Общее устройство, техническое обслуживание и ремонт бульдозера Т130
Содержание
Введение
. Общее устройство бульдозера Т130
.1 Устройство машины
.2 Устройство узла (детали)
. Эксплуатация и техническое обслуживание
бульдозера Т130
.1 Эксплуатация и ТО машины
.2 Эксплуатация и ТО узла (детали)
.3 Возведение земляного полотна
. Ремонт дорожных машин
.1 Ремонт бульдозера на базе Т-130
.2 Ремонт рабочего оборудования бульдозера
.3 Ремонт вала (шестерни)
. Охрана труда
. Промышленная экология
Список использованных источников
Введение
Интенсивное развитие строительного производства и сокращение
сроков ввода в эксплуатацию новых жилых домов, заводов и фабрик, железных и
автомобильных дорог, газо- и нефтепроводов требуют ускоренного выполнения
больших объемов и комплексной механизации земляных работ, значительную долю
которых выполняют бульдозеры, бульдозеры-рыхлители, бульдозеры-погрузчики,
скреперы и грейдеры. Существенное значение придается применению этих машин при
добыче полезных ископаемых, производстве строительных материалов и в
сельскохозяйственном строительстве.
Отраслью строительного и дорожного машиностроения проводится
работа по усовершенствованию конструкций бульдозеров, бульдозеров-рыхлителей,
бульдозеров-погрузчиков, скреперов и грейдеров, улучшению технико-экономических
показателей, повышению единичной мощности, гидрофицированию управления,
увеличению надежности и ресурса в эксплуатационных условиях, облегчению
технического обслуживания и ремонта, улучшению условий труда машиниста и
эргономических показателей.
В связи с необходимостью освоения богатств Крайнего Севера,
Сибири, Дальнего Востока особое значение придается бульдозерам,
бульдозерам-рыхлителям, скреперам ввода в эксплуатацию промышленных объектов,
добыче полезных ископаемых, строительных материалов в тяжелых климатических
условиях при температуре воздуха до -60 'С и разработке вечномерзлых грунтов.
Бульдозеры, скреперы и грейдеры - это землеройно-транспортные
и планировочные машины. Они разрабатывают, транспортируют и формируют грунты и
материалы, перемещают их на определенное расстояние, роют котлованы, образуют
насыпи дорог и плотин. Основное различие этих машин состоит в том, что
бульдозер разрабатывает грунты отвалом и после образования призмы земли
перемещает ее волоком по рабочей поверхности к месту отсыпки или планировки.
Наибольшее расстояние, на которое перемещают грунт
бульдозером, достигает 100-150 м. При большей дальности эффективность работы
бульдозеров снижается и им на смену приходят скреперы. Они разрабатывают грунты
и материалы режущей ей кромкой, набирают их в ковш, закрывают заслонку, поднимают
ковш над поверхностью рабочей площадки, перевозят его с высокой транспортной
скоростью (до 10 м/с) на расстояние до 5 км. Затем скреперы отсыпают грунт в
насыпь или отвал равномерным слоем. Планировочные работы на рабочей площадке
магма осуществлять бульдозером и грейдером. При смерзании грунтов зимой или
разработке прочных материалов их рыхлят бульдозерами-рыхлителями. Таким
образом, машины взаимно дополняют одна другую при производстве многих видов
земляных работ в различных климатических и грунтовых условиях.
Особое внимание при создании бульдозеров, скреперов и
грейдеров придают улучшению условий и облегчению труда машинистов, что снижает
их утомляемость и повышает производительность труда.
С этой целью введен электростартерный запуск или управление
пусковым двигателем дизеля из кабины; снижены усилия на органах управления;
применены удобные подрессоренные сиденья, регулируемые по высоте и массе
машинистов, остекленные кабины с круговой обзорностью; существенно снижены шум
и вибрация на рабочем месте; установлены вентиляция, отопительные приборы,
кондиционеры, аптечки, термос. Комплекс приборов позволяет контролировать
работу агрегатов и заправку топливом с рабочего места машиниста.
Облегчению условий работы машинистов способствуют внедрение
гидромеханических и электрических трансмиссий на базовых тракторах и тягачах,
применение автоматизированных систем при планировке, которые сводят к минимуму
затраты энергии для управления машиной и утомляемость машинистов.
Повышение надежности и срока службы машин обусловлено
применением более высококачественных и высокопрочных конструкционных сталей и
материалов, повышением качества изготовления механизмов и деталей,
своевременным диагностированием и техническим обслуживанием бульдозеров,
скреперов, грейдеров, соблюдение сроков проведения профилактических работ,
инструкций по эксплуатации. Строгое выполнение правил эксплуатации сокращает
количество неисправностей машины и повышает готовность ее к выполнению рабочих
операций.
Эффективное использование техники требует высокой
квалификации от машиниста, знания устройства машин, правил технического
обслуживания и ремонта, безопасной эксплуатации, постоянного повышения знаний и
профессионального мастерства, овладения передовыми методами управления и
эксплуатации.
Условия перестройки в промышленности, введение нового
механизма хозяйствования, переход на полный хозрасчет строительных организаций
и управлений механизации, использование арендного подряда при выполнении
землеройно-транспортных работ позволяют молодым машинистам значительно
увеличить дневную выработку, повысить личный интерес в результатах труда,
материальное стимулирование обслуживающего персонала.
В настоящее время машинисты бульдозеров, скреперов, грейдеров
получают образование и практические навыки в профессионально технических
училищах и на предприятиях. На решении этой важной задачи необходимо
сконцентрировать внимание работников системы профессионально-технического
образования, учебно-производственной сети отраслей народного хозяйства.
Следует и далее развивать профессионально-технические училища
при базовых предприятиях, способные готовить квалифицированных рабочих для
эксплуатации новой техники, автоматизированных производств с применением
компьютеров, роботов, микропроцессорных средств и гибких технологий.
Здесь рассмотрены бульдозеры, скреперы, грейдеры с двигателем
мощностью до 150 кВт, на которых в основном проходят практику и работают
молодые машинисты.
Назначение.
Бульдозер представляет собой самоходную
землеройно-транспортную машину, предназначенную в основном для срезания
планировки и перемещения на расстояние до 150 м грунтов и материалов.
Состоит бульдозер из базового трактора или тягача, впереди
которого в поперечной плоскости навешен рабочий орган - отвал. Бульдозер - это
машина цикличного действия: сначала осуществляется рабочий ход (разработка и
перемещение грунта, засыпка траншей, срезка кустарника и т.п.), затем холостой
ход (возвращение в исходное положение), после чего цикл повторяется.
При установке на бульдозер в задней части трактора рыхлителя
получают бульдозер-рыхлитель. Бульдозеры-рыхлители разрабатывают грунты более
высокой прочности и смерзшиеся материалы после их предварительного рыхления.
Классификация.
Бульдозеры классифицируют по назначению, типу ходовой части,
конструкции рабочего оборудования, форме и назначению рабочего органа, типу
привода рабочего оборудования, тяговому классу базовой машины (мощности
двигателя).
По назначению различают бульдозеры общего назначения и
специальные.
Бульдозеры общего назначения используют для выполнения
основных видов землеройно-транспортных и вспомогательных работ на различных
грунтах и в климатических условиях умеренной зоны с температурой окружающей
среды :+ 40'С, холодного климата с температурой воздуха до -60 'С, а также в
условиях тропиков с температурой до.50 С.
Специальные бульдозеры предназначены для выполнения целевых
работ в специфических грунтовых или технологических условиях. Выпускают
бульдозеры-путепрокладчики, используемые при прокладке дорог и путей,
бульдозеры-толкачи - для работы со скреперами, трюмные бульдозеры - для
штабелирования материалов и полезных ископаемых в трюмах теплоходов, подземные
бульдозеры - для работы в шахтах и штольнях, подводные бульдозеры - для работы
вводе.
По типу ходовой части выпускают гусеничные и колесные
бульдозеры.
Гусеничный бульдозер распространен наиболее широко, так как
может быть использован в тяжелых грунтовых условиях.
Колесный бульдозер применяют при работе в более легких
дорожных условиях и необходимости часто перебазироваться с объекта на объект.
По конструкции рабочего оборудования различают бульдозеры с
неповоротным отвалом, поворотным отвалом в плане, универсальные и
бульдозеры-погрузчики.
В бульдозерах с неповоротным отвалом он установлен
перпендикулярно продольной оси машины неподвижно или с небольшим угловым
качанием в поперечной плоскости.
В бульдозерах с поворотным отвалом его можно поворачивать на
определенный угол в обе стороны от основного положения.
Универсальные бульдозеры оборудованы и шарнирно-сочлененным
отвалом из двух одинаковых частей, которые могут быть установлены
перпендикулярно продольной оси машины, под углом в одну сторону или под углом в
разные стороны. Бульдозеры-погрузчики характеризуются тем, что на подъемной
стреле шарнирно установлен отвал; вместо него можно навешивать грузовой ковш
или другие виды сменного рабочего оборудования (например, крюк), по форме
рабочего органа различают прямой, полусферический, сферический отвалы.
У прямого отвала - одинаковая форма по всей ширине. Концы
полос сферического отвала загнуты вперед на ширину боковых ножей. В сферическом
отвале боковые секции выдвинуты вперед на 1/3 ширины.
По назначению отвалы подразделяют на землеройный, снежный,
угольный, а также отвалы для толкания скреперов, уборки древесных отходов,
мусора.
Землеройный отвал используют при разработке грунтов и
насыпных, материалов. Скальный отвал с лобовым листом большей толщины и
усиленной металлоконструкцией предназначен для перемещения горных пород и
крупнокусковых материалов. Снежный отвал, состоящий из двух половин,
установленных под определенным углом один к другому, применяют при уборке
снега. Угольный отвал используют при складировании материалов. Отвал для
толкания скреперов усиливают в средней части толстым листом. Отвалы для уборки
древесных отходов и мусора изготовляют больших размеров и снабжают прорезным
козырьком.
1. Общее устройство бульдозера Т130
1.1 Устройство машины
Бульдозер-рыхлитель характеризуется тем, что на тракторы,
оборудованные бульдозером с неповоротным или поворотным отвалом, сзади навешивают
гидравлический однозубый или многозубый рыхлитель. К заднему мосту базового
трактора крепят на шпильках опорную раму, на которой внизу шарнирно установлена
рама, а вверху - тяга. К тягам шарнирно прикреплена рабочая балка так, что
образуется параллелограммный четырехзвенник.
По диагонали четырехзвенника установлены гидроцилиндры. В
рабочей балке закреплен зуб прямоугольного сечения, на конце которого
установлен быстросъемный наконечник.
Выдвигая шток гидроцилиндра, поднимают рабочую балку и зуб в верхнее
положение, втягивая шток - заглубляют рыхлитель в грунт. Благодаря
параллелограммному четырехзвеннику, зуб перемещается при подъеме по траектории,
близкой к вертикали. На тяжелых бульдозерах-рыхлителях применяют рыхлители, у
которых вместо верхней тяги устанавливают гидроцилиндры, обеспечивающие угловые
перемещения рабочей балки и зуба для получения больших разрушающих усилий
машин.
Бульдозер-погрузчик агрегатируют с колесным трактором или
шасси. На базовом тракторе неподвижно закреплена рама, представляющая собой две
вертикальные наружные стойки, жестко соединенные между собой. К раме шарнирно
подвешивают стрелу. Одна сторона стрелы поднимается и опускается в вертикальной
плоскости двумя гидроцилиндрами. На противоположном конце стрелы на двух шарнирах
прикреплена рамка, которая поворачивается относительно стрелы двумя
гидроцилиндрами. К рамке крепят бульдозерный отвал, погрузочный ковш или другие
виды сменного рабочего положения.
У бульдозера-рыхлителя рабочий цикл складывается из циклов
работы бульдозера и рыхлителя.
В начале участка движения рыхлителя передним ходом стойка с
зубом опускается в прочный грунт на определенную глубину t. Машина во время
движения вперед со скоростью Vp рыхлит грунт зубом. При подходе к концу
разрыхляемого участка рыхлитель углубляется из грунта и машина останавливается.
Затем включается задняя передача, бульдозер-рыхлитель со скоростью откатывается
в исходное положение и смещается в сторону на некоторую величину, называемую
шагом движения. После этого операция повторяется.
У бульдозера-погрузчика цикл работы зависит от типа
устанавливаемого рабочего оборудования. При оборудовании погрузочным ковшом
бульдозер-погрузчик, перемещаясь со скоростью Vp, внедряет рабочий орган в
штабель материала и одновременно поворачивает ковш в сторону базовой машины до
момента наполнения. Затем машина отходит назад со скоростью Vo, и в это же
время поднимает ковш на высоту, необходимую для разгрузки. После этого
транспортное средство подходит поперек движения бульдозера-погрузчика и он, перемещаясь
вперед, приближается к транспортному средству и поворачивает ковш для разгрузки
материала. Далее бульдозер-погрузчик отходит на некоторое расстояние назад,
опускает ковш и поворачивает его для внедрения в штабель. Последняя операция -
подход машины к штабелю на расстояние L, после чего цикл повторяется.
Операции, выполняемые машиной с грузом в ковше, называют
рабочим ходом; движение бульдозера-погрузчика с порожним ковшом - холостым
ходом.
Аналогичные операции происходят при работе машины с грузоподъемными
крюком, вилами, но вместо штабеля насыпного материала перемещают штучные грузы,
разгружаемые в транспортные средства или на место установки (например, склад).
1.1 - Бульдозеры и их разновидности
У неповоротного бульдозера ДЗ 110 А
(рис.1.2) отвал 1 крепится посредством универсальных шарниров 8 к толкающему
устройству в виде двух брусьев 7 коробчатого сечения, задние концы которых
соединены с помощью упряжных шарниров 6 с балками 5 ходовою устройства базового
трактора 4. Шарниры позволяют толкающим брусьям поворачиваться в вертикальной и
горизонтальной плоскостях при перекосе отвала.
Подъем и опускание отвала осуществляются с
помощью двух гидроцилиндров двойного действия 3, штоки которых шарнирно
прикреплены к отвалу через кронштейны. Отвал в рабочем положении удерживают
гидрораскос 2 и винтовой жесткий раскос 10, которые установлены в плоскостях
соответственно левого и правого толкающих брусьев. Нагрузка между толкающими брусьями
равномерно распределяется механизмом 9 компенсации перекоса, обеспечивающим
устойчивость отвала в горизонтальной плоскости.
Рис1.2 - Неповоротный бульдозер ДЗ 110 А
Рассмотрим конструктивные особенности яро воротных и
поворотных бульдозеров. Гидрораскос осуществляет перекос отвала в поперечной
плоскости путем поворота его на угол до ± 12° и представляет собой гидроцилиндр
двойного действия с гидрозамком, который включен в гидросистему трактора.
Винтовой раскос служит для механического изменения угла резания ножей в
диапазоне ± 10° от среднего угла установки, составляющего 55°.
У поворотного бульдозера ДЗ-109Б отвал /
монтируется на универсальной толкающей раме 7, охватывающей снаружи трактор 4 и
состоящей из двух жестко соединенных между собой полурам прямоугольного
сечения.
Рама крепится к ходовым тележкам трактора
с помощью упряжных шарниров 5. На раме вместо отвала может быть установлено
различное сменное оборудование с гидравлическим управлением - кусторез, древовал,
корчеватель-собиратель, плужный снегоочиститель и др.
Поворотный отвал соединен с толкающей
рамой посредством центрального шарового шарнира 10 и двух боковых толкателей 8
с винтовыми раскосами 2, обеспечивающих различное положение отвала относительно
рамы.
При одинаковом изменении длины раскосов от
среднего положения регулируют угол резания ножей. Угол поперечного перекоса
отвала в вертикальной плоскости регулируется путем изменения межцентрового
расстояния проушин раскосов.
Отвал может быть установлен в плане под
углом у в обе стороны от продольной оси машины и под прямым углом к ней. Для
установки отвала в три положения (прямое, правое и левое) на верхней полке
каждой полурамы установлены по три опорных кронштейна 6, в которых шарнирно
крепятся толкатели. На скошенной части полурам установлены кронштейны 9 для
крепления гидроцилиндров 3 подъема-опускания отвала.
У некоторых моделей бульдозеров изменение
угла поворота отвала в плане и регулировка угла перекоса отвала осуществляются
с помощью гидроцилиндров. При продольном движении бульдозера с повернутым в
плане отвалом грунт перемещается вбок по отвалу.
Способность поворотных бульдозеров
перемещать грунт в сторону определяет их широкое использование при засыпке
каналов, рвов, траншей коммуникаций, а также очистки строительных площадок и
дорог от снега.
Гидравлическая система управления рабочим
оборудованием обеспечивает с помощью гидроцилиндров подъем и принудительное
опускание отвала, его плавающее и фиксированное положения, поворот отвала в
плане (у поворотных бульдозеров), поперечный двусторонний перекос (до 12°)
отвала в вертикальной плоскости, регулировку угла резания ножей отвала (среднее
значение 55°) путем поворота (наклона) отвала вперед и назад относительно
толкающего устройства.
Принудительное заглубление ножей отвала в
грунт под действием гидроцилиндров, развивающих усилие до 40 % и более веса
тягача, позволяет бульдозерам с гидравлическим управлением разрабатывать
прочные грунты, а возможность установки отвала в определенное фиксированное
положение обеспечивает срезание слоя грунта заданной толщины. Поперечный
перекос отвала повышает универсальность машины и ее эксплуатационные
возможности на планировочных работах, облегчает разработку тяжелых грунтов и т.
п.
Гусеничные бульдозеры могут оснащаться
дополнительным быстросъемным оборудованием, значительно расширяющим их
технологические возможности: неподвижными или гидроуправляемыми уширителями 1 и
удлинителями отвала, открылками, передними и задними рыхлительными зубьями,
кирковщиком для взламывания асфальтовых покрытий, гребенчатыми ножами для
разработки мерзлых грунтов, надставкой для рытья канав, откосником с жестким
креплением и гидроуправляемым откосником-планировщиком, передними и задними
лыжами, грузовыми вилами, подъемным крюком и т. п.
Аппаратура автоматического управления
отвалом обеспечивает повышение качества обработки грунтовой поверхности,
повышение производительности машины за счет уменьшения числа проходов
бульдозера по планируемому участку, и снижение утомляемости машиниста.
1.2 Устройство узла
(детали)
Бульдозерное оборудование с шарнирным
креплением отвала к толкающим брусьям состоит (рис. 1.3.) из отвала, двух
толкающих брусьев и, гидрораскоса, винтового раскоса, механизма компенсации
(подкоса) и двух упряжных шарниров, которыми оборудование крепят к рамам
гусеничных тележек базового трактора. Шарнир представляет собой крестовину, к
которой на двух взаимно перпендикулярных пальцах шарнирно установлены отвал и
толкающие брусья. Шарниры позволяют толкающим брусьям поворачиваться в
вертикальной и горизонтальной плоскостях при перекосе отвала.
Рис.1.3 - Рабочее оборудование бульдозера
с неповоротным отвалом и гидроперекосом
- нож; 2 - щека; 3 - козырек; 4 - пояса
жесткости; 5, 16 - кронштейны; 6 - винтовой раскос; 7 - рукоятка; 8 - механизм
компенсации перекоса; 9, 12 - толкающие брусья; 10 - упряжной шарнир; 11 -
гидрораскос; 13 - крестовина; 14, 18, 19 - пальцы; 15 - отвал; 17 - серьга; 20
- втулка; 21 - полусфера; 22 - крепежный болт; 23 - прокладки.
Отвал представляет собой лобовой лист
криволинейного профиля, обеспечивающего минимальную энергоемкость копания и
снижающего заливание грунта. Сзади по всей длине листа приварены верхний и
нижний пояса жесткости, а также соединительный лист, в результате чего
образуется объемная металлоконструкция.
Торцы отвала закрыты боковыми щеками, к
которым приварены вертикальные ножи со скошенной режущей кромкой. Сзади
приварены кронштейны. В зоне установки ножей боковая щека усилена накладкой.
Нижняя часть лобового листа образует подножевую плиту, которая сзади отвала
подперта рядом продольных привареных косынок.
На подножевую плиту с помощью болтов с
потайными головками, гаек и пружинных шайб установлены два средних и два литых
боковых ножа. Верхняя часть лобового листа переходит в козырек со скошенными
краями по профилю призмы.
Толкающие брусья и служат для передачи
тягового усилия от трактора к отвалу. Они имеют коробчатое сечение и сварены из
уголков. К передним торцам брусьев приварены литые проушины для крепления через
крестовины к отвалу, сзади - полусферы опоры упряжных шарниров. Сверху на
коробке брусьев приварены кронштейны для установки винтового раскоса и
гидрораскоса. С наружной стороны балки усилены накладками, которые одновременно
предохраняют брусья от абразивного изнашивания. С внутренней стороны левого
бруса приварен кронштейн, к которому шарнирно крепят механизм компенсации.
Гидрораскос и винтовой жесткий раскос,
которые установлены в плоскостях соответственно левого и правого толкающих брусьев,
удерживают отвал в рабочем положении. Одна сторона раскосов прикреплена к
толкающим брусьям, другая - к отвалу с помощью двух пальцев. Пальцы фиксированы
от поперечного смещения цилиндрическими штифтами со шплинтами. Гидрораскос
осуществляет перекос отвала в поперечной плоскости и представляет собой
гидроцилиндр двойного действия, который включен в гидросистему трактора с
помощью шлангов и трубопроводов.
При выдвижении штока гидрораскоса
бульдозерный отвал поворачивается в поперечной плоскости направо по ходу машины
(по часовой стрелке) на угол до 12°: при втягивании его - налево на тот же
угол. Упряжной шарнир выполнен в виде цилиндрического пальца, на котором
закреплена сферическая втулка с помощью шайбы и болтов. Втулку охватывают две
разрезные полусферы, одна из которых приварена к концу толкающего бруса, другая
прикреплена к втулке двумя болтами с гайками. Для регулирования зазора в
упряжном шарнире между полусферами размещены регулировочные прокладки. С целью
защиты поверхностей трения от попадания абразивных частиц шарнир защищен
резиновыми кольцами. Смазочный материал подается в шарнир через пресс-масленку.
Гидрораскос состоит из гидроцилиндра, гидрозамка, защищенного кожухом, и
штуцеров для подсоединения к гидросистеме базового трактора.
Винтовой раскос служит для механического
изменения угла резания ножей в диапазоне ± 10° от среднего угла установки,
равного 55°, и выравнивания отвала в прямое положение после сборки. Раскос
представляет собой трубу, с одной стороны которой выполнено резьбовое отверстие,
а с другой - вставлена свободно вращающаяся проушина с шестигранником,
фиксируемым от свободного проворачивания пружинным стопором.
В резьбовую часть трубы ввернут винт с
головкой, в отверстие которой запрессован шарнирный подшипник. Поверхности трения
винта и проушины смазываются с помощью масленок. Винт защищен от грязи
уплотнением. При навинчивании трубы на винт с помощью рукоятки, установленной в
патрубок, уменьшают угол резания отвала. Повышая межцентровое расстояние
раскоса, соответственно увеличивают угол резания, при разработке тяжелых и
липких материалов - уменьшают. Стружка грунта самостоятельно отделяется от
верхнего козырька отвала в случае подбора оптимального угла резания.
Механизм компенсации представляет собой цилиндрическую тягу с
проушинами, которая одной стороной шарнирно связана с правым толкающим брусом,
другой - с поперечным шарниром, размещенным в зоне продольной оси на кронштейне
левого толкающего бруса. В кронштейне установлен палец с резьбовым концом.
Для облегчения сборки деталей используют монтажные прокладки.
Палец с помощью серьги шарнирно связан с отвалом. Механизм компенсации
обеспечивает устойчивость отвала в горизонтальной плоскости и позволяет
передавать поперечные нагрузки равномерно двум толкающим брусьям. Оборудование
поднимают и опускают с помощью двух гидроцилиндров двойного действия. Их штоки
прикреплены к отвалу шарнирно при помощи кронштейнов. Противоположные штокам
концы гидроцилиндра присоединены к трактору.
Режущие ножи бульдозерного отвала. Ножи бульдозеров режут
грунт в процессе его разработки. От конструкции ножа, формы режущей кромки,
сохранения ее заострения в процессе работы, износостойкости зависит
производительность машины. Применяют два типа ножей (рис.1.4): средние и
боковые.
Средний нож изготавливают из полосового проката. Выполненные
по его краям параллельные кромки скошены под углом 30°. Для повышения
долговечности режущие кромки ножей наплавляют сормайтом или сталинитом. Два
рада квадратных отверстий ножа с двух сторон развенкованы под углом 90°.
Отверстия удерживают крепежные болты с квадратным оголовником от поворачивания
при навинчивании гаек. Коническая головка болта входит в отверстие таким
образом, что оказывается заподлицо с плоской рабочей поверхностью ножа и не
мешает движению грунта по нему. Отверстия расположены на расстоянии а и б.
Схема смещения и перестановки средних ножей показана на рис. 5а. На заводе
средний нож 1 прикрепляют к подножевой плите 3 болтами 2 с гайками в нижнем
ряду отверстий (положение I).
После изнашивания режущей кромки на межцентровое расстояние Ь
гайки отвертывают, нож опускают до совмещения верхнего ряда отверстий
(положение И) и сверлений в плите 3 и затягивают нож болтами. Когда режущая
кромка снова изнашивается, нож снимают с отвала, переворачивают на 180° и закрепляют
в нижнем ряду отверстий (положение III).
а - средний; б - боковой
Рисунок 1.4 - Режущие ножи бульдозерного отвала
После дальнейшего изнашивания его снова смещают вниз и крепят
на верхнем ряду отверстий (положение IV). Если режущая кромка выступает на 15...25 мм
над нижним краем подножевой плиты, то нож заменяют новым. Четырехкратная
перестановка среднего ножа значительно повышает срок его службы. На
бульдозерный отвал устанавливают два-три средних ножа для облегчения их
перестановки.
а - среднего; б - бокового; 1,4 - ножи; 2 - болт;
- надножевая плита бульдозерного отвала.
Рисунок 1.5 - Схема перестановки режущих
ножей бульдозера
Левым и правым боковыми ножами 4 (рисунок 1.5) защищают края
отвала. Отлиты ножи из износостойкой стали. Каждый нож представляет собой
плоскую пластину, боковая и нижняя наружные кромки которой утолщены для
повышения срока их службы. Нижние и боковые кромки скошены под задним углом
60°. Верхний край ножа срезан под углом 45°, чтобы уменьшить залипание грунта.
В ноже сделаны четыре ряда квадратных отверстий с конической зенковкой с
наружной стороны для установки конических головок крепежных болтов. Ножи
прикреплены к подножевой плите 3 двумя рядами болтов 2 (положение V). Два других ряда
используют для смещения ножей вниз после их изнашивания (положение VI).
2. Эксплуатация и техническое обслуживание
бульдозера Т130
2.1 Эксплуатация и ТО
машины
Бульдозеры и бульдозеры-погрузчики выполняют операции
следующим образом (рисунок 2.1). Послойную разработку и перемещение материалов
производят при расстоянии транспортирования 50... 150 м. Большие расстояния
экономически выгодны для тяжелых бульдозеров. При поверхностной разработке
грунтов и полезных ископаемых характерны челночные движения машины, чередующие
рабочий ход и отъезд назад порожняком. Грунт целесообразно набирать и
перевозить по одному проходу с образованием боковых валиков, траншейным
способом, спаренной работой бульдозеров, образованием нескольких призм. В
легких грунтовых условиях применяют дополнительное сменное оборудование
бульдозера (открылки, уширители, удлинители, съемные козырьки).
Рис. 2.1. Основные
земляные работы бульдозера
Возведение насыпей осуществляют двумя
способами: поперечными проходами из резерва (I) и продольными
односторонними движениями машины (II).
При поперечном перемещении грунта из
резервов целесообразно использовать траншейный способ разработки материалов и
спаренную работу нескольких машин. Первые призмы подают в центр насыпи,
последующие - ближе к ее краям.
Призмы волочения укладывают в прижим.
Подъемы откосов насыпи, по которым подается грунт, не должны превышать 30%. При
больших подъемах насыпи работа неэффективна.
Продольными движениями бульдозера в
направлении продольной оси насыпи целесообразно подавать грунт под уклон.
Высота насыпи в этом случае может быть до 4...5 м.
Разработку выемок производят продольными
двусторонними проходами (III) и поперечными ходами (IV). Продольный
двусторонний способ обеспечивает большую производительность бульдозеров. Его
применяют при небольшой протяженности выемок и в случаях, когда грунт, вынутый
из выемки, полностью укладывают в прилегающие насыпи. Поперечный способ
разработки выемки применяют, когда излишки грунта укладывают в кавальеры вдоль
будущего полотна дороги.
Отрывку каналов, ирригационных сооружений,
траншей, котлованов производят поперечными ходами бульдозера с постепенным
смещением машины вдоль сооружений (У). Грунт укладывают в кавальеры по всей
протяженности каналов, создавая с обеих сторон валы земли. Разрабатывают грунт
в параллельных траншеях глубиной не более габаритной высоты машины. Расстояние
между траншеями до 0,4...0,6 м. После отрывки разрушают межтраншейную перемычку.
В этом случае эффективна групповая работа машин спаренными параллельными
ходами.
Планировочные работы проводят на ровной
поверхности, срезая небольшие бугры и засыпая впадины, ямы, овраги. Большие
впадины засыпают с соседних косогоров продольными проходами (VI). Последние проходы
делают со смещением на 3/4 ширины отвала, чтобы исключить
появление боковых валиков. После грубой передней планировки целесообразно
провести отделку поверхности при заднем ходе бульдозера и "плавающем"
положении отвала. Для большей точности целесообразно применять взаимно
перпендикулярные проходы бульдозеров.
Пробивку террас и полок на косогорах
осуществляют бульдозерами с неповоротным и поворотным отвалами. Наиболее
эффективен и безопасен способ перемещения грунта с косогора в полунасыпь
(рис.2.1.) поперечными проходами машины под уклон (I).
Такой способ целесообразен на пологих
склонах косогоров. При больших углах наклона используют продольный способ (II). В этом случае отвал
бульдозера, установленный с перекосом, пробивает сначала проход 1, затем 2, 3,
4 и 5. Работа продольными проходами более производительна, однако необходимо
проявлять особую осторожность, так как возможно поперечное сползание или
опрокидывание машины по склону. Поэтому в целях безопасности проведения работ
учитывать поперечную устойчивость бульдозера.
Засыпку траншей (рис.2.2.) производят
бульдозерами с неповоротным или поворотным отвалом. Эту операцию выполняют
прямыми проходами, перпендикулярными оси траншеи, или косыми движениями под
некоторым углом к ней.
Бульдозер с неповоротным отвалом краем
захватывает часть грунта из насыпи и перемещает его в траншею. Если глубина
траншеи 1,5 м и более, то грунт ссыпают через одну или две призмы, чтобы не
допускать обвала стенок траншеи и сползания в нее бульдозера. После первого
прохода бульдозер смещается при заднем ходе и операция повторяется.
У бульдозера с поворотным (более широким)
отвалом его устанавливают под углом направо к продольной оси машины и косыми
хода- ми под углом 30...40е сталкивают грунт в траншею. Применение
бульдозеров с поворотным отвалом на этой работе более эффективно, так как грунт
частично смещается в сторону при сталкивании.
Толкание скреперов осуществляют бульдозеры
при наборе грунта и выходе груженого скрепера из забоя с большим уклоном
подъездных путей.
Рисунок 2.2 - Разработка косогоров
бульдозером
а - неповоротный, б - поворотный, 1 -
насыпь грунта, 2 - траншея
Рисунок 2.3 - Засыпка траншей бульдозером
с отвалом
Погрузку грунта в транспорт с эстакады
производят преимущественно в песчаных карьерах. Эстакаду устраивают в траншее,
отрытой бульдозером. Продольными ходами бульдозер подвигает материал к бункеру
эстакады и загружает самосвалы. Бульдозер работает через одну или две призмы,
чтобы не вызвать обвала эстакады.
Погрузка грунта в транспорт с лотка.
Валку деревьев осуществляют, упираясь
максимально поднятым отвалом в ствол.
Корчевку пней выполняют прямым отвалом или
отвалом с пере косом. Сначала наибольшим заглублением отвала средними или
угловыми ножами подрезают корни пня и раскачивают его повторными включениями
муфты сцепления. Затем одновременным поступательным движением машины и подъемом
рабочего оборудования выкорчевывают пень. Аналогичным образом удаляют из земли
крупные камни и валуны, частично находящиеся на поверхности.
Срезку кустарника и мелколесья производят
прямым отвалом, опущенным в грунт на глубину 10...20 см, при поступательном
движении вперед всего бульдозера. По мере накопления кучи кустарников, корней,
мелких деревьев поворотным движением перемещают в сторону от очищаемой трассы.
а - продольно-кольцевая, б - спиральная, в
- челночная со смещением, г продольно-поперечная
Рисунок 2.4 - Схемы рыхления грунтов
а - траншейный с подачей в автотранспорт погрузчиком, б - под
уклон с погрузкой из штабеля в транспорт экскаватором, в - двумя
бульдозерами-рыхлителями; 1 - бульдозеры-погрузчики, 2 - погрузчик, 3 -
автотранспорт, 4- экскаватор
Рисунок 2.5 - Способы разработки фунтов и
добычи полезных ископаемых
Снегоочистку выполняют для содержания
автомобильных дорог в хорошем состоянии. Наиболее эффективен в этом случае
бульдозер с поворотным отвалом с косопоставленным рабочим органом.
Бульдозеры-рыхлители разрушают скальные и
мерзлые породы под воздействием двух сил: сжатия зубом и разрыва массива
наконечником и стойкой. Лучше всего рыхлить этими машинами трещиноватые и
слоистые породы: известняки, песчаники, сланцы, фосфориты, бурые и каменные
угли.
Выбор схемы рыхления зависит от прочности
и природы разрабатываемых пород.
При рыхлении грунтов IV категории и прочных
пород целесообразно работу машин организовывать по продольно-кольцевой и
спираль ной схемам, так как они обеспечивают наибольшую производительность
машины.
Челночную и продольно-поперечную схемы
применяют при рыхлении скальных пород и вечномерзлых грунтов. Последнюю схему
используют, когда необходимо получить разрыхленную породу меньших размеров. Ее
дополнительно дробят гусеницы трактора.
Площади мерзлых грунтов разрабатывают
послойно на максимально возможную глубину.
При глубине промерзания пород 50...70 см
можно рыхлить массив тремя зубьями; если глубина разработки пород больше, то
одним зубом за два или три прохода с глубиной рыхления 30...40 см за каждый
цикл. При работах на мерзлых породах сила тяги машины снижается на 35...45% за
счет уменьшения коэффициента сцепления ходовой части с грунтом.
Грунты рыхлят на рабочей передаче
трактора, перемещающегося со скоростью 0,9...2,7 км/ч. По окончании рабочего
цикла выглубляют рыхлитель и проверяют наличие съемного наконечника. При его
утере можно повредить носок стойки, и он не будет удерживать наконечник. В этом
случае стойку заменяют.
Разрыхленные грунты и породы убирают
землеройно-транспортными машинами.
Существует несколько рациональных схем организации работы
бульдозера-рыхлителя в сочетании с погрузчиками и экскаваторами.
При разработке массива траншейным способом
бульдозер-рыхлитель послойно рыхлит породу на дне траншеи. Затем бульдозерным
оборудованием при приподнятом рыхлителе порода перемещается в штабель
челночными движениями машины. Из штабеля одноковшовым погрузчиком раздробленный
материал погружается в автотранспорт и отвозится к месту складирования или
переработки.
Более рациональная схема разрыхления и
уборки пород бульдозером под уклон. Штабель материала образуют у подошвы
уклона. Из штабеля экскаватор или погрузчик загружает породу в автотранспорт.
Производительность агрегата в этом случае выше.
Чтобы согласовать производительность
погрузочных средств, иногда применяют два бульдозера-рыхлителя, которые сначала
продольно-поперечными ходами рыхлят дно траншеи, затем один бульдозер подает
материал к месту складирования, а другой заталкивает его в штабель, из которого
погрузчик забирает породу и заполняет автотранспорт.
При добыче полезных ископаемых открытым
способом применяют комплексный отряд машин, в который входят 3...5
бульдозеров-рыхлителей, экскаватор или погрузчик и несколько самосвалов. Чтобы
не было простоев, один бульдозер-рыхлитель только рыхлит площадку. Несколько
бульдозеров параллельно сдвигают разрыхленную пустую породу в штабель, из
которого экскаватор загружает ее в автотранспорт и транспортирует в отвал.
После уборки пустой породы аналогичным способом разрабатывают полезные
ископаемые.
Особенности эксплуатации бульдозеров и
бульдозеров-рыхлителей в различных грунтовых и климатических условиях.
Почвенно-геологические и климатические
условия нашей страны отличаются большим разнообразием. Бульдозеры и
бульдозеры-рыхлители эксплуатируют на увлажненных, несвязных, глинистых
грунтах, скальных породах, добыче руд, полезных ископаемых, золотоносных
песков, при разработке смерзшихся и вечномерзлых грунтов.
На увлажненных и несвязных грунтах
эксплуатация затруднена в связи с их уменьшенной несущей способностью,
повышенным сопротивлением перекатыванию, снижением коэффициента сцепления с
грунтом и соответственно силы тяги бульдозеров. При положительной наружной
температуре рыхлитель снимают, так как грунты легко можно разрабатывать
бульдозерным отвалом. Демонтаж рыхлителя снижает массу машины, в связи, с чем
сокращаются потери на перекатывание.
Отвал бульдозера наполняют на 2/3
высоты. Характерный признак перегрузки отвала - это буксование гусениц и колес.
Так как несущая способность грунтов и сопротивление сдвигу ниже, то почвозацепы
гусениц и шин при меньшей силе тяги срывают уплотненные участки почвы и
движители буксуют. Другой причиной буксования является резкое изменение частоты
вращения коленчатого вала двигателя. Во время буксования почва быстро
выбирается из-под гусениц, и трактор опирается на корпус заднего или ведущего
моста.
Не следует также резко изменять частоту
вращения коленчатого вала двигателя во избежание буксования гусениц и колес.
При буксовании ходовой части бульдозера выжимают сцепление, включают заднюю
передачу, поднимают отвал и задним ходом выезжают из образовавшейся колеи.
Застрявший бульдозер вытаскивают на буксире. Если предварительно вывесить
машину на отвале и положить в образовавшуюся колею подсобные материалы (доски,
бревна), то бульдозер может выехать самостоятельно.
Бульдозер не должен работать по одному и
тому же следу. При разработке траншей и котлованов их ширина должна быть в два
раза больше ширины отвала. Нельзя использовать бульдозеры, у которых износились
гребни траков или почвозацепы шин. Изношенные детали ходовой части заменяют
новыми.
При движении задним ходом грунт планируют
и перемещают на низшей передаче.
На заболоченных участках можно работать
только бульдозерами, базовыми машинами которых служат тракторы болотных
модификаций с уширенными гусеницами и удельным давлением на грунт 0,02...
...0,03 МПа. Колесные машины на заболоченных грунтах применять нецелесообразно,
так как они буксуют и могут проваливаться.
На грунтах со слабой несущей способностью
можно использовать колесные машины со всеми ведущими колесами и низким
давлением воздуха в шинах.
Бульдозеры широко эксплуатируют при
разработке мерзлых грунтов и в условиях низких температур, при которых резко
изменяются свойства материалов. Металлоконструкции и резиновые уплотнения
становятся хрупкими, смазочные материалы густеют, затрудняется запуск
двигателей и увеличивается интенсивность их изнашивания, охлаждение топлива
ухудшает его воспламенение, качество распыла и приводит к потере мощности
двигателя, расход топлива увеличивается, емкость аккумуляторных батарей падает
и ухудшаются условия работы электрической системы бульдозера, загустевшая
рабочая жидкость не позволяет четко управлять рабочим оборудованием. Кроме
того, ухудшаются условия труда водителя за счет снижения температуры в кабине,
уменьшения видимости рабочих органов и фронта работ через замороженные стекла,
увеличиваются усилия на рукоятках и педалях управления, повышается количество
отказов.
Для работы в условиях холодного климата
используют бульдозеры, которые изготовлены из специальных сталей и
резинотехнических материалов. В индексы этих машин добавляют буквы ХЛ, например
бульдозер ДЗ-141ХЛ. При эксплуатации бульдозеров в таких условиях соблюдают
следующие правила.
До наступления холодного периода в
соответствии с инструкцией по эксплуатации, в агрегаты заливают масло зимних
сортов, а в систему охлаждения двигателя - незамерзающую жидкость типа антифриз
или тосол, повышают плотность электролита в аккумуляторных батареях до 1,31 и
утепляют их пенопластом, проверяют работу гидросистемы, отопительных приборов,
уплотнения кабины, подтягивают все соединения. В гидросистему рекомендуют
заливать зимние сорта масел типа ВМГЗ.
Подготовка топливной системы заключается в
промывке баков, сливе отстоя из фильтров, отстойников для удаления влаги,
регулирования топливной аппаратуры и форсунок, утепления баков, фильтров и
топливопроводов. Чтобы конденсат не собирался на внутренних стенках топливных баков
и отстойников, их утепляют обмазками, листами асбеста, чехлами из парусины и
ватина. Применяют только зимнее топливо (3 или А), которое обязательно сливают
после работы.
Перед заправкой смазочной системы
материалами зимних сортов ее промывают, прочищают фильтры, отключают радиаторы.
Трансмиссию промывают дизельным топливом и
заливают маслом зимних сортов. Затем проверяют работу бортовых фрикционных муфт
и тормозов гусеничных машин и рулевого управления у колесных.
Для улучшения теплового баланса двигателя
устанавливают утеплительный чехол на его капот, закрывают передние шторки и
перед решеткой радиатора дополнительно укладывают лист железа или фанеры. На
зиму снимают вентилятор.
Кабину утепляют, подводят теплый воздух из
подкапотного пространства для обогрева стекол, готовят антиобледенитель стекол
(раствор из 30 % соли и 70 % глицерина). Целесообразно изнутри устанавливать
накладные стекла из плексиглаза, которые наклеивают резиновым клеем на
резиновую прокладку. Щели в полу и дверях заделывают войлоком, на рукоятки
управления надевают войлочные чехлы. К стенкам кабины прикрепляют тканевые
утеплители, уменьшающие потери теплоты в окружающую среду.
Постоянный подогрев используют на
стоянках, для чего поток горячего воздуха нагнетается вентилятором по пневмопроводу
к механизмам машины. Возможен подогрев масла и рабочей жидкости электрическим
способом от постоянной электросети.
Предпусковой подогрев осуществляют с
помощью котлов, которые работают на бензине или дизельном топливе. Бензиновый
пусковой подогреватель ПЖБ-400 (рисунок 2.6.) применяют для разогрева
двигателей тракторов Т-170. Его устанавливают на двигатель перед зимней
эксплуатацией.
- кронштейн, 2 котел, 3 - горелка, 4 -
свеча накаливания, 5 - бензопровод, 6 - вентилятор, 7 - бензобак, 8 - клапан, 9
- трубопровод, 10 - труба, 11 - сливной кран
Рисунок 2.6 - Предпусковой подогреватель
ПЖБ-400
Перед эксплуатацией машины предварительно
обогревают кабину электропечами мощностью 2...2,5 кВт. При этом надо соблюдать
правила электробезопасности. В процессе работы машины кабину постоянно
обогревают отопителем. Иногда выхлопную трубу пропускают через кабину для
дополнительного использования теплоты выхлопных газов. Возможен ее подвод от
радиатора с помощью трубы.
Запуск двигателя в зимнее время требует
большого внимания от машиниста. Известны три системы запуска: холодный, при
постоянном подогреве, и с предпусковым подогревателем.
Предпусковой подогрев осуществляют с
помощью котлов, которые работают на бензине или дизельном топливе. Бензиновый
пусковой подогреватель ПЖБ-400 (рисунок 2.6.) применяют для разогрева
двигателей тракторов Т-170. Его устанавливают на двигатель перед зимней
эксплуатацией.
Подогреватель представляет собой котел 2,
который прикреплен с помощью кронштейна 1 к дизелю. К котлу подведена горелка
3, в которую воздух нагнетается вентилятором 6. Первоначально воздух
нагревается свечой накаливания 4. Бензин подается через электромагнитный клапан
8 и бензопровод 7 из бачка пускового двигателя. Котел подогревает охлаждающую
жидкость двигателя и по трубопроводу 9 она поступает в систему охлаждения.
Жидкость заливают через трубу 10, сливают с помощью крана 11. Одновременно
горячими газами подогреваются масляный картер двигателя и дизельное топливо.
Снегозадержание на сельскохозяйственных
полях и вдоль дорог осуществляют одиночными проходами бульдозеров (рисунок 2.7.
а), после чего остаются уплотненные снежные валы.
Рисунок 2.7 - Снегозадержание (а) и снегоочистка
(б), выполняемые бульдозером
Холодный запуск выполняют при температуре
-30° С, применяя эфирные пусковые жидкости, впрыскиваемые в распыленном
состоянии во всасывающий трубопровод двигателя. Для карбюраторных двигателей -
это пусковая жидкость "Арктика", для дизельных - "Холод
Д-40".
Постоянный подогрев используют на
стоянках, для чего поток горячего воздуха нагнетается вентилятором по
пневмопроводу к механизмам машины. Возможен подогрев масла и рабочей жидкости
электрическим способом от постоянной электросети.
При использовании на мерзлых грунтах
бульдозера-рыхлителя увеличиваются масса и сила тяги машины, затрудняется
управление механизмами и агрегатами за счет снижения температуры конденсата в
шарнирных и подвижных соединениях. Поэтому необходимо плавно выполнять рабочие
операции, чтобы избежать разрушения сварных швов и металлоконструкций.
Рекомендуют чаще очищать ходовую часть от намерзшего льда и грунта, чтобы не
поломать механизм натяжения, опорные и направляющие катки.
Снегоочистку дорог выполняют бульдозерами
с поворотным отвалом в сочетании с роторно-винтовыми снегоочистителями.
Последовательность очистки приведена на рисунок 2.7, б. Снег отвалом бульдозера
отгребают от оси дороги к периферии, а затем отбрасывают снегоочистителем на
обочину. Аналогичным образом очищают и другую полосу. Если нет снегоочистителя,
то проходы бульдозера по одной полосе повторяют и снег отбрасывают ближе к
кювету дороги.
Эксплуатация бульдозеров,
бульдозеров-рыхлителей и бульдозеров-погрузчиков в южных районах, в условиях
жарких пустынь и влажных тропиков, имеет свои характерные особенности. Грунт и
металлические части машин в жаркое время нагреваются до температуры 50...70 °С.
Пересохший грунт превращается в пыль, и запыленность воздуха может достигать
4...5 г/м3, а видимость снижаться до 5...10м.
В условиях жаркого климата следят за тем,
чтобы в смазочной системе двигателя, сборочных единицах трансмиссии, элементах
ходовой части, гидросистеме были залиты материалы летних сортов, которые
отличаются большей несущей способностью и лучшими смазочными свойствами.
Боковые капоты и шторку радиатора двигателя снимают, чтобы он не перегревался.
Систематически промывают систему охлаждения, так как собирающиеся там ржавчина
и шлам ухудшают тепловой режим двигателя. Особенно следят за уровнем воды в
радиаторе.
После работы в запыленных условиях
ежедневно промывают под напором воды из шланга двигатель, радиатор и машину в
целом, так как налеты пыли на пластинах и трубках радиатора, на поверхности
двигателя ухудшают его охлаждение и приводят к преждевременному изнашиванию
сборочных единиц.
Ежесменно осматривают и продувают
воздухоочиститель, проверяют герметичность крышек заливных горловин двигателя,
радиатора, коробки передач, задних мостов, бортовых редукторов. Систематически
снимают налет пыли и чистят сапуны на механизмах базовых машин. При их
загрязнении возможна утечка масла через сальники.
Для улучшения условий работы в кабине
машиниста ее переднюю стенку и крышку с внутренней стороны закрывают
дополнительной теплоизоляцией, чтобы теплота от двигателя и прямые лучи солнца
меньше проникали во внутреннее пространство кабины. Необходимо следить за
герметичностью уплотнения дверей и стекол кабины, особенно при работе в
запыленных условиях, работой стеклоочистителя и омывателя стекол. Вентилятор,
воздухоохладитель или транспортный кондиционер в жаркое время года должны быть
всегда в рабочем состоянии.
Чтобы удалять абразивные частицы с
поверхностей трения, необходимо чаще смазывать шарнирные соединения рабочего
оборудования пластичными смазочными материалами. В жаркое время особенно
тщательно следует проверять герметичность соединений топливных гидролиний
двигателя, чтобы исключить возгорание машины.
Подготовка машин к
эксплуатации. Использование по назначению. Учет работы машин
Подготовка к эксплуатации заключается в
получении машины от завода-изготовителя или регионального представителя завода
(диллера) и последующем ее вводе в эксплуатацию.
При получении машины завод-изготовитель
(дилер) обязан: предоставить будущему владельцу эксплуатационно-техническую
документацию согласно перечню в паспорте передаваемой модели и совместно с
получателем сверить принадлежность документации передаваемой машины по
заводскому номеру в паспорте и на фирменной табличке, обычно прикрепляемой
снаружи на кабине машиниста; проверить осмотром совместно с получателем
целостность сборочных единиц и наличие пломб, отсутствие повреждений,
комплектность согласно упаковочному листу, провести краткий инструктаж
получателя в объеме раздела «ВНИМАНИЕ» инструкции (руководства) по эксплуатации
машины; продемонстрировать получателю работу предъявляемого образца на холостом
ходу без нагрузки по всем рабочим операциям и работу приборов безопасности,
сигнализации, блокировки; проверить с получателем прикладываемые к машине
запасные части, инструмент и принадлежности (ЗИП), в том числе базовой машины,
на соответствие их упаковочным листам. Проверяют также эксплуатационные
документы - техническое описание и инструкцию по эксплуатации, паспорт.
Техническое описание и инструкция по
эксплуатации объединены в один документ, содержащий данные об эксплуатационных
качествах машины, описание устройства составных частей и сборочных единиц,
раздел по техническому обслуживанию, монтажу, демонтажу и транспортированию
крана. К техническому описанию и инструкции по эксплуатации, как единому
документу, прилагаются аналогичные материалы по базовой машине, электро- и
гидромашинам, контрольно-измерительным приборам и приборам безопасности.
В паспорте содержатся сведения об
изготовлении машины, ее техническая характеристика, чертеж с указанием основных
размеров, кинематическая схема механизмов, характеристика приборов,
электрические и гидравлические схемы, другие сведения в соответствии с
требованиями «Правил устройства и безопасной эксплуатации сосудов, работающих
под давлением», «Правил устройства и безопасной эксплуатации трубоукладчиков»,
«Положения о паспорте самоходной машины и других видов техники».
Паспорт, техническое описание и инструкция
по эксплуатации вместе с эксплуатационными документами базовой машины,
комплектующих изделий и ведомостью быстроизнашивающихся деталей, схемой
погрузки машины на железнодорожную платформу хранятся у главного инженера
организации-владельца машины - в несгораемом ящике, о котором должны знать
машинист и лицо, ответственное за содержание машины в исправном состоянии.
Перед транспортированием машины по
железной дороге или водным путем на заводе-изготовителе после ее погрузки
пломбируют двери кабины, капот двигателя, ящик аккумуляторных батарей,
топливные баки, инструментальные ящики.
Вся эксплуатационная и
товаросопроводительная документация укладывается в пакет из полихлорвиниловой
пленки. Запасные части - инструмент и принадлежности (ЗИП), упаковываются в
парафиновую бумагу.
В случае обнаружения несоответствия
записям в сопроводительных документах, отсутствия или порчи пломб, повреждения
самой машины необходимо составить коммерческий акт о размерах фактической
недостачи и повреждений прибывшей техники.
На станции получения машины, прибывшей к
владельцу по железной дороге или водным путем, проверяют сопроводительные
документы, наличие и исправность пломб, целостность и комплектность по
внутренней описи (приклеивается к боковому стеклу в кабине изнутри),
устанавливают снятые при отгрузке сборочные единицы и комплектующие изделия,
производят зарядку аккумуляторной батареи, заправляют топливно-смазочными мате
риалами и охлаждающей жидкостью. После этого приступают к опробованию
механизмов на холостом ходу и транспортируют, машину на эксплуатационную базу.
Прибывшая на эксплуатационную базу, другое
место хранения и технического обслуживания дорожно-строительная машина подлежит
приемке технической комиссией, назначенной указом руководителя предприятия -
владельца машины.
В процессе приемки члены комиссии
проверяют комплектность машины, техническое состояние ее составных частей и
сборочных единиц, оформляют акт приемки машины на баланс предприятия для
присвоения ей инвентарного номера. Трубоукладчики, кроме того, проходят
регистрацию в органах Госгортехнадзора с получением регистрационного номера и
разрешения на пуск в работу.
Осмотр дорожно-строительных машин
проводится также согласно «Правилам про ведения государственного технического
осмотра тракторов, самоходных дорожно-строительных и иных машин и прицепов к
ним органами государственного надзора за техническим состоянием самоходных
машин и других видов техники (Госгортехнадзора)».
Использование по назначению представляет
собой вид эксплуатации машины, при котором производится выбор модели для
использования на объекте применения (строительной площадке), подготовка к
ежесменному использованию, управление машиной в транспортном положении,
установка машины у объекта приме нения, перевод из транспортного положения в
рабочее, выполнение рабочих движений и операций, монтаж и демонтаж сменного
рабочего оборудования.
По назначению дорожно-строительные машины
используются при выполнении операций из состава технологических комплектов
строительной площадки.
Подготовке выбранной машины к
использованию предшествует обоснование включения ее в технологический комплект
средств механизации. Дальнейшая подготовка машины к использованию заключается в
проведении ежесменного обслуживания на эксплуатационной базе перед выездом на
строительную площадку или в месте межсменного хранения (стоянки) машины, транспортировании
к рабочей зоне, проверке состояния площадки и трассы для размещения и
передвижения машины в процессе выполнения работ. Перед пуском в работу на
строительной площадке необходимо еще раз осмотреть расположение всех органов
управления машиной, приборов безопасности и контроля качества выполнения
технологических операций, а также необходимо ознакомиться с проектом
производства работ (технологической картой) с применением данной машины.
Учет работы подъемно-транспортных и
строительных машин осуществляется с целью проведения правильных расчетов между
владельцами машин и предприятиями, получающими их в аренду, а также для
контроля за использованием и наработкой используемой техники. В практике
эксплуатации машин учет их работы ведется путем занесения необходимых сведений
в первичные документы.
В соответствии с постановлением
Правительства РФ от 8 июля 1997 г. № 835 «О первичных учетных документах» учет
работы дорожно-строительных машин теперь ведется с занесением требуемых
сведений в следующие учетные документы: путевой лист строительной машины (форма
ЭСМ-2), рапорт о работе строительной машины (форма ЭСМ-3), рапорт-наряд о
работе строительной машины (форма ЭСМ-4), карта учета работы строительной
машины (форма ЭСМ-5), журнал учета работы строительной машины (форма ЭСМ-6).
2.2 Эксплуатация и ТО
узла (детали)
Техническое обслуживание основных систем и
сборочных единиц.
Техническое обслуживание двигателя и его
систем. Наибольший объем работ по техническому обслуживанию машины приходится
на двигатель внутреннего сгорания и его системы (топливную, смазочную,
охлаждения, воздухоочистки).
В двигателях к наиболее сложным работам по
обслуживанию относят регулирование распределительного механизма, давления
впрыска топлива форсунками, угла опережения подачи топлива.
Зазор между клапанами и бойками коромысел
распределительного механизма проверяют щупом, а регулируют ключом или
специальными приспособлениями.
Для проверки и регулирования давления
впрыска и угла опережения подачи топлива также имеются специальные приспособления.
При обслуживании топливной системы
обращают внимание на степень загрязнения и сорт применяемого топлива, не
допускают попадания воды и пыли в топливный бак, систематически удаляют отстой
из бака и корпуса фильтра грубой очистки, регулярно промывают топливный бак.
Засорение фильтров ведет к снижению мощности двигателя и падению давления
топлива в системе.
После первого засорения фильтрующих
элементов тонкой очистки снимают с них верхний слой фильтрующей бумаги, а после
повторного засорения - заменяют элементы. Предварительно промывают в чистом
дизельном топливе внутренние полости корпусов фильтров и остальных деталей. В
фильтрах грубой очистки топлива при сильном загрязнении промывают внутренние
полости и сетчатые элементы.
Периодически снимают форсунки и прочищают
распыливающие отверстия иглой. Следят за тем, чтобы форсунки, топливный насос и
трубки были чистыми. Прокладки под форсунки рекомендуется использовать не более
двух раз, после чего их заменяют новыми или отжигают. Если топливо подтекает
через соединения трубок высокого давления, то подтягивают накидные гайки.
Обслуживание смазочной системы заключается
в систематическом наблюдении за температурой и давлением, своевременной
промывке масляного фильтра, смене отработавшего смазочного материала,
ежесменной проверке его уровня. Для нормальной работы поддерживают температуру
масла в пределах 7О...9О°С, а давление при номинальной частоте вращения -
0,3...0,5 МПа.
В системе охлаждения температура жидкости
должна быть в пределах 85...90 °С. Для поддержания указанного теплового режима
следят за уровнем охлаждающей жидкости, устраняют ее течи, при ТО-2 для
самоходных скреперов и ТО-3 для гусеничных машин промывают систему и удаляют
осадки и накипь, при ТО-2 регулируют натяжение ремня привода вентилятора.
Признаки сильного загрязнения радиатора -
быстрый подъем температуры и кипение воды при нормальной эксплуатации машины.
Для удаления накипи в радиатор заливают
содовый раствор (150 г соды на 1 л воды) и работают в течение смены. После
этого раствор сливают и промывают систему чистой водой. Снаружи радиатор
периодически очищают от пыли и грязи мягкой металлической щеткой.
При обслуживании системы воздухоочистки натяжение ремня 1
привода вентилятора (рис.2.8.) регулируют перемещением натяжного ролика 2 с
помощью регулировочного винта 7.
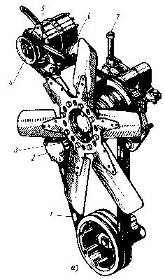
Рисунок 2.8 - Устройство для натяжения ремней привода
вентилятора и генератора: а - общий вид, б - схема регулирования; 1,6- ремни
вентилятора и генератора, 2-ролик, 3 - кронштейн, 4 - генератор, 5 -планка, 7 -
винт
Прогиб нормально натянутого ремня при
усилии 50...70 Н составляет 20... 25 мм. Проверяют натяжение ремня через каждые
60... 100 ч работы машины. Чрезмерное натяжение сокращает срок службы
подшипников шкивов привода и самих ремней, а слабое - вызывает буксование
шкивов и перегрев двигателя.
Рис. 2.9. Вторая ступень
воздухоочистителя:1,2 - основной и дополнительный фильтры-патроны, 3, 5 -
выходной и входной патрубки, 4 - корпус
Большое влияние на работу двигателя
оказывает состояние фильтров-патронов воздухоочистителей. Загрязнение
фильтрующей бумаги повышает сопротивление воздухоочистителя и может послужить
причиной дымления двигателя, падения его мощности. Засоренные бумажные
фильтры-патроны 1 (рис. 2.9.) через 500 ч заменяют чистыми или продувают сжатым
воздухом струей, направленной изнутри наружу. Ориентировочный срок службы
фильтров-патронов с проведением продувок и промывок не более 1500 мото-ч. при
нормальной запыленности воздуха. В случае повышенной запыленности срок
сокращается.
Кроме указанных операций в соответствии с
инструкцией по эксплуатации двигателя регулируют форсунки, клапанные зазоры,
проверяют угол начала подачи топлива и т.д. Все перечисленные работы выполняют
в объеме и в сроки, указанные инструкцией. В противном случае
завод-изготовитель может отказаться от рекламации в случае неисправности
двигателя, выявленной в гарантийный период.
Техническое обслуживание трансмиссии.
Обслуживание муфты сцепления при ТО-2 и
ТО-3 сводится к периодической проверке зазоров между рабочими поверхностями
дисков для определения отхода среднего ведущего диска и регулирования
свободного хода педали, подтягиванию резьбовых соединений и смазыванию.
Кроме того, предотвращают пробуксовку
дисков, которая происходит либо от изнашивания фрикционных накладок, либо от их
замасливания. Пробуксовку дисков при их износе до определенной величины
устраняют регулированием муфты. Замасленные диски промывают керосином сразу
после остановки машины, пока диски нагреты, и масло легко смывается с них.
В муфтах сцепления смазывают выжимные
подшипники и подшипники ведущего вала, шарнирные соединения осей и рычагов
механизмов управления.
В соединительных валах и карданных
передачах смазывают подшипники и шлицевое соединение, проверяют и подтягивают
крепления фланцев. Игольчатые подшипники и шлицевое соединение карданных валов
смазывают через масленки 3. После выработки крестовин 8 появляются стуки при
троганье машины с места. Износ крестовин и подшипников проверяют через
500..1000 ч.
В механической коробке передач
периодически проверяют уровень смазочного материала. В сроки, установленные
инструкцией, заменяют его. Отработавший материал удаляют через сливную пробку
сразу после остановки машины, пока он не остыл. Перед заливкой свежего
смазочного материала коробку передач и редуктор конических шестерен (для
тракторов) промывают, заполнив керосином (у трактора Т-170) или веретенным
маслом (у тягача МоАЗ 6442). Затем, запустив двигатель, дают ему поработать
5...8 мин.
Ежесменно проводят наружный осмотр коробки
для выявления и устранения течи через манжетные уплотнения валов и прокладки в
разъемах.
В коробках передач тракторов, смазываемых
насосом, по манометру на щитке приборов контролируют давление в системе,
которое должно быть не ниже 0,05 МПа. Причиной падения давления может быть
выход из строя насоса, повреждения в соединениях или засорение гидролиний.
В гидромеханической передаче следят за
уровнем смазочного материала, устраняют его утечки через соединения гидролиний,
систематически промывают или заменяют фильтрующие элементы, контролируют по
приборам давление в гидросистеме при работе машины. Через 2000 ч работы
смазочный материал заменяют и промывают всю систему.
В механических коробках передач регулируют
блокировочный механизм переключения передач, а также зацепления главной
передачи гусеничных тракторов. В системах питания гидротрансформатора,
управления и смазывания гидромеханической коробки передач регулируют рабочее
давление.
В заднем мосту гусеничного трактора при техническом
обслуживании регулируют ход рычагов и педалей управления тормозами планетарного
механизма поворота и остановочными тормозами и зазоры тормозных лент.
Для поддержания нормальной работы
механизмов заднего моста трактора типа ДТ-75НР следят за отсутствием
перетекания смазочного материала из отсеков главной передачи и конечных передач
в сухие отсеки планетарного и остановочного тормозов, для чего периодически
отвертывают пробки тормозных отсеков. Картер заднего моста промывают дизельным
топливом в течение 3...5 мин при работающем тракторе. Допускаемая температура
смазочного материала и деталей заднего моста во время работы трактора под
нагрузкой до 90 0С. Чтобы предотвратить перегрев заднего моста, а
также нарушение герметичности его уплотнений, емкости заправляют до
определенного уровня.
Нагрев заднего моста может быть вызван
неправильным регулированием тормозов.
При замене тормозных лент или изношенных
накладок новыми ленту рихтуют на шкивах. Неприлегание накладок к поверхности
шкива не должно превышать 0,5 мм.
Боковой зазор между зубьями конических
шестерен не регулируют и при увеличении его свыше 2 мм шестерни заменяют.
В конечном редукторе своевременно
проверяют уровень смазочного материала, доливают или заменяют его, промывают
корпус редуктора и периодически подтягивают крепления, особенно его корпус к
мосту.
При обслуживании заднего моста трактора
Т-170 устраняют пробуксовку дисков бортовых фрикционных муфт, т.е. регулируют
механизм управления поворотом или промывают накладки дисков.
В случае изнашивания фрикционных накладок
регулируют свободный ход рычага управления. Ленты тормозов периодически
подтягивают по мере изнашивания накладок. Слишком тугое затягивание лент
приводит к их нагреву, а слабое - к недостаточному торможению. Замасленные ленты
тормозов промывают.
В конечных редукторах периодически
проверяют уровень смазочного материала. За первые 100 ч работы трактора
ежемесячно, а затем периодически подтягивают гайки крепления ведущего колеса и
кожухов.
В ведущем мосту колесного трактора и одноосного
тягача через 1000 ч регулируют зацепление главной передачи, конические
подшипники подтягивают резьбовые соединения, заменяют смазочный материал в
полостях главной и конечной передач.
Качество зацепления зубьев конических
шестерен главной передачи проверяют по отпечатку краски на рабочей стороне
зубьев. Для этого смазывают 3...4 зуба ведущей шестерни краской по всей
поверхности и после поворота ее измеряют отпечатки (пятно контакта) на ведомой
шестерне. Зацепление считают хорошо отрегулированным, если отпечаток краски
покрывает более 50 % длины зуба и располагается на расстоянии 4...6 мм от его
наружных кромок.
К внешним признакам нарушения зацепления
шестерен главной передачи и разрегулирования подшипников относятся повышенный
шум и нагрев корпуса.
Техническое обслуживание ходовой части.
Рамы тракторов и тягачей в процессе эксплуатации периодически осматривают,
обращая особое внимание на состояние лонжеронов и места их стыковки с
поперечными. При обнаружении трещин и других повреждений рамы своевременно
ремонтируют. Ходовая часть гусеничного трактора работает в исключительно
тяжелых условиях и подвергается значительному изнашиванию. Поэтому техническому
обслуживанию ходовой части уделяют особое внимание. При этом регулярно очищают
ее от грязи, периодически подтягивают все крепления, смазывают балансиры,
опорные катки, натяжные колеса и поддерживающие ролики, а также регулируют
натяжение гусениц.
Нельзя допускать к работе трактор Т-170 с
ослабленным креплением башмаков, которое в первые 100...200 ч работы проверяют
ежедневно.
На тракторе типа ДТ-75НР через каждые 2000
ч работы переставляют каретки подвески по перекрестной схеме: переднюю левую
каретку меняют местами с задней правой, а переднюю правую - с задней левой.
Благодаря этому опорные катки изнашиваются равномерно. Осевой зазор каретки
должен быть не более 2 мм. При увеличении зазора заменяют прокладку под крышкой
более тонкой (0,5 мм).
Слабо натянутое полотно гусеницы вызывает
частый сход ее с катков, направляющих и ведущих колес, а сильно натянутое -
значительно сокращает сроки службы звеньев, соединительных пальцев и других
деталей гусеничной ходовой части. Кроме того, в обоих указанных случаях
увеличиваются непроизводительные потери мощности трактора. Натяжение гусениц
проверяют при замере провисание верхней ветви, которое должно быть у трактора
типа ДТ-75НР 30...50 мм, а у трактора Т-4АП2 -20...30 мм.
Рисунок 2.10 - Проверка провисания цепи
ТО2
Для замера провисания верхней ветви цепи
гусеницы (рис.2.10.) трактор устанавливают на ровной площадке так, чтобы нижние
ветви были натянуты. На выступающие концы пальцев звеньев гусеницы,
расположенных над поддерживающими роликами, кладут ровную планку и замеряют
расстояние от планки до пальцев наиболее провисшего звена. Если провисание
превышает норму, натягивают гусеницу винтовым механизмом
Натяжение гусениц у трактора Т-170
проверяют по провисанию гусеничной цепи между ведущим колесом и задним
поддерживающим катком, которое должно составлять 7... 15 мм. На этом тракторе
установлен гидравлический механизм натяжения гусеницы. При техническом
обслуживании рессорной подвески тягача МоАЗ 6442 через 100 ч работы подтягивают
крепления, смазывают рессоры и пальцы, периодически заменяют рабочую жидкость в
амортизаторах. Рессоры смазывают при приподнятом краном тягаче, заполняя
зазоры, образовавшиеся между листами. Рабочую жидкость в амортизаторах меняют
не реже одного раза в год.
Обслуживание колес и пневматических шин
заключается в проверке через 500... 1000 ч крепления обода к ступице,
смазывании и регулировании подшипников ступицы.
Правильная эксплуатация шин требует
ежесменный до начала работы проверки давления воздуха, которое должно строго
соответствовать норме, указанной в инструкции.
Уменьшенное давление в шинах приводит к
повышенному внутреннему трению и быстрому перегреву покрышки, в результате чего
наступает расслоение резины. Повышенное давление увеличивает жесткость шины и
тем самым приводит к неравномерному и ускоренному ее изнашиванию.
Шины предохраняют от попадания на них
топлива и масла, оказывающих разрушающее действие на резину.
Для проверки и регулирования конических
подшипников ступиц вывешивают колесо над грунтом. Конические подшипники
регулируют при осевом зазоре или боковой качке колеса. После регулирования
подшипников колеса должны проворачиваться от руки без ощутимого осевого зазора.
Техническое обслуживание тормозов.
Тормоза относятся к важнейшим элементам
управления машиной и связаны с безопасностью работы на ней. Поэтому поддержание
исправного состояния тормозной системы - одна из основных задач технического
обслуживания. Оно заключается в контроле крепления механизмов и деталей
тормоза, очистке от грязи и замасливания поверхностей трения, смазывании втулок
разжимных кулаков, осей колодок, своевременном регулировании свободного хода
механизмов управления, зазоров между барабаном и тормозными накладками по мере
их изнашивания.
Техническое обслуживание тормозов
гусеничных тракторов проводят одновременно с техническим обслуживанием задних
мостов.
При техническом обслуживании стояночных
тормозов колесных машин периодически осматривают тормозные накладки. Если от
поверхности накладок до головки заклепок остается менее 5 мм, то накладки
заменяют. Основная неисправность стояночного тормоза -низкая эффективность торможения,
причиной которой может быть изнашивание или замасливание накладок, а также
нарушение регулировок тормоза.
Техническое обслуживание колесных тормозов
заключается в периодическом их осмотре, регулировании зазоров, смазывании
шарнирных соединений. Замасленные колодки промывают бензином и просушивают.
Изношенные колодки, у которых расстояние от поверхности трения до головок
винтов крепления накладок меньше 1 мм, заменяют.
Для безотказной работы тормозов большое
значение имеет техническое обслуживание пневмопривода.
У компрессора своевременно регулируют
натяжение ремня, очищают клапаны и седла, проверяют герметичность прилегания
клапанов, подтягивают крепежные детали. Через каждые 500 ч работы снимают
головку блока цилиндров компрессора для очистки деталей и проверки
герметичности. Одновременно проверяют состояние уплотнительных колец плунжера и
заменяют изношенные. Клапаны, не обеспечивающие герметичности, притирают к
седлам.
Регулятор давления периодически проверяют
на герметичность. Утечку воздуха можно обнаружить на слух при неработающем
двигателе.
Тормозной кран проверяют на надежность
крепления и герметичность. Утечка воздуха через корпус крана, корпуса пружин
клапанов, поршни и соединения не допускается. Через клапаны допускается
незначительная утечка воздуха (за 5 с образуется один мыльный пузырек размером
до 25 мм). Для устранения утечки воздуха прочищают клапаны и седла.
При ежесменном техническом обслуживании из
ресивера через краники сливают конденсат. Компрессор считают неисправным, если
за сутки в конденсате скапливается более 15...20 см3 смазочного
материала. Сливают конденсат также при наличии воздуха в системе.
В процессе эксплуатации периодически
проверяют герметичность воздухопроводов. Падение давления в системе тормозов
при неработающем компрессоре допускают не более 0,05 МПа в течение 30 мин при
свободном положении органов управления и 15 мин при работе органов управления.
Техническое обслуживание
электрооборудования. Его обслуживание заключается в содержании приборов в
чистоте и своевременной проверке и подзарядке аккумуляторной батареи.
Аккумуляторную батарею через каждые 100 ч
работы очищают от пыли и грязи, окислившиеся выводы и наконечники проводов
чистят и смазывают техническим вазелином, прочищают деревянной палочкой
вентиляционные отверстия в пробках элементов. Через 1000 ч работы проверяют
уровень и плотность электролита и при необходимости подзаряжают батареи.
К основным показателям, характеризующим
техническое состояние аккумуляторных батарей, относятся плотность электролита, электродвижущая
сила (ЭДС) и напряжение.
Плотность электролита определяют с помощью
ареометра (рис. 2.11, а), который представляет собой стеклянную трубку с
резиновой грушей на конце и поплавком со шкалой. Ареометр опускают в горловину
аккумулятора и с помощью груши набирают в трубку электролит. Поплавок при этом
всплывает на определенный уровень, соответствующий плотности электролита, что и
видно по шкале. Плотность электролита при температуре 15 °С должна составлять
следующие значения.
Полностью заряжена..... 1,31 1,29 1,27
1,25
Разряжена на 25 %....... 1,27 1,25 1,23
1,21
Разряжена на 50 %....... 1;23 1,21 1,19
1,17
Рисунок 2.11 - Проверка технического
состояния батареи:
а - измерение плотности электролита
ареометром, б - измерение напряжения нагрузочной вилкой
В случае повышения или понижения
температуры электролита на каждые 15 °С плотность должна быть увеличена или
уменьшена на 0,01 по отношению к показанию ареометра.
Степень разряженности батареи можно также
определить, замеряя ее напряжение с помощью нагрузочной вилки (рис. 2.11, б).
При замере контакты вилки плотно прижимают в течение 5 с к выводам батареи, и
вольтметр показывает напряжение аккумуляторов. Если напряжение отдельных
аккумуляторов при замере отличается более чем на 0,2 В или быстро падает, то
батарею подзаряжают, пропустив через нее ток.
Генератор, стартер при ежесменном
техническом обслуживании проверяют на надежность крепления. Затем определяют
состояние контактных соединений. Если после пуска двигателя стрелка амперметра
показывает ток или устанавливается на нулевом делении, то это указывает на
исправность генератора и всей зарядной цепи. Натяжение ремня привода генератора
регулируют так же, как и ремень вентилятора.
Генератор периодически снимают, очищают от
пыли и грязи, проверяют высоту щеток, которая должна быть не менее 8 мм. Новые
щетки притирают к коллектору шлифовальной шкуркой. Коллектор и щеткодержатели
очищают от угольной пыли. Нормальный вид коллектора при эксплуатации -
полированная поверхность темно-вишневого или фиолетового цвета.
Изоляцию, соединения проводов проверяют на
целостность. Загрязненные провода тщательно очищают и протирают. Запрещается
использовать для предохранителей проволоку, так как она не может предотвратить
повреждения приборов и короткие замыкания.
Приборы освещения очищают, подтягивают
крепления, проверяют качество установки оптических элементов в корпусах фар,
поддерживают чистоту и плотность соединений контактов и выводов.
Техническое обслуживание рабочего оборудования.
Рабочее оборудование очищают от грязи, периодически контролируют сварные швы и
соединения деталей металлоконструкций, а также смазывают поверхности трения.
Выявленные трещины сварных соединений и поломки ответственных элементов
металлоконструкции (например, толкающего бруса, хобота, поперечины тяговой
рамы, седельно-сцепного устройства) оперативно устраняют.
Применение изношенных отвалов и режущих
ножей резко снижает производительность машины. Затупленный нож сдвигают по
отверстиям или переворачивают на 180°, используя для работы вторую режущую
кромку. Полностью затупленные ножи заменяют новыми или наплавляют режущие
кромки.
Техническое обслуживание гидравлической
системы. Ежесменно перед началом работы проверяют уровень рабочей жидкости в
гидробаке, устраняют подтекание жидкости в соединениях. Основой надежной работы
гидравлической системы является постоянное поддержание чистоты рабочей
жидкости. Загрязнение жидкости и несвоевременная промывка фильтра, гидробака и
других элементов системы приводят к быстрому изнашиванию поверхностей трения
насоса, клапанов, гидрораспределителей, гидроцилиндров, а также к нечеткой их
работе. В соответствии с инструкцией тщательно промывают в дизельном топливе
фильтр, сапун заливной горловины и заменяют отработавшую жидкость.
Для проверки и регулирования давления в
гидросистеме создают и замеряют максимальное давление, например, подняв отвал
до упора и удерживая гидрораспределитель во включенном положении. Если
давление, замеренное манометром, не соответствует норме, то его регулируют
предохранительным клапаном. Неисправности сборочных единиц гидросистемы,
требующие разборки, устраняют только в условиях, исключающих попадание в них
песка, пыли, грязи и воды.
Особенности сезонного технического
обслуживания основных сборочных единиц машин. Эксплуатация бульдозеров и
скреперов в разное время года обусловливает особые требования к обслуживанию.
Для подготовки к осенне-зимнему периоду проводят внеочередное техническое
обслуживание (СО), промывают систему охлаждения, топливный бак и заправляют
емкости жидкостями и смазочным материалом зимних сортов. В систему охлаждения
заливают (если это допускает инструкция) низкозамерзающую смесь (антифриз).
Аккумуляторные батареи подзаряжают электролитом повышенной плотности и утепляют
войлочными или фанерно-бумажными прокладками. На машинах устанавливают или
готовят к эксплуатации пусковой подогреватель и подключают отопитель кабины.
Проверяют работу термостата и указателя температуры воды, так как в холодное
время года необходимо соблюдать температурный режим.
На тракторах и тягачах устанавливают
утеплительные чехлы, предусмотренные в комплекте ЗИП.
При подготовке машины к весенне-летнему
периоду также проводят внеочередное СО заменяют рабочие жидкости, смазочный
материал и охлаждающую жидкость летними сортами, заливают электролит пониженной
плотности. Учитывая, что в летний период возрастает запыленность воздуха,
особое внимание уделяют обслуживанию воздухоочистителя.
Заправка систем и механизмов топливом и
смазочным материалом
Большинство подвижных контактирующих
деталей машин, например зубчатые передачи, подшипниковые опоры, плунжеры, не
могут работать без нанесенного на их поверхности смазочного материала. В случае
отсутствия смазочного материала в зоне контакта детали быстро изнашиваются.
На надежность и долговечность машин
существенное влияние оказывает выбор смазочного материала с учетом конструкции
сопряженных пар, условий их работы и степени изношенности. Например, детали,
работающие под большим давлением, смазывают более вязким маслом во избежание
его выдавливания. При высоких скоростях используют масла меньшей вязкости,
которые способствуют сохранению масляной пленки на поверхностях.
У изношенных деталей увеличиваются зазоры,
что требует применения более вязких масел. Такое же масло выбирают для деталей,
работающих при повышенной температуре. Для эксплуатации машин при низких
температурах необходимо менее вязкое масло. По этой причине для смазывания
машин в летний и зимний периоды назначают сорта масел с разной вязкостью.
Различают два основных смазочных материала
- жидкие и пластичные.
К жидким относят моторное,
трансмиссионное, веретенное масло. Такими маслами смазывают, погружая
вращающиеся детали в масляные ванны, из которых масло разбрызгивается по всему
корпусу сборочной единицы и смазывает остальные детали, или с помощью насоса,
который подает масло из вацны по каналам и трубам к смазываемым деталям.
Пластичные смазочные материалы (литол,
солидол) при обычных для работы машины температурах сохраняют свою несущую
способность.
Рисунок 2.12 - Точки смазывания
бульдозера-рыхлителя.
Материал с помощью ручных шприцев наносят
на поверхности разобранных механизмов (например, шлицевое карданных валов) или
закладывают его в полости (ступицы колес, подшипники качения).
При смазывании шприцем его наконечник
накладывают на головку пресс-масленки, через которую смазочный материал под
давлением поступает по каналам и зазорам к смазываемым поверхностям. Новый
смазочный материал нагнетают до тех пор, пока старый материал не выйдет из
зазоров и не покажется свежий.
Перед нанесением свежего смазочного
материала рабочие поверхности и полосы деталей промывают керосином или
дизельным топливом.
Надежная работа агрегатов и сборочных
единиц в значительной мере зависит от своевременной и правильной заправки и
смазывания машины, а также строгого применения только рекомендованных
инструкцией сортов топлива и смазочных материалов.
Соблюдение правил заправки и хранения топлива влияет на
безотказность работы двигателя. Топливный бак рекомендуется заправлять
отстоявшимся топливом, что исключает попадание в топливную систему двигателя
посторонних частиц и воды. Перед заправкой обязательно протирают горловины и
крышки баков от грязи, пыли и остатков топлива. Топливные баки допускается
заправлять только через раздаточную колонку или от передвижных заправочных
станций.
Смазывание занимает до 50 % общего объема
работ по техническому обслуживанию и является одной из обязанностей машиниста.
В инструкции по эксплуатации каждой
конкретной машины включены карты и таблицы смазывания, в которых указаны места
и количество точек смазывания, его периодичность в часах, марки и наименование
смазочного материала для летней и зимней эксплуатации, способ смазывания. В
табл. 15 и на рис. 2.12. указаны наиболее характерные точки смазывания и
рекомендуемые смазочные материалы. Большое влияние на качество смазывания
оказывает соблюдение чистоты при смазочных работах. Предварительно тщательно
очищают от грязи и пыли смазочный инвентарь (пресс-масленки, воронки), а также
пробки заливных отверстий, масленки и поверхность около них. Выдавившийся после
нагнетания смазочный материал удаляют. Если процесс нагнетания затруднен, и
смазочный материал через зазоры не выдавливается, такую сборочную единицу
разбирают и промывают. Из подшипников качения предварительно удаляют старый
материал и при необходимости промывают детали керосином или дизельным топливом.
Из картеров коробок передач, редукторов и
ведущих мостов смазочный материал сливают сразу после остановки машин, пока
отработавшее масло находится в разогретом, разжиженном состоянии и легко
вытекает через сливное отверстие.
Для промывки в картер заливают веретенное
масло или дизельное топливо, которое сливают после работы сборочной единицы
вхолостую в течение 3...5 мин. Затем картер заправляют свежим материалом.
При заливке следят за уровнем материала.
Его избыток так же вреден, как и недостаток. Уровень определяют по контрольным
пробкам, щупу, на котором указаны отметки минимального и максимального
количества смазочного материала, и масломерному стеклу, установленному на
боковой стенке снаружи корпуса.
Машинист обязан бережно относиться к
топливу и смазочным материалам и по возможности экономить их. Достигают
экономии за счет предотвращения потерь при заправке машины, а также в
результате технически грамотной эксплуатации. Например, при отказе в работе
одной из форсунок дизеля перерасход топлива может составить 8...25%. К
излишнему расходу топлива могут привести, например, неудачно выбранные маршруты
транспортирования грунта скрепером, длительная работа двигателя на холостом
ходу.
Значительные потери топлива и рабочей жидкости гидросистемы
вызывают подтекание через неплотные соединения трубопроводов. Переполнение
емкостей картеров маслом выше предусмотренных уровней также приводит к
неоправданному перерасходу этого ценного материала. Поэтому своевременное и
тщательное выполнение технического обслуживания, устранение выявленных
неисправностей, периодическая проверка и регулирование топливной аппаратуры,
применение рациональной схемы работы и правильная загрузка двигателя создают
реальные условия для успешной экономии топлива и смазочных материалов.
Организация системы технического
обслуживания и ремонта дорожно-строительных машин
Все работы, входящие в состав технических
обслуживаний, разделены на моечно-очистные, крепежные,
контрольно-регулировочные, заправочно-смазочные. ЕО выполняют перед началом, в
течение или после рабочей смены. Цель его - поддержание работоспособности и
безопасности машины в течение каждой рабочей смены.
В состав ЕО входят контроль технического
состояния машины, заправка топливно-смазочными материалами, рабочей и
охлаждающей жидкостью.
ТО назначается для снижения интенсивности
изнашивания сборочных единиц машины путем своевременной их очистки от пыли и
грязи, смазывания и регулирования.
ТО подразделяется на ТО-1, ТО-2, ТО-3
которые выполняют через определенные, установленные
предприятиями-изготовителями величины наработки.
СО выполняют два раза в год при подготовке
машины к использованию в периоды летнего и зимнего сезонов. Если время
проведения очередного ТО по периодичности совпадает со временем выполнения
планового ремонта, ТО и ремонт выполняют одновременно.
ЕО перед выездом машины с эксплуатационной
базы и перед началом работы на объекте выполняет машинист; по окончании рабочей
смены, а также плановое ТО выполняет персонал специализированного участка
планово-предупредительного технического обслуживания и ремонта машин. ЕО
характеризуется определенным обязательным составом работ.
Обязательный состав работ может быть
дополнен другими операциями, необходимость выполнения которых возникла в
процессе ЕО или выявлена во время эксплуатации техники.
Перед выездом с базы (места хранения)
выполняют ЕО и проверяют: крепление элементов опорно-ходовой части и рабочего
оборудования; системы питания охлаждения и смазки; комплектность и состояние
комплекта ЗИП машиниста; надежность крепления всех сборочных единиц и
механизмов, гидроцилиндров; наличие топлива в баке и уровень рабочей жидкости в
гидробаке; надежность закрывания сливных и заливных пробок всех механизмов и
систем; крепление колес, состояние шин и давление в них; работу трансмиссии и
рулевого управления.
Заканчивают ЕО перед началом выполнения
операций на объекте: проверяют работу органов управления машиной, исправность
приборов и тормозов, герметичность воздуховодов и магистралей.
Кроме того, необходимо убедиться в
отсутствии стуков и ненормальных шумов в двигателе, трансмиссии, исполнительных
механизмах. По окончании смены рабочее оборудование землеройных машин опускают
на основание, двигатель заглушают, очищают и моют машину, осматривают ее и
устраняют обнаруженные неисправности; полностью дозаправляют систему двигателя
топливом, смазкой и охлаждающей жидкостью; очищают аккумуляторные батареи от
грязи и электролита, проверяют их крепление; проверяют гидроцилиндры и их
крепление; исправность элементов рабочего оборудования; наличие смазки во всех
механизмах; отсутствие механических повреждений воздуховодов и
гидрооборудования, утечек через соединения гидросистемы, состояние тяг и
рычагов тормозов и корпусов механизмов, приводов управления рабочими операциями
и двигателем. Образовавшийся в маслосборнике компрессора конденсат сливают,
открыв вентиль, затем проверяют натяжение приводного ремня вентиляторов.
При ТО-1 выполняют операции ЕО и, кроме
того, проверяют: состояние металлоконструкции, рабочего оборудования, блоков,
элементов крепления опорной рамы к раме машины; надежность крепления
опорно-поворотного круга и противовеса; |состояние зубчатого венца опорно-поворотного
круга и приводной шестерни механизма поворота у экскаваторов; состояние и износ
тормозных накладок, колодок, ленты и тормозов, натяжение гусениц; надежность
крепления фланцев карданных валов; крышек подшипников, крестовин карданных валов,
электрооборудования, гидрокоммуникаций, осветительных приборов, аккумуляторных
батарей; уровень и плотность электролита батареи, степень разряженности; работу
осветительных приборов и сигнализации; состояние гидрокоммуникаций (разбирают
масляный фильтр, промывают его элементы, настраивают перепускные и
предохранительные клапаны, заменяют вышедшие из строя уплотнения и
грязесъемники гидроцилиндров), резиновых колец, фар и задних фонарей.
Очищают и моют машину. Сливают из
топливного бака, фильтров грубой и тонкой очистки топливо. Смазывают
консистентной смазкой подшипники, опорно-поворотное устройство, шарниры
управления гидрораспределителей, шаровые пальцы шарнирных тяг. Подтягивают
гайки и болты крепления сборочных единиц. Проверяют уровень масла и при необходимости
доливают его в картеры. Заправляют машину топливо-смазочными материалами.
Проверяют давление в сливной магистрали и в системах управления. Очищают
аккумуляторную батарею, вентиляционные отверстия, воздухозаборник.
При ТО-2, ТО-3 выполняют работы ЕО и ТО-1,
а также проверяют состояние элементов двигателя, осматривают пульт управления
машиной, заменяют масло в картерах, очищают и моют двигатель, сливают
скопившееся масло в картере муфты сцепления, заменяют рабочую жидкость в
гидросистеме, промывают ее гидрораспределители и фильтры, регулируют элементы и
систему силовой установки и гидрооборудования, правильность работы приборов
безопасности трубоукладчиков, контрольно-измерительных приборов, установку фар
и габаритных огней.
Кроме того: проверяют карданные шарниры на
отсутствие осевого и углового зазоров; подтягивают наружные болты и гайки
ведущего моста; снимают ступицы ведущих колес с тормозных барабанов, очищают
тормоза от загрязнений, проверяют состояние рабочей поверхности барабанов и
накладок, убеждаются в отсутствии течи жидкости из колесных цилиндров,
промывают в керосине и осматривают подшипники, смазывают все точки в
соответствии со схемой смазки; закладывают необходимое количество смазки в
ступицы, регулируют зазоры в подшипниках; проверяют состояние
металлоконструкций рабочего оборудования и рам; осматривают вентилятор
охлаждения рабочей жидкости.
СО: промывают систему охлаждения
двигателя, топливный бак и топливопроводы, заменяют рабочие жидкости в
соответствии с условиями эксплуатации предстоящего сезона; заменяют масла на
сорта, соответствующие предстоящему сезону эксплуатации машины; доводят
плотность электролита в аккумуляторной батарее до нормы, рассчитанной на
предстоящий сезон эксплуатации; включают или выключают подогреватель двигателя
и устройств для обогрева кабин водителя и машиниста; очищают от загрязнений
стояночный тормоз и смазывают тонким слоем солидола детали разжимного и
регулировочных механизмов, опорные поверхности концов тормозных колодок.
Возможные неисправности и способы их
устранения. Техническая диагностика машин
Состояние машины, при котором она не
соответствует хотя бы одному из требований нормативно-технической документации,
называется неисправным.
Основными причинами возникновения
неисправностей деталей и сборочных единиц являются некачественное изготовление,
нарушение правил эксплуатации, перегрузка деталей при передвижении и выполнении
рабочих операций на объектах применения, несоблюдение периодичности и объема
работ по техническому обслуживанию и ремонту машин. Вследствие этого
значительно ухудшаются условия работы деталей, повышается интенсивность их
изнашивания, увеличиваются зазоры в сопряжениях, возрастают динамические
нагрузки, что приводит к преждевременному выходу деталей из строя, отказу
сборочных единиц, нарушению работоспособности машины.
В процессе эксплуатации машин возможны
неисправности, вызванные износом, заеданием, нарушением регулировки,
ослаблением пружин, попаданием воздуха в гидросистему.
Возможные неисправности
дорожно-строительных машин и способы их устранения характеризуются признаками,
приведенными в инструкциях по эксплуатации конкретных моделей машин.
Цель технической диагностики - выявить
неисправности машины без ее разборки и определить ресурс безотказной работы
сборочных единиц, фактическую потребность в производстве работ при техническом
обслуживании и ремонте в момент возникновения отказа или неисправности
сборочных единиц.
Таким образом, диагностирование является
неотъемлемым технологическим элементом всей системы технического обслуживания и
ремонта дорожно-строительных машин и позволяет: снизить количество отказов и
простоев машины, повысить безопасность ее работы; увеличить продолжительность
эксплуатации машины и сократить расход запасных частей; уменьшить трудоемкость
технического обслуживания и ремонта; обеспечить ресурсосбережение
эксплуатационных материалов.
Основа диагностики - определение
показателей технического состояния сборочных единиц, их замер и сравнение со
значениями параметров, установленными нормами на создание машины.
В связи с тем, что техническую диагностику
проводят без разборки машин, особое значение приобретают симптомы (признаки),
которые характеризуют техническое состояние составных частей и сборочных
единиц: внешние признаки (вмятины, сколы, задиры, следы подтекания жидкости, а
также зазоры, люфты, свободный и рабочий ходы), а также биение, удары, стуки,
шумы, вибрации.
Процесс диагностирования машин состоит из
трех последовательно выполняемых этапов: анализ технического состояния машины и
результатов диагностирования, определение вида и объема работ по техническому
обслуживанию и ремонту, направление машины в соответствующие рабочие зоны
технического обслуживания или ремонта. Для каждой сборочной единицы
разрабатывают методы, средства и условия диагностирования, позволяющие наиболее
точно и полно определить техническое состояние машины.
Для диагностики оборудуют специальные
участки, оснащенные контрольно-измерительными средствами. По конструктивному
исполнению контрольно-измерительные средства диагностики подразделяют на
внешние и встроенные в машину системы. Внешние средства диагностики размещают в
передвижной диагностической станции и на стационарном посту эксплуатационной
базы. В состав встроенных в машину систем диагностики входят датчики,
показывающие приборы, индикаторы. Средства диагностирования используют в
отапливаемых пространствах на всех режимах работы машины. Сначала диагностируют
гидрооборудование и электрооборудование, затем основные сборочные единицы
машины, начиная с двигателя, трансмиссии и заканчивая тормозами. На постах
должна храниться документация по проверке диагностических средств измерений
параметров.
На участке диагностирования размещают
стационарный пост со стендами, где диагностированию подвергаются машины,
проходящие техническое обслуживание и текущий ремонт непосредственно на
территории эксплуатационной базы. В дополнение к стационарному посту на участке
диагностирования предусматривают мобильные передвижные станции, с помощью
которых диагностирование машин может проводиться на местах их эксплуатации во
время технического обслуживания.
Кроме того, на участке диагностирования
оборудуется лаборатория по контролю за качеством рабочей жидкости, используемой
в гидрооборудовании машин.
Очистно-моечные и смазочно-заправочные
работы.
В состав работ по очистке
дорожно-строительных машин входят операции: уборка кабины, приведение в порядок
ходового устройства, удаление пыли, налипании и грязи с рабочего оборудования.
Перед мойкой машины необходимо проверить
наличие и крепление крышек ее топливных баков и маслоналивных горловин. При
необходимости подтягивают их крепление и закрывают плотнее. Доставленную на
моечную площадку машину осматривают. Имеющиеся на ее поверхности почвенные и
растительные остатки удаляют скребками. Грязь с поверхности машины смывают
водой температурой 15-25° С и под давлением 1,6-2 мПа, без моющего раствора.
Поверхности, загрязненные грязью и маслом, очищают пароводяной струей и водой,
нагретой до температуры 85° С, под давлением до 10 мПа. Для повышения
эффективности струи применяют насадки различных типов. Универсальной является
насадка с цилиндрическим соплом. С ее помощью очищают поверхности сложной
конфигурации. Струя из насадки с коническим соплом быстро разрушает засохшую
грязь и отделяет ее от поверхности металла. Для очистки больших поверхностей
применяют насадки с щелевым соплом.
Для ускорения очистки поверхности машин
при наличии на них масляных отложений или консервационной смазки применяют
моющие средства. Начинают мыть машину сверху. Чтобы хорошо очистить нижнюю и
верхнюю поверхности ходового устройства и базовой машины, применяют
соответственно сосредоточенную и распыленную струю воды.
Части машины с относительно гладкими
поверхностями моют капроновыми щетками, закрепленными на полой рукоятке, к
которой под напором по гибкому шлангу подается вода. Поверхности, очищенные с
применением специальной моющей жидкости, ополаскивают водой. В зимнее время для
мойки используют горячую воду. Топливо, масла, которые смываются с поверхности машин,
и моющие растворы оказывают вредное влияние на окружающую среду. Поэтому машины
следует мыть на специально оборудованных постах, обеспечивающих сбор
использованных моющих растворов и их очистку. Такие посты создаются в здании
производственного корпуса эксплуатационной базы или в отдельном здании. На них
должно быть оборотное водоснабжение.
При мойке машин моющими растворами
необходимо соблюдать меры предосторожности, так как некоторые из применяемых
моющих средств, например растворяюще-эмульгирующие, обладают токсичностью и
пожароопасностью. При очистке машин необходимо обращать внимание на
герметичность смазочной системы, систем охлаждения и питания двигателей,
гидросистемы и картеров. На сухих пыльных поверхностях хорошо видны места
подтекания топлива, масел, рабочей и охлаждающей жидкостей. Места подтекания
необходимо удалять сразу же по окончании мойки, так как даже самые минимальные
утечки вызывают ощутимые потери топлива, масел и рабочих жидкостей. Кроме того,
смоченные утечками поверхности машин быстрее и сильнее загрязняются. В процессе
мойки машин проверяют также комплектность машин - все ли сборочные единицы и
детали находятся на своих местах и в каком они состоянии. Это позволяет
ускорить обслуживание машины. Закрытые каналы гидросистемы и двигателя,
топливные и масляные баки, полости картеров и коробок передач очищают
циркуляционной промывкой постоянно обновляющимися моющим составом из
взрывобезопасной жидкости или смеси дизельного топлива и дизельного масла в
соотношении 4:1. При промывке смазочной системы периодически (через каждые 5
мин.) прокручивают коленчатый вал двигателя стартером, пусковым двигателем или
вручную. Систему охлаждения двигателя промывают методом жидкостно-воздушной
очистки. При промывке радиатора на нижний патрубок подаются вода и сжатый
воздух. Водно-воздушная смесь проходит через трубку радиатора и по спусковому
шлангу, надетому на патрубок верхнего бачка радиатора, выливается на
бетонированную площадку моечного пункта, а затем в колодец-отстойник.
Смазывание сборочных единиц и деталей
машин производят специально подобранными смазочными материалами.
Основные назначения смазочного масла -
снижать износ соприкасаемых деталей за счет создания на трущихся поверхностях
прочной масляной пленки, уменьшать потери на трение, предохранять соприкасаемые
поверхности от коррозии, хорошо прилипать к поверхности деталей, отводить от
них тепло, уносить продукты износа, устранять заедание трущихся поверхностей.
Места смазывания составных частей машины,
периодичность смазывания и применяемый при этом смазочный материал определены в
таблице и время для мойки используют горячую воду. Топливо, масла, которые
смываются с поверхности машин, и моющие растворы оказывают вредное влияние на
окружающую среду.
Поэтому машины следует мыть на специально
оборудованных постах, обеспечивающих сбор использованных моющих растворов и их
очистку. Такие посты создаются в здании производственного корпуса
эксплуатационной базы или в отдельном здании. На них должно быть оборотное
водоснабжение.
При мойке машин моющими растворами
необходимо соблюдать меры предосторожности, так как некоторые из применяемых
моющих средств, например растворяюще-эмульгирующие, обладают токсичностью и
пожароопасностью. При очистке машин необходимо обращать внимание на
герметичность смазочной системы, систем охлаждения и питания двигателей,
гидросистемы и картеров. На сухих пыльных поверхностях хорошо видны места
подтекания топлива, масел, рабочей и охлаждающей жидкостей. Места подтекания
необходимо удалять сразу же по окончании мойки, так как даже самые минимальные
утечки вызывают ощутимые потери топлива, масел и рабочих жидкостей.
Кроме того, смоченные утечками поверхности
машин быстрее и сильнее загрязняются. В процессе мойки машин проверяют также
комплектность машин - все ли сборочные единицы и детали находятся на своих
местах, и в каком они состоянии. Это позволяет ускорить обслуживание машины.
Закрытые каналы гидросистемы и двигателя, топливные и масляные баки, полости
картеров и коробок передач очищают циркуляционной промывкой постоянно
обновляющимися моющим составом из взрывобезопасной жидкости или смеси
дизельного топлива и дизельного масла в соотношении 4:1. При промывке смазочной
системы периодически (через каждые 5 мин.) прокручивают коленчатый вал
двигателя стартером, пусковым двигателем или вручную.
Систему охлаждения двигателя промывают
методом жидкостно-воздушной очистки. При промывке радиатора на нижний патрубок
подаются вода и сжатый воздух. Водно-воздушная смесь проходит через трубку
радиатора и по спусковому шлангу, надетому на патрубок верхнего бачка
радиатора, выливается на бетонированную площадку моечного пункта, а затем в
колодец-отстойник.
Смазывание сборочных единиц и деталей
машин производят специально подобранными смазочными материалами. Основные
назначения смазочного масла - снижать износ соприкасаемых деталей за счет
создания на трущихся поверхностях прочной масляной пленки, уменьшать потери на
трение, предохранять соприкасаемые поверхности от коррозии, хорошо прилипать к
поверхности деталей, отводить от них тепло, уносить продукты износа, устранять
заедание трущихся поверхностей.
Места смазывания составных частей машины,
периодичность смазывания и применяемый при этом смазочный материал определены в
таблице и схеме смазывания, содержащихся в инструкции по эксплуатации машины.
Кроме того, таблицы смазывания заводы
изготовляют на металлических пластинках и прикрепляют на кабине. Подшипники
смазывают через пресс-масленки с помощью шприца. В стационарных и передвижных
мастерских для этой цели применяют солидолонагнетатели с пневматическим или
электрическим приводом. Перед смазыванием, если машину не мыли, необходимо
тщательно очистить масленки от грунта чистиком, затем протереть чистой тканью
или обдуть сжатым воздухом. Некоторые подшипники смазывают маслом, поливая из
масленки, а в мастерских - из наконечника раздаточного крана. Открытые зубчатые
передачи, канаты и цепи смазывают пластичной смазкой лопаточкой или кистью,
равномерно нанося ее по всей поверхности детали. Канаты для ускорения
смазывания пропускают через специальное приспособление. При картерном
смазывании подшипников и шестерен периодически требуется проверять уровень
масла в картерах и при необходимости доливать его, используя для этого
маслозаправщики, маслораздаточные колонки и передвижные мастерские.
Перед открытием контрольного или заливного
отверстия необходимо тщательно вытереть пробку или крышку. Не допускается
доливать масло в картеры выше установленного уровня. У передвижных компрессоров
применяется система смазки разбрызгиванием с принудительным поддержанием
постоянного уровня в верхних ваннах поддона. При работе компрессора шестерня
коленчатого вала приводит во вращение текстолитовую шестерню, установленную в
картере. Вращающаяся текстолитовая шестерня забрасывает масло из нижней ванны
поддона в специальный карман картера, откуда масло перетекает в малый отсек
канала, образованного внутренними стенками картера и выступающей частью
поддона.
Канал разделен на две части двумя
пластинчатыми пружинами, укрепленными на боковых стенках выступающей части
поддона. Из малого отсека масло вытекает в верхнюю ванну поддона, находящуюся
под разбрызгивателями шатунов цилиндров. Разбрызгиватели шатунов и вращающиеся
части коленчатого вала создают во внутренней полости картера и в нижней части
цилиндров масляный туман, который смазывает стенки цилиндров, поршневые пальцы,
коренные и шатунные подшипники. К шатунным шейкам масло поступает через
отверстия в нижних головках шатунов, к поршневым пальцам - через отверстия в
верхних головках шатунов и в бобышках поршней. Масло, стекающее со стенок
картера, собирается в большом отсеке канала, из которого через прямоугольное
отверстие поступает во вторую половину верхней масляной ванны поддона.
Текстолитовая шестерня подает масла значительно больше, чем расходует его компрессор,
поэтому свежее масло вытесняет отработавшее из второй половины верхней масляной
ванны поддона.
Вытесненное отработавшее масло стекает в
нижнюю половину ванны поддона, где оно охлаждается. В процессе охлаждения на
дно ванны оседают металлические частицы, образующиеся от приработки движущихся
деталей компрессора. Далее циркуляция масла повторяется. Для обеспечения
нормальной смазки компрессора необходимо поддерживать уровень масла в картере в
пределах верхней и нижней рисок масломера.
Рабочая жидкость за счет заполнения
объемов гидрооборудования одновременно выполняет функции его смазки и
охлаждения. Для дорожно-строительных машин применяют смазочные масла
минерального происхождения. Основными показателями масел являются: вязкость,
содержание водорастворимых кислот и щелочей, содержание механических примесей и
воды, температура застывания и вспышки.
Смазочные масла должны отвечать следующим
основным требованиям:
обладать высокими вязкостными свойствами и
хорошей смазочной способностью для обеспечения жидкостного трения деталей,
не изменять физико-химических свойств и не
образовывать смол при заданных режимах работы машины,
защищать детали от коррозии даже при
продолжительной остановке,
не застывать при низких температурах, не
содержать воды и механических примесей,
не менять свойства при продолжительном
хранении.
Обозначение смазочных масел выполняют
«Обозначение нефтепродуктов». Обозначение моторных масел по первый буквенный
индекс М обозначает моторное масло; следующий за индексом М цифровой индекс указывает
класс вязкости; буквы А, Б, В, Г указывают на группу по эксплуатационным
свойствам; цифра 1 позади букв обозначает назначение масла для карбюраторных
двигателей, цифра 2 - для дизельных двигателей.
Пример обозначения моторного масла: М-10-В
моторное масло, класса вязкости 10 для дизельных двигателей. Обозначение
трансмиссионных масел по первой группе знаков обозначается буквами ТМ
(трансмиссионные масла); вторая группа знаков обозначается цифрами и
характеризует принадлежность масел по эксплуатационным свойствам; третья группа
знаков в виде цифр характеризует класс кинематической вязкости.
Пример обозначения трансмиссионного масла:
ТМ-5-93 трансмиссионное масло с противозадирочными присадками
высокой эффективности и многофункционального действия (5), 9 класса вязкости,
содержащее заглушающую присадку (3). Сорта смазочных масел и места смазывания
машины указываются в картах смазки, содержащейся в инструкции (руководстве) по
эксплуатации.
Заправка машин заключается в наполнении
при ежесменном обслуживании (ЕО) рабочей жидкостью и топливом соответствующих
емкостей (баков), охлаждающей жидкостью радиатора двигателя.
В качестве рабочей жидкости для заполнения
гидрооборудования дорожно-строительных машин применяют масла: всесезонное
гидравлическое ВМГЗ, веретенное АУ, гидравлическое МГ-ЗОУ, индустриальное
И-30А.
Эксплуатационные свойства рабочей жидкости
определяются вязкостью, плотностью и температурой применения. Вязкость
характеризует силы внутреннего трения при работе гидросистемы во всем диапазоне
рабочих температур.
С повышением температуры вязкость
понижается и в результате уменьшается сопротивление движению элементов
гидрооборудования, но в то же время возрастают внутренние утечки рабочей
жидкости.
При низких температурах вязкость рабочей
жидкости повышается, что ухудшает ее прокачиваемость. Показатель плотности
рабочей жидкости характеризует ее смазывающие свойства. При оптимальной
плотности в рабочей жидкости образуется прочная масляная пленка, отсутствуют
противозадирные и противоизносные присадки, уменьшается трение, между
элементами гидрооборудования. Среди показателей эксплуатационных свойств
рабочей жидкости важнейшим является температура окружающего воздуха, при
которой ее применяют. Диапазон температуры должен обеспечивать работоспособность
гидрооборудования в различных климатических зонах.
Температура застывания рабочей жидкости -
это температура, при которой жидкость теряет подвижность и загустевает
настолько, что при наклоне пробирки под углом 45° уровень жидкости в ней
остается неизменным в течение 1 мин. Обозначение рабочих жидкостей первая
группа знаков обозначается буквами ВМГ (всесезонное минеральное
гидравлическое), вторая группа знаков обозначается цифрами и характеризует
класс кинематической вязкости. Пример обозначения гидравлического масла: МГ-30
- минеральное гидравлическое масло (МГ) класса вязкости 15.
Рабочую жидкость заливают в масляный бак
через заливной фильтр с помощью заливной воронки, в которую вкладывают два слоя
батиста. При заполнении удаляют из гидросистемы воздух, отвинчивая штуцеры в
наивысших точках заполняемых участков. После заполнения рабочей жидкостью всей
гидросистемы бак дозаправляют. Рабочую жидкость, предназначенную для заправки
гидросистемы, получают в чистой опломбированной таре и хранят в закрытом отапливаемом
помещении или перед заправкой предварительно разогревают трубчатыми
подогревателями. В процессе технического обслуживания масло подают в бидонах,
канистрах и банках, а также с помощью механизированных установок.
Условия применения дизельного топлива для
эксплуатации дорожно-строительных машин при температуре окружающего воздуха
следующие: от 0° и выше - летнее 20° С и выше -зимнее Г; ниже -20° С до -50° С
- арктическое А. В процессе хранения и работы двигателя масло не должно
изменять своих свойств под действием температур. Заправку машин топливом
производят на стационарных, передвижных и контейнерных автозаправочных
станциях.
Стационарные заправочные станции
располагаются на эксплуатационных базах, на автодорогах, по пути следования
машины к объекту.
Передвижные заправочные станции размещают
в местах сосредоточения техники с двигателем внутреннего сгорания, на
территории крупных строительных площадок, в других местах, где отсутствуют или
вышли из строя стационарные заправочные станции. Контейнерные заправочные
станции располагаются на рассредоточенных объектах.
В качестве охлаждающей жидкости для
двигателей применяют чистую и мягкую воду, не содержащую механических примесей
и растворимых солей. Не содержит больших примесей и загрязнений и используется
для заправки кипяченая вода, а также вода, бывшая в системе охлаждения
двигателей. Зимой вместо воды систему охлаждения можно заправлять антифризом,
приготавливаемым из незамерзающей технической жидкости этиленгликоля,
разбавленной наполовину водой. Антифриз ядовит, поэтому с ним надо обращаться
крайне осторожно.
2.3 Возведение земляного полотна
На эффективность эксплуатации строительно-дорожных машин в
основном влияет качество организации и решения следующих задач:
· Оптимизация режимов работы машин в
зависимости от особенностей объектов и условий работы;
· Оптимальное комплектование машин в
механизированные отряды с учетом конкретных условий и особенностей выполняемых
работ;
· Обеспечение топливосмазочными и
эксплуатационными материалами и рациональное их использование;
· Выбор способа перебазирования машин с
объекта на объект, обеспечивающего минимальные затраты и потери времени;
· Сбережение, хранение машин в периоды,
когда они не используются по назначению.
Данные задачи являются управляемыми и, их приходиться решать
на разных условиях управления эксплуатации машин.
Дорожно-строительные работы относятся к линейным, которые
характеризуются распределением объемов земельных работ вдоль строящейся дороги.
Это способствует успешному применению поточного метода организации
строительства. Для выполнения линейных работ комплектуются специализированные
отряды дорожных машин для строительства элементов дорог.
Правильная организация производства работ характеризуется
применением передовых методов труда, обеспечением полной занятости машин в
течении смены, их своевременное и качественное техническое обслуживание
позволяет снизить затраты труда и повысить темпы строительства.
Определение оптимального и качественного состава СОДМ.
При возведении земляного полотна определяет его поперечное
сечение. При этом необходимо задаться заложением откосов.
Отношение b=H/L
называется заложением откоса. Для связных грунтов-супесей и суглинков b принимают 1/2.
b=H/L=1/2=0,5
По принятому значению b и заданной средней
высоте H
насыпи определим длину откоса насыпи L по формуле:
L=H/b=2,0/0,5=4,0
м.
Тогда ширина насыпи по основанию будет равна:
где A - ширина земляного полотна поверху.
Определяем площадь поперечного сечения земляного полотна:
S=
*Н=
*2,0=38 м2
По вычисленной площади поперечного сечения элемента дороги и ее
длине определяем объем работ V в плотном теле
в метрах кубических по формуле:
м3
где Lд - длина строящейся дороги в метрах.
Сооружение земляного полотна необходимо провести в сроки с 12
апреля по 25 октября 2004 года. Количество рабочих дней путем отбрасывания
выходных и праздничных будет равно 140 дней.
Зная объем работ и установленное количество рабочих дней, задаемся
количеством рабочих дней в сутки и определяем необходимую сменную
производительность СОДМ:
где Тр - количество рабочих дней;
n - количество смен в сутки.
Выбираем два отряда, которые будут работать в две смены, по 8
часов в сутки и сменная производительность каждого будет составлять 2035,71 м3/см.
Оптимальный вариант СОДМ для выполнения заданного вида работ при
строительстве автомобильных дорог определяется путем сравнения различных
вариантов взаимосвязанных отрядов дорожных машин.
При возведении насыпи из боковых двух сторонних резервов средняя
дальность транспортирования грунта lср определяется по формуле:
где
- ширина резерва по низу, м;
hр -
средняя глубина резерва, принимается 0,8м;
Ширина растительного слоя будет равна:
Длина создаваемая земляного полотна в смену будет равна:
В курсовой работе достаточно сравнить два варианта СОДМ с
различными ведущими машинами.
Рисунок - 1. Поперечное сечение земляного полотна:
А - ширина земляного по верху; В - ширина по основанию; Н -
средняя высота насыпи;
Отряд
1) Срезка растительного слоя
Выбираем бульдозер типа ДЗ-28 (Т-130).
Нормативная производительность ведущей машины будет равна:
где Vн , tн - соответственно, нормативные объем
грунта в м3 и время в часах по ЕНир;
tсм -
продолжительность смены в часах.
Количество ведущих машин Nвед для выполнения линейных земляных работ
определяется по формуле:
Вычисленное значение Nвед округляется до целого
числа в большую сторону.
Принимаем одну машину. Машина имеет коэффициент использования
0,32, значит, её можно использовать при выполнении других работ.
2) Разработка и перемещение грунта
Выбираем бульдозер ДЗ-28 (Т-130).
Нормативная производительность будет равна:
Количество ведущих машин будет равно:
Принимаем одну машину.
3) Предварительное разравнивание грунта в теле насыпи
Выбираем бульдозер типа ДЗ-8 (Т-100)
Нормативная производительность машины будет равна:
Количество машин будет равно:
Принимаем одну машину.
4) Послойное уплотнение грунта
Выбираем каток типа ДУ-29А
Нормативная производительность ведущей машины будет равна:
Количество ведущих машин будет равно:
Принимаем одну машину.
5) Профилирование земляного полотна
Выбираем автогрейдер типа ДЗ-99
Площадь горизонтальных участков будет равна:
Площадь откосов будет равна:
Нормативная производительность машины будет равна:
Количество ведущих машин будет равно:
Принимаем одну машину.
б) Окончательная планировка площадей автогрейдерами ДЗ-99.
Нормативная производительность ведущей машины будет равна:
Количество ведущих машин будет равно:
Принимаем одну машину.
2 Отряд
1) Срезка растительного слоя
Выбираем автогрейдер типа ДЗ-99.
Нормативная производительность ведущей машины будет равна:
Количество ведущих машин будет равно:
Принимаем одну машину.
) Разработка и перемещение грунта
Выбираем бульдозер типа ДЗ-24А (Т-180).
Нормативная производительность ведущей машины будет равна:
Количество ведущих машин будет равно:
Принимаем одну ведущих машины.
3) Предварительное разравнивание грунта в теле
насыпи
Выбираем бульдозер типа ДЗ-24А (Т-180).
Нормативная производительность ведущей машины будет равна:
Количество ведущих машин будет равно:
Принимаем одну машину.
4) Послойное уплотнение грунта
Выбираем каток типа ДУ-31А
Нормативная производительность ведущей машины будет равна:
Количество ведущих машин будет равно:
Принимаем одну машину.
5) Профилирование земляного полотна
Выбираем бульдозер типа ДЗ-24А (Т-180)
а) Планировка откосов
Нормативная производительность ведущей машины будет равна:
Количество ведущих машин будет равно:
Принимаем одну машину.
б) Окончательная планировка площадей.
Нормативная производительность машины будет равна:
Количество ведущих машин будет равно:
Принимаем одну машину.
При выборе оптимального СОДМ из двух вариантов по наименьшим
затратам суммарным удельным приведенным затратам необходимо вычислить удельные
приведенные затраты для каждой машины по формуле:
где Ссм - стоимость машино-смены;
Цоп - оптово-отпускная стоимость машины;
Ен - нормативный коэффициент эффективности капитальных
вложений (Ен=0,15);
а - коэффициент, учитывающий затраты на доставку машины с завода
изготовителя потребителю (а=1,07 - 1,08).
Удельные приведенные затраты для машины типа бульдозер ДЗ-28
(Т-130) будут равны:
Удельные приведенные затраты для машины типа бульдозер ДЗ-8
(Т-100) будут равны:
Удельные приведенные затраты для машины типа каток ДУ-29А будут
равны:
Удельные приведенные затраты для машины типа автогрейдер ДЗ-99
будут равны:
Удельные приведенные затраты для машины типа бульдозер ДЗ-24А
будут равны:
Удельные приведенные затраты для машины типа каток ДУ-31А будут
равны:
Рассчитанные варианты двух отрядов машин представим в виде
таблиц по следующей форме:
Таблица 2.1. Специализированный отряд дорожных машин (вариант
1) для возведения земляного полотна
Наименование
машины
|
Модель
|
Количество
|
Оптово-отпускная
цена, (тг)
|
Стоимость
маш.-смен, (тг)
|
Удельные
приведенные затраты, м3/тг
|
Бульдозер
|
ДЗ-28 (Т-130)
|
2
|
530000
|
450
|
1.48
|
Бульдозер
|
ДЗ-8 (Т-100)
|
1
|
625000
|
330
|
0,68
|
Каток
|
ДУ-29
|
1
|
2350000
|
460
|
1,79
|
Автогрейдер
|
ДЗ-99
|
1
|
618000
|
320
|
0,67
|
|
|
|
|
4,62
|
Таблица 2.2. Специализированный отряд дорожных машин (вариант
2) для возведения земляного полотна
Наименование
машины
|
Модель
|
Количество
|
Оптово-отпускная
цена, (тг)
|
Стоимость
маш.-смен, (тг)
|
Удельные
приведенные затраты, м3/тг
|
Бульдозер
|
ДЗ-24А (Т-180)
|
2
|
2240000
|
500
|
3,53
|
Каток
|
ДУ-31А
|
1
|
1600000
|
390
|
1,29
|
Бульдозер
|
ДЗ-24А
|
1
|
2240000
|
500
|
1,76
|
|
|
|
|
|
6,58
|
Так как ∑Zуд1 < ∑Zуд2, для
дальнейших расчетов принимаем первый вариант отряда, так как общие удельные
приведенные затраты меньше, чем во втором варианте отряда.
. Описание схемы возведения земляного полотна бульдозером
Срезку растительного слоя производим бульдозером ДЗ-28.
Нормами учтена срезка грунта при отсутствии корней кустарника за один два
прохода по одному следу на глубину до 15 см.
В том случае, когда на объекте имеются корни кустарника, а
также небольших деревьев, срезку растительного слоя производят за два-три
прохода по одному следу на общую глубину до 25 см.
Ширину участка расчистки принимают до 30 м. Уборка грунта с
границ участка при необходимости нормируется отдельно в зависимости от способа
уборки.
Разработку и перемещение грунта, предварительное
разравнивание его в теле насыпи производим бульдозером ДЗ-8. При этом состав
работы следующий:
1. Приведение агрегата в рабочее положение.
2. Разработка грунта с перемещением его и выгрузкой.
3. Возвращение бульдозера в забой поражняком.
Послойное уплотнение грунта в теле насыпи производим
самоходными катками. При этом состав работы следующий:
1. Приведение агрегата в рабочее положение.
2. Уплотнение грунта.
. Повороты катка и переходы на соседнюю полосу укатки.
Планировку верха земляных сооружений производим автогрейдером
ДЗ-99. нормами предусмотрено планировка земляных сооружений при отклонении
отметок от проектных до 0,15 м.
В том случае, когда эти отклонения превышают 0,15м необходимо
произвести предварительную планировку земляного полотна бульдозерами или
срезать грунт скреперами.
Планировку откосов насыпи производим также автогрейдером
ДЗ-99. при этом состав работы следующий:
1. Приведение автогрейдера в рабочее положение.
2. Планировка откосов автогрейдером со срезкой грунта.
. Перемещение автогрейдера вхолостую по дну выемки или
по берме.
. Поворот автогрейдера с переездом через насыпь
. Перестановка ножа автогрейдера.
Рисунок 2.14. Схема возведения землянного полотна
бульдозером.
1. Схема замлянного полотна.
2. Срезка растительного слоя и укладка его в валики.
3. Разработка и перемещение грунта бульдозером и
предварительное разравнивание его в теле насыпи.
4. Послойное уплотнение грунта в теле насыпи самоходными
катками.
. Планировка горизонтальных поверхностей и откосов
автогрейдерами.
3. Расчеты годового плана и месячного
плана-графика ТО и ТР машин, входящих в состав СОДМ
С целью содержания парка машин в работоспособном состоянии и
получения высокой эффективности и надежности его работы дорожно-строительные
организации и управления механизации должны разрабатывать и использовать при
технической эксплуатации парка: годовые планы технического обслуживания ремонта
машин; месячные планы графики ТО и ТР машин.
Наработка в планируемом году будет равна:
где kc - поправочный коэффициент.
Количество капитальных ремонтов
где Нф - фактическая наработка;
Нпл - планируемая наработка,
К - количество выполненных ремонтов.
Для первой машины наработку определим по формуле:
, ч
Количество капитальных ремонтов за планируемый период эксплуатации
для бульдозера ДЗ-28 (1) будет равна:
принимаем Кт=0
Количество ТР и ТО-3
принимаем Кто-3=2
Количество ТО-2
принимаем Кто-2 =5
Количество ТО-1
принимаем Кто-1=23
Планируема наработка машины за период времени с 12 апреля по 11
мая будет равна:
День проведения ТО определяется по формуле:
Дтор=
,
где Кдр - число рабочих дней на данный период;
Тп - периодичность ТО и Р, ч.
Рассчитываем дни проведения ТО-1:
Рассчитываем дни проведения ТО-2:
т.к. день проведения второго ТО-2 является 33, а рабочих дней 22,
то второй ТО-2 проводиться не должен.
Рассчитываем дни проведения ТО-3:
т.к. день проведения второго ТО-3 является 52, а рабочих дней 22,
то второй ТО-3 проводиться не должен.
Количество капитальных ремонтов за планируемый период эксплуатации
для бульдозера ДЗ-28 (2) будет равна:
принимаем Кт=0
Количество ТиТО-3
принимаем Кто-3=1
Количество ТО-2
принимаем Кто-2 =6
Количество ТО-1
принимаем Кто-1=23
Рассчитываем дни проведения ТО-1:

Рассчитываем дни проведения ТО-2:

т.к. день проведения второго ТО-2 является 35, а рабочих дней 22,
то второй ТО-2 проводиться не должен.
Рассчитываем дни проведения ТО-3:
т.к. день проведения ТО-3 является 72, а рабочих дней 22, то ТО-3
проводиться не должен.
Количество капитальных ремонтов за планируемый период эксплуатации
для бульдозера ДЗ-8 (3) будет равна:
принимаем Кт=0
Количество ТиТО-3
принимаем Кто-3=2
Количество ТО-2
принимаем Кто-2 =5
Количество ТО-1
принимаем Кто-1=22
Рассчитываем дни проведения ТО-1:

Рассчитываем дни проведения ТО-2:

т.к. день проведения второго ТО-2 является 38, а рабочих дней 22,
то второй ТО-2 проводиться не должен.
Рассчитываем дни проведения ТО-3:

т.к. день проведения ТО-3 является 94, а рабочих дней 22, то ТО-3
проводиться не должен.
Количество капитальных ремонтов за планируемый период эксплуатации
для катка ДУ-29 (4) будет равна:
принимаем Кт=0
Количество ТиТО-3
принимаем Кто-3=2
Количество ТО-2
принимаем Кто-2 =6
Количество ТО-1
принимаем Кто-1=22
Рассчитываем дни проведения ТО-1:


Рассчитываем дни проведения ТО-2:

т.к. день проведения второго ТО-2 является 23, а рабочих дней 22,
то второй ТО-2 проводиться не должен.
Рассчитываем дни проведения ТО-3:
т.к. день проведения ТО-3 является 41, а рабочих дней 22, то ТО-3
проводиться не должен.
Количество капитальных ремонтов за планируемый период эксплуатации
для автогрейдера ДЗ-99 (5) будет равна:
принимаем Кт=0
Количество ТиТО-3
принимаем Кто-3=2
Количество ТО-2
принимаем Кто-2 =6
Количество ТО-1
принимаем Кто-1=22
Рассчитываем дни проведения ТО-1:

Рассчитываем дни проведения ТО-2:

т.к. день проведения второго ТО-2 является 25, а рабочих дней 22,
то второй ТО-2 проводиться не должен.
Рассчитываем дни проведения ТО-3:
т.к. день проведения ТО-3 является 63, а рабочих дней 22, то ТО-3
проводиться не должен.
Результаты расчетов для остальных машин оформляются в планах
и графике ТО и ТР на листах формата А3.
План технического обслуживания и ремонта машин на 2004 г.
_____________________________
(наименование организации)
Наименование и
марка (индекс) машины
|
Заводской №
машины
|
Фактическая
наработка, ч
|
Наработка в
планируемом году
|
Количество ТО и
ремонта в планируемом году
|
|
|
С начала
эксплуатации
|
Со времени
проведения
|
|
К
|
ТО-3 и ТР
|
ТО-2
|
ТО-1
|
|
|
|
К
|
ТР и ТО-3
|
ТО-2
|
ТО-1
|
|
Кол-во
|
Месяц
проведения
|
|
|
|
Бульдозер ДЗ-28
|
|
7038
|
1278
|
318
|
78
|
18
|
1792
|
0
|
--
|
2
|
5
|
23
|
Бульдозер ДЗ-28
|
|
7722
|
1962
|
42
|
42
|
42
|
1792
|
0
|
--
|
1
|
6
|
23
|
Бульдозер ДЗ-8
|
|
8406
|
2646
|
726
|
6
|
6
|
1792
|
0
|
--
|
2
|
5
|
22
|
Каток ДУ-29
|
|
9090
|
3330
|
450
|
210
|
30
|
1792
|
0
|
--
|
2
|
6
|
22
|
Автогрейдер
ДЗ-99
|
|
9774
|
3054
|
174
|
174
|
54
|
1792
|
0
|
--
|
2
|
6
|
22
|
План-график технического обслуживания и ремонта машин на
апрель-май месяц 2004 г.
________________________________________
(наименование организации)
Наименование и
марка (индекс) машины
|
Заводской №
машины
|
Фактическая
наработка на начало месяца, ч
|
Планируемая
наработка на месяц, ч
|
Числа месяца и
виды ТО и ремонтов
|
|
|
С начала
эксплуатации
|
Со времени
проведения
|
|
12
|
13
|
14
|
15
|
16
|
17
|
18
|
19
|
20
|
21
|
22
|
23
|
24
|
25
|
26
|
27
|
28
|
29
|
30
|
1
|
2
|
3
|
4
|
5
|
6
|
7
|
8
|
91011
|
|
|
|
К
|
ТР и ТО-3
|
ТО-2
|
ТО-1
|
|
|
|
|
|
|
|
|
|
|
|
|
|
|
|
|
|
|
|
|
|
|
|
|
|
|
Бульдозер ДЗ-28
|
|
7038
|
1278
|
318
|
78
|
18
|
282
|
|
|
|
|
То-1
|
|
|
|
|
|
То-1
|
|
|
|
|
|
То-2
|
|
|
|
|
|
То-1
|
|
То-1
|
Бульдозер ДЗ-28 |
|
7722
|
1962
|
42
|
42
|
42
|
282
|
|
|
То-1
|
|
|
|
|
|
То-1
|
|
|
|
|
|
То-1
|
|
|
|
То-2
|
|
|
|
|
|
То-1
|
Бульдозер ДЗ-8 |
|
8406
|
2646
|
726
|
6
|
6
|
282
|
|
|
|
|
|
|
|
То-1
|
|
|
|
То-1
|
|
|
|
|
|
То-1
|
|
|
|
|
|
То-2
|
То-1
|
Каток ДУ-29 |
|
9090
|
3330
|
450
|
210
|
30
|
282
|
|
|
|
То-2
|
|
|
|
|
|
То-1
|
|
|
|
|
|
То-1
|
|
|
|
|
|
То-1
|
|
|
То-2
|
Автогрейдер ДЗ-99 |
|
9774
|
3054
|
174
|
174
|
54
|
282
|
|
То-1
|
|
|
|
|
|
То-2
|
|
|
|
То-1
|
|
|
|
|
|
То-2
|
|
|
|
|
|
То-1
|
То-2
|
|
|
|
|
|
|
|
|
|
|
|
|
|
|
|
|
|
|
|
|
|
|
|
|
|
|
|
|
|
|
|
|
|
|
|
|
|
|
|
|
|
|
|
|
|
|
|
|
|
4. Таблица смазки ведущей машины (2.3.)
Место смазки
|
Кол-во точек
|
Смазочный
материал
|
Указания по
смазке
|
При ТО-1 (60
ч) бульдозера
|
Шарнир
гидравлического цилиндра
|
2
|
Масло
индустриальное 45
|
Смазать при
помощи масленки
|
Шарниры
рычагов и тяг управления гидравлическим приводом
|
5
|
тоже
|
То же
|
Шарниры штока
цилиндров и отвала
|
2
|
тоже
|
Тоже
|
Подшипники
валика коробки управления
|
4
|
литол 24
|
Солидоло-нагнитателем
через масленку
|
При ТО-2 (240
ч)
|
Подшипники
цапф гидравлического управления
|
4
|
Литол 24
|
Набить под
крышки
|
Бак системы
гидравлического управления
|
|
Всесезонное
масло ВМГ 3
|
Слить
отработавшее масло, промыть систему и залить свежее масло
|
5 расчеты потребности в
горюче-смазочных материалах на период работы СОДМ
и рекомендации по их экономии
Топливо смазочные материалы существенно влияют
на стоимость производства дорожных работ машинами. Поэтому расход их строго
регламентирован по видам и номенклатуре машин, по установленным на них
двигателям, применению в различных климатических зонах страны и режимах их
производственного использования. Средние нормы расхода топлива, рабочих
жидкостей и смазочных материалов определяют с учетом использования машин по
времени и мощности установленных на них двигателей.
Индивидуальную норму расхода топлива g на единицу рабочего
времени машины определяют по формуле:
g=0,001qеNеkо, кг/маш.-ч.
где qе - удельный расход топлива при номинальной
мощности двигателя, г/(кВт. ч.);
Nе - номинальная мощность двигателя машины, кВт;
Kо - интегральный нормативный коэффициент;
0.01 - переводной коэффициент граммов в
килограммы.
Интегральный нормативный коэффициент К учитывает
средние условия эксплуатации машин в течение рабочей смены при расчете
индивидуальных норм. Значение его определяют по формуле:
Kо=kдвkднkтнkтз,
где kдв - коэффициент использования двигателя по
времени;
kдн - коэффициент использования двигателя по
мощности;
kтн - коэффициент, учитывающий изменение удельного
расхода топлива в зависимости от степени использования двигателя по мощности;
kтз - коэффициент, учитывающий расход на запуск и
регулировку работы двигателя, а также ежесменное техническое обслуживание
машин в начале смены, kтз=1.03 для всех видов машин.
Нормируемый расход топлива на работу машины Qн, в строительных
организациях для расчета с машинистами определяют на основании установленных
индивидуальных норм и нормативных коэффициентов по формуле:
где g - индивидуальная норма расхода топлива,
л/маш.-ч;
Т - время работы машины, маш.-ч.
Индивидуальную норму расхода топлива g на единицу рабочего времени бульдозером ДЗ-28 определят по
формуле:
,
Нормируемый расход топлива на работу бульдозера ДЗ-28 будет
равна:
Индивидуальную норму расхода топлива g на единицу рабочего
времени бульдозером ДЗ-8 определят по формуле:
Таблица 2.4. Исходные данные для расчета
нормируемых расходов топлив, масел и смазок для машин СОДМ.
Наименование
машин, модель
|
Для расчета
топлив
|
Для расчета
масел и смазок
|
|
kдв
|
kдн
|
kтн
|
qе
|
Моторные, %
|
Трансмиссионные,
%
|
Индустриальные,
%
|
Смазки, %
|
Бульдозер
ДЗ-28
|
0,86
|
0,4
|
1,68
|
238
|
4,1
|
0,8
|
0,1
|
0,06
|
Бульдозер ДЗ-8
|
0,86
|
0,4
|
1,68
|
259
|
4,6
|
0,9
|
0,1
|
0,06
|
Каток ДУ-29
|
0,79
|
0,5
|
1,19
|
252
|
4,5
|
0,9
|
0,02
|
0,06
|
Автогрейдер
ДЗ-99
|
0,9
|
0,5
|
1,18
|
252
|
4,9
|
0,7
|
0,02
|
0,5
|
Нормируемый расход топлива на работу бульдозера ДЗ-8 будет равен:
Индивидуальную норму расхода топлива g на единицу рабочего времени катком ДУ-29 определят по формуле:
Нормируемый расход топлива на работу катка ДУ-29 будет равен:
Индивидуальную норму расхода топлива g на единицу рабочего
времени автогрейдера ДЗ-99 определят по формуле:
Нормируемый расход топлива на работу автогрейдера ДЗ-99 будет
равен:
Дорожно-строительные организации ежегодно
расходуют тысячи тонн нефтепродуктов. Эффективность их использования зависит
от надежной экономной работы двигателей и систем, потребляющих нефтепродукты.
Экономия топлива в процессе эксплуатации может быть достигнута следующим
путем: снижения времени работы машины вхолостую: сокращением порожних
пробегов; поддержание нормальных тепловых режимов работы двигателя;
своевременное регулирование топливной аппаратуры и т.д.
Нормы расхода топливно-смазочных
материалов и пути их экономии.
Нормой расхода топливно-смазочных материалов
(ТСМ) называют плановый показатель их расхода на единицу объема выполненных
работ. Нормы расхода ТОМ разделяют на индивидуальные и групповые.
Индивидуальная норма устанавливается применительно качество конкретным
условиям работы отдельной машины
Таблица 2.5. Нормируемый расход топлива, масел и
смазок на период работы СОДМ
Наименование
машин, модель
|
дизельное
топливо кг
|
Масла
|
Пластинчатые
смазки, кг
|
|
|
Моторное, кг
|
Трансмиссионное,
кг
|
Индустриальное,
кг
|
|
Бульдозер
ДЗ-28
|
32236,8
|
1321,7
|
257,9
|
32,2
|
19,3
|
Бульдозер
ДЗ-28
|
32236,8
|
1321,7
|
257,9
|
32,2
|
19,3
|
Бульдозер ДЗ-8
|
25016,64
|
1150,8
|
225,1
|
25,0
|
15,0
|
Каток ДУ-29
|
25833,6
|
1162,5
|
232,5
|
5,2
|
15,5
|
Автогрейдер
ДЗ-99
|
19020
|
932,0
|
3,8
|
95,1
|
Всего
|
134343,8
|
5888,7
|
1106,5
|
98,4
|
164,2
|
Групповая учитывает разнообразные условия
группы машин. Она является средней величиной индивидуальных норм.
В строительной отрасли каждое
министерство (ведомство) утверждает свои нормы расхода ТСМ. В таблице 2.5
приведены индивидуальные нормы расхода дизельного топлива на работу
бульдозеров, скреперов и грейдеров.
Приведенные в таблице 2.5 нормы расхода
топлива установлены для условий эксплуатации машин при положительных температурах.
При работе машин в зимнее время (средняя температура воздуха ниже О0 С),
в южных районах нормы повышают до 5%, в районах с умеренным климатом - до 10%,
в северных районах - до 15%, асфальтоукладчик в районах Крайнего Севера и
приравненных по условиям к ним - до 20%.
Нормы расхода масел, смазок для машин и
бензина для пусковых двигателей установлены в процентах от расхода дизельного
топлива в следующих размерах: моторного масла - 5, трансмиссионного масла - 1,
пластичной смазки - 1,5, бензина - 3 летом и 4,5 зимой.
Соблюдение установленных норм расхода ТСМ
на работу машин оценивают по данным учета отработанного ими времени и
израсходованного топлива. Количество заправляемых в машину ТСМ измеряют
счетчиками, мерными линейками и мерными кружками и записывают в ведомость
учета, которую ведет заправщик, и сменный рапорт машиниста.
В конце каждого месяца, квартала и года
подсчитывают фактический и нормативный расход ТСМ.
Основными направлениями экономического и
социального развития СССР на 1986-1990 годы и на период до 2000 года
определена задача по усилению режима экономии. В них содержится требование о
том, чтобы настойчиво добиваться рационального и экономного расходования всех
видов ресурсов и снижения их потерь. Это требование относится и к качеству ТСМ.
Хорошие основы для экономного расходования ТСМ создаются при правильном их
применении. Для этого необходимо соблюдать требования о том, чтобы каждую
машину заправляли и смазывали только предназначенными для нее ТСМ.
Основными путями экономии ТСМ бульдозеров,
скреперов и грейдеров являются устранение их потерь и снижение расходования.
Потери дизельного топлива при заправке
баков машин открытой струей (ведром) достигают 1,2%, при переполнении
топливного бака- 0,1-0,3%, при заправке через шланг без раздаточного крана -
0,18-0,2%, асфальтоукладчик через неплотности в соединениях средств заправки -
0,4-0,5%.
Заправка машин маслами с помощью
различных мелких предметов может вызвать потери от 3,5 до 10%.
3. Ремонт дорожных машин
3.1 Ремонт бульдозера на
базе Т-130
Дорожно-строительные машины ремонтируют
через определенные промежутки времени, установленные в зависимости от срока
службы групп деталей. Для каждой модели машин предусматривается
последовательность выполнения и состав ремонтных работ, состав звена рабочих,
продолжительность выполнения работы. Если время проведения очередного ТО по
периодичности совпадает со временем выполнения планового ремонта, техническое
обслуживание и ремонт выполняют одновременно.
Ремонт может быть текущим, выполняемым на
эксплуатационных базах, и капитальным, который производится на
специализированных ремонтных предприятиях.
Текущий ремонт, осуществляемый в процессе
эксплуатации для гарантированного обеспечения работоспособности машины до
очередного планового ремонта, включает в себя диагностирование, замену и
устранение неисправностей отдельных сборочных единиц и их регулирование.
При текущем ремонте заменяют изношенные
детали, срок службы которых равен межремонтному периоду, а также выполняют
ремонтные работы: заваривают трещины в металлоконструкциях, правят вмятины.
Кроме того при текущем ремонте машин проверяют размеры посадочных мест
ответственных соединений: замеряю зубья зубчатых зацеплений; заменяют
уплотнения, где обнаружена течь масла; проверяют корпуса редукторов и при
выявлении дефектов ремонтируют их или заменяют; проверяют подшипники и
штифтовые соединения, рамы, опорно-поворотное устройство.
Текущий ремонт организуют одним из трех
способов: индивидуальным, агрегатным и смешанным.
При небольшом числе эксплуатируемых
однотипных машин (например катков) применяют индивидуальный способ, при
котором сборочные единицы, снимаемые с машины, подвергаются ремонту и вновь
устанавливаются на нее, сохраняя принадлежность к отремонтированным составным
частям.
Агрегатный способ заключается в замене на
ремонтируемой машине неисправных сборочных единиц новыми или заранее
отремонтированными в условиях эксплуатационной базы и строительной площадки.
Дорожно-строительные машины
предпочтительно ремонтировать агрегатным методом, так как их легко расчленить
на сборочные единицы, которые имеют свойства полной взаимозаменяемости, легкой
отделяемости от составных частей, независимой сборки без сложных
регулировочных операций. Для выполнения ремонта агрегатным способом необходим
оборотный фонд исправных деталей и сборочных единиц, а также ремонтное
предприятие.
Оборотный фонд образуется из сборочных
единиц, получаемых от заводов-изготовителей, а также из восстановленных
деталей и сборочных единиц. Потребность в оборотном фонде определяется для
каждой эксплуатационной организации в зависимости от числа однотипных машин,
времени оборачиваемости деталей и сборочных единиц и времени их ремонта.
При небольшом парке машин и наличии
оборотного фонда деталей и сборочных единиц применяют смешанный способ
ремонта, Сущность смешанного способа ремонта состоит в том, что все сборочные
единицы с одинаковыми ресурсами группируют в ремонтные комплекты на заводах, а
их установку на машине взамен неисправных проводят на эксплуатационных базах.
Перед остановкой машины на текущий
ремонт, машинист вместе с механиком устанавливают по фактическому техническому
состоянию, а также по записям в журнале учета ремонтов перечень необходимых
ремонтных работ, определяют потребность в запасных частях, материалах и
дополнительной рабочей силе.
Текущий ремонт выполняют
специализированные бригады с участием машиниста, что обеспечивает высокое
качество ремонтных работ. После текущего ремонта машину испытывают.
3.2 Ремонт рабочего
оборудования бульдозера
Капитальный ремонт, выполняемый по
ремонтной документации для восстановления исправности и полного, или близкого
к полному, восстановления ресурса машины предусматривает полную разборку
машины, дефектацию, восстановление и замену деталей, сборку, регулирование и
испытание.
В капитальный ремонт машины направляют на
основании тщательного анализа их предельного технического состояния.
Критерии предельного состояния:
усталостные трещины, зазоры по посадкам подшипников, деформации, люфты, износ,
выработка поверхности катания, обломы, удлинение детали, уменьшение диаметра
детали. Подлежащие капитальному ремонту машины предварительно очищают от
загрязнений; консервируют штоки цилиндров; охлаждающую жидкость и топливо
сливают, кабину и капот опломбируют; шины должны быть накачаны.
Поступающие в капитальный ремонт машины
на ремонтных предприятиях не обезличивают. Отремонтированные машины поступают
к тем же владельцам, от которых они прибыли в ремонт. Сборочные единицы и
детали в них при капитальном ремонте могут обезличиваться, за исключением
базовых составных частей, сборочных единиц механической, гидравлической и
электрической систем, зубчатых колес, колец разобранных подшипников, взаимно
приработанных и совместно обработанных.
Все составные части, приборы и детали
должны быть закреплены, как это предусмотрено конструкцией.
Собранные после ремонта сборочные единицы
подвергают стендовой обкатке и испытанию. Сборочные единицы, выдержавшие
испытания и принятые ОТК, заправляют свежим маслом и подают на пост общей
сборки, где их устанавливают на составные части. Отремонтированная машина
поступает на пост стационарных испытаний в объеме, определяемом специальной
программой испытаний.
Испытанную машину комплектуют ЗИП и
передают на площадку готовой продукции. Межремонтный ресурс отремонтированных
машин должен быть не менее 80% ресурса до первого капитального ремонта. Выдачу
из капитального ремонта машин оформляют актом, который подписывают
одновременно представители ремонтного предприятия и владельца машин.
3.3 Ремонт вала (шестерни)
Служебное назначение и анализ работы сборочной
единицы.
Назначение, конструкция и принцип работы
сборочной единицы.
Коробка передач является неотъемлемым механизмом
трактора и автомобиля в случае установки на них двигателя внутреннего
сгорания. С помощью коробки передач можно изменять величину крутящего момента,
передаваемого на ведущие органы трактора или автомобиля, что способствует
преодолению изменяющихся сопротивлений при движении.
Коробка передач дает возможность машине
двигаться задним ходом, передавать часть мощности приводным машинам,
обеспечивает необходимый разгон при трогании с места и затем движении.
По принципу действия коробки передач
подразделяются на составные, бесступенчатые и ступенчатые.
Бесступенчатые коробки передач в определенном
интервале обеспечивают получение бесконечного числа передач; изменение передач
в этих коробках происходит автоматически в зависимости от сопротивления
дороги.
Составные коробки передач применяются в тех
случаях, когда необходимо получить большое число передач или увеличить крутящий
момент. Эти коробки состоят из двух последовательно соединённых передач или
механизмов.
Ступенчатые коробки передач представляют собой
редукторы с набором шестерен. В таких коробках передач изменение передаточных
чисел сочетанием зацепления шестерен осуществляется не плавно, а ступенями.
По числу валов коробки передач подразделяются на
двухвальные (без учета валика заднего хода), трехвальные и четырехвальные,
составные и специальные.
На рисунке 3.1. изображена двухвальная коробка
передач. Она состоит из двух основных валов: первичного и вторичного, и вала
заднего хода. Первичный вал 2 соединяется через муфту сцепления с двигателем;
вал имеет шлицы, на которых размещены каретки 3. На вторичном валу 5 жестко
закреплены шестерни 1. Этот вал передает усилие на центральную передачу и
затем к ведущим колесам. Вал заднего хода на рисунке не показан.
Картер 4 коробки передач, внутри которого
размещены шестерни, валы и подшипники, является одновременно резервуаром для
масла, которым смазываются все детали коробки.
Рисунок 3.1-Кинематическая схема
десятиступенчатой коробки передач
Назначение, конструкция и анализ работы деталей.
Валы предназначены для передачи вращающих
моментов и в большинстве случаев для поддержания вращающихся вместе с ними
относительно подшипников различных деталей машин. Валы, несущие на себе
детали, через которые передаются вращающий момент, воспринимают от этих
деталей нагрузки и, следовательно, работают одновременно на изгиб и кручение.
При действии на установленные на валах детали осевых нагрузок валы
дополнительно работают на растяжение или сжатие. Некоторые валы не
поддерживают вращающиеся детали, поэтому эти валы работают только на кручение.
По назначению различают валы передач, на которых
устанавливают зубчатые колеса, звездочки, муфты и прочие детали передач, и
коренные валы, на которые устанавливают не только детали передач, но и другие
детали, например маховики, кривошипы и т. д.
Технологический процесс ремонта деталей
Дефекты деталей и разработка карты дефектации.
Основными дефектами вертикального вала являются:
) износ рабочих поверхностей Б и В;
)повреждение резьбы Д.
В связи с этим в соединении возникают зазоры,
что приводит к потере машиной работоспособности.
Определим размеры деталей в сопряжении
“вал-отверстие” допускаемые без ремонта
1. Размеры по чертежу
,
Размеры деталей
для вала
мм,
мм;
для отверстия
мм,
мм.
Максимальный зазор
мм.
мм.
Допустимый зазор
мм.
мм.
Допустимый износ в сопряжениях
мм.
мм.
Допустимые без ремонта размеры вала и отверстия:
размеры вала, считая, что отверстие новое:
мм,
размеры отверстия, считая, что вал новый:
мм,
мм,
размеры вала и отверстия, считая, что они износились одинаково
мм,
мм.
мм.
. Размеры по чертежу
,
.
Размеры деталей:
для вала
мм,
мм,
для отверстия
мм,
мм.
Максимальный зазор
мм.
мм.
Допустимый зазор
мм.
мм.
Допустимый износ в сопряжении
мм.
мм.
Допустимые без ремонта размеры вала и отверстия:
размеры вала, считая, что отверстие новое
мм,
мм,
размеры отверстия, считая, что вал новый
мм,
мм,
размеры вала и отверстия, считая, что они износились одинаково
мм,
мм,
мм.
мм.
Выбор способа ремонта отдельных поверхностей
деталей
Износ деталей связан с изменением их
геометрической формы и номинальных размеров, что вызывает изменение
первоначальной посадки сопряжения. Таким образом, ремонт сводится к
восстановлению работоспособности деталей и обеспечению первоначальной посадки
сопряжения, т. е. зазора или натяга, устанавливаемых техническими условиями.
При выборе способа ремонта необходимо учитывать
следующие факторы:
материал восстанавливаемой поверхности;
характер и размеры износа;
конструктивные особенности детали;
условия работы детали в узле;
затраты на восстановление.
Проанализировав данные факторы и изучив основные
виды ремонта отдельных поверхностей детали, выбираем автоматическую наплавку.
Наплавку рабочих поверхностей Б и В производят по винтовой линии. Изношенную
шлицевую поверхность Г наплавляют продольными валиками. Изношенную резьбовую
поверхность Д заплавляют заподлицо.
Проектирование
технологического процесса ремонта
Вид детали: вал вертикальный
Материал: сталь 40Х
Таблица 3.1-Технологический процесс ремонта
детали
№ операции
|
Наименование и
содержание операции
|
Оборудование и
оснастка
|
005 010 015
020 025 030 035 040 045 050 055
|
Очистка и
мойка детали Подготовка изношенной поверхности к наплавке Зачистка ремонтной
поверхности Точить поверхность Б и В до размеров Æ72 и Æ48 Наплавить поверхности Б и В до размеров Æ82 и Æ52 Наплавить поверхность Д Проточить поверхности Б и В
до размеров Æ80 и Æ50 Проточить поверхность Д и нарезать
резьбу Фрезерование Термическая обработка Шлифовать поверхности Б, В
Промывка детали Технический контроль Нанесение антикоррозионного покрытия
|
Моечная машина
ОМ-837 Токарный автомат Установка для наплавки А-580 Токарный автомат
Горизонтально-фрезерный станок Круглошлифовальный станок 3У10В Моечная
машина ОМ-837
|
Проектирование ремонтной операции
Рассчитать наплавку вала, если известно:
- Для поверхности Б
мм,
мм,
мм.
Наплавка проводится по винтовой линии;
- Толщина наплавляемого
слоя
мм,
где
мм - величина износа,
мм - припуск;
мм,
Принимаем диаметр электродной проволоки
мм;
Выбираем наплавочный аппарат А-580;
Определяем силу тока и коэффициент наплавляемости:
А,
А,
;
;
Скорость наплавки
м/ч,
Где
г/см3 - плотность материала,
- площадь наплавляемой поверхности
м/ч,
мм2.
мм2.
Скорость подачи электродной проволоки
м/ч;
м/ч;
Объём расплавленного металла
см3;
см3;
Масса израсходованной электродной проводки
г.
г.
- Для поверхности В
- Для поверхности Б
мм,
мм,
мм.
Наплавка проводится по винтовой линии;
Толщина наплавляемого слоя
мм,
где
мм - величина износа,
мм - припуск;
мм,
Принимаем диаметр электродной проволоки
мм;
Выбираем наплавочный аппарат А-580;
Определяем силу тока и коэффициент наплавляемости:
А,
А,
;
;
Скорость наплавки
м/ч,
где
г/см3 - плотность материала,
- площадь наплавляемой поверхности,
м/ч,
мм2.
мм2.
Скорость подачи электродной проволоки:
м/ч;
м/ч;
Объём расплавленного металла
см3;
см3;
Масса израсходованной электродной проводки
г
г
Таблица 3.2. Карта технологического процесса
ремонта
|
Наименование,
марка материала
|
Обозначение
изделия
|
Наименование
изделия
|
Код, вид
ремонта
|
|
Сталь 40Х
|
|
|
|
номер
|
Наименование,
содержание операции
|
Контролируемые
параметры
|
Приспособление,
измерительный инструмент
|
Код профессии
|
Код рабочих
|
Код тарифной
ставки
|
Тпз
|
Особые
указания
|
участка
|
операции
|
|
Номинальное
допустимое значение
|
Измеренное
значение
|
|
|
Разряд работы
|
Код вид норм
|
Тшт
|
|
|
1
|
Износ рабочей
поверхности
|
0,174
|
|
Штангенциркуль
|
|
|
|
|
|
|
2
|
Износ
шлицевого соединения
|
0,423
|
|
Штангенциркуль
|
|
|
|
|
|
|
|
|
|
|
|
|
|
|
|
|
4. Охрана труда
бульдозер ремонт эксплуатация вал
шестерня
Требования безопасности при бульдозерных,
скреперных и грейдерных работах.
Общие требования. Безопасности людей и
машин, предотвращению аварий и несчастных случаев в нашей стране придается
большое значение. С этой целью постоянно совершенствуются конструкции машин,
улучшаются условия труда машиниста, разработаны специальные требования и
правила безопасности, которые машинист должен знать и выполнять
неукоснительно. Залогом безопасной работы являются отличное знание машинистом
устройства и правил работы на машине и ее исправность.
При эксплуатации бульдозеров и скреперов
необходимо руководствоваться правилами, приведенными в СНиПШ-4- 80 и системе
стандартов ССТБ.
На бульдозерах, скреперах и грейдерах
разрешается работать лицам, достигшим 18 лет, прошедшим специальное обучение и
имеющим удостоверения на право управления этими машинами. Машинистам
самоходных скреперов, кроме того, необходимо иметь права водителя автомобиля,
выданные Госавтоинспекцией.
Допуск к работе на машине оформляют
приказом по строительной организации. Запрещается работать на неисправной машине.
Перед выездом на работу машинист и механик должны проверить техническое
состояние машины и при обнаружении неисправностей устранить их.
Особое внимание должно быть обращено на
исправность рулевого управления, тормозов и сигнализации. До начала работы прораб
или механик должен довести до сведения машиниста условия выполнения работы -
схемы движения, способы взаимодействия с другими машинами и мероприятия по
обеспечению безопасности труда. Перед началом движения следует убедиться, что
путь свободен, и подать сигнал.
При перемещении машин своим ходом или на
транспортном средстве, особенно с выездом на автомобильные дороги, необходимо
строго выполнять требования правил дорожного движения. Особую осторожность
следует проявлять при переездах через железнодорожные пути, мосты и
искусственные сооружения с учетом указанных на них допускаемых нагрузок и
габаритов.
На рабочей площадке должны быть приняты
меры, предотвращающие опрокидывание или сползание машин. Откосы и косогоры, на
которых предстоит работать машине, не должны превышать значений, допускаемых
техническим паспортом. Приближение к откосам насыпи или выемки во избежание их
обрушения ближе расстояний, указанных, не допускается как во время работы, так
и при остановке машины.
В случае расположения рабочей площадки
около линии электропередач (НЭП) необходимо учитывать требования
электробезопасности. В этих зонах можно работать только при письменном
разрешении и под наблюдением лиц, ответственных за безопасность.
При работе в темное время суток следует
периодически очищать от грязи и пыли отражатели фар и плафонов.
Во время перерывов и по окончании работ
машина должна быть установлена на ровной площадке и заторможена. Рычаги
органов управления ставят в нейтральное положение, а кабину запирают. Не
допускается оставлять машину с работающим двигателем. Во время осмотра машины
рабочий орган (отвал, ковш) должен быть опущен на грунт, двигатель выключен
или отключен привод.
Чтобы предотвратить несчастные случаи,
запрещается:
допускать к работе необученных рабочих и
посторонних лиц;
приступать к работе или продолжать ее при
обнаружении любой неисправности;
устанавливать машину на свеженасыпанном,
не утрамбованном грунте;
переезжать через кабели, трубопроводы без
специальных защитных укрытий;
перевозить посторонних людей в кабинах;
запускать двигатель, используя движение
под уклон;
останавливать машину на уклонах; в случае
вынужденной остановки на уклоне необходимо выключить двигатель, затормозить
машину ручным тормозом или подложить под колеса (гусеницы) упоры;
находиться под поднятым рабочим органом
(отвалом, ковшом, заслонкой), удерживаемым гидроцилиндром или канатом;
пользоваться открытым огнем для ускорения
пуска двигателя или разогрева масла в картерах коробок передач и ведущих
мостов, а также эксплуатировать машину при течи в топливных и масляных
системах.
Особенности безопасной работы
бульдозеров.
Во время работы с заглубленным отвалом
или зубьями рыхлителя запрещается делать повороты машины. В случае сброса
грунта под откос или засыпки траншей поперечными ходами нельзя выдвигать отвал
за край насыпи, так как это может привести к сползанию бульдозера. При заднем
ходе бульдозера отвал должен быть приподнят. Во время движения запрещается
становиться на раму и отвал.
Особенности безопасной работы скреперов.
При работе скреперов наиболее опасен поворот в процессе движения под уклон. В
это время возможно боковое внешнее опрокидывание машины. Поворот следует
производить на пониженных скоростях и по кривым радиусам, в 2,5...3 раза
превышающим минимальные. Значения уклонов дорог действительны только для
прямолинейного движения.
Запрещается во время работы кому-либо
находиться между трактором и рабочим оборудованием прицепного скрепера.
В момент толкания скрепера не допускаются
резкие удары отвалом по буферу.
При транспортировании скрепера своим
ходом на большие расстояния необходимо закрепить ковш к тяговой раме
специальными стопорами.
Особенности безопасной работы грейдеров.
При работе грейдером запрещается посторонним лицам находиться вблизи отвала
или задних колес, так как может произойти неожиданный занос машины в сторону.
Не допускается работать грейдером на
участках, не очищенных от крупных пней, камней и металлического лома.
Запрещается также движение грейдера задним ходом при опущенном отвале или
кирковщике. В связи с довольно сложной траекторией движения агрегата повороты,
развороты в конце участка следует осуществлять на первой передаче трактора.
Требования безопасности
при техническом обслуживании и ремонте машин.
К техническому обслуживанию и ремонту
допускаются машинисты, слесари, сварщики, электрики и другие рабочие,
прошедшие обучение и знающие устройство ремонтируемых машин, а также
требования безопасности выполнения ремонтных работ.
Обслуживаемую или ремонтируемую машину
перед началом работ надежно затормаживают, подложив под гусеницы или колеса
упоры, рабочие органы опускают на подкладки или устанавливают на фиксаторы.
Находиться под рабочими органами либо составными частями машины, поднятыми
грузоподъемным средством, гидравлическим или канатным приводом, запрещается.
Во время мойки машин, предшествующей
обслуживанию и ремонту, рабочий должен быть одет в непромокаемый костюм,
резиновые перчатки и сапоги. При ручной мойке источники освещения и силовые
двигатели должны быть герметически изолированы.
Запрещается производить обслуживание и
устранять неисправности машины при работающем двигателе. Исключение составляют
только регулирование системы питания, электрооборудования двигателя и
опробование тормозов.
Приступая к работе, необходимо убедиться
в исправности инструментов, приспособлений, подъемных механизмов. Не
допускается применять ключи, зевы которых не соответствуют размерам гаек, а
также наращивать ключи другим ключом или трубой. Нельзя ударять по ключу при
отвертывании или завертывании плотно затянутых болтов и гаек. Пользуясь
различными съемниками, необходимо проверять надежность захвата детали лапами.
Если невозможно применять съемники или
прессы для демонтажных операций, то используют выколотки с медными
наконечниками и молотки с медными бойками. Проводить эти работы кувалдами не
допускается.
Для крепежных работ целесообразно
использовать ручные машины. Включать их можно только после установки в рабочее
положение. Инструменты нельзя направлять в сторону руки, поддерживающей
обрабатываемую деталь.
Для безопасного монтажа и демонтажа
сборочных единиц со сжатыми пружинами необходимо применять специальные
приспособления, щипцы или стяжные болты.
Перед демонтажем гидравлической,
смазочной и других систем необходимо слить рабочую жидкость и топливо в
специальную емкость, не допуская расплескивания их, особенно в горячем
состоянии.
При подъеме тяжелых деталей или составных
частей необходимо убедиться в соответствии грузоподъемных средств и чалочных
приспособлений. Запрещается пользование сращенными канатами или цепями,
соединенными с помощью болтов. Поднимать или опускать груз следует строго
вертикально, плавно без рывков. Необходимо следить за тем, чтобы чалочные
канаты не перекручивались.
При работе с электроинструментом, который
находится под напряжением 220 В и выше, обязательно пользуются
диэлектрическими перчатками, сапогами, ковриками. Инструмент должен быть
заземлен.
Сверла, головки ключа допускается
заменять в ручной машине только после ее полной остановки.
Работать с аккумуляторной батареей можно
только в резиновых перчатках. Доливать электролит необходимо резиновой грушей.
При заправке машин или проверке уровня
топлива запрещается курить и пользоваться открытым огнем.
На участке технического обслуживания и
текущего ремонта машин должно быть установлено противопожарное оборудование
согласно нормам пожарной безопасности. Запрещается загромождать доступ к этому
оборудованию и использовать его в других целях.
Не допускается подтекание нефтепродуктов.
Пролитые огнеопасные жидкости следует немедленно убирать. Запрещается курить
возле мест хранения нефтепродуктов.
5. Промышленная экология
Охрана окружающей среды.
Вопросы экологии в настоящее время
рассматриваются как важнейшая государственная проблема.
Большое внимание должно быть уделено
охране природы в процессе земляных работ. При подготовке трассы сооружения
необходимо очищать ее от леса и кустарника с максимально возможным сохранением
лесного массива. Деревья ценных пород должны быть пересажены. По возможности
следует избегать использования грунта из боковых резервов или ограничивать их
глубину до 1... 1,5 м.
В соответствии с действующим
законодательством строительные организации, работающие на сельскохозяйственных
землях и лесных угодьях, должны за свой счет приводить эти участки в
состояние, пригодное для дальнейшего использования (рекультивировать). Работы
выполняют в ходе строительства или не позднее чем в течение года после их
завершения. При рекультивации растительный слой грунта, срезанный во время
расчистки полосы под будущее сооружение и перемещенный в сторону, возвращают
на открытые грунтовые участки резервов.
При эксплуатации машин необходимо также
соблюдать следующие правила.
Гусеничные машины во время
транспортирования собственным ходом должны перемещаться по обочинам дорог, а в
случае пересечения асфальтированных покрытий следует использовать временные
настилы.
Запрещается работа на машинах с
повышенной дымностью, при утечках топлива, масел, рабочих жидкостей. Попадая в
грунт, эти материалы отрицательно влияют на окружающую природу. Категорически
запрещается сливать отработавшие нефтепродукты на землю, в водоемы и
канализационную сеть. Эти материалы следует собирать и сдавать на нефтебазы
или уничтожать методами, согласованными с Госсанинспекцией.
Требования безопасности труда при
транспортировании и хранении машин.
При погрузке машины на прицеп и разгрузке
с прицепа требуется следить за тем, чтобы не находились люди в зоне возможного
ее падения (сползания).
После погрузки машины на прицеп следует
проверить надежность ее крепления.
Перед транспортированием машин
собственным ходом необходимо поднять ковш скрепера и закрепить его
транспортной подвеской к раме скрепера, отключив гидропривод или лебедку, а у
прицепных грейдеров - поднять тяговую раму в верхнее положение и закрепить
цепью подвеса.
При транспортировании машин по дорогам
следует передвигаться по правой их стороне с соблюдением интервала между
машинами или транспортными агрегатами не менее 20 м.
В случае плохой видимости на буксируемой
машине при жесткой сцепке необходимо включить габаритные огни, при гибкой
сцепке - передние.
Железнодорожные пути следует переезжать
только через переезды, на пониженной передаче, при открытом шлагбауме. При
отсутствии на переезде шлагбаума и сигнализации необходимо остановиться перед
ним и убедиться в отсутствии приближающегося к переезду поезда.
При подъезде к мостам, плотинам
необходимо убедиться в возможности проезда по ним.
Машины, остановившиеся на дороге на
длительное время, необходимо огородить в дневное время красными флажками, а в
ночное время - красными фонарями.
Запрещается транспортировать машины в
ночное время без фар освещения и задних световых сигналов.
Площадки, на которых ведется подготовка
машин к хранению, должны быть ровными, хорошо освещенными, не иметь
посторонних предметов, обеспечивать хороший доступ к машине и возможность
использования грузоподъемных средств, установки снятых с машины составных ее
частей.
Гусеничные машины должны опираться на
подкладки всей опорной поверхностью гусениц. Подставки, используемые под
пневмоколесные машины, должны быть прочными и устойчивыми.
Чтобы машина самопроизвольно не
откатывалась при подъеме ее домкратом, следует под колеса подложить колодки.
Снятые с машин сборочные единицы и детали
необходимо укладывать на стеллажи: на нижние полки следует укладывать тяжелые
детали, а на верхние - легкие.
Рабочие, выполняющие операции по
нанесению защитных покрытий на детали машин, допускаются к работе после
проведения инструктажа и освоения правил пользования защитными
приспособлениями с очками, респираторами и др.
Список использованных
источников
1. Устройство и эксплуатация
дорожно-строительных машин: Учебник для на. проф .образования / Раннев А.В.,
Полосин М.Д.;-2-е издание., стер.-М,: Издательский центр «Академия»,2003.-488с
. Строительные машины и оборудование:/Добронравов
С.С. Справочник для на. проф. образования, строит. спец. вузов и инж.-техн.
работников.-М,.Высш. Школа,1991.-456 с.:ил.
. Бульдозеры, скреперы, грейдеры: Учеб. для
ПТУ.-2-е изд., перераб.и доп.-М.: Высш.шк.,1991.-334с.:ил.
. Строительство автомобильных дорог: Справочник
инженера-дорожника / Под ред. В.А. Бочина.- М.: Транспорт, 1980,-511с.
. Указания по организации и проведению
технического обслуживания и ремонта дорожных машин (ВСН 6-79) / Минавтодор
РСФСР. М.: Транспорт, 1980.-136с.
. ЕНир. Сборник Е 2. Земляные работы. Вып. 1.
Механизированные и ручные земляные работы/Госстрой СССР. - М.: Стройиздат,
1988. - 224с.
. Киселев М.М. Топливосмазочные материалы для
строительных машин: Справочник. М.: Стройиздат, 1988.-217с.