Проект технічного переобладнання сульфатного відділення ПАТ 'Авдіївський КХЗ'
Пояснювальна записка
до дипломного проекту
на тему „ Проект технічного
переобладнання сульфатного відділення ПАТ «Авдіївський КХЗ» ”
Об’єкт вивчення - сульфатне
відділення цеху уловлювання №1 Авдіївського коксохімічного заводу.
Ціль проекту - переобладнання
сульфатного відділення підприємства хімічної технології.
У дипломному проекті наведена
технологічна схема сульфатного відділення та піридинової установки, креслення
основних апаратів: абсорберу, барабанної сушарки, випарника та нейтралізатора.
Розрахунки усіх основних апаратів: абсорберу, випарника, сушарки,
нейтралізатора та всієї піридинової установки.
Наведені фізико-хімічні основи
процесу уловлення аміаку з коксового газу та отримання піридинових основ,
описані основні апарати та технологічні схеми. Розрахунок випарника виконаний
за допомогою ЕОМ.
СУЛЬФАТНЕ ВІДДІЛЕННЯ, ПІРИДИНОВА
УСТАНОВКА, АБСОРБЕР, СУШАРКА, СУЛЬФАТ АМОНІЮ, НЕЙТРАЛІЗАТОР, ВИПАРНИК
Объект изучения - сульфатное
отделение цеха улавливания №1 Авдеевского коксохимического завода.
Цель проекта - переоборудование
сульфатного отделения предприятия химической технологии.
В дипломном проекте приведена
технологическая схема сульфатного отделения и пиридиновой установки, чертежи
основных аппаратов: абсорбера, барабанной сушилки, испарителя и нейтрализатора.
Расчеты всех основных аппаратов: абсорбера, испарителя, сушилки, нейтрализатора
и всей пиридиновой установки.
Приведенные физико-химические основы
процесса улавливания аммиака из коксового газа и получения пиридиновых оснований,
описаны основные аппараты и технологические схемы. Расчет испарителя выполнен с
помощью ЭВМ.
СУЛЬФАТНОЕ ОТДЕЛЕНИЕ, ПИРИДИНОВАЯ
УСТАНОВКА, АБСОРБЕР, СУШИЛКА, СУЛЬФАТ АМОНИЯ, НЕЙТРАЛИЗАТОР, ИСПАРИТЕЛЬ
The object of study - sulfate
separation recovery shop number 1 Avdiivka Coke.purpose of the project - the
conversion of sulfate chemical separation technology.the thesis project
presented flow sheet separation of sulfate and pyridine installation drawing
main unit: absorbers, drum dryer, evaporator and converter. Payments all major
units: the absorber, evaporator, dryer, converter and all pyridine
installation.physic-chemical basis of process capture ammonia from coke oven
gas and receipt of pyridine bases, describes the main technological devices and
circuits. Calculation of the evaporator is made by computer.
SULFATE DEPARTMENT, PYRIDINE INSTITUTIONS, ABSORBERS, DRIERS,
AMMONIUM SULFATE, CONVERTES, VAPORIZERS
ЗМІСТ
ВСТУП
. ТЕХНІКО-ЕКОНОМІЧНЕ ОБҐРУНТУВАННЯ
. ХАРАКТЕРИСТИКА СИРОВИНИ ТА ГОТОВОЇ
ПРОДУКЦІЇ
.1 Характеристика вхідної сировини
.2 Характеристика продукції,що
випускається
. ФІЗИКО-ХІМІЧНІ ОСНОВИ ПРОЦЕСІВ
.1 Уловлювання аміаку з коксового
газу з отриманням сульфату амонію
.2 Уловлювання піридинових основ з
коксового газу
. ВИБІР ТЕХНОЛОГІЧНОЇ СХЕМИ
. ВИБІР ОБЛАДНАННЯ
.1 Конструкція абсорберу
.2 Конструкція випарника
.3 Конструкція барабанної сушарки
.4 Конструкція конденсатору
. МАТЕРІАЛЬНІ РОЗРАХУНКИ
БЕЗСАТУРАТОРНОГО МЕТОДУ ОТРИМАННЯ СУЛЬФАТУ АМОНІЮ
.1 Матеріальний баланс аміаку
6.2 Розподіл поглинання аміаку по ступеням абсорберу
7. РОЗРАХУНОК АБСОРБЕРУ
7.1 Матеріальний розрахунок
.2 Матеріальний і тепловий баланси збірки абсорбера
1-го ступеня
.3 Розрахунок 2-го ступеня абсорберу
.4 Матеріальний і тепловий баланси збірки 2-го ступеня
абсорбера
.5 Визначення розмірів абсорберу
8. РОЗРАХУНОК КОНДЕНСАТОРУ
.1 Тепловий розрахунок
8.2 Визначення поверхні теплопередачі
9. РОЗРАХУНОК СУШАРКИ
9.1 Матеріальний розрахунок
.2 Тепловий розрахунок сушарки
.3 Визначення розмірів сушильного барабану
10. ПРОЕКТ ПІРИДИНОВОЇ УСТАНОВКИ
.1 Обґрунтування необхідності
уловлювання піридинових основ
.2 Опис схеми піридинової установки
.3 Вибір обладнання
.4 Розрахунок нейтралізатору
.5 Розрахунок конденсатору легких
піридинових основ
. РОЗРАХУНОК ВИПАРНИКА НА ЕОМ
11.1 Постанова задачi
.2 Математичний опис
.3 Ідентифікація змінних
.4 Аналіз результатів розрахунку
12. ЕКОНОМІЧНЕ ОБҐРУНТУВАННЯ ПРОЕКТУ
УЛОВЛЮВАННЯ ПІРИДИНОВИХ ОСНОВ
12.1 Визначення капітальних витрат
.2 Розрахунок чисельності працівників
.3 Розрахунок фонду оплати праці основних виробничих
працівників.
.4 Визначення собівартості продукції виробництва
.5 Визначення виробничої собівартості уловлювання
піридинових основ.
.6 Розрахунок економічної ефективності технологічного
рішення
13. АВТОМАТИЧНИЙ КОНТРОЛЬ І РЕГУЛЮВАННЯ
ПРОЦЕСУ
. ОХОРОНА ПРАЦІ ТА БЕЗПЕКА ПРИ
НАДЗВИЧАЙНИХ СИТУАЦІЯХ
.1 Стисла характеристика виробництва
та його шкідливі фактори
.2 Заходи щодо поліпшення праці
.2.1 Розрахунок заземлення насосної
установи
.2.2 Розрахунок витяжної вентиляції
.2.3 Пожежна безпека
14.3 Безпека при надзвичайних ситуаціях
ВИСНОВКИ
ПЕРЕЛІК ПОСИЛАНЬ
ВСТУП
Аміак утворюється в процесі
коксування з азоту і водню кам'яного вугілля. Велика частка азоту вугілля (до
60%) залишається в коксі у вигляді термічно стійких азотистих поєднань, а
остання частка видаляється з вугілля разом з леткими продуктами коксування -
газом, смолою і надсмольною водою.
Утворення аміаку при коксуванні
вугілля починається при температурі біля 600°С, а максимальний вихід його
досягається при температурах 800-900°С.
За даними [1] вихід аміаку від сухої
шихти для донецького вугілля варіюється в межах 0,25-0,30%, а для кузнецьких
може досягати 0,45 %.
Вміст аміаку в газі для різного
вугілля [1] може варіюватися в межах 5,5 - 12,5 г/м3 (0 °С).
Вилучення аміаку з коксового газу -
обов'язкова технологічна операція при підготовці газу до його подальшого
використання. Норми допустимого вмісту аміаку в газі: не більше 0,03 г/м3[2],
тобто повнота витягання аміаку з газу повинна складати 99,7 - 99,8 % мас. Такі
серйозні вимоги визначаються чисто технологічними причинами [3]:
необхідність видалення компонента,
який призводить до корозії газопроводів та обладнання;
для попередження виникнення
відкладань в газопровідних комунікаціях і регулюючих пристроях коксових
батарей;
для нормальної експлуатації
бензольно-скруберних відділень і цехів сірко очистки;
аміак з ціаністим воднем, що
знаходиться в газі, різко посилює корозію устаткування, утворюючи добре
розчинне комплексне з'єднання - гексацианферрат - (NH4)4[FeCN6];
аміак, що залишається в газі, при
спалюванні перетворюється переважно на токсичні і корозійно-небезпечні оксиди
азоту;
аміак стабілізує емульсії води і олії
при уловлюванні бензольних вуглеводнів.
У результаті уловлювання аміаку
сірчаною кислотою утворюється сульфат амонію.
Сульфат амонію виробляється на
коксохімічних заводах у великих кількостях. На 1 т сухої шихти виробництво
сульфату амонію (сухого) складає 11,0-11,5 кг.
Сульфат амонію являється дуже
ефективним азотним добривом. Особливістю цього вигляду добрива є ті, що він
дозволяє підпитувати ґрунт не лише азотом, але і сіркою. Остання входить до
складу білків і амінокислот рослин і тому разом з азотом є одним з важливих
елементів живлення сільськогосподарських культур. По мірі важливості для рослин
сірку можна поставити на третє місце після азоту і фосфору. Продукт володіє
важливою для життєдіяльності рослин властивістю. Він переводить фосфор, що
знаходиться в ґрунті з нерозчинної форми в розчинну і тим самим підсилює процес
поглинання рослиною цієї речовини. Це дозволяє понизити кількість фосфорних
добрив, що вносяться до ґрунту.
Не дивлячись на те, що продукт
найширше використовується в сільському господарстві, він також застосовується і
в інших галузях. Наприклад, у біохімії переосадження сульфатом амонію є загальним
методом очищення білків. Використовується в технології хлорування води з
амонізацією, вводиться в оброблювану воду за декілька секунд до хлору, з хлором
утворює хлораміни - зв'язуючи вільний хлор, завдяки чому значно скорочується
утворення хлорорганіки шкідливої для організму людини, скорочується витрата
хлору, зменшується корозія трубопроводів. В харчовій промисловості його
використовують як харчову добавку Є517 (речовини проти злежування). В
промисловості сульфат амонію використовують як сировину при виробництві
акумуляторів, у виробництві віскозного волокна і як основу при виробництві
вогнезахисних просочень для дерева.
Так як сатураторний метод не дає
можливості регулювати розмір отримуваних кристалів, то пропонується для
впровадження безсатураторний метод отримання сульфату амонію на ПАТ
«Авдіївський КХЗ», у якому на стадії абсорбції отримують ненасичений розчин солі, що
піддається вакууму, - випарці в умовах інтенсивної циркуляції, що забезпечує
незначне пересичення і керований ріст кристалів.
1. ТЕХНІКО-ЕКОНОМІЧНЕ ОБҐРУТУВАННЯ
ПРОЕКТУ
Авдіївський коксохімічний завод має у
своєму складі сульфатне відділення для очистки коксового газу від аміаку з
отриманням сульфату амонію.
До складу сульфатного відділення
входить також аміачне відділення, призначення якого полягає у витяганні аміаку
з надлишкової аміачної води для переробки його у сульфат амонію.
Може стати можливим впровадження
піридинової установки для уловлювання легких піридинових основ. Ця установка
призначена для витягання піридинових основ (які містять піридин
і його гомологи: піколіни, лутідини,
колоїдини та хінолін) з маточного розчину сульфатного відділення. Таким чином
ще буде додаткове очищення маточного розчину для більш кращого уловлення аміаку
з коксового газу.
Ця установка вже на заводі є, бо
піридинові основи раніше уловлювалися, але собівартість не окупалася і
керівництво вирішило не робити цього. Тому не треба великих капітальних затрат,
треба тільки пересвідчитися у справності обладнання, і якщо ми збільшимо ринки
збуту, то прибуток буде досить великий (він наведений у розділі економічне
обґрунтування проекту, у таблиці 16.7).
Піридинові основи досить цінні, тому
треба їх уловлювати, тому що основним джерелом отримання легких піридинових основ
є коксовий газ і частково надсмольна аміачна вода, що містить 0,3-0,4 г/л
піридинових основ.
Піридин і його гомологи легко
розчиняють багато органічні і мінеральні речовини і тому використовуються як
розчинник на заводах гумової і лакофарбової промисловості і заводах пластмас.
Піридинові основи використовуються при виробництві фарб і деяких хімікатів; при
виробництві речовин, які надають водонепроникність тканин і шкіри; для
денатурації спирту; у виробництві отрутохімікатів для боротьби з шкідниками сільського
господарства; для виробництва цінних синтетичних продуктів, що використовуються
в медицині; для отримання фунгіцидів, тобто речовин, які застосовуються для
боротьби з паразитним грибом і бактеріями, що викликають захворювання
культурних рослин.
Піридин є вихідною речовиною для
виробництва лікарських та фармацевтичних препаратів і вітамінів. Джерелом
отримання протитуберкульозних препаратів - фтевазида, салюзида та ін. служить g-піколін. Комплексні сполуки
піридину можуть застосовуватися в якості інгібіторів.
Не достовірно відомо скільки ще ми
зможемо робити кокс з вугілля, тому що вугілля це вичерпна сировина, а так як
основним джерелом отримання легких піридинових основ є коксовий газ, дуже
важливо вилучати всі цінні компоненти з нього.
Може зараз і піридинові основи не
дуже затребувані на ринку, бо ціна висока, але дуже скоро можуть стати взагалі
дефіцитом. Не варто упускати можливості їх отримувати.
. ХАРАКТЕРИСТИКА СИРОВИНИ І ГОТОВОЇ ПРОДУКЦІЇ
2.1 Характеристика вихідної сировини
У хімічно чистому сульфаті амонію аміак становить 25,76%,
залишок 74,24% припадають на частку сірчаної кислоти. На вітчизняних
коксохімічних для виробництва сульфату амонію використовується сірчана кислота
наступних видів: баштова, контактна технічна (привізна і з власних цехів
мокрого каталізу); відпрацьована з підприємств органічного синтезу ;
регенерована після мийки фракцій сирого бензолу та інших коксохімічних
продуктів. Якість сірчаної кислоти нормується стандартом [2].
Для виробництва сульфату амонію вищого і першого сортів
використовується контактна сірчана кислота поліпшеної марки Б концентрації
92,5-94,0% з вмістом заліза не більше 0,015%, оксидів азоту та миш'яку 0,0001%;
для виробництва сульфату амонію другого сорту використовуються контактна
технічна кислота концентрації ≥ 92,5 %, що містить 0,02 % заліза; баштова
кислота марки А концентрацією ≥ 75% і вмістом 0,02 % заліза.
Регенерована сірчана кислота цехів ректифікації сирого
бензолу зі змістом моногідрату до 50% забруднена органічними домішками
(сульфокислотами і продуктами полімеризації). Ці домішки негативно впливають на
хід сатураторному процесу і знижують якість сульфату амонію. Однак економічно
необхідно використовувати цю кислоту, як найбільш дешеву.
Крім того, в сірчаній кислоті містяться і інші домішки -
оксиди азоту, миш'як, хлористі сполуки, свинець, кадмій, алюміній та інші, які
також впливають на роботу сатуратора і якість сульфату амонію. Вміст цих
домішок нормується стандартом.
Велике значення для роботи сульфатного відділення має
організація прийому і зберігання сірчаної кислоти. Зберігання сірчаної кислоти
( ≥ 75%) здійснюється у вертикальних сховищах з вуглецевої сталі
місткістю не більше 400 м3. Сховища забезпечуються повітряками з
волого уловлювачами. Для регенерованої кислоти застосовують сховища з
внутрішньою кислототривкою футерівкою. Ємність складу сірчаної кислоти залежить
від розмірів виробництва сульфату амонію і від того, на якій кислоті працює
сульфатне відділення (на привізної або власної). Ємність складу становить від
15 до 20 доз добової потреби.
Температура плавлення концентрованої сірчаної кислоти -10,3
°С.
2.2 Характеристика продукції, що
випускається
Сульфат амонію [
SO4] отримують на
коксохімічних заводах у сульфатному відділенні цеху уловлювання. Початковою
сировиною для отримання сульфату амонію служить аміак, що міститься в коксовому
газі.
Отримання сульфату амонію засноване на реакції нейтралізації
аміаку сірчаної кислотою в сатураторах або абсорберах:
.
Сульфат амонію являє собою білі, прозорі кристали форми
подовженого ромба величиною від сотих і десятих часток міліметра до 6-8мм і
більше. Щільність кристалічного сульфату амонію при 20°С становить 1,768 г/см3.
Насипна маса в залежності від крупності кристалів і змісту вологи коливається в
межах 780-830 кг/м3. Сульфат амонію, добре розчиняється у воді. З
підвищенням температури розчинність його у воді збільшується. Хімічно чистий
сульфат амонію містить 21,237 % азоту[3].
За державним стандартом (ГОСТ-9097-74) сульфат амонію повинен
характеризуватися такими показниками (таблиця 2.1):
Важливим показником якості сульфату амонію є розмір кристалів
Дрібнокристалічна структура солі з сильно розвиненою поверхнею являє собою
причиною підвищеного вмісту в ній вологи і сірчаної кислоти, що
Таблиця 2.1 - Показники сульфату амонію
Показник
|
Сорт
|
|
Вищий
|
I
|
II
|
Вміст азоту в перерахунку на суху речовину,%
|
21
|
20,8
|
20,8
|
Вміст вологи,%, не більше
|
0,2
|
0,3
|
0,3
|
Вміст H2SО4,%, не більше
|
0,025
|
0,050
|
0,050
|
Колір
|
Білий
|
Білий або слабо окрашений
|
Не нормується
|
Гранулометричний склад, вміст фракції > 0,25 мм,
%, не менше
|
95
|
70
|
Не нормується
|
Залишок на ситі 6мм
|
Відсутній
|
-
|
Не нормується
|
призводить до злежування при зберіганні і зрощенню її в
агломерати. Крупнокристалічна сіль менш схильна злежуванню і рівномірно
розподіляється в ґрунті при використанні її в якості добрива.
Сульфат амонію містить близько 24% сірки, яка у вигляді
сульфат-іона надходить у ґрунт разом з добривом. Сульфат амонію є добривом для
сільськогосподарських полів. У світовому виробництві азотних добрив на частку
сульфату амонію припадає більше 20% від усього виробництва азоту, в нашій
країні 6-7% від усієї кількості випущених азотних добрив.
. ФІЗИКО-ХІМІЧНІ ОСНОВИ ПРОЦЕСІВ
3.1
Уловлювання аміаку з коксового газу з отриманням сульфату амонію
Отримання сульфату амонію засноване
на поглинанні аміаку з коксового газу розчином сірчаної кислоти і протіканні
реакції нейтралізації.
NH3+H2SO4→(NH4)2SO4+q.
Процес нейтралізації сірчаної кислоти
аміаком протікає в дві стадії:
утворення кислої солі - бісульфату
амонію
2SO4+NH3→NH4HSO4;
перетворення кислої солі на середню у
міру перенасичення розчину аміаком
4HSO4+NH3→(NH4)2SO4.
Ці реакції протікають з виділенням
тепла, кількість якого залежить від умов ведення процесу. При взаємодії чистого
аміаку і насиченого розчину сульфату амонію що містить 7-8% вільної кислоти,
тепловий ефект сумарної реакції складає при 47,5°С 815 кДж/кг сульфату амонію,
а при 66,3°С 1855 кДж/кг При поглинанні аміаку з коксового газу тепловий ефект
процесу значно менший оскільки частина аміаку знаходиться у вигляді летких
з'єднань з сірководнем, вуглекислотою і іншими кислими газами, на розкладання
яких витрачається тепло. Для практичних розрахунків можна приймати тепловий
ефект сумарної реакції рівним 1180 кДж/кг сульфату амонію.
Співвідношення між сульфатом та
бісульфатом в розчині визначається кислотністю останнього. При низькій
кислотності (1-2%) в розчині переважає сульфат, який випадає з пересиченого
розчину у вигляді кристалів. При підвищенні кислотності розчину до 34% середня
сіль переходить практично повністю в кислу, яка має кращу розчинність у воді і
в кислих розчинах. При 60°С розчинність сульфату амонію у воді складає 46,6%,
при підвищенні кислотності до 19% вона практично не міняється, а потім
поступово росте і при кислотності 34% досягає максимуму (близько 52%) після
чого починає знижуватися.
Утворення кристалів сульфату амонію
відбувається при пересиченні маткового розчину за рахунок безперервного процесу
поглинання аміаку сірчаною кислотою або в результаті упарювання розчину.
Кристалізація розпочинається з утворення центрів кристалізації - зародків
кристалів. Для отримання великих кристалів необхідно забезпечити умови для їх
росту, інтенсивність якого залежить від швидкості дифузії сульфату амонію з
розчину до граней кристалів швидкості переходу молекул солі з рідкої фази в
тверду і швидкості відведення прихованої теплоти кристалізації від поверхні
кристалів в розчин. При інтенсивному перемішуванні розчинів процеси дифузії
сульфату амонію з розчину до граней кристалів і відведення тепла кристалізації
настільки інтенсифікуються, що практично не роблять впливу на процес
кристалізації. При цьому швидкість переходу речовини з рідкої фази в тверду
пропорційна другому ступеню різниці концентрації пересиченого і насиченого
розчинів
Коефіцієнт швидкості кристалізації К
залежить в сильній мірі від умов кристалізації. Експериментально встановлено,
що основними чинниками, що роблять вплив на ріст кристалів, являються
інтенсивність перемішування температура і кислотність маткового розчину, а
також концентрація різних домішок в нім.
Шляхом перемішування розчинів можна
прискорити ріст дрібних кристалів, затримати утворення нових зародків або
розчинити центри кристалізації, що вже утворилися. Для отримання великих
кристалів необхідно підтримувати їх тривалий час в зваженому стані в
пересиченому розчині, що може бути забезпечено за наявності висхідного потоку
розчину в кристалізаторі. При такому русі розчину створюються сприятливіші
умови для росту великих кристалів, оскільки вони мають більшу енергію
кристалізації і розташовані в нижній частині кристалізатора, куди підводиться
свіжий пересичений розчин.
Дрібніші кристали і зародки в таких
умовах поступово розчиняються, оскільки вони мають більшу розчинність і
знаходяться у верхній частині кристалізатора, де міра пересичення маткового
розчину незначна. Коли розмір кристалів досягає певної величини, вони осідають
на дно кристалізатора і виводяться в якості продукту.
Утворенню великих кристалів сприяють нижча
температура і кислотність маткового розчину. У виробничих умовах розчин
постійно контактує з холодними стінками апаратів й трубопроводів, внаслідок
чого він стає пересиченим і в цих зонах утворюються нові зародки кристалів. При
накопиченні їх в системі не можуть бути отримані великі кристали через нестачу
пересиченого розчину. Чим вище температура маткового розчину, тим значніше
вплив місцевих переохолоджень розчину, тим більше зміст дрібних фракцій в
отримуваному продукті.
Для отримання великокристалічного
продукту процес кристалізації повинен проводитися при можливо низькій
температурі, а апарати і трубопроводи мають бути теплоізольовані.
Підвищення кислотності розчину
призводить до збільшення змісту бісульфату амонію зростанню в'язкості і
щільності розчину, припиненню росту кристалів. Бісульфат піридину, що
утворюється при цьому, також перешкоджає росту кристалів і сприяє збільшенню
тієї солі, що злежується при зберіганні.
Найбільш великі кристали виходять при
кислотності розчину 1-2%. Проте, якщо кристалізація сульфату амонію робиться в
апараті для поглинання аміаку сірчаною кислотою при такій кислотності
відбувається інтенсивне відкладення кристалів на стінках апарату і в
трубопроводах, порушується нормальна робота установки. З цієї причини в таких установках
підтримується кислотність маткового розчину на рівні 4-5%. При цьому дуже
важливо підтримувати однакову кислотність в усьому об'ємі розчину і виключати
утворення нейтральних зон, в яких виходить сіра або чорна сіль (перепал).
Істотний вплив на ріст кристалів і їх
форму роблять різні домішки в матковому розчині. При змісті більше 1 г з'єднань
окисного (трьохвалентного) заліза в 1 кг розчину збільшується зміст дрібних
фракцій в продукті. Наявність в розчині хрому, алюмінію, кадмію сприяє утворенню
голчастих кристалів, які при зберіганні легко ламаються, утворюючи пил, і
схильні до злежування. Наявність в розчині ціанідів і хлоридів також
перешкоджає росту кристалів.
Негативна дія названих домішок може
бути обмежена при введенні в розчин щавлевої кислоти, сульфату магнію і
щавлевокислого кальцію, сечовини, з'єднань закисного (двовалентного) заліза,
марганцю, кобальту.
Домішки в матковому розчині не лише
перешкоджають росту кристалів, але і надають їм різне забарвлення. Сірий колір
сульфату амонію обумовлений наявністю смолянистих речовин, сірчистих з'єднань
заліза, міді, свинцю. Жовте забарвлення дають з'єднання миш'яку. Роданисті
з'єднання у присутності слідів заліза дають червоне або рожеве забарвлення.
Блакитний колір надає сульфату берлінська лазур. Крім того, ціаністі з'єднання
утворюють із залізом комплексні з'єднання, які в суміші з іншими речовинами
надають сульфату колірні відтінки від зелено-жовтого до фіолетового.
Для отримання сульфату амонію білого
кольору необхідно робити попереднє очищення коксового газу від смолянистих
речовин ціаністого водню і сірководню, застосовувати чисту сірчану кислоту та
апаратуру з корозійностійких матеріалів.
Ефективними антизлежувальними
добавками можуть бути відхід коксохімічного виробництва-відпрацьований розчин
сірко чистки і деякий металургійний пил.
3.2
Уловлювання піридинових основ з коксового газу
Піридинові основи, що утворюються при коксуванні кам'яного
вугілля, являють собою суміш гетероциклічних сполук ароматичного ряду з
загальною формулою
. Вихід піридинових основ залежить від вмісту азоту у вугіллі
і температури коксування. На утворення витрачається в середньому 1,2-1,5%
вмісту у вугільній шихті азоту. На заводах Кузбасу, вугілля яких містять
1,8-3,0% азоту, вміст піридинових основ в прямому газі становить 0,5-0,7 г/
проти 0,25-0,4 г/
на заводах Донбасу, коксівного
вугілля, що містять 1,2-1,8% азоту. Утворилися при коксуванні піридинові основи
містять піридин
і його гомологи, а також інші азотовмісні сполуки основного
характеру і більш складного складу (хінолін, ізохінолін, хінальдін та ін).
Піридинові основи це безбарвна з
різким запахом рідина. Піридинові основи щільністю при 20
дорівнює 923-982 кг/
і киплячі в межах 115-160
, називають легенями; Піридинові
основи з щільністю 1055-1100 кг/
і киплячі в межах 160-300°С називають важкими.
Піридинові основи добре розчиняються
у воді, смолі і в сирому бензолі. При охолодженні коксового газу вони
розчиняються в надсмольній води і в смолі, але більша частина їх залишається в
коксовому газі. Розподіл піридинових основ між газом, надсмольної водою і
смолою залежить від температури газу після первинних холодильників та їх
конструкції. Чим краще первинне охолодження газу, тим вище зміст піридинових
основ у конденсаті холодильників і менше в газі. У надсмольній аміачній воді
розчиняється до 15-25% легких піридинових основ від їх ресурсів в газі. Важкі
піридинові підстави розчиняються в кам'яновугільній смолі, а потім виділяються
сірчаною кислотою з кам'яновугільних фракцій і масел. Піридинові основи можна
виявити на всіх технологічних ділянках цеху уловлювання, в тому числі і у воді
кінцевих холодильників, поглинальному маслі, в сирому бензолі, в сепараторній
воді бензольного відділення, так як володіють підвищеною летючістю і хорошу
розчинністю у воді й інших рідинах.
Легкі піридинові основи являють собою
найбільш цінну частину основ, містить піридин
і його гомологи: піколіни, лутідини,
колоїдини (рис. 3.1). Основним джерелом отримання легких піридинових основ є
коксовий газ і частково надсмольна аміачна вода, що містить 0,3-0,4 г/л
піридинових основ.
Піридин і його гомологи легко розчиняють
багато органічні і мінеральні речовини і тому використовуються як розчинник на
заводах гумової і лакофарбової промисловості і заводах пластмас. Піридинові
основи використовуються при виробництві фарб і деяких хімікатів; при
виробництві речовин, які надають водонепроникність тканин і шкіри; для
денатурації спирту; у виробництві отрутохімікатів для боротьби з шкідниками
сільського господарства; для виробництва цінних синтетичних продуктів, що
використовуються в медицині;
- піридин; 2 - піколіни; 3 -
лутідіни; 4 - колоїдини
Рисунок 3.1 - Піридин та його
гомологи
для отримання фунгіцидів, тобто
речовин, які застосовуються для боротьби з паразитним грибом і бактеріями, що
викликають захворювання культурних рослин.
Піридин є вихідною речовиною для
виробництва лікарських та фармацевтичних препаратів і вітамінів. Джерелом
отримання протитуберкульозних препаратів - фтевазида, салюзида та ін. служить g-піколін. Комплексні сполуки
піридину можуть застосовуватися в якості інгібіторів.
. ВИБІР ТЕХНОЛОГІЧНОЇ СХЕМИ
В залежності від схеми охолодження прямого коксового газу і
уловлювання з нього аміаку розрізняють три способи отримання сульфату амонію:
непрямий, прямий і напівпрямий.
При непрямому способі частина аміаку (20-30% від загальних
ресурсів) вилучається з коксового газу конденсатом, який утворюється при
охолодженні газу у первинних газових холодильниках до 25-35
, а інша частина (80-70%) зворотної
води при промиванні газу в аміачних скруберах. Надсмольна вода (газовий
конденсат) і слабо аміачна вода з скруберів потім переробляються в аміачних
колонах з отриманням парогазової суміші, що складається з водяної пари,
газоподібного аміаку, вуглекислоти, сірководню, ціаністого водню та інших компонентів.
Ця суміш поступає в сатуратор, де аміак зв'язується з сірчаною кислотою з
утворенням насиченого розчину сульфату амонію і кристалів солі, які виводяться
з дна апарата з частиною розчину на центрифугу, а після промивання і сушіння
передаються на склад.
Цей спосіб отримання сульфату амонію має велику гнучкість
процесу, що дозволяє проводити в залежності від умов ринку сульфат амонію або
концентровану аміачну воду, або одночасно два продукту в одному цеху. Важливою
перевагою цього способу є виробнича надійність. Крім того, цей спосіб дозволяє
виробляти сірчану кислоту і піридинові підстави з парогазової суміші, яка
виходить з сатуратора з простої технології.
Однак непрямий спосіб має ряд недоліків: великі капітальні
витрати, велика кількість стічних вод, значні втрати аміаку із зворотним газом.
З-за всіх цих недоліків непрямий спосіб не знайшов
застосування на заводах України, але в поєднанні з аміачною очищення коксового
газу від сірководню може бути перспективним.
Прямий спосіб полягає в тому, що весь аміак, який утворюється
при коксування, що вилучається з коксового газу сірчаною кислотою до
охолодження в первинних газових холодильниках. З газозбірника гарячий коксовий
газ надходить в електрофільтр для очищення від туманно образної смоли, а потім
в сатуратор, де аміак зв'язується сірчаною кислотою з утворенням насиченого
розчину і кристалів сульфату амонію.
Особливістю цього способу є те, що при охолодженні коксового
газу після сатуратора в первинних газових холодильниках конденсат, що
утворюється, не містить аміаку і амонійних солей і тому відпадає необхідність
переробки його в аміачний колоні. Відсутність аміачного відділення дозволяє
знизити витрату пари, вартість обладнання, а також зменшити до мінімуму обсяг
стічних вод.
Проте широкого поширення цей спосіб не отримав з-за значних
недоліків: наявність великої кількості апаратів, що працюють під розрідженням,
що підвищує можливість підсосу повітря і утворення вибухонебезпечної суміші,
збільшує витрата електроенергії на транспортування газу; інтенсивна корозія
обладнання, яка обумовлена наявністю в газі хлористого водню і хлористого
амонію; труднощі очищення газу від смоли при високих температурах і освіти в
сатураторе великої кількості кислої смолки; великий обсяг апаратури з-за
високої температури і вологовмісту газу; неможливість уловлювання в сатуратор
легких піридинових підстав з-за високої температури розчину та відсутність
аміачної пари для його нейтралізації в піридинової установки.
Найбільше поширення на заводах України отримав напівпрямий спосіб
виробництва сульфату амонію, який має переваги, а іноді і недоліки прямого та
непрямого методів. За цим методом коксовий газ після газозбірника охолоджується
в первинних газових холодильниках до 25-35
, в результаті чого водяна пара
конденсується практично повністю, а газовий конденсат, що утворюється, розчиняє
до 20-30% аміаку, що міститься в прямому коксову газі. Охолоджений газ
подається нагнітачами в абсорбер, де решті аміак поглинається сірчаною кислотою
з утворенням сульфату амонію.
Отримані при переробці надлишкової надсмольної води аміачні пари подаються
частково до нейтралізатор піридинової установки, де аміак також зв'язується
сірчаною кислотою. Таким чином, весь аміак прямого коксового газу внаслідок
переробляється на сульфат амонію.
Недоліками цього способу виробництва сульфату амонію є
необхідність переробки надлишкової надсмольної води в аміачних колонах, яка
вимагає значної витрати пари і луги, а також утворення значного обсягу стічних
вод, які в свою чергу вимагають складної очищення.
В залежності від апаратурного оформлення процесів поглинання
аміаку сірчаною кислотою і кристалізації сульфату амонію розрізняють два
різновиди напівпрямого способу, які отримали найбільше поширення в
промисловості, - сатураторний і безсатураторний. Слід зазначити, що в
літературі немає жодних тлумачень цих термінів, вони не відображають
особливостей апаратурних оформлення процесів.
По термінології, яка прийнята в коксохімічній промисловості,
сатураторним називається процес, при якому поглинання аміаку з коксового газу
сірчаною кислотою і утворення кристалів сульфату амонію здійснюється в одному
апараті барботажного типу, який називається сатуратором. При безсатураторному
способі поглинання аміаку сірчаною кислотою здійснюється в форсуночному (або
насадковому) скрубері, який може зрошуватися як пересиченим розчином, який
містить кристали сульфату амонію, так і ненасиченим розчином. У першому випадку
кристалізація сульфату амонію відбувається одночасно з поглинанням аміаку в скрубері,
а в другому утворення пересиченого розчину в спеціальному апараті -
кристалізаторі.
Перевагою безсатураторних процесів є менший гідравлічний опір
форсуночних абсорберів і можливість проведення окремих стадій процесу
(абсорбції аміаку, кристалізації сульфату амонію та ін.) при найбільш
сприятливих умовах.
Таку схему і відображає даний дипломний проект.
Після нагнітачів коксовий газ, що
містить 6-10 г/
аміаку, надходить у колектор входу газу в аміачні абсорбера.
Як і ПГС, абсорбери включені в газову схему паралельно. Продуктивність одного
абсорбера по газу становить 100000
/час .
Коксовий газ надходить у нижню
частину абсорбера, де зрошується маточним розчином через 3 яруси бічних форсунок,
по 4 штуки в кожному, і одну центральну. Очищений до вмісту аміаку не вище 0,03
г/
коксовий газ надходить в кислотну
пастку, де очищається від яких віднесло з абсорбера дрібних бризок розчину.
Після цього газ прямує в КГХ бензольного відділення.
Розчин на зрошення абсорбера
подається з циркуляційного збірника подачі, в якому підтримується заданий зміст
вільної сірчаної кислоти і питома вага. З нижніх двох ярусів форсунок розчин
стікає на днище абсорбера і через гідрозатвор потрапляє до збірки повернення.
Вміст вільної сірчаної кислоти в цьому розчині повинно бути 0,8-1%. З верхнього
ярусу форсунок і з центральної форсунки розчин, пройшовши через абсорбер,
потрапляє на розділову тарілку, яка перешкоджає змішуванню повертаються з 1,2 і
з 3 ярусів розчинів. З тарілки, через гідрозатвор, розчин з вмістом вільної
= 1,2-1,4% повертається до збірки
подачі.
Збірники подачі і повернення з'єднані
за типом «сполучених посудин» трубопроводом діаметром 500мм. Необхідний вміст
вільної сірчаної кислоти в збірнику подачі підтримується додаванням сірчаної
кислоти з напірного бака. Питома вага підтримується додаванням «брудного»
конденсату з напірного бака води.
Із збірки повернення розчин з кислотністю
0,8-1% виводиться в живильні збірники для додаткового відстою перед подачею в
випарники.
З кислотної пастки розчин через
гідрозатвор виводиться в збірник подачі. У циркуляційних збірниках у верхній
частині накопичується кисла смолка, яка уловлюється в абсорбері з коксового
газу. Періодично кисла смолка відкачується в спеціальну автоцистерну і
вивозиться в цех Уловлювання №2 на установку з переробки відходів
коксохімічного виробництва.
Маточний розчин з живильних збірників
містить 40% сульфату амонію подається в випарники живильними насосами.
Випаровування і кристалізація розчину відбуваються під вакуумом. Трубчаста
система випарника підігрівається парою, а вакуум підтримується двоступінчатим
паровим ежектором, який працює в поєднанні з поверхневим конденсатором.
При досягненні необхідної
концентрації кристалів в випарнику, отримана пульпа безперервно подається
насосом в центрифугу. Маточний розчин відділяється в центрифузі від кристалів і
самопливом повертається в циркуляційний збірник подачі, а кристали сульфату
після центрифуги транспортерами подаються в сушильне відділення.
Конденсат після поверхневих
конденсаторів і конденсаторів ежекторів надходить до збірки брудного
конденсату, а потім в напірний бак брудного конденсату.
У процесі роботи випарників
сульфатного відділення в міжтрубному просторі кожного утворюється від 5
/год до 9
/год конденсату, який являє собою
конденсат глухого пари низького тиску. Загальна кількість утворився конденсату
складе від 10 м3/год до 25 м3/год. Конденсат після
нагрівального пристрою випарника самопливом надходить до збірки чистого
конденсату, звідки насосом подається в центрифугу для промивання сульфату
амонію від вільної сірчаної кислоти, для поповнення напірних баків води і на
зволоження пара, подається у випарники. На ці цілі використовується приблизно
від 3 м3/год до 6 м3/год. Надмірна кількість конденсату
може використовуватися на технологічні потреби підприємства.
Сушіння і склад сульфату амонію.
Сульфат амонію після центрифуги надходить на стрічковий транспортер вологого
сульфату амонію, а потім в приймальний бункер сушарки. У сушильні агрегати
подається нагнітає вентилятором гаряче повітря, нагріте в калориферах глухим
пором. З сушарки сульфат амонію надходить на склад для навантаження в ж/д
напіввагони.
Сушарка обладнана також витяжним
вентилятором, на всмоктуючому трубопроводі якого встановлений скрубер
знепилювання, що перешкоджає попаданню пилу сульфату амонію в навколишнє
середовище. Це досягається шляхом зрошення повітря, що виходить з сушарки водою
(чистим конденсатом), що подається насосом зі збірки знепилювання через
форсунку. Зі скрубера вода повертається до збірки, тобто знаходиться в
замкнутому циклі.
При насиченні води кристалами сульфату
амонію виробляється викачка її в циркуляційні збірники, а збірник поповнюється
свіжим чистим конденсатом.
Для запобігання віднесення води в
атмосферу, в скрубері передбачена осушуваних насадка. У міру забивання насадки
проводиться її промивка через промивальну форсунку.
Аміачні колони. Велика частина аміаку
в аміачної воді знаходиться у вигляді різних солей. Наявність їх пояснюється
тим, що одночасно з аміаком розчиняється сірководень, вуглекислий газ,
хлористий водень, синильна кислота і т.д. Деякі з цих солей неміцні і легко
розкладаються при нагріванні, виділяючи при цьому аміак. Що міститься у вигляді
таких солей аміак називається летючим. Інші солі більш стійкі при нагріванні не
руйнуються, що міститься у вигляді таких солей аміак називається зв'язаним.
Зв'язаний аміак знаходиться, головним чином, у вигляді хлористого
), роданистого
), і сірчанокислого (
) амонію.
Аміачна вода зі сховища надлишкової
аміачної води №8 подається в міжтрубний простір теплообмінників аміачних колон,
де нагрівається аміачною водою, пройшла очищення. Після теплообмінника вода
надходить у аміачні колони №1,2, де відбувається віддувка летючого аміаку
гострою парою. Пароаміачна суміш по аміакопроводу направляється в газопровід
входу газу в ПГС. Очищена від аміаку вода після колони надходить у пекопастку,
де під дією відцентрової сили відбувається очищення її від пеку.
Потім вода надходить у відстійник V =
60
для додаткового відстою від
смолистих речовин. З верхньої частини відстійника вода з переливу надходить у
промсборнік V = 60
, звідки насосом подається в трубний простір теплообмінника.
З метою утилізації відпрацьованого
содового розчину цехів сіркоочищення, а також для часткового розкладання солей
пов'язаного аміаку в стічних водах відділення хімустановки, в змішувачі
розташованому перед аміачної колоною №3 змішується 600-1000 г/л содового
розчину і 10-14 м3/час надсмольної води.
Розкладання відбувається по реакції:
.
Утворені солі летючого аміаку
розкладаються в колоні і пароаміачна суміш виводиться в 5ту зверху царгу
аміачної колони №2 для додаткового насичення летючим аміаком.
. ВИБІР ОБЛАДНАННЯ
5.1 Конструкція абсорберу
При безсатураторному методі отримання сульфату амонію
очищення газу від аміаку здійснюють в двоступінчатому абсорбері зрошувального
типу (рис. 5.1).
Корпус апарату складається з циліндричної обичайки, конічного
днища і кришки. Внутрішній простір апарату розділений на дві секції за
допомогою кільцевої перегородки з обичайкою, у верхній частині якої змонтована
(суворо горизонтально) ковпачкова барботажна тарілка з кільцевим переливанням
на рівні кромок обичайки. Штуцери, а також встановлені над ними ковпаки мають
трапецеїдальну форму і на тарілці розташовані радіально.
Усередині обичайки встановлений краплевідбійник, виконаний із
зігнутих смуг листового матеріалу. Верхня і нижня секції абсорбера обладнані
індивідуальними системами зрошування і виконують функції першого і другого
ступеня абсорбції аміаку. Нижня секція (перший ступінь) обладнана двома ярусами
форсунок по шість штук в кожному. Верхня секція (другий ступінь) має один ярус
форсунок, крім того, уздовж осі апарату розташована форсунка з крупнокаплевим
зрошуванням призначена також для зменшення бризковиносу газовим потоком. Верхня
секція обладнана люками.
Коксовий газ поступає в нижню секцію апарату через патрубок,
промивається кислим розчином циркуляційного циклу першого ступеня абсорбції за
допомогою форсунок, потім звільняється від бризок розчину в краплевідбійнику і
поступає в штуцери 3 ковпачкової тарілки, яка заповнена рідиною до рівня кромок
обичайки. При цьому в нижній секції абсорбера з газу витягається близько 95 %
аміаку, що міститься в ньому.
Циркулюючий розчин кислотністю близько 1% після контакту з
газом поступає в конічне днище і виводиться через патрубок.
Вхід газу у верхню секцію абсорбера здійснюється в режимі
барботажу завдяки наявності занурених в рідину ковпаків. Далі газ піддається
повторному контакту з рідкою фазою в режимі зрошування за допомогою форсунок. В
процесі рециркуляції в контурі зрошувальної системи другого ступеня розчину
кислотністю 10-12% з газу витягаються залишки аміаку і легкі піридинові основи.
Очищений коксовий газ виводиться з абсорбера через патрубок, а розчин
накопичується в кільцевому проміжку між стінками абсорбера і обичайки і
виводиться через патрубок.
Рисунок 5.1 - Конструкція двоступінчатого тарілчастого
абсорберу зрошувального типу
5.2 Конструкція випарника
Випарник є поверхневим теплообмінником, де випаровується
вода, утворюючи вторинну пару, конденсат якої (дистилят) заповнює втрати
робочого тіла в паросиловому циклі (рис. 5.2). Дистилят майже вільний від
домішок і за якістю близький до конденсату турбін. Кипляча вода (концентрат)
внаслідок випарювання має дуже високий солевміст, що у багато разів перевершує
солевміст початкової води. Підігрів і випар води у випарнику здійснюються за
рахунок тепла пари, що поступає з відбору турбіни (первинна пара). Конденсація
вторинного пари робиться в спеціальних поверхневих теплообмінниках, включених в
теплову схему турбіни і охолоджуваних основним конденсатом. Такий теплообмінник
називається конденсатором.
Попри те, що тепло, зате, що витрачається на пароутворення
вихідної води у випарнику, за винятком втрати розсіяння, повністю повертається
в цикл в конденсаторі випарної установки, тут має місце енергетична втрата, обумовлена
теплопередачею через стінку при певному температурному натиску (10-25°С).
Внаслідок цього вторинна пара має нижчий тиск в порівнянні з первинним.
Енергетичну втрату можна значно зменшити раціональним
включенням випарника і його конденсатора в регенеративну схему турбіни. Крім
того, економічність установки можна підвищити при переході на двоступінчату
схему випарювання. При цій схемі вторинна пара першого випарника є первинною
(що гріє) парою другого випарника. Зі збільшенням числа східців випарної
установки кількість дистиляту, що отримується з 1 кг пари, відібраної з турбін,
віз¬розтане. Тому очевидно, що при зрівнянні одноступінчатою і
багатоступінчастою установок, працюючих при одному і тому ж температурному
перепаді, більш економічною виявляється багатоступінчаста установка.
Проте збільшення числа східців призводить до ускладнення і
дорожчання установки і може бути виправдане тільки при значних втратах
конденсату. На сучасних великих електростанціях, де втрати конденсату не
перевершують 1,5 застосовуються в основному одноступінчаті установки. B ряду
випадків два одноступінчатих випарника встановлюються на різних відборах
турбіни.
Поверхневі випарники за конструктивним виконанням
розділяються на горизонтальні та вертикальні. По компонувальним міркуванням
нині заводами випускаються для електричних станцій тільки випарники
вертикального типу.
Рисунок 5.2 - Конструкція поверхневого трубчастого
теплообмінника
5.3 Конструкція конденсатору
Корпус конденсатора являє собою сталеву суцільно зварену
обичайку прямокутного перерізу з привареним до неї днищем. Зварювання корпусу
проводиться на монтажному майданчику. Для додання жорсткості корпусу
конденсатора до його днища приварена рама, що складається з поперечних балок двотаврового
перерізу. Під крайніми поздовжніми балками розташовані пружинні опори
конденсатора
Трубна система конденсатора складається з:
– трубного пучка;
– двох кінцевих одинарних трубних дощок;
– проміжних трубних дощок.
Трубний пучок складається з гладких прямих трубок Ø28x1.5,
для розміщення
яких в трубних дошках застосована стрічкове компонування. Компонування трубного
пучка у вигляді багаторазової згорнутої стрічки та розміщення на виступаючих
ділянках пучка «зубців» істотно збільшує загальний периметр трубного пучка, і
тим самим досягається низька швидкість пара в периферійних рядах трубок - 50-60
м/с. Хоча величина вхідної швидкості і невелика, для запобігання ерозійного
зносу трубок і поліпшення їх вібраційних характеристик товщина стінки трубок першого
ряду збільшена до 2 мм.
Теплообмінні трубки развальцовані на глибину 50 мм у двох
одинарних трубних дошках.
Опорами трубного пучка є проміжні трубне дошки, розташовані
на рівних відстанях один від одного, в проміжних трубних дошках є круглі вирізи
для вирівнювання тиску по довжині конденсатора, а також вирізи в нижній частині
для вільного протікання конденсату в бік конденсатосбірників. У центрі трубних
дощок виконані вирізи для проходження пароповітряної суміші в трубі
відсмоктування повітря.
Конденсат, що надходить у зливні трубки з вище розташованих
рядів труб, відводиться до трубних дощок і стікає в нижню частину конденсатора,
без переохолодження на нижніх рядах трубок. Уловлювання конденсату сприяє
зменшенню загального парового опору конденсатора, так як при цьому
забезпечується вільний прохід пари в тупикові проходи трубного пучка
(конструкція конденсатору приведена на рис.5.3).
Рисунок 5.3 - Конструкція конденсатору.
5.4 Конструкція барабанної сушарки
Барабанна сушарка є зварним циліндром - барабаном, на
зовнішній поверхні якого укріплені бандажні опори, кільцями жорсткості і
приводним зубчатим вінцем. Вісь барабана може бути нахилена до горизонту на
4-6°С (рис. 5.3).
Барабанні атмосферні сушарки безперервної дії призначені для
сушки сипких матеріалів топочними газами або нагрітим повітрям.
Усередині барабана встановлюють насадки, конструкція яких
залежить від властивостей висушуваного матеріалу. З боку завантажувальної
камери багатозамочна гвинтова насадка, з числом спіральних лопатей від шести до
шістнадцяти залежно від діаметру барабана. При сушці матеріалу з великою
адгезією до поверхні на початковій ділянці останнього закріплюють ланцюги, за
допомогою яких руйнують камки і очищають стінки барабана. Для цієї ж мети
можуть застосовувати ударні пристосування, розташовані із зовнішньої сторони
барабана.
У сушарках діаметром 1000-1600 мм для матеріалу з хорошою
сипучістю і середнім розміром частинок до 8 мм встановлюють секторну насадку. У
тих же сушарках, для матеріалів, що володіють підвищеною адгезією або сипких
матеріалів з середнім розміром частинок більше 8 мм встановлюють підйомний -
лопатеві пристрої. У сушарках діаметром 1000- 3500 мм для матеріалів схильних
до налипання, але поновлюючих сипкі властивості в процесі сушки спочатку
встановлюють підйомний - лопатеві перевалочні пристрої, а потім секторні
насадки.
Основний матеріал для виготовлення барабанів сушарок,
завантажувальних і розвантажувальних камер - вуглецеві стали. У технічно
обґрунтованих випадках додаткове виготовлення барабанів, розвантажувальних і
розвантажувальних камер частково або повністю з жаростійких сталей спеціальних
марок.
Барабанні вакуумні сушарки працюють, як правило, періодично і
їх застосовують для сушки теплочутливих матеріалів від води і органічних
розчинників, а також для сушки токсичних матеріалів. Залежно від властивостей
матеріалу і вимог до готової продукції застосовують сушарки середнього або
глибокого вакууму. Вакуумні барабанні сушарки застосовують в основному у виробництві
полімерних матеріалів.
Принципова схема барабанної сушарки. Вологий матеріал з
бункера за допомогою живильника потрапляє в сушильний барабан, що обертається.
Паралельно матеріалу в сушарку подається сушильний агент, що утворюється при
згоранні палива в топці і змішення газів в камері змішувача. Повітря в топку і
камеру змішувача подається вентиляторами. Висушений матеріал з протилежного
кінця сушильного барабана, а з нього на транспортуючий пристрій.
Відпрацьований сушильний агент перед викидом в атмосферу
очищається від пилу в циклоні. При необхідності виробляється додаткове, мокре
пиловловлювання у скрубері.
Транспортування сушильного агента через сушильну камеру
здійснюється за допомогою вентилятора. При цьому установка знаходиться під
розрідженням 50 - 250 Па, що виключає витік сушильного агента через нещільність
установки.
Барабан приводиться в обертання електродвигуном через зубчату
передачу.
Рисунок 5.3 - Конструкція барабанної сушарки
. МАТЕРІАЛЬНІ РОЗРАХУНКИ БЕЗСАТУРАТОРНОГО МЕТОДУ ОТРИМАННЯ
СУЛЬФАТУ АМОНІЮ
6.1 Матеріальний баланс аміаку
Згідно з виробничими даними ПАТ «Авдіївський коксохімічний
завод» об`єм коксового газу дорівнює 100000 м3/год, вміст аміаку у
газі - 564 кг/год, з аміачно-водяними парами потрапляє аміаку - 200 кг/год.
Кількість аміаку, яка уноситься з коксовим газом складає 3 кг/год. Матеріальний
баланс аміаку приведено в таблиці 6.1.
Таблиця 6.1- Матеріальний баланс аміаку (кг/год)
Прихід
|
Витрата
|
З коксовим газом 564
|
З коксовим газом 3
|
З аміачно-водяними парами 200
|
Реагує з кислотою 761
|
Разом 764
|
Разом 764
|
Для поглинання Gам.=761 кг/год аміаку необхідно
подати сірчаної кислоти в моногідраті (Gк-ти):
, (6.1)
де
- молярна маса сірчаної кислоти, 98 кг/моль;(NH3)
- молярна маса аміаку.

кг/год;
при цьому утворюється сухого сульфату амонію:
сух. =
Gам. + Gк-ти; (6.2)
сух. =
761 +2193 = 2954 кг/год,
а з вологістю 2 %:
вл .=
(6.3)
вл =
кг/год.
Витрата 92,5 %- вої сірчаної кислоти складе:
=
(6.4)
кг/год,
із них моногідрату сірчаної кислоти 2193 кг/год, води 178 кг/год.
Для спрощення розрахунку нехтуємо вмістом сірчаної кислоти і
піридинових основ у відфугованому сульфаті амонію.
6.2 Розподіл поглинання аміаку по ступеням
абсорберу
У абсорбер надходить наступна кількість коксового газу з нагнітача і
аміачно-водяної пари з дефлегматора (таблиця 6.2).
Таблиця 6.2 - У абсорбер надходить наступна кількість
коксового газу з нагнітача і аміачно-водяної пари з дефлегматора.
Компоненти
|
З нагнітача кг/год
|
З дефлегматора кг/год
|
Всього
|
|
|
|
кг/год
|
м3/год
|
Сухий коксовий газ Бензольні вуглеводні Сірководень
Двоокис вуглецю Піридинові основи Аміак Водяна пара
|
45600 2600 1120 - 40 564 2920
|
- - 38 48 6 142 696
|
45600 2600 1158 48 46 706 3616
|
100000 702 763 24 13 930 4500
|
Разом
|
52844
|
930
|
53744
|
106932
|
Кількість поглиненого аміаку в 1-му ступені абсорберу можна
визначити виходячи з умови рівності поверхні контакту або об`ємів обох ступенів
абсорберів і коефіцієнтів абсорбції, що приводить до рівняння:
,
де a1, a2 и a3 - вміст аміаку в газі
до 1-й, до 2-ї і після 2-го ступеня абсорберу.
Величини a1 і a3 дорівнюють:
г/м3,
г/м3,
де кількість аміаку у газі після абсорберу дорівнює 3 кг/год.
Тоді:
г/м3.
Таким чином, в 1-му ступені абсорбера поглинається аміаку:
=
;
де
- загальний об’єм коксового газу, який надходить з
нагнітача і аміачно-водяної пари з дефлегматора (з табл. 6.2
106932 м3/год).
кг/год.
Надходить аміаку в другий ступінь:
кг/год,
і поглинається аміаку в другому ступені:
=
-
,
де
- кількість аміаку у газі після абсорберу дорівнює 3
кг/год.
=
46 - 3 = 43 кг/год.
Для поглинання 660 кг/год аміаку в 1-му ступені абсорберу необхідно
витратити сірчаної кислоти в моногідраті (за формулою 6.1):
кг/год,
при цьому утворюється сульфату амонію (6.2):
660
+ 1902 = 2562 кг/год.
У другому ступені поглинається аміаку 43 кг/год, витрачається сірчаної
кислоти (6.1):
кг/год,
і утворюється сульфату амонію (6.2):
43
+124 = 167 кг/год.
Крім того, в 2-ий ступінь надходить сульфат амонію, що утворюється в піридинової
установці в кількості:
,
де
- кількість аміаку, що йде з дефлегматора в
нейтралізатор,
=58 кг/год.
кг/год.
Таким чином, всього накопичується сульфату амонію в 2-му
ступені абсорбера (6.2):
167 +225 = 392 кг/год.
Загальна кількість сульфату амонію:
;
2562 + 392 = 2954 кг/год.
Кількість розчину, що перетікає з абсорбера 2-го ступеня в
абсорбер 1-го ступеня має бути такою, щоб вивести в 1-ий ступінь абсорберу
сульфат амонію в кількості, що утворюється в 2-му ступені абсорбції і в
піридиновій установці.
Кількість сульфату амонію, що утворюється в 2-му ступені й в
піридинової установці дорівнює
392 кг/год.
Так як розчин містить 28 % (NH4)2SО4,
то кількість цього розчину дорівнюватиме:
;
кг/год,
або за об`ємом
Таким чином, розчин, що перетікає містить, кг/год (див. табл. 6.3).
Таблиця 6.3 - Склад розчину, що перетікає
Найменування
|
Вміст, кг/год
|
Сульфат амонію
|
1400 0,28 = 392
|
Сірчаної кислоти
|
1400 0,12 = 168
|
Сульфату піридину
|
|
Води по різниці
|
732
|
Разом
|
1400
|
Зі 108 кг/год сульфату піридину (
), що надходить в 1-й ступінь
абсорберу, десорбується зворотно 48 кг/год (
) піридинових основ і звільняється:
;
108 - 48 = 60 кг/год сірчаної кислоти.
Кількість розчину, що виводиться із 1-го ступеня абсорберу у
випарник повинно бути таким, що після випаровування води і виділення всього
вироблюваного сульфату амонію залишився насичений розчин сульфату амонію певної
концентрації.
Кількість розчину, що виводиться із 1-го ступеня абсорбера у
випарник, визначимо наступним чином.
Позначимо кількість цього розчину через G і вміст у ньому
сульфату амонію 40 % і H2SO4 1 %. Тоді в ньому міститься
сульфату амонію 0,4G кг/год.
Після випаровування W кг/год води в випарники в центрифузі
входить пульпа в кількості (G-W) кг/год, в якій знаходиться 0,4G кг/год
сульфату амонію.
Після видалення вологого сульфату амонію в центрифузі в
кількості:
;
де 0,98 - вміст сухого сульфату амонію;
кг/год,
залишиться маточного розчину (G -W- 3014), з них сульфату амонію (0,4G
- 2954).
Оскільки вміст сульфату амонію в маточному розчині після центрифуги
дорівнює 47%, тому можна скласти рівняння:
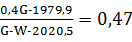
.
Кількість води, що видаляється в випарники, можна визначити за такою
формулою:

,
де С0 - вміст (NH4)2SO4 у
сульфаті амонію, С0 = 98 %;
С1 - в тій же, в пульпі після випарника; приймаємо, що
пульпа містить 50 % за масою викристалізованої солі, а насичений матковий
розчин містить 47 % сульфату амонію; тоді:
С1=50+0,5∙47=73,5%;
С2 - той же, в маточному розчині після центрифуги, С2
= 47 %;
С3 - той же, в розчині, що виводиться із 1-го ступеня
абсорбції у випарник, С3 = 40 %;
-
кількість вологого сульфату амонію, кг/год.
Тоді:
кг/год.
Підставляючи W, отримаємо:
звідки об'єм розчину дорівнюватиме:
р-ну=
,
де
- кількість розчину, що виводиться з абсорбера у
випарник, 10655 кг/год;
-
щільність розчину 1,24 кг/л.
м3/год.
Вміст піридинових основ в цьому розчині можна визначити за рівнянням:
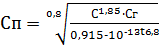
Приймаємо температуру розчину після 1-го ступеня абсорбції 58
С (надалі ця температура перевіряється по тепловому
балансу збірника 1-го ступеня абсорбції) і концентрацію сірчаної кислоти 1 %.
Вміст піридинових основ дорівнює:
г/м3.
Тоді максимальний вміст піридинових основ у виводимому в випарник
розчині:
=5,83
г/л.
Фактичний вміст визначаємо приймаючи, що рівновага відповідає 50 %
вмісту піридинових основ в газі, тоді:
=3,07
г/л.
Таким чином, в розчині, що направляється у випарник, міститься, кг/год
(табл. 6.4).
Таблиця 6.4 - Вміст розчину, що направляється у випарник
Найменування
|
Вміст, кг/год
|
Сульфат амонію
|
0,4 10655 = 4262
|
Сірчана кислота
|
0,01 10655 = 106,6
|
Сульфат піридину
|
=51,4
|
Води по різниці
|
6235
|
Разом
|
10655
|
З цієї кількості розчину, спрямованого у випарник, після
випаровування води в кількості 4858 кг/год (
) і відділення вологого сульфату
амонію в центрифузі в кількості 3014 кг/год (з них сухого 2954 кг/год і вологи
60 кг/год) залишиться маткового розчину:
10655 - 4858 - 3014 = 2783 кг/год.
Після додавання промивної води в кількості 170 кг/год (
) повертається маточного розчину до
збірки 1-го ступеня абсорбції
;
2783 +170 = 2953 кг/год.
Склад цього розчину і кількість (кг/год) наступні (таблиця
6.5).
Таблиця 6.5 - Склад розчину
Найменування
|
Вміст, кг/год
|
Сульфат амонію
|
4262 - 2954 = 1308
|
Сірчана кислота
|
106,6
|
Сульфат піридину
|
51,4
|
Вода
|
6235 - 4858 - 60 +170 =1487
|
Разом
|
2953
|
. РОЗРАХУНОК АБСОРБЕРУ
7.1 Матеріальний розрахунок
Прихід
У абсорбер 1-го ступеня надходить коксовий газ з нагнітача і
аміачно-водяні пари з дефлегматору у кількості, кг/год (дивиться таблицю 7).
Таблиця 7.1 - Склад надходячего коксового газу
Найменування
|
Вміст, кг/год
|
Сухий коксовий газ
|
45600
|
Бензольні вуглеводні
|
2600
|
Аміак
|
706
|
Сірководень
|
1158
|
Двоокис вуглецю
|
48
|
Піридинові основи
|
46
|
Водяна пара
|
3616
|
Разом
|
53774
|
У абсорбер надходить циркулюючий розчин зі збірника 1-го
ступеня абсорберу. Позначимо цю кількість через G1.
Таким чином, загальний прихід дорівнює:
+ G1
кг/год
Витрата
З коксового газу із 706 кг/год аміаку поглинається 660 кг/год
і залишається в газі 46 кг/год.
Кількість піридинових основ в газі після 1-го ступеня
абсорбції збільшується за рахунок десорбції їх з перетікання, що надійшов з
2-го ступеня абсорбції. Кількість десорбуючих піридинових основ в 1-му ступені
абсорберу дорівнює 48 кг/год. Таким чином, у вихідному газі буде міститися
піридинових основ:
+48 = 94 кг/год
Кількість водяної пари, що виходять з газом з 1-го ступеня
абсорбції, можна визначити виходячи з того, що за рахунок тепла нейтралізації
відбувається нагрів газу до 58 °С, тобто до температури потрапляючого розчину,
і випаровування відповідної кількості води. Позначимо цю кількість через
:
кг/год,
де Q1- тепло, внесене коксовим газом, кДж/год;2 -
тепло, внесене амоніачно-водяними парами, кДж/год;3- тепло реакції
нейтралізації, кДж/год;4-тепло, що відноситься сухим газом, кДж/год;
температура
газу на виході з абсорбера, t = 58 °С.
Тепло, що вноситься коксовим газом при 50 °С:1=15868750
кДж/год
Тепло, що вноситься аміачно-водяними парами з дефлегматора при 95 °С,
дорівнює:
Q2= ((142∙0,508+38∙0,24+48∙0,418+6∙0,246)∙95+696∙(595+0,44∙95))∙4,19=
=1897980 кДж/год
Тепло реакції нейтралізації аміаку:
Q3 =
кДж/год,
де 195675 - тепло реакції нейтралізації, кДж/год сірчаної кислоти.
Тепло, що відноситься сухим коксовим газом при температурі 58
°С:
Q4=((46∙0,508+1158∙0,298+48∙0,418+94∙0,246+2600∙0,246+45600∙0,7)∙58)∙4,19=
8012670 кДж/год.
Тоді:
кг/год.
Загальна кількість газів, що виходять з 1-го ступеня абсорберу в 2-й,
наведена в таблиці 7.2.
Таблиця 7.2 - Загальна кількість газів, що виходять з 1-го ступеня
абсорбера в 2-й
Найменування
|
Витрата по газу
|
|
кг/год
|
м3/год
|
Сухий коксовий газ
|
45600
|
100000
|
Бензольні вуглеводні
|
2600
|
702
|
Аміак
|
46
|
61
|
Сірководень
|
1158
|
763
|
Двоокис вуглецю
|
48
|
24
|
Піридинові основи
|
94
|
27
|
Водяна пара
|
4982
|
6200
|
Разом
|
54528
|
107777
|
Кількість циркулюючого розчину, що виходить з 1-го ступеня
абсорбера, позначимо G2 кг/год. Тоді загальна витрата дорівнює:
+ G2,
Дорівнюючи прихід і витрату, отримаємо:
+G1=51528+G2;
або G1=G2+754
Друге рівняння для визначення G1 і G2
отримаємо виходячи зі значень концентрацій сірчаної кислоти на вході і виході з
1-го ступеня абсорбції і кількості сірчаної кислоти, що витрачається, в 1-му
ступені.
Приймаючи концентрацію розчину, що поступає, 1,6 % і що
виходить 1 %, отримаємо рівняння:
де
- кількість кислоти, що витрачається в 1-му ступені
абсорбера, кг/год.
Для зв'язування в 1-му ступені абсорберу 660 кг/год аміаку потрібне
використати сірчаної кислоти 1902 кг/год . Проте при розкладанні сульфату
піридину, що поступив з 2-го ступеня, звільняється сірчаної кислоти 60 кг/год.
Тому:
= 1902 - 60 = 842 кг/год,
Таким чином,
,6
G1 = G2 + 184200.
Вирішуючи приведені два рівняння з невідомими G1 і G2,
отримаємо G1=305744 кг/год
і G2=304990 кг/год.
Об'єм розчину, що поступає, при щільності 1,24 кг/л буде:
м3/год
Матеріальний баланс 1-го ступеня абсорбції наведений у таблиці 7.3, а
тепловий баланс - у таблиці 7.4.
Таблиця 7.3 - Матеріальний баланс 1-го ступеня абсорбції
Прихід
|
кг/год
|
Витрата
|
кг/год
|
Коксовий газ
|
52844
|
Коксовий газ
|
54528
|
Аміачно-водяна пара
|
930
|
Циркулюючий розчин
|
304990
|
Циркулюючий розчин
|
305744
|
|
|
Разом
|
359518
|
Разом
|
359518
|
Таблиця 7.4 - Тепловий баланс 1-го ступеня абсорбції
Найменування
|
кДж/год
|
Найменування
|
кДж/год
|
Тепло коксового газу
|
15868750
|
Тепло коксового газу
|
8012670+(595+ +0,438 58) 4,19 4982==20963343
|
Тепло аміачної водяної пари
|
1897580
|
Тепло, що втрачається назовні
|
552000
|
Тепло нейтралізації 3797654 Тепло циркулю-
ючого розчину 304990
2,93
t
=
=894536 t
|
|
Тепло циркулю- ючого розчину
|
305744 2,93 58,9=52011335
|
|
|
Разом
|
73575719
|
Разом
|
21018543+894536 t
|
Дорівнюючи прихід і витрату тепла, отримаємо температуру розчину, що
виходить з 1-го ступеня абсорбера, рівну 58,8
°С,
тобто приблизно таку ж, як і що поступає.
7.2 Матеріальний і тепловий баланси збірки
абсорбера 1-го ступеня
Матеріальний розрахунок
Прихід. У збірку абсорбера 1-го ступеня поступають: циркулюючий розчин
з абсорбера, маточний розчин з центрифуги, перетік з 2-го ступеня абсорберу,
сірчана кислота, вода для поповнення циклу.
Визначаємо кількість цих потоків :
. Кількість розчину, що поступає з 1-го ступеня абсорбера:
-10655=29433 кг/год.
. Кількість маточного розчину, що поступає з центрифуги, дорівнює 2953
кг/год.
. Кількість розчину, що поступає з 2-го ступеня абсорбера
(перетікання), дорівнює 1400 кг/год.
. Кількість кислоти, що поступає, позначимо x1.
. Кількість води для поповнення циклу позначимо y1.
Загальна витрата дорівнює:
+ x1 + y1.
Витрата. Кількість розчину, що виводиться зі збірки в циркуляцію,
дорівнює 305744 кг/год.
Дорівнюючи прихід і витрату, отримаємо:
1 + y1 = 7056 кг/год.
Для визначення x1 і
y1 складемо баланс моногідрату сірчаної кислоти (дивиться таблицю
7.5).
Таблиця 7.5 - Баланс моногідрату сірчаної кислоти
Прихід
|
кг/год
|
З кислотою при концентрації 92,5 %
|
0,925· x1
|
З маточним розчином з центрифуги
|
106,6
|
У перетіканні з 2-го абсорбера
|
168
|
Утворюється при розкладанні піридинових основ
|
60
|
Разом
|
0,925· x1 +334,6
|
Витрата
|
кг/год
|
У розчині, що йде у випарник
|
106,6
|
На реакцію з NH3 в 1-му ступені
|
1902
|
Разом
|
2008,6
|
Дорівнюючи прихід і витрату, отримаємо:
0,925·
x1+334,6=2008,6
Звідси кількість розчину кислоти
x1=1674
кг/год, з них: моногідрату
·0,925=1548 і води 126 кг/год.
Кількість води, необхідної для поповнення циклу:
y1 = 7056 - 1674 = 5382 кг/год
Тепловий баланс збірки 1-го ступеня
Прихід
. Тепло, внесене циркулюючим розчином:
Q1=294335∙2,93∙58,8=50761132
кДж/год
. Тепло, внесене маточним розчином при 50
°С:
Q2=2953∙2,68∙50 = 395938
кДж/год,
де 2,68 - теплоємкість маточного розчину, кДж/(кг∙град).
3. Тепло,внесене перетоком розчину з 2-го ступеня абсорберу:
Q3=1400∙3,31∙50 =231707
кДж/год,
де 3,31 - теплоємність цього розчину кДж/(кг∙град).
.Тепло, внесене кислотою:
Q4=1674∙1,55∙20 = 51904 кДж/год,
де 1,55 - теплоємність сірчаної кислоти, кДж/(кг∙град).
.Тепло, внесене водою поповнення:
Q5=5382∙20∙4,19=451012 кДж/год
6. Тепло розведення сірчаної кислоти від 92,5 до 1,6 %.
Тепло розведення, що доводиться на 1 моль H2SO4:
кДж/кмоль H2SO4;
кДж/кмоль H2SO4,
і на 1548 кг моногідрату:
кДж/год.
Загальний прихід тепла:прих=52891085 кДж/год.
Витрата.
. Тепло, що втрачається назовні (за практичними даними):7=55200
кДж/год.
. Тепло, що відноситься циркулюючим розчином:8=305744
2,93t.
Разом витрата тепла:
+ 896747 t.
Прирівнюючи прихід і витрату, отримаємо:
= 55200 + 896747t.
Звідси температура розчину, що встановилася t=58° С.
7.3 Розрахунок 2-го ступеня абсорберу
Прихід. У абсорбер 2-го ступеня поступає коксовий газ з абсорбера 1-го
ступеня в кількості, наведеній в таблиці 7.6.
Таблиця 7.6 - Склад коксового газу з абсорберу 1-го ступеня
Найменування
|
Прихід, кг/год
|
Сухий коксовий газ
|
45600
|
Бензольні вуглеводні
|
2600
|
Сірководень
|
1158
|
Аміак
|
46
|
Двуокис вуглецю
|
48
|
Піридинові основи
|
94
|
Водяна пара
|
4982
|
Разом
|
54528
|
Циркулюючий розчин зі збірки 2-го ступеня абсорбера.
Позначимо цю кількість через G3.Тоді загальний прихід дорівнює:
+ G3.
Витрата.
Коксовий газ.
Із аміаку в коксовому газі 46 кг/год поглинається 44 кг/год і
залишується в газі 2 кг/год.
Кількість піридинових основ, які залишуються після абсорбції,
дорівнює 2 кг/год і поглинається піридинових основ:
- 2=92 кг/год
Кількість водяних парів, які виходять з газом із 2-го ступені
абсорбції GВ визначаємо виходячі з того, що за рахунок тепла
нейтралізації і охолодження газу від температури 58°С до 52°С відбувається
випарення води.
Велічина Gв може бути визначена по рівнянню:
,
де Q1 - тепло, внесене коксовим газом, кДж/год;2 -
тепло реакції нейтралізації, кДж/год;3 - тепло, яке уноситься сухим
коксовим газом із абсорберу при= 52° С.
Тепло, яке вноситься коксовим газом:1= 20963343 кДж/год.
Тепло реакції нейтралізації:
кДж/год,
де 193586 - тепло реакції нейтрализації H2SO4.
Тепло, яке уноситься сухим коксовим газом:3=(45600∙0,7+2600∙0,246+1158∙0,238+3∙0,508+43∙0,418+2∙0,246)∙4,19·52=7158945
кДж/год
Тоді:
кг/год
Загальна кількість газів, які виходять із 2-ї ступені абсорберу
наведене в таблиці 7.7.
Таблиця 7.7 - Загальна кількість газів, які виходять з 2-го ступеня
абсорберу
Найменування
|
кг/год
|
м3/год
|
Сухий коксовий газ
|
45600
|
100000
|
Бензольні вуглеводні
|
2600
|
702
|
Аміак
|
3
|
4
|
1158
|
763
|
Двоокис вуглецю
|
48
|
24
|
Піридинові основи
|
2
|
0,6
|
Водяна пара
|
5429
|
6756
|
Разом
|
54840
|
108249,6
|
Циркулюючий розчин.
Кількість циркулюючого розчину, що виходить з 2-го ступеня
абсорбера, позначимо G4
кг/год.
Тоді загальна витрата дорівнює 54840+ G4.
Дорівнюючи прихід і витрату, отримаємо:
+ G3=54840+
G4
Або:
3= G4+312
Кількість розчину, абсорбера, що поступає в 2-й ступінь,
приймаємо по об’єму рівним кількості розчину, що поступає в 1-й ступінь
абсорбції, що забезпечує однакову щільність зрошування.
Оскільки об’єм розчину, що поступає в 1-й ступінь, 247 м3/год,
то маса розчину G3 при
щільності 1,2 кг/л буде:
G3=247
1200=296400 кг/год.
Тоді:
G4=296400 - 312 = 296088 кг/год.
Матеріальний та тепловий баланси 2-го ступеня абсорбера
наведені в таблицях 7.8 і 7.9.
Таблиця 7.8 - Матеріальний баланс 2-го ступеня абсорбера
Прихід
|
кг/год
|
Витрата
|
кг/год
|
Коксовий газ
|
54528
|
Коксовий газ
|
54840
|
Циркулюючий розчин
|
296400
|
Циркулюючий розчин
|
296088
|
Разом
|
350928
|
Разом
|
350928
|
Таблиця 7.9 - Тепловий баланс 2-го ступеню абсорберу
Прихід
|
кДж/год
|
Витрата
|
кДж/год
|
Тепло коксового газу
|
20963343
|
Тепло коксового газу
|
21210929
|
Тепло нейтралізації
|
247586
|
Тепло нейтралізації
|
173475
|
Тепло циркулюючого
|
296400 52 2,93= =45205742
|
Тепло циркулюючого
|
296088 2,93t= =868426t
|
Разом
|
66416671
|
Разом
|
21384404 +868426t
|
Прирівнюючи прихід і витрату тепла, отримаємо температуру
розчину абсорбера, що виходить з 2-го ступеня, в циркуляцію t=51,9 °С.
.4 Матеріальний і тепловий баланси
збірки 2-го ступеня абсорбера
Матеріальний розрахунок
Прихід. У збірку абсорбера 2-го ступеня поступають:
циркуляційний розчин з абсорбера, розчин з піридинової установки, сірчана
кислота, вода для поповнення циклу.
Визначимо кількість цих потоків:
. Кількість розчину, що поступає з піридинової установки,
дорівнює 1247,5 кг/год.
. Кількість кислоти, що поступає x2.
. Кількість розчину, що поступає з абсорбера, дорівнює:
- 961 - 1400 =293727 кг/год.
.Кількість води, що поступає, для поповнення циклу у2..
Загальний прихід:
,5+x2.+у2..
Витрата. Кількість розчину, що виходить зі збірки в
циркуляцію, дорівнює 296400 кг/год.
Прирівнюючи прихід і витрату, отримуємо:
х2+у2=1425,5 кг/год
Для визначення складаємо баланс моногідрату сірчаної кислоти
(таблиця 7.10).
Таблиця 7.10- Баланс моногідрату сірчаної кислоти
Прихід
|
Кількість, кг/год
|
З кислотою при концентрації 92,5 %
|
0,925· х2
|
Витрата
|
кг/год
|
Переток розчину у 1 ступінь
|
168
|
У піридинову установку
|
115
|
На реакцію з NH3, що йдуть з піридинової
установки
|
|
На реакцію з NH3 в другому ступені
|
124
|
На реакцію з піридиновими основами в 2-му ступені
абсорбції
|
|
Разом
|
524
|
Прирівнюючи прихід і витрату, отримаємо:
,925∙х2=524,
звідси кількість розчину сірчаної кислоти х2=566,5
кг/год, з них: моногідрату:
,925
566,5=524 кг/год,
та води:
,5-524=42,5 кг/год.
Тоді кількість води, необхідна для поповнення циклу:
у2=1425,5 - 566,5=859 кг/год.
Тепловий баланс збірки 2-го ступеня
Прихід.
. Тепло, що вноситься циркулюючим розчином:1=293727
3,31
52 = 50557819 кДж/год
. Тепло, що вноситься розчином з піридинової установки:2=1247,5
0,537
50
4,19=80662 кДж/год,
де 2,25-теплоємність розчину, кДж/(кг
град).
. Тепло, що вноситься кислотою:3=566,5
1,55
20 =17565 кДж/год
. Тепло, що вноситься водою поповнення циклу:4=859
20
4,19=71984 кДж/год
.Тепло розбавлення сірчаної кислоти від 92,5 % до 12 %:
кДж/год
де теплота розбавлення від 92,5 % до 12 % на 1 кмоль дорівнює:
;
кДж/кмоль H2SO4.
Загальний прихід тепла 51112567 кДж/год.
Витрата:
. Тепло, що втрачається назовні:
Q6=173475 кДж/год
. Тепло, що виноситься розчином:
7=296400∙0,79t∙4,19=981114t
Загальна витрата тепла
Qвит=173475+981114t
Дорівнюючи прихід і витрату тепла, отримаємо
=173475+981114t,
Звідси температура розчину, що встановилася t= 51,9 °С.
Баланс кислоти і води поповнення приведений в таблиці 7.11.
Таблиця 7.11- Баланс кислоти і води поповнення
Компоненти
|
Збірка1
|
Збірка2
|
Всього
|
Разом
|
|
H2SO4
|
H2O
|
H2SО4
|
H2O
|
H2SO4
|
H2O
|
|
Розчин кислоти Вода поповнення циклу
|
1548 -
|
126 5382
|
524 -
|
42,5 989,5
|
2072 -
|
178 6371,5
|
2250 6371,5
|
Всього
|
1548
|
5508
|
524
|
1032
|
2072
|
6549,5
|
8621,5
|
Матеріальні баланси сульфатної і піридинової установок
наведені у таблицях 7.12 та 7.13.
Таблиця 7.12 - Матеріальний баланс сульфатної установки
Прихід
|
кг/год
|
Витрата
|
кг/год
|
Коксовий газ
|
52844
|
Коксовий газ
|
54840
|
Аміачно-водяні пари
|
930
|
Розчин для піридинової установки
|
961
|
Сірчана кислота
|
2371
|
Сульфат амонію
|
3014
|
Промивна вода
|
170
|
Випаровується у випарники
|
4858
|
Вода для поповнення циклів
|
6371,5
|
|
|
Знепіридинений розчин
|
1247,5
|
|
|
Разом
|
63673
|
Разом
|
63673
|
Таблиця 7.13 - Матеріальний баланс піридинової установки
Прихід
|
кг/год
|
Витрата
|
кг/год
|
Розчин з абсорберу
|
961
|
Розчин у збірник абсорберу
|
1247,5
|
Аміачно-водяні пари з дефлегматору
|
380
|
Піридинові основи (водні)
|
57,5
|
|
|
Неконденсуючі гази
|
36
|
Разом
|
1341
|
Разом
|
1341
|
7.5 Визначення розмірів абсорберів
Кількість газів і пари, що поступають в абсорбер, наведено в
таблиці 7.14.
Таблиця 7.14 - Кількість газів і пари, що поступають в
абсорбер
Компоненти
|
З нагнітача
|
З дефлегматору
|
|
кг/год
|
м3/год
|
кг/год
|
м3/год
|
Сухий коксовий газ Бензольні вуглеводні Сірководень
Двоокис вуглецю Піридинові основи Аміак Водяна пара
|
45600 2600 1120 - 40 564 2920
|
100000 702 738 - 11 743 3643
|
- - 38 48 6 142 696
|
- - 25 24 1,7 187 866
|
Разом
|
52844
|
105828
|
930
|
1103,7
|
Об’єм газів, що поступають, за фактичних умов складемо
м3/год,
де 906-тиск перед абсорбером, мм рт.ст.
Приймаємо швидкість газів в абсорбері 4 м/с. Тоді необхідний перетин
абсорберу:
м2
і діаметр абсорбера:
м.
Приймаємо діаметр абсорберу 3,2 м.
Об’єм абсорберу визначаємо з умов абсорбції амоніаку по рівнянню:
м3,
де
- об’єм газів, що поступають
;
К - коефіцієнт абсорбції аміаку сірчаною кислотою в розпорошувальних
апаратах, за практичними даними К=5000 1/год;
вміст
аміаку в газі, що поступає і виходить, г/м3
.
Об’єм абсорбера 1-го ступеня дорівнює:
м3,
тоді необхідна висота робочої частини абсорбера:
м.
Приймаємо висоту кожної ступені по 8 м.
Розміри робочої частини абсорбера 2-го ступеня абсорбції залишаються
такими ж, як і 1-го ступені,так як
,
8. РОЗРАХУНОК КОНДЕНСАТОРУ
8.1 Тепловий розрахунок
Прихід.
. Тепло, яке вноситься водяною парою з випарника:1
= 12536657 кДж/год.
Витрати.
. Тепло, яке уноситься конденсатом пару при температурі конденсації
50 °С:2
=4858·50·4,19=1017751 кДж/год.
. Тепло, яке уноситься охолоджуючою водою: Q3
Дорівнюючи прихід та витрату, одержимо:3 =
11518906 кДж/год.
Витрату води визначаємо приймаючи температуру входу та виходу
води 25 і 40 °С:
W =
м3/год.
8.2 Визначення поверхні
теплопередачі
Швидкість води при турбулентному руху
визначаємо по рівнянню:
υ=10
,
де Z - в’язкість води при середній
температурі,
ρ
- густина води;- внутрішній діаметр
трубок.
υ=10
м/с.
Приймаємо швидкість води 0,6 м/с,
тоді необхідний перетин для проходу води:
S=
м2.
Необхідна кількість труб в одному ході:=
шт.
При чотирьох ходах:=299·4=1196 шт.
Приймаємо 4 - ходову трубчатку з числом труб 1303, які розміщуються на
19 шестикутниках.
Тоді фактична швидкість води:
υ=
м/с.
Поверхня теплопередачі:
,
де Q - кількість тепла, Q3 = 11518906 кДж/год;
∆tср
- середня логарифмічна різниця температур в теплопередачі:
∆tср=
°С
К - коефіцієнт теплопередачі:
,
де
коефіцієнт теплопередачі від пари, приймаємо 41900;
термічний опір стінок трубок; цією величиною нехтуємо;
термічний опір забруднень, приймаємо рівним
0,0002385;
коефіцієнт теплопередачі від стінки до киплячого розчину
визначуваний по рівнянню:
Критерій Нуссельта:
Критерій Рейнольдса:
Критерій Прандтля:
.
Тоді:
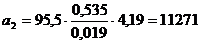
.
Коефіцієнт теплопередачі:
Необхідна поверхня теплопередачі:
Довжина труб:
l =
=
м.
Тоді діаметр трубчатки буде:
,
де
число шестикутників;
крок розміщення трубок;
відстань від кожуха,
Приймаємо:=1,3·0,022=0,029 м;`=0,022 м.
Тоді:=2·(19·0,029+0,022)=1,726 м
9. РОЗРАХУНОК БАРАБАННОЇ СУШАРКИ
9.1 Матеріальний розрахунок
Виходячи з вихідної вологості сульфату амонію 2 %,
встановлюємо кількість вологи, що видалена з матеріалу по рівнянню:
де
- кількість солі , що виходить з сушарки;
,
- відповідно початкова і кінцева вологість сульфату
амонію, %.
Тоді:
коксовий газ сульфат амоній
9.2 Тепловий розрахунок сушарки
Як паливо використовується сухий коксовий газ наступного складу (%
об.): CH4 - 26,0; C2H6 - 2,5; H2 -
60,0; CO - 6,5; N2 - 1,5, О2 - 0,6, CО2 - 2,9.
Для спалювання 1 кг цього газу необхідно L0 кг сухого
повітря. Розрахунок L0 за наступною формулою:
,
де СО, Н2,
-
об’ємні долі компонентів, що горять.
Звідси:
кг/кг.
Виходячи з теплових ефектів реакцій згоряння компонентів палива:
+
10810 кДж/м3;
+
12680 кДж/м3;
+
35741 кДж/м3;
+
63797 кДж/м3.
Розрахуємо кількість тепла, що утвориться при згорянні 1 м3
газу:
,
де ω
- об’ємна доля компоненту, %;-
питома теплота згоряння компоненту, кДж/м3.
Отримуємо:
кДж/м3
Щільність паливного газу визначимо за формулою:
,
де
- мольна маса компоненту;
-
температура палива;
-
мольний об’єм газу.
Підставивши у формулу значення отримаємо:
кг/м3.
Кількість тепла, що виділяється при спалюванні 1 кг газу:
Маса газів, що подається до барабану у розрахунку на 1 кг палива, що
горить визначається загальним коефіцієнтом надлишку повітря α, необхідного для горіння палива та розбавлення
топочних газів до температури 130 °С. Значення α знаходять з рівнянь теплового та матеріального
балансів:
,
де η
- ККД топки (дорівнює 0,95);
-
теплоємність палива при 20°С, (дорівнює 1,34 кДж/(кг· К));
-
ентальпія свіжого повітря, кДж/кг;
-
вологовміст свіжого повітря, кг/кг;0 - теплота випаровування води
при 0°С, 2500 кДж/кг;
-
середня теплоємність водяної пари, 1,97 кДж/(кг· К);вп - температура
пари на вході у барабан tвп=130°С.
Для розв’язання цього рівняння необхідно розрахувати кількість вологи,
що утвориться при згорянні газу. Перерахуємо об’ємні долі компонентів у масові:
Кількість вологи, що утвориться при згорянні 1 кг палива дорівнює:
кг/кг.
Вологовміст свіжого повітря знаходимо по даних вологості повітря φ0=70%, та температурі tпов=20°С за формулою:
де Р - атмосферний тиск (101 кПа);
-
парціальний тиск насиченої водяної пари при 20°С, (2340 Па).
Звідси:
Загальна питома маса сухих газів, що утворюються при згорянні 1 кг
палива та розбавлені топічних газів повітрям до температури 130°С дорівнює [3]:
Питома маса водяної пари у газовій суміші при спалюванні 1 кг палива:
Вологовміст газів на вході у барабан сушарки:
Ентальпія газів на вході у барабан сушарки:
У процесі сушіння тепло витрачається на нагрівання та випаровування
вологи, нагрівання матеріалу, та непродуктивні втрати теплоти у оточуюче
середовище. З рівняння теплового балансу сушіння:
Для теоретичної сушарки Δ=0. Для реальної сушарки:
,
де
- питома витрата тепла на нагрівання матеріалу;
-
втрати тепла у оточуюче середовище віднесені до 1 кг випареної вологи. Згідно з
ГОСТу 26-01-450-78 приймаються для барабанних сушарок у межах 85 - 120 кДж/кг.
Приймаємо
= 120 кДж/кг.
де
,
-
температура матеріалу на вході та на виході з сушарки.
Звідси:
Ентальпія водяної пари на виході з сушарки:
,
де
- температура газів на виході з сушарки.
2500+1,97*75=2647,75
кДж/кг.
Ентальпія вологих газів на виході з барабану сушарки:
Звідси:
Вологовміст газу на виході з барабану:
В процесі сушіння волога з матеріалу випаровується та уноситься агентом
сушіння. При цьому вологовміст газів збільшується з х1 до х2. Тому:
Витрата теплоносія:
Витрата тепла на сушіння:
Витрата паливного газу:
З цього:
9.3 Визначення розмірів сушильного барабану
Основні розміри сушильного барабану вибирають виходячи з об’єму
сушильного простору. Цей об’єм складається з об’єму, необхідного для прогріву
матеріалу до температури при котрій починається інтенсивне випаровування (
), та об’єму необхідного для процесу випаровування
вологи (
).
Об’єм простору в який випаровується волога може бути знайдений з
модифікованого рівняння масопередачі:
де
’- середня рушійна сила масопередачі, кг/м3;
-
об’ємний коефіцієнт масопередачі.
Якщо рух матеріалу та агенту сушіння прямоточний, то коефіцієнт
масопередачі Кυ
чисельно рівний коефіцієнту
масовіддачі βυ.
Для барабанної сушарки коефіцієнт
масовіддачі βυ
може бути розрахований за
емпіричним рівнянням:
де ρср - середня цільність сушильного агенту, кг/м3;
с - теплоємність сушильного агенту при середній температурі в барабані
(1 кДж/кг*К);
β - коефіцієнт заповнення барабану матеріалом (12%);
Р0 - тиск при якому проводиться процес, Па;
р - середній парціальний тиск водяної пари, Па;- частота обертів
барабану, об/хв. приймаємо n=1,5 об/хв;
ω - швидкість газового потоку в барабані, м/с.
Середня щільність сушильного агенту при середній температурі в барабані
розраховується за формулою:
Середню температуру знаходимо як середньоарифметичну між температурою
сушильного агенту на вході (
)
та на виході (
) з сушарки:
Тоді:
Розрахуємо середній парціальний тиск парів води у барабані по значеннях
вологовмісту на вході та на виході з барабану:
Значення парціальних тисків розрахуємо за формулами:
Звідси:
Згідно:
Маючі усі вихідні дані розрахуємо коефіцієнт масовіддачі βυ:
Рухаючу силу масопередачі
визначимо
через рівняння:
де
- середня рухаюча сила масопередачі, Па. Її можна
розрахувати за рівнянням:
Для прямоточних сушарок
=
-
-
рухаюча сила в началі процесу та
=
-
-
рухаюча сила наприкінці процесу. р* - тиск водяної пари над вологим
матеріалом.(
= 17153 Па;
=
16063 Па). Звідси:
Розрахуємо рухаючу силу масопередачі
:
Об’єм простору необхідний для процесу випаровування:
Об’єм необхідний для прогріву матеріалу знаходимо з модифікованого
рівняння теплопередачі:
де Qп - витрата тепла на прогрів матеріалу, кВт;
Кυ - об’ємний коефіцієнт теплопередачі, кВт/м3*К;
Δtср - середня різниця температур теплоносія
та матеріалу.
Витрата тепла Qп дорівнює:
де t - температура матеріалу на вході в сушарку;
θ - температура матеріалу на виході;
см - теплоємність сухого сульфату амонію.
Отже:
Об’ємний коефіцієнт теплопередачі знаходимо за емпіричним рівнянням:
Звідси:
Для розрахунку Δtср
необхідно знайти температуру, до якої охолодиться сушильний агент віддаючи
тепло матеріалу сушіння. Цю температуру можна знайти з рівняння:
де tх - шукана температура.
Звідки:
Підставляючи розраховані значення отримуємо:
Звідси об’єм сушильного простору барабану:
Відношення довжини барабану до його діаметру повинно знаходитися у
межах 3,5÷7.
Приймаємо L/D = 5.
З формули:
Звідси діаметр барабану:
Довжина барабану:
За ГОСТом 26-01-437 - 85 вибираємо барабан сушарки 1200×6000
мм, об’єм його сушильного
простору 6,78м3.
Визначимо швидкість газів в барабані за формулою:
,
де
- коефіцієнт заповнення барабану насадкою;
-
об’ємна витрата вологого сушильного агенту на виході з барабану, м3/с.
Він дорівнює:
,
де
- середній вологовміст сушильного агенту, кг/кг
сухого. Розраховується як середньоарифметичне між
та
:
Тоді:
Швидкість газів в барабані:
Перевіримо, чи є дана швидкість припустимою, виходячи з того, що
кристали сульфату амонію більші 0,35 мм не повинні виноситися током газів з
барабану. Швидкість виносу рівну швидкості витання знайдемо з формули:
,
де
- в’язкість газу при середній температурі, (рівна
0,022 мПа*с);
-щільність агенту сушіння при середній температурі;-
діаметр часток матеріалу;- критерій Архімеду, рівний:
де
- щільність часток матеріалу.
Звідси:
Розрахуємо критерій
Архімеду:
Швидкість витання:
Вона є меншою за
фактично розраховану швидкість газів у барабані
=2,23
м/с, тому розрахунок основного обладнання закінчуємо [1].
Кількість матеріалу,
що знаходиться у сушарці:
Час перебування
матеріалу у барабані:
Кут нахилу барабану
розраховується за формулою:
Звідси:
10. ПРОЕКТ УЛОВЛЮВАННЯ ПЫРИДИНОВИХ ОСОВ
10.1Обґрунтування важливості
уловлювання піридинових основ
Піридин (С5Н5N) - Це речовина разом з
цілим рядом аналогічних з'єднань, взагалі званих піридиновими основами, було
відкрито в 1846 р. Андерсоном при дослідженні кісткового масла, виходить сухою
перегонкою не знежирених кісток. З моменту свого відкриття піридин вельми
зацікавив хіміків своїми властивостями, багато в чому нагадують властивості
бензолу, і тим, що починав собою цілий ряд гомологів. У 1869 р. Кернер у
приватному листі до Каниццаро висловив думку, що піридин може бути розглянутим,
як бензол, в якому одна група СН заміщена азотом, тобто що піридин має будову:
<#"810213.files/image293.gif"> <#"810213.files/image294.gif"> <#"810213.files/image295.gif"> <#"810213.files/image296.jpg"> <#"810213.files/image297.gif">;
Обидві ці солі знаходяться в робочому розчині в розчиненому
вигляді. Вони є нестійкими сполуками, схильними при певних умовах дисоціювати з
виділенням піридину у вільному вигляді. В маточному розчині абсорберу в
основному міститься кислий сульфат піридин. Будучи термічно стійким з'єднанням
у водних розчинах навіть при високій концентрації (200-260 г/л) і високих
температурах (75-80°С), кислий сульфат піридину, проте, легко дисоціює під дією
сульфату амонію з утворенням вільного піридину, який при певних умовах
видувається газом з маточного розчину абсорберу і втрачається.
Найбільш суттєвими факторами, що впливають на ступінь
уловлювання піридинових основ з газу, є температура розчину у абсорбері, його
кислотність і концентрація в ньому піридинових основ. При цьому вирішальним
фактором є температура. Вона визначає ступінь дисоціації піридину і, отже,
пружність парів піридину над маточним розчином. Висока температура маточного
розчину порушує умови одночасного уловлювання в абсорбері аміаку і піридинових
основ. В результаті підвищення кислотності розчину порушується процес утворення
крупнокристалічних солей сульфату амонію.
Оптимальний технологічний режим сатуратора, що забезпечує
нормальне протікання процесу одночасного уловлювання в ньому аміаку і
піридинових основ, характеризується наступними параметрами: температура
абсорберу 50-55°С, кислотність маткового розчину 4,5-5,0%, концентрація
піридинових основ у розчині 12-15 г/л. Це дозволяє довести ступінь уловлювання
піридинових основ до 90%. Необхідна концентрація піридинових основ в маточному
розчині підтримується шляхом безперервного виведення з абсорберу постійної
кількості розчину на переробку в піридинових відділеннях.
Низька концентрація піридинових основ в маточному розчині
обумовлена необхідністю переробки великої кількості його, що вимагає більш
ємною апаратури і, отже, збільшення капітальних витрат.
В установках отримання сульфату амонію безсатураторним
способом в результаті роздільного уловлювання аміаку і піридинових основ
концентрація піридинових основ в матковому розчині досягає 100-120 г/л, що
сприятливо позначається на техніко-економічних показниках роботи піридинової
установки.
Виділення піридинових основ з маточного розчину здійснюється
в піридиновій установці.
Частина маточного розчину з кристаллоприймача 1 через
відстійник і витратомір маточного розчину 3 безперервно надходить в
нейтралізатор, в який постійно подається концентрована пароаміачна суміш після
дефлегматора аміачної колони. Барботируя через шар маточного розчину в
нейтралізаторі, більша частина аміаку витрачається на нейтралізацію вільної
сірчаної кислоти, решті аміак реагує з сульфатами піридину та його гомологами.
При цьому піридинові підстави виділяються у вільному вигляді по реакції:
5H5NH × HSО4 + 2NH3 -® (NH4)2SО4
+ C5H5N.
Виділилися в нейтралізаторі вільні піридинові основи
випаровуються за рахунок теплоти нейтралізації розчину і часткової конденсації
парів.
Температура розчинів нейтралізаторі утримується на рівні
100-101°С. Випарувалися при цій температурі піридинові заснування в суміші з
водяними парами, частиною аміаку, який не прореагував, вуглекислотою,
сірководнем, частиною фенолів і парами нейтральних масел, а також з газами
направляються, які не скондесувалися в міжтрубний простір
конденсатора-холодильника, де пари конденсуються і конденсат охолоджується до
30-35°С протікає по трубах технічною водою.
Пари, які не сконденсувалися і гази через повітровідвідники
відводяться в газопровід перед первинними газовими холодильниками. Цим
зменшуються втрати легких піридинових основ.
Сконденсована і охолоджена рідина з конденсатора-холодильника
надходить у сепаратор, в якому піридинові основи відділяються від води
внаслідок різниці їх густини. Верхній шар, що представляє собою сирі піридинові
основи, відводиться в один з мірників, а звідти в сховище.
Обезпіридинений розчин з нейтралізатора через гідрозатвор надходить у проміжний
збірник реактор-підкислювач, де відстоюється від шламу, а потім підкислюється
сірчаною кислотою до кислотності 10-12% і повертається в сатуратор. Лужність
маточного розчину після нейтралізатора повинна знаходитися в межах 0,3-0,5 г/л
летючого аміаку.
Якість сирих піридинових основ оцінюється по їх утриманню в
сирому продукті, яка визначається кількістю і складом органічних речовин, що
знижують вміст 100%-них піридинових основ в перерахунку на безводний продукт.
Так як органічні речовини, що складаються в основному з
легких погонів смоли, нафталіну та фенолів, що потрапляють в нейтралізатор
піридинової установки з маточним розчином сатуратора і з аміачними парами, то
якість сирих піридинових основ знаходиться в прямій залежності від режиму
роботи цих відділень, від роботи відділення конденсації, очищення газу від
туманообразної смоли в електрофільтрах. Якість сирих піридинових основ
визначається також температурою аміачної пари, що надходять в нейтралізатор.
Висока температура аміачної пари пов'язана з підвищеним вмістом в їх складі
водяних парів, які, пройшовши нейтралізатор, повністю конденсуються в
конденсаторі і потрапляють в сепаратор. При цьому зменшується концентрація
розчинних солей в сепараторной воді знижується її щільність, збільшується
розчинність в ній піридинових основ, в результаті чого вони погано відстоюються
в сепараторі і погіршується їх якість.
Наявність у сепараторній воді великої кількості розчинених
амонійних солей (NH4)2СО3 і (NH4)2S
досить позитивний фактор, тому що це збільшує її щільність, сприяючи швидкому і
чіткому відстоювання більш легких піридинових основ. Якщо щільність
сепараторній води більш висока, зменшується кількість розчиняються піридинових
основ. Для збільшення вмісту амонійних солей в сепараторній воді її зазвичай
замикають в циклі сепаратор-нейтралізатор-сепаратор.
На деяких заводах сепараторна вода використовується як
зрошення, що подається на аміачну колону. В результаті пари, що йдуть в
нейтралізатор, збагачуються важливими компонентами (аміак, піридинові основ,
вуглекислота і сірководень). Крім того, на 3-5°С знижується температура пари
після колони, різко зменшуючи вміст у них води.
Вивід сепараторній води у вигляді зрошення на аміачну колону
сприятливо позначається на водному балансі нейтралізатора і сатуратора,
зменшуючи кількість води, яка потрапляє в ці апарати.
Важливий результат виводу сепараторній води для зрошення
полягає в тому, що стає можливим видалити зі стічними водами після аміачної
колони значну частину агресивних ціаністих з'єднань, які при замкнутому циклі
сепараторній води поступово накопичувалися в нейтралізаторі і сепараторі, руйнуючи
апаратуру і комунікацію сульфатно-піридинового відділення. Потрапляючи в
сатуратор, комплексні сполуки ціаністого водню та заліза (ферроцианиды),
нерозчинні в кислому середовищі, негативно впливають на гранулометричний склад
сульфату амонію.
Основним апаратом піридинової установки є нейтралізатор. Він
являє собою вертикальний циліндр з конічним днищем, виготовлений з чавуну або
вуглецевої сталі, діаметром 1800 мм, загальною висотою 2600 мм. Внутрішня
поверхня нейтралізатора для захисту від корозії гомогенно освинцовується,
зовнішня поверхня теплоізольована. Аміачні пари надходять у центральній трубі і
розподільного пристрою (барботеру), виготовленому з чавуну або нержавіючої
сталі. Матковий розчин надходить по трубопроводу, занурений в розчин, утворюючи
гідрозатвор. Пари відводяться в конденсатор-холодильник через верхній штуцер.
Для конденсації парів піридинових основ застосовують
конденсатори трубчастого типу з поверхнею теплообміну 20
, виготовлені з сталі. Застосовуються
конденсатори поглибленого типу, виготовлені з нержавіючої сталі, вони
громіздкі, але надійні в роботі.
10.3 Вибір обладнання для
піридинової установки
Конструкція конденсатору представлена у розділі 5.3, ця
конструкція співпадає з конденсатором, який використовується у піридиновій
установці.
Конструкція нейтралізатору:
Гіпрококсом розроблена більш досконала конструкція
нейтралізатора, наведена на рис. 12.1. Він являє собою вертикальний
циліндричний апарат, розділений сферичним днищем на дві секції, у кожній з яких
встановлено по дві ковпачкові тарілки. Обидві секції з'єднані між собою
переточними трубами для парів і маточним розчином.
Маточний розчин з абсорберів подається на верхню тарілку, а
аміачні пари під нижню тарілку верхньої секції нейтралізатора. Нейтралізований
розчин перетікає по трубі 6 в нижню секцію апарату, куди надходять також
аміачні пари з верхньої секції. В результаті взаємодії розчину з парами на
тарілках піридинові основи переходять практично повністю в парову фазу і
виводяться з апарату через штуцер 7 в конденсатор-холодильник.
Обезпіридинений розчин виводиться знизу апарату по трубі 8 у
сульфатне відділення. Важливою перевагою вдосконаленої конструкції нейтралізатора
гіпрококсу є більш ефективне використання аміаку для нейтралізації розчину і
зниження його витрати.
Рисунок 10.1 - конструкція нейтралізатору
10.4 Розрахунок нейтралізатору
Матеріальний розрахунок
Прихід. В нейтралізатор піридинової установки надходять:
. Аміачно-водяна пара з дефлегматора в наступній кількості
(табл. 10.1).
Таблиця 10.1 - Кількість аміачно-водяної пари з дефлегматора
Найменування
|
Кількість, кг/год
|
Аміак
|
60
|
Сірководень
|
17
|
Двуокис вуглецю
|
22
|
Водяна пара
|
279
|
Піридинові основи
|
2
|
Разом
|
380
|
. Розчин з абсорберу в кількості 961 кг/год.
. Вода з сепаратора. Позначимо цю кількість через х.
Разом 3483, 9 + х.
Витрата. З нейтралізатора виходять:
. Розчин у збірник в абсорбері в кількості 1247,5 кг/год.
. Пари в конденсатор в кількості (табл. 10.2):
Таблиця 10.2 - Кількість парів в конденсатор
НайменуванняКількість, кг/год
|
|
Сірководень
|
16
|
Двуокис вуглецю
|
20
|
Піридинові основи
|
51,5
|
Водяна пара
|
у
|
Разом
|
1335 + у
|
Дорівнюючи прихід і витрату отримаємо х + 6 = у.
Тепловий розрахунок
Прихід тепла. 1. Тепло, внесене розчином з абсорберу:1=
961. 64 . 48 . 4,19 = 123697 кДж/год,
де 48 - температура розчину, °С.
. Тепло, внесене аміачно-водяними парами:2= ((60 .
0,508 + 17 . 0,24 + 22 . 0,21 + 2 . 0,246) ·
95 +
+ 279·(595+0,438 . 95))· 4,19 = 759995 кДж/год.
. Тепло, внесене конденсатом з сепаратора, приймаючи
температуру конденсату 30 °С:3 = 125,7 х кДж/год.
. Тепло хімічних реакцій:) тепло розчинення аміаку
кДж/год.
б) тепло розкладання сульфату
піридину і нейтралізації вільної сірчаної кислоти:
кДж/год.
Разом Q3 = 366426 кДж/год
Загальний прихід тепла:прих = 1250118 +125,7х
Витрата тепла. 1. Тепло, що уноситься розчином:4 =
1247,5 . 0,75 . 102·4,19 = 399867 кДж/год,
де 102 - температура в нейтралізаторі, °С.
. Тепло, що уноситься парами в конденсатор:5 =((16
. 0,24 + 20 . 0,21)·100+51,5·( 102+0,3 . 100 )
+
+ у · ( 595+0,438 . 100 ))·4,19 = 31852,38 +
2676,57 у,
де 100 - температура парів, що виходять із нейтралізатору,
°С;
- тепло випаровування піридинових основ, ккал/кг.
. Тепло, що втрачається нейтралізатором назовні, приймаючи 1
% від приходу:6 = 0,01·( 1250118 +125,7х ) = 12501,18 + 1,257х.
Загальна витрата тепла:витр = 444220,56 + 2676,57у
+ 1,257х,
Дорівнюючи прихід і витрату тепла, отримаємо:
1250118 +125,7х = 444220,56 + 2676,57у + 1,257х,
або
,44 = 2676,57у-124,443х.
Вирішуючи це рівняння з рівнянням матеріального балансу х + 6
= у, отримаємо:
х = 309 кг/год ; у = 315 кг/год.
Матеріальний баланс нейтралізатору (табл. 10.3):
Таблиця 10.3 - Матеріальний баланс нейтралізатору
Прихід
|
кг/год
|
Витрата
|
кг/год
|
Аміачно-водяні пари
|
380
|
Розчин
|
689
|
Пари в конденсатор
|
572,5
|
Розчин
|
961
|
Вода з сепаратора
|
309
|
|
|
Разом
|
1650
|
Разом
|
1650
|
Тепловий баланс нейтралізатору (табл.
10.4).
Таблиця 10.4 - Тепловий баланс
нейтралізатору
Прихід
|
кг/год
|
Витрата
|
кг/год
|
Тепло маточного розчину
|
123697
|
Тепло маточного розчину
|
399867
|
Тепло аміачно-водяних парів
|
759995
|
Тепло парів, що йдуть в конденсатор
|
874972
|
Тепло конденсату
|
38841
|
Тепло, що втрачається назовні
|
14120
|
Тепло хімічних реакцій
|
366426
|
|
|
Разом
|
1288959
|
Разом
|
1288959
|
10.5 Розрахунок конденсатору легких
піридинових основ
Матеріальний розрахунок
Прихід. В конденсатор надходять пари з нейтралізатору в
кількості (табл. 10.6)
Таблиця 10.5 - Пари в конденсатор з нейтралізатору
Найменування
|
Кількість, кг/год
|
Сірководень
|
16
|
Піридинові основи
|
51,5
|
Двоокис вуглецю
|
20
|
Водяні пари
|
315
|
Разом
|
402,5
|
Витрата. З конденсатора виходить
конденсат в кількості:
Вода - 315 кг/год;
Піридинові основи - 51,5кг/год;
Разом - 366.5 кг/год.
Неконденсовані гази, кг/год:
Сірководень - 16;
Двоокис вуглецю - 20;
Разом - 36;
Всього - 402,5.
У сепараторі конденсатора відбувається поділ рідких фаз і
утворюються легкі піридинові основи в кількості 57,5 кг/год (з них: піридинових
основ 51,5 кг і води - 6 кг) і сепараторна вода в кількості:
- 6 = 309 кг/год,
повертаємо в сепаратор.
Тепловий розрахунок
Прихід. Тепло, внесене парами з нейтралізатора:
Q1 = 874972 кДж/год.
Витрата. 1. Тепло, що уноситься конденсатом:2 =
(315+51.5 . 0,43)30. 4.19 = 42379 кДж/год.
. Тепло, що уноситься неконденсованими газами:з = (20 .
0,204+16 . 0,235)30. 4.19 = 985 кДж/год.
. Тепло, що уноситься технічною охолоджуючою водою Q4.
Разом витрата 43364 + Q4.
Прирівнюючи прихід і витрату, отримаємо
= 43364+ Q4,
Приймаючи температуру води, що надходить на охолодження,
рівний 24 °С, і виходить 45 °С, отримаємо витрату води:
кг/год,
або 9.451 м3/год
Тепловий баланс конденсатору (табл.
10.6)
Таблиця 10.6 - Тепловий баланс
конденсатору
Прихід
|
кг/год
|
Витрата
|
кг/год
|
Тепло, внесене паром
|
874972
|
Тепло конденсату
|
42379
|
|
|
Тепло неконденсованих газів
|
985
|
|
|
Тепло, відбираємо технічною водою
|
831608
|
|
|
|
|
Разом
|
874972
|
Разом
|
874972
|
Визначення поверхні теплопередачі і розмірів конденсатору
Приймаємо трубки діаметром 38/2,5 мм. Критична швидкість води
в трубках :
м/с.
Необхідний перетин трубок в одному ході
м2.
Приймаємо трубчатку з 6 ходами по воді, тоді перетин всіх ходів:= 6 .
0,0515 = 0,309 м3.
Необхідну кількість трубок:
шт..
Приймаємо п=367 шт., що розміщуються на тринадцяти
шестикутниках.
Тоді фактична швидкість води буде дорівнювати:
м/с.
Число Рейнольдса:
.
Число Прандтля:
,
де 0,998 - теплоємність води при 34,5 С, кДж/(кг .
град);
,518 - коефіцієнт теплопровідності води при 34,5 °С,кДж/(м.год.град).
Критерій Нуссельта:= 0,023 . 22850,8 .
4,840,4 . 0,45 = 9,46,
звідси коефіцієнт тепловіддачі до води буде дорівнювати:
кДж/(м2
. год . град).
Коефіцієнт тепловіддачі від конденсующейся пари води до
стінки приймаємо а1 = 41900 кДж/(м2 . год .
град) .
Коефіцієнт теплопередачі в період конденсації пари при обліку
опору забруднень з боку води 0,00024 м2.год.град /кДж
буде дорівнювати:
кДж/(м2
. год . град).
Загальна кількість тепла, що відбирається водою, дорівнює
831608 кДж/год.
Тепло охолодження конденсату:П = (315+0,43 .
51,5) . (100 - 30) . 4,19 = 98885 кДж/год.
Тепло конденсації пари:1 = 831608 - 98885 =
73272,3 кДж/год.
Визначаємо різницю температур за періодами:
°С 100 °С 30 °С
Період конденсації______ Період охолодження
°С 26,5 °С 24 °С
Проміжна температура води:
°С.
Середня різниця температур в період конденсації:
°С.
Середня різниця температур в період охолодження:
°С.
Необхідну поверхню теплопередачі для періоду конденсації парів:
м2.
Коефіцієнт тепловіддачі від конденсату до стінки визначаємо за
рівнянням:
кДж/(м2
. год . град).
Коефіцієнт теплопередачі в період охолодження конденсату:
кДж/(м2
. год . град)
Перевіряємо температуру стінки:
°С
Необхідна поверхня теплопередачі для періоду охолодження конденсату:
м2.
Загальна поверхня охолодження конденсатора:= 21,2+8,2 = 29,4 м2.
Довжина труб:
м.
Діаметр трубчатки:= 2(xt + t),
де х - число шостикутників, дорівнює 13 шт.;- крок розміщення
трубок, рівний 50 мм4- відстань центру крайньої трубки від кожуха, дорівнює 38
мм.
Тоді:= 2(10 . 0,05+0,038) = 1,076 м.
. РОЗРАХУНОК ВИПАРНИКА НА ЕОМ
11.1 Постанова задачi
Розрахунки з застосуванням ЕОМ дозволяють заощадити час і
провести більш точні розрахунки.
Необхідно провести розрахунок випарника. Розрахунок випарника
полягає в складані матеріального балансу; теплового балансу з визначенням необхідної
кількості пари, а також конструктивного розрахунку з визначенням діаметру.
Розрахунок проведено за допомогою програми Turbo Pascal 7.0.
В основі розрахунків покладено матеріальні та теплові
баланси, які базуються на законах збереження маси та енергії. Для розрахунку
діаметру використані аналітичні залежності.
11.2 Математичний опис
Матеріальний розрахунок:
У випарник поступає розчин з 1-го ступеня абсорбера
наступного складу (таблиця 11.1).
Таблиця 11.1 - Розчин що поступає у випарник
Найменування
|
кг/год
|
Сульфат амонію
|
Gс1=4262
|
Сірчаної кислоти
|
Gк1=106,6
|
Сульфату піридину
|
Gп1=51,4
|
Води
|
Gв1=6235
|
Разом
|
∑G1=Gс1+Gк1+Gп1+Gв1
|
У випарнику випаровується вода у кількості Gп=4858
кг/год. Тому з випарника виходить пульпа наступного складу (таблиця 11.2).
Таблиця 11.2 - Вхід пульпи з випарника
Найменування
|
Вміст, кг/год
|
Сульфат амонію
|
Gс1
|
Сірчаної кислоти
|
Gк1
|
Сульфату піридину
|
Gп1
|
Води
|
Gв2=Gв1-Gп
|
Разом
|
∑G2=Gс1+Gк1+Gп1+Gв2
|
При відділенні кристалів сульфату амонію у кількості Gсв=3014
кг/год після центрифуги залишиться маточного розчину:
м=∑G2 - Gсв.
Маса сухого сульфату амонію Gсс=2954 кг/год, маса
води Gвп=60 кг/год.
Склад маточного розчину наведений в таблиці 11.3.
Таблиця 11.3 - Склад розчину
Найменування
|
Вміст, кг/год
|
Сульфат амонію
|
= -
|
Сірчаної кислоти
|
|
Сульфату піридину
|
|
Води
|
Gв3=Gв3-Gвп
|
Разом
|
∑G3=Gс3+Gк1+Gп1+Gв3
|
Тепловий розрахунок:
Прихід.
.Тепло, що вноситься розчином при температурі t1=58,9
°С:
1 =∑G1 c1· t1.
.Тепло кристалізації сульфату амонію:
2 = q1 · Gсс/М.
.Тепло гріючої пари Q3.
Разом прихід:
=Q1 +Q2 +
.
Витрата.
.Тепло, що відноситься парами води з випарника:
4=(Gм
0,64+Gсп
0,34)
t1
4,19.
.Тепло, що відноситься парами води з випарника:
5= Gп · qп,
де qп =2580 -tнтальпsя парe, кДж/кг.
. Тепло концентрації сірчаної кислоти незначне (від 1 % до
3,8 %) і їм нехтуємо.
. Тепло, що втрачається назовні:6=173475 кДж/год.
Загальна витрата тепла
∑Qв=Q4+Q5+Q6.
Прирівнюючи прихід і витрату, отримаємо тепло горючої пари
3=Q- ∑Gв.
Втрати тепла назовні:6=173475 кДж/год.
Витрата пару:
Визначення поверхні теплопередачі:
Поверхню теплопередачі випарника визначаємо по формулі:
,
де
кількість тепла, що передається:
=Q3-Q6
різниця
температур в теплопередачі між парою і розчином,
коефіцієнт
теплопередачі визначаємо по формулі
,
де
коефіцієнт теплопередачі від пари, приймаємо 41900
кДж/год;
термічний
опір стінок трубок; цією величиною нехтуємо;
термічний
опір забруднень, приймаємо рівним 0,000477;
коефіцієнт
теплопередачі від стінки до киплячого розчину визначуваний по наближеному
рівнянню:
,
де
тепловий потік.
= К· ∆tср
Задаємося
q=79685.
Обчислюємо
.
Перевіряємо значення q.
Необхідна поверхня теплопередачі:
Приймаємо трубки діаметром 57/4 мм і завдовжки 1,5 м.
Тоді необхідне число трубок:
=
Приймаємо 613 трубок, що розміщуються на 13 шестикутниках.
Тоді діаметр трубчатки буде:
,
де
число шестикутників;
крок розміщення трубок;
відстань від кожуха,
.3 Ідентифікація змінних
Таблиця 11.4 - Ідентифікація змінних та констант
Змінна в описі
|
Змінна в програмі
|
Фізичний сенс змінної, її розмірність
|
Значення змінної
|
1
|
2
|
3
|
4
|
Gс1
|
Gс1
|
Маса сульфату амонію, кг/год
|
4262
|
Gк1
|
Gк1
|
Маса сульфатної кислоти, кг/год
|
106,6
|
Gп1
|
Gп1
|
Маса сульфату піридину, кг/год
|
51,4
|
Gв1
|
Gв1
|
Маса води, кг/год
|
6235
|
Gп
|
Gп
|
Маса пару, кг/год
|
4858
|
∑G1
|
∑G1
|
Маса разом, кг/год
|
визначається
|
∑G2
|
∑G2
|
Маса разом, кг/год
|
визначається
|
∑G3
|
∑G3
|
Маса разом, кг/год
|
визначається
|
Gсс
|
Gсс
|
Маса сухого сульфату амонію, кг/год
|
2954
|
α1
|
α1
|
Коефіцієнт тепловіддачи, кДж/(м2·год·град)
|
41900
|
t1
|
t1
|
Температура розчину °С
|
58,9
|
Мса
|
Mса
|
Молярна маса сульфату амонію, кг/кмоль
|
132
|
К
|
K
|
Коефіцієнт теплопередачі, кг/(м2·год·град)
|
визначається
|
F
|
F
|
Плоша поверхні теплопередачі
|
визначається
|
D
|
D
|
Діаметр трубчатки, м
|
визначається
|
11.4 Аналіз результатів розрахунку
В результаті розрахунку ЕОМ були знайдений основні показники
випарника, а також основні баланси процесу.
Проводячи аналіз приведених вище результатів, можна
однозначно говорити про повну працездатність програми, правильності складання
алгоритму розрахунку.
Значення результатів не виходять за межі похибки.
. ЕКОНОМІЧНЕ ОБҐРУНТУВАННЯ ПРОЕКТУ УЛОВЛЮВАННЯ ПІРИДИНОВИХ
ОСНОВ
12.1 Визначення капітальних витрат
Витрати на створення нових і реконструкцію діючих основних
фондів прийнято вважати капітальними витратами. З огляду на пропоновані вимоги
до диплома в розділі дипломного проекту розраховуємо тільки прямі витрати на
створення основних виробничих фондів.
У відповідності Закону України «Про оподаткування прибутку
підприємств» під терміном «основні фонди» варто розуміти матеріальні цінності,
використовувані у виробничій діяльності платника податків протягом періоду, що
перевищує 365 календарних днів з дати введення в експлуатацію таких
матеріальних цінностей, і вартість яких поступово зменшується у світлі з
фізичним або моральним зношуванням.
Відомо, що складові величини прямих капітальних вкладень
включають:
витрати на будівництво будинків і споруджень,
вартість складських і підсобних приміщень,
вартість основного технологічного устаткування,
витрати на монтаж, футеровку, приладів КВП.
Шукані величини капітальних вкладень, основу яких становлять
основні виробничі фонди проектованого підрозділу, визначаємо за укрупненими
показниками. За укрупненими показники приймаємо дані реально діючого
підприємства ПАТ «Авдіївський КХЗ» цех уловлювання продуктів коксування, такі
як: норми амортизації, первісну вартість основних фондів, термін служби
устаткування, ліквідаційну вартість устаткування та ін. З огляду на дані
галузевої структури основних фондів, а також, рекомендованої Законом України
їхньої класифікації, визначаємо балансову вартість основних виробничих фондів.
Виконаний розрахунок зводимо в таблицю 12.1.
Таблиця 12.1-Балансова вартість основних фондів
Типові класифікаційні групи основних виробничих
фондів
|
Балансова вартість, грн
|
Питома вартість,%
|
1 група - Піридинова установка: нейтралізатор,
сепаратор, мірник, кристалоприймач, конденсатор-холодильник, сховище
піридинових основ.
|
1004632
|
92
|
2 група - автомобільний транспорт і вузли,
електромеханічні прилади, агрегати та ін.
|
342789
|
5
|
3 група - будь-які інші основні фонди, які не
включені в 1 та 2 групи
|
52693
|
2
|
4 група - системи й кошти ЕОМ, ТV, селекторного
зв'язку та ін.
|
44150
|
1
|
Усього балансова вартість
|
1444264
|
100
|
Визначивши балансову вартість активної частини основних
коштів, розрахуємо амортизаційну суму.
У відповідності зазначеного вище Закону України,
амортизаційна сума визначається за формулою:
,
де А - річна амортизаційна сума, грн;
Б - балансова вартість основних фондів на момент розрахунку
амортизаційної суми, грн;
п- середня норма амортизації, %.
грн,
12.2 Розрахунок чисельності працівників
При виконанні цього розділу треба керуватися принципом забезпечення
планового обсягу випуску продукції економічно обґрунтованою чисельністю
працюючих за рахунок застосування прогресивних норм часу, багатоверстатного
обслуговування, поєднання професій.
Приймаємо режим роботи первинний, умови шкідливі, режим 1-змінний.
Необхідно скласти баланс часу одного працівника (табл. 12.2):
Таблиця 12.2 - Визначення робочого часу одного працівника
Стаття балансу
|
Дні
|
Число календарних днів
|
365
|
Кількість неробочих днів: святкових вихідних
|
- 91
|
Максимальний фонд часу роботи одного працівника
|
274
|
3.Заплановані невиходи з причин: - чергова і
додаткова відпустка - невиходи із-за хвороби та відпустка по вагітності -
виконання державних і громадських обов’язків - учбова відпустка без відриву
от виробництва
|
30 12 1 1
|
Всього за статтею 3
|
44
|
Всього плановий номінальний фонд У тому числі годин:
нічних вечірніх
|
230 607 313
|
Розрахунок чисельного складу основних виробничих робітників
ведемо по нормах обслуговування робочих місць, машин, апаратів. На
підприємствах розрізняють обліковий й явочний склад основних робітників Явочний
склад - це та чисельність, що зайнята роботою в зміні або змінах. Облікова чисельність
основних робітників більше явочної на, так називану, величину підмін.
Коефіцієнт величини підмін визначаємо за формулою:
,
де
- плановий фонд часу роботи основного технологічного
устаткування, днів;
- номінальний фонд часу роботи одного середньооблікового
робітника, днів.
Явочну чисельність основних виробничих робітників визначаємо за
формулою:
,
де Ряв - явочна чисельність основних робітників, чол.;-
кількість робочих місць, що обслуговують;
п - норма обслуговування робочого місця, чол.;
с - кількість змін.
чол.;
Прийняте число робочих 13 чоловік.
Облікову чисельність основних робітників визначимо за формулою:
чол.,
Прийняте число робочих 21 людина.
Отриману чисельність основних робітників зводимо в таблицю 16.3
штатного розкладу.
Таблиця 12.3-Плановий штатний розклад основних робітників
Перелік основних професій
|
Тариф, розряд
|
Обліковий склад
|
I. Піридинова установка 1. Апаратник виробництва
малотоннажної продукції
|
5
|
6
|
Разом по Ι
|
|
6
|
II. Сульфатне відділення 1. Апаратник отримання
сульфату амонію 2. Апаратник отримання сульфату амонію
|
6 5
|
5 10
|
Разом по ΙΙ
|
|
15
|
III. Чергова група 1. Електрослюсар із ремонту й
обслуговуванню 2. Слюсар-ремонтник
|
5 5
|
4 4
|
Разом по ΙΙI
|
|
8
|
IV. Ремонтна група 1. Водій навантажувача 2.
Електрослюсар із ремонту й обслуговуванню електроустаткування 3.
Електрослюсар із ремонту й обслуговуванню електроустаткування 4.
Електрослюсар із ремонту й обслуговуванню електроустаткування 5.Інший
ремонтний персонал групи
|
4 6 5 4
|
3 2 4 5 43
|
Разом по IV
|
|
57
|
Усього основних робітників
|
5,38
|
Усього основних й обслуговуючого персоналу
|
|
86
|
12.3 Розрахунок фонду оплати праці
основних виробничих працівників
В основу розрахунку планового фонду оплати праці основних
виробничих працівників приймаємо тарифну систему з почасово - преміальною
формою її розрахунку. Система преміювання основних працівників базується на
«положенні о преміюванні…» розроблений на підприємстві. В основі вказаного
положення лежить :
виконання плану по виробництву;
дотримування технологічних режимів;
відсутність рекламацій зі сторони споживача товарної
продукції;
дотримання вимог з ОП і ТБ.
У розрахунках приймаю середню величину преміювання у розмірі
40%.
Плановий фонд оплати праці робочих проектувального підрозділу
знаходимо з обліком усіх складових його утворюючих.
В основу укладені рекомендації заводських та галузевих вимог
при обчислюванні фонду оплати праці (ФОП), а також дотримання положень КЗоПа,
рішень уряду України.
Звісно ФОП включає заробіток по тарифу (Зт) та
доплат к тарифному заробітку. Так у загальному вигляді фонд оплати праці може
бути наведений у формулі:
ФОП = Зт + Здоп, грн
Визначаємо заробіток по тарифу за формулою:
Зт = Тст ∙ Вн ∙
Ш ∙ С , грн,
де Зт - заробіток по тарифу;
Тст - середньо година тарифна ставка;
Вн - номінальний фонд часу роботи одного
середньоспискового працівника;
Ш - штатна кількість основних виробничих працівників;
С - тривалість змін в годинах.
Визначення заробітку по тарифу потребує розрахунку середнього
тарифного розміру та відповідно середньої тарифної ставки. Розрахунки
показують, що середній тарифний розряд одного середньоспісочного робітника
відповідає 5, тоді, тарифна ставка вказаного розряду відповідає 10,27 грн/год.
Допоміжна заробітна плата - це винагородження за працю зверх
встановлених норм, за особливі умови праці. Вона складається з доплати,
надбавок, гарантованих та ком пенсійних виплат встановлених законодавством,
премії.
Зт = 10,27∙230∙28·8 = 529110 грн
Визначимо доплату за роботу нічний час за формулою:
Зніч = (Тст ∙ Вніч ∙
Ш) ∙
;
Зніч = (10,27 ∙607 ∙ 28) ∙
= 69819 грн.
Доплата за роботу у вечірні часи:
Звеч = (Тст ∙ Ввеч ∙
Ш) ∙
;
Звеч= (10,27∙ 313 ∙28) ∙
= 18001 грн.
Визначимо суму премій по виробництву:
Зпрем = (Зг+Звеч+Зніч)
∙
;
Зпрем= (529110+18001+69819) ∙
= 246772 грн.
Визначимо доплату до тарифного заробітку за переробітку по
графіку:
Згпер = 0,5(Тст ∙ Впер
∙ Ш);
Згпер= 0,5∙10,27∙62∙28
= 8914 грн.
Доплата за роботу у святкові дні:
Зсв = Тст ∙ Всв ∙
Ш;
Зсв= 10,27∙80∙28 =2240 грн.
Визначимо суму оплати чергової та додаткової відпуски:
Звід = (Зг+Зніч+Звеч+Згпер+Зпрем+Зсв)
∙
;
529110+69819+18001+8914+246772+2240)
114112 грн.
Визначимо суму доплати за навчання без відриву від
виробництва:
Знавч = (Зг+Зніч+Звеч+Згпер+Зпрем+Зсв)
∙
= 3804 грн;
Знавч
529110+69819+18001+8914+246772+2240)
=3804 грн.
Отримані розрахунки позволяють визначити ФОП, який
відповідає:
ФОП = Зт+Здопл;
ФОП= 529110+345746 = 874856 грн.
Таким чином, отриманий розрахунком плановий ФОП робітників
проектованого відділення, відповідає значенню реально діючого виробництва, про
що свідчать заводські данні, так середньомісячна величина заробітку з
урахуванням відчислень, відповідає порядку 2700грн. Дані розрахунку ФОП наведені
в таблиці 12.4
Таблиця 12.4 - Данні розрахунку фонду оплати праці
Найменування
|
Сума, грн.
|
Заробітна плата по тарифі
|
529110
|
Додаткова заробітна плата: доплата за роботу вночі
доплата за роботу ввечері оплата виробничої премії доплату за переробітку по
графіку доплата за роботу у святкові дні:
|
69819 18001 246772 8914 2240
|
Всього
|
345746
|
Разом
|
874856
|
Таким чином, отриманий розрахунком плановий ФОП робітників
проектованого відділення, відповідає значенню реально діючого виробництва, про
що свідчать заводські данні, так середньомісячна величина заробітку з
урахуванням відчислень, відповідає порядку 2700грн.
12.4 Визначення собівартості
продукції виробництва
Собівартість - це сукупність витрат, пов’язаних з
виробництвом і збутом продукції. Ціль планування собівартості є визначення
напрямку, складу й рівня витрат на виробництво продукції в плановому періоді.
Головним завданням планування собівартості є збільшення прибутку, зниження
собівартості й підвищення рентабельності підприємства. Розрахунок калькуляції
собівартості продукції проводиться на основі обсягу виробництва, норм
використання матеріалів, палива, енергії й планово-заготівельних цін,
розрахункового фонду заробітної плати працівників, кошторису цехових витрат і
інших показників. Розрахунок собівартості продукції здійснюється на весь випуск
і на калькуляційну одиницю. У хімічних виробництвах калькуляційними одиницями
є: вагові, об’ємні, штуки, метри й ін.. Вагові одиниці приймають із певним
змістом речовини. Вагові одиниці в натурі (технічна вага) проставляються без
вказівки змісту корисної речовини (наприклад: синтетичний каучук і ін.).
Калькуляція собівартості групи однорідних виробів вимога
встановлення коефіцієнта перерахування натуральної кількості виробів даної
групи в умовні одиниці. Основні техніко-економічні показники виробництва
сульфату амонію на 2013 р. представлені в табл.. 12.5 (дані взяті в
економічному відділі Авдіївського КХЗ).
Таблиця 12.5 - Основні показники виробництва сульфату амонію
на 2013 р. (на одиницю виробництва 1000 шт.).
Статті витрат
|
Виготовлено підприємством, грн.
|
1 Сировино та матеріали: Газ очищений від смоли
Сірчана кислота: Кислота сірчана-с/сч №1 Кислота сірчана зі сторони Кислота
сірчана с/оч №2 Разом сірчаної кислоти Відпрацьований содовий розчин Сульфат
амонію 1 сорт кисла смолка Залишки від чистки обладнання
|
19501716 2255915,7 616729 2872644,7 37983 387924
3546 287
|
2 Паливо та енергія: Електроенергія Теплоенергія
Вода зворотна стиснене повітря електрогазодувки
|
76222 593541 232061 2368 347788
|
Осн. Заробітна плата виробничим робочим
|
26789
|
Додаткова заробітна плата
|
30751
|
Відчислення на соціальні заходи
|
22245
|
Загальновиробничі витрати
|
66808
|
Амортизація
|
101130
|
Усього виробнича собівартість
|
24107181
|
12.5 Визначення виробничої
собівартості уловлювання піридинових основ
Витрати на виробництво та збиту виробничої продукції
регламентується галузевим та заводськими нормативними документами. Як правило,
інструкції визначають типовий документ (форму) по якому визначають витрати на
виробництво продукції. Такий документ називається калькуляцією собівартості.
У якості прикладу складемо калькуляцію собівартості
уловлювання піридинових основ та отриманні дані складемо в таблицю 12.6 витрат
на одиницю продукції піридину.
Таблиця 12.6 - Калькуляція собівартості по уловлюванні легких
піридинових основ і хіноліну.
Найменування статей витрат
|
од. вим.
|
На весь обсяг виробництва
|
На одиницю
|
|
|
кіль-кість
|
ціна, грн.
|
сума, грн.
|
норма витрат
|
сума, грн.
|
1
|
2
|
3
|
4
|
5
|
6
|
7
|
1. Сировина, напівфабрикати й основні матеріали Власного
виробництва:
|
|
|
|
|
|
|
- маточний розчин
|
т.м3
|
4300
|
21,995
|
94579
|
1,0944
|
24,073
|
- аміачна вода
|
т
|
2404,9
|
5,3
|
12746
|
0,067
|
0,35
|
Разом по ст. 1
|
грн
|
|
|
107325
|
|
24,423
|
2. Енергія на технологічні цілі:
|
|
|
|
|
|
|
Електроенергія
|
квт/г
|
3302150
|
0,12746
|
420885
|
17,183
|
2,190
|
Теплоенергія з ТЭЦ
|
г/кал
|
32055
|
29,6560
|
950623
|
0,1668
|
4,947
|
Вода оборотна
|
т.м3
|
6730
|
109,183
|
734804
|
0,0350
|
3,824
|
Разом по ст. 2
|
грн
|
|
|
2106312
|
|
11,741
|
3. Оплата праці - основна - додаткова
|
грн грн.
|
|
|
78301 80955
|
|
0,407 0,421
|
4. Відрахування на соціальні заходи
|
грн
|
|
|
63002
|
|
0,328
|
5. Амортизація основних засобів і нематеріальних
активів
|
грн
|
|
|
|
|
3,106
|
6. Затрати на ремонт основних засобів 7. Затрати на
утримання основних засобів 8. Інші цехові витрати
|
грн грн грн
|
|
|
103478 262535 623634
|
|
3,244 3,089 3,245
|
Разом
|
грн
|
|
|
716150
|
|
50,497
|
9. Непрямі витрати у тому числі: - зміні - постійні
|
грн грн
|
|
|
339700 228597
|
|
1, 768 1,19
|
Разом
|
грн
|
|
|
568297
|
|
28,539
|
Разом виробнича собівартість готової продукції
|
грн
|
|
|
3498084
|
|
115,2
|
12.6 Розрахунок економічної
ефективності технологічного рішення
Цей підрозділ передбачає розрахунок
суми прибутку від реалізації запропонованого рішення і обґрунтування показників
його економічної ефективності на найближчі 3 роки.
Обсяг реалізації (V) розраховується в
такий спосіб:
,
де n - кількість найменувань (видів) продукції;
-
планована до продажу продукція кожного виду продукції
,
;
-
передбачувана ринкова ціна кожного виду продукції
,
.
грн/р
Приймаємо ринкову ціну для продажу 250 грн/кг піридину та 180 грн/л
хіноліну, виходячи з бажаного рівня рентабельності
Так, якщо підприємство буде випускати продукцію
більш високої якості, то ринкова ціна може бути збільшена.
На підставі прогнозів обсягів реалізації і
розрахунків за собівартістю продукції складається план доходів і витрат на 3
роки, який
дозволяє оцінити перспективи отримання позитивних економічних результатів за
проектованим технічним рішенням. Результати розрахунків вносяться у таблицю 12.7.
Таблиця 12.7 - Прогноз доходів і витрат на 3 роки
установки уловлювання піридинових основ, тис. грн.
Статті витрат/доходів
|
Роки
|
|
1 рік
|
2 рік
|
3 рік
|
1. Дохід від продажу продукції:
|
955260
|
955260
|
955260
|
2. Повна собівартість
реалізованої продукції
|
530726,4
|
530726,4
|
530726,4
|
3. Фінансовий результат до
оподаткування: - прибуток - збиток
|
424533,6
|
424533,6
|
424533,6
|
4. Сума податку на прибуток
|
80661,384
|
80661,384
|
80661,384
|
5. Фінансовий результат після
оподаткування: -
чистий прибуток - чистий збиток
|
343872,22
|
343872,22
|
343872,22
|
Економічна ефективність впровадження
пропонованих технічних рішень передбачає розрахунок показника:
Оцінка періоду окупності капітальних
вкладень, пов’язаних із впровадженням даного технічного рішення:
,
де ТОК - період окупності, роки;
КВ - капітальні витрати, пов’язані із реалізацією технічного рішення,
грн.;
ЧП - середньорічний чистий прибуток від виробничої діяльності, грн.
В результаті техніко-економічного обґрунтування була розрахована
собівартість продукції, яка склала 115,2 грн. При реалізації об’єму продаж
955260 грн/р, загальна сума об’єму та витрат 343872,22 грн, що дозволило
визначити період окупності
4,2
роки, виходячи з цього можна вважати, що впровадження даного проекту установки
уловлення легких піридинових основ у сульфатне відділення цеху уловлювання №1
Авдіївського КХЗ являється економічно обґрунтованим.
. ОХОРОНА ПРАЦІ ТА БЕЗПЕКА ПРИ НАДЗВИЧАЙНИХ СИТУАЦІЯХ
14.1 Стисла характеристика виробництва та його
шкідливі фактори
Призначення сульфатного відділення - вилучення із коксового газу
аміаку, отримання сульфату амонію, переробка надлишкової аміачної води,
утилізація відпрацьованого содового розчину цехів сіркоочищення №1,2.
Після нагнітачів коксовий газ, що
містить 6-10 г/
аміаку, надходить у колектор входу газу в аміачні абсорбера.
Коксовий газ надходить в нижню частину абсорбера, де зрошується матковим
розчином.
Розчин на зрошення абсорбера
подається з циркуляційного збірника подачі, в якому підтримується заданий зміст
вільної сірчаної кислоти і питома вага. З нижніх двох ярусів форсунок розчин
стікає на днище абсорбера і через гідрозатвор потрапляє до збірки повернення.
Вміст вільної сірчаної кислоти в цьому розчині повинно бути 0,8-1%. З верхнього
ярусу форсунок і з центральної форсунки розчин, пройшовши через абсорбер,
потрапляє на розділову тарілку, яка перешкоджає змішуванню повертаються з 1,2 і
з 3 ярусів розчинів. З тарілки, через гідрозатвор, розчин з вмістом вільної
= 1,2-1,4% повертається до збірки
подачі.
Зі збірника повернення розчин з
кислотністю 0,8-1% виводиться в живильні збірники для додаткового відстою перед
подачею у випарники.
Маточний розчин, який містить 40%
сульфату амонію з живильних збірників подається у випарники живильними
насосами. Випар і кристалізація розчину відбуваються під вакуумом.
При досягненні необхідної
концентрації кристалів в випарнику, отримана пульпа безперервно подається
насосом в центрифугу. Маточний розчин відділяється в центрифузі від кристалів і
самопливом повертається в циркуляційний збірник подачі, а кристали сульфату
після центрифуги транспортерами подаються в сушильне відділення.
Вологий сульфат амонію за температури
35
та вологістю в 5% надходить до
бункеру вологого матеріалу. У якості теплоносію застосовується повітря, що
нагрівається парою в калорифері.
Нагрітий теплоносій із температурою
125
крізь газорозподільну коробку
сушарки подається під решітку сушильної зони із швидкістю, що забезпечує
утворення стійкого киплячого шару солі.
Частки сульфату амонію, що виносяться
крізь газовідвідні труби, надходять до циклону та періодично передаються на
стрічковий конвеєр.
Висушений та охолоджений сульфат
амонію надходить до бункеру сухого матеріалу та періодично передається на
стрічковий конвеєр. За допомогою стрічкового конвеєра сульфат амонію надходить
на склад.
Початковою сировиною є коксовий газ з
вмістом аміаку (6
10)г/
.
Кінцевою продукцією є сульфат амонію
першого сорту.
Сульфат амонію не пожежонебезпечний.
Шкідливим фактором є пил. Гранично припустима концентрація в робочій зоні 10
мг/
. Періодичність контролю шкідливих
речовин у повітрі робочої зони - не рідше 1 разу у квартал.
При здійсненні технологічних процесів
у повітрі робочої зони на різних робочих місцях можливе виділення шкідливих
речовин і вплив на працюючих шкідливих факторів. Наприклад, апаратник отримання
сульфату амонію знаходиться під впливом сірчаної кислоти, сірководню, аміаку,
нафталіну, пилу сульфату амонію.
Фенол, нафталін володіють високою
летючістю. Пари їх уражають слизисту оболонку ока і дихальних шляхів. При
контакті з шкірою ці речовини викликають запальні реакції, а проникаючи в
організм викликають загальну токсичну дію на ряд органів і систем. Фенол надає
в основному місцеву дію й у меншій мірі впливає на функції центральних відділів
нюхового аналізатора. Навпаки, нафталін у першу чергу приводить до порушення
відповідних нервових процесів у кірковому відділі аналізатора в бік первинного
гальмування при відносно слабкій місцевій дії.
Сірководень надає як місцеву (на
слизисті оболонки), так і загальнотоксичну дію. При концентраціях близько 1,2
мг/л і вище спостерігається блискавична форма отруєння. Смерть наступає
унаслідок кисневого голодування, яке викликається блокуванням тканинного
дихання в зв’язку з пригнобленням клітинних окислювально-відновних процесів.
При концентраціях сірководню в межах від 0,02 до 0,2 мг/л і вище наголошуються
симптоми отруєння з боку нервової системи, органів дихання і травлення.
З’являється головний біль, запаморочення, безсоння, загальна слабкість, зниження
пам’яті, чхання, кашель, ускладнення дихання й в окремих випадках гострий
набряк легенів із смертельним наслідком. Спостерігається гіперсалівація,
нудота, блювота, пронос. Характерна поразка слизистої оболонки очей -
кон’юктивіт, світлобоязнь. Суміш сірководню з повітрям, що містять від 4 до 45
об’ємних відсотків цього газу, вибухонебезпечні.
Характерними ознаками аміачного
токсикозу є звичайне підвищення збудливості, розвиток судом, пригноблення
дихального центру. Невеликі дози аміаку приводять до підвищення
умовно-рефлекторної збудливості. Великі дози аміаку, навпаки, викликають
зникнення умовних рефлексів.
Сірчана кислота викликає хімічні
опіки шкіри, око.
Пил сульфату амонію порушення життєве
важливих функцій органів дихання, викликає кашель, кисневе голодування
організму.
Процес виробництва сульфату амонію
також супроводжується значним шумом і вібраціями, джерелами яких є
нейтралізатори, сушарки, насосні установки, апарати з пристроями, що
перемішують.
Підвищення рівня шуму і вібрації на
робочих місцях впливає на організм людини.
У результаті тривалого впливу шуму
порушується нормальна діяльність серцево-судинної і нервової системи, травних і
кровотворних органів, розвивається професійна приглухуватість, прогресування
якої може привести до повної втрати слуху.
Вібрація впливає на центральну
нервову систему, шлунково-кишковий тракт, органи рівноваги (вестибулярний
апарат), викликає запаморочення, оніміння кінцівок, захворювання суглобів.
Тривалий вплив вібрації викликає професійне захворювання - вібраційну хворобу,
ефективне лікування якої можливо лише на ранніх стадіях, причому відновлення
порушених функцій протікає вкрай повільно, а за певних умов в організмі можуть
наставати необоротні процеси, що приводять до повної втрати працездатності.
Під впливом інтенсивного шуму і
вібрації настають стомлюваність, дратівливість, поганий сон, головний біль,
ослаблення пам’яті, уваги, гостроти зору, що веде до зниження продуктивності
праці (у середньому на 10
15 %) і часто є причиною травматизму.
Крім можливого впливу шуму і вібрацій
робітники під час виробничого процесу можуть піддаватися впливу інфрачервоного
випромінювання, підвищених і знижених температур, вологості навколишнього
середовища.
У літній період робітники можуть
піддаватися впливу підвищених температур, а в зимовий період впливу знижених
температур атмосфери.
14.2 Заходи щодо поліпшення праці
Вимоги, щодо поліпшення праці,
передбачають:
усунення безпосереднього контакту
робітників з вихідними матеріалами, готовою продукцією і відходами виробництва,
що роблять шкідливий вплив;
застосування систем контролю і
керування технологічним процесом, що забезпечує захист працюючих і аварійне
відключення виробничого устаткування;
своєчасне видалення і знешкодження
відходів виробництва, що є джерелами шкідливих і небезпечних виробничих
факторів;
застосування засобів колективного
захисту працюючих.
Робітникам, які працюють у відділенні
забороняється:
працювати на устаткуванні з
виділенням пари і газів, з пропусками кислоти, розчину.
знижувати щільність розчину
циркуляції нижче 1,22 г/
.
подавати кислоту в збірники
циркуляції на шар смоли.
приймати зі складу сірчану кислоту з
концентрацією нижче 91% і вище 94% (зимовий час), а також зі вмістом окислів азоту
вище 0,001%.
спорожняти гідрозатвори циркуляції
без відключення скруберів по газу.
працювати при наявності газових
виділень з апаратури і комунікацій в атмосферу, особливо в приміщеннях.
Усе технологічне обладнання,
електричне, вентиляційне та металеві трубопроводи повинні бути заземлені шляхом
з'єднання струмопровідними перемичками на всьому протязі даної системи в
безперервний електричний ланцюг і приєднані не менш, ніж у двох місцях до
контурів заземлення електрообладнання і блискавкозахисту з дотриманням вимог
ПУЕ. Застосування безпечної напруги (12 В) при чищенні апаратури.
14.2.1 Розрахунок заземлення
насосної установи
Розрахунок заземлення проводиться для
того, щоб визначити опір споруджуваного контуру заземлення при експлуатації,
його розміри і форму. Як відомо, контур заземлення складається з вертикальних
заземлювачів, горизонтальних заземлювачів і заземлюючого провідника.
Вертикальні заземлювачі забиваються в ґрунт на визначену глибину.
Горизонтальні заземлювачі з'єднують
між собою вертикальні заземлювачі. Заземлюючий провідник з'єднує контур
заземлення безпосередньо з електрощитом.
Розміри і кількість цих заземлювачів,
відстань між ними, питомий опір ґрунту - всі ці параметри безпосередньо
впливають на опір заземлення.
Розрахунковий питомий опір:
,
де -
- еквівалентний питомий опір ґрунту,
Ом·м;
- сезонний кліматичний коефіцієнт
(за довідником
);
- опір однієї фази відносно землі (
Ом)
,
Опір розтікання струму одного
вертикального заземлювача (стрижня):
,
де l - довжина
заземлювача, (l=2-3)м;- його діаметр, (3-5)см;- відстань від поверхні землі до
середини заземлювача (
), м.
Ом
Кількість паралельно
з’єднаних одиночних заземлювачів визначається за формулою:
,
де
- коефіцієнт корисної дії заземлювачів (за довідником
0,7);
(1000в)
.
.
Довжина
горизонтальної з'єднувальної полоси:
,
де а - відстань між
заземлювачами (а=5
8), м;
.
Опір з’єднувальної
полоси:
,
де
- коефіцієнт попиту горизонтальних заземлювачів (з
довідника 0,7);
- діаметр полоси (
=2
4), см;
- глибина закладення полоси (0,8-0,9).
Ом.
Визначимо
результуючий опір заземлюючого пристрою:
,
Якщо
чи
не
можна проводити подальший розрахунок (розрахунок невірний), треба повернутися
до розрахунку довжини горизонтальної з’єднувальної полоси.
Ом
Розрахунок заземлення
обладнання:
,
де
- опір тіла людини (1000 Ом);
- фазова напруга (380 В);
- опір однієї фази відносно до землі.
1,55 А.
Коефіцієнт
використання показує, як впливають один на одного струми розтікання з одиночних
заземлювачів при різному розташуванні останніх. При з'єднанні паралельно,
струми розтікання одиночних заземлювачів роблять взаємний вплив один на одного,
тому чим ближче розташовані один до одного заземлюючі стрижні тим загальний
опір заземлюючого контуру більше.
14.2.2 Розрахунок витяжної
вентиляції
Процес отримання сульфату амонію
супроводжується виділенням великої кількості пилу, тому приміщення обов’язкове
повинно бути оснащене вентиляцією. Найбільш ефективної в даному випадку буде
приточно-витяжна вентиляція.
Для створення нормальних
санітарно-гігієнічних умов праці в приміщенні, де відбувається пресування,
передбачена приточно-витяжна і природна вентиляція, що здійснюється за рахунок
передбачених у конструкції будинку вентиляційних ліхтарів.
Кількість повітря, що подається в
приміщенні при боротьбі зі шкідливими виділеннями, визначається по формулі:
де L - повітрообмін,
;- кількість шкідливих виділень, що
виділяються за одну годину;
- гранична припустима концентрація
пилу сульфату амонію,
мг/
;
- гранично припустима концентрація
шкідливості в зовнішнім повітрі.
Отже, при проектуванні необхідно забезпечити в системі
вентиляції даної ділянки подачу чистого повітря в кількості
.
Визначимо сумарні втрати тиску воздуховода:
∑P =
,
де
- утрати тиску при терті повітря об стінки воздуховода;
- утрати тиску в місцевій частині воздуховода.
;
,
де
- коефіцієнт тертя, що залежить від шорсткості стінок;
- щільність повітря,
;
- довжина воздуховода,
-
діаметр воздуховода, м;- швидкість руху повітря.
,
де F - гідравлічний
радіус поперечного перерізу воздуховода,
;
;
;
Па;
Па;
.
За знайденим
значенням P і L визначимо ККД вентилятора:
.
Визначимо потужність
вентилятора:
;
квт.
14.2.3
Пожежна безпека
В усіх випадках
виникнення пожежі на підприємстві чи появи гару й інших ознак горіння
обслуговуючий персонал цеху чи установки зобов’язаний вжити заходів для
ліквідації вогню, використовуючи наявні в наявності засобу пожежогасіння, і по
встановленому зв’язку викликати пожежну охорону. Пожежний зв’язок поділяють на
зв’язок оповіщення, ціль якого - своєчасний виклик на пожежу, диспетчерську -
для керування силами і засобами пожежогасіння і зв’язок на пожежі - для
керівництва пожежними підрозділами при гасінні пожежі. Ці види зв’язку
забезпечують телефонами, радіопередавачами і пожежною сигналізацією.
Вогнегасні засоби
можуть бути рідкими (вода, розчин солей), газоподібними (водяники пари,
газоподібна вуглекислота), пінотипними, твердими (суха земля, пісок, тверда
вуглекислота). Найбільш розповсюдженим способом боротьби з вогнем є вода, що
застосовують для гасіння більшості пожеж.
Для посилення
вогнегасних властивостей води в неї додають кислотно-лужний порошок. У цьому
випадку утвориться хімічна піна, при введенні якої в зону вогню виникає хмара
інертного газу, що перешкоджає доступу повітря в сферу вогню. Хімічну піну
використовують для гасіння всіх нафтопродуктів (з температурою спалаху до 45
) і твердих пальних речовин.
Кожен працівник
повинен дотримувати наступні правила пожежної безпеки:
проведення тимчасових
вогневих робіт на території й у приміщенні цеху, розведення багать і інших
випадків застосування відкритого вогню дозволяється тільки після оформлення
плану проведення вогневих робіт і твердження його головним інженером заводу.
постійні вогневі
роботи проводити у встановлених наказом директора місцях і виробництвах.
при роботах у пожеже
і вибухонебезпечних місцях користуватися інструментом не дає іскріння.
не курити на
території й у приміщеннях цеху. Курити дозволяється тільки в спеціально
відведених місцях.
первинні засоби
пожежогасіння на робочих місцях повинні бути в наявності і міститися в чистоті
і справності, передаватися по зміні.
забороняється
застосовувати бензол, бензин, розчинники й інші легкозаймисті рідини для миття
рук, підлог, стін, вікон і чищення спецодягу в приміщеннях цеху.
систематично стежити
за герметичністю устаткування, апаратів і комунікацій, не допускаючи витоку
пар, рідин.
збереження газу,
бензину, мастильних матеріалів, карбіду кальція дозволяється тільки в
спеціально відведених місцях.
балони з газом
установлювати удалині від джерел тепла.
категорично
забороняється працювати з кисневими балонами в промаслених рукавицях і
спецодязі, чи забрудненими олією руками.
категорично
забороняється гасити електроустаткування водою, піною, пінними вогнегасниками.
при загорянні
усередині приміщення негайно зупинити виробництво, відключати вентиляційні
системи від електропостачання.
використання
пожежного устаткування й інвентарю для виробничих, господарських і інших
нестатків, не зв’язаних з пожежогасінням, забороняється.
для внутрішнього
висвітлення апаратів, цистерн, ємкостей під час їхнього огляду, чищення і
ремонту повинні застосовуватися тільки вибухозахищені акумуляторні переносні
лампи напругою не вище 12 В з захисними ковпаками і сітками
14.3
Безпека при надзвичайних ситуаціях
Аналіз умов
виникнення та розвитку аварії технологічного блоку (таблиця 14.1)
Таблиця 14.1 - Умови
виникнення та розвитку аварій
Найменування стадії розвитку аварійної ситуації
(аварії)
|
Основні принципи аналізу умов виникнення (переходу
на іншу стадію) аварійної ситуації (аварії) та її наслідків
|
Способи і засоби попередження, локалізації аварії
|
1
|
2
|
3
|
1. Вихід параметрів за критичні значення
|
Перевірка вивченості властивостей звертаються
продуктів; їх аналіз; виявлення особливо небезпечних речовин; виявлення
параметрів, що визначають небезпеку технологічних процесів і їх критичні
значення; оцінка достатності оснащення засобами, що виключають вихід
параметрів за допустимі межі, їх ефективність, надійність
|
Дооснащення технологічних процесів засобами
контролю, управління і протиаварійного захисту, підвищення їх надійності й
ефективності; удосконалення технологічних процесів
|
2. Вибух в апаратурі
|
Наявність постійних і випадкових джерел запалювання
і їх характеристики в порівнянні з температурою самозаймання і мінімальною
енергією запалювання. Наявність вибухонебезпечної суміші
|
Виключення джерел запалювання, застосування засобів
контролю і регулювання по запобіганню утворення вибухонебезпечної суміші
|
3. Руйнування апаратури
|
Аналіз кількісних енергетичних характеристик вибух
(надлишковий тиск, швидкість зростання тиску) і порівняння їх з
характеристиками міцності апаратури. Наявність засобів захисту обладнання від
руйнування при вибуху (запобіжні клапани, розривні мембрани, агрегати тощо)
|
Оснащення запобіжними пристроями, автоматичними
системами придушення вибуху, підвищення міцнісних характеристик апаратури
|
4. Знос, втома матеріалу, апарату
|
Перевірка вивченості корозійних властивостей
звертаються речовин; наявність даних про швидкості корозії та зносу;
відповідність матеріалу обладнання (трубопроводів), захисного покриття
ущільнювальних матеріалів. Наявність умов для механічного пошкодження
обладнання (трубопроводів) від зовнішніх і внутрішніх джерел впливу
|
Застосування устаткування підвищеної надійності,
ефективного захисного покриття і захисних пристроїв
|
5.Розгерметизація апаратури
|
Перевірка відповідності обладнання, трубопроводів,
запірної арматури, запобіжних і ущільнювальних пристроїв і т.д. вимогам
нормативів (проекту, регламентами); оцінка технічного стану апаратури (якість
зварних з'єднань, складання роз'ємних з'єднань, ступінь зносу тощо); оцінка
порядку і повноти діагностичного контролю, ефективності
планово-попереджувальних ремонтів і т.п.
|
Розвиток бази діагностування та дефектоскопії
устаткування; вдосконалення системи планово-попереджувального ремонту; заміна
морально застарілого, зношеного і не відповідає нормативам обладнання
|
6. Травмування людей
|
Аналіз кількісних енергетичних характеристик пожежі
(енергія випромінювання) і вибуху; наявність і чисельність людей у зоні
можливого ураження
|
Раціональне планування промислового майданчика.
Розміщення поза зоною можливого впливу пожежі будівель адміністративного,
побутового і допоміжного призначення;
|
ВИСНОВОК
Сульфат амонію являється дуже
ефективним азотним добривом. Особливістю цього вигляду добрива є ті, що він
дозволяє підпитувати ґрунт не лише азотом, але і сіркою. Остання входить до складу
білків і амінокислот рослин і тому разом з азотом є одним з важливих елементів
живлення сільськогосподарських культур. По мірі важливості для рослин сірку
можна поставити на третє місце після азоту і фосфору. Продукт володіє важливою
для життєдіяльності рослин властивістю. Він переводить фосфор, що знаходиться в
ґрунті з нерозчинної форми в розчинну і тим самим підсилює процес поглинання
рослиною цієї речовини. Це дозволяє понизити кількість фосфорних добрив, що
вносяться до ґрунту.
Не дивлячись на те, що продукт
найширше використовується в сільському господарстві, він також застосовується і
в інших галузях. Наприклад, у біохімії переосадження сульфатом амонію є
загальним методом очищення білків. Використовується в технології хлорування
води з амонізацією, вводиться в оброблювану воду за декілька секунд до хлору, з
хлором утворює хлораміни - зв'язуючи вільний хлор, завдяки чому значно
скорочується утворення хлорорганіки шкідливої для організму людини,
скорочується витрата хлору, зменшується корозія трубопроводів. В харчовій
промисловості його використовують як харчову добавку Є517 (речовини проти
злежування). В промисловості сульфат амонію використовують як сировину при
виробництві акумуляторів, у виробництві віскозного волокна і як основу при
виробництві вогнезахисних просочень для дерева.
Так як сатураторний метод не дає
можливості регулювати розмір отримуваних кристалів, то пропонується для
впровадження безсатураторний метод отримання сульфату амонію на ПАТ
«Авдіївський КХЗ», у якому на стадії абсорбції отримують ненасичений розчин солі, що
піддається вакууму, - випарці в умовах інтенсивної циркуляції, що забезпечує
незначне пересичення і керований ріст кристалів.
У дипломному проекті наведена
технологічна схема сульфатного відділення та піридинової установки, креслення
основних апаратів: абсорберу, барабанної сушарки, випарника та нейтралізатора.
Розрахунки усіх основних апаратів: абсорберу, випарника, сушарки,
нейтралізатора та всієї піридинової установки.
Наведені фізико-хімічні основи
процесу уловлення аміаку з коксового газу та отримання піридинових основ,
описані основні апарати та технологічні схеми. Розрахунок випарника виконаний
за допомогою ЕОМ.
ЛІТЕРАТУРА
1. Берсудский
В.Е., Крысин В.Н., Лесных С.И. Технология изготовления конструкций. -М. : Машиностроение,
1975
. Кардашов
Д.А. «Синтетические клеи»
. Інформаційні
технології в освіті, науці та виробництві. Вип 1(2): I-74 наук. Праць. О.: А.
О. Бахва, 2013, - 344 с.
. Процес
і обладнання струминно-лазерного різання: Монографія. - Харків. - В-во «Точка»,
2013. - 288 с. - іл..
5. Билик Ш. М. Макрогеометрия деталей машин. М.,
«Машиностроение», 1973. 344 с.
6. Борисов М. В., Павлов И. А., Постников В. М.
Ускоренные испытания машин на износостойкость, как основа повышения их
качества. М., Издательство стандартов, 1976. 352 с.
7. Бруевич Н. Г., Сергеев В. И. Основы нелинейной теории
точности и надежности устройств. М., «Наука», 1976. 136 с.
8. Бусленко Н. П. Моделирование сложных систем. М.,
«Наука», 1969. 576 с.
9. Гнеденко Б. В., Беляев Ю. К., Соловьев А. Д.
Математические методы в теории надежности. М., «Наука», 1965. 524 с.
10. Гоулдстейн Дж. Растровая электронная микроскопия и
рентгено-скопический анализ. - М.: Мир, 1995. - 432 с. - ил.
11. Дальский А. М. Технологическое обеспечение надежности
высокоточных деталей машин. М., «Машиностроение», 1975. 224 с.
12. Коваленко
В.С. Лазерная технология. - К.: Вища школа, - 1989. - 280 с.
. Коваленко
В.С., Романенко В.В., Олещук Л.М. Малоотходные процессы резки лучом лазера. -
К.: Техника, 1987. - 112 с. - ил.
14. Кузнецов Ю.Н. и др. Компоновки
станков с механизмами параллельной структуры. - Киев-Херсон: ПП «Вишемирский» -
2010. - 471 с.
15. Лыков, А.В. Теория тепло- и массопереноса / А.В.Лыков,
Ю.А.Михайлов. - М. - Л.: Госэнергоиздат, 1963. - 535 с.
16. В.А. Крижанівський, Ю.М. Кузнєцов, І.А. Валявський,
Р.А. Скляров. - Технологічне обладнання з паралельною кінематикою. - імекс ЛТД
Кіровоград 2004р. - 449с.
17. Методы испытания, контроля и исследования
машиностроительных материалов. Справочное пособие /под ред. Туманова А.Т. - М.:
Машиностроение, 1973. - т.3. - 282 с.
18. Михайлов А.Н. Разработка технологий на основе
функционально ориентированного похода. - Донецк, из-воДонНТУ, 2008. - 450 с. -
ил.