Расчет параметров и обзор принципа работы пуансонного овощерезательного механизма МС28-100
Министерство Образования и науки Российской Федерации
Новосибирский
Государственный Технический Университет
Кафедра проектирования технологических машин
Расчетно-графическая работа по дисциплине:
механическое оборудование
предприятий общественного питания.
Расчет параметров и обзор принципа работы пуансонного
овощерезательного механизма МС28-100
Новосибирск
Содержание
Введение
1. Сущность
и назначение процесса: измельчения
2. Обзор
технологических машин для проведения измельчительно-режущего процесса
.1
Виды режущих инструментов и способы резания
.2
Пуансонный овощерезательный механизм
.3
Дисковые овощерезки
.4
Роторная овощерезательная машина
Расчетная
часть
.
Исходные данные для расчета параметров пуансонной овощерезки
.Расчет
технологических параметров
Список
используемой литературы
Введение
Предприятия общественного питания, оснащены производственным
оборудованием, служащим для механизации ручного труда и автоматизации его
управления.
Производственное оборудование, предназначенное для выполнения
технологических операций по переработке сырья в пищевые продукты, называют
технологическим оборудованием.
Технологическое оборудование, в котором обрабатываемый
продукт, не изменяя своих физико-химических и других свойств, изменяет только форму,
размеры, и т.п., называют машиной. Конструктивная особенность машин - наличие
движущихся исполнительных органов, которые механически воздействуют на
обрабатываемый продукт.
Технологическое оборудование, в котором обрабатываемый
продукт изменяет свои физико-химические свойства или агрегатное состояние,
называют аппаратом. Конструктивная особенность аппарата - наличие определенного
пространства (объема) - рабочей камеры (резервуара), в котором происходит
воздействие на продукт с целью изменения его свойств. Кроме того, для работы
аппаратов применяют различные рабочие жидкости (холодную и горячую воду), газ,
пар, паровоздушную смесь, дым и т.д., которые называются тепло - и
хладагентами.
В зависимости от характера цикла работы оборудования оно
бывает периодического и непрерывного действия. В оборудование непрерывного
действия загрузка продукта осуществляется по средствам какого-либо
автоматического транспортирующего устройства. В оборудование периодического
действия транспортирующее устройство отсутствует.
Работа технологического оборудования заключается в
последовательном выполнении вспомогательных (загрузка, выгрузка, перемещение
т.п.) и основных (перемешивание, измельчение, формование и т.п.) операций. В
зависимости от соотношения вспомогательных и основных операций оборудование
может быть неавтоматического, полуавтоматического и автоматического действия. В
неавтоматическом оборудование вспомогательные и операции выполняют с
применением ручного труда. В полуавтоматах основные операции выполняет оборудование,
а вспомогательные - рабочий. В автоматах все операции выполняются
оборудованием.
На предприятиях общественного питания значительное место в
технологическом процессе механической обработки пищевых продуктов занимает
измельчение продуктов резаньем. Резание продуктов осуществляют режущими
инструментами с целью придания продуктам заданных формы, размера и качества
поверхности. Режущими инструментами служат ножи различной конструкции и формы.
1. Сущность и назначение процесса: измельчения
Процесс измельчения пищевых продуктов, т.е. разделение их на
части, широко применяется на предприятиях общественного питания при
изготовлении сахарной пудры, панировочных сухарей, дробленых орехов, кофе,
пюреобразных продуктов из вареных овощей, фруктов, творога, при нарезке сырых
овощей и фруктов, мяса, хлеба, сыра, колбасы, масла сливочного и других
продуктов.
Измельчение - механический процесс, при котором воздействие
рабочих органов на обрабатываемый продукт сопровождается переходом последнего
за пределы упругих деформаций. Поэтому при выборе способа измельчения
первостепенное значение приобретают такие свойства продукта, как упругость,
вязкость, пластичность. Под упругостью понимается свойство продукта
восстанавливать свои форму и размеры после прекращения воздействия на него
внешней нагрузки, под влиянием которой они были изменены. Это свойство
характеризуется модулем упругости. Исходя из этого, все продукты подвергаемые
измельчению, не могут рассматриваться как упругие. Наличие у них таких явлений,
как релаксация (падение напряжения при неизменной деформации) и ползучесть
(рост деформации при постоянных нагрузках), позволяет отнести эти продукты к
упруго-вязким и вязкопластическим телам.
По характеру применяемых усилий измельчение производят
следующими способами: разрыванием - разрушением при растяжении; раздавливанием
- разрушением при сжатии; размалыванием- разрушением при изгибе; сдвиганием
одного слоя продукта относительно другого - разрушением при сдвиге; созданием
на малых участках поверхности продукта больших контактных напряжений -
разрушением лезвием.
Разнообразие пищевых продуктов требует и различных способов
их измельчения. На практике, как правило, применяются одновременно несколько
способов измельчения, например изгиб и сдвиг, сжатие и сдвиг и др.
В зависимости от физико-механических свойств продуктов,
особенностей технологического процесса, требований к дисперсности, качеству
поверхности раздела, форме конечного продукта этот процесс осуществляют на
различных измельчающих машинах.
По функциональному назначению режущее оборудование
классифицируется на следующие виды:
ü для измельчения твердых пищевых продуктов
(размолочные машины и механизмы);
ü для измельчения мягких пищевых продуктов
(протирочные машины и механизмы);
ü для резания пищевых продуктов (овощерезательные
машины, мясорубки, мясорыхлители, хлеборезки, машины резки гастрономических
товаров и др.)
режущий инструмент овощерезка роторная машина
2. Обзор технологических машин для проведения
измельчительно-режущего процесса
.1 Виды режущих инструментов и способы резания
Значительное место в технологическом процессе механической
обработки пищевых продуктов предприятий общественного питания занимает
измельчение продуктов способом резания.
Способ резания применяется для разрезания различных продуктов
ломтиками, дольками, кубиками, прямоугольными и квадратными пластинками,
кружочками, а также для шинкования.
Разрезание продуктов осуществляется режущими инструментами с
целью придания продуктам заданных формы, размера и качества поверхности. При
этом каждый исходный кусок продукта должен быть разделен на более мелкие части
без остатка и отходов. Существенным требованием к конечному продукту является
одинаковость формы его частиц, а чаще всего их массы.
На предприятиях общественного питания разрезанию подвергают
овощи, фрукты, мясо, рыбу, хлебобулочные изделия, гастрономические товары
(колбасы всех видов, ветчина, буженина, сыр и т. д.).
В зависимости от вида обрабатываемого продукта все
оборудование, предназначенное для разрезания пищевых продуктов, подразделяется
на четыре группы:
Ø овощерезки;
Ø мясорубки, рыхлители;
Ø хлеборезки;
Ø машины для нарезки
гастрономических товаров.
Виды режущих рабочих инструментов. В качестве режущих рабочих
инструментов на предприятиях общественного питания применяют ножи, имеющие
различную конструкцию и форму.
У всех ножей режущая сторона (лезвие) имеет форму двугранного
одностороннего или двустороннего клина (рис. 2.1). Грань лезвия Б,
которая совпадает с плоскостью движения ножа, называется опорной.
Рис. 2.1
Двугранный клин: а-односторонний;
б - двусторонний
Грань лезвия А расположенная под углом к плоскости движения
ножа, называется рабочей или лицевой. Эта грань производит деформирование,
например отгибание продукта и вытеснение его из пространства, занимаемого
впоследствии ножом.
Линия пересечения опорной и рабочей граней носит название
режущей кромки лезвия. Поскольку двугранный клин имеет одну режущую кромку,
резание продуктов он может производить только в. одной плоскости.
Угол а, образованный опорной и рабочей гранями, называется
углом заточки лезвия. Клин (рис. 2.1, а) называется односторонним, если имеет
рабочую А и опорную Б грани. Клин (рис. 2.1, б) называется двусторонним, если
не имеет опорной грани, поскольку обе его грани являются рабочими. Такой клин
можно представить в виде двух сложенных вместе по опорным граням односторонних
клина. Углом заточки для двустороннего клина является угол, образованный
рабочими гранями. Для двустороннего симметричного клина (рис. 2.1, б) угол заточки
равен удвоенному углу заточки одностороннего клина.
Помимо ножей для разрезания твердых продуктов применяют
режущие инструменты, лезвия которых выполнены в форме клина с явно выраженными
зубцами и углом заточки, равным нулю или отрицательным (рис. 2.2). Такие
инструменты называют пилами. Кроме того, для разрезания пластичных продуктов в
отдельных случаях применяют режущие инструменты в виде проволоки. Для
осуществления процесса разрезания необходимо относительное перемещение рабочего
инструмента и продукта. В общем случае скорость этого перемещения направлена
под некоторым углом φ к режущей кромке лезвия
и ее можно разложить по двум направлениям: по нормали к режущей кромке и вдоль
нее.
Рис. 2.2. Схема резания продукта пилой с разведенными
зубьями: а - с отрицательным углом заточки; б- с углом заточки, равным 0
В частном случае скорость может быть направлена по одному из
этих направлений (рис. 2.3). Если скорость направлена вдоль режущей кромки, то
проникновение ножа в продукт будет отсутствовать и резания не произойдет.
Рис. 2.3. Схема относительного перемещения ножа и продукта:
а-под углом к режущей кромке; б - по нормали к режущей
кромке; в - вдоль режущей кромки
ОСНОВНЫЕ СПОСОБЫ РЕЗАНИЯ ПРОДУКТОВ
Kак уже отмечалось, резание может быть осуществлено при
относительном перемещении режущего инструмента и продукта. В зависимости от
направления этого перемещения резание принято подразделять на рубящее и
скользящее.
При рубящем резании режущий инструмент перемещается
относительно продукта перпендикулярно режущей кромке лезвия, при скользящем
резании - под острым углом к режущей кромке лезвия.
При рубящем резании лезвие ножа, перемещаясь перпендикулярно
режущей кромке, деформирует продукт и уплотняет его поверхностный слой, в
котором возникают контактные напряжения, имеющие максимальное значение в зоне
контакта с острой кромкой ножа. По мере возрастания силы воздействия ножа на
продукт увеличивается деформирование последнего и возрастают контактные
напряжения. Как только контактные напряжения достигают некоторой предельной
величины, происходит разрушение продукта острой кромкой ножа.
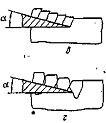
Рис. 2.4. Схема деформации различных продуктов при рубящем
резании: а - пластичных продуктов; б - волокнистых пластичных продуктов - клин
направлен поперек волокон; в - неволокнистых твердых продуктов; г - твердых
хрупких продуктов
Характер разрушения зависит от структурно-механических свойств
продукта: у пластичных продуктов имеет место срез уплотненных частиц продукта,
у твердых хрупких, у пластичных волокнистых, разрезаемых поперек волокон,
твердых волокнистых и неволокнистых продуктов - скалывание.
При резании пластичных продуктов (овощи, фрукты, хлеб мягкий,
сыр, мясо и рыба сырые) при небольшом угле заточки клина под действием
касательных напряжений, возникающих вследствие воздействия рабочей грани
лезвия, происходит деформирование частей продукта вдоль рабочей грани ножа. При
этом отрезаемый слой плавно отгибается рабочей гранью клина и отделяется от
основной части продукта, которая остается за опорной гранью ножа. Поверхности
срезанных кусочков получаются достаточно ровными и гладкими (рис. 2.4, а).
У всех волокнистых пластичных и твердых продуктов, а также у
неволокнистых твердых и хрупких продуктов в процессе резания происходит
скалывание, т.е. разрушение материала под действием касательных напряжений, при
котором одна часть продукта смещается относительно другой по какой-либо поверхности.
Так, у волокнистых пластичных продуктов (вареное мясо, рыба),
если клин направлен поперек волокон, а также у неволокнистых твердых продуктов
(черствый хлеб, вареная печень), скалывание происходит под острым углом к
плоскости среза (рис. 2.4, б, в). При этом поверхности срезанных кусочков имеют
неровности (зазубрины), а сам отрезанный кусочек не сохраняется целиком и чаще
всего распадается на отдельные части.
При резании твердых хрупких продуктов, например костей, даже
при незначительных углах заточки клина происходит двойное скалывание: в
направлении движения ножа и под некоторым углом к плоскости среза (рис. 2.4,
г). Часто поверхности скалывания у таких продуктов располагаются ниже опорной
грани клина. Поверхности кусочков получаются неровными, ломаными, со
значительной шероховатостью.
При скользящем резании в результате движения ножа
перпендикулярно режущей
кромке происходит проникновение его в толщу продукта, а при
движении ножа вдоль режущей
кромки-перепиливание мельчайшими микрозубчиками лезвия
волокон и стенок продукта.
В отличие от рубящего резания при скользящем резании для
разрезания продукта требуются меньшие уплотнение и усилие, так как перерезание
продукта осуществляется отдельными микрозубчиками, причем суммарная длина
микрозубчиков, одновременно участвующих в разрезании продукта, всегда меньше
длины режущей кромки лезвия Поэтому при скользящем резании величина контактных
напряжений, необходимая для разрезания продукта, а следовательно, и требуемое
усилие, значительно меньшие, чем при рубящем резании. При скользящем, резании
для осуществления разрезания продукта не требуется, чтобы все зубчики лезвия на
полную глубину проникали в продукт. Поверхности среза при скользящем резании
получаются, более гладкими и ровными, чем при рубящем резании. Происходит это
потому, что при скользящем резании продукт подвержен меньшему силовому
воздействию со стороны, режущего инструмента.
Скользящее резание применяют для разрезания пластичных
продуктов с невысокой механической прочностью.
Для разрезания твердых продуктов, имеющих значительную
механическую прочность, применяют зубчатые режущие инструменты (пилы).
Применение рубящего или скользящего резания определяется физико-механическими
свойствами продукта, требованиями, предъявляемыми к качеству поверхности
отрезаемых кусочков, а также энергетическими показателями.
Рубящее резание рекомендуется использовать для тех продуктов,
у которых разрушающие контактные напряжения невелики и разрезание происходит
без значительного уплотнения. Вследствие этого поверхность среза получается
достаточно ровной и продукт не деформируется. К таким продуктам можно отнести
сыры, масло сливочное. Для тех продуктов, у которых разрушающие контактные.
напряжения достигаются только после того, как продукт претерпел наряду с
упругой и пластическую деформацию, рубящее резание не рекомендуется. У таких
продуктов отрезанные кусочки остаются в деформированном состоянии. Пористые
продукты (хлеб мягкий ржаной и пшеничный, бисквиты) утрачивают частично свою
пористость, ухудшается их товарный вид. Сочные продукты (помидоры, лимоны,
огурцы свежие, сырое мясо, рыба, фрукты и т. д.) вследствие деформации теряют
часть сока и становятся малопригодными к употреблению.
При скользящем резании продукт значительно меньше
деформируется. Пористые продукты не крошатся и не утрачивают своей пористости.
Сочные продукты не теряют сока, а их ломтики не разваливаются и не
деформируются.
На предприятиях общественного питания для нарезки плодов и
овощей используют овощерезательные машины и механизмы. Наиболее распространенная
форма нарезки -ломтики, брусочки, соломка, стружка, дольки
Ломтики имеют две параллельные поверхности среза, расстояние
между которыми равно толщине ломтика h; длина и ширина ломтика определяются размерами
разрезаемого плода. Брусочки и соломка имеют, как правило, два определенных
размера - толщину h и ширину b.
.2 Пуансонный овощерезательный механизм
В пуансонном овощерезательном механизме нарезку овощей
осуществляют путем продавливания продукта пуансоном через неподвижную ножевую
рамку. По такому принципу работает сменный механизм МС28-100 (рис. 2.6.),
присоединяемый к универсальной кухонной машине ПУ-0,6.
Рис. 2.6. Механизм МС28-100 для нарезки
сырых овощей: а - разрез; б - общий вид
Рабочей камерой механизма служит неподвижный пустотелый
цилиндр 3, выполненный как одно целое с загрузочным каналом 19. Нижним торцом
камера опирается на ножевую рамку 2, которая крепится к корпусу редуктора 7 с
помощью двух стоек 4 и гаек 1. Стойки закреплены в корпусе редуктора штифтами
11. Внутри рабочей камеры перемещается пуансон 12. К нижнему торцу пуансона
прикреплена пластинка с выступами 13, предназначенными для проталкивания
продукта в неподвижную ножевую рамку. Находясь в крайнем нижнем положении,
пуансон своим выступом 18 закрывает загрузочный канал, предотвращая тем самым
попадание продукта в пространство камеры над пуансоном. Пуансон совершает
возвратно-поступательное движение, которое передается ему следующим образом.
Привод кухонной машины передает вращение входному валу б, от которого через
червяк 10 и червячное колесо 14 движение передается коленчатому валу 16. Оба
вала опираются на графито-баббитовые подшипники. Шейка коленчатого вала
установлена в прорези рамки-кулисы 8. Последняя имеет две пары роликов 9
(подшипников качения), движущихся по направляющим корпуса, и шток 5, к которому
прикреплен пуансон. При вращении коленчатого вала его шейка совершает движение
по окружности, в то время как связанная с ней рамка-кулиса совершает
возвратно-поступательное движение. За один оборот коленчатого вала рамка-кулиса
делает один двойной ход (вверх-вниз). Корпус редуктора закрыт крышкой 15и
пробкой 17.
Работа механизма заключается в следующем. В загрузочный канал
вручную подают по одному корнеклубнеплоду. В тот момент, когда пуансон
находится в верхнем положении, клубень скатывается на ножевую рамку, при
движении пуансона вниз клубень продавливается через ячейки ножевой рамки. Форма
нарезки определяется конструкцией ножевой рамки. Для нарезки продукта
брусочками применяют ножевую рамку 21 с квадратными ячейками, для нарезки
дольками (чесночком) рамку 20.
Технические характеристики пуансонного
овощерезательного механизма МС28-100
Машина, сменный
механизм
|
Марка
|
Производительность,
кг/ч
|
Мощность
электро-двигателя, кВт
|
Габаритные
размеры, мм.
|
Число двойных
ходов пуансона, 1/м
|
Ход поршня, мм.
|
Масса, кг.
|
Пуансонный
овощерезательный механизм
|
МС28-100
|
100
|
0,6
|
318x242x360
|
28
|
100
|
20
|
.3 Дисковые овощерезки
Дисковые овощерезки предназначены для нарезки овощей и
фруктов ломтиками, брусочками, соломкой. Устанавливают их, как правило, в
заготовочных цехах предприятий общественного питания. Овощерезки выпускаются с
индивидуальным приводом (МРО50-200, МРО400-1000, МУ-1000) или в качестве
сменных механизмов (МС10-160, УММ-10, МОП-II-1) к приводам
универсальных кухонных машин.
Рабочей камерой овощерезок служит пустотелый цилиндр,
расположенный вертикально или горизонтально. Рабочая камера имеет загрузочное и
разгрузочное устройства. Рабочим органом овощерезок являются ножи, закрепленные
на вращающемся опорном диске и имеющие прямолинейную или криволинейную форму.
Для нарезки овощей и фруктов ломтиками ножи устанавливают параллельно плоскости
опорного диска на некотором расстоянии от него, 'равном толщине отрезаемого
ломтика. Для нарезки плодов и овощей брусочками применяют комбинированные ножи,
состоящие из ножевой гребенки с лезвиями, расположенными перпендикулярно
плоскости опорного диска, и ножа, установленного параллельно плоскости опорного
диска. Для получения соломки применяют рабочие органы в виде стального листа с
отверстиями, один край которых отогнут, и заострен.
Нарезку плодов ломтиками осуществляют следующим образом:
плоды из загрузочного устройства поступают на вращающийся опорный диск и
движутся вместе с ним до тех пор, пока не будут остановлены стенкой камеры,
имеющей форму кругового клина «улитки» либо цилиндра. К опорному диску продукт
прижимается за счет его заклинивания между наклонной поверхностыо камеры и
опорным диском или вручную с помощью толкателя. Ножи врезаются в неподвижные
плоды и отрезают от них ломтики, которые проваливаются в отверстия опорного
диска. Оставшаяся часть плода опускается на опорный диск, вновь останавливается
стенкой камеры и прижимается к опорному диску, после чего с нее срезается
следующий ломтик. Процесс повторяется до тех пор, пока продукт полностью не
измельчится.
Рис. 2.7. Универсальная овощерезательная
машина МРО 50-200
Универсальная овощерезательная машина МРО50-200. Машина (рис.
2.7) предназначена для нарезки сырых овощей ломтиками, брусочками, соломкой и
шинковки капусты. Устанавливается машина на амортизаторах на рабочем столе в
заготовочном цехе. Состоит она из приводной части, сменных рабочих органов и
съемного загрузочного устройства 7. В состав приводной части входят литой
алюминиевый корпус 5, электродвигатель 12, укрепленный на плите, имеющей пазы
для натяжения ремней клиноременной передачи 13, и вертикальный приводной вал 1,
установленный на конических роликовых подшипниках 3. Натяг в подшипниках
регулируется с помощью гайки 14. Подшипники закрыты крышками. На верхней
половине вала, на шпонке установлена втулка 9 с двумя выступами, передающими
вращение рабочим органам. Положение втулки относительно цилиндрической части
корпуса, в которой расположены рабочие органы, регулируется гайкой 10 и
фиксируется винтом 4. На втулке 9 с помощью левой резьбы закреплен трехлопастный
сбрасыватель 11, предназначенный для продвижения нарезанного продукта к
разгрузочному устройству 2. На верхний конец приводного вала насажен опорный
диск 6 с ножами, закрепленный на валу с помощью специального винта 8 и имеющий
в нижней части два паза для зацепления с втулкой 9.
В комплект машины входят следующие рабочие органы: опорный
диск с серповидными ножами для нарезки овощей ломтиками, кольцами и
полукольцами толщиной 2 мм и шинковки капусты, два опорных диска с
комбинированными ножами для нарезки овощей брусочками сечением 10X10 мм и
соломкой сечением 3X3 мм, два терочных диска для нарезки овощей стружкой
сечением 0,8x1,2 мм и 3X3 мм. Регулировка толщины нарезки в данной машине не
предусмотрена.
Опорный диск с ножами размещен в цилиндрической расточенной
части литого корпуса машины. Сверху на эту часть корпуса устанавливается
съемное загрузочное устройство 7, закрепляемое с помощью зацепа и фиксатора.
Для обеспечения безопасной работы в машине предусмотрен блокировочный
выключатель, который разрывает цепь питания электродвигателя при снятом
загрузочном устройстве.
Загрузочное устройство 7 имеет литой корпус с двумя круглыми
и одним серповидным отверстиями. В отверстия вставляются соответствующей формы
толкатели. В серповидном отверстии продукт прижимается к опорному диску
посредством кронштейна, который является рычагом второго рода. Серповидный
толкатель шарнирно закреплен на кронштейне, который в свою очередь шарнирно
закреплен на корпусе загрузочного устройства. При повороте кронштейна вокруг оси
серповидный толкатель перемещается внутри отверстия. Серповидное отверстие в
загрузочном устройстве предназначено для подачи к ножам разрезанных на части
кочанов капусты, круглые отверстия - для овощей других видов (картофеля,
моркови, свеклы, редиса, репы и т.д.).
Нарезку продуктов на овощерезке производят следующим образом.
Включив машину, закладывают овощи вручную в одно из отверстий загрузочного
устройства и прижимают толкателями к вращающемуся опорному диску. Ножи,
вращающиеся вместе с опорным диском, отрезают от плодов последовательно слой за
слоем в виде ломтиков, колец, полуколец, брусочков, соломки. В момент отрезания
продукт удерживается от перемещения стенкой загрузочного отверстия и
толкателем. Отрезанные частицы продукта проходят в отверстия опорного диска,
расположенные под ножами, захватываются вращающимся сбрасывателем и подаются в
разгрузочный лоток.
.4 Роторная овощерезательная машина
Роторная овощерезка так же, как и дисковая, входит в комплект
универсальной овощерезательной машины МРО400-1000. Особенность этой овощерезки
состоит в том, что ее ножи в процессе резания остаются неподвижными, а продукт
перемещается вращающимся ротором с лопастями. На роторной овощерезке овощи
нарезаются ломтиками толщиной 3 мм и брусочками сечением 3X3; 6X6 и 10X10 мм.
Камерой обработки этой машины (рис. 2.9, а) служит
вертикально расположенный литой цилиндр 5, который крепится к корпусу 9 с
помощью зацепа 13 и фиксирующей защелки 12. Сверху на рабочую камеру
устанавливается откидная загрузочная воронка 5, которая поворачивается вокруг
оси 10 и стопорится фиксатором 11. В боковой стенке рабочей камеры имеется
проем, куда вставляется сменный ножевой блок 3.
Для нарезки продукта ломтиками (рис. 2.9, б) ножевой блок
имеет литую щеку 14 и нож 16. При установке ножевого блока в рабочей камере
внутренняя поверхность щеки совмещается с внутренней поверхностью камеры, а
лезвие ножа выступает внутрь камеры на расстояние, равное толщине отрезаемых
ломтиков. Острая кромка ножа располагается параллельно образующей рабочей
камеры. Для нарезки продукта брусочками ножевой блок дополнительно оснащается
ножевой гребенкой 15, лезвия которой расположены перпендикулярно стенке камеры.
Ножевые блоки закрепляются в стенке рабочей камеры с помощью вилки 17 и
откидного болта.
Рис. 2.9 Универсальная овощерезательная
машина МРО400-1000: а - общий вид машины; б - блок инструмента для нарезки
продукта ломтиками и брусочками; в - ротор
Внутри рабочей камеры расположен ротор (рис. 2.9, б), имеющий
литое основание в виде диска, к которому прикреплены три вертикальные лопасти
6, расположенные под углом 65° к касательной окружности основания 7 ротора,
проведенной через точку пересечения лопасти с этой окружностью. Ротор
устанавливается на верхнем конце выходного вала 1 приводного устройства машины
и закрепляется винтом 4 с левой резьбой. С внешней стороны рабочей камеры
напротив режущих инструментов расположен разгрузочный канал 2, переходящий в
разгрузочное устройство машины. Работает овощерезка следующим образом. Продукт
через загрузочное устройство загружают в рабочую камеру, где он захватывается
вращающимися лопастями ротора и подается к неподвижным ножам. При этом продукт
под действием центробежной силы прижимается к внутренней стенке рабочей камеры
и скользит по ней. При нарезке ломтиками выступающий над поверхностью рабочей
камеры нож, расположенный параллельно образующей рабочей, камеры, за каждый
оборот отрезает от продукта слой, равный толщине ломтика. При нарезке
брусочками продукт сначала надрезается ножевой гребенкой, а затем отрезается
ножом, расположенным перпендикулярно ножам ножевой гребенки. Отрезанные частицы
продукта поступают сначала в разгрузочный канал, а затем в разгрузочное
устройство машины. Для обеспечения безопасной работы машина снабжена
блокировочным выключателем, предотвращающим включение электродвигателя при
снятых рабочей камере и загрузочном устройстве.
. Исходные данные для расчета параметров пуансонной
овощерезки
Показатели
|
Условные обозначения
|
Размерность
|
Исходные
данные
|
1. Ширина
брусочка
|
а
|
м
|
0,01
|
2. Высота хода
пуансона
|
h
|
м
|
0,08
|
3. Толщина
ножей
|
δ
|
м
|
0,001
|
4. Высота ножей
|
h1
|
м
|
0,016
|
5. Число ходов
пуансона
|
n4
|
об/мин
|
26
|
6. Коэффициент
трения продукта о ножи
|
f
|
-
|
0.25
|
7. Модуль упругости
картофеля
|
Е
|
Па
|
2,5*106
|
8.Удельное
сопротивления продукта резанию
|
qв
|
Н/м
|
700
|
9.
Производительность
|
Q
|
кг/ч
|
70
|
10. Количество
зубьев
|
Z1
|
-
|
18
|
|
Z3
|
-
|
20
|
|
Z5
|
-
|
15
|
|
Z6
|
-
|
18
|
11. Коэффициент использования рабочей
камеры
|
φ
|
-
|
0,2
|
12. Число оборотов
двигателя
|
n1=nЭ
|
об/мин
|
1440
|
13.Насыпная
масса продукта
|
ρ
|
кг/м3
|
700
|
2. Определение основных параметров
Из формулы производительности находим скорость продвижения
продукта через ножевую решетку:
где, h-высота хода пуансона, м;
n4- число
двойных ходов пуансона, 1/мин;
Находим площадь ножевой рамки:
где, Q-производительность пуансонной овощерезки,
кг/ч;
ν0- скорость продвижения продукта через ножевую рамку, м/с;
ρ- насыпная масса продукта, кг/м3;
φ - коэффициент использования объема
рабочей камеры;
Находим диаметр ножевой рамки: принимаем, что ножевая рамка
круглого сечения
Усилие направленное на разрезание продукта режущими кромками
ножевой рамки:
где, qв - удельное сопротивление продукта резанью, 700 Н/м;
∑l - общая длинна лезвия, м;
Ψ - коэффициент использования длинны
лезвия.
Для брусочков с сечением (а×а, а=0,01 м):
Определяем мощность электродвигателя:
Где, Р4 - сила трения продукта о ножи ножевой
решетки, Н;
η - КПД всего привода и
механизма
Где, δсж - напряжение сжатия, возникающее в
продукте в результате продавливания его через ножевую решетку, Па;
Е* - относительная деформация продукта при его сжатии;
а - ширина брусков, м;
Е - модуль упругости продукта, 2,5·106 Па;
F - площадь соприкосновения продукта с боковыми поверхностями
ножей, м2.
Где, h1 - высота ножей, м;
f -коэффициент трения продукта о ножи, 0,25.
Найдем силу трения продукта о ножи ножевой рамки:
где, δ - толщина
ножей в ножевой рамке, м;
E- модуль упругости продукта, Па;
∑l- общая длина лезвий, м;
ψ- коэффициент трения продукта о ножи.
Мощность равна:
Выбираем двигатель:
N= 0,06 кВт. Двигатель серии 4А типоразмер А50А4 с синхронной
частотой вращения 1500 об/мин.
Частота вращения вала двигателя при номинальной нагрузке: nном= 0,98·nc
Номинальная частота вращения: nном = 0,98·1500
= 1470 об/мин
Найдем общее передаточное отношение механизма:
Цилиндрическая зубчатая передача сменного механизма И0
= 3,15
Передаточное число редуктора быстроходной ступени Иб =
4,15
Передаточное число для тихоходной ступени Иm = 4,15
Уточненное общее передаточное число:
И = И0 ·Иб ·Иm = 3,15· 4,15· 4,15 = 54,25
Для дальнейших расчетов примем обозначения для зубчатых колес и
для валов, на которых они закреплены:
Ø ведущее колесо
быстроходной ступени редуктора - 1;
Ø ведомое колесо
быстроходной ступени редуктора - 2;
Ø ведущее колесо тихоходной
ступени редуктора - 3;
Ø ведомое колесо тихоходной
ступени редуктора - 4;
Ø шестерня сменного
механизма - 5;
Ø колесо сменного
механизма.
При расчете используем:
Ø значение передаточных
чисел;
Ø моменты на валах
определяем без учета КПД;
Ø используем значение
потребной мощности N1 = 60 Вт.
Частота вращения валов:
Находим угловые скорости:
Находим моменты на валах:
3. Расчет зубчатых колес редуктора
Материал: сталь 45.
Твердость: шестерня- НВ=210; колесо- НВ=190.
Допустимое контактное напряжение:
Где, δН limв - предел контактной выносливости при базовом числе циклов, при
твердости < НВ 350 => [δ]Н = 2НВ+70;
КHL - коэффициент безопасности 1,1…1,2 =>
принимаем 1,15;
Допустимое контактное напряжение шестерни:
Допустимое контактное напряжение колеса:
Принимаем допустимое контактное напряжение по колесу: [δ]Н = 391 Н/мм2
Расчет тихоходной ступени редуктора
Межосевое расстояние:
Где, ИТ - 4,15;
Ψва- коэффициент ширины венца по межосевому расстоянию для
прямозубых колес 0,0125…0,25 => принимаем Ψва = 0,17;
КН - коэффициент нагрузки.
КН = КHα · KHβ · KHυ
Где, КHα - коэффициент, учитывающий
неравномерность распределения нагрузки между зубьями, принимаем равным 1;
KHβ - коэффициент, учитывающий
неравномерность распределения нагрузки по ширине венца, принимаем равным 1,25;
KHυ - динамический коэффициент, принимаем
равным 1,1.
КН = 1·1,25·1,1=1,375
Принимаем стандартное значение аω = 63 мм
Модуль зацепления: m = (0,01…0,02)
аω =
0,63…1,26 мм => принимаем m = 1 мм
Суммарное число зубьев:
Число зубьев шестерни:
Принимаем Zз = 24
Число зубьев колеса:
Проверка межосевого расстояния:
Уточняем передаточное число тихоходной ступени редуктора:
Расхождение составляет 2,4 %, что допустимо
Основные размеры шестерни и колеса тихоходной ступени редуктора.
Диаметры делительных окружностей:
Диаметры вершин зубьев:
Диаметр впадин:
Окружная скорость колеса:
Ширина колеса:
Принимаем в4 = 12 мм
Ширина шестерни:
Силы, действующие в зацеплении:
окружные:
-радиальные:
Проверочный расчет зубьев тихоходной ступени редуктора на
выносливость по контактным напряжениям:
КН = КHα · KHβ · KHυ
КHα =
1,06
KHβ = 1,06
KHυ = 1,05
КН = 1,06·1,06·1,05=1,17
[δ]Н =
391 Н/мм2
δН ≤ [δ]Н , условие прочности
выполнено.
3.2 Расчет быстроходной ступени редуктора
Модуль зацепления: m = 1 мм
Суммарное число зубьев:
Число зубьев шестерни:
Принимаем Zз = 24
Число зубьев колеса:
Уточняем передаточное число быстроходной ступени редуктора:
Расхождение составляет 2,4 %, что допустимо
Основные размеры шестерни и колеса быстроходной ступени редуктора.
Диаметры делительных окружностей:
Диаметры вершин зубьев:
Диаметр впадин:
Окружная скорость колеса:
Ширина колеса:
Принимаем в4 = 12 мм
Силы, действующие в зацеплении:
-окружные:
радиальные:
Проверочный расчет зубьев тихоходной ступени редуктора на
выносливость по контактным напряжениям:
КН = КHα · KHβ · KHυ
КHα =
1,09
KHβ = 1,06
KHυ = 1,05
КН = 1,09·1,06·1,05=1,21
[δ]Н =
391 Н/мм2
δН ≤ [δ]Н , условие
прочности выполнено.
4. Расчет зубчатой цилиндрической передачи сменного
механизма
Межосевое расстояние:
Где, И0 - передаточное число зубчатой передачи сменного
механизма, равное 3,15;
М6 = 20,5·103 Н/мм;
ψва = 0,17;
КН = 1,37
Материал 30 ХГС, твердость: -колесо 250 НВ, -шестерня 260 НВ.
Для зубьев колеса:
КHL
=1;
[n]H =1,15;
m = 1,5 мм
Диаметры делительных окружностей:
Окружная скорость колеса:
Ширина колеса:
Ширина шестерни:
Диаметры вершин зубьев:
Диаметр впадин:
Силы, действующие в зацеплении:
-окружные:
радиальные:
Проверочный расчет зубьев на выносливость по контактным
напряжениям:
КН = КHα · KHβ · KHυ
КHα =
1,06
KHβ = 1,05
KHυ = 1,05
КН = 1,06·1,05·1,05=1,17
[δ]Н =
495,65 Н/мм2
δН ≤ [δ]Н , условие
прочности выполнено.
Предварительный расчет валов
Ведущий вал редуктора: МК1 = 0,38·103 Н·мм,
при [τ]к = 20 Н/мм2, допустимое напряжение на
кручение.
Принимаем диаметр выходного конца ведущего вала равен диаметру
вала двигателя dв1 = 10 мм.
Под подшипниками принимаем: dп1 =10 мм.
Под шестерни принимаем: dш1 = 12 мм.
Промежуточный вал редуктора: МК2 = 1,57·103 Н·мм,
при [τ]к
= 20 Н/мм2.
Диаметр вала под зубчатыми колесами:
Принимаем под зубчатыми колесами: dк2=10 мм.
Под подшипниками принимаем: dп =10 мм.
Выходной вал редуктора: МК4 = 6,51·103 Н·мм,
при [τ]к
= 25 Н/мм2.
Диаметр выходного конца:
Принимаем диаметр выходного конца: dв4 = 12
мм.
Под подшипниками принимаем: dп4 = 13
мм.
Под зубчатым колесом принимаем: dк4 = 15
мм.
Ведомый вал сменного механизма: МК5 = 20,5·103
Н·мм, при [τ]к
= 25 Н/мм2.
Принимаем: dв5 = 20 мм.
Под подшипниками принимаем: dп5 = 21
мм.
Диаметр ступицы:
Длина ступицы:
Предварительный выбор подшипников
Выбираем шарикоподшипники радиальные однорядные легкой серии.
Ø Ведущий вал: № 201; d =10 мм; D = 30 мм; В = 9 мм; С =
4,6 кН.
Ø Выходной вал: № 202; d =12 мм; D = 32 мм; В = 10 мм; С =
4,7 кН.
Ø Промежуточный вал: № 200;
d =10 мм; D = 30 мм; В = 9 мм; С =
4,6 кН.
Проверка подшипников на долговечность
Ведущий вал редуктора
В плоскости x-y:
В плоскости х-z:
Суммарная реакция опор:
Расчет долговечности подшипников:
Промежуточный вал редуктора
l1 = 23,5 мм
l2 = 61 мм
l3 = 25,5 мм
Реакции опор в плоскости х-z:
Проверка:
Реакции опор в плоскости у-z:
Проверка:
Суммарные реакции опор:
Расчет долговечности подшипников:
Ведомый вал редуктора
Реакции опор в плоскости х-z:
Суммарные реакции опор:
Так как в предыдущих расчетах получены результаты в несколько раз
превышающие допустимые нагрузки, а нагрузки на подшипники ведомого вала меньше,
проверку на долговечность можно не проводить.
Выбор шпонок
Ø ведомый вал редуктора,
соединенный с колесом 4: шпонка 5×5×16мм;
Ø ведущий вал сменного
механизма: шпонка 5×5×20мм;
Ø ведомый вал сменного
механизма: шпонка 6×6×25мм;
Ø выходной конец ведущего
вала редуктора: шпонка 4×4×14мм;
Ø ведущий вал редуктора,
соединенный с шестерней: 5×5×12мм;
Ø промежуточный вал
редуктора, соединенный с колесом 2: шпонка 3×3×10мм, с шестерней 3 : шпонка 3×3×14 мм.
Проверяем соединение промежуточного вала редуктора с колесом
2:
Условие прочности:
где δсм - напряжение сжатия Н/мм2;
[δ]см
- допустимое напряжение сжатия, равно 100 Н/мм2
Материал - сталь 45 нормализованная.
d - диаметр, в месте установки шпонки = 10 мм;
h - высота шпонки.
Условие прочности выполнено.
. Определение изгибающих моментов
Для построения эпюр изгибающих моментов определяем значение
изгибающих моментов в характерных сечениях: опора 3.4. по оси зубчатого колеса
2 и по оси шестерни 3.
Из предыдущих расчетов получаем, что:
В проекции x-z:
Опора 3: Му=0;
Опора 4: Му=0;
Сечение по оси зубчатого колеса 2:
Му = Rx3 ·23,5 = 5,38·23,5=126,43 Н·мм
Сечение по оси шестерни 3:
Му = Rx4 ·25,5 = 91,48·25,5=2332,74Н·мм
В проекции y-z:
Опора 3: Мх=0;
Опора 4: Мх=0;
Сечение по оси зубчатого колеса 2:
Мх = Rу3 ·23,5 = 19,53·23,5=458,95Н·мм
Сечение по оси шестерни 3:
Мх = Rу4 ·25,5 = 37,97·25,5=968,23 Н·мм
В проекции х- у: от колеса 2 до шестерни 3 действует крутящий
момент:
Мк=М2=1,57·103 Н·мм.
Опасное сечение - по оси шестерни 3. Здесь действует максимальный
изгибающий момент, крутящий момент. Сечение вала ослаблено наличием шпоночной
канавки.
В сечении А-А изгибающие моменты:
Му = 2332,74 Н·мм
Мх=968,23 Н·мм
Суммарный изгибающий момент:
Коэффициент запаса хода:
Где, nδ -коэффициент
запаса прочности по нормальным напряжениям;
nτ - коэффициент запаса прочности по
касательным напряжениям;
Где, δ-1- предел
выносливости при симметричном цикле изгиба;
К δ -
коэффициент концентрации нормальных напряжений;
β - коэффициент, учитывающий внешние
шероховатости = 0,9;
δv - амплитуда цикла нормальных напряжений,
равная наибольшему напряжению изгиба в рассматриваемом сечении;
δм - среднее напряжение цикла нормальных напряжений =0.
τ-1- предел выносливости при симметричном
цикле кручения = 0,58;
τv = τm
Материал - сталь 45
Кδ
= 590 Н/мм2
δ-1=0,43· Кδ
τ-1=0,58· δ-1
δ-1=0,43·590=254 Н/мм2
τ-1=0,58·254=147 Н/мм2
Основной момент сопротивления сечения (момент сопротивления
сечения изгибу):
Померный момент сопротивления сечения (момент сопротивления
сечения кручению):
- диаметр вала в
сечении = 10 мм
b - ширина шпоночного паза = 3 мм
c - глубина шпоночного паза = 1,8 мм
Амплитуда
нормальных напряжений изгиба:
Амплитуда и
средние напряжение цикла:
τv = τm =
. Выбор муфты
Для соединения
вала электродвигателя с выходным концом ведущего вала и редуктора выбираем
упругую муфту со звездочкой комбинированного исполнения.
Муфта упругая со
звездочкой 6,3-П-1-11-2 ГОСТ 14084-76
Диаметры
отверстий в полумуфтах для соединения с валами электродвигателя и редуктора d=11 мм.
Передаваемый
крутящий момент: Мкр = 0,38 Н·мм.
Спецификация
Сборочные
единицы:
· редуктор -1;
· сменный механизм - 1.
Детали:
· кожух - 1;
· корпус - 1;
· фиксатор - 1.
Стандартные детали:
· винт М4×12 ГОСТ 17475-72 - 12;
· гайка М5 ГОСТ 5927-70 - 4;
· гайка М8 ГОСТ 5927-70 - 4;
· шайба 5 65Г ГОСТ 6402-70 - 4;
· шайба 8 65Г ГОСТ 6402-70 - 4;
· шпилька М5×4 ГОСТ 22038-76 - 4;
· шпилька М8×22 ГОСТ 22038-76 -4.
Прочие изделия:
· муфта упругая со звездочкой 6,3-11-1-11-2
ГОСТ 14084-76 - 1;
· электродвигатель А50А4 - 1.
Список используемой литературы
1. Жуков
В.И. Процессы и аппараты пищевых производств - Новосибирск: Издательство НГТУ,
2003.
2. Елхина
В.Д. и др. Механическое оборудование предприятий торговли и общественного
питания - М.: Экономика, 1987.
3. Ботов
М.И., Елхина В.Д., Голованов О.М. Тепловое и механическое оборудование
предприятий общественного питания - М.: Издательский центр «Академия», 2002.
4. Н.А Предтеченский Механическое оборудование предприятий
общественного питания. - М.: Экономика, 1974
5. С.А. Чернавский Курсовое проектирование деталей
машин. -М.: Машиностроение, 1980-351 с.