Проектирование линии транспортировки известково-доломитовой пыли с целью оптимизации производства мусоросжигательного завода
Содержание
Введение
Литературный обзор
Оборудование для сжигания отходов
1. Анализ состояния вопроса, постановка цели и задач проекта
2. Конструкторская часть
2.1 Расчет и конструирование шнекового транспортера установки
2.1.1 Техническое задание
2.1.2 Энергокинематический расчет привода (рисунок 2.1)
2.1.3 Выбор электродвигателя
2.1.4 Определение энергокинематических параметров привода
2.1.5 Выбор мотор-редуктора
2.2 Расчет и проектирование приводного приводного вала установки
2.2.1 Предварительный расчет вала
2.2.2 Предварительный выбор подшипников
2.2.3 Подбор и проверочный расчет муфт
2.2.4 Подбор шпонок и проверка прочности шпоночных соединений
2.2.5 Силовой расчет приводного вала представлен на рисунке 2.3
2.2.6 Проверочный расчет подшипников
2.2.7 Проверочный расчет приводного вала
2.3 Расчет и проектирование гидропривода перемещение гильотинной
двери установки
2.3.1 Определение нагрузочных и скоростных параметров
гидродвигателя
2.3.2 Определение геометрических параметров и выбор ГД
2.3.3 Составление принципиальной схемы привода
2.3.4 Расчет и выбор насосной установки
2.4 Расчет и выбор гидроблока управления и трубопроводов
2.4.1 Расчет и выбор гидроаппаратуры
2.4.2 Расчет трубопровода по участкам
2.4.3 Разработка конструкций гидроблока управления
2.4.4 Определение потерь давления в аппаратах и трубопроводах
Расчет производим для быстрого подвода.
2.5 Разработка рамы шнекового конвейера
2.5.1 Техническое задание для построения рамы шнекового конвейера
2.5.2 Проверочный расчет на прочность от действия изгибающего
момента в сечении А-А
2.5.3 Проверочный расчет на прочность от действия изгибающего
момента в сечении Б-Б
2.5.4 Расчет сварного шва на прочность
3. Технологическая часть
3.1 Разработка технологического процесса изготовления детали
"зубчатого колеса"
3.2 Выбор типового оборудования и типовых универсальных
приспособлений
3.2.1 Токарная операция
3.2.2 Горизонтально-фрезерная операция
3.2.3 Вертикально-сверлильная операция
3.2.4 Зубофрезерная операция
3.2.5 Горизонтально-протяжная операция
3.2.6 Внутришлифовальная операция
3.3 Расчет режимов резания и техническое нормирование операций
3.3.1 Определяем тип производства
3.3.2 Выбор режущих инструментов
3.3.3 Выбор режимов резания
3.3.4 Уточненное нормирование времени операции
3.3.5 Составление управляющей программы для станка с ЧПУ
3.4 Расчет и конструирование фрезы для нарезания зубьев на детали
"колесо зубчатое"
3.4.1 Расчёт дисковой зубофрезерной модульной фрезы. Определение
эвольвентного участка
3.4.2 Определение профиля неэвольвентного участка
3.4.3 Конструктивные параметры дисковых фрез
4. Организационно-экономическая часть
4.1 Оценка затрат на проведение модернизации
4.2 Затраты на оказание услуг
4.2.1 Материальные
4.2.2 Оплата труда
4.2.3 Амортизационные отчисления
4.2.4 Прочие затраты
4.3 Определение экономической эффективности
5. Безопасность и экологичность проекта
5.1 Анализ опасных и вредных производственных факторов при
эксплуатации мусоросжигательной печи
5.2 Меры по обеспечению безопасных и здоровых условий труда
5.3 Расчет системы кондиционирования в помещение пульта управления
5.4 Меры по обеспечению устойчивости работы мусоросжигательного
завода в условиях чрезвычайных ситуаций
5.5 Меры по охране окружающей среды
Заключение
Список использованных источников
Введение
Во всем мире все более острой становится проблема утилизации
бытовых и промышленных отходов. Основным преимуществом сжигания отходов
считается то, что объем отходов, идущих на захоронение, уменьшается в десять
раз.
Долгое время считалось, что термические технологии позволяют
эффективно обезвреживать токсичные отходы с образованием нетоксичных веществ.
Между тем, данные последних 20-25 лет свидетельствуют, что сжигание отходов -
это источник постоянного поступления вредных веществ в окружающую среду [1].
Поэтому во многих странах были приняты законодательные акты, которые наложили
запрет почти на все способы термического уничтожения отходов, содержащих
токсичные вещества. В частности, в США в 1984 году были приняты поправки к
"Закону о сохранении и восстановлении ресурсов". Согласно этим
поправкам, опасные отходы должны перерабатываться в безопасные и только затем
вывозиться на свалки или сжигаться. Тем не менее, даже в США общее количество
отходов, подвергшихся сжиганию, в середине 90-х годов составляло более 4 млн.
тонн в год [1].
Проблема отходов исключительно актуальна и для
России. На территории страны в отвалах, полигонах, хранилищах и свалках
накоплено более 100 млрд. тонн твердых бытовых и промышленных отходов. Ежегодно
в Российской Федерации образуется более 140 млн. м 3 таких отходов, из них лишь
5-10 % перерабатываются, а остальные вывозятся на полигоны для хранения [29].
Несмотря на строительство во многих странах вблизи крупных городов
мусоросжигающих заводов (МСЗ), ни одна из применяемых технологий сжигания не
соответствует экологическим требованиям. Главный аргумент противников
технологий сжигания - загрязнение атмосферного воздуха высокотоксичными
веществами и образование новых, потенциально опасных отходов (зола, шламы),
требующих специального хранения или захоронения. Многие ученые считают, что
печи для сжигания отходов - это те же свалки, но представляющие еще большую
экологическую угрозу. По данным Агентства по охране окружающей среды США (ЕРА),
при сжигании бытовых отходов в атмосферу выбрасывается более сотни токсичных
соединений.
В процессе сжигания твердых бытовых отходов
образуются и другие вещества. Например, при сжигании хлороформа образуются
хлорированные ароматические углеводороды и ПАУ. Установлено, что если исходная
смесь содержит пять веществ, то при сжигании образуется более 20 соединений,
представляющих собой неполные продукты сгорания. В частности, диоксины
образуются в результате реакций, протекающих на стенках очистных установок в
зоне охлаждения дымовых газов.
Эмиссия вредных веществ от печей сжигания
уменьшается с ростом их качественного уровня. Низкий фактор эмиссии характерен
для небольших (< 500 кг/ч) и простых печей, работающих при загрузке твердых
бытовых отходов (ТБО) партиями без какой-либо системы контроля подачи воздуха в
зону горения и полноты сжигания [2].
Особых мер предосторожности требуют медицинские
отходы, которые содержат также кровь, фармацевтические препараты, перевязочные
материалы и т.п. Наряду с вирусами, бактериями и патогенными микроорганизмами
они могут содержать токсичные химические вещества. Во многих странах, в том
числе и в России, их сжигают на месте в больнице или каком-либо другом
медицинском учреждении в небольших печах. Крупные печи, работающие в
непрерывном режиме, встречаются крайне редко. Это является причиной более
высоких эмиссионных факторов поступления вредных веществ в воздух при сжигании
медицинских отходов по сравнению с ТБО.
Литературный
обзор
Мусоросжигательный завод - предприятие, использующее
технологию переработки твёрдых бытовых отходов, посредством термического
разложения в котлах или печах [28]. После высокотемпературного разложения
образуются продукты сгорания: пепел, шлаки и летучие газы. Этот метод позволяет
снизить объём бытовых отходов для захоронения примерно в 10 раз. Однако
сжигание хлоросодержащих полимерных материалов ведёт к образованию токсичных
веществ. Существуют различные технологии сжигания отходов в мусоросжигательных
заводах, в основном их разделяют по типу печей, в которых производят сжигание.
. Слоевое сжигание - для слоевого сжигания характерна подача
горячих воздушных потоков на слой отходов, загруженный на колосниковую решётку.
Различают несколько разновидностей слоевого сжигания: с неподвижной
колосниковой решёткой, сжигание с неподвижным слоем отходов, с подвижной цепной
решёткой, с неподвижной.
. Технология кипящего слоя - в технологии псевдоожиженного
слоя отходы предварительно разделяют на гомогенные фракции, а затем сжигают в
специальных камерах в присутствии песка, доломитовой крошки или другого
абсорбента, который обладает высокой теплопроводимостью. Известняк и доломит
являются основным сырьем, нашедшим коммерческое применение в промышленности.
Эти углеродосодержащие соединения используются при осуществлении контроля за
вредными выбросами в окружающую среду (например, при десульфурации отходящих
газов). В кипящий слой вводят значительное количество инертных наполнителей -
шлак, песок, доломит, известняк; они повышают теплоотдачу. Доломит и известняк,
помимо этого, связывают в карбонаты до 90 % оксидов серы. В циркулирующий
кипящий слой также дозировано добавляют известняк для подавления оксидов серы.
Мусоросжигательный завод утилизация промышленный
3. Пиролиз и газификация - отходы под давлением нагревают в
бескислородной среде. В результате образуются жидкости и газы с высокой
удельной теплотой сгорания, которые можно использовать в качестве топлива.
Все термические методы переработки и утилизации отходов
помимо их обезвоживания направлены на получение энергии, а также твердого,
жидкого или газообразного топлива при их пиролизе.
Оборудование
для сжигания отходов
Сжигание производится в специальных печах, которые бывают
нескольких видов. Для сжигания твердых бытовых отходов используются установки
ТБО, для отходов сельского хозяйства, например, шелухи семечек подсолнечника,
котлы-утилизаторы.
Установки-утилизаторы повсеместно применяются в
промышленности. Это целые комплексы, которые уничтожают шламы, отходы целлюлозы
и нефтеперерабатывающей промышленности в больших объемах. Тепло, которое
вырабатывается во время горения, используют для обогрева помещений, и других
технических нужд.
В развитых странах часть ТБО уничтожается в специальных
мусоросжигательных установках. При этом в одних случаях вырабатывается
электроэнергия, в других - пар, которым отапливаются близлежащие предприятия
или жилые кварталы. В России этот метод мало распространен, главным образом
потому, что используемые на этих заводах зарубежные технологии не справляются с
неотсортированными российскими отходами [29]. В основе технологий -
контролируемое сжигание отходов при высокой температуре в специальном
оборудовании - инсинераторе, оснащенном системой многоступенчатой газоочистки.
Инсинераторы на базе подовых, вращающихся и циклонных печей
предназначены для утилизации различных отходов. Подовая печь используется для
утилизации твердых бытовых, жидких отходов и стоков, промышленных отходов (в т.
ч. нефтешламов), а также для обезвреживания медицинских и биологических
отходов. Циклонный реактор предназначен для утилизации жидких и газообразных
отходов. Вращающаяся печь используется для уничтожения твердых бытовых и
пастообразных отходов, старогодних шпал. Их преимущества:
· От первоначального объема отходов остается
лишь 5% золы.
· Газообразные продукты первичного горения
дожигаются в специальной камере инсинератора, что обеспечивает разложение
образующихся в процессе инсинерации диоксинов.
· Существует возможность рекуперации
тепловой энергии (пар, горячая вода, электроэнергия).
1. Анализ
состояния вопроса, постановка цели и задач проекта
Целью данной ВКР является проектирование линии
транспортировки известково-доломитной пыли с целью оптимизации производства
мусоросжигательного завода города Череповца. Задача автора - провести
правильный анализ проекта, рассчитать привод транспортера для подачи
известково-доломитной пыли, разработать гидропривод гильотинной двери и
технологический процесс изготовления колеса зубчатого, произвести
технико-экономическое обоснование мероприятия и обозначить меры по обеспечению
безопасных и здоровых условий труда.
Человек не может жить, не оставляя после себя твёрдые бытовые
отходы (ТБО). Количество их зависит различных факторов. В среднем принято
считать, что на одного жителя в год может накапливаться до 350 кг мусора.
На общее накопление ТБО влияют следующие факторы:
- Степень благоустройства зданий (наличие
мусоропроводов, системы отопления, тепловой энергии для приготовления пищи,
водопровода и канализации);
- Развитие сети общественного питания и
бытовых услуг;
- Уровень производства товаров массового
спроса и культура торговли;
- Уровень охвата коммунальной очисткой
культурно-бытовых и общественных организаций;
- Климатические
условия.
Отходы собираются как на специализированных
(санкционированные места), так и на стихийно возникающих свалках (неразрешенные
места). Сконцентрированные в отвалах, на свалках отходы - опасные источники
загрязнения поверхностных и подземных вод, атмосферного воздуха, почв и
растений. Сложившаяся ситуация представляет реальную угрозу здоровью людей -
современным и будущим поколениям страны.
Проблема твердых бытовых отходов (ТБО) является
остроактуальной, поскольку ее решение связано с необходимостью обеспечения нормальной
жизнедеятельности населения, санитарной очистки городов, охраны окружающей
среды и ресурсосбережения.
ТБО включают разнообразные вещества органического и
минерального происхождения: пищевые отходы, использованную бумагу и картон,
текстиль, древесину, кости, кожу, резину, пластмассу, металл, стекло, камни и
др. Мусор является благоприятной средой для развития микроорганизмов,
вызывающих некоторые инфекционные заболевания. Поэтому необезвреженные отходы
могут быть источником массового загрязнения окружающей среды.
Ни один из применяемых в настоящее время способов сбора и
удаления отходов не является полностью удовлетворительным ни по
санитарно-гигиеническим, ни по технико-экономическим показателям.
Твердые бытовые отходы (ТБО) являются отходами
сферы потребления, образующимися в результате бытовой деятельности населения.
Они состоят из изделий и материалов, непригодных для дальнейшего использования
в быту.
Это отходы, которые накапливаются в жилом фонде, учреждениях,
предприятиях общественного назначения (школах, зрелищных и детских учреждениях,
гостиницах, столовых и т.п.) [28].
К твердым бытовым отходам, учитываемым нормой накопления,
относятся отходы, образующиеся в жилых зданиях, включая отходы от текущего
ремонта квартир, отходов продуктов сгорания в устройствах местного отопления,
смет, опавшие листья, собираемые с дворовых территорий и крупногабаритные
предметы домашнего обихода.
Состав и объем отходов чрезвычайно разнообразны и зависят не
только от страны и местности, но и от времени года и от многих других факторов.
Как известно, подавляющая масса ТБО в мире пока складируется
на мусорных свалках, стихийных или специально организованных в виде
"мусорных полигонов". Однако это самый неэффективный способ борьбы с
ТБО, так как мусорные свалки, занимающие огромные территории часто плодородных
земель и характеризующиеся высокой концентрацией углеродсодержащих материалов
(бумага, полиэтилен, пластик, дерево, резина), часто горят, загрязняя
окружающую среду отходящими газами. Кроме того, мусорные свалки являются
источником загрязнения как поверхностных, так и подземных вод за счет дренажа
свалок атмосферными осадками.
Например, в Москве ежегодно образуется 10 млн. т промышленных
и бытовых отходов, которые вывозятся на специализированные свалки. Таких свалок
в Подмосковье свыше 50, каждая площадью от 3 до 10 га. В целом в России под
мусорные свалки отчуждено 0,8 млн. га земель, среди которых не только пустыри,
овраги и карьеры, но и плодородные черноземы.
Зарубежный опыт показывает, что рациональная организация
переработки ТБО дает возможность использовать до 90% продуктов утилизации в
строительной индустрии, например в качестве заполнителя бетона. По данным
специализированных фирм, осуществляющих в настоящее время даже
малоперспективные технологии прямого сжигания твердых бытовых отходов,
реализация термических методов при сжигании 1000 кг ТБО позволит получить
тепловую энергию, эквивалентную сжиганию 250 кг мазута. Однако реальная
экономия будет еще больше, поскольку не учитывают сам факт сохранения первичного
сырья и затраты на добычу его, т.е. нефти и получения из нее мазута.
В мировой практике нашли промышленное применение четыре
метода переработки ТБО:
- термическая обработка (в основном
сжигание);
- биотермическое аэробное компостирование (с
получением удобрения или биотоплива);
- анаэробная ферментация (с получением
биогаза);
- сортировка (с извлечением тех или иных
ценных компонентов для вторичного использования).
Наиболее рациональным методом переработки ТБО является
мусоросжигание. Его зарождение относится еще к 1870 г. Основное его
преимущество - сокращение объемов отходов более чем в 10 раз, а их массы - в 3
раза. Главный же недостаток прямого сжигания необработанных ТБО связан с
серьезной опасностью загрязнения атмосферы вредными выбросами.
Сложность непосредственной утилизации ТБО обусловлена, с
одной стороны, их исключительной многокомпонентностью, с другой - повышенными
санитарными требованиями к процессу их переработки. В связи с этим сжигание до
сих пор остается наиболее распространенным способом первичной обработки бытовых
отходов.
Сжигание требует предварительной обработки ТБО (с получением
т. н. топлива, извлеченного из отходов). При разделении из ТБО стараются
удалить крупные объекты, металлы (как магнитные, так и немагнитные) и
дополнительно его измельчить. Для того чтобы уменьшить вредные выбросы, из
отходов также извлекают батарейки и аккумуляторы, пластик, листья. Сжигание
неразделенного потока отходов в настоящее время считается чрезвычайно опасным.
Таким образом, мусоросжигание может быть только одним из компонентов
комплексной программы утилизации.
Сжигание позволяет примерно в 3 раза уменьшить вес отходов,
устранить некоторые неприятные свойства: запах, выделение токсичных жидкостей,
бактерий, привлекательность для птиц и грызунов, а также получить
дополнительную энергию, которую можно использовать для получения электричества
или отопления.
Сжигание можно разделить на два вида:
непосредственное сжигание, при котором получается только
тепло и энергия;
пиролиз, при котором образуется жидкое и газообразное
топливо.
Экологические воздействия МСЗ в основном связаны с
загрязнением воздуха, в первую очередь - мелкодисперсной пылью, оксидами серы и
азота, фуранами и диоксинами. Серьезные проблемы возникают также с захоронением
золы от мусоросжигания, которая по весу составляет до 30% от исходного веса
отходов и которая в силу своих физических и химических свойств не может быть
захоронена на обычных свалках. Для безопасного захоронения золы применяются
специальные хранилища с контролем и очисткой стоков.
В настоящее время уровень сжигания бытовых отходов в
отдельных странах различен. Так, из общих объемов бытового мусора доля сжигания
колеблется в таких странах, как Австрия, Италия, Франция, Германия, от 20 до
40%; Бельгия, Швеция - 48-50%; Япония - 70%; Дания, Швейцария 80%; Англия и США
- 10%. В нашей стране сжиганию подвергаются пока лишь около 2% бытового мусора,
а в Москве - около 10% [29].
Для повышения экологической безопасности необходимым условием
при сжигании мусора является соблюдение ряда принципов. К основным из них
относятся температура сжигания, которая зависит от вида сжигаемых веществ;
продолжительность высокотемпературного сжигания, зависящая также от вида
сжигаемых отходов; создание турбулентных воздушных потоков для полноты сжигания
отходов.
Различие отходов по источникам образования и
физико-химическим свойствам предопределяет многообразие технических средств и
оборудования для сжигания.
В последние годы ведутся исследования по совершенствованию
процессов сжигания, что связано с изменением состава бытовых отходов,
ужесточением экологических норм. К модернизированным способам сжигания отходов
можно отнести замену воздуха, подаваемого к месту сжигания отходов для
ускорения процесса, на кислород. Это позволяет снизить объем горючих отходов,
изменить их состав, получить стеклообразный шлак и полностью исключить
фильтрационную пыль, подлежащую подземному складированию. Сюда же относится и
способ сжигания мусора в псевдоожиженном слое. При этом достигается высокая
полнота сгорания при минимуме вредных веществ.
Мусоросжигание обеспечивает минимальное содержание в шлаке и
золе разложимых веществ, однако оно является источником выбросов в атмосферу.
Мусоросжигательными заводами (МСЗ) выбрасываются в газообразном виде хлористый
и фтористый водород, сернистый газ, диоксин, а также твердые частицы различных
металлов: свинца, цинка, железа, марганца, сурьмы, кобальта, меди, никеля,
серебра, кадмия, хрома, олова, ртути и др.
В последнее время все более распространяется метод
совместного сжигания твердых бытовых отходов и шламов сточных вод. Этим
достигается отсутствие неприятного запаха, использование тепла от сжигания
отходов для сушки осадков сточных вод.
В настоящее время в г. Череповце мусор вывозится на мусорные
полигоны, чем наносит огромный вред окружающей среде. Даже не смотря на то, что
по технологии предусмотрена прокладка дна мусорного котлована материалами не
пропускающими продуктов гниения. На самом же деле по прошествии n-го количества времени
материал прорывается и происходит активное заражение грунтовых вод продуктами
долговременного гниения, опасных бактерий и микробов. А так как объемы мусора
из года в год не уменьшаются, а только увеличиваются возникла крайняя
необходимость в поиске новых методов утилизации бытовых отходов, то есть строительстве
мусоросжигательного завода (МСЗ).
Поэтому целью проекта является разработка системы
транспортирования и загрузки известково-доломитной пыли (ИДП) для уже
существующего проекта МСЗ.
Исходя из поставленной цели необходимо решить следующие
задачи:
- рассчитать и спроектировать привод
транспортера;
- спроектировать
план цеха;
- рассчитать гидропривод гильотинной двери и
раму конвейера;
- разработать технологический процесс
изготовления колеса зубчатого;
- рассчитать экономическую эффективность от
внедрения проекта;
- проанализировать и предложить меры по
обеспечению безопасных и здоровых условий труда.
2.
Конструкторская часть
2.1 Расчет и
конструирование шнекового транспортера установки
2.1.1
Техническое задание
Мощность на приводном валу, кВт: 1 кВт;
Частота вращения приводного вала nПР = 17 об/мин.
Рисунок 2.1 - Кинематическая схема привода
- мотор-редуктор, 2 - муфта, 3 - подшипники, 4 - вал шнека.
2.1.2
Энергокинематический расчет привода (рисунок 2.1)
Определение КПД привода [7, стр.178].
КПД привода определяется по формуле 2.1:
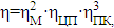
(2.1)
где 
КПД муфты;

КПД цилиндрической передачи;

КПД одной пары подшипников [6, стр.43].
Следовательно, КПД привода составит:
Определение требуемой мощности электродвигателя определяется по
формуле 2.2, кВт:
(2.2)
2.1.3 Выбор
электродвигателя
В качестве привода шнекового конвейера выбираем
мотор-редуктор.
Электродвигатель мотор-редуктора выбираем по значению
номинальной мощности РНОМ в соответствие с условием:
(2.3)
Принимаем значение номинальной мощности электродвигателя РНОМ
= 1,5кВт.
Наиболее предпочтительным является двигатель 4АМ100L8У3 номинальной мощности РНОМ = 1,5 кВт,
номинальной частоты вращения nНОМ = 700 об/мин [7, стр.407, табл. К9, К10].
Принимаем передаточное число привода 40.
2.1.4
Определение энергокинематических параметров привода
Мощность на быстроходном валу редуктора определяется по
формуле 2.4, кВт:

(2.4)
Мощность на тихоходном валу редуктора определяется по формуле 2.5,
кВт:
(2.5)
Мощность на приводном валу определяется по формуле 2.6, кВт:
(2.6)
Частота вращения выходного вала электродвигателя, об/мин:

.
Частота вращения быстроходного вала редуктора, об/мин:
Частота вращения тихоходного вала редуктора определяется по
формуле 2.7, об/мин:
Частота вращения приводного вала, об/мин:
Угловая скорость выходного вала электродвигателя определяется по
формуле 2.8, с-1:
(2.8)
Угловая скорость быстроходного вала редуктора, с-1:
Угловая скорость тихоходного вала редуктора определяется по
формуле 2.9, с-1:
(2.9)
Угловая скорость приводного вала, с-1:
Крутящий момент на выходном валу электродвигателя определяется по
формуле 2.10, Нм:
(2.10)
Крутящий момент на быстроходном валу редуктора определяется по
формуле 2.11, Нм:
(2.11)
Крутящий момент на тихоходном валу редуктора определяется по
формуле 2.12, Нм:
(2.12)
Крутящий момент на приводном валу определяется по формуле 2.13,
Нм:
(2.13)
2.1.5 Выбор
мотор-редуктора
На основании выполненных расчетов выбираем
мотор-редуктор4МЦ2С-140-1,5-G110-ЦУ3 ГОСТ 15150-69, номинальное передаточное число i = 40, диаметр выходной
ступени тихоходного вала d2 =45 мм, межосевое расстояние АW = 140 мм.
2.2 Расчет и
проектирование приводного приводного вала установки
2.2.1 Предварительный
расчет вала
В качестве материала быстроходного и тихоходного валов
выбираем
сталь 45, термообработка - улучшение, твердость 269…302 НВ
[7, стр.153].
Предел прочности
;
Предел текучести
Предел выносливости
;
Допускаемые напряжения кручения
[5, стр.160].
Диаметр первой ступени вала определяется по формуле 2.14, мм:
(2.14),
Принимаем d1 = 45 мм по ряду нормальных линейных
размеров ГОСТ 6636-69. Длина 1-й ступени под полумуфту определяется по формуле
2.15, мм:
(2.15)
Диаметр ступени под подшипник и корпус подшипникового узла
определяется по формуле 2.16, мм:
(2.16)
где t = 2,5 мм.
Принимаем d2 = 50 мм.
Длина ступени выбирается конструктивно в соответствие с шириной
подшипника и габаритами корпуса подшипникового узла.
Диаметр ступени вала под звездочки и ролик определяется по формуле
2.17, мм:
(2.17)
Длина третьей ступени выбирается конструктивно в соответствии с
конструкцией ролика.
Диаметр ступени под подшипник, мм:
.
Длина ступени выбирается конструктивно в соответствие с шириной
подшипника и габаритами корпуса подшипникового узла (рисунок 2.2).
Рисунок 2.2 - Конструкция приводного вала
2.2.2
Предварительный выбор подшипников
В качестве опор приводного вала рабочей машины выбираем
сферические роликовые подшипники № 53609 ГОСТ 24969-81: d = 45 мм; D = 100 мм; В = 35 мм; Cr= 104 кН, С0 = 63кН. [7,
стр.432].
В соответствие с выбранными подшипниками выбираем крышки
торцевые с отверстием для манжетного уплотнения: крышка 11-72.30 ГОСТ 18512-73.
Манжетные уплотнения ГОСТ 8752-79 1.1-50.70-1 [6, стр.119].
Подшипники приводного вала помещены в корпуса типа РУ для
подшипников качения ГОСТ 13218.10-80.
2.2.3 Подбор
и проверочный расчет муфт
Подбор муфты для тихоходного вала редуктора. Для соединения
тихоходного вала с приводным валом выбираем муфту упругую втулочно-пальцевую
500-45-1.25-11 ГОСТ 21425-93 [6, стр.249], номинальный момент Т=500 Нм,
посадочный диаметр d1=45 мм.
2.2.4 Подбор
шпонок и проверка прочности шпоночных соединений
Подбор призматической шпонки и проверочный расчет соединения под
полумуфту на приводном валу. Для соединения приводного вала с полумуфтой
принимаем призматическую шпонку
ГОСТ23360-78, t1 = 4 мм [7,
стр.450].
Условие прочности соединения определяется по формуле 2.18, Н/мм2:
(2.18)
где d = d1 =45 мм. Т = 5,07 Нм.
[2, стр.266].
Следовательно,
Условие прочности соединения выполняется.
Проверяем прочность шпоночного соединения на срез определяется по
формуле 2.19:
, (2.19)
где kA - коэффициент внешней динамической
нагрузки. Принимаем kA=1,1для нагрузок средней неравномерности.
допускаемое напряжение среза. Следовательно,
Прочность соединения обеспечена.
2.2.5 Силовой
расчет приводного вала представлен на рисунке 2.3
Рисунок 2.3 - Схема нагружения приводного вала
Проверка:
+3245-2.1857-6194=0.
Строим эпюру изгибающих моментов относительно оси OY, Нм:
Крутящий момент
Суммарные реакции опор, Н:
Суммарные моменты в опасных сечениях, Нм: М2 = 399,7Нм; М3 =
891Нм; М4 = 195Нм.
2.2.6
Проверочный расчет подшипников
Эквивалентная нагрузка Re учитывает характер и
направление нагрузок, действующих на подшипники, условия работы зависит от типа
подшипника определяется по формуле 2.20.
(2.20)
где Rr - суммарная реакция подшипника, Н;
Х=0,4 коэффициент радиальной нагрузки;
V=1 коэффициент вращения,
где Rr = RА = 6194Н;
Определяем базовую долговечность подшипника № 53609 ГОСТ 24969-81
по формуле 2.21.
(2.21)
Следовательно,
Подшипник № 53609 ГОСТ 24969-81 пригоден.
2.2.7
Проверочный расчет приводного вала
Проверочный расчет валов на прочность выполняют, учитывая
совместное действие изгиба и кручения. Целью расчета является определение
коэффициентов запаса прочности в наиболее опасном сечении вала и сравнение его
с допускаемым коэффициентом запаса прочности определяется по формуле 2.22.
, (2.22)
где s - общий коэффициент запаса прочности в
опасном сечении вала;
[s] = 1,6…2,1 допускаемый коэффициент запаса
прочности.
Нормальные напряжения в опасных сечениях вала изменяются по
симметричному циклу и определяются, Н/мм2:
(2.23)
где М - момент изгиба в опасном сечении вала, Гм.
На приводном валу моменты изгиба испытывают 2 и 3 сечения. М2 =
399,7Нм; М3 = 891Нм; М4 = 195Нм.
WНЕТТО -
осевой момент сопротивления сечения вала, мм3.
Для 2-го сечения:
(2.24)
Для 3-го и 4-го сечения:
(2.25)
Касательные напряжения изменяются по от нулевому циклу и
определяются:
(2.26)
где 
- полярный момент инерции сопротивления сечения вала, мм3. МК2 =
МК3 = 710,4Нм; МК4 = 76,3Нм.
Для 2-го сечения:
(2.27)
Для 3-го и 4-го сечения:
(2.28)
Касательные напряжения для 2-го сечения, Н/мм2:
Касательные напряжения для 3-го и 4-го сечения, Н/мм2:
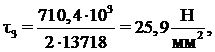
Во 2-м сечении нормальные и касательные напряжения имеют
наибольшее значение по сравнению с другими сечениями вала. Дальнейший расчет
ведется только для 2-го сечения вала, которое называется расчетным. Коэффициент
концентрации нормальных напряжений в расчетном сечении вала определяется по
формуле 2.29:
(2.29)
где Кσ - коэффициент концентрации нормальных напряжений.
Принимаем Кσ = 2,3 [6,
стр.271-272]. Кd = 0,75 - коэффициент влияния абсолютных
размеров поперечного сечения; КF = 1,5
коэффициент влияния шероховатости; КУ = 1,6 коэффициент влияния поверхностного
упрочнения.
Коэффициент концентрации касательных напряжений в расчетном
сечении вала определяется по формуле 2.30:
(2.30)
Принимаем Кτ
= 1,75;
Пределы выносливости по нормальным напряжениям в расчетном сечении
определяется по формуле 2.31, Н/мм2:
(2.31)
где
- предел выносливости.
Следовательно,
Пределы выносливости по касательным напряжениям в расчетном
сечении определяется по формуле 2.32, Н/мм2:
(2.32)
Следовательно,
Коэффициент запаса прочности по нормальным напряжениям
определяется по формуле 2.33:
(2.33)
Коэффициент запаса прочности по касательным напряжениям
определяется по формуле 2.34:
(2.34)
Общий коэффициент запаса прочности в расчетном сечении
определяется по формуле 2.35:
(2.35)
Следовательно,
Условие прочности
выполняется.
Дальнейшее снижение коэффициента запаса прочности вала в опасном
сечении считаю нецелесообразным, т.к. это повлечет за собой уменьшение диаметра
цапфы вала. Это, в свою очередь, отрицательно повлияет на грузоподъемность
подшипников приводного вала.
2.3 Расчет и
проектирование гидропривода перемещение гильотинной двери установки
2.3.1
Определение нагрузочных и скоростных параметров гидродвигателя
В мусоросжигательной печи отрезание мусора осуществляется с помощью
ножа гильотинной двери. Рабочий ход ножа осуществляется с помощью двух
гидроцилиндров (левого и правого). Возврат ножа осуществляется с помощью двух
возвратных гидроцилиндров. При расчете и выборе исполнительных гидроцилиндров
необходимо знать осевое усилие, необходимое для перемещения рабочих органов.
Суммарное осевое усилие, приложенное к гидроцилиндрам: R=320000Н
Осевое усилие, приложенное к каждому возвратному гидроцилиндру:
По условиям конструкции и работы гильотинной двери выбираем левый
и правый гидроцилиндры двухстороннего действия с односторонним штоком. В
качестве возвратных гидроцилиндров выбираем плунжерные гидроцилиндры.
На основании параметров привода определяются максимальная скорость
и максимальное осевое усилие:
Vдmax= Vmax= 0,03 м/с, Rдmax= Rmax= 3,2·105 Н
2.3.2
Определение геометрических параметров и выбор ГД
В качестве исполнительного гидродвигателя выбираем
гидроцилиндр двухстороннего действия с односторонним штоком.
Основными параметрами гидроцилиндра являются диаметры поршня
и рабочее давление.
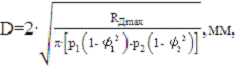
(2.36)
где р1 и р2 - давление соответственно в
напорной и сливной полостях гидроцилиндра;
р1 = 2/3×pн, МПа, (2.37)
Предварительно выбираем насос, у которого pн=16 МПа; р1 = 2/3×6=10,67 МПа; Принимаем: р2 = 0,3…0,9 МПа;
- коэффициенты, которые принимаются с
учетом выбранной конструкции ГЦ с односторонним штоком.
Принимаем во внимание, что в гидросхеме используются два
гидроцилиндра, поэтому в качестве расчетного возьмем ½ осевого усилия, необходимого по заданию.
По полученному значению D из
справочника [1] выбирается стандартный гидроцилиндр, у которого диаметр поршня Dст>D; Dст = 140 мм. Диаметр штока определяется по формуле 2.38:
(2.38),
По справочнику [1] принимаем стандартное значение, ближайшее
большее к расчетному: dст = 100 мм
Основные параметры гидроцилиндра по ТУ 2.0221050.004-88:
гидроцилиндр с односторонним штоком;
Dст=140 мм,
dст=100 мм, ход поршня s=1000 мм;
Рном=16 МПа.
Обозначение: ГЦП 140´100´1000
ТУ 2.0221050.004-88
Определяем диаметры поршней возвратных гидроцилиндров по формуле
2.39:
(2.39)
где
- осевое усилие, приложенное к поршню
возвратного гидроцилиндра, Н (
=22600 Н);
- давление в напорной полости возвратного
гидроцилиндра,
МПа (
=4,5МПа),
По ГОСТ 6540-68 выбираем плунжерные гидроцилиндры с диаметром
поршня D=80 мм и ходом поршня S=250 мм.
2.3.3
Составление принципиальной схемы привода
Составление принципиальной схемы гидропривода начинаем от
гидроцилиндра, то есть наносим на схему гидроцилиндр, а затем на его гидролинии
устанавливаем регулирующие и направляющие гидроаппараты в соответствии с
циклограммой работы привода и способом регулирования скорости. После этого
объединяем напорную, сливную и дренажную линии отдельных участков схемы.
Последним этапом является изображение гидросхемы насосной установки, размещение
фильтра, обратного клапана, регулятора расхода.
Принципиальная схема ГП выполняется в соответствии с ГОСТ на
правила выполнения гидравлических схем и условные графические изображения их
элементов [5]. Комплексы гидроаппаратов, входящих в состав насосных установок,
гидроблоков управления, гидропанелей и других узлов, выделяются на схеме
штрихпунктирными линиями.
Способы управления распределителями и соответственно их
обозначения определяются при выборе гидроаппаратов и после этого указываются на
принципиальной схеме. На схеме цифрами указываются характерные сечения (входы и
выходы из гидроаппаратов, места соединения линий). Схема насосной установки
окончательно определяется после выбора её модели. Принципиальная схема привода
гильотины представлена на рисунке 2.4
Рисунок 2.4 - Схема работы гидропривода
Быстрый подвод: БП:
ПП(ГЦ1)/ШП(ГЦ1)
Н -Ф-Д - Р(РР)А- КО2- - В(РР)Т -
ГБ _________ГБ
ПП(ГЦ2)/ШП(ГЦ2)
КП
Быстрый отвод БО:
включены ЭМ1, ЭМ3
ШП(ГЦ1)/ПП(ГЦ1)
Н-Ф-Д - Р(РР)В -- Р3 - А(РР)Т -
ГБ ______________ГБ
ШП(ГЦ2)/ПП(ГЦ2)
КП
Стоп:
все ЭМ выключены
Н-Ф-Д - Р(РР)Т - ГБ
КП
Принятые на схеме обозначения:
Н - насос;
Ф - фильтр;
Д - дроссель;
РР1 - реверсивный распределитель;
Р2, Р3 - распределители;
ЭМ1, ЭМ2, ЭМ3 - электромагниты распределителей;
КП1, КП2 - предохранительные клапаны;
ГЦлев - левый гидроцилиндр;
ГЦправ - правый гидроцилиндр;
ГЦ1, ГЦ2 - возвратные гидроцилиндры;
ГЦ3 - прижимные гидроцилиндры;
КО1, КО2 - клапаны обратные.
2.3.4 Расчет
и выбор насосной установки
Выбор насосной установки осуществляется исходя из требуемых
расхода жидкости и давления в гидроприводе.
Для гидроцилиндра с односторонним штоком определяется по
формуле 2.40:
(2.40)
(2.41)
где QБО, QБО - максимальные расходы жидкости
соответственно при быстром подводе и отводе;
F1ст, F2ст - эффективные площади стандартного
гидроцилиндра соответственно в напорной и сливной полостях гидроцилиндра определяется
по формуле 2.42; VДmax= 0,03 м/c (по заданию)
(2.42)
(2.43)
Определяем максимальные расходы жидкости:
Номинальная подача насоса должна превышать QБП:
Qн >QБП, л/мин, (2.44)
Величина требуемого давления на выходе из насоса:
рн=р1+Δрн, МПа, (2.45)
где Δрн - суммарные потери давления в линии, соединяющей насос с
гидроцилиндром при обратном ходе.
Потери давления могут быть определены только после разработки
гидропривода, поэтому предварительно выбор насосной установки производится,
приняв:
(2.46),
На основании полученных значений из справочника выбираем модель
насосной установки и насоса:
ТУ2-053-1535-80, где 3 - исполнение по высоте гидрошкафа; Н =
1850 мм; А - исполнение по способу охлаждения: с теплообменником и
терморегулятором; М - исполнение по расположению и количеству агрегатов:
агрегат за щитом; Л - расположение насосного агрегата: левое; Г48-8 -
обозначение насосной установки; 4 - исполнение по вместимости бака: 160 л; УХЛ
- климатическое исполнение; НПл56-5/16 - тип комплектующего насоса
(пластинчатый двухпоточный), pн=16 МПа;
4А160М6 - электродвигатель; 9Г49 - 33 - номер насосного агрегата; Qн=61 л/мин=1,02·10-3 м3/с.
Подача насоса данной установки удовлетворяет условию:
Qн >Qmax, м3/с, (2.47)
>55,44м3/с.
2.4 Расчет и
выбор гидроблока управления и трубопроводов
.4.1 Расчет и
выбор гидроаппаратуры
Параметрами для выбора гидроаппаратуры является величина
расхода жидкости и рабочего давления в той линии, где установлен аппарат.
Номинальные значения расхода и давления - ближайшие большие к расчетным
значениям. Выбранные аппараты должны соответствовать заданному способу монтажа,
в данном случае резьбового, а для блока управления - встраиваемого. Выбор
аппаратуры производим из справочника [9]. При выборе направляющей аппаратуры
предпочтение отдаём распределителям типа В, отличающимся меньшими габаритами и
металлоёмкостью.
РР1 (схема 14) - распределитель реверсивный;
Qном=100 л/мин=1,67·10-3 м3/с;
Рном=32 МПа
ВЕХ16.14.30/ОФ.А. В220-50НД.Н. ЕТ ГОСТ 24679-81
В - гидрораспределитель золотниковый;
ЕХ - управление электрогидравлическое;
- диаметр условного прохода, мм;
- исполнение по схеме 14 [1];
/ - номер конструкции;
ОФ - без пружинного возврата с фиксатором;
Л - тип магнита: маслонаполненный;
В220 - 50 - вид тока; В - переменный, напряжение 220В,
частота 50Гц;
Н - наличие кнопки для ручного переключения на
электромагнитное;
ЕТ - соединение линий управления с основными: линии
соединены;
Ф - фильтр;
Qном=63 л/мин=1,05·10-3 м3/с; Рном=32
МПа
ФГМ32 ТУ-053-1778-86Е
Номинальная пропускная способность 100 л/мин;
Номинальная тонкость фильтрации 10 мкм;
Р3 (схема 573) - распределитель;
Qном. =160 л/мин=2,67·10-4 м3/с; Рном=32
МПа
РХ20.573.3.00. В220-50 ТУ2-053-1436-79Е
РХ - гидрораспределитель; 20 - диаметр условного прохода, мм;
573 - исполнение по гидросхеме 573; 3 - вид управления: электрогидравлическое;
00 - без регулирования времени переключения;
В220 - 50 - вид тока; В - переменный, напряжение 220В,
частота 50Гц;
КП1 - клапан предохранительный встраиваемого исполнения
Qном=63 л/мин=1,05·10-3 м3/с; Qmax=200 л/мин=3,33·10-3
м3/с;
Pном=32 МПа, МКПВ16/3Ф4В1УХЛ4 ТУ2-053-1737-85;
МКПВ - клапан предохранительный на базе встраиваемых
элементов с международными присоединительными размерами;
- условный проход, мм;
- номинальное давление 32 МПа;
Ф исполнение по способу монтажа: вставной;
- исполнение по функционально-конструктивному признаку;
В - исполнение по виду регулировки: винт с квадратной
головкой;
- исполнение по давлению;
УХЛ - климатическое исполнение;
- категория размещения.
КО1, КО2 - клапаны обратные;
Qном=63 л/мин=1,05·10-3 м3/с; Рном=20
МПа
Г51-33 ТУ2-053-1649-83Е
Д - дроссель встраиваемого исполнения;
Qном=63 л/мин=1,05·10-3 м3/с; pном=32 МПа
МДВ16/3Ф1ВУХЛ4 ПТУ2-053-614-83;
МДВ - дроссель встраиваемый с международными присоединительными
размерами по DIN 24342; 16 - условный проход, мм; 3 - номинальное давление 32 МПа;
Ф - вставной монтаж; 1 - конструктивное исполнение; К - исполнение по виду
регулировки: винт с квадратом под ключ; УХЛ - климатическое исполнение; 4 -
категория размещения.
Внутренний
диаметр трубопровода определяется по формуле 2.48:
где Q - максимальный расход жидкости в трубопроводе, м3/с;
- рекомендуемая скорость течения жидкости в трубопроводе, м/с;
Максимально допускаемая толщина стенки трубопровода определяется
по формуле 2.49:
где р - максимальное давление жидкости в трубопроводе;
- предел прочности на растяжение
материала трубопровода:
= 340 МПа; Кб - коэффициент безопасности,
Кб = 4;
2.4.2 Расчет
трубопровода по участкам
Трубопроводы разбиваем на участки и производим расчёт для
каждого участка.
Напорные трубы: участки 1-4, 36-37
Qmax= 61 л/мин=1,02·10-3 м3/с;
Выбираем ближайшее большее стандартное значение:
Dуст=20 мм,
Для данного участка выбираем стальные бесшовные трубы 25´3 по ГОСТ 8734-75
Соединение с шаровым ниппелем: 2-25-К3/4" ОСТ 2 Г 91-26-78.
где: 2 - конструктивное исполнение на давление;
- наружный диаметр трубы dн, мм;
К3/4”-резьба коническая;
Напорные трубы: участки 17-18, 19-20
Qmax = 55,44 л/мин=9,24·10-4 м3/с;
Выбираем ближайшее большее стандартное значение:
Dуст=20 мм,
Для данного участка выбираем стальные бесшовные трубы 22´2,5 по ГОСТ 8734-75. Соединение с шаровым
ниппелем: 2-22-К3/4" ОСТ 2 Г 91-26-78. Напорно-сливные трубы: участки
15-16, 25-25а
Выбираем ближайшее большее стандартное значение: Dуст=25 мм,
Для данного участка выбираем стальные бесшовные трубы 32´3,5 по ГОСТ 8734-75
Соединение с шаровым ниппелем: 2-32-К1" ОСТ 2 Г 91-26-78.
Напорно-сливные трубы: участки 26-27, 28-29
Qmax =55,44/2= 27,72 л/мин=4,62·10-4
м3/с;
Выбираем ближайшее большее стандартное значение: Dуст=20 мм,
Для данного участка выбираем стальные бесшовные трубы 22´2,5 по ГОСТ 8734-75
Соединение с шаровым ниппелем: 2-22-К3/4" ОСТ 2 Г 91-26-78.
Напорно-сливные
трубы: участки 30-31, 32-33
Qmax
=27,14/2=13,57 л/мин=2,26·10-4 м3/с;
Выбираем ближайшее большее стандартное значение: Dуст=12 мм,
Для данного участка выбираем стальные бесшовные трубы 16´2 по ГОСТ 8734-75. Соединение с шаровым ниппелем: 2-16-К1/2"
ОСТ 2 Г 91-26-78. Напорно-сливные трубы: участок 34-35
Qmax
= 27,14 л/мин=4,52·10-4 м3/с;
Выбираем ближайшее большее стандартное значение: Dуст=20 мм,
Для данного участка выбираем стальные бесшовные трубы 22´2,5 по ГОСТ 8734-75
Соединение с шаровым ниппелем: 2-22-К3/4" ОСТ 2 Г 91-26-78.
Сливные трубы: участки 38-39,13-22, 23-24
Qmax = 55,44 л/мин=9,24·10-4 м3/с;
уст=25 мм,
Для данного участка выбираем стальные бесшовные трубы 32´3,5 по ГОСТ 8734-75
Соединение с шаровым ниппелем: 2-32-К1" ОСТ 2 Г 91-26-78.
Сливные трубы: участок 43-44
Qmax= 61 л/мин=1,02·10-3 м3/с;
Выбираем ближайшее большее стандартное значение: Dуст=25 мм,
Для данного участка выбираем стальные бесшовные трубы 32´3,5 по ГОСТ 8734-75
Соединение с шаровым ниппелем: 2-32-К1" ОСТ 2 Г 91-26-78.
2.4.3
Разработка конструкций гидроблока управления
В гидроблок управления входят следующие аппараты: РР -
распределитель реверсивный стыкового исполнения ВЕХ16.14.30/ОФ.А. В220-50НД.Н.
ЕТ ГОСТ 24679-81; Д - дроссель встраиваемого исполнения МДВ16/3Ф1ВУХЛ4
ПТУ2-053-614-83; КО - клапан предохранительный встраиваемого исполнения
МКПВ16/3Ф4В1УХЛ4 ТУ2-053-1737-85.
Данные аппараты компонуются на специальном корпусе, к
которому прикрепляются посредством стандартных крепёжных деталей. При проектировании
корпуса гидроблока управления обеспечивается максимальная простота,
компактность и технологичность конструкции, удобство сборки, а также
возможность установки его на оборудование (на задней стенке корпуса
предусмотрены резьбовые крепёжные отверстия). Диаметры отверстий в корпусе
соответствуют диаметрам отверстий в аппаратах, которые к нему присоединяются.
Толщина перемычек между отверстиями не превышает 3…5 мм. Аппараты располагаем
таким образом, чтобы иметь возможность их беспрепятственной настройки и
регулировки. Трубопроводы подключаем так, чтобы конструкция была эргономичной.
На основе компоновки выполняется сборочный чертеж гидроблока
управления, на котором проставляются габаритные, присоединительные и
установочные размеры. На основании сборочного чертежа блока управления
выполняется рабочий чертеж корпуса. Учитывая сложность конструкции корпуса,
отверстия пронумеровываются (обозначаются).
2.4.4
Определение потерь давления в аппаратах и трубопроводах
Определение потерь давления в аппаратах
Потери давления D р ГА в гидроаппаратах
определяются по формуле 2.50:

(2.50)
где Dро -
давление открывания или настройки аппарата;
А и В - коэффициенты аппроксимации экспериментальной зависимости
потерь давления в аппарате от расхода жидкости через него;
Qmax-расход жидкости через аппарат на данном
этапе цикла.
Величина Dро для обратных клапанов приводится в справочнике [9], а для
напорных, редукционных и переливных клапанов выбирается при расчете
гидродвигателя и насосной установки. Для распределителей, фильтров и дросселей Dро=0. Коэффициенты А и В определяются по
формулам 2.51 и 2.52:
(2.51)
(2.52)
где Qном - номинальный расход аппарата;
Dрном - потери давления в
аппарате при номинальном расходе.
Величина Dрном для стандартных гидроаппаратов указывается в
справочнике [9] в таблицах основных параметров.
Расчет производим для быстрого подвода.
Напорная линия
Фильтр Ф: Qном=63 л/мин=1,05·10-3 м3/с;
Дроссель Д: Qном=63 л/мин=1,05·10-3 м3/с,
Распределитель РР: Qном=100 л/мин=1,67·10-3 м3/с;
Клапан обратный КО2: Qном=63 л/мин=1,05·10-3 м3/с;
Сливная линия
Распределитель РР: Qном=100 л/мин=1,67·10-3 м3/с;
Расчет потерь давления в гидроаппаратах сводим в таблицу 2.1
Таблица 2.1 - Потери давления в гидроаппаратах
Наименование и
модель аппарата
|
DРо (ΜПа)
|
А (МПа·с/м3)
|
В (МПа·с2/м6)
|
Этап цикла
|
Qmax (м3/с)
|
DРг а (ΜПа)
|
Фильтр Ф 2ФГМ32
|
0
|
47,6
|
45351,5
|
БП
|
0,001017
|
0,095288
|
Дроссель Д
МДВ16
|
0
|
123,8
|
117913,8
|
|
0,000924
|
0,215072
|
Распределитель
РР ВЕХ16
|
0
|
60
|
36000
|
БП
|
0,000924
|
0,086176
|
Клапан обратный
КО2 Г51-33
|
0,15
|
47,6
|
45351,5
|
БП
|
0,000924
|
0,23272
|
Распределитель
РР ВЕХ16
|
0
|
60
|
36000
|
БП
|
0,000452
|
0,034506
|
Потери в гидроаппаратах: напорная линия: DРгаН = 0,629256ΜПа; сливная линия: DРгаС = 0,034506ΜПа; суммарные потери в
ГА: DРгаS = 0,034506ΜПа.
Определение потерь давления в трубопроводах.
Потери давления по длине.
Потери давления по длине обусловлены вязким трением жидкости
при ее течении в трубопроводе. Существенное влияние на величину этих потерь
оказывает режим течения жидкости. Различают два режима: ламинарный и
турбулентный, причем переход из одного режима в другой происходит при критическом
числе Рейнольдса (Reкр). Поэтому прежде всего для каждого трубопровода определяется
число Рейнольдса (Re).
Re=U·dст/n, (2.53)
где U - фактическая скорость движения жидкости в трубопроводе;
n - кинематический
коэффициент вязкости жидкости.
Затем сравниваем это число с Reкр:
если Re<Reкр, то режим течения ламинарный,
если Re>Reкр, то режим течения турбулентный.
Для гладких круглых труб, а так же для отверстий в корпусе
гидроблока управления Reкр=2300, для рукавов Reкр=1600.
При расчете потерь давления трубопроводы разбиваются на
участки, имеющие одинаковый диаметр и расход жидкости. Потери давления D
Ре на вязкое трение:
(2.54)
где ρ - плотность рабочей жидкости;
λi - коэффициент гидравлического трения на i-м участке;
ni - число участков.
Для гладких цилиндрических трубопроводов коэффициент λi
определяется по формулам:
при ламинарном режиме λi=64/Rei
при турбулентном режиме λi=0,3164/ (Rei) 0,25,где Rei - число
Рейнольдса на i-м участке.
Расчет производим для быстрого подвода.
Участок 1-4:
f1-4=π (d) 2/4=π (0,019) 2/4=2,84·10-4 м2,U1-4=Q/f1-3=1,02·10-3/2,84·10-4
=3,59 м/с,-4=U1-4·d/γ=3,59
·0,019/19·10-6=3585,8.
Режим течения турбулентный.
λi=0,3164/ (3585,8) 0,25=0,040888
Для остальных участков трубопровода расчет производим аналогично.
Результаты расчетов сводим в таблице 2.2:
Таблица 2.2 - Потери давления по длине
Этап цикла
|
Линия
|
Qmax (м3/с)
|
Учас-ток
|
dст; (м)
|
fст; (м2)
|
U (м/с)
|
Rei
|
λi
|
Li (м)
|
ΔРi (МПа)
|
ΔРе (МПа)
|
1
|
2
|
3
|
4
|
5
|
6
|
7
|
8
|
9
|
10
|
11
|
12
|
БП
|
Н
|
0,00102
|
1-4
|
0,019
|
0,000284
|
3,59
|
3585,8
|
0,040888
|
0,9
|
0,010957
|
0,050629
|
0,097984
|
|
Н
|
0,000924
|
5-13
|
0,02
|
0,000314
|
2,94
|
3096,0
|
0,042417
|
0,15
|
0,001211
|
|
|
|
Н-С
|
0,000924
|
14-15
|
0,02
|
0,000314
|
2,94
|
3096,0
|
0,042417
|
0,07
|
0,000565
|
|
|
|
Н-С
|
0,000924
|
15-16
|
0,025
|
0,000491
|
1,88
|
2476,8
|
0,04485
|
1,6
|
|
|
1
|
2
|
3
|
4
|
5
|
6
|
7
|
8
|
9
|
10
|
11
|
12
|
БП
|
Н
|
0,000924
|
17-18-20
|
0,017
|
0,000227
|
4,07
|
3642,3
|
0,040728
|
0,9
|
0,015722
|
0,050629
|
0,097984
|
|
Н-С
|
0,000924
|
25-25a
|
0,025
|
0,000491
|
1,88
|
2476,8
|
0,04485
|
0,4
|
0,001119
|
|
|
|
Н-С
|
0,000462
|
26-27
|
0,017
|
0,000227
|
2,04
|
1821,2
|
0,035142
|
2,2
|
0,00829
|
|
|
|
Н-С
|
0,000462
|
28-29
|
0,017
|
0,000227
|
2,04
|
1821,2
|
0,035142
|
2,2
|
0,00829
|
|
|
|
Н-С
|
0,000226
|
30-31
|
0,012
|
0,000113
|
2,00
|
1263,0
|
0,050673
|
1,9
|
0,014117
|
0,047355
|
|
|
Н-С
|
0,000226
|
32-33
|
0,012
|
0,000113
|
2,00
|
1263,0
|
0,050673
|
1,9
|
0,014117
|
|
|
|
Н-С
|
0,000452
|
34-35
|
0,017
|
0,000227
|
1,99
|
1783,1
|
0,035893
|
4,8
|
0,017709
|
|
|
|
Н-С
|
0,000452
|
35-36
|
0,02
|
0,000314
|
1,44
|
1515,6
|
0,042227
|
0,1
|
0,000193
|
|
|
|
С
|
0,000452
|
37-38
|
0,02
|
0,000314
|
1,44
|
1515,6
|
0,042227
|
0,1
|
0,000193
|
|
|
|
С
|
0,000452
|
38-39
|
0,025
|
0,000491
|
0,92
|
1212,5
|
0,052784
|
1,3
|
0,001026
|
|
|
Напорная линия: D Рlн = 0,050629ΜПа
Сливная линия: D Рlс = 0,047355ΜПа
Суммарные потери по длине при БП: D РlS
= 0,097984ΜПа
Местные потери давления
Местные потери давления
складываются из потерь в различных местных сопротивлениях
и определяются по формуле 2.55:
(2.55)
где ζj - коэффициент j-го
местного сопротивления;
nм - число местных сопротивлений;
fстj - площадь внутреннего сечения
трубопровода перед j-м сопротивлением.
Коэффициент ζj определяется по справочнику [1].
Расчет местных потерь производим для быстрого подвода.
Участок 1-4:
изгиб трубы R/do=4 ζ=0,2 (2 изгиба)
вход в емкость ζ=1
вход в трубу R/do=0,04 ζ=0,26
тройник ζ=0,1
ζ1-4=
2·0,2+1+0,26+0,1=1,76,
Для остальных участков трубопровода расчет производим аналогично.
Результаты расчетов сводим в таблице 2.3.
Таблица 2.3 - Местные потери давления
Этап цикла
|
Линия
|
Qmax [м3/с]
|
Учас-ток
|
fст; [м2]
|
Вид местного
сопротивления
|
Кол-во
|
ζi
|
Σζi
|
Δ Рмj [МПа]
|
1
|
2
|
3
|
4
|
5
|
6
|
7
|
8
|
9
|
10
|
БП
|
Н
|
0,00102
|
1-4
|
0,000284
|
изгиб трубы
R/d0=4
|
2
|
0,2
|
1,76
|
0,010033
|
0,049476
|
|
|
|
|
|
вход в ёмкость
|
1
|
1
|
|
|
|
|
|
|
|
|
вход в трубу
|
1
|
0,26
|
|
|
|
|
|
|
|
|
Тройник
|
1
|
0,1
|
|
|
|
|
Н
|
0,00102
|
4-6
|
0,000314
|
Тройник
|
1
|
0,1
|
0,1
|
0,000464
|
|
|
Н
|
0,000924
|
6-13
|
0,000314
|
Тройник
|
1
|
0,1
|
0,1
|
0,000381
|
|
|
Н-С
|
0,000924
|
14-15
|
0,000314
|
колено 900
|
1
|
1,2
|
1,6
|
0,006096
|
|
|
|
|
|
|
резкое
расширение d0/d=0,8 Æ20/Æ25
|
2
|
0,2
|
|
|
|
БП
|
Н-С
|
0,000924
|
15-16
|
0,000491
|
изгиб трубы
R/d0=6
|
2
|
0,18
|
2,76
|
0,004307
|
0,049476
|
|
|
|
|
|
резкое сужение
d0/d=0,55 Æ25/Æ17
|
2
|
0,2
|
|
|
|
|
|
|
|
|
Тройник
|
1
|
2
|
|
|
|
|
Н
|
0,000924
|
17-18-25
|
0,000227
|
изгиб трубы
R/d0=6
|
2
|
0,18
|
2,96
|
0,021605
|
0,049476
0,049476
|
|
|
|
|
|
резкое
расширение d0/d=0,55 Æ17/Æ25
|
2
|
0,3
|
|
|
|
|
|
|
|
|
Тройник
|
1
|
2
|
|
|
|
|
Н-С
|
0,000924
|
25-26
|
0,000491
|
изгиб трубы
R/d0=6
|
2
|
0,18
|
2,96
|
0,004619
|
|
|
|
|
|
|
резкое сужение
d0/d=0,55 Æ25/Æ17
|
2
|
0,3
|
|
|
|
|
|
|
|
|
Тройник
|
1
|
2
|
|
|
|
|
Н-С
|
0,000462
|
26-27
|
0,000227
|
изгиб трубы
R/d0=6
|
3
|
0,18
|
0,54
|
0,000985
|
|
|
Н-С
|
0,000462
|
28-29
|
0,000227
|
изгиб трубы
R/d0=6
|
3
|
0,18
|
0,54
|
0,000985
|
|
|
Н-С
|
0,000226
|
30-31
|
0,000113
|
изгиб трубы
R/d0=6
|
3
|
0,18
|
0,54
|
0,00095
|
0,010049
0,010049
|
|
Н-С
|
0,000226
|
32-33
|
0,000113
|
изгиб трубы
R/d0=6
|
3
|
0,18
|
0,54
|
0,00095
|
|
|
Н-С
|
0,000452
|
33-35
|
0,000227
|
изгиб трубы
R/d0=6
|
5
|
0,18
|
3
|
0,00524
|
|
|
|
|
|
|
резкое
расширение d0/d=0,8 Æ12/Æ17
|
2
|
0,3
|
|
|
|
|
|
|
|
|
Тройник
|
1
|
1,5
|
|
|
|
|
Н-С
|
0,000452
|
35-36
|
0,000314
|
колено 900
|
1
|
1,2
|
1,2
|
0,001094
|
|
|
С
|
0,000452
|
37-38
|
0,000314
|
резкое
расширение d0/d=0,8 Æ20/Æ25
|
1
|
0,3
|
1,5
|
0,001368
|
|
|
|
|
|
|
колено 900
|
1
|
1,2
|
|
|
|
|
С
|
0,000452
|
38-39
|
0,000491
|
изгиб трубы
R/d0=4
|
6
|
0,2
|
1,2
|
0,000448
|
|
Напорная линия: DРМн =0,049476ΜПа;
Сливная линия: DРМс =0,049476ΜПа;
Суммарные местные потери давления: D РМΣ=0,059525.
По результатам расчетов потерь давления в гидроаппаратах,
потерь по длине, местных потерь рассчитываются суммарные потери в напорной и
сливной линиях. Результаты сводятся в таблице 2.4
Таблица 2.4 - Суммарные потери давления
Линия
|
Этап цикла
|
DРга (МПа)
|
DРl (МПа)
|
DРм (МПа)
|
D РΣ (МПа)
|
Н
|
БП
|
0,629256
|
0,050629
|
0,729361
|
С
|
БП
|
0,034506
|
0,047355
|
0,049476
|
0,1313
|
По полученным данным уточняем расчет насосной установки по
давлению:
Рнтреб= Р1+DРн=10,67+0,729361=11,399361
(МПа)
,399361<16
Условие выполняется.
2.5
Разработка рамы шнекового конвейера
2.5.1
Техническое задание для построения рамы шнекового конвейера
Рама шнекового конвейера представляет собой сварную
конструкцию. Каркас рамы состоит из швеллеров №22. Сверху к каркасу приварен
лист толщиной 6 мм. Внутри выполнена плита с пластинами для установки шнекового
конвейера. Произведем расчеты рамы передаточной тележки на изгиб для наиболее
нагруженных сечений А-А и Б-Б (рисунок 2.5).
Рисунок 2.5 - Каркас рамы тележки
2.5.2
Проверочный расчет на прочность от действия изгибающего момента в сечении А-А
В целях упрощения расчета нагрузку от собственного веса
тележки и нагрузку от веса груза примем равномерно распределенными по раме
тележки. При этом схема для расчета нагрузок в сечении А-А (рисунок 2.6)
Рисунок 2.6 - Расчетная схема сечения А-А
Распределенную нагрузку от веса тележки и веса груза
определим по формуле 2.56 [20]:
(2.56)
где
- нагрузка от веса рамы, Н;
- нагрузка от веса груза, Н;
- динамический коэффициент (
);
- расстояние между опорами (
)
(2.57)
Изгибающий момент от распределенной нагрузки определяем по
формуле:
(2.58)
Рассчитаем момент сопротивления сечения состоящего из настила
(лист 6×5231×280) и швеллеров №22
Определяем площадь сечения настила
по формуле 2.57:
(2.57)
где l - длина настила, (l=523,1 см);
h - толщина настила, (h=0,6
см).
Площади сечений швеллеров №22 по ГОСТ 8240-72 находим из
справочных таблиц:
[20].
Определяем суммарную площадь сечения по формуле 2.58:
(2.58)
Определяем статический момент сечения относительно оси 0XS
по формуле 2.59:
(2.59)
где
- статический момент настила 1
относительно оси X, см
, определяем по формуле 2.60;
- статические моменты швеллеров 2,3,4,5,6,7 относительно оси X, см
.
(2.60)
α=11+0,4=11,4 см,
(2.61)
Определяем статический момент сечения
А-А относительно оси Y по формуле 2.62:
(2.62)
где статический момент относительно оси Y определяется по формуле 2.63:
(2.63)
где
- расстояние от центра тяжести детали до
оси 0Y, см.
Определяем статические моменты настила 1 и швеллеров 2,3,4,5,6,7:
Определяем координаты центра тяжести
и
всего сечения А-А по формулам 2.64 и 2.65:
(2.64),
(2.65),
Определяем осевой момент инерции
относительно центральной оси
по формуле 2.66 [20]:
(2.66)
где
- момент инерции сечения листа настила,
см
;
- расстояние ЦТ листа 1 до оси
(
);
- момент инерции швеллера №22 (
);
- расстояние от оси
до оси
(
см).
(2.67)
Определяем сопротивление сечения
для волокон верхнего пояса по формуле 2.68:
(2.68)
Определяем сопротивление сечения
для волокон нижнего пояса по формуле 2.69:
(2.69)
Определяем напряжение изгиба в нижнем поясе, как наиболее
нагруженном, по формуле 2.70:
(2.70)
Определим коэффициент запаса прочности по формуле 2.71 [20]:
(2.71)
где
- допускаемое напряжение для стали Ст3, (
);
- допускаемый коэффициент запаса прочности, (
).
Следовательно, необходимый запас прочности обеспечен.
2.5.3
Проверочный расчет на прочность от действия изгибающего момента в сечении Б-Б
Нагрузку от собственного веса тележки и нагрузку от веса
груза принимаем также, как и в сечении А-А, равномерно распределенной по раме
тележки. При этом схема для расчета нагрузок в сечении Б-Б будет иметь вид
согласно рисунке 2.7 Распределенную нагрузку от веса тележки и веса груза
определяем по формуле 2.72 [20]:
(2.72)
где
- нагрузка от веса тележки, Н;
- нагрузка от веса груза, Н;
- динамический коэффициент, учитывающий ударный характер
приложения нагрузки (
).
Изгибающий момент от распределенной нагрузки определяем по формуле
2.73:
(2.73)
Рисунок 2.7 - Расчетная схема сечения Б-Б
Определяем площадь сечения настила по формуле 2.74:
(2.74)
где
- длина настила,
;
- толщина настила,
см.
Площади сечений швеллеров 2,3,4, и 5 составляют 26,7 см
(швеллер №22 ГОСТ 8240-73).
Определяем суммарную площадь сечения Б-Б по формуле 2.75:
(2.75)
Определяем статический момент сечения относительно оси 0XS
по формуле 2.76:
(2.76)
где
- статический момент настила 1
относительно оси Х, см
, определяется по формуле 2.77;
- статические моменты швеллеров 2,3,4,5 относительно оси Х, см
.
(2.77)
(2.78)
Определяем статический момент сечения Б-Б
относительно оси Y по формуле 2.79:
(2.79)
где
статический момент относительно оси Y определяется по формуле 2.80:
(2.80)
где
- расстояние от центра тяжести детали до
оси 0Y, см.
Подставляя числовые значения, определяем статические моменты
настила 1 и швеллеров 2,3,4,5:
Определяем координаты центра тяжести
и
всего сечения А-А, определяется по формуле 2.81 и 2.82:
(2.81)
(2.82)
Определяем осевой момент инерции
относительно центральной оси 
по формуле 2.83 [20]:
(2.83)
где
- момент инерции сечения листа настила,
см
, определяется по формуле 2.84;
- расстояние ЦТ листа 1до оси 
(
);
- момент инерции швеллера №22 (
);
- расстояние от оси
до оси
(
).
(2.84)
Определяем сопротивление сечения
для волокон верхнего пояса определяется по формуле 2.85:
(2.85),
Определяем сопротивление сечения
для волокон нижнего пояса определяется по формуле 2.86:
(2.86)
Определяем напряжение изгиба в нижнем поясе, как наиболее
нагруженном, по формуле 2.87:
(2.87)
Определяем коэффициент запаса прочности по формуле 2.88:
(2.88)
где
- допускаемое напряжение для стали Ст3 (
);
- допускаемый коэффициент запаса прочности (
).
.
Следовательно, необходимый запас прочности обеспечен.
Спроектированная металлоконструкция передаточной тележки обладает необходимой
прочностью.
2.5.4 Расчет
сварного шва на прочность
Проверочный расчет соединений деталей и узлов рамы производим
в соответствии с требованиями [20] по формуле 2.89:
(2.89)
где
- расстояние от оси Х до верхней кромки
вертикального листа (
);
- допускаемое напряжение для сварных швов на срез определяется по
формуле 2.90, МПа.
(2.90)
Необходимая прочность сварного шва передаточной тележки
обеспечена.
3.
Технологическая часть
3.1
Разработка технологического процесса изготовления детали "зубчатого
колеса"
Колесо зубчатое представляет собой обод со ступицей
соединенное в единое целое диском. В ступице зубчатого колеса проточено
посадочное отверстие Ø45Н7, а также просверлено
два отверстия Ø13,7мм и отверстие М10 для
фиксирования зубчатого колеса на валу от осевого смещения. На диске зубчатого
колеса нарезано 36 зубьев модулем 4 мм. Колесо зубчатое является основным
элементом зубчатой передачи и служит для передачи вращающего момента с одного
вала на другой. Зубчатые передачи составляют наиболее распространённую и важную
группу механических передач. Их применяют в широком диапазоне областей техники
и условий работы. Зубчатые передачи в сравнении с другими механическими
передачами обладают существенными достоинствами, а именно: малыми габаритами,
высоким К.П.Д., большой долговечностью и надёжностью в работе, постоянством
передаточного отношения из-за отсутствия проскальзывания, возможностью
применения в широком диапазоне моментов, скоростей, передаточных чисел.
Наиболее сложными для обработки поверхностями в смысле точности и
ответственности являются поверхность, на которой нарезаются зубья, внутреннее отверстие
в ступице Ø 45Н7, а также торцевые поверхности
зубчатого колеса. Выбранная для изготовления зубчатого колеса сталь 45 ГОСТ
1050-88 вполне соответствует тяжёлым условиям работы механизма. Химический
состав стали 45 представлен в таблице 3.1
Таблица 3.1 - Химический состав стали 45, %
С
|
Si
|
Mn
|
S
|
P
|
Ni
|
Cr
|
0.40-0.50
|
0.17-0.37
|
0.50-0.80
|
0.045
|
0.045
|
0.3
|
0.3
|
Таблица 3.2 - механические свойства стали 45
σт МПа
|
σвр МПа
|
σ5
|
Y
|
Dн Дж/см
|
НВ (не более)
|
360
|
610
|
16
|
40
|
50
|
241
|
Одним из факторов влияющих на характер технологического
процесса является технологичность конструкции. Выполним оценку технологичности
по элементам конструкции детали и технологическим условиям на ее изготовление.
Колесо зубчатое - цельной конструкции.
Материал детали - сталь 45
Выбранная заготовка предусматривает оптимальную механическую
обработку.
Деталь достаточной жесткости при обработке.
Заготовка доступна для обработки и контроля.
Базы технологические и измерительные совмещены.
Контроль размеров производится универсальными средствами
измерения.
При изготовлении колеса зубчатого используется действующее
оборудование.
. При изготовлении зубчатого колеса, применяются
универсальные приспособления.
Применяется стандартный режущий инструмент.
Способ изготовления заготовки имеет решающее значение при
выборе первых операций технологического процесса. На выборе заготовки и метода
её получения значительное влияние оказывают характеристики материала из
которого должна изготовляться деталь, её конструктивные формы и размеры,
программа выпуска деталей в год. Метод получения заготовки должен обеспечивать
наименьшую себестоимость изготовления детали среди предлагаемых вариантов. Для
обеспечения правильности выбора рассмотрим два варианта получения заготовки для
изготовления колеса зубчатого:
Вариант 1 - Заготовка из круглого проката (рисунок 3.1):
Рисунок 3.1 - Эскиз заготовки
В соответствии с ГОСТ 2590-88 "Прокат стальной
горячекатаный круглый", выбираем заготовку Ø 170 мм, длиной L=102 мм. Объём заготовки
определяем по формуле 3.1:
(3.1)
где D - диаметр заготовки, мм, L - длина заготовки, мм
Массу заготовки определяем по формуле 3.2:
Mз = ρ · Vз, кг, (3.2)
где ρ - удельный вес стали, равный 7,85 г/см3
Мз = 7,85 · 2314 = 18165г = 18,2кг.
Вариант 2 - Заготовка поковка - цилиндр ступенчатой формы с осевым
отверстием Ø 35мм
длиной 102мм (рисунок 3.2).
Рисунок 3.2 - Деталь изготовленная методом штамповка
Объем поковки определяем по формуле 3.3:
Vп = V1 + V2 - V3, см3, (3.3)
где V1, V2, V3 - объемы отдельных частей заготовки, см3,
Vп = 3,14·172 /4·4+3,14·11/4·6,2-3,14·3/4·10,2 = 1405см3
mп = 7,85·1405 = 11030г = 11кг
Таким образом, наиболее экономичной с точки зрения расхода металла
является заготовка - поковка.
Выбор плана (маршрута) обработки детали.
На основании типовых технологических маршрутов, исходя из выбранной
заготовки (поковка) разработаем маршрут изготовления колеса зубчатого.
Операция 1 - Токарная
.1 Подрезать торец ступицы на Ø 114
.2 Проточить наружный диаметр ступицы до Ø104 на длину 60мм.
.3 Проточить торец зубчатого венца.
Переустановить деталь.
.4 Проточить торец зубчатого венца в размер 28мм.
.5 Проточить наружный диаметр зубчатого венца Ø 152мм.
.6 Снять фаски 1,6х45 на наружном диаметре зубчатого венца Ø152мм.
Операция 2 - Токарная
.1 Расточить внутреннее отверстие Ø 44 Н11 на длину 90мм.
.2 Снять фаски 1,6х45 во внутреннем отверстии Ø 44 Н11.
Операция 3 - Горизонтально - Фрезерная
.1 Фрезеровать квадрат 80 на ступице колеса зубчатого.
Операция 4 - Вертикально - Сверлильная
.1 Сверлить 2 отверстия Ø 13,7мм в ступице колеса зубчатого на
длину 80мм.
.2 Сверлить отверстие Ø 8,5мм под резьбу М10.
.3 Нарезать резьбу М10.
Операция 5 - Зубофрезерная
.1 Нарезать 36 зубьев модулем 4 мм с углом зацепления 20.
Операция 6 - Горизонтально - Протяжная
.1 Протянуть отверстие Ø 45 H7 на длину 90мм.
Операция 7 - Внутришлифовальная
.1 Шлифовка внутренней поверхности Ø45.
Операция 8 - Контроль
Расчёт припуска на обработку (рисунок 3.3).
Рисунок 3.3 - Схема допусков отверстия
Величина припуска на обработку и допуски на размеры заготовок
зависят от следующих факторов:
. Материал заготовки.
. Конфигурация и размеры заготовки.
. Вид заготовки и способы её получения.
. Требования в отношении механической обработки.
. Технические условия в отношении качества и класса шероховатости
поверхности, точности размеров заготовки.
Из этого следует, что величина общего припуска зависит от толщины
дефектного слоя, подлежащего снятию, припусков на промежуточные операции,
погрешности установки, шероховатости поверхности. Выполним расчёт припуска на наружный
диаметр заготовки по методу профессора Кована. Минимальный припуск на диаметр
при обработке наружной поверхности вращения определяем по формуле 3.4:
(3.4)
где Rz - высота микронеровностей (параметр
шероховатости поверхности поковки), Rz
=0,32мм
Rt - глубина дефектного поверхностного слоя. Выбираем по таблице на
поковку Rt= 3мм
Рi - суммарное значение поверхностных
отклонений для расчётной поверхности. Поверхностные отклонения - это сумма
допусков формы и расположения поверхностей. Выбираем по ГОСТ 24643-81
"Числовые значения допусков формы и расположения поверхностей"
следующие данные в зависимости от размера заготовки.
Допуск формы цилиндрической поверхности 0,6мм
Допуск цилиндричности, округлости 1,5мм
Допуск торцевого биения 0,4мм
Допуск соосности, симметричности 1,6мм
Отсюда,
Рi= 0,6 + 1,5 + 0,4 + 1,6 = 4,1мм,
Ey - погрешность установки на выполняемом переходе - сумма
погрешностей базирования Eb и закрепления
Ез.
Погрешность базирования Eb = 0,
так как измерительная база совмещена с установочной, значит Еy = Ез.
Принимаем Еy = 0,5мм,
Рассчитаем максимальный припуск:
Zmax = Zi + Тп. п. + Тв. п.,
где Тп. п. - допуск на предшествующем переходе, принимаем для
поковки
Тп. п. = 1,5мм.
Тв. п. - допуск на выполняемом переходе, принимаем для токарной
операции Тв. п. = 0,08мм
Zmax = 14,9 + 1,5 + 0,08 = 16,48мм.
Определяем размеры заготовки:
Поковка Ø 170 -
0,6мм
Для остальных размеров заготовки колеса зубчатого припуски и допуски
определяем из справочников и заносим в таблицу 3.3.
Таблица 3.3 - Выбор припусков и допусков по таблицам
Размер, мм
|
Припуск, мм
|
Допуск, мм
|
Размер
заготовки, мм
|
Ø104
h14
|
6
|
4
|
Ø 114
h14
|
Ø 45 H7
|
6
|
4
|
Ø 35
H14
|
28 h 14
|
6
|
6
|
40 h14
|
90 h 14
|
6
|
6
|
102 h14
|
3.2 Выбор
типового оборудования и типовых универсальных приспособлений
Выбор станочного оборудования является одной из важнейших
задач при разработке технологического процесса механической обработки
заготовки.
От правильного его выбора зависит производительность
изготовления детали, экономное использование производственных площадей,
механизации и автоматизации ручного труда, электроэнергии и в итоге
себестоимость изделия.
На основании маршрута изготовления колеса зубчатого по
справочникам выбираем необходимое оборудование и приспособления.
3.2.1
Токарная операция
Для выполнения токарной операции выбираем токарно-винторезный
станок с ЧПУ, модели 16К20Ф3С5, который имеет следующие технические
характеристики (таблица 3.4):
Таблица 3.4 - Характеристики токарно - винторезного станка
Класс точности
по ГОСТ 8-82, (Н, П, В, А, С)
|
П
|
Диаметр
обрабатываемой детали, мм
|
400
|
Диаметр детали
над суппортом, мм
|
220
|
Длина
обрабатываемой детали, мм
|
1000
|
Мощность
двигателя главного движения, кВт
|
11
|
Габарит станка:
Длина_Ширина_Высота, мм
|
3360_1710_1750
|
В качестве
приспособления принимаю 3-х кулачковый патрон 7102-0077 по ГОСТ 24351-80
|
|
3.2.2
Горизонтально-фрезерная операция
Для выполнения фрезерной операции выбираем консольный
вертикально - фрезерный станок модели 6Н82, который имеет следующие технические
характеристики (таблица 3.5):
Таблица 3.5 - Характеристики консольного вертикально -
фрезерного станка
Размер рабочей
поверхности стола (ширина х длина), мм
|
250Х1000
|
Расстояние от
оси шпинделя до поверхности стола, мм
|
0-340
|
Наибольшее
расстояние от вертикальных направляющих станины до середины стола, мм
|
370
|
Расстояние от
оси шпинделя до хобота, мм
|
150
|
Число
Т-образных пазов
|
3
|
Расстояние
между Т-образными пазами, мм
|
50
|
Наибольший угол
поворота стола, град
|
±45
|
Наибольшее
перемещение стола, мм продольное поперечное вертикальное
|
600 200 340
|
Число ступеней
оборотов шпинделя
|
16
|
Число оборотов
шпинделя в минуту
|
65-1800
|
Подача стола,
мм/мин продольная поперечная вертикальная
|
35-1020 28-790
14-390
|
Скорость
быстрого перемещения стола, м/мин продольного поперечного вертикального
|
2,9 2,3 1,15
|
Мощность
электродвигателей, кВт привода главного движения привода насоса охлаждения
|
4 0,125
|
Габариты станка
(длина х ширина х высота), мм
|
2060Х1940Х1600
|
2100
|
В качестве
приспособления принимаю универсально делительную головку УДГ-160 и 3-х
кулачковый патрон 7102 - 0077 по ГОСТ 24351-80
|
|
3.2.3
Вертикально-сверлильная операция
Для выполнения сверлильной операции выбираем вертикально -
сверлильный станок модели 2Р135 Ф2, который имеет следующие технические
характеристики (таблица 3.6):
Таблица 3.6 - Характеристики вертикального - сверлильного
станка
Наибольший
условный диметр сверления в стали, мм
|
35
|
Расстояние от
торца шпинделя до плиты, мм наибольшее наименьшее
|
1100 750
|
Расстояние от
оси шпинделя до вертикальных направляющих станины, мм
|
300
|
Наибольшее
расстояние от торца шпинделя до рабочей поверхности стола, мм
|
750
|
Наибольшее
перемещение шпинделя, мм
|
225
|
Число ступеней
чисел оборотов
|
9
|
Пределы чисел
оборотов в минуту
|
68 - 1100
|
Число ступеней
подач
|
11
|
Пределы подач
на один оборот шпинделя, мм
|
0,115 - 1,6
|
Наибольшее
усилие, допускаемое механизмом подач, кг
|
1600
|
Размеры
рабочей поверхности стола, мм
|
450 х 500
|
Наибольшее
перемещение стола (вручную), мм
|
325
|
Мощность
электродвигателя главного движения, кВт
|
4,5
|
Габариты станка
(длина х ширина х высота), мм
|
1240Х810Х2565
|
Вес станка, кг
|
1528
|
3.2.4
Зубофрезерная операция
Для выполнения зубофрезерной операции выбираем станок
зубофрезерный вертикально одноколонный с неподвижной колонной и подающим столом
модели 5А32Б. его характеристики представлены в таблице 3.7
Таблица 3.7 - Характеристика зубофрезерного станка модели
5А32Б
Наибольший
диаметр нарезаемого колеса, мм
|
750
|
Наибольшая ширина
нарезаемого колеса, мм
|
300
|
Диаметры
фрезерных оправок, мм
|
27, 32, 40
|
Наибольшие
размеры фрез, мм Диаметр Длина
|
200 155
|
Конус Морзе
шпинделя, N
|
5
|
Мощность
электродвигателей, кВт
|
8
|
Габариты
станка, мм Длина Ширина
|
3200 1600
|
Вес станка, кг
|
8100
|
3.2.5
Горизонтально-протяжная операция
Для выполнения протяжной операции выбираем
горизонтально-протяжной станок 7523, который имеет следующие технические
характеристики (таблица 3.8):
Таблица 3.8 - Характеристики горизонтального -
протяжного станка
Номинальная
тяговая сила, Т·С
|
10
|
Количество
плунжеров
|
1
|
Длина рабочего
хода ползуна, мм
|
1250
|
Скорость
рабочего хода, м/мин
|
11,5-1,5
|
Скорость
обратного хода, м/мин
|
20
|
Мощность
электродвигателя, кВт
|
18,5
|
Габаритные
размеры, мм Длина Ширина Высота
|
6340 2090 1910
|
.2.6
Внутришлифовальная операция
Для выполнения внутришлифовальной операции выбираем
внутришлифовальный станок3К229А, который имеет следующие характеристики
(таблица 3.9):
Таблица 3.9 - Характеристики внутришлифовального
станка
Диаметр
шлифуемого отверстия наибольший, мм
|
500
|
Наибольшая
длина шлифования, мм
|
500
|
Наибольший
наружный диаметр устанавливаемого изделия, мм
|
800/630
|
Наибольший угол
шлифуемого конуса, град
|
60
|
Расстояние от
оси шпинделя изделия до зеркала стола, мм
|
410
|
Мощность
привода главного движения, кВт
|
7.5
|
Суммарная
мощность электродвигателей, кВт
|
14.63
|
Габариты станка
длина. ширина. высота, мм
|
4165Х1780Х2000
|
Масса, кг
|
7300
|
Показатель
точности обработки образца изделия: постоянство диаметра в продольном
сечении, мкм круглость, мкм
|
3 1.6
|
Шероховатость
поверхности образца-изделия: цилиндрической внутренней Ra, мкм плоской
торцевой
|
0,08 0,32
|
3.3 Расчет
режимов резания и техническое нормирование операций
3.3.1
Определяем тип производства
Тип производства определяем по коэффициенту штучного времени
по формуле 3.4:
К = Тшт. ср N / Fд · 60, (3.4)
где
Т шт. ср. - среднее штучное время по операциям, мин
N - годовая программа выпуска деталей
Fд - действительный годовой фонд времени работы оборудования,
час. Для односменной работы Fд = 2015 час
Нормы времени определяем по приближённым формулам.
Операция 1 - Токарная
.1 Подрезать торец ступицы
Черновое подрезание определяется по формуле 3.5:
to = 0.037 (D - d) · 0,001, мин, (3.5)= 0,037
(114 - 30) ·0,001 = 0,45мин.
Чистовое подрезание определяется по формуле 3.6:
to = 0.052 (D - d) · 0,001, мин, (3.6)= 0.052 (D
- d) · 0,001 = 0,052 (114 - 30) · 0,001 = 0,63 мин,
Σto = 0,45 + 0,63 = 1,1 мин.
.2 Проточить наружный диаметр ступицы
Черновая проточка определяется по формуле 3.7:
to = 0.17 · d · l · i · 0.001, мин, (3.7)=
0.17·114·60·1·0.001=1,2мин.
Чистовая проточка определяется по формуле, 3.8:
to = 0.1 · d · l · i · 0.001, мин, (3.8)= 0.1 ·
114 · 60 · 1 · 0,001 = 0,7 мин,
Σto= 1.2 + 0.7 = 1.9 мин.
.3 Проточить торец диска
Черновая проточка
to = 0,037 (170 - 130) · 0,001 = 0,5 мин,
Чистовая проточка
to = 0,052 (170 - 130) · 0,001 = 0,7 мин,
Σto = 0,5 + 0,7 = 1,2 мин.
.4 Проточить торец диска
Черновая проточка
to = 0,037 (170 - 30) · 0,001 = 1,1 мин,
Чистовая проточка
to = 0,052 (170 - 30) · 0,001 = 1,5 мин,
Σ to = 1,1 + 1,5 = 2,6 мин.
.5 Проточить наружный диаметр диска
Черновая проточка
to = 0.17 · 152 · 30 · 2 · 0,001 = 1,6 мин,
Чистовая проточка
to = 0,1 · 152 · 30 · 2 · 0,001 = 1 мин,
Σ to = 1,6 + 1
= 2,6 мин.
Операция 2 - Токарная
Расточить внутреннее отверстие Ø 45 Н11 определяется по
формуле 3.9:
to = 0.18 · d · l · i · 0.001, мин, (3.9)=0,18 ·
45 · 90 · 5 · 0,001 = 3,7 мин,
Σtток = 1,1 + 1,9 + 1,2 +
2,6 + 2,6 + 3,7 = 13,1 мин.
Тшт.к. ток = К · Σ t ток, мин, (3.10)
Тшт.к. ток = 2,14 · 13,1 = 28 мин.
Операция 3 - Горизонтально-фрезерная
Фрезерование квадрата 80 на ступице колеса зубчатого
Черновое фрезерование определяется по формуле 3.11:
to = 6 · l · i · 0.001, мин, (3.11)= 6 · 120 · 2
·4 · 0,001 = 5,8 мин.
Чистовое фрезерование определяется по формуле 3.12:
to = 4 · l · i · 0,001, мин, (3.12)= 4 · 120 · 2
· 4 · 0.001 = 1,9 мин,
Σtфр = 5,8 + 1,9 = 7,7 мин.
Т шт.к. фр = К · Σ t фр, мин, (3.13)
Т шт.к. фр = К · Σ t фр = 1,84 · 7,7 = 14,2
мин.
Операция 4 - Вертикально-сверлильная
.1 Сверлить два отверстия Ø13,7 мм в ступице колеса
зубчатого определяется по формуле 3.14:
to = 0.52 · d · l · 0,001, мин, (3.14)= 0,52 ·
13,7 · 80 · 2 · 0, 001 = 1,2 мин.
4.2 Сверлить отверстие Ø8,5 мм для нарезания резьбы
М10
to = 0,52 · 8,5 · 40 · 0,001 = 0,2 мин.
.3 Нарезание резьбы М10
to = 0,4 · d · l · 0.001, мин, (3.15)
to = 0,4 · 10 · l · 0.001 = 0,2 мин,
Σtcв = 1,2 + 0,2 + 0,2 = 1,6
мин.
Т шт.к. св = К · Σ t cв, мин, (3.16)
Т шт.к. св = 1,72 · 1,6 =2,8 мин.
Операция 5 - Зубофрезерная
to = 18 · D · l · 0,001, мин, (3.17)= 18 · 144 ·
28· 0,001 = 72 мин.
Тшт.к. з. = К · Σ to, мин, (3.18)
Т шт.к. з. = 72 · 1,66 = 120 мин.
Операция 6 - Горизонтально-протяжная определяется по формуле
3.19:
to = 0.1 · d · l · 0,001, мин, (3.19)= 0.1· 45 ·
90 · 0.001 = 0,405мин.
Операция 7 - Внутришлифовальная
Шлифовка внутренней поверхностиØ45 определяется по формуле
3.20
to=0.2d·l· 0,001, мин, (3.20)=0.2 · 45 · 90·
0,001=0,81 мин,
Общее время на операцию
to = 28 + 14.2 + 120 + 2.8 + 0,405+0,81= 165,4 мин.
Определяем среднее штучное время пор формуле 3.21:
tшт. Ср = to / n, мин, (3.21)шт. Ср = 165,4/4 =41,35
мин,
где n - число операций.
Определяем коэффициент штучного времени
К = 41 · 25/2015 · 60 = 0,01.
Значит производство - мелкосерийное
3.3.2 Выбор
режущих инструментов
При разработке технологического процесса механической
обработки заготовки выбор режущего инструмента, его вида, конструкции и
размеров в значительной мере предопределяется методами обработки и качества
обрабатываемой поверхности заготовки. Выбор материала для режущего инструмента
зависит от формы и размеров инструмента, материала обрабатываемой заготовки,
техники резанья и типа производства. Для обработки стали рекомендуется
применять инструмент, режущая часть которого изготовлена из титановольфрамовых
твердых сплавов (Т5К10, Т15К6), быстрорежущих инструментальных сталей (Р6М5). Выбранный
инструмент заносим в таблицу 3.10.
Таблица 3.10 - Выбор режущего инструмента
№
|
Операция
|
Маршрут
обработки
|
Режущий инструмент
|
1
|
2
|
3
|
4
|
1
|
Токарная
|
подрезать торец
|
Токарный
подрезной отогнутый правый резец с пластинкой из твердого сплава Т15К6 ГОСТ
18880-73
|
|
|
Проточить
наружный диаметр
|
Токарный
проходной упорный резец ГОСТ 18879-73 из твердого сплава Т15К6
|
1
|
Токарная
|
Подрезать торец
|
Токарный
подрезной отогнутый правый резец с пластинкой из твердого сплава Т15К6 ГОСТ
18880-73
|
|
|
Проточить
наружный диаметр
|
Токарный упорно
- проходной отогнутый резец с углом в плане 45º и с пластинками из твердого сплава
Т15К6 ГОСТ 18880-73
|
|
|
Точить фаски
|
Токарный упорно
- проходной отогнутый резец с углом в плане 45º и с пластинками из твердого сплава
Т15К6 ГОСТ 18880-73
|
2
|
Токарная
|
Расточить
отверстия
|
Резец токарный
расточной Т15К6 ГОСТ 18882-73
|
|
|
Точить фаски
|
Токарный
упорно-проходной отогнутый резец с углом в плане 45º и с пластинками из твердого сплава
Т15К6 ГОСТ 18880-73
|
3
|
Горизонтально-фрезерная
|
Фрезеровать
квадрат
|
Фреза торцовая
насадочная
|
4
|
Вертикально-сверлильная
|
Сверлить одно
сквозное отверстия
|
Сверло
спиральное с коническим хвостовиком ГОСТ 10903-77; Æ 13,7мм, L=140мм.
|
|
|
Рассверлить
одно отверстия
|
Сверло
спиральное с коническим хвостовиком ГОСТ 10903-77; Æ 8,5мм, L=50мм.
|
4
|
Вертикально-сверлильная
|
Нарезать резьбу
|
Метчик машинный
из быстрорежущей стали ГОСТ 17933-72, d=10мм, Р=1,25 мм.
|
5
|
Зубофрезерная
|
Нарезать зубья
|
Фреза червячная
Р6М5, однозаходная. D =225 мм,Z=12, ГОСТ 9324-75, класс Б
|
6
|
Горизонтально-протяжная
|
Протянуть
отверстие
|
Цилиндрическая
протяжка Р18 ГОСТ 18217-80
|
7
|
Внутришлифовальная
|
Шлифовать
отверстие
|
Круг ПП25.10.
d24А,10ПС2 К5 35м/с А1 ГОСТ2424-83
|
3.3.3 Выбор
режимов резания
По справочникам выбираем режимы резания и заносим их в
таблицу 3.11
Таблица 3.11 - Режимы резания
Операция
|
Скорость
резания V м/мин
|
Подача S мм/об
|
Глубина резанияt
мм
|
Токарная 1.
Подрезать торцы черновая чистовая 2. Проточить наружный диаметр черновая
чистовая 3. Расточить отверстие Черновая чистовая
|
172,78 245,35
115,98 231,97 138,23 152,32
|
0,6 0,15 0,7
0,05 0,7 0,2
|
3 2 3 2 2 0,5
|
Горизонтально-фрезерная
Фрезеровать 80
|
231,97
|
0,2
|
4
|
Вертикально-сверлильная
Сверлить отверстие Нарезать резьбу
|
20,5 В ручную
|
0,15
|
|
Зубофрезерная
Нарезать зубья черновая чистовая
|
20 28
|
3 0,5
|
4 1
|
Горизонтально-протяжная
Протянуть отверстие
|
1,8
|
|
|
Внутришлифовальная
Шлифовать отверстие
|
20
|
|
|
3.3.4
Уточненное нормирование времени операции
Норма штучного времени считается по формуле 3.22:
Tшт = То + Тв + Тоб + Тф, мин, (3.22)
где Тшт - штучное время, мин.
То - основное (технологическое) время, мин.
Тв - вспомогательное время, мин.
Тоб - время на обслуживание рабочего места, мин.
Тф - время на физические надобности, мин.
Т об = Тт. об + Т о. об, мин, (3.23)
где Т т. об - время на техническое обслуживание, мин.
Т о. об - время на организационное обслуживание, мин.
То = Тв + Топ, мин, (3.24)
где Топ - операционное время, мин
В условиях мелкосерийного производства нормативы на
обслуживание рабочего места и естественные надобности можно объединить и
принять в зависимости от размеров обрабатываемой детали в размере 4,6%.
Расчет основного (технологического) времени:
Расчет основного (технологического) времени определяем по
формуле 3.25:
То = L · I / S · n, мин, (3.25)
где L - расчетная длина обработки определяется по формуле 3.26, мм
I - число проходов
S - подача, мм/об
N - число оборотов в минуту.
Расчетная длина обработки детали, мм
L = L1 + L2 + L3, мм, (3.26)
где L1 - длина обрабатываемой детали, мм
L2 - длина врезания и подвода инструмента, мм
L3 - длина перебега, мм
Длину врезания и подвода и длину перебега выбираем по
справочникам.
Для расчета основного времени выбираем по справочникам режимы
резания для технологических операций.
По формуле n = 1000·V / π · d и по таблицам режимов
резания рассчитаем число оборотов детали (или инструмента) в минуту (округлим
до ближайшего стандарта), по припуску определяем примерное число проходов и
заносим все данные в таблицу 3.12.
Таблица 3.12 - Токарная операция
Операция
|
L. мм
|
П об/мин
|
i
|
Токарная1 1.
Подрезать торец ступицы черновая чистовая 2. Проточить наружный диаметр ступицы
черновая чистовая
|
70 70 80 80
|
500 710 355
710
|
2 1 2 1
|
3. Проточить
торец диска черновая чистовая 4. Проточить торец диска черновая чистовая 5.
Проточить наружный диаметр диска черновая чистовая 6. Снять две фаски 1,6 х
45
|
50 50 100 100
50 50 1,6
|
355 560 355
560 280 500 500
|
1 1 2 1 2 1 1
|
Токарная 2
7. Расточить отверстиеÆ 44Н11
Черновая 8. Снять две фаски 1,6 х 45
|
110 1,6
|
1000 1000
|
3 1
|
Подставив данные в формулу, для расчёта основного времени и
составим таблицу для технологического времени по переходам (таблица 3.13).
Таблица 3.13 - Технологическое время для токарной операции
Операция
|
То, мин
|
1. Подрезать
торец ступицы черновая чистовая
|
tо=70х2/0,6 х
500 = 0,47 to = 70 х1/0,4 х 710 =0,25
|
2. Проточить
наружный диаметр ступицы черновая чистовая
|
To = 80 х2/0,7
х 355 = 0,65 to = 80 х 1/0,3 х 710 = 0,4
|
3. Проточить
торец диска черновая чистовая
|
To = 50х 1/0,6
х355 = 0,3 to = 50 х 1/0,4 х 560 = 0,25
|
4. Проточить
торец диска черновая чистовая
|
To = 100 х
2/0,6 х 355 = 1,2 to = 100 х 1/0,4 х 560 = 0,5
|
5. Проточить
наружный диаметр диска черновая чистовая
|
To = 50 х
2/0,7 х 280 = 0,5 to = 50 х 1/0,3 х 500 = 0,35
|
6. Снять две
фаски 1,6х45
|
To= 0.25 х 2 =
0,5
|
7. Расточить
отверстиеÆ 44Н11 черновая
|
To = 110 х3/0,7
х 1000 = 0,5
|
8. Снять две
фаски 1,6х45
|
To = 0.25 х 2 =
0,5
|
9. Итого
|
То1 = 5,9 То2 =
1
|
Вспомогательное время выберем по справочнику:
Tв1 = 5,05мин
Tв2 = 0,6 мин
Рассчитаем штучное время по полученным данным определяем по
формуле 3.27:
Тшт= (То + Тв) · (1 + (α +β + γ) / 100), мин, (3.27)
Тшт1 = (5,9 + 5,05) · (1 + 4,6/100) = 11,4мин,
Тшт2 = (1+0,6) · (1 + 4,6/100) = 1,67мин.
Таблица 3.14 - Фрезерная операция
Операция
|
L. мм
|
П. об/мин
|
i
|
Фрезеровать
квадрат 80
|
120
|
400
|
4
|
Подставив данные в формулу для расчёта основного времени и
составим таблицу 3.15 для технологического времени фрезерной операции.
Таблица3.15 - Технологическое время для фрезерной операции
Операция
|
То. мин
|
Фрезеровать
квадрат 80
|
То = (120 ·
4/0,2 ·400) · 4 = 24
Рассчитаем штучное время по полученным данным по формуле
3.28:
Тшт = (То + Тв) (1+ (α + β + γ) / 100, мин, (3.28)
Тшт = (24 + 3,12) · (1 + 4,6/100) = 28,3 мин.
Расчет штучного времени для зубофрезерной операции.
Рассчитаем штучное время для зубофрезерной операции по
формуле 3.29:
Тшт = Тп. з. + То + Тв + Тоб. + Тф, мин, (3.29)
где Тшт - штучное время, мин;
Тп. з. - подготовительно - заключительное время, мин.
Тп. з. = 0,2 мин;
То - основное (технологическое) время, мин;
Тв - вспомогательное время, мин.
Тв = 1,25 мин;
Тоб. - время на обслуживание рабочего места, мин;
Тф. - время на физические надобности, мин.
Тоб. = Тт. об. + То. об., мин, (3.30)
где Тт. об. - время на техническое обслуживание, мин;
То. об. - время на организационное обслуживание, мин.
То= Тв + Топ, мин, (3.31)
где Топ - оперативное время, мин;
Так как норма времени на техническое и организационное
обслуживание и физические надобности принимается в процентах от оперативного
времени - (α + β + γ) = 8%, то формулу
штучного времени можно записать в виде:
Тшт = Тп. з. + (То + Т) (1 + (α + β + γ) /100), мин, (3.32)
Время может быть определено через скорость резания
определяется по формуле 3.33
То = π d (L + l) z /1000 V S, мин, (3.33)
где L - длина нарезаемого зуба, мм;
l - величина врезания червячной фрезы, мм;
n - частота вращения червячной фрезы, об/мин;
S - подача на один оборот нарезаемой детали, мм/об;
z - число нарезаемых зубьев;
V - скорость резания, м/мин;
d - диаметр червячной фрезы, мм.
Основное время при черновой обработке:
Tо2 = 3,14 · 125 (28 + 40) · 36 /1000 · 20 · 3 = 16
мин,
Основное время при чистовой обработке:
Tо2 = 3,14 · 125 (28 + 40) · 36/1000 · 28 · 0,5 = 68
мин,
Основное время для операции:
То = 16 + 68 = 84 мин,
Штучное время для зубофрезерной операции:
Тшт = 0,2 + (84 + 1,25) · (1+ 8/100) = 92,3 мин.
Рассчитаем штучное время для сверлильной операции
определяется по формуле 3.34:
Тшт = Тпз + То + Тв + Тоб + Тф, мин, (3.34)
где Тшт - штучное время, мин; Тпз - подготовительное - заключительное
время, мин; Тпз - 0,2 мин; То - основное (технологическое) время, мин; Тв -
вспомогательное время, мин; Тоб - время на обслуживание рабочего места, мин; Тф
- время на физические надобности, мин.
Тоб. = Тт. об. + То. об, мин, (3.35)
Так как норма времени на техническое, организационное
обслуживание и физические надобности принимается в процентах от оперативного
времени (α + β + γ) = 8%, то формулу
штучного времени можно записать в виде:
Тшт=Тпз + (То + Тв) · (1 + (α + β + γ) /100, мин, (3.36)
Основное время сверления определяется по формуле 3.37:
То = L / nS = l + l1/nS, мин, (3.37)
где L - длина отверстия, мм;
l1 - величина врезания, мм;
S - подача инструмента на один оборот;
n - число оборотов инструмента в минуту.
А так как n = 1000V/π·d, то технологическое
время может быть определено через скорость резания определяется по формуле
3.38:
То = π· d· (l + l1) / 1000·V· S, мин, (3.38)
Технологическое время для сверления двух отверстий Ø13,7:
То = 2 · 3,14 ·13,7· (80 + 20) / 1000 · 20,5 · 0,4
= 1,1мин,
Технологическое время для сверления отверстия под резьбу М10
диаметром Ø 8,5мм:
То = 3,14 · 8,5 (40 + 20) / 1000 · 20,5 · 0,4 =
0,2мин,
Тшт = 0,2 + (1,1 + 0,2) (1 + 0,08) = 1,4мин,
Для нарезания резьбы в отверстии:
То = 3,04 мин, Тв = 3,02мин, Тшт = 3,04 + 3,02 = 6,06мин,
Штучное время по всей операции:
Тшт = 1,4 + 6,06 = 7,46мин.
Рассчитаем штучное время для протяжной операции определяется
по формуле 3.39:
Тшт = Тпз + То + Тв + Тоб + Тф, мин, (3.39)
где Тшт - штучное время, мин;
Тпз - подготовительное - заключительное время, мин;
Тпз - 0,2 мин;
То - основное (технологическое) время, мин;
Тв - вспомогательное время, мин;
Тоб - время на обслуживание рабочего места, мин;
Тф - время на физические надобности, мин;
Тоб. = Тт. об. + То. об, мин, (3.40)
Так как норма времени на техническое, организационное
обслуживание и физические надобности принимается в процентах от оперативного
времени (α + β + γ) = 8%, то формулу
штучного времени можно записать в виде:
Тшт=Тпз + (То + Тв) · (1 + (α + β + γ) /100, мин, (3.41)
Основное время протягивания определяется по формуле 3.42:
Tо= (Lр. х/ 1000·V) ·к, мин, (3.42)
где Lр. х - длина рабочего хода, мм;
V - скорость резания, м/мин.;
К - поправочный коэффициент в зависимости от обратного хода.
Определяем скорость резания по нормативам:V=4 м/мин.;
Принимаем по паспорту станка: V=3,6 м/мин;
Проверочный расчет по мощности резания определяется по
формуле 3.43:
P=FΣb, Н, (3.43)
где Σb - суммарная длина
режущих кромок всех зубьев, мм; одновременно участвующих в резании определяется
по формуле 3.44;
F - сила резани, приходящая на единицу длины режущей кромки
зуба, кГ;
Σb= (bun/zс) ·ri, мм, (3.44)
Σb= (10.1/1).4=40 мм,
P=23,5.40=940кГ ≈9400Н.
Корректируем скорость резания по мощности двигателя:
Vкор. =1,8 м/мин.
Определяем длину рабочего хода по формуле 3.45:
Lр. х=. lu. + ln + lдоп, мм, (3.45).
где lu. - длина протягивания, мм;
ln - длина рабочей части протяжки, мм;
lдоп. - дополнительная длина хода, мм;
Определяем длину рабочей части протяжки по формуле 3.46:
ln=L - l1, мм, (3.46)
где L - Общая длина протяжки, мм;
l1 - длина протяжки до первого режущего зуба, мм;
ln= 628-320 = 308мм;
Lр. х=.90+308+30=428мм;
Определяем основное время:
Tо= (428/1000·1,8) ·2=0,47 мин.;
Штучное время для протяжной операции:
Тшт = 0,2 + (0,47+ 1,28) · (1+ 8/100) = 2,05мин,
Штучно - калькуляционное время на изготовление колеса
зубчатого:
Тшт = 11,4 + 28,3 + 7,46+1,67+92,3+ 2,05 = 143,18 мин.
Полученные результаты свожу в таблицу 3.16
Таблица 3.16 - Технологическое время на изготовление колеса
зубчатого
Операция
|
Тпз мин.
|
Тв мин.
|
То мин.
|
Тшт мин.
|
Токарная
Горизонтально-фрезерная Вертикально-сверлильная
|
0,2 0,2 0,2
|
5,05 3,12 3,22
|
5,9 24 4,14
|
11,4 28,3 7,46
|
Токарная
|
0,2
|
0,6
|
1 84 0,47
|
1,67 92,3 2,05
|
Зубофрезерная
Горизонтально-протяжная
|
0,2 0,2
|
1,25 1,28
|
|
|
Итого
|
|
|
|
143,18
|
3.3.5
Составление управляющей программы для станка с ЧПУ
Порядок проектирования:
- Выбор состава
переходов
- Выбор режущих
инструментов
- Выбор режимов
резания
- Составление
геометрической информации
- Составление
текста управляющей программы
Выбор состава переходов на операцию №2, согласно маршруту
обработки:
1. Точить торец
2. Точить поверхность
. Точить торец
. Расточить отверстие
. Фрезеровать квадрат
6. Сверлить отверстие Ø13,7 мм, Ø8,5 мм
7. Нарезать резьбу
. Фрезеровать зубья
. Протянуть отверстие Ø45 мм
. Шлифовать отверстие Ø45 мм.
Режущие инструменты:
. Резец подрезной проходной Т5К6
2. Фреза торцевая насадная Т5К10 Ø160 мм
. Сверло спиральное Ø13,7; Ø8,5 мм Р6М5
4. Метчик машинный Ø10 мм Р6М5
. Резец расточной Т5К6
. Фреза червячная Р6М5
7. Круг ПП25.10. d24А,10ПС2 К5 35м/с А1 ГОСТ2424-83
Выбор геометрической информации:
- Координаты
начальной точки: 100; 141
- Траектории
движения инструментов
Текст управляющей программы:
%G27T101S041M104G58Z+000000F70000X+000000G26G01F10100L31Z−14100F70000X−02500X−07500F10013Z+14100F70000X+10000G40F10100L31T102S041G26G01F10100L32Z−14300F70000X−02500X−03900F10013Z+00200F70000X+03900Z−00200X−03900F10013Z+00200F70000X+03700Z−09100F10013X+00200F70000Z+09100X−00380Z−09100F10013X+02880F70000Z+13200G40F10100L32T111G26G01F10100L21Z−14000F70000Z−20000F10054Z+34000F70000G40F10100L21T104S044G26G01F10100L34X−07670F70000Z−14000Z−09200F10025X−00100F70000Z+09200X+00180Z−09200F10025X−00100F70000Z+09200X+00150Z−09200F10025X−00100F70000Z+23200X+07540G40F10100L34T105S044G01F10100L35X−07370F70000Z−14000Z−00100F10011X−00150Z−00150Z−09050X−00100F70000Z+23300X+07620G40F10100L35T106S043G01F10100L36X−07600F70000Z−14100X+00970F10013X+00150Z−00150Z−00250G03X+00100Z−00100I+00200G01X+03200X+00300Z−00300Z−08300X+00100F70000Z+23200G40F10100L36G25X+999999F70000M105G25Z+999999M002
.4
Расчет и конструирование фрезы для нарезания зубьев на детали "колесо
зубчатое"
3.4.1 Расчёт
дисковой зубофрезерной модульной фрезы. Определение эвольвентного участка
Исходные данные, необходимые для расчета фрезы.
Модуль m=2,25
Число зубьев колеса Z=42
Угол исходного контура α=200, Х=0.
Так как дисковая зуборезная модульная фреза имеет нулевой
передний угол и при нарезании цилиндрического прямозубого колеса работает
методом копирования, то профилирование ее режущих кромок сводится к определению
формы впадин зубьев обрабатываемого изделия. Согласно ГОСТ 10996-64 профиль
зуба фрезы состоит из эвольвентного, неэвольвентного участков и прямой.
Радиус основной окружности [16] определяется по формуле 3.47,
мм:
 (3.47)
 мм.
Радиус делительной окружности определяется по формуле 3.48, мм:
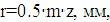 (3.48)
Радиус вершины зубьев колеса определяется по формуле 3.49, мм:
 (3.49)
 мм.
Радиус окружности впадин колеса определяется по формуле 3.50, мм:
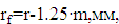 (3.50),  мм.
Координаты Х и Y любой точки
эвольвенты можно определить по формуле 3.51, 3.52, 3.53:
(3.51)
(3.52)
(3.53)
где Sg - ширина впадины зуба по делительному
диаметру определяется по формуле 3.54:
Т. к Х=0;
 (3.54)
 .
На эвольвентном участке профиля условно отмечаем десять точек
так, чтобы выполнялось условие:
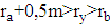 , мм, (3.55)
где  - радиус произвольных окружностей, проведенных через выбранные
точки.
 , мм, (3.56)
 .
Для получения координат различных точек эвольвенты задают
несколько значений rх. Для определения соответствующих им углов aх используют формулу 3.57, 3.58:
(3.57)
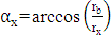 , (3.58)
 ,

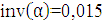 ;
 ,
 ,
 .
Расчет остальных точек производим аналогично, результаты заносим в
Таблицу 3.17
Таблица 3.17 - Расчетные значения точек эвольвенты
диаметр
|
50,625
|
49,23
|
48,54
|
47,85
|
47,16
|
46,47
|
45,78
|
45.09
|
44,4
|
Х, мм
|
3,497
|
2,695
|
2,342
|
2,02
|
1,731
|
1,477
|
1,263
|
1,084
|
0,999
|
Y, мм
|
50,504
|
49,156
|
48,483
|
47,807
|
47,128
|
46,477
|
45,763
|
45,017
|
44,389
|
3.4.2
Определение профиля неэвольвентного участка
В зависимости от числа зубьев нарезаемого
колеса устанавливают два типа профилей зуба. У нас z =42, поэтому в этом
случае профиль зуба колеса будет эвольвентным только на протяжении АВ - от
окружности выступов до основной окружности. Участок же О1В от основной
окружности до окружности впадин будет неэвольвентным. Профилирование фрезы
представлено на рисунке 3.4
Рисунок 3.4 - Профилирование фрезы
Учитывая, что зубчатые колеса, нарезанные стандартными
дисковыми фрезами, требования высокой точности не удовлетворяют, радиус
закругления вершины зубьев инструмента можно находить по формуле 3.59:
 (3.60)
где  - нормальный модуль, мм;
 - коэффициент, зависящий от числа зубьев нарезаемого колеса и
угла зацепления  .
Согласно [17]  .
 .
3.4.3
Конструктивные параметры дисковых фрез
Угол a подбирают с таким
расчетом, чтобы обеспечить на боковых сторонах профиля задние углы a1
не менее 3°. Угол в точке М,jм и a1
связаны между собой следующим соотношением [16] определяется по формуле 3.60:
(3.60)
Угол φ для любой точки можно определить, построив касательную к
профилю в этой точке. Он должен быть не менее 30°, тогда угол получится равным 10-15°.
(3.61)
Принимаем K=3мм. [2]
Передний угол g= 0°.
Размер Н фрез с зубьями без подфрезерования (рис.3.4) определяют
по формуле 3.62:
(3.62)
где - высота профиля, мм, определяется
построением.
Ширину В определяют после расчета профиля фрезы
определяется по формуле 3.63:
(3.63)
где Ха - ширина впадины зуба на окружности вершин;
DВ0 - коэффициент, учитывающий увеличение
ширины фрезы по сравнению с шириной впадины зуба на окружности вершин (DВ0=35% - для m=1мм; DВ0=15% -
для m=8мм). Для промежуточных значений модуля данный
коэффициент находится интерполированием).
Принимаем 7 мм.
Угол и радиус r впадины
определяют по формулам для обычных затылованных фасонных фрез т.е. r=1.5мм,  .
Наружный диаметр фрезы D, число
зубьев Z и диаметр отверстия dотв следует выбирать по ГОСТ 10996 - 64 в зависимости от
модуля зубчатого колеса.
Поэтому принимаем D=63мм, Z=12, dотв=22мм.
Для изготовления дисковой зубофрезерной модульной фрезы, по ГОСТ
19265 - 73, принимаем сталь инструментальную быстрорежущую Р6М5.
4.
Организационно-экономическая часть
4.1 Оценка
затрат на проведение модернизации
По принятой технологической схеме в настоящее время
известково-доломитная пыль подается вручную с использованием электрического
тельфера. Подача осуществляется при помощи фронтального погрузчика. Во всем
процессе задействовано 7 человек обслуживающего персонала, которые постоянно
работают во вредных условиях.
Под инвестициями в данной работе подразумеваем сумму денежных
средств, необходимую на проектные работы и строительство объекта, покупку
основных средств для его дальнейшей эксплуатации, а также начальный оборотный
капитал, необходимый для покрытия текущих затрат при начальной эксплуатации
объекта до тех пор, пока выручка не будет покрывать текущие расходы.
Проведем экономический расчет системы автоматической подачи
известково-доломитной пыли в бункер мусоросжигательной печи.
В данном случае величина капитальных вложений ∆С будет
состоять из следующих элементов (рисунок 4.1):
1. Стоимость проектных работ - Спр;
2. Стоимость общестроительных работ (земляные работы,
устройство фундамента) - Сстр;
. Стоимость изготовления металлоконструкций (в т. ч.
стоимость металла) - Сизг;
4. Стоимость монтажа металлоконструкций -
См;
. Стоимость оборудования - Соб;
6. Стоимость монтажа и пуско-наладки оборудования - См.
об.
1. Стоимость проектных работ Спр определяется:
Спр=Цл∙Nл, руб, (4.1)
где Цл - цена одного условного листа, взятая по средним ценам
по г. Череповцу - 6000 руб.,
Nл - количество условных листов, равное 30 по экспертным
оценкам аналогичных работ.
Спр=6000∙30=180 000 руб.
. Стоимость общестроительных работ Сстр определяется:
Сстр=Цстр∙Nз, руб, (4.2)
где Цстр - средняя сметная стоимость земляных и фундаментных
работ, 17 000 руб. за куб. м по г. Череповцу,
Nз - общее количество куб метров работ, 10 куб. м в
соответствии с объемом работ.
Сстр=17 000∙10=170 000 руб.
. Стоимость изготовления металлоконструкций Сизг определяется
следующим образом:
Сизг= (Цм+Уизг) ∙Nм, руб, (4.3)
где Цм - средняя стоимость металла, 28 000 руб. за 1 тонну,
Уизг - стоимость услуги по изготовлению металлоконструкций,
26 000 руб. за тонну по г. Череповцу,
Nм - количество тонн металлоконструкций, 2,5 т по проекту.
Сизг= (28 000+26 000) ∙2,5=125 000 руб.
4. Стоимость монтажа металлоконструкций См:
См=Ум∙Nм,руб, (4.4)
где Ум - стоимость услуги по монтажу металлоконструкций,
принимается по средним городским показателям 22 000 руб. за тонну,
См=22 000∙10=220 000 руб.
. Стоимость оборудования Соб определяется как сумма
всего закупаемого оборудования: транспортера, датчики уровня пыли,
электрического привода и составляет 400 000 руб.
6. Стоимость монтажа и пуско-наладки оборудования См. об
определяется в размере 15% от стоимости самого оборудования и составляет:
См. об= Соб∙0,15=400 000∙0,15=60 000 руб.
Таким образом, величина капитальных вложений (рисунок4.1):
∆С= Спр+Сстр+Сизг+См+Соб+ См. об, руб, (4.5)
∆С=240 000+170 000+125 000+220 000+400 000+60 000=1 155
000 руб.
Рисунок 4.1 - Величина капитальных вложений в проект
4.2 Затраты
на оказание услуг
Затраты на подачу известково-доломитной пыли в бункер
включают в себя следующие элементы:
- Материальные
затраты;
- Оплата труда;
- Текущее
обслуживание и ремонт;
- Амортизационные
отчисления;
Электроэнергия и прочие расходы (на охрану труда, спецодежду,
ГСМ и т.д.). К эксплуатационным или текущим затратам относятся следующие
затраты:
4.2.1
Материальные
Затраты на текущий ремонт, руб/год принимаются в размере
25-30% затрат на амортизацию:
Sт. р= (0,2-0,3) Sам, руб. /год, (4.6)
До внедрения проекта затраты на текущий ремонт составляли:
Sт. р.0=0,25∙28400=7 100 руб. /год,
После внедрения проекта затраты:
Sт. р.1=0,25∙74010=18 503 руб. /год.
Расчёт затрат на электроэнергию:
Sэ= Р∙hгод∙Сэл, руб, (4.7)
где Р - установленная мощность электродвигателей, кВт;
hгод - число часов использования установленной мощности в году;
Сэл - стоимость электроэнергии за 1 кВт/ч потребляемой мощности.
До модернизации проекта потреблялась энергия электрическим
тельфером в объеме 3,5 кВт/ч в течение 1620 часов в год. Стоимость
электроэнергии - 2766 руб. за 1000 кВт/ч (по данным бухгалтерии).
После внедрения проекта электроэнергия потребляется
электродвигателем привода в объеме 1,5 кВт/ч в течение такого же количества
времени.
Sэ= (3,5-1,5) ∙1620∙2,766=8961руб.
4.2.2 Оплата
труда
Sз=S1з∙ n∙12∙1,3,руб.,
(4.8)
где S1з - средняя заработная плата 1 человека,
обслуживающего оборудование, в месяц (15 500 рублей). До внедрения проекта в
технологическом процессе было задействовано 7 человек обслуживающего персонала,
а после проекта число обслуживающего персонала сократилась до 3 человек, тогда
экономия на затраты а заработной плату составит:
Sз=15500∙4∙12∙1,3=967200руб.
4.2.3
Амортизационные отчисления
Амортизационные отчисления рассчитываются с использованием
линейного метода по формуле:
(4.9)
где - стоимость объекта, руб.;
- норма амортизации.
Значение определяется по формуле:
(4.10)
где - срок полезного использования
оборудования, равен 6 лет,
Затраты на амортизационные отчисления, руб/год:
Sам=Р1Сстр+Р2Соб, руб/год, (4.11)
где Р1 - процентные отчисления стоимости общестроительных работ
(принимаются равными 3.2%); Сстр - стоимость общестроительных работ; Р2 -
процентные отчисления от стоимости оборудования с монтажом и наладкой (в
среднем могут быть приняты 8.2%); Соб - стоимость оборудования с монтажом и
наладкой.
До внедрения проекта амортизационные затраты:
S0ам=0,032∙0+0,082∙346000=28 400 руб. / год,
После внедрения проекта амортизационные затраты:
S1ам=0,032∙170000+0,082∙460000=74 010 руб. / год,
Sам=28400-74010=-45610руб.
/год.
4.2.4 Прочие
затраты
1,3 - 30% страховые взносы по оплате труда.
Затраты на прочие расходы, руб. /год, можно принимать в
размере 30% от суммы амортизационных отчислений, годового фонда заработной
платы и затрат на текущий ремонт:
Sпр=0.3 (Sам+Sзат+Sт. р), руб. /год, (4.12)
До внедрения проекта:
S0пр=0,3 (28400+708660+7100) =223 248 руб/год,
После внедрения проекта:
S1пр=0,3 (74010+236220+18503) =96 620 руб/год.
Результаты всех расчетов приведены в таблице 4.1.
Таблица 4.1 - Суммарные затраты на оказание услуг
|
Значения
показателей
|
Примечание
|
|
До внедрения
проекта
|
После внедрения
проекта
|
Изменение
|
|
Материальные
затраты, руб. /год
|
23 883
|
26 495
|
- 2 612
|
За счет
автоматизации процесса
|
Затраты на
оплату труда руб. /год
|
708 660
|
236 220
|
+472 440
|
за счет
сокращения штата на 4 человека
|
Затраты на
амортизационные отчисления, руб. /год
|
28 400
|
74 010
|
- 45 610
|
За счет
удорожания оборудования и строительных материалов
|
Прочие
затраты, руб. /год
|
223 248
|
98 620
|
+124 628
|
Спецодежда,
ГСМ, охрана труда и за счет смены оборудования
|
Суммарные
производственные затраты, руб.
|
984 291
|
385 345
|
+605 859
|
|
На основе проведенных расчетов мы можем сравнить
распределение затрат до и после внедрения инвестиционного проекта на рисунке
4.2 и на рисунке 4.3.
Рисунок 4.2 - Структура затрат до внедрения проекта
Рисунок 4.3 - Структура затрат после внедрения проекта.
Так, исходя из приведенных выше структур, видно, что в
результате внедрения инвестиционного проекта существенно снизились затраты на
заработную плату с отчислениями - порядка 17%, возросли амортизационные
отчисления и затраты на текущий ремонт, электроэнергия и прочие затраты в
процентном отношении от всей суммы затрат не изменились.
4.3
Определение экономической эффективности
Экономический годовой эффект от внедрения проекта
определяется по формуле:
Э= (∑Э1-∑Э2) - Ен∆С, руб., (4.11)
где Ен - нормативный коэффициент эффективности капитальных
вложений, равный 0,15;
Рассчитаем предполагаемую операционную прибыль после
модернизации:
По = В - З,руб. /год, По = 650245 -
385345 = 264900руб. /год,
где В - выручка, З - общие производственные затраты;
Рассчитаем прибыль:
Чистая прибыль составляет:
Пч = По - 0,2П,руб. /год,
Пч = 264900 - 0,2 ∙ 264900 = 211920руб. /год
Годовой доход составляет:
Д = Пч + За,руб,/год,
Д = 211920 + 385345 = 592265руб,/год.
Сравнивая годовые доходы до и после модернизации, сделаем
вывод, что данные изменения являются с экономической точки зрения.
Срок окупаемости модернизации (без учета инфляции):
∑Э1 - суммарные эксплуатационные затраты до внедрения
проекта;
∑Э2 - суммарные эксплуатационные затраты после
внедрения проекта;
∆С - величина капитальных вложений.
Э= (984 291-385 345) - 0.15·1 155 000=428 696 руб.
5.
Безопасность и экологичность проекта
При эксплуатации мусоросжигательной печи на производственный
персонал действуют разнообразные опасные и вредные производственные факторы.
5.1 Анализ
опасных и вредных производственных факторов при эксплуатации мусоросжигательной
печи
1) Движущееся оборудование, подвижные части.
Опасность травмирования присутствует. Рядом с
мусоросжигательной печью есть зольный конвейер открытого типа, который
перемещает золу на выходе из печи. Повышенная запыленность и загазованность
воздуха рабочей зоны.
Работники МСЗ подвергаются риску воздействия выбросов, так
как летучая зола, оседающая на их одежде и открытых частях тела, содержит
значительные количества диоксинов и других токсичных веществ. Риск возрастает
при проведении процесса очистки печей. Выдаваемые средства индивидуальной
защиты предохраняют только дыхательную систему, но не защищают кожу.
В группу риска входят операторы и рабочие, отвечающие за сбор
и транспортировку золы. В цехе постоянно работает вытяжная вентиляция, которая
не допускает превышения запыленности выше предельно допустимой концентрации
вредных веществ определенный по ГОСТ12.1.005-88.
) Повышенная температура поверхностей оборудования.
Наружная поверхность мусоросжигательной печи имеет температуру
порядка 80
С, что не исключает опасность ожогов.
Технологический проем печи закрывается стальной дверью, которая не имеет
ограждений и представляет опасность термических ожогов. Обслуживающему
персоналу в соответствии с инструкциями по технике безопасности запрещено
подходить к проему печи во время ее работы, он предназначен только для ремонта
агрегата в остановочный период.
) Повышенная температура воздуха рабочей зоны.
В цехе, возможно, присутствует незначительное повышение
температуры, но обслуживающий персонал находится там непродолжительное время,
для загрузки печи.
) Повышенный уровень шума на рабочем месте.
Отсутствует
) Повышенный уровень вибрации.
Источников вибрации нет.
) Повышенный уровень электромагнитных излучений.
В модуле управления основным источником электромагнитного
излучения являются мониторы компьютеров. В случае постоянного нахождения
источника излучения в непосредственной близости от человека, возможны
патологические изменения в органах зрения, нарушение обмена веществ.
) Отсутствие или недостаток естественного света, недостаточное
освещение рабочего места. Часто естественное и искусственное освещения
несоответствует установленным нормам. Слабое освещение приводит к напряжению
глаз, что при длительном воздействии ведет к ухудшению зрения. Также возникает
головная боль, нервное напряжение.
Биологические опасные и вредные производственные факторы
1) Бактерии, вирусы, грибы, простейшие и т.п.
Скапливаются в местах, труднодоступных для проведения уборки:
например, клавиатура. Влияние незначительное.
Психофизиологические опасные и вредные производственные факторы
1) Физические перегрузки.
Печь и пульт управления в рабочем состоянии при нормальных
условиях труда не являются источником статических и динамических физических
перегрузок. Постоянное воздействие на персонал рассмотренных факторов может
привести к травмам и профессиональным заболеваниям.
5.2 Меры по
обеспечению безопасных и здоровых условий труда
Цех представляет собой помещение высотой 10 метров, площадью
около 1500 м2. На данной территории, кроме печи, расположены
мастерские электрослужбы, механослужбы, пульт управления, санитарно-бытовые
помещения, изолированный склад химических реактивов.
В рабочей зоне периодически присутствует источник выделения
вредных веществ, установлена местная вытяжная вентиляция. В помещении пульта
управления ежедневно проводиться влажная уборка.
Уровень естественного и искусственного освещения в помещениях
регламентируется СНиП 23-05-95 в зависимости от характера зрительной, системы и
вида освещения, фона, контраста объекта с фоном. Цех по задачам зрительной
работы, согласно СНиП, относится к первой группе (помещение, в котором
производится различение объектов зрительной работы при фиксированном
направлении линии зрения работающих на поверхность). Выполняемый тип работ
принадлежит к зрительным.
При работе с ЭВМ, как правило, применяется естественное
освещение. Желательно чтобы световые проемы располагались слева от оператора
ЭВМ, допускается и правостороннее естественное освещение. В тех случаях, когда
одного естественного освещения не хватает, устанавливается совмещенное
освещение. При этом дополнительное искусственное освещение применяется не только
в темное, но и в светлое время суток.
Для искусственного освещения помещения используются главным
образом люминесцентные лампы. Наиболее приемлемыми являются люминесцентные
лампы белого и тепло - белого света. Рекомендуемая освещенность для работы с
экраном дисплея составляет 200 лк, а при работе с экраном в сочетании с работой
над документами - 400 лк. Освещение достаточно равномерно распределено на
рабочих поверхностях и в окружающем пространстве; не должно быть резких теней,
прямой и отраженной блеклости; освещение должно быть равномерно во времени;
направление излучаемого осветительными приборами светового потока должно быть
оптимальным [23].
Важное значение для предотвращения электротравматизма имеет
правильная организация обслуживания действующих электроустановок, проведение
ремонтных, монтажных и профилактических работ. В зависимости от категории
помещения необходимо применять определенные защитные меры, обеспечивающие
достаточную электробезопасность при эксплуатации, техническом обслуживании и ремонте.
В помещениях с повышенной опасностью электроприборы, переносные светильники
выполнены с двойной изоляцией или напряжение питания не превышает 42В.
Оператору запрещается приступать к работе при обнаружении
любой неисправности оборудования до ее устранения [23].
Помещение оборудовано ручными средствами пожаротушения. К ним относят:
. Оборудование противопожарных щитов.
2. Пожарные краны
. Ручные огнетушители.
Персонал, работающий в помещении лаборатории, знает
последовательность действий в случае пожара, а также умеет пользоваться ручными
средствами пожаротушения.
При организации рабочего места оператор обеспечивает взаимное
расположение всех его элементов в соответствии с эргономическими требованиями,
с учетом характера выполняемого оператором исследования, комплексности
технических средств, форм организации труда и наиболее оптимального для данного
исследования рабочего положения.
Угол поворота монитора регулируется для лучшего обзора
выводимых данных. При этом экран находиться от глаз пользователя на оптимальном
расстоянии 600-700 мм, но не ближе 500мм с учетом размеров алфавитно-цифровых
знаков и символов.