Детали машин
Содержание
Введение
. Определение срока службы
приводного устройства
. Выбор двигателя.
Кинематический расчет привода
. Выбор материала червячной
передачи
. Расчет закрытой червячной
передачи
. Расчет открытой
поликлиноременной передачи
. Нагрузки валов редуктора
. Разработка чертежа общего
вида редуктора
. Определение реакций в
опорах подшипников
. Проверочный расчет
подшипников
. Проверочные расчеты
. Тепловой расчет червячного
редуктора
. Расчет технического уровня
редуктора
Литература
приводной двигатель
редуктор подшипник
Введение
Целью данной работы является проектирование
привода к качающемуся подъемнику на основании комплексного технического
задания. Привод включает в себя электродвигатель, соединенный при помощи
ремённой передачи с червячным одноступенчатым редуктором, который, в свою
очередь, при помощи муфты и цепной передачи соединен с валом исполнительного
механизма.
В рамках данной расчетно-графической работы
проводится расчет и выбор требуемого электродвигателя, проектный расчет
редуктора и открытой передачи, проверочный расчет редуктора, валов, расчет
подшипников.
Червячный одноступенчатый редуктор предназначен
для передачи мощности между валами электродвигателя и исполнительного
механизма.
Муфта служит для компенсации неточности
установки валов и ограничения нагрузок в приводе.
Ремённая передача служит для передачи движения с
увеличением крутящего момента от двигателя на редуктор.
1. Определение срока службы приводного
устройства
Устанавливаем качающийся подъемник на
железнодорожную станцию для обработки товарных вагонов. Работа в две смены,
нагрузка маломеняющаяся, режим реверсивный, продолжительность смены 8 часов.
Определяем ресурс привода Lh
= 365·Lτ·tc
·Lc
где Lτ
= 4 года - срок службы привода;
tc
= 8 ч. - продолжительность смены;
Lc
= 2 - число смен;
h
= 365·4·8·2 = 23360 ч
Принимаем время простоя 15% ресурса. Тогда Lh
= 23360·0,85 = 19856 ч
Рабочий ресурс привода принимаем Lh
= 20·103 ч
Таблица 1.1. Эксплуатационные характеристики
машинного агрегата
Место
установки
|
Lτ
|
Lc
|
tc
|
Lh, ч
|
Характер
нагрузки
|
Режим
работы
|
железнодорожная
станция
|
3
|
2
|
8
|
20·103
|
с
малыми колебаниями
|
реверсивный
|
. Выбор двигателя. Кинематический расчет привода
Определяем требуемую мощность привода: Ррм
= Fυ,
где F
= 1,2 кН - грузоподьемность;
υ = 0,60 м/с - скорость
подъема.
Ррм = 1,2·0,60 = 0,72 кВт
Определяем КПД привода:
η = ηзп·ηоп·ηм·
ηпк2,
где ηзп
= 0,85 - КПД закрытой червячной передачи;
ηоп
= 0,97 - КПД открытой поликлиноременной передачи;
ηм
= 0,98 - КПД муфты;
ηпк
= 0,99 - КПД подшипников качения;
η = 0,85·0,97·0,98·0,992
= 0,79
Находим требуемую мощность двигателя:
Рдв = Ррм/
η = 0,72/0,79 = 0,91 кВт
Определяем частоту вращения вала:
= 37,5
об/мин
Находим передаточное число привода u
для
каждого варианта:
Проводим разбивку передаточного числа привода u,
принимая uзп
= 10, тогда передаточное число
Принимаем u
= 24,53 при nном
= 920 об/мин.
По справочным таблицам выбираем электродвигатель
4АМ80В6У3 с мощностью 1,1 кВт и частотой вращения 920 об/мин.
При
выбранном двигателе уточняем общее передаточное число привода:
Определяем максимально допустимое отклонение
частоты вращения приводного вала:
Δnрм
= nрмδ/100=
37,5.7/100=2,62 об/мин.,
где δ- допускаемое
отклонение скорости приводного вала рабочей машины.
Определяем допускаемую частоту вращения
приводного вала, приняв Δnрм
=
-0,7 об/мин:
[nрм]=
nрм+-
Δnрм=37,5-0,7=36,8
об/мин.
Фактическое передаточное число привода uф:
ф=
nном/[nрм]=920/36,8=25
Передаточные числа закрытой и открытой передач:
оп=
uф/uзп=25/10=2,5
Таблица 2.1. Силовые и кинематические параметры
привода
Тип
двигателя 4АМ80В6У3 Рном = 1,1 кВт, nном = 920
об/мин
|
Параметр
|
Передача
|
Параметр
|
Вал
|
|
закрытая
|
открытая
|
|
двигателя
|
редуктора
|
приводной
рабочей машины
|
|
|
|
|
|
быстроходный
|
тихоходны
|
|
Передаточное
число u
|
10
|
2,5
|
Расчетная
мощность Р, кВт
|
0,91
|
0,86
|
0,72
|
0,70
|
|
|
|
Угловая
скорость ω,
1/с
|
96,3
|
38,5
|
3,85
|
3,85
|
КПД
η
|
0,85
|
0,97
|
Частота
вращеня n, об/мин
|
920
|
368
|
36,8
|
36,8
|
|
|
|
Вращающий
момент Т, Н·м
|
9,45
|
22,45
|
187
|
183,26
|
. Выбор материала червячной передачи
Выбираем материал для червяка и червячного
колеса: сталь 40Х; улучшение; твердость 269…302НВ;
σв =900 Н/мм2;
σт =750 Н/мм2;
σ-1
=410 Н/мм2; Dпред=
125 мм.
Выбираем материал для зубчатых венцов червячных
колес:
vs=4,3.
ω2 .uзп/103
. 
4,3.3,85.103/103.
=0,94
м/с
Материал для червячного колеса СЧ18, способ
отливки в землю σви
= 355 Н/мм2. Определяем
допускаемые контактные [σ]H,
Н/мм2 , и изгибные [σ]F,
Н/мм2
напряжения:
[σ]H
=175-35.vs=175-35.
0,94=142,1 Н/мм2
[σ]F
=0,075
. σви
. КFL=0.075.
355.0.656=17.46 Н/мм2
КFL=
N=573.
ω2 .Lh=573.3,85
.20.103=44,121.106
число циклов переменных напряжений за весь срок
службы (наработка);
Таблица 3.1. Механические характеристики
материалов червячной передачи
Элемент
передачи
|
Марка материала
|
Dпред
|
Термообработка
|
HRC
|
σв
|
σт
|
σ-1
|
[σ]н
|
[σ]F
|
|
|
|
|
HRC
|
Н/мм2
|
|
|
|
Способ
отливки
|
|
|
Червяк
|
40Х
|
125
|
У
|
269…302НВ
|
900
|
750
|
410
|
-
|
-
|
Колесо
|
СЧ18
|
-
|
З
|
-
|
355
|
-
|
-
|
142,1
|
17,46
|
4. Расчет закрытой червячной передачи
Проектный расчет
Определяем главный параметр - межосевое
расстояние аw
:
аw
=
мм
Определяем число витков червяка:
2
= z1.uзп=4.10=40
Определяем модуль зацепления m
= (1,5…1,7)аw/z2=(1,5…1,7)125/40=5
мм,
Коэффициент диаметра червяка: q=(0,212…0,25)z2=(0.212…0.25)40=10
Коэффициент смещения инструмента х=(аw/m)-0,5(q+z2)=(125/5)-0.5(10+40)=0
Определяем фактическое передаточное число uф
и определяем его отклонение Δu
от заданного u: uф
= z2/
z1
= 40/4 = 10;
Δu
=
0%
≤ 4%
Определяем фактическое межосевое расстояние:
w
= 0,5m(q+z2+2x)
= 0.5.5(10+40)=125 мм.
Основные геометрические размеры передачи, мм:
а) Основные размеры червяка:
Делительный диаметр d1=qm=10*5=50
Начальный диаметр dw2=m(q+2x)=5(10)=50
Диаметр вершин витков da1=d1+2m=50+2*5=60
Диаметр впадин витков df1=d1-2.4m=50-2.4*5=38
Делительный угол подъема линии витков
Длина нарезаемой части при х
= 0; c = 0
б) Основные геометрические размеры червячного
колеса:
- делительный диаметр:
- диаметр вершин:
диаметр впадин:
- начальный диаметр:
- наибольший диаметр:
,
- ширина венца: b2
= 0.315 aw
= 0.315*125=40 (при z1
= 4),
- радиусы закруглений зубьев:
f
= 0,5d1
+ 1,2m
= 0,5∙50 + 1,2∙5 = 31 мм;
Ra
= 0,5d1
- m
= 0,5∙50 - 5 = 20 мм;
- условный угол обхвата червяка венцом колеса

Проверочный расчет
Проверяем КПД:
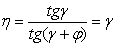
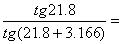
vs=uф.
ω2 .d1/2cos
103
Проверяем контактные напряжения σн:
σн
=
Н/мм2t2
=
=
1870 H
Перегрузка 1%
при v2=0.385≤
3 м/с К=1
Допускается перегрузка до 5%
Проверяем напряжение изгиба зубьев колеса σF,
Н/мм2
:
σF=
0,7*YF2·
·К=0,7·1,45·
1
= 9,5F2=
1,45;
zυ2
= z2/cos3
=
40/0,8=50;
σF
= 9,5 Н/мм2 ≤ [σ]F
= 17,46 Н/мм2;
Таблица 4.2. Параметры червячной передачи
Проектный
расчет
|
Параметр
|
Значение
|
Параметр
|
Значение
|
Межосевое
расстояние aw, мм
|
125
|
Диаметр
делительный: червяка d1, мм
колеса d2, = dw2мм
|
50 200
|
Модуль
зацепления m, мм
|
5
|
|
|
Длина
нарезаемой части червяка b1
|
70
|
|
|
|
|
Начальный
диаметр dw1
|
50
|
Ширина
зубчатого венца: колеса b2, мм
|
40
|
Диаметр
вершин витков: червяка dа1, мм
колеса dа2, мм
|
60
210
|
Угол
обхвата черв. Венцом колеса
|
880
|
Наибольший
диаметр dам2
|
215
|
Число
витков червяка z1, мм Число
зубьев колеса z2, мм
|
4
40
|
Диаметр
впадин витков : червяка df1, мм
колеса df2, мм
|
38
188
|
Делительный
угол витков червяка
|
2108ʹ
|
Коэффициент
диаметра червяка q
|
10
|
Проверочный
расчет
|
Параметр
|
допускаемые
значания
|
Расчетные
значения
|
примечание
|
КПД
|
0,85
|
0,85
|
-
|
σн, Н мм2
|
142.1
|
147
|
3.4%
|
σF, Н мм2
|
17.46
|
9.5
|
45%
|
. Расчет поликлиноременной передачи
Проектный расчет
В зависимости от мощности, передаваемой ведущим
шкивом Р1=1,1 кВт и частоте вращения n1
= 920 об/мин, выбираем поликлиновый ремень нормального сечения К. Минимально
допустимый диаметр ведущего шкива d1min
= 40 мм. В целях повышения срока службы ремня принимаем из стандартного ряда d1
= 80 мм.
Определяем диаметр ведомого шкива d2:
2 = d1·u·(1 - ε) = 80·2,5·(1 -
0,01) = 198 мм.
Принимаем
стандартное значение d2 = 200 мм.
Определяем
фактическое передаточное число uф и
определяем его отклонение Δu от заданного u:
ф =
= 2,5;
Δu =
0 ≤ 3%
Определяем
ориентировочное межосевое расстояние а:
а ≥ 0,55(d1
+ d2)
+ Н = 0,55·(80 + 200) + 4 = 158 (мм),
где Н = 4 мм - высота сечения поликлинового
ремня.
Определяем расчетную длину ремня l:
= 2a
+
=
778 мм;
Принимаем стандартную длину l
= 800 мм.
Уточняем межосевое расстояние по стандартной
длине а:
а = 
{2·800 - 3,14(200 +
80) +
}
= 197 мм.
Определяем угол обхвата ремнем ведущего шкива α1:
α1=
1800 - 570
= 1450 ≥
1200.
Определяем скорость ремня: υ
=
=
3,85 м/с ≤ [υ] = 40 м/с.
Определяем
частоту пробегов ремня: U
= 1000·υ/l
= 1000·3,85/800 = 4,8 с-1
= 4,8 с-1 ≤ [U]
= 30 с-1.
Определяем допускаемую мощность, передаваемую
одним поликлиновым ремнем с десятью клиньями [Рп]. Принимаем [Р0]
= 1,3 кВт; Ср=0,8; Сα
=0,9; Сl=1;
[Рп] = [Р0]СрСαСl
= 1,3·0,8·0,9·1 = 0,936 кВт.
Определяем число клиньев поликлинового ремня z:
= 10Рном/[Рп] = 10·1,1/0,936
= 11,75; принимаем z = 12.
Определяем силу предварительного натяжения F0
поликлинового ремня:
0
=
=
337,5 Н.
Определяем окружную силу Ft,
передаваемую поликлиновым ремнем:
t
=
=
285 Н.
Определяем силы натяжения ведущей F1
и ведомой F2
ветвей:
1
=
=
337,5 +
=
480 Н; F2
=
=
337,5 -
=
194 Н.
Определяем силу давления на вал Fоп
для поликлинового ремня:
оп
= 2 F0sin α1/2
= 2·337,5·sin 145/2 = 641 Н.
Проверочный расчет
Проверяем прочность поликлинового ремня по
максимальным напряжениям в сечении ведущей ветви σmax:
σmax=
σl
+ σи + συ
= 4,42 + 4 + 0,0029 = 8,42 (Н/мм2) ≤ [σ]р
= 10 Н/мм2.
σl
=
=
4,42 Н/мм2; σи
= Еи
= 4 Н/мм2;
συ = ρυ2·10-6
= 1250·3,852·10-6 = 0,0029 Н/мм2.
Таблица 5.1. Параметры поликлиноременной
передачи
Параметр
|
Значение
|
Параметр
|
Значение
|
Тип
ремня
|
поликли-новый
|
Частота
пробегов ремня U, 1/с
|
4,8
|
Сечение
ремня
|
К
|
Диаметр
ведущего шкива d1, мм
|
80
|
Число
клиньев
|
12
|
Диаметр
ведомого шкива d2, мм
|
200
|
Межосевое
расстояние а, мм
|
197
|
Максимальное
напряжение σmax, Н/мм2
|
8,42
|
Длина
ремня l, мм
|
800
|
Предварительное
натяжение ремня F0
|
337,5
|
Угол
обхвата малого шкива α1
|
1450
|
Сила
давления ремня на вал Fоп, Н
|
641
|
6. Нагрузки валов редуктора
Таблица 6.1. Определение сил в зацеплении
закрытой передачи
Вид передачи
|
Силы
в зацеплении
|
Значение
силы, Н
|
|
|
на
шестерне(червяке)
|
на
колесе
|
Червячная
|
Окружная
|
Ft1 = 898
|
Ft2= 1870
|
|
Радиальная
|
Fr1 = 680
|
Fr2 = 680
|
|
Осевая
|
Fa1 = 1870
|
Fa2 = 898
|
Ft1 =
=
898
H; Ft2=
=
=
1870
H;r1 = Fr2 = 680 Н;
Fr2 = Ft2tg α
= 1870tg 20 = 680 Н;a1
= Ft2= 1870 H; Fa2 = Ft1 = 898 H.
Вид
передачи
|
Силы
в зацеплении
|
Значение
силы, Н
|
Поликлиноременная
|
Радиальная
|
Fоп = 641
|
Муфта
|
Радиальная
|
Fм = 3418
|
Fоп
= 2F0sinα1/2
= 2·337.5·sin 145/2 = 641
Н;м = 250
= 3418
Н
. Разработка чертежа общего вида редуктора
Определяем размеры ступеней редуктора.
Тихоходный вал:
36 мм,
Согласовываем d1 с диаметром муфты
упругой с торообразной оболочкой , для этого определяем расчетный момент,
передаваемый муфтой:
Тм = 200 Н∙м.м = 60
мм - длина полумуфты;
d2
= d1 + 2∙t = 36 + 2∙2,5 = 40 мм;2 ≈
1,25d2 = 1,25∙40 ≈ 50 мм;3 = d2 +
3,2·r = 40 + 3,2∙2,5 = 48 мм,
l3
- определяется графически;
d4
= d2 = 40 мм.4 = Т + с = 25,5 + 20 = 45 мм.
Назначаем
предварительно подшипники роликовые конические однорядные средней серии по d =
36 мм подшипник № 7308.
Подшипник
7308 ГОСТ 27365-87
Размеры:
d = 40 мм, D = 90 мм, Т = 25,5 мм, b = 23, с =20
мм
Грузоподъемность:
Сr = 61 кН, Сr0 = 46 кН
Факторы
риска: e = 0.28 Y = 2.16 Y0=1,19
Принимаем:
lст=
(1,1…1,5)d =
(1,1…1,5)·48 = 70 мм - длина ступицы колеса:
Принимаем
dст= (1,55…1,6)d
=(1,55…1,6)48 = 75 мм.
Быстроходный
вал:
d1 =
= 22.39 мм;
Принимаем
d1 = 22 (мм);
1 = (1,2…1,5) d1 = (1,2…1,5)
22 = 28 мм;
d2 = d1 + 2·t = 22 + 2·2
= 26мм,
l2 ≈ 2 d2 = 2·30 ≈
60 мм;
d3 = d2 + 3,2·r = 30 +
3,2·1.6 = 35 мм, принимаем d3 = 30 мм;
3 - определяется графически;
4 = d2 = 26 мм;
l4 = Т + с =
21 + 17 = 38 мм.
Назначаем
предварительно подшипники роликовые конические однорядные средней серии по d =
26 мм подшипник № 7306.
Подшипник
7306 ГОСТ 27365-87
Размеры:
d = 30 мм, D = 72 мм, Т = 21 мм, b = 19, с =17 мм
Грузоподъемность:
Сr = 40 кН, Сr0 = 29,9 кН
Факторы
риска: e = 0.34 Y = 1.78 Y0=0.98
lт = 105 мм;
lБ = 190 мм;
lОП = 61 мм;
lм = 79 мм;
Таблица 7.1. Материалы валов. Размеры ступеней.
Подшипники
Вал
(материал… σв=…Н/мм2
σт=…Н/мм2 σ-1=… Н/мм2)
|
Размеры
ступеней, мм
|
Подшипники
|
|
d1
|
d2
|
d3
|
d4
|
Типо-размер
|
dхDхТ,мм
|
Сr, кН
|
С0t, кН
|
|
l1
|
l2
|
l3
|
l4
|
|
|
|
|
Быстроходный:
сталь 40Х; σв=900 σт=750 σ-1=410
|
22
|
26
|
30
|
26
|
7306
|
30х72х21
|
40
|
29,9
|
|
28
|
60
|
180
|
38
|
|
|
|
|
Тихоходный:
сталь 45; σв=890 σт=650 σ-1=380
|
36
|
40
|
48
|
40
|
7308
|
40х90х25,5
|
61
|
46
|
|
60
|
50
|
92
|
45
|
|
|
|
|
. Определение реакций в опорах подшипников
Быстроходный вал.
Дано: Ft1
= 898 H; Fr1
= 680 H; Fa1
= 1870 H; Fоп
= 641 H;
d1
= 0,05 м; lоп
= 0,061 м; lБ
= 0,19 м
. Вертикальная плоскость
а. определяем опорные реакции:
;
;
= 380,26Н.
;
;
=
= 940,74 Н.
Проверка:
-
FОП
+ RВZ
- Fr + RAZ
= -641+940.74-680+380.26 = 0
б. строим эпюру изгибающих моментов относительно
оси X (рис.1) в
характерных сечениях 1…4:
-39.1
Н·м;
Н·м;
-10.6 Н·м.
2. Горизонтальная плоскость
а. определяем опорные реакции: RBX
= RAX =
449
Н
б. строим эпюру изгибающих моментов относительно
оси Z (рис.1) в
характерных сечениях 1…3:
-
42.6 Н·м;
. Строим эпюру крутящих моментов (рис. 1):
= 11.2 Н·м.
4. Определяем суммарные радиальные реакции:
= 588.386 Н;
= 1042.3975 Н.
5. Определяем суммарные изгибающие моменты в
наиболее нагруженных сечениях:
= 55.896 Н·м;
-39.1
Н·м.
Тихоходный вал.
Дано:
Ft2 = 1870 H; Fr2 = 680 H; Fa2 = 898 H; Fм = 3418 H;2
= 0,2 м; lм = 0,079 м; lТ = 0,105 м.
1.Вертикальная
плоскость
а.
определяем опорные реакции:
;
=0;
= -515 Н;
;
;
= 1195 Н;
Проверка:
; RDZ
- Fr2
+ RCZ
= -515-680+1195 = 0
б. строим эпюру изгибающих моментов относительно
оси Y (рис 2) в
характерных сечениях 1…4:
МY1
= 0;
МY3
=
63 Н·м; МY2
= 0;
-27 Н·м. МY4
= 0
. Горизонтальная плоскость
а. определяем опорные реакции:
;
;
= -5054.6 Н;
;
;
3506.6 Н.
Проверка:
;
б. строим эпюру изгибающих моментов относительно
оси Z (рис 2) в
характерных сечениях 1…4:
МZ1
= 0;
МZ3
=
184.1 Н·м; МZ4
= 0;
МZ2
= FM*lM=3418*0.079=270
Н·м
. Строим эпюру крутящих моментов (рис 2)
= 187 Н·м.
4. Определяем суммарные радиальные реакции:
= 3544 Н;
= 5194 Н.
. Определяем суммарные изгибающие моменты в
наиболее нагруженных сечениях:
= 194.58 Н·м; М2
= МZ2
= 270 Н·м.
9. Проверочный расчет подшипников
Проверяем пригодность подшипников 7306
быстроходного вала. Осевая сила в зацеплении Fа
= 1870 Н. Реакции в подшипниках R1
= 588.4 H; R2
= 1042.4 H. Характеристика
подшипников: Сr
= 40000 Н; С0r
= 29900 Н, Х = 0,4; V = 1; КТ
= 1; а1 = 1; а23 = 0,7; Кб = 1.
Требуемая долговечность подшипников Lh
= 19856 часов. Подшипники установлены по схеме враспор.
S1=0.83*e*Rr1=0.83*0.34*588.4=166
HS2=0.83*e*Rr2=0.83*0.34*1042.4=294 HS1< RS2
FA> RS2- RS1
RA1=RS1=166 HA2=RA1+FA=166+1870=2036
H
Определяем отношения:
=0,282 < e
=1.953 > e
RЕ1 =
V∙Rr1∙Кs∙Кт
= 1∙588.4∙1.3∙1 = 764.92 Н.Е2 = (XV∙Rr2+Y
RA2 )Кs∙Кт
= (0.4*1*1042.4+1.78*2036)*1.3*1 = 5253.35 Н.rp
=
=36334
Н. < Сr
L10h
= a1a23
27352
ч > Lh
-
подшипник пригоден.
Проверяем пригодность подшипников 7308
тихоходного вала. . Осевая сила в зацеплении Fа
= 1870 Н. Реакции в подшипниках R1
= 5194 H; R2
= 3544 H. Характеристика
подшипников: Сr
= 61000 Н; С0r
= 46000 Н, Х = 0,4; V = 1; КТ
= 1; а1 = 1; а23 = 0,7; Кб = 1.
Требуемая долговечность подшипников Lh
= 19856 часов. Подшипники установлены по схеме враспор.
S1=0.83*e*Rr1=0.83*0.28*5194=1207
HS2=0.83*e*Rr2=0.83*0.28*3544=823.6 HS1 > RS2
FA> 0A1=RS1=1207
HA2=RA1+FA=1207+898=2105
H
Определяем отношения:
=0,232 < e
=0.594 > eЕ1
=
V∙Rr1∙Кs∙Кт
= 1∙5194∙1.3∙1 = 6752.2 Н.Е2 = (XV∙Rr2+Y
RA2 )Кs∙Кт
= (0.4*1*3544+2.16*2105)*1.3*1 = 7753.7 Н.
Crp
=
=26858
Н. < Сr
L10h
= a1a23
304889
ч > Lh
-
подшипник пригоден.
Таблица 9.1. Основные размеры и эксплуатационные
характеристики
подшипников
Вал
|
Подшипник
|
Размеры
dxDxT, мм
|
Динамическая
грузоподъемность
|
Долговечность
|
|
принят
предварительно
|
принят
окончательно
|
|
Cгр
|
Сr
|
L12h
|
Lh
|
Б
|
7306
|
7306
|
30x72x21
|
24013.6
|
40000
|
27352
|
19856
|
Т
|
7308
|
7308
|
40x90x25.5
|
26858
|
61000
|
304889
|
19856
|
10. Проверочные расчеты
Проверочный расчет шпонок.
sсм =
≤
[s]см,
где Ft
- окружная сила, Н;
Асм = (0,94h
- t1)lp
- площадь смятия, мм2,
lp
= (l - b)
- рабочая длина шпонки.
Быстроходный вал:
шпонка под шкивом поликлиноременной передачи
8х7х30, t1
= 4 мм.
p
= (30 - 8) = 22 мм; Асм = (0,94h
- t1)lp
= (0,94∙7 - 4)∙22 = 56,76 мм;
sсм =
=
35.95 Н/мм2 ≤ [s]см
Тихоходный вал:
шпонка под муфтой 10х8х45, t1
= 5 мм.
p
= (45 - 10) = 35 мм; Асм = (0,94h
- t1)lp
= (0,94∙8 - 5)∙35 = 88.2 мм;
sсм =
=
117.78 Н/мм2 ≤ [s]см
Тихоходный вал:
шпонка под колесом 14х9х60, t1
= 5,5 мм.
p
= (60 - 14) = 46 мм; Асм = (0,94h
- t1)lp
= (0,94∙9 - 5,5)∙46 = 136,16 мм;
sсм =
=
57,22 Н/мм2 ≤ [s]см
Таблица 10.1. Результаты проверочных расчетов
Детали
|
Напряжение,
Н/мм2
|
|
расчетное
σ
|
Допускаемое [σ]
|
Шпонки
|
Б
|
35,95
|
110…190
|
|
Т
|
117,78
|
|
|
Т
|
57,22
|
|
11.
Тепловой расчет червячного редуктора
м=
Температура воздуха вне корпуса редуктора tВ=
20
Кt=
9…17 Вт/(м2*град)-коэффициент теплопередачи
А - площадь теплоотдающей поверхности корпуса, м2=0,36
м
≤ [t]M=80…95
12. Расчет технического уровня редуктора
а. Определяем массу редуктора:
= φρd1
*10-9=7.6·7,4·103·1570000·10-9
= 88.3 кг,
где φ = 7.6,
- коэффициент заполнения;
= L
x B
x H
= 310·105·255 = 8300250 мм3;
ρ = 7,4·103
кг/м3 - плотность чугуна.
б. Определяем критерий технического уровня:
γ = m/Т2
= 88,3/187 = 0,47 кг/Н·м
Таблица 12.1. Технический уровень редуктора
Тип
редуктора
|
Масса
m, кг
|
Момент
Т2, Н·м
|
Критерий
γ
|
Вывод
|
Червячный
|
88,3
|
187
|
0,47
|
Технический
уровень редуктора - низкий
|
Литература
. Шейнблит А.Е. Курсовое
проектирование деталей машин: Учеб. пособие для техникумов. - М.: Высш. Шк.,
1991. - 432 с.: ил.
. Куклин Н.Г., Куклина Г.С., Житков
В.К. Детали машин: Учебник для техникумов - М.:Илекса, 1999.- 392 с.:ил.