Реконструкция технологии обработки медных концентратов на Надеждинском металлургическом заводе (НМЗ)
Оглавление
ВВЕДЕНИЕ
. ТЕХНОЛОГИЧЕСКАЯ ЧАСТЬ
.1 Общая характеристика
автогенных процессов
.2 Обоснование выбранной
технологии
.3 Структура
пирометаллургического процесса
.4 Сущность плавки
сульфидного сырья во взвешенном состоянии
.5 Физико-химические основы
процесса
.6 Теплообмен в рабочем
пространстве печи
.7 Конструкция печи
.8 Подготовка и сушка
концентратов
.9 Процесс плавки
концентратов
.10 Утилизация тепла
отходящих газов в котлах-утилизаторах
.11 Общая характеристика печи
во взвешенном состоянии на подогретом дутье как объекта управления
.12 Общие условия обжига
сульфидных материалов
.13 Технологический расчёт
автогенной плавки во взвешенном состоянии
.13.1 Вещественный состав
концентрата
.13.2 Состав и количество
пыли; безвозвратные потери при плавке
.13.3 Состав и количество
штейна, шлака и флюса
.13.4 Количество дутья и
технологических газов
.13.5 Исходные данные для
технологического расчёта взвешенной плавки
.14 Методика расчёта
теплового баланса автогенной плавки во взвешенном состоянии на подогретом дутье
.14.1 Теплота реакций
процесса
.14.2 Энтальпия материалов и
продуктов плавки
.14.3 Расчёт теплового
баланса печи взвешенной плавки на подогретом дутье
.15 Выбор размеров печи
. АВТОМАТИЗАЦИЯ
.1 Печь взвешенной плавки как
объект управления
.2 Структура АСУ ТП ПВП
.3 Цели создания АСУТП
.4 Функции АСУТП
.5Аппаратурный синтез
.5.1 Технические
характеристики системы
.5.2 Выбор контроллерной
аппаратуры, подбор персональных компьютеров и настройка сетевого подключения
.5.3 Контрольно-измерительные
приборы
.6 Программное обеспечение
АСУТП
. СПЕЦИАЛЬНАЯ ЧАСТЬ
. ОХРАНА ОКРУЖАЮЩЕЙ СРЕДЫ
.1 Характеристика предприятия
как источника нарушения и загрязнения природной среды
.1.1 Район расположения и
природные климатические условия
.2 Охрана атмосферного
воздуха
.2.1 Санитарно-защитная зона
.2.2 Источники, загрязняющие
вещества, выбрасываемые в атмосферный воздух
.3 Охрана подземных и
поверхностных вод
.4 Охрана земельных ресурсов
. БЕЗОПАСНОСТЬ
ЖИЗНЕДЕЯТЕЛЬНОСТИ
.1 Безопасность в условиях
производства
.1.1 Анализ вредных и опасных
факторов производства
.1.2 Анализ травматизма
.1.3 Техника безопасности
.1.4 Промсанитария
.1.5. Противопожарная
безопасность
.2 Безопасность
жизнедеятельности в условиях чрезвычайных ситуаций (ЧС)
.2.1 Анализ потенциально
возможных ЧС
.2.2 План предупреждения и
ликвидации ЧС
. ЭЛЕКТРОТЕХНИЧЕСКАЯ ЧАСТЬ
.1 Электроснабжение участка
цеха
.2 Характеристики
потребителей
.3 Расчётная нагрузка
потребителей
.4 Выбор трансформатора
.5 Потери напряжения в сети
.6 Выбор коммутационной
аппаратуры
.ЭКОНОМИЧЕСКАЯ ЧАСТЬ
.1 Общая характеристика
плавильного отделения
.1 Калькуляция себестоимости
продукции
.2 Расчёт экономической
эффективности
ЗАКЛЮЧЕНИЕ
БИБЛИОГРАФИЧЕСКИЙ СПИСОК
ВВЕДЕНИЕ
Металлургия меди, а также других тяжелых цветных металлов является
ведущим звеном отечественной цветной металлургии. На долю тяжелых цветных
металлов в РФ приходится значительная часть валовой продукции отрасли.
Значение меди из года в год возрастает, особенно в связи с бурным
развитием энергетики, электроники, машиностроения, авиационной, космической и
атомной техники. Дальнейшее развитие и технический уровень медного производства
во многом определяют технический прогресс многих отраслей народного хозяйства
нашей страны, в том числе микропроцессорной техники.
Повышение требований к защите окружающей среды привело к значительному
удорожанию строительства и эксплуатации предприятий цветной металлургии. Это в
свою очередь вызвало активное совершенствование существующих процессов
производства металлов и разработку новых, более интенсивных процессов,
обеспечивающих охрану окружающей среды, комплексное использование всех
компонентов и теплотворной способности сырья, снижение капитальных и
эксплуатационных расходов, позволяющих широко использовать автоматические
системы управления технологическими процессами (АСУТП).
Разработка и внедрение взвешенной плавки для переработки сульфидных
концентратов имеет большую историю. Впервые этот процесс в печи, состоящей из
шахты и отражательной камеры для проведения обжига и плавки, был предложен в
1908 г. в России Броуном. Исследовательские работы по взвешенной плавке на
воздушном дутье были проведены в нашей стране в 1928-1929 гг. под руководством
проф. В.А. Ванюкова в Московском институте цветных металлов и золота и на
Московском электролитном заводе. Испытания процесса затем были продолжены в
1932-1933 гг. на московском опытном и Карабахшском медеплавильных заводах.
Крупные полупромышленные испытания были проведены в 1932 г. на заводе
«Анаконда» (США) и в 1935 г. - в г. Дегтярке под руководством инженера Г.Я.
Лейзеровича.
Наиболее интенсивно процесс взвешенной плавки медных концентратов начал
разрабатываться в послевоенные годы в Финляндии и Канаде, испытывавших
серьезные затруднения в угле и электроэнергии. Финские металлурги после
длительных испытаний процесса взвешенной плавки на горячем дутье на
полупромышленной установке в г. Поти внедрили в 1949 г. эту технологию на
заводе «Харьявалта». С момента пуска первых печей взвешенной плавки медных
концентратов прошло уже около 50 лет. За этот период финский процесс получил
наиболее широкое распространение.
В настоящее время в мире имеется около 20 печей взвешенной плавки на
горячем воздушном дутье, которые перерабатывают не только медные, но и
никелевые, и полиметаллические концентраты. Значительному совершенствованию
подвергнуты печи, горелки, котлы-утилизаторы и воздухоподогреватели, стало
использоваться воздушно-кислородное дутье, много сделано по совершенствованию
процесса и конструкции печей японскими металлургами, применившими оригинальные решения
по шихтоподготовке, глубокой сушке, воздухонагреву, повышению стойкости
огнеупоров.
Наиболее широкое распространение среди новых интенсивных автогенных
процессов получили плавки во взвешенном состоянии, разработанной фирмой
«Оутокумпу» (Финляндия) для сульфидного медного сырья.
Основными преимуществами взвешенной плавки по сравнению с отражательной
плавкой являются:
· высокая производительность;
· возможность получения богатых штейнов;
· возможность получения богатых по SO2 (10-15%)
газов, обеспечение высокой степени извлечения серы из отходящих газов и
сокращение выбросов сернистого газа в атмосферу (включая газы конвертирования,
которые смешивают с богатыми газами взвешенной плавки);
· низкий суммарный расход энергии в результате использования
тепла экзотермических реакций при плавке сульфидной шихты и высокой степени
утилизации тепла отходящих газов для выработки энергии, возвращаемой в процесс
(примерно 80 % тепла отходящих газов полезно используется с помощью
котла-утилизатора, применяемого фирмой «Оутокумпу»);
· высокая степень механизации и автоматизации.
При плавке во взвешенном состоянии на подогретом дутье успешно решены
вопросы тепловой энергетики и использования серы в газах.
Процесс взвешенной плавки позволяет существенно снизить энергозатраты по
сравнению с традиционными (отражательной плавкой и электроплавкой). Это
преимущество процесса «Оутокумпу» является следствием не столько принципиальных
особенностей самой взвешенной плавки, сколько результатом успехов фирмы в
решении вопросов конструктивного оформления всего плавильного комплекса и, в
первую очередь, котла-утилизатора.
В замыкании энергетического баланса важную роль играет содержание
кислорода в дутье. Если температура в газовом пространстве печи не превышает
определённого уровня, определяемого стойкостью огнеупоров, и избыточная теплота
отнимается охлаждаемыми элементами, то и температура отходящих из печи газов
при различном содержании кислорода будет оставаться практически постоянной.
Данный проект разрабатывается для реконструкции существующей технологии
обработки медных концентратов на Надеждинском Металлургическом Заводе (НМЗ)
входящего в состав заполярного филиала горной металлургической компании
«Норильский Никель».
1. ТЕХНОЛОГИЧЕСКАЯ ЧАСТЬ
Наиболее широкое распространение среди новых интенсивных автогенных
процессов получили плавки во взвешенном состоянии, разработанной фирмой
«Оутокумпу» (Финляндия) для сульфидного медного сырья.
Плавка во взвешенном состоянии на подогретом дутье была осуществлена в
промышленном масштабе финской фирмы «Оутокумпу» на заводе «Харьявалта». В
первоначальном варианте для плавки применяли воздушное дутьё, подогретое до 400
- 5000С. Начиная с конца 60-х годов, этот процесс по лицензии фирмы
«Оутокумпу» стали широко применять на металлургических заводах многих стран. В
настоящее время он внедрён более чем на 30 предприятиях для переработки медных,
никелевых и пиритных концентратов. Финскую плавку на сегодня можно считать
самым распространённым в промышленности и наиболее технологически и аппаратурно
отработанным автогенным процессом плавки сульфидных концентратов.
С момента возникновения плавка во взвешенном состоянии на подогретом
дутье претерпела существенные изменения, особенно в дутьевом режиме.
Температура нагрева дутья колеблется от 200 до 1000 0С.
1.1 Общая характеристика автогенных процессов
Принцип автогенности уже в течение более 100 лет широко используют при
окислительном обжиге сульфидных руд и концентратов и конвертировании штейнов.
Широкое внедрение процессов обогащения привело к получению более богатых,
но мелких материалов, не пригодных для шахтной плавки. Это вызвало к жизни
сначала отражательную плавку, а затем и электроплавку.
Однако в обоих случаях широко распространенных в современной
металлургической практике процессах плавка сульфидного концентрата ведётся за
счёт поступающих извне источников энергии. Однако в связи с ростом стоимости
энергетических ресурсов, проблема эффективного использования теплоты от
сжигания сульфидов становится более актуальной.
В основе любого автогенного способа плавки сульфидных медных концентратов
лежат экзотермические реакции окисления сульфидов шихты и в первую очередь
сульфидов железа:
2FeS + 3O2 + 2SiO2 = Fe2SiO4
+ 2SO2 + 1030290 кДж (1)
FeS + 3O2 = 2FeO + 2SO2 + 937340 кДж (2)
2FeO + 2SiO2 = Fe2SiO4 + 92110
кДж (3)
Таким образом, автогенная плавка по своей сущности является окислительным
процессом. При её осуществлении степень десульфуризации можно регулировать в
любых заданных пределах, изменяя соотношение между количествами
перерабатываемого материала и дутья.
Тепловая
работа печей автогенных плавок характеризуется тем, что температура отходящих
газов превышает температуру плавления шлаков, составляя не менее 1200 - 1250
. Высокая температура отходящих газов обуславливает
большие потери с ними теплоты. Если в пиритном процессе даже при использовании
холодного воздушного дутья теплоты от сжигания сульфидов практически достаточно
для ведения процесса плавки, то при автогенной плавке флотационных концентратов
обнаруживается значительный её дефицит. Недостаток теплоты может быть восполнен
как увеличением статей прихода, так и уменьшением статей расхода в тепловом
балансе плавки. Дополнительная теплота для процесса может быть получена за счёт
предварительного подогрева дутья.
Необходимая
температура подогрева дутья определяется количеством сульфидов, которое может
быть окислено по условиям технологии. Как правило, достаточно нагревать
воздушное дутьё до 500 - 600
. При
этом следует иметь в виду, что подогрев дутья может и должен быть осуществлён
за счёт теплоты отходящих газов самой плавки.
На
основе автогенных процессов могут быть созданы технологические схемы,
обеспечивающие минимальные энергетические затраты, высокую комплексность
использования сырья и предотвращающие загрязнение воздушного и водного
бассейнов.
Применительно
к флотационным концентратам автогенные металлургические процессы могут быть
организованы по-разному как технологически, так и аппаратурно. С
технологической точки зрения эти процессы в первую очередь различаются методом
сжигания сульфидов. Мелкие сульфидные концентраты можно сжигать как в
распыленном состоянии в газовой фазе (в факеле), так и в расплавах.
Плавками
во взвешенном состоянии называют процессы, при осуществлении которых мелкие
сульфидные концентраты сжигают в факеле, образующемся при горении сульфидов
шихты, подаваемой в раскаленное пространство печи через специальные горелки
вместе с дутьём. За счёт теплоты, выделяющейся при горении сульфидов,
распыленная шихта нагревается и плавится. Образовавшиеся капли падают на
поверхность шлакового расплава, находящегося в отстойной камере, где происходит
разделение штейна и шлака.
При
осуществлении автогенной плавки в расплаве шихтовые материалы тем или иным
способом вводятся вначале в ванну уже имеющегося сульфидно-оксидного расплава,
плавятся и растворяются в нём, а затем сульфиды, находясь в жидком состоянии,
окисляются подаваемым в расплав дутьём.
Первоначально
казалось, что использование при плавке во взвешенном состоянии сильно развитой
поверхности мелких концентратов, позволяющее осуществлять процесс окисления
распыленных сульфидов с очень большими скоростями, является достаточным
преимуществом, чтобы считать это направление наиболее перспективным. Однако
этого условия оказалось недостаточно для создания высокопроизводительного
метода плавки, так как производительность агрегатов в конечном итоге
определяется не скоростью окисления сульфидов, а другими, более медленными
стадиями в сложном комплексе процессов, протекающих при плавке.
Идея
использования автогенного процесса для плавки флотационных концентратов на
штейн возникла и была впервые почти одновременно опробована в CCCР
и в США на заводе «Анаконда», получив в дальнейшем широкое распространение во
всем мире. В настоящее время можно назвать не менее двух десятков освоенных
промышленностью, внедряемых и предлагаемых автогенных процессов.
Первые
исследования плавки сульфидных концентратов при сжигании их во взвешенном
состоянии были начаты в начале 30-х годов прошлого столетия. Одним из
направлений этих исследований предусматривалось сжигание сухих концентратов при
вдувании их в газовое пространство печи по образцу сжигания угольной пыли в
отражательных печах. Работы выполнялись Рыковым и другими под руководством
доктора технических наук В.А. Ванюкова. Предложенный ими вариант автогенной
плавки получил название «газ-процесс».
Г.Я.
Лейзерович позднее предложил сжигать и плавить сульфидные концентраты в вертикальной
шахте с последующим разделением продуктов плавки в горизонтальной части печи.
Опытный образец комбинированной печи некоторое время работал на одном из
опытных металлургических заводов Урала. Результаты исследований, к сожалению,
не доведенных до конца, в дальнейшем были использованы как отечественными, так
и зарубежными фирмами, в том числе фирмой «Оутокумпу» (Финляндия), для создания
современного процесса плавки во взвешенном состоянии.
1.2 Обоснование выбранной технологии
В настоящее время, наиболее важным из направлений развития
металлургического производства является внедрение ресурсосберегающих технологий
и оборудования, а также их дальнейшее развитие и усовершенствование. С
внедрением в промышленное производство микропроцессорной техники настал новый
период современного развития металлургии. Как показывает опыт развития
металлургического производства, в течение последних нескольких десятилетий
технология переработки медного и никелевого сырья во всем мире совершенствуется
на основе разработки и освоения автогенных процессов.
Под автогенным понимается пирометаллургический процесс, в котором
необходимый для технологии уровень температур обеспечивается только за счет
теплоты, вносимой исходными материалами, и теплоты от экзотермических реакций
самого процесса. Автогенный процесс, таким образом, проходит без затрат
углеродистого топлива или электроэнергии непосредственно в рабочем пространстве
агрегата. Практически в производстве металлов единственной группой реакций,
которые могут дать достаточный экзотермический эффект для автогенности
процесса, являются реакции окисления компонентов исходного сырья кислородом.
Поэтому все автогенные пиропроцессы являются окислительными, для их
осуществления требуется подача газообразного кислорода, т.е. кислородосодержащего
дутья.
В настоящее время автогенная плавка в производстве меди и никеля получила
широкое распространение и на сегодняшний день является одним из наиболее
перспективных процессов переработки сульфидного сырья.
Современный металлургический процесс должен обеспечивать:
высокую степень комплексности использования перерабатываемого сырья;
высокую удельную производительность металлургических аппаратов;
минимальные энергетические затраты;
высокую степень комплексной автоматизации;
максимально безопасные и безвредные условия труда;
минимальный выброс в атмосферу вредных газов;
наибольшую экономическую эффективность.
Высокая степень комплексности использования сырья является основным и
едва ли не самым важным требованием к современной технологии, причем она должна
пониматься в самом широком смысле.
Понятие комплексности использования перерабатываемого сырья включает в
себя максимально высокое извлечение всех ценных составляющих (медь, никель,
цинк, кобальт, сера, железо, благородные металлы, редкие и рассеянные
элементы), использование силикатной составляющей руды.
Перерабатываемые сульфидные руды и концентраты обладают достаточно
высокой теплотворной способностью и являются не только источником ценных
компонентов, но и технологическим топливом, следовательно, в понятие
комплексного использования сырья включает в себя использование его внутренних
энергетических возможностей.
Сульфиды по своей теплотворной способности незначительно уступают таким
видам топлива, как торф, углистые сланцы, дрова. А если сопоставить количество
добываемых в год сульфидных руд, с количеством тепловой энергии, которая может
быть получена при их сжигании, то можно получить цифру порядка нескольких
миллионов единиц условного топлива.
Конечным итогом увеличения комплексности использования сырьевых
материалов должно привести к созданию так называемых безотходных технологий,
высшей ступени развития промышленности.
Важным элементом дальнейшего повышения комплексности использования сырья
является также использование вторичных энергоресурсов, создающихся при
осуществлении главным образом пирометаллургических процессов - физической
теплоты отходящих газов, расплавленных шлаков и других нагретых до высоких
температур продуктов и полупродуктов.
С повышением комплексности использования перерабатываемого сырья
неразрывно связано решение проблемы устранения вредных выбросов в окружающую
среду (таких как, накопление всякого рода отвалов (шлаки, хвосты и др.),
выбросы SO2 и других вредных газов, пыли и возгонов, сброса
технологических вод фабрик и заводов).
Важную роль в совершенствовании технологии получения цветных металлов
играет удельная производительность металлургического оборудования. Перспективно
создание непрерывных поточных линий (ряд последовательно установленных
агрегатов, работающих в едином непрерывном потоке), тогда степень их
автоматизации будет обеспечивать наибольшую удельную производительность
металлургического производства.
При выборе технологических и аппаратурных решений возможность создания
непрерывных поточных линий должна являться важным критерием их оценки. На
основе автогенных процессов могут быть созданы технологические схемы,
обеспечивающие минимальные энергетические затраты, высокую комплексность
использования сырья и предотвращающие загрязнение воздушного и водного бассейнов.
Анализ тенденций развития взвешенной плавки с подогретым дутьем и
кислородно-взвешенной плавки показывают, что различия между этими процессами
постепенно сглаживаются. В кислородно-взвешенном процессе исследуется
возможность перехода на вертикальный факел горения. В плавке с подогретым
дутьем начато использование обогащения дутья кислородом. Таким образом, отличия
сохраняются лишь в содержании кислорода, степени нагрева дутья и аппаратурном
оформлении. При повышении содержания кислорода в дутье увеличивается содержание
в газах SO2 и в принципе могут быть снижены затраты на их
переработку. Однако при этом снижается коэффициент использования теплоты и
возрастают затраты на получение кислорода. Выбор оптимального содержания
кислорода в дутье должны окончательно решать экономические расчёты для условий
конкретного предприятия. Что касается аппаратурного оформления, то и здесь в
конечном итоге должны быть найдены близкие оптимальные решения.
Принципиальное единство технологических основ двух разновидностей плавки
во взвешенном состоянии порождает общность их достоинств и недостатков.
Основными достоинствами процесса являются использование тепла сжигания
сульфидов и высокое извлечение серы в газы, богатые по содержанию SO2. Главнейшие недостатки процесса: низкая удельная
производительность, высокое содержание ценных компонентов в шлаках
необходимость глубокой сушки исходной шихты и связанный с этим большой
пылеунос.
Основные технико-экономические показатели взвешенной плавки с
использованием подогретого дутья приведены в таблице 1.1.
Таблица 1.1
Основные технико-экономические показатели работы ряда заводов,
использующих взвешенную плавку с подогретым дутьем
Показатель
|
«Харьявалта» (Финляндия)
|
«Саганосеки» (Япония)
|
«Тамано» (Япония)
|
Производительность печи, т/сут
|
900
|
3330
|
1280
|
Удельный проплав, т/м2*сут
|
11,9
|
10,9
|
9,3
|
Содержание О2 в дутье, %
|
35-40
|
22,1
|
Воздух
|
Температура дутья, 0С
|
200
|
900-1000
|
450
|
Содержание меди, % в штейне в шлаке (после обеднения)
|
60 0,85
|
60 0,52
|
50 0,56
|
Содержание SO2 в газах,
%
|
18-20
|
10,3
|
8-10
|
Пылеунос
|
8-10
|
8-10
|
8-10
|
Метод обеднения шлака
|
Флотация
|
Флотация
|
В электрообогреваемом отстойнике
|
Таким образом, наиболее экономически выгодным путем развития
металлургического производства является реконструкция действующих предприятий
при максимальном использовании уже имеющегося вспомогательного хозяйства,
существующих фундаментов, зданий, сооружений, в частности складов, отделений
подготовки и транспортировки шихты, газоходного хозяйства, транспорта продуктов
плавки и т. д. В этом случае переход на новую технологию будет связан только с
заменой старой аппаратуры на новую и установкой, при необходимости, некоторой
дополнительной вспомогательной аппаратуры. Если при этом удельная
производительность новой технологии и аппаратов будет существенно выше старой,
то на тех же производственных площадях мощность завода может быть значительно
увеличена при минимальных капитальных затратах.
1.3 Структура пирометаллургического процесса
Любой пирометаллургический процесс характеризуется
одновременным или последовательным протеканием многочисленных физико-химических
превращений - элементарных стадий. При плавке сульфидных руд и концентратов,
каким бы методом она не проводилась, важнейшими элементарными стадиями
являются:
1) нагрев шихты;
2) диссоциация неустойчивых химических
соединений;
) окисление сульфидов;
) расплавление легкоплавких составляющих шихты
с образованием первичных расплавов;
) растворение наиболее тугоплавких компонентов
в первичных расплавах;
) разделение продуктов плавки.
Скорость и полнота протекания этих процессов зависят
от физико-химических свойств компонентов шихты, температуры, интенсивности
массо- и теплообмена, а производительность агрегатов в целом определяется
скоростью завершения наиболее медленной из элементарных стадий.
Считаем необходимым рассмотреть важнейшие стадии
процесса плавки и их кинетические закономерности.
Нагрев шихты практически полностью лимитируется процессами теплопередачи.
Условиями теплопередачи и размерами кусков определяется также в значительной
степени начало термического разложения неустойчивых химических соединений.
В настоящее время, когда на плавку поступают преимущественно флотационные
концентраты с малыми размерами частиц (70 мкм и меньше), можно легко достичь
очень высоких скоростей их нагрева, если будут созданы благоприятные условия
для интенсивного массо- и теплообмена. Одним из приемов, обеспечивающих высокие
скорости нагрева, является распыление шихты в нагретом до высокие температуры
газовом пространстве при высокой степени турбулентности потока. В этом случае
мелкая шихта нагревается за считанные доли секунды. Исключительно быстро
протекает нагрев шихты также при загрузке ее в расплав. В автогенных процессах,
где источником теплоты служат реакции окисления сульфидов концентрата, теплота
выделяется непосредственно на поверхности частиц или в ванне расплава, т. е.
там, где она расходуется на процессы плавления. Поэтому нагрев мелких частиц
шихты в условиях интенсивного массообмена осуществляется быстро и не лимитирует
производительности плавильных агрегатов.
Окисление сульфидов. Окисление сульфидов кислородом является
экзотермическим процессом и протекает на границе раздела фаз.
Многочисленные исследования кинетики реакций окисления сульфидов
показали, что скорость их протекания зависит от многих факторов: температуры,
природы фаз, их физико-химических свойств и агрегатного состояния, крупности
сульфидных частиц, размеров поверхности контакта реагентов и т. п.
С момента воспламенения окисление (горение) сульфидов идет очень
интенсивно и ускоряется с ростом температуры. Однако скорость гетерогенных
процессов, протекающих на границе раздела фаз (твердой, жидкой и газообразной),
не может неограниченно расти с температурой, так как начинает зависеть от
процессов массообмена. Это обусловлено тем, что суммарная скорость в данном
случае будет определяться соотношением скоростей собственно химической реакции
и подвода реагентов к реакционной поверхности.
Таким образом, для обеспечения высоких скоростей окисления необходимы
большая реакционная поверхность и интенсивный массообмен.
Плавление шихты и формирование расплавов. Конечная цель любого вида
плавки - перевод всей перерабатываемой шихты в расплавленное состояние с
получением штейна и шлака с их последующим разделением.
Значительные различия в физико-химических свойствах соединений, в первую
очередь в их температурах плавления, приводят при нагревании шихты только к
постепенному формированию расплава конечного состава. Сначала идёт образование
первичного расплава из наиболее легкоплавких компонентов с последующим
растворением в них более тугоплавких веществ. Следовательно, процессы штейно- и
шлакообразования включают в себя две элементарные стадии: расплавление
легкоплавких составляющих шихты и растворение в первичных расплавах более
тугоплавких веществ.
Из числа присутствующих в сульфидных шихтах химических соединений
наиболее легкоплавкими являются сульфиды. При этом природные сульфидные
эвтектики по сравнению с отдельными сульфидами имеют еще меньшие температуры
плавления. Поэтому процессы штейнообразования начинаются раньше, чем процессы
шлакообразования, и идут с большими скоростями.
Шлакообразование начинается позднее из-за более высоких температур
плавления не только свободных оксидов, но и оксидных эвтектик. Образование
первичных шлаковых расплавов - процесс достаточно быстрый и скорость его
практически совпадает со скоростью нагрева шихты до температуры плавления
легкоплавких компонентов. При ограниченных температурах в плавильных агрегатах
особо важное значение приобретают процессы растворения тугоплавких оксидов в
первичных шлаковых расплавах.
Процессы растворения являются значительно более медленными по сравнению с
прямым расплавлением легкоплавких компонентов и лимитируются малой скоростью
диффузии.
В реальных условиях растворение твердой фазы в жидком растворителе (при
плавке растворителем является первичный расплав) проходит в три этапа: диффузия
растворителя к поверхности твердой фазы, химическое взаимодействие реагентов с
образованием растворимого соединения и его диффузия в массу раствора. Поэтому конечная
скорость шлакообразования существенным образом зависит от гидродинамических
условий, то есть от интенсивности массообмена между компонентами твердой шихты
и жидкими продуктами плавки, устраняющей диффузионные сопротивления.
Образование шлаков в металлургических печах начинается, как правило, с
получения железо-силикатных эвтектик фаялитового состава или более сложных
многокомпонентных легкоплавких композиций на основе силиката оксида железа. В
дальнейшем в них растворяются более тугоплавкие оксиды и в первую очередь
кремнезём, содержащийся в рудном сырье или вводимый в шихту в качестве
кварцевого флюса.
Возможность значительного ускорения процесса растворения тугоплавких
составляющих в первичных расплавах путем интенсивного их перемешивания не вызывает
никаких сомнений. Так, автогенные плавки, осуществляемые в барботируемых
расплавах, отличаются очень высокими скоростями формирования шлаков. В
существующих процессах, в частности при отражательной плавке и плавках во
взвешенном состоянии, скорость растворения флюсов может быть увеличена только
путем очень тонкого их измельчения и перемешивания расплава в зонах
отстаивания.
Таким образом, скорость растворения тугоплавких составляющих (скорость
формирования конечного шлака) в отдельных случаях, когда перемешивание
расплавов в плавильных печах отсутствует или происходит очень медленно, может
существенно влиять на скорость плавки в целом.
Скорость и полнота разделения фаз. Медь находится в шлаке частично в
растворённом состоянии и частично в виде мелких взвешенных частиц штейна.
Решающее влияние на её содержание в шлаке оказывает степень его окисленности,
т. е. содержание в нем трехвалентного железа.
Следовательно, полнота перевода меди в штейн в
значительной степени определяется полнотой восстановления магнетита при его
взаимодействии с сульфидами. В ряде случаев целесообразно даже восстанавливать
магнетит углеродистыми восстановителями. Процесс восстановления магнетита
сульфидами протекает относительно медленно и, хотя он и не определяет общей
производительности печи, влияние магнетита на содержание растворенной меди и
разделение фаз необходимо учитывать при создании современной технологии и
принимать все возможные меры для обеспечения максимально полного его
восстановления. Для обеспечения достаточной скорости восстановления магнетита
прежде всего необходимо вести процесс при повышенной температуре (не менее
1300-1350 °С) и энергичном перемешивании расплава газами для снятия
диффузионных сопротивлений и снижения парциального давления SО2.
Нужно также обеспечить необходимое время контакта шлака с сульфидами. Очевидно,
что эти требования наиболее полно реализуются при осуществлении процесса
плавления в барботируемых расплавах.
Значительная часть меди находится в шлаках в виде
мелкой штейновой эмульсии. Кроме того, при восстановлении или сульфидировании
металлов в шлаковом расплаве обычно выпадает дополнительное количество очень
мелкой взвеси металлсодержащей фазы, отстаивание которой происходит крайне
медленно и не успевает завершиться за приемлемое с практической точки зрения
время. Поэтому одновременно с восстановлением шлака необходимо обеспечить
укрупнение штейновых или металлических частиц.
Можно однозначно утверждать, что именно медленное протекание процессов
укрупнения мелкой штейновой (металлической) взвеси и ее отделение от шлака
являются одними из самых медленных этапов, лимитирующих скорость процесса
плавки в целом. Из этого вытекает важный практический вывод - необходимо
изыскивать такие методы ведения плавки, которые обеспечивали бы быстрое
протекание процесса коалесценции штейновой взвеси. Наиболее эффективным приемом
ускорения этого процесса является перемешивание шлака с получающимся в самом
процессе плавки штейном. Известно, что даже загрузка сульфидов на поверхность
шлаковой ванны и однократная промывка шлака каплями штейна приводят к заметному
обеднению шлака. Если же перемешивание шлака вести с большим количеством штейна
(при малом его расходе), то это позволит многократно повторять промывку и
практически полностью собрать мелкую взвесь штейна или металла в донную фазу.
При этом важно, чтобы извлекающая фаза имела высокие плотность, поверхностное
натяжение и растворяющую способность по отношению к меди. Чем больше будет
межфазное натяжение, тем крупнее будут образующиеся при перемешивании капли металлсодержащей
фазы, что в сочетании с той ее плотностью обеспечит быстрое разделение фаз при
последующем отстаивании.
Сочетание процессов восстановления и перемешивания
шлака со штейном позволяет резко интенсифицировать процесс укрупнения штейновых
частиц и разделение фаз. Доказано, что крупность частиц при этом возрастает
настолько, что для разделения штейна и шлака вместо 10-15 ч требуется менее
одного часа.
Правильная организация процесса разделения фаз создает
предпосылки для резкой интенсификации работы плавильных агрегатов и повышения
их удельной производительности.
1.4 Сущность плавки сульфидного сырья во взвешенном состоянии
Печь взвешенной плавки применяется при автогенной
плавки медного концентрата на штейн.
Пылевидные частицы медного концентрата вместе с
оборотной пылью печи взвешенной плавки вдуваются подогретым дутьём через четыре
шихтовые горелки, расположенные в центре свода реакционной шахты, в печь. В
горелках происходит перемешивание шихты с дутьем.
Шихтовоздушная смесь из горелок поступает в раскалённое подсводовое
пространство плавильной шахты, где сульфиды воспламеняются, пока шихта
находится во взвешенном состоянии. За время падения сульфиды успевают в должной
степени окислиться, а легкоплавкие сульфиды и железистые силикаты расплавиться.
На поверхность шлаковой ванны, находящейся в отстойной камере печи, из
вертикальной шахты падают капли расплава раскаленные частицы тугоплавких
компонентов. В этих условиях процессы формирования шлака и штейна продолжаются
и заканчиваются в ванне печи.
Продукты плавки: штейн и шлак выпускаются из печи периодически и
поступают на конвертирование и обеднение соответственно.
1.5 Физико-химические основы процесса
Процесс окисления сульфидов меди в реакционной шахте печи происходит в
переходном режиме: то есть когда на скорость процесса влияют одновременно
диффузия и кристаллохимическое превращение сопровождается воспламенением
частиц, которое длится доли секунды. При этом скорость реакции достигает своего
максимального значения и здесь возможно кратковременное протекание процесса в
кинетическом режиме.
В
области более высоких температур, характерных для реакционной зоны плавильной
шахты печи (температура 1500-1550
С),
процесс окисления сульфидных частиц с большей вероятностью протекает в
диффузионном режиме. По мере развития химической реакции на поверхности
сульфидной частицы образуется твердый слой продуктов окисления. Транспорт
кислорода к реакционной зоне в этом случае затрудняется, и процесс переходит в
область, лимитируемую внутренней диффузией. Для этого режима характерно
отсутствие зависимости скорости окисления от интенсивности движения газа. Кроме
того, диффузионное сопротивление возрастает со временем по мере увеличения
толщины оксидной пленки.
Процесс
окисления сульфидных частиц после их расплавления состоит из следующих основных
стадий:
1. Окисление серы на поверхности сульфидного расплава адсорбированным
кислородом газовой фазы;
2. Окисление двухвалентного железа на поверхности капли адсорбированным
кислородом;
3. Окисление серы трехвалентным железом в объеме жидкой фазы.
1.6 Теплообмен в рабочем пространстве печи
Основу теплового баланса процесса плавки в печи взвешенной плавки
составляет теплота экзотермических реакций окисления сульфидов. На кинетические
закономерности, как отдельных этапов, так и в целом процесса окисления
существенное влияние оказывает теплопередача. Количество теплоты, выделяемой на
поверхности, определяется макроскопической скоростью реакции, а количество теплоты,
отводимой от поверхности, условиями теплопередачи.
Достигнув определенной температуры, при которой тепло, выделяемое при
окислении, достаточно для протекания автогенного процесса, сульфидная частица
воспламеняется. В результате интенсивного окисления на поверхности сульфидной
частицы температура может быть более 1500 °С при температуре газового потока
1300-1350°С.
Температура воспламенения и удельная поверхность сульфидов находятся в
одинаковой гиперболической зависимости от среднего размера частиц. Удельная
поверхность при уменьшении размере зерен возрастает, а температура
воспламенения снижается.
Помимо реакций окисления, по мере прогрева твердой частицы начинают
протекать реакции диссоциации высших сульфидов. Интенсивно процесс начинается
при температуре 550°С и заканчивается при температуре 850°С. Наиболее низкую
температуру диссоциации имеет пирит (550°С), наиболее высокую борнит (850°С).
Особенностью диссоциации является то, что процесс сопровождается
значительным поглощением теплоты, протекает как на поверхности, так и внутри
зерна сульфида. Таким образом, при окислении и диссоциации на одной и той же
частице протекало два конкурирующих процесса: окисление с выделением теплоты,
диссоциация с ее поглощением. Результирующая величина может быть определена из
теплового эффекта реакций и скорости их протекания.
В результате процессов окисления и диссоциации, теплоты выделяется
значительно больше, чем поглощается.
Особенностью высокотемпературного взаимодействия кислорода с сульфидными
расплавами является то, что их окисление осуществляется как за счет кислорода
газовой фазы, так и кислорода оксидов железа.
В условиях процесса плавки во взвешенном состоянии доставка окислителя из
объема газовой фазы к поверхности частицы может осуществляться с помощью конвективной
диффузии за счет наличия скорости потока и вследствие молекулярной диффузии.
Общее уравнение массопередачи в данном случае имеет вид:
,
где
первый член уравнения
учитывает законы молекулярной диффузии,
второй
член
учитывает законы конвективного массообмена,
-
скорость перемещения газа относительно твердого тела.
При
плавке в печах взвешенной плавки скорости движения сульфидных частиц шихты и
окислителя (газа) сравнимы друг с другом, поэтому
стремится к нулю и соответственно конвективной
составляющей уравнения можно пренебречь.
В
данном случае процесс окисления можно рассматривать с позиции диффузионной
кинетики микрогетерогенных реакций, т.е. реакций, протекающих на поверхности
дисперсных частиц, взвешенных в другой фазе. Конвективная диффузия в
микрогетерогенных системах практически не оказывает влияния на скорость
реакции, так как частицы перемещаются вместе с потоком. Однако общая скорость
массопереноса в таких системах достаточно высока из-за того, что диффундирующие
реагенты имеют незначительные размеры. Таким образом, если пренебречь влиянием
конвекции на диффузию кислорода к поверхности сульфидной частицы, а, также
допуская, что она имеет форму сферы диаметром d, коэффициент массоотдачи
может быть определен по формуле:
,
где
Nu - критерий Нуссельта, характеризующий массоперенос.
С
учетом того, что для сферических частиц, взвешенных в неограниченной покоящейся
среде, Nu = 2, данное выражение приобретает вид:
Когда
кинетика реакции окисления на поверхности первого порядка, то для каждой
отдельной частицы зависимость эффективной константы скорости
, отнесенной к единице поверхности дисперсной частицы,
можно перейти к эффективной константе скорости
,
отнесенной к единице объема газовой фазы:
где
F - средняя поверхность дисперсной частицы;- число частиц, диспергированных в
единице объема газа.
Зная
, N, F и гранулометрический состав концентрата, а
также концентрацию окислителя на поверхности, от которой происходит диффузия,
можно оценить скорость процесса на единицу объема газовой фазы. При слабом
развитии конвекции массоперенос кислорода к реакционной поверхности происходит
за счет молекулярной диффузии, в основе которой лежит градиент концентрации.
В
соответствии с представлениями о механизме массопереноса реагента из объема
фазы к реакционной поверхности различают две области: ядро (основной объем газа)
и пограничный слой у поверхности раздела фаз. Перенос компонентов в основном
объеме при интенсивном перемешивании в основном происходит вследствие
конвективной диффузии; роль молекулярной диффузии в этом случае не столь
велика. По мере приближения к поверхности раздела фаз конвективные потоки
затухают, и возрастает значение молекулярной диффузии. В непосредственной
близости от границы раздела фаз существует пограничный слой, через который
массоперенос осуществляется только молекулярной диффузией.
Природа
пограничного диффузионного слоя сложна и его возникновение обусловлено наличием
вязкости потока и силами притяжения между молекулами твердого компонента и
окружающей среды. Толщина слоя зависит от вязкости газа, характера поверхности,
условий перемешивания и размера частицы. Чем меньше размер частицы, тем больше
толщина слоя. Для частиц диаметром не более 0,5 мм этот параметр составляет
10-20 радиусов частицы.
Для
условий взвешенной плавки, где основное количество частиц флотационного
концентрата имеет размеры менее 0,07 мм, толщина слоя может составлять
0,35-0,70 мм.
Проникновение
молекул газа через диффузионный пограничный слой осуществляется молекулярной
диффузией.
Скорость
молекулярной диффузии зависит от коэффициента диффузии, толщины диффузионного
слоя, поверхности частицы и разности концентраций.
Использование
подогретого дутья позволяет повысить количество окислителя, поступающего к
реакционной поверхности. Соответственно, снижается продолжительность этапа
молекулярной диффузии. Это приводит к увеличению общей скорости окисления,
лимитируемой диффузией.
Высокое
содержание дисперсных частиц в дутье (до 4 кг/м3) приводит к тому,
что толщина газовой прослойки между ними составляет 0,5-1,0 мм, т.е. становится
соизмеримой с толщиной диффузионного слоя. При низкой относительной скорости
газового потока, обтекающего реакционную поверхность взвешенной частицы,
толщина слоя сохраняется. Это дает возможность сосредоточения в нем основного
сопротивления массопереносу и появления диффузионных затруднений со стороны
газовой фазы.
Удаление
диоксида серы в объем газового потока происходит со скоростью:
Поскольку
концентрация SО2 в зоне реакции выше, чем в турбулентной области
газового потока, то движущей силой диффузии газообразных продуктов здесь
является разность их концентраций у поверхности раздела фаз
и в объеме газа
.
При
протекании процесса окисления сульфидного концентрата во внешне диффузионной
области оперативное удаление SО2 от поверхности твердой частицы
приводит к увеличению общей скорости взаимодействия.
1.7 Конструкция печи
Конструкция печи для плавки во взвешенном состоянии на подогретом дутье
достаточно сложна - она сочетает в себе две вертикальные шахты (плавильную и
газоход-аптейк) и горизонтальную камеру-отстойник (рис. 1.1.).
Рис. 1.1. Печь взвешенной плавки на штейн с
вертикальным расположением технологического факела: 1 - реакционная шахта; 2 -
отстойник; 3 - вертикальный газоход (сепарационная камера)
Тонкоизмельченная шихта, предварительно высушенная до
содержания влаги менее 0,2%, подается в бункер шихты. Из бункера шихта двумя
скребковыми транспортерами "Редлер" подается через свод реакционной
камеры с помощью четырех специальных горелок (рис. 1.2). Основное назначение
горелки - приготовление и подготовка шихтововоздушной смеси для ускорения
процесса горения сульфидов. Перемешивание шихты с дутьем достигается
разбиванием струи шихты о конус-рассекатель и подачей дутья через воздушный
патрубок и распределительную решетку.
Рис. 1.2. Схема горелки печи для плавки во взвешенном
состоянии
- дутьё; 2 - шихтовая воронка; 3 - загрузочный
патрубок; 4 - воздушный патрубок; 5 - конус-рассекатель; 6 - распределительная
решётка; 7 - диффузор.
Вся печь финской плавки выполнена в виде кладки из магнезитового кирпича.
Футеровка плавильной шахты и аптейка заключена в металлические кожухи из
листовой стали. В кладку всех элементов печи заложено большое количество
водоохлаждаемых элементов, что позволяет значительно удлинить срок службы агрегата.
Аптейк непосредственно сочленён с котлом-утилизатором туннельного типа. В
боковой стенке отстойной камеры установлены две медные водоохлаждаемые плиты с
отверстиями для выпуска шлака, а в передней торцевой стене - чугунные шпуры для
выпуска штейна.
Основным элементом печи является плавильная шахта, представляющая собой
цилиндрическую камеру с внутренним диаметром 3-8 м, высотой 7-12 м и толщиной
стен 250-380 мм. Реакционная камера выложена из хромомагнезитового кирпича и
заключена в металлический кожух из листовой стали. Чтобы исключить смещение
кладки, кожух жестко скреплен с футеровкой и установленными в ней медными
водоохлаждаемыми кессонами, которые расположены на стыке шахты со сводом
отстойника. Шахта может иметь арочный или распорно-подвесной свод, выложенный
из термостойкого кирпича. Свод обычно двухслойным. Второй слой состоит из
легковесного шамота толщиной 75-150 мм. Общая, толщина свода 525 мм. Сверху
кладка закрывается стальным листом, что улучшает герметичность свода и
исключает возможность попадания пыли на его поверхность. В своде имеются 4
отверстия для установки шихтовых горелок. Кроме того, в центре свода
расположено отверстие для установки горелки, предназначенной для сжигания
традиционных видов топлива, и ряд отверстий по периферии для подачи в печь
конвертерной пыли.
Отстойная зона печи имеет площадь пода от 40 до 300 м2. В
конструктивном отношении отстойник аналогичен анодным печам стационарного типа.
Внутреннюю футеровку печи отстойника выполняют из хромитопериклазового кирпича.
Для наружной кладки применяют шамот. Между шамотной и хромитопериклазовой
кладкой по всему периметру печи на уровне ванны установлены медные
водоохлаждаемые кессоны. Общая толщина кладки на уровне расплава составляет
около 800 мм. Над ванной толщину стен ступенчато уменьшают до 450-600 мм, В
торцевой и боковых стенках печи предусмотрено несколько (9-11) шпуровых
отверстий для выпуска продуктов плавки. Штейн выпускают в головной части печи,
шлак - со стороны вертикального газохода. Выпускные отверстия обычно расположены
на разных уровнях; высота шлаковых шпуров над подом составляет 500-600 мм,
штейновых шпуров-25, 100 и 250 мм. В кладке стен предусмотрено 18-20 отверстий
для установки горелок природного газа и наблюдения за ходом технологического
процесса, расположенных на расстоянии около 4 м от основания подины.
Под печи сооружают из хромитопериклазового термостойкого кирпича в виде
многослойной обратной арки. Для его теплоизоляции используют легковесный шамот.
Свод отстойной камеры имеет арочную или, распорно-подвесную конструкцию.
Его кладку ведут в два слоя: нижний слой состоит из хромитопериклазового
кирпича, верхний - из легковесного шамота или другого теплоизоляционного
материала. В кладке свода размещены 8 отверстий диаметром 300 мм для загрузки
чугунного скрапа и 4 контрольных отверстия диаметром 120 мм для проведения
замеров уровня расплава в ванне печи. Отстойник имеет сварной металлический
кожух и снаружи заключен в подвижный металлический каркас стоечного типа.
Вертикальная сепарационная камера значительно выше
плавильной и имеет прямоугольную форму. Ее длина составляет 9 м, ширина 7 м и
высота 17 м. К торцевой стенке камеры примыкает газоход для отвода продуктов
сгорания топлива и технологических газов, имеющий в поперечном сечении форму
прямоугольника шириной 7 и высотой 6 м. В кладке стен размещены также 2
контрольных люка для осмотра футеровки и несколько (8-10) отверстий для
установки фурм, через которые подают газ для восстановления сернистого
ангидрида.
Сверху сепарационная камера ограничена распорно-подвесным
сводом, который выкладывают из хромитопериклазового кирпича, образующего
огнеупорную футеровку толщиной порядка 300 мм. Для утепления свода футеровку
покрывают слоем теплоизоляции из легковесного шамота. В центре кладки размещено
отверстие для аварийного отвода газов, при нормальной работе печи закрытое
крышкой из огнеупорных материалов.
Процесс окисления сульфидов шихты проходит с большим
выделением тепла. Поэтому части печи, температура в которых достигает наивысших
значений, кессонируют закладными кессонами.
Для кессонного охлаждения применяют химически чистую
воду. Несмотря на предпринимаемые меры и кессонное охлаждение огнеупорной
кладки печи, она довольно быстро изнашивается. Как показала практика, в течение
первых 6-8 месяцев работы: происходит разгар футеровки шахты до достаточной
толщины 50-70 мм. В газовом объеме отстойной части печи толщина футеровки в
течение 1,0-1,5 лет становится равной0-100 мм с полным выкрашиванием в связи с
потерей связки. Кессоны этой части печи работают в гарнисажном режиме.
Наиболее перспективным для агрегатов автогенной плавки
являются охлаждаемые элементы, полученные из высокотеплопроводного материала, с
увеличенной толщиной стенки со стороны расплава. Достаточная толщина стенок и
высокая теплопроводность медного проката предотвращают или значительно снижают
возможные последствия кратковременных отклонений от стационарных тепловых
условий - локальных тепловых ударов, обеспечивая быстрое растекание тепла по
всей массе кессона.
Расположение и число кессонов на агрегате должны
отвечать некоторому оптимуму, поскольку чем чаще поставлены кессоны в
футеровке, тем больше кладка выдержит воздействие со стороны рабочего
пространства печи и тем значительнее теплопотери с охлаждением, что
неблагоприятно действует на тепловой баланс и технико-экономические показатели
плавки. Удачно выбранные расстояния между кессонами и режимы охлаждения на
финских печах взвешенной плавки продлевают кампанию до 3-4 лет без остановки на
капитальный ремонт. Однако после выработки футеровки до определенной толщины
износ ее значительно замедляется, так как образуется гарниссаж (пропитка
остаточной толщины расплавом), который продолжает исполнять роль футеровки.
В большинстве случаев механические усилия в футеровке
возникают вследствие изменения теплового режима печи, включая режим сушки и
разогрев воды в огнеупорах. В инерционный период разогрева печи, когда тепловой
импульс еще не достиг противоположной стороны стенки, внутренняя (прогретая)
часть огнеупорной кладки испытывает температурную деформацию, а со стороны
непрогретой части кладки -реактивное противодействие этой деформации. Величина
теплового импульса, определяющего температурную деформацию, размер прогретых
зон кладки, термомеханические свойства материалов футеровки, при определенных
ситуациях способствуют разрушению кладки.
Вследствие этого сушка и разогрев материалов должны
осуществляться согласно расчётному графику. Критическая скорость разогрева
огнеупорных образцов, превышение которых образует сколы:
для магнезитовых огнеупоров - 3 град/мин,
для хромомагнезитовых - 8 град/мин.
С целью продления межремонтной кампании разработана
методика защиты внутренних поверхностей печи и составы защитных покрытий.
Определены оптимальные режимы, при которых происходит образование гарниссажа.
Принятые меры позволили продлить работу печи от одного капитального ремонта до
другого.
Разработан торкрет-аппарат со смачиванием огнеупорной
массы на выходе из сопла. Его основные характеристики:
давление воздуха 0,58-0,6 МПа;
объем камеры сухой массы 0,2 м3
давление жидкости в сопле 0,28-0,32 МПа.
Огнеупорный слой толщиной 50-70 мм наносят в ячейки
кожуха печи путем подачи торкрет-массы через специально предусмотренные
ремонтные люки в горизонтальном направлении с расстояния 8-9 м.
Решающее влияние оказывает правильно подобранный
состав торкрет-массы, обеспечивающий хорошую прилипаемость к кожуху при большом
расстоянии торкретирования, удовлетворительную стойкость при определенной
толщине слоя, обеспечивающего защиту металлических полок.
Положительные результаты были получены при
использовании торкрет-массы на шве хромомагнезита. Жидкая масса состоит из
жидкого стекла и воды.
Наибольшая толщина при торкретировании за один раз
получена при следующих условиях:
. отношение основных составляющих: мертель - хромомагнезитовый
порошок - кремнефтористый натрий =1:15:0,003.
. жидкость для смачивания: жидкое стекло: вода =1:3.
. плотность массы 2,50 г/см3 . При данных
плотности и толщине слоя в 58-65 мм получается максимальной коэффициент
прилипания 85%. Содержание в слое крупных частиц45% (2-3 мм), средних 20%
(2-0,5 мм) и мелких 35% (< 0,5 мм).
Исследования поведения торкрет-слоя показали, что в
зонах с максимальной температурой (шахта) торкрет-слой в течение первых часов
работы скалывается на 0,25-0,3 толщины от резкого термического напряжения при
нагреве, затем во вторую, третью декаду работы происходит его покрытие
гарнисажем (10 мм); далее слой, уложенный в ячейке, не разрушается. На кожухах
с меньшими тепловыми нагрузками торкет-слой деформируется в меньшей степени,
скалывается 0,2 части толщины, далее идет замещение на настыль (гарнисаж),
затем стабилизируется и не разрушается.
1.8 Подготовка и сушка концентратов
Качественная подготовка исходного сырья оказывает решающее влияние на
конечные технико-экономические показатели металлургического производства.
В металлургическую переработку, как правило, поступает не один
металлосодержащий материал, а смесь разных сортов рудного сырья с флюсами с
оборотами.
Общие требования качеству металлургических шихт:
постоянство химического состава;
- однородность по химическому, минералогическому и
гранулометрическому составу;
оптимальная крупность компонентов шихты;
оптимальная влажность.
Основой перерабатываемых в печи взвешенной плавки с подогретым дутьём
шихтовых материалов являются сульфидные флотационные концентраты.
При этом концентрат, вдуваемый в реакционную зону печи вместе с
технологическим воздухом, должен быть абсолютно сухим.
Влажность исходных сульфидных концентратов может изменяться от 7-8 до
27-28%. Традиционные схемы обезвоживания концентратов с малой влагоемкостью
включают сгущение, фильтрацию на дисковых фильтрах и сушку в барабанных
сушилках с противотоком концентрата и сушильного газа. Такое технологическое
решение приемлемо для хорошо фильтрующихся крупнозернистых концентратов, не
содержащих мелкой фракции и глинистых частиц.
Для сушки мелкодисперсных влагоемких концентратов используются
распылительные сушилки, принцип действия которых заключается в диспергировании
пульпы концентрата в потоке нагретого осушающего агента (отходящие газы
металлургических печей, подогретых воздух, горячие продукты сгорания топлива).
Пульпу концентрата в распылённом состоянии специальным устройством подают в
рабочее пространство сушилки.
1.9 Процесс плавки концентратов
Высушенную шихту (концентрат в смеси с измельченным кварцевым флюсом) до
влажности 0,1 % подают в бункер, расположенный над печью, из которого
дозирующими устройствами направляют в горелки, установленные в своде шахты.
Основное назначение горелок - приготовление и подготовка шихтовоздушной смеси
для ускорения процесса горения сульфидов.
Горелки работают по принципу эжектора шихты, которая
увлекается подогретым дутьём, поступающим в горелку со скоростью 80 - 130 м/с.
Степень нагрева дутья зависит от характера выплавляемого материала, теплового
баланса процесса и колеблется от 200 0С до 1000 0С.
Перемешивание шихты с дутьём достигается разбиванием струи шихты
конус-рассекатель и подачей дутья через воздушный патрубок и распределительную
решётку.
Обогащение дутья кислородом интенсифицирует процесс плавки и позволяет
получать более концентрированные по SO2 отходящие газы. Это может быть наиболее целесообразным при получении из
этих газов элементарной серы.
Плавка во взвешенном состоянии позволяет в широких пределах варьировать
степень десульфатизации, которая может достигать в отдельных случаях 85-90%. На
заводе «Харьявалта» при плавке медного концентрата степень десульфуризации
составляет около 77%. В связи с этим штейны взвешенной плавки более богаты по
содержанию цветных металлов, чем штейны отражательной плавки. Обычно в штейнах
взвешенной плавки содержится 40-50% меди, 20-30% железа, 20-30% серы.
Для дальнейшей переработки богатых штейнов требуется меньшее число
конвертеров и меньшие эксплуатационные затраты. Температура штейна при
взвешенной плавке поддерживается около 12000С, шлака 1250 - 13000С,
температура отходящих газов 1300-14000С. Пылевынос в процессе
взвешенной плавки составляет в среднем 5-10%.
Шлак взвешенной плавки не является отвальным и требует дополнительной
обработки. Шлаки плавки медного концентрата содержат 1-2% меди, 30-40% железа,
1,5-2% серы, SiO2 = 34-40%. Обеднение этих шлаков
проводится в основном в электропечах или флотацией.
.10 Утилизация тепла отходящих газов в котлах-утилизаторах
Известно, что одним из основных преимуществ процесса Оутокумпу является
снижение общих энергозатрат за счёт выработки вторичных энергоресурсов при
утилизации тепла отходящих газов.
Это достигается использованием специальных котлов-утилизаторов
туннельного типа, с помощью которых используется около 80 % тепла отходящих
газов. В котлах-утилизаторах туннельного типа движение газов горизонтальное.
Котёл совершенно герметичен, так как стенки его выполнены цельносварными
трубчатыми панелями. Подсосы воздуха в системе составляют до 15% конверт
1.11. Общая характеристика печи во взвешенном состоянии на подогретом
дутье как объекта управления
Важной задачей научно-технического прогресса в цветной металлургии
является разработка и внедрение высококачественных и компактных технологических
процессов, обеспечивающих комплексное использование сырья и снижение вредных
выбросов в атмосферу. К таким процессам можно отнести плавку во взвешенном
состоянии на подогретом дутье.
Задачей исследования является интенсификация, оптимизация и управление
процессом автогенной плавки на подогретом дутье.
Протекание определённого технологического процесса и поведение
технического устройства характеризуется некоторыми переменными величинами. Если
речь идет об управлении, то процессы и устройства рассматриваются как объект
управления (ОУ), желаемое поведение которого должно быть обеспечено.
Переменные, которые характеризуют состояние объекта управления, называют
выходными величинами. Иногда их называют выходными координатами.
В реальных условиях на объект управления оказывает воздействие внешняя
среда. Всё многообразие этого воздействия учесть невозможно. Поэтому в поле
зрения оставляют лишь величины, которые оказывают влияние на выходные
координаты, их называют входными воздействиями. Эти воздействия подразделяются
на две группы: управляющие и возмущающие. Управляющие воздействия обеспечивают
желаемое функционирование объекта, и должны быть, прежде всего, измеряемыми.
Если таких воздействий нет, то задача управления не имеет решения. Возмущающие
воздействия препятствуют нормальному функционированию объекта управления.
В данном случае объектом управления выступает печь для плавки во
взвешенном состоянии на подогретом дутье.
Необходимо исследовать влияние входных переменных на состав продуктов
переработки процесса взвешенной плавки во взвешенном состоянии медного
концентрата для целей управления.
При рассмотрении печи как объекта управления входными переменными могут
выступать состав и количество медного концентрата, состав и количество флюса,
загружаемые в печь, количество подаваемого дутья, температура дутья, выходными
переменными могут выступать давление в печи, температура штейна, температура
шлака, выходящие из печи, возмущающими воздействиями могут быть состав сырья,
изменение концентрации в дутье кислорода и так далее.
Управление металлургическим процессом представляет собой по существу
управление режима работы металлургического аппарата (печи), поэтому объектом
управления является именно металлургический аппарат.
Всякий металлургический аппарат представляет собой в первом приближении
емкость, в которой поддерживаются определённые концентрации химических веществ,
распределения температур, давлений - определённый режим работы.
В аппарат поступают потоки исходных материалов (концентраты, флюсы,
реагенты), а из него отводится потоки продуктов процесса (штейн, шлак), причем
соблюдается определенный режим потоков.
В связи с изложенным существуют непрерывный режим потоков на входе
(загрузке) и выходе (разгрузке), дискретный режим на входе (загрузка разделенными
во времени порциями) и непрерывный на выходе, непрерывный режим на входе и
дискретный на выходе, режим дискретный и на входе и на выходе.
Соблюдение режима работы аппарата, то есть с одной стороны, режима
потоков, а с другой - регламентированного разделения режимных параметров в
объёме аппарата, должно обеспечивать развитие нужных физико-химических
превращений в материалах, загруженных в аппарат и совокупность этих
превращений, составляющих основное содержание технологии, реализуемой в данном
аппарате, называется технологическим процессом.
1.12 Общие условия обжига сульфидных материалов
Целью окислительного обжига медных концентратов
является частичное удаление серы и перевод сульфидов железа в формы легко
шлакуемых окислов.
В состав концентрата входят минералы различных
металлов: меди, железа.
Каждый сульфид имеет специфические физические и
химические свойства, которые - определяют температуру процесса обжига, степень
десульфуризации при обжиге и производительность печи.
Начальная температура, или нижний температурный предел
обжига зависит от температуры воспламенения сульфидов концентрата. Температуры
воспламенения сульфидов различных металлов различны, поэтому и воспламенение
концентратов происходит при различных температурах.
Максимальная температура в процессе подового обжига
материалов зависит от температур плавления входящих материалов в состав
сульфидов. Во всех случаях максимальная температура обжига должна быть ниже
температур плавления присутствующих в концентрате сульфидов.
На результаты обжига оказывает большое влияние размер
зерен или частиц обжигаемого материала. Тонкое измельчение увеличивает
поверхность руды и дает возможность интенсифицировать процесс обжига, так как
химические взаимодействия кислорода с сульфидами происходят на границе соприкосновения
печных газов с сульфидами, а величина этой поверхности зависит от степени
дробления или измельчения руды и ее особенностей (трещиноватости, степени
шероховатости поверхности, пористости и т. п.).
С повышением температуры печи возрастает скорость
реакций окисления сульфидов и увеличивается производительность печи. Однако при
подовом обжиге имеется известный верхний предел температурного режима, который
определяется прежде всего спеканием материала и образованием нежелательных
соединений.
Надлежащая степень обжига сульфидных материалов
зависит от количества воздуха, поступающего в печь. При окислительном обжиге в
подовой печи, т. е. при ограниченном контакте твердых материалов с печными
газами, в некоторых случаях для получения удовлетворительных результатов
десульфуризации требуется подача, в печь избытка воздуха в 4-5 раз больше
теоретического количества. Это связано с переходом процесса окисления сульфидов
при достижении их температуры воспламенения из кинетической области в
диффузионную, где скорость реакции окисления определяется количеством
подводимого в единицу времени кислорода к горящей поверхности сульфида. При
данном количестве воздуха, поступающего в печь, последнее условие может быть
обеспечено в результате обогащения воздуха кислородом.
Повышение расхода воздуха при подовом обжиге связано
со значительным разубоживанием обжиговых газов по содержанию сернистого
ангидрида и в некоторых случаях требует увеличения расхода топлива на
поддержание необходимой температуры в печи.
Сульфатизирующий обжиг, требующий максимальных
концентраций сернистых газов в атмосфере печи, как правило, проводится при
минимально возможном избытке воздуха против теоретически необходимого его
количества.
Большим преимуществом обжига во взвешенном состоянии
следует считать возможность вести процесс при расходе воздуха, близком к
теоретическому. Эта возможность обусловливается подвижностью отдельных частиц
сульфидов и большой степенью контакта их с печными газами, т. е. увеличенной
поверхностью реакционной зоны.
Скорость реакций окисления сульфидов зависит от
температуры, крупности зерна, скорости газового потока, наличия катализаторов и
некоторых других условий. При прочих равных условиях продолжительность обжига
определяет полноту протекания реакций окисления сульфидов. С увеличением
продолжительности процесса реакции окисления протекают полнее, но вместе с тем
происходит и более полное завершение нежелательных при обжиге реакций
ферритообразовапия. С повышением продолжительности процесса пропорционально
уменьшается производительность обжигового агрегата.
Сульфатизирующий обжиг требует продолжительного
времени пребывания материалов в печи, так как процесс осуществляется при
минимальном расходе воздуха и умеренной температуре. Поэтому производительность
обжиговой печи при сульфати-зирующем обжиге значительно меньше, чем при
окислительном обжиге.
Реакция окисления сульфида возникает на свободной его
поверхности, т. е. на границе соприкосновения с печным газом, содержащим
кислород, и сопровождается образованием окисла или сульфата и выделением
сернистого ангидрида, образующим снаружи твердой частицы газовую пленку или
оболочку. Эта пленка задерживает процесс дальнейшего окисления частиц сульфида
и может быть в той или иной степени удалена при перемешивании или перегребании
материала. Перегребание материала имеет большое значение при подовом методе
обжига. В последнем случае условия процесса осложняются еще тем, что твердые
частицы сульфида не изолированы одна от другой и не имеют со всех сторон
свободного доступа воздуха, так как концентрат располагаются па поду плотным
слоем толщиной от 30 до 150 мм.
При перегребании материала вскрываются и приходят в
соприкосновение с кислородом воздуха все новые внутренние слои материала.
Одновременно при перегребании осуществляется механическое удаление
поверхностной газовой пленки на отдельных зернах сульфидов. Однако большая
интенсивность перемешивания невыгодна, так как получается слишком большой унос
пыли из печи и заметно сокращается служба гребков вследствие их быстрого
износа. При этом увеличивается также расход электроэнергии.
Печи для обжига во взвешенном состоянии выгодно
отличаются отсутствием быстро изнашивающегося перегребного механизма;
вследствие разобщенности отдельных частиц сульфидов в этих видах обжига
достигается достаточно полный контакт их с кислородом печных газов и
необходимость механического перемешивания или перегребания материалов в этих
видах обжига исключается.
Окислительный и сульфатизирующий виды обжига
представляют сложные гетерогенные процессы, связанные с явлениями адсорбции,
десорбции, реакционной диффузии и рядом сложных химических взаимодействий.
Протекание этих процессов и их результаты в основном
зависят от свойств исходных материалов, подвергаемых обжигу, т. е. от свойств
сульфидов, а также и от свойств продуктов их окисления, т. е. сульфатов и
окислов.
Процесс плавки во взвешенном состоянии позволяет
получить штейны различной степени обогащения.
Заданное извлечение меди можно поддерживать:
. изменением количества загружаемой шихты в единицу
времени;
2. изменением соотношения в шихте
сульфидсодержащих шихтовых компонентов и песчаника при неизменных показателях
дутья.
Необходимо следить за соотношением дутье-загрузка
шихты во избежании переокисления шлака.
Чем больше подают кислорода на единицу массы проплавляемой
шихты, тем дольше окисляется и переводится в шлак железо, тем богаче по
содержанию меди штейн и наоборот, чем меньше подают кислорода, тем быстрее
окисляется и переводится в шлак железо, что в свою очередь, приводит к бедным
штейнам.
Чем больше содержание магнезита, тем больше потери
меди в шлаке.
Чем больше вводят в шихту песчаника, тем больше
окисленного железа надо перевести в шлак, тем богаче штейн и наоборот, чем
беднее штейн, тем меньше песчаника должно быть.
Из приведенного выше следует, что изменение расхода
дутья, содержания кислорода в дутье, состава сырья приводит к существенным
изменениям выходных параметров.
Таким образом, задача управления должна обеспечивать:
. снижение влияния возмущений по составу сырья;
2. управление потоками шихты и дутья;
. стабилизация соотношения потоков.
Главным фактором, обеспечивающим эффективность
технологического процесса, является соблюдение оптимальных условий его ведения.
Обеспечение высокой точности поддержания параметров, характеризующих
технологический процесс и качество получаемого продукта, на оптимальном уровне
возможно только при помощи высокоэффективных систем автоматического контроля и
управления процессом.
1.13 Технологический расчёт автогенной плавки во взвешенном состоянии
Методика технологического расчёта автогенной плавки во взвешенном
состоянии приведенена ниже.
1.13.1
Вещественный состав концентрата
Сначала
находим вещественный состав концентрата. Принимая во внимание, что медь в
концентрате присутствует в формах CuFeS2 и Cu2S, для определения их содержаний вводим промежуточное
неизвестное
- содержание меди в концентрате в форме CuFeS2. Тогда:
содержание
меди в Cu2S (Cu)k -
;
содержание
железа: в CuFeS2 0,8790
;
в
FeS2 (А)k = (Fe)k - 0,8790
- (Fe)
;
содержание
серы: в CuFeS2 1,0091
;
в
Cu2S 0,2523*[(Cu)k -
)];
в
FeS2 1,1481(А)k
.
Уравнение
для определения
будет иметь следующий вид:
(S)к
= 1,0091
+0,2523*[(Cu)k -
)]+1,1481(А)k .
Отсюда
можно найти
:
=
(4)
Содержание:2 …2,8881
2S…1,2523*[(Cu)k -
)]2 … 2,1481(А)k
Fe2O3 …1,4297(Fe)
.
Учитывая
небольшое содержание в концентрате Al2O3 и CaO, принимаем условно Al2O3 в форме корунда, а CaO - в форме
кальцита. Содержание CaCO3
составляет 1,7848(CaO)к. Содержание «прочих» определяем по разности
100 - (
)к. Вещественный анализ концентрата
представлен в таблице 1.2.
Таблица 1.2
Вещественный состав концентрата в обобщенном виде, % (по массе)
Соединения
|
Всего
|
Cu
|
Fe
|
S и CO2
|
Остальное
|
CuFeS2
|
2,8881 0,8790 1,0091 -
|
|
|
|
|
Cu2S
|
1,2523*[(Cu)k- )](Cu)k - -0,2523*[(Cu)k - )]-
|
|
|
|
|
FeS2
|
2,1481(А)k
|
-
|
(А)k
|
1,1481(А)k
|
-
|
Fe2O3
|
1,4297(Fe) -(Fe) -0,4297(Fe)
|
|
|
|
|
SiO2
|
(SiO2)к
|
-
|
-
|
-
|
(SiO2)к
|
Al2O3
|
(Al2O3)
|
-
|
-
|
-
|
(Al2O3)к
|
CaCO3
|
1,7848(CaO)к
|
-
|
-
|
0,7848(CaO)к
|
(CaO)к
|
Прочие
|
100 - ( )к---100 - ( )к
|
|
|
|
|
Итого
|
100
|
(Cu)k
|
(Fe)к
|
(S)к+0,7848(CaO)к
|
( )ост
|
.13.2 Состав
и количество пыли; безвозвратные потери при плавке
При расчёте пыли взвешенной плавки исходим, прежде всего, из того, что в
концентрате отсутствуют компоненты, обладающие повышенной летучестью в условиях
плавки. Поэтому химического уноса (возгонов) в данном случае нет, и пыль
является результатом только механического уноса. Считаем, что все компоненты
концентрата подвержены механическому уносу в одинаковой степени, а их окисление
происходит уже в составе унесённой пыли. Тогда соотношение в пыли металлов,
шлакообразующих и «прочих» будет таким же, как в концентрате.
Основываясь
на данных заводской практики, принимаем величину пылеуноса концентрата как долю
количества поступающего на плавку концентрата а, % и содержание серы в пыли (S)
. Тогда количество пыли m
= mк * 0,01а.
В
пыли медь и железо представлены простыми сульфидами и оксидами. Считаем, что
они находятся в формах Cu2S, Cu2O, FeS2, Fe3O4, Fe2O3 и
принимаем соотношение между сульфидной и оксидной формами соединений меди и
железа:
=
= n,
=
= m.
В
пыли концентрата также содержатся SiO2, Al2O3, CaO и
«прочие».
Обозначим
количество меди в пыли как промежуточное неизвестное
. Тогда, исходя из принятой пропорциональности
пылеуноса металлов, шлакообразующих и «прочих», найдём количество этих
компонентов в пыли:
Fe
=
; SiO
=
; Al2O
=
; CaO
=
;
П
=
.
Находим
выраженный через v количественный вещественный состав пыли.
Количество
пыли:
Cu в Cu2S…
; Cu в Cu2O…
;
Cu2S
=1,2523
; в том числе S…0,2523
;
Cu2O
=1,1259
; S
=
(S)
*0,01m
;в FeS
…
= S
- 0,2523
= (S)
*0,01a*0,01
mк - 0,2523
;
= 2,7420
;
Fe в FeS
…1,7420
.
Железа
в окисленной форме:
Fe
= Fe
-1,7420
;
Fe в Fe3O4… Fe
;
Fe в Fe2O3… Fe
;
Fe3O
= 1,3820 Fe
; Fe2O
= 1,4297Fe
.
Количество
пыли концентрата:
mк * 0,01а = 1,2523
+1,1259
+2,7420(S)
*0,01a*0,01 mк - 0,6918
+1,3820 Fe
+1,4297Fe
+
+
+
+
+
(5)
Из
уравнения (5) после подстановок и преобразований находим количество меди в пыли
Cu
=
:
=
(6)
Как
видно, выражение (6), хотя и является начальной стадией составления модели,
довольно громоздкое. Поэтому при дальнейшем составлении и решении модели
придётся отказаться от конечных формул для неизвестных. По результатам расчётов
составляем таблицу (2) количественного вещественного состава пыли в обобщенном
виде.
Таблица 1.3
Количественный вещественный состав пыли концентрата в обобщенном виде
Соединения
|
Всего
|
Металлы
|
S
|
O
|
Остальное
|
Cu2S
|
1,2523 0,2523 --
|
|
|
|
|
Cu2O
|
1,1259 -0,1259 -
|
|
|
|
|
FeS
|
2,7420 1,7420 --
|
|
|
|
|
Fe3O4
|
1,3820 Fe Fe -0,3820 Fe -
|
|
|
|
|
Fe2O3
|
1,4297Fe Fe -0,4297Fe -
|
|
|
|
|
SiO2
|
---
|
|
|
|
|
Al2O3
|
---
|
|
|
|
|
CaO
|
---
|
|
|
|
|
П
|
---
|
|
|
|
|
Итого
|
0,01аmk
|
(S) *0,01a*0,01mк ост
|
|
|
|
Пыль взвешенной плавки является оборотным продуктом - после улавливания в
системе газоочистки печи она шихтуется вместе с концентратом и вновь поступает
на плавку. Однако часть пыли при газоочистке не улавливается, что приводит к
безвозвратным потерям некоторого количества исходной шихты. Помимо газоходной
пыли, безвозвратные потери обусловлены и другими факторами: потерями
концентрата в системе подачи его в печь, проливами расплавов и тому подобное.
При составлении заводских балансов безвозвратные потери учитываются только для
цветных металлов. Поскольку при взвешенной плавке основная часть безвозвратных
потерь обусловлена неулавливаемым пылеуносом, отнесём за счёт этой статьи все
безвозвратные потери и будем их учитывать по всем составляющим пыли.
Массу безвозвратных потерь принимаем по данным заводской практики как
долю от количества поступающего на плавку концентрата (b %). Тогда общая масса безвозвратных потерь:
m
= 0,01b*mk
Безвозвратные
потери сказываются на количестве улавливаемой пыли, которая возвращается в
плавку. С учётом этого масса оборотной пыли, поступающей на плавку, составит:
m
= m
- m
=0,01а*mk -
0,01b*mk = 0,01mk (а-b) = 0,01mkа (1-
); (7)
где
= b/a - отношение массы безвозвратных потерь к массе пыли.
Поскольку
состав безвозвратных потерь принят таким же, как и состав пыли, то масса
каждого компонента пыли, возвращаемой в плавку, будет меньше массы этого
компонента mi в уходящей из печи пыли на величину
mi.
Количество компонентов в теряемой пыли (безвозвратные потери):
Cu2S
=
Cu2S
; Cu2O
=
Cu2O
и так
далее.
Если
бы потерь оборотной пыли не было, то количество её в приходе и в расходе было
бы одинаковым, и тогда рудная шихта, непосредственно поступающая на плавку и
образующая штейн и шлак, формально (с точки зрения расчёта) была бы
представлена исходным концентратом. При этом количество и качество пылеуноса
никак не влияло бы на расчёт количества и состава штейна и шлака. В нашем же
случае, с учётом потерь пыли, количество её в приходе меньше, чем в расходе.
Это означает, что в расчёте необходимо учесть ту часть концентрата, которая
идёт на образование безвозвратно теряемой пыли; лишь оставшаяся его часть
явится рудной шихтой, непосредственно участвующей в плавке.
Требуется
найти, таким образом, количество концентрата за вычетом теряемой пыли. При этом
приходится учитывать, что в составе пыли есть соединения, которых нет в
концентрате (Cu2O, FeS, Fe3O4),
поэтому простое вычитание количеств соединений пыли в данном случае невозможно.
В связи с этим следовало бы провести полный расчёт реакций образования
безвозвратно теряемой пыли из исходного концентрата - в материальном балансе в
любом случае необходимо учитывать расход дутья и количество газов,
соответствующее указанным реакциям.
Учёт
теряемой пыли в концентрате, непосредственно поступающем на плавку, будем
производить исходя из количества элементов в пыли (в данном случае меди и
железа), а не их соединений. При этом безразлично, количество каких конкретно
соединений будет уменьшено за счёт потерь с пылью состава концентрата.
Количество
меди и железа в теряемой пыли:
Cu
=
; Fe
=

.
Полагая,
что количество меди и железа в безвозвратных потерях почти наверняка меньше
количества Cu2S и Fe2O3 в
концентрате, вычтем Cu
и Fe
из масс металлов в этих соединениях.
Останется
в концентрате (поступит непосредственно в плавку):
Cuпл = (Cu)k*0,01mk - Cu
;в Cu2S…Cu
= [(Cu)k -
]0,01mk
- Cu
;2Sпл =1,2523Cu
;пл = (Fe)k*0,01mk - Fe
;в Fe2O3 … Fe
= [(Fe)
0,01mk
- Fe
;2O
=
1,4297 Fe
;
= (SiO2)k *0,01mk -
SiO
.
Аналогично
последнему выражению получим значения:
Al
O
= (Al2O3)k *0,01mk
-
Al2O
;
П
= (П)k *0,01mk -
П
.
При
этом надо, однако, учесть, что CaO находится в концентрате в виде CaCO3, а в пыли - в виде CaO.
Поэтому CaCO
определяется по выражению:
CaCO
= (CaCO3)k
*0,01mk -
1,7848CaO
,
где
1,7848 - стехиометрический коэффициент пересчёта CaO в CaCO3.
Количество
CuFeS2 и FeS2
остаётся в концентрате,
непосредственно поступающем в плавку, без изменений, например: CuFeS
= (CuFeS2 )k *0,01mk .
1.13.3 Состав
и количество штейна, шлака и флюса
В составе штейна автогенной плавки медного концентрата целесообразно
задавать содержание меди (Cu)шт.
Исходными промежуточными данными будут при этом (Fe2O3)шт и (П)шт.
Самоплавкие шлаки взвешенной плавки почти всегда получаются сильно
основными, с высоким содержанием железа, что определяется глубоким его
окислением при плавке (получением богатых штейнов). Поэтому для взвешенной плавки
требуется, прежде всего, применение кислого, кремнийсодержащего флюса. При этом
с целью экономии, уменьшения массы шлака и улучшения теплового баланса, плавки
окончательный шлак выбирают также основным, чаще всего с содержанием SiO2 до 35-37%. При таких шлаках вводить в качество флюса
известняк обычно нецелесообразно, так как положительное влияние увеличения (CaO)шт на содержание меди в
основном шлаке и его температуру плавления существенно не проявляется. В связи
с этим при составлении модели взвешенной плавки можно в большинстве случаев
сразу принять к использованию только один кислый флюс.
Выбор конкретного содержания кремнезёма в шлаке взвешенной плавки зависит
от ряда условий: состава концентрата и флюса, содержания меди в штейне, способа
последующей переработки шлаков с целью извлечения из них меди, аппаратурного
оформления взвешенной плавки. Для обоснованного выбора (SiO2)шт с учётом этих условий целесообразно
вначале оценить свойства самоплавкого шлака, получаемого при плавке без
использования флюса. Поэтому при составлении модели технологии взвешенной
плавки пойдем по пути предварительного определения состава самоплавкого шлака.
На основании результатов анализа его состава выберем окончательный состав.
Поскольку для свойств самоплавкого шлака не имеют определяющего значения
содержания таких компонентов, как цветные металлы, сера и «прочие», в
предварительном расчёте учитывать их не будем.
Количество штейна (предварительное):
m
=
=
.
Количество
в штейне:
Cu2S
=
1,2523*Cuпл ;
Fe3O4
=
(Fe3O4)шт*0,01m
;
= m
-
Cu2S
- Fe3O4
;
= 0,6353FeS
+
0,7236 Fe3O4
= 0,6353 m
-
0,7956 Cuпл -
,6353(Fe3O4)шт*0,01m
+ 0,7236(Fe3O4)шт*0,01m
= 0,6353 m
-
,7956Cuпл +
0,0883(Fe3O4)шт*0,01m
=
Cuпл {[0,6353+
0,0883*0,01
(Fe3O4)
)/0,01(Cu)шт] - 0,7956}.
Обозначим
предварительное количество самоплавкого шлака через промежуточное неизвестное u.
Количество
в шлаке:
Fe
= Feпл
- Fe
;
SiO2
=
SiO
; Al2O3
= Al2O
;
CaO
= CaO
;
П
=
П
.
В
шлаках взвешенной плавки имеется высокое содержание магнетита (обычно 10-15%);
ориентировочно примем это содержание Fe3O4
.
Fe в Fe3O4
… 0,7236(Fe3O4)
*0,01u;в FeO
…
Fe
- 0,7236(Fe3O4)
*0,01u;
= 1,2865[Fe
- 0,7236(Fe3O4)
*0,01u].
Для
ориентировочного учёта суммы содержаний меди и серы в самоплавком шлаке (на
практике она чаще всего не превышает 2-3 %) примем её (d)
, %:
d
= (d)
*0,01u.
Масса самоплавкого шлака:
u = Fe
+
Fe3O4
+
SiO2
+ Al2O3
+ CaO
+
П
+
d
.
После
подстановок и преобразований получим:
u ={1,2865Feпл - Cuпл {[81,73+
0,1136(Fe3O4)
]/(Cu)
- 1,0235}+ SiO2
+ Al2O3
+ CaO
+
П
}/[1-
0,0691(Fe3O4)
*0,01-(d)
*0,01]. (8)
Зная
количества компонентов в самоплавком шлаке mi и
количество шлака m
= u, находим содержание каждого компонента в шлаке (%),
например,
(FeO)
= FeO
/u*100. (9)
Подставляя
соответствующие числовые значения в полученные выражения, находим состав шлака
по основным шлакообразующим, затем, оценивая свойства полученного самоплавкого
шлака, выбираем окончательный состав шлака, который может быть получен в
результате применения кислого флюса. При выборе принимаем следующие
промежуточные данные: (SiO2)ш;
(Cu)ш; (S)ш;
(Fe3O4)ш.
Учитываем, кроме того, что медь в шлаках взвешенной плавки частично содержится
в оксидной форме: принимаем, что она содержится целиком в форме Cu2O.
Обозначим величину отношения содержания меди в форме Cu2O к
общему содержанию меди в шлаке буквой р.
(Cu в Cu2O)ш
/ (Cu)ш = p.
Перед
определением окончательных количественных составов штейна и шлака рассчитываем
вещественный состав флюса.
В
качестве флюса задан песчаник с содержанием следующих компонентов: (SiO2)Ф; (Fe2O3)Ф; (Al2O3)Ф; (CaO)ф.
Минералогический состав флюса задан несколько упрощённо такими соединениями:
кварцем, каолином, лимонитом и моносиликатом кальция.
В
песчанике содержится:
каолинита
(Al2O3* 2SiO2*2H2O) Ф = 2,5320(Al2O3)Ф, в том числе
SiO2…1,1785(Al2O3)Ф;2O…0,3535(Al2O3)Ф;
моносиликата
кальция (CaO* SiO2) Ф =
2,0713(CaO)ф, в том числе
SiO2…1,0713(CaO)Ф;
кварца
(SiO2)
= (SiO2)Ф
- 1,1785(Al2O3)Ф
- 1,0713(CaO)ф;
лимонита
(Fe2O3*2H2O)
Ф = 1,2257(Fe2O3)Ф,
в том числе
Fe…0,6994(Fe2O3)Ф;…
0,3006(Fe2O3)Ф;2O…0,2257(Fe2O3)Ф;
«прочие»
по разности 100 -
.
Вещественный
состав флюса представлен ниже в таблице 1.4.
Таблица 1.4
Вещественный состав флюса, % (по массе)
Соединения
|
Всего
|
SiO2, Fe
|
Al2O3, CaO, O
|
H2O, прочие
|
SiO2
|
(SiO2)Ф - 1,1785(Al2O3)Ф- - 1,0713(CaO)ф
|
( SiO2)Ф -1,1785(Al2O3)Ф- -1,0713(CaO)ф
|
-
|
-
|
Al2O3* 2SiO2*2H2O
|
2,5320(Al2O3)Ф
|
1,1785(Al2O3)Ф
|
(Al2O3)Ф
|
0,3535(Al2O3)Ф
|
CaO* SiO2
|
2,0713(СаО)Ф
|
1,0713(СаО)Ф
|
(СаО)Ф
|
-
|
Fe2O3*2H2O
|
1,2257(Fe2O3)
Ф
|
0,6994(Fe2O3)
Ф
|
0,3006(Fe2O3)
Ф
|
(Fe2O3) Ф
|
П
|
100 - --100 -
|
|
|
|
Итого
|
100
|
(SiO2)Ф
+0,6994* (Fe2O3) Ф
|
-
|
-
|
Затем производим полный расчёт количественных составов штейна и шлака и
количество флюса.
Обозначим
массы штейна х, шлака y, флюса z. Величина флюса z в данном
случае будет представлять количество флюса, непосредственно участвующего в
плавке (в образовании штейна и шлака). Поскольку мы рассчитываем безвозвратные
потери как долю от всех компонентов оборотной пыли, то необходимо учесть,
наряду с потерями компонентов концентрата, потери компонентов флюса, поскольку
он также частично уносится в пыль. Обозначим количества компонентов флюса,
которые участвуют в плавке, как m
.
Количество
штейна:
mшт = x = Cuшт /
[0,01(Cu) шт].
Количество
в штейне:
Cuшт = Cuпл - Cuш
= Cuпл - (Cu)ш*0,01y;
Cu2S
=
1,2523*Cuшт;3O
= (Fe3O4)
*0,01x;
Пшт = (П)шт*0,01х;шт = mшт - Cu2S
- Fe3O
-
Пшт; Feшт =
0,6353 FeSшт + 0,7236 Fe3O
.
Количество
в шлаке:
Cu в Cu2Oш… pCuш = p(Cu)
ш *0,01y;
Cu2Oш = 1,1259(Cu) ш *0,01y;
Cu в Cu2Sш… (1-p)Cuш = (1-p)(Cu)
ш *0,01y;
Cu2Sш = 1,2523(1-p)Cuш;
S в FeSш … (S)ш*0,01y
- 0,2523(1-p)(Cu) ш *0,01y;ш
= 0,6918(1-p)(Cu) ш *0,01y;в FeSш
… 1,7429(S)ш*0,01y - 0,4395(1-p)(Cu) ш *0,01y;в Fe3O
… 0,7236(Fe3O4)
*0,01y;ш = Feпл + Feф
- Feшт = Feпл +0,6994(Fe2O3)Ф*0,01z
- Feшт ;в FeOш … Feш - 1,7420(S)ш*0,01y
+ 0,4395(1-p)(Cu) ш *0,01y
-
,7236(Fe3O4)
*0,01y;ш =
1,2865 Feш - 2,2411(S)ш*0,01y
+ 0,5654(1-p)(Cu) ш *0,01y
-
,9309(Fe3O4)
*0,01y;
=
(SiO2)ш *0,01y;2O
= Al2O
+
(Al2O3)Ф*0,01z;ш = CaO
+
(CaO)ф*0,01z;
Пш
= П
+ (П)ф*0,01z - (П)шт*0,01х.
Уравнения
модели:
x = Cuшт
/ [0,01(Cu) шт ];
(10)
y = Cu2Oш + Cu2Sш + FeSш + Fe3O
+ FeOш + SiO
+ Al2O
+ CaOш
+ Пш ;
z = (SiO
-
SiO
) / [0,01(SiO2)ф ]. (12)
После
нахождения неизвестных примем во внимание, что найденная величина z не
учитывает безвозвратные потери флюса. Более того, в найденном количестве и
составе пыли не учтён пылеунос флюса. Поэтому внесем соответствующие коррективы
в количественные составы пыли, безвозвратных потерь и флюса. При этом доля
уноса в пыль флюса от подаваемого его количества на плавку иная, чем доля
концентрата. Это обусловлено, помимо разницы в плотностях частиц концентрата и
флюса, разной крупностью этих материалов; поскольку флюс не поступает на
флотационное обогащение, схема измельчения у флюса своя.
Обозначим
долю уноса в пыль флюса f%, а долю безвозвратных потерь g%.
Обе величины берём от массы поступающего в печь флюса, которую обозначим mф; она и представляет собой искомое количество флюса,
входящее в материальный баланс плавки. Поскольку пыль флюса, как и пыль
концентрата, является оборотным продуктом, она будет фигурировать как в
приходной, так и в расходной части баланса, однако в приходе её масса m
будет
меньше расхода m
на величину потерь. Поэтому найденная величина z,
представляющая собой количество непосредственно участвующего в плавке флюса,
будет меньше необходимого количества флюса mф только на величину безвозвратных потерь:
mф = z + m
.
Учитывая
значения f и g, получаем:
m
= 0,01*f* mф; m
= 0,01*g* mф; mф = z /
(1-0,01*g);
m
= z [f / (100 - g)]; m
= m
(g / f) = m
*
, (13)
где
величина
- отношение массы безвозвратных потерь флюса к массе
флюса.
В
составе заданного флюса в отличие от концентрата нет окисляющихся компонентов,
поэтому состав пылеуноса флюса аналогичен составу самого флюса. Однако во флюсе
протекают при нагревании реакции диссоциации минералов, содержащих влагу. Ввиду
этого пыль будет представлена оксидами SiO2, Al2O3, CaO, Fe2O3, а также «прочими» и не содержать влаги.
Соответственно, содержание этих простых компонентов в пыли будет иным (выше),
чем во флюсе.
Пересчёт
состава флюса на состав пыли производим таким же образом, как и при расчете,
пыли концентрата. Обозначим h - неизвестное количество SiO2 в пыли флюса SiO
(промежуточное неизвестное). Тогда количество других компонентов в этой пыли:
Al2O
= h (Al2O3)т / (SiO2)ф ; CaOпФ = h [(CaO)ф /(SiO2)ф ] и т. д. (14)
Количество
пыли во флюсе:
m
= z*f / (100 - g) = h + h*[(Al2O3)Ф + (CaO)ф
+ (Fe2O3)Ф
+ (П)ф] /
(SiO2)ф = h [100 - (H2O)Ф
/(SiO2)ф ];
отсюда
= z*f (SiO2)ф /{(100 - g)*[100 - (H2O)Ф]}.
(15)
Найдя
h, определим далее по формуле (14) количество
компонентов в пыли.
Количество
компонентов в безвозвратных потерях флюса находим из соотношений:
m
= 0,01g*0,01c
,ф
= g*z /(100 - g)* 0,01 c
= g / f (m
*0,01c
) =
*
m
* c
,
то
есть
SiO
=
* m
*(SiO2)ф ,
H2Oбпф =
* m
*(H2O)ф, и т. д. (16)
Найденные
количества компонентов пылеуноса флюса необходимо прибавить к количествам
одноименных компонентов пылеуноса концентрата; таким образом, мы получили общий
количественный состав пыли в расходной части материального баланса плавки.
Общее количество всей этой пыли:
mп = m
+ m
, причём m
= m
+ m
.
В
приходной части баланса количество каждого компонента пыли должно быть
уменьшено по сравнению с расходной его частью на величину безвозвратных потерь
этого компонента. При этом m
= m
+ m
. Общее количество пыли (оборотная пыль) в приходе m
будет,
следовательно, равно:
m
= mп -
m
,
где
m
- сумма количеств всех компонентов потерь флюса, за
исключением влаги.
Таким
образом, статьями материального баланса автогенной плавки в данном случае будут
(без учёта дутья и газов):
в
приходе mк , mф , m
;
в
расходе mшт (или
х), mш (или у),
mп.
В
явном виде безвозвратные потери в этом варианте составления материального
баланса отсутствуют, так как они учтены в разнице между приходом и расходом
пыли. Такой подход определяется тем, что в целом безвозвратные потери при
взвешенной плавке в основном обусловлены потерями пыли, вследствие чего эти
потери сказываются преимущественно на количестве оборотной пыли, и их
рассчитывают, исходя из состава пыли.
.13.4 Количество
дутья и технологических газов
В данном разделе количество дутья и технологических газов будем
рассчитывать по общему балансу кислорода и серы в материалах и продуктах, а не
по отдельным реакциям процесса.
Поскольку в материальном балансе процесса количество оборотной пыли в
приходе меньше количества ее в расходе величину безвозвратных потерь, нет
надобности учитывать отдельно разные количества пылей в балансе кислорода;
вместо этого в расходной части баланса будем учитывать безвозвратные потери.
Количество серы в материалах и продуктах:
в
концентрате
;
в
штейне
;
в
шлаке
;
в
безвозвратных потерях
Переходит
серы в газы:
.
Считаем,
что вся сера в газах автогенной плавки находится в форме SO2 (количество SO3 пренебрежимо мало). Масса SO2 в газах
.
Количество
кислорода в материалах и продуктах:
в
концентрате
;
во
флюсе
;
в штейне
;
в
шлаке
;
в
безвозвратных потерях
Обп
=
в
SO2 газов
.
Требуется
кислорода для дутья (теоретически необходимое количество кислорода):
(17)
Примем
по данным практики степень использования кислорода дутья при плавке η[%]. Действительное количество кислорода и количество
свободного кислорода в газах, соответственно:
В
печь подается не чистый кислород, а смесь технического кислорода и воздуха,
содержащая, помимо кислорода, другие газы, в основном азот. Пренебрегая другими
газовыми составляющими, исходим из известного объемного содержания кислорода в
техническом кислороде, подаваемом в реакционную шахту {О2}тк%;
остальное - азот.
Объём
собственно кислорода и азота в техническом кислороде соответственно составят:
Масса
собственно кислорода и азота в дутье:
O
=32,0/22,39[O2]
=1,429[O2]
, N
=28,02/22,40[N2]
=1,251[N2]
.
Помимо
SO2, O2 и N2 в
технологических газах автогенной плавки содержатся СО2 и пары воды
от разложения минералов флюса и от остаточной внешней влаги концентрата и
флюса, которой соответственно равно
и
(сверх 100 %).Поскольку в безвозвратных потерях СО2
и Н2О нет, то всё их количество из концентрата и флюса
переходит в газы: СО
= 0,7848(СаО)к;
Н2Ог
=(Н2О)Ф0,01 mф +
0,01 mк +
0,01 mф.
.13.5
Исходные данные для технологического расчёта взвешенной плавки
Для решения поставленной модели примем следующие исходные и промежуточные
данные, которые представлены в таблице 1.5.
Таблица 1.5
Исходные данные
|
(Сu)k
|
19
|
(Fe)k
|
31,6
|
(S)k
|
35,5
|
(SiO2)k
|
5,5
|
(Al2O3)k
|
5,8
|
(CaO)k
|
0,5
|
(Fe) ok k
|
2
|
(SiO2)ф
|
73,3
|
(Al2O3)ф
|
6,3
|
(CaO)ф
|
2
|
(Fe2O3)ф
|
13
|
mk
|
100
|
a
|
9
|
(S)k п
|
10
|
n
|
0,6
|
m
|
0,4
|
b
|
0,45
|
(Cu)шт
|
50
|
(Fe3O4)шт
|
8
|
(П)шт
|
1,6
|
(Fe3O4)пр ш
|
12
|
(d) пр ш
|
2,5
|
8
|
g
|
0,4
|
(Прочие)к
|
0,1
|
Величины
(SiO2)шт,
(Cu)шт, (S)шт,
(Fe3O4)
и р выберем после определения состава самоплавкого
шлака.
Вначале подсчитываем вещественный состав концентрата. Полученные данные
занесены в таблицу 1.6.
Таблица 1.6
Вещественный состав концентрата, % (по массе)
Соединения
|
Всего
|
Cu
|
Fe
|
S и CO2
|
Остальное
|
CuFeS2
|
37,517
|
12,990
|
11,418
|
13,109
|
-
|
Cu2S
|
7,526
|
6,010
|
-
|
1,516
|
-
|
FeS2
|
39,057
|
-
|
18,182
|
20,875
|
-
|
Fe2O3
|
2,859
|
-
|
2,000
|
-
|
0,859
|
SiO2
|
5,5
|
-
|
-
|
-
|
5,5
|
Al2O3
|
5,8
|
-
|
-
|
-
|
5,8
|
CaCO3
|
0,892
|
-
|
-
|
0,392
|
0,5
|
Прочие
|
0,849
|
-
|
-
|
-
|
0,849
|
Итого
|
100,000
|
19,000
|
31,600
|
35,892
|
13,508
|
Затем находим количество и состав пыли концентрата (таблица 1.7).
Таблица 1.7
Количество и состав пыли концентрата
Соединения
|
Всего
|
Металлы
|
S и O
|
Остальное
|
|
кг
|
%
|
кг
|
%
|
кг
|
%
|
кг
|
%
|
Cu2S
|
1,648
|
18,31
|
1,316
|
14,62
|
0,332
|
3,69
|
-
|
-
|
Cu2O
|
0,889
|
9,88
|
0,789
|
8,77
|
0,100
|
1,11
|
-
|
-
|
FeS
|
1,557
|
17,30
|
0,989
|
10,99
|
0,568
|
6,31
|
-
|
-
|
Fe3O4
|
2,479
|
27,54
|
1,794
|
19,94
|
0,685
|
7,61
|
-
|
-
|
Fe2O3
|
1,026
|
11,40
|
0,718
|
7,98
|
0,308
|
3,42
|
-
|
-
|
SiO2
|
0,609
|
6,77
|
-
|
-
|
-
|
-
|
0,609
|
6,77
|
Al2O3
|
0,643
|
7,14
|
-
|
-
|
-
|
-
|
0,643
|
7,14
|
CaO
|
0,055
|
0,61
|
-
|
-
|
-
|
-
|
0,055
|
0,61
|
Прочие
|
0,094
|
1,04
|
-
|
-
|
-
|
-
|
0,094
|
1,04
|
Итого
|
9,000
|
100,000
|
5,606
|
62,30
|
1,993
|
22,14
|
1,401
|
15,56
|
Рассчитываем количественных состав безвозвратных потерь концентрата и
оборотной пыли концентрата (таблица 1.8.).
Таблица 1.8
Количественный состав безвозвратных потерь концентрата и оборотной пыли
концентрата, кг
Соединения
|
Безвозвратные потери
|
Оборотная пыль
|
|
Всего
|
Металлы
|
S,O,остальное
|
Всего
|
Металлы
|
S,O,остальное
|
Cu2S
|
0,082
|
0,066
|
0,016
|
1,566
|
1,250
|
0,316
|
Cu2O
|
0,044
|
0,039
|
0,005
|
0,845
|
0,750
|
0,095
|
FeS
|
0,078
|
0,050
|
0,028
|
1,479
|
0,939
|
0,540
|
Fe3O4
|
0,124
|
0,090
|
0,034
|
2,355
|
1,704
|
0,651
|
Fe2O3
|
0,051
|
0,035
|
0,016
|
0,975
|
0,683
|
0,292
|
SiO2
|
0,031
|
-
|
0,031
|
0,578
|
-
|
0,578
|
Al2O3
|
0,032
|
-
|
0,032
|
0,611
|
-
|
0,611
|
CaO
|
0,003
|
-
|
0,003
|
0,052
|
-
|
0,052
|
Итого
|
0,450
|
0,280
|
0,170
|
8,550
|
5,326
|
3,224
|
Зная безвозвратные потери концентрата, рассчитываем далее количество
компонентов концентрата, непосредственно поступающих в плавку на образование
штейна и шлака (таблица 1.9.). Поскольку концентрат, непосредственного
поступающий на плавку, не является конечным продуктом процесса, а служит лишь в
качестве промежуточного элемента модели, процентный состав его не приводим.
Таблица 1.9
Количественный состав концентрата, непосредственно поступающего на
плавку, кг
Соединения
|
Всего
|
Cu
|
Fe
|
S, CO2
|
Остальное
|
CuFeS2
|
37,517
|
12,990
|
11,418
|
13,109
|
-
|
Cu2S
|
7,395
|
5,905
|
-
|
1,490
|
-
|
FeS2
|
39,057
|
-
|
18,182
|
20,875
|
-
|
Fe2O3
|
2,609
|
-
|
1,825
|
-
|
0,784
|
SiO2
|
5,470
|
-
|
-
|
-
|
5,470
|
Al2O3
|
5,768
|
-
|
-
|
-
|
5,768
|
CaCO3
|
0,887
|
-
|
-
|
0,390
|
0,497
|
Прочие
|
0,844
|
-
|
-
|
-
|
0,844
|
Итого
|
99,547
|
18,895
|
31,425
|
35,864
|
13,363
|
Производим предварительный расчёт штейна и шлака с целью определения
требуемого состава шлака и выбора флюса. Поскольку предварительный расчёт
является упрощенным и приблизительным, таблиц не составляем. По формуле (8)
находим u = 42,53. Затем определяем
предварительный состав самоплавкого шлака, %:
(FeO)
=55,9;
(SiO2)
= 12,9; (Al2O3)
=13,6; (CaO)
=1,2;
(П)
=1,9;
(Fe3O4)
=12,0; (d)
=2,5.
Самоплавкий
шлак взвешенной плавки концентрата оказался чрезвычайно железистым, и поэтому
процесс нуждается в применении кремнийсодержащего флюса. Примем (SiO2)
=36 %. Для шлака принятого содержания SiO2
и штейна с 50 % Сu,
учитывая также среднее качество заданного флюса (73,3 % SiO2), недостающие промежуточные данные для окончательного
расчета могут быть приняты следующими:
(Сu)ш =
1,0; (S)ш =
1,5; (Fe3O4)ш =
12,0; p = 0,3.
Перед
окончательным расчётом штейна и шлака рассчитаем вещественный состав флюса
(таблица 1.10.).
Таблица 1.10
Вещественный состав флюса, % (по массе)
Соединения
|
Всего
|
SiO2
|
Fe
|
O
|
H2O
|
Прочие
|
SiO2
|
63,740
|
63,740
|
-
|
-
|
-
|
-
|
Al2O3*2SiO2*2H2O
|
15,950
|
7,420
|
-
|
-
|
2,230
|
6,3
|
CaO*SiO2
|
4,140
|
2,140
|
-
|
-
|
-
|
2
|
Fe2O3*2H2O
|
-
|
9,090
|
3,910
|
2,930
|
-
|
Прочие
|
0,240
|
-
|
-
|
-
|
-
|
0,240
|
Итого
|
100,000
|
73,300
|
9,090
|
3,910
|
5,160
|
8,540
|
Приводим результаты поэтапного расчёта количеств компонентов штейна и
шлака, составляющих уравнения модели.
mшт = x = 37,79-0,020*у; Сu2Sшт = 23,662-0,0125*y; Fe3O
=
0,080*х; П
шт = 0,010*х; FeS
шт = 14,128 - 0,007477*у - 0,090*х;
Feшт =
8,9754 -
,00475*у
+ 0,00071*х; Cu в Cu2Oш …0,0030*у;
Cu2Oш =
0,003378*у; Cu
в
Cu2Sш …0,0070*у;
Cu2Sш =
0,008766*у; S в FeSш …
0,01323*у; FeSш =
,03629*у;
Fe в FeSш
…0,02305*у; Fe в Fe3O4
…0,08683*у; Feш =
,4496
- 0,00071*х + 0,00475*у + 0,0909*z; FeOш =
28,8814 -
,000913*х
- 0,13526*у + 0,011697*z; SiO
=0,360*у; Al2O
= 5,768 +
,063*z; CaO
ш =0,497 + 0,020*z; Пш
=0,844 - 0,01*х + 0,0025*z.
Уравнения
модели:
x = 37,79 -
0,020*y;
у
= 35,9904 - 0,01091*x + 0,39317*у + 0,20247*z;
z = 0,49113*y -
7,4625.
Решив
составленную систему уравнений, найдем значения неизвестных:
х
= 36,447, у = 67,171, z = 25,527.
Подставим
найденные значения х, у, z в выражения, определяющие количества компонентов в
штейне, шлаке и флюсе, получим их количественные составы (таблицы 1.11-1.12.).
Таблица 1.13.
Количественный состав флюса,
непосредственно участвующего в плавке, кг
SiO2
|
Всего
|
SiO2
|
Fe
|
O
|
H2O
|
Прочие
|
Al2O3*2SiO2*2H2O
|
16,268
|
16,268
|
-
|
-
|
-
|
-
|
CaO*SiO2
|
4,072
|
1,895
|
-
|
-
|
0,569
|
1,608
|
Fe2O3*2H2O
|
1,057
|
0,546
|
-
|
-
|
-
|
0,511
|
Прочие
|
4,066
|
-
|
2,320
|
0,998
|
0,748
|
-
|
SiO2
|
0,064
|
-
|
-
|
-
|
-
|
0,064
|
Итого
|
25,527
|
18,709
|
2,320
|
0,998
|
1,317
|
2,183
|
Таблица 1.14.
Количественный состав пыли флюса, безвозвратных потерь флюса и оборотной
пыли флюса, кг
Составная часть флюса
|
Всего
|
SiO2
|
Fe2O3
|
Al2O3
|
CaO
|
Прочие
|
H2O
|
Пыль
|
2,05
|
1,585
|
0,281
|
0,136
|
0,043
|
0,005
|
-
|
|
|
|
Fe 0,197
|
|
|
|
|
|
|
|
O 0,084
|
|
|
|
|
Безвозвратные
|
0,101
|
0,074
|
0,013
|
0,007
|
0,002
|
-
|
0,005
|
потери
|
|
|
Fe 0,009
|
|
|
|
|
|
|
|
O 0,004
|
|
|
|
|
Оборотная пыль
|
1,953
|
1,51
|
0,268
|
0,129
|
0,041
|
0,005
|
-
|
|
|
|
Fe 0,188
|
|
|
|
|
|
|
|
O 0,080
|
|
|
|
|
Таблица 1.15
Количественный состав флюса, загружаемого в печь, кг
Соединения
|
Всего
|
SiO2
|
Fe
|
O
|
H2O
|
Прочие
|
SiO2
|
16,333
|
16,333
|
-
|
-
|
-
|
-
|
Al2O3*2SiO2*2H2O
|
4,088
|
1,902
|
-
|
-
|
0,571
|
1,615
|
CaO*SiO2
|
1,061
|
0,548
|
-
|
-
|
-
|
0,513
|
Fe2O3*2H2O
|
4,082
|
-
|
2,329
|
1,002
|
0,751
|
-
|
Прочие
|
0,064
|
-
|
-
|
-
|
-
|
0,064
|
Итого
|
25,628
|
18,783
|
2,329
|
1,002
|
1,322
|
2,192
|
Таблица 1.16
Количество и состав уходящей пыли
Соединения
|
Всего
|
Металлы
|
S и O
|
Остальное
|
|
кг
|
%
|
кг
|
%
|
кг
|
%
|
кг
|
%
|
Cu2S
|
1,648
|
14,91
|
1,316
|
11,91
|
0,332
|
3
|
-
|
-
|
Cu2O
|
0,889
|
8,05
|
0,789
|
7,14
|
0,1
|
0,9
|
-
|
-
|
FeS
|
1,557
|
14,09
|
0,989
|
8,95
|
0,568
|
5,14
|
-
|
-
|
Fe3O4
|
2,479
|
22,43
|
1,794
|
16,24
|
0,685
|
6,2
|
-
|
-
|
Fe2O3
|
1,307
|
11,83
|
0,915
|
8,28
|
0,392
|
3,55
|
-
|
-
|
SiO2
|
2,194
|
19,86
|
-
|
-
|
-
|
-
|
2,194
|
19,86
|
Al2O3
|
0,779
|
7,05
|
-
|
-
|
-
|
-
|
0,779
|
7,05
|
CaO
|
0,098
|
0,89
|
-
|
-
|
-
|
-
|
0,098
|
0,89
|
Прочие
|
0,099
|
0,9
|
-
|
-
|
-
|
-
|
0,099
|
0,9
|
Итого
|
11,05
|
100
|
5,803
|
52,52
|
2,077
|
18,8
|
3,17
|
28,69
|
.14 Методика расчёта теплового баланса автогенной плавки во взвешенном
состоянии на подогретом дутье
Составим модель расчета теплового баланса для переработки медного
концентрата. Основными статьями приходной части баланса является тепло
экзотермических реакций окисления диссоциирующей серы и сульфида железа.
Таблица 1.17
Количественный состав оборотной пыли, кг
Соединения
|
Всего
|
Металлы
|
S и O
|
Остальное
|
|
кг
|
%
|
кг
|
%
|
кг
|
%
|
кг
|
%
|
Cu2S
|
1,566
|
14,91
|
1,250
|
11,90
|
0,316
|
3,01
|
-
|
-
|
Cu2O
|
0,845
|
8,04
|
0,750
|
7,14
|
0,095
|
0,90
|
-
|
-
|
FeS
|
1,479
|
14,08
|
0,939
|
8,94
|
0,540
|
5,14
|
-
|
-
|
Fe3O4
|
2,355
|
22,42
|
1,704
|
16,22
|
0,651
|
6,20
|
-
|
-
|
Fe2O3
|
1,243
|
11,83
|
0,870
|
8,28
|
0,373
|
3,55
|
-
|
-
|
SiO2
|
2,089
|
19,89
|
-
|
-
|
-
|
2,089
|
19,89
|
Al2O3
|
0,740
|
7,04
|
-
|
-
|
-
|
-
|
0,740
|
7,04
|
CaO
|
0,093
|
0,89
|
-
|
-
|
-
|
-
|
0,093
|
0,89
|
Прочие
|
0,094
|
0,89
|
-
|
-
|
-
|
|
0,094
|
0,89
|
Итого
|
10,504
|
100,00
|
5,513
|
52,48
|
1,975
|
18,80
|
3,016
|
28,71
|
Аппаратурным оформлением тепла обуславливаются потери тепла печью во
внешнюю среду за счет теплопередачи через футеровку, излучения через открытые
отверстия и отвода тепла системой охлаждения конструктивных узлов агрегата.
Перейдем к расчету статей баланса.
.14.1 Теплота
реакций процесса
Из сопоставления вещественных составов исходных материалов и продуктов
следует, что подлежащими учету при расчете технологии являются следующие
результирующие реакции:
Из
перечисленных реакций все, кроме реакции (III), являются
бесспорными по своим конечным результатам, то есть из исходных компонентов
обязательно получаются конечные соединения. Реакция же (III)
может и не иметь места, если в исходных материалах имеется большое количество
и количество магнетита
,
образующегося из этого
по реакции (IV), равно всему магнетиту,
содержащемуся в продуктах (штейне и шлаке). При этом может быть избыточное
(сверх необходимого для образования
)
количество
, которое должно восстанавливаться по реакции:
Таким
образом, вместо реакции (III) в приведенном перечне появляется реакция (VI).
Указанная
неопределенность в реакциях не имеет, однако, в данном случае значения,
поскольку конечные количества
и
в продуктах плавки однозначно определены.
Приведенными
выше реакциями (I) ч (VI) не исчерпываются все реакции процесса автогенной
плавки. Ранее мы не учитывали шлакование образующихся оксидов, поскольку эти
превращения не влияют на количество и состав дутья и газов. В тепловом балансе
эти реакции следует учитывать.
В
нашем примере единственной реакцией шлакообразования, которая может внести
заметный вклад тепловой баланс, является взаимодействие
с кремнеземом шихты с образованием фаялита:
Известно,
что в шлаках типа конвертерного количество образующегося фаялита определяется
количеством имеющегося
, так как
имеется в
избытке по отношению к
. Поэтому реакцию (VII)
рассчитываем по
.
Рассчитываем
реакции.
(I) Количество образующихся:
(IV)
Всего поступает в процесс
с исходными материалами:
Образуется
:
.
На
это требуется
:
(III)
Всего образуется
при плавке и переходит в штейн и шлак:
.
Образуется
по реакции (IV)
, а по реакции (III)
образуется:
.
При
этом окисляется
; требуется кислорода
;
образуется SO2
.
(II) Количество
в шлаке:
.
Где
Fe
= Fe в FeS,
Fe
= Fe в Fe3O4.
Расходуется
по реакции (IV)
; всего образуется
при
плавке по реакции (II):
. При
этом окисляется 
;
требуется кислорода
; образуется SO2
.
(V) В
результате диссоциации высших сульфидов по реакции (I) выделяется
элементарной серы
; требуется кислорода на ее окисление
. Образуется SO2
.
Обозначим
тепловые эффекты
(Дж/моль) учитываемых нами реакций буквой q с
индексом, отвечающим номеру реакции, а количество тепла (кДж), выделяемого или
поглощаемого в процессе автогенной плавки по этим реакциям, - соответственно Q1, Q2 и так
далее.
Тепло
реакции (I) подсчитаем по количеству, содержащемуся в
, меди:
Остальные
реакции просчитываем по количествам участвующих в них соединений:
Общее
количество теплоты Qр,
выделяющееся в результате реакций процесса равно
(18)
1.14.2
Энтальпия материалов и продуктов плавки
Материалами рассчитываемой автогенной плавки являются концентрат, флюс и
дутье. Концентрат и флюс поступают в плавку без предварительного подогрева,
вследствие чего их энтальпия весьма незначительна, так что ей можно пренебречь.
Дутье в реализованном в заводских условиях процессе взвешенной плавки подается
ненагретым. Не исключена, однако, возможность его предварительного подогрева в
рекуператоре для снижения расхода технического кислорода на плавку - увеличения
доли воздуха в дутье. В случае подогрева энтальпия дутья будет значительной, и
она должна быть учтена в балансе. Однако и без целенаправленного подогрева
дутья энтальпия дутья в тепловом балансе процесса может быть заметной
вследствие того, что в процессе сжатия в нагнетателях или компрессорах дутье может
разогреваться до значительной температуры. Степень разогрева зависит от типа
газоподающей машины, температуры засасываемого ею газа, степени его сжатия и
др. На температуре дутья при входе его в печь существенно сказывается также
охлаждение его на трассе от газоподающей станции до печи. Поскольку в общем
случае подаваемое в процесс дутье может вносить заметное количество теплоты,
учитываем его в балансе.
Зная объемы технического кислорода дутья, найденные в материальном
балансе, найдем теплоту, вносимую техническим кислородом дутья:
,
где
, кДж/(м3·єС) - средняя объемная
теплоемкость технического кислорода и интервале температур от 0 єС до
.
Продуктами
плавки являются штейн, шлак и технологические отходящие газы. Теплоту, уносимую
штейном и шлаком, выражаем через энтальпии
и
, которые находим из справочной литературы для
определенных температур и непосредственно для тех составов этих продуктов,
которые получены в результате числового расчета технологии. При этом необходимо
принять температуру штейна и шлака на выходе из печи. Теплота штейна и шлака:
Теплоту
технологических газов рассчитываем по отдельным газовым составляющим. Теплота,
уносимая технологическими газами (за исключением паров воды) равна:
где
,
и
- соответствующие средние объемные теплоемкости
газовых составляющих от 0 до tг.
Теплота,
затрачиваемая на нагрев и испарение внешней влаги концентрата и флюса и нагрев
паров воды:
где
2674 - теплота, затрачиваемая на нагрев 1 кг воды от 0 до 100 єС и испарение
влаги при этой температуре и нормальном атмосферном давлении, кДж / кг
-
средняя теплоемкость паров воды в интервале температур от 100 до tг, кДж / (м3·єС)
1.14.3 Расчёт теплового баланса печи взвешенной плавки на подогретом
дутье
Тепловой баланс печи взвешенной плавки после произведенных расчетов будет
выглядеть следующим образом:
На
этом тепловой баланс печи взвешенной плавки является завершенным.
Прежде
всего, подсчитаем тепловые эффекты реакций. Справочные данные дают следующие
значения теплот образования (энтальпий) соединений, участвующих в реакциях:
Таблица 1.19
Теплоты образования некоторых соединений
Соединение
|
   FeO   
|
|
|
|
|
|
|
|
|
|
190,37
|
100,42
|
128,66
|
79,50
|
264,44
|
1116,74
|
821,34
|
296,81
|
1473,64
|
910,46
|
|
Пользуясь данными таблицы 1.19., подсчитываем теплоты образования
приведенных выше реакций по формуле:
Тепловой баланс печи взвешенной плавки после произведенных расчетов будет
выглядеть следующим образом:
Рассмотрим статьи прихода
Значит, тепловые эффекты реакций qi , МДж / кмоль будут равны
:
Тепло
реакции (I) подсчитаем по количеству, содержащемуся в
, меди:
Остальные
реакции просчитываем по количествам участвующих в них соединений:
Общее количество теплоты Qр, выделяющееся в результате реакций
процесса равно
Q1=-0,2839*19=-5,3941
МДж
Q2=6,4148*24,588=157,727
МДж
Q3=7б3695*0,888=6,544
МДж
Q4=0,1337*5,369=0,718
МДж
Q5=14,5021*4,7937=69,519
МДж
Q7=0,2387*22,922=5,471
МДж
Qр=234585 кДж.
Зная объемы технического кислорода дутья, найденные в материальном
балансе, найдем теплоту, вносимую техническим кислородом дутья:
,
где
, кДж/(м3·єС) - средняя объемная
теплоемкость технического кислорода и интервале температур от 0 єС до
.
Масса и объем технического кислорода в дутье равны mткз, Vтк
Примем Vтк в качестве промежуточных переменных:
Объем
собственно кислорода и азота в техническом кислороде соответственно составят:
Объемы
кислорода и азота в техническом кислороде и воздухе (содержание кислорода в
воздухе 21 % по объему):
Промежуточная
система уравнений:
Решив
эту систему получим:
Так
как
то мы получим, что
=25,334-0,221s
Зная
объемы технического кислорода дутья, найденные в материальном балансе, найдем
теплоту, вносимую техническим кислородом дутья:
,
где
, кДж/(м3·єС) - средняя объемная
теплоемкость технического кислорода и интервале температур от 0 єС до
.
Qтк =1,339*200*(25,334-0,221*s)
Таким образом,
Qприхода = 234585 +6673,805-59,091*s.
Рассмотрим статьи расхода тепла.
Продуктами
плавки являются штейн, шлак и технологические отходящие газы. Теплоту, уносимую
штейном и шлаком, выражаем через энтальпии
и
, которые находим из справочной литературы для
определенных температур и непосредственно для тех составов этих продуктов,
которые получены в результате числового расчета технологии. При этом необходимо
принять температуру штейна и шлака на выходе из печи. Теплота штейна и шлака:
где
iшт = 960, iш
= 1460.
Qшт = 34990,08 кДж, Qш = 97729,48 кДж.
Теплоту
технологических газов рассчитываем по отдельным газовым составляющим. Теплота,
уносимая технологическими газами (за исключением паров воды) равна:
где
,
и
- соответствующие средние объемные теплоемкости
газовых составляющих от 0 до tг.
Теплота,
затрачиваемая на нагрев и испарение внешней влаги концентрата и флюса и нагрев
паров воды:
=9461,71
кДж.
где
2674 - теплота, затрачиваемая на нагрев 1 кг воды от 0 до 100 єС и испарение
влаги при этой температуре и нормальном атмосферном давлении, кДж / кг,
-
средняя теплоемкость паров воды в интервале температур от 100 до tг, кДж / (м3·єС).
Рассчитываем потери в окружающую среду.
Запишем уравнения теплопроводности для данной стенки:
где
- тепловое сопротивление стенки.
Принимаем
значение tн=275єС,
огнеупор
- шамот,
Теплоизоляционный
материал-шлакобетон
кожух
- стальной
Затем
находим среднюю температуру:
=(275+25)/2=150єС
При
полученной температуре из справочной литературы ищем значение критерия Прандтля
(Pr = 0,684).
Теперь
необходимо рассчитать критерий Грасгофа:
Gr=
Находим произведение полученных критериев Gr*Pr=6,698*109 и
в справочной литературе находим вспомогательные коэффициенты c=0.135 и n=0.33
Теплоотдача при естественном движении газа в свободном пространстве печи
можно рассчитать по формуле Михеева:
Nu = c(Gr*Pr)n=235,99
С
другой стороны, критерий Нуссельта равен: Nu =
Следовательно,
коэффициент теплоотдачи равен:
=(235,99*0,336)/1=8,432
q =
8,432*(275-25)=2108 кДж.
Находим
t1= t2+
єС
пот = q*l = 213,309Дж
Qрасхода= Qприхода
234585
+6673,805-59,091*s = 34990,08+ 97729,48 +54498,75+1416,25*s
+9461,71+0,213
Таблица 1.20
Тепловой баланс взвешенной плавки
Q реакции
|
Q техн.кислорода
|
|
|
|
Приход
|
234585
|
4888,324628
|
|
|
|
239473,3
|
Q штейна
|
Q шлака
|
Q O2
|
Q H20
|
Q потерь
|
Расход
|
34990,08
|
97729,48
|
97291,84163
|
9461,71
|
0,213
|
239473,3
|
.15 Выбор размеров печи
Для расчёта теплового баланса принимаем предварительные размеры печи
взвешенной плавки.
Шахта реакционная:
Диаметр шахты принимаем равным, м 10,3
Высоту факела исходя из длины факела горения
(по опытным данным), м 20,5
высота кессонированной части стен, м 13,7
высота некессонированной части стен, м 6,8
толщина футеровки кессонированных стен, м 0,79
толщина футеровки некессонированных стен, м 1,18
толщина футеровки свода, м 1,18
объем шахты, м3 579,9
Отстойная часть:
Площадь пода, м2 259,1
Ширину отстойной части принимаем
по диаметру реакционной шахты, м 10,3
длина пода, м 25,25
высота пода, м 4,5
толщина футеровки подины, м 1,57
толщина футеровки верхних стен свода, м 0,59
толщина футеровки стен на уровне расплава, м 0,79
Аптейк
Высоту аптейка принимаем по высоте
установленного за печью котла-утилизатора, м 24,00
длина аптейка, м 10,3
ширина аптейка равна ширине отстойной части печи, м 10,3
толщина футеровки стен, м 0,79
толщина футеровки свода, м 0,59
площадь сечения на входе в аптейк, м2 79,71
объем шахты, м3 1209,2
2. АВТОМАТИЗАЦИЯ
Важной задачей научно-технического прогресса в цветной металлургии
является разработка и внедрение высококачественных и компактных технологических
процессов, обеспечивающих комплексное использование сырья и снижение вредных
выбросов в атмосферу. К таким процессам можно отнести плавку во взвешенном
состоянии на подогретом дутье.
.1 Печь взвешенной плавки как объект управления
Печь взвешенной плавки предназначена для
перерабатывания сульфидного медного концентрата на штейн и шлак с заданными
извлечениями цветных металлов и железа. В печи выделяют две зоны: зону
теплогенерации и зону технологическую. Каждая из зон имеет своё назначение,
которое определяет во многом построение и особенности узлов автоматического контроля и управления.
Для автоматического управления теплогенерацией и
технологическими реакциями необходимо контролировать целый ряд теплотехнических
и технологических параметров: расходы и давление топлива, воздуха, состав и
температуру продуктов сгорания, покидающих печь, массу исходных материалов,
температуру и состав шлака и штейна.
Для обеспечения высокопроизводительной работы печи
взвешенной плавки необходимо непрерывно контролировать ряд величин,
характеризующих состояние конструктивных элементов и узлов агрегата, например
температуру свода реакционной шахты, газоходов, температуру пода, температуру
кладки аптейка и прочее.
Управление процессом плавки может осуществляться
изменением входных параметров:
· расхода и состава загружаемой шихты;
· расхода дутья, при этом удаётся
регулировать температуру, однако одновременно изменяется и состав штейна.
Состав штейна регулируют поддержанием на определенном
уровне соотношения загрузка шихты - расход дутья; нарушение этого соотношения
может привести к переокислению шлака. При первых признаках переокисления шлака
с помощью корректировки дутьевого режима печь выводится на нормальный режим.
Правильность хода процесса плавки и условий работы
печи оценивается плавильщиком, а также системой автоматики по измеренным
значениям контролируемых параметров. Однако при современном развитии
вычислительной техники есть возможность получить расчётные показатели плавки.
Отклонения от расчётных показателей плавки вносят следующие возмущения:
· колебание состава шихты и оборотных продуктов, поступающих в плавку,
· колебания состава и давления дутья и другие возмущения.
Параметрами, определяющими ход технологического процесса в отстойной
части печи, являются температура и состав штейна и шлака. В штейне
контролируется содержание меди, железа и других элементов.
Температура штейна и содержание извлекаемых металлов в нём - это главные
параметры плавки. Определяющими характеристиками шлака служат содержание в нем
флюсующих элементов и содержание закиси железа.
Параметрами, определяющими теплообменные процессы в печи и состояние
агрегата, являются температура свода, газоходов, давление в рабочем
пространстве и разрежение в котле-утилизаторе, состав продуктов сгорания.
автоматизация медный взвешенный плавка
2.2 Структура АСУ ТП ПВП
Цветная металлургия относится к крупным отраслям сферы промышленности
народного хозяйства Российской Федерации. По характеру производства предприятия
цветной металлургии относятся к непрерывным производствам с тяжелыми условиями
труда, так как включают в себя горячие цехи и переделы с выделениями паров,
пыли и токсичных газов. Эти заводы оснащены агрегатами большой единичной
мощности, обычно выпускают химически чистую продукцию в больших объемах и
являются энергоемкими производствами, так как потребляют значительную долю
топливно-энергетических ресурсов, вырабатываемых в народном хозяйстве. Все эти
обстоятельства делают проблемы механизации и автоматизации производственных
процессов особенно актуальными для цветной металлургии.
Управление вообще и управление металлургическим производством, в
частности, это информационный по своей природе процесс, обеспечивающий
реализацию материального процесса при условии достижения сформулированной
заранее цели функционирования производства и системы управления им. Управление
технологическим процессом это комплекс мероприятий, обеспечивающих стабильное
протекание процесса, повышение эффективности производства в соответствии с
выбранным критерием или критериями оптимальности при заданных экономических и
технологических условиях. Основными критериями эффективности управления
являются повышение технологической дисциплины и производительности труда,
улучшение качества продукции, экономия материальных ресурсов, снижение
себестоимости продукции, улучшение условий труда и культуры производства.
АСУТП - это человеко-машинная система, предназначенная для обеспечения
эффективного функционирования технологического объекта управления (ТОУ) путем
автоматизированного выполнения функций управления.
Состав АСУ ТП ПВП приведен на рис. 2.1.
Состав АСУТП печи взвешенной плавки представляет собой:
. входная информация (потоки сырья и материалов);
2. выходная информация (качество и количество продукции);
. оперативный персонал (технологи, инженеры);
. техническое обеспечение (комплекс технических средств);
5. Организационное обеспечение (технологические инструкции, описания и
инструкции по эксплуатации системы).
Комплекс ПВП включает в себя следующие системы контроля и управления,
обеспечивающие функционирование комплекса в заданном технологическом режиме:
· автоматическая система подачи шихтовоздушной смеси в горелки;
· автоматическая система охлаждения печи;
· система контроля отходящих газов.
Также имеется система промышленного телевидения и система аварийной
сигнализации.
Структура АСУТП трехуровневая:
. Нижний уровень. Обеспечивает выдачу информации о состоянии
технологических параметров технологического оборудования (датчиков),
запорно-регулирующей арматуры и электропровода, а также прием управляющих
сигналов;
2. Средний уровень. Обеспечивает сбор и первичную обработку
информации от измерительных преобразователей и датчиков, выдачу управляющих
воздействий и передачу на верхний уровень системы параметров сигнализации и
измерения;
. Верхний уровень - автоматизированное рабочее место (АРМ).
Обеспечивает взаимодействие с оператором, передачу управляющих команд на нижний
уровень, накопление данных, их архивирование, формирование отчётов, передачу и
прием потоков информации с уровня предприятия.
Сигналы нижнего уровня системы поступают по линиям связи на контроллер,
который преобразует средний уровень системы. В контроллере поступающая
информация обрабатывается и далее по скоростной шине передачи данных передается
на АРМы оператора. Информация на операторских АРМах используется для
формирования видеоинтерфейса, обеспечивающего возможность наблюдения за
технологическими процессами управления протеканием этих процессов.
При необходимости эта связь с другими системами может быть организована
стандартными техническими средствами (модемная связь, радиоканал и др.) с
использованием стандартных протоколов обмена.
Для повышения «живучести» системы контроллер и АРМы оператора
комплектуются источниками бесперебойного питания.
Управление регулирующими, запорными органами и электроприводами в местном
пусконаладочном режиме осуществляется от кнопок, расположенных непосредственно
у приводов.
В основном режиме работы управление регулирующей,
запорной арматурой и электроприводами осуществляется автоматически от
контроллеров, в соответствии с заданными алгоритмами, либо дистанционно с
клавиатуры рабочей станции оператора-технолога. Режимы управления выбираются
оператором-технологом.
Перечень средств низовой автоматики приведён в таблице
2.4., обусловлен их надежностью, высоким метрологическими характеристиками,
быстродействием, наличием систем диагностики и мониторинга, а также имеющимся
опытом их эксплуатации на металлургических предприятиях в условиях действующего
производства.
Средний уровень базируется на серии контроллеров RSLogix 5000 фирмы Allen-Bradley
(США), объединенных сетью Control Net. Контроллерные
шасси и шасси устройств связи с объектом (УСО) размещены в шкафах напольного
типа (шкафы управления).
Верхний уровень базируется на АРМ, установленных в
помещениях операторов и объединенных сетью Ethernet. Для повышения оперативности
управления в операторной предусмотрены 3 станции операторов-технологов, 5
видеомониторов промышленного телевидения.
Повышение стабильности и высокой надежности системы в
тяжелых промышленных условиях достигается использованием дублированной сети и
"горячим" резервированием процессов, а также степенью защиты
оборудования.
2.3 Цели создания АСУТП
Автоматизированная система предназначена для контроля
и управления технологическим процессом взвешенной плавки медного сырья и
производственно-хозяйственной деятельностью плавильного на основе применения
современных программно-технических средств и технологий сбора, обработки,
хранения и передачи информации.
Целью создания АСУ ТП ПВП является разработка
человеко-машинного интерфейса обеспечивающего управление, как технологическим
процессом, так и основным и вспомогательным оборудованием печи во всех режимах
ее работы. Так же должна обеспечиваться выработка и реализация управляющих
воздействий на основное и вспомогательное оборудование на основе анализа информации
о ходе технологического процесса и о состоянии оборудования.
Внедрение автоматизированной системы позволит повысить
технико-экономические показатели производственного процесса взвешенной плавки,
улучшить условия труда за счет оперативности получения информации о техническом
состоянии технологического оборудования и технологических параметрах, повышения
качества управления и принятия соответствующих организационно технических мер.
.4 Функции АСУТП
Функции АСУ ТП ПВП разделяются на информационные и управляющие.
Информационные функции АСУ ТП:
контроль за основными параметрами процесса, т.е.
непрерывная проверка соответствия параметров допустимым значениям;
измерение и регистрация по вызову оператора тех
параметров процесса, которые его интересуют в ходе управления процессом;
вычисление некоторых комплексных показателей,
неподдающихся непосредственному измерению;
вычисление технико-экономических показателей работы
объекта.
Управляющие функции АСУ ТП:
стабилизация управляемых величин технологического процесса
на некоторых постоянных значениях;
программное изменение режимов процесса;
формирование и реализация управляющих воздействий,
обеспечивающих оптимальное течение технологического процесса;
защита оборудования от аварий;
управление пусками и остановками агрегатов.
2.5 Аппаратурный синтез
Структурная схема АСУТП ПВП представлена на рис. 2.5.1.
.5.1
Технические характеристики системы
АСУТП ПВП представляет собой специализированную
систему, что позволяет обеспечить максимальный учет специфики реального объекта
управления и условий эксплуатации при минимальной стоимости системы и
габаритно-массовых характеристиках аппаратуры за счет отсутствия избыточности.
Аппаратура системы разработана с учетом требований максимальной внутри- и
межприборной унификации на уровне конструктивных элементов, функциональных
электронных узлов и модулей, требований ремонтопригодности и эргономики и имеет
единый дизайн и конструктивный стиль.
Аппаратура системы не требует специальных помещений и
может быть установлена в помещении операторских или щитовых. Аппаратура системы
(шкафы автоматизации и местные пульты управления) имеет исполнение IP65 (6 - полная защита против пыли, 5
- защита от брызг воды всех направлений) и предназначена для круглосуточной
работы в условиях плавильного цеха. Исключением являются случаи плановых
профилактических остановок.
За счёт небольших габаритных и весовых характеристик
контроллеров восстановление работоспособности аппаратуры в условиях помещений
плавильного цеха в случае отказа осуществляется путем замены неисправного
прибора исправным из состава ЗИП (запасное имущество и принадлежности) в
течение 10 мин, при этом работоспособность исправной части системы сохраняется
за счет соответствующих алгоритмов живучести.
В аппаратуре системы применена периодическая
автоматическая калибровка измерительных трактов контроллеров, парирующая
технологические, временные и температурные воздействия на их точностные
характеристики.
.5.2 Выбор
контроллерной аппаратуры, подбор персональных компьютеров и настройка сетевого
подключения
В качестве основы комплекса технических средств
применена серия контроллеров RSLogix
(Allen-Bradley). Серия контроллеров представляет собой 6-, 8-, 10-,
12- и 17-местные шасси, в каждом из которых устанавливаются модули питания,
процессорные модули и (или) модули сопряжения, модули ввода/вывода (Input/Output (I/O) модули). Эффективному применению контроллеров
способствует возможность использования нескольких типов центральных процессоров
различной производительности, наличие широкой гаммы модулей ввода - дискретных
и аналоговых сигналов, функциональных моделей и коммуникационных процессоров.
В зависимости от степени сложности решаемой задачи в
контроллерах могут быть использованы различные типа центральных процессоров,
отличающиеся производительностью, объемом памяти, наличием или отсутствием
встроенных входов/выходов и специальных функций, наличием или отсутствием
коммуникационных интерфейсов.
Принцип действия контроллеров базируется на взаимодействии процессора с
памятью программ. В памяти программ хранится программа пользователя. Процессор
обеспечивает управление технологическим процессом в соответствии с этой
программой.
Процессор работает циклически. Каждый цикл начинается
со считывания входных сигналов и записи их значений в область памяти
отображения входных сигналов. Затем шаг за шагом выполняется программа
пользователя. Расчетные значения выходных сигналов записывают в область памяти
отображения выходных сигналов, откуда передаются на выходы контроллера.
Для сбора и обработки сигналов, а также формирования и
выдачи управляющих воздействий будем использовать программно-логический
контроллер (ПЛК) RSLogix5OOO.
Процессоры RSLogix имеют память до 7,5 мбайт и способны обрабатывать до 4000
аналоговых или 128000 дискретных сигналов. Быстродействие процессоров 0,08
мсек/1К битовых инструкций. Процессоры имеют многозадачную операционную
систему, позволяющую выполнять 32 задачи по 32 программы каждая. Модули
ввода/вывода и сетевые адаптеры, и процессоры имеют встроенные средства
самодиагностики.
Контроллер позволяет:
устанавливать процессоры, модули ввода/вывода, сетевые
адаптеры в любое место шасси;
устанавливать процессоры в любом шасси;
нет разделения на шасси вводов/выводов и процессорные;
создавать многопроцессорные системы управления, путем
установки в одно или разные шасси нескольких процессоров;
создавать на базе сети ControlNet распределенные системы управления
протяженностью до 6 км (до 30 км на оптоволокне), причем скорость работы сети
не зависит от длины линии;
организовать МОСТ между двумя сетями, например между
двумя локальными сетями ControlNet, Ethernet, DeviceNet.
заменять модули под напряжением;
задавать индивидуально для каждого модуля ввода/вывода
требуемую периодичность отправки данных и гарантировать ее выполнение.
Принцип организации программируемого контроллера
RSLogix: Шасси контроллера представляет собой сегмент сети ControlNet; каждый
модуль в шасси является станцией. Модули ввода/вывода, процессоры и другие
модули могут быть установлены на любое место в шасси. Обмен данными между
модулями в шасси контроллера ControlLogix осуществляется по принципу
источник-потребитель, как в сети ControlNet. Подключения к "внешним"
сетям ControlNet, Ethernet и др. осуществляется через специальные модули -
коммуникационные процессоры, обеспечивающие передачу данных между внешней сетью
и сетью шасси контроллера. Каждый коммуникационный процессор является узлом
сети, и может самостоятельно передавать и принимать информацию. Их количество в
шасси не ограничено.
Все шасси ControlLogix в системе управления на базе
сети ControINet являются участками сети, а каждый модуль в такой системе
является самостоятельным узлом сети, это в частности, позволяет свободно
распределять процессоры по разным шасси системы управления.
Модули входов/выходов контроллера ControlLogix
отличаются высокой точностью и перегрузочной способностью, развитыми
диагностическими и защитными функциями. Аналоговые входы 16 или 8 каналов, 16
битные, точность 0,1...0,3 %, с контролем обрыва датчика, защита от перегрузки
30 Vdc для входов по напряжению, 8 Vdc для входов по току, оптическая развязка
с шиной обеспечивает защиту по напряжению 2550 Vdc в течение 1 с.
Аналоговые модули входов обеспечивают:
- задание реального диапазона изменения входного
сигнала;
- масштабирование значения входного сигнала в
инженерные единицы;
фильтрацию входного сигнала по выбираемой
частоте;
контроль выхода сигнала за пределы заданного
диапазона;
контроль выхода сигнала за пределы
допустимого диапазона;
контроль превышения допустимой скорости
изменения сигнала;
- обнаружение обрыва провода; простую калибровку с помощью
стандартного пакета программирования. Аналоговые выходы 8, 6, или 4 канала, 15
битные, точность 0,15...0, 3%, с контролем обрыва датчика, защита от перегрузки
24 Vdc, электронное ограничение выходного тока до 21 mА, оптическая развязка с шиной обеспечивает защиту по
напряжению 2550 Vdc в течение 1 с.
Аналоговые модули выходов обеспечивают:
- задание реального диапазона изменения выходного
сигнала;
- масштабирование из инженерных единиц в
значения выходного сигнала;
эхо данных, измерение реального значения
сигнала на выходных клеммах;
ограничение скорости изменения выходного
сигнала;
ограничение допустимого диапазона выходного
сигнала;
обнаружение обрыва провода;
переход в заданное "безопасное
состояние" в случае потери связи с процессором;
- простую калибровку с помощью стандартного пакета
программирования.
Дискретные модули входов имеют исполнения:
стандартное, с изолированными каналами, с диагностикой обрыва линии. Модули
имеют оптическую развязку между каналами / группами и шиной, обеспечивающую
защиту по напряжению 2550 Vdc в течение 1 с.
Модули с электронной защитой обеспечивают защиту от
короткого замыкания, модули с диагностикой обеспечивают определение обрыва
линии, определение короткого замыкания и электронную защиту от него. Модули
выходов с диагностикой обеспечивают контроль срабатывания выходного каскада.
Выходы модулей могут быть программированы на переход в "безопасное
состояние" в случае потери связи с процессором.
В системах управления на базе контроллеров RSLogix предусмотрено аппаратное
резервирование:
- процессоров;
блоков питания шасси контроллеров;
линий связи сети ControlNet.
Программирование контроллера осуществляется с помощью
пакета RSLogix5OOO, реализованного в соответствии со стандартом IEC 61131-3.
Программирование осуществляется на языках релейно-контактных символов,
структурированного текста, функциональных блоков, языке графов. Дружественный
интерфейс, включает все стандартные функции редактирования Microsoft Windows.
Языки программирования поддерживают символьную адресацию, что позволяет
создавать программы с последующей привязкой к реальным объектам.
В составе языка имеются инструкции по работе с
массивами (вплоть до трёхмерных) и структурами (в том числе создаваемыми
пользователем), математические и логические функции, а также специальные
функции для программирования управления процессами.
Программирование всех функций контроллера (включая
контуры регулирования ПИД), а также конфигурирование модулей ввода/вывода и
сетевых адаптеров осуществляется стандартными средствами RSLogix5OOO.
Количество внутренних переменных, контуров регулирования и других инструкции в
рабочей программе ограничено только объёмом памяти процессора. В пакет встроена
функция графического отображения состояния до 16 переменных в виде трендов.
Программа может быть документирована на русском языке.
На верхнем уровне выбрано сетевое оборудование,
которое обеспечивает интеграцию системы в общезаводскую ЛВС. Компьютеры и
мониторы, встроенные в секционированные столы, образуют АРМ операторов. Для
выхода в общезаводскую ЛВС используется оптоволоконный кабель и устанавливается
коммуникационный шкаф.
АРМ - оператора представляет собой персональный
компьютер, выполненный на базе процессора Intel Pentium IV. Для данной схемы
управления достаточным количеством персональных компьютеров будет наличие
одного сервера, трех клиентов (АРМы операторов) и одного ПК программиста.
Архитектура используемых ПК приведена в таблице 2.1.
Таблица 2.1
Технические характеристики персональных компьютеров
Принадлежность
|
CPU
|
RAM
|
Hard Drive
|
Сервер
|
Intel, 3200 MHz
|
512 Mb
|
200 Gb
|
Клиент
|
Intel, 1600 MHz
|
128 Mb
|
20 Gb
|
ПК программиста
|
Intel, 2400 MHz
|
256 Mb
|
40 Gb
|
Так же в комплекте каждого ПК имеется настольный
монитор (не менее 17"), клавиатура и манипулятор типа «мышь» для ввода
команд, громкоговорители акустической системы и установлена операционная
система MS Windows 2000. Питание системных блоков осуществляется от устройств
бесперебойного питания.
Конфигурация контроллеров представлена в таблицах 2.2.
и 2.3.
Таблица 2.2
Конфигурация контроллера АСУ подачи шихтовоздушной
смеси
|
Наименование
|
Количество
|
1
|
Программируемый контроллер RSLogix5OOO 1.5 МВ памяти
|
1
|
2
|
Блок питания контроллерной корзины, 220 В
|
1
|
3
|
Контроллерная корзина, 10 мест для установки модулей
ввода-вывода
|
1
|
4
|
Модуль ввода дискретных сигналов, 24 В, 32 канала
|
1
|
5
|
Модуль вывода дискретных сигналов 24 В, 16 каналов с
электронными предохранителями
|
2
|
6
|
Модуль ввода аналоговых сигналов 4-20 мА, 16 каналов
|
2
|
7
|
Модуль вывода аналоговых сигналов, 4-20 мА, 8 каналов
|
1
|
8
|
Модуль связи по сети Control Net
|
1
|
9
|
Модуль связи по сети EtherNet
|
1
|
Таблица 2.3
Конфигурация контроллера АСУ охлаждения печи
|
Наименование
|
Количество
|
1
|
Программируемый контроллер RSLogix5OOO 1.5 МВ памяти
|
1
|
2
|
Блок питания контроллерной корзины, 220 В
|
1
|
3
|
Контроллерная корзина, 18 мест для установки модулей
ввода-вывода
|
1
|
4
|
Модуль ввода дискретных сигналов, 24 В, 32 канала
|
2
|
5
|
Модуль вывода дискретных сигналов 24 В, 16 каналов с
электронными предохранителями
|
3
|
6
|
Модуль ввода аналоговых сигналов 4-20 мА, 16 каналов
|
7
|
7
|
Модуль вывода аналоговых сигналов, 4-20 мА, 8 каналов
|
1
|
8
|
Модуль связи по сети Control Net
|
1
|
9
|
Модуль связи по сети EtherNet
|
1
|
Сигналы системы контроля отходящих газов поступают на
корзину удаленного ввода-вывода Flex IO. По сети Control Net корзина удаленного ввода-вывода соединена с
контроллером.
Конфигурирование контроллера происходит в среде
RSLogix5OOO. После того как определено количество необходимых модулей и
подобрано шасси, производим конфигурирование контроллерной корзины. Первый шаг
- устанавливаем 10 слотовое шасси и указываем выбранный процессорный модуль.
Далее поочередно набираем корзину:
1. устанавливаем модуль ввода дискретных сигналов;
2. устанавливаем два модуля вывода дискретных
сигналов;
. устанавливаем два модуля вывода аналоговых
сигналов. Для каждого канала (их восемь) указывается тип входного сигнала, и
выполняется градуировка (задается шкала и диапазон сигналов);
. устанавливаем модуль вывода аналоговых
сигналов;
. устанавливаем модуль сети Ethernet и выполняем конфигурирование;
. устанавливаем модуль сети Control Net.
Далее производим аналогичным образом конфигурацию
второго контроллера (АСУ охлаждения) и корзины удаленного ввода-вывода.
Система управления реализована в виде распределенной
контроллерной системы. Все контроллеры объединены посредством технологической
сети, построенной с использованием двух протоколов обмена данных.
На базе индустриального стандарта Ethernet реализована связь для
информационного обмена между компонентами системы и верхним уровнем. Связь
осуществляется по стандартному кабелю категории 5. Сеть предназначена для
передачи информации о состоянии технологического оборудования и технологического
процесса с контроллеров на сервер данных верхнего уровня, и получения команд и
параметров управления с системы верхнего уровня.
На базе стандарта ControlNet реализована связь между компонентами
системы. Связь осуществляется по коаксиальному кабелю. Сеть предназначена для
осуществления связи между контроллерами и связи контроллеров с блоками
распределенной периферии.
Сеть ControlNet основана на топологии общей шины, однако её можно сконфигурировать как в
виде звезды, так и в виде древовидной структуры.
Сеть ControlNet - управляющая сеть, удовлетворяющая
требованиям приложений реального времени с высокой пропускной способностью.
Сеть объединяет функциональность сети ввода-вывода и сети обмена точка-точка,
обеспечивая высокую производительность для обеих функций.
Сеть ControlNet обеспечивает детерминированные,
периодические пересылки всех критических управляющих данных в дополнение к
пересылке некритичных по времени данных. Фирменный метод доступа к носителю,
используемый в сети ControlNet, приводит к детерминированной доставке критичных
ко времени данных запланированных, назначая им более высокий приоритет, чем для
некритичных незапланированных. В результате обновления входов-выходов и
взаимные блокировки контроллеров всегда имеют приоритет перед загрузкой-сохранением
программ и обменом сообщениями.
Все устройства ControlNet имеют прямой доступ к данным
в сети Foundation Fieldbus. Сеть
ControlNet обеспечивает избыточность носителя, что позволяет поддерживать
функционирование системы при повреждении кабеля и взрывобезопасность при
обеспечении оптоволоконного канала передачи.
К сети могут быть подключены программируемые
логические контроллеры (ПЛК), датчики, исполнительные механизмы (ИМ), частотные
привода (ЧП) и др. Запланированные данные передаются со скоростью 5 Мбит/с, что
улучшает как производительность ввода-вывода, так и связи процессор-процессор.
Гибкая архитектура системы может работать с несколькими процессорами, в любом
месте кабеля шины сегмента сети можно установить до 99 адресуемых узлов (через ответвители).
На сегменте ControlNet можно осуществить как
дискретные, так и недискретные посылки данных входов-выходов. Дискретная
передача данных ввода-вывода происходит, когда единственный блок данных
ввода-вывода (8, 16 или 32 бита, соответствующие образу модуля ввода-вывода)
передается и принимается одновременно от всех модулей в шасси. Таким образом,
за одну дискретную пересылку обновляется образ ввода-вывода для всех дискретных
модулей, установленных в шасси. Недискретная передача данных происходит, когда
блок данных (до 64 слов в пакете) пересылается в один или из одного иска
ввода-вывода.
Каждая таблица отображения входов-выходов процессора
ControlNet может содержать ограниченное число данных. Каждое вхождение в сеть
соответствует одной запланированной пересылке данных входов-выходов между
процессором ControlNet и шасси ввода-вывода или же сообщение другому процессору
ControlNet. Поскольку добавления вхождения к таблице отображения входов-выходов
создает запланированную пересылку данных входов-выходов на периодической
основе, которую определяет пользователь, то для запланированных пересылок
данных не требуется программная логика. Для не дискретных передач ввода-вывода
существует возможность программирования их как незапланированных пересылок,
чтобы сделать их пересылками по событию.
Конфигурирование сети ControlNet производится в среде
RS NetWorx for ControlNet. Аналогично конфигурированию контроллерной корзины
производится настройка сети Control Net. Сначала указывается модуль
подключения, затем указывается шасси и происходит набор корзины. На рисунке
2.3. представлен этап выбора модуля и корзины.
Рис. 2.3 Конфигурирование подключения по ControlNet
После того как корзина собрана, подключаем по сети ControlNet корзину удаленного ввода-вывода Flex IO. Конфигурирование происходит аналогично (8 слотовое шасси и
два модуля ввода аналоговых сигналов). На рисунке 2.4. общий вид окна
приложения RS NetWorx for ControlNet.
Рис. 2.4 Окно приложения RS NetWorx for ControlNet
2.5.3
Контрольно-измерительные приборы
Используемые измерительные приборы для реализации
проекта представлены в табл. 2.4.
Контроль основных параметров осуществляется следующим
образом:
Температура расплава.
Для измерения температуры расплава по ходу плавки служат пирометры
спектрального отношения, которые относятся к бесконтактным средствам измерения,
т. е. при измерении отсутствует непосредственное соприкосновение исследуемой
среды и датчика. Пирометры спектрального отношения предназначены для
определения цветовой температуры путем измерения отношения спектральных
энергетических яркостей, соответствующим двум длинам волн.
Температура в печи, котле-утилизаторе, газоходах.
Температура кладки реакционной шахты в районе факела
горения шихтововоздушной смеси должна сохраняться в пределах от 12000С
до 13500С, измеряется радиационным пирометром, измерение температуры
которым основано на улавливании теплового излучения и концентрировании его на
термочувствительном элементе с помощью собирательной линзы, установленном в
специальной арматуре в реакционной шахте печи после горелки. Для контроля
температуры кладки котла-утилизатора радиационный пирометр в защитной арматуре
через визирную трубу, установленную в кладке стены котла-утилизатора,
визируется на переднюю стенку котла-утилизатора. Температура отходящих газов в
газоходе после котла-утилизатора составляет 310 - 4000С. Измерение
данной температуры производится стандартной хромель-алюмелевой термопарой в
металлической чехле.
Давление в шихтовоздушных горелках, разрежение в
газоходе.
Отбор давления в шихтовоздушных горелках
осуществляется импульсной трубкой со свода печи в центральной его части.
Давление в этой точке зависит от конструкции и режима работы печи и составляет
в среднем 0,1 МПа. Для контроля разрежения в газоходной системе импульсную
трубку устанавливают в газоходе после котла-утилизатора и соединяют трассой с
показывающим тягомером на щите автоматики печи.
Система охлаждения конструкций печи.
Для обеспечения оптимальной температуры нагрева кладки
реакционной шахты печи используют систему испарительного охлаждения с
применением кессонов.
2.6 Программное обеспечение АСУТП
Современные распределительные системы управления (РСУ) характеризуются
территориальной и функциональной распределенностью систем сбора данных и
управления. Контроль хода технологического процесса и управление низовой
автоматикой осуществляется оператором автоматизированного рабочего места
оператора (АРМ-оператора).
Представление данных в реальном масштабе времени в ходе технологического
процесса, визуализации процесса в виде мнемосхем, составление отчетов и
графиков, сигнализация отклонений параметров и др. функции осуществляются с
помощью специального программного обеспечения SCADA (Supervisory Control And Data Acquisition) - система
сбора данных и оперативного диспетчерского управления, разрабатывалась как
универсальное многофункциональное программное обеспечение систем верхнего
уровня, позволяющее оперативному персоналу наиболее эффективно управлять технологическим
процессом.
Основные функции, выполняемые практически любой из многих представленных
на рынке промышленной автоматизации SCADA - систем:
· сбор данных о параметрах процесса, поступающих от контроллеров или
непосредственного от датчиков и исполнительных устройств (значения температуры,
давление и других параметров, положение клапан или вала исполнительного
механизма);
· обработка и хранение полученной информации. Под обработкой информации
понимается выполнение функций фильтрации, нормализации, масштабирования и др.;
· графическое представление в цифровой, символьной и иной форме
информации о ходе технологического процесса;
· сигнализация изменений хода технологического процесса,
особенного в предаварийных и аварийных ситуациях в виде системы алармов. При
этом может осуществляться регистрация действий обслуживающего персонала в
аварийной ситуации;
· формирование сводок, журналов и других отчётных документов о ходе
технологического процесса на основе информации, собранной в архивах;
· формирование команд оператора по изменению параметров настройки и режима
работы контроллера, исполнительных устройств (пуск-останов, открытие -
закрытие).
Автоматическое управление ходом технологического процесса в соответствии
с имеющимся в SCADA - системах алгоритмами управления (ПИ-, ПИД-регулирование,
позиционное, нечеткое регулирование и др.). Данные функции рекомендуется
использовать для решения задач невысокого быстродействия.
Таким образом, SCADA - системы являются мощным инструментом для
разработки ПО верхнего уровня АСУ ТП. При этом от разработчика не требуется
больших знаний в области программирования на языках высокого уровня.
Необходимо подвести итог:
в качестве программного обеспечения выбраны следующие программы фирмы Allen-Bradley:
· Программа связи RSLinx
· Пакет RSView32
(SCADA - система)Дополнения к RSView32:
1RSActive Display System
2RSSql
3RSView32 Historian
4RSLoop Optimaizer.
Программные продукты Rockwell Automation позволяют создавать системы
человеко-машинного интерфейса различной сложности, решать задачи по сбору и
архивированию данных, обмену информацией между системами управления и с
программами верхнего уровня. Внедрение в программные продукты стандартов
Microsoft делает их простыми в освоении, удобными в использовании и
эффективными в работе.
Программа связи RSLinx организует через ОРС -, DDE -, Advance DDE серверы
связь программ верхнего уровня (пакеты программирования, SCADA, и др.) с
программируемыми контроллерами. Обмен информацией с контроллерами
осуществляется по сетям. RSLinx выполняет оптимизацию трафика путем группировки
передаваемой информации в пакеты.
Пакет RSView32 позволяет реализовать полнофункциональную SCADA, включая
отображение графиков, "тревог", архивацию данных и вывод отчетов,
обработку "рецептов" и т.п. Создание проекта не требует
программирования. Пакет позволяет работать с векторными и битовыми графическими
изображениями созданными в других программах.
Дополнения к RSView32.SPC (поставляется бесплатно) обеспечивает
возможность статистического контроля за отдельными тегами.Messenger
(поставляется бесплатно) позволяет организовать передачу сигналов тревоги и
коротких отчетов по электронной почте, на пейджер, на факс, а также
синтезировать звуковое сообщение через звуковую карту.Trend (поставляется
бесплатно) обеспечивает отображение исторических данных, полученных из
различных источников. Может рисоваться до 100 графиков.RecipPro (поставляется
бесплатно) позволяет создавать и редактировать файлы "рецептов",
которые могут содержать до 5000 ингредиентов, 1000 наборов данных, 500 тегов в
виде электронной таблицы.Webserver позволят обеспечить доступ через интернет с
помощью любого стандартного web-браузера к технологической информации.
RSView32.Display System позволяет организовать SCADA на базе клиент-серверной
структуры. Поддерживается до 20 клиентов.обеспечивает обмен данными между
тегами программируемого контроллера и базами данных, соответствующих стандартам
ODBC 2.0, Oracle OCI, SAP и др. Пакет позволяет выполнять транзакции по
заданным условиям, таким как событие (изменение значение тега), периодически и
т.п. Допускает двунаправленный обмен.Historian предназначен для проведения
статистического анализа данных и подготовки отчетов. Позволяет создавать архивы
и сохранять данные на CD, магнитных лентах и т.п.Optimaizer анализирует
процесс, автоматически создает модель для всех контуров регулирования и
позволяет на основании этой модели подбирать и тестировать параметры PID
регуляторов. Программа позволяет определять взаимное влияние контуров
регулирования, настраивать каскадированные регуляторы, выбирать параметры
исходя из необходимости более "спокойной" или более
"агрессивной" работы регуляторов и многое другое.
Программирование контроллера осуществляется с помощью пакета RSLogix5000,
реализованного в соответствии со стандартом IEC 61131-3. В этом стандарте
описаны:
два текстовых языка:
5IL -
список инструкций
6ST -
структурированный текстдва графических языка:
7LD - язык лестничных диаграмм
8FBD -
язык диаграмм функциональных блокова так же язык графических схем:
- SFC - язык последовательных функциональных схем
Стандарт IEC 61131-3 не устанавливает правил взаимодействия программного
обеспечения, поставляемого изготовителем, что позволяет повысить гибкость
представления и сделать программирование более удобным для пользователя.
3. СПЕЦИАЛЬНАЯ ЧАСТЬ
Математическую модель процесса разрабатывали на основе
экспериментально-аналитических методов. Структуру модели при этом определили с
позиций детерминистического подхода.
Химизм процесса окисления шихты правомерно представить основными
стехиометрическими уравнениями:
1. 2 CuFeS2
Cu2S + 2 FeS + S
. FeS2
FeS + S
. 2 FeS + 3O2
2 FeO + 2 SO2
. 4 FeO + O2
2Fe2O3
. S + O2
SO2
Данные уравнения отражают в общем, виде суммарное действие различных
химических реакций и представлены в виде, позволяющем учесть основные продукты,
получающиеся в процессе плавки шихты на штейн. Скорость окисления сульфидных
компонентов шихты лимитируется диффузионными стадиями, а кинетика химических
реакций не оказывает существенного влияния на скоростные характеристики
процесса. В этих условиях правомерно процесс представить суммой реакций
псевдопервого порядка.
При математическом описании плавки шихты дополнительно к рассмотренным
положениям использовали ряд упрощающих допущений: все химические реакции
протекают в пределах печи и их скорость не зависит от массовых концентраций
продуктов окисления; образованием SO3
в отходящих газах пренебрегаем, так как содержание его в отходящих газах
составляет доли процента; скорость окисления не зависит от концентрации
сульфидных компонентов в расплаве, так как плавка шихты ведется с получением
штейна, то есть процесс окисления протекает со значительным избытком сульфидов.
Математическая модель процесса плавки шихты во взвешенном состоянии на
подогретом дутье получили в виде системы уравнений материальных балансов по
участвующим в процессе веществам и привели к виду:
С
*Gш - 2*К3*С
*О
- G
= 0
2*К3*С
*О
- 4*К4*С
*О
- G
= 0
Gш*alfaO2*0,3 + Gш*0,02609-2*К3*С
*О
*0,86-0,1434*С
*Gш-0,437*
С
*Gш = 0
В
основе процессов расслаивания расплавов на шлак и штейн лежат явления
разделения двух фаз на основании разности удельных масс и коагуляции
полидисперсных систем (укрупнение частиц).
При
математическом описании разделения расплава на шлак и штейн использовали
следующие основные положения и упрощающие закономерности.
Закономерности
осаждения сульфидных частиц из окисленного расплава описываются следующим
уравнением:
,
где
Сi -
концентрация i-того сульфидного компонента в расплаве;
v - скорость
осаждения сульфидных частиц;
- высота
слоя окисленного расплава.
Скорость
осаждения сульфидных частиц в определенных пределах может быть выражена
уравнением Стокса:
v =
,
где
- плотность частиц штейна;
-
плотность частиц окисленного расплава (шлака);
g - ускорение
свободного падения;
-
вязкость шлака;
r
- приведенный (эквивалентный) радиус оседающих частиц.
Полидисперсную систему рассматривали как бидисперсную и при этом
динамикой осаждения крупных частиц пренебрегли. Тогда кинетика осаждения мелких
частиц за счёт ортокинетической коалесценции (исчезновение мелких частиц за
счёт слияния с крупными при осаждении последних с большой скоростью) может быть
выражена следующим уравнением:
,
где
n/ -
содержание мелких частиц в единице объема;
В
- аттракционный объем, создаваемый крупными частицами в единицу времени в
процессе их осаждения.
Потоки
сульфидных частиц при таком представлении рассматриваемых явлений представили
как суммы потоков крупных частиц, потоков мелких частиц, не изменяющихся в
процессе осаждения, и потоков мелких частиц, осаждаемых при слиянии с крупными
частицами. При этом соотношение потока крупных частиц приняли пропорциональным:
р
= р0 - р1*С
.
Математическую
модель разделения расплава на шлак и штейн получили в виде системы уравнений
материальных балансов по участвующим в процессе веществам:
В
этом уравнении в квадратных скобках представлены потоки сульфидных частиц из
зоны разделения в штейн, они определяют состав штейна по уравнению:
Для
определения вязкости расплава необходимо дополнительно определять текущее
значение содержания SiO2 в
расплаве и его температуру.
Материальный
баланс по двуокиси кремния для зоны разделения расплава имеет вид:
Полученная
система уравнений материальных балансов по участвующим в процессе веществам
представлена ниже на рис. 3.1.
При исследовании полученной модели процесса плавки
сульфидного сырья, мы установили следующее:
при увеличении содержания меди в шихте, содержание
меди в штейне возрастает (рис.3.2.).
Рис. 3.1 Математическая модель процесса плавки сульфидного сырья в ПВП
Рис. 3.2 Характеристика изменения содержания меди
вштейне при изменении содержания меди в шихте
- при увеличении содержания меди в шихте, содержание меди в шлаке
возрастает (рис.3.3).
Рис. 3.3 Характеристика изменения содержания меди в
шлаке при изменении содержания меди в шихте
- при уменьшении содержания меди в шихте, содержание
меди в штейне уменьшается (рис.3.4).
Рис. 3.4 Характеристика изменения содержания меди в
штейне при изменении содержания меди в шихте
- при уменьшении содержания меди в шихте, содержание
меди в шлаке уменьшается (рис.3.5).
Рис. 3.5. Характеристика изменения содержания меди в
шлаке при изменении содержания меди в шихте
- при увеличении содержания SiO2
в шихте, содержание меди в штейне уменьшается (рис.3.6).
Рис. 3.6 Характеристика изменения содержания меди в
штейне при изменении содержания SiO2 в шихте
при увеличении содержания SiO2 в шихте,
содержание меди в шлаке уменьшается (рис.3.7).
Рис. 3.7 Характеристика изменения содержания меди в
шлаке при изменении содержания SiO2 в шихте
Необходимо построить статические характеристики процесса плавки
сульфидного сырья.
Таблица 3.1
Содержание Cu шихты
|
Содержание Сu штейна
|
15,2
|
43,53
|
17,1
|
46,85
|
19
|
50,01
|
20,9
|
53,02
|
22,8
|
55,91
|
Рис.
3.8 Статическая характеристика содержание Cu штейна = f
Таблица 3.2
Содержание Cu шихты
|
Содержание Cu шлака
|
15,2
|
0,737
|
17,1
|
0,883
|
19
|
0,9995
|
20,9
|
1,115
|
22,8
|
1,23
|
Рис.
3.9 Статическая характеристика содержание Cu шлака = f
(содержание Cu шихты)
Таблица 3.3
Содержание SiO2 шихты
|
Содержание Сu штейна
|
0,15
|
50,12
|
0,17
|
50,06
|
0,19
|
50,01
|
0,21
|
49,95
|
0,23
|
49,9
|
0,25
|
49,84
|
0,27
|
49,79
|
0,29
|
49,74
|
0,31
|
49,69
|
0,33
|
49,64
|
0,35
|
49,59
|
0,37
|
49,54
|
0,39
|
49,49
|
Рис.
3.10 Статическая характеристика содержание Cu штейна = f
(содержание SiO2 шихты)
Таблица 3.4
СодержаниеSiO2 шихты
|
Содержание Сu шлака
|
0,15
|
1,013
|
0,17
|
1,006
|
0,19
|
0,9995
|
0,21
|
0,9929
|
0,23
|
0,9865
|
0,25
|
0,9801
|
0,27
|
0,9738
|
0,29
|
0,9676
|
0,31
|
0,9615
|
0,33
|
0,9554
|
0,35
|
0,9494
|
0,37
|
0,9436
|
0,39
|
0,9377
|
Рис.
3.11 Статическая характеристика содержание Cu шлака = f
(содержание SiO2 шихты)
Таким
образом, при исследовании полученной модели плавки сульфидного сырья в печи
взвешенной плавки при увеличении содержания меди в шихте, содержания меди в
штейне и в шлаке возрастает и, наоборот, при уменьшении содержания меди в
шихте, содержания меди в штейне и в шлаке уменьшается. Однако при увеличении
содержания SiO2 в шихте,
содержание меди в штейне и в шлаке уменьшается.
Это
соответствует справочным данным, значит, исследования были проведены верно.
Технологический процесс плавки сульфидного сырья в печи ПВП относится к
высокоскоростным процессам переработки сырья. При этом формировать типовую
структуру управления по возмущению, а именно - состав продуктов переработки
(входные управляющие параметры) не представляется возможным по причине большого
транспортного запаздывания в системе получения информации о составе продуктов и
дискретности получения этой информации. Следовательно, систему управления
строим по принципу компенсации возмущений на входе. Структурную схему
управления можно разбить на две подсистемы:
Рис. 3.12 Блок-схема системы управления процессом плавки ПВП с
использованием ЭВМ
Таким образом, из приведённого выше следует, что структурную схему
управления можно разбить на две подсистемы:
. систему шихтовки материалов, которая должна обеспечивать паспортный
состав шихты для плавки на оптимальный состав шлака;
2. режим плавки, с помощью которого мы задаём режим управления
процессом плавки из условий получения заданного состава штейна по меди, что
обеспечит ритмичную переработку штейна на последующих стадиях.
Для обеспечения автогенности процесса требуется система регулирования
теплового режима.
В связи с тем, что процессы, протекающие в факеле, практически
безинерционны, а жестко выдержать подачу шихты с практически нулевой влажностью
затруднительно, следовательно, возникают также ситуации, в которых если расход
шихты в какой-нибудь период времени получается меньше заданного, то происходит
переокисление расплава, а, следовательно, что ведёт к потерям меди со шлаками.
При избытке шихты по отношению к заданному получается медный по меди
штейн. Это приводит к более продолжительному времени переработки такого штейна,
а следовательно, к дополнительным расходам. Значит, основная задача заключается
в организации управления соотношения шихта - дутьё.
Для организации температурного режима необходимо вводить определённое
количество теплового потока с дутьём, то есть при заданном расходе дутья
температура дутья должна быть постоянной. Следовательно, температура в печи в
факельной зоне должна быть постоянной.
Для того чтобы отработать возмущения, необходима система регулирования,
которая бы обеспечивала компенсацию температуры и корректировала расход
штеиного потока с дутьем по температуре в факельной зоне. Данная система
приведена ниже на рис. 3.13.
Рис. 3.13. Схема управления соотношения шихта - дутьё: ДТ - датчик температуры,
Р-Р - регулятор; 1 - весоизмеритель, 2 - пульт управления, 3- электродвигатель,
4 - датчик расхода
Приведенная выше схема является каскадной системой управления
температуры, предусматривающая стабилизацию температуры дутья с коррекцией
температуры в факельной зоне. Данная система является типовой.
4. ОХРАНА ОКРУЖАЮЩЕЙ СРЕДЫ
.1 Характеристика предприятия как источника нарушения и загрязнения
природной среды
Охрана природы и рациональное использование природных
ресурсов - одна из важнейших задач, стоящих перед металлургами при
строительстве и эксплуатации производств.
Надеждинский металлургический завод производит
переработку медного сульфидного сырья путем плавки во взвешенном состоянии. К
наиболее мощным источникам загрязнения окружающей среды на промышленном объекте
относят плавильный и рафинировочный передел. Основным источником выбросов в
атмосферу в медном производстве отделения печей взвешенной плавки является
дымовая труба, установленная после сернокислотного цеха с системой очистки газов
от серы, и аэрационные фонари зданий основного производства и газоочистки.
Дымовая труба используется для централизованных выбросов отходящих газов
сернокислотного цеха. Дымовая труба выполнена из железобетона (несущий ствол),
изнутри футерована шамотом. Высота трубы 70 м; внутренний диаметр устья 3 м;
температура выбрасываемой смеси 100-180 °С. Загрязнение окружающей среды
линейными источниками (здания пиропроцессов и газоочистки) происходит
вентиляционными выбросами через короба и иные проёмы, расположенные вдоль
отделения. Компоненты пыли и газов появляются в вентиляционных выбросах при
нарушении технологии процесса плавки медного концентрата в печах взвешенной
плавки, нарушении правил эксплуатации агрегатов и оборудования газоочистки;
загрузке в агрегат концентратов, оборотной пыли.
Чтобы предотвратить отрицательное воздействие металлургического
производства на окружающую среду, к нему предъявляются следующие требования:
- комплексность использования сырья;
улавливание, очистка и утилизация выбросов;
применение систем оборотного водоснабжения, методов
глубокой очистки сточных вод, безводных технологий;
складирование шлаков на непригодных для сельского
хозяйства землях, рекультивации шлаковых отвалов, утилизация шлаков.
4.1.1 Район
расположения и природные климатические условия
Надеждинский металлургический завод относится к заполярному филиалу ГМК
«Норильский Никель» и расположен на юге Таймырского полуострова, где
биогеографическим центром является плато Путорана., которое занимает большую
часть обширного прямоугольника, образованного реками Енисей, Хета, Котуй и
Нижняя Тунгуска и простирающегося примерно на 650 км как с севера на юг, так и
с запада на восток. Площадь плато - более 250 тыс. кв. км. Плато представляет
собой ряд базальтовых покровов мощностью 2000 м и более, формировавшихся с
каменноугольного периода. Оно куполообразно приподнято и имеет высшую отметку
1701 м; это поднятие - гора Камень - самое высокое на Среднесибирском
плоскогорье. От наивысшей точки купола водораздельные пространства радиально
понижаются до 800-1000 м. На западе и севере плато резко обрывается
300-800-метровыми уступами, которые образуют четкую границу с Приенисейской
(Западно-Сибирской) и Северо-Сибирской низменностями и Котуйским шито. На юге и
северо-востоке плато постепенно понижается до 500-700 м, плавно переходя к
общему уровню Среднесибирского плоскогорья.
Некоторые особенности рельефа (отпрепарированность трапповых ступеней,
выработанность долин крупнейших озер, присутствие моренного материала) в тех
или иных районах плато можно рассматривать как следствие оледенения.
Тектонические разломы, выветривание, деятельность рек сформировали современный
рельеф плато, придав ему облик гор.
Во многих тектонических трещинах возникли реки, а в наиболее глубоких
разломах сформировались озера. Уникальные по красоте тектонические озера
Путораны, которые нередко называют "внутренними пресноводными
фьордами", почти не имеют аналогов в мире. Больше всего озер находится в
центральной и северо-западной части плато, где глубина эрозионного расчленения
превышает 800 м. Реки врезались в плато на глубину 1000-1300 м, образуя узкие
извилистые долины с крутыми склонами, многочисленными порогами и водопадами.
Характер рек типично горный. Питание рек и ручьёв преимущественно снеговое.
Наибольший сток рек приходится на период интенсивного таяния снега (май-июнь).
Зимой сток практически прекращается, часто реки промерзают до дна. В летнее
время обычны дождевые паводки.
Озера освобождаются ото льда поздно, а на реках образуются мощные наледи.
Огромные массы льда и холодной воды создают особый микроклимат в озерных
котловинах и речных долинах.
По температурным показателям климат Путораны близок к климату горных
районов Якутии, отличаясь от последнего гораздо большей влажностью. Годовая
сумма осадков на плато составляет 473-671 мм, в среднем 586 мм. На долю дождя и
тумана приходится 70% годовой суммы осадков, на долю снега - 30%. Число
дождливых дней достигает 60, особенно сильные и продолжительные дожди бывают в
августе, когда за трое-четверо суток выпадает более 50 мм осадков. Высота
снежного покрова изменяется в среднем от 80 см у подножия склонов до 50 см на
вершине плато. Выпуклые и равнинные участки часто почти лишены снежного
покрова. На подветренных частях трапповых ступеней мощность снежных забоев
может достигать нескольких метров. Зима на плато очень холодная, среднесуточные
температуры часто достигают -44°С, абсолютный минимум -68°С зарегистрирован в
феврале (метеостанция Агата). В летний период абсолютный максимум 30°С.
Заморозки на почве нередко случаются даже в разгар лета. Вегетационный период в
среднем длится около 90 дней, период активной вегетации 52 дня, в среднем с 26
июня по 16 августа. Краткость этого периода компенсируется круглосуточным
освещением с 11 июня по 2 августа и близким к круглосуточному в остальное время
лета. Суточное количество радиации на плато Путорана превышает данный
показатель для субтропиков, что создает здесь особо благоприятные условия для
фотосинтеза. Плато Путорана находится в области сплошного распространения вечной
мерзлоты. Для всех почв плато характерны высокая глинистость и связанное с ней
мерзлотное рельефообразование. Из-за суровости климата на высотах более
1000-1200 м выражены лишь начальные этапы почвообразовательного процесса. Здесь
физическое выветривание преобладает над химическим. Значительные площади
гольцовых пространств плато заняты крупноглыбовыми и мелкокаменистыми
россыпями. На этих высотах отсутствуют не только почвы, но и скопления
мелкозема. С уменьшением абсолютной высоты появляются грубоскелетные
фрагментарные почвы. Ниже они сменяются горно-тундровыми почвами.
.2 Охрана атмосферного воздуха
.2.1
Санитарно-защитная зона
Согласно СанПиН 2.2.1/2.1.1. 1200-03 санитарно-защитная зона предприятия
составляет 1000 м (класс I). В санитарно-защитную зону предприятия не попадают
жилые строения индивидуального пользования. Вокруг территории предприятия нет
лесных массивов, нет болот. Нормирование качества воды рек, озёр, водохранилищ
проводят в соответствии с «санитарными правилами и нормами охраны поверхностных
вод от загрязнений». Правила устанавливают нормированные значения для следующих
параметров воды водоёмов: содержание плавающих примесей и взвешенных веществ,
запах, привкус, окраска, температура воды, значение рН, состав и
предельно-допустимые концентрации (ПДК) ядовитых и вредных веществ. Качество
атмосферного воздуха нормируется также ПДК загрязняющих веществ (для населённых
пунктов).
Состав отходящих газов после печи ПВП приведён ниже в таблице 4.1.
(состав приведен из расчёта переработки 100 кг сухого концентрата).
Таблица 4.1
Состав отходящих газов
Газ
|
Всего при н. у., м3
|
Всего, % по объему
|
Всего, кг
|
Всего, % по массе
|
С02
|
0,36
|
1,65
|
0,71
|
1,95
|
S02
|
6, 68
|
30,53
|
19,12
|
52,47
|
02
|
0,70
|
3,20
|
1,00
|
2,74
|
N2
|
9,26
|
42,28
|
11,58
|
31,78
|
Н20
|
4,89
|
22,34
|
3,93
|
10,78
|
Всего
|
21,89
|
100,00
|
36,44
|
100,00
|
Рассмотрим сернистый ангидрид (SО2) - бесцветный газ с острым
запахом, тяжелее воздуха в 2,26 раза; ПДК его 20 мг/м3. Образуется
SО2 и выделяется в плавильном цехе при окислении сульфидного сырья.
Раздражает преимущественно верхние, а при длительном воздействии также и
глубокие дыхательные пути. Вдыхание более высоких концентраций ведет к
охриплости, болям, чувству стеснения в груди и к бронхиту. Является ценным
компонентом и служит для получения серной кислоты и элементарной серы. Однако
при низком его содержании производство кислоты экономически не выгодно и
технологические газы в обход трубы сернокислотного цеха сбрасываются в
атмосферу.
Технологические газы содержат до 30-50 мг/м3 пыли, которая
улавливается (сначала котлом-утилизатором, а затем осаждается в сухих
электрофильтрах) и идёт в оборотное производство. Газы после очистки
выбрасываются в атмосферу, чем вызывают загрязнение атмосферного воздуха.
Концентрацию загрязняющих веществ в атмосфере в жилой зоне контролирует
городская СЭС, ежедневно. Отчёты о проведении анализов направляются заводу в
отдел охраны природы ежемесячно. В случае превышения установленных нормативов
выясняются причины и, чаще всего, за этим следует штраф.
На заводе разработан проект норм предельно допустимого выброса (ПДВ), в
нем предложен список загрязняющих веществ, по которому АО "ГМК Норильский
никель " контролируется СЭС, районным комитетом по охране окружающей среды
и другими инспектирующими органами:
· окись углерода;
· сернистый ангидрид;
· диоксид углерода.
На заводе проведена инвентаризация выбросов.
Инвентаризация выбросов (ГОСТ 17.2.1.04-77) представляет собой
систематизацию сведений о распределении источников по территории, о количестве
и составе воздуха. Основной целью является получение исходных данных для:
оценки степени влияния выбросов загрязняющих веществ предприятия
наокружающую природную среду;
установление предельно допустимых норм выбросов загрязняющих веществ ватмосферу,
как целым предприятием так и отдельными источниками загрязняющими атмосферу;
оценка состояние пыли газоочистного оборудования предприятия; -
планирование природоохранных работ на предприятие.
4.3 Охрана подземных и поверхностных вод
Основными потребителями воды и источниками сброса в плавильном цехе
являются системы водяного и испарительного охлаждения, котлы-утилизаторы,
отделение подготовки шихты. В цехе сконструирована система оборотного
водоснабжения, обеспечивающая подачу и отведение воды для всех технических
нужд. Система водообеспечения в идеале не предусматривает сброс сточных вод в
природные водоёмы и водотоки. Оборотная вода после использования поступает на
очистные сооружения, а затем возвращается потребителям.
Однако на практике часть воды поступает в промышленно-ливневую
канализацию. Расход воды в промышленно-ливневой канализации колеблется от 80 до
305 м3/час, средний расход составляет 193 м3/час.
Содержание цветных металлов в канализации оставляет в среднем, мг/литр: 0,04
меди, 0,013 кобальта. Суммарный сток комбината колеблется от 1100 до 1600 м3/час.
60 % этого стока формируют сточные воды цехов комбината, 26 % сток плавильного
цеха, 14 % сток очистных сооружений.
В эксплуатации находится промышленный участок очистки сточных вод общего
цеха комбината. Однако вода в контрольном створе остается загрязненной,
особенно тяжелыми цветными металлами, это связано, прежде всего, с воздушным
переносом пыли производства.
Контроль за сбросами ведется по схеме-графику. График ведомственного лабораторного
контроля за составом сточных вод и их влияние на гидрохимический режим
выполняется аккредитованной лабораторией завода.
4.4 Охрана земельных ресурсов
Основными отходами производства являются пыль и шлаки. Пыль,
выбрасываемая в приземный слой атмосферы через дымовую трубу и аэрационные
фонари, близка по химическому составу к исходному сырью и составляет 10-12 % от
него. Поэтому экономически выгодно подвергать отходящие газы пылеочистке. По
методике расчёта процесса плавки и в связи с конструктивными особенностями печи
пыль практически шестью улавливают и возвращают в производство. Однако из-за
разного рода факторов (в основном технологических) существует значительный
пылевыброс в атмосферу, а затем его осаждение на поверхность
Шлаки печи взвешенной плавки идут на обеднение в электрические
обеднительные печи и лишь потом в отвал. Обеднение способствует максимально
снизить опасность загрязнения почвы цветными металлами. Шлаковые отвалы
находятся на небольшом состоянии от промплощадки комбината.
5. БЕЗОПАСНОСТЬ ЖИЗНЕДЕЯТЕЛЬНОСТИ
.1 Безопасность в условиях производства
.1.1 Анализ
вредных и опасных факторов производства
Технологический процесс взвешенной плавки по совокупности факторов
производственной среды, оказывающих влияние на здоровье и работоспособность
человека, относится к производству с вредными условиями труда. Многие работы -
выдача шлака, штейна, горячий ремонт кладки - производится вручную в районе
интенсивного выделения тепла и концентрированных сернистых газов, что создает
тяжелые условия труда.
Особенностями ведения технологического процесса являются: работа с
расплавами, применение технического и технологического кислорода, природного
газа, механизмов с вращающимися деталями, возможность выделения газа и пыли в
атмосферу отделения.
Обслуживающий персонал печей взвешенной плавки производит различные
операции с расплавами - выдача шлака, штейна, неправильное и небрежное
выполнение этих операций может привести к выплеску расплава, взрывам и в
отдельных случаях к авариям.
При взвешенной плавке используют кислород, дутье, неправильное обращение
с которыми может привести к пожарам, взрывам, отравлениям.
Возможны ожоги лица и других частей тела расплавом. Особенно часто это
случается при прожиге шпуров или при закрытии шпуров, когда нарушаются
правильные приемы работы и не используются соответственные спецодежда и
защитные средства, а так же при взрывах и хлопках при попадании штейна в сырые
ковши и чаши; ожоги рук раскаленным инструментом (ломики, шуровки и т.д.) при
работе без рукавиц или в изношенных рукавицах, а также ожоги лица и других
частей пламенем при работе печи под давлением.
Возможны засорение глаз и их ожоги при работе без очков при выгребке пыли
из систем пылеулавливания и ремонте аэрационного и пневматического транспорта.
Происходят тяжелые травмы рук и головы при нарушении правил обслуживания
скребковых и ленточных конвейеров и отсутствии средств аварийного их
отключения. Эти травмы наблюдаются в основном при попытках устранения на ходу
неисправностей работающего оборудования - пробуксовки транспортной ленты,
укрепление скребков на цепи скребкового конвейера; травмы рук, ног и головы
несправным инструментом и кирпичом при большом скоплении рабочих во время
производства текущих и шальных ремонтов печей.
Воздействие опасных производственных факторов может вызвать у работающих
в отделении:
термические ожоги расплавом металла и шлака;
ожоги и поражения электрическим током при обслуживании
электрооборудования в случае нарушения правил техники безопасности при
обслуживании и ремонте движущихся частей механизмов, оборудования и при работе
исправным инструментом.
Для безопасной работы обслуживающего персонала и обеспечения необходимых
санитарно-технических н противопожарных норм должны быть предусмотрены
следующие мероприятия:
· аспирационные установки должны быть в исправном рабочем состоянии;
· вращающиеся части механизмов должны быть ограждены:
· все электродвигатели должны быть заземлены;
· рабочие отделения должны иметь индивидуальные средства
защиты.
5.1.2 Анализ
травматизма
Наиболее часто несчастные случаи происходят с молодыми, малоопытными
рабочими.
Таблица 5.1
Анализ травматизма в плавильном цехе за 2005-2006 год
Год
|
Количество
|
Проценты
|
Коэффициент тяжести
|
2005
|
12
|
20,2
|
34,6
|
2006
|
6
|
9,7
|
24,3
|
Критериями оценки состояния техники безопасности на производстве являются
коэффициенты частоты и количество несчастных случаев.
Коэффициент частоты - это количество несчастных случаев, отнесенное к
1000 работающих, коэффициент тяжести - это отношение количества дней
нетрудоспособности к количеству несчастных случаев.
Основные причины травматизма:
неудовлетворительная организация работ - 40,5 %
нарушение технологических процессов и технологии производства - 23,2 %
нарушение правил безопасности - 20,1 %
нарушение производственной и трудовой дисциплины (в том числе нахождение
на рабочем месте в состоянии алкогольного опьянения) - 16,2%.
Основными травмирующими факторами являются:
машины и механизмы, технологическое оборудование - 41,2%
падение с высот людей и предметов - 27,2 %
отравление газом - 19,4 %
хлопки и выбросы расплавленного металла и шлака -15,1%.
Более 50% несчастных случаев приходится на долю ремонтного персонала.
Здесь также основными причинами травматизма являются: неудовлетворительная
организация работ, отсутствие нарядов-допусков, недостаточная обученность
персонала, неудовлетворительное состояние оборудования (особенно газоходной
системы), отравление газами при чистке газоходной системы.
5.1.3 Техника
безопасности
Техника безопасности при взвешенной плавке имеет следующую особенность:
комплекс взвешенной плавки насыщен большим количеством оборудования и
механизмов - ленточные, скребковые и цепные конвейеры, вентиляторы, дымососы и
насосы, котлы высокого давления и электрофильтры, штейно- и шлаковозы, мостовые
краны и т.п. Эти механизмы работают вблизи от рабочих мест, и обслуживающий
персонал должен быть внимательным и выполнять требования техники безопасности.
Главными причинами производственного травматизма являются нарушения
технологического режима, несоблюдение рабочими правил техники безопасности,
слабый контроль за их выполнением со стороны инженерно-технических работников и
низкое качество оградительных приспособлений.
На каждом предприятии, в каждом цехе должен производиться анализ
травматизма, а все причины и обстоятельства несчастных случаев - обсуждаться с
рабочими. Взвешенная плавка связана с вредными условиями труда, в связи с этим
для рабочих и ИТР, работающих на комплексах взвешенной плавки, установлен
восьмичасовой рабочий день и дополнительный двенадцатидневный отпуск.
К работе на комплексах взвешенной плавки допускаются физически и
психически здоровые люди в возрасте от 18 лет после соответствующего заключения
медицинской комиссии. Вновь поступающие рабочие в обязательном порядке проходят
вводный инструктаж в отделе техники безопасности завода, а затем их
инструктирует на рабочем месте администрация цеха или передела. После этого
рабочий проходит десятичасовое обучение практическим приемам работы под
руководством опытного рабочего, а по истечении установленного срока обучения
сдает экзамен на знание правил техники безопасности специальной комиссии,
назначенной администрацией цеха.
Все рабочие один раз в квартал проходят инструктаж по правилам техники
безопасности, инструктаж проводят сменные мастера и руководители служб.
Администрация цеха и передела обеспечивает ежегодное обучение рабочих на курсах
технического минимума, где наряду с техническими вопросами изучаются правила
техники безопасности.
Один раз в год проводится проверка знаний правил техники безопасности
рабочими и ИТР передела. Рабочие сдают экзамены комиссии под председательством
начальника передела, ИТР - цеховой комиссии под председательством начальника
цеха.
Все виды инструктажа и результаты экзаменов оформляются в соответствующих
журналах. Машинисты и сигналисты (строгальщики) мостовых кранов,
подведомственных Госгортехнадзору, дежурные и ремонтные электрики, а также
рабочие, имеющие дело с природным газом, кроме экзаменов по знанию общих правил
по ТБ, сдают экзамены на знание специальных правил Госгортехнадзора и
Госэнергонадзора. После сдачи экзаменов рабочим выдаются соответствующие
удостоверения.
Администрация предприятия обеспечивает всех работающих инструкциями по ТБ
по данной специальности, а общие инструкции вывешивает в раскомандировочных помещениях
и на рабочих местах.
Большое внимание следует уделять правильной эксплуатации оборудования,
своевременному его ремонту и испытаниям. Движущиеся механизмы должны быть
докрашены так, чтобы они хорошо были видны и выделялись на общем фоне цеха. Все
движущиеся части должны быть надежно ограждены.
Переделы взвешенной плавки насыщены значительным количеством
электрического оборудования, которое должно иметь заземление и
эксплуатироваться в соответствии с требованиями Госэнергонадзора.
Все рабочие передела обеспечиваются спецодеждой и средствами
индивидуальной защиты в зависимости от выполняемой работы. Плавильщики получают
суконные рукавицы, валенки, войлочные шляпы, очки и щитки из оргстекла, рабочие
других профессий, не связанных с работой с расплавами, - хлопчатобумажную
спецодежду. Вид спецодежды и срок ее носки для рабочих различных профессий
определяется типовыми отраслевыми нормами.
Администрация предприятия обеспечивает своевременный ремонт, сушку и
стирку спецодежды, а администрация цехов и переделов - контроль за соблюдением
правил её ношения. При проведении горячих ремонтов, кроме суконной одежды,
рабочие используют асбестовые халаты, рукавицы. Спецодежда и чистая одежда
рабочих хранится в отдельных шкафах в бытовом комбинате, в котором также располагаются
душевые, прачечная и мастерские по ремонту спецодежды и обуви.
В целях предотвращения травматизма необходимо тщательно принимать смену,
следить за чистотой рабочих мест и проходов,
исправностью лестниц, площадок, ограждений. Применение бирочной или жетонной
смены приема и сдачи основного оборудования повышает ответственность
обслуживающего и ремонтного персонала за выполнение правил техники
безопасности.
Наряду с требованиями безопасности, описанными выше,
существуют определенные нормы, которые снижают опасность факторов имеющих место
на данном производстве. К ним можно отнести следующие общие правила:
территория, помещения, отделения должны содержаться в
чистоте и систематически очищаться от отходов производства;
накопление пыли на стенках, конструкциях и
оборудовании не допускаются;
электрическое оборудование должно быть заземлено и
эксплуатироваться в соответствии с требованиями правил. Освещение территории,
проходов, проездов, во всех помещениях и отдельных рабочих местах должны
соответствовать установленным нормам (не менее 30 лк на 1 м2
площади): для переносного электрического освещение должны применяться
светильники напряжением не выше 36 В; при работе внутри металлических ёмкостей
и в сырых местах напряжение осветительной сети не должно превышать 12 В;
все эксплуатационное оборудование, а так же
используемые инструменты и приспособления для обслуживания должны быть
исправны;
аспирационные системы должны включаться в работу до
пуска технологического оборудования, а отключаться после его остановки и
обеспечивать удаление пыли и газа от места их образования; аспирационные
системы должны быть максимально герметичны;
все открытые движущие части машин и механизмов,
расположенные на высоте 2,5м и менее уровня пола или доступные для случайного
прикосновения с рабочих площадок, должны быть ограждены сплошными или сетчатыми
ограждениями с размерами ячеек 20x20 мм; зубчатые, ременные, цепные передачи
независимо от высоты их расположения н скорости вращения должны иметь сплошные
ограждения;
площадки, расположенные на высоте более 0,6 м,
переходные мостики и так далее должны иметь ограждения высотой не менее 1 м со
сплошной обшивкой по низу 0,14 м;
проверка плотности кислородопроводов, арматуры и
кислородного оборудования должна производиться мыльным раствором;
ремонт кислородопроводов и узлов оборудования проводят
только после их отключения и продувки воздухом до содержания в них кислорода
23%, что должно контролироваться двукратным анализом;
все работы ведутся по наряду-допуску не менее чем
двумя лицами.
Кроме средств индивидуальной защиты (СИЗ) должна
обеспечиваться и работать приточно-вытяжная вентиляция, кроме той, что по
технологическому регламенту не должна на определенном этапе работать.
5.1.4
Промсанитария
Вентиляция является эффективным средством обеспечения
нужных гигиенических качеств воздуха, соответствующих требованиям Санитарных
норм проектирования промышленных предприятий (СН 245-71). Приточная вентиляция
должна подводиться непосредственно к рабочим местам, а подаваемый воздух должен
быть кондиционированным. Приточной вентиляцией с подачей кондиционированного
воздуха должны быть оборудованы кабины машинистов мостовых кранов.
Тепловое излучение печей взвешенной плавки, особенно в
местах выпуска расплавов, вызывают у рабочих значительное потовыделение, с
которым теряются необходимые организму соли. Для регулирования вводно-солевого
равновесия организма и поддержания его работоспособности в горячих цехах
устанавливают аппараты газированной воды. Вода подсаливается поваренной солью
из расчета 5 г/л, норма расхода воды на одного рабочего составляет 4-5 л/день.
Для обеспечения безопасности труда при работе в
механической мастерской плавильного отделения, необходимо обеспечить
достаточную освещенность рабочих мест.
Произведём расчёт освещения механической мастерской
плавильного отделения. Размеры помещения:
длина а = 5м,
ширина b =
12м,
высота H =
6м.
Потолок, стены и пол имеют коэффициенты отражения 50,
30 и 10 %. Контраст объекта с фоном малый, фон - темный. Для освещения
мастерской используются светильники УПМ-15 с лампами накаливания Г
220-235-300-1 с мощностью 300 Вт. Коэффициент запаса Кз = 1,5.
При высоте помещения Н = 6 м и высоте расчётной
поверхности над поломр = 0,8 м, величине hc = 1,2 м
высота подвески светильников равна:
h = H - hр - hc = 6 - 0,8 - 1,2 = 4 м.
Для заданного расположения контрольных точек А и В
величины d1, d2, d3 будут соответственно равны 3,2 м, 2,69 м и 7,56 м.
Для
точки А определяем величину tg
= 3,2/4 = 0,8. Этому значению тангенса соответствует
угол
= 38,7 0С.
По
характеристике светораспределения для светильника УПМ-15 и угла 38,7 0С
находим I
= 110 кд.
Рассчитываем
освещённость, создаваемую одним светильником с условной лампой в точке А:
ЕА
=
лк.
Суммарная
освещённость в точке А при работе четырех светильников:
4*4,33 =
17,32 лк.
Затем
определяем значение коэффициента для ламп накаливания типа Г 220-235-300-1, при
этом световой поток Фл в соответствии со справочными данными будет
равен 4000 лм.
Рассчитываем
коэффициент, учитывающий тип конкретного источника чвета:
=
= 2,67.
Тогда
освещенность в точке А от светильников с принятым типом ламп равна:
ЕгА
= m *
= 2,67*17,32 = 46,24 лк.
Аналогично проводим расчет для точки В, получаем
4,1*2+0,74*2
= 9,68 лк.
Тогда
освещенность в точке В от светильников с принятым типом ламп равна:
ЕгВ
= m *
= 2,67*9,68 = 25,85 лк.
Рассчитываем
значения яркости в точках А и В:
LcA = 4 *
2,67/(180*cos38,70) = 0,072 кд/м2.
LcB =
0,081 кд/м2.
Нормативное
значение освещенности для данных условий составляет 150 лк.
Фактическое
значение освещённости в точке В равно 25,85 лк, то есть меньше нормируемой
величины. Таким образом, по справочным данным условия труда относятся к классу
3.1.
Затем
рассчитываем индекс помещения:
=
.
При
заданных коэффициентах окружающих поверхностей находим коэффициент
использования светового потока
= 51 %.
При
площади пола S = 180 м2, коэффициенте запаса Кз
= 1,3 и коэффициенте неравномерности освещенности Z = 1,1,
вычисляем суммарный световой поток при N=1:
Флн
= 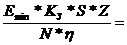
75705,88
лм.
Тогда
необходимое число ламп равно:
N = 
21,8 шт.
Таким
образом, для создания на рабочей поверхности освещенности 150 лк, необходима
установка 22 светильников УПМ-15 с лампами Г 220-235-300-1.
Произведём
расчёт суммарной мощности осветительной установки и числа ламп методом удельной
мощности.
Для
светильников типа УПМ-15 при S = 180 м2, высоте подвеса 4-6 м и
освещенности 25 лк находим по справочным данным w/ = 5,05 Вт/ м2.
Рассчитываем
необходимую удельную мощность для создания нормальной освещённости:
w =
= 7,58 Вт/ м2.
Рассчитываем
мощность осветительной установки:
РЛ
= w*S = 7,58*180 = 1,364 кВт.
Определяем
количество светильников при мощности одной лампы 0,06 кВт и n=1:
N =
= 21,9 шт.
Таким
образом, результаты расчётов количеств ламп, осуществленных различными
методами, практически совпадают.
.1.5
Противопожарная безопасность
Согласно нормам СН-245-71, предприятия,
перерабатывающие горячие расплавы по оценке пожарной безопасности относятся к
категории «Г», а здания цеха к первой степени опасности.
Для предупреждения и локализации пожаров проводится
комплекс организационных и технических мероприятий. К ним относится:
установка пунктов с противопожарным инструментом и
ящиком с песком;
монтаж электрической сигнализации;
наличие пенных огнетушителей типа ОП-5; для тушения
загораний в электропечах (огнетушитель ОУ-7);
наличие водопровода, находящегося под давлением воды,
предусмотренным инструкциями;
при каждом внутреннем пожарном кране должен быть
выкидной рукав длинной не менее 10 м и ствол, который размещен в специальном
шкафу. Напор в сети обеспечивает в получении струи воды 6 м; расход воды на
внутреннее пожаротушение 5 л/с, на наружное -20 л/с.;
наличие пожарных лестниц;
обеспечение свободных проходов к инвентарю и средствам
сигнализации.
Противопожарный водопровод объединён с хозяйственным и
производственным водопроводом. Для обеспечения бесперебойной подачи воды при
разрыве, замерзании или других аварий трубопровода, сети противопожарных
водопроводов делают кольцевыми с диаметром труб наружного трубопровода не менее
100 мм. Пожарные краны устанавливаются на высоте 1,35 м от уровня пола, внутри
помещений у входа, на площадках отапливаемых лестничных клеток.
Все трудящиеся цеха регулярно проходят инструктаж по
противопожарной профилактике. Организуется добровольная пожарная дружина,
которая осуществляет систематический контроль за выполнением противопожарных
правил.
5.2 Безопасность жизнедеятельности в условиях чрезвычайных ситуаций (ЧС)
.2.1 Анализ
потенциально возможных ЧС
Чрезвычайная ситуация - быстрое изменение условий
окружающей среды и жизнедеятельности человека, обусловленное природными или
техногенными факторами. Для города потенциально возможными ЧС являются:
· чрезвычайная ситуация климатогенного происхождения
(город расположен на севере Европейской части страны, что обуславливает
продолжительную зиму и короткое лето, большое скопление снега, заносы, морозы и
т.д.);
· пожары;
· чрезвычайная ситуация техногенного характера,
обусловленные производственной деятельностью комбината.
5.2.2 План
предупреждения и ликвидации ЧС
Одним из наиболее опасных факторов для возникновения
ЧС на комбинате является использование агрессивных и ядовитых веществ: хлора,
кислоты, аммиака и др.
Хлор используется в качестве реагента при
гидрометаллургическом производстве меди. Он поступает на комбинат в
железнодорожных цистернах в сжиженном состоянии, затем сливается в расходные
«танки» и по хлоропроводам направляется на технологию.
В процессе этих операций возможно возникновение
непредвиденных аварийных ситуаций с утечками хлора в промышленной зоне. При
неблагоприятных погодных условиях (юго-восточный ветер) хлорное облако будет
двигаться в сторону жилых районов, что вызовет чрезвычайное положение во всем
районе.
В связи с этим на комбинате штабе ГО разрабатываются
планы «Предупреждения» и «Ликвидации» хлорной аварии. Они включают в себя:
- порядок транспортировки, слива и использования
хлора;
требования к оборудованию (его расположение в стороне
от наиболее вероятногоскопления людей, доступность к ремонту, предупреждающая
окраска и т.д.);
1организацию системы отсечных клапанов, позволяющих дистанционно вывестииз
работы аварийный участок;
2организацию при производстве военизированной «Газоспасательной службы»
идобровольной газоспасательной дружины» - оперативных отрядов,
непосредственнопредназначенных для предупреждения и ликвидации хлорных аварий;
- систему оповещения (сирены, объявления по радио) об
утечках хлора;
-действия промышленного персонала предприятия и
жителей города приобъявлении «Хлорной аварии».
После принятия этих планов администрацией города и
комбината они принимаются к обязательному исполнению всеми службами и
организациями города, проводятся тренировки по отработке и согласованию
действий спасательных и аварийных отрядов по ликвидации аварии.
6. ЭЛЕКТРОТЕХНИЧЕСКАЯ ЧАСТЬ
.1 Электроснабжение участка цеха
Существующая цеховая понизительная трансформаторная
подстанция находится в некотором удалении от плавильного участка цеха. По
конструктивным особенностям, для электроснабжения оборудования участка цеха
принимаем наружные кабельные линии, проложенные по трубам в кабельных нишах.
Длину кабелей принимаем равной 200 метрам для всех потребителей из-за
особенностей расположения оборудования.
6.2 Характеристики потребителей
В отделении печей взвешенной плавки основными потребителями
электроэнергии являются электродвигатели машин и механизмов с напряжение
питания 0,4 кВ. Потребители электроэнергии приведены в таблице 6.1.
Таблица 6.1
Характеристики потребителей
Электропотребители
|
Количество п, шт
|
Установленная мощность Рн, кВт
|
Cos Коэффициент спроса, Кс
|
|
Привод скребкового транспортёра
|
3
|
8,5
|
0,7
|
1,0
|
Воздуходувка
|
1
|
80
|
0,8
|
0,8
|
Насосная
|
1
|
80
|
0,7
|
0,7
|
Вентиляционная
|
1
|
30
|
0,7
|
0,8
|
Освещение
|
-
|
30
|
1
|
1
|
Прочие
|
-
|
70
|
0,5
|
0,3
|
6.3 Расчётная нагрузка потребителей
Активная мощность электропотребителей рассчитывается
следующим образом:
РР = РН *n* Кс = 8,5* 3*1,0 = 25,5
кВт.
Реактивная мощность электропотребителей рассчитывается
следующим образом:
QP
= РР*tg
= 25,5 *1,02 = 26 квар.
Полная
мощность электропотребителей рассчитывается следующим образом:
S =
= 36,4 кВA.
Результаты
расчётов сводим в таблицу 6.2.
Таблица 6.2
Расчётная нагрузка потребителей
Электропотребители
|
Мощность
|
|
Активная мощностьРР, кВт
|
Реактивная мощность, QP, квар
|
Полная мощность,S, кВA
|
Привод скребкового транспортёра
|
25,5
|
26
|
36,4
|
Воздуходувка
|
60
|
52,9
|
80
|
Насосная
|
56
|
57,1
|
79,9
|
Вентиляционная
|
24
|
24,5
|
34,3
|
Освещение
|
30
|
-
|
30
|
Прочие
|
21
|
36,4
|
42
|
Итого
|
216,5
|
196,9
|
302,6
|
6.4 Выбор трансформатора
Потери в сети низкого напряжения.
Активные потери:
,
где
= 216,5 кВт - суммарная активная мощность
электропотребителей;
= 4,3 кВт.
Реактивные потери:
,
где
= 196,9 квар - суммарная реактивная мощность
электропотребителей;
= 5,9 квар.
Мощность трансформатора:
,
где
= 220,8 кВт,
= 202,8
кВт.
Тогда
=
= 299,8 кВА.
Номинальная мощность трансформатора:
,
где
= 1,3 - коэффициент допустимой перегрузки,
n= 2 -
количество трансформаторов.
Тогда
номинальная мощность трансформатора равна:
кВА.
Выбираем трансформатор ТМ-250/10, номинальные данные
которого:
Uвн/Uнн = 10/0,4 - высокое напряжение/низкое
напряжение;
Uк = 4,5 % - напряжение короткого замыкания;
Рхх = 0,82 кВт - мощность холостого хода;
io= 2,3 %*Iн .
Выбор сечения токопроводящих жил кабеля проводим по
условию нагрева:
= 166 А.
Таблица 6.3
Выбор сечения токопроводящих жил кабелей
Электропотребители
|
Потребляемый ток, А
|
Сечение токопроводящей жилы кабеля, мм2
|
, % , %
|
|
Привод скребкового транспортёра
|
166
|
150
|
1,2
|
2,9
|
Воздуходувка
|
364
|
185
|
1,9
|
4,9
|
Насосная
|
364
|
185
|
1,9
|
4,9
|
Вентиляционная
|
156
|
150
|
1,1
|
2,8
|
Освещение
|
137
|
50
|
4,2
|
-
|
Прочие
|
191
|
150
|
1,0
|
По условиям нагрева выбираем кабель марки КШВГ,
сечения жил которых были рассчитаны ранее.
6.5 Потери напряжения в сети
Потери напряжения в сети обуславливаются линейным
сопротивлением кабельной линии. При больших значениях длин кабелей, потери
могут достигать недопустимых значений, при которых невозможна нормальная работа
электроустановок. По ГОСТу, падение напряжения на зажимах самых удаленных от
подстанции потребителей не должно превышать 5 %. При падении напряжения ниже 5
%, необходимо повышать напряжение на низкой стороне подстанции, что может
негативно сказаться на работе других потребителей, расположенных ближе к
подстанции. Другим, более перспективным решением проблемы, является увеличение
сечения токоведущих жил кабеля, на котором наблюдается недопустимое падение
напряжения. Для этого проводим проверочный расчёт кабелей на падение напряжения
по формуле:
,
где
IP - ток, протекающий по кабелю (А);
l - длина кабеля
(м);
= 58
-
удельная проводимость;
Uн = 380 В - напряжение питания; s - сечение
проводника (мм2).
,
где
Iп = 5* IP - пусковой ток (А); cos
= 0,5*cos
Результаты
расчётов приведены выше в таблице 6.3.
6.6 Выбор коммутационной аппаратуры
Коммутационная аппаратура выбирается по условию
рабочего тока электроприёмников. Она должна обеспечивать бесперебойное питание
электроприёмников в нормальных условиях и быстрое отключение агрегатов от сети
а аварийной ситуации. Принципиальная схема электроснабжения участка цеха
приведена на рис. 6.1.
Для подключения к сети насосной, а так же двигателей компрессорной
(воздуходувной) станции выбираем комплексное распределительное устройство КРУ2
-10-20, с номинальными данными:
номинальный ток - 630 А; ток термической стойкости -
20 кА;
электрическая стойкость - 52 кА; выключатель - ВМПЭ
-10;
Для остального оборудования принимаем
распределительное устройство К-ХП/ВАК с номинальными данными:
номинальный ток - 320 А; ток термической стойкости -
20 к А;
электрическая стойкость - 40 кА; выключатель - ВНВ
-10/320.
7. ЭКОНОМИЧЕСКАЯ ЧАСТЬ
.1 Общая характеристика плавильного отделения
Плавильное отделение цеха предназначено для плавки сульфидных медных
концентратов с получением богатого штейна и отвального шлака, а также очищенных
и охлажденных газов плавильной зоны, пригодных для производства элементарной
серы и серной кислоты. Производительность по концентрату 34,25 т/сут. (годовая
производительность комплекса - 300 тыс. т/год).
В состав оборудования входят:
1. печь взвешенной плавки;
2. теплообменный аппарат (газоохладитель);
. аптейк;
. загрузочный тракт печи.
Богатый штейн, образующийся при плавке, периодично выпускают из печи и
передается на варку металлов. Шлак непрерывным потоком поступает в
обеднительные электропечи и далее на грануляцию и откачивается в виде пульпы на
шлакоотвал с последующим возвратом воды на грануляцию. Газовые потоки
плавильной зоны применяются для производства элементарной серы и серной
кислоты.
7.1
Калькуляция себестоимости продукции
Себестоимость выпускаемой продукции определяется на основании приведенных
расчётов сырьевых и топливно-энергетических затрат, расходов на содержание и эксплуатацию
оборудования и цеховых расходов.
Для определения себестоимости продукции составляется калькуляция.
Таблица 7.1
Калькуляция себестоимости продукции
Наименование статей затрат и материалов
|
Единица измерения
|
Цена за единицу, тыс. руб.
|
По проекту
|
Фактически
|
|
|
|
Количество
|
Сумма, тыс. руб.
|
Количество
|
Сумма, тыс. руб.
|
Концентрат
|
т
|
31
|
1,25
|
38,75
|
1,25
|
38,75
|
Флюс
|
т
|
5
|
0,05
|
0,25
|
0,05
|
0,25
|
Вода
|
тыс. м3
|
1,21
|
0,003
|
0,0036
|
0,003
|
0,0036
|
Дутьё
|
тыс. м3
|
12,1
|
0,20
|
2,42
|
0,20
|
2,42
|
Энергозатраты
|
МВт*час
|
0,6
|
0,3
|
0,18
|
0,38
|
0,228
|
Основная заработная плата производственных рабочих
|
тыс. руб.
|
|
|
0,16
|
|
0,21
|
Дополнительная заработная плата производственных рабочих
|
тыс. руб.
|
|
|
0,02
|
|
0,04
|
Единый социальный налог
|
тыс. руб.
|
|
|
0,05
|
|
0,05
|
Содержание оборудования
|
тыс. руб.
|
|
|
0,70
|
|
0,72
|
Цеховые расходы
|
тыс. руб.
|
|
|
0,20
|
|
0,24
|
Итоговая стоимость
|
тыс. руб.
|
|
|
42,73
|
|
42,91
|
7.2 Расчёт
экономической эффективности
Экономический эффект достигается за счёт внедрения автоматизированной
системы управления, а также за счёт внедрения более современных ПЛК.
Экономическая эффективность определяется как разница между фактической и
проектируемой себестоимостью:
Эс = (С1 - С2)*А = (42,91 - 42,73)* 300
= 54 тыс. руб.
Экономический эффект определяется по формуле:
Э = Эс * (1-0,24) = 54 * (1-0,24) = 41,04 тыс. руб.
Срок окупаемости оборудования вычисляется по следующей формуле:
года.
где
К1 - капитальные вложения базового варианта;
К2
- капитальные вложения по проектируемому объекту;
С1
- себестоимость годового выпуска базового варианта;
С2
- себестоимость годового выпуска по проектируемому объекту.
Таблица 7.2
Сводные технико-экономические показатели проекта
Наименование
|
Единица измерения
|
Значение показателей
|
|
|
По проекту
|
Фактически
|
Годовой выпуск продукции
|
тыс. т
|
300
|
300
|
Капитальные вложения в основные фонды
|
тыс. руб.
|
176,93
|
-
|
Численность трудящихся
|
чел
|
50
|
52
|
В том числе:
|
|
|
|
рабочих
|
чел
|
40
|
42
|
ИТР
|
чел
|
10
|
10
|
Себестоимость продукции
|
тыс. руб
|
42,73
|
42,91
|
Экономический эффект
|
тыс. руб
|
41,04
|
-
|
Срок окупаемости
|
год
|
3,3
|
-
|
ЗАКЛЮЧЕНИЕ
Для плавки на штейн медного рудного сырья и концентратов в настоящее
время используется множество пирометаллургических процессов. В дипломном
проекте проведен расчет комплекса печи для плавки медного сульфидного
концентрата во взвешенном состоянии (печь взвешенной плавки).
В дипломном проекте произведён расчёт материального баланса взвешенной
плавки, теплового баланса взвешенной плавки, так же рассчитаны некоторые
конструктивные размеры печи.
В данном проекте была разработана математическая модель процесса плавки
шихты, получены статические характеристики процесса, разработана структурная и
функциональная схема автоматизации.
В экологической части произведена оценка вредного воздействия данного
передела на окружающую среду, определена санитарно-защитная зона, показаны
источники, загрязняющие вещества, выбрасываемые в окружающую среду.
Для обеспечения электроэнергией комплекса печи взвешенной плавки по
предварительным расчетам выбрали трансформатор, кабели и распределительные
устройства.
Описали комплекс мер по технике безопасности, противопожарной
безопасности и промсанитарии при работе в отделении печей взвешенной плавки.
БИБЛИОГРАФИЧЕСКИЙ СПИСОК
1. Анашкин
А.С., Кадыров Э.Д. Техническое и программное обеспечение распределенных систем
управления / под ред. Харазова В.Г. СПб, 2004 г.
2. Ванюков
А.В., Уткин Н.И. Комплексная переработка медного и никелевого сырья. Челябинск,
изд. «Металлургия», 1988, 432 с.
. Гальнбек
А.А., Шалыгин Л.М., Шмонин Ю.В. Расчёты пирометаллургических процессов и
аппаратуры цветной металлургии: Учебное пособие для ВУЗов, Челябинск, изд.
«Металлургия», 1990, 448 с.
. Грацерштейн
И.М., Малинова Р.Д. организация, планирование и управление на предприятиях
цветной металлургии. М: изд. «Металлургия», 1987, 416 с.
. Гудима
Н.В., Швейц Я.П. Краткий справочник по металлургии цветных металлов. М: изд.
«Металлургия», 1975, 536 с.
. Диомидовский
Д.А. Металлургические печи цветной металлургии, М: изд. «Металлургия», 1970,
704 с.
. Диомидовский
Д.А. Контроль и автоматизация процессов в цветной металлургии, М: изд.
«Металлургия», 1967, 403 с.
8. Иванов
В.А., Юбдеев Ю.М. АСУП и АСУ ТП цветной металлургии. Тематический сборник
научных трудов. М, 1980.
9. Кобахидзе
В.В. Тепловая работа и конструкции печей цветной металлургии. М:изд. «МИСиС»,
1994, 356с.
7. Левин
М.В. Автоматизация пиро- и гидрометаллургических производств: Учебное пособие.
Л.: изд. ЛГИ, 1986, 98 с.
8. Шмонин
Ю.Б. Анализ и синтез систем автоматизации металлургического производства:
Учебное пособие, Л.: изд. ЛГИ, 1986, 106 с.
. Шмонин
Ю.Б. Проектирование, монтаж и эксплуатация систем автоматизации
металлургического производства. Учебное пособие. Л: ЛГИ, 1984 с.
10. Охрана
окружающей среды / под ред. Белова С.В. М.: изд. «Высшая школа», 1991,
11. Техника
безопасности и производственная санитария. Краткий справочник металлурга / под
ред. Зиньковского М.М. изд. 2-е М.: изд. «Металлургия», 1983, 256с.
12. Электроснабжение
и электрооборудование заводов цветной металлургии и обогатительных фабрик.
Методическое указание. Л: ЛГИ, 1985.
. Организация,
планирование, управление производством и основы АСУП. Кудасов В.И., Шульгин
А.И. Методические указания. Л.: изд. ЛГИ, 1989, 35 с.