Технологические возможности станков
Аннотация
Целью данной курсовой работы является закрепление необходимых будущему
инженеру теоретических знаний по металлорежущим станкам.
В данной курсовой работе рассматривается изучение конструкций и подсистем
станков. Также подробно изучены конструкции отдельных узлов станка, движения в
станке, основные технические характеристики, а также кинематика станка. На
основе материалов патентного поиска, обзора технической литературы и
документации представлены станки аналоги с подробным описанием технических возможностей.
Содержание
Введение
1. Технологические
возможности станков
1.1 Назначение станков
1.2 Эскизы выполняемых
операций
1.3 Эскизы типовых деталей
2. Компоновки станков
2.1 Схемы компоновок
2.1.1 Токарный
обрабатывающего центра модели SPU 20 МС
2.1.2 Токарный многоцелевой
станок модели ИРТ180ПМФ4
2.1.3 Станок токарный с ЧПУ SPU
40 CNC
2.1.4 Токарный многоцелевой
станок GMX 400
2.1.5 Прутковый многоцелевой
станок моделей LG-71, LG-81 и LG-83 фирмы «Яшино» (Япония)
2.2 Функциональное назначение
узлов
3.
Конструктивные схемы привода полярной. Координаты токарных многоцелевых станков
4. Привод
вращения инструмента токарных многоцелевых станков
5.
Инструментальная оснастка токарных многоцелевых станков
6. Выводы и
рекомендации
7. Конструкции
пружинно-зубчатых муфт
7.1 Область
применения
7.2 Конструкции муфт
7.2.1 Пружинно-зубчатая муфта
7.2.2 Пружинно-зубчатая муфта
(разновидность 2)
Литература
Введение
Современные металлорежущие станки - это высоко развитые машины,
включающие большое число механизмов и использующие механические, электрические,
электронные, гидравлические, пневматические и другие методы осуществления
движений и управления циклом. По конструкции и назначению трудно найти более
разнообразные машины, чем металлорежущие станки. На них обрабатывают
всевозможные детали - от мельчайших элементов часов и приборов до деталей,
размеры которых достигают многих метров, - турбин, теплоходов, прокатных
станов.
Современное станочное оборудование является базой для развития гибкого автоматизированного
производства, резко повышающего производительность труда в условиях средне- и
мелкосерийного производства.
Использование гибких производственных систем, состоящих из набора
станков, манипуляторов, средств контроля, объединенных общим управлением от
ЭВМ, дает возможность и в многономенклатурном крупносерийном производстве
стимулировать научно-технический прогресс, быстрый и с минимальными затратами
переход к новым, более совершенным образцам выпускаемой продукции. Переход от
использования набора станков и других технологических машин к машинным системам
в виде гибких производственных систем технологического оборудования помимо
повышения производительности труда коренным образом изменяет весь характер
машиностроительного производства. Создаются условия постепенного перехода к
трудосберегающему производству при наивысшей степени автоматизации.
Совершенствование современных станков должно обеспечивать повышение
скоростей рабочих и вспомогательных движений при соответствующем повышении
мощности привода главного движения. Исключительное значение приобретает
повышение надежности станков за счет насыщения их средствами контроля и
измерения, а также введения в станки систем диагностирования
Повышение скоростей рабочих и вспомогательных движений связано с
дальнейшим совершенствованием привода станков, шпиндельных узлов, тяговых
устройств и направляющих прямолинейного движения. Применение композиционных
материалов для режущих инструментов позволяет уже сейчас реализовать скорость
резания до 1,5-2 км/мин, а скорость подачи довести до 20-30 м/мин. Дальнейшее
повышение скоростей потребует поиска новых конструкций, использующих иные
физические принципы и обеспечивающих высокую работоспособность ответственных
станочных узлов.
Применение станочных модулей возможно только при полной автоматизации
всех вспомогательных операций за счет широкого использования манипуляторов и
промышленных роботов. Это относится к операциям, связанным со сменой заготовок,
режущих инструментов, технологической оснастки, с операциями измерения
заготовки, инструмента, с операциями дробления и удаления стружки из рабочей
зоны станка.
Оснащение станков гибкого автоматизированного производства различными
контрольными и измерительными устройствами является необходимым условием их
надежной работы, особенно в автономном и автоматизированном режиме. В
современных станках используют широкий набор средств измерения, иногда очень
точных, таких, например, как лазерные интерферометры, для сбора текущей
информации о состоянии станка, инструмента, вспомогательных устройств и для
получения достоверных данных о исправной работе.
Современные металлорежущие станки обеспечивают исключительно высокую
точность обработанных деталей. Ответственные поверхности наиболее важных
деталей машин и приборов обрабатывают на станках с погрешностью в долях
микрометров, а шероховатость поверхности при алмазном точении не превышает
сотых долей микрометра. Требования к точности в машиностроении постоянно
растут, и это, в свою очередь, ставит новые задачи перед прецизионным станкостроением.
Специалисты в области технологии машиностроения, металлорежущих станков и
инструментов находятся на одном из самых ответственных участков всего
научно-технического прогресса. Задача заключается в том, чтобы в результате
коренного совершенствования технологии обработки, создания новых металлорежущих
станков с микропроцессорным управлением, станочных модулей для гибких
производственных систем обеспечить техническое и организационное перевооружение
всех отраслей машиностроения и на этой основе обеспечить существенное повышение
производительности труда. Для успешного творческого труда
инженеры-станкостроители должны быть фундаментально подготовлены в области
математики, физики, вычислительной техники, иметь фундаментальные знания и
навыки по общим инженерным дисциплинам и, наконец, хорошо знать свою будущую
специальность. Необходимо ясно представлять общие важнейшие свойства и
качества, определяющие технический уровень металлорежущих станков, с тем, чтобы
создавать лучшие образцы и новые модели станков.
В настоящее время и в обозримом будущем потребуется создание новых
моделей станков, станочных модулей, гибких производственных систем, поэтому
будущие специалисты-станкостроители должны владеть основами конструирования
станков и их важнейших узлов. Для успешного применения вычислительной техники
при конструировании необходимо хорошо знать содержание процесса проектирования
всех видов станочного оборудования, владеть методами его моделирования и
оптимизации.
Современный станок органически соединил технологическую машину для
размерной обработки с управляющей вычислительной машиной на основе
микропроцессора. Поэтому специалист станкостроитель должен хорошо понимать
принципы числового программного управления станками, владеть навыками
подготовки и контроля управляющих программ. Он должен знать устройство
микропроцессорных средств управления, основные их характеристики и возможности
применительно к станочному оборудованию.
Для большинства машиностроительных
производств детали типа тел вращения по номенклатуре и трудоемкости
технологических операций являются преобладающими. Анализ технологических
процессов обработки деталей указанной группы показывает, что при достаточно
удовлетворительном решении задачи автоматизации процессов формообразования
основного контура (при первичной обработке) на станках токарной группы
достаточно острой является проблема быстрого перехода и осуществления вторичных
операций - фрезерования, сверления, шлифования и т. д. Это объясняется, в
первую очередь, большими материальными затратами, обусловленными необходимостью
создания оснастки для вторичных операций, временными потерями, которые
вызываются перемещениями обрабатываемых деталей к станкам и неизбежным их
пролеживанием в межоперационный период.
Разработка и внедрение токарных многоцелевых
станков позволяет в значительной мере решить задачу общего повышения уровня
автоматизации технологических процессов, а также повышения точности и
производительности обработки рассматриваемых деталей.
При создании многоцелевых токарных станков
наиболее важными являются технологические аспекты применения этого
высокоэффективного и дорогого вида оборудования, выбор компоновочных схем,
проектирование наиболее характерных узлов - привода полярной координаты
шпинделя, инструментальной системы, в первую очередь, привода вращающихся
инструментов, инструментальных блоков.
Технологический анализ позволяет помимо
всего определить количество основных координат, необходимых для обработки всех
элементов детали при осуществлении первичных и вторичных операций, уточнить
компоновку станка с учетом максимальной концентрации операций, а также
определить основные требования к исполнению привода полярной координаты
шпинделя, емкости и конструкции инструментальной системы.
В настоящем обзоре рассмотрены вопросы
технологии обработки деталей на токарных многоцелевых станках, в частности,
статистика применяемости вращающихся инструментов, характеристика и
конструктивные схемы привода полярной координаты шпинделя, основные схемы
привода вращающихся инструментов и инструментальных блоков.
1. Технологические возможности станков
1.1 Назначение станков
Многооперационные (многоцелевые) станки предназначены
для комплексной обработки деталей с автоматической сменой инструментов.
Токарные многоцелевые станки,
предназначенные для обработки общемашиностроительных деталей, изготовляются на
базе аналогичных токарных станков с ЧПУ и их технические характеристики в
основном соответствуют базовым моделям. Дополнительные функции обеспечиваются
за счет оснащения шпинделя станка приводом его углового позиционирования
(приводом полярной координаты С) с соответствующим блоком управления и приводом
вращения инструмента (сверл, фрез, разверток, метчиков, многошпиндельных
насадок и т. п.).
Станки для обработки «отраслевых» деталей
отличаются большим числом управляемых координат, создаются, как правило, на
оригинальной базе и, следовательно, при наличии расширенных технологических
возможностей более дороги. Компоновка и конструктивные решения токарных
многоцелевых станков определяют области их применения.
Условиям мелкосерийного производства в
наибольшей степени отвечают одношпиндельные станки, оснащенные одним крестовым
суппортом с одной (двумя) револьверными головками или инструментальным
магазином.
Для средне- и крупносерийного производства
целесообразна разработка одношпиндельных многосуппортных станков или
многошпиндельных станков. Большая часть токарных многоцелевых станков имеют
наклонную или прямоугольную станину заднего расположения, что обеспечивает
оптимальные условия доступа в рабочую зону оператору и загрузочному устройству,
а также схода стружки, С0Ж и возможность установки автономных транспортеров для
уборки стружки.
Современные токарные многоцелевые станки,
как правило, снабжены ограждениями и кожухами кабинетного типа, позволяющими
полностью изолировать рабочую зону станка при высоких режимах обработки и
большой подаче С0Ж (до 40-50 л/мин) при давлении 3-4 атм. Станки оснащены также
вытяжными устройствами.
Устройства ЧПУ размещаются с учетом
габаритов станка на поворотной консоли, в стационарной или подвижной части
ограждения; лицевая часть панели управления имеет наклонное и вертикальное
расположение.
1.2 Эскизы выполняемых операций
Как показывает технологический анализ, более 70% деталей типа
тел вращения кроме токарной обработки требуют проведения дополнительных
операций. К ним относятся (рисунок 1): обработка отверстий (сверление,
зенкерование, развертывание, расточка, нарезка резьбы), оси которых расположены
параллельно, перпендикулярно или под углом к оси детали; фрезерование под разными
углами лысок, пазов (в том числе шпоночных); объемная фрезерная обработка
(фрезерование профильных канавок, полостей переменной глубины, профильных
кулачков).
Рисунок 1 - Примеры дополнительной
обработки деталей типа тел вращения.
Создание многоцелевых токарных станков, обеспечивающих полную
комплексную обработку деталей типа тел вращения на одном станке за одну
установку, позволяет существенно повысить точность и производительность
обработки, сократить производственный цикл, обеспечить повышение общего уровня
автоматизации технологических процессов, а также быструю переналадку при
переходе на обработку другой детали.
1.3 Эскизы типовых деталей
Многооперационные станки в основном используют для обработки корпусных и
призматических деталей, имеющих большое число гладких, ступенчатых и резьбовых
отверстий различных диаметров и расположенных с разных сторон детали. Кроме
того, возможна обработка плоскостей и сложных контуров. Типовые детали,
выполняемые на станке, приведены на рисунке 2.

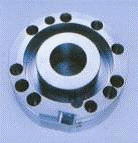
Рисунок 2 - Типовые детали
2. Компоновки станков
Компоновка токарных многоцелевых станков в
значительной мере определяется типом загрузочных устройств заготовок,
исполнением инструментальной системы, системы эвакуации стружки, защиты.
Прутковые станки обычно снабжены магазином
для автоматической подачи прутка.
В зависимости от требуемого уровня
автоматизации многоцелевые станки патронного и патронно-центрового типа
оснащаются роботами пристыковочного, напольного, портального или мостового
типов.
Большинство токарных многоцелевых станков, предназначенных
для мелкосерийного производства, имеет одну револьверную головку, установленную
на крестовом суппорте, или инструментальный магазин. Отдельные станки снабжены
двумя револьверными головками, размещенными на поперечных салазках, причем одна
из головок оснащена приводом вращающегося инструмента, а другая содержит только
неподвижный инструмент.
Ось револьверной головки с вращающимся инструментом может
быть расположена перпендикулярно или параллельно оси рабочего шпинделя,
определяя тем самым размещение вращающегося инструмента относительно обрабатываемой
детали. Отличительные особенности токарных многоцелевых станков от станков с
ЧПУ приведены в приложении 1.
2.1
Схемы компоновок
2.1.1 Токарный обрабатывающий центр модели SPU 20 МС
Рисунок 3 - Общий вид токарного обрабатывающего центра модели SPU 20 МС
Предназначен для комплексной обработки
фасонных деталей с преимущественным выполнением операций сверления и
фрезерования. Для этого в SPU 20 МС серийно предусмотрены:
• Ось С (В) на обоих шпинделях (привод
полярной координаты);
• Приводные инструменты в верхней инструментальной головке;
• Интегрированная с верхним суппортом ось Y для сложного
внецентрового сверления и фрезерования.
Наличие инструментов с приводом для операций сверления и
фрезерования и правый шпиндель под обработку противоположной стороны заготовок
в токарных центрах создают предпосылки для комплексной обработки при
максимальной производительности.
• Точение по двум или четырем координатам
на левом шпинделе.
• Прием заготовки от левого шпинделя
подвижной правой шпиндельной бабкой.
• Независимая обработка на левом или
правом шпинделях.
• Точение по двум или четырем координатам на правом шпинделе.
2.1.2 Токарный многоцелевой станок модели
ИРТ180ПМФ4
Рисунок 4 - Общий вид токарного многоцелевого
станка модели ИРТ180ПМФ4
- станина; 2 - револьверная головка; 3 -
привод вращающегося инструмента револьверной головки; 4 - поперечные салазки; 5
- сменный диск револьверной головки; 6 - тумба с поворотной стойкой; 7 - диск
револьверной головки в позиции обработки; 8 - промышленный робот; 9 - тактовый
стол; 10 -шпиндельная бабка
Токарный многоцелевой станок модели
ИРТ180ПМФ4 (рис. 2) с роботом пристыковочного типа выполнен по схеме с задним
размещением суппорта, установленного на горизонтальных направляющих станины. На
поперечных салазках станка установлена револьверная головка со сменным диском
(накопителем), имеющим 12 гнезд для неподвижного и вращающегося инструмента.
Ось вращения револьверной головки параллельна плоскости горизонтальных
направляющих поперечных салазок и перпендикулярна оси шпинделя станка. У
правого торца станины станка установлена тумба с поворотной двухпозиционной
стойкой, на одной стороне которой размещается новый сменный диске
подготовленным инструментом. В случае необходимости диск с отработанным
инструментом с помощью гидропривода по специальным направляющим перемещается на
свободную позицию стойки, а новый диск (после поворота стойки на 180°)
автоматически перемещается в рабочую зону станка и закрепляется на поворотной
части головки.
Технические характеристики станка модели
ИРТ180ПМФ4:
Максимальный диаметр обрабатываемой
детали, мм 180
Максимальная длина обрабатываемой детали, мм 200
Диапазон частот вращения шпинделя, мин-1
20 - 4000
Мощность привода главного движения, кВт 22
Диапазон частот вращения инструментального
шпинделя
револьверной головки, мин-1 45-45000
Мощность привода вращающегося инструмента
револьверной головки, кВт 3,7
Дискретность по координатам:
линейным (X и Z), мм 0,01
полярной (С), град 0,01
2.1.3 Станок токарный с ЧПУ SPU 40 CNC
Рисунок 5 - Общий вид cтанка
токарного с ЧПУ SPU 40 CNC
Токарный станок SPU 40 CNC с ЧПУ современной конструкции является
экономичным технологическим решением для обработки длинномерных валов,
позволяет вести точную и высокопроизводительную обработку валов и фланцев
диаметром максимум 500 мм и длиной максимум 2500 мм. Варианты конструкционного
исполнения в зависимости от числа управляемых линейных осей верхнего и нижнего
суппортов и длин точения позволяют заказчику выбрать оптимальный вариант
решения технологических проблем.
SPU 40 CNC с двумя управляемыми координатами (простейший вариант станка,
оснащенный лишь верхним суппортом с управляемыми координатами Z, X)
SPU 40 CNC с управлением по двум координатам и неподвижным люнетом (на
нижней управляющей установлен самоцентрирующийся люнет, с подачей от задней
бабки)
SPU 40 CNC с управлением по 3 координатам (2 управляемые координаты Z, X
верхнего суппорта и ЧПУ-координата люнета с отдельным сервоприводом)
SPU 40 CNC с управлением по 4 координатам (наиболее сложный вариант
станка с двумя суппортами независимого управления по двум координатам Z, X и W,
U)
SPU 40 CNC 1000/1500/2500 с различными межцентровыми расстояниями.
Рисунок 6 - Станина
Верхняя 12-позиционная инструментальная
головка с возможностью применения приводных инструментов для фрезерования
плоскостей и расточки вне осевых отверстий как параллельно, так и
перпендикулярно оси точения.
Задняя бабка всех станков SPU 40 CNC автоматически
перестанавливается с помощью отдельного электродвигателя и ходового винта.
Нижняя 8-позиционная инструментальная
головка предназначена для непосредственного крепления токарных резцов.
Рисунок 7 - Рабочая зона станка
Подвижный люнет установлен на продольных
салазках нижнего суппорта с ЧПУ движением в оси точения.
Неподвижный люнет в принципе не отличается
от подвижного люнета. Однако перемещение осуществляется путем тяги при помощи
задней бабки.
2.1.4 Токарный многоцелевой станок GMX 400
Рисунок 8 - Общий вид токарного многоцелевого
станка модели GMX 400
Компоновка многооперационного станка модели GMX
400 приведена на рисунке 9. Особенностью компоновки данного станка
является наличие контр-шпинделя и скоростной фрезерной головки
Рисунок 8 - Компоновка токарного многоцелевого
станка модели GMX 400
2.1.5 Прутковый многоцелевой станок моделей LG-71, LG-81 и LG-83 фирмы «Яшино»
(Япония)
Инструментальные системы относятся к линейному типу (рисунок
8). Характерной их особенностью является размещение на удлиненных поперечных
салазках 5 крестового суппорта 6 ряда инструментальных блоков 3 для токарной
обработки.
Рисунок 8 - Общий вид пруткового многоцелевого
станка моделей LG-71, LG-81 и LG-83 фирмы «Яшино» (Япония)
- основная шпиндельная бабка; 2 - патрон;
3 - блоки с неподвижным инструментом; 4 - фрезерная головка; 5 - поперечные
салазки; 6 - суппорт; 7 - дополнительная шпиндельная головка; 8 - зажимное
устройство; 9 - обрабатываемая деталь; 10 - блок с инструментом для обработки
со стороны отрезки
На салазках установлены одношпиндельная
фрезерная головка 4 и дополнительная шпиндельная головка 7, оснащенная
индивидуальным приводом вращения ее шпинделя и зажимным устройством.
Дополнительная шпиндельная головка используется при отрезке полуобработанной
детали отрезным резцом суппортов от прутка, размещенного в главном шпинделе
станка и закрепленного в патроне 2 основной шпиндельной бабки 1, и при
обработке детали 9 со стороны отрезки инструментом из блока 10, закрепленного
на шпиндельной бабке 1.
Достоинства данной компоновки - повышенная жесткость,
производительность обработки, обеспечиваемая за счет сокращения
вспомогательного времени на смену инструментов.
Недостатком описанной схемы
инструментальной системы, как и в случае размещения двух револьверных головок
на одних поперечных салазках, является резкое уменьшение размера
обрабатываемого изделия (диаметра изделия, устанавливаемого над станиной) - 320
мм для станка модели LG-71 и 460 мм для станка модели LG-81; номинальные размеры
обработки соответственно составляют 0 100Х 100 мм и 0 120Х 120 мм.
Линейное размещение неподвижных и
вращающихся инструментов на поперечных салазках использовано на токарном
многоцелевом станке модели CNC 143 фирмы Ebosa (Швейцария) и др.
Необходимость обеспечения полной обработки
на токарных многоцелевых станках, в том числе обработки деталей со стороны
отрезки на прутковых станках и задней части детали на станках патронного типа
предопределяет большое разнообразие конструктивных решений, в первую очередь
количества рабочих органов станков, оснащения их приводами перемещений, способов
размещения и их взаимодействия.
Самыми распространенными решениями данной
задачи, которые могут быть рекомендованы с учетом наиболее важных факторов
(серийности производства, исполнения и типоразмера станка и т. д.), являются:
оснащение накопителя (тактового стола)
патронного токарного многоцелевого станка кантователем;
оснащение станка кантователем, размещенным
на неподвижном узле (например, на шпиндельной бабке) патронного станка
небольшого типоразмера, или кантователем, размещенным в непосредственной
близости от станка. При этом передача заготовок осуществляется с помощью
манипулятора или робота;
выполнение станка с двумя шпиндельными
узлами, размещенными в одном корпусе или в отдельных шпиндельных бабках,
установленных рядом. Для передачи полуобработанных заготовок из патрона одного
шпинделя в патрон другого для обработки обратной стороны детали может быть
использован либо робот с поворотным захватом (ротацией), либо револьверные
головки с захватными устройствами, размещенные на поворотной стойке поперечных
салазок суппорта;
оснащение патронного токарного
многоцелевого станка двумя оппозитными поворотными шпиндельными бабками
(основной и дополнительной), при этом дополнительная шпиндельная бабка имеет
возможность продольного перемещения по координате Z для захвата
полуобработанной на основной бабке заготовки для последующей ее обработки с
другой стороны. При повороте шпиндельных бабок на 90° осуществляются операции
внецентровой отработки поверхностей на правом и левом торцах заготовки;
оснащение станков пруткового или
патронного типов двумя оппозитно расположенными шпиндельными бабками-основной и
дополнительной, причем последняя выполнена подвижной для осуществления захвата
полуобработанной в основной бабке заготовки для последующей обработки заготовки
со стороны отрезки (или второй стороны). Возможно неподвижное исполнение обеих
бабок, тогда передача полуобработанной детали с одной бабки на другую
осуществляется с помощью робота;
оснащение одного из гнезд револьверной
головки станка неподвижным схватом (для патронного станка) или вращающимся
цанговым зажимом для последующей обработки заготовки с обратной стороны (левого
торца) неподвижным и вращающимся инструментом, размещенным в отдельном узле.
Все другие схемы, обеспечивающие решение
задачи обработки с двух сторон, в той или иной мере включают элементы указанных
выше решений.
Широкие возможности для получения
различных вариантов исполнения токарных многоцелевых станков (патронных и
патронно-центровых) обеспечивает угловая компоновочная схема (рис. 9). В этом
случае станина станка снабжена верхними направляющими, расположенными под углом
к горизонтальной плоскости, и нижними направляющими, расположенными в
вертикальной плоскости. В зависимости от исполнения станки могут оснащаться
одним (см. рис. 9, а) или двумя (см. рисунок 9, б) крестовыми суппортами,
задней бабкой (при патронно-центровом исполнении), устанавливаемой на нижних
направляющих. В случае необходимости на этих же направляющих могут быть
смонтированы стационарный или подвижный люнеты, оснащенные автономным приводом,
управляемым ЧПУ.
Рисунок 9 - Варианты исполнения
токарного многоцелевого станка:
а - с двумя крестовыми суппортами, б - с
одним крестовым суппортом; 1 - шпиндельная бабка; 2 - верхние направляющие; 3 -
нижние направляющие; 4 - верхний крестовый суппорт; 5 -. револьверная головка;
6 - задняя бабка; 7 - нижний крестовый суппорт
2.2
Функциональное назначение узлов
Опишем функциональное назначение узлов на примере токарного многоцелевого станка модели GMX
400.
Станина.
Несет на себе основные подвижные и неподвижные узлы станка. Форма
поперечного сечения горизонтальной станины определяется требованиями жесткости,
расположением направляющих, условиями удаления стружки и охлаждающей жидкости,
размещением в ней различных механизмов, агрегатов и резервуаров. Увеличение
жесткости станины добиваются с помощью поперечных и продольных ребер. В связи с
тем, что момент сил, действующих на станину у основания, больше, чем момент
сил, действующих сверху, станину выполняют расширяющейся книзу.
Инструментальный магазин(цепной).
С целью обеспечения полной обработки сложных корпусных деталей, включая
точную финишную обработку за одну установку, станок оснащается «накопителем»
инструментов, т.е. инструментальным магазином. Смена инструмента осуществляется
автооператором с двумя захватами в течение 5 секунд.
Рисунок 10 - Цепной инструментальный магазин многоцелевого
станка модели GMX 400
Двухзахватный автооператор сложнее однозахватнего, но обеспечивают
значительно меньшую длительность цикла смены инструмента. Применение
инструментального магазина гарантирует малое вспомогательное время и
максимальную производительность.
Рисунок 11 - Автооператор многоцелевого станка модели GMX 400
Салазки.
Предназначены для перемещения инструмента, заготовки или других базовых
деталей станка. Салазки имеют две системы направляющих. Конструктивные формы
салазок определяются формой и расположением направляющих, конструкцией
регулирующих элементов и механизма привода, требованиями к размерам по высоте.
Плоские направляющие скольжения покрыты пленкой из материала с малым
коэффициентом трения, обладающего способностью к гашению колебаний,
обеспечивающего минимальный момент холостого хода и движение на малых скоростях
без скачков. При этом обеспечивается повышение плавности перемещений стола и
салазок, увеличивается точность позиционирования и снижается необходимая
мощность привода подач.
Пульт управления.
Рисунок 12 - Пульт управления многокоординатного обрабатывающего центра
модели DMU 50
Предназначен для управления станком: ввода или изменения исходных
параметров, задания определенных режимов обработки, а также контроля за
процессами обработки.
3. Конструктивные схемы привода полярной. Координаты токарных
многоцелевых станков
Одной из основных задач при создании
токарных многоцелевых станков является обеспечение двух режимов обработки:
обычного точения неподвижным инструментом
(в этом случае шпиндель приводится во вращение от электродвигателя главного
привода);
периферийной обработки вращающимся
инструментом (вне-центровых отверстий, шпоночных пазов, сложных поверхностей и
пр.).
Во втором случае шпиндельные узлы вместе с
соответствующим приводом образуют механизм полярной (круговой) координаты,
которая в зависимости от условий обработки может иметь:
непрерывное управление с дискретностью
угловых перемещений шпинделя порядка 0,001° - при контурном фрезеровании
поверхностей типа коноидов, кулачков и других фасонных элементов;
позиционное управление с дискретностью
1-2° - при сверлении, нарезании резьб, зенкеровании и развертывании
внецентровых отверстий, цековке и др.
Расчеты показывают, что при осуществлении
фрезерных переходов на детали диаметром 200 мм частота вращения шпинделя должна
составлять 0,20-0,25 об/мин при крутящем моменте 200 Нм (N= 1,5 кВт). Привод
полярной координаты при окружной скорости позиционирования 25 м/мин детали
диаметром 400 мм должен обеспечивать частоту вращения шпинделя 20 об/мин.
Являясь в данном случае механизмом привода
подачи станка с ЧПУ, узел полярной координаты должен обеспечивать: высокую
точность и отсутствие люфтов; высокую осевую, изгибную и крутильную жесткость;
высокую надежность работы (при смене режимов обработки); высокий КПД, малые
габариты; блочное исполнение.
Указанные требования обусловливают высокую
точность изготовления элементов привода круговой координаты. Известные решения
конструктивных схем механизма привода, имеющие те или иные недостатки, во
многих случаях позволяют получать вполне работоспособные конструкции.
Блочное выполнение привода полярной
координаты при минимальных его габаритах позволяет использовать базовый узел
шпиндельной бабки в различных исполнениях станка - обычном с ЧПУ, многоцелевом
или гибком производственном модуле.
Высокое качество привода полярной
координаты может быть достигнуто, в частности, за счет: использования коротких
кинематических цепей повышенной точности и жесткости; применения передач с большим
передаточным числом и высоким КПД (волновые передачи); применения в
кинематической связи привода полярной координаты со шпинделем беззазорных пар;
установки точного роторного датчика на выходном звене привода.
Фиксирование механизма привода полярной координаты
в положениях «сцеплено» и «расцеплено», соответствующих режимам периферийной
(сверление, фрезерование и др.) и токарной обработки, должно осуществляться
соответствующими устройствами и контролироваться конечными выключателями,
связанными с системой управления.
Механизм перемещения привода полярной
координаты должен автоматически производить надежное сцепление кинематической
пары, обеспечивающей связь привода полярной координаты со шпинделем, исключая с
помощью блокировок возможность одновременного включения привода быстрого
вращения и привода полярной координаты шпинделя.
Известны следующие варианты исполнения
привода полярной координаты шпинделей:
однодвигательное - для станков малых и
средних типоразмеров, в этом случае инерционные нагрузки ротора (двигателя)
оказывают малое влияние на точность позиционирования шпинделя;
двухдвигательное - для крупных станков,
более мощный двигатель используется при точении, а меньший - при периферийной
обработке. Включение-отключение привода полярной координаты может
осуществляться посредством электромагнитных или зубчатых муфт, работающих по
командам ЧПУ и сцеплением - расцеплением кинематических пар, обеспечивающих
связь привода полярной координаты со шпинделем станка.
Первый вариант исполнения не обеспечивает
высокой надежности работы привода, а при втором варианте имеет место снижение
жесткости привода, обусловленное наличием большого количества подвижных
элементов и стыков. На рисунках 12-20 представлены кинематические схемы привода
полярной координаты шпинделя токарных многоцелевых станков. Приводы, схемы
которых изображены на рисунках 13-20, являются непрерывными. На рисунке 12
показана схема однодвигательного привода шпинделя, обеспечивающего режимы
точения и внецентрового сверления и фрезерования. При втором режиме шпиндель
индексируется с дискретностью 1-2,5°, точность позиционирования ±0,01°,
повторяемость ±0,005°. Фиксация шпинделя 1 в заданном положении осуществляется
посредством зубчатого колеса 2 и сектора 3, перемещаемого штоком гидропривода
4. Шпиндельная бабка снабжена тормозным устройством 7. На рисунке 13 дана схема
однодвигательного привода главного движения, обеспечивающего в режиме
периферийной обработки в сочетании с перемещениями по линейным координатам X и Z формирование сложных
поверхностей. Дискретность углового перемещения шпинделя по координате С
составляет 0,001°. Положение шпинделя контролируется роторным датчиком 5.
Рисунок 12 - Однодвигательный
позиционный привод:
1 - шпиндель; 2 - зубчатое колесо (z = = 144); 3 -
фиксирующий зубчатый сектор; 4 - гидропривод; 5 - приводной электродвигатель; 6
- ременная передача
Рисунок 13 - Однодвигательный
регулируемый привод:
- шпиндель; 2 - зубчатая передача; 3 -
ременная передача; 4 - приводной электродвигатель; 5 - роторный датчик
(преобразователь)
Рисунок 14 - Двухдвигательный привод
1 - шпиндель; 2 - зубчатое колесо; 3 -
подвижное колесо; 4-5 - зубчатые колеса; 6 - тормоз; 7 - роторный датчик
(преобразователь); 8 - приводной электродвигатель скоростного вращения; 9 -
ременная передача; 10 - регулируемый электродвигатель привода полярной
координаты; 11 - роторный преобразователь
Рисунок 15 - Двухдвигательный привод:
1 - шпиндель; 2 - электродвигатель
скоростного вращения; 3 - ременная передача; 4 - регулируемый электродвигатель
привода полярной координаты; 5 - редуктор; 6 - червячная передача; 7 -
электромагнитная муфта; 8 и 9 - роторные преобразователи
Рисунок 16 - Двухдвигательный привод:
1 - шпиндель; 2 - регулируемый электродвигатель привода
полярной координаты; 3 - поворотный рычаг; 4 - гидроцилиндр; 5-6 - зубчатые
колеса; 7 и 10 - роторные преобразователи; 8 - двигатель скоростного вращения;
9 - ременная передача
Рисунок 17 - Двухдвигательный привод
1 - шпиндель; 2 - подвеска; 3 -
шпиндельная бабка; 4 - корпус привода полярной координаты; 5 - гидропривод; 6 и
10 - электродвигатели скоростного вращения и привода полярной координаты
шпинделя; 7 и 11 - роторные преобразователи; 8 - размыкаемая червячная пара; 9
- ременная передача
Рисунок 18 - Двухдвигательный привод:
1 - шпиндель; 2 и 9 - электродвигатели
привода полярной координаты и скоростного вращения; 3 - промежуточный редуктор;
4 - червяк; 5 - корпус привода полярной координаты; 6 - гидропривод; 7 -
червячное колесо; 8 и 10 - роторные преобразователи
Рисунок 19 - Двухдвигательный привод:
1 - шпиндель; 2 - привод полярной
координаты; 3 - червяк; 4 - червячное колесо; 5 - ось поворота привода; 6 -
механизм поворота привода полярной координаты; 7 и 10 - электродвигатели
скоростного вращения и привода полярной координаты; 8 и 11 - роторные
преобразователи (датчики); 9 и 12 - ременные передачи
Рисунок 20 - Двухдвигательный привод:
1 - шпиндель; 2 - корпус привода полярной
координаты; 3 - кронштейн; 4 - шпиндельная бабка; 5 - вал; 6 и 8 - зубчатые
колеса; 7 - гидроцилиндр; 9 - червячная пара; 10 и 11 - электродвигатели
привода полярной координаты и скоростного вращения; 12 и 13 - ременные
передачи; 14 - перебор; 15 и 16 - роторные преобразователи
Кинематические схемы двухдвигательных
приводов даны на рисунках 14-20. В варианте, приведенном на рисунке 14,
скоростное вращение шпинделя 1 при точении осуществляется от привода, основой
которого является электродвигатель 8, от которого вращение на шпиндель 1
передается посредством ременной передачи 9. Шпиндель оснащен тормозным
устройством 6 и роторным преобразователем 7. Перемещение шпинделя на меньших
скоростях при периферийной обработке осуществляется с помощью привода полярной
координаты, содержащего регулируемый электродвигатель 10 с роторным
преобразователем 11 и зубчатые колеса 2-3 и 4-5. Отключение привода полярной
координаты осуществляется посредством шестерни 3, выводимой из зацепления с
зубчатым колесом 2 соответствующим механизмом.
Наличие роторных датчиков перемещения 7 и
11 соответственно в приводах скоростной цепи и полярной координаты позволяет
контролировать угловое положение колес 2 и 3 и исключить возможность
столкновения вершин зубьев указанных элементов.
Оснащение шпинделя 1 тормозным устройством
6 обеспечивает надежную фиксацию шпинделя и детали при обработке в режиме
позиционирования, выборку люфтов в цепи привода полярной координаты (при
включении тормозного устройства 6 в режим «подтормаживания»).
В приводе, схема которого изображена на рисунке 13, режим
точения осуществляется при передаче вращения шпинделю 1 от двигателя 2 через
ременную передачу 3. Программируемое угловое
перемещение шпинделя в режиме позиционирования и контурной обработки от
электродвигателя 4 передается через промежуточный редуктор 5 и червячную
передачу 6, колесо которой установлено на опорах качения на шпинделе 1. Связь
червячного колеса со шпинделем осуществляется через электромагнитную муфту 7
при отключенном скоростном приводе. Повышение надежности работы привода
главного движения при этом может быть достигнуто путем использования различных
конструктивных схем связи привода полярной координаты, снабженного элементами
передачи (зубчатое колесо, червяк), взаимодействующими в требуемый момент с
элементом передачи (зубчатое колесо, червячное колесо), установленным на шпинделе
станка. Перемещения привода полярной координаты в крайние, фиксированные
положения «сцеплено» и «расцеплено» осуществляются автономным приводом,
управляемым устройствами ЧПУ.
На рисунке 16 приведена схема перемещения
привода полярной
координаты шпинделя 1 станка. Привод размещен на поворотном рычаге 3,
перемещение которого осуществляется от гидроцилиндра 4. В положении «сцеплено»
движение от привода на шпиндель 1 передается через зубчатое колесо 5,
смонтированное на приводе, и колесо 6, закрепленное на шпинделе 1. Для
исключения попадания зуб в зуб колес 5 и 6 используются датчик резьбонарезания
7 шпинделя 1 и роторный датчик привода 10. В край
них положениях рычаг 3 взаимодействует с упорами и контролируется конечными
выключателями. В приводе используется волновой редуктор с передаточным
отношением i=
80. '
На рисунке 15 показана схема полярной
координаты шпинделя, выполненная также с угловым перемещением привода в
положения «сцеплено» и «расцеплено». Сам привод 1 размещен в подвеске 2,
закрепленной на корпусе шпиндельной бабки 3 станка. Перемещение корпуса 4
привода осуществляется с помощью гидропривода 5. В крайних положениях привода,
контролируемых конечными выключателями, корпус 4 взаимодействует с упорами,
один из которых в положении «сцеплено» выполнен регулируемым.
В схеме привода полярной координаты,
представленной на рисунке 16, автономный узел 2 кинематически связан со
шпинделем 1 станка посредством расцепляемой пары червяк-червячное колесо 3-4.
Угловое перемещение узла 2 относительно оси 5 осуществляется в автоматическом
режиме механизмом 6, выполненным в виде унифицированного узла, который
обеспечивает ввод в зацепление червяка 3, кинематически связанного с приводом
узла 2.
Включение привода полярной координаты
шпинделя блокируется конечными выключателями при «утыкании» вершин зубьев
червяка и червячного колеса.
Режим сцепления осуществляется при
медленном вращении привода, 2, чтр позволяет гарантированно обеспечить надежное
сцепление червячной пары 3-4. Положение «сцеплено» фиксируется датчиком углового
положения шпинделя. По завершению операций периферийной обработки расцепление
червячной пары 3-4 производится реверсированием механизма 6, после чего
поворотный корпус с узлом 2 отводится в положение «расцеплено» с помощью
соответствующего устройства.
Достоинством данного варианта исполнения
привода полярной координаты являются высокая жесткость, точность и надежность
работы.
Привод полярной координаты шпинделя содержит электродвигатель
2 постоянного тока или переменного тока с частотным регулированием,
промежуточный редуктор 3 и червяк 4, которые размещены в корпусе 5, имеющем
возможность перемещения в направлении, перпендикулярном оси шпинделя станка от
гидропривода 6. При периферийной обработке червяк 4 сцеплен с червячным колесом
7, закрепленным на шпинделе 1 станка.
Перед точением привод полярной координаты
отключается за счет осевого перемещения корпуса 5 гидроприводом 6, при этом
червяк 4 выводится из зацепления с червячным колесом 7.
Недостаток рассмотренной схемы -
увеличенные массогабаритные характеристики узла.
Схема привода полярной координаты,
изображенная на рисунке 18, выполнена в виде автономного узла, содержащего
червячный редуктор, размещенный в корпусе 2, вертикальные направляющие которого
установлены на кронштейне 3, закрепленном на шпиндельной бабке 4 станка. На
валу 5 червячного колеса насажено зубчатое колесо 6, которое при перемещении
корпуса 2 посредством гидроцилиндра 7 по направляющим в вертикальной плоскости
вводится в зацепление с зубчатым колесом 8, закрепленным на шпинделе 1 станка.
Движение при внецентровой обработке от
электродвигателя 10 посредством червячной пары 9 и зубчатой пары 6-8 передается
шпинделю 1 . Крайние положения корпуса 2 контролируются конечными
выключателями.
Достоинством данной схемы является
возможность регулировки величины люфта в конечном звене передачи и червячной
паре, а также беззазорное соединение вала ротора электродвигателя с входным
валом редуктора и червячного колеса с выходным валом.
Скоростное вращение шпинделя
осуществляется от регулируемого электродвигателя 11 через две поликлиновые
ременные передачи 12, 13 и перебор 14.
Контроль угловых положений шпинделя 1 и
шестерни 6 с помощью преобразователей 15 и 16 исключает возможность «утыкания»
вершин зубьев колес 6 и 8.
При выборе конструктивного решения привода
полярной координаты шпинделя следует принимать во внимание следующие факторы:
типоразмер станка; сложность, жесткость и точность работы привода; надежность
работы; габариты и металлоемкость привода..
Необходимо оснащать привод полярной
координаты шпинделя тормозным устройством и размещать роторный датчик привода
на ближайшем к шпинделю кинематическом звене, что позволит исключить влияние на
точность обработки погрешности промежуточных звеньев, уменьшить люфт механизма
и повысить его жесткость.
4. Привод вращения инструмента токарных
многоцелевых станков
К инструментальной системе токарных
многоцелевых станков предъявляются следующие основные требования:
высокая точность фиксации инструмента
(0,5-1 мкм);
высокая жесткость фиксации корпуса
инструментодержателя;
минимальное время смены инструмента от «реза» до «реза» (в
пределах 0,5-2,5 с);
наличие вращающегося инструмента,
обеспечивающего обработку элементов детали в радиальном и осевом направлениях,
а также под произвольным углом к оси вращения на оптимальных режимах резания;
возможность обработки детали после ее
отрезки или кантования;
возможность «подпитки» (ручной или
автоматической) основного накопителя инструментом из дополнительного накопителя
для обеспечения работы станка без вмешательства оператора в течение 12-16 ч.
Конструктивно инструментальная система
токарных многоцелевых станков реализуется в виде:
инструментальных магазинов, связанных
посредством манипуляторов или роботов с инструментальными головками,
закрепленными на поперечных салазках станка стационарно или с возможностью
программируемого поворота, обеспечивающего последовательный ввод в обработку
радиального или осевого неподвижного и вращающегося инструмента, а также
инструмента для обработки детали под углом;
револьверных многопозиционных головок,
оснащенных неподвижными и вращающимися (радиальными и осевыми) инструментами, а
также вращающимся инструментом для обработки деталей под углом.
Системы с инструментальными магазинами по
сравнению с многопозиционными головками обладают следующими преимуществами:
большей емкостью накопителя; большей универсальностью (что позволяет ограничить
номенклатуру применяемой оснастки); большей жесткостью и точностью фиксации;
габариты инструментальных головок систем с магазинами значительно меньше
габаритов револьверных многопозиционных головок. Относительным недостатком
инструментальных систем с магазинами следует считать меньшую надежность,
обусловленную их большей сложностью.
Анализ конструкции инструментальных систем
с револьверными многопозиционными головками позволяет сделать следующие выводы:
увеличение емкости головки ограничивает технологические
возможности станка, что обусловлено уменьшением диаметров зажимного патрона и
обрабатываемой детали, снижением режимов резания;
наличие в головке нескольких вращающихся
осевых и радиальных инструментов с большим вылетом затрудняет программирование,
исключающее возможность столкновения инструмента с патроном или обрабатываемой
деталью;
наличие в головке нескольких вращающихся
инструментов с большим вылетом вызывает скапливание стружки;
необходимость размещения в одном блоке
инструментов с оправками, фиксирующих элементов, приводов вращения инструмента
и поворота приводит к значительному увеличению габаритов головки и станка;
уменьшение габаритов головки неизбежно
связано с уменьшением емкости накопителя, изменением типоразмера применяемого
инструмента, ограничением технологических возможностей станка.
Инструментальные головки систем с
магазином имеют следующие исполнения: в зависимости от количества одновременно
установленных инструментов - одно- и двухинструментальные; в зависимости от
числа управляемых координат - стационарного типа, с одной и двумя поворотными
координатами. Конструктивные исполнения головок, разработанные за последнее
время, обеспечивают существенное расширение технологических возможностей
станка.
Рисунок 21 - Кинематическая схема
одноинструментальной головки:
зажимной сухарь блока; 2 - зубчатая муфта;
3 - приводная шестерня инструментального шпинделя; 4 - инструмент; 5 -
инструментальный блок; 6 - поворотный корпус; 7 и 8 - плоскозубчатые колеса; 9
и 10 - косозубые колеса; 11- электродвигатель привода вращения инструмента; 12
- зубчатое колесо; 13 - шток-рейка; 14 - гидроцилиндр поворота головки; 15 -
неподвижный корпус; 16 - гидроцилиндр зажима зажимного блока; 17 - гидропривод
закрепления инструментального блока; 18 и 19 - конические зубчатые колеса
На рисунке 21 показана
одноинструментальная головка, входящая в инструментальную систему
патронно-центрового.токарного многоцелевого станка. Головка, имеющая ось
вращения, расположенную под углом 45° к оси Z станка, фиксируется в
двух положениях, что обеспечивает возможность установки инструмента в осевом и
радиальном направлениях. Единая система базирования для неподвижного и
вращающегося инструмента обеспечивает унификацию применяемой оснастки.
Привод вращающегося инструмента содержит
регулируемый электродвигатель 11 с номинальной мощностью 4,5 кВт и максимальной
частотой вращения 4500 об/мин, пару косозубых 9, 10 и пару конических зубчатых
колес 18, 19, а также муфту 2 с внутренними зубьями, сцепленную с шестерней 3
инструментального шпинделя 4.
Изменение положения оси гнезда корпуса 6
производится при размыкании плоскозубчатых колес 7 и 8 штоком 13 гидроцилиндра,
сцепленным с зубчатым колесом 12 и контролируемым конечными выключателями.
Дисковый инструментальный магазин, ось которого параллельна
оси шпинделя, установлен сзади станины станка с возможностью перемещения по
круглой направляющей, закрепленной на кронштейнах станины за кареткой, с
которой он связан захватом.
Поворот диска инструментального магазина
осуществляется программируемым электроприводом, поиск нужного инструмента -
автоматический по программе.
Инструментальные блоки для всех видов
работ снабжены базирующим цилиндрическим хвостовиком диаметром 50 мм с рейкой,
выполненным по ОСТ 2 416-2-78.
В корпусах инструментальных блоков для
вращающихся инструментов на подшипниках установлены шпиндели для выполнения
«нецентровых» работ, на хвостовиках которых смонтированы муфты-шестерни для
сцепления с приводом.
Передача инструментов из магазина в
головку и обратно производится манипулятором (имеющим прямоугольный цикл
перемещений) при параллельном расположении оси шпинделя и гнезда головки, когда
суппорт отведен в заднее положение. Гидроцилиндр продольного перемещения
манипулятора размещен на каретке станка.
Недостаток данной инструментальной системы
- размещение инструментального шпинделя внутри цилиндрического хвостовика, что
ограничивает величину передаваемого на инструмент крутящего момента.
Разработана конструкция головки
патронно-центрового станка с двумя гнездами - для неподвижного и вращающегося
инструмента. Базовые поверхности гнезд неподвижного и вращающегося инструмента
отличаются по форме, что не позволяет унифицировать вспомогательный инструмент.
Достоинствами инструментальной системы
данного исполнения являются: большая жесткость и точность установки блоков
вращающихся инструментов; меньшие потери времени на смену инструментов
(загрузка инструментов совмещена с процессом обработки) .
На рисунке 22 приведена схема
инструментальной головки, имеющей две полярные координаты и оснащенной двумя
гнездами для неподвижного и вращающегося инструмента. Полярная координата А с
осью вращения диска 3, перпендикулярной плоскости поперечных направляющих
салазок, обеспечивает обработку отверстий и пазов, расположенных под углом к
оси вращения, кратным 2,5°. Другая полярная координата головки Б, ось поворота
корпуса 4 которой параллельна плоскости направляющих поперечных салазок,
обеспечивает, возможность обработки на детали шпоночных пазов и подобных
элементов «вразгонку» немерным инструментом.
Помимо расширенных технологических
возможностей, инструментальная головка подобного исполнения обладает высокой
жесткостью и точностью, исключает возможность столкновения с узлами станка и
обрабатываемой деталью.
Рисунок 22 - Схема инструментальной головки с двумя
круговыми координатами:
- суппорт; 2 - поперечные салазки; 3 - поворотный
инструментальный блок; 4 - поворотный корпус головки; 5 и 6 - гнезда дли
вращающегося и неподвижного инструментов
Накопителем инструментальной системы станка служит кассета
с инструментами, установленная на тележке, размещенной у правого торца станины
станка с возможностью перемещения с шагом, равным расстоянию между гнездами
кассеты. Емкость кассеты - 48 инструментов. При необходимости кассета с помощью
робокара автоматически заменяется на новую с подготовленным комплектом
инструментов.
Базирующие поверхности вращающихся
инструментов выполнены по разработкам фирмы Hertel (ФРГ) или с крутым конусом.
Мощность электродвигателей привода
вращения инструмента в зависимости от типоразмера станка составляет 6,9, 8,7 и
12,6 кВт. | Диапазон частот вращения инструментальных шпинделей головок -
30...2200 (30...3000) об/мин.
В инструментальных системах рассмотренных
ранее станков серии WNC 500C и WNC 700C фирмы Voest-Alpine (Австрия) одновременно могут быть использованы револьверные
многопозиционные головки и дисковый магазинный накопитель емкостью 15
инструментов, из которого требуемый инструмент с помощью манипулятора
передается в гнездо шпинделя головки, установленной на поперечных салазках
(компоновка станков описана выше).
Привод вращения инструмента головки 4
(рисунок 23) содержит
электродвигатель 11, связанный клиноременной 9, 10 и конической зубчатой
передачами с инструментальным шпинделем 2. Угловое положение последнего
контролируется роторным преобразователем 7.
Линейное перемещение головки в
направлении, перпендикулярном плоскости направляющих салазок, осуществляется
приводом, содержащим регулируемый электродвигатель 13, связанный клиноременной
передачей 12 с винтом шарико-винтовой пары 14. Дискретность перемещения головки
по оси Y-0,001
мм.
Угловое перемещение инструментальной
головки 4 осуществляется электродвигателем 11 с дискретностью 0,01° при
зафиксированном посредством пальца 20 шпинделе 2. При обкатке ведущей
конической шестерни сцепленного с ней ответного зубчатого колеса, жестко
связанного со шпинделем 2, происходит поворот головки, угловое положение
которой при этом контролируется роторным преобразователем 15, сцепленным с
корпусом головки зубчатой парой 10. При обработке головка 4 подтормаживается
гидротормозом 5. Угловое положение головки через 90° фиксируется пальцем 17,
перемещаемым штоком гидроцилиндра 75. Мощность электродвигателя 11 - 5,4 кВт.
Диапазон частот вращения инструментальных шпинделей - 12...3000 мин. Линейное
перемещение головки по оси У - 160 мм. Приводы вращения инструментального
шпинделя и линейного перемещения головки по координате У снабжены устройствами
натяжения ремней.
Две последние рассмотренные схемы
инструментальных систем свидетельствуют об устойчивой тенденции расширения
технологических возможностей оборудования применительно к условиям серийного
производства.
Рисунок 23 - Кинематическая схема
инструментальной головки с двумя (линейной и круговой) координатами:
1 - гидроцилиндр фиксации шпинделя
головки; 2 -инструментальный шпиндель; 3 - коническая зубчатая передача; 4
-поворотная головка; 5 - гидротормоз; 6 и 16 - зубчатые передачи; 7 и 15 -
роторные преобразователи; 8 - электромагнитные муфты; 9 и 10 - клиноременные
передачи; 11-электродвигатель привода вращения инструмента и углового
перемещения головки; 12 - ременная передача; 13-электродвигатель привода
линейного перемещения головки; 14 - шариковая пара винт-гайка линейного
перемещения головки; 17 - палец-фиксатор головки; 18 - гидропривод фиксации
головки; 19 - гидроцилиндр разжима шпинделя; 20 - палец-фиксатор шпинделя
Ниже приведены основные параметры инструментальных систем
токарных многоцелевых станков с магазинами.
Следует отметить, что наметившаяся одно
время тенденция отказа в конструкциях токарных станков с ЧПУ от применения
инструментальных систем с магазинами не получила своего развития при создании
токарных многоцелевых станков, поскольку концепция таких станков именно с
магазинными питателями и различными инструментальными головками обеспечивает
большую жесткость конструкции и точность обработки, а также гибкость и
мобильность оборудования.
Конструктивные схемы инструментальных
систем с револьверными многопозиционными головками различаются:
количеством установленных на суппортах
головок;
формой накопителя головки и расположением
оси вращения накопителя относительно базовых поверхностей станка;
количеством накопителей в головке;
расположением инструментальных блоков на
поверхностях накопителя;
количеством вращающихся инструментов в
одной головке;
наличием или отсутствием индивидуального
двигателя в приводе вращения инструментов, а также типом установленного двигателя;
местом связи инструментальных шпинделей с
приводом (в поворотном накопителе-диске или в корпусе головки);
компоновкой, формой присоединительных
элементов и базирующими поверхностями инструментальных блоков с вращающимся
инструментом;
степенью автоматизации смены и установки
инструментальных блоков с неподвижными и вращающимися инструментами.
Важнейшим конструктивным элементом
револьверных многопозиционных головок является узел фиксации и базирования,
реализуемый обычно на плоских зубчатых парах.
В последнее время наиболее широко
применяются головки без осевого перемещения диска накопителя, требующего вывода
из зацепления неподвижного и подвижного плоских зубчатых колес. В этом случае
перед поворотом диска, жестко связанного с плоским зубчатым колесом, в осевом
направлении перемещается ответное базирующее зубчатое колесо, обеспечивая тем
самым возможность свободного поворота диска в заданную позицию по кратчайшему
пути, при этом угловой поворот диска контролируется роторным датчиком
(преобразователем) перемещения.
В последнее время при разработках револьверных головок
прослеживается тенденция к отказу от традиционных схем базирования и фиксации с
использованием плоских зубчатых шестерен, отличающихся высокой сложностью
технологических процессов изготовления. Компоновка и конструктивное исполнение
головок все более приближается к прецизионным шпиндельным узлам.
На рисунке 24 показана схема револьверной
многопозиционной головки, в приводе которой установлен регулируемый
электродвигатель 2, связанный с датчиком 1. Ротор электродвигателя 2 жестко
соединен с генератором волновой зубчатой передачи 3, гибкое колесо которой
закреплено на валу 13 диска 6, установленном на подшипниках 5 и 7 в корпусе 4
головки. Закрепленный с помощью разжимных пружинных колец на валу 13 диск 6
выполнен с пазами, число которых равно количеству
Рисунок 24 - Схема револьверной головки
с периферийной фиксацией:
1 - роторный датчик; 2 - регулируемый
электродвигатель; 3 - волновая зубчатая передача с остановленным жестким
колесом; 4 - корпус головки; 5 и 7 - опорные подшипники; 6 - диск; 8 - фланец;
9 - тормозные элементы; 10 - диск; 11 - гидропривод фиксации головки; 12 -
фиксирующий палец; 13 - вал
инструментальных гнезд диска 10 и с
которыми взаимодействует фиксирующий палец 12, оснащенный гидроприводом 11. К
корпусу 8 крепится фланец 8, в котором с возможностью периодического
взаимодействия с диском 10 размещены тормозные элементы 9; перемещение их
осуществляется при подаче давления.
Поворот диска 10 с инструментами из
позиции в позицию производится при отведенном фиксирующем пальце 12 приводом,
включающим электродвигатель 2 и волновую передачу 3. В заданном положении диск
10 фиксируется пальцем 12 и тормозится элементами 9.
Конструкция головки обеспечивает
реверсирование и установку заданного инструмента при угловом перемещении диска
10.
Частота вращения диска 5-20 мин-1.
Передаточное отношение волновой зубчатой передачи - 20.
К достоинствам рассмотренной схемы головки
следует отнести простоту конструкции, обусловленную использованием
унифицированных элементов, высокую жесткость и точность.
Следует ожидать в перспективе отказ от механических фиксирующих
устройств и переход на следящий привод, обеспечивающий получение
неограниченного количества позиций, высокую точность и жесткость.
Обычно револьверные головки токарных
многоцелевых станков имеют индивидуальный привод вращающихся инструментов,
оснащенный автономным электродвигателем; значительно реже применяются приводы
совмещенного типа, когда движение инструменту передается с главного привода
станка (модель 11Б40ПФ4 Новосибирского станкозавода, модель TNC 30D и др. фирмы Traub). Последняя схема позволяет
осуществлять резьбофрезерование и обработку многогранников.
При размещении вращающихся инструментов на
головках оси инструментальных шпинделей, установленных в головках или блоках, в
зависимости от выполняемых операций имеют следующие положения, по отношению к
оси вращения шпинделя и другим базовым поверхностям станка: осевое; радиальное
(перпендикулярное к оси шпинделя и параллельное плоскости направляющих
поперечных салазок); перпендикулярное к оси шпинделя и к плоскости направляющих
поперечных салазок; под произвольным углом к оси шпинделя.
В дисковых накопителях револьверных
многопозиционных головок гнезда для неподвижного и вращающегося инструмента
располагаются на торце (зеркале) или на периферии диска. Последнее решение
обычно применяется в головках, установленных в патронно-центровых станках. Б
некоторых случаях на периферии головок применяется двухрядное расположение
гнезд - один ряд для неподвижных инструментов, другой - для вращающихся.
Анализ показывает, что для 95% деталей,
обрабатываемых на станках, вполне достаточно 5-6 вращающихся инструментов,
используемых в одной наладке. Наличие в накопителе 8-10 и более гнезд для
установки вращающихся инструментов является во многих случаях избыточным и
создает «страховочный запас» технологических возможностей, часто не реализуемых
в работе и удорожающих конструкцию.
Ниже приведены данные об общем числе
установленных в револьверных головках инструментов и количестве вращающихся
инструментов для многоцелевых станков различных изготовителей.
Привод инструментальных шпинделей по месту
размещения ведущих звеньев (по отношению к шпинделю) может реализоваться по
двум схемам: с размещением ведущих звеньев: в поворотном диске (накопителе)
револьверной головки (с внутренним размещением привода); с внешним приводом,
размещенным в неподвижном корпусе револьверной головки.
В первом случае (рисунок 25, а) движение от электродвигателя
посредством ременной зубчатой передачи передается на центральный вал, от
которого через конические зубчатые передачи - на инструментальные шпиндели или
промежуточные валы с муфтами, с которыми сцепляются приводные муфты
инструментальных блоков. Максимальное число вращающихся инструментов а
головке-4 .
Недостаток данной схемы привода -
повышенный уровень шума, вращение инструментальных шпинделей в незагруженных
позициях. Такими же недостатками обладает и схема, в которой движение от
электродвигателя передается на инструментальные шпиндели посредством ременной
зубчатой передачи, ремень которой охватывает одновременно несколько ведомых
шкивов", соединенных с инструментальными шпинделями накопителя (рисунок
25, б).
В схеме привода, размещенного в
неподвижном корпусе блока (рисунок 25, в), шпиндель инструментального блока,
находящегося в позиции обработки, сцепляется с ведущим валом привода посредством
включаемой или подпружиненной муфты. Такое выполнение привода вращающегося
инструмента обеспечивает значительное упрощение конструкции, уменьшение уровня
шума, а также повышение точности и жесткости механизма при одновременном
увеличении количества устанавливаемых в головке вращающихся инструментов (во
всех ее позициях), возможность передачи на инструментальный шпиндель большого
крутящего момента.
Рисунок 25 - Кинематические схемы привода вращения
инструмента револьверных головок:
а - центральный привод: б и в - прямой и угловой
инструментальные блоки; 2 - диск головки; 3 и 4 - конические зубчатые колеса; 5
- промежуточный вал с полумуфтами,; 7 - электродвигатель привода инструмента; 8
и 10 - шкивы; 9 - зубчатый ремень; 11 - корпус головки; 12 - центральный вал; 6
- боковой привод (с одновременным охватом нескольких ведомых шкивов): 1 и 6 --
шкивы; 2 и 4 - угловой и прямой инструментальные блоки; 3 - диск головки; 5 -
зубчатый ремень; 7 - электродвигатель привода инструмента; 8 - корпус головки;
в - привод, размещенный в корпусе головки: 1 - промежуточный вал с полумуфтой;
2 и 4 - прямой и угловой инструментальные блоки; 3 - диск головки; 5 - зубчатые
ремни; 6, 7, 10 - шкивы; 8 - электродвигатель приводи инструмента; 9 - корпус
головки
Для вращения инструментов револьверных многопозиционных
головок используется, как правило, регулируемый привод на базе
электродвигателей постоянного тока или асинхронных электродвигателей с
частотным регулированием. В ряде случаев используются электродвигатели
специального исполнения, позволяющие повысить технологические возможности
оборудования.
На рисунке 26 приведена характеристика
привода с асинхронным регулируемым электродвигателем серии 1ГТ 5102-ОАСО с
встроенным редуктором, устанавливаемым в револьверных головках типа 05.472
упомянутого выше изготовителя.
Ниже даны основные технические параметры револьверных головок
зарубежного производства, схемы исполнения' которых рассмотрены выше (параметры
головок других фирм аналогичны упомянутым [10];), а также технические данные
револьверных многопозиционных головок отечественного производства.
Сравнительный анализ показывает, что эти параметры достаточно близки.
Револьверные головки отечественных станкозаводов уступают пока зарубежным аналогам
главным образом по времени поворота из позиции в позицию, верхнему пределу
частот вращения инструментальных шпинделей, надежности их работы.
n, мин
Рисунок 26 - Характеристика привода
вращающегося инструмента
5. Инструментальная оснастка токарных многоцелевых станков
К инструментальной оснастке токарных
многоцелевых станков предъявляются следующие основные требования:
унификация основных элементов блоков и
других деталей для неподвижного и вращающегося инструментов;
высокая жесткость и точность
конструктивных элементов инструментальных блоков и других деталей;
высокая стабильность и надежность фиксации
блоков и инструмента;
передача высокой скорости и крутящего
момента на вращающийся инструмент;
возможность регулирования частоты вращения
инструментального шпинделя блока;
возможность смены инструмента в блоке в
ручном и автоматическом режимах;
подача СОЖ к инструменту и обдув сжатым
воздухом (обмыв СОЖ) посадочных поверхностей при автоматической смене блоков.
За рубежом разработки по созданию
инструментальной оснастки ведутся как станкостроительными
фирмами-разработчиками токарных многоцелевых станков, так и фирмами,
специализирующимися в данной области.
Среди первых следует отметить фирмы Okuma, Ikegai, Tochiba, Mitsubishi (Япония), Gildemeister, Traub, Index (ФРГ), к их числу
относятся также американские, австрийские и французские фирмы.
Среди специализированных фирм следует выделить разработки
фирм Sauter, Krupp-Widia, Hertel (ФРГ), Illinois Tool Works,-General Electric, Kennametal (США), Sandvic (Швеция), Baruf-faldi Frizioni (Италия) и др.
Точность позиционирования инструментальных
блоков составляет ±2...±3 мкм при усилии зажима 1500-2500 кгс.
Конструкция блоков допускает использование
привода с мощностью до 8 кВт при частоте вращения инструмента до 5000- 6000 мин-1
и крутящем моменте до 100-150 Н-м.
Базирование инструментальных блоков
осуществляется по цилиндрическим (ОСТ 2 416-2-78) или коническим хвостовикам
или торцовым зубьям.
При автоматической смене блоков
используются пружинные V или гидравлические устройства зажима, применяется
автоматическая система опознания блоков с использованием электронного
устройства и кода блока. Закрепление блока производится перемещающимся в
поперечном направлении под воздействием пакета тарельчатых пружин или
гидроцилиндра стержня, на торце которого выполнена мелкомодульная зубчатая
нарезка, взаимодействующая с нарезкой блока и обеспечивающая поджим базового
торца блока к корпусу головки и фиксацию цилиндрического хвостовика. При
наличии конического хвостовика закрепление блока осуществляется осевым
перемещением последнего с помощью пакета тарельчатых пружин. Разжим
инструментальных блоков осуществляется с помощью отдельного гидропривода.
Инструментальные блоки станков с револьверными
многопозиционными головками снабжены базирующими элементами, выполненными также
либо в виде цилиндрических хвостовиков с рейкой (по ОСТ 2 416-2-78), либо в
виде центрирующих цилиндрических хвостовиков в сочетании с фланцами,
закрепляемыми на зеркале или периферии диска головки.
Система инструментальной оснастки
создается с учетом технологических возможностей станка и конструктивных
особенностей его узлов. Обычно она включает держатели-блоки вращающегося и
неподвижного инструмента, причем эти блоки должны быть максимально
унифицированы по присоединительным поверхностям, элементам, взаимодействующим с
захватными устройствами робота (манипулятора).
Номенклатура блоков должна обеспечивать
закрепление инструментов и оправок, имеющих различные присоединительные
поверхности (цилиндрические, нормальные и укороченные конусы и т. д.).
Номенклатура инструментальной оснастки
токарных многоцелевых станков включает: прямые и угловые блоки для
сверлильно-фрезерных работ; прямые и угловые блоки для резьбонарезания; прямые
и угловые блоки для дисковых фрез; план-суппортные блоки; многошпиндельные
головки блоки для шлифовальных кругов.,
На рисунке 28 показаны схемы блоков для отдельных видов
инструментов, при этом предусмотрена передача крутящего момента на инструментальный
шпиндель или ведущий вал блока через муфту, размещенную на валу или шпинделе,
установленных в расточке центрирующего элемента. Такое решение может быть
рекомендовано
Рисунок 27 - Инструментальный блок:
1 - цанга; 2 - корпус; 3 -
инструментальный шпиндель; 4 - зажимной палец с «мышиным» зубом; ,5 - зубчатая
муфта; 6 - подшипники опор инструментального шпинделя; 7 - упор
Рисунок 28 - Кинематические схемы
инструментальных прямых и угловых инструментальных блоков
для небольших станков, поскольку в данном случае габариты
центрирующего элемента в значительной мере ограничивают размеры
инструментального шпинделя (рисунок 27). При выполнении блока с внешним
расположением ведущего вала и муфты возможно обеспечить передачу на инструмент
больших крутящих моментов и существенно повысить жесткость и точность
инструментального шпинделя (рисунок 29).
Рисунок 29 - Инструментальные блоки с
внешним расположением ведущего вала и муфты
Недостатками рассмотренных решений
инструментальной системы являются невысокая универсальность, уровень
автоматизации и невозможность «подпитки» в ряде случаев инструментом при работе
в «безлюдном» режиме. Весьма успешной попыткой устранения упомянутых
недостатков является разработка гибкой системы инструментов (FTS) фирмы Hertel (ФРГ), которая включает
следующие основные элементы: сменные головки с неподвижным и вращающимся
инструментом, накопители (магазины) различного исполнения, расположенные вне
рабочей зоны станка манипулятор, обеспечивающий передачу сменных головок к
станку и обратно, инструментальная многопозиционная головка самого станка с
механизмами поворота и приводом вращения инструмента. Торцовое зубчатое
соединение типа «Хирт» обеспечивает высокую точность фиксации сменных
инструментальных головок и восприятия нагрузок при резании .
Базирующие элементы блоков выполнены либо
в виде цилиндрических хвостовиков с рейкой, либо в виде центрирующих
цилиндрических хвостовиков с фланцами. В последнем случае блоки крепятся к
головке винтами. Предусмотрено исполнение сменных головок с наружными
диаметрами зубчатых муфт 40, 63 и 80 мм.
В корпусах блоков имеются каналы для
подвода СОЖ к режущему инструменту, а также жидкости и воздуха для очистки
зубьев муфты.
Посадочные места головок с неподвижным и
вращающимся инструментом унифицированы, что позволяет устанавливать в рабочие
позиции сменные головки с различными инструментами, в зависимости от вида
выполняемой операции.
На станок головки с инструментами
передаются с помощью роботов или манипуляторов из питателя, емкость которого
может составлять от 12 до 240 инструментов. Применяется кодирование гнезд
питателя. Управление системой FTS, осуществляемое на основе программируемого
контроллера, обеспечивает выполнение следующих функций: перемещение
инструментов при их смене; обмен данными с системой управления, включающими
обозначение накопителя, номер инструмента, идентификацию кода инструмента,
кодирование и идентификацию гнезд накопителя, величину коррекции, радиус
закругления пластины, стойкость (число обработанных деталей), режимы обработки.
Инструментальная система типа BTS [12], разработанная
фирмой Sandvic (Швеция), содержит те же основные элементы, которые включены в
систему FTS, и отличается только конструктивным исполнением элементов
базирования и крепления.
6. Выводы и рекомендации
Одним из основных направлений развития
машиностроения является создание гибких производств, способных обеспечивать
изготовление новых изделий в заданные сроки при оптимальных затратах. Такие
производства, наряду с гибкостью и мобильностью, должны обеспечивать полный
цикл обработки деталей на минимальном количестве станков.
Токарные многоцелевые станки в наибольшей
степени отвечают требованиям как гибких производств, так условиям современного
машиностроения в целом. Опыт внедрения и эксплуатации токарных многоцелевых
станков показал, что более высокая по сравнению с обычными станками с ЧПУ
загрузка этого оборудования сопровождается ростом производительности и качества
обработки, уменьшением потребности в площадях, экономией основных фондов.
Внедрение токарных многоцелевых станков позволит в значительной степени решить
задачу уменьшения дифицита станочников.
Разработка токарных многоцелевых станков
должно проводиться на основе тщательного технологического анализа номенклатуры
обрабатываемых деталей, с учетом перспективы изменения параметров точности,
сложности, материалов, а также совершенствования технологических процессов
механической обработки, в т. ч. возможности повышения уровня концентрации
разнородных технологических операций (включая термообработку, сборку и т. д.).
Анализ показывает, что большая часть
токарных многоцелевых станков, предназначенных для обработки
общемашиностроительных деталей, создается на базе токарных станков с ЧПУ путем
оснащения их дополнительным приводом полярной координаты (С) и приводом
вращающегося инструмента, размещенным на инструментальной головке.
Изменение положения детали для полной
обработки осуществляется с помощью кантователей - автономных, размещенных на
станке (на тактовом столе) или встроенных в руку робота, а также револьверной
головки, снабженной захватным вращающимся устройством.
Расширение технологических возможностей
токарных многоцелевых станков, предназначенных для обработки отраслевых деталей
повышенной сложности и точности, обеспечивается посредством компоновочных
решений, предусматривающих оснащение станков дополнительными управляемыми
координатами (линейными и полярными) с возможностью обработки детали под
произвольным углом к оси вращения, нарезания крупных резьб и т. д.
Для унификации узла шпиндельной бабки в различных исполнениях
станка рекомендуется выполнять привод полярной координаты шпинделя в виде
автономного блока, легко стыкуемого с приводом главного движения (скоростного
вращения) шпинделя. Привод полярной координаты должен обеспечивать высокую
жесткость и точность, отсутствие люфтов, высокую надежность и КПД. Выбор схемы
привода полярной координаты должен осуществляться с учетом областей применения
станков и его конструктивных параметров (точности, жесткости, надежности,
габаритов и металлоемкости).
Рекомендуется оснащать шпиндельные узлы
токарных многоцелевых станков тормозными устройствами, работающими в двух
режимах - подтормаживания (для выборки люфта при позиционировании и контурном
фрезеровании) и полного торможения (при позиционной обработке - внецентровом
сверлении и рассверливании, нарезании резьб и т. д.).
Инструментальные системы токарных
многоцелевых станков выполняются в виде:
инструментальных головок (с одним или
двумя гнездами), связанных роботом (манипулятором) с магазином неподвижных и
вращающихся инструментов;
линейных накопителей инструментов и
головок, размещенных на поперечных салазках станка;
револьверных многопозиционных головок;
комбинированных устройств, включающих
установленные на поворотной стойке револьверную головку с неподвижным
инструментом и инструментальную головку (с одним гнездом) для вращающегося
инструмента.
Головки снабжены приводом вращения
инструментов. Головки инструментальных систем с магазинами могут быть выполнены
с двумя полярными или с одной полярной и одной линейной управляемыми
координатами, обеспечивающими значительное расширение технологических
возможностей станка путем осуществления обработки немерным инструментом или под
произвольным углом.
Рекомендуется оснащать инструментальные
головки приводом с регулируемым электродвигателем, позволяющим оптимизировать
режимы обработки с использованием современных высокопроизводительных режущих
инструментов.
Емкость дисковых револьверных головок
токарных многоцелевых станков в нормальном исполнении составляет 12-18
инструментов (из них 6 и более вращающиеся). Такое исполнение вполне достаточно
для обработки номенклатуры общемашиностроительных деталей в обычных условиях.
Исходя из анализа разработанных схем
привода вращающегося инструмента, рекомендуется в револьверных головках в
основном применять схему с внешним вводом, обеспечивающим вращение инструмента,
находящегося в рабочей позиции. Данная схема привода обеспечивает большую
точность, существенное повышение нагрузочных характеристик привода, упрощение
конструкции при одновременном снижении уровня шума.
Широкая номенклатура инструментальных блоков токарных
многоцелевых станков, а также необходимость автоматической «подпитки»
инструментальной системы при работе в «безлюдном» режиме обусловливают переход
к унифицированной конструкции базирующих поверхностей (цилиндрические
хвостовики с рейкой по ОСТ 2-416-78; укороченные конусы и т. д.) для
вращающихся и неподвижных инструментов.
Унификация базирующих поверхностей и других элементов
инструментальных блоков является основой серийного производства высокоточной
оснастки специализированными предприятиями отрасли.
7. Конструкции пружинно-зубчатых муфт
7.1 Область применения
По количеству конструктивных
разновидностей группа пружинных предохранительных муфт является наиболее
разнообразной и обширной.
Общим для всех конструкций является то, что замыкание
кинематической цепи осуществляется с помощью пружин, поставленных с начальным
натяжением. Почти все пружинные предохранительные муфты работают по одному
принципу - при превышении расчетной величины крутящего момента происходит
относительное перемещение полумуфт и разрыв силовой цепи. Рабочие элементы
полумуфт обычно выполняют в виде зубьев, кулачков, шариков или роликов. Поэтому
разрыв силовой цепи происходит скачкообразно и сопровождается сильным износом
соприкасающихся поверхностей, резкими колебаниями, нагрузки в приводе и большим
шумом. Мероприятия, направленные на уменьшение износа рабочих элементов муфты
(изготовление контактных поверхностей рациональной формы, введение
ограничителя, обеспечивающего срабатывание муфты при одном скачке, ускорителя,
дополнительно воздействующего на отключаемые части, и др.), приводят к
усложнению конструкции таких муфт и их удорожанию.
При конструировании пружинных
предохранительных: муфт необходимо предусматривать возможность их регулировки,
позволяющей изменять коэффициенты запаса сцепления, а значит, и величину
передаваемого крутящего момента. Это достигается регулировкой первоначального
сжатия пружин. Величина крутящего момента, передаваемого муфтой, зависит также
от угла контакта рабочих элементов полумуфт и коэффициента трения между
подвижными элементами.
Пружинные предохранительные муфты
применяют, как правило, для передачи небольших крутящих моментов и в приводах с
малыми инерционными массами.
Расчет таких муфт, в основном, сводится к определению
размеров пружины, которая должна обеспечивать передачу максимального крутящего
момента и выключение муфты,-при перегрузке привода.
7.2 Конструкции муфт
7.2.1 Пружинно-зубчатая муфта
На рисунке 30 показана конструкция пружинно-зубчатой муфты.
Устройство муфты следующее. Крутящий момент от звездочки с полумуфтой 3 на вал 1 передается через
зубья полумуфты 2, фланцевую втулку 4 и шпонку 5. При превышении расчетной
величины крутящего момента осевая составляющая усилия, действующего на зубья,
сожмет
пружину 7, и зубья выйдут из зацепления, в результате чего будет прервана
кинематическая цепь (механизм остановится). При устранении перегрузки, зубья
полумуфт 2 и 3 снова войдут в зацепление, и кинематическая цепь будет
восстановлена.
Рисунок
30 - Пружинно-зубчатая муфта
-
вал;
-
полумуфта;
-
звездочка с полумуфтой;
-
фланцевая втулка;
-
шпонка;
,8
- упорные шайбы;
-
пружина;
-
гайка.
станок токарный муфта инструмент
7.2.2 Пружинно-зубчатая муфта (разновидность 2)
Полумуфта 1 (рисунок 31, а) с радиально
расположенными зубьями неподвижно установлена на валу 2. Форма профиля зубьев
представлена на рисунке 31,6.
Рисунок 31 - Пружинно-зубчатая муфта
В существующих конструкциях муфт угол а равен
30-40° На ступице полумуфты 1 свободно посажена полумуфта 3 выступы радиально
расположенных зубьев которой входят во впадины зубьев полумуфты 1. В
рассматриваемой конструкции полумуфта 3 представляет собой зубчатое колесо,
входящее в основную кинематическую цепь привода. Полумуфты 1 и З прижаты друг к
другу пружиной 4, предварительное натяжение которой регулируется гайкой 5.
При возрастании передаваемого крутящего
момента до величины, превышающей предельное значение, усилие пружины становится
недостаточным для того, чтобы уравновесить осевую силу, возникающую при этом на
зубьях полумуфт. Происходит деформация пружины за счет перемещения полумуфты 3
вдоль оси вала, а при значительной перегрузке - размыкание силовой цепи.
Расчетные формулы для пружинно-зубчатых муфт выводятся из условия равновесия
сил, действующих на полумуфту 3.
Литература
1. Ельчанин Ю.М., Итин А.М., Карякин В.Н.,
Федоров В.И. Применение и конструктивные особенности токарных многоцелевых
станков. - М.: ВНИИТЭМР, 1987, 48 с. 25 ил. (Технология, оборудование,
организация и экономика машиностроительного производства. Серия 1.
Металлорежущее оборудование и средства технологического оснащения. Обзорн.
информация, вып. 6.).
2. Металлорежущие станки: Учебник для
машиностроительных втузов./ Под ред. В.Э. Пуша. - М.: Машиностроение, 1985. -
256 с., ил.
. Обработка на станках с числовым программным
управлением: Справ. пособие./ Под ред. И.А. Каштальяна, В.И. Клевзовича. - Мн.:
Выш. шк., 1989. - 271 с.: ил.
. Приспособления для металлорежущих станков. Расчеты и
конструкции./ Под ред. М.А. Ансерова. - М.: Машиностроение, 1966. - 651 с.: ил.
. Проектирование металлорежущих станков. - 3-е изд.,
перераб. и доп./Под ред. Г.А. Тарзиманова. - М.: Машиностроение, 1980. - 288с.,
ил.
. Станочное оборудование автоматизированного
производства: Учебник / Под ред. В.В. Бушуева. - М.: Станкин, 1993.
. Каталог «gildemeister».
. http://www.gildemeister.com/