Перспективные методы производства стали
Курсовая работа
на тему: Перспективные методы
производства стали
План
сталь производство
выплавка
Введение
. ОБЩИЕ СВЕДЕНИЯ О КЛАССИФИКАЦИИ И ПРОИЗВОДСТВЕ СТАЛИ
.1 Классификация и маркировка стали
.2 Краткая характеристика способов производства стали
. ОСНОВЫ ПРОИЗВОДСТВА СТАЛИ
.1 Современное состояние сталеплавильного производства
.2 Основы технологии выплавки стали в мартеновских печах
.2.1 Общие сведения
.2.2 Основы технологии выплавки стали в мартеновской печи
.3 Основы технологии выплавки стали в конверторе
.4 Выплавка стали в дуговых и индукционных печах
.5 Технологическая схема производства стали в дуговой печи
3. Новые современные технологии
получения стали
3.1 Перспективные методы обработки стали при разливке
.2 Универсальный агрегат «Conarc»
.3 Отечественные агрегаты ковш-печь для внепечной обработки
стали
Выводы
Литература
Введение
Сталь - это железоуглеродистый сплав, содержащий до 2,0 % углерода, и ряд
других элементов (марганец, кремний, фосфор, сера и др.).
По химическому составу стали можно разделить на две основные группы:
углеродистые и легированные. В зависимости от содержания углерода различают
стали низко- (до 0,25% С), средне- (0,25-0,6 % С) и высокоуглеродистые- (более
0,6 % С). Сталь была и остается базисным материалом промышленности, о чем
говорят цифры роста в последние годы объемов производства стали в мире и роста
цен на металлопродукцию. Если мировое производство стали в 2004 году
перешагнуло рубеж в 1 млрд. т (1024 млн.т.), то в 2006г. оно выросло на 80-90
млн.т.
Производство стали - это сложный физико-химический процесс, при котором
протекают химические реакции в жидком металле и шлаке, а также на границах
между жидким металлом и шлаком, между шлаком и газовой печной средой.
Сталь производят в мартеновских и электрических печах, а также в
конвертерах. Если еще недавно 80% стали производили в мартеновских печах,
сейчас производство стали идет по пути применения новых прогрессивных
технологий.
Цель настоящей работы - ознакомиться с методами производства стали в современных
условиях, рассмотреть перспективные технологии получения стали на основании
анализа материалов трудов и статей различных авторов.
Работа состоит из четырех разделов, листов 54, рис.8, табл 2,
использованы материалы 15 источников. Первый раздел посвящен общим сведениям о
классификации и производстве стали и в нем даются общие сведения о сталях и
краткая характеристика способов их производства на основании источников [1,2],
их свойства и классификация; во втором разделе рассматриваются основные технологии
производства стали на основе материалов различных источников [3-12], он состоит
из пяти подразделов: в первом подразделе второго раздела представлено
современное состояние сталеплавильного производства, во втором подразделе
второго раздела освещаются особенности мартеновского процесса производства
стали, третий подпункт второго раздела посвящен основам конвертерного
производства, четвертый подпункт второго раздела дает представление о выплавке
стали в дуговых и индукционных печах, в пятом подпункте второго раздела
освещается процесс производства стали в дуговых печах. Третий раздел имеет три
подраздела и освещает особенности современного технологического процесса
получения стали [13-15]. Итог по данной теме дается в разделе: выводы.
1. ОБЩИЕ
СВЕДЕНИЯ О КЛАССИФИКАЦИИ И ПРОИЗВОДСТВЕ СТАЛИ
.1
Классификация и маркировка стали
Для улучшения качества стали и придания ей особых свойств в ее состав
вводят легирующие элементы. Такие стали называются легированными и по
содержанию легирующих компонентов они делятся на низко-, средне- и
высоколегированные. В низколегированной стали содержится обычно до 2,5 %
легирующих элементов, в среднелегированной - от 2,5% до 10%, в
высоколегированной- более 10 %.
В нашей стране установлены единые условные обозначения химического
состава стали. Обозначение марки стали состоит из букв, указывающих, какие
компоненты входят в состав стали (табл. 1) и цифр, характеризующих среднее
содержание этих компонентов.
Первые две цифры маркировки стали обозначают среднее содержание углерода,
выраженное в сотых долях процента для конструкционных сталей и в десятых долях
- для инструментальных и нержавеющих сталей.
Таблица 1.1.-Условные обозначения компонентов стали
Название компонента
|
Химический символ
|
Условное обозначение
|
Название компонента
|
Химический символ
|
Условное обозначение
|
Алюминий
|
Al
|
Ю
|
Медь
|
Cu
|
Д
|
Бор
|
B
|
Р
|
Молибден
|
Mo
|
М
|
Ванадий
|
V
|
Ф
|
Никель
|
Ni
|
Н
|
Вольфрам
|
W
|
В
|
Ниобий
|
Nb
|
Б
|
Кобальт
|
Co
|
К
|
Титан
|
Ti
|
Т
|
Кремний
|
Si
|
С
|
C
|
У*
|
Марганец
|
Mn
|
Г
|
Хром
|
Cr
|
Х
|
*Обозначение используется лишь в марках качественной углеродистой
инструментальной стали. [1, с.135]
Затем буквой указан легирующий элемент и цифрой справа от буквы - его
содержание. Например, если сталь назначена маркой 3X13, это значит, что она содержит 0,3 % углерода и 13 % хрома.
Если сталь легирована несколькими элементами, то все они указываются в
обозначении марки: сталь 2Х17Н2 - 0,2% углерода, 17% хрома и 2 % никеля. Если
за буквой не стоят цифры, это значит, что содержание легирующего элемента не
превышает 1,5 %. Например, сталь 12ХНЗА содержит менее 1,5 % хрома. Буква А в
конце обозначения марки указывает на высокое качество стали.
По назначению стали делят на конструкционные; инструментальные; стали и
сплавы с особыми физическими и химическими свойствами.
Конструкционные стали применяют для изготовления ответственных
строительных конструкций, деталей различных сложных машин, авиационных моторов,
подшипников и других изделий. Эти стали могут быть углеродистыми или
легированными. Основными легирующими элементами конструкционных сталей являются
хром и никель.
Инструментальные стали применяют для изготовления резцов, фрез, кувалд,
калибров и другого режущего, ударно-штампового и мерительного инструмента.
Стали этой группы также могут быть углеродистыми (содержание углерода - от 0,7
до 1,2%) или легированными. Важнейшие легирующие элементы инструментальных
сталей - хром, марганец, кремний, вольфрам, ванадий.
К сталям и сплавам с особыми физическими свойствами относятся
кислотостойкие, нержавеющие, жаропрочные, окалиностойкие, износоустойчивые,
электротехнические стали, а также сплавы с высоким электрическим
сопротивлением. Для химического состава сталей этой группы характерно низкое
содержание углерода и высокое содержание легирующих элементов.
Помимо указанных элементов в стали находятся и растворенные в ней газы -
кислород, водород, азот, которые ухудшают свойства стали, что проявляется в
склонности к старению, то есть постепенному изменению механических свойств с
течением времени (уменьшается пластичность и ударная вязкость с одновременным
повышением пределов прочности, текучести и твердости металла).
1.2 Краткая
характеристика способов производства стали
Получение стали из чугуна и скрапа происходит путем удаления (окисления)
примесей из расплавленных шихтовых материалов. Такие процессы имеют место при
производстве стали в мартеновских и двухванных печах; в кислородных конвертерах
с верхней, донной и комбинированной продувкой; в дуговых и индукционных печах
при плавке с применением кислорода.
Дуплекс-процесс - это процесс производства стали, ведущийся
последовательно в двух сталеплавильных агрегатах, позволяющий наиболее
эффективно использовать возможности каждого из них. Например, основная
мартеновская печь - дуговая печь, конвертер - дуговая печь, основная - кислая
мартеновская печь. Особые условия плавки в кислой мартеновской печи требуют
очень низкого содержания серы и фосфора в шихте. Однако все дуплекс-процессы
имеют наряду с преимуществами и существенные недостатки, выражающиеся в
уменьшении производительности сталеплавильных агрегатов и в появлении
организационных трудностей синхронизации работы различных сталеплавильных
агрегатов.
Совершенствование внепечных способов обработки стали, обработка
синтетическими шлаками, вакуумирование, продувка аргоном предопределяют
развитие других видов дуплекс-процессов. Электропечь в этих процессах
используется только как плавильный агрегат, доводка же металла осуществляется
вне печи, в ковшах или реакторах конвертерного типа. Имеет перспективу развития
и производство стали методом смешения, когда в одном из сталеплавильных
агрегатов расплавляют углеродистый полупродукт, в другом - лигатуру, затем их
сливают в один ковш.
В зависимости от назначения сталь производится одним из следующих
способов. Стали массового назначения и часть низколегированных выплавляется,
как правило, в конвертерах, мартеновских и двухванных печах. Это объясняется
высокой производительностью указанных сталеплавильных агрегатов и большой
потребностью народного хозяйства в таком металле.
Легированные и высоколегированные стали, в которых содержание легирующих
элементов колеблется от нескольких сотых до нескольких десятков процентов,
производят в основном в дуговых электропечах. Это объясняется меньшим угаром
дорогостоящих легирующих элементов (наличие восстановительного периода), достижением
высоких температур и получением более чистого металла по сере, фосфору и газам.
Стали, сплавы с особыми физическими свойствами выплавляют в дуговых
сталеплавильных и индукционных печах. Для улучшения свойств этих сталей
применяют методы переплава и специальной электрометаллургии,
аргонно-кислородное (АОД) и вакуум-кислородное (ВОД) обезуглероживание. [2, с.9]
2. ОСНОВЫ
ПРОИЗВОДСТВА СТАЛИ
.1
Современное состояние сталеплавильного производства
За последние полтора столетия в производстве стали произошло много
изменений. Отошли в прошлое такие способы, как тигельная плавка, пудлинговый
процесс и многие другие, которые хотя и обеспечивали получение качественной
стали, но были трудоемки, малопроизводительны. Их вытеснили конвертерные и
мартеновские способы получения стали. В текущем столетии начали широко
применять электрометаллургические способы, позволяющие выпускать наиболее
высоколегированные стали. Основным способом выплавки стали в 80-х годах
двадцатого века являлся конвертерный, которым выплавляли более 55 % стали; постепенно сокращается доля
стали, выплавленной в мартеновских печах (~20 %), и непрерывно возрастала выплавка стали в дуговых
электропечах (которая достигла уже 25 %).
Мартеновское производство занимает еще значительное место в общем
производстве стали и, кроме России, сохранилось на Украине и в некоторых
странах Европы и Азии, %:
Кислородно-конвертерный процесс прошел сложный и долгий путь создания и
развития. Потребовалось около 150 лет
с момента возникновения идеи до ее применения в промышленности, и, в конце
концов, эта идея оказалась революционной.
В 1855 г Генри Бессемер в заявке на патент № 1292 предложил глубокопогруженную продувку
сверху воздухом через трубу из огнеупорной глины.
Первым технологическим прорывом стала донная продувка воздухом в
асимметричном поворотном конвертере. Это получило известность как
бессемеровский процесс и/или как основной бессемерово-томасовский
технологический процесс. Со времен создания бессемеровского процесса на
воздушном дутье (1855
г.) были предприняты
многочисленные попытки его усовершенствования.
Со временем в ходе исследований в лабораторных и полупромышленных
агрегатах были опробованы технологические варианты верхнего, бокового и донного
газокислородного дутья, использование при продувке газовых смесей,
парокислородного дутья, кислородно-углекислотного, вдувание в конвертер
порошкообразной извести в струе кислорода, комбинированная продувка кислородом
сверху и воздухом снизу и др. Из всех апробированных вариантов на том этапе
развития техники для первого промышленного внедрения был выбран технологический
процесс с верхней кислородной продувкой, как наиболее технологичный, надежный и
простой в управлении. Именно этот вариант затем и получил широкое промышленное
развитие. Комплексная технология конвертерной плавки в сочетании с непрерывной
разливкой потребовала специальной подготовки металла (доводки и стабилизации
его по химическому составу и температуре). В этих условиях стало целесообразным
проводить рафинировочные и корректировочные операции не в конвертере, а в
ковше. Таким образом, конвертер стал агрегатом для выплавки стандартного
металлического полупродукта с последующим получением в ковше методами внепечной
обработки качественной стали любого состава со стабилизацией свойств для
условий непрерывной разливки. Такая технологическая схема позволила значительно
упростить и стандартизировать режим кислородной продувки, увеличить
производительность конвертеров, стабилизировав состав и температуру металла в
ковше. Впоследствии эта схема была заложена в проектах всех новых конвертерных
цехов, а также получила широкое развитие в зарубежной практике. Так зарождалась
внепечная обработка стали как самостоятельное технологическое звено
сталеплавильного производства. [5]
.2 Основы технологии выплавки стали в мартеновских печах
2.2.1
Общие сведения
До появления кислородно-конверторного способа производства стали в
основном всю сталь выплавляли в мартеновских печах. Широкое распространение
мартеновского способа производства стали было обусловлено возможностью
использования в качестве шихты чушкового чугуна, металлического лома, а также
расплавленного чугуна. Преимуществом мартеновских печей является также
возможность выплавки в них широкого сортамента углеродистых, качественных,
легированных сталей и использования топлива различных видов.
С появлением производительных и экономически более выгодных агрегатов - конверторов - строительство мартеновских печей прекращено. Однако многие
существующие печи, главным, образом наиболее крупные мартеновские, будут
эксплуатироваться еще долго.
Мартеновский процесс получения стали представляет собой переработку
жидкого чугуна и металлолома на поде отражательной печи.
Для плавления твердых шихтовых материалов и нагрева жидкого металла и,
шлака до заданной температуры, а также для покрытия значительных неизбежных
тепловых потерь, вызываемых большой продолжительностью плавки в мартеновском
процессе, недостаточно физического и химического тепла шихтовых материалов.
Поэтому в отличие от конверторного способа; выплавки, стали мартеновский
процесс осуществляется при подводе в печь определенного количества тепла,
получаемого при сжигании топлива.
В зависимости от химического состава огнеупоров футеровки, используемых
исходных шихтовых материалов в мартеновском производстве применяют кислый и
основной процессы плавки, а также комбинацию этих процессов, называемую
дуплекс-процессом.
Кислый мартеновский процесс протекает в печах, футеровка которых
выполнена из кислых огнеупорных материалов (динасовый кирпич, кварцевый песок,
кварциты). При плавке в кислой печи образуются кислые шлаки, при которых из
расплава плохо удаляются сера, фосфор. Поэтому кислый процесс ведут только на
качественной шихте с небольшим содержанием вредных примесей и применяют для
выплавки наиболее ответственных сталей, так как в результате получают сталь с
большой степенью чистоты. В настоящее время кислые мартеновские печи применяют
сравнительно редко.
Основной мартеновский процесс осуществляется в печах, футеровка которых
выполнена из основных огнеупорных материалов (магнезитовый, хромомагнезитовый
кирпич, магнезитовый порошок, доломит). Плавку в этом случае ведут под
основными, шлаками, которые образуются при использовании в качестве
шлакообразующего материала известняка. После окисления кремния, марганца и
частично углерода происходит окисление содержащегося в шихте фосфора до Р2О5,
который переходит в шлак, где связывается с известью, в соединение 4СаО-Р2О5.
Основной процесс более универсален и наиболее распространен, так как позволяет
использовать шихту с повышенным содержанием фосфора и серы.
Дуплекс-процессом называют комбинированный способ плавки, применяемый в
определенных условиях для улучшения качества получаемой стали. В этом случае
плавку ведут в двух печах. Вначале шихту плавят в основной мартеновской печи с
удалением фосфора и серы до необходимых пределов. После этого полученный жидкий
полупродукт выпускают из печи и заливают во вторую кислую мартеновскую печь,
где доводят сталь до заданного химического состава.
.2.2 Основы технологии выплавки стали в
мартеновской печи
Шихтовые материалы и топливо. Шихтовые материалы при мартеновском, как и
при других способах производства стали, состоят из металлической части,
неметаллической части - сыпучих
материалов и добавок - раскислителей и
легирующих.
Металлическая часть состоит из чугуна и металлолома. Чугун используют в
жидком или твердом состоянии (в виде чушек).
Соотношение жидкого чугуна и металлолома в исходной металлической части
шихты может изменяться в широких пределах- от 100% жидкого чугуна до 100% твердых материалов. Поэтому в
зависимости от содержания в шихте жидкого чугуна и металлолома основной
мартеновский процесс подразделяют на скрап-, скрап-рудный и рудный процессы
плавки.
При скрап-процессе металлическая часть шихты состоит из 60-85% металлолома и 40-15% жидкого чугуна. Скрап-процесс осуществляют на заводах,
где выплавка чугуна мала или вообще отсутствует и где скапливается большое
количество отходов производства в виде стального и чугунного лома.
В зависимости от состояния шихтовых материалов этот процесс делят на:
1) скрап-процесс на твердом чугуне, при
котором чугун используют в виде чушек;
2) скрап-процесс с добавлением жидкого
чугуна к металлолому;
3) карбюраторный процесс, при котором
шихта состоит полностью из стального лома. Карбюраторный процесс является
вынужденным и играет незначительную роль в общем объеме производства стали.
При скрап-рудном процессе шихта в основном состоит из жидкого чугуна (55-80%). В качестве дополнительных материалов
используют металлолом и железную руду (15-20% массы металлической части шихты). Скрап-рудный процесс
получил наибольшее распространение.
При рудном процессе шихта полностью (100%) состоит из жидкого чугуна с большим использованием
железной руды, которую добавляют для окисления примесей. Рудный процесс
широкого распространения не имеет.
Сыпучие материалы разделяют на шлакообразующие и окислители.
В качестве шлакообразующих материалов в основных мартеновских печах
применяют известняк, известь, плавиковый шпат, боксит и шамотный бой, а в
кислых печах - кварцевый песок, динасовый или
шамотный бой и известь. В качестве окислителей и добавок используют те же
материалы, что и в дуговых печах.
Наряду с шихтовыми материалами большое значение для мартеновской плавки
имеет топливо, которое при сгорании, выделяет тепло и тем самым обеспечивает
необходимые условия протекания процесса выплавки стали.
В мартеновских печах используют газообразное или жидкое топливо.
Газообразное топливо может быть высококалорийным, не требующим предварительного
подогрева, или низкокалорийным, которое предварительно подогревают до 900-1200° С. Из высококалорийных топлив
наиболее часто применяют природный газ или смесь природного газа с мазутом; из
низкокалорийных топлив - смесь коксового
и доменного газов.
В качестве жидкого топлива используют мазут или смолу и смоляные масла,
которые являются побочными, продуктами коксования каменного угля.
Для повышения тепловой мощности печи в современных мартеновских цехах
воздух, подаваемый для сжигания топлива, обогащают кислородом. Для
интенсификации технологического процесса жидкий металл продувают кислородом при
помощи фурмы, вводимой в рабочее пространство печи через свод. [6, с.269]
Технологическая схема производства стали в мартеновской печи. Процесс
производства стали в мартеновской печи состоит из следующих основных периодов
(рис. 2.1): заправки, загрузки шихты, прогрева,
заливки чугуна, окисления примесей, скачивания шлака, раскисления и
легирования, выпуска стали.
Заправка предшествует каждой плавке и заключается в исправлении
изношенных мест футеровки пода и откосов ванны печи. Заправку откосов ванны
начинают во время выпуска стали, из печи по мере понижения уровня стали и
шлака. К концу выпуска производится заправка задней стенки и торцевых откосов ванны,
а после выпуска -
заправка пода.
Изношенные места восстанавливают наваркой обожженного мелкого доломита,
магнезита. При местных повреждениях пода их очищают от металла и шлака выдувкой
сжатым воздухом или кислородом с последующей заправкой тонкомолотым
магнезитовым порошком.
На малых печах заправку выполняют вручную, а на больших применяются
заправочные и торкрет-машины. Одновременно с заправкой пода заделывают
сталевыпускное отверстие.
Подготовленная к плавке шихта транспортируется из шихтового отделения в
загрузочный пролет в мульдах, установленных на тележках. С тележек мульды
снимаются загрузочной машиной и подаются в печь через загрузочные окна.
Прогрев шихты осуществляют как во время загрузки шихты, так и после ее
окончания, сжигая топливо в рабочем пространстве печи. Шихту нагревают до 1300-1400° С, чтобы чугун не затвердевал во
время заливки.
Заливка чугуна в мартеновскую печь осуществляется с помощью заливочного
крана из ковшей через подвесные желоба, устанавливаемые в загрузочные окна.
Ковши с чугуном подаются из миксерного отделения на чугуновозах. При заливке
чугуна происходит бурное окисление углерода чугуна, вследствие чего из ванны
выделяется большое количество окиси углерода, сгорающей над поверхностью ванны
с выделением значительного количества тепла, которое способствует расплавлению
шихты.
Окислительные процессы начинаются уже в период расплавления шихты за счет
окислителей, введенных в шихту при загрузке, и кислорода атмосферы печи. Для
ускорения окислительных процессов на современных печах дополнительно вводят
технический кислород, вдуваемый в ванну через фурму.
Образующиеся окислы элементов шихты, плавящиеся шлакообразующие
материалы, пустая порода твердых окислителей создают шлак, который участвует в
окислении примесей шихты (углерода, кремния, марганца, фосфора, серы).
Удаление первичного шлака, содержащего окислы фосфора и кремния,
осуществляется самотеком при его вспенивании газообразными окислами углерода.
Шлак через порог загрузочного окна идет сквозь шлаковое отверстие в задней стенке
печи стекает в шлаковые ковши, установленные под печью. При уменьшении
вспенивания шлак удаляют с помощью загрузочной машины или же вручную
деревянными гребками. После этого введением шлакообразующих «наводят» новый
шлак, способствующий дальнейшему окислению примесей. Операции удаления и
наведения шлака в течение плавки могут проводиться неоднократно до получения
стали, а требуемым содержанием углерода, фосфора, серы.
Раскисление и легирование ведут в два приема: предварительно в ванне
печи, окончательно в ковше при выпуске стали. Выпуск стали из мартеновской печи
осуществляется в зависимости от вместимости печи - в один ковш или по
раздвоенному желобу в два сталеразливочных ковша. Оставшийся в печи шлак
вытекает в конце выпуска стали в сталеразливочный ковш, откуда он по сливному
желобу стекает в рядом установленный шлаковый ковш.
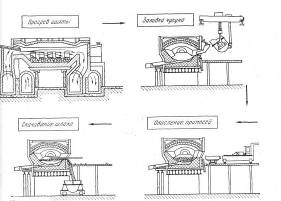
Рисунок 2.1. Технологическая схема производства стали в мартеновской печи
[7, с.58]
Из ковша сталь разливают в изложницы. В изложнице сталь не может
затвердевать одновременно во всем объеме, так как скорость отвода теплоты
различна. Поэтому процесс кристаллизации начинается с холодных (относительно
температуры раскаленной стали) стенок и дна изложницы, а затем уже
распространяется внутрь жидкого металла. Плотность твердой стали несколько выше
расплавленной, поэтому в слитке в верхней части вследствие уменьшения объема
стали образуется усадочная раковина. Кроме того, химический состав стали в
различных зонах зерна (кристаллита) стали будет неоднородным, что называется
внутрикристаллической ликвацией. Различие химического состава по зонам слитка
называют зональной ликвацией.
Недостатки, возникающие при разливке стали в изложницы, устраняются при
получении слитков на установках непрерывной разливки стали. Ее принципиальная
схема дана на рис. 2.2.
Рис. 2.2.
- Схема установки для
непрерывной разливки стали:
а - -вертикальная разливка; б - радиальная разливка; 1 - ковш; 2 - разливочное устройство; 3- водоохлаждаемый кристаллизатор; 4 - форсунка- 5 - зона
вторичного охлаждения; 6 - тянущие ролики; 7 - слиток; 8 - газорез; 9 - кантователь
При таком способе разливки жидкий расплав поступает в сквозную
изложницу-кристаллизатор 3 прямоугольного
сечения с глубиной 20-30 м. Стенки
кристаллизатора, изготовленные из меди, интенсивно охлаждают холодной водой. В
начале работы шахту кристаллизатора перекрывают брусом-затравкой, он выполняет
роль искусственного центра кристаллизации и дна. Металл затвердевает у стенок
кристаллизатора и у поверхности бруса-затравки и начинает извлекаться из
кристаллизатора с определенной скоростью (обычно 0,5-1,5 м/мин). В кристаллизатор непрерывно
подают металл, так что его уровень в кристаллизаторе постоянен в процессе
разливки. Поверхность жидкого металла защищают от высокотемпературного
окисления слоем синтетического шлака или атмосферой инертного газа. Для
получения мелкозернистой структуры заготовка, выходящая из кристаллизатора,
орошается распыленной водой из форсунок. После затвердевания по всему сечению
заготовка разрезается на части стандартной длины. Преимущества способа
непрерывной разливки стали очевидны - заготовки
получают небольшого сечения, сокращается время их выдачи и обработки, большая
степень однородности по длине и поперечному сечению заготовок обеспечивает
стабильные механические свойства и повышает надежность металлоизделий. [8, с.21-22]
Металлическую часть составляют жидкий чугун (основной компонент) и
металлолом или скрап (20-30% массы чугуна).
Металлолом - это некачественные слитки, отлитые в сталеплавильных цехах,
обрезь, образующаяся в процессе прокатки, отходы металлообработки, изношенное и
устаревшее оборудование, инструмент, вышедшие из строя металлоконструкции и
другие изделия из стали и чугуна.
Металлолом в специальном - скрапоразделочном
- цехе завода очищают от посторонних
примесей и подготавливают для загрузки в конвертор: крупный металлолом
разделывают на части, а мелкий и легковесный прессуют в пакеты. Металлолом
подается к конверторам в специальных совках.
Сыпучие материалы разделяют на охладители и шлакообразующие. Охладители
применяют для понижения температуры металла в процессе продувки, так как
окисление кислородом примесей чугуна сопровождается выделением большого
количества тепла. Основным охладителем является металлолом, добавляемый в шихту
в таком количестве, чтобы тепла, выделившегося в процессе продувки, было
достаточно для его расплавления. Однако при избыточном количестве тепла, кроме
металлолома, в качестве охладителей могут быть использованы железная руда,
агломерат, окатыши и известняк. Охладители подают в конвертор отдельными
порциями по ходу плавки.
Шлакообразующие шихтовые материалы применяют для наведения в конверторе
шлака, участвующего в процессах окисления примесей чугуна. В качестве
шлакообразующих материалов в кислородно-конверторном процессе используют
свежеобожженную известь и известняк.
Применение извести и известняка для конверторной плавки вызвано
необходимостью в очень короткий срок получить шлак заданного состава. Это
необходимо для быстрого удаления примесей серы и фосфора и получения
качественной стали. Количество шлакообразующих материалов зависит от содержания
кремния в чугуне, количества чугуна, количества и состава охладителя. Общий
расход шлакообразующих составляет 5 - 9 % от массы металлической шихты.
Для ускорения шлакообразования применяют разжижающие добавки, к которым
относятся боксит и плавиковый шпат.
Добавочные материалы (раскислители и легирующие) вводят в сталь во время
слива ее из конвертора в сталеразливочный ковш. Раскислители служат для
удаления избыточного кислорода, содержащегося в стали в конце продувки,
легирующие добавки - для получения
стали требуемого химического состава.
Эти материалы используют обычно в виде чистых металлов (алюминия,
марганца, никеля, хрома, молибдена, кобальта, титана) или сплавов этих металлов
с железом - ферросплавов (ферросилиция,
ферромарганца, феррохрома, феррованадия, ферромолибдена, ферротитана и др.),
или в виде сплавов этих металлов друг с другом (силикомарганец, силикокальций,
си-ликоалюминий и др.) Все добавочные материалы при введении в сталь не должны
содержать влагу. Влага резко ухудшает качество стали вследствие растворения в
металле водорода. Поэтому гигроскопичные материалы, т. е. материалы, способные
поглощать влагу, перед введением в ковш сушат или прокаливают в сушильных
печах.
Технологическая схема производства стали в конверторе. Процесс
производства стали в конверторе состоит из следующих основных периодов:
загрузки металлолома, заливки чугуна, продувки кислородом, взятия пробы и
замера температуры Подготовленный к плавке металлолом подается из шихтового
отделения в загрузочный пролет в совках, установленных на самоходных тележках
(скраповозах). С тележек совки снимаются специальной загрузочной машиной и
подаются к конвертору. Перед загрузкой металлолома конвертор поворачивается в сторону загрузочного пролета на 15 - 20°, носок совка вводится в горловину
конвертора, наклоняется и металлолом ссыпается в конвертор.
Заливка чугуна в конвертор осуществляется заливочным краном из ковшей,
подаваемых в загрузочный пролет из миксерного отделения на чугуновозах. (рис.2.3.)
В период продувки конвертор устанавливают в вертикальное положение,
опускают фурму и включают подачу кислорода.
Рисунок 2.3.
Технологическая схема
производства стали в конверторе
В начале продувки в конвертор загружают основную массу шлакообразующих
добавок. Остальную их часть загружают отдельными порциями в течение всего
периода продувки. Шлакообразующие подаются в конвертор из расходных бункеров,
установленных над конвертором, с помощью питателей, весов-дозаторов, ленточных
транспортеров, промежуточных бункеров и желобов.
При подаче шлакообразующих и кислорода на поверхности металлической ванны
возникает шлак, состоящий из свободных или химически связанных окислов железа,
магния, марганца, кремния, кальция, алюминия, фосфора и других элементов,
входящих в состав шихтовых материалов.
Шлак участвует в химических реакциях окисления и восстановления железа,
дефосфорации, десульфурации и других процессах, протекающих в металлической
ванне. Шлак воспринимает и удерживает вредные примеси, перешедшие в него из
металла, а также частицы плавильной пыли при прохождении их с потоками газов;
при посредстве шлака осуществляется перенос кислорода от струи к металлической
ванне.
Подаваемая под большим давлением струя кислорода углубляется в ванну,
растворяется в жидком металле, частично дробится и переходит в пузыри, которые,
поднимаясь вверх, вызывают циркуляционное движение металла в ванне.
В металле, в зоне входа струи кислорода развиваются очень высокие
температуры (~2500° С). В этой зоне происходит интенсивное окисление железа,
углерода и частичное окисление других примесей металла.
Образующимися при окислении углерода газообразными окислами СО и СО2, а
также струей кислорода металл перемешивается и дробится на капли, шлак
вспенивается и перемешивается с металлом. При этом значительная часть объема
конвертора заполняется металло-шлаковой эмульсией.
Взятие пробы и замер температуры металла осуществляют по окончании
продувки. Для этого конвертор наклоняют в горизонтальное положение. В новых
конверторных цехах устанавливают специальные машины, замеряющие температуру и
отбирающие пробы металла по ходу продувки без наклона конвертора.
Готовая сталь из конвертора сливается в сталеразливочный ковш,
установленный под конвертором на самоходной тележке (сталевозе). Одновременно со сливом стали из
приемной воронки по специальному поворотному желобу в сталеразливочный ковш подают
добавки - раскислители и легирующие.
Шлак из конвертора сливают в шлаковый ковш, установленный под конвертором
на шлаковозе.
Для этого конвертор
наклоняют горловиной вниз. Продолжительность плавки мало зависит от вместимости
конвертора и составляет примерно 35 - 40 мин. [9, с.112]
.4 Выплавка стали в дуговых и
индукционных печах
Современные дуговые сталеплавильные печи имеют механизированную загрузку
шихты с помощью бадьи, для чего свод печи поворачивается вокруг вертикальной
оси примерно на 90°. Печи вместимостью 25 т и более снабжены механизмами для
поворота кожуха с футеровкой для ускорения процесса плавления и предохранения
подины от разрушения. Все эти печи оборудованы устройствами для
электромагнитного перемешивания металла. Печи вместимостью 25-200 т
спроектированы с учетом механизированной загрузки шлакообразующих и легирующих
материалов, механизированной заправки откосов и подин печей, уборки шлака от
печи с помощью шлаковоза.
Основное преимущество индукционных печей - чистота источника тепла, не
компенсировало ряда серьезных недостатков этих печей, в том числе невысокого
уровни нагрева шлака и эксплуатационных трудностей с футеровкой, поэтому они в
дальнейшем были вытеснены дуговыми печами.
Индукционные тигельные печи широко используются для переплава чугуна,
цветных металлов и их сплавов, при этом обычно применяется ток промышленной
частоты, что значительно уменьшает капитальные и эксплуатационные расходы.
Индукционные печи наиболее широко применяются в литейных цехах. Это
малогабаритные агрегаты, в которых можно быстро выплавлять металл небольшими
порциями. На металлургических предприятиях индукционные печи применяются только
для выплавки специальных сталей и сплавов, которые невозможно или экономически
невыгодно производить в дуговых агрегатах. В первую очередь это относится к
процессам переплава или сплавления сталей с дорогими и легко окисляющимися
легирующими элементами.
Основными преимуществами индукционных печей в сравнении с дуговыми
сталеплавильными электропечами являются: получение стали с низким и особо
низким содержанием углерода; исключение возможности науглероживания стали;
интенсивное перемешивание ванны, способствующее выравниванию температуры
металла, его химического состава и ускорению процесса рафинирования в целом;
легкость регулирования температурного режима. Индукционные печи имеют высокую
производительность. Выдачу металла из них можно производить небольшими порциями
через малые промежутки времени. Для этих печей характерны небольшие габариты,
относительно бесшумный режим работы, незначительное выделение пыли, слабое и
направленное вверх излучение улучшает условия работы сталеваров.
К недостаткам индукционных печей следует отнести: высокую стоимость и
сложность электрооборудования; низкую температуру шлака, его высокую вязкость,
что практически исключает осуществление десульфурации и дефосфорации; низкую
стойкость футеровки тиглей.
Современные тигельные печи делятся на печи повышенной частоты,
применяемые преимущественно для плавки стали и специальных сплавов из кусковой
шихты, и печи промышленной частоты для плавки чугуна, цветных металлов и их
сплавов. Такое разграничение индукционных тигельных печей обусловлено тем, что
печи промышленной частоты из-за чрезмерного перемешивания ванны металла могут
работать при ограниченных значениях мощности, недостаточных для быстрого
плавления стальной шихты.
При нагреве шихты в тигельной индукционной печи в каждом куске ее
индуктируется вихревой индукционный ток, так как контактные сопротивления между
отдельными кусками очень велики и куски шихты можно рассматривать как
изолированные друг от друга. По мере нагрева отдельные куски группируются в
более крупные объединения и постепенно плавятся, образуя ванну жидкого металла,
в которой индуктируется кольцевой индукционный ток, имеющий в каждый момент
времени противоположное направление по сравнению с током индуктора.
Плавки в индукционных печах проводят методом переплава - сплавления.
Состав шихты должен обеспечивать пo расплавлении анализ сплава, близкий к заданному. Относительно холодные
вязкие шлаки являются надежной защитой металла от газопоглощения и окисления. В
индукционных печах выплавляют все марки сталей. Но особенно перспективно их
применение для получения сталей с особо низким содержанием углерода и
высоколегированных. При этом содержание углерода в шихте может быть доведено до
необходимых концентраций при практически полном сохранении таких дефицитных
легирующих как никель, молибден, вольфрам, ванадий.
Обычно окислительные процессы в индукционных печах не проводят, однако
при выплавке стали с особо низким содержанием углерода успешно применяется
продувка кислородом. Длительность плавки в индукционных печах минимальная,
доводка плавки после расплавления обычно не превышает 30 мин.
На территории бывшего СССР на ряде заводов качественной металлургии
работают вакуумные индукционные печи (ИСВ) различных типов вместимостью от 0,01 до 2,5 т. В вакуумных печах выплавляются стали и сплавы
широкого сортамента - нержавеющие,
низколегированные и конструкционные стали, прецизионные сплавы. Вакуумно-индукционные
печи (ВИП) применяют для получения металлов предназначенных для переплава в
вакуумно-дуговых печах. Для вакуумно-индукционной плавки разработаны различные
конструкции установок периодического и полунепрерывного действия. Работа печей периодического действия
характеризуется тем, что после каждой плавки вакуумную плавильную камеру
необходимо разгерметизировать для замены изложницы или формы с отливкой и
загрузки следующей порции шихты.
Печи периодического действия в конструктивном отношении проще и поэтому
затраты на их сооружение меньше. Однако ввиду необходимости откачивать в начале
каждой плавки большое количество газов, понижая давление от атмосферного до
рабочего, установки периодического действия оборудованы более мощными вакуумными
насосами. Кроме того, металл, выплавленный в печах периодического действия,
может содержать большее количество кислорода и газов, по сравнению с металлом,
полученным в печах полунепрерывного действия. Это связано с тем, что при
нарушении вакуума стенки тигля пропитываются оксидами, образующимися из
остатков металла, а поверхность печи, вакуумной камеры и расположенных в ней
устройств поглощают газы.
В печах полунепрерывного действия смену изложниц и загрузку шихты
осуществляют через шлюзовые устройства без нарушения вакуума в плавильной
камере. Поэтому в таких печах можно проводить без разгерметизации несколько
плавок, число которых обычно определяется стойкостью тигля.
В печах полунепрерывного действия уменьшаются колебания температуры тигля
и возрастает его стойкость. Сокращение простоев на ремонтах тигля, а также
исключение затрат времени на откачку камеры между плавками, замену изложниц и
совмещение конца одной плавки с началом другой обеспечивает более высокую
производительность печей этого типа. Все это обусловило более широкое
распространение в промышленности индукционных тигельных печей полунепрерывного
действия.
Недостаточная стойкость тиглей является основной причиной ограниченного
использования ВИП. Для печей вместимостью до 2 т стойкость футеровки составляет 40-65 плавок, а для печей вместимостью более 2 т стойкость футеровки меньше 30 плавок.
Преимущества вакуумной плавки более полно реализуются при бесшлаковом
процессе, поэтому ВИП обычно ведется без шлака и отличается сравнительной
простотой: получение требуемого состава достигается переплавом соответствующих
отходов или сплавлением чистых
материалов. Так как плавка проводится в герметическом кожухе и процессы
плавления и нагрева в индукционных печах достаточно быстротечны, то возможности
корректировки состава металла по ходу плавки ограничены. В связи с этим при ВИП
обычно необходим точный расчет и тщательное взвешивание шихты.
Вакуумной индукционной плавке свойственны два существенных недостатка:
во-первых, расплав контактирует с огнеупорной футеровкой, являющейся источником
загрязнения металла кислородом, включениями и металлическими примесями;
во-вторых, условия кристаллизации слитка в обычной изложнице способствуют
развитию ликвационных процессов и обогащению отдельных зон слитка ликвирующими
примесями, как и при кристаллизации металла обычной выплавки. Эти недостатки
были устранены с появлением печей вакуумно-дугового переплава (ВДП).
Печи ВДП делятся на печи с нерасходуемыми и расходуемыми электродами.
Печи с нерасходуемыми электродами применяются для выплавки тугоплавких металлов
из шихты соответствующего состава и имеют сравнительно небольшие размеры. Для
выплавки стали, титана и ряда сплавов применяются печи с расходуемыми
электродами, выплавляемыми из переплавляемой стали или сплава.
Плавка в печах ВДП с расходуемым электродом позволяет получать металл
высокой степени чистоты, так как при этом устраняются возможные источники
загрязнения и имеются благоприятные условия для рафинирования металла вакуумом.
Что же касается условий кристаллизации металла в водоохлаждаемом
кристаллизаторе, то при последовательном наплавлений слитка можно в значительной мере ослабить ликвационные
процессы.
Сущность ВДП заключается в следующем (рис. 2.4.). Металлическая «затравка», с помощью которой
первоначально зажигается электрическая дуга, располагается на водоохлаждаемом
поддоне. Электрическая дуга горит между
электродом и лункой жидкого (исключая печи с керамическим тиглем) металла.
Разряд происходит через пары металла, находящегося в промежутке между катодом и
анодом. Применение постоянного тока обу-словлено большой устойчивостью
электрической дуги. Для концентрации дуги и предотвращения перехода разряда на
стенку кристаллизатора он окружен соленоидом с продольным магнитным полем.
Расплавленный на электроде
(катоде) металл образует
капли, которые стекает в лунку жидкого металла.
По мере расплавления нижней части электрода электрододержатель
автоматически перемещает электрод вниз. Вся система уплотняется и в ней
создается соответствующий вакуум (0,7-6,65 Па). Расплавление металла в вакууме
способствует дегазации стали и раскислению ее углеродом, что существенно
снижает содержание газов и неметаллических включений. Металл кристаллизуется в
водоохлаждаемом кристаллизаторе. Быстрое охлаждение металла обеспечивает
получение химически однородного слитка с мелкозернистой структурой, и мелкими
неметаллическими включениями, благодаря чему свойства стали в результате ВДП
существенно улучшаются. Этим способом можно переплавлять стали и сплавы,
содержащие легкоокисляющиеся элементы, такие как титан, цирконий и другие.
Наиболее крупные печи ВДП работают в странах СНГ и США, они рассчитаны на
выплавку слитков массой 40-60т.
Методом ВДП переплавляют легированные конструкционные стали и стали со
специальными свойствами. Электрошлаковый переплав (ЭШП) получил широкое
распространение в мире для производства высококачественных сталей и сплавов
ответственного назначения в слитках массой до 300 т.
Метод ЭШП основан на переплаве твердого стального электрода под
электропроводным рафинирующим флюсом. Для ЭШП используется сравнительно простое
оборудование, легкое в обслуживании и надежное в процессе работы (рис. 2.5.). Преимущества метода ЭШП
способствовали его быстрому освоению во всех передовых странах.
Рисунок 2.4. Схема
вакуумной дуговой печи с расходуемым электродом:
- механизм подачи электрода; 2 - электрододержатель;
3- уплотнение; 4-электрод; 5 - кристаллизатор;
6 - вакуумная камера; 7-подвод тока к кристаллизатору
Принцип метода сформулирован еще в 1882 г. русским изобретателем электродуговой сварки А. Г. Славяновым. Первая
установка ЭШП конструкции института электросварки им. Е. О. Патона АН УССР,
позволявшая получать слитки массой до 300 кг, была установлена на заводе «Днепроспецсталь» в 1958 г. На территории бывшего СССР методом ЭШП выплавляют
стали свыше 100 марок - конструкционные, подшипниковые, кислотостойкие, жаростойкие,
инструментальные, жаропрочные и др.
Рисунок 2.5.
Схема электрошлакового
переплава:
- расходуемый
электрод; 2 - медный водоохлаждаемый
кристаллизатора 3
- расплавленный шлак;
4-слиток
Сущность электрошлакового переплава заключается в следующем. На дне
кристаллизатора устанавливают металлическую затравку, на которой начинается
процесс и которая предохраняет водоохлаждаемый поддон от повреждения в момент
зажигания. По составу затравка полностью или приблизительно такая же, как и
переплавляемый электрод. Поверх затравки насыпается смесь рабочего флюса и
магниевого или алюминиевого порошка для ускорения зажигания и формирования
жидкой ванны. Переплавляемый
электрод опускают в
кристаллизатор (он должен касаться смеси), после чего вокруг электрода насыпают
рабочий флюс в количестве 6-8 % от
массы заготовки. Напряжение подводится к электроду и плите. Электропроводный
флюс расплавляется. Жидкая флюсовая ванна выполняет роль электросопротивления,
в которой протекают процессы плавления и рафинирования металла.
Переплавляемый электрод продвигается постепенно вниз, так что его конец
всегда погружен в шлаковую ванну. Капли жидкого металла стекают с конца
электрода, проходят через флюсовую ванну, где рафинируются от газовых и
неметаллических включений. Под слоем флюса образуется жидкая металлическая
ванна. Вследствие интенсивного охлаждения плиты и кристаллизатора протекает
направленная кристаллизация металла. Дендриты располагаются под углом к оси
кристаллизатора и жидкой металлической ванны, из которой происходит непрерывная
подпитка затвердевающего слитка. Характер кристаллизации создает условия для
получения плотной бездефектной структуры.
Большое влияние на температуру шлаковой и металлической ванны оказывает
состав электропроводного флюса. Чаще всего используют флюс на основе 70 % CaF2+30 % А12О3.
В зависимости от цели переплава (определенная структура, уменьшение содержания
серы, неметаллических и газовых включений) состав флюса можно менять в широких
пределах.
Температура флюсовой ванны определяется главным образом содержанием его
основных составляющих (Аl2Оз, CaF2, CaO).
При увеличении концентрации оксидов алюминия и кальция происходит
соответственное повышение температуры ванны. Температура флюсовой ванны при ЭШП
значительно выше, чем в других металлургических процессах и составляет обычно 1730- 18700С. Перегрев стали выше
температуры ликвидуса составляет 260-490 °С, а флюсовой ванны - 420- 5700С.
После ЭШП характер и распределение неметаллических включений в полученной
заготовке существенно изменяются. Количество включений уменьшается в 2- 2,5 раза после первого переплава и в 3-4 раза после повторного переплава. В
результате повышения чистоты металла возрастают его технологические и
эксплуатационные свойства, особенно пластичность, длительная прочность при
высокой температуре, полируемость, свариваемость и др. Повышение
технологической пластичности после ЭШП позволяет дополнительно легировать
металл и тем самым увеличивать характеристики жаропрочности.
ЭШП, ВДП, плазменно-дуговой (ПДП) и электронно-лучевой (ЭЛП) переплавы
являются дополнительными в технологическом цикле производства стали. Такой же
операцией является и ВИП, если используется специально выплавляемая заготовка.
Естественно, что любая дополнительная операция связана с увеличением затрат.
Стоимость указанных способов передела колеблется в широких пределах и зависит в
первую очередь от степени освоения и
объема производства, а также стоимости применяемых материалов.
Механические свойства и длительная прочность жаропрочных сплавов после
ЭШП превышают требования: технических условий и от свойств металла ВДП
отличаются несущественно. В то же время технологическая пластичность сплавов
после ЭЛП выше, чем после ВДП. Пластичность сплавов ЭЛП по сравнению с металлом
обычной выплавки при температурах горячей деформации получается более высокой.
Имеются сведения, что стойкость подшипников из стали ШХ15, полученной ЭШП, в 10 раз выше, чем из обычной.
Для правильной оценки развития того или другого нового способа передела
важно провести технико-экономические сравнения между ними. Анализ полученных
результатов позволяет следующим образом ориентировочно расположить различные
способы по возрастанию эффективности воздействия на качество металла: ЭШП, ВДП,
ВИП комбинированные методы. Стоимость передела находится в обратном
соотношении, т. е. наименьшая при ЭШП. [10, с.59]
Для обозначения отдельных типов электропечей в странах бывшего СССР
принята следующая система. Первая буква - тип печи: Д - дуговая; И - индукционная; С - сопротивления; Р - рудовосстановительная;
Э - электронно-лучевая; Ш - электрошлаковая. Для плавильных печей
(кроме рудовосстановительных) вторая буква обозначает металл, для выплавки
которого предназначены печи: А - алюминий
и его сплавы, Б -бронза; Г - магний;
Д - молибен; К - цирконий; Л - латунь;
М - медь и ее сплавы; Н - ниобий; О - олово, свинец, баббит; Р - вольфрам; С - сталь
и жаропрочные сплавы; Т - титан,
титанистые шлаки; X - тантал; Ц - цинк; Ч - чугун.
Третья буква определяет основной конструктивный признак печи: для дуговых
сталеплавильных печей П - поворотный
свод; В - выкатываемый кожух печи; для
индукционных печей К - канальные, Т - тигельные; для печей сопротивления Т - тигельные; К - камерные; Б- барабанные;
для вакуумных и дуговых индукционных печей В- вакуум; для электронно-лучевых П - плавильная; для электрошлаковых - поперечное сечение слитка Ц - цилиндрическое; К - квадратное;
П - прямоугольное. Четвертая
вспомогательная буква добавляется для обозначения миксеров (М), агрегатов (А),
гарниссажных печей (Г).
Цифра после буквенного обозначения указывает вместимость печи в тоннах,
за исключением дуговых вакуумных или электрошлаковых печей, для которых она
означает максимальный диаметр выплавляемого слитка (в дециметрах). Для первых
из них через тире ставится вторая цифра - масса слитка в тоннах. Для электронно-лучевых печей - первая цифра указывает число пушек (излучателей электронов).
Печи сопротивления имеют довольно сложную систему обозначений,
учитывающих основные конструктивные признаки печи, характер среды в рабочем
пространстве, размеры рабочего пространства, максимальную рабочую» температуру и другие показатели.
У рудовосстановительных печей вторая буква характеризует форму ванны: К - круглая; П - прямоугольная; третья
буква обозначает основной конструктивный, признак печи: О - открытая, 3 - закрытая.
После букв через тире пишется цифра, показывающая мощность печи (в мегавольт-амперах).
У индукционных установок для нагрева и термообработки вторая буква
определяет технологическое назначение установки, третья буква - вид нагреваемого изделия. Последующие
цифры указывают мощность установки (в
десятках киловатт), частоту тока (в герцах), максимальные размеры заготовки и
длину индуктора (и сантиметрах), а буквы - систему питания и режим нагрева.
В высокочастотных установках с ламповыми генераторами первые три буквы
обозначают вид нагрева: ИМИ - высокочастотный
индукционный, ВЧД - высокочастотный
диэлектрический. Далее в виде дроби указывается колебательная мощность (в
киловаттах) и рабочая частота (мегагерцах), и буквами - технологические установки: ЗП - закалка поверхностная; ИГ - ионизация газа; ПЗ - плавка зонная; НС - нагрев
сквозной и другие.
Для плазменных дуговых печей обычно употребляется обозначение ПДП. Другие
виды нагрева не имеют пока установленных обозначений.
Приведем несколько примеров обозначений электрических печей, применяемых
для плавки стали и ферросплавов: ДСП-50 - дуговая сталеплавильная печь с поворотным сводом вместимостью 50 т, ИСТ-1 - индукционная сталеплавильная тигельная печь вместимостью 1 т, ИЧТ-6 - индукционная чугуноплавильная тигельная печь вместимостью 6 т, РКЗ-16,5 - рудовосстановительная круглая закрытая
печь для выплавки ферросплавов мощностью 16,5 МВА, ЭЛП-1А-250 - электронно-лучевая
печь, агрегат с одной аксиальной пушкой мощностью 250 кВт.
Увеличение производства электростали будет достигнуто за счет повышения
производительности существующих печей и строительства новых.
В дальнейшем основная масса электростали будет выплавляться в крупных
электропечах (100,
200, 300 и 400-т).
Электропечи вместимостью 50 т и
ниже предполагается использовать для выплавки высоколегированных сталей и
сплавов, а также для выплавки стали на машиностроительных заводах для фасонного
литья. [11, с.115]
2.5 Технологическая схема производства
стали в дуговой печи
Процесс производства стали в дуговой электропечи состоит из следующих
основных периодов: заправки, завалки, плавления, окисления, раскисления и
легирования, слива стали (рис. 2.6.). Заправка
выполняется для восстановления изношенных участков футеровки печи. Осуществляют
заправку с помощью специальных заправочных машин сухим магнезитовым порошком.
Загрузку металлолома в дуговую печь ведут сверху при помощи загрузочной бадьи.
Рисунок 2.6.- Технологическая схема производства стали в дуговой печи
Одновременно с металлоломом в небольших количествах в печь загружают и
шлакообразующие окислители и науглероживатели. После загрузки печь накрывают
сводом и начинают расплавлять шихту.
Плавление шихты осуществляется под действием тепла, выделяющегося при
горении электрической дуги между опускающимися электродами и расплавляемым
металлоломом.
Дуга прожигает в твердой шихте колодцы. Расплавленный металл постепенно
стекает на под. Электроды опускаются до поверхности скопившегося на поде
жидкого металла и останавливаются. Тепло электрических дуг при этом
аккумулируется жидким металлом, он перегревается и в нем расплавляется
оставшаяся твердая шихта. По мере непрерывного увеличения слоя жидкого металла
электроды автоматически поднимаются кверху.
Окислительные процессы начинаются уже в период расплавления шихты за счет
окислителей, введенных в шихту во время загрузки. После полного расплавления
шихты в печь с помощью специальной загрузочной машины равномерными порциями
вводят окислители. При этом начинается окисление углерода и кипение металла,
обусловленное выделением из металла окиси углерода. При кипении ванны
происходит перемешивание и удаление растворенных в металле газов (водорода,
азота). Окисляется и переходит в шлак фосфор. Шлак вспенивается и самотеком
удаляется из печи через рабочее окно или печь слегка наклоняют в сторону
рабочего окна и шлак скачивают деревянными гребками в шлаковый ковш,
установленный на тележке под печью.
Вместе со шлаком удаляется и фосфор. После скачивания 60 - 70 % шлака в печь вновь вводят
шлакообразующие.
Образующийся новый шлак ускоряет процессы дефосфорации стали. Углерод
окисляется в течение всего окислительного периода. Скорость окисления углерода
и интенсивность кипения ванны регулируют добавками железной руды.
В последнее время значительное увеличение скорости окислительных
процессов достигается продувкой металла газообразным кислородом.
В течение всего окислительного периода берут пробы стали для определения
содержания в ней углерода, фосфора и других элементов.
Во время окислительного периода наряду с окислением вредных примесей
происходит окисление и потеря полезных компонентов- марганца, хрома, ванадия, вольфрама, титана. В стали остаются
растворенные сера и кислород, ухудшающие ее свойства. Удаление кислорода и серы
из стали, а также корректировка ее химического состава и температуры
достигаются при помощи раскисления.
Раскисляющие добавки, выбираемые в зависимости от марки стали, растворяются
в металле и взаимодействуют с растворенным в нем кислородом. Образующиеся при
этом окислы всплывают на поверхность металла и поглощаются шлаком. Для
доведения содержания углерода до нормы в соответствии с выплавляемой маркой
стали одновременно с введением раскис-лителей проводят также науглероживание
стали. Для этого на открытую ее поверхность после удаления шлака загружают
дробленый кокс или электродный бой и сталь перемешивают. После науглероживания
стали и введения в нее раскислителей в печь загружают шлакообразующие
материалы. Образовавшийся шлак раскисляется вследствие добавки на его
поверхность молотых кокса, ферросилиция, ферромарганца, силико-кальция,
порошкообразного алюминия и других сплавов. Одновременно с раскислением шлака
происходит диффузионное раскисление стали и удаление серы, которая содержится в
расплаве в соединении с железом и марганцем в виде сульфидов (FeS и MnS). Вместе с тем шлак препятствует поступлению
кислорода из атмосферы в сталь, способствует удалению продуктов глубинного раскисления.
Электромагнитное перемешивание ускоряет переход серы и неметаллических
включений из стали в шлак. Для получения необходимого химического состава в
сталь вводят легирующие добавки.
Для слива стали печь наклоняют. Сталь и шлак стекают через сливное
отверстие по желобу в сталеразливочный ковш. В процессе слива происходит
перемешивание стали и шлака, что способствует дополнительному удалению из нее
серы и кислорода. Шлак во время слива всплывает на поверхность, что в
определенной степени препятствует охлаждению металла. Если это необходимо, то
при сливе в ковше дополнительно проводят раскисление и легирование. [12, с.60]
3. Новые
современные технологии получения стали
.1
Перспективные методы обработки стали при разливке
Достижения в области материаловедения и возрастающие требования к
металлам и сплавам, которые эксплуатируются в экстремальных условиях,
обусловили необходимость разработки новых технологических процессов и
электротехнологического оборудования для их плавки, внепечной обработки, разливки
и кристаллизации.
Приоритетным направлением в решении этих проблем в промышленно развитых
странах мира является использование в металлургических технологиях средств
магнитной гидродинамики. Малоинерционное бесконтактное воздействие
электромагнитных полей на жидкий и кристаллизующийся металл дает возможность
управлять его температурой и скоростью движения и, соответственно, процессами
тепло- и массопереноса на всех металлургических переделах. В частности,
позволяет перераспределять тепло и вещество в различных зонах
электротехнологических установок (ЭТУ), интенсифицировать межфазные
взаимодействия в системе металл-реагент, изменять интенсивность прямого или
косвенного силового воздействия массовых электромагнитных сил в одно- и
многофазных системах. Представляется возможность также осуществлять
регулируемую электромагнитную транспортировку металлических расплавов по
герметичным трубопроводам.
Наложение электромагнитных полей на затвердевающий металл позволяет
кардинально влиять на характер процессов кристаллизации. Это связано как с
возможностью изменения условий теплоотвода с поверхности литых заготовок, так и
с обеспечением управления конвекционными потоками на фронте затвердевания
металла и в межкристаллитном пространстве Разработка ЭТУ для применения в
металлургических технологиях ставит также вопрос о создании специальных
источников для их электропитания.
Конечными целями использования внешних воздействий в металлургических
технологиях являются получение высокого качества изделий из металлов и сплавов,
а также энерго- и ресурсосбережение.
В связи с этим целесообразно рассмотреть несколько примеров применения
ЭТУ в литейных и металлургических технологиях. В частности, в
Физико-технологическом институте металлов и сплавов (ФТИМС) НАН Украины
разработан новый класс не имеющих аналогов за рубежом электромагнитных
устройств, получивших название «магнитодинамические насосы и установки». Их
особенностью является то, что в одном агрегате конструктивно и функционально
совмещены индукционная канальная печь и электромагнитный насос. Для этого
наряду с каналом и индукторами предусмотрен дополнительный электромагнит,
создающий на одном из участков канала внешнее магнитное поле. В результате
индукторы индуцируют ток в жидком металле, находящемся в канале, а электромагнит
- магнитное поле, направленное по
нормали к току. При взаимодействии тока и поля по закону Ленца в жидком металле
возникает электромагнитная сила, вызывающая его движение. При этом можно в
широких пределах управлять температурой жидкого металла изменением режимов
индукционного нагрева путем регулирования напряжения на обмотках индукторов.
Кроме того, изменением напряжения на обмотках электромагнита, обеспечивается
управление интенсивностью и направлением движения расплава в каналах и тигле
установки. Это позволяет бесконтактно осуществлять электромагнитное
перемешивание жидкого металла и его разливку.
На таком принципе созданы и эксплуатируются в промышленности
магнитодинамические миксеры-дозаторы для сплавов черных и цветных металлов.
Такие миксеры-дозаторы, в частности, для чугуна и стали, используют для
получения, выдержки и разливки железоуглеродистых сплавов на формовочных
линиях, карусельных автоматах, комплексах получения мелющих тел и других
литейных машинах.
Перспективной областью применения магнитодинамических миксеров-дозаторов
является непрерывная разливка стали. Во-первых, такие агрегаты функционально
подходят для применения в составе литейно-прокатных модулей при валковой
разливке стали, так как могут обеспечить ее требуемый химический состав и
температуру как в процессе выдержки, так и разливки по заданному режиму.
Во-вторых, они могут быть использованы в качестве промежуточных ковшей
принципиально нового магнитодинамического типа при непрерывной разливке стали,
особенно для получения тонких широких слябовых заготовок. В данном случае
устраняются недостатки, присущие традиционно применяемым промежуточным ковшам:
сложность организации стабильного истечения струи из него в кристаллизатор МНЛЗ
вследствие низкой надежности стопорных и шиберных затворов; необходимость
дополнительного применения специальных систем перемешивания расплава (продувка
инертными газами, установка электромагнитных перемешивателей и др.); трудность
эффективного подогрева стали с целью компенсации теплопотерь при внепечной обработке
и транспортировке металла к МНЛЗ, достигающих 50-100°С, а также соблюдения оптимальных
температурных условий разливки и обеспечения возможности выпуска стали из
плавильной печи с более низкой температурой для уменьшения продолжительности
плавки, снижения расхода огнеупоров, угара легирующих элементов и
энергопотребления; высокие скорости потоков стали в кристаллизаторе, что
ухудшает качество непрерывнолитых заготовок и обусловливает необходимость
применения специальных сложных и дорогостоящих устройств для торможения таких
потоков.
В настоящее время применяют различные способы нагрева стали в
промежуточном ковше, в основном с помощью плазмы или электрической дуги, а
также химическим способом при вводе алюминия. Недостатком плазменного и
дугового способов является повышение угара элементов, так как нагрев металла
осуществляется с поверхности. Поэтому, даже учитывая сравнительно небольшую
глубину ванны расплава в промежуточном ковше (порядка 0,7-0,8 м), необходимо осуществлять
интенсивное перемешивание всего объема стали для усреднения температуры.
Известен опыт применения индукционного промежуточного ковша в Японии на
заводе фирмы Kawasaki Steel, который позволил резко сократить брак
непрерывнолитых заготовок по причине нестабильности температуры разливки,
создать необходимые тепловые и гидродинамические условия для внепечной
обработки расплава в ковше. Однако, к сожалению, указанная разработка не нашла
широкого промышленного применения, что объясняется в первую очередь
несовершенством систем управления расходом стали, основанных на использовании
механических устройств - стопоров и
шиберов.
Поэтому предлагается применить в технологиях непрерывной разливки стали
вместо традиционного промежуточного ковша - магнитодинамический промежуточный ковш, созданный на базе
апробированного промышленности, в том числе в условиях НКМЗ,
магнитодинамического миксера-дозатора стали. Анализ особенностей непрерывной
разливки стали, предусматривающей использование магнитодинамического
промежуточного ковша по сравнению с традиционным показывает, что он имеет
следующие преимущества: исключена необходимость применения стопоров и шиберных
затворов, что упрощает процесс разливки стали и устраняет потребность в
применении инертных газов для защиты рабочей зоны затворов; бесстопорная разливка
металла позволяет перейти к безнапорной, снизить динамический напор,
создаваемый струей стали, поступающей в кристаллизатор, уменьшить интенсивность
циркуляционных потоков металла в кристаллизаторе и улучшить условия
кристаллизации слитка; обеспечивается возможность независимого и активного
управления температурными и расходными параметрами процесса разливки; выдача
расплава из верхней зоны миксера повышает надежность процесса разливки металла
и уменьшает вероятность прорывов жидкой стали в области промежуточного ковша;
индукционный подогрев металла производится в нижней зоне миксера, что в
комплексе с управляемой электромагнитной циркуляцией улучшает условия
теплопередачи, позволяет точно выдерживать температурный режим разливки,
снизить энергозатраты, существенно повысить эффективность внепечной, в том
числе реагентной и фильтрационной обработки расплава; сокращение расхода
основных и вспомогательных материалов.
На рис.3.1. представлены принципиальные схемы реализации непрерывной
разливки стали с использованием традиционного промежуточного ковша и
магнито-динамического, обладающего отмеченными выше преимуществами.
В настоящее время вышеперечисленные ведущие фирмы-производители имеют
свои высокоскоростные кристаллизаторы с оригинальным профилем гильзы, что
позволяет существенно повысить скорость разливки.
Так, для квадратных сечений 100x100 и 150x150 мм фирмой Voest-Alpine
на настоящий момент времени достигнуты скорости 6,0 и 3,8-4 м/мин
соответственно, что обеспечивает высокую производительность установки,
удовлетворяющую современным требованиям заказчика и, как следствие, ряд
конкурентных преимуществ для производителя оборудования. Таким образом,
скорости разливки выросли в 1,5-2 раза
по сравнению с аналогичными показателями 15-20 лет назад.
Также нужно отметить наметившиеся тенденции повышения емкости
сталеразливочного ковша до 200-360
т и, как следствие, увеличения продолжительности разливки плавки до 2-3 ч. На комбинатах стран СНГ сортовые
МНЛЗ, как отмечалось, наиболее вероятно будут устанавливаться взамен части
устаревших блюмовых, МНЛЗ в
существующих отделениях непрерывной разливки, оснащенных преимущественно
конвертерами большой емкости.
Технические вопросы перехода на ковш большой емкости уже решены:
увеличение емкости и высоты промежуточного ковша, применение крышки, аргонной
защиты, непрерывного измерения температуры и подогрев.
В двух предыдущих десятилетиях XXв. в промышленно развитых странах активно совершенствовали разливку в
кристаллизаторе и повышали производительность МНЛЗ. Эта тенденция продолжает
сохраняться и в первом десятилетии XXI в. Кроме того, также не менее активно будет совершенствоваться ковшевая
разливка.
Рисунок 3.1. - Схемы традиционной (а) и новой (б) технологий непрерывной
разливки стали: 1
- сталеразливочный ковш;
2 - стопор; 3 - промежуточный ковш; 4 - шиберный затвор; 5 - кристаллизатор; 6 - магнитодинамический промежуточный ковш; 7 - индуктор; 8 - электромагнит;
9 - металлопровод [13]
3.2
Универсальный агрегат «Conarc»
В силу роста требований к качеству
металлопродукции в условиях оптимизации экономических показателей за счет
рационального выбора сырьевых материалов и энергетических ресурсов в недалеком
будущем сталеплавильные цеха будут оснащаться универсальными агрегатами.
Универсальным агрегатом является процесс «Conarc», предложенный фирмой SMS-Demag
и представляющий собой комбинацию процессов дуговой сталеплавильной печи и
кислородного конвертера. Процесс «Conarc» позволяет работать с различными сырьевыми материалами (жидкий чугун,
скрап, чугун и заготовка прямого восстановления). Двухкорпусной агрегат
включает комбинацию верхней кислородной фурмы с электродами дуговой печи,
которые могут альтернативно применяться в двух одинаковых корпусах печи.
(рис.3.2.) Процесс начинается с фазы
кислородного конвертера, которая потом переходит в фазу электродуговой печи.
Полный цикл включает последовательную загрузку шихты в оба корпуса печи,
которая начинается с заливки жидкого чугуна, после чего вводится кислородная
фурма и начинается процесс продувки. В конце продувки кислородом в печь
загружают твердые шихтовые материалы (скрап и (или) металлизованное сырье), и
затем электроды устанавливают в рабочее положение и включают дугу. В конце фазы
дуговой плавки удаляется шлак, а готовая сталь сливается в ковш, который
передается для обработки на установке ковш-печь.
На печи «Conarc» (две
170-тонные печи) металлургического завода «Saldanha Steel» (ЮАР), запущенной в эксплуатацию в 1998г.,
соотношение в завалке жидкого чугуна и твердой металлизованной шихты
варьируется в широком диапазоне от 30:70 до 75:25. На печи достигнут расход
энергии менее чем 200кВт час/т при годовом производстве 1,35млн.т. [14]
Рисунок 3.2.-Технологический процесс выплавки стали в двухкорпусной печи «Соnarс» [14]
.3
Отечественные агрегаты ковш-печь для внепечной обработки стали
Значительное ужесточение требований к качеству и сортаменту сталей,
необходимость увеличения производительности металлургических комплексов
инициировали переход сталелитейных цехов на новую технологию. Она
предусматривает выплавку в электропечах полупродукта с заданным содержанием
углерода и требуемой температурой и перенос рафинировочных и доводочных
операций в ковшовые установки или агрегаты ковш-печь (АКП). Обработка на АКП
обеспечивает выполнение комплекса технологических операций: нагрева металла со
скоростью до 5 0С/мин и стабилизации его температуры
в ковше перед разливкой; доводки химического состава; раскисления металла;
глубокой десульфурации; гомогенизации расплава; удаления неметаллических
включений; введения шлакообразующих материалов и легирующих добавок.
Эти технологические задачи выполняются с применением электродугового
нагрева и продувки аргоном через донную пористую фурму (пробку) ковша с помощью
системы газопроводов и управления газовым режимом; дозированного введения через
специальный водоохлаждаемый фланец в крышке кусковых шлакообразующих, легирующих
материалов и раскис-лителей. а также подачи на поверхность металла
порошкообразных реагентов в потоке аргона; продувки аргоном через верхнюю
погружную фурму; ввода в расплав алюминиевой и порошковых проволок с помощью
трайб-аппарата; автоматизированного определения уровня металла и его
температуры, диагностики содержания кислорода в металле и отбора проб металла и
шлака.
Для перечисленных
технологических операций используются агрегаты ковш-печь типа АКП с ковшами
вместимостью от 12
до 320 т, спроектированные совместно с челябинскими
организациями и предприятиями; НТ ЗАО «АКОНТ», ООО «НТЦ «Приводная техника» и
ООО «ИСК». С 1994
г. ОАО «Сибэлектротерм»
изготовлено 16 комплектов агрегатов типа АКП для
отечественных металлургических заводов.
Циклограмма внепечной обработки на АКП сопрягается с циклом работы
плавильного агрегата и технологическим оборудованием дальнейшей обработки
расплава для каждого производства и, как правило, включает следующие этапы:
· выпуск металла из плавильного агрегата в ковш, присадку в
него кремния, ферросплавов и шлакообразующих, продувку аргоном;
· подачу ковша под свод, присоединение газового продувочного
тракта;
· опускание свода, начато продувки аргоном;
· включение печи, подачу шлакообразующих, формирование жидкого
шлака;
· отключение печи, измерение температуры, отбор проб металла и
шлака;
· включение печи, подачу шлакообразуюших, корректировку
химического состава металла;
· отключение печи, измерение температуры, отбор проб,
определение окисленности
металла;
· включение печи, подачу шлакообразующих и раскислителей,
корректировку химического состава и температуры металла;
· отключение печи, окончательное раскисление порошковой и
алюминиевой проволокой, отбор проб, подъем свода;
· выведение ковша из установки АКП для транспортировки на разливку.
Приведенное описание циклограммы включает операции обработки
углеродистых, качественных углеродистых и легированных конструкционных сталей.
Предусмотрена возможность изготовления и поставки заказчикам новых конструкций
агрегатов ковш-печь с разным уровнем комплектации. Благодаря модульному
унифицированию технических решений узлов АКП упрощаются модернизация установок,
работающих на металлургических заводах, и создание новых агрегатов для
внепечной обработки с использованием металлоконструкций имеющихся электропечей.
Разработанная серия установок АКП имеет несколько вариантов исполнения: в
частности, одно- и двухпостовое, с токопроводяшим рукавом электрододержателя
(сталь - медь) иди шинно-трубчатыми
токоподводами.
Для введения в ковш всех необходимых для обработки стали технологических
материалов и диагностических средств измерения используются следующие
устройства и механизмы:
· автоматизированная машина для измерения уровня металла в
ковше, температуры шлака и металла, измерения содержания кислорода и отбора
проб;
· специальный стенд и система газопроводов управлення газовым режимом для продувки аргоном
через донную пористую фурму (пробку) ковша или верхнюю специальную фурму;
· механизм (манипулятор) подачи, опускания в ковш и подъема
верхней фурмы;
· погружные футерованные огнеупорные сменные фурмы (каждая из
них рассчитана для определенной операции) для обеспечения подачи в металл
аргона либо порошкообразных материалов в струе аргона, контейнер для установки
фурм (рассчитан на восемь фурм);
· задатчик-позиционер (устройство, позволяют поворачивать
контейнер с фурмами на определенный угол для взятия очередной фурмы и установки
отработанной при помощи механизма подъема, поворота и опускания);
· машина (трайб-аппарат) для подачи в металл алюминиевой или
порошковой проволоки из соответствующих бунтов;
· бунтоприемники с установленными на них бунтами проволоки;
· установка для подачи порошкообразных материалов;
· водоохлаждаемая труботечка. соединенная наклонной труботечкой
с конвейером бункерной эстакады, а также с
системой весодозирования и ввода в ковш кусковых шлакообразующих, раскислителей
и легирующих материалов.
Агрегат ковш-печь дополнительно оснащается системами и оборудованием:
· самоходным сталевозом, оборудованным шлепперным подводом энергоносителей и газовых сред;
· автоматизированной системой дозирования и транспортировки
кусковых материалов, включающей бункеры-хранилища, весодозирующие устройства,
транспортеры; системой подачи порошковых материалов (угля, кокса) в струе
инертного газа; стендом для наращивания электродов; системой улавливания и
очистки технологических газов; системой водоохлаждения элементов конструкции;
гидросистемой с насосно-аккумуляторной станцией и электрогидравлическим
регулятором вводимой в ковш-печь мощности; пневмосистемой; системой
трубопроводов и системой управления режимом подачи газов при продувке; стендом
наклона ковша, снабженным машиной скачивания шлака скребкового типа; стендом высокотемпературною
нагрева ковша, ремонта его футеровки и замены продувочных донных фурм (пробок)
и шиберных затворов; системами промышленного телевидения, телефонной и
оперативной связи, а также пневмотранспорта (пневмопочты); цеховой системой
газоочистки и респирации; системой отопления и вентиляции помещений, в которых
установлены агрегаты и сопутствующее оборудование; системами освещения и
сигнализации, а также кондиционирования главного поста управления агрегатом.
Основные параметры агрегатов ковш-печь приведены в таблице 3.1.
АСУТП обеспечивает повышение производительности агрегата, сокращение
расхода энергоресурсов, ферросплавов и легирующих элементов. Эффективность
управления достигается использованием современных надежных средств
автоматизации, математических моделей и методов управления, обеспечением
точности выполнения технологических операций и повышением информированности
технологического персонала. В числе задаваемых критериев работы
технологического оборудования - обеспечение
требуемого темпа нагрева металла; уменьшение удельного расхода материальных и
энергетических ресурсов; улучшение качества стали.
Разработанная серия отечественных агрегатов ковш-печь обеспечивает
выполнение современных технологических требований обработки сталей и имеет
энергетические параметры, соответствующие лучшим образцам установок для доводки
стали до требуемых стандартов.
Выводы
Современные промышленные технологии производства и разливки стали
представляют собой определенную высокоэффективную систему технологий и
операций, базирующихся на весьма малом количестве мощных технологических
парадигм, составляющих некоторое метатеоретическое единство. Это обеспечивает
металлургам сравнительно высокую стабильность и гармонизацию большинства
металлургических процессов и систем. При этом следует особо подчеркнуть, что
большинство из этих процессов окончательно оформились в качестве базовых в
конце 20-го века, а их функциональные возможности и энергетические показатели
находятся на границе известных физических законов и ограничений. Эти
технологические процессы представляются хорошо продуманными и научно
обоснованными в части их соответствия современным сырьевым материалам,
энергетическим источникам и требованиям взаимодействия с окружающей средой. В
конечном счете, это обеспечивает производство металлопродукции более высокого
качества при минимальных затратах при условии ее высокой конкурентоспособности.
Научный и технологический прогресс, наблюдаемый в производстве и разливке
стали, в целом можно представить в виде пяти основных тенденций (направлений)
реструктуризации черной металлургии.
1. Совмещение
в единую максимально совмещенную замкнутую систему основных технологических
операций и процессов производства металлопродукции, что обеспечивает сокращение
временных затрат на управление (уменьшение цикла прохождения от сырья до
продукции во времени) и ускоряет возможности по оперативному выполнению заказов
клиентов.
Примером таких построений являются различного рода мини-металлургические
заводы. Прогресс в области создания оборудования для мини-заводов достиг крайне
высоких темпов: только в последние полтора десятилетия были разработаны новые
конструктивные подходы и созданы оригинальные технологические решения,
обеспечивающие существенный рост удельной производительности дуговых
сталеплавильных печей; отработана концепция высокоэффективного агрегата для
внепечной обработки стали, получившего в литературе название»ковш-печь»; а
также реализована на практике концепция высокопроизводительной многоручьевой
сортовой МНЛЗ, позволившая обеспечить совмещение дискретного цикла выплавки
стали и ее непрерывной разливки.
Можно с уверенностью утверждать, что в ближайшее десятилетие будет
развиваться тенденция повышения удельной производительности дуговых печей и
машин непрерывной разливки стали. Для этого созданы все условия.
2. Стремление
приблизить профиль получаемой при непрерывной разливке заготовки к профилю
конечной металлопродукции, что обеспечивает существенный энергосберегающий
эффект.
В первую очередь, это относится к плоской металлопродукции, где
совершенно четко обозначена тенденция создания высокотехнологичных
литейно-прокатных модулей (ЛПМ) с разливкой на тонкие слябы и последующей
прокаткой до тонкой полосы. Это фактически исключает из технологической системы
этап производства слябов, их подогрева перед последующей прокаткой и прокатку
слябов на толстолистовых станах.
3. Создание
сталеплавильных агрегатов на базе основных кислородных конвертеров, оснащеных
токоподводящими электродами, обеспечивающими интенсификацию подвода тепла, что
обеспечит цикл плавки (от выпуска до выпуска) на уровне 18-22 минут.
Правильный выбор сталеплавильного процесса в основном определяется
ограничениями по содержанию сопутствующих (вредных) примесей и составом шихты
исходной завалки. Не менее важным фактором при этом является степень совмещения
дискретного процесса выплавки стали с квазинепрерывным процессом ее разливки.
Используемые в практике сталеплавильного производства кислородные конвертеры
(КК) и дуговые сталеплавильные печи (ДСП) имеют весьма жесткие ограничения по
содержанию сопутствующих (вредных) примесей и составом шихты исходной завалки.
Не менее важным фактором при этом является степень совмещения дискретного
процесса выплавки стали с квазинепрерывным процессом ее разливки. Используемые
на практике сталеплавильного производства кислородные конвертеры (КК) и дуговые
сталеплавильные печи (ДСП) имеют весьма жесткие ограничения по интенсивности
подвода тепла и составу шихты.
В недалеком будущем сталеплавильные цеха будут оснащаться универсальными
агрегатами типа процесса «Conarc».
. Уравновешенный и всеобъемлющий контроль за воздействием
металлургических выбросов и отходов на окружающую среду.
Фактически это означает, что в ведущих промышленных странах все большим
приоритет будут приобретать программы развития черной металлургии с учетом
требований минимизации возможных отрицательных воздействии на окружающую среду.
При этом приоритетное развитие получат процессы, обеспечивающие рециклинг
технологических отходов и скрапа.
С того момента, когда с появлением установок «ковш-печь» основная
технологическая нагрузка по поддержанию требуемых температурных режимов для
протекания необходимых физико-химических процессов в расплаве, доводка
химического состава, причем широчайшими возможностями и др. операции вынесены
из сталеплавильного агрегата, его роль уже несколько иная. Главное - это
получить качественный расплав. В классической схеме: сталеплавильный агрегат -
«ковш-печь» - МНЛЗ (машина непрерывной разливки стали) требует четкого графика
подачи стали, чтобы обеспечить непрерывную разливку. Конвертеры и электропечи
обеспечивают эти условия, с мартенами сложнее, однако постепенно намечается
тенденция перехода с мартеновского способа производства стали к конвертерному и
электродуговому, а также к новым технологиям производства и разливки стали.
. Интеллектуализация системы технологических процессов и операций путем
широкого интегрирования применения компьютерного мониторинга и внедрения в
производство управляющих моделей, динамично реагирующих на любую
производственную ситуацию, начиная с получения и разгрузки сырья и заканчивая
отгрузкой металлопродукции за ворота завода. В этом ракурсе максимальные
конкурентные преимущества будут приобретать технологические решения,
направленные не просто на решение производственных задач и обеспечивающие
максимальное энерго- и ресурсосбережение, но в тоже время и максимально
адаптированные к современным системам автоматического управления производством.
При таком подходе вряд ли возможно сохранение консервативных схем производства
и разливки стали (мартеновские печи, разливка в слитки и пр.)
Таким
образом, одной из передовых технологий является производство стали, включающее
выплавку стали в агрегате типа «Conarc»,
применение затем обработки в установке «ковш-печь», с последующей разливкой
МНЛЗ.
Литература
1. Жадан В.Т., Гринберг Б.Г., Никонов В.Я. Технология
металлов и других конструкционных материалов. М.: В.ш., 1970. - 704с.
2. Горобец В.Г., Гаврилова М.Н. Производство стали в
дуговой печи. М.: Металлыргия, 1986. - 208с.
. Блаутцик Х. Замена мартеновского производства в
России на электросталеплавильные комплексы фирмы «ФАИ-Фукс»// «Сталь» №7,
2006г., С.35-36
. Колпаков С.В., Шахпазов Е.Х., Югов П.И. Создание и
развитие кислородно-конвертерного процесса в мире.// «Сталь» №8, 2006. -
С.31-34
. Гуненков В.Ю., Тищенко В.А., Пивцаев В.В., Карпович
Ю.В. Совершенствование технологии внепечной обработки стали на Белорусском
металлургическом заводе//ОАО «Черметинформация». Бюллетень «Черная металлургия»
№11, 2004. - С.26-30
. Кудрин В.А. Металлургия стали. М.: Металлургия,
1981. - 488с.
. Кнорозов Б.В. и др. Технология металлов. М.:
Металлургия, 1978. - 904с.
. Жуков А.П., Малахов А.И. Основы металловедения и
теории коррозии. М.: В.ш., 1991. - 168с.
. Арсентьев П.П., Квитко М.П. Конвертерный процесс с
донным дутьем. М.: Металлургия, 1983. - 128с.
. Глебов А.Г., Мошкевич Е.И. Электрошлаковый
переплав. М.: Металлургия, 1985. - 343с.
. Юзов О.В. Эффективность новых сталеплавильных
процессов и агрегатов. М.: Металлургия, 1977. - 240с.
. Ловчиновский Э.В., Вагин В.С. Машины и механизмы
сталеплавильного производства. М.: Металлургия, 1982. - 271с.
. Дубоделов В.И. Применение электротехнических систем
в литейных и металлургических технологиях.// «Металлургические процессы и
оборудование» №2, 2006. - С.23-26
. Смирнов А.Н. Современные тенденции развития
процессов производства и разливки стали.// «Металл и литье Украины» №1, 2006. -
С.7-10
. Кузьмин М.Г., Чередниченко В.С. Отечественные
агрегаты ковш-печь для внепечной обработки стали.// «Сталь» №6, 2006. - С.68-70