основного циркуляционного конвейера и примыкаюших к нему ответвлений
вспомогательных конвейеров. Конвейер имеет подвесные четырехколесные каретки,
передвигаемые толкающим кулаком тянущей цепи со скоростью примерно 7 м/мин. На
подвесном стержне кареток расположены три штифта для адресования груза.
Разгрузка контейнера происходит с помощью опрокидывателя с которого
каучук попадает на приемный транспортер и далее на весовой транспортер, а затем
на питательный транспортер резиносмесителя.
.2.2 Подготовка и доставка технического углерода
В настоящее время используют техуглерод в гранулированном
виде. Он поступает на завод обычно железнодорожными вагонами, выгрузка из
которых осуществляется через нижние люки, затем с помощью элеватора техуглерод
загружают в высотные бункера для хранения техуглерода.
Транспортировка техуглерода со склада в подготовительный цех
осуществляется по пневмотранспортной системе всасывающего типа.
В цехе для каждого типа техуглерода предусмотрен свой
расходный бункер с циклоном - осадителем, из которого по шнековому питателю
технический углерод поступает к весам для техуглерода, которые располагаются
непосредственно над резиносмесителем. После взвешивания навеска техуглерода
загружается в воронку, расположенную в задней стенке резиносмесителя.
4.2.3 Подготовка и развеска светлых сыпучих ингредиентов
Светлые порошкообразные компоненты для эластомерных
композиций поступают на заводской склад в бумажных мешках или другой таре
завода-изготовителя. Все порошкообразные ингредиенты должны поступать в виде,
удобном для применения и не требующем дополнительной обработки, поэтому
производится контроль соответствия поступающих ингредиентов требованиям ГОСТа.
Для устранения несоответствий, на заводе предусмотрены специальные сушилки для
просушивания материалов и сита для просеивания некоторых компонентов.
Подача светлых сыпучих ингредиентов со склада в расходные
бункера осуществляется автоматически с помощью ПТК при сигнале от расходного
бункера на склад. Расходные бункера каждого резиносмесителя предназначены для
определенного материала и снабжены верхним и нижним уровнемерами. Из расходных
бункеров сырье по шнековым питателям подается к весам, откуда на питательный
транспортер резиносмесителя.
Некоторые светлые сыпучие ингредиенты, расходуются в малых
количествах (менее 100 кг/сут.), при загрузке их в бункер, время их хранения
будет составлять порядка нескольких суток, что нецелесообразно. В этом случае
ингредиенты дозируются на участке полуавтоматической развески и упаковываются в
полиэтиленовые мешки с помощью установок АУ-3.
Установка АУ-3 использует полиэтиленовую пленку для упаковки
готовых навесок ингредиентов, подготавливая полиэтиленовый мешок подходящего
размера для каждого ингредиента. Производительность автомата АУ-3 = 600
пакетов/час.
Пакеты с готовыми навесками компонентов электрокарами
доставляются к питательным конвейерам резиносмесителей. Ингредиенты загружаются
в резиносмеситель прямо в полиэтиленовой пленке.
.2.4 Прием, хранение и дозирование жидких ингредиентов
Жидкие материалы обычно транспортируются в железнодорожных
цистернах, но гибким трубопроводам через воронку их сливают в заводские емкости
для хранения. В зимнее время перед опорожнением вагона-цистерны в ее «рубашку»
подают пар или горячую воду для предварительного разогрева материала.
Хранение осуществляется в подземных отапливаемых хранилищах,
откуда материалы гидронасосами перекачиваются к месту применения. Для подачи
жидких мягчителей из емкостей для хранения в подготовительный цех, применяются
обогреваемые трубопроводы типа «труба в трубе».
Жидкие материалы транспортируют по системе трубопроводов под
давлением. Для поддержания необходимой температуры в трубопроводах применяют
паровой или электрический обогрев. Далее жидкие материалы подаются к дозаторам.
От дозаторов точное количество материала вводится в резиносмеситель при
закрытом верхнем затворе с помощью инжектора под давлением 0,6 - 0,8 МПа.
.2.5 Описание процесса смешения
Приготовление таких смесей как ПД-167, ПД-168, ПД-169, КД-46,
ИД-19, ФД-20, БЛД-21, 9ЛО-53, ЕКД-39, ЕВД-40, ДД-7 осуществляется в две стадии,
но некоторые смеси (БД-57, БД-56, НШ-18) требуют трехстадийного смешения.
При двухстадийном смешении первая стадия производится в резиносмесителе
РС 270/40. При этом получают маточную смесь, которая не содержит вулканизующую
группу, реакционноспособные модификаторы и стабилизаторы, не стойкие к высокой
температуре (температура: 1 стадия-140ºС.).
После первой стадии резиновая смесь гранулируется и
опрыскивается каолиновой суспензией для охлаждения и предотвращения слипания
гранул. Излишки антиадгезива удаляются на вибрационном транспортере, после
которого гранулы маточной смеси элеватором загружаются в барабанную
охладительную установку. В барабанной установке смесь охлаждается и
пневмотранспортом доставляется в усреднительные барабаны вместимостью 15 тонн,
где происходит промежуточное хранение, вылежка смеси, усреднение заправок.
Для второй стадии смешения гранулы маточной смеси подаются на
третий этаж по пневмотранспортной системе всасывающего типа. В циклонах
-осадителях происходит разделения гранул смесей и всасываемого воздуха, смеси
подаются в расходные бункера, а воздух, пройдя через рукавный фильтр
выбрасывается в атмосферу.
Из расходных бункеров смеси попадают в дозаторы, откуда на
питательный транспортер резиносмесителя, где к гранулам маточной смеси
добавляются вулканизующая группа и реакционоспособные компоненты, вводимые на
последней стадии.
Процесс смешения второй стадии осуществляется в
резиносмесителе РС 270/З0 (температура: 2 стадия-108-110ºС). После смешения, смесь выгружается в воронку червячной машины
типа АЧВЛ-1200 с листовальной головкой. Полученная готовая резиновая смесь
ленточным транспортером подаются в охлаждающую установку фестонного типа
УФТ-3600, после которой установлен маятниковый укладчик, после которого смеси в
поддонах отправляются к складу готовых резиновых смесей ленточным
транспортером.
При трехстадийном смешении первую стадию производят в
резиносмесителе РС 270/30, вторую - в РС 270/40, а третью вновь в РС 270/30
(температура: 1 стадия-140ºС, 2 стадия-140ºС, 3 стадия-108ºС). Вторая стадия при
трехстадийном смешении является дорабатывающей.
После второй стадии, смесь как и после первой подвергается
грануляции (гранулятор МЧТ 380/450) и вылежке, а вулканизующая группа и
реакционоснособные компоненты вводятся на третьей стадии.
Многостадийные процессы смешения применяются потому, что
процесс диспергирования порошкообразных компонентов наиболее интенсивно осуществляется
на начальной стадии смешения, когда смесь еще не успела разогреться и
присутствуют большие сдвиговые напряжения.
.2.6 Контроль процесса приготовления резиновых смесей
Для контроля процесса смешения резиносмесители оснащаются
комплектом контрольно - измерительных приборов. В процессе работы
резиносмесителя контролируют и автоматически регулируют температуру резиновых
смесей, продолжительность смешения, давление сжатого воздуха, подаваемого в
цилиндры верхнего и нижнего затворов, расход охлаждающей воды.
Для контроля температуры в смесительной камере и
продолжительности смешения применяемся специальная термопара, расположенная в
корпусе смесительной камеры, и электронный самопишущий потенциометр ЭПД. С
помощью ЭПД может производиться автоматическое открытие нижнего затвора при
достижений заданной температуры в смесительной камере.
Давление сжатого воздуха контролируют самопишущими приборами,
первичными датчиками которых являются манометры и динамометры, установленные в
пневмосистеме. Для бесперебойного снабжения сжатым воздухом в сети необходимо
установить накопительную емкость, из которой через клапан будет сбрасываться
давление, на случай перебоя в расходе воздуха.
Наблюдение за работой приборов и контроль над соблюдением
режима смешения производит оператор. Контроль осуществляется за пультом
оператора, на который вынесены вторичные приборы всех датчиков.
После окончания смешения, производят контроль качества
резиновых смесей.
.2.7 Контроль качества резиновых смесей
Для контроля качества резиновых смесей применяют приборы для
измерения вулканизационных характеристик резиновых смесей по ГОСТ 12535-78 на
реометрах типа «Монсанто-100». Приборы такого типа имеют цилиндрическую камеру,
в которой совершает синусоидальные колебания с амплитудой +1 ~ +3° биконический
ротор. Запрессовка в камеру и испытания при 100-200 °С резиновой смеси
позволяют получить кривую кинетики вулканизации смеси (рисунок 1) в виде
зависимости сопротивления резиновой смеси колебательным движениям ротора в
камере с момента ее закрытия.
Рисунок 1 - Реометрические кривые (1-3) вулканизации
резиновых смесей различных типов
Холодная смесь показывает повышенный крутящий момент Мнач.
характеризующий начальную вязкость смеси при низких температурах (в переработке).
После разогрева вязкость смеси при температурах вулканизации характеризует (и
может приниматься для количественного описания течения смеси в канатах
пресс-форм) минимальный крутящий момент Ммин. Время сохранения вязкотекучего
состояния до начала вулканизации резиновой смеси с ростом крутящего момента на
0,1 Н*м от минимального значения определяется как время Ts, характеризующее
индукционный период в начале вулканизации. Максимальный крутящий момент Ммакс
определяет жесткость вулканизованной резины. При испытании резиновых смесей
возможны три типа кривых вулканизации:
Крутящий момент уменьшается после достижения максимального
значения,которое и принимается далее за величину Ммакс;
2 Крутящий момент достигает равновесного значения и его
максимальное значение выбирают по равновесной величине;
Крутящий момент монотонно возрастает (зачастую наблюдается
для СКЭП, БСК, БНК) с переходом кривой в участок с переменной скоростью
увеличения крутящего момента; в этом случае Ммакс определяют по времени
перегиба кривой в участке с переменной скоростью роста крутящего момента.
Оптимальное время вулканизации t90 рассчитывают,
принимая оптимальной степень вулканизации по достижении 90 %-го крутящего
момента в ходе вулканизации, т. е. М90 = Ммин + 0,9(Ммакс - Ммин).
Скорость вулканизации Vs (в %/мин) вычисляют по
формуле:
s = 100 / (t90 - ts), %
/мин,
которая определяет темпы роста крутящего момента на наиболее
активном этапе вулканизации.
.3 Описание технологического процесса изготовления шины
размера 21.00 Р33
.3.1 Обработка текстильного корда
Обработка и обрезинивание корда производится на поточной
кордной линии ЛОК-80-1800. Она состоит из трёх участков и соответствующих им
агрегатов: АПК-80-1800 (пропитка и сушка); АТК-80-1800 (термообработка),
АОК-80-1800 (обрезинивание).
Технологический процесс обработки корда включает в себя ряд
операций: раскатка рулонов корда, пропитка корда, сушка пропитанного корда,
термическая вытяжка и нормализация корда, дополнительная сушка корда в малой
сушильной камере, обрезинивание корда на каландре.
Корд суровье с раскаточного устройства через питающие валки
непрерывно поступает в компенсатор (натяжение в компенсаторе 1,5 кН).
Компенсатор предназначен для создания запаса корда с целью непрерывной работы
кордной линии при стыковке концов рулонов корда на стыковочном прессе. В
процессе стыковки концы рулонов корда накладывают друг на друга внахлест,
проложив между ними и с каждой стороны стыка ленту резиновой смеси толщиной
0,7-0,8 мм и шириной 120-150 мм, затем стык вулканизуют между плитами пресса
при 170°-190
°С
в течении 60-90 секунд. После компенсатора кордное полотно проходит между
соплами вакуумного очистителя, где очищается от пыли и ворсинок и поступает в
ванну для пропитки агрегата АПК-80-1800, заполненную пропиточным составом ПР-01-02-01-308
с концентрацией 15 %. Участок приготовления пропиточных составов
располагается в блоке складов. Пропиточные составы представляют собой
многокомпонентные смеси латекса, резорцинформальдегидных смол и других целевых
добавок. Для приготовления пропиточных составов используют реакторы емкостью
1000 л с мешалками. При перемешивании через мерники загружают латекс,
конденсированную резорцинформальдегидную смолу и воду. Дозировка воды зависит
от заданной концентрации пропиточного состава и от концентрации его компонентов
(латекса, смолы). Для повышения устойчивости состава и повышения рН, если это
необходимо добавляют аммиачную воду; рН пропиточного состава 9,5 - 10,5.
Затем корд проходит устройство для удаления избытков
пропиточного состава, состоящего из специальных скребков и вакуумного отсоса.
Пропитанный корд подается в сушильную камеру и сушится при температуре 120-160 °С в течение нескольких
минут. Корд сушат под натяжением до 45 Н/нить. Влажность корда после сушки не
должна превышать 0,5-1,0 %.
После сушки корд по транспортирующим роликам направляется на
агрегат АТК-80-1800 для термообработки и вытягивания. Основной частью агрегата
является термобашня, которая включает в себя камеру термовытяжки и камеру
нормализации. Термическая вытяжка корда осуществляется при температуре 190 °С при натяжении 20-50
Н/нить, продолжительностью 20 секунд. Для закрепления эффекта вытяжки корд
поступает в камеру нормализации. Натяжение корда в камере нормализации
снижается и составляет 5-10 Н/нить и при температуре 190 °С. При термической
обработке корд вытягивается на 12 %, а на стадии нормализации усаживается на 4
%, то есть вытяжка составляет 8 %. После термообработки и нормализации корд по
направляющим роликам поступает в компенсатор участка каландрования. Перед обрезиниванием
корд направляют в сушилку. После сушки при 177 °С до влажности 1,0-1,5% корд поступает на
агрегат АОК-80-1800 и подвергается обрезиниванию на четырёхвалковом каландре.
Температура валков каландра равна 85-100°С, скорость обрезинивания
40 м/мин. При обрезинивании происходит заполнение резиновой смесью промежутков
между нитями корда, а также наложение с каждой стороны полотна слоя резины
толщиной 0,2-0,3 мм. Далее обрезиненный корд проходит прибор контроля толщины
обкладки (калибромер). Затем корд проходит через охлаждающие барабаны и
компенсатор, и поступает на закаточный станок, где закатывается в бобины с
прокладочным полотном.
Хранение бобин обрезиненного корда осуществляется на
складских стеллажах. Приём бобин с кордом на склад и подача его со склада к ДРА
выполняется по монорельсовой полуавтоматической дороге с самоходными подвижными
составами.
.3.2 Обработка и обрезинивание металлокорда
Металлокорд применяют для изготовления брекерных браслетов и
дополнительных бортовых крыльев. На завод нити металлокорда поступают на
шпулях. Получение металлокордного полотна и его обрезинивание, раскрой,
стыковка, продольный раскрой полосы и закатка ее в прокладку осуществляют ни
линии ИТ 7464.
Линия ИТ 7464 состоит из шпулярника, червячной машины МЧХ-90-Л-СБ,
трех холодильных барабанов, раскроечно-стыковочного устройства и закаточных
устройств.
Нити металлокорда поступают в Т-образную головку МЧХ, туда же
поступает резиновая смесь. Рабочая скорость обрезинивания не менее 5-15 м/мин.
Температура корпуса МЧХ 80 °С, головки 100 °С, червяка 70 °С. Температура
обрезиненного металлокордного полотна на выходе из головки машины 85-90 °С.
Далее металлокорд поступает на три холодильных барабана, откуда через
компенсатор на раскроечно-стыковочный агрегат, который включает в себя
подающее, режущее, стыковочное и отборочное устройства.
Подающее устройство включает механизм зажима транспортерной
ленты, а так же механизм фиксации брекерной ленты. Режущее устройство состоит
из траверсы, на которую установлен пневмоцилиндр, приводящий в движение ножи,
которые раскраивают металлокорд на величину ширины брекерной заготовки. Далее
включается стыковочное устройство.
Металлокордная полоса с отборочного устройства подается на
дисковые ножи, а затем на закаточное устройство, закатывается в катушки через
прокладочный материал и отправляется на сборочный станок 2СТ 33.
.3.3 Изготовление и обертка бортовых колец
Процесс изготовления бортовых крыльев включает следующие
операции: раскатка и обрезинивание проволоки, навивка бортовых колец, обертка
кольца промазанной бязевой ленточкой, наложение наполнительного шнура и
крыльевой ленты.
Бортовое кольцо служит для придания нерастяжимости,
необходимой прочности и жесткости бортовой части покрышки.
Бортовые кольца изготавливаются на кольцеделательном агрегате
АКД 80/1300. Проволока поставляется на шинные заводы в металлических катушках
массой до 500 кг, которые устанавливаются в раскаточные стойки шпулярника без
перемотки и рихтовки. Число катушек в шпулярнике зависит от числа проволок (ширины
проволочной ленты) в одном витке проволочного кольца. По выходе из него
отдельные проволоки собираются в прядь в собирающем узле, представляющего собой
ролик с выемками или гребенку из вертикальных роликов (число проволок - 12).
Для увеличения прочности связи между резиновой смесью и
поверхностью проволоки при обрезинивании ее пропускают через установку для
нагрева, в которой ее подогревают до 50-80 ºС. Применяют
электрический обогрев током большой силы при малом напряжении. При прохождении
проволоки между блоками включается ток и проволока нагревается. Температура
подогрева регулируется изменением силы тока. Недопустим сильный перегрев
проволоки, так как это может привести к уменьшению ее твердости.
Нагретые нити проволоки протягиваются через головку червячной
машины холодного питания с Т-образной головкой. В головке червячной машины
проволока изолируется резиновой смесью и образует обрезиненную ленту, которая
проходит через охладительную ванну, обдувается воздухом для удаления капель
воды с поверхности, протягивается с помощью протяжных барабанов через
компенсатор и подается в замок шаблона кольцеделательного автомата,
закрепляется и наматывается на шаблон для получения заданного числа витков
(количество витков - 20). По окончании намотки шаблон автоматически
останавливается, лента обрубается пневматическим ножом, замок открывается,
готовое кольцо сбрасывается с шаблона. Стык закрепляют ленточкой из бязи
шириной 15 мм, промазанной с двух сторон на каландре резиновой смесью. Готовое
бортовое кольцо подается в агрегат для подвулканизации стыка.
Стык бортового кольца укрепляют путем местной подвулканизации
на полуавтоматических станках карусельного типа. Для колец диаметром 381-1095
мм применяют полуавтомат ИЖ-25162 с 18 прессформами с электрическим обогревом.
Бортовое кольцо после снятия с шаблона намоточного станка кольцеделательного
агрегата закладывают в нижнюю половину прессформы по ходу вращения, затем
полуформы закрывают и стыки подвулканизовывают при температуре 180-190 ºС в течении 1-2 минут. Раскрытие и выгрузка колец осуществляется
автоматически. Производительность автомата ИЖ-25162 составляет 11-12 шт/мин.
Обертка бортовых колец рекомендуется для шин, в конструкции
которых предусмотрен наполнительный шнур или требуется повышенная монолитность
борта. Она осуществляется ленточкой из промазанной бязи, предварительно
раскроенной под углом 45º на
диагонально-резательном агрегате. Стыкованные полосы подаются к
продольно-резательной машине ПР-68, где раскраиваются в продольном направлении
на ленты шириной 130 мм для продольной обертки и шириной 15 мм - для
спиральной, которые наматываются на металлические шпули (диаметр намотки около
120 мм).
Спиральную обертку бортовых колец ведут на станке 101-04,
принцип действия которого основан на вращении шпули с ленточкой вокруг кольца,
поворачивающегося по мере обмотки. Когда бортовое кольцо сделает один оборот,
лента с катушки полностью обернет его по спирали. Обернутое кольцо снимают со
станка и, проверив его качество, навешивают на стойку.
Наложение крыльевой ленты. После обертки на бортовое кольцо
покрышки накладывают наполнительный шнур и обрезиненную кордную ленту - так
называемую крыльевую ленту - флиппер. Крыльевые ленты изготавливают из
обрезиненного корда, который с продольно-резательных машин, при помощи валиков
транспортируется к крыльевым станкам.
Сборку крыльев грузовых покрышек осуществляют на крыльевом
станке СКФ-5. Он состоит из стойки и несущей станины, на которой смонтированы
подающий механизм прикаточных роликов. Привод работает от асинхронного электродвигателя.
Станок работает следующим образом: бортовое кольцо устанавливают на
поддерживающие ролики (левый прикаточный ролик при этом отведен). Затем к
кольцу подводятся наполнительный шнур и крыльевая лента, которая при помощи
системы роликов и направляющих лотков обертывается вокруг бортового кольца.
В шинах конструкции радиальных шин предусматривается
усиленный борт, для чего кроме наполнительного шнура применяют дополнительное
крыло, содержащее сердечник из двух витков обрезиненной металлокордной нити
22л15 и перегнутую со ступенькой металлокордную крыльевую ленту. Дополнительные
крылья изготавливают на крыльевых станках СДК-1. На полосу обрезиненного
металлокорда накладывают сердечник, края металлокордной ленты заворачивают
вокруг сердечника и дублируют.
.3.4 Изготовление профилированных деталей и наполнительного
шнура
Шприцевание профилированных деталей, наполнительного шнура
производится на шприц-машине холодного питания МЧХ-160. Резиновая смесь
температурой не ниже 18 °С подается в червячную машину. Температура головки
червячной машины не ниже 80-85 °С, температура корпуса машины I зоны 45-50 °С, II зоны 60-75 °С, червяка 65-70 °С.
Заготовка в виде непрерывной ленты выходит из головки машины
с температурой (110±5) °С. Далее поступает в
охладительную ванну, где охлаждается до температуры (30±6) °С. После охлаждения
профилированные детали и наполнительные шнуры обдуваются сжатым воздухом для
удаления влаги и подаются на отборочный транспортёр, который двигается со
скоростью 12 м/мин. Затем профилированная резиновая смесь режется ножом
гильотинного типа на заготовки и укладывается на стеллажи-тележки, на которых
они хранятся и транспортируются к станкам для сборки покрышек.
.3.5 Изготовление бортовых и крыльевых лент
Бортовые ленты изготавливаются из обрезиненного корда 232КНТС
и 22Л15, крыльевые ленты из 232КНТС. Текстильный корд раскраивается под углом
45°на
ДРА-3-0-45°. После стыковки полосы подаются на продольно-резательную машину
ПР-68, где они раскраиваются вдоль на узкие ленты.
Бортовые ленты, изготовленные из металлокорда марки 22Л15
методом обрезинивания металлокорда на ИТ-7464.
Бортовые ленты шприцуются на шприцмашине холодного питания
МЧХ-160 и режутся на заготовки.
Готовые крыльевые ленты подаются к крыльевым станкам, а
готовые бортовые ленты поступают к питателям станков для сборки покрышек.
.3.6 Изготовление заготовок боковин
Боковины КГШ выпускают на протекторных агрегатах различных
типов. Схема агрегата для выпуска протекторной ленты работает следующим
образом.
Резиновая смесь непрерывно подается к червячной машине
МЧХ-250 и шприцуется в виде профильной ленты. Температура головки червячной
машины 80-90 ºС, скорость шприцевания 8 м/мин. Затем
резиновая лента отбирается приемным транспортером, маркируется валиком и
направляется на весовой транспортер, где она с помощью весов непрерывно
взвешивается. При отклонении от массы (единицы длины ленты) от заданной
производится автоматическое регулирование скорости шприцевания червячной
машины.
Далее боковины подвергаются шероховке и промазке клеем.
Боковина с помощью транспортера подается на барабан шероховального устройства.
Поверхность барабана покрыта кардной лентой. Барабан вращается со скоростью 8
м/с в направлении движения протекторной ленты. Промазка клеем отшерохованной
ленты с температурой 75-80 ºС производится с помощью
барабана, обтянутого войлоком; барабан свободно вращается в ванне с клеем.
Уровень и концентрация клея в ванне поддерживается постоянными с помощью
циркуляционного насоса.
После шероховки и промазки клеем лента транспортером
пропускается через короб с вытяжной вентиляцией. В коробе поверхность боковины
просушивается в течение 30-40 с. Просушенная лента поступает на усадочный
рольганг, который состоит из роликов с постепенно уменьшающимися в направлении
движения резиновой ленты диаметрами, но с одинаковой частотой вращения.
Благодаря этому лента при движении по поверхности рольганга подвергается
принудительной усадке. С усадочного рольганга лента подается в охладительные
ванны, температура охлаждающей воды 15-20 ºС.
Охлажденная лента обдувается воздухом и подается на
транспортер, где с помощью дискового ножа разрезается под углом 15-20º на заготовки 3850 мм. Концы отрезанных заготовок промазываются
клеем. Затем заготовки отбираются быстро движущимся транспортером, взвешиваются
на весах с рольгангом и с помощью транспортерных средств направляются на
промежуточный склад, где они выдерживаются в течение не менее 2 ч для
обеспечения их полной усадки, но не более 2 суток для предотвращения снижения
клейкости. Со склада заготовки боковин направляют к станкам I стадии сборки КГШ
(СПД4-1170-2200).
.3.7 Процесс сборки покрышек
Процесс сборки покрышек очень трудоемкий. Он включает в себя
ряд операций: предварительно заготовленные детали покрышек по транспортным
системам направляют на участок сборки, где производится их наложение на
барабаны сборочных станков, склеивание, дублирование и прикатка в определенной
последовательности до получения сырых покрышек.
КГШ собирают в три стадии. Сначала на диагонально-резательной
машине производят раскрой корда на полосы заданной ширины, которые затем
стыкуют в ленту на верхнем транспортере питающего устройства. Остатки корда
укладывают на стеллаж для дальнейшего использования. По ходу выполнения
операций лента отбирается на нижние транспортеры - накопители питающего
устройства П-2000 и направляются к сборочному станку СПД 4-1170-2200 на первую
стадию сборки. При этом собирается каркас с посадкой бортовых крыльев и
обработкой борта. Так же на каркас накладываются боковины протектора. Затем
сборочный барабан складывается, каркас покрышки снимается со станка первой
стадии и устанавливается на формующий барабан станка второй стадии сборки при
помощи трансфера.
Вторая стадия сборки производится на станке 2СТ33, который
состоит из станка сборки брекерного браслета и станка окончательной сборки.
Разжав брекерный барабан и опустив лоток питателя, на станке
сборки брекерного браслета собирают брекерный браслет. На трансфер при помощи
кран-балки устанавливается каркас покрышки. По готовности брекерного браслета
лоток питателя поднимается. Переносчик браслета заходит на брекерный барабан.
После захвата браслета брекерный барабан сжимается. После этого трансфер
каркаса перемещается к станку окончательной сборки, надвигая каркас на
формующий барабан. Одновременно трансфер уводит с брекерного барабана
переносчик с брекерным браслетом. После фиксации каркаса на формующем барабане
трансфер освобождает рабочую зону для переносчика. После этого переносчик
заходит на формующий барабан, совмещая плоскости симметрии брекерного браслета
и каркаса.
В процессе формования каркас покрышки дублируется с брекерным
браслетом (то есть под давлением склеивается с ним). После этого переносчик
освобождает рабочую зону для лотков двухслойного питателя и прикатчика. Затем
лотки питателя опускаются, а прикатчик отводится от станины станка
окончательной сборки. Производится наложение слоев брекера из двухслойного
питателя и других деталей (материалов) из технологических тележек, прикатка
отдельных частей и покрышки в целом. По окончании сборки покрышки прикатчик
отводится к станине станка окончательной сборки, лотки двухслойного питателя
поднимаются, и трансфер подхватывает собранную покрышку. После сжатия и
разведения заплечников и вакуумирования диафрагмы формующего барабана трансфер
снимает покрышку с формующего барабана.
Собранная на II стадии покрышка кран-балкой транспортируется
к агрегату навивки протектора узкой лентой АНПР - 2200.
Сформованная покрышка с наложенными боковинами и брекером
устанавливается при помощи кран-балки на фланцы обода. С начала покрышка
заводится на левый фланец, затем правый фланец подводится к покрышке, все время
покрышка поддерживается кран-балкой. После установки покрышки на фланцы обода,
кран-балка уводится с рабочей зоны агрегата и, во внутрь покрышки подается
сжатый воздух. В воронку червячной машины МЧХ-160Л-СБ подается резиновая лента
с питателя ПЧ-250, которая профилируется формообразователем в необходимый
профиль шириной 200 мм и толщиной 12 мм. Далее профилированная резиновая лента
подается на узел накладывателя/прикатывателя. С помощью этого узла
профилированная лента подается на вращающуюся покрышку, на которой происходит
наложение и прикатывание протектора по заранее введенной программе. После
наложения протектора по профилю покрышки резиновая лента отрезается. Кран-балка
подводится под покрышку. Спускается воздух из покрышки, фланцы разжимаются
(правый фланец отводится), покрышка снимается с фланцев обода и подается для
окраски внутренней поверхности перед вулканизацией.
.3.8 Процесс вулканизации покрышек
Вулканизация покрышек происходит в форматоре-вулканизаторе ФВ
1-1250-2500-735/1300 (100”).
Собранные покрышки с участка сборки подают на горизонтальные
ролики станка SV-14 для окраски (скорость окрашивания 6 шт./час) и приводят во
вращение. При вращении покрышки вдоль ее внутренней полости перемещается
штанга, на которой установлены форсунки для разбрызгивания смазки по всей
внутренней поверхности. Покрышка после окраски поступает на сверление беговой
части протектора. Сверление производится пневмодрелью ИП 1010.С, с частотой
вращения 3000 мин-1. После сверления заготовка поступает на станцию
навешивания, которое осуществляется во время непрерывного движения конвейера.
Для обеспечения бесперебойного питания 100 - дюймовых
форматоров - вулканизаторов сырыми покрышками в сборочном цехе принят 4-х
часовой запас покрышек, который должен храниться на специально отведенных для
этих целей складских петлях питающего конвейера.
Транспортная система состоит из главного циркуляционного
конвейера, складских конвейерных петель и рабочих конвейерных петель. Главный
циркуляционный конвейер и складская конвейерная петля имеют самостоятельные
приводы. Складская петля имеет загрузочную станцию для сырых покрышек. На
загрузочной станции предусмотрен один стационарный загрузчик - манипулятор, с
помощью которого сырые покрышки вместе со специальными челюстными захватами ее
за борта навешиваются на подвески грузонесущих тележек, курсирующих по данной
петле толкающего конвейера.
Подача свободных от покрышек грузонесущих тележек под
загрузку осуществляется автоматически. Нагруженные тележки по вызову от
форматоров, передаются со складских конвейерных петель на главный
циркуляционный конвейер, а затем на рабочую петлю толкающего конвейера.
Грузонесущие тележки разгружаются передвижным манипулятором,
то есть манипулятором с ходовой тележкой, обеспечивающей его перемещение вдоль
ряда форматоров - вулканизаторов. Ходовая тележка манипулятора представляет
собой раму, на осях которой смонтированы 8 катков. Разгрузка осуществляется
следующим образом. Оператор перемещает манипулятор с подвеской к загружаемому
форматору - вулканизатору, одновременно опуская и поворачивая каретку стрелы в
положение, обеспечивая возможность загрузки форматора. При достижении
необходимого положения оператор разжимает захваты подвески, и покрышка
сбрасывается на диафрагму пресса.
Разгруженная тележка автоматически передается на главный
циркуляционный конвейер и оттуда поступает под загрузку.
После вулканизации покрышек их отбор осуществляется с задней
стороны форматоров - вулканизаторов при помощи ленточных транспортеров,
расположенных между рядами вулканизаторов. Далее покрышки поступают на
собирающий конвейер, а затем системой подвесных толкающих конвейеров, ленточных
транспортеров и гравитационных рольгангов транспортируются на участок
заключительных операций.
После разбраковки специальным подъемным столом покрышки
поднимают до уровня отборочного цепного конвейера и навешиваются на подвески,
по которым они транспортируются на склад готовой продукции.
Таблица 4.31 - Режим вулканизации покрышек размера 21.00-Р33
Наименование
операции
|
Параметры
|
Продолжительность
операции, мин
|
Время с начала
цикла, мин
|
|
Температура, °С
|
Давление, Мпа
|
|
|
1
|
2
|
3
|
4
|
5
|
Напуск пара в
диафрагму “в тупик
|
193±3
|
1,6
|
6
|
0
|
Отключить пар и
включить подачу перегретой воды циркуляцией
|
180
|
2,5
|
219
|
6
|
Напуск пара в
паровую камеру до температуры вулканизации
|
|
|
15
|
12
|
Вулканизация
при температуре в паровой камере
|
145
|
|
198
|
27
|
Отключить
подачу пара в паровую камеру. Сброс открыт
|
|
|
|
225
|
Отключить напуск
перегретой воды в диафрагму и включить подачу охлаждающей воды
|
40
|
2,5
|
9
|
225
|
Спуск
охлаждающей воды из диафрагмы
|
|
|
6
|
234
|
Общая продолжительность вулканизации, мин - 240
Продолжительность перезарядки, мин - 20
4.3.9 Заключительные операции
Покрышки после вулканизации имеют выпрессовки резины, которые
требуются удалять. Для этих целей применяют станок ПО “Днепро-шина”.Станок
представляет собой два вогнутых ролика, вращающихся на осях, расположенных на
станине; один из них приводится во вращение от электродвигателя мощностью 1
кВт. Привод включается при помощи фрикционной муфты. Покрышка устанавливается
на ролики и сверху прижимается специальным вогнутым роликом, нагружаемым
пневмоцилиндром. Обрезка выпрессовок производится путем автоматического прижимания
ножей касательно к поверхности покрышки. Ножи упруго прижимаются
пневматическими цилиндрами. После нескольких оборотов покрышки ножи отходят и
покрышка выталкивается.
Далее покрышки поступают на разбраковку. После разбраковки
специальным подъемным столом покрышки поднимают до уровня отборочного цепного
конвейера и навешиваются на подвески, по которым они транспортируются на склад
готовой продукции.
.3.10 Изготовление ездовых камер
Автокамерные рукава выпускаются на камерных линиях. Линия
оборудована МЧТ с диаметром червяка 400 мм и предназначена для профилирования
заготовок шириной до 560 мм. Резиновая смесь температурой (85±6) °С, в виде
ленты с питательных вальцев транспортером, подается в загрузочную воронку
червячной машины типа МЧТ-400, выпускающей заготовку, снабжена форсункой, через
которую внутрь рукава впрыскивается смесь талька в воздухе для предотвращения
слипания стенок рукава. Температура головки червячной машины составляет (75±5)
°С, корпуса - (30±5) °С, скорость шприцевания 8 м/мин. Выходящий из машины
камерный рукав температурой не выше 110 °С поступает на приёмный транспортер,
проходит через автоматические весы, обеспечивающие его непрерывное взвешивание,
и по наклонному рольгангу поступает в ванну для охлаждения. В ванне камерный рукав
охлаждается водой (температура охлаждающей воды 18 °С) до 25-30 °С, здесь же происходит и
его усадка. Из ванны рукав подается на рольганг для обдувки воздухом и через
поворотный шкив поступает на рабочий транспортер, расположенный над ванной для
промазки рукава клеем по месту крепления вентиля. Слой клея, нанесенный на
рукав, просушивают инфракрасными лампами, а затем в рукаве приспособлением
пробивают отверстие под вентиль, одновременно камеры маркируют. Затем вентиль
опускают по стержню до соприкосновения со стенкой камеры, стержень вынимают и
пятку вентиля прессуют к камерному рукаву пневматическим прикатчиком. Камерный
рукав опудривают тальком в камере и ножом автоматически режут на заготовки
длиной (2400±10) мм с допуском на усадку. Для облегчения реза нож нагревают
электрическим током до температуры 250 °С.
Расправленные камерные заготовки укладывают на
книжки-тележки, на которых их выдерживают 3-4 часа до полного остывания
заготовок, усадки, так как в этом случае прочность стыка будет более высокой.
Далее заготовки по транспортёру подают к стыковочным станкам ССКБ-670. Концы
рукавов обрезают (температура ножей 250 °С), сближают и
выдерживают под давлением 9,8 МПа в течение 15 секунд. Состыкованную камеру
снимают со станка и укладывают на полки конвейера, который подаёт её на
вулканизацию.
Для увеличения прочности стыка его охлаждают в течение 15
минут. Для этого камеру кладут на трубу, в которой циркулирует хладоагент
(хлорид кальция с температурой (-10…-15) °С).
Формование камерных заготовок перед вулканизацией
осуществляется на шаблонах в наклонном положении. Формование проводят в две
стадии путем подачи в камеру сжатого воздуха (максимального давления 0,8 МПа).
Камеру надевают на шаблон, центрируют и вентиль камеры соединяют с механизмом
для подачи сжатого воздуха. Воздух подают до тех пор, пока стенки камеры не
достигнут первого ограничителя, автоматически отключаемого подачу воздуха в
камеру. После выдержки заготовки на шаблоне вторично подают сжатый воздух, пока
стенки камеры не достигнут второго жёстокого ограничителя. Вентиль камеры
герметизируют, камеру осматривают для выявления посторонних включений и
пузырьков.
Вулканизация осуществляется в одноформовых прессах
ВК-180-1870 (75”).
Таблица 4.32 - Режим вулканизации автокамеры размера
21.00-Р33
Наименование
операции
|
Параметры
|
Продолжительность
операции, мин
|
Время с начала
цикла, мин
|
|
Температура, °С
|
Давление, Мпа
|
|
|
Напуск воздуха
в камеру
|
|
0,8
|
30
|
0
|
Продувка форм
воздухом
|
|
|
2
|
0
|
Продувка форм
паром
|
|
|
3
|
2
|
Подача пара и
прогрев форм до температуры вулканизации
|
|
|
6
|
5
|
|
|
|
|
|
Вулканизация
при температуре
|
170
|
|
14
|
11
|
Спуск воздуха
из камеры
|
|
|
10
|
30
|
Охлаждение форм
до температуры
|
70
|
|
15
|
25
|
Общая продолжительность вулканизации, мин - 40
Продолжительность перезарядки, мин - 5
После вулканизации автокамеры подают на пневматические станки
для изгиба вентиля ИРО-2440РП и далее на станок для вставки золотника в корпус
вентиля.
При разбраковке автокамеры подвергают визуальному осмотру и
испытывают на герметичность методом вакуумирования. Негерметичные камеры с
ввернутым золотником вакуумируются с использованием вакуум-насоса до полного
слипания их стенок, а затем визуально наблюдают за разъединением стенок камеры
при проникновении в них воздуха. Время вылежки камеры для выявления
негерметичности составляет 3-4 часа.
После маркировки годных камер и навинчивания колпачка готовые
камеры на крючковом конвейере направляются на комплектование.
.3.11 Обработка вентилей
Герметичное и прочное крепление вентиля к камере является
одним из наиболее важных факторов, определяющих эксплуатационные качества
камер. Для повышения прочности связи с резиной вентили изготавливают из латуни,
а перед креплением к камерному рукаву после очистки от антикоррозийной смазки и
загрязнений их обрезинивают.
Заготовки для резиновой пятки нарезают дисковым ножом РЗП-1
из шприцованного толстостенного рукава, шприцуемого на червячной машине
МЧХ-160. Металлические корпуса вентилей устанавливают в гнезда пресс-форм
(пресс гидравлический 600×600) и сверху накладывают
резиновое кольцо. Формование пятки и ее прочное крепление к латунированному
корпусу вентиля обеспечивается за счет создания давления прессования около 15
МПа. Вулканизацию проводят при 143 °С в течение 12 мин.
По окончании вулканизации пятки вентиля осматривают не забито
ли отверстие в корпусе вентиля, шерохуют на станке ИТЭД-69, затем пятки
промазывают клеем, сушат и подают к камерному агрегату.
4.3.12 Изготовление ободных лент
Для профилирования ободных лент используют МЧХ с диаметром
червяка 160 мм.
Резиновая смесь экструдируется в виде профилированной ленты
со скоростью 12 м/мин. Шприцевание происходит при температуре головки
червячного пресса 70-90 °С, планки - 70-80 °С, корпуса - не выше 40 °С и
заготовки на выходе - не выше 110 °С. Далее заготовка поступает на приемный и
весовой транспортеры и далее в ванну с водой для охлаждения до 40 °С. По выходе из ванны
лента обдувается сжатым воздухом и автоматически режется на заготовки длиной 2600
мм.
Вулканизация ободных лент производится в горизонтальных
котлах на жестких дорнах. Шприцованные заготовки с заданным профилем стыкуют и
надевают на плоские или фигурные дорны с некоторым натяжением, затем дорны с
заготовками ободных лент помещают на полки вагонетки, которую по рельсам
закатывают в котел. Вулканизация длится 30 минут. Давление пара в котле
поддерживается равным 4,6 МПа.
покрышка шинный резиновый корд
Таблица 4.33 - Режим вулканизации ободных лент
Наименование
операции
|
Параметры
|
Продолжительность
операции, мин
|
Время с начала
цикла, мин
|
|
Температура, °С
|
Давление, Мпа
|
|
|
Подача пара в
котел до температуры вулканизации
|
|
|
12
|
0
|
Вулканизация
при температуре
|
155
|
4,6
|
13
|
12
|
Выпуск воздуха
|
|
|
5
|
25
|
Оборудование: автоклав вулканизационный АВТМ 1600*5000-12,5
Общая продолжительность вулканизации, мин - 30
Продолжительность перезарядки, мин - 5
Затем ободную ленту направляют на пробивку отверстий под
вентиль. После чего ленты поступают на разбраковку и комплектацию.
.3.13 Изготовление диафрагм
Диафрагмы изготавливают методом литьевого формования в
специальных прессах К 25.243.02. Резиновые смеси на основе бутилкаучука
изготавливают в две стадии с очисткой смеси в червячных прессах - фильтрах.
Затем смеси подаются в червячную машину холодного питания МЧХ-250 и
экструдируются в виде монолитного шнура прямоугольного сечения; скорость
шприцевания 2 м/мин. Температура головки червячной машины составляет 80-85 °С,
корпуса - 70-75 °С. Полученный шнур режут автоматическим ножом (угол закроя
60°) на заготовки длиною 3450 мм с учётом усадки при хранении. Затем заготовки
подают транспортёром на весы, где проверяют массу и размеры.
С весов годные заготовки заворачивают в полиэтиленовые плёнки
для предохранения от загрязнения и укладывают на стеллажи, где они хранятся не
менее двух, но не более 24 часов. По мере надобности заготовки транспортируют
на участок вулканизации диафрагм.
Перед вулканизацией в литьевом прессе заготовки взвешиваются
вторично и предварительно подогреваются до 70-100 °С. Резиновые заготовки перед
формованием стыкуют в кольцо. Заготовку закладывают в нижнюю полуформу,
опускают сердечник, поднимают нижнюю полуформу вверх. Под действием высокой
температуру и усилия прессования резиновая смесь заполняет зазор между
сердечником и стенками формы. Вулканизация происходит при температуре 180 °С в течение 70 минут, при
давлении 0,9 МПа. Пресс-форму обогревают паром. По окончании вулканизации
нижняя половина формы вместе с сердечником начинается двигаться вниз,
освобождая диафрагму из верхней половины формы. С помощью выталкивателя
диафрагму поднимают из нижней половины формы.
Таблица 4.34 - Режим вулканизации диафрагм 21.00Р-33
Наименование
операции
|
Параметры
|
Продолжительность
операции, мин
|
|
Температура, °С
|
Давление, Мпа
|
|
Вулканизация
при температуре
|
180
|
0,9
|
70
|
Оборудование: пресс гидравлический вулканизационный для
диафрагм ус. 20КН, инд. К25.243.02
Продолжительность перезарядки, мин - 15
После выгрузки диафрагму охлаждают, обрезают выпрессовки,
подшлифовывают и проверяют на отсутствие дефектов на специальном станке,
рабочей частью которого является резиновая камера; камера раздувается и
натягивает диафрагму, что позволяет обнаружить в ней трещины и другие дефекты.
Мелом проставляется дата и смена изготовления.
От партии отбирают одну диафрагму для проверки размеров,
механических показателей и степени вулканизации. Через 15 дней диафрагмы
поступают в цех вулканизации.
5. Расчётная часть
.1 Расчёт материального баланса
Таблица 5.1 - Расчет выпуска товарной продукции
Наименование
изделия
|
Выпуск товарной
продукции, шт
|
Отбор на
испытание готовой продукции
|
Расчетный
выпуск товарной продукции в сутки, шт
|
|
|
|
|
|
в год
|
в сутки
|
проценты
|
количество в
сутки, шт
|
|
|
|
|
|
|
|
Шина 21.00.R33
|
60000
|
186,91
|
0,025
|
0,046
|
186,95
|
|
|
|
|
|
|
Таблица 5.2 - Материальный баланс резиновых смесей
Наименование
смеси
|
Норма расхода
на 1000 шт. шин, кг
|
Потери
|
Расход с
потерями на 1000 шт. шин, кг
|
Расход смеси в
сутки, кг
|
|
|
|
|
|
|
|
%
|
кг
|
|
|
|
|
|
|
|
|
1
|
2
|
3
|
4
|
5
|
6
|
Каркас слой 1
кд-46
|
6733,15
|
3,6
|
242,41
|
6975,52
|
1304,07
|
Каркас слой 2-7
кд-46
|
35953,20
|
3,6
|
1294,30
|
37247,41
|
6962,40
|
Каркас слой 8
кд-46
|
6141,04
|
3,6
|
221,10
|
6362,12
|
1189,39
|
Каркас слой 9
кд-46
|
12905,13
|
3,6
|
464,60
|
13369,71
|
2499,46
|
Профилированная
деталь каркаса кд-46
|
11748,80
|
1,05
|
423,40
|
11872,16
|
2219,50
|
Прослойка
каркаса кд-46
|
11315,52
|
1,05
|
118,80
|
11434,31
|
2137,64
|
Бортовое кольцо
ИД-19
|
3198,30
|
6,25
|
199,90
|
3387,57
|
633,29
|
Бортовое кольцо
для дополнительного крыла БД-56
|
43,86
|
6,25
|
2,70
|
46,60
|
8,71
|
Обертка кольца
ФД-20
|
59,13
|
2,4
|
1,42
|
60,55
|
11,31
|
Наполнительный
шнур НШ-18
|
7721,45
|
1,25
|
96,52
|
7817,97
|
1461,57
|
Крыльевая лента
КД-46
|
1255,76
|
3,6
|
45,20
|
1300,97
|
243,21
|
Бортовая лента
БЛД-21
|
2628,10
|
1,55
|
40,70
|
2668,87
|
498,94
|
Бортовая лента
под дополнительное крыло БЛД-21
|
991,20
|
1,55
|
15,40
|
1006,56
|
188,07
|
Крыльевая лента
БД-57
|
1893,92
|
3,55
|
67,23
|
1961,15
|
366,6
|
Резиновая лента
для изоляции кромок БД-57
|
196,56
|
1,05
|
2,06
|
198,62
|
37,13
|
Бортовая лента
выше пятки борта КД-46
|
878,49
|
3,6
|
31,60
|
910,11
|
170,14
|
Брекер слой 1-3
БД-57
|
20901,02
|
3,55
|
742,00
|
21643,01
|
4046,16
|
Брекер слой 4-5
БД-57
|
11107,85
|
3,55
|
394,30
|
11501,97
|
2150,29
|
Прослойка
брекера БД-57
|
9126,33
|
1,05
|
95,83
|
9222,36
|
1724,12
|
Профилированная
деталь БД-57
|
37521,20
|
1,05
|
393,97
|
37915,17
|
67088,24
|
Подканавочный
слой ПД-168
|
42200,00
|
1,35
|
569,7
|
42769,70
|
7995,79
|
Беговая часть
ПД-167
|
102800,00
|
1,35
|
1387,80
|
104187,80
|
10477,9
|
Боковина ПД-169
|
42552,51
|
1,35
|
574,50
|
43126,97
|
8062,58
|
Автокамера
ЕКД-39
|
20459,32
|
3,85
|
787,70
|
21247,21
|
3972,16
|
Ободная лента
9ЛО-53
|
7708,06
|
1,0
|
77,08
|
7785,14
|
1455,43
|
Диафрагма
(ходимость 40) ДД-7
|
1440,60
|
3,0
|
43,22
|
1483,80
|
277,39
|
Обрезинка пятки
вентиля ЕВД-40
|
30,23
|
1,25
|
0,38
|
30,61
|
5,72
|
Таблица 5.3 - Сводная таблица расхода резиновых смесей
Наименование
смеси
|
Шифр
|
Расход смеси в
сутки, кг
|
1
|
2
|
3
|
Слои каркаса,
прослойка каркаса, крыльевая лента, бортовая лента
|
КД-46
|
16726,81
|
Бортовое кольцо
|
ИД-19
|
633,29
|
Бортовое кольцо
для дополнительного крыла
|
БД-56
|
8,71
|
Обертка кольца
|
ФД-20
|
11,31
|
Наполнительный
шнур
|
НШ-18
|
1461,57
|
Бортовая лента
|
БЛД-21
|
681,01
|
Бортовая лента
под дополнительное крыло, брекер слой 1-3, брекер слой 4-5, прослойка
брекера, профилированная деталь
|
БД-57
|
15412,54
|
Подканавочный
слой
|
ПД-168
|
7995,79
|
Беговая часть
|
ПД-167
|
19477,9
|
Боковина
|
ПД-169
|
8062,58
|
Автокамера
|
ЕКД-39
|
3972,16
|
Ободная лента
|
9ЛО-53
|
1455,43
|
Диафрагма
(ходимость 40)
|
ДД-7
|
277,39
|
Обрезинка пятки
вентиля
|
ЕКД-40
|
5,72
|
Таблица 5.4 - Материальный баланс ингредиентов резиновой
смеси
Наименование
ингредиентов
|
Массовые
проценты
|
Расход на
суточную программу, кг
|
Потери
|
Расход на
суточную программу с потерями, кг
|
|
|
|
%
|
кг
|
|
1
|
2
|
3
|
4
|
5
|
6
|
КД-46
(обрезинивание слоев каркаса, бортовой ленты, крыльевой ленты, для
изготовления каркаса)
|
НК, RSS1-3,
SHR-10.вязкость по Муни(60±5)усл.ед.
|
58,48
|
9781,83
|
0,16
|
15,65
|
9797,48
|
Сера
|
1,29
|
215,77
|
0,85
|
1,83
|
217,6
|
Сульфенамид Ц
|
0,47
|
78,62
|
0,50
|
0,39
|
79,01
|
Малеимид Ф
|
1,46
|
244,21
|
0,50
|
1,22
|
245,43
|
Ультрасил VN3
|
2,92
|
488,42
|
1,00
|
4,88
|
493,3
|
Цинковые белила
|
2,92
|
488,42
|
0,70
|
3,42
|
491,84
|
Стеариновая
кислота
|
1,17
|
195,7
|
0,30
|
0,58
|
196,28
|
Канифоль
сосновая
|
244,21
|
0,50
|
1,22
|
245,43
|
Масло ПН-6Ш
|
2,92
|
488,42
|
0,50
|
2,44
|
490,86
|
Мягчитель АСМГ
|
2,92
|
488,42
|
0,50
|
2,44
|
490,86
|
Диафен ФП
|
0,58
|
97,01
|
0,50
|
0,48
|
97,49
|
Углерод
технический П-323
|
23,41
|
3914,11
|
1,00
|
39,14
|
3953,25
|
Итого
|
100,00
|
16726,81
|
|
73,69
|
16800,5
|
ИД-19
(обрезинка бортовой проволоки)
|
НК, RSS1-3,
SMR-5, SМR-10, SМR-20.вязкость по Муни(60±5)усл.ед.
|
50,49
|
319,53
|
0,16
|
0,511
|
320,04
|
Сера
|
0,61
|
3,86
|
0,85
|
0,03
|
3,89
|
Сера полимерная
|
2,42
|
15,31
|
0,85
|
0,13
|
15,44
|
Сульфенамид Ц
|
0,30
|
1,9
|
0,50
|
0,01
|
1,91
|
Тиазол 2МБС
|
0,10
|
0,63
|
0,50
|
0,003
|
0,633
|
Цинковые белила
|
5,05
|
31,96
|
0,70
|
0,22
|
32,18
|
Сантогард PVI
|
0,15
|
0,95
|
0,50
|
0,004
|
1,00
|
Стеариновая
кислота
|
1,01
|
6,39
|
0,30
|
0,02
|
6,41
|
Канифоль
сосновая
|
1,51
|
9,56
|
0,50
|
0,04
|
9,6
|
Масло ПН-6Ш
|
2,52
|
15,96
|
0,50
|
0,08
|
16,04
|
Мягчитель АСМГ
|
5,05
|
31,96
|
0,50
|
0,15
|
32,11
|
Диафен ФП
|
0,51
|
3,2
|
0,50
|
0,016
|
3,21
|
Углерод
технический П-245
|
15,14
|
95,83
|
1,00
|
0,95
|
96,78
|
Углерод
технический П-514
|
15,14
|
95,83
|
1,00
|
0,95
|
96,78
|
Итого
|
100,00
|
633,29
|
|
3,11
|
636,4
|
БД-56
(изготовление бортового кольца)
|
НК, RSS1-3,
SMR-5, непластикат
|
52,33
|
4,55
|
0,16
|
0,007
|
4,56
|
Сера
|
1,78
|
0,15
|
0,85
|
0,001
|
0,15
|
Сера полимерная
|
0,47
|
0,04
|
0,85
|
0,0003
|
0,04
|
Сульфенамид М
|
0,31
|
0,03
|
0,50
|
0,0001
|
0,03
|
Модификатор РУ
|
1,05
|
0,09
|
0,50
|
0,0004
|
0,09
|
Ультрасил VN3
|
5,23
|
0,46
|
1,00
|
0,004
|
0,47
|
Нафтенат
кобальта
|
1,05
|
0,09
|
1,00
|
0,0009
|
0,09
|
Сантогард PVI
|
0,1
|
0,01
|
0,50
|
0,000
|
0,01
|
Цинковые белила
|
4,19
|
0,36
|
0,70
|
0,003
|
0,36
|
Стеарат натрия
|
0,52
|
0,05
|
1,00
|
0,0005
|
0,05
|
Смола SP - 1077
|
2,62
|
0,23
|
1,00
|
0,002
|
0,23
|
Масло ПН-6Ш
|
2,1
|
0,18
|
0,50
|
0,00
|
0,18
|
Мягчитель АСМГ
|
1,57
|
0,14
|
0,50
|
0,00
|
0,14
|
Диафен ФП
|
0,52
|
0,05
|
0,50
|
0,00
|
0,05
|
Углерод
технический П-323
|
26,16
|
2,28
|
1,00
|
0,03
|
2,31
|
Итого
|
100
|
8,71
|
|
0,05
|
8,76
|
ФД-20 (обертка
борта)
|
НК, RSS1-3,
SMR-5, SМR-10, SМR-20.вязкость по Муни(60±5)усл.ед.
|
22,84
|
2,58
|
0,16
|
0,004
|
2,58
|
СКИ-3 II группа
|
22,84
|
2,58
|
0,03
|
0,001
|
2,58
|
Регенерат РКТ
|
13,70
|
1,55
|
1,00
|
0,01
|
1,55
|
Сера
|
1,10
|
0,12
|
0,85
|
0,00
|
0,12
|
2-меркаптобензтиазол
|
0,18
|
0,02
|
0,50
|
0,00
|
0,02
|
Сульфенамид Ц
|
0,28
|
0,03
|
0,50
|
0,00
|
0,03
|
Модификатор РУ
|
1,37
|
0,15
|
0,50
|
0,001
|
0,15
|
Цинковые белила
|
2,28
|
0,26
|
0,70
|
0,002
|
0,26
|
Стеариновая
кислота
|
0,46
|
0,05
|
0,30
|
0,00
|
0,05
|
Канифоль
сосновая
|
1,37
|
0,15
|
0,50
|
0,001
|
0,15
|
Углеводородные
смолы
|
6,85
|
0,7
|
1,95
|
0,01
|
0,78
|
Масло ПН-6Ш
|
3,66
|
0,41
|
0,50
|
0,002
|
0,41
|
Диафен ФП
|
0,23
|
0,03
|
0,50
|
0,00
|
0,03
|
Мел
природообогащенный
|
9,14
|
1,03
|
1,50
|
0,02
|
1,05
|
Углерод
технический П-514
|
13,70
|
1,55
|
1,00
|
0,02
|
1,57
|
Итого
|
100
|
11,31
|
|
0,071
|
11,38
|
НШ-18
(наполнительный шнур)
|
НК, RSS1-3,
SMR-5, непластикат
|
50,84
|
743,35
|
0,16
|
1,18
|
744,53
|
ТЭП ДСТ-30Р
|
2,54
|
37,12
|
0,03
|
0,01
|
37,13
|
Сера полимерная
|
2,54
|
37,12
|
0,85
|
0,31
|
37,13
|
Сульфенамид М
|
0,46
|
6,72
|
0,50
|
0,03
|
6,75
|
Тиазол 2МБС
|
0,10
|
1,46
|
0,50
|
0,007
|
1,467
|
2,54
|
37,12
|
1,00
|
0,37
|
37,49
|
Модификатор РУ
|
1,02
|
14,9
|
0,50
|
0,07
|
14,97
|
Бензойная
кислота
|
0,15
|
2,19
|
0,70
|
0,01
|
2,2
|
Цинковые белила
|
2,54
|
37,12
|
0,70
|
0,25
|
37,37
|
Сантогард PVI
|
0,15
|
2,19
|
0,50
|
0,01
|
2,2
|
Стеариновая
кислота
|
1,02
|
14,9
|
0,30
|
0,04
|
14,94
|
Канифоль
сосновая
|
1,02
|
14,9
|
0,50
|
0,07
|
14,97
|
Мягчитель АСМГ
|
2,54
|
37,12
|
0,50
|
0,18
|
37,3
|
Ацетонанил Р,
РГ
|
0,25
|
22,5
|
0,50
|
0,43
|
22,93
|
Углеводородные
смолы
|
1,53
|
3,65
|
1,95
|
0,005
|
3,65
|
Диафен ФП
|
0,25
|
3,65
|
0,50
|
0,018
|
3,65
|
Углерод
технический П-514
|
20,34
|
297,28
|
1,00
|
2,97
|
300,25
|
Углерод
технический П-323
|
10,17
|
148,49
|
1,00
|
1,48
|
149,97
|
Итого
|
100
|
1461,57
|
|
7,43
|
1469,00
|
БЛД-21
(бортовая лента)
|
НК, RSS1-3,
SMR-5.вязкость по Муни(60±5)усл.ед.
|
35,33
|
244,02
|
0,16
|
0,39
|
244,41
|
СКМС-30 АРКМ
|
19,13
|
131,35
|
0,03
|
0,39
|
131,74
|
ТЭП ДСТ-30Р
|
2,73
|
18,82
|
0,03
|
0,006
|
18,82
|
Сера полимерная
|
1,53
|
10,51
|
0,85
|
0,08
|
10,59
|
Сульфенамид М
|
0,49
|
3,36
|
0,50
|
0,016
|
3,376
|
Цинковые белила
|
1,64
|
11,26
|
0,70
|
0,07
|
11,33
|
Сантогард PVI
|
0,16
|
1,1
|
0,50
|
0,005
|
1,105
|
Стеариновая
кислота
|
1,09
|
7,49
|
0,30
|
0,02
|
7,51
|
Канифоль
сосновая
|
1,09
|
7,49
|
0,50
|
0,03
|
7,52
|
Масло ПН-6Ш
|
2,73
|
18,82
|
0,50
|
0,09
|
18,91
|
Углеводородные
смолы
|
1,09
|
7,49
|
1,95
|
0,14
|
7,63
|
Диафен ФП
|
2,73
|
18,82
|
0,50
|
0,09
|
18,91
|
Углерод
технический П-234
|
30,06
|
206,45
|
1,00
|
2,06
|
208,51
|
Итого
|
100
|
687,01
|
|
3,38
|
690,39
|
БД-57 (бортовая
лента, брекер)
|
НК, RSS1-3,
SMR-5, непластикат
|
52,67
|
8116,24
|
0,16
|
12,98
|
8129,22
|
Сера
|
1,79
|
275,88
|
0,85
|
2,34
|
278,22
|
Сера полимерная
|
0,47
|
72,43
|
0,85
|
0,61
|
73,04
|
Сульфенамид М
|
0,32
|
49,32
|
0,50
|
0,24
|
49,56
|
Малеимид Ф
|
2,63
|
406,89
|
0,50
|
2,03
|
409,0
|
Модификатор
НФА-К
|
0,4
|
60,10
|
0,50
|
0,3
|
60,40
|
Нафтенат
кобальта
|
1,05
|
161,83
|
1,00
|
1,61
|
163,44
|
Сантогард PVI
|
0,11
|
16,90
|
0,50
|
0,08
|
17,00
|
Цинковые белила
|
4,21
|
650,40
|
0,70
|
4,55
|
655,0
|
Стеарат натрия
|
0,53
|
81,68
|
1,00
|
0,81
|
83,0
|
Смола SP - 1077
|
2,63
|
406,89
|
1,00
|
0,40
|
407,2
|
Масло ПН-6Ш
|
2,11
|
325,20
|
0,50
|
1,62
|
327,0
|
Мягчитель АСМГ
|
1,28
|
243,51
|
0,50
|
1,21
|
244,72
|
Диафен ФП
|
0,53
|
81,68
|
0,50
|
0,40
|
82,08
|
Углерод
технический П-323
|
28,97
|
4463,47
|
1,00
|
44,63
|
4508,10
|
Итого
|
100
|
15412,54
|
|
73,81
|
15486,35
|
ПД-168
(подканавочный слой протектора)
|
НК, RSS1-3,
SMR-5.вязкость по Муни(60±5)усл.ед.
|
57,8
|
4621,56
|
0,16
|
7,39
|
4628,95
|
Сера
|
0,58
|
46,38
|
0,85
|
0,39
|
46,77
|
Сульфенамид Ц
|
0,58
|
46,38
|
0,50
|
0,23
|
46,61
|
N,N'-дитиодиморфалин
|
0,87
|
69,56
|
0,50
|
0,34
|
69,90
|
Фталевый
ангидрид
|
0,29
|
23,18
|
0,50
|
0,11
|
23,20
|
Цинковые белила
|
4,05
|
323,82
|
0,70
|
2,26
|
326,08
|
Стеариновая
кислота
|
1,45
|
115,93
|
0,30
|
0,34
|
116,27
|
Канифоль
сосновая
|
1,73
|
138,32
|
0,50
|
0,69
|
140,01
|
Масло ПН-6Ш
|
2,31
|
183,9
|
0,50
|
0,91
|
184,81
|
Диафен ФП
|
0,58
|
46,38
|
0,50
|
0,23
|
46,61
|
Ацетонанил Р,
РГ
|
0,87
|
69,56
|
0,50
|
0,34
|
69,9
|
Углерод
технический П-323
|
28,9
|
2310,70
|
1,00
|
23,10
|
2333,8
|
Итого
|
100
|
7995,79
|
|
36,33
|
8032,12
|
ПД-167 (беговая
часть протектора)
|
НК, RSS1-3,
SMR-5, SМR-10.вязкость по Муни(60±5)усл.ед.
|
39,85
|
7761,90
|
0,16
|
12,41
|
СКИ-3 I группа
|
17,08
|
3326,80
|
0,03
|
0,99
|
3328,0
|
Сера
|
0,57
|
111,02
|
0,85
|
0,94
|
112,0
|
Сульфенамид М
|
0,57
|
111,02
|
0,50
|
0,55
|
111,57
|
N,N'-дитиодиморфалин
|
0,85
|
165,56
|
0,50
|
0,82
|
166,38
|
Гексол ЗВ, ЗВИ
|
0,28
|
54,53
|
0,50
|
0,27
|
55,0
|
Бензойная
кислота
|
0,28
|
54,53
|
0,70
|
0,38
|
55,5
|
Сантогард PVI
|
0,09
|
15,58
|
0,50
|
0,07
|
15,65
|
Цинковые белила
|
2,28
|
444,09
|
0,70
|
3,1
|
447,19
|
Стеариновая
кислота
|
1,71
|
333,07
|
0,30
|
0,9
|
334,0
|
Канифоль
сосновая
|
1,14
|
222,04
|
0,50
|
1,11
|
223,15
|
Масло ПН-6Ш
|
2,28
|
444,09
|
0,50
|
2,22
|
446,31
|
Диафен ФП
|
0,57
|
111,02
|
0,50
|
0,55
|
112,0
|
Ацетонанил Р,
РГ
|
1,14
|
222,04
|
0,50
|
1,11
|
223,158
|
Ультрасил VN3
|
5,69
|
1108,29
|
1,00
|
11,08
|
1119,37
|
Углерод
технический П-245
|
25,62
|
4992,18
|
1,00
|
49,92
|
5042,10
|
Итого
|
100,00
|
19477,90
|
|
196,31
|
19674,21
|
ПД-169
(боковина протектора)
|
НК, RSS1-3,
SMR-5, SМR-10.вязкость по Муни(60±5)усл.ед.
|
44,44
|
3628,16
|
0,16
|
5,8
|
3634,0
|
СКМС-30 АРК
|
19,05
|
1535,11
|
0,03
|
0,46
|
1535,57
|
Сера
|
0,63
|
50,79
|
0,85
|
0,43
|
51,22
|
Сульфенамид Ц
|
0,95
|
76,59
|
0,50
|
0,38
|
76,97
|
Фталевый
ангидрид
|
0,32
|
24,90
|
0,50
|
0,12
|
25,02
|
Масло ПН-6Ш
|
3,81
|
255,58
|
0,50
|
1,78
|
257,36
|
Цинковые белила
|
3,17
|
80,62
|
0,70
|
0,24
|
81,0
|
Стеариновая
кислота
|
0,95
|
161,25
|
0,30
|
0,8
|
162,05
|
Канифоль
сосновая
|
1,90
|
322,50
|
0,50
|
1,61
|
324,11
|
Защитный воск
ЗВ-1
|
1,28
|
104,81
|
0,70
|
0,73
|
106,0
|
Диафен ФП
|
1,28
|
104,81
|
0,50
|
0,73
|
106,0
|
Углерод
технический П-323
|
22,22
|
1789,80
|
0,10
|
17,89
|
1807,69
|
Итого
|
100,00
|
8062,58
|
|
30,63
|
8093,21
|
ЕКД-39 (ездовая
камера)159,22
|
Бутилкаучук БК
1675Т
|
53,05
|
2107,23
|
0,030
|
0,63
|
2107,86
|
ХБК НТ-1066
|
1,06
|
42,10
|
0,030
|
0,01
|
42,11
|
Сера
|
1,06
|
42,10
|
0,850
|
0,35
|
42,45
|
Тиазол 2МБС
|
0,26
|
10,72
|
0,500
|
0,05
|
10,77
|
Тиурам Д
|
0,53
|
21,05
|
0,500
|
0,1
|
21,15
|
Цинковые белила
|
2,65
|
105,26
|
0,700
|
0,73
|
105,90
|
Стеариновая
кислота
|
0,53
|
21,05
|
0,300
|
0,06
|
21,11
|
Октофор N, Na
|
1,06
|
42,10
|
0,500
|
0,21
|
42,31
|
Стабилойл 18
|
10,60
|
421,44
|
0,500
|
2,1
|
423,54
|
Углерод
технический П-514
|
29,20
|
1159,07
|
0,100
|
11,59
|
1170,66
|
Итого
|
100,00
|
3972,16
|
|
15,83
|
3987,99
|
9ЛО-53 (ободная
лента)
|
СКИ-3
|
24,16
|
356,43
|
0,030
|
0,1
|
356,53
|
СКД
|
14,37
|
213,90
|
0,030
|
0,06
|
213,96
|
СКМС- 30 АРКМ
15
|
9,78
|
142,48
|
0,030
|
0,04
|
142,51
|
Регенерат РКТ
|
14,69
|
213,80
|
1,000
|
2,13
|
215,93
|
Сера
|
0,64
|
9,31
|
0,850
|
0,07
|
9,38
|
Сульфенамид Ц
|
0,59
|
8,58
|
0,500
|
0,04
|
8,62
|
Тиазол 2МБС
|
0,10
|
1,45
|
0,500
|
0,007
|
1,457
|
Фталевый
ангидрид
|
0,24
|
3,49
|
0,500
|
0,01
|
3,5
|
Цинковые белила
|
1,47
|
21,39
|
0,700
|
0,14
|
21,53
|
Стеариновая
кислота
|
1,48
|
7,13
|
0,300
|
0,02
|
7,15
|
Канифоль
сосновая
|
0,98
|
14,26
|
0,500
|
0,07
|
14,33
|
Масло ПН-6Ш
|
5,88
|
85,57
|
0,500
|
0,42
|
85,90
|
Защитный воск
ЗВ-1
|
0,49
|
7,13
|
0,700
|
0,04
|
7,17
|
Диафен ФП
|
0,24
|
3,49
|
0,500
|
0,01
|
3,50
|
Ацетонанил Р,
РГ
|
0,73
|
10,62
|
0,500
|
0,05
|
10,67
|
Углерод
технический П-514
|
24,16
|
356,43
|
1,000
|
3,56
|
359,90
|
Итого
|
100,00
|
31455,43
|
|
6,76
|
1462,19
|
ДД-7
(диафрагма)
|
Бутилкаучук
БК-1675Т
|
57,38
|
159,22
|
0,030
|
159,26
|
Наирит ДН
|
2,87
|
7,93
|
0,030
|
0,002
|
7,93
|
Амберол St-137
|
4,59
|
12,73
|
0,500
|
0,06
|
12,79
|
Гексол ЗВ, ЗВИ
|
0,17
|
0,47
|
0,500
|
0,002
|
0,47
|
Цинковые белила
|
1,72
|
4,77
|
0,700
|
0,03
|
4,80
|
Стеариновая
кислота
|
1,72
|
4,77
|
0,300
|
0,01
|
4,78
|
Стабилойл 18
|
2,87
|
7,93
|
0,500
|
0,03
|
7,96
|
Углерод
технический П-514
|
14,34
|
39,77
|
1,000
|
0,39
|
40,16
|
Углерод
технический П-234
|
14,34
|
39,77
|
1,000
|
0,39
|
40,16
|
Итого
|
100,00
|
277,39
|
|
0,954
|
278,34
|
ЕКД-40
(вентильная резина)
|
СКИ 3-01
|
39,54
|
2,28
|
0,030
|
0,00
|
2,28
|
Хлорбутилкаучук
ХБК НТ-1068
|
13,18
|
0,75
|
0,030
|
0,0002
|
0,75
|
Сера
|
1,58
|
0,09
|
0,850
|
0,0007
|
0,09
|
Сульфенамид Ц
|
0,64
|
0,03
|
0,500
|
0,0001
|
0,03
|
Белая сажа
БС-120
|
13,18
|
0,74
|
1,000
|
0,007
|
0,747
|
Цинковые белила
|
10,54
|
0,62
|
0,700
|
0,004
|
0,624
|
Бензойная
кислота
|
0,26
|
0,01
|
0,700
|
0,00
|
0,01
|
Модификатор РУ
|
0,53
|
0,03
|
0,500
|
0,0001
|
0,03
|
Мягчитель АСМГ
|
1,05
|
0,06
|
0,500
|
0,0003
|
0,06
|
Защитный воск
ЗВ-1
|
1,05
|
0,06
|
0,700
|
0,0004
|
0,06
|
Углерод
технический П-514
|
18,45
|
1,08
|
1,000
|
0,01
|
1,09
|
Итого
|
100,00
|
5,72
|
|
0,022
|
5,74
|
Таблица 5.5 - Сводная таблица расхода ингредиентов
Наименование
ингредиентов
|
Наименование
смесей
|
Итого, кг
|
|
ПД-167
|
ПД-168
|
ПД-169
|
БД-57
|
КД-46
|
БЛД-21
|
НШ-18
|
ФД-20
|
ИД-19
|
ЕКД-39
|
ЕКД-40
|
9ЛО-53
|
ДД-7
|
БД-56
|
Расчет
|
Принято
|
1
|
2
|
3
|
4
|
5
|
6
|
7
|
8
|
9
|
10
|
11
|
12
|
13
|
14
|
15
|
16
|
17
|
2
Меркаптобензтиазол
|
|
|
|
|
|
|
|
0,02
|
|
|
|
|
|
|
0,02
|
1,0
|
N,N-'дитиодиморфолин
|
166,38
|
69,69
|
|
|
|
|
|
|
|
|
|
|
|
|
236,28
|
237,0
|
АФФС типа
Амберол ST-137
|
|
|
|
|
|
|
|
|
|
|
|
|
12,79
|
|
12,79
|
13,0
|
Ацетонанил Р
|
223,15
|
69,9
|
|
|
|
|
3.,65
|
|
|
|
|
10,.67
|
|
|
307,37
|
308,0
|
Бензойная
кислота
|
55,0
|
|
|
|
|
|
2,2
|
|
|
|
0,01
|
|
|
|
57,21
|
58,0
|
Мягчитель АСМГ
|
|
|
|
244,72
|
490,81
|
|
37,3
|
|
32,13
|
|
0.06
|
|
|
0,14
|
805,19
|
806,0
|
БК-1675Т
|
|
|
|
|
|
|
|
|
|
2107,86
|
|
|
159,26
|
|
2267,12
|
2268,0
|
Гексол 3В
|
55,0
|
|
|
|
|
|
|
|
|
|
|
|
0,47
|
|
55,47
|
56,0
|
Диафен ФП
|
112,0
|
46,61
|
106,0
|
82,08
|
97,49
|
18,91
|
3,65
|
0,03
|
3,21
|
|
|
3,5
|
|
0,05
|
473,53
|
474,0
|
Защитный воск
ЗВ-1
|
|
|
106,0
|
|
|
|
|
|
|
|
0,06
|
7,17
|
|
|
113,23
|
114,0
|
Канифоль
сосновая
|
223,15
|
140,01
|
162,05
|
|
245,43
|
7,52
|
14,97
|
0,15
|
9,6
|
|
|
14,33
|
|
|
817,21
|
818,0
|
Кислота
стеариновая техническая (стеарин)
|
334,0
|
116,27
|
81,0
|
|
196,28
|
7,51
|
14,94
|
0,05
|
6,41
|
21,11
|
|
7,15
|
4,78
|
|
789,50
|
790,0
|
Кремнекислотный
наполнитель Ультрасил VN3
|
1119,37
|
|
|
|
493,3
|
|
37,49
|
|
|
|
|
|
|
0,47
|
1650,26
|
1651,0
|
Малеимид Ф
|
|
|
|
409,0
|
245,43
|
|
|
|
|
|
|
|
|
|
654,43
|
655,0
|
Масло ПН-6Ш
|
446,31
|
184,81
|
324,11
|
327,0
|
490,86
|
18,91
|
|
0,41
|
16,04
|
|
|
85,9
|
|
0,18
|
1894,53
|
1895,0
|
Мел природный
обогащенный
|
|
|
|
|
|
|
|
1,05
|
|
|
|
|
|
|
1,05
|
2,0
|
Модификатор
Н-ФАК
|
|
|
|
60,4
|
|
|
|
|
|
|
|
|
|
|
60,4
|
61,0
|
Модификатор РУ
|
|
|
|
|
|
|
14,97
|
0,15
|
|
|
0,03
|
|
|
0,09
|
15,24
|
16,0
|
Наирит ДН
|
|
|
|
|
|
|
|
|
|
|
|
|
7,93
|
|
7,93
|
8,0
|
Нафтенат
кобальта
|
|
|
|
163,44
|
|
|
|
|
|
|
|
|
|
0,09
|
163,53
|
164,0
|
НК, RSS1-3,
SMR-5, непластицированный
|
|
|
|
8129,22
|
|
|
744,53
|
|
|
|
|
|
|
4,56
|
8878,31
|
8879,0
|
НК, RSS1-3,
SМR-5,SMR-10, SMR-20 вязкость по Муни (60±5) усл.ед
|
7774,31
|
4628,95
|
3634,0
|
|
9797,48
|
244,41
|
|
2,58
|
320,04
|
|
|
|
|
|
26401,77
|
26402,00
|
Октофор N
|
|
|
|
|
|
|
|
|
|
42,31
|
|
|
|
|
42,31
|
43,0
|
Регенерат РКТ
|
|
|
|
|
|
|
|
1,55
|
|
|
|
215,93
|
|
|
217,48
|
218,0
|
Сажа белая
БС-120
|
|
|
|
|
|
|
|
|
|
|
0,747
|
|
|
|
0,747
|
1,0
|
Сантогард РVI
|
15,65
|
|
|
17,0
|
|
1,105
|
2,2
|
|
1,0
|
|
|
|
|
0,01
|
36,96
|
37,0
|
Сера
|
112,0
|
46,77
|
51,22
|
278,22
|
217,6
|
|
|
0,12
|
42,45
|
0,09
|
9,38
|
|
0,15
|
761,89
|
762,0
|
Сера полимерная
|
|
|
|
73,04
|
|
10,59
|
37,43
|
|
15,44
|
|
|
|
|
0,04
|
136,54
|
137,0
|
СКД 2 марка
|
|
|
|
|
|
|
|
|
|
|
|
213,96
|
|
|
213,96
|
214,0
|
СКИ-3
|
3328,0
|
|
|
|
|
|
|
2,58
|
|
|
|
356,53
|
|
|
3687,1
|
3688,0
|
СКИ-3-01
1группа
|
|
|
|
|
|
|
|
|
|
|
2,28
|
|
|
|
2,28
|
3,0
|
СКМС-3ОАРК
|
|
|
1535,57
|
|
|
131,74
|
|
|
|
|
|
|
|
|
1667,31
|
1668,0
|
СКМС-30 АРКМ-
15,1 группа
|
|
|
|
|
|
|
|
|
|
|
|
142,51
|
|
|
142,51
|
143,0
|
Смола SР-1077
|
|
|
|
407,3
|
|
|
|
|
|
|
|
|
|
0,23
|
407,53
|
408,0
|
Стабилоил 18
|
|
|
|
|
|
|
|
|
|
423,54
|
|
|
7,96
|
|
431,5
|
432,0
|
Стеарат натрия
|
|
|
|
80,0
|
|
|
|
|
|
|
|
|
|
0,05
|
83,05
|
83,0
|
Сульфенамид М
|
111,57
|
|
|
49,56
|
|
3,376
|
6,75
|
|
|
|
|
|
|
0,03
|
171,28
|
172,0
|
Сульфенамид Ц
|
|
46,61
|
76,97
|
|
79,01
|
|
|
0,03
|
1,91
|
|
0,03
|
8,62
|
|
|
213,18
|
214,0
|
Тиазол 2МБС
|
|
|
|
|
|
|
1,467
|
|
0,633
|
10,77
|
|
1,457
|
|
|
14,32
|
15,0
|
Тиурам Д
|
|
|
|
|
|
|
|
|
|
21,15
|
|
|
|
|
21,15
|
22,0
|
ТЭП ДСТ-30Р
|
|
|
|
|
|
18,82
|
37,13
|
|
|
|
|
|
|
|
55,95
|
56,0
|
УВС
|
|
|
|
|
|
7,63
|
22,93
|
0,78
|
|
|
|
|
|
|
31,34
|
32,0
|
Углерод
технический П-234 (245)
|
5042,1
|
|
|
|
|
|
|
|
96,78
|
|
|
|
40,16
|
|
5179,04
|
5180,0
|
Углерод
технический П-245 (234)
|
5039,85
|
|
|
|
|
|
|
|
|
|
|
|
|
|
5039,85
|
5040,0
|
Углерод
технический П-323 (324)
|
|
2333,8
|
1807,69
|
4508,1
|
3953,25
|
|
|
|
|
|
|
|
|
2,31
|
12605,15
|
12606,0
|
Углерод
технический П-514
|
|
|
|
|
|
|
300,25
|
1,57
|
96,78
|
1170,66
|
1,09
|
359,9
|
40,16
|
|
1970,41
|
1971,0
|
Фталевый
ангидрид
|
|
23,2
|
25,02
|
|
|
|
|
|
|
|
|
3,5
|
|
|
51,72
|
52,0
|
ХБК НТ-1068
|
|
|
|
|
|
|
|
|
|
42,11
|
0,75
|
|
|
|
42,86
|
43,0
|
Цинковые белила
|
447,19
|
326,08
|
257,36
|
655,0
|
491,84
|
11,33
|
37,37
|
0,26
|
32,18
|
105,9
|
0,624
|
21,53
|
4,80
|
0,36
|
2391,82
|
2392,0
|
Каучук в виде
латекса ДБА-1 (100%)
|
|
|
|
|
|
|
|
|
|
|
|
|
|
|
71,55
|
72,0
|
Каучук в виде
латекса СКД-1с (100%)
|
|
|
|
|
|
|
|
|
|
|
|
|
|
|
71,55
|
72,0
|
Смола СФ-282
(100%)
|
|
|
|
|
|
|
|
|
|
|
|
|
|
|
22,68
|
23,0
|
Таблица 5.6 - Материальный баланс пропиточного состава
Наименование
|
Норма расхода
на 1000 шт. шин, кг
|
Потери
|
Расход на
суточную программу, кг (на сухой остаток)
|
|
|
%
|
кг
|
|
ПР-01-02-01-308
|
904,64
|
-
|
-
|
169,13
|
Таблица 5.7 - Материальный баланс ингредиентов на
приготовление пропиточного состава (на сухой остаток)
Наименование
ингредиентов
|
Весовой %
|
Расход в сутки,
кг
|
Потери
|
Расход в сутки
с потерями, кг
|
|
|
|
%
|
кг
|
|
Каучук в виде
латекса ДБА-1 (100%)
|
40,30
|
68,15
|
5
|
3,4
|
71,55
|
Каучук в виде
латекса СКД-1с (100%)
|
40,30
|
68,15
|
5
|
3,4
|
71,55
|
Смола СФ-282
(100%)
|
13,28
|
22,46
|
1
|
0,22
|
22,68
|
Формальдегид
(100%)
|
5,32
|
9,01
|
5
|
0,45
|
9,45
|
Едкий натр
(100%)
|
0,80
|
1,35
|
5
|
0,06
|
1,41
|
Итого
|
100,00
|
169,13
|
|
|
176,64
|
Таблица 5.8 - Материальный баланс клеев и смазок
Наименование
операций
|
Шифр смеси
|
Единица
измерения, кг
|
Расход на
1000шт. шин
|
Расход в сутки,
кг
|
автопокрышка
|
Для промазки
заплечиков барабана
|
КЯ-67
|
кг
|
7,50
|
1,40
|
Для промазки
бортовой части покрышек перед вулканизацией
|
СК-75
|
кг
|
254,25
|
47,53
|
Для промазки
новых диафрагм
|
СК-75
|
кг
|
6,00
|
1,12
|
Для окраски
пресс-форм цеха вулканизации КГШ
|
СК-9в (СК-9д)
|
кг
|
495,00
|
92,54
|
Для окраски
внутренней поверхности покрышек
|
СК-92
|
кг
|
584,33
|
109,24
|
Для
опрыскивания гранул маточных смесей
|
СК-96
|
кг
|
14800,00
|
2766,86
|
ездовая камера
|
Для промазки
рукава под фланец
|
КЯ-79
|
кг
|
3,72
|
0,69
|
Промазка фланца
вентиля
|
КЯ-78
|
кг
|
1,59
|
0,29
|
Для маркировки
сырых заготовок камер
|
КЯ-68
|
кг
|
4,41
|
0,82
|
ободная лента
|
Для промазки
стыка ленты
|
КЯ-83
|
кг
|
4,86
|
0,9
|
Таблица 5.9 - Материальный баланс текстильных материалов
Наименование
материала
|
Расход на 1000
шт. шин
|
Коэффициент
изменения площади (КИП)
|
Расход
материала суровья в сутки, м2
|
|
Обрезиненного,м2
|
Суровья, м2
|
|
|
слои каркаса
|
352 КНТС
|
7268,21
|
6904,78
|
0,95
|
1290,85
|
|
|
|
|
|
35 КНТС
|
43581,44
|
41184,46
|
0,945
|
7699,43
|
352КНТС
|
6629,29
|
6297,82
|
0,95
|
1177,38
|
123 КНТС
|
6663,75
|
6263,93
|
0,94
|
1171,04
|
крыльевая лента
|
232 КНТС
|
1531,26
|
1454,69
|
0,95
|
271,95
|
обертка
|
Бязь
|
400,10
|
400,10
|
-
|
74,79
|
бортовая лента
|
232 КНТС
|
1071,22
|
1017,65
|
0,95
|
190,24
|
Таблица 5.10 - Материальный баланс металлической арматуры
Наименование
|
Ед.изм.
|
Норма расхода
на 1000 шт. шин
|
Потери
|
Расход на
суточную программу
|
|
|
|
%
|
кол-во
|
|
слои брекера
|
Металлокорд 52л
15/23
|
м²
|
5690,45
|
2,5
|
142,26
|
1090,42
|
21л 22
|
м²
|
3588,9
|
2,5
|
89,72
|
687,71
|
бортовое кольцо
для дополнительного крыла
|
22л 15
|
кг
|
152,40
|
5,0
|
7,62
|
29,91
|
|
п.м
|
21928,80
|
5,0
|
1096,44
|
бортовая лента
|
22л 15
|
м²
|
1120,00
|
2,5
|
28,00
|
214,61
|
Проволока
|
Проволока1л
|
п.м.
|
227736,00
|
5,0
|
11386,80
|
44704,0
|
|
кг
|
17353,48
|
5,0
|
867,67
|
3406,44
|
Вентиль
|
шт
|
1000,00
|
-
|
-
|
186,95
|
.2 Расчет количества оборудования
Таблица 5.11 - Расчет количества резиносмесителей
Наименование
смеси
|
Цикл смешения,
мин
|
Объем загрузки,
дм3
|
Расчетная
плотность, кг/м3
|
Производи-тельность,
кг/ч
|
Расход смеси в
сутки, кг
|
Машино-часы
|
Расчетное
количество
|
1
|
2
|
3
|
4
|
5
|
6
|
7
|
8
|
КД-46
|
|
|
|
|
|
|
|
1 стадия
|
3,0
|
170
|
|
3243,6
|
16091,2
|
4,96
|
0,21
|
2 стадия
|
3,0
|
160
|
|
3168,0
|
16726,81
|
5,27
|
0,22
|
ИД-19
|
|
|
|
|
|
|
|
1 стадия
|
3,0
|
170
|
1,16
|
3519,0
|
607,44
|
0,17
|
0,007
|
2 стадия
|
3,0
|
160
|
1,17
|
3369,6
|
633,29
|
0,18
|
0,007
|
БД-56
|
|
|
|
|
|
|
|
1 стадия
|
5,0
|
170
|
1,11
|
2037,96
|
8,34
|
0,004
|
0,00017
|
2 стадия
|
3,5
|
170
|
1,11
|
2911,37
|
8,34
|
0,002
|
0,00009
|
3 стадия
|
3,0
|
160
|
1,12
|
3225,60
|
8,71
|
0,002
|
0,00004
|
ФД-20
|
|
|
|
|
|
|
|
1 стадия
|
3,0
|
170
|
1,15
|
3488,4
|
10,7
|
0,003
|
0,00013
|
2 стадия
|
3,0
|
160
|
1,16
|
3312,0
|
11,31
|
0,003
|
0,00013
|
НШ-18
|
|
|
|
|
|
|
|
1 стадия
|
5,0
|
170
|
1,15
|
2305,38
|
1354,76
|
0,58
|
0,025
|
2 стадия
|
3,5
|
170
|
1,15
|
2963,82
|
1354,76
|
0,45
|
0,019
|
3 стадия
|
3,0
|
160
|
1,17
|
3340,8
|
1461,57
|
0,43
|
0,018
|
БЛД-21
|
|
|
|
|
|
|
|
1 стадия
|
3,0
|
170
|
1,12
|
3396,6
|
653,22
|
0,19
|
0,008
|
2 стадия
|
3,0
|
160
|
1,13
|
3225,6
|
687,01
|
0,21
|
0,009
|
БД-57
|
|
|
|
|
|
|
|
1 стадия
|
5,0
|
170
|
|
1982,88
|
14449,34
|
7,28
|
0,31
|
2 стадия
|
3,5
|
170
|
|
2832,68
|
14449,34
|
5,10
|
0,21
|
3 стадия
|
3,0
|
160
|
|
3139,2
|
15412,54
|
4,90
|
0,21
|
ПД-168
|
|
|
|
|
|
|
|
1 стадия
|
4,0
|
170
|
1,13
|
2881,72
|
7717,53
|
2,67
|
0,116
|
2 стадия
|
3,25
|
160
|
1,14
|
3004,06
|
7995,79
|
2,66
|
0,115
|
ПД-167
|
|
|
|
|
|
|
|
1 стадия
|
4,0
|
170
|
1,13
|
2593,35
|
18687,13
|
7,2
|
0,31
|
2 стадия
|
3,25
|
160
|
1,14
|
3030,64
|
19477,9
|
6,4
|
0,27
|
ПД-169
|
|
|
|
|
|
|
|
1 стадия
|
4,0
|
170
|
1,08
|
2455,65
|
7830,39
|
3,18
|
0,13
|
2 стадия
|
3,25
|
160
|
1,09
|
2871,13
|
8062,58
|
2,80
|
0,12
|
ЕКД-39
|
|
|
|
|
|
|
|
1 стадия
|
6,0
|
210
|
1,10
|
2060,1
|
3898,29
|
1,89
|
0,082
|
2 стадия
|
3,0
|
160
|
0,10
|
3168,0
|
3972,16
|
1,25
|
0,054
|
9ЛО-53
|
|
|
|
|
|
|
|
1 стадия
|
3,0
|
170
|
1,12
|
3774,3
|
1421,98
|
0,37
|
0,016
|
2 стадия
|
3,0
|
160
|
1,12
|
3225,6
|
1455,43
|
0,45
|
0,019
|
ДД-7
|
|
|
|
|
|
|
|
1 стадия
|
6,0
|
210
|
1,10
|
2041,2
|
264,19
|
0,12
|
0,005
|
2 стадия
|
3,0
|
160
|
1,10
|
3110,4
|
277,39
|
0,08
|
0,003
|
ЕКД-40
|
|
|
|
|
|
|
|
1 стадия
|
6,0
|
210
|
1,24
|
2343,6
|
5,57
|
0,002
|
0,00009
|
2 стадия
|
3,0
|
160
|
1,25
|
3600,0
|
5,72
|
0,001
|
0,00004
|
Пластикация
|
7,0
|
180
|
0,92
|
1281,65
|
26401,77
|
20,59
|
0,89
|
Таблица 5.12 - Распределение смесей по
резиносмесителям
Резиносмеситель
|
Наименование
смеси
|
Загрузка
|
Резиносмеситель
№1 270/40
|
пластикат
|
0,89
|
Итого
|
|
0,89
|
КД-46 (1ст. - 2
ст.)
|
0,21
|
|
ИД-19 (1ст. - 2
ст.)
|
0,007
|
|
ФД-20 (1ст. - 2
ст.)
|
0,00013
|
|
БЛД-21 (1ст. -
2 ст.)
|
0,008
|
|
ПД-168 (1ст. -
2 ст.)
|
0,116
|
|
ПД-167 (1ст. -
2 ст.)
|
0,31
|
|
ПД-169 (1ст. -
2 ст.)
|
0,13
|
|
ДД-7 (1ст. - 2
ст.)
|
0,005
|
|
ЕКД-39 (1ст. -
2 ст.)
|
0,082
|
|
ЕКД-40 (1ст. -
2 ст.)
|
0,00009
|
|
9ЛО-53 (1ст. -
2 ст.)
|
0,016
|
Итого
|
|
0,89
|
Резиносмеситель
№3 270/40/30
|
БД-56 (1ст. -
3ст.)
|
0,00017
|
|
НШ-18 (1ст. -
3ст.)
|
0,025
|
|
БД-57 (1ст. -
3ст.)
|
0,31
|
|
БД-56 (2ст. -
3ст.)
|
0,00009
|
|
НШ-18 (2ст. -
3ст.)
|
0,019
|
|
БД-57 (2ст. -
3ст.)
|
0,21
|
|
БД-56 (3ст. -
3ст.)
|
0,00009
|
|
НЩ-18 (3ст. -
3ст.)
|
0,018
|
|
БД-57 (3ст. -
3ст.)
|
0,21
|
Итого
|
|
0,8
|
Резиносмеситель
№4 270/30
|
КД-46 (2ст. -
2ст.)
|
0,22
|
|
ИД-19 (2ст. - 2
ст.)
|
0,007
|
|
ФД-20 (2ст. - 2
ст.)
|
0,00013
|
|
БЛД-21 (2ст. -
2 ст.)
|
0,009
|
|
ПД-168 (2ст. -
2 ст.)
|
0,115
|
|
ПД-167(2ст. - 2
ст.)
|
0,27
|
|
ПД-169 (2ст. -
2 ст.)
|
0,12
|
|
ДД-7(2ст. - 2
ст.)
|
0,003
|
|
ЕКД-39 (2ст. -
2 ст.)
|
0,054
|
|
ЕКД-40(2ст. - 2
ст.)
|
0,00004
|
|
9ЛО-53(2ст. - 2
ст.)
|
0,019
|
Итого
|
|
0,82
|
Таблица 5.13 - Расчёт количества бункеров для
резиносмесителей
Наименование
ингредиентов
|
Насыпная масса,
кг/м3
|
Суточ-ный
расход, кг
|
Объем суточного
расхода, м3
|
Время
хране-ния, час
|
Объем хранения,
м3
|
Объем бункера,
м3
|
Коли-чество
бунке-ров
|
1
|
2
|
3
|
4
|
5
|
6
|
7
|
8
|
Резиносмеситель
№ 1
|
Ренацит 7
|
423
|
184,0
|
0,43
|
24
|
0,61
|
1,16
|
1
|
Резиносмеситель
№ 2
|
Ультрасил VN3
|
120
|
1650,09
|
13,75
|
2
|
1,6
|
2,08
|
1
|
Цинковые белила
|
531
|
1699,09
|
3,19
|
10
|
1,89
|
2,08
|
1
|
Стеариновая
кислота
|
508
|
774,56
|
1,52
|
12
|
1,08
|
1,48
|
1
|
Канифоль
сосновая
|
637
|
802,24
|
1,25
|
12
|
0,89
|
1,48
|
1
|
Мягчитель АСМГ
|
542
|
523,03
|
0,96
|
12
|
0,68
|
1,48
|
1
|
Углерод
технический П-323
|
400
|
8094,74
|
20,2
|
6
|
7,21
|
8,0
|
1
|
Углерод
технический П-234
|
400
|
208,51
|
0,52
|
24
|
0,74
|
4,5
|
1
|
Фталевый
ангидрид
|
729
|
51,72
|
0,07
|
-
|
-
|
-
|
п/а
|
Бензойная
кислота
|
311
|
55,01
|
0,17
|
-
|
-
|
-
|
п/а
|
Защитный воск
ЗВ-1
|
510
|
113,23
|
0,22
|
24
|
0,31
|
1,48
|
1
|
Углерод
технический П-514
|
400
|
1669,5
|
4,17
|
24
|
5,9
|
8,0
|
1
|
Углерод
технический П-245
|
400
|
5179,04
|
12,94
|
8
|
6,16
|
8,0
|
1
|
Октофор N
|
640
|
42,31
|
0,06
|
-
|
-
|
-
|
п/а
|
Мел
природообогащенный
|
610
|
1,05
|
0,001
|
-
|
-
|
-
|
п/а
|
Белая сажа
БС-120
|
120
|
0,747
|
0,006
|
-
|
-
|
-
|
п/а
|
Углеводородные
смолы
|
570
|
8,41
|
0,014
|
-
|
-
|
-
|
п/а
|
Резиносмеситель
№ 3
|
Ультрасил VN3
|
120
|
37,96
|
-
|
-
|
-
|
-
|
п/а
|
Нафтенат
кобальта
|
580
|
163,53
|
0,28
|
24
|
0,4
|
0,67
|
1
|
Цинковые белила
|
531
|
692,73
|
1,3
|
24
|
1,8
|
2,08
|
1
|
Стеарат натрия
|
|
83,05
|
-
|
-
|
-
|
-
|
п/а
|
Смола SP 1077
|
470
|
407,53
|
0,86
|
24
|
1,22
|
1,48
|
1
|
Мягчитель АСМГ
|
542
|
247,72
|
0,45
|
24
|
0,64
|
1,48
|
1
|
Углерод
технический П-323
|
400
|
4510,41
|
11,27
|
11
|
7,37
|
8,0
|
1
|
Бензойная
кислота
|
311
|
2,2
|
-
|
-
|
-
|
-
|
п/а
|
Стеарин
|
508
|
14,94
|
-
|
-
|
-
|
-
|
п/а
|
Канифоль сосновая
|
637
|
14,97
|
-
|
-
|
-
|
-
|
п/а
|
Углеводородные
смолы
|
570
|
22,93
|
-
|
-
|
-
|
-
|
п/а
|
Углерод
технический П-514
|
400
|
300,25
|
0,75
|
24
|
1,07
|
4,5
|
1
|
Углерод
технический П-234
|
400
|
0,37
|
24
|
0,52
|
4,5
|
1
|
Сера
|
787
|
278,37
|
0,35
|
24
|
0,5
|
0,67
|
1
|
Сера полимерная
|
797
|
110,51
|
-
|
-
|
-
|
-
|
п/а
|
Сульфенамид М
|
560
|
56,34
|
-
|
-
|
-
|
-
|
п/а
|
Модификатор РУ
|
500
|
15,06
|
-
|
-
|
-
|
-
|
п/а
|
Сантогард PVI
|
703
|
19,21
|
-
|
-
|
-
|
-
|
п/а
|
Диафен ФП
|
|
85,78
|
-
|
-
|
-
|
-
|
п/а
|
Тиазол 2МБС
|
365
|
1,467
|
-
|
-
|
-
|
-
|
п/а
|
Модификатор
НФА-К
|
580
|
60,4
|
-
|
-
|
-
|
-
|
п/а
|
Ацетонанил Р,
РГ
|
460
|
3,65
|
-
|
-
|
-
|
-
|
п/а
|
Малеимид Ф
|
703
|
409,0
|
0,58
|
24
|
0,82
|
1,16
|
1
|
Резиносмеситель
№ 4
|
Сера
|
787
|
483,52
|
0,61
|
24
|
0,87
|
1,16
|
1
|
Сульфенамид Ц
|
530
|
213,18
|
0,4
|
24
|
0,57
|
1,16
|
1
|
Малеимид Ф
|
703
|
245,43
|
0,34
|
24
|
0,48
|
1,16
|
1
|
Диафен ФП
|
510
|
387,75
|
0,76
|
24
|
1,08
|
1,16
|
1
|
Сера полимерная
|
797
|
26,03
|
-
|
-
|
-
|
-
|
п/а
|
Тиазол 2МБС
|
365
|
12,86
|
-
|
-
|
-
|
-
|
п/а
|
Сантогард PVI
|
703
|
17,755
|
-
|
-
|
-
|
-
|
п/а
|
2-меркаптобензтиазол
|
389
|
0,02
|
-
|
-
|
-
|
-
|
п/а
|
Модификатор РУ
|
500
|
0,18
|
-
|
-
|
-
|
-
|
п/а
|
Сульфенамид М
|
560
|
114,94
|
0,2
|
24
|
0,28
|
0,67
|
1
|
N,N'-дитиодиморфалин
|
280
|
236,28
|
0,84
|
12
|
0,6
|
1,16
|
1
|
Ацетонанил Р,
РГ
|
460
|
303,72
|
0,66
|
24
|
0,94
|
1,16
|
1
|
Гексол ЗВ, ЗВИ
|
470
|
55,47
|
-
|
-
|
|
|
п/а
|
Амберол St-137
|
460
|
12,79
|
-
|
-
|
-
|
-
|
п/а
|
Тиурам Д
|
364
|
21,15
|
-
|
-
|
-
|
-
|
п/а
|
Таблица 5.14 - Подбор весов для резиносмесителя №1
Наименование
ингредиентов
|
Шифр смеси и
навеска, кг
|
Тип весов
|
|
Пластикат
|
|
Ренацит 7
|
1,16
|
ВАД 2-292
|
Таблица 5.15 - Подбор весов для резиносмесителя №2
Наименова-ние
ингредиентов
|
Шифр смеси и
навеска, кг
|
Тип весов
|
|
КД-46(1)
|
ИД-19(1)
|
БЛД-21(1)
|
ПД-167(1)
|
ФД-20(1)
|
ПД-168(1)
|
ПД-169(1)
|
9ЛО-53(1)
|
ДД-7
|
ЕКД-39
|
ЕКД-40
|
|
1
|
2
|
3
|
4
|
5
|
6
|
7
|
8
|
9
|
10
|
11
|
12
|
13
|
Ультрасил VN3
|
5,72
|
|
|
11,48/2
|
|
|
|
|
|
|
|
ВАД 10-253
|
Цинковые белила
|
5,72
|
10,36
|
3,26
|
4,59
|
5,0
|
8,04
|
5,99
|
2,86
|
4,12
|
6,21
|
28,27/3
|
|
Стеариновая
кислота
|
2,29
|
2,07
|
2,17
|
3,44
|
0,92
|
2,87
|
1,8
|
0,95
|
4,12
|
1,24
|
|
ВАД 5-318
|
Канифоль
сосновая
|
2,86
|
3,11
|
2,17
|
2,29
|
2,8
|
3,46
|
3,59
|
1,9
|
|
|
|
|
Мягчитель АСМГ
|
5,72/2
|
10,36/2
|
|
|
|
|
|
|
|
|
2,83
|
|
Защитный воск-1
|
|
|
|
|
|
|
2,39
|
0,95
|
|
|
2,83
|
|
Углерод
технический П-234
|
|
|
55,91
|
|
|
|
|
|
|
|
|
ВАД 80-341
|
Углерод
технический П-514
|
|
31,08
|
|
|
27,57
|
|
|
|
34,37
|
|
|
|
Углерод
технический П-245
|
|
31,08
|
|
51,62
|
|
|
|
47,51
|
34,37
|
68,36
|
47,51
|
|
Углерод
технический П-323
|
45,75
|
|
|
|
|
57,46
|
41,9
|
|
|
|
|
|
Продолжение
таблицы 5.15
|
1
|
2
|
3
|
4
|
5
|
6
|
7
|
8
|
9
|
10
|
11
|
12
|
13
|
Масло ПН-6Ш
|
5,72
|
5,18
|
5,44
|
4,59
|
7,35
|
4,60
|
7,19
|
11,4
|
|
|
11,4
|
ВАД 15-288
|
Стабилойл
|
|
|
|
|
|
|
|
|
6,87
|
24,86/2
|
|
|
Таблица 5.16 - Подбор весов для резиносмесителя №3
Наименование
ингредиентов
|
Тип весов
|
|
БД-56
|
НШ-18
|
БД-57
|
|
1
|
2
|
3
|
4
|
5
|
Сера
|
1,0
|
|
3,1
|
ВАД 10-253
|
Цинковые белила
|
8,29
|
5,29
|
8,3
|
|
Нафтенат
кобальта
|
|
2,08
|
|
Малеимид Ф
|
|
|
4,6
|
|
Смола SP-1077
|
5,18
|
|
5,19
|
ВАД 10-253
|
Мягчитель АСМГ
|
3,11
|
5,29
|
3,11
|
|
Углерод
технический П-323
|
51,71
|
|
57,11
|
ВАД 80-341
|
Углерод
технический П-514
|
|
41,09
|
|
|
Углерод
технический П-234
|
|
20,5
|
|
|
Масло ПН-6Ш
|
4,14
|
|
4,15
|
ВАД 5-318
|
Таблица 5.17 - Подбор весов для резиносмесителя №4
Наименование
ингредиентов
|
Шифр смеси и
навеска, кг
|
Тип весов
|
|
НШ-18
|
КД-46
|
ИД-19
|
ФД-20
|
БЛД-21
|
ПД-167
|
ПД-168
|
ПД-169
|
9ЛО-53
|
|
1
|
2
|
3
|
4
|
5
|
6
|
7
|
8
|
9
|
10
|
11
|
Сульфенамид М
|
0,85
|
|
|
|
0,91
|
1,04
|
|
|
|
ВАД 2-292
|
Диафен ФП
|
0,47
|
1,04
|
0,95
|
0,42
|
5,06
|
1,04
|
1,05
|
2,20
|
0,44
|
|
Ацетонанил Р,
РГ
|
0,47
|
|
|
|
|
2,08
|
1,57
|
|
1,32
|
|
Сульфенамид Ц
|
|
0,83
|
0,57
|
0,51
|
|
|
1,05
|
1,65
|
1,05
|
|
Сера
|
4,75
|
2,28
|
1,14
|
2,03
|
|
1,04
|
1,05
|
1,10
|
1,14
|
ВАД 5-318
|
Малеимид Ф
|
|
2,60
|
|
|
|
|
|
|
|
|
N,N' -
дитиодиморфалин
|
|
|
|
|
|
1,56
|
1,57
|
|
|
|
Таблица 5.18 - Расчет количества каландровых линий
Марка корда
|
Ширина корда, м
|
Расход корда
суровья, м2/сутки
|
Расход корда
суровья, п.м./сутки
|
Скорость
обрезинки корда, м/мин
|
Производи-тельность
каландра, м/ч
|
Машино-часы
|
Расчетное
количество каландровых линий
|
352КНТС
|
1,5
|
1290,85
|
860,56
|
40,00
|
2160,00
|
0,39
|
0,017
|
35 КНТС
|
1,5
|
7699,43
|
5132,95
|
|
|
2,37
|
0,103
|
352 КНТС
|
1,5
|
1177,38
|
784,92
|
|
|
0,36
|
0,015
|
123 КНТС
|
1,5
|
1171,04
|
780,69
|
|
|
0,36
|
0,015
|
232 КНТС
|
1,5
|
271,95
|
181,30
|
|
|
0,08
|
0,003
|
232КНТС
|
1,5
|
190,24
|
126,82
|
|
|
0,05
|
0,0025
|
Таблица 5.19 - Расчет количества диагонально-резательных
машин
Марка корда
|
Тип ДРМ
|
Выпуск
покры-шек в сутки, шт
|
Длина слоя на
одну покры-шку, м
|
Суточная длина
слоев, м
|
Шири-на
полот-на корда, м
|
Угол закроя
|
Длина
закра-иваемой полосы, м
|
Число ре- зов в
мину-ту
|
Произ-водитель-ность
ДРМ, м/ч
|
Маши-но-часы
|
Расчет-ное
коли-чество ДРМ
|
352 КНТС
|
ДРА 3-0-45
|
186,95
|
3,71
|
694,51
|
1,5
|
3,0
|
1,5
|
15,00
|
1204,53
|
0,57
|
0,025
|
35 КНТС
|
|
|
11,20
|
2094,70
|
|
3,0
|
1,5
|
|
1204,53
|
1,73
|
0,075
|
35 КНТС
|
|
|
11,31
|
2114,40
|
|
5,0
|
1,5
|
|
1207,50
|
1,75
|
0,075
|
352 КНТС
|
|
|
3,79
|
708,54
|
|
5,0
|
1,5
|
|
1207,50
|
0,58
|
0,025
|
123 КНТС
|
|
|
3,81
|
712,27
|
|
5,0
|
1,5
|
|
1207,50
|
0,58
|
0,025
|
232 КНТС
|
|
|
5,38
|
1005,7
|
|
45,0
|
2,12
|
|
1701,10
|
0,59
|
0,025
|
232 КНТС
|
|
|
2,58
|
482,33
|
|
45,0
|
2,12
|
|
1701,10
|
0,59
|
0,025
|
Таблица 5.20 - Расчет количества продольно-резательных машин
Марка корда
|
Тип ПРМ
|
Длина слоя на 1
покрышку, м
|
Суточная длина
слоев, м
|
Ширина полотна
корда, м
|
Производи-тельность
ПРМ, м/ч
|
Машино-часы
|
Расчетное
количество ПРМ
|
232 КНТС (крыльевая
лента)
|
ПР-68
|
2,8
|
2093,84
|
520
|
1800,0
|
1,16
|
0,05
|
232 КНТС
(бортовая лента)
|
ПР-68
|
2,58
|
964,66
|
400
|
1800,0
|
0,53
|
0,023
|
Таблица 5.21 - Расчет количества линий изготовления
металлобрекера
Тип линии
|
Суточный расход
металлобрекера, м2
|
Производительность,
м2/ч
|
Машино-часы
|
Количество
линий
|
ИТ 7464
|
Слои брекера
|
|
52л 15/23
|
46
|
23,70
|
1,03
|
|
21л 22
|
|
14,95
|
0,60
|
|
|
|
22л 15
|
46
|
4,66
|
0,20
|
итого
|
|
|
|
1,87
|
Таблица 5.22 - Расчет количества шприц-машин
Наименование
оборудования
|
Наимено-вание
смеси
|
Расход смеси в
сутки, кг
|
Возврат
|
Расход смеси в
сутки с учетом возврата, кг
|
Ско-рость
шприце-вания, м/мин
|
Масса одного
метра профиля, кг
|
Коли-чество
шприцуемых ручьев
|
Произво-дитель-ность
шприц-машины, кг/ч
|
Машино-часы
|
Количе-ство
машин
|
|
|
|
%
|
кг
|
|
|
|
|
|
|
|
Боковина МЧХ-250
|
ПД-169
|
8062,58
|
10
|
80,625
|
8143,20
|
8
|
6,80
|
1
|
2937,60
|
2,77
|
0,12
|
Наполнитель-ный
шнур МЧХ-160
|
НШ-18
|
1461,57
|
10
|
14,61
|
1476,18
|
12
|
0,66
|
2
|
855,36
|
1,72
|
0,074
|
Проф. детали
МЧХ-160
|
БД-57
|
7088,24
|
5
|
354,41
|
7442,65
|
12
|
0,51
|
2
|
660,96
|
0,53
|
0,023
|
Бортовая лента МЧХ-160
|
БЛД-21
|
1053,61
|
5
|
52,68
|
1106,29
|
12
|
0,65
|
2
|
842,4
|
1,313
|
0,057
|
9ЛО-53
|
1455,43
|
5
|
72,77
|
1528,2
|
12
|
2,93
|
2
|
3797,28
|
0,40
|
0,017
|
Диафрагма
МЧХ-250
|
ДД-7
|
277,39
|
10
|
27,73
|
305,12
|
2
|
16,5
|
1
|
1782,0
|
0,17
|
0,0074
|
Камера МЧТ-400
|
ЕКД-39
|
3972,16
|
10
|
39,72
|
4011,88
|
8
|
6,84
|
1
|
2954,88
|
1,35
|
0,059
|
Таблица 5.23 - Расчет количества кольцеделательных агрегатов
Тип агрегата
|
Выпуск покрышек
в сутки, шт
|
Количество
колец в покрышке, шт
|
Количество
колец в сутки, шт
|
Производительность
агрегата, шт/ч
|
Машино-часы
|
Количество
агрегатов
|
АКД 80-1300
|
186,95
|
4
|
747,8
|
65
|
11,50
|
0,50
|
СДК-1 (для
дополн. крыла)
|
|
2
|
373,90
|
18
|
20,77
|
0,90
|
Таблица 5.24 - Расчет количества крыльевых и оберточных
станков
Тип станка
|
Суточный выпуск
покрышек, шт
|
Количество
колец в покрышке, шт
|
Количество
колец в сутки, шт
|
Производитель-ность
станка, шт/ч
|
Машино-часы
|
Количество
станков
|
СКФ-5
|
186,95
|
4
|
747,80
|
32
|
23,36
|
1,01
|
Спиральная
обертка. станок 101-04
|
|
4
|
747,80
|
60
|
12,46
|
0,54
|
Таблица 5.25 - Расчет количества сборочных станков, станков
для окраски покрышек
Тип станка
|
Суточный выпуск
покрышек, шт
|
Производительность
станка, шт/ч
|
Машино-часы
|
Количество
станков
|
1 стадия сборки
|
СПД 4-1170-2200
|
186,95
|
0,85
|
219,94
|
9,56
|
2 стадия сборки
|
2СТ-33
|
186,95
|
8
|
23,36
|
1,01
|
3 стадия сборки
(навивка протектора)
|
АНПР-2200
|
186,95
|
1,9
|
98,39
|
4,27
|
для окраски
покрышки
|
SV-14
|
186,95
|
6
|
31,15
|
1,35
|
Таблица 5.26 - Расчет количества форматоров- вулканизаторов,
прессов для вулканизации диафрагм, ободных лент, автокамер
Наименование
оборудования
|
Марка
оборудования
|
Суточный выпуск
покры-шек, шт
|
Общий режим
вулканизации с перезарядкой, мин
|
Производи-тельность,
шт/ч
|
Потребное
количество машино-часов
|
Расчетное
количество оборудования, шт
|
Пресс
гидра-влический вулканизационный для диафрагм
|
К25.243.02
|
186,95
|
85
|
0,70
|
6,67
|
0,27
|
Камера
|
ВК180-1870
|
|
45
|
1,33
|
140,56
|
5,85
|
Автоклав
вул-канизационный для ободных лент
|
АВТМ
1600*5000-12,5
|
|
35
|
1,71
|
10,93
|
0,45
|
Форматор-вул-канизатор
|
ФВ1-1250-2500-735/1300
(100")
|
|
260
|
0,23
|
812,82
|
33,86
|
Таблица 5.27 - Расчет количества станков для обрезки
выпрессовок
Тип станка
|
Суточный выпуск
покрышек, шт
|
Производительность
станка, шт./ч (по каталогу)
|
Машино-часы
|
Количество
станков
|
Обработка
выпрессовок, по типу ПО "Днепрошина"
|
186,95
|
15
|
12,46
|
0,54
|
Таблица 5.28 - Расчет количества станков для стыковки камер,
резки заготовок пятки вентиля и изгиба вентиля
Тип станка
|
Суточный выпуск
покрышек, шт
|
Производительность
станка, шт/ч
|
Машино-часы
|
Количество
станков
|
Стыковка камер:
ССКБ-670
|
186,95
|
75
|
2,49
|
0,11
|
Изгиб вентиля:
ИРО-2440 РП
|
|
1800
|
0,10
|
0,004
|
Резка заготовок
пятки: РЗП-1
|
|
100
|
1,86
|
0,008
|
Шероховка:
ИТЭД-69
|
|
100
|
1,86
|
0,008
|
Таблица 5.29 - Расчет количества прессов для вулканизации
пяток вентиля
Тип пресса
|
Суточный выпуск
камер, шт.
|
Общий цикл
вулканизации, мин
|
Число плит
|
Число гнезд на
плите, шт.
|
Производительность
пресса, шт./ч
|
Машино-часы
|
Количество
прессов
|
Пресс
гидравлический 600*600
|
186,95
|
12
|
1
|
36
|
180,0
|
0,96
|
0,04
|
Таблица 5.30 - Расчет количества сквидж-каландров
Тип агрегата
|
Суточный выпуск
покрышек, шт
|
Длина слоя, м
|
Суточная длина
слоя, м
|
Скорость, м/мин
|
Производи-тельность,
м/ч
|
Машино-часы
|
Количество
|
3-710*1800
|
186,95
|
11,15
|
2084,49
|
16
|
864
|
2,62
|
0,2
|
.3 Конструкторский расчет
Расчет запаса прочности каркаса
1 Внутреннее давление для покрышки размера 21 00 R33:=5,6
кг/см2;
Усилие, которое выдерживает материал до разрыва:разр.=35
кг;
Радиус покрышки:

Дн - наружный диаметр покрышки, мм;- толщина покрышки в
середине беговой части протектора, мм;
Полуширина профиля покрышки в поддутом состоянии:

где В - ширина профиля покрышки в поддутом состоянии, мм.
4 Общая толщина покрышки по боковине:
общ=hk+hбок=12,51+13,5=26,01
мм;k=(1,5*0,8)+(1,3*0,8*7)+(2*0,8) +(0,9*3*0,9)=12,51 мм;бок=15*0,9=13,5
мм;
где hk - толщина слоев каркаса;бок -
толщина слоев боковины;
5 Ширина профиля:

где hобщ.- толщина слоев с учетом прессовок;

- полуширина профиля покрышки в поддутом состоянии;
Отсюда отношение 
: 
Значение 1-l0 находим графически, с помощью номограмм:
-l0=0,31 мм;
Находим l0:
l0=
1-0,31=0,69 мм;
Так как l0=
, следовательно:0=l0*R=0,69*878=605,82
мм;
Находим sinβk:
sinβk= 
c= 
где Дсбор.бар. - диаметр сборочного барабана, мм;
α-угол закроя нити корда по первому слою
каркаса;
α=3°; sin 3°=0,052;
δ1-коэффициент вытяжки нити корда;
δ1=0,05;
sinβk= 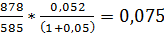
;
уголβk=4°;
Плотность нитей по короне (экватору) находится:
k1=i0*
нитей/100 мм;
k2=i0*
нитей/100 мм;k3=i0*
нитей/100 мм;
Sik=(62,69*6)+(62,85*2)+(36,77*1)=544,78 нитей/100 мм;
где i0-количество нитей на 100 мм ширины полотна;c-
внутренний радиус по сборочному барабану;
, 2, 1- число слоев в каркасе;
Максимальное усилие, возникающее в нити от действия внутреннего
давления:
Nmax=p* 
где p- внутреннее давление для покрышки размера 21 00 R33, 5,6
кг/см2;2- наружный диаметр покрышки;02-
определяем по номограмме;
bk =4°; cosbk=0,9976;
Запас прочности каркаса:

где Nразр.- усилие, которое выдерживает материал до
разрыва, 35 кг;
Расчет запаса прочности бортового кольца
15 D бортового кольца покрышки размера 21 00 R33 =865 мм;
Радиус середины бортового кольца:

Количество проволок в бортовом кольце:=количество проволок в ряду*
H;
=12*20=240;
где H - количество витков, 20;
количество проволок в ряду=12;кольца=1,5*20 =30 мм;
Площадь поперечного сечения одной проволоки:
¦=p*R2=3,14*0,52=0,78
мм2;
Угол наклона нитей по середине бортового кольца (находим по
таблице Брадиса): уголbс=20;

где 
=0,0750;
20 Усилие, возникающее в бортовом кольце:
P0=p*
кг/см;
cos 20=0,9994;
21 Напряжение в одной проволоке:
s=
кг/см2
где P0- усилие, возникающее в бортовом
кольце;количество проволок в бортовом кольце;площадь поперечного сечения одной
проволоки;
Запас прочности бортового кольца:
=
где sврем.пред.проч.=180-200 кг/мм2;
6. Строительная часть
При проектировании промышленного здания параметры выбраны,
прежде всего, из условия функционирования технологической схемы производства и
создания необходимых условий труда. Размеры здания определены с учетом
рационального размещения основного и резервного оборудования для проведения
процесса, рассчитанного в технологической части.
Для производственного корпуса используется одноэтажное
здание. Многоэтажное здание используется для производства в вертикальном
направлении потока технологического процесса (подготовительный цех).
Подготовительный цех располагается в трехэтажном здании, состоящем из кранового
пролета, сетка колонн 12х24 и этажной части с отметками 0,000; 7,200; 13,800
метров, сетка колон 6х6.
Основной корпус проектируемого завода состоит из одноэтажного
здания с сеткой колон 12х24 метров и имеет три пролета. В основном корпусе
применяются столбчатые фундаменты. Сборочный железобетонный фундамент
столбчатой конструкции состоит из нескольких элементов: подколоника со стаканом
для установки колонны, опорной фундаментной плиты и бетонного столба для
фиксирования фундаментных балок.
Для проектируемого завода применяются железобетонные колоны
квадратного сечения размером 800х800 мм. Заделка колон в стакан фундамента
производится на 750 мм.
Все несущие конструкции промышленных зданий данного завода
выполнены посредством использования типовых сборных железобетонных элементов.
Стены производственного здания выполнены из панелей размером
12х16 и марки ПСЛ-160. Толщина наружных стен 0,6 м, на участках дверных проемов
кирпичные вставки, в бытовых помещениях стены оштукатурены цементным раствором
марки М-50. Стены производственных помещений и складов белятся известью. Панели
окрашиваются на высоте 1,8 м огнестойкой краской, в коридорах и лестничных
площадках на высоте 1,5 м. Предусматривается температурный шов, предупреждающий
деформацию конструкции.
Полы одноэтажного здания и подготовительного цеха устраивают
по железобетонным плитам. Пол состоит из покрытия, стяжки, гидроизоляции и
основания.
Оборудование устанавливается на армированные или
прочнобетонные фундаменты, в зависимости от массы и специфики работы.
Окна производственного здания - стальные, переплетены по
серии ПР-05-50, остекление глухое, размером 6х1,2. Тип проема - ленточный.
Стекла в железобетонных переплетах закреплены в четверти
глубиной 12мм. Крепление ферм и колон выполняются анкерными болтами с
последующей сваркой опорных деталей.
Для подготовительного цеха используются безраскосные фермы
арочного типа, для основного производственного корпуса - скатные покрытия.
Безчердачные крыши состоят из железобетонных плит со следующими основными
элементами:
водоизоляционный ковер;
основание под ковер (стяжка);
утеплитель;
- пароизоляция;
Кровлю изготавливают из мягких водонепроницаемых материалов.
В производственном цехе полы выполнены из бетона (мраморная
крошка). Такие полы более прочны и эстетичны. В бытовых помещения полы
выполняются из керамической плитки по бетонному основанию, перекрытия
выполняются по железобетонным фермам длиной 24 м, плитами из железобетонной
серии ПК-01-74162.
Кровля выполняется в следующей последовательности: устройство
пароизоляции из одного слоя рубероида, утепление кровли фибролитом 160 мм,
цементная стяжка слоем 25 мм, кровля рулонная слойная (три слоя).
По всему периметру здания для отвода атмосферных осадков от
стен с наружной стороны выполняется асфальтовая отмостка шириной 1 м.
7. Безопасность и экологичность проекта
.1 Безопасность проекта
7.1.1 Анализ опасных и вредных производственных
факторов
На проектируемом производстве имеются место опасные и вредные
производственные факторы.
Факторы имеют различную природу действия. К группе физически
опасных и вредных производственных факторов относятся вращающиеся части
технологического оборудования (валки каландров и вальцев, сборочные барабаны),
повышенная температура поверхности технологического оборудования (головки
шприц-машин, форматоры-вулканизаторы, валки каландров и вальцев), острые части
технологического оборудования (лезвие дискового ножа, ножи резки протекторов,
обрезки выпрессовок), повышенная напряжённость электрического поля, опасный
уровень напряжения в электрической цепи (каландры, вальцы,
форматоры-вулканизаторы, вулканизационные котлы).
К группе химически опасных и вредных факторов на
проектируемом производстве относятся запыленность и загазованность рабочей зоны
(загрузка и выгрузка ингредиентов из резиносмесителя, пыль сыпучих
инредиентов), канцерогенные вещества (техуглерод), Раздражающие вещества
(каолин, стеарин).
К группе психофизиологически опасных и вредных факторов
относятся:
физические (статические и динамические) перегрузки: ручной
труд при работе на вальцах, каландре, сборочном станке; ходьба от станка к
станку;
нервно-психические перегрузки: умственное перенапряжение;
монотонность работы на ДРМ, каландре; эмоциональные перегрузки; перенапряжение
анализаторов (зрительных при работе с компьютерами, слуховых от повышенного
уровня шума).
К группе профессий подверженных данным факторам, относят:
операторы технических систем, руководители цехов, отделов, непосредственные
участники производства[1,4,37].
Таблица 7.1 - Характеристика токсичных веществ на
производстве шин [4,23,37,43,50]
Наименование
вещества
|
Наименование
участка
|
ПДК, мг/м³
|
Характер
воздействия на организм человека
|
Средства
индивидуальной защиты
|
1
|
2
|
3
|
4
|
5
|
Технический
углерод
|
Склад и
подготовительный цех
|
4
|
Канцерогенен;
раздражает кожные покровы обладает фиброгенными свойствами, действует на
верхние дыхательные пути
|
Респиратор
|
Канифоль
|
―”―
|
―”―
|
|
Спецодежда
|
Белая сажа
|
―”―
|
―”―
|
Обладает
фиброгенными свойствами, действует на верхние дыхательные пути
|
Респиратор
|
Диафен ФП
|
―”―
|
2
|
Воздействие на
ЦНС, органы дыхания желудок
|
Респиратор
|
Сера
|
―”―
|
4
|
Воспаление
слизистых оболочек и верхних дыхательных путей
|
Защитные очки,
респиратор
|
Бензойная
кислота
|
―”―
|
―
|
Пары вызывают
раздражение слизистых оболочек гортани, носоглотки, глаз
|
Перчатки,
защитные очки, респиратор
|
Каолин
|
―”―
|
6
|
Действует на
органы дыхания. Фиброзные изменения лёгких; вызывает экземы
|
Респиратор,
защитная одежда
|
Белила цинковые
|
―”―
|
0,5
|
Респиратор
|
Тальк
|
Комплектование
|
4
|
Раздражает
слизистые оболочки верхних дыхательных путей, глаз; канцерогенен
|
Защитные очки,
респиратор
|
Углеводороды
|
Вулканизационный
протекторный, каландровый
|
300
|
Действует на
ЦНС, кровь, вызывает остановку дыхания в больших концентрациях
|
Респиратор
|
Амминосоединения
|
Вулканизационный
обрезка выпрессовок
|
0,5
|
Вызывает
заболевания органов дыхания, желудочно-кишечного тракта
|
Респиратор
|
Сернистый
ангидрид
|
Вулканизационный
|
10
|
Раздражает
сли-зистые оболочки дыхательных путей, глаз носоглотки
|
Защитные очки,
респиратор
|
Бензин
|
Сборочный,
балансировочный ремонтный
|
100
|
На кровотворные
органы, ЦНС, печень, кожу и органов дыхания; обладает наркотическим действием
|
Респиратор,
защитная одежда
|
Оксид углерода
|
Обрезка
выпрессовок, протекторный, каландровый
|
20
|
На ЦНС, кровь,
остановка дыхания при высоких концентрациях
|
Респиратор
|
Фталевый
ангидрид
|
Склад и
подготовительный цех
|
1
|
Раздражает
верхние дыхательные пути и глаза; действует на органы дыхания
|
Респиратор,
спецодежда
|
N-нитрозодифенил-амин
|
―”―
|
2
|
Действует на
лёгкие, печень, почки, сердце; обладает свойствами канцерогенов
|
Респиратор
|
Гексол ЗВ
|
―”―
|
100
|
Действует на
кожные покровы
|
Перчатки
|
Октофор N
|
―”―
|
10
|
Раздражает
слизистые оболочки глаз
|
Защитные очки,
респиратор
|
Ацетонанил Р
|
―”―
|
1
|
Действует на
ЦНС, слизистые оболочки глаз
|
―”―
|
Сульфенамид М
|
―”―
|
1,5
|
Действует на
кожу, слизистые верхних дыхательных путей, глаз
|
―”―
|
СКИ-3
|
―”―
|
40
|
Раздражение
глаз, гортани
|
―”―
|
СКМС-30-АРКМ
|
―”―
|
5
|
Сильное
раздражение слизистых оболочек глаз, носоглотки; действие на печень,
желудочно-кишечный тракт
|
Защитные очки,
респиратор, спецодежда
|
Таблица 7.2 - Характеристика веществ и материалов, обладающих
взрывопожароопасными свойствами [35,37,40]
Наименование
вещества
|
Группа
горю-чести
|
Температура, 0С
|
Концентрацион-ные
пределы распро-странения пламени, г/м3
|
Температур-ный
предел распростра- нения пламени, 0С
|
|
|
вспышки
|
воспламенения
|
самовоспламенения
|
|
|
Обрезиненный
корд
|
ГВ
|
260
|
335
|
400
|
-
|
-
|
МаслоПН - 6
|
ГВ
|
368
|
310
|
381
|
-
|
-
|
Альтакс
|
ГВ
|
-
|
-
|
570
|
37,8
|
-
|
Стеарин
|
ГВ
|
196
|
223
|
320
|
-
|
-
|
Диафен ФП
|
ГВ
|
182
|
192
|
550
|
32,5
|
-
|
Канифоль
|
ГВ
|
202
|
250
|
-
|
12,6
|
-
|
Технический
углерод
|
ГВ
|
-
|
180-210
|
250 - 400
|
не взрывоопасен
|
|
Защитный воск
|
ГВ
|
240-320
|
260
|
345
|
-
|
-
|
Бензин
|
ЛВЖ
|
-18
|
-
|
300
|
-
|
-
|
Резиновые смеси
|
ГВ
|
255-260
|
310
|
320-380
|
-
|
-
|
Бензойная
кислота
|
ГВ
|
121
|
146
|
532
|
-
|
-
|
Таблица 7.3 - Анализ опасных и вредных производственных
факторов [1,2,3,4,50]
Поме-щение,
учас-ток
|
Наименова-ние
оборудо-вания
|
Наименование
производственного фактора
|
Продолжительность
действия в смену, час.
|
Фактическая
величина фактора
|
Нормативная
величина фактора
|
|
|
опасный
|
Вредный
|
|
|
|
|
|
|
|
|
|
|
Загото-вительный
|
Сквидж-каландр;
ДРА; ЛИМБ-300; протектор-ный агрегат
|
Работа
механизмов; горючесть полуфабрикатов; выделение токсичных веществ при работе
|
Травмы, шум,
выделение токсичных веществ (углеводоро-дов).
|
8
|
79 дБА 18мг/м³
|
80 дБА 20мг/м³
|
Учас- ток сборки
|
Сборочные
станки
|
Работа
механизмов, взрывопожаро-опасность (бензин), горючесть полуфабрикатов
|
Травмы,
токсичные выделения паров бензина, шум
|
8
|
74 дБА 50мг/м³
|
80 дБА 100мг/м³
|
Вулканизационный
|
Форматоры-вулканиза-торы
(ФВ)
|
Горючесть
изделий, работа ФВ
|
Нарушение
микроклимата, выделение летучих органических веществ (аминосоедине-ний),
ожоги, шум
|
8
|
79 дБА
|
80 дБА
|
Учас- ток
заклю-чительных опера-ций
|
Баланси-ровка,
обрезка
|
Работа
механизмов, пожароопасность готовой продукции
|
Травмы, наличие
в рабочей зоне летучих органических веществ (бензин, оксид углерода), талька
|
8
|
79 дБА 4 мг/м³
|
80 дБА 0,3-0,39
мг/м³
|
7.1.2 Общая
характеристика опасности проектируемого завода
На проектируемом шинном заводе выпуск покрышки
осуществляется в трех промышленных зданиях. В первом корпусе (подготовительном
цехе) происходит изготовление резиновой смеси из поступивших ингредиентов, во
втором корпусе располагается технологическое оборудование, третий корпус - цех
вулканизации, где происходит подготовка покрышек к вулканизации и их формование.
Подготовительный цех представляет собой
трёхэтажное здание, которое состоит из высотной части, высотой 20,8 м шириной
18 м. и этажной части с отметками 0,0 м.; 7,2 м.; 13,8 м, с сеткой колонн 6*6
метров. По технологическим условиям, резиносмесители, на эстакадах высотой 4,85
м, установлены в высотной части корпуса.
Разбивка сетки колонн, шаг и пролёты несущих
конструкций принята в соответствии с типовыми схемами одноэтажной и
многоэтажной части зданий. Шаг колонн- 6 м., пролёта- 6м., а в подготовительном
цехе- 18 м.; в производственном цехе шаг колонн- 12 м., пролёта- 24м.
По количеству выделяемых вредных веществ, проектируемый
шинный завод относится к III санитарному классу. Ширина защитно-санитарной зоны
не менее 300 метров.
Помещение вулканизационного цеха относится по степени
опасности поражения людей электрическим током ко 2 классу - особо опасных
помещений, так как характеризуется одновременно наличием условий, создающих
опасность, а именно, высокая температура и повышенная относительная влажность.
Остальные помещения двух корпусов классифицируются, по
степени опасности поражения людей электрическим током, как помещения с
повышенной опасностью. Они характеризуются наличием одного из признаков:
токопроводящей пыли (подготовительный и основной цеха); возможности
одновременного прикосновения человека к имеющим соединение с землёй
металлоконструкциям зданий, технологическим аппаратам с одной стороны и к
металлическим корпусам электрооборудования - с другой (все цеха); повышенной
относительной влажности (все цеха); токопроводящих полов - железобетонных (все
цеха) [15,20,29,42].
Таблица 7.4 - Общая характеристика опасности проектируемого
производства [21,25,29,35,42]
Наименование
помещений, участков
|
Вещества и
материалы, применяемые в производстве
|
Категория
помещений по взрывопожарной и пожарной опасности
|
Степень
огнестойкости зданий и сооружений
|
Класс помещений
по ПУЭ
|
1
|
2
|
3
|
4
|
5
|
Подготовительный
цех
|
Горючие,
трудногорючие, жидкие материалы
|
В-1
|
II
|
с повышенной
опасностью
|
Каландровый цех
|
Горючие, твердые
материалы
|
В-1
|
II
|
с повышенной
опасностью
|
Участок
заготовитель-ных операций
|
Горючие,
твёрдые материалы
|
В-1
|
II
|
с повышенной
опасностью
|
Сборочный цех
|
Горючие,
твёрдые материалы
|
В-1
|
II
|
с повышенной
опасностью
|
Цех
вулканизации
|
Горючие,
твёрдые материалы
|
В-1
|
II
|
с повышенной
опасностью
|
Автокамерный
цех
|
Горючие,
твёрдые материалы
|
В-1
|
II
|
с повышенной
опасностью
|
Степень огнестойкости - ΙΙ,
так как
производственные здания проектируемого завода относятся к Ι категории. К таким зданиям предъявляются наиболее высокие
требования по прочности и долговечности, срок их службы - не менее 100 лет.
Пожароопасная зона класса П-IIа - зона, где находятся твердые
горючие вещества: резина, каучуки, обрезиненные текстильные материалы.
В производственных цехах находятся в обращении горючие и
трудногорючие вещества и материалы (в том числе пыли, волокна), в связи с чем
данные помещения по взрывопожарной и пожарной опасности относятся к
пожароопасной категории В-1 (участки основных технологических операций и
складских помещений) [18,21,25,42,46].
7.1.3 Производственная безопасность
Организационные мероприятия, направленные на устранение
опасных и вредных производственных факторов.
На проектируемом предприятии будет создана служба охраны
труда.
В обязанности руководства предприятия, несущего
ответственность за охрану труда, входит разработка системы управления охраной
труда. Нормативной и методологической основой системы управления охраной труда
являются законодательные акты о труде, постановления и распоряжения
правительства, система стандартов безопасности труда, нормативная и нормативно
- техническая документация, а также локальные нормативно-правовые акты.
На руководителя предприятия возлагается ответственность за
своевременную и качественную организацию проведения инструктажей (вводный,
первичный, повторный, внеплановый, целевой). Ответственность за проведение
инструктажей возлагается на специалиста по охране труда или работника, на
которого приказом работодателя возложены эти обязанности.
Для всех принимаемых на работу лиц независимо от квалификации
и стажа, а также для работников, переводимых на другую работу, проводится
вводный инструктаж по охране труда. Который проводит специалист по охране труда
в кабинете охраны труда или специально оборудованном помещении с использованием
современных технических средств и наглядных пособий.
Первичный инструктаж проходят все вновь принятые на
предприятие, работники организации, переведенные в установленном порядке из
другого структурного подразделения, командированные работники сторонних
организаций, на рабочем месте до начала самостоятельных работ руководителями
структурных подразделений организации по программам, разработанным и
утвержденным в установленном порядке.
Повторный инструктаж проходят все работающие на предприятии
не зависимо от квалификации, образования и стажа работы, на рабочем месте не
реже 1 раза в 6 месяцев с целью проверки и повышения уровня знаний, правил и
инструкций по охране труда, по программам, разработанных для проведения
первичного инструктажа.
Внеплановый инструктаж проводится при введении в действие
новых или изменении законодательных нормативных правовых актов; при изменении
технологических процессов, замене или модернизации оборудования; при нарушении
работниками требований охраны труда, если эти нарушения создали реальную угрозу
наступления тяжких последствий; по требованию должностных лиц органов
госнадзора; при перерывах в работе долее 30 календарных дней; по решению
работодателя.
Целевой инструктаж проводится при выполнении разовых работ,
не связанных с прямыми обязанностями по специальности; при ликвидации
последствий аварий, стихийных бедствий и катастроф; производстве работ, на
которые оформляется наряд-допуск, разрешение и другие документы; проведение
экскурсий на предприятии;
Результаты проведения вводного инструктажа регистрируются в
журнале вводного инструктажа по охране труда, который хранится в службе охраны
труда. Результаты проведения первичного инструктажа на рабочем месте
регистрируются в журнале регистрации первичного инструктажа по охране труда и
хранятся у руководителей структурного подразделения. Результаты повторного,
внепланового инструктажей регистрируются в журнале первичного инструктажа по
охране труда на рабочем месте и хранятся у руководителя структурного
подразделения.
Разработка инструкций по охране труда для работников
осуществляется на основании приказов и распоряжений работодателя. В цехах
обеспечение инструкциями по охране труда возложено на начальников цехов. Целью
разработки инструкций по охране труда является обеспечение безопасных условий
труда на рабочем месте. Периодичность пересмотра инструкций не реже одного раза
в пять лет.
Для рационального режима труда и отдыха проектом предусмотрен
трёхсменный рабочий день по восемь часов в смену. В рабочее время предусмотрены
одночасовые перерывы на обед; время на курение составляет пять минут, через
каждые два часа. Один раз в год предоставляется оплачиваемый отпуск равный
двадцати восьми календарным дням
Так же в обязанности руководства входит организация
проведения предварительных (при поступлении на работу) и периодических (в
течение трудовой деятельности) медицинских осмотров. Перед заключением
трудового договора с работником работодатель предприятия должен определить
необходимость направления его на медосмотр с целью предотвращения
профессиональных заболеваний и несчастных случаев.
На предприятии предусмотрено социальное страхование
работников от несчастных случаев на производстве и профессиональных заболеваний
[51].
Инженерно-технические
средства безопасности
Для безопасности и защиты работающих от опасных
производственных факторов применяются ограждения, предохранительные, тормозные
и блокировочные устройства, сигнализации, сигнальные цвета, знаки безопасности,
а также предупредительные плакаты и надписи.
Таблица 7.5 - Инженерно-технические средства безопасности
[7,8,9,10]
Наименование
оборудования
|
Применяемые
средства безопасности
|
Бункера
расходные
|
Сигнализаторы
верхнего предела уровня механической подачи сыпучих ингредиентов
|
Вальцы и
каландры
|
Ограждения,
предохранительные устройства для регулировки зазора между валками
|
Резиносмесители
|
Предохранительные
устройства, обеспечивающие фиксацию верхнего затвора, световая и звуковая
сигнализации перед выгрузкой резиновой смеси из резиносмесителей
|
Установка
охлаждающая фестонного типа
|
Ограждения по
всей длине
|
Диагонально-резательный
агрегат (ДРА)
|
Ограждения,
световая сигнализация и звуковая сигнализация перед пуском и при аварийной
остановке
|
Агрегат
кольцеделательный (АКД)
|
Ограждения по
всей длине
|
Станки
сборочные
|
Остановочные
дуги, педали. Кнопки красного цвета грибкового типа
|
Форматоры-вулканизаторы
|
Лампы синего
цвета, указывающие на отсутствие давления в диафрагме
|
Для подачи каучука и других ингредиентов в резиносмеситель на
проектируемом заводе предусмотрена транспортная система - ленточный конвейер,
имеющий оградительные перила. Данный вид конвейера также применяется для
транспортирования сырых и готовых покрышек, автокамер.
На проектируемом предприятии предусмотрена система подвесных
толкающих конвейеров (ПТК), необходимых для транспортировки ингредиентов в
подготовительном цехе, а также для транспортировки покрышек в основном
производстве, на некоторых участках.
Использование автоматизированных средств для развески
ингредиентов и других технологических процессов создаёт безопасную работу
персонала [7,8,9,10].
Блокировочное устройство вальцов
Предохранительные устройства на вальцах должны обеспечивать
безопасные условия работы, исключающие травматизм. Основная опасность при
работе на вальцах - возможность попадания руки вальцовщика в зазор между
валками. Поэтому вальцы снабжены устройством для аварийного останова. Оно
выполнено в виде двух штанг, расположенных параллельно образующим валков на
высоте 1200 мм от уровня пола. При нажатии на штангу (2) концы ее через систему
рычагов (3) действуют на выключатели (10), укрепленные на траверсах вальцов,
которые прекращают подачу тока к электродвигателю привода (11). Одновременно
выключается электромагнит колодочного тормоза на валу электродвигателя, и
тормоз (под действием пружины (5) или груза) зажимает тормозной шкив.
При незагруженных вальцах путь торможения не должен превышать
1/4 оборота переднего валка, начиная с момента нажатия на аварийный
выключатель. При нагруженных вальцах система торможения должна обеспечить
практически мгновенную остановку валков. В современных вальцах при аварийном
торможении передний валок автоматически отодвигается от заднего, увеличивая тем
самым зазор между ними до 25 мм. На станине вальцов предусмотрена кнопка «Стоп
раздвижки», останавливающая механизм раздвижки при необходимости.
Аварийное отключение агрегата вальцов производится без
предупреждения технологического персонала об останове нажатием на штангу, в
следующих случаях:
- угроза несчастного случая с людьми, попавшими под напряжение;
- предупреждение поломки механических частей
агрегата;
- при появлении ненормального шума в двигателе или
в подшипниках;
- при появлении огня или дыма из двигателя.
В соответствии с действующими нормативами по технике
безопасности аварийный выключатель должен обеспечить безопасную работу на
вальцах.
Вальцы являются одним из опасных устройств. Рабочие должны
знать как пользоваться блокировочными устройствами и как они устроены
[9,36,48].
На графическом листе № представлена схема блокировочного
устройства вальцов.
Защита от статического электричества
Заряды статического электричества образуются при трении
одного диэлектрика о другой или диэлектриков о металлы. Например, участок
развески, изготовление резиновой смеси, каландровый участок, клеевой участок и
другие. Статическое электричество может нарушать нормальное течение
технологических процессов.
Для защиты от разрядов статического электричества проектом
предусмотрены мероприятия, направленные на предупреждение возникновения и
накопления зарядов. Предотвращение накопления зарядов статического
электричества достигается:
· заземлением оборудования и коммуникаций
(бункера, транспортёры, резиносмесители и другое оборудование);
· подбор скорости движения веществ
(транспортировка технического углерода в пневмотранспорте);
· нейтрализация зарядов ионизацией воздуха.
Для отвода статического электричества с тела человека
предусматривают токопроводящие полы или заземлённые зоны, токопроводящая обувь
с сопротивлением не более 10е+8 Ом [12].
Электробезопасность
Для защиты людей от поражения электрическим током в условиях
производства проектом предусматриваются следующие меры защиты: имеющиеся на
предприятии электрооборудование обладает покрытием, обеспечивающим защиту от
воздействия окружающей среды, является коррозионностойким, металлические части
надёжно защищены лакокрасочным покрытием. Применяются провода и кабели с
поливинилхлоридной изоляцией, а также провода с резиновой изоляцией и бумажной
изоляцией в свинцовой или поливинилхлоридной оболочке. Rдоп=не менее
500 кОм, Iутечки=0,001 А.
Для обеспечения защиты при прикосновении к нетоковедущим
частям, которые случайно оказались под напряжением используется защитное
заземление, выполненное преднамеренным электрическим соединением металлических
частей электроустановок (резиносмесители, вальцы, форматоры-вулканизаторы) с
“землёй” или её эквивалентом. Так как на производстве используется
железобетонный фундамент, то применяются естественные заземлители
(предусматриваются закладные детали для присоединения электрического и
технологического оборудования). Наряду с этим на проектируемом предприятии
применяется контурное заземляющее устройство. Электроды заземляющего устройства
расположены по контуру (периметру) и внутри площадки на которой установлено
заземляемое оборудование.
Для обеспечения автоматического отключения электроустановки
при возникновении в ней опасности поражения током предусмотрено защитное
отключение [6,29].
Молниезащита производственных зданий
На проектируемом предприятии для защиты от прямого удара
молнии используются двойные стержневые молниеотводы, расположенные на крыше
высотной части здания подготовительного цеха. Молниеотводы выполняются из
стержневого молниеприемника, двух токоотводов. В качестве заземлителей
используются электропроводящие части строительных и производственных
конструкций и коммуникаций.
На крыше одноэтажного корпуса здания под слой
гидротеплоизоляции укладывается молниеприемная сетка. Она изготавливается из
стальной проволоки диаметром не менее 6 мм, шаг ячеек 12х12 метров. Сетка
соединена двумя токоотводами, расположенными на противоположных стенах здания,
присоединённых к наружному контуру системы защитного заземления [24].
.1.4 Производственная санитария и гигиена труда
Защита от нарушения теплового баланса организма
В связи с тем, что на проектируемом предприятии постоянно
выполняются физические работы средней тяжести, категории 2 а (это работы,
связанные с постоянной ходьбой, выполняются стоя или сидя, но не требующие
перемещения тяжестей), необходимо предусмотреть параметры производственного микроклимата.
Таблица 7.6 - Нормативные параметры микроклимата воздуха
рабочей зоны [3]
Нормативные
параметры
|
Оптимальные
|
Допустимые
|
|
холодный период
года (+10°С и ниже)
|
тёплый период
года (+10°С и выше)
|
холодный период
года (+10°С и ниже)
|
тёплый период
года (+10°С и выше)
|
Температура
воздуха, °С
|
18-20
|
21-23
|
15-21
|
20-22
|
Относительная
влажность воздуха, %
|
40-60
|
40-60
|
не более 75
|
не более 65
(при 26 °С)
|
Скорость
движения воздуха, м/с
|
не более 0,2
|
0,3
|
не более 0,4
|
0,2-0,5
|
Для того, чтобы эти параметры микроклимата поддерживались,
необходимо применение центральной системы отопления с изолированным воздушным и
водным теплоносителем.
Применение вентиляции создаёт благоприятные и комфортные
условия для труда.
В подготовительном и вулканизационном цехах используется
приточная и вытяжная вентиляции. Вытяжная вентиляция располагается в местах
наибольшего скопления вредных веществ (а именно, в подготовительном цехе - у
резиносмесителей и участке развески, в вулканизационном - у
форматоров-вулканизаторов). Местная приточная вентиляция применяется над
вальцами в подготовительном цехе и в сборочном цехе [3,11,16,17].
Таблица 7.7 - Применение вентиляции
|
Вытяжная
вентиляция
|
Местная
приточная
|
Подготовительный
цех
|
Резиносмеситель
Развеска
|
Вальцы
|
Цех
вулканизации
|
Форматоры-вулканизаторы
|
-
|
Цех сборки
|
-
|
Сборка
|
Защита от шума и вибрации
Некоторые производственные процессы, а именно смешение в
резиносмесителях, вальцевание резиновых смесей, вулканизация в форматорах-
вулканизаторах, сопровождается значительным шумом и вибрацией. Допустимый
уровень звука на рабочих местах составляет 80 дБА. На предприятии уровень шума
значительно выше допустимого. Основные источники шума- редукторы,
электродвигатели.
Для того, чтобы снизить уровень шума предусмотрено установить
редукторы и электродвигатели на фундаменте с прокладкой из войлока,
использовать для данного оборудования специальные кожухи. Между цехами
устанавливаются звукоизоляционные экраны. Над резиносмесителями,
устанавливаются звукопоглотители.
На предприятии производственные процессы смешения,
вальцевания, изготовления резиновых заготовок сопровождаются значительной
вибрацией. Для снижения вибрации предусмотрена виброизоляция. Амортизаторы
(демпферы) вибраций при работе резиносмесителей, вальцев.
Для защиты работающих от воздействия шума применяют
индивидуальные средства защиты: наушники, противошумные вкладыши. Для защиты
рук от локальной вибрации применяют рукавицы или перчатки с
упруго-демпфирующими вкладышами [2,5].
Защита органов зрения от перенапряжения
В корпусах проектируемого предприятия выполняются зрительные
работы малой точности, относящиеся к V а разряду зрительных работ.
В вечернее и ночное время предусмотрено использование
искусственного освещения. Источники света при искусственном освещении -
люминесцентные лампы. В подготовительном цехе - пылевлагозащищённые светильники
типа ПВЛ-1, ПВЛ-6. Взрывозащищённые светильники типа НОГЛ-80 применяются в
помещении клеевого участка.
Для общего освещения производственных помещений с нормальной
влажностью и с небольшой запылённостью применяют светильники прямого света типа
ОДО. Высоты расположения светильников над рабочей поверхностью: для ПВЛ-1 - 1,5
метра; для НОГЛ-80 и ОДО - 1,4 метра. Норма освещённости для V а разряда - 300
лк.
В случае внезапного отключения рабочего освещения
предусматривается аварийное освещение пониженного напряжения 36 и 12 В [22].
Водоснабжение
На проектируемом предприятии для хозяйственно-бытовых нужд, с
расчётом 25 литров воды на человека в смену, используются внутренние
водопроводные сети. Норма расхода воды в душевых - 30-60 литров на одного
человека в смену. Для умывальников - 3-5 литров.
Устройства питьевого водоснабжения расположены на расстоянии
не более 75 метров от рабочего места и представляют собой устройство фонтанного
типа с раковинами для воды [14,19,41,42].
Обеспечение санитарно-бытовыми помещениями и устройствами
Производство шин по санитарной характеристике относится к
группе 1в производственных процессов. Это процессы, вызывающие загрязнение,
веществами 3 и 4 классов опасности, спецодежды и тела. На проектируемом
предприятии предусмотрены санитарно-бытовые помещения: гардеробные, душевые,
умывальные, уборные, курительные, устройства питьевого водоснабжения, помещения
для хранения и выдачи спецодежды, обработки, обогрева, и охлаждения. Умывальные
и душевые помещения предусмотрены из расчёта 15 человек на 1 душевую сетку и 10
человек на 1 питьевой кран.
Гардеробные помещения предусмотрены общие с двумя отдельными
шкафами на 1 человека [20,41,42].
Организация питания Питание на предприятии осуществляется в
столовых. Предусмотрены буфеты, продовольственные магазины, пункты выдачи
молока. В случае, если в цехе работает не более 20 человек, предусмотрены
комнаты для приёма пищи [41,42].
Противопожарные мероприятия
На проектируемом предприятии предусмотрена пожарная часть, на
вооружении которой три автоцистерны (одна в боевом расчёте и две в резерве).
Кроме этого имеются пожарные машины, спецодежда, телефонная связь, специальное
оборудование. Также размещены следующие средства пожаротушения:
водяное пожаротушение - включает спринклерную установку,
расположенную в сборочном цехе.
паровое - используется для тушения загораний в сушильных
камерах каландровой линии;
газовое - применяется на протекторных агрегатах
(автоматический или ручной пуск газа);
воздушно-пенное пожаротушение используется на пожароопасных
участках, например, в вулканизационном цехе.
Для тушения небольших очагов пожара используются первичные
средства пожаротушения: ОУП-10, ОУ-2, ОУ-5, ОП-2, ОП-5.
На проектируемом предприятии предусмотрены средства
автоматической пожарноохранной и пожарной сигнализации; необходимы для передачи
сообщений о пожаре (его месте) на пульт пожарной охраны, в виде звуковой или
оптической сигнализации (ТОПАЗ).
Применение извещателя ПКИЛ-9 (пожарный кнопочный извещатель
лучевой) и автоматического извещателя ДТЛ (датчик тепловой легкоплавкий)
позволит оперативно и точно получать информацию о случившемся пожаре.
Для более удобного доступа к месту возгорания, для пожарных
машин предусмотрены проезды шириной 6 метров. Расстояние между оборудованием и
проездом не менее 1,5 метра. Чтобы пожар не распространялся от здания к зданию,
применяют противопожарные разрывы. Минимальное расстояние между жилыми домами и
предприятием 1000 метров [21,26,27,28,35].
.2 Экологичность проекта
.2.1 Охрана атмосферного воздуха
На проектируемом предприятии основным источником загрязнения
атмосферного воздуха является подготовительный цех, который оборудован
аспирационными установками.
Таблица 7.8 - Источники загрязнения атмосферного воздуха в
подготовительном цехе
Наименования
источников загрязнения и загрязняющих веществ
|
Причина
загрязнения
|
Количество выбросов
м³/час
|
Ожидаемая
концентрация выброса, мг/м³
|
ПДК в
атмосферном воздухе населённых мест, мг/м³
|
Резиносмеситель
- окись углерода - пыль ингредиентов
|
техуглерод,
порошкообраз-ные ингредиенты
|
0,785
|
0,55
|
4,0 5,0
|
Гранулятор -
окись углерода - каолин
|
техуглерод
|
|
0,25
|
4,0 6,0
|
Также источником загрязнения атмосферного воздуха служат: на
сборочном участке - агрегаты по изготовлению деталей покрышек; протекторный
агрегат; каландр. Для выбрасываемых вредных веществ: толуол, гептан, бензин,
оксид углерода, стирол и другие, в воздушное пространство, предусмотрен метод
рассеивания газов и паров в атмосфере.
Не менее загрязняющим источником воздуха является
вулканизационный цех с выбросами диоксида серы, аминносоединений,
диэтилбензола, пентана, стирола, циклопентана и другие.
Для очистки атмосферного воздуха от пыли применяются циклоны
(производительность 4700 м3/ч, степень очистки 98%). Перед выбросом
загрязнённый воздух очищают в рукавных фильтрах типа БФМ-90 (производительность
3500 м3/ч, степень очистки 84-92%) [13,11,51].
Таблица 7.9 - Устройства по очистке воздуха [51,54].
Наименование
очистного устройства
|
Тип, модель,
марка
|
Производитель-ность,
м3/ч
|
Степень
очистки, %
|
Рукавный фильтр
|
БФМ-90 (ФРО)
|
3500
|
до 98
|
.2.2 Охрана естественных водоёмов и рациональное
использование водных ресурсов
В технологических процессах производства шин вода
используется, в основном, для охлаждения оборудования, заготовок, приготовления
пропиточных составов, получения теплоносителей. Однако, вода на предприятии
расходуется и для хозяйственно-питьевого назначения.
В результате технологических процессов техническая вода будет
содержать примеси: взвешенных веществ, мельчайших частиц резины и корда, а
также нефтепродукты [19,54].
Таблица 7.10 - Показатели водопотребления и отвода воды на
предприятии [53]
Наименование
потребителей
|
Водопотребление
|
Водоотвод
|
|
Свежая вода
|
Оборотная вода
|
|
|
м³/час
|
м³/сут
|
м³/час
|
м³/сут
|
м³/час
|
м³/сут
|
1.На
хозяйственные и технологичес-кие нужды 2. Сточные воды в приёмник
|
1200 ―
|
28800 ―
|
400 ―
|
9600 ―
|
490 328
|
11760 7872
|
В специальных очистных сооружениях сточные воды очищаются от
крупных механических загрязнений специальными решётками, а мелкие удаляются
очисткой в отстойниках. После того, как вода очистилась некоторая часть
направляется в систему оборотного водоснабжения, а другая в городские
очистительные сооружения и в приёмники.
Таблица 7.11- Анализ очистных устройств и систем [18,54]
Наименование
очистительных устройств
|
Тип устройства
|
Степень
очистки, %
|
Производи-тельность,
см/час
|
1. Решётки для
улавливания крупных частиц
|
Механический
|
80
|
Прямоток
|
2. Отстойник
для стока сточных вод и распределения взвешенных частиц
|
Механический
|
76
|
60
|
.2.3 Утилизация отходов. Защита почвы от загрязнения
На шинном заводе основными видами отходов являются:
бракованные («сырые») резиновые смеси, перевулканизованная и
недовулканизованная резина, резинотканевые материалы, обрезиненный металлокорд
и непосредственно сами корда и металлическая проволока.
Все виды отходов проектируемого предприятия можно разделить
на три группы. К первой группе относятся: резиновые смеси, обрезиненные корда,
вулканизованные выпрессовки, брак автокамер и ободных лент. Ко второй группе
относят: отработанные диафрагмы, необрезиненные корда и металлопроволоку. К
третьей: обрезиненная металлическая проволока, бракованные покрышки и покрышки
после испытаний.
Первая группа полностью подлежит переработке. Отходы второй
группы полностью не могут перерабатываться на проектируемом предприятии. Третья
группа отходов тоже полностью не перерабатывается, так как не разработаны
эффективные методы их переработки.
В качестве решения утилизации отходов являются сжигание в
специальных печах или вывоз на полигоны [51,54].
7.2.4 Благоустройство и озеленение территории предприятия
Для благоустройства и озеленения проектируемого предприятия
необходимо: посадка деревьев, разбивка газонов и клумб, создание
санитарно-защитных зон на предприятии, наличие асфальтированных дорог,
организация мест отдыха во время перерывов.
Площадка, для размещения предприятия, должна быть расположена
на ровном месте с небольшим уклоном, обеспечивающим отвод поверхностных вод.
Ровная поверхность территории обеспечивает удобство и повышает безопасность
движения людей и транспортных средств.
На территории проектируемого предприятия предусмотрена
простая схема проездов для удобства и кратчайшей связи между зданиями и
сооружениями. Транспортные магистрали не совмещаются с дорожками, по которым
ходят люди [15,18,54].
.3 Безопасность жизнедеятельности в чрезвычайных ситуациях
Наше поколение постоянно живёт в окружении угроз - глобальных
и частичных, реальных и вымышленных, устойчивых и проходящих.
Говоря о характере и тенденциях рисков природно-техногенных
чрезвычайных ситуаций, необходимо признать, что с каждым годом они приобретают
все более масштабный и устойчивый характер.
В целом, если учитывать самые массовые чрезвычайные ситуации
локального характера, в том числе пожары и дорожно-транспортные происшествия,
есть основание говорить о том, что в России ежегодно они уносят более 50 тысяч
человеческих жизней и наносят увечья более 250 тыс. человек.
Для решения проблем безопасности в России существует Единая
государственная система предупреждения и ликвидации чрезвычайных ситуаций.
Организации и предприятия определены как низший уровень структуры.
На проектируем предприятии, должны быть созданы структуры ГО
и ЧС. Согласно постановлению правительства РФ №1113 от 05.11.95 г. [30]
органами управления по делам ГО и ЧС на объекте являются:
· руководящий состав;
· формирования общего назначения;
· службы;
· формирования служб.
В соответствии с Федеральным законом РФ №68 “О защите
населения в чрезвычайных ситуациях природного и техногенного характера” [31]
предприятия должны осуществлять следующие мероприятия в области защиты
населения и территории от чрезвычайных ситуации:
· планировать и осуществлять необходимые
меры в области защиты работников организаций и подведомственных объектов
производственного и социального назначения от чрезвычайных ситуаций.
· обеспечивать создание, подготовку и
поддержание в готовности к применению сил и средств предупреждения и ликвидации
чрезвычайных ситуаций, обучение работников организаций способам защиты и
действиям в чрезвычайных ситуациях.
· обеспечивать организацию н проведение
аварийно-спасательных и других неотложных работ на подведомственных объектах
производственного н социального назначения н на прилегающих к ним территориях в
соответствии с планами предупреждения и ликвидации чрезвычайных ситуаций.
Шинный завод проектируется в Кемеровской области, в районе
города Кемерово.
На проектируемом предприятии используются вещества,
отнесенные к разряду веществ с повышенной опасностью: ГЖ и трудногорючие
жидкости, твердые горючие и трудногорючие вещества и материалы (в том числе
пыли и волокна), вещества и материалы, способные при взаимодействии с водой,
кислородом, воздухом или друг с другом только гореть.
Взрывы в промышленности являются одними из проявлений
аварийных событий.
Одной из основных причин возникновения чрезвычайной ситуации
на проектируемом предприятии может стать возникновение пожара из-за повышенной
температуры поверхностей оборудования и обрабатываемых материалов.
В условиях мирного времени завод может оказаться в довольно
тяжелой ситуации, как от собственных (внутренних) источников возникновения ЧС,
так и от внешних.
При работе завода возможны пожары, которые могут привести к
разрушению зданий, сооружений, коммуникаций, человеческим жертвам.
Дестабилизирующее действие на данный завод могут оказывать
внешние источники ЧС - землетрясения, ураганы, снежные заносы, изменение уровня
воды в реке, ядерные взрывы, аварии на железной дороге, теракты, резкое
колебание температур и давления.
Проектируемый завод предполагается построить в зоне
сейсмической активности. Поэтому заводские здания выполняются из железобетонных
плит и панелей с металлическим каркасом, способным выдержать землетрясение
малой и средней разрушительной силы.
Землетрясения вызывают разрушение зданий, выводят из строя
технологическое оборудование, коммуникации.
Поскольку проектируемый завод располагается на реке Томь, то
возможно возникновение подтоплений, в результате подъема воды в реке в весенний
период.
В результате ядерного взрыва вероятны различной степени
тяжести разрушения зданий, сооружений, технологического оборудования, массовые
пожары и другие поражения. Кроме того, железная дорога является источником
возникновения ЧС, вследствие опасности перевозимых по ней грузов (токсических,
радиоактивных), в связи с возможными авариями.
Завод - скопление большого количества людей, где возможно
проведение теракта, быстрое распространение различных эпидемий.
Основными причинами техногенной опасности являются: износ
оборудования, грубое нарушение норм и правил техники безопасности при
обслуживании оборудования, ошибки персонала.
Для людей опасность взрыва может проявляться в виде:
· ударной волны, давление во фронте которой
превышает допустимое
значение;
· пламени и пожара;
· обрушения коммуникаций, конструкций зданий
и сооружений и разлетания их осколков;
· образования при взрыве и(или) выходе из
поврежденных аппаратов, содержащихся в них вредных веществ и содержания этих
веществ в воздухе в количествах, превышающих предельно допустимые концентрации.
Для структур ГО и ЧС существует следующий план действий,
согласно Федеральному закону РФ №68 “ О защите населения и территорий от
чрезвычайных ситуаций природного и техногенного характера”[31]:
В режиме повседневной деятельности:
• совершенствование подготовки органов управления по
делам гражданской обороны и чрезвычайным ситуациям, сил и средств к действиям
при чрезвычайных ситуациях, организация обучения населения способам защиты и
действиям при чрезвычайных ситуациях; применения средств индивидуальной защиты
и ПРУ.
• создание и восполнение резервов финансовых и
материальных ресурсов для ликвидации чрезвычайных ситуаций;
• изучение состояния окружающей среды и
прогнозирование чрезвычайных ситуаций;
• сбор и обработка информации о сценариях развития
чрезвычайных ситуаций;
• планирование действий органов управления и сил
структуры ГО ЧС предприятия, организация подготовки и обеспечения их
деятельности;
• подготовка производственного персонала к действиям в
чрезвычайных ситуациях;
В режиме повышенной готовности:
• усиление контроля за состоянием окружающей среды,
прогнозирование возникновения чрезвычайных ситуаций и их последствий;
• введение при необходимости круглосуточного дежурства
руководителей и должностных лиц органов управления и сил структуры ГО ЧС на
стационарных пунктах управления;
• непрерывный сбор, обработка и передача органам управления
и силам структуры ГО ЧС предприятия данных о прогнозируемых чрезвычайных
ситуациях, информирование населения о приемах и способах защиты от них;
• уточнение планов действий (взаимодействия) по
предупреждению и ликвидации чрезвычайных ситуаций и иных документов;
• принятие на себя комиссиями по чрезвычайным ситуациям
непосредственного руководства функционированием ГО и ЧС, формирование при
необходимости оперативных групп для выявления причин ухудшения обстановки
непосредственно в районе возможного бедствия, выработки предложений по ее
нормализации;
• усиление дежурно-диспетчерской службы;
• усиление наблюдения и контроля за состоянием
окружающей природной среды, обстановкой на потенциально опасных объектах и
прилегающих к ним территориях, прогнозирование возможности возникновения
чрезвычайных ситуаций и их масштабов;
• приведение в состояние готовности сил и средств,
уточнение планов их действий и выдвижение при необходимости в предполагаемый
район чрезвычайной ситуации;
В режиме чрезвычайной ситуации:
• непрерывный контроль за состоянием окружающей среды,
прогнозирование развития возникших чрезвычайных ситуаций и их последствий;
• оповещение органов местного самоуправления и
организации, а также производственный персонал о возникших чрезвычайных
ситуациях;
• проведение мероприятий по защите производственного
персонала и территорий от чрезвычайных ситуаций;
• организация работ по ликвидации чрезвычайных
ситуаций и всестороннему обеспечению действий сил и средств единой системы,
поддержанию общественного порядка в ходе их проведения, а также привлечению при
необходимости в установленном порядке общественных организаций и населения к
ликвидации возникших чрезвычайных ситуаций.
Федеральный закон РФ №68 “ О гражданской обороне”//
Нормативные правовые акты. Гражданская оборона. Предупреждение и ликвидация ЧС
природного и техногенного характера [32] включает комплекс основных защитных
мероприятий:
· своевременная и полная информация о
возникновении ЧС;
· накопление фонда защитных сооружений и
содержание их в режиме готовности, и наличие третьего режима работы ФВО;
· планирование и качественное осуществление
эвакомероприятий;
· накопление, своевременное обеспечение и
правильное использование средств индивидуальной защиты.
В случае угрозы поражения, население эвакуируется в
кратчайшие сроки пешим порядком и всеми видами имеющегося транспорта.
Наиболее целесообразным способом защиты людей является
рассредоточение и эвакуация в загородную зону производственного персонала и
населения, проживающего вблизи предприятия. В работе по организации и
проведению рассредоточения и эвакуации придерживаются плана и указаний
начальника ГО объекта. Создается эвакуационная комиссия и сборные эвакуационные
пункты (СЭП).
При проведении эвакуации и рассредоточения обязательно должно
быть организованно медицинское обслуживание, транспортное обеспечение, связь,
обеспечение средствами индивидуальной защиты: противогазами, респираторами,
защитными одеждами и обувью, а также убежищами; а также питание и отдых
эвакуируемых людей.
Особое внимание нужно уделить подготовке и обучению личного
состава эвакуационных комиссий, сборных эвакуационных пунктов и всех структур
гражданской обороны, а также должно быть запланировано проведение
тактико-специальных учений и тренировок для лучшего взаимодействия между собой
с целью успешного решения всех вышеуказанных задач в случае возникновения ЧС.
Весь комплекс организационно- технических мероприятий по ГО и
ЧС осуществляется для предотвращения потерь и ликвидации последствий в очаге
поражения.
Заблаговременное создание структуры ГО ЧС и
высокая степень их готовности и выполнению функциональных обязанностей
обеспечат защиту производительных сил и основных производственных фондов, что
является в свою очередь положительно скажется на устойчивости работы
проектируемого предприятия в чрезвычайных ситуациях мирного и военного времени.
8. Экономика, организация и планирование производства
.1 Режим работы цеха, эффективный фонд времени работы
оборудования
Режим работы цеха характеризуется прерывным или непрерывным
технологическим режимом, числом смен в сутки и продолжительностью рабочей
смены.
Календарный фонд времени работы оборудования (Тк) равен
количеству календарных дней в году. Тк = 365 дней или 365дн * 24ч = 8760 часов.
Номинальный фонд времени работы оборудования (Тн) равен
календарному фонду за вычетом простоев оборудования в выходные и праздничные
дни. В случае непрерывного технологического процесса Тн = Тк.
Эффективный фонд времени (Тэф) равен номинальному за вычетом
простоев оборудования в плановых ремонтах и регламентированных
(запланированных) простоях. Тэф = Тн - Трем.
Таблица 8.1- Баланс рабочего времени оборудования
Наименование
|
Вид
производства
|
|
Непрерывное
|
|
дни
|
часы
|
1
|
2
|
3
|
1. Календарный
фонд времени 2. Выходные 3. Праздничные 4. Номинальный фонд времени Простои в
ремонтах 5. Капитальный ремонт 6. Средний ремонт 7. Текущий ремонт Итого
простои в ремонтах 8. Эффективный фонд времени
|
365 - - 365 22
12 9 44 321
|
8760 - - 8760
528 288 240 1056 7704
|
8.2 Расчет стоимости основных фондов
.2.1 Расчет стоимости зданий и сооружений
Единовременные затраты (капитальные вложения) включают в себя
стоимость строительства необходимых зданий и сооружений, а так же затраты на
закупку, доставку и монтаж оборудования. Расчет сводится в таблице 8.2.
Таблица 8.2 - Расчет затрат на производство зданий и
сооружений
Наименование
строения
|
Стоимость, руб.
|
1
|
2
|
Подготовительный
цех
|
84048,0
|
Основное
производство
|
339669,7
|
Сооружения и
передаточные устройства
|
127115,3
|
Итого
|
550833,0
|
Таблица 8.3 - Расчет стоимости технологического оборудования
Наименование
|
Цена, тыс. руб.
|
Кол-во, шт.
|
Стоимость, тыс.
руб.
|
1
|
2
|
3
|
4
|
Резиносмеситель
РС 270/40/30
|
8750,0
|
1
|
8750,0
|
Резиносмеситель
РС 270/40
|
7200,0
|
2
|
14400,0
|
Резиносмеситель
РС 270/30
|
7200,0
|
1
|
7200,0
|
Пресс 600*600
|
5000,0
|
1
|
5000,0
|
Кран мостовой
г/п 50 т
|
25000,0
|
1
|
25000,0
|
Кран мостовой
г/п 20 т
|
10000
|
4
|
40000,0
|
Каландр
универсальный 3-710-1800-005
|
17010,0
|
1
|
17010,0
|
Линия для
изготовления боковин с МЧХ-250
|
37300,0
|
1
|
37300,0
|
Линия для
изготовления наполнительного шнура и профилированных деталей с МЧХ-160
|
4500,0
|
2
|
9000,0
|
Линия для
изготовления автокамер с МЧХ-400
|
15000,0
|
1
|
15000,0
|
Линия для
изготовления ободных лент с МЧХ-160
|
4000,0
|
1
|
4000,0
|
МЧХ-250 для
изготовления заготовок диафрагм
|
31000,0
|
1
|
31000,0
|
ВК 180-1870
|
6500,0
|
6
|
39000,0
|
АВТМ
1600-5000-12,5
|
30000,0
|
1
|
30000,0
|
ПР-68
|
400,0
|
2
|
800,0
|
СКД-1
|
400,0
|
1
|
400,0
|
СКФ-5
|
2300,0
|
2
|
4600,0
|
101-04
|
380,0
|
1
|
380,0
|
РЗП-1
|
4000,0
|
1
|
4000,0
|
ИТЭД-69
|
3000,0
|
1
|
3000,0
|
К25.243.02
|
35000,0
|
1
|
35000,0
|
Установка
фестонного типа
|
950,0
|
2
|
1900,0
|
Установка
аспирационная
|
689,90
|
2
|
1379,80
|
Установка
барабанного типа
|
689,90
|
3
|
2069,70
|
Машина
червячная МЧТ-380/450
|
2500,0
|
2
|
5000,0
|
Машина
червячная АЧВЛ-1200
|
2550,0
|
1
|
2550,0
|
Машина
червячная со сменной головкой
|
2550,0
|
1
|
2550,0
|
ДРА 3-0-450
|
14780,0
|
2
|
29560,0
|
Станок для
обрезки выпрессовок по типу «Днепрошина»
|
275,0
|
1
|
275,0
|
Станок для
сборки СПД 4-1170-2200 с питателем и сборочным барабаном
|
10950,0
|
10
|
109500,0
|
Станок для
сборки 2СТ-33
|
12800,0
|
2
|
25600,0
|
Станок для
сборки АНПР-2200
|
14400,0
|
5
|
72000,0
|
Станок ИТ -7464
|
12500,0
|
2
|
2500,0
|
Кольцеделательный
агрегат АКД-80-1300
|
3100,0
|
1
|
3100,0
|
Форматор-вулканизатор
ФВ-1-1250-2500-735/1300 (100”)
|
18000,0
|
34
|
612000,0
|
Пресс
гидравлический для диафрагм
|
8400,0
|
1
|
8400,0
|
Станок для
окраски SV-14
|
200,0
|
2
|
АПК-80-1800
|
42000,0
|
1
|
42000,0
|
АТК-80-1800
|
31000,0
|
1
|
31000,0
|
АОК-80-1800
|
31000,0
|
1
|
31000,0
|
ИРО-2440 РП
|
3700,0
|
1
|
3700,0
|
Станок для
стыковки камер ССКБ-670
|
2000,0
|
1
|
2000,0
|
Итого основные
затраты
|
|
|
1318424,5
|
Дополнительные
затраты
|
Вспомогательное
оборудование (бункера для хранения ингредиентов, транспортные системы и т.п.)
- 20% от основных затрат
|
|
|
263684,9
|
Транспортные,
монтажные и спецработы - 17% от основных работ
|
|
|
224132,1
|
Итого
дополнительные затраты
|
|
|
487817,0
|
Итого
|
|
|
1806241,5
|
|
|
|
|
|
Таблица 8.4 - Амортизация основных фондов
Группы основных
фондов
|
Стоимость, тыс.
руб.
|
Норма
амортизации
|
Сумма
амортизационных отчислений, тыс. руб.
|
Здание
|
423717,7
|
2,0
|
8474,3
|
Сооружение и
передаточное устройство
|
127115,3
|
5,0
|
6355,7
|
Технологическое
оборудование
|
1806241,5
|
10,0
|
180624,1
|
Транспортные
средства
|
90312,0
|
15,0
|
13546,8
|
Инструмент и
инвентарь
|
36124,8
|
20,0
|
7224,9
|
Итого
|
2483511,3
|
|
216225,8
|
Расчет суммы амортизационных отчислений рассчитывается по
формуле:
А = (Ф*На)/100,
где
А - годовая сумма амортизационных отчислений, тыс. руб.;
Ф - стоимость соответствующих основных фондов, тыс. руб.;
На - норма амортизационных отчислений, %
А = (423717,7*2,0)/100 = 8474,3 тыс. руб.
8.3 Расчет численности персонала
.3.1 Расчет численности рабочих
Таблица 8.5 - Годовой баланс рабочего времени
среднесписочного рабочего
Наименование
|
Непрерывный
режим
|
Прерывный режим
|
|
8-ми часовая
смена, 4-х бригадный график
|
5-ти дневная
рабочая неделя
|
1 Календарный
фонд времени, дни
|
365
|
365
|
2 Выходные, дни
|
91
|
104
|
3 Праздничные,
дни
|
−
|
12
|
Номинальный
фонд времени, дни
|
274
|
251
|
I Планируемые
невыходы:
|
30
|
30
|
1 Очередные и
дополнительные отпуска, дни
|
|
|
2 Болезни, дни
|
7
|
5
|
3 Учебный
отпуск, дни
|
1
|
1
|
4 Прочие, дни
|
1
|
1
|
Итого
невыходов, дни
|
39
|
37
|
II Эффективный
фонд времени, дни
|
235
|
214
|
III
Продолжительность рабочей смены, часы
|
8,0
|
8,0
|
IV Эффективный
фонд времени, часы
|
1880
|
1712
|
Таблица 8.6 - Расчет численности рабочих при 8-ми часовой
смене и 4-х бригадном графике работы
Наименование
|
Разряд
|
Число рабочих в
смену, чел.
|
Число смен
|
Явочное число
рабочих, чел.
|
Штатная
численность рабочих, чел.
|
К резерва
|
Списочная
численность рабочих человек
|
1
|
2
|
3
|
4
|
5
|
6
|
7
|
8
|
1. Основные
рабочие
|
Подготовительный
цех
|
|
|
|
|
|
|
|
Машинист
резиносмесителя
|
6
|
2
|
3
|
6
|
8
|
1,17
|
9
|
Перезарядчик на
подачу сыпучих ингредиентов
|
4
|
2
|
3
|
6
|
8
|
1,17
|
9
|
Составитель
навесок
|
4
|
2
|
3
|
6
|
8
|
1,17
|
9
|
Рабочий по
загрузке разгрузке каучуков
|
4
|
1
|
3
|
3
|
4
|
1,17
|
5
|
Грануляторщик
|
6
|
2
|
3
|
6
|
8
|
1,17
|
9
|
Оператор по
изготовлению резиновых смесей
|
5
|
1
|
3
|
3
|
4
|
1,17
|
5
|
Каландровый
участок
|
Перезарядчик
транспортной системы раскатки
|
4
|
3
|
3
|
9
|
12
|
1,17
|
14
|
Стыкрвщик
текстиля
|
4
|
3
|
3
|
9
|
12
|
1,17
|
14
|
Машинист
пропиточного агрегата
|
6
|
1
|
3
|
3
|
4
|
1,17
|
5
|
Оператор
термообработки
|
5
|
1
|
3
|
3
|
4
|
1,17
|
5
|
Машинист
каландра
|
6
|
1
|
3
|
3
|
4
|
1,17
|
5
|
Машинист
шприцмашины
|
5
|
1
|
3
|
3
|
4
|
1,17
|
5
|
Заготовительно-сборочный
цех
|
Сборщик
(1стадии)
|
6
|
25
|
3
|
75
|
100
|
1,17
|
117
|
Перезарядчик
сборочных станков
|
5
|
2
|
3
|
6
|
8
|
1,17
|
9
|
Закройщик корда
|
6
|
2
|
3
|
6
|
8
|
1,17
|
9
|
Шприц-машинист
протекторного агрегата
|
5
|
5
|
3
|
15
|
20
|
1,17
|
23
|
Оператор
протекторного агрегата
|
5
|
5
|
3
|
15
|
20
|
1,17
|
23
|
Оператор
сборочного станка (2 стадии)
|
6
|
2
|
3
|
6
|
8
|
1,17
|
9
|
Изготовитель
колец
|
3
|
1
|
3
|
3
|
4
|
1,17
|
5
|
Флипперовщик
|
3
|
1
|
3
|
3
|
4
|
1,17
|
5
|
Изолировщик
колец
|
3
|
1
|
3
|
3
|
4
|
1,17
|
5
|
Машинист линии
изготовления проф.деталей
|
5
|
1
|
3
|
3
|
4
|
1,17
|
5
|
Машинист линии
изготовления боковин
|
5
|
1
|
3
|
3
|
4
|
1,17
|
5
|
Машинист линии
изготовления ободных лент
|
5
|
1
|
3
|
3
|
4
|
1,17
|
5
|
Машинист линии
изготовления камер
|
5
|
1
|
3
|
3
|
4
|
1,17
|
5
|
Стыковщик камер
|
5
|
3
|
3
|
9
|
12
|
1,17
|
14
|
Каландровщик
металлокорда
|
5
|
3
|
3
|
9
|
12
|
1,17
|
14
|
Цех
вулканизации
|
Вулканизаторщик
покрышек
|
6
|
3
|
15
|
20
|
1,17
|
23
|
Обрезчик
выпресовок
|
4
|
1
|
3
|
3
|
4
|
1,17
|
5
|
Вулканизаторщик
камер
|
5
|
3
|
3
|
9
|
12
|
1,17
|
14
|
Вулканизаторщик
ободных лент
|
5
|
1
|
3
|
3
|
4
|
1,17
|
5
|
Вулканизаторщик
диафрагм
|
6
|
1
|
3
|
3
|
4
|
1,17
|
5
|
Итого
|
|
|
|
255
|
340
|
|
399
|
2. Дежурный
персонал
|
Слесарь-ремонтник
|
5
|
3
|
3
|
9
|
12
|
1,17
|
14
|
Слесарь КиПиА
|
5
|
3
|
3
|
9
|
12
|
1,17
|
14
|
Электромонтер
|
5
|
3
|
3
|
9
|
12
|
1,17
|
14
|
Итого
|
|
|
|
27
|
36
|
|
42
|
3. Ремонтный
персонал
|
Слесарь-ремонтник
|
5
|
3
|
1
|
3
|
3
|
1,17
|
4
|
Электрогазосварщик
|
6
|
3
|
1
|
3
|
3
|
1,17
|
4
|
Электромонтер
|
6
|
3
|
1
|
3
|
3
|
1,17
|
4
|
Итого
|
|
|
|
9
|
9
|
|
12
|
4. Прочие
рабочие
|
Подготовительный
цех
|
Уборщица
производственных помещений
|
-
|
2
|
1
|
2
|
2
|
1,17
|
3
|
Кладовщик
|
-
|
1
|
1
|
1
|
2
|
1,17
|
2
|
Приемщик сырья
|
-
|
2
|
1
|
2
|
2
|
1,17
|
3
|
Транспортный
рабочий
|
3
|
2
|
3
|
6
|
8
|
1,17
|
9
|
Крановщик
|
4
|
1
|
3
|
3
|
4
|
1,17
|
5
|
Лаборант ФМИ
|
4
|
4
|
3
|
12
|
16
|
1,17
|
19
|
Каландровый
участок
|
Перекатчик
ткани и прокладки
|
3
|
1
|
3
|
3
|
4
|
1,17
|
5
|
Уборщик
|
-
|
3
|
1
|
3
|
3
|
1,17
|
4
|
Кладовщик
|
-
|
1
|
1
|
1
|
1
|
1,17
|
2
|
Транспортный
рабочий
|
3
|
2
|
3
|
6
|
8
|
1,17
|
9
|
Заготовительно-сборочный
цех
|
Промазчик
деталей
|
3
|
1
|
3
|
3
|
4
|
1,17
|
5
|
Приемщик
полуфабрикатов
|
-
|
1
|
1
|
1
|
1
|
1,17
|
2
|
Кладовщик
|
-
|
1
|
1
|
1
|
1
|
1,17
|
2
|
Уборщицы
|
-
|
3
|
1
|
4
|
4
|
1,17
|
5
|
Транспортные
рабочие
|
3
|
4
|
3
|
12
|
16
|
1,17
|
19
|
Крановщик
|
4
|
2
|
3
|
6
|
8
|
1,17
|
9
|
Цех
вулканизации
|
Рабочий по
разборке и сборке диафрагм
|
5
|
2
|
3
|
6
|
8
|
1,17
|
9
|
Рабочий по
смене диафрагм
|
5
|
3
|
3
|
9
|
12
|
1,17
|
14
|
Кладовщик
|
-
|
1
|
1
|
1
|
1
|
1,17
|
2
|
Уборщик
|
-
|
3
|
1
|
3
|
3
|
1,17
|
4
|
Рабочий по
чистке пресс-форм
|
4
|
2
|
1
|
2
|
2
|
1,17
|
3
|
Транспортные
рабочие
|
3
|
3
|
3
|
9
|
12
|
1,17
|
14
|
Крановщик
|
4
|
4
|
3
|
12
|
16
|
1,17
|
19
|
Итого
|
|
|
|
108
|
138
|
|
168
|
Всех рабочих
|
|
|
|
397
|
523
|
|
621
|
|
|
|
|
|
|
|
|
|
|
|
|
|
|
|
|
|
8.4 Расчет фондов заработной платы персонала
.4.1 Расчет фонда заработной платы рабочих
Расчет фондов зарплаты рабочих производят раздельно по каждой
группе рабочих, основой для расчета является тарифные ставки рабочих, их
списочный состав и эффективный фонд времени.
Таблица 8.7 - Расчет тарифного фонда зарплаты рабочих
Наименование
профессии
|
Спи-сочная
численность, чел
|
Часовая
тариф-ная ставка, руб
|
Эффективный
фонд времени, часы
|
Тарифный фонд
зарплаты, тыс. руб.
|
|
|
|
Одного рабочего
|
Всех рабочих
|
|
1
|
2
|
3
|
4
|
5
|
6
|
1. Основные
рабочие
|
Подготовительный
цех
|
Машинист
резиносмесителя
|
9
|
61,13
|
1880
|
16920
|
1034,32
|
Перезарядчик на
подачу сыпучих ингредиентов
|
9
|
47,22
|
1880
|
16920
|
798,96
|
Составитель
навесок
|
9
|
47,22
|
1880
|
16920
|
798,96
|
Рабочий по
загрузке разгрузке каучуков
|
5
|
47,22
|
1880
|
9400
|
443,87
|
Грануляторщик
|
9
|
61,13
|
1880
|
16920
|
1034,32
|
Оператор по
изготовлению резиновых смесей
|
5
|
57,16
|
1880
|
9400
|
Каландровый цех
|
Перезарядчик
трвнспортой системы раскатки
|
14
|
47,22
|
1880
|
26320
|
1242,83
|
Стыковщик
текстиля
|
14
|
47,22
|
1880
|
26320
|
1242,83
|
Машинист
пропиточного агрегата
|
5
|
61,13
|
1880
|
9400
|
574,62
|
Оператор
термообработки
|
5
|
57,16
|
1880
|
9400
|
537,30
|
Машинист
каландра
|
5
|
61,13
|
1880
|
9400
|
574,62
|
Машинист
шприцмашины
|
5
|
57,16
|
1880
|
9400
|
537,30
|
Заготовительно-сборочный
цех
|
Сборщик
(1стадии)
|
117
|
61,13
|
1880
|
219960
|
13446,15
|
Перезарядчик
сборочных станков
|
9
|
57,16
|
1880
|
16920
|
967,15
|
Закройщик корда
|
9
|
61,13
|
1880
|
16920
|
1034,32
|
Шприцмашинист
протекторного агрегата
|
23
|
57,16
|
1880
|
43240
|
2471,60
|
Оператор
протекторного агрегата
|
23
|
57,16
|
1880
|
43240
|
2471,60
|
Оператор
сборочного станка (2 стадии)
|
9
|
61,13
|
1880
|
16920
|
1034,32
|
Изготовитель
колец
|
5
|
39,76
|
1880
|
9400
|
373,74
|
Флипперовщик
|
5
|
39,76
|
1880
|
9400
|
373,74
|
Изолировщик
колец
|
5
|
39,76
|
1880
|
9400
|
373,74
|
Машинист линии
изготовления проф. деталей
|
5
|
57,16
|
1880
|
9400
|
537,30
|
Машинист линии
изготовления боковин
|
5
|
57,16
|
1880
|
9400
|
537,30
|
Машинист линии
изготовления ободных лент
|
5
|
57,16
|
1880
|
9400
|
537,30
|
Машинист линии
изготовления камер
|
5
|
57,16
|
1880
|
9400
|
537,30
|
Стыковщик камер
|
14
|
57,16
|
1880
|
26320
|
1504,45
|
Каландровщик
металлокорда
|
14
|
57,16
|
1880
|
26320
|
1504,45
|
Цех
вулканизации
|
Вулканизаторщик
покрышек
|
23
|
61,13
|
1880
|
43240
|
2643,26
|
Обрезчик
выпресовок
|
5
|
47,22
|
1880
|
9400
|
443,87
|
Вулканизаторщик
камер
|
14
|
57,16
|
1880
|
26320
|
1504,45
|
Вулканизаторщик
ободных лент
|
5
|
57,16
|
1880
|
9400
|
537,30
|
Вулканизаторщик
диафрагм
|
5
|
61,13
|
1880
|
9400
|
574,62
|
Итого
|
399
|
|
|
|
42765,19
|
2. Дежурный
персонал
|
Слесарь-ремонтник
|
14
|
48,21
|
1880
|
26320
|
1268,89
|
Слесарь КиПиА
|
14
|
48,21
|
1880
|
26320
|
1268,98
|
Электромонтер
|
14
|
84,21
|
1880
|
26320
|
1268,89
|
Итого
|
42
|
|
|
|
3806,67
|
3. Ремонтный
персонал
|
Слесарь-ремонтник
|
4
|
47,70
|
1712
|
6848
|
340,35
|
Электрогазосварщик
|
4
|
54,67
|
1712
|
6848
|
374,38
|
Электромонтер
|
4
|
54,67
|
1712
|
6848
|
374,38
|
Итого
|
12
|
|
|
|
1089,11
|
4. Прочие
рабочие
|
Подготовительный
цех
|
Уборщица
производственных помещений
|
3
|
31,06
|
1712
|
5136
|
159,52
|
Кладовщик
|
2
|
31,06
|
1712
|
3424
|
106,35
|
Приемщик сырья
|
3
|
31,06
|
1712
|
5136
|
159,52
|
Транспортный
рабочий
|
9
|
34,79
|
1880
|
16920
|
588,65
|
Крановщик
|
5
|
39,76
|
1880
|
9400
|
373,74
|
Лаборант ФМИ
|
19
|
39,76
|
1880
|
35720
|
1420,23
|
Каландровый
участок
|
Перекатчик
ткани и прокладки
|
5
|
34,79
|
1880
|
9400
|
327,03
|
Уборщик
|
4
|
31,06
|
1712
|
6848
|
212,70
|
Кладовщик
|
2
|
31,06
|
1712
|
3424
|
106,35
|
Транспортный
рабочий
|
9
|
34,79
|
1880
|
16920
|
588,65
|
Заготовительно-сборочный
цех
|
Промазчик
деталей
|
5
|
34,79
|
1880
|
9400
|
327,03
|
Приемщик
полуфабрикатов
|
2
|
31,06
|
1712
|
3424
|
106,35
|
Кладовщик
|
2
|
31,06
|
1712
|
3424
|
106,35
|
Уборщик
|
5
|
31,06
|
1712
|
8560
|
265,87
|
Транспортные
рабочие
|
19
|
34,79
|
1880
|
35720
|
1242,70
|
Крановщик
|
9
|
39,76
|
1880
|
16920
|
672,74
|
Цех
вулканизации
|
Рабочий по
разборке и сборке диафрагм
|
9
|
43,24
|
1880
|
16920
|
731,62
|
Рабочий по
смене диафрагм
|
14
|
43,24
|
1880
|
26320
|
1138,08
|
Кладовщик
|
2
|
31,06
|
1712
|
3424
|
106,35
|
Уборщик
|
4
|
31,06
|
1712
|
6848
|
212,70
|
Рабочий по
чистке пресс-форм
|
3
|
39,76
|
1712
|
5136
|
204,21
|
Транспортные
рабочие
|
14
|
34,79
|
1880
|
26320
|
915,67
|
Крановщик
|
19
|
39,76
|
1880
|
35720
|
1420,23
|
Итого
|
|
|
|
11492,64
|
Всех рабочих
|
621
|
|
|
|
59153,61
|
|
|
|
|
|
|
|
|
|
|
В производстве занято 621 человек.
Фонд оплаты труда проектируемого завода составляет 59153,61
тыс. руб.
.4.2 Цеховой персонал рассчитывают, исходя из типовых схем
управления цехом с учетом их совершенствования. Расчет фонда зарплаты цехового
персонала производят на основе схемы должностных окладов.
.4.3. Цеховой персонал рассчитывают, исходя из типовых схем
управления цехом с учетом их совершенствования. Расчет фонда зарплаты цехового
персонала производят на основе схемы должностных окладов.
Таблица 8.9 - Расчет фонда зарплаты цехового персонала
Должность
|
Числен-ность,
чел.
|
Должност-ной
оклад, руб.
|
Доплата за
вредность, руб.
|
Общий оклад,
руб.
|
Годовой фонд
зарплаты, руб.
|
Годовой фонд
зарплаты с учетом РК, тыс. руб.
|
1.
Руководители:
|
|
|
|
|
|
|
Начальник цеха
|
3
|
23000
|
2300
|
25300
|
910800
|
1366,2
|
Заместитель
начальника цеха
|
3
|
18500
|
1850
|
20350
|
732600
|
1098,9
|
Начальник
участка по производству КГШ
|
2
|
17300
|
1730
|
19030
|
456720
|
685,08
|
2. Специалисты:
|
|
|
|
|
|
|
Инженер-технолог
|
4
|
15000
|
1500
|
16500
|
792000
|
1188,0
|
Механик
|
3
|
13300
|
1330
|
14630
|
526680
|
790,02
|
Энергетик
|
3
|
13300
|
1330
|
14630
|
526680
|
790,02
|
Мастер смены
|
9
|
16500
|
1650
|
18150
|
1960,20
|
2940,30
|
Инженер по
нормированию труда
|
2
|
14700
|
1470
|
16170
|
388080
|
582,12
|
Экономист
|
3
|
12400
|
1240
|
13640
|
491040
|
736,56
|
Табельщик
|
3
|
8700
|
870
|
9570
|
344520
|
516,78
|
Бухгалтер
|
3
|
9000
|
900
|
9900
|
356400
|
534,60
|
Итого
|
38
|
|
|
|
|
11228,58
|
.5. Планирование себестоимости продукции
.5.1 Расчет сметы расходов по содержанию и эксплуатации
оборудования
Таблица 8.10 - Расчет сметы расходов по содержанию и
эксплуатации оборудования
Статья расходов
|
Сумма расходов,
тыс. руб.
|
Пояснение к
расчету
|
1
|
2
|
3
|
1. Содержание
оборудования и других рабочих мест
|
|
|
а) Зарплата
дежурного персонала
|
10113,93
|
Из табл.8.8
|
б) Отчисления
на социальные нужды
|
2629,62
|
26% от ст. 1 а
|
в) Смазочные и
обтирочные материалы
|
9031,21
|
0,5% от ст. 4
табл.8.3
|
г) Услуги
мастерских
|
54187,25
|
3% от ст.4
табл.8.3
|
Итого
|
75962,01
|
|
2. Текущий
ремонт оборудования
|
|
|
а) Зарплата
ремонтного персонала
|
2128,5
|
Из табл. 8.8
|
б) отчисления
на социальные нужды
|
553,41
|
26% от ст.2а
|
в) Материалы
для ремонта
|
36124,83
|
2% от ст.4
табл.8.3
|
г) Услуги
вспомогательных цехов
|
54187,25
|
3% от ст.4
табл.8.3
|
Итого
|
92993,99
|
|
3. Амортизация
оборудования и других активных фондов
|
201395,8
|
Ст.3-5
табл.8.4, гр. 4
|
4. Содержания
транспорта и расходы по его эксплуатации
|
9031,2
|
10% от ст.4
табл.8.4, гр.2
|
5. Износ
малоценного инвентаря
|
1083,74
|
3% от ст.5
табл.8.4, гр2
|
Итого
|
211510,7
|
|
Всего
|
380466,7
|
|
Таблица 8.11 - Расчет сметы цеховых расходов
Статья расходов
|
Сумма расходов,
тыс. руб.
|
Пояснение к
расчету
|
|
1. Содержание
цехового персонала:
|
|
|
|
а) зарплата
цехового персонала 2470,2
|
11228,58
|
Из табл. 8.9
|
|
б) отчисление
на социальные нужды 642,2
|
2919,43
|
26% от ст. 1а
|
|
в) зарплата
прочих вспомогательных рабочих 53907,7
|
22460,7
|
Табл.8.8
|
|
г) отчисления
на социальные нужды
|
5839,78
|
26% от ст. 1 в
|
|
Итого
|
42448,49
|
|
|
2. Содержание
здания цеха и сооружений
|
16525,0
|
3% от ст. 1-2
табл.8.4
|
|
3. Текущий
ремонт здания цеха и сооружений
|
5508,3
|
1% от ст. 1-2
табл.8.4
|
|
4. Амортизация
цеха и сооружений
|
14830,0
|
Ст. 1-2
табл.8.4 гр.4
|
|
5. Расходы по
охране труда и технике безопасности
|
13299,10
|
10% от зарплаты
всех рабочих
|
|
6. Прочие
расходы
|
5508,33
|
1 -2% ст. 1-2
табл.8.4
|
|
Итого
|
55670,73
|
|
|
Всего по смете
|
98119,22
|
|
|
8.6 Расчет себестоимости продукции
Наименование продукции: покрышка «БелАЗ» 21.00Р-33
Калькуляционная единица: шт.
Годовой выпуск: 60000
Действующая оптовая цена: 58000
Таблица 8.12 - Калькуляция себестоимости продукции
Статьи
калькуляции
|
Ед. изм.
|
Расходы на
единицу
|
Расходы на весь
выпуск
|
|
|
Коли- чество
|
Цена, руб.
|
Сумма, руб.
|
Количество
|
Сумма, тыс.
руб.
|
1
|
2
|
3
|
4
|
5
|
6
|
7
|
1. Сырье и
основные материалы:
|
|
|
|
|
|
|
2
Меркаптобензтиазол
|
кг
|
0,0001
|
72,5
|
0,00725
|
6,0
|
0,435
|
N,N-'дитиодиморфолин
|
кг
|
1,26
|
176,0
|
221,76
|
75600
|
13305,6
|
АФФС типа
Амберол ST-137
|
кг
|
0,06
|
148,44
|
8,91
|
3600
|
534,38
|
Алетонанил Р
|
кг
|
1,46
|
76,60
|
111,84
|
87600
|
6710,16
|
Бензойная
кислота
|
кг
|
0,31
|
49,90
|
15,47
|
18600
|
928,14
|
Мягчитель АСМГ
|
кг
|
4,3
|
10,28
|
44,20
|
258000
|
2652,24
|
БК-1675Н
|
кг
|
12,12
|
142,88
|
1731,71
|
727200
|
103902,3
|
Гексол ЗВ
|
кг
|
0,29
|
67,93
|
19,70
|
17400
|
1181,98
|
Диафен ФП
|
кг
|
2,53
|
115,4
|
292,0
|
151800
|
17517,72
|
Защитный воск
|
кг
|
0,6
|
15,0
|
9,0
|
36000
|
540,0
|
Канифоль
|
кг
|
4,37
|
38,0
|
166,06
|
262200
|
9963,6
|
Стеарин
|
кг
|
4,22
|
49,50
|
208,9
|
253200
|
12533,4
|
Ультрасил VN3
|
кг
|
8,82
|
15,0
|
132,3
|
529200
|
7938,0
|
Малеимид Ф
|
кг
|
3,49
|
420,0
|
1465,8
|
209400
|
87948,0
|
Масло ПН-6Ш
|
кг
|
10,1
|
23,70
|
239,37
|
606000
|
14362,2
|
Мел природный
обогащенный
|
кг
|
0,005
|
2,42
|
0,0121
|
300
|
0,726
|
Модификатор
Н-ФАК
|
кг
|
0,32
|
170,0
|
54,4
|
19200
|
3264,0
|
Модификатор РУ
|
кг
|
0,08
|
175,0
|
14,0
|
4800
|
840,0
|
Наирит ДН
|
кг
|
0,04
|
123,75
|
4,95
|
2400
|
297,0
|
Нафтенат
кобальта
|
кг
|
0,87
|
230,48
|
52200
|
12031,06
|
НК
|
кг
|
188,7
|
80,0
|
15096,0
|
11322000
|
905760,0
|
Ренацит
|
кг
|
0,98
|
67,0
|
74,48
|
58800
|
4468,8
|
Октофор N
|
кг
|
0,22
|
32,0
|
7,04
|
13200
|
422,4
|
Регенерат РКТ
|
кг
|
1,16
|
15,0
|
17,4
|
69600
|
1044,0
|
БС-120
|
кг
|
0,004
|
33,10
|
0,1324
|
240
|
7,94
|
Сантогард PVI
|
кг
|
0,19
|
158,0
|
30,02
|
11400
|
1801,2
|
Сера
|
кг
|
4,07
|
7,0
|
28,49
|
244200
|
1709,4
|
Сера полимерная
|
кг
|
0,73
|
63,3
|
46,209
|
43800
|
2772,54
|
СКД-2
|
кг
|
1,14
|
60,76
|
69,27
|
68400
|
4155,98
|
СКИ-3
|
кг
|
19,72
|
62,74
|
1237,23
|
1183200
|
74233,97
|
СКИ-3-01
1группа
|
кг
|
0,01
|
70,15
|
0,7
|
600
|
42,09
|
СКМС-30АРК
|
кг
|
8,91
|
54,16
|
482,57
|
534600
|
28953,94
|
СКМС-30АРКМ-15
|
кг
|
0,76
|
51,66
|
39,26
|
45600
|
2355,7
|
Смола SP
|
кг
|
2,18
|
90,0
|
196,2
|
130800
|
11772,0
|
Стабилойл-18
|
кг
|
2,31
|
39,71
|
91,73
|
138600
|
5503,8
|
Стеарат натрия
|
кг
|
0,44
|
22,98
|
10,11
|
26400
|
606,7
|
Сульфенамид М
|
кг
|
0,91
|
120,0
|
109,2
|
54600
|
6552,0
|
Сульфенамид Ц
|
кг
|
1,13
|
105,0
|
118,65
|
67800
|
7119,0
|
Тиазол 2МБС
|
кг
|
0,07
|
115,0
|
8,05
|
4200
|
483,0
|
Тиурам Д
|
кг
|
0,11
|
28,2
|
3,1
|
6600
|
186,12
|
ТЭП ДСТ-30Р
|
кг
|
0,29
|
57,0
|
16,53
|
17400
|
991,8
|
УВС
|
кг
|
0,16
|
23,05
|
3,67
|
9600
|
221,3
|
ТУ П-234 (245)
|
кг
|
1,92
|
36,21
|
69,52
|
115200
|
4171,4
|
ТУ П-245 (234)
|
кг
|
27,7
|
36,21
|
1003,01
|
1662000
|
60181,02
|
ТУ П-323 (324)
|
кг
|
67,42
|
34,91
|
2353,63
|
4045200
|
141217,9
|
ТУП-514
|
кг
|
10,53
|
31,56
|
332,33
|
631800
|
19939,61
|
Фталеавй
ангидрид
|
кг
|
0,27
|
45,78
|
12,36
|
16200
|
741,66
|
ХБКНТ-1068
|
кг
|
0,23
|
126,0
|
28,98
|
13800
|
1738,8
|
Белила цинковые
|
кг
|
12,79
|
74,0
|
946,46
|
767400
|
56787,6
|
Латекс ДБА-1
|
кг
|
0,38
|
157,47
|
59,84
|
22800
|
3590,31
|
Латекс СКД-1с
|
кг
|
0,38
|
69,91
|
26,57
|
22800
|
1593,94
|
Смола СФ-282
|
кг
|
0,12
|
149,95
|
18,0
|
7200
|
1074,64
|
Формальдегид
|
кг
|
0,05
|
16,0
|
0,8
|
3000
|
48,0
|
Едкий натр
|
кг
|
0,007
|
25,96
|
0,181
|
420
|
10,90
|
Проволока 1Л
|
Кг
|
18,22
|
33,39
|
608,37
|
1093200
|
36501,92
|
Корд232 КНТС
|
Пм
|
1,65
|
55,35
|
91,33
|
99000
|
5479,65
|
Корд 352 КНТС
|
пм
|
8,805
|
68,53
|
603,40
|
528300
|
36204,4
|
Корд 35 КНТС
|
пм
|
27,46
|
76,82
|
2109,47
|
1647600
|
126568,6
|
Корд 123 КНТС
|
пм
|
4,18
|
42,29
|
176,8
|
250800
|
10606,3
|
Бязь
|
пм
|
0,26
|
28,93
|
7,52
|
15600
|
451,3
|
Вентили Д-13
|
шт
|
1,0
|
43,43
|
43,43
|
60000
|
2605,8
|
Металлокорд
21л22
|
кг
|
2,03
|
107,82
|
218,9
|
121800
|
13132,5
|
Металлокорд
22л15
|
кг
|
1,30
|
105,30
|
136,9
|
78000
|
8213,4
|
Металлокорд
52л15
|
кг
|
3,98
|
110,43
|
439,51
|
238800
|
26370,7
|
Итого
|
|
|
|
31914,26
|
|
1914850,0
|
2. Вода, пар,
эл.энергия на технологические нужды
|
|
|
|
|
|
|
Вода
|
м3
|
3,11
|
8,37
|
26,03
|
186600
|
1561,84
|
Пар
|
Гкал
|
2,52
|
401,74
|
1012,4
|
151200
|
60743,0
|
Электроэнергия
|
КВт/час
|
1713
|
0,89
|
1524,57
|
102780000
|
91474,2
|
Итого
|
|
|
|
2563,0
|
|
153779,04
|
3. Заработная
плата основных производственных рабочих
|
|
|
|
712,75
|
|
42765,19
|
4. ЕСН
|
|
|
|
185,31
|
|
11118,95
|
5. Расходы на
содержание и эксплуатацию оборудования
|
|
|
|
6341,11
|
|
380466,7
|
6. Цеховые
расходы
|
|
|
|
1635,32
|
|
98119,22
|
|
|
|
43351,76
|
|
2601098,9
|
7.Общезаводские
расходы
|
|
|
|
4335,17
|
|
260109,9
|
Итого
производственная себестоимость
|
|
|
|
47686,9
|
|
2861209,0
|
8.Внепроизводствен-
ные расходы
|
|
|
|
476,9
|
|
28612,09
|
Итого полная
себестоимость
|
|
|
|
48163,6
|
|
2889821,0
|
.7 Планирование прибыли
.7.1 Расчет прибыли от реализации продукции
Таблица 8.13 Расчет прибыли от реализации
продукции
Наименование
продукции
|
Реализуемая
продукция
|
Прибыль,
тыс.руб.
|
|
По полной
себестоимости
|
По оптовым
ценам
|
|
|
Количество, шт
|
Себестоимость
единицы, руб.
|
Сумма, тыс.руб
|
Цена, руб.
|
Сумма, тыс.руб.
|
|
21.00-33
|
60000
|
48163,6
|
2889816,0
|
8000
|
3480000,0
|
590184,0
|
Расчет рентабельности производства
Р=Пр*100 %/(Фо+Ос)
=590184,0* 100 %/ (4346144,77+434614,48) =12,34 %
Р - рентабельность производства, %,
Пр - прибыль от реализации, тыс.руб.,
Фо - стоимость основных фондов, тыс.руб.,
Ос - стоимость оборотных средств, тыс.руб.
Из расчета следует, что предприятие является рентабельным.
Рентабельность составляет 12,34 %
Ф=РП/ Фо =3480000,0/4346144,775=0,8 руб
Ф - фондоотдача, руб.
РП - реализованная продукция, тыс. руб.
Фо - стоимость основных фондов, тыс. руб.
ПТР= РП/Ч=3480000,0/659=5280,73 тыс.
руб.
ПТР - производительность труда, руб.,
РП - реализованная продукция, тыс. руб.,
Ч - общая численность персонала, чел.
З=С/РП=2889816,0/3480000,0=0,830 руб.
З - затраты на рубль товарной (реализованной) продукции,
руб.,
С - полная себестоимость продукции, тыс.руб.,
РП - реализованная продукция, тыс.руб.
Ток= Фо/ Пр=4346144,775/590184,0=7,36
лет
Ток - срок окупаемости предприятия, лет,
Фо - полная стоимость основных фондов, тыс. руб.,
Пр - прибыль от реализации продукции за вычетом
налога на прибыль (24%), тыс.руб.
Таблица 8.14 - Основные
экономические показатели
Наименование
показателей
|
Показатели
|
1. Годовой
выпуск продукции:
|
|
а) в
натуральном измерении, шт.
|
60000
|
б) в денежном
измерении, тыс. руб.
|
3480000
|
2. Численность
персонала:
|
|
а) всего
|
659
|
б) рабочих
|
621
|
3.
Производительность труда, тыс. руб.
|
5280,73
|
4.
Себестоимость единицы продукции, руб.
|
48163,6
|
5.
Себестоимость годового выпуска, тыс. руб.
|
2889816,0
|
6. Стоимость
основных фондов, тыс. руб.
|
4346144,775
|
7. Фондоотдача,
руб.
|
0,8
|
8. Затраты на
рубль товарной продукции, руб.
|
0,830
|
9. Прибыль от
реализации, тыс. руб.
|
590184,0
|
10.Рентабельность
производства, %
|
12,34
|
11.Срок
окупаемости предприятия, лет
|
7,36
|
Заключение
Данный проект шинного завода по производству покрышек
спроектирован с учётом максимальной автоматизации производства. При описании
технологических процессов подготовки и транспортирования сырья рассмотрены
современные системы подачи и дозирования, изготовления смесей.
Описаны основные тенденции совершенствования технологии и
оборудования для изготовления деталей, сборки, вулканизации изделий, связанные
с полной автоматизацией операций, снижением энергозатрат, интенсификацией режимов
вулканизации.
Разработаны мероприятия по защите работников предприятия и
окружающей среды.
Также был произведен экономический расчет предприятия, в
котором была рассчитана рентабельность, она составила 12,34% и срок окупаемости
предприятия - 7,36 лет.
Библиографический список
1 ГОСТ
12.0.003 - 74* Опасные и вредные производственные факторы. Классификация. -
Введ. 01.01.76.- М.: Изд-во стандартов, 1974.-16с.
2 ГОСТ
12.1.003 - 83* Шум. Общие требования безопасности. - Взамен ГОСТ 12.1.003-76;
введ. 01.07.84.- М.: Изд-во стандартов, 1983.-18с.
3 ГОСТ
12.1.005 - 88* Общие санитарно-гигиенические требования к воздуху рабочей зоны.
- Взамен ГОСТ 12.1.005-76; введ. 01.01.89.- М.: Изд-во стандартов, 1988.-16с.
ГОСТ
12.1.007 -90 Вредные вещества. Классификация и общие требования безопасности. -
Взамен ГОСТ 12.1.007-78; введ. 01.01.91.- М.: Изд-во стандартов, 1990.-20с.
ГОСТ
12.1.012 - 01 Вибрационная безопасность. Общие требования. - Введ. 01.01.02.-
М.: Изд-во стандартов, 2001.-18с.
ГОСТ
12.1.030 - 81* Электробезопасность. Защитное заземление. Зануление. - Введ.
01.07.82.- М.: Изд-во стандартов, 1981.-14с.
ГОСТ
12.2.003 - 91 Оборудование производственное. Общие требования безопасности. -
Введ. 01.07.92.- М.: Изд-во стандартов, 1991.-18с.
ГОСТ
12.2.046 - 80 Оборудование для производства резинотехнических изделий. Общие
требования безопасности. - Введ. 01.01.81.- М.: Изд-во стандартов, 1980.-20с.
ГОСТ
12.2.062 - 81 Оборудование производственное. Ограждения защитные. - Введ.
01.07.82.- М.: Изд-во стандартов, 1981.-16с.
10 ГОСТ
12.4.026 - 01 Цвета сигнальные, знаки безопасности и разметка сигнальная.
Назначения и правила применения. Общие технические требования и характеристики.
Методы испытаний. - Введ. 01.01.02.- М.: Изд-во стандартов, 2001.-22с.
11 ГОСТ
12.4.121 - 83 Системы вентиляционные. Общие требования безопасности. - Введ.
01.01.84.- М.: Изд-во стандартов, 1983.-16с.
ГОСТ
12.4.124 - 83 Средства защиты от статического электричества. Общие технические
требования. - Введ. 01.01.84.- М.: Изд-во стандартов, 1983.-24с.
ГОСТ
17.2.3.02 - 78 Охрана природы. Атмосфера. Правила установления допустимых
концентраций вредных веществ. - Введ. 01.07.79.- М.: Изд-во стандартов,
1978.-16с.
СанПиН
2.1.5.980-00 Водоотведение населенных мест. Санитарная охрана водных объектов.-
М.: Федеральный центр Госкомсанэпиднадзора Минздрава России, 2000.-20с.
15 СанПиН
2.2.1/2.1.1.1200 - 03 Санитарно-защитные зоны и санитарная классификация
предприятий, сооружений и иных объектов. - СПб.: типография «Авангард», 2003.
-38с.
16 СанПиН
2.2.548 - 96 Гигиенические требования к микроклимату производственных
помещений. - М.: Госкомсанэпиднадзор России, 1996. - 20с.
17 СНиП
41.01.03 Отопление, вентиляция и кондиционирование.- М.: Госстрой России,
2003.-54с.
18 СНиП
11-89-80* Генеральные планы промышленных предприятий.-М.: Госстрой России,
1980.-50с.
19 СНиП
2.04.02 - 02 Водоснабжение. Наружные сети и сооружения.- М.:Госстрой России,
2002.-159 с.
СНиП
2.09.04 - 01 Административные и бытовые здания.- М.: Минстрой России,
2001.-19с.
СНиП
21-01- 02 Пожарная безопасность зданий и сооружений.- М.: Госстрой России,
2002.-23с.
СНиП
23-05- 03 Естественное и искусственное освещение.- М.: Госстрой России,
2003.-50с.
23 ГН
2.2.5.686 - 98 Предельно-допустимые концентрации вредных веществ в воздухе
рабочей зоны.- М.: из-во «НЦ ЭНАС»,1998.-58с.
24 И-72
Инструкция по устройству молниезащиты зданий, сооружений и промышленных
коммуникаций.- М.: из-во «НЦ ЭНАС», 2004. -46 с.
НПБ
105 - 03 Определение категорий помещений, зданий и наружных установок по взрывопожарной
и пожарной опасности.- СПб.: из-во «НЦ ЭНАС», 2003. -170с.
НПБ
166 - 97 Пожарная техника. Огнетушители. Требования к эксплуатации. Основные
показатели и методы испытаний. М.: ГПС МВД РФ,1997.-54с.
НПБ
88 - 2001 Установки пожаротушения и сигнализации. Нормы и правила
проектирования. - М.: ГПС МВД РФ, 2001. - 44с.
ППБ
01 - 03 Правила пожарной безопасности в Российской Федерации. - СПб.: изд-во
«ДЕАН». 2003. -192с.
Правила
устройства электроустановок.- М.: изд-во «НЦ ЭНАС», 2002. - 170с.
30 Постановление
правительства РФ от 05 ноября 1995 г. №1113 «О Единой государственной системе
предупреждения и ликвидации ЧС». - Красноярск, 2003.-с.38-51.
Федеральный
закон РФ №68 “ О защите населения и территорий от чрезвычайных ситуаций
природного и техногенного характера”. - Красноярск, 2000.-с.6-14.
Федеральный
закон РФ №68 “О гражданской обороне”// Нормативные правовые акты. Гражданская
оборона. Предупреждение и ликвидация ЧС природного и техногенного характера. -
Красноярск, 2000.-с.30-35.
33 Андрашников,
Б.И. Интенсификация процессов приготовления и переработки резиновых смесей
[Текст] / Б.И. Андрашников. - М.: Химия, 1986. - 224с.
34 Андрашников,
Б.И. Справочник по автоматизации и механизации производства шин и РТИ [Текст] /
Б.И. Андрашников. - М.: Химия, 1981. - 296с.
35 Баратов,
А.Н. Взрывопожарность веществ и материалов и средств их тушения. Справочное
издание в 2-х книгах [Текст] / А.Н. Баратов, А.Я. Корольченко и др. - М.:
Химия,1990. - 201с.
36 Барсков,
Д.М. Машины и аппараты резинового производства [Текст] / Под ред. Д.М.
Барскова. - М.: Химия, 1975. - 600с.
37 Вредные
вещества в промышленности. Справочник [Текст] / Под ред. Лазарева Н.В., Левиной
Э.И. - Л.: Химия, 1977. Том 3 - 608с.
38 Гончарова,
Л.А. Технология шинного производства: Учебное пособие для дипломного
проектирования студентами специальности 250600 всех форм обучения [Текст] /
Л.А. Гончарова, Д.В. Ершов, В.М. Гончаров. - Красноярск.: СибГТУ, 2005. - 32с.
39 Горчакова,
В.Г. Безопасность и экологичность проекта: Методические указания к выполнению
раздела в дипломных проектах (работах) для студентов химико-технологических
специальностей всех форм обучения [Текст] / В.Г. Горчакова, Е.С. Ставиский,
В.С. Петров. - Красноярск.: СибГТУ, 2003. - 22с.
40 Кошелев,
Ф.Ф. Общая технология резины [Текст] / Ф.Ф. Кошелев, А.Е. Корнев, А.М. Буканов
- М.: Химия, 1978.-528с.
41 Москаленко,
В.Н. Охрана труда. Учебное пособие. Законодательные и нормативно-правовые акты
по охране труда [Текст] / под ред. В.Н. Москаленко, 2-е изд., испр. и дополн. -
Красноярск: СибГТУ, 2006. - 686 с.
42 Макаревич,
В.А. Строительное проектирование химических предприятий [Текст] / В.А.
Макаревич. - М.: «Высшая школа», 1977. - 208с.
43 Гончарова,
Л.А. Основы рецептуростроения эластомерных композиций. Часть 1. Принципы
составления и оптимизация рецептур резиновых смесей [Текст] / Л.А. Гончарова,
В.М. Гончаров, С.И. Левченко. - Красноярск.: СибГТУ, 2002. - 84с.
44 Гончарова,
Л.А. Основы рецептуростроения эластомерных композиций. Часть 2. Основные
принципы построения рецептур шинных резин [Текст] / Л.А. Гончарова, В.М.
Гончаров, С.И. Левченко.- Красноярск.: СибГТУ, 2002. - 93с.
45 Осошник,
И.А. Технология пневматических шин [Текст] / И.А. Осошник, О.В. Карманова, Ю.Ф.
Шутилин. - Воронеж.: гос. технол. акад. воронеж, 2004. - 508с.
46 Пожарная
безопасность. Взрывобезопасность [Текст]: справочник / А.Н. Баратов [и др.].-
М.: Химия,1987.-272с.
47 Пневматические
шины [Текст]: учеб. пособие для вузов / С.М. Цукерберг [и др.]. - М.: Химия,
1973. - 264с.
48 Рагулин,
В.В. Технология шинного производства [Текст] / В.В. Рагулин - М.: Химия, 1975.
- 352с.
49 Салтыков,
А.В. Основы современной технологии автомобильных шин [Текст] / А.В. Салтыков.-
М.: Химия, 1974.-294с.
50 Справочник
резинщика [Текст] / П.И. Захарченко [и др]. - М.: Химия, 1971. - 608с.
51 Степановских,
А.С. Охрана окружающей среды [Текст] / А.С. Степановских. - Курган.:
«Звуралье», 1998. - 512с.
Технология
резиновых изделий [Текст]/Ю.О. Аверко-Антонович, [и др.]. - Л.: Химия, 1991. -
352 с.: ил.
Технологический
регламент производства шин 21.00.R33
Экологический
паспорт санитарно-технического состояния условия труда. Утверждено генеральным
директором ООО «ПО Красноярский шинный завод» Р.М. Давыдовым 25.04.2005 г.
Свод
технических нормативов на производство шин / ФГУП «НИИШП» - 2001.-260с.