Выпаривание раствора аммиачной селитры
Содержание
Введение
1. Аналитический обзор литературы
.1 Сырье и методы производства аммиачной селитры
.2 Технические требования к готовой продукции
1.3
Применение аммиачной селитры
.
Характеристика исходного сырья и готового продукта
.1
Характеристика исходного сырья
.2
Физико-химические свойства аммиачной селитры
.2.1
Слеживаемость и меры ее предотвращения
.2.2
Термическое разложение NH4NO3, огне- и взрывоопасность
.
Теоретические основы производства NH4NO3
.
Технологическая схема производства NH4NO3 и ее описание
. Основная
аппаратура
.1 Выпарной
аппарат
.2 Аппарат
ИТН
.3 Аппарат КС
6.
Выпаривание растворов аммиачной селитры
6.1
Технологическое оформление узла выпаривания
. Расчет
.1
Материальный баланс
.2 Тепловой
баланс
8. Техника
безопасности
Выводы
Список
используемой литературы
Введение
Химическая промышленность выпускает широкий ассортимент азотных
удобрений, которые различаются содержанием азота, также получают кальциевую и
натриевую селитры. Азотная промышленность нашей страны развивается высокими
темпами, превышающими темпы прироста продукции всей промышленности страны в
2-2,1 раза. Темпы роста отечественной азотной промышленности значительно выше
темпов роста мировой азотной промышленности. Основными азотными удобрениями,
выпускаемыми нашей промышленностью, являются аммиачная селитра и карбамид. В
настоящее время производство последнего развивается более высокими темпами, чем
производство аммиачной селитры. Весьма быстро растет производство комплексных
удобрений и, следовательно, получение их азотсодержащих компонентов. Развитие
производства сульфата аммония, основанного на использовании аммиака из
коксового газа и растворов, получаемых при производстве капролактама, зависят в
значительной степени от развития коксохимической промышленности и промышленности
синтетического капронового волокна. Твердые азотные удобрения выпускаются
только в гранулированном виде. В связи с ростом производства аммиака
увеличивается и объем выпускаемых жидких азотных удобрений [2].
Подавляющая часть продукции мировой азотной промышленности используется в
сельском хозяйстве в виде удобрений, для промышленных целей потребляется
примерно 15-20% вырабатываемых соединений азота. Азотные удобрения, выпускаемые
промышленностью, содержат питательный элемент - азот в виде аммиака, ионов
аммония NH4+, ионов NО3- и
аминогруппы NH2-. Все соли аммония и аммиак относятся к
физиологически кислым удобрениям. Минеральные соли поглощаются (сорбируются)
корнями растений из разбавленных почвенных растворов, в которых соли
диссоциированы на ионы. Корни растений быстрее усваивают щелочные ионы аммония,
чем кислые нитрат-ионы, вследствие чего повышается кислотность почвенного
раствора. Подкисление почвы объясняется также способностью некоторых почвенных
бактерий окислять аммиак до азотной кислоты. Этот процесс носит название
нитрификации, обусловливающей биологическую кислотность удобрений. Наибольшее
подкисление почвы наблюдается при внесении в нее сульфата аммония. Под влиянием
почвенных бактерий карбамид в течение 2-3 суток превращается в карбонат
аммония, который постепенно нитрифицируется, т.е. превращается в нитрат.
В связи с этим карбамид тоже относится к физиологически и биологически
кислым удобрениям. Кальциевая и натриевая селитра увеличивают почвенную
щелочность и, следовательно, являются физиологически щелочными удобрениями [1].
Применение минеральных удобрений в сельском хозяйстве не только повышает
урожайность культур, но и улучшает качество сельскохозяйственной продукции. Тем
самым повышается рентабельность сельскохозяйственного производства и
сокращается потребность в рабочей силе [2].
1. Аналитический обзор литературы
.1 Сырье и методы производства аммиачной селитры
Производство аммиачной селитры состоит из нейтрализации азотной кислоты
газообразным аммиаком и кристаллизации продукта. Аммиак не должен содержать
более 1% влаги, в нем не допускается присутствие масла. Азотную кислоту берут
концентрацией более 45% HNO3; содержание окислов азота в ней не
должно превышать 0,1%. Для получения аммиачной селитры могут быть использованы
также отходы аммиачного производства - например, аммиачная вода и танковые и
продувочные газы, отводимые из хранилищ жидкого аммиака и получаемые при
продувках систем синтеза аммиака. Состав танковых газов: 45-70% NH3,
55-30% Н2+ N2 (со следами метана и аргона); состав
продувочных газов: 7,5-9% NH3, 92,5-91% Н2+ N2
(со следами метана и аргона). Кроме того, для производства аммиачной селитры
используются также газы дистилляции с производства карбамида, их примерный
состав: 55-57% NH3, 18-24% СО2, 15-20% Н2О.
Тепловой
эффект реакции NH3(г)+НNО3(ж)
NH4NO3 составляет 35,46
ккал/(г·моль). При производстве аммиачной селитры обычно применяют 45-58%-ную
кислоту. В этом случае тепловой эффект реакции нейтрализации соответственно
уменьшается на величину теплоты разбавления азотной кислоты водой и на величину
растворения аммиачной селитры.
При рациональном использовании тепла нейтрализации можно получить за счет
испарения воды концентрированные растворы и даже плав аммиачной селитры.
В соответствии с этим различают схемы с получением раствора аммиачной
селитры с последующим выпариванием его (так называемый многостадийный процесс)
и с получением плава (одностадийный или безупарочный процесс). Для выбора рациональной
схемы нейтрализации необходимо сравнить четыре принципиально различные схемы
получения аммиачной селитры с использованием тепла нейтрализации:
) установки, работающие при атмосферном давлении (избыточное давление
сокового пара 0,15-0,2 ат);
) установки с вакуум-испарителем;
) установки, работающие под давлением, с однократным использованием тепла
сокового пара;
) установки, работающие под давлением, с двукратным использованием тепла
сокового пара (получение концентрированного плава).
В промышленной практике нашли широкое применение как наиболее эффективные
установки, работающие при атмосферном давлении, с использованием тепла
нейтрализации и частично установки с вакуум-испарителем [3].
.2 Технические требования к готовой продукции
Согласно существующему в России ГОСТ 2-85, производят гранулированный
нитрат аммония двух марок: А - высшей категории качества и Б - высшей категории
качества (высший сорт) и первой категории качества (первый сорт). Показатели
качества выпускаемой промышленностью аммиачной селитры представлены в таблице
1.
Таблица 1
селитра аммиачная ГОСТ 2-85
|
Марка А
|
Марка Б
|
|
|
Высший
|
I сорт
|
II сорт
|
внешний вид
|
Гранулированный продукт без посторонних механических
примесей
|
Суммарная массовая доля нитритного и аммонийного
азота в пересчёте:
|
|
|
|
|
|
на NH4NO3 в сухом веществе, % не менее
|
98
|
не нормируется
|
на азот в сухом веществе, %, не менее
|
не норм
|
34,4
|
34,4
|
34
|
Массовая доля воды, %, не более
|
0,3
|
0,3
|
0,3
|
0,3
|
PH 10%-ного водного раствора, не менее
|
5
|
5
|
5
|
5
|
Массовая доля веществ, нерастворимых в 10%-ном
растворе азотной кислоты, %, не более
|
не нормируется
|
|
|
|
Гранулометрический состав:
|
Массовая доля гранул
|
|
|
от 1 до 3 мм, %, не менее
|
93
|
не нормируется
|
от 1 до 4 мм, %, не менее
|
не норм
|
95
|
95
|
95
|
от 2 до 4 мм, %, не менее
|
не норм
|
80
|
50.
|
не норм
|
менее 1 мм, %
|
4
|
3
|
3
|
4
|
более 6 мм, %
|
0
|
0
|
0
|
0
|
Статистическая прочность гранул н/гранулу
(кг/гранулу), не менее
|
5(0,5)
|
8(0,8)
|
7(0,7)
|
5(0,5)
|
|
|
|
|
|
Рассыпчатость, %, не менее
|
100
|
100
|
100
|
100
|
Кондиционирующая добавка
|
нитрат магния
|
Предприятия, выпускающие аммиачную селитру, должны гарантировать
потребителю, что предусмотренные ГОСТ 2-85 качественные показатели продукта
будут сохраняться в течение 6 месяцев при соблюдении потребителем условий
хранения, установленных стандартом.
.3 Применение аммиачной селитры
Аммиачная селитра относится к тому виду минеральных удобрений, без
которого практически немыслимо современное сельское хозяйство. Принадлежность к
семейству азотных удобрений, универсальность применения, возможность
промышленных объемов производства и поставок, отработанная технология
производства - вот плюсы, которые сохраняют непоколебимыми позиции селитры
аммиачной на рынке удобрений.
Азот совершенно необходим растениям. Хлорофилл, благодаря которому
используется солнечная энергия и производится строительный материал для живых
клеток, содержит азот. Внешне аммиачная селитра представляет собой гранулы
белого цвета. Гранулированное вещество хорошо растворяется в воде и содержит
34,4% азота. Ее вносят в качестве подкормки для всех видов сельскохозяйственных
культур, в условиях любых типов почв и для подготовки почвы к посеву. В
промышленности аммиачная селитра используется как сырье для производства
взрывчатых веществ и дальнейшего применения в химической, горнодобывающей и
строительной отрасли.
Существует проблема, связанная с высокой гигроскопичностью аммиачной
селитры. Гранулы теряют твердость, расползаются при повышении влажности
воздуха. Однако, современные технологические разработки позволяют учесть этот
нюанс и искоренить его еще на стадии производства.
Одним из достоинств аммиачной селитры традиционно считают то, что почва в
полном объеме поглощает аммиачную часть, благодаря быстрой растворимости
удобрения. При этом аммиачная селитра обладает более длительным действием по
сравнению с нитратной. Дробное внесение аммиачной селитры позволяет снизить
потери нитратного азота от вымывания. Успешно применяется в производстве
тукосмеси как наиболее оптимальный азотный компонент. В настоящее время на
рынке химии наблюдается стабильный рост спроса на аммиачную селитру и как на
удобрение, и как на промышленное химическое сырье. Это связано и с поддержкой,
оказываемой государством сельскохозяйственной отрасли и развитием отечественной
промышленности в целом.
2. Характеристика исходного сырья и готового продукта
.1 Характеристика исходного сырья
Исходное сырье для производства аммиачной селитры должно иметь
характеристики, представленные в таблице 2.
Таблица 2
Характеристика исходного сырья [2]
Аммиак
|
Содержание влаги, %, не более
|
1
|
Присутствие масла
|
не допускается
|
Концентрация, %
|
100
|
Начальная температура, оС
|
50
|
Плотность, кг/м3
|
0,771
|
Температура кипения при атмосферном давлении, оС
|
-33,19
|
Температура затвердевания, оС
|
-77,75
|
Средняя теплоемкость, кДж/(кг·К)
|
4,19
|
Азотная кислота
|
Концентрация, %
|
46
|
Содержание окислов азота, %, не более
|
Начальная температура, оС
|
35
|
Теплоемкость 46%-ой НNО3 при 35оС,
кДж/(кг·К)
|
3,2
|
.2 Физико-химические свойства аммиачной селитры
Нитрат аммония, или аммиачная селитра, NH4NO3,
белое кристаллическое вещество, содержащее 35% азота в аммиачной и нитратной
формах. Нитрат аммония плавится при 169,6оС, его теплота плавления
16,2 ккал/кг, теплоемкость при 20-28оС 0,422 ккал/(кг·град),
температура кипения 235оС.
При атмосферном давлении в интервале от -50оС до температуры
плавления нитрат аммония существует в пяти кристаллических формах I-V (табл.
3), различающихся структурой, удельным объемом и другими свойствами кристаллов
[5]
Таблица 3
Кристаллические формы аммиачной селитры [3]
Условные обозначения кристаллических форм
|
Системы
|
Температурные интервалы стабильного существования, оС
|
Плотность, г/см3
|
Теплота превращения, кал/г
|
I
|
Кубическая
|
169,6-125,2
|
-
|
16,75
|
II
|
Тригональная (α-ромбоэдричаская)
|
125,2-84,2
|
1,69
|
12,24
|
III
|
Моноклинная (ß-ромбоэндрическая
|
84,2-32,3
|
1,66
|
4,17
|
IV
|
Ромбическая
|
От 32,3 до -16,9
|
1,726
|
4,99
|
V
|
Тетрагональная
|
Ниже -16,9
|
1,725
|
1,6
|
Каждая модификация существует лишь в определенной области температур, и
переход (полиморфный) из одной модификации в другую сопровождается изменениями кристаллической
структуры, выделением (или поглощением) тепла, а также скачкообразным
изменением удельного объема, теплоемкости, энтропии и т.д. полиморфные переходы
являются обратимыми т.е. энантиотропными [4].
ΔН0 полиморфных переходов IV
III 1,7
кДж/моль, III
II 13 кДж/моль. В процессах перехода II
III, IV
III, IV
V объем элементарной ячейки увеличивается. Удельная
теплоемкость Ср (в кал/г·град) водных растворов нитрата аммония для
температур 16-52о составляет для концентрации 9,18% - 0,929; 28,5% -
0,7227; 47,1% - 0,697; 63,9% - 0,61; 88% - 0,47; 92% - 0,45; 96% - 0,43; 98,5%
- 0,42 [3].
Для
жидкого нитрата аммония уравнения температурной зависимости давления пара [5]:
р
(мм рт. ст.) = 10,708-4670/Т, (349-438 К),р (мм рт. ст.) = 9,987-4360/Т,
(373-513 К).
В процессе нагревания при 200-270 оС разлагается по реакции:
NH4NO3
N2О+2Н2О+36,8 кДж/моль
Выше
270оС разлагается со взрывом по реакции:
NH4NO3
N2+0,5О2+2Н2О+112,6 кДж/моль
Нитрат
аммония очень гигроскопичен. Гигроскопичность нитрата аммония и скорость
процесса поглощения им влаги из воздуха, как установлено, растут при участии
растворимых минеральных солей.
Значительная
растворимость в воде и высокий температурный коэффициент растворимости,
гигроскопичности и имеющие место полиморфные превращения являются причиной
слеживаемости нитрата аммония. Это в конечном итоге затрудняет фактическое его
применение. Нитрат аммония является концентрированным азотным удобрением. Его
применяют в производстве взрывчатых веществ - аммонитов и гранулитов, в
качестве реагента для растворения циркониевых оболочек-твэлов в процессе
регенерации облученного ядерного топлива [5].
.2.1
Слеживаемость и меры ее предотвращения
Аммиачная
селитра обладает способностью сильно слеживаться. Этому благоприятствует
сравнительно большая растворимость аммиачной селитры в воде, высокий
температурный коэффициент растворимости, гигроскопичность соли и полиморфные
превращения. При остывании горячей аммиачной селитры в таре, а также при ее
длительном хранении, когда изменяется ее температура (нагрев и охлаждение),
происходит кристаллизация аммиачной селитры из маточного раствора. Кристаллы,
выделившиеся из раствора, находящегося на поверхности частиц, связывают смежные
частицы; в результате этого селитра слеживается. Кроме того, при охлаждении
горячей соли в мешках селитра претерпевает модификационное превращение при 32,30С
с перестройкой кристаллической решетки; при этом слеживаемости способствует
давление, развиваемое весом вышележащей массы соли.
По
другим данным, полиморфное превращение NH4NO3(IV)
NH4NO3(III) ведет к разрыхлению структуры и само по себе не
может являться причиной слеживаемости аммиачной селитры [3].
Для
получения практически неслеживающейся селитры, пригодной для длительного
хранения, применяют следующие мероприятия:
1) продукт выпускают в виде однородных гранул, что уменьшает поверхность
соприкосновения с воздухом;
2) сплав селитры, поступающий на гранулирование, должен содержать
минимально возможное количество воды (0,2-0,3%);
) гранулы селитры охлаждают в аппаратах с кипящим слоем до
температуры ниже 48оС, т.е. до температуры существования IV
модификации, упаковывают, транспортируют и хранят при температурах, исключающих
переход в другую модификацию;
) в раствор аммиачной селитры вводят добавки (магнезиальную-нитрат
магния, доломитную, фосфатно-сульфатную и др.);
) поверхность гранул обрабатывается поверхностно-активными
веществами, в частности диспергатором НФ, защищающим продукт от увлажнения при соприкосновении
с воздухом, относительная влажность которого выше гигроскопической точки
селитры. В случае применения нитрата магния обработка ПАВ не требуется [2].
Влияние неорганических добавок на уменьшение слеживаемости аммиачной
селитры в основном определяется:
1) понижением содержания свободной влаги в частицах;
2) понижением гигроскопической точки соли, что ведет к уменьшению
количества испарившейся межчастичной влаги;
) ослаблением связи между кристаллами;
) изменением удельного объема маточного раствора [3].
.2.2 Термическое разложение NH4NO3, огне- и
взрывоопасность
Длительный опыт производства и применения аммиачной селитры показал, что
при соблюдении установленных правил аммиачная селитра безопасна. Чистая
аммиачная селитра не чувствительна к толчкам, ударам или трению. Однако при
определенных условиях нитрат аммония обладает взрывчатыми свойствами. На этом
основании его используют и как сырье в производстве аммиачно-селитренных
взрывчатых веществ. Они взрывают только от детонатора. Взрывы чистой аммиачной
селитры могут быть вызваны в основном или воздействием детонаторов, или
термическим разложением соли в замкнутом пространстве.
Взрывоопасность нитрата аммония возрастает в присутствии минеральных
кислот и легко окисляющихся материалов, таких как органические вещества и
некоторые металлы, особенно в порошкообразном состоянии (например, алюминий,
цинк, свинец, сурьма, висмут, никель, медь, кадмий). В большинстве случаев в
присутствии этих металлов (особенно кадмия и меди) образуется неустойчивый, легко
разлагающийся нитрит аммония.
При увеличении размера частиц и повышении влажности взрывоопасность
аммиачной селитры значительно уменьшается. Влажная соль, содержащая более 3%
воды, не взрывает даже при взрыве детонатора.
При нагревании нитрат аммония начинает разлагаться согласно уравнению:
NH4NO3
NН3+НNО3-41,7
ккал
Это
разложение становится заметным выше 150 оС, но, даже при 165 оС,
потеря в весе аммиачной селитры не превосходит 6% за сутки. При более высоких
температурах нитрат аммония разлагается интенсивно по следующим реакциям:
NH4NO3
N2О+2Н2О+8,8 ккал
При
быстром нагревании до высокой температуры:
NH4NO3
N2+0,5О2+2Н2О+28,5 ккал
(Теплоты
этих реакций даны для 18оС и для газообразного состояния продуктов
реакции). Последнее уравнение соответствует взрывному разложению NH4NO3. Термическое разложение NH4NO3 может происходить одновременно по нескольким
реакциям, причем одна из них может доминировать над другими.
Стабилизаторами,
предотвращающими самопроизвольное разложение аммиачной селитры, могут быть
вещества, связывающие образующиеся при ее разложении азотную кислоту и NО2,
или выделяющие при взаимодействии с NH4NO3
аммиак. Последний нейтрализует
азотную кислоту и восстанавливает окислы азота до элементарного азота.
Стабилизаторами являются, например, карбамид (0,05-0,1% от веса селитры),
карбонат кальция или магния (5%), хлориды, уротропин и др. [3].
селитра сырье аппаратура выпаривание
3. Теоретические основы производства NH4NO3
Наиболее распространенные способы производства аммиачной селитры основаны
на реакции нейтрализации азотной кислоты аммиаком:
NH3(г)+НNО3(ж)
NH4NO3+144,9 кДж
На
1 кг 100%-ной НNО3 теоретически расходуется 17:63 = 0,27 кг
NH3.
Химическое взаимодействие газообразного аммиака и растворов азотной кислоты
протекает с большой скоростью, но лимитируется массообменом и
гидродинамическими условиями. Поэтому большое значение имеет интенсивность
смешения реагентов, которая в основном зависит от соотношения между скоростями
движения азотной кислоты и аммиака в реакторе. Наиболее тесное соприкосновение
реагентов достигается при условии, что линейная скорость газообразного аммиака
превышает линейную скорость раствора азотной кислоты не более чем в 15 раз.
Процесс нейтрализации протекает с выделением тепла. В производственных условиях
применяется азотная кислота концентрацией 45-60% НNО3.
Известно,
что разбавление азотной кислоты протекает с выделением тепла. В производстве
аммиачной селитры используются уже готовые растворы азотной кислоты, поэтому
количество тепла, выделяющегося при нейтрализации таких растворов, уменьшается
на величину теплоты разбавления кислоты. Чем выше концентрация применяемой
азотной кислоты, тем меньше значение теплоты ее разбавления и тем больше
тепловой эффект нейтрализации растворов азотной кислоты аммиаком.
В
результате нейтрализации раствора азотной кислоты образуется не твердый нитрат
аммония, а его раствор. Поэтому нужно учитывать также теплоту растворения
нитрата аммония, которая имеет отрицательное значение, так как нитрат аммония растворяется
с поглощением тепла. Этот эффект тоже уменьшает количество тепла нейтрализации
азотной кислоты.
Таким
образом, суммарное количество тепла Q
, выделяющегося в результате реакции нейтрализации
растворов азотной кислоты газообразным аммиаком определяется из следующего
уравнения:
= Qреак
- (q1 + q2),
где
Qреак - теоретический тепловой эффект нейтрализации, равный 144,9
кДж;1 - теплота разбавления НNО3;2
- теплота разбавления NН4NО3.
Для
определения суммарного теплового эффекта в процессе нейтрализации часть воды
испаряется, и раствор концентрируется. С целью более полного выделения воды
целесообразно предварительно подогревать азотную кислоту и аммиак. При
одинаковой концентрации азотной кислоты с повышением температуры реагентов на
каждые 10 оС концентрация полученного раствора нитрата аммония
увеличивается примерно на 1%.
При
подогревании аммиака увеличивается скорость его поступления в реакционную массу
и улучшается перемешивание реагентов. Это ускоряет процесс нейтрализации и тем
самым снижает возможные потери аммиака с отходящим соковым паром.
Положительное
влияние на технологический процесс оказывает повышение (4,5-5,5 ат или 4,5·105-5,5·105
н/м2) давления в реакторе-нейтрализаторе. С увеличением общего
давления уменьшается парциальное давление паров азотной кислоты; в этих
условиях она кипит при более высокой температуре, вследствие чего снижаются
потери азотной кислоты с соковым паром. Соковый пар повышенного давления может
быть с успехом использован для последующего упаривания растворов нитрата
аммония. При увеличении давления уменьшается объем реакционного аппарата и
соответственно снижаются тепловые потери в окружающую среду. Экономическая
целесообразность применения повышенного давления зависит от дополнительного
расхода энергии на сжатие аммиака и азотной кислоты и от затрат на специальное
оборудование [1].
4. Технологическая схема производства NH4NO3 и ее
описание
Аммиачную селитру получают нейтрализацией азотной кислоты газообразным
аммиаком по реакции:
NH3(г)+НNО3(ж)
NH4NO3+144,9 кДж
Эта
практически необратимая реакция протекает с большой скоростью и с выделением
значительного количества тепла. Обычно ее ведут при давлении, близком к
атмосферному; в некоторых странах работают установки нейтрализация протекает
под давлением 0,34 МПа. В производстве аммиачной селитры используется
разбавленная 47-60%-ная азотная кислота.
Тепло
реакции нейтрализации используется на испарение воды и концентрирование
раствора.
Промышленное
производство включает следующие стадии: нейтрализацию азотной кислоты
газообразным аммиаком в аппарате ИТН (использование тепла нейтрализации);
упаривание раствора селитры, гранулирование плава селитры, охлаждение гранул,
обработка гранул ПАВ, упаковку, хранение и погрузку селитры, очистку газовых
выбросов и сточных вод. Добавки вводят при нейтрализации азотной кислоты.
На
рис.1 приведена схема современного крупнотоннажного агрегата АС-72 мощностью
1360 т/сут.
Рис.
1. Схема агрегата по производству аммиачной селитры АС-72:
-
подогреватель кислоты; 2 - подогреватель аммиака; 3 - аппараты ИТН; 4 -
донейтрализатор; 5 - выпарной аппарат; 6 - напорный бак; 7, 8 - грануляторы; 9,
23-вентиляторы; 10 - промывной скруббер; 11 - барабан; 12,14 - транспортеры; 13
- элеватор; 15-аппарат кипящего слоя; 16 - грануляционная башня; 17 - сборник;
18, 20 - насосы; 19 - бак для плава; 21-фильтр для плава; 22 - подогреватель
воздуха
Поступающая
58-60%-ная азотная кислота подогревается в подогревателе 1 до 70-80оС
соковым паром из аппарата ИТН 3 и подается на нейтрализацию. Перед аппаратами 3
в азотную кислоту добавляют термическую фосфорную и серную кислоты в количестве
0,3-0,5% Р2О5 и 0,05-0,2% сульфата аммония, считая на
готовый продукт.
Серная
и фосфорная кислоты подаются плунжерными насосами, производительность которых
легко и точно регулируется. В агрегате установлены два аппарата нейтрализации,
работающие параллельно. Сюда же подается газообразный аммиак, нагретый в
подогревателе 2 паровым конденсатом до 120-130оС. Количество
подаваемых азотной кислоты и аммиака регулируют таким образом, чтобы на выходе
из аппарата ИТН раствор имел небольшой избыток азотной кислоты, обеспечивающий
полноту поглощения аммиака.
В нижней части аппарата происходит нейтрализация
кислот при температуре 155-170°С с получением раствора, содержащего 91-92% NH4NO3. В верхней части аппарата водяные пары (так называемый
соковый пар) отмываются от брызг аммиачной селитры и паров HN03. Часть тепла сокового
пара используется на подогрев азотной кислоты. Далее соковый пар направляют на
очистку в промывные скрубберы и затем выбрасывают в атмосферу.
Кислый раствор аммиачной селитры направляют в
донейтрализатор 4, куда поступает аммиак в количестве, необходимом для донейтрализации
раствора. Затем раствор подают в выпарной аппарат 5 на доупарку, которая
ведется водяным паром под давлением 1,4 МПа и воздухом, нагретым примерно до
180°С. Полученный плав, содержащий 99,8-99,7% селитры, при 175 °С проходит
фильтр 21 и центробежным погружным насосом 20 подается в напорный бак 5, а
затем в прямоугольную металлическую грануляционную башню 16 длиной 11 м,
шириной 8 м и высотой от верха до конуса 52,8 м.
В верхней части башни расположены грануляторы 7 и 8; в
нижнюю часть башни подают воздух, охлаждающий капли селитры, которые
превращаются в гранулы. Высота падения частиц селитры 50-55м. Конструкция
грануляторов обеспечивает получение гранул однородного гранулометрического
состава с минимальным содержанием мелких гранул, что уменьшает унос воздухом
пыли из башни. Температура гранул на выходе из башни равна 90-110°С, поэтому их
направляют для охлаждения в аппарат кипящего слоя 15. Аппарат кипящего слоя -
прямоугольный аппарат, имеющий три секции и снабженный решеткой с отверстиями.
Под решетку вентиляторами подается воздух, при этом создается кипящий слой
гранул селитры высотой 100-150 мм, которые поступают по транспортеру из
грануляционной башни. Происходит интенсивное охлаждение гранул до температуры
40°С (но не выше 50°С), соответствующей условиям существования IV модификации. Если температура
охлаждающего воздуха ниже 15°С, то перед поступлением в аппарат кипящего слоя
воздух подогревают в теплообменнике до20°С. В холодный период времени в работе
могут находиться 1-2 секции.
Воздух из аппарата 15 поступает в грануляционную башню
для образования гранул и их охлаждения.
Гранулы аммиачной селитры из аппарата кипящего слоя
подают транспортером 14 на обработку поверхностно-активным веществом во
вращающийся барабан 11. Здесь гранулы опрыскивают распыленным 40%-ным водным
раствором диспергатора НФ. После этого селитра проходит электромагнитный
сепаратор для отделения случайно попавших металлических предметов и
направляется в бункер, а затем на взвешивание и упаковку в бумажные или
полиэтиленовые мешки. Мешки транспортером подают для погрузки в вагоны или на
склад.
Воздух, выходящий из верхней части грануляционной
башни, загрязнен частицами аммиачной селитры, а соковый пар из нейтрализатора и
паровоздушная смесь из выпарного аппарата содержит непрореагировавшие аммиак и
азотную кислоту и частицы унесенной аммиачной селитры. Для очистки в верхней
части грануляционной башни установлены шесть параллельно работающих промывных
скрубберов тарельчатого типа 10, орошаемых 20-30%-ным раствором аммиачной селитры,
которая подается насосом 18 из бака. Часть этого раствора отводится в
нейтрализатор ИТН для промывки сокового пара, а затем подмешивается к раствору
аммиачной селитры и, следовательно, идет на выработку продукции.
Из цикла непрерывно отводится часть раствора (20-30%),
поэтому цикл обедняется и восполняется добавкой воды. На выходе из каждого
скруббера установлен вентилятор 9 производительностью 100000 м3/ч,
который отсасывает воздух из грануляционной башни и выбрасывает его в атмосферу
[2].
5. Основная аппаратура
.1 Выпарной аппарат
Выпарной аппарат (рис. 2) - вертикальный цилиндр,
состоящий из теплообменной и очистной зон. Диаметр зон соответственно 2,8 и 3,8
м и высота 15,9 м; поверхность теплообмена 710 м2. Раствор селитры
подается внутрь трубок 3, обогреваемых водяным паром, и стекает по их
внутренней поверхности в виде пленки. При этом происходит упаривание раствора.
Далее он поступает на доупарку в тарельчатую часть аппарата 5 и выходит с
конечной концентрацией 99,8% NH4N03.
Рис. 2. Выпарной аппарат: 1 - сетчатый отбойник; 2 -
очистные тарелки; 3 - трубчатка; 4 - змеевики; 5 - провальные барботажные
тарелки
На трех верхних тарелках расположены змеевики,
обогреваемые паром. В нижнюю часть аппарата из подогревателя 22 нагнетают
горячий воздух (15-25 тыс. м3/ч) при температуре 185оС,
который проходит тарелки и трубки противотоком раствору. Происходит
доупаривание и воздух насыщается водяным паром. Полученную паровоздушную смесь
отмывают от брызг раствора в верхней части аппарата, где расположены две
тарелки 2, орошаемые конденсатом водяного пара. Аппарат изготовлен в основном
из кислотостойкой стали [2].
.2 Аппарат нейтрализации ИТН
Аппарат нейтрализации ИТН (рис. 3) представляет собой
вертикальный цилиндрический аппарат, состоящий из реакционной и сепарационной
зон диаметром соответственно 1,6 и 3,8 м и высотой 10,1 м.
Рис. 3. Аппарат ИТН: 1-реакционный стакан; 2-барботер
аммиака; 3- барботер азотной кислоты; 4-диффузор; 5-завихритель; 6-колпачковая
тарелка; 7-брызгоотбойник; 8-промыватель
В реакционной зоне имеется стакан 1 диаметром 1,2 м и
высотой 4,3 м, в нижней части которого расположены отверстия для циркуляции
раствора. Несколько выше отверстий внутри стакана размещен барботер 2, подающий
газообразный аммиак, над ним - барботер азотной кислоты 3. Реакционная
парожидкостная смесь выходит из верхней части реакционного стакана; часть
раствора выходит из аппарата ИТН и поступает в донейтрализатор, а остальная
часть (циркуляционная) - вновь идет вниз. Выделившийся из парожидкостной смеси
соковый пар отмывается на колпачковых тарелках 6 от брызг раствора аммиачной
селитры и паров азотной кислоты 20%-ным раствором селитры, а затем конденсатом
сокового пара.
Аппарат изготовлен из кислотостойкой стали, а
барботеры аммиака и азотной кислоты - из титана [2].
.3 Аппарат КС
Аппарат КС для охлаждения селитры длиной 15 м, шириной
2,4 м и высотой 7 м; состоит из трех секций. Каждая секция снабжена
индивидуальным подводом охлаждающего воздуха (70-90 тыс-м3/ч).
Производительность аппарата 60 т/ч селитры.
Рис. 4. Аппарат кипящего слоя
На рис. 4 изображен односекционный аппарат КС.
Поступающий воздух проходит воздухораспределительную решетку 8 для обеспечения
равномерного потока воздуха. Поэтому на решетке 5 создается равномерный кипящий
слой охлаждаемой селитры без застойных зон и проскока воздуха, что обеспечивает
хорошее перемешивание частиц и эффективный теплообмен. Аммиачная селитра,
подаваемая в аппарат КС ленточным транспортером, поступает на грохот 2,
вмонтированный в аппарат КС.
Крупные куски селитры отбирают и отводят на
растворение и возвращаются в производственный цикл. Гранулы, прошедшие грохот,
поступают на вход в первую секцию аппарата; образующийся здесь кипящий слой
имеет высоту 100-150 мм. Гранулы в кипящем слое движутся также в горизонтальном
направлении со скоростью до 0,1 м/с.
Каждая секция аппарата имеет индивидуальные течки для
выгрузки селитры, поэтому она может охлаждаться в одной, двух или в трех
секциях. Три секции аппарата работают в летнее время при повышенной температуре
воздуха [2].
6. Выпаривание растворов аммиачной селитры
6.1 Технологическое оформление узла выпаривания
Непременным условием улучшения качества аммиачной селитры является
обеспечение высокой степени упаривания ее растворов в выпарных аппаратах
последней ступени с достижением остаточного содержания влаги в готовом продукте
не более 0,3% (определяется методом сушки согласно ГОСТ 2-75).
До недавнего времени основным типом выпарной аппаратуры в производстве
аммиачной селитры являлись вертикальные и горизонтальные конструкции (выпарки
АС) с рабочими элементами в виде труб, по которым упариваемый раствор и
образовавшийся из него вторичный пар двигаются прямотоком в виде парожидкостной
смеси. Последняя, как правило, на большей части длины труб имеет кольцевую
структуру: сплошная жидкая пленка на стенках (восходящая пленка), а в центре
паровой «стержень», несущий большое количество брызг.
Такая организация процесса позволяет достичь высоких коэффициентов
теплоотдачи от обогреваемой поверхности к кипящему раствору. Однако при столь
интенсивном процессе кипения происходит значительное выравнивание концентраций
вдоль потока за счет переноса по его оси больших масс раствора с повышенным
содержанием легколетучего компонента в ядре потока в виде брызг. Это
обстоятельство проявляется тем сильнее, чем выше концентрация конечного плава и
чем больше разность концентраций раствора на входе в рабочие трубы и на выходе
из них. В результате в таких аппаратах не приходится при интенсивной нагрузке
рассчитывать на получение плавов концентрацией 99,3-99,5% NH4N03. Для столь высокой степени отделения растворов
селитры от воды необходимо обеспечить более организованное протекание массообмена
при упаривании, потребовавшее разработки принципиально отличных конструкций.
Достаточно четко такой процесс удается провести в падающей пленке, что и было
принято за основу при разработке в ГИАПе, доупарочного аппарата (рис. 5) и
выпарного аппарата типа «труба в трубе».
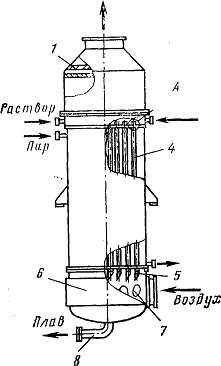
Рис. 5. Доупарочный аппарат с падающей пленкой:
- жалюзийный сепаратор; 2 - кольцевые перегородки; 3 - зубчатый колпачок;
4 - рабочие трубы- 5 -хвостовик; 6- кольцевая распределительная камера; 7 -
отверстие для ввода воздуха; 8 - штуцер для вывода упаренного раствора (плава).
Сущность процесса в аппарате, изображенном на рис. 5 состоит в следующем:
доупариваемый раствор подается на верхний срез вертикально расположенных
рабочих труб 4. В межтрубное пространство аппарата поступает
теплоноситель - греющий пар давлением примерно 1,1 МПа (11 кгс/см2).
Массообмен - отвод паров из раствора обеспечивается подачей воздуха снизу
внутрь рабочих труб, по стенкам которых стекает навстречу ему упариваемая
пленка. Поток воздуха предварительно нагревается до температуры около 180°С с
тем, чтобы при контакте воздуха с плавом не оказывалось охлаждающее воздействие
на пленку плава.
Так как при обычных температурах атмосферного воздуха парциальное
давление паров воды в нем составляет всего 2,7-5,4 кПа (20-40 мм рт. ст.), то
оказывается возможной работа под общим давлением на стороне испарения, равным
атмосферному, поскольку создается значительная движущая сила для массообмена и обеспечивается
большой удельный вынос влаги.
Упомянутый выше аппарат типа «труба в трубе» был рассчитан не как
дополнительный, а для замены существующих аппаратов второй ступени выпаривания.
В нем сочетается выпаривание в восходящей пленке - на первых стадиях процесса
(от 82 до 98°/, NH4N03), где требуется
повышенная интенсивность теплообмена, лимитирующего упаривание основных
количеств воды, с выпаркой и падающей пленке - на последних стадиях процесса,
где необходимо удаление малых количеств воды (от 2 до 0,5%), а удельный вес
массообмена резко возрастает.
Промышленный образец такого аппарата производительностью 30-35 т/ч
длительно эксплуатировался в действующем цехе. Ведение процесса в аппарате
требует поддержания стабильно низкого остаточного давления над упариваемым
раствором - порядка13,3 кПа (100 мм рт. ст.), что вызвало необходимость
установки дополнительного вакуумного оборудования. Поскольку эксплуатация
агрегата оказалась при этом более сложной, чем в случае работы низконапорных
вентиляторов, подающих воздух в доупарочный аппарат (рис. 5), то аппарат типа
«труба в трубе» не был рекомендован для широкого внедрения в производство
аммиачной селитры.
Дальнейшее снижение влажности плава не может быть осуществлено на
аппаратах трубчатой конструкции (рис. 5) без уменьшения их производительности.
При удалении следов влаги. движущая сила процесса - разность парциальных
давлений воды над стекающим раствором и во встречном потоке воздуха -
уменьшается и для завершения процесса необходимо значительное увеличение массообменной
поверхности, но при этом требуется весьма малое количество тепла. Такой процесс
может быть обеспечен при создании в нижней части доупарочного аппарата
массообменного устройства, например в виде одной или нескольких барботажных
тарелок [5].
Рис. 6. Комбинированный выпарной аппарат:
I -
очистная часть; II - трубчатая
часть; III - концентрационная часть; 1 -
сетчатый отбойник; 2 - штуцер для ввода конденсата; 3 - очистные переточные
тарелки; 4, 5 - змеевики; 6 - провальные барботажные тарелки.
Раствор аммиачной селитры концентрацией не ниже 87% по обогреваемому
коллектору поступает в выпарной аппарат 1. Стекая по трубкам, раствор
упаривается, попадает в нижнюю тарельчатую часть и проходит последовательно
несколько концентрационных тарелок провального типа, при этом его концентрация
повышается до 99,7-99,8% NH4N03.
В нижнюю часть аппарата вентилятором непрерывно подается атмосферный
воздух, нагретый в подогревателе 3 до 185°С теплом, выделяющимся при
конденсации насыщенного пара давлением до 1,4 МПа (14 кгс/см2).
Воздух, проходя вверх по тарелкам и трубкам, вступает в контакт с раствором,
отводит влагу, а затем поступает под очистные тарелки переточного типа.
На
верхнюю очистную тарелку подается паровой конденсат, а с нижней отводится
раствор аммиачной селитры (
20% NH4NO3). Паровоздушная смесь, проходя последовательно две
тарелки, охлаждается, промывается и через выхлопную трубу выбрасывается в
атмосферу. В схеме предусмотрена возможность подачи исходного раствора
аммиачной селитры (для предварительного упаривания) на нижнюю очистную тарелку,
где расположены змеевики, после чего он направляется в трубчатую часть
аппарата.
Для подвода тепла и испарения влаги из раствора селитры в межтрубное
пространство аппарата и в змеевики нa тарелках подается пар давлением до 1,4 МПа. Обогрев днища выпарного
аппарата, буферного бака и паровых рубашек на линиях плава аммиачной селитры
осуществляется паром давлением 0,8 МПа.
Следует отметить, что условия проведения конечной стадии процесса
упаривания плава ограничены узким температурным диапазоном. С одной стороны,
это температура 163- 170°С, соответствующая кристаллизации расплавов селитры
концентрацией 99,3 - 100%, с другой - температура 180-190 °С, установленная из
соображений безопасного ведения процесса, поскольку нагревание аммиачной
селитры до более высоких температур приводит к ее повышенному термическому
разложению.
ъ
Рис. 7. Схема установки комбинированного выпaрного аппарата:
- комбинированный выпарной аппарат; 2 - вентиляторы; 3 -
воздухоподогреватель; 4 - буферный бак; 5 - разбрызгиватель плава.
Кроме того, необходимо учитывать, что степень разложения аммиачной
селитры значительно возрастает при нагревании в присутствии кислот, хлоридов и
некоторых органических веществ (например, масла). Изложенные обстоятельства
требуют точного ведения технологического режима в пределах заданных значений
температуры плава, а также соблюдения некоторых других регламентных показателей
его работы (кислотность плава, содержание масла и хлоридов, поступающих в цех с
аммиаком, газами дистилляции кислотой).
Внедрение выпарного аппарата (рис. 6) позволяет модернизировать
существующее в действующих цехах производства аммиачной селитры выпарное
отделение путем ликвидации вакуумной ступени выпаривания (предшествующей
доупариванию) или перевода ее в режим работы под атмосферным давлением [6]. В
случае сохранения ступени выпаривания под вакуумом, число концентрационных
тарелок может быть уменьшено до двух (благодаря повышенной концентрации
исходного раствора) и отпадает необходимость в установке на них змеевиков. При
этом окончательное упаривание плава в массообменной части осуществляется за
счет его теплосодержания, что приводит к небольшому (примерно на 4°С)
охлаждению раствора. При использовании в такой схеме доупарочного аппарата с
пятью тарелками работа всего отделения может быть интенсифицирована на 30-50%.
В производстве аммиачной селитры по схемам АС-67 и АС-72 доупаривание
раствора осуществляется в одном аппарате с пятитарельчатой массообменной
частью, куда исходные щелока концентрацией 90-92% поступают из аппарата ИТН.
7. Расчет
В качестве греющего пара используется соковый пар с давлением 0,14 МПа из
аппарата ИТН. Количество этого пара составляет 350 кг на 1 т раствора аммиачной
селитры. В первую ступень поступает 1,4 т раствора NH4NO3 с концентрацией 68% и температурой
1150С. Выпаривание ведется под давлением 0,025 МПа.
Во вторую ступень выпаривания поступает 1,2 т раствора с концентрацией
85% NH4NO3 при 1050С. Греющим агентом служит насыщенный
водяной пар с давлением 0,1 МПа. Давление в аппарате 0,03 МПа. Конечная
концентрация получаемого плава 98,8%.
Рис. 8. Схема двухступенчатой выпарки раствора аммиачной селитры:
- выпарной аппарат первой ступени; 2 - сепаратор; 3 - сборник; 4 - насос;
5 - напорный бак; 6 - выпарной аппарат второй ступени.
.1 Материальный баланс
Для составления материального баланса первой ступени выпарки
дополнительно к заданным необходимо вычислить количество выпариваемой воды.
При давлении пара, поступающего из аппарата ИТН, равном 140 кПа (1,4
кгс/м2), теплота конденсации сокового пара 2244 кДж/кг.
Следовательно, количество тепла, отдаваемого соковым паром:
кДж
785,4 МДж
(Допускаем,
что конденсат, удаляющийся от греющих камер выпарного аппарата, имеет температуру
сокового пара).
Соковый
пар, выходящий из выпарных аппаратов первой ступени при давлении 25,0 кПа (0,25
кгс/м2), имеет энтальпию 2617 кДж/кг. Поэтому количество испаренной
в первой ступени воды равно:
/2617
= 300,11 кг
300 кг
Это
соответствует количеству воды, которое необходимо удалить из раствора, для
упаривания его до концентрации 85 % NH4NO3. Действительно, количество раствора после упарки
равно:
-
300 = 1100 кг
Следовательно,
концентрация NH4NO3 равна:
%
Разница
в 0,5% концентрации раствора между исходным и вычисленным значениями лежит в
пределах точности технических расчетов.
Составляем
материальный баланс первой ступени выпарки аммиачной селитры:
Таблица 1
Материальный баланс первой ступени выпарки аммиачной селитры
Приход, кг
|
Расход, кг
|
%-ный раствор NH4NO3…………1400
|
%-ный раствор NH4NO3………...1100
|
в том числе 100 %-ный раствор NH4NO3…….1000 Н2О………………………………....400
|
в том числе 100 %-ный раствор NH4NO3……1000 Н2О………………………………...100
соковый пар……………………….300
|
Всего……………………………....1400
|
Всего……………………………..1400
|
.2 Тепловой баланс
С раствором аммиачной селитры поступает:
кДж
370,78 МДж
где
2,303 - теплоемкость %-ного раствора NH4NO3, кДж/(кг
К).
Приход
теплоты с соковым паром, поступающим из аппарата ИТН:
кДж
785,4 МДж
Расход
теплоты с упаренным раствором аммиачной селитры составляет:
где
1,989 - теплоемкость 85%-ного раствора NH4NO3, кДж/(кг
К).
Температура
кипения раствора, содержащего 85% NH4NO3 при давлении 25,0 кПа (0,25 кгс/м2):
,
где
- температура насыщенного водяного пара при 25,0 кПа
(0,25 кгс/м2), равная 60 0С;
-
температурная депрессия; она определяется как разность между температурой
кипения 85%-ного раствора (0С) и воды при 98,07 кПа (1 кгс/м2)
и равна:
,5
- 100 = 46,5 0С
-
коэффициент температурной депрессии, равной 0,763 при 60 0С.
Следовательно:
0С
кДж
208,92МДж
Расход
теплоты с соковым паром, уходящим из первой ступени выпарки:
кДж
785,4МДж
где
2617 - энтальпия насыщенного водяного пара при 25,0 кПа (0,25 кгс/м2),
кДж/кг.
Теплопотери
в первой ступени выпарки определяем по разности между приходом и расходом:
кДж
161,8 МДж
По
отношению к приходу тепла это оставляет:
%
что
соответствует произведенным данным.
Тепловой баланс первой ступени выпарки раствора аммиачной селитры
Приход, Дж
|
Расход, МДж
|
с раствором %-ной NH4NO3…..370,78
|
с упаренным раствором %-ной NH4NO3…………………………..208,92
|
с соковым паром из ИТН……..785,40
|
с соковым паром из первой
ступени..........................................785,38
теплопотери………………………161,8
|
Всего…………………………1156,18
|
Всего……………………………1156,18
|
8. Техника безопасности
Особенностью в производстве аммиачной селитры является возможность ее
разложения. Чтобы это исключить, необходимо контролировать перегрев раствора
или плава выше максимально допустимой температуры, т.е. 190оС. Для
этого предусмотрены блокировки, автоматически перекрывающие подачу пара на
обогрев трубчатой части выпарного аппарата или подогрев воздуха. Емкость
резервуара плава должна быть минимальной. Конструкция выпарного аппарата должна
исключать возможность застоя в нем плава, так как при увеличении времени пребывания
плава снижается температура его разложения.
Плав селитры должен быть слегка щелочным, так как в кислой среде
температура его разложения снижается. Недопустимо загрязнение раствора и плава,
поскольку примеси снижают температуру разложения раствора или плава. Особую
важностью является точность дозировки фосфорной и серной кислот при
нейтрализации, из-за опасности разложения раствора.
При хранении аммиачной селитры не допускается загрязнение ее примесями,
бумагой и др. Необходимо удерживать установленные нормы, регламентирующие
максимально допустимое количество аммиачной селитры, хранимое в одном отсеке
заводского склада [2].
Выводы
В данном курсовом проекте были рассмотрены основы технологии
производства, а также применение широко распространенного азотного удобрения -
аммиачной селитры. Особое внимание уделено сырью и методам производства
аммиачной селитры, техническим требованиям к готовой продукции.
Представлена характеристика исходного сырья и готового продукта,
приведены физико-химические свойства аммиачной селитры, особенно важными из
которых являются слеживаемость и меры ее предотвращения, а также термическое
разложение NH4NO3, огне- и взрывоопасность.
Подробно рассмотрены теоретические основы производства и различные схемы
получения аммиачной селитры с использованием тепла нейтрализации, из которых
выбрана и описана наиболее эффективная технологическая схема крупнотоннажного
агрегата АС-72, а также рассмотрена основная температура технологического
процесса. Целью курсового проекта был расчет материального и теплового балансов
процесса выпаривания раствора аммиачной селитры.
Также изложены данные о контроле и автоматизации технологического
процесса, технико-экономические показатели и техника безопасности в
производстве аммиачной селитры.
Список используемой литературы
1. Павлов
К.Ф., Романков П.Г. Примеры и задачи по курсу процессов и аппаратов химической
технологии.- М.: ООО ТИД «Альянс», 2005.-576 с.
. Основные
процессы и аппараты химической технологии: Пособие по проектированию / Под ред.
Ю.И. Дытнерского. - М.: Химия, 2008.
. Мельников
Е.А. и др. Технология неорганических веществ и минеральных удобрений. - М.:
Химия, 1983. - 432 с.
. Соколовский
А.А., Яшке Е.В. Технология минеральных удобрений и кислот. - М.: Химия, 1971. -
456 с.
5. Позин М.Е.
и др. Технология минеральных солей (удобрений, пестицидов, промышленных солей,
окислов и кислот), ч.1, изд. 4-е, испр. Л., Изд-во «Химия», 1974. - 768с.
6. Касаткин
А.Г. Основные процессы и аппараты химической технологии. - М.: ООО ТИД
«Альянс», 2005.
. Кафаров
В.В. Основы массопередачи.- М.: Высшая школа, 1972.- 494 с.
. Процессы и
аппараты химической технологии / Под ред. Захаровой А.А. - М.: Издательский
центр «Академия», 2006.- 528 с.
. Лыков М.В.
Сушка в химической промышленности. - М.: Химия, 1970.
. Справочник
азотчика. Кн. 2. - М.: Химия, 1987. - 404 с.