Проект модернизации системы управления подъёмной установки в условиях ш. 'Западно-Донбасская'
СОДЕРЖАНИЕ
шахта
выработка подъемная установка
Введение
1. Общая
часть
.1 Краткие
сведенья о шахте «Западно-Донбасская»
1.2 Краткая
геологическая характеристика месторождения
.3 Вентиляция
.4 Вскрытие
шахтного поля
1.5 Способ
подготовки разрабатываемых пластов
1.6 Система
разработки добычных участков
1.7
Технология проведения участковых подготовительных выработок
1.8
Технология очистных работ. Общие сведения
1.9 Шахтный
подъем
.10 Транспорт
.11 Водоотлив
.12
Электроснабжение шахты
1.13
Электроснабжение подъемных машины ЦШ 5х4
2.
Специальная часть
.1 Исходные
данные для проектирования
2.2
Последовательность расчета
2.2.1 Расчет
и выбор емкости подъемного сосуда
2.2.2 Расчет
и выбор подъемного каната
.2.3 Расчёт и
выбор основных размеров органа навивки
.3 Кинематика
подъемной установки
.3.1 Расчет
продолжительности подъемной операции
.3.2 Расчет
максимальной скорости подъема
.4 Динамика
подъемной установки
.5 Расчет
диаграммы усилий
.6 Расчет
приводного двигателя
.7 Расход
энергии и КПД подъемной установки
2.7.1
Расчет мощности на валу двигателя и потребляемой из сети
.7.2
Расход энергии на один подъем
2.7.3
КПД подъемной установки
2.8
Автоматизированная система управления и комплексной защиты шахтной подъемной
установки, регистрации и визуализации режимов ее работы ЗДКР
.8.1 Функции
и возможности системы
.8.2 Опыт
внедрения и эксплуатации
.8.3 Состав и
массогабаритные параметры
. Монтаж,
наладка и эксплуатация подъемной установки
.1
Планово-предупредительные осмотры и ремонты
.
Электроснабжение шахтной подъемной установки
.1 Расчет
нагрузки участка
.2 Расчет
электрической сети участка
.3 Расчет
токов короткого замыкания
.4 Выбор
аппаратуры управления и защиты
5.
Технико-экономические параметры эксплуатации угольного подъема
5.1 Расчет
численности работников участка
.2 Расчет
себестоимости по элементам «Заработная плата» и «Отчисления на социальные
нужды»
.3 Расчет
себестоимости по элементу «Материалы»
5.4 Расчет
себестоимости по элементу «Электроэнергия»
5.5 Расчет
себестоимости по элементу «Амортизация»
5.6 Сводная
смета эксплуатационных затрат
6. Охрана
труда
6.1 Анализ
опасных и вредных производственных факторов. Техника безопасности при
эксплуатации и обслуживании подъемной установки. Разработка
инженерно-технических мероприятий по охране труда
.2
Противопожарное оборудование подъёмной установки
ВВЕДЕНИЕ
Задачи дальнейшего повышения эффективности работы предприятий
горнодобывающей промышленности невозможны без автоматизации производственных
процессов. Вследствие этого повышаются требования к системам управления и
электроприводам подъемных установок, являющихся одной из основных частей
технологического комплекса по добыче полезного ископаемого подземным способом.
В связи с ростом производственных мощностей горных предприятий,
увеличением глубины подъема основной тенденции развития шахтного подъема
являются повышения грузоподъемности и скорости движения подъемных сосудов
Перспективы развития электропривода шахтных подъемных машин определяются
достижениями электромашиностроения, силовой преобразовательной техники и
техники автоматического регулирования.
Реализация надежности работы скипового угольного подъема с учетом
применения более совершенного привода управления и регулирования скоростью
подъемного двигателя постоянного тока на современной элементной базе рассмотрено
в данном проекте.
В условиях перехода Украины к рыночным отношениям, когда уголь является
практически единственным энергоносителем, вопросы энергосбережения и экономии
при эксплуатации горно-шахтного оборудования приобретают большое
народно-хозяйственное значение.
Учитывая, что основные потребители электроэнергии на предприятиях -
шахтные подъёмные, вентиляционные, водоотливные и пневматические установки (на
их долю приходится до 65-80% общего объёма энергопотребления), исследования и
анализ режимов их работы в целях изыскания резервов для снижения энергетических
и эксплуатационных расходов представляют теоретический и практический интерес.
1. ОБЩАЯ ЧАСТЬ
.1 Краткие сведенья о шахте «Западно-Донбасская»
Шахтное поле расположено в Павлоградско-Петропавловском углепромышленном
районе Западного Донбасса.
В административном отношении шахта расположена на территории
Павлоградского района Днепропетровской области Украины.
Шахта «Западно-Донбасская» №16/17 ГХК «Павлоградуголь» сдана в
эксплуатацию в 1979 году с проектной мощностью 1.5 млн.т добычи угля в год.
Четыре года (1981- 1984 г.г.) шахта выполняла установленный на уровне
графика освоения мощности план по добыче угля. С 1985 г., когда план достиг
проектной мощности, он шахтой не выполняется.
Основной причиной снижения достигнутого объема добычи являются весьма
сложные горно-геологические условия, выявленные в процессе эксплуатации шахты.
Из-за усиленного горного давления и интенсивного пучения пород почвы от влияния
очистных работ, капитальные горные выработки находятся в неудовлетворительном
состоянии, не соответствуют требованиям Правил безопасности, что привело к
ухудшению проветривания и осложнению работы подземного транспорта шахты.
В 1995 году производственная мощность шахты пересмотрена и установлена
1,2 млн.т. угля в год, а период реконструкции капитальных горных выработок,
включая главный и вспомогательный стволы, нормативный объём добычи установлен
810 тыс.т. угля в год.
Размеры шахтного поля составляют для блока №1:
- по простиранию - 6.0 км.,
по падению - 2.2…3.0 км.
Режим работы принят следующий:
1. число рабочих дней в году для шахты - 300;
2. пятидневная рабочая неделя для трудящихся с одним общим выходным
и одним выходным по скользящему графику;
. продолжительность рабочей смены:
на подземных работах - 6 часов;
на поверхности - 8часов.
. количество рабочих смен:
в очистных забоях - три смены по добыче угля и одна
ремонтно-подготовительная,
в подготовительных забоях - три смены по проведению горных выработок и
ремонтно-подготовительная,
на поверхности - три смены.
1.2 Краткая геологическая характеристика месторождения
В геологическом строении шахтного поля принимают участие продуктивные
отложения нижнего карбона и перекрывающие их осадочные образований
триас-юрского, палеогенового, неогенового и четвертичных возрастов.
В тектоническом отношении участок характеризуется неспокойным залеганием
пород и угольных пластов.
Из крупных тектонических нарушений отмечен Богдановский сброс с
амплитудой до 300 м., являющийся границей шахтного поля со стороны восстания,
вдоль южной границы шахты.
В пределах шахтного поля промышленное значение имеют 7 угольных пластов:
с10в,с9, с8в,с8н,с7,с5
и с1.
По данным геологического отчета газоносность пластов
изменялась от 0.9 до 59 м3/т и в среднем составляла 8…15 м3/т.
Для отдельных групп пластов установлена следующая природная метаноносность
пластов (на горную массу):
с8в и с8н
- от 9 до 25 м3/т, на большей части поля максимальная - 14 м3/т.;
с7в, с7н,
с6, с5 - от 11до25 м3/т,
на большей части максимальная -15 м3/т.;
с4 и с1 - от 18 до 25м3/т,
на большей части поля 19 м3/т.
Шахта «Западно-Донбасская» отнесена к сверхкатегорной по метану, по
взрывчатости угольной пыли - опасна. Относительная газообильность шахты
составляет 25,7м3/т, абсолютная - 32,5 м3/т. Суфлярные
выделения метана и внезапные выбросы угля и газа отсутствуют. Газоносность
вмещающих пород достигает 2 м3/т.
В гидрогеологическом отношении шахтное поле отнесено к закрытому типу, а
поэтому обводнение горных выработок ожидается за счет статических запасов
подземных вод, содержащихся в песчаниках и угольных пластах карбона. При
отработке пластов с10 и с8
возможны кратковременные притоки воды до 1-3 м3/ч за счет
статических запасов воды в песчаниках кровли, поэтому отработка этих пластов
столбами по падению не рекомендуется. Общий приток воды в шахту при
максимальном удалении горных работ, составит 250…350 м3/час. В
отдельных случаях повышенные притоки возможны у зон тектонических нарушений и
при подработке некачественно затампонированных скважин.
Осушение шахтного поля не производится из-за незначительного притока.
Внезапных прорывов воды в очистные выработки не ожидается. Приток воды в лаву
возможен до 3м3/ч.
Нормальный приток воды составляет 43 м3/ч, максимальный - 63 м3/ч.
В дальнейшем, при вскрытии нижней свиты пластов, нормальный приток ожидается до
120 м3/ч, максимальный - до140 м3/ч.
Откачка этого притока на поверхность осуществляется главной водоотливной
установкой на горизонте 585 м, оборудованной тремя насосами типа ЦНС 300-600,
по двум трубопроводам, проложенным в главном стволе.
1.3 Вентиляция
Схема проветривания - высасывающая. Суфлярных выделений метана и
внезапных выбросов угля и газа на шахте не отмечалось. Угли не склонны к
самовозгоранию. По вспомогательному стволу происходит подача свежей струи
воздуха в шахту, по главному стволу выводится исходящая струя воздуха.
На шахте установлены два центробежных вентилятора типа ВРЦД-1,5 с
асинхронным двигателями:
АКС 16-44-24 (240 об/мин., 500 кВт, 6000 В);
СДС 3-17-41-16 (375 об/мин., 1600 кВт, 6000 В).
В прирезанной части - 2 вентилятора ВРЦД-4,5 с двигателями СДС 3-17-41-16
(375 об/мин., 1600 кВт, 6000 В).
Депрессия шахты Н=330 кГс/м2 и расход воздуха составляет Q=305 м3/с.
Схема проветривания выемочных участков - возвратноточная, а там где удается
удержать за лавой штрек применяется прямоточная схема проветривания с
подсвежением исходящей струи воздуха.
1.4 Вскрытие шахтного поля
Шахтное поле вскрыто двумя центрально-расположенными сдвоенными стволами
глубиной 680м. и диаметром 7,5м. и квершлагами на горизонте 480м.
Пласты с8в и с8н
в центре поля шахты вскрыты непосредственно стволами. В месте пересечения
стволами пласта с8н сооружён околоствольный
двор на горизонте 480м,от которого пройдены на запад и восток магистральные
выработки. Этими выработками шахтное поле разделено на уклонное и бремсберговое
части поля.
Действующие горизонты: 480, 530, 585, 680. Основные рабочие: 480 и585м.
Основными выработками по подготовке шахтного поля являются магистральные штреки
(откаточные, конвейерные и вентиляционные), пройденные от околоствольного двора
горизонта 480м в западном и восточном направлениях к границам шахтного поля.
Горизонт 480м производит обслуживание горных работ на пластах с8в,
с8н и с10в по
выдаче угля и породы и выполнению вспомогательных операций.
Горизонт 585м - дренажный, на нём расположен главный водоотлив шахты и
загрузочное устройство для выдачи породы. Горизонт 680 м - для чистки зумпфа
главного ствола от просыпающейся горной массы и породы. Шахтное поле вскрыто
двумя вертикальными центрально-сдвоенными стволами: главным и вспомогательным.
Главный ствол оборудован подъёмными машинами ЦШ5х4 (двух - скиповой
подъем для выдачи горной массы ) и ЦШ4х4 (одно-скиповой подъем с противовесом
для выдачи породы ) и обслуживает горизонты 480 м и 585 м, кроме выдачи угля и
породы он служит для вывода исходящей струи воздуха.
Вспомогательный ствол оборудован двумя подъёмными машинами ЦР6х3,2/0,5.
Тип подъёмов - двухклетевой и одноклетевой с противовесом. Клети двухэтажные
неопрокидные. Он служит для спуска - подъёма людей, материалов и оборудования,
при необходимости - для выдачи породы, а также для подачи свежей струи воздуха
в шахту. Вспомогательный ствол обслуживает горизонты 480м, 585м и 680м. В этом
стволе имеются засечки на горизонтах 510м, 550м, 615м и 630м, а в главном - на
горизонтах 530м, для камер угольного загрузочного устройства, а также на
горизонте 585м для камеры породного загрузочного устройства.
Горная масса с горизонта 585м передается в настоящее время конвейерным
транспортом на горизонт 480м и далее к угольному загрузочному устройству
главного ствола на этом горизонте.
Характеристика ствола блока №1 приведена в таблице 1.1.
Таблица 1.1. Характеристика стволов блока №1
Показатели
|
Наименование ствола
|
|
Главный
|
Вспомогательный
|
Абсолютная отметка устья
ствола, м
|
+139,2
|
+139,8
|
Абсолютная отметка головки
Рельсов околоствольного двора, м :
|
|
гор. 480 м
|
-320
|
-320
|
гор. 510 м
|
-350
|
-350
|
гор. 585 м
|
-425
|
-425
|
гор. 680 м
|
-520
|
-520
|
Глубина зумпфа ствола, м
|
-
|
35
|
Полная глубина ствола,
включая зумпф, м
|
680
|
715
|
Площадь сечения ствола в
свету, м
|
44,2
|
44,2
|
Вид крепи ствола: а) в
наносах б) в коренных породах
|
|
|
чугунные тюбинги
|
|
бетон, железобетон
|
Толщина крепи ствола, мм
|
500
|
500
|
Армировка ствола
|
Металлическая
|
металлическая
|
Назначение стволов
|
Предназначен для выдачи
угля, породы и отработанной струи воздуха.
|
Предназначен для
спуска-подъема людей, материалов, оборудования, подачи в шахту свежей струи
воздуха.
|
1.5 Способ подготовки разрабатываемых пластов
Для отработки пластов принята панельная схема подготовки.
Система разработки - длинными столбами по восстанию в уклонной части поля
и по протиранию в бремсбергов ой части поля одинарными и сдвоенными лавами.
Длина выемочных стволов 800-1500м.
Первоочередные сближенные пласты с8в и с8н
в блоках №1 и №2 намечается отрабатывать одновременно в уклонных и
бремсберговых полях в направлении от стволов к границам блоков столбами по
падению и восстанию спаренными лавами.
Первоочередные пласты с8в и с8н
в блоке №1 первоначально отрабатывать в уклонном поле в направлении от стволов
к границам блока.
Сближенные пласты с8ви с8н
в пределах участка отрабатывать раздельно. Отработка пластов - одинарными
лавами.
Для независимой работы одинарных лав, отработка пластов на крыльях
ведется отдельными фронтами работ. Число фронтов работ на крыле соответствует
числу лав.
Для отработки пластов в уклонном поле от околоствольного двора горизонта
480 м. по пласту с8н проходятся панельные
откаточные и конвейерные штреки, а от квершлага горизонта 585 м, которым
подсекается пласт с8н у нижней границы уклонного
поля - дренажный штрек.
В связи с тем, что пласты с8в и с8н
залегают друг от друга на расстоянии 6-7 м панельные и дренажные штреки,
расположены по пласту с8н, являются общим и для пласта
с8в.
Между панельными и дренажными штреками пройдены выемочные конвейерные и
грузо-людские штреки, которыми оконтуриваются столбы по падению.
1.6 Система разработки добычных участков
Система разработки принята - смешанная. Для пласта с8в
и с8н уклонная часть поля отрабатывается
длинными столбами по восстанию. Длина лавы Lл = 180 - 210 м. Длина
столба Lст = 1400 - 1200 м. Бремсберговая часть
поля разбита на 4 панели, в составе панели 1 этаж. Отработка этой части поля
производится длинными столбами по простиранию. Длина лавы Lл= 180 - 225 м. Длина столба Lст = 1200- 2300 м.
Основными подготовительными выработками являются: восточный магистральный
откаточный штрек №1, восточный магистральный откаточный штрек №2, восточный
магистральный конвейерный штрек, восточный магистральный вентиляционный штрек,
восточный дренажный штрек, западный магистральный откаточный штрек №1, западный
магистральный откаточный штрек №2, западный магистральный конвейерный штрек,
западный магистральный вентиляционный штрек №2, западный дренажный штрек, южный
магистральный откаточный штрек, южный магистральный конвейерный штрек, западный
магистральный конвейерный штрек №2, южный магистральный откаточный штрек №2,
откаточный квершлаг, конвейерный квершлаг.
Штрека пройдены сечением Sсв.= 17,7 м2 и закреплены
крепью КШПУ 17.7.
В местах сопряжения и особых пучений, штрека перекреплены кольцевой
крепью с диаметром 4,5 м. С шагом от 0,3- 0,8 м, затянуты ж/б затяжкой и
затомпанированы тампонажом за рамочного пространства.
Выемочные штрека пройдены сечением Sсв.= 11,7 м2,
закреплены крепью КШПУ 11,7 с затяжкой:
борт - армокаркас;
кровля - колотая руд/стойка.
Начиная с 1999 года, на выемочных штреках применяется крепь АППК с
сечением Sсв.= 14,4 м2, шаг установки
от 0,3 - 0,8 м.
Для доставки материалов в лаву применяется напочвенная канатная дорога,
для транспортировки горной массы с лавы на конвейерный штрек применяются
скребковые и ленточные конвейера.
Схема проветривания добычного участка возвратноточная с подсвежением.
.7 Технология проведения участковых подготовительных
выработок
Выемка горной массы осуществляется проходческим комбайном П110, 4ПП-2М в
комплексе с ленточным перегружателем ППЛ-1.
Выработки крепятся крепью КШПУ-14.4, шаг крепи - 0.5 м. Выработка
крепиться с перетяжкой кровли колотой руд/стойкой бортов армокаркасом.
Горная масса грузится в вагоны ВГ-3.3 и электровозами АМ-8Д
транспортируется в околоствольный двор горизонта 480 м, составами не более 5-6
вагонов.
Выемка горной массы осуществляется заходками. Заходка начинается углубления
резцовой короны на требуемую глубину. Затем перемещением рабочего органа в
горизонтальной или вертикальной плоскости производится выемка горной массы по
всему сечению забою. Машинист комбайна находится у пульта управления и
управляет работой комбайна.
Звеньевой находится на конце навесной стрелы скребкового конвейера
комбайна, следит за перегрузкой горной массы на прицепной перегружатель ППЛ-1,
поправляет кабель и руководит работой звена.
Проходчики находятся с обеих сторон комбайна на расстоянии не менее 2-х
метров от его питателя. Производят зачистку почвы выработки и подготавливают
элементы крепи к установке. Один проходчик находится на конце прицепного
перегружателя ППЛ-1 и следит за погрузкой горной массы в вагон.
Один проходчик подготовляет и доставляет материалы.
При падении больших кусков породы на питатель, комбайн оттесняет под
прикрытие постоянной крепи, рабочий орган поднимают вверх. Комбайн выключается
и по разрешению комбайнёра, проходчики кувалдами разбивают упавшие куски
породы.
Возведение крепи производится при отставании постоянной крепи от груди
забоя не более 0.3 м после установки рамы, и 0.8 м - до установки. Комбайн
зарубывается режущим органом в грудь забоя на нужную глубину. Пускатель
комбайна отключается. Проходчики, находясь под защитой постоянной крепи,
производят тщательную уборку кровли, боков и груди забоя. Затем разделываются
лунки глубиной 200 мм под ножки крепи. На последней раме устанавливается
межрамные стяжки. После в лунки укладывается подпятники, на которые устанавливаются
ножки крепи и хомутами крепится к ранее установленным межрамным стяжкам. На
установленные ножки укладывается верхняк проходчиками и крепится к верхняку
последней рамы межрамной стяжки. Установка верхняка производится с ранее
установленного полка. На редуктор исполнительного органа комбайна одним концом
укладывается деревянный полок из досок толщиной 60 мм, а другим на лестницу
установленную на расстрелы ранее установленных рам.
Установка рамы проверяется по макшейдерскому направлению. При возведении
крепи необходимо постоянно следить и при необходимости производить уборку
кровли, боков и груди забоя от отломившихся кусков породы. Проходчики
производят перетяжку кровли, бортов выработки. Машинист комбайна во время
установки рамы постоянной крепи проверяет узлы комбайна. Производит смазку.
Подтягивает болтовые соединения, находясь в закрепленной части выработки.
Основные технико-экономические показатели по проведению выработок
приведены в таблице 1.2.
Таблица 1.2 Технико-экономические показатели
Показатели
|
Значение
|
Сечение выработки: в
проходке в свету
|
12.2 м3 12.2 м3
11.7 м3
|
Способ проведения
|
комбайновый
|
Тип комбайна
|
4ПП-2М
|
Число заходок за смену за
сутки
|
2 6
|
Проведение выработки
|
|
Продвигание за заходку
|
0,8 м
|
Продвигание за сутки
|
5 м
|
Продвигание за месяц
|
145 м
|
1.8 Технология очистных работ. Общие сведения
Для анализа очистных работ возьмем отработку 841 лавы ш.
«Западно-Донбасская».
лава подготовлена горными работами для выемки угля пл.с8н
в бремсберговом поле блока №1 восточного крыла шахты.
Длина лавы 194 м. Полезная длина столба 1484 м. Средняя геологическая
мощность 0,97 м.
Выемка угля в лаве производится комбайном К-103 с механизированной крепью
КД-80 и скребковым конвейером СП-250. Управление кровлей - полное обрушение.
Система разработки - длинными столбами по простиранию.
Вынимаемая мощность 1,05 м.
Приводные головки конвейера с ВСП вынесены на штрек и закреплены на
столах.
Сопряжения лава - штрек, до разработки компактных промышленных и надежных
крепей сопряжения, закреплены гидравлическими стойками ГСК под прогоны из
спецпрофиля.
1.9 Шахтный подъем
В течение всего срока службы шахты уголь выдается с горизонта 585 м.
через главный ствол, порода выдается породным подъемом по этому же стволу.
Главный ствол оборудован двухскиповым угольным и односкиповым породным
подъемами.
Подъемные машины угольного и породного подъемов многоканатные,
соответственно, типа ЦШ 5х4 и ЦШ 4х4, установленные на башенном
копре.
Вспомогательный ствол оборудован двухклетевой и одноклетевой с
противовесом подъемными установками с одноканатными подъемными машинами типа
ЦР-6хЗ,2 / 0,5.
Двухклетевой подъем обслуживает горизонты 585 и 680 м. Клети обоих
подъемов двухэтажные с максимально поднимаемым грузом в одной вагонетке ВГ-3,3
с породой массой 6300 кг.
Вспомогательный ствол прирезанной части оборудован двумя
одноклетьевыми противовесами подъёмными установками, предназначенными для
спуска-подъёма людей и выполнения вспомогательных операций. Подъёмы обслуживают
горизонты 480м и 585м. Подъёмные машины каждого подъёма типа ЦР4-3210,6 с
редукторным приводом от электродвигателя асинхронного мощностью 630кВт, 500
об/мин; 6000 В, обеспечивают максимальную скорость подъёма 8,9м/с. Клети
2-этажные на одну вагонетку ВГ-3,3 в этаже.
1.10 Транспорт
Транспортировка угля на шахте конвейеризирована от очистных забоев до
загрузочного устройства главного ствола. Уголь из лавы скребковым конвейером
выдается на сборный штрек, по которому он транспортируется до магистральной
конвейерной выработки.
Далее конвейерной цепочкой он доставляется до конвейерной сбойки на
главный ствол и далее через углеспускной гезенк уголь поступает к питателям для
загрузки в скип.
Для транспортировки породы, материалов оборудования по магистральным
откаточным штрекам (квершлагам) на шахте применяется локомотивный транспорт.
Порода от проведения и ремонта горных выработок доставляется в околоствольные
дворы гор.480м и 585м. на круговые опрокиды, где выгружается в породные
загрузки и в породные скипы. В проходческих забоях с уклоном более 0,050 для
откатки породы, доставки материалов используются напочвенные канат-ные дороги
типа ДКНУ и ДКНЛ или ленточные конвейеры до места погрузки (выгрузки) на
магистральной выработке.
На поверхности шахты для доставки материалов и оборудования используется
локомотивный транспорт или автотранспорт.
Доставка материалов и оборудования по горизонтальным выработкам
произ-водится при помощи локомотивной откатки в шахтных вагонетках, или
транспор-тным оборудованием системы «Пакод».
В выработках с уклоном, превышающим 0,050, доставка производится в этих
же транспортных средствах при помощи напочвенных канатных дорог.
Конвейерные цепочки по магистральным выработкам для транспортировки угля
оборудованы конвейерами 1Л-100К, 1Л-120К, 1ЛУ-120
По выемочным штрекам очистных забоев и проходимых выработках используются
конвейеры типа 1Л-80 и 1ЛТ-80.
Откатка по горизонтальным выработкам осуществляется электровозами АМ- 8Д
и дизелевозами ДГ-35 в вагонетках УВГ-3,3.
Выработки с уклоном более 0,050 оборудованы напочвенными дорогами с
колеей 900 и 600 мм. на базе лебедок ДКНУ, ДКНЛ и ТКС. Для откатки породы и
материалов этими дорогами используются вагонетки УВГ-3,3, ВДК-2,5 и
транспортные средства «Пакод».
Люди по магистральным выработкам доставляются составами из вагонеток
ВЛ-18.
1.11 Водоотлив
По данным доразведки шахтного поля общий нормальный приток воды в шахту
при максимальном развитии горных работ в блоках №1 и №2 составит 350 м3/час.
Максимальный приток 440м3/час.
Главная водоотливная установка распологается в околоствольном дворе горизонта
585 м в специальной камере.
При отработке первоочередных пластов Св8 и Сн8
вода с уклонного поля по дренажному штреку пл. Сн8 и по
квершлагу гор. 585 м самотеком, по водоотливным канавкам поступает в
водосборики главного водоотлива. С бремсбергового поля вода по откаточным и
вентиляционным штрекам самотеком, по канавкам поступает в околоствольный двор
гор. 480 м, с которого по скважине переспускается на гор. 585 м и по канавкам
поступает в водосборники.
Насосная камера соединена трубным ходком с главным стволом и ходком с
выработкой околоствольного двора.
В соответствии с заданым притоком и геодезической высотой главная
водоотливная установка оборудуется пятью насосами. Существующая камера,
пройденая по рабочим чертежам на три насоса 8МС-10 расширяется дополнительно на
два насоса ЦНС 300-700. Дополнительно к трем насосам 8МС-10 устанавливаются два
насоса ЦНС 300-700 на семь колес. Приводом к насосам служат асинхронные
взрывобезопасные электродвигатели серии АТД-2 типа 2АЗМВ-800 мощностью по 800
кВт, 3000 об/мин, 6 кВ. В качестве подкачивающих насосов устанавливаются насосы
ВП-340.
Зумпфы главного и вспомогательного стволов блока №1 сбиваются между собой
на гор. 680 м. Вода из зумпфа главного ствола переспускается во вспомогательный
ствол. Для откачки общего притока 30 м3/ч оборудована зумпфовая
водоотливная установка у вспомогательного ствола. В камере зумпфовой
водоотливной установки, расположенной на 23 м ниже горизонта 680 м установлены
два насоса 4МС-10 на пять колес с асинхронными электродвигателями с
короткозамкнутым ротором типа КО 42-2 по 50 кВт, 3000 об/мин, 660 В. Напорные
трубопроводы диаметром 100 мм прокладываются от насосов до места сбора воды в
водоотливную канавку на гор. 585 м, по которой вода самотеком направляется в
водосборник.
1.12 Электроснабжение шахты
Внешнее электроснабжение шахты выполнено напряжением 150 кВ от
энергосистемы «Днепроэнерго».
На промплощадке шахты (блок №1) сооружена подстанция глубокого ввода
150/35/6 кВ с двумя силовыми трансформаторами ТДТН-25000/150. Ее питание предусмотрено
ответвлениями от действующей двух цепной ВЛ 150 кВ шахты «Павлоградская», 330
кВ шахты «Днепровская» общей протяженностью (ВЛ 150 кВ и ответвление) 14 км.
Шахта относится к потребителям 1 категории. Питание подаётся от 2 и более
независимых источников. Подстанция имеет два трансформатора ТДТН один из которых
является рабочим, другой резервным комутируемым относительно высоковольтных
линий разъединителем наружной установки РНДВ 220/1000 на напряжении 154 кВ.
Для надежного электроснабжения группы шахт построены резервные связи по
линиям электропередачи между подстанциями «Петропавловская» 110 кВ,
«Терновская» 35 кВ, «Самарская» 35 кВ.
ГПП состоит из воздушных линий, воздушных отделителей и разъединителей,
масляных выключателей разрядников, трансформаторов напряжения 35/0,4 кВ, для
собственных нужд, трансформаторов35/0,4 шин 6кВ, распределительных ячеек,
конденсаторных установок, аккумуляторных помещений, комнат автоматики и
управления. Мощность к.з. на шинах ГПП равна 126,6 МВА.
Далее питание от 1 и 2 секции и трансформаторы ТМ-400 6/6,3 запитаны ЦПП
гор.480 и ЦПП гор. 585 м. ЦПП гор 480 и 585 расположеныв околоствольной
выработки. Каждое ЦПП обеспечено 4 вводами. Марки кабелей применяемые для
вводов на ЦПП - ЦСКН 3´150 и ВЭВБбШВ 3´150.
В ЦПП применяются ячейки типа РВД-6. Ячейки следующих вариантов
исполнения: вводные, отходящего фидера.
Мощность к.з. на шинах ЦПП гор. 480 равно 51,2 МВА
Мощность к.з. на шинах ЦПП гор. 585 равно 39,9 МВА.
Питание поверхностного электрооборудования шахты осуществляется от 1 и 2
секций ГПП 6кВ через высоковольтные выключатели разъединители к потребителям 6
кВ, это стационарное оборудование и через трансформаторы ТМ3-1000/10 и КТП
6/0,4-0,23 для питания блоков вспомогательного, и главного ствола, котельной и
ремонтно-складских помещений.
Для компенсации реактивной мощности применяются реакторы Р5-10-630-0,25 и
БСК
Электроснабжение шахты «Западно-Донбасская» (блок №3) осуществляется от
ГПП, расположенной на территории шахты. Питание ГПП блока №3 поступает по двум
воздушным линиям от шахты «Героев Космоса» подстанции 150/35/6 кВ.
Протяжённость линии 8,5 км. На ГПП напряжение понижается с 35 до 6 кВ. Далее
пониженное напряжение по каналам прокладывается к потребителям кабелем маркой
ААШвУ и ААБлУ с повышенной температурой нагрева.
Мощность короткого замыкания на шинах 6 кВ подстанции 35/6 кВ составляет
82,2 МВА.
С ГПП от высоковольтных ячеек двух секций шин напряжение 6 кВ по двум
кабельным линиям СК-6-3х120 подаётся по вспомогательному стволу к ЦПП горизонта
420 м на вводные ячейки КРУВ-6. От ячеек напряжение по кабельным линиям
поступает к потребителям: высоковольтным установкам ЦНС и понижающим
трансформаторным подстанциям участковых РП.
Мощность короткого замыкания на шинах ЦПП горизонта 420 м составляет 45,6
МВА.
Потребляемую мощность шахты сведем в таблицу 1.3.
Таблица 1.3. Мощность потребителей
Наименование потребителей
|
Потребляемая мощность, кВт
|
Добычные участки
|
4720
|
Подготовительные участки
|
960
|
Подземный транспорт:
электровозный конвейерный
|
8 5470
|
Подземные установки:
вентиляция технологический комплекс поверхности Выработка сжатого воздуха
Освещение
|
2009 7966 730 419 61
|
Прочие электроприемники
Первая группа Вторая группа
|
67 995
|
1.13 Электроснабжение подъемных машины ЦШ 5х4
Согласно правил технической эксплуатации в угольных и сланцевых шахтах
односкиповой угольный подъем относится к I категории по бесперебойности электроснабжения.
Питание силового трансформатора ТМПД-3200/10У2 преобразовательного
агрегата ТП3-2500/1050Т, принято двумя вводами: ячейки №51 и №45 ГПП 150/35/6
кВ.
Для видимого разрыва линий во время проведения ремонтных и наладочных
работ предусмотрены разъединители ( камеры КСО-366), располагающиеся на отметке
6,6 башенного копра (ру-5кВ).
От трансформатора тиристорного преобразователя (отметка 0 башенного
копра) до тиристорного преобразователя(отметка 66,6 башенного копра) и от
последнего до приводного электродвигателя (отметка 80,7 башенного копра)
приложены многоамперные кабели постоянного тока типа АСВВ-000 сечением 1500 мм2.
Питание вспомогательных приводов осуществляется по одному вводу
напряжением 380В от распределительного щита 0,4/0,23 кВ кабелем 3х150+1х50мм2.
Для защиты и управления вспомогательными приводами принята станция типа
ШГЕ5903 с вводными автоматами типа А314 и АП50-3МТ.
Защита приводов и линий осуществляется автоматическими выключателями с
выполнением условия, при котором защитные аппараты имеют к длительным токовым
грузовым нагрузкам проводников кратность, не более приведенной в ПУЭ глава III-1, пункт III-1-7.
На отметках башенного копра приняты кабели марки АВВГ-660, ВВБГ-660,
ААГ-660. Прокладка кабелей предусмотрена на сварных лотках и кабельных блоках,
в металлорукавах и трубах.
Вывод:
Работа на горном предприятии ведется в сложных горно-геологических
условиях. Все производственные и вспомогательные участки работают согласно
плану по шахте. Шахтный подъем требует модернизации системы управления, чтоб в
условиях рыночной экономики снизить себистоимость угля.
2. СПЕЦИАЛЬНАЯ ЧАСТЬ
.1 Исходные данные для проектирования
Годовая производительность по выдаче угля - 1,25 млн.т в год;
Число рабочих горизонтов - 1;
Число рабочих дней в году - 300;
Продолжительность работы подъёмной установки в сутки - 18;
Коэффициент резерва производительности подъёмной установки - 1,5;
2.2 Последовательность расчета
.2.1 Расчет и выбор емкости подъемного сосуда
а) определяется часовая производительность подъемной установки
т/ч
(2.1)
где
С = 1,5 - коэффициент резерва производительности подъемной установки; N
= 300 - расчетное число рабочих дней подъемной установки в году; t
= 18 - продолжительность работы подъемной установки в сутки, ч;
т/ч
б)
рассчитывается оптимальная грузоподъемность подъемного сосуда
QП =1.3Аг
кг (2.2)
где
Н - высота подъема, м. Для скипового подъема
м
(2.3)
где hПБ =40 м
- высота приемного бункера; hЗБ = 40 м - глубина загрузочного бункера; Һ=0,3 м - высота рамы скипа над уравнем приемного бункера в момент
разгрузки скипа с донной
разгрузкой.
Н=585+40+40+0,3=665,3, м,
QП =1,3·347
665,3=11635,4, кг,
, кН,
По полученному значению QП
выбираем скип СНМ-15-223-1,1.
Таблица 2.1 Технические характеристики скипа СНМ-15-223-1,1
Емкость кузова, м3
|
Грузоподъем-ность, кН
|
Высота скипа, м
|
Путь разгрузки, м
|
Масса скипа, кг
|
Пауза, с
|
геометри-ческая
|
полезная
|
|
|
|
|
|
15
|
813
|
140,1
|
13,7
|
2.6
|
16020
|
15
|
2.2.2 Расчет и выбор подъемного каната
Для
шахты глубиной НШ
600 м
Длинна
отвеса каната:
м (2.4)
где
- высоту копра, которая расчитываеться для
многоканатной подъемной установки по формуле:
м,
м,
Рассчитаем
суммарную массу груза приходящуюся на один канат по формуле:
кг (2.5)
где
n = 4 - число головных канатов;
QП=
кг,
кг,
Расчетное
суммарное разрывное усилие всех проволок каната:
кН (2.6)
где
- кратность расчетного разрывного усилия к концевому
грузу без учета собственной массы каната, для многоканатных грузовых подъемных
установок;
кН,
Принимаем
стальной трехграннопрядный подъёмный канат.
Таблица
2.2 Технические характеристики стального трехграннопрядного каната
Диаметр, мм
|
Расчетная масса 100 м
каната, кг
|
Расчётное суммарное разрывное
усилие всех проволок в канате при МН/м2, кН
|
33
|
539,2
|
801
|
Выбранный по каталогу подъемный канат проверяется на фактический запас
прочности
(2.7)
где
QZ = 1135 кН - расчетное суммарное разрывное
усилие всех проволок каната, p = 8.233 кг/м - расчетная масса одного
метра каната, выбранного по каталогу,
,
.
Условие
выполняется.
Примем
4 стальных хвостовых каната с характеристиками:
Таблица
2.3 Технические характеристики стального плоского каната для уравновешивания
Расчетная масса 100 м
смазанного каната, кг
|
Расчётное суммарное
разрывное усилие всех проволок в канате при МН/м2, кН
|
572
|
2.2.3 Расчёт и выбор основных размеров органа навивки
Расчетный диаметр многоканатного органа навивки:
мм (2.8)
где
- диаметр головного каната;
мм,
Принимаем
многоканатную подъемную машину ЦШ5-4 с
м.
Также
выбираем отклоняющий шкив ШКФ-3Б с DШВ = 3м.
Таблица
2.4 Технические характеристики многоканатной подъемной машины ЦШ5-4.
Параметр
|
|
Диаметр барабана, м
|
5
|
Максимальное статическое
натяжение ветви каната, кН
|
1450
|
Максимальная разность
статических натяжений канатов, кН
|
350
|
Максимальный диаметр
каната, мм
|
50
|
Максимальная скорость, м/с
|
16
|
Маховой момент машины,
приведенный к тихоходному валу (без редуктора и электродвигателя), кН∙м2
|
6250
|
Выбранная подъемная машина проверяется по удельному давлению на
футеровку.
Н/м2 (2.9)
Максимальное
статическое натяжение набегающей ветви каната:
Н (2.10)
где
- число головных канатов;
Максимальное
статическое натяжение сбегающей ветви каната:
Н (2.11)
где
кг/м - массы одного метра хвостовых канатов;
, Н,
, Н,
, Н/м2
Условия
выполняются.
Рис 1. Расположение многоканатной подъемной установки
2.3 Кинематика подъемной установки
.3.1 Расчет продолжительности подъемной операции
По известной часовой производительности подъемной установки и выбранной
грузоподъемности подъемного сосуда время его движения определяется в следующей
последовательности:
количество подъемов в час:
(2.12)
продолжительность
одного цикла подъема:
с (2.13)
время
движения подъемных сосудов:
с (2.14)
где
θ = 15 с - продолжительность паузы, принимается в зависимости
от грузоподъемности угольного скипа.
,
с,
с.
2.3.2 Расчет максимальной скорости подъема
Для расчета принимается прямолинейная пятипериодная диаграмма скорости.
Принятые значения ускорения а1 = 0.7 м/с2 и а3 = 0.7 м/с2 замедления предварительно должны быть проверены на
допустимые значения против скольжения канатов:
при подъеме груза:
(2.15)
при
спуске груза:
(2.16)
где
- коэффициент трения каната о футеровку шкива;
- угол
охвата канатом барабана;
,кг -
масса движущихся элементов сбегающей ветви;
, кг
- масса движущихся элементов набегающей ветви;
кг (2.17)
, м -
длина обвивки канатом барабана;
, кг
- масса отклоняющего шкива;
кг
(2.18)
кН/м2
- маховый момент отклоняющего шкива;
кг
кг
, кг
- масса движущихся элементов сбегающей ветви;
кг (2.19)
кг
Запас
по нескольжению выполняется.
Кроме
того, подъемная установка проверяеться на отсутствие скольжения каната в
статическом режиме:
(2.20)
Условие
выполняеться.
В
соответствии с рекомендациями ПБ примем а1 = 0.7
м/с2, а3 = 0.7 м/с2,
а’1 = 0.3 м/с2, а’3 = 0.3 м/с2
При
этом проверяются:
скорость
схода порожнего скипа с кривых
м/с (2.21)
где
h0 =
2.65 м - путь
движения в кривых;
м/с
скорость
входа груженого скипа в кривые
м/с (2.22)
м/с.
В
результате расчета необходимо определить Vmax,
t1, t2, t3, h1, h2, h3.
Для
расчета максимальной скорости движения фактическая пятипериодная диаграмма
скорости заменяется условной трехпериодной с параметрами:
высота
подъема - HУ, м;
время
движения - ТУ, с;
максимальная
скорость движения - Vmax.У, м/с.
Максимальная
скорость условной трехпериодной диаграммы
м/с (2.23)
где
а - модуль скорости, определяемый по скорости
(2.24)
Vср.У - средняя скорость условной диаграммы:
м/с (2.25)
Время
условной диаграммы
с (2.26)
с
Высота
подъема НУ условной диаграммы определяется выражением:
м (2.27)
м
м/с
м/с.
Максимальная
скорость фактической пятипериодной диаграммы скорости равна:
м/с (2.28)
, м/с.
Далее
расчетная максимальная скорость согласуется с Vmax
по ПБ и корректируется по выбранному оборудованию в следующей
последовательности:
а)
определяется число оборотов двигателя, соответствующее расчетному значению
максимальной скорости
об/мин (2.29)
где
i = 1 - передаточное отношение для безредукторного
привода.
об/мин;
Оставляем двигатель принятый на шахте П2-800-256-8КУ4
Таблица
2.5 Технические характеристики тихоходного двигателя постоянного тока
П2-800-256-8КУ4
Номинальная мощность на
валу, кВт
|
Номинальное напряжение, В
|
Скорость вращения, об/мин
|
КПД, %
|
Маховый момент ротора, кН·м2
|
4000
|
750
|
40
|
90.5
|
2630
|
б) фактическая максимальная скорость подъема
м/с (2.30)
м/с.
После
установления значения фактической максимальной скорости определяются:
время
и путь ускоренного движения порожнего скипа вне разгрузочных кривых:
с (2.31)
м (2.32)
с,
м;
время
и путь замедленного движения груженого скипа перед разгрузочными кривыми:
с (2.33)
______________м (2.34)
с,
м;
время
и путь равномерного движения:
с (2.35)
м (2.36)
м,
, с;
фактическая
продолжительность движения подъемных сосудов:
с (2.37)
фактический
коэффициент резерва производительности подъемной установки
(2.38)
.
2.4 Динамика подъемной установки
Расчет приведенной к окружности органа навивки массы
движущихся частей подъемной установки.
Приведенная к окружности органа навивки масса движущихся элементов
подъемной установки рассчитывается:
кг (2.39)
где mП - масса элементов
подъемной установки, совершающих поступательное движение, истинно равная
суммарной массе груза, подъемных сосудов и канатов, кг;
mвр - масса элементов подъемной установки, совершающих
вращательное движение, условно приведенная к окружности органа навивки, кг.
Масса
элементов, совершающих поступательное движение, определится как
кг (2.40)
где
LГ.К -
длина одной ветви головного каната, м,
м (2.41)
м
, м -
длина хвостового каната;
м (2.42)
м
кг
Приведенная
к окружности органа навивки масса вращающихся элементов подъемной установки
м (2.43)
где
mМК,
mОТ.Ш,
mР -
приведенные к окружности органа навивки массы соответственно многоканатной
машины, отклоняющего шкива и ротора электродвигателя;
КЗ.П = 1 - коэффициент, учитывающий приведенный к
окружности органа навивки вес редуктора (для безредукторного привода);
кг (2.44)
где
= 6250 кН·м2 - маховый момент
машины, приведенный к тихоходному валу (принимается из технической
характеристики подъемной машины);
кг
кг (2.45)
где
кН/м2 - маховый момент отклоняющего шкива;
кг
кг (2.46)
где
кН/м2 - маховый момент ротора;
кг;
кг;
кг.
2.5 Расчет диаграммы усилий
Расчет движущих усилий на окружности органа навивки производится по
уравнению академика М. М. Федорова (применительно к рассматриваемому случаю) :
(2.47)
где
K = 1.15 -
коэффициент, учитывающий вредные сопротивления движению.
По
результатам расчета строят диаграмму движущихся усилий.
)
а =
=0.3
H;
)
а =
=0.3
H;
)
а =
=0.7
H;
)
а =
=0.7
H;
)
а =
=0
H;
)
а =
=0
H;
)
а = -
= -0.7
H;
)
а = -
= -0.7
H;
)
а =
= 0.3
H;
)
а =
= 0.3
H.
2.6 Расчет приводного двигателя
Точный расчет мощности приводного двигателя производится на основании
диаграммы движущих усилий и выполняется в следующей последовательности:
Определяется эквивалентное усилие по выражению
(2.48)
Для пятипериодной
диаграммы:
(2.49)
ТЭ - эквивалентное время работы двигателя и для
приводных двигателей с самовентиляцией определяется:
с (2.50)
где
α
= 2/3 и β = 1/3 - коэффициенты, учитывающие ухудшение
условий охлаждения двигателя в периоды неустановившихся движения и пауз.
с
Определим
эквивалентное усилие:
H,
Определяется
эквивалентная мощность приводного двигателя
кВт (2.51)
Она
может оказаться большей или меньшей мощности двигателя, ранее выбранного по
ориентировочному расчету.
кВт
Окончательно
принимаем тихоходный двигатель постоянного тока П2-800-256-8КУ4
Выбранный
по каталогу двигатель проверяется по условиям пусковой перегрузки
(2.52)
где
Fmax -
максимальное усилие из диаграммы движущих усилий;
FH
- номинальное усилие выбранного двигателя, рассчитываемое по выражению
Н (2.53)
Н
Н
.
Условие
выполняется.
2.7 Расход энергии и КПД подъемной установки
.7.1 Расчет мощности на валу двигателя и потребляемой из сети
Для определения расхода энергии за подъем рассчитывают мощности на валу
двигателя и потребляемой из сети.
Мощность на валу двигателя и потребляемая из сети рассчитывается на базе
диаграмм скорости и движущих усилий.
Мощность на валу двигателя
кВт (2.54)
кВт,
кВт,
кВт,
кВт,
кВт,
кВт,
кВт,
кВт,
кВт,
кВт,
Мощность,
потребляемая из сети:
кВт (2.55)
где
- КПД двигателя.
кВт,
кВт,
кВт,
кВт,
кВт,
кВт,
кВт,
кВт,
кВт,
кВт.
По
рассчитанным данным строим диаграммы мощности на валу и мощности, потребляемой
из сети.
2.7.2 Расход энергии на один подъем
Действительный расход энергии на один подъем представляет собой площадь
диаграммы мощности, потребляемой из сети, рассчитывается:
кВт·ч (2.56)
где
(2.57)
кВт·ч
Удельный
расход энергии на одну тонну
кВт·ч/т (2.58)
кВт·ч/т,
Расход
энергии на тонно-километр
_____________кВт·ч/т·км (2.59)
, кВт·ч/т·км.
2.7.3 КПД подъемной установки
КПД подъемной установки определяется как отношение полезного расхода
энергии на один подъем WП к
действительному расходу Wд
(2.60)
Полезный
расход энергии на один подъем определяется:
кВт·ч/подъем (2.61)
кВт·ч/подъем,
или 83,4%.
2.8
Автоматизированная система управления и комплексной защиты шахтной подъемной
установки, регистрации и визуализации режимов ее работы ЗДКР
Сотрудниками
ООО НТФ «Автоматуглерудпром» и ОАО «Гипроруда» разработана автоматизированная
система управления и комплексной защиты шахтной подъемной установки,
регистрации и визуализации режимов ее работы, сокращенно система ЗКДР (защиты,
контроля движения и регистрации) [148].
Система
предназначена для решения на современном уровне задач повышения экономической
эффективности и безопасности работы ШПУ, расположенных на поверхности. Решение
этих задач распадается на следующие составляющие:
— непрерывный контроль всех параметров безопасности ШПУ;
— повышение качества контроля параметров и оперативности срабатывания защит
от недопустимых режимов работы;
— повышение надежности работы ШПУ;
— постоянный мониторинг ситуации и обеспечение условий для своевременного
принятия предупредительных и защитных мер по обеспечению безопасной работы ШПУ;
— регистрация, хранение и автоматизированное воспроизведение исторической
информации о работе установки за требуемый интервал времени, разработка и
реализация рациональных управленческих решений по результатам ее анализа.
В соответствии с этим главными функциями системы управления и комплексной
защиты ШПУ являются контроль движения, защита от недопустимых режимов работы,
выдача путевых команд, регистрация текущих данных, визуализация текущей и
накопленной информации о режимах работы и параметрах ШПУ.
Требования, определяющие технические решения: универсальность системы,
дублирование технических средств отбора и обработки информации о параметрах
безопасности, а также взаимный контроль правильности функционирования этих
средств.
Дублирование технических средств обработки информации выполнено в виде
двухканального аппарата контроля хода и защиты АКХЗ.
Для полного дублирования функций защиты к каждому из двух резервированных
одновременно работающих каналов, образованных контроллерами с соответствующим
набором модулей ввода-вывода, подключены дублированные средства отбора
информации о параметрах безопасности ШПУ, а дублированные каналы запитаны от
отдельных источников бесперебойного питания.
Таблица 2.6 Требования к системе, определяющие выбор поворотного
шифратора приращений
Параметр
|
Значение
|
Относительная погрешность
контроля скорости движения
|
Не более 5%
|
Время реакции системы на
превышение заданной скорости
|
Не более 0,1 с
|
Относительная погрешность
контроля превышения заданной скорости
|
Не более 10%
|
Абсолютная погрешность
формирования путевых команд
|
Не более 0,1 м
|
В системе задействованы датчики следующих типов:
— датчики давления Sitrans
Р серии MS фирмы Siemens;
— преобразователи измерительные напряжения постоянного тока Е 857 ЭС;
— датчики положения ДКПУ-22.
В качестве датчиков тока используются стандартные шунты, которые входят в
состав системы управления электроприводом шахтной подъемной машины.
Алгоритм работы подсистемы контроля хода и защиты реализуется на уровне
контроллеров АКХЗ двумя программами: «Ввод данных» и «Управление».
Программа «Ввод данных» написана на языке С и по предъявлению пароля в
диалоговом режиме предоставляет возможность ввода, редактирования и записи в
память контроллеров постоянных данных и уставок срабатывания защит, а также
вызова и просмотра записанных данных. При выборе любой из позиций меню на экран
выводятся формы для заполнения соответствующими данными.
Программа «Управление» разработана с использованием инструментальной
системы программирования Ultra Logik. В нее
включены две внешние процедуры, написанные на языке С и свернутые в
функциональные блоки системы.
Программа подсистемы регистрации и визуализации режимов работы (данная
подсистема состоит из сети АРМ машиниста и АРМ механика ШПУ) создана с
использованием Scada-системы Genesis532 (фирма lconics) версии 7.0.
Обмен информацией между двумя подсистемами производится по сети Ethernet с протоколом 1РХ.
2.8.1 Функции и возможности системы
Разработанная система выполняет следующие основные функции:
— защита ШПУ при выходе значений параметров безопасности за допустимые
пределы, заданные в виде уставок срабатывания;
— контроль исправности элементов, узлов и блоков, выход из строя которых
приводит к потере защитных функций системы;
— выдача сообщений машинисту о проскальзывании каната по результатам
ведения соответствующего контроля;
— блокировка, не допускающая самовосстановления системы после исчезновения
или устранения причины срабатывания защит;
— автоматическая установка в режим «Ревизия» при восстановлении ранее
снятого напряжения питания;
— выдача в заданных точках пути путевых команд, необходимых для безопасного
управления и защиты ШПУ;
— контроль цепи тормоза предохранительного (ТП) и определение причин его
срабатывания:
— формирование сигнала рассогласования фактической и заданной скоростей
движения и вывод его для визуального контроля на соответствующий прибор,
представленный на АРМ машиниста;
— контроль состояния и положения оборудования ШПУ по сигналам
соответствующих датчиков и выдача сообщений;
— контроль идентичности работы резервированных каналов АКХЗ и выдача
сигнала запрета пуска очередного цикла подъема;
— визуализация заданных режимов работы, местоположения подъемных сосудов в
стволе, скорости движения подъемных сосудов (тахограмм), а также значений
заданной и фактической скоростей движения, пройденного пути, токов якоря и
возбуждения электродвигателя, давления в системах ТП и ТР (тормоза
предохранительного и рабочего);
— регистрация, хранение, архивирование и документирование информации о
состоянии и режимах работы ШПУ;
— воспроизведение исторической информации за указанный период времени.
Возможности системы характеризуются показателями, представленными в табл.
Таблица 2.7 Показатели, характеризующие возможности системы
Показатель
|
Значение
|
Глубина подъема, м
|
До 1500
|
Максимальная скорость
движения сосуда, м/с
|
До 20
|
Диапазон значений
контролируемых ускорений, м/с2
|
0..5
|
Количество формируемых
путевых команд, шт.
|
40
|
Погрешность контроля
превышения заданной скорости, %
|
Не более ± 10
|
Погрешность формирования
путевых команд, м
|
Не более ^ 0,1
|
Количество точек отбора
информации о положении сосуда в стволе, шт.
|
4 (на один горизонт)
|
Время реакции системы на
превышение заданной скорости движения, с
|
Не более 0,1
|
Минимальное значение
контролируемой скорости пробуксовки шкива и проскальзывания каната, м/с
|
0,2
|
Периодичность контроля
идентичности каналов, с
|
До 5
|
2.8.2 Опыт внедрения и эксплуатации
Для решения задач комплексной защиты, регистрации и визуализации режимов
работы ШПУ опытный образец системы ЗКДР был установлен на Центральном руднике
ОАО «Апатит» (Мурманская область), налажен и поставлен комиссией на приемочные
испытания.
После успешного завершения приемочных испытаний и доводки по замечаниям и
предложениям приемочной комиссии система ЗКДР была сертифицирована (сертификат
соответствия № РОСС RU. МЕ92. В00316),
получила разрешение Федерального горного и промышленного надзора России № РРС
04-11720 на право применения на ШПУ и введена в эксплуатацию [148].
Разработанная система ЗКДР. М по принципу построения также представляет
собой многоуровневую распределенную сетевую структуру и функционально состоит
из следующих подсистем:
— контроля движения и защиты;
— регистрации и визуализации информации;
— автоматизированного управления.
Система ЗКДР имеет три модификации ЗКДР.1, ЗКДР.2 и ЗКДР. 3.
Модификация системы ЗКДР. 1 содержит в своем составе двухканальный
аппарат АКХЗ, средства отбора информации и функционально состоит из двух
подсистем:
— контроля движения и защиты;
— регистрации и визуализации информации.
Модификация системы ЗКДР.2 содержит в своем составе пульт управления
шахтной подъемной машиной ПУШПМ, двухканальный аппарат АКХЗ, контроллер
управления КУПМ, средства отбора информации и функционально состоит из
следующих подсистем:
— контроля движения и защиты;
— регистрации и визуализации информации;
— автоматизированного управления.
Модификация системы ЗКДР. 3 содержит в своем составе аппарат регистрации
АР и средства отбора информации о значениях регистрируемых параметров ШПУ,
состоянии и режимах работы оборудования, а также специальное прикладное
обеспечение (ПО) для стандартной ПЭВМ, периодически или постоянно подключаемой
к аппарату регистрации. Функционально ЗКДР. 3 состоит из следующих подсистем:
— регистрации информации;
— формирования базы данных и визуализации информации. Модификация системы
ЗКДР. 3 фактически представляет собой регистратор параметров и режимов работы
ШПУ, (в дальнейшем по тексту регистратор РПР), применение которого
предусматривается требованиями ПБ.
Модификации ЗКДР.1 и ЗКДР.2 системы ЗКДР предназначены для
автоматизированного управления шахтными подъемными установками ШПУ и выполнения
комплекса мер по обеспечению необходимого уровня их производственной
безопасности за счет непрерывного выполнения следующих операций в ходе цикла
подъема:
непрерывное управление электроприводом подъемной машины и
дискретное управление оборудованием ШПУ;
— отбор, ввод, обработка и представление информации о параметрах и режимах
работы, выявление и индикация недопустимых отклонений от установленных значений
основных параметров безопасности, обеспечение оперативной защиты ШПУ от
превышения скорости, переподъема, пробуксовки шкива, выхода за допустимые
пределы давления в системе предохранительного тормоза и недопустимых режимов
силовых цепей электропривода и цепей управления;
— ввод от соответствующих датчиков, обработка и представление информации о
других параметрах ШПУ, выявление и индикация недопустимых или опасных
отклонений от установленных значений параметров и обеспечение либо оперативной
зашиты ШПУ, либо блокировки очередного цикла подъема до устранения выявленных
отклонений;
— регистрация, архивирование, хранение и воспроизведение исторической
производственной информации о работе ШПУ;
— выдача путевых команд управления и защиты.
Регистратор РПР предназначен для непрерывной регистрации значений
параметров и режимов работы ШПУ, накопления и хранения информации и обеспечения
возможности считывания как текущей, так и исторической информации для
дальнейшего анализа и принятия обоснованных и эффективных управленческих решений,
касающихся как штатных, так и, главным образом, нештатных ситуаций, возникающих
при работе ШПУ.
Система ЗКДР предназначена для применения на ШПУ, расположенных на
поверхности шахт, работающих в регионах с умеренным и холодным климатом, и
пригодна для использования на ШПУ с барабанными и многоканатными подъемными
машинами со всеми системами электропривода.
2.8.3 Состав и массогабаритные параметры
Техническое обеспечение модификации системы ЗКДР. 1 представляет собой
следующий набор технических средств:
— средства отбора информации подсистемы контроля движения и защиты (датчики
перемещения барабана или канатоведущего и отклоняющего шкивов подъемной машины
(эн- кодеры), датчики давления рабочей среды в системах предохранительного и
рабочего тормозов, датчики тока в главной цепи и в обмотках возбуждения
электродвигателей);
— аппарат контроля хода и защиты АКХЗ, представляющий собой два
контроллерных канала контроля хода и защиты со взаимным контролем идентичности
их работы;
— АРМ машиниста подъема на базе ПЭВМ, конфигурация которой включает
системный блок, клавиатуру, монитор, сетевая карта, устройство записи на
компакт диски (CD-ROM), источник бесперебойного питания;
— АРМ механика подъема на базе ПЭВМ, конфигурация которой включает
системный блок, клавиатуру, монитор, сетевую карту, источник бесперебойного
питания, принтер, устройство записи на компакт диски (CD-ROM).
Техническое обеспечение модификации системы ЗКДР.2 представляет собой
следующий набор технических средств:
— средства отбора информации подсистемы контроля движения и защиты (датчики
перемещения барабана или канатоведущего и отклоняющего шкивов, подъемной машины
(эн- кодеры), датчики давления рабочей среды в системах предохранительного и
рабочего тормозов и датчики тока в главной цепи и в обмотках возбуждения
электродвигателей);
— средства отбора информации подсистемы управления (датчики напряжения и
тока в главных цепях и цепях управления, датчики давления и температуры);
— аппарат контроля хода и защиты АКХЗ;
— пульт управления шахтной подъемной машиной ПУШПМ;
— контроллер управления КУПМ;
— АРМ механика подъема на базе ПЭВМ, конфигурация которой включает
системный блок, клавиатуру, монитор, сетевые модули, источник бесперебойного
питания, принтер, устройство записи на компакт диски (CD-ROM).
Техническое обеспечение модификации системы ЗКДР. 3, то есть регистратора
РПР, представляет собой следующий набор технических средств:
— аппарат регистрации АР;
— средства отбора информации.
Основные массогабаритные параметры технических средств системы ЗКДР
соответствуют нормам, указанным в табл.
Таблица 2.8 Массогабаритные параметры технических средств
системы ЗДКР
Наименование параметров
|
Норма
|
Габаритные размеры, мм, не
более
|
|
- аппарат контроля хода и
защиты АКХЗ
|
1800x1200x500
|
- контроллер управления
КУПМ
|
1800x600x500
|
- аппарат регистрации АР
|
1300x600x320
|
- датчики
|
145x216x175
|
- пульт ПУШПМ
|
|
высота
|
1500
|
ширина
|
2200
|
глубина
|
1200
|
Масса, кг, не более
|
|
- аппарат контроля хода и
защиты АКХЗ
|
75
|
- контроллер управления
КУПМ
|
50
|
- аппарат регистрации АР
|
50
|
- датчики
|
10
|
- пульт ПУШПМ
|
100
|
.8.4 Показатели функционального назначения
Система ЗКДР имеет двухуровневую структуру. Первый уровень систем ЗКДР. 1
и ЗКДР.2 представлен подсистемами управления и контроля движения и защиты,
второй - подсистемой регистрации и визуализации информации.
Первый уровень системы ЗКДР. 3 представлен подсистемой регистрации
информации, второй - подсистемой формирования базы данных и визуализации
информации.
Функционирование подсистемы контроля движения и защиты обеспечивается
аппаратом контроля хода и защиты АКХЗ и датчиками, входящими, как в состав
системы, так и в состав оборудования ШПУ.
Функционирование подсистемы управления обеспечивается пультом управления
ПУШПМ, контроллером управления КУПМ и средствами отбора информации о параметрах
и состоянии оборудования ШПУ, контролируемых подсистемой.
Функционирование подсистемы регистрации и визуализации информации
обеспечивается АРМ машиниста и АРМ механика подъема или пультом управления
ПУШПМ и АРМ механика подъема.
Функционирование подсистемы регистрации информации модификации ЗКДР. 3
обеспечивается аппаратом регистрации АР и средствами отбора информации о
параметрах и состоянии оборудования ШПУ, контролируемых подсистемой.
Функционирование подсистемы формирования базы данных и визуализации
информации модификации ЗКДР. 3 обеспечивается специальной прикладной программой
для стандартной ПЭВМ, периодически или постоянно подключаемой к аппарату
регистрации АР.
Пульт управления ПУШПМ выполнен на основе промышленной мебели, состоящей
из двухтумбового стола с двумя монтажными секциями и регулируемого поворотного
кресла. На столешнице стола установлены два манипулятора (джойстика), ряд
кнопок управления оборудованием и переключателей цепей управления
оборудованием, в тумбах стола - два персональных компьютера с источниками
бесперебойного питания и клавиатурой, а в монтажных секциях - два монитора,
клеммники.
Система ЗКДР может иметь модификацию, предусматривающую применение
выделенного сервера, поставляемую по специальным заказам.
В процессе работы модификации ЗКДР.1 и ЗКДР.2 системы выполняют набор
функций, состоящий из функций, которые должна выполнять каждая из их подсистем.
Подсистема контроля движения и защиты выполняет следующие функции:
— размыкание цепи защиты при недопустимом отклонении от установленных
значений параметров безопасности ШПУ;
контроль пробуксовки канатоведущего шкива и проскальзывания канатов по
канатоведущему шкиву на многоканатных ШПУ и выдачу соответствующих команд
машинисту подъемной машины или на срабатывание защиты;
— автоматический непрерывный контроль исправности (самоконтроль) элементов,
узлов и блоков, выход из строя которых приводит к потере защитных функций
системы;
— блокировку, не допускающую самовосстановление схемы (замыкание контакта
исполнительного устройства в цепи защиты подъемной машины) после исчезновения
или устранения причины его срабатывания;
— выдачу в заданных точках пути сигналов (путевых команд), необходимых для
управления и защиты ШПУ;
— контроль сигналов устройств и событий, вызывающих срабатывание
предохранительного тормоза ШПУ;
— световую индикацию с запоминанием, сигнализирующую раздельно о
срабатывании реле защиты или реле контроля исправности;
— формирование сигнала рассогласования между фактической скоростью движения
и скоростью, заданной защитной тахограммой, и вывод его для визуального
контроля на соответствующий прибор (отклономер), представленный на мониторе АРМ
машиниста;
— контроль сигналов датчиков стопорения, точной остановки сосуда, стволовых
дверей и других технологических устройств.
Подсистема управления обеспечивает:
— задание режима работы на предстоящий цикл подъема;
— дискретное управление (запуск в работу и останов) оборудования ШПУ;
— непрерывное управление электроприводом шахтной подъемной машины;
— управление рабочим тормозом;
— наложение и снятие предохранительного тормоза;
— предупредительную сигнализацию при выходе значений технологических
параметров из номинального диапазона;
— ввод и запись в память контроллера значений уставок срабатывания
предупредительной сигнализации.
Подсистема регистрации и визуализации информации производит обработку и отображение
на мониторах значений и сообщений о:
— заданном режиме работы и сигналах стволовой сигнализации;
— состоянии элементов цепи предохранительного тормоза;
— положении стволовых дверей, посадочных и других технологических
устройств;
— местоположении подъемных сосудов ШПУ в стволе шахты;
— скорости движения подъемных сосудов (тахограмма движения);
— токе подъемного двигателя;
— токе возбуждения двигателей (для электропривода постоянного тока);
— снижении сопротивления изоляции;
— напряжении сети;
— напряжении внешних цепей управления ВЦУ;
— давлении маслостанции;
— давлении в цилиндре предохранительного тормоза;
— давлении в цилиндре рабочего тормоза;
— давлении в тормозной системе;
— температуре деталей оборудования, а также регистрацию, хранение и
архивирование информации о состоянии и работе оборудования ШПУ.
Модификации системы ЗКДР.1 и ЗКДР.2 характеризуются показателями
назначения и соответствуют нормам, приведенным в табл.
Таблица 2.9. Показатели назначения
системы ЗДКР
Наименование показателя
|
Значение, норма
|
Напряжение питания,
номинальное, В
|
220 переменного
тока(50±1)Гц
|
Потребляемая мощность, ВА,
не более
|
1000
|
Количество каналов ввода
сигналов, шт., не менее:
|
|
ЗКДР.1
|
|
аналоговых
|
8
|
дискретных
|
80
|
ЗКДР.2
|
|
аналоговых
|
27
|
дискретных
|
92
|
Количество каналов вывода
управляющих сигналов, шт., не менее: ЗКДР.1 аналоговых дискретных ЗКДР.2
аналоговых дискретных
|
48 2 52
|
Высота отображаемых цифр и
знаков на дисплеях, мм, не менее
|
9
|
Наличие гальванической
развязки в каналах ввода-вывода
|
Обязательно
|
Прочность изоляции
гальванической развязки, В, не менее
|
500
|
Характер выходных сигналов
управления
|
Релейные, типа «сухой
контакт»
|
Коммутационная способность
выходных реле: напряжение переменного тока, В, не менее ток, А, не менее
напряжение постоянного тока, В, не менее ток, А, не менее
|
220 1 30 5
|
Диапазон изменения
выходного сигнала непрерывного управления электроприводом, В
|
от-10 до+10
|
Диапазон изменения
выходного сигнала непрерывного управления регулятором давления рабочего
тормоза, мА
|
от 0 до 200
|
Гп\/биня ППГП.РМЯ м пп
|
ЧООП
|
Максимальная скорость
движения сосуда, м/с, до
|
20
|
Диапазон значений
контролируемых ускорений, м/с
|
от 0 до 5
|
Количество формируемых
путевых команд, шт.
|
40
|
Погрешность контроля
превышения заданной скорости, %, не более
|
±10
|
Погрешность формирования
путевых команд, м, не более
|
±0,1
|
Количество точек отбора
информации о положении сосуда в стволе, шт., на один горизонт
|
4
|
Быстродействие защиты по превышению
скорости и переподъему, с,
|
0,1
|
Минимальное значение
контролируемой скорости пробуксовки шкива и проскальзывания каната, м/с
|
0,2
|
Периодичность контроля
идентичности каналов, с, до
|
1,0
|
Вывод:
В данном разделе рассчитаны: подомный сосуд, канаты, орган навивки,
двигатель. Построены диаграммы скоростей и усилий. Рассчитан расход энергии на
один подъем. Выбрана автоматизированная система управления и комплексной защиты
шахтной подъемной установки, регистрации и визуализации режимов ее работы ЗДКР
3. МОНТАЖ, НАЛАДКА И ЭКСПЛУАТАЦИЯ ПОДЪЕМНОЙ УСТАНОВКИ
Все вновь монтируемые и реконструируемые шахтные подъёмные установки
независимо от их назначения, типа и места установки перед вводом в эксплуатацию
должны быть подвергнуты ревизии, наладке и испытанию.
Ревизию, наладку и испытание эксплуатируемых подъёмных установок
производят в соответствии с требований Правил безопасности в угольных шахтах
(ПБ) и Правил технической эксплуатации угольных шахт (ПТЭ) специализированные
наладочные бригады один раз в год по графикам, согласованных с шахтами,
производственными объединениями по добыче угля и местными органами
Госгортехнадзора. Электрическая часть и аппаратура автоматизированных подъёмных
установок подлежит ревизии и наладке через 6 мес.
Наладочные работы производятся с целью:
проверки соответствия установки проекту, ПБ, ПТЭ, Правилам устройства
электроустановок (ПУЭ);
устранения обнаружение дефектов и выявленных отклонений от проекта
действующих правил, инструкций и нормативов;
обеспечения бесперебойной и безаварийной работы подъёма;
улучшения технико-экономических показателей подъёмной установки
(увеличение срока службы оборудования, повышение производительности, снижение
расхода электроэнергии и пр.) путем модернизации оборудования на основе
последних технических достижений;
проверки соблюдения обслуживающим персоналом ПБ, ПТЭ, Правила технической
эксплуатации электроустановок потребителей и Правил техники безопасности при
эксплуатации электроустановок потребителей, действующих инструкций и
нормативов;
инструктирования обслуживающего персонала по уходу и эксплуатации
подъёмной установки.
В наладочных работах на установке принимает участие шахтный персонал,
закрепленный за наладочной бригадой на весь период работ.
Наладочные работы на установке осуществляют в соответствии с графиком
проведения ревизии, наладки и испытания подъёмной установки, составленным и
согласованным с главным механиком предприятия и лицом, ответственным за
эксплуатацию подъёмной установки и утвержденным руководством шахты.
Одновременно с ревизией и наладкой шахтный персонал производит
маркшейдерскую проверку копровых шкивов, копра и установки подъёмной машины в
соответствии с требованиями ПТЭ.
При вводе в эксплуатацию новых подъёмных машин, кроме перечисленных выше
работ, необходимо произвести:
1) проверку фундамента до начала монтажа и в процессе монтажа;
2) проверку геометрической правильности установки машины,
горизонтальности валов и подшипников (производится маркшейдером шахты);
3) маркшейдерскую проверку правильности установки копровых шкивов и
определение углов девиации каната (производится маркшейдером шахты).
) испытание электрооборудования в соответствии с требованиями
Правил устройства электроустановок;
) прокручивание машины, обкатку ее на холостом ходу и под
нагрузкой продолжительностью 72 ч, после чего повторно осмотреть копровые
шкивы, навивки, тормозные устройства, валы и подшипники, соединительные муфты,
указатель глубины, двигатели и т.п. при необходимости произвести наладку
соответствующих узлов, а также подтяжку болтов, шпилек, жимков и т.п.
В соответствии с требованиями ПБ и ПТЭ после ревизии и наладки необходимо
провести контрольные испытания подъёмной установки комиссией в составе главного
механика шахты и представителя наладочной бригады.
Главный механик шахты обеспечивает необходимы технологический режим
работы установки при испытаниях, а руководитель наладочной бригады -
методическое и метрологическое обеспечение проведения испытания.
О проведении контрольных испытаний составляется протокол по установленной
форме в четырех экземплярах (для шахты, производственного объединения по добыче
угля, РГТИ и наладочного управления), который утверждает начальник
энергомеханической службы производственного объединения. Утверждение протоколов
обеспечивает главный механик шахты. В протоколе фиксируются сведенья о
неустраненных дефектах с указанием сроков устранения и наименования
организации, силами которой рекомендуется производить работы.
Машинный зал цилиндрической установки располагается на копре. В машинном
зале размещают органы навивки, двигатель, распределительное устройство,
реверсор, пульт управления.
В здании подъёмной машины для монтажных и ремонтных работ имеется
подъёмный кран грузоподъёмностью 60 т.
В здании должно быть рабочее и аварийное освещение. Рабочее освещение
осуществляется от сети 220 В, а аварийное - от аккумуляторных батарей
напряжением 12 В. При ремонтах дополнительное освещение осуществляют
переносными лампами напряжением 12 В.
Температура в здании должна быть не ниже 12 °С и поддерживается зимой с помощью
центрального отопления. Здание подъёмной машины должно быть обеспечено
противопожарными средствами.
Для каждой подъёмной установки необходимо иметь: паспорт подъёмной
машины, схему тормоза, принципиальную и монтажную схему коммутации, инструкцию
для машиниста подъёмной установки, схемы парашютных устройств, прошнурованные
журналы: «Книга осмотра подъёмной установки», «Книга осмотра подъемных канатов
и их расхода» и «Книга приемки и сдачи смен». В машинном зале в рамке под
стеклом вывешивается инструкция для машиниста, принципиальная электрическая
схема управления, схемы тормоза и парашютных устройств.
Подъёмная установка находится в ведении главного механика шахты. К
машинистам подъёмных установок (операторам) предъявляются определенные
требования, касающиеся стажа их работы на шахте, медицинского
освидетельствования, сдачи экзаменов на право управления подъёмной машиной и
стажировки по специальности. В обязанность машиниста входит прием - сдача
смены, управление, уход и надзор за машиной. Каждый непонятый сигнал должен
быть воспринят машинистом как сигнал «Стоп», после чего он выясняет причины
неясного сигнала.
Каждая аварийная остановка машины, а также все замеченные повреждения
должны быть записаны машинистом в журнал. Машину можно пускать в ход после
того, как установлена причина предохранительного торможения.
Для каждой установки в резерве должны быть: подъёмный сосуд, направляющий
шкив, секции обмотки подъёмного двигателя, двигатель тормозного компрессора,
комплект футеровки и тормозных колодок, быстроизнашивающиеся узлы и детали,
части к аппаратам управления и защиты, испытанный подъёмный канат,
уравновешивающий канат (полный комплект канатов).
Особенности эксплуатации одноканатных установок, определяются меньшими
размерами машины, расположением её на копре и необходимостью контроля
равномерного распределения нагрузки между всеми подъёмными канатами. Этот
контроль производится еженедельно при помощи динамометров одновременно с
измерением потери сечения канатов. Выравнивание усилий производят специальными
регулировочными устройствами на подъёмных сосудах.
Особое внимание при эксплуатации должно быть обращено на точность
проточки канавок футеровки на цилиндрическом барабане. При несоблюдении этого
радиусы обхвата будут различными, а распределение нагрузки в канатах
неравномерным, в связи с чем возникает опасность прогрессирующего аварийного
износа футеровки.
3.1 Планово-предупредительные осмотры и ремонты
Представляют систему периодически повторяющихся мероприятий по проведению
запланированных во времени профилактических работ по осмотру, уходу и надзору с
устранением неисправностей, а также ревизий и ремонтов, восстанавливающих
работоспособность оборудования установки.
Виды и периодичность осмотров, объёмы работ и нормативы времени на их
выполнение регламентируются ПБ, ПТЭ и отраслевыми инструкциями.
Для подъёмных установок приняты следующие виды осмотров:
- ежесменный осмотр (приемка-сдача смены), производится машинистами с
участием дежурного слесаря; продолжительность осмотра 15…20 мин;
ежесуточный осмотр, производится бригадой под руководством механика
подъёма; осмотру подлежат подъёмные сосуды, проводники, загрузочные и
разгрузочные устройства, направляющие шкивы, все агрегаты и узлы подъёмной
машины; результаты осмотра записывают в «Книгу осмотра подъёмной установки»,
которая имеет два раздела. В первом разделе против каждого объекта осмотра
отмечаются: Н - объект неисправен; У - объект исправен; «-» - осмотра не было;
во втором разделе записывают характер и степень неисправности объекта; главный
механик должен наметить мероприятия по устранению неисправностей и
ответственных за это лиц; продолжительность осмотра устанавливается в
зависимости от глубины ствола и должна быть не менее 2,5 ч.
Текущий ремонт производят еженедельно бригадой по осмотру и ремонту и ремонту
установки под руководством механика подъёма. Ремонт проводят на месте установки
оборудования, он заключается в восстановлении или замене быстроизнашивающихся
деталей, устранение всех дефектов, замеченных при осмотрах. Для
текущего ремонта отводится 2 ч в неделю.
Не реже одного раза в 15 дней главный механик шахты проверяет
правильность работы предохранительного тормоза и конечных выключателей защиты
от переподъёма путем искусственного переподъёма на малой скорости.
Ревизию и наладку подъёмной установки производят один раз в год
специализированной бригадой при участии представителя энергомеханической службы
шахты.
Технический осмотр и испытания проводят через 6 мес. после ревизии
и наладки. Объём этой работы, выполняемой
комиссией под руководством главного механика шахты, определен «Инструкцией по
техническому осмотру и испытанию эксплуатационных и проходческих подъёмных
установок».
Капитальный ремонт из-за и длительности работ предусматривает остановку на
длительное время по графику, составленному главным механиком производственного
объединения. При составлении графика руководствуются нормативными сроками
службы элементов подъёмных установок. Полный срок службы до списания
одноканатной подъёмной машины - 20 лет, такие же сроки службы имеют подъёмные
электродвигателя. Период до капитального ремонта для подъёмной машины равен 10
лет и для всех подъёмных двигателей он равен 10 годам. Остальное
электрооборудование имеет полный срок службы 12…15 лет и до капитального
ремонта 6…7 лет.
Таблица 3.1 График ППР
Числа
|
Месяцы года
|
|
I
|
II
|
III
|
IV
|
V
|
VI
|
VII
|
VIII
|
IX
|
X
|
XI
|
XII
|
1
|
4ТО, ТО2
|
ТО4
|
ТО4
|
4ТО, ТО2
|
4 ТО, ТО2
|
4 ТО, ТО2
|
4 ТО, ТО2
|
4 ТО, ТО2
|
4 ТО, ТО2
|
4 ТО, ТО2
|
4 ТО, ТО2
|
4 ТО,ТО2
|
2
|
4 ТО, ТО2
|
4 ТО, ТО2
|
4 ТО, ТО2
|
ТО3
|
4 ТО, ТО2
|
4 ТО, ТО2
|
4 ТО, ТО2
|
4 ТО, ТО2
|
РО1
|
4 ТО, ТО2
|
4 ТО, ТО2
|
4 ТО, ТО2
|
3
|
4ТО, ТО2
|
4 ТО, ТО2
|
4 ТО, ТО2
|
4 ТО, ТО2
|
4 ТО, ТО2
|
4 ТО, ТО2
|
4 ТО, ТО2
|
4 ТО, ТО2
|
4 ТО, ТО2
|
ТО3
|
4 ТО, ТО2
|
ТО4
|
4
|
4 ТО, ТО2
|
4 ТО, ТО2
|
4 ТО, ТО2
|
4 ТО, ТО2
|
4 ТО, ТО2
|
Т2
|
4 ТО, ТО2
|
4 ТО, ТО2
|
4 ТО, ТО2
|
4ТО, ТО2
|
4 ТО, ТО2
|
4 ТО, ТО2
|
5
|
4 Т, ТО2
|
ТО3
|
ТО3
|
4 ТО, ТО2
|
4 ТО, ТО2
|
4 ТО, ТО2
|
4 ТО, ТО2
|
4ТО, ТО2
|
4 ТО, ТО2
|
4 ТО, ТО
|
ТО4
|
4 ТО, ТО2
|
6
|
4 ТО, ТО2
|
4 ТО, ТО2
|
4 ТО, ТО2
|
4 ТО, ТО2
|
4 ТО, ТО2
|
4 ТО, ТО2
|
4 ТО, ТО2
|
ТО3
|
4 ТО, ТО2
|
4 ТО, ТО2
|
4 ТО, ТО2
|
4 ТО, ТО2
|
7
|
4 ТО, ТО2
|
4 ТО, ТО2
|
4 ТО, ТО2
|
4 ТО, ТО2
|
РО1
|
4 ТО, ТО2
|
4 ТО, ТО2
|
4 ТО, ТО2
|
4 ТО, ТО2
|
4 ТО, ТО2
|
4 ТО, ТО2
|
4 ТО, ТО2
|
8
|
ТО4
|
4 ТО, ТО2
|
4 ТО, ТО2
|
4 ТО, ТО2
|
4 ТО, ТО2
|
4 ТО, ТО2
|
4 ТО, ТО2
|
4 ТО, ТО2
|
4 ТО, ТО2
|
ТО4
|
4 ТО, ТО2
|
4 ТО, ТО2
|
9
|
4 ТО, ТО2
|
4 ТО, ТО2
|
4 ТО, ТО2
|
РО1
|
4 ТО, ТО2
|
4 ТО, ТО2
|
ТО1
|
4 ТО, ТО2
|
4 ТО, ТО2
|
4 ТО, ТО2
|
4 ТО, ТО2
|
4 ТО, ТО2
|
10
|
4 ТО, ТО2
|
4 ТО, ТО2
|
4 ТО, ТО2
|
4 ТО, ТО2
|
4 ТО, ТО2
|
4 ТО, ТО2
|
4 ТО, ТО2
|
Т2
|
4 ТО, ТО2
|
4 ТО, ТО2
|
ТО3
|
11
|
4 ТО, ТО2
|
РО1
|
4 ТО, ТО2
|
4 ТО, ТО2
|
4 ТО, ТО2
|
ТО3
|
4 ТО, ТО2
|
4 ТО, ТО2
|
4 ТО, ТО2
|
4 ТО, ТО2
|
4 ТО, ТО2
|
4 ТО, ТО2
|
12
|
4 ТО, ТО2
|
4 ТО, ТО2
|
Т2
|
4 ТО, ТО2
|
4 ТО, ТО2
|
4 ТО, ТО2
|
4 ТО, ТО2
|
4 ТО, ТО2
|
4 ТО, ТО2
|
4 ТО, ТО2
|
ТО3
|
4 ТО, ТО2
|
13
|
4 ТО, ТО2
|
4 ТО, ТО2
|
4 ТО, ТО2
|
4 ТО, ТО2
|
4 ТО, ТО2
|
4 ТО, ТО2
|
4 ТО, ТО2
|
ТО4
|
4 ТО, ТО2
|
4 ТО, ТО2
|
4 ТО, ТО2
|
4 ТО, ТО2
|
14
|
4 ТО, ТО2
|
4 ТО, ТО2
|
4 ТО, ТО2
|
4 ТО, ТО2
|
ТО3
|
4 ТО, ТО2
|
4 ТО, ТО2
|
4 ТО, ТО2
|
4 ТО, ТО2
|
4ТО, ТО2
|
4 ТО, ТО2
|
4 ТО, ТО2
|
15
|
РО1
|
4 ТО, ТО2
|
4 ТО, ТО2
|
4 ТО, ТО2
|
4 ТО, ТО2
|
4 ТО, ТО2
|
4 ТО, ТО2
|
4 ТО, ТО2
|
4 ТО, ТО2
|
ТО3
|
4 ТО, ТО2
|
4 ТО, ТО2
|
16
|
4 ТО, ТО2
|
4 ТО, ТО2
|
4 ТО, ТО2
|
ТО3
|
4 ТО, ТО2
|
4 ТО, ТО2
|
ТО4
|
4 ТО, ТО2
|
4 ТО, ТО2
|
4 ТО, ТО2
|
4 ТО, ТО2
|
4 ТО, ТО2
|
17
|
4 ТО, ТО2
|
4 ТО, ТО2
|
4 ТО, ТО2
|
4 ТО, ТО2
|
4 ТО, ТО2
|
4 ТО, ТО2
|
4 ТО, ТО2
|
4 ТО, ТО2
|
ТО3
|
4 ТО, ТО2
|
4 ТО, ТО2
|
ТО4
|
18
|
4 ТО, ТО2
|
4 ТО, ТО2
|
4 ТО, ТО2
|
4 ТО, ТО2
|
4 ТО, ТО2
|
ТО4
|
4 ТО, ТО2
|
4 ТО, ТО2
|
4 ТО, ТО2
|
4 ТО, ТО2
|
4 ТО, ТО2
|
4 ТО, ТО2
|
19
|
4 ТО, ТО2
|
ТО4
|
ТО3
|
4 ТО, ТО2
|
4 ТО, ТО2
|
4 ТО, ТО2
|
4 ТО, ТО2
|
4 ТО, ТО2
|
4 ТО, ТО2
|
4 ТО, ТО2
|
4 ТО, ТО2
|
4 ТО,ТО2
|
20
|
4 ТО, ТО2
|
4 ТО, ТО2
|
4 ТО, ТО2
|
4 ТО, ТО2
|
4 ТО, ТО2
|
4 ТО, ТО2
|
4 ТО, ТО2
|
ТО4
|
4 ТО, ТО2
|
4 ТО, ТО2
|
4 ТО, ТО2
|
4 ТО, ТО2
|
21
|
4 ТО, ТО2
|
4 ТО, ТО2
|
4 ТО, ТО2
|
4 ТО, ТО2
|
ТО4
|
4 ТО, ТО2
|
4 ТО, ТО2
|
4 ТО, ТО2
|
4 ТО, ТО2
|
4 ТО, ТО2
|
4 ТО, ТО2
|
4 ТО, ТО2
|
22
|
ТО3
|
4 ТО, ТО2
|
4 ТО, ТО2
|
4 ТО, ТО2
|
4 ТО, ТО2
|
4 ТО, ТО2
|
4 ТО, ТО2
|
4 ТО, ТО2
|
4 ТО, ТО2
|
РО1
|
4 ТО, ТО2
|
4 ТО, ТО2
|
23
|
4 ТО, ТО2
|
4 ТО, ТО2
|
4 ТО, ТО2
|
ТО3
|
4 ТО, ТО2
|
4 ТО, ТО2
|
4 ТО, ТО2
|
4 ТО, ТО2
|
4 ТО, ТО2
|
4 ТО, ТО2
|
4 ТО, ТО2
|
4 ТО, ТО2
|
24
|
4 ТО, ТО2
|
4 ТО, ТО2
|
4 ТО, ТО2
|
4 ТО, ТО2
|
4 ТО, ТО2
|
4 ТО, ТО2
|
4 ТО, ТО2
|
4 ТО, ТО2
|
ТО3
|
4 ТО, ТО2
|
4 ТО,ТО2
|
ТО3
|
25
|
4 ТО, ТО2
|
4 ТО, ТО2
|
4 ТО, ТО2
|
4 ТО, ТО2
|
4 ТО, ТО2
|
ТО3
|
4 ТО, ТО2
|
4 ТО, ТО2
|
4 ТО, ТО2
|
4 ТО, ТО2
|
4 ТО, ТО2
|
4 ТО, ТО2
|
26
|
4 ТО, ТО2
|
ТО4
|
ТО4
|
4 ТО, ТО2
|
4 ТО, ТО2
|
4 ТО, ТО2
|
4 ТО, ТО2
|
4 ТО, ТО2
|
4 ТО, ТО2
|
4 ТО, ТО2
|
ТО3
|
4 ТО, ТО2
|
27
|
4 ТО, ТО2
|
4 ТО, ТО2
|
4 ТО, ТО2
|
4 ТО, ТО2
|
4 ТО, ТО2
|
4 ТО, ТО2
|
4 ТО, ТО2
|
РО1
|
4 ТО, ТО2
|
4 ТО, ТО2
|
4 ТО, ТО2
|
4 ТО, ТО2
|
28
|
4 ТО, ТО2
|
4 ТО, ТО2
|
4 ТО, ТО2
|
4 ТО ТО2
|
ТО3
|
4 ТО, ТО2
|
4 ТО, ТО2
|
ТО3
|
4 ТО, ТО2
|
4 ТО, ТО2
|
4 ТО, ТО2
|
4 ТО, ТО2
|
29
|
ТО4
|
4 ТО, ТО2
|
4 ТО, ТО2
|
4 ТО, ТО2
|
4 ТО, ТО2
|
4 ТО, ТО2
|
4 ТО, ТО2
|
4 ТО, ТО2
|
4 ТО, ТО1
|
ТО3
|
4 ТО, ТО2
|
4 ТО, ТО2
|
30
|
4 ТО, ТО2
|
|
4 ТО, ТО2
|
4 ТО, ТО2
|
4 ТО, ТО2
|
4 ТО, ТО2
|
РО1
|
4 ТО, ТО2
|
4 ТО, ТО2
|
4 ТО, ТО2
|
4 ТО, ТО2
|
4 ТО, ТО2
|
31
|
4 ТО, ТО2
|
|
4 ТО, ТО2
|
|
4 ТО, ТО2
|
|
4 ТО, ТО2
|
4 ТО, ТО2
|
|
4 ТО, ТО2
|
|
4 ТО,ТО2
|
- ТО-1-ежесменное техническое обслуживание.
ТО-2-еженедельное техническое обслуживание.
ТО-3-еженедельное техническое обслуживание.
ТО-4-двухнедельное техническое обслуживание.
Т-2 (НРП)- полугодовая ревизия-наладка.
Т-3 (НРГ)-предмет на ревизия-наладка.
Таблица 3.2 Виды ТО
Вид -ТО
|
Названия работ
|
Последовательность
выполнения работ
|
Технические условия
работоспособности
|
ТО-1
|
- Проверка защиты от
обратного хода. - Проверка защиты от превышения заданного времени
пуску и подтягивания. - Проверка блокирования перехода с ручного режима на
автоматический. - Проверка положения сосуда в стволе. - Проверка
защиты от превышения скорости. - Проверка блокирования позволяющего
включения подъемного двигателя при переподъеме только в сторону ликвидации
переподъема.
|
Для этого при подъеме груза
в автоматическом режиме во время нахождения подъемного сосуда в середине
ствола поставить рукоятку командоконтролера в положение «0». Для этого
установить рукоятку рабочего торможения в положение «заторможено», а
командоконтролер в «0». Для этого во время стоянки при «заряженной» машине
перевести рукоятку выбора режимов в положения «Автоматика» Для этого сосуд
поставить в промежуточное положение, ключ выбора режимов поставить в
положение «Автоматика» кнопку зарядка в положение «Заряженная» Согласно с
инструкцией про проверку РОС. Обеспечивает контактами ПО в цепочки 1ТП и
цепочки катушек контактов реверсора.
|
После остановки машины и
начала движения в обратном направлении включается предохранительное
Торможение. После включения реверсора с задержкой времени, согласно с
вставкой защиты, применяется предохранительное торможение. Применяется
предохранительное торможение. Машина «заряжается» только в конечных
положениях сосуда (точная остановка). В других положениях сосуда машина «не
заряжается» Накладывается предохранительное торможение при превышении
заданной скорости. При переподъеме сосуда больше чем на 0.5 м накладывается
предохранительное торможение.
|
ТО-2
|
- Проверка
работоспособности аппаратуры контроля температуры подшипников. - Проверка блокирования
подъемной установки при заполненом прийомном бункере. -Проверка защиты
контроля работоспасобности обмотки регулятора давления. - Проверка
блокирования выключающяя влияния тока в обмотке управления регулятора
давления тормозного момента. - Проверка работоспособности реле дуговой
блокировки.
|
Во время стоянки машины
уменьшить температурную уставку датчика до срабатывания. Для этого
выключить питание ВГРП. Через реле 2 РКЦ. При предохранительном
торможении контакт КРТ 2 1ТП в цепи 2СН. Для этого быстро перевести
рукоятку командо-контролера через «0» при реверсировании.
|
Включается световая и
звуковая сигнализация. Накладывается предохранительный тормоз.
Накладывается предохранительный тормоз. Накладается предохранительноетторможение.
Контакторы реверсора включаются с выдержкой во времени.
|
ТО-3
|
- Проверка блокировки
замыкания на «землю» в цепях управления и защиты. - Проверка защиты
работоспасобности дугового блокирования. - Проверка блокирования от
залипания контактов ускорения и отсутсвия давления в системе маслосмазки. -
Проверка защиты от короткого замыкания у входных цепях аппарату управления
контакторами.
|
Релиазовано через реле Р3,
которое включается при замыкании на «Землю». Реализуется через реле 2РВ,
контакт которого введено в цепь (1ТП). Котакт 1РБ включен в цепь статорных
контактов в цепи реле РЗД. Через контакт в цепи 1ТП.
|
Размыкается цепь реле
направления, включит светловой сигнал. Накладывается предохранительный
тормоз. Котакторы ускорения не включится при залипании хотябы одного из
них. Накладывается предохранительное торможение.
|
ТО-4
|
Выполнить все виды работ
ТО-1, ТО-2, ТО-3под руководством главного механика.
|
|
|
Т-3 (НРГ)
|
Выполнить работы которые
предусмотрены «Руководством по ревизии, наладки и испытанию шахтных подъемных
установок» (М. Надра, 1980 г.)
|
|
|
4. ЭЛЕКТРОСНАБЖЕНИЕ ШАХТНОЙ ПОДЕМНОЙ УСТАНОВКИ
Для всех типов шахтных подъёмных машин с электроприводом по системе Г-Д с
тиристорным возбуждением применяется единый комплект электрооборудования,
обеспечивающий управление скиповыми подъёмами.
В комплект входят: электродвигатель постоянного тока серии П или ПБК
независимого возбуждения, применяемый в качестве подъёмного двигателя. К
двигателю пристроены тахогенераторы, центробежное реле и преобразовательный
агрегат, состоящий из синхронного двигателя, который является приводным
двигателем агрегата, и генератора постоянного тока ГП, осуществляющего питание
подъёмного двигателя.
Комплектно с преобразовательным агрегатом поставляют возбудитель,
регулятор возбуждения с ручным дистанционным приводом, разрядное сопротивление
с синхронному электродвигателю и маслостанцию ; два сухих трансформатора ТС для
питания возбудителей двигателя и генератора (напряжение 380 - 230 - 133 В);
реверсивный тиристорный преобразователь мощностью 60 кВт (напряжение питания
230В, напряжение цепей управления 380В и выпрямленное напряжение 230В),
предназначенный для для питания обмотки возбуждения обмотки генератора;
нереверсивный тиристорный преобразователь аналогично типа для питания обмотки
возбуждения подъёмного двигателя; станцию управления автоматическим
выключателем на ток главной цепи 6000А; шкаф линейного контактора привода Г- Д
; шкаф управления пуском и защитой синхронного двигателя; три шкафа управления вспомогательными
приводами.
4.1 Расчет нагрузки участка
Исходные данные:
Двигатель постоянного тока - П2-800-256-8КУ4
Напряжение,

Мощность,
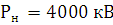
Частота
вращения, n=40 об/мин
Ток
якоря, 
Коэффициент
спроса, 
Коэффициент
мощности, 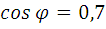
Рисунок 4.1 Схема электроснабжения угольного подъема
Расчетные электрические нагрузки определяются методом коэффициента
спроса.
Расчетная активная мощность определяется по формуле:

,кВт (4.1)
где
Pн -
номинальная мощность потребителя, кВт;
Kс - коэффициент спроса потребителя.

кВт
Реактивная
мощность определяется по формуле:

;
кВАр (4.2)
где
tgφ - соответствует
характерному для электроприемника cosφ, определяемому по справочникам.

; кВАр
Полная
мощность определяется по формуле:
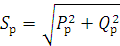
; кВА
(4.3)

; кВА
Из
каталога выбираем трансформатор ТДГД 8000/10У2, с следующей технической
характеристикой:
Uвн=6 кВ; Pк.з.=33,2
кВт; Pх.х.=8,2
кВт;
Uнн=0,59 кВ; Uк.з.=8,2 %; Iх.х.=39 %.
4.2
Расчет электрической сети участка
Выбираем
сечение проводов и кабелей по длительно-допустимому току нагрузки. Расчетный ток
для каждого участка определяется по формуле:

(4.4)
где
Sру -
расчетная мощность потребителей получающих питание по данному участку, кВА;
Uну - номинальное напряжение участка, кВ.
Принимаем
два кабеля КШВГ 3×95+1×35
с Iд=265 А, х0=0,071 Ом/км, r0=0,076, Sк.з. ГПП=59,9 МВА, l=20м.
Проверяем
кабель по термической устойчивости к току к.з.
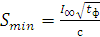
(4.5)
где
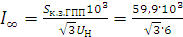
=5770 А
(4.6)
tф=0,15
с=165

мм2

(4.7)
где
cosφс.в. -
средневзвешенный cosφ;
l
- длина участка, км;
r0 и x0 -
активное и индуктивное удельное сопротивление кабелей Ом/км.

%
Принимаем
кабель к ГПП АС-240 с Iдоп=610 А, r0=0.132 Ом/км, х0=0,121, l=220м.
Проверяем
кабель по термической устойчивости к току к.з.(ф-ла 4.5)
где
с=105

мм2
Потери
напряжения в кабелях определяются по формуле (4.7):

%
Все
выбранные кабеля удовлетворяют условиям потери напряжения и не превышают 5%.
4.3
Расчет токов короткого замыкания
Расчет токов короткого замыкания необходим для проверки устойчивости при
к.з. выбранных уставок защиты и отключающей способности пускозащитной
аппаратуры.
Рисунок 4.2 - Схема замещения сети
Ток трехфазного к.з. для любой точки сети может быть определен по
формуле:
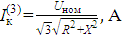
(4.8)
где
Uном -
напряжение источника ток, В;
R и X
- соответственно сумма активных и индуктивных сопротивлений цепи до
определенной точки к.з., Ом.
Ток
двухфазного к.з. можно определить из соотношения.

(4.9)
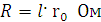
(4.10)

(4.11)

(4.12)

(4.13)
4.4
Выбор аппаратуры управления и защиты
Выбираем КРУВ по номинальному напряжению и по предельному отключающему
току.

В

(4.14)
9,6

(4.15)
кА ≥ 7,585 кА
Принимаем КРУВ-6,основные характеристики указаны в таблице 4.1
Таблица 4.1 Основные характеристики КРУВ-6
Параметры
|
КРУВ-6
|
Номинальное напряжение, В
|
6000
|
Номинальный ток (А) ячеек:
вводных и секционных отходящих присоединений
|
100; 160; 200;
320; 400; 630; 20; 32; 80; 100; 160; 200; 320; 400
|
Мощность отключения, МВ∙А
|
100
|
Предельный сквозной ток КЗ, кА: амплитудное
значение действующее значение
|
25 -
|
Предельный односекундный
ток термической стойкости при
КЗ, кА
|
9,6
|
Уровень и вид взрывозащиты
|
РВ, 4В, И
|
Тип выключателя
|
ВЭВ-6
|
Вывод:
В данном разделе осуществлен расчет
электроснабжения угольной
подъемной машины, приняты мероприятия по экономии электроэнергии. Выбран
трансформатор ТДГД 8000/10У с 
=8000
кВА. Выбраны кабели типа:
Принимаем два кабеля типа:
КШВГ
3×95+1×35
с 

, 
АС-240
с

, 
Также
был произведен расчет комплектного распределительного устройства КРУВ-6.
5. ТЕХНИКО-ЭКОНОМИЧЕСКИЕ ПАРАМЕТРЫ ЭКСПЛУАТАЦИИ УГОЛЬНОГО ПОДЪЕМА
.1 Расчет численности работников участка
Расчет численности работников участка произведем на основе
суммарной нормативной трудоёмкости планового суточного технического
обслуживания и ремонта оборудования подъёмных комплексов главного ствола.
Таблица 5.1 Нормативная трудоемкость
планового ТО по борудованию подъёмной установки
Номер работы
|
Наименование работы
|
среднее число подз. эл.
слесарей
|
Средняя продолж. выполнения
работ, мин.
|
Кол-во оборудования
|
Общее время
|
1
|
2
|
3
|
4
|
5
|
6
|
МЕХАНИЧЕСКОЕ ОБОРУДОВАНИЕ ТО -2 (ЕЖЕСУТОЧНОЕ)
11.1.2.1 11.1.2.3 11.1.2.4
11.1.2.6 11.1.2.8 11.1.2.9
|
Получение информации о
состоянии оборудования Осмотр приводного и отклоняющего шкивов Осмотр
тормоза завода ЛКУ Осмотр соединительной муфты Осмотр воздушной системы
Осмотр воздушного фильтра
|
1 2 2 1 1 1
|
5 10 20 5 10 5
|
1 4 2 2 3 3
|
5 80 80 10 30 15
|
Итого по ТО-2 220 мин.
|
ТО-3 (ЕЖЕНЕДЕЛЬНОЕ)
11.1.3.1 11.1.3.2 11.1.3.4
11.1.3.6 11.1.3.7 11.1.3.9 11.1.3.10
|
Проверка крепления
футировки приводного шкива Смазка тормоза завода ЛКУ Проверка воздушного
фильтра Проверка воздушной маслёнки Очистка водомаслоотделителя Очистка
фильтра компрессора Смазка бронзовых втулок отклоняющих шкивов
|
2 2 1 1 1 2 2
|
50 90 30 10 10 20 20
|
2 2 3 3 4 4 2
|
200 360 90 30 40 160 80
|
Итого по ТО-3 960 мин.
на сутки 13,7 мин.
|
ТО-4 (ДВУХНЕДЕЛЬНОЕ)
11.1.4.2 11.1.4.4
|
Проверка крепления
футировки барабана Проверка правильности работы предохранительного тормоза
|
2 1
|
90 10
|
2 2
|
360 20
|
Итого по ТО-4 380 мин.
на сутки 27 мин.
|
РО-1 (ЕЖЕМЕСЯЧНОЕ)
11.1.5.1 11.1.5.2 11.1.5.6
11.1.5.8 паспорт
|
Проверка приводного шкива
Проверка и смазка отклоняющих шкивов Проверка и смазка зубчатой муфты Проверка
регулятора давления панели тормоза Проверка компрессора
|
2 2 2 2 1
|
60 60 40 180 100
|
2 2 2 3 4
|
240 240 160 1080 400
|
Итого по РО-1 2120 на
сутки 71 мин
|
Т-1 (ЕЖЕКВАРТАЛЬНЫЙ)
|
11.1.7.1 11.1.7.2 11.1.7.4
11.1.7.6 паспорт
|
Проверка и смазка подшипников
отклоняющих шкивов Проверка электромагнитного клапана Очистка воздушного
фильтра Проверка износа футировки приводного шкива Проверка компрессора
|
2 2 2 2 1
|
60 90 45 30 480
|
4 15 3 2 4
|
480 2700 270 120 1920
|
Итого по Т 5490 на сутки
61 мин
|
Т-2(ПОЛУГОДОВОЙ)
11.1.8.1. 11.1.8.3
|
Проверка и смазка
подшипников качения органа навивки Очистка компрессора
|
3 3
|
180 360
|
4 4
|
2160 4320
|
Итого по Т-2 6480 на сутки
36 мин.
|
Т-3 (ГОДОВОЙ)
11.1.8.1.
|
Проверка зубчатой муфты с
заменой смазки
|
3
|
240
|
2
|
1440
|
Итого по Т-3 1440 на
сутки 4 мин. мин.
|
Всего за сутки по механическому оборудованию 556 мин. - 9,27 час
ЭЛЕКТРИЧЕСКОЕ ОБОРУДОВАНИЕ ТО-2 (ЕЖЕСУТОЧНОЕ)
11.2.2.1 11.2.2.2 11.2.2.3
11.2.2.4 11.2.2.5 11.2.2.6 11.2.2.7 11.2.2.8 11.2.2.9 11.2.2.11 11.2.2.12
11.2.2.15 11.2.2.17 11.2.2.18 11.2.2.19
|
Получение информации о
состоянии оборудования Осмотр и проверка ограничителя скорости ОСЭРП Осмотр
и проверка ограничителя скорости ЭОС-3 Осмотр аппарата задания АЗК Осмотр и
проверка концевых выключателей и блокировочных устройств Осмотр и проверка
аппаратуры сигнализации Проверка исправности АЗП Осмотр и проверка скоро
стимера Осмотр и проверка работы подъёмного двигателя Осмотр
высоковольтного распред.устройства Осмотр быстродействующего выключателя ВАТ
Осмотр и проверка командоаппаратов Осмотр пульта управления ПМ Проверка
исправности аппаратуры управления и автоматизации Проверка исправности
ап-туры КТЭУ
|
1 1 1 1 1 1 2 1 1 1 2 1 1
2 2
|
5 10 20 10 10 10 10 5 10
10 10 5 5 20 30
|
1 2 2 2 2 2 2 2 2 2 3 4 2
3 2
|
5 20 40 20 20 20 40 10 20
20 60 20 10 120 120
|
Итого по ТО-2 545 мин.
|
ТО-3 (ЕЖЕНЕДЕЛЬНОЕ)
11.2.3.1 11,2.3.2 11.2.3.3
|
Осмотр подъемного
электродвигателя Осмотр и проверка аппарата АЗК Осмотр и проверка
тиристорных преобразователей КТЭУ
|
2 2 2
|
30 20 30
|
2 2 3
|
120 80 180
|
Итого по ТО-3 380 мин. на
сутки 54 мин.
|
ТО-4 (ДВУХНЕДЕЛЬНОЕ)
11.2.4.1 11.2.4.2 11.2.4.4
|
Осмотр и проверка
быстродействующего выключателя ВАТ Проверка правильности работы защитных
устройств Проверка исправности блокировочных устройств
|
2 2 2
|
90 60 40
|
3 2 2
|
540 240 160
|
Итого по ТО-4 940 мин. на
сутки 67 мин.
|
РО-1 (ЕЖЕМЕСЯЧНОЕ)
11.2.5.1 11.2.5.2 11.2.5.3
11.2.5.4 11.2.5.6 11.2.5.7 11.2.5.8 11.2.5.9
|
Осмотр подъёмного
электродвигателя Осмотр и проверка релейной станции Осмотр и проверка
тиристорных преобразователей КТЭУ Осмотр и проверка быстродействующего
выключателя ВАТ Осмотр командоаппаратов Осмотр и проверка ограничителя
скорости ОСЭРП Осмотр и проверка ограничителя скорости ЭОС-3 Осмотр и проверка
аппарата АЗК
|
2 2 2 2 2 2 2 2
|
90 120 120 90 60 60 40 120
|
2 2 3 3 4 2 2 2
|
360 480 720 540 480 240 160
480
|
Итого по РО-1 3460 мин.
на сутки 115 мин.
|
Т-2 (ПОЛУГОДОВОЙ)
11.2.8.1 11.2.8.2 11.2.8.4
11.2.8.5 11.2.8.6 11.2.8.7 11.2.8.8
|
Проверка состояния и ремонт
подъёмного двигателя Проверка состояния и ремонт быстродействующего
выключателя ВАТ Проверка состояния пульта управления ПМ Проверка состояния
и ремонт релейной станции Проверка состояния и ремонт тиристорных
преобразователей КТЭУ, ТП-3, ТПР-9 Проверка состояния и ремонт ограничителя
скорости ОСЭРП Проверка состояния и ремонт аппарата АЗК
|
2 2 2 2 2 2 2
|
180 90 90 120 120 60 90
|
2 3 2 2 3 2 2
|
720 540 360 480 720 240
360
|
Итого по Т-2 3420 мин. на
сутки 19 мин.
|
Всего за сутки по электрическому оборудованию 801 мин. - 13.35 час
ОБОРУДОВАНИЕ ВЕРТИКАЛЬНЫХ СТВОЛОВ ТО-2 (ЕЖЕСУТОЧНОЕ)
11.3.2.2 паспорт подв устр
11.3.2.7 11.3.2.11 11.3.2.16 11.3.2.17 11.3.2.18 11.3.2.19 11.3.2.20
11.3.2.21 11.3.2.22 11.3.2.23
|
Осмотр и проверка состояния
металлоконструкции скипа Осмотр и проверка состояния подвесного устройства
ККБ Осмотр и проверка состояния подвесных устройств Осмотр и проверка
роликовых направляющих Осмотр подъёмных канатов Проверка элементов жёсткой
армировки Проверка разгрузочного устройства Осмотр уравновешивающих
канатов Проверка состояния колодцев, амортизационных рам Осмотр
загрузочного устройства Осмотр трубопроводов Осмотр кабельных линий
|
2 2 2 2 2 2 2 2 2 2 1 1
|
20 30 20 10 45 45 20 45
40 40 45 45
|
4 4 4 16 2 1 2 2 2 3 1 1
|
160 240 160 320 180 90 80
180 160 240 45 45
|
Итого по ТО-2 1900 мин.
|
ТО-3 (ЕЖЕНЕДЕЛЬНОЕ)
11.3.3.2 11.3.3.3 11.3.3.5
11.3.3.8 11.3.3.9
|
Осмотр и проверка состояния
подъёмных канатов Осмотр и проверка состояния уравновешивающих канатов
Контроль распределения нагрузки между подъемными канатами Осмотр
разгрузочного устройства Осмотр загрузочного устройства
|
2 2 1 2 2
|
45 45 10 30 30
|
2 2 2 3 3
|
180 180 20 180 180
|
Итого по ТО-3 740 мин. на
сутки 106 мин.
|
РСИ (ЕЖЕМЕСЯЧНОЕ)
11.3.5.1 11.3.5.3 11.3.5.5
11.3.5.8 11.3.5.11 паспорт прицепи. паспорт 11.3.5.12 11.3.5.13 11.3.5.16
11.3.5.17 11.3.5.18
|
Осмотр подъёмных канатов Контроль распределения нагрузки между
подъёмными канатами Осмотр уравновешивающих канатов Осмотр элементов жесткой армировки Осмотр и
проверка состояния скипов Осмотр и проверка состояния прицепных устройств
головных канатов Осмотр и проверка состояния прицепных устройств
уравновешивающих канатов Осмотр и проверка состояния трубопроводов Осмотр и
проверка состояния кабельных линий Осмотр разгрузочного устройства Осмотр
загрузочного устройства Осмотр и проверка состояния проводников
|
2 2 2 2 3 2 2 2 2 2 2 2
|
180 30 180 180 30 50 40
360 180 30 50 45
|
8 2 6 1 4 4 4 1 1 3 3 1
|
2880 120 2160 360 360 400
320 720 360 180 300 90
|
Итого по РО-1 8250 на
сутки 275 мин.
|
РО-2 (ДВУХМЕСЯЧНОЕ)
11.3.6.2
|
Контроль распределения
нагрузки между подъёмными канатами
|
2
|
30
|
2
|
120
|
Итого по РО-1 120 на сутки
2 мин.
|
Всего за сутки по вертикальным стволам 2283 мин. - 38.05 час
Таблица 5.2 Нормативная численность
электрослесарей по техническому обслуживанию и ремонту оборудования породного подъёма
№п/п
|
Наименование
|
Годовая нормативная
трудоемкость технического обслуживания
|
В ШАХТЕ:
|
1 2 3
|
Маслостанция СНУ-5 Лебедки
1ЛГКН Кран мостовой с К=1 / 0,65 = 1,53, где К - коэффициент при работе в
шахте
|
2043 1019 680
|
|
ПОВЕРХНОСТЬ:
|
1 2 3 4 5 6 7 8 9
|
Лебедки стационарные Кран
мостовой Бойлер Лифт Насосы Внутренняя отопительная магистраль, включая радиаторы,
на 1 км Внутренняя канализация, на 1 км Внутренняя разводка питьевой
противопожарной воды, на 1 км Душевые краны, на 10 шт.
|
756 445 154 230 80 150 300
150 150
|
|
|
|
|
|
|
Нормативная численность электрослесарей на работе в шахте определяется по
формуле
Нч. = (К1´К2´К3´ТОР)/ (357´ tсм.) (5.1)
где К1= 0,4 К2 =1,15 К3 = 1,1
tсм. = 6ч
Нч. =0,4´1,15´1,1´(1019´4+2043´3+680´2)/357´6= 2,73 чел.
Нормативная численность электрослесарей для работы на поверхности
определяется по формуле
Нч.= 1,15´(756´3+154´3+230+7´80+0,6´150+0,2´300+0,2´150+150)/ (357´8)= 1,29 чел.
Таблица 5.3 Расчёт комплексной нормы выработки
Наименованию работ
|
ед. изм.
|
Объём работ
|
Норма выработки
|
Поправочный коэф. На
|
Норма вы- работки с учётом
поправки
|
Тарифная или средняя ставка
|
кол-во чел-см на объём
работ
|
Сумма зарплаты
|
Суточное ТО механической
части ПУ
|
ком
|
1
|
9.27
|
1,0
|
9.27
|
4,78
|
1,54
|
44,17
|
Суточное ТО электрической
части ПУ
|
ком
|
1
|
13.35
|
1,0
|
13.35
|
5,37
|
2,22
|
71,52
|
Суточное ТО оборудования
вертикальных стволов главного подъема
|
ком
|
1
|
38.05
|
1,0
|
38.05
|
5,37
|
6.34
|
204,28
|
Суточное ТО дополнительного
оборудования главного подъёма:
|
ком
|
|
|
|
|
|
|
|
в шахте
|
ком
|
1
|
16.38
|
1,0
|
16.38
|
4,43
|
2.73
|
72,56
|
на поверхности
|
ком
|
1
|
10.32
|
1,0
|
10.32
|
2,19
|
1.29
|
22,6
|
Дежурство электрослесарей
главного подъёма
|
ч/см
|
1
|
18
|
1,0
|
18
|
5,34
|
3.00
|
96,66
|
ИТОГО 511,79
Численность машинистов подъёма установлена ЕНЧ за 1995 §25 п.2. Если
ствол оборудован автоматизированной грузовой подъёмной установкой и согласно
ПЛА является запасным выходом из шахты, то численность машинистов
устанавливается исходя из норматива - 1 человек в смену на подъёмную машину.
Явочная численность рабочих на подъёме принимается в зависимости от
необходимости количества обслуживающего персонала.
Итого явочная численность рабочих в сутки:
машинистов - 4;
дежурных электрослесарей - 3;
электрослесарей - 17;
ИТР - 2.
Численность руководящих работников на подъёме:
- начальник -1;
- зам. начальника - 1;
механика - 1.
Списочная численность определяется в зависимости от коэффициента
списочного состава.
Rспис.
= (Тр -
Тк) / ((Тр - Тк - ТВД - Тот.)´Ку) (5.2)
где Тр - Тк - календарное число дней в году и
праздничных;
Тк - ТВД - Тот. - число праздничных,
выходных и отпускных дней в году;
Ку - коэффициент, учитывающий число невыходов.
Rспис.
=
(365-12)/((365-12- 90 -62)´ 0,96) =1,83
Чсп.(маш.)= 4´1,83= 7 чел.
Чсп.(эл.сл.)=17´1,83=32 чел.
Чсп.(деж.эл.сл.)=3´1,83= 6 чел.
Сводная ведомость численности работников представлены табл.4.4
5.2 Расчет себестоимости по элементам «Заработная плата» и
«Отчисления на социальные нужды»
Прямая зарплата по месячным окладам равна
Зокл.= Qмес´Исп. (5.3)
Зокл. маш.= 1738 ´ 7 = 12166, грн.
Зокл. эл. сл.5= 2990 ´ 16 = 47840, грн.
Зокл. эл. сл.4= 2740´10=27400, грн.
Зокл. эл. сл.3=2490´6=14940, грн.
Зокл.д. эл. сл.= 2990 ´ 6 = 17940, грн.
Зокл. нач.= 4650, грн.
Зокл.з.н.= 4426, грн.
Зокл.мех.=4077, грн.
Доплата в ночное время за одну рабочую смену 25% от тарифной ставки.
Дн(маш.) = 6,9 ´ 30 ´ 8 ´0,25 =
414, грн.
Дн(д.эл.сл.) = 10,4 ´ 30 ´ 8´0,25= 624, грн.
Премия за выполнение плана - 100% выплачивается : 25 % для дежурных
электрослесарей и 25% для машинистов от прямой зарплаты с учетом ночных.
Для начальника, зам. начальника и механика установлена премия в размере
50%.
Дп(маш.) = (Зок + Дн)´% = (1738+ 59,1)´0,25=449,3 грн.
Дп(эл.сл.5р.) =Зок ´ % = 2990´0,25 = 747,5 грн.
Дп(эл.сл.4р.) =Зок ´ % = 2740´0,25 = 685 грн.
Дп(эл.сл.3р.) =Зок ´ % = 2490´0,25 = 622,5 грн.
Дп(д.эл.сл.)= (Зок + Дн)´ % = (2990+104)´0,25= 773,5 грн.
Дп(нач.) = Зок´ % = 4650´0,5=2325 грн.
Дп(зам.нач.) = Зок´ % =4426´0,5 =2213 грн.
Дп(мех.) = Зок´ % = 4077´0,5=2038,5 грн.
Прочие неучтенные доплаты 1% от прямой заработной платы.
Суммарную прямую заработную плату, премия и доплаты получаем общий фонд
заработной платы по участку
Списочная численность
|
Основная
|
Доплаты
|
S зарплаты, грн
|
Таблица 5.4 Определение планового фонда оплаты труда
|
|
Прямой оклад
|
Премия
|
Ночные
|
Прочие доплаты
|
|
Машинист
|
7
|
12166
|
449,3
|
414
|
121,66
|
13150,96
|
Электрослесарь
|
16 10 6
|
47840 27400 14940
|
747,5 685 622,5
|
- - -
|
478,4 274 149,4
|
49065,9 28359 15711,9
|
Деж. электрослесарь
|
6
|
17940
|
773,5
|
624
|
179,4
|
19516,9
|
Начальник участка
|
1
|
4650
|
2325
|
-
|
46,5
|
7021,5
|
Зам. начальника
|
1
|
4426
|
2213
|
-
|
44,26
|
6683,26
|
Механик
|
1
|
4077
|
2038,5
|
-
|
40,77
|
6156,27
|
ИТОГО
|
|
|
|
|
|
145665,69
|
Себестоимость по элементу «Заработная плата» рассчитывается:
Sз.п.= SЗз.пл./ Дмес., грн./т., (5.4)
Sз.п.= 145665,69/104166,7 = 1,39 грн./т
Отчисления на социальные нужды планируется в размере 39,3% от
суммы месячного фонда заработной платы и рассчитывается:
Зотч. = 0,393´SЗЗ.П., грн. (5.5)
Зотч. = 0,393´145665,69=57246,62 грн.
Себестоимость по элементу «Отчисление на социальные нужды»
рассчитывается:
Sотч.
=SЗотч. / Дмес.,
грн./т., (5.6)
Sотч.
= 57246,62/104166,7
= 0,55 грн./т.
.3 Расчет себестоимости по элементу «Материалы»
Таблица 5.5 В приведенной таблице все цены на материалы
договорные
Наименование Материала
|
Количество, шт.
|
Расход в натуральном
исчислении
|
Цена за единицу
исчисляемого, грн.
|
Затраты в год, грн.
|
Подъёмный канат
|
4
|
660 м
|
120
|
316800
|
Уравновешивающий канат
|
3
|
610 м
|
87
|
159210
|
Масло И-40
|
|
0,4 т
|
7517
|
3006,8
|
Смазка 1:13
|
|
0,2 т
|
14380
|
2876
|
Ролики НКП-320
|
1
|
в зборе
|
6834
|
6834
|
Металл 8…10 мм
|
|
3 т
|
4267
|
12801
|
ИТОГО
|
|
|
|
488726,8
|
Себестоимость по элементу «Материалы» определяется:
Sм.= Зм. / Дгод.,
грн./т., (5.7)
Sм.
=
488726,8/1250000= 0,39 грн./т.
5.4 Расчет себестоимости по элементу «Электроэнергия»
Потребляемая мощность определяется умножением количества единиц
оборудования на установленную мощность и на количество часов работы в месяц.
Стоимость электроэнергии определяется умножением потребляемой
электроэнергии на тариф за 1 кВт./ час.
Потребляема мощность подъёмной машины составляет 1,64 кВт´ч./т по подъёму груза (из ранее
рассчитанного раздела 2.8.) и примем еще 10% от потребляемой мощности подъёмной
машины, т.к. они не учитывались для подъёма груза. Неучтенные 10% потребляемой
мощности используются для ежедневной проверки подъёмной установки и
оборудования ствола. Таким образом, потребляемая мощность подъёмной машины с
учетом 10% составит 1,804 кВт´ч./т.
На обслуживание подъёмной установки еще используется 1,66 кВт´ч./т.
Итого 3,464 кВт´ч./т
Оплата за электроэнергию на шахте производится почасово:
с 6:00 до 8:00 - 1кВт=0,59 грн.;
с 8:00 до 10:00 - 1кВт=1,2 грн.;
с 10:00 до 16:00 - 1кВт=0,59 грн.;
с 16:00 до 18:00 - 1кВт=1,2 грн.;
с 18:00 до 22:00 - 1кВт=0,59 грн.;
с 22:00 до 6:00 - 1кВт=0,2 грн.
значит
с 6:00 до 8:00 - 3,464 кВт´ч./т = 2,04 грн´ч./т ; за 2 часа - 4,08 грн´ч./т
с 8:00 до 10:00 - 3,464 кВт´ч./т = 4,15 грн´ч./т ; за 2 часа - 8,3 грн´ч./т
с 10:00 до 16:00 - 3,464 кВт´ч./т = 2,04 грн´ч./т ; за 6 часа - 12,24 грн´ч./т
с 16:00 до 18:00 - 3,464 кВт´ч./т = 4,15 грн´ч./т ; за 2 часа - 8,3 грн´ч./т
с 18:00 до 22:00 - 3,464 кВт´ч./т = 2,04 грн´ч./т ; за 4 часа - 8,16 грн´ч./т
с 22:00 до 6:00 - 3,464 кВт´ч./т = 0,69 грн´ч./т ; за 8 часа - 5,52 грн´ч./т
Себестоимость по элементу «Электроэнергия» рассчитывается:
Sэл. = S / 24, грн./т. (5.8)
эл. = 46,6 / 24= 1,94 грн./т.
С использованием ЗКДР Sэл. = S / 24, грн./т.
Sэл.
= 37,28 / 24= 1,55
грн./т.
5.5 Расчет себестоимости по элементу «Амортизация»
Амортизационные отчисления за месяц определяется по каждому виду
принятого вида оборудования:
Амес.= Пп ´(НА/(100´12)), грн./ мес. (5.9)
где Амес. - сумма амортизационных отчислений за месяц, грн.;
Пп. - полная начальная цена, грн.;
НА. - годовая норма амортизации, принимается по сборнику норм
амортизации.
Таблица 5.5.1 Расчет себестоимости по элементу «Амортизация»
Наименование оборудования
|
Коли-чество, шт.
|
Стоимость единицы
оборудования, грн
|
Ставка амортизационного
отчисления, %
|
Сумма отчислений, грн./год
(грн./мес.)
|
Подъёмная машина
|
1
|
1092270
|
15(1,25)
|
163840,5(13653,38)
|
Компрессор
|
2
|
17500
|
15(1,25)
|
5250(437,5)
|
Маслостанция
|
1
|
70000
|
15(1,25)
|
10500(875)
|
Двигатель ПМ
|
1
|
2500000
|
15(1,25)
|
375000(31250)
|
Пускатель ПВИ-125
|
4
|
3700
|
15(1,25)
|
2220(185)
|
Лебедка ЛП-5
|
3
|
14600
|
15(1,25)
|
6570(547,5)
|
Лебедка ЛП-18
|
3
|
51200
|
15(1,25)
|
23040(1920)
|
Лебедка 1ЛГКН
|
1
|
6200
|
15(1,25)
|
930(77,5)
|
Кран мостовой КМС-60
|
1
|
57300
|
15(1,25)
|
8595(716,25)
|
Кран мостовой
|
2
|
51400
|
15(1,25)
|
15420(1285)
|
Скип СНМ
|
2
|
35000
|
15(1,25)
|
10500(875)
|
ИТОГО
|
|
|
|
621865,5(51822,13)
|
Таблица 5.5.2 Расчет себестоимости по элементу «Амортизация»
Наименование оборудования
|
Коли-чество, шт.
|
Стоимость единицы
оборудования, грн
|
Ставка амортизационного
отчисления, %
|
Сумма отчислений, грн./год
(грн./мес.)
|
Подъёмная машина
|
1
|
1092270
|
25(2,08)
|
163840,5(13653,38)
|
Компрессор
|
2
|
17500
|
25(2,08)
|
5250(437,5)
|
Маслостанция
|
1
|
70000
|
25(2,08)
|
10500(875)
|
Двигатель ПМ
|
1
|
2500000
|
25(2,08)
|
375000(31250)
|
Пускатель ПВИ-125
|
4
|
3700
|
25(2,08)
|
2220(185)
|
Лебедка ЛП-5
|
3
|
14600
|
25(2,08)
|
6570(547,5)
|
Лебедка ЛП-18
|
3
|
51200
|
25(2,08)
|
23040(1920)
|
Лебедка 1ЛГКН
|
1
|
6200
|
25(2,08)
|
930(77,5)
|
Кран мостовой КМС-60
|
1
|
57300
|
25(2,08)
|
8595(716,25)
|
Кран мостовой
|
2
|
51400
|
25(2,08)
|
15420(1285)
|
Скип СНМ
|
2
|
35000
|
25(2,08)
|
10500(875)
|
ЗКДР
|
1
|
495000
|
25(2,08)
|
74250(6187,5)
|
ИТОГО
|
|
|
|
696115,5(58009,63)
|
Себестоимость по элементу «Амортизация» рассчитывается:
SА= SАмес. / Дмес., грн./т. (5.10)
А=
51822,13/104166,7= 0,5 грн./т.
С ЗКДР SА= SАмес. / Дмес., грн./т.
SА= 58009,63/104166,7= 0,56 грн./т.
5.6 Сводная смета эксплуатационных затрат
Таблица 5.6.1 Сводная смета эксплуатационных затрат без ЗКДР
Элемент затрат
|
Сумма затрат за год, грн.
|
Себестоимость 1 т угля
|
Удельный вес, %
|
Затраты на материалы
|
488726,8
|
0,39
|
8,2
|
Расходы на зарплату
|
1747988
|
1,39
|
29,1
|
Расходы на соц. нужды
|
686959
|
0,55
|
11,5
|
Амортизация
|
621865,5
|
0,5
|
10,5
|
Затраты на эл.энергию
|
2425000
|
1,94
|
40,7
|
ИТОГО
|
5970539,3
|
4,77
|
100
|
Таблица 5.6.2 Сводная смета эксплуатационных затрат с ЗКДР
Элемент затрат
|
Сумма затрат за год, грн.
|
Себестоимость 1 т угля
|
Удельный вес, %
|
Затраты на материалы
|
488726,8
|
0,39
|
8,8
|
Расходы на зарплату
|
1747988
|
1,39
|
31,3
|
Расходы на соц. нужды
|
686959
|
0,55
|
12,4
|
Амортизация
|
696115,5
|
0,56
|
12,6
|
Затраты на эл.энергию
|
1937500
|
1,55
|
34,9
|
ИТОГО
|
5557289,3
|
4,44
|
100
|
Вывод:
Условная годовая экономия равна 413250 грн.
Дополнительных инвестиций за счет привлеченных средств в сумме 495000
грн. Которые будут иметь срок окупаемости:
Ток. = (DКВ)
/ Эуг. = 495000 / 413250 = 1,2 года или 1 год 2 мес 7 дней. Без
учета роста цен на электроэнергию.
6. ОХРАНА ТРУДА
6.1 Анализ опасных и вредных производственных факторов.
Техника безопасности при эксплуатации и обслуживании подъемной установки.
Разработка инженерно-технических мероприятий по охране труда
При эксплуатации подъемной установки возникают следующие вредные
производственные факторы:
Пыль - мелкие твёрдые тела органического или минерального происхождения.
Пыль - это частички среднего диаметра 0,005 мм и максимального - 0,1 мм. Под
действием влаги пыль обычно превращается в грязь.
Шум - беспорядочные колебания различной физической природы, отличающиеся
сложностью временной и спектральной структуры. С физиологической точки зрения
шум - это всякий неблагоприятный воспринимаемый звук.
Вибрация - механические колебания, оказывающее ощутимое влияние на
человека. В этом случае подразумевается частотный диапазон 1,6-1000 Гц. Понятие
вибрация тесно связано с понятиями шум, инфразвук, звук.
Электромагнитные поля - это фундаментальное физическое поле,
взаимодействующее с электрически заряженными телами, представимое как
совокупность электрического и магнитного полей, которые могут при определённых
условиях порождать друг друга.
Недостаток природного осветления. Так как здание подъемных машин
расположено в ангарном, практически не имея естественного освещения, в силу
своих конструктивных особенностей вынужденно применятся искусственное освещение
даже в дневное время суток. Что однозначно влияет на работу обслуживающего
персонала подъемной установки. Падения зрения, замедления реакции, усталость
глаз.
Микроклимат
К опасным производственным факторам относятся: оборудование, которое
работает под давлением, выше чем атмосферное; электрооборудование; обрыв
каната; пробуксовка и скольжение каната по канатоведущему шкиву; открытые
вращающиеся части подъемной машины и элементы подъемной установки.
Шахтная подъёмная установка должна быть оборудована следующими защитными
и блокировочными устройствами:
максимальной и нулевой защитой;
защитами от провисания струны и напуска каната в ствол;
устройством блокировки, позволяющим включать двигатель после переподъёма
сосуда только в сторону ликвидации переподъёма;
устройством блокировки, не допускающим снятия предохранительного тормоза,
если рукоятка рабочего тормоза не находится в положении «заторможено», а
рукоятка аппарата управления - в нулевом положении;
устройством, подающим сигнал машинисту при недопустимом поднятии петли
уравновешивающего каната;
дублирующим ограничителем скорости или устройством, обеспечивающим
контроль целостности передачи от вала подъёмной
машины к указателю глубины, если ограничитель скорости не имеет полного
самоконтроля;
На случай поломки подъёмной машины или застревания подъёмных сосудов в
стволе оборудовать аварийно-ремонтную подъёмную установку. В связи с наличием в
стволе двух подъёмных установок дополнительная аварийно-ремонтная установка
отсутствует.
Запрещается переход людей через подъёмные отделения ствола. На всех
горизонтах шахты перед стволами установить предохранительные решетки для
предупреждения перехода людей через подъёмные отделения.
Подъёмную машину снабдить аппаратом (индикатором), показывающим машинисту
положение сосуда в стволе.
Подъёмная машина должна имеет исправно действующие:
самопишущий скоростимер. Тахограммы должны хранится в течение 3 месяцев;
вольтметр и амперметр;
манометры, показывающие давление сжатого воздуха в тормозной системе.
В подъёмной машине исправное механическое, рабочее и предохранительное
торможение с независимым друг от друга включением привода, воздействующее на
орган навивки.
Рабочий тормоз в неподвижном состоянии подъёмной машины обеспечивает
получение момента, не менее создаваемого предохранительным тормозом.
После замены элементов тормозной системы (тормозные колодки, тяги,
цилиндры, и др.) необходимо произвести ее испытания специализированной
наладочной бригадой. Результаты испытаний оформляются актом.
Подъёмные сосуды, подвесные устройства, направляющие башмаки, загрузочные
и разгрузочные устройства, направляющие и отклоняющие шкивы, их футеровка и
подшипники, тормозная система и другие элементы подъёмной машины, аппаратура
защиты и система управления осматриваются и проверяются ежесуточно лицом,
имеющим соответствующую квалификацию и назначенным приказом руководителя
предприятия для этой цели, и еженедельно - механиком подъёма. Этим же лицом
армировка ствола ежесуточно осматривается при скорости движения сосудов до 1
м/с и не реже одного раза в неделю при скорости движения 0,3 м/с. Участки
стволов, находящиеся в ремонте, осматриваются ежесуточно при скорости 0,3 м/с.
Одновременно с осмотром армировки ствола производиться осмотр крепи назначенным
приказом руководителя предприятия специально обученным лицом.
Главный механик шахты ежемесячно, а старший механик не реже одного раза в
15 дней производит проверку правильности работы предохранительного тормоза,
защитных устройств и исправность всех остальных вышеуказанных элементов
подъёмной установки. Результаты осмотров заносятся в Книгу осмотра подъёмной
установки.
Копры осматриваются комиссией под председательством главного инженера
шахты.
Производить осмотр копра один раз в год.
Машинистами подъёмных машин назначены лица, прошедшие специальное
обучение, получившие соответствующее удостоверение и прошедшие 2-месячную
стажировку и получившие соответствующее удостоверение.
Машинистами многоканатных подъёмов назначены лица, проработавшие не менее
1 года на грузовых подъёмных машинах.
Перед вводом в эксплуатацию и в дальнейшем один раз в год
специализированная наладочная организация с участием представителей
энергомеханической службы шахты производить ревизию и наладку подъёмной
установки в объёмах, предусмотренных Руководством по ревизии, наладке и
испытанию шахтных подъёмных установок, утвержденным Минуглепромом СССР
26.07.79.
Электрическая часть подъёмных установок подлежит ревизии и наладке через
6 месяцев.
Не реже одного раза в год маркшейдерская служба шахты или
специализированная организация, имеющая на это право, выполняет проверку
геометрической связи шахтного подъёма и копра в соответствии с инструкцией по
производству маркшейдерских работ, утвержденной Госгортехнадзором СССР
20.02.85. По проверки инженером шахты. Один экземпляр этого акта передается
главному механику шахты.
После ревизии и наладки подъёмной установки главный шахты и представитель
наладочной организации производят ее контрольные испытания. О проведении
контрольных испытаний составляется протокол, который утверждается директором
или главным инженером шахты. Через 6 месяцев после ревизии и наладки каждая
эксплуатационная установка подвергается техническому осмотру и испытанию
комиссией под руководством главного механика шахты.
Объём технического осмотра и испытания определяется Инструкцией по
техническому осмотру и испытанию эксплуатационных и проходческих подъёмных
установок, утвержденной Минуглепромом СССР 26.08.76.
О проведенном осмотре и испытании составляется акт.
На подъёмную установку на участке составить следующие документы:
график работы подъёма, утвержденный главным инженером шахты, с указанием
времени, необходимого для производства ежесуточных осмотров элементов подъёмной
установки;
паспорт подъёмной машины;
детальная схема тормозного устройства с указанием основных размеров;
инструкция для машинистов подъёмных установок;
прошнурованные книги: Книга осмотра подъёмной установки, Книга осмотра
каната и их расхода, Книга приема и сдачи смен, Книга осмотра стволов,
утвержденные приказом Госнадзорохрантруда от 18.01.96 №7.
Схема тормозного устройства, исполнительная электрическая схема и
инструкция для машиниста вывешена в машинном помещении.
В качестве расчетной части приводится определение расхода воды на
орошение и необходимое число форсунок для загрузочного бункера угольного
подъема.
Суточный
расход воды 
(м³/сут) для комплексного обеспылевания вычисляется по
формуле:

(6.1)
Где
v - суточный объем работы по отдельным производственным
процессам, принимаем 3360 т/сут;
q - удельный
расход воды по отдельным производственным процессам, принимаем равным 3 л/т.
Необходимое
число форсунок n для обеспечения нормативных параметров орошения
рассчитываются по формуле:

(6.2)
где
Q - расход воды на орошение, л/мин;
a - коэффициент
расхода воды форсункой;
Р
- давление воды у форсунки, принимаем равную 1,5 Мпа.
Принимаем
форсунку:
тип
КФ-1.6-75
конусная
угол
раствора факела75
±10°
6.2
Противопожарное оборудование подъёмной установки
От пожарных резервуаров к каждому стволу шахты должен прокладываться
трубопровод, диаметр которого равен диаметру трубопровода, проложенного в стволе,
но не менее 150 мм, а между зданиями и сооружениями - не менее 100 мм.
На подшкивной площадке и у шкивов копров должны быть установлены
оросители, которые размещают по контуру защищаемого объекта, с тем, чтобы по
всей защищаемой поверхности создавалась водяная завеса.
Требованиями п. п. 21 - 22 "Инструкции по противопожарной защите
угольных шахт" к § 553 ПБ установлено, что вентили и задвижки, подающие
воду к разбрызгивающим установкам на подшкивных площадках копров и в устьях
стволов, должны располагаться вне помещений, в которых могут распространиться
продукты горения (дым, высокая температура).
Разбрызгиватели установок для защиты подшкивных площадок копров
располагаются по периметру подшкивных площадок, т.е. мест, где могут отлагаться
смазочные материалы. Суммарный расход воды должен соответствовать требованиям
ПБ. Часть воды должна подаваться на канаты для их охлаждения. Система
трубопроводов и органов управления должна быть сухотрубной, а задвижки для
подачи воды в систему - предохранены от замерзания. Они также должны
располагаться в местах, не подверженных задымлению и действию высоких
температур при пожарах в стволах, надшахтных зданиях и др. сооружениях.
Расход воды на нужды пожаротушения на шахтных копрах в соответствии с
требованиями ПБ должен быть не менее 25 куб. м/ч (7 л/с).
В устьях всех вертикальных стволов и шурфов ниже уровня расположения
пожарных ляд по периметру поперечного сечения и на элементах армировки
монтируется трубопровод, оборудованный оросителями. Форма (разводка) трубопровода
должна обеспечивать создание плотной водяной завесы, перекрывающей все
поперечное сечение выработки.
Удельный расход воды в поперечном сечении ствола должен составлять 2 куб.
м/ч на 1 кв. м поперечного сечения выработки для стволов, закрепленных негорючей
крепью, и 6 куб. м/ч на 1 кв. м - для выработок, закрепленных горючей крепью.
Водяные завесы в устьях вертикальных стволов называют также кольцевыми
завесами, однако это не значит, что конструктивно установка должна иметь форму
кольца. Трубопроводы и разбрызгиватели установки в поперечном сечении ствола
должны быть расположены таким образом, чтобы разбрызгиваемая вода создавала
сплошную завесу с удельным расходом в соответствии с требованиями ПБ. Установка
должна располагаться в стволе ниже пожарных ляд. Подача воды в установку должна
осуществляться от пожарного водопровода на поверхности, так как при пожарах в
стволах и других основных объектах, как правило, производится отключение
электроэнергии в шахту. Задвижки для пуска воды в установку должны располагаться
в помещениях (сооружениях), в которые не могут попасть газообразные продукты
горения (дым), где бы ни возник очаг пожара и какой бы режим проветривания
шахты при этом не применялся. Все трубопроводы и органы должны быть
предохранены от замерзания.
Правилами безопасности в угольных шахтах допускается не сооружать
пожарные ляды в устьях вертикальных стволов при многоканатных подъемах. Это
обусловлено только тем, что при наличии в поперечном сечении большого
количества канатов (иногда до нескольких десятков) создать достаточно
герметичную ляду затруднительно. Если устройство ляды (моста - ляды) проектом
не предусматривается, то на случай поступления продуктов горения (дыма) из
ствола в башенный копер (надшахтное здание) в проекте необходимо предусмотреть
устройство герметизирующих дверей, клапанов, заслонок на всех проемах,
соединяющих помещения башенного копра с его внутренней шахтой. Если проектом
предусматривается устройство ляды (моста - ляды), то необходимо предусмотреть
наличие заранее подготовленных, опробованных и подогнанных приспособлений для
герметизации ляд после их закрытия.
Эти приспособления должны храниться вблизи устья ствола или в складе
пожарных материалов, для чего должно быть предусмотрено специальное место.
Для проектирования всех герметизирующих устройств и сооружений, которые в
зимнее время находятся постоянно или могут оказаться в результате
реверсирования вентиляционной струи в условиях отрицательных температур, должны
быть разработаны меры, облегчающие их открывание (закрывание), на случай
примерзания, образования наледей.
При решении вопросов эвакуации людей из зданий и помещений необходимо
выполнить расчеты количества эвакуационных выходов из зданий с учетом наличия
людей на этажах и в помещениях, обязательно нужно принять во внимание
возможность задымления помещений не только в случае пожара в данном или
соседних помещениях, но также в случае выполнения общешахтного реверсирования
вентиляционной струи при пожаре в одной из основных горных выработок,
возможность самопроизвольного опрокидывания вентиляционной струи при
значительном развитии пожара в выработке или остановке вентиляторов главного
проветривания.
При конструктивном оформлении путей эвакуации решаются вопросы
использования тех или иных строительных материалов (металл, железобетон),
расположения выходов (открытые лестницы, закрытые лестничные клетки, уклоны) и
ширины эвакуационных лестниц, протяженности путей эвакуации, материала и
направления открывания дверей и т.п.
В необходимых случаях, особенно в башенных копрах, должен решаться вопрос
об обеспечении работников средствами индивидуальной защиты дыхания
(самоспасателями) и индивидуальными светильниками.
Вывод:
В данном разделе были описаны и проанализированы опасные и вредные
производственные факторы, которые возникают при эксплуатации проектируемого
объекта. Произведен расчет мероприятия по пылеподавлению в загрузочном бункере
угольного подъема. Дано описание противопожарного оборудования.