Разработка технологии выплавки стали 35ХМЛ
1. Введение
Сталь 35ХМЛ - легированная конструкционная
сталь, которая содержит:
С=0,3-0,4%;
Мn=0,4
- 0,9%;
Cr=0,8 - 1,1%;
Si=0,2-0,4%;
Мо=0,2-0,3%;
Р< 0,04%;
S<0,04%.
Режимы термической обработки конструкционных
сталей определяются главным образом содержанием углерода, т.к. сталь 35ХМЛ
содержит 0,35% С, следовательно по ГОСТ 977-88 она проходит следующие режимы
термической обработки:
а)нормализациям 860 - 880°С;
б)отпуск 600 - 650 °С.
Механические свойства стали зависят от ее
структуры и состава. После термической обработки стали механические свойства
повышаются.
Механические свойства стали 35ХМЛ после
нормализации и отпуска приведены в таблице 1.
Таблица 1. Механические свойства стали 35ХМЛ.
Предел
текучести от, МПа
|
Временное
сопротивление оВ9 МПа
|
Относительное
удлинение 5,%
|
Относительн.
сужение VI/,%
|
Ударная
вязкость КСИ, кДж/м2
|
392
|
589
|
12
|
20
|
294
|
2. Разработка технологии плавки
стали в кислой печи с окислением
2.1 Подбор шихты для выплавки кислой
электростали
Набор компонентов шихты, их состав, нормы
расхода:
возврат собственного производства - 40%
пакеты стали - 12%
стружка стальная - 6%
стружка чугунная - 5%
чугун передельный
-
?
лом стальной
-
?
ферросплавы - ?
Расчет.
1. Определим средний состав стали для расчета.
Сталь 35ХМЛ по ГОСТ 977-88 содержит С=0,3-0,4%;
Мn=0,4-0,9%; Cr=0,8
- 1,1%; Si=0,2 - 0,4%;
Р< 0,04%; S<0,04%; Mo=0,2-0,3%.
Принимаем для расчета, что С=0,35%; Mn=0,6%;
Cr=1%; Si=0,3%;
Р=0,04%; S=0,04%; Mo=0,25%;.
. Проводим анализ технологии плавки.
В окислительном периоде должно выгорать 0,20% С.
Марганец Mn
угорает до 10%,
Хром Cr
угорает до 15%.
Молибден Mo
угорает до 5%
Кремний Si
угорает до 5%
Конечное содержание серы и фосфора определяется
шлаковым режимом. т.к. футеровка кислых ДСП состоит из почти чистого кремнезема
и шлаки в процессе плавления шихты образуются кислые и невозможно проводить в
печи операции десульфурации и дефосфорации, следовательно необходимо выбирать
шихту с наименьшим содержанием фосфора и серы.
. Определяем количество возврата в шихте и
количество углерода
вносимого
возвратом.
Содержание углерода в возврате
. В шихту сталеплавильных печей фосфор и сера в
основном переходят из чугуна, следовательно стружку чугуна исключаем из
расчетов.
. Определяем количество стружки стальной Хс.с в
шихте.
Считаем, что стружка стальная принадлежит стали
марки 20Л, которая по ГОСТ 977-88 содержит С=0,17-0,25%, Мn=0,45
- 0,9%; Cr<0,3%; Si=0,2
- 0,52%; Р< 0,035%; S<0,035%.
Для расчета принимаем, что стальная стружка
содержит С=0,2%; Мn=0,7%; Cr=0,3%;
Si=0,35%; Р= 0,025%; S=0,025%.
Содержание углерода в стальной стружке
. Определяем количество пакетов стали Хп.с и
количество углерода вносимого ими
В качестве стальных пакетов используем отходы
листовой стали СтЗКП по ГОСТ 380-2005, которая содержит С=0,14 - 0,22%, Мn=0,3
- 0,6%;Cr<0,3%; Si<0,05%;
Р< 0,04%; S<0,04%.
Для расчета принимаем:
С=0,18%; Mn=0,45%;
Cr<0,3%; Si=0,05%;
Р<0,03%; S<0,03%.
Содержание углерода в пакетах стали:
. Определяем суммарное количество передельного
чугуна и стального лома в шихте.
. Определяем суммарное количество углерода,
вносимого чугуном и ломом
. Определяем количество передельного чугуна в
шихте и количество углерода вносимого чугуном.
В качестве передельного чугуна выбираем чугун
марки ПВК2 (группы 2, класса А, категории 1), содержащий: Si=0,5
- 0,9%; Мn=0,5 - 1,0%; Р<
0,020%; S<0,015%, С=4,0 -
4,5%.
Для расчета принимаем:
Si=0,7%; Мn=0,75%;
Cr<0,04%Р<
0,015%; S<0,01%, С=4,3%.
Принимаем, что лом стальной соответствует стали
30Л, содержащий по ГОСТ 977-88 С=0,27 - 0,35%, Мn=0,45
- 0,9%; Cr<0,3%; Si=0,2
- 0,52%; Р< 0,035%; S<0,035%.
Для расчетов принимаем:
С=0,3%; Mn=0,7%;
Cr<0,3%;Si=0,35%;
Р< 0,025%; S<0,025%.
. Определим количество стального лома в шихте и
количество углерода вносимого им.
. Определяем количество элементов вносимых
возвратом, стружкой стальной, пакетами стали, передельным чугуном и стальным
ломом.
Возвратом вносится:
Стружкой стальной вносится:
Пакетами стали вносится:
Чугуном передельным вносится:
Ломом стальным вносится:
Всего шихтой вносится:
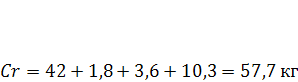
. Определяем угар элементов из шихты:
Кремний Si
- 5%.
Марганец Мn
-10%.
Хром Cr-15%.
Сера S
и фосфор Р - не угорают. С =0,2% от металлозавалки.
Угар углерода составляет:
Перешло в сталь : 55 - 20 = 35 кг.
Угар марганца:
Перешло в сталь: 64,57-6,45 = 58,12 кг.
Угар хрома:
Перешло в сталь:57,7-8,65=49,04 кг.
Угар кремния:
Перешло в сталь: 32,62-1.059= 20.12 кг.
Угар молибдена:
Перешло в сталь: 10,5-0,52=9,98 кг.
Сера S
и фосфор Р не угорают, значит Р = 3,16 кг и S
= 3,107 кг - перешли в сталь.
. Доводка стали по химическому составу сводится
к определению количества раскислителей и легирующих.
Требуемое количество кремния в стали
С учетом остатков хрома в металлозавалке
необходимо ввести в виде ферросплавов 9,88 кг. Используем для этих целей
ферросилиций ФС75 ГОСТ 1415-93, содержащий С=0,1%,Mn=0,4%;
Cr=0,3%; Si=74,0-80,0%;
Р=0,04%; S=0,02%.
Принимаем Si=76%.
Требуемое количество марганца:
Нет необходимости применять ферросплавы.
Требуемое количество хрома:
С учетом остатков хрома в металлозавалке
необходимо ввести в виде ферросплавов 50,95 кг. Используем для этих целей
феррохром низкоуглеродистый ФХ004 ГОСТ 4757-91 (класс фосфора А), содержащий
С=0,05%, Cr=68%; Si=1,5%;
Р=0,02%; S=0,02%.
Требуемое количество молибдена в стали
С учетом остатков молибдена в металлозавалке
необходимо ввести в виде ферросплавов 15 кг. Используем для этих целей
ферромолибден ФМо60 ГОСТ 4759-91, содержащий С=0,05%, Mo=60%;
Si=0,8%; Р=0,05%; S=0,05%.
14. Находим массу основных элементов и примесей,
которые вносятся с ферросплавами.
ФХ004
ФМо60
ФС75
. Определим угар легирующих элементов из
ферросплавов.
Общее содержание углерода в ферросплавах:
Углерод не угорает из ферросплавов.
Общее содержание молибдена в ферросплавах:
Молибден угорает из ферросплавов на 6%.
Общее содержание хрома в ферросплавах:
Хром угорает из ферросплавов на 7%.
Общее содержание кремния в ферросплавах:
Кремний Si
угорает из ферросплавов на 5%.
Общее содержание фосфора Р:
Фосфор Р не угорает из ферросплавов.
Общее содержание фосфора Mn:
Фосфор Mn
не угорает из ферросплавов.
Общее содержание серы:
Сера S
не угорает из ферросплавов.
Перешло легирующих элементов в сталь из
ферросплавов:
С
= 0,063 кг.
Мо=
15-0,9=14,1 кг.
Cr=50,98-3,57=47,41
кг.
Si
= 11.2-0,56=10,64 кг.
Р
= 0,025 кг.
S
= 0,023 кг.
Mn=0,052
кг
Всего в стали:
С
=35+0,063=35,063 кг.
Мо
= 9,98+14,1=24,08 кг.
Cr=49,04+47,41=96,46
кг
Si
=20,12+10,64=30,76 кг.
Р
= 3,16+0,02=3,18 кг.
S
=3,107+0,02= 3,127 кг.
Mn=58,17
кг
16. Проверяем расчет содержания основных
компонентов в стали 35ХМЛ
С
10025,88
- 100%
,063
- Х%= 0,35%
Мо
10025,88
- 100%
,08
- Х%
Х=
0,24%
Мn
10025,88
- 100%
,17
- Х%
Х=
0,58%
Cr
10025,88
- 100%
,46
- Х%
Х=
0,96%
Si
10025,88
- 100%
.76
- Х%= 0,31%
Р
10025,88
- 100%
,18
- Х%
Х
= 0,032%
S
10025,88
- 100%
,127
- Х%
Х
= 0,03%
Данный состав шихты обеспечивает получение стали
заданной марки.
.2 Описание технологии выплавки
стали в кислой электродуговой печи
Футеровка кислых ДСП аналогична футеровке кислых
мартеновских печей и состоит из почти чистого кремнезема; соответственно шлаки
кислых печей насыщены
.Ни серу, ни фосфор
удалить из металла под кислым шлаком нельзя, и это должно учитываться при
шихтовке плавки. В кислых печах сталь обычно выплавляют методом переплава с
проведением короткого периода кипения для дегазации расплава. Кислые шлаки
менее проницаемы для газов, чем основные; растворимость газов в кислых шлаках
низка активность
(основного
оксида). При повышении температуры восстанавливается кремний, например, по реакциям
;
,
откуда
.
В кислых шлаках, насыщенных
,
приближается
к единице, поэтому скорость восстановления кремния может быть весьма заметна
(до 0,01%/мин), особенно при высоком содержании углерода.
В связи с отсутствием условий для десульфурации
и дефосфорации удельная (на 1 т стали) поверхность контакта металл - шлак для
кислых печей не имеет такого значения, как для основных, поэтому для уменьшения
тепловых потерь можно иметь более глубокую ванную. Меньшая теплопроводность
кислых огнеупоров также способствует снижению тепловых потерь и более быстрому
нагреву металла. Из-за отсутствия длительных периодов рафинирования металла от
фосфора и серы все это приводит к получению более высокого теплового КПД,
сокращению длительности плавки, уменьшению расходов электроэнергии и
электродов. Кислая футеровка и кислые шлаки, большая глубина ванны кислых
печей, невысокая стоимость материалов, из которых формируется футеровка (песок,
динасовый кирпич), - вот неполный перечень достоинств кислых печей. К
недостаткам относится невозможность проводить в печи операции десульфурации и
дефосфорации.
В настоящее время емкость кислых печей не
превышает 10 т. Число кислых печей достаточно велико; их устанавливают в
литейных цехах и используют в основном для производства фасонного литья.
3. Разработка технологии выплавки
стали в основной электродуговой печи с окислением
.1 Подбор шихты для выплавки
электростали с окислением
Набор компонентов шихты, их состав, нормы
расхода:
возврат собственного производства - 40%
пакеты стали - 12%
стружка стальная - 6%
стружка чугунная - 5%
чугун передельный
-
?
лом стальной
-
?
ферросплавы - ?
Расчет.
1. Определим средний состав стали для расчета.
Сталь 35ХМЛ по ГОСТ 977-88 содержит С=0,3-0,4%;
Мn=0,4-0,9%; Cr=0,8
- 1,1%; Si=0,2 - 0,4%;
Р< 0,04%; S<0,04%; Mo=0,2-0,3%.
Принимаем для расчета, что С=0,35%; Mn=0,6%;
Cr=1%; Si=0,3%;
Р=0,04%; S=0,04%; Mo=0,25%;.
. Проводим анализ технологии плавки.
В окислительном периоде должно выгорать 0,3%
углерода.
Mn из
металлозавалки -3%, кремний Si
до15%, хром Cr до 20%,
молибден Мо до 6%, кремний Si
до 15%.
Фосфор не восстанавливается из шлака, но
полностью восстанавливается из ферросплавов.
Конечное содержание серы и фосфора определяется
шлаковым режимом, поэтому концентрации данных элементов исключаем из расчетов.
Результаты расчетов сводим в таблицу 2.
. Определяем количество возврата в шихте и
количество углерода
вносимого
возвратом.
Z-металлозавалка.
Содержание углерода в возврате:
. Определяем количество стружки чугунной в шихте
и количество углерода, вносимого чугунной стружкой.
Считаем, что стружка чугунная соответствует
чугуну марки СЧ20, который по ГОСТ 1412-85 содержит С =3,3-3,5%; Si=l,4-2,2%;
Мn=0,7 - 1,0%; Р<
0,3%; S<0,15%.
Для расчета принимаем, что стружка чугунная
содержит С=3,4%; Si=l,5%;
Mn=0,8%; Р=0,3%; S=0,12%.
Содержание углерода в стружке чугунной
5. Определяем количество стружки стальной Хс.с в
шихте и количество углерода вносимого стружкой стальной.
Считаем, что стружка стальная принадлежит стали
марки 20JI, которая по
ГОСТ 977-88 содержит С=0,17- 0,25%, Мn=0,45
- 0,9%; Cr<0,3%; Si=0,2
- 0,52%; Р< 0,035%; S<0,035%.
Для расчета принимаем, что стальная стружка
содержит С=0,21%; Mn=0,7%;
Cr=0,3%; Si=0,35%;
Р=0,035%; S=,035%.
Содержание углерода в стальной стружке
6. Определяем количество пакетов стали Хп.с и
количество углерода вносимого ими
В качестве стальных пакетов используем отходы
листовой стали СтЗКП по ГОСТ 380-2005, которая содержит С=0,14 - 0,22%, Мn=0,3
- 0,6%; Cr<0,3%; Si<0,05%;
Р< 0,04%; S<0,04%.
Для расчета принимаем:
C=0,18%; Mn=0,45%;
Cr=0,3%; Si=0,05%;
P=0,04%; S=0,04%.
Содержание углерода в пакетах стали:
7. Определяем суммарное количество передельного
чугуна и стального лома в шихте.
8. Определяем суммарное количество углерода,
вносимого чугуном и ломом
9. Определяем количество передельного чугуна в
шихте и количество углерода вносимого чугуном.
В качестве передельного чугуна выбираем чугун
марки ПЛ1 (группы 1, класса А, категории 2) ГОСТ 805 - 95, который содержит:
С=4,0-4,5%; Si=0,9-1,2%;
Мn=0,3-0,5%; Р<
0,08%; S<0,02%.
Для расчета принимаем:
С=4,3%; Si
=1%; Mn=0,4%; Р =
0,08%; S = 0,02%.
Принимаем, что лом стальной соответствует стали
25JI, содержащий
С=0,22-0,30%, Мn=0,45-0,9%; Cr<0,3%;
Si=0,20-0,52%; Р<
0,04%; S<0,04%.
Для расчетов принимаем:
С=0,26%; Mn=0,70%;
Cr=0,3%; Si=0,35%;
Р= 0,04%; S=0,04%.
10. Определим количество стального лома в шихте
и количество углерода вносимого им.
11. Определяем количество элементов вносимых
возвратом, стружкой стальной, стружкой чугунной, пакетами стали, передельным
чугуном и стальным ломом.
Возвратом вносится:
Стружкой чугунной:
Стружкой стальной:
Пакетами стали:
Чугуном передельным:
Лом стальной:
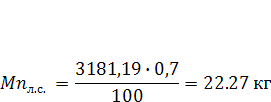
Всего шихтой вносится:
. Определяем угар элементов из шихты
Угар кремний Si
- 15%.
Угар марганца Мn
- 10%.
Угар молибдена Мо - 6%.
Угар хрома Cr
- 20%.
С =0,3% от металлозавалки.
Угар углерода составляет:
Перешло в сталь :
Угар кремния из завалки:
Перешло в сталь :
Угар марганца:
Перешло в сталь:
Угар хрома:
Перешло в сталь:
Угар молибдена:
Перешло в сталь:
. Доводка стали по химическому составу сводится
к определению количества раскислителей и легирующих.
Требуемое количество кремния в стали
С учетом остатков кремния в металлозавалке
необходимо ввести в виде ферросплавов 8,63 кг. Используем для этих целей
ферросилиций ФС70 (ГОСТ 1415-93), содержащий С=0,1%; Si=70%;
Mn=0,4; Cr=0,4%;
P=0,04%; S=0,02.
0,9 степень усвоения кремния из ферросплавов в
основной печи
Требуемое количество марганца:
С учетом остатков марганца в металлозавалке
необходимо ввести в виде ферросплавов 4,25 кг. Используем для этих целей
ферромарганец ФМн90 ГОСТ 4755- 91, содержащий С=0,5%; Si=l,8%;
Р=0,05 - 0,3%; S=0,02%; Мn=90%;.
Требуемое количество молибдена:
С учетом остатков молибдена в металлозавалке
необходимо ввести в виде ферросплавов 15,2 кг. Используем для этих целей
ферромолибден ФМо60 ГОСТ 4759- 89, содержащий С=0,05%; Si=0,8%;
Р=0,05%; S=0,1%; Мо=60%.
Требуемое количество марганца:
С учетом остатков хрома в металлозавалке
необходимо ввести в виде ферросплавов 56.05 кг. Используем для этих целей
феррохром низкоуглеродистый ФХ001А ГОСТ 4757- 91, содержащий С=0,01%; Si=0,8%;
Р=0,02%; S=0,02%; Cr=68%;.
14. Находим массу основных элементов и примесей,
которые вносятся с ферросплавами с учетом их угара.
ФС70
ФМn90
ФМо60
ФХ001А
15. Определим угар легирующих элементов из
ферросплавов.
Общее содержание марганца в ферросплавах:
Угар
Общее содержание кремния в ферросплавах:
Угар
Общее содержание молибдена в ферросплавах:
Угар
Общее содержание хрома в ферросплавах:
Угар
Перешло легирующих элементов в сталь из
ферросплавов:
С
= 0.054 кг.
Мn
= 4.67 - 0.23=4.44 кг.
Si
= 11.04 - 0.55 = 10.49 кг.
Cr
= 56.03-5.6 = 50.43 кг.
Mo
= 15.18 - 2.28 = 12.9 кг.
Всего в стали:
С=35+0.054=35.05
кг.
Мn
= 55.75+4.44 = 60.19 кг.
Si
=26.37+10.49=36.86 кг.
Mo=9.4+12.9=22.3
кг.
Cr=43.95+50.43=94.38
кг.
16. Проверяем расчет содержания основных
компонентов в стали 35ХМЛ
С
10025,87
-100%
,05
- Х%= 0,35%
Мn
10025,87
-100%
,19
-Х%
Х=
0,6%
Si
10025,87
-100%
,86
-Х%
Х=0,37%
Mo
10025.87
-100%
.3
-X%
X=0,22%
Cr
10025.87
-100%
.38
-X%
X=0.94%
Содержание элементов в шихте соответствует
составу стали 35ХМЛ
3.2 Описание технологии выплавки
стали в основной печи с окислением
сталь шихта электродуговая печь
Плавка состоит из следующих периодов:1) заправка
печи; 2) загрузка шихты; 3) плавление; 4) окислительный период; 5)
восстановительный период; 6) выпуск стали.
Заправка печи.
Заправка - это исправление изношенных и поврежденных участков футеровки пода.
После выпуска очередной плавки с подины удаляют остатки металла и шлака. На
поврежденные места подины и откосов забрасывают магнезитовый порошок или же
магнезитовый порошок, смешанный с каменноугольным пеком (связующим).
Длительность заправки 10 - 15 мин.
Загрузка шихты.
Загрузку шихты ведут бадьями или корзинами, а в некоторых старых печах
небольшой емкости - завалочными машинами.
Плавление.
После окончания завалки электроды опускают почти до касания с шихтой и пускают
ток. Под действием высокой температуры друг, шихты под электродами плавиться,
жидкий металл стекает вниз, накапливаясь в центральной части подины. Электроды
постепенно опускаются, проплавляя в шихте «колодцы» и достигают крайнего
нижнего положения. В дальнейшем по мере увеличения количества крайнего нижнего
положения. В дальнейшем по мере увеличения количества жидкого металла электроды
поднимаются, так как автоматические регуляторы поддерживают длину дуги
постоянной.
В начале периода расплавления дуги горят большую
часть времени в холодной шихте, при этом свод и стены печи защищены от прямого.
излучения дуг. Поэтому в этот период используется полная номинальная
(максимальная) мощность печного трансформатора. Режим горения дуг в этот период
крайне нестабильный, окруженные холодной шихтой дуги горят неустойчиво, длинна
их очень мала (10...25 мм), они легко перебрасываются с одного куска на другой,
результате чего возникают резкие колебания мощности. В конце периода плавления
длинна дуг увеличивается. Расплавленная поверхность ванны отражает значительную
энергию на свод и стены, поэтому для защиты кладки от сильного излучения
мощность печного трансформатора снижают на 20...30%.
Для ускорения плавления куски нерасплавившейся
шихты с откосов следует сталкивать в зону электрических дуг. В период плавления
необходимо обеспечить раннее образование шлака, предохраняющего металл от
насыщения газами и науглероживания электродами. С этой целью, если в завалку не
давали известь, в проплавляемые электродами колодцы несколькими порциями
присаживают известь (1-3% от массы металла).
Во время плавления происходит частичное
окисление составляющих шихты, формируется шлак, происходит частичное удаление в
шлак фосфора и серы. Окисление примесей осуществляется за счет кислорода
воздуха, окалины и ржавчины, внесенных металлической шихтой.
За время плавления полностью окисляется кремний,
40 - 60% марганца, частично окисляется углерод и железо. В формирование шлака
наряду с продуктами окисления (SiO2,
MnO, FeО)
принимает участие окись кальция, содержащаяся в извести. Шлак к концу периода
плавления имеет примерно следующий состав, %: 35-50 СаО; 15-25 SiO2;
8-15 MgO;5-10 MnO;
3-7 Al2O3;
0,5-1,2 P2O5.
Низкая температуры и наличие основного железистого шлака благоприятствует
дефосфации. В зоне электрических дуг за время плавления испаряется от 2 до 5%
металла, преимущественно железа.
Для ускорения плавления иногда применяют
газокислородные горелки, вводимые в рабочее пространство через свод или стенки
печи. За счет теплоты, выделяющейся от сжигания газа, сокращается длительность
плавления и расход электроэнергии (на 10-15%).
Для уменьшения продолжительности плавления часто
применяют продувку кислородом, вводимым в жидкий металл после расплавления 3/4
шихты с помощью фурм или стальных футерованных трубок. Окисление железа, а также
марганца, кремния и других примесей металла газообразным кислородом протекает с
выделением значительного количества теплоты, которое ускоряет расплавление
остатков металлического лома. При расходе кислорода 4-6 м/т длительность
плавления определяется в первую очередь мощностью трансформатора и составляет
от 1,1 до 3,0 ч. Расход электроэнергии за время плавления составляет 400- 480
кВт∙ч/т. В конце периода плавления длинна дуг увеличивается.
Расплавленная поверхность ванны отражает значительную энергию на свод и стены,
поэтому для защиты кладки от сильного излучения мощность печного трансформатора
снижают на 20...30%.
Окислительный период.
Задача окислительного периода плавки:
а) уменьшить содержание в металле фосфора до
0,01-0,015%;
б) уменьшить содержание в металле водорода и
азота;
в) нагреть металл до температуры близкой к
температуре выпуска (на 120-130°С выше температуры ликвидуса).
Наряду с этим за время периода окисляется
углерод до нижнего предела его требуемого содержания в выплавляемой стали. За
счет кипения (выделения пузырьков СО при окислении углерода) происходит
дегазация металла и его перемешивание, что ускоряет процессы дефосфорации и
нагрева.
Окислительный период начинается с того, что из
печи сливают 65-75% шлака, образовавшегося в период плавления. Шлак сливают не
выключая ток, наклонив печь в сторону рабочего окна на 10-12°С. Слив шлака
производят для того, чтобы удалить из печи перешедший в шлак фосфор. Удалив
шлак, в печь присаживают шлакообразующие: 1-1,5% извести и при необходимости
0,15-0,25% плавикового шпата, шамотного боя или боксита.
После сформирования жидкоподвижного шлака в
ванну в течение всего окислительного периода вводят порциями железную руду с
известью либо ведут продувку кислородом; печь для слива шлака в течении периода
наклона в сторону рабочего окна.
При кипении вместе с пузырьками СО из металла
удаляются водород и азот. Этот процесс имеет большое значение для повышения
качества электростали, поскольку в электропечи в зоне электрических дуг идет
интенсивное насыщение металла азотом и водородом. Это насыщение ускоряется в
результате диссоциации молекул азота и водорода в зоне дуг, имеющих температуру
свыше 3000 °С. В связи с этим электросталь обычно содержит азота больше, чем
мартеновская и кислородно-конвертерная сталь.
Кипение и перемешивание обеспечивает также
ускорение выравнивания температуры металла и его нагрев. За время
окислительного периода необходимо окислить углерода не менее 0,2-0,3% при
выплавке высокоуглеродистой стали (содержащей более 0,6% С) и 0,3-0,4% при
выплавке средне- и низкоуглеродистой стали (нижний предел указанных значений
относится к большегрузным печам).
Окислительный период заканчивается тогда, когда
углерод окислен до нижнего предела его содержания в выплавляемой марке стали, а
содержание фосфора снижено до 0,010-0,015%. Период заканчивают сливом
окислительного шлака, который производят путем наклона печи в сторону рабочего
окна, а также вручную с помощью деревянных гребков, насаженных на длинные
металлические прутки. Полное скачивание окислительного шлака необходимо, чтобы
содержащийся в нем фосфор не перешел обратно в металл во время
восстановительного периода. Окислительный период длится от 30 до 90 минут.
Восстановительный период.
Задачами периода являются:
а) раскисление металла;
б) удаление серы;
в) доведение химического состава стали до
заданного;
г) корректировка температуры.
Все эти задачи решаются параллельно в течении
всего восстановительного периода; раскисление металла производят одновременно
осаждающим и диффузионным методами.
После удаления окислительного шлака в печь
присаживают ферромарганец в количестве, необходимом для обеспечения содержания
марганца в металле на его нижнем пределе для выплавляемой стали, а также
ферросилиций из расчета введения в металл 0,10 - 0,15% кремния и алюминий в
количестве 0,03 - 0,1%. Эти добавки вводят для обеспечения осаждающего
раскисления металла. Далее наводят шлак.
Для улучшения перемешивания шлака и металла и
интенсификации медленно идущих процессов перехода в шлак серы, кислорода и
неметаллических включений в восстановительный период рекомендуется применять
электромагнитное перемешивание, особенно на большегрузных
печах, где величина удельной поверхности
контакта металл-шлак значительно меньше чем в печах малой емкости. Длительность
восстановительного периода составляет 40-100 минут.
В восстановительный период условия работы
футеровки печи наиболее тяжелые, мощность снижается и доходит до 30-40%
номинального значения.
4. Вопросы техники безопасности при
выплавке стали в электродуговых печах
1. Электропечи должны быть оборудованы
устройствами для удаления отходящих дымовых газов и очистки их от пыли.
. Конструкция фундамента печи должна обеспечить
удобный осмотр кожуха подины и ремонт механизма наклона.
. Наклоняющиеся и качающиеся электропечи с
электроприводом должны иметь ограничители наклона, самотормозящие устройства и
блокировку для автоматического отключения тока от нагревательных элементов при
наклоне печи на выпуск металла.
. Пускатели наклона печей должны быть
установлены в таком месте чтобы с него видно было струю жидкого металла, идущую
из печи и крановщика, участвующего в разливе металла.
. В случае применения для наклона печи
гидравлического привода должны быть приняты меры, исключающие возможность
попадания расплавленного металла и шлака на гидравлические устройства.
. На щитах и пультах управления электропечей
должна быть установлена световая сигнализация, а на рабочей площадке печи
установлена кнопка аварийного отключения.
. Включать электропечи для просушки или плавки
металла можно только после их тщательного осмотра дежурным электромонтером
квалификации не ниже 4 группы по электробезопасности. Крепление электродов
должно быть надежным, а трубопроводы охлаждающей системы должны находиться в
исправном состоянии.
. Установка электродов, осмотр печи и другие
работы, связанные с непосредственным соприкосновением с электродами, а также
замена заслонок допускаются только при снятом напряжении.
. Для сборки электродов и установки заменяемых
электродов возле электропечи должен быть установлен специальный станок.
Допускается производить наращивание электродов на печах. Перед началом
наращивания электродов печь должна быть отключена.
. Крепление головок электродов должно
систематически проверяться и во всех случаях его ослабления печь должна быть
немедленно отключена.
. Зажатие и освобождение электродов в
электродержателях должны быть механизированы. Управление механизмом зажима
электродов должно производится с площадки у печи.
. Отверстие для электродов в своде печи должны
иметь уплотняющие кольца для уменьшения выделения газов в рабочее помещение.
. Находиться людям под печью в период плавления
шихты запрещается.
. Рабочая площадка печного пролета по всему
периметру должна иметь перильное ограждение и сплошную обортовку по низу.
15. Заправка подины, откосов и стен электропечей
должна быть механизирована.
. Электропечи емкостью 20т и более должны иметь
специальные устройства для перемешивания расплавленного металла.
. Для установки газокислородной горелки в
завалочное окно электропечи в крышке окна должно быть устроено специальное
отверстие, соответствующее размерам горелки.
18. Газокислородные горелки должны быть
оборудованы запорной арматурой, а также приборами, контролирующими расход и
давление газа, кислорода и охлаждающей воды.
19. Горелка перед включением должна быть продута
кислородом, после чего должен подаваться газ. Отключение горелки должно
производиться в обратном порядке.
. В случае прогара водоохлаждаемой горелки она
должна быть отключена и выведена из рабочего пространства печи в крайнее
верхнее положение.
. Во время работы газокислородной горелки крышка
завалочного окна должна быть закрыта.
. Для скачивания шлака под завалочным окном
должен быть устроен спускной желоб под рабочую площадку. Отверстие в рабочей
площадке должно перекрываться съемной футерованной крышкой.
23. Устройство желоба для выпуска металла из
печи должно исключать возможность переполнения его металлом, а также разъедание
футеровки желоба и прорыва металла при выпуске плавки.
. Для обслуживания выпускного желоба возле него
должна быть устроена металлическая площадка с перилами.
. Для приема скачиваемого шлака должны
применяться шлаковые ковши и шлаковни. Шлаковни должны быть обеспечены
устройством для их транспортирования и кантовки.
. Ковши и шлаковни должны быть сухими и изнутри
покрыты известковым раствором.
. Переполнение ковшей и шлаковень шлаком не
допускается.
. Водоохлаждаемые элементы печей перед их
установкой должны подвергаться гидравлическому испытанию.
. Соединение водоохлаждаемых элементов должно
допускать возможность отключения отдельных элементов от системы охлаждения.
. Вода, подаваемая для охлаждения, должна быть
очищена от механических примесей.
. Подвод охлаждающей воды должен производиться в
нижнюю часть охлаждаемых элементов, и отвод нагретой воды - от верхней их
части.
. Запорная арматура для отключения
водоохлаждаемых элементов системы охлаждения печи должна размещаться в
доступных и безопасных для обслуживания местах.
33. Отвод охлаждающей воды должен производиться
в водосборные резервуары, установленные в местах, исключающие попадание в них
жидких металла и шлака.
. Температура воды, отходящей от водоохлаждаемых
элементов, должна быть ниже температуры выпадения осадков временной жесткости
предусматриваться инструкцией предприятия.
. Все элементы охлаждения печи и подвода воды
должны быть герметичными. Подача охлаждающей воды должна быть бесперебойной.
. Располагать подводы и отводы охлаждающей воды
под завалочным окном и выпускным желобом строго запрещается.
5. Список использованных источников
1.
Отливки стальные ГОСТ 977-88
.
Чугун передельный ГОСТ 805-95
.
Ферросилиций ГОСТ 1415-93
.
Ферромарганец ГОСТ 4755-91
.
Ферромолибден ГОСТ 4759- 89
.
Феррохром ГОСТ 4757- 91
.
Кудрин В.А. Теория и технология производства стали. Учебник для вузов. - М.:
ОАО «Издательство АСТ»,2003.-528с.
.
Гуляев А.П. Металловедение. Учебник для вузов. 6-е изд., перераб. и доп. М.:
Металлургия, 1986- 544с.
.
Электрометаллургия стали и ферросплавов. Еднерал Ф. П. - М.: Металлургия,
1987.- 487с.