Средняя
твёрдость поверхности зубьев
|
|
200
|
250
|
300
|
350
|
400
|
450
|
500
|
550
|
600
|
|
|
-
|
25
|
32
|
38
|
43
|
47
|
52
|
56
|
60
|
|
10
|
16,5
|
25
|
36,4
|
50
|
68
|
87
|
114
|
143
|
2) Определяем
допускаемое контактное напряжение 
, Н/
:
Находим число циклов перемены напряжений за весь
срок службы:
N1
= 573 * 
* Lh2 =
573 * 
* Lh1 =
573 * 32,07 * 15000 = 2756416502 = 573 * 8,017 * 15000 = 68906115
Для улучшенных колёс:
1 ≤ 
≤ 2,6
Если N
> 
, то принять 
;
3) Определяем
допускаемые контактные напряжения 
, Н/
:
4) Определяем
допускаемые контактные напряжения для зубьев шестерни и колеса 
, Н/
:
Для косозубых передач дальнейший расчёт ведут по
среднему контактному напряжению:

=0,45 * (
5) Определение
допускаемых напряжений изгиба 
, Н/
:
6) Определение
долговечности для зубьев шестерни и колеса:
Далее расчёт ведём по наименьшему значению.
Результаты расчётов зубчатой передачи редуктора
занести в таблицу №5:
Механические характеристики зубчатой передачи:
Таблица №5
Элемент
передачи
|
Марка
стали
|
Дпред
|
Термо-
обработка
|
НВ1ср
|
σв
|
σ-1
|
[σ]н
|
[σ F
|
|
|
Sпред
|
|
НВ2ср
|
Н/мм2
|
Шестерня
|
40Х
|
125/80
|
У
|
285,5
|
900
|
410
|
580,9
|
135,27
|
Колесо
|
40Х
|
200/125
|
У
|
248,5
|
790
|
375
|
514,3
|
148,48
|
Проектный расчёт зубчатой передачи.
1. Определяем
главный параметр - межосевое расстояние 
, мм:

,
а) 
- вспомогательный
коэффициент.

- косозубая
передача.

- прямозубая
передача.
б)

в) U
- передаточное число редуктора.
U
= 4
г) 
- вращающий момент
на тихоходном валу.
д) 
- среднее
допускаемое контактное напряжение.
е) 
- коэффициент
неравномерности нагрузки по длине зуба.

m
≥

а) 
- вспомогательный
коэффициент.

- косозубая
передача.

- прямозубая
передача.
б)

- делительный
диаметр колеса, мм.

= 
= 248 мм
в)

- ширина венца
колеса, мм.
г)

- допускаемое
напряжение изгиба, Н/
≥

3,14 ≈ 3,5;
Полученное значение округляем в большую сторону
из ряда стандартных чисел:
Таблица
№6
m, мм
|
1
|
1,5
|
2
|
2,5
|
3
|
4
|
5
|
6
|
8
|
10
|
m, мм
|
1,25
|
1,75
|
2,25
|
2,75
|
3,5
|
4,5
|
5,5
|
7
|
9
|
|
Значения первого ряда предпочесть второму ряду;
3. Определяем
угол наклона зубьев 
:
Угол наклона принимаем 
4. Определяем
суммарное число зубьев шестерни и колеса для косозубого колёса:

;
5. Уточняем
действительную величину угла наклона зубьев:
6. Определяем
число зубьев шестерни:

;

;
Принимаем 
≥ 18; 20 ≥
18;
7. Определяем
число зубьев колеса:

;
8. Определяем
фактическое передаточное число 
:

;
9. Определяем
фактическое межосевое расстояние для косозубой передачи:

;

;
10.
Определяем основные геометрические параметры передачи:
Таблица №7
Проверочный расчёт зубчатой
передачи.
. Проверяем
межосевое расстояние:
2. Проверяем
пригодность заготовок колёс:

; 
;

;

;
,91 ≤
120 мм; 48 ≤ 80 мм;
3. Проверяем
контактные напряжения:
а) K
- вспомогательный коэффициент
K
= 376 - косозубые передачи.
K
= 436 - прямозубые передачи
б)

- окружная сила в
зацеплении, Н
в)

- коэффициент
нагрузки:

г)

- коэффициент
динамической нагрузки.
д)

- окружная
скорость колёс, м/с

;

;
4. Проверяем
напряжение изгиба зубьев шестерни и колеса 
, Н/
:
а) 
- коэффициент,
учитывающий распределение нагрузки между зубьями:
б) 
- неравномерность
нагрузки по длине зуба:
в) 
- коэффициент
динамической нагрузки:
г) 
и 
- коэффициенты
формы зуба шестерни и колеса. Определяются по таблице №8, интерполированием в
зависимости от числа зубьев шестерни 
и колеса 
для прямозубых
колёс. Для косозубых - в зависимости от эквивалентного числа зубьев шестерни:
где 
- угол наклона
зубьев.

;

;

;

;
Коэффициенты формы зуба:
Таблица №8
z или 
|
|
|
|
|
|
|
|
|
|
|
|
16
|
4,28
|
24
|
3,92
|
30
|
3,80
|
445
|
3,66
|
71
|
3,61
|
180
|
3,62
|
17
|
4,27
|
25
|
3,90
|
32
|
3,78
|
50
|
3,65
|
80
|
3,61
|
∞
|
3,63
|
20
|
4,07
|
26
|
3,88
|
35
|
3,75
|
60
|
3,62
|
90
|
3,60
|
|
|
22
|
3,98
|
28
|
3,81
|
40
|
3,70
|
65
|
3,62
|
100
|
3,60
|
|
|
Примечание. Коэффициенты формы зуба 
соответствуют
коэффициенту смещения инструмента x
= 0.
Если при проверочном расчёте 
значительно меньше

, то это допустимо,
так как нагрузочная способность большинства зубчатых передач ограничивается
контактной прочностью. Если 
свыше 5% то надо
увеличить модуль m,
соответственно пересчитать число зубьев шестерни 
и колеса 
и повторить
проверочный расчёт на изгиб. При этом межосевое расстояние 
не изменяется, а
следовательно, не нарушается контактная прочность передачи.
д) 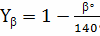
- коэффициент,
учитывающий наклон зуба:

;
,82 
; 63,82 
153,57;
,36 
; 70,36 
135,27
Результаты заносим в таблицу №9:
Параметры зубчатой цилиндрической передачи.
Таблица №9
Таблица №10
Проверочный
расчёт
|
Параметр
|
Допускаемые
значения
|
Расчётные
значения
|
Примечания
|
Контактные
напряжения  ,Н/
|
492,84
Н/
|
424,88
Н/
|
-
|
Напряжение
изгиба
|
|
135,27 Н/
|
97,05
Н/
|
-
|
|
|
148,48
Н/
|
85,89
Н/
|
-
|
2.3
Выбор и расчёт муфт
1. Определяем
расчётный момент и выбираем муфту:

;
Где 
- коэффициент
режима нагрузки;

- вращающий момент
на соответствующем валу редуктора, Н*м;

- номинальный
момент - Т = 1000;
Значение коэффициента режима нагрузки:
Таблица №11
Тип
машины
|
|
Передаточные
тележки
|
1,25…1,50
|
Моторные
шлейфовые тележки
|
1,5…2,0
|
Краны,
лебёдки, элеваторы
|
2,0…3,0
|
Муфту выбираем по таблицам по значению
номинального момента при условии:

;
Результаты подбора записываем в конце пункта с
указанием основных характеристик муфты:

; 
Результаты подбора муфты:

;

;

.
Смещение валов осей не более:
Радиальное: 
;
Угловое: 
.
2.4
Выбор и расчёт системы смазки
1. Смазывание
зубчатого зацепления:
а) Способ
смазывания.
Для редукторов общего назначения применяют
непрерывное смазывание жидким маслом картерным непроточным способом
(окунанием). Этот способ применяют для зубчатых передач при окружных скоростях
от 0,3 до 12,5 м/с;
б) Выбираем
сорт масла:
Зависит от значения расчётного контактного
напряжения в зубьях 
, Н/
.
Циркуляционные системы жидкой смазки
предназначены для автоматической подачи в узлы трения очищенного и охлажденного
минерального масла под давлением. В черной металлургии наибольшее
распространение получили системы с ротационно-поршневыми и шестеренными
насосами.
Основными узлами системы жидкой
смазки являются рабочая и резервная насосные установки /, резервуар, дисковые
самоочищающиеся фильтры, маслоохладитель, напорный и сливной трубопроводы,
перепускной клапан.
Резервуар служит для подогрева и
очистки масла от механических примесей и воды. Перегородки делят резервуар на
отдельные отсеки. Масло, возвращающееся из узлов трения по-сливному
трубопроводу, предварительно очищается сетчатыми фильтрами и магнитными
сепараторами 2. В левом отсеке благодаря изменению направления скорости из
масла выпадают крупные механические примеси. Объем среднего отсека составляет
примерно 50% объема резервуара. Поэтому скорость движения масла резка
уменьшается и из него осаждается большая часть взвешенных примесей. Из правого
отсека очищенное масло по всасывающей трубе и трубопроводу 6 поступает к
насосным установкам. Поплавок и
шарнирное соединение 8 позволяют постоянно забирать масло из верхних слоев.
Полезную вместимость резервуара
рассчитывают по формуле V - (25 - 60)Р, где Р - подача насосной установки.
Сорт масла выбираем по таблице №12:
Рекомендуемые сорта смазочных масел для передач
(ГОСТ 17479.4-87);
Таблица №12
Передача
|
Контактные
напряжения  , Н/
|
Сорт
масла
|
Зубчатая
|
До
600 Св. 600 до 1000 Св. 1000
|
ИГА
- 68; ИГА - 46 ИГС - 100; ИГС - 68; ИГС - 150; ИГС - 100
|
Условные обозначения:
И - индустриальное; Г - предназначается для
гидравлических систем; А - масло без присадок; С - масло с антиокислительными
присадками; число - класс кинематической вязкости.
Выбрал сорт масла: ИГА-68;
в) Определяем
количество масла:
Для двухступенчатых редукторов при смазывании
окунанием объём масляной ванны определяют из расчёта 0,4…0,8 л масла на 1 кВт
передаваемой мощности.
г) Определяем
уровень масла:
При окунании в масляную ванну колеса:

;
При нижнем расположении шестерни:

;
д) Контроль
уровня масла.
Уровень масла, находящегося в корпусе редуктора,
контролируют различными маслоуказателями.
Наибольшее распространение имеют железовые
маслоуказатели, так как они удобны для осмотра, конструкция их просто и
достаточно надёжна.
3.
Организация производства
3.1
Требования к эксплуатации
Управление передаточной тележкой:
Перед началом работы:
.Перед началом работы для приёмки смены, осмотра
и проверки работы тележки непосредственный или оперативный руководитель, должны
выделить работнику необходимое время.
.Прибыть на место стоянки тележки, на котором поручено
работать.
.Проверить наличие и исправность оборудования и
приспособлений тележки.
.Произвести осмотр рельсового пути на предмет
отсутствия посторонних предметов.
.Не приступать к работе, если складирование
груза не обеспечивает полную безопасность выполнения работ на участке.
.Незамедлительно ставить в известность
непосредственного или оперативного руководителя в случае, если отсутствует
возможность самостоятельно устранить факторы, создающие опасность при
выполнении работ на участке.
В процессе работы:
.Не допускать превышения грузоподъёмности
тележки и нарушения габаритов груза установленного на тележке: груз не должен
выступать более чем на 1/3 размера платформы, расстояние между наиболее
выступающими частями тележки или груза и конструкциями здания, оборудования или
складируемыми материалами должно быть не менее 0,7 метра по обе стороны
тележки.
.Устанавливать груз равномерно по всей
платформе, начиная от центра.
.Крупногабаритные детали большой массы
устанавливать только по центру тележки во-избежании её опрокидывания.
.Неустойчивые и круглые предметы надёжно крепить
на платформе.
.Круглые детали большого диаметра и массы
устанавливать на специальные подставки.
.Находиться у пульта управления и внимательно
следить за движением тележки и состоянием груза.
.Работнику занимающемуся эксплуатацией тележки
не разрешается:
допускать нахождение людей в зоне движения
тележки;
перевозить людей на платформе;
находиться на платформе во время подъёма или
опускания груза, а также во время движения тележки;
брать на буксир и толкать с помощью тележки
другие транспортные средства;
пользоваться концевыми выключателями как рабочим
органом для остановки тележки;
допускать удары тележки о тупики;
заклинивать органы управления;
прыгать с платформы.
По окончании работы:
.Произвести разгрузку передаточной тележки
выполняя требования изложенные в инструкции.
.Установить передаточную тележку на постоянное
место стоянки.
.Пользоваться соответствующей ключ - биркой для
управления передаточной тележкой.
.Взятие ключ - бирки от тележки с собой, при
любом уходе от пульта управления.
.Не допускать превышения грузоподъёмности
тележки и нарушения габаритов груза перевозимого на тележке.
Погрузка и разгрузка передаточной
тележки:
Перед началом работы:
.Перед началом работы для приёмки смены, осмотра
и проверки работы тележки непосредственный или оперативный руководитель, должны
выделить работнику необходимое время.
.прибыть на место стоянки тележки, на котором
поручено работать.
.Выполняя требования изложенные в инструкциях:
Ознакомиться с характерными особенностями груза,
подлежащего погрузке, выгрузке.
Ознакомиться со схемами строповки и
складирования груза.
Проверить наличие свободных мест (участка
склада) и их состояние, а также состояние проходов.
Подготовить места для складирования груза и
проходы (освободить от посторонних предметов, обеспечить наличие
вспомогательных средств для фиксации положения груза, восстановить габариты).
Проверить наличие и исправность креплений на
тележке, исключающих падение и скатывание груза.
.Подобрать необходимые грузозахватные
приспособления для строповки, произвести их визуальную проверку (при
использовании ГПМ).
.Определить машинисту крана порядок выполнения
работы (при использовании ГПМ).
.Не приступать к работе, если складирование
груза не обеспечивает полную безопасность выполнения работ на участке.
.незамедлительно ставить в известность
непосредственного или оперативного руководителя в случае, если отсутствует
возможность самостоятельно устранить факторы, создающие опасность при
выполнении работ на участке.
В процессе работы:
.Погрузку, разгрузку осуществлять с
использованием электромостовых кранов. При этом выполнять требования,
изложенные в технической документации на погрузку, разгрузку данного вида
груза.
.Погрузка, разгрузка тележки:
подвеску крана установить строго над грузом;
произвести строповку груза, убедившись в том,
что он надёжно закреплён стропами и ничем не удерживается, рукой подать команду
машинисту крана на подъём груза;
приподняв груз на высоту 200-300 мм прекратить
подъём, убедится в надёжности строповки. Осмотреть груз на наличие дефектов и
продолжить подъём;
перемещение груза осуществляется после подъёма
груза на высоту, превышающую высоту находящихся на пути движения предметов на
0,5 м.
.При перемещении груза находиться впереди, с
боку или сзади груза на расстоянии не менее 5 м. Не допускать появления людей в
зоне перемещения груза. Запрещается находиться между стеллажами во время
складирования груза.
.Для подъёма и спуска с платформы тележки
использовать специальную стационарную лестницу, при её отсутствии применять
приставную лестницу.
.Устанавливать груз равномерно по всей
платформе, начиная от центра.
.Крупногабаритные детали большой массы устанавливать
только по центру тележки во-избежании её опрокидывания.
.Неустойчивые и круглые предметы надёжно крепить
на платформе.
.Не допускать удара груза о платфрму.
.Разгрузку тележки производить в направлении от
краёв к центру.
При складировании соблюдать:
расстояние от груза до оборудования, оснастки и
т.п. не менее 1,5 м.
расстояние от груза до стен здания, помещений и
колонн не менее 1,5 м.
По окончании работы:
.Выполнять требования изложенные в технической
документации.
.Предупредить машиниста крана об окончании
работ.
.Убрать грузозахватные приспособления.
.Наличие и исправность креплений на тележке,
исключающих падение и скатывание груза.
3.2
Техническое обслуживание
Приёмка смены
Эксплуатационный персонал при приёмке смены
обязан:
.Очистить путь тележки от посторонних предметов,
а также головки рельсов от попавшей на них смазки.
.Прокачать с помощью ручной станции смазку к
узлам трения.
.Опробовать работу тележки без загрузки.
.Проверить исправность действия сигнализации и
при необходимости вызвать дежурного электрика для устранения неисправностей.
Дежурный персонал приёмку смены обязан проводить
в соответствии с п.п. 1.11-1.13 (см. приложения), обратив при этом особое
внимание на состояние и крепление муфт и редукторов, на наличие смазки в редукторах
и при необходимости долить в них масло; на состояние уплотнений, работу
тормозов.
Текущее обслуживание
Уход за тележкой в течении смены проводить в
соответствии с указаниями 1.16-1.18 (см. приложения), кроме того, следить:
. Не перегружена ли тележка.
. Чтобы при остановке тележки у подъёмного стола
выдерживался зазор между тележкой и столом 150 мм;
. Чтобы при подходе тележки к столу скорость не
превышала 1,0 м/с.
Ревизии и ремонты
Ревизии и ремонты тележки проводить не реже
одного раза в два месяца в соответствии с указаниями п. 1.20, 1.21, 1.24 (см.
приложения), кроме того:
.Осмотреть сварные швы, рамы; обнаруженные
трещины расчистить и заварить;
.Обеспечить жестокость опор концов рельс со
стороны подхода тележки к столу;
.Заменять скаты при наличие трещин или износе
реборд колеса по толщине более чем на 40%.
3.3
Рабочая жидкость и способы подвода
Рабочая жидкость соединяет в себе как проточный,
так и циркуляционный способы. При работе движущихся частей машин и механизмов
возникает трение, ведущее к их износу. Для снижения трения и, следовательно,
износа трущихся частей служит различная смазка, которая способствует длительной
и безаварийной работе машин и механизмов.
Эффективная смазка трущихся поверхностей зависит
главным образом от способа подачи смазочных материалов и сорта смазки,
учитывающего условия эксплуатации данной машины.
Смазочные материалы, применяемые в машинах и
механизмах металлургического оборудования, разделяются на две основные группы:
жидкие (минеральные) масла и густые (консистентные) смазки и мази.
В зависимости от назначения и конструкции
механизма, отдельных его узлов и приборов выбирают способ подачи смазки.
Системы индивидуальной смазки обеспечивают подачу смазки только к одной точке,
централизованные же системы - к нескольким точкам.
Индивидуальную и централизованную систему смазки
в свою очередь подразделяют на ряд способов подачи жидких и густых смазочных
материалов. К основным способам как индивидуальной, так и централизованной
подачи жидкой и густой смазок относятся, например, периодическая и непрерывная
подачи, без принудительного давления, или под давлением.
Периодической называется смазка, которая
осуществляется через определенные промежутки времени в зависимости от
устройства смазываемого механизма и условий его эксплуатации.
Непрерывная - смазка, действующая непрерывно или
через короткие, заранее установленные промежутки времени в течение всего
периода работы смазываемого механизма.
Смазкой под давлением называют подачу масла с
помощью насосного устройства, которая может приводиться в действие от руки,
движущихся частей самого смазываемого механизма или специального двигателя.
По характеру циркуляции масла различают:
проточный, циркуляционный и смешанный способы подачи смазки.
При поточном способе смазки отработанное масло
не возвращается к первоначальной точке подачи. В отличие от проточного, при
циркуляционном способе отработанное масло автоматически и многократно
возвращается к трущимся поверхностям.
Жидкая смазка минеральными маслами широко
применяется во многих агрегатах металлургического оборудования. При этом
одновременно со смазкой трущихся поверхностей отводится тепло. Расход масла в
циркуляционных системах смазки сокращается до минимума, в то время как густая
смазка теряется безвозмездно. Вместе с тем применение жидких минеральных масел
не всегда целесообразно, так как усложняется конструкция смазываемых узлов,
требуются надежные уплотнения, устраняющие утечки масел. В таких случаях
применяют густую смазку.
Такую смазку применяют также, когда необходимо
защитить поверхности трения от попадания в них окалины и воды; ее применяют для
смазки тяжело нагруженных подшипников скольжения и качения, работающих при
небольшом количестве оборотов, с частыми реверсами или на
повторно-кратковременном режиме; смазки подшипников вертикальных и наклонных
валков, плоских и цилиндрических направляющих.
4.
Охрана труда
.1
Техника безопасности при ремонте и техническом обслуживании
Работоспособность, исправность оборудования и
его использование по назначению приводит к преждевременным отказам
оборудования, цель предупреждения преждевременного износа путём смазки,
регулировки, своевременного обнаружения дефектов и их устранения, а также
совершенствования оборудования. Техническое обслуживание выполняется по
графикам в соответствии с инструкциями. Периодичность и продолжительность
работы устанавливается цехом, согласовывается и утверждается главным инженером,
оборудование в цехах закрепляется за отдельными бригадами персонала цеха.
В течении смены эксплуатационный и дежурный
персонал несёт ответственность за оборудование и его работоспособность, также
отмечает в журналах приёмку и сдачу смен, журналом фиксируются результаты
осмотра закреплённого оборудования по графику состояния в течении смены:
дефекты, нарушения по технике безопасности, меры принятые для устранения
дефектов, нарушение правил технической эксплуатации оборудования, а также при
остановке оборудования на плановый ремонт.
Дежурный персонал в течении смены ведёт
наблюдение за работой оборудования проверяет показания приборов, нагрев узлов,
поступление смазки, регулярные записи в журналах.
Анализ опасных и вредных
производственных факторов при работе сортоправильной машины.
При правке проката на сортоправильных машинах
возможны следующие факторы: шум, электрический ток, вращающиеся механизмы,
горячий металл, прокат, перемещающийся с большой скоростью, загрязненный
воздух. Все эти виды факторов относятся к группе физических и технологических
факторов.
Следовательно, в данных
производственных условиях человек подвергается многократному воздействию,
эффект которого может оказаться более значительным, чем при изолированном
действии того или иного фактора.
Рассмотрим каждый из опасных и
вредных факторов. На охлаждения и правки сортового проката составляет примерно1-
90 дБ. По спектральному составу - это среднечастотный и низкочастотный шум
различной продолжительности. Интенсивный шум на производстве способствует
снижению внимания и увеличению числа ошибок при выполнении работ.
Исключительно сильное влияние шум
оказывает на быстроту реакции, что негативно сказывается на производительности
труда технологического персонала.
Шум затрудняет своевременную реакцию
работающих на предупредительные сигналы внутрицехового транспорта (электрокар,
мостовых кранов, передаточных тележек и т.д.), что способствует возникновению
несчастных случаев на производстве.
Шум оказывает влияние на весь
организм человека: угнетает центральную нервную систему, вызывает изменение
скорости дыхания и пульса, способствует нарушению обмена веществ, может
привести к профессиональным заболеваниям. Высокая индивидуальная
чувствительность может быть одной из причин повышенной утомляемости и развития
различных неврозов.
Движущиеся механизмы являются
наиболее опасными факторами для рабочего персонала. Механические опасности могут
возникнуть у любого объекта, способного причинить человеку травму в результате
не спровоцированного контакта объекта или его частей с человеком. Риск
подвергнуться такому контакту может произойти при взаимодействии человека с
механизмом в трудовом процессе и при случайном прохождении человека в пределах
действия механизма. Минимальный контакт человека с вращающимися или движущимися
механизмами может привести к серьезной травме или даже к смертельному исходу.
На участок правки металл поступает
охлаждённый только до 400- 500 С, поэтому существует опасность ожога при
касании близко расположенных
ограждений, рабочих механизмов и бурежки (бракованного проката), а также
опасность получения теплового., удара при долгом нахождении в зоне воздействия
температуры проката.
Прокат поступающий в сортоправильную
машину и выходящий из него, перемещается с большой скоростью. В случае бурежки
проката металл может устремиться в любую сторону и нанести травмы различной
тяжести, включая летальный исход, персоналу, находящемуся в районе поражения.,
В процессе правки проката в воздухе
оказывается большая концентрация пыли, окалины и различных аэрозолей.
Загрязненный воздух отрицательно воздействует на организм человека в целом и на
органы дыхания, зрения и кожный покров в частности.
Загрязненный воздух вызывает кашель, слезоточение, а
также зуд кожных покровов.
4.2
Пожарная безопасность
При возникновении на тележке возгорания
(пожара), работник занятый эксплуатацией обязан немедленно работу, вытащить
ключ-бирку, окриком оповестить о пожаре людей, находящихся вблизи очага
возгорания, вызвать пожарную охрану по телефону 56-66-61 или 01, сообщить
оперативному или непосредственному руководителю и приступить к тушению пожара,
пользуясь первичными средствами пожаротушения, с учётом личной безопасности.
При невозможности безопасного тушения, покинуть тележку.
Пожарная профилактика
предусматривает мероприятия по предупреждению и ликвидации пожаров, включая
ограничения сферы распространения огня и обеспечение успешной эвакуации людей и
имущества из горящих помещений. Источниками
воспламенения могут быть: тепло нагретых частей оборудования и металла, искры
различных типов, неисправность электрооборудования.
Причины возникновения пожара могут
быть следующие: недостатки в планировке помещения и конструкции здания, дефект
оборудования, нарушение режима технологического процесса, нарушение техники
безопасности персоналом.
Основные меры предупреждения пожаро-
и взрывоопасности производственных процессов, включают:
- предотвращение образования горючей
и взрывоопасной среды;
- контроль качества горючей среды;
- применение герметичного
оборудования;
- отвод и изоляция горючей и
взрывоопасной среды;
- применение рабочей и аварийной
вентиляции;
- оптимизация, механизация и
автоматизация процессов.
При возникновении пожара необходимо:
привести в действие подручные
средства тушения, отключить подачу энергии, эвакуировать огнеопасные и ценные
материалы, перекрыть коммуникации, по которым возможно распространение пожара,
сообщить о пожаре.
4.3
Электробезопасность
Если элементы тележки и ворот оказались под
напряжением, работник занятый эксплуатацией должен принять меры личной
безопасности, чтобы не попасть под действие напряжения.
Источником электрического тока на участке
охлаждения и правки сортового проката являются электродвигатели, пульты
управления и кабеля электропроводки. Действие электрического тока на живую
ткань носит разносторонний и своеобразный характер.
Электробезопасность представляет
собой систему организационных и технических мероприятий и средств,
обеспечивающих безопасность от вредного и опасного влияния на людей
электрического тока. Оно обеспечивается конструкцией электроустановок,
техническими способами и средствами защиты, организационными мероприятиями.
Но опасности поражения электрическим
током цех является помещением с особой опасностью, т.к. здесь присутствует
токопроводящая пыль, возможен контакт человека с металлоконструкциями,
технологическими агрегатами и корпусами электродвигателя.
Все токоведущие части заизолированы
и заземлены металлическими штырями или металлической полосой с сопротивлением
К=4 Ом, в соответствии с правилами и ГОСТами в местах, где возможно разрушение
или повреждение изоляции, она должна быть закрытой или двойной.
Для предотвращения короткого
замыкания необходимо: правильный выбор, монтаж, эксплуатация сетей, машин и
аппаратов, соблюдение правил эксплуатации, осмотров, ремонта электрических
установок. Для локализации
короткого замыкания используют
быстродействующую релейную защиту и выключатели, установочные автоматы, плавкие
вставки, предохранители.
Применяемые кабеля и провода должны
соответствовать условиям эксплуатации оборудования. Конструктивные детали
электрооборудования выполнены из изолирующих материалов.
При обслуживании электрооборудования
имеются средства индивидуальной защиты и инструмент, который надежно
заизолирован. Для безопасного обслуживания электроустановок сети, необходимо
систематически проверять изоляцию на
электропрочность, чтобы определить утечки в сети и предупредить возможность
пробоя на корпусе. Также устанавливаются молниеотводы.
Молниеотводы предназначены для
защиты производственных помещений от молний. Устанавливаются изолируемые от
здания отдельно стоящие молниеотводы стержневого типа, расположенные равномерно
по площади горизонтальной проекции. Каждый из молниеотводов имеет заземление.
4.4
Бирочная система
Бирочная система - это система допуска к
работам, связанным с эксплуатацией, техническим обслуживанием и ремонтом
оборудования и механизмов с электроприводом, гидроприводом и пневмоприводном,
направленная на обеспечение безопасной организации труда и установление
правильных производственных отношений между лицами, выполняющими эти работы.
Общие требования:
. Бирочная система применяется при эксплуатации
оборудования и механизмов, а также при их техническом обслуживании и ремонте,
выполняемом как без нарядов - допусков, так и по нарядам - допускам, когда
безопасность работ обеспечивается выполнением требований бирочной системы и
наряда-допуска.
. Ответственность за организацию функционирования
бирочной системы и контроль за соблюдением её требований возлагается на
руководителя структурного подразделения Общества, а внутри структурных
подразделений - на руководителей участков.
. В каждом подразделении должны быть выполнены
следующие мероприятия:
а) составлен перечень механизмов,
укомплектованных ключ-бирками и жетон-бирками;
б) внесены необходимые изменения в
технологическую документацию (чертежи, электросхемы и т.д.) электроприводов
механизмов и цепей управления с помощью электромагнитов, гидро - ,
пневмораспределителей, на которых установлены замки - выключатели с
ключ-бирками;
в) укомплектованы замки - выключатели и
ключ-бирками пульты управления механизмами в соответствии с перечнем;
г) определены места навешивания (хранения) жетон-бирок
для механизмов с электроприводом при их эксплуатации в соответствии с перечнем;
д) определены места хранения жетон-бирок для
механизмов с гидроприводом и пневмоприводном при эксплуатации соответствии с
перечнем;
е) определён порядок передачи ключ-бирок и
жетон-бирок при эксплуатации механизмов;
ж) определены места хранения ключ-бирок от
периодически используемых механизмов, находящихся в эксплуатации;
з) требования бирочной системы при эксплуатации
механизмов, касающихся конкретных профессий рабочий и видов работ, доведены до
рабочего персонала в инструкциях по охране труда по профессиям и видам работ ;
и) назначены допускающие при проведении работ по
техническому обслуживанию и ремонту механизмов;
к) определены места хранения журналов выдачи-приёма
бирок;
л) назначено лицо, ответственное за изготовления
жетон-бирок, бирок к ключам и их дубликатов;
м) требования бирочной системы при техническом
обслуживании и ремонте механизмов, касающиеся конкретных профессий рабочий и
видов работ, доведены до рабочего персонала в инструкциях по охране труда по
профессиям и видам работ.
. Механизмы с электроприводом, коммутационная
аппаратура которых находится в Машинных залах (электрических помещениях,
запираемых шкафах), а пульты управления располагаются в постах управления или к
пультам управления располагаются в постах управления или к пультам управления
возможен свободный доступ посторонних лиц, оборудуются и жетон-биркой, и
ключ-биркой.
. Изменение в электрической схеме действующего
оборудования при введении бирочной системы должны быть сделаны по проекту.
. Лицами, ответственными за соблюдением бирочной
системы и безопасное проведение работ с применением бирочной системы, являются:
- лицо,
выдающее наряд-допуск;
- допускающий
к работе;
- электромонтёр
или слесарь по обслуживанию механизмов;
- лицо из
технологического персонала, управляющего механизмом;
-
производитель работ;
- члены
бригады.
Бирочная система предусматривает применение
следующих типов бирок:
ключ-бирка (ключ с навешенной биркой);
жетон-бирка для механизмов с электроприводом;
жетон-бирка для механизмов с гидроприводом;
жетон-бирка для механизмов с пневмоприводном.
Ключ-бирка предназначена для подготовки цепей
управления электроприводов механизмов к включению или отключению с помощью замка-выключателя,
устанавливаемого на пультах управления механизмами, а также цепей управления с
помощью электромагнитов и гидро - , пневмораспределителей. Бирка к ключу имеет
прямоугольную форму, окрашена в белый цвет, изготовлена из пластмассы, оргстекла,
текстолита.
На бирку наносят порядковый номер и наименование
механизма, сокращённое наименование участка, подразделения.
Заключение
В ходе выполнения данного мне дипломного проекта
я изучил назначение, принцип действия, устройство и техническую эксплуатацию
передаточной тележки. Изучил систему смазки, возможную модернизацию
передаточной тележки склада слябов стана 2000. Наблюдал, как проводят
техническую эксплуатацию, текущее обслуживание и ремонт агрегата.
Произвел основные расчеты редуктора, смазки. Выполнил
чертежи привода, редуктора, рамы с приводом передаточной тележки на формате А1.
Прокатное производство является завершающим
звеном металлургического цикла. В современных прокатных цехах технологические
операции осуществляются по поточному и непрерывному циклу, позволяющие широко
применять комплексную механизацию и автоматизацию.
В связи с этим, модернизация
передаточных тележек склада слябов, как это видно на данном производстве очень
актуальна и представляет большой практический интерес в плане повышения
производительности цеха, снижения простоев основного оборудования, увеличения
автоматизации технологических процессов, снижения затрат и времени на ремонты.
Литература:
1.
Королев А.А. Механическое оборудование прокатных черной и цветной металлургии,
- М.: Металлургия, 2009;
.
Королев А.А. Конструкция и расчет машин и механизмов прокатных станов, - М.:
Металлургия, 1985;
3.
Осипов В.К., Чекмарев А.А. Справочник по машиностроительному черчению - М.:
Высшая школа, 1994;
4.
Писаренко Г.С. Справочник по сопротивлению материалов, - Киев: Наукова Думка,
2008;
5.
Целиков А.И. и др. Машины и агрегаты металлургических заводов.- Том 1
Машины
и агрегаты доменных цехов. - М. :Металлургия, 1987;
6.
Целиков А.И. и др. Машины и агрегаты металлургических заводов.- Том2
Машины
и агрегаты сталеплавильных цехов .- М.: Металлургия, 1988;
7.
Целиков А.И. и др. Машины и агрегаты металлургических заводов .- Том3
Машины
и агрегаты для производства и отделки проката: Металлургия,1988;
8.
Четвериков В.С. Методические рекомендации к курсовой работе. Расчет
экономической эффективности проводимых технических мероприятий. -
9.
Череповец: Череповецкий металлургический колледж, 2002;
10.
Шейнблит А. Е. Курсовое проектирование деталей машин - Калининград: Янтарный
сказ, 2001;
11.
Единая система конструкторской документации ГОСТ 2.105-95, ГОСТ 2. 301,-М.,
2005;
12.
Дешина М.А., Методика организации дипломного проектирования, 2006.
Приложение
1.11 - Передача смен производится в следующем
порядке:
1.11.1 - По окнчании смены машинисты постов
управления, операторы и слесари по ремонту оборудования, сдающие смену, обязаны
записать в журнал приёмки-сдачи смен данные о состоянии обслуживаемого
оборудования, неисправностях которые были обнаружены во время работы или
нарушениях Правил и мерах, принятых для их устранения, а также поставить в
известность об этом принимающему смену.
.11.2 - Принимающий смену и сдающий совместно
осматривают обслуживаемое ими оборудование, устраняют обнаруженные
неисправности, после чего докладывают мастеру (бригадиру) о том, что смена
принята и в каком состоянии находится оборудование.
.11.3 - Неисправности, обнаруженные при приёмке
смены и не записанные в журнале сдающим смену, записывает персонал, принимающий
смену.
В случае обнаружения неисправностей, при которых
работа оборудования запрещается, принимающий смену сообщает об этом
руководителю сменного ремонтного персонала или начальнику смены (оборудование
может быть пущено в работу только после полного устранения неисправностей и
получения разрешения на пуск).
.11.4 - Передача смены подтверждается в журнале
приёмки-сдачи смен подписями лиц, принимающих и сдающих смену, после чего смена
считается переданной (принятой).
.13 - Мастера, механик, начальник смены и
начальник стана обязаны ежесуточно проверять записи в журналах приёмки и сдачи
смен и принимать меры по устранению неисправности оборудования.
.16 - Эксплуатационный персонал обязан выполнять
ремонтные работы по устранению неисправностей, появляющихся при работе
обслуживаемого им оборудования, для чего он должен пройти специальное обучение
второй профессии (слесаря по ремонту оборудования) и иметь необходимый
инструмент.
.18 - Инженерно-технический персонал цеха обязан
периодически проверять техническое состояние оборудования стана. Проверку
проводить согласно графику, утверждённому главным механиком (инженером) завода.
Оборудование должны осматривать:
.18.1. - Начальник (заместитель) цеха и помощник
(заместитель) начальника цеха по оборудованию - не реже одного раза в месяц.
.18.2. - Механик цеха - не реже двух раз в
месяц.
.18.3. - Мастер - не реже одного раза в неделю.
.20 - Эксплуатационный персонал должен содержать
контрольно-измерительную аппаратуру в соответствии с действующими инструкциями
цеха контрольно-измерительных приборов (КИП). Обслуживание и ремонт
электроконтактных термометров и манометров, электрических указателей потока
масла и других приборов (логометров, самопишущих манометров, термометров
сопротивления и т.п.) осуществляется цехом КИП.
.21 - При передаче смен, текущем обслуживании,
периодических осмотрах, ревизиях и ремонтах оборудования необходимо соблюдать
действующие на заводе бирочную систему и систему допусков, а также
противопожарные меры безопасности.
.24 - Приёмка оборудования в ремонт, проведение
ремонта и сдача в эксплуатацию после окончания ремонтных работ производятся в
соответствии с Положением о ППР (г. Харьков ВНИИОчермет, 1973).